SAFETY FIRST
The crucial importance of machinery and workplace safety

Designing for safety & security
Good design + technology = safe home environments
Cersaie 2024 wrap up NKBA Excellence in Design Awards 2024
Sharpening your personal saw Vale Simon Hodgson
We pay tribute to a true mentor and friend to all
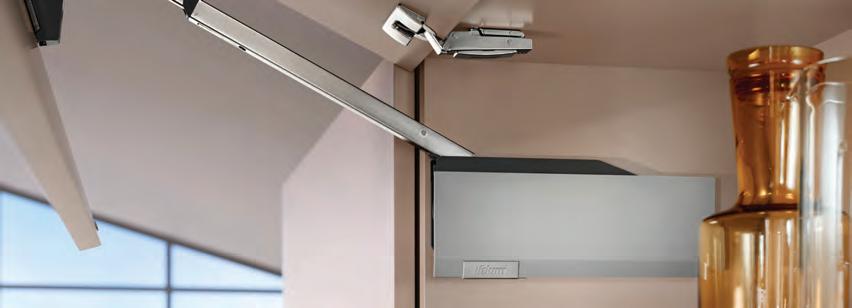

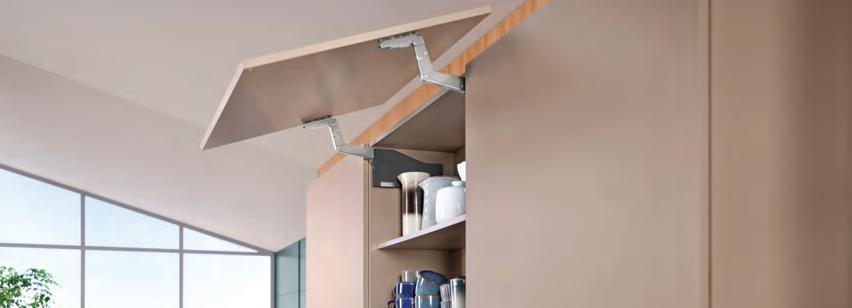
From the editor

Welcome to issue 2 of Connect magazine and thank you to all our readers and advertisers who provided such amazingly positive feedback after issue 1.
As we kick off 2025, it’s time to tackle the serious issue of machinery and workplace safety. In researching this topic and speaking to all the wonderful industry members who willingly gave their time and expertise to assist me, I’ve realised it’s so much more than just doing what “has” to be done.
Workplace accidents don’t just affect those who are injured. The flowon effect to family, friends, work mates and colleagues (and the business) is insurmountable. To deep dive into this topic, I spoke to a variety of representatives from the machinery sector as well as factory owners and operators. I hope you find their input as insightful as I did.
As an extension of that theme, we have a Silica ban update from the ACFA Workplace Advice team and a summary of the key insights from the recent ACCI National Business WHS Survey. Plus, Ben Fewtrell from Max My Profit shows us how the 5S principles are about more than just efficiency — they are also about safety.
Writer Pam Kershaw looks at safety in the home and how the design process can incorporate elements to keep homeowners safe and secure. Rob Ditessa delves into the realm of training and speaks to a variety of individuals in the cabinet-making and joinery fields about their road to success.
We’re grateful to the team at HIA Economics for their Home Building Outlook update (hint: it’s looking up!). Selina Zwolsman walks us through the ins and outs of safe interior design principles. And our friends at KBDi share how to play it safe with white, while still staying stylish.
Also in this issue, enjoy a report from Cersaie 2024, wrap up of the ACFA Industry Conference, the fabulous major winners from the 2024 NKBA NZ Awards, plus so much more!
On a personal note, I wrote what was probably the most challenging piece of content I’ve ever undertaken in crafting a tribute to Simon Hodgson. Simon was my life partner, my business partner and my whole world. Coming to terms with his loss is one of the hardest things I’ve ever done, and I don’t know that I will ever truly do so. But I am grateful for the opportunity to celebrate the best of him and recognise his immense contribution to our industry.
Enjoy!
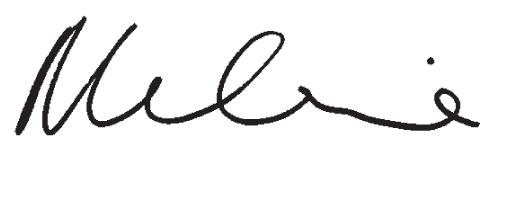
Connect magazine is published by the Australian Cabinet & Furniture Association.
ABN 80 000 071 787
Publisher: Dean Brakell, CEO, ACFA
Editor: Melanie Gardener
Advertising Sales: Fiona Joynes
Art Director: Liza Jane Smith, liza@monava.com.au
Contributing Writers: Rob Ditessa, Pam Kershaw, Selina Zwolsman, Ben Fewtrell, Dean Brakell, Monique Penton, Tom Devitt (HIA)
Social Media: Brandshake Pty Ltd
Printer: Neo Pty Ltd
Correspondence to: PO Box 157, Gosford NSW 2250
Front cover: Danielle Victoria Design Studio
Subscriptions: Connect magazine is produced as a hard-copy print publication as well as an online digital magazine. If you wish to subscribe please visit connectmagazine.com.au/
@connectmagazineaus @connect-magazine-aus
Copyright © Connect magazine (Property of the Australian Cabinet and Furniture Association). All rights reserved. The magazine or any part thereof may not be copied or reproduced without written permission from the publisher. Any specifications and/or claims here within are those of the manufacturer and/or supplier. Disclaimer: Statements by advertisers, expressed editorial opinion and/or contributors’ comments are not necessarily representative of those of ACFA Ltd or its members unless expressly stated. The publisher and editor assume no responsibility for errors or omissions or any consequence of reliance on this publication.
The Australian Cabinet and Furniture Association Ltd is a trade association that represents the interests of the cabinet making, kitchen, design, joinery, furniture, fit-out, and other wood, timber, stone and panel processing industries. Membership and advertising enquiries are welcome.
FEATURES
6 Safety First
The crucial importance of workplace safety in the cabinet-making, renovation and stone industries. By Melanie Gardener.
18 Home Safety and Security
Where good design meets new technology to create safe living environments. By Pam Kershaw.
28 Training for Success
In today's world, traditional apprenticeships, formal education programs, and cutting-edge digital courses offer a variety of options to suit different learning styles and career goals. By Rob Ditessa.
34 Designing for Safety
Essential kitchen design tips to prevent fires, falls and injuries. By Selina Zwolsman.
44 Vale Simon Hodgson
We pay tribute to a member of our industry who is remembered as an inspirational force, a true mentor and a friend to all. By Melanie Gardener.
48 Product Update
Give your next project a lift with our editor’s pick of the latest kitchen, bathroom and interior products.
50 Transform your business with the 5S Methodology
To remain competitive, deliver high-quality craftsmanship, and meet deadlines, optimising every aspect of your operations is crucial. By Ben Fewtrell.
54 Furniture & Wall Coverings
Interior and exterior product inspiration for rooms and walls to create an outstanding end result.
56 Cersaie 2024
The international exhibition for ceramic tile and bathroom furnishings was held last September in Bologna, Italy.
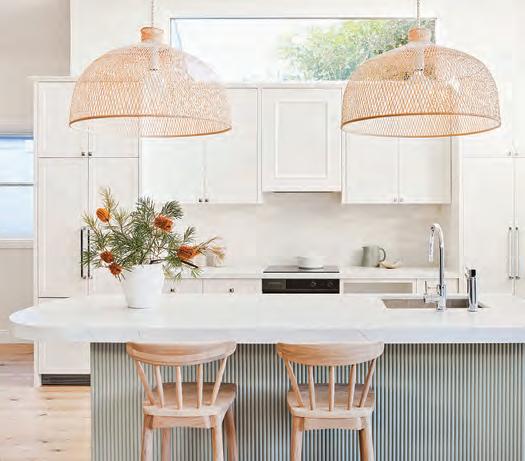
81 The Last Word: Sharpening Your Personal Saw
Few of us have sufficient time to do everything in our businesses but better management and supervisory training can significantly improve productivity and safety. By Dean Brakell.
ASSOCIATION UPDATES
22 Playing it safe (and stylishly) with white
We love colourful kitchens at KBDi, but we'll never tire of the crisp, clean, classic appeal of a white working space.
36 NKBA Excellence in Design Awards 2024
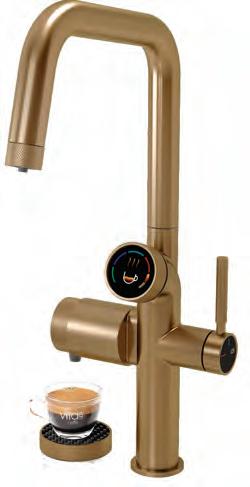
The best kitchens and bathrooms in New Zealand were announced at a gala ceremony in September 2024.
40 Home Building Outlook
The outlook for home building is brighter heading into 2025, with on-the-ground activity showing clear signs of improvement. By Tom Devitt, HIA senior economist.
46 ACFA Industry Conference 2025
Industry members came together in Sydney on 7 March for a day of learning and personal development.
INDUSTRY NEWS
53 Key Insights from the ACCI National Business WHS Survey
The Australian Chamber of Commerce and Industry's 2024 National Business WHS Survey sheds light on the evolving challenges faced by businesses in workplace health and safety (WHS).
58 Engineered Stone Ban Update
With all jurisdictions now finished their transitional arrangements, the complete ban on all materials containing at least one per cent crystalline silica, including engineered stone, came into effect on 1 January 2025.
60 Incentive Payment for Apprentices
The Australian Government has announced a $10,000 incentive payment to attract apprentices into the residential construction and clean energy sectors.
61 A Modern Qld Reimagining with Hettich
This project sought to create a home that is both immediately welcoming and equally impressive.
62 A Global Creative First: The Boston Oak Collection
The Boston Oak Collection is an innovative milestone, offering a broad spectrum of 12 colours inspired by traditional methods of staining natural timber.
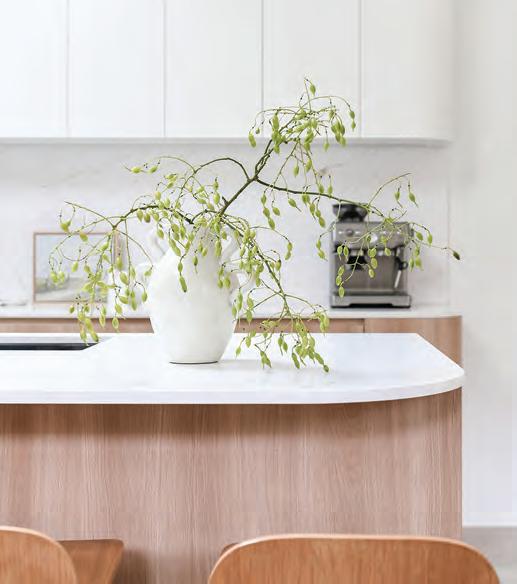
64 Australian-Made Solutions with Multicam Systems
The commitment to innovation, quality, and customer satisfaction is shown through Multicam’s dedication to providing solutions to Australian businesses.
66 Introducing AVENTOS top and AVENTOS HKi
Blum’s AVENTOS top and AVENTOS HKi lift systems offer a perfect blend of style and functionality.
68 Lincoln Sentry + Oliveri sink and tap update
Expanding its partnerships with premium product suppliers, Lincoln Sentry is proud to announce it is now a major distributor for Oliveri sinks and taps.
70 Enhancing Manufacturing Efficiency
The role of Material Handling Machines and CABINET VISION to streamline operations and create efficient workplaces.
71 Grass Nova Pro Scala
Creating your dream design is now easier than ever with the Nova Pro Scala drawer system, which offers a wide range of customisation options to bring your vision to life.
72 Introducing All About Labels
Australia’s leading manufacturer of removable labels to the cabinetry industry.
73 Fair Work Commission Update
Rising applications to the Fair Work Commission highlight the need for small business compliance.
74 Striking the Balance: Upgrade Machinery or Increase Employee Headcount?
When managing a business, one of the crucial decisions involves allocating resources between capital investment and the level of employee wages.
75 MSF30322 Certificate III in Cabinet Making and Timber Technology
ACFA's unique workplace-based training model is designed to meet the evolving needs of our industry.
76 Cutting-edge Tech Propels ASC Flatpacks to New Heights
Initially a modest operation, today ASC Flatpacks is a thriving enterprise, thanks to the transformative power of Cabinetry.Online technology.
77 New Wage Theft Laws
Important changes to workplace laws regarding underpayment of wages came into effect on 1 January 2025.
78 Effortless Expansion
goCabinets is a game-changer for growing cabinet makers.
79 Simply the Best CRM for the Kitchen Industry
Ayrmont Technologies' ARMS is the ultimate business solution designed specifically for kitchen, bathroom, and joinery companies.
80 Make Recycling Easy with Hideaway Bins
With an increasing demand for easier ways to separate waste and recycling, Hideaway Bins offers a simple colour coding system which can have a huge impact.
82 Index
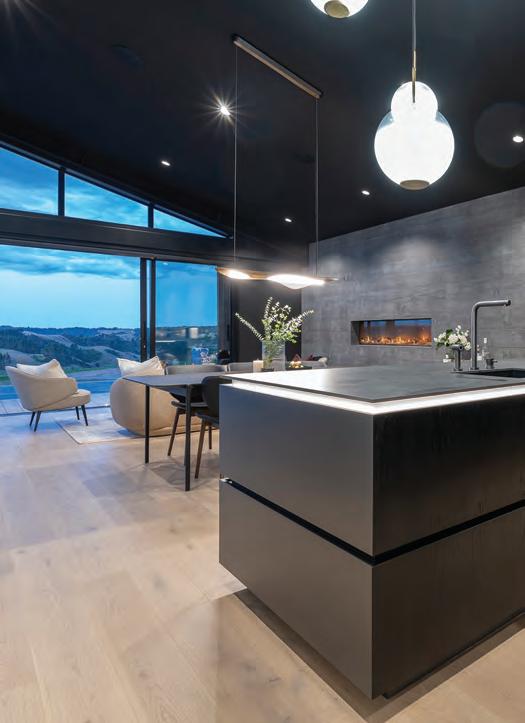
Safety First Workplace
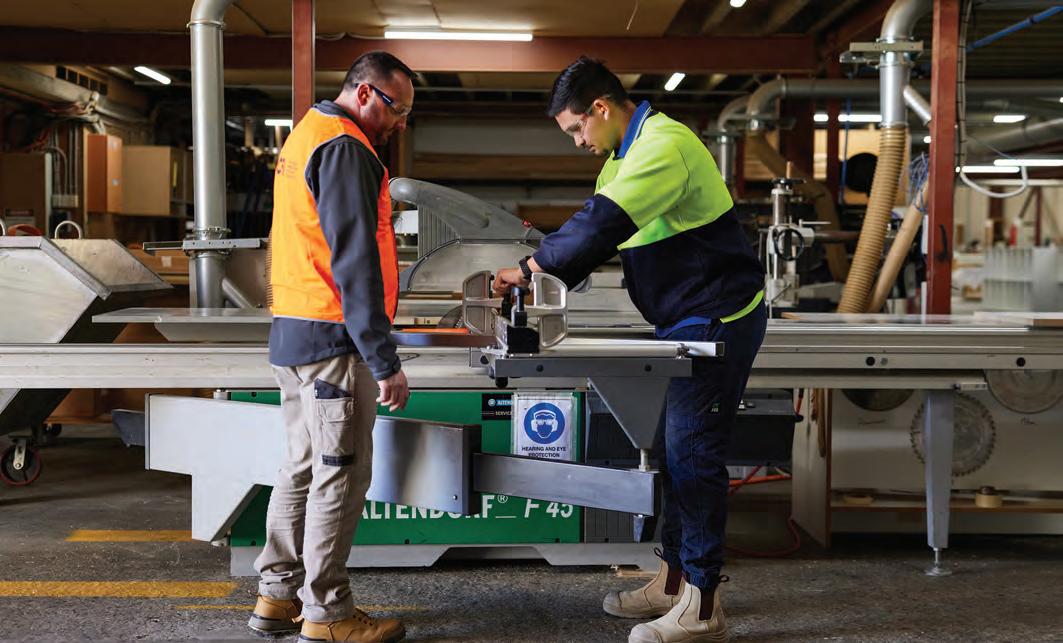
The crucial importance of workplace safety in the cabinet-making, renovation and stone industries
By Melanie Gardener
Workplace safety should never be just a matter of regulatory compliance. It's a fundamental aspect that ensures both the wellbeing of workers and the sustainability of businesses. The intricate processes involved in crafting cabinets, furniture, stone and bespoke woodwork, as well as building and renovation works, require a keen focus on safety measures to prevent accidents, promote efficiency, and uphold quality standards.
Connect spoke to several representatives from the machinery industry as well as factory owners and operators to better understand the design and development of today’s machines plus the implementation of safety processes within various work sites.
Understanding the Risks
Cabinetmaking, building/renovation and stone fabrication involve a variety of tools and materials that, if not handled properly, can pose significant risks
to workers. From table saws and routers to sharp hand tools and hazardous materials such as adhesives and finishes, each component of the process presents its own set of potential hazards. Splinters, cuts, abrasions, and exposure to dust and fumes are common risks that must be mitigated through proper safety protocols.
Legal and Ethical Obligations
Beyond the moral imperative to protect workers, there are legal requirements that mandate workplace safety in every industry, including cabinetmaking, building and stone fabrication. Workplace Health & Safety guidelines and other regulatory standards set forth specific measures to ensure the safety of employees. Compliance with these regulations not only prevents legal repercussions but also fosters a culture of responsibility and care within the workplace.
There has been a considerable shift in perception within an industry that once saw workplace injuries as “battle scars” which were worn with pride. Thankfully, this old-school attitude has no place in today’s factories and work sites.
“Safety is a core design consideration of all our products and is integral to the design process,” explains Darren Faulkner from Multicam. “At the
forefront of this is operator safety but we also look at ergonomics, compliance with standards, integration with third-party safety devices and many other factors.”
At SCM Group, safety is paramount at every stage of the machinery design process. “It’s not an afterthought, but a core principle integrated from initial concept to final production,” explains Matthew Saad, service manager. “SCM’s goal is to create machinery that is not only efficient and productive but also is inherently safe to use.”
Enhancing Productivity and Efficiency
A safe work environment is inherently more productive. When workers feel secure in their surroundings, they can focus entirely on their tasks without the distraction or fear of accidents. Properly trained employees are more likely to work efficiently, reducing downtime due to injuries or mistakes. This efficiency directly translates into improved output and higher-quality products, benefiting both the company and its clients.
Protecting Workers' Health
Factory environments can expose workers to a range of health hazards, such as respiratory issues from dust, or skin problems from contact with chemicals. Implementing safety measures such as dust collection systems, ventilation, and personal protective equipment (PPE) such as respirators, gloves and eye/ear protection is crucial to safeguarding the long-term health of employees. Regular health screenings and education on the risks associated with factory work further contribute to maintaining workers' wellbeing.
Preventing Accidents and Injuries
Accidents in a factory can have serious consequences, ranging from minor injuries to lifealtering incidents. Machine-related injuries, in particular, can be severe if safety precautions are overlooked. Utilising machine guards, implementing lockout/tagout procedures, and providing comprehensive training on equipment usage are effective strategies to minimise these risks. Additionally, fostering a culture where employees feel empowered to report safety concerns ensures that potential hazards are addressed promptly.
“As a European company we simply will not compromise on safety as we operate in worldwide
Workplace Safety
markets,” explains Con Badenhorst from Felder. “Most accidents happen when procedures are not followed, or when operators are under-trained, pressured, tired or distracted, so we see machinery training as a crucial element of creating safe workspaces.”
“Extensive analysis is conducted to evaluate all possible interactions between operator and machines during normal operation and maintenance, but also unintentional actions of bad habits that may be adopted,” explains Michael Bullock, Biesse Oceania CEO. “This goes beyond fences, photocell and access gates and includes devices and additional protections aimed to safeguard the operator.”
Safety When Using Machinery
Machinery is central to factory operations. From precision panel saws, edgebanders, jointers, and CNC machines to gangsaws and slab polishers, these tools are indispensable for producing high-quality work. However, their power and complexity also make them significant sources of risk. Ensuring safety when using machinery involves a combination of proper training, equipment maintenance, and adherence to established protocols.
Jon Chamberlain from Wood Tech explains that safety is a foundational principle for all Wood Tech machinery. “Every machine is tested and reviewed to ensure it meets safety standards,” he says. “Depending on the machine type, this may include the introduction of additional safety features such as emergency stops, safety barriers and intuitive user interfaces that make its use safer for operators.”
Matthew from SCM Group says the company’s commitment to operator wellbeing is reflected in
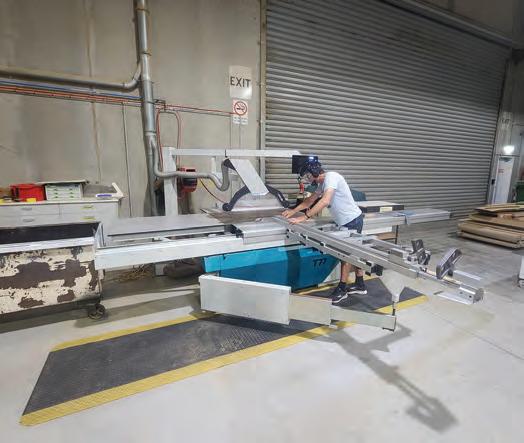
Workplace Safety
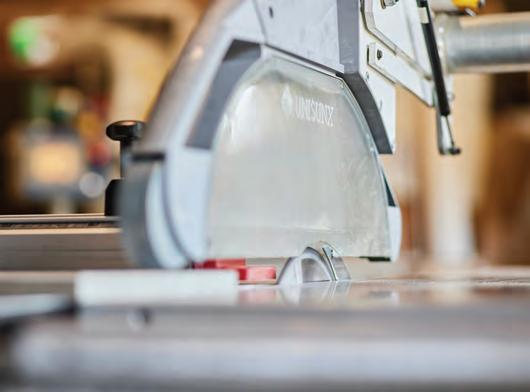
several key ways. “Physical guarding is meticulously designed and implemented to prevent access to hazardous areas of the machinery during operation,” he explains. “Sophisticated electronic protection systems are incorporated to detect and mitigate potential risks with automated shutdowns in unsafe situations. Clear and prominent safety signage provides operators with crucial warnings and instructions.”
Automation and Safety
The advancement of automation within machinery has significantly contributed to creating a safer work environment in cabinet-making, joinery and stone fabrication workshops. Automated machines, such as CNC routers and robotic saws, reduce direct human interaction with cutting tools, thereby lowering the risk of accidental injuries. Additionally, automation helps ensure consistency and precision, reducing errors that can lead to dangerous situations. Features such as automated shut-off mechanisms, motion sensors, and real-time monitoring systems further enhance safety by preventing misuse and detecting potential hazards before they escalate.
All manufacturers agreed that automation plays an integral role in the workplace safety aspect of machine operations.
Jon from Wood Tech provides the example of the Panel Storage System. “Not only does the system manage stock levels but it seamlessly loads the CNC with the correct size material for the job at hand without any user intervention. Features such as automatic tool changes and remote monitoring systems further enhance safety by managing these tasks without the need for any direct physical involvement,” he says.
For Con from Felder, removing the human element increases safety by default. “It’s simple,” he explains. “If you don’t touch it, it cannot hurt you. Automation removes human input and creates reliability, efficiency and speed. If you can touch it, then it should have options for a system such as the Felder PCS saw safety system."
Darren from Multicam says the majority of its automation features revolve around material handling, clamping and processing. “The development of automatic loading, automatic alignment, and automatic unloading has taken a lot of the physicality out of machine operation. This also greatly reduces setup times, increases accuracy and improves the operator experience,” he adds.
At SCM Group, the incorporation of automation into its machines was driven by a desire to stay ahead of the curve in technology as well as safety. “The machinery takes on more of the workload which improves cost-effectiveness and optimises resource utilisation,” says Matthew from SCM. “Automation helps create a safer working environment by taking humans out of the most dangerous situations and providing more reliable control over machine operations."
Biesse has been progressively integrating automation into its machinery design to enhance both efficiency and precision. “Automation enhances safety by reducing the need for manual intervention, thereby minimising the risk of human error and accidents,” adds Michael from Biesse. “Automated systems can perform repetitive and hazardous tasks, allowing operators to focus on supervision and control, assisted by software and interfaces."
Training and Competence
Every worker operating machinery must be adequately trained in its use. This includes understanding how to start, operate, and shut down the equipment safely. Workers should also be trained to recognise potential signs of malfunction and understand the importance of routine maintenance. Comprehensive and ongoing training not only prevents accidents but also boosts confidence and efficiency when using machinery.
“Machinery training at Wood Tech covers a broad range of safety topics including proper machine operator training, identification of potential hazards and emergency protocols. We emphasise the
Case Study: Castlewood Kitchens
We spoke to: Pat Abela, managing director
Employees: 40 (27 in the factory including four apprentices)
In business: More than 40 years
Manufactured goods: Project builders/custom residential joinery, high-end
Why is workplace safety important? What benefit does it bring to your business?
A person’s life and livelihood are in your hands. If you care about people, you want them to be looked after in the workplace. Trauma after an accident can express itself at any time and in so many ways and it doesn’t just affect the person who is injured — it affects everyone mentally and physically around them.
What are some workplace safety strategies currently in place?
Our factory foreman oversees the team but, overall, we seek to create a good culture where we look after one another and look out for each other. We like to get involved in awareness days as well and ask for feedback from the team to see what works, and what doesn’t. We also maintain good communication with our tradies to make sure their younger people are looked after. And training — lots of training as there is always something new to learn.
We have employed a specific person in our office to oversee safety and utilised the expertise of an external HR company to audit our safety measures and produce a safety report with recommendation which we have since implemented. In addition, we do our own audits each year to look at how we can improve.
What methods do you use to communicate safety strategies to the team? And is this part of ongoing training and development?
Regular meetings and safety updates, plus lots of signage in the factory, are key factors. But we don’t rely solely on signage as we feel it’s vital to make sure we also show what we expect. We have an induction process for all new team members, and in addition, we try hard to empower the team to speak up if they see something that requires attention or if they want to suggest an improvement.
What role does ergonomics play in maintaining workplace safety?
We don’t use adjustable-height benches, but we ensure they are at the correct height for our team members. Each
Workplace Safety
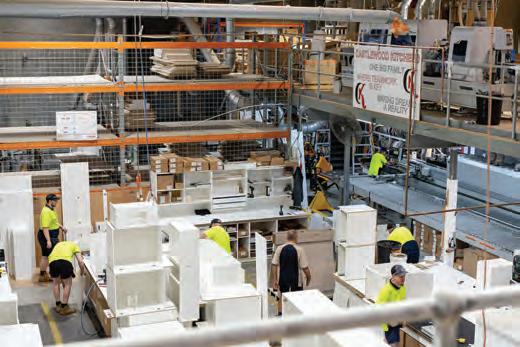
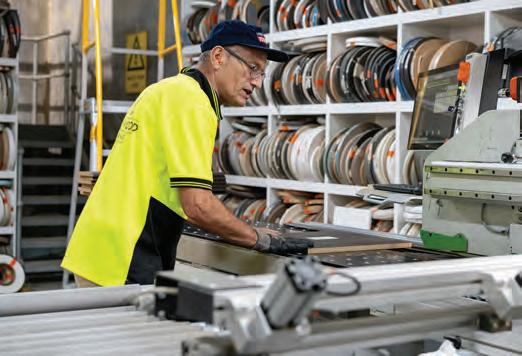
person designs their bench to suit their preferred layout — we find this gives them ownership and autonomy over their station. Workflow design in the factory is also really important — it’s good to have everything close but not too close, because it’s beneficial to keep up some movement. Efficiency is the main area we address but we also want to find a balance of moving/not moving.
What does your program of machinery maintenance look like and what process do you implement to make sure this stays on track?
We opted for the extra maintenance package for our Biesse machines to ensure we can take fast action if something needs to be addressed. But we also have pre-booked services every year which includes a full check over of the machine and action on anything that needs to be updated or fixed. Before any machine is turned on, we have a full safety check list which must be completed. The machines are designed so well that you can’t even get close to the cutting areas as sensors will turn the machine off straight away, and they are completely fenced off for added safety.
Anything else to add?
Our focus is on making sure the team are aware of what they need to do to protect themselves. Of course, as a director, I am personally liable but that’s not our main driver. We work with tools that can be dangerous so it’s a team effort — no one wants to be injured so we take responsibility as a collective to create a better environment
Workplace Safety
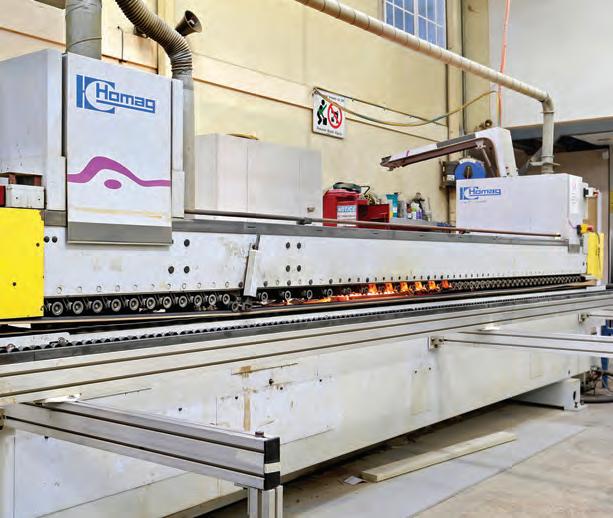
importance of regular maintenance and adherence to manufacturer guidelines to mitigate risks during use,” Jon from Wood Tech adds.
“Training is essential in fostering a culture of safety within the workplace,” he says. “It equips operators with the knowledge and confidence to use the machinery correctly which reduces accidents and downtime.”
At Felder, machinery training focuses on correct use and understanding of the machine as well as the principles of production. “Understanding how a machine is designed to operate will always lead to a much safer environment,” says Con. “We want to mitigate any work or time pressures that drive behaviour that leads to accidents.”
Darren from Multicam says their safety training focuses on operator safety and the safety of those interacting with the machinery. “This includes material handling (heavy items), material holding (suction or manual clamping methods, handling of cutting tools (sharp objects), machine and tool guarding, use of PPE, suitability of products, noise, swarf and dust control, plus safety during maintenance,” he explains.
“Training plays an imperative role in workplace safety,” agrees Matthew from SCM Group. “Effective training not only equips employees with the knowledge and skills to perform their jobs safely, but also fosters a safety-conscious culture within the workplace. By understanding potential risks, employees are better prepared to identify and mitigate dangers, preventing accidents and injuries.”
Michael from Biesse says the company’s training programs cover a variety of safety aspects including equipment inspection, proper operation procedures and maintenance protocols. “The training combines theory and practice to ensure complete mastery of the equipment, emphasising the importance of safety in all aspects of machine use,” he adds.
Regular Maintenance and Inspections
Well-maintained machinery is safer and more reliable. Scheduled inspections and maintenance routines help identify potential issues before they become hazards. Ensuring blades, belts, and other components are in good condition reduces such risks and enhances overall performance.
Regular maintenance tasks should include:
• Daily Checks: Inspect machines at the start of each shift to ensure they are clean, lubricated, and free of debris. Check for visible signs of wear or damage, such as frayed belts or cracked components.
• Blade and Tool Sharpening: Maintain sharp blades and tools to ensure clean cuts and reduce strain on machinery, which can lead to overheating or malfunction.
• Dust Extraction Systems: Regularly clean and inspect dust collection systems to prevent blockages that can reduce efficiency and pose fire hazards.
• Calibration: Periodically calibrate machines to ensure they operate within specified tolerances, especially for precision equipment such as CNC machines.
• Record Keeping: Maintain a detailed log of maintenance activities, including dates, tasks performed, and any parts replaced. This helps track performance and identify recurring issues.
• Professional Servicing: Schedule professional servicing for complex machinery at recommended intervals to ensure optimal performance and safety compliance.
“Our comprehensive training programs ensure operators are not only skilled but also understand the importance of vigilance and proper machine care in maintaining a safe working environment,” says Jon from Wood Tech. “We advocate for a proactive approach to machinery maintenance and provide
Case Study: Debrich Custom Joinery
We spoke to: Richard Curley, director
Employees: 25 (11 in the factory including two apprentices)
In business: More than 30 years
Manufactured goods: Custom residential joinery, high-end
Why is workplace safety important? What benefit does it bring to your business?
We run a site with potential dangers, so our first priority has to be safety. I want my staff to all go home the same way they arrived. No one wants to lose someone to a workplace accident — the costs are so much more than just financial.
What are some workplace safety strategies currently in place?
Every day we make sure the factory is pristine — swept clean, no trip hazards, and off-cuts dealt with. We use nonslip, rubber matting and eye/hearing protection is a must. We carry out toolbox talks every three months and all our machinery is serviced twice per year, plus we use vacuum lifters to look after our backs, and ensure the machine guards are always in place. All our machines have “no-go” areas clearly marked around them.
All our apprentices are on a workbench between two senior people so they benefit from both checking on them and overseeing their work.
What methods do you use to communicate safety strategies to staff? And is this part of ongoing training and development?
We have a sign board in the lunchroom which is regularly updated with any new or relevant information. Every staff member has a tablet (we’re aiming for a paperless office!) and any relevant updates are also sent out to each tablet. We find a day-to-day generalised format of training works best as that allows us to be responsive to changing conditions but we do constantly review all our safety procedures and policies with the input of our factory manager who generally oversees this area.
What role does ergonomics play in maintaining workplace safety?
We aim to keep everything off the ground — all our leads and air come from above so this minimises trip hazards. To minimise bending, all tools are in drawers at the work

