
who
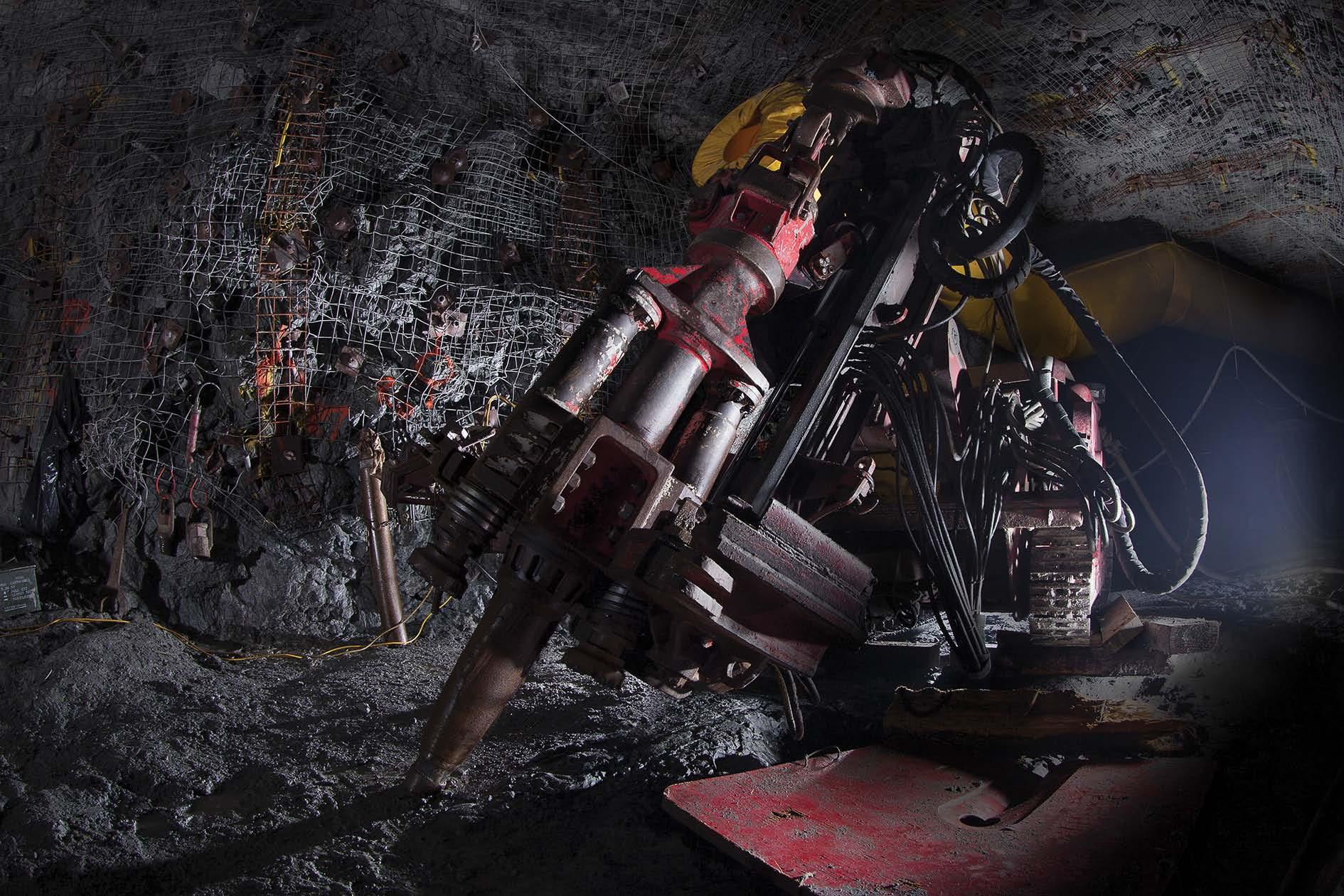
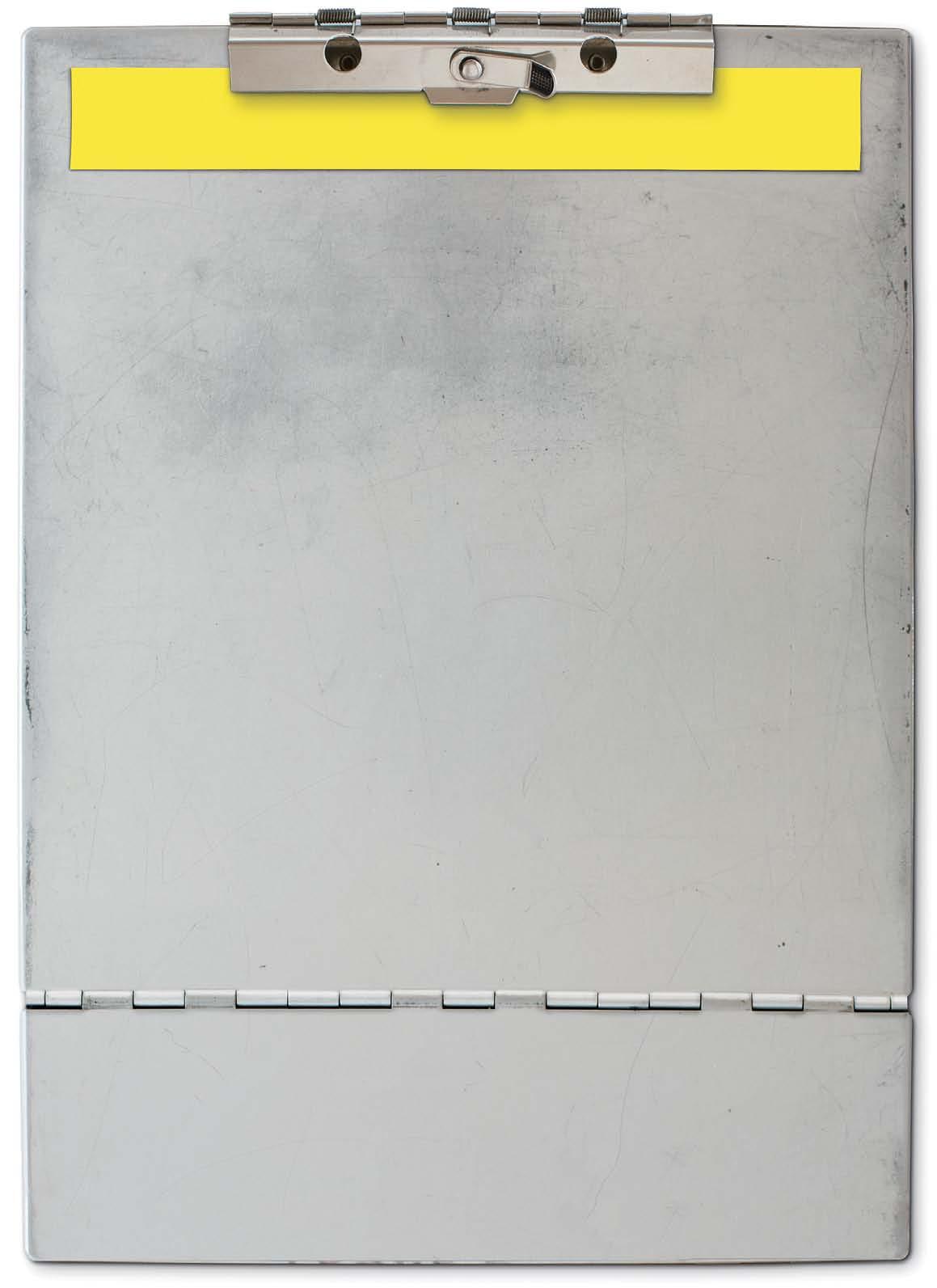
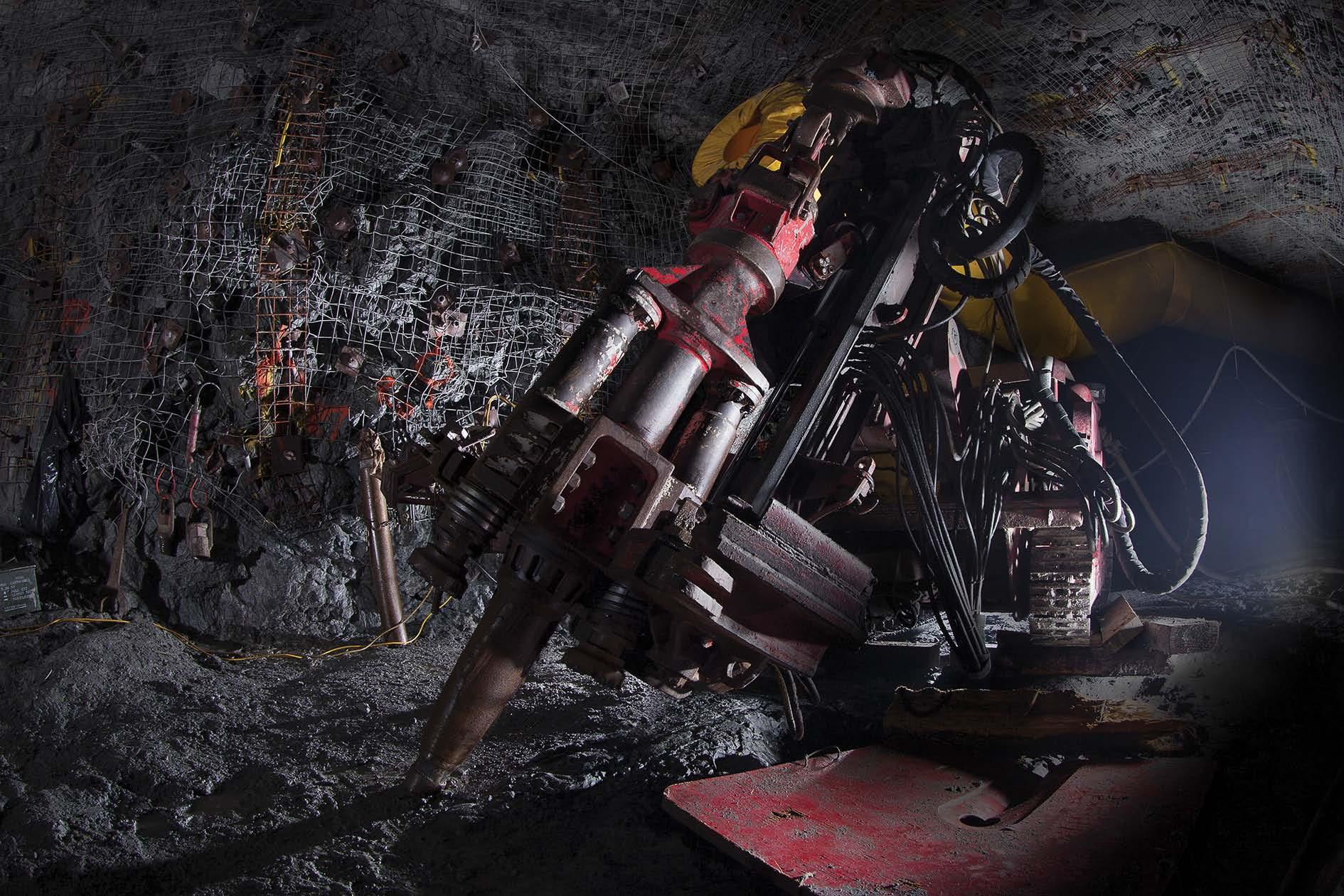
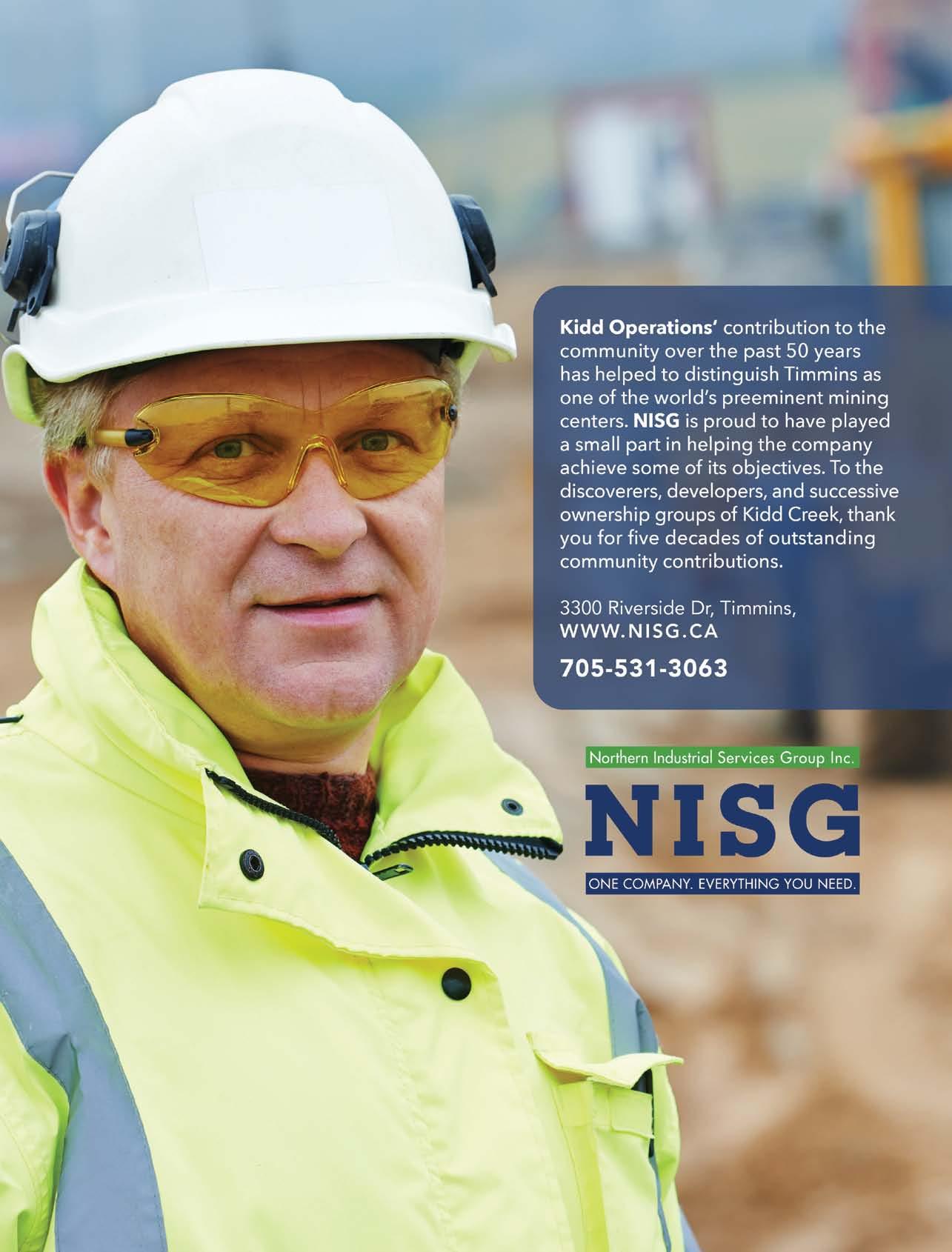
who
journey from core to ore has many challenges. When engineering commenced on the Kidd Mine D No. 4 Shaft, we knew this was a special project. Sinking concurrently from two horizons in an operating mine made this project as complex as it was technically challenging. Cementation is very proud to have played a key role in the development of Kidd’s Mine Deep operation as the engineering company and sinker for the Kidd Mine D No. 4 Shaft. Congratulations Glencore and everyone at the Kidd Mine on your 50th anniversary.
Process
Materials
In-plant,
Most mining executives would dance in the streets if they got 50 good years out of their orebody. With five de cades in its rear-view mirror, Kidd Creek can not only rejoice, but revel in the fact that the world’s deepest base metal mine has life in it still. That life to date has led to an unimag inable production record – extraordi nary engineering accomplishments - homespun expertise that is shared around the world – an unwavering commitment to environmental stew ardship - and a commitment to the highest standards of safety that other industrial operations can merely envy. In the pages that follow you will read about the mine’s discovery in the ear ly 1960s; a royal photo opportunity; a herd of majestic mammals that de lighted children and adults alike; the mysterious prospector who vanished after erecting a ramshackle home stead above the orebody; one of many multi-generational Timmins families who have been part of the payroll; and
much, much more.
Today, as the company advances deep underground to the 9600 foot level, the man in charge of that undertaking is balancing both short and long term expectations for the workforce and the community.
“A resource has a finite end,” says Kidd Creek’s Mine Manager Steve Badenhorst, who took over the post in January of 2016 from Tom Semadeni. He points out that a decision late in 2015 to target the 9600 level extends the mine’s life an extra year to 2022.
“Unlike an agricultural business, you can’t hope that the gold or copper or zinc from a mine is going to stay there (and sustain itself) forever. After 50 years Kidd definitely has an orebody that extends deeper, but the infrastruc ture was developed to extract the top 1100 feet. We have extended that over a long period of time to where we are now reaching the end of that infra structure.”
Badenhorst says there is more to the
Kidd Creek orebody, but the company would need to develop an expensive new infrastructure and a new hoisting system to go after that material.
Even if prices for copper and zinc rose dramatically, the ore is so deep, and so expensive to extract that it would be counter-intuitive to engage in the pursuit just because it’s there.
In the interim, the company is taking time out in 2016 to reflect on the ex traordinary impact Kidd has made on the city of Timmins and surrounding area over the past 50 years.
And while the final chapters have yet to be written, the opening chapters, all five decades, are remarkable indeed. With more than 20,000 employees over those years, and a staggering in vestment in equipment, contractors, and the community – Kidd Creek has been a multi-generational economic engine for a city that once believed it would live and die on gold and a mod est lumber industry.
“The articles in this magazine are but a fraction of the many thousands of unique and engaging stories that will be shared for generations to come,” says Badenhorst.
While the future of Kidd has an im pending and inevitable finish date – its past is timeless.
There is no other mine in the world like Kidd Creek.
Steve Badenhorst says he recently described the Kidd mine to his 17-yearold son by characterizing it as a large building that takes years to constructbut it’s never finished.
“Imagine a scenario where you keep going higher and higher and adding scaffolding and someone says: ‘Okay, that’s the height’, and someone else says, ‘No, no – with the right technology we can go higher’.” Indeed. The prevailing attitude is “Look what we’ve al ready done – we can do more.”
While the pride, the ingenuity, and the determination may be in abundance, the reality is that the cost of extending the mine’s life would far exceed the return on that investment.
“Even now there are people who are telling us we can go a bit deeper and that’s driven by this sense of achieve ment around the challenge that has al ready been met.
Most of the longer-serving employees have been part of that challenge for many decades,” says Badenhorst who took over as Kidd Operations Gener al Manager in January of 2016 from Tom Semadeni who held the post for eight years.
“They’ve taken Kidd through these major capacity gaps where others sug gested you could never get through that,” he adds. “It’s remarkable.”
When it comes to the short-term fu ture of Kidd, he is careful not to proj ect any false expectations.
“You can’t farm a resource. In essence it’s the next seven or so years that we have to manage to get the best pos sible extraction - and then if we look
wick Mine in Bathurst, New Bruns wick. The lead-zinc-copper mine was discovered in 1953 and started production in 1964 before closing in 2013 just short of its 50th anniversary.
“In the Brunswick case they mined everything out over the course of its life to a point where there are limits to what you can mine economically,” said Badenhorst.
“At the final stage of the mine, they went back and said ‘can we mine what is left and still make money?’ For ex ample, are there any areas above us where we can possibly go through and access economic ore?
I think it gave Brunswick an extra two years of life. Whatever you do, it is still finite, it will end at some point.”
What about commodity prices? “The realistic one (chance of keeping the mine open longer) is if there is a rise in commodity prices. We don’t be lieve that energy prices will drop –
so input costs are largely where they are.
If we go to where com modity prices are now, we are looking at 2005/2006 levels, and when you com pare that to 2015 levels, if you want to be economic you would have to ask staff to undertake paycuts back to 2005/2006 levels and that is not attainable.”
Badenhorst says that on the other hand, if com modity prices were to rise, then you could think about going after the deeper material.
He cautions however, that a jump in prices would be counter-intuitive because the deeper you get, the higher the cost.
“For example, a skip that we use to pull material from the bottom of the mine, if it can handle 40 tons on the upper levels, it might only take 17 tons on the lower levels. You can’t keep mining economically at those lower depths.”
“The second biggest cost we have in terms of energy consumption is our ventilation fan system. It’s very hot down there. To ventilate it to make it safe for people to work is going to consume a lot of energy.”
Badenhorst says you can do many things on the input side of costs. Kidd is always looking for ways to reduce ventilation costs which in turn will re duce energy consumption.
In the interim, technology advance ments are focused on reducing hu man interaction by remote mining or scooping. “We can remove the opera tors and put them on surface (9600 feet above) while the machines are on the lower levels. It reduces the cost of normal breaks and shift change times,” says Badenhorst.
New Mines:
• Research and development laboratories providing customized ready mix, cement and cementitious solutions
• Solutions for quicker construction times for concrete headframes, concrete lined shafts and underground structures
• Worldwide logistics services delivering cement and ready mix to hard to get at locations
• Backfill solutions including: cement products, plant operation, portable plant possibilities and technical support
Mobile ready mix and wet shotcrete services and products provider
Portable crushing and screening plant capabilities
Mine Closure:
• Providing assistance, support and screening solutions for mine tailings reclamation projects
• Products and technical expertise for soil remediation, solidification and stabilization solutions
A strong commitment to health, safety, and environmental standards.
By partnering with Lafarge
to bring innovation, performance and certainty to your new mine, operating mine and mine closure projects.
more information,
years
operations!
There’s an ancient truism about min ing. To find an orebody, pitch your tent in the shadows of another.
