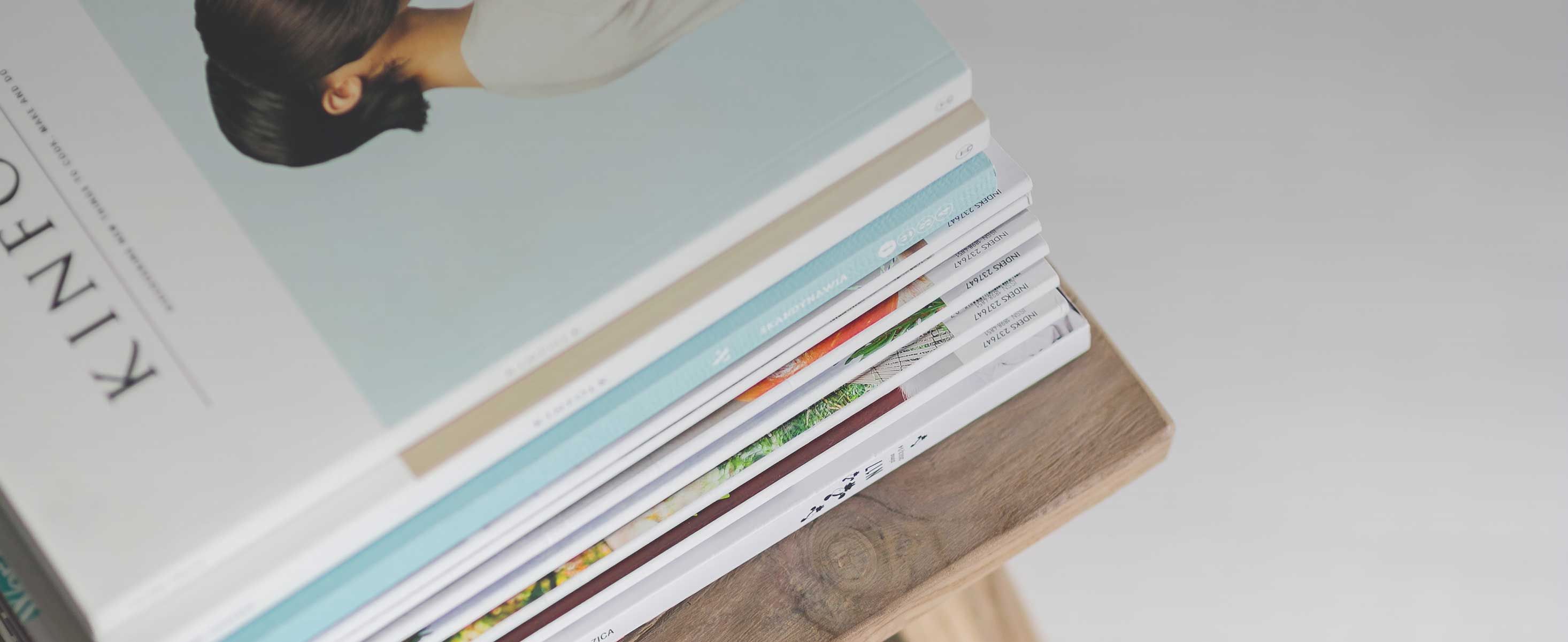
10 minute read
5. Management Procedures and Mitigation Measures
5.1 Bentonite Plant
The main environmental risks associated with the bentonite plant are the discharge of chemicals from the operation of the plant and/or the discharge of sediment laden water to stormwater drains within the main works area, which in turn discharge into the Waitematā Harbour.
To avoid or minimise any discharges from the bentonite plant to the surrounding environment, each plant is designed and operated as follows:
The entire bentonite plant is bunded to contain any spilt material or bentonite slurry in the event of a pipe or pump failure during transfer of the slurry. Any surface water collected in the bund is pumped out to the on-site WTP. Sodium bicarbonate and bentocyrl are added to the bentonite slurry. Neither chemicals are classified under HSNO as hazardous and are stored within the bunded bentonite plant area. No other environmentally hazardous substances are required as part of the bentonite plant operation. In the event of a spill outside of the bunded area, the standard spill control procedures will be implemented to contain and manage the spill (refer to Section 6 of this ITA EMP). In addition, a Bentonite Plant Spill Response Plan has been prepared and will be implemented (refer Appendix C). This Plan outlines the environmental controls and spill response procedures specific to the operation of the plant detailed in Section 2.3 of this ITA EMP. The extent of the bunded areas of the bentonite plant that will be sealed off during the works are shown in the Stormwater Drainage Plan in the Bentonite Plant Spill Response Plan.
