CBRE DATA CENTRES
Global network of experts, exchanging information to remain one step ahead.
SOCOTEC UK
Expanded offering for the construction & asset management sectors.
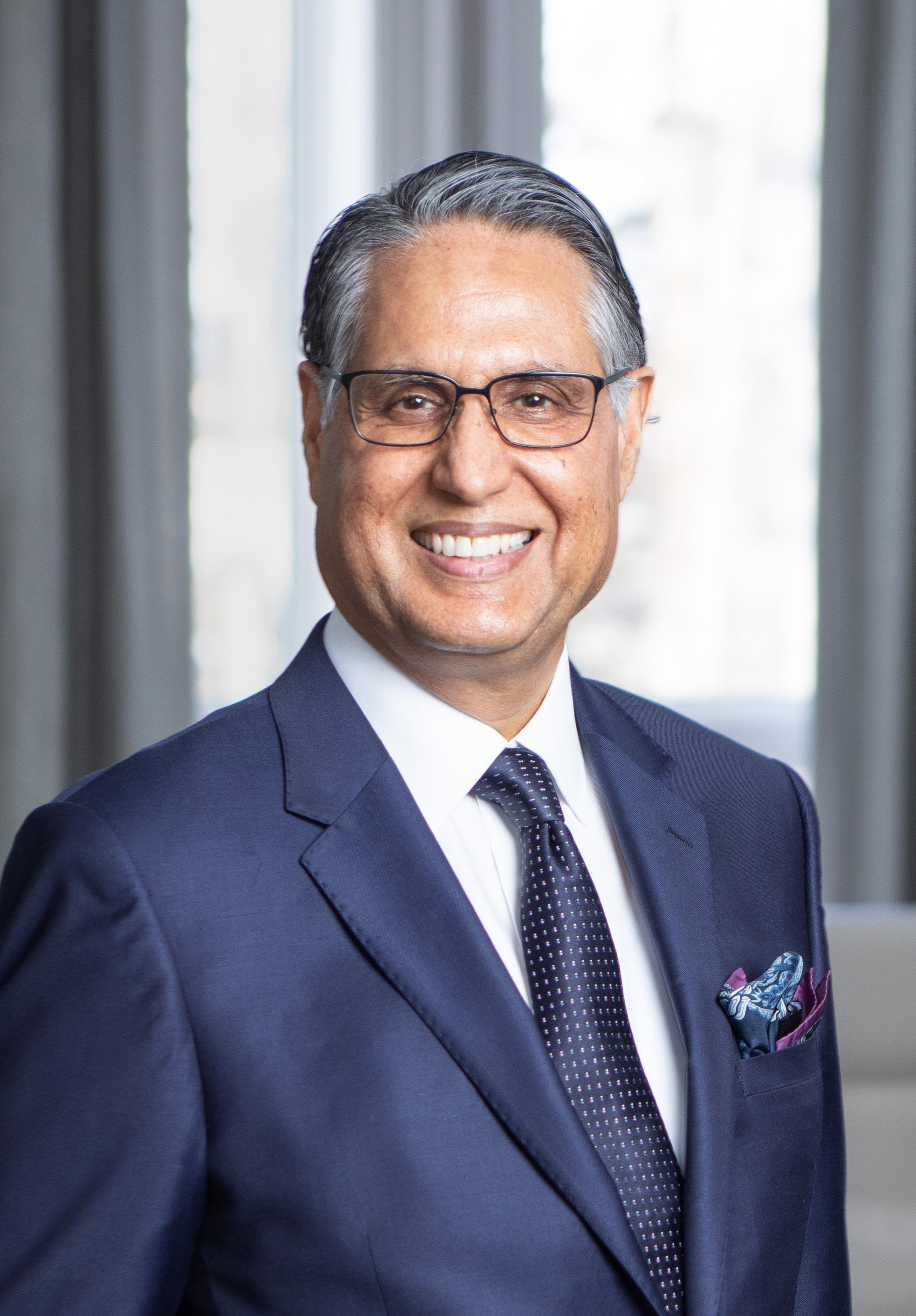
Global network of experts, exchanging information to remain one step ahead.
Expanded offering for the construction & asset management sectors.
Exclusive interview with CEO, Sukhdev Toor, on their journey from a single motel to a chain of hotels & residencies.
Entering its 150TH year, a proud legacy that is set to continue.
A strategy that aims to strengthen their position while improving environmental credentials.
MILLER KNIGHT Specialist regeneration and refurbishment, making buildings safer.
PROJECT MANAGERS
NIK AHUJA n.ahuja@ceomediagroup.com
CAMERON BEAZER c.beazer@ceomediagroup.com
ANDREW BOURKE a.bourke@ceomediagroup.com
BENJAMIN CROWSON b.crowson@ceomediagroup.com
DAVID GARNER d.garner@ceomediagroup.com
DAVID HAYVIS d.hayvis@ceomediagroup.com
JOHN HOLLIMAN j.holliman@ceomediagroup.com
DECLAN JONES d.jones@ceomediagroup.com
JOSH MALIN j.malin@ceomediagroup.com
ROBERT NAPIER SMITH r.smith@ceomediagroup.com
LIAM PYWELL l.pywell@ceomediagroup.com
JAKE REEMAN j.reeman@ceomediagroup.com
ALBERT RUSU a.rusu@ceomediagroup.com
HAYDEN TURNER h.turner@ceomediagroup.com
RASH UDDIN r.uddin@ceomediagroup.com
TYLER WARNER t.warner@ceomediagroup.com
DESIGN
SCOTT ANDREWS design@ceomediagroup.com
ACCOUNTS
MIKE ASHER accounts@ceomediagroup.com
PRODUCTION
KAMILA KAJTOCH production@ceomediagroup.com
EDITORIAL
CHRIS FARNELL cfarnell@ceomediagroup.com
SALES & MARKETING DIRECTOR
TREVOR GRETSINGER t.gretsinger@ceomediagroup.com
SUBSCRIPTIONS, PRESS RELEASES AND GENERAL ENQUIRIES: info@ceomediagroup.com
The list of jobs that do not involve using a computer is shrinking all the time, and the list of promises made about the technology is only growing. But it can all sound like a lot of buzzwords until you see the applications of this technology in practice, and it can take you to some truly places you did not expect.
In this issue, we talk with Lavie Bio, a company using artificial intelligence to find biological alternatives to synthetic chemicals in the agriculture sector. We have also talked with Viralgen, whose research into treatments for genetic diseases has been driven by the latest digital technologies.
We have learned about the cutting-edge digital and simulation tools behind the construction of the new Dakhla Atlantic Port, and Eton Systems’ state-of-the-art production lines. Eton Systems is just one of the high profile manufacturers featured in this article, including HansaMatrix, Hoberg & Driesch, and International Cookware, the company behind the world famous Pyrex brand.
And we have also had an indepth discussion with CBRE Data Centers France, learning not only about the immense data infrastructure necessary to support the latest technological innovations and applications, but also about the preparations it is making for breakthroughs yet to come.
One of the side effects of rapidly developing technology is a rapidly developing regulatory environment, which means there is a demand for consultants who can guide businesses through
that environment. In our feature on SOCOTEC, we learn how they provide that support.
But no matter how advanced the technology becomes, there are some areas where a human touch is still necessary. In our article on Poltrona Frau’s Interiors In Motion arm, we learn about the craftwork that goes into creating their high-class luxury vehicle interiors for the automotive and aerospace sectors.
Whether you are using the latest technology, or timehonoured traditional techniques, the skills of your people remain your most valuable investment.
ON THE COVER
Manga Hotel Group
Go to page 16
EVENT
London Climate Technology Show 2024
ExCeL London, United Kingdom
27th - 28th November 2024
An unparalleled platform for climate technology innovators, policymakers and businesses at large to accelerate the net zero economy transition.
NEWS
Digital Tools
A Broader Digital Frontier
LEADING FEATURE
Manga Hotel Group
Taking Canadian Hospitality to the Next Level
AGRICULTURE
Lavie Bio
Biologicals for a Greener Future
AUTOMOTIVE
Poltrona Frau
The Seat of Luxury
AVIATION,
Julius
COMMUNICATIONS & TECHNOLOGY
CBRE Data Centre Solutions France Making Data Happen
CONSTRUCTION
Creagh Concrete Casting Call
Höganäs Borgestad Smart Refractory Solutions
Meldrum Group Following Quality
Miller Knight Elevating Building Safety
SOCOTEC UK An Expanding Service Offering
ENERGY & UTILITIES
EGENCO The Power to Unlock Potential
FINANCE & CONSULTING
Absa Bank Botswana One Story at a Time
Helsinki Partners The Happiest Place on Earth
HEALTHCARE &
Eton Systems
Where Quality Inspires Trust
HansaMatrix
Customer-Focused, Expert-Driven
Hoberg & Driesch Continuity in Change
METALS & MACHINERY
AYS
SHIPPING, PORT & MARINE
Dakhla Atlantic Port A New Gateway to Africa
Damen Naval Mission Ready
Port of Aberdeen
Port of Opportunities
We put fervour in our work to make it happen!
• Renewable energy solutions & supply of generators
• Civil engineering
• Machine tools
• Technical, technological & strategic advice
• New communication & information technologies
LONDON CLIMATE TECHNOLOGY SHOW 2024
WHERE: EXCEL LONDON, UNITED KINGDOM WHEN: 27TH - 28TH NOVEMBER 2024
An unparalleled platform for climate technology innovators, policymakers and businesses at large to accelerate the net zero economy transition.
Helping accelerate the global net zero economy transition, the London Climate Technology Show is the most sought after exhibition & conference focused on the fast developing climate technology value chain, where stakeholders from across the world assemble to experience two days of high value content and unparalleled business opportunities. The London Climate Technology Show aims to be the largest climate technology exhibition and conference in the world for advancing the global net zero economy transition and shaping a sustainable future with ground breaking and collaborative technologies.
contact_salesEMEA@paloaltonetworks.com +966 800844 5418
www.paloaltonetworks.com
THE RANGE OF DIGITAL TOOLS AND WHAT THEY ARE CAPABLE OF IS CONSTANTLY WIDENING, AND THEY ARE FINDING APPLICATIONS IN SOME SURPRISING PLACES.
It seems like you can’t turn a corner without running into a story about Artificial Intelligence these days. The term is used so widely, and so broadly, that you could be forgiven for being increasingly uncertain about what the term actually means.
While we could easily argue at length about definitions, perhaps it is more useful to have a look at how these tools are being applied in practice. Once we start looking into that, we find the technology in some surprising places.
BRINGING DIGITAL TO LIFE
Some of the most innovative applications of digital solutions are taking place in the life sciences sector.
Agriculture, for instance, is not an industry sector commonly associated with the cutting edge of technology. Lavie Bio is a firm that leverages cuttingedge computational technology to develop the next generation of ag-biological products that will represent a leap forward in improving agriculture practices and the environment. As we learn in our profile of the company this issue, AI is one of the key tools it uses, and perhaps unexpectedly, it is being used to drive a more natural sort of farming.
“This AI system enables us to identify the microbes that we want to turn into two types of products – bio-pesticides, which are intended to replace some chemical applications in a biological-based solution, and bio-stimulants that bring additional capabilities to the plant in order to help it grow better,” says Amit Noam, Lavie Bio’s CEO.
By deploying this technology here, Lavie Bio hopes to push for farming practices that move away from chemical and synthetic-based solutions as consumers worldwide demand healthier food for themselves and the planet.
The medical sector is one where you might be less surprised to find cutting-edge technology. In our conversation with Jimmy Vanhove, CEO of Viralgen, we learn about the company’s new MSAT laboratory, an investment of over 10 million euros.
“This laboratory strengthens our mission to bring hope to patients through science and innovation, reaffirming our commitment to improving
people’s health and wellbeing,” Vanhove emphasised at the facility’s inauguration ceremony.
Every aspect of MSAT’s operations is set to feature stateof-the-art facilities, operated by a highly skilled team with an innovative approach to the integration of digital technology. It is implementing tools and systems such as electronic lab notebooks and advanced data management systems to ensure efficient real-time data capture, analysis and visualisation. The facility is one that has been built around data, ensuring that its integrity is maintained and can be traced to its source.
While the technology is made to serve and protect the data, it ultimately exists to empower the researchers who are doing the work, enabling interdisciplinary collaboration, which in turn drives informed decisionmaking. MSAT’s research team is at the forefront of digitalisation applications in gene therapy production, paving the way for more effective and accessible treatments for rare genetic diseases.
“OUR KEY STRENGTH IS OUR KNOW-HOW, THE COMBINATION OF HARDWARE AND SOFTWARE; WE OFFER A NEW PRODUCTION MINDSET TO A FACTORY.”
The big questions around some of the applications known as “artificial intelligence” are based on the energy costs of image generators and LLMs, but digital tools have also been deployed to help reduce the environmental impact of large facilities and infrastructure.
We can see this in practice in our profile of Dakhla Atlantic Port, one of Morocco’s biggest infrastructure construction projects. As the Port’s Construction Director, Nisrine Iouzzi points out, “Morocco has embarked on a comprehensive strategy for digital and environmental transition. Aligning with these national strategic orientations, we
have ensured their integration throughout the various phases of the project, from the study phase to the construction phase."
During the study phase of the project, Dakhla Port used technologies at the forefront of what is possible in digital and physical modelling, calculation, and sizing.
“This approach continued into the execution phase, where we employed intelligent control and monitoring systems, such as semi-automatic welding systems, drone-based work monitoring, and the use of new blocks for the breakwater armour," Iouzzi says.
Similarly, powerful digital systems are being employed in the manufacturing sector, as we see with Eton Systems. As with Viralgen’s MSAT laboratory, the power is not just in gathering data, but in being able to do so on a real-time basis, informing the necessary tools to improve manufacturing processes with powerful software programmes. In our discussion with Eton System’s CEO, Jerker Krabbe, he points out that Eton Systems’ material handling systems are
almost unique in the industry, with the flexibility to fit different production lines at different production sites.
"Eton Systems is the Rolls Royce of conveyor systems,” says Krabbe. “Our key strength is our know-how, the combination of hardware and software; we offer a new production mindset to a factory. As such, we can't just install the system and run; we have life-long relationships with our customers, who rely on us to improve their productivity and profitability."
All of these tools, applications and solutions depend on data, and as our reliance on data increases, it is less practical and increasingly risky to store vital data on-site. This is why the role of companies such as CBRE Data Centre Solutions has already become incredibly vital to modern business. In this issue’s feature of CBRE Data Centre Solutions in France, we see that the sector is set to grow exponentially, and data centre providers are already looking to see what the next big thing will be.
“We are trying to be ahead of the market,” says Séraphin Bravard, Director of CBRE Data Center Solutions France. “At the moment we are working on data centre opportunities dedicated to cloud applications, but we are also looking at what will be next. We are brainstorming, with our customers and internally, on what new requirements, specifications, and solutions will be necessary. That is why we are part of local data centre associations where we can share our clients’ view of the market with the industry.”
Exactly what form the next phase of digital solutions will take remains to be seen, but one thing we can be sure of is that it will have an impact in every possible business sector.
“AT THE MOMENT WE ARE WORKING ON DATA CENTRE OPPORTUNITIES DEDICATED TO CLOUD APPLICATIONS, BUT WE ARE ALSO LOOKING AT WHAT WILL BE NEXT."
Manga Hotel Group is an impressive venture by any measure, with 5,800 rooms across 31 hotels and 3,000 purpose-built rental units. Some of those hotels and residences are ones that Manga Hotel Group has acquired, while others it has built itself. It is also affiliated with well-known hotel brands including Marriott, Hilton, Hyatt, and the InterContinental Hotel Group. Manga also has involvement in expanding into several high-rise building developments with approximately 500 units each, in various stages of construction and operation.
We have been in this business for a very long time,” says Sukhdev Toor, founder and CEO of Manga Hotel Group. “I started the business 34 years ago, when there were not as many big franchises as there are now.”
Toor has mastered the hotel industry floor by floor, building on that foundation of knowledge of the industry to the heights Manga Hotel Group has reached today. He started out working in one small hotel, and there he grew the business
to nine hotels by 1997. From there, Toor began building hotels in 1998.
“The Hampton Inn that we built and opened in 1999 was our first construction and the first Hampton Inn in Canada, and now the Hampton chain has more than 3,000 hotels worldwide,” Toor says. “We have built hotels from the ground up for Marriott, Hilton, Hyatt and the InterContinental Hotel Group.”
In addition to building, Manga has grown through acquisition. The Group has acquired 8 new hotels in the last twelve months,
& Surrounding
Commercial & Residential Buildings Cleaning Services Specializing in Hotels & Condominiums
Main Services Provided:
∙ Daily/Nightly Cleaning Services (Cleaning to Reset Designated Pubic & Service Areas for Next Day)
∙ Multi-Surface Cleaning/Disinfection/Sanitation
∙ Commercial Grade Restroom Cleaning Services
∙ Commercial Grade Culinary Stations (Commercial Kitchens) Cleaning Services
∙ Specialized Floor Maintenance (Stripping/Refinishing, Impregnating, Sealing, Natural Stone Polishing, Pressure Washing)
∙ VLM (Dry) Carpet Cleaning/Wet 4 Stage Carpet Shampoo Cleaning
Global Cleaning & Consulting Solutions is a professional cleaning and maintenance company that has been servicing commercial, industrial and residential properties/buildings in the Greater Toronto and Surrounding Areas since 2010.
We are a very versatile company that can adapt and integrate our services to suit the needs of any client regardless of what type of property they are; from hotels to condominiums, office buildings to manufacturing plants, entertainment facilities to product showrooms to convention/banquet facilities. The types of cleaning services we offer are vast and can vary depending on the frequency of which they are utilized, from daily/nightly, weekly, monthly, quarterly, annually services.
Since our inception, it was our mandate to ensure that our clients felt less like customers and more like members of our community. With this approach, we treat all of the facilities under our care like they are our own, going beyond expectations to service them with the care and attention they rightly deserve. We also make sure that we service all of our clients’ properties with the most effective cleaning products that are eco-friendly, tough on grime but gentle to the planet.
Our success is solely rooted in the business success of our clients. Our operations are driven by this belief; whereby our best work at cleaning our client’s property making them pristine, will help give an unforgettable first impression to their clients.
www.gccsinc.ca
www.gccsinc.ca
• CANADIAN OWNED SINCE 1961
• PROFESSIONAL LAUNDRY ROOM DESIGN & SUPPORT
• FULL SERVICE & PARTS DEPARTMENTS
• REDUCE COSTS & INCREASE PRODUCTION
CANADA’S LEADING DISTRIBUTOR OF INDUSTRIAL & COMMERCIAL LAUNDRY MACHINES
Harco Co Ltd. is the Canadian leader for On-Premise laundry equipment, with state-of-the-art brands such as UniMac, Chicago Dryer, Maytag Commercial, and other specialty lines for all your laundry needs. Our expert team will assist with design and equipment selection while Harco’s awardwinning service department will ensure you will receive the best after-sales support in the industry. Our fully stocked parts distribution center cuts down on long wait times for critical parts, guaranteeing your equipment is always operational.
www.harcoco.com +1-800-387-9503 / sales@harcoco.com
opened two new properties and is continuously renovating properties in its existing portfolio with constant capital reinvestment.
As Manga Hotel Group has evolved, it has also entered new territory, learning lessons along the way. For a brief period, the Group ran limited-service
hotels such as Comfort Inns, before the Group underwent a streamlining process to focus on upscale brands, the kind of hospitality facilities that have a high barrier of entry for other builders.
It is this ability to recognise and move with the times that has made Manga Hotel Group a leader in the sector. Currently, what makes Manga
Hotel Group a real trendsetter in the field is its approach to improving the sustainability of the hospitality industry.
“We were the first hotel developer in Canada to be LEED-certified which stands for Leadership in Energy and Environmental Design,” Toor tells us proudly. “Right now we are building hotels in downtown Toronto with solar panels and geothermal power. Hotels with lower carbon emissions.”
Speaking on the Group’s expansion outside of Ontario, Toor states “In Canada, we have opened up brand new horizons. We took the first Hilton hotel to the province of Nova Scotia, where we own eight hotels now, four of which are Hilton properties. We also brought the first Hilton hotel to the province of Newfoundland and have two Hilton properties there.”
While the company has always led the way, there have also been challenges to overcome.
“There are various challenges when you try to grow any business,” Toor is the first to point out. “You have to not only be aware of your own financial situation, but also be careful about where the economy is going on a worldwide scale. We have seen recessions. We have seen the financial crash in 2008. You need to be resilient and sustainable to have a longterm strategy that works.”
Covid-19 presented a similar challenge for the hospitality industry, coming on very suddenly. During lockdown, the rules were changing rapidly and hotels struggled to keep up. It was a challenging time, and even as lockdown lifted, hotels had to continue to adapt to a constantly changing regulatory environment.
“Post-Covid we were not allowed to go into the guests’ rooms to clean. Since then we have trained our staff to adapt their cleaning routines to suit the customers’ preferences,”
Toor tells us. “We are very careful in sanitising the rooms.”
To adhere to the standards that Manga Hotel Group holds itself to, it needs staff who are fully on board with those standards and the culture that Manga Hotel Group has built.
“Our staff are crucial,” Toor says. “Without them, we cannot be successful. We have incentive programs and benefits. We retain our staff by giving them bonuses. We look after each other. It is very hard to find good people and retain them. That is an important part of the whole business.”
Under Toor’s vision, Manga Hotel Group has become a completely vertically integrated business, from land acquisition, to construction, to hotel operations and management.
“We don’t manage for third parties,” Toor says. “Our head office covers all accounting, property management, and construction, all in-house.”
As Toor steers Manga Hotel Group towards its future, it is clear that he is planning ahead. But he is also conscious that the correct approach is to move one step at a time. The Group has already performed exceptionally well with other prestigious brands. Now Toor is planning to launch his own.
“There is no final destination, you just continue growing,” he tells us. “We have recently launched our new TOOR Hotel in Toronto, but soon it will be coming to some of the biggest cities in the world. We are
working to create our own brand and hotel collection under which we are building three new hotels in downtown Toronto, before moving into other markets like London, New York and Chicago. We are looking for opportunities to acquire and build.”
Toronto is historically a great place to launch a hotel brand. As Toor points out, this is also where the Four Seasons first emerged, starting on the same street as TOOR Hotel. It is the perfect location to meet the needs of a rapidly changing customer segment.
“Consumers are looking for different experiences these days. Boutique style, upscale hotels for cities,” Toor shares.
“Starting a brand is about consistency and service. Brands can start from anywhere these days. So we are creating a niche product for the market in the upscale lifestyle segment and growing that into major cities.”
The TOOR Hotel in Toronto will soon be just one of four hotels in the TOOR Hotel collection, a new, fundamentally Canadian brand.
“There is a uniqueness to Canadian hospitality that is recognised globally,” Toor says.
“That, combined with the legacy of operational excellence we have built, is what we are rooting our eponymous hotel brand in before taking it worldwide.”
That legacy is not just the legacy of the company, however. It is also the legacy of Sukhdev Toor himself.