On Nov. 8, 1963, a young Canadian geologist, Ken Darke, hauled a 2-ton diamond drill 25 kilometres north of the prolific gold mining town of Tim mins, Ontario into Kidd Township. One of the first holes he spotted was logged as Kidd 55-1; and when the core was pulled the following day, Darke and his drill crew stared in amazement. It contained a foot of solid copper. More than 3,000 kilometres to the south, a struggling American com pany, Texas Gulf Sulphur, was poised to become the operator of one of the world’s richest deposits of zinc, cop per, lead, silver, tin, cadmium and in dium.
When Darke shared the news with senior Texas Gulf officials, they couldn’t get on a plane fast enough. Vice President and Manager of Ex ploration Richard Mollison and Se nior Geologist Walter Holyk quietly
flew to Timmins; arranged a swamp buggy; and headed off to view the drill core at the site.
They were equally amazed. The pair agreed it was a major discovery. They ordered drilling to be put on hold; the discovery site disguised; and the drill moved to the north where a dummy hole was drilled.
Seven additional holes were drilled in early 1964 before the news was of ficially announced on April 16, 1964.
Only the discovery core was ever as sayed (in a U.S. lab) before the news. It wasn’t until December that assays on 55-1 were released. The official as say was extraordinary. That discovery hole was included 602 ft. averaging 1.18% copper, 8.1% zinc and 3.8 oz./ton silver.
Subsequent drill holes delivered even better results.
In a published interview a decade af ter the discovery of the Kidd Creek orebody was announced, P. Ray Clarke, vice-president, Texasgulf Inc. and Vice-president and General Man
ager of Ecstall Mining Limited, (then Kidd’s name) reflected on 1964.
“The news on April 16 of the large, rich deposit of zinc, copper and sil ver beneath the muskeg near the Town of Timmins created excitement across several nations. It started one of the wildest land rushes ever seen in the quiet Northern Ontario woods. It caused hysterical activity on the American and Canadian stock ex changes. It changed Texasgulf from a sulphur-fertilizer company into one of diversified international magnitude,” said Clarke.
And it changed Timmins in a dozen different ways, all for the better.
The company’s story began in 1909 when a small operation was created to mine sulphur in the southwestern United States.
Texas Gulf Sulphur Company Ltd. grew into a major sulphur producer, but by the 1950s, it faced hard times and declining reserves.
It decided to look elsewhere for sul
Unifor Local 599-T On-site Office
P.O. Box 1931, Timmins, Ontario, P4N 7X1 Tel: 705 235 8121 ext. 7599 Unifor599@glencore ca.com www.timmins599.blogspot.ca/
For a base metals mine, with finite resources at depths seen nowhere else in the world, to exist 50 years is a remarkable achievement. Kidd continues to thrive, and still proves to be a decent and safe place for all to earn a living.
One of the main drivers for Kidd’s success for the past 50 years and counting has been its employees. A more diversified and innovative group you would be hard pressed to find! From the late 1960’s up to the present, whether you worked underground or in any plant, you could always feel a sense of comradery. This is self evident by the numerous generations of families that have enjoyed long careers here. More than 20,000 employees have walked through our gates as this was and still is one of the city’s biggest employers. Both Kidd’s employees as well as our employer have been major contributors in many ways to the success of this community and look forward to continuing that tradition.
On behalf of Unifor Local 599 current and past membership, I would like to congratulate Kidd Operations on reaching this golden anniversary.
Paul Fillion Unit Chairsights on Canada under the Canadian Shield Project.
The program was a failure and had been sharply reduced when Darke was sent to Timmins in early 1963 to supervise a drilling program.
The main target was a large anomaly in Kidd Township. Anomalies occur when material in the ground gives off a reading different from the surround ing area when geophysical equipment passes overhead.
The readings were so strong that for years airplanes and helicopters hired by mining companies in the area used them to set their instruments before flying off to do surveys. Apparently no one thought the anom aly worth investigating until Texas Gulf came along.
Remarkably, Mclntyre Porcupine Mines Ltd. was cutting trees on the site for use in its Mclntyre Gold Mine, one of the largest in Canada and a mainstay of the area economy since its discovery in 1909.
When drill crew foreman Rene Ger vais brought Darke part of the core on that night of Nov. 9th, the young ge-
first was to perform more drilling to prove the first hole wasn’t a ‘fluke’ and the second to keep the find secret until it could acquire the land around it.
What became one of the most impor tant mineral discoveries in the history of the world was on land the discover er didn’t own; Texas Gulf merely had an option on the four-claim, 160-acre property.
In fact, there were three major owners to contend with, as well as numerous small pieces of property to acquire and Crown land to be staked.
In the months that followed, Texas Gulf managed to acquire 60,000 acres by staking and buying property. While Darke confined the drill crew to the site for weeks, the men needed food and other supplies.
Diamond drill core was shipped to the U.S. for storage even though there was a laboratory within 143 km of Timmins.
Still, speculation grew as what was going on in Kidd Township. Eventu ally, prospectors and other companies started to tie up ground near the find
and in the adjoining townships. The Jungle Telegraph in Africa has nothing over the rumor grapevine in mining circles.
The bible of Northern American mining journals, the Northern Miner weekly in Toronto, got wind of the story and managed to put together enough facts that the company agreed
The story was written on April 13 and carried in the edition of April 16. On the same day, Texas Gulf made a for mal announcement in New York City. The news sparked the biggest, wildest mining rush in Canadian history.
That the find was made in an area where gold had been found as early as 1906, where the three giants of Ca nadian gold mining, the Dome, Hol linger and Mclntyre were still in pro duction; and where more than 50 gold mines had been born and died just added color and excitement to events.
There were huge areas that couldn’t be staked because they were held by mining companies, individual pros pectors and veterans of wars around the turn of the century but every square inch of open ground in eight 36-square mile townships was staked or bought (sometimes flipped several times for ever higher amounts) and soon every diamond drill rig in Can ada and the northern U.S. was punch ing holes into the ground.
Darke had managed to stake all the open ground he thought the company needed and he told it as far as he was concerned there was nothing of value on the land he passed up.
History was to prove him right. To day, a half century later, no one has found another major base metal ore body in the Timmins area.
At the time of the rush and with penny stocks soaring in value with the mere announcement that companies had
Whether your equipment is highly complex or fairly simple, you need your machines to work.
NTN has a solution that puts your mine at ease.
Whether you work on top of the world or deep in it…
Cont’d from pg. 14 acquired ground near Kidd Creek (of ten 15 and 20 miles away), the theory was that the orebody was a ‘splash’ and there had to be other parts of it to be found.
A study conducted by the Geological Survey of Canada, the Ontario Geo logical Survey and Falconbridge Ltd. was released in 1995, proving the ore body was a geologic ‘tear,’ a self-con tained and isolated occurrence. The millions of dollars bet in the stock market frenzy of the remainder of 1963 and throughout 1964 on specu lation that there were more Texas Gulf orebodies around Timmins proved pointless.
Experts determined the Kidd Creek deposit was originally formed on the seafloor around hot springs 2.7 billion years ago, similar to how black smok ers form on the seafloor today. While exploration was occurring all around it, Texas Gulf was busy se lecting a site for a concentrator 17 miles east of the find. They needed to build a highway from Timmins north through the muskeg to the discov ery, along with a railway between the mine and metallurgical site that would be home to the concentrator and the many good-paying jobs that went along with it.
The railway started hauling ore on November 7, 1966 and nine days later, the first ton of ore went through the new concentrator.
The orebody was so unusual, yielding copper, zinc, lead, silver, cadmium, tin, as well as sulphuric acid and in dium as by-products, that people from Russia, China, Chile, U.S., Mexico
and other mining nations came to study it.
Not surprisingly, gold was found near the metallurgical property and for a few years it created an additional rev enue stream for the owners.
Nothing like Kidd Creek has been found anywhere else but numerous other mining companies continue to explore in and around Timmins and the rest of the Precambrian Shield.
Despite its wealth and reserves, Kidd Creek has had six owners. Texas Gulf (by then Texasgulf Inc.) sold in 1981 to France-based Society National Elf.
It immediately sold the Canadian mineral properties to the Canada De velopment Corporation (controlled by the federal government) and in 1986 Canadian mining giant Falcon bridge acquired the mine.
Swiss-based Xstrata plc acquired Fal conbridge in August 2006.
It merged with fellow Swiss-based Glencore plc in May of 2013 and be came Glencore Xstrata.
The merger created one of the world’s largest natural resources groups, ex tending through more than 90 com
modities from copper to barley and from oil to vanadium. The company employs roughly 181,000 people across 50 countries.
Glencore Xstrata plc subsidiary, Xstrata Canada Corp., announced that effective July 30, 2013, it had changed its name to Glencore Canada Corporation.
Glencore Xstrata was renamed Glen core plc at the AGM in May 2014. Glencore plc is an Anglo–Swiss mul tinational commodity trading and mining company headquartered in Baar, Switzerland, with its registered office in Saint Helier, Jersey. It is one of the largest commodity traders in the world.
On July 16, 1996, Frank Pickard, 62, president and CEO of Falconbridge told a gathering of Timmins civic and political leaders he hoped the Kidd Creek Mine will be here “30 years from now.
I won’t be here but the mine could be.” He was out by just four years, the fabulous mine is slated to close in the first quarter of 2022, after 56 years of production.
was $270.5 mil lion.
In 1974 more than 60 per cent of the company’s earn ings came from Canada. Yet, Fogarty saw a potential for the mine that would have again changed the com pany. In a speech on July 19, 1974 to the New York So ciety of Security Analysts, Fogarty revealed his vi sion.
“New opportuni ties include ship
Were it not for a tragic plane crash in 1981 and the loss of several senior Texas Gulf officials, North Ameri ca’s most prolific mining community might have been so much more.
Dr. Charles (Chuck) Fogarty was a vi sionary businessman who spent eight years at the helm of Kidd Creek. His biggest dream would have changed the mining community of Timmins into an industrial giant. Fogarty was chairman of the board and CEO of Texas Gulf Sulphur from October 1973 until 1981, the com pany that had already changed the fortunes of Timmins with the discov ery of a world-class orebody of zinc, copper, silver, lead and several other minerals in 1963. Timmins area gold mines had dwin dled to 13 by 1959 and there were only six left a decade later. To add salt to the wound, several of the town’s sawmills had closed, reducing the size of the region’s second major industry.
Texas Gulf literally pulled Timmins and a number of small nearby com munities out of an economic tailspin, becoming the town’s biggest employ er and largest taxpayer.
In a 1996 public address, then Tim mins Mayor Victor Power said “To those who were responsible for the investment and the exploration that led to this find we all owe a deep debt of gratitude.”
In 15 short years, the Kidd Creek Mine helped transform Texas Gulf from a one product company, sulphur, to a multinational giant with five divi sions, chemicals, metals, oil and gas, international and exploration. The cash flow from the Kidd Mine fu eled a majority of that expansion over the years.
As Fogarty said: “In 1960, sales of our one product, sulphur, were $59 million, net income was $13 million and total assets were $125 million.”
By 1972 the company’s gross revenue
ping pyrite from Timmins to Lee Creek in North Carolina and return ing phosphate rock to Timmins. A Timmins fertilizer complex would be based on North Carolina rock and sulphuric acid from the mine’s zinc and copper smelting facilities. At Lee Creek, Kidd Creek pyrite would be used to produce sulphuric acid.”
He also said, “Plans are in the for mulation stage for further expansion at Kidd Creek to eventually process about 75 per cent of the zinc concen trate production.”
On Sept. 30, 1980, Fogarty spoke in Toronto at the A.E. Ames Metal Conference and once again he talked about vertical opportunities. The company had two gold mines on its property, Owl Creek and Hoyle Pond, and he said a precious metals refinery was planned.
“We would like to build a cement plant at Kidd Creek. Large amounts
of cement are required for un derground backfill in order to achieve 100 per cent ore recov ery,” said Fogarty.
He told the conference that en gineering work and some piledriving was then underway for the expansion of the new copper smelter and refinery to increase capacity from 65,000 to 100,000 tons per year by using more oxy gen in the smelting process.
The project would include “new oxygen and sulphuric acid plants and an expansion of the refin ery. Construction is scheduled to start in early 1982,” he said.
But it was not to be.
A small corporate jet, returning through rain and ground fog to company headquarters in Stam
ford, Conn., crashed on approach to Westchester County Airport on Feb. 11, 1981. Executives had been attending a meeting in To ronto.
Richard D. Mollison, the vice chairman of Texas Gulf, is sued a statement confirming that Charles F. Fogarty, the company’s 59-year-old chairman and chief executive officer, three of the company’s 12 vice-presidents, the chief corporate communications officer and two pilots were killed on impact.
Five months later, Elf Aquitaine, a French development corpora tion acquired ownership of Texas Gulf in a $5 billion deal.
The two gold properties were eventually sold off and Fogarty’s dreams were forgotten.
Did you know that Canada’s most iconic folk country singer wrote a song about the discovery of the Kidd Creek Mine?
Well it’s true, the now legendary Stompin’ Tom Connors was living in Timmins at the time of the nations largest staking boom created by the announcement of the discovery of a rich copper and zinc deposit in Kidd Township.
So in 1965, the 29 year old Tom Con nors sat with Murdo Martin who was Member of Parliament for Timmins,
and Gerry Quinn and the three men wrote a song about the bright future the mine would bring to Timmins, even correctly forecasting a smelter and refinery.
Local radio station CKGB knew Tom was a star in the making and recorded his second 45 rpm single. Side 1 of that vinyl record features “The Birth of the New Dragon Mine” which was the Kidd Creek Mine. When the mine’s name changed from the New Dragon Mine to Kidd Creek Mine, Tom stopped singing the song. He
eventually re-recorded it in 2008 on his album The Ballad of Stompin’ Tom and re-titled it “The Birth of the Texas Gulf Mine”
In addition to Timmins – Birth of the Texas Gulf Mine, other Stompin Tom Songs related to mining include Sudbury Saturday Night (Inco Nickel Miners), Dam Good Song for a Miner (Elliot Lake Uranium Miners), Fire in the Mine (Timmins Gold Miners, 1965 McIntyre Mine Fire), Coal Boat Song (Cape Breton Coal), Long Gone to the Yukon (Yukon Gold).
In Timmins that great northern place of renown
The Hollinger mine was about to close down Was enough to strike fear to the hearts of the bold Wondering just what their future would hold Nobody knew it was time
For the birth of the new Dragon mine
But a copter flew daily from Timmins they say To land in Kidd township just 12 miles away Still no one paid heed as they walked down the streets Engrossed with the problems they’d soon have to meet Then just a few heard it was time
For the birth of the new Dragon mine
There was a mere handful who found out the score
The Texas Gulf Sulfur had struck some good ore
Together they staked every claim to be found Is said some made millions for holding good ground Guess somebody knew it was time
For the birth of the new Dragon mine
At last word leaked out of this rich copper find And the people of Timmins went out of their mind
A well beaten path to the stock brokers door Was trodden by thousands never seen there before
Now everyone knew it was time
For the birth of the new Dragon mine
From Reid to Carscallen and eastward to Teck The bush filled with stakers who daily would trek And the moose had to hide themselves most of the day
While claims stakers rushed in to make the bush pay All the papers proclaimed it was time
For the birth of the new Dragon mine
To Timmins came people from south east and west
From thousands of miles they all came to invest
Some mortgaged their homes just to try out their luck
A few struck it rich while the others got stuck But the hopes of the north made a climb
At the birth of the new Dragon mine
So nobody’s worried the future looks bright
For a smelter in Timmins we’ve all joined the fight
A smelter with lots of rich ore to refine Will start a new life for the old Porcupine
And the eyes of the world are in line Well fixed on the new Dragon mine
They’re all watching this new Dragon mine
Ask anyone connected with the Kidd discovery if luck was involved and you’ll likely get the same answerluck had very little to do with it. The more poignant response would be - it was hard work, it took huge sums of money and a new explora tion theory arrived at separately by four groups of geologists along with several individuals who collectively pursued that theory with an unwaver ing determination. The discovery would not have been possible without Texas Gulf Sulphur Company Limited accepting and ulti mately agreeing to act on the theory. How it all happened was diarized by chief mine geologist Brian W. Hester. He was hired by Texas Gulf on May 1st, 1964 to replace geologist Ken Darke who was leaving. Darke was the man who spotted the famous Kidd 55-1 diamond drill hole that pierced the massive orebody. What follows is an abridged version of events as recalled by Hester, with additions from other documents.
‘replacement.’ At the time, little inter est was shown in volcanic processes. Geology of the Precambrian structure in the Canadian Shield was widely considered to be too complicated and poorly exposed to allow interpretation in anything more than general terms. Work in Japan and Norway led to ge ologists to debate a new theory, that massive sulphides were related to vol canogenic processes (VMS). Corporations that employed geolo gists working on this new interpreta tion of VMS deposits included Fal conbridge, Texas Gulf, Anaconda, and Consolidated Zinc Corporation. Hester worked for each company except Anaconda. His experience al lowed him the opportunity to develop a broad network of contacts. The four corporations regarded their in-house interpretations as confiden tial - but in the field, ideas were often
and routinely exchanged informally. Some geologists argued that drilling records showed that sulphides seemed
Geologists are notorious for jumping from one project to another. After all, they have to go where there’s workand where there is mining work to be done - alcohol and professional banter is sure to follow.
In 1950, Canadian Walter Holyk joined Texas Gulf Sulphur as a ge ologist and was given the mandate to locate pyrite deposits from which sulphur could be produced. He per suaded company management that it would be more beneficial to try to lo cate base metal sulphides than pyrite bodies and with that theory in mind, he initiated exploration in Eastern Canada. Called the Shield Project, the hunt concentrated on the Precambrian Shield.
It was the early development days of electromagnetic (EM) geophysical methods - which had yet to be adapted
posit.
Holyk -Texas GulfRichard Mollison, the Texas Gulf vice president and manager of exploration, quickly arrived and met with Holyk who introduced him to Cheriton. Mollison met with both geologists and they eagerly filled him in about their updated VMS theory. Holyk and Mollison reasoned they now had a powerful exploration model with a more general application. Why not try it out on the Canadian Shield? Texas Gulf had recently hired another geologist, Leo Miller. Holyk briefed him on the plan. Miller was told to make a compilation of Canadian Shield geology. His task was to catalog the areas not underlain by granite between Chibougamou, Quebec in the northeast and Kenora, Ontario in the southwest. With a back ground in uranium, Miller was sent on a tour of base metal mines. It was the winter of 1956-57 so field work was not possible.
to aircraft. TGS’s head geophysicist, Van Donohoo, designed a system that could be used on a helicopter. Working in the old copper district in the Eastern Townships of Quebec, Holyk ran into a former classmate from the University of British Co lumbia, Cam Cheriton. While em ployed by separate companies, the pair shared their ideas and developed a rough concept of VMS. In 1953, a deposit of massive base metal sulphides was discovered using helicopter-assisted e-m near Bathurst, New Brunswick. Holyk and Cheriton raced to the site as soon as they heard about it.
Working independently, they applied their new theory and on the first day, Cheriton found the Caribou deposit for Anaconda and on the second day Holyk found the Half Mile Lake de
As a result of Miller’s research, he recommended three areas for further work - an area near Gowganda, one near Kenora, and another that would become the Kidd Creek Mine site north of Timmins.
The effectiveness of the TGS helicop ter-borne EM system had been proven in New Brunswick, so the unit was moved to Timmins.
Holyk recruited a team of researchers tasked with combing through gov ernment records to pinpoint areas in which he believed massive sulphide orebodies would occur. The geologi cal targets were then surveyed using the Texas Gulf airborne system. Flights were made over the three se lected sites but only the Timmins one responded well to the new equipment. Flying in the Timmins area eventually resulted in about 2,000 anomalies. The
one in Kidd Township was the darling of the day’s geologists - but the area’s land ownership issues forced it low on the priority list.
Work continued throughout the 1950s, and 69 anomalies were drill-tested in the Timmins area alone, with little success.
A slump in the price of sulphur forced TGS to send its exploration crews to Calgary to hunt for oil and gas. There was no money for mineral exploration.
The company’s financial picture im proved and money was found to re sume work in the Timmins area.
For years, Holyk, Mollison and even tually Darke pushed to drill that strong anomaly in Kidd Township.
A number of critics and observers sug gest the discovery of the Kidd Creek deposit was the result of the Canadian Shield program initiated by Holyk for Texas Gulf in 1958.
TGS on the other hand, always took the position that it was a team effort, supported by multi-million dollar budgets and the faith that top officials had in their field personnel. Only the persistence of Texas Gulf staff enabled the company to acquire permission to drill their favoured tar get on Nov.8, 1963, the strong anom aly which, for years had been so dif ficult to option from several owners. In technical terms, drilling revealed that Kidd Creek, a 100 million ton volcanic massive sulphide (VMS) deposit, occurred at a domed rhyolite sediment contact.
In the end, it was the contribution of a great many geologists and an adven turous yet focused corporate board of directors, who had pieced together a working hypothesis that led to the discovery one of the world’s greatest zinc, copper, lead, and silver mines.
66 holes of the Timmins project had
In 1963 when Texas Gulf had cash flow, Darke wrote a memo urging the company to resume its search in the
Mollison, who later became president of the company, flew to Toronto from his Timmins office and got the money
Darke ordered Hole K55-l drilled on
The core that was drawn from that hole on Nov. 9 changed the histories of Timmins, the company, and the
There was much more to the story than just two stubborn and determined
First, Darke was lucky to be alive. Originally from British Columbia, he graduated from the University of BC in 1956 with a degree in geological
In an unusual move, Timmins city council welcomed an “old friend” back to the community on Sept. 12, 1983. Council paid official recogni tion to Mollison for his contribution to the quality of life in Timmins. Mollison was returning after being appointed as chairman of the board of Kidd Creek Mines Limited.
mine - but two men deserve special recognition - mining engineer Richard (Dick) Mollison and geologist Ken neth (Ken) Darke.
