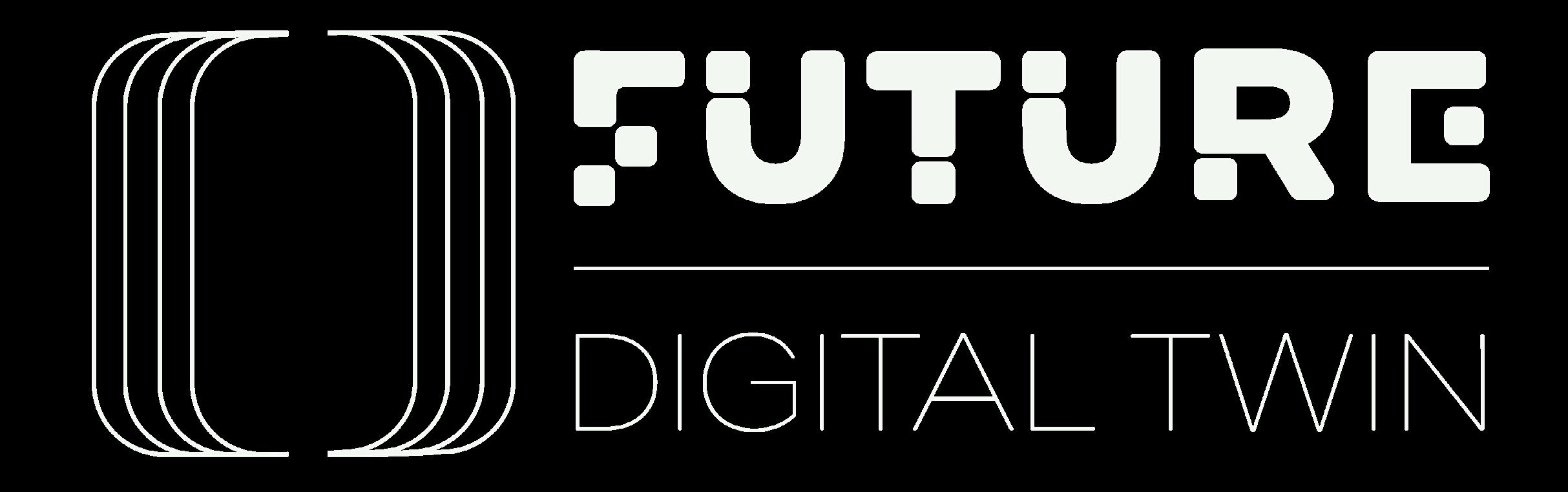
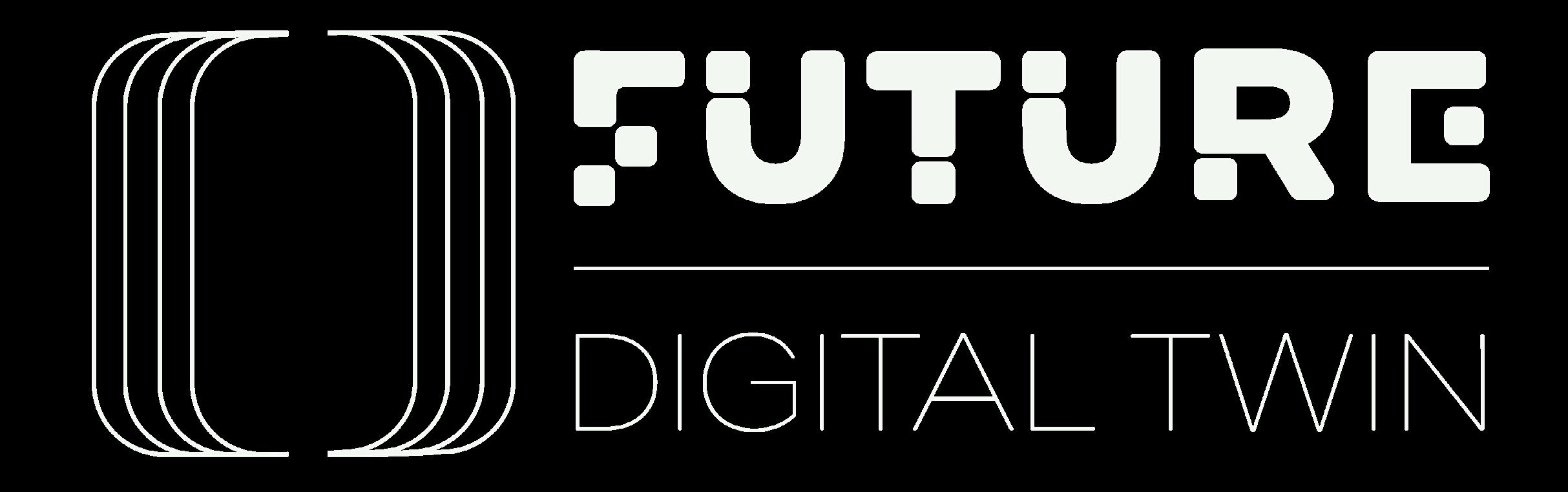
The Rise of Digital Oilfields
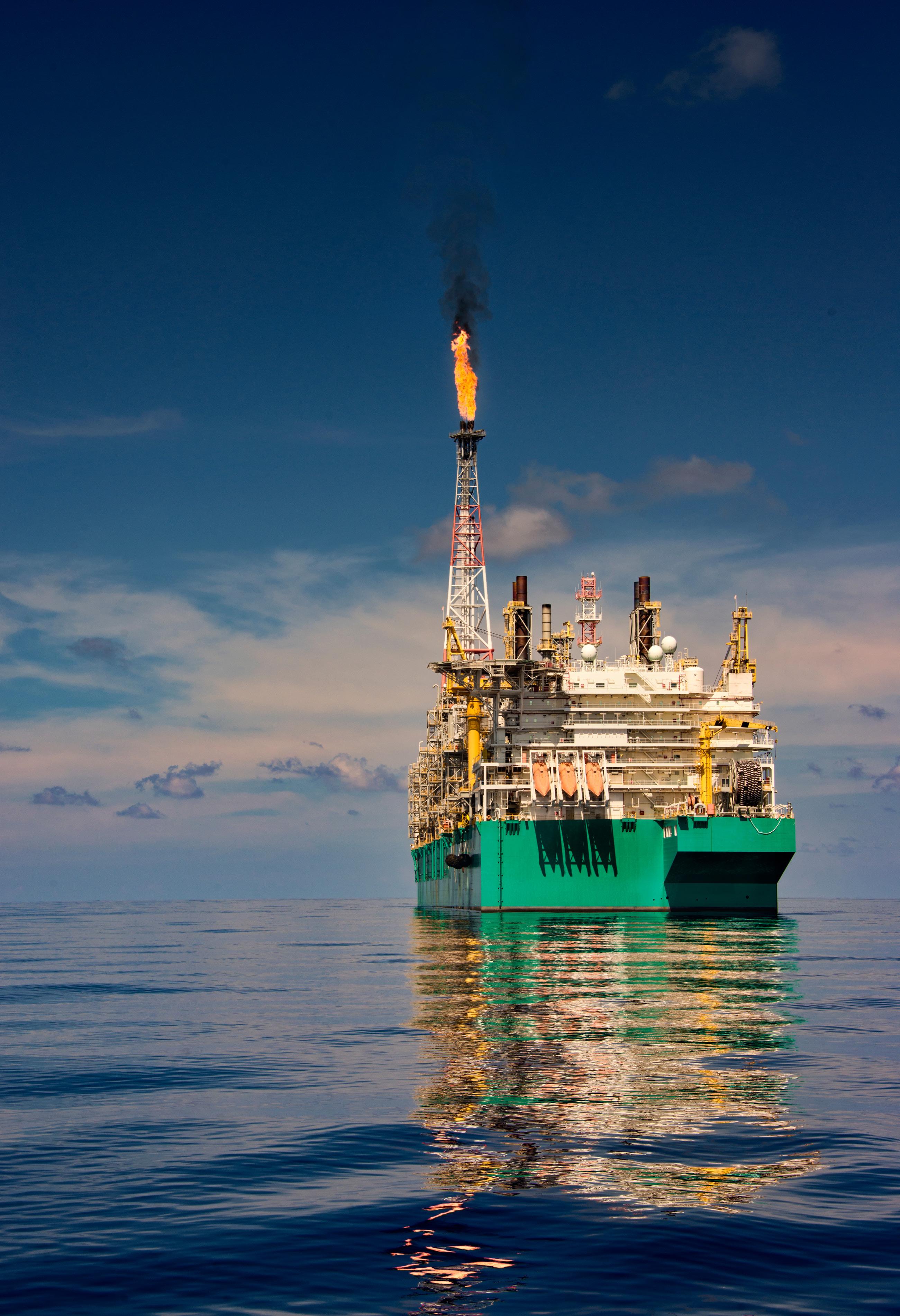
Predictive AI and the Path to Net Zero
The Power of Data
Analytics
Cyber Preparedness
Enhancing Wellbore Integrity
Walking the Data Tightrope
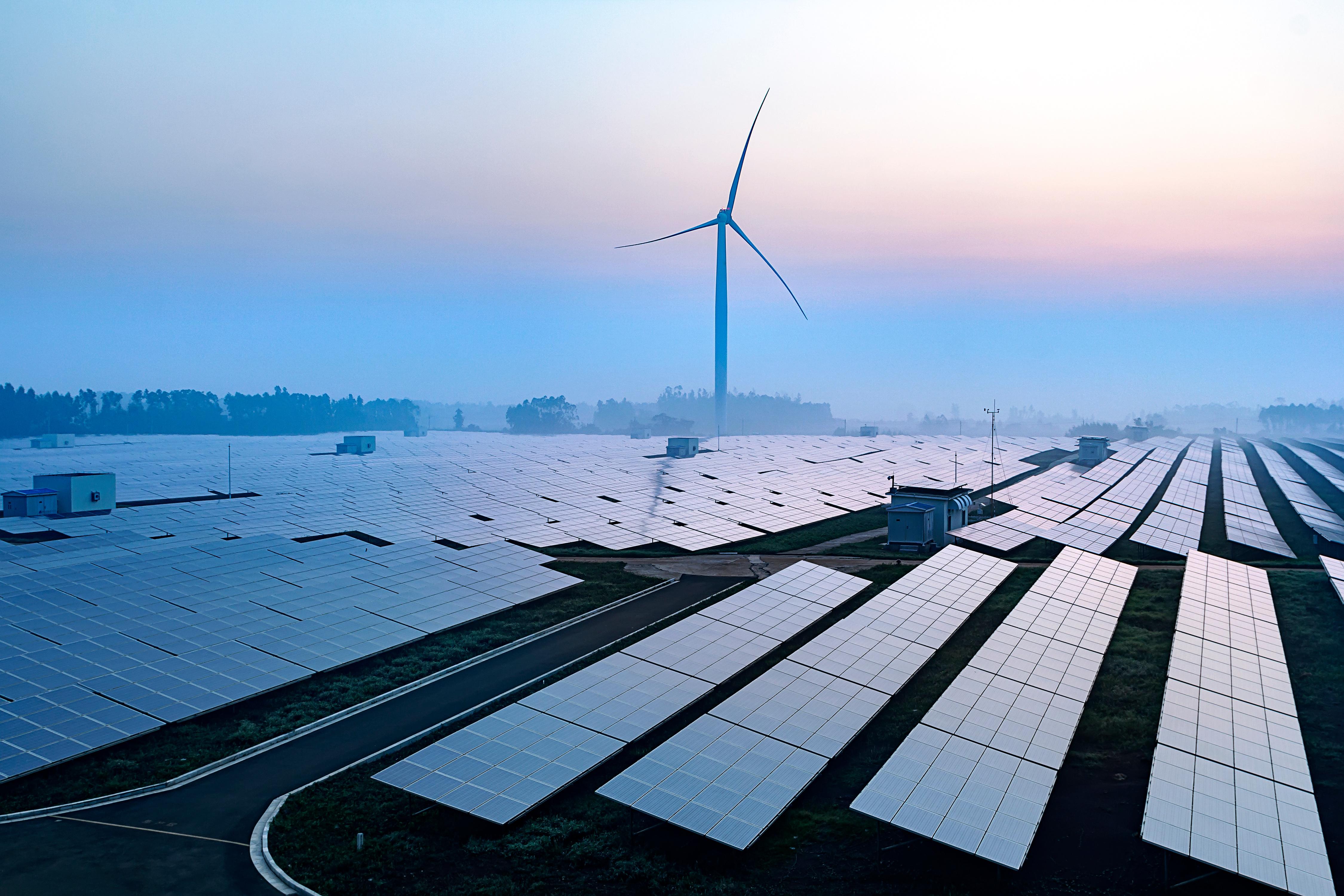
CEO
Mark Venables – Editor in Chief mark.venables@cavendishgroup.co.uk
Managing Director
Adam Soroka
Advertising Director
Mike Smith mike.smith@cavendishgroup.co.uk
Harnessing Gen AI’s Potential in the Oil and Gas Sector
Genetic algorithms (Gen AI) represent a promising frontier in reshaping the landscape of the oil and gas sector, offering a suite of innovative applications poised to revolutionise operations across the entire value chain. These applications harness the power of artificial intelligence and evolutionary computation to tackle complex challenges, optimise processes, and drive efficiency in various facets of the industry.
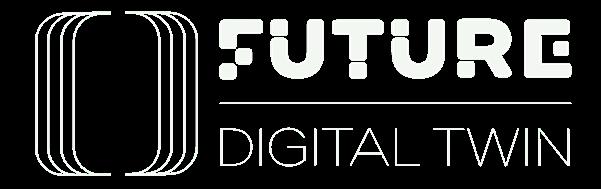
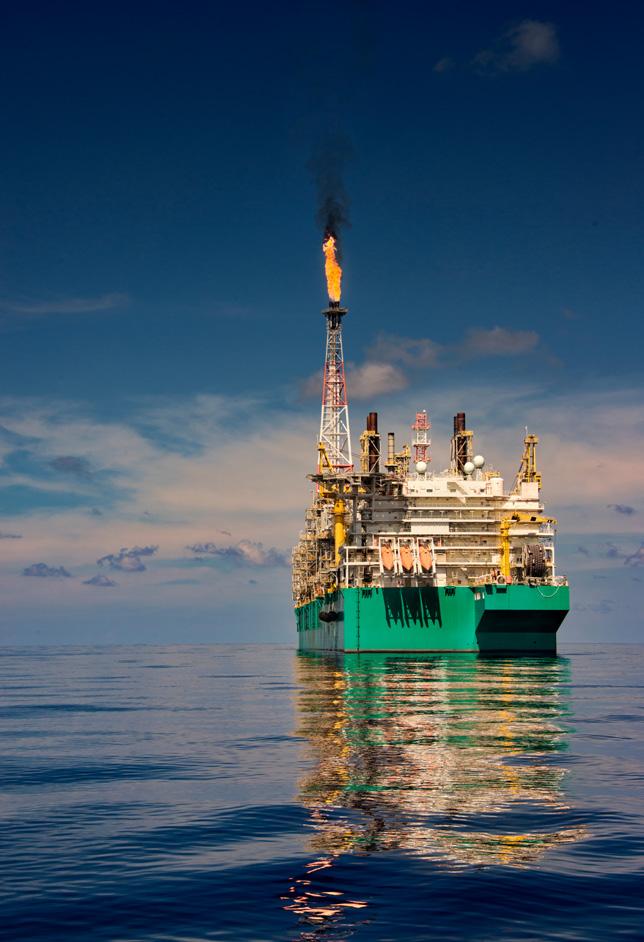
Second Floor Front 116-118 Chancery Lane London WC1A 1PP
Tel: +44 (0)203 675 9530
At the forefront of Gen AI’s potential lies reservoir management and optimisation. By assimilating vast datasets encompassing geological formations, production histories, and reservoir characteristics, Gen AI algorithms can discern patterns, identify optimal drilling locations, and formulate strategies to enhance hydrocarbon recovery rates. Through continuous adaptation and evolution based on real-time data inputs, these algorithms can refine reservoir management practices, optimise well placement, and maximise production yields.
Gen AI also holds significant promise in drilling and wellbore optimisation. By examining historical drilling data, geomechanical properties, and real-time sensor feedback, Gen AI algorithms can optimise drilling parameters, such as trajectory and speed, to minimise drilling time, reduce costs, and mitigate risks associated with wellbore instability or formation damage. This enables drilling engineers to make proactive decisions, enhancing operational efficiency and safety.
In the realm of predictive maintenance and asset management, Gen AI offers invaluable insights for optimising equipment performance and longevity. By analysing sensor data from machinery and equipment, Gen AI algorithms can predict impending failures or malfunctions, enabling preemptive maintenance interventions to minimise downtime, reduce maintenance costs, and optimise asset utilization.
When it comes to production optimization by analysing production data and operational parameters GenAI can identify inefficiencies and opportunities for improvement. By optimising production workflows, minimising downtime, and maximising production rates, Gen AI algorithms enhance overall operational efficiency and profitability.

Supply chain optimisation represents another frontier for Gen AI applications in the oil and gas sector. By studying historical data, market trends, and logistical parameters, Gen AI algorithms can optimise inventory management, procurement processes, and logistics operations. This ensures streamlined supply chain operations, minimized costs, and enhanced resilience against disruptions.
Additionally, Gen AI can support environmental monitoring efforts by analysing environmental data and predicting the potential impact of oil and gas operations on ecosystems. By identifying risks and recommending mitigation measures, Gen AI contributes to environmental sustainability and regulatory compliance.
Overall, the integration of Gen AI technologies holds immense potential to drive innovation, efficiency, and sustainability in the oil and gas sector, paving the way for transformative advancements and competitive differentiation in a rapidly evolving industry landscape.
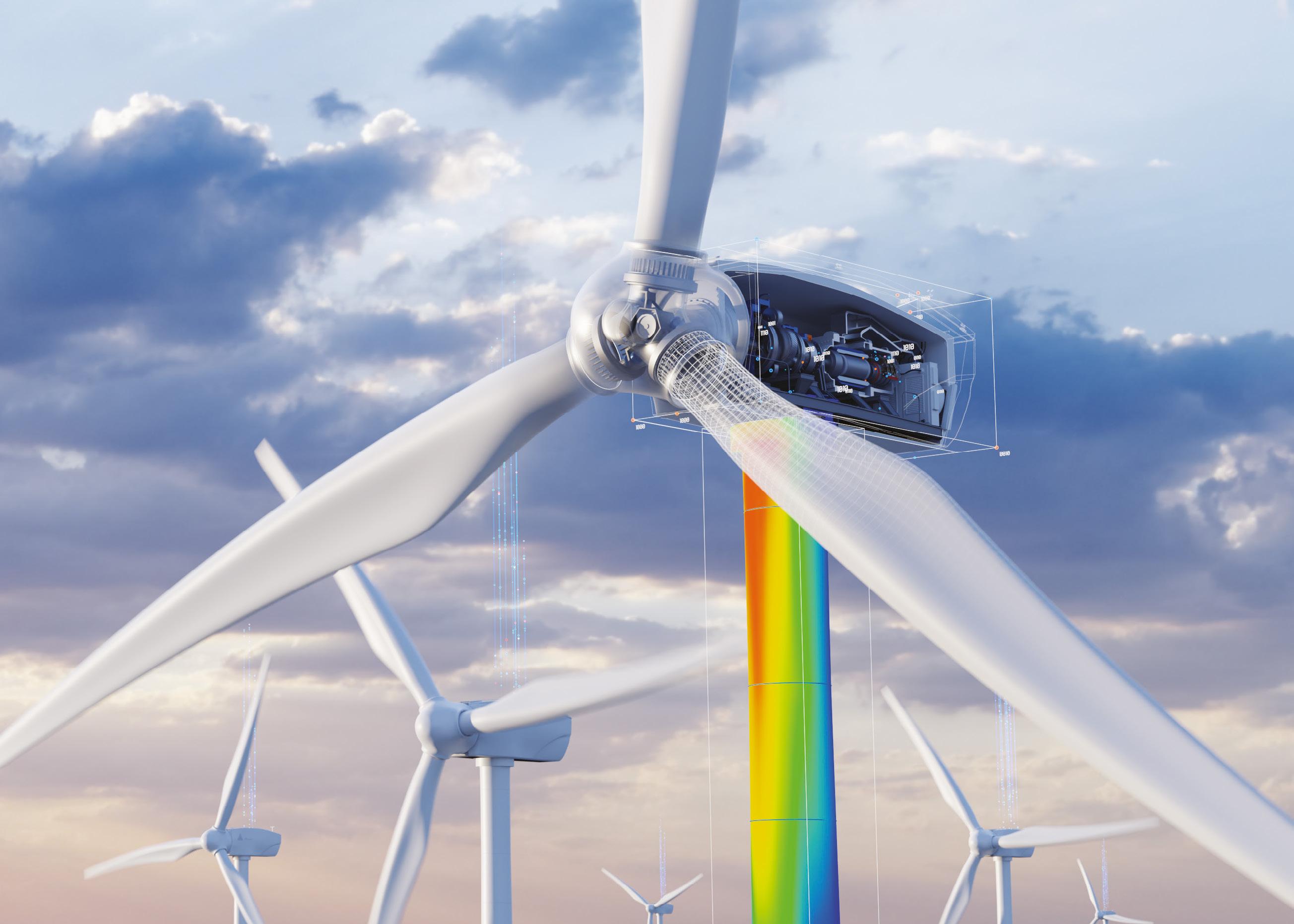

Amidst a wave of innovation, the fusion of digital twins and generative AI emerges as a game-changer for asset owners in the oil and gas industry, enabling smarter decisions, optimized processes, and a transformative journey toward efficiency, sustainability, and resilience
of cloud
Often hailed as the harbinger of revolutionary change, AI has ridden a wave of hype and fascination.
Predictive artificial intelligence (AI) has rapidly emerged as a transformative force in the energy industry, offering actionable insights to optimize asset management
The right mix of supportive policies, financial mechanisms, and technological innovation can de-risk investments in carbon capture, utilisation and storage (CCUS)
In the dynamic realm of the oil and gas industry, the integration of digital twin technology is reshaping operations, driving efficiency gains, and paving the way for a sustainable future amidst evolving environmental and economic imperatives
In today’s energy sector, the efficient management and maintenance of offshore assets is more crucial than ever to ensure sustained operations and long-term viability
Amidst a staggering performance gap in the oil and gas industry, the strategic implementation of data analytics systems promises to revolutionize operations, drive efficiency gains, and mitigate environmental impacts, ushering in a new era of sustainable growth
At look at how Aramco are harnessing power of AI, Big Data, and the Industrial Internet of Things (IIoT)
How digital twins are reshaping the oil and gas industry, from enhancing safety and efficiency to accelerating growth and innovation
the Oil and Gas Sector’s Cyber Preparedness
As cyberattacks escalate in frequency and sophistication, Siemens Energy underscores the urgent need for enhanced cybersecurity measures in the oil and gas industry
Wellbore Integrity with Intelligent Deployment and Advanced Well Architecture
Conventional multi-zone completions in the world of offshore oil and gas often use a technique of cementing the wellbore space between the casing and the formation, and then perforating the cement to initiate production
With increasing adoption of digital twins across the industry, the quality and ongoing maintenance of data is coming under the spotlight.
the Industrial Sector Use Digital and AI as a Competitive Advantage?
In the rapidly evolving landscape of AI integration the transformative power of human-centered AI, emphasizing trust, collaboration, and maximizing opportunities to propel industries towards a sustainable and efficient future
Final Word: Harnessing Digitalization and Data Optimization in Upstream Oil and Gas
How remote telemetry solutions could help oil and gas operators greatly improve their sustainability measures
In the upstream oil and gas sector, the integration of digitalization and data optimization is revolutionizing operations, driving efficiency, safety, and sustainability to unprecedented heights.
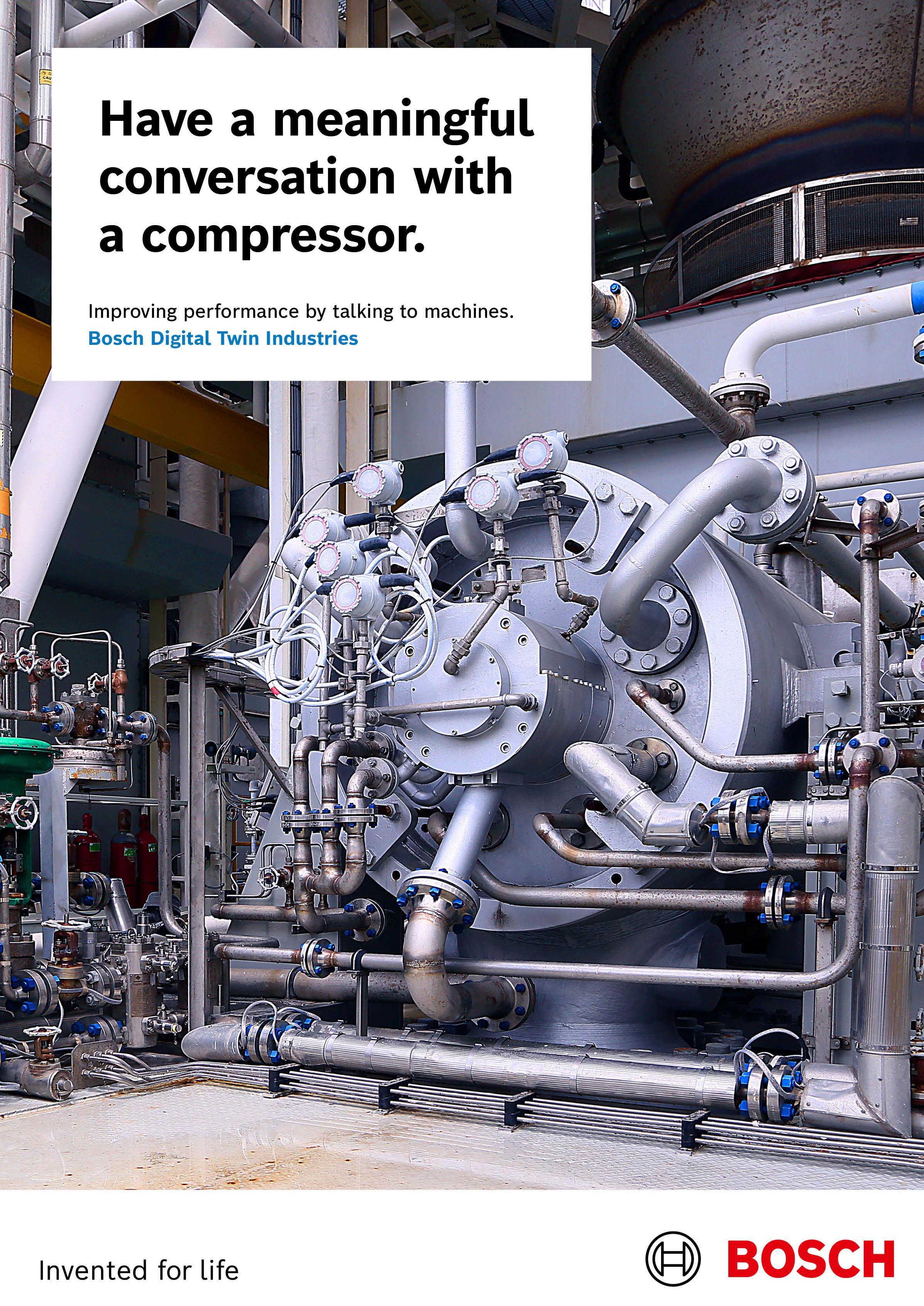
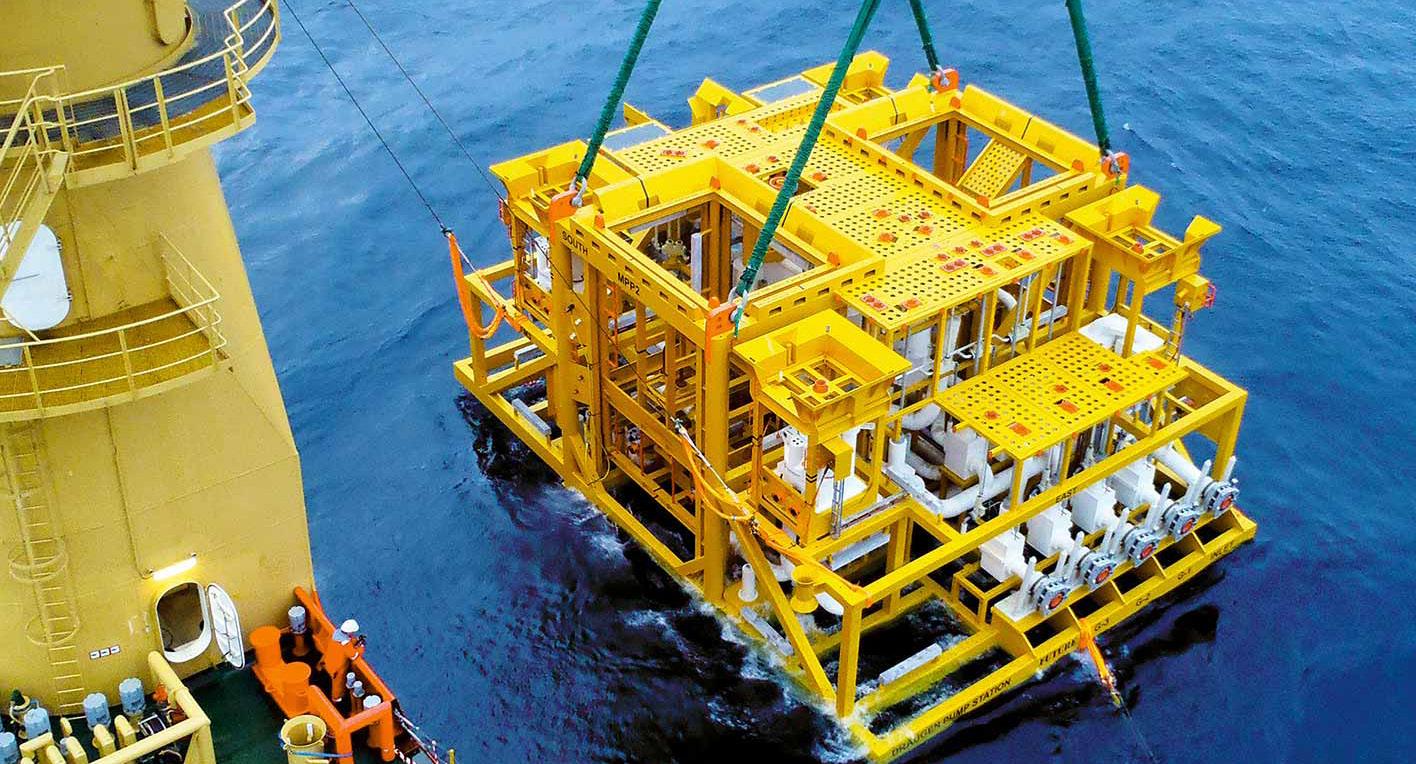
SLB OneSubsea and Subsea7 Sign LongTerm Strategic Collaboration Agreement with Equinor
SLB has announced the signing of a new long-term strategic collaboration agreement between Equinor ASA and the Subsea Integration Alliance (which comprises OneSubsea and Subsea7). The agreement paves the way for exploratory work to begin on two projects: the Wisting field offshore Norway and Bay Du Nord, off Newfoundland and Labrador, Canada. The agreement represents an innovative, integrated way of working. It enables early information sharing, technology innovation and other collaborative benefits critical to unlocking more subsea projects by making them economically viable. Building on their experience as members of the Subsea Integration Alliance, this agreement also further cements OneSubsea and Subsea7’s positions as trusted contractors to Equinor. “Equinor is working hard to improve
and mature the Wisting and Bay du Nord projects,” Trond Bokn, senior vice president for Project development in Equinor, said. “Selecting the supplier at this early stage, is a new way of approaching project development for us, and a vote of confidence to Subsea Integration Alliance. We look forward to developing concepts together, in a process with full visibility on profitability, and joint efforts to make these challenging projects sanctionable.”
