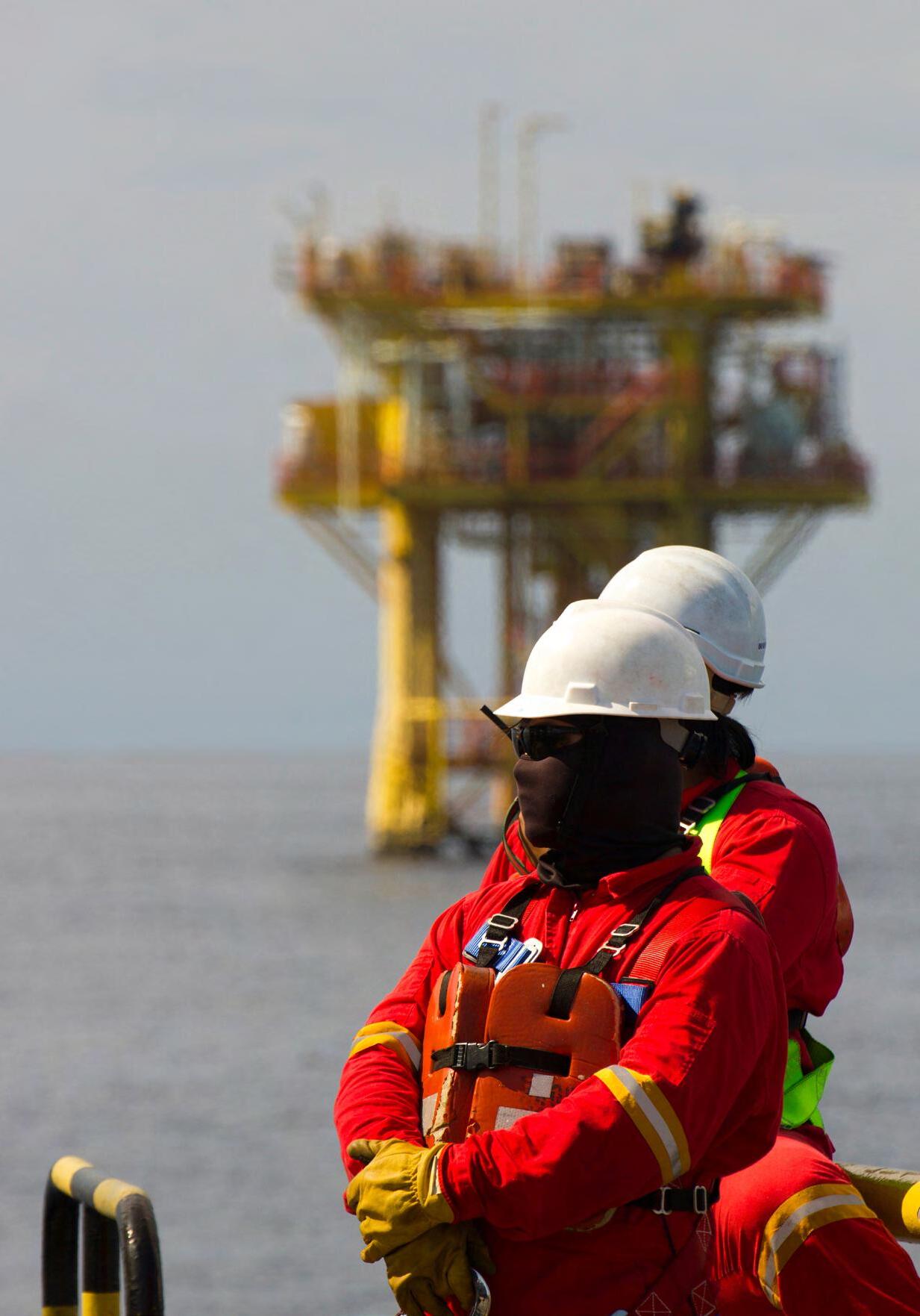
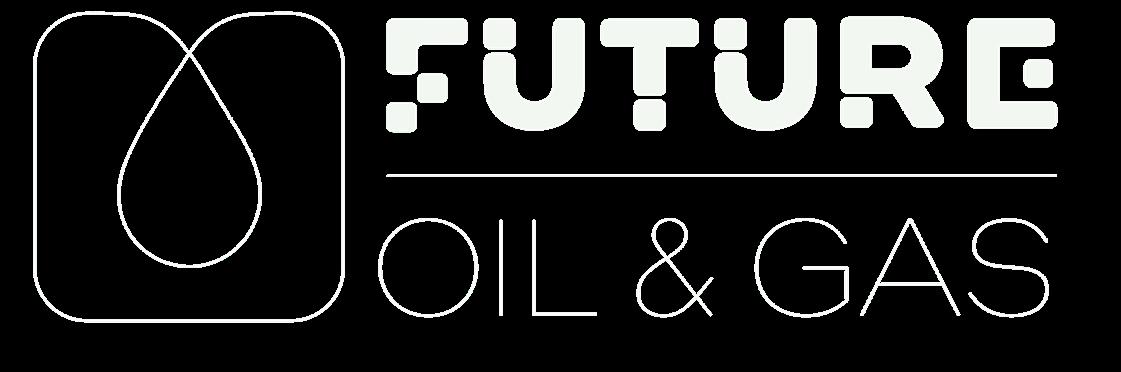
Autonomy Requires More Than Just Data
Edge Computing Powers Oil Efficiency
Rethinking Safety In A Connected World
AI Is Now Critical In Oil And Gas
Building Trust In Digital Operations
Managing Director
Adam Soroka
Editor in Chief
Mark Venables
There was a time when the term ‘digital twin’ sounded like a marketing gimmick, an impressive label for something vaguely virtual, indefinitely postponed, and questionably useful. That time is over. The stories in this issue leave no doubt: digital twins are no longer a futuristic concept for oil and gas. They are the defining feature of a new operational paradigm.
What has changed is not just the maturity of the technology, but the clarity of its purpose. Early digital twin efforts often suffered from an obsession with visual fidelity and data completeness. The thinking seemed to be that if we could replicate every bolt, pump, and pipe in perfect 3D, the value would emerge on its own. But replication is not transformation. The real power of a digital twin lies not in its ability to mirror the physical world but in its ability to interpret it, making operational complexity comprehensible and actionable.
This issue examines that shift in thinking from several angles. On one hand, we explore how digital twins have become integral to managing asset performance, safety, and emissions in real time. They are no longer isolated dashboards or highend simulators. They are operational engines, living, learning systems that evolve with the asset, absorbing data from sensors, logs, documents, and human input. From upstream reservoir management to downstream logistics, twins are reshaping decision-making across the value chain.
But just as important as the technological evolution is the human one. As we highlight in this edition, the digital twin must serve people, not just machines. A model that satisfies control systems but ignores the technician at 2am or the graduate engineer on their first offshore assignment has failed its most important test. We must build systems that empower users with role-specific insight, contextual navigation, and actionable knowledge, because in oil and gas, performance and safety still depend on the quality of human judgement.
That means designing digital twins not as monoliths, but as dynamic interfaces that grow with the organisation. It means investing in architecture that prioritises flexibility over perfection and traceability over data hoarding. It means recognising that the real return on a digital twin is not a
visualisation, it is a decision made faster, a repair made earlier, a risk understood before it escalates.
Perhaps most critically, it means reframing the digital twin as a long-term asset in its own right, a digital spine connecting people, systems, and strategy. It is not a one-off project but a continuous capability. Every time an operator tags an insight, every time a process is simulated, every time a decision is logged, the twin becomes more useful and more trusted.
This issue of Future Oil and Gas is a snapshot of that evolution. It shows what is possible when we stop asking whether digital twins are ready for the industry and start asking whether the industry is ready for the scale of change, they make possible.
Welcome to the twin-enabled future.
Mark Venables, Editor, Future Oil and Gas
Driven by best-in-class health and safety standards, Suncor is committed to transforming its operations across its diverse business units. A key element of this transformation involved optimizing Control of Work processes: such as permit-to-work, hot work, and isolation management/LOTO. To support this initiative, Suncor selected Enablon Control of Work as part of its broader digital transformation strategy. Standardizing these critical processes not only helped meet rigorous health and safety standards but also improved efficiency and provided frontline workers with better access to essential information directly in the field.
Data-driven decision-making is transforming oil and gas, but success depends as much on people and processes as on technology. As autonomous operations mature, companies must align culture, connectivity, and computing to achieve real value.
Oil and gas companies are under pressure to reduce costs, operate more safely, and deliver on sustainability promises. Edge computing offers a powerful tool to help meet these challenges by enabling realtime data insights in even the harshest operational environments.
As the oil and gas sector confronts disruption on multiple fronts, digital twins are emerging as the key to reducing downtime, enhancing safety, and optimising asset performance across complex operations. By mirroring real-world systems with real-time data and simulation, they are reshaping how companies manage infrastructure, streamline operations, and respond to volatility.
AI is redefining the role of digital twins from isolated replicas to intelligent, interconnected agents. As oil and gas operations become more complex, AIenabled twins are shifting from visualisation tools to real-time decision-makers that support safety, sustainability, and systemwide optimisation.
Senior leaders in oil and gas face mounting pressure to extend asset life, enhance cyber resilience and cut emissions. Industrial autonomous operations promise to deliver gains across all three, but require a fundamental rethink of how data, systems and people work together.
Decarbonization of the UK’s energy system requires increased interaction and cooperation between all energy stakeholders. Therefore, alongside electrification, digitalization remains a key enabler in the pathway towards net zero against a backdrop of volatility, unpredictability, and complexity.
From dynamic PHAs to live barrier management, Ruben Mejias of Enablon outlines how integrated platforms are helping energy and petrochemical operators reduce incidents, cut emissions, and stay compliant. As safety, productivity, and sustainability converge, the industry must rethink how risk is managed in real time.
Data handover failures in oil and gas projects are still far too common, often undermining the performance of even the most sophisticated digital assets. By appointing a Main Digital Contractor, operators can embed data integrity from the outset and ensure the transition from project to operations is seamless, efficient and value-driven.
Murray Callander, CEO of Eigen, reflects on 25 years of digital transformation in oil and gas, from floppy disks and Excel hacks to cloud-native deployments and AIpowered workflows. He explores the cultural, technological, and organisational shifts that have shaped the digital oilfield, and the lessons that still need learning.
Real-world applications and use cases have emerged beyond the buzz and hype of AI. Natural language processing (NLP), large language models (LLM), hybrid machine learning (ML), generative and agentic AI, all represent a litany of transformational technologies.
In the oil and gas sector, performance is not merely a concept, kit is a calculation. As the industry convenes in Aberdeen for the Future of Oil and Gas 2025, the dialogue is shifting from theoretical innovation to proven transformation in the field. As Katarzyna Chrzan, Senior Marketing Manager at Cohesive explains, the question is no longer whether we should modernise, but how we can do so in a way that delivers measurable, scalable impact.
Digital twins are becoming essential for operational insight in oil and gas, but a narrow focus on assets and automation risks missing the bigger picture. To deliver real value, twins must serve the connected worker as much as they serve the control system.
For too long, the oil and gas sector has treated artificial intelligence as a future consideration, something to be explored in labs and pilot projects, rather than deployed at scale.
Data-driven decision-making is transforming oil and gas, but success depends as much on people and processes as on technology. As autonomous operations mature, companies must align culture, connectivity, and computing to achieve real value.
