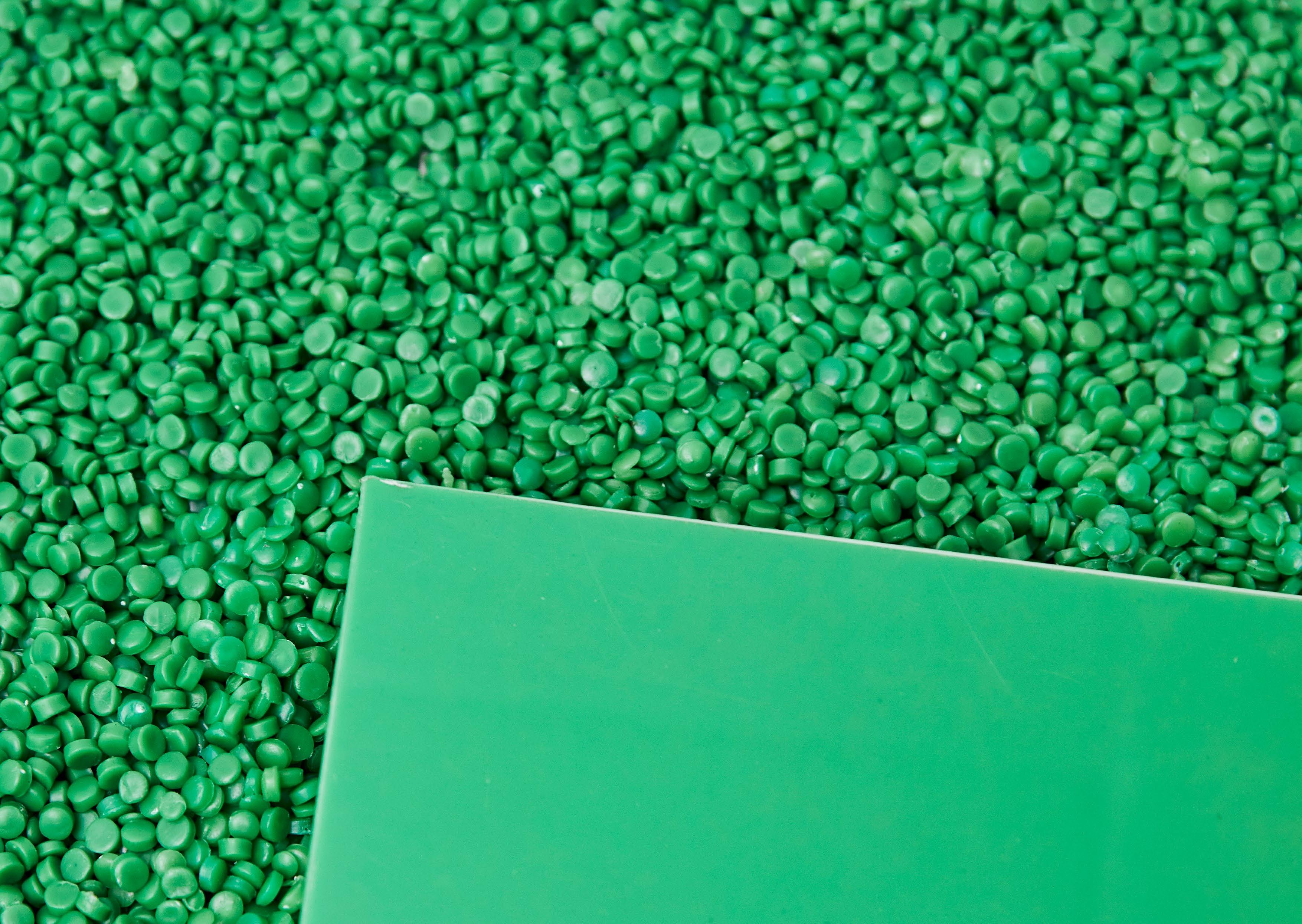
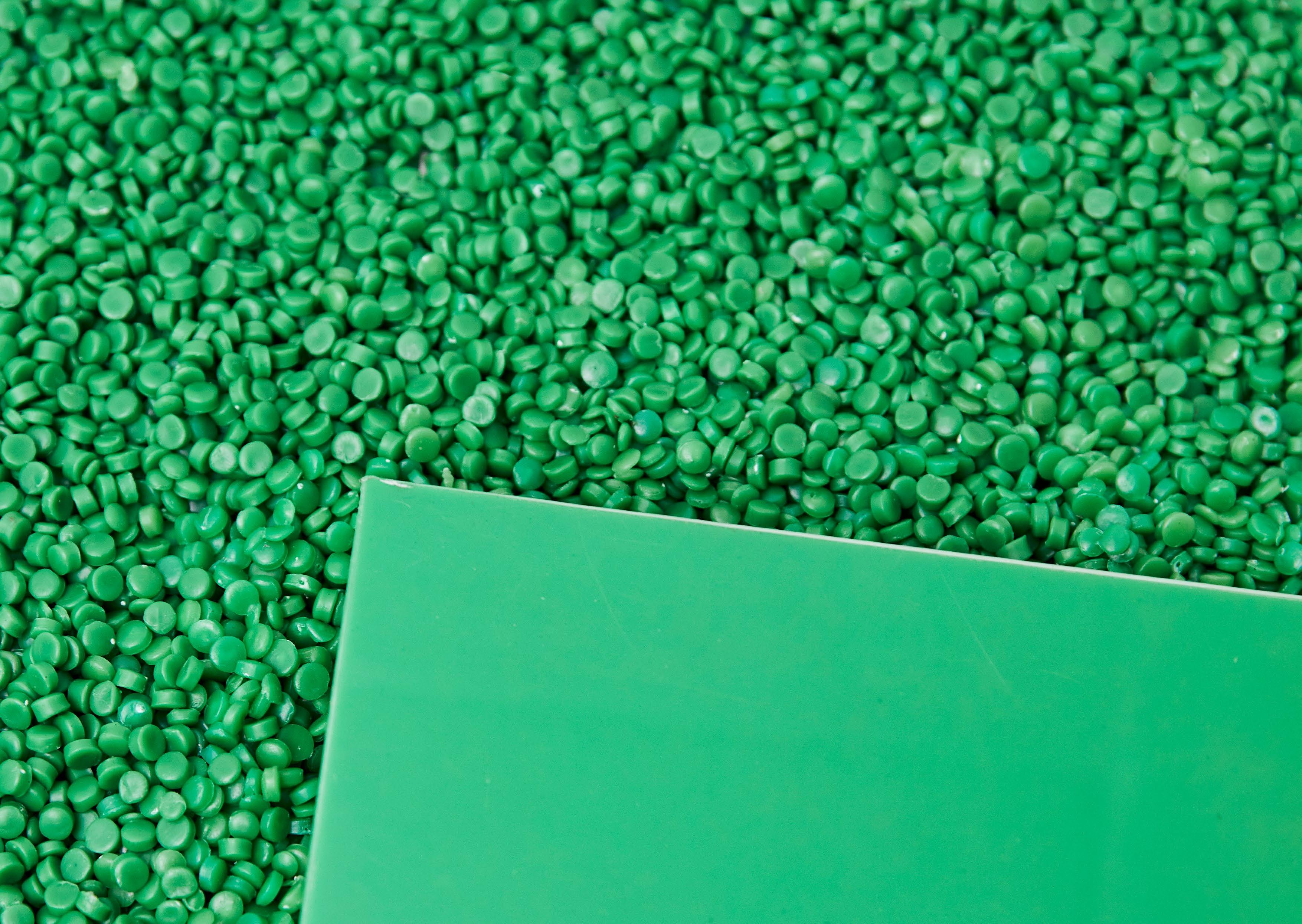
SUSTAINABILITY REPORT 2024
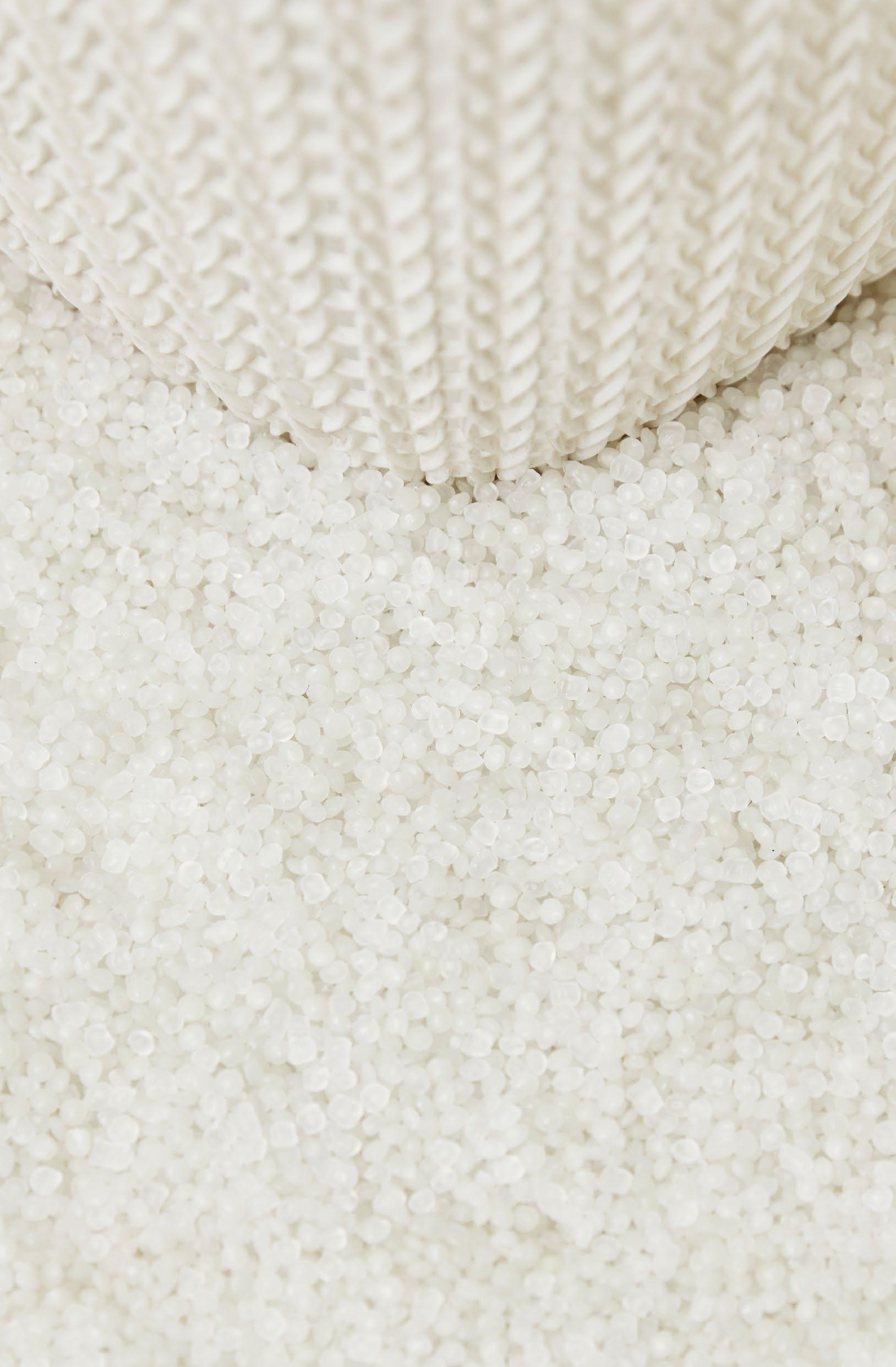
DEAR READER,
At RAFF Plastics, plastic waste gets a new life as a raw material for numerous products. For almost 50 years, we have been pioneers in recycling industrial and consumer waste. We want to continue playing this pioneering role to reduce waste and make a circular economy a reality.
Over the past year, we have firmly embedded our sustainable objectives in our corporate strategy by preparing for the Corporate Sustainability Reporting Directive (CSRD). As our first CSRD report is due in 2026, we are particularly proud of the gold medal that we have been awarded by Ecovadis, recognising the efforts we are already making every day.
After all, circularity is not a distant goal for us, but a daily reality. Our big bag project, which we recycle and have manufactured in a completely closed loop, is a recent example of this.
Our impact extends further, however. By recycling plastic waste into high-quality raw materials for industry, we support a more sustainable production process for our customers so they can also reduce their carbon footprint. Since the beginning of this year, we have been issuing customers with a Recycled Plastic Climate Impact Certificate, showing their CO2 reduction.
An important milestone in reducing our own carbon footprint was the purchase and commissioning of our first electric truck. This has reinforced our role as a forerunner in sustainable logistics.
Our strength lies in our strong and diverse team. We attach great importance to our employees’ well-being and we want to make a positive contribution to society together with them. Among other things, we have been recycling plastic caps for almost 20 years to raise money for the Belgian Guide Dog Centre, and we organised a beach clean-up on our coast as a teambuilding activity.
This report is not only an overview of our efforts and achievements, but also a starting point for the sustainable path we want to take together with all our customers, suppliers, employees, partners and stakeholders. Our resolute aim is to keep moving forward. For example, we are currently investigating how to recycle fishing nets and ocean waste.
We are continuing to innovate and inspire with processes that benefit not only our business but also our society and planet. We are thus tangibly striking a balance between People, Planet and sustainable Profit.
Together, we are building a sustainable world, for now and for future generations.
CAROLINE VAN DER PERRE CEO, RAFF PLASTICS
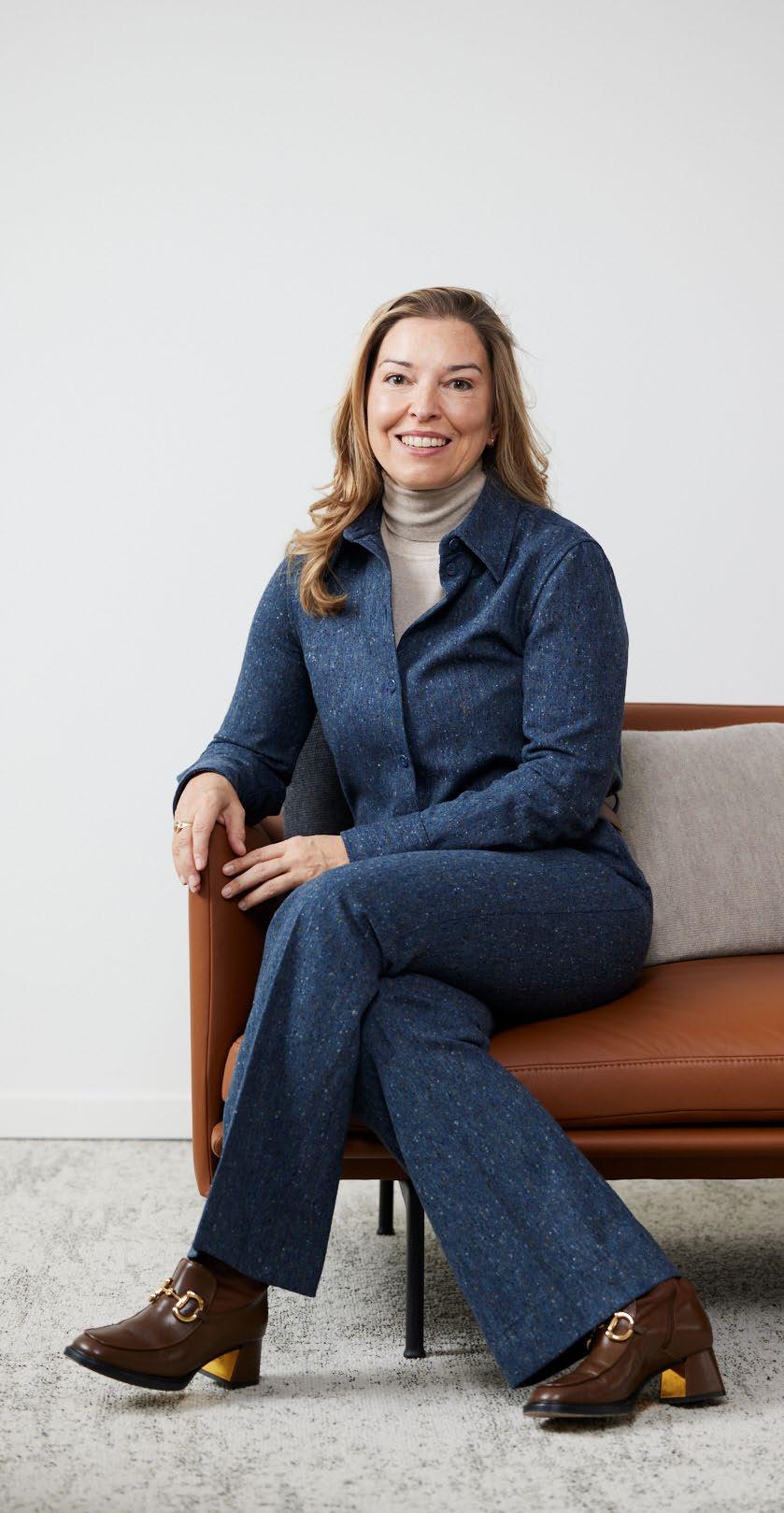
ALMOST 50 YEA RS OF RECYCLING FOR A BETTER FUTURE
PIONEERS IN RECYCLING
1976 Raf Van der Perre, Caroline’s father, establishes RAFF Plastics, which originally manufactured PVC compounds from virgin material. The company soon started recycling PVC and other plastics, becoming a pioneer in the sector.
