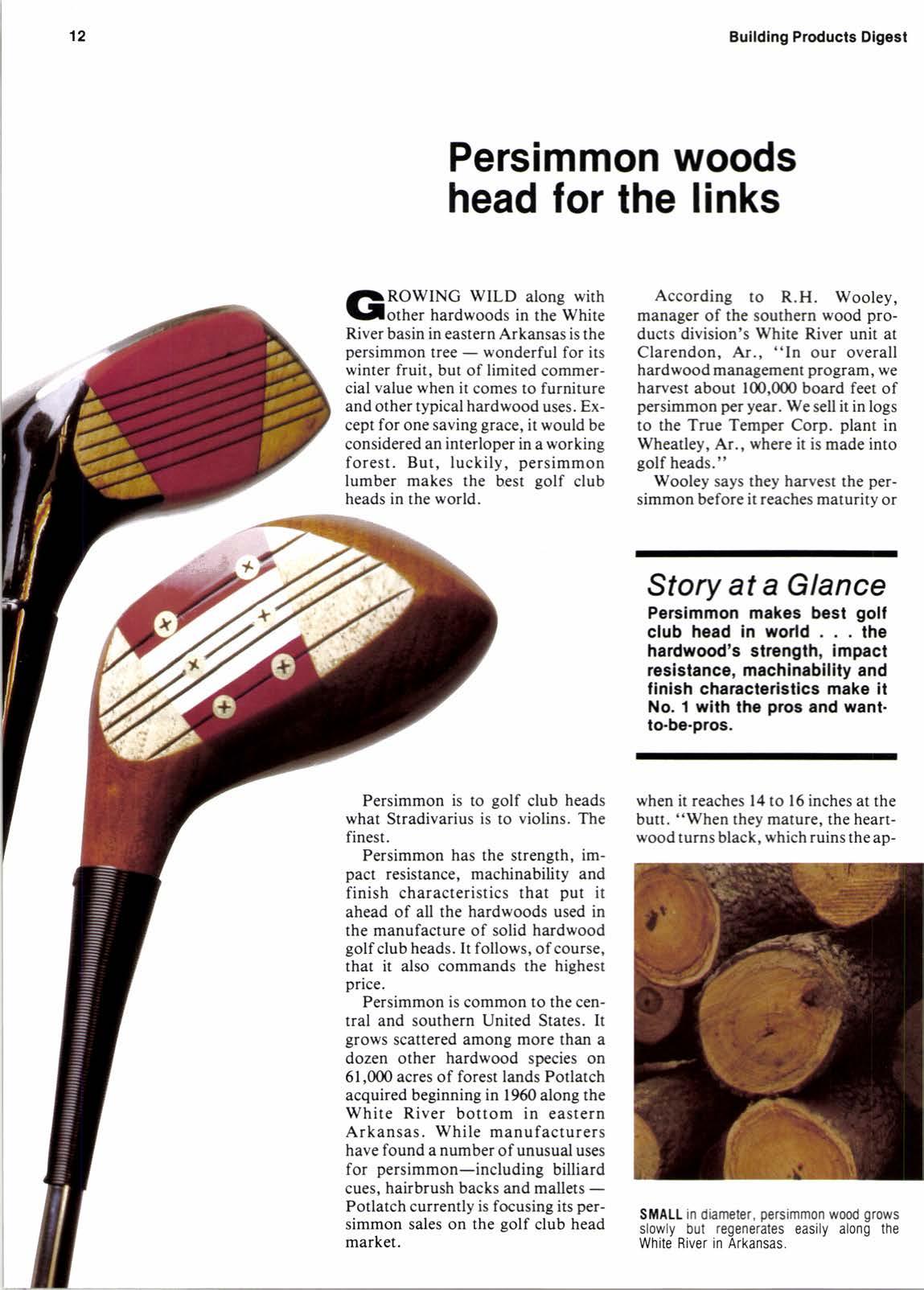
3 minute read
Persimmon woods head for the links
aEROWING WILD along with llotner
narowooos m rne wnrte River basin in eastern Arkansas is the persimmon treewonderful for its winter fruit, but of limited cornmercial value when it comes to furniture and other typical hardwood uses. Except for one saving grace, it would be considered an interloper in a working forest. But, luckily, persimmon lumber makes the best golf club heads in the world.
According to R.H. Wooley, manager of the southern wood products division's White River unit at Clarendon, Ar., "In our overall hardwood management program, we harvest about I(X),(XX) board feet of persimmon per year. We sell it in logs to the True Temper Corp. plant in Wheatley, Ar., where it is made into golf heads."
Wooley says they harvest the persimmon before it reaches maturity or
Story at a Glance
Perslmmon makes beet golf club head in world . the hardwood's stnnglh, impact reslslance, machlnrblllty and finlsh chancterlstlcs make it No. 1 with the pros and wanttobe-pros.
Persimmon is to golf club heads what Stradivarius is to violins. The finest.
Persimmon has the strength, impact resistance, machinability and finish characteristics that put it ahead of all the hardwoods used in the manufacture of solid hardwood golf club heads. It follows, of course, that it also commands the highest price.
Persimmon is common to the central and southern United States. It grows scattered among more than a dozen other hardwood species on 6l,000 acres of forest lands Potlatch acquired beginning in llXO along the White River bottom in eastern Arkansas. While manufacturers have found a number ofunusual uses for persimmon-including billiard cues, hairbrush backs and malletsPotlatch currently is focusing its persimmon sales on the golf club head market.
when it reaches 14 to 16 inches at the butt. "When they mature, the heartwood turns black, whichruinsthe ap- pearance of a golf head," he explains.
"Persimmon grow kinda slow, and sometimes they're hard to get at," Wooley says. But regeneration is easy. "They just keep on growing and coming back. The contractor assigned to logging the persimmon takes off through the woods on a skid tractor. When he finds one big enough, he'll cut it and move on to find the next one. In a half day, he'll get maybe l0 or 12 trees."
Wooley estimates that in the l8 years since he first set foot on the White River unit, more than 1.5 million board-feet of persimmon has been sent over to the True Temper plant to be converted into golf club heads. The Wheatley complex is one of only three plants in the world that produce solid hardwood golf heads. It ships out more than 500,000 semifinished club heads annuallv to sporting goods manufacturers in the United States and Japan.
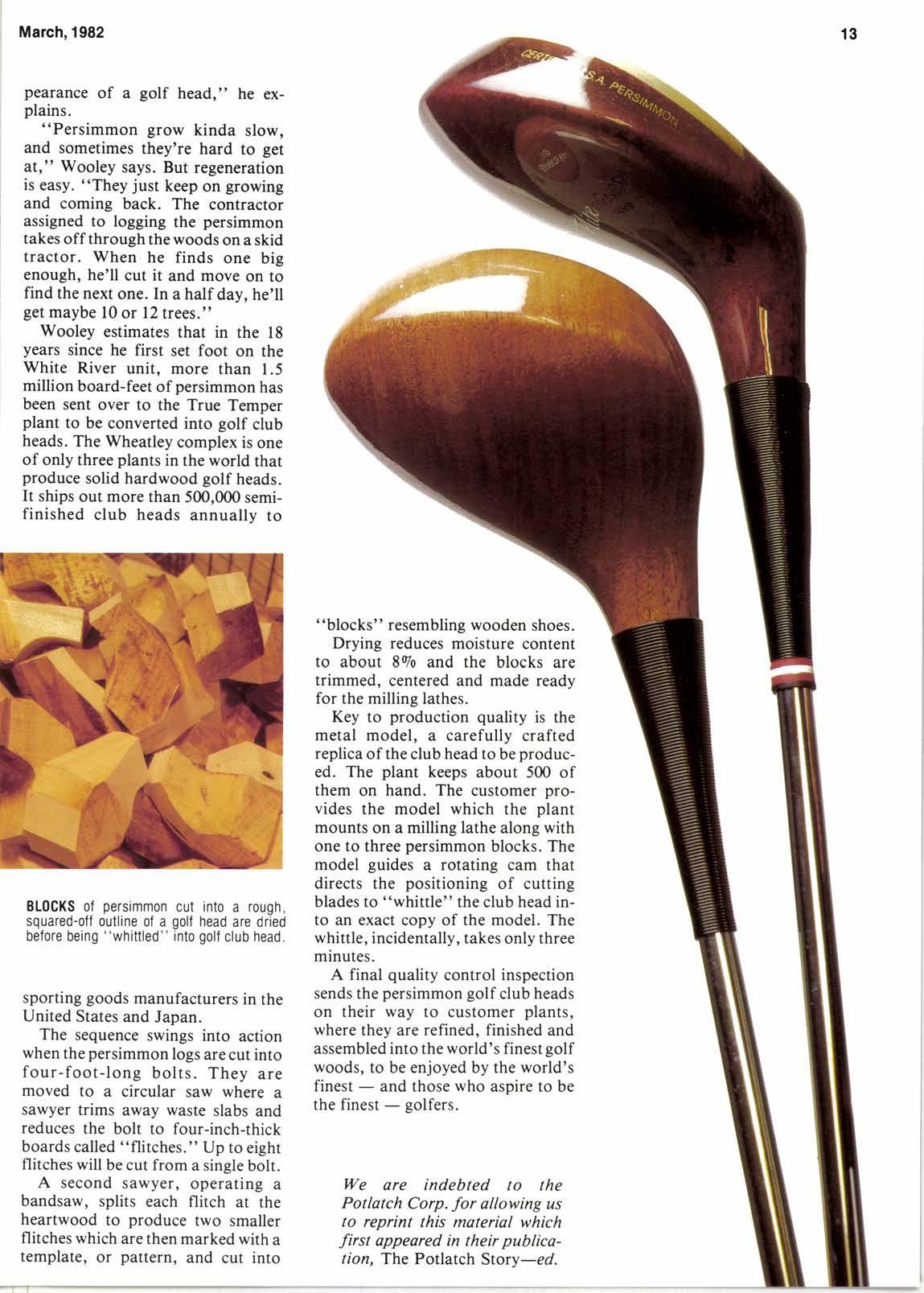
BL0CKS of persimmon cut into a rough, squared-off outline of a golf head are dried before being "whittled" into golf club head.
The sequence swings into action when the persimmon logs are cut into four-foot-long bolts. They are moved to a circular saw where a sawyer trims away waste slabs and reduces the bolt to four-inch-thick boards called "flitches." Up to eight flitches will be cut from a single bolt.
A second sawyer, operating a bandsaw, splits each flitch at the heartwood to produce two smaller flitches which are then marked with a template, or pattern, and cut into
"blocks" resembling wooden shoes. Drying reduces moisture content to about 890 and the blocks are trimmed, centered and made ready for the milling lathes.
Key to production quality is the metal model, a carefully crafted replica of the club head to be produced. The plant keeps about 500 of them on hand. The customer provides the model which the plant mounts on a milling lathe along with one to three persimmon blocks. The model guides a rotating cam that directs the positioning of cutting blades to "whittle" the club head into an exact copy of the model. The whittle, incidentally, takes only three minutes.
A final quality control inspection sends the persimmon golf club heads on their way to customer plants, where they are refined, finished and assembled into the world's finest golf woods, to be enjoyed by the world's finestand those who aspire to be the finestgolfers.
We are indebted to the Potlatch Corp. for allowing us to reprint this material which first appeared in their publication, The Potlatch Story-ed.