It was Darke’s unwavering belief in the potential of the Timmins area to host base metals that allowed him to be the right man, at the right time, in the right place back in 1963.
It was Mollison as vice-president and manager of exploration who had faith in Darke and fought the corporate battle to get the exploration budget restored after the company wanted to give up.
Darke spotted the drill that penetrated the massive copper-zinc-lead-silver deposit in Kidd Township, just 16 miles north of the then Town of Tim mins.
He was a field geologist for Texas Gulf Sulphur Co. when the explora tion budget was exhausted in 1962 and field work was cut back. The first
He went to work for Texas Gulf and in May of 1958 he was sent on a flight over Baffin Island. The plane crashed. Darke’s back was broken and his jaw severely damaged.
Despite two dislocated ankles, ge ologist George Podolsky dragged Darke and two others to safety from the burning plane. The four lay in a snowbank for 87 hours before being rescued.
While recuperating at his home in Trail, B.C. Darke prepared a paper on “type situations” where mineral de posits might be found in the Canadian Shield.
Five years later, K55-1 proved to be the ultimate “type situation”.
Born in Minnesota in 1916, Mollison was a brilliant man who won many awards during his educational period and in his professional life, but it was his personality that earned him friend ships and respect.
Mollison met with council and then with local business leaders, many of whom he had met during a relation ship stretching back two decades when he was with Texas Gulf.
Timmins Mayor Victor Power told other council members that Molli son was “fondly remembered for the many gifts the company bestowed upon the community over the years.” Mayor Power told a VIP reception that “I’m confident under the lead of the chairman of the board of directors that Kidd Creek will continue to in vest in Timmins and take an interest in the community as a good corporate citizen.”
Mollison worked out of Timmins for several years before moving up the Texas Gulf corporate ladder to the po sition of president and director 197379 and then chairman and CEO 198182 after the death of chairman Charles Fogarty.
He visited the mine nearly every month and always kept Timmins council aware of company activities and plans.
Today Highway 655 is the vital link that interconnects commerce and healthcare in the Cochrane Territorial District of Northern Ontario with over 1,150 vehicles using it per day.
This secondary highway begins at the intersection of Highway 101 and Algonquin Boulevard, near the iconic Hollinger Mine office building in Timmins and stretches 75 kilometres north, generally paralleling a high-volt age transmission line to intersect Highway 11 between the communities of Cochrane and Smooth Rock Falls. It has the distinction of being Ontario’s only secondary highway that features a 90 km/h (55 mph) speed limit due to its importance and high design standards.
This highway we take for granted today, was not always there. The highway’s beginning is a result of the Texas Gulf Sulphur Company building a permanent paved access highway to their Kidd Creek Mine property located 21 kilometres north of Timmins.
Major highway construction by Miller Paving began in June 1965, which allowed pre-production ore to be trucked and milled at Kam-Kotia and Broulan Reef Mines. This pilot plant test work helped figure out the right metallurgical settings to use in the Hoyle Concentrator. The highway to the mine was fully paved by October 1966.
Prior to the Texas Gulf Highway, access into Kidd Township for exploration was primarily by helicopter, Bom bardier bush buggy, or by foot for those who dared to trek through the woods. For many years prior to the dis
covery at Kidd Creek access into those flat swampy lands north of Timmins was from seasonal logging roads and gravel roads originating off the Ice Chest Lake Road near Connaught and Frederickhouse Lake. One could also elect to travel by water craft on the back waters of the Mattagami River created by the Lower Sturgeon Generating station built in 1923.
Highway 655 follows a long esker formation, which actually for much of the length is the watershed dividing line for the Mattagami River to the west, and the Porcupine River system to the east. As a result there are no major creek or river crossings.
The highway skirts Bigwater Lake where a campground was developed by Texas Gulf for its employees that hosted many summer family picnics.
The route also passes Noted Lake and Feldman Lake, the later serves as the main water supply source for the Kidd Mine and replaced an original 8-inch well system as the operation moved underground.
In 1978, the Ontario Ministry of Transportation completed the extension of the Kidd Creek (Texas Gulf) Highway northwards to Highway 11. With the advent of 911 call services, the mine site address became 11335 Highway 655 North.
No highway construction was required to access the Concentrator in Hoyle because Highway 101 east was pre-existing. Significant work though was required in 1966 within the right of way of Highway 101 for 6 ki lometres to install a 30 inch water pipeline from the Frederickhouse River.
To think of 50 years’ worth of boot prints across both the Kidd mine and concentrator sites is almost unimaginable considering that Kidd has employed more than 20,000 peo ple since 1966. And many of those boot prints have been made by generations of the same families.
When you think of “the family business,” you probably think of a store or an auto dealership. Anything but a mine. However, some of Kidd’s employees working for the opera tions today are following in the boot steps of their fathers and grandfathers. The Spehars are an example of a multigenerational “family business” in mining.
Nearly three kilometres underground, two brothers, Ivo and Mikka Spehar, take turns installing steel bolts into the fresh ly exposed rock walls.
“We’re the first ones in, breaking new ground to extend the mine,” says Ivo. They call it ground support, and 9600 feet above them, their father, Miro Spehar, is part of a team that develops the intricate operational plans that determine, in part, where his two sons will be working on any given day. Miro’s job as a designer is part of yet another operational plan of sorts, keeping the Spehar name attached to Kidd Op erations’ mining legacy.
Miro’s father Ed Spehar was here when Kidd Creek first started in the early 1960’s. He came to Canada as a political refugee and eventually settled in Timmins where he went to work for Kidd as the chief draftsman. Ed was part of the team that developed the early mine models and simultaneously, thanks to his love of photography, became Kidd’s de facto historian.
Ed’s grandson, Ivo started at Kidd Creek as a summer student in 2011. After getting his common core training, he landed a full-time job with Kidd. He and his brother Mikka are not only on the same shift, they are on the same crew. Mikka started at Kidd in 2010 as a “nipper”, the nickname used to describe what amounts to a miner’s helper.
“When the crews needed stuff done, it was our job to go and fetch what was needed,” he says. “You have to start some where and now my brother and I are part of the deep de velopment team. I guess you could say we started from the bottom up.”
Mika and Ivo’s maternal grandfather Matti Kangas also worked as a “shaft man” at Kidd for many years.
Some of the three-generation families that have worked at Kidd include the Rivas, Del Bels, Toners, and Laurins.
Prospectors, geologists, and mine-seekers may not all be spiri tual men and women - but when it comes to mining communities like Timmins, there is little doubt that many prayers were answered when news of the Kidd discovery was shared with the world back in 1964.
Attendees to a global conference on mining practices in Ottawa on Nov.7, 2014 heard praise about one company in particular. Canadian Conference of Catho lic Bishops president Paul-André Durocher spoke of growing up in the mining town of Timmins, On tario.
The Gatineau, Quebec Archbish op was 10 years old when the town’s largest gold mine, the Hol linger, announced it would close
because it had run out of gold. The mine closure created a “huge economic blow,” said Durocher. Many families found themselves without a source of income and there were genuine fears Timmins would become a ghost town. Not long afterwards, a major dis covery led to the opening of a new mine, Kidd Creek, in the mid1960s.
Prayers had been answered. Owner Texas Gulf arrived with the intent of contributing to the overall good of the community, the arch bishop said. Durocher told the con ference how Kidd offered the best salaries; it promised to lay off no one during the course of the min ing operation; and it bought prop erty around a lake (known today as BigWater) to create camp sites its
employees could use. The company then built a metal lurgical facility to process the ore, “integrating the most advanced systems for the ecological treat ment of ore,” he said.
The company continued to moni tor water downwind of the site, even though no one lived there. It also kept a herd of bison - because bison are so sensitive to air pollu tion, he said.
Their presence was a sign of the quality of the air.
Durocher went on to praise the way Texas Gulf and its successive owners have spent untold millions of dollars to protect the environ ment around its mine.
Today, Glencore carries on that commitment to environmental legacy.
I arrived on the job on the third day of January, 1964.
The company had been doing a lot of drilling in the area, and they had struck that good hole back in Novem ber of 1963. After that, they moved off the property; because they didn’t have all the holdings yet; all the deals weren’t closed.
We started moving equipment back in to the property on Good Friday, which I believe that year was the 27th of March. We continued to move equipment in over the Easter holiday, by equipment, I’m talking drills and camp equipment.
We got into the property through the back of Dugwall, out by Hoyle. A winter road went out to the hydro line on which we could go by truck, an ice road. They were hauling pulp (cut
trees) out at the time. From there we used swamp buggies to pull the drills across country to the property, about two-and-a-half-miles.
Throughout the winter months we were staking. I had a bunch of guys staking for me, laying out the claims. And I had to spend a lot of time at the mining recorder’s office, registering the claims.
That winter, we staked about 240 claims, but scattered about the area. You must remember that the mine site was not staked land. Much of it was patented land. Much of the mine site land was in the hands of different fam ily estates, which the company had to negotiate with. This was land that was given to veterans of the Boer War back around the turn of the century. I doubt if anybody ever lived on the land. There was nothing there but bush. We
put up the tents immediately, at least to get going, I think there were four of them. We eventually ended up with 12 tents. Then we hauled in plywood and built a cook room, a totally wooden room.
A core shack came in a little bit later, about a month later, and that was ply wood too. That was where we stored the core and split it. But all the sleep ing quarters were all tents.
The drilling contractor was Canadian Longyear from North Bay. We kept the crews in the bush until the an nouncement was made.
But before that happened, one of the guys took sick, and I personally es corted him to the Bon-Air Motel, took him to see a doctor, then took him to a drug store to get a prescription, then back to the Bon-Air Motel to spend
the night, and back into work the next day.
I never let him out of my sight. That was so nobody could talk about the drilling results. We kept it that way until the 16th of April (date of the official announcement of the find by Texas Gulf).
But it wasn’t such a long period. We only moved in at the end of March on this particular property. We set up the first drill to start working on April 1, in the morning.
It was a late spring, so we didn’t get too much water. In fact, we moved in and set up even before the snow start ed to melt.
We got set up with one drill and in about a week or so we had seven drills at work. And we had seven drills go ing all spring, and all summer, right up until about November. They pro duced a lot of core, and I’d say about 90 per cent of that core produced was ore.
I was kept pretty busy that first sum mer because I had the seven drills to look after. Our geologist was only out to the site a few times after we got started and then he quit. It was a lot of activity concentrated in one small area, considering that the company had catalogued more than 2,000 anomalies in its Canadian Shield Project. Out of that, only sev en, including Kidd, were picked for more study. Aerial surveys were car
ried out over Kidd in 1958 and 1959, and I believe even in 1960.
And this was the one of seven select ed for further study that turned out to be an orebody.
My first affiliation with Texas Gulf Sulphur was back in 1954. They had contracted a geophysical survey through Newmont Explorations, and I worked as a contractor for them cut ting picket (mining claim) lines. This was in New Brunswick.
My family came up here in February of 1964. Up to the end of March I was with them, but from the end of March throughout the summer, I was lucky to get home briefly once a week.
Every Tuesday afternoon I’d take a load of split core to the airport, and stay there until it was actually loaded on the aircraft, and the aircraft had taken off. It went to the Colorado School of Mines for assay.
There were a lot of rumours going around then, actually, they had started after the first hole drilled the previ ous November. The drillers had gone away, and you couldn’t stop them from talking.
Most of the core was kept hidden from them, but the initial footage wasn’t. Some of them recognized it as good ore.
When we were drilling that summer, the geologist would log the core, turn it over to me, and I would section it off. Then my splitters would split it in two, put half of it back into the core
box, and put the other half into canvas bags.
Life was interesting in the camp. We didn’t have too good facilities, so we’d just get up and go straight for breakfast at 6:15 in the morning. We took a bath when we got out.
I would never stop working before 9 or 9:30 at night, about 14-hour days, seven days a week, for a six-month period. I was younger then, I don’t know if I’d want to work like that again.
From about the time I arrived here Jan. 3, until about a week before Christmas, I hadn’t had a day off. Never had a day I didn’t work. But a week didn’t go by that Richard Mol lison (vice-president of exploration) wasn’t up here too. And decisions were made very quickly.
Dick came in to see me one morning, we had a coffee, and then he said we were going to take the helicopter to see where we could put a road.
We flew over the area with mosa ics and plotted the road pretty much where it is now. By the end of June, Miller Paving had started building the road. By working 6 days a week from day break to dusk, Miller Paving rushed the highway’s construction to completion.
By the 10th of October of that same year, the first Texasgulf employee was me, who drove a company truck right up to the core shack.
That was how things got done.
For more than 100 years people from all walks of life have found their way to the Timmins area. Some turned around and left. The majority stayed. None more interesting than long-time Kidd employee Wayne Kidd. He told his story in 1984 and recounted how he was asked by a helicopter company to snoop around the Town of Timmins for a single day while delivering a chopper to the nearby Town of Co chrane.
A fevered mining rush was happening in and around Timmins thanks to the April 16, 1964 announcement by Tex as Gulf Sulphur Company of the huge Kidd Creek base metal find. Dozens of companies were scrambling to send men into the bushland but there were very few roads and planes and heli
copters were scarce.
I didn’t know all that much about mining, but I did know how to pilot a helicopter, and that’s how I came to Kidd Creek. I learned to fly in the air force, going in in 1955 and coming out in 1959. Then I went to Dominion Helicopters.
In April 1964, I came to Timmins on the way to deliver a helicopter to Co chrane. The machine was due there May 1 so I was ordered to stop in Tim mins on the way through to see what was going on in the mining scene. There were rumours about something big in a mining rush going on. Domin ion had a helicopter here on contract. It had arrived in November of 1963. Texas Gulf had drilled its big hole in early November, then set out to cov er its tracks. They put drills back in
Prosser Township to look like they were going back where they had been. They were actually drilling anoma lies, so they weren’t really dummy holes.
Texas Gulf originally didn’t have its own helicopter here. It had one in the Arctic and one in storage in Churchill, Man. The one in the Arctic was on Baffin Island, where Nanisivik is. I was at the Bon-Air Motel and got commandeered (hired) by a bunch of (mining claim) stakers.
Texas Gulf then brought in one heli copter, and sent a pilot to Churchill to bring back the one in storage. Then they offered me a job, about the third week in April. I started May 7.
At that time there wasn’t much at the discovery site except trees and
swamp. There was a little communi ty of tents for the drill crews and the slashers (tree cutters).
The centre of the orebody domed and came to within 12 feet of surface, so a dragline was brought in one day be cause Dick Mollison (vice-president and manager of exploration) wanted to have a look at the orebody. All we had seen was (drill) core. The dragline cleaned off just the dome. Some holes were put in and they blew off the top of the dome.
On September 18, 1964 Mollison walked the trench and then told me to fly into town and buy two cases of #1 Mumm’s champagne. Then the others were allowed into the trench.
By the first of June I was on my way to Nanisivik to bring the other heli
copter back.
I was supposed to fly right back into Timmins, but the helicopter wasn’t in very good shape. It had been sitting there all winter. It had a canvas han gar on it, but it had blown off.
I talked to my boss in New York and he said since I was there to do what I thought best. I had it taken apart and shipped to Montreal and had it back together in two days and on its way to Timmins.
I was up in the Arctic until July and when I got back they had started to survey the road, and it was probably into the property by September. They built it awfully fast.
Before the road was built, everything went in through the muskeg from the power line, all the food and that. I
used to fly in some of the people in volved, such as geologist Hugh Clay ton and the surveyors.
I’d service the drills and fly in and out seven days a week. I think I went for something like two months without a day off.
Then I had a day off and went for an other two months.
We built the hangar behind the BonAir that Fall and did all the flying out of there until 1971. Finally, we had to move to the airport.
I moved to Timmins in the summer of 1964. I had been living in Bramp ton, but the company said I had a per manent job, based in Timmins. Been here ever since.
I had come up here for one day, and never left.
highly-skilled workforce to run a mine, but it also takes some type of safe and technically-sound hole in the ground, whether that is an open pit or a mine shaft. At Kidd Creek, you will find both those types: pit and shafts.
“Kidd Creek was twice blessed when the gigantic orebody was discovered in 1963,” said Keith Youngblut, a former mine manager for the Kidd Creek One, Two and Three Mines. “For one thing, the ore was close to the surface and for another, since the orebody was virtually vertical, mining could begin right at the sur face. Open pit mining, of course, is infinitely less expensive than un derground mining. That’s why most mine developers hope against hope that there will be an open pit mine developed, at least for the first few years.
Because the pit area was covered with muskeg and dense spruce forest with no rock outcrops, the first task was to clear the trees and excavate
The 1.5 to 1.8 metres of muskeg at the surface was underlain by considerable depths of brown boulder clay, varved clays and silty material at the rock sur face. Overburden depths ranged from 3.6 metres at the center of the pit area to 27.4 metres at the north and south rims of the pit. Finished clay banks were to have a 5:1 slope, with a 3:1 back slope on the 12.2 metre berms, giving an over-all slope of 10:1, which would be was a major undertaking due to the large volume, the instability of the material and the containment of the stripped material to prevent environ mental damage to surrounding streams. First the muskeg was removed down to the clay around the perimeter of the proposed stripping area. A water-tight dike of rock and clay was constructed in this trench and the stripping area was drained.
A fleet of fifty-five large motor scrap ers, twelve bulldozers, three draglines and ten 35-ton trucks were used. Strip ping took place mainly in the winter when the frozen clay could be ripped,
more economically by scrapers. The draglines were used during the summer by building rock roads over the soft clay. Final clean-up in the hollows of the rock surface was com pleted with the draglines and a 6-cu. yd rubber-tired loader.
Then the surface of the ore was washed, removing all traces of clay to minimize problems in the concen trator. A total of 8.5 million yards of overburden was removed during the five winters of stripping.
The finished clay areas were seeded with a mixture of timothy and rye grasses and crown vetch for stability and the prevention of erosion.
“We started mining the open pit in the fall of 1966,” said Youngblut. “The first copper-zinc circuit in the concen trator started in November, 1966, and two more circuits were added in early 1967.”
Little by little, a gaping hole was be ing dug into the earth - and the hole would keep getting bigger and deeper
“We stopped open pit mining in the spring of 1977,” said Youngblut. “By that time, we had already removed more than 30 million tonnes of ore from the pit. Added to that, we ex tracted 69.8 million tonnes of waste.”
When the decision was made to de velop an underground mine, access was made by drifting from the second bench of the open pit to where the No. One Mine shaft was to be collared. The pit, upon its closure, ended up be ing 792.6 metres long by 400 metres wide and over 200 metres deep.
Cont’d from pg. 36 as time went on.
In the end, the pit went down over 200
metres. There were 18 benches, each about 10 metres higher than the one below it.
On the technical side, Kidd had to fig ure out how to mine the two orebod ies discovered – the North and South orebodies, as well as how to blend the different ores prior to sending them to the concentrator. The two orebodies had a combined length of 670.6 me tres and a maximum width of 192.9 metres. They strike almost due north, dip about 85 degrees east and rake to
Cont’d from pg. 38
the north.
Mining plans were based on comput erized analysis of the drill core spac ing and the location of the mineraliza tion data.
The ores at Kidd Creek are massive, stringer and disseminated sulphides varying widely in metal content and distribution.
The South Orebody, which contained sphalerite, chalcopyrite and a minor amount of silver, provides most of the higher-grade zinc and some highgrade copper for the copper-zinc ‘A’ ore milling circuits. The North Ore body had both ‘A’ type ore and the lead-zinc-silver ore which provides feed for the ‘C” milling circuit.
On the hanging-wall side, a cherty breccia containing chalcopyrite and minor amounts of sphalerite is mined as ‘A’ ore and a massive to semimassive sulphide material containing galena, pyrite, sphalerite and silver is mined as ‘C’ ore.
The two distinct ore types are handled and treated separately throughout the entire operation. In addition, each ore type is blended within itself to provide ore feeds for the concentrator with rea sonably consistent grades and mineral characteristics.
The preliminary evaluation of the two orebodies was computerized for tonnages and grades on a 6.1 by 6.1 metre grid. The evaluation was based on drill-core intersections over 12.2 metre vertical projections coinciding with the proposed bench intervals, taking the deviations of the drill holes into account. The computer print-outs gave an ore distribution and evaluation bench-by-bench and indicated the areas of varying mineralization.
For every truckload of ore, two-andhalf to four truckloads of waste rock needed to be removed.
The pit was tear-drop shaped, with the narrow end to the south, and at the surface was 792.5 metres long by 400
metres wide. Ramps were 30.5 me
tres wide, with a 10% grade.
The south ramp was left-handed, started at the southeast and contin ued to the bottom of the pit. A second ramp on the west and north walls ran from surface to join the south ramp at No.7 bench. The surface crusher was in close proximity to the south ramp minimizing the hauling distance to the crusher. This ramp handled the total pit pro
duction when part of the south ramp, from No. 4 bench to surface, was lost due to the underground operation. Over-all wall slopes were 53 degrees, and were laid out to avoid prominent protuberances which could relax and become unstable and potentially dan gerous.
In the years 1969 and 1970, with a peak waste rock stripping ratio of four waste to one ore, the relatively small
Cont’d on pg. 40
complicated by the forced mining of certain ore types to maintain orderly pit development.
By operating the pit 21 shifts per week and doublehandling some ore on and off stockpiles, the tight period was traversed very successfully. During 1972, the situation re versed itself as the waste-ore ra tio dropped dra matically and massive stock piles were built outside of the pit, resulting in a much simpler situation with regard to grade control and a re turn to a 15-shift work week. The open pit was relatively dry, even though it was located in a muskeg area.