“Equinor has long been a crucial customer to our business and to the Alliance. We couldn’t be more proud to be embarking on this collaboration,” Mads Hjelmeland, CEO of OneSubsea, said. “Today’s agreement underlines the trusted relationship that we have built over many years and enables us to take our collaboration further by sharing and aligning on goals and values, improving performance and learnings across projects, and unlocking new opportunities to enhance safety, risk management and sustainability results.”
John Evans, CEO of Subsea7 added: “Subsea7 has been collaborating with Equinor for many years to optimize challenging subsea developments ranging from bundle solutions for the Snorre Expansion to the integrated Bacalhau development in Brazil. We look forward to extending and deepening this relationship as we work together to unlock the value in Wisting and Bay du Nord.”
The agreement paves the way for collaboration to begin immediately on early, joint concept studies for two major projects. Under the same agreement, any resulting EPCI execution would be directly awarded to the alliance, if a final investment decision (FID) is made.
Wisting is located in the Barents Sea, offshore Norway. Bay Du Nord is approximately 500 km northeast of St John’s, Newfoundland and Labrador, Canada. Bringing together the expertise, experience and capabilities of Equinor, OneSubsea and Subsea7 has enabled further exploratory work across both projects, with the potential for additional opportunities to be unlocked in the short- to medium-term.
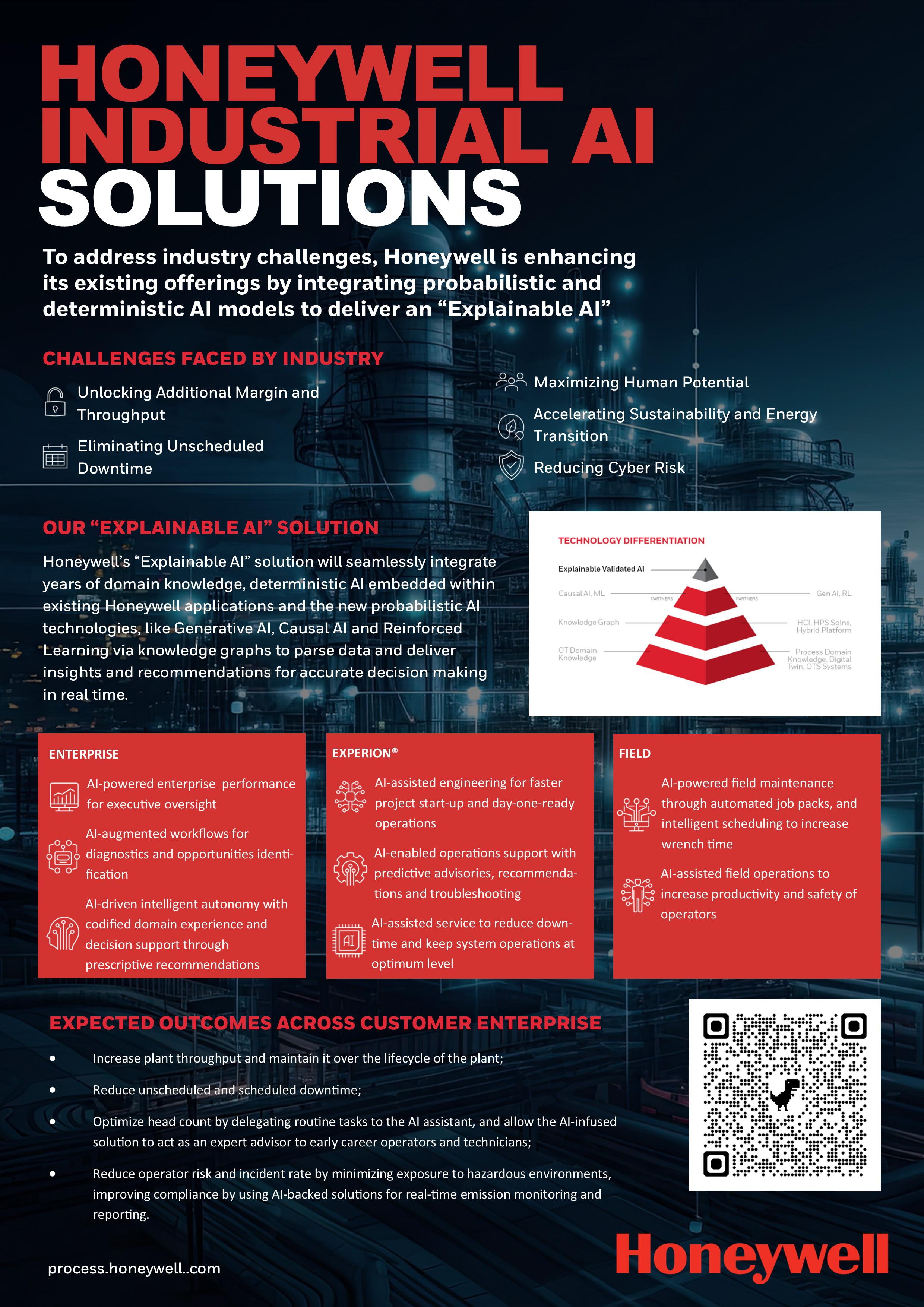
bp begins oil production from major new platform offshore Azerbaijan
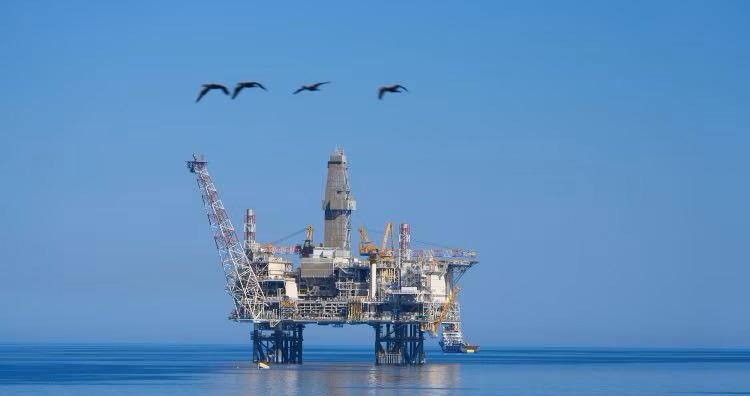
bp, as operator of the AzeriChirag-Gunashli (ACG) project, has announced the start-up of oil production from the new Azeri Central East (ACE) platform as part of the ACG field development in the Azerbaijan sector of the Caspian Sea. bp’s strategy is to invest in the energy system of today – such as in the development of ACE – as well as the energy system of the future.
The ACE platform is the seventh oil producing platform installed on the giant ACG field in the Caspian Sea. ACG first began production in 1997 and has since produced over 4.3 billion barrels of oil. The bp-operated Shah Deniz gas field has two further platforms in the Caspian.
The ACE platform and related facilities are designed to process up to 100,000 barrels of oil per day
(bpd) and the project is expected to produce up to 300 million barrels over its lifetime. Oil will pass through the processing facilities on the platform and then be exported around 130 kilometres to the onshore Sangachal terminal via a new in-field pipeline linked to an existing 30-inch subsea export line.
Initial production from ACE comes from the first well that was initiated from the platform at the end of last year. ACE production is expected to increase through 2024 to around 24,000bpd as two more planned wells are drilled, completed, and brought online.
Ewan Drummond, bp’s senior vice president, projects, said: “I’m incredibly proud of the team at bp for safely delivering the first bp-operated offshore platform fully controlled from onshore. This establishes a new benchmark for innovative engineering and competitive project delivery for our company and the wider industry.”
The ACE platform is technologically and digitally the most advanced bp-operated platform in the world. Its innovative engineering allows automation of labour-intensive processes, enabling safer and more efficient operations. The platform has a state-of-the-art fully automated drilling rig. The use of modern technology and new processes also helps lower operational emissions.
Gary Jones, bp’s regional president for Azerbaijan, Georgia and Turkiye, said: “This successful start-up is testament to the ongoing close collaboration between bp, SOCAR and the Government of Azerbaijan, together with the support of our partners. First oil from ACE – in the year of the thirtieth anniversary of the agreement to develop ACG – marks the beginning of this world-class field’s next development phase.”
“This is the ninth world-class production platform that we have built, installed, and are operating offshore Azerbaijan. ACE really stands out with its engineering creativity, advanced digital technology, and automation. We are proud to have delivered what we believe is the ‘platform of the future’.”
The safe start-up of ACE delivers on the first major investment decision made by the ACG partnership since the signing of the extended ACG production sharing agreement in 2017.

ExxonMobil Guyana moves forward with sixth offshore development
ExxonMobil has made a final investment decision for the Whiptail development offshore Guyana, after receiving the required government and regulatory approvals. Whiptail, the sixth project on the Stabroek block, is expected to add approximately 250,000 barrels of daily capacity by the end of 2027.
“Our sixth multi-billion-dollar project in Guyana will bring the country’s production capacity to approximately 1.3 million barrels per day,” said Liam Mallon, president of ExxonMobil Upstream Company. “Our unrivaled success in developing the Guyana resource at industry-leading pace, cost and environmental performance is built on close collaboration with the government of Guyana, as well as our partners, suppliers, and contractors. The Stabroek block developments are among the lowest emissions intensity assets in ExxonMobil’s upstream portfolio and will provide the world with additional reliable energy supplies now and for years to come.”
The $12.7 billion Whiptail project will include up to 10 drill centers with 48 production and injection wells. “We are committed to helping spread the benefits throughout the country by investing in local Guyanese communities and projects to support the
country’s phased and sustainable development,” Mallon said.
Production from the six Stabroek block developments will generate tens of billions of dollars of revenue and significant economic development for Guyana. Since first production in 2019, more than $4.2 billion has been paid into the Guyana Natural Resource Fund. There are currently 6,200 Guyanese working in support of Stabroek block operations—which is 70% of the workforce. The cumulative spend of ExxonMobil Guyana and its contractors with Guyanese suppliers since 2015 surpassed $1.5 billion at the end of 2023.
The Floating Production Storage and Offloading (FPSO) vessel for the Whiptail project, to be named Jaguar, is under construction. Three FPSOs – the Liza Destiny, Liza Unity and Prosperity – are currently operating offshore Guyana and are safely producing more than 600,000 barrels of oil per day. Construction is underway on FPSOs for the Yellowtail and Uaru projects, with Yellowtail anticipated to start production in 2025 and Uaru targeted in 2026.
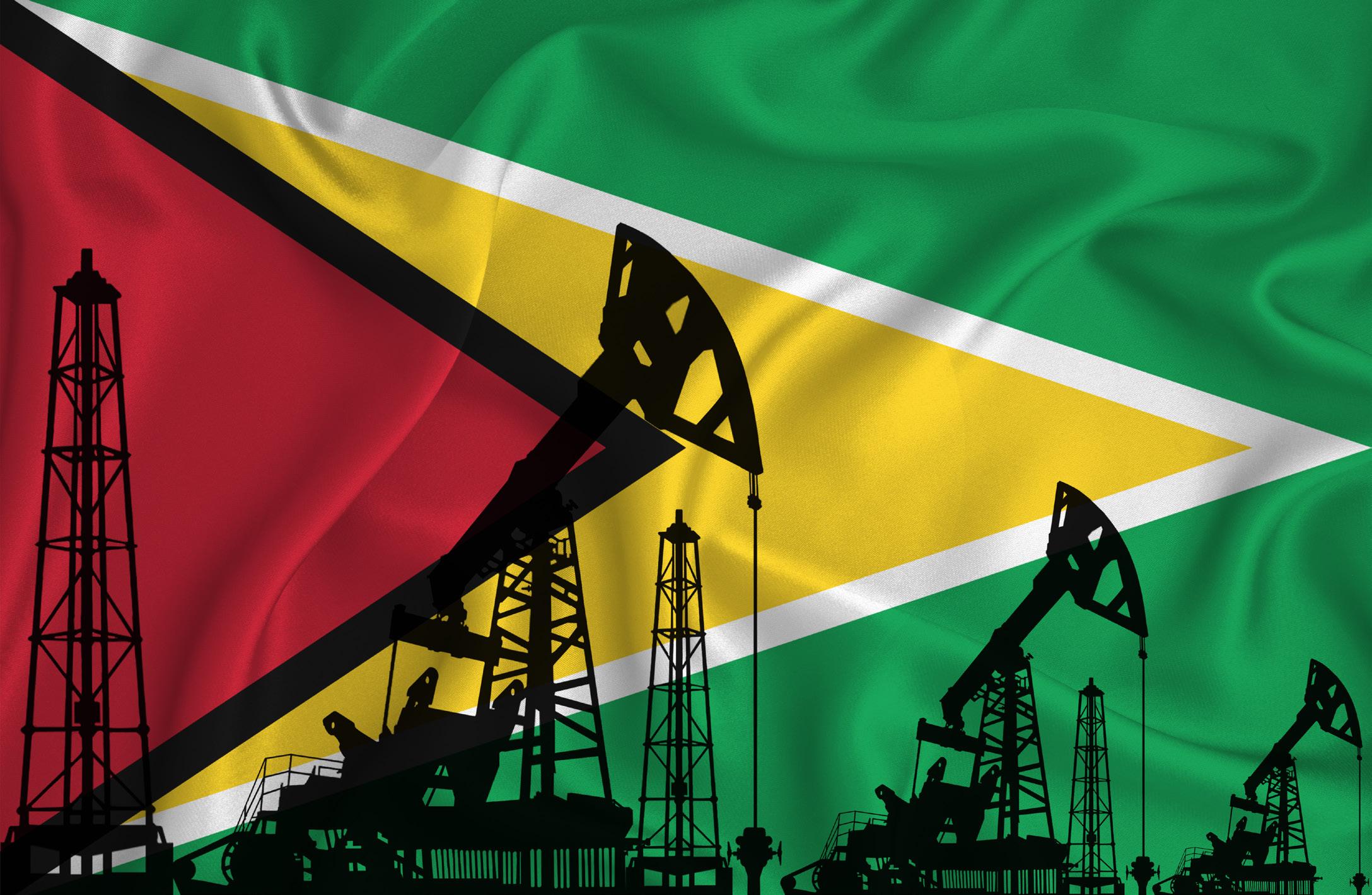
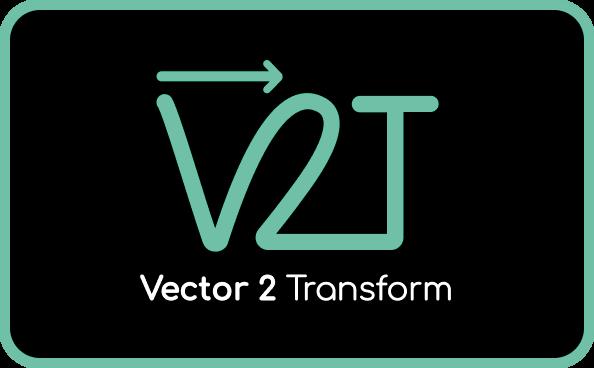
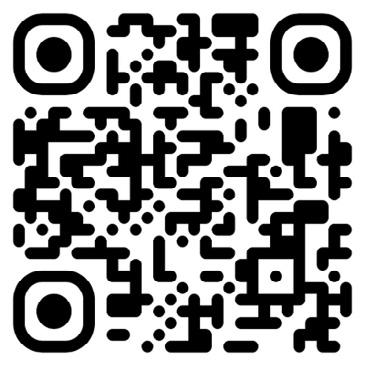
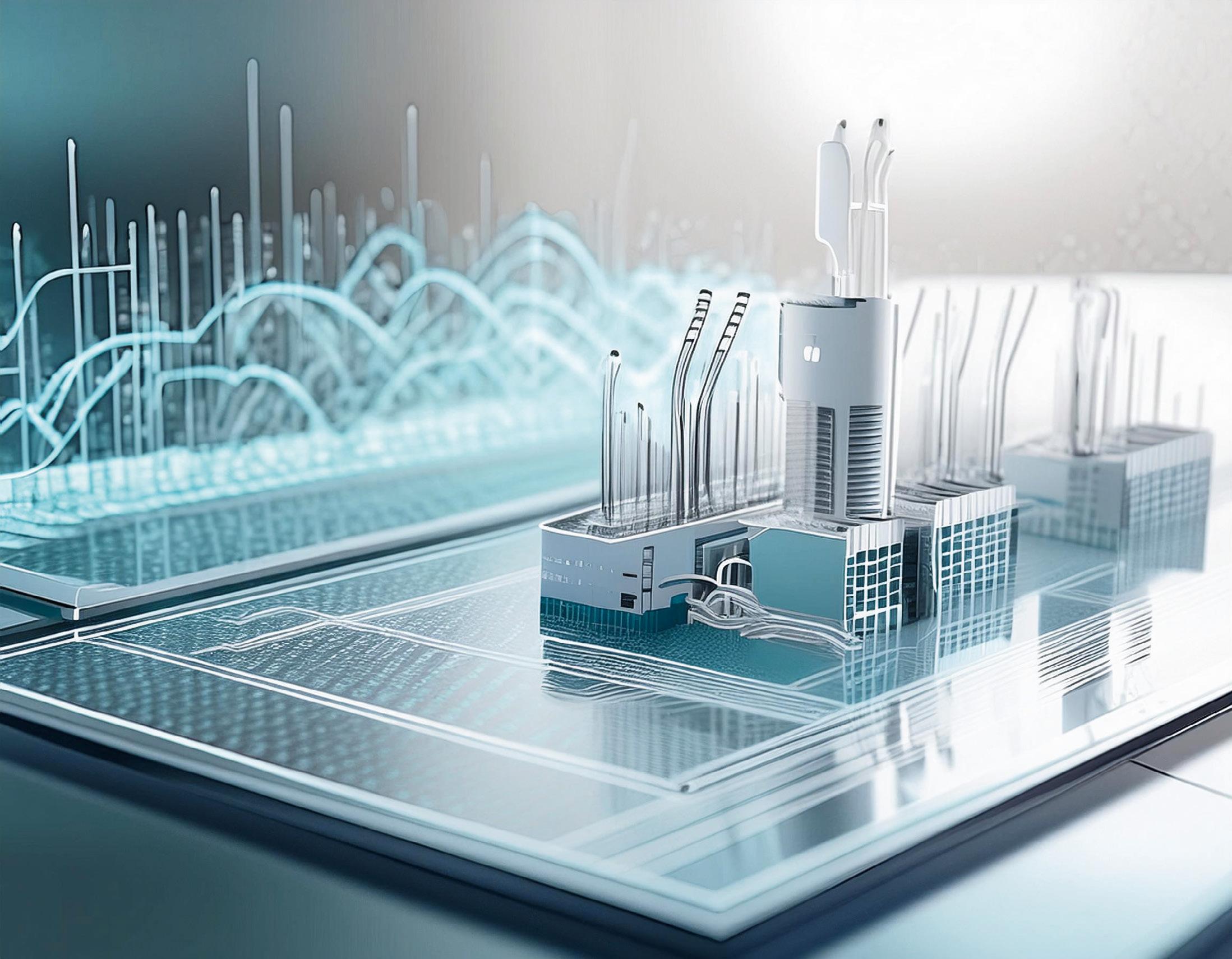
Rhino Resources and Halliburton to sign contract for integrated deep-water services offshore Namibia
Halliburton has announced it has been awarded a deep water integrated multi-well construction contract by Rhino Resources, a private company engaged in both onshore and offshore energy exploration in Africa.
This collaboration between Halliburton and Rhino Resources marks a strategic milestone to harness the full potential of Namibia’s oil and gas sector. Halliburton, with its collaborative approach and solutions engineering, is uniquely positioned to maximize asset value in this block with Rhino Resources. Together, we will establish a standard for innovation and economic growth in the industry.
“Under this agreement, Halliburton will provide complete solutions to construct exploration and appraisal wells, along with testing services,” Jean Marc Lopez, senior vice president, Europe, Eurasia, and Sub-Saharan Africa at Halliburton, said. “Halliburton will also extend its country operation facilities to support all product service lines from Namibia to enhance collaboration and maximize asset value for Rhino Resources and Namibian customers.”
With more than a decade of exploration in Namibia, Rhino Resources holds operatorship of Block 2914A (PEL 85). This block, located in the shallower portion of the Orange Basin, boasts significant potential. It is strategically located less than 20km from the nearest discovery and amidst multiple Namibian discoveries made over the last two years. The block’s proximity to other international operators further
underscores its strategic relevance.
In late 2022, Rhino conducted a 3D seismic survey that reinforced the block’s potential with multiple viable plays and drillable prospects. In addition, Halliburton and Rhino Resources will uphold the emphasis on localization in Namibia’s oil and gas sector, with the aim to distribute the economic advantages of Namibia’s resources to the local community.
“Rhino is pleased to have established a collaboration with Halliburton and views this as an important driver in the continued growth of the Namibian oil and gas industry,” said Travis Smithard, chief executive officer at Rhino Resources Ltd. “The opportunity for catalysing local services and the broadening of positive economic influence in Namibia are expected to establish a valuable legacy for the Namibian people well beyond our initial exploration campaign.”
As Halliburton and Rhino Resources approach operational commencement in the fourth quarter of 2024, the agreement underscores the importance of integration of global expertise with local resources to foster economic resilience and progress in Namibia’s growing energy sector.

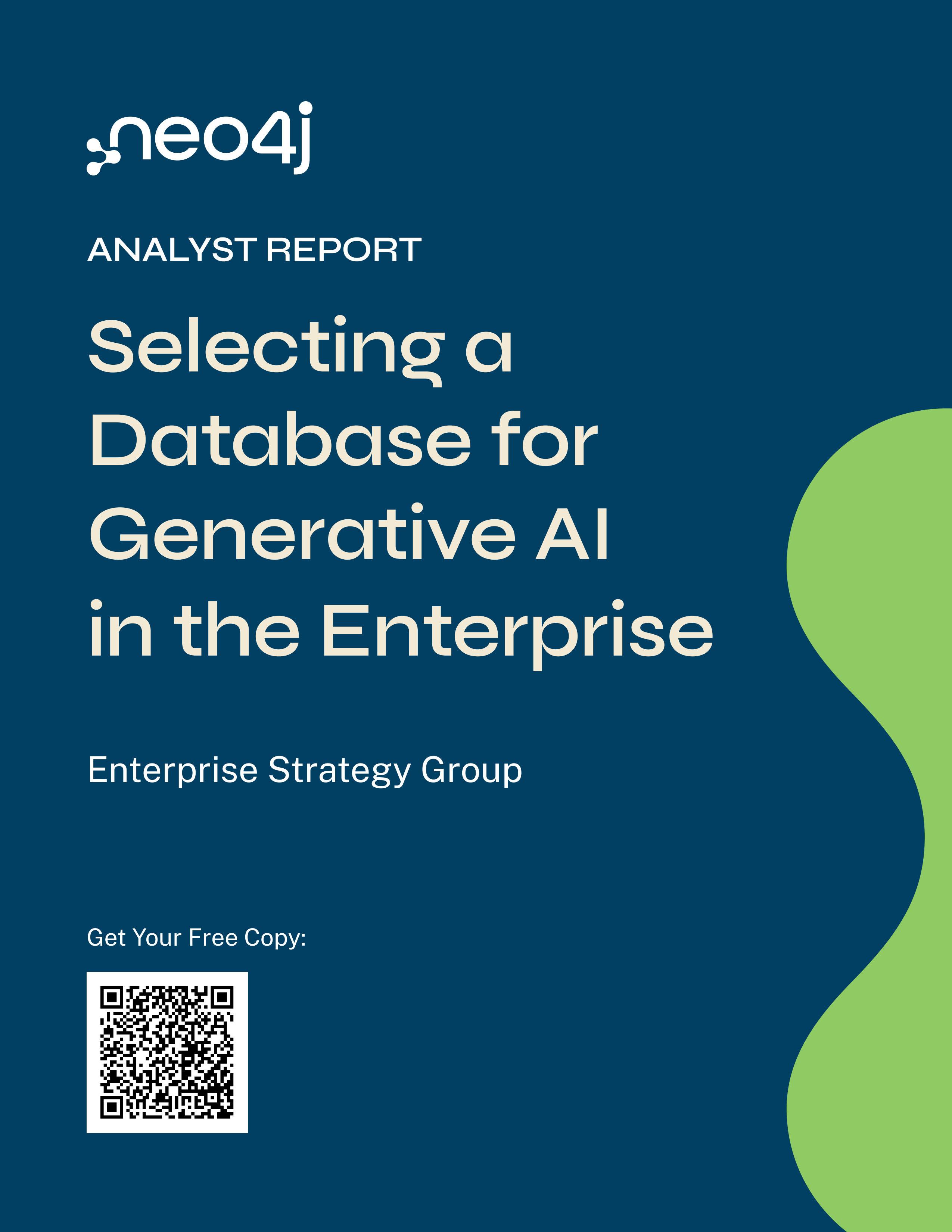
Kongsberg Digital awarded contract with Equinor to rebuild its Life Cycle Simulators for the Sleipner Field
Kongsberg Digital has secured a significant contract with Norwegian energy company Equinor. The agreement entails rebuilding the Sleipner Life Cycle Simulators using Kongsberg Digital’s K-Spice and LedaFlow simulation technologies. The estimated worth of the agreement exceeds 25 million NOK. Kongsberg Digital is proud to collaborate with Equinor on this significant project, which will significantly increase the simulation capabilities of the Sleipner area in the North Sea. By leveraging the latest simulator technologies from Kongsberg Digital, Equinor aims to enhance operational efficiency, improve training programs, and ensure the highest level of fidelity in simulator-based engineering.
To provide the multidisciplinary operation and engineering teams with a complete Life Cycle Simulator engineering and training tool environment, three simulators will be developed using K-Spice and LedaFlow simulation technologies. The silulators are an Engineering Study Simulator (ESS), an Engineering Test Simulator (ETS), and an Operator Training Simulator (OTS).
The simulators will model the processes of all wells, pipelines, and offshore production facilities for three different assets of the Sleipner installations. These assets include the Processing, Drilling, and Living quarter platform (A), the Unmanned Production platform (B), and the Processing and CO2 removal platform (T). Additionally, the project will involve modelling the power grid using K-Spice Power.
The Sleipner Life Cycle Simulator project is scheduled to commence in the first quarter of 2024, with an estimated completion by the end of 2025. This two-year project will develop a dynamic simulator model incorporating topside process simulation models using K-Spice and multiphase flow models of production wells and flowlines using LedaFlow software.
“We are honoured to be collaborating with Equinor on the Sleipner Life Cycle Simulator project. Our commitment to this project underscores our dedication to providing comprehensive, trustworthy, and reliable 1st principle Digital solutions to the energy sector. We are confident that the Sleipner asset will greatly benefit from the enhanced operational efficiency, troubleshooting analysis and training opportunities our technologies offer.”, says Shane McArdle, Chief Executive Officer of Kongsberg Digital
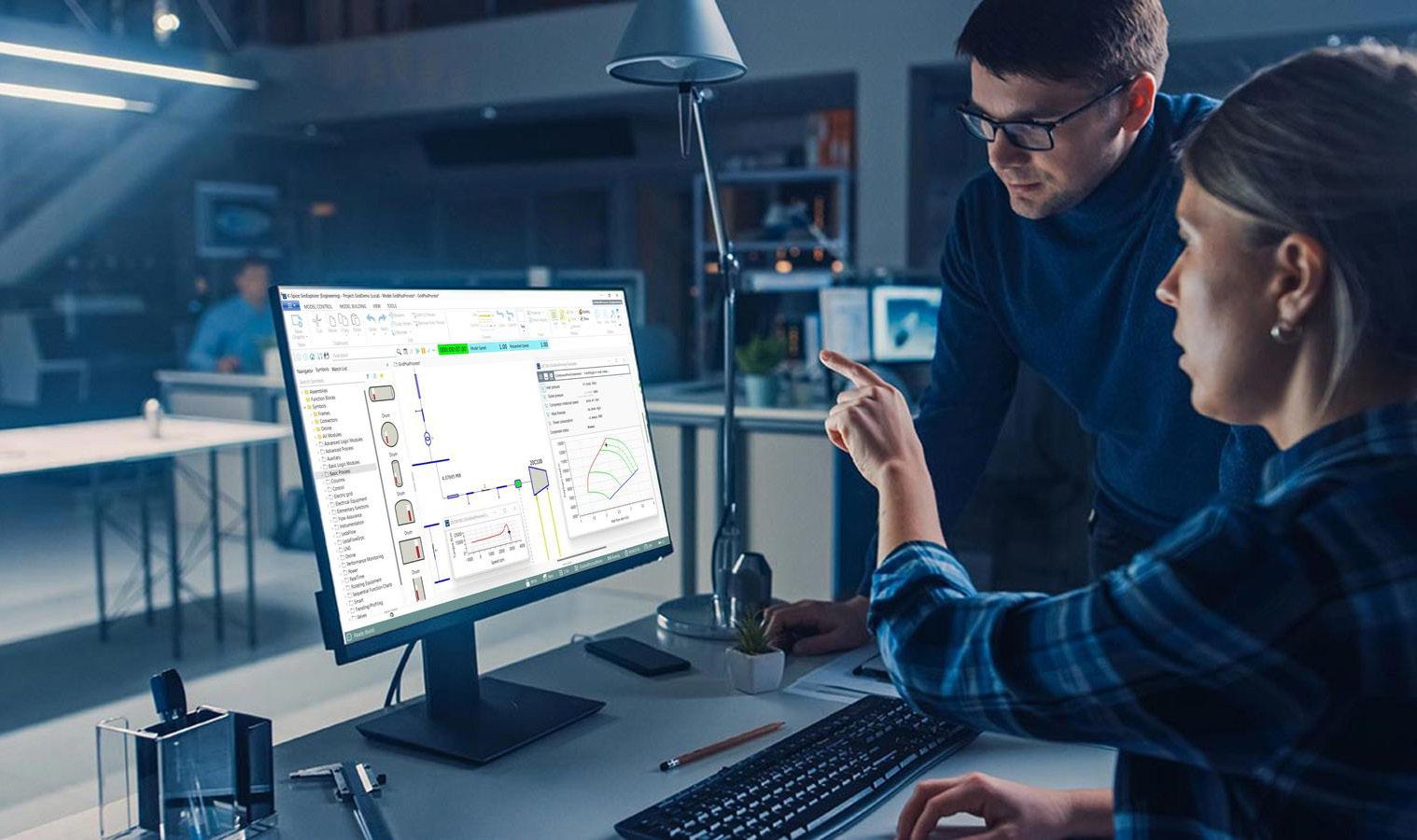
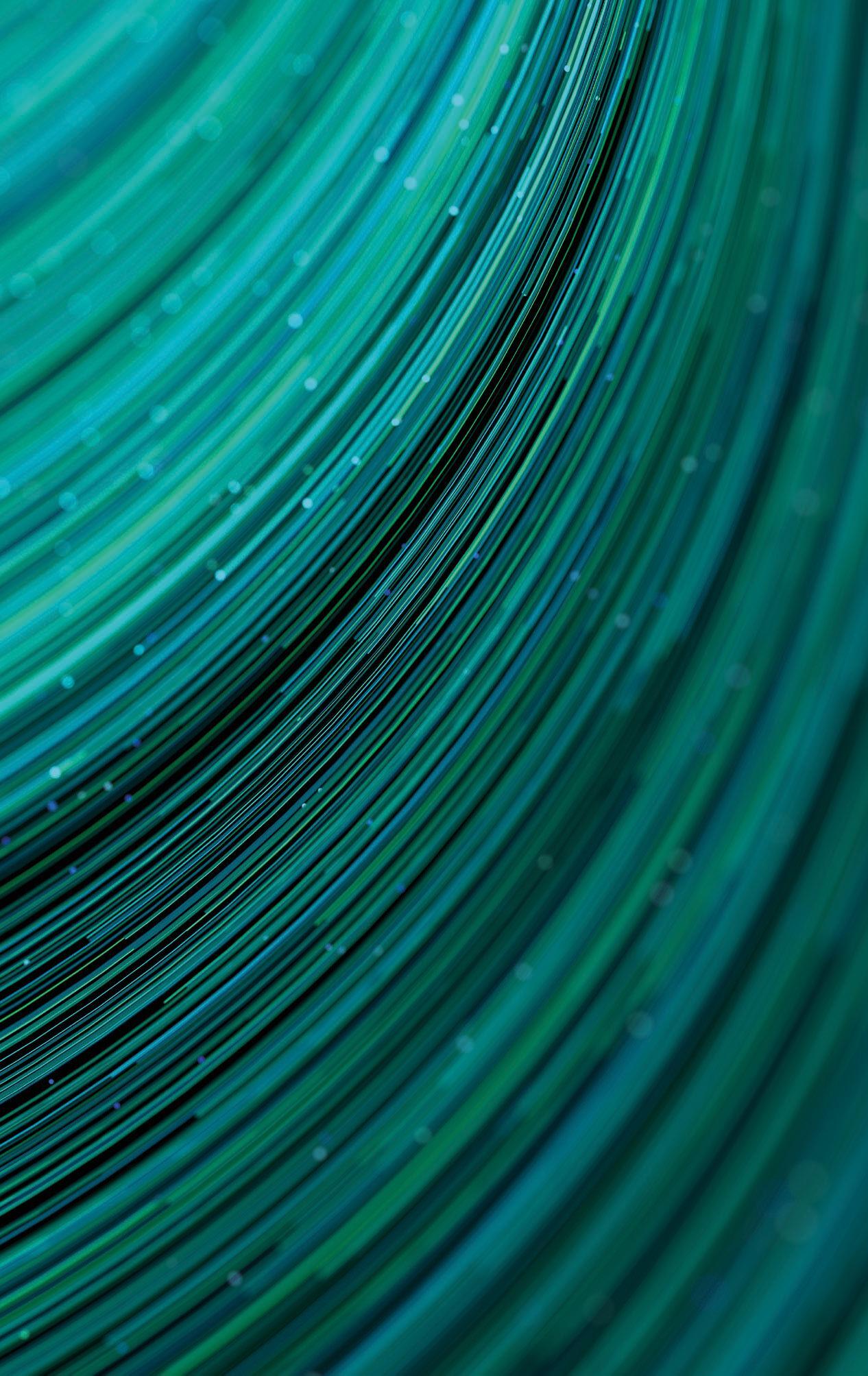
At Wood, we are designing the future by decoding digital to transform industry.