There is no shortcut to autonomous operations. The journey is as much about shifting attitudes as adopting technologies. While the sector increasingly invests in AI, robotics, and edge computing, IDC’s Research Manager for Operational Technology, Carlos Gonzalez, argues that none of it matters without cultural commitment.
“IDC believes it is essential that there is complete buy-in from the top down when we address any sort of digital transformation strategy,” Gonzalez explains. “If you do not have the people on the ground floor willing to undergo training or adopt new tools, or people at the C-suite level willing to invest time, money, resources, and also their patience, you are not going to see a high level of success.”
Oil and gas operators are already under pressure to modernise legacy assets and futureproof remote sites. But without a workforce that understands and supports the shift, even the most advanced systems fall short. Leaders who succeed tend to be those that foster a shared belief that transformation is necessary, not optional.
Many executives mistakenly see autonomous operations as a linear technology upgrade. In practice, it is circular and continuous, with data as both input and output. AI and machine learning depend on data to function, but autonomy also generates new data, fuelling real-time optimisation, predictive maintenance, and strategic scaling.
“Data is fuel for autonomous operations. Without data, there is no way they can proceed,” Gonzalez states. “The cloud, in IDC’s perspective, is one of those inevitable tools that companies will need to embrace in some capacity if they want to scale and deploy data at a larger level.”
For distributed operations typical in oil and gas, spanning onshore, offshore, subsea, and desert environments, the cloud is
not merely a storage mechanism. It is the connective tissue that allows insights to be shared across facilities and functions. However, its effectiveness depends on how well organisations democratise access to data internally. Cloud-native strategies that enable secure, scalable, and decentralised decision-making are increasingly the differentiator between cautious adopters and digital leaders.
If cloud is the brain, edge is the reflexes. Autonomous systems thrive on responsiveness, but latency kills performance in real-time scenarios. That is why edge computing is now a priority in environments where decisions must be taken faster than a human can act.
“Edge devices are where the operation meets the cloud. If we have learned anything along this industry 4.0 journey, it is that edge computing is beneficial,” Gonzalez explains. “It helps with what data gets transmitted to the cloud. It is not a data dump. You are being very effective in how you communicate and transform your data.”
The distinction between data collection and data utility becomes vital here. Advanced sensor technologies, combined with edge computing, enable only the most relevant, compressed, or contextualised information to reach the cloud. This ensures agility without overwhelming storage or bandwidth, critical in harsh or bandwidthconstrained environments such as offshore rigs or remote gas processing plants.
Technology adoption is never purely technical. Gonzalez stresses that digital transformation is ultimately a human process, and the biggest bottleneck is rarely the system, it is the skills gap.
“Among the leaders that believe digital technology gives them an edge, 36% of them have a culture of buy-in. They have an understanding that this is where we need to invest, and they are all behind it,” he says. “At the end of the
day, you are introducing all this technology, but if the human workers and employees are not fully invested, the success rate is diminished.”
According to IDC’s Future of Operations survey, nearly half of respondents cite education and training as the biggest challenge in deploying digital technology. This is closely followed by recruitment and retention. As experienced workers retire, their knowledge departs with them, leaving a vacuum that new tools are only beginning to fill.
AI, machine learning, and generative tools like ChatGPT are being integrated into training environments. Virtual reality enables immersive instruction, while augmented reality connects younger engineers with senior specialists from miles away. These tools do not replace human insight, but they can retain, replicate, and relay it more efficiently than traditional handovers or static documentation ever could.
Remote operations are a proving ground
Autonomous operations are not an abstract goal. In sectors where access is limited and conditions are extreme, they are already essential. Oil and gas, like agriculture, covers vast and often hazardous territories. Travel time, safety risks, and environmental exposure make remote operations a practical imperative, not a future aspiration.
“Oil and gas have several sites that are only accessible by helicopter or some sort of hazardous mode of travel,” Gonzalez points out. “By setting up remote operations and letting them run autonomously, it is essential for companies to maintain connectivity and safety. These are the organisations leading the way in wireless networks and distributed data strategies.”
Remote operations depend on robust connectivity, but also on automation maturity. AI must be able to make and adapt decisions without human input in real time. In oil and gas, where a minor delay can cascade into major losses or safety risks, this capability is not merely valuable, it is existential.
As these systems scale, edge computing allows decisionmaking to stay localised, while cloud infrastructure ensures strategic alignment across geographies. The result is a distributed model of autonomy, where data, decisions, and deployment are harmonised rather than centralised.
The future is flexible and federated
The post-pandemic industrial world no longer tolerates rigidity. Market fluctuations, regulatory shifts, and geopolitical risks have all exposed the fragility of inflexible systems. The modern expectation, from both customers and shareholders—is for resilience and responsiveness, not just efficiency.
“Making advanced decisions in real time that are flexible, being able to respond—that is the goal of autonomous operation,” Gonzalez says. “AI, cloud technology, edge devices—these are all driven by data, and it is about using that data to make decisions in real time.”
This vision of autonomy is not about removing humans from the loop. It is about putting people in the right part of the loop, where creativity, judgment, and oversight are most valuable, and automating the rest. It is a model of human-machine collaboration that prioritises speed, safety, and sustainability.
For oil and gas, the implications are significant. Sites become safer by removing personnel from hazardous zones. Operations become more efficient by minimising manual interventions. And organisations become more adaptive by embedding intelligence at every level, from the field device to the executive dashboard.
Tomorrow’s leaders are building today’s infrastructure
The technologies of autonomy are already available. AI, robotics, cloud, and edge computing are no longer experimental. But the companies realising value are those that understand the full equation: data plus culture plus connectivity equals autonomy.
Gonzalez is clear about the stakes. “Tomorrow’s success will be artificial and machine learning driven. These tools are going to help with upskilling, with training, with assisted programming, and with the real-time adjustments that need to happen in operations.”
Executives in oil and gas now face a strategic choice. Continue to see digitalisation as a bolt-on initiative, or embrace it as the foundation of operational resilience and innovation. Autonomous operations are not the end goal. They are the infrastructure for the next era of industrial competitiveness.
Cintoo is the all-in-one platform for reality and 3D scan data synergy. When scan data is trapped in siloed desktop tools, disconnected from EDMS, BIM, and digital twins, its value is lost.
Cintoo changes that—making data accessible, collaborative, and actionable for faster, safer and more sustainable decisions. In turn, empowering teams to streamline inspections, planning, maintenance, and asset lifecycle management. Join us for an exclusive webinar with our partner Neonex on July 8
Reimagine P&IDs – Safer, Smarter, More Accurate. Discover today’s practical use cases for enhancing ROI.
cintoo.com sales@cintoo.com
As the oil and gas sector confronts disruption on multiple fronts, digital twins are emerging as the key to reducing downtime, enhancing safety, and optimising asset performance across complex operations. By mirroring real-world systems with realtime data and simulation, they are reshaping how companies manage infrastructure, streamline operations, and respond to volatility.
The oil and gas industry is undergoing a structural recalibration. Long defined by boom-and-bust commodity cycles and complex physical infrastructure, operators are now required to navigate persistent volatility, decarbonisation targets, and investor demands for leaner, more transparent operations. The appetite for short-term gain has been replaced by a need for long-term adaptability, built on foundations of operational intelligence, real-time data, and advanced analytics.
This environment leaves little room for reactive, siloed approaches. Operational resilience is no longer a back-office conversation, it is a boardroom imperative. Digital twins, once experimental and confined to high-fidelity modelling of isolated components, have evolved into strategic enablers that support enterprise-wide transformation. By creating dynamic, virtual replicas of physical assets, systems, and processes, digital twins provide operators with a continuous feedback loop between real-world operations and digital simulation.
This capability changes not only how assets are maintained and operated but also how decisions are made. It removes the guesswork from complex optimisation problems, allowing multidisciplinary teams to test scenarios, forecast risks, and simulate improvements before making physical changes on the ground. In an industry where decisions carry significant safety, environmental, and financial consequences, that precision is vital.
A fully functioning digital twin is far more than a visual model. It is a dynamic system that integrates sensor data, engineering documentation, operational parameters, and real-time performance metrics. It incorporates the digital DNA of an asset, geometry, process flows, material properties, and control logic—alongside real-time feeds from IoT devices, DCS systems, and historian databases. It also contains the operational memory of the asset, including maintenance records, incident histories, and contextual information such as environmental constraints or safety-critical tolerances.
This convergence of static and dynamic data creates a system that does not just reflect reality but learns from it. The digital twin evolves alongside the physical asset, ingesting new data, recalibrating predictions, and refining simulations over time. It becomes not only a single source of truth but also a system of insight.
The digital twin’s value is unlocked when this insight is made actionable. Engineers must be able to query the twin for diagnostics, operators must receive timely alerts, and executives must gain dashboards that support capital allocation and strategy development. This requires a robust infrastructure of data standardisation, integration middleware, cloud platforms, and userfriendly visualisation tools. Without these, the digital twin remains a passive model. With them, it becomes an operational command centre.
In the context of asset performance, the benefits of a digital twin are immediate and tangible. Predictive maintenance, energy efficiency, and throughput optimisation can all be managed with greater precision and lower cost. Real-time condition monitoring enables earlier detection of degradation,
allowing planned interventions rather than emergency repairs. Heat exchangers, pumps, and compressors, assets that traditionally fail without warning—can now be monitored for subtle patterns of failure behaviour, informed by years of historical data and advanced analytics.
This has measurable impacts on OPEX and CAPEX. Maintenance budgets can be allocated based on condition rather than calendar. Spare part inventories can be calibrated to actual failure probabilities. High-value assets can remain in service longer without compromising safety or performance. In complex environments such as offshore platforms, this also reduces the risk exposure of personnel, who are no longer dispatched reactively but based on data-driven risk profiles.
What differentiates digital twins from conventional monitoring is the ability to simulate potential interventions in advance. Before a valve is replaced, engineers can run a simulation within the twin to understand the impact on process dynamics, energy use, and system balance. This accelerates root cause analysis and shortens the time from problem detection to resolution.
While rotating equipment and surface assets are natural candidates for twin implementation, some of the most valuable applications occur upstream, within reservoir modelling and production planning. By integrating geophysical models, well logs, flow simulations, and historical production data, operators can develop digital twins of
reservoirs that continuously adapt as new data is captured. This enhances the accuracy of forecasts, optimises field development plans, and supports adaptive reservoir management.
The ability to run synthetic simulations—testing different injection rates, lift strategies, or well trajectories, within a digital twin environment means decisions are no longer constrained by static assumptions. Machine learning models can identify early signs of water breakthrough or pressure anomalies, suggesting new workover strategies or real-time choke management.
For brownfield assets, this capability enables enhanced recovery at minimal additional cost. For greenfield projects, it ensures that development decisions are informed by a living model, not a onetime simulation. In both cases, production efficiency improves, and environmental impact is reduced.
Safety and risk management are embedded in every layer of oil and gas operations. Digital twins provide a powerful platform for managing these obligations more proactively. They allow safety systems to be stress-tested in silico, revealing interlocks that might fail under pressure or alarms that might conflict in cascade
scenarios. Operators can visualise the sequence of events that would lead to loss of containment or equipment failure and adjust control logic accordingly.
Real-time monitoring of safety-critical parameters, such as gas concentrations, vibration thresholds, or pressure limits, allows the digital twin to serve as a predictive risk engine. Rather than responding to breached limits, operators can act on trend data that shows a deviation is emerging. This enhances compliance with regulatory frameworks while also reducing downtime due to false alarms or over-engineered trip points.