The history of agricultural biologicals – a diverse group of products derived from naturally occurring microorganisms as the primary active ingredients – is as old as agriculture itself, as humans have been working in tandem with living organisms to grow crops for centuries. However, only recent advancements have made them competitive with chemical substances in terms of improving yields, with the added benefit of generating healthier crops and preserving the soil.
Amit Noam, CEO, Lavie Bio.
Leading the way in this exciting development is Lavie Bio, a subsidiary of Evogene, a pioneer in the field of applied computational predictive biology. Lavie Bio’s ag-biological products under development are based on the naturally occurring microbial population and aim at improving food quality, sustainability, and agriculture productivity.
The company uses a proprietary computational predictive system, the Biology Driven Design platform (BDD), powered by Evogene’s proprietary MicroBoost AI tech engine, harnessing the power of big data, artificial intelligence, and advanced informatics for the discovery, optimization and development of bio-stimulant and bio-pesticide products.
Company CEO Amit Noam summarises the core business: “We leverage cutting-edge computational technology to develop the next generation of ag-biological products that will represent a leap forward in improving agriculture practices while protecting the environment.
The AI system enables us to identify the microbes that we want to develop into two types of products – bio-pesticides, which are intended to replace some chemical applications in a biological-based solution, and bio-stimulants that bring additional capabilities to the plant in order to help it grow better.”
Noam points out that structuring and controlling the microbiome composition in the field is a “game changer” in crop performance. “We are trying to understand which microbes have which effect on the plant, and if it is possible to isolate that microbe and turn that into a product – change the microbiome composition in the field using the right microbes.”
“This is done in a natural way, as the world is set to move away from chemical, synthetic-based solutions – a macro trend that is now happening on a global scale as consumers demand healthier food. As such, biologicals seem to be the right solution, one that is more sustainable, cleaner, better for the environment, the soil, and ourselves.”
From fermentation process development to production
Up to 10 m3 in-house fermentation volume
Access to up to 150 m3 fermentation volume
Versatile in drying and formulation techniques
He points out that today, the biologicals market is around $12 billion p.a. While still accounting for only 5% of the entire ag inputs market which includes chemicals, it is by far the fastest growing industry, expected to increase to $30 billion in less than a decade.
Importantly, when developing a new product, Lavie Bio benchmarks it against the chemical product already in the market. “We can easily be better than the other biological products, but still not win the market. You need to set the bar at where the chemicals are, and if you’re able to bring a solution that is not only on par with the chemical but also brings the whole sustainability solution, that’s where the market will erupt, and that’s where biologicals will move from the 5% to the 25% of this entire $200B market,” says Noam.
Over the last few years, the company has achieved several significant milestones. Last year, Lavie Bio launched its first product to be commercialised. Yalos®, a leading-edge bio-inoculant for hard red spring wheat, durum, and barley, was introduced in the United States, followed by Canada in 2024. Taking advantage of a combination of two microbes, Yalos enhances nutrient availability and uptake, improving a plant’s natural defence mechanism and its ability to mitigate stress.
“Yalos, a bio-inoculant for a range of crops, has been proven to improve yield by six per cent on average, and the index has been constant over 250 trials. This consistency across five different years, different climatic areas, different soil types based on a huge amount of data, is unique for a biological agent” says Noam.
More recently, the company has announced the commercial expansion of Yalos to winter wheat, following successful trials. This expansion effectively doubles the potential market for Yalos compared to the markets in which Lavie Bio already operates. In addition, Lavie Bio is expecting to expand Yalos into other key crops, such as soybean and canola, with ongoing field trials in North America and an expected commercial launch in 2025.
Noam points out that the company currently has 8 products in the pipeline to be marketed within two business models – either sold directly by Lavie Bio’s own sales team, or licenced to global players.
“Cooperation is key for our growth,” he says. “A small company with unique capabilities needs partners to disrupt the market. We are a partnershipled company and we are also impact-driven, we want our products to make a difference, to reach as many farmers as possible. The only way to do that is through cooperation with other organisations.”
That is already happening. In July 2023, Lavie Bio signed a licencing agreement for a bio fungicide with Corteva, and has just recently announced a partnership with Syngenta, a leader in agricultural innovation, to develop a novel bioinsecticide. The company has also announced a collaboration
with Bayer on another product, and with ICL will develop yieldincreasing bio-stimulants for key row crops facing various abiotic stresses.
“Lavie Bio is unique in that we are the preferred partner of choice for all these big players in the industry, as our technology is so special and we do things very differently,” says Noam, adding that Lavie Bio is at the very intersection of biology, sustainability and artificial intelligence.
“On the one side, we have the ability to be on the cutting edge of computational technology, and on the other to be fully sustainability-driven. That’s the magic of our company, and that is what attracts the best minds to us – biologists, agronomists or the computational scientists who look for exciting challenges that can make a difference to the planet.”
“I feel very privileged to be part of what I believe is one of the best teams in the industry, with the motivation and with the capabilities to make a positive impact on our environment: to make it safer, cleaner and healthier for generations to come.”
Looking forward, he reflects that while Lavie Bio is currently focusing on organic growth, the company is also looking at opportunities for investments, for acquisitions, to be able to increase its capabilities. “I believe we live in the most exciting times for agricultural biologicals as we will see this market erupt over the next few years. Biologicals have matured; there are new technologies, new companies, new capabilities to be able to make the move. The industry is ready to make that leap.”
IN ITALY, POLTRONA FRAU HAS BEEN A NAME ASSOCIATED WITH LUXURY FOR OVER 110 YEARS. NOW ITS MANUFACTURING KNOW-HOW IS COMING TO THE UK.
Poltrona Frau is an Italian company that manages over a dozen flagship stores in many of the most important cities in the world, and boasts a network of over 450 points of sale across the globe. It belongs to Haworth Group, a US Company that has been leading the office furniture market since 1948. The story of Poltrona Frau begins in 1912, when the Sardinian entrepreneur Renzo Frau registered the name in the city of Turin.
He was in love with the style of furniture that was typical of the English style aristocracy at the time. The sort of furniture you would see in gentlemen’s clubs and so on,” says Giovanni Maiolo, Director of the Business Unit Interiors in Motion sector of Poltrona Frau. “He founded this company to design his own collection, and it rapidly gained popularity. Soon Poltrona Frau was the official furniture provider for the Italian Royal Family, and continued to grow for many years. It became the standard for luxury while we still had a monarchy.”
Of course, a lot changed with the Second World War and after a series of crises, the company was facing bankruptcy by 1963. But in the face of that crisis, one of Poltrona Frau’s major creditors, a family-owned Italian tannery, saw an opportunity.
“They were well-known in the small leather goods industry, and they decided to buy the Poltrona
Frau brand, employing a single member of staff to put together a new collection,”
Maiolo says. “That person trained a new generation to produce furniture.
They convinced a firsttime designer, that until that period had never designed furniture, to create a collection to be sold in the luxury market segment all over the world.”
In 1968, Poltrona Frau embraced the opportunity to collaborate with some acclaimed Italian designers. It was a venture that led to some iconic products, among them the Dezza armchair, designed by Giò Ponti, and the Lullaby bed, designed by Luigi Massoni. This radical transformation of Poltrona Frau’s product range, coexisting with the brand’s more traditional designs, generated the distinctive trademark identity of the Poltrona Frau brand that persists today.
Giovanni Maiolo, Director of Interiors in Motion, Poltrona Frau.
MAGG was born from the ideas of Andrea Merlitti and Gianluca Giovine: to develop and produce materials capable of maintaining sustainable mobility.
MAGG produce interior and exterior trim for electric, luxury and special vehicles. Where possible with natural fibre and recycled materials.
It is led by two young entrepreneurs, Andrea Merlitti and Gianluca Giovine, who had the happy intuition to turn an idea into a manufacturing company: the industrial area of Pineto is now home to the production of prototypes.
The development of innovative solutions and serial production of new, lightweight, sustainable materials capable of guaranteeing the present and future demands of the market.
“Over the years, we have developed and produced various innovative components” explains Andrea, “thermoset, thermoplastic composites using natural, mineral and thermoplastic fibres.” Gianluca further supports him: “MAGG is a dynamic company, in step with customer needs, no new challenge catches up unprepared. The competence, flexibility of our team and our facilities allow us to be competitive in the market.”
www.maggsrl.com 0039 0858 126 296
The collection was a hit, and once again Poltrona Frau was a byword for luxury, this time intrinsically associated with high quality leather. Even today, the majority of customers desire Poltrona Frau for their product lines in leather. From there the company has continued to expand, launching three key business units. The first, and most well-known, is the Residential Business Unit, famous for its luxury furniture, accessories and compliments. The second business unit, Custom Interiors, is specialized in small to large scale public spaces and collaborate with the world’s most prestigious architects and studios. This unit is less well-known, but no less prestigious, producing seating systems and interior solutions for many public buildings such as the European Parliament, the Shakespeare Theatre in Stratford Upon Avon, the Walt Disney concert hall in Los Angeles and several Opera houses. Last but not least is the Interiors in
Motion Business Unit, led by Giovanni Maiolo. This segment of the business was born in 1984. Its first project was the Lancia Thema with an 8.32 Ferrari Engine, where Gianni Agnelli, FIAT’s former owner, wanted to reach the same elegance and comfort he had seen in the Poltrona Frau armchairs of his own living room.
Today this business unit covers several sectors, from Automotive where it manufactures and upholsters interior components such as headliners, pillars, dashboards, door panels, and centre consoles, to Yachting and Aviation luxury classes for seating.
“We have collaborated with Singapore Airlines for their firstclass cabins. We do the seating systems for all the top-end manufacturers in the automotive sector,” says Maiolo. “We can say we are probably one of the most important producers of interiors in the luxury field. We have supplied the interiors for most cars over £100,000. Ferrari is historically our most important customer in that market. We have also worked with Land Rover since 2008, and we are
supplying important products for the new Range Rovers. In the UK we are also working with Maclaren and Aston Martin.”
Poltrona Frau Interiors in Motion is responsible for providing a complete range of services, from design to product development, from test validation to project management, and offering innovative technical solutions for the creation of products of the highest quality.
It helps its customers create exclusive and unique interiors for cars, aircraft and boats.
Poltrona Frau has grown to dominate the luxury sector of the market. The Interiors in Motion business unit is now worth 120 million euros and employs approximately 600 people. But the luxury sector also comes with unique challenges. While the production runs may be significantly shorter than in the mass-market sector, maintaining the necessary quality levels at volume is still a challenge.
“In the luxury segment, you need to be able to handle complexity, providing high quality at sufficient volumes,” Maiolo points out. “In a single day, you might need to do the interiors for three fully bespoke cars, but we have to do that to the highest production standards. When you want to do personalisation and volume simultaneously, we are the only ones who can manage that.”
Poltrona Frau is able to provide these levels of complexity and volume because it carries out most of its activities manually.
“We have automated some processes which allow us to be competitive, but for the personalisation, we provide manual work,” Maiolo tells us. “We look for areas where we can add value and create distance between ourselves and the competition.”
When it comes to providing that level of hands-on skill, Poltrona Frau’s location is a huge boon. Its facilities are in close proximity to those of Gucci and Prada. They work at the cross section of several supply chains providing unique and specific applications around luxury leatherware, with a lot of opportunities to add value.
“Poltrona Frau facilities are located in a region imbued with manufacturing tradition in the world of leather,” Maiolo says.
While Poltrona Frau is a quintessentially Italian company, in recent years it has established a new facility in the UK.
“Joining forces with Poltrona Frau and Haworth Lifestyle makes me very confident that the skills, know-how and credibility I have built over 40 years of work in the sector have found the best possible platform to be nurtured and expanded in the future,” said KJ Ryan Founder Kevin Ryan.
“With this acquisition, we will be able to replicate the same organisation we have in Italy in the UK,” Maiolo tells us. “There will be a few synergies in terms of safety parameters, but at the
same time, we have carried out so much investment in Italy that it will be necessary to keep some of our parts production on our side. We aim to replicate those processes and that expertise here, working with the local supply chain and with most of our staff employed locally. The goal is to create an autonomous branch to supply UK customers with the same philosophy we have in Italy.”
Italy and Great Britain both have firmly established manufacturing cultures. Bringing those cultures together opens up some exciting opportunities.
“I believe there are a lot of advantages in merging British and Italian manufacturing culture,” Maiolo says. “Basically only Italy and the UK have that experience manufacturing for
the luxury segment. Elsewhere, the maximum standard you will get is premium. So it was a natural part of our strategy to establish a presence in the UK after Brexit because it makes it easier to approach the customers here.”
Maiolo is passionate about the opportunities for crossfertilisation between Italian and British manufacturing that could open up new possibilities for innovation and service.
“It makes it possible to get in contact with the best professionals with a lot of experience, and from our side, that means we can provide a different offering to many of our competitors,” Maiolo says. “What we have in the UK are small companies that can support low volume one-offs, or multinational companies that are used to working with much larger volumes, and the natural impact that has on service and cost. We can be much more flexible than the bigger firms in the UK but produce in volumes that smaller competitors cannot.”
The lessons learned from this cross-pollination are ones that can be taken further afield, as Maiolo points out, “Moving into Britain is a chance to build up new knowledge and new practices that we can then share around Europe.”
JULIUS NYERERE INTERNATIONAL AIRPORT, THE INTERNATIONAL AIRPORT OF DAR ES SALAAM, HAS UNDERGONE EXTENSIVE EXPANSION AND MODERNISATION OVER THE LAST DECADE, WITH MORE TO COME.
Named after Tanzania’s first president, Julius Nyerere International Airport (JNIA) is the largest and busiest international airport in Tanzania, located in Dar es Salaam, the largest and fast-growing city in Tanzania.
The airport is one of the 59 government-owned airports and airstrips, operated, developed, and managed by the Tanzania Airports Authority (TAA). “JNIA currently employs some 1,000 staff directly across its various functions and departments,” says Airport Director Rehema Myeya, adding that over the last few years, the airport has undergone extensive modernisation and expansion to handle increasing traffic volumes.
She explains that JNIA is one of the oldest international airports; it started to operate in 1954, with a capacity of 500,000 passengers per year at its Terminal 1. In 1984, Terminal 2 was opened, adding infrastructure and facilities with the capacity of 1,500,000 passengers and 30,000 tonnes of cargo annually.
accredited international airport professional, got involved in JNIA, first within the Terminal construction project, and gradually moving up all the way to the position of Airport Director.
Rehema reflects that the airport business itself is demanddriven, hence the continued capacity expansion. “As we are speaking, JNIA is now handling almost 1.4 million international passengers, in addition to 1.4 million domestic passengers, on both scheduled flights and private charters.”
[Opposite Page]
Rehema Myeya, Airport Director, Julius Nyerere International Airport
The biggest expansion so far begun in 2014 with the construction of a state-of-theart Terminal 3, designed to raise passenger capacity from 2.5 million to 9 million annually, and completed in 2019. That was also the time when Rehema, a professional civil engineer and
JNIA is a hub for Air Tanzania, the national carrier, and the growth of Air Tanzania since its restructuring in 2016 has boosted the airport. The range of destinations has expanded and now includes cities in Europe, Africa, Asia, and the Middle East.
“JNIA’s role for the region’s development is undeniable. Unlike the other two popular airports of Zanzibar and Mount Kilimanjaro, where 90% of passengers are tourists, we cater for a mix of businessmen, corporate clients, and investors,
For 24 years, Equity Aviation has been a leading aviation services provider as Ground Handler for Business Jets and General Aviation in Tanzania, East Africa and beyond. Our extensive partnership with our partners and clients we ensures seamless operations through the major International Airports.
With more than two decades of experience and a commitment to quality standards and exceptional service, Equity Aviation is your trusted partner for all your aviation needs. We offer a comprehensive range of services, including:
• VIP, Crew & passenger Handling
• Meet & Assist
• VIP & CIP lounges
• Surface Transportation
• Permits
• Fuel
• Charter
T: +255 739 923 721 (24hrs) E: occ@equityaviation.co.tz
M: +255 767 845 448 www.equityaviation.co.tz
as well as tourists. Given its unique position, JNIA also provides excellent access to those destinations, as well as to the national parks, the northern highlands and other popular attractions.”
“We are also a very competitive airport with the cheapest A1 jet fuel, and most of the airlines prefer to stop here to refuel,” she continues, adding that the airport also serves as an alternative aerodrome for many island airports, including Nairobi in neighbouring Kenya.
Rehema admits that the continued expansion presents a certain challenge in terms of human resources. “Aviation is a specialized sector that requires trained personnel. Aviation skills outside the airport are scarce, so for us training is key. Last year, over 1 billion shillings (over $370,000) was spent on training – mandatory, professional as well as benchmarking.”
“With the current Director General Mr Mussa Mbura, we have seen a seamless transformation journey across all areas of the airport, especially in prioritizing human capital to improve operations, information technology, ICT and development projects.”
The new Terminal 3 has been designed for the anticipated growth of international air traffic, leaving the existing international Terminal 2 to cater for domestic flights. “JNIA is now one of the most modern airports in East Africa. Parking, shops, bars, and air-conditioned halls allow passengers to wait for their flight in the best conditions. With a flight punctuality greater than 90%, the airport guarantees a seamless air travel experience,” affirms Rehema.
“Everybody loves Terminal 3. It has a very simple, clear design and employs the latest technology to make our passengers’ experience as enjoyable as possible, and their moving through the airport as easy as possible.”
“We have digitised security systems and installed modern self-check-in counters and e-passport gates so that movement is fast and efficient. We are one of the very few airports in Africa to have
installed intelligently designed, high-speed baggage handling systems (BHS) to improve overall service for airlines and their passengers.”
She points out that Terminal 3 was also designed with every
aspect of sustainability taken into consideration. It has a skylight roof, so no lighting is needed during the day, and only switches on automatically at certain times when darkness falls.
Waste is segregated to be incinerated at site and water treatment ponds have been installed with a water screening system in place.
“On the airside, we encourage aircraft to switch off their engines when parked and to plug into ground power units to reduce emissions, and only to switch their engines back on when taxiing.”
Under Rehema’s management, the airport is adding new airlines and achieving international recognition for its outstanding performance. Since the end of the pandemic, Saudia Airlines and Air France have started new routes to JNIA, followed by Zambia Airways in June 2024; South Africa Airlines are expected to join in October.
The airport has also recently scored excellent results in an ICAO security audit, becoming No 4 in Africa, and has been recognized as CIEV Fresh Certified in cargo handling. To further improve passenger comfort, the airport supports intermodal transport development linking the airport to the city as well as other parts of the country.
Further expansion is planned, with the major upcoming project being the renovation of Terminal 2. “We have started with the preliminary design and are in discussions with the stakeholders to finalise the financial arrangements. The plan is to turn Terminal 2 into a modern national hub for Air Tanzania, ready to handle bigger volumes of traffic of up to 3.5 million passengers.”
“Our thanks go to the exemplary leadership of Her Excellency Dr Samia Suluhu Hassan for the financial support we receive to execute strategic projects to enhance connectivity across the country and regional.
She says that the management is also focused on increasing non-aeronautic revenue streams. In 2022, the Tanzania Airports Authority announced its plans to develop a four-star hotel and commercial complex at Julius Nyerere International Airport (JNIA) and the procurement process has now started through a publicprivate partnership.
Apparently, there are busy times ahead. Rehema agrees:
“We have several major projects to go ahead in the near future and more is to come. We have space for hangars, for a private jet terminal and further facility modernisation.” Overall, the development of JNIA reflects the economic development of the country, which is set to continue to rise to new heights.
LOT POLISH AIRLINES, POLAND’S NATIONAL AIRLINE, IS IMPLEMENTING ITS GROWTH STRATEGY, ONE THAT AIMS TO STRENGTHEN THE COMPANY’S POSITION WHILE FURTHER IMPROVING ITS ENVIRONMENTAL CREDENTIALS.
LOT Polish Airlines, the flag carrier of Poland, remains one of the world’s oldest operational airlines – in 2024 the company commemorates its 95th anniversary and this impressive legacy is set to continue: LOT survived the challenging years of the global pandemic with flying colours and is determined to translate its recent record financial results into ambitious growth.
Krzysztof Krolak, VP Technical Operations, explains that last year the company defined a new strategy for 2024–2028. Key objectives include expanding the aircraft fleet by around 50% (110 in 2028 versus 79 today), increasing passenger numbers by around 70% (16.9 million in 2028 versus 10.3 million today) as well as increasing service quality and passenger satisfaction, for example by setting new interior standards on wide-body aircraft
and introducing Wi-Fi access on long-haul flights.
“Growing passenger numbers and opening new destinations clearly require more aircraft,” says Krolak.
“The fleet expansion is already being implemented with the planned delivery of three new Embraer E195-E2 alongside with additional Boeing 7378 MAX. The first jet arrived in July with the remaining aircraft deliveries expected to be completed in Q4 2024.”
Designed to accommodate up to 136 passengers, these jets will feature a single-class configuration and support the airline’s growth strategy. Today LOT has a fleet of 45 E-jets making it one of the largest operators of E-jets in Europe, and the Embraer E195-E2 will further enhance the airline’s operational flexibility.
“We also plan to expand our fleet of regional aircraft and expect the final decision to be made by the end of the year. This is in line with our plans to fully modernise the fleet by 2035,” says Krolak. The airline is considering both Embraer E2s and Airbus A220s for its fleet renewal.
Also as part of the new strategy, LOT wants to introduce nearly 20 new scheduled destinations, both medium- and long-haul. Bearing in mind the growing importance of pro-environmental attitudes in the world and passengers’ expectations, an
Destination ECO project has been introduced, aimed at reducing CO2 emissions, finding alternative aviation fuels and recycling.
“Needless to say, sustainability is very important to us and is an integral part of the new strategy. We are striving to optimise flight operations, reducing the quantity of plastics on board and in our offices, and we are also working to protect the environment by restoring habitats, to name just a few of the environmental measures that we have launched,” says Krolak.
Despite the fact that LOT has been one of the aviation companies severely affected by the war in Ukraine, the company has been achieving outstanding results over the last few years, as traffic volumes are slowly starting to return to pre-pandemic levels. “People want to fly and our load factor is going up. We don’t have any aircraft grounded due to a shortage of passengers,”
affirms Krolak, adding that the summer season in particular has been extremely busy. With its extensive flight network, LOT already reaches the most remote corners of the world. “Outside Europe, we operate direct flights to Canada and the US and we are also re-opening flights to Asia, which had many routes closed during the pandemic,” says Krolak. “In Europe, new routes are being continuously added to the list of destinations.”
For example, LOT aircraft will now be serving the Cyprus route 4 times per week in the winter season and 6 times a week in the summer. The connection to the French city of Lyons, operating six times a week, will be re-launched in September. Another destination included in the
carrier’s 2024-2028 expansion strategy is Larnaca, which will re-start in October, following a two-year pause. Further afield, earlier this year the company started to fly to Riyadh, which has become the second city on the Arabian Peninsula in the national carrier’s flight network, after Dubai. The company did not lay off any staff during the pandemic, so the increased volume of business will not hinder a smooth and efficient operation, although Krolak admits that a shortage of skilled manpower has been an ongoing challenge. “We note a lack of qualified aviation and aeronautical engineering resources, from ground personnel and mechanics to office engineers. This issue is further accentuated by the
fact that the older generation is now leaving for retirement, creating a gap in much-needed skill transfer.”