As a trusted advisor and partner, we empower our clients by designing digital strategies and integrating solutions that drive advancements across the asset lifecycle.
woodplc.com/solutions/digitalisation
Saudi Aramco’s AI innovation dominance places company ahead of the curve
The oil and gas industry is confronted with an array of disruptive challenges, which stem from rising energy demands, frequent threats to the supply chain, geopolitical tensions, and the transition to alternative and sustainable fuel sources. In response to these pressures, there is a compelling need to fervently embrace innovation.
Leading this charge is Saudi Aramco, the world’s largest oil production company. Aramco is spearheading the innovations by embracing cutting-edge technologies like artificial intelligence (AI), both within its core operations and beyond, which places the company ahead of the curve.
This strategic approach has been unveiled by Technology Foresights, an innovation intelligence platform by GlobalData, a leading data and analytics company.
The Saudi state-owned oil company has significantly invested in research and development (R&D) compared to its industry peers, allocating approximately $3.5 billion in 2023, representing a 15% annual increase despite global challenges. This investment is reflected in its innovative efforts, which extend beyond its primary operations.
GlobalData’s Technology Foresights identifies over 250 areas of innovation involving Aramco, spanning technologies poised to disrupt the oil and gas sector, such as AI, drones, robotics, electric vehicles (EVs), and hydrogen technology. Additionally, Aramco has internally developed cybersecurity capabilities to safeguard against cyber threats encountered in recent years.
“Technology Foresights throws light on Aramco’s AI innovation strategy.” Sourabh Nyalkalkar, Practice Head of Innovation Products at GlobalData, said.
“The innovation leadership map reveals how the company is employing AI in its core operations and selectively prioritizing the adoption of AI innovations in specific areas of its business. For instance, utilizing AI for oil exploration and underwater operations is a significant strategic focus where the company clearly holds a strong leadership position.
“A recently published patent application clearly demonstrates this usage, describing the deployment of drones in sub-surface terrain to capture images. These images are then analyzed using machine learning (ML) algorithms to detect oil spills and pollutants. Another application showcases the use of AI/ML for automating seismic data processing and providing real-time updates for sub-surface reservoir models.”
Aramco is expanding its innovation initiatives beyond patents. In late 2023, the company launched a digital innovation ecosystem named Saudi Accelerated Innovation Laboratory (SAIL). Its goal is to engage with a broader ecosystem, including government organizations and startups, to foster the development of digital innovation products. In March 2024, the company introduced its own LLM through SAIL. Known as Aramco METABRAIN, the generative AI model is trained on data accumulated by the company over the past 90 years.
“Aramco is also betting on futuristic technologies,” Nyalkalkar added. “The company is closely monitoring the startup ecosystem and has in the recent past invested in several companies such as Pragmatic, which develops flexible semiconductor chips, and Sunrate, a fintech company.
“From the perspective of industry watchers and stakeholders, Saudi Aramco’s initiatives in adopting cutting-edge technologies, particularly AI, provide valuable insights into strategic navigation within a disruptive environment. For startups and other vendors developing industry-specific solutions, the insights gained from the in-depth innovation analysis of Aramco and its peers can assist in prioritizing areas that can enhance the value proposition.
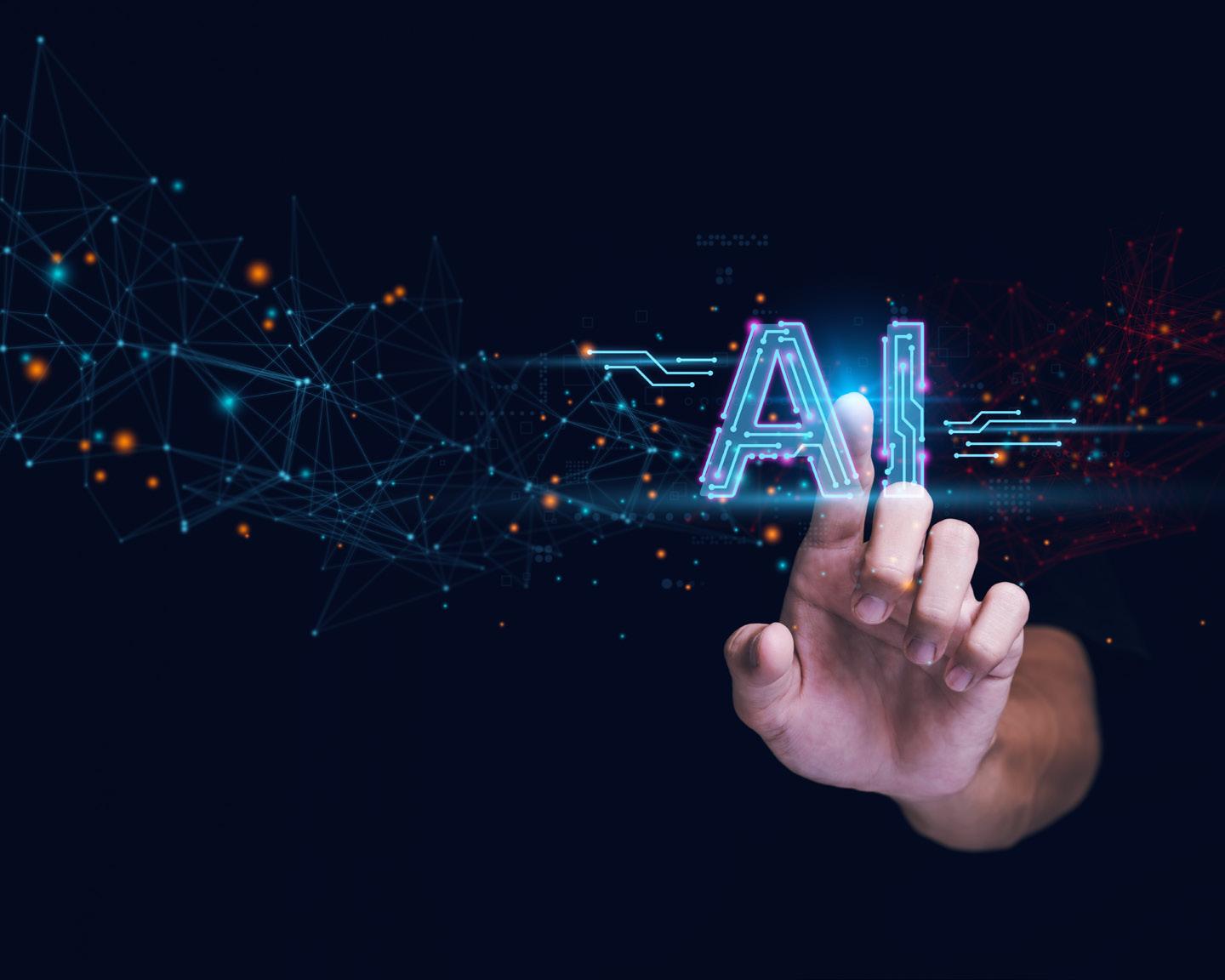
Future Conference
In collaboration with Shell

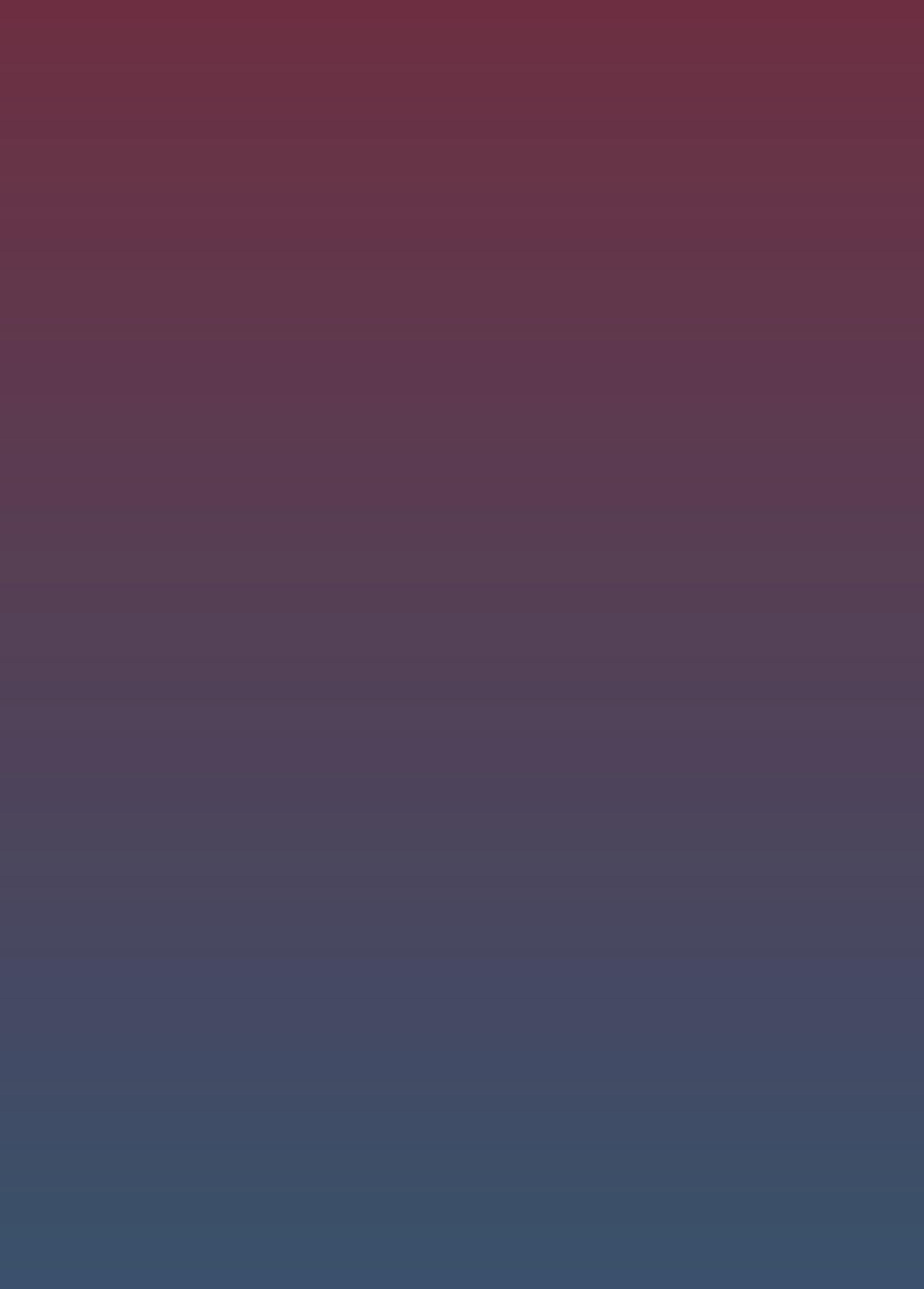
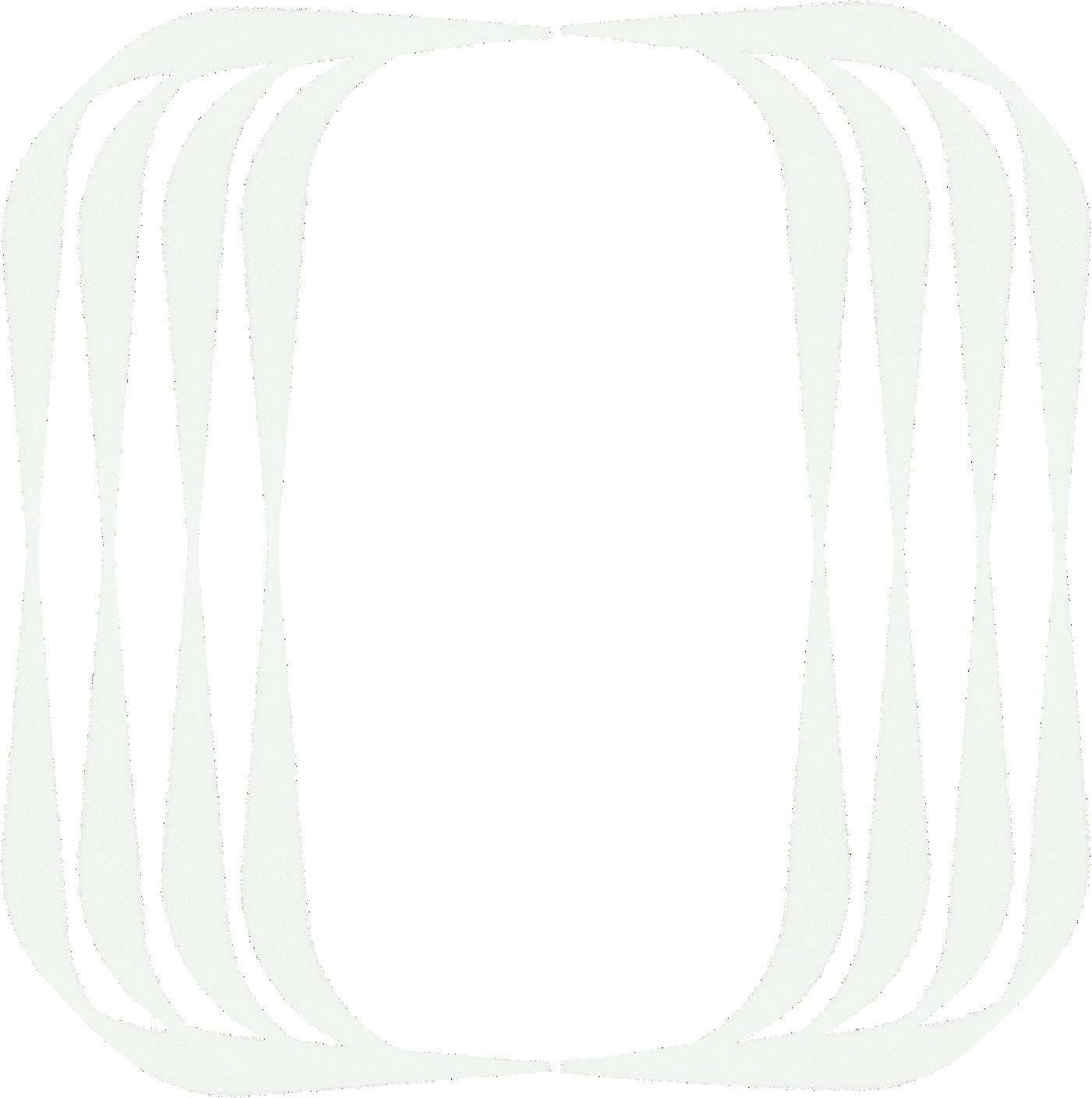
Exploring Open Collaboration, Innovation & Energy Transition
AMSTERDAM | ENERGY TRANSITION CAMPUS
7-8TH OCTOBER, 2024
The Role of Digital Oilfields in Improving Efficiency and Safety
Discover how the convergence of cloud computing and big data analytics is revolutionising oil and gas operations, ushering in a new era of real-time monitoring, predictive maintenance, and collaborative decision-making
The advent of digitalization has spurred a transformative shift in the oil and gas (O&G) industry, transcending mere incremental advancements to pave the way for the emergence of the ‘digital oilfield’. Leveraging cutting-edge technologies such as cloud computing and big data analytics, the digital oilfield revolutionizes traditional operational paradigms by enabling the real-time monitoring, analysis, and utilization of all pertinent operational data. This heralds a new era characterized by enhanced safety, sustainability, and efficiency in O&G operations.
The Genesis of the Digital Oilfield Historically, O&G operations were largely reliant on manual processes and disparate data sources, leading to inefficiencies, delays, and increased risk exposure. Recognising the need for innovation, industry pioneers began exploring the integration of digital technologies to optimise operations. The digital oilfield
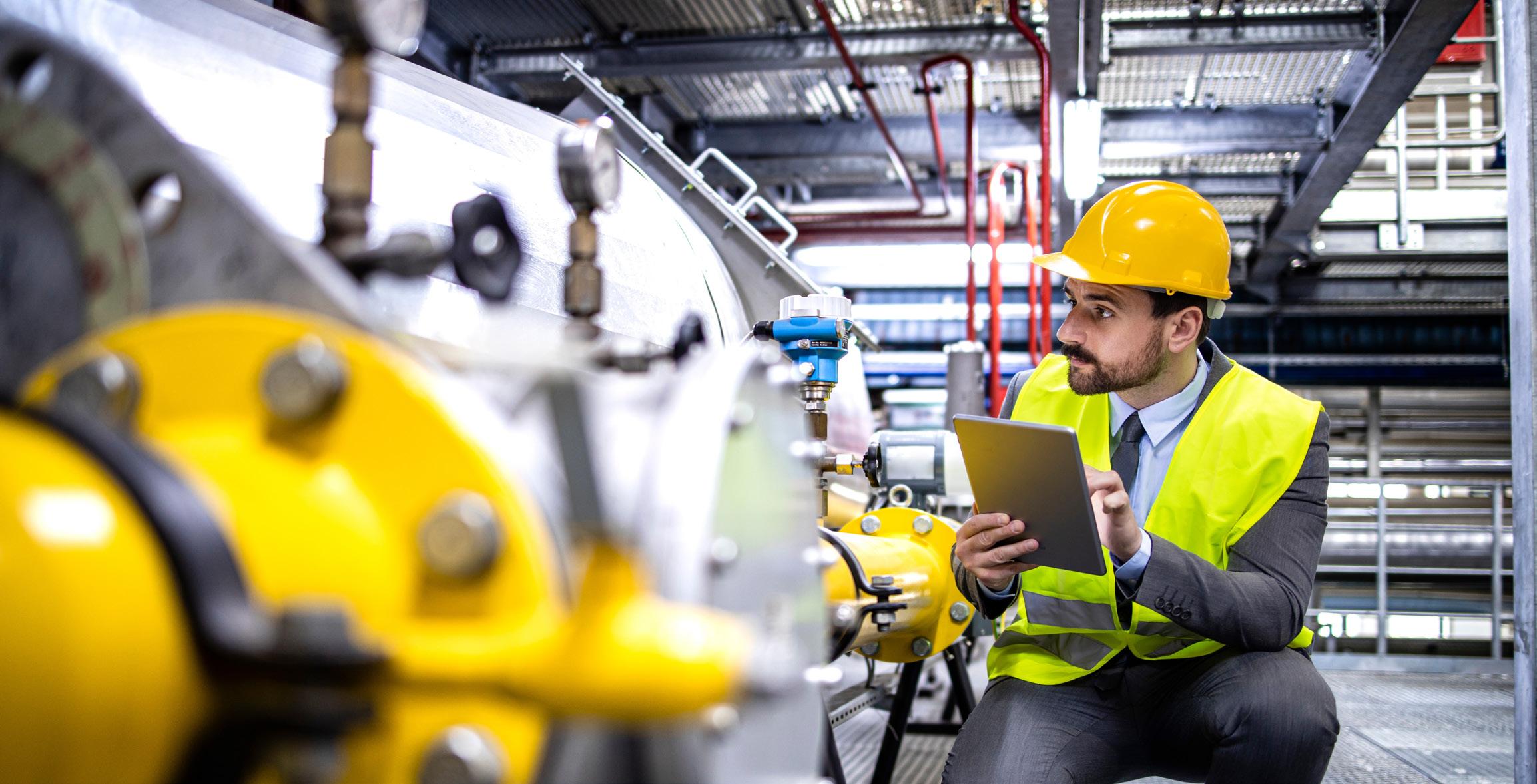
concept emerged as a holistic solution, aiming to harness the power of data-driven insights to streamline workflows, enhance decision-making, and drive operational excellence.
Core Technologies Driving Digital Transformation
At the heart of the digital oilfield lie advanced technologies that empower real-time data acquisition, processing, and visualisation. Cloud computing infrastructure serves as the backbone, providing scalable, on-demand access to computing resources for data storage, processing, and analysis. Big data analytics tools leverage machine learning algorithms and predictive modelling techniques to extract actionable insights from vast volumes of operational data, enabling proactive decision-making and trend forecasting.
Real-Time Data Integration and Visualization
A cornerstone of the digital oilfield is the seamless integration of diverse data sources, including sensor data, production metrics, geological surveys, and equipment telemetry. Through interconnected IoT devices and sensor networks, realtime data streams are aggregated and transmitted to centralized cloud-based platforms for processing. Advanced visualization tools transform raw data into intuitive dashboards and interactive reports, empowering stakeholders to gain comprehensive insights into operational performance and identify optimisation opportunities.
Enhancing Safety and Sustainability
The digital oilfield’s real-time monitoring capabilities play a pivotal role in enhancing safety and sustainability across O&G operations. By continuously monitoring environmental conditions, equipment performance, and personnel activities, operators can proactively identify potential hazards and mitigate risks before
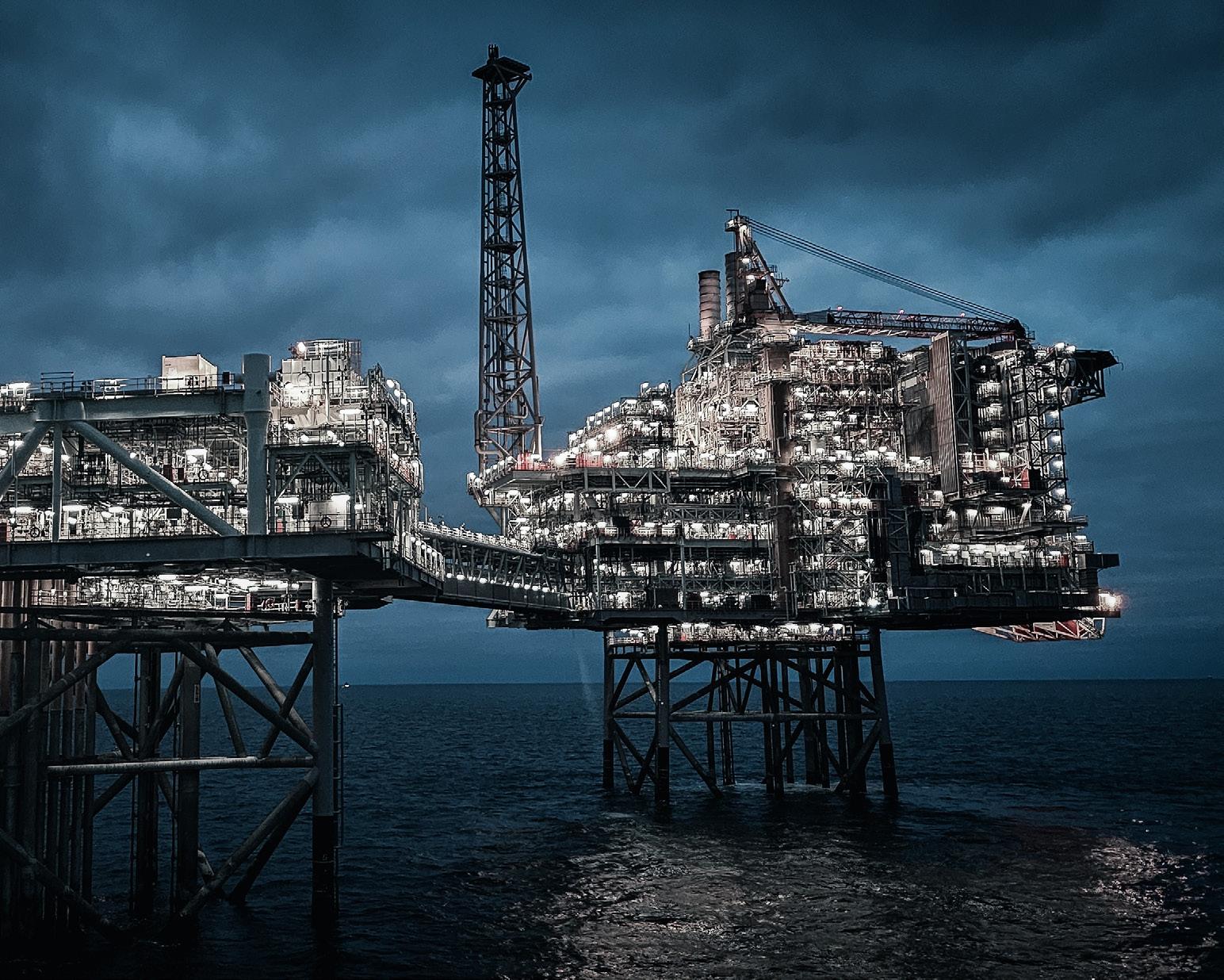
they escalate. Furthermore, predictive analytics models enable the early detection of equipment failures and operational anomalies, minimizing downtime and preventing costly accidents.
Optimizing Production and Asset Management
One of the primary objectives of the digital oilfield is to optimise production efficiency and asset management. Through predictive maintenance algorithms, operators can anticipate equipment failures and schedule proactive maintenance interventions, maximizing uptime and extending asset lifespan. Additionally, advanced reservoir modelling and simulation tools enable precise reservoir characterization and production forecasting, facilitating informed decision-making regarding drilling, well placement, and reservoir management strategies.
Driving Operational Excellence Through Collaboration
The digital oilfield fosters a culture of collaboration and knowledge sharing among diverse stakeholders, including engineers, geoscientists, and field personnel. By providing centralised access to real-time data and collaborative workspaces, the digital oilfield enables cross-functional teams to collaborate seamlessly, share insights, and cocreate innovative solutions to complex operational challenges. This collaborative approach accelerates decisionmaking processes, drives continuous improvement, and fosters a culture of innovation within the organization.
The Path Forward: Embracing Digital Transformation
As the O&G industry continues to embrace digital transformation, the digital oilfield represents a paradigm shift in operational practices, empowering organisations to adapt and thrive in an increasingly complex and dynamic environment. By harnessing the power of cloud technologies, big data analytics, and real-time data integration, operators can unlock new opportunities for efficiency gains, cost savings, and sustainable growth. The journey towards a fully digitalized oilfield is ongoing, but the potential benefits are undeniable, heralding a future characterized by safer, smarter, and more sustainable O&G operations.
Unlocking Synergies: Digital Twins and Generative AI
Amidst a wave of innovation, the fusion of digital twins and generative AI emerges as a game-changer for asset owners in the oil and gas industry, enabling smarter decisions, optimized processes, and a transformative journey toward efficiency, sustainability, and resilience
As a researcher focused the last five years on better understanding the value of digital twins throughout the lifecycle of complex facilities, I have been amazed by the countless recent innovations being put to the work of mitigating significant challenges for asset owners, particularly in the operational context.
For example, Enhanced Predictive Maintenance involves integrating digital twin technology with predictive artificial intelligence (PAI) models. This enables operators to monitor equipment health in real time. By integrating sensor data, historical performance, and environmental conditions,
digital twin human-machine interfaces can be programed to predict maintenance needs based on actual usage rather than solely relying upon the equipment manufacturers’ proposed maintenance schedule.
At an enterprise level, sharing of these large data sets, Generative Artificial Intelligence (Gen AI) algorithms can analyze vast amounts of data to identify patterns and anomalies. It predicts equipment failures, recommends maintenance schedules, and optimizes resource allocation at scale; helping operators reduce downtime, extend asset lifespan, and prevent catastrophic failures.
