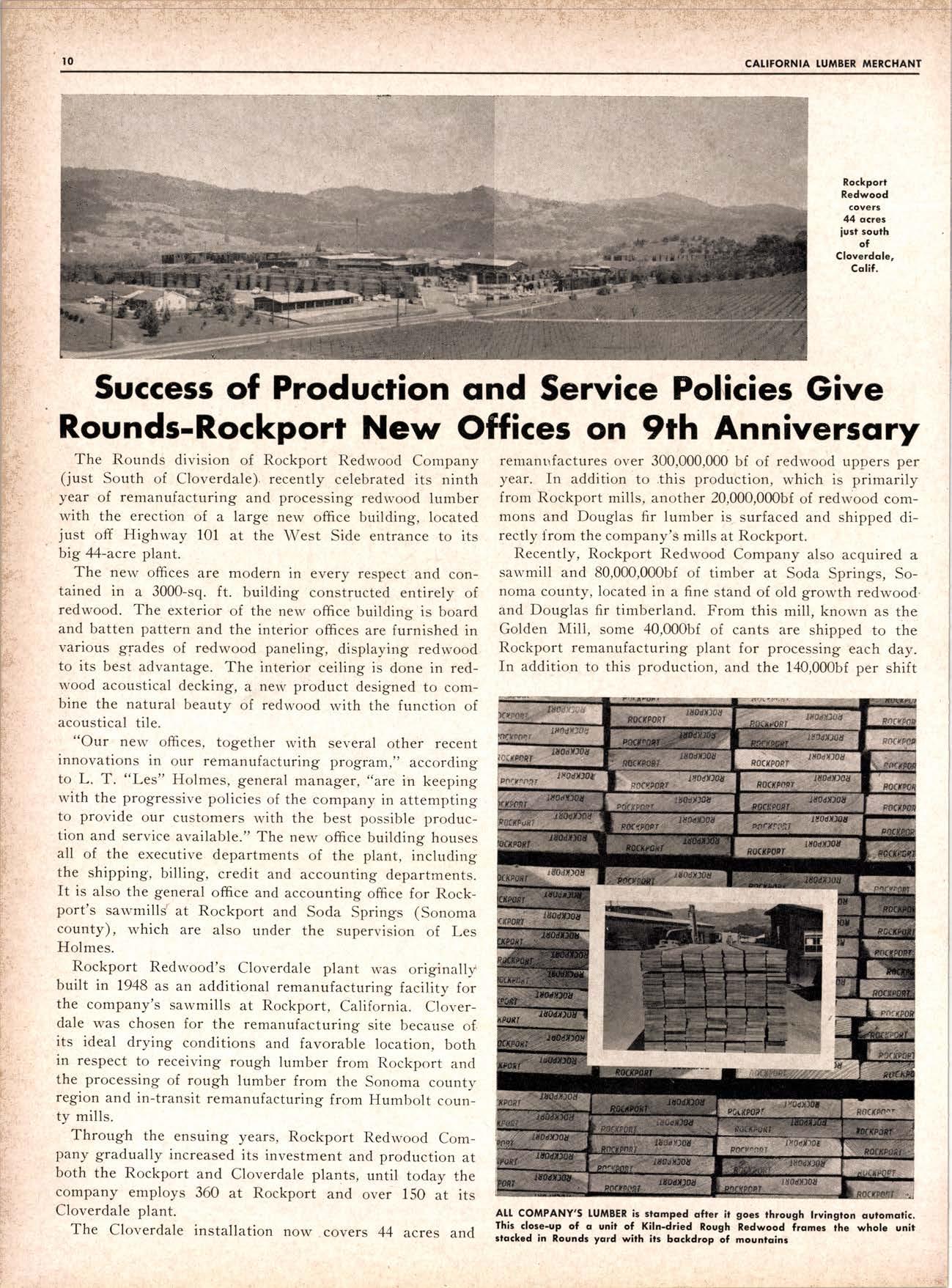
3 minute read
Success of Production qnd Service Pol'icies Give Rounds-Rockport New Offices on 9rh Anniversqry
The Rounds division of Rockport Redwood Company (just South of Cloverdale), recently celebrated its ninth year of remanufacturing and processing redwood lumber with the erection of a large new office building, located just off Highway 101 at the West Side entrance to its big 44-acre plant.
The new offices are modern in every respect and contained in a 3000-sq. ft. building constructed entirely of redwood. The exterior of the new office building is board and batten pattern and the interior offices are furnished in various grades of redwood paneling, displaying redwood to its best advantage. The interior ceiling is done in redwood acoustical decking, a new product designed to combine the natural beauty of redwood with the function of acoustical tile.
