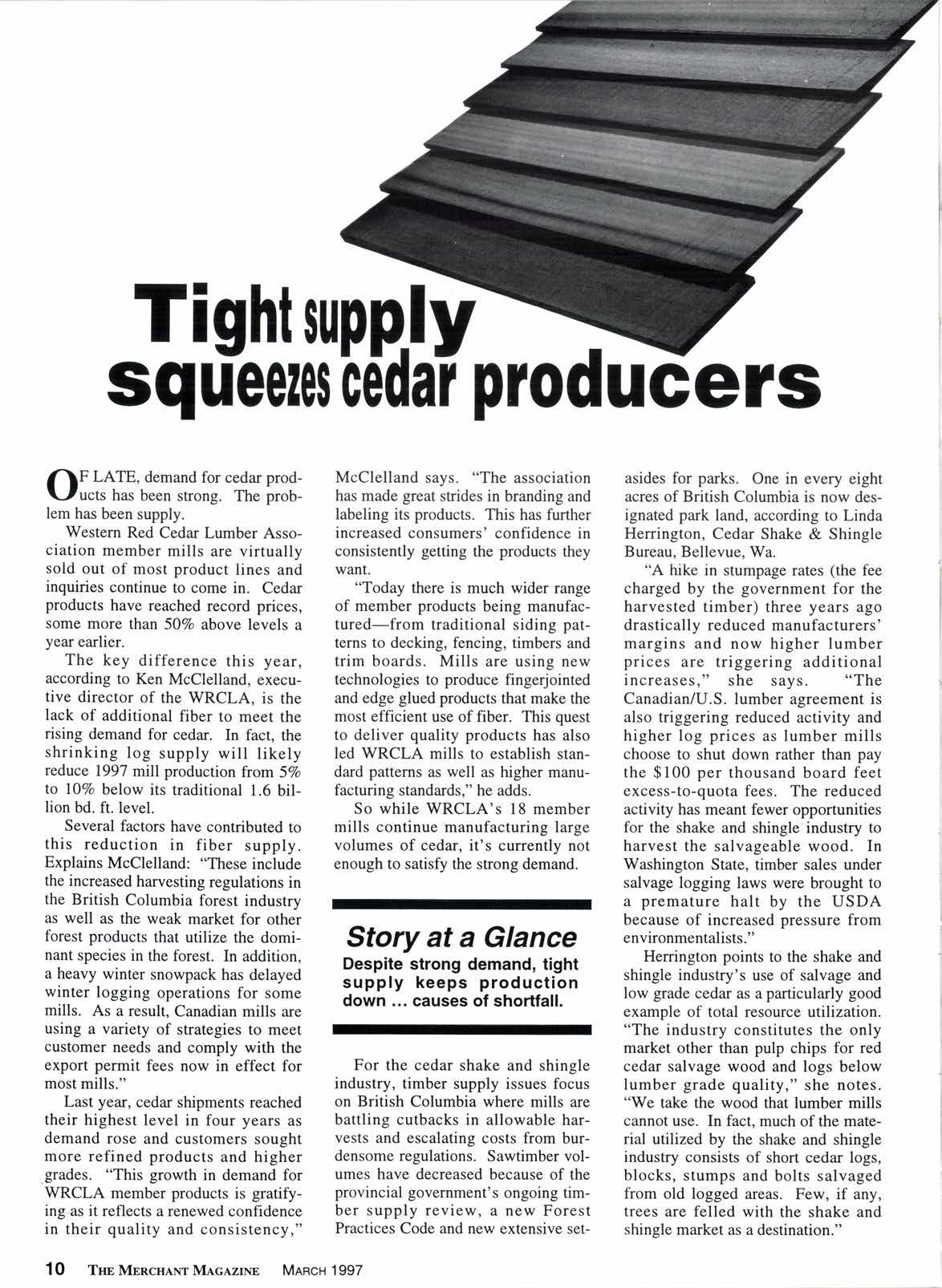
6 minute read
Tight supp.ll squeere$ceoar produders
nF LATE, demand for cedar prod\-fucts has been strong. The problem has been supply.
