PLUS: A construction ‘thrill ride’ Ascension’s industrial tsunami Trucker blues
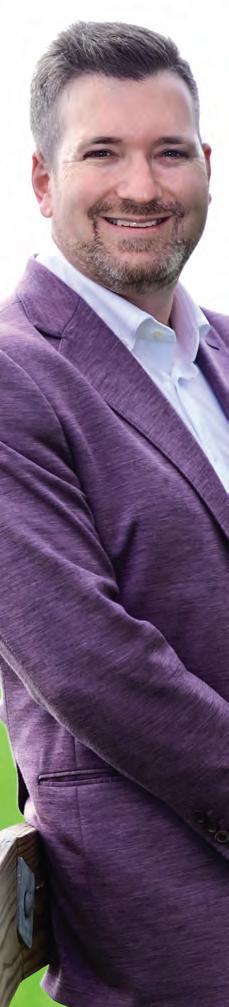
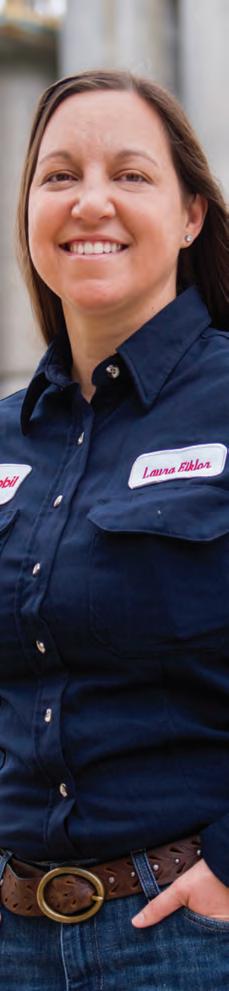

PLUS: A construction ‘thrill ride’ Ascension’s industrial tsunami Trucker blues
Meet the next generation driving Louisiana’s industrial future.
As a leading Louisiana manufacturer of custom pipe supports, piping accessories, and plate products, we’ve been providing unparalleled customer support for four decades. We’re large enough to ship thousands of custom products each month and small enough to ramp up quickly and decisively whenever you need us.
You can rely on the Delta Machine and Ironworks team of experienced fabricators, welders, and machinists for all your industrial construction project needs. We’re committed to quality, integrity, and, above all, being the most loyal partner any customer could ever want.
When your company is able to focus on its core competencies, great things can happen. That's where Brown Eagle can help. Having our team as your partner for logistics operations lets your team focus on what they do best. And when they do, the sky's the limit. That’s why some of the most demanding Fortune 500 clients rely on Brown Eagle. To discover how Brown Eagle can help your company soar, contact our service team today.
TRANSFORM YOUR TRAINING WITH PYVOT VERIFY – AN AI-DRIVEN TOOL THAT HELPS VERIFY IDENTITY AND MONITOR
• ASC staff validates AI.
• Eliminate travel. Reduce risk.
• Proof of training provided via digital badge.
DOES ASC HOST YOUR TRAINING? Wrap it with Pyvot Verify in 24 hours!
CONTACT US: (877) 345-1253 | info@alliancesafetycouncil.org
6
9 ICYMI
13 Executive Spotlight
How STEM Day inspired Regina Davis’ rise
13 Emerging Leaders
Meet the next generation driving Louisiana’s industrial future.
NEWS
23 Buckle up
Venture Global kicks off Louisiana’s construction ‘thrill ride’ as more projects reach the final investment decision stage.
28 Ground Zero
Ascension and St. James parishes are bracing for the strain of an industrial investment tsunami.
37 Trucker blues
The transportation industry is charged with meeting rising demand for drivers. Here’s what stands in the way.
44 The forgotten variable
‘Scope 3’ emissions are often overlooked in the quest for carbon neutrality.
50 The Boom at a Glance
Our maps of the projects driving industrial growth.
54 The Toughest Challenge
Paola Alvarado on being Louisiana’s fastest growing company
33 Leaders of Industry
10/12 Industry Report shines a light on regional companies and organizations that make an impact in their fields and in their communities.
Send your ideas and company news to editor@1012industryreport.com.
eople skills” don’t often come naturally to a detail-oriented engineer or bottom-line minded industrial owner. The beneficial trait often must be learned.
As one emerging leader in this issue’s cover story put it, there’s no one-size-fits-all approach to leadership that will work for all teams. Leaders must adapt their message to the inclinations and personalities of the individuals they manage.
Of course, being able to “read the room” is just one trait of a good leader. Transparency, authenticity, approachability