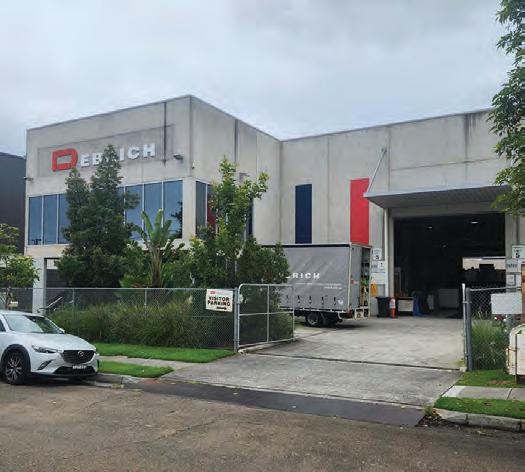
stations in the most ergonomic position, and each bench has fatigue matting to offset any long periods of time standing.
What does your program of machinery maintenance look like and what process do you implement to make sure this stays on track?
In addition to our regular, scheduled service program we ensure staff know to immediately report any issues to the factory foreman so it can be dealt with. We also bring this up during our toolbox talks and the tablets can be used to report issues.
Anything else to add?
My main goal is to have an environment that is clean, safe and free from as many hazards as possible — I have extremely high standards for cleanliness and rubbish removal as well as dust extraction. On site is our greatest challenge as there is so much that is out of our control, so we do our best to work with builders who have similar standards and are more proactive rather than meeting minimal criteria.
Workplace Safety
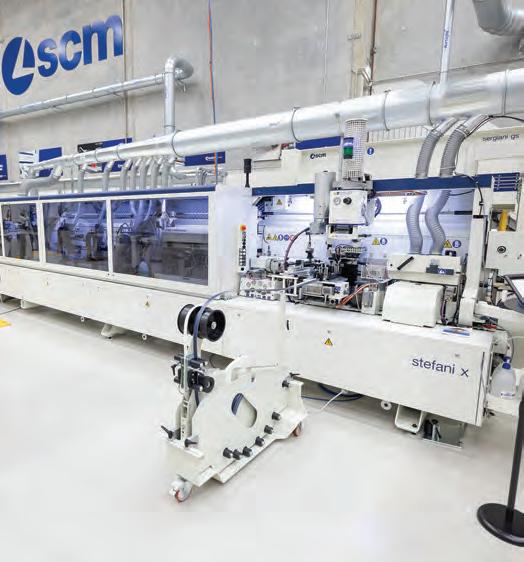
regular inspections and scheduled servicing to all customers."
“We educate our operators on the maintenance requirements for the safe and reliable operation of the machine,” says Darren from Multicam. “This encompasses general daily maintenance, which can be easily carried out by the operator, through to scheduled maintenance and servicing which is carried out by our factory-trained technicians. Maintenance is emphasised as the single most important factor in keeping the machine productive and the operators protected."
Matthew from SCM Group says regular checks and servicing of machinery, including all safety features, are essential. “Machinery maintenance is a key factor in ensuring safe usage,” he explains. “Our approach prioritises preventative maintenance to prevent malfunctions and breakdowns that could lead to safety hazards. A well-maintained machine is a safe machine."
“We emphasise the importance of regular and preventative maintenance to ensure the longevity and safe operation of our machines,” says Michael from Biesse. “Regular maintenance helps identify potential issues before they become hazardous, thereby contributing to the safe usage of machines. Machines have controllers with different levels of passwords that enable changing certain parameters depending on the operator level. The highest access password is available to Biesse engineers."
Machine Guards and Safety Features
Modern woodworking and stone fabrication machinery is equipped with a range of safety features designed to protect operators. Machine guards, fencing, emergency stop buttons, and sensors that detect and prevent accidental contact with cutting tools are essential. Employers must ensure these safety features are functional and never bypassed for convenience.
Lockout/Tagout Procedures
Lockout/tagout procedures are critical when maintaining or repairing machinery. These procedures ensure that equipment is completely de-energised and cannot be accidentally started while repair or upgrade work is being performed. Clear signage and training on these protocols are essential to prevent potentially fatal accidents.
This specific issue was highlighted recently in the case of a Victorian industrial plastics manufacturer who pleaded guilty to “failing to maintain plant that was safe and without risks to health”1. A supervisor at the plant was significantly injured while undertaking repair work to a machine which had its interlock system disconnected and the sensors which should have activated it were covered with tape.
Dust and Noise Control
Machinery in cabinetmaking and stone fabrication can generate significant dust and noise. Prolonged exposure to dust and particles can lead to respiratory problems, while excessive noise can cause hearing damage. Implementing effective dust and noise control measures is essential to safeguard workers' health and wellbeing.
Key strategies for dust control include:
• Centralised Dust Collection Systems: Install a highcapacity dust extraction system to capture and contain airborne particles directly at their source, such as saws, sanders, polishers and routers.
• Air Filtration Units: Use air purifiers equipped with HEPA filters to remove fine dust particles from the factory atmosphere.
• Regular Cleaning Protocols: Establish strict cleaning schedules to prevent the buildup of dust on surfaces, machinery, and floors. Use industrial vacuums instead of brooms to avoid stirring up dust.
Case Study: Marquis
We spoke to: Phillip Gray, general manager Employees: 40 (30 in the factory including three apprentices)
In business: More than 40 years
Manufactured goods: Custom residential bathroom vanities
Why is workplace safety important? What benefit does it bring to your business?
Workplace safety is about looking after our people. If our team feels safe, they are more confident and more productive. When we run a safe factory, we avoid downtime, keep morale high and build trust. At the end of the day, it’s about creating a workplace where everyone feels valued and protected.
What are some workplace safety strategies currently in place?
We conduct regular safety audits and risk assessments. All our machinery has modern safety features such as emergency stop buttons and guards. Our board storage system has been completely automated both for efficiency as well as safety of staff. We organise all our tools and machinery to keep workspaces clutter free and PPE is non-negotiable for certain tasks. And we hold regular emergency drills to ensure all our staff know what to do.
What methods do you use to communicate safety strategies to staff? And is this part of ongoing training and development?
Simple and consistent is the key to success for our team. Each shift kicks off with toolbox talks to go over safety reminders and any updates. Clear signage is all through the factory and posters to reinforce key messages. Our internal systems are used to share updates digitally to ensure everyone stays informed. We offer regular refresher training and sessions tailored to specific risks such as handling heavy materials or machinery operation. External experts are brought in when needed — it’s never a “set and forget” for us.
What role does ergonomics play in maintaining workplace safety?
This is a huge focus for us — all our workstations have been designed to minimise strain with height-adjustable benches and organised workflows as well as fatigue-reducing mats
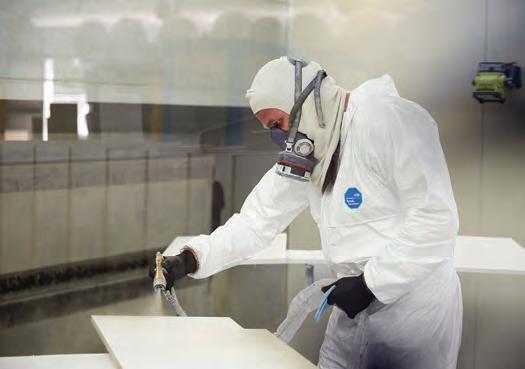

at each workstation. Our wrapping station has a specially designed tilt table so no vanity need be lifted. Plus, we encourage regular breaks to help reduce fatigue.
What does your program of machinery maintenance look like and what process do you implement to make sure this stays on track?
We work on a preventative maintenance program so our machines are inspected and serviced regularly, based on a detailed schedule. This allows us to catch potential issues early and take action if needed. Our team knows to report problems straight away and all issues are logged digitally so nothing can be missed.
Anything else to add?
We’re passionate about combining safety with sustainability so we’ve invested in energy-efficient machinery and we work extremely hard to reduce waste. This is not only good for the environment but it also creates a safer and more efficient workplace for our team.
Workplace Safety
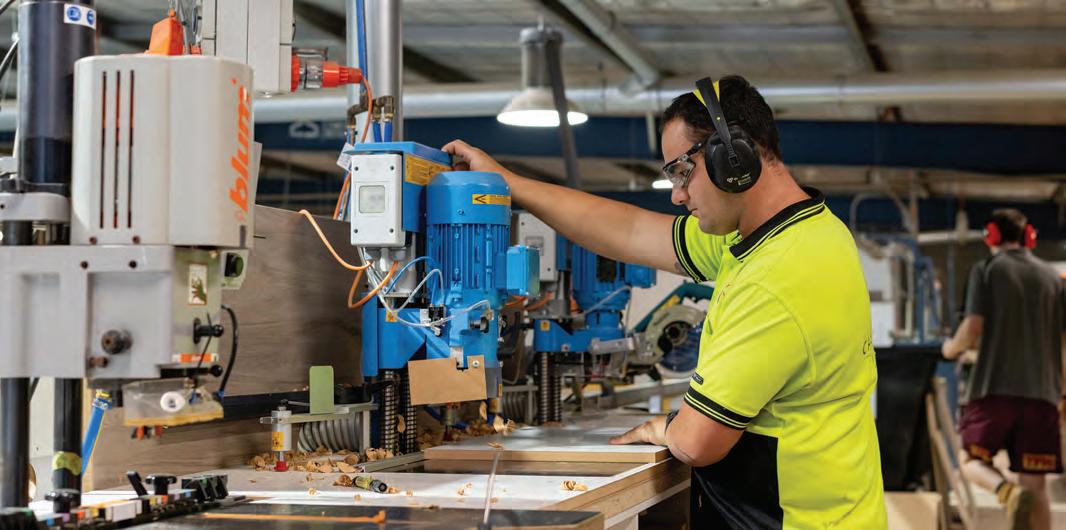
• Sealed Workspaces: Designate specific areas for high-dust activities and isolate them with physical barriers or enclosures.
Key strategies for noise control include:
• Soundproofing: Use sound-dampening materials on walls, ceilings, and floors to reduce the echo and transmission of noise within the workspace.
• Machine Maintenance: Ensure all machinery is well-maintained, as worn or damaged components can generate excessive noise during operation.
• Hearing Protection: Provide workers with highquality earmuffs or earplugs rated for the noise levels present in the factory.
• Noise Zoning: Identify areas where noise levels are highest and limit access to essential personnel only.
The implementation of these strategies helps business owners create a safer and more comfortable working environment and reduces the risk of long-term health issues associated with dust and noise exposure.
Ergonomics and Workflow Design
Improper workflow or poorly designed workstations can lead to repetitive strain injuries and fatigue. Machinery should be positioned and adjusted to reduce unnecessary bending, reaching, or awkward postures. Ergonomic considerations improve worker comfort, reduce the risk of injury, and enhance productivity.
Key strategies to optimise ergonomics and workflow design:
• Workstation Setup: Ensure workbenches, machinery, and tools are at an appropriate height or adjustable to minimise bending or stretching.
• Tool Accessibility: Arrange tools and materials within easy reach to reduce awkward movements and improve efficiency.
• Seating and Support: Provide ergonomic chairs and anti-fatigue mats for tasks that require prolonged standing or sitting.
• Workflow Analysis: Evaluate the flow of materials and tasks to minimise unnecessary movement or duplication of effort. Position workstations in a logical sequence that supports efficient workflow and production.
• Adjustable Equipment: Invest in height-adjustable workbenches and equipment to accommodate workers of varying heights and preferences.
• Lighting: Use adequate lighting to reduce eye strain and improve precision during detailed work
Promoting Quality and Reputation
For cabinet-making, renovation and stone fabrication businesses, reputation is everything. A commitment to workplace safety demonstrates professionalism and reliability to clients, collaborators and stakeholders. Clients are more likely to trust companies that prioritise safety, knowing that their products are crafted with
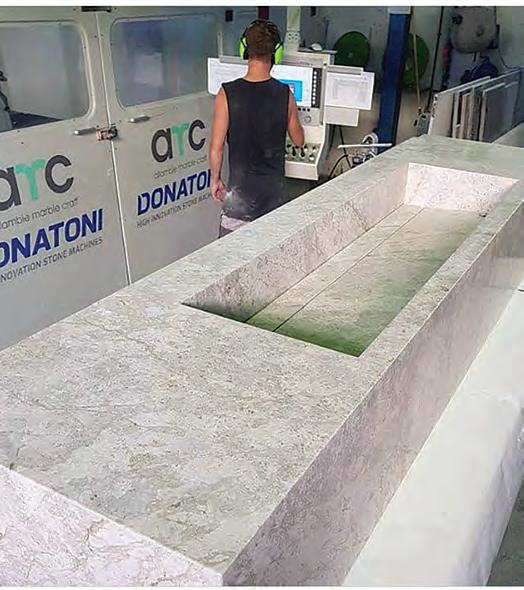
Case Study: Allambie Marble Crafts
We spoke to: Andrew McMonnies, owner
Employees: 12 (five in the factory including one apprentice, two installers & two check measurers) In business: Almost 30 years
Manufactured goods: Kitchen benchtops, splashbacks and vanity tops in natural stone and reconstituted stone
Why is workplace safety important? What benefit does it bring to your business?
Safety is a primary priority in our business. Not only does it minimise the risk of injuries, accidents and illness, but we think it is important that our employees feel safe at work and know they are being looked after. We are a family business and some of our employees have been with us for 25 years. A focus on safety increases productivity, produces a better performance and helps us create a great relationship with our staff.
What are some workplace safety strategies currently in place?
Procedures and Safe Work Method Statements are an integral part of our WHS plan. These have been developed with the input of our workers to make sure
we document each step of their day-to-day tasks and ensure safety at every stage. We make sure all employees read, fully understand and sign off on the procedures. These documents are updated annually plus we maintain an annual risk assessment of all procedures and work methods. An external WHS company oversees the general OHS side of our business. Daily safety strategies include a Silica Risk Control Plan, twice-a-day hosing of the workshop, compulsory mask wearing, plus we provide a laundry service for staff workwear. All our machines run with water (no dust) and the slurry is filtered multiple times and reused with the excess slurry compacted into bricks.
What methods do you use to communicate safety strategies to staff? And is this part of ongoing training and development?
Bi-monthly talks and Safe Work Review meetings with the WHS appointed team. These can cover a wide range of topics including First Aid, bullying, work-related mental health issues, manual tasks in the workshop etc … These meetings help to identify and rectify hazards, as well as keep employees informed about updates to legislation. Toolbox Talks help involve staff which leads to greater job satisfaction and team building. All staff benefit from annual health checks and all our masks are regularly tested.
What role does ergonomics play in maintaining workplace safety?
We implement safety measures to prevent and avoid injury from lifting and manual handling and we see ergonomics as important both in the factory as well as in the office. We minimise heavy lifting with three cranes in the factory and our installation truck has also been fitted with a crane. We also utilise anti-fatigue floor mats in the factory.
What does your program of machinery maintenance look like and what process do you implement to make sure this stays on track?
All our machines are serviced annually through external companies which is in addition to our own annual checks. We contract a company to undertake testing and tagging of all electrical equipment and power tools both in the factory and in the office as well as the toolbox on the truck.
Anything else to add?
We’re conscious of the numerous changes in our industry recently and it’s important that we stay on top of new information and legislation. We’re proud to be a dust-free factory and our recycling and re-use of slurry water helps the environment. Our most recent air monitoring study conducted by Safe Work put us below the standard and we’re proud that’s the result of our actions.
Workplace Safety
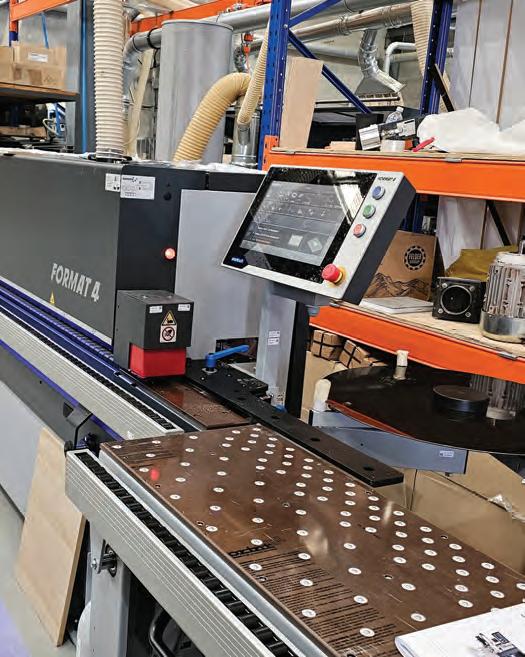
care by a workforce that is protected and respected. Furthermore, adhering to safety standards enhances the overall quality of workmanship, reducing errors and reworks while maintaining high standards of craftsmanship.
Training and Education
Central to maintaining a safe workplace is ongoing training and education. New employees should receive comprehensive safety training before they begin work, covering topics such as tool operation, hazard recognition, and emergency procedures. Regular refresher courses and updates on safety protocols ensure all workers remain informed about the latest practices and equipment.
In addition to basic safety training, ongoing professional development plays a crucial role in fostering a culture of safety and excellence. This includes advanced training on emerging technologies and updates on changes to safety regulations and industry standards. Providing opportunities for workers to enhance their skills ensures they remain competent and confident in their roles.
The training of apprentices is particularly important. Apprentices must be closely supervised and mentored to develop both technical skills and a strong awareness of safety protocols. Structured
programs that combine hands-on experience with theoretical knowledge help instil good habits from the outset of their careers.
All employers must demonstrate documented training on machines and power tools in the workplace for all employees. This includes standard operating procedures in writing to ensure the safe operation of both machinery and power tools (under supervision) and sign off on training completed. Employers cannot rely on training of apprentices by Registered Training Organisations alone.
Supervisory staff overseeing work on machinery also require specialised training. These individuals must be equipped to identify potential hazards, enforce safety protocols, and provide guidance to less experienced workers. Effective supervisors act as role models, demonstrating best practices and ensuring that all team members adhere to safety standards.
Investing in the knowledge and skills of employees not only enhances safety but also fosters a sense of professionalism and dedication within the workforce. A well-trained team is more likely to work cohesively, efficiently, and safely, contributing to the overall success of the business.
Creating a Culture of Safety
Ultimately, workplace safety is not just a set of rules; it's a culture that starts from the top. Management's commitment to safety sets the tone for the entire organisation, influencing attitudes and behaviours at all levels. Encouraging open communication, providing resources for safety improvement, and recognising and rewarding safe practices all contribute to cultivating a culture where safety is prioritised and valued.
Prioritising workplace safety in our industry is not only a legal and ethical responsibility but also a strategic investment in the longevity and success of businesses. By safeguarding employees from harm, businesses can enhance productivity, protect their reputation, and ensure the wellbeing of their workforce. Through continuous education, proactive measures, and a commitment to fostering a culture of safety, businesses in our industry can thrive in an environment where safety and excellence go hand in hand. The integration of safety protocols in machinery operation further underscores the importance of vigilance and responsibility in creating a secure and productive workspace.■
Workplace Safety
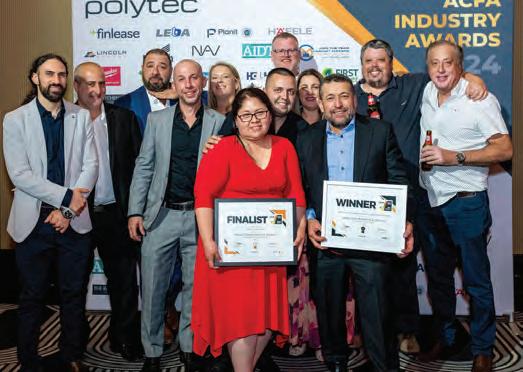
Case Study: Betta Style Kitchens & Joinery
We spoke to: Nino Strangio, managing director Employees: 19 (12 in the factory including two apprentices)
In business: More than 30 years
Manufactured goods: Kitchens and joinery — retail, commercial and residential, laminate benchtops and panels, bathroom renovations
Why is workplace safety important? What benefit does it bring to your business?
Safety is paramount for any business, including ours, and it brings various benefits such as increased efficiency and production, and more profitable operations. We also see a reduction in absenteeism and workers' compensation claims with translates to fewer disruptions and lesser costs to the business.
What are some workplace safety strategies currently in place?
We provide employee training, undertake regular equipment inspections, keep up-to-date health and safety records, and ensure prompt investigation of any incidents. We have regular staff meetings where we address safety issues, promote wellness and wellbeing and generally create a culture of teamwork. We also encourage regular breaks to manage fatigue.
What methods do you use to communicate safety strategies to staff? And is this part of ongoing training and development?
Our main day-to-day communication is through our regular staff meetings, but we also document all our safety policies
and procedures which are shared with staff and revised or updated as required. We also check on how the strategies are implemented to ensure we are complying with best industry practices. We see this ongoing approach to safety as an investment in our business as any costs associated with injuries are hugely detrimental to the business, and far outweigh any costs involved in prevention activities.
What role does ergonomics play in maintaining workplace safety?
Ergonomics are a crucial part of maintaining workplace safety. If our workers are comfortable at work, this lowers stress and reduced the chance of any injury due to awkward positions or physical strain. This, in turn, improves productivity and ensures all our staff feel valued and looked after.
What does your program of machinery maintenance look like and what process do you implement to make sure this stays on track?
Each machine has a planned maintenance program which is scheduled at regular intervals to ensure their longevity, reduce breakdowns and minimise production downtime. To ensure we stay on track, we have a dedicated staff member whose job is to oversee the maintenance program which consists of completing individual checklists, making a list of priorities, managing maintenance intervals, keeping detailed records of all work and inspections completed, and regular reviews as needed.
Anything else to add?
Because we work for the trade industry, as well as for builders and the retail/commercial sector, we find it’s important that our clients know we run a safe workspace. This gives them the confidence in our ability to produce on time and within budget, as well as reassurance of the high quality of our products.

Home safety and security
Where good design meets new technology
By Pam Kershaw
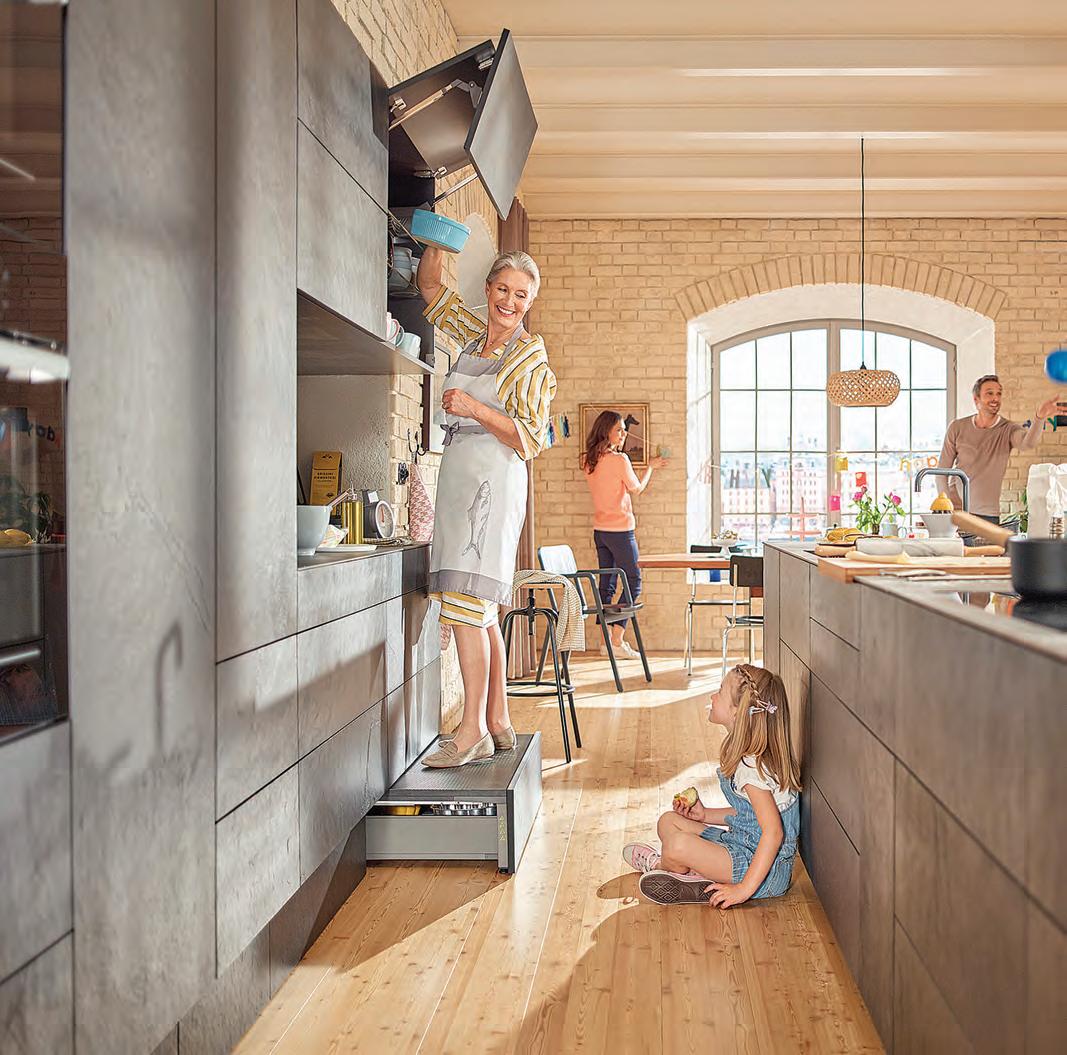
Home sweet home. Or is it?
Every year, thousands of Australians realise their home safety and security aren’t up to scratch. In 2022-23, government reports showed that 8.5 per cent of households experienced crimes such as break-ins or attempted break-insi. The home was also the most commonly reported place for fallsii — and falls were the leading cause of injury hospitalisations that year.
Home safety and security involve two aspects: physical safety through good design, building and manufacture; and security through increasingly sophisticated surveillance and alarm systems.
So, let’s start at the front door.
Keyless entry systems are well established, but biometric authentication is becoming increasingly common because of its high security and ease of use, according to Jason Elbayeh, head of operations at home automation specialist, Blutek.
“Brands such as Lockwood and Samsung are integrating fingerprint scanners into smart locks which can store multiple family fingerprints,” he says. “The Samsung SHP-DS705 is a good example, offering access via a fingerprint, PIN code or traditional key. The risk of lock picking or traditional key theft is significantly reduced.”
Enhanced smart locks
These come with advanced security features, including tamper detection, automatic locking and encrypted communication accessed via a smartphone app. Brands such as Nuki and Schlage have added layers of protection, such as antitampering alarms and automatic locking when the door is closed.
“Smartphone integration has revolutionised keyless entry, allowing homeowners to unlock doors from their phones from anywhere in the world,” Jason says.
For example, the August Smart Lock Pro integrates with various smart home platforms such as Google Assistant, Amazon Alexa and Apple HomeKit, offering voice command control and the ability to grant temporary access to family members, guests or service providers.
The rise of keyless entry systems is closely tied to the growing trend of home automation.
“Smart locks are increasingly being integrated with other home automation devices, such as security cameras, lighting systems and alarms. This provides more control over security while enhancing overall convenience,” Jason adds.
Ring, a company known for its video doorbells, now offers the Ring Alarm Security Kit which integrates with Ring's smart locks, enabling remote door operation, viewing of real-time footage from cameras and visitor communication via smartphone app.
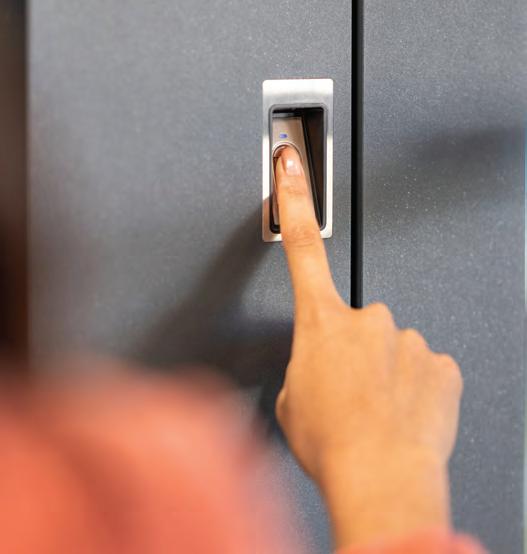
Safety & Security
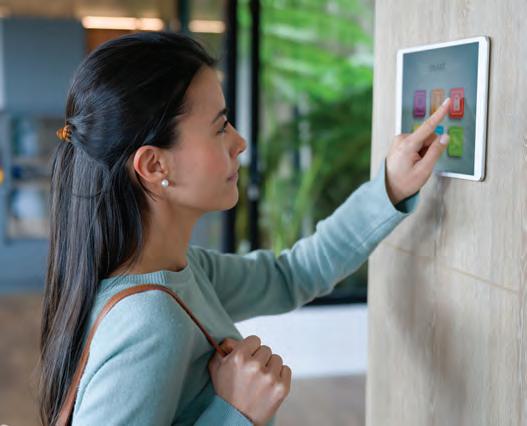
Perimeter surveillance
Ideally, home security systems should stop intruders before they even reach the front door.
John Frost, founder of The Home Automation Company, says cameras for perimeter surveillance are now highly sophisticated.
“Cameras are now much better at differentiating between different kinds of objects,” he says. “Once, they were merely motion detectors and would respond to a tree blowing next door as much as someone walking into your front yard.”
Today’s systems can flash red and blue lights and turn on bright white lights to enable full-colour images if a potential intruder enters a front yard. The property owner is notified via an app and can warn that the police have been called, or a recorded message can advise that the area is under surveillance.
John says surveillance is usually set up during a new build or as part of home automation systems installation which can include integration of lighting, power management, blinds and curtains, audiovisual and watering systems.
“People have become more attuned to home security because they might own the best or newest house on the street, because they or a neighbour have been burgled, or because of media exposure of security and surveillance,” he adds.
Cameras are usually placed at the front and rear of the home, and at the side of the property or laneway if these areas are vulnerable. Internally, entry foyers, family rooms and kitchens may be included.
In planning home security, his company will look for vulnerabilities.
Safety & Security
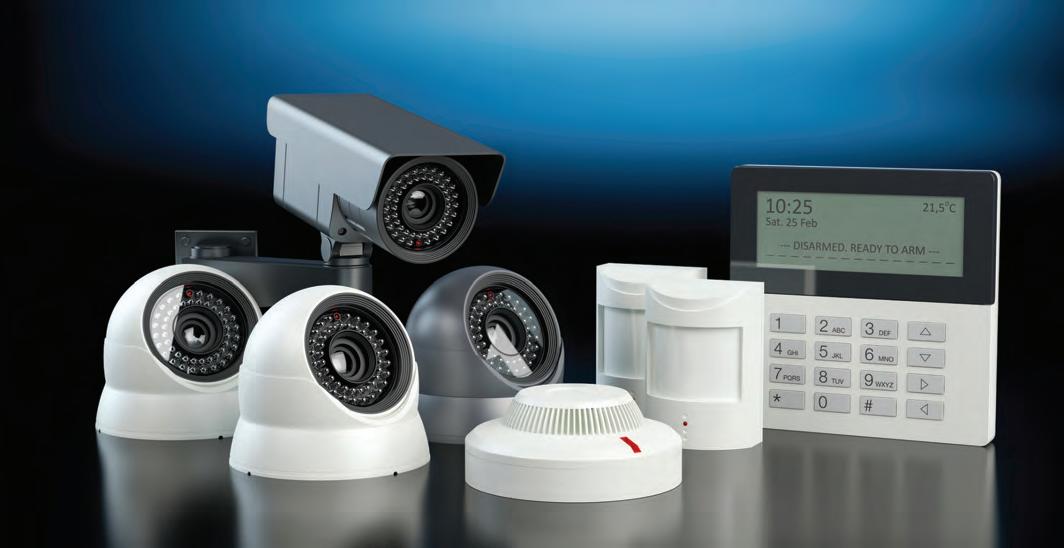
“We look for the points of entry: front doors, back doors, sliding doors, whether the glass in windows is laminated or old glass. Laminated glass is pretty hard to break, whereas ordinary glass is easy,” John explains.
Cameras work with alarm systems internally, so if an alarm sensor is triggered the camera will show the intruder’s location.
“The other factor in alarms — and it’s often ignored — is the internal siren. Most people in the industry call it a ‘screamer’ — and if it goes off you want to get out of the house.
“It’s painful, it makes you want to vomit. That’s deliberate. By the time police get to the house, it’s going to be 10 to 20 minutes. If the screamer is going
off, intruders will probably get out much faster,” John says.
Designing for safety
The National Construction Code (NCC) 2022iii sets out requirements for design and construction of buildings in Australia, including the minimum required level for safety, health, amenity, accessibility and sustainability.
The Australian Building Codes Board, on behalf of the Australian Government and each state and territory government, produces and maintains the NCC.
Falls prevention is a key factor in good design but falls still occur regularly.
“According to the Australian Institute of Health and Welfare, falls were the leading cause of injury hospitalisations in 2022–23 and the leading cause of injury deaths in 2021–22,” says Melbourne architect David Francis.
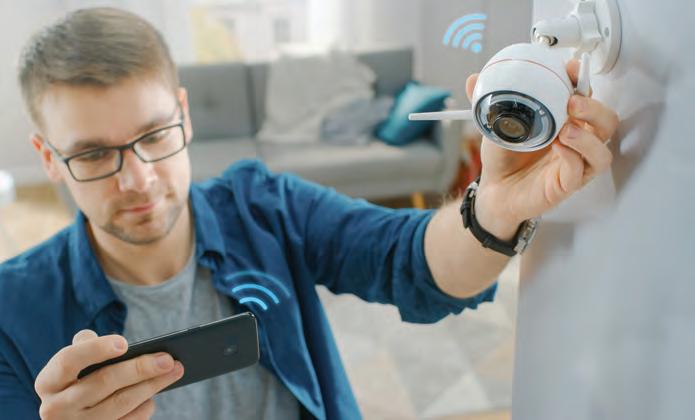
“And while you might think that staircases pose the greatest risk, falls on the same level from slipping, tripping or stumbling accounted for four times as many hospitalisations as falls on stairs and steps,” he adds.
Passive safety design, where the broad bones of the house do most of the work, is essential in new
builds and should be optimised wherever possible in major renovations, David says.
“Ideally, architects, interior designers and cabinet makers should work closely to ensure they produce the optimum safety profiles for homeowners and occupiers, particularly the elderly, children and those with compromised mobility,” he adds.
Passive safety design includes factors such as an open floor plan that provides better sightlines for supervising children and keeping an eye on the elderly. Blind spots and corners should be minimised, as should changes of level.
Where doors lead to garden areas, landscaping and external paving should ideally be on the same level as internal floors.
Non-slip surfaces are essential in wet areas, and steps into showers should be eliminated for the elderly (for details on liveable design, see Connect’s Summer 2024 issue https://connectmagazine.com.au/ connect-magazine-issue-1/ ).
Grab rails double as towel rails
“Safety rails are important in homes for older people, but they’re usually not particularly attractive. Some designs can double as towel rails, improving the



