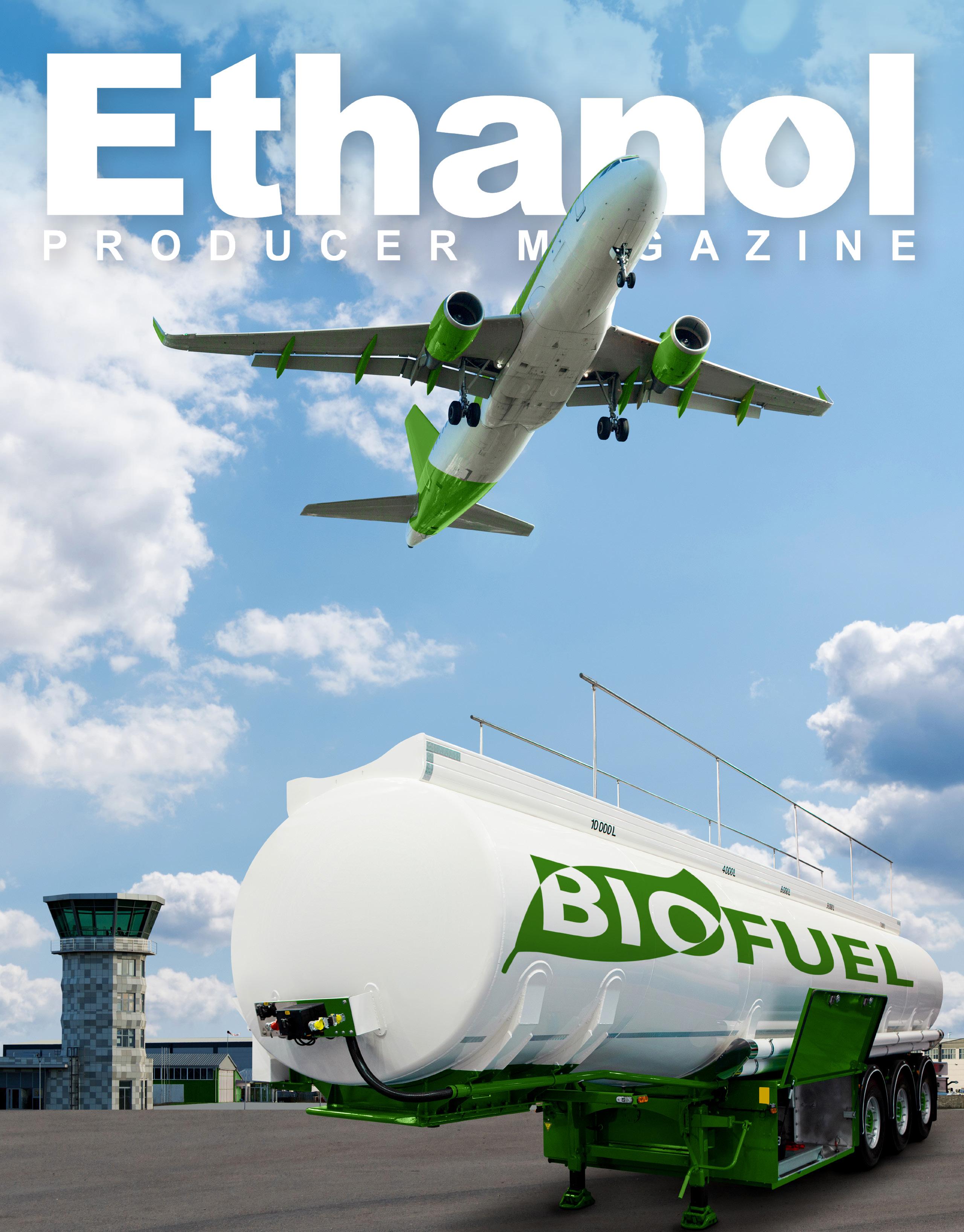
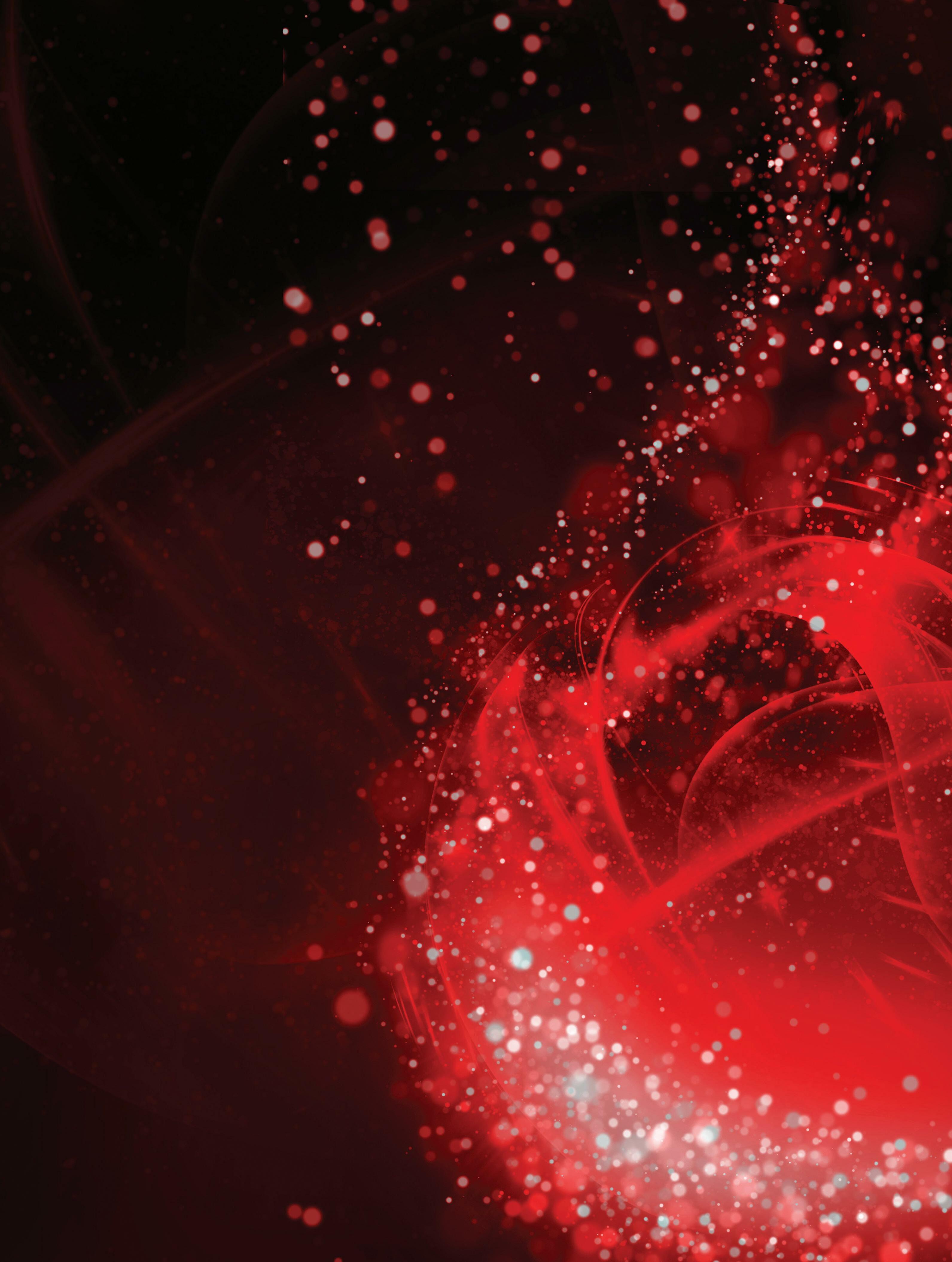
Cobb Galleria Centre, Atlanta, GA (866) 746-8385 | BiomassConference.com
Now in its 16th year, the International Biomass Conference & Expo is expected to bring together more than 800 attendees, 140 exhibitors and 65 speakers from more than 21 countries. It is the largest gathering of biomass professionals and academics in the world. The conference provides relevant content and unparalleled networking opportunities in a dynamic business-to-business environment. In addition to abundant networking opportunities, the largest biomass conference in the world is renowned for its outstanding programming—powered by Biomass Magazine—that maintains a strong focus on commercial-scale biomass production, new technology, and near-term research and development.