Western Red Cedar Lumber Association member mills are virtually sold out of most product lines and inquiries continue to come in. Cedar products have reached record prices, some more than 50Vo above levels a year earlier.
The key difference this year, according to Ken McClelland, executive director of the WRCLA, is the lack of additional fiber to meet the rising demand for cedar. In fact, the shrinking log supply will likely reduce 1997 mill production from 5Vo to l0Vo below its traditional 1.6 billion bd. ft. level.
Several factors have contributed to this reduction in fiber supply. Explains McClelland: "These include the increased harvesting regulations in the British Columbia forest industry as well as the weak market for other forest products that utilize the dominant species in the forest. In addition, a heavy winter snowpack has delayed winter logging operations for some mills. As a result, Canadian mills are using a variety of strategies to meet customer needs and comply with the export permit fees now in effect for most mills."
Last year, cedar shipments reached their highest level in four years as demand rose and customers sought more refined products and higher ,grades. "This growth in demand for WRCLA member products is gratifying-as it reflects a renewed confidence in their quality and consistency,"
McClelland says. "The association has made great strides in branding and labeling its products. This has further increased consumers' confidence in consistently getting the products they want.
"Today there is much wider range of member products being manufactured-from traditional siding patterns to decking, fencing, timbers and trim boards. Mills are using new technologies to produce fingerjointed and edge glued products that make the most efficient use of fiber. This quest to deliver quality products has also led WRCLA mills to establish standard patterns as well as higher manufacturing standards," he adds.
So while WRCLA's 18 member mills continue manufacturing large volumes of cedar, it's currently not enough to satisfy the strong demand.
Story at a Glance
Despite strong demand, tight supply keeps production down ... causes of shortfall.
For the cedar shake and shingle industry, timber supply issues focus on British Columbia where mills are battling cutbacks in allowable harvests and escalating costs from burdensome regulations. Sawtimber volumes have decreased because of the provincial government's ongoing timber supply review, a new Forest Practices Code and new extensive set- asides for parks. One in every eight acres of British Columbia is now designated park land, according to Linda Herrington, Cedar Shake & Shingle Bureau, Bellevue, Wa. nEDWOOD and westl\ern red cedar, while often preferred for siding, decks and other outdoor structures because of their beauty, stability and durability, will, if left natural or poorly maintained, begin to show their age. Retailers should have ready answers for customers anxious to restore woods discolored by sunlight, moisture, temperature, microorganisms. dirt or soot.
"A hike in stumpage rates (the fee charged by the government for the harvested timber) three years ago drastically reduced manufacturers' margins and now higher lumber prices are triggering additional increases," she says. "The Canadian/U.S. lumber agreement is also triggering reduced activity and higher log prices as lumber mills choose to shut down rather than pay the $100 per thousand board feet excess-to-quota fees. The reduced activity has meant fewer opportunities for the shake and shingle industry to harvest the salvageable wood. In Washington State, timber sales under salvage logging laws were brought to a premature halt by the USDA because of increased pressure from environmentalists."
Herrington points to the shake and shingle industry's use of salvage and low grade cedar as a particularly good example of total resource utilization. "The industry constitutes the only market other than pulp chips for red cedar salvage wood and logs below lumber grade quality," she notes. "We take the wood that lumber mills cannot use. In fact, much of the material utilized by the shake and shingle industry consists of short cedar logs, blocks, stumps and bolts salvaged from old logged areas. Few, if any, trees are felled with the shake and shingle market as a destination."
The first step toward suggesting a remedy is identifying the source of discoloration. The wood maY have turned driftwood gray due to ultraviolet radiation and precipitation, or nearly black as a result of mildew growth, soot accumulation, extractive staining, or iron in fasteners. contaminated finishes or airborne particles.

Mildew is often the culPrit on decks and siding in moist environments, often in areas with restricted air flow, high humidity or too much shade. While unsightly, mildew is a superficial fungus growth that does not degrade the wood's structure. It commonly appears as numerous small dark spots on the wood's surface with gray, fan-shaped areas sPreading below as spores from the original colony multiply and are washed down the surface.