“To this end, we are actively working on establishing and promoting internal training programmes, and also are working with technical schools to attract youngsters to the aviation sector. Being a national carrier is significant and LOT is seen as an attractive employer. Indeed, we are a brand that counts and that certainly helps to raise interest in aviation in the young generation.”
“ALTHOUGH THE SUPPLY CHAIN WAS HEAVILY AFFECTED DURING THE PANDEMIC, IT IS CONTINUOUSLY IMPROVING. AS WE GROW, WE WANT OUR SUPPLIERS TO GROW WITH US.”
Being one of the most important companies in Poland, with a long European
heritage, also means that LOT’s role in the country’s economy is undisputed. “Wherever possible we try to hire Polish contractors and suppliers to support the market. However, aviation is an international sector so we naturally work with international companies as well,” says Krolak.
“Although the supply chain was heavily affected during the pandemic, it is continuously improving. As we grow, we want our suppliers to grow with us. As such we will be helping to create a positive environment to support the development and rise of the aviation business.”
That is already happening. While at the beginning of 2024 the company had 75 aircraft in its fleet, the number is set to increase to 86 by end of the year, says Krolak and affirms that to experience the actual execution of a clear strategy is very motivating.
“Seeing us deliver on our promise makes everybody in the company proud. There is a lot of work involved, requiring a huge amount of effort from all of us, but at the same time it is fun. Seeing that our hard work is bringing about the desired results is, indeed, very exciting.”
CREATED A FORCE TO BE RECKONED WITH
The Saab Group was founded in 1937, but the UK branch of the company dates back only to the dawn of the Covid pandemic. It was a tough time to establish a new arm of the company, but since then Saab UK has seen impressive expansion.
It’s an enterprise that is seeing significant growth. We have doubled our headcount in the last 18 months,” says Andy Fraser, Group Managing Director of Saab UK. “It means that we are really well positioned to take advantage of our Swedish engineering roots, while bringing that together with the best of British engineering.”
Fraser believes that engineering knowledge is needed now more than ever, as there is rising demand for high tech defence technology that can help keep the world safe. This is why Saab has made a £100 million investment in Saab UK over the last year alone.
“We are growing our own IP here in the UK, making mergers and acquisitions such as our purchase of drone developer BlueBear last year,” Fraser says. “BlueBear in particular offers Saab a significant manufacturing presence that builds on Saab’s long-term growth and expanding presence in the UK.”
Saab UK, he has seen the country became a real focus area for the Group as a whole.
But the keystone of its approach is that Britain is not just a market full of potential, but a talent pool that compliments Saab Group’s own.
“There is a professional way to approach engineering. We have tried and tested methods to go through a product life cycle, and that method has matured in both the UK and Sweden,” Fraser explains. “You can follow the steps from bright idea to product maturity, into manufacturing and out to market. That process and methodology are quite international and relatively easy to follow through. But the specific technologies developed in the UK and Sweden are complementary. The different approaches and cultures let us unlock different technologies that marry together well.”
[Opposite Page]
It is something that Fraser is clearly passionate about. In his previous career in the British army, Fraser first came across Saab in a training environment. As Group Managing Director of
That technology is backed up by a robust supply chain and industry network. Saab UK has around 1,000 partners across its supply chain, 99% of which are SMEs, and Fraser tells us he expects that to grow significantly over the coming years.
For instance, the vehicle that is arguably Saab’s signature piece, the Gripen fighter jet, draws 37% of its total supply chain from the UK, a £3 billion endeavour that will support 6,000 jobs over the next ten years.
At the same time, the Nextgeneration Light Anti-tank Weapon (NLAW) has already proven absolutely crucial in the early stages of repelling the Russian invasion of Ukraine, and 66% of those weapons come from the UK supply chain.
“Saab’s products have been a significant part of the support for Ukraine, and that is important to us,” Fraser emphasises. “The majority of NLAW’s final assembly has been done in the UK in partnership with Thales, at their manufacturing facility in Belfast. When we saw the urgency of the situation, we redoubled our
efforts to increase manufacturing volumes.”
Saab UK’s technology also includes the Barracuda Mobile Camouflage System (MCS), a multispectral camouflage solution that protects its wearer from visual, infrared and radar detection, which is being supplied through collaboration with the Abbey Group in Liverpool.
In all of these projects, across the supply chain and within Saab UK’s own recruitment and retention drives, one belief ties those people and projects together.
“One thing I have learned is the power of a sense of purpose,” Fraser says. “Keeping people and society safe is fundamental. It speaks volumes to me personally, because I have served in Afghanistan. I have seen what it is like when you do not have the opportunity to feel safe. That underpins everything we do throughout Saab.”
To aid in that sense of purpose, Fraser has simplified and narrowed-down Saab UK’s purpose to two key goals.
“Firstly, make sure our people love their career. Not just enjoy the job - love their career,” Fraser says. “Secondly, to delight our customers. Bringing those two goals together is what I feel we should be doing as business leaders.”
It means Saab UK is well positioned to attract that special blend of Swedish and British engineering expertise, particularly as Saab invests 17% of its sales revenue back into research and development. Saab UK have also been developing its new site in Fareham, to be the base of production for its Seaeye underwater systems and Sensor Systems’ Centre of Radar Excellence. The whole
site in Fareham supports 400 jobs at Saab UK, in established and future roles across various business activities. It makes Saab UK an exciting place to work, allowing it to retain people by giving them new and exciting things to work on.
“We have a really high-end workforce with fantastically intelligent people doing incredible things,” Fraser says.
That workforce informs what Fraser refers to as “the Triple Helix”, the best of government, industry and academia coming together to create the Saab UK Innovation Network. Centred at Imperial Collage’s Scale Space in White City, the network seeks to identify and apply for relevant UK research funding opportunities within Saab UK’s focus technology areas; Radar Solutions, Electronic Warfare, Underwater Defence and Public Safety. Part of this includes developing UK IP which directly supports Saab UK’s growth. It is this Innovation Network that Saab UK seeks to build on with its acquisitions and partnerships
of companies such as BlueBear and Abbey Group.
“We have been supporting the British army for 30 years with training and simulation technology. We have a good heritage, and we are doing exciting things while growing significantly,” Fraser reports.
Looking to the future, Fraser adds, “In some ways the future is simple. In some ways, it is complex.
Saab will grow further in the UK. We have work ahead to bring everyone together, creating a sense of firmly embedded identity.”
Saab UK is set to continue to invest in the country and its manufacturing and engineering capabilities here.
“We plan to grow and expand along with the demand our customers place in front of us,” says Fraser. “The world is a dangerous place right now. We think that will be the case for some time. What drives us is our desire to make the world a safer place by delivering cutting edge technology.”
CBRE DATA CENTRES IS A GLOBAL NETWORK OF LOCALLY GROUNDED EXPERTS IN DATA CENTRE NEEDS, EXCHANGING INFORMATION TO REMAIN ONE STEP AHEAD OF THE MARKET.
As the digital revolution steams forward, with exploding demand for cloud computing and a host of functions that have fallen under the umbrella label “artificial intelligence”, it can sometimes be easy to forget that all of these virtual assets have very real feet of clay. Our online world needs to be stored on hard drives in the real world, built on real land, kept running by real power, built, and operated by real people.
CBRE Data Centre Solutions’ job is to identify, locate and provide those resources. Working to its clients’ exacting specifications, CBRE’s Site Selection business identifies and sources assets including land, power, and buildings, and collaborates with architects, engineers, and consultants to give the client the finished data centre they need. Once that data centre is operating, CBRE helps market those data halls to colocation providers through its enduser-oriented Occupiers and Digital Infrastructure Advisory lines. The Digital Infrastructure Advisory Line also carries out
IT infrastructure audits and provides recommendations, while CBRE’s Occupiers line advises the end user about which data centres can best host its servers, and then negotiate a contract for them with the colocation provider. CBRE’s Capital Market team provides transaction services to investors dedicated to the data centre sector, while CBRE GWS handles Project Management and Facility Management services for users.
“We are an American-based company with 130,000 people working around the world,” says Séraphin Bravard, Director of CBRE Data Centre Solutions in France. “Most of the data centre
Reid Brewin Architects (RBA) leads innovative architectural design for data centres, focusing on sustainability and adaptability since 2006. Our designs are not just about data centres; they are about the future of our planet. The future of data centres relies on sustainable design, energy consumption, sourcing, and integration into communities. RBA minimises environmental impact through heat and water recovery systems, promoting green spaces and local food production with urban farming initiatives. Our designs adhere to LEED, BREEAM, and WELL standards, enhancing air quality and reducing carbon footprints.
Incorporating greenery reduces urban heat islands, improves air quality, and supports biodiversity. Green roofs, vertical gardens, and extensive landscaping help cool urban areas naturally, reducing energy use and emissions. Green spaces also create habitats for pollinators and beneficial insects, improving residents’ quality of life.
Despite challenges, the benefits of reusing waste heat and rainwater harvesting are substantial. Successful implementation requires regulations, research investment, and innovative energy transfer approaches. Public and stakeholder education is crucial for overcoming obstacles and realising these initiatives’ full potential.
The rising demand for IT capacity necessitates extensive planning. RBA integrates urban greenhouses and rooftop gardens into data centres, reducing environmental impact and contributing to urban communities. Our master planning maximises site yield and flexibility, ensuring optimal use of space for future growth and technological advancements. We engage local communities, creating benefits and fostering positive relationships.
A contemporary and collaborative workplace is essential for success. At RBA, we create high-quality work environments that promote wellness and innovation. Our designs include wellness-driven amenities, fostering a culture of collaboration. Creating attractive workspaces, we help our clients attract and retain skilled professionals, ensuring project success.
Leveraging Building Information Modelling (BIM) technology, Reid Brewin Architects designs sustainable, efficient, and community-focused data centres. BIM improves collaboration, reduces risks, and ensures precise execution, allowing us to meet the highest standards. Our commitment to sustainability, innovative planning, and high-quality work environments sets us apart.
Reid Brewin Architects is not just another architectural firm. We are dedicated to designing sustainable, efficient, and community-focused data centres. Our commitment to sustainability is unwavering, and we invite you to visit us at RBA Architects to learn more about our projects and vision.
www.rb-architectes.com
players are American, and here we have very good, established relationships with the US while serving as a European hub.” Bravard operates out of France, with his own team occupying the CBRE Data Centre European Hub, while remaining connected with CBRE’s presence in France, Germany, Iberia, Italy, the Netherlands, and Nordic countries, and CBRE’s historic European headquarters in Europe. It is this wide spread that gives CBRE its most powerful advantage on the market.
“We have a lot of people dedicating their time to data centres, enabling us to not only collect a lot of information from across Europe, but to crossreference that information to provide a detailed vision of the market,” Bravard says. “That is also thanks to our workplace solutions company, CBRE WGS (Global Workplace Services), dedicated Project Management and Facility Management for data centres. This represents 6,000 people around the world, allowing us to extend our network in the data centre industry and providing good market visibility.”
Because CBRE has dedicated data centre teams all around the world working for the same clients, the company is able to maintain a good understanding of its clients’ international strategies and needs.
“We know what they are looking for and what they can do,” Bravard tells us. “It’s nice to have this perspective on the market compared to our competitors.”
This perspective is born of CBRE’s position, primarily as a broker company. Each of CBRE’s brokers operates as an independent data centre specialist in their own countries.
“Thanks to that we have people who know the local market, obviously in terms of real estate market but also of all the providers that are needed during the life of a data centre and all the legislation which applies,” Bravard says. “Our strength is to be able to understand the strategy of our customers at a global level, giving us the necessary insight to implement that strategy at a local level. You are like an entrepreneur running a company inside a company.”
That freedom is important for a company serving such a wide spread of international markets.
CBRE’s management gives each operational team the freedom to implement new types of services and ways of
Séraphin
Director of
working to adapt to the needs of a fast-changing industry.
As Bravard points out, to expand in Western Europe you need a presence in many different countries, each with their own cultures and regulatory frameworks.
“YOU ARE LIKE AN ENTREPRENEUR RUNNING A COMPANY INSIDE A COMPANY.”
“It is difficult to expand in all these countries at once because they are all different and even multinational companies do not have enough human resources to address them all at once,” Bravard says. “During these last few years, data centre operators grew in Europe by acquiring other European data centre operators, but now, because of the explosion in the industry, data centre operators have to grow organically. To do that, we are given the liberty to conduct business how we see fit because you do not do business the same way in the UK, Italy, or Germany. It makes us a global company with local knowledge.”
“AT THE MOMENT WE ARE WORKING ON DATA CENTRE OPPORTUNITIES DEDICATED TO CLOUD APPLICATIONS, BUT WE ARE ALSO LOOKING AT WHAT WILL BE NEXT.”
The market has certainly been active in recent years. Bravard began working in the data centre sector in 2018, when the market was not yet what it is today.
“What we needed was to invest,” Bravard recalls. “When you see a possibility, you have to allocate resources to be a part of it. We started the data centre business line in France in 2018, when the market was not as active as it was today. But even then, CBRE as a whole, from local teams to the top management in France, Europe, and the US, were willing to allocate the necessary resources to support the project. They were saying ‘We believe in what you are doing and there is a future in this market.”
Soon enough, that investment paid off.
“There was much less demand, and then after Covid, the market exploded,” Bravard recalls. “With the new requirements demanded by AI, the market is due to grow even further. The question I set to figure out was ‘How would I get in touch with these big players like Amazon and Microsoft?’ I quickly found that CBRE opens doors, thanks to the reputation its data centre teams had established in the US and Europe via London over more than 20 years.”
But more than being a recognisable name that could open doors, Bravard found that CBRE was a network of dedicated people from around the world. More than a list
of useful contacts, he found that it was a valuable learning resource.
“I have learned a lot from those members around the world,” he recalls. “Even now, we have possibilities no other competitor has. At CBRE there is a culture which makes you feel part of a big family. CBRE gives its people support and a lot of liberty in terms of how to run their business. We have worldwide leadership in real estate and data centres, supported by a deep understanding of the market that allows us to implement data centre projects for everyone from first-class data centre players to local actors.”
While there is no denying the market is following a steep growth now, CBRE is already looking at where the market could be going next.
“We are trying to be ahead of the market,” Bravard states. “At the moment we are working on data centre opportunities dedicated to cloud applications, but we are also looking at what will be next. We are brainstorming, with our customers and internally, on what new requirements, specifications, and solutions will be necessary. That is why we are part of local data centre associations where we can share our clients’ view of the market with the industry. We educate people internally and outside of CBRE, especially with local administration and in the States. At CBRE we try to be as updated as possible on what is happening in the market while maintaining the broadest view of the sector.”
Creagh Concrete is a family-owned business, employing 800 people across five locations in the UK and Northern Ireland. Creagh works in the precast concrete construction industry, manufacturing its products in its three factories in Northern Ireland, as well as one in Scotland and another in Nottingham. But the firm’s offering goes beyond manufacturing, to include the design and construction of precast cement elements.
We take everything from small jobs such as farm buildings to precast floors for housing and apartment blocks, highrise buildings and multi-storey car parks,” says Seamus McKeague, Creagh Concrete’s Managing Director. “We have geographical coverage from Dorset to Aberdeen, from Wales to East Anglia, and of course, here in Northern Ireland.”
That wide geographic footprint, combined with Creagh’s holistic service offering, sets the firm apart in the sector.
“We see ourselves as a service provider. We pride ourselves on being the client’s lead partner,” McKeague shares. “We are involved from the design stage onwards, with a team of engineers and designers. We then see that project through manufacturing, transportation to the site, and final construction. It is a complete package that guarantees the clients will meet their deadlines and budget.”
By investing in the correct training and looking after its people Creagh Concrete ensures a solid foundation for its workers to offer a full turnkey solution. It is a company built around recognising the value of its people and the relationships they go on to form with their customers.
“We have people who can price the work, see it through manufacturing and get an overarching feel for where the market is while building good relationships with customers,” says McKeague. “We are a people company. Internally and externally, we have always been this way.”
To get the most out of those people and relationships, Creagh Concrete ensures that they have the best tools and facilities at their disposal, and that the work they do means something.
“Our factories are modern, our equipment is good, our reputation is strong,” McKeague says. “We are also involved in the wider community. We are part of business associations and leadership institutes, such as the Northern Ireland manufacturing group; CBI. We play our part in the industry and the environment. So many of our workers are in local groups, and we support them in all sorts of ways, such as sponsorships for local sports teams. We help and bring benefits to the whole community.”
McKeague has been in the business for 43 years and has seen the company grow and contribute to local communities while also overcoming numerous challenges.
“How do you bring a good culture into the company, and apply good governance? That is a real challenge,” McKeague shares. “We need to keep the quality high as we develop the business. We have sought out a range of accreditations for safety, environmental impact, and quality. Then we make sure we follow through on that. Values are a huge part of this company.”
One of those key values is diversity, and this is a value lived throughout Creagh Concrete.
“If you are in our company canteen, you can see that diversity for yourself,” McKeague says. “We have 110 non-UK nationals working with us. Creagh Concrete has good gender diversity and cultural diversity, and that has been a really positive thing for us. We embrace it.”
However diverse that team is, however, there is one thing they all have in common. Accountability.
“We seek out those who can take on responsibility,” McKeague tells us. “We want good, genuine, helpful people. Those are our core values.”
The search for those people is an ongoing process. Creagh Concrete is continuously recruiting for different roles. The firm does not have a big turnover, beyond the natural attrition that comes from construction site work. Part of this search means recruiting people from outside, and the other part of the solution is developing from within.
“We have our own internal development and good people come through that,” McKeague says. “But we also look outside.
We have taken 30 to 40 young Indian engineers and Bim technicians over the last three years, because we were struggling to find that level of talent. It has improved the quality of the business and our reputation.”
At the same time, to develop the skills base that Creagh Concrete relies on the company founded its own academy ten years ago. The business had been struggling to find the young design engineers and CAD technicians it relied on, and so set out to develop its own. In the first year the academy recruited 15 young people, funded with sponsorship from the Department of Educational Learning.
“We have run the academy in different ways over the last ten years. Its graduates are guaranteed a job at the end of it. It has been really good for us,” McKeague says. “We are also teaching joiners, electricians and engineers to meet skill shortages by developing our own skills.”
To further that work, Creagh has also partnered with Belfast Metropolitan College. This partnership forms part of a greater growth strategy for the company.
“We are always looking to the future, and it is very positive,” McKeague tells us. “We see an opportunity to double the size of the business in terms of turnover over the next five years. We are growing our employment numbers by 50%. We are developing our skills in IT, and training the next generation of designers and technicians. Our order book has never been so strong, and our turnover rose by ten per cent last year, against the grain.”
Creagh Concrete sees itself as a leading player in the industry. McKeague himself is the president of the Academy of Engineering, as well as sitting on the Board of Manufacturing in Northern Ireland. But even in this busy period of growth and expansion, McKeague remains hands-on with Creagh Concrete itself.
“I like to get out around the sites twice a month,” says McKeague.
The company is now investing in a new factory, and is seeing an influx of young people who see a future in Creagh Concrete.
“Everyone feels very positive because they have all made a strong contribution to turning the company around,” McKeague says. “Enjoy the business, enjoy the people you are with, and be ambitious. That’s where the fun comes into the business.”
HÖGANÄS BORGESTAD, A SWEDISH COMPANY THAT HAS SUPPLIED REFRACTORY PRODUCTS FOR 200 YEARS, IS ENTERING A NEW CHAPTER IN ITS HISTORY WITH A MAJOR INVESTMENT.
Designing refractories is an art, developed over the centuries –material composition, grain size and density are combined with precision; thermal conductivity, permeability, abrasion resistance and thermal expansion are measured meticulously. For close to 200 years, Höganäs Borgestad has mastered this art to perfection.
[Opposite Page]
Hanna Landell, Managing Director, Höganäs Borgestad.
We are a company with a long tradition, producing refractories since 1825,” says Managing Director Hanna Landell. “The Nordics have been our main market, but we have established a global presence over the years, serving customers in more than 70 countries. Many times, we have followed our customers to apply the concept used in their Nordic operations in their global production units around the world.”
The Höganäs Borgestad Group today employs 300 people across several companies within the refractory and insulation sector. The focus is on providing a comprehensive solution that enhances the productivity and competitiveness of its customers; solutions that will deliver long lasting value. To this end, Höganäs offers turnkey solutions, working closely with customers all the way from design through to installation and support.
“We are a concept supplier, a solution provider offering a well-defined range of refractory products and installation that are applied across a range of industries. Our know-how in the development of refractories and high-temperature solutions, acquired over two centuries, is our main differentiator,” says Landell.
“With our technical expertise we focus on developing concepts that create added value for our customers. As a relatively small company, we can be close to them and provide a high level of service suited to their needs, responding swiftly and flexibly to their requirements.”
As for any company in Europe, one of Höganäs’s challenges is the shortage of human resources, specifically within the refractory sector. However, the company strives to handle the challenge from a long-term perspective, looking for people with the right mindset and training them internally.
Mattias Ganslandt Founder and CEO, Primrock
Primrock is a leading provider of capacity and balancing services to the Nordic electricity market. We work to make the electricity system more scalable, reliable and sustainable. We offer services to transmission system operators as well as industrial and commercial end-users of electricity. Our investments are 100% compliant with the EU taxonomy for sustainable activities and we are a Nasdaq Green Equity Designation - Private Company.
Primrock, a leading supplier of capacity services to the Nordic electricity market, is expanding with power quality as a service to industrial end-users in the Scandinavian countries. This is part of Primrock’s user-centric strategy to make the power system more reliable and scalable for energy-intensive businesses with critical needs and plans to electrify processes over the coming decades.
Founded in Stockholm – the capital of Sweden - in 2020, Primrock works to change the topology of the electricity market with distributed assets installed in proximity of end-users. Innovative solutions and services are provided from systems built on proven technologies and components from leading international manufacturers.
To meet the challenges with changing and growing needs, Primrock designs and invests in systems which can adapt to new and varying requirements over time. Scalability and reliability are obtained through multi-functionality, modularity and mobility.
Primrock’s physical assets are multi-functional with several technical interfaces that allow for delivery of services with different specifications and features. Simultaneously providing services to industrial needs as well as capacity and reserves to grid operators offer strategic flexibility and is a source of costefficiency and long-term competitiveness.
A modular design and modular installation make Primrock’s systems highly scalable with cost-efficient and standardized units. Modularity in combination with proximity and redundant distribution to critical needs make the technical systems more reliable and tolerant to faults. With increasing risks associated with geopolitical challenges and a greater occurrence of extreme weather events, new functionality is vital to obtain continuous and reliable power supply.
With a goal to deploy capacity rapidly and at a pace compatible with the needs of its customers, Primrock builds systems that are transportable and, if needed, re-located to new geographies. This mobility allows for rational production of units while sites and grid connections are prepared. In addition, mobility of modules has the advantage of mitigating location-specific risk and facilitating re-use of assets, should local demand conditions change.
In sum, the strategy to deploy multi-functional, modular and mobile systems is based on the assessment that electricity markets, both demand and supply, will change dramatically over the coming decades. Primrock’s way to handle this forthcoming transition is to have the options to adapt and continuously re-optimize.