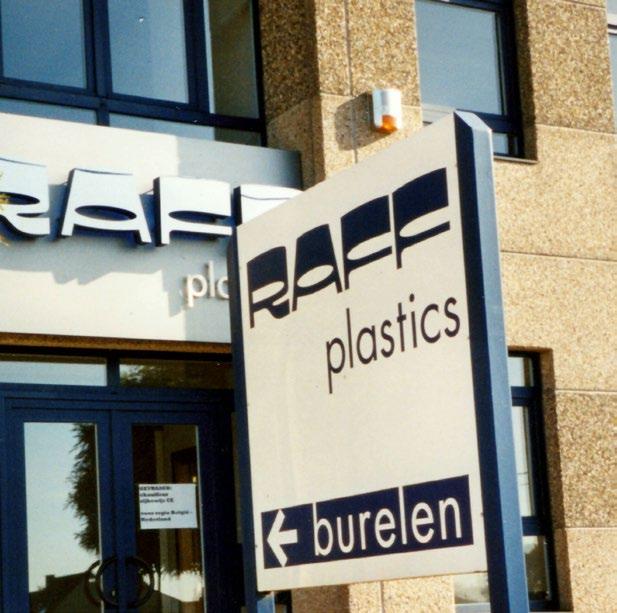

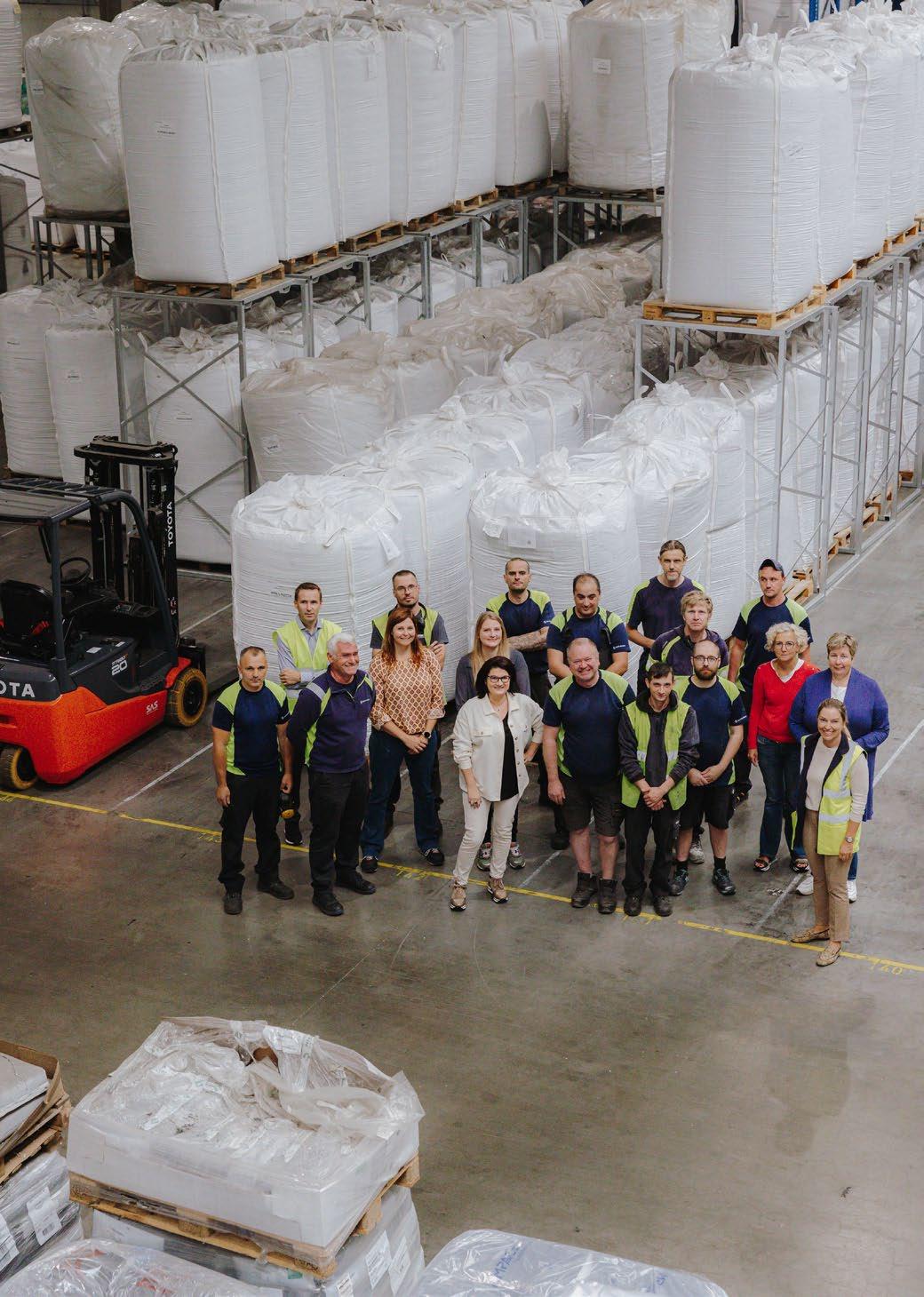
SUSTAINABLE GROWTH
The company site expands to 80,000 square metres and has 7,128 solar panels to reduce its carbon footprint.
2021 Signing of a declaration of intent for Operation Clean Sweep to prevent environ mental pollution from granulate spills.
2023 RAFF Plastics starts preparing for the CSRD and develops its sustainability strategy. The company receives an Ecovadis gold medal for the sustainable efforts it has already made.
2023 Start of collaboration with Go Forest.
2023 Circular big bag project with LC Packaging.
2024 Commissioning of first all-electric truck.
2024 Partnership with Go Ocean.
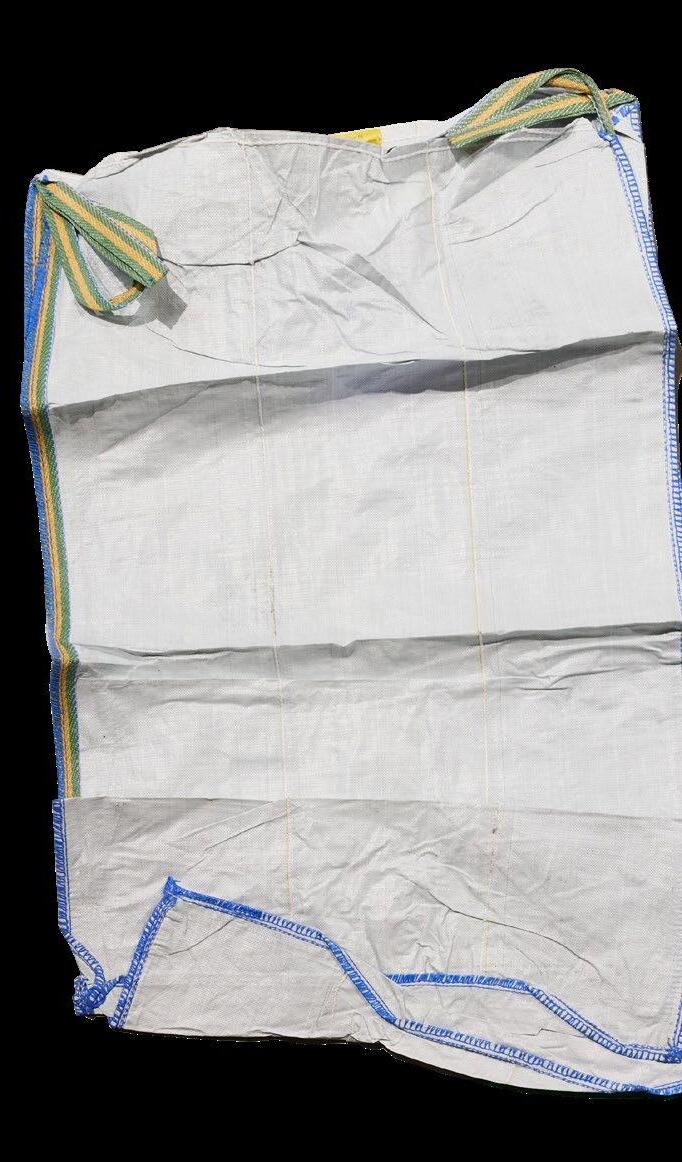
EXPANSION AND INNOVATION
2001 RAFF Plastics increases its production capacity and continues to innovate.
2005 The company starts recycling plastic caps for the Belgian Guide Dog Centre.
2012 The company expands further through a merger and Caroline becomes joint CEO, together with Christophe Dehouck.
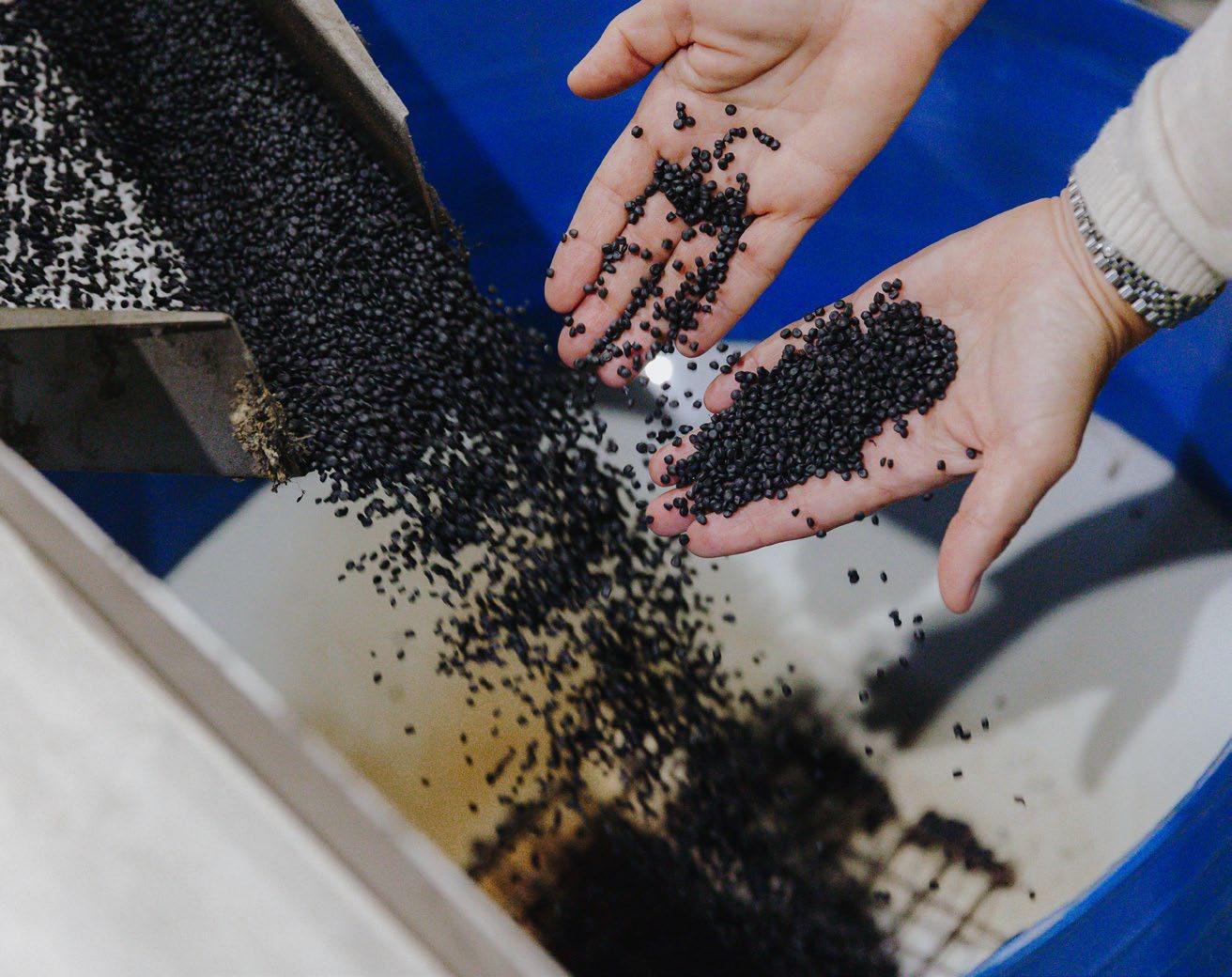
A NEW LIFE FOR PLASTIC WASTE
Every material that enters RAFF Plastics’ plant is plastic waste, which is then processed and delivered to customers as a new raw material suitable for various applications. Over the years, the company has processed increasing volumes of consumer waste, thereby reducing the amount of landfill waste.