Safety & Security
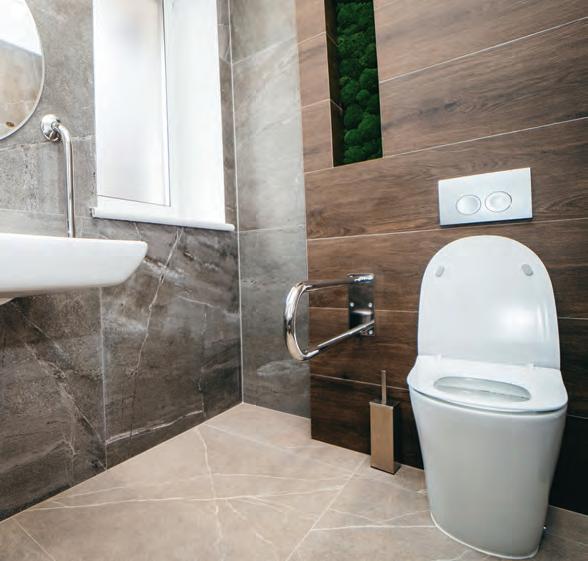
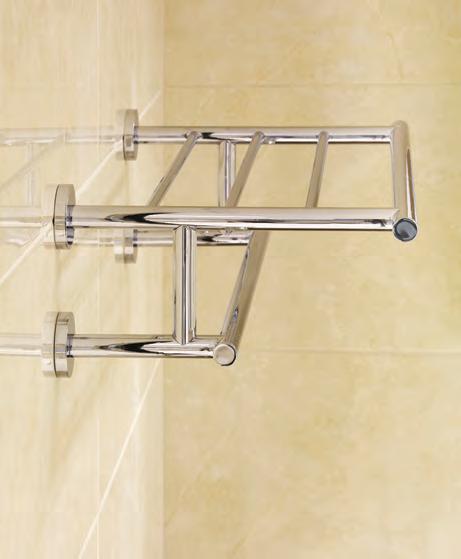
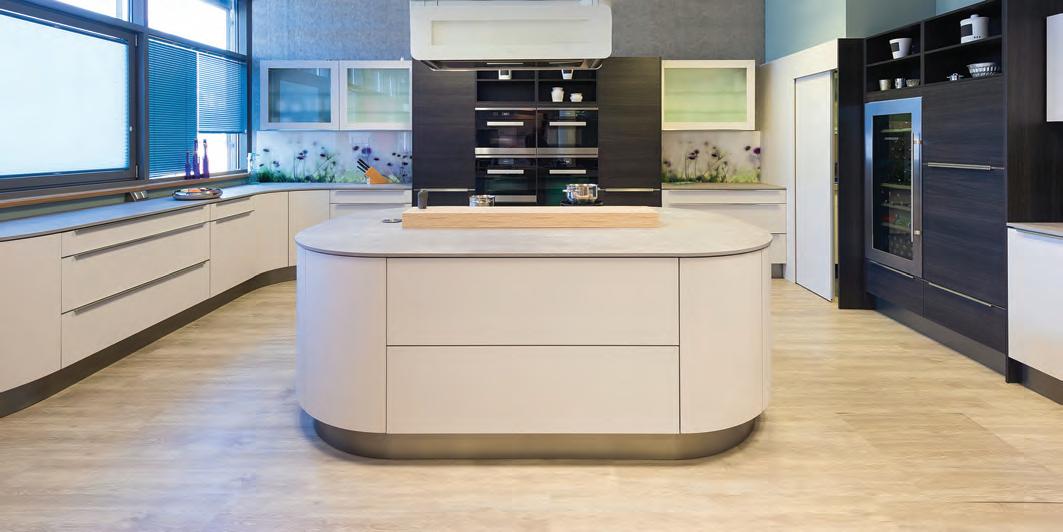
aesthetics as well as the safety of bathrooms,” David says. “And for health safety, hand basins should be included in all toilet compartments.”
In multi-storey homes and apartments, the NCC specifies that staircases must be designed to minimise fall risk, with uniform treads and risers and a minimum width of 600mm. Handrails must meet specific heights and eliminate gaps that small children could slip through.
“Handrails must be ergonomically designed so they’re easy to grip, and it’s a good idea to minimise
the length of stair flights to reduce the distance of any falls,” David says. “Ideally, you’d avoid split-level living areas and changes of level of less than three steps, as these are invitations to falls.”
Passenger lifts are a sensible consideration for homes occupied by elderly people and babies in prams.
All home areas need good lighting, particularly for the elderly whose eyesight is dimming. Stairs and steps must be well-lit to highlight changes in level, good task lighting is essential in kitchens, and movementactivated lighting gives better nighttime safety.
Other electrical precautions include keeping power points a safe distance from sinks and basins and, if they can’t be kept out of reach of infants, safety covers should be used.
And it’s a given that switchboards and smoke alarms are up to date and comply with building codes.
Special considerations for cabinetry
In the kitchen, bullnose or rounded edges are far safer than sharp edges on countertops, while heatresistant countertops can reduce the danger of burns. High-traffic areas also need rounded or chamfered edges on cabinetry, providing better protection for careening toddlers at benchtop height.
“Knobs and handles may be an issue in many households,” David says. “Soft-close mechanisms reduce the risk of pinched fingers, and push-toopen systems eliminate the need for handles that can catch on clothing or prove difficult for less able occupants. D-shaped handles provide better grip for those with reduced hand strength, but recessed handles are safer.”
Kitchen work is easier when countertops and cabinetry reduce the need for bending or reaching, while pull-out or rotating shelves give better access. Step ladders are potentially dangerous, so
consider pull-out steps that create extra storage behind kickboards and provide easy access to higher cabinets.
Glass or mirrors incorporated in cabinetry can make a good play on light and space, but tempered or laminated glass is the safest solution if they’re at child height.
Ensuring the safety of little ones who are curious but unaware of home dangers is a top priority in many households.
“Sophisticated electronic safety devices include baby monitors, smart cameras and motion sensors that enable remote monitoring of activities, and smart sensors on doors and windows that can alert parents when they are opened,” David says.
There are many more aspects to consider, including childproof locks on cupboards and electrical appliances, gates at the top of stairs, and dangling curtain and blind cords.
Home sweet home? It should be, provided there’s safety in design and technology. ■
i) www.abs.gov.au/statistics/people/crime-and-justice/crime-victimisation /latest-release ii) www.aihw.gov.au/reports/injury/injury-in-australia/contents/summary#trends iii) www.ncc.abcb.gov.au/

Playing it withsafewhite
and stylishly
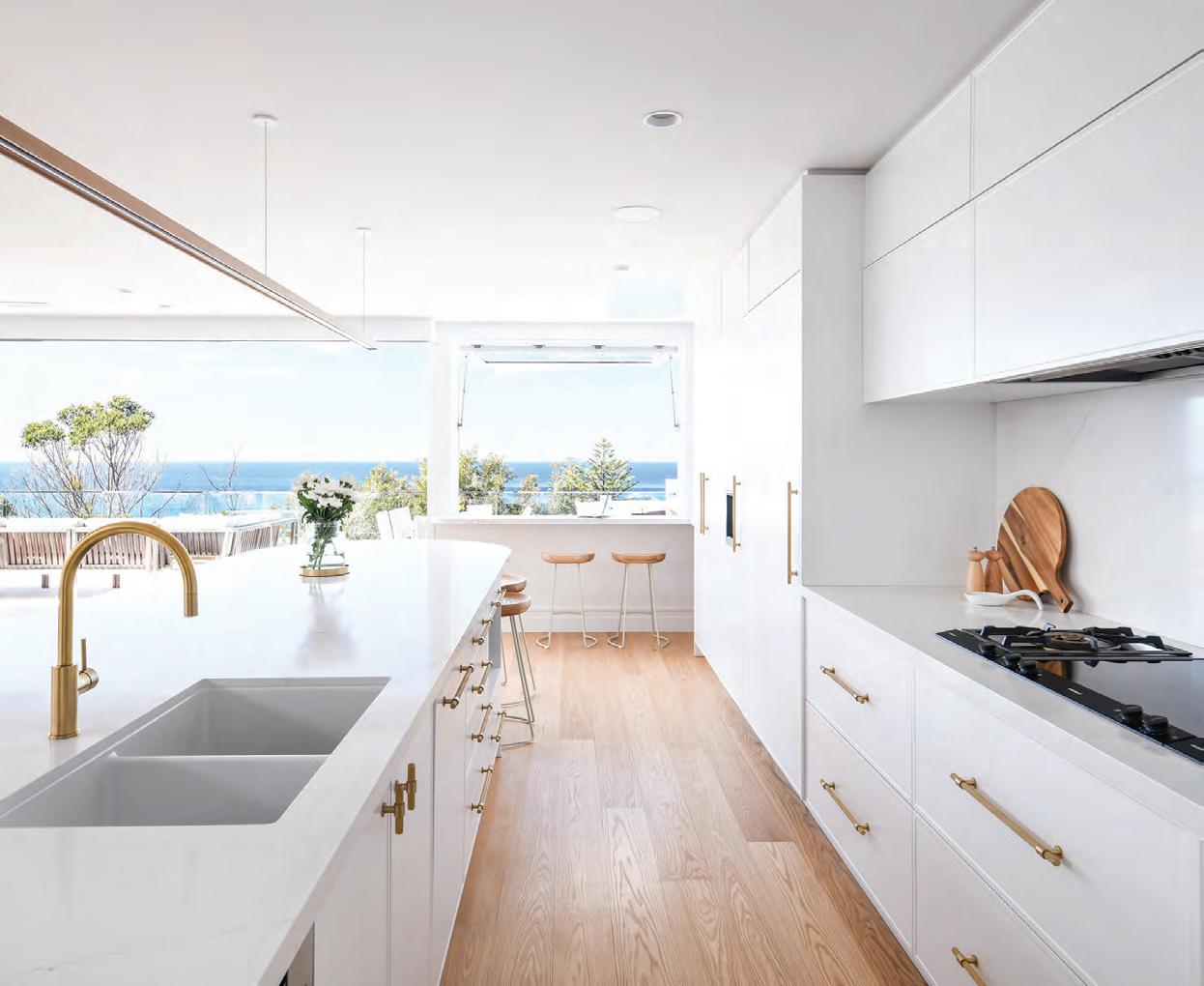
We love colourful kitchens at KBDi, but we'll never tire of the crisp, clean, classic appeal of a white working space
With its timeless appeal, cleanliness qualities, and general market safety, white has long been popular in Australian kitchen and bathroom designs. In this feature, we'll expand on the reasons why white is always a go-to and share the five favourite whites of KBDi kitchen and bathroom designers.
The top three reasons why white is a safe choice
#1 Timelessness and Versatility
White offers a neutral canvas that complements various design styles, from modern minimalism to classic elegance. This adaptability allows
homeowners to easily update or accessorise their spaces without clashing with existing elements. White's neutrality ensures that kitchens and bathrooms remain stylish and relevant even as design trends evolve.
#2 Perception of Space and Cleanliness
In areas such as kitchens and bathrooms, where cleanliness is crucial, white surfaces can emphasise hygiene and foster a sense of purity. Furthermore, by reflecting light, white can make smaller spaces seem larger and more open, resulting in an airy and roomy atmosphere.
#3 Market Trends and Preferences
While recent trends have shifted towards bolder colours and earthy tones in interior design, white remains a staple in many Australian homes. Various tints, tones, and shades of white routinely appear on the top-selling list for big brands such as Dulux and Laminex, and on the KBDi Awards image gallery.
The Five Favourite Whites of Australia's Best Kitchen Designers
As we comb through the specifications of our award entries, we see that a few whites regularly appear in the two-pack selections. Following are the top five:
Dulux Natural White™
This warm and neutral white is often used for its adaptability in both traditional and contemporary settings. Danielle Bonello-Dunsford (Danielle Victoria Design Studio) applied it beautifully in this stunning small kitchen entry (pictured next page).
Dulux Lexicon® Half (and Dulux Lexicon® Quarter)
This crisp, cool white is ideal for modern interiors and those seeking a clean, minimalist style. Nina Di Marco (YDM Design Studio) combined Lexicon Half with Plantation Ash detailing for a cool, calm look (pictured next page).
Dulux Whisper White
One of Dulux's most popular warm whites, Whisper White is perfect for creating inviting, tranquil spaces. Sari Munro (INSIDESIGN) used it to great effect in this airy kitchen, adding some Diamond White Mountain Oak detailing for extra warmth and texture.
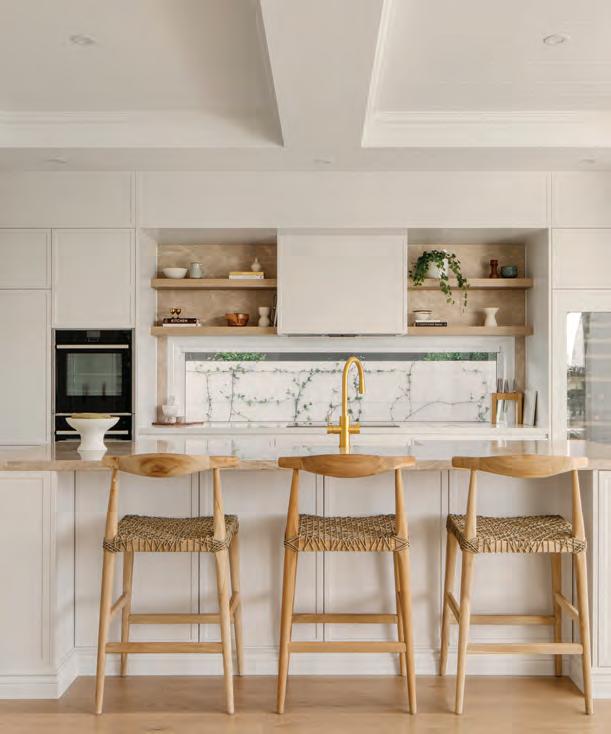
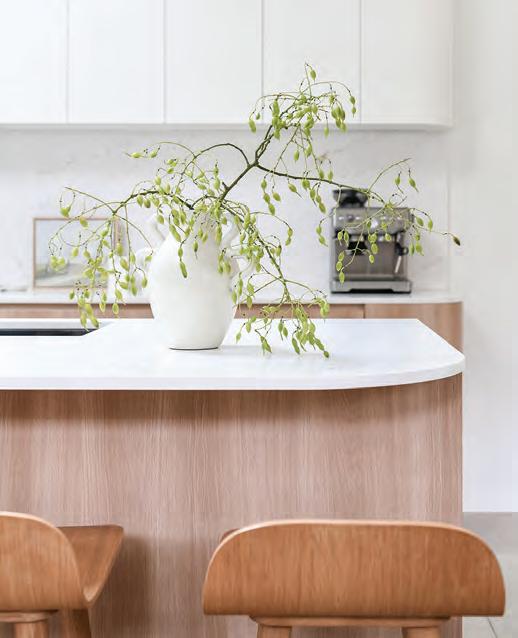
Dulux Vivid White™
This bright, pure white is often used to maximise light and space. Alex Stone (Revamper Pty Ltd) did just this, combining the cool white with Florence Oak features (opposite page).
Dulux Casper White Quarter
We're seeing more of this beautiful neutral white. Gold Coast designer Chloe Elliott (Wood Marble & White) applied it beautifully in this striking kitchen. Paired with Polytec's Casentino Beech, it's a winner.
When is White Warm, Cool or Neutral?
White can be warm, cool, or neutral, depending on its undertones and the context in which it is used. Here's how to distinguish them:
Warm Whites
With their subtle peach, pink or yellow undertones, warm whites offer a creamy, soft, inviting appearance.
Examples of warm whites:
• Dulux Whisper White
• Dulux Antique White USA
• Dulux White Dune Half
• Dulux Hog Bristle Quarter
• Dulux White Beach Quarter
• Laminex White
• Laminex Chalk White
• Laminex White Linen
• Laminex Calm White
Design
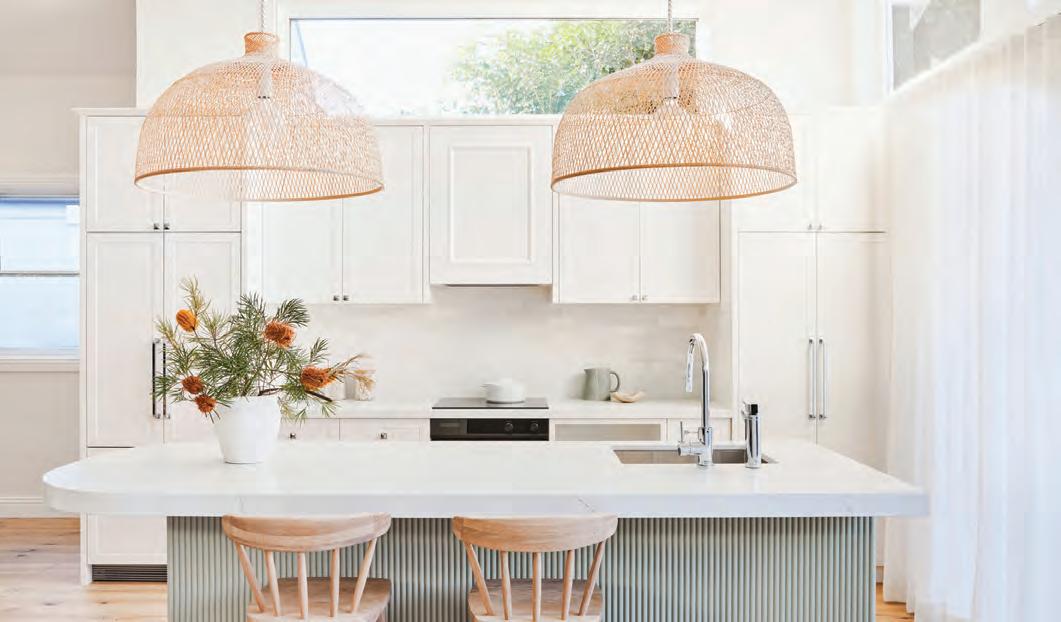
Cool Whites
Cool whites generally carry blue or grey undertones and are helpful in tempering bright light. They offer a crisp, clean and modern appearance.
Examples of cool whites:
• Dulux Vivid White (with some cautions — scroll down for more info)
• Dulux White on White
• Dulux Lexicon Quarter
• Dulux Lexicon Half
• Dulux Lexicon
• Dulux Terrace White
• Laminex Polar White
• Formica Snowdrift
Neutral Whites
Neutral whites have balanced undertones, making them neither too warm nor too cool. They’re the most versatile whites and are adaptable to many different settings.
Examples of neutral whites:
• Dulux White Polar Quarter
• Dulux Natural White
• Dulux Snowy Mountains Half
• Dulux Casper White Quarter
• Dulux Charmed White
• Dulux White Exchange Half
• Laminex Aries
Factors Influencing Perception of Colour Temperature
Lighting
Warm lighting (incandescent or yellow-toned) can make whites appear warmer. Cool lighting (LED or daylight bulbs) can make whites look cooler.
Surrounding Colours
Whites may shift in perception depending on adjacent colours. Consider how adjoining or nearby colours may reflect upon the white and change its tone or value. For example, light reflected from a terracotta-toned external wall could add a tint of apricot to your white kitchen. Conversely, light bouncing off a blue-tiled pool can add an unexpected cool change to your neutral interiors.
More about specifying pure whites
Dulux Vivid White™ is a highly reflective and bright pure white often chosen for its ability to create a clean, modern aesthetic. However, there are several potential downsides to using pure whites such as Vivid White as a wall colour:
Harshness in Natural Light: In spaces with abundant natural light, a pure, tint-free white can appear overly stark or glaring, making the environment feel cold and sterile rather than inviting. This is equally (or
potentially more) relevant in external applications — consider this if working on selections for a sunny alfresco area.
Shows Imperfections: The high reflectivity of pure whites can make wall imperfections, such as dents, uneven textures, or plaster cracks, more noticeable. Accordingly, the surfaces to be painted will require comprehensive (often time-consuming) preparation to achieve a flawless finish.
Lack of Warmth: Without undertones, pure whites can lack the warmth that other whites such as Dulux Natural White™ or Antique White U.S.A.® offer. This can make spaces feel more sterile, especially in areas with cooler lighting.
Compatibility with Furniture and Décor: The starkness of a pure white may not pair well with specific colour schemes or natural materials. Warm or earthy tones in furniture and décor might clash with crisp, tint-free whites, leading to a disjointed look.
Maintenance Challenges: Bright, reflective whites can easily show dirt, scuffs, and stains, requiring frequent cleaning to maintain their pristine appearance. Paint touch-ups may not be easy, either. Walls or panels often require a complete repaint to conceal marks or blemishes well.
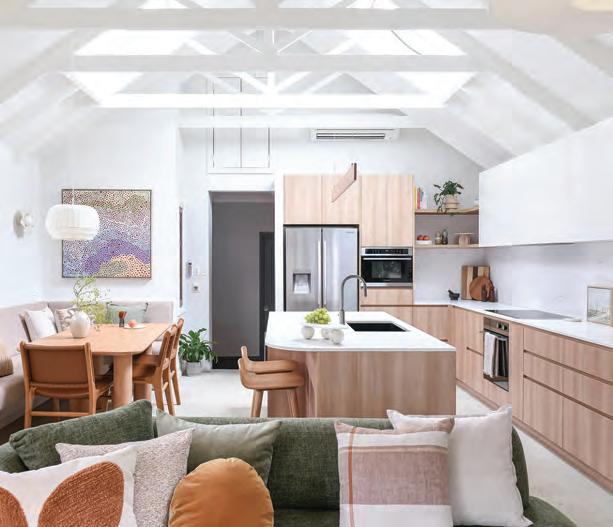
(i.e., polyurethane-coated surfaces), ceilings, and trim rather than walls.■
kbdi.org.au/home 1300 253 223
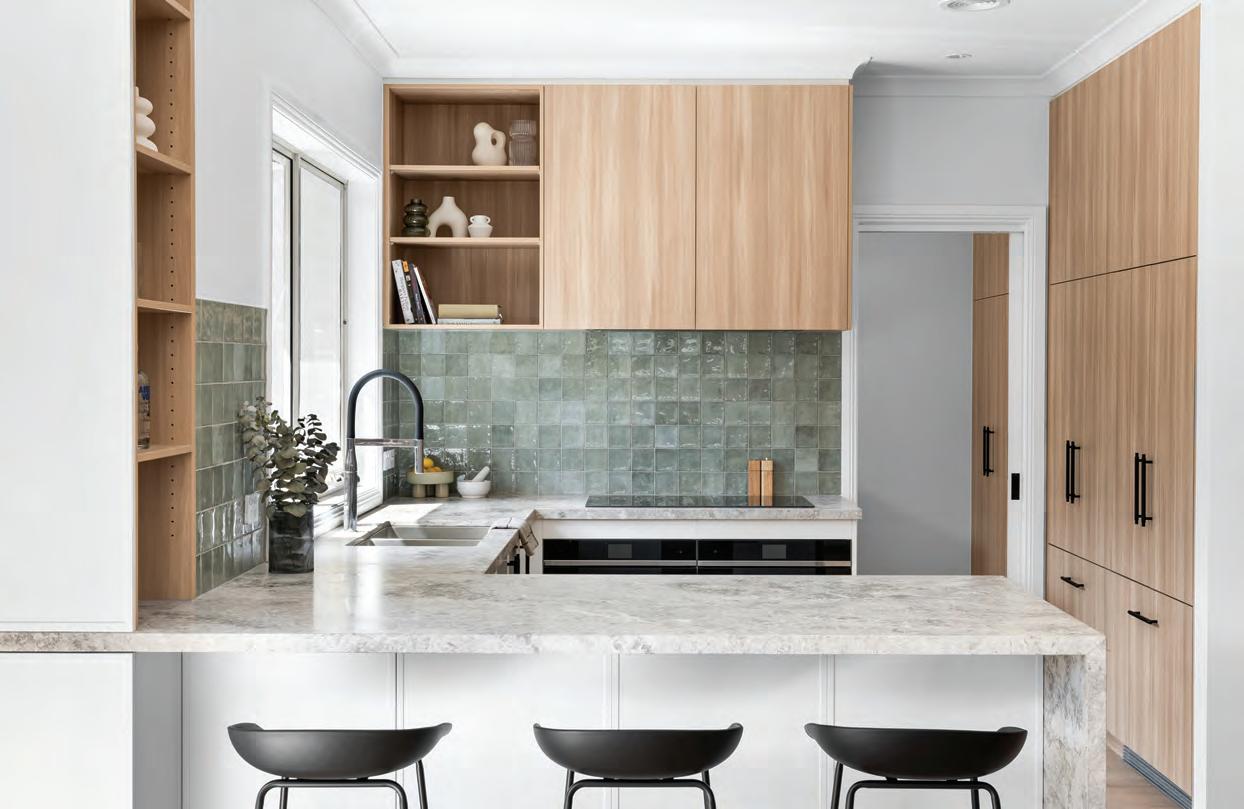
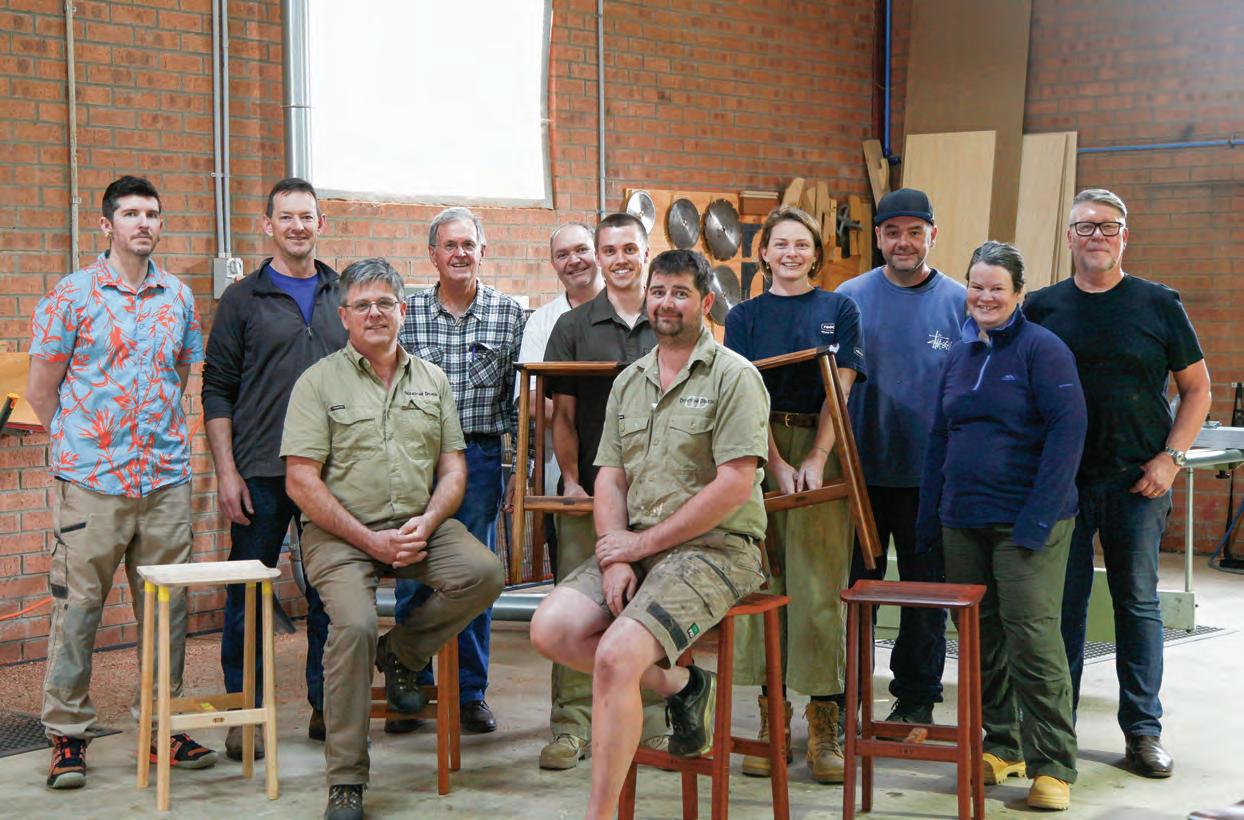
Training for success
In today's world, traditional apprenticeships, formal education programs, and cutting-edge digital courses offer a variety of options to suit different learning styles and career goals. Here, we speak to a variety of individuals in the cabinet-making and joinery fields about their road to success
By Rob Ditessa
On his road to success, Charles Sandford missed the turn to a formal apprenticeship. “I learned on a needto-know basis, just by the jobs I was doing. I did all sorts of woodwork. I also did a lot of furniture restoration which taught me a lot. Definitely, if you can, do a course. It’s a good idea. In my case I did all that the hard way.”
While studying medicine at university, Charles got a holiday job at a woodwork factory and discovered his talent for woodwork. “I found that it satisfied a creative need in me.” He set himself up in a garage in a business, making furniture that featured woodturning.
Travelling in Britain, he got a job in a furniture factory where he found a mentor. This inspired him to re-
establish himself back in Australia in a woodwork business that evolved into Charles Sandford Turning and Joinery, a large wood fabrication services business that includes crafting bespoke high-end fine woodwork furniture.
He tells Connect, “If you make something you’re proud of, it’s the same as an artist painting a picture. You get that same sense of satisfaction, that you’ve made something beautiful, even if you didn’t design it, because there’s another level of skill required to make it. When I’m interviewing for apprentices, it’s important that they’re good with their hands, and that they’re able to conceptualise.”
Phoebe Everill agrees about the value of training courses. She explains to Connect that TAFE’s infrastructure gives it the ability to find and employ
multiple tutors for specific areas in this incredibly diverse craft. The Certificate IV in Furniture Design and Technology she completed at the Sturt School for Wood is a brilliant base grounding in skills acquisition. She adds that what is required to complement initial training is a good mentor.
Today, Phoebe owns and runs a boutique business designing and making bespoke high-end fine woodwork furniture and conducting woodwork courses. As a teenager, she felt an impulse to fulfil her inner potential by becoming a woodworker. “I would take every opportunity possible to work or observe my father in the workshop.”
Phoebe completed her basic training working in his furniture and joinery business, then worked independently as a renovator before successfully applying to attend the prestigious Sturt school.
She wants to help people realise their maker potential by offering wood craft courses, and she wants it to be fun. “If we are encouraged to have fun, we are less afraid of taking risks, and that opens up the creative vein. We are hard-wired to make,” she says.
Craig Bennett, TAFE NSW Furnishings and Cabinet Making head teacher, tells Connect: “Our teachers offer personalised support to learners studying these qualifications, including those looking to venture into the high-end furniture sector. Our teachers, often still working in the industry themselves, foster learner’s creativity, support skill development and expertise and we’ve seen many graduates go on to start their own business.”
He says, “TAFE NSW is seeing a growing trend of more women looking to study furniture and woodworking courses. For example, at TAFE NSW Newcastle, there are three female students in one class. We help female high school students identify potential career pathways in the furniture and woodworking industry through vocational taster courses, delivered at a local TAFE NSW campus.
“For example, we’ve delivered such initiatives as the ‘Furniture Making Girls Can Too’ programs at a number of TAFE NSW campuses. This type of vocational taster programs allows students from all backgrounds to experience the TAFE learning environment.”
According to statistics provided to Connect by the National Centre for Vocational Education Research (https://www.ncver.edu.au), at 31 December 2023
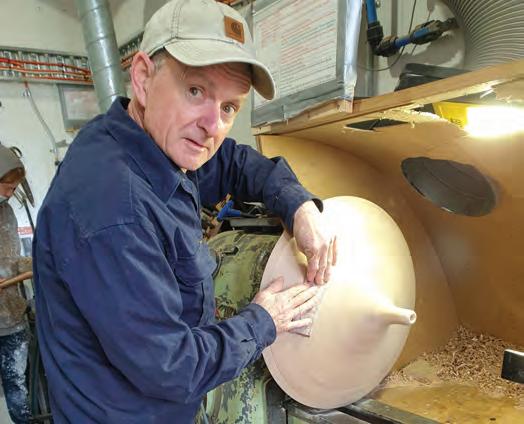
The business of business
“I can’t underestimate the need for small business training. No matter how good you are as a maker, you need to be able to access markets and sell your work,” says Phoebe Everill.
Charles Sandford reflects, “It’s important to know what you’re good at, and what you’re not good at. I’m not a very organised sort of person, and I’ve got people who do that for me at the moment. I got ripped off a few times. That makes you harden up, and getting paid is very important. There are plenty of rip-off merchants out there, so you’ve got to be aware of all those things.”
Evan Dunstone says “Strategies and business studies specific to woodworking should be a vital part of any long course. This will be met with resistance from some students. Most fine woodworkers fail to survive financially because they don’t understand what the ‘job’ is. They like woodwork, but they don’t like running a woodworking business.”
He makes this comparison, “The difference between a cook and a chef is largely professional speed and accountability. A home cook can spend all day cooking a dinner party for six people without really caring about the cost or time. A professional chef does the same thing in 20 minutes and knows the price of every ingredient, their fixed and variable overheads and they can do it six nights a week for 30 years.”
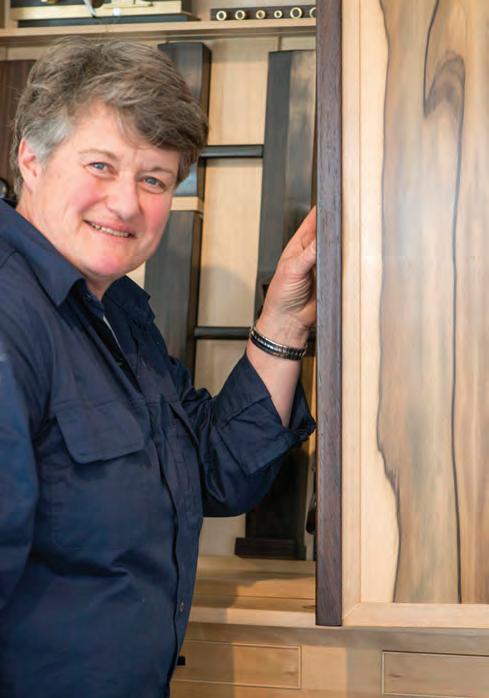
“I feel incredibly privileged to practise a craft that also supports me financially, but the genuine gold of this career is about the work that I make, and the people who I spend time with.
there were 2875 apprentices and trainees in-training as cabinet and furniture makers at TAFE. University training accounted for 210, and private training providers 1645. There were 4355 males, and 375 females. (See table below for full details.)
The Australian Cabinet and Furniture Association (ACFA) is the largest private Registered Training Organisation (RTO) for cabinet making in NSW. (ACFA is the publisher of Connect).
Kristy Cole, ACFA training manager, says, “Over the past five years, ACFA has seen a steady rise in the number of female apprentices entering the cabinetmaking, furniture, and joinery industries. Trainers consistently praise their exceptional attention to detail, strong commitment, and high unit completion rates, qualities which are highly valued in the trade.
“This trend was proudly celebrated at the recent 2024 ACFA Industry Awards, where a talented female apprentice, Stevie-Lee Harding from Ross Thompson Furniture, was named Apprentice of the Year for Furniture Making.”
Evan Dunstone is one of a handful of woodworkers who own and run businesses solely designing and making high-end fine woodwork furniture. Evan trained as an informal apprentice under David MacLaren at the prestigious Bungendore Woodworks Gallery.
In establishing Dunstone Design in 1998, he employed makers who had trained through the ANU Canberra School of Art, or Sturt. He quickly realised that they had sound knowledge, but not pace-ofwork, decision-making skills, or experience making other people’s designs.
“I thought I was the problem,” he says.
“Then a Swedish maker, the late Rasmus Malbert, visited my workshop in 2006. He had trained at the Malmstens University in Stockholm and, despite never
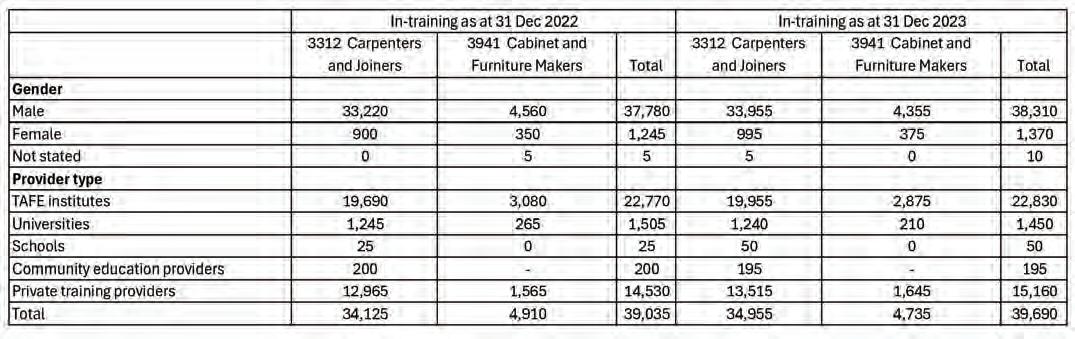
having worked professionally, as he was right at the end of his training, he could do everything.
“When I discussed the depth and breadth of his training, I realised what a gulf there was between Australia’s and Sweden’s approach to training. From that day forward, I decided to train all Dunstone Design employees in-house, basically the way I had been trained.”
Like most serious craftspeople, Evan wants to pass on his knowledge. “I employ talented people and I mentor talented people. I won’t employ or mentor people I don’t believe in. Obviously, the results are going to be good, because I am putting energy into fertile soil. But I can only take on apprentices at the rate that my work sells. The best way to train woodworkers in Australia is for businesses to thrive. My client base allows me to train and mentor,” he states.
He says the elephant in the room is always productivity. The elephant comes in two but related parts, workshop efficiency, and personal productivity. Considering this, he has developed a Production Masterclass.
He says: “In our last one, we had nine students make 24 Waterfall stools as a group in five days. The students got to see how we plan for productivity, and work as a team. We use a commercial design that’s been in production for 25 years. We use all the jigs, equipment, machines, methods and strategies that we normally use to make those stools.
“A student can leave a wood school without ever having made another person’s commercial design, or used a spindle moulder, or have worked as part of a team, or have been pace-set by a professional maker, or seen how processes can evolve over time through experience, new equipment or innovative jigs.
“Woodwork is about problem solving, and time management. The discipline it takes to plan and execute a production run, carries through to one-off projects.”
One recent session saw the Woodworkers Association of NSW and the Gottstein Trust each sponsor one student, and Britton Timbers supply the native timbers.
Learning to make sound, timely decisions is a skill, and a critical part of productivity, says Evan. “In fact, a bad decision done well will often trump a good decision done badly. But it’s surprisingly difficult to put a student under real time pressure. When I’ve taught at Sturt, or the Australian School of Fine Furniture, or
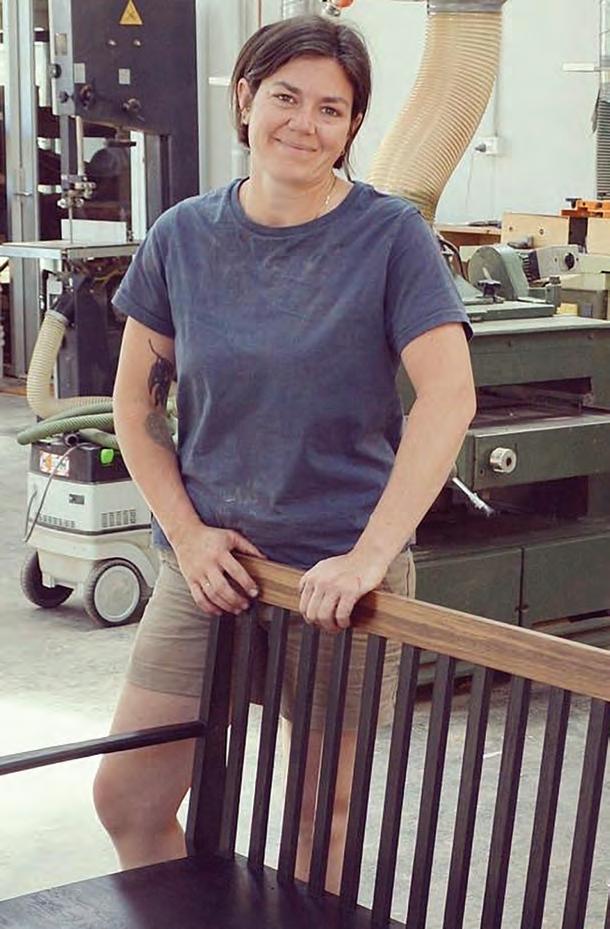
ANU’s School of Art, I have noticed that the most productive students were the ones with the most real pressure on them.”
He says that a student with a baby at home, rent to pay or a partner who needs them to be back at a specified time has real-world pressure on them. They will use their time well. One of the advantages of a one- or two-week Masterclass is that time is short. People want to cram in as much information and experience as possible. They will arrive on time, work hard and have to leave at a set time because the lights are turned off. Many of the longer courses open the workshop early and allow a student to stay late.
In his lengthy and generously open conversation with Connect, Evan offers an insight that culturally, Australia has always wanted to train people for a specific job-role in the shortest time, and at the lowest cost. “We want to train for ‘wood machinist’, ‘joiner’,
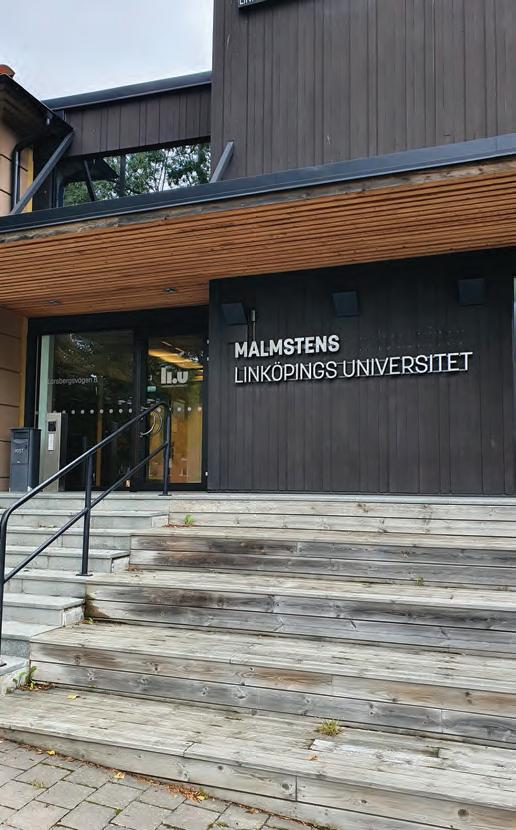
or ‘cabinetmaker’ with just enough knowledge to do each job,” he laments. “We also take a perverse pride in being self-taught.” But he acknowledges the value of the current training providers including Registered Training Organisations, and an impetus for more integrated approaches across the country.
Evan is impressed by the woodwork industry training available at Sweden’s Malmstens University (https://liu.se/en/article/campus-lidingo). It delivers intensive, deep, and comprehensive training in all aspects of wood technology.
He would like to see the introduction here of a similar three-year course with high standards, objective testing, and the potential for students to fail, covering all aspects of woodwork and making the student workready across a wide range of roles. A graduate would understand the responsibilities and requirements for being both an employee and an employer.
Evan says, “We would have a cohort of equally well-trained people across a wide range of related fields able to talk to each other with a common baseline of knowledge, and would raise the general understanding and appreciation of woodwork, forestry, and respect for this wonderful natural material.”
Musing that there is no appetite in Australia to fund a school as comprehensive as Malmstens, Evan suggests that the Australian government could fund one new
Australian Government and the Strategic Review of the Australian Apprenticeships Incentive System
“The Strategic Review of the Australian Apprenticeships Incentive System has recently been provided to the Australian Government, and the findings are currently under consideration,” a spokesperson for the Department of Employment and Workplace Relations informed Connect, at time of writing.
Justice Iain Ross AO and Ms Lisa Paul AO PSM, two eminent experts in the field, conducted the review.
The Terms of Reference said, “Considering the long-term trend of declining completion rates and skill shortages across the Australian economy, the Government has decided to commission a Strategic Review of the Incentive System (the Review), to ensure that incentives and other non-financial support are designed
to optimise completion rates and address skill shortages to provide the skilled workers needed for Australia’s growing economy."
In a speech about the review to the National Manufacturing Workforce Forum in April last year, Dr Iain Ross, said, “The apprenticeship system faces a number of challenges. It’s clear that we will not successfully address skill shortages simply by increasing commencements. We must do more to increase retention and completion. Apprenticeship completion rates have been in steady decline for more than a decade to the current rate of about 56 per cent, though there’s significant variance between particular trades and traineeships.”
Statements from ITECA and ACFA in response to the announcement can be read on page 60.
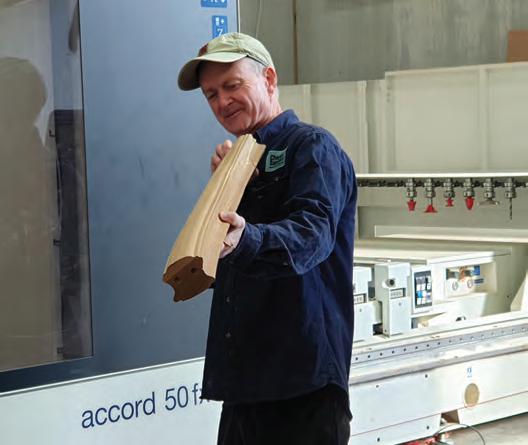
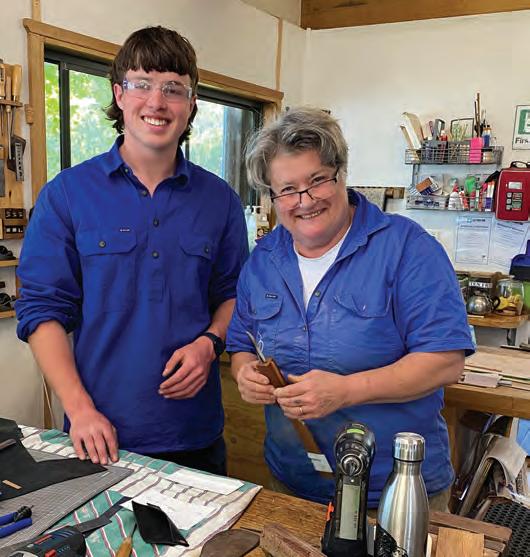
student per annum so that there would always be three Australians per year at the school, one starting, one mid-studies, and one finishing.
Ultimately, Evan puts down Australia’s success in turning out many fine furniture makers to having compelling timber. He says, “We take it for granted because we have grown up with it. Our timber is fascinating, and many of the prominent makers, including me, were drawn to the craft because the materials are so wonderful. We can literally find an old fencepost and find beauty in it. Nobody ever got excited about a piece of pine. I reckon the system has little to do with it. I just think that Australians love timber, and enough of us work at understanding it because of that love.” ■
Stop Press!
As this issue of Connect goes into production, the federal government has announced it will double the apprenticeship incentive payment to $10,000 for eligible trainees in construction occupations.
The move is in response to the findings of the Strategic Review of the Australian Apprenticeship Incentive System.
The announcement comes in a joint statement from Prime Minister Anthony Albanese, Skills and Training Minister Andrew Giles, and Housing Minister Clare O’Neil.
The government “is also taking additional immediate steps to support the Review’s most urgent recommendations:
*Maintain the 2025 Priority List and extend current Australian Apprentice Training Support and Priority Hiring Incentive payment settings by six months until 31 December 2025. This will provide consistency for employers and cost of living relief to apprentices in priority occupations during the consultation process.
*Increase the Living Away From Home Allowance from 1 July 2025 so apprentices can meet the costs associated with moving to take up an apprenticeship.
*Increase the Disability Australian Apprentice Wage Support payment from 1 July 2025 to support employers taking on apprentices with disability,” says the statement.
The government is considering the Review’s findings and will consult stakeholders on longerterm reforms recommended by the Review to inform its response, says the statement.
The Review’s final report is available at https:// www.dewr.gov.au/australian-apprenticeships/ resources/strategic-review-australianapprenticeship-incentive-system-final-report
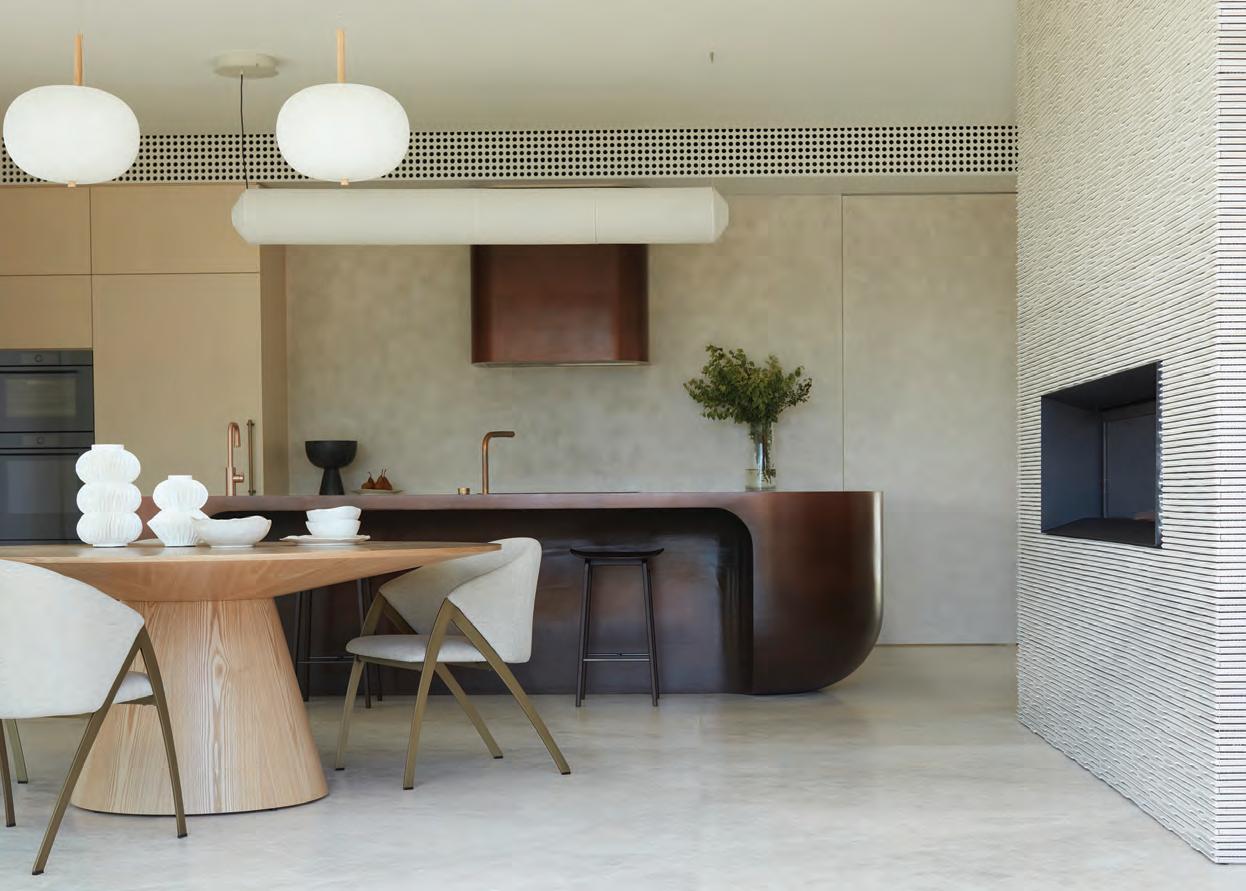
Designing for Safety
Essential kitchen design tips to prevent fires, falls and injuries
By Selina Zwolsman
Akitchen is often considered the heart of the home. It is where meals are prepared, families gather, and friends get together to break bread.
However, it’s also one of the most hazardous areas in any household setting. Poorly designed kitchens can lead to house fires, burns and scalds, slips and falls and more. Accordingly, it is crucial to consider various safety aspects when designing a kitchen to create a functional, efficient, and secure space. This article will explore four essential safety issues to keep in mind when planning a kitchen.
Fire Safety
According to Fire Rescue Victoria, cooking in the kitchen is the single largest cause of fires in Australian homes. In fact, it suggests that 40 per cent of house fires start in the kitchen. Most incidents occur when cooking is left unattended, and many could potentially be avoided with some sensible design decisions. Keep the following top of mind when preparing plans for your clients.
Placement of Cooking Appliances — Gas Cooktops and Rangehoods
As set out in Australian Standard AS/NZS 5601.1:2022 Gas installations Part 1: General installations, the minimum clearance requirement between a gas cooktop (top of trivet) and the lowest part of a rangehood is 650mm.
The minimum clearance between a gas cooktop and the lowest part of an exhaust fan is 750mm.
What is the difference between rangehood and an exhaust fan?
A rangehood is a ventilation system designed to extract smoke, steam, grease, and cooking odours. They feature a filtration mechanism and varying controls (fan speed, lighting etc.), enhancing cooking and safety.
An exhaust fan, on the other hand, has the more simplified role of expelling indoor air outside. They’re often installed on walls or windows and are budgetfriendly and space-saving. They’re less than ideal when it comes to kitchen ventilation needs, however,
so we’ll only outline requirements for rangehoods from here on.
New Installations
For new building work, rangehoods and exhaust fans must be installed in accordance with the appliance manufacturer’s instructions.
Where a difference occurs between the Standard and the installation instructions, the greater clearance shall apply.
Kitchen Renovations with New Cabinets and Rangehoods
For kitchen renovations in an existing property where new cabinets and rangehoods have been fitted, gasfitters will be expected to install the gas cooking appliance per the new gas installation clearances (650mm minimum) or the clearance prescribed in the gas appliance installation instructions or rangehood installation instructions — again, whichever is greater.
Existing Installations — Appliance Replacement only
Where only the appliance is being replaced, the overhead clearance from the highest part of the highest burner of the appliance or the hob to the rangehood shall not be less than 600mm unless the appliance manufacturer’s instructions specify a greater clearance.
Minimum Clearance to Any Other Downward-facing Combustible Surface
AS/NZS 5601 notes that any other downward-facing combustible surface fixed at a height less than 650mm above the supporting surface of a cooking vessel (i.e. top of trivet) must be protected for the full width and depth of the cooking surface. The standard sets out suitable methods of protection (i.e. facing materials and associated backing), and it’s imperative that these requirements are met.
The absolute minimum clearance between the top of the trivet and any overhead surface shall be not less than 450mm.
Trivet Measurements
It should be noted that as of 30 March 2023, the measurements will be taken from the top of the trivet of a gas cooking appliance. (This is a change from previous editions of the Standard, which was measured from the top of the highest burner.)
Removable accessories, such as wok trivets that sit upon a hob trivet or minor elevations in trivets for wok burners, are not considered when measuring from the gas cooking appliance.
Distance between Gas Cooktop and Vertical Surfaces
AS/NZS 5601 sets out requirements for side and rear clearances of gas cooktops, too.
Where the distance from the periphery (edge) of the nearest burner to any vertical combustible surface is less than 200mm, that surface must be protected in accordance with the Standard’s requirements to a height of no less than 150mm above the edge of the nearest burner for the full dimension (width or depth) of the cooking surface area. If the gas cooking appliance has a fitted splashback, protection of the rear wall is unnecessary, as long as the splashback

