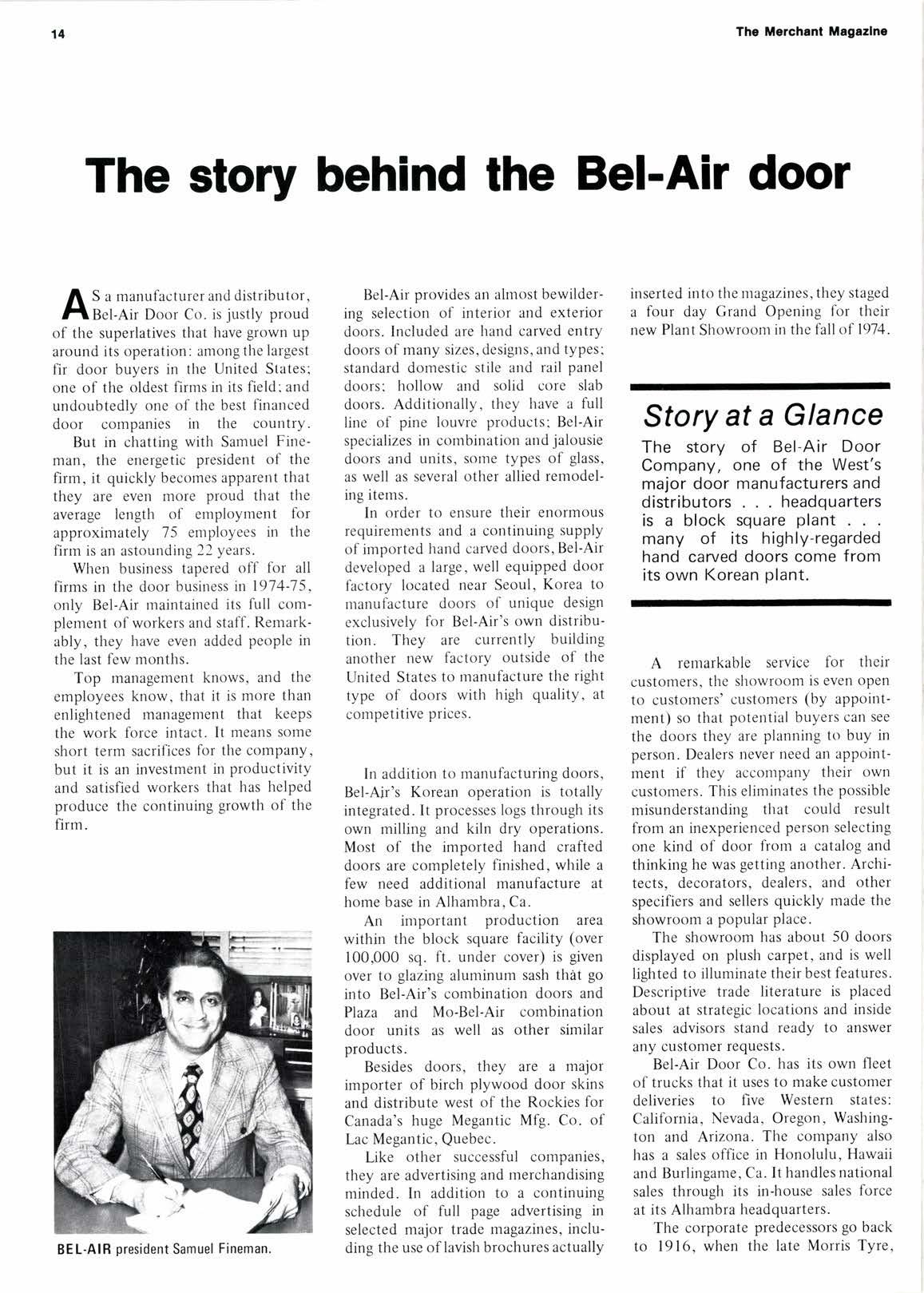
6 minute read
The story behind the Bel-Air door
S a manufacturer and distributor, Bel-Air Door Co. is justly proud of the superlatives that have grown up around its operation: among the largest fir door buyers in the United Statesi one of the oldest firms in its field: and undoubtedly one of the best financed door companies in the country.
But in chatting with Samuel Fineman, the energetic president of the firm, it quickly becomes apparent that they are even more proud that the average length of employment for approximately 75 employees in the firm is an astounding 22 years.
When business tapered off for all firms in the door business in 1974-75, only Bel-Air maintained its full complement of workers and staff Remarkably, they have even added people in the last few months.
Top management knows, and the employees know, that it is more than enlightened management that keeps the work force intact. It means some short term sacrifices for the company, but it is an investment in productivity and satisfied workers that has helped produce the continuing growth of the firm.
Bel-Air provides an almost bewildering selection of interior and exterior doors. Included are hand carved entry doors of many sizes, designs, and types: standard domestic stile and rail panel doors: hollow and solid core slab doors. Additionally, they have a full line of pine louvre products: Bel-Air specializes in combination and jalousie doors and units, some types of glass, as well as several other allied remodeling items.
In order to ensure their enormous requirements and a continuing supply of imported hand carved doors, Bel-Air developed a large, well equipped door factory located near Seoul, Korea to manufacture doors of unique design exclusively for Bel-Air's own distribution. They are currently building another new factory outside of the United States to manufacture the right type of doors with high qualitY, at competitive prices.
In addition to manufacturing doors, Bel-Air's Korean operation is totally integrated. It processes logs through its own milling and kiln dry operations. Most of the imported hand crafted doors are completely finished, while a few need additional manufacture at home base in Alhambra, Ca.
An important production area within the block square facility (over 100,000 sq. ft. under cover) is given over to glazing aluminum sash thAt go into Bel-Air's combination doors and Plaza and Mo-Bel-Air combination door units as well as other similar products.
Besides doors, they are a major importer of birch plywood door skins and distribute west of the Rockies for Canada's huge Megantic Mfg. Co. of Lac Megantic, Quebec.
Like other successful companies, they are advertising and merchandising minded. In addition to a continuing schedule of full page advertising in selected major trade magazines, including the use oflavish brochures actually inserted into the magazines, they staged a four day Grand Opening for their new Plant Showroom in the fall of 1974.
Story at a Glance
The story of Bel-Air Door Company, one of the West's major door manufacturers and distributors headquarters is a block square plant many of its highly-regarded hand carved doors come from its own Korean plant.
A remarkable service for their customers, the showroom is even open to customers' customers (by appointment) so that potential buyers can see the doors they are planning to buy in person. Dealers never need an appointment if they accompany their own customers. This eliminates the possible misunderstanding that could result from an inexperienced person selecting one kind of door from a catalog and thinking he was getting another. Architects, decorators, dealers, and other specifiers and sellers quickly made the showroom a popular place.
The showroom has about 50 doors displayed on plush carpet, and is well lighted to illuminate their best features. Descriptive trade literature is placed about at strategic locations and inside sales advisors stand ready to answer any customer requests.
Bel-Air Door Co. has its own fleet of trucks that it uses to make customer deliveries to five Western states: California, Nevada, Oregon, Washington and Arizona. The company also has a sales office in Honolulu, Hawaii and Burlingame, Ca. It handles national sales through its in-house sales force at its Alhambra headquarters.
The corporate predecessors go back to 1916, when the late Morris Tyre,
D00R INSPECTOR-repairman (1) is on fulltime duty to insure quality. (2) One of three door glazers who install a variety of types of glass in doors. (3) 0ne of several combination door production lines. Installer is using automatic screw driver. (4) Sash assembly operator on automatic sash assembly machine, part of a $l/4 million sash tooling. (5) Screening operation in the Bel-Air panel production line. Line operates fulltime, every day, year round.
Samuel Fineman's father-in-law, founded a company dealing in the glass business. The firm evolved over the years, moved away from concentrating on glass (though they still do a healthy business in glass) and now concentrates on doors. Starting with the company in early 1954, Fineman learned all phases of the business and in 1959 began a sister company, Alhambra Metal Products, which today does the bulk of its business supplying Bel-Air Door with jalousies and aluminum sash. The dollar value of the Alhambra, Ca., plant is put in excess of one and one-half million dollars with the worth of the machinery being an additional one-half million dollars.
Innovations in production, nrarketing, advertising and promotion have always rnarked the firrn as it has moved deftly through an ever-changing business world. Under the leadership of its able president, the future augers well for this experienced, solidly based exarnple of aggressive American free en terDnse.

ENOUGH hemlock to make a small hill (note size of workers on barge) backdrops (l-r) Daryl Bond, All-Coast Forest Products, and Clem Twombley, Doman Timber Sales, Ltd. In lower left picture, two cranes and a number of forklifts work away at unloading. Even its ocean going tug, right hand picture, is topped by huge mass of hemlock dimension. Lumber was loaded at Cowichan Bay. Vancouver lsland; Westcan was the shipper.
Another Record load of hemlock
S the biggest lumber market in the world, the greater southern California area understandably consumes lumber in gargantuan quantities and the barge pictured here qualifies as a biggie in anyone's league.
Loaded with 5.1 million gross footage of hemlock dimension lumber, enough to build more than 500 homes; it was valued at approximately S800,000. It is the largest single barge of lumber ever landed at Los Angeles Harbor, eclipsing the previous record setabout a month previous by the Ed Fountain Lumber Co. (see The Merchant, Jan. p. l3 ).
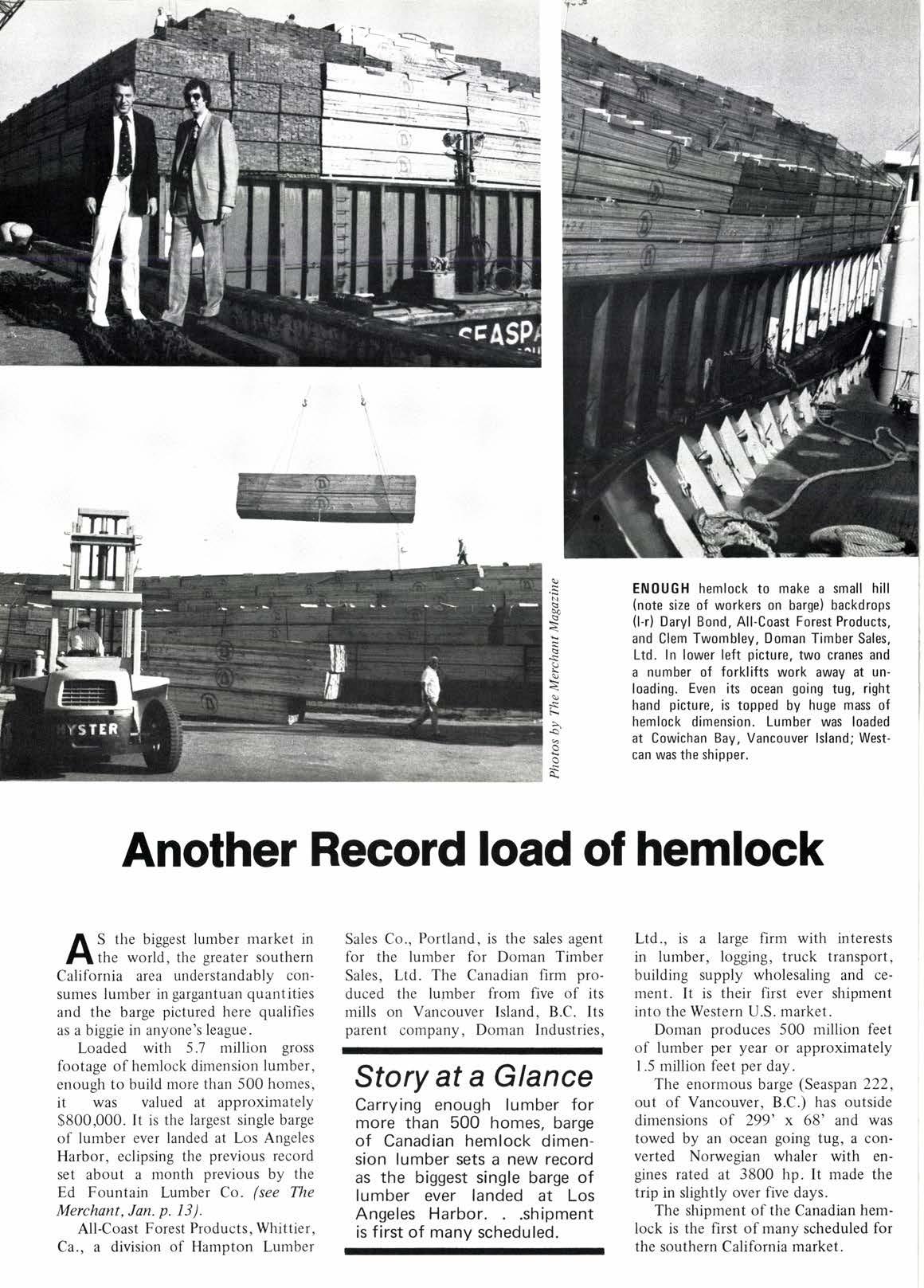
All-Coast Forest Products, Whittier, Ca., a division of Hampton Lumber
Sales Co., Portland, is the sales agent for the lumber for Doman Timber Sales, Ltd. The Canadian firm produced the lumber from five of its mills on Vancouver Island, B.C. Its parent company, Doman Industries,
Story at a Glance
Carrying enough lumber for more than 500 homes, barge of Canadian hemlock dimension lumber sets a new record as the biggest single barge of lumber ever landed at Los Angeles Harbor. .shipment is first of many scheduled.
Ltd., is a large firm with interests in lumber, logging, truck transport, building supply wholesaling and cement. It is their first ever shipment into the Western U.S. market.
Doman produces 500 million feet of lumber per year or approximately 1.5 million feet per day.
The enormous barge (Seaspan 222, out of Vancouver, B.C.) has outside dimensions of 299' x 68' and was towed by an ocean going tug, a converted Norwegian whaler with engines rated at 3800 hp. It made the trip in slightly over five days.
The shipment of the Canadian hemlock is the first of many scheduled for the southern California market.
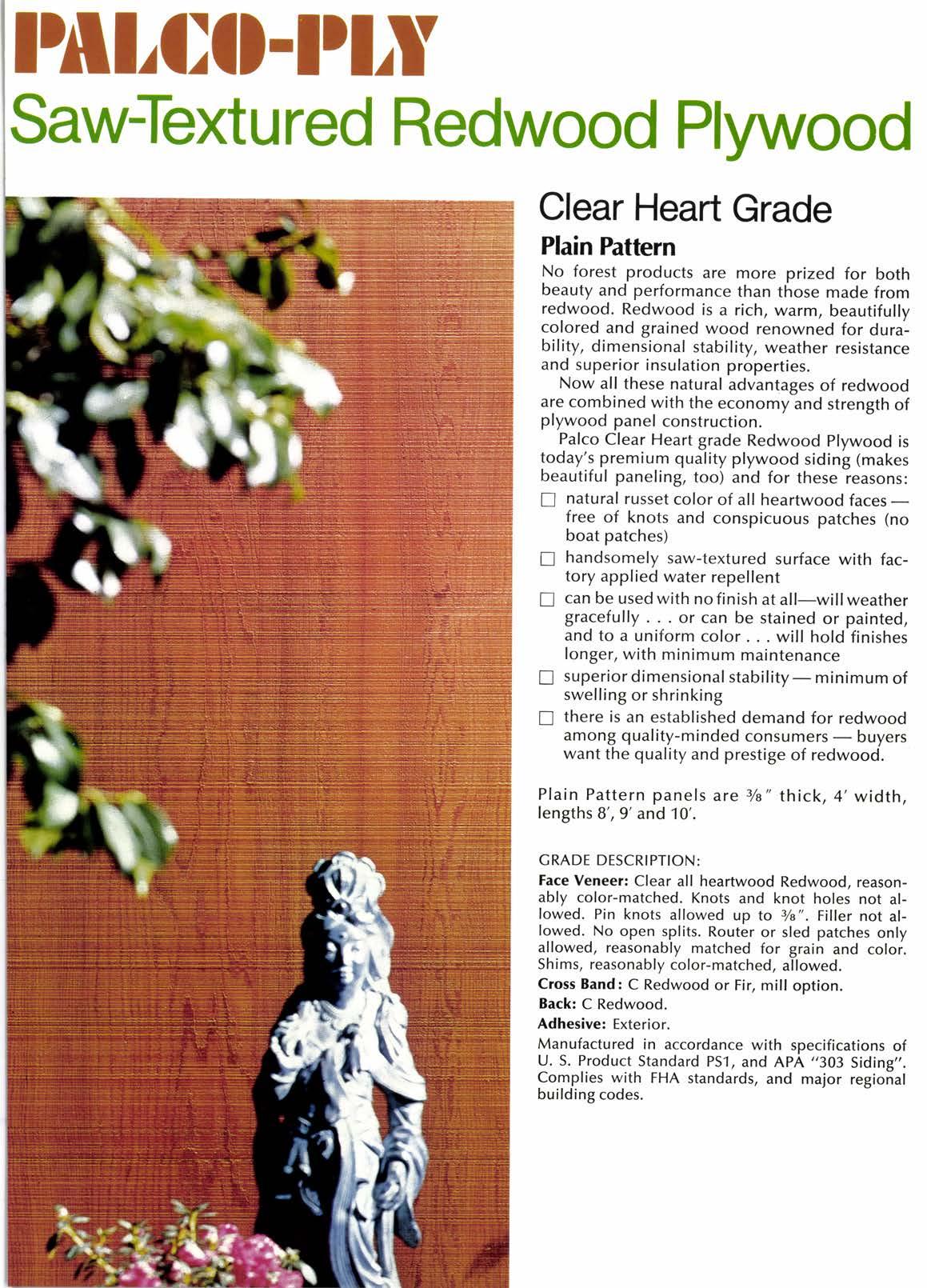
EXTERIORS:
Uses: Provides quality and prestige exteriors for all types of constructionf rom the most expensive custom homes to vacation cottages. ldeal also for commercial buildings where beauty of wood and ease of maintenance is required. Uses: siding, soffits, patio dividers, garden structures, carports, etc. Appf ication: The 3/a" panels may be nailed direct to studs 16" o.c.serves as both sheathing and siding in one application. Eliminates need for wall bracing and building paper. Or may be applied over any type of wall sheathing. In either case use corrosion-resistant 6d siding nails: hot dipped galvanized (not electro galvanized), stainless steel, or aluminum. Space nails 6" o.c, on panel edges, and 12" on intermediate studs, Drive flush but do not set. lmportant: leave 1/s" space at panel edges and ends; do not butt up tight.
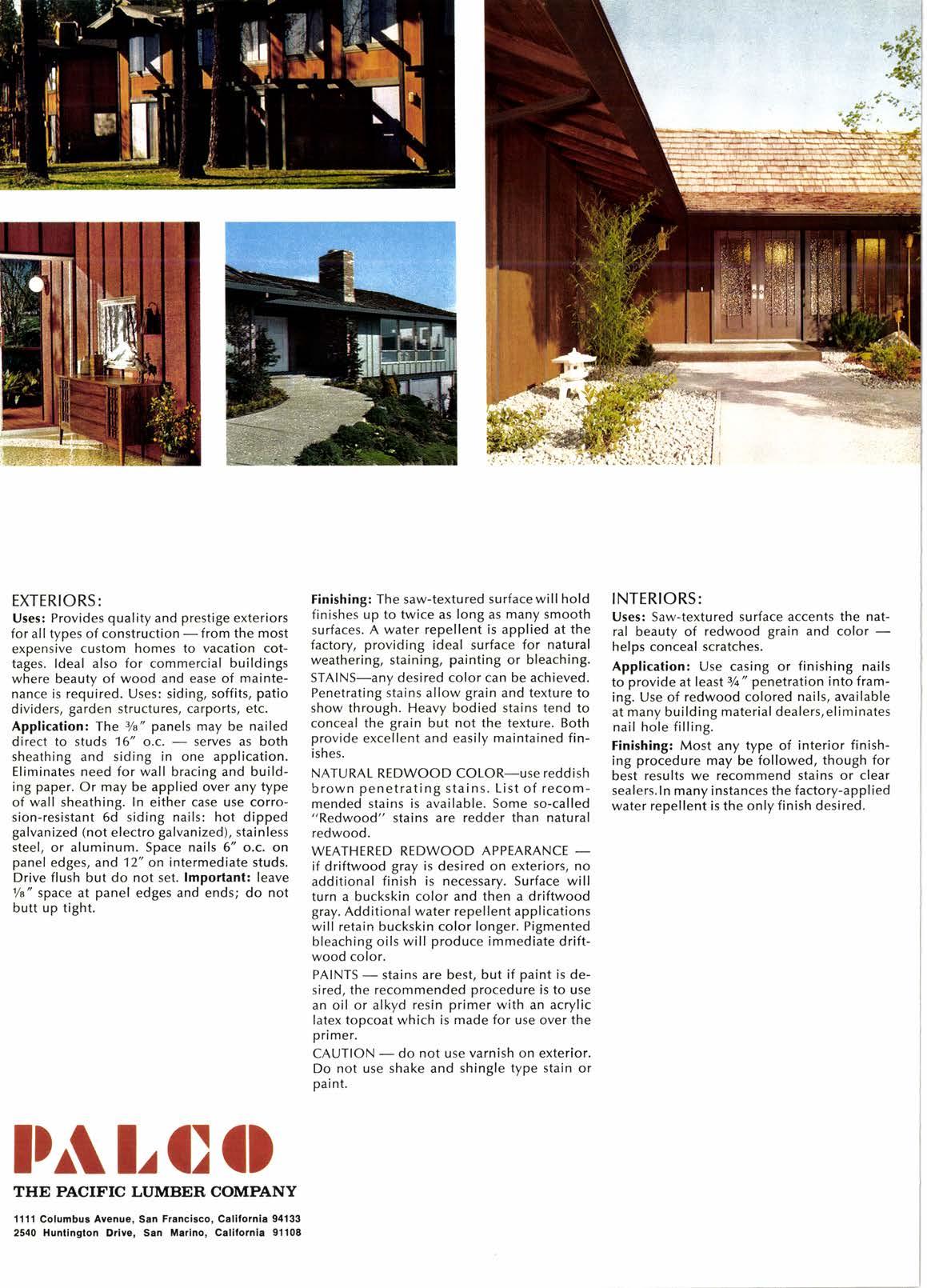
Finishing: The saw-textured surface will hold finishes up to twice as long as many smooth surfaces. A water repellent is applied at the factory, providing ideal surface for natural weathering, staining, painting or bleaching.
STAINS-any desired color can be achieved. Penetrating stains allow grain and texture to show through. Heavy bodied stains tend to conceal the grain but not the texture. Both provide excellent and easily maintained finishes.
NATURAL REDWOOD COLOR-use reddish brown penetrating stains. List of recommended stains is available. Some so-called "Redwood" stains are redder than natural redwood.
WEATHERED REDWOOD APPEARANCE if driftwood gray is desired on exteriors, no additional finish is necessary. Surface will turn a buckskin color and then a driftwood gray. Additional water repellent applications will retain buckskin color longer. Pigmented bleaching oils will produce immediate driftwood color.
PAINTSstains are best, but if paint is desired, the recommended procedure is to use an oil or alkyd resin primer with an acrylic latex topcoat which is made for use over the orimer.
CAUTIONdo not use varnish on exterior. Do not use shake and shingle type stain or paint.
INTERIORS:
Uses: Saw-textured surface accents the natral beauty of redwood grain and colorhelps conceal scratches.
Application: Use casing or finishing nails to provide at least 3/n " penetration into framing. Use of redwood colored nails, available at many building material dealers,eliminates nail hole filling.
Finishing: Most any type of interior finishing procedure may be followed, though for best results we recommend stains or clear sealers. I n many instances the factory-appl ied water repellent is the only finish desired.