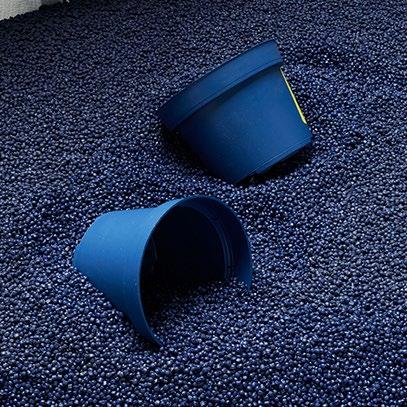
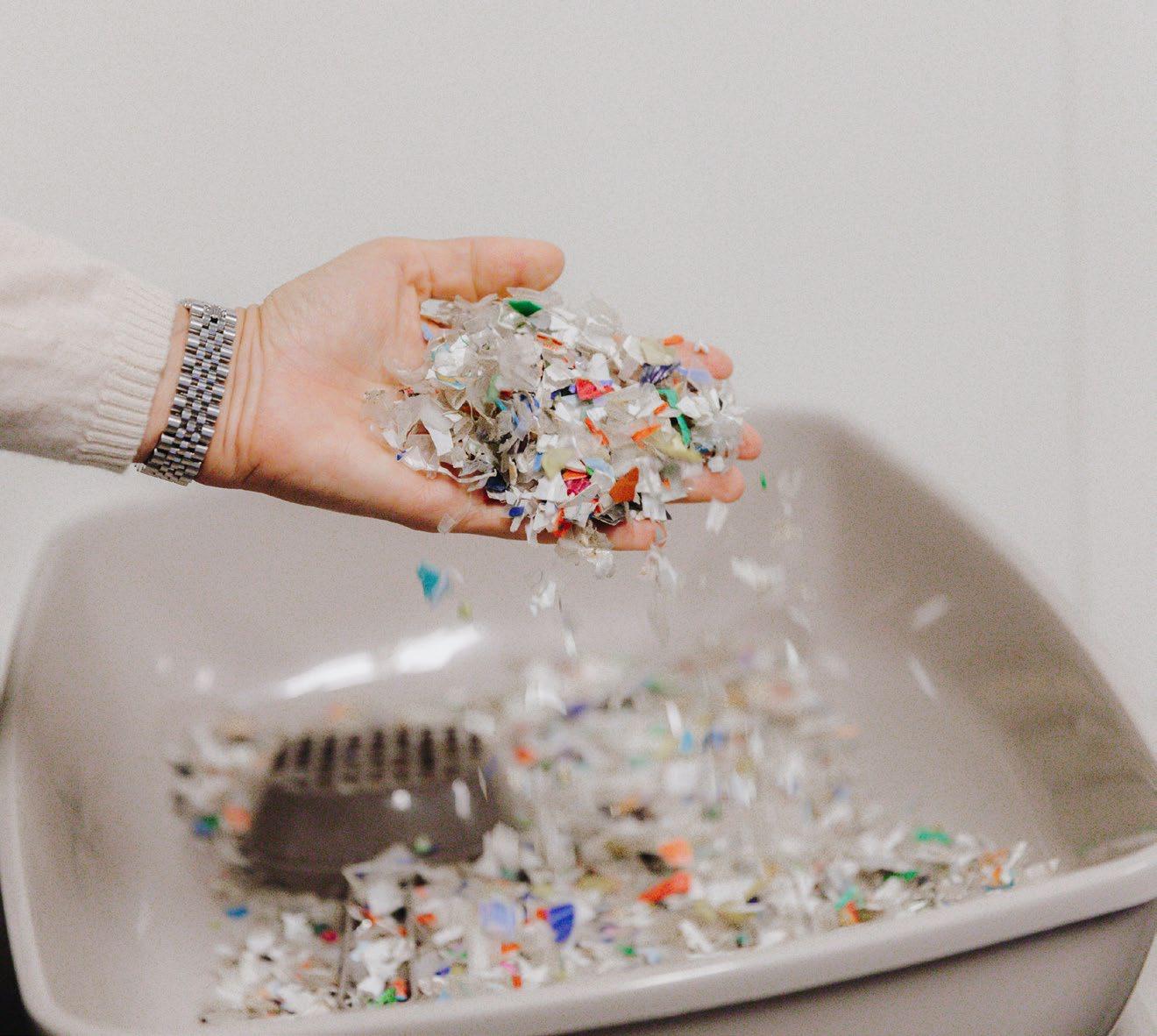
PLASTIC WASTE AS A SOURCE OF INNOVATION AND INSPIRATION
RAFF Plastics has been a recycling pioneer for almost 50 years. The company is able to recycle some 70,000 tonnes of plastic waste, 80% of which comes from consumer waste, into new raw materials. “Meanwhile, we are already looking further ahead and want to be able to recycle ocean and river waste as well,” Caroline Van der Perre and Christophe Dehouck tell us.
Constantly reinventing yourself to create a sustainable and healthy future, not only for the company, but also for the planet and society: that is the clear vision of Caroline Van der Perre and Christophe Dehouck and has since become part of RAFF Plastics’ DNA. “Moving forward is the only option. That is why we stand ready to face every challenge, despite the obstacles they may present,” says Caroline.
INNOVATION THROUGH AMBITIOUS PROJECTS
Caroline and Christophe love to innovate and experiment and are not swayed by arguments about something being too expensive, too cumbersome or not efficient. For instance, they are focusing on multimodal transport and energy-saving measures for the company, such as an electric truck, more energy-efficient machinery and a solar panel park that allows the company to meet part of its own energy needs. And the ambitions extend further: RAFF Plastics wants to be a pioneer in the future of recycling.
“We can only achieve our ambitions by continuing to look ahead and innovate in our operations. A recent example is the circular project we set up for the production of big bags, together with our partner and supplier LC Packaging. The big bags that
we buy from them are made from old big bags that we ourselves have recycled into raw material. That way, our customer is our supplier and vice versa.” The circular big bag project was nominated for the Trends Impact Awards in the Circular Economy category last year.
The company is also fully exploring how it can recycle waste from oceans and rivers in the future. “That will be a complex process because such waste is very contaminated. But I am intrigued by it – and ambitious about what we can achieve,” adds Caroline.
TURNING ENVIRONMENTAL CHALLENGES INTO ECONOMIC ADDED VALUE
Caroline is sometimes asked whether such initiatives are not too expensive. “A sustainable transition costs money, that is true. Today, I cannot demonstrate the profitability of recycling ocean waste. In the short term, it would be easier to run higher volumes on our existing lines, if we were going purely for profit.”
“But at RAFF Plastics, we take a long-term perspective. If we can also recycle ocean waste in the future, we will be able to process more waste, attract new customers and automatically grow as a company, and
“THINKING ABOUT INNOVATIVE PROCESSES FOR A SUSTAINABLE FUTURE INTRIGUES ME AND MAKES ME AMBITIOUS.”
TOGETHER, WE BUILD A WORLD WHERE PLASTIC WASTE BECOMES A SOURCE OF INNOVATION AND INSPIRATION, FOR NOW AND FOR FUTURE GENERATIONS.
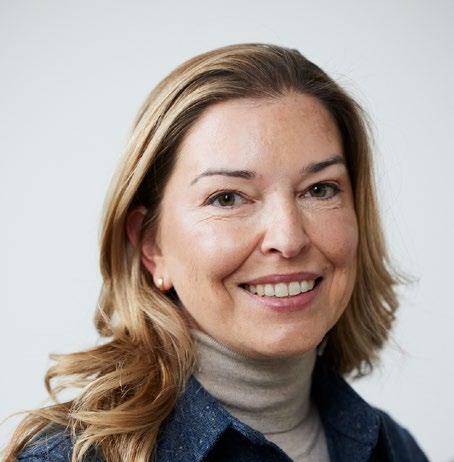
CAROLINE VAN DER PERRE
“IT IS BY JOINING HANDS ACROSS SECTORS THAT WE CAN BUILD A WORLD IN WHICH PLASTIC WASTE CREATES SUSTAINABLE ADDED VALUE FOR FUTURE GENERATIONS.”
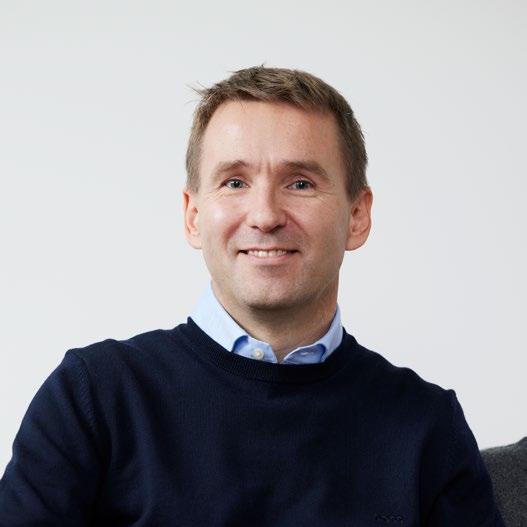
therefore make more profit. That profit will allow us to focus on innovation again. So, we turn environmental challenges into economic added value.”
INVESTING IN SUSTAINABLE GROWTH
To help finance their sustainable initiatives, RAFF Plastics are looking to public bodies and financial institutions. “Some projects, such as the electric truck, receive government subsidies. We are also looking for parties that believe in us.”
“That is why we have enshrined our sustainable ambitions in our corporate strategy and want to demonstrate that our efforts are making a substantial difference.” The launch of our CSRD preparation process with a double materiality analysis and CO2 measurement last year was the basis for future reporting under the European CSRD standards.
“We did not want to wait until we were legally obliged to issue a report,” Caroline and Christophe explain. “Going through the process has already ensured that we can demonstrate a number of efforts in the short term as part of a standardised framework and that we have developed a sustainability strategy with concrete longerterm objectives.”
INSPIRING INDUSTRY AND POLICYMAKERS
Ecovadis, the internationally recognised organisation which assesses companies’ sustainability efforts, awarded RAFF Plastics a gold medal on its first assessment. “Such recognition confirms our vision and provides national and international visibility,” explains Caroline.
She wants to leverage this visibility to positively influence policymakers. For instance, she participates in the sounding board group of the Public Waste Agency
of Flanders (OVAM) and speaks at several conferences, including those organised by industry federation Denuo. “I explained our big bag project at Plastic Matters, a meeting organised every year by Denuo and Essenscia Polymatters, the industry federation for plastic manufacturers. This helps RAFF Plastics to reach like-minded people,” Caroline says.
WORKING TOGETHER ACROSS SECTORS
RAFF Plastics also finds those like-minded people in other organisations, such as Go Forest and Go Ocean. Caroline: “Because of the high-profile recognition we recently received thanks to Ecovadis’ gold medal, the WOMED Award I picked up as female entrepreneur of the year, and a nomination by Trends Gazellen, I have met entrepreneurs with the same vision.”
One such entrepreneur is Sarah Parent of Go Forest, an organisation that wants to work together with a number of partners to focus on reforestation. Sister company Go Ocean works to preserve and restore coastlines and oceans. Caroline and Sarah quickly discovered their common vision, interests and concerns. “So, in early 2024, we entered into a structural partnership. We are investing in Go Ocean and contribute expertise and a new network to explore how to recycle ocean waste in the future.”
Caroline and Christophe strongly believe in the power of collaboration to bring about change. “It is by joining hands across sectors that we can build a world in which plastic can act a source of inspiration and innovation and create sustainable added value for future generations. It is no coincidence that this is our new corporate mission,” they conclude.
CHRISTOPHE DEHOUCK
GOLD STRAIGHT AWAY FOR SUSTAINABILITY PERFORMANCE
A specific question from a client about RAFF Plastics’ sustainability strategy got the ball rolling. “We assumed that we had already come a long way in terms of ESG, but we wanted to document our efforts in a demonstrable ESG policy,” Christophe Dehouck and Caroline Van der Perre explain.
MATERIALITY ANALYSIS
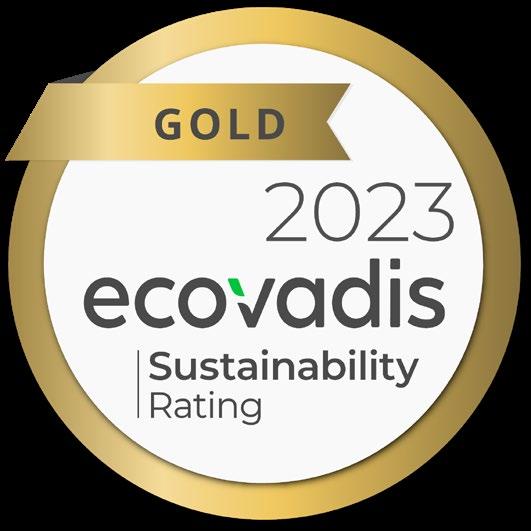
RAFF Plastics therefore started an Environment, Social and Governance (ESG) process in 2023, mapping out its sustainability ambitions and carrying out a double materiality analysis, among other things. That analysis revealed the aspects on which RAFF Plastics’ activities have an impact: Environment (E), Social (S), and Governance (G). It also examined which sustainability issues and trends in turn have an economic impact on RAFF Plastics.
The process resulted in a number of targets for the coming years, so that from 2026 the company can meet the reporting requirements of the Corporate Sustainability Reporting Directive (CSRD) within the European ESG regulations, which grew out of the European Green Deal.
In the short term, it has already led to specific actions, such as investments in sustainable production processes, greener transport and renewable energy. “Last year, we resolutely chose to keep moving forward, even though this involved quite a few drastic changes and investments,” Caroline Van der Perre explains. “On the other hand, it also provided us with subsidies, and recognition and visibility both inside and outside our sector,” Christophe Dehouck adds.
GOLD STRAIGHT AWAY
RAFF Plastics also wanted to test all the sustainability efforts it had already made against the internationally recognised Ecovadis standards. Ecovadis is an organisation that meticulously assesses companies on their sustainability performance, based on policy documents, action plans and reports. The assessment involves a comprehensive analysis that focuses on four main topics: environment, labour and human rights, ethics and sustainable procurement.
Using the information obtained, Ecovadis generates a scorecard showing a company’s strengths and weaknesses.
DOUBLE MATERIALITY ANALYSIS
“We submitted more than 50 pieces of evidence during this process,” says Philip Dooms (Partner, ESG and Sustainability at Baker Tilly), who co-led the Ecovadis process. “We demonstrably mapped RAFF Plastics’ sustainability policy and procedures already in place in a structured and formal manner.”
Within the recycling sector, Ecovadis has now assessed 556 companies worldwide, including RAFF Plastics. The company was awarded a gold medal, which placed it “among the top 6% of all companies in the sector. It is exceptional for a company to achieve this in its first assessment. It is a clear confirmation and recognition of RAFF Plastics’ ambitious sustainability vision.”
HOW DOES ECOVADIS WORK? THE FOUR MAIN TOPICS IN THE ASSESSMENT
1. ENVIRONMENT
Assessment of the company’s environmental impact, including energy consumption, waste management and emissions reduction.
2. LABOUR & HUMAN RIGHTS
Analysis of how the company deals with workers’ rights, working conditions and human rights within the organisation and in the supply chain.
556 COMPANIES
FROM THE RECYCLING SECTOR WORLDWIDE HAVE BEEN ASSESSED BY ECOVADIS + 50
PIECES OF EVIDENCE
WERE SUBMITTED BY RAFF PLASTICS TO ECOVADIS
TOP 6%
RAFF PLASTICS IS AMONG THE TOP 6% OF ALL RECYCLING COMPANIES ASSESSED GLOBALLY
3. ETHICS
Review of the company’s ethical policies and practices, including anti-corruption, fair business practices and data protection.
4. SUSTAINABLE PROCUREMENT
Assessment of how the company integrates sustainability principles into its procurement policies and practices, and the extent to which it encourages its suppliers to also act sustainably.
OPERATION CLEAN SWEEP PREVENTS

ENVIRONMENTAL POLLUTION FROM GRANULATE
In 2021, RAFF Plastics signed a declaration of intent for Operation Clean Sweep (OCS) to prevent pollution from spills (loss of granulate during the production process).
OCS is an international programme for all stakeholders in the plastics and recycling industry to help companies address and prevent granulate losses. It aims to ensure less plastic granulate from the industry ends up in the environment and oceans.
Prime plastic producers are already subject to a mandatory OCS audit, but it is not yet mandatory for transport companies and recyclers. Nevertheless, RAFF Plastics is already going ahead with it. Among other things, the declaration of intent sets out that the company is optimising its site to prevent granulate spills, that its employees are being trained to catch spills and that internal procedures are in place to prevent granules from entering the environment.