This was probably because the rock surface was sealed by the overlying clays, giving the surface waters little chance to penetrate to bedrock. The normal inflow of water was about 325 gallons per minute, however, during the spring thaw or at times of heavy rainfall several million gallons of water may enter the pit.
A series of pumps with a capacity of 3,000 gallons per minute were used to lift water out of the pit.
A unique feature was the location of de-watering pumps and electrical substations in underground excavations in the walls of the pit. All pumps were controlled automati cally by float or probe switches. Even though pit ceased operation in 1977, it still plays an important role in Kidd’s underground mining pro duction. Through the pit, Kidd draws some fresh air for ventilation as well as for maintaining the ice stopes that help cool the deeper levels in the sum mer. An automated system monitors any movement of the pit walls. Upon closure, plans are to allow the pit to naturally fill with water. In the interest of public safety, a several-metre high boulder fence will be erected around the entire perimeter of the open pit.
An orebody as large and complex as Kidd Creek presented developers, engineers and the mine’s ownership team with a unique set of challenges. The realization that the Kidd Creek orebody was actually two deposits with different values forced the com pany to undertake extensive testing before decisions were made regarding a concentrator.
Following the announcement of the discovery on April 16, 1964, limited testing was done by several companies as soon as drill core was available. During 1965, bench-scale and pilotplant programs were pursued at Lake field Research of Canada Limited and at the federal Mines Branch in Ottawa. When the bench-scale testing was fin ished, the decision was made that the company would mine two types of ore. By then, enough information was available to start designing the con centrator (more commonly known as a mill).
When the decision was made in March 1965 to go ahead with the pit-railwayconcentrator complex, it soon became obvious that two of the major prob lems were soils and transportation. The whole vicinity of the pit was cov ered with muskeg, glacial till and clay. Soil tests proved the clays to be very weak and inclined to flow. In most cases they were deeply de
posited on steeply inclined sub-strata. Only two small bedrock outcrops, one on each side of the pit, were found. One of these had to be reserved for the pit primary crusher.
It soon became evident that there was no site near the pit suitable for the large building and equipment identi fied for the concentrator.
Furthermore, the transportation of large quantities of cement, steel and machinery would be impossible, be cause neither the permanent road nor the railway had been started.
The choice of a concentrator site was therefore primarily dictated by the proximity to an existing railway and highway and the presence of a suit able expanse of surface bedrock for foundations.
An area of stable bedrock situated adjacent to Highway 101 and the On tario Northland Railway, inside the City of Timmins but 15 miles east of City Hall was picked. The location would eventually become commonly known as “The Met Site”, a nickname for what would more technically be called the metallurgical complex. The good news is that there was suf ficient bedrock for the entire con centrator and for future expansions. The main pipeline of Northern and Central Gas was only a few hundred yards away and an excellent source of
power was close at hand.
The site was 17 miles from the pit by railway but the company already knew that a railway would have to be built regardless of which site was chosen.
Thus, the metallurgical site 34 miles by road from the pit was selected.
On completion of the Lakefield pilotplant testing, two full-scale produc tion pilot-plant programs were started in the Timmins area, at the Kam-Ko tia copper mine and Broulan Reef gold mine.
At Kam-Kotia, 1,100 tons per day of copper-zinc ore was milled for 10 days a month between October, 1965 and October, 1966.
At Broulan Reef, a 400-tpd flotation plant was installed to process silverlead-zinc ores. The Broulan Reef operation was run from April to De cember, 1966. Production started at the Kidd concentrator in November, 1966.
The Kam-Kotia and Broulan Reef programs proved to be quite valuable, because the information obtained was used to verify and modify the concen trator design.
They also served as an excellent train ing ground for the staff being acquired to operate the concentrator. A wel come bonus was that the concentrates
Cont’d from pg. 42 produced at the two local mines were sold at a profit. Primary crushing was performed at the Kidd Creek Mine, also inside the city. Run of mine ore was delivered to the concentrator at the metallurgical site by train Power and fuel were obtained from the hydro and natural gas lines which pass close to the concentrator site. Water was obtained from the Frederickhouse River, 6 miles east of the concentrator.
The main concentrator building was a large structure 500 by 640 feet by 90 feet high and contained facilities for fine crushing, crushed ore storage, grinding, flotation, concen trate handling and reagent handling.
Located in the same building were the machine shop, ware house, metallurgical laboratory, pilot plant, men’s change room, sample preparation area and an assay laboratory. The first copper-zinc circuit was started up in November 1966 followed shortly after by the second copper-zinc circuit the following January and the lead-zinc circuit in February.
It was operating at capacity by March 1967.
Originally designed to handle 9,000 tons per day, the con centrator was quickly expanded to treat 10,000 tons per day.
Two different ore types were processed by selective flota tion in the three individual circuits to recover copper, lead and zinc concentrates.
In 1973, a smaller circuit was added to recover pyrite and tin concentrates from the combined zinc tailings of the three main circuits.
A fourth circuit was completed in May 1978 to handle in creased feed tonnage from the expanded mining operation.
By 1981, the concentrator treated 12,250 tonnes per day. Normally, three circuits treated copper-zinc ore at a com
Cont’d from pg. 42 bined rate of 6,500 tons per day; the third circuit treated 3,500 tpd of sil ver-lead-zinc ore.
With the start-up of the tin plant in December 1973, seven concentrates were produced: high silver copper, low silver copper, lead, low silver zinc, high silver zinc, pyrite and tin. At 1974 market prices, the pyrite con centrate had no value so it was stock piled for future use. Concentrate pro duction, exclusive of pyrite, averaged 2,400 tpd.
Recycling of mill water was imple mented in 1975. The concentrator underwent many revisions and improvements since it was built.
Some of the changes in the concentra tor made after start-up were anticipat ed in the original design. Here are the highlights: •1982 tin plant decommissioned •1985 hit peak throughput of 4.53M tonnes ore •1988 ‘C’ ore depleted, all divisions
treating the same ore •1993 Distributed control system (DCS) installed •1993 Custom milling of a copper-gold ore from Wisconsin (Flambeau) begins; ends in 1997 •1995 Outotec high rate thickener in stalled in the tailings area to increase underflow density for spigotting on cone •1996 PI System installed for sharing of process information •1998 ore tonnage drops to 2 division demand, A division shut down •2001 Pond E water polishing pond in stalled in tailings area •2004 Begin custom milling a Copper, nickel ore in D division after re-design of process and equipment (Montcalm ore body)
•2009 Custom milling of Montcalm ore body ceases •May 2010 Copper and Zinc Smelters on Kidd Metallurgical Site close, con centrates shipped by rail for further pro cessing in Canada. •2014 Dropping tonnage results in 2nd division cycling on and off
The whole plant was highly automat ed and control was coordinated from a central control room.
The treatment process followed con ventional practices, although fine grinding was required for optimum flotation recoveries.
Central control, located between the grinding and flotation sections, housed the main control room, the shift foreman’s office, the rotameter room, the X-ray analyzer room and an instrument repair shop.
With the exception of the concen trate drying section, all functions of the concentrator are operated and coordinated from the central control room that contained the essential control panels, operator’s desk, Xray read out typewriters, remote con trols for the mill water pumps, and tailings thickener, process computers and their auxiliary equipment.
Today, the Kidd Operations’ concen trator remains an efficient operation with a blend of old and new technol ogies working hand in hand.
Most mining companies are faced with an either/or decision as it relates to the extraction of their orebody. It boils down to two basic choicesopen pit or underground. It is unusual to see both choices executed at the same time.
Then again - Kidd Creek was not your typical mine property. The massive amounts of copper, zinc and other base metals mined until 1972 from Kidd Creek were extracted by open-pit methods. To assure continuity of production, preliminary planning for an under ground operation was started in 1968 only four years after the start of the
open pit and a full-time planning staff was in place by the following year.
The Kidd Creek No. 1 Mine shaft was located on the footwall of the ore zone, about 400 ft. from the edge of the pit.
The company wanted to use the under ground operation to replace the high ore tonnages, about 10,000 tons per day, that were coming from the Kidd Creek pit. The challenge and ultimate goal was to execute the underground operation without interfering with or disrupting operations in the pit.
In order to achieve a balanced ore mix to the concentrator, engineers de cided in 1971 that some of the under
ground ore would be mixed with ore from the open pit.
Underground development began in mid-1969. Vertical access to the mine was to be through a single vertical shaft and a 17% declining ramp from the second bench of the open pit. The need for early development of un derground ore was important. It was a significant factor in the selection of a ramp as one way to access the mine.
The single shaft was chosen because it offered the lowest construction and operating costs of all the options at that time.
Yet the tremendous value of the ore
vided free laundering of work clothes. In the dry, clothes baskets were sus pended beneath the change benches instead of being pulled up to the ceil ing, giving the changing room an open, brightly lit appearance. The room beneath the dry was heated and well ventilated to remove cloth ing moisture and odors.
body allowed planners to provide for a high degree of mechanization in a completely trackless operation. The company spent millions on equipment, rubber-tired jumbos, loading and hauling equipment, raise borers, and a large fleet of utility and service vehicles.
The fleet of mostly diesel vehicles presented the company with another challenge. The high degree of diesel ization prompted planning for a ven tilation system that would eventually circulate up to 750,000 cfm of air per day.
Once the major pieces of the planning puzzle were assembled, shaft sinking began in March of 1970. What follows is a detailed description of how the underground mine was fo rumlated.
The 24-ft diameter concrete-lined shaft was 3,050 ft. deep and was com missioned in March 1972. The 17-ftwide x 10-ft-high ramp was advanced to the 1,200 level and eventually reached the bottom of the shaft. Some production ore began to move in the shaft in June 1972 through skip loading from a lip pocket on the 800-
ft level.
Prior to the commissioning of the shaft, as much as 20,000 tpm of de velopment muck was moved out of the ramp in 20-ton Wagner MTT-420 Teletrams.
Engineers were given another task. An underground crushing plant was com pleted by the end of 1972. That way, all underground ore and development waste would be crushed underground before being hoisted to surface. Mining manager Bart Thompson had been specifically hired in 1965 by Texas Gulf to phase out the open pit and to develop underground opera tions. He served as general manager from 1974-80.
He spoke enthusiastically in 1972 of service facilities the company was providing for its underground work ers. Each main level service area in the mine included a heated lunchroom with fluorescent lighting, a washroom with hot and cold running water, and flush toilets - a vastly different envi ronment that Kidd’s mining brethren in nearby gold mines were unaccus tomed to.
Above ground in the change house, there was a laundry facility that pro
Shaft hoisting units included two 27V4-ton skips traveling at 3,250 fpm; a main cage, 17 ft. 9 in. x 7 ft. 9 in. x 24 ft. 6 in. high, on steel guides; and an auxiliary cage on wooden guides. Galvanized steel compo nents were used throughout the shaft to minimize the effects of corrosion, wear, and oxidation.
The minimum thickness for the con crete lining of the shaft was 12 inches. The Kidd Creek ramp was collared in the wall of the second bench of the open pit, 80 ft. below surface. The ramp broke through to the shaft at the 800 and 1,200 levels. (Main levels for the underground operation were de veloped at 400-ft. intervals). When it reached the bottom of the shaft, the ramp heading had required an advance of 21,000 feet. Development ore and waste were moved up the ramp prior to the com missioning of the main shaft.
Ventilation at the ramp face was sup plied by 34-in., 30-hp axial vane fans pulling through a 30-in. ventilation duct.
Concreting was used on main road ways to provide clean surroundings and low maintenance costs - it also al lowed higher-speed haulage. The mine shaft and headframe were equipped with three hoists supplied by Canadian Westinghouse. The production hoist was a 168-in. four-rope friction winder powered by
a 6,000-hp dc motor that lifted a 27.5-ton skip at a rate of 3,250 fpm. A second four-rope friction winder powered by an 800-hp motor handled the main cage. A small drum hoist handled the auxiliary man cage.
The headframe was a 235 ft. 6 in. high concrete structure. Construction began in June 1969 and the slip-formed walls were completed in October of that year.
The headframe included a large hydraulically powered ship-type crane on the top floor to erect and service equipment, eliminating the need for heavy steel and crane rails that would normally be used in this application.
The shaft and hoists were rated at about 1,000 tph. The 24 ft. diameter shaft was collared beginning in June 1969. The shaft was sunk to 3056 ft. and the headframe was slip-formed to a height of 235 ft. 6 in. The first 300 ft. of the shaft were sunk full face with a 10 boom jumbo beneath a Galloway stage. The remainder of the shaft was benched with hand held machines and mucked with two wall-mounted Cryderman units.
The shaft was equipped with two Westinghouse friction hosts to provide 15,000 tpd hoisting capacity, 20 ton main cage service and a small auxiliary cage. Levels were established at 400 ft. intervals and a single loading pocket built at the 2860 level.
The haulage system and the 42 x 65 in. Allis-Chalmers gyratory crusher became operational in June 1973. Two addition al 5000 ton loadout bins, a new change-house, office, compressor and powerhouse facilities were also built at this time. All in all, the underground operation is an engineering marvel and a testament to the determination of the mine’s owners, the talent and ingenuity of staff, and of course, the star of the show, the orebody itself.
The extraordinarily unique Kidd Creek orebody tested some of the best mining engineers in the world. Its abundant mineral content led to some of the most innovative operational plans the industry has ever witnessed. Who in their right mind for example, would ever contemplate building a mine under another mine?
November 3, 1978 was a special day in the history of Kidd Creek as it marked the completion of the shaft for Kidd’s No.2 mine.
Today, the 50-year-old operation is comprised of four mines, No.1, No.2, No.3, and the Deep or ‘D’ Mine. The first two are traditional mines topped with familiar headframes while the third is an internal mine that starts on the 4700-foot level. ‘D’ Mine, as it is known, is also an internal mine, it sits under the other mines.
The 1978 ceremony marked what at the time was believed to be the largest mine shaft in North America in terms of rock volume removed.
The 5,105-foot deep, $31 million dol lar, 3,407,850 cubic foot hoisting in stallation for the second underground mine was part of an ambitious expan
sion program.
The Kidd Creek Mines were operated by Texasgulf Metals Company, an unincorporated division of Texasgulf Inc.
On November 3, a shaft crew com prised of Texasgulf and Maclsaac Mining and Tunnelling Co. Ltd. of Sudbury personnel completed the equipping of the shaft.
All of the materials were purchased in Canada by Texasgulf’s own purchas ing personnel in Timmins.
Soon after the sinking of the No. 1 shaft was completed in 1972, Texas gulf started a program of exploratory diamond drilling from 2800 level in No. 1 Mine.
The drilling outlined sufficient ore be low the level to justify a second shaft. Feasibility studies demonstrated that production could be increased by one third exclusively from this deep ore.
The study called for a 25-foot diam eter shaft to the 5,000 foot horizon to service a mine producing 5,000 tons of ore per working day.
Throughout the shaft and headframe construction, Texasgulf acted as gen eral contractor and with the exception of the headframe, which was designed
by V.B. Cook Ltd., was also its own engineer and designer.
Heading up the engineering and con struction team was David L. McKay, superintendent of No. 2 Mine. In volved in the shaft design was David Porteous, assistant superintendent of engineering, minesite, who was as sisted by John Wearing, project en gineer, Pascal Malone, design drafts man, and the late Seppo Sorsa, senior design technician.
Although Texasgulf engineers and supervisors were involved through out the project, the company became much more directly involved in the construction when its own personnel were used to install the shaft steel.
During the steel installation and the shaft commissioning, all personnel were on the Texasgulf payroll.
At the time, the circular concrete shaft had a total of 20 stations, two load ing pockets, four lip pockets and a fu ture mid-shaft dumping facility which were excavated during the sinking phase.
This required removal of 3,407,850 cubic feet of rock weighing 280,000 tons - the opening created being sup
celebrating 75 years of operation
and would like to thank the
support over the
its humble
the SGS facility in Lakefield
market leader
trusted
Lakefield
grown into
Cont’d from pg. 50
ported by 25,000 rock bolts, 11,000 steel straps and 34,830 cubic yards of concrete.
The shaft was equipped with 13 miles of pipe, 19 miles of power and control cables, and 5,100 tons of galvanized steel to provide a facility through which four friction hoists were to move men, rock and materials in four counterweighted conveyances sus pended with 20 miles of wire rope at speeds of 3,000 feet per minute and 1,500 feet per minute respectively. An unusual feature is that all the struc tural steel and pipe were hot-dipped galvanized.
The site selected required the removal of 70 feet of unconsolidated overbur den using a freezing technique. Freez ing was supervised by Cementation Company of Canada and Foraky Ltd. of England.
Inside the freeze wall, which was in sulated as excavation proceeded, Gorf Contracting and Leo Alarie and Sons Ltd., both of Timmins, excavated and secured a 69 x 52 foot area, 70 feet to bedrock.
Preparatory work for shaft sinking consisted of a six-foot diameter bore
hole from the 200 to 2800 foot lev els and an alimak raise from 200 to surface executed by the No. 1 Mine crews during the period of surface construction.
Maclsaac Mining and Tunnelling commenced excavation of the shaft in April 1975.
Phase 1 of the sinking consisted of slashing to final shaft diameter into the borehole in ten-foot lifts with the removed material being handled through No. 1 Mine at appropriate levels as sinking advanced.
On reaching the 2800 foot level, Phase II began with standard benching pro cedures utilizing eight-foot benches. Broken material was handled with two Cryderman clams, suspended from a five-deck Galloway stage, into 180 cubic foot buckets and hoisted to surface.
The five-deck Galloway stage was suspended by four one-inch lock coil ropes in double purchase. The four drums of the Galloway stage hoist had a capacity of 3,000 feet each but when these ropes were in double purchase the working depth was halved. In order to overcome this deficiency
and reach the 5,105 feet required, four magazine winches, each with a stor age capacity of 11,000 feet of rope, were installed.
This installation, believed unique in the industry, was engineered by G. Ti ley and Associates.
Concreting of the shaft, concurrent with sinking, was carried within 50 to 20 feet from the shaft bottom. Speci fication for the monolithic wall lin ing called for a minimum of one-foot thickness of 4,000 pounds per square inch strength concrete.
All concrete was mixed on site in a batch plant operated by Texasgulf, transported to the shaft site and poured to the bottom via pipelines. Upon completion of sinking, the Galloway stage was modified to accommodate the equipping phase. An initial run from surface to the shaft bottom was made with the modified stage to install pipes, power and con trol cables.
The facility allowed the installation of five pipes and 13 cables in one pass. All power and control cables were supplied by Canada Wire in cut
Cont’d from pg. 52
lengths, capped and wound for instal lation from point to point.
Horizontal runs at stations were an chored and wound on storage reels to facilitate future station development and subsequent cable junctions.
Prior to returning the stage to surface for the equipping phase survey control lines were established for the length of the shaft and anchored at collar and shaft bottom.
As the stage returned to surface azi muths were established in stations us ing a gyro-theodolite.
Two loading pockets manufactured by Mining Machinery and Equipment Ltd. of North Bay were installed - one at the 2800 level to provide back-ups for the No. 1 Mine in case of hoist fail ure in that facility and one at the 4900 level.
These units were sandblasted and coal-tar epoxy coated by Gorf Con tracting prior to installation.
Four lip pockets, designed by Tex asgulf and manufactured by Stewart Machine Works of Noranda are in stalled at the 3400, 4000, 4400 and 4800 levels. These units allowed for initial level development until such time as the ore and waste pass sys tems of the mine were established.
Crash beams, station steel, mid-shaft dump and other special steel was variously fabricated by Tri-Steel and Lord & Cie of Montreal and Suntract and Canron of Toronto.
Footings for the headframe and as sociated structures (designed by V.B. Cook Ltd. of Thunder Bay) were es tablished and the concrete headframe, extending 70 feet below and 210 feet above collar was slip-formed by Am
plex Ltd. of Thunder Bay.
After slip-forming, Roy Construction and Supply Company of Timmins was contracted to complete the headframe floors, bin walls and support founda tions for the hoists. Once the control floor level, 105 feet above the collar, was established, steel support for con veyance compartments from the collar to the sheave deck was installed and barricaded off from the main area of the head frame.
The separation allowed for concur rent completion of the headframe and sinking of the shaft.
As the sinking operations were iso lated, equipping of the headframe was conducted simultaneously to the sink ing phase allowing ample time for the installation of the hoists and associ ated controls by Levert Industries of Sudbury.
Before its multi-billion dollar discovery, the anomalous stretch of land north of Timmins that contained the Kidd Creek orebody was well-trampled by the local mining fraternity in Timmins. One woeful man literally lived on top of it.
A legendary and recluse individual, who went by the single name of Martin, endured the quintessential life of a lone pros pector in a shack above what Texas Gulf eventually would call the South Outcrop.
It’s believed Martin spent many unsuccessful years wandering the area in search of gold. A majority of the gold mines in the Timmins area were discovered as a result of surface outcrop pings along the famous Porcupine-Destor Fault Zone. Unfortunately for Martin, there were no such visible indicators around his ramshackle dwelling.
In fact, given his limited means and equipment, he could not have found the huge base-metal orebody that was to become the Kidd Creek Mine because it was under several feet of muskeg. Years before the Texas Gulf discovery, Martin disappeared walking through the bush to Timmins to obtain supplies. There were no roads into the area at that time.
Local police failed to find him. They made the decision to burn his animal and insect-infested shack to the ground.
As time passed, pulp wood started to be harvested in the area. A cutter found a human leg bone inside a boot. A search of the immediate area uncovered a pair of spectacles that had been prescribed for Martin by a Timmins optician.
The discovery closed the final chapter of his mysterious disap pearance.
No relatives of the old prospector were ever located, so it is believed Texas Gulf paid for a simple burial service for his re mains.
For a period of time, the ridge where his cabin had been located was known as ‘Martin’s Outcrop’ but that moniker ended when the term ‘South Outcrop’ was assigned to the area by the com pany.