"Our new offices, together with several other recent innovations in our remanufacturing program," according to L, T. "Les" Holmes, general manager, "are in keeping with the progressive policies of the company in attempting to provide our customers rvith the best possible production and service available." The new office building houses all of the executive departments of the plarrt, including the shipping, billing, credit and accounting departments. It is also the general office and accounting office for Rockport's sawmills at Rockport and Soda Springs (Sonoma county), which are also under the supervision of Les Holmes.
Rockport Redwood's Cloverdale plant was originally built in 1948 as an additional remanufacturing facilitv for the company's sawmills at Rockport, California. Cloverdale was chosen for the remanufacturing site because oi its ideal drying conditions and favorable location, both in respect to receiving rough lumber from Rockport and the processing of rough lumber from the Sonoma county region and in-transit remanufacturing from Humbolt county mills.
Through the ensuing years, Rockport Redwood Company gradually increased its investment and production at both the Rockport and Cloverdale plants, until today the company employs 36O at Rockport and over 150 at its Cloverdale plant.
The Cloverdale installation now covers 44 acres and remanrrfactures over 300,000,000 bf of redwood uppers per year. In addition to .this production, which is primarily from Rockport mills, another 20,000,000bf of redwood commons and Douglas fir lumber is surfaced and shipped directly irom the company's mills at Rockport.
Recently, Rockport Redwood Company also acquired a sawmill and 80,000,00obf of timber at Soda Springs, Sonoma county, located in a fine stand of old growth redwood. and Douglas fir timberland. From this mill, known as the Golden Mill, some 40,000bf of cants are shipped to the Rockport remanufacturing plant for processing each day. In addition to this production, and the 140,000bf per shift
FIRST PANEI (1. lo r.): Horry Mcrlo, vicc-pre:idenl ond gonelol msnoger of Round: Lumber Go., Sqn Froncisco (l.fr in left photo) ond 1,. l. Holmer, Rockport Redwood Co. generol monoger; sacond photo: plont interior seen frgm top of dry kilnr; green chain to dght, ploning mill lo rcor; third photo: Chorlie Moikin, residcnt monqger of Rockporr Redwood ol Rockport, Colif.
SECOND PANEL: Borery of eighr dry kilns with totol copocity of 500,000 bf per chcrge; moncgement insists on neol plcnt, one of big reosons for minimum of plonf sccidenls ond wcsle; second pholo: fire-prolection syttem includes
$250,000 sprinkler fed by reservoir of plonl reor (i/s olso stocked with trour); third: f,otcar ol end of big spur line, lorge truck-looding oreo ot righr; besides controct houlers, Rockport uses its own nine semis for prompt mixed or 3troight ship-
INEN'S. THIRD PANET: NEW WOOdS molcher cnd lrvington sutomotic R/L end surfscer ond end printer bolster quolity-mi!ling progrom; :econd: Elmer Oben, in chorge of dry kilns, 3ticking, re:ow, soiling of green ond receiving of oll redwood (lefr), Horrv lflerlo ond Elm.i Rodgerr, in chorge of ploner produclion qnd shipping; third: l2-ccr spur with "window.ehode" convor coverg for eoch locding dock ollowr oll-weather corlooding. FOURTH
PANEI: Bcvel-siding mill where qll kiln-dried riding ir produced ond bundled, ond (righr) V.-P. Merlo inspecr q bundle of bevel riding being looded for eart€rn cu3tomer,
New ofiice building u3e3
Redwood to best odvonlcge throughout, houscs lhe enlire odminislrqlive stofi of pl6nt lnlerior views of lhc new oficer ql Roundr rhow how thcy ore poncled in voriety of beautiful Redwood pollern3 ond cover sorne 3,01X, squcre feel produced at Rockport, California, the Cloverdale plant also remanufactures 100,000bf of controlled production daily.
The Cloverdale plant maintains a redwood inventory of approximately 20,000,000bf, of which around 12,000,000bf is on sticks at all times ;70% of this inventory is in upper grades. Kiln facilities include eight dry kilns with a total capacity of 500,000 bf of 1" lunrber per charge. In addition to drying all upper grades of redwood, Rockport Redwood also dries some of its common grades. Diversified shipments are the rule rather than the exception-any combination of rough green or dry finish lumber in straight or mixed truck-and-trailer or carload lots. The firm employs nine of its own big semi rigs for truck and trailer shipments and it maintains a twelve-car spur line to facilitate car shipments.