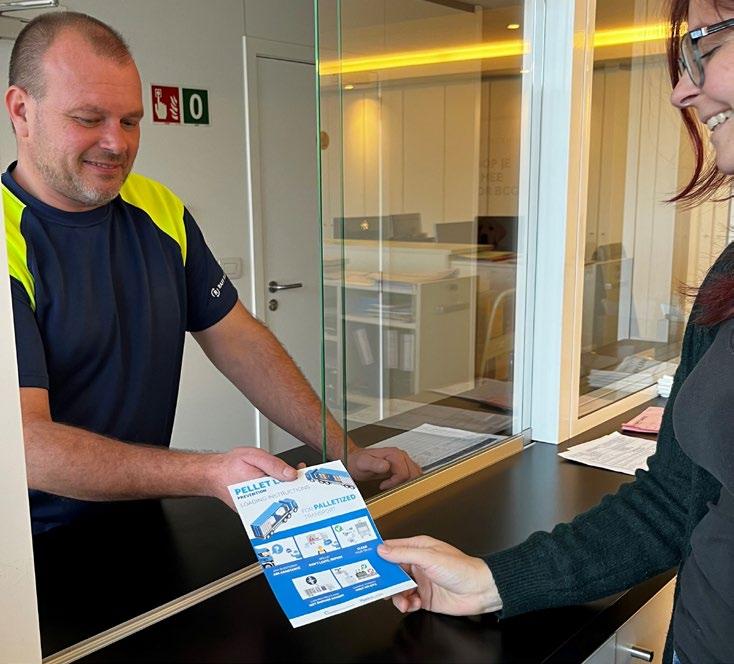
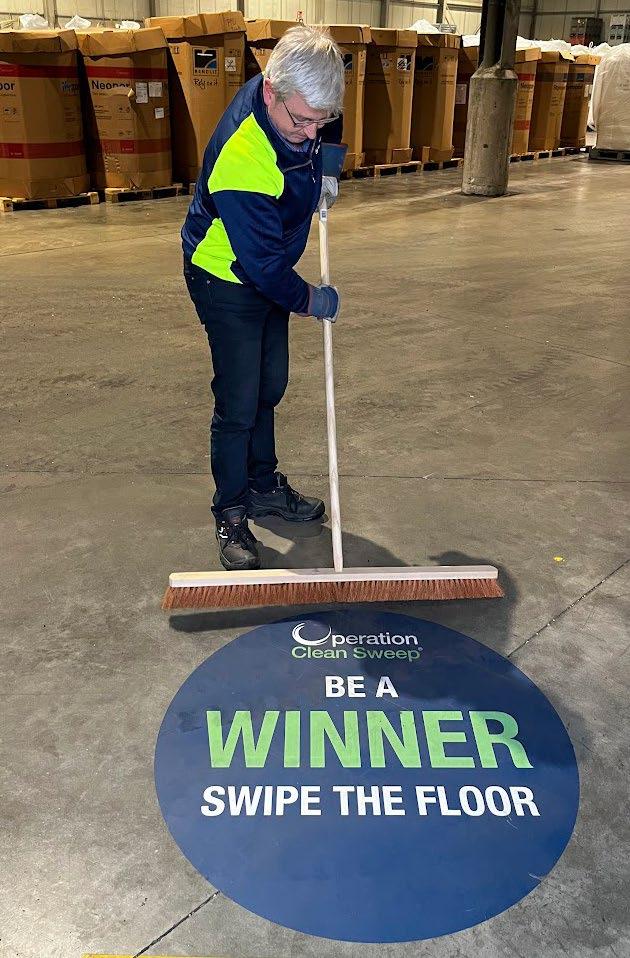
CIRCULAR INNOVATION: BIG BAGS IN A CLOSED LOOP
A customer who becomes your supplier, and vice versa: that is the dream of circular value chains. Such a closed loop is closer to reality than we think, however, as RAFF Plastics and LC Packaging have developed a fully closed loop recycling system for big bags together, based on the common drive to make a difference in the sector through sustainable innovation.
SIMON LAUWERS, KEY ACCOUNT MANAGER
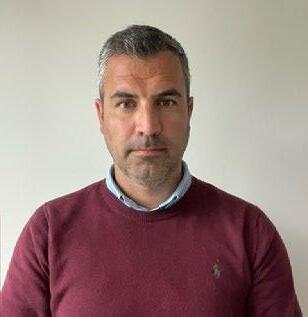
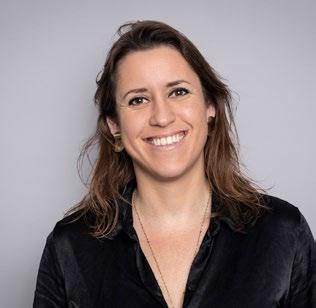
LOTTE MASTWIJK, HEAD OF SUSTAINABILITY
VAN LC PACKAGING
Since 2008, RAFF Plastics has been purchasing some 60,000 big bags a year from LC Packaging, to deliver its granulates
“WE NEED PIONEERS LIKE RAFF PLASTICS TO ACHIEVE THE SUSTAINABILITY AMBITIONS IN OUR SECTOR.”
to customers. “For some time, Caroline and Christophe had indicated that they were interested in purchasing big bags made from recycled materials, as part of their sustainability mission,” explains Simon Lauwers of LC Packaging.
CLOSED LOOP
RAFF Plastics also recycles big bags itself to turn them into new raw materials, and the idea soon arose to collaborate with LC Packaging to create a completely closed loop for big bag recycling.
This is exemplary of the good cooperation between the two companies, fuelled by their shared sustainability ambitions.
LC PACKAGING PRODUCES BIG BAGS.
RAFF Plastics purchases big bags from them to transport recycled granules.

WHAT IS A BIG BAG?
A big bag, or Flexible Intermediate Bulk Container (FIBC), is a large, sturdy bag made of woven polypropylene, intended for storing and transporting large quantities of dry, liquid or granular materials. These bags can hold 1,000 to 1,500 kg and are widely used in the agricultural, chemical and construction industries. A filled big bag is 1.5 to 1.9 metres high and fits on a Europallet.
The results have been impressive: the first container of 7,000 to 8,000 recycled big bags was delivered to RAFF Plastics in early 2024. LC Packaging manufactured them with raw materials sourced from RAFF Plastics, which had been recycled from bags that came from... LC Packaging.
In the meantime, LC Packaging has achieved European QA-CER certification for the use of recycled polypropylene (rPP) in big bags, qualifying the company as an approved rPP-PCR supplier.
“As a supplier we can offer added value to customers like RAFF Plastics, as it enables them to comply with European sustainability standards,” explains Simon Lauwers. “Although the cost of big bags made from PCR is still higher at the moment, the certificate entitles customers to compensation and there is an obvious positive environmental impact due to circularity as wastage and related CO2 emissions are avoided.”
HIGH QUALITY
“Not many raw materials suppliers can provide recycled materials of such high quality as RAFF Plastics,” explains Lotte Mastwijk, Head of Sustainability at LC Packaging.
“They can make a big difference for us in the long run, given that one of our goals is for 80% of our sales to come from circular packaging by 2030.” This is how RAFF Plastics became not only a customer, but also a supplier of LC Packaging.
THE CIRCLE IS COMPLETE... AND EXPANDING
But that’s not where the story ends, as both RAFF Plastics and LC Packaging intend to expand the project further and produce as many big bags as possible in the closed loop system. “Moreover, we are using it as a test case for our other customers to show that a closed loop is really achievable. We need pioneers like RAFF Plastics to help achieve this,” Lotte and Simon conclude.
EUROPEAN SUBSIDIES
For the big bag project, RAFF Plastics can count on funding under the European Union’s Recovery and Resilience Facility (RRF)..

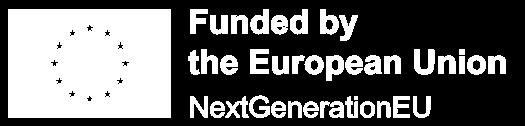
TRENDS IMPACT AWARD
The big bag project was nominated for the Trends Impact Award 2023 in the Circular Economy category.

10.000 TONNES OF BIG BAGS PER YEAR
RAFF PLASTICS PROCESSES USED BIG BAGS
into recycled polypropylene (rPP) and supplies it as a raw material to LC Packaging.

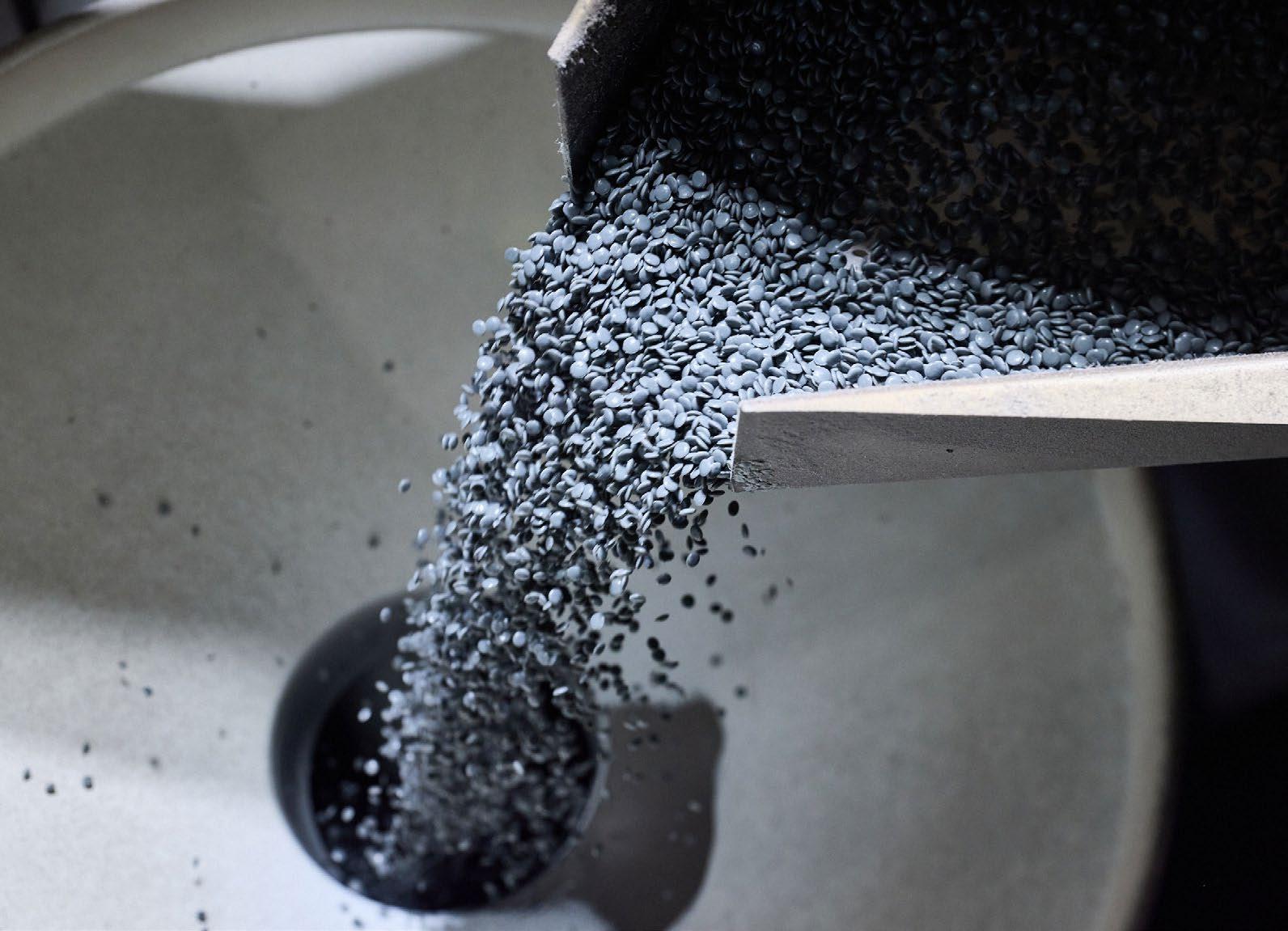
WORKING WITH CUSTOMERS TO ACHIEVE A POSITIVE CLIMATE IMPACT
When companies use RAFF Plastics’ recycled materials in their production processes, they automatically reduce their carbon footprint. To further encourage them and to recognise their efforts, RAFF Plastics awards its customers a CO2 certificate, based on calculations using the Greenhouse Gas Protocol.
By recycling plastic waste into a new raw material, RAFF Plastics creates a positive impact on the climate within the value chain. Customers are of course the driving force behind this process as they are the ones who achieve CO2 gains by purchasing recycled granulate from RAFF Plastics instead of using virgin material: granulate made directly from oil using chemical processes.
CERTIFICATE BASED ON CO2 MEASUREMENT DATA
“Many customers wanted to know by exactly how much they were reducing their emissions by using recycled raw materials sourced from us. After all, they themselves all have the mission and ambition to drastically reduce their carbon footprint by 2050,” Caroline Van der Perre and Christophe Dehouck explain. “That is why we wanted to create a certificate for them based on verified data.”
In 2023, RAFF Plastics had its own CO2 footprint assessment carried out by an independent consultant, as part of the preparation for its sustainability reporting under the European CSRD.

GREENHOUSE GAS PROTOCOL
The assessment was performed in accordance with the globally recognised Greenhouse Gas Protocol standard. This is the most widely used standard for accounting and reporting greenhouse gas emissions under which emissions are expressed as CO2 equivalents and are considered within the company’s entire value chain.
RECYCLED PLASTIC CLIMATE IMPACT CERTIFICATE
Using data from that analysis, RAFF Plastics calculates a customer’s net gain in emissions reduction when they use recycled granulate rather than virgin material. To make it more tangible, this gain is converted to the equivalent mileage of a diesel car needed to arrive at the same emissions. The Recycled Plastic Climate Impact Certificate is the result of those calculations and has been issued to every customer since the beginning of 2024.
THE FORMULA
CO2 REDUCTION =
CO2 EMISSIONS FROM VIRGIN PLASTICS -
CO2 EMISSIONS FROM RECYCLED GRANULATE
• CO2 emissions from the production of virgin plastics are compared with CO2 emissions from RAFF Plastics’ operations.
• This takes into account all the steps from raw material to transport to the customer (from cradle to gate).
• The CO2 emissions of recycled granulate are based on the Carbon Footprint calculation of RAFF Plastics’ recycling activities, supplemented by the CO2 emission factors from the CE Delft study (www.CE.nl).
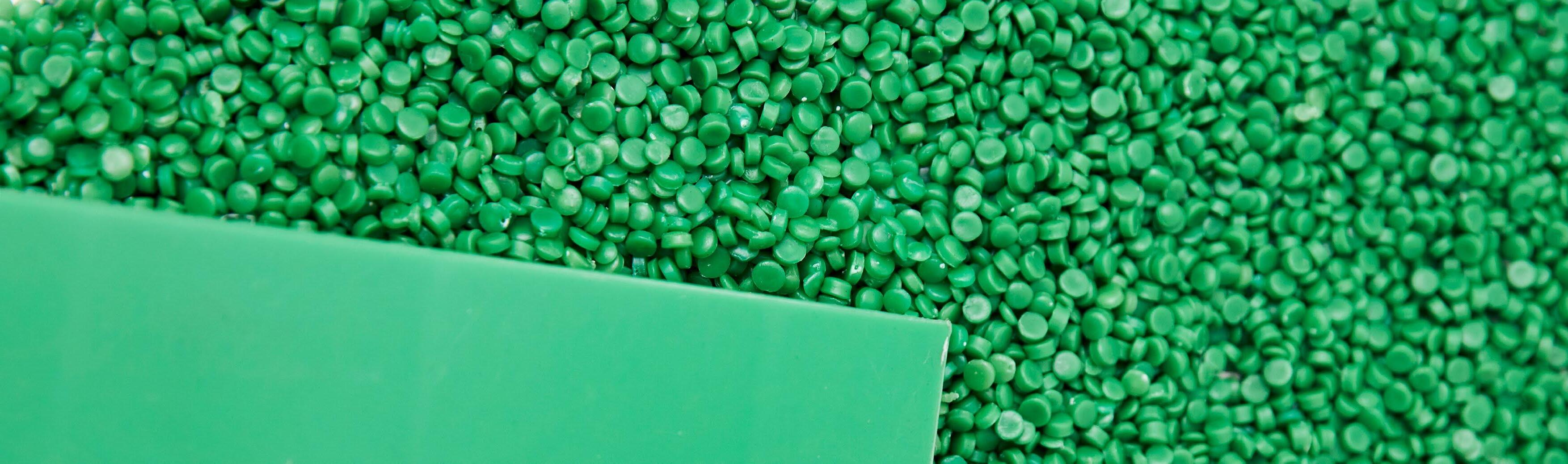
• To calculate the CO2 emissions from virgin plastics, the average of Base Carbone V23 and Ecoinvent 3.9.1 emission factors is used.
FIRST ALL-ELECTRIC TRUCK: AN INVESTMENT IN THE FUTURE
RAFF Plastics started using its first all-electric truck at the beginning of this year. This signals a new step in the company’s sustainability strategy, which is exploring how it can further reduce its CO2 emissions.