CHI Health Center, Omaha, Nebraska (866) 746-8385 | FuelEthanolWorkshop.com
From its inception, the mission of this event has remained constant: The FEW delivers timely presentations with a strong focus on commercial-scale ethanol production—from quality control and yield maximization to regulatory compliance and fiscal management. The FEW is the ethanol industry’s premier forum for unveiling new technologies and research findings. The program is primarily focused on optimizing grain ethanol operations while also covering cellulosic and advanced ethanol technologies.
CHI Health Center, Omaha, Nebraska (866) 746-8385 | BiodieselSummit.com
The Biodiesel Summit: Sustainable Aviation Fuel & Renewable Diesel is a forum designed for biodiesel and renewable diesel producers to learn about cutting-edge process technologies, new techniques and equipment to optimize existing production, and efficiencies to save money while increasing throughput and fuel quality. Produced by Biodiesel Magazine, this world-class event features premium content from technology providers, equipment vendors, consultants, engineers and producers to advance discussion and foster an environment of collaboration and networking through engaging presentations, fruitful discussion and compelling exhibitions with one purpose, to further the biomassbased diesel sector beyond its current limitations.
2023 Int'l Fuel Ethanol Workshop & Expo 39
BASF Enzymes LLC 21 CTE Global, Inc. 7 D3MAX, LLC 22-23 Fagen, Inc. 31
Fluid Quip Mechanical 12 Fluid Quip Technologies, LLC 26 Growth Energy 13 ICM, Inc. 19
J.C. Ramsdell Enviro Services, Inc. 37
Lallemand Biofuels & Distilled Spirits 3 Mole Master Services Corporation 27 Novozymes 11
Phibro Ethanol 9
Premium Plant Services, Inc. 33
Renewable Fuels Association 2 Trucent 40 Victory Energy Operations, LLC 20 Zenviro Tech US Inc. 17
President & Editor
Tom Bryan | tbryan@bbiinternational.com
Online News Editor
Erin Voegele | evoegele@bbiinternational.com
Staff Writer
Katie Schroeder katie.schroeder@bbiinternational.com
Vice President of Production & Design Jaci Satterlund jsatterlund@bbiinternational.com
Graphic Designer
Raquel Boushee rboushee@bbiinternational.com
CEO
Joe Bryan | jbryan@bbiinternational.com
Vice President of Operations/Marketing & Sales
John Nelson | jnelson@bbiinternational.com
Senior Account Manager/Bioenergy Team Leader Chip Shereck | cshereck@bbiinternational.com
Account Manager
Bob Brown | bbrown@bbiinternational.com
Circulation Manager
Jessica Tiller | jtiller@bbiinternational.com
Marketing & Advertising Manager Marla DeFoe | mdefoe@bbiinternational.com
Ringneck Energy Walter Wendland Little Sioux Corn Processors Steve Roe Commonwealth Agri-Energy Mick Henderson Aemetis Advanced Fuels Eric McAfee
Western Plains Energy Derek Peine Front Range Energy Dan Sanders Jr.
Customer Service Please call 1-866-746-8385 or email us at service@bbiinternational.com. Subscriptions Subscrip tions to Ethanol Producer Magazine are free of charge to everyone with the exception of a shipping and handling charge for anyone outside the United States. To subscribe, visit www.EthanolProducer.com or you can send your mailing address and payment (checks made out to BBI International) to: Ethanol Producer Magazine Subscriptions, 308 Second Ave. N., Suite 304, Grand Forks, ND 58203. You can also fax a subscription form to 701-746-5367. Back Issues, Reprints and Permissions Select back issues are available for $3.95 each, plus shipping. Article reprints are also available for a fee. For more information, contact us at 866-746-8385 or service@bbiinternational.com. Advertising Ethanol Producer Magazine provides a specific topic delivered to a highly targeted audience. We are committed to editorial excellence and high-quality print production. To find out more about Ethanol Producer Magazine advertising opportunities, please contact us at 866-746-8385 or service@bbiinternational.com. Letters to the Editor We welcome letters to the editor. Send to Ethanol Producer Magazine Letters to the Editor, 308 2nd Ave. N., Suite 304, Grand Forks, ND 58203 or email to editor@bbiinternational.com. Please include your name, address and phone number. Letters may be edited for clarity and/or space.
Please check our website for upcoming webinars www.ethanolproducer.com/pages/webinar
Despite the doom and gloom often expressed about the future of renewable fuels amid the rise of electric vehicles, ethanol’s future is bright. Yes, it looks imminent that domestic gasoline use will steadily diminish in the years ahead—a 135-billion-gallon market may become 110 billion gallons over time—and that seems like trouble for ethanol on the surface, but it’s certainly not a death knell. Beyond E10—and even E15—current production levels can easily be maintained in a future full of EVs through the adoption of higher ethanol blends like E30, possible EV-biofuel hybrids, maintaining current exports, seizing niche opportunities like high-purity alcohol and aggressively pursuing new markets in the hard-to-electrify space like diesel and sustainable aviation fuel (SAF).
The latter opportunity, most agree, is enormous, especially if new incentives for SAF production can be modified to include corn ethanol by more fairly representing the biofuel’s real carbon intensity (CI) as well the CI diversity of different production facilities, feedstocks and associated farming practices. As we report in our page-14 cover story, “Adding Thrust To Ethanol-Based SAF,” the International Civil Aviation Organization estimates that more than 80 SAF offtake agreements have already been signed (some involving alcohol-based SAF) representing nearly 9 billion gallons of proposed, contracted-to-deliver production. The thing is, beyond a few billion gallons of SAF that will be made from existing low-CI wastes like used cooking oil, the massive quantities of feedstock needed for several more billion gallons of SAF will need to come from an almost ubiquitous source: ethanol. With companies like Southwest Airlines, LanzaJet (now backed by Bill Gates capital), Green Plains, Honeywell, BASF and others betting large on alcohol-based SAF, it’s hard to see this opportunity not achieving lift.
Incentives related to SAF production in the U.S. are multi-part and stackable. Producers can collect an attractive pergallon tax credit ($1.25-$1.75) while picking up a premium for their bio-jet fuel in low-carbon markets like California and also generating RINs. However, questions about RINs tied to next-gen fuels like SAF made from intermediate feedstocks at a different location—like biocrude, biomass-based sugars or undenatured ethanol—were largely unanswered until the U.S. EPA clarified its provisions on biointermediates earlier this year. On page 24, we do our best to explain the agency’s rules elucidation in “Shedding Light On Biointermediates.”
We jump into a plant-level dialogue in “Stepping Down Water Use,” on page 28, but the story maintains a certain relevance to the low-carbon threads preceding it. While carbon intensity reduction almost always overshadows water use reduction in our headlines—perhaps because the industry has already lowered water use so much—it remains critical. Plus, with much of the world (including the Southwest U.S.) growingly water constrained, the idea of water intensity ratings could become as common as CI scores, one source tells us.
Finally, anchoring this issue is a nice-fitting story about two policy initiatives (one already introduced in both houses of Congress, the other a coalition-based proposal with early legs). “Advancing Policy In Parallel,” on page 34, stacks up the Next Generation Fuels Act with the still-budding Drive Clean Initiative, two potential approaches to backstopping the RFS in its post-2022 existence. Both efforts seek to introduce higher-level ethanol blends with related but different levers—high octane and low carbon. For unique reasons, both paths are compelling.
Enjoy the read.