To meet expanding needs from electricity end-users, new assets and functions must be added to the power system. These changes require investment from traditional as well as new market participants. A wider range of private and institutional investors, providing financing to scalable capacity, is vital to the development of the electricity markets and the power system.
Primrock strategy is to channel more financing from capital markets to the future of the power system. In line with Primrock’s strategy and as an important step to provide transparency and reduce transaction costs for investors, Primrock – as the first company ever – has obtained Nasdaq Green Equity Designation - Private Company.
www.primrock.eu
Market uncertainty remains another major challenge, admits Landell. “Potential geopolitical risks may impact any business today, including ours, but this does not hinder us from pursuing a number of initiatives, including a preliminary study for a new plant. Making sure these initiatives do not interfere with daily operations is also a challenge, but an exciting one!”
To remain competitive, continued investment in technologies is a must. In 2016 the company launched a monolithic production line in its Bjuv site, the most modern of its kind in Europe at that time. Now a major project in under way that will fundamentally change the shape and form of the company, preparing it for future development.
In October 2023, Höganäs Borgestad announced the decision to build a new, advanced refractory plant to allow for more sustainable production. The company has shared a long and rich history with the municipality of Bjuv, going back almost two centuries.
As the site is located right in the town centre, the current factory blocks further development of the town and its infrastructure.
Against this backdrop, a decision was made to relocate and build a modern production plant in the immediate vicinity. The new plant, the biggest investment in the Höganäs Borgestad Group’s history, is expected to commence production in three to five years.
“We will continue to offer the company’s wide range of products and competitive offerings, throughout and after the construction process. The project presents a great opportunity for both the municipality of Bjuv and our company; it will allow Bjuv to grow and will allow us to expand
our product range with new solutions for the future,” says Landell.
She reflects that while the Nordic market may be small, it is in many ways driving the green shift. “Refractory technology is developing fast, with focus on innovative ways to minimize its environmental impact in order to make the refractory process more sustainable.”
“Refractories are sometimes seen as commodities but they are high-value products that need to be durable while providing high performance and environmental credentials. Advances in AI technologies continue to drive innovation across multiple sectors, including the refractory industry, and these will be also utilised in our company to stay competitive.”
“Our advantage is that we are both producer and installer, providing a total solution from concept and design to
installation, across the whole value chain. Together with our customers we can make a bigger impact,” she affirms, adding that sustainability is a top priority for both the company and its customers as they strive to becoming carbon-neutral in the future.
A great example of how a joint effort can make a big difference is Höganäs’s recent project with Interwell, a renowned Norwegian oil service company and a pioneer in the field of temporary and permanent closure of oil and gas wells - its RockSolid technology, a ground-breaking sustainable innovation for the oil and gas industry of the future and the past, involves developing and testing very high temperature molten materials.
For Interwell, Höganäs became a natural partner of choice, not only contributing in-
depth expertise and customized refractory products but also continuing to lead key R&D projects that help to push the limits of this novel technology to widen the scope of its application.
“While the increasing pressure on greener solutions and related legislation may be regarded as a challenge, we see it as an opportunity as well,” says Landell. “We are currently strengthening the team and increasing our presence in the northern parts of Sweden and Finland to make use of the numerous opportunities arising in that part of the Nordics, especially in the steel industry.”
“Apart from that, we have a number of interesting projects and new products that are coming to their execution phase at the end of the year. With a positive outcome to these, I would expect the business to grow next year.”
MELDRUM GROUP HAS BEEN CONTINUOUSLY GUIDED BY ITS PRINCIPLES SINCE IT WAS FOUNDED, AND THOSE SAME PRINCIPLES GUIDE ITS PLANS FOR THE FUTURE AS WELL.
Meldrum is an expanding and innovative UK construction company based in the Northeast of England. Much like its founder and Group CEO, civil engineer Dave Meldrum, the company has a strong bias towards civil projects, but as it has grown over the last 23 years it has developed into a multi-faceted construction group.
We developed a facilities business to offer facilities management services, but also so that we could hand over projects to it once construction is complete,” Meldrum tells us. “Our facilities arm will then manage the new building during the retention period, and that has worked really well. They have 24/7 support with their own plumbers, electricians and handymen.”
By having this handover in place, Meldrum Group is able to ensure that its customers receive a building that will meet their standards down to the smallest detail.
“If there are any latent defects on a job, such as a door handle rattling, our facilities management team are there within hours to put it right,” Meldrum observes. “It is a great way to handle the service after handover.”
That the facilities management company is an arm of Meldrum Group itself rather than a subcontractor reflects the “If it
is worth doing, do it yourself” philosophy that percolates through Meldrum’s entire business. That same attitude gave rise to the firm’s steel fabrication arm when, many years back, Meldrum struggled to get steelwork to site on schedule.
“We have our own draftsman in the office, so we can get designs drawn up on Friday, manufactured over the weekend and delivered to site on the Monday!” Meldrum says. “It is all about satisfying the needs of service to the site.”
That said, haste is far from the only reason Meldrum brings jobs in-house, as can be seen in the Group’s fire stopping business.
“After Grenfell, people paid a lot more attention to this,” Meldrum says. “We saw a couple of projects that had been handed over more than 12 years ago were found to be defective in this area, and when we went to the subcontractor, if they still existed at all, there was a clear reluctance to return to site.”.
Edmundson Electrical is the UK’s largest Electrical Wholesaler, distributing an extensive range of top branded products from the world’s leading manufacturers.
Operating daily from over 240 locations across the UK, with quality customer service at the core of our operations, we provide you with access to over 800,000 items and same-day delivery.
Our service doesn’t end there - our unique approach to service means that our teams are empowered to become experts within their field, meaning that we don’t just give you access to the items that you need, but also the in-depth knowledge you deserve from your wholesaler.
Complete
Newton Cap House Toronto Bishop Auckland County Durham DL14 7SB United Kingdom
Tel: 01388 606 569
Email: enquiries@completecladding.co.uk www.completecladding.co.uk
Meldrum Group responded by launching its own fire stopping business, which is now a yearand-a-half old, and the work it is doing is already receiving fantastic plaudits. The Group’s fire stopping work is signed off through an exclusive agreement with a local fire brigade.
“We de-risk by selfdelivering,” Meldrum points out. “We are not just packaging subcontractors, because that does not guarantee you the quality you need.”
The company’s attention to detail has also helped it navigate crises that other organisations have been hit hard by. In 2020,
at the height of Covid, Meldrum Group was one of many companies and organisations hit by a wave of cyberattacks. The NHS and EasyJet were among the groups who, like Meldrum Group, found themselves locked out of their software and issued with a ransom.
“98% of those hit paid the ransom. We didn’t,” Meldrum tells us. “Our IT department had us up and running in just over a week. I was really proud of how we behaved through all that. As a company, we have been in recession more than out of it, and we are pretty resilient as a result.
“WE DEVELOPED A FACILITIES BUSINESS TO OFFER FACILITIES MANAGEMENT SERVICES, BUT ALSO SO THAT WE COULD HAND OVER PROJECTS TO IT ONCE CONSTRUCTION IS COMPLETE.”
The different elements of the Meldrum Group have evolved as the company has found need, forming a unique business structure to ensure quality and innovation for its customers.
“To drive commercialism, accountability and responsibility, we have them as separate companies within the group structure, which we developed three-and-a-half years ago,” Meldrum says. “They trade with each other just like any domestic subcontractor. It is a structure that drives the right kinds of behaviour, preventing familiarity even as they all work out the same office. Everything is in order, and everyone knows who is doing what, and they are all separate legal entities but cross-guaranteed financially.”
Across those entities Meldrum Group has grown a turnover of £70 million, employing 230 people as well as offering 180
LPW Steelcraft Ltd are a family-run steel manufacturer/ erectors working under the governance of EN 1090 standards, based in Houghton-Le-Spring, County Durham covering works nationwide.
With a strong team of fabricators and steel erectors with combined experience totaling over 200 years, we specialise in the fabrication and installation of all steelwork such as steel structures, mezzanine floors, staircases/fire escapes, balustrades, handrails and secondary steelwork.
LPW Steelcraft Ltd have built our brand and reputation on providing quality service and solutions for our clients, we provide a full design, manufacture and installation service for our customers.
LPW Steelcraft 19 Philadelphia Complex, Houghton-Le-Spring DH4 4UQ United Kingdom
+44 (0)191 722 1363
info@lpwsteelcraft.co.uk www.ipwsteelcraft.co.uk
apprenticeships. Two-thirds of the company’s staff have never worked for anyone else, driving a loyal workforce that is fully imbued with the culture and integrity that Meldrum aspires to.
“It is very easy to teach technical skills,” Meldrum says. “It is harder to teach integrity. So, we recruit people with that quality and promote a culture that allows people to maintain it.”
“IT IS HARDER TO TEACH INTEGRITY. SO, WE RECRUIT PEOPLE WITH THAT QUALITY AND PROMOTE A CULTURE THAT ALLOWS PEOPLE TO MAINTAIN IT.”
As we talk with Meldrum, it is clear that this combination of integrity and loyalty is important to him, and more than that, he believes it should not go unrewarded.
“We have put a lot of work and time into this,” Meldrum tells us.
“We have a strong succession plan in place, and some great young directors here and I am very confident, as a result, of the future of the business.”
“I am a firm believer that rather than saying ‘Let’s turnover £100 million’, you should focus your efforts on turning over a quality product,” he says. “That will lead to organic growth and attract the right people into the company. The numbers are important, but if the focus is on quality I am convinced the numbers follow. I get stats on every site we run. We consistently find the sites with the top health and safety scores produce the most profit. That is not by chance. It is because they are very well-run sites.”
“I AM A FIRM BELIEVER THAT RATHER THAN SAYING ‘LET’S TURNOVER £100 MILLION’, YOU SHOULD FOCUS YOUR EFFORTS ON TURNING OVER A QUALITY PRODUCT.”
MILLER KNIGHT, A SPECIALIST IN BUILDING REGENERATION AND REFURBISHMENT, HAS A CLEAR OBJECTIVE – TO MAKE BUILDINGS SAFER FOR THEIR OCCUPANTS.
PROJECT MANAGED BY: BENJAMIN CROWSON
In the UK, the construction environment has changed dramatically over the last 10 years, specifically as a result of the devastating Grenfell tragedy, with fire safety within the built environment, as well as the combustibility of certain modern building materials, becoming a major consideration for both the public and the authorities.
So it comes as no surprise that the capabilities and competence of specialist companies providing first-class services to respond to these considerations are increasingly required. One such company is Miller Knight, a multi-discipline Principal Contractor providing complex and sensitive regeneration and refurbishment projects, with specialist divisions dedicated to remedial passive and structural fire protection.
The company is also a leading UK domestic construction and fire compliance provider and demand for its services is increasing. “The last seven years have been a period of steep growth for the company, as fire protection requirements have become stricter, with building safety becoming a top priority for developers, builders and asset managers,” says CEO David Dickson. “What was accepted before, is not accepted anymore. Over
those seven years, we have helped many clients to remedy issues that they didn’t know they even had.”
He explains that the company provides a one-stop solution that may include cladding replacement, passive fire protection, intumescent coatings, cavity barriers, fire curtains, structural boarding and more. In addition, Miller Knight also offers fire safety facility management as well as building regeneration.
“We carry most of the work out in-house. We have all the relevant accreditations to certify our works and sign the building off as safe at the end of the project. With the exception of a few specialized types of work, we don’t need to sub-contract anything. This allows us not only to be cost-effective and cost-competitive but also to be fast, efficient and streamlined as we have direct control over the resources.”
“WE HAVE ALL THE RELEVANT ACCREDITATIONS TO CERTIFY OUR WORKS AND SIGN THE BUILDING OFF AS SAFE AT THE END OF THE PROJECT. WITH THE EXCEPTION OF A FEW SPECIALIZED TYPES OF WORK, WE DON’T NEED TO SUB-CONTRACT ANYTHING.”
Dickson himself joined Miller Knight in 2016 when the company was facing liquidation and effectively turned the business around. “With the exception of a few years during the pandemic, we have never stopped growing since then, improving the business and winning prime clients.”
“We will turn over in the region of £50 million this year, which is nearly double the amount we achieved last year. Looking at the size of the business compared to what it was in 2016, with just under a million in turnover, we can be proud of the impressive progress we have made, a testament to our dedication and commitment to providing exceptional work for our clients.”
He points out that Miller Knight works for a limited number of large clients such as insurers, portfolio managers, asset managers, developers and pension funds, in other words entities that have a large portfolio of assets to remediate.
The list of projects that the company has completed is long and varied. Dickson highlights the recent remedial work at the Gateway student accommodation in Lincoln, an eight-storey establishment, accommodating 500 bed spaces for students at the University of Lincoln.
The project, in which Miller Knight was the Principal Contractor, involved installing remedial fire protection features to the entirety of the building to meet building compliance and fire safety regulations.
“The project included a large package of internal and external works ranging from
remediating non-compliant compartmentation, fire door renewal and new sprinklers, to fire alarm system installations, external facade modifications and the installation of compliant fire barriers and insulating material,” says Dickson.
All the works were conducted to a high standard and in line with current fire safety standards, certified with a FIRAS certificate of conformity and monitored through audit trails, for the building to welcome students in the next academic year.
SPECIALIST FACADE REMEDIATION & THROUGH WALL CONSTRUCTION SYSTEMS WITH COMPLIANCE AT THE CORE.
FULLY TESTED & CERTIFIED A1/A2 SYSTEMS OFFERED
LEARN MORE
IF YOU WOULD LIKE TO FIND OUT HOW WE CAN MAKE A DIFFERENCE TO YOUR PROJECT PLEASE FEEL FREE TO CONTACT US.
Dickson affirms that the company strives to work in an environmentally friendly manner as much as possible, with a focus on carbon reduction, minimizing emissions and sourcing materials and labour locally. “As a business, we are trying to improve our carbon footprint and to make sure that we are using the most efficient and economic methods and skills to effectively carry out the projects.”
He further points out that when it comes to digitization, the company is ahead of the curve. For quite some time, every item of the remedial work has needed to be digitally recorded so the information on
what has been installed, where it has been installed, how it was designed, who it was approved by could be available and ready to be handed over to the client and to be used throughout the life cycle of the building.
“The challenge that we are facing now is the new Building Safety Act that has introduced sweeping reforms changing the way buildings are designed, constructed and managed. The Act applies to all new or
ENSURING EXCELLENCE: CORE GROUP’S COMMITMENT TO MILLER KNIGHT
At the heart of Core Group’s partnership with Miller Knight lies a commitment to excellence and quality. Every supporting operative we supply boasts a minimum of an NVQ Level 2 qualification or equivalent and possesses at least five years of experience in their chosen trade. This ensures that each worker is not only highly skilled but also seasoned in their field, ready to meet the demands of any project.
Compliance with industry standards is a cornerstone of our operations. Every operative is required to have a CSCS card, and many of Miller Knight’s projects necessitate additional qualifications such as DBS checks and Asbestos Awareness certification. We facilitate these checks and courses seamlessly, ensuring that our workforce meets all the specific requirements of our clients.
On average, we supply approximately one hundred general tradesmen weekly to Miller Knight for projects spread across the UK. Our relationship with Miller Knight spans over six years, during which we have become their number one talent provider. This long-standing collaboration is a testament to the trust and reliability we have built over time.
Our expertise extends beyond just supplying skilled labour; we possess extensive knowledge of the fire protection industry and the broader construction sector. This expertise has enabled us to fulfill labour requests even in the most challenging areas and at very short notice. Whether it’s a brief project or a long-term engagement spanning over five years, we have consistently delivered top-notch operatives to meet Miller Knight’s needs.
In a rapidly evolving industry, our dedication to quality and compliance sets us apart, making us a trusted partner for Miller Knight and a leader in providing exceptional workforce solutions.
www.coregroup.org.uk
existing occupied buildings over 18 metres high, which is basically the area where we operate. We are now in the process of understanding what is required to effectively proceed with those works that we had already started before the Act came into force.”
“ULTIMATELY BUSINESSES ARE ALL ABOUT PEOPLE WORKING TOGETHER. WE WILL FOCUS ON DELIVERING A GOOD JOB, A QUALITY PRODUCT.”
“However, we are confident that once we get through that learning curve over the next six months or so, we’ll be able to really get on with the schemes and keep delivering high-value projects. We already meet many of the new requirements anyway, so we are fairly
comfortable that what we’re doing now will satisfy the Safety Regulator.”
Speaking about the future, Dickson affirms that while opportunities are manifold and will be increasing, this will not
necessarily result in an increase in the size of his business.
“Ultimately businesses are all about people working together. We will focus on delivering a good job, a quality product. We are not going after expansion, as we may lose the connection that we all have at the moment. That connection drives our culture, and that is why we are different.”
He acknowledges that Miller Knight has been investing substantially in training, in order to secure a capable, homegrown workforce. “The market
out there is massive, but our turnover has been increasing primarily because the projects are generally getting bigger, not purely because we increase staff numbers.”
That is also the anticipated pattern in the coming months and years. “We will strive to deliver high-quality schemes for the large clients that we work for, and to continue to grow the business as we have done so far, i.e. on the basis of our ability to complete large, complex fire safety projects to our clients’ utmost satisfaction.”
AS SOCOTEC UK GROWS, SO DOES ITS OFFERING FOR THE CONSTRUCTION AND ASSET MANAGEMENT SECTORS.
PROJECT MANAGED BY: DAVID HAYVIS
SOCOTEC is a multinational, private equity-owned Testing, Inspection, and Certification (TIC) business, headquartered in France. The overall Group’s annual revenue is currently valued at approximately 1.4 billion euros.
Despite its French origins, SOCOTEC has established a significant international presence, with platforms in the USA and throughout Europe. SOCOTEC UK is the second-largest platform within the Group, making it a critical component of the company’s global operations. Looking ahead, SOCOTEC has set ambitious targets for the 2024 to 2028 period. The Group aims to grow its annual revenues from the current 1.4 billion euros
to 2.4 billion euros over the next four years. This demonstrates SOCOTEC’s strategic focus on expanding its market share and solidifying its position as a leading global TIC provider. The combination of SOCOTEC’s strong French heritage, diverse international footprint, and bold growth objectives highlights the company’s commitment to delivering high-quality testing, inspection, and certification services to clients around the world. As the second-largest
Excellent battery performance
Continuous monitoring for several months
Rubust and weather-proof design
Complete with color display and keypad
Time- and cost-effective
Manage remotely from your device
INFRA Net Measurement Management System
Wireless Triaxial Vibration Monitor
INFRA C50
Wireless Sound Level Meter
Class 1 design
At the forefront of remote monitoring Sigicom offers a complete and compact wireless solution for measuring vibrations and noise. Thanks to exceptional battery life, and remote monitoring your work will be both simplified and more cost-effective.
Founded in Sweden in 1981, Sigicom is a leading provider of advanced measurement systems for environmental monitoring, focusing on critical parameters like vibrations, noise, and dust.
Sigicom’s commitment to innovation and research keeps our products at the cutting edge, helping customers meet strict regulations. Our reliable instruments provide accurate data in tough environments, reducing the environmental impact of projects. We deliver practical solutions that ensure projects are compliant, safe, and sustainable.
Sigicom has expanded across Europe, the USA, and Canada, becoming a global player while maintaining a local, personal approach. Along with our topquality products we prioritize customer care, recognizing its importance in maintaining our high standards.
Through our long-running collaboration with SOCOTEC, we contribute to the infrastructure and construction sectors by managing environmental and safety aspects comprehensively.
Customer care and industry expertise are the heart of Sigicom’s mission, driving us to not only meet but exceed expectations, ensuring every project is a step toward a safer, more sustainable future. Together with our customers, we shape the world we build.
SEE THE WORLD LIKE SOCOTECH
The quote “Never assume anything” has never been more important for structural health and longevity. From mega construction projects, to the testing of existing assets, reliable structural data is key for informed decision making. Assumptions at any stage can be costly.
Thanks to advancements in non-destructive testing (NDT) technologies like ground penetrating radar (GPR), ultrasonics, and Eddy-current, it’s now possible to inspect concrete structures with unrivalled clarity, leaving nothing to guesswork.
Proceq, a Screening Eagle brand and leading manufacturer of NDT equipment, has been at the forefront of the new advancements with their technologies being used extensively across the UK by companies such as Socotec and National Highways, to assess and test existing structures and new infrastructure.
As pictured (above), Proceq GPR can swiftly identify steel placement issues or areas of concern in existing structures. With real-time data visualization and augmented reality views, the technology makes it easier than ever to collect reliable data. And better yet, it’s understandable for all stakeholders.
When you can see bridges, buildings and roads with a data driven perspective like Socotec, you gain valuable insights that others miss. This enables detection of defects as early as possible, helping to avoid costly repairs or replacements.
With an increase in construction projects expected in 2025, and the current global stock of existing structures aging by the day, Screening Eagle Technologies are driven by their mission to protect the built world with sensors, software and data. Don’t let hidden defects surprise you, contact Screening Eagle for tailored solutions.
www.screeningeagle.com
platform, the UK division will play a pivotal role in SOCOTEC’s ability to achieve its long-term aspirations.
The UK entity has an annual revenue of approximately £200 million, with a growth trajectory going to £300 million by 2028. It has four key divisions: Environment, Building & RealEstate, Disputes & Advisory, and Infrastructure.
Richard Hildick-Smith, managing director of Infrastructure said: “It is great to lead Socotec UK’s Infrastructure division, I’m proud of SOCOTEC’s ability to bring together all of its business units to provide clients with a single, integrated provider of multiple products and services. Our ambition as a company is to build trust and contribute to a safer, more sustainable world.”
SOCOTEC has seen impressive growth, and in the UK twothirds of that growth has been through acquisition. This is in accordance with SOCOTEC’s ongoing strategy to become the partner of choice for megaprojects in the UK.
“The elevator pitch for SOCOTEC is increasingly, through organic and inorganic growth, to become a single supplier for construction companies, projects, asset owners and operators,” HildickSmith says. “We want to be a supplier that will deliver testing, inspection and compliance
services, as well as asset management and integrity services.”
Hildick-Smith is the first to admit that there is nothing unique about a company that can offer a broad range of services. But while most of those companies will rely on decentralised acquisitions or their supply chains to manage projects and support asset operations, SOCOTEC’s strategy sees it bringing more and more of those services in-house and really integrating the acquisitions into a single core offering and execution.
“We have provided support to megaprojects like HS2, Silvertown Tunnel, Lower Thames Crossing, and this morning I was at the A147 Missing Link Project,” Hildick-Smith tells us. “We are doing a lot of work for the Principal Contractor on that Project, Kier. We have a materials testing site lab up there and are increasingly supporting other areas of the execution, from asbestos management to geotechnical monitoring. Similar to other megaprojects we are able to simplify their delivery of scope technically and commercially. “
But while SOCOTEC has established itself as a valued partner of choice for these projects, it is not focused on the megaproject/construction market exclusively.
“There is certainly a current reduction on mega Projects” Hildick-Smith acknowledges. “There are some very public examples of mega projects being either cancelled, paused or descoped. Things like HS2 and Stonehenge are examples of this.”