The Volvo FG truck is an example of RAFF Plastics’ long-term vision. The company has been using electric vans and forklifts for some time. The electric truck is the first in its fleet of 11 transport trucks and also the first of its kind in Belgium. “It was a logical step for us, but not an obvious one. We see this as an opportunity to explore how we can further reduce our operational footprint through transport, even if it involves a considerable investment,” Caroline Van der Perre and Christophe Dehouck tell us.
COMPENSATION
“Fortunately, our investment is partly compensated by subsidies. Such government interventions can ultimately persuade family businesses to introduce changes, because the transition to sustainable processes requires effort and costs money. But as a company, you should also dare to look ahead: this is an investment in the future, from which we can learn a lot,” they go on.
7,128
SOLAR PANELS
meeting 10% of RAFF Plastics’ total power needs, including for its own charging infrastructure 300 KM range for the electric truck

“SUBSIDIES CAN HELP WHEN YOU MAKE INVESTMENTS LIKE THESE, BUT YOU SHOULD ALSO DARE TO LOOK AHEAD AS A COMPANY.”
CHARGING INFRASTRUCTURE AND LOGISTICS PLANNING
After all, the electric truck presents several challenges. “To start with, we installed our own charging infrastructure because the public facilities for charging trucks are not yet optimal. They do not always charge fast enough and tall trucks often do not fit under the canopy,” Caroline Van der Perre explains.
When fully charged, the truck has a range of 300 kilometres. By comparison, a diesel truck with a full tank has a range of 3,000 kilometres. The logistical planning was adjusted to allow the electric truck to transport as many goods as possible and recharge on its own charging platform between deliveries.
TRAINING FOR DRIVERS
Drivers also need to undergo specific training to be allowed to drive the trucks.
“This training was provided by Volvo Trucks. Electric trucks are very different to drive compared to
diesel trucks,” explains Caroline Van der Perre, who is a truck driver herself and runs her own transport company Carotrans. “But Jurgen, one of our experienced drivers, was up for the challenge.”
A complete renewal of the truck fleet with electric trucks is not on the agenda just yet.
“First, we want to investigate the operational impact and the contribution to our carbon footprint. This is just one piece of the puzzle in our sustainability strategy,” Caroline and Christophe conclude.
Elektrische pionier met diesel in het bloed
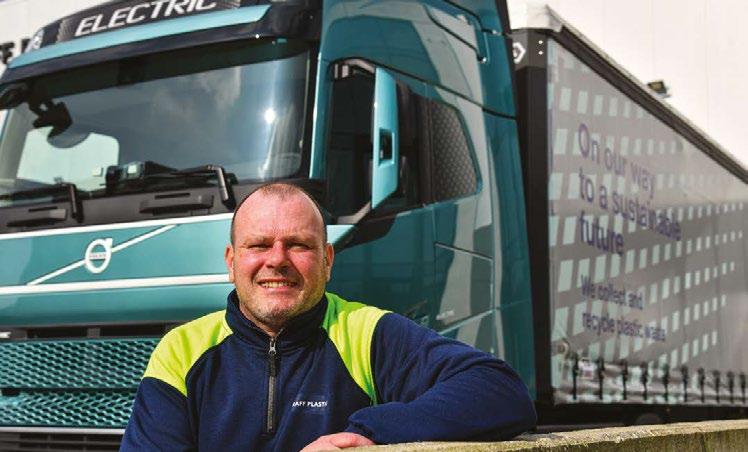
Jurgen Bruneel is een pionier. Als een van de eerste chauffeurs in België gaat hij dagelijks de baan op met een volledig elektrische trekker-oplegger voor zijn werkgever RAFF Plastics. En dat voor ween ervaren routier die naar eigen zeggen
Michiel Leen
tellende vloot van het plasticrecyclagebedrijf, het is ook een van de eerste in zijn soort op de Belgische wegen. Dat brengt zowel voor het bedrijf als voor een ervaren chauffeur als Jurgen een aantal aanpassingen met zich mee, maar de eerste indrukken zijn positief. En Jurgen kwijt zich met enthousiasme van zijn rol als ambassadeur van het nieuwe rijden.
“Ik werk al 25 jaar als chauffeur, maar van opleiding ben ik slager,” zegt Jurgen. “Ik kreeg al snel de smaak te pakken voor het rijden met de vrachtwagen. Geef toe, op de baan zijn is toch geestiger dan binnen zitten. Ik heb lang internationale transporten gedaan en heb
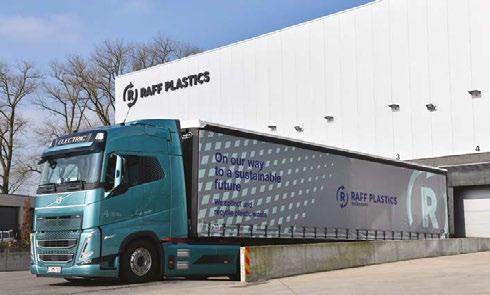

“Oudere collega’s zijn soms sceptisch. Een truck moet lawaai maken, hé.”
grote bekommernis: dan rij je zonder problemen heen en weer naar Parijs. Intussen weet ik ook hoeveel percent van de batterij ik op bepaalde trajecten nodig heb. En ik probeer mijn zuinigheidsrecords
klop-
een goede planning.”
scepsis. “Daar heb je hem, met zijn stofzuiger”, lachen ze. “Ook op sociale media zijn de reacties weleens heftig. Maar dat zie je in het debat over elektrische personenwagens ook.” Voor oudere collega’s moet een vrachtwagen lawaai maken, hé. Het onbekende schrikt af, en een oude boom verplant je niet zomaar. Ik denk dat een jongere generatie er sneller mee weg zal zijn. En na een kijkje in de cabine zijn ze vaak al minder sceptisch. Ik zou zeggen: probeer het een keer!”
behulp
toch zonder stroom vallen onderweg, komt
mocht
Action je depanneren of naar de dichtstbijzijnde laadpaal slepen. Straaljager Achter het stuur valt vooral het grote comfort op. “Tijdens het rijden valt op dat de truck veel minder lawaai maakt dan een klassiek model,” zegt Jurgen. “Het geluid heeft iets van een straaljager. De trekker is ook zo’n vier ton zwaarder dan een dieseltrekker, dus hij ligt vaster op de baan. En met 770 pk kun
dingen
een klassieke truck niet mogelijk zijn. Met negentig
uur
helling aan het einde van de Kennedytunnel oprijden, bijvoorbeeld. Dan geef je de collega’s het nakijken.” Een full-option-uitrusting, adaptive cruise control, verschillende camera’s en een luchtgeveerde cabine zorgen dat er weinig te klagen valt achter het stuur. Ook slaapmogelijkheid is in de cabine aanwezig, maar daar heeft Jurgen nog geen gebruik van hoeven te maken. Scepsis De boventoon is dus positief. Het lijkt wel alsof hij zelf staat te kijken van zijn enthousiasme over het elektrische rijden. “Ik ben geboren met diesel in mijn bloed. Als je me tien jaar geleden had gezegd dat ik met een elektrische vrachtwagen zou rijden, had ik het niet geloofd.” Jurgen heeft alvast veel bekijks als hij met de FH een parking op rijdt. “Iedereen komt er eens naar kijken, ook kantoorwerkers die hun middagpauze houden.” Bij collega’s is er soms
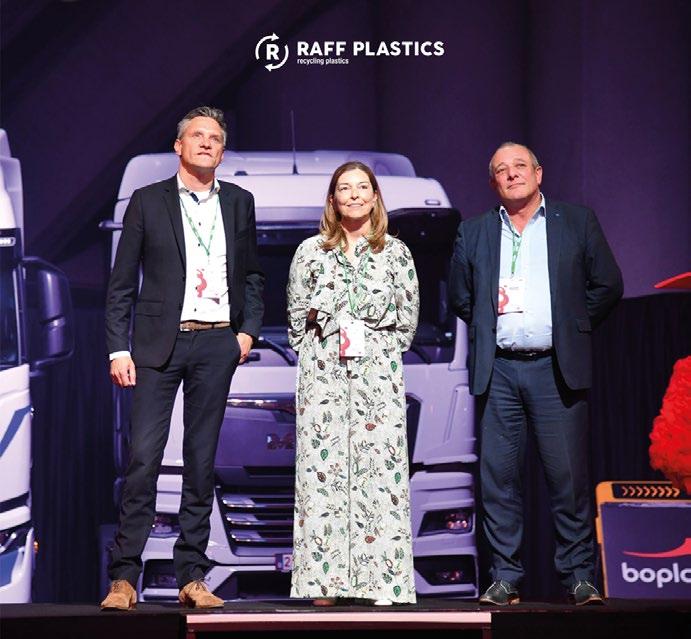
GREEN TRUCK AWARD
The Green Truck Award was presented at Transportmedia’s Transport & Logistics Awards 2024 in May 2024. RAFF Plastics won a great second place with Carotrans, for commissioning its first electric truck.
Eigen laadpaal RAFF Plastics geeft alvast het goede voorbeeld door zijn laadinfrastructuur open te stellen voor wagens van andere bedrijven. “Als er een online raadpleegbaar netwerk zou ontstaan van dergelijke laadpunten, valt er alvast één drempel weg om elektrisch rijden mogelijk te maken,” zegt zaakvoerder Caroline Van der Perre. Ze geeft ook mee dat zonder ondersteuning van de Vlaamse overheid de economische case voor elektrisch vrachtvervoer nog problematischer zou zijn. De personen- en bestelwagens van het bedrijf zijn al volop geëlektrificeerd, maar de aankoop van een tweede elektrische truck is nog een twijfelgeval. Ook omdat op de andere bedrijfsvestiging in Londerzeel niet dezelfde laadinfrastructuur voorhanden is als in Houthulst.
Jurgen Bruneel in een notendop > 42 jaar > Woont in Ardooie > Slager van opleiding > 25 jaar ervaring als chauffeur, waarvan 11 bij RAFF Plastics
TRANSPORT MANAGEMENT MAGAZINE (TRANSPORTMEDIA) INTERVIEWS DRIVER JURGEN BRUNEEL
In the interview, Jurgen Bruneel explains the challenges and benefits of driving an electric truck.
Levensecht
Jurgen Bruneel
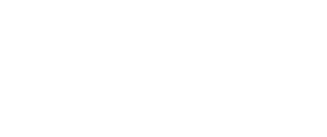
Go Forest will plant a tree for every new visitor to RAFF Plastics who registers via a QR code. Last year’s results:
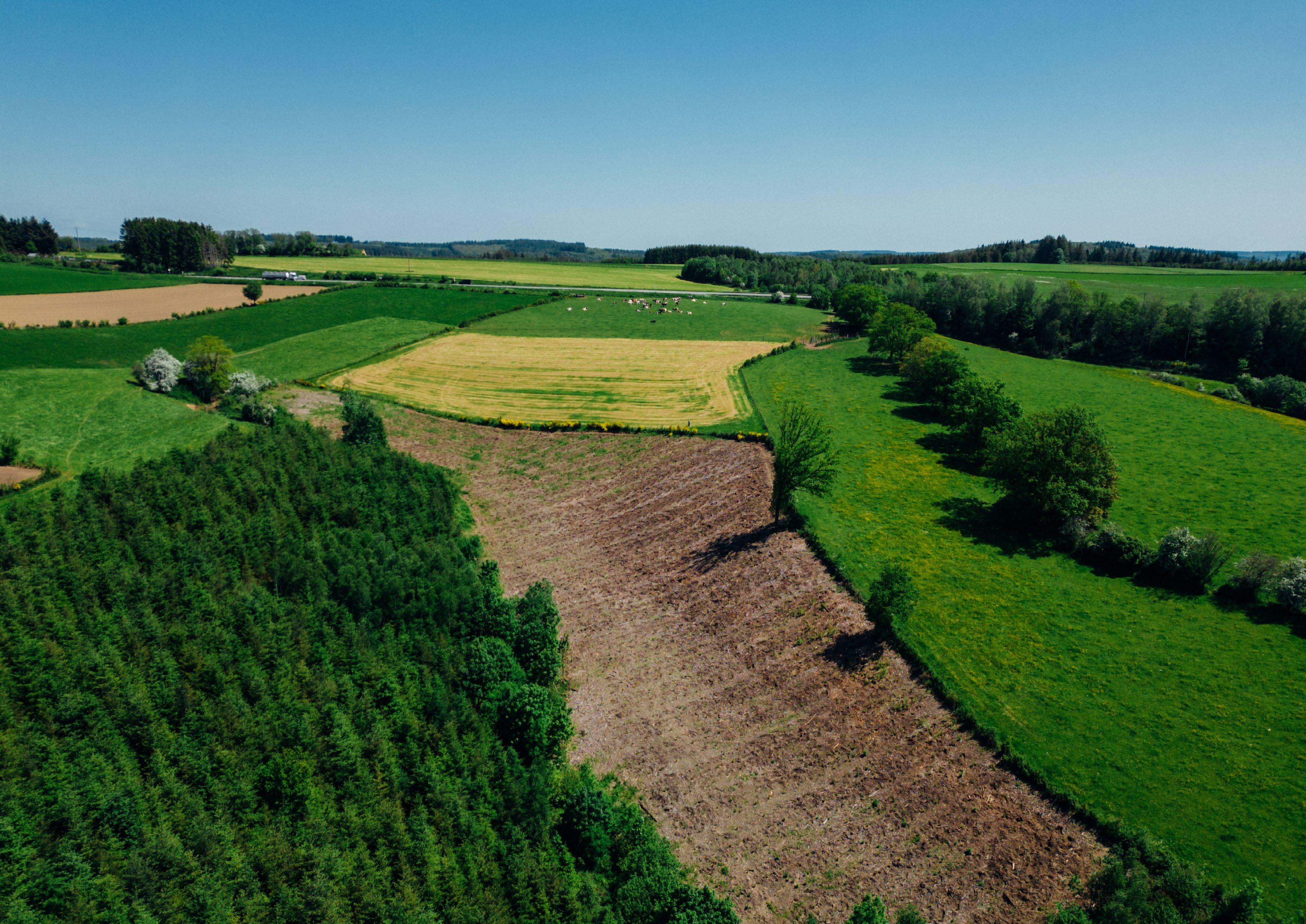
RAFF PLASTICS SUPPORTS NATURE RESTORATION AND REFORESTATION WITH GO FOREST
In 2023, RAFF Plastics contacted Go Forest, which aims to restore nature by planting suitable tree species in different countries and regions around the world. The organisation not only focuses on reforestation, but also actively works to prevent deforestation.
RAFF Plastics supported this project last year by handing out business cards with QR codes. Visitors to the company received a card and were able register via the QR code. As a bonus, the visitors received a linen bag containing flower seeds they could plant at home. For every visitor who registered, Go Forest planted a tree on behalf of RAFF Plastics.
154 TREES PLANTED VIA 3 PROJECTS IN BELGIUM 26.95
TONNES
OF CO2 ABSORBED DURING THEIR LIFETIME
THE POWER OF A DIVERSE AND FAMILY-LIKE SOCIAL FABRIC
To achieve its sustainable vision for the future, RAFF Plastics builds on a closeknit team of 64 employees who consider the company to be their second home, whether they come from Poland, Romania, France or Belgium. What is more: they all attach great importance to the company’s values and shared sustainability mission.
“We have created a workplace where diversity, family values and attention to safety prevail,” Caroline Van der Perre explains. The management is strongly committed to a dynamic and positive corporate culture, focusing on employee welfare and a shared mission to create a better future for the next generations.” As part of our ESG process, we commissioned a stakeholder survey using a standardised questionnaire. Our own employees were also surveyed. The results revealed that a surprisingly large majority of our people, some 80 per cent, attach very high importance to our sustainability mission.”
BETTER STRUCTURES AND MONTHLY TEAM MEETINGS
To keep the team working together smoothly and processes running efficiently, RAFF Plastics is investing in shared workflow platforms, advanced ERP systems and ongoing digital transformation. “This requires an effort from the whole team, which is why we support them with training and coaching. Technology helps to streamline the way we work and measurements help us reduce our impact on the environment,” says Caroline Van der Perre.