5.2 D-Wall Construction
The main environmental risk associated with D-wall construction is the discharge of sediment laden water and high pH to the stormwater networks.
To avoid or minimise any discharges from the construction of D-walls at CSA 5, the works are managed as follows:
The entire D-wall construction area drains to a low point from which any runoff is pumped to the on-site WTP. All stormwater catchpits within the works areas have been removed or diverted to the WTP. In the event of a spill outside of the bunded area, the standard spill control procedures will be implemented to contain and manage the spill (refer to Section 6 and Appendix B of this ITA EMP). 5.3
Soil Mixing Plant
The main environmental risk associated with operation of the soil mixing plant is the discharge of sediment laden water and elevated pH from cement used in the grout slurry mix.
To avoid or minimise any discharges from the jet grout plant into the surrounding environment, the plant will be designed and operated as follows:
The soil mixing plant is bunded, with any surface water collected in the bund being pumped out to the on-site water treatment plant.
Page 33
Mt Eden Main Works
In the event of a spill outside of the bunded area, the standard spill control procedures will be implemented to contain and manage the spill (refer to Section 6 of this ITA EMP). The extent of the bunded areas of the soil mixing plant is shown in the CSA 5 site layout in Figure 2-
1.
5.4 Ground Improvement
The main environmental risk associated with ground improvement works is the discharge of sediment laden water and high pH to the stormwater networks.
To avoid or minimise any discharges from the ground improvements, the works are managed as follows:
Regular inspection of hoses and connections from the soil mixing plant area for leaks. All stormwater catchpits have been removed or diverted. The ground improvement works form an excavation and any contaminated water that collects in the area will be pumped back to the WTP. In the event of a spill outside of the bunded area, the standard spill control procedures will be implemented to contain and manage the spill (refer to Section 6 of this ITA EMP).
5.5 TBM Component A Plant
The main environmental risk associated with the TBM “Component A” plant in the Technical Area of CSA 4 is the discharge of sediment laden water with elevated pH from the cement, pulverised fly ash and bentonite used in the Component A slurry mix.
To avoid or minimise any discharges from the Component A plant to the surrounding environment, the plant is designed and operated as follows: • The entire Component A plant including all raw material silos is bunded to contain any spilt material or slurry mix in the event of a pipe or pump failure during preparation or transfer to the TBM. Any surface water collected in the bund is pumped out to the on-site WTP. • All raw material silos are fitted with high level sensors, interlocks and alarms to prevent overfilling, and all bulk material raw material refills and plant operations are supervised by staff trained in standard operating procedures and emergency response. • Regular inspection of hoses and connections from the Component A plant area for leaks. • In the event of a spill outside of the bunded area, the standard spill control procedures will be implemented to contain and manage the spill (refer to Section 6 and Appendix B of this ITA EMP).
5.6 Tunnel Segment Storage
The main environmental risk associated with the tunnel segment storage at CSA 4 is the discharge of elevated pH from stormwater in contact with the concrete segments.
To avoid or minimise any discharges from the segment storage to the surrounding environment, the plant is designed and operated as follows: • The segment storage area drains toward the excavation of the tunnel entrance. Any accumulated stormwater is contained and pumped back to the WTP at CSA 4.
Page 34
Mt Eden Main Works
All stormwater catchpits have been removed and diverted to beyond the CSA 4 area.
5.7 Muck Bin Area
The main environmental risk associated with the storage of material at the muck bin at CSA 5 is the discharge of sediment laden water and high pH to the stormwater networks.
To avoid or minimise any discharges from the muck bin area the works are managed as follows:
The muck bin area is graded to a low point sump which is pumped to the on-site water treatment plant. In the event of a spill outside of the bunded areas in the CSA, the standard spill control procedures will be implemented to contain and manage the spill (refer to Section 6 and Appendix B of this ITA EMP).
5.8 Diesel Tank and Generator
A key environmental risk associated with the diesel tank at CSA 4 and diesel fuelled generator at CSA 5 is the discharge of hydrocarbons to the stormwater networks.
To avoid or minimise any discharges from the diesel tank or generator, the works are managed as follows:
Both the diesel tank and generator are located within bunded areas, and any runoff that collects in the bund is pumped to the on-site water treatment plant. All refuelling of the tank or generator will be supervised by workers trained in emergency response. Drip trays are in place during refuelling activities for reduction of incidental contamination of runoff in the bund. All stormwater catchpits have been removed and diverted to beyond the CSA 4 and CSA 5 areas. In the event of a spill outside of the bunded areas in each CSA, the standard spill control procedures will be implemented to contain and manage the spill (refer to Section 6 and Appendix B of this ITA EMP).