Despite this reduction in new infrastructure, there is an increasing need to manage the existing Infrastructure. This is where SOCOTEC UK’s extensive offering comes into its own.
As well as construction in the megaprojects space, SOCOTEC UK is heavily involved in existing asset projects.
“National Highways is not just a government agency for building new highways, it also maintains existing highways. The same is true of the rail network, and water companies,” HildickSmith points out.
“Various divisions of SOCOTEC UK support National Highways directly and indirectly in supporting those operations, be it through road testing, bridge maintenance, or other services.”
That list of services is expanding. Last month SOCOTEC acquired Impulse Geophysics, a major supplier directly and indirectly to National Highways for 4K video surveys and Ground Penetrating Radar (GPR).
“It was an element we could not do in-house and we knew this capability was a major part of the offering to clients needing to maintain their highways assets” Hildick-Smith says. “When we bought them, it was not to add revenue and profit, but to bring those services in-house and thus offer a better-integrated service to clients.”
It is this approach that makes SOCOTEC stand out even during a period of consolidation in the sector.
“There is a lot of acquisition in the industry, often the purpose is to buy companies almost just to grow in size. Hildick-Smith points out. “Our strategy is about adding additional services to the buffet.”
However, Hildick-Smith is also adamant that SOCOTEC will not become a holding company for its acquisitions.
“If you have a simple model of buying quantity and they operate independently, that’s easy to do. But we acquire companies with the goal of fully integrating
them over time to become one team,” he says. “We are one company with multiple services, not an umbrella organisation for multiple companies. As a result, the client gets a better more integrated output”
Achieving that vision and ensuring SOCOTEC remains a single team might be the company’s biggest challenge. Last year, the added a strategic role to its executive team to take on that challenge directly, in the form of a Business Integration Director.
“The operational owners are delivering day-to-day, so having someone there to proactively aid
that integration was a big step for us,” Hildick-Smith says. “The process is completed over a bespoke period of time. We work with the new entity to understand what the best timeframes are for what we call a ‘hive up’ into the base business. There’s no onesize-fits-all approach.”
SOCOTEC UK also places a great deal of importance on bringing the whole team together face-to-face, with a UK committee meeting every two months, and a UK-wide conference.
“Patrick Lencioni wrote something called The Five Dysfunctions of a Team, it’s a triangle about how to develop a high-performing team” HildickSmith explains. “We have all
gone through a similar team concept, and building trust is the bottom rung.”
A higher rung is investment in the company’s people, and this is an area where SOCOTEC UK excels, particularly around training and apprenticeships.
“Investing in all levels of training and apprenticeships is a huge part of our strategy,” Hildick-Smith says. “Over the last three years, we have put hundreds of people through various forms of technical and management training. I have personally done a Level 7 NVQ Management Apprenticeship alongside other members of the senior Socotec team. I learnt a lot from that, but the best part of it was building relationships with other managers and leaders from other Business Units. Building
those bonds is key. We know have a great network to identify where we can work together to deliver for clients.”
Building and strengthening personal and team relationships is how a collection of acquisitions becomes a single team, working together to further drive growth even as the environment is challenging.
“There are headwinds in the economy, but as we go into 2025 and onwards, we know there will be a resurgence in infrastructure and construction projects, alongside an ever-increasing need to better manage the existing asset and infrastructure base,” Hildick-Smith says. “We will continue to partner with companies involved in that, supporting them with a growing range of services.”
MALAWI’S PREMIER ENERGY PROVIDER IS SEEKING TO GENERATE THE POWER MALAWI’S ECONOMY NEEDS TO THRIVE.
Malawi has a population of over 20 million people, with an economy worth more than $7.5 billion and all of those people and businesses need power. That is the mission of the Electricity Generation Company (Malawi) Ltd, EGENCO. EGENCO is the state-owned company responsible for generating Malawi’s electricity. Originally part of the Electricity Supply Corporation of Malawi (ESCOM), in 2016 the country’s energy sector underwent major reforms leading to the firm being separated into three companies, one responsible for transmission, another acting as a single buyer buying from the other generators that was dissolved in 2022, and one responsible for generation. As the firm responsible for power generation, EGENCO occupies a foundational position in Malawi’s prospects for growth.
We are responsible for generating power, which we sell to ESCOM, who sell it to the customers,” explains Dr Maxon Chitawo, Acting CEO of EGENCO. “We operate four hydropower stations, augmented by thermal generators when we face high demand.”
Of these core power stations, three are based along the Shire River in the southern part of the country, the Nkula, Kapichira, and Tedzani Power Stations. The fourth is a smaller plant, with a capacity of only 4.5 megawatts, Wovwe Power
Station based on the Wovwe River in the Karonga District. Alongside these river plants, EGENCO operates thermal power plants in Lilongwe, Mzuzu and Mapanga, Blantyre. Overall, the company has a total installed generation capacity of 441.95 megawatts, with 390.55 megawatts from hydropower plants and 51.4 megawatts from standby diesel power plants.
With these facilities behind them, EGENCO has been able to position itself as the leader in power generation in Malawi.
“In Malawi, as the leading state-owned company, we generate most of the power
that the grid uses,” Chitawo tells us. “There are other players in the sector, with smaller capacities drawn from solar generation. Together they add a total of 101 megawatts to the grid. Then there are two other companies generating power from hydro that provide less than ten megawatts. So, we are the leading company on the market, supplying 80% of Malawi’s energy. We anchor the grid because our systems are bigger. That is the reason that we are the leading company power generator for Malawi today.”
But just because EGENCO is the leading power generator in the country does not mean that it is happy to stop there. In our conversation with Chitawo, it is clear that he has plans for growth far beyond what EGENCO has already achieved.
“WE ANCHOR THE GRID BECAUSE OUR SYSTEMS ARE BIGGER. THAT IS THE REASON THAT WE ARE THE LEADING COMPANY POWER GENERATOR FOR MALAWI TODAY.”
“Currently the key challenge is to expand our generation capacity,” he tells us. “We want to finance new projects. There are so many sites that we believe have the potential for hydropower generation. Hydropower is a capital-intensive source of power, but if you make the necessary investment to develop it, hydro plants can run for a much longer period – often as much as 40 years.”
But to unlock that long-term potential, EGENCO needs capital, a great deal of capital, and that is the challenge that Chitawo is setting out to meet. However, it is only one of the ways that EGENCO is seeking to generate the capacity that meets Malawi’s needs.
“Our tariff is lower compared to other companies in the region, and we are able to network and utilise systems to recover what we invest in the system,” Chitawo tells us. “We are currently looking at two or three different ways to expand capacity. We are looking for partners and investors who will work with us and invest in power generation for Malawi. We are interested to hear from
anyone willing to discuss joint ventures or public-private partnerships to build new power stations. We are also looking to talk with institutions who can lend us money. The government can guarantee our loans, and we will be able to quickly pay back what we borrow once we start selling power.”
In pursuit of Chitawo’s growth agenda, EGENCO places a great deal of value on its team. In the company’s long history, it has always had a very low staff turnover, as the firm sees its people as much of an investment as its power plants.
“When we recruit people, they stay with us,” Chitawo says. “We source many of our staff, particularly engineers, through our universities in Malawi. Our public universities run engineering programmes, and we have other universities training people in renewable energy systems. These recruits fit our culture very well, because they have been trained by institutions that work closely with us.”
The work does not stop there, however. The training the recruits have had before they join EGENCO is only a foundation for a career of learning.
“Once people have come into the company, we frequently send them for further training,” Chitawo says. “We send our engineers to places such as Zambia, Ghana, Egypt and even India for further training, which can run for approximately one to three weeks.”
That knowledge will be brought to bear to realise EGENCO’s mission to further grow Malawi’s electricity production capacity. But for
Chitawo this is not just about capacity for the capacity’s sake. He believes it is the key to unlocking the potential of Malawi’s economy.
“Currently we are not yet at 1 gigawatt capacity, and that is affecting our economic growth,” Chitawo tells us. “You cannot grow and thrive in the dark. Energy is an enabler for economic growth.”
The goal is simple. Generate more electricity to sell into the grid, so that Malawi’s businesses can use that energy to grow its businesses, power its projects, and create a better future for Malawi as a whole.
“We want to grow capacity to meet the demand and ensure our country can find enough power to do business. That is our mission now.”
THE BOTSWANAN SUBSIDIARY OF ABSA GROUP IS CHANGING TO REFLECT THE BANK’S NEW, MORE CUSTOMER-CENTRIC BRAND POSITIONING.
JOHN HOLLIMAN
Absa Group Limited is an African financial services group that is working to be a leading light in the sector across the continent. As one of Africa’s largest diversified financial services groups, it is listed on the Johannesburg Stock Exchange in South Africa and maintains a presence in 12 countries across Africa through its 42,000 employees. Despite its pan-African perspective, the Group is locally-minded in its approach, applying local solutions to local challenges and adding value to everything it does.
Absa’s clients will be offered a range of retail, business, corporate, investment, and wealth management solutions.
In Botswana, Absa is represented by Absa Bank Botswana Limited. Absa Bank Botswana is publicly listed on the Botswana Stock Exchange, meaning Botswana’s citizens have a real stake in the business. It also means that Absa Bank Botswana’s accounts are available to the public, and that it must satisfy investors and regulators that its business is sound. The organisation follows stringent governance guidelines to meet the Botswana Stock Exchange listing requirements.
The bank’s story dates back to 1950, when the bank opened its first branch in Lobatse. From there the bank expanded its network to the point where it became an incorporated Botswanan company in 1975.
Throughout the long history of the company, Absa Bank Botswana has believed in, and practised integrity in all its business dealings. The bank is overseen by independent, nonexecutive directors who have been chosen for their fearless commitment to integrity, as well as their business ability to ensure that Absa stays true to its values.
But while those values remain unchanged, recently Absa Bank Botswana has been working with the Group as a whole to redefine the Absa brand, recentring the pan-African organisation around its internal corporate purpose, “Empowering Africa’s tomorrow, together ...one story at a time.”
Absa’s newly repositioned brand signals a commitment to become more human-focused and empathetic in its approach to banking, creating a seamless and intuitive customer experience.
Absa’s new brand positioning is built on the promise that “Your Story Matters”. It is a promise intended to launch the bank on a clear trajectory towards ensuring Absa’s entire suite of services and offerings follows this more accessible, and responsive banking ethos.
“Empowering Africa’s tomorrow, together, one story at a time” and “Your story matters” are two halves, internal and external, of a common philosophy. As a full-service bank, Absa Bank Botswana’s mission is to cater for customers from every walk of life, from digital-only clients to those who prefer to talk in-branch.
“We are a bank for all seasons,” said Arrie Rautenbach, Group CEO of Absa when the brand repositioning was announced.
“Your Story Matters is more than a strapline, it is a declaration of our intent that our customers are much more than mere account numbers, they matter to us and so do the stories behind the individuals. Gaining this context will allow Absa to serve them in a more meaningful manner.”
The reimagining of Absa’s brand is the result of a detailed review of customer insights, feedback and research.
Let Incepta be your partner in crafting a brand with a meaningful impact.
Services available:
“A very consistent message comes across in research into perceptions of banks and banking,” said Sydney Nhlanhla Mbhele, Absa’s Group Chief Marketing and Corporate Affairs Officer. “Customers feel that the relationship is one-sided and that banks don’t understand either their life situations or their individual needs. This often leaves them feeling helpless as well as disconnected from opportunities to improve their individual or business prospects.”
In pursuing this more humancentric approach, Absa Bank Botswana is adapting the best digital offerings of the Absa ecosystem, infusing them with a bit more of a human touch. Those digital tools exist side-byside with an extensive physical network, the combination of both systems has been central to Absa’s new approach.
“Essentially, we’re making a step-change throughout the organisation; one that will
involve enhancing the value of our products, improving our levels of customer service, and vastly improving our capacity to deliver banking solutions that will be timely and relevant to our customers throughout their lives,” Mbhele said at the announcement of this new brand position.
Among those tools are Absa Mobi Tap, a tool that Absa Group has recently launched in key markets across the African continent. The tool allows small businesses to accept card-based payments on NFCenabled Android smartphones. This means the creation of a new, convenient, and seamless solution that allows businesses to grow their sales opportunities.
By leveraging an innovative partnership with the Mastercard Foundation in Ghana, Absa has gone on to roll out a gamechanging SME offering. This comes with an unprecedented interest rate of ten per cent, 60% lower than the market
average. It is not just a boost for small businesses, but a complete transformation of the way particularly women and young people can access financing.
As well as rolling out these new digital tools, in January of this year Absa listed the first ever Sustainable Bond on the Botswana Stock Exchange. Through financial inclusion and job creation that aims to promote women and young people, this new bond will create opportunities for companies to drive meaningful social impact.
“This repositioning is not just a marketing exercise – it is a company-wide business transformation and reaffirmation of a more humancentred approach to banking coupled with a seamless experience across our touchpoints,” Mbhele said. “The entire company has bought into this renewed vision, and we have worked tirelessly to take our colleagues, particularly our frontline, on this journey. While this is the beginning of the journey, customers can expect improved levels of service experience, underpinned by empathy.”
“WHILE THIS IS THE BEGINNING OF THE JOURNEY, CUSTOMERS CAN EXPECT IMPROVED LEVELS OF SERVICE EXPERIENCE, UNDERPINNED BY EMPATHY.”
At a time of immense complexity and market contradictions for financial institutions, navigating the current regulatory and economic environment is a pervasive challenge, as Rautenbach has pointed out.
“Some of these paradoxes include the fact that our collective informal economies are as diverse as our formal economies, while there are numerous geographic hurdles,” Rautenbach said. “These challenges have ultimately forced Absa to innovate
rapidly. This was the genesis of ‘Your Story Matters’ and a more human-centred approach – and these will be our guiding principles going forward as the new brand positioning takes root.”
2024 marks five years since Absa Group became a standalone African bank. This is a significant point in the growth and development of the Group as a whole. This new brand positioning is more than a PR exercise, it is a declaration of where Absa is heading in Botswana and beyond.
“Ultimately Your Story Matters positions us as a bank that values individual customers and wants to be part of their personal and financial narratives,” Mbhele said. “It suggests a customer-centric approach in which the bank listens to and cares about the unique journey of each person they serve. It defines Absa as a bank of the future; one that is more than just a financial services institution but also a partner on each customer’s life journey.”
HELSINKI IS KNOWN FOR MANY THINGS; ELEGANT DESIGN, CLEAN AIR, AND AN ENVIABLE WORK-LIFE BALANCE. YET SELLING THIS CITY’S POTENTIAL TO THE WORLD IS STILL A GREAT TASK.
PROJECT MANAGED BY: RASH UDDIN
Helsinki Partners is a city marketing, investment and talent attraction company, working for, and owned by the City of Helsinki. The first rule of any marketing company is to believe in your product, and Helsinki Partners has no issues on that score.
Iwould say our unique selling point is Helsinki itself,” says Leena Lassila, Helsinki Partners’ Director of Visitor Attraction. “Helsinki is a unique city, it is big enough to have a vivid city culture, business ecosystem, large start-up community and to function as a testbed for new innovations but small enough to make everything work smoothly – people are well connected and there is low bureaucracy.”
These are qualities that are reflected in Helsinki Partners itself. As a company,
it opens doors for its clients and matches people with possibilities.
“Our staff are helpful, motivated and highly committed to serving our clients,” Lassila says. “Our mission is to promote the city’s sustainable growth and build Helsinki’s global reputation and brand. We do this by attracting international investments, businesses, congresses, business events, talent and visitors, and by conducting international sales and marketing.”
Saarinen Tours offers private, bespoke tours in and around Helsinki focusing on the life and works of architect Eliel Saarinen. We are happy to tailor our tours according to your wishes, from a one hour walking tour of Helsinki to a week long architectural tour of Finland.
+358 40 508 9928
info@saarinentours.com www.saarinentours.com
Helsinki Partners has been doing well in that mission, with a record year in 2019, and a very good sales funnel for the following years. As demand was rising, international hotel investors saw big potential in Helsinki. But then 2020 happened.
“During the pandemic, conferences were all postponed or switched to virtual and only now are we starting to see the same sales flow again,” Lassila shares. “It took several years to recover. During those years, our city invested in expanding hotel capacity to the point where we can now easily accommodate conferences.’”
Anybody who takes advantage of what Helsinki has to offer has immediately come to appreciate it. Yet Helsinki Partners has still faced obstacles in its mission to get the word out.
“One big challenge is simply general awareness of Helsinki. Based on research, we know that our product is ahead of the brand,” Lassila points out. “Every
time we have clients visiting Helsinki, they seem to be very positively surprised. 80% of our conference delegates report that this is their first visit to Helsinki, which shows our huge potential for growth.”
Lassila believes the city of Helsinki is only now beginning to realise that potential. During the summer of 2024, Helsinki recovered to the pre-pandemic levels in terms of overnights. During this year Helsinki has also seen an upswing in big international concerts and business events.
“2025 seems to be a very good year for congresses and business events again,” Lassila says. “Conferences organised in Helsinki usually overperform when it comes to delegate attendance and expectations. For
example, in July the European Academy of Neurology EAN congress’ estimated 6,000 participants and in the end saw an attendance of 7,000 delegates.”
With results like that, Helsinki Partners has a strong foundation to build the brand even further.
“Our brand is developing in the right direction. By accurately measuring awareness and visitor satisfaction across a number of metrics, we can see the development of a positive public image for the city,” Lassila says. “There are no shortcuts, but we are heading in the right direction, and we are already seeing some heartening results.”
Looking forward, Lassila has big ambitions for the future of Helsinki and the whole metropolitan area. She believes it has the potential to be the most sustainable destination for conferences and business events in the world.
“Last year, Helsinki managed to raise its position in the GDS Index, and we are now in fourth place worldwide,” Lassila says proudly. “This year, we have started a very comprehensive two-year program where we help local companies to promote all the fantastic sustainability work they are doing internationally.”
One of the strongest selling points for Helsinki as a place to do business is the reservoir of talent that can be found there, and that talent is attracted by the excellent working conditions that Helsinki can provide.
Helsinki Partners itself is just one example of that.
“Our USPs as a city, and as a company, are strongly connected to Nordic work-life balance,” Lassila says. “We invest in our employees’ wellbeing and measure it systematically. We also develop our leadership teams and devote a great deal
of concentration to building our company culture. As a company we attract people who are passionate about the product; Helsinki.”
By offering interesting career opportunities alongside an opportunity to promote the city of Helsinki, the company attracts members of staff who are very passionate about the city.
“It is all about balancing your work and free time,” Lassila tells us. “After office hours there is plenty of free time to spend with your friends and family and enjoy the things the city has to offer; the closeness to the sea and nature, the art and design, and an interesting food scene.”
Despite all Helsinki has to offer and all the progress that Helsinki Partners has made, Lassila is the first to point out that the company has a great deal of work ahead of it.
“Destination branding and sales promotion is long-term
work and our sights are on the city’s sustainable growth and building Helsinki’s global reputation and brand,” she tells us. “Year after year, Finland and Helsinki top the World Happiness Index.”
Lassila is right. In fact, this year marks the seventh year that Helsinki has been awarded the top spot on the list.
“We want to bring that up and welcome visitors, talents, businesses and events with open arms,” Lassila says. “We are not perfect; this is a real place with real people. In Helsinki, we enjoy simple pleasures: clean air, pure water, relaxing saunas, unique food, walking around in the woods and on the seashore, experiencing local events and celebrations, and enjoying design in everyday life. Helsinki Happiness is calm and peaceful; it’s an appreciation for how things work and the ability to pause and admire the little things in life.”
VIRALGEN IS CONTINUING ITS MISSION TO GIVE PEOPLE WITH GENETIC DISEASES ACCESS TO CURATIVE GENE THERAPY, WITH A NEW LABORATORY UNLOCKING EVEN MORE POTENTIAL.
Viralgen was founded by Asklepios BioPharmaceutical (AskBio), one of America’s leading gene therapy pharmaceutical companies, and Columbus Venture Partners, a Spanish venture capital company that focuses on biotech companies. Both companies recognised the value of collaboration to serve the needs of the growing gene therapy sector. From the very beginning, its aim has been to give people with genetic diseases access to curative gene therapy.
It is a company whose story is defined by being ahead of its time, investing in a platform for the industrial production of clinical trials that will lead to the eventual marketing of new treatments.
The company was first established in the Gipuzkoa Science and Technology Park in San Sebastian, Basque Country, Spain, in October 2017. This strategic location gave Viralgen access to the knowledge and talent in the region, so within just two years it was accredited by the Spanish Agency of Medicines and Medical Devices (AEMPS). This enabled it to manufacture and provide cGMP (Good Manufacturing Practice) services in accordance with regulations and ensured its production and marketing met the required standards for use in human patients.
This would prove to be the foundation for rapid and exponential growth that would establish Viralgen as an emerging leader in the production of AAV for clinical trials.
But with that growth comes challenges. It meant that Viralgen needed the capacity for industrial-scale manufacturing of treatments that were only in the clinical trial phase, and then the capabilities to subsequently put those products on the market.
Viralgen then went on to be acquired by the German multinational, Bayer, in October 2020. Bayer preserved Viralgen’s original brand, philosophy, and management team, allowing it the managerial independence it needed to respond to the challenges of the genetic medicine sector.
Peptide and protein analysis with the new Agilent ExD cell
More in-depth data about sequence, structure, modifications, and purity can help you make better decisions about your candidate molecules.
The new Agilent ExD cell with Agilent ExDViewer software easily and cost-effectively adds electron capture dissociation to the capabilities of the Agilent 6545XT AdvanceBio LC/Q-TOF. So, you can elevate your peptide and protein analyses and minimize costly delays in your research.
What’s more, the Agilent ExDViewer analysis software allows you to interpret top-down and targeted bottom-up characterization data, providing a clearer perspective on your protein’s structure.
www.agilent.com/chem/innovation-that-drives-breakthroughs
Agilent is a global leader in life sciences, diagnostics, and applied markets. The company provides laboratories worldwide with instruments, services, consumables, applications, and expertise, enabling customers to gain the insights they seek. Agilent’s expertise and trusted collaboration give them the highest confidence in our solutions.
Agilent has one of the broadest solutions portfolios of any company serving the pharmaceutical industry. Our solutions provide precise answers for every segment of the industry, from disease research and drug discovery to drug development, manufacturing and quality control. Agilent can be a trusted partner providing expertise and complete solutions to help get products to market faster.
The development of nucleic acid therapeutics requires robust analytical methods for the accurate characterization of the gene delivery products such as adeno-associated virus vectors (AAV). Accurate characterization requires robust analytical methods to ensure high quality delivery systems. Advanced analytical techniques such as LC/MS and capillary electrophoresis are indispensable tools.
The characterization of capsid proteins is critical to ensure the quality of the gene therapeutic. Peptide mapping by LC/MS enables reliable and accurate assessment of AAV capsid proteins. Agilent automates and simplifies peptide mapping with a broad portfolio of systems, consumables, software and services for the complete and sensitive determination of peptide sequences as well as their PTMs.