Renewable Fuels Association 202-289-3835
gcooper@ethanolrfa.org
When President Biden announced emergency summertime waivers for E15 in April, some misinformed pundits wrote off the move as “political posturing” or “a gimmick” to satisfy Midwest voters. But now that the summer is over, we’re able to look at what the data say about the real impact of the emergency waivers. In short, the data provide two clear takeaways: First, E15 sales volumes skyrocketed over the summer (rather than dropping sharply, as they had done in past summers when no waiver was in place). Second, for drivers who had access to E15, the savings at the pump were substantial.
In fact, recent analysis by RFA shows E15 sales rose to record levels in the summer months, rather than falling by half (as they did prior to the summertime E15 barrier being removed in 2019). The analysis also shows drivers choosing E15 saved an average of 30 cents per gallon over the summer. That means a typical household that used E15 in place of regular gasoline (E10) this summer saved roughly $90-$100 on their fuel bill between June 1 and September 15. Altogether, American drivers who fueled with E15 this summer saved nearly $60 million.
These savings could not have come at a better time. Following the Russian invasion of Ukraine in February, crude oil and retail gasoline prices surged, and the Biden administration banned imports of crude oil and petroleum products from Russia.
By mid-June, the national average price of gasoline hit $5 per gallon for the first time, giving consumers more need for the availability of lower-cost ethanol blends at the pump. Gasoline supplies were very tight and oil refineries were operating at very high utilization rates, making E15 an effective option for delivering price relief at the pump. That’s because lower-cost ethanol, produced at facilities across the country, is blended to produce finished gasoline close to filling stations, whereas additional crude oil processing was constrained by the tight refinery capacity. Over the course of the summer, ethanol prices were, on average, 89 cents below wholesale gasoline prices.
In addition to the economic benefits, using E15 reduces greenhouse gas emissions even further than E10, by about 3 percent, and E15 also similarly reduces emissions of the pollutants that lead to groundlevel ozone and smog.
While the emergency waivers were a win for American drivers in 2022, we need a solution to make year-round E15 permanent, and RFA and its allies are working on this along several tracks. For example, in April, a number of state governors notified EPA that they are establishing regulations in their state for parity between all fuel blends when it comes to vapor pressure, as is their right under the Clean Air Act. And in Congress, bills like the Next Generation Fuels Act and the Lower Food and Fuel Costs Act would also make E15 available year-round.
E15 is approved for use in more than 96 percent of the cars and trucks on the road. It saves drivers money, and it reduces emissions. E15 isn’t just good for America in emergency situations, like we saw this past summer. It’s good for America all the time. That’s why we need a permanent solution to ensure E15 is offered at filling stations around the country—every single day of the year. And RFA won’t stop working until we’ve achieved that goal.
leticia@unica.com.br
The California Air Resources Board (CARB) is undergoing its regular review to ensure the state is deploying the most cost-effective and technologically-advanced ways to achieve its aggressive climate goals. The “Scoping Plan” is updated every five years and it is an opportunity to assess what is working, and what’s not, in the fight to reduce greenhouse gases.
One thing we know is working is the Low Carbon Fuel Standard. Since its inception, the LCFS has driven down the carbon intensity of the fuels used to power California’s cars and trucks. This is a policy success other states—and countries—can and should emulate.
As the Scoping Plan review unfolds, it is important to remember CARB’s storied history of environmental leadership. Created in 1967, the Board soon adopted the first nitrogen oxides standards for cars and led the way for the development of the catalytic converter, a groundbreaking advance in reducing auto-created smog.
Similarly, California was far ahead of the curve in 2011 when it put ethanol to work by deploying biofuels like Brazilian sugarcane ethanol to improve octane levels and lowering greenhouse gases emitted from cars and trucks, reducing the carbon intensity of the transportation market as part of the LCFS program. As a result, carbon intensity in transportation fuels has plummeted and CARB is slightly ahead of its goals.
Some may be inclined to discount biofuels in the ambitious push to electrify the California fleet, but biofuels remain a proven environmental tool that must be part of the plan to manage the decades-long transition away from petroleum.
It is easy to understand the appeal and promise of electric vehicles, but any impartial accounting of Brazilian sugarcane ethanol’s performance will reaffirm what we know to be true: Biofuels are essential to meeting California’s GHG goals and will continue to be so. It is important to note that hybrid flex cars using sugarcane ethanol have CO2 emission levels on par with electric vehicles.
Sugarcane ethanol’s efficiency has evolved over the last decade as has the harvesting and transportation that brings the biofuel to market. Innovative farming, mechanized harvesting, regenerative land use and improved shipping and supply processes all represent a commitment to constant improvement.
The future is bright for sugarcane ethanol as it is the best available option to reduce the carbon intensity in many hard-to-electrify sectors such as aviation and shipping. And new technologies are underway to use sugarcane to power some of the tens of thousands of electric vehicle recharging stations required for the EV revolution. Sugarcane ethanol is proving to be a solution for mobility and carbon emissions challenges now and in the future. One fascinating development is the possibility of producing green hydrogen through ethanol reforming processes.
Policymakers around the world are taking note of CARB’s work, and its end product will have implications far beyond California. States just now considering ways to reduce the carbon intensity of transportation fuel with clean, high-quality fuels should be afforded the opportunity to leverage biofuel’s benefits as California did over the last decade. This will be made easier with an uninterrupted import market and incentives for importing this energy source at scale.
As CARB leaders proceed with their important deliberations, we only ask that Brazilian ethanol be scored fairly and accurately so that California residents can continue to enjoy the environmental benefits derived from the world’s most efficient and climate-friendly biofuel while electrification slowly begins to ramp up.
Consistently
be a
achieve
BASF has introduced a new dehydra tion catalyst to process renewable feed stocks. The novel star-shaped catalyst, dubbed CircleStar, reportedly achieves a 99.5 percent electivity for ethanol-to-ethyl ene conversion. BASF says CircleStar will lower the carbon footprint of bioethylenebased products ranging from jet fuel to plastics by more than 10 percent, while matching the performance of convention al fossil-based ethylene.
Honeywell is rolling out a new etha nol-to-jet fuel (ETJ) processing technol ogy that allows producers to convert cornbased, cellulosic or sugar-based ethanol into sustainable aviation fuel (SAF). De pending on the type of ethanol feedstock
fuel produced from Honeywell's
fuel process can reduce
emissions by 80 percent
Carbon America has formed an agree ment with Bridgeport Ethanol LLC to de velop a carbon capture and storage (CCS) project at the 53 MMgy ethanol plant in western Nebraska. The project is currently expected to be operational in 2024.
The agreement with Bridgeport Etha nol is the third such agreement announced by Carbon America this year to finance,
“Our novel CircleStar for bioethanol to bioethylene conversion has excellent product properties and helps our custom ers significantly increase their production efficiency while reducing carbon emissions and supporting their net-zero targets,” said Detlef Ruff, senior vice president, process catalysts at BASF.
on a total lifecycle basis, compared to pe troleum-based jet fuel.
According to Honeywell, demand for SAF continues to grow, but limited sup plies of traditional SAF feedstocks such as vegetable oils, animal fats and waste oils present a supply challenge. “Ethanol offers producers a widely available, economically viable feedstock,” the company stated.
build, own and operate CCS systems at ethanol plants. In May, the company an nounced similar agreements with Sterling Ethanol LLC and Yuma Ethanol LLC to develop CCS projects at their respective Colorado-based biorefineries. All three ethanol plants are affiliated with Colorado Agri Products.
Fuel ethanol is second only to coal as the most-transported fuel by rail, accord ing to the U.S. EIA. The agency recently found that 95 percent of all U.S. fuel etha nol deliveries between regions in the first half of 2022 were by rail.
Also, in the same time period, 97 per cent of the fuel ethanol delivered by rail in the U.S. originated in the Midwest. Rail accounted for 96 percent of the Midwest’s
The U.S. EPA has approved an effi cient producer pathway for Green Plains Inc.’s 116 MMgy ethanol plant in Central City, Nebraska. The approval allows the fa cility to generate renewable identification numbers (RINs) for non-grandfathered volumes of ethanol.
