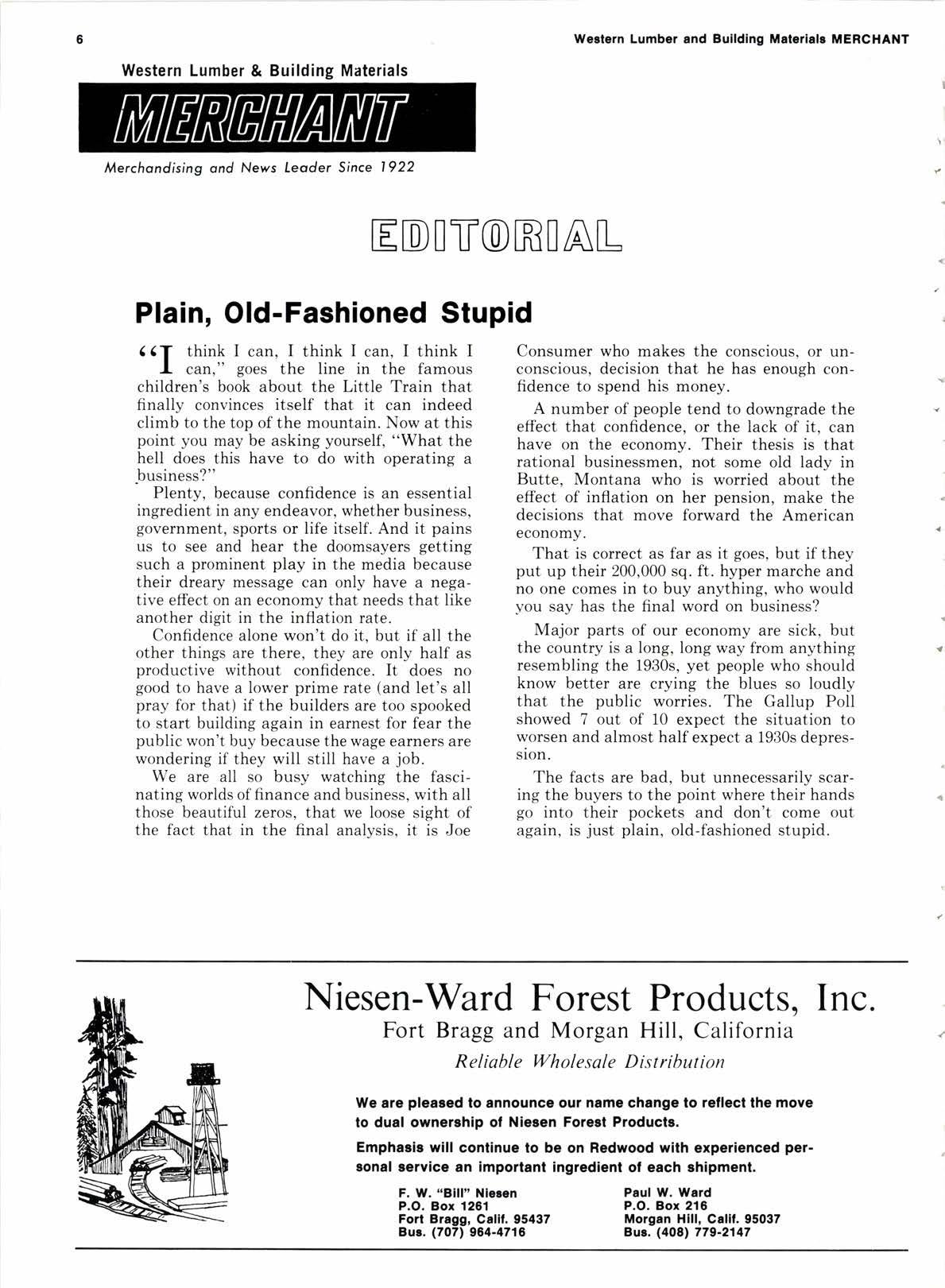
2 minute read
Niesen-Ward Forest Products, Inc.
Fort Bragg and Morgan Hill, California Reliable Wholesale Distribution
We are pleased to announce our name change to reflect lhe move to dual ownership ol Nieren Fored Producta.
Emphaais will continue lo be on Redwood with experienced perronal service an important ingredient of each shipment.
"ARCO supplies lOOo/o Old-Growth Redwood?"
"No problem with long term timber supply?" "hlgEtB"
"Finest Kiln Dried OualityT"ccwrt
"Any problem with pool car or truck & trailer orders?"