Scenario planning is another key benefit. Entire facilities can be subjected to virtual emergency drills, with process upsets, electrical failures, or blowdown events simulated in full. This improves not only system design but also human readiness, as operators are trained in digital replicas that reflect the actual layout and behaviour of their plant.
Supply chains that see around corners
Beyond the plant boundary, digital twins are helping operators better understand and manage their supply chains. By modelling the flow of goods, spare parts, chemicals, and products from source to site and beyond, companies gain visibility into bottlenecks, inefficiencies, and vulnerabilities.
These models incorporate data from suppliers, logistics providers, and internal ERP systems, allowing simulations that account for lead times, regional risks, weather events, and demand fluctuations. What emerges is a predictive model that can anticipate delays and recommend countermeasures before they impact production schedules.
This is particularly valuable for LNG operations, where supply chains are long, constrained, and capital-intensive. Being able to model storage constraints, shipping delays, or feedstock quality variations in a single digital environment supports more agile decision-
making and reduces the bullwhip effects that plague energy logistics.
Human insight through simulation and training
Digital twins are not simply operational tools. They are also learning environments. In an industry facing a widening skills gap, the ability to train personnel using live data and real-world scenarios is invaluable. Operators can rehearse startup, shutdown, and emergency procedures in a safe, controlled setting. Technicians can visualise system layouts and maintenance workflows before setting foot on site.
This improves not only knowledge transfer but also confidence. By simulating infrequent or hazardous events, digital twins accelerate learning and reduce the risk of human error. Simulation data can be used to benchmark competence and identify training needs, ensuring that workforce development is continuous and datainformed.
Scaling across the enterprise
The true impact of digital twins emerges when they are scaled from point solutions to platform capabilities. This requires standardisation of data formats, alignment of engineering practices, and cultural shifts toward data-driven operations. It also requires investment in the supporting infrastructure, edge devices, connectivity, cloud platforms, and cybersecurity.
Companies that succeed in this transition are those that treat the digital twin not as a product, but as an evolving digital asset. Each new project adds fidelity. Each integration expands capability. Each user interaction generates insight. Over time, the digital twin becomes the digital spine of the enterprise—connecting planning to execution, engineering to operations, and people to processes.
The oil and gas industry is often characterised as slow to adopt change. Yet, when the stakes are clear and the value is demonstrable, it has shown an ability to move fast and decisively. Digital twins represent one of those inflection points, a convergence of technologies that offers a fundamentally different way of operating.
They do not replace human expertise but augment it. They do not eliminate risk but make it visible and manageable. They do not promise perfection but deliver improvement at scale. For leaders tasked with steering their organisations through a period of profound transition, the digital twin is not just a tool. It is a lens, a way of seeing operations as they are, understanding them as they behave, and improving them as they evolve.
That perspective, more than any single metric or application, is the real value of the digital twin. It is not a mirror of the present. It is a preview of what is possible.
Oil and gas companies are under pressure to reduce costs, operate more safely, and deliver on sustainability promises. Edge computing offers a powerful tool to help meet these challenges by enabling real-time data insights in even the harshest operational environments.
Few sectors generate as much data under such extreme conditions as oil and gas. Remote assets such as offshore platforms, pipelines and liquefied natural gas (LNG) plants rely on thousands of sensors.
Yet most of that data remains unused or is delayed by transmission bottlenecks and bandwidth limits. In many cases, valuable insights are simply lost.
Edge computing provides a way to reverse that trend. By processing data locally, on or near the asset itself, operators gain the ability to act on information in real time without relying on distant cloud infrastructure. This is particularly important in environments with limited connectivity or high latency.
“The industry has long been rich in data but poor in insight,” explains Miran Gilmore, Senior Consultant at STL Partners. “By moving compute resources closer to where data is generated, edge infrastructure allows operators to extract meaning and value from information that was previously wasted or delayed. It is about turning raw data into decisions.”
Edge is not just about speed. It enables safer operations by flagging anomalies before they become incidents and supports more efficient production through continuous feedback and adjustment. The shift from reactive decision-making to predictive optimisation has become a strategic imperative.
Traditional IT infrastructure is rarely designed for the harsh realities of oilfield operations. Edge
architecture must contend with heat, vibration, corrosion and isolation, all while operating reliably and autonomously.
“Latency is not just a technical inconvenience,” Gilmore adds. “In upstream production or gas processing, a few seconds can be the difference between early intervention and equipment failure. Edge computing makes it possible to act on those early signals without waiting for a round trip to the cloud.”
For an LNG plant, where downtime can cost upwards of $25 million per day, these delays matter. Edge allows equipment monitoring, process control and predictive diagnostics to take place on site, dramatically reducing the time to detect and respond.
There are also economic benefits. A single oil platform can generate over a terabyte of data each day, but transmitting this data via satellite is both slow and costly. By analysing it at the edge, network traffic and associated costs are reduced.
One of the clearest benefits of edge computing is improved condition monitoring. As sensors become cheaper and more capable, they are being deployed across critical systems, from compressors and turbines to subsea valves and wellheads.
“There is a growing maturity in the ecosystem,”
says Gilmore. “With more compute power available on site, operators can now run real-time analytics to detect unusual behaviour, isolate faults and even trigger automated responses.”
That enables predictive maintenance to be embedded within operations. Rather than responding to alarms or periodic inspections, operators can anticipate failures, schedule maintenance efficiently, and reduce unplanned downtime.
The improvements go beyond cost and efficiency. Edge analytics contribute to safer working conditions by identifying issues early and reducing the need for manual intervention in hazardous areas. They also provide a buffer for critical infrastructure, protecting against cascading failures.
Integration and governance remain key challenges
Despite the advantages, integrating edge solutions is not straightforward. Oil and gas remains a conservative industry, with significant investment in legacy systems and established workflows. There is also a persistent gap between IT and operational technology (OT) environments.
Gilmore warns that adoption will require more than new equipment. “Edge is not just a technical bolt-on. It demands changes in how data is managed, how teams collaborate, and how decisions are made. That means rethinking budgets, processes and even training.”
Skills are a major barrier. Many field personnel are unfamiliar with edge architecture, while data scientists and engineers often lack domain
experience in oil and gas operations. Closing this gap will be critical to scaling successful deployments.
There are also unresolved questions around data ownership. As machine learning models are increasingly embedded at the edge, it is not always clear who owns the insights, or the value they create. Collaboration between operators and vendors will need clearer governance frameworks.
Edge computing also has a role to play in sustainability. Real-time monitoring of flaring, emissions, and energy consumption enables operators to measure and improve environmental performance. In remote or off-grid areas, edge systems can support integration with renewable energy and microgrid infrastructure.
“Edge provides the visibility and responsiveness needed to operate more sustainably,” says Gilmore. “It supports compliance and reporting, but more importantly, it enables better control over environmental impact.”
As the energy transition accelerates, edge technology may prove essential for balancing new demands with existing assets. By enabling smarter, cleaner operations, it supports both short-term performance and long-term strategic goals.
The oil and gas sector is under no illusions about the complexity of adopting new technologies at scale. Edge computing will not replace cloud infrastructure or traditional SCADA systems overnight. But it offers a complementary layer of intelligence, one that is increasingly vital.
“There is growing interest and real investment happening,” Gilmore concludes. “But edge will only deliver value if it is embedded into how companies operate day to day. It must be treated as a strategic capability, not a peripheral experiment.”
As the industry continues to navigate volatile markets, operational risk, and environmental scrutiny, edge computing offers a rare combination of agility, insight and resilience. For forwardlooking operators, it could prove to be one of the most important enablers of digital transformation over the coming decade.
AI is redefining the role of digital twins from isolated replicas to intelligent, interconnected agents. As oil and gas operations become more complex, AI-enabled twins are shifting from visualisation tools to real-time decision-makers that support safety, sustainability, and system-wide optimisation.
Digital twins have long played a vital role in asset-heavy industries, enabling engineers to monitor performance, simulate conditions, and predict maintenance needs. But the traditional twin has always been tethered to a specific function or dataset. A model of a single compressor, for example, might help identify performance anomalies, but it cannot contextualise what those anomalies mean across an entire platform or pipeline. That is where artificial intelligence is changing the game.
Rick Standish, Executive Industry Consultant at Hexagon Asset Lifecycle Intelligence, has witnessed the evolution of digital twins over more than two decades. The technology has matured, but the turning point now lies in AI’s ability to deepen, scale, and interconnect twin functionality across assets and systems. “Initially, digital twins were primarily used for monitoring and simulation of a physical asset and focused on a specific business interest,” he explains. “Today, we are really seeing the beginning of a transformative shift. Thanks to the ever-growing availability of real-time and retrofitted sensor data, more powerful generative AI models, and deep learning analytics, digital twins are becoming more proactive and increasingly autonomous.”
This progression is not just about technical capacity. It is about realigning how twins function in the wider decision-making environment. Instead of mirroring an individual pump, AI-powered twins are now being designed to simulate and optimise process-
wide behaviour, integrating structured and unstructured data from engineering documents, maintenance records, and sensor feeds. That, says Standish, gives operators a real opportunity to simulate and optimise entire workflows, so long as they can trust the intelligence behind the insights.
The issue of trust is not a peripheral concern. As twins become more intelligent, the consequences of acting on flawed data become more significant. Martin Bergman, Lead Strategist for AI and Enabling Technologies at Hexagon, emphasises the foundational role of data quality in digital twin success. “An impactful and trustdriven digital twin relies on a solid, up-todate data foundation,” he says. “If the data does not represent the status quo of the physical asset, it is of little value.”
According to Bergman, AI can help address
this by ingesting and contextualising previously inaccessible information. Around 90 per cent of industrial data is unstructured, buried in PDFs, diagrams, logs, and handwritten records. AI, especially large language models, is enabling companies to turn this material into structured, machine-readable context. This is not a one-off project. “We are now seeing the move from project-based contextualisation to continuous services that keep the twin up to date in real time,” he explains. “That makes the digital twin a living, trustworthy source of truth.”
The importance of this shift is compounded by the fact that many assets, especially offshore, change ownership over their lifetime. The result is a patchwork of engineering records, maintenance systems, and data gaps. AIpowered contextualisation creates consistency where previously there was confusion, enabling what Standish describes as “a consistent record of the asset’s engineering data” that can then be used for process safety and asset integrity management.
Importantly, contextualised data is not simply about locating the right document or verifying a specification. It also underpins the ability to automate verification processes across entire data ecosystems. With the correct contextual layer, companies can run large-scale consistency checks between technical drawings, P&IDs, and maintenance logs to verify accuracy, identify discrepancies, and trigger corrective workflows before those inconsistencies manifest as operational risks.
Once trusted data is in place, the next step is making it actionable. Today’s digital twins do not simply serve up insights; they support decision-making through interfaces that resemble consumer AI. Natural language interaction is becoming a core capability, allowing engineers to ask complex questions about the twin’s behaviour or the asset’s condition without navigating through multiple dashboards.
Bergman outlines a three-tier evolution of this capability. The first is the AI intern, searching, summarising, and
organising relevant data. The second is the AI engineer, assisting in analysis, running root cause assessments, and suggesting optimisations. The third is the AI agent, an autonomous participant in operational workflows that can communicate with other digital systems, such as ERP or safety monitoring tools. “The idea is that users no longer need to go into multiple subsystems,” he explains. “Instead, agents communicate with each other to surface insights or initiate tasks. It is about turning passive data into intelligent action.”