For a powerful solution for comprehensive biomolecule analysis
Agilent offers the 6545XT AdvanceBio LC/Q-TOF system. This instrument offers the flexibility of everything you need to prepare, separate, detect, and analyze biomolecules—with dedicated reports to share your results. Easily dig deeper into peptide digests with the iterative MS/MS mode of operation.
We offer HPLC columns and workflows for capsid identity confirmation, empty/full ratio determination, and aggregate analysis. We utilize a variety of solutions, ranging from size exclusion and ion exchange chromatographic methods to peptide mapping-based protein identification.
The newest Agilent AdvanceBio SEC columns offer larger 500 Å and 1000 Å pore sizes, developed and optimized for robust, highresolution aggregate analysis of adeno-associated viruses (AAVs) and virus-like particles (VLPs).
Discover more about the comprehensive Agilent portfolio of analytical tools, cell analysis solutions, translational, and molecular biology solutions for rapid development of safe, consistent, and potent gene therapy products.
www.agilent.com/en/solutions/biopharma-pharma/gene-therapeutics
AAV LNP and mRNA Analytical Characterization | Agilent Agilent Tools for Peptide Mapping and PTM Analysis | Agilent
From here, Viralgen has expanded into a new facility which will unlock the commercial manufacturing capabilities it needs. In June 2021, the first of three modules of the new facility opened, representing Viralgen’s first step towards a fivefold increase in production capacity. Utilising the manufacturing scalability of the Pro10 platform, Viralgen has achieved a seamless transition from R&D production to commercial cGMP manufacturing.
When we last spoke with Jimmy Vanhove, Viralgen’s CEO, he told us, “What is important for us is that we have fully integrated operations to develop and manufacture vectors all the way from clinical to commercial scale, including in-house quality control testing as well as formulation and filling. We believe that is a great competitive advantage.”
Vanhove also pointed to Viralgen’s second unique selling point; the firm’s proprietary cell line that significantly shortens the time to market for new treatments.
“We can provide our clients with cGMP clinical material in under nine months, which is exceptional when compared to the standard time of over 12 months,” Vanhove said last year. That speed to market is backed up by an astounding level of in-house expertise. As Vanhove pointed out in our last feature, “Because we’re so focused on AAVs, and work with
AskBio, we have a high level of scientific understanding, development experience and regulatory expertise that we believe is unrivalled by most other Contract Development Manufacturing Organisations (CDMOs). We think that combination of process development and regulatory expertise is unique in the market.”
“WE CAN PROVIDE OUR CLIENTS WITH CGMP CLINICAL MATERIAL IN UNDER NINE MONTHS, WHICH IS EXCEPTIONAL WHEN COMPARED TO THE STANDARD TIME OF OVER 12 MONTHS,”
Of the 400 people Viralgen employs, over 75% have advanced degrees, with 25% holding doctorate degrees and over 50% with master’s degrees. Viralgen values and retains that knowledge pool, ensuring a turnover level of only 3% since the company’s inception.
“So not only do we attract but we also retain that knowledge,” Vanhove told us. “There’s a continuity of knowledge that we keep in the company, and also a continuity where we interact with clients.”
That continuity is set to stretch far into the future with this year’s inauguration of Viralgen’s new MSAT (Manufacturing, Science and Technology) laboratory at the Science and Technology Park of the Basque Country in Donostia. The new laboratory is a milestone for Viralgen’s ongoing state-ofthe-art research and production of advanced therapies. It is a facility that combines clinical development activities with commercial production,
increasing the rate of development and delivery of new treatments for rare genetic diseases. It is a mission that is set to improve the lives of millions of patients around the world.
Vanhove was at the inauguration ceremony himself, alongside the Mayor of Donostia, Eneko Goia, Arantxa Tapia, the Basque Government’s Minister of Economic Development and Competitiveness, and Eider Mendoza, General Deputy of Gipuzkoa.
The presence of these officials underscored a joint commitment to advancing research and technological development, that in turn will fuel the future economic growth of the Basque Country.
“THIS LABORATORY STRENGTHENS OUR MISSION TO BRING HOPE TO PATIENTS THROUGH SCIENCE AND INNOVATION, REAFFIRMING OUR COMMITMENT TO IMPROVING PEOPLE’S HEALTH AND WELL-BEING.”
Building trust in the therapies of tomorrow by making the invisible visible today.
QuTEM is a world-leading provider of GMP-certified TEM services and quality control analyses of nanoparticles for the life science industry.
Our expert team partners with clients, delivering reliable, traceable data and insights for informed decision-making, ensuring global patient safety. We’re committed to building trust in tomorrow’s therapies by making the invisible visible today.
QuTEM is a world-leading provider of GMP-certified Transmission Electron Microscopy (TEM) services and nanoparticle quality control analyses. Our diverse team of 27 experts from around the globe specializes in structural biology, nanotechnology, virology, and more. Together, we provide solutions and support throughout the entire value chain to our global life science partners in both research and commercial settings.
We offer reliable cryogenic TEM (cryoTEM) and negative stain TEM (nsTEM) analyses using our proprietary software, helping clients to visualize and assess the purity and stability of their gene therapy and drug delivery vector products. In close collaboration with our clients, we develop innovative methods to meet industry demands for characterizing key quality attributes, like genome length or aggregation, for example. Our services, often delivered within 4-10 business days, are crucial in time-sensitive situations, particularly in the biopharmaceutical vector manufacturing industry.
We prioritize client needs, offering expedited services for regulatory filings and production issues. Our long-term partnership with Viralgen exemplifies our commitment to quality and innovation, having validated their cryoTEM analytical procedure according to ICH Q2 (R1) guidelines.
We continue to support the biopharmaceutical manufacturing industry and look forward to advancing vector-based therapies, including AAVs, lentiviruses, liposomes, and more.
www.qutem.com
Email: info@qutem.com www.qutem.com
Kyfora Bio, Polysciences bioprocessing brand, supporting development of cell and gene therapy (CGT) breakthroughs from bench to clinic. Kyfora provides research grade through cGMP transfection reagents and excipients for viral vectors, mRNA vaccines, and other drug delivery applications. Our cost-effective and scalable cGMP processes empower advanced therapies to improve patients’ lives.
Polysciences Europe GmbH T: +49 (0)6201 845 200 - E: info@polysciences.de www.kyfora.com www.polysciences.com
“This laboratory strengthens our mission to bring hope to patients through science and innovation, reaffirming our commitment to improving people’s health and wellbeing,” Vanhove emphasised at the facility’s inauguration ceremony.
The MSAT laboratory itself is the product of over 10 million euros of investment, alongside the Analytical Centre of Excellence (ACE), another specialised analytical laboratory. That investment will not only boost the local economy, but also demonstrate a vital commitment to the improvement of public health and scientific advancement. Through its combination of clinical development activities and the production of Adenoassociated Virus (AAV) for advanced therapies, MSAT will play a crucial role in fulfilling that commitment. Every aspect of its
operations will feature stateof-the-art facilities, a highly skilled team, and an innovative approach to the integration of digital technology.
MSAT’s implementation of electronic lab notebooks and advanced data management systems ensures the efficient real-time capture, analysis, and visualisation of critical information. It means that data integrity and traceability are ensured and enhanced. This digitalisation also empowers interdisciplinary collaboration, driving informed decisionmaking.
MSAT, like Viralgen as a whole, is staffed by a highly skilled research team at the forefront of digitalisation applications in gene therapy production. This is the work that will pave the way for more effective and accessible treatments for rare genetic diseases.
ORIGINATING IN THE GARMENT INDUSTRY, SWEDEN-BASED ETON SYSTEMS NOW PROVIDES SOME OF THE MOST EFFICIENT
Located in Borås, the textile region of Sweden, Eton Systems was founded in 1967 when the conveyor business was divested from Eton Fashion, a Swedish company making shirts since 1928. Early on, the company founder Inge Davidson realised the benefits of streamlining production process, minimizing downtime and maximising efficiency and invented a novel system.
‘When the needles are moving – we’re creating value,’ that was Inge Davidson’s notion that became the basis of the world’s first Unit Production System (UPS),” says CEO Jerker Krabbe. “He designed a hanging conveyor system that didn’t waste valuable floor space and required no major modification to existing machines. His system allowed all the material needed for a specific garment to be moved as a unit directly from the sewing machine of any workstation to the next, substantially increasing efficiency.”
Over the years, the Eton system has grown into one of the most versatile conveyor systems available, and one that can automate almost any kind of industry. Today, there are more than 4,500 Eton systems installed in more than 75 countries and in different production areas, including garment, home textiles, furniture, plastic, and automotive industries.
the wake of a global pandemic, and in the middle of a turbulent geopolitical and economic situation was a challenge but given the brand strength and its global reach, we have steered the business through the difficult times better than most,” affirms Krabbe.
Eton Systems provides material handling systems consisting of individually addressable product carriers, automatically finding its way to the correct operation. The systems are designed to eliminate manual transportation and minimize handling, radically increasing the time for adding value to the products.
The material handling solution from Eton Systems increases efficiency in all kinds of industrial production and the aim is to minimize work in progress. Some even say that Eton Systems started practicing Lean Manufacturing even before it became a concept.
[Opposite Page]
Jerker Krabbe, CEO, Eton system.
In 2022, the company experienced an important milestone with a management buyout that initiated enhancements to make the business better suited for the future. “Completing changes in
Crucially, the systems include a real-time information function and the necessary tools to improve the manufacturing processes through powerful software programs. Krabbe points out that almost all material
Inca is your reliable partner when it comes to injection molding. We work in close partnerships with our customers, adding value all the way from R&D to a delivered product.
Injection molding is our main focus but we strive to be a one-stop supplier where we help our customers with product development, tooling, marking, customized packing and distribution.
handling systems from Eton Systems are unique and designed to fit different production lines at different production sites.
“Eton system is the Rolls Royce of a conveyor system. Our key strength is our know-how, the combination of hardware and software; we offer a new production mindset to a factory. As such, we can’t just install the system and run; we have life-long relationships with our customers, who rely on us to improve their productivity and profitability.”
“Similarly as with our customers, we foster long-term, close relationships with our suppliers that start in the very first stages of product developmentwe developed the understanding and knowledge together. Quite simply, without trusted suppliers we would not be able to secure the high quality of our systems.”
Krabbe points out that Eton Systems is welcoming the reshoring of textile industry back to Europe and USA, as manufacturers are seeking to reduce their environmental footprint and ensure reliability of supplies, while striving to reduce cost by means of automation. Something that Eton Systems can certainly provide.
“Digitalisation and the push for more sustainable, shorter and less expensive supply chains are currently making manufacturing in high-cost countries within Europe and North America more attractive and our technologies are very much a part of making reshoring a feasible option for our customers”
“The automation trend is very strong, and our systems connects all elements to be in line with the Industry 4.0 concept, so that the processes can be monitored remotely from anywhere in the world. Our system also enables
tracking and tracing of individual operators’ performance, providing manufacturers with full transparency of the factory environment. These are only some of the benefits that our systems offer.”
He acknowledges that to meet the rising demand for its automated fabric and part handling solutions, the company has just implemented a strategic investment in a new production facility in Borås. The new premises were officially opened in May.
“Staying here in Borås, we are staying true to our roots and heritage,” he says. “In addition to a pleasant working environment for our people, the new factory offers many benefits - we have optimised production flows to match those of our customers, and introduced hardware and software demo systems so that customers can see Eton systems’ benefits for themselves. We demonstrate that if we can do production in Sweden and be profitable, so can they. It only needs the right quality and the right brand.”
Krabbe insists that reducing carbon footprint is very important for Eton Systems and that the new factory reflects environmental considerations in terms of using less energy and less chemicals and a much more efficient production flow in general. “Externally, we have been working with customers to move away from fast fashion, developing systems that can track and help recycle garments.”
Looking ahead, he affirms that although Eton Systems was born in the textile industry, the systems are applicable to any type of business. The most recent incarnation of the original Eton UPS concept is
now gaining recognition as the industry standard for precise and comprehensive production control by leading global manufacturers, as the system offers unparalleled level of flexibility, quality, and return on investment
‘Our challenge is now to prioritize our resources across the segments that could profit
from an Eton system. It could be plastics, it could be bicycles, it could be anything that needs to be transported. It’s about getting the word out there and spreading our reputation. Our system, manufactured to the highest quality, is one of a kind and the future looks very exciting.”
WITH ITS CUSTOMER FOCUSED AND ENGINEERING DRIVEN APPROACH, HANSAMATRIX HAS MADE ITSELF INTO A POWERFUL ALLY.
HansaMatrix is a Latvian-based provider of electronics manufacturing services, offering precise mechanical parts manufacturing alongside electronic manufacturing services.
We are an electronics manufacturing services company with 500 employees and a proud history behind us,” says Andrius Luinys, Chief Business Development Officer for HansaMatrix. “This July, we celebrate our 25th anniversary. We are not new in the market, so we bring both history and competence, with a focus on the industrial, energy and connectivity sectors.”
Most of HansaMatrix’s work is with OEMs that have decided to outsource all or part of their production to electronics manufacturing service companies such as HansaMatrix. However, in offering these services,
HansaMatrix also faces a great deal of competition. There are 2,000 electronics manufacturing service companies in Europe, all competing for the same business.
“We stand out in this competition on our differentiation factors,” Luinys informs us. “Size-wise, we stand at close to one-hundredth place among these 2,000 companies. We have a lean and flat organisation structure, which means that our customers are only ever one phone call away from our top management. At the same time, we are quite flexible and customer-oriented. Our focus is on customer satisfaction.”
Andrius Luinys, Chief Business Development Officer, HansaMatrix.
We offer comprehensive cross-border packaging development services. Simply send us a sample of your product, and we’ll create a customized packaging solution tailored to your needs.
You’ll receive a 3D file with precise measurements, along with an assembly animation, and we’ll also produce a prototype for you to review with your product packed inside.
Contact us today for a free consultation.
E-mail: sales@austrapak.lv www.austrapak.lv
Cardboard packaging and displays: Design & Production
For nearly three decades, Austra Pak has been a reliable partner in the packaging and advertising production industry in Latvia. Based in Riga, we have earned our reputation by delivering comprehensive solutions that meet the diverse needs of our clients, from design development to final production. Our portfolio includes an array of products such as packaging, POS displays, and printed advertisements, all crafted to the highest standards.
One of our proudest partnerships is with HansaMatrix, a leading innovator in high-tech product manufacturing. This collaboration highlights our shared commitment to quality and environmental responsibility. Within HansaMatrix projects, our talented engineering team has successfully replaced plastic inlays and other packaging elements with custom-developed cardboard alternatives, significantly reducing environmental impact while maintaining high functionality. As an FSC-certified company, Austra Pak is dedicated to responsible forestry practices and ensuring that our products contribute to a healthier planet.
Whether it’s designing inlays for secure product transport or crafting eye-catching POS displays for retail environments, we are dedicated to providing solutions that exceed our clients’ expectations. As we approach our 30th anniversary, we continue to expand our capabilities and enhance our services, always striving to be a trusted partner in your business’ success.
www.austrapak.lv
“WE ARE QUITE FLEXIBLE AND CUSTOMER-ORIENTED. OUR FOCUS IS ON CUSTOMER SATISFACTION.”
That focus on customer satisfaction is supported by the generous volume of extra capacity HansaMatrix possesses. Just recently the company has opened a newly built facility to support HansaMatrix’s growth and the ramp-up of demand from both new and existing customers.
“We have 3,500 square metres of new floor space to offer our customers and onboard their projects,” Luinys shares. “We are ready to help. We don’t need an extra one or two years of greenfield development for our capacity to match our customers’ demand. We call ourselves a onestop-shop supplier. In practice, that means if a customer needs electronics, mechanics, and assembly services for a box-built
project, we can provide nearly everything required.”
HansaMatrix can manufacture printed circuit boards, machined metal or plastic injection moulded parts to precise specifications, all in one place.
“The message to our customers is that they don’t need five or ten different suppliers,” Luinys tells us. “We can be the only one to support all of their company’s needs.”
That support is made even more valuable by being close at hand. HansaMatrix’s facilities are positioned close to its customers in the Nordic region, and the rest of Europe, allowing it to support them quickly and efficiently.
The collaborative nature of HansaMatrix’s relationship with its customers begins at the inception of any project.
“When we deal with a new project or product, we strive to go the extra mile. We focus on the engineering and purchasing sides of the project and finding potential improvements,” Luinys says. “It makes no sense to us for the customer to just transfer their design to us if we do not question it. We aim for an efficient manufacturing process with no production stops. Better manufacturing yield is
beneficial for our customers as well as us.”
That closeness has proven particularly valuable during challenging times, which HansaMatrix has seen its fair share of over the last 25 years. Most recently, the company has navigated the pandemic and, in the aftermath of that, a global shortage of the electronic components HansaMatrix’s business relies on.
“We are not the only ones who faced this issue, but what helped us in these difficult times was close cooperation and relationships with our end customers,” Luinys says.
The strength of these relationships meant that real discussion over potential solutions was possible.
ANYONE WHO HAS MONEY CAN BUY EQUIPMENT, BUT EQUIPMENT ALONE IS NOT ENOUGH. YOU NEED SKILLED PEOPLE TO OPERATE IT, AND WE HAVE THAT.
“We do not have our own products,” Luinys points out. “We manufacture products for our customers, to their specific designs. While we have some influence over the bigger picture because we are buying the parts and manufacturing the components, the design belongs to the customer. So, when there were component shortages, we cooperated very closely with our customers and their designers to find the right solutions. We proposed a lot of ideas from our side, including alternative suppliers and different options for managing stockkeeping and forecasting.”
The ideas HansaMatrix has contributed satisfied their customers, and allowed them to avert any stops in production, one of the top priorities for any manufacturer.
“We see ourselves as customer-oriented and this can be seen in every aspect of the company,” Luinys tells us. “We are not a very big company, so we do not need to get ten signatures just to make a decision or get approval. We value our customers because we understand that only with high customer satisfaction can we maintain growth.”
In addition to its relationships with customers, HansaMatrix values its relationship with its staff. In acquiring new talent, HansaMatrix trades on the reputation it has built over the last 25 years.
“Each new product we are awarded needs to attain a certain level of quality,” Luinys says. “That requires talented engineers, who are not easy to recruit, but we are well known in Latvia as an employer. We rank among the top five EMS suppliers in the Baltics, which helps. We also have tight connections with the universities and colleges that
offer engineering degrees, which plays a significant role as well.”
Finding the right people is crucial to Luinys’s vision for the future of HansaMatrix.
“Everyone describes their own company with nice words, but in all honesty, HansaMatrix has everything it needs to grow,” Luinys says. “We have big ambitions for growth, and most importantly we have the right people. Anyone who has money can buy equipment, but equipment alone is not enough. You need skilled people to operate it, and we have that. With our history, our competence, and our extra capacity, we are now putting more focus on business development, knocking on more and more doors to have discussions about what we can offer.”
Find out more at: www.hansamatrix.com
HOBERG & DRIESCH IS A COMPANY THAT KNOWS HOW TO ADAPT QUICKLY WHILE ALWAYS STAYING TRUE TO ITS CORE VALUES.
Hoberg & Driesch was founded in 1948 by Peter Hoberg and Tony Driesch, operating for more than 60 years exclusively in the German market as a family-owned company. When the founders retired without any other family members ready to take over the company, it began employing Managing Directors as CEOs, including current CEO, Hanns Westendorf.
From the beginning, we were one of the leading stockholders in Germany in steel tubes, but around the millennium we realised there was no space for growth anymore because our market share was close to 30% to 35%,” Westendorf says. “I joined the company in 2009 and my strategy was to take part in the consolidation of the German steel tube stockholding market and take the company international.”
Today, Hoberg & Driesch is one of Europe’s leading wholesalers of steel piping. The firm stores 80,000 tons and sells over 200,000 tonnes of steel tubing a year and has grown its presence to servicing nine countries with three international processing plants across three countries. Furthermore, in its central
warehouse in Düsseldorf, Hoberg & Driesch runs one of the biggest automated highbay systems with 8,500 storage units and approximately 11,000 tons of seamless tubes.
“In 2015 we took a further step into the processing business,” Westendorf says. “We decided to invest in adding value to attract business, especially in the direction of the automotive industry. Meanwhile, we offer almost complete solutions to automotive suppliers.”
From there the company has grown to a team of 650 people, and a turnover of 650 million euros, with three-quarters of its turnover in stockholding for steel tubes and the remaining quarter in processing.
It has established itself as a business that is able to adapt and change, without ever losing sight of what is important.
“I have always called it ‘continuity in the change’,” Westendorf says. “There are changes in the markets, and in products, and the challenges we and our customers face, but throughout that, the company always stands for continuity. We have very little fluctuation in terms of staff. I am only the
• One of the Top-3 largest seamless pipe producers in Europe and Top-5 railway wheel manufacturers worldwide.
• Deliveries to more than 80 countries all around the world.
Our production facilities are located in the center of Ukraine, close to main roads and seaports. We control quality at all stages of production – from steel melting to finished goods’ delivery.
A wide network of trade offices around the world allows us to provide quality services to customers in Ukraine, Europe, the Middle East, and North America.
Interpipe manufactures steel pipes for oil and gas production and transportation, mechanical engineering, power generation, and construction purposes. The company offers a wide selection of pipes and tubes from 21 mm to 457 mm in diameter with wall thickness up to 80 mm.
What is the goal as a leading manufacturer of steel tubes? Providing maximum quality and reliability for customers and the climate.
With CliMore®, BENTELER Steel/Tube is making an important contribution to a more climate friendly future. For more sustainability in industry, business, and society. www.benteler.com/climore
fourth CEO in 76 years. That is a long time with only four people running the company. That stands for continuity and that is very much appreciated by our customers.”
Part of that continuity comes from Hoberg & Driesch’s clear product policy and the partnership with their main suppliers. The firm works across eight big product groups, in the carbon steel tubes market.
“We are a big company, we have a big assortment of products, and that makes the company strong,” Westendorf tells us. “We are not changing our policies year by year, but we remain clear that our products have traceability. That is the recipe to be successful down the decades.”
It is this ability to balance change and stability that has allowed the company to navigate the challenges of the industry. First, there was Covid, when the industry went from one extreme to the other and Hoberg & Driesch had to adapt quickly to keep up. Then, when the Russian invasion of Ukraine began, energy prices skyrocketed, and Hoberg & Driesch had to adapt again.
“At the end of the day, that we are able to do that is due to the very few layers we have in the company,” Westendorf explains.
“There is always a quick response to questions from staff. Personally, I think other companies are much slower in their reaction to changing environments.”
It is an approach that is seen most clearly in the company’s approach to acquisitions.
“That is also something we always see when it comes to an opportunity to buy a company, we don’t run around the houses for years,” Westendorf says. “We have very quick, fast coordination with our supervisory board, and decisions are taken in a very short time.”
Of course, to make decisions quickly, you need the right people to make those decisions. The company maintains a low rate of replacement, which is part of where its stability comes from.
“We have very little turnover within the company, so we do not often need to replace people,” Westendorf says. “When you invest in a company, it keeps the turnover low. We pay people fairly, and we create a good atmosphere across all our different departments. We have a policy from the top to the shop floor that people know what is expected of them and what they can expect from the company.”
It also helps that Hoberg & Driesch takes care of its employees – particularly during times of crisis such as the Covid pandemic.