Ethanol plants that have approved ef ficient producer pathways are able to gen
PROtect LLC, which has a significant customer base in ethanol production, has announced that it has achieved over 1 mil lion work hours without a lost time inci dent.
“Every single individual in our com pany should be extremely proud of PRO tect reaching [this milestone],” said Nathan VanderGriend, PROtect president and CEO. “Our business [provides] safety
fuel ethanol deliveries to the East Coast and 90 percent of deliveries to the Gulf Coast. In addition to rail, ethanol is also shipped by truck and barge. Unlike oil and gas, however, it is not transported via pipeline.
erate RINs for production volumes above those grandfathered under current Renew able Fuel Standard regulations. To qualify for compliance, any new production above the grandfathered gallons must meet a 20 percent greenhouse gas reduction thresh old when compared to the baseline GHG of gasoline.
reliability and compliance services to a variety of high-hazard industries. The ser vices we provide help keep our customers’ team members and communities safe, their equipment and operations from experi encing catastrophic failure and unplanned downtime. This milestone is proof of our dedication to applying what we deliver ex ternally to our customers, and internally with our team.”
Policy
By Luke GeiverThe sky is no longer the limit for ethanol. From the world’s top airlines to the highest-GDP countries, the race to get more sustainable aviation fuel (SAF) is in the air—and ethanol is on board.
Before understanding the technolo gies, big-name partnerships and genera tional volume demand projections related to SAF, it’s important to understand how we got here, by both government push and private sector pull.
Although SAF was making headlines well before the landmark U.S. Inflation Re duction Act was signed into law this past August, the bill provided immediate ampli fication to the biobased jet fuel movement. The IRA includes several provisions that incentive the use or production of SAF, including a two-year tax credit for blend ers, a three-year tax credit for producers, and a grant program worth $290 million over four years to carry out projects that produce, transport, blend/store, develop, demonstrate or apply low-emission avia tion technologies. To be eligible, the SAF must achieve at least a 50 percent improve ment in GHG emissions performance on a lifecycle basis as compared with conven tional jet fuel, according to the bill. And the tax credit—which starts at $1.25 per gallon of SAF—increases with every percentage point of improvement in lifecycle emis sions performance, up to $1.75 a gallon.
In mid-2021, the European Union passed its own version of the IRA, includ ing robust SAF incentives and firm targets. Through the EU’s “Fit for 55” package, the share of sustainable fuels at EU airports will increase from a minimum of 2 percent in 2025 to at least 63 percent by 2050.
Back in the U.S., just a few months after the passage of Fit for 55, the U.S. Department of Energy rolled out its SAF Grand Challenge to meet 100 percent of U.S. aviation fuel demand with sustainable, low-carbon fuel—also by 2050.
The Grand Challenge is a U.S. govern ment-wide approach to make and use more
SAF. The immediate goal is to domestically produce 3 billion gallons of SAF by 2030. The DOE’s long-term goal is to produce 35 billion gallons of SAF by 2050, or essen tially all the jet fuel used domestically.
Despite what seem to be lofty goals, the DOE believes the U.S. has everything it needs to begin ramping up SAF now to achieve its vision. The Billion-Ton Report provided by the U.S. Department of Ag riculture shows that 1 billion dry tons per year of biomass can be grown or collected sustainably in the country. That amount of biomass can be converted into roughly 50 to 60 billion gallons of advanced biofuel (in this case, lots of SAF) without impacting agriculture, trade or current uses of bio mass. Furthermore, the DOE believes that as ground transport electrifies, SAF pres ents a potential market for existing biofuels including ethanol.
In September, when the U.S. DOE released an updated roadmap for the SAF
Grand Challenge, DOE Secretary Jennifer Granholm said that not only is the initiative critical to decarbonizing the airline industry and reaching U.S. climate goals, but helping “American companies corner the market on a valuable emerging industry.”
SAF news from the aviation front shows airlines of all sizes and types are well past just considering their involvement with SAF. The headlines are no longer about airlines studying the potential of biobased fuel. They’re about offtake deals being signed now.
The International Civil Aviation Or ganization, a leading aviation group recog nized across the world, has started track ing and publishing the rise of SAF offtake agreements on its website. The numbers explain it all. In 2013, ICAO showed there
was only one offtake agreement by a major airline with an SAF provider. In 2016, the agreement trends show a discernible spike, reaching six agreements. But then in 2021 and 2022, offtake agreement signings for SAF have been nothing but wheels up. Last year, there were 23 offtake agreements an nounced. This year, there have already been 30.
United Airlines (6) and Delta (7) have led the way among major airlines signing offtakes in 2022. For producers of SAF, Gevo Inc. (10), Neste (12) and World En ergy (10) are all in the double-digit range for offtake agreements, with Aemetis (9) also right there. In total, ICAO currently says there are 80 offtake agreements for SAF in place.
The International Air Transport Asso ciation is a trade association for the world’s airlines. With 290 airlines represented, the IATA member list accounts for 83 percent of total air traffic. “We support many ar eas of aviation activity and help formulate industry policy on critical aviation issues,” Sebastian Mikosz, senior vice president for environment and sustainability, tells Ethanol Producer Magazine.
About a year ago, IATA released its Net Zero commitment, a goal of its mem bers to reach net-zero carbon emissions by 2050, through four different decarboniza tion pathways. “We know that achieving net-zero carbon emissions from aviation by 2050 will be extremely difficult,” Mikosz says.
According to Mikosz and his team, however, there is a plan. The scale of the aviation industry in 2050 will require the mitigation of 1.8 gigatons of carbon. IATA knows that. The association believes that roughly 65 percent of that carbon will be abated through sustainable aviation fuels. Hydrogen-based new propulsion technol ogy may account for another 13 percent; efficiency improvements will help at 3 per
cent; and the remaining 19 percent will be handled through carbon capture and stor age (11 percent) and/or offsets (8 percent).
“The actual split, and the trajectory to get there, will depend on what solutions are the most cost-effective at any particular time,” IATA’s Net Zero plan states. “What ever the ultimate path to net zero will be, it is absolutely true that the only way to get there will be the value chain and govern ments playing their role.”
IATA knows it plays an important role in achieving 65 percent of its net-zero com mitment through the use of SAF. Mikosz explains that the association understands that the market needs to get a clear signal from its members about SAF. “We take it seriously, and we intend to deliver on it.”
“We need policymakers and SAF pro ducers to keep producing more SAF to make it available to airlines,” he says. Ev ery single drop of SAF produced last year was used by airlines around the world, and it will be no different this year, according to IATA.
“In our analyses,” Mikosz says, “we determined that scaling up production and availability of SAF is key to decarbonizing a notoriously hard-to-abate sector. Scenarios vary, but one thing is clear: SAF will repre sent the biggest share of the solution ... We expect to rely on SAF so strongly because at this time, it is the only reliable avenue to decarbonize the sector without disrupting the air connectivity that drives the global economy.”
IATA is also stressing that SAF isn’t a new or novel product. “SAF has been in use for several years, with more than 450,000 flights powered by a combination of SAF and conventional fuel already having oc curred.”
The association also believes that by 2025, the number of SAF producing facili ties will jump dramatically in the next eight years. Although IATA describes the num ber of operating facilities involved with SAF this year as a “handful,” there will be nearly 100 by 2025. By 2030, there will be several hundred. Volumes of SAF pro
duced and used by 2030 could reach at least 7.4 billion gallons.
Even with 30 offtake agreements signed this year, airlines and current or fu ture SAF producers alike will not be able to
keep pace with demand in the near term. That doesn’t mean both aren’t trying. SAF FiRE Renewables LLC, a company formed by D3MAX LLC, as part of a DOE-backed project to develop and produce scalable, sustainable aviation fuel, is in the early stag es of commercializing its SAF production
platform. The company announced a joint venture with Southwest Airlines earlier this year and is pursuing a proven, potentially game-changing production method capable of utilizing corn stover-based ethanol as a feedstock for SAF.