What differentiates this new generation of tools from earlier dashboard-style solutions is their interactivity and their autonomy. Instead of waiting for human queries, these agents can trigger alerts or suggest optimisations based on observed changes in behaviour, asset conditions, or operational context. This moves the model from a reactive posture to a proactive one, anticipating faults, analysing scenarios, and even suggesting economic trade-offs between maintenance timing, resource allocation, and production targets.
One of the most promising outcomes of this shift is the ability to align digital twin capabilities with broader corporate priorities, especially sustainability. Historically, digital twins have been perceived as efficiency tools: reducing downtime, extending equipment life, and streamlining maintenance. Now, AI integration is allowing them to support ESG goals in a far more tangible way.
For example, AI-enhanced twins can monitor and simulate emissions, identify energy inefficiencies, and even help with regulatory reporting. “We are moving into a phase where digital twins are critical to environmental compliance,” says Standish. “Whether it is reducing fugitive emissions with sensor analytics or using AI-powered monitoring for carbon capture and storage, these are becoming core operational capabilities.”
This is especially relevant for offshore platforms where the stakes for both environmental performance and uptime are high. One operator, Standish explains, used a digital twin to analyse vibration and temperature trends from gas compressors and predict early bearing wear. The AI model forecast failure within weeks, triggering a proactive intervention that avoided unplanned shutdown. At the same time, remote teams accessed the same cloud-based twin to simulate outcomes and validate next steps.
As operators take on growing regulatory and shareholder pressure to decarbonise operations, the role of AI will only become more integral. Bergman sees a future where digital twins can simulate
energy consumption across an entire network of facilities, model the effect of switching to alternative fuels, or predict how adjusting operating parameters could reduce carbon intensity without sacrificing throughput. This is not science fiction, it is already beginning to happen in pilot projects across the sector.
Scaling responsibly and avoiding the AI lock-in trap
Despite the clear potential, success is not guaranteed. Digital twins fail more often from governance issues than technical ones. Both Bergman and Standish caution that earlystage projects can fall into the trap of overpromising, underdelivering, or building models that are not scalable. “The first question companies should ask is not what technology they need, but what outcome they want to achieve,” says Bergman. “Digital twins must solve specific problems or unlock specific value, or they will not be used.”
He also stresses the need for architectural flexibility. AI tools and models are evolving rapidly, and solutions that look promising today may be outdated within a year. “You cannot afford to be pinned to a single ecosystem,” he says. “Stay agnostic. Choose architectures that allow you to plug in best-in-class tools as they emerge.”
Standish highlights the importance of involving users at every stage. “Digital transformation is not just about deploying technology, it is about ensuring people understand it, are not threatened by it, and know how to use it to improve their work,” he says. “We need to bring operations, engineering, and IT together from day one.”
A paradigm shift for human-machine collaboration
Looking ahead, both experts are convinced that the next phase of industrial digitalisation
will involve far deeper collaboration between human users and intelligent systems. Digital twins are becoming not just smarter, but more empathetic, designed to reflect how people actually work, think, and make decisions under pressure.
In high-stakes environments like offshore oil platforms, the ability to quickly simulate a ‘what if’ scenario or ask a digital assistant to identify failure correlations across a complex dataset is more than a convenience. It is a necessity. With labour shortages growing and operational complexity increasing, AI-powered twins offer a way to capture institutional knowledge, reduce risk, and deliver decisions that are traceable and explainable.
Bergman puts it simply: “If we can make digital twins easier to use, more trustworthy, and more responsive, they will not just be used by data scientists or engineers. They will be used by everyone who needs to make fast, reliable decisions about the assets they are responsible for.”
The implication is clear. As AI becomes embedded in the DNA of digital twins, the boundaries between data, insight, and action will blur. And for operators seeking to remain competitive while navigating energy transition, economic volatility, and operational risk, that convergence may be the most valuable transformation of all.
Senior leaders in oil and gas face mounting pressure to extend asset life, enhance cyber resilience and cut emissions. Industrial autonomous operations promise to deliver gains across all three, but require a fundamental rethink of how data, systems and people work together.
Even before oil and gas executives reach for AI-enabled tools, they are being forced to answer more pressing operational questions. How can they improve asset utilisation without triggering downtime? Which legacy infrastructure must be upgraded to meet new emissions targets? And what happens when their most experienced engineers retire, taking decades of domain knowledge with them?
According to Sunil Pandita, Vice President and General Manager for Connected Cyber and Industrial at Honeywell, these questions are not isolated. They all stem from a confluence of pressures shaping the sector. Global macroeconomic uncertainty, the energy transition, infrastructure modernisation, and cybersecurity are now interdependent problems, and demand an equally integrated response. That response, Pandita argues, is industrial autonomous operations.
The convergence of four pressures
Each of these challenges is well known individually. Many organisations are deferring investment due to interest rate volatility and inflationary pressure, choosing instead to sweat existing assets. But this introduces new problems around ageing
equipment and unplanned downtime, which, according to Honeywell research, affects around 10 per cent of turnover across the industry.
The second pressure comes from sustainability mandates. “Electrification and emissions reduction are non-negotiable,” Pandita explains. “We are seeing a rise in Chief Sustainability Officers at the most senior levels. That is a clear signal that net-zero is no longer a reporting obligation. It is a strategic priority, with operational consequences.”
The third challenge relates to infrastructure, both physical and digital. “The real challenge is not just adding more sensors or connecting machines to the cloud,” Pandita continues. “It is extracting intelligence from that data at the right time, in the right context, and making it useful to the people who need it most. With advances in edge computing, machine learning, and GenAI, we can now separate signal from noise at scale.”
The final pressure is cybersecurity, where the stakes have never been higher. Honeywell estimates that 80 per cent of industrial organisations have experienced a cyberattack in the past year, with nearly half resulting in operational downtime. OT cybersecurity has become a board-level concern. But the response cannot be limited to perimeter defences alone. It must be embedded in every layer of the industrial technology stack, from sensor to cloud. “Industrial autonomous operations offer a systemic answer to all four pressures,” Pandita adds. “But autonomy is not just about technology. It is about rearchitecting how data, applications and people interact, across the entire asset lifecycle.”
For oil and gas, the traditional use of AI has been rooted in machine learning models built
on structured data, vibration signals, flow rates, temperature curves. That approach still has value, but Pandita believes the real transformation lies in AI’s ability to mine unstructured data, much of it previously untapped.
“We are talking about AI that can read equipment manuals, maintenance logs, video feeds, shift reports,” Pandita explains. “That is the unstructured layer, and GenAI is surfacing insights from it that were simply inaccessible before. We call this AI 3.0, intelligent context at scale.”
In practical terms, that opens entirely new use cases. A technician can ask a digital assistant how to safely isolate a valve based on hundreds of past procedures. A field engineer can receive real-time guidance drawn from manuals and prior incident reports, without leaving the worksite. Search becomes intelligent, decision-making becomes
faster, and experience is no longer a bottleneck.
According to Honeywell’s estimates, these developments could contribute to a 26 percent increase in industrial GDP by 2030, largely driven by the fusion of domain knowledge with generative AI.
The shift to industrial autonomy also changes the role of digital twins. Once used primarily for training or design validation, they are now becoming operational systems in their own right. “We use high-fidelity digital twins not just for simulation, but for real-time optimisation,” Pandita explains. “It is the same digital twin used to train an operator that is now running online, monitoring live plant data, testing scenarios, and advising on optimal process adjustments.”
This is not theoretical. Honeywell has already deployed operational twins that can analyse flow conditions, test what-if cases during upsets, and identify pathways to achieve maximum throughput with minimal emissions. These models can balance performance across competing objectives, production volume, cost, energy consumption, and environmental compliance, in real time.
What makes this possible is not just the model itself, but the cloud-native architecture that supports it. “The digital twin lives in the cloud, it is fed by edge data, and it is accessed remotely,” Pandita continues. “This enables collaboration between experts located anywhere, supporting faster response and broader knowledge sharing.”
Autonomy does not mean removing people. It means augmenting them with better tools, insights, and interfaces. That philosophy applies not only to operations, but to workforce development.
There are two major challenges. First, the sector’s most experienced professionals are nearing retirement. Second, their successors learn differently. Traditional training rooms and static manuals are no longer effective. “New operators want learning to be mobile, on-demand, and
contextual,” Pandita says. “We have built training platforms that allow them to access immersive simulations on a tablet, on a bus, or at home. They can replay actual plant operations, pause, rewind, and experiment in a safe environment.”
AR and VR have become essential to this shift. But just as important is the ability to capture expert knowledge from the existing workforce before it is lost. Honeywell does this by recording workflows and integrating them into digital twins, preserving expertise in a format that is interactive and persistent.
It is not only trainees who benefit. These tools empower internal teams to troubleshoot, collaborate, and adapt more effectively. When data is organised, accessible, and contextualised, it becomes an equaliser. “Technology becomes the co-pilot,” Pandita explains. “It does not replace human judgement, but it supports it with real-time advice and richer data sets. And increasingly, that advice includes insights from unstructured sources, videos, logs, and emails, that were invisible before.”
Many executives fall into the trap of thinking that more data equals more value. But Pandita cautions that the goal is not simply to increase volume. It is to deliver relevance.
“When we deploy new platforms, it is common to discover problems the business did not even know existed,” Pandita says. “Machine number five has been underperforming for six months, but nobody noticed because there was no insight. Once data is captured and analysed, inefficiencies become visible.”
The value then comes from turning that visibility into action. Whether it is predictive maintenance, dynamic scheduling, or process reconfiguration, the system must be able to recommend and support decisions across departments and functions. “Connecting existing applications through APIs
is one way we do this,” Pandita adds. “It allows insights from one domain, such as asset health, to inform another, like supply chain or production planning.”
In this sense, the autonomy is not only in machines, but in the information itself. When insights move freely between systems and stakeholders, they accelerate alignment, reduce conflict, and enable faster course correction.
Despite the technical complexity, the deployment of industrial autonomous operations hinges on trust. Systems must be explainable, resilient, and secure. That means embedding cybersecurity at every level and ensuring human oversight is never removed from the loop.
“Cyber risk is not just a control system problem anymore,” Pandita says. “It is a business continuity risk. The more connected we become, the more important it is to ensure every device, every edge node, every cloud instance is protected.”
That is why Honeywell builds security into the architecture from the outset, not as an add-on. And it is also why autonomy must remain transparent. Decision logic should be traceable, assumptions documented, and human operators empowered to intervene when needed.
“Ultimately, industrial autonomy is not a technology project,” Pandita concludes. “It is a leadership decision. It requires a clear vision for how your organisation wants to work, how it values data, and how it empowers people.”
Those who succeed will not only run safer and more efficient operations. They will shape the future of the energy transition itself, one informed decision, one intelligent system, and one empowered team at a time.
At Wood, we are designing the future by decoding digital to transform industry.
Our Digital Asset and DataOps solution applies decades of operating experience and digital expertise to deliver the building blocks of digital transformation.
As your Main Digital Contractor, we drive digitalisation across capital projects by setting the lifecycle strategy and building the digital asset. We then embed technology in operations to advance ways of working, enable operational excellence and deliver lasting value.