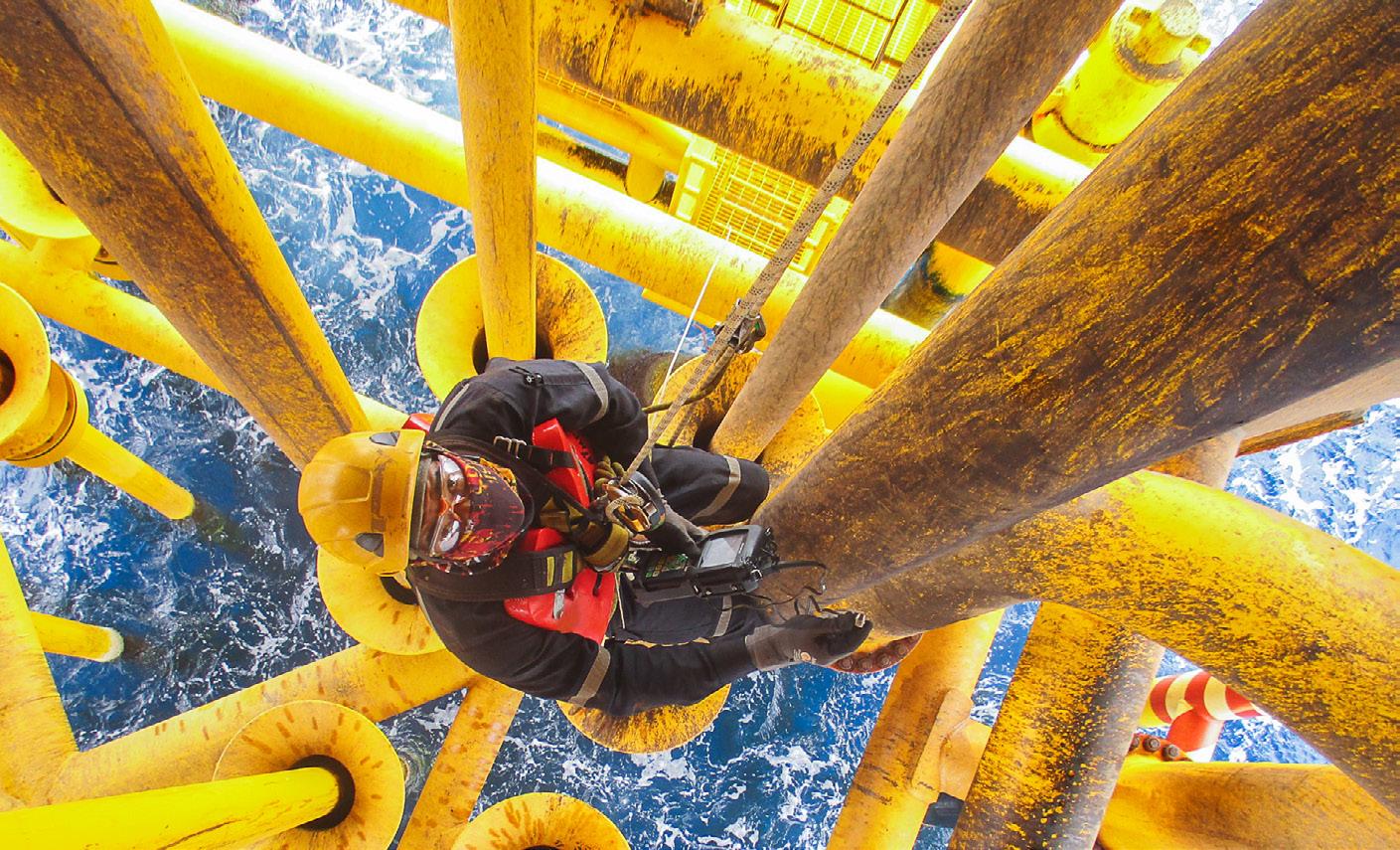
Optimized Production Scheduling
By incorporating virtual ‘guardrails’ into production operations decision criteria, the PAI can warn the operator of potential unintended consequences of operational settings by estimating the outcomes across multiple configuration scenarios leveraging latent insights from prior operational activities. Digital twins have been used to simulate production processes, considering variables like reservoir pressure, well flow rates, and equipment availability. Gen AI allows operators to optimize production schedules dynamically. Gen AI algorithms can suggest adjustments to schedules based on real-time data, market demand, and supply chain constraints. This evolving technology, released within the past 18 months, is a major turning point in terms of value realization. The value proposition includes increased production efficiency, reduced waste, and better alignment with market demand.
Resilient Supply Chain Management
Considering the many vulnerabilities exposed by the recent COVID-19 pandemic, another tangible benefit of Digital Twins is how they can model an entire supply chain, from raw material extraction to final product delivery. Operators gain visibility into interdependencies and vulnerabilities that their specific organization’s inputs require to reliably deliver their products across a complex global network of suppliers and stakeholders. Gen AI is frequently tasked with analyzing supply chain
data, identifying bottlenecks, and suggesting alternative routes or suppliers. This results in improved supply chain resilience, reduced disruptions, and better risk management.
Energy Efficiency and Emissions Reduction
Another key benefit of Digital Twins is their ability to simulate energy consumption across facilities and product transport & distribution systems. Operators can identify energyintensive processes and optimize operations energy usage to better align with fluctuations between peak demand and excess supply, particularly when managing power available from renewable energy sources and storage devices. Gen AI is particularly well suited for these types of challenges as it can be prompted to explore optimization scenarios, suggesting more energy-efficient configurations. The value from this integration includes lower operational costs, reduced carbon emissions, and transparent compliance with ever- changing environmental stewardship guidelines and regulations.
Real-Time Decision Support
One key benefit of Digital Twins is that they provide a virtual sandbox for testing various proposed operational configuration scenarios. The capacity to highlight unintended outcomes beyond the immediate results of a configuration change is a great way to incorporate wisdom based on actual past experiences into the decision-making process. Too often, past errors in judgement are seldom incorporated as ‘lessons learned’. Economist Adam Smith suggested that the greatest economic benefit for all can be accomplished when individuals are acting in their own self-interest. I disagree, modern humans serving their own interests tend to ashamedly bury their mistakes, failing to capitalize on the insights those failures could bring to the enterprise.
Complex data systems that accurately capture and record prior decisions and their outcomes enable operators to simulate typical human responses to emergency conditions, market fluctuations, or equipment failures. This is where Gen AI can be used as a guardrail to process real-time data, providing actionable insights with instant consideration of past
performance against present circumstances and future operational objectives. It enhances decision-making by recommending optimal decisions based on changing conditions. This results in faster response times, better strategic alignment, improved safety, and better resource allocation.
Personalized Training and Skill Development
With recent innovations in 3D Virtual/Augmented Reality immersive geospatial environments, digital twins can be segmented from live systems to provide a safe but realistic environment for training operators. Orientation of new operators has long-included simulated exposure to complex situations, but now it can be done with digital twins in near-real time without risking real assets. Gen AI is employed in developing customized training modules, adapting to each individual learning style and experience level. The value from this approach includes reduced training costs, faster skill acquisition, and improved operator competence.
Innovating Beyond Boundaries
Digital Twins of complex facility assets provide a foundation for directed innovation. Operators can experiment with novel approaches without affecting physical assets. Gen AI can be prompted to propose alternative solutions to wicked problems and enable research and development (R&D) teams to focus their iterative approach to instantiate viable solutions while exploring otherwise uncharted territories. This intentional use of Digital Twins with Gen AI in R&D translates into accelerated innovation, potential opportunities to create competitive advantage, and breakthrough discoveries.
In summary, the fusion of digital twins and generative AI empowers operators to make smarter decisions, optimize processes, and navigate the energy transition successfully. As the oil and gas industry embraces these technologies, it embarks on a transformative journey toward a more efficient, sustainable, and resilient future. If you are ready to take the next step in that journey, collaborate with us at the Future Digital Twin & Generative AI conference in Houston.
About the author: After more than three decades as a technology management specialist in the Oil & Gas industry, Randell McNair, D.B.A. is now an adjunct instructor, author, conference speaker, and practitionerscholar researching stewardship of insights from information assets such as digital twins, engineering databases, and document management systems. #informingpossibilities
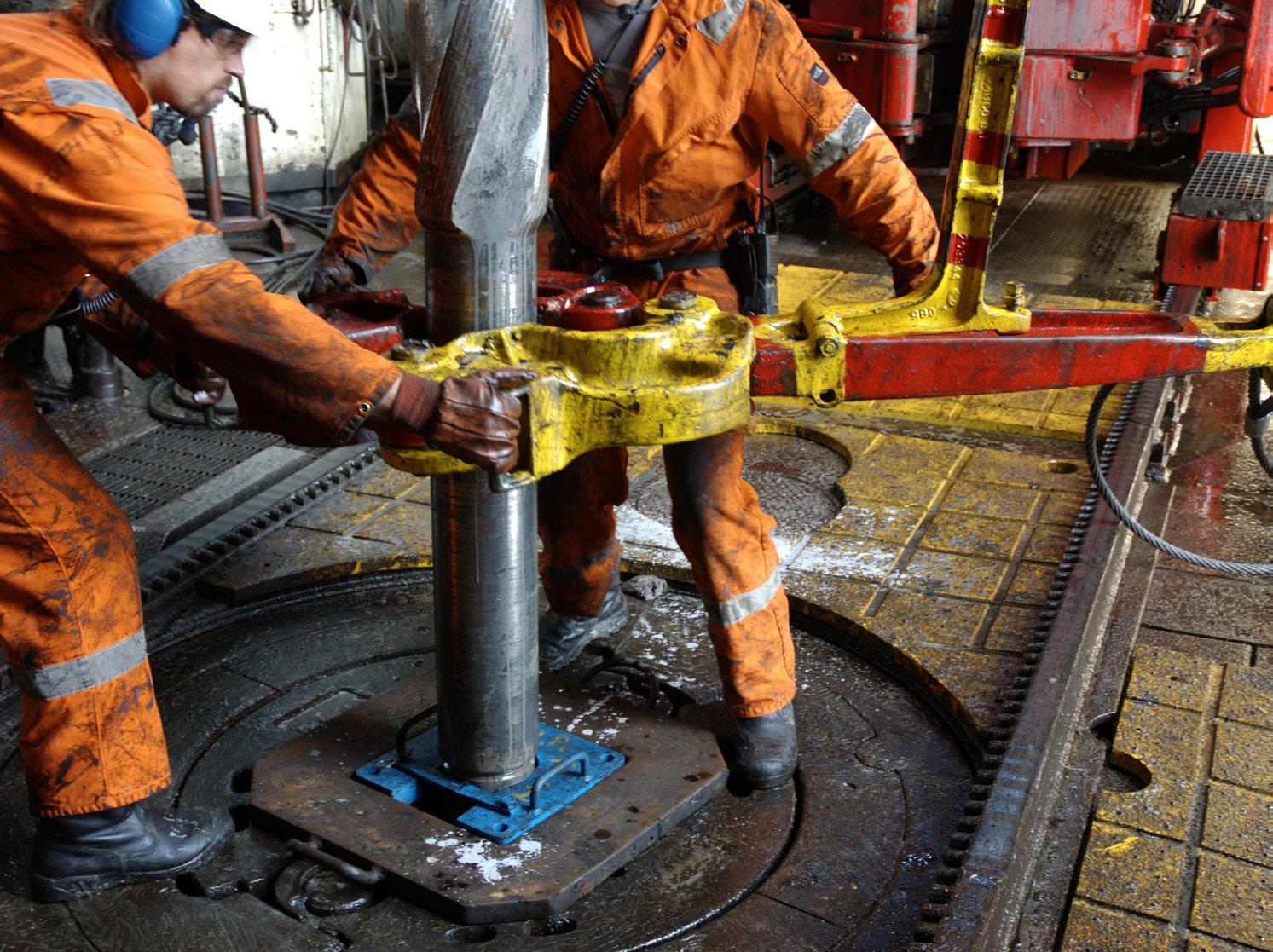
Transforming the Future of Work in Energy: From Buzz to Business-as-usual?
Often hailed as the harbinger of revolutionary change, AI has ridden a wave of hype and fascination. Few trends have captured as much attention and speculation, yet beyond the buzz, AI is starting to become entrenched in real-world applications – and this time, it’s more than just business as usual.
AI and its compatriots—including natural language processing (NLP), large language models (LLM), hybrid machine learning (ML), and generative AI—comprise a formidable team of transformational technologies.
Within the broader energy industry, the possibilities are endless:
Faster, more reliable data processing and verification, with more sophisticated data-sharing infrastructures
Connected data sources as a foundation for accelerated innovation and collaboration
Increased autonomy and automated services in operations and maintenance
Integrated physics-based and datadriven digital twin models that together with AI augment human decisionmaking
Improved asset performance management and reliability for plants from upstream to downstream Bi-directional data flows between systems and equipment, with Generative AI enhancing interaction to increase situational and operational awareness
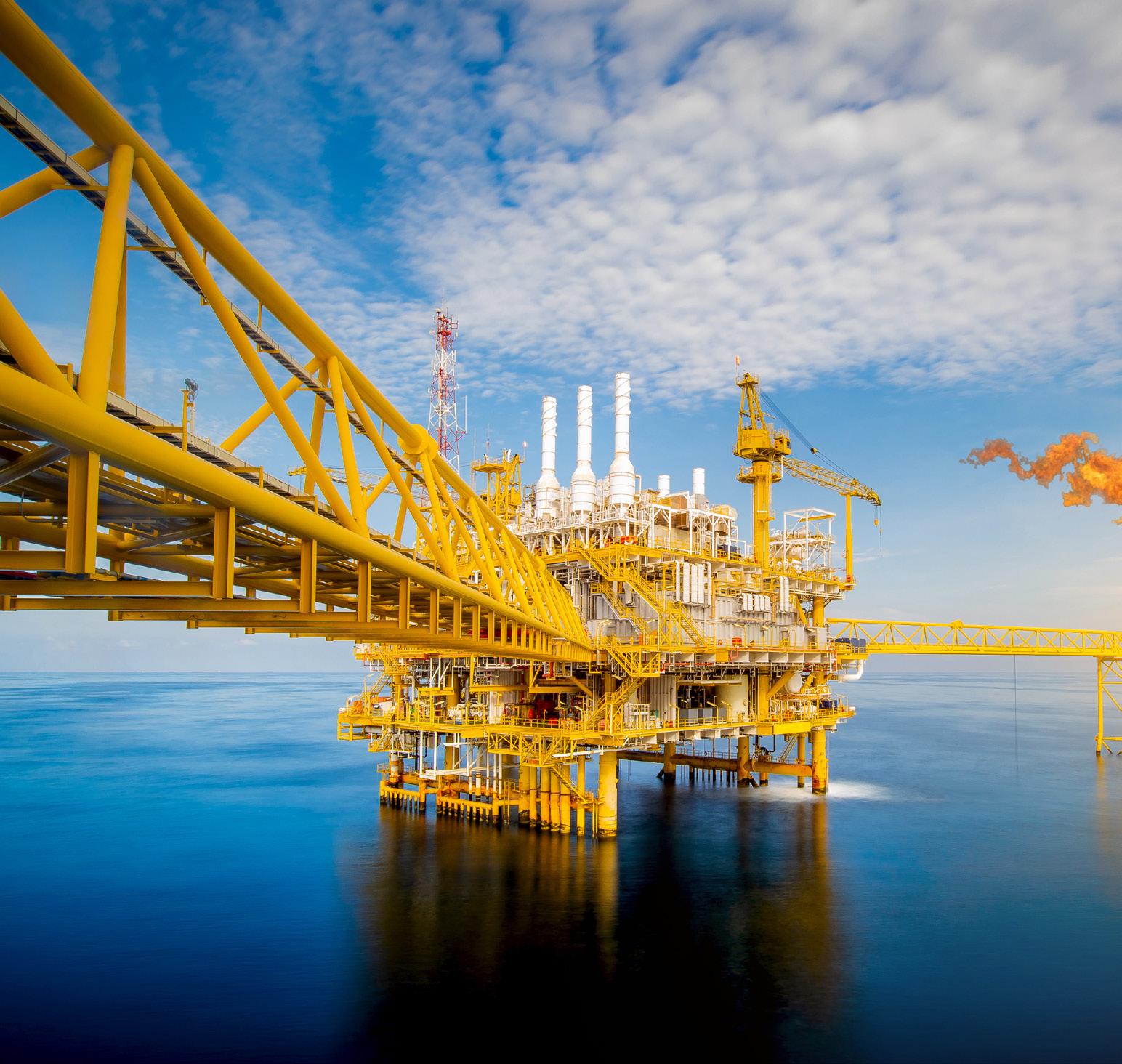
Supply chain transparency and traceability across the energy value chain
Predictive analytics for improved energy efficiency
When we look at the value that can be extracted from a transformed digital strategy driven by AI, it’s easy to envision the short- and longterm benefits that are sure to follow – faster information flows and data processing, less risk, improved communication and accelerated automation. What’s difficult is identifying the path to push past the buzz and embed these sophisticated technologies into future ways of working in a way that makes sense for the industry. How will AI fit in as part of day-to-day operational processes?
As Kongsberg Digital explain It is not just about data and dashboards
We have heard it before that what matters most is not the data you have but how you use that data. Data standards are an important part of our digital future, enabling companies to collaborate and coinnovate through system interfaces that integrate in the back end. Many progressive companies have put in place a solid data infrastructure and added select applications like a digital twin on top, making data more contextualised and accessible through simplified dashboards that make data easy to find, filter and apply.
However, data and dashboards are not enough of a springboard for AI to have the measurable value or ROI that companies expect. Instead, we need to start with a value-focused approach that zooms in on the specific use cases and services where AI can have the most influence through a digital operating model that builds on digital twin technology backed by physics-based and data-driven models. The successful implementation of an AI-infused digital strategy needs to be driven by desired business outcomes.
Driving transformation with a value-focused approach
The ability to identify the areas where AI can evolve into more than business as usual requires a degree of familiarity with today’s complex energy landscape. As a technology provider with domain and technical expertise, we can point to
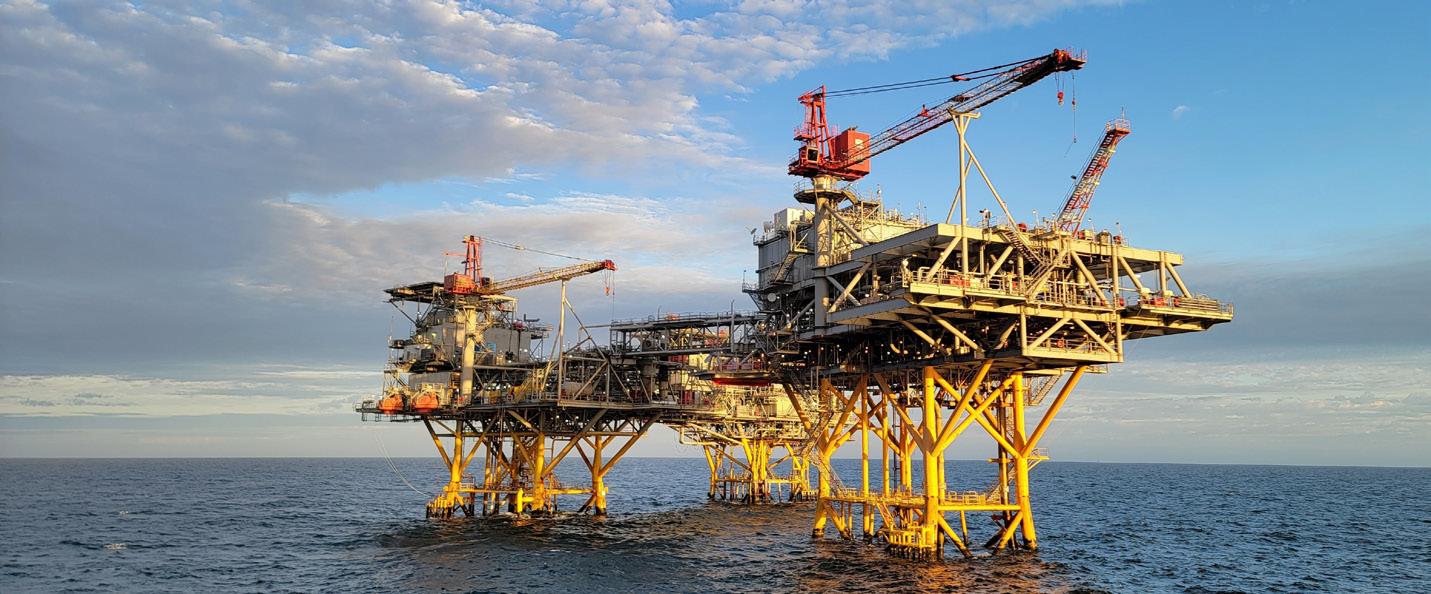
areas where we see the biggest potential for the industry: Safety
• Operations and Maintenance
• Performance Monitoring Supply Chain Management Design and Engineering
• Emissions Management
Once specific services within these potential impact areas have been identified – typically those that occur frequently and thus create identifiable, repeatable data patterns that can be used for learning and incremental automation – it becomes easier to understand how AI and its cohorts can be used to build out value-driven applications that extract information, process it and provide informed recommendations for actionable items that can be executed independently to contribute to overall improved energy efficiency.
Beyond the buzz, it is important to keep humans at the center of work but augmented by technology that is agnostic to different data types and sources. That way, technology is a supporting function that puts the right information – not too much, and not too little, just what is necessary – in front of the right user to enable decision-making at a faster pace, with lower risk. The cascading effects can be exponential depending on the use case, leading to everything from minimized emissions to earlier intervention on predicted maintenance failures.
A glimpse into the AI-driven future of energy operations
Let us take the example of an emissions management workflow for methane emissions. Imagine an emissions reduction team manages ten assets for a large E&P company, monitoring these facilities continuously to trend both the
individual and overall carbon footprint of operations. Their primary work tool: a cloud-based dynamic digital twin, where they can access an emissions management cockpit that has been configured to show the biggest energy consumers at any given time. More than just dashboards, this cockpit shows not only where there are trends towards heightened consumption but also critical incidents that need intervention, along with recommended courses of action based on continuous real-time data feeds and informed by historical and synthetic data.
The cockpit shows a main gas turbine in one of the facilities that is consuming more energy than it should, increasing the asset’s overall carbon score. An investigation kicks off, and the team dives into the data available in the twin. Using a built-in AIpowered chat function, they make a few queries to locate the correct information in just a few clicks.
Armed with these insights, they fly to different locations virtually, looking at the flare stack or vents to identify the troublesome consumer. Data flows back and forth behind the scenes, masking the complexity of these queries. The team investigates the simulator view, seeing simulated versus actual values to get prescriptions on where to intervene. With these prescriptive outputs, they have exactly what they need: instructions on what to do and the reasoning for why.
Transforming the future of work in energy
Data turns to insights, insights turn to actions, actions turn to outcomes, and outcomes turn to prescriptive tasks that the team can execute with full transparency into the reasoning process – for almost any use case driven by business needs and expected value-based outcomes. Some customers are already starting this journey. It’s better than business as usual.
How Predictive AI is Helping Smooth the Energy Sector’s Path to Net Zero
Predictive artificial intelligence (AI) has rapidly emerged as a transformative force in the energy industry, offering actionable insights to optimize asset management and enhance the reliability of energy systems amidst evolving demand patterns and renewable integration, although as Colin Gault, Head of Product at POWWR, explains, challenges in data quality and governance persist
Predictive artificial intelligence (AI), which uses patterns in historical data to forecast future outcomes or classify future events, is on everybody’s lips right now. And for good reason. The technology can be used to provide actionable insights and aids in decisionmaking and strategy formulation.
In the past year or so, we have seen the emergence of many new and exciting applications for predictive AI within the energy industry to better maintain and optimise energy assets. Advances in the technology have been nothing short of rapid. The challenge, though, has been in supplying the ‘right’ data to make them effective.
Today, we not only see the use of predictive AI to inform when an asset is at a higher risk of sustaining damage and in need of preventative maintenance but combined with weather and traffic data so as to
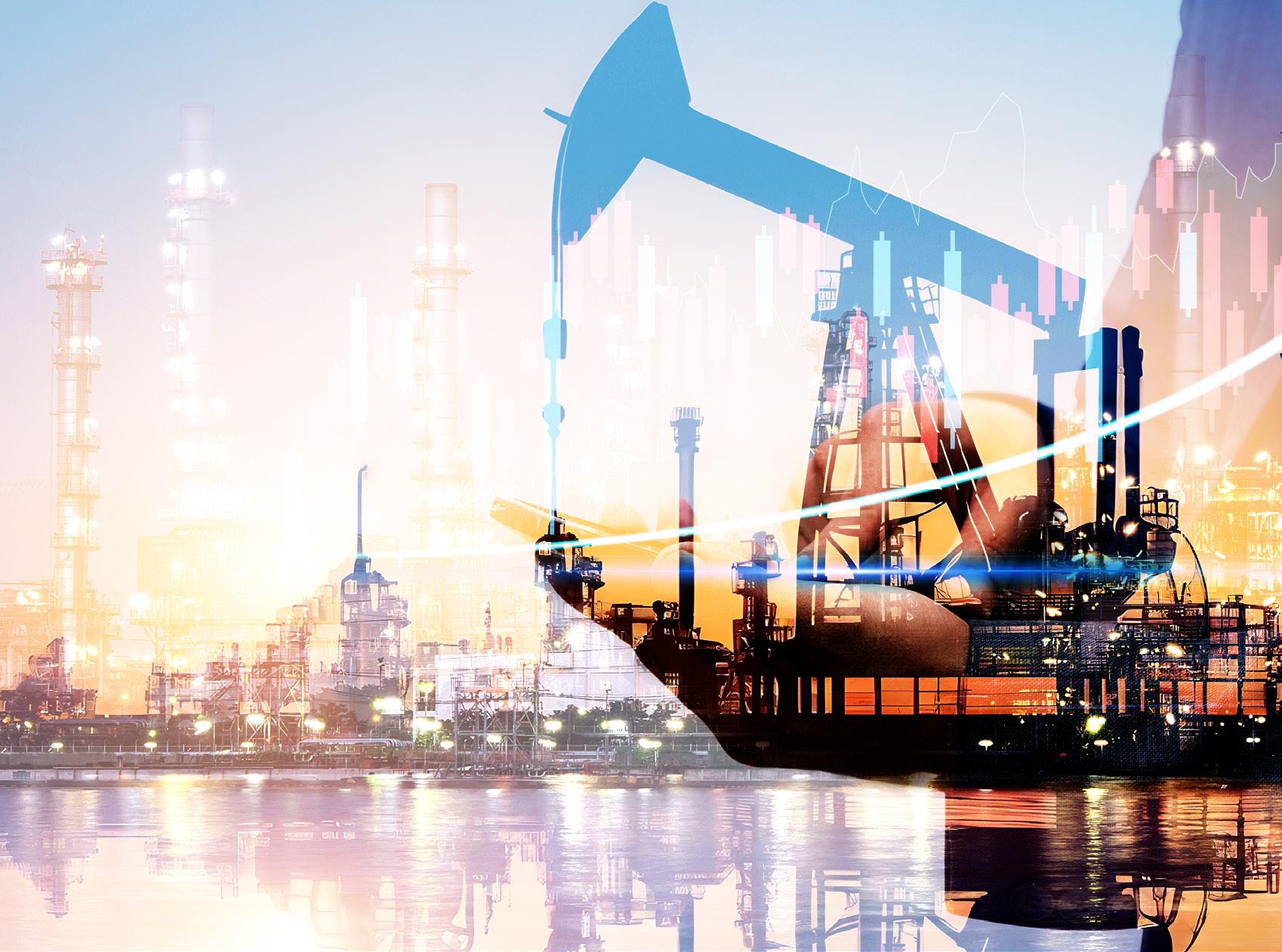
support dispatching engineers to a site optimally. This is helping to increase the reliability of the entire energy system.
Continuously changing supply and demand
Whilst further transitions towards net-zero have to be applauded, it does disrupt both the supply side and the demand side of the energy system. Electric vehicles (EVs), residential solar, and electric heating are all continuously changing demand patterns. At the same time, an increase in renewables on the grid is causing fluctuations in supply capacity. After all, a wind farm is not particularly useful without wind, and a solar farm is not especially useful without the sun.
A lot of what is grabbing headlines right now in the media is the use of predictive AI to learn these new patterns and deploy models into use rapidly to support demand flexibility. Yet, matching demand to available supply is the inverse of the traditional energy system.
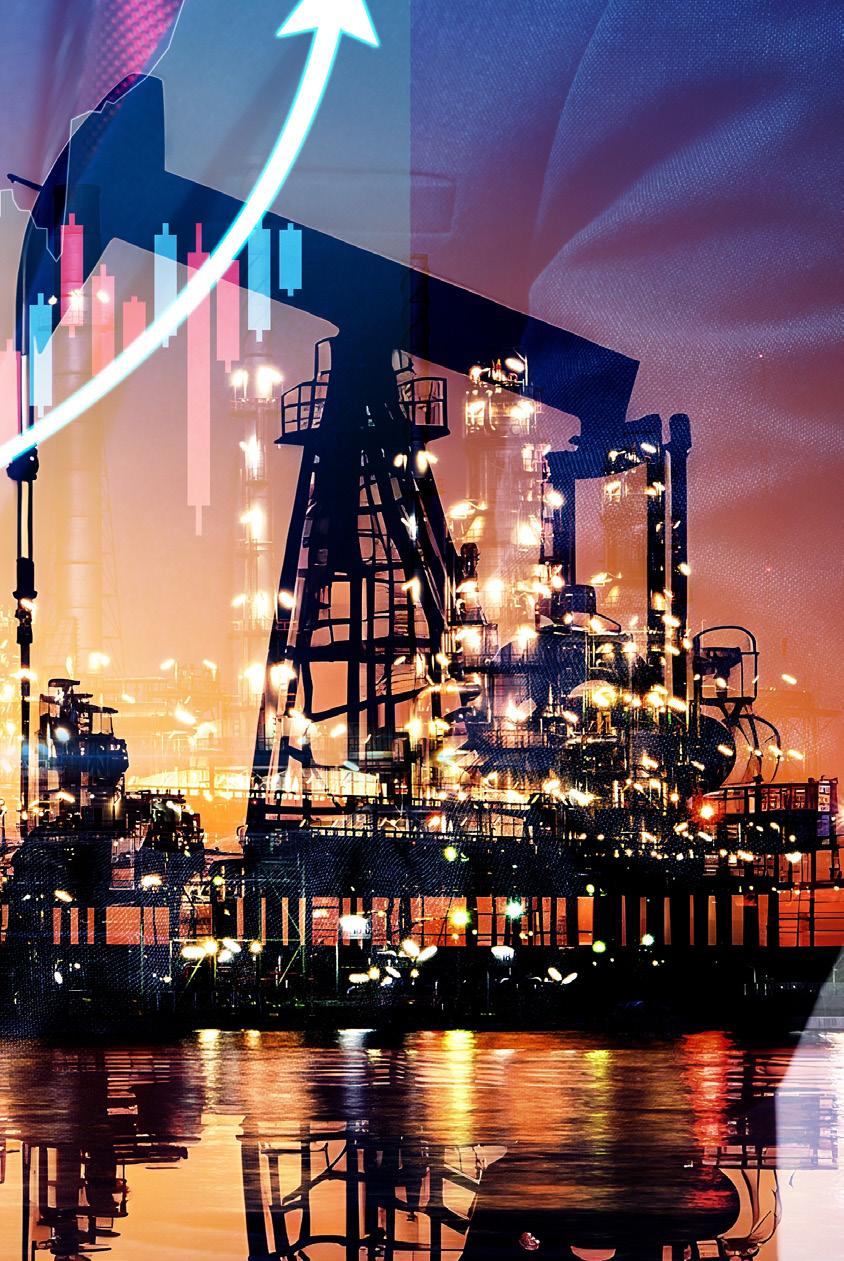
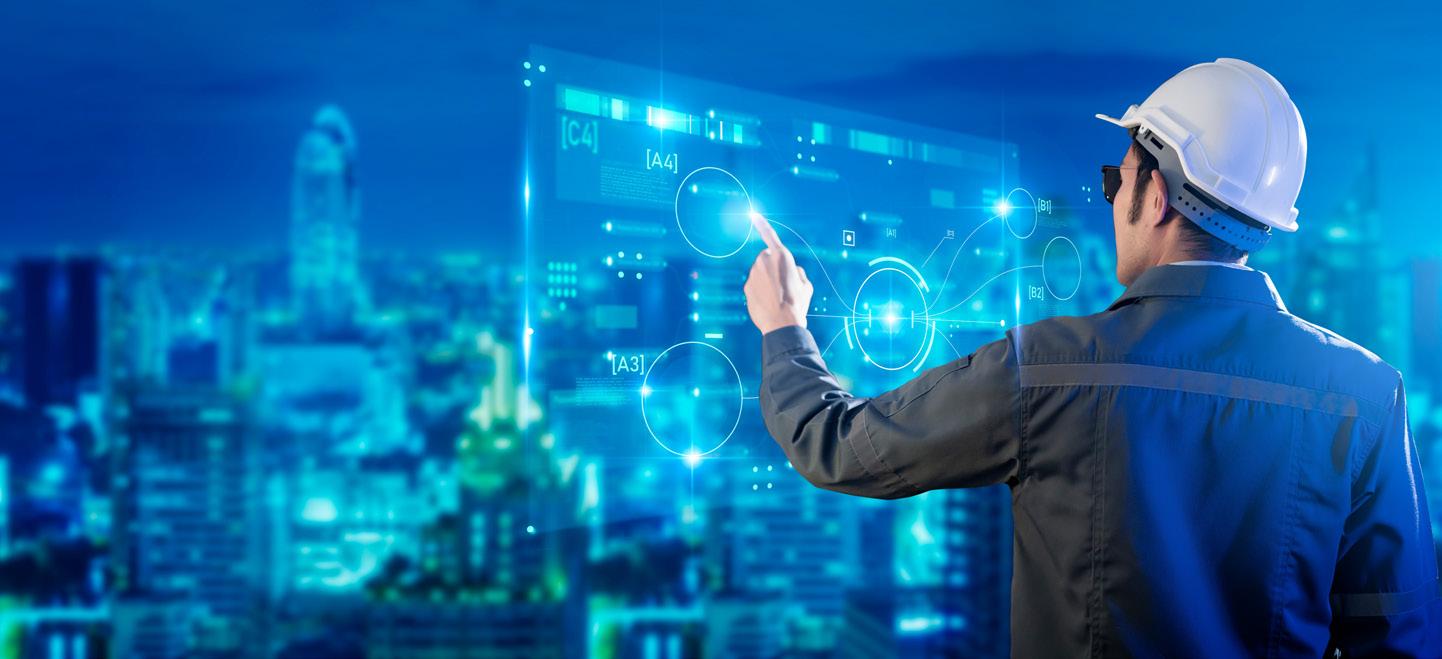
By being able to better predict when the energy system will experience an imbalance in supply and demand means that the charging of EVs, for example, can be scheduled better to ensure the balancing of the grid. The reward is cheaper electricity for all.
The ability to learn
A big risk to the energy sector is, of course, energy imbalance as this could lead to blackouts. The ability to accurately forecast is imperative to being able to mitigate supply-demand imbalance.
Balancing the energy system has always relied on being able to accurately predict customer behaviour. But this was always at the aggregate level when suppliers could turn up and down energy supply at will. Now, though, there is a greater need for localised predictability as distribution grids become more active with twoway power flows caused by distributed energy resources, and grids are balanced at an increasingly granular level.
Thankfully, with predictive AI, it is now not only possible to learn customer demand patterns at the individual consumer level but even at the appliance level. Although not widely utilised yet, predictive AI is being used more and more to support demand side flexibility, particularly with things like electric heating and EVs – often the largest loads in a house or building. If a building has an energy storage system, that too is more likely to come with optimisation algorithms informed by predictive AI that can learn usage patterns to schedule battery import and export.
A change for the better
According to a recent GlobalData report, predictive AI is already driving measurable improvements in renewable energy forecasting, grid operations and optimisation, the coordination of distributed energy assets, and demand-side management within the energy industry. This has been good to see. Further, the report predicts that predictive AI will play a major role in enhancing asset optimisation and customer segmentation in the years to come.
There is no doubt that it is changing the energy sector for the better, whether it be detecting and repairing faults, better predicting weather patterns, or providing more accurate usage monitoring. It will be interesting to see what the future holds for the technology. Whilst the future is exciting, it is still in the emerging technologies phase and needs to overcome the challenges often seen when scaling up.
To truly become successful, though, there also needs to be new robust governance procedures added to ensure the quality of data used to train the new predictive models are up to scratch. It will be important to confirm the integrity of all training data through detailed logging, auditing trails, verification frameworks, and oversight procedures. And then to continuously evaluate the datasets for emerging issues. In my view, that is where a lot of digitalisation of the energy sector will focus over the coming year. For example, the industry has already started to envision a digital twin of the energy system where predictive AI and open data combine to better plan and operate a much more distributed and flexible energy system.
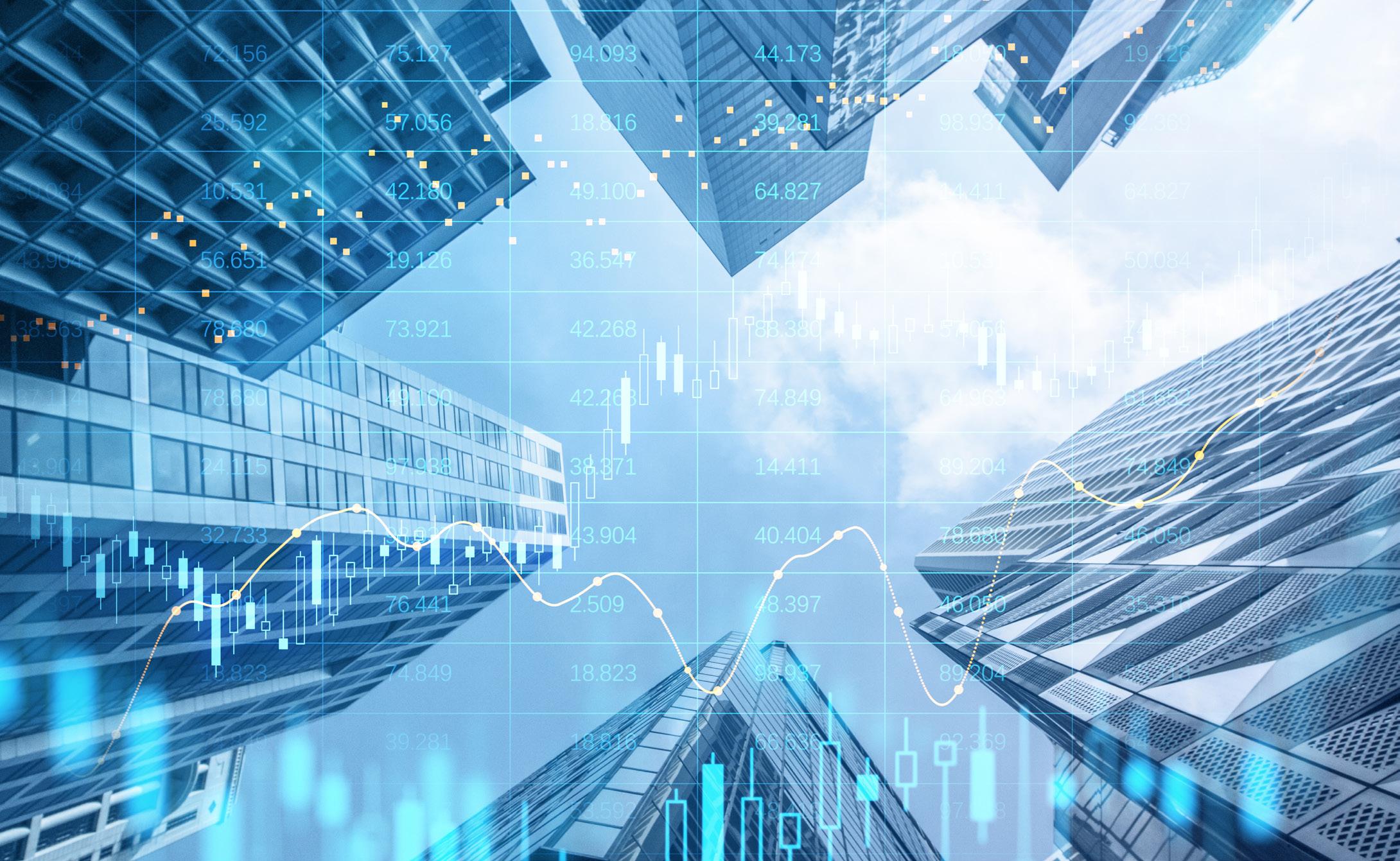
Navigating the energy transition: The critical mix of finance, technology and policy for green investment
Dr Valentina Dedi, Lead Economist at KBR, explores how the right mix of supportive policies, financial mechanisms, and technological innovation can de-risk investments in carbon capture, utilisation and storage (CCUS) and maximise the potential for green investment amid uncertain times, while also addressing the role of oil and gas in the transition.
The global community finds itself at a pivotal moment in the battle against climate change. As the urgency to transition from a fossil fuel-dominated energy system, heavily reliant on oil and gas, to one driven by greener sources intensifies, governments and investors alike are managing the challenges and opportunities presented by this shift.
Governments around the world have acknowledged the urgency of accelerating the energy transition and have prioritised capital allocation in their national and energy policies. The Paris Agreement sets ambitious targets for reducing greenhouse gas emissions and limiting global temperature rise to well below 2°C above pre-industrial levels. Meeting these targets requires an unprecedented level of investment in clean energy technologies and infrastructure.
According to S&P Global Platts, if the targets agreed by the world’s major economies under the Paris Agreement were to be met by 2050, it would mean more than $5 trillion in investment each year between now and 2050. To put this into perspective, this is equivalent to investing more than today’s size of Germany’s entire economy every year for the next two and a half decades. This scale of investment is well beyond what government budgets can afford. Large-scale private sector engagement will be critical too, including from the oil and gas industry.
In recent years, significant capital has been directed towards energy transition projects. However, these investments have been largely constrained to commercially viable projects, primarily favouring renewable power generation, such as wind and solar. These technologies have matured and are now market-ready thanks to a continuous decline in technology costs and the advances in efficiency over the past decade. While they are crucial to the energy transition, they alone cannot address the full scope of the challenge, and especially in decarbonising the hard-to-abate sectors.

The decarbonisation potential of CCUS projects CCUS has the scope to play a pivotal role in the latter sectors. It can be readily deployed at fossil fuel power plants and industrial facilities, such as cement, iron and steel, and chemicals, where CO2 is captured and stored or used to create products such as fuels and chemicals (CCU). CCUS can also provide a low-cost pathway for low-carbon hydrogen production, which can further contribute to the decarbonisation of the industry and transportation sector, or it can enable the removal of CO2, which is unavoidable or technically difficult to abate, directly from the atmosphere through Direct Air Capture with Storage (DACS) or Bioenergy with CCS (BECCS). This technology is particularly relevant for the oil and gas industry, as it can help mitigate emissions from their operations and products.
Although the adoption of CCS has lagged behind initial projections, there has been a substantial increase in activity and interest in recent years. Across the globe, novel technologies are being piloted with the goal of driving down expenses for both the power generation and industrial sectors. In addition to chemical absorption and physical separation, the two most advanced capture technologies, other separation technologies are also being tested, including membranes and looping cycles.
To meet net-zero targets, CCUS deployment must increase by several orders of magnitude within the next two to three decades. In the case of the US, it would mean a scale up to as much as 100 times today’s levels, according to the US Department of Energy’s Office of Clean Energy Demonstrations (OCED). While an ever-increasing number of projects across the entire value chain are being announced, only a fraction of them can take a final investment decision.
CCS is not a new technology, but the challenge lies in its economically large-scale deployment as investors face several uncertainties and risks. These can entail technology failures, cost overruns, extended timeframes, and high capital costs, among others. Another significant risk factor is the lack of clarity with respect to the demand outlook, which makes it challenging for investors to understand the scale of opportunity, and, thus, for projects to reach a financial investment decision. Scaling up the infrastructure needed to transport and store captured CO2 also requires the development of new business models which secure the required revenue streams, as well as partnerships between emitters, technology providers, and storage operators. The oil and gas industry, with its expertise in managing large-scale infrastructure projects and subsurface storage, can play a key role here.
The importance of policy and regulation
Realising the full potential of the CCUS technology, especially at these early stages, will require continued policy support and collaboration between governments, industry, and investors.
Coming up with the right policy framework and financing and incentive mechanisms will be critical. Governments and policymakers must establish an environment which creates stability and revenue predictability to attract the required investment and support the acceleration of the technology.
Thus, setting clear targets and priorities over the short-, medium- and long-term, including legally binding policy and regulatory frameworks, will be crucial to minimise policy uncertainty. At the same time, policy efforts should centre around the introduction of de-risking mechanisms and incentives that support green growth and foster green investment. This is especially pertinent for technologies and infrastructure, such as CCUS, which stand at a risky point of their deployment curve. This can be achieved through a wide range of instruments and approaches, including innovation funding, carbon pricing
instruments, carbon credits, tax incentives, guarantees, and low interest loans, among others.
Recent policy developments in the US, such as the Inflation Reduction Act and the Infrastructure Investment and Jobs Act, have started driving investment in clean energy technologies. The Inflation Reduction Act, in particular, is expected to be a game-changer for the CCS industry as it provides significant tax incentives for capturing and storing carbon dioxide. At the same time, as the UK envisions to become a global technology leader for CCUS, the government announced a funding of £20 billion to support the initial deployment of projects, aiming to unlock further investment from the private sector as it provides the much-needed certainty to investors. Back in 2011 and 2015, a lack of agreement on government budgeting and capital allocation, in tandem with a lack of understanding of the commercial risks had led to CCUS project cancellations in the UK.
The path forward
Mobilising the capital needed to achieve the ambitious targets will require careful design of policies, financing mechanisms & incentives, and innovation funding. These measures must work together to de-risk investments, boost capital availability, and ultimately make clean energy technologies economically sustainable. The oil and gas industry has a critical role to play in this transition, by leveraging its expertise, infrastructure, and financial resources to support the deployment of CCUS and other low-carbon technologies.
The path to a sustainable energy future is complex and challenging, but it is also filled with opportunity. By harnessing the power of policy, technology, and finance, we can unlock the vast potential of green investment and accelerate the transition to a low-carbon economy. Governments must continue to lead the way, while at the same time, the private sector steps up and embraces its role as a catalyst for change, channelling capital towards innovative technologies. Recent policy developments in the US and Europe are a promising sign of the growing momentum behind the energy transition. However, much more needs to be done.
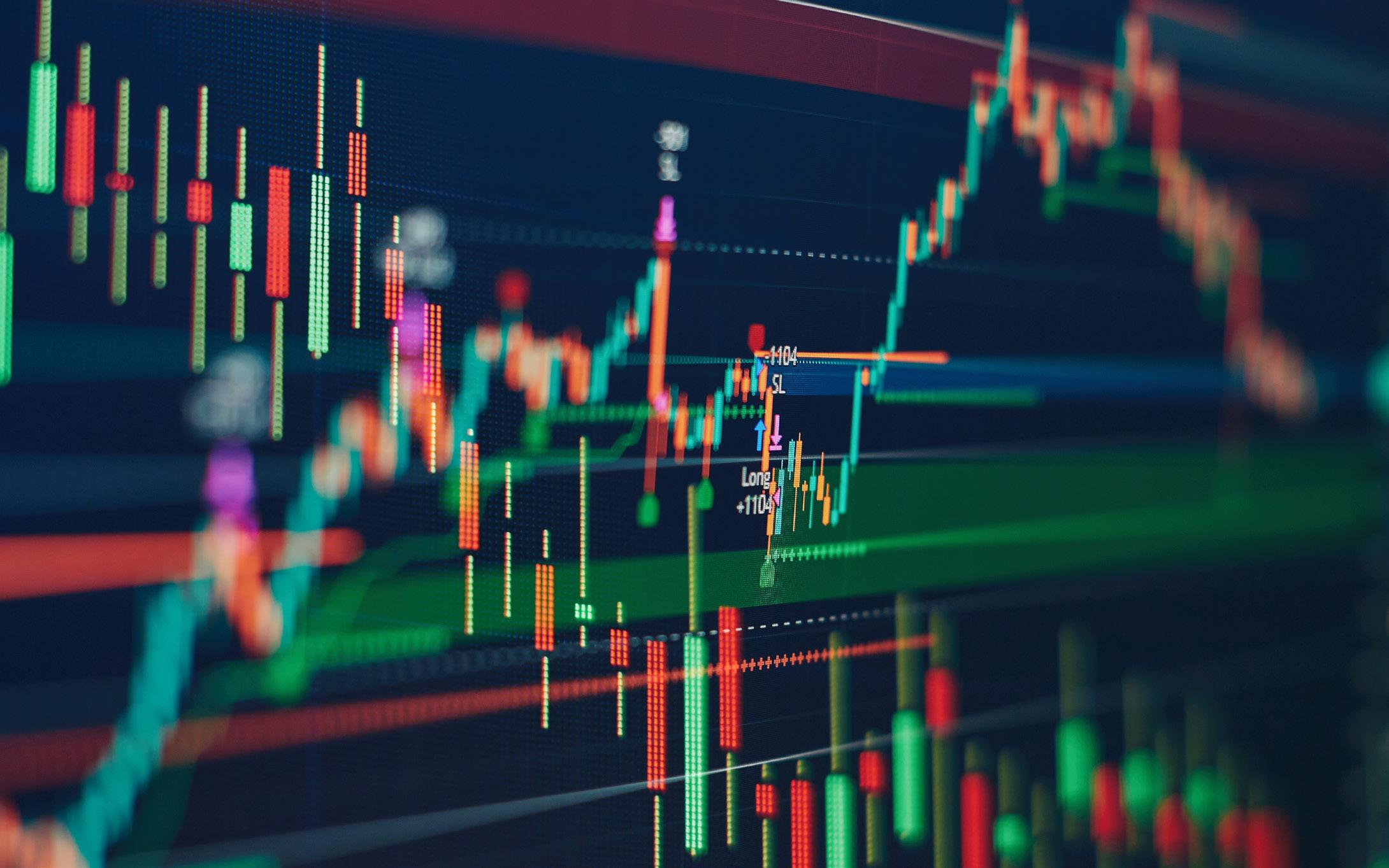
Greening the black gold with digital twins
In the dynamic realm of the oil and gas industry, the integration of digital twin technology is reshaping operations, driving efficiency gains, and paving the way for a sustainable future amidst evolving environmental and economic imperatives as Shweta Saxena, CEO,
MachineMax, explains
The oil and gas industry is a dynamic sector driven by the imperative for enhanced productivity and performance. Amidst its digital transformation, the adoption of technologies like artificial intelligence (AI) and the Industrial Internet of Things (IIoT) is central to this evolution. Digital twin technology, an innovative advancement from IIoT, is revolutionising how the industry manages assets, optimises operations, and reduces both costs and unplanned downtime.
In today’s competitive landscape, oil and gas companies are focused on transforming their operations to improve the reliability of assets while reducing costs and emissions. The move towards carbon neutrality is crucial, and digital twin technology offers a promising pathway to addressing these challenges by significantly enhancing operational efficiencies. These technologies include smart sensors, mobile connectivity devices, cloud computing and AI, which collectively enable a robust integration of operation technologies with information technologies.
Digital twins provide a comprehensive digital representation of physical assets, capturing essential data like machine performance and environmental conditions. This virtual testing
ground facilitates real-time adjustments and improved decision-making, enabling facility operators to simulate various operational scenarios without halting production. This is particularly effective for minimising environmental impacts while maintaining costeffective operations.
For instance, digital twins can model the effects of adjusting pump speeds to alter flow rates in pipelines or optimise compressor operations to reduce energy consumption without affecting output. Another key application is in leak detection, where digital twins simulate pipeline systems to identify potential failure points, preventing environmental contamination.
Meanwhile, digital twins can also test emission control technologies, such as carbon capture and storage, helping to choose the most effective method to reduce greenhouse gas emissions. They can also support resource management, like water recycling in hydraulic fracturing or minimising chemical use to reduce waste.
This proactive approach enables the identification and refinement of the best possible strategies to implement sustainable practices. However, the deployment of digital twins is not without challenges. Siloed information systems are
still a significant barrier. With intelligent sensor technology, advanced telematics and collaborative cloud management, seamless integration and real-time data processing across platforms are achievable. These technologies enhance the granularity of data necessary to model and simulate complex operational scenarios while making a single source of data accessible to a variety of stakeholders, thereby enabling real-time interventions.
Looking ahead, the strategic deployment of digital twin technology holds immense potential for transforming the oil and gas industry. Beyond immediate operational improvements, digital twins are pivotal for long-term planning and strategic decision-making. They allow companies to simulate future scenarios, evaluate the impact of operational changes and plan technological upgrades. This not only bolsters sustainability but also secures a competitive advantage in an increasingly environmentally conscious market.
Offering more precise control over emissions and a unified platform for continuous improvement, digital twin technology will play a pivotal role in the industry’s future, transforming challenges today into opportunities for sustainable growth tomorrow.
Unlocking offshore asset integrity through innovative technologies
In today’s energy sector, the efficient management and maintenance of offshore assets is more crucial than ever to ensure sustained operations and long-term viability. Essential to achieving this is integrity assessments, which play a pivotal role in ensuring the prolonged and reliable functioning of installations throughout their lifecycle.
Oil and gas platforms in particular, are exposed to harsh environmental conditions and complex challenges, necessitating regular inspections to maintain their integrity and operational efficiency. The goal of these assessments is to minimise the need for disruptive interventions, thereby reducing downtime, costs, and potential safety risks.
The sorting and curation of data is playing an increasingly important role in this activity, providing insights that support more effective maintenance planning for safety-critical
equipment, while reducing the requirement for unnecessary inspections. However, there are several hurdles to overcome to gather and extract full value from the available data. This is partly due to the extreme volume of data which can span decades for mature assets, including information from various sources.
The existing approach in large physical asset management revolves around sporadic data collection, periodically analysed by
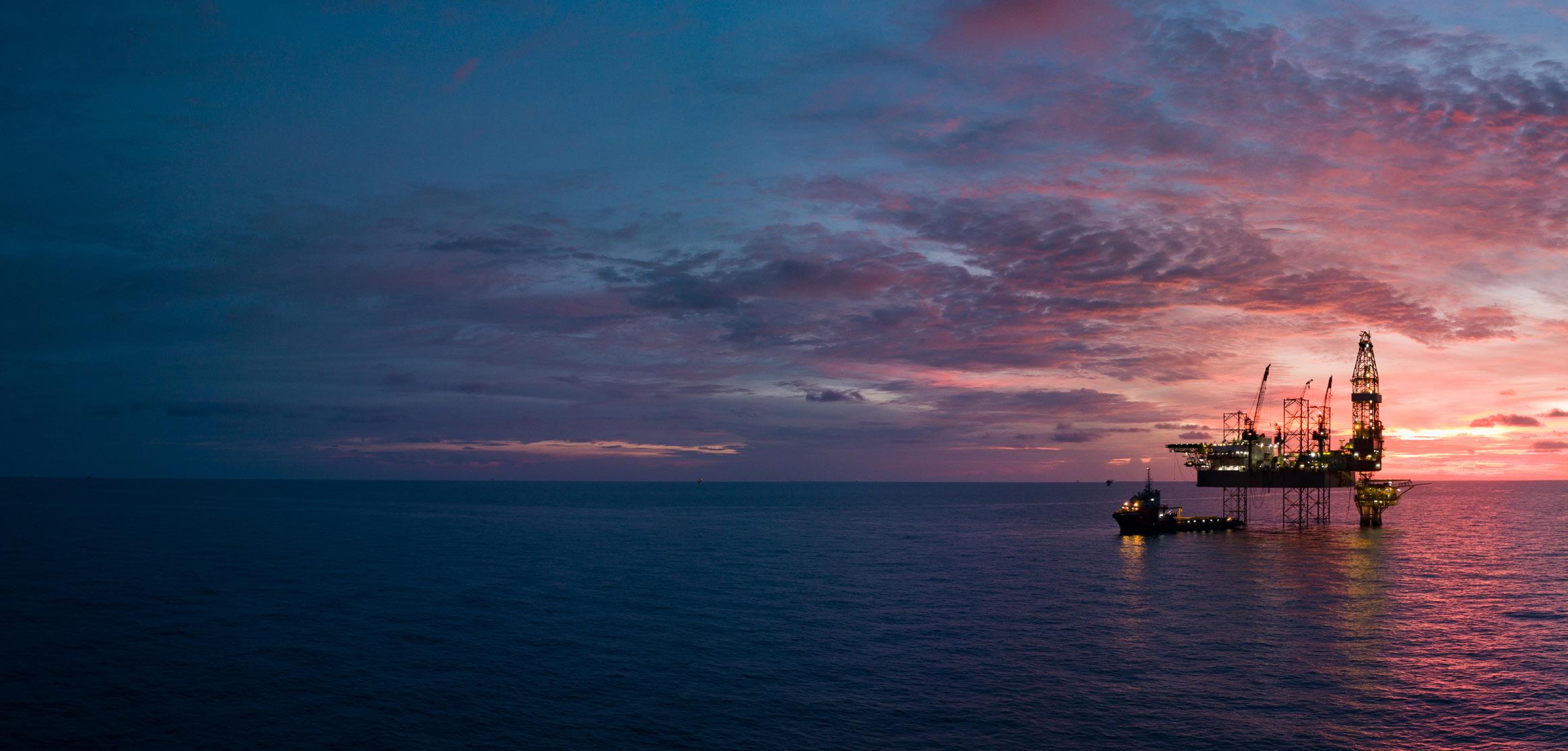
humans. This method results in reactive and lagging decision-making, where the full commercial picture is not always considered. This can lead to operational disruptions and further technical, operational, and logistical complexities if not addressed.
However, these challenges highlight opportunities for change where digitalization is a key player. Advanced data analytics, artificial intelligence, and the Internet of Things (IoT) empower operators to optimize production, predict equipment failures, and streamline maintenance processes. To fully leverage the potential of data, it is imperative for the energy industry to ensure robust data management and integrity.
Understanding your data
Imrandd specialize in industrial data solutions, helping clients in energy and other sectors to make fast and efficient business decisions in line with commercial and environmental, social and governance (ESG) strategies.

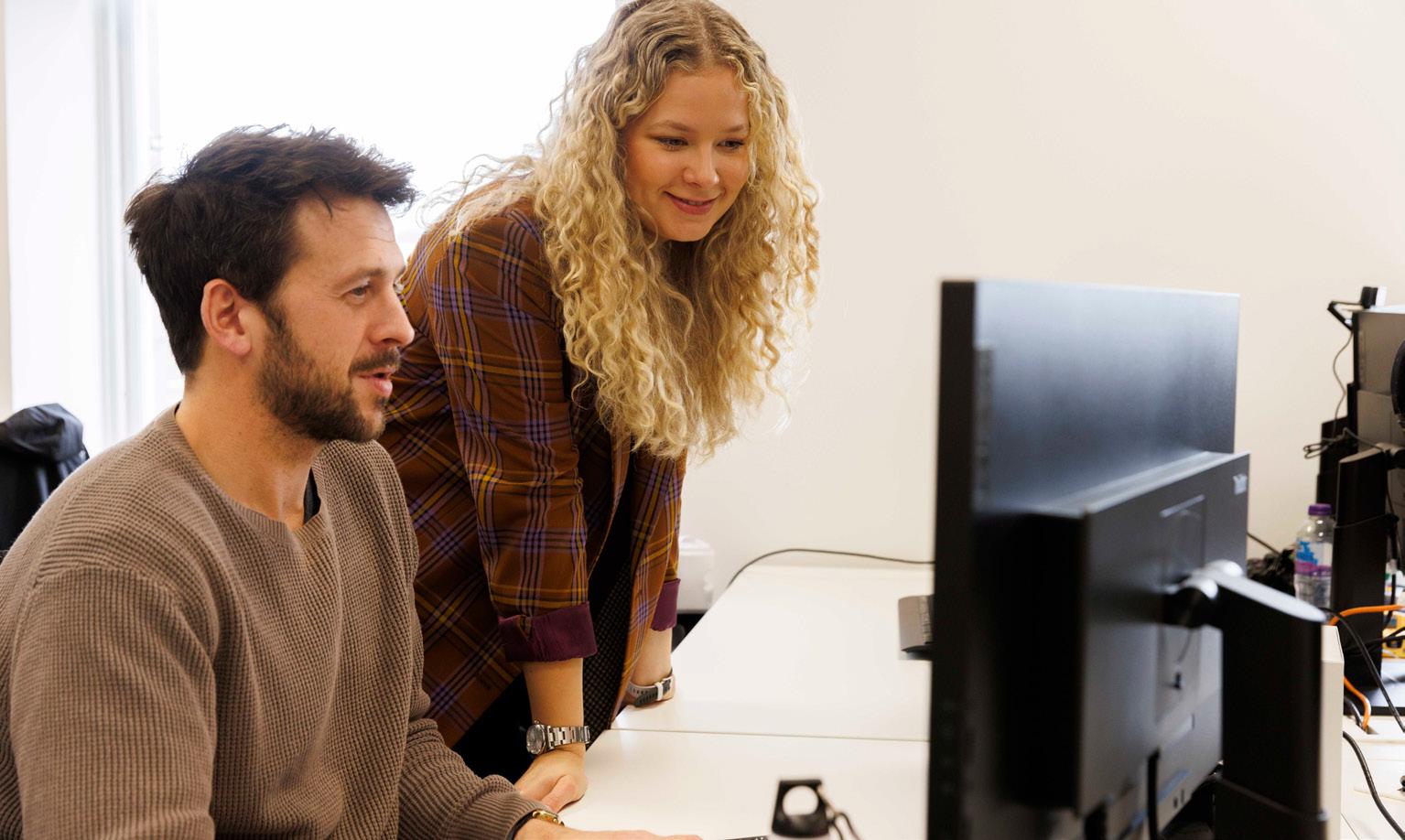
The company was recently approached by a North Sea operator to carry out a comprehensive integrity assessment on a floating production storage offloading (FPSO) vessel. The FPSO was undergoing modifications and upgrades to accommodate new field operation conditions and required identification of equipment for replacement, repair, or fabric maintenance. The organisation also requested details for prioritising the order in which they were replaced based on their condition. The aim was to ensure minimal need for offshore intervention from an integrity standpoint to extend the operational life of the field, up to cessation of production (CoP) in 2035.
Imrandd collaborated with a digital asset management specialist to bring combined capabilities across asset scanning, data extraction and data analysis, allowing for large volumes of inspection data to be efficiently obtained, processed, and analysed. The partnership set out to make optimal use of the FPSO’s large dataset which consisted of external asset scans and internal inspection reports.
The partner company’s web-based technology was first utilised for inspection of all pressure systems which included pipework, vessels, heat exchangers, tanks, and filters, in addition to topside structures, hull, and marine elements. The visual inspection tool utilises accurate inspection and engineering data to rapidly detect and quantify defects, providing functionality to facilitate support and manage the integrity management cycle.
Steven Saunders, global head of new business explains how Imrandd then gathered all non-destructive testing (NDT) reports including crucial integrity assessment data which was then sorted, curated and cleansed for further analysis using semi-automated QA/QC processes, before employing its EXTRACT software.
“EXTRACT automatically ingests and gathers data which is essentially inaccessible, and consolidates it into one digestible format, ready for analysis,” he says. “The technology utilises a combination of techniques including Optical Character Recognition (OCR) and computer vision to enable limitless volumes of data to be processed rapidly. With the ability to pull data from multi-format sources and different report types, extraction of large datasets delivers accurate digitized data.
“From the data processed, our proprietary solution obtained 2,976 topside pipework wall thickness readings from over 480 inspection reports from 2017 onwards. This produced considerable time savings, taking a matter of days in comparison to what would have previously taken a team of engineers’ weeks, and ensured that there was a clear picture of the asset’s condition history.”
Prioritised insights
The extracted data was then processed using Imrandd’s EXACT analytical tool which cleanses, corrects and interprets large data sets, then maps and predicts equipment degradation. It delivers actionable insights to significantly reduce OPEX and improve asset integrity management and plant reliability. Utilizing these insights, corrosion rates were calculated and remaining life predictions from trendable data were identified and formed the basis for recommended inspection intervals and integrity interventions. This ensured that failure patterns and corrosion hotspots and risks were known, with the software identifying threats which were potentially unknown or reveal inspection blind spots.
“EXACT provided further analysis of the data which helped to provide large scale statisticsbased trending corrosion rates, and predicted the remaining operational life to ensure key maintenance priorities were identified,” Saunders adds.
Providing valuable outcomes
The next step involved an external condition assessment by integrating Imrandd’s methodology with the partner’s technology for all pressure systems, structures, hull, and marine elements.
Data was gathered from master and reference sources such as the equipment register and piping specifications, and scanned data was assigned corrosion categories for each line, calculating corrosion rates based on operating conditions and recommended practices. The extraction collected a 100% external visual inspection report and established a baseline for integrity evaluations for pipework and vessels.
“Both the internal and external results were validated through a site inspection of areas of concern and unquantifiable areas with threat potential,” Saunders continues. “The findings were fed back into the analyses as a means of ‘calibrating’ to ensure the most up to date actual condition was reported. This allowed optimization of final recommendations to minimize the number of in-scope items requiring integrity action or any future in-operation inspection.”
From the data acquired, cleansed, and analysed, Imrandd was able to provide the operator with valuable recommendations equating to a significant reduction of 40-50% in anticipated maintenance and repair costs, and ultimately extended the operational life of the FPSO.
The importance of innovation Innovation and advancements in technology
are critical in supporting effective inspection and maintenance programmes. Integrating advanced data solutions seamlessly with digital asset management systems can deliver comprehensive assessments that surpass the outputs of traditional methods. Imrandd recently invested £1 million in developing a revolutionary asset management solution, harnessing artificial intelligence (AI) to reduce inspection time and costs for offshore operators. The propriety monitoring and intervention software, ALERT, has been designed to go beyond traditional approaches to routine asset integrity monitoring. Despite the challenges presented by vast volumes of data and the limitations of traditional approaches, digital transformation such as this offers promising solutions.
The importance of data lies in its ability to provide actionable insights for effective maintenance planning and risk mitigation, not only supporting the identification of potential threats but also aids in predicting equipment degradation, enabling asset owners and operators to adopt a preventative rather than a corrective stance.
Looking ahead, continued investment in innovative technologies integrated with digital asset management solutions will be a transformative force in the future of energy and industrial industries.
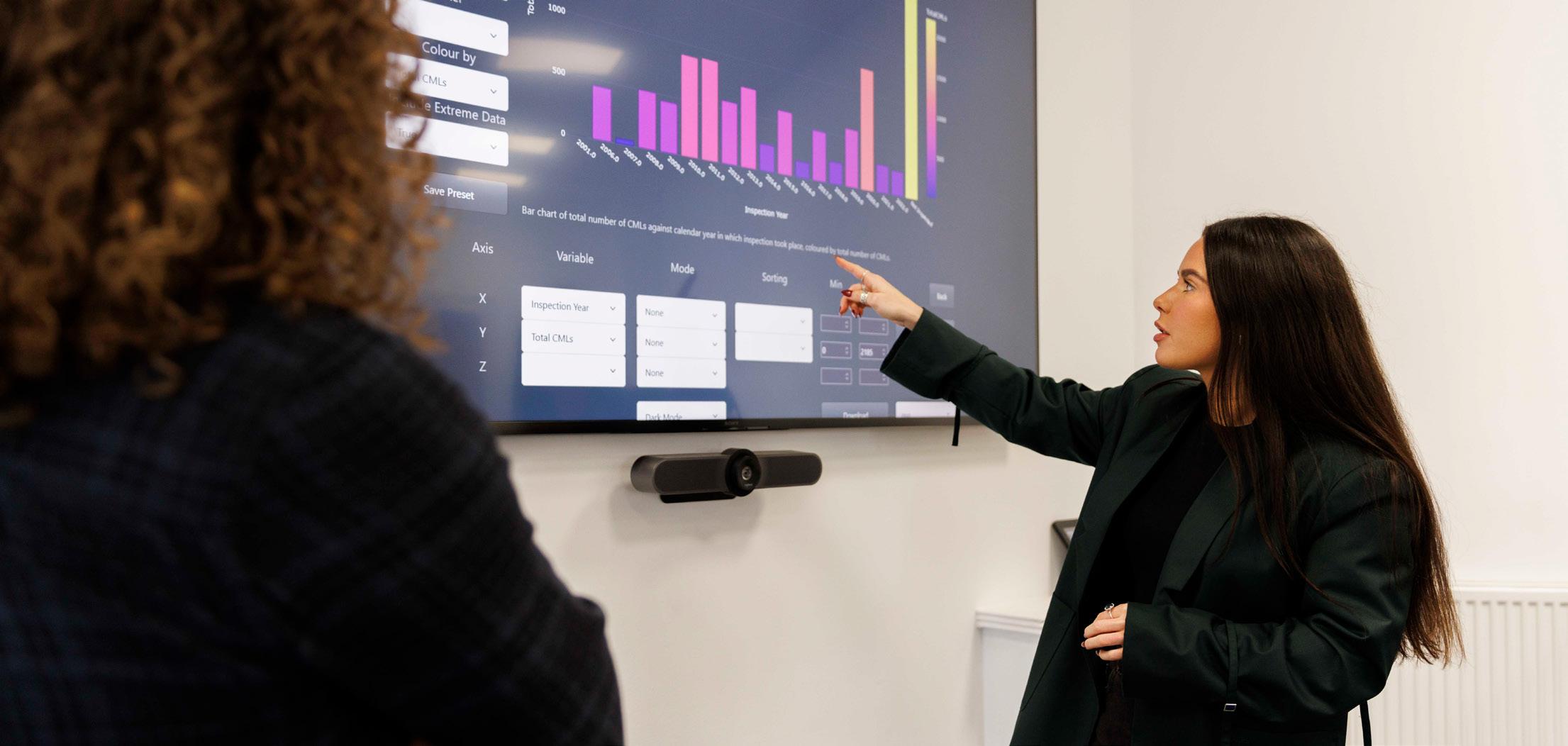
The Transformative Power of Data Analytics
Amidst a staggering performance gap in the oil and gas industry, the strategic implementation of data analytics systems promises to revolutionize operations, drive efficiency gains, and mitigate environmental impacts, ushering in a new era of sustainable growth
The oil and gas (O&G) industry stands at a critical juncture, facing unprecedented challenges amid fluctuating market conditions, evolving regulatory landscapes, and mounting environmental concerns. At the end of last year, McKinsey highlighted a glaring performance gap within the sector, estimating it at a staggering $200 billion. Their research underscores a significant discrepancy between the actual and potential production levels of offshore platforms, revealing that, on average, these platforms operate at a mere 77% of their maximum production potential.
This revelation emphasizes the urgent need for transformative solutions to bridge this performance gap and unlock the industry’s full potential. One such solution lies in the effective utilization of data analytics systems and tools, which have the capacity to revolutionise O&G operations, optimise efficiency, and drive sustainable growth.
Correctly implemented data analytics systems offer a powerful mechanism to navigate the operational complexity inherent in O&G operations. By harnessing the vast amounts of data generated across exploration, production, refining, and distribution processes, these systems can provide invaluable insights into every facet of operations, from reservoir management to asset maintenance and supply chain logistics.
The potential benefits of leveraging data analytics in the O&G industry are profound. Notably, the rapid adoption of these technologies can yield substantial returns on investment, with McKinsey estimating returns of as much as 30-50 times the original investment. These returns stem from enhanced operational efficiency, reduced downtime, and optimized asset performance, all of which translate into tangible cost savings and improved profitability for industry players.
The strategic implementation of data analytics holds the promise of addressing environmental concerns by minimising wastage, preventing accidents, and alleviating bottlenecks within operations. By leveraging real-time data insights, O&G companies can identify and mitigate potential risks, thereby reducing their ecological footprint and fostering a culture of
environmental stewardship.
Data analytics enables O&G companies to embrace predictive maintenance strategies, allowing for the early detection of equipment failures and the proactive scheduling of maintenance activities. This proactive approach not only minimizes downtime and production losses but also enhances worker safety by averting potentially hazardous incidents.
In addition to operational benefits, the effective use of data analytics can drive innovation and facilitate informed decision-making across the entire value chain. By leveraging advanced analytics techniques such as machine learning and artificial intelligence, O&G companies can uncover hidden patterns, optimize processes, and identify new opportunities for growth and diversification.
The O&G industry stands to reap substantial rewards from harnessing the power of data analytics. By embracing these transformative technologies, industry players can bridge the performance gap, drive efficiency gains, and achieve sustainable growth in an increasingly competitive and dynamic landscape. As the industry continues to evolve, the strategic deployment of data analytics will remain a cornerstone of success, enabling O&G companies to thrive in the face of evolving challenges and capitalize on emerging opportunities.
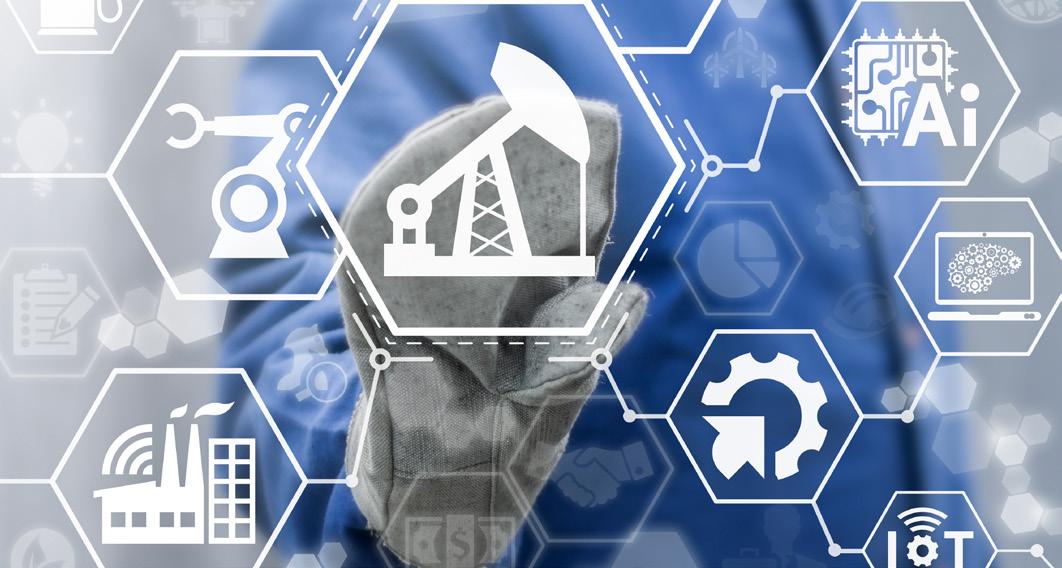
Unlocking the potential of remote telemetry solutions in oil and gas pipelines
Etienne Clauw, Associate Product Line Manager – RTUs at Ovarro, explains how remote telemetry solutions could help oil and gas operators greatly improve their sustainability measures.
The oil and gas industry faces demands to adopt more sustainable practices. But, given that fossil fuels will remain essential to global growth for the next 10-20 years, can the industry ever be truly sustainable and reduce its carbon dioxide (CO2), methane (CH4) and other greenhouse gas emissions? Investments in new and sustainable technologies hold the answer to this question.
Sustainability initiatives in the oil and gas industry
include the ‘Global Decarbonization Alliance’, a group of oil and gas companies — including Siemens Energy, Tata Steel, Enel Green Power and others — with a goal to achieve net-zero scope one and two emissions by 2050. The industry is also seeing an increase in interest in alternative energy sources, such as the use of hydrogen, which has the potential to be more sustainable compared to traditional fossil fuels like coal, oil and natural gas. Alongside these broader initiatives, the oil and
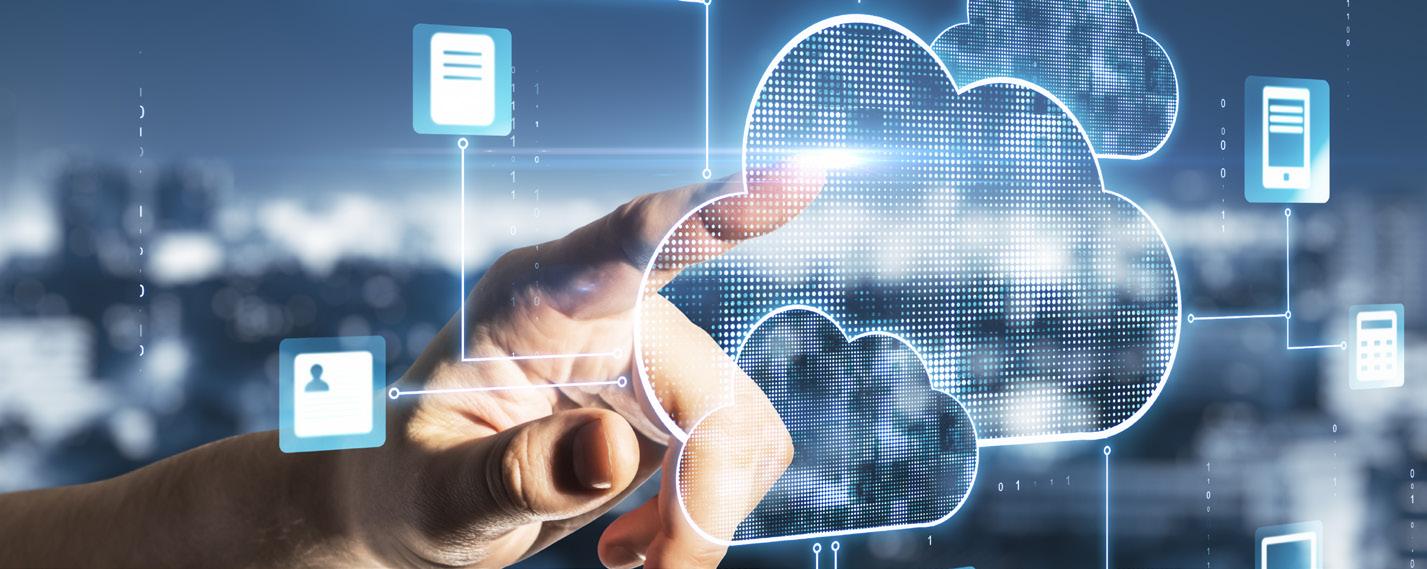

gas industry is making better use of sustainable technologies. A report by the World Future Energy Summit highlights eight ways in which, with cleantech innovations, oil and gas companies are striving to minimise costs and reduce their carbon footprint across operations. Key initiatives include the better use of data analytics to optimise production, decrease freshwater use, improve water recycling efforts, and reduce methane leaks.
Additionally, companies are exploring used oil recycling, streamlining processes, creating digital oilfields — similar to digital twins — for real-time monitoring and analysis and investing in renewable energy sources. All these efforts signal a shift towards sustainability in the oil and gas sector.
Nevertheless, the use of cleantech innovations also presents operational challenges. First, there may be significant upfront costs for the technology itself. Second, challenges might relate to the complexities of integrating and maintaining

these advanced solutions, including infrastructural developments or the logistical hurdles of applying the technologies in remote or offshore locations.
Third, it is necessary to comply with evolving environmental regulations. Lastly, the workforce must be trained in using the new systems. Oil and gas companies must navigate these obstacles while driving the industry towards a more sustainable future — but how?
Safe areas
One solution lies in the increased use of data and artificial intelligence (AI) for the monitoring and control of crucial assets. After all, oil and gas are among the highest value assets passed through a pipe or transported via land and sea. The main goal of remote control and monitoring is to improve efficiency in oil and gas operations, which is essential for reducing emissions.
Safety is another consideration due to the hazardous nature of the sector. Specific areas within oil and gas facilities are designated as “safe areas” or “non-hazardous areas” where the risk of fire or explosion is minimised. These safe areas typically house communications equipment such as control systems, instrumentation, and networking infrastructure.
However, changes in design philosophies — including the “keep it simple” ethos — and cost-saving measures have led to the removal of safe areas from many locations. For operators, this makes it more difficult and expensive to install control and communications equipment and the power systems to operate them. Furthermore, remote locations often have little to no power and rely on solar panels or small production powered gensets.
How can oil and gas network operators improve monitoring and control of crucial assets, while also overcoming these challenges? Fortunately, remote telemetry solutions have emerged as a pivotal tool.
Ovarro’s remote telemetry units (RTUs) are equipped with cellular wireless connectivity and are designed to empower operators with real-time insights and control over their assets. By excluding wired components and opting for compact, lower power designs with smart communication protocols, companies can not only lower installation costs but also minimise the footprint of control systems. Integrating RTUs in series or parallel with control equipment allows remote access without the need for additional modems, streamlining installation processes and reducing expenses. The added flexibility also helps overcome the absence of safe areas.
Industry players leveraging remote telemetry solutions include Beijing City Gas Group, PetroChina and Distrigas. With over 100,000 telemetry, automation and remote monitoring solutions deployed worldwide, including in critical oil and gas applications, the impact of these technologies is growing.
Remote monitoring
In one case, PetroChina Pipeline Company Limited, a subsidiary of PetroChina Limited, undertook the ambitious project of constructing over 800 kilometres of pipeline within 180 days, setting a new record in a challenging high-latitude and extremely cold environment. Facing extreme temperatures ranging from -52.3 degrees Celsius in winter to 39.8 degrees Celsius in summer, the project required robust control systems.
Implemented by Ovarro’s partner ZKCiT, a systems integrator, 22 TBox-MS Modular RTUs facilitated pipeline monitoring and control, operating reliably despite temperatures as low as -43 degrees Celsius. Crucially, the remote telemetry systems exceeded the customers’ specified operational limits and ensured continuous operation of the pipeline.
This example shows how wireless communication technologies, leveraging specialised devices like RTUs, can enhance the monitoring and control of crucial assets. The result is more efficient, sustainable oil and gas operations.
The Rise of AI and Big Data
At look at how Aramco are harnessing power of AI, Big Data, and the Industrial Internet of Things (IIoT), which is any system of interrelated computing devices that are connected digitally to enhance industrial processes, to optimize many aspects of its operations, from reservoir management to power consumption, and to achieve a variety of goals, from improving workers’ safety to reducing CO2 emissions.
The rapid expansion of AI benefits owes much to Big Data, which encompasses the creation and capture of vast datasets containing diverse information produced at remarkable speeds. Through processing and analysing these datasets, AI algorithms are now instrumental in tackling complex problems. When combined, AI and Big Data offer an extensive array of potential applications. In manufacturing, AI optimizes product design, inventory management, and logistics, while online platforms leverage it for virtual assistants, advertising, language
translation, and cybersecurity. On the roads, AI algorithms power Sat-Nav systems and regulate traffic flow to minimize congestion. Across various aspects of modern life, AI drives cost reduction, time efficiency, and operational optimization.
At Aramco, AI stands as a cornerstone of our Digital Transformation initiative, where we continuously innovate smart tools and digital solutions to enhance decision-making processes and elevate business performance. Leveraging the synergies of
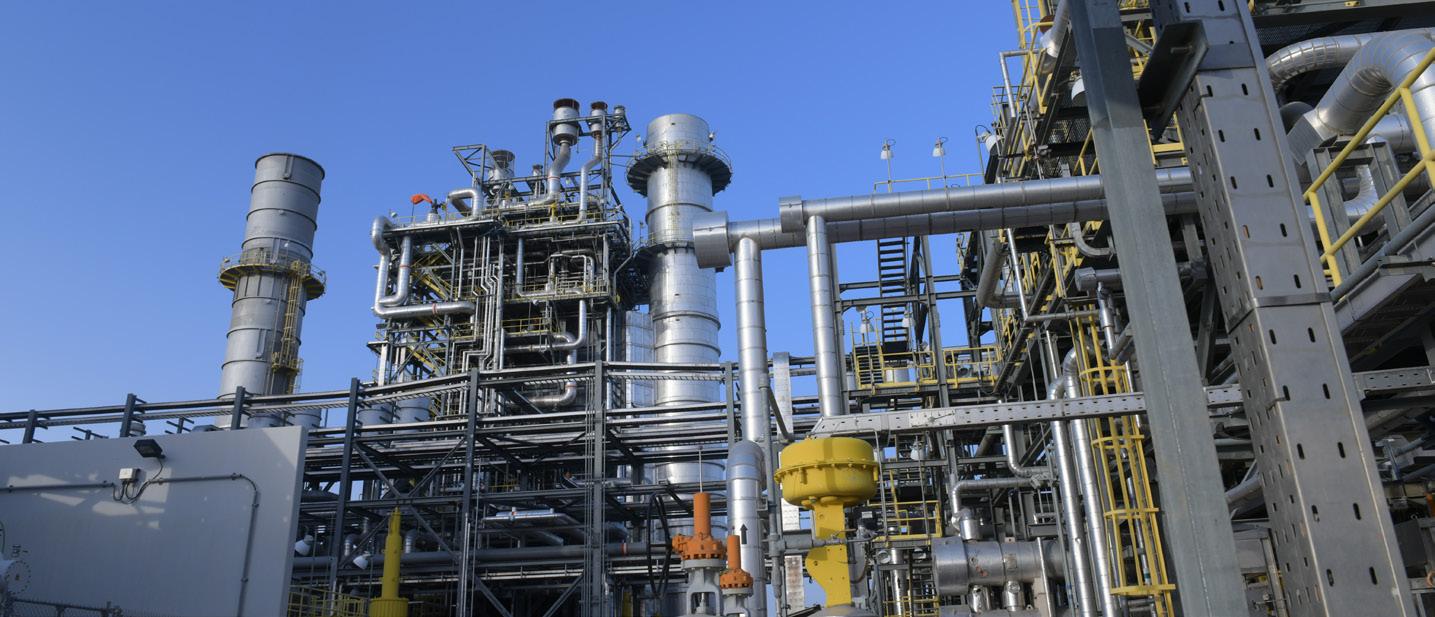
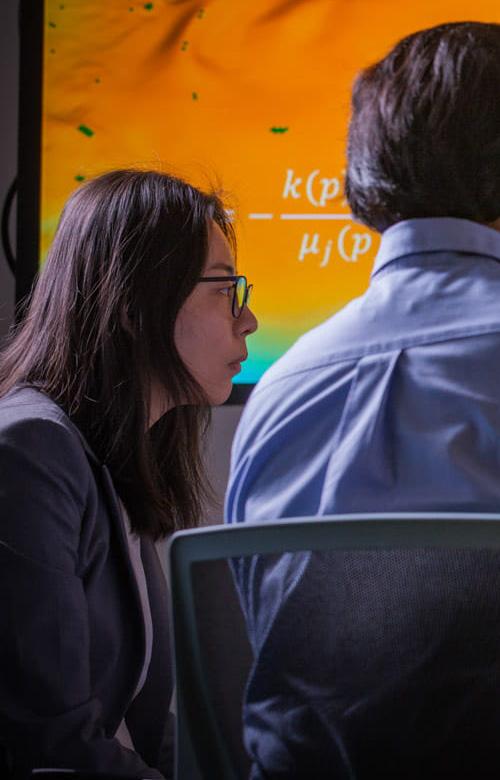
AI and Big Data, we are committed to maintaining our leadership position in meeting the world’s escalating demand for reliable, affordable, and environmentally conscious energy solutions.
How Aramco use AI and Big Data
Utilizing AI and Big Data solutions can enhance diverse operations in the energy sector, fostering heightened efficiency, reliability, and sustainability. Aramco has committed to positioning itself as a premier digitalized energy enterprise, recognizing the pivotal role of industrial AI in realizing this objective. Presented below are five instances illustrating how Aramco harnesses the potential of these sophisticated digital technologies in practical applications.
Flare monitoring
Flaring occurs when hydrocarbon gases are released and combusted due to pressure buildup in pipelines and processing facilities. Aramco utilises Big Data to provide engineers with a comprehensive
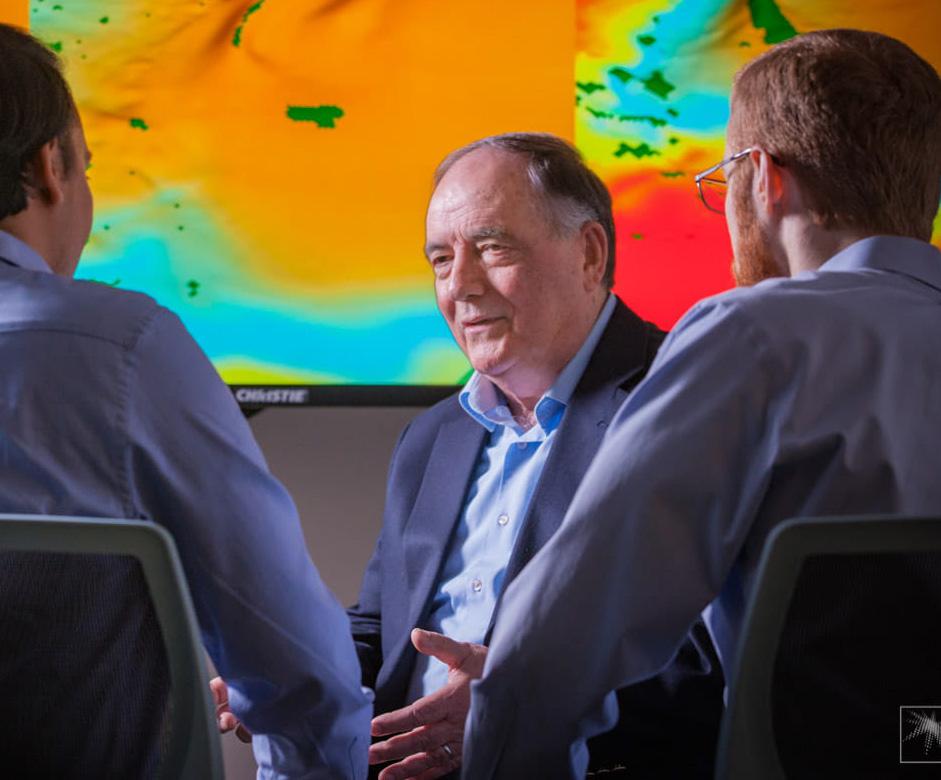
visualisation of the entire gas processing system, enabling swift identification of flaring sources and the generation of potential solutions. With access to 18,000 data sources for monitoring and forecasting flaring, Aramco compares real-time data with models constructed using diverse Big Data processing techniques. This allows their in-house-developed AI systems to anticipate when a facility might exceed flaring targets, enabling pre-emptive remedial measures. The integration of Big Data and AI has been instrumental in Aramco achieving over a 50% reduction in flaring since 2010, maintaining a flare volume of below 1% of total raw gas production for the past decade, thus establishing industry-leading standards.
Reservoir modelling
Reservoir simulation uses state-of-the-art digital visualization tools to model our reservoirs, and their management challenges, and thereby guide decisionmaking to achieve optimal development plans. For example, TeraPOWERS, which is Aramco’s reservoir and basin simulator, utilises Big Data to simulate the entire hydrocarbon system of the Arabian Peninsula, using models that are continually updated with new drilling and production data. Sophisticated algorithms then analyse this data to maximize our access to these hydrocarbon resources.
Camera-Based Well Space Out system
This innovative project utilises a platform connected to the Industrial Internet of Things (IIoT) to automatically space out the drillstring assembly, which is an
important component used to make the drill bit turn at the bottom of a wellbore. The platform consists of smart and waterproof high-resolution wireless cameras, and other sensors, that use AI and machine learning to process and analyse the video and imagery captured. These technologies automate and optimise the placement of the drillstring assembly — a critical step in the process of drilling new hydrocarbon wells, as correct placement allows for easy and fast shutdown in the event of a well control issue caused by unexpected changes in pressure.
Khurais oil field
At Khurais, one of Aramco’s largest oil fields, it has deployed 40,000 sensors to monitor more than 500 oil wells — creating the world’s first Advanced Process Control (APC) for a conventional oil field. Harnessing the latest advances in Big Data analytics, machine learning, smart sensors, and robotics, has delivered several significant benefits at Khurais. These include the development of an in-house AI solution for optimizing fuel gas consumption in boilers; using robotics to make maintenance operations safer, cheaper and more efficient; and deploying a pipeline management system to detect possible leaks using fibre optics as a sensor. These digital solutions have helped to achieve a 15% increase in oil production and a 100% improvement in troubleshooting response times.
Abqaiq plant
Abqaiq, which has been in operation for more than 70 years, is Aramco’s biggest oil processing facility and the largest crude stabilisation plant in the world. The digital transformation of Abqaiq has led to significant operational improvements in three key areas. First, the use of robots and smart drones to perform nearly a third of routine operations has reduced the reliance on manual field checks. Second, the introduction of machine learning and AI algorithms has enabled the automatic adjustment of the oil stabilization process, leading to increased power generation performance and a reduction in CO2 emissions. Third, the expanded use of data, analytics, and predictive modelling, has helped engineers to anticipate potential system failures more effectively.
Revolutionising Oil and Gas Operations with the Power of Digital Twins
Nate Bridges, Oil & Gas Specialist at NavVis explores how digital twins are reshaping the oil and gas industry, from enhancing safety and efficiency to accelerating growth and innovation
Oil and gas companies are perpetually innovating to enhance safety, increase accuracy, save time, and reduce costs. This is achieved not only by redefining production capabilities and advancing clean energy technologies, but also through introducing transformative technologies and efficiency-boosting practices in their operations.
However, there is immense potential for future innovation, as many companies in the industry are still utilising traditional methods and older technologies. This presents a significant opportunity to usher in a new era of technology advancement and modern methodologies that could revolutionise the entire industry.
For example, current methods of physically searching and manually documenting a site – still a common practice in the sector – are time-consuming, expensive and introduce unnecessary safety risks. A lot of process drawings are schematic, so it can be labourintensive to simply locate a specific area. However, when producing a digital alternative, it can still take organisations more than a year to capture a site if they rely on the more traditional static scanning technologies. This means data from the beginning of the project can already be outdated before the project is over. For scanning technologies to be truly effective, they need to be fast and easy to update and rescan. Capture also needs to be scalable, so that it can be done across multiple sites, enabling organisations to conform to more efficient ways of working.
This is where cutting-edge reality capture technologies, such as digital twins, come to the forefront, revolutionising the way companies operate. Digital twins – the output –enable organisations to replicate physical assets within a digital environment, allowing for accurate as-is conditions, remote collaboration, and detailed analysis. Such a transformation offers unique insights into how best to enhance, expand, and optimise operations, irrespective of geographic constraints. Here, we explore the impact of outdated and inefficient technology solutions on the innovation capacity of the oil and gas industry. Digital twins can be pivotal in ushering in genuine innovation, and this article will offer insights on how organisations can implement novel strategies to fast-track their plans.
Outdated technology is holding the industry back Outdated technology is one of the key factors preventing parts of the oil and gas industry from unlocking its true potential. Oil and gas sites are constantly evolving, and it can be difficult for an organisation to plan efficiently without accurate and up-to-date virtual information that reflects the physical reality.
Laser scanning is a key technology that the industry has embraced in a bid to gain a clear understanding of their sites. But while popular methods of laser scanning provide an organisation with remote access to a site – and are a step forward from having to physically walk around the entire location – the traditional approaches in the sector have their own challenges. They can be difficult to implement at scale and depend on many hundreds or even thousands of individual scans.