“We had to go on short work, paying to fill the gap between what people got from the state and their full salary. That was highly appreciated by our workers,” Westendorf recalls.
“WE HAVE A POLICY FROM THE TOP TO THE SHOP FLOOR THAT PEOPLE KNOW WHAT IS EXPECTED OF THEM & WHAT THEY CAN EXPECT FROM THE COMPANY.”
When the company does need to recruit new talent, it takes people at the start of their careers and offers them a promising path forward.
“We have people from school starting here in the stock rooms, the machining shop or the offices, and learning from there,” Westendorf tells us.
Hoberg & Driesch is also seeking out new skills as the company expands and changes.
“We are looking for people who are good with languages,”
BEHRINGER GROUP
Complete supplier for sawing systems, customised material handling solutions, steel plate and profile machining centers.
BEHRINGER is one of the world leading complete suppliers for sawing systems. Our product range spans from bandsawing and circular sawing machines to plants for steel construction. At the same time, we provide our customers with specialist expertise in the field of material handling.
The second pillar of BEHRINGER is our own in-house foundry. We supply most of the cast iron for our own machine production, but our foundry also produces components for well-known German manufacturers of lathes & milling machines.
BEHRINGER looks on a strong relationship with Hoberg & Driesch for many years. Hoberg & Driesch is located at numerous sites in Germany and Europe. In more than 40 years, we have developed and realised dozens of projects together.
BEHRINGER’s high-performance bandsawing machines and automatic circular saws are used to cut standard pipes, thick-walled pipes, hollow sections, welded pipes and special pipes straight or mitred as well as solid material.
MATERIAL HANDLING SYSTEMS
For a fully automated production and for an efficient material flow, the sawing systems are equipped with various handling devices in the infeed and outfeed section. Loading and unloading zones, loading magazines, buffer areas, cross conveyors and cut-off grippers, material tables for short parts as well as a sensible trim and remnant disposal system ensure a smooth production process.
Our goal is to develop solutions for the market that exceed both our customers and our own expectations.
www.behringer.net
Westendorf says. “We need people with two or three languages, which we did not need when we were only based in Germany.”
Looking to the future, Hoberg & Driesch’s pillars of stability and flexibility remain central to its strategy. When we talk with Westendorf, he is looking to use those pillars to support big plans for future growth.
“The total mechanic engineering market is mature in Europe,” he says. “I believe there will always be a need for a strong partner in logistics who can supply just in time, and I believe people want partners who are loyal to them. They want partners who are not changing their sales policies from one year to the next. We offer a steady partnership on both the purchasing side and the sales side to our customers. Moreover, our investments during the last 15 years have certainly made us one of the most efficient partners in the industry.”
As well as expanding its market presence, Hoberg & Driesch is looking to work on solidifying its foundations to provide a strong platform for future growth with new acquisitions.
“We feel there is a need for consolidation in the European steel tube stockholding market,” Westendorf shares. “We want to play a major role in that. We are in the market looking for opportunities to buy companies in Germany and elsewhere. Poland is one potential target for us.”
Westendorf explains that Hoberg & Driesch is not only growing in terms of turnover and geographic footprint. It is also expanding its market coverage, growing its presence in the processing sector for the automotive industry and looking at ways to move along the supply chain to add further value.
“We want to grow in the components sector of the automotive industry, as well as consolidating in steel tube stockholding,” Westendorf says. “We are going to be actively looking for companies to acquire
while enlarging our processing business. It all comes down to what I said at the beginning, the key for us is continuity in change. The market is changing, and requirements are changing, but the company needs to show continuity for its customers.
To this end, Hoberg & Driesch supports the sustainability ambitions of our partners and customers in the tube industry. Customers are increasingly seeking sustainable solutions. Therefore, we do a lot to improve the carbon footprint of our company and the products we offer.”
PYREX AND DURALEX ARE INTERNATIONALLY RECOGNISED BRANDS. BUT WHEN THEY CAME TOGETHER THEY CREATED SOMETHING EVEN STRONGER.
The term “household name” gets used a lot, but few brands can claim to have been in as many households as the glassware lines Pyrex and Duralex. But while you are doubtlessly familiar with both brands, you may not know the difference between them.
Both brands manufacture glass kitchenware, but Duralex uses tempered soda-lime glass, while Pyrex uses low-thermal-expansion borosilicate glass.
And you might not have heard that a couple of years ago the owner of both brands underwent a major rebranding exercise itself. In 2022, the parent company International Cookware became La Maison Française du Verre, bringing the Pyrex and Duralex brands into one company with shared values and ambitions.
Those values include incomparable quality, tradition, innovation and sustainability, as well as a shared goal to build an internationally recognised centre of excellence for the glass industry. Combined, the brands have created a company with over 750 people, producing 100 million pieces each year across 133 countries.
Leading the charge for the new brand has been the company’s CEO, Jose-Luis Llacuna. Llacuna has been with International Cookware since 2015, leading
its takeover of Duralex in January 2021. When the firm’s new name was announced, Llacuna committed to investing €17 million by 2024, to maintain approximately 250 jobs.
“Pyrex and Duralex are two brands that are as essential as they are timeless,” he said when the change was announced.
“Thanks to their know-how, these two companies design simple everyday products that are adapted to consumer needs and have incomparable quality.”
But this year, Llacuna has handed over the CEO position to a new leader, Géraldine Fiacre. Fiacre joined La Maison Française du Verre (LMFV) in January this year. From the outset, her mission has been to lead the Group through a complex international environment while strengthening the success of the Duralex and Pyrex brands.
Fiacre graduated from ESSEC Business School, before jumping into a career at the PepsiCo Group. From there she has gone on to have a wide range of positions in marketing and sales, gaining experience across the sector in Europe.
SEFPRO is the only refractory group worldwide fully dedicated to and streamlined for offering top-of-the-line solutions specifically to the glass industries. For nearly a hundred years, SEFPRO has played a key role in the evolution of the offer available to glassmakers over the world.
Our industry is entering a new era. Beyond the sustainability imperative, glass must achieve decarbonization and circularity.
As an enabling partner that embraces every challenge and supports you in your journey to carbon neutrality, at SEFPRO, we provide future-proof refractory solutions to the glass industry.
Because you – our glassmaking customers - face the challenges of producing high-quality low-carbon glass. Because our solutions are critical to your performance and impact, we support you to build the future of our daily life and our planet through carbon-neutrality.
From the birth of the idea in your mind until the next furnace rebuild: we are the end-to-end enabling partner through 4 pillars:
PREMIUM QUALITY: We are committed globally to deliver reliable solutions over the complete lifecycle of furnaces. We are continuously improving our processes for better quality and services.
INNOVATION: We provide leading high-tech materials and solutions that meet the challenges of our industry.
CUSTOMER CENTRICITY: We always are by your side, collaborating hand in hand with our experts and manufacturing at a global level to deliver above expectations. Our worldwide presence ensures proximity with our customers.
SUSTAINABILITY: We enable glassmakers both to reduce emissions of current furnace designs and to build the furnace of tomorrow with new melting technologies towards carbon neutrality. www.sefpro.com
She has come to LMFC with over 19 years of significant contributions to the Barilla Group, where she was pivotal to the development of its brands, especially in France. She served as Barilla Group’s Marketing Director for the French and Western European markets, as well as the General Manager of Barilla’s Swiss subsidiary. From June 2019, Fiacre went on to hold the CEO position at Bolton Food (Saupiquet), the food subsidiary of the eponymous Italian multinational group.
On arriving in her position at LMFV, Fiacre said, “It is an honour for me to bring my international experience in brand management within a competitive global environment, expertise in steering industrial activities and team management to the LMFV Group. The renowned brands Duralex and Pyrex, symbols of ‘Made in France,’ have all the necessary resources to fulfil the Group’s ambitions for industrial sovereignty and sustainable performance.”
As well as a new name, and new leadership, LMFV has also been investing heavily in rebuilding a new furnace facility.
Larger glass manufacturers can have several furnaces to trial innovations and new products, but LMFV makes smart use of just one, whilst collaborating with companies such as Glass Service and F.I.C. UK. This allows LMFV to retain their innovational approach to glass in kitchens whilst building partnerships in the sector. Instead, LMFV
studies carefully to determine what it can put inside its furnace, while collaborating with companies such as Glass Service and FIC UK.
The rebuilding and modernisation of LMFV’s furnace is taking place simultaneously with a huge maintenance project, the scope of the entire operation meaning work will take several years. One of the furnace facilities’ four presses is being entirely retrofitted during the rebuilding, and LMFV has invested in robotic stacking for its dishes.
“PYREX AND DURALEX ARE TWO BRANDS THAT ARE AS ESSENTIAL AS THEY ARE TIMELESS. THANKS TO THEIR KNOW-HOW, THESE TWO COMPANIES DESIGN SIMPLE EVERYDAY PRODUCTS THAT ARE ADAPTED TO CONSUMER NEEDS AND HAVE INCOMPARABLE QUALITY.”
While this might sound like a relatively straightforward job to automate, the massive variety of shapes and sizes among the dishes LMFV produces means that it took the company some time to find the right technology provider – Prototig, a firm based in Limoges, also in France. Prototig has supplied customised machines for two of LMFV’s four production lines.
A single Pyrex product takes 28 to 30 hours to produce. The broad range of weight, shapes and dimensions it manufactures means that staff on three of its four production lines need
to switch from one product to another each day. The shapes created on that production line are so complex that LMFV has had to search long and hard for the right automatic inspection solution.
Finding the right supplier for this solution has meant trying numerous specialists and a variety of camera models. It involves technical challenges such as finding the right perspective to view the dish, because unlike with a bottle, it is hard to look at a dish on the conveyor from above.
Like many industries, the glass sector is currently undergoing a transition to the use of renewable energy in its manufacturing process. Several potential energy sources have been discussed through the sector, including biofuels, a greater reliance on electricity, and finally, hydrogen. LMFV has been investigating the potential of hydrogen through a project in collaboration with Air Liquide and SEFPRO
The project, called “Hyrex”, has focused on the use of hydrogen in glass furnaces during LMFV’s furnace rebuild, trialling hydrogen injection processes inside the new furnace’s burners. The study’s
mission was to observe the impact these burners will have on glass quality. From there, LMFV intends to assess that impact and lay the ground for preparations for the use of hydrogen in the furnace rebuilds of 2027 or 2032.
Glass Service’s modelling has proven positive, but LMFV is taking a step-by-step approach to assessing how this new furnace behaves with a greater use of electricity.
The company was founded when Bessie Littleton, the wife of physicist Jessie Littleton, first thought of using the material “Nonex” to create a pie plate. So even now, it is a company that understands the benefit of both collaboration and the scientific approach.
Herbert Pfab, Chief Technical Officer, Liebherr-Werk Bischofshofen GmbH.
GMBH BRINGS GROUND-BREAKING INNOVATIONS TO THE MARKET THAT BOAST BOTH PERFORMANCE & SUSTAINABLE CREDENTIALS.
Liebherr-Werk Bischofshofen GmbH is a member of the Liebherr Group, the global leader offering pioneering machine solutions across 13 product segments, employs over 50,000 employees in more than 150 companies on every continent. Managed by the Liebherr family to this day, the Group continues to thrive on this family spirit that has always determined its corporate culture, and which continues to provide a firm foundation for global success.
n 2024, Liebherr has reached a significant milestone, as it celebrates its 75th anniversary – a journey of steady growth and expansion. Founded in 1960 as the first Austrian plant in the Liebherr Group, LiebherrWerk Bischofshofen GmbH is a specialist in the development, production and sales of the Group’s wheel loaders, which are offered in four size classes: compact loaders, stereo loaders, mediumsized wheel loaders and the XPower wheel loader. The products reflect decades of experience and advanced know-how.
“Since its foundation, Liebherr-Werk Bischofshofen
GmbH has grown steadily through high-quality standards, sustainable innovations and creative solutions. Today, we are the competence and development centre for wheel loaders of the Liebherr Group, employing around 1,100 people,” explains Herbert Pfab, Chief Technical Officer.
Liebherr-Werk Bischofshofen GmbH is well-known for its continuous innovation. For example, the company’s XPower wheel loaders have been designed to represent a holistic wheel loader concept, which sets new standards in terms of fuel efficiency, performance, robustness and comfort. The core feature of the XPower wheel loader is its innovative power-split travel drive, which allows operators to save up to 30% on fuel.
The Bischofshofen plant is closely integrated into the international group of companies and cooperates with other Liebherr plants.
“We work particularly closely with the Liebherr production sites in Dalian (China) and Guaratinguetá (Brazil) where modified wheel loader models are produced for emerging markets outside Europe and North America. LiebherrWerk Bischofshofen GmbH is responsible for the product lines at both manufacturing facilities. This expansion underlines the professional competence and international orientation of the Liebherr plant.”
Liebherr’s innovation efforts are focused on future-facing technology solutions. “As part of our product responsibility, it is both our goal and our challenge to offer customers safe, efficient and high-performance products that are also environmentally friendly in the long term,” says Herbert Pfab. “The basis for
this is, among other things, our technology-open research into alternative drive technologies in order to reduce wheel loader emissions and promote decarbonization.”
To this end, the company has developed its first batteryelectric wheel loader, the L 507 E. Thanks to its alternative drive concept, it operates locally emission-free, is lownoise and just as powerful as conventionally powered wheel loaders. Depending on the operating conditions, the L 507 E offers a running time of up to eight hours. A modular battery concept makes it possible to install a second lithium-ion battery, which increases the running time. When driving
downhill and braking, energy is fed back into the battery through recuperation. It has been available in several European countries since February 2024.
As large vehicles with an operating weight of up to 40 tonnes are more difficult to electrify due to their high energy requirements, the company has been looking at different solutions, says Pfab. “Extensive studies have shown that the hydrogen reciprocating piston engine is the optimal solution for many applications. Here, we have achieved a major milestone in June 2024, presenting our first prototype of a large loader with a hydrogen engine, the L 566 H.”
“The hydrogen engines enable almost zero greenhouse gas emissions, will emit almost no nitrogen oxides in the future and at the same time offer a high level of efficiency,” he continues, adding that in the course of developing the hydrogen wheel loader, Liebherr-Werk Bischofshofen GmbH has also commissioned the first hydrogen filling station on factory premises – the first of its kind in the state of Salzburg, and another milestone on the company’s path towards the decarbonization of construction machinery.
Pfab further explains that Liebherr-Werk Bischofshofen GmbH is also preparing mobile refuelling options so that construction machinery can also be refuelled directly on site. “This is particularly important for remote construction sites and less-mobile construction machinery.”
Digitalisation is another priority topic for Liebherr-Werk Bischofshofen GmbH and the company is developing solutions
to make wheel loaders and their operation more efficient and safer. These include a variety of assistance systems that support operators in their daily work, such as active person recognition, an integrated tyre pressure monitoring system or the ‘Truck Payload Assist’ weighing system.
“With these and other assistance systems, LiebherrWerk Bischofshofen GmbH offers holistic solutions to optimize operator safety and comfort and increase performance. These assistance systems have been developed by Liebherr-Werk Bischofshofen GmbH and are fully integrated into the machine control system.”
However, even the best technology would be useless without the core ingredient –the people. Pfab affirms that Bischofshofen’s employees identify strongly with Liebherr and its products. “Many of our people remain loyal to the company for years. This is supported by our corporate culture based on mutual respect, fairness, trust and long-term relationships.
‘One Passion. Many Opportunities’, LiebherrWerk Bischofshofen GmbH offers a diverse range of professional fields.
True to its motto ‘One Passion. Many Opportunities’, LiebherrWerk Bischofshofen GmbH offers a diverse range of professional fields – from logistics and purchasing to human resources and marketing, through to quality management and production planning. Apprentices, trainees and students can choose from a wealth of different options for starting their careers. Every employee has a wide range of opportunities for career development and self-realization, regardless of their position – be it as an industrial designer or engineer.
Going forward, Liebherr-Werk Bischofshofen GmbH is pushing ahead with the phase-out of fossil fuels and is preparing solutions to decarbonize construction sites and gravel works. Following the first electrified Liebherr wheel loader, the company will be looking at expanding the electric drive to other small- and medium-sized devices. Series production of the large wheel loader with a hydrogen engine is planned for the second half of the decade, and focus on digitisation of mobile work machines will intensify.
Operator’s comfort also remain a priority. “While driver assistance systems have long been part of the programme, the company is particularly researching tele-operation –functions that can offer a high level of safety, especially in monotonous and dangerous operations,” acknowledges Pfab. He affirms that overall, Liebherr-Werk Bischofshofen GmbH continues to strive to develop innovative, efficient and comfortable solutions for customers; solutions that at the same time meet the market’s environmental and sustainability requirements.
Last year Osho Chemical Industries Ltd celebrated 30 years of selling Agro Chemical, Animal Health and Public Health products. The firm is based in Kenya but operates across Tanzania, Uganda, Zambia, and Malawi amongst others. But the company has more to celebrate than longevity. Over the last 30 years, Osho Chemical Industries has grown from a team of six employees to a company with 536 staff across the range of countries it operates in.
It is impressive growth, built on a foundation of caring about the people and the animals it works with.
“We are customer-focused and employee-centric,” says Rushabh Shah, Head of Sales and Marketing at Osho Chemical Industries. “We take the time to understand our customers and their requirements. We have a field team of 88 specialists who visit the farmers’ and ensure they have the products they need. We offer free advice on challenges such as disease and pests, supported by a strong country-wide network of 500 distributors with 5,000 stockists. It is a comprehensive, fully working chain from Osho as the manufacturers, to the farmers.”
Osho Chemical Industries has built its position in the market by catering for all farmers’ requirements, from public health products, to its animal health range and a comprehensive agrichemical offering. The goal is to create a one-stop shop for farmers.
[Opposite Page]
Rushabh Shah, Head of Sales and Marketing at Osho
But in many ways, Osho Chemical Industries is more than a onestop shop. It is also the first port
of call when challenges arise. This could be seen nowhere more clearly than in 2020. While most people remember 2020 for Covid-19, for many farmers in Kenya that year was memorable because of a different outbreak – an outbreak of locusts that threatened food security across the region.
“We were able to come up with products that could be used to control the locusts,” Shah says. “We rapidly developed the in-house manufacturing of ULV products including biological controls. The locust invasion gave us an opportunity to really showcase our local manufacturing in terms of speed to market and the development of new products.”
Osho Chemical Industries found itself in a position to supply products to Ethiopia, Djibouti, Yemen, Tanzania, Uganda, and Kenya that could help mitigate the locust invasion. This is exactly the sort of challenge that gives Osho Chemical Industries the opportunity to show what it can do.
“We have a product development department that looks at the challenges farmers are facing and what solutions we
Safepak Limited, based in Kenya with a presence across East and Central Africa, is a market leader in the design and manufacture of rigid plastic packaging solutions.
Since its founding in 1991, Safepak has developed an extensive portfolio of high quality and innovative products. These include preforms, bottles, jars, closures, jerrycans, and other packaging solutions for clients across a wide range of FMCG industries. Safepak is an ISO 9001 & ISO 22000 accredited organization.
SAFEPAK LTD. P.O. Box 63150 - 00619, Muthaiga, Nairobi, Kenya, Maasai Rd, Behind Libra House, Off Mombasa Rd.
(+254 20)2 403 222 | 2 403 223 | 2 403 224 (+254) 724 390 700 | 738 999 046 (+254) 720 657 254 | (+254) 703 843 861 admin@ke.safepakgroup.com
can come up with,” says Shah. “We also work together with local universities to research and develop new products.”
Indeed, Osho Chemical Industries has working partnerships with the top three universities in Kenya, taking the products of their research to see if Osho can find commercially viable applications for them. The agro chemical product company also has its own trial site, a specialised area for testing new innovations to see which products will work to its customers’ needs and expectations.
One area that Osho Chemical Industries has paid particular attention to is sustainability, with the firm’s field teams training farmers on the best use of pesticides and chemicals in general.
“What we find is that through education we can teach farmers to use products safely,” Shah tells us. “We ensure they use the right amount and do not over-spray. We train more than
three thousand farmers a month in groups, teaching them how to use these products safely and effectively. On top of that we are also pushing our biological range as well, so farmers not only use less chemicals but increase the uptake of biological solutions.”
Osho Chemical Industries works with small-scale farmers, training them in the tools, techniques and solutions that will promote sustainability and
food security. At the same time, the company has committed to planting 30,000 trees by the end of next year.
But as we said at the beginning, what sets Osho Chemical Industries apart is its focus on the needs of its customers and its employees, and the firm invests in the training of its employees as much as the farmers it works with.
“We launched the Osho Training Academy two years ago,” Shah says. “It is essentially a training academy for all of our staff. It has been built to equip them with the skills they need. We run a range of programs every year.”
This year the theme Osho is pursuing is wellness. The company is taking a closer look at the mental and physical health of its employees, providing full-body check-ups, ultrasounds, and counselling for those who require it.
“Through these initiatives, we are able to really retain our talent,” Shah says. “This is why we were voted for as a Great Place to Work in Kenya. It is the first time a family-owned business has been in the top three for the award.”
Among the workers, Osho Chemical Industries has been particularly focussing on investment in its machine operators.
“These are people who typically do not have a formal educational background, so what we were able to do was work with our National Institute of Training to come up with a whole course for them. We gave them a certificate in machine
training that they could use to build their job profiles and grow their careers.”
The certificate proved to be one of the first in Kenya certifying on-the-job skills for people without a formal education background, paving the way for a brighter future.
And Osho Chemical Industries has a bright future ahead of it as well.
“We are expanding geographically, quite rapidly,” Shah tells us. “In the next two years, we will be looking to expand into Ethiopia, Congo and Zimbabwe. We have also set up our own biological production. Our teams are looking at biological strains found in the soils of the countries we operate in, seeking out control agents. That is quite exciting! We will soon be offering products derived from natural pathogens found in the countries we operate in.”
AS A RELATIVELY NEW GROUP CEO, JESS OH HAS A STRONG VISION FOR THE LONG-TERM FUTURE OF AYS GROUP.
Ann Yak Siong Hardware Sdn Bhd was established in Malaysia in 1982, founded by Mr. Oh Chiew Ho, starting with a modest 2,000 sq. ft. hardware shop and a small team of three employees. Over the years, the company evolved beyond its origins in hardware trading, expanded its operations as a trader, stockist, and distributor of steel and construction materials, with a particular focus on structural steel sections and culminating in AYS VENTURES BERHAD listing on the Main Market of Bursa Malaysia Securities Bhd (stock code: AYS 5021) in 2012. The AYS group now generates an annual turnover of RM 1.3 billion.
Today the business is overseen by its new Group CEO, Mr Oh Chiew Ho’s daughter, Ms Jess Oh Pooi Foon. AYS Group has built itself a reputation as a large-scale steel and building materials distributor working across Malaysia and Singapore.
“Over the past 40 years, our founder has leveraged his efforts and experience in the industry to bear on the growth of the business,” Jess Oh tells us. “Throughout the years, we have also continuously built our team, attracting the people and talent that contribute to our business’s success. This combination of new talent and established experience is our strength.”