See what’s possible: woodplc.com/digital
From dynamic PHAs to live barrier management, Ruben Mejias, Senior Technology Sales Support Specialist, Wolters Kluwer Enablon outlines how integrated platforms are helping energy and petrochemical operators reduce incidents, cut emissions, and stay compliant. As safety, productivity, and sustainability converge, the industry must rethink how risk is managed in real time.
To start off, please tell us a little more about Enablon and what you do. Wolters Kluwer Enablon provides industry leaders across complex, hazardous industries with a fully integrated platform that supports them in managing risk, drive operational excellence and boost productivity across their entire value chain – from digital permit to work to incident management, and from interactive bowties to process safety management. In my role as Senior Technology Sales Support Specialist, I support clients in implementing advanced software solutions that enhance risk management and elevate safety standards in their organizations.
In our opinion, what are the key challenges faced by your target audience in the energy and petrochemical industries?
One of the key challenges is maintaining robust process safety management (PSM) in increasingly complex and high-risk operating environments. As facilities age and operational demands rise, companies must rigorously manage hazards associated with hazardous substances and extreme operating conditions to prevent catastrophic incidents. Ensuring compliance with evolving regulations, integrating digital monitoring technologies, and fostering a strong safety culture across all levels of the organization are essential but resource-intensive tasks.
I understand that Enablon covers quite an expansive range of solutions offered for the energy and petrochemicals industries. Could you tell us a little more about this?
Within our platform, we have designed our interconnected solutions to support three core goals: increasing safety, boosting productivity, and maintaining compliance. The Enablon platform is tailored to the maturity level and the expectations of our customers. We support a wide range of use cases – from digital Permit to Work for a single refinery, all the way to a fully integrated PSM, EHS and sustainability management system for an entire enterprise. Whether
our customers need to view live barrier health information in dynamic bowties that deliver data for predictive risk in their plant visualization – or if they want to manage all process safety incidents across operations. This is all made possible by our core data platform, which uses more than two decades of expertise to operationalize all this risk data into useful outcomes. This has led to our customers achieving stunning results, from reducing incidents by 94%, to reducing maintenance backlogs by 60%, to preventing thousands of tonnes of CO2 releases.
Why is dynamic management of barriers and safeguards critical?
Organizations that don’t use dynamic barrier management must understand that all barriers can potentially degrade over time, and they might not be aware of the status of their safety critical controls and the cumulative risk associated with their degradation. Dynamic barrier management software provides real-time management and continually informs users of the current state of risk, including whether there is barrier degradation. It gathers data and provides analysis that helps organizations make informed decisions.
What is the main problem with PHAs today?
Traditionally, PHA has been an activity documented on paper or through a standalone solution, which is typically built, managed, and accessed only by a select few within a company. The problem is that PHA are static documents and workers in the field may find challenging or time consuming to make operational decisions based on extensive and static PHA studies. Most organizations only review and update PHAs based on schedules or when an incident/event demands a review of existing hazards and controls.
What should companies be aware of regarding the management of safeguards and dynamic PHAs?
A holistic approach is needed for managing risk effectively and remain compliant, safe and competitive. Risk data should be easily accessible and visible to key decision makers so they can prioritize and take appropriate actions. . The best-in-class Process Safey Management system can address that issue because it fully integrates PHA studies, risk databases, and control of work software. It also provides a single platform for complete visibility and can be easily updated.
What are some changes in trends that you have observed?
I am seeing a strong push towards consolidation and connection – both in people as well as in tech. People expect a stronger connection to the work they do and the planet they inhabit, and technology is expected to work seamlessly to support both company and workforce goals. I see these as positive trends, which are driving more harmonious development, and more holistic innovation across, safety, productivity and sustainability.
What are some of the benefits that your clients have seen from working with Enablon?
Prioritize long-term vision. Even in a rapidly changing landscape, a wellsupported long-term strategy always wins over ad-hoc solutions. Increased safety will generally support increased productivity (and thus increased value), and sustainability will drive a better future for all of us.
Murray Callander, CEO of Eigen, reflects on 25 years of digital transformation in oil and gas, from floppy disks and Excel hacks to cloud-native deployments and AI-powered workflows. He explores the cultural, technological, and organisational shifts that have shaped the digital oilfield, and the lessons that still need learning.
Let’s start with your background. Can you tell us a bit about yourself and your journey in the industry? Where were you when the digital oilfield revolution began over 25 years ago?
Well, I started working in oil and gas right at the very end of 1999. I graduated from university in July 1999 and began working in September with Foster Wheeler Energy Limited. Back then, everything was incredibly manual; I remember being given a calculation pad and strict instructions on numbering and initialling every page for traceability – everything was done on paper. My desk didn’t even have a computer on it in 2000. I got my first desktop later that year for specific tasks like air dispersion modelling. Most work, however, was still on paper, like marking up huge P&IDs laid out on desks. I was given a massive stack of paper to check in two weeks, and that was actually the trigger for me to learn to program. I figured automating it would be faster than doing it by hand. I managed to get a digital copy on a floppy disk and taught myself Visual Basic, wrote an algorithm, and finished the check in about nine days. From then on, I used code more and more, and I saw everyone eventually getting computers and then laptops on their desks. By 2005, I was working at Halliburton in a consultancy called Granherne and was invited onto one of the early digital projects with BP because I was seen as the “engineer that could do digital”. I was linking simulations with Excel and automating reports to speed up concept studies.
Looking back, what were the biggest challenges in those early digital oilfield initiatives?
Looking back, especially at those BP projects we did in the Caspian starting in 2005, the biggest challenges were definitely cyber security, networking, and infrastructure. It was all so new. There wasn’t a standard way to connect control systems to data historians and then to business systems. We had to work extensively with others to figure out and establish secure templates for these multi-tier architectures.
What limitations did you face back then — technologically, organizationally, and from a management perspective?
We faced limitations across the board. Technologically, a big one was the sheer speed and rate of change in
IT technology compared to the very slow, deliberate pace of major oil and gas projects. We had to lock in technology decisions early on, like the version of Windows (I think it was XP initially), which would often be obsolete by the time the platform was actually live. We simply couldn’t afford to keep up with those rapid IT changes within the structure of a major project.
Organizationally, there was a significant disconnect between the IT world and the operational technology (OT) world. These are two vastly different worlds with very different domain expertise and ways of working. The IT world often moved extremely quickly, seeing mistakes as relatively cheap and technology as almost disposable. This clashed with the careful, slow process of major projects where mistakes are very costly. There was a real cultural mismatch. Often, IT didn’t understand what the business or users needed, leading to them optimizing their own world potentially at the expense of operations. This sometimes pushed intelligent engineers back to simple tools like Excel rather than engaging with IT, which they saw as complicated. Central IT structures weren’t always compatible with the needs of major projects either. From a management perspective, a key challenge was the lack of understanding between specialist areas. It was hard for those outside of IT to grasp why digital projects took so long. There was also a major misunderstanding about the difference between a minimum viable product (MVP) or proof of concept and a full enterprise-grade, supported product. People would see a simple proof of concept working and think the project was done, not realizing the ten times more work required to make it robust, secure, and supported for industrial operations. This made getting proper funding and schedules challenging. There was also perhaps an expectation, influenced by consumer software and open source, that digital solutions should be free or cheap, not recognizing the significant costs involved in enterprise software development and customization for unique company challenges.
Fast-forward to today — how has the digital oilfield landscape evolved over the past 25 years? What’s truly different now?
The landscape has evolved dramatically. A huge shift happened around 2008 with the iPhone, which accelerated changes in behaviour and technology adoption. Now, we have a new generation that grew up with technology always available, so they have higher expectations and are comfortable using it. What’s truly different? Firstly, the amount of data we generate is enormous now, partly because projects are designed with digital tools in mind and are better instrumented. We can handle and store much more data. Cloud systems have been a game changer, allowing us to manage vast amounts of data and make it far more accessible. Remote access is now much easier and more secure from anywhere on any device, thanks to cloud technology, which was a major headache early on.
Secondly, the quality and availability of web technology have improved immensely. We have standardized browsers and excellent open-source libraries that make developing secure apps
with good user experiences much quicker than coding everything from scratch. Finally, infrastructure as code is a major shift. Instead of installing on physical servers, we use code and pipelines to build and deploy applications rapidly into virtual environments. Deployment speed is huge, and it’s incredibly flexible –we can spin up environments quickly and even rebuild everything from code in minutes if there’s a security issue.
AI is transforming industries across the board. In your view, how is AI shaping or accelerating digitalisation in oil and gas?
AI is definitely another game changer. There’s a huge expectation around it, but I think the reality, like with any tool, will be a bit different from the initial hype. It will provide value in ways we might not have thought of, but perhaps not in others we initially expected. I see it primarily as an extremely valuable tool for improving efficiency. I use it a lot as an assistant, and it makes me and my team more efficient. However, it’s not at a level where it can replace people because it makes mistakes. It can also be misused if relied on blindly. If we’re going to trust AI outputs, there’s a huge responsibility on us to verify them. It needs to be explainable and auditable. While autonomous operation might be a future possibility, I think we’ll see AI used in an assistive way much more in the near term. It will take significant time, checking, verification, and legal frameworks to build the trust needed for full autonomous operation, similar to how we still have pilots and train drivers even though the technology for automation exists. So, it will accelerate things, but likely with humans remaining in the loop for a long time.
Based on your experience, what are the top three lessons you’ve learned from implementing digital
Based on my experience, here are the top three lessons: Get into the detail early. Concepts are great, but you need to start looking at real data, real systems, how things connect, the infrastructure, data structures, and what the users actually need as soon as possible.
Focus relentlessly on the user. You need a laser focus on delivering value to the user. It might feel boring or too simple, like just reducing clicks, but if it makes their daily work easier and they are delighted, it will be adopted and successful. Trying to force adoption rarely works.
Break the project down into manageable steps. Industrial digital projects are often unique, so you can’t cost them like building a standard house. Cut them into small, costable, deliverable steps. Use a phased approach – discovery, de-risking, and several delivery stages – to get something working early, verify it with users, and then add the enterprise features. This minimizes rework and keeps the organization on board. Trying a big bang approach is very difficult and risky.
your
what are the
Building on those lessons learned, the key success factors are really about breaking projects down into stages and critically, making sure all your stakeholders are on board. You need to communicate clearly what you’re delivering and give users the chance to provide input as early as possible. This is crucial because rework is one of the most expensive things in digital projects. Getting feedback early helps avoid misunderstandings where you deliver exactly what was asked for, only to find out it wasn’t actually what was needed. By showing users what’s possible early on, they can better define a scope that they will be delighted with at the end.
digital transformation across operations and design
Augmented engineering applications and services to fundamentally improve the way you work through intelligent, data-driven approaches
In the oil and gas sector, performance is not merely a concept, kit is a calculation. As the industry convenes in Aberdeen for the Future of Oil and Gas 2025, the dialogue is shifting from theoretical innovation to proven transformation in the field. As Katarzyna Chrzan, Senior Marketing Manager at Cohesive explains, the question is no longer whether we should modernise, but how we can do so in a way that delivers measurable, scalable impact.
Despite decades of investment in SCADA, DCS, EAM, and ERP systems, many oil and gas operators still lack a unified, real-time perspective on asset performance. Data silos between operational technology (OT) and enterprise IT environments continue to obscure visibility, delay decisionmaking, and restrict proactive action.