A laser scan is a snapshot in time and the longer it takes to secure that snapshot, the less value it can provide to businesses. What significant parts of the oil and gas sector lack at the moment are solutions that work reliably and quickly so businesses can have continuous access to the accurate data they need to successfully operate, maintain, and develop their site.
Failure to leverage more innovative technology can lead to missed opportunities for streamlining processes, reducing costs, and maximising results. It can also hamper decision-making, as data analysis and insights become more time-consuming and prone to human error.
Enhance operations with digital twins
As mentioned, of the best ways oil and gas companies can leverage
technology to enhance their operations is by creating “digital twins” of their facilities. A digital twin is a virtual replica or simulation of a physical asset, such as drilling rigs, production facilities, pipelines, petrochemical plants, refineries, and even entire oil fields. Creating a digital twin allows organisations to bring this physical asset into the digital world, so they can determine how best to develop, expand, and optimise the asset.
Digital twins play a large role in both the maintenance and optimisation of a physical asset. They enable real-time monitoring and analysis, providing a comprehensive view of the asset’s performance and
condition and allow for both predictive maintenance and early detection of anomalies.
Digital twins can also be a significant part of the exploration process, allowing oil and gas companies to simulate and model complex reservoirs. By integrating geological and production data, as well as real-time monitoring, companies can, for example, optimise drilling strategies, predict production rates, and improve hydrocarbon recovery. The technology can then facilitate real-time adjustments and optimisation of production processes, helping to maximise output and minimise operational costs.
Along with helping companies get the most out of their assets, digital twins have the potential to aid the wellbeing of their workforce through safety planning and training. The technology enables companies to simulate various scenarios and assess potential risks associated with operations. By creating virtual replicas of their facilities and equipment, companies can conduct virtual safety drills, train employees for emergency situations, and develop robust risk-mitigation strategies.
Best way to create digital twins
The most efficient way to produce a reliable, up-to-date digital twin of a given site is by using advanced mobile

laser scanning. This innovative form of mapping technology uses simultaneous localisation and mapping (SLAM) algorithms and cloud-based processing to enable reality capture at the speed of walking as well as more automated processing and alignment. This approach provides a more complete digital representation of the space in much less time than any traditional versions of scanning methods could realistically achieve.
Plant safety can be improved by limiting the amount of people and time on-site for data collection, meaning workers don’t need to be sent to dangerous or remote locations until they are fully trained and prepared. Producing a copy of the site using mobile mapping can improve project performance and employee productivity, both in the design phase all the way through to informing
the supply chain in the operations phase. For example, using the NavVis VLX mobile mapping system, one of Australia’s leading oil and gas producers was able to capture its fleet of facilities across the Australian continent comprehensively – an area covering around three million square metres.
By using VLX, the oil and gas producer can capture its assets three times faster than would be the case with a terrestrial scanner, while still producing highly accurate measurements. And with the VLX data, anyone can open a 360° view and check measurements quickly, all from their desk. This ability to check measurements for all facilities in a single system is still very rare in the oil and gas industry and can dramatically change the way oil and gas facility owners operate.
Accelerating growth
Legacy systems and processes hinder experimentation, data-driven decision-making, and the implementation of transformative technologies. Consequently, many firms find themselves grappling with the implementation of their innovative digital twin strategies, primarily because of the lack of rapid and comprehensive data capture at a scalable level.
The oil and gas industry is at the beginning of its digitisation journey, and companies need to consider how the technologies they implement today will lay the foundations for processes and technologies of the future. This will help organisations boost project resilience as well as provide good insight into infrastructure and assets and seamlessly accelerate business growth.
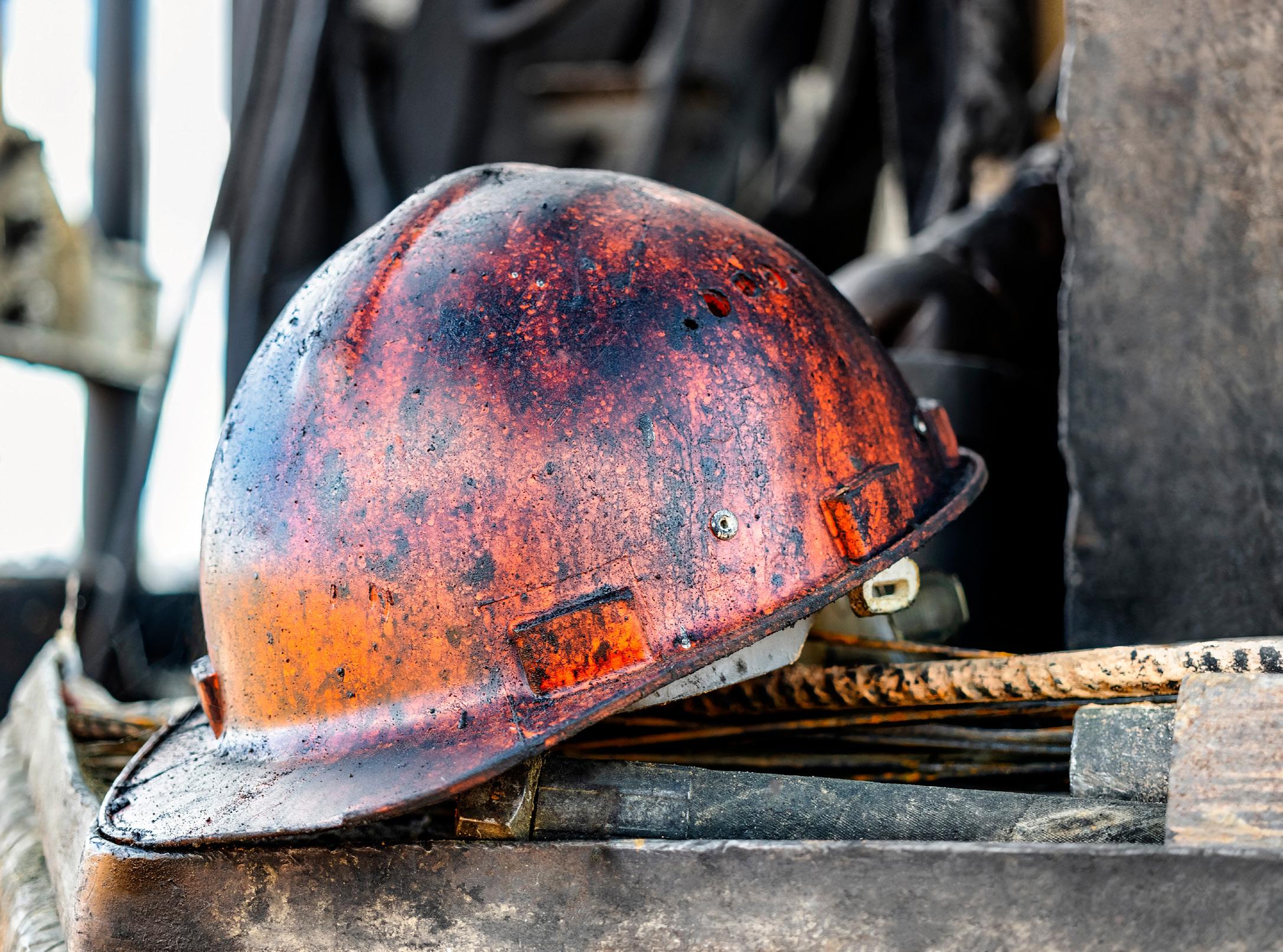
Assessing the Oil and Gas Sector’s Cyber Preparedness
As cyberattacks escalate in frequency and sophistication, Siemens Energy underscores the urgent need for enhanced cybersecurity measures in the oil and gas industry, highlighting the imperative to protect critical systems, data, and personnel against evolving threats to ensure operational resilience and safety
Cybersecurity threats pose a significant risk to the oil and gas industry, with potential consequences ranging from compromised data integrity to jeopardising human lives. The recent ransomware attack on U.S. pipeline operator Colonial Pipeline highlights the escalating frequency and sophistication of such attacks, underlining the urgent need for enhanced cyber resilience measures across the sector.
According to experts, the vulnerability of oil and gas companies to cyberattacks extends beyond digital applications to encompass information systems (IT) and operational technology (OT). In light of this, Siemens Energy stresses the imperative for immediate action to safeguard critical systems, data, and personnel against cyber threats.
Ahmed Bakr, a senior cybersecurity officer (CSO) based in Jeddah, Saudi Arabia, underscores the industry’s susceptibility to cybercrime, emphasising the pressing need for proactive defence mechanisms. The Colonial Pipeline incident serves as a stark reminder of the devastating impact a single cyberattack can inflict, with the company compelled to halt operations along its extensive pipeline network, incurring significant economic losses.
A study commissioned by Siemens in 2017 revealed alarming statistics regarding cyber incidents in the U.S. oil and gas sector, with 68% of respondents reporting incidents of confidential data breaches or operational disruptions within a year. However, many organisations demonstrated a lack of awareness regarding the associated risks, highlighting the urgent need for heightened vigilance and cybersecurity preparedness.
Bakr underscores the evolving motives of cyber criminals, who are increasingly driven not only by financial gain but also by the desire to inflict physical harm and disrupt critical operations. Consequently, ensuring the security of operational technology assumes paramount importance in protecting human lives and preserving essential infrastructure.
The concept of layered defence, characterised by overlapping cybersecurity controls, emerges as a cornerstone of effective cybersecurity strategy. Siemens Energy advocates for a comprehensive approach to cybersecurity, encompassing product development, project execution, and supplier partnerships, to uphold stringent industry standards and fortify defences against evolving threats.
Siemens Energy offers a suite of cybersecurity solutions tailored to the unique challenges of the oil and gas sector, ranging from product certification to comprehensive consultancy services. By leveraging its global expertise and strategic partnerships, the company equips oil and gas companies with the necessary tools and knowledge to navigate the complex cybersecurity landscape effectively.
Ahmed Khalifa, technical sales manager for Cybersecurity in Dubai, highlights the importance of employee training and awareness in mitigating cybersecurity risks, citing studies that attribute a significant proportion of data breaches to human error. By fostering a culture of cybersecurity awareness and upskilling personnel, organisations can bolster their defences against cyber threats.
Despite the inherent risks associated with digitalisation, Siemens Energy contends that the benefits for the oil and gas industry far outweigh the potential drawbacks. Leveraging digital technologies such as artificial intelligence (AI) and remote monitoring enhances operational efficiency and asset management while mitigating cybersecurity risks.
AI-driven solutions such as Plant Security Monitoring represent a proactive approach to cybersecurity, enabling oil and gas companies to detect anomalies and deviations in plant behaviour indicative of cyber intrusions. By harnessing the power of digitalisation and AI, Siemens Energy aims to empower oil and gas companies to safeguard their critical infrastructure and embrace the transformative potential of digital technologies.
Enhancing Wellbore Integrity with Intelligent Deployment and Advanced Well Architecture
Conventional multi-zone completions in the world of offshore oil and gas often use a technique of cementing the wellbore space between the casing and the formation, and then perforating the cement to initiate production. This process is time-consuming, costly, and inefficient. Advanced Well Architecture (AWA) optimizes the well construction process, reducing risk and variability to provide operators with a more cost-effective basis for an open hole intelligent completion design that can be adopted for single or multizone scenarios.
The problem with cement
Cementing wells comes with a set of risks. In deep well environments, achieving cement seal integrity is challenging for a multitude of reasons, including losses, a depleted reservoir, quality of cement, and equivalent circulating densities limitation. There is also a prohibitive cost to pay in terms of sustainability both from the cement itself – which is carbon intensive in production – and from the explosives used to perforate the casing. Due to the need for installation of an even smaller casing within the casing that has been cemented and perforated, the net result is a relatively small production area.
Advanced Well Architecture (AWA)
The completion concept of Advanced Well Architecture (AWA) drastically reduces risk and variability in operations by delivering flexibility to the number of zones, thus mitigating for reservoir uncertainties, and optimizing well construction through standardized structural design.
AWA is comprised of multiple components, with award-winning technologies like the Welltec Annular Barrier (WAB) at the heart of the concept. Instead of drilling
an oversize hole to accommodate cement, a new wellbore can be drilled to the required dimension and the production casing then utilizes a WAB to ensure zonal isolation. Zones can then be controlled by opening and closing the flow valve which is mounted on the downhole actuator in the upper completion. This system provides full zonal isolation and zonal control, delivering a far simpler completion than could otherwise be achieved in a multizone cement scenario.
The architecture of the architecture
In addition to the industry proven WAB for zonal isolation, AWA is comprised of the Welltec Flow Valve (WFV) with Dual Position (DP) for inflow control, with the option for addition of a Downhole Actuator (DHA) onto the upper Intelligent Completion (IC) extended inner string, which engages with and mechanically shifts open the WFV-DP just prior to landing off the upper completion, providing flow access to the previously isolated zones.
The WFV is a full bore valve that can be used for both production and injection purposes within the lower completion, and its rugged design enables rotation during liner deployment. With specially designed inlets and sealing system, the WFV is qualified to open and close multiple times under differential pressure whilst maintaining flow, for both injection and production. The full bore design of the WAB provides high pressure zonal isolation and creates a completion which facilitates more efficient and smooth intervention in the future.
The DHA is a robust, bi-directional shifter, designed to be deployed on the tailpipe of the upper or intermediate completion to facilitate the mechanical opening and closing of the WFV. The DHA provides controlled access to multiple zones isolated during the safe deployment of the upper and intermediate completion. Run in combination across an open hole reservoir section, this system facilitates full bore, cementless, zonal isolation and control.
Tried and tested in the most challenging deepwater setting
The operational flexibility and equipment standardization provided by AWA has been a key factor in proving the concept’s worth in some of the most challenging environments. Of more than 50 completions made on behalf of multinational operator Petrobras, several AWA systems have been installed in the ultra-deepwater Brazilian pre-salt. Reservoir uncertainties and limited data can make it difficult to predict the number of zones required. Additionally, in the deepwater case, severe loss scenarios made it challenging for initial intelligent completion designs as they were not compatible with the managed pressure drilling (MPD) techniques being applied to drill the well.
Petrobras decided to design and implement a new intelligent completion
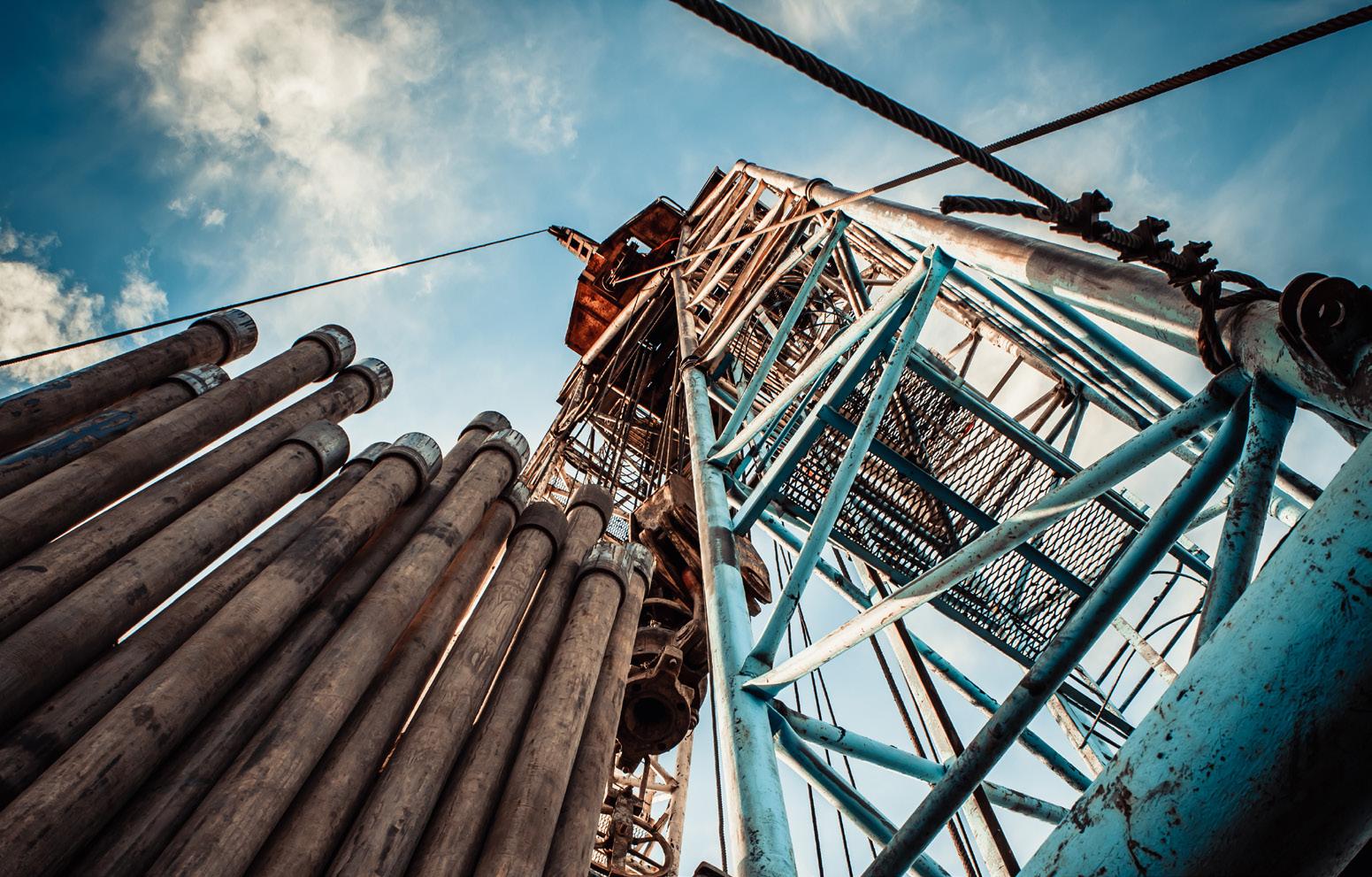
design to reduce the time and cost per well. Usually, the well architecture associated with intelligent completion wells in pre-salt areas would preclude a separate run for perforation after cementing. AWA allows the steps of cemented then perforated casing to be skipped and facilitates a single operation for deployment of a simple and reliable full completion – this totally eliminates the cost of cementing the reservoir section.
Utilizing the AWA system, Petrobras was able to tailor their completion design as per their required specifications and gain several benefits. The open hole intelligent completion applied with the AWA system enabled operational flexibility and equipment standardization, meaning the same completion design could be adopted for either a single or multi-zone completion. This further allowed the operator to optimize and finalize the completion design based on reservoir data gathered during the drilling and logging phase, essentially at a much later stage than normal, thus giving them best production capability with full flexibility and minimal inventory.
In this case, a directional injection well was constructed in approximately 15 days less than the most recent configuration well (including drilling and completion). In a more complex five-phase well scenario, the savings would be in excess of 25 days.
Continued product development – Welltec Expandable Anchor (WEA)
Metal Expandable Packer (MEP) technology developed by Welltec has an established and proven track record across the globe. The forthcoming introduction of an all-metal Welltec Expandable Anchor (WEA) will assist operators at various stages of drilling and completion, offering a reliable, robust solution for application as a liner hanger, anchor, or tie-back.
With the modular addition of metal slips, the expandable anchor can be incorporated into designs to help overcome challenges with highly deviated wells, high-pressure-high-temperature conditions, challenging geometry of new or existing wells, enabling hang-off and anchoring of the liner or casing with a previous casing or open hole.
The high expansion capability of the new product helps cover a wide range of applications with one solution, covering different size casings. The WEA is qualified to API19LH and V0 high pressure and temperature standards, which can be used for injection and production wells with the possibility of modification to address specific requirements.
Walking the data tightrope
With increasing adoption of digital twins across the industry, the quality and ongoing maintenance of data is coming under the
spotlight. Rob
Kennedy, Global Director – Digital Twin Solutions, Wood and Shirley Ike, Global Director – Data Management Consultancy, Wood explain that with many competing drivers at play, achieving and sustaining a valuable and trusted data foundation for an asset requires a balanced approach.
The last couple of years has seen most of the oil and gas majors scaling digital twin solutions across their global assets. In addition to creating a data foundation for their assets, these digital twins are providing insights that de-risk project delivery, reduce maintenance burden, safeguard production, and reduce emissions.
When you consider that operators’ portfolios contain a mix of new, recent, and aging assets, with some even delivered in the days when paper copies were the norm, it is no surprise that this widespread adoption of digital twins has started to highlight numerous data challenges.
While the industry has generally been effective at managing dynamic operational data, for example by utilising process data historians and maintenance management systems, it is the lessdynamic engineering and asset data, 3D models and reality capture data that are proving to be the most challenging.
Standards only get you so far
The industry is collaborating to develop and mature data standards and interchange formats. Not only do these standards enable a level of consistency and predictability across the supply chain, but they also enable operators to decouple

data from authoring systems and proprietary solutions.
Current data standards are tailored to capital project delivery and the subsequent handover to operations, but not the operating phase itself. They define the data to be collected for each type or class of equipment, with the aim of achieving a complete and compliant dataset at the point of handover. But trying to sustain this level of data quality through decades of operations is impracticable.
Finally, while data handover standards contain attributes to indicate the criticality of certain equipment, a framework for applying similar criticality ratings to individual data attributes is currently lacking.
Considering data criticality
The operations phase requires an unwavering focus on keeping people safe, reducing emissions and minimising expenditure, all while maximising reliability and production. In this context, it’s not always apparent what data is the most critical. Is it the data that can enable the greatest potential impact on the bottom line? Or the data that can help you to mitigate a risk? Or is it the data that could have the greatest potential consequence if it were incorrect and led to an incorrect decision?
The criticality of data will change depending
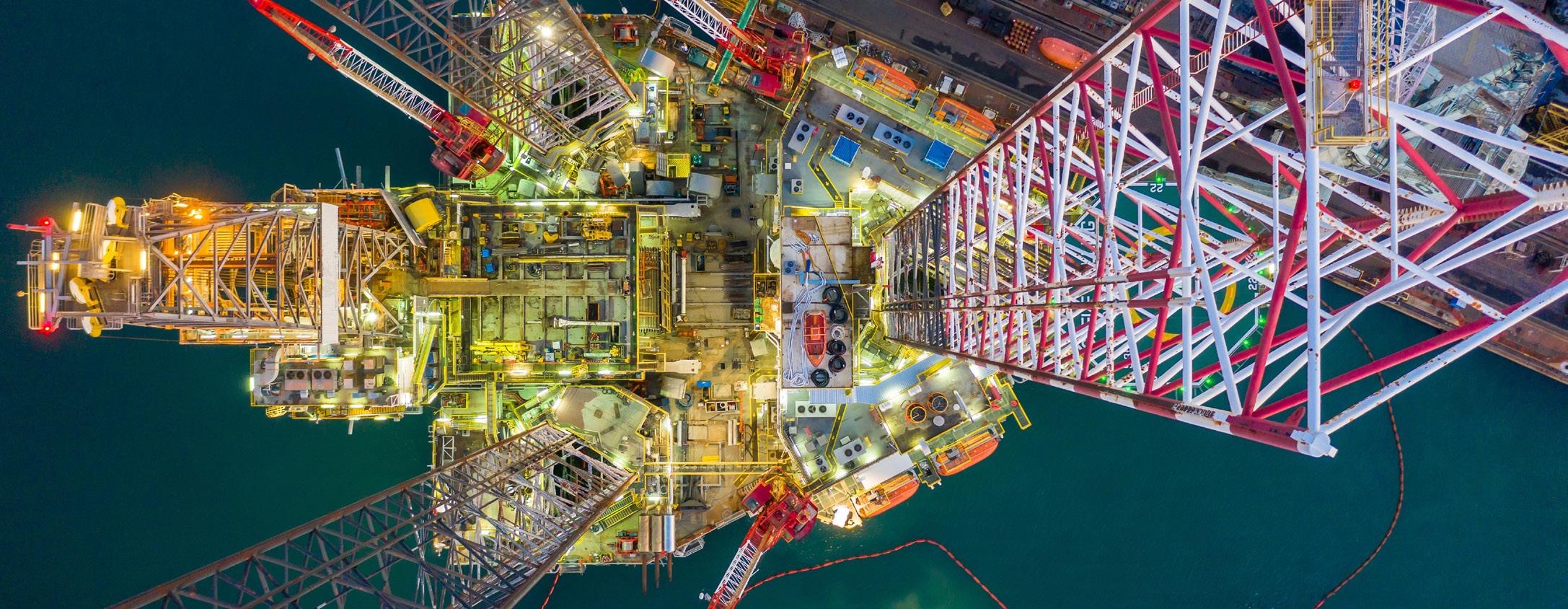
on the particular asset, the lifecycle phase, ongoing activities, and risks being managed. For example, on a recent project Wood deployed a reliability solution that supported removal of over 75,000 hours of maintenance, but this solution was wholly dependent on us integrating crucial sampling and monitoring data from ten standalone systems.
Given the dynamic nature of operations, it is simply not practicable to foresee all the data you may need and to know it will be up to date all the time. But might it be possible to define and focus efforts on a core set of data most critical for asset operations, and likewise identify other data sets as less critical?
Maintaining and sustaining digital assets
Current industry philosophies towards data maintenance are varied, ranging from the blanket approach of striving to keep all data up to date, to extremely targeted approaches that only update data on request when it is needed. Anecdotally, regardless of the approach there is still a widespread challenge with keeping critical data up to date, particularly when changes are made to the physical asset.
Just as how physical assets are maintained, might it be beneficial to take a more balanced
approach to maintaining digital assets that strikes a balance between criticality, reliability, the potential consequences of failure, and cost?
Reframing users’ relationship with data
Digital twin users are exposed to large amounts of data, information, and insights. While only some of it influences decisions about how to operate and maintain the asset, our experience shows that any data errors (even those that are not critical) can cause user distrust of the entire digital twin.
To support a more balanced approach to data management, it is imperative that users have visibility of the provenance of each piece of data, including when it was last updated and validated, enabling them to gauge its reliability. We have found that supporting this with a process that enables users to query data and request updates helps to build trust and gain buy-in from users, enhancing digital twin adoption.
Conclusion
Digital twin solutions are a powerful way for organisations to gain insights, improve decision-making and optimise the operation and maintenance of their assets. However, realising these potential benefits not only requires the right technology and data, but also needs operating teams to integrate them effectively into their work.
At Wood, we take a transformation-led approach to digital twin that combines decades of project delivery and operating experience with deep domain knowledge and digital expertise. Moving to the balanced data maintenance approach outlined in this article requires this clear understanding of users, the jobs they perform and the decisions they need to make.
Just like we do on their physical counterparts, we need to focus the maintenance of our digital assets on the areas that have the biggest impact on safety, risk, reliability, and the bottom line. Only then can we sustain digital twins and the value they deliver over the long term.
Digital twin is just one of Wood’s core digital solutions that we are applying to transform industry. Discover how we can solve your data challenges and decode your digital future: woodplc.com/solutions/digitalisation
Can the Industrial Sector Use Digital and AI as a Competitive Advantage?
In the rapidly evolving landscape of AI integration, Heather Cykoski, Senior Vice President, Industrial and Process Automation, Schneider Electric highlights the transformative power of human-centered AI, emphasizing trust, collaboration, and maximizing opportunities to propel industries towards a sustainable and efficient future
It is quite the understatement to say that AI experienced tremendous growth over the last year and a half, charged by the maturation of large language models (LLMs). Every industry has been affected—whether directly by use cases that are ready to go to market or indirectly by transformations that are happening fast and furiously to ensure business sustainability and growth in the AI world.

While Schneider Electric has been a leader in digitization and early applications of artificial intelligence (AI), I like to think of AI as already being everywhere. It’s in our living rooms, our homes, our buildings, and our factories. We have watched AI progress exceptionally with unprecedented speed. Now the question most companies have to ask themselves is not, “When are we going to leverage AI.” Instead, it is, “How fast are we going to leverage AI?”
The industrial sector is not immune from this widespread AI buzz and figuring out what to do about it in a way that aligns to a company’s core business strategy. At Schneider Electric, we innovate ways already-digitized applications can become AI-infused to deliver even greater insights and business intelligence from data. Harnessing decades of data, some form of AI is inherent in all Schneider technologies, whether on the plant floor, inside an asset, or part of an entire enterprise. From machine learning algorithms that serve up predictive analytics to integrated LLMs that act like copilots, AI is accelerating Schneider’s industrial automation and energy
management playbook.
For instance, Schneider recently entered a memorandum of understanding (MOU) with Hy Stor Energy to advance integrated, off-grid green hydrogen production and energy storage at scale. Though this MOU, Schneider is providing the company not only with automation and safety solutions and AVEVA process operation platforms, but also with AI optimization software that improves weather analysis, enables predictive operations, and finetunes digital energy management solutions. This digital AI-driven coalition will enable Hy Stor Energy to deliver 100% carbon-free energy to its customers, providing safe and reliable renewable energy on-demand.
For any AI project to succeed, there are three elements that must be considered: The human element of AI
At CERA Week earlier this year, Schneider Electric CEO Peter Herweck said, “As far as I am concerned, every AI begins and ends with the human
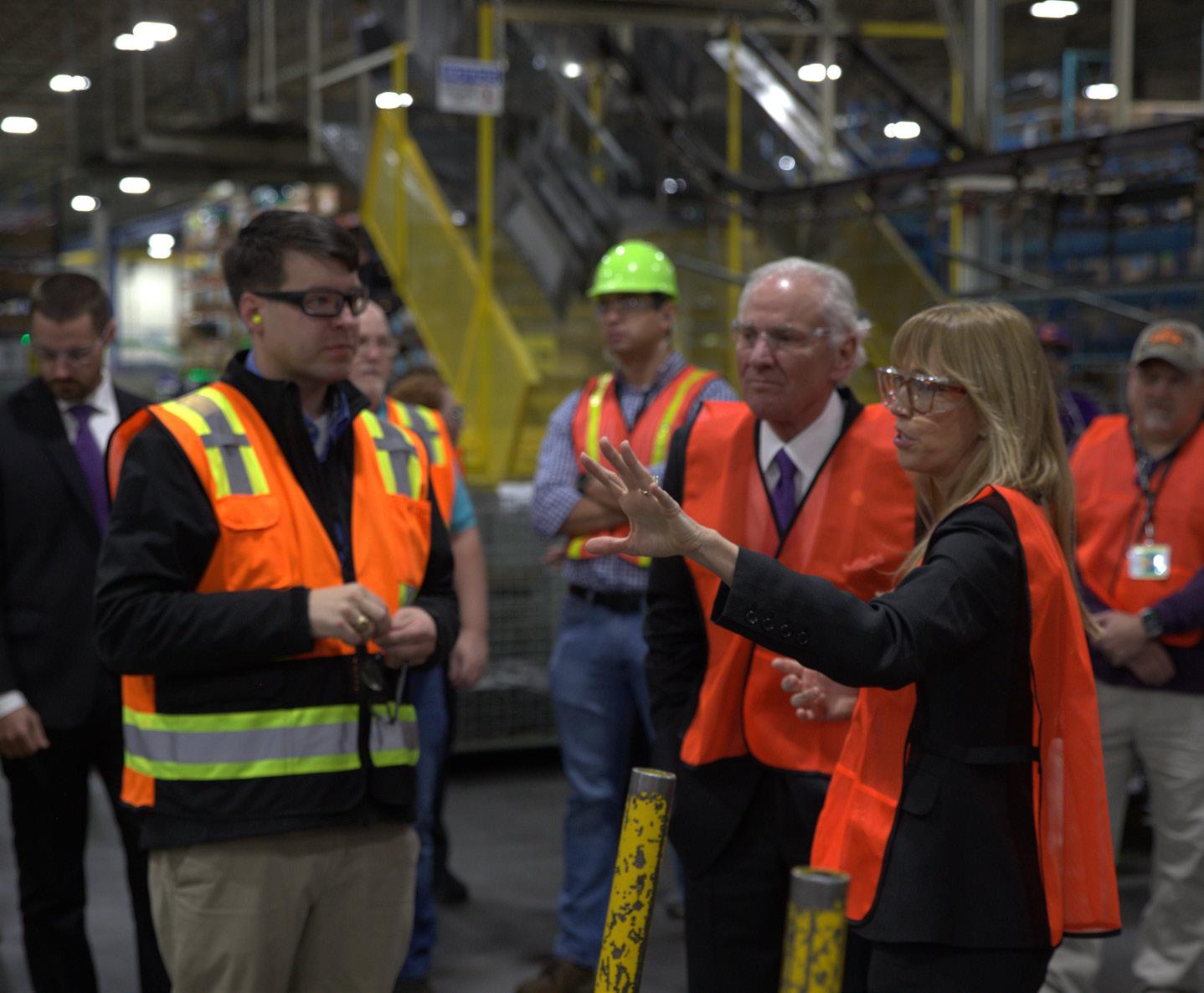
element”. He describes this aspect of AI as human intelligence with AI, or “HI with AI.” Hi, humans!