That talent forms the foundation of a strong network of suppliers and the wide customer base that AYS Group has built up. As well as supplying raw materials, AYS Group’s service offerings include 3D engineering design with Building Information Modelling (“BIM”), manufacturing of steel purlins, and truss decks, project management services
and providing one-stop solution-based steel services to support our customers in the construction, oil & gas and shipbuilding industries.
Jess Oh says. “What sets us apart is our focus on large scale projects. We have a highly project-orientated team, and we package our services into a one-stop-shop solution. When our customers tender a project, we ensure they receive the materials they need on time, enabling them to complete the job efficiently, and at competitive prices.”
It is an offering that makes AYS Group a powerful partner to have, but also places them in a potentially vulnerable position regarding changes in the economy.
“We need to be highly dynamic, because we are in very close contact with economic changes,” Jess Oh shares. “Currency fluctuations, such as the softening of the US dollar, directly impact the cost of our stockholding. We are also facing challenges from the slowdown in the Chinese economy. Given China’s proximity to our country,
the capacity of Chinese steel production has a direct impact on our business. We have to manage price fluctuations very closely to continue securing orders and procuring materials in a price competitive way.”
“IN TERMS OF SUCCESSION PLANNING, WE HAVE OVERCOME THE FIRST MAJOR CHALLENGE, THE TRANSITION FROM THE FIRST GENERATION TO THE SECOND GENERATION”
However as Jess Oh points out, AYS Group’s ability to meet these challenges is closely linked to its ability to attract and retain talent.
“Attracting new talent is a challenge that is faced by the entire industry,” Jess Oh points out. “Nowadays we find the younger generation is reluctant to enter the construction industry, with many turning to the financial and IT sectors.”
However, as AYS Group has successfully transitioned to its second generation with Jess Oh assuming the Group CEO position, the company is ready to address this challenge.
“In terms of succession planning, we have overcome the first major challenge, the transition from first generation to second generation,” Jess Oh explains. “My father identified successors for the lead positions
in the company, helping us navigate one of the significant stepping stones we faced.”
What was particularly special about this succession planning was that Mr Oh Chiew Ho marked his daughter, Jess, out among her three brothers as the one to succeed him as Group CEO, particularly in a very maleled industry.
“The steel industry is generally very male-orientated, and appointing a daughter instead of one of the sons in a Chinese
family is not so easy,” Jess Oh says. “My father is still my Executive Chairman and is well respected across the market and in the industry. At the same time, my three brothers have agreed to take on other key positions in the company. Ultimately our objective is to identify the most talented people for the right positions. The disparity between male and female employment is decreasing, with an emphasis now on capability, regardless of gender.”
AYS’s Board of Directors.
Jess Oh herself joined the industry 20 years ago, and through the early years of her career, she was used to being the only woman in an environment heavily populated by men.
“I have become comfortable and used to it,” she says. “My business partners respect me, and if you know what you are doing and can instill confidence in your business partners, then your clients, suppliers, and staff will allow you to lead. The support will be there because they believe in your ability to deliver on your promises.”
It is this ability not only to acquire new talent, but also to accurately assess that talent and its potential, that lies at the heart of AYS Group’s strategy going forward.
“We continually invest in human resources, aligning our KPI with the perspective we need,” Jess Oh says. “We are identifying potential and considering how to implement out succession planning in a professional and sustainable manner.”
“I believe everyone has their strengths and weaknesses, the important thing is to identify the strengths of our people and address the gaps in our available skillset through training,” Jess Oh says. “These are the areas we continue to invest resources and time into, building a stronger team.”
That goal has been the driving force behind all of Jess Oh’s decisions. Talking with her, it is clear she is taking a long-term perspective in her leadership of the company.
The future of AYS is firmly anchored in its core valuesAlliance, Yield, Sustainability. These values not only define the company’s identity but also shape its strategic direction and long-term goals.
AYS’ priority is to build a sustainable company. This means empowering employees
and not relying on a single leader to carry forward the company’s vision.
“Even though we have been in business for 42 years, we consider ourselves a young company, embracing a youthful mindset, with significant untapped potential. There are a lot of things we think we can do to drive the team to another level and make the company stronger.”
“We will continue forging strategic alliances with our business partners to diversify our offerings, but those diversifications will be corelated and in line with our corelated business area allowing AYS in creating new avenues for growth,” Jess Oh says.
In short, AYS is poised for continued success and growth, driven by the company’s dedication to employee empowerment, sustainability and strategic partnerships.
THE DAKHLA ATLANTIC PORT IS ONE OF THE MOROCCO’S BIGGEST INFRASTRUCTURE PROJECT, SET TO SERVE AS AN ECONOMIC CATALYST IN THE RE-SHAPING OF AFRICA.
Currently under construction, the new Dakhla Atlantic Port (DAP), located in southern Morocco, is expected to boost trade across West Africa and beyond. The $1.2 billion megaproject is due to complete in 2028 and will include a trade port, a fishing port and a shipyard. The port is set to support economic, social and industrial development in all productive sectors as well as providing the region with a modern and scalable logistic tool in line with the development aspirations of the region.
Once operational, the port, occupying 650 hectares, is expected to handle 35 million tonnes of goods a year, and also serve as a key infrastructure element operating in the field of transportation and storage of green hydrogen. In the vicinity of the port, one thousand hectares will be allocated for economic activities, including a logistic pole, a general industrial zone, a marine competitiveness pole, a commercial zone and a shared public services pole.
“As its name suggests, the Dakhla Atlantic Port embodies a royal vision for the Atlantic African alliance, an alliance based on development and shared prosperity for African countries,” says Nisrine Iouzzi, Director of Dakhla Atlantic port Construction.
“Proximity to the African and Latin American markets was one of the key factors when selecting the location for this green field development.”
She further points out that the port will integrate Sahel countries without a coastline,
allowing them to benefit from the advantages of the Atlantic coast. “Like the Tanger Med port, the Dakhla Atlantic Port will enhance maritime connectivity between Morocco and other African countries, reaffirming Morocco’s significant role in the international maritime transport market. The Dakhla Atlantic Port will significantly contribute to inclusive economic and social development in the southern regions of Morocco.”
She further notes that the Dakhla Atlantic Port is the largest port planned within the country’s 2030 National Port Policy that began to be implemented in 2012. Within the policy, two major ports have already been completed on the Mediterranean coast, with the new port on the Atlantic coast expected to attract more port traffic coming to and from Africa, and also to strengthen the connectivity between Morocco and the countries of Americas.
Given the port’s location, a lot of preparatory work had to be done, including the development of the complete infrastructure counting roads and cement and steel plants to provide crucial raw materials.
“We are proud to note that for the construction phase, the companies responsible for execution, monitoring, and control of the project are 100% Moroccan. This is thanks to the numerous port infrastructure projects completed over the past 12 years as part of the National Port Strategy for 2030.”
“WE ARE PROUD TO NOTE THAT FOR THE CONSTRUCTION PHASE, THE COMPANIES RESPONSIBLE FOR EXECUTION, MONITORING, AND CONTROL OF THE PROJECT ARE 100% MOROCCAN.”
During the construction phase, the port is set to directly employ more than 2,500 people. As a hub for economic activity in the future, it is expected to have a positive impact on local communities, attracting businesses and creating jobs in construction, logistics, transportation, and related industries.
“The project is designed with scalability in mind, in order to meet the future needs of the region and Africa in terms of traffic demand and maritime connectivity,” affirms Iouzzi. “It also includes the construction of a maritime bridge to provide a deep-water port and regulate the project’s impact on the site’s hydro-sedimentary dynamics.”
Given the strategic importance of the new port and its size, challenges are an integral part of the process but these are being handled well. “The challenges can be summarized by the project management triangle – balancing scope, cost, and time to maintain highquality construction. Addressing these challenges requires a comprehensive approach that combines strategic planning, technological innovation, and effective management,” says Iouzzi.
“The recruitment of the project team members was based on strict criteria, emphasizing experience and personal and professional skills to ensure the tasks are carried out effectively. Additionally, as part of project management, the project leadership has established a value system that the entire team adheres to.”
The same rigorous approach applies to managing suppliers –crucial partners for the project. Daily deliveries are required of high-quality materials and equipment that meet the
standards specified in the contract in compliance with international regulations. “Just to give you an idea of the sheer size of the project – constructing the port will require 20 million kg of steel for piles, 29 million kg of steel for concrete reinforcements, 314,000 tonnes of cement, 1.2 million cubic meters of concrete, and 20 million tonnes of materials for dikes and embankments,” says Iouzzi.
in April 2024, Morocco launched the Green Hydrogen Offer, a sustainable energy development plan, and the entire port will focus on the shift towards ecofriendly policies. Indeed, as soon
as hydrocarbons are no longer needed, the port administration will convert the oil products terminal over to green energy.
In terms of sustainable development, an environmental preservation and monitoring plan has been implemented, along with a clean energy production system. Solar plants are already providing electricity to the construction site and other environmental measures have been implemented.
“Morocco has embarked on a comprehensive strategy for digital and environmental transition. Aligning with these national strategic orientations, we have ensured their integration
throughout the various phases of the project, from the study phase to the construction phase,” says Iouzzi.
“During the study phase, we used cutting-edge technologies in digital and physical modelling, calculation, and sizing. This approach continued into the execution phase, where we employ intelligent control and monitoring systems, such as semi-automatic welding systems, drone-based work monitoring, and the use of new blocks for the breakwater armour.”
It seems that progress is well under control and construction is continuing according to plan. Following the preparatory works, some 25% of the port construction is now completed. “Over the next 12–18 months, we will focus on the completion of the maritime bridge and the ramping up of the main breakwater construction, along with the start of the quay block fabrication – on schedule for the port to be delivered in 2028 and open in 2029,” Iouzzi affirms in concluding.
DAMEN NAVAL, THE DEDICATED NAVAL SHIPBUILDING DIVISION OF THE DAMEN SHIPYARDS GROUP, WILL BE CELEBRATING ITS 150TH ANNIVERSARY NEXT YEAR –A PROUD LEGACY THAT IS SET TO CONTINUE.
Damen Naval is the largest division of the Damen Shipyards Group and covers all the naval activities of the Group. With an impressive history going back to 1875, when the Royal Schelde Yard was founded in Vlissingen, Damen Naval is today the only naval original equipment manufacturer (OEM) in the Netherlands.
Managing Director Roland Briene explains that while the company was active over the years across a variety of sectors, and employed some 5,000 in its heyday, becoming a member of the global Damen Shipyards Group in 2000 sharpened its focus on shipbuilding services alone.
He affirms that the company is getting ready for the big celebration next year. “Reaching 150 years of being a privately owned naval shipbuilder, still alive and kicking, is something to be proud of. This history is part of our heritage, but we are also looking into the future, embracing new opportunities.”
The company has a long tradition of serving the Royal Netherlands Navy and this relationship is set
to continue with the contract to build the RNLN’s new Combat Support Ship and the new Anti-Submarine Warfare Frigates (ASWF) for both the Netherlands and Belgium.
Damen Naval was also selected for the design and build of the German Navy’s F126 frigates. This contract, awarded to Damen Naval in June 2020, represents a significant upgrade to the German navy. At 166 meters in length and with a displacement of up to 10,000 tonnes, these frigates are set to be the largest in the fleet. Designed as versatile multimission platforms, the F126 frigates can operate globally across diverse conditions, from tropical climates to polar regions.
At Mehler Protection, our mission is simple yet profound: protecting lives and securing peace of mind. We offer a comprehensive range of solutions, meticulously engineered to protect both individuals and diverse operational platforms like naval vessels.
info@mehlerdefence.de @
mehler-protection.com
Mehler Protection is a subsidiary within Mehler Systems, deeply committed to upholding the values and principles that have defined the Mehler brand for decades. This connection provides a unique advantage – the synergy of a specialized focus on protective solutions with the broader capabilities and resources of Mehler Systems. It allows to leverage a wide array of expertise, technological innovation, and global reach, reinforcing the position as a trusted leader in protecting lives and assets.
Mehler Protection is the technology and market leader for naval protection systems in Europe. With the M-RACC product family (Multirole Armour Composite Components), Mehler Protection offers a modern, modular protection system with a low basis weight, which is specially tailored to the requirements of maritime mission scenarios. M-RACC systems offer reliable protection against ballistic projectiles and fragments as well as shaped charges and anti-tank weapons in maritime threat scenarios, tested according to STANAG 4569 AEP-55, Vol. 1. The protection of critical areas of the ship, such as the bridge, command-and-control centre, machine gun positions and ammunition depots, ensures the operational capability of the overall system and significantly increases the crew´s probability of survival. The individual protection solutions are designed by Mehler Protection on the basis of extensive threat analyses depending on the intended use and the resulting threat scenario. Based on decades of experience, Mehler Protection offers the expertise as a system consultant for the design of marine protection systems and is therefore an important long year partner of Damen Naval.
www.mehler-protection.com
Read more at www.wartsila.com/marine/customer-segments/navy
Wärtsilä SAM Electronics is responsible for the electrical system integration package for the F126 program.
The package comprises the integration of all electrical systems on the platform and the supply of numerous electrical systems, such as switchboards, power distribution, lighting and degaussing systems as well as the installation of the entire cable plant.
We are proud to contribute to the success of Damen Naval as one of the most trusted leading electrical system integrators for newbuild and service.
Briene points out that Damen Naval’s order book is at a record high. “Important new contracts were signed before the pandemic as a result of the planned investment by the Dutch and German Navies, and the current geopolitical situation means that demand for our vessels is increasing.”
“In total, we are now building eight frigates, four for the German Navy and four for the Royal Netherlands Navyand Belgian Navy,” he says, adding that the German Navy chose to exercise its option for two additional frigates so the company now has a total of 10 frigates under contract, in addition to other projects ongoing for the Royal Netherlands Navy and other parties.
These major contracts, which began to be implemented right in the middle of a pandemic, brought significant changes to
Naval. The company had to increase staff numbers from 400 to 1,200 and implement a number of new IT systems. Needless to say, successfully integrating all these new engineers, and making sure that all programmes and systems were effectively in place, was a significant challenge in a ‘locked down’ world but one that was handled successfully.
“We managed to find new people, not only from the Netherlands, but also from Spain, Portugal, France and other countries who relocated to work with us. Ensuring that these new people did not feel isolated was key,” affirms Briene. “Ever since then, the wellbeing of our people – our core asset – has become one of management’s priorities.”
Following the Russian invasion of Ukraine, it was clear that there is more to come, says Briene, and more changes would be needed.
“That was the moment where, in 2022, we decided to restructure the company and re-define our strategy. In 2023, a completely new structure was implemented with new systems and procedures, setting us up for the large contracts that were to come, making Damen Naval ready for the future.”
“REACHING 150 YEARS OF BEING A PRIVATELY OWNED NAVAL SHIPBUILDER, STILL ALIVE & KICKING, IS SOMETHING TO BE PROUD OF.”
With its proven track record, Damen Naval stands out with several strengths. Supply chain management is one of them. Some 150 to 200 suppliers and co-makers are needed for a
large frigate, so coordinating the work requires skilled hands.
“As the national OEM for naval shipbuilding, we work with many subcontractors, suppliers and comakers and are experienced in integrating a lot of such systems into a single system,” explains Briene.
“For example, within a single contract with a customer, we integrate all the weapon systems, all the sensors, and other equipment into our own systems to produce a functioning warship that can fight and win at sea. Basically, we engineer and build a ship by integrating a lot of components with co-makers. That is quite a special capability.”
Damen Naval is currently building Combat Support Ship Den Helder at its shipyard Damen Galați in Romania.
“The other differentiator, from the bigger perspective within the Damen Shipyards Group, is our capability to provide a full range of ships to navies from a small patrol craft up to fully fledged frigates.”
The company can also leverage the advantage of Damen Shipyards Group’s global sales organization. “Where in the world there is water, Damen is there also. This geographical spread has boosted our exports and helped us to sign contracts with
clients in Indonesia, Morocco and quite recently, Colombia, where we will work closely with a local shipyard to build a frigate for the Colombian Navy.”
To meet all this emerging demand, utilisation of capacities has to be carefully considered while making sure that the demanding requirements of the company’s long-standing customer, the Royal Netherlands Navy, are duly met, says Briene.
a
and parts
“We are now looking into the 30’s horizon for new contracts. We have to carefully assess the efficiency of our yards to make sure that we are ready to produce what our clients need in order to prepare for the worst – that’s what naval shipbuilding is about,” he says.
In concluding, he reflects that over the 150 years of
the
its existence, the company has gone through major changes and has survived in robust shape – a remarkable achievement. “The flexibility and adaptability to new developments has been an integral part of Damen Naval and will continue. With the new efficient business structure, we are fit for the future.”
“THE FLEXIBILITY AND ADAPTABILITY TO NEW DEVELOPMENTS HAS BEEN AN INTEGRAL PART OF DAMEN NAVAL AND WILL CONTINUE.
RECENTLY
Port of Aberdeen, Scotland’s largest berthage port, has always played a major role in the country’s development. The port handles a substantial volume of Scotland’s seaborne freight traffic and is an important supporter of the country’s energy sector as well as tourism. As a multimodal port, it offers a strategic location, worldclass facilities and an expert supply chain.
Chief Executive Officer
Bob Sanguinetti points out that the impressive legacy is set to continue. “We are the oldest existing business in the UK and with the recent transformational investment in the port’s expansion we are making sure that we stay relevant and continue to grow for the next 100 years.”
With its 119 direct employees, Port of Aberdeen is a relatively small company but it facilitates and supports a huge amount of business. “The importance of Port of Aberdeen for the local as well as regional economy is undeniable,” says Sanguinetti. “We contribute £1.5 billion gross value added (GVA) to the economy, and we support 12,000 jobs in the supply chain.”
“The port is a key logistics hub for the offshore sector in the North Sea, and this will remain as we transition from fossil fuels to renewables, and
as the oil and gas platforms are replaced over time by floating and fixed offshore wind farms.”
Sanguinetti explains that as a Trust Port, the long-term vision can be supported by major investment without expecting immediate return. To this end, South Harbour – the largest marine infrastructure project in Trust Port history - was officially opened in September 2023.
The new harbour offers 1,500 metres of deep-water berths, extensive heavy-lift capabilities, 125,000 sq. m. of flexible laydown space, and ample project areas for vessels up to 300 m in length. As such, it offers unparalleled capacity to support projects of all sizes and requirements.
“Opening South Harbour has made us the largest port by berthage in Scotland with 7000 vessels calling in every year.
Beattie FRC Ltd are a leading civil engineering construction company based in the Central belt of Scotland that specializes in formwork, reinforcement, concrete, scaffolding and groundworks. Our long established leadership teams have a vast experience in major civil engineering projects over the last 25 years throughout the UK. Latest Major projects include Harbours, Service Trench, Copes & Capping beams, Crown walls, Retaining walls, Swing bridges, Nuclear tanks, Fracking tanks, Tram extension, Viking wind power plant, A9 bridges to name but a few.
In the dynamic energy hub of Aberdeen, the Aberdeen Harbour Expansion Project (AHEP) addressed the critical need for expanded port facilities to accommodate larger vessels. As the project manager, cost consultant, and quantity surveyor, Doig + Smith played a pivotal role in this transformative endeavour.
The D+S team navigated significant challenges, including minimising disruptions to ongoing operations and adhering to stringent environmental standards. The project required careful planning to protect local wildlife and manage the site’s proximity to sensitive areas, such as a Site of Special Scientific Interest and a dolphin habitat.
projects.
www.doigandsmith.co.uk
The construction involved extensive dredging and the creation of new quays and breakwaters, utilising innovative techniques like the incorporation of precast concrete caissons to enhance the port’s heavy lift capacity. Despite unforeseen challenges, including the departure of the initial contractor and COVID-19-related delays, Doig + Smith’s strategic project management contributed to the project’s success.
Doig + Smith have a wealth of experiencer in port, harbour and marine projects including current roles with Ardesier Port and Stornoway Deep Water Port.
www.doigandsmith.co.uk
This accounts for about 43% of Scotland’s overall marine traffic,” says Sanguinetti, adding that with these enhanced capabilities and capacity, the port can now attract much larger vessels – such as the 290 m-long cruise ship, Costa Favolosa, that was welcomed to the Port of Aberdeen in June, the longest vessel ever to visit the port.
“South Harbour has been the single most important achievement in the last 10 years,” says Sanguinetti.
“We are now very well placed to continue consolidating and growing our business across the energy, trade and tourism sectors, our three core business streams.”
The port is also making impressive progress on the sustainability front. “We were delighted to launch our net zero strategy last year, aiming
to become the UK’s first net zero port by 2040,” says Sanguinetti.
“Our net zero strategy has three work streams – reducing emissions, facilitating future fuels, and supporting the energy transition. These guide all projects, investment, and decision-making. Over the next decade, we will invest £55 million to become a leading
exemplar in environmental stewardship and sustainability, pioneering green port innovation and facilitating energy transition solutions.”
He points out that this cannot be achieved in isolation, and the port will be working very closely with government and with the private sector. Tangible progress is already visible –the ‘Shore Power in Operation’
demonstrator project, started in August 2024 as part of a £4 million project designed to supply clean electricity to vessels at seven berths. As one of the first of its kind in the UK, the project is scheduled to deliver its first power in March 2025.
“THE IMPORTANCE OF THE PORT OF ABERDEEN FOR THE LOCAL AS WELL AS REGIONAL ECONOMY IS UNDENIABLE.”
Sanguinetti points out that the port is in a privileged position to provide key support to the shipping sector to help it transition from fossil fuels to renewables. “We are talking to all stakeholders including the government to see what we can do to provide the infrastructure for new green fuels as they come along.”
Environmental initiatives are considered a priority also internally, he further affirms. The port has an extensive replacement programme in place to replace all vehicles and equipment with electric versions and is continuing the roll-out of LED replacements for lighting. “Our pilot vessels and work boats are now all running on HVO which has allowed us to reduce our CO2 emissions significantly.”
Sustainability is not the only priority on the agenda –digitisation is also at the focus of attention. Port of Aberdeen is set to become the smartest port in the UK with a significant £1 million investment in new technology to improve the safety, connectivity, and sustainability of the port. The view is to upgrade and expand the port’s CCTV and security systems and the deployment of a private 5G, public Wi-Fi and IoT networks to support a range of solutions to improve operations and the customer experience.
The port’s efforts towards a greener future and business enhancement have been duly recognised – in 2023, Port of Aberdeen was voted Business of the Year in the north-east of Scotland, and earlier this year, it won Business of the Year at the Maritime UK Awards, in recognition of its outstanding performance.
The recent investments will, no doubt, further increase the Port of Aberdeen’s importance for the country. “We have been around for almost 900 years due to our ability to adapt, identify trends and change accordingly. We are now doing the same as we go through the energy transition,” says Sanguinetti.
Excellent business performance and a commitment to advancing the maritime sector in the United Kingdom will remain key tasks for the future.
Sanguinetti affirms that for the next 12 to 18 months, the focus will be on consolidating the existing business and continuing on the growth path with existing and new customers.
“We will strive to make tangible progress on our net zero strategy, and to work with our partners to see how we can further reduce emissions, while pursuing our diversification strategy to the benefit of the port and the development of the region.”
www.linkedin.com/company/ceo-media-group twitter.com/businessfocus_