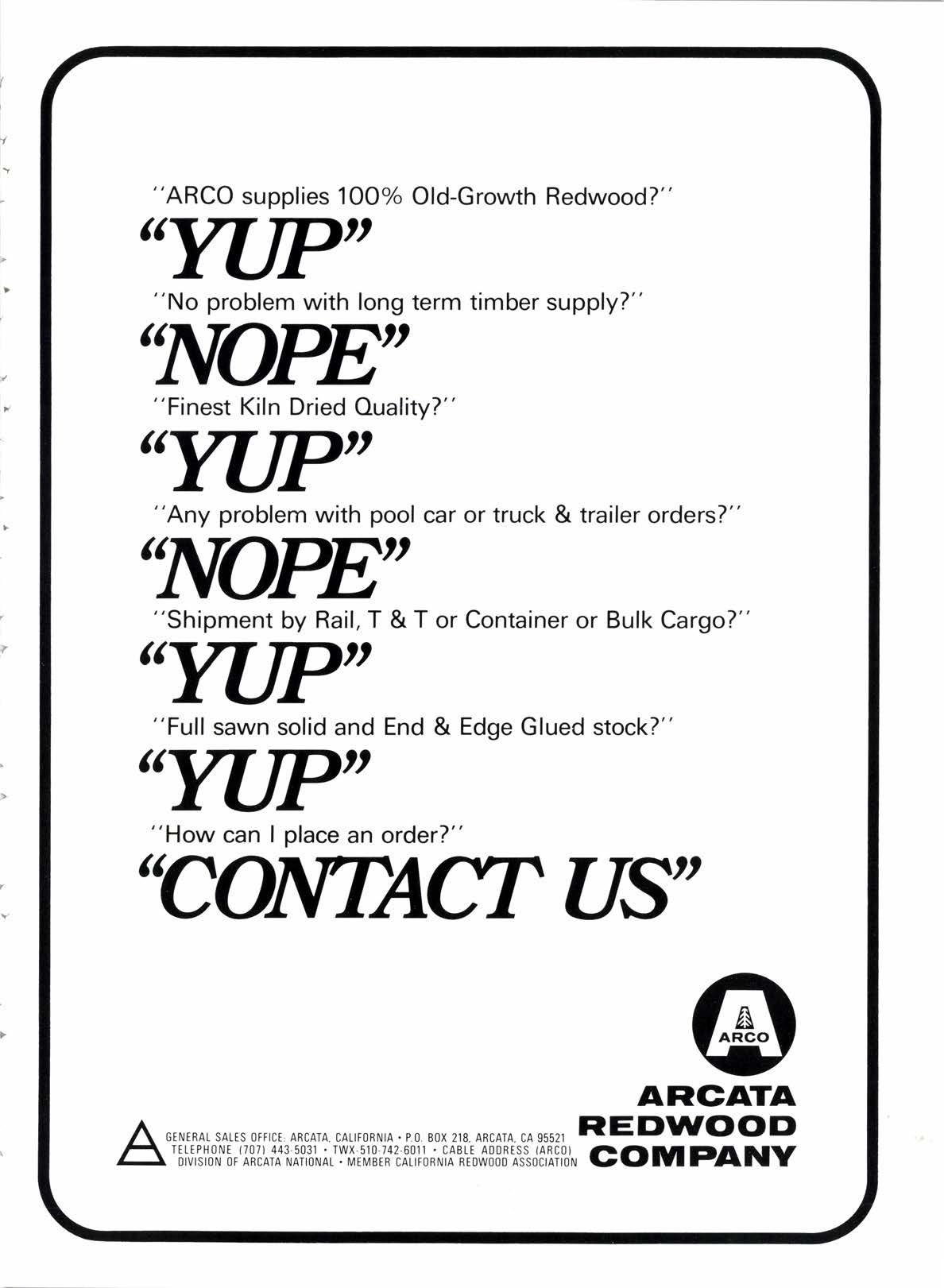
"Shipment by Rail, T & T or Container or Bulk Cargo?"
"Full sawn solid and End & Edge Glued stock?"
"How can I place an order?"
EASY ACCESS Post-and-beam design, with posts separated as widely as required, allows Jor unimpeded movement of all types ol materials handling equipment at wholesale lumber section, Ward & Harrington Home lmprovement Center. Posts, aparl from other advantages, proved uniquely applicable for loundation use because ol special soil problem created by high clay conlenl.
Entirely apart from substantial cost savings over tilt-up concrete or pre-fab steel, for comparable square footage, the poles proved uniquely applicable in the Costa Mesa project because of a serious soil problem, according to Leon R. Durham, of Treated Pole Builders, Inc., Ontario, Ca.