Selina Zwolsman CKD Au, CBD Au is a qualified interior designer and experienced writer specialising in design and building-related content. She produces technical and editorial content for industry and training organisations, and assists small to medium business owners with web and media copy, email marketing campaigns and more. Selina has shared many design-related presentations with trade and consumer audiences and loves to promote the work of Australia’s best designers and manufacturers. Contact Selina via her website at nicelysaid.com.au.
Design
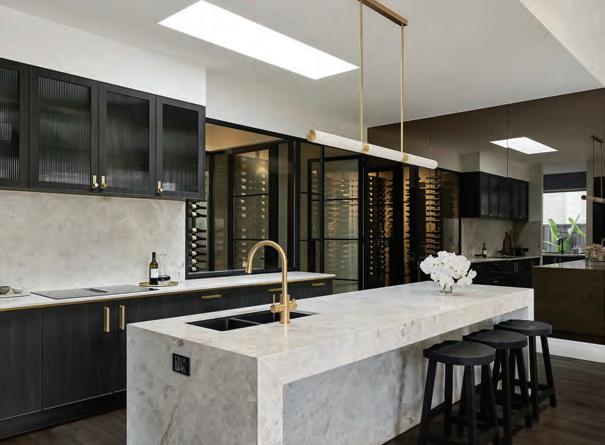
adequately protects any combustible surface within 200mm of the edge of the nearest burner to a height of at least 150mm above the edge of the nearest burner.
Additional Requirements for Down-draught Extraction Systems
With down-draught extraction systems becoming increasingly popular, it’s important to be aware of the regulations related to these appliances.
Appliances with integral down-draught extraction systems shall only be installed if the design conforms to Australian requirements. That is, they must be certified or be acceptable to the Technical Regulator.
Appliances shall only be installed with separate down-draught extraction systems if they meet the following requirements:
• The appliance installation instructions state the appliance may be used with the down-draught extraction system, and
• The down-draught extraction system installation instructions state that the downdraught extraction system may be used with the appliance.
Cooktops Near Windows
A cooktop should be placed at least 300mm horizontally from an openable window, with 500mm clearance preferred for a gas appliance. The most obvious consequence of having a cooktop too close to a window is that a fire on the stove or cooktop could easily jump to curtains. Less obvious but equally dangerous is the potential for a breeze to blow out
the flame on a gas burner. This could allow gas to accumulate unnoticed and cause a potential explosion.
Fire Extinguishers and Smoke Detectors
Fire Rescue Victoria recommends that a fire extinguisher and fire blanket should be stored within easy reach but away from the cooking area.
All states and territories have particular requirements for smoke alarms. Fire and Rescue NSW suggests that the ideal location for detectors is on the ceiling between sleeping and living areas; smoke alarms should not be fitted in or near the kitchen.
Avoiding Burns and Scalding
Around 6000 Australians are hospitalised every year as a result of a burn or scald. Almost half of these are caused by contact with hot drinks, foods, fats, cooking oils and hot water, so, unsurprisingly, the kitchen is often the site of injury.
• Thoughtful design can certainly help avoid these burns and scalds. Following are a few safety tips to consider.
• Take note of the distance between the cooktop and the sink. How far will your client need to travel with their boiling pot of pasta and water? Will they potentially cross paths with others in the home?
• When your client removes a steaming hot dish from the microwave, how accessible will the nearest set-down point be?
• Install microwaves so that the base sits no higher than 1250mm from the floor and always check the installation instructions for a new (or existing) microwave. Most manufacturers set specific dimensions regarding the minimum installation height of the appliance, too, and you'll want to ensure you comply.
• Will an under-bench oven prove awkward for the client? Will telescopic runners make checking on food easier? Where is the closest set-down bench in relation to the oven?
• Is the cooktop located too close to the edge of a bench or adjacent to a thoroughfare in the kitchen? Is there a risk of a passerby bumping or knocking a saucepan handle?
Slip and Fall Prevention
According to the Australian Institute of Health and Welfare, falls are the leading cause of injury and injury deaths in Australia. Of course, not all of these falls occur in the kitchen, but there are things we can do as kitchen designers to minimise the risk to our clients.
Slippery floors are a common cause of injuries in the kitchen. A steady build-up of oil in the area in front of a cooktop can slowly but surely create a slip hazard. This may be less obvious to the eye than a pool of oil or water, and a non-slip kitchen mat for this area may be a wise investment for an aging or unsteady client.
If you’re helping your client select a floor for their new kitchen, consider ease of cleaning alongside slip resistance — both are equally important as far as slip prevention goes.
Thoughtful storage planning can help prevent falls. Work closely with your client to determine which items they access most often. Provide space for these items at a convenient height, and consider lift-up or pulldown shelving for overhead cabinets.
Knife Cuts
While falls are the leading cause of injury generally, when it comes to kitchen-related presentations at emergency rooms around the country, cutting and piercing injuries win. We certainly can’t control
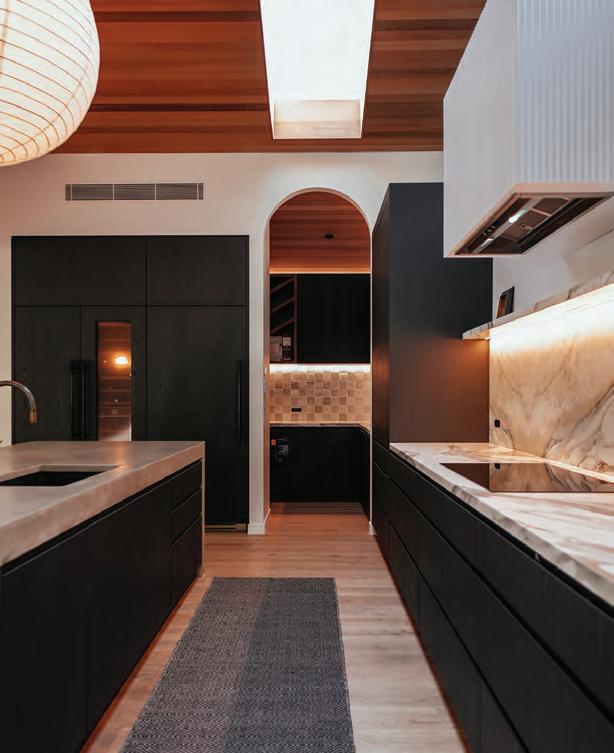
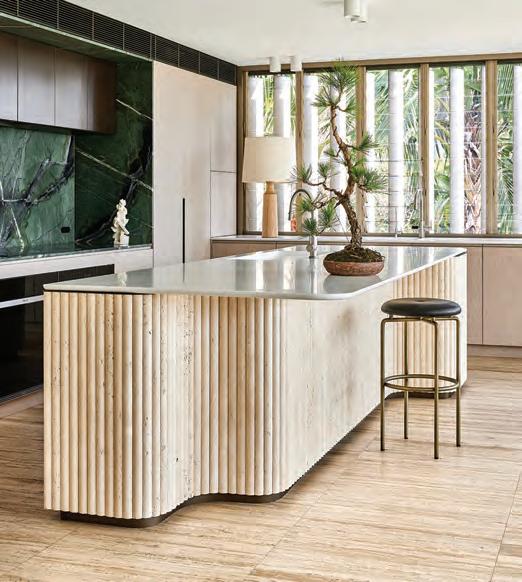
the way our clients use their knives, but we can consider the following when designing a ‘safe space’ for meal preparation.
• A well-lit preparation zone is an essential part of a kitchen. Ambient and mood lighting are great, but a high level of lux is required to safely use a knife. Determine where your client will do their chopping (meal preparation) and light up the space accordingly.
• Provide a dedicated space for knife storage. Does your client prefer to store knives in a drawer? Make sure your cutlery inserts accommodate neat and organised storage. Do they prefer a magnetic, wall-mounted knife holder? Determine a location for this and ensure it’s noted on your elevations.
• Facilitate knife sharpening. Ironically, blunt or dull knives can be more dangerous than sharp utensils. What kind of knife sharpener does your client prefer? Where can this be stored for ease of access?
• An informed kitchen designer prioritises safety as highly as aesthetics and functionality. By addressing the above as a minimum, designers can create a kitchen that reduces risks and enhances usability. Whether designing a home kitchen or a commercial space, integrating these safety considerations will ensure a safer environment for everyone. ■
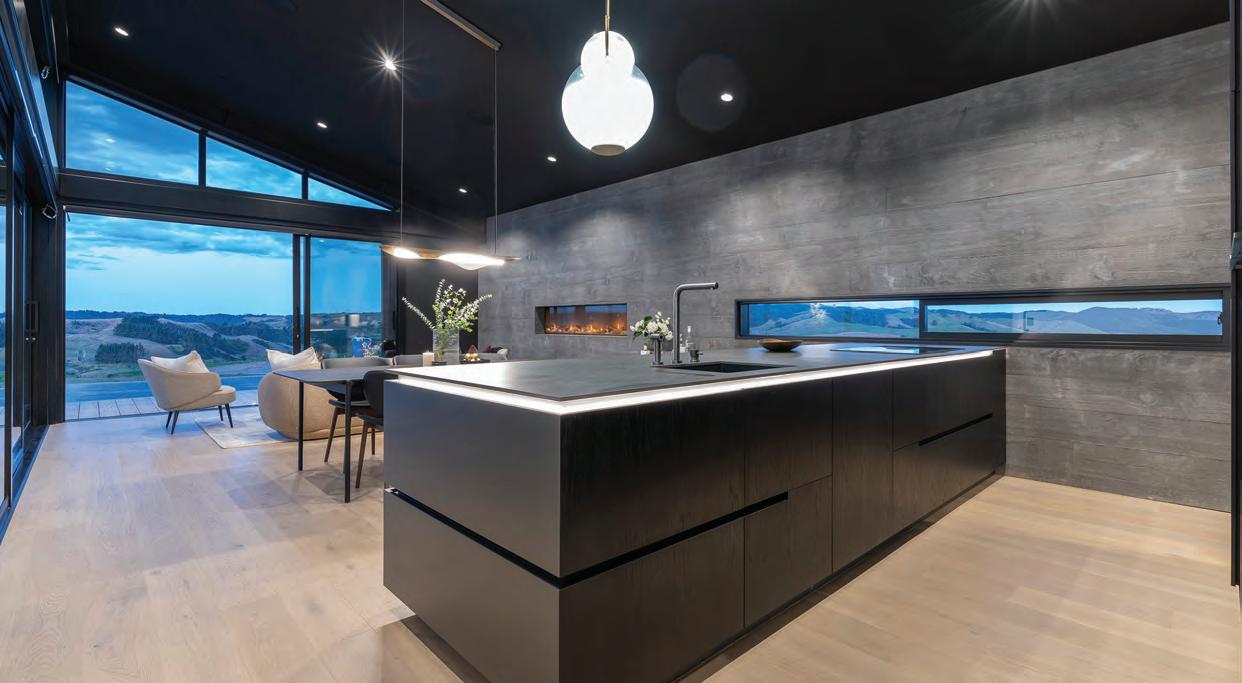
NKBA Excellence in Design Awards 2024
The best kitchens and bathrooms in New Zealand were announced at a gala ceremony in September 2024
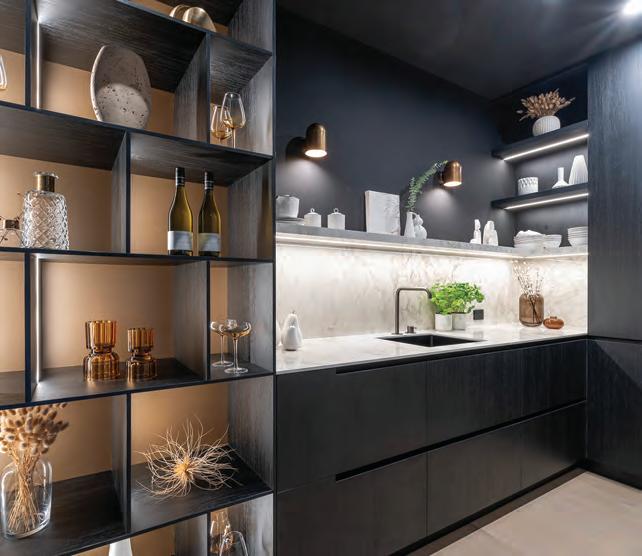
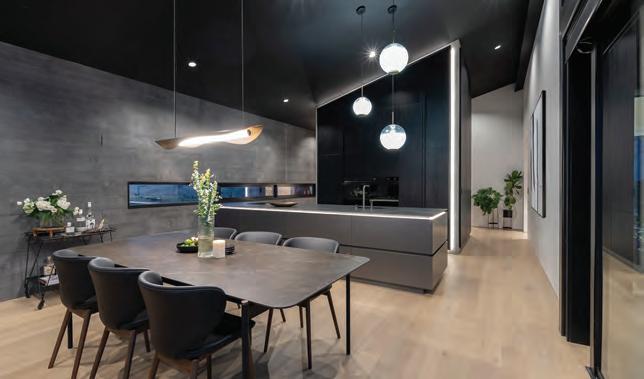
Designer of the Year Award
Alina Cuchiliuc, Cube Dentro, Auckland
The judges said they were extremely impressed with this first-time entrant and recent NZ Diploma in Kitchen Design graduate, praising her high calibre of design execution, from the aesthetics to the quality of plans.
“Alina has produced some lovely details and the delivery of beautiful and creative spaces. She has used play on scale to intrigue and encourage guests to ask, ‘what is beyond?’ This is a designer with clever and elevated thinking,” they said.
Alina’s $120K+ kitchen was designed for an experienced property developer who desired a modern kitchen and scullery design for his family of six in their newly built holiday retreat in Maramarua.
Alina says the key to the success of the project was involvement in the early planning stages.
“Being part of a project before construction starts is very important. It helps to understand the project's goals and design plans from the beginning, making sure they match what the client wants. It also helps to solve problems early on and to work well with the whole team, which keeps things running smoothly and avoids delays. Being involved early also lets us add interesting design ideas, maximise the space, and find costeffective solutions, ensuring an optimal result,” she says.