There are two additional events associated with Martin’s activi ties in the area. He blasted a small rock cut and exposed one of the cherty beds between the basic flows.
Without any visible gold, he simply did not know what he was looking at and ceased work.
A few metres away from where the outcrop ended, Martin cleared a small patch of ground and planted a vegetable garden. About seven metres below his little stretch of carrots and po tatoes - Texas Gulf would eventually find some of the highest grade zinc and copper mineralization on the planet.
Kidd Creek has had a lot to celebrate over the past 50 years including some memorable staff and family get-togethers - none more so than the company’s first Christmas party.
Ray Jones was the first general manager of Texas Gulf Sulphur’s Timmins operations. His shared his recollection of the first Christmas staff party in 1964 in the company’s eight-page 20th anniversary newspaper in 1984. The party was held in Jones’ hotel room
By Ray Jones (1984)My first contact with Texasgulf peo ple was made in New York in 1964 and arranged completely by others. Stanrock Uranium Mines (Elliot Lake) was in the process of closing. My current concern was to do my utmost to help the lean and hungry Stanrock crew to relocate. I was for tunate to have had my last five jobs come looking for me. I had given little thought to my own relocation. Following the Stanrock business meeting, I was casually asked if I would like to accompany George Rowe, Stanrock’s president, to lunch. He was lunching with Dick Mollison (vice-president of explora tion) and Chuck Fogarty (executive vice-president) of Texas Gulf Sul phur Company.
At the end of the meal, Dick Mol lison asked if I would stay to talk to him and Dr. Fogarty. Not being scheduled to return to Elliot Lake until the next morning, I had the
time. I assumed they wanted to talk about some of our interesting Stan rock history and perhaps discuss ideas for starting up a major mining enterprise.
Great was my surprise when they suggested I might join them to man age the Texas Gulf project at Tim mins. Needless to say, it didn’t take long for an about-to-be unemployed 48-year-old miner to go for the handshake.
By mid-October 1964 I was a resi dent of the Senator Motor Hotel in Timmins, and joined Don Taylor, Sylvia Porter, Hugh Clayton and others working out of a little office on Pine Street south.
The proposed mining area was by then a vast cleared space crisscrossed with trails kept well mud died by busy muskeg tractors, with tiny collections of temporary struc tures - mine office, core storage, drill camp, eatery - at its edge.
Harry Coott and Ray Pigeon were
busy collecting numbers for Frank Kobe to translate into lines on My lar, while Norm Doucet was herding a group of contractors and/or tem porary employees clearing bush for a waste disposal area.
Bob Tait was already on staff as chief metallurgist and was spending most of his time at the Lakefield Re search Centre. Don Taylor was chief accountant and slated to head up the administration group. My priority was to devise an orga nization that could carry the project into operation, and bring into it the right people at the right time and with appropriate direction and guid ance.
At the same time, I must keep ac tively involved with the Texas Gulf (no, not yet Ecstall or Tg) support group (including such familiar names as Earl Huntington, Gino Giusti, Walter Meyer); keep Dick Mollison, my immediate superior,
all times informed, and obtain the
required approvals of all decisionshopefully in advance.
There were good times and fun times - lots - and frustrating times, too. It was fortunate that Dick and I had generally similar attitudes, philosophies and oper ating goals (I suppose that had it not been so, I wouldn’t have been there).
We had frequent differences in our appreciation of how to trans form the philosophies into policy, the goals into attained realities. With all that was going on, it was inevitable that there would be breakdowns in communication.
I can recall most vividly Dick winding up the most serious and painful reprimand with a hearty handshake and “Have a cigar!”
The first of our Christmas parties took place in my hotel room. It was not overly crowded, although I believe all the people then forming the Timmins operational group attended.
Lacking my notes, I’m probably missing somebody, but I believe the participants were Sylvia Porter, Irene Parke, Don Taylor, Don Stewart, Harvey Mitton, Harry Coott, Ray Pigeon, Norm Doucet, Hugh Clayton, Gerry O’Halloran, Bal Shannon, and last (but not shortest) Frank Kobe.
We had a jolly time, and I hated to be the first to leave to catch my plane to Toronto enroute to Elliot Lake. The party carried on, as was evidenced by the completely dry state of my room when I got back after Christmas! Note: Harvey Mitton later described the party this way: Ray had to leave early, so when we ran out of refresh ments, we just charged some more to Ray. We left his room dry.
Congratulations Kidd Operations on 50 years of productive mining! We are proud of your history and the many contributions you made to the communities in the North. Staff & Management Mining Life Magazine
Whenever outside investors put their fingerprints on a natural resource, pol iticians find themselves in the cross hairs of public opinion and the spot light of competing interests.
In April 1972, Timmins’ mayor, Leo Del Villano, would look back over the eight years since the 1964 announce ment of the Kidd Creek Mine and de clare them a boom period for his min ing town.
“Economically,” the mayor said, “the development of the Kidd Creek mine has been a godsend. In 1963, many viewed Timmins as not having much of a future. Now there is Texas Gulf, and there are off-shoots and support ing industries. That’s been a big help.” His proclamation was an understate ment. The mayor dismissed as unim portant the question of development of the mine with US capital. “Ordi nary people like me don’t care,” the former postman turned liquor sales man stated.
“If it weren’t for Texas Gulf, where would we be? Texas Gulf has done a lot for the town.”
Proud of his growing 28,000-person com munity, the mayor added, “We don’t have problems. And if we do, we take care of them! Well, some people com
plain about the paving. That’s our most serious problem,” he added with his trademark smile.
The prosperity afforded the commu nity as a result of the extraordinary economic benefits of the Kidd Creek operation had spinoffs of another kind according to Del Villano.
For example he stated, “We don’t have a problem with crime. And we are working to build more housing.”
Known as Leo the Lion, Mayor Del Villano liked to travel with, or with out, the permission of town council.
To the surprise of many, he would of ten pop up at events throughout On tario and across Canada.
His colourful nature and unique den tal structure was certain to get his picture and an accompanying story about Timmins in the local media of whatever city he visited.
In 1964, the mayor quietly travelled to Houston for the annual meeting of Texas Gulf Sulphur Company Lim
ited, the owner of Kidd Creek. When he returned to Timmins, he said he was highly impressed with the com pany’s plans for the community.
Del Villano was born in Timmins in 1913, just one year after the birth of the town of Timmins, on Jan. 1, 1912. His father was a blacksmith at the Hollinger Gold Mine - a producer of more than 19.3 million ounces of gold before it closed operations in 1968. The Hollinger resumed production at the site as an open pit in 2014. The celebrated working man’s politi cian believed the main job of a mayor was to be a booster for his community and he was known far and wide for his colourful description of his home town’s future.
This not only earned him respect in Timmins but a loyal following at the ballot box. Del Villano occupied the mayor’s office, with one two-year in terruption, for 14 years, prior to that he sat as a councillor on Timmins town council for eight years. Among the many publicity stunts he orchestrated in order to put Timmins on the world map, he most famously offered in 1959 to replace the bearskin hats of the Queen’s guards at Buck ingham Palace.
The ensuing black bear hunt he or ganized led to massive publicity and he delivered 62 hides to the Palace to underscore the point that Timmins was much more than gold, zinc, and copper.
Ask any old-time male miner what he thinks about women going under ground and you’ll get the same an swer - it’s bad luck. However, when it comes to royalty, superstitions are quickly and easily set aside out of re spect.
Precedent was set when Queen Eliza beth became the first woman to set foot underground in a Sudbury, On tario mine along with King George VI during their 1939 Royal Tour of Canada.
A continuation of Royal tradition in 1959 saw Her Majesty Queen Eliza beth II and His Royal Highness Prince Philip visit the same Frood Mine just as her parents had done twenty years earlier.
In 1981, the Royal tradition contin ued when Princess Margaret, the then 50-year-old sister of Queen Elizabeth II, and her daughter Lady Sarah Arm strong Jones, 17, took an underground tour of the base-metal Kidd Creek Mine in Timmins, Ontario. Lady Sar ah would later serve as a bridesmaid at the wedding of Prince Charles and Lady Diana Spencer. It was Princess Margaret’s fifth tour of Canada since 1958. The Royal Tour included visits to Toronto, Cam bridge, Timmins, and Muskoka. For Timmins, it was the third time a mem ber of the royal family had visited the community. The first was in 1919 when the Prince of Wales visited the Town of Timmins and the Hollinger Gold Mine. The second was in 1941 when the Duke of Kent, Princess Margaret’s uncle, visited the commu nity and both the Hollinger and Mc Intyre Gold Mines.
The four-hour 1981 Timmins visit be gan on Thursday July 9, when a Ca
Princess Margaret tours the Kidd Creek Mine in “royal” red coveralls, white hardhat, miner’s belt with lamp and knee-high rubber safety boots. Photo credit: Ed Spehar / Timmins Museum Collection
nadian Forces Cosmopolitan aircraft touched down at the Timmins Airport at 1:10 pm. Greetings were provided by local dignitaries including Min ister of Natural Resources and lo cal Cochrane South MPP Alan Pope, Timmins-Chapleau MP Ray Chenier, and Mayor Victor Power. An honourary police escort com prised of Royal Canadian Mounted Police, Ontario Provincial Police, and Timmins police led the RCMP-chauf
feured royal car and motorcade along with a media bus down Airport Road, to Laforest Road, and up the Texas Gulf Highway (now Highway 655) to the Kidd Creek zinc and copper mine. The group was running a half hour late of its expected 1:30 pm arrival at the mine due to an unscheduled stop to see the new fixed wing air ambu lance stationed at the airport that had a dedication ceremony earlier in the
day.
Upon arrival at the mine a logistics issue developed as the me dia bus was not able to fit under the haul truck overpass on the main entrance road endan gering reporters’ ability to fully cover the event. The media forcefully argued the underground tour was the most newsworthy part of the tour because of the un conventional work at tire and location. An al ternate route for the bus was quickly found which allowed the media to conduct on-site coverage. Princess Margaret and her daugh ter ducked into a private room and changed into matching maroon red coveralls, white hard hats, miners’ belts and lamps, and knee-high rubber safety boots in order to comply with Ontario’s mining safety regulations. Then there were the white gloves that served as a reminder that these were no ordinary guests. As the media re ported, everyone else was in drab green coveralls.
1980 employee recognition reward, brass belt buckle, for Kidd Creek Mine achieving safest metal mine in Canada and receiving the John T. Ryan National Trophy.
brought the group for a 30-minute tour through the maze of 12-foot high tunnels which comprise the mine’s working. The group had an opportu nity to witness operating drills and a scooptram in action.
their “street” clothes and were presented with gifts such as a lighter fashioned from Kidd Ore for Princess Margaret and a mineral collection for Lady Sarah before being driven to Timmins’ City Hall where they were officially received by mayor and council. Mayor Vic Power did not attend the mine tour. Over 1000 crowded outside to get a glimpse of the royal party and hear the public addresses during the beautiful summer day. The last stop was a brief visit to the Waferboard Corporation Ltd. oriented strand board plant on Highway 101 west before flying back to Toronto. The story of the royal visit ran in the local paper for days after ward.
A short meeting was held with Tex asgulf Metals Company president Ray Clarke and vice president Eric Belford. The pair guided the Princess and her daughter, lady in waiting Mrs. Whitehead, MPP Pope, three police officers and three photographers to the elevator cage.
The group descended to the 1,600 foot level of the 2,960-foot deep mine. A service car was waiting and
Very little conversation took place because of the noisy environment. Clarke commented to the media a day prior to the tour that there was no need to clean the mine, as it was spot less already! The company went out of its way to give off a good impres sion. Fresh white paint covered the rock walls on 1600 level. The gesture went largely unnoticed.
After returning to surface Princess Margaret laughed when one employ ee helping her out of the cage asked “Well, would you like to make it a ca reer?” By this time a group of some 50 smiling miners and employees had lined the hallway and waved and ap plauded as the entourage passed. The royal visitors changed back into
The tour was arranged by the Gov ernment of Ontario and was intended to help celebrate an excellent safety performance, as the mine had just been awarded the Canadian Institute of Mining’s John T. Ryan National Trophy for Metal Mines with the lowest accident frequency during the previous year in all of Canada. As for that timeworn superstitionthat women would bring bad luck if they were permitted underground? Turns out it couldn’t be further from the truth. It could be argued that Prin cess Margaret’s underground visit definitely brought good luck, because the Kidd Creek Mine won the Na tional Trophy again that year, the year that followed, and compiled quite the record winning National recognition five out of six years (1980, 81, 82, 84, 85).
From left are: Richard Mollison, vice-president of the new metals division of Texas Gulf; James Auld, Ontario Minister of Tourism and Development; George Wardrope, Ontario Minis ter of Mines; Timmins Chamber president William Scott.
In June of 1966, Kidd Creek execu tives, local politicians and the Tim mins Chamber of Commerce took part in a time-honored tradition of burying a time capsule that would give the future community a glimpse into the past.
And while the company in 2016 is basking in the benchmark of its 50th year of production, it will be another 50 years before company officials, politicians, and residents will get to see what’s buried under the 10-ton boulder of Kidd Creek ore that is planted near the doorstep of the Tim mins Chamber of Commerce.
The time capsule contains a small treasure trove of artifacts about the mine and its beginnings.
The capsule is not to be opened until 2066.
The history, however, will be incom plete, in that it refers only to the Kidd open pit operation.
The Number One Mine was only a distant thought when the capsule was buried in 1966, and there was no zinc plant, no copper smelter or refinery, not even a Number Two Mine.
The Kidd Creek ore-find had been an nounced April 16, 1964, less than two years before the capsule was prepared. In fact, neither the pit nor the concen trator was in operation when the cap sule was assembled and buried. It does however contain newspaper,
tapes about Kidd Creek’s impact on the local mining scene.
It lies in the concrete base of a 10ton Kidd Creek ore sample. The time capsule was buried in the hope that it would provide a snapshot into history as it was in Timmins in June of 1966, unsullied by hindsight.
The plaque attached to the large boul der reads:
“Ore from the Kidd Creek Mine of Texas Gulf Sulphur Company erected by Timmins-Porcupine Chamber of Commerce in June 1966 to commem orate development of this important zinc, copper, lead, silver discovery (time capsule in base).”
William Scott, who was president of the chamber of commerce, said at a dedication ceremony: “To those who open this capsule in the future, I am sure that Canada and even this area will be great in the eyes of the world, but this area has only achieved this greatness and prominence through hard work and a dogged determina tion in the future.”
Attending the dedication ceremony
president of the new metals division of Texas Gulf; George Wardrope, On tario Minister of Mines, and James Auld, Ontario Minister of Tourism and Development.
The chamber’s tourist committee, led at that time by businessman Lorne Rowe, took responsibility for the idea and contents of the display.
For fifty years now, visitors to the Chamber office could read about and touch a genuine Kidd Creek ore speci men from a mining operation that is famous worldwide. The Kidd discov ery was a remarkable story in more ways than one as it came at a time when the area’s prolific gold mining industry was in decline. Besides news media records, the cap sule also contains wood specimens, coinage, transportation timetables and letters from civic leaders. Would-be-thieves and troublemak ers beware, the capsule cannot be ac cessed without machinery capable of lifting a 10-ton piece of ore. Anyone anxious to get a glimpse inside will have to wait another 50 years.
Startup in 1972 of a new $70 million, 120,000-tpy electrolytic zinc plant near Timmins put Texas Gulf Inc. squarely in the middle of the North American zinc market. The new source came on stream at an opportune time for US zinc buy ers. Six US zinc plants were forced to shut down over the previous two years, and consumers found zinc in tight supply.
The first carload of zinc was shipped from the new plant on May 1. “We took some pictures of it, but we didn’t tie it up in ribbons,” Texas Gulf’s manager of metal sales, Kent Hoffman, said of the occasion. “It was too badly needed.” The new zinc plant was to process about half of the zinc concentrates produced from Texas Gulf’s huge Kidd Creek Mine, located 17 miles away.
Output from the mine in 1971 to taled 582,000 tons of 52% zinc con centrates, 172,000 tons of 25% cop per concentrates, 70,400 tons of lead concentrates, 13 million oz of silver in concentrates, and 3.2 million lb of
cadmium in concentrates. The mine had, until 1972, been operated entire ly as an open pit. Development for an underground op eration was near completion, assur ing continuity in the flow of ore after open-pit operations were completed. The Kidd Creek mine and concentra tor and the new zinc plant were owned and operated by Texas Gulf’s wholly owned subsidiary, Ecstall Mining Limited.
Zinc from the new plant were to be marketed from Texas Gulf Metals Di vision offices in Toronto.
In April 1971, Texas Gulf acquired the sales organization of the Ameri can Zinc Co., which had shut down its electrolytic plant in Illinois. This ac quisition gave the company valuable contacts in the huge US zinc market, and after the buyout, Texas Gulf kept the market alive until the new plant was started up by importing zinc from Europe to supply its US customers. The US was to be the principal mar ket for Texas Gulf’s zinc metal. Texas Gulf hoped to supply a part of the Canadian zinc market, but that was
expected to be a tough nut to crack. Canada was the world’s largest zinc producer in terms of mine output - about 1.2 million tpy - and its do mestic consumers took only about one-tenth of this production. Cana da’s older zinc producers were long established.
In addition to 120,000 tpy of zinc, the plant was designed to produce about one million lb per year of cadmium, 230,000 tpy of sulphuric acid, 24,000 tpy of silver-lead residue, and 1,000 tpy of cement copper.
A five-year contract for sale of all of the plant’s production of sulphuric acid had been negotiated with Cana dian Industries Ltd., Canada’s largest producer of chemicals.
The Ecstall zinc plant was designed around two brick-lined Lurgi turbu lent bed roasters having a combined rated capacity of 758 tpd of concen trates.
Lurgi roasters had predominated at zinc plants constructed during the previous 10 years, and no other roast er was seriously considered for the
Ecstall plant.
Ecstall concentrates were put through commercial tests in Lurgi roasters at the Balen, Belgium, plant of Soc. des Mines et Foundries de Zinc de la Vi elle Montagne, because none of the plants taking these concentrates on a regular schedule was roasting concen trates from Ecstall exclusively. The roasters at the Ecstall plant were sup plied by Lurgi Canada Ltd.
The initial design for the Ecstall plant called for a standard neutral leach of the roaster product, but during prepa ration for construction, Texas Gulf learned of the development of the jarosite leach process by the Electro lytic Zinc Co. of Australasia, Ltd.; Det Norske Zink-kompani, of Norway; and Asturiana de Zinc, of Spain. Texas Gulf obtained a license to use the process at Ecstall and designed it into the plant.
The jarosite process yields a more complete recovery of zinc by largely eliminating the disposal of zinc fer rites in tailings, as was common at neutral leach plants. These ferrites can be dissolved by hot acid leaching.
However, past attempts to precipitate the dissolved ferric ions had yielded slurries that were difficult to filter, that entrained zinc-rich solution after filtration, and in which the zinc oxide present in the calcines was inefficient ly used in neutralization.
In the jarosite process, ferric ions were precipitated as a jarosite, and these problems were avoided. The Ec stall plant used a sodium jarosite pre cipitation; however, the process could also use potassium or ammonium as the precipitating agent.
Jarosites are a group of com pounds of the general formula ZnFe2(SO4)2(OH), where X can be Na, K, Rb, NH4, Ag, or Pb/2.
At Ecstall, use of the jarosite process was expected to raise zinc recoveries from about 88% to about 93%. Engineering, design, procurement, and construction of the Ecstall plant were managed by a team headed by Dr. James R. West, Texas Gulf’s vice president of research and engineering, and including H. G. Bocckino, R. J. Boyle, and A. Gloster, assistant man agers for research and engineering. Overall responsibility for Ecstall at
Timmins - the mine, the concentrator, and the electrolytic zinc plant - was held by P. Ray Clarke, vice president and general manager of Ecstall. Frank S. Gaunce was zinc plant superinten dent, and George Freeman was assis tant zinc plant superintendent.
Three engineering companies, Lurgi Canada Ltd., Simon-Carves of Can ada Ltd., and the Ralph M. Parsons Construction Co. of Canada Ltd., coordinated the design, engineering, procurement, and construction of the plant. Construction was supervised by A. G. Perry, superintendent of en gineering and technical services for Ecstall Mining Limited.
The zinc plant was located next to the Ecstall concentrator (mill), about 17 miles east of the Kidd Creek Mine. Concentrate was delivered from the concentrator to the roasting plant by conveyor belt. At the roaster, a re versible shuttle discharged the con centrates to four 750-ton concentrate storage bins - a four-day supply of concentrate storage ahead of the roasters.
An elevator which fed the conveyor
belt between the concentrator and the roasters provided a method of trans ferring concentrates from an outdoor storage area to the storage bins. Concentrates were taken primarily from the concentrator’s “C” flotation circuit, which produced a relatively low-zinc, high-silver product. “A” circuit concentrates had a higher zinc and a lower silver content. They were more valuable in the open mar ket and were expected to account for the bulk of Ecstall’s concentrate sales from the electrolytic zinc plant.
There were two parallel roasting lines in the roast ing plant. Each line was equipped with two concen trate storage bins, an air blower, a roaster, a waste heat boiler, a precipitator, cyclones, a calcine cooler, and a ball mill for calcine grinding.
The plant was completely enclosed in a building 226’ x 106’x 108’ high at the feed end and 70’ high above the dust precipita tors. The roasters were 27’ 8” ID in the lower section and 37’ diameter in the up per section and rose from ground floor almost to the top of the building. Concentrates fed out of storage bins onto a vari able speed extractor belt, then to a weightometer belt, and then to the two slinger belts which fed each roaster.
Allis-Chalmers air blow ers supported the turbulent bed in the roaster, forcing 23,000 cfm of air through tuyeres in the roaster floor. Oil burners were used to preheat the roasters to ig
nition, starting the exothermic oxida tion of the concentrates.
Excess heat was largely removed by water flowing through coils in the tur bulent bed section of the roaster. The desired operating temperature was 930°C.
Calcine product from the roasters was
conveyor to a Hardinge ball mill for grinding and air classification.
All mechanical calcine convey ers in the roasting plant were kept under vacuum, with vent through a filter bag, for air quality control. A baghouse at each ball mill provided further dust control.
A liquid effluent treatment sys tem, along with the acid plant and numerous dust control devices throughout the Ecstall plant, al lowed it to meet the highest stan dards of environmental quality control.
With over 40 years of
only tire service
Historically, the Kidd Creek under ground mining complex can be di vided into four main areas, resulting from phased development of the de posit.
These are the Nos. 1, 2, 3 and D Mines. The company knew the ore body ran deep and a great deal of preplanning had to be done and many known problems solved in advance. Each of the mines extended the life of the operation, helping both the com pany and the community of Timmins. The benefits from going deep always exceeded the costs.
The No. 1 Mine extended from the 800 level (pit bottom) to 2800 level. The remaining ore in the No. 1 mine was exhausted in 2008.
The No. 2 Mine stretched from the 2800 level to the 4600 level and was mined out in 2005.
No. 3 Mine started operation in Oc tober 1990. It was developed in two stages, Phase 1 from 4600 to 6000 level, and Phase 2 from 6000 to 6800
level.
Mine D opened up ore from 6800 to 9600 level.
Prior to 2004 all mining took place above the 6800 level.
Mine No. 3’s Phase 1 was exhausted in 2010, while Phase 2 was mined un til 2015.
The No. 1 and No. 3 shaft are pres ently used for ventilation only. Going underground meant having to deal with many problems, with safety for the workers and corrosion being major.
Corrosion is a major nuisance at Kidd Creek. Underground, the mine is es sentially a high sulphide environment with mild sulphuric acid collecting just about everywhere.
Sulphuric acid loves copper and cor rodes exposed electrical connections. That’s one of the reasons why the mine preferred the sealed junction box with terminal strips.
Greg Mascioli, mobile maintenance superintendent said in 2008 “during
the first year, you typically had mini mal problems with plug-in connec tors.
During the second year everything went to pot and by the third year it was a complete disaster. You would open the dash and it would be a rat’s nest where 50 guys had been pulling wires.
The current Kidd Creek standards specify that every wire is numbered and that it correlates with the terminal strip. We also specified that a heatshrink covering be used to protect the numbering.
The technicians would test from ter minal strip to terminal strip. With all of the numbers in front of them, they could identify the problem within minutes.”
Safety is never forgotten.
One example of the company’s pol icy is to include contractor incidents along with the mine’s statistics. Consolidating its safety figures made
7700, 8300 and 9000 levels in the No. 4 shaft are used to transfer ore to skips for hoisting up the shafts.
On surface, the ore is conveyed to load-out bins, from which it is hauled by rail to the Kidd Metallurgical Site. Scientists and mining people from all over the world have come to tour the mine.
In 2011, Ryan Anderson, a research geologist at the U.S. Geological Sur vey Astrogeology Science Center, was part of a group of U.S. scientists who toured the mine. Ryan had a background in Physics and Astrono my and received his PhD in Planetary Science from Cornell University. Ryan is interested in deciphering the history of Mars through quantitative geomorphology and spectroscopy.
The following is part of a report he wrote about the tour that took him to the bottom of the mine:
As newcomers, every noise, every light was strange and startling, and it was mentally taxing just being down there.
the mine realize that there was room for improvement with contractors on the site.
Christian Bruneau, then manager of mining operations, said in 2008: “Kidd Creek employs numerous con tractors, but there is now only one set of numbers when it’s time to refer to safety.
A mine must take responsibility for any person who comes on site. Our relationship with the contractors has improved greatly. We have regular meetings with them to make sure that their strategy is aligned with our strategy —to reduce the accident rate. It makes me proud to report that we have seen a 25% improvement in
safety results from 2006 to 2007 and an incredible 75% improve ment in 2008. We have an excellent safety record and a good working relationship with contractors.”
The Mine D, Stage 1 project be tween 6800 and 8800 levels pro duced more than one-half of the required ore.
The majority of personnel and bulk supplies are moved between sur face and underground via the No. 2 shaft, running to the 4700 level, and the No. 4 shaft, reaching from 4700 to 9600 levels.
Transfer between the shafts on 4700 level is by train and ore is moved between the shafts by conveyor. Loading pockets on 2800 and 4700 levels in the No. 2 shaft, and 6800,
As one of the guys in my car put it, it felt like “people just weren’t meant to be that far underground.” But humans are ingenious, and we specialize in finding ways to live where we were never meant to. We learned to wear warm cloth ing and store food to survive bitter winters. We learned to sail the seas for months at a time without sight of land. We ride submersibles to the bottom of the sea, and rockets into the void of space, and return to tell the tale.
And, in our search for resources we plumb the depths of the Earth, under taking phenomenal feats of engineer ing to extract metals from the stone. To me it’s a reminder of how adapt able we are, how capable, and how unstoppable.
We are a species that can do anything if we put our minds to it. The ques tion is, what will we put our minds to next?
“D” is for dreams. And at Kidd, these dreams are huge- the kind that result in monumental techno logical feats such as the creation of Kidd’s Mine “D” making the Operations the deepest base-metal mine in the world.
Over its 50-year history, Kidd has had a number of teams driven by the belief that they could extend the life of the Kidd Creek Mine by pushing deeper. They first started with extending the world-famous ore body from the 6800 Level underground to the 8800 Level (or 8,800 feet be low surface). Before they finished dreaming, the mine had reached 9,600 feet below surface – the closest point to the center of the earth anywhere in the world. Operating at nearly 3km under
ground is not without its challeng es, but Kidd has proven that it can be done and safely at that.
The deepening project, approved by the Falconbridge Board of Di rectors in 2000, was called Mine D (for Deep) and was the fourth of ficial mine on the Kidd Creek site. The project moved ahead in stages. Stage I saw the sinking of #4 shaft to 9,889 feet and deepened the mine from 6800 to 8800 level and took a little over six years to complete at a cost $679 million. Stage II, which occurred between 2007 to 2011, extended mine pro duction further down to the 9500foot level at a cost of $125 million. The deepening of the mine continues to this day, with a further $15 million invested in 2015 to com plete the deepening project down
to the 9600 level.
In today’s dollars, Kidd’s Mine “D” project would likely exceed $1 billion. It was an ambitious project bringing together a num ber of internal and external experts and specialized construction com panies like AMEC, Hatch, Cementation, Redpath and Dumas among many others.
When the Kidd orebody first went into production in 1966, nobody would have guessed that the same orebody would still be producing 50 years later from nearly 3km underground. Today, Kidd Mine hoists 2.25 million tonnes from an average depth of 2.5km below sur face (8300 level) with the deepest stopes currently producing from the 9500 level. The current life of the operation is 2022.
For almost half of Kidd Mine’s 50year history, a Sandvik loader has been used to muck ore through the mine, or a Sandvik drill has been drill ing deep into the rocks thousands of meters below the ground.
“Sandvik supplies the majority of our equipment – all of our long hole drills and the scoop fleet at Kidd are from Sandvik,” says Ryan Roberts, Manag er of Mine Operations at Kidd Mine. “We have partnered with them for a long time and continue to do so be cause they listen to our needs, espe cially on the automation side of the operation. Automation only works if a mine really buys into it and Sandvik has the expertise to train onsite em ployees to ensure the system works.” This partnership began 25 years ago when Kidd Mine purchased its first ten Sandvik loaders – seven Toro 501s and three Toro 400 loaders - complete with a maintenance contract in the early Nineties. These ten ‘old-timers’ – and the Sandvik 1400 loaders which later replaced them - were lovingly rebuilt by Sandvik in 1999 and were “almost better than new afterwards” according to Greg Mascioli, Super intendent of Mobile Maintenance at Kidd Mine.
As the mine expanded its operations, the relationship between the two com panies also stepped up a pace. Gradu ally, more Sandvik equipment includ ing two 1009 Data Solo drills, began
to appear in the mine.
And, as the mine began to rely increasingly on Sandvik’s technical sup port, a Sandvik service technician became a per manent fixture on site.
2003 marked another milestone with the Mine D extension project, pro longing the mine’s life. Flexibility was the name of the game in this me ga-million-dollar invest ment project.
By 2008, Kidd Mine had been extended to almost 3,000 meters, making it the deepest base metal mine in the world. Because it was so hot and deep un derground, the decision was taken to automate part of its scoop fleet. This would improve safety for the mine staff and at the same time boost effi ciency. In 2013, Sandvik’s AutoMine Lite – an automated loading and haul ing system for underground hard rock mining - was installed.
“Automating part of our fleet in creased our effective facetime by re ducing the effect of travel time and allowed us to operate through seismic closures and gas checking. Initially we only used automation in transfers but have progressed to muck stopes with automated loaders. This allows us to muck seismically sensitive stopes by safely removing the opera tor from the area,” explains Roberts.
“We have recently invested further in our infrastructure to operate certain areas in continual automation. Today, we have the biggest automated scoop fleet in North America.”
Terry Smith, Account Manager at Sandvik, has managed the Kidd Mine account for over 10 years. He says it is a very special customer which is close to his heart. “Typically the em ployees at Kidd are lifetime dedicated employees and the mine has been an important part of the local community for half a century. In our industry, it’s something special to have such lon
gevity.”
Smith recalls Gil Babin, the mine’s former maintenance specialist. “In my opinion, he was a forward thinker in the Canadian mining industry and really knew how to make his suppli ers perform better. He forced people to rethink their engineering to make operations safer.”
He was also a man who kept his sup pliers on their toes. “He often dug in his heels when a piece of equipment – and he didn’t care who the supplier was - came onsite with known safety or reliability issues unaddressed. He could identify safety issues from an incident or accident and would pass this information on to the supplier who often used it to make their ma chines better and safer,” says Mas cioli.
Sandvik took many of Kidd Mine’s suggestions on board, using them to make improvements. “We appreciat ed their feedback and fully endorsed most of the changes especially when we rebuilt their equipment,” says Smith.
For Mascioli, uptime is critical. Equipment must be reliable and op erators properly trained to maintain valuable production time. He says Sandvik has provided consistent sup port. “They offer quick turn around on repair items. They keep a good inventory supply with quick parts de livery. And, they provide 24-hour-aday parts and technical services when needed,” he explains.
According to Roberts, the current economic downturn in the mining industry makes it more important than ever to optimize the efficiency of the mine’s equipment.
“With the current low metal price, it is essential that we continue to improve the utilization of our fleet, so that we don’t need a bigger fleet. Automation has enabled us to reduce our scoop fleet by four loaders but we have had to learn how to maximize the poten tial of each unit; planning the setup and scheduling the areas is key to the success.”
On June 25, 1981, a new era in cop per smelting was ushered in, not just in Timmins but in North America.
On that date, the most modern copper smelter and refinery in the world was officially commissioned at the Kidd Creek met site, at a cost of around $292 million, under the original $300 million estimate.
The decision to install a copper smelt er and refinery was made in the early 70s, and, in 1975, after an exhaustive study of the available technologies, Japanese technology was chosen.
The Mitsubishi Continuous Smelting Process was selected for the smelter and Onahama #3 Tankhouse design as the basis of the copper refinery. Both technologies were state-of-theart and best met all of the stringent design requirements, not the least of which was to ensure that the most environmentally-sound facility be in stalled and operated in Timmins. It was originally intended to install two furnace lines, capable of produc ing 118,000 tonnes of blister copper/ year. After a further review, the scope of the project was reduced and a sin gle furnace line was installed, such that the installed capacity was 59,000
tonnes/year.
It is interesting to note that in 1990, the original design capacity of 118,000 tonnes/year was achieved through the single furnace line.
Construction started in 1976, but was slowed during 1977 and 1978. Nor mal progress resumed in 1979, and construction of the facilities were completed in early 1981.
At the time of commissioning, the op erating and maintenance complement of the copper smelter and refinery was around 310 workers.
Of this total, fewer than 15 had had previous experience in a smelter or refinery. In fact, the majority of the workforce were transfers from other Kidd departments.
After some early and expected diffi culties during the plant commission ing, the effectiveness of the smelting operation improved, as problem areas were identified and resolved. By 1983 the design capacity of 59,000 tonnes/ year had been achieved.
Further equipment modifications and additions were subsequently made to increase the smelting capacity, at a to tal cost of about $40 million, in order to process the excess copper concen
trate produced. Otherwise it would have been smelted on a ‘custom’ basis at other smelters.
In the copper refinery, production capacity was increased from 59,000 tonnes/year by 1981 to about 95,000 tonnes/year of cathode. This capac ity increase resulted from a number of improvements, the most significant of which was the implementation of stainless steel electrode technology in the tankhouse, in 1986, using the pat ented Kidd Process®.
In addition to increasing plant capac ity, this technology also allowed Kidd to produce a higher quality cathode product.
The increase in smelter and refinery capacity had a marked and beneficial effect on the overall operating costs, allowing Kidd to achieve and main tain a highly competitive global po sition. This was a testament to both the installed technology at the smelter and refinery and also to the abilities of the operating and maintenance per sonnel in Copper Operations. Due regard for the environment was also maintained, both inside and out side of the plant. The Kidd smelter
was recognized as being one of the cleanest plants in North America, and one of the best in the world. In 1990, the level of sulphar dioxide (S02) emitted to atmosphere from the smelt er acid plant was only 1,700 tonnes.
Beginning in 1989, the smelter began processing copper and zinc-bearing ‘secondary’ material from other com panies, so-called ‘custom smelting’or recycling.
The characteristics of the smelting process, together with the on-site availability of the zinc plant which processes smelter dust, allowed Kidd, through the Custom Materials and Resource Management Group, to bid aggressively for such materials. Pro cessing of this material improved the overall plant economics.
A specialized computer system was used to regulate the many functions in the smelting process.
The computer system called Mod comp, which was an acronym for Modular Computer Systems, was used to regulate the many Sanctions in the smelting process at the metal lurgical plants.
The mini-computers performed such functions as regulating the feeds and flows to the smelting furnaces and reagent additions in the concentrator flotation circuits.
The smelter acid plant also had a liq uid SO2 operation.
The Kidd smelter normally produced about one per cent of the world’s cop per and zinc, as well as more than half a million tonnes of sulfuric acid per year.
Xstrata Copper Canada announced on Dec. 7, 2009 “that it will permanently cease operation of its copper and zinc metallurgical plants at the Kidd Met allurgical Site in Timmins on May 1, 2010, in a rationalization of its Cana dian metallurgical operations. The Kidd mine and concentrator will re main in operation.”
Claude Ferron, then Chief Operat ing Officer for Xstrata Copper Can
ada, commented: “Global smelting overcapacity is driving treatment and refining charg es to record lows while the costs to operate and maintain these fa cilities continue to increase. Our situ ation in Canada is exacerbated by a strengthening Ca nadian dollar. The requirement for further capi tal investment in these plants and lower sale prices for some by-prod ucts including sul phuric acid have also negatively impacted the vi ability of these op erations.”
Timmins Mayor Tom Laughren commented at the time that “high electricity prices here in Ontario are
killing businesses that rely on cheap power. Xstrata’s annual hydro bill for the smelter is $70 million. In Quebec, the price is 40-50% lower.” Xstrata expected that approximate ly 670 employees and 450 contract workers would be impacted as a result of this decision.
An early retirement incentive was offered to all eligible employees. Unionized employees were treated in accordance with the collective agree ment. Where possible, employees were of fered the possibility to work at other Xstrata operations. Xstrata continued to honour existing commitments to communities in the region.
Xstrata’s Copper Canada division will focus on integrating the remaining
CCR refinery, in order to improve the overall financial competitiveness of the division, it said.
In 2012, steel recycling company Del san dismantled 36 industrial buildings and ancillary infrastructure. Accord ing to an Xstrata newsletter, more than 50,000 tonnes of steel were re moved over a 10-month period.
Most of the material went to Canadi an steel recyclers. Electronics, trans formers and other items were also recycled, reducing the amount of ma terial destined for a landfill.
Equipment, furniture and trucks were donated to community groups and or ganizations.
in the Timmins operation capable of completing the project.”
The smelter cost $292 million and was operational three months early, he recalled.
Japanese technology was acquired and there were 64 Japanese technical people on the site when the job was completed June 18, 1981 but then a hitch developed.
The head of the Japanese group said the moon was in the wrong phase and asked for the start up to be delayed a week. Texasgulf agreed and the switch was thrown on June 25. Laforest recalled that he missed the ceremony.
be proud of,” he said.
He is a 1965 graduate of McMaster University in Hamilton with a degree in civil engineering. He was born in Timmins and still resides here.
He joined Texasgulf in September 1969. Prior to that, he was with M. S. Yolles & Associates of Toronto, con sultants in design and construction, for four years.
He began his engineering efforts at the mine site when work was being done on Mine No.1’s headframe and the underground service facilities. He then shifted from the mine to the metallurgical site where he was proj ect engineer on the tin circuit, the cen tral warehouse, shops and laboratory. He was assigned to the smelter project in July, 1975.
Picking a site for the smelter and re finery was a problem because there was no rock big enough at the mine site so an area was picked 17 miles to the east.
asgulf Inc., entrusted him with the $300 million smelter and electrolytic refinery project in Timmins.
Laforest recalls to this day his sur prise when as construction manager in 1977 his suggestion was accepted that the staff in Timmins could complete the project on budget and before the estimated completion date. Work had started in 1976 but a slump in metal markets led to the company slowing the project down. Laforest had been acting as the liaison person between Texasgulf and SNC/GECO Canada Inc.
“The slowdown lasted eight months and during that period SNC/GECO was project manager but pulled their people out. That’s when I went to Fogarty.
“I certainly appreciated the trust Fogarty and other company officials placed in me. I had made the point that there were a lot of good people
He had committed to being in Toronto for the swearing in of Cochrane South MPP Alan Pope as a cabinet minister and he shared a taxi going to Queen’s Park with Gregory Reynolds and sev eral other Timmins residents.
“Look out the back window and see if there is a flash in the sky,” he said to Reynolds. “Why?” asked Reynolds as he cranked his neck.
“Because it is 10 a.m. and they are pushing the start button on the smelter in Timmins. I want to know if it blows up,” Laforest replied.
When told there was nothing in the sky, Laforest laughed and said “now it is safe to fly home tonight.”
Laforest praised the team he worked with on the project, Joe Campbell, now a Timmins city councillor, was the accountant; Greg Berlingeri; Doug Pretsell from Iroquois Falls, mechanical supervisor; Doug Kelly handled health and safety duties; and there were others.
“Most of the complex was built by local workers and contractors and it was great for Timmins, something to
“Yes, there was rock in Hoyle Town ship with a railway and a provincial highway close but it was 80 feet down under bad soil and muskeg,” Laforest recalled.
“We had to dig out the site, about 2 million tons, and back fill it. Then we had to sink 60 miles of steel piles into the new ground.
“The smelter, refinery and acid plant all sit on piles,” he said.
Since there was only two plant in the world using the technology Texasgulf bought, Laforest was sent to Japan for two weeks to study a smelter opera tion in Naoshima and a refinery in Yo kohama.
“I didn’t like the food and I only had one good meal. That was when one of the training people took me home for teriyaki steak,” he recalled with a laugh.
During the construction phase, there were eight Japanese consulting on the smelter and 56 on the refinery.
“We needed the 56 because we had to put PVC on top of rubber to line the electrolytic tanks and they were the
rectors of the Timmins and District Hospital.
He has always performed community work, serving while at Kidd on the Timmins Police Commission and the board of Northern College. He also served in 1970-74 as a councillor for the City of Timmins.
“I never worked for any company that treated its employees as well as it did and was as community minded as Kidd Creek. It encouraged its em ployees to be active and in my case
I was allowed as much time off as I needed for activities of the various boards and city council work.
“When council was building the Mountjoy Arena, the company had a lot of material in its warehouses it deemed surplus. When I asked for some things to be donated to the arena project, I was told to take what was needed.
big banquet that evening.
only ones in the world who knew how to do it.
“The Japanese worked in small groups and each group had at least one English speaking person. We had no language problems.
“All of them stayed in one hotel and they had a great time here,” said La forest.
There were five different unions working on the smelter project but he recalls it as a trouble free period.
There was one slowdown and picket lines at the entrance to the met site in 1978 but the dispute was quickly settled.
“SNC/GECO created a policy of meeting with the unions on a regu lar basis and we continued it after we took over the project.
“If a problem was raised, it was tack led immediately and things continued smoothly,” he said.
Things did not go as smoothly when members of the Texasgulf board showed up with their wives at a pre viously announced inspection of the smelter.
“The women were wearing high heeled shoes as they were going to a
“The floors of the smelter were cov ered with steel gratings. There was a chance a woman would catch a heel in a grating and be injured.
“The inspection was held up un til we found work boots for the wom en.”
Laforest left in September 1983 to start his own con struction company. He explained there were no challeng es left in his field at Kidd Creek.
“All the big proj ects had been com pleted. I thought I could create a bet ter future going out on my own.”
He is semi-retired now, just doing some consulting work, but is chair of the board of di
“Kidd did that a lot, helping commu nity projects and groups. It was great that way.”
A single announcement in 1964 made world headlines and at the same time, it gave renewed hope to the Town of Timmins and a level of communitywide prosperity that exceeded the residents’ wildest dreams. That event was the discovery of the massive Kidd Creek orebody.
For the past 50 years, Kidd Opera tions has been contributing to local prosperity by providing high-paying jobs to over 20,000 individuals in cluding multi-generational families. In addition, the company has contrib uted hundreds of millions of dollars in local taxes and millions more in the purchase of goods and services. However, that is just one aspect - the business side, of how Kidd and its successive domestic and global own ers have helped to make Timmins a better place.