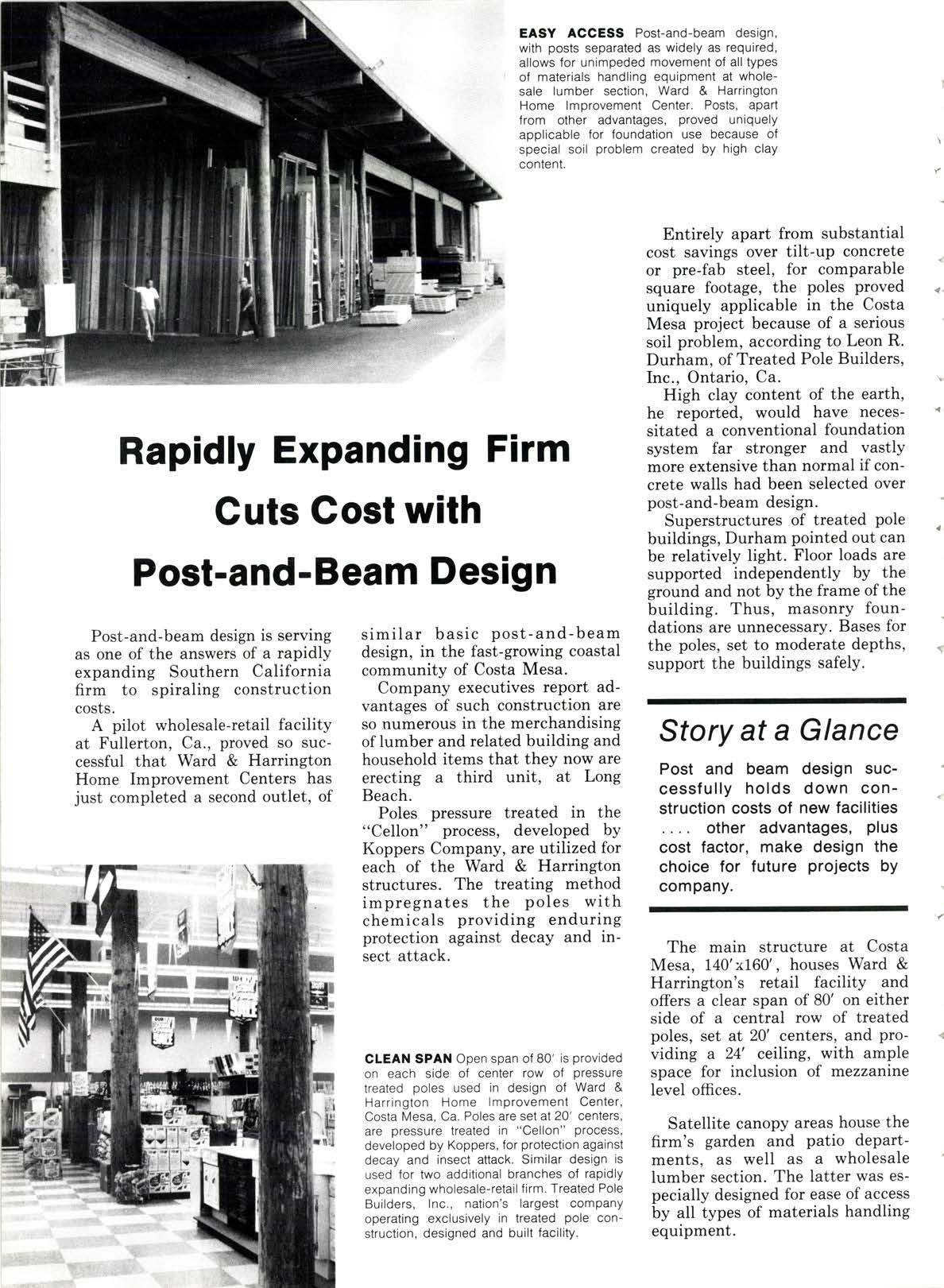
Rapidly Expanding Firm Guts Cost with Post-and-Beam Design
Post-and-beam design is serving as one of the answers of a rapidly expanding Southern California firm to spiraling construction costs.
A pilot wholesale-retail facility at Fullerton, Ca., proved so successful that Ward & Harrington Home Improvement Centers has just completed a second outlet, of similar basic post-and-beam design, in the fast-growing coastal community of Costa Mesa.
Company executives report advantages of such construction are so numerous in the merchandising of lumber and related building and household items that they now are erecting a third unit, at Long Beach.
Poles pressure treated in the "Cellon" process, developed by Koppers Company, are utilized for each of the Ward & Harrington structures. The treating method impregnates the poles with chemicals providing enduring protection against decay and insect attack.
High clay content of the earth, he reported, would have necessitated a conventional foundation system far stronger and vastlY more extensive than normal if concrete walls had been selected over post-and-beam design.
Superstructures of treated pole buildings, Durham pointed out can be relatively light. Floor loads are supported independently by the ground and not by the frame of the building. Thus, masonry foundations ate unnecessary. Bases for the poles, set to moderate depths, support the buildings safely.
Story at a Glance
Post and beam design successfully holds down construction costs of new facilities other advantages, plus cost factor, make design the choice for future projects by company.
CLEAN SPAN Open span of B0' is provided on each side of center row of pressure treated poles used in design of Ward & Harrington Home lmprovement Center, Costa Mesa, Ca. Poles are set at 20' centers, are pressure treated in "Cellon" process, developed by Koppers, for prolection against decay and insect attack. Similar design is used for two additional branches of rapidly expanding wholesale-retail iirm. Treated Pole Builders, Inc., nation's largest company operating exclusively in treated pole construction, designed and built facility.
The main structure at Costa Mesa. 140'x160', houses Ward & Harrington's retail facility and offers a clear span of 80' on either side of a central row of treated poles, set at 20' centers, and providing a 24' ceiling, with ample space for inclusion of mezzanine level offices.
Satellite canopy areas house the firm's garden and patio dePartments, as well as a wholesale lumber section. The latter was especially designed for ease of access by all types of materials handling equipment.