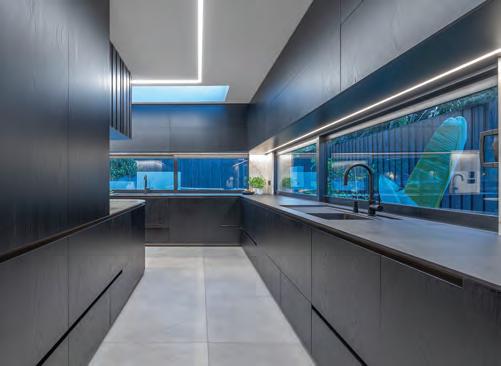
Supreme Kitchen Design Award
Leonie Hamill, Cube Dentro, Oceanside Residence, Auckland
Located in the Auckland suburb of Hillsborough, this kitchen was celebrated for the strong values on which it was designed.
“Family values, centred around traditional Indian culture and cuisine, were key to the design. There was a strong emphasis on a well-organised storage system for the heavy use of spices and other ingredients. Daily meals are prepared by Mum and Grandma, and it was therefore important for the layout to reflect how the pair like to work. For example, the rear zone, behind the hob wall, is mainly used for food preparation, while the front of the kitchen with island is for showcasing, serving, and enjoying cuisine,” says Leonie.
The judges of the 2024 NKBA Excellence in Design Awards said the kitchen was phenomenal and a standout in the 2024 awards, stating that “from a design detailing perspective, this kitchen is a level above. It is beautiful and it looks great from every angle. The designer hasn’t missed any detail, just look at the leg on the island, it is visually stunning. Another area of success in this space is the interpretation of the brief, they haven’t overdone it, but have designed a superb kitchen that works very well for multiple cooks. It is clever, clean, modern and the main island is just exceptional. We love it.”

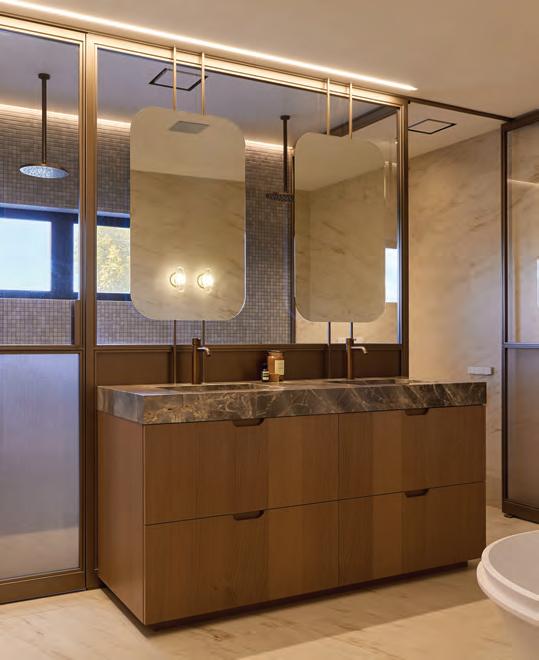
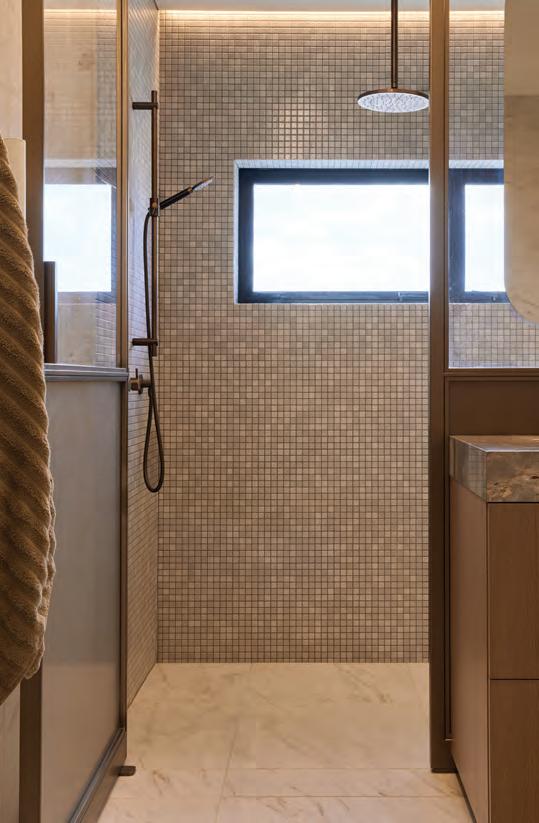
Supreme Bathroom Design Award
Georgia Langridge, Modi Design, Parisian Stay, Canterbury
Georgia’s project, ‘Parisian Stay’, has a light and bright atmosphere during the day, while allowing moody vibes in the evening. The NKBA judges said the bathroom showcased unique features, alongside stunning materials and tones.
“This is a lovely space that walks the delicate line between masculine and feminine. There are so many incredible design details. The texture, the consistent use of metallics and the luxurious materials are all very successful. The bath is an interesting and stunning feature, as is the giant walk-in shower. This designer has a very good understanding of bathroom design, they know how to define a space, and we applaud the technical design. One particularly successful aspect is the way the space allows for communication and solitude; the zones are separate and at the same time connected, which allows for varying degrees of privacy,” they added.
The 2024 Excellence in Design judging panel included leading local and international kitchen designers, alongside fashion designer Karen Walker. NKBA would like to thank Karen Walker, Davinia Sutton, Morgan Cronin, Trudi Rabbitte, Gavin Hepper, and Glen Johns.
Rachael Kwok, executive officer of the National Kitchen and Bathroom Association of New Zealand (NKBA), says 2024 was a year of fresh faces. “NKBA is committed to supporting emerging designers, so it was encouraging to see new designers step into the awards arena in 2024. With all this year’s entrants creating beautiful, innovative and functional spaces, it’s clear that the future of New Zealand’s kitchen and bathroom design industry is in safe hands. Well done to all our award winners,” she says.
The National Kitchen and Bathroom Association of New Zealand is the only membership organisation for kitchen and bathroom designers of New Zealand. Celebrating success in the kitchen and bathroom industry, the NKBA Excellence in Design awards have been running for more than 30 years.
For a full list of all award winners, visit nkba.org.nz/
The 2024 NKBA Excellence in Design Award Winners are:
Designer of the Year Award, Alina Cuchiliuc, Cube Dentro, Hilltop Residence/Moody Elegance, Auckland
Supreme Kitchen Design Award, Leonie Hamill, Cube Dentro, Oceanside Residence, Auckland
Supreme Bathroom Design Award, Georgia Langridge, Modi Design, Parisian Stay, Canterbury
DNKBA Elite Kitchen Design Award, Natalie Du Bois, Du Bois Design, Snakes and Ladders, Auckland
DNKBA Elite Bathroom Design Award, Celia Visser, Celia Visser Design, Contemporary Rococo, Auckland
DNKBA Platinum Kitchen Design Award, Melanie Sa'u, Melanie Sa’u Design Studio, Mellon’s Bay Residence, Auckland
DNKBA Platinum Bathroom Design Award, Emma Morris, Eternodesign, Tranquil Paradise, Canterbury
DNKBA Gold Kitchen Design Award, Jenny Holmes, Designmarked Kitchens, Moana Heights, Waikato
DNKBA Gold Bathroom Design Award, Lacey Exton, Comber and Comber, Manor House — Master Suite Retreat, Canterbury
DNKBA Silver Kitchen Design Award, Georgia Langridge, Modi Design, Urban Tenor, Canterbury
DNKBA Silver Bathroom Design Award, Georgia Langridge, Modi Design, Stone Cocoon, Canterbury
DNKBA Bronze Kitchen Design Award, Alina Cuchiliuc, Cube Dentro, Hilltop Residence, Auckland
Kitchen Distinction Award — up to $30k, Karen Harlen, Bays Joinery, Black Elegance, Top of South Kitchen Distinction Award — $30–$60k, Anna Thomas, Bays Joinery, Arabescato Reverie, Top of South Kitchen Distinction Award — $60–$90k, Anna Thomas, Bays Joinery, Elevated Beach House, Top of South Kitchen Distinction Award — $90–$120k, Emma Gourdie, Spatial Co, Refined Industrial, Top of South Kitchen Distinction Award — $120k+, Alina Cuchiliuc, Cube Dentro, Hilltop Residence, Auckland
Bathroom Distinction Award — up to $50k, Michelle Lamb, Michelle Lamb Interior Architecture, Seaside Sanctuary, Canterbury
Bathroom Distinction Award — $50k+, Lacey Exton, Comber and Comber, Manor House — Master Suite Retreat, Canterbury
Creative Excellence Kitchen Design Award, Na Ni, Aurora Australis Interior, Shades of Silence: The Ultimate Minimal in Grey and Black, Auckland
Outstanding Kitchen Renovation Award, Melanie Sa'u, Melanie Sa’u Design Studio, Maraetai Residence, Auckland
Outstanding Bathroom Renovation Award, Michelle Lamb, Michelle Lamb Interior Architecture, Seaside Sanctuary, Canterbury
Visual Impact Award, George Molnar, Bays Joinery, Luxe Living Kitchen, Top of South
First Time Entrant Award, Katherine Lightfoot, Kella Design Co., Gulf View Muse, Auckland
Residential Spatial Innovation Design Award, Alina Cuchiliuc, Cube Dentro, Moody Elegance, Auckland
Character Kitchen Design Award, Natalie Du Bois, Du Bois Design, Small but Mighty, Auckland
Auckland Kitchen Design Recognition, Celia Visser, Celia Visser Design, Hidden Gem, Auckland
Auckland Bathroom Design Recognition, Katie Scott, Sticks+Stones Design, Access + Relax, Auckland
Auckland Alternative Design Recognition, Jordana Gurney, Cube Dentro, Bucklands Beach Residence, Auckland
Bay of Plenty Kitchen Design Recognition, Michelle McAnulty, Beaver Kitchens, Pohutukawa Retreat, Bay of Plenty
Canterbury Kitchen Design Recognition, Georgia Langridge, Modi Design, Bronze Echo, Canterbury
Canterbury Bathroom Design Recognition, Emma Morris, Eternodesign, Tranquil Paradise, Canterbury
Southern Kitchen Design Recognition, Hub Design Interiors, Hub Design Interiors, Arrowtown Hills, Southern
Waikato Kitchen Design Recognition, Jenny Holmes, Designmarked Kitchens, Moana Heights, Waikato
Wellington Kitchen Design Recognition, Simone van der Plas, Simone van der Plas PDINZ, Rakau Road
Radiant Harbour Haven Kitchen, Wellington
Taranaki Kitchen Design Recognition, Kitchen Studio New Plymouth, Kitchen Studio New Plymouth, Magnolia Cottage, Taranaki
Top of the South Bathroom Design Recognition, Anna Thomas, Bays Joinery, Midnight Retreat, Top of South
Top of the South Kitchen Design Recognition, George Molnar, Bays Joinery, Ebony Elegance, Top of South

Home Building Outlook Improving
The outlook for home building is brighter heading into 2025, with on-the-ground activity showing clear signs of improvement
By Tom Devitt, HIA senior economist
The Reserve Bank’s rate hiking cycle weighed heavily on housing demand from mid-2022. This eventually produced a 12-year low in housing commencements in the 2023/24 financial year.
From this trough, indicators of future home building activity such as new home sales and housing loans have slowly picked up nationally. Despite interest rates remaining elevated, the Reserve Bank hasn’t increased interest rates in more than a year and, in fact, delivered only one hike in the last 20 months.
This stability and expectations that the next move will be a cut, combined with strong population growth, low unemployment rates and incredibly tight rental markets, has helped improve confidence and bring investors and owner-occupiers back to the market.
Markets are also starting to diverge once again. Western Australia led the nation with a recovery beginning in 2023. Buyer interest here has been driven by the strongest population growth in the country, from both overseas and interstate, together with relatively affordable land. Queensland and South
Australia showed signs of improvement in 2024 for similar reasons. This contrasts with Sydney, where the highest land costs in the country have continued to constrain new buyer interest. With even Victoria showing early signs of improvement, this leaves Sydney as arguably the only large market still to see a pick-up in on-the-ground activity.
Higher-density housing also remains much more constrained than detached housing. In addition to recent pressures that the entire home building sector has faced, labour constraints caused a number of already-approved larger apartment developments to stall before commencement.
Larger apartment projects take much longer than detached houses to complete and so require a great deal of certainty around the cost and availability of materials and labour. Without this certainty, developers could not be confident enough to proceed. Competition for skilled trades from public infrastructure projects is creating a great deal of uncertainty around resourcing.
Local government restrictions on density and punitive state government taxes on foreign investors are also constraining higher density housing development. The result is that multi-unit commencements are still around decade lows, half of what was being commenced in the mid-2010s, with no sign yet of their much-needed recovery.
Policy choices at a state and local level will determine the nature and magnitude of the divergence between jurisdictions and housing types. States and territories that are able to provide more

affordable shovel-ready land will be best placed to support home building.
The policy levers available at all levels of government to address the barriers to home building — taxes, planning, approvals, regulations, skills and labour — mean there is tremendous upside potential to the home building outlook across Australia. These reforms will be essential to meeting the Australian government’s 1.2 million homes target over the coming five years, addressing the housing crisis and supporting more Australians into homeownership. ■
Housing Industry Association hia.com.au/
New Home Commencements, Moving Annual Total, Australia

Vale Simon Hodgson
We
pay tribute to a member of our industry who is remembered as an inspirational force, a true mentor and a friend to all
By Melanie Gardener
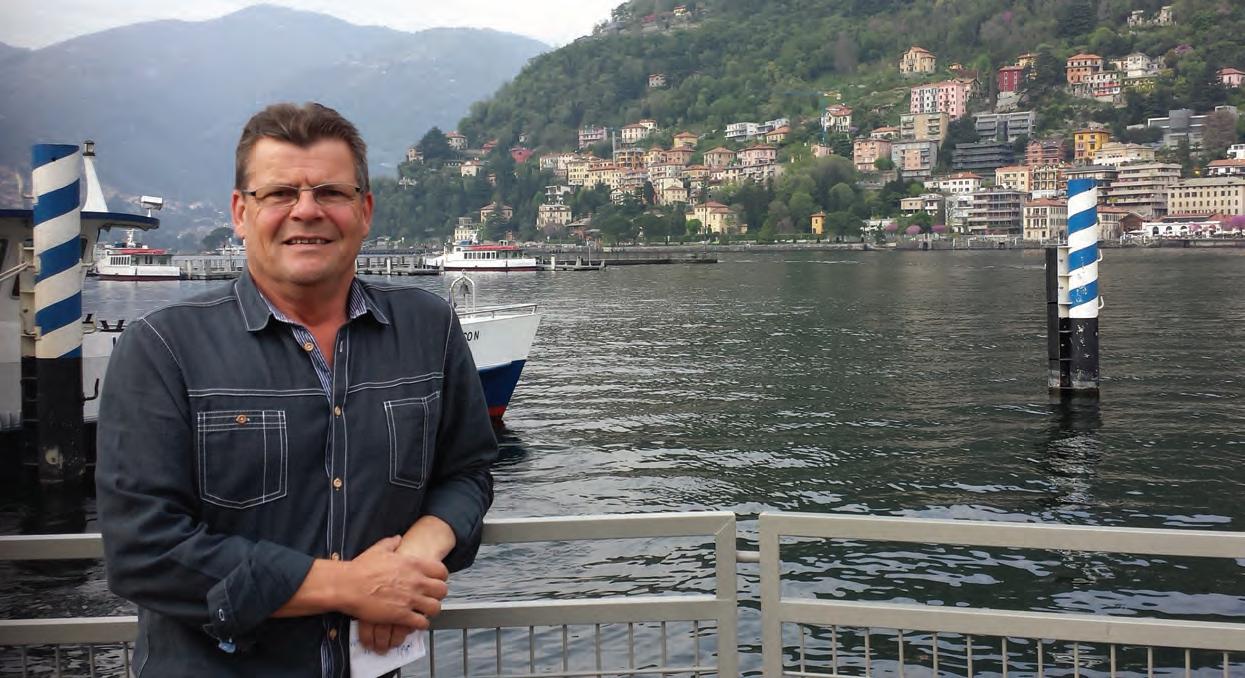
Simon Hodgson unexpectedly passed away in October 2024 following a short illness. He was a well-known character within the cabinet-making and design sectors and his enthusiasm and genuine love for this industry was obvious in his every interaction.
Simon held various roles within the industry, including as a director of Impala Kitchens and Nouvelle Kitchens in Sydney. He established his own consulting business which saw him undertake stints with Artline Kitchens, Harvey Norman Kitchens & Bathrooms and, most recently, Exclusive Cabinetry, among others.
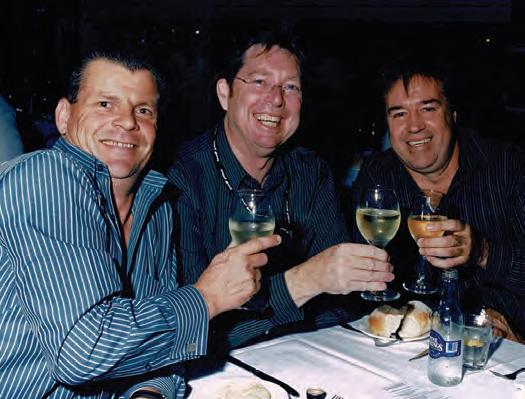
He was best known for his commitment to industry associations, starting with his role as HIA NSW K&B Committee chair from 2001 to 2008 which also saw him sit on the HIA NSW Regional Executive Committee over the same period. Simon became the HIA National K&B Committee vice-chair from 2003 to 2004 then was promoted to HIA National K&B Committee chair from 2004 to 2008. He also sat on the HIA National Policy Congress from 2003 to 2008.
One of his proudest accomplishments was being one of a small group of founders who worked tirelessly to establish KBDi (Kitchen & Bathroom Designers Institute), work on which began in 2005/2006. Simon subsequently sat on KBDi’s Board of Directors until 2014.
Simon’s knowledge and understanding of the design and cabinet-making industries was vast and this saw him join ACFA’s (Australian Cabinet & Furniture Association) Board of Directors in 2020 — a position he would hold until his death.
Those who met Simon will remember his boundless energy and willingness to share his experience for the benefit of all. To that end, he helped to establish The Kitchen & Bathroom Blog, a resource for the industry, in 2013. As an extension of this, he was also instrumental in creating Australian International Design Tours
(AIDT) in 2015 to facilitate the Australian design community’s attendance at significant international trade shows.
Rex Hirst, past president of KBDi had this to say: “Simon made friends wherever he went through his honesty, commitment, work ethic and, most of all, his ability to connect with people. Simon was a person who never wasted a minute and made sure that everyone who met him went away knowing that they had just been with an inspirational, caring, loyal and humorous person, as a recipient of his devoted support."
Dean Brakell, CEO of ACFA, agrees. “Simon’s contributions extended beyond projects and roles; he was a mentor, a colleague, and a friend to many of us. His legacy will continue to inspire us to strive for excellence and unity within our industry. Simon’s leadership and passion were evident in every endeavour he undertook,” he says.
Peter Fry, past HIA National K&B chair and fellow National Committee member with Simon, says “Simon was an inspiring visionary whose passion challenged the kitchen and bathroom industry to evolve and change. Simon was always generous with his time and knowledge assisting and supporting those in and around the industry. He could always see the positive side to every situation and left those around him feeling they were heard and a part of the discussion. We have lost an authentic, open-minded leader of the industry, and great friend."
Ron Redman, from Blum Australia (retired) and a close friend of Simon, as well as co-tour leader on some of AIDT’s early trips, says “Our industry has lost one of the most dynamic, passionate, inclusive, inspirational and supportive people we will ever know. Throughout our lives, we sometimes encounter people who have vision and passion as well as a unique ability to inspire others to come together in meaningful productive ways, to achieve extraordinary results. Simon was one of those people."
Simon’s passing has left an unfillable hole in the industry, but his legacy continues on in the numerous industry members he has inspired and in the collaborative relationships he helped establish between the design and cabinet-making sectors. He will be sorely missed by all. ■
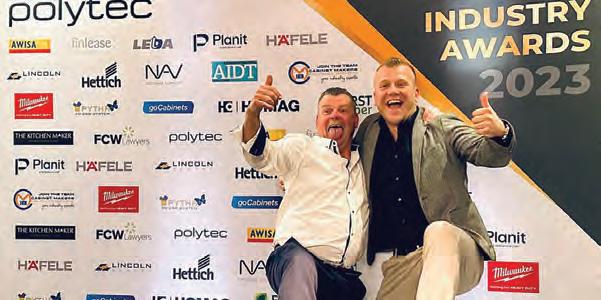

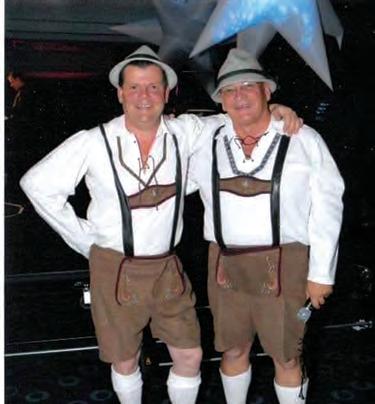
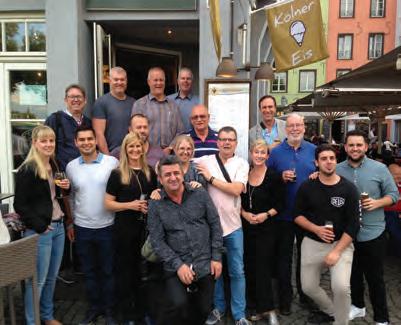
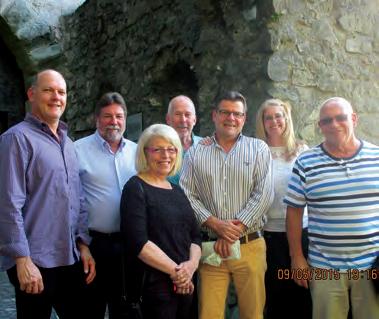

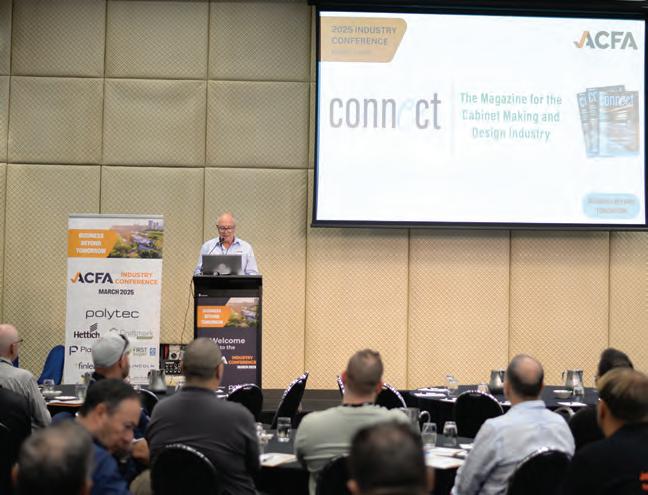
ACFA 2025 Industry Conference
Industry members came together in Sydney on 7 March for a day of learning and personal development
Members of the cabinet-making, joinery and design industry attended the ACFA Industry Conference, held at the magnificent Waterview in Bicentennial Park in March. The theme for the event was “Business Beyond Tomorrow” and attendees were able to discover innovative practices, learn from industry leaders and challenge their personal and professional development.
Keynote speaker Julian Moore opened proceedings with an insightful presentation on “Harnessing Artificial Intelligence to Drive Business Success”. Julian is a renowned expert in AI solutions and attendees benefitted from his extensive experience in utilising AI to streamline manual processes, reduce costs, and drive growth and innovation. Julian’s presentation
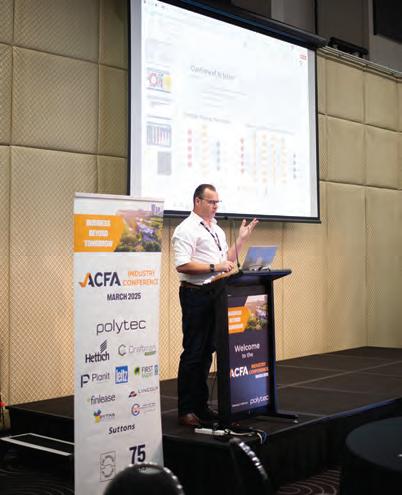
wowed the crowd with live demonstrations of how AI has developed and some of the incredible advancements in the technology in just a few years.
The next session took a serious look into the legal side of business management with “Essential Legal Insights: Understanding Consumer Rights, Contracts 101, Warranties and Payment Protection”. Andrew Seaton, managing partner with Easton Belle Lawyers, walked attendees through the legal minefield that is consumer guarantees, looking closely at unfair contract terms, home statutory warranty insurance, contracts (both verbal and in writing), and how to write contracts to ensure you get paid. All agreed this was an incredibly eye-opening session with plenty of valuable take-aways. There were plenty of
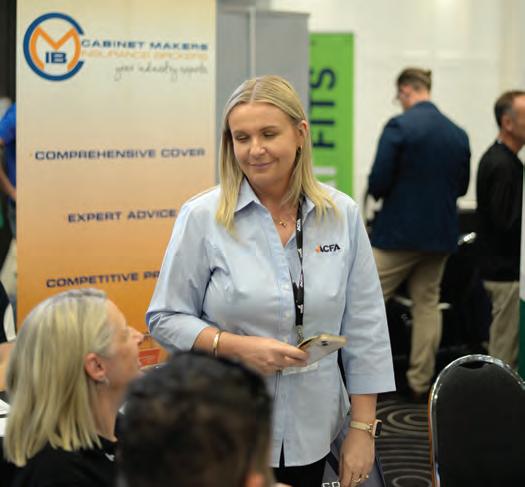

questions from the floor which continued well into the lunch break.
Ben Fewtrell from MaxMyProfit took to the stage to present on his topic “Built to Last: Creating a Business that Thrives Without You”. Ben took attendees on a deep dive into how to set up a business to run smoothly, concentrating on setting KPIs and not being afraid to hold employees and systems to accountability. He covered off on practical ways to structure a business for growth, with a clear path to creating systems to keep things running smoothly. Ben’s presentation broke down the figures to show business owners how small changes or increases compound over time to create meaningful profitability and business longevity.
One of the most interesting sessions of the day was the presentation of the “Future Tradie Report”. Developed by Trout Creative Thinking and Next, the report is the first of its kind in Australia. Presented by Seana Glover and Anthony Bologna from Trout Creative Thinking, the importance of this session cannot be understated. With Millennials and Gen Z expected to make up 75 per cent of the workforce within the next decade, the findings of the report provided valuable insight into emerging ambitions, diverse team management approaches and retention strategies, helping attendees understand and engage with the next generation of tradies.
The final session of the day was an engaging panel discussion on the Future Training Package and delved into some of the challenges and opportunities in training apprentices. The panel had an opportunity to share their experiences and provide commentary on how training can better align with the needs of today’s businesses. Members of the panel were Dean Brakell — ACFA CEO, Glen Cannon — industry trainer/ assessor, Tim Cleary — stakeholder engagement lead/

skills insight and Darren McKavanagh — director, The Kitchen Maker. There were a number of salient points made by attendees which led to a robust discussion with the panel and the crowd.
Thank you to our conference sponsors and for supporting our industry to have the opportunity to take time out to learn and grow. Thanks to Polytec, Hettich, Craftmark Surfaces, Planit, Leitz, First Super, Lincoln Sentry, Finlease, Cabinet Makers Insurance Brokers, Pytha Partners and Suttons. ■
acfa.net.au/key-takeaways-2025-acfa-conference/
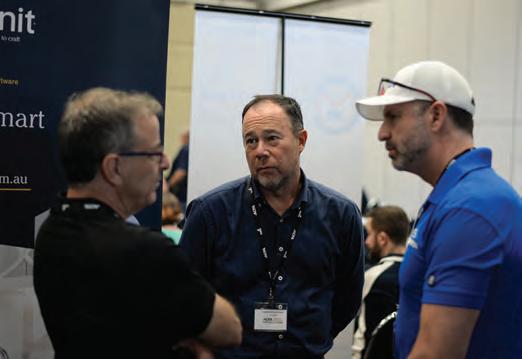
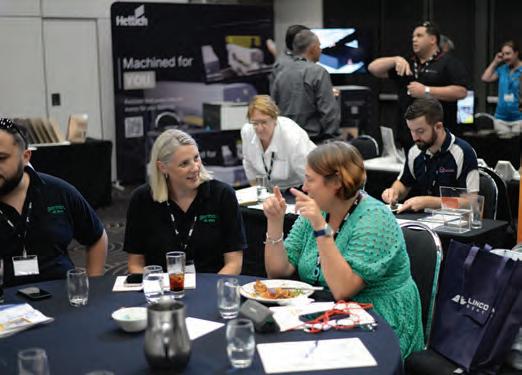
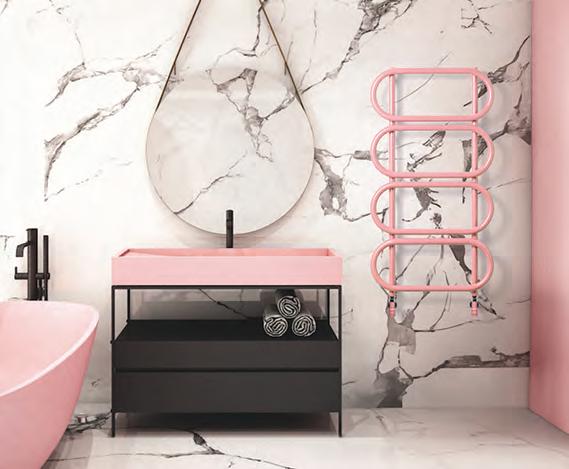
Oltremateria® ErailCaffe
Scirocco H Chain
Designed by Libero Rutilo from DesignLibero, Chain is a steel radiator that is available in two options (round or square), three heights and 79 colours including new matte shades such as Pink (pictured).
sciroccoh.it/en
Oltremateria® has been awarded the Archiproducts® ADA 2024 Sustainable Design Award for ErailCaffe, a new continuous surface for cladding and flooring made from recovered coffee grounds, out-of-date ground coffee and coffee beans. Available in Australia through Wellness Surfaces. wellnesssurfaces.au

Product Update
Give your next project a lift with our editor’s pick of the latest kitchen, bathroom and interior products
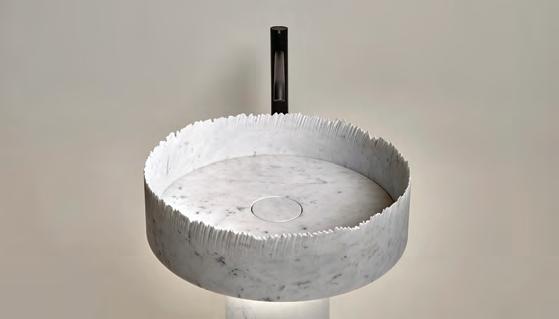
48 Round
The ZETR 48 Round has been named a Good Design Award Gold winner in the Product (Furniture & Lighting) category. Designed in Australia, the ZETR 48 is a small, flush outlet and switch with complementary matching button covers and metal finish faceplates. zetr.com.au/round-single-outlet-flat-black
antoniolupi Flow
The Flow washbasin by antoniolupi has been included in the ADI Design Index 2024. Designed by Paolo Ulian, Flow is made of white Carrara marble and features a unique fringed and pleated effect created by a numerically controlled waterjet cut.
antoniolupi.it/en/
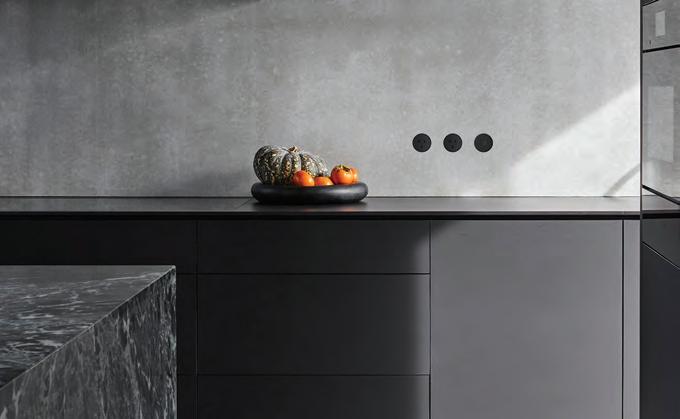
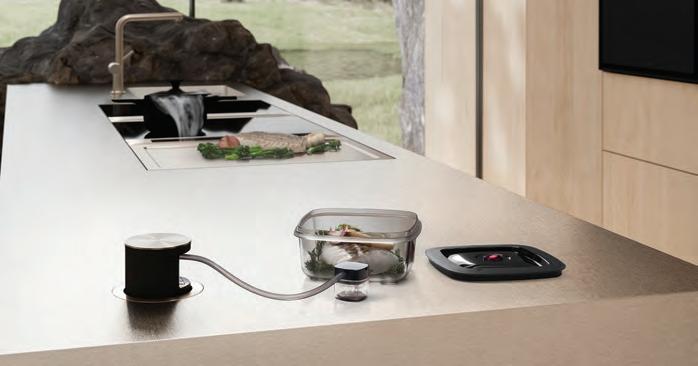
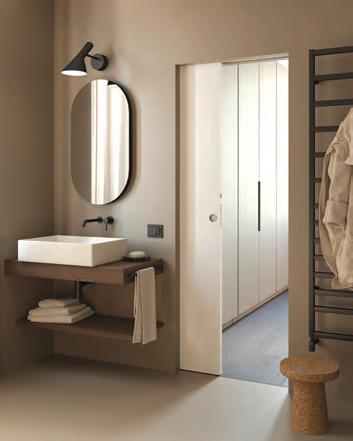
Lapalma WOD Panels
Protek® Magic Box Linear
Protek® Magic Box Linear includes spaces for electrical and water systems on both sides of the pocket frames, using a special expanded polystyrene mould. The Linear pocket frames are available in three options: Magic Box Linear Elektro for electrical systems, Magic Box Linear Hydra for water systems, and Magic Box Linear Domotika for both.
protek-controtelai.com/en/home/
The WOD Panel system by Lapalma was designed by Raffaella Mangiarotti and consists of a succession of elements in timber or felt, joined by hide hinges which allows it to fully adapt to a linear or curved position.
lapalma.it/en
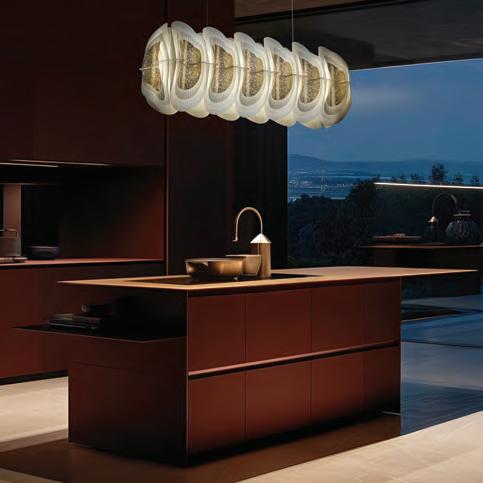
Bora QVac
The new BORA QVac is an effective and compact built-in vacuum sealer which can be used to vacuum seal food. The BORA QVac can be flush-mounted in worktops or surfacemounted on top to suit the design of the kitchen and the needs of the homeowner.
bora.com/au/au/
Vita Gessi Caffè™
The Vita Gessi™ multifunction system, in addition to providing still and sparkling water, cold and boiling, with different levels of customisation, is now available with an integrated coffee function using capsules. gessi.com/en

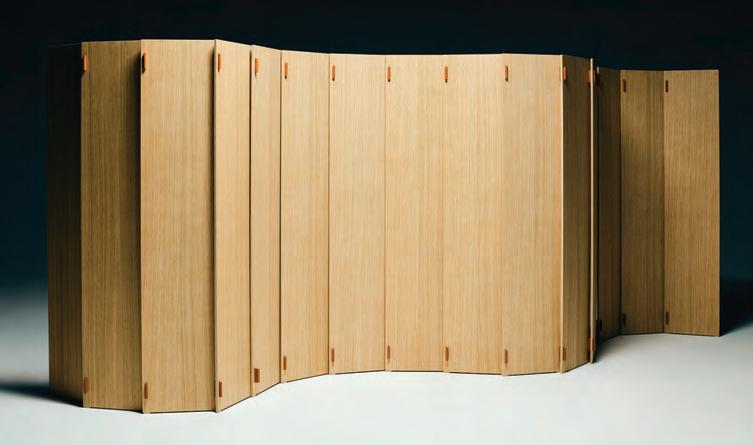
Slamp Fiordlys Collection
Designed by Paolo d’Arrigo, this new sculptural design takes its inspiration from the sinuous waves of the Aurora Borealis and the moving silhouettes of Nordic cliffs.
slamp.com/en

Transform Your Business with the 5S Methodology
Efficiency isn't just a 'nice to have'—it’s essential. To remain competitive, deliver high-quality craftsmanship, and meet deadlines, optimising every aspect of your operations is crucial
By Ben Fewtrell
One proven strategy to achieve this is the 5S methodology. Originating from Japan's lean manufacturing principles, 5S stands for Sort, Set in Order, Shine, Standardise, and Sustain. By adopting these principles, you can streamline your operations, reduce waste, and improve the overall quality of your work. Additionally, a well-organised workshop is a more attractive and safer place to work, which can help you retain skilled craftspeople and attract new talent.
Here’s how you can apply the 5S methodology to transform your business.
1. Sort: Eliminate the Unnecessary
The first step in the 5S methodology is to sort through all the tools, equipment, and materials. The goal is to remove anything that is not essential to your current operations.
Begin by categorising items into three groups: necessary, occasionally needed, and unnecessary. Use colour-coded tags or stickers to visually represent your decisions for each item. Start by removing unnecessary items. For instance, if you have outdated jigs, worn-out tools, or offcuts that you’ll never use, it’s time to clear them out.
Reducing clutter not only creates more workspace but also makes it easier to find the tools and materials you need when you need them. Take a walk through your workshop with a clipboard and note what doesn’t belong, you might be surprised at what you find.
2. Set in Order: Organise for Efficiency
Once you’ve sorted out the essentials, the next step is to organise them efficiently. Designate specific areas for tools and materials based on their frequency of use.
For example, place commonly used hand tools within easy reach of your primary workbench. Use labelled storage bins, pegboards, or shelving for other items. You can also paint or tape colour-coded outlines on your work surfaces to indicate where tools belong, ensuring they are always returned to the right spot.
For larger equipment that is portable, consider marking specific areas on the workshop floor to keep everything neatly in its place. Colour-coding based on type or stage of production (e.g., raw timber, cut pieces, and finished products) can further streamline operations and make it easier for your team to work efficiently.
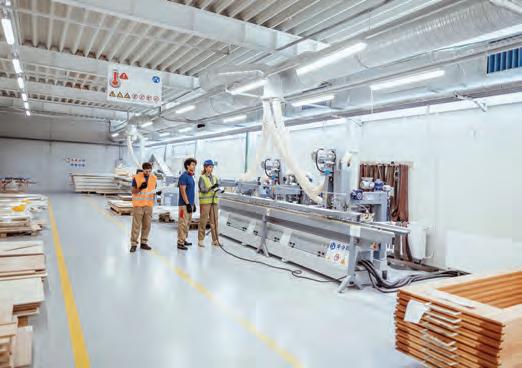
3. Shine: Keep the Workshop Clean
A clean workspace is essential for safety and productivity. Dust, scraps, and spills can create hazards and slow you down.
Implement a daily cleaning routine to keep your workshop spotless. This can include wiping down benches, vacuuming sawdust, and emptying bins. Encourage your team to take a few minutes at the end of each day to tidy up their areas.
A clean workshop not only creates a more pleasant environment but also reduces the risk of accidents

Business & Finance
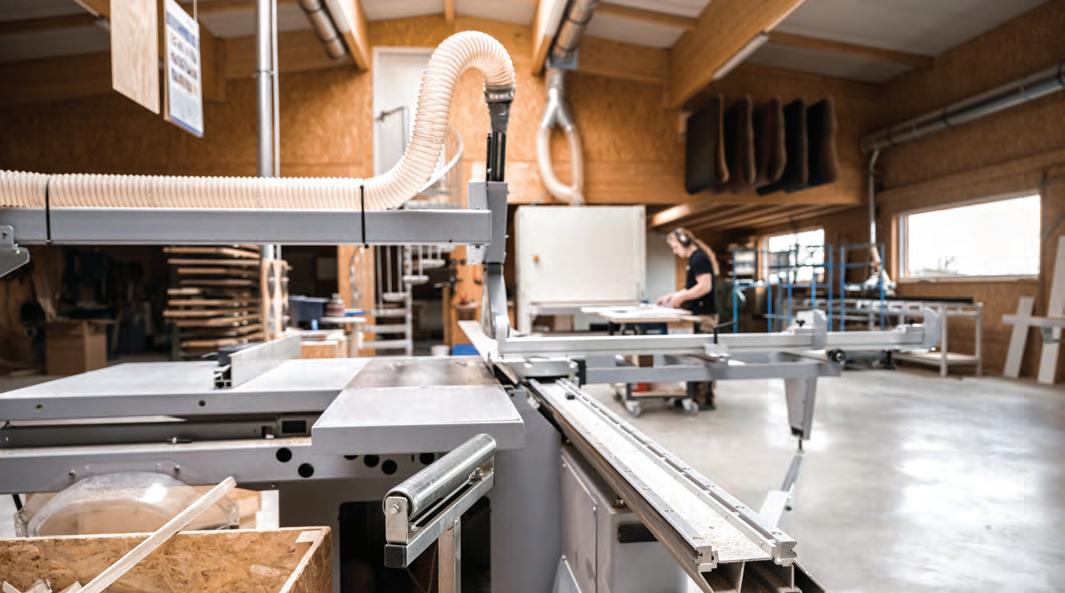
and ensures tools and equipment remain in good working condition. Plus, a tidy workspace reflects your commitment to quality and professionalism when clients visit your shop.
4. Standardise: Create Consistent Procedures
Standardisation ensures that the improvements made in the first three steps become part of your daily workflow. Develop Standard Operating Procedures (SOPs) for key tasks, such as material handling, machinery maintenance, and assembly processes.
For example, create a checklist for end-of-day clean-up, detailing tasks such as returning tools to their designated spots, clearing workbenches, and ensuring everything is ready for the next day. When everyone follows the same processes, it leads to consistent quality and fewer errors.
You can also establish routines for inspecting tools and equipment, ensuring they remain in top condition and are ready for use when needed.
5. Sustain: Maintain and Improve
The final step is to sustain the changes by making 5S a permanent part of your workshop culture. Regularly schedule audits to assess how well the 5S principles are being maintained.
Engage your team with ongoing training sessions to reinforce best practices. Hold monthly meetings to
review progress, address challenges, and celebrate successes. Recognise and reward employees who actively contribute to maintaining the 5S standards. By embedding 5S into your daily routine, your workshop will remain organised, efficient, and ready to handle even the most complex projects.
Adopting the 5S methodology in business can lead to significant improvements in efficiency, safety, and overall productivity. By sorting, setting in order, shining, standardising, and sustaining, you can create a workspace that supports high-quality craftsmanship while enhancing team morale and satisfaction.
Start small, focus on one area of your workshop and gradually implement each step. Before long, you’ll see the impact of 5S on your workshop’s efficiency, effectiveness, and reputation for excellence. ■
Ben Fewtrell is the co-founder and managing partner at MaxMyProfit. With more than 20 years of experience in business growth, Ben is also the cocreator of the "Business Exceleration™ Blueprint" and co-hosts the Max Your Business Podcast. He’s known for his dynamic presentations and effective business coaching, helping companies boost their sales and efficiency.
maxmyprofit.com.au/
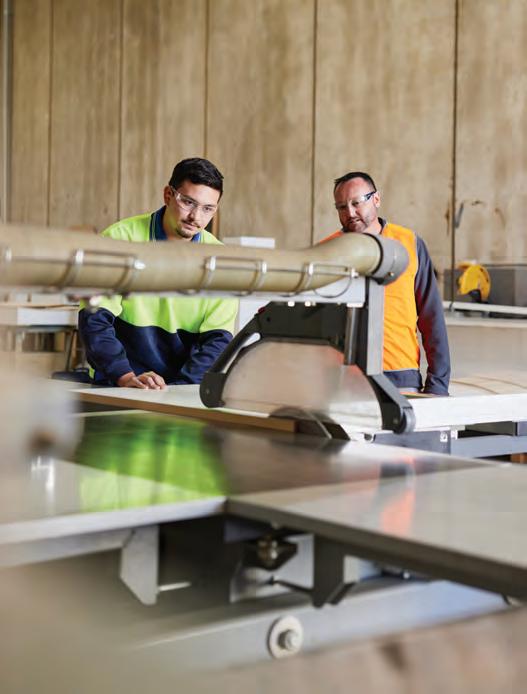
Key Insights from the ACCI National Business WHS Survey 2024
The Australian Chamber of Commerce and Industry's 2024 National Business WHS Survey sheds light on the evolving challenges faced by businesses in workplace health and safety (WHS). Representing 324 businesses across various industries and regions, the survey captures critical concerns and trends.
1. Complexity in Compliance: Businesses of all sizes reported feeling overwhelmed by increasing WHS regulations. Small businesses specifically highlighted the need for simpler, more practical guidance tailored to their industries.
2. Rising Mental Health Challenges: A striking 34 per cent of small business owners were diagnosed with a mental health condition in the past
year, underscoring the growing pressures in today’s business environment. Many businesses confuse general mental health concerns with psychosocial risks, pointing to a need for clearer education.
3. Psychosocial Risks Remain a Blind Spot: Businesses struggle with managing workplace issues such as poor relationships, conflict, and lack of support. Confidence in addressing these hazards varies by industry and business size, with larger organisations often grappling with conflict management and organisational justice.
4. Barriers to Effective WHS:
The top obstacles cited were time constraints, high costs, and conflicting sources of information. Small businesses were most affected by time and cost, while larger organisations sought consistency across jurisdictions.
5. Chemical and Biological Hazards:
Approximately one-third of businesses manage hazardous substances. Larger businesses typically implement thorough air and health monitoring, but small businesses often lack resources or awareness to do so.
6. Industry-Specific Challenges:
Key industries such as construction and manufacturing reported difficulties in applying standard WHS practices to specific risks such as silica dust and welding fumes, further emphasising the need for tailored approaches.
Empowering Businesses through Support
The report reinforces the critical role of industry associations in guiding businesses through WHS compliance. Tailored resources and accessible tools can alleviate the burden, enabling businesses to maintain safe and healthy workplaces.
ACFA is a proud member of the Australian Chamber of Commerce and Industry and ACFA representatives sit on the ACCI Workplace Policy Committee and Silica Reference Group to provide advocacy for ACFA members. ACFA members were encouraged to participate in the survey to provide insight relevant to our specific industry area. ■
ACFA Workplace Advisory Team Membership@acfa.net.au 1300 342 248
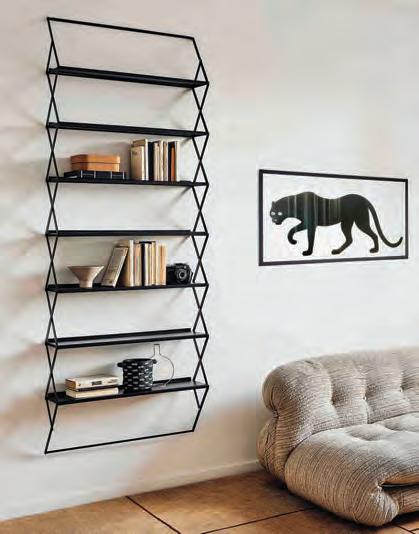
Eta Beta bookcase
Designed by Paolo Ulian and Cinzio Ianiro, the bookcase connects the horizontal shelves by means of pantograph-style lateral struts that work like an accordion. Eta Beta is available in two different heights — seven shelves and 212cm high or four shelves and 134cm high. The shelves are 20cm deep and 82cm wide and the units are available in matte black or matte white.
kriptonite.com/it

Bloomery Décor
From artist Julie Coste, based in the Netherlands, the Vintage Pink Cranes wallpaper is part of the Bloomery Décor designer wallpaper collection. With a stunning, neutral colour palette, this wall covering brings a timeless flair to traditional and modern homes. wallsauce.com
Furniture & Wall Coverings
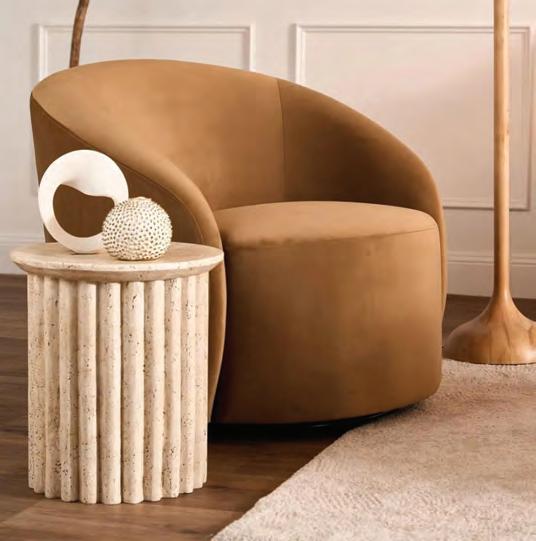
Evoking tranquillity, Wild Wild Woods is from the Rewilding collection and invites a strong connection to nature. Printed on Eco-wallpaper with 79 per cent renewable fibres, and also available as a bespoke Grasscloth wallpaper, recycled velvet or linen, handmade-to-order lampshades and recycled velvet cushions. divinesavages.com
Interior and exterior product inspiration for rooms and walls to create an outstanding end result
Tivoli Side Table
Introduce a touch of glamour with the Tivoli Side Table. Crafted with faux travertine and fluted sides, this pillar-column-inspired table exudes luxury. Its resin finish adds a polished touch, making it the perfect statement piece for any room.
kiraandkira.com.au/
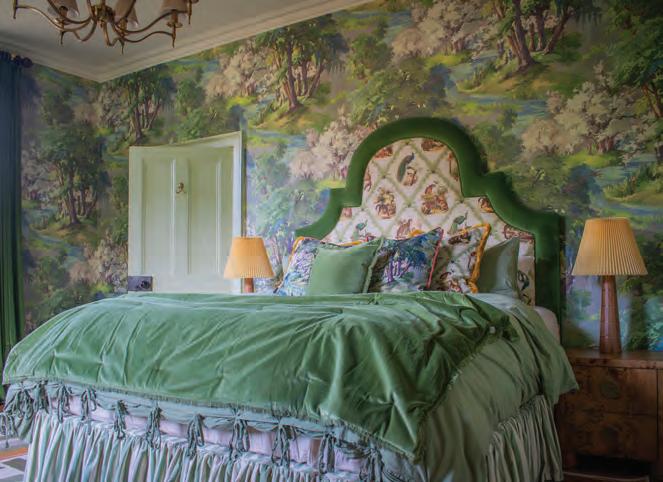
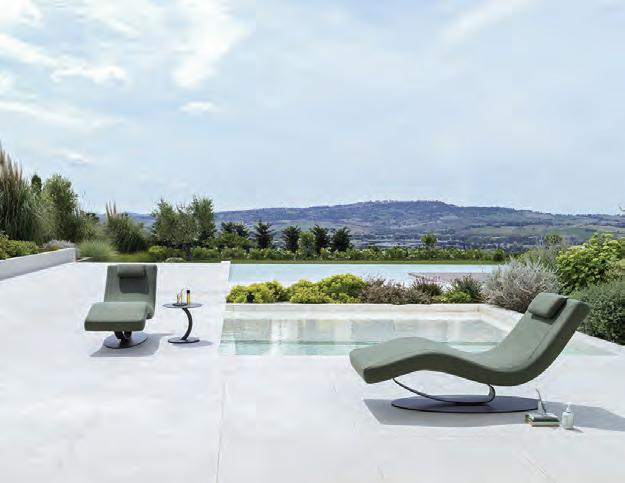
Salix Breeze
Salix Breeze is a sublime cream and green Japanese willow tree wallpaper mural, where the serene world of chinoiserie meets modern Japandi sensibilities. Whether as a statement piece in a living room or a soothing backdrop in a bedroom, the cream and green Japanese willow tree wallpaper mural infuses spaces with timeless elegance and a breath of Zen.
feathr.com/

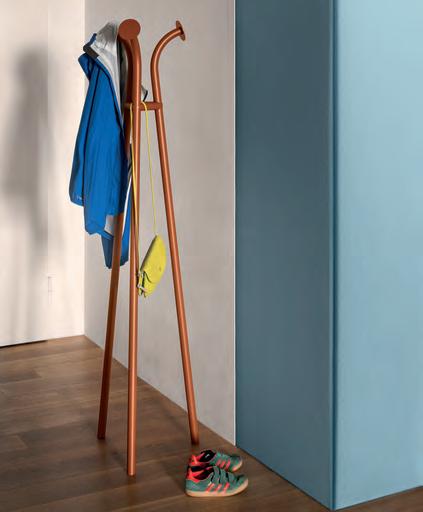
Wellness Therapy
Designed by Alberto Apostoli from Studio Apostoli for Varaschin, the Wellness Therapy collection includes a chaise lounge (pictured), single and double beds, and a side table. Focused on outdoor wellbeing and the idea of ultimate relaxation, the collection is ideal for residential projects, spas or hospitality establishments. albertoapostoli.com/?lang=en
The Mixer
The Mixer was designed with hosting in mind! She’s perfectly proportioned to make the most of her storage potential. Whether it’s cocktails, kitchen utensils or storing your most prized possessions, The Mixer will surprise you with how much can be hidden inside! mustardmade.com/
Bobbi Bar Stool

The Bobbi Bar Stool combines contemporary style with modern design, featuring a slender frame that adds a sleek touch to any kitchen. Designed for comfort, it provides excellent back support and comes upholstered in two colours (Boho Chai pictured), offering versatility to suit various styles.
satara.com.au
Hug coat stand
Designed by Giulio Iacchetti, the Hug coat stand is part of the Hug collection and is designed to make a visual impact. Its simple design of three static vertical pieces held together by a horizontal tube belies the cleverness of its design. The collection is available in 35 finishes including 11 new colours introduced in 2024. fantin.com/en/
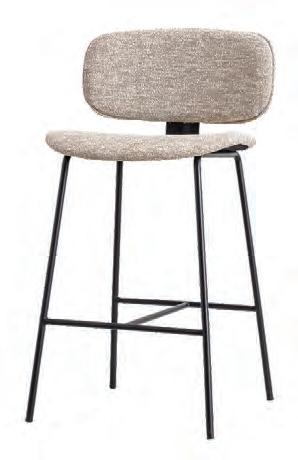
Cersaie 2024
The international exhibition for ceramic tile and bathroom furnishings was held last September in Bologna, Italy
Held from 23-27 September 2024, the 41st edition of Cersaie saw 15 fully occupied halls and a total exhibition floor space of 145,000m2, with more than 95,000 local and international visitors. The show hosted 606 companies with 38 per cent non-Italian exhibitors from 25 countries. Here are some of the highlights.
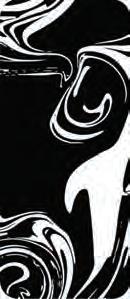

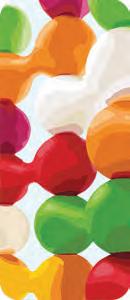

Casalgrande Padana
The new Terrae collection provides a contemporary reinterpretation of the traditional ceramic tile. Terrae is available in six colours and six sizes as well as a natural matte finish and a grip finish, all with a thickness of 9mm. Terrae is also available with a thickness of 20mm with an anti-slip surface for use outdoors. These tiles can be laid on screed or directly on earth or grass and Terrae is made entirely from natural raw materials. casalgrandepadana.com
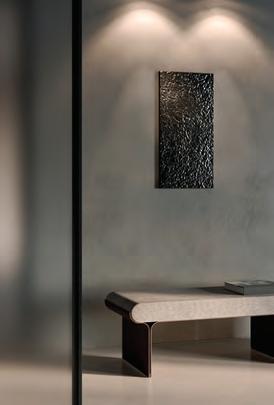
Lovelight39
The “Urban Garden” collection is designed by architect Simone Micheli and is a manifesto for the revisitation of urban space. Each slab tells the stories of community and sharing, and invites a deep reflection on urban planning and contemporary living. The collection stands out for its mix of materials, organic lines, bright colours, blacks and whites, interspersed with silver and gold finishes.
Lovelight39.it
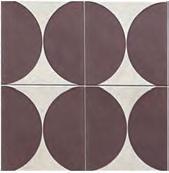

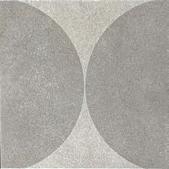
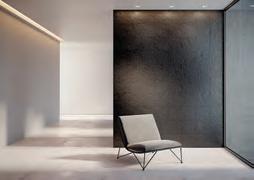
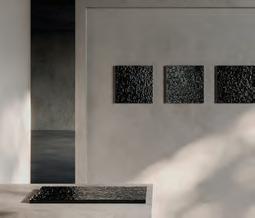
Ceramiche Refin
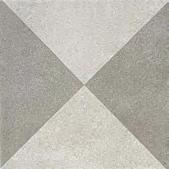
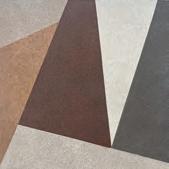
Designed by Quayola, each 20mm-thick piece seeks to represent the ripples of water on the surface of the porcelain stoneware. Glint Variation 30cm x 30cm consists of four subjects which can be used as a composition of pieces or to create scenographic full-wall coverings. Glint Variation 30cm x 60cm is proposed as a single piece of art, produced in a limited edition of 99 pieces and delivered with a numbered certificate of authenticity.
refin.com


SICIS
The Elisyan collection is a series of furniture pieces with integrated backlighting. Each element is designed to enhance the beauty of Vetrite, SICIS’ iconic laminated glass. The collection includes baths and washbasins, mirrors and shower cubicles each with a refined harmony between aesthetics and technical execution. sicis.com/
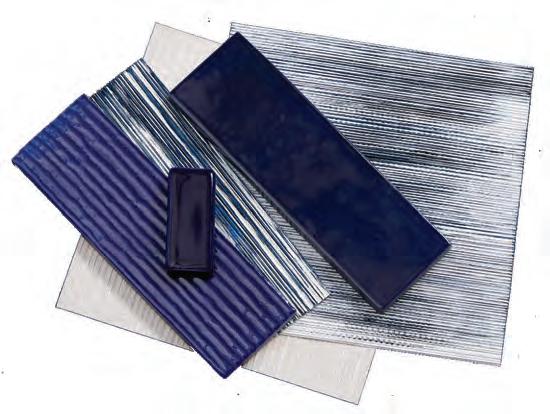
Sapienstone
Ceramica Sant’Agostino
Introducing eight new collections: Novart combines the fragmented and decorative nature of mosaics; Iro is inspired by textural, sinuous plaster for a vibrant colour effect; Windstone represents wind moving across a surface; Bit is a cotto-effect brick tile; Glow is a silky, neutral terrazzo, Invictus Cross has a cross-cut vein inspired by travertine; Gracewood is a timber-effect collection; and Extra has been expanded with three new colours from the Bergstone series in slab format.
ceramicasantagostino.it/en/
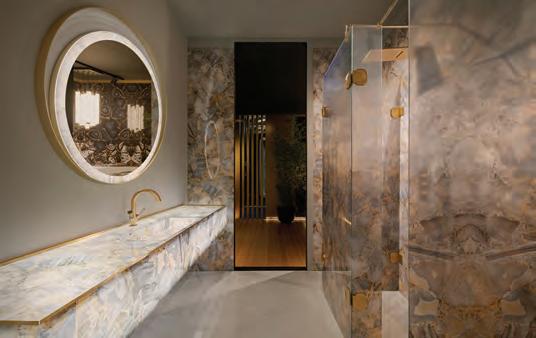
Decoratori Bassanesi
Two new surfaces designed by Federica Biasi were presented. Kimono features bold, vibrant colours and takes cues from the intricate knots and folds of a traditional Japanese robe. Wă reflects the uneven terracotta tiles seen throughout the architecture in rural villages in China.
decoratoribassanesi.it/en/
Silver Wave 4D features a lapped finish that accentuates the natural beauty of the granite while being smooth to the touch. Crema Avorio and Breccia Imperiale are available in a natural finish that highlights the structure and veining. The warm, velvety hues of Crema Avorio brighten up spaces with a subtle elegance, while Breccia Imperiale, with its rich brown colour and sinuous veins, adds warmth and character to any space. sapienstone.com/
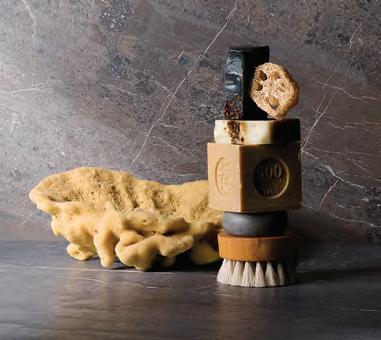
cersaie.it
Workplace Health & Safety
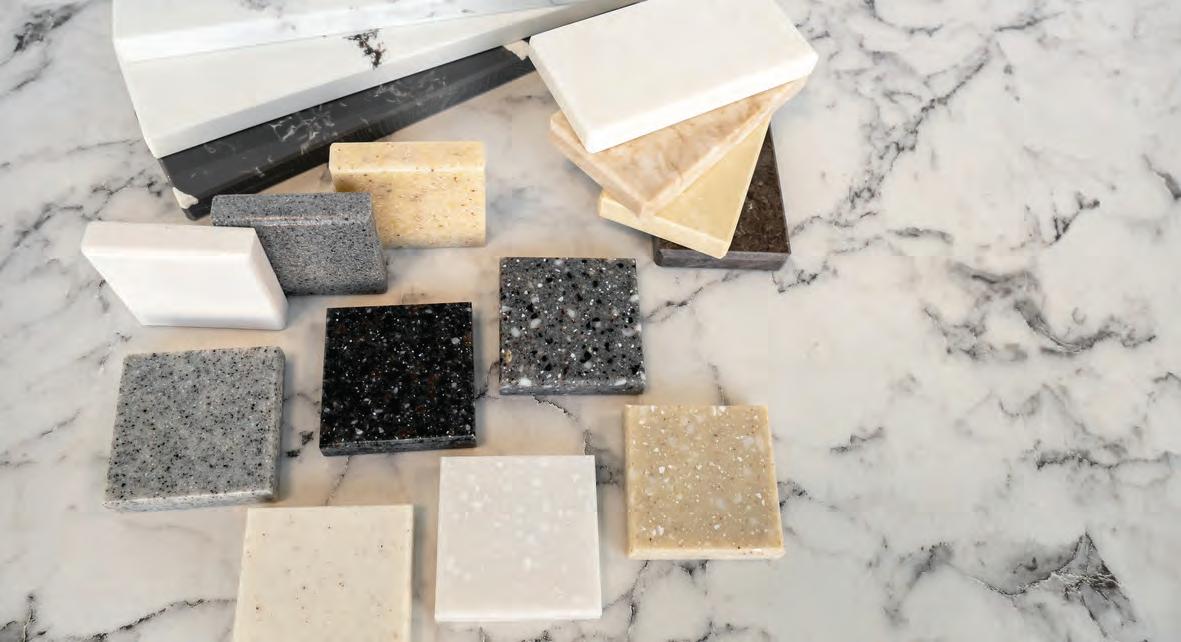
With all jurisdictions now finished their transitional arrangements, the complete ban on all materials containing at least one per cent crystalline silica, including engineered stone, came into effect on 1 January 2025.
From 1 July 2024 a ban on the manufacture, supply, processing and installation of engineered stone benchtops, panels and slabs was implemented. A number of jurisdictions were granted a transitional period between 1 July 2024 and 31 December 2024 (with the exception of Queensland, Victoria and the ACT).
The engineered stone prohibition only applies to engineered stone benchtops, panels and slabs. Engineered stone products not in these forms are not prohibited under this ban. In addition, sintered stone and porcelain products that do not contain resin do not meet the definition of engineered stone so the ban does not apply to those products.
To allow for the management of legacy engineered stone benchtops, panels and slabs, allowances have been made for processing under certain circumstances, such as disposal. Under WHS Regulations, application can be made for exemption from the ban and this may be granted if certain criteria are met and strict safety processes followed.
SafeWork Australia has developed a guide to support persons conducting a business or undertaking
Engineered Stone Ban
(PCBUs) to understand how the WHS Regulations will affect them. This can be found on the SafeWork Australia website.
The guide references WHS Regulation 529D and details the scope of the engineered stone prohibition and explains in detail why it was implemented. It provides further guidance around the limited circumstances in which work with engineered stone is permitted and how to make an application, if required, to request an exemption. A PCBU must notify the WHS regulator before any permitted work with legacy stone is carried out.
Some crystalline silica substances, such as natural stone, are not covered by the ban but PCBUs still owe a duty of care to the health and safety of workers who are processing natural stone products. A “Working with Crystalline Silica Substances: Guidance for PCBUs” document is also available from SafeWork Australia.
Members can also view and download resources from the ACFA Member Portal in the WHS/Crystalline Silica Tab — please remember to enter your username and password to be able to access the member-only resources. ■
ACFA Workplace Advisory Team Membership@acfa.net.au 1300 342 248
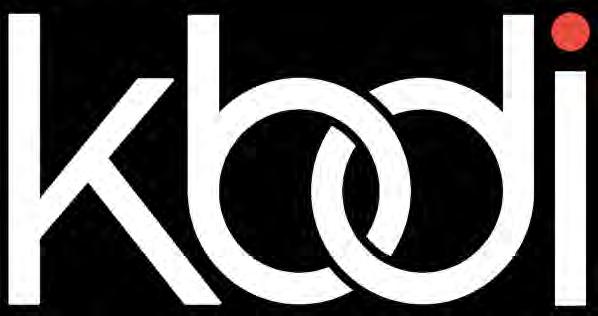
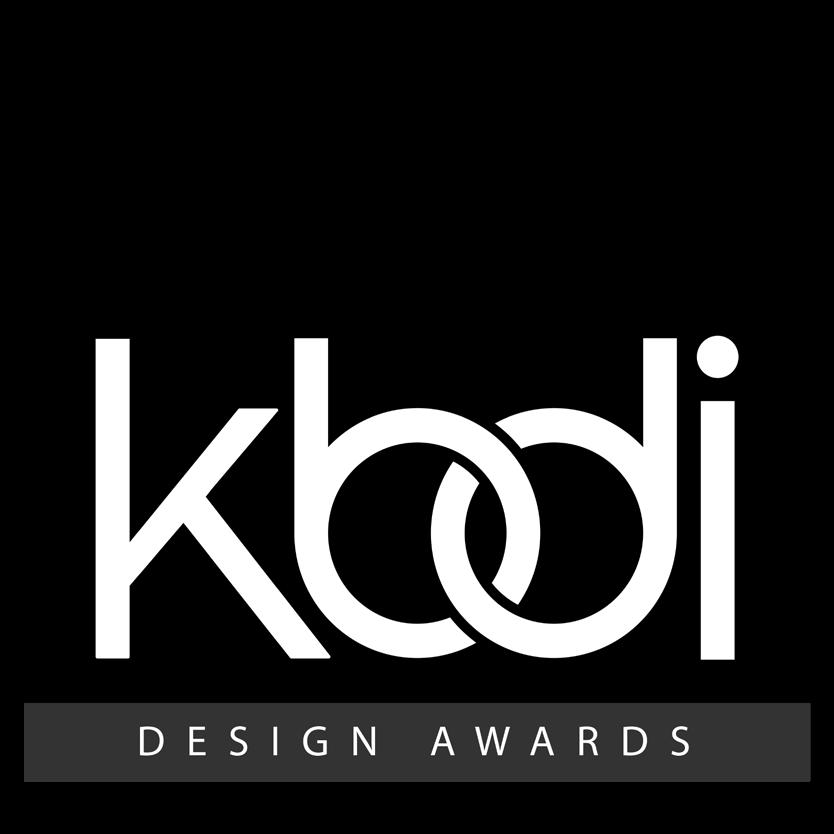
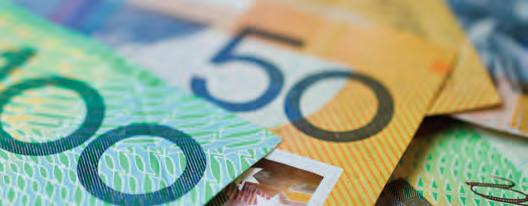
Incentive Payment for Apprentices
The Australian Government has announced a $10,000 incentive payment to attract apprentices into the residential construction and clean energy sectors
The Independent Tertiary Education Council Australia (ITECA), of which ACFA is a member, has released a statement in response to the Australian Government’s announcement of a $10,000 incentive payment for apprentices, specifically in the residential construction and clean energy industries. While the organisation welcomes the focus on retention of apprentices in these sectors, it notes that the announcement fell short of addressing skills shortages in other key industries.
“This initiative is a welcome boost for apprentices entering residential construction and clean energy careers, but it does little for people aspiring to work in industries outside these sectors, where the skills gap is just as urgent,” says Troy Williams, ITECA chief executive.
It is also unclear (at time of printing) whether cabinetmaking would fall into the “residential construction” definition to allow cabinet-making apprentices to be eligible for the incentive payment. ACFA has made, and will continue to make, enquiries to obtain further information on this matter.
According to ITECA, the government’s investment of $627 million in this initiative may encourage some new apprenticeships and help retention in those two industry sectors. However, the organisation says the scheme is unlikely to reverse the sharp decline in apprentice recruitment seen in recent years.
“While it’s positive to see measures that aim to support apprentice recruitment and retention, we
cannot ignore the glaring gaps in the Australian Government’s approach and the industries left behind,” adds Mr Williams.
The scheme will come into effect from 1 July 2025 and will see eligible apprentices receive a $2000 lump sum at six, 12, 24 and 30 months, with a final payment on completion of their apprenticeship for a total of $10,000 on top of their wages.
The announcement was made as a response to the Strategic Review of the Australian Apprenticeship Incentive System, which commenced in February 2024 and was led by Dr Iain Ross AO and Ms Lisa Paul AO PSM. The review particularly pinpointed apprentices as being highly vulnerable to cost-ofliving pressures and identified this as a reason for falling enrolment numbers.
At the time of the announcement, Minister for Skills and Training, Andrew Giles, said, “it is essential that we get the Australian Apprenticeships system right. We need to have a system with more apprentices finishing their training and gaining the skills and qualifications that we need in our workforce."
ITECA will continue to lobby the Australian Government to broaden the scope of the scheme to address systemic skills shortages facing businesses across the entire economy. It identified support of small businesses which employ apprentices as well as greater collaboration with independent RTOs as being essential to ensure Australia’s workforce is equipped to meet future demand. “Ensuring apprentices start and complete their training is vital,” says Mr Williams. “But it is only one piece of the puzzle."
ACFA CEO Dean Brakell welcomes the initiative and says, “We are glad to see a focus from the Government on redressing the shortfall in apprenticeship commencements and completions, and we are keen to receive further clarification on exactly how the scheme will be administered and implemented, and which sectors are eligible.
“We note the scheme is not due for implementation until after the next federal election and we remain optimistic that the scheme will provide the incentives needed to ensure an increased uptake in the number of apprentices, not just in our sector, but across the broader construction industry.
“On behalf of our members, we will continue to work with various stakeholders to provide further clarity and information as it comes to hand,” he adds. ■
A Modern Qld Reimagining
This project sought to create a home that is both immediately welcoming and equally impressive
By combining thoughtful design with a focus on comfortable living, Sunshine Coast home builders AUSMAR achieved a space that is both beautiful and functional.
This project highlights the power of focused design. By strategically selecting areas for premium finishes (such as the Illumination Design Profile on key cabinetry) AUSMAR, in collaboration with the skilled joiners at Format Kitchens, achieved a sophisticated aesthetic without over-capitalising. This thoughtful approach is something that it applies to its many projects, maximising the importance of both impact and value.
This AUSMAR custom home brings a modern twist to the classic Queenslander style, embodying a vision of warmth and sophistication. A thoughtfully curated colour palette and meticulously designed elements create an inviting and refined atmosphere. The kitchen, bathroom, and wardrobe spaces are cleverly designed with abundant storage solutions. Rich dark timber-toned cabinetry provides a striking contrast