RAFF Plastics has also introduced regular monthly team meetings, in which employees can share their ideas and personal concerns with management. “It is essential for us that everyone feels heard and valued. These meetings strengthen the group feeling, ensure that everyone is involved and that we work together towards the same goals.”
DIVERSITY AS AN ASSET
The close-knit atmosphere perhaps typifies RAFF Plastics the most. The team is one big family with employees of multiple nationalities, ages, genders, origins and job levels. “Communicating with each other in multiple languages is the norm here,” confirms Mieke Leeman, HR Manager at RAFF Plastics.
RAFF Plastics embraces the company’s diversity as a strength and supports all foreign employees in several areas. “We help them with administration, banking and insurance applications, and we are happy to do so: for us it is a small effort, we are used to it, but for them it is a huge support that often allows them to stay on board here longer and come and live in the region,” adds Mieke.

“WE EMBRACE DIVERSITY IN OUR TEAM AND HELP OUR FOREIGN WORKERS WITH THEIR ADMIN.”
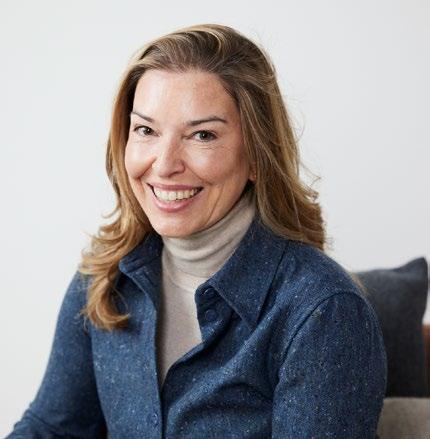
“MONTHLY TEAM MEETINGS PROVIDE A FORUM FOR OUR EMPLOYEES TO SHARE IDEAS AND CONCERNS WITH MANAGEMENT.”
- MIEKE LEEMAN HR MANAGER
- CAROLINE VAN DER PERRE
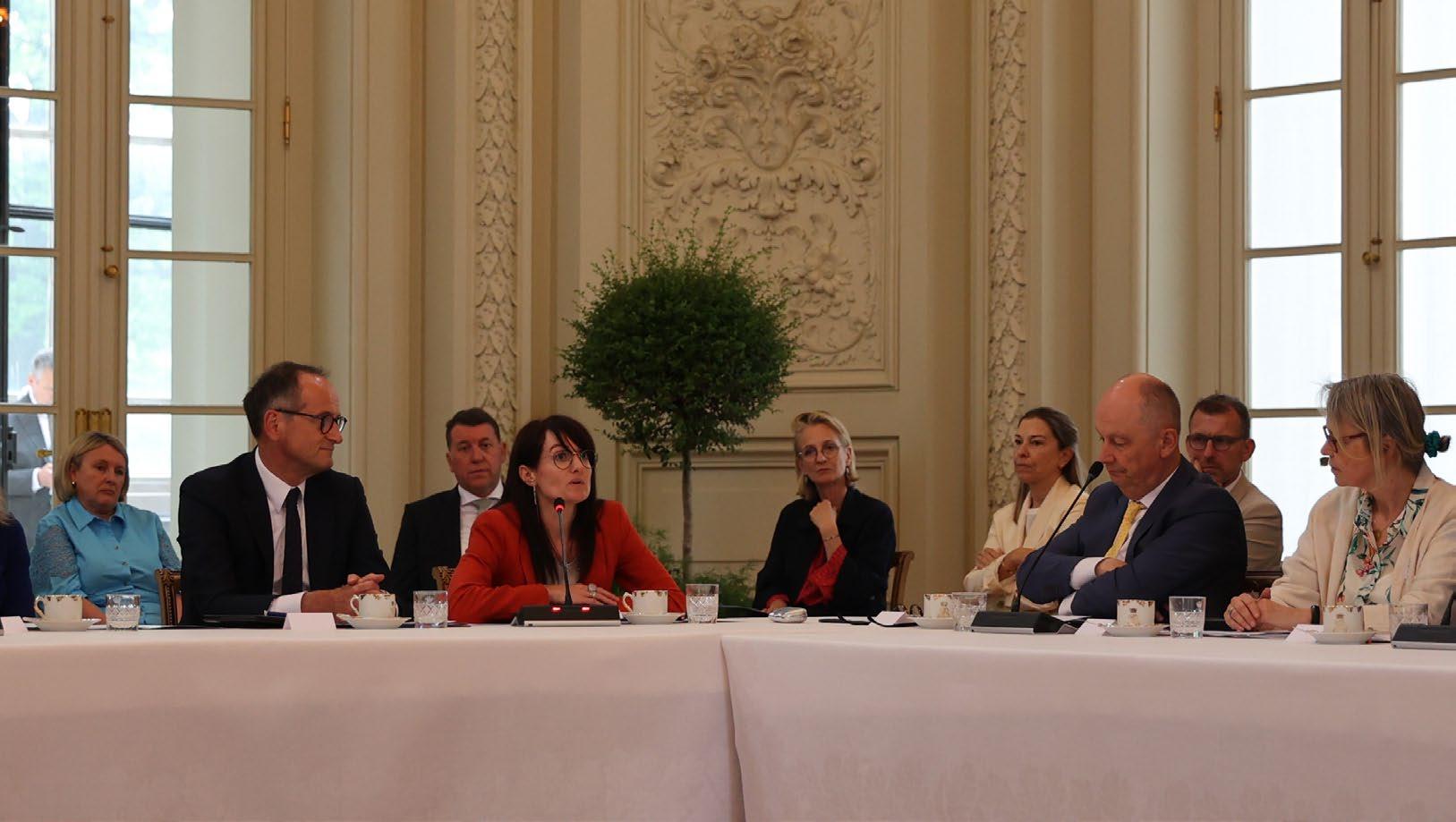
BUSINESS UNITING TALENTS 2030
Convinced that diversity in the workplace is an asset, RAFF Plastics is participating in the Business Uniting Talents (BUT) 2030 project. This CSR Europe initiative, funded by the Prince Philippe Fund in cooperation with the King Baudouin Foundation, promotes dialogue between employees and managers to reduce inequality and build inclusive business models.
A total of 30 Belgian companies and nine employer federations are taking part. Between 2020 and mid-2024, they collaborated on the Multicultural Diversity & Inclusion Assessment.
On 28 May 2024, representatives of all the companies and federations, including Caroline Van der Perre, met King Philippe at a roundtable on multicultural diversity and inclusion to conclude the project.
* Figures based on total number of employees at RAFF Plastics, Carotrans and RCC Plast.
WELL-BEING AS CORPORATE CULTURE: MORE THAN A SAFE WORKING ENVIRONMENT
2023-2024 INITIATIVES
WORK EMPLOYEES WORKPLACE
• Introduction of MONTHLY TEAM MEETINGS
• Systems and technology to promote collaboration: launch of TEAMIFY platform to share working procedures with each other and with other departments.
• LEAN LEADERSHIP: management and employees are trained to have more autonomy in their work and introduce a systematic approach to their tasks.
• SUPPORT for administrative questions from foreign workers.
• In-house CODE 95 TRAINING for truck drivers.
• SAFETY TRAINING and evacuation drills for all employees.
• TEAMBUILDING: Beach Clean-up.
• NEW OFFICE with communal meeting rooms, a space to have lunch with the whole team and meeting rooms for confidential individual meetings.

SAFETY
As a manufacturing company, RAFF Plastics guarantees the safety of its employees. It has an occupational health and safety policy and occupational health and safety advisor for this purpose. “Our advisor is currently taking a level 2 refresher course, which is not compulsory, but we want them to have the certification anyway,” Caroline Van der Perre explains.
In addition, an annual audit identifies safety and fire risks. The company has sprinkler systems, smoke and fire alarms across all departments and carries out weekly evacuation drills. RAFF Plastics even has its own fire truck.
A TEAM WITH A GREEN MISSION
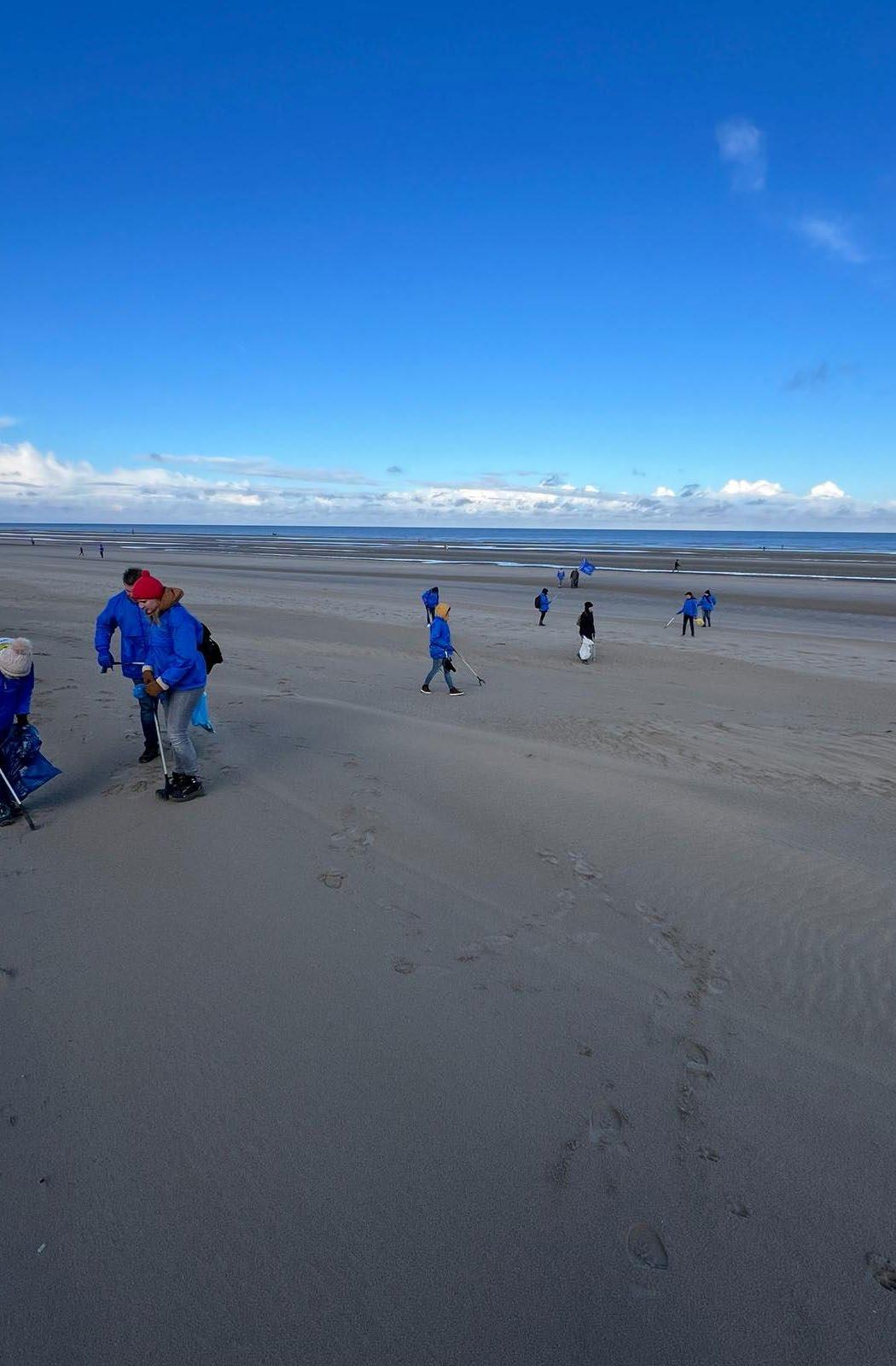
In February 2024, RAFF Plastics organised its first teambuilding event with all employees. “We went to clean up a stretch of beach, given our sustainable business strategy and mission to reduce plastic waste everywhere, including on beaches,” Caroline Van der Perre explains.
Employees were divided into two teams: one led by Caroline and one led by Christophe Dehouck. “There had been a storm the night before, so the people from River Cleanup, who organised the activity for us, had warned that there probably would not be much rubbish to pick up as rubbish is often pulled back into the sea during a storm. Still, it was surprising how much we picked up in an hour and a half: about 61 kilograms, including a lot of plastic that was tangled up with organic waste.”
The clean-up was not only a bonding team activity with an environmental purpose. “We also got to know the River Cleanup team this way and the beach clean-up helped to support them,” Caroline says. “I am continuing to speak with the people from the organisation to see if and how we could work together in the future.”
“IT WAS SURPRISING HOW MUCH WASTE WE PICKED UP IN ABOUT 1.5 HOURS.”
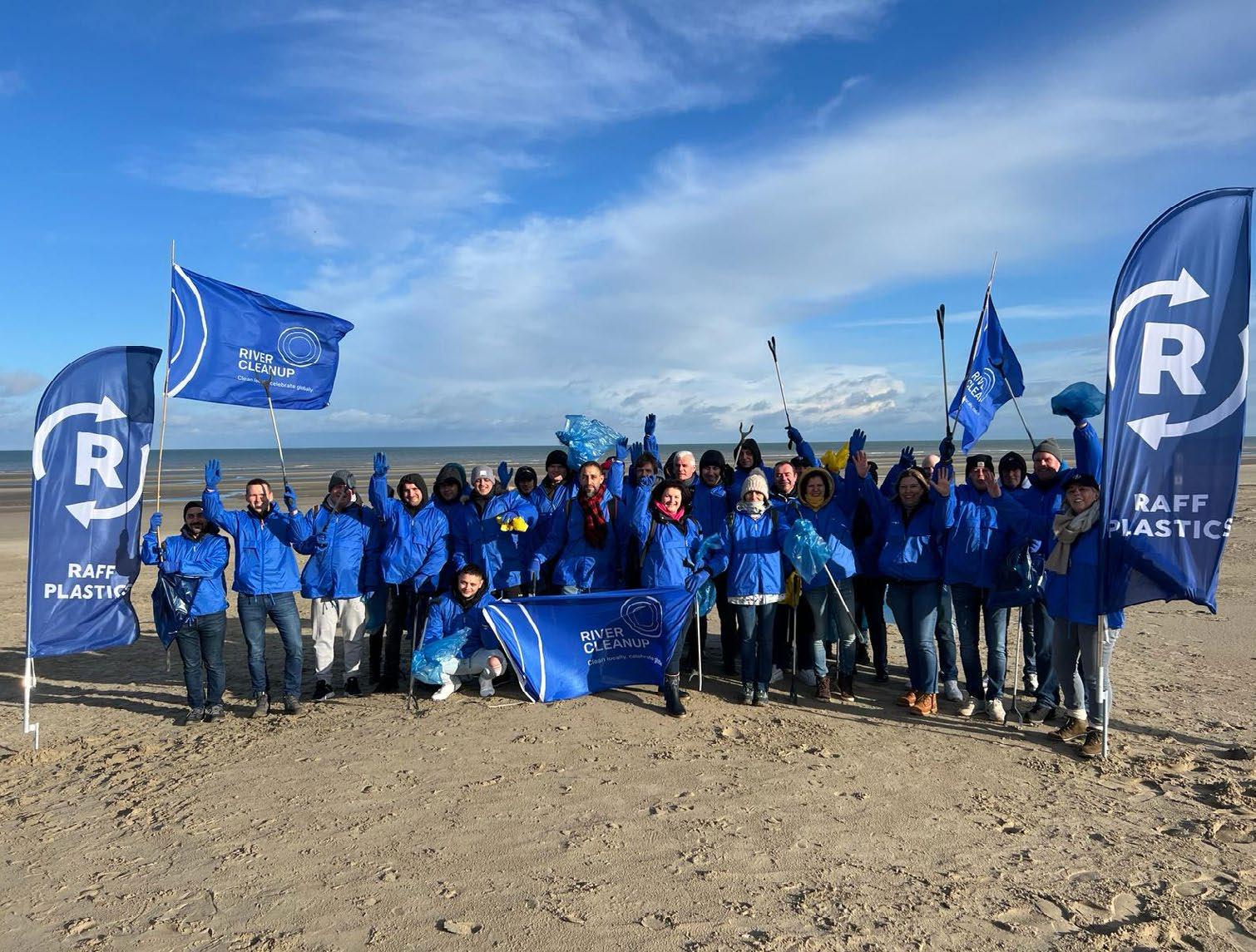
A WORD FROM OUR EMPLOYEES
TOMA NICOLAE (34) TEAM LEADER

“I AM THINKING OF OUR CHILDREN’S FUTURE”
“I am from Romania and started working for RAFF Plastics in 2021. They are a very nice employer: we are like one big family. My wife has since moved to Belgium too and found work here. We are thinking of starting our own family. That is why I think RAFF Plastics’ sustainability mission is so important. We need to secure our children’s future and a company like this can help with that.”
