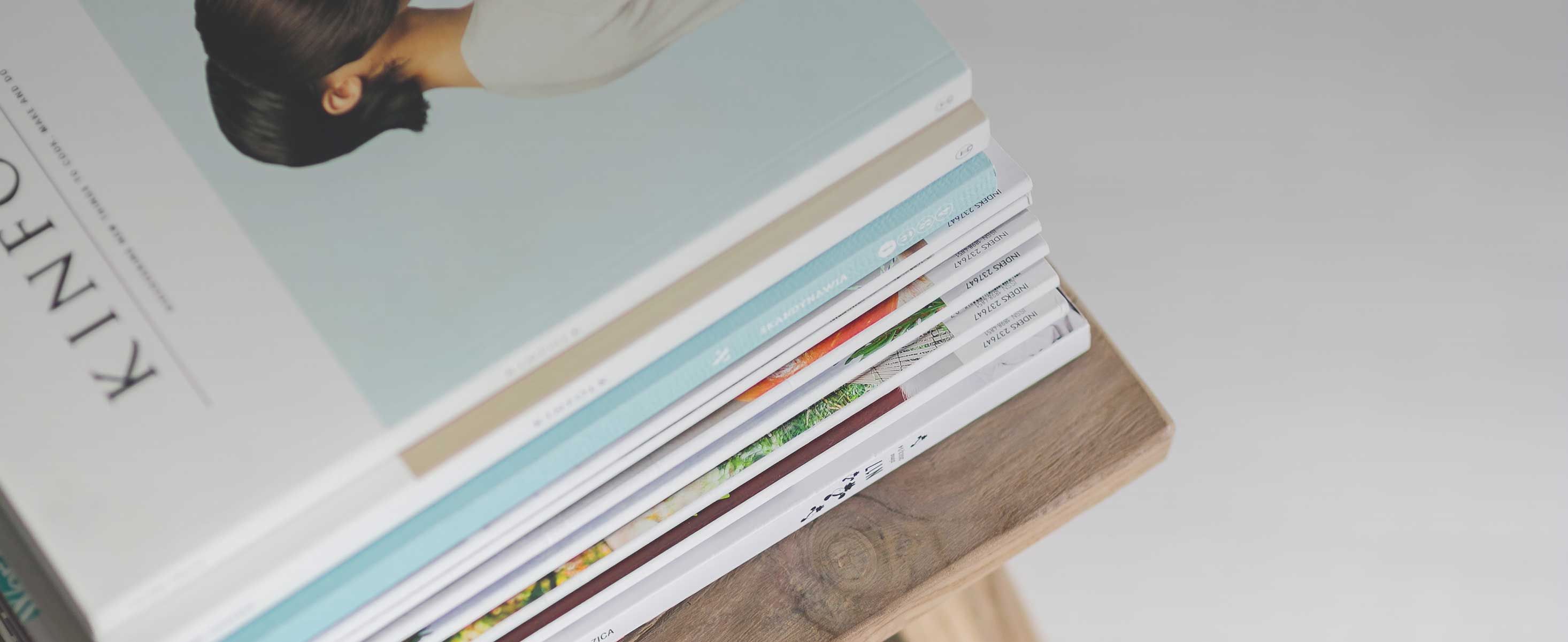
5 minute read
Appendix C: Bentonite Plant Spill Response Plan
Purpose and Objective of Plan
The bentonite plant is located within CSA5. This Bentonite Plant Spill Response Plan (BPSRP) relates to the management of spills of liquid bentonite slurry and/or additives from within the bentonite plant.
The objective of this BPSRP is to ensure that emergency spills are handled in an appropriate manner to ensure safety of all personnel and to prevent damage to the environment.
Bentonite components and additives
The fresh bentonite slurry is composed of water from the main fire hydrant and of bentonite and additives (sodium bicarbonate and bentocryl).
Mixing of bentonite with water and additives (sodium bicarbonate and bentocryl) to make a bentonite slurry, which will be temporarily stored within the silos before being used in the diaphragm wall construction.