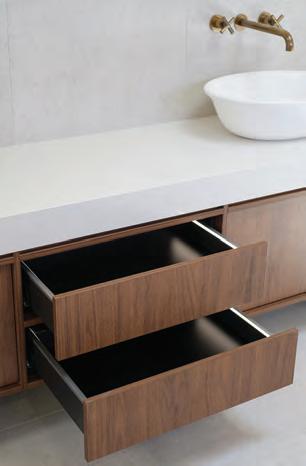
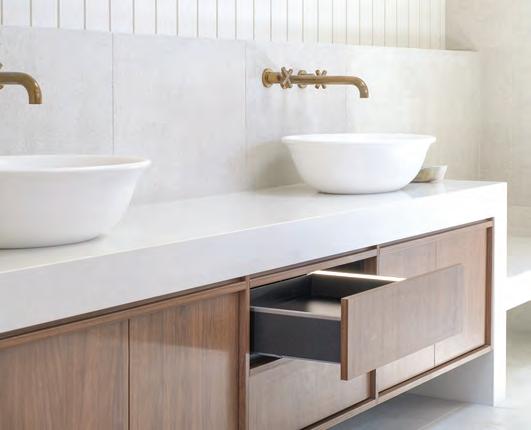
to the neutral white marble textures, achieving a seamless balance of elegance and practicality in every room.
“What is really great about the Hettich eShop website is that you can download and import the 3D hardware files into Sketchup, which can give the clients a good idea of what they are going to get come production time” — Format Kitchens on the benefits of the Hettich eShop.
Illumination Everywhere
Design and technology are key features integrated into the cabinetry of this home. The AvanTech YOU Illumination drawers from Hettich add a stunning glow when opened, enhancing both the kitchen and bathroom spaces.
With encouragement from Hettich and collaboration with its joiners, AUSMAR incorporated them into this project with outstanding results. The team was particularly impressed by the hardware's quality and the sleek, slimline design, making it a feature they plan to specify in future projects.
Intentional Thinking
Complementing the Anthracite drawers, the Obsidian Black hinges paired beautifully with the black cabinetry carcass, creating a cohesive and sophisticated look throughout the home.
Waste bins provide another practical and welcome addition, sitting beside the sink for a seamless waste solution. ■
Hettich Australia designwithhettich.au
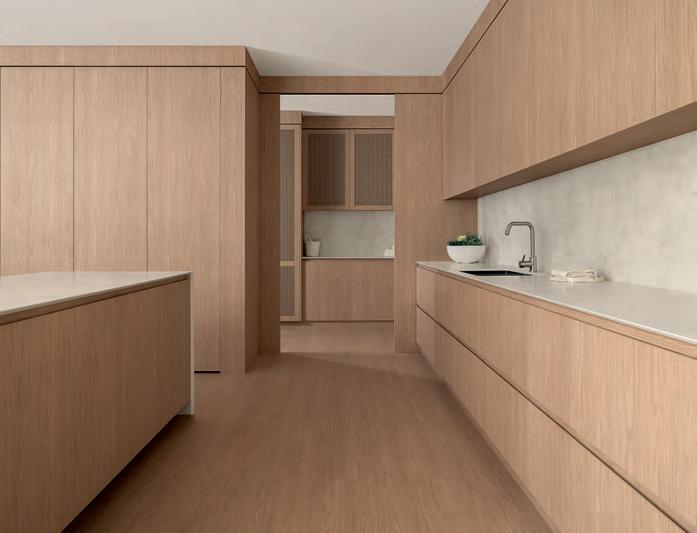
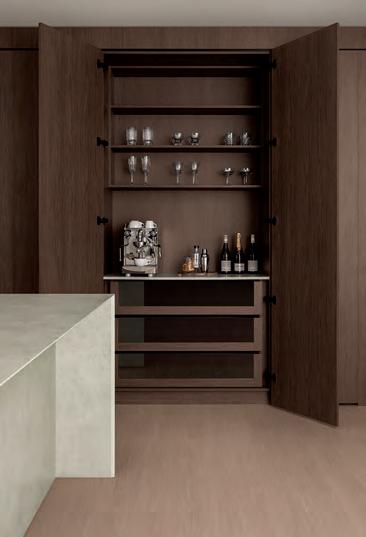
A global creative first: The Boston Oak Collection
The Boston Oak Collection is an innovative milestone, offering a broad spectrum of 12 colours inspired by traditional methods of staining natural timber, using the original Boston Oak structure as its base in polytec’s signature Woodmatt finish.
This collection is more than just new colours; it represents a significant evolution in design, setting new standards for versatility and functionality within the industry. The collection ensures the ultimate mixand-match aesthetic available in 18mm decorative board, 25mm panels, laminate, and 18mm Surano doors with an expanded product offer to come.
In observing the evolving trends of design, polytec recognised a need for a greater synergy in materials. Designers were often faced with the challenge of mismatched timbers and incompatible colours, especially when working with mixed materials in high-end joinery projects. The Boston Oak Collection was developed to provide a harmonious range of products that connect both in structure, aesthetic appeal, and functionality.
The Boston Oak Collection equips joiners with products for high-traffic areas; laminate to build benchtops and curves, 18mm decorative board
to create ceiling-to-floor cabinets, wall linings, and custom joinery.
You can achieve a high-end, cohesive look with the Boston Oak Collection without compromising on functionality. For those seeking a sophisticated and versatile solution for their design projects, the Boston Oak Collection offers a truly unparalleled choice. ■
polytec.com.au/ polytec.com.au/the-boston-oak-collection 1300 300 547
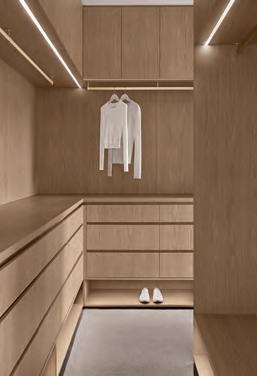

Expert Guidance, Stronger Business
Your HR & Workplace Support Team

ACFA membership offers businesses access to a wide array of industry resources, including tailored templates, checklists, policies and a personal HR advisory call services.
www.acfa.net.au
Expert guidance from hiring to HR compliance; protecting your business at every stage.
Hear from one of our members
“The ACFA team is a fantastic source of knowledge and always goes the extra mile to find answers and provide support.
What I really appreciate is how easy it is to call and speak to someone directly, and they always follow up with an email summarising the conversation and sharing any extra info or documents needed.
Every experience I’ve had with ACFA has been positive”
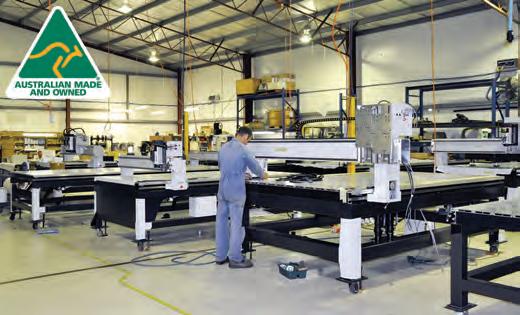
AustralianMade Solutions with Multicam Systems
The commitment to innovation, quality, and customer satisfaction is shown through Multicam’s dedication to providing solutions to Australian businesses
Australian-owned and operated, Multicam Systems has been an industry leader in providing Australian manufactured CNC routing solutions to a diverse range of industries for more than 35 years.
Unpredictable changes in import and export costs due to fluctuations in currency exchange rates can have an impact on costs and complicate budgets for businesses and customers. Multicam Systems offers a clear advantage in the market, with its CNC routing machines manufactured in Australia.
By designing, manufacturing, and supporting CNC machines locally, Multicam can provide its customers with a level of stability and reliability that is needed in today's landscape. The company’s production process does not depend on international imports or overseas manufacturing, and changes in the global market do not impact the prices of its machines.
When the Australian dollar fluctuates against international currencies, companies which source machinery from overseas often face increased product costs, which must be absorbed or passed on to the purchaser. In contrast, Multicam Systems and its
customers can rely on consistent pricing which avoids the complications associated with unpredictable exchange rates.
Multicam’s focus on local production ensures faster turnaround times for machine orders, spare parts, and servicing. One major focus has been on advances in machinery footprint to suit workshops with smaller floor space; some imported machines are manufactured without taking this into consideration.
Companies reliant on imported goods may also experience significant delays caused by disruptions in the supply chain. Multicam Systems' local manufacturing and servicing teams are always prepared to assist with prompt support, providing Australian businesses with a dependable partner that recognises the importance of maintaining uninterrupted production.
Selecting a Multicam Systems machine represents not only a practical decision but also an investment in the Australian economy. By supporting domestically produced goods, customers contribute to the advancement of Australian manufacturing and aid in the creation of jobs for skilled workers within the country.
During challenging economic times, Multicam's commitment to local production and customerfocused solutions enables it to provide stability, reliability, and peace of mind to consumers. When forming a partnership with Multicam Systems, businesses gain access to world-class CNC technology and support an Australian-made solution that mitigates the uncertainties and fluctuations of the global economy.
Multicam Systems continues to provide quality, reliability, and the lasting benefits of local expertise, building a strong future for the Australian economy. ■
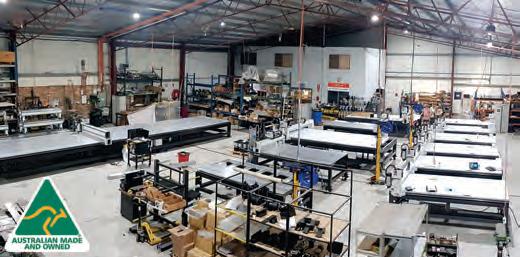


Introducing AVENTOS top and AVENTOS HKi
Blum’s AVENTOS top and AVENTOS
HKi lift systems offer a perfect blend of style and functionality
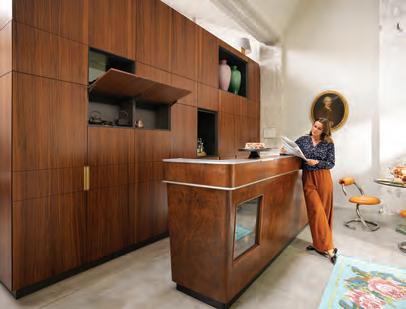
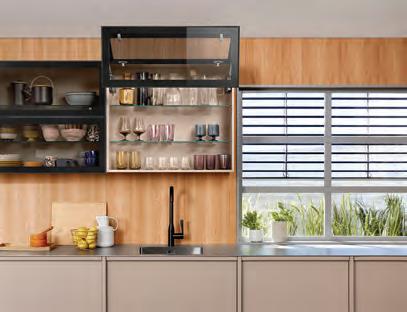
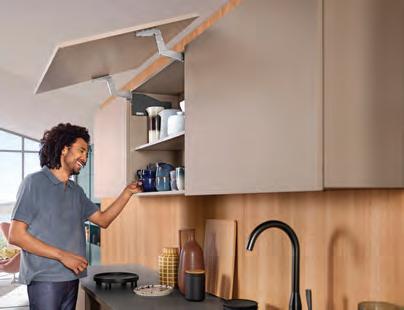
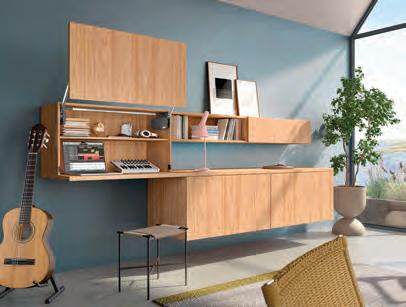
Blum has launched AVENTOS top and AVENTOS HKi lift systems into the Australian market — innovative solutions that combine efficiency, aesthetics, and convenience.
The new lift systems offer cutting-edge options for cabinetry that go beyond the traditional hinged door. These revolutionary systems combine seamless integration, aesthetic appeal and exceptional performance.
AVENTOS top The Latest Generation of Lift Systems
The AVENTOS top range impresses with its compact design. With its sleek, minimalist look, the range features clean lines and subtle elegance. The lift mechanisms are concealed behind silk white, light grey, or dark grey cover caps, blending seamlessly with the furniture or standing out as a charming contrast.
Ideal for overhead wall cabinets, AVENTOS top provides freedom of movement and easy access without occupying too much space. Be it fold up, swing up and over, lift up or pivot up — there is a lift type to suit nearly any design requirement.
The AVENTOS top range comes with Blum’s BLUMOTION soft-close as standard. Or, for an enhanced experience, choose Blum’s SERVO-DRIVE electrical opening support system.
AVENTOS HKi — The Integrated Stay Lift
AVENTOS HKi is the first of its kind and is able to fully integrate into the cabinet side thanks to its extremely slim construction. This lift system fits perfectly into cabinet sides with a thickness of 16mm or more, making it virtually invisible from the outside. It creates a seamless, uncluttered appearance without sacrificing the same high-quality motion, symmetrical fittings, opening angle stop, easy adjustment, and easy assembly that the AVENTOS lift system range is known for.
The integrated lift system remains invisible when closed, even with glass fronts. The visible parts of AVENTOS HKi, seen when the front is open, show elegant onyx black hardware. Fronts can be made from various materials, such as timber, MDF, and glass, featuring narrow or wide aluminium frames.
Overhead Cabinets — Enhancing Design Possibilities
Both AVENTOS top and AVENTOS HKi lift systems push the boundaries of design. These systems align perfectly with current trends towards concealed hardware, ensuring maximum accessibility and customisability.
Whether you’re drawn to the visible elegance of the AVENTOS top or the subtle integration of the AVENTOS HKi, these systems provide the tools to create truly remarkable interiors. ■
Blum Australia blum.com/au/en/
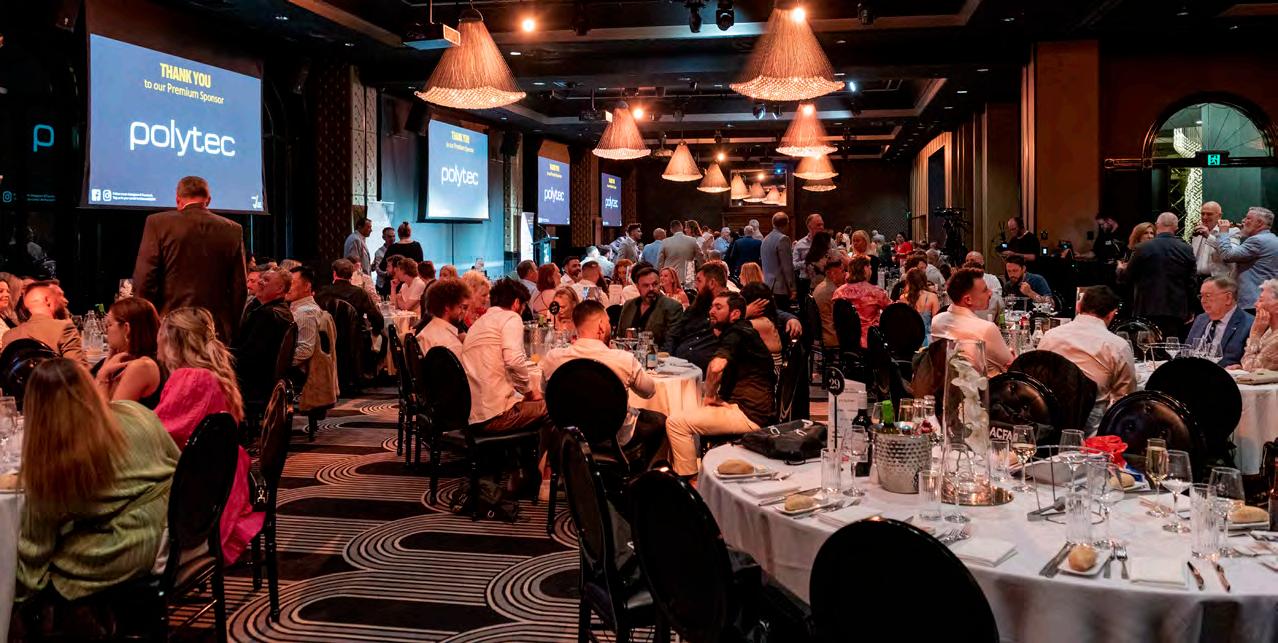
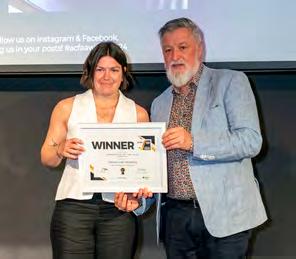
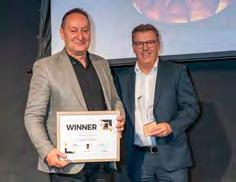
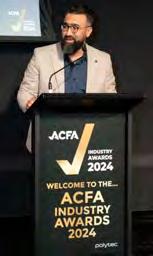
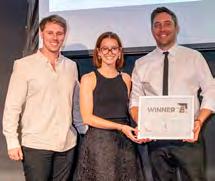


AWARD ENTRIES NOW OPEN
EARLY BIRD CLOSES ENTRIES CLOSE AWARDS DINNER
30th May 2025
31st July 2025 19th September 2025
Recognising Craftsmanship, Design & Innovation
The ACFA Industry Awards celebrate the outstanding craftsmanship, innovation, and leadership across the cabinet, furniture and design industry. Whether you’re an emerging talent or a seasoned professional, this is your chance to showcase your talent, gain industry-wide recognition, and elevate your business.
Don’t miss the opportunity to boost your profile, attract new clients and stand out!
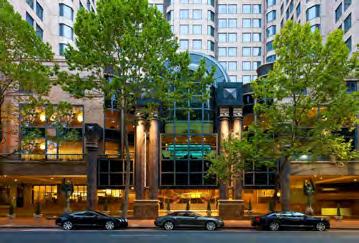
Lincoln Sentry + Oliveri sink and tap update
Growing its partnerships with premium product suppliers, Lincoln Sentry is proud to expand its offering of quality Oliveri sinks and taps
A commitment to quality and support of the Australian design and cabinet-making industries are just two of the many synergies between Lincoln Sentry and Oliveri which makes this range expansion a natural progression.
Lincoln Sentry is one of Australia's leading suppliers and distributors of hardware and components to the cabinet- and furniture-making industry, having been established in 1986. The company specialises in offering a selection of quality products, backed by expert knowledge and advice, with a focus on the trade market of Australia.
Oliveri has been designing and manufacturing products in Australia since 1947 and its investment in high-quality sinks and tapware is a perfect fit with Australia’s design-conscious community. The company also sources a comprehensive range of sinks and taps from around the globe, in addition to its range of locally made products.
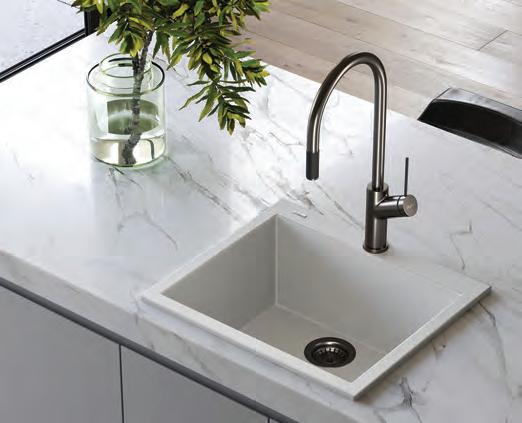
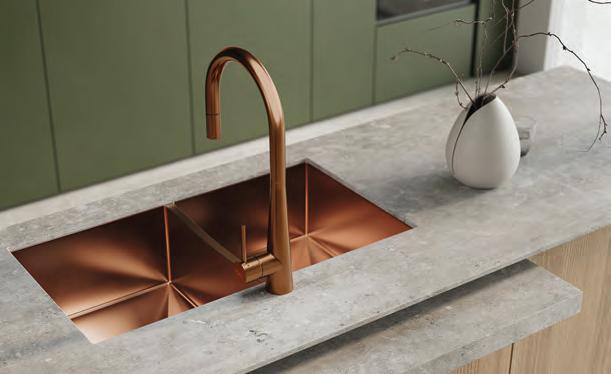
Oliveri’s sink and tap ranges provide solutions to suit all kitchen and laundry environments, whether in premium luxury homes or to help with budgetconscious renovations. All Oliveri sinks are backed by a lifetime warranty.
Contemporary and durable, the Santorini range of Italian-made granite sinks are scratch, heat and impact resistant. Available in a full range of design configurations including both undermount and topmount installations, Santorini can be specified in black, white or new matte black finishes.
The Spectra range is designed for luxury projects, with its sleek 5mm radius corner and square-bowl design. Choose from five striking colour finishes including gold, stainless steel, gunmetal, copper or black. Made from 1.2mm stainless steel, Spectra is available as a single, one-and-a-half bowl, and double-bowl configuration.
For a modern, soft-square design, consider the Sonetto Project range, available in 1.2mm stainless steel. With multiple bowl configurations available, Sonetto is a lovely addition to any interior space.
Australian-made, the Flinders Project and Finista® ranges round out the new product offerings. Both are available as a single, one-and-three-quarter, or double-bowl-with-drainer configurations. The Flinders Project range provides a contemporary drainer design while the Finista® range is perfect for those looking for a great quality solution at a budgetfriendly price.
Check out the new great range of laundry sinks and matching tapware on the Lincoln Sentry website. ■
Lincoln Sentry lincolnsentry.com.au/ls-resources-blog/ catalogues-ch-sinks-and-accessories
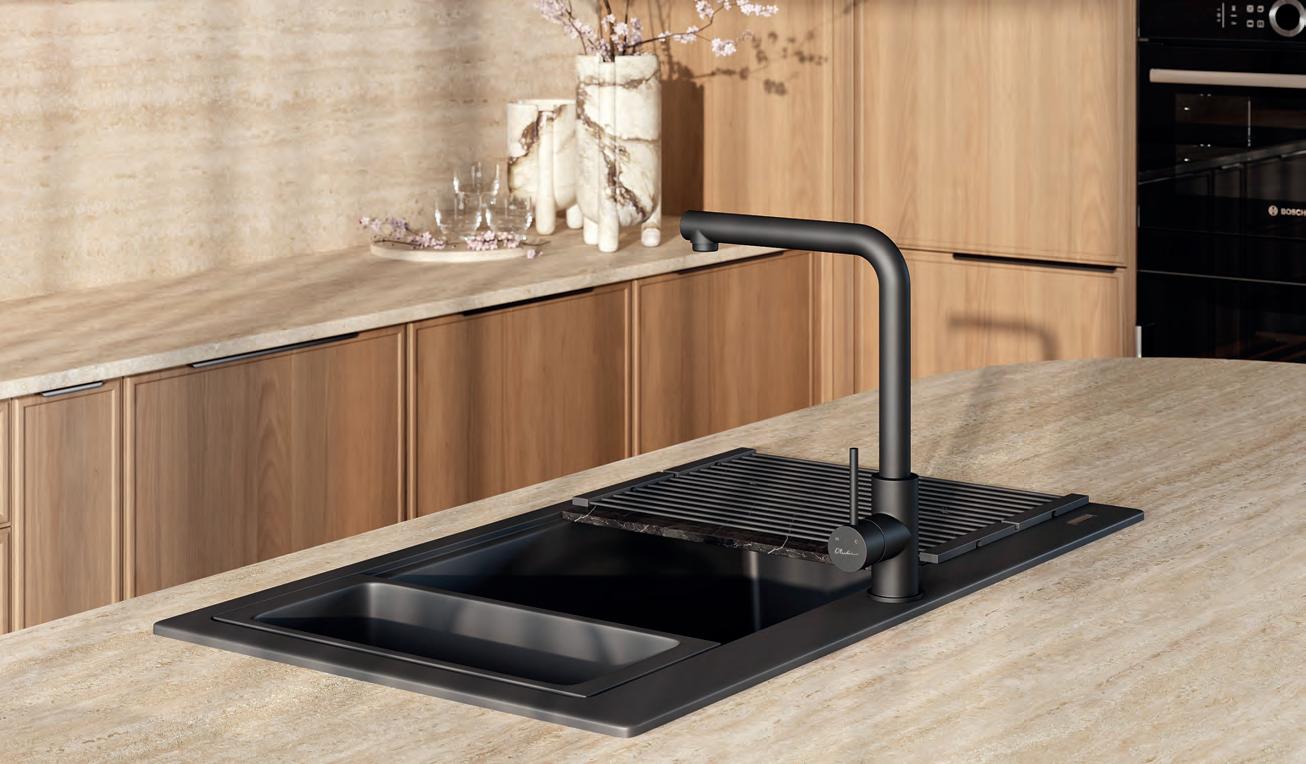
Enhancing Manufacturing Efficiency
The Role of Material Handling Machines and CABINET VISION
Staying competitive requires continuous improvement in productivity, workflow optimisation, and safety. Advanced technologies such as Material Handling Machines (MHS) integrated with CABINET VISION can streamline operations.
Transforming Workflow and Productivity
Brett, operations manager at Supreme Kitchens in Adelaide, described the productivity improvements as “transformative!”. Supreme Kitchens is now running at full capacity with a consistent output and adjustments made in real time, ensuring that workflows are continuously improved.
The integration of MHS with CABINET VISION has allowed Brett’s team to automate many of the inefficient, manual tasks which has simplified the process and reduced unnecessary handling, allowing operators to meet production demands, even during peak times.
For Leevi, setout coordinator at Universal Cabinets & Designs in Western Australia, the new system is a “game-changer!”. “The integration of CABINET VISION and MHS has significantly improved efficiency by reducing errors and minimising wastage,” he says.
The system’s requirement for precise cut requests fosters greater accountability and cuts down on common mistakes. The time saved by eliminating manual tasks is substantial, allowing Leevi’s team to focus more on critical front-end tasks.
Meeting Deadlines and Managing Larger Projects
Brett (Supreme Kitchens, SA), explains that streamlined workflows and material handling have created fewer delays in production so the team can work faster and more efficiently, even when dealing with large volumes of work.
Leevi (Universal Cabinets & Designs, WA) shares similar sentiments. “The seamless nesting capabilities
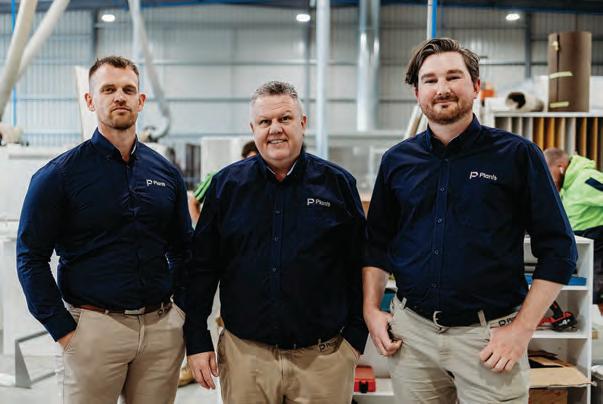
in CABINET VISION also contribute to significant reductions in errors and inefficiencies, particularly when handling complex designs,” he says.
Automated back-end processes allow the team to focus on the tasks that require human expertise, while the software takes care of the repetitive, timeconsuming tasks. This enhanced ability to scale operations allows the company to grow with confidence.
Improved Workplace Safety
Brett notes that automation of material handling processes reduces and better organises the overall movement of workers and materials through the facility, leading to a safer working environment.
Leevi’s company has experienced similar safety benefits. The automation of material handling has led to a more organised factory floor, with fewer materials left in high-traffic areas, which clears up space for additional workstations.
A Seamless Integration for Future Growth
Brett’s team has embraced the changes, with operators becoming more proficient in their use of the systems. Leevi has seen his company transform from a smaller, more informal operation to a professional, highly efficient manufacturing business.
The integration of Material Handling Machines and CABINET VISION software has proved to be a powerful combination that not only improves day-to-day operations but also positions cabinet makers and joiners for long-term success. ■
Planit Australia planitaustralia.com.au/ 1300 855 411
Grass Nova Pro Scala
Creating your dream design is now easier than ever with the Nova Pro Scala drawer system, which offers a wide range of customisation options to bring your vision to life
The innovative design features a step on the side (Scala means "step" in Italian) and true high-side steel sides, allowing you to use almost any material to elevate the drawer aesthetics to new heights. This flexibility makes it possible to achieve a personalised, unique look that suits your style and preferences.
One of the standout techniques for customisation involves simply rebating the back of the material being used and incorporating strip magnets. This technique enhances the functionality and visual appeal of the drawer system while offering a clean, modern finish.
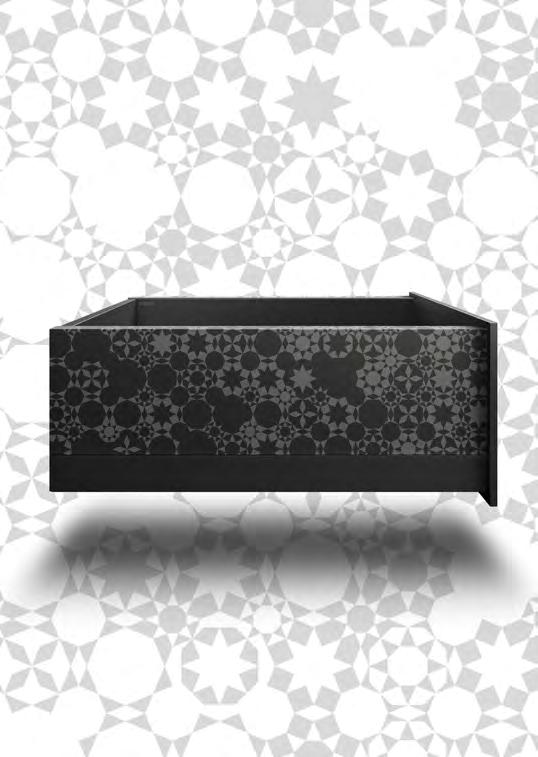
The beauty of the Nova Pro Scala system lies in its versatility — the options are virtually limitless. Whether you want to incorporate timber, glass, or other materials into your design, this system accommodates it all.
This approach is frequently used in European markets, where it has become a signature feature of many industry-leading kitchen manufacturers. With the Scala drawer system, you can easily elevate your designs and create a sophisticated and functional space that will stand the test of time. ■
Grass grass.eu
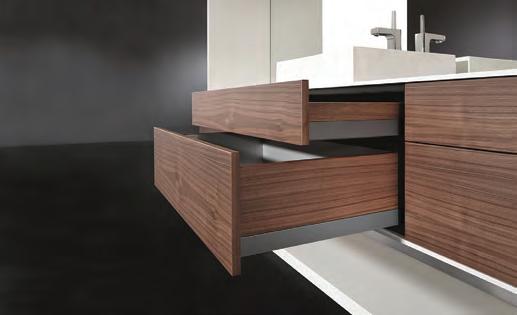
Nova Pro Scala
Moved by Art
Introducing All About Labels
Australia’s leading manufacturer of removable labels to the cabinetry industry
Established in 2003, this family-run business has grown to become Australia's leading manufacturer of blank labels, serving a diverse clientele from small businesses to large corporations across Australia and New Zealand.
Operating from its premises in Rocklea, Brisbane, All About Labels has built a reputation for providing high-quality, customised label solutions tailored to the unique needs of various industries, including cabinetry, nursery, logistics, retail, food, and manufacturing.
All About Labels strives to offer a different experience, especially for those who may have felt like "just a number" in the past. By providing bespoke solutions and budget-conscious options, it ensures that every customer feels valued and supported in achieving their labelling goals.
An example of its industry-specific focus is the company’s dedication to the cabinetry and joinery sector. All About Labels understands the critical role this sector plays in the building industry and the need to provide the high-quality, removable adhesive labels that are essential for seamless production and
installation processes. The company’s labels are industry tested to be easily removable without leaving any residue, saving labour and preventing costly damage during installation.
As a member of the Australian Cabinetry and Furniture Association (ACFA) and the Australian Woodworking Industry Supplier Association (AWISA), All About Labels has been a trusted partner to this industry for many years. ■
All About Labels allaboutlabels.com.au 1300 762 603
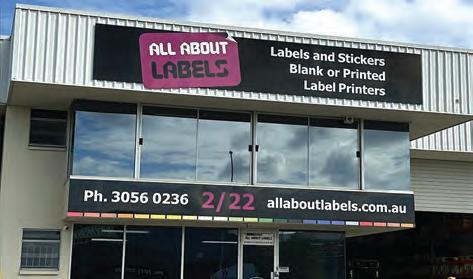
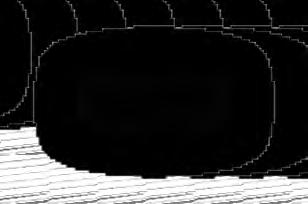