HAS WORKED FOR RAFF PLASTICS FOR 3 YEARS AND HAS SINCE MOVED TO BELGIUM. RECENTLY BECAME TEAM LEADER
MUSTAPHA AIT SALM (36) OPERATOR

“RECYCLING
IS CARING ABOUT THE ENVIRONMENT”
“I live across the border, in Dunkirk, and happily commute every day to come to work. We are working for a better future and the company is very conscious about the environment and our surroundings. I love working here, which is why I returned after having been employed here as a student in 2013. The atmosphere in the team is very nice and RAFF Plastics gives us a lot of help with all the administration.”
HAS WORKED FOR RAFF PLASTICS FOR 2 YEARS. ALSO WORKED FOR RAFF PLASTICS FOR ONE YEAR AS A STUDENT IN 2013 AND RETURNED
ADAM NICOLAE-BOGDAN (41) TEAM LEADER
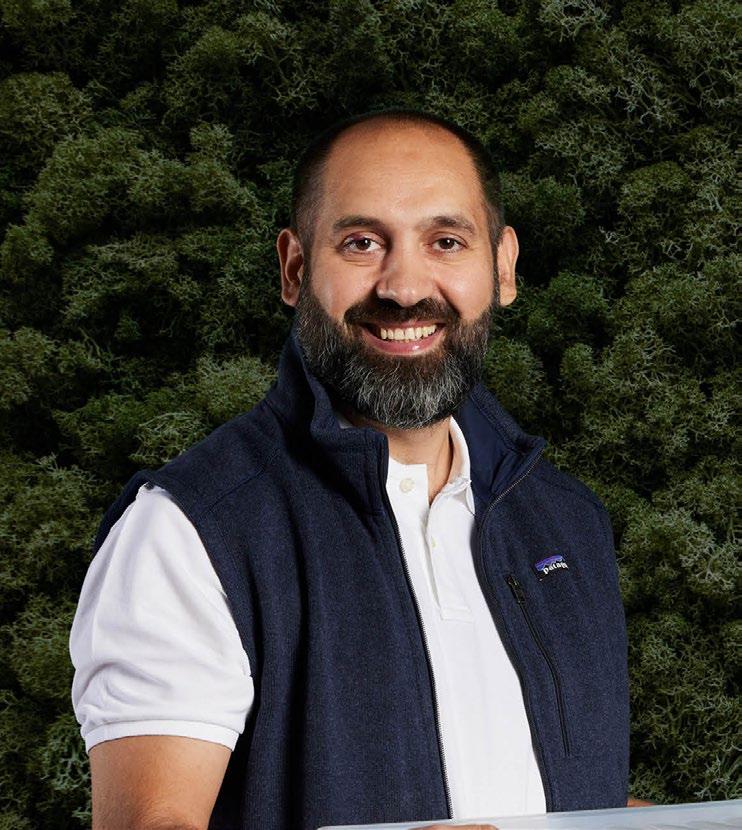
“EVERY
YEAR WE CONTINUE TO INVEST IN INNOVATION”
“I started working for RAFF Plastics as an operator in 2014. Initially, I did not plan to stay here for so long, but I liked the work so much that my wife eventually moved here too. We have been living here for ten years and I have been promoted to team leader. The reason I have been here for so long is because we want to do better every year. We now also recycle big bags, push for innovation and invest in increasingly better machines. This is challenging but at the same time gives me great satisfaction. Here, I can use my experience to work towards a better future.”
HAS WORKED FOR RAFF PLASTICS FOR 10 YEARS AND WAS ITS VERY FIRST FOREIGN EMPLOYEE
RECYCLING PLASTIC CAPS TO FUND GUIDE DOG TRAINING
The Belgian Guide Dog Centre (BCG) has been working with RAFF Plastics to collect plastic caps and recycle them into new raw material. The proceeds from the caps are used to train new guide dogs, which are essential for visually impaired people.
The cooperation started 10 years ago, when someone with a visual impairment came to speak at the school where Ann Asselman of “Ternat Dopt Mee” worked. “He told us that his dog would be retired soon and that getting a new dog would cost at least 40,000 EUR. So, we came up with the idea of collecting plastic caps as a school and selling them for recycling, using the proceeds to finance a new dog. I then reached out to the Belgian Guide Dog Centre (BCG) and Caroline from RAFF Plastics, who were immediately very friendly and enthusiastic.”
FORTY TRUCKLOADS
Since then, the volunteers of Ternat Dopt Mee and the Belgian Guide Dog Centre in Tongeren together collect about 40 truckloads of plastic caps every year. Before going to RAFF Plastics, the caps are carefully sorted by dozens of volunteers at the centres in Tongeren and Ternat. The sorted caps are then sold to RAFF Plastics for recycling. All the proceeds go to BCG.
305,780 CAPS collected in 2023
40 TRUCKLOADS of caps are recycled annually at RAFF Plastics
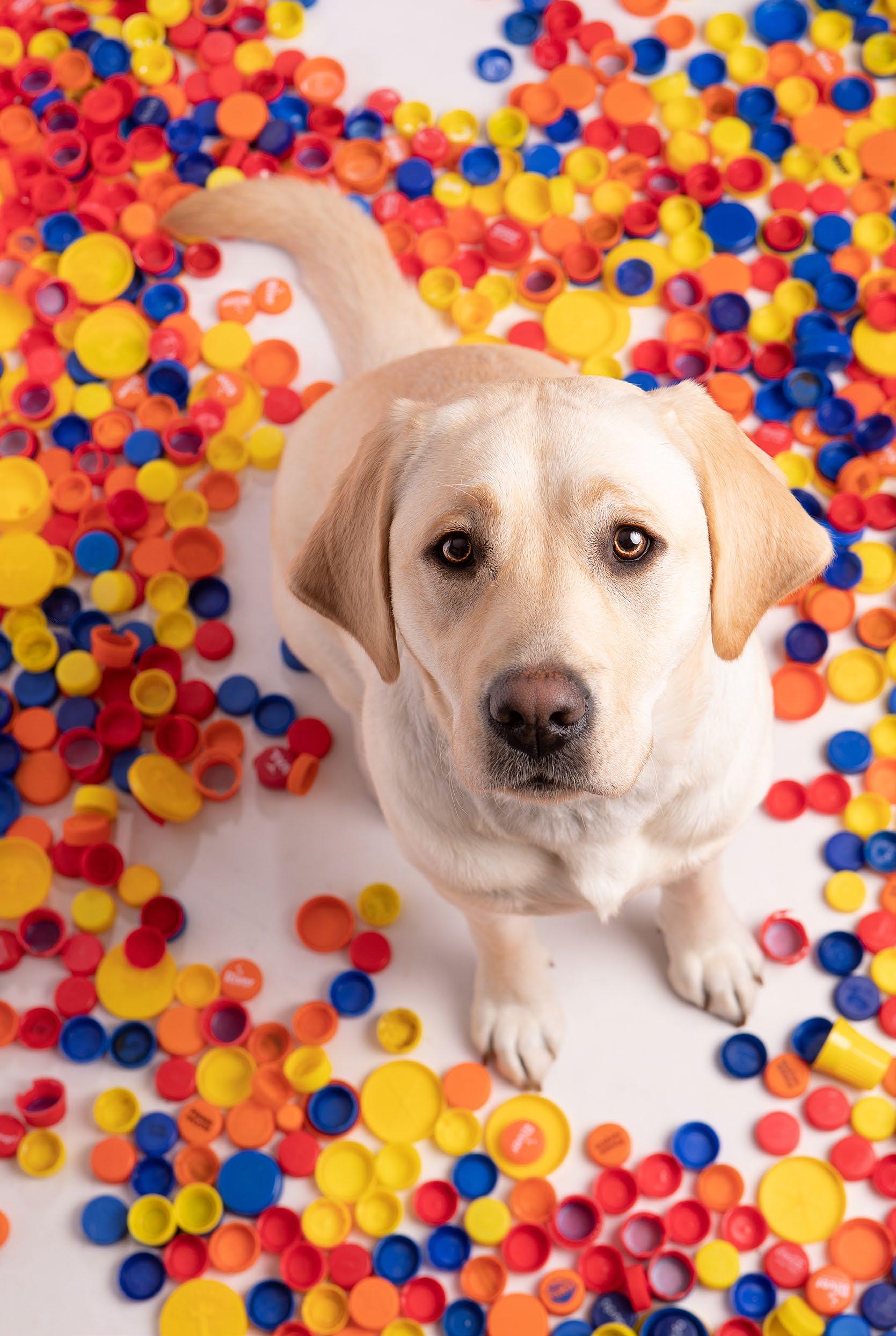
2-3 GUIDE DOGS