Mark Yancey, CEO of SAFFiRE, be lieves the market for SAF by 2050 will be in the 10 billion gallons per year range, if not more. And his optimism in the quickly emerging SAF space is not singular. Gevo
Inc., Aemetis, World Fuels, Neste and oth ers have publicly stated that the volume potential for SAF in the years ahead is mas sive—in the billions of gallons per year range.
LanzaJet, an emerging superstar in the SAF sector, has transformed its work with technology from the DOE’s Pacific North west National Laboratory that was started years ago, into offtake agreements or invest
ments spanning the world. Since 2020, Lan zaJet has announced projects totaling 300 million gallons of SAF in the U.S., U.K., Sweden, Central Europe, Canada and Japan.
Highly motivating alcohol-to-jet news in the SAF space also came from Honey well in late 2022. In October, the company announced a new, innovative ethanol-to-jet fuel processing technology allowing pro ducers to convert corn-based, cellulosic or sugar-based ethanol into SAF.
“Ethanol offers producers a widely available, economically viable feedstock,” the global technology entity said. “Hon eywell’s ready-now technology uses highperformance catalysts and heat manage ment capabilities to maximize production efficiency resulting in a cost-effective, lower carbon intensity aviation fuel.”
Barry Glickman, vice president and general manager of Honeywell Sustain able Technology Solutions, says the new ethanol-to-jet fuel process can be used as
- Honeywella standalone platform or be coupled with carbon capture technology.
The SAF tech plants can be modular ized off site, enabling lower installed costs and faster, less labor-intensive installation compared to job site construction. The technology can give producers SAF capac ity up to a year faster than what is possible with traditional construction approaches, Honeywell says. In addition, Honeywell be lieves petroleum refiners and transportation fuel producers can convert current or idle facilities into SAF production plants, “to meet growing market demand.”
For corn-based ethanol producers, SAFFiRE and Honeywell clearly have op tions for entering and thriving in the ex
ploding SAF market. For producers eyeing alternative feedstocks, there are also several opportunities—from tech to investors. The airstrip needed to give lift to alcohol-based aviation fuel has been cleared, accord ing to multiple aviation associations. Tech providers are here and proven. Airlines are in. Government entities and policymakers have made their position in favor of SAF clear. So, for SAF production this year and decades into the future, the flight towards a new era of multi-billion-gallon per year volumes is no longer just taxiing toward the runway—it's already taken off.
Author: Luke Geiver Contact: editor@bbiinternational.com'Ethanol offers producers a widely available, economically viable feedstock.'
Stephanie Schmidt Ph.D. is a plant chemist and process analyst at Badger State Ethanol. She talks about her love for her job, her experience in the ethanol industry and pushing the limits of the industry every day.
Stephanie Schmidt Ph.D. is a plant chemist and process analyst at Badger State Ethanol. After earning a doctorate in Applied Mathematical and Computational Sciences from the University of Iowa, Schmidt started working as a scientist at a cellulosic ethanol plant right out of college. Throughout her career, Schmidt has developed her talent in data analysis and trending.
Born and raised in Portland, Oregon, Schmidt says that there was a lot of emphasis on care for the environment where she grew up. “There were all sorts of just little environmental things we had done as long as I can remember,” she says. “The big reduce-reuse-recycle…kind of being just conscious about the environment was part of our life at school and at home and my parents’ work. And so, when I went to college and I graduated, I knew I wanted to do something environmentally bene cial.”
In 2010, her pastor introduced a man who was starting a cellulosic ethanol plant near Cedar Rapids, Iowa, that turned trash into ethanol. Schmidt introduced herself and went in for an interview two days later. A couple years later, when the R&D portion of the company moved to Virginia, Schmidt changed jobs to stay in the Midwest, working as a vendor for an enzyme provider. In 2015, after two tragedies with her daughters, she took a job at an ethanol plant near Ames, Iowa to travel less. Soon after, Badger State Ethanol reached out with a job offer, which she took and moved to Wisconsin
At Badger State Ethanol, there is no typical day for Schmidt. The plant is constantly trying to push the industry forward. They led the industry in developing protein fractionation among other technologies and continue to try new things. “Our board and our CEO very much drive this because they are not afraid of making mistakes,” Schmidt says. “If we try something new and it doesn't work, we gure out what went wrong, we learn from this and then we improve it and we try again.” Her favorite thing about her job is the people she works with every day.
BASF has gone above and beyond in providing quality service for Badger State, Schmidt says. They were a strong supporter of Badger State in the hard times of the pandemic, “Just watching out and helping us, whatever they could do to make our lives easier at that time,” she says. “And they do that all the time, it wasn’t just during the pandemic.”
Outside of working hours, Schmidt loves to travel with her family, especially to national parks since they plan to visit every U.S. national park. So far, Schmidt’s favorite has been Death Valley National Park. They also like visiting amusement parks and trying new restaurants. Besides travel, Schmidt also spends her free time coaching her daughters’ sports teams and cheering for the Hawkeyes and Packers.
Shoring up its provisions on biointermediates, the EPA is catching up with new and envisioned biofuel production goals. Following a workshop on the topic, Ethanol Producer Magazine spoke with a policy expert to learn more.
By Katie SchroederBiointermediates have po tential to give ethanol produc ers a chance to access other renewable fuel markets, such as sustainable aviation fuel (SAF). The U.S. Environmental Pro tection Agency published biointermedi ate provisions in July that came into ef fect August 30. “Parties may now begin submitting registration requests and qual ity assurance plans for biointermediates,” said Mary Manners, deputy director of the compliance division with the EPA, in a Biointermediates Workshop hosted on line September 29. She and other EPA policy staff gave guidance to producers
on how to navigate the provisions in place for biointermediate use, including com pliance reporting, engineering reviews, transfer credits, biointermediate identifi cation and more.
At the workshop, Robert Anderson from the Office of Transportation and Air Quality, and team lead on the regu latory development part of the biointer mediates proposal, provided background on the development of the biointerme diate provisions. “When we originally wrote the RFS2 regulations ... the focus of those regulatory provisions were on single facilities,” he said. “The idea being that all the feedstocks and all the process ing to turn those feedstocks into a renew able fuel would occur in one place. And
we built the program that way because that single point of regulation would allow us to more easily oversee the program and ensure that valid RINs were generated. Almost as soon as we ... finalized RFS2, we started getting inquiries from regulated parties that highlighted the opportunities for advanced cellulosic fuels that would require process ing at more than one facility. And these so-called ‘proto-renewable’ fuels, or inter mediate products, are what we call biointer mediates.”
Chris Bliley, senior vice president of policy with Growth Energy, explains that the EPA’s earlier regulations viewed an ethanol production facility as a “onestop-shop” for transforming biomass into biofuel. However, with the evolution of
the biofuel industry there was a need for a regulatory pathway for producers to use their product to make something new. For example, processing corn or corn stover to make ethanol, but then using that ethanol to make SAF. “Essentially, the regulations had to catch up with the innovations in the industry and provide a regulatory pathway for somebody who may make something that would then be used again to produce a different biofuel,” Bliley says.
One of the key things the EPA pro visions accomplish is defining what a bio intermediate is. During the EPA’s Biointer
mediate Workshop, Anderson described the regulatory criteria that define a biointerme diate as found in 40 CFR 80.1401 of the RFS. First, a biointermediate is a feedstock used to make a renewable fuel made from biomass. Secondly, he explained that bioin termediates cannot generate RINs; the bio intermediate must be produced at a differ ent facility than the one that produces the finished renewable fuel. “If all the produc tion happens at a single [renewable] fuel fa cility it’s not a biointermediate,” Anderson said.
The biointermediate also must use an approved pathway, used in the production of the renewable fuel listed in the pathway and follow the approved process. It also must be listed in the provisions the EPA
released. The various biointermediates that currently have eligible pathways under the EPA’s provisions include: biocrude, bio diesel distillate bottoms, biomass-based sugars, digestate, free fatty acid feedstock, glycerin, soapstock, and—importantly for the ethanol industry—undenatured etha nol. “[Finished] renewable fuels are not biointermediates, and neither is renewable biomass that has not been substantially al tered,” Anderson explained. Finally, it can not be a feedstock material in an approved renewable fuel pathway already used to produce that fuel.