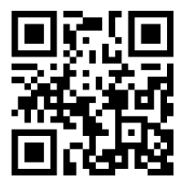
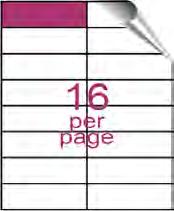
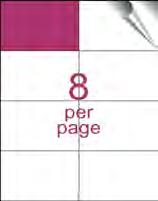
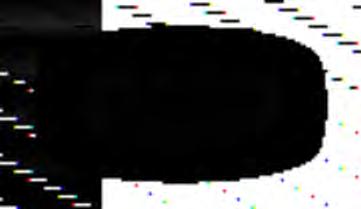
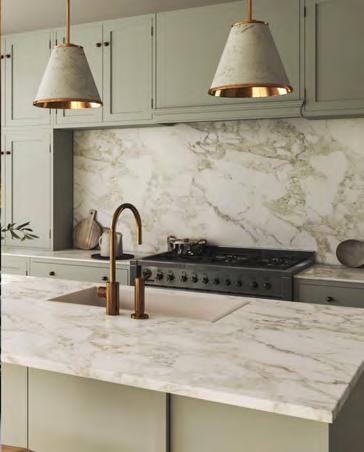
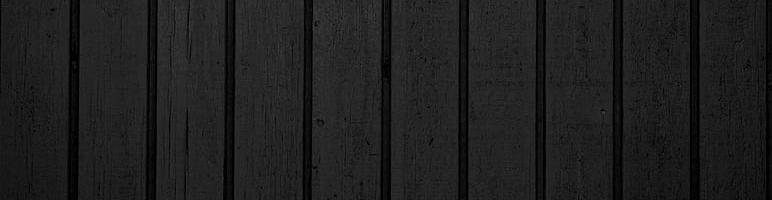



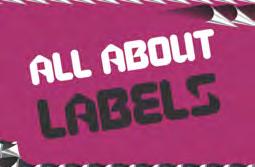


Fair Work Commission Update
Rising applications to the Fair Work Commission highlight the need for small business compliance
With recent legislative changes broadening the Fair Work Commission’s scope, the importance of compliance has never been clearer. The Commission's latest statistics for 2023–24 reveal a significant increase in applications across key areas.
Here’s a quick look at the current landscape:
• 40,190 applications lodged, a 27 per cent increase from 2022–23, reflecting heightened vigilance and enforcement.
• Unfair dismissal applications led the way, comprising 37 per cent of all lodgements with a total of 14,772.
• General protections involving dismissal applications made up 14 per cent, with Supported Wage System Agreements closely behind at 13 per cent.
• Workplace bullying and sexual harassment accounted for 987 lodgements — showcasing the increased scrutiny around these areas.
These figures highlight the real cost of noncompliance — not only financially but also in terms of reputation. All members of our industry should be


taking proactive steps to stay compliant and protect your businesses. The best way to do this is to stay updated on the latest legislative changes and have access to expert advice on workplace matters to ensure compliance remains straightforward and manageable.
ACFA has developed a number of resources to assist members in all areas of compliance including:
• Downloadable casual and apprentice employment contracts
• Award snapshots specific to our industry
• FAQs and fact sheets
• Detailed employer guides — essential tools for staying compliant and informed
• Customised employment contracts — for tailored needs, the Workplace Advice Team can create specific employment contracts, giving you peace of mind that your documentation is compliant
These resources help to simplify complex requirements, making it easier to navigate employment standards, minimise risk, and ensure your business is prepared for any workplace challenge.
With unlimited workplace advice, the ACFA Workplace Advisory Team is only a phone call or email away — just one of the many benefits of being an ACFA member. ■
ACFA Workplace Advisory Team Membership@acfa.net.au 1300 342 248
Source: Fairwork Commission Annual Report 2023-24.

Striking the Balance: Upgrade Machinery or Increase Employee Headcount?
When managing a business, one of the crucial decisions involves allocating resources between capital investment and the level of employee wages.
This is particularly relevant as organisations look to increase their production capacity and/or production efficiencies as well as maintaining acceptable margins on the finished goods.
Upgraded machinery may achieve both increased capacity and production efficiencies leading to great margins, however, they come at a cost. How does such a cost compare to utilising existing machinery in combination with increased staffing levels?
To put it in simple dollar terms, the finance cost on a $200,000 machine fully paid off over five years is less than paying for an additional employee at $1000 per week.
Depending on the machinery capability, gains can be significant compared to a simple increase in
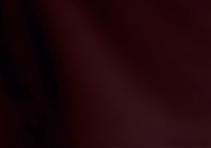
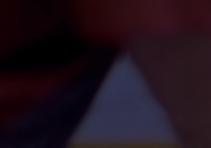

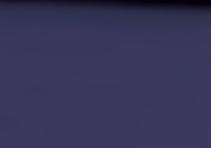
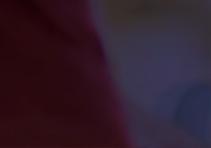

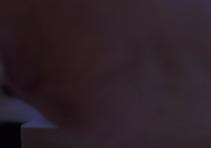
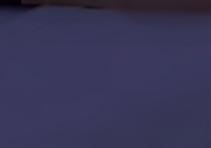
employee headcount. These gains may also include the ability to reduce human error in the process, leading to an overall increase in quality as well as increased margin, where a well-designed production facility has the capacity to reduce the overall cost per component.
The potential downside of opting for equipment upgrades is the long-term commitment to debt as opposed to the flexibility to expand and contract the labour force.
By carefully balancing these strategies, businesses can create a sustainable and thriving operation to maximise the benefits across both variables. ■
For more information, get in touch with senior equipment finance specialist Michael Ryan on 0417 279 891 or michael@finlease.com.au
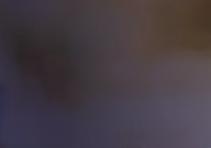

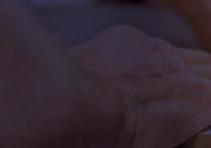
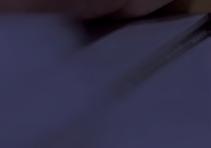
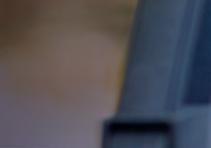
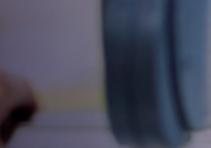
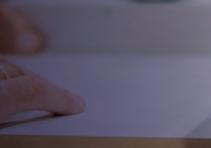
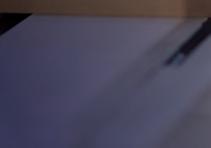
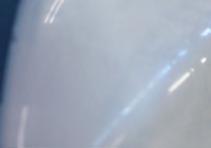
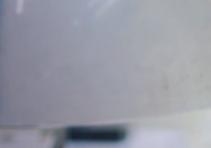
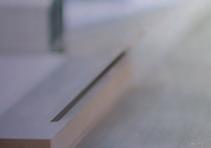
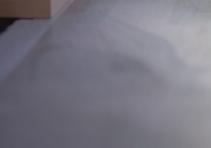

MSF30322 Certificate III in Cabinet Making and Timber Technology
The Australian Cabinet and Furniture Association (ACFA) has proudly delivered industry-focused training to the cabinet-making, furnishing, kitchen, and bathroom sectors for more than 26 years

ACFA’s unique workplace-based training model is designed to meet the evolving needs of our industry. A personalised and flexible approach sets the RTO apart, allowing it to adapt to the specific needs of your business. Expert trainers and assessors, all with industry backgrounds, bring their knowledge directly to your workplace. Hands-on training and assessment using your everyday machinery and equipment, ensures that learning is practical, relevant, and aligned with your operational requirements.
MSF30322 Certificate III in Cabinet Making and Timber Technology
ACFA is proud to be authorised in training the latest qualification for our industry. The Certificate III equips learners with skills in designing, manufacturing, and assembling cabinetry and other timber-based products. It covers various aspects of cabinet making, including interpreting drawings, selecting materials, using hand and power tools, using various static machines, assembling components, using CAD/CAM technology, installation of cabinetry and completing work-based projects throughout the course.
Nationally Recognised Qualifications
Workplace-based training qualifications obtained through ACFA are nationally recognised.
Industry Specialised Trainers
ACFA trainers and assessors are qualified industry tradespeople with years of industry experience who maintain currency to ensure delivery of best practice training and assessment.
Collaborative Support
ACFA's workplace-based training model fosters a close relationship between business owners/supervisors and trainers, allowing them to work together to support and develop apprentices' needs. Regular workplace visits and open communication ensure personalised training in a real-world environment.
Enrol Anytime
ACFA takes enrolments on demand, no need to wait for semester beginning and end dates.
Flexible Delivery
Training is accompanied by an online learning platform removing the need for textbooks. Online learning is supplemented by workplace projects and observations.
Custom Fit Delivery
Training is customised to be delivered at your premises on your machinery.
Training Subsidies*
You may be eligible to complete your course fee-free through government funding. *Eligibility criteria apply
Certificate III Qualifications
MSF30322 Certificate III in Cabinet Making and Timber Technology — Kitchens and Bathrooms
MSF30322 Certificate III in Cabinet Making and Timber Technology — Furniture
MSF30322 Certificate III in Cabinet Making and Timber Technology — Wood Machining ■
ACFA-Training-Brochure_NSW-CertIII_Web.pdf RTO National Code: 90432
Software Cutting Mistakes, Increasing Efficiency, and Maximising Profits
How ASC Flatpacks Scaled Successfully with Order Automation
In 2014, Andrew Steel was a foreman at a cabinetmaking business, tackling full-time work while taking on weekend side job in the hope of building his own business. After years of long hours, he decided it was time to go all in.
Unlike other cabinet makers in his area, relying on paperwork and manual processes, Andrew embraced a smarter approach. He’s built ASC Flatpacks with the support of Cabinetry.Online.
“With the online system, it’s clear what they order is what they get,” Andrew explains. No more backand-forths, no more miscommunications — just clear, accurate, and automated orders.
Avoiding the Pain Points of Traditional Cabinetry Business
By adopting Cabinetry.Online Andrew found a way to avoid typical frustrations:
• Minimising miscuts and waste
• Reducing client calls
• Avoiding inefficiencies, allowing a focus on growth.
Andrew plans to double or triple ASC Flatpacks' output, leveraging the efficiency of Cabinetry.Online to handle higher order volumes without increasing complexity.
“We are now signing on with an advertising agency to chase even more opportunities,” he says.
Andrew’s success story proves that automating the ordering process isn’t just about innovation — it’s about making business easier, reducing stress, and staying profitable. If you’re tired of dealing with the same daily frustrations, Cabinetry.Online might be the solution that helps you take control and grow your business.
Want to see how it works? Book a demo today.
Cabinetry.Online 1300 783 997
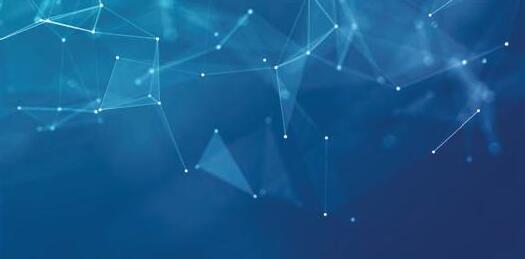
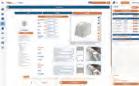


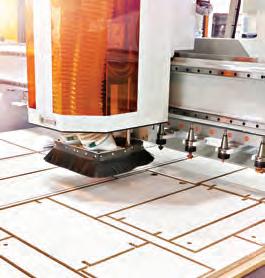


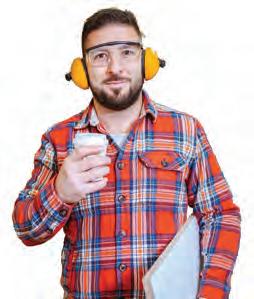
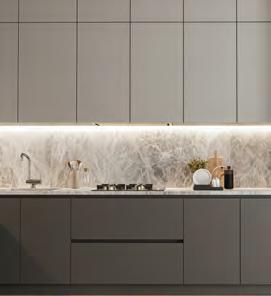
New Wage Theft Laws
Important changes to workplace laws regarding underpayment of wages came into effect on 1 January 2025
From 1 January 2025, deliberate underpayment of wages is deemed a criminal offence, and it’s essential to understand how these laws apply and the steps you can take to remain compliant.
What Do the New Laws Mean?
From 1 January 2025, any intentional underpayment of wages, superannuation, or entitlements can lead to criminal penalties, including fines and potential prosecution: If a person is convicted of a criminal offence, a court may impose a maximum of 10 years in prison for an individual. They can also impose significant penalties for the individual or a company, or both.
Maximum Penalty for a Company
If the court can determine the underpayment amount, the maximum penalty will be the greater of: three times the underpayment amount OR $8,250,000. If the court can’t determine the underpayment amount, the maximum penalty is $8,250,000.
Maximum Penalty for an Individual
If a court can determine the underpayment amount, the maximum penalty will be the greater of: three times the underpayment amount OR $1,650.000. If the court can’t determine the underpayment amount, the maximum penalty is $1,650.000.
Intentional conduct includes:
• Purposefully paying less than the required minimum.
• Failing to act, such as deliberately not paying an employee.
Note: The criminal offence does not apply for underpayments that happen because of a genuine mistake but they must be corrected promptly.
How Can Small Businesses Stay Compliant?
To assist small businesses, the Fair Work Ombudsman has introduced the Voluntary Small Business Wage Compliance Code. This code provides practical steps to ensure employees are paid correctly. Importantly, small businesses that follow the Code and make an error will not be referred for criminal prosecution.
Please Note: Even if an employer has complied with the Code, civil actions such as issuing a compliance
notice or an enforceable undertaking may still be taken, and civil penalties may still apply.
To ensure compliance, ACFA recommends the following steps:
1. Follow Your Pay Slip and Record-Keeping Obligations
• Provide pay slips within one working day of payday.
• Ensure pay slips include all required information, such as hours worked, pay rates, and deductions.
• Keep accurate, accessible, and legible records of time worked and wages paid.
2. Stay Up to Date with Workplace Laws
• Stay informed by subscribing to and regularly reading the ACFA Member Bulletins, which provide updates on key topics such as minimum wage increases, award classifications, and workplace laws.
• Make adjustments promptly on any of these changes.
3. Get Help If You Need It
• Seek advice from ACFA’s Workplace Advice Team for award rate information and compliance guidance.
• Use ACFA member resources, including FAQs and checklists, to simplify payroll and recordkeeping processes.
4. Address Issues Quickly
• If an underpayment is identified, act promptly by:
• Correcting the error and backpaying employees.
• Identifying the cause to prevent future occurrences.
• Communicating transparently with affected employees about the resolution.
Resources to assist members have been loaded to the ACFA Member Portal including FAQs explaining the new laws, a checklist to help assess compliance and a Fact Sheet on how to fix an underpayment. ■
ACFA Workplace Advisory Team Membership@acfa.net.au 1300 342 248
Software Expand Without the Overheads: How goCabinets Can Transform Your Business
While growth is exciting, the costs and complexities of scaling up can often be overwhelming. But, what if there was a way to grow without having to invest in factories, machinery, staff or other daunting overheads?
Enter goCabinets: The Smarter Way to Scale goCabinets is an online ordering system that allows tradespeople to customise, quote, and order cabinetry directly from a local manufacturer without needing to invest in expensive CNC machinery or manage the production process themselves.
With goCabinets, you get instant quotes and can quickly respond to client needs. Feel confident knowing your cabinets are cut by trusted local cabinet makers, using high-quality materials from Australian manufacturers.
Why Choose goCabinets?
Simplify Operations: No need for your own factory or CNC machine — goCabinets connects you with trusted local manufacturers who handle production for you.
Boost Profitability: Reduce overhead costs and maximise your earnings by outsourcing production while maintaining full control over your projects.
Accelerate Turnaround: Provide clients with fast, accurate quotes and secure more jobs with a seamless ordering process.
Flexible Growth: Scale your business on your terms without the financial risks of traditional expansion.
Trusted Craftsmanship: Work with reputable CNC manufacturers to ensure precision cutting and high-end finishes.
Expand Smarter in 2025
With goCabinets, you can streamline your business, increase profitability, and grow with confidence without the usual financial and operational challenges.
Ready to take the next step? Let goCabinets be your partner in success this year. ■
goCabinets goCabinets.com.au
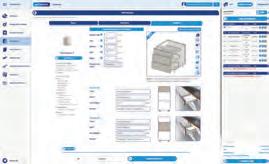
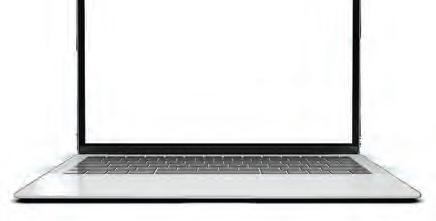
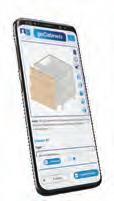
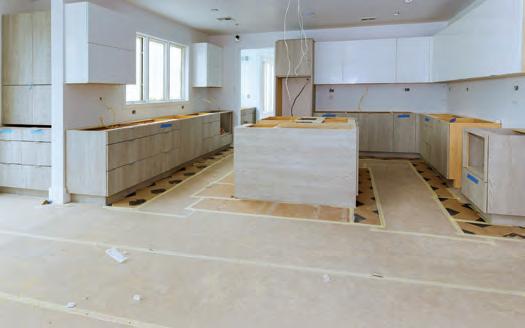
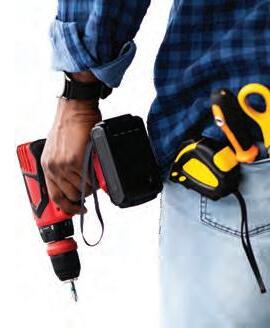
Simply The Best CRM for the Kitchen Industry
Ayrmont Technologies' ARMS is the ultimate business solution designed specifically for kitchen, bathroom, and joinery companies. This competitively priced Australian platform enhances efficiency, productivity, profitability, and keeps you organised and in control of your business, helping you stay ahead in a fastpaced, dynamic industry.
Why Choose ARMS?
Tailored for Renovators: ARMS is built by industry experts, inspired by renovators and cabinet makers, and powered by cutting-edge developers.
All-in-One Automation: Automate key tasks such as quoting, manufacturing cost estimation, project management, scheduling, trade resource management, supplier and trade work orders, and customer invoicing.
Seamless Integration: Works with accounting platforms such as Xero for effortless financial management.
Mobile-First Access: Access critical documents, plans, and project details anytime, anywhere — right from your tablet or mobile.
CRM Features That Drive Sales Lead and Sales Management: Capture and convert more leads with dedicated modules.
Marketing Automation: Run smarter campaigns to grow your customer base.
Calendar and Appointment Scheduling: Never miss an opportunity with streamlined calendars.
Optimise Operations with Powerful Reporting: Gain full visibility of your business performance with comprehensive operational and profit management reports — all accessible on desktop, tablet, or mobile.
ARMS transforms your business into a well-oiled machine, giving you control of your operations and showrooms. Take the next step in efficiency, growth, and profitability. Visit our website now to learn more or book a demo. ■
ayrmont.com.au/
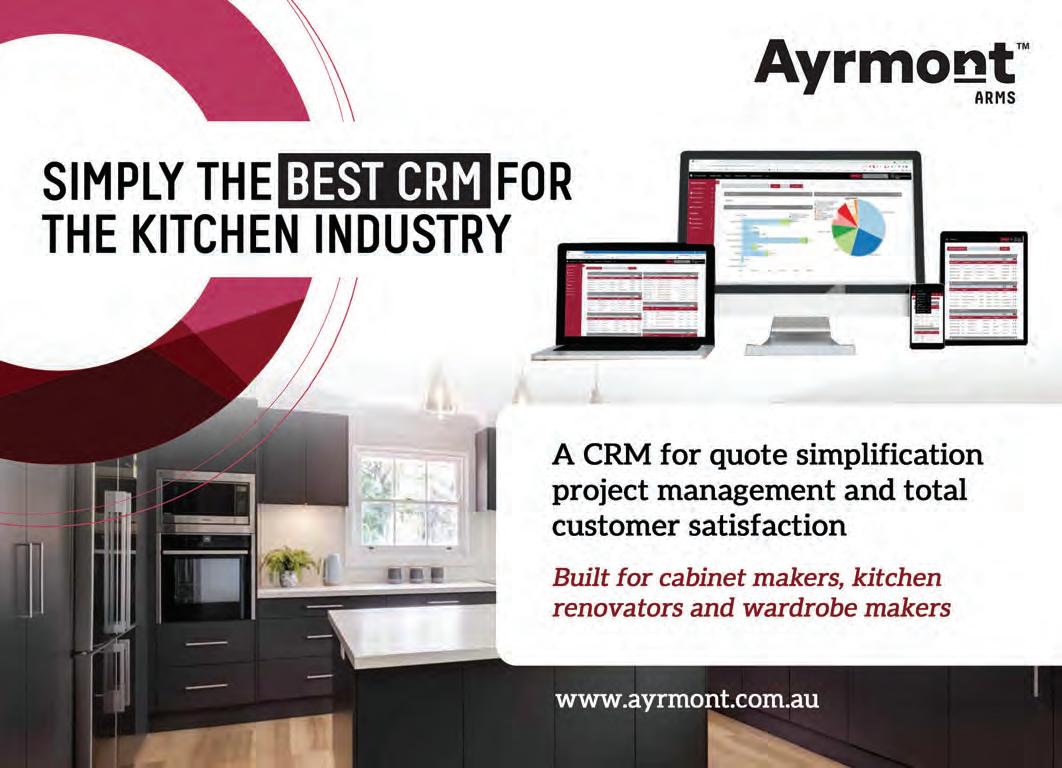
Make Recycling Easy with Hideaway Bins
With an increasing demand for easier ways to separate waste and recycling, Hideaway Bins offers a simple colour-coding system which can have a huge impact

Recycling can be confusing, especially if you are unsure which bin to put your rubbish or recycling into. Colour-coded bins offer a visual cue that simplifies the process of waste separation.
Whether in the home or the office environment, colour-coded recycling bins promote awareness about the importance of recycling and waste reduction. The visible differentiation of bins helps
everyone, even children, understand the significance of separating waste and the positive impact it can have on the environment.
One of the most significant advantages of colourcoded bins is the reduction of contamination in recyclable materials. Contaminated recycling often means those materials cannot be recycled at all. Colour-coded bins help by separating waste correctly at the start, which leads to improved recycling rates and a more efficient use of resources.
Hideaway colour-coded liner holders are in four new colours — Red, Green, Yellow and Blue — and are available to suit all Concelo bins and most of the Hideaway Compact range. The liner holders can be purchased separately, either to be installed with new bin units or as an upgrade to existing Hideaway Bins.■
Hideaway Bins hideawaybins.com.au/sustainability

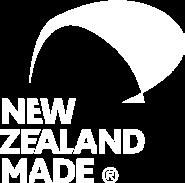
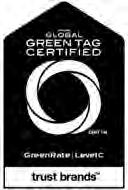
Sharpening Your Personal Saw
Few of us have sufficient time to do everything in our businesses, but better management and supervisory training can significantly improve productivity and safety
By Dean Brakell
Time management is a universal problem, especially for small to medium Australian businesses in light manufacturing sectors. When time poor, it’s common for business owners to downgrade the importance of personal and business development for themselves and their management/supervisory staff.
Many in our industry gain our trade qualifications at a young age, but not enough of us take the time to develop our skills further. And, often, the default position is to provide supervision that reflects the same style and standard under which we were trained — also known as “training by osmosis”. This can mean past inefficiencies or bad practices are passed down to the next generation.
Ineffective Supervisors/Mid-Level Managers
Supervisors/mid-level managers generally have good technical skills and can problem solve most issues as they occur on a day-to-day basis. The challenge arises when they are asked to identify why the problem or issue occurred in the first place. They are often too busy or lack the insight to see the root cause of the problem, which means the problem will occur again and again.
Ineffective supervisors/middle management will impact:
• The welfare and safety of employees (high likelihood of more workplace accidents and time off due to injuries)
• Reduced productivity (staff not motivated or mentored to perform to their potential)
• Workplace culture (unable to set a good example or uphold the company’s vision and values)
• Absenteeism (staff taking days off as they couldn’t be bothered going to work)
Effective Supervisors/Middle Managers
I have visited a significant number of businesses in our industry and I can tell immediately when I walk into a well-run business.
I see planning and thought behind the layout of machinery and production areas (reduced material movement = increased productivity). I notice a controlled urgency in the way people work and a
general good vibe in the workplace (good workplace culture = staff value their jobs and the company).
Safety in the workplace is not a secondary consideration but is incorporated in all processes so it becomes the accepted norm (fewer accidents = less time lost to injuries and workers' compensation premiums stabilise). Visual cues include a production board or scheduling board for work (great communication = a well-organised and efficient workplace).
Effective Supervisors/Mid-Level Managers impact:
• Workplace culture (set standards, walk the talk, don’t accept poor behavior)
• Increased productivity (motivate staff to meet their full potential, have a sense of urgency in the way they work)
• Work Health & Safety awareness (consult with staff on a regular basis, safety is incorporated in all processes, PPE worn where required, designated walkways)
• Reduce reworks (commitment to continual improvement and best practice)
• Good people skills (good communicator, shows respect to all staff, shows enthusiasm, can influence and mentor)
One of the most significant pressures ACFA members tell us about is the struggle to balance day-today business activity with business development. Owners and managers know they need to keep their management skills up to date and improve on them to maximise productivity.
This is the main reason associations focus so much of our energy on business leadership, management development and business skills. It is also why we put so much emphasis on mentoring and supporting your team as they develop the skills of your apprentices and trainees.
Business owners, managers and supervisors need to do the same, in the pursuit of a sharper personal saw that can help improve productivity and profitability, and ultimately create a stronger, more profitable business. ■

Company Name Page Number
ACFA 63, 67
All About Labels 72
Ayrmont 79
Blum IFC, 66
Cabinetry.Online 76
Finlease 74
GoCabinets 78
Grass 71
Hettich 61, OBC
HIA Economics 42
Hideaway Bins 80
KBDi 24, 59
Lincoln Sentry 68, 69
Multicam 64, 65
NKBA 38
Planit 70, IBC
Polytec 62
Australian Cabinet and Furniture Association Ltd (ACFA)
Connect The Magazine
Connect magazine will be published quarterly and distributed free to end users involved in the cabinetmaking, kitchen, design, furnishing and joinery industries. Every issue of Connect magazine brings you the most relevant and impactful stories from the cabinet-making, furniture and design sectors. Our content is curated to keep you informed and be inspired. The Summer Edition — Industry Awards & Design; Autumn Edition — Machinery & Safety; Winter Edition — Business Insights, the Economy and Finance; Spring Edition – Design Trends & Sustainability.
ACFA The Association
ACFA, formerly named the Furnishing Industry Association of Australia (FIAA), is a not-for-profit industry association. ACFA, incorporated since June 1948, has a proud history of representing the needs of businesses in the sector. FIAA and the Cabinet Makers and Designers Association (CMDA) merged in 2018 and ACFA was born.
ACFA is a membership organisation with members located all around Australia. ACFA’s altruistic existence is to assist members in trade and commerce throughout Australia and to deliver high-quality education, training, information and resources to those who are involved in the cabinetmaking, kitchen, furnishing and joinery industries.
Membership information can be located at: acfa.net.au/membership/
ACFA The Registered Training Organisation (RTO) RTO National Code:
90432
ACFA has been a Registered Training Organisation for more than 25 years. In that time, ACFA has served the needs of the furnishing, cabinet-making and kitchen sector with structured, flexible, accredited, and nationally recognised trade training. ACFA exists purely for the industry — the organisation speaks as a united voice to the community, consumers and all levels of Government to ensure the best interests of the industry.
ACFA offers both accredited and non-accredited training and more information can be found at: acfa.net.au/training/
Distribution
Connect magazine is distributed free of charge to ACFA and KBDi members, subscribers, ACFA database, and client databases of major suppliers and partners of ACFA. To be added to the distribution list, please visit the Connect magazine website: connectmagazine.com.au/


AVANTECH YOU BY HETTICH
The AvanTech YOU platform concept delivers exceptional flexibility and customisation, enabling the creation of tailor-made drawer solutions that meet customer needs, while upholding manufacturing efficiencies and preserving the premium quality and sleek design.
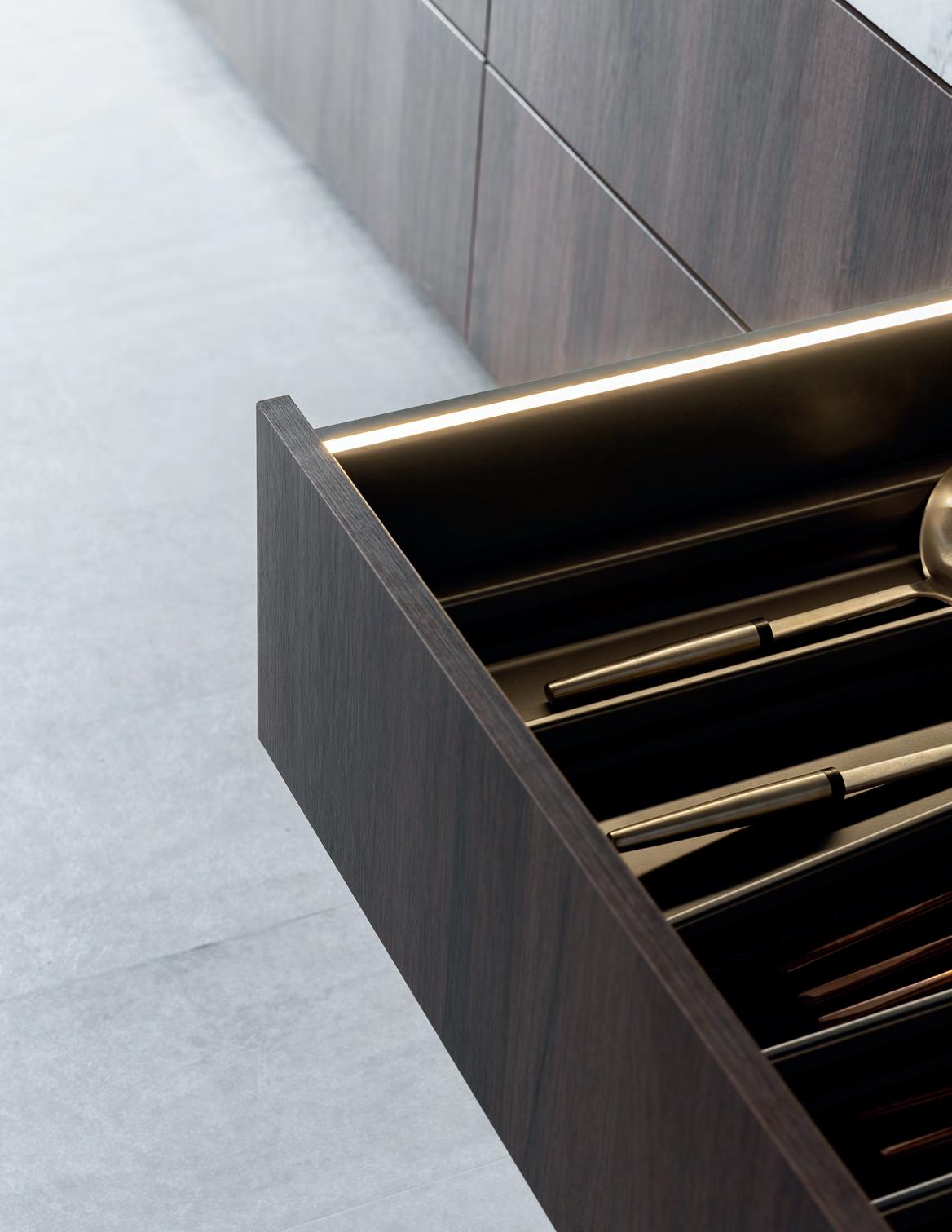
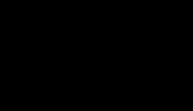