The result? Reactive maintenance, inefficient planning, and missed opportunities for optimisation.
This is where a comprehensive Asset Performance Management (APM) strategy becomes vital. It’s not simply about deploying a platform, it’s about creating an integrated ecosystem that connects data, people, and processes.
Delivering Tangible Value Through Integrated Asset Strategies:
• Advisory services to evaluate the current digital landscape, identify integration gaps, and
define a roadmap for a unified APM architecture aligned with business objectives.
Data services to classify, standardise, and integrate fragmented asset data across systems, transforming it into actionable intelligence for real-time monitoring and advanced decision support.
• Technology platforms such as the IBM Maximo Application Suite (MAS) serve as unified solutions that integrate data from SCADA, DCS, EAM, and ERP data into a single operational layer, eliminating silos and enabling predictive insights at scale.
Together, these capabilities establish the foundation for scalable, insight-driven asset strategies that go beyond dashboards and deliver measurable impact in the field.
An example of this comes from Scotia Gas Network (SGN), a leading UK gas distributor. By unifying operations in a single Maximo system, SGN cut infrastructure complexity, removed fragile custom integrations, and reduced maintenance costs. The transition was completed with zero downtime for thousands of users—proving that large-scale digital transformation can be seamless and effective. The unified platform now enables shared communication, decision-making, and reporting across the organization.
Inconsistent failure coding and reliability data across onshore, offshore, and regional sites continue to hinder effective root cause analysis and benchmarking. Without a unified taxonomy, continuous improvement efforts often rely on assumptions rather than evidence. Aligning asset hierarchies with ISO 14224 and harmonising historical failure data unlocks analytics-ready datasets—enabling RCA, MTBF/MTTR tracking, and global reliability benchmarking. This creates a solid foundation for consistent, data-driven decisionmaking across the enterprise.
At the same time, operators face growing pressure from ageing workforces and rising labour costs, particularly in remote or offshore environments where skilled labour is scarce. AI-powered workforce analytics and intelligent scheduling tools to help organisations optimise resource
allocation, identify skill gaps, and support longterm workforce planning. The goal isn’t just to reduce OPEX—it’s to embed resilience and agility into day-to-day operations.
In high-risk industrial environments, safety and operational continuity go hand in hand. Yet many oil and gas operators still rely on manual or fragmented systems to manage critical activities such as shutdowns, commissioning, and high-risk maintenance. This not only increases exposure to incidents but also limits the ability to respond quickly and confidently when it matters most. Digital tools are transforming how operators plan and execute complex operations.
A real-world example shows the value of this approach:
This case comes from the gas-to-power sector, where natural gas (LNG) is converted into electricity. At a major power plant in Indonesia, Cohesive implemented a digital Permit-toWork (PTW) system in IBM Maximo during the commissioning of a new combined cycle gas turbine (CCGT) unit. The high-risk “first fire” phase—when the plant begins generating power— was managed without a single incident or minute of downtime.
The system ensured consistent safety procedures, real-time permit tracking, and better coordination—critical in such environments. It also supported the plant’s sustainability goals by reducing the risk of unplanned emissions and reinforcing its reputation as a responsible employer.
Many facilities still rely on fixed-interval or reactive maintenance—even when condition monitoring tools are available. This results in unnecessary interventions, unplanned outages, and increased lifecycle costs.
In the UK, the number of active production hubs could fall dramatically—from 46 today to just 4 by 2040. But this trajectory is not set in stone. With the right digital strategies, including AI-powered predictive maintenance, operators can extend the productive life of existing assets, reduce unplanned downtime, and extract more value from mature
fields—delaying decommissioning and improving return on investment.
The future of oil and gas is not solely about technology—it’s about transformation that delivers in the field. By addressing deep operational challenges with AI-powered solutions, the industry can move from fragmented data to unified intelligence, from reactive maintenance to predictive strategy, and from complexity to clarity.
The UK’s North Sea sector is entering a new phase. While the government has not formally banned new oil and gas exploration licences, recent policy direction—particularly through the Great British Energy Act 2025—signals a strategic shift away from fossil fuel expansion and towards clean energy investment. In this context, the ability to safely and efficiently operate mature infrastructure is essential—not only to maintain domestic energy supply, but also to buy time for the build-out of low-carbon alternatives.
In this evolving landscape, AI and Asset Performance Management are more than tools for operational efficiency—they are strategic enablers. By extending asset life, improving reliability, and creating a digital foundation for future repurposing, operators can not only maximise today’s output, but also prepare infrastructure to support tomorrow’s low-carbon energy systems.
Some operators are already on this journey. For the rest, the time to begin is now.
www. cohesivesolutions.com www.ibm.com/products/maximo
Decarbonization of the UK’s energy system requires increased interaction and cooperation between all energy stakeholders.
Therefore, alongside electrification, digitalization remains a key enabler in the pathway towards net zero against a backdrop of volatility, unpredictability, and complexity.
In the UK’s first Energy Digitalisation Strategy, the Government set out how only a digitalized energy system can withstand the distributed nature of low-carbon technologies connecting to the grid in the coming years. A number of subsequent use cases - many now being realized as actual projects - are emerging across the UK energy sector. For example, the National Energy System Operator (NESO) is leading on the Virtual Energy System which aims to enable an ecosystem of connected digital twins. However, introducing digital technology, enabling data sharing, and increasing automation, inherently introduces additional risk into safety-critical systems.
How can the energy industry adopt digital technology, deploy sensor systems,
share data and enable the introduction of computational models (including artificial intelligence and digital twins) to command their assets and be confident in their safe, secure and economical operation in addition to meeting the legal and regulatory requirements?
A substantial green prize lies ahead for the UK as it decarbonizes its economy.
As we enter 2025, the energy industry stands at a pivotal moment in its history. Despite global economic headwinds and geopolitical uncertainties, we’ve witnessed unprecedented momentum in clean energy deployment and DNV forecasts that the world will hit peak emissions this year.
The UK’s energy landscape is transforming rapidly, with record-breaking renewable energy generation and falling costs of clean technologies setting new benchmarks for what is possible. The past year has demonstrated the UK’s potential on this transition journey. We’ve seen wind power generation reach historic highs, battery storage capacity expand significantly and Electric Vehicle (EV) adoption show signs of recovery. However, these achievements, while significant, are merely the initial steps toward the UK’s 2050 net-zero goal.
The ambitious new transition pathway mapped out by the UK government includes three critical milestones that will shape our journey towards net zero. DNV’s UK Energy Transition Outlook 2025 reveals a mixed picture of progress and challenges against these three targets:
• First, by 2030, we expect to see a dramatic expansion of clean power infrastructure, with installed renewable capacity forecast to double, reducing our reliance on gas to less than 12%, but falling just short of the Clean Power 2030 target of 95%.
Second, DNV’s forecast of a 35% reduction of today’s emissions by 2035 highlights that progress is being made, but that the UK will still fall short of its new Nationally Determined Contributions (NDC) target of at least 81%.
Third, our forecast for 2050 sees the UK successfully decoupling economic growth from energy consumption, reducing the UK’s energy demand by 25% and emissions by 82% compared with 1990 levels. But clearly the UK is not reaching net zero.
Looking ahead, we see enormous opportunities in this transition. The green economy promises new jobs, reduced energy costs for consumers, enhanced energy security, and technological leadership. However, these opportunities can only be realized through continued policy support, strategic investment, and strong collaboration across all sectors. The
technologies and opportunities. Together, we
that is not just cleaner and more efficient, but also more equitable and resilient.
At DNV, we firmly believe that digital transformation is key to safeguarding energy supply in its current form; whilst at the same time helping to decarbonize and electrify society. We also expect our energy system to comprise connected digital twins, with AI baked into this smart, Cyber Physical Infrastructure (CPI). This will address the significant increase in complexity we foresee across the entire energy system which is becoming increasingly digitalized and connected. Only with trusted digital systems managing this complexity will the UK’s energy supply remain safe, secure and sustainable.
The chasm between theory and reality in terms of where the sector is today and where it needs to be to realise this digitalisation is significant but not unbridgeable. Through controlled research and testing, which includes stress testing the full envelope of potential future scenarios and demonstrating compliance, trust in digital assets can be gained: unlocking their investment and adoption across the energy industry.
Establishing trust in digital assets is vital for the industry, which is used to managing high-risk assets and critical infrastructure essential for society. As the energy sector transitions toward cleaner and smarter technologies, digital trust ensures seamless integration of these cross-vector systems to enable efficient energy production, distribution, and consumption. However, whilst digital technologies offer significant opportunities, they also introduce complexities and risks.
Some examples include:
Smart energy adoption: With the proliferation of smart energy technologies (such as smart grids, sensors, and IoT devices), there will be a substantial increase in the quantity of data produced and exchanged. Maintaining
trust in the accuracy and validity of this data is paramount for reliable decision-making.
Data management: Interoperability is essential for systems to facilitate new and existing data sources. Effective data handling through measurable data quality, secure storage and seamless exchange are critical for optimizing energy operations.
Cybersecurity: Operational technology must be robust against cyber threats which act as a significant hurdle for the adoption of digitalized assets on critical national infrastructure. It is therefore imperative that systems are rigorously tested against cyber threats, and that thorough cyber-security strategies with incident response plans are in place prior to adoption to instil trust that the energy system will remain safe, controlled and resilient. Regulatory compliance: Trustworthy systems need to adhere to industry regulations and standards. Compliance builds confidence among stakeholders and ensures responsible energy practices.
In summary, digitalization is essential but it introduces new complexity and risks. Digital trust is paramount in underpinning a reliable and resilient energy system which supports a sustainable energy transition.
Awareness and reduction of digital technology risk is imperative to accelerating the energy transition. Without appropriate assurance of technical risk, new energy technologies – and specifically, digital and cyber-physical technologies – are, at best, expensive to scale, operate, insure and/or finance. Technical confidence is a critical building block for the deployment of energy technologies. Independent assurance can give investors the confidence needed to finance and ultimately deploy these technologies at scale.
According to DNV’s latest Energy Industry Insights report, a survey of over 1,000 C-level executives across power, renewables, oil and gas and industrial
energy use sectors, a total of 91 % of respondents reported that they will increase or maintain investment in digitalization in the year ahead. Associated with that, 68% will focus on automation; whilst 71% report that improving data quality and ensuring data availability is high on the agenda. 60% of respondents suggest that they will use AI-driven applications in their operations.
The automation piece is of particular interest, as industry tells us that it is investing significant amounts into AI and other digital technologies but, according to the detail in our research, few can demonstrate the trustworthiness of these technologies to stakeholders for critical decisionmaking. Although only 12% of the industry’s C-level respondents say they are in an advanced stage of AI development – or have live AI projects – this is set to change with 73% stating they are piloting or planning activities for the future.
The struggle for many companies is the transition from pilot innovation projects and lab-based demonstrations to actual projects with businessas-usual implementation. DNV’s learnings, from assisting customers across the energy sector in this transition to implement trustworthy AI, can be summarised in three key highlights:
• There needs to be a better understanding of how AI technology will deliver value by being sustainably integrated into work processes; Digital assets that are created require a structured change management approach throughout any digitalization process to ensure value is realized;
• Given the different assurance requirements of digital technologies compared to physical assets, a comprehensive approach to data management and data quality is required to leverage sustainable value.
For many organisations in the sector, all three of those items remain challenges that need to be solved to ensure a more meaningful return on investment from assets. Establishing digital trust is vital to the future of the sector.