Rockport's never-ending cycle of mill modernization and improvement was recently capped by the installation of a new Woods Matcher equipped with an Irvington automatic R/L end surfacer and end printer-insuring smooth, even-end milling and end stamping of the brand name "ROCKPORT" on every piece of lumber that goes through the plant.
"We are proud of our lumber and milling and we rvant to identify it as "ROCKPORT" brand forallto see," Holmes pointed out. "This installation, together with our present Glz-A Stetson-Ross and additional surfacing equipment and moulders, is a part of our continuing effort
(Continued on Page 14)
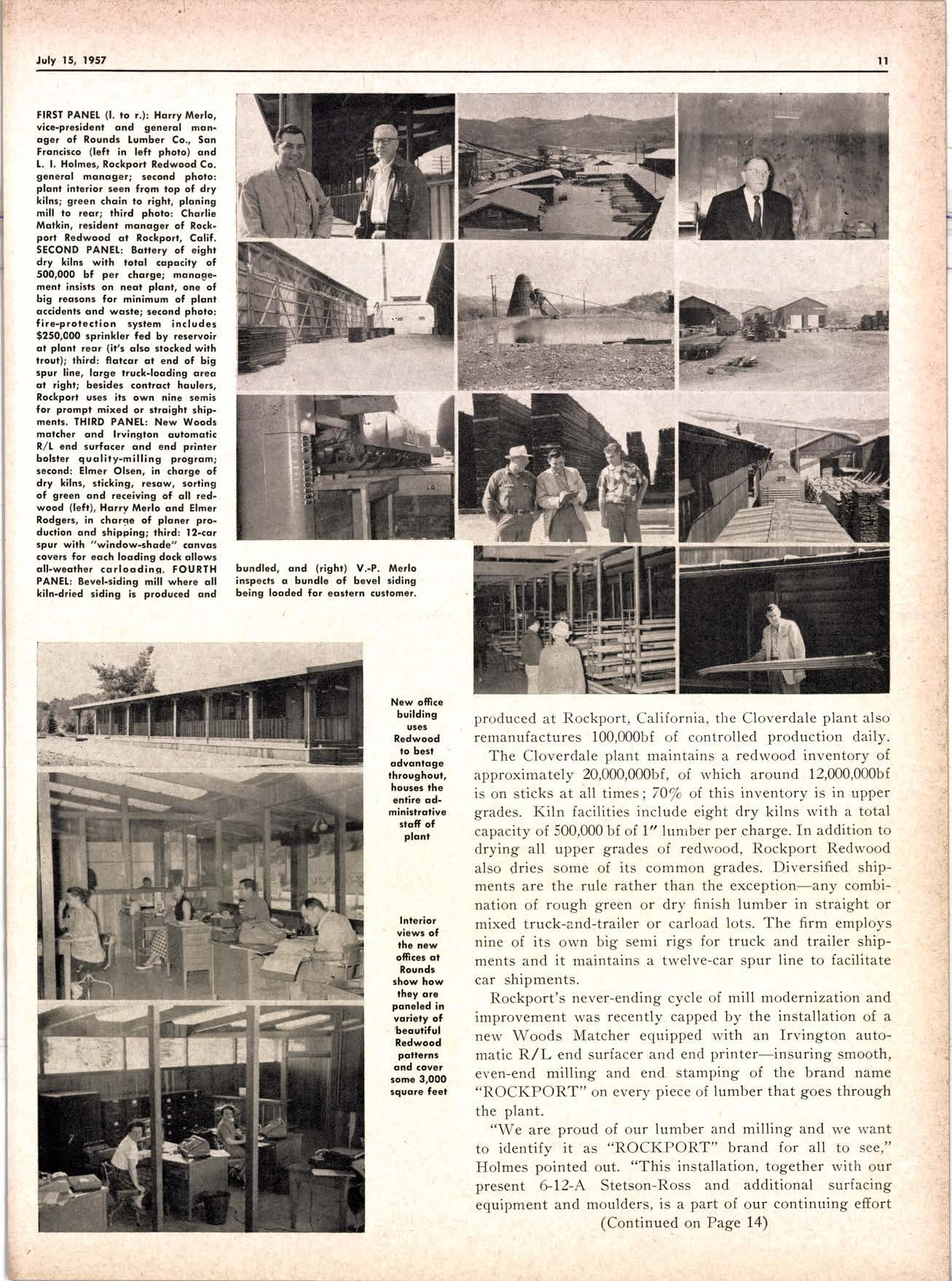