Safety Data Sheets for the Bentonil, the Sodium Bicarbonate and the Bentocryl are held at the site office. These additives are not classified under HSNO as hazardous. Irrespective of this, all of these additives will be stored within the bunded bentonite plant area. No other hazardous substances will be required as part of the bentonite plant operation.
Structural Controls
The entire bentonite plant is bunded to contain any spilt material or bentonite slurry in the event of a pipe or pump failure during transfer of slurry. A surface pump will be used to manually pump any surface water that collects within the bund to an onsite water tank or to the water treatment plant. The bund will be checked on a daily basis for water accumulation, to determine whether pumping is required.
Once the water treatment plant has been commissioned, surface water from the bunded area will be pumped to the plant for treatment. This water will be treated prior to discharge to the stormwater system.
Washwater
At the end of each shift the plant is washed down. Any washwater will be contained within the bunded area and pumped to the onsite water tank or the water treatment plant once commissioned.
Contingency Measures
To prevent overflow from the silos:
• The float switches have been positioned to 2.5 m below the top of the silos, providing extra capacity in the top of the silos in the event of heavy rain • The level alarms have been tested during a trial run • The silos supply circuit has been checked and tested during a trial run • The levels of slurry inside the silos will be lowered down to a minimum level during any long weekend and/or holiday periods (e.g., during Christmas and New Year)
Page 46
Mt Eden Main Works
To prevent the slurry line from bursting:
The slurry line network shall be tested and checked The slurry lines have been bought specifically for this project and are not second hand use The slurry lines materials and fittings have been procured considering a safety factor for slurry pressure. The pumps have a maximum working pressure of 5 bars, and the hoses are designed for 10 bars working pressure with a safety factor of 3:1, with their connections being crimped
Spill Response Procedure –Within the bunded area
The crew at the bentonite plant is composed of 1 plant operator and 2 plant assistants. The full plant will be checked by one member of the crew every 20 minutes to confirm no spillage/leakage has occurred.
In the event of a minor spill of bentonite slurry within the bunded area, the platform has been equipped with a slurry pump to suck the slurry back into the de-sanding plant. Two spare pumps have been provided for.
In the event of a major spill from the overflow or rupture of one or more silos the bund walls have been designed to contain the equivalent of 2 silos.
The spill will be sucked up with the slurry pump and pumped to an appropriate location (e.g., back into one of the silos).
Spill Response Procedure –Spills outside of the bunded area
In the event of a bund breach or other spill (pipe burst) outside the bunded area the following process will be followed:
Additional sand bags are available onsite. Depending on location of the spill, sand bags will be placed in key locations to contain the spill within the site boundary.
In the event of a spill beyond the site boundary the following process will be followed:
Confine the spill with sandbags, booms or other suitable material Block off the closest stormwater catchpits Contact a waste disposal contractor to clean up the spill Notify the STMS who would decide whether the road needed to be closed, or if not they would direct traffic around the spill Notify the Environmental Manager (Sarah Sutherland 021 956 397). The Environmental Manager will notify the Auckland Council 24 hour pollution hotline.
Spill Response Procedure –Oil
The oil at the plant is present in the enclosed gear box of the pumps. An oil spillage could potentially occur during the re-filling of the pump oil container. In addition a hydraulic oil spill could potentially occur if one of the hydraulic oil hoses to the Hydrofraise machine burst.
In the event of any oil spillage site staff will use the spill kit and follow the general emergency spill response procedure (ESRP) to contain and manage the spill (refer to Appendix B).
Page 47
Mt Eden Main Works
One general purpose, and one oil only spill kit will be located adjacent to the plant. Each kit will have a register of contents, and an inspection sheet. Each bin will be inspected monthly to ensure all contents are present. Stocks of sand bags will also be checked during the monthly inspection.
Spill Response Procedure –Drills
On a two-monthly basis the site will schedule and run a spill deployment exercise on the site related to the Bentonite Plant and/or Hydrofraise machine. These drills will enable staff to become knowledgeable and proficient in the response procedures outlined in this plan and spill response equipment available on the site. Any lessons learnt from these drills will be used to improve this spill response plan.
Page 48
Mt Eden Main Works