Anderson clarified that the EPA in tends to add more biointermediates to the list moving forward. If someone would like to have a potential biointermediate added, he advises them to reach out to the EPA’s support line and submit a description of it, which will allow the EPA to examine it and determine if it fits into a qualifying category. Next, Anderson recommends that the submitter puts in a petition for rulemaking, allowing the EPA to add it to the regulations so that it can be used to generate RINs. “The biointermediate pe tition should contain a legal and technical justification for why we should include the potential biointermediate in the program,” he said.
The petition should include informa tion on the biointermediate process, which feedstocks are used to make the biointer mediate and what renewable fuel it makes.
“We would also like a discussion of the pathways that it could fall under or wheth er it needs a new pathway,” Anderson said. “And then ... to help us prioritize work, the description of the timeline for its ultimate development and production.”
Biointermediates fit into a unique pro duction process for making renewable fu els. The process starts with renewable bio mass, which may be harvested at a variety of locations, Anderson explains. Typically, the biomass goes through a “form change” before reaching the biointermediates facil ity. When it reaches the facility, it is con
verted into a “proto-renewable fuel or bio intermediate.” The biointermediate is then taken to a renewable fuel facility where it is further transformed into a finished renew able fuel and distributed for use.
Under the provisions, biointermediate processing must take place at one facility and be shipped to a single renewable fuel facility, however the renewable facility can receive biointermediates from multiple sources. “There are [aspects of] the logis tics [and aggregation] that are a little bit more specialized,” Bliley says. “I think, im portantly, this provides some certainty to the marketplace. This provides a regulatory path forward, and I think people will work through that.”
It was also key for the EPA to define what biointermediates are and how they fit into the RFS. “There had to be some clarity about, for instance, how a product is handled, where and when the RINs are generated and what really qualifies as a bio intermediate,” Bliley says.
In the workshop, Aaron Levy from the Office of Transportation and Air
'Now that biointermediates are allowed in the program, it allows for a supply chain where biocrude is produced from crop residue via pyrolysis at one facility and then upgraded to renewable gasoline at another facility.'
- Aaron Levy, EPA Office of Transportation and Air Quality
Quality, discussed how biointermediates fit into the EPA’s “gen erally applicable” pathways. “We call those generally applicable because any party can submit a registration application to produce fuel through any of the pathways listed in that table,” Levy said. He explained that no changes were made to these pathways in the biointermediates provisions other than adding esterification, which allows for the use of free fatty acids as a feedstock for biodiesel production. The pathways do not change, but the provi sions simply allow the production process to be split between two facilities. Levy gave the example of renewable gasoline produc tion from crop residue. “Now that biointermediates are allowed in the program, it allows for a supply chain where biocrude is produced from crop residue via pyrolysis at one facility and then upgraded to renewable gasoline at another facility,” he said. “Pro vided that those two pieces of the production process meet the production process requirements.”
The provisions admitting biointermediates under the RFS give needed clarity for ethanol producers who are pursuing SAF or other innovations in the ethanol industry, Bliley explains. “I think [the provisions] are very important because they provide a regulatory path forward for our producers to [support] new in novations in renewable fuels,” he says, alluding to new market op portunities for ethanol such as SAF production. “This provides a great deal of certainty in how our producers can help meet those goals.”
“These provisions are designed to provide traceability, ac countability, a chain of evidence, all of that, so that we can prop erly implement the program,” Manners said at the workshop. Bli ley further explains that the provisions in the EPA’s recent ruling create a regulatory system, allowing the agency to ensure that the renewable fuels produced utilizing biointermediates meet the re quirements of the RFS. Other key provisions are focused on RIN generation, he says. “You want to make sure that if I’m producing ethanol, that it’s undenatured and going as a feedstock for sustain able aviation fuel, for example, and so there’s not already a RIN generated when I produce it,” Bliley says.
The provisions also outline the ways in which biointermedi ate producers and the renewable fuel producers each must dem onstrate compliance with the RFS. These requirements include attest engagement, product transfer documents and other record keeping requirements, as well as a mandatory quality assurance plan conducted by a third-party auditor to verify that RINs were generated correctly by the final biofuel producer.
At the facility level, water experts and engineers deal with issues big and small—from advanced cooling water analyses to sealing solutions and RO membranes—to reduce the use of H2O at ethanol plants.
WaterDeploying efficient and cost-effective water manage ment solutions at ethanol plants is a topic that might not seem as important as carbon inten sity score talk, and understand ably so. But at this past summer’s Inter national Fuel Ethanol Workshop and Expo, the world’s largest gathering of ethanol pro ducers, a panel on water was popular. Three panelists provided invaluable insight, help ing plant engineers and others understand water-related issues—big and small—that ethanol plants and their service providers deal with.
For the big-picture view, Quinn Han son-Pollock, industry technical consultant from Nalco Water, provided a deep-dive into optimizing the utility water balance at an ethanol plant. Thinking about the world’s water challenges as a whole helps to explain water usage issues at the plant level.
By 2030, if nothing changes, global water demand will outpace supply by 56 percent, he noted in his presentation. More than 40 percent of the global population is affected by water stress. Nearly threefourths of all companies have water use re duction goals, but 85 percent lack the tools to achieve them. That is where Hanson-Pol lock and his team can help.
His team works under the following understanding. Cooling tower water needs make up well over half (60 percent) of an ethanol plant’s utility water use. Next is re verse osmosis feed water for steam (19 per cent), followed by scrubber water (17 per cent) and then backwash/miscellaneous (4 percent).
Water consumption is also affected by the limitations of the production process itself. A cooling tower must reject heat via evaporation. From Nalco Water’s Cooling
Tower Engineering Evaluations, a typical ethanol plant cooling tower rejects 13,500 Btu/gal of ethanol produced. A 100 MMgy plant has a cooling water evaporation rate of 314 gallons per minute (gpm), which results in 1.62 gallons of water use per gal lon of ethanol. Scrubber water accounts for roughly 0.62 gallons of water per gallon of ethanol. Direct injection steam and deaerator venting accounts for 0.42 gallons of water per gallon of ethanol. Backwash and miscel laneous accounts for 0.13 gallons of water per gallon of ethanol.
To optimize all of those numbers, Han son-Pollock says an ethanol plant’s water treatment provider should help formulate the facility’s strategy to maximize reverse osmosis recovery (increasing recovery from 65 percent to 80 percent reduces the water intensity of a plant by 0.13); maximize cool ing tower cycles (increasing cycle times from 4 to 5 reduces water intensity by 0.14); op timize softener run-lengths or formulate a plan to recover clean water from the regen cycle; and evaluate creative solutions.
Managing the percentages related to water usage starts with recognizing the cur
rent state of the industry. While most plants are focused on carbon intensity (CI) scores, the time will come when they need to look at water intensity grading or something akin to it, Hanson-Pollock says. Right now, ethanol plants are modern facilities that have their water makeup streams metered. The next step is to totalize and trend that data to iden tify areas to optimize. In the future state of ethanol, he says, water will have continuous monitoring of water distribution, utilization and cooling tower performance.
In fact, Naclo has already started per forming cooling tower analysis work. The main issues they’ve found, so far, are related to fermentation temperature, especially dur ing hot and humid conditions. There are also typical issues with recirculation flow rate, water distribution among heat exchangers, water distribution at the tower, nozzle per formance, air flow through tower, biofoul ing and scale or iron deposition. “Improving visibility on cooling water flow will allow for plants to maximize performance and pro duction,” Hanson-Pollock says.
Terry Roberts, Midwest regional man ager for SEPCO, an industrial fluids sealing solution provider that serves multiple sec tors, says a seal is like a book. His presenta tion dialed down to a water related issue on a much smaller physical footprint area than that of Hanson-Pollock’s.
“A seal will tell you its story if you let it,” he said, explaining the information avail able after a failed seal is analyzed, especially in the case of ethanol evaporation opera tions. The mechanical seal itself is very sim ple. However, Roberts explains, there are hundreds of variables that can contribute to a failure. Examination of a failed seal can offer insight into failure prevention in the future, he says.
During his presentation, “Water Con servation In Ethanol Evaporation Opera tions: A Systems Approach to Sealing Im
proves Asset Uptime in Difficult-to-Seal Processes,” Roberts offered a real case study to highlight SEPCO’s expertise. And, how effective its failure analysis team is at reading a seal like a book.
Roberts’ case study story starts with the evaporation stage at an ethanol plant. Spe cifically, after distillation where the remain ing stillage goes through the process of re moving the liquid, leaving the solids (i.e., the DDGS).
“One plant engineer had struggles with pump and seal failures,” he says. “The slurry flowing through the evaporator pumps was problematic for many reasons. In addition to the fluid complications, the engineer had problems with premature seal failure, detect ing inboard seal leaks, setting up the environ mental controls correctly and proper train ing of the maintenance team.”
The premature seal failures could have been from improper installation, pump misalignment or mismanagement of the seal chamber environment, according to Roberts. But the only way to know was to perform the failure analysis. Most analyses show that despite what many might believe, mechanical seals are not always the cause of larger failures. Instead, most failures are caused by systemic problems or poor seal se lection. And, by design, the seal is the weak link in the system.
Seal analysis can reveal the following: if the right seal was selected for the application; if operating conditions are optimized; if the team set up the flush system properly; and if the barrier fluid is performing effectively.
For the ethanol plant issue in this par ticular case study, Roberts’ failure analysis team found three issues. First, the wrong mechanical seal design was used. Second, the environmental controls installed were not effective. And third, a more robust bar rier fluid was needed.
For the new, appropriate seal, Roberts’ team selected a dual cartridge mounted seal. The new seal helped to provide a more ro bust and balanced design that allowed for
• Water Intensity Ratio - gallons of water used per gallon of ethanol produced
• Typical range is 3.5 - 4.0 gal H2O / gal EtOH
• Example 100 MMgy plant at “Standard” Operating Conditions
• 1,011,000 gallons of fresh water per day
• Water intensity of 3.62 gal H2O / gal EtOH
Cooling Tower Makeup (gpm)
RO Feedwater for Steam (gpm)
Scrubber Water (gpm)
MMF Backwash/Misc. (gpm)
higher barrier fluid and process pressures. The new seal also provided an integral pumping ring in the seal that helped to move the barrier fluid from the seal gland to the convection tank for cooling. The tangential flush connections also provided more effec tive cooling in the seal gland.
The team also upgraded the barrier flu id. A synthetic oil specifically formulated for these applications was used. The main ben efits of the new barrier fluid include its resis tance to thermal and oxidative degradation, along with its ability to provide excellent heat transfer resulting in longer seal life.
Finally, the team installed a convec tion tank, commonly referred to as a seal pot. The convection tank provided a closed loop system that let the barrier fluid move heat from the seal gland to the tank for cool ing and then back to the mechanical seal to provide the necessary lubrication to the seal forces.
The failure analysis and resulting work showed that reviewing the seal itself really did yield a good ending with the plant, up ping its mean time between repairs (MTBR) to 37 months after previously needing to do maintenance work every four months. “Don’t underestimate how much each me chanic (on the SEPCO team) understands about seals,” said the ethanol plant engineer cited in the case study.
Brad Thompson, a water expert from Veolia (he presented under Suez which re cently merged with Veolia), spoke extensive ly about the importance of selecting the right reverse osmosis (RO) membrane, a common and extremely important element of every plant’s water treatment and usage plan. RO membranes are typically used for purifica tion across the process and, as Thompson
shows, most membranes only last three to five years. But, Thompson says, “membrane life can be extended by changing your ap proach.”
It’s important to understand why mem branes fail first. The common causes include microbiological growth, degradation, scale formation, pretreatment fouling and struc tural fouling related to the previous reasons. The most predominant cause of failure is microbiological fouling (roughly 75 percent of all failures). Nearly half of all autopsies performed to look at RO membrane issues show the existing damage to be significant (42 percent).
To fix microbiological fouling issues, Thompson says removal includes aggres sive clean-in-place practices. The process requires increased cleaner at higher pH, in creased time, increased temperature and in creased frequency. The ideal pH to remove microbiological fouling is 12.0.
There are two options to extend mem brane life: non-chemical solutions or chemi cals. For the non-chemical approach, the proper membrane needs to be selected from the start and then flushes need to be per formed. Engineers need to know the mem brane spec sheet. For example, a membrane at 99.0 percent rejection rate will let 1 per cent salt passage, while a membrane at 98.5 percent rejection rate will let 1.5 percent salt passage. Thompson says the difference can be important. Fouling-resistant membranes should also be used. The No. 1 membrane he recommends is the fouling resistance op tion in 34-mil.
Chemical solutions involve stage-bystage CIP, knowing when to clean, and the use of enzymatic cleaners. For staged CIP steps, it starts with a 160 gallon per minute CIP followed by a 80 gpm CIP. To prevent degradation, an engineer needs to improve dechlorination by getting the strokes per minute of the system right. Overfeeding the system will create microbiological growth. Underfeeding the vessels will cause mem brane degradation.
For membranes fouled with biofilm, there are new enzymatic cleaners that are comparable to conventional cleaners but won’t clean non-biofilm elements, Thomp son says.
Overall, extending the life of a mem brane includes on-time CIP, knowing the membrane specs, and stage-by-stage clean ing. Thompson’s presentation, like the others,
highlighted the importance of understanding the modern-day solutions for everyday water issues at the plant level.
Author: Luke Geiver Contact: editor@bbiinternational.comThe Drive Clean Initiative and Next Generation Fuels Act are simultaneously finding support in the ethanol industry. Both aim to usher in higher blends of ethanol, but via different mechanisms.
By Katie SchroederThe Inflation Reduction Act, arguably the most sweep ing clean energy legislation in U.S. history, is poised to con siderably benefit the ethanol industry and bioenergy writ large. The bill’s passage in August was hailed as a watershed moment for clean energy, climate and, specifically, CO2 capture and sequestration—the key stone of ultra-low-carbon ethanol pro duction. But for all that the IRA deliv ers—which is, to say, a lot—it does not address several of the U.S. ethanol in dustry’s most pressing needs and obsta cles to future growth. More is needed.
Shepherding federal legislation is difficult and tricky—compromising on new policy can have unwanted effects on existing law. That’s why trade groups representing biofuels in Washington D.C. have, for years, been very careful to not back proposals that might jeop ardize the Renewable Fuel Standard, the nation’s longtime biofuels program. But as the RFS enters a new phase of
its existence, with the U.S. Environ mental Protection Agency exercising a “reset” of the legislation this fall, and the electric vehicle movement gain ing critical mass, the ethanol industry’s policy guardians are entertaining federal legislation that would, if not replace the RFS, backstop it with a national lowcarbon fuel standard, a high-octane fuel requirement, or both.
The favored vehicle for an octanebased biofuel program is the Next Gen eration Fuels Act, a bill that raises the octane content for fuel, increasing en gine efficiency and reducing emissions by requiring higher blends of ethanol. The bill was introduced by U.S. Rep. Cheri Bustos of Illinois in both the 2021 and 2022 Congresses. Bustos tells Ethanol Producer Magazine her reason for supporting and presenting the bill is rooted in her family’s heritage of farm ing, and her service to the rural, cornproducing part of Illinois she serves. She says that even though the IRA should boost higher ethanol blends—it provides $500 million for biofuels infra structure—it does not accomplish what
the Next Generation Fuels Act would. Bustos says interest in the proposed bill has been strong; it gained bipar tisan support at its introduction with 17 Republican representatives and 12 Democrat representatives cosponsor ing it. The bill was also introduced to the Senate this year by Republican Sen. Chuck Grassley of Iowa, longtime sup porter of the biofuels industry.
“I really see this as a win-win-win. And what I mean by that is, obviously we are facing the challenges of higher gas prices. This can help bring down a gallon of gas by 50 cents a gallon by blending ethanol,” Bustos says. “Num ber two, we have a climate disaster on the horizon, and this helps bring down the carbon that is emitted into the air. And [third], it supports rural America, specifically our family farmers. So, I think when you look at those three wins, we just think this has great potential.”
On a different but related path, a national low-carbon fuel standard push is being organized as the Drive Clean Initiative. Already, the initiative is a sur prisingly diverse group of transporta
tion industry stakeholders—from ethanol producers to EV companies—interested in achieving net-zero emissions from trans portation by 2050. Geoff Cooper, president and CEO of the Renewable Fuels Associa tion, says the RFA has been involved with the initiative since its inception and is a founding member. The Drive Clean Initia tive, he says, is made up of ethanol produc ers, environmental groups, electric vehicle stakeholders and more, all united around the common belief that the best way to reach net zero emissions by 2050 is through the implementation of a national low-car bon fuel standard.
Whether the Drive Clean Initiative complements, competes against or overlaps with the Next Generation Fuels Act is best explained by what each proposal is primar ily championing. Both are aimed at support ing the proliferation of higher-level ethanol blends, albeit through different but related “stick-and-carrot” mechanisms—one fo cused more on the internal combustion en gine vehicles on the road today, the other casting a wider net big enough for ethanol, EVs and all other low-carbon transporta tion sources.
Doug Durante, executive director of the Clean Fuels Development Coalition, outlines what the Next Generation Fuel Act is and how it can help the ethanol in dustry. “The key to all of this is not just low carbon, but octane,” he says. “Ethanol’s highest value proposition is octane. There’s nothing like it; there’s nothing that adds oc tane the way it does, and then, now, with the [sequestration] of carbon, there’s definitely nothing that does it in a low-carbon way.”
The act would raise the octane require ment on fuel and requires that the octane added reduces greenhouse gas emissions by 40 percent to guarantee that the octane will not be increased through the use of toxic aromatics, Durante explains. The minimum amount of octane needed in a fuel to propel a vehicle is 87 AKI (anti knock index, made
up of the average of a fuel’s research octane number, or RON, and motor octane num ber), Durante explains. Refiners generally make an 84 AKI fuel and then add ten per cent ethanol to add three points of octane to make the 87 AKI fuel that drivers find at the pump. The bill would increase the oc tane requirement to 90/91 AKI, gradually increasing it over the years, thereby increas ing the percentage of ethanol in the fuel.
Durante explains that the automotive industry has been calling for higher octane ratings for years, since this would allow them to make more fuel efficient, high-per formance engines. Companies within the automotive industry such as General Mo tors and United Autoworkers, and compa nies within the machinery industry like John Deere and Case International are support ers of the NGFA. Durante explains that the bill would address issues such as the soonto-be diminishing number of FFVs on the road. It would also require automakers to warranty their vehicles for high-octane fuel and RVP waivers, while giving ethanol pro ducers an opportunity for volume growth in the domestic transportation market.
The bill provides a “systematic knock down of the obstacles,” Durante explains, by ensuring that the high-octane fuel would be low carbon through the increased use of ethanol as an octane additive. The bill also puts limits on aromatics, otherwise known as mobile source air toxics, chemicals used in gasoline to raise octane, Durante ex plains. Limiting these aromatics would al low ethanol to step in and fill the gap as a clean, low carbon option for increasing octane. “The whole point is to make clean octane, and this goes all the way back to the Clean Air Act of 1990, when they passed a lot of these initial clean fuel provisions, they were calling for clean octane from eth anol all the way back then,” he says. “So, this is very important. It would control these aromatics and make sure that not only the octane additives and such have to meet a low-carbon standard. And, just by virtue of being ethanol, they’re nontoxic.”
The other obstacle it knocks down is the need for vehicles designed to burn high er octane fuels. The bill would address this by reestablishing flex-fuel vehicle credits for automakers. “I used to do a lot of work in the FFV area, and right now the automak ers just aren’t making [them],” Durante says. “There’s not a market for it; there’s no in centive for them to make it, so we reestab lish those credits, and I’m a big fan of those credits because they don’t cost anything. They don’t cost the consumer anything ... Just give those guys a little credit for using a fuel that doesn’t emit as much carbon or use as much gasoline.”
This legislation has the potential to in crease demand for ethanol by another 4 to 5 billion gallons, as well as increasing corn use by another billion and a half bushels, Du rante says. He calls this increase a co-benefit as it reduces greenhouse gases (which is a potential low-carbon fuels standard tie-in).
Durante believes ethanol’s most unique and valuable attribute is its ability to add octane to fuel. “The octane would be able to start at this 95 [RON] and then increase over the years even more to a 98 RON, which would be a 93 or a 94 premium, it would almost be like a super-premium,” he says. “You’re talking about being able to [sell] 20 percent ethanol blends at the 95 level and 25 or 30 at this 98 RON level. So, that would be a significant increase over where we are now, we’re only using 10 or 15 percent now, so that’s important.”
The ultimate goal of the Drive Clean Initiative is to create a national clean fuel standard—based on carbon intensity—that is technology neutral. “The guiding prin ciple here is that we need to remain focused on the overall objective of reducing carbon emissions rather than trying to prescribe what technologies or what fuels need to be used to reduce emissions,” Cooper says. With California recently implementing an
electric vehicle mandate that bans internal combustion engines beginning in 2035, the Drive Clean Initiative wants to demonstrate that there is more than one way to reach net zero emissions. The goal, Cooper explains, is to set carbon reduction targets and create “a market mechanism to drive investment and creativity in the marketplace” to reach those goals without dictating one technol ogy as the solution.
This technology-neutral framework would allow for ethanol, electricity, hydro gen and other technologies to all play a role in meeting the net zero goal. “We think that’s a much better approach than being prescriptive and mandating certain technol ogies,” Cooper says. “And it’s certainly bet ter than choosing technology winners and losers and forcing certain technologies on consumers who may not want those tech nologies.”
Allowing the consumer to find the best solution for them could help decarboniza tion happen more quickly. The Drive Clean initiative has been educating lawmakers on the benefits of such a policy as well as high lighting “lessons learned” from clean fuel standards at the state level, Cooper says. “The point is to build momentum for the conversation and get more people talking about this policy solution and get more people up to speed on why, we believe, this is the most efficient and most economically attractive path forward for decarboniza tion,” he says. Currently, he expects a bill to be introduced in Congress sometime in the next 12 months.
The technology-neutral nature of this policy solution is evident in the indus tries represented; ethanol producers such as POET and Calgren Renewable Fuels, electrical charging companies like Charge Point, automakers such as Alliance for Au tomotive Innovation, environmental group involvement from the New York League of Conservation Voters, SAF producers such as Alder Fuels, biodiesel and renew able diesel producers, and more. “For the
last several years we have spent a lot of time just building trust with groups who share this common interest of reducing carbon emissions from transportation, and doing it in a way that is market-based and incentivebased, rather than using mandates and dra conian measures to force certain technolo gies,” Cooper says.
In order to ensure the program is fair, the Drive Clean Initiative supports utiliz ing the GREET model developed by the Department of Energy’s Argonne National Laboratory. Cooper explains that this mea surement fills the necessary role of being science-based, data driven and not politi cized.
These two policy approaches both have their benefits, and elements of each may ul
timately influence final policy. “We strongly believe that we need to be pursuing any op portunity to advance the dialogue and ad vance the discussion around ethanol’s role in reducing carbon emissions, and both of these concepts do that,” Cooper says. “We’ll get to a point where it's clear that one ap proach has more appeal than the other, and at that juncture we’ll make a decision on how we want to proceed, but we’re a long way from being there, and that’s why we think it’s foolish to promote one policy at the expense of the other when we should be promoting both.”
Author: Katie SchroederContact: katie.schroeder@bbiinternational.com
has been protecting
both since 1988.