First, humans are essential in the loop of building and training AI models to ensure greater accuracy and relevance of the data feeding the models, drawing on their very human domain experience. Second, humans are at the core of the workplace change that is necessary for ensuring a successful AI roll out. This kind of change management could mean bringing new people into the workforce or supporting educating and upskilling the existing workforce to help accelerate today’s AI advancements. Focusing on this crucial human element creates a more efficient operation, not only for Schneider as we leverage these innovations in our own factories, but also for our customers. Keep in mind that employees across generations will want to turn to AI as an easy button of sorts. I personally grew up watching “The Jetsons,” where George Jetson could just push some buttons that took care of everything. Wouldn’t that be cool if employees could have the Jetson equivalent of AI in a very safe, responsible, and a sustainable way?
Without change management on AI integration and usage, even the best and most seamless AI models are destined to fail. That brings up my second point: AI will never succeed unless it is trustworthy.
Trust in AI
For a mission-critical sector, such as energy, trust in AI is imperative and must be treated at the same level of cybersecurity. While the quality of the data used to build and train the model is the starting point, trust in AI also is borne from a secure-by-design approach. What does this mean? It’s simple. Cybersecurity protocols must be built into AI tools, solutions, and processes instead of being regarded as an afterthought.
Strengthening trust in AI also means protecting intellectual property and the enterprise’s crown
jewels. For the energy sector, this level of trust is paramount as the sector invests in R&D to create or mature new technologies and sources of energy needed to accelerate the energy transition.
For example, Schneider’s EcoStruxure Automation Expert is a software-defined industrial automation solution that creates a safe environment where customers can take data or pull assets from Schneider or other parts of their enterprise to make improvements throughout the operational lifecycle within a cybersecure environment.
Collaboration on AI projects
As I have said, AI is in everything that Schneider does. To be successful with full vertical integration, however, collaboration with partners is essential. In fact, collaboration is how to start to make AI transformations to remain competitive in an AI-first world.
For instance, Schneider is partnering with Intel for providing the AI modules as part of the aforementioned EcoStruxure Automation Expert solution. Working with Intel, we can push the boundaries of software-led automation to optimize industrial operations from design to maintenance. Indeed, partnership is a path forward for AI for many companies.
If you are a company, like Schneider Electric, that has been gathering data for decades, you have to make sure that you are contextualizing that data. That is an area where we also work with our customers as partners to ensure the data is empowering them to make the right decisions to solve their most pressing problems.
Maximize AI opportunities
There is no question that AI — done right — can level up productivity, operational efficiency, and agility by connecting automation hardware and industrial software to work together seamlessly, even if they come from different suppliers. The key to success is finding a partner with deep domain experience paired with industrial tech leadership to help you maximize the opportunities that AI presents for you, your business, and the future of both.
Harnessing Digitalization and Data Optimization in Upstream Oil and Gas
As Mark Venables explains, in the upstream oil and gas sector, the integration of digitalization and data optimization is revolutionizing operations, driving efficiency, safety, and sustainability to unprecedented heights.
In the dynamic and ever-evolving landscape of the upstream oil and gas sector, the integration of digitalisation and the effective utilisation of data have emerged as gamechangers, revolutionising traditional operational paradigms and driving efficiency, safety, and sustainability to unprecedented heights. As the industry continues to navigate through various challenges, including fluctuating commodity prices, regulatory pressures, and the imperative to reduce environmental impact, leveraging advanced technologies and harnessing the power of data analytics have become imperative for companies seeking to remain competitive and resilient in the face of evolving market dynamics.
Digitalisation in the upstream oil and gas sector encompasses a broad spectrum of technologies, ranging from Internet of Things (IoT) devices and sensors to artificial intelligence (AI), machine learning (ML), and advanced analytics platforms. These technologies enable realtime monitoring and control of operations, predictive maintenance, and optimisation of asset performance, thereby enhancing operational efficiency and asset reliability while minimizing downtime and reducing costs.
One of the primary advantages of digitalisation in upstream operations is its ability to streamline exploration and production processes through enhanced data-driven decision-making. By integrating data from various sources, including subsurface data, production data, and equipment sensor data, companies can gain deeper insights into reservoir characteristics, optimise well placement, and maximise hydrocarbon recovery
rates. Additionally, advanced modelling and simulation techniques powered by AI and ML algorithms enable more accurate reservoir modelling and production forecasting, mitigating risks and uncertainties associated with exploration and production activities.
In addition to optimizing reservoir management, digitalisation facilitates remote monitoring and control of offshore platforms and production facilities, thereby improving operational safety and reducing the exposure of personnel to hazardous environments. Through the deployment of IoTenabled sensors and predictive analytics, operators can proactively identify and address potential equipment failures or operational anomalies, minimising the risk of incidents and ensuring compliance with stringent health, safety, and environmental regulations.
Furthermore, digitalisation enables the implementation of predictive maintenance strategies, allowing operators to anticipate equipment failures before they occur and schedule maintenance activities during planned downtime windows, thereby maximising asset uptime and extending equipment lifespan. By transitioning from reactive to proactive maintenance practices, companies can reduce maintenance costs, optimise resource allocation, and enhance operational efficiency across their asset portfolios.
Another key advantage of digitalisation and data optimisation in the upstream oil and gas sector is their role in driving sustainability and environmental stewardship. By leveraging
advanced monitoring and control systems, operators can minimise greenhouse gas emissions, reduce flaring and venting, and optimise energy consumption across their operations. Furthermore, by utilising data analytics to optimise production processes and reduce water usage, companies can mitigate their environmental footprint and contribute to the industry’s transition towards a more sustainable energy future.
Moreover, digitalisation enables the integration of renewable energy sources, such as solar and wind power, into upstream operations, further reducing reliance on fossil fuels and lowering carbon emissions. By leveraging data analytics to optimise the integration of renewables and enhance energy efficiency, companies can reduce operating costs, enhance resilience to energy price volatility, and position themselves as leaders in the transition towards a low-carbon economy.
In conclusion, the adoption of digitalisation and the effective utilisation of data represent transformative trends in the upstream oil and gas sector, offering significant advantages in terms of operational efficiency, safety, sustainability, and competitiveness. By embracing advanced technologies and harnessing the power of data analytics, companies can optimise exploration and production processes, enhance asset performance, and drive innovation across the value chain. As the industry continues to evolve, digitalisation will play an increasingly critical role in shaping its future trajectory, driving value creation, and ensuring long-term success in a rapidly changing global energy landscape.
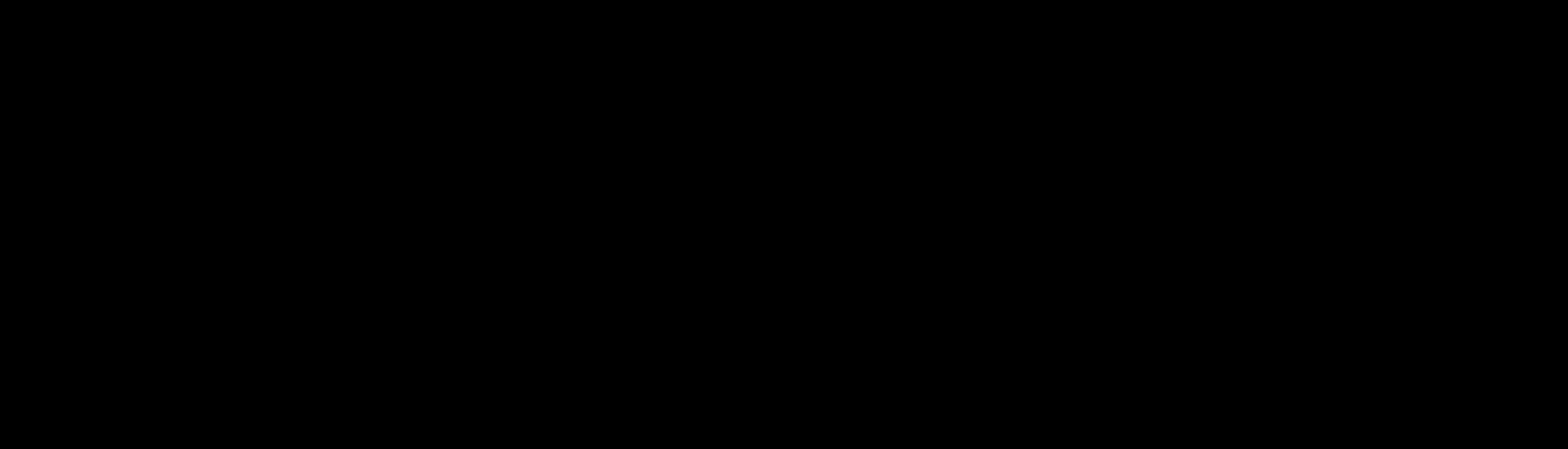
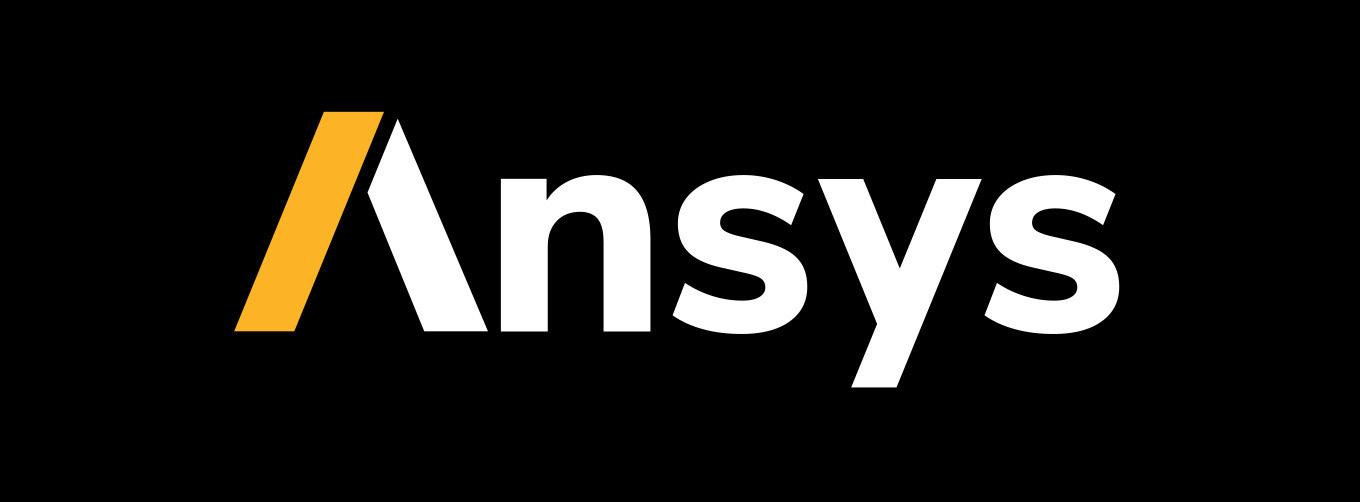
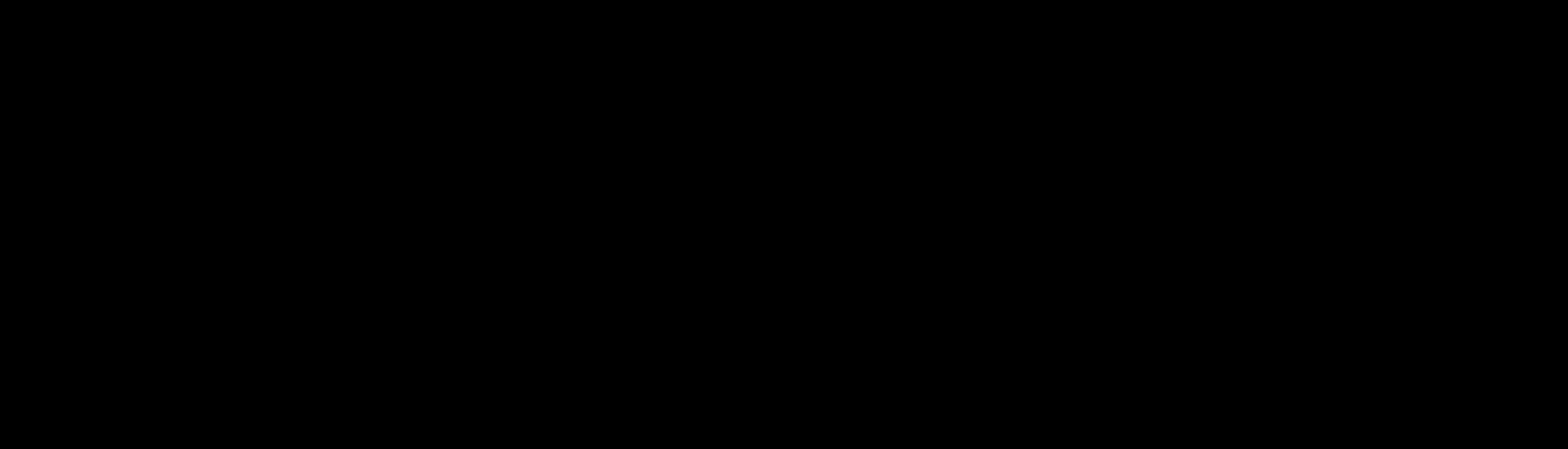
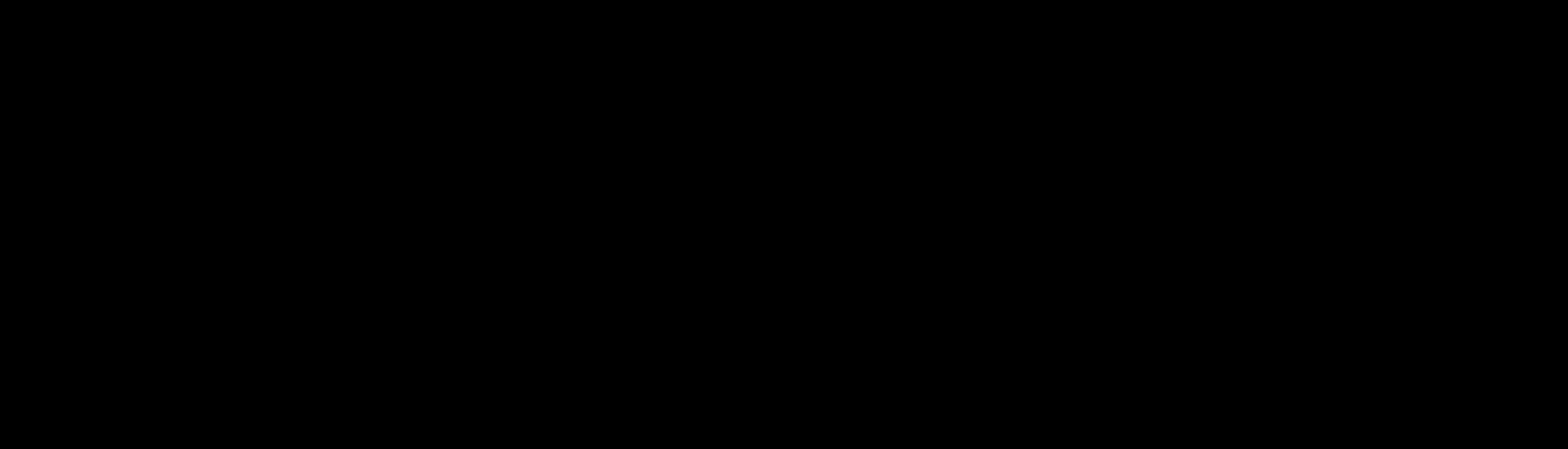
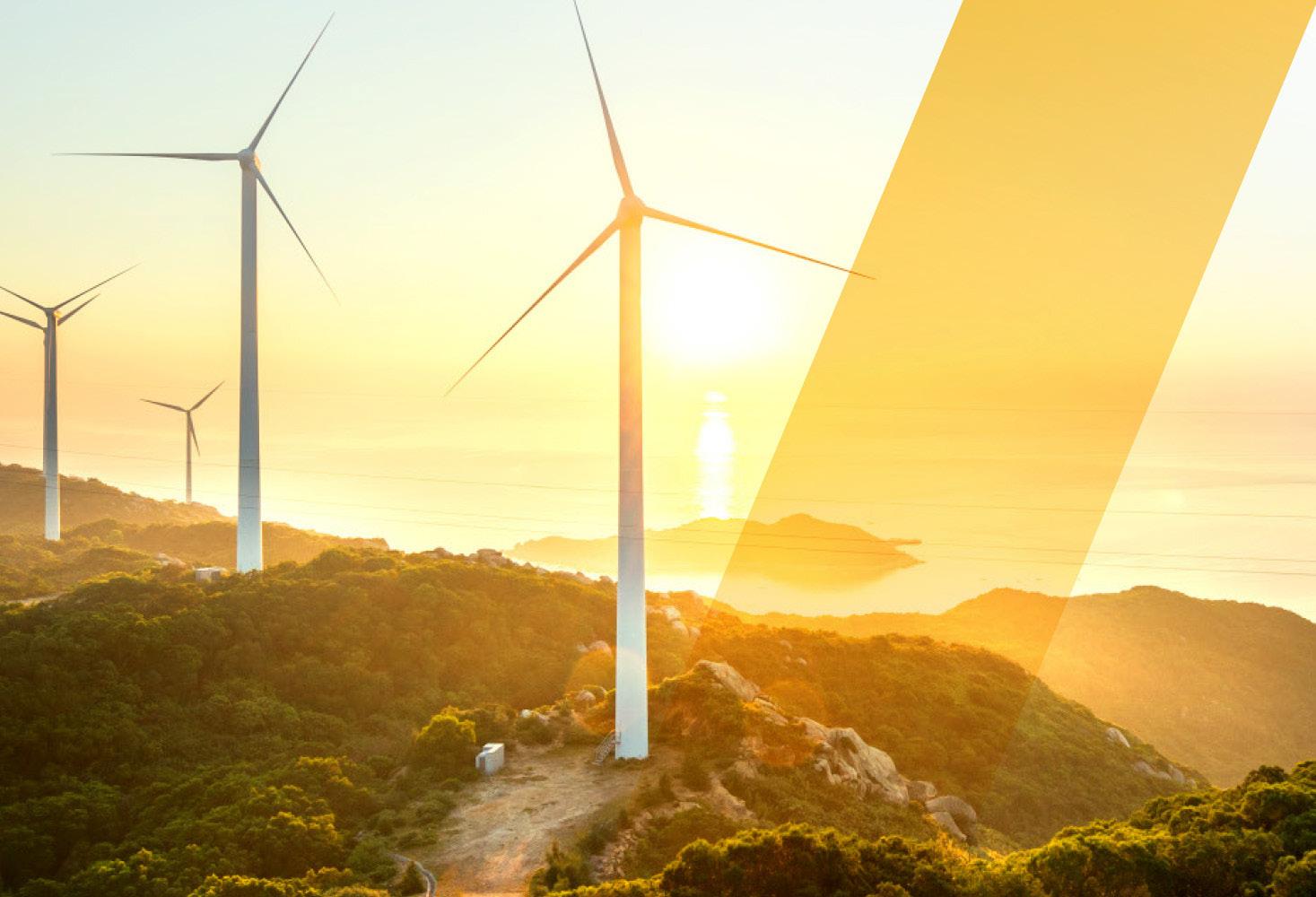
For over 50 years, Ansys software has enabled innovators to push boundaries with the predictive power of simulation. From sustainable transportation to advanced semiconductors, from satellite systems to lifesaving medical devices, our software will power the next great leaps in human advancement.
ANSYS COM
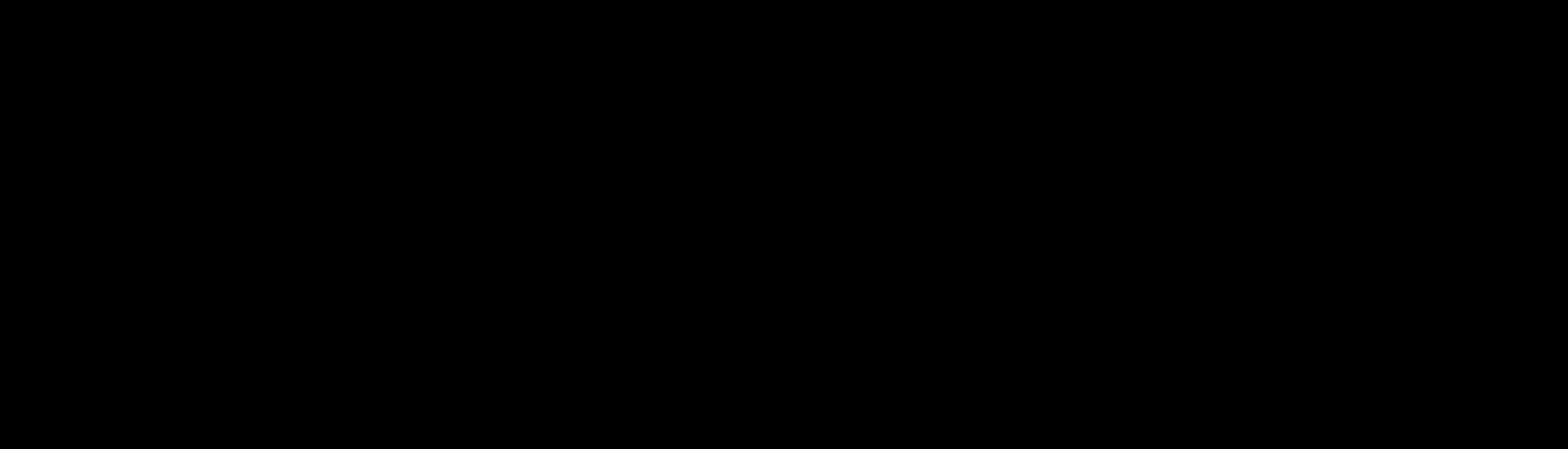
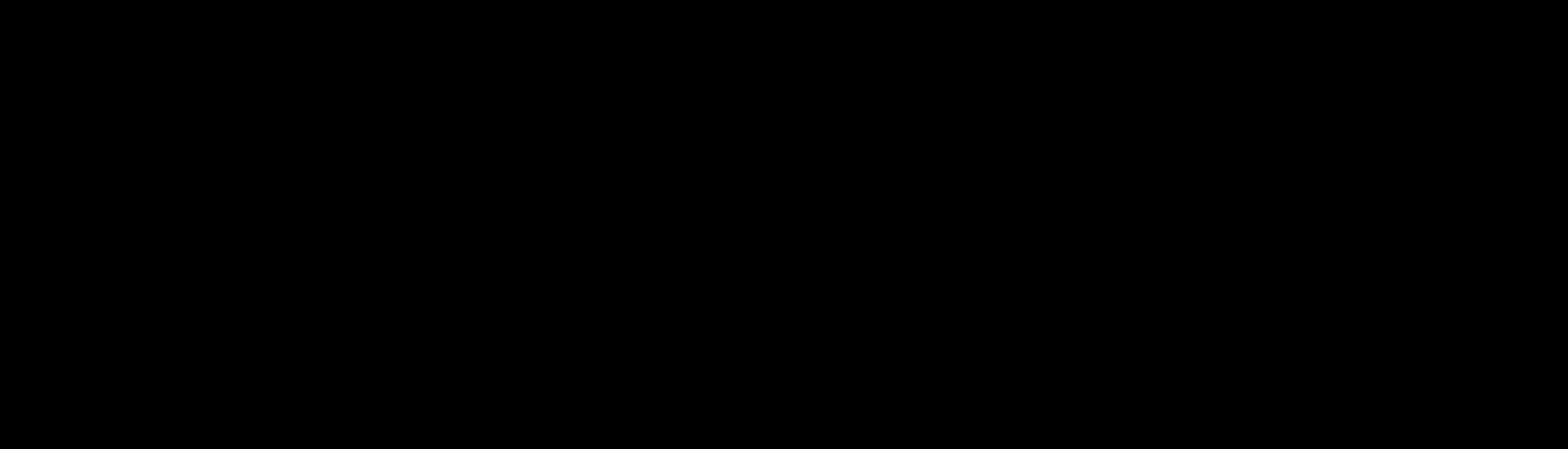
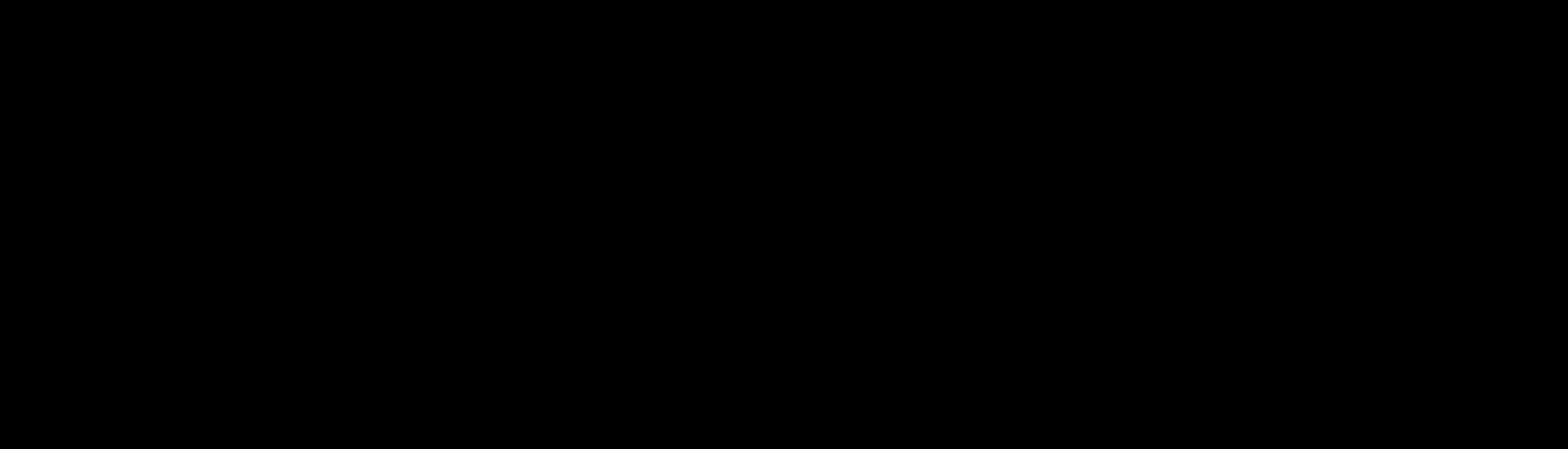




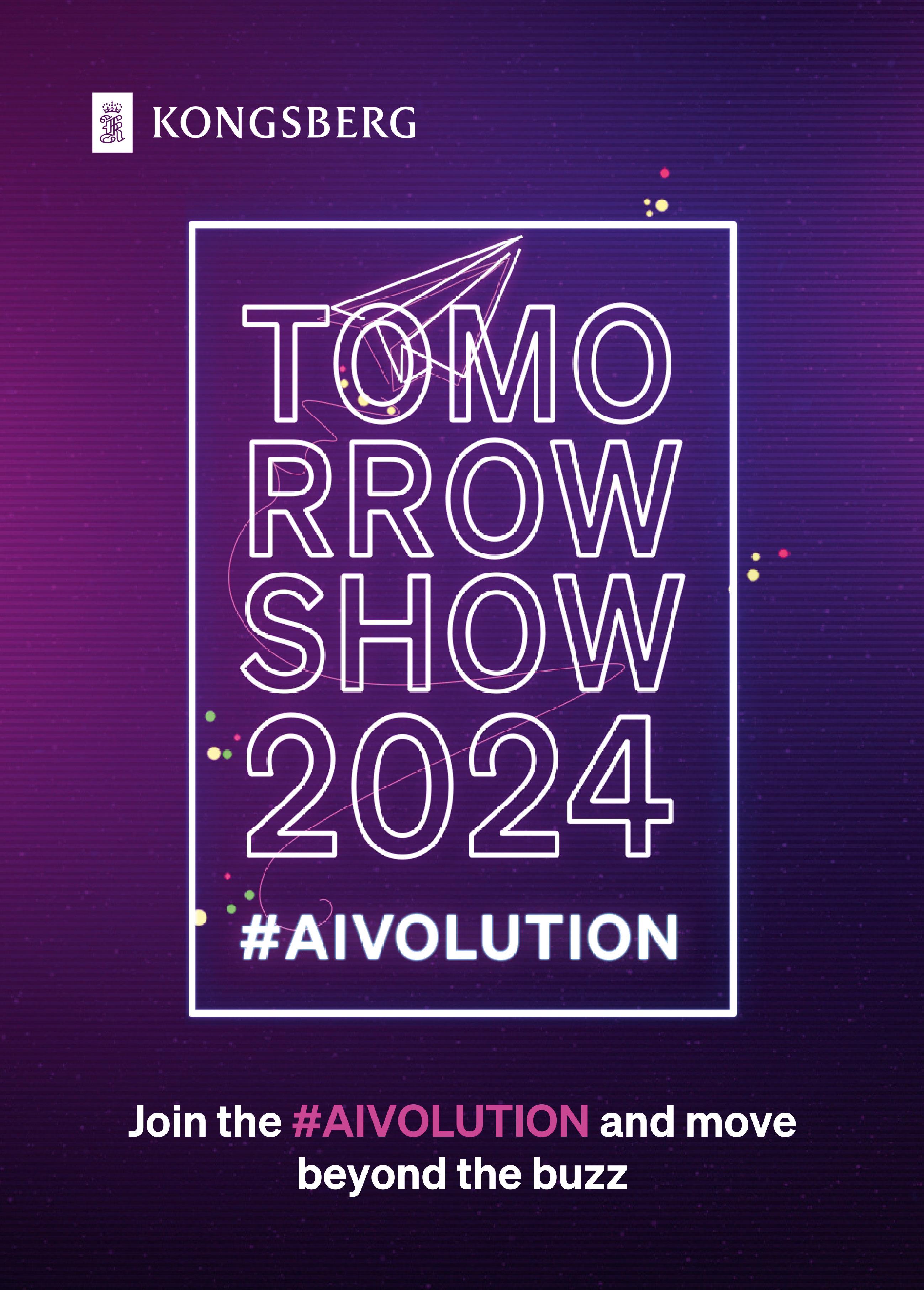