can be trained each year thanks to this collection
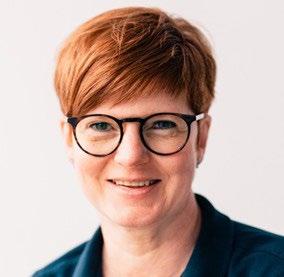
ANN SMETS, BELGIAN GUIDE DOG CENTRE (BCG)
100,000 EUR
is the average annual donation for the BCG from caps recycled at RAFF Plastics
“THE CAPS THAT ARE COLLECTED FOR RAFF PLASTICS ALLOW US TO TRAIN 2-3 GUIDE DOGS A YEAR TO HELP VISUALLY IMPAIRED PEOPLE.”
“RAFF Plastics provides logistical support and transport for the caps,” explains Ann Smets of the BCG. All caps that have been collected and sorted are then processed at RAFF Plastics into industrial granules. “In May, the volunteers from Tongeren visited the factory in Houthulst so they could see how all those caps are given a new life.”
2-3 GUIDE DOGS ANNUALLY THANKS TO CAP COLLECTION
The caps add up to about 100,000 euros a year for the BCG. “Training a guide dog is an expensive process. The cost can be as much as 40,000 EUR,” explains Ann Smets. “So, thanks to the proceeds from the caps, we can train two to three dogs every year. Without this cooperation with RAFF Plastics, a lot of people would be left without a guide dog.”
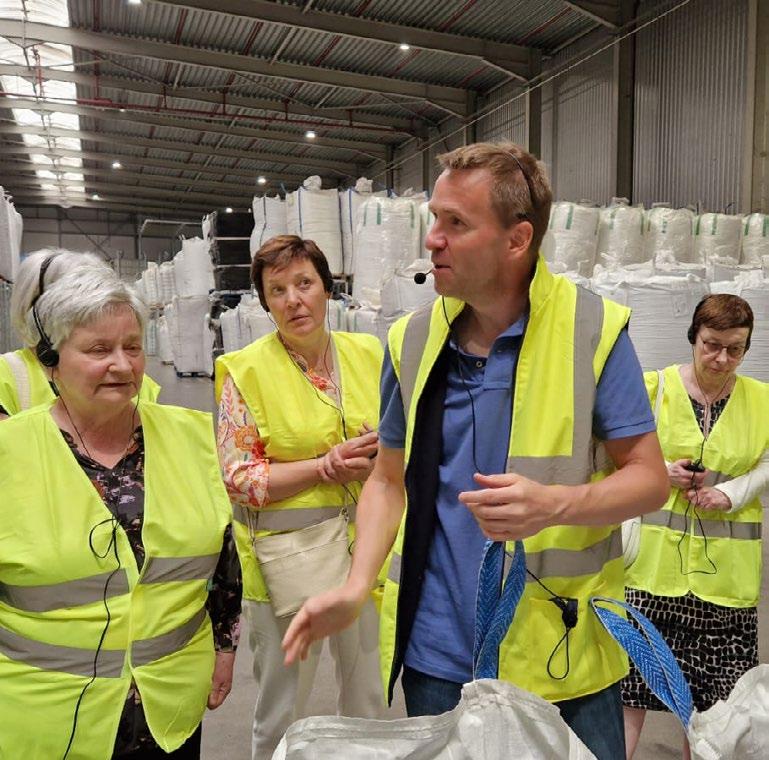
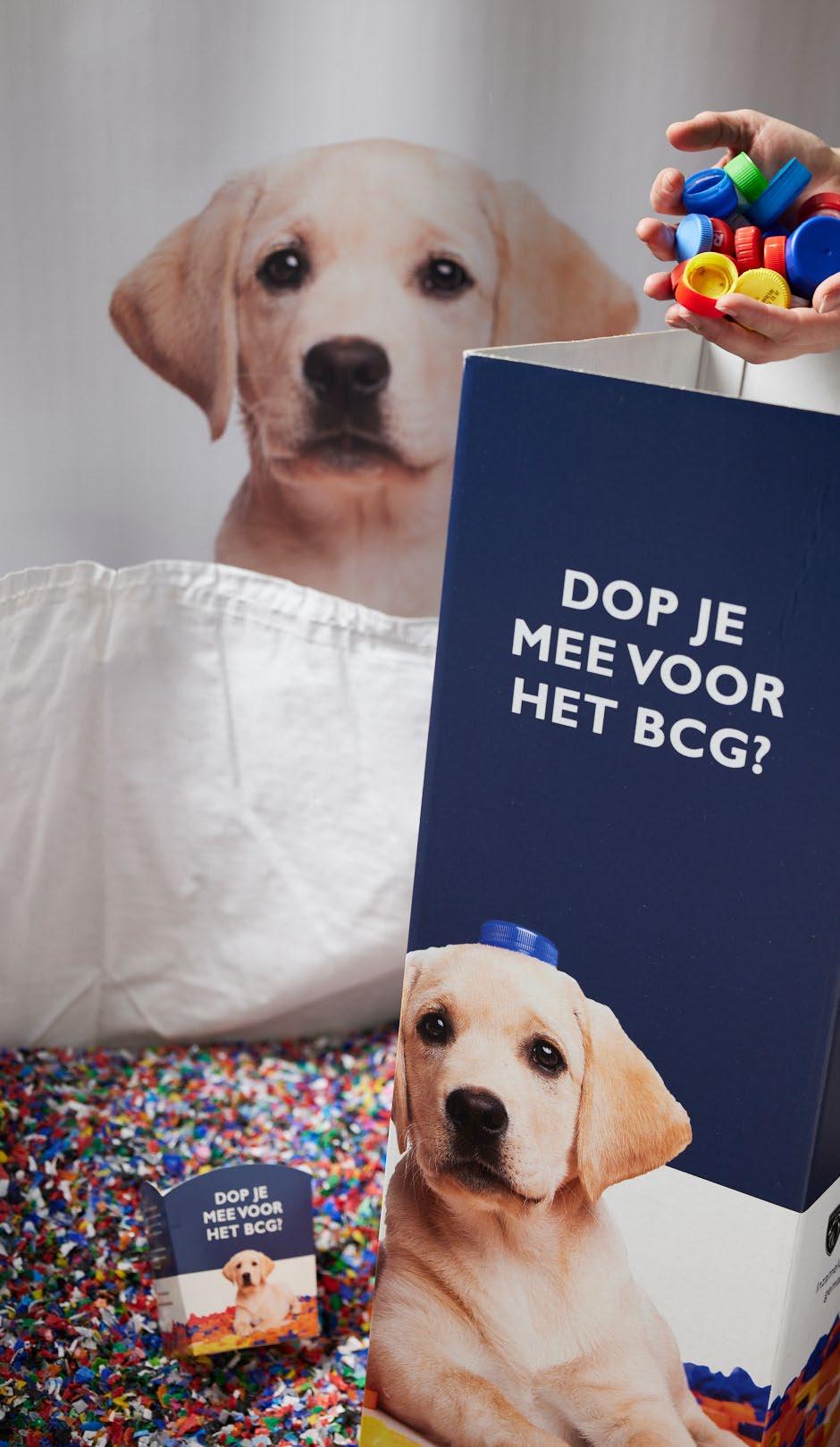
30
CORAL FRAGMENTS
transplanted in Indonesia with funding from RAFF Plastics in
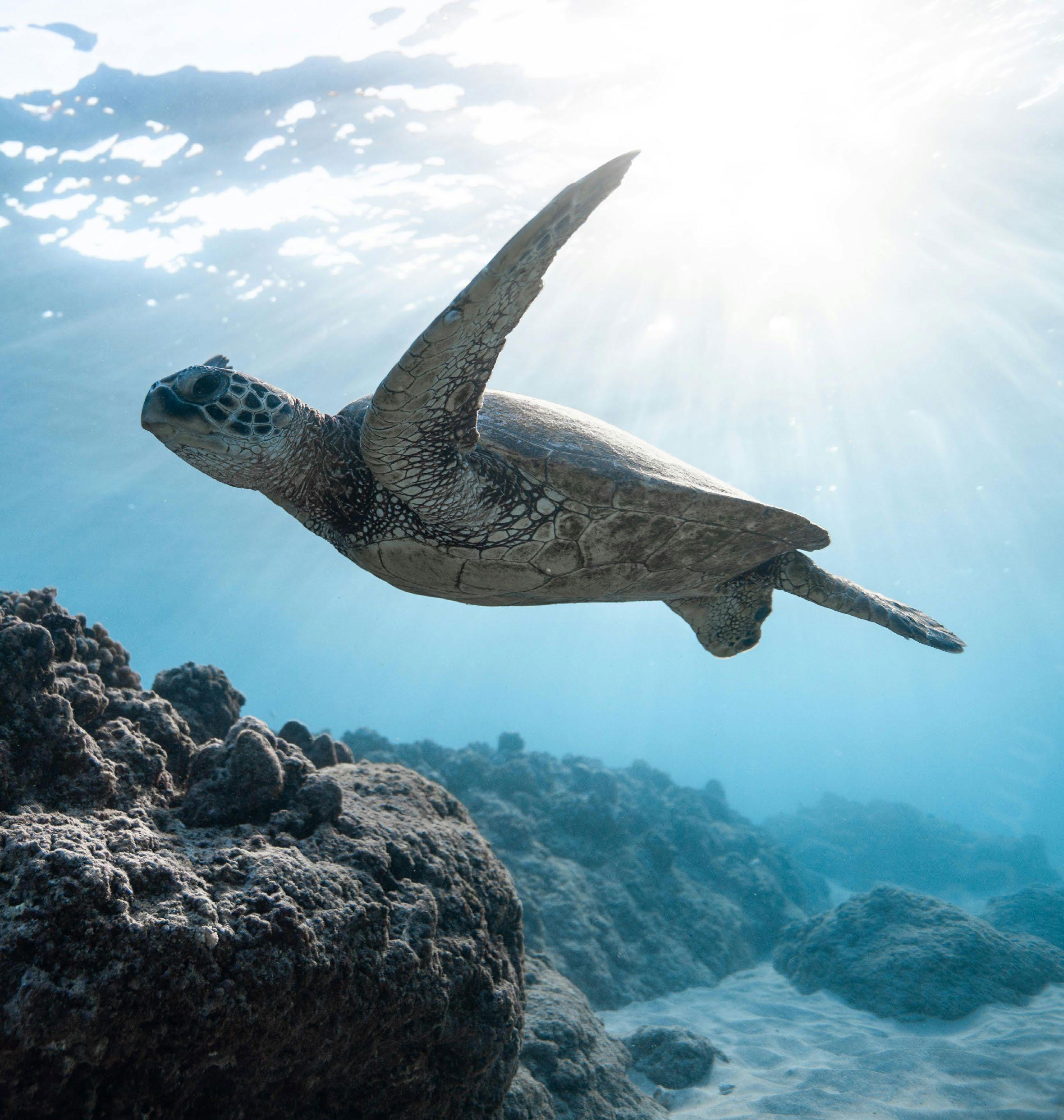
THE FUTURE OF RECYCLING IN THE FIGHT AGAINST OCEAN WASTE
In January 2024, RAFF Plastics entered into a strategic partnership with Go Ocean, an organisation committed to restoring coastlines and ocean ecosystems to strengthen resilience to climate change. As a partner, RAFF Plastics provides not only funding but also expertise to further develop Go Ocean, with Caroline Van der Perre as a member of the board of directors.
“At RAFF Plastics, we are investigating how to recycle plastic ocean waste into new raw materials. It is a challenge because this waste is highly contaminated. But together with the restoration of underwater ecosystems, it is essential for the future of our planet,” Caroline explains.
Dozens of companies have since joined Go Ocean. Their investments are used by the organisation to plant seagrasses in the UK, restore coral reefs in Indonesia and plant mangrove forests in Madagascar, to mention just a few initiatives. Recently, Go Ocean launched two new projects to restore biodiversity in the North Sea: the restoration of oyster reefs at offshore wind farms and the nature-friendly reconstruction of the harbour dam in Blankenberge.
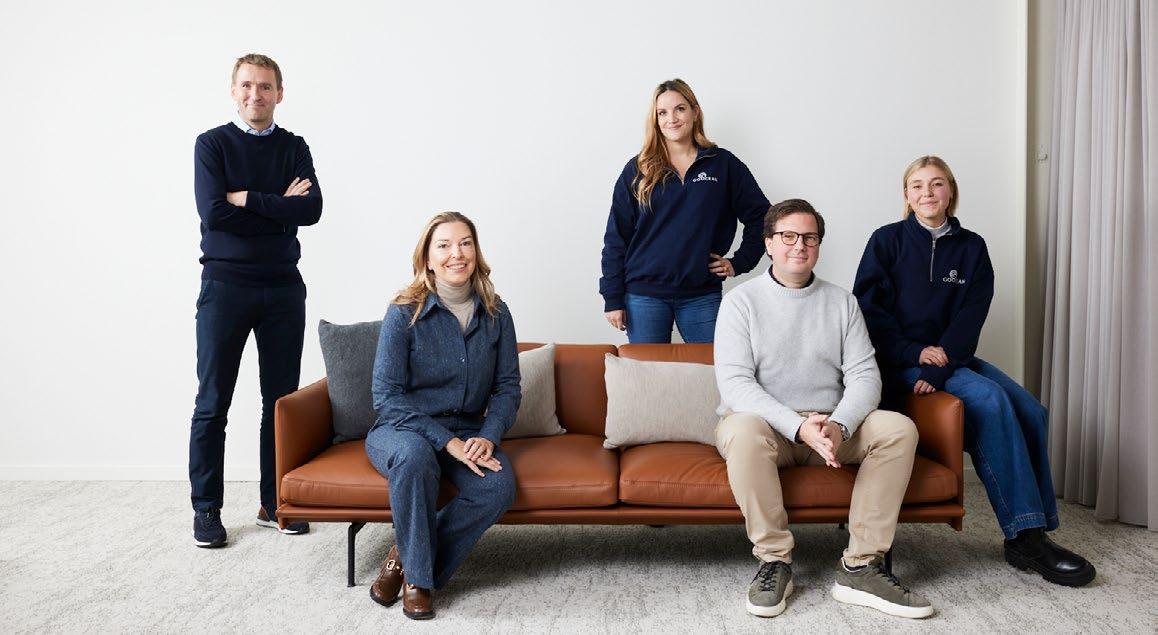

COLOPHON
2024 RAFF PLASTICS SUSTAINABILITY REPORT
RAFF Plastics
Melanedreef 16
Houthulst raffplastics.be
facebook.com/RAFFPlastics.Carotrans linkedin.com/company/raff-plastics instagram.com/raffplastics_carotrans
CONCEPT, LAY-OUT & COPYWRITING
cantilis.be
IN ASSOCIATION WITH bakertilly.be
PHOTOS
RAFF Plastics
Baker Tilly
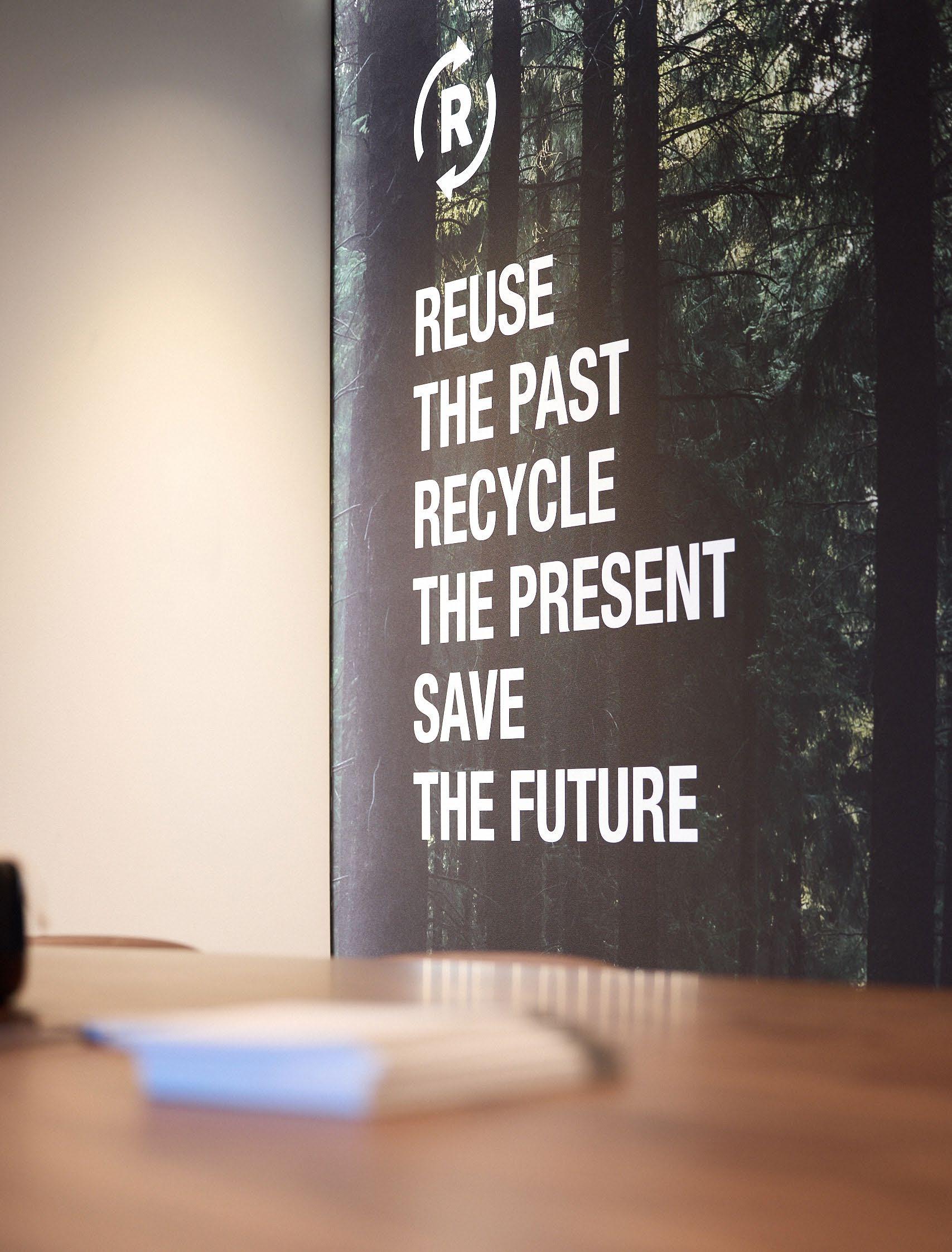
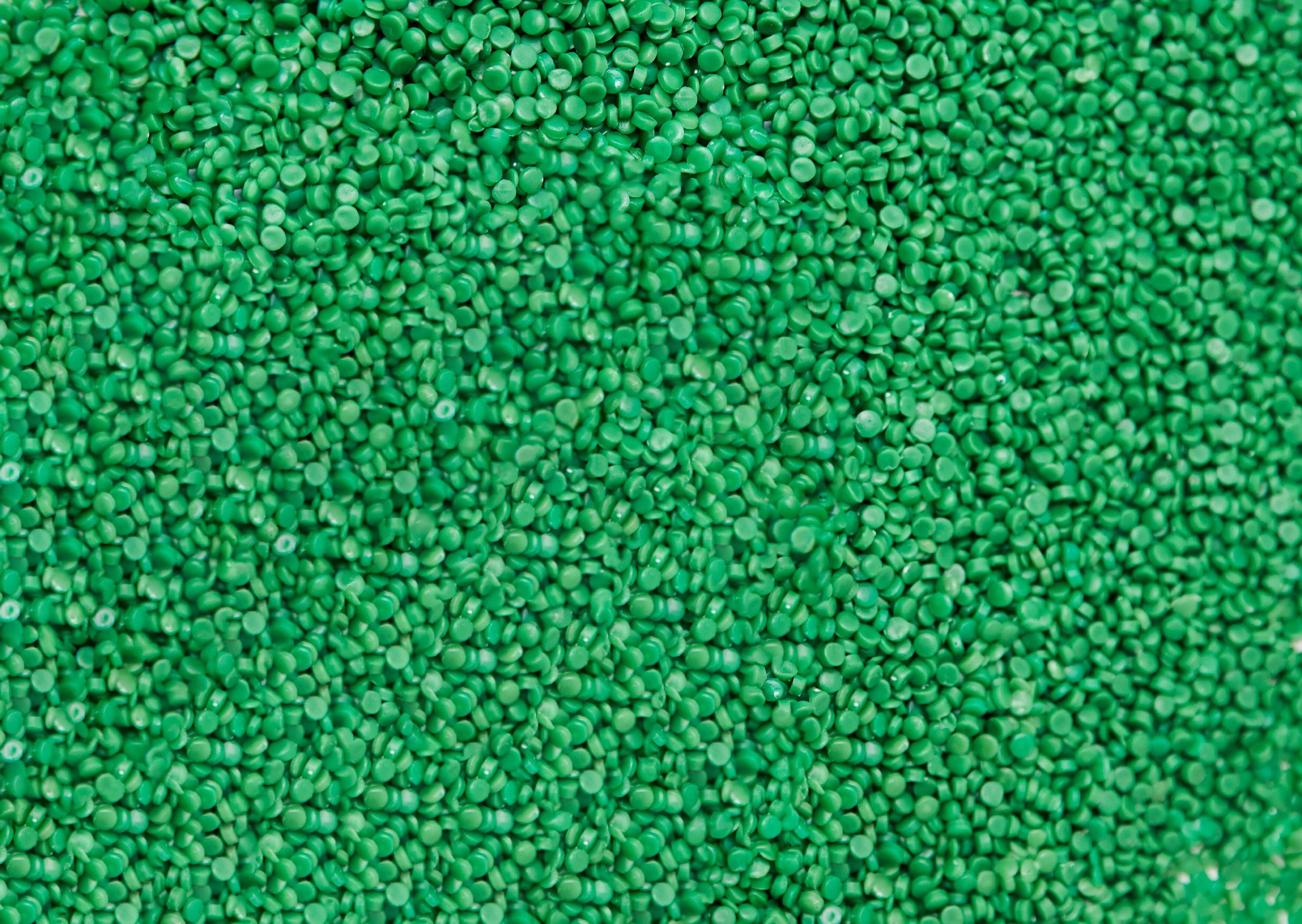