5.9 Stormwater and Groundwater Treatment
Groundwater and stormwater which collects in the excavation areas and bunded areas during construction works will be treated as detailed in the ESCP and the FTMP (refer to Appendix H of the CEMP). Flocculants (both chemical or non-chemical) will be used to settle out sediment. Dosing for pH treatment will also be undertaken in the WTP as required to ensure water discharged from the system will not result in adverse effects on the receiving environment. The WTP at CSA 4 is located to the northeast of the Technical Area and the WTP at CSA 5 is located adjacent to the entrance off Water Street.
The WTP operation is outlined in detail in Section 3 of the FTMP for the main works (Appendix C of the ESCP).
Page 35
Mt Eden Main Works
Discharge to sewer network may also be undertaken where water quality requirements for stormwater cannot be met. Any discharges to the sewer network will be in accordance with the terms of a Trade Waste Agreement to be established with WaterCare.
The principal environmentally hazardous substances that are stored and used at CSA 4 and CSA 5 during the construction works will include:
Fuel (e.g. petrol, diesel); Oils and greases; Dry grout, cement, pulverised flyash and bentonite; Sodium silicate accelerator (Component B); Concrete and asphalt (use only, will not be stored on site); and Water treatment chemicals (for sediment settling and pH adjustment e.g. flocculation agents and sulfuric acid). All chemicals are stored in a secure area with secondary containment sized to contain at least 110% of the largest container in the event of a spill. The main storage area at each site is the hazardous goods storage area indicated on each CSA layout provided in Figures 2-1 to 2-4. The main chemical store at CSA 4 is on the western side of the Technical Area and at CSA 5 is to the northeast of the site adjacent to the muck bin. There is also some local storage of chemicals at each WTP. For all local storage, chemicals must be stored on spill pallets to provide appropriate secondary containment.
Safety Data Sheets (SDS) for all of the chemicals used or stored in the main works area are kept in the main works site office with a sub-set on file at each storage location relevant to the specific materials being stored. A Hazardous Substances and SDS register shall be kept on-site at each CSA and regularly maintained to ensure it is up to date with the chemicals and volumes of chemicals used and stored on-site. An indicative inventory of hazardous substances has been provided as Section 5.15 of the CEMP.
Spill kits and associated spill response equipment are to be located as follows:
For CSA 4: at the spoil store, the water treatment chemical storage area, the Technical Area vehicle entrance, the A Component plant and the workshops; For CSA 5: at the soil mixing and bentonite plant bunded area, the water treatment chemical storage area and the workshop.
5.11 Waste Management
For the purpose of the main works, waste material refers to items removed from worksites and road carriageways, such as surplus or reject spoil, excavated seal, pipes, rubbish detritus and any other unwanted materials. Appropriate disposal shall be arranged for any material that requires off-site disposal.
If hazardous material requires off-site disposal, it will be disposed of safely, through an appropriate contractor authorised to handle, transport, process or safely dispose of the waste concerned to an approved disposal facility.
Any waste bins on-site will either be stored undercover or will be installed with covers to prevent rainwater ingress.
Page 36
Mt Eden Main Works
5.12 Wash-down
A wheel wash is provided at the site exit of both CSA4 and CSA5 to minimise tracking of sediments off site. The wheel wash water is contained and drains to the associated WTP or collected and removed off-site via sucker truck.
No road vehicle wash-down will be undertaken on-site at either CSA outside of the designated wheel wash. The location and nature of the construction works, along with the construction methodology serves to minimise the potential for site vehicles to drive over areas of open excavation or unpaved areas and track dirt onto the surrounding road network.
In the event of material being spilled onto the ground around the tunnelling excavation or from trucks transporting the spoil from the spoil store at CSA 4, the material will be cleaned prior to the vehicle leaving the site. This may involve some localised washing of vehicles and tyres. Any runoff from the wash down area will be directed to sediment control devices with associated sediment settling and monitoring prior to discharge.
Some washing of machinery within the excavation areas may be required. In this instance, washing of machinery is undertaken using a hose or water blaster on-site within areas of excavation only. All runoff within these areas is either drained to ground or captured and pumped to the WTP.
Page 37
Mt Eden Main Works