After all, what good is all that prosperity if it isn’t felt in the heart of the community?
Kidd’s approach to good corporate citizenship has always been predi
a difference in the lives of those it touches.
When providing grants to a non-profit organization, Kidd’s community rela tions staff carefully look for projects and programs that are aligned with well-established community goals. To find out what these goals are, Kidd consults with community stakeholders to identify gaps and needs, and regu larly uses the City of Timmins’ 2020 Strategic Plan as one of its guides. In this way, the company knows that their grants and investments are actu ally aligned with community priorities and that they will have broad positive impact on sustainable community de velopment…long after Kidd Opera tions ceases production. One example among hundreds is Kidd’s investment in the Spruce Hill Lodge Retirement Home, Timmins’ only non-profit seniors’ assisted liv ing residence. The City of Timmins, social agencies, seniors and their fam
cial and transitional housing for vul nerable populations. Waiting lists for affordable seniors’ housing were long. Therefore, Kidd approved a grant that allowed Spruce Hill to expand and provide six additional rooms in their facility.
Timmins knows only too well that a resource-based economy is cyclical by nature. Commodity prices rise and fall with global supply and demand, resulting in ‘boom and bust’ cycles for communities. Too often, the cor porate giving of many companies and businesses, large and small, mirrors this pattern.
Financial support may rise at a time when a community is already doing well and then decrease when the com munity is not doing as well and the need is actually greater. In addition, mining projects are finite. When a mine must be closed, there is another shrinkage of spending, jobs and cor
porate giving.
Kidd’s approach to corporate giving, which is through strategic social invest ment, aims to ease the impact of min ing’s cyclical nature on the community. The company looks to support non-profit organizations and projects that contrib ute to both capacity-building and the
sustainability of organizations and the broader community. The two main goals are to support organi zations and projects that will have long-term benefits for the commu nity and to help the non-profit sector become more financially self-reliant in a highly competitive fundraising environment.
“Teach a man to fish” is a simple way to describe Kidd’s approach to corpo rate giving.
One example of this approach was Timmins’ first “Working Towards Sustainability Conference for the Non-Profit Sector” held in 2013. This project was initiated and supported by Kidd in direct response to the notfor-profit sector’s need for help in understanding and exploring ways to become less reliant on public and pri vate-sector donors and more self-sus taining for the long-term. Nearly three years later, non-profits still refer to the conference and what they learned.
“Through Kidd Operations’ Work ing Towards Sustainability Confer ence, we gained valuable insight into key considerations for continuing to develop social enterprise models of service delivery that will increase our ability to withstand a diminish ing charitable giving landscape,” says Rena Keenan Buhler, Chair, AntiHunger Coalition Timmins.
This commitment to the community through strategic social investment has also captured the attention of the Ontario Trillium Foundation (OTF), an agency of the Government of On tario and Canada’s largest publicsector grant maker. Under new lead ership, the Foundation had begun to refocus its community investment strategy on grant making for collec tive impact and sustainability and saw the opportunity to establish the Foun dation’s first partnership with indus try and thus chose Kidd Operations based on both organizations’ aligned strategy.
This partnership resulted in the cre ation of a $1 Million Kidd Opera tions – Ontario Trillium Foundation Legacy Fund which will be adminis tered by the Foundation and will be
Cont’d
gin making grants when Kidd ceases operations in Timmins in or around early 2022. This collaborative ef fort, the first for the Government’s Ontario Trillium Foundation, also breaks ground for future partnerships between the Foundation and industry in benefit to communities across On tario. And it started right here in Tim mins with Kidd.
When you’re one of the “big players in town”, it’s natural that people focus on the financial aspect of your com munity support. Stakeholders tend to remember and highlight those “wowfactor” community investments whether they be million-dollar invest ments in X-Ray machines or legacy funds.
But the reality is that the greatest com munity impact is made by people, not money. It is the people who work and volunteer with our many local nonprofit organizations and groups that make Timmins a better place to live.
From the ventilation technician who, as a Harley Davidson group member, collects toys for needy kids, to the business analyst who fosters rescued dogs, from the driller who coaches hockey to the tailings metallurgist who volunteers with a community fire department, Kidd employees contrib
ute thousands of hours of their time each year to several dozen organiza tions, associations and groups.
As a company, Kidd encourages, rec ognizes and celebrates its employees’ invaluable community contributions. Since 2007, Kidd Operations has proudly contributed nearly $4 Million to over 50 local non-profits and proj ects.
Every living be ing, whether it flies, lopes, walks or crawls, on the two sites operated by Kidd Operations in Timmins are moni tored and recorded.
Knowing where humans are and what they are do ing, whether staff or visitors, is a matter of safety - but track ing non-humans is part of Glencore’s global Biodiversity Conservation com mitment to protect ing wildlife and their habitat at their operations around the planet.
In Timmins, the pro gram has resulted in Kidd taking a lead role in the Matta gami River sturgeon restoration project, in addition to pro tecting peregrine falcons, bats and bank swallows.
Each site is comprehensively moni tored and the company encourages all employees and contractors to doc ument if they see any creature, living or deceased. The practice gives Kidd a robust picture of the property’s many unique inhabitants, provides important information on the health of the surrounding environment and allows the company to communi cate timely safety concerns, such as watching out for a family of bears or moose.
It also provides Kidd with a vital dossier to take action and adhere to its biodiversity protection initiatives
W. Warren Holmes, General Manager, Kidd Creek Div., Falconbridge Ltd., in 1993 holds a falcon chick with heavy mitts for protection.
falcon) were spotted at the Kidd mine site.
Working with the On tario Ministry of Natu ral Resources, Kidd en vironmental staff took steps to make certain the family was left un disturbed.
Through a number of sightings, it was as sumed the trio was us ing a ledge in an unused open pit as their home. The pit walls mimic the steep cliff habitat pre ferred by falcons.
In 2012 and 2013 there were additional sight ings of a single fal con, but a mate never showed up. In 2014 and 2015 however, breed ing seems to have been re-established and new eyasses were observed.
that not only involve its own opera tions, but the community as well. For example, if a particular animal is spotted, and Kidd staff determine that it is on the protected list, then the company takes specific measures to safeguard the species well-being.
At one point, peregrine falcons were an endangered species in Ontario. In fact, by the mid-1960s there was little evidence of breeding activity across the province.
A ban on the use of DDT in 1972 and the implementation of a national rear ing program restored the bird’s popu lation.
In 2011, a pair of peregrine falcons and their eyass (the name for a baby
In 2015, Kidd teamed up with Highline Power Inc., and local teacher Tim Brooks, along with his R. Ross Beattie Senior Public School students, to erect two new raptor nesting platforms. They are mounted on 25-foot wooden poles.
“With the decline of certain raptor species, such as eagles and osprey, we decided to help them out with the installation of nesting boxes,” said Corey McLister, Kidd Environmental Coordinator.
Since 2011, Kidd Operations has been involved in the sturgeon project when it provided funding and personnel to support fish transfers, as well as, mi gration and breeding monitoring pro grams.
The sturgeon project was established
101 in the eastern part of the City of Timmins were equally perplexed to see a herd of buffalo as they passed by the Hoyle metallurgical operations of the Kidd Creek Mine.
Environmental awareness across North America has been at the fore front of modern mining operations, as it was back in 1972 when Kidd Creek opened its zinc plant in Hoyle Township just east of Timmins.
Oh, give me a home where the Buffalo roam. Where the Deer and the Antelope play; Where seldom is heard a discouraging word, And the sky is not cloudy all day.
Brewster Higley, the man who penned the immortal “Home on the Range” American pioneer anthem in 1870 likely never imagined that buf-
falo would roam in the shadows of a multinational mining giant in a land known as The Porcupine.
Yet, for 25 years, drivers on Highway
Cont’d from pg. 86
in 2002 in an effort to reintroduce them in the local watershed.
With financial assistance from Kidd Operations, the Timmins Natural ists Club was able to publish a poster of birds found in the area, which is available for purchase at the Matta gami Region Conservation Authority office.
The poster project was of mutual benefit since the company started monitoring different bird species around its sites. The company con ducted a nocturnal owl survey, with help from the naturalist group.
Nocturnal owl surveys are still conducted by environmental staff biannually and a third party migratory bird survey was conducted again in 2015.
“We know that the bank swallow is considered threatened in Ontario and the rest of Canada, and we do have them on site. We have been monitoring them for a few years,” said McLister.
“They are in a sand pile, and we use the sand to cover our landfill site as daily cover. We have communicated to employees on site to be aware and to not touch the area of the sand pile that is being used by the bank swallow colony.
In the past few years, we have been establishing buffer zones with sig nage to avoid disturbing the areas that they colonize.”
Other projects have included the construction of bat houses, with the help of a local high school and the Monteith Correctional Facility.
The company was eager to prove to local residents and the growing envi ronmentalist movement that the zinc plant was not upsetting the area’s eco system. The buffalo were brought in shortly after the zinc plant began op erations in 1972.
Grazing on what can easily be de scribed as the front lawn on the com pany’s massive metallurgical com plex, the healthy, thriving buffalo herd served as a reminder to detractors that the smelter was not a threat to the lo cal environment.
As for the herd itself, six plains buffa lo were acquired in 1973 from a farm in southern Ontario - part of a herd from the Elk Island National Park in Alberta.
For a quarter century, thousands of young couples would hop in the fam ily vehicle and take their children for the short drive to the eastern outskirts of Timmins where they would park on the shoulder of Highway 101 or pull into the visitor area to point and mar vel at the size of the adult buffalo. Word would spread quickly and fami lies would flock to the site as adults and children alike would squeal with delight to catch a glimpse of a new born member of the Kidd buffalo herd. The herd kept growing over the years, but in order to keep things man ageable, the company made a decision that 60 was the acceptable population number.
Sadly, a slowdown in the economy
Oxygen and nitrogen gases are commonly used in hydrometallurgy processes for the flotation of molyb denum, gold leaching or pH reduction in water. Regardless of the applica tion, the question inevitably arise how much gas is required for the job and how to optimize its use.
The BoostAL GoldTM offer from Air Liquide Canada was specifically developed to address such crucial issues when the time comes to choose between air and oxygen for pre-oxidation or leaching.
the herd in 1998 and its members were donated to various farms. Administration of the herd was un der the long-term direction of Lloyd Netherton, superintendent of lands and timber. Providing day-to-day management and feeding of the herd was Irene Brunet of Barber’s Bay. Not unlike Jane Goodall who studied chimpanzees for many, many years, Lloyd and Irene built a personal file of buffalo habits that many hoped might
Launched in 2012, the BoostALTM mining offer has already sparked widespread interest in the Canadian industry, with six projects completed to date.
For instance, higher dissolved oxygen is known to speed up kinetics in gold leaching, but what is the best level of oxygen to maximize gold recovery and reduce reagents consumption? Some processes will require oxygen for oxi dation of sulfur or redox (Fe2+) com pounds in acid or alkaline medium: should this be done under pressure? high temperatures? and what type of gas disperser would work best given the particular amount of gas involved. Questions abound.
BoostALTM provides the critical input required to make an accurate assessment of the economics of gold extraction for a particular project, enabling operators to reduce energy consumption and optimize their manufacturing processes. Key para meters such as the dissolved oxygen profile and oxygen-uptake rate can be precisely measured on site by Air Liquide specialists. The data obtained, combined with mineral analysis, is used to verify the likely impact on yields.
to domesticate the animals, but their welfare was of top concern and every effort was made to ensure they were happy in their industrial environment. They received regular medical atten tion and meticulous records were kept of the animals’ feed requirements. The grazing area started at 30 acres but ended up at 300. Four separate fenced enclosures were eventually required. At the beginning, the animals had three stands of trees
was needed so one was obtained from a farm in Sundridge, Ontario to help extend the herd bloodline.
Depending on your consumption volume and activity requirements, our team will help you make the right supply mode choice (cylinders, micro-bulk, bulk, on-site, pipeline).
Dennis Bordin, superintendent, envi ronmental services, made the decision to stage a special ceremony. The bull had to undergo a period of quarantine before joining the herd, so Dennis used the time to locate a book of in cantations and a jar of “powder” from an unspecified source.
Air Liquide Canada
working hard to provide solutions
At the bull’s coming out party, Bordin recited the sexual prowess incantation as onlookers eagerly awaited the out come.
Liquide’s BoostALTM solution
some of the most important challenges faced by the industry
Acid mine drainage
O2
Pre-oxydation
CN recovery or
out more about how Air Liquide
The incantation went well enough, but the powder sprinkling was less successful. The bull refused to burst through ceremonial streamers that had been strung across the gate. The four-year-old bull eventually decided to skip all the attention and ducked under the streamers and qui etly assimilated with the rest of the herd.
The air is so pure and the breezes so fine, The zephyrs so balmy and light, That I would not exchange my home here to range, Forever in azures so bright.
They’re huge, they’re yellow, they’re powerful, and they never sleep.
According to rail supervisor Roger Lachance, these leviathans of the rail way are an integral part of Kidd Op erations.
“Kidd is one of a few mines that have its own surface railway,” Lachance says.
“A lot of mines have underground railways, but we have a standard gauge, 27 kilometre surface rail link between the mine in Kidd Township and the concentrator site at Hoyle.”
The railway is important because it is the only source of transport for ore coming to the concentrator. When the railway stops hauling, as it did once following a derailment, it doesn’t take long for the concentrator to go on short rations.
Kidd’s rails are the standard gauge 56 ½ inches apart, the same as the Ontar io Northland Railway and other major railroads in North America.
In addition to the 27 kilometres of mainline track between the mine and the met site, Kidd’s Railway has about 13 kilometres of yard track.
The railroad division is comprised of 29 side-dump ore cars, each of 112.5 tonnes (125 ton) capacity, although
Lachance says they are seldom filled beyond the 90 tonnes target mark.
The powerful GP-38-2 General Motors locomotives, each rated at 2,000 horsepower, generally haul 25 car trains. The number of cars may vary from time to time, depending on how many are sidelined for maintenance, says Lachance, however 25 car trains are the norm.
The company has two of the big GM locomotives, but it also has one GP9, rated at 1750 horsepower, and one RS-23, with a 1,000-horsepower en gine manufactured by Montreal Loco motive Works.
With its ease of maintenance and extreme versatility the (General Pur pose) GP-9 locomotive can be used for yard work or as a spare locomotive for the ore haul. The (Road Switcher) RS-23 is used for yard work at the concentrator site, where most of the yard shunting is located.
“There is an amount of local traffic for these engines at the concentrator site. For example, we shunt empty gondola rail cars from the ONR yard to the concentrator load-out for load ing copper and zinc concentrates. Ap proximately 7,000 to 8,000 tonnes of concentrate are loaded each week into
the rail cars and shipped out to our sister companies for processing, each gondola rail car holds 88 tonnes,” says Lachance.
Lachance says the Kidd Railway team is highly efficient. Most of its 18 em ployees are cross-trained, so they can fill different positions when, for ex ample, trainmen (locomotive opera tors) and switchmen take their vaca tions.
The trains make four runs a day be tween the mine site and the met site.
“Because the trains operate only at about 48 kilometres per hour, and be cause the loads are so heavy, it takes time for the train to reach that speed. It usually takes about 45 minutes for the trip between the mine and the met site,” he says.
With loading and unloading added to the mainline rolling time, it makes the turnaround time for one run about two hours and 40 minutes.
When it was built in 1966, the rail line between Kidd Township and Hoyle cost about $7 million. The company spends over $300,000 on improvements and upgrading each year.
Since the Kidd Railway was built, the bright yellow locomotives have
hauled an estimated 150 million tonnes of ore from the mine to be milled.
One small group of Kidd employees never takes a break because of the weather. That’s the Railway Crew. A raging January blizzard or a punish ing August rainstorm doesn’t keep them off the track.
In fact, the crew is more likely to be hard at work amid the raging elements than away from them. A blizzard can stop a railroad dead in its tracks if switches are fouled and inoperable. To borrow the theme of a time-worn letter carrier phrase, neither driving snow, nor biting wind and numbing cold will keep the track crew indoors, they have to keep things moving.
A lot of equipment helps the crew do its job. There are plows and snow throwers to speed snow removal but it still takes a man with a wire broom to clean the narrow space between switch points and the flange space on road crossings.
During the summer months, if rail or ties are being replaced, neither biting flies nor driving rain can bring things to a halt, because the ore trains have to keep running. And they can’t run if a section of rail is missing.
There have been a lot changes since Nov. 7, 1966 when the tracks had been laid by Ontario Northland Rail way crews and the first Texas Gulf train rolled.
There were 16 side-dump ore cars and
two 1,000 horsepower locomotives used on the run, holding at 56 kilo metres per hour. Four additional cars were kept on standby.
A third locomotive was kept in the concentrator rail yard to handle switching.
At the end of the line, contents of the cars were dumped into a 2,500 ton live storage pit. It was a fast opera tion; three cars were handled simultaneously every three minutes.
There was a traffic superintendent, a railway foreman, a clerk, three train men- switchmen crews and a mainte nance foreman and six crewmen. Trains made four round trip per day as crews worked two-eight hour shifts on a five-day week.
Despite the occasional news story to the contrary, today’s mining compa nies have environmental stewardship built into their DNA. Kidd Operations’ unwavering commitment to the environment was recognized in 2014. Glencore Canada Corporation earned the 2014 Tom Peters Memorial Rec lamation Award for the closure plan design and reclamation of its Kidd Operations’ Metallurgical Site jarosite pond and adjacent Three Na tions Creek.
The jarosite (iron sulphate mud pro duced from zinc refining) pond was built in 1971 and it operated from 1972 until refining operations at the Metallurgical Site ceased in 2010. In all, 50 hectares were reclaimed. Re habilitation activities included cap ping of the pond, removal of soils, revegetation and a remedial action plan for the aquatic ecosystem in Three Nations Creek. The project was led by
Glencore Canada Corporation (for merly Xstrata Copper) Closed Sites in partnership with AMEC Earth and Infrastructure. The award was presented in Peterbor ough, Ontario at the seventh annual Ontario Mine Reclamation Sympo sium and Field Trip organized by the Canadian Land Reclamation Associa tion and the Ontario Mining Associa tion.
The Canadian Land Reclamation As sociation (CLRA), the Ontario Min ing Association (OMA), the Ontario Ministry of Northern Development and Mines (MNDM) and mining com pany Vale established the Tom Peters Memorial Mine Reclamation Award in 2007.Tom Peters was a founding member of the Canadian Land Rec lamation Association (CLRA) - es tablished in 1975. He was President of the Association in 1981 – 82. In 1984, he won the CLRA’s prestigious
Noranda Land Reclamation Award for outstanding achievement in the field of land reclamation.
The purpose of the award is to encour age the pursuit of excellence in mine reclamation and to recognize and pro mote to the mining industry and en vironmental community at large, out standing achievement in the practice of mine reclamation in Ontario.
“It is a great honor to receive this award. We are proud of this accom plishment and it wouldn’t have been possible without the dedication and hard work of all those involved, and their contribution to the successful execution of the project,” said John Stroiazzo, Manager, Reclamation and Projects, Glencore Canada Corpora tion.
“Kidd Operations is proud to see what the implemented remedial action plan for Three Nations Creek has accom
plished over the years in terms of im proved ecosystem health and water quality.
It demonstrates the commitment that we have to restoring the environment after our operations cease, and should be reassuring to all stakeholders,” said Tom Semadeni, then General Manager, Kidd Operations. “Over the past three years, we have invested over $30 million in environmental risk reduction at both our mine and mill sites as we pursue continuous improvement in all areas of our opera tion, including health, safety, environ ment and community.”
Tom Peters graduated from the Uni versity of Guelph in 1948 and moved to Copper Cliff, Ontario where he worked in the agricultural department of Inco Limited (now Vale), becom
ing their Agriculturist in 1973. Tom utilized his agricultural background to assist Inco with their tailings re vegetation and overall land reclama tion programs.
He pioneered the use of agricultural practices in re-greening mine tailings, including the basic recipes for the ad dition of limestone, fertilizer, seed and the planting of fall rye as a cover crop. His work yielded excellent re sults on Inco’s Copper Cliff tailings and his methods became the standard practice for mines all over the world.
Tom was a well-respected and gifted leader for environmental causes and was internationally recognized in the field of land reclamation.
He made major contributions to the City of Greater Sudbury Land Rec lamation Program. He taught agri cultural courses at the University of
Guelph and Cambrian College, and contributed to reclamation courses at Laurentian University. He received an honorary doctorate from Laurentian for his outstanding leadership in re-greening Sudbury. Tom retired in 1985, and in 1987, became the first non-American to be named “Reclamationist of the Year” by the American Society for Surface Mining and Reclamation.
Following his death in 2007, the Ca nadian Land Reclamation Associa tion (CLRA) in cooperation with the Ontario Mining Association (OMA), the Ontario Ministry of Northern Development, Mines and Forestry (MNDMF) and Vale established the Tom Peters Memorial Mine Reclama tion Award to recognize outstanding achievement in the practice of mine reclamation in Ontario.
The impact of Kidd Operations on Timmins over its first 50 years has been well documented and it hasn’t gone unnoticed by the local business community. Whether it’s innovation, technology or the environment, Kidd Operations is a standout in the region.
Over the years, Kidd has been nomi nated for several awards through the Timmins Chamber of Commerce annual NOVA Business Excellence Awards, the city’s premier business recognition event.
One example is the NorthernTel Pro ductivity, Innovation & Diversifica tion Award given to a business that has improved productivity through the use of an innovative product, technology or system.
As a 2015 nominee in that category, the company was recognized for in vesting in leading-edge technology, such as automated scoop trams (“auto scoops”) one of the ways in which Kidd Operations is maximizing the ore body to extend the life of mine to 2022. Currently, Kidd has two auto mated scoop trams in operation under ground with an additional two ready
for implementation. Not only will this make Kidd’s fleet of automated scoop trams the biggest in North America, but also the only fleet to be used in open blast hole stopes.
Over the course of 2014, Kidd ex panded the use of the “auto scoops” from operating them between shifts to transfer ore only to mucking stopes around the clock. As a result, the ma chines operate 21 hours per day ver sus eight hours per day for regular scoop resulting in a 50% increase in productivity. Furthermore, the two “auto scoops” each moved 350,000 tonnes in 2014, whereas regular pro duction scoops moved just under 200,000 tonnes each resulting in a whopping increase of 180% in tonnes moved through the use of automation.
The Automation Project at Kidd was a $10.2 million investment in increased safety, productivity and econom ic contributions to the community through an extended life of mine.
Next to labour, energy is the second highest operating expense for Kidd.
With the goal of extending mine life to 2022, Kidd has been implementing
various energy conservation methods and technologies.
Ventilation-on-Demand (VoD) is one such system to reduce energy con sumption and costs. Mining at depths of 3km below surface requires large and powerful ventilation fans to push fresh air down to the deepest levels. Manually adjusting or modifying short-term air flow is both labourintensive and impractical. Ventila tion-on-Demand consists of the in stallation of 28 automated louver regulators controlled from surface to automatically monitor and adjust airflow to meet ventilation needs on demand thereby reducing delays and improving working conditions and productivity, as well as reducing en ergy consumption. The conservation technology represents an investment of $9.3 million.
Operating the deepest base-metal mine in the world at depths of 9600 feet requires tremendously large and numerous ventilation fans. Installing and handling these large and bulky fans is a comprehensive operation that
must first and foremost take workers’ safety into consideration. In 2012, Kidd Operations began looking for a diverse utility vehicle that could be used in the installation and handling of fans, as well as one that could per form a variety of other underground functions. Because of Kidd’s unique needs and stringent safety criteria, a multi-purpose unit had to be custom designed. Kidd worked with Marcotte Mining Machinery Services to de velop and build the Multi-Minejack, a single unit capable of performing the
sidered a “game changer”, this single unit can complete more functions than any other piece of equipment in the underground utility vehicle mar ket, from fan, pipe and screen installa tion to scissor lift, tire changer, boom truck and flat deck. The vehicle offers increased safety, lower consumable cost, higher de gree of equipment utilization, and lower emissions. Safety features in clude four lanyard anchors and a mobile lighting system on the deck, tethered remote and fixed controls, a fire suppression system, a 180-de
that must be deployed for boom and deck functions, and a safety interlock programmed into the PLC to reduce boom speed when the deck is lifted from the deck stops. The one vehicle does the job of five different machines without the additional emissions from multiple units. Since the machine can be used for many different tasks, it doesn’t sit idle for long periods of time, which greatly improves its uti lization value. The single vehicle has only one engine, one set of tires, and one transmission that needs servicing, which keeps its consumable cost low. Kidd Operations has showcased the many benefits of the Multi-Minejack for other mines and created opportu nities for Marcotte Mining Machinery Services to custom-build and export various other pieces of mining equip ment to South America and the U.S.
In addition to innovations in technol ogy, the company has won NOVA awards in the following categories: President’s Award (2013); Produc tivity, Innovation and Diversification (2012); Environmental Award (2009 and 2003); Business Contribution to the Community Award (2008); Life long Learning Award (2005).
1952, February
Texas Gulf Sulphur (TGS), a major American sulphur producer, consid ered a Canadian Shield exploration program for sulphur.
1957
TGS began designing an electromag netic device on a helicopter.
1958
The general area of Kidd Creek was mapped geologically on the ground.
1959
Three years of aerial exploration was started, covering 15,000 miles of flying and recording several thousand anomalies.
1959, March 3
The “Kidd-55” electromagnetic anomaly was recorded.
1963 Early
The option was obtained to purchase the first of four half lots overlying the orebody.
1963, October
Field crews carried out ground geo physical surveys of this land to locate a drill site.
1963, November 9
One hole was drilled and the core showed copper-zinc mineralization.
1964, March
All four tracts of land overlying the orebody were contracted and drilling started.
1964, April 16
With eight drill holes to confirm its existence but only the original core analysed, the orebody discovery was announced and the diamond-drilling program accelerated. Limited metal lurgical testing was started and car ried on for about six months.
1964, November
A bench metallurgical testing pro gram using drill core was started at Lakefield, Ontario by the nucleus of a TGS metallurgical staff.
1964, December
Clay removal was started in the pit.
Initial bench metallurgical tests using drill core were completed at Lake field and a mill flowsheet was ready. Mill design was started by TGS staff at Parsons-Jurden, New York, who supplied the engineering services.
May 3, 1965
Pilot-plant tests were started at Lake field on copper-zinc ore from test pits and carried on for three months. Pilot-plant tests were started at Ot tawa on lead-zinc ore from test pits and carried on for two months.
1965, June
The construction of a permanent road from Timmins to the mine site was started. The clearing of a concentra tor (mill) site 17 miles east of Tim mins, near the community of Hoyle, was started.
1965, August Concentrator foundations were com pleted. September, 1965 concentrator steel erection was started. Construc tion of the mine site crushing plant began. Pilot plant tests continued at Lakefield for three months on cop per-zinc and lead-zinc surface ore. 1965, October Copper-zinc ore was available from the pit on bench 1 in large tonnages. The surface diamond-drilling program was terminated. The pilot-plant program on copper-zinc ore at KamKotia Mine was started at 1,000 tons per day for 10 days per month for one year.
1965, November Steel erection was finished and the concentrator building enclosed so that equipment installation could continue during the winter. 1966, March
The construction of the railroad from the mine site to the concentrator site was started. 1966, April The Broulan Reef Gold Mine pilot
plant was started on lead-zinc surface ore at 400 tons per day and continued for 9 months.
1966, September Mine site crusher began operating. 1966, October Mine site road paving completed. 1966, Nov.ember 4
The railroad was finished and ready for operation.
1966, November 16
The first copper-zinc circuit was started and was up to design capacity in two weeks.
1967, January 13
The second copper-zinc circuit was started and was up to design capacity in 2 shifts.
1967, February 14
The lead-zinc circuit was started, but tonnage was restricted because one ball mill head was faulty and the re placement was not delivered on time. 1967, March 18
The concentrator was up to full ton nage and treated over 3 million tons of ore in 1967, with good metallurgy. 1967, May 24 Bench 2 in the pit was producing ore. 1967, October Bench 3 in the pit was producing. 1968, February Bench 4 was producing. 1968, June Tin recovery pilot plant had started. 1969, June
Collaring of the underground shaft was started and completed in 40 days. In August the underground ramp was started from Bench 2 in the pit.
1969, September
The construction of the concrete No. 1 head frame began. 1969, November
The concrete No. 1 headframe was completed. Site preparation for the zinc plant was started. Clay removal in the pit was completed.
1970, January
The zinc plant construction started. 1970, March 14
No. 1 shaft sinking was started. 1970, December
The 800-level development was started from the ramp. 1972, March 14
The shaft was bottomed at 3,050 feet. 1972, March
The 1,200-level development was started from the ramp. 1972, April
The zinc plant consisting of roaster, acid plant, leach plant, electrolytic cell house and casting plant begins operation.
1972, May Mine shaft was ready for hoisting. 1972, November
The tin plant construction started. 1973, June 22
The underground crusher and ore handling facilities were operational. 1973, October
The zinc plant continuous leaching circuit was installed and operating. 1973, December
The tin plant operation started. 1974, October 21 Headframe for No.2 Mine is com pleted. Shaft sinking at No.2 Mine bottoms out at 5,105 feet. 1974-1975 Construction completed on back fill plant, analytical laboratory and warehouse and purchasing building. Fourth circuit added to concentrator. 1975
Thickened tailings disposal technol ogy as developed by E. Robinsky begins.
1976, June Copper smelter and refinery con struction begins. 1981, June Copper operations begin production at 59,000 tonnes annually. 1981, June
Societe National Elf of France ac quires all of the outstanding shares of Texasgulf Inc. and sells its mining interests to Canada Development Corporation.
1981, November Kidd Creek Mines Limited is created with CDC holding a 34% interest. 1982
Tin plant decommissioned. 1983
Zinc sulphide presure leaching auto clave based on the Sherritt Gordon Mine Ltd. process commissioned in Zinc Plant. 1985
Hits peak throughput of 4.53M tonnes ore.
1986, March Falconbridge Limited buys Kidd Creek Mines Ltd. 1988
‘C’ ore depleted, all divisions treating the same ore. Noranda Inc. and Trel leborg AB of Sweden acquire Fal conbridge Limited for $2.9 billion. 1989, January 1
Two Kidd gold mines, Owl Creek and Hoyle Pond, become Falcon bridge Gold Corp. 1990, October
Work begins on Mine No. 3 internal shaft. 1991, April 16
Official opening of indium plant, processing electrostatic precipita tor “cottrell” dust from the copper smelter. 1992
No. 3 Shaft sunk to 6,916 feet. 1993
Custom milling of copper-gold ore from Wisconsin (Flambeau) begins; ends in 1997. Outotec high rate thickener installed in the tailings area to increase underflow density for spigotting on cone. 1996
Kidd Creek Division is divided into
two independent divisions- the Kidd Mining Division and the Kidd Metallurgical Division.
1998
Ore tonnage drops to 2 division de mand, A-division shut down.
2000
Mine D developement aproved by Board.
2002
Mining starts on 6,800 foot level.
2004
Concentrator begins milling Mont calm Copper-Nickel ore.
Zinc plant modifiesd to treat ZincPrecious metals concentrate. Mining starts on 7,500 foot level.
2005
Falconbridge merges with Noranda. Mining starts on 8,200 foot level.
2006
Xstrata purchases 100% of Falcon bridge.
No. 4 Shaft sunk to 9,882 feet.
2007 Board aproval to mine at 9,000 and 9,100 levels.
2009
Custom milling of Montcalm ore body ceases.
2010, May
Copper and Zinc Smelters on Kidd Metallurgical Site close.
2011
Decline reaches 9,800 foot level shaft bottom.
2013 Glencore buys Xstrata.
2014
Kidd Operations wins the Tom Peters Memorial Reclamation Award for its closure plan design and reclamation of the Met Site jarosite pond.
2015
Board aproval to mine at 9,500 foot level.
2016 Kidd Operations celebrates 50 years of production.
How will the eventual windup of Kidd Operations impact Timmins?
This is something the community will have to adapt to.
Kidd Operations’ two sites, the mine property and the metallurgical com plex are in their sunset years, but as the company continues toward an impending closure date some time in 2022, the short and long-term fate of those assets will shift toward commu nity economic developers.
The Timmins Economic Development Corporation has been planning for the closure of Kidd for many years, knowing full well that replacing the world-class mining operation will not be easy nor quick to accomplish.
General Manager Steve Badenhorst, who assumed his new role at the be ginning of 2016, acknowledges that there are some possibilities and a few ideas for the mining operation itself that have been floated as trial balloons for discussion purposes, but how those ideas become reality is mostly out of the company’s hands.
“One of the challenges I have in my
role is to lower some of the expec tations because the community has become very dependent on Kidd through the employment base we have and the direct spend, as well as the philanthropic spend.”
Badenhorst also cautions that the time horizon is relatively short.
“Over time, and particularly with current metal prices we have to make a decision whether it is a ‘go’ or a ‘no-go’ as far as facility-use is con cerned. We are engaging with the community all the time looking for alternative uses to get a sense of val ue of certain assets.”
So what if genuine interest is shown?
It is unlikely that Glencore will as sume any joint responsibility if a proponent emerges that takes a direct interest in either the minesite or the met site.
“If there is interest, then certainly the proponent would need to take on the liability of running that facility as well,” says Badenhorst.
“For example, if they are only going to use 10% of the facility, you can’t
leave the other 90% so we will have to go through a staged process over the next few years of lowering the ex pectation in the community of what Kidd will still contribute.”
What are some of the possibilities?
Suggestions are plenty, but planning and feasibility are another matter al together.
“One idea, for example, is that we have these extreme temperatures down there – we are closer than any one has ever gotten to the center of the earth. By putting in a few holes deeper down we could generate geo thermal energy. So, put a few holes down, pump water which we have an abundance of, turn it into steam and run turbines. Nice idea, but at some point you need to make a decision about whether it is feasible or not in the remaining life of the mine. Ideally you want a walkaway situation where you hand that to some power produc er. We are looking at whether that is feasible or not.”
Badenhorst isn’t shy about putting the
ball squarely back in the court of local economic developers.
“Over time where is the alternative industry in Timmins that is going to employ people?” he asks. “There’s a perception that Timmins is always going to have mining. There will be some mines but will there be enough to sustain the kind of employment lev els that are present right now – I don’t think that’s going to be the case.”
As for Kidd Operations he says the company is working on a progressive mine closure. “We have a multi-year plan of how we are going to tackle that and the Met Site is a good exam ple where the progressive closing of structures has already started happen ing. In 2010 the copper smelter was dismantled and all the infrastructure associated with that and the adminis tration building – each of those objec tives are to try to bring the land back as near to its original condition by not waiting until the final year.”
Badenhorst says there are certain things the company is trying to do on the tailings facility site as well, which
is also going to be progressive. “So we are not waiting until the final 2022 date. The progressive rehabilitation of the underground structure, you can’t start filling it with water at the mo ment, so we have started with some of the surface areas.”
Mining communities around the globe are always fearful that mining companies will pack up and sneak off in the middle of the night, leaving a mess behind for everyone to clean up. When it comes to Kidd Operations, morally and legislatively, that is not possible.
Letters of credit in the hundreds of millions have been submitted to the Ministry of Northern Developement and Mines as assurance the closure will get done as planned.
“The philosophy around closure that we have is we will never walk away,” Badenhorst adds. “Glencore will stay with the requirement to stay here in a limited presence, maintaining what ever the final land use has been de termined to look like. At the tailings facility, that whole thing will eventu ally be capped and we are looking at
alternate means of how we can reduce acid generation, how we can control the water, what chemical reagents we can add to the water to keep it safe to discharge into the nearby creek. All of those things will be done but only at the final closure. Then you can main tain for many years past that.
“The closure plan could be four to five years. There’s a feasibility plan that has only just started of which there are a number of conceptual models. Those plans need to be submitted to the Ontario government to say this is what we are going to be doing. The feasibility study is being done to de cide which concept we want to work with.”
“One was to cover it with a biomass – bring gold tailings in and cover the whole tailings dam – and then use gold tailings and cover the top of it and then return it to vegetation use. Another concept is to cover it with granular sand.”
Those closure plans are several years away and it is the company’s sincere intention to return the land to as near to its original condition.
While the majority of Kidd Creek production has always been copper and zinc, there was a relatively brief period when the company flirted with becoming a serious gold producer.
After all, Timmins’ first 50 years were based almost exclusively on the pre cious metal – why should Kidd Creek be any different?
In 1981, the company developed the Owl Creek Gold Mine, a small pre cious metals orebody four kilometres northwest of the metallurgical com plex.
At the time, the company felt it could process 200,000 tons of gold ore per year and deliver an impressive 20,000 ounces annually as a return on that in vestment over about six years. The decision likely gave the compa ny some anguish as the price of gold in 1980 was just under $600 US per ounce. The price plummeted in 1981 to an average of $400 an ounce. Nev ertheless, the decision to go ahead stood firm.
A decision was made to convert the D circuit in the Kidd Concentrator to accommodate the gold ore – even though it wasn’t a part of the compa ny’s core strategy.
Despite the diminishing price of gold, the company also put plans in motion to do some underground drilling at Owl Creek.
Production at Owl Creek’s open pit operation began in April 1982 with Peter Blakey as mine superintendent. A pyrite gold concentrate produced at the Kidd Concentrator was refined at
the McIntyre Gold Mine in Schum acher.
The mine produced nearly 250,000 tons of gold ore that year. The com pany’s expectations about Owl Creek were more than met.
While additional exploration was underway at Owl Creek, company geologists were focusing even more attention on another gold property called Hoyle Pond – just two and a half kilometres away.
The small, high grade Hoyle Pond deposit was assessed as having sig nificant potential to increase the amount of gold ore that could be put through the Concentrator.
By 1985, the company was no longer referring to gold as a hobby. In their annual report, Owl Creek and Hoyle Pond were referred to as “increas ingly important” to Kidd Creek. Owl Creek’s orebody was close to surface and Hoyle Pond was deeper under ground.
Hoyle Pond development work be gan in 1984 and was in full produc tion by 1986. The ore grade in 1986 was slightly above 4 grams per tonne Company officials estimated that the two little gold mines might have enough life in them to produce about 600,000 grams of gold per year through the late 1980s.
A quote from the company’s 1985 newsletter stated: “At Kidd Creek, we believe gold has a strong future, not just a glorious past”. This com mitment to increased gold produc tion became more visible as spend
ing of $6.6 million Canadian was put towards building a new gold mill and upgrade crushing facilities at the Cop per Smelter. A 300 tonnes-per-day gravity and flotation facility was in stalled in the southeast corner of the Smelter Feed Prep building.
To put Hoyle Pond into perspective at the time, the Canadian Mining Journal reported in May of 1986 that Hoyle Pond produced 790,000 grams of gold at an average of 15 grams per ton, nearly four times the amount of gold coming out of Owl Creek. Now Falconbridge Gold Corpora tion entered the picture. It had been created in 1988 as a spin-off by Fal conbridge Ltd. As the owner of Kidd since 1986, it moved the Owl Creek and Hoyle Pond mines into Falcon bridge Gold.
Falconbridge Gold went public in 1989 with a share offering, thus be coming an independent company with its own board of directors answerable only to its shareholders.
Owl Creek had been mined out in 1989 but Hoyle Pond was still going strong and was expected to produce gold for another 4-5 years despite the fact gold was now selling for well be low $400 an ounce.
In 1992, Falconbridge Gold bought the nearby Bell Creek Gold Mine and Mill from Canamax Resources, thus ending its milling contract with Kidd.
By May of 1993, the fate of Owl Creek and Hoyle Pond would be in new hands. Kinross bought Bell Creek and Hoyle Pond in 1994. Hoyle Pond would eventually wind up in the hands of Goldcorp, the dominant player in the Timmins gold mining landscape. After spending $194 mil lion to go deep, Goldcorp says the mine is the richest in the history of the Timmins Gold Camp and has a long life ahead of it. Thanks to those early efforts by Kidd Creek, the Hoyle Pond Mine continues to be a pillar in the Timmins economy.
conbridge) was he called Rev enue Canada.
The discovery hole at the Hoyle Pond Mine was drilled by Texas Gulf Sul phur Company Inc. in 1969 with hole DDH 69-17 intersecting 6.5 grams gold / tonne over 3.0m (0.18 oz / ton / 9.8 feet). Subsequent drill programs in 1980 and 1982 outlined a deposit containing 199,600 tonnes grading 15.1 g / t Au (97,670 oz gold).
Construction of ramp access was completed in 1984, and mining began by Kidd Creek Mines in 1985 with the production of 64,400 tonnes grading 13.0 g / t Au
For a period of time, all of the Hoyle Pond ore was custom milled at a near by gold mine, the Aquarius Project, owned by New York based Asarco. Jim Francis, Kidd Operations Risk Coordinator overseeing the Mine and Concentrator sites, has been there since the beginning. He worked in the Concentrator for 20 years before be coming superintendent of the rail and yard services group. Today he is the only person left who had anything to do with the company’s gold milling. The gold concentrates once produced by Kidd were part of a more nefari ous piece of Timmins history. In 1986
four men were charged in connec tion with a major gold robbery at the Aquarius Mine.
Francis, then 24 years old, was about to start a new job with Falconbridge after finishing a short but productive career with Asarco, the company that was custom-milling Falconbridge Gold’s ore.
In late January of that year, two masked men, a security guard, and an inside employee were charged in connection with the theft of $375,000 worth of gold concentrates. After a lengthy investigation and two trials, only the security guard was found guilty.
Most of the gold was recovered by in termediaries who sold it back to Fal conbridge’s insurance company.
“Instead of going in to work (at Kidd) Monday morning and going through orientation, I had to do some calcu lations on how much gold was lost because I had processed most of it (at Aquarius) and we would have re ceived it that week to ship it.”
“It was quite a shock. The insurance guy, the first thing they did when the gold had been sold back to us (Fal
He (the insurance agent) want ed to make sure the intermedi ary paid his income taxes on it,” Francis chuckles. “That put the screws to the intermediate guy which was pretty appropriate.” Francis started underground with Redpath and with a metallurgy background, Asarco moved him into the mill to run the gold room and the gold table. The company processed its own ore until the price of gold dropped and it be gan custom-milling the gold from Kidd Creek’s Hoyle Pond. Kidd Creek Mines designed a gold mill circuit within the Kidd Metallurgical Copper Smelter feed prep building nearly identical to the one at Aquarius so he was hired on to do the same work.
“We used to trip the metal detector with gold,” Francis explains. “The metal detectors are normally there to prevent tramped steel from going into your crusher. There was so much gold in the rock that it would trip out the metal detector.
There were times when we had rock that looked like it had a bunch of grapes attached to it – it was all gold. We used to pull nuggets the size of your thumb out of the ball mill feed chute. This was cleaned once a month to keep the volume down, it was that rich.”
Mining activities continued through 1989 under Falconbridge Gold Cor poration and continued until the purchase of Falconbridge Gold by Kinross Gold Corporation in 1994.
In Hoyle Pond’s first 20 years it pro duced two million ounces of gold. Goldcorp acquired 51% of the Porcu pine Joint Venture (PJV) from Placer Dome in May 2006. In 2007, Gold corp acquired the remaining 49%.