Mildew can be treated with sPecialty cleaners or common household bleach, later rinsing off mild cases or scrubbing off more severe infestations with a stiff bristle brush and a solution of one cup of trisodium Phosphate (TSP), one cup of liquid bleach and one gallon of water.
Naturally occurring chemical extractives in cedar and redwood contribute to their beauty, stability and durability; but sometimes migrate to the wood's surface. High concentrations cause discoloration, which may appear in several forms: boards, high in extractive content, that turn very dark if unprotected by finishes and exposed to moisture; extractives bleeding through paint if stain-blocking oil or alkyd primers weren't used; condensation on the unPrimed back side of boards.
A warm water detergent solution that includes a specialty brightener or oxalic acid can be used to diagnose and remove extractive stains. If extractives have bled through paint or stain and aren't readily removed by the solution, the surface may have to be repainted, using a stain-blocking primer.
Tannins may also react to iron and water to form a dark, blue-black iron tannate precipitate. Long-term iron exposure can cause deterioration which appears similar to charring or decay. Iron stains maY be easy to detect since they are often near nail heads, screw heads or other hardware.
Scattered discrete, dark flecks maY result from the use of steel wool or wire brushes, or from airborne iron dust from machinerY. occurring almost immediately after the ironcontaminated wood becomes wet. Rough or surfaced green wood sometimes has inky black marks where it has come in contact with forklift blades, rollers, strapping or other iron materials. Iron-contaminated finishes or water may result in a more uniformly distributed, gray-to-black discoloration.
Most iron stains can be removed by using the same solutions as for removing extractive stains. It may be more difficult, however, to remove and prevent recurrence of nail stains, since they penetrate deePlY. The nails should be replaced or countersunk, the holes swabbed with a water repellent and filled with a durable exterior wood filler.
Lime found in mortar and concrete mixes can cause severe stains when spilled or tracked onto redwood. Unfortunately, sanding or bleaching will not remove these black stains.
Many commercial Products are available for removing discolorations and restoring the new appearance of cedar and redwood. These Products are offered in powder or liquid concentrate form and are typically based upon non-chlorine bleaches, detergents and/or oxalic acid' Selling points are: they are intended for a specific use, come with detailed instructions and are quite effective.
Story at a Glance
First step is identifYing cause of discoloration ... sell cleaners, brighteners and finishes to avoid future Problems.
Powerwashing is a PoPular aPPlication method, saving time and labor, but is a choice better suited for experienced contractors. Water and pressure are fundamental enemies of wood, so improper powerwashing can do more harm than good.
And make sure once the wood has been cleaned and restored, a protective finish is applied. High quality products containing mildewcides, water repellents and ultraviolet protection provide the best performance.
ll /I'OISTURE is a notorious enemy IVtof fingerjointed wood products. Yet one manufacturer has found a way to fingerjoint lumber before it's ever dried.
After more than a year of research and development, and a rigorous, months-long testing approval process, Wood Fiber Products, Inc., Lockeford, Ca., has devised a new process to fingerjoint green lumber. Their secret is in the adhesive. "I don't know of anybody else that's doing this," explains WFP's Bob Prouty. "No one else could find a glue that would hold. The problem with fingerjointing is when you get the lumber wet, it will reject the glue. The moisture is absorbed, and the lumber might fall apart."
Last year, Wood Fiber Products began working with a glue manufacturer familiar with adhesives which use fiber as a filler. Their unique new adhesive allows WFP to fingerjoint both green and dry without end shrinkage. The joint reportedly is as strong as the wood itself.
He says the process is user friendly and environmentally friendly, devoid of any carcinogens, contaminants, pollutants or other toxic emissions.
The testing on green lumber also provided the company with horizontal structural approval for fingerjointing kiln dried lumber.
WFP plans to fingerjoinr both green and kiln dried blocks in redwood, hem-fir and Douglas fir. New products include redwood decking, fascia, siding and fencing products green or dry to specified lengths, hem-fir and Douglas fir dry plate and treated stock to specified lengths with approved grade stamps. WFP is even working with the same manufacturer to develop stains to go with the redwood decking.
The company also produces finger- joint blanks and studs, edge-glued products, box shook and cut stock.
Prouty attributes the need for such new engineered wood products to the curtailment of federal government timber sales. "New processes such as fingerjointing green lumber will provide yet another way to increase the utilization of what timber that is available," he says.
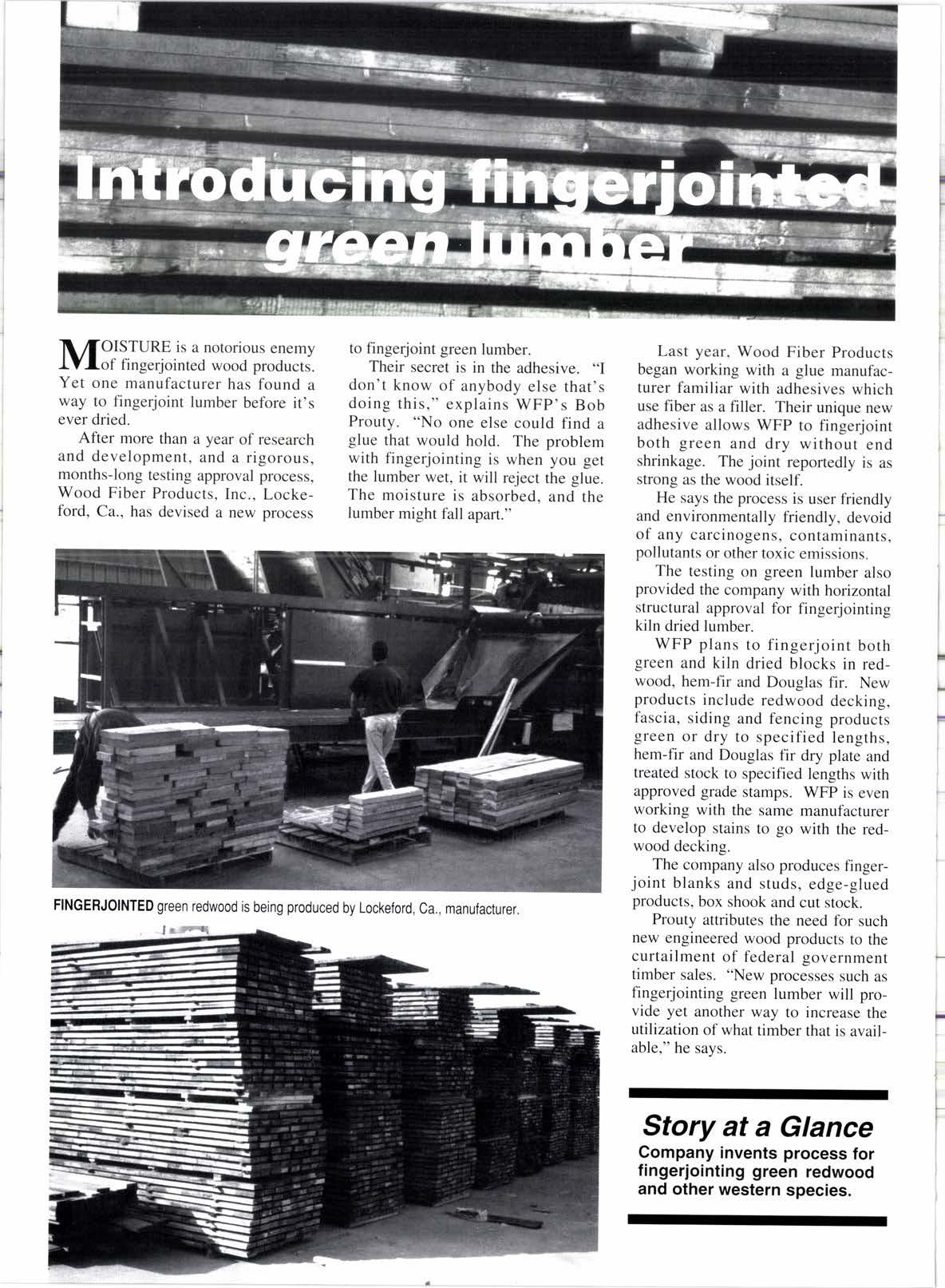