Cloud-powered insights for upstream performance.
In upstream oil and gas, unseen flow assurance risks and underperforming wells reduce output and threaten asset integrity. KBC Acuity™ Upstream Operations Monitor transforms your production visibility by combining real-time data with predictive analytics to optimize performance and meet production targets.
Data handover failures in oil and gas projects are still far too common, often undermining the performance of even the most sophisticated digital assets. By appointing a Main Digital Contractor, operators can embed data integrity from the outset and ensure the transition from project to operations is seamless, efficient and value-driven.
By Rob Kennedy, Global Director, Digital Asset and DataOps, Wood, and Michael Edwards, Head of Data Partnerships and Platforms, Wood
Successful oil and gas capital projects aren’t just about delivering on time and within budget. They also require a flawless start-up and ramp-up of the asset. As operations become increasingly digitalised, the need for complete and trusted data has never been greater. Yet, data handover from project to operations remains a significant challenge. By engaging a Main Digital Contractor and treating the digital asset as a critical element of the physical asset, the quality of the data handover can be significantly enhanced.
Capital projects are leveraging increasing levels of digital technology to enhance efficiency, reduce rework and mitigate risk. Despite the growing adoption of data standards and data-centric practices, challenges with handover to operations remain, with incomplete datasets, inaccuracies and inconsistencies adding to late delivery.
Many operators have successfully integrated digital twins into their operational workflows, where they are key enablers for safe, reliable, optimised and profitable operations. For new assets, the start-up, ramp-up and early operations period is crucial, with delays potentially costing millions of dollars per day. Data handover issues can impede the proactive management and optimisation of the asset during this critical period, creating knock-on consequences.
Operations teams are often left to address data issues from handover. The cost to rework datasets, extract additional data from documentation and rectify the 3D model can be substantial, and is a hidden cost that isn’t budgeted for.
The industry must find a better way to manage data on capital projects that simultaneously benefits the project and ensures a high-quality and timely handover to operations.
Data standards alone are not enough
Selecting an appropriate data standard is clearly important, but its successful implementation is imperative, requiring buy-in and prioritization across the project. However, many project teams, contractors and suppliers view data handover as a burden, perhaps due to a lack of understanding of how that data will be used to deliver value.
Work to achieve a successful data handover should start in the select phase. A lifecycle digital strategy for the asset should be developed, shaping activities in the project phase and into operations. Early engagement of project stakeholders and contractors is essential and aims to foster a mindset change whereby data is treated as an important deliverable.
In the define phase, data use cases in the project and in operations should be identified, including any unique or particularly valuable areas for the specific asset. This allows an appropriate data standard to be selected, and any additional attributes to be incorporated as needed. Data requirements then need to be cascaded across the project, implemented by engineering teams and incorporated into contracts. Importantly, there must be sufficient commercial incentive (or penalty) to ensure that contractors meet these requirements.
Data gathering and assurance begins in the execute phase. In addition to the existing practice of validating data against the standard and checking completeness, it’s critical to ensure that there are no data gaps due to missing tags. Field verification of data and models should also be performed to enable as-building.
Finally, to prepare operations to receive the data handover, a suite of dedicated processes and procedures are required to sustain and maintain data over the asset life.
A successful data handover requires significant effort and strong engagement from all parties involved, including contractors and suppliers. Having a dedicated data team to drive this process across the project and supply chain will significantly improve the quality of the data handover, and help to mitigate the risk and cost of re-work.
A Main Automation Contractor (MAC) is often employed on capital projects to provide a unified approach to control systems from the define phase through to operations. Similarly, a Main Digital Contractor can enhance digitalisation on the project by coordinating all stakeholders and managing all digital and data activities.
Starting in the select phase, the Main Digital Contractor leads the creation of the lifecycle digital strategy for the asset, with significant influence from operations. Then, in the define phase, they identify and prioritize digital initiatives and document the associated data requirements, overseeing adoption by the project and inclusion in contracts. In readiness for execute, a ‘pre-operations’ digital twin is deployed. This serves as the central data hub for the duration of the project, enabling data exchange with completions and commissioning contractors and operations readiness teams, before facilitating a seamless transition to operations.
The pre-ops twin is utilized by the Main Digital Contractor throughout the execute phase to gather, manage and validate data from each contractor, utilizing data pipelines between the pre-ops twin and each contractor’s own digital environment.
Data validation, completeness and consistency issues are highlighted in the pre-ops twin to enable their prioritized close-out. Then, to assure data accuracy, verification tasks are incorporated into commissioning inspection test records, with findings being used to asbuild data and models.
As the operations phase approaches, the pre-ops twin is utilized to prepare data and models for handover, accelerate the maintenance and integrity builds and load data into operational systems. This enables these systems, and their connection to the operational digital twin, to be tested in readiness for start-up.
Finally, before handover the Main Digital Contractor establishes a data operations, or DataOps, team to govern, update, maintain and manage change to data, ensuring that
operations teams receive high-quality, actionable data.
To ensure successful data handover from the project, operations need to actively influence the lifecycle data requirements and processes from the outset. A Main Digital Contractor is essential in this process, engaging project and operations stakeholders and driving a consistent digital approach across the project.
As oil and gas operations become increasingly digitalised, the value of high-quality, trusted data is becoming more evident. Remediating existing data for operating assets to achieve the necessary level of data quality requires considerable cost and effort – for new assets it is therefore imperative that we gather and handover the right data. Just as we wouldn’t accept a physical asset requiring extensive rework before operations, we must hold digital assets to the same standard.
As your Main Digital Contractor, we drive digitalisation across your capital projects, delivering digital-native assets that advance ways of working, enable operational excellence and deliver lasting value. See
woodplc.com/digital
Real-world applications and use cases have emerged beyond the buzz and hype of AI. Natural language processing (NLP), large language models (LLM), hybrid machine learning (ML), generative and agentic AI, all represent a litany of transformational technologies.
The possibilities for our digital future within the energy industry are endless:
• Faster, more reliable data processing and verification, with more sophisticated data-sharing infrastructures
Connected data sources as a foundation for accelerated innovation and collaboration
• Increased autonomy and automated services in operations and maintenance
Integrated physics-based and data-driven digital twin models that together with AI augment human decision-making
• Improved asset performance management and reliability for plants from upstream to downstream Bi-directional data flows between systems and equipment, with Generative AI enhancing interaction to increase situational and operational awareness
• Supply chain transparency and traceability across the energy value chain
Predictive analytics for improved energy efficiency
Considering the potential unlocked by an AI-driven digital transformation strategy, both immediate and long-term advantages become clear - ranging from faster data processing and improved information flow to reduced risk, enhanced communication, and greater automation. But the real challenge lies in moving beyond the hype to thoughtfully integrate these advanced technologies into daily operations in a way that aligns with industry needs. The key question is how AI will become embedded in routine business processes, supporting everything from workflow automation and data analysis to decision-making and
customer engagement, ultimately reshaping how organizations operate and deliver value.
Moving beyond data and dashboards
What matters most is not just the data you have but how you use that data. Data standards are an important part of our digital future, enabling companies to collaborate and co-innovate through system interfaces that integrate in the back end. Many progressive companies have put in place a solid data infrastructure and added select applications like a digital twin on top, making data more contextualised and accessible through simplified dashboards that make data easy to find, filter and apply.
However, data and dashboards are not enough of a springboard for AI to have the measurable value or ROI that companies expect. Instead, we need to start with a value-focused approach that zooms in on the specific use cases and services where AI can have the most influence through a digital operating
model that builds on digital twin technology backed by physics-based and data-driven models. The successful implementation of an AI-infused digital strategy needs to be driven by desired business outcomes.
Driving transformation with a value-focused approach
Effectively leveraging AI to move beyond “business as usual” in the energy sector requires deep familiarity with the industry’s evolving landscape. As a technology provider with both domain and technical expertise, we see the greatest potential for AI-driven value creation in several key areas
• Safety
Operations and Maintenance
Performance Monitoring
Supply Chain Management
Design and Engineering
Emissions Management
Once specific services within the potential high-
impact areas are identified—typically those that are frequent and generate consistent, repeatable data patterns—they can serve as ideal candidates for AI-driven automation. These patterns enable AI and related technologies to support the development of value-focused applications that extract and process information, generate insights, and provide actionable recommendations. Many of these actions can be executed autonomously, ultimately contributing to greater energy efficiency.
Beyond the hype, it’s essential to keep people at the core of operations, supported by technology that can seamlessly handle diverse data types and sources. In this model, technology serves as an enabler—delivering the right amount of information to the right person at the right time. This enhances decision-making speed while reducing risk. Depending on the use case, the resulting benefits can scale significantly, from reduced emissions to earlier interventions in
predictive maintenance scenarios.
Consider a methane emissions management workflow.
An emissions reduction team oversees 10 assets for a major exploration and production company, continuously monitoring each site’s carbon footprint. Their central tool: a cloud-based, dynamic digital twin that provides access to a configurable emissions management cockpit. This cockpit goes far beyond static dashboards—it highlights the highest energy consumers in real time, flags critical incidents requiring immediate attention, and suggests recommended actions based on live data streams enriched with historical and synthetic datasets.
At one facility, the cockpit detects that a main gas turbine is consuming significantly more energy than expected, pushing up the site’s overall emissions profile. The team initiates an investigation by querying the digital twin through an integrated AI-powered chat interface, retrieving targeted insights in seconds.
With the relevant data in hand, they virtually navigate to various system components—such as flare stacks and vents—to pinpoint the issue. Behind the scenes, complex data processing and integration are handled seamlessly, allowing the team to focus on decision-making. They consult a simulator view within the twin to compare realtime and modeled values, receiving prescriptive guidance on where and how to intervene. Armed with this clarity, the team can act quickly, supported by both actionable instructions and transparent rationale
Data becomes insight. Insight drives action. Action delivers outcomes. And outcomes evolve into prescriptive tasks—clear, traceable, and executable—enabling teams to move with confidence and transparency. This cycle supports a wide range of use cases, each aligned with business goals and value-driven outcomes. Forwardthinking energy companies are already embracing this shift. It’s not just better than business as usual—it’s the foundation for a smarter, more sustainable future.
The term ‘digital twin’ is often misunderstood, not least because it conjures the image of a flawless replica, an exact virtual likeness of a physical system that can be monitored, queried, and controlled. But oil and gas operations are not idealised environments. They are dynamic, high-risk, and deeply human systems. The true purpose of a digital twin is not replication, but translation. It must translate complexity into clarity, offering operational insight to both systems and people.
Digital twins are becoming essential for operational insight in oil and gas, but a narrow focus on assets and automation risks missing the bigger picture. To deliver real value, twins must serve the connected worker as much as they serve the control system.
As technologies mature and digital initiatives expand, this distinction becomes critical. A twin that simply mirrors asset states and process flows may satisfy the control room, but it offers little value to the technician tasked with diagnosing a valve issue at 2am, or the new engineer trying to understand how a safety system interacts with surrounding equipment. In reality, the digital twin is not a finished product, it is an evolving interface, shaped as much by human need as by data flow.
Hexagon’s Asset Lifecycle Intelligence division argues that the future of the digital twin lies in its ability to support operational roles, not just technical functions. “We want every operator to function as our best operator on his or her best day,” the company states. This goal reflects a fundamental shift in thinking. Rather than focus solely on automated optimisation, digital twin strategies must also empower the connected worker to make informed, safe, and timely decisions. Without this human-centric perspective, the technology risks becoming another underused layer in an already fragmented information landscape.
Most oil and gas organisations already sit atop vast repositories of information. Engineering documents, sensor data, procedural guides, maintenance records, equipment hierarchies, and compliance manuals, none of this is new. The problem is not one of data scarcity but of information utility. Too often, critical knowledge is trapped inside static files, legacy systems, or siloed applications.
Hexagon describes this as a failure of digitisation. “Valuable information, which is often a section of these larger documents, is not indexed or searchable, rendering it unusable and unfindable in
Capture inspection data using tablets
Input inspection media using cameras
Integrates with UAVs for media capture
Integrates with ROVs for media capture
Streamlined management of asset integrity
Integration with AI
End-to-end digital integrity management
Marine Technical Limits (MTL) specialises in FPSO integrity management and on-station repairs, delivering full-spectrum services - from risk-based integrity management and life-extension studies to end-to-end offshore inspection and repair campaigns.
With over 20 years specialising in FPSO integrity, MTL has developed the PYXIS platform - a cutting-edge digital tool to manage structural integrity with precision. PYXIS supports anomaly and asset management, inspection planning, repair oversight and lightship-weight control all in a single end-to-end system.
Surveys and inspections are fully digitised via the PYXIS Inspector application deployed on suitable zone-rated tablets. Inspection data is captured and synchronised in near real time, reducing reporting time by approximately 30%. Engineers can remotely review findings immediately, enabling faster, data-driven decisions.
Trusted by major FPSO operators globally, MTL empowers operators to extend asset life, minimise downtime and bolster operational certainty. Their commitment to innovation continues to keep them at the forefront of FPSO integrity management.
a digital system.” The result is that operators face a paradox: despite being surrounded by data, they cannot find what they need in the moment of need.
Eigen has tackled this issue with its Ingenuity platform, built around a data model that behaves more like a knowledge graph than a conventional hierarchy. Rather than forcing users to know where to look, the system allows them to navigate by context, jumping from a well to its valves, from those valves to their sensor data, from that data to its documentation, and so on. This relational structure ensures that workers are not just consuming information but working within a digital environment that reflects how the physical plant actually functions.
“When the user accesses an object in the Data Model, the full context is immediately available,” Eigen explains. “All the properties and all the related information and objects.” What emerges is not a digital library or an engineering database, but an operational tool, a living interface that delivers insight based on relevance, not on guesswork or keyword matches.
The twin as a training ground, not just a
The skills gap in oil and gas is no longer a looming threat, it is a present reality. As experienced engineers retire and recruitment struggles to keep pace with attrition, knowledge transfer becomes both urgent and difficult. Traditional methods, classroom training, manuals, and mentorship, cannot scale quickly enough. Here, the digital twin offers a unique opportunity to embed learning directly into operational systems.
Hexagon makes the case for a new approach to industrial learning. “We want operators to learn in the flow of work,” the company notes. “Truly digitised content contains links and metadata that directs users to knowledge that supports efforts to perform work at the highest level.” This model is closer to how people learn in their personal lives, typing a query into a search engine, watching a video tutorial, or following step-by-step guidance on a mobile device. In the industrial context, it means offering context-rich, role-specific content, accessible on any device, in any location, and always up to date.
Eigen reinforces this approach through templated displays and model-driven visuals. A wellbore
object, for instance, can drive a dynamic visualisation that automatically populates with the most relevant data points, document links, and performance metrics. This not only aids operational decision-making but accelerates on-the-job learning by showing how systems interrelate in practice, not just in theory.
The digital twin, when fully realised, becomes a continuous training platform. It reduces the time to competency, improves procedural adherence, and preserves institutional knowledge in a usable, discoverable form. For the incoming generation of workers, many of whom expect digital-native experiences, this could be the difference between engagement and attrition.
One of the most dangerous assumptions in digital
twin projects is that they must begin with a comprehensive model. The pursuit of perfection often delays deployment and deters adoption. What matters is not how much the twin knows, but how well it can adapt.
Eigen recognises this and has built its data model to grow incrementally. “The Data Model can be as small or as large as you like,” the company notes. “It could just model the Production Wells on a facility to start with and then be expanded over time.” The underlying architecture supports extensions, updates, and new relationships without breaking what already exists. This ensures that early investment continues to deliver value even as use cases evolve.
Hexagon takes a similar view, arguing that digital twins must evolve with the operational reality. As procedures change, incidents occur, and equipment
is upgraded, the twin must reflect those changes, not as a periodic manual update, but as a continuous feedback loop. Real-time annotations, operator input, and contextual updates all contribute to keeping the twin relevant and trusted.
This adaptability is not merely technical. It aligns with how people actually work, starting with what they know, solving immediate problems, and building confidence over time. A rigid, monolithic twin that tries to do everything from day one is more likely to be rejected than adopted. A flexible, responsive system that grows with the organisation will generate lasting engagement and measurable impact.
In a high-consequence environment like oil and gas, decisions must be backed by confidence. Whether investigating a process deviation or confirming a maintenance task, operators need to know not just the data, but where it came from. This is where traceability becomes essential.
Eigen’s model embeds links to source systems—such as data historians, document control systems, or engineering databases, so that users can trace each insight to its origin. “The Data Model should not also be a data store,” the company explains. “The Eigen Ingenuity Data Model includes pointers to the source data wherever possible.” This approach preserves trust and reduces duplication while allowing for dynamic interaction across systems.
Hexagon extends this concept to human data—capturing how people interact with systems and procedures and feeding that insight back into the operational model. By linking human performance data to system outcomes, organisations can identify procedural gaps, training needs, or design flaws that would otherwise remain invisible. In this way, traceability becomes a strategic asset, not just a compliance measure.
At its core, the digital twin must bridge the gap between technical systems and human expertise. It should translate the abstract into the actionable, the complex into the comprehensible. Too often, technology initiatives focus on instrumentation and integration but neglect interpretation and interaction. Hexagon’s framework acknowledges this by placing equal emphasis on automation, analytics, and the connected worker. The goal is not just to enable better system performance, but to create conditions in which people can perform better too. By integrating simulations, real-time tracking, interactive learning, and scenario-specific guidance, the twin becomes an operational partner rather than a digital ornament.
Eigen’s use of graph technology further supports this goal by offering a nonlinear, intuitive path through operational complexity. Instead of navigating through rigid folder structures or abstract taxonomies, users can move fluidly through contextual relationships, mirroring how experienced engineers build mental models of systems over time.
Together, these approaches suggest a new paradigm for digital twin development. It is not enough to model the plant. We must model how the plant
is understood, used, and improved by the people who run it.
The oil and gas industry is no stranger to technology. It has adopted some of the most advanced engineering, control, and data systems in the world. But as the sector pushes further into digitalisation, the success of these initiatives will be determined not by how clever the algorithms are, but by how effectively they serve the people on the ground.
Digital twins must do more than visualise data. They must contextualise knowledge, support action, and accelerate learning. They must evolve with operations, adapt to new challenges, and remain trusted by those who rely on them daily. And above all, they must close the gap between insight and impact, ensuring that the right decision is not only possible, but obvious.
The future of digital twins will not be defined by fidelity to physical systems, but by their utility in human workflows. When the model is built for the worker as much as for the asset, the twin becomes a true partner in performance, safety, and sustainability.
For too long, the oil and gas sector has treated artificial intelligence as a future consideration, something to be explored in labs and pilot projects, rather than deployed at scale. That mindset is not only outdated, it is dangerous. In an industry built on razor-thin margins, volatile markets, and high-risk environments, failing to embrace AI is not a cautious move, it is an existential threat.
The era of incremental improvement is over. Operators cannot afford to wait for perfect conditions or unassailable evidence. The technology is ready. The business case is clear. AI has proven its value in real-world scenarios, from predictive maintenance and drilling optimisation to emissions monitoring and supply chain intelligence. What remains is the will to act.
This is not about replacing people. It is about augmenting human capabilities to make faster, better decisions at scale. The average offshore platform generates terabytes of data daily, much of it unused. Teams cannot manually process this flood of information in real time, let alone extract insight. AI does not get tired, distracted or overwhelmed. It sifts, correlates, and learns, turning noise into actionable intelligence. That is not just a productivity gain; it is a safety imperative.
Consider predictive maintenance. Instead of reacting to failures, AI allows operators to anticipate and prevent them. This is not theory. Operators are already seeing maintenance response times slashed by up to 40 per cent and equipment lifespans extended significantly. In an environment where downtime costs millions per day, these are not marginal gains, they are game changers.
And yet, too many organisations are still dabbling. They invest in proofs of concept but fail to scale. They silo AI initiatives in IT or R&D, disconnected from operations. Or worse, they cling to legacy systems and processes that actively resist innovation. The result is a widening gap between digital leaders and laggards, a divide that will only grow more punishing as AI becomes more embedded in the competitive fabric of the industry.
Those still sitting on the fence must recognise the cost of inaction. AI is not just about driving efficiencies, it is about staying relevant. As net-zero targets tighten, capital becomes more discerning, and geopolitical shocks reshape supply and demand, agility becomes the most precious asset. AI is a force multiplier for agility. It enables faster decision cycles, more adaptive operations, and a data-driven approach to everything from reservoir modelling to logistics planning.
Take emissions management. With AI, operators can detect leaks faster, model carbon intensity across operations, and optimise energy usage at every level. This is critical not only for regulatory compliance but for stakeholder credibility. ESG is no longer a box-ticking exercise. Investors, governments and the public are watching, and AI provides the tools to meet their expectations with transparency and rigour.
Then there is generative AI, which is just beginning to find its place in the industry. While many dismiss it as hype, the reality is that large language models and synthetic data tools are already showing value in
accelerating geological interpretation, automating documentation, and supporting decisionmakers with context-rich insights. These are not toys. They are enterprise-grade tools that will increasingly underpin core workflows.
Of course, AI adoption is not without risks. Poor data quality, weak governance, and fragmented infrastructure can undermine even the most promising initiatives. But these are not reasons to delay. They are reasons to invest intelligently, to build the foundations that make AI effective and scalable. This means breaking down data silos, investing in cloud-native infrastructure, and building the internal capabilities to integrate AI into operational DNA.
It also means challenging cultural inertia. AI will not thrive in organisations where failure is feared, experimentation is punished, or success is measured by adherence to the status quo. It requires a shift in mindset, from control to collaboration, from hierarchy to autonomy, from instinct to evidence.
Leadership must own this shift. Delegating AI to innovation teams or external consultants is not enough. Executives must understand the technology, champion its use, and align incentives to encourage adoption. This is a strategic imperative, not a technical experiment. Companies that treat it as such will lead. Those that do not will fall behind.
The future of oil and gas belongs to the digitally mature. AI is the lever that can pull this industry into a new era—safer, cleaner, faster, and smarter. But the window for early advantage is closing. The question now is not whether AI will transform oil and gas. It is who will lead that transformation,and who will be left behind.
Join delegates from Shell, Vår Energi, OMV, Equinor and more at Kongsberg
Digital’s annual tech event. Explore the trends that are shaping the future of work in oil and gas, chemicals, offshore wind and the grid.
TOPICS
Agentic AI
Assets of the future
Smart manufacturing
Future-proof operations
Net-zero and CCUS
Workflow automation
Operational agility
Digital twin technology
Follow the QR link to learn register for free: