

KEEP IT SAFE
MARCH / APRIL 2025
Foreword
Simon Brentnall CMIOSH PIEMA AIFSM
BFFF were recently asked to speak at the International Food Event (IFE) in London on the topic of Artificial Intelligence (A.I).
According to research, the Food and Drink industry has been the fourth fastest adopter of A.I technology. In this session I provided successful examples of how A.I is being practically implemented within BFFF membership.

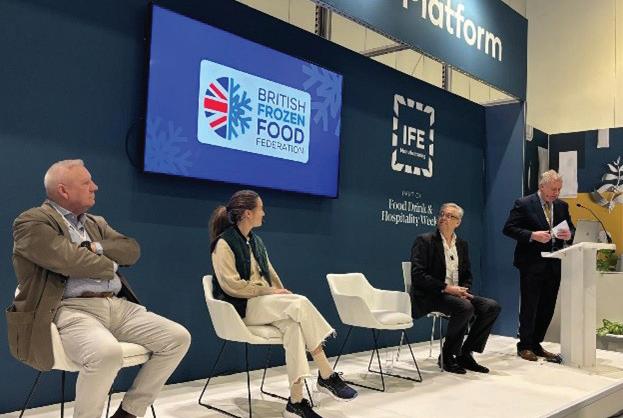
The first example showed how a national food wholesaler has utilised A.I in its 2000 strong HGV fleet to identify driver distractions, this has resulted in a 40% reduction in road traffic accidents within the first 3 months of implementation and all insured risks down by 15% together with a reduction in civil claims.
The second example showed how a national retailer has reduced employee accidents in its East Midlands site by 80% in the first 10 weeks of deployment. The system can detect people running, blocked fire exits, workers in close proximity to workplace transport and incorrect manual handling technique.
With the food industry losing so many experienced workers of the baby boomer generation through retirement, A.I technology provides exiting an opportunity for young people to step up being somewhat tech savvy already.
The session was a great success with standing room only.
To raise a query simply e-mail me at: simonbrentnall@BFFF.co.uk
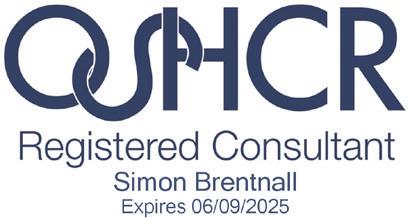
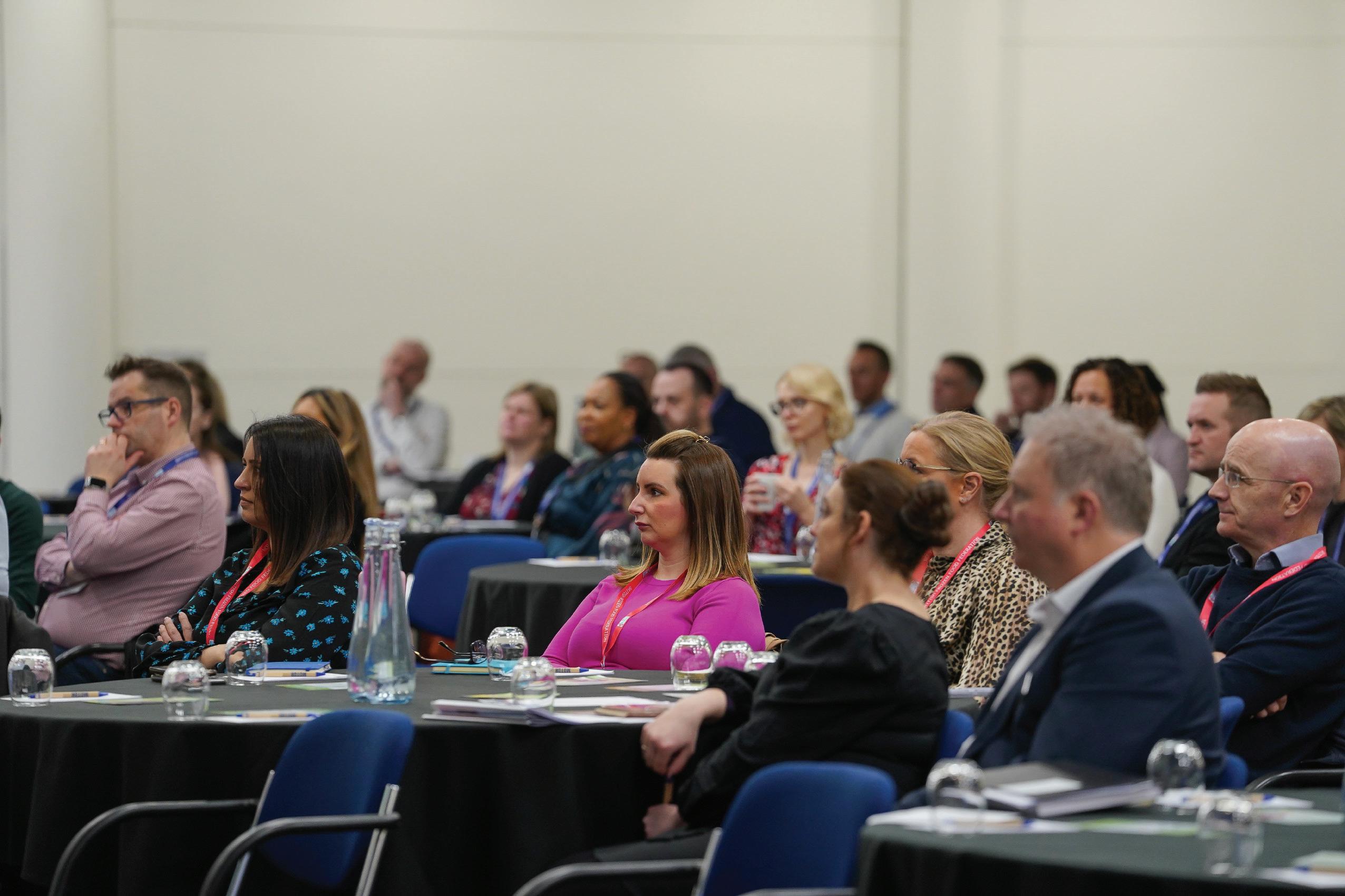
HEALTH & SAFETY CONFERENCE

13TH MAY 2025
BFFF INITITIVES
BFFF MEMBERS, ARCO, UNVEILS NEW STATE OF THE ART CENTRE, INVESTING IN THE FUTURE OF SAFETY INNOVATION – BOOK YOUR VISIT!
Arco, the UK and Ireland’s leading safety expert, opens its doors on a cutting-edge Customer Discovery Centre, marking a bold investment designed to transform customer experience and drive industry innovation.
This state-of-the-art facility brings together product expertise, advanced safety training, and industry collaboration under one roof. Designed to engage with customers and suppliers, the Discovery Centre showcases Arco’s integrated safety solutions featuring its independent UKAS and SATRA accredited Product Assurance Lab with a dedicated space for product innovation.
As part of this investment, Arco has also expanded its training offering with a brand-new practical training facility, broadening its national coverage of training centres for workers in the highest risk industries. Specialising in confined space and working at height ‘hands-on’ training alongside a multitude of classroom-based courses, this Safety Services centre of excellence increases accessibility to critical safety education.
With three flexible learning spaces, innovative displays, and cutting-edge technology, the Discovery Centre is designed to adapt to the needs of customers and colleagues alike, making it a premier destination for training, collaboration, and knowledge-sharing. Now operational, customers can explore the latest advancements in safety, PPE and work wear, undertake training courses and receive expert guidance on product selection and development under one roof.
CEO of Arco, Guy Bruce said: “We’re thrilled to open our new state of the art Customer Discovery Centre. It’s our way of giving customers fresh inspiration and ultimate safety confidence day in day out.
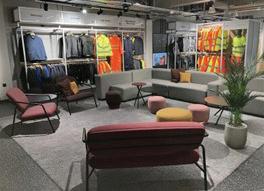
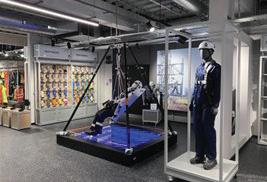
“By investing in world-class facilities and smarter ways to engage with our customers, this is more than an upgrade to our services, it’s a strategic shift in how our customers interact with Arco and how our safety solutions are developed, shared, and experienced. The future of safety is here, and this immersive space truly demonstrates the value available to all customers when they have the best in the safety business at their side. We’re looking forward to hosting our customers and partners here for years to come.”
To arrange a visit to the new innovation centre, please contact simonbrentnall@bfff.co.uk
BFFF INITITIVES
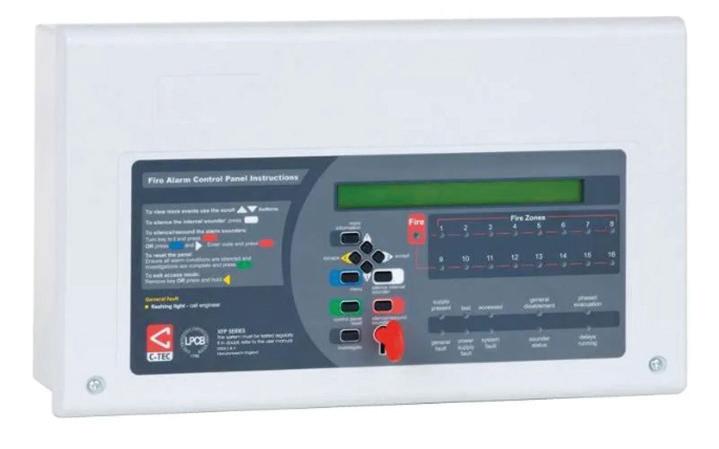
Analog Addressable Fire Alarm Systems: Similar to addressable systems, but they provide more detailed information about the status of each device, such as sensitivity levels and maintenance needs.
Wireless Fire Alarm Systems, Hybrid Fire Alarm Systems and Voice Evacuation Systems are all variations in systems that cover specific circumstances.
Finally, I should mention that standards around fire alarm requirements, design, installation, commissioning and maintenance all fall within the Recommendations within BS5839 Part 1: 2017. Alarm categories range from a ‘full cover’ through to a manual system without the need for detection. I will briefly explain the first three categories:

L1
Systems
• Coverage : L1 systems are designed to provide the highest level of protection for life. It includes automatic fire detection in all areas of a building, including all rooms, escape routes, and voids over 800mm in height.
• Purpose : This comprehensive coverage ensures early detection of fire, allowing for prompt evacuation and minimizing risk to occupants.
L2 Systems:
• Coverage: L2 systems require automatic fire detection on all escape routes and rooms leading onto escape routes. Additionally, they include
areas deemed as high risk, such as boiler rooms
• Purpose: The primary goal is to ensure early detection and warning to facilitate safe evacuation, especially in areas where the risk of fire is higher
L3 Systems:
• Coverage: L3 systems mandate automatic fire detection on all escape routes and rooms opening onto escape routes. Unlike L2 systems, L3 systems do not necessarily cover high-risk areas beyond escape routes
• Purpose: The focus is on ensuring that occupants are alerted to a fire in time to evacuate safely, with emphasis on escape routes
Recommendations:
• System Design: Ensure the fire alarm system design is based on a thorough fire risk assessment, considering the specific needs and risks of the building
• Installation: Follow best practices for installation, including proper placement of detectors, manual call points, and alarm sounders in accordance with British Standard BS5839 Part 1.
• Maintenance: Regular maintenance and testing are crucial to ensure the system remains functional and reliable, also in accordance with British Standards
By adhering to these guidelines, buildings can achieve effective fire protection, ensuring the safety of occupants and compliance with British Standards.
For further information, please contact: jonathan.dixson@essex-fire.gov.uk
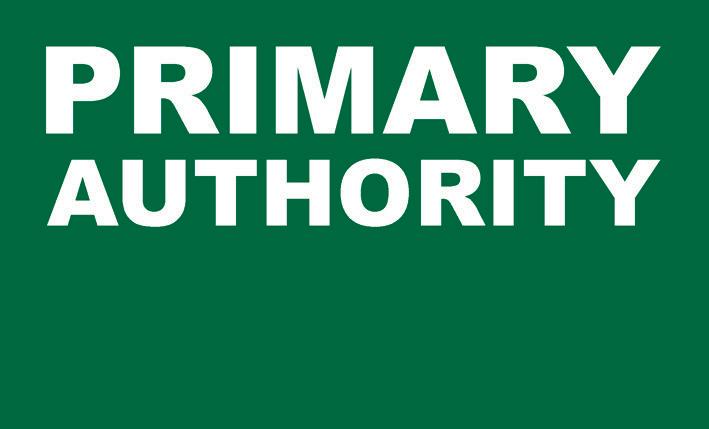
SAFETY FOCUS

ACORN WAREHOUSE SOLUTIONS LTD HAS RECENTLY JOINED BFFF AS MEMBERS, THEY EXPLAIN MORE ABOUT THE LEGAL REQUIREMENTS FOR RACKING INSPECTIONS.
What is a PRRS?
A PRRS is a ‘Person Responsible for Racking Safety’. It is a position designated by SEMA and the HSE in HSG76 (HSG 76 The HSE Manual on Warehousing and Storage) to oversee the use, operation and maintenance of your storage racks ensuring that the system remains serviceable and safe. They need to ensure that the racking is correctly installed, operated and maintained in accordance with SEMA guidelines and that the hierarchical approach to inspections is followed:
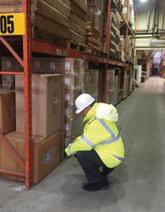
1. All damage is reported when it happens or as soon as it is seen.
2. Internal inspections are carried out on a weekly basis or some other regular interval based on a risk assessment.
3. ‘Expert’ inspections by a technically competent person are carried out at least once a year. A written report should be submitted to the PRRS detailing damage and action required.
For all this to happen you need to have formal documented systems for reporting damage, defects and any other issues that may affect the safety of the operation, and then a follow up process to ensure the safe and timely offloading of damage according to its severity, and finally that repairs are undertaken as soon as possible.
Employees should receive training, information, and instruction on the safe operation of storage racks with particular attention paid to those parts that affect their safety and the safety of others. The person responsible for rack safety should help to educate staff on recognising potential risks, the importance of damage reporting as soon as it occurs and to create and promote a culture of safety within the workplace. Acorn Warehouse Solutions Ltd can supply onsite training to meet this need.
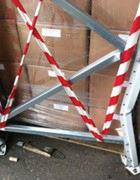
Normally your inspections will be conducted from ground level with the racking loaded, unless problems are detected at higher levels when a more detailed high-level investigation may be necessary. Alternatively, the level of occupancy may restrict the scope of inspection where damage is detected requiring offloading of the racks to allow a more detailed inspection and in such cases, you may also need to seek professional help. Automated and high bay systems also require inspection but given their nature and height a more specialised tailored programme can be adopted, and for this you should seek specialist advice.

As such the PRRS can be seen as an administrative role, but it makes sense that they have undergone some basic training to ensure they are aware of the needs and requirements for inspections so book them onto a rack safety and awareness training course where they will find out all about internal inspections and how to conduct them.
Should you require any information on racking standards or inspection, please contact us as below:
Acorn Warehouse Solutions Ltd
Suite 8, Newmarket Business Centre 341 Exning Road, Newmarket, Suffolk CB8 0AT
Tel: 01799 532024
Email: admin@awsltd.biz
Registered in England No. 5866480
VAT Reg No 985 7286 54
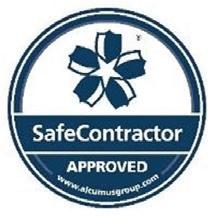

GUIDANCE
WTW SURVEY SHOWS HEALTH AND SAFETY REMAINS TOP
CONCERN FOR DIRECTORS AND OFFICERS WORLDWIDE

Recently WTW joined as BFFF members, their recent survey shows 80% of directors and officers consider health and safety risks to be very important or extremely important to their organisation.
The latest Directors and Officers Liability Insurance Survey by Willis found that physical workplace risks were deemed the most important by 43% of respondents, followed by employee mental health and wellbeing consequences stemming from work (28%) and from personal matters (12%).
For the first time since 2018 civil litigation and third party claims were included among the top seven concerns, with 63% of directors and officers surveyed considering these significant risks to their Directors and Officers. Smaller organisations (<$50 million in revenue) and those with revenues between $1 and $5 billion mentioned litigation more often. The largest organisations surveyed (>$5 billion in revenue) included diversity, equity and inclusion as well as bribery and corruption as top risks, while excluding the financial distress, bankruptcy and insolvency concerns of smaller organisations.
Climate change is no longer considered a top seven risk in several regions, including Asia, North America and the Middle East. In contrast, diversity, equity and inclusion, a risk that was included in the survey for the first time this year, has made its way into the top seven for Great Britain, North America and Africa. Social risks as a whole feature prominently in the list of concerns and, when looked at over a five-year period, the increase in concern is notable. For example, breach of human rights within or by business operations has risen from 23% of responders considering it a very or extremely important concern in 2021 to 62% in 2025. Similarly, concern about supplier business practices has risen from 27% in 2021 to 59% in 2025.
In general, there is a strong alignment between perceived material risks and board expertise and priorities. However, there is a notable exception when it comes to cybersecurity
and data privacy, with many boards indicating more time is needed. Data loss and cyber-attacks, including extortion, are considered to be very important or extremely important for 77% of those surveyed. Artificial intelligence lags behind (only 51% of respondents consider it to be very or extremely important and considered by the fewest number of respondents to be material to the business while also being the lowest ranked issue on which respondents considered the board to have the relevant expertise), but this perception may change in the future as new use cases and regulations develop.
Angus Duncan, global D&O coverage specialist at Willis, said: “The latest survey results underscore the diverse challenges directors and officers face today, highlighting how fraught the landscape has become. Despite increasing concerns over litigation risks, cost remains the dominant driver for D&O insurance purchasing decisions. This trend persists even as regulatory scrutiny and shareholder activism increase global liability exposures. By taking a proactive approach, companies can optimise their D&O coverage while mitigating financial and reputational risk. Our data helps clients anticipate emerging risks before they become serious exposures.”
To find out more about the services of WTW, see below:
BFFF URGES ITS MEMBERS TO ENSURE ADEQUATE CONTROLS ARE IN PLACE FOR EQUIPMENT FITTED WITH LITHIUM-ION BATTERIES
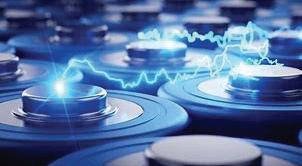
With more equipment being introduced into the food industry with Lithium-Ion technology, BFFF urge its members to ensure adequate controls.
TRANSPORT HUB
CALL FOR DROWSY DRIVING TEST AS FLEETS WARNED OF DANGERS
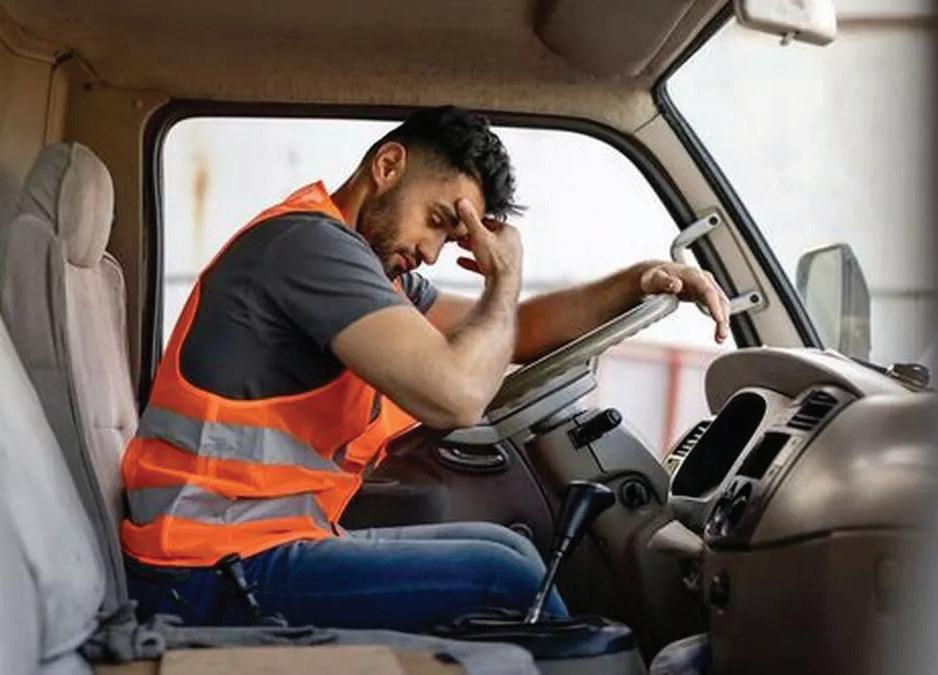
Fleets and their drivers are being warned about drowsy driving, with more than 430 people killed or seriously injured and 1,276 collisions, linked to tiredness in 2023.
The Royal Society for the Prevention of Accidents (RoSPA) is working with the Fatigue Group, a non-profit organisation led by NHS anaesthetists, to provide advice on managing the risk of fatigue, the importance of regular rest and recognising when people are too tired to drive. The message came ahead of this year’s World Sleep Day on 14 March.
RoSPA also wants government to introduce standardised tests for assessing fatigue at the scene of road traffic collisions, similar to breathalyser tests for alcohol, establish a national registry of drowsy driving incidents, and run public awareness campaigns targeting high-risk groups such as shift workers.
Caitlin Taylor, road safety manager at RoSPA, said: “Drowsy driving is responsible for many serious and fatal collisions each year. Fatigue impairs driving ability similar to drink or drug driving but gets much less attention. This must change.
“Fatigue slows reaction times, reduces awareness, and affects decision-making, putting everyone at risk.
“RoSPA calls on employers, policymakers, and the Government to act now by improving workplace fatigue management, investing in public awareness campaigns, and collecting better data on fatigue-related crashes. No one should lose their life due to preventable driver fatigue.” Fatigue presents a risk across the entire workforce and that
is most apparent in physically demanding industries such as haulage and construction, but can also affect people putting in long hours at an office before driving home.
RoSPA emphasises that anyone who begins to feel tired when they are driving stop as soon as is safe and possible, and ideally try and find somewhere safe to sleep until they feel rested.
Although two strong coffees and a 15-minute nap might help in the short-term, this should never be done more than once per journey.
EU BACKS DOWN ON NEW RULES TO ALLOW TEENAGERS TO DRIVE HGVS
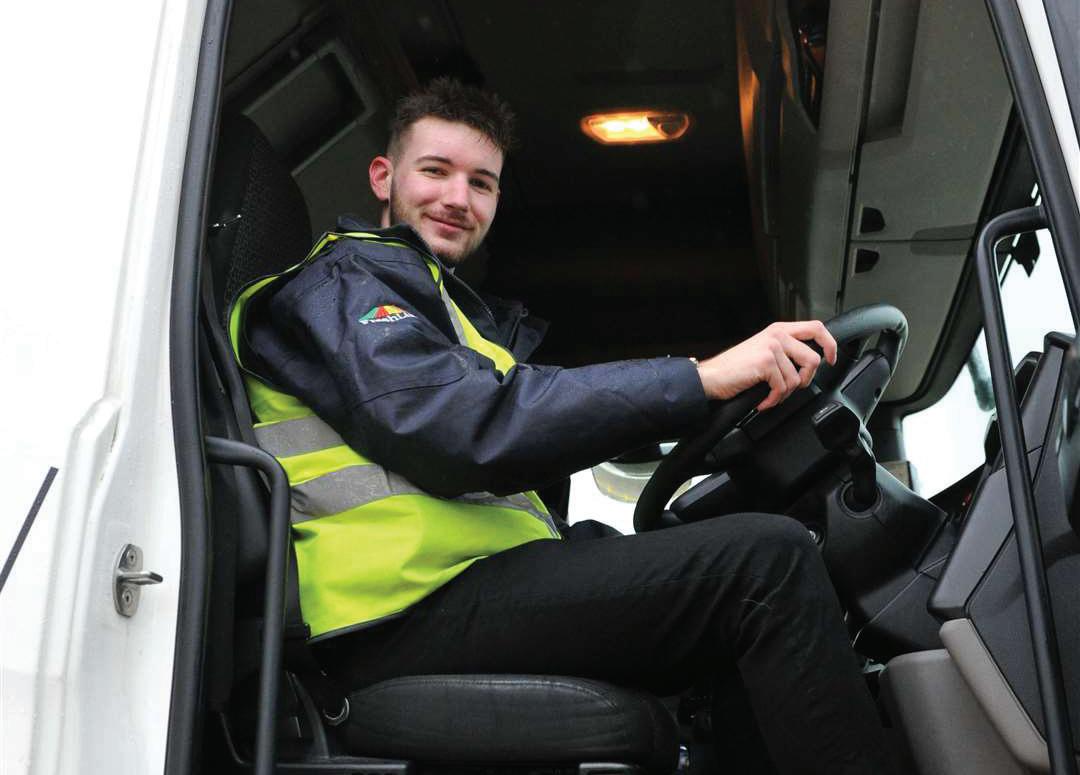
The EU has decided against forcing member states to allow 17-year-olds to be able to drive a heavy goods vehicle (HGV).
The initial proposal from the European Commission, published in 2023, would have required all EU countries to allow 17-year-olds to train to drive a lorry. However, EU negotiators struck a final deal on 25 March, which now makes this optional for member states.
Currently, only five EU countries allow teenagers as young as 18 to drive a lorry: Finland, Germany, Ireland, Poland and Spain.
Ellen Townsend, policy director of the European Transport Safety Council (ETSC), said: “Allowing teenagers to drive lorries at 17 is and always was a terrible idea. Data from several countries show that younger drivers of heavy goods vehicles are much more likely to crash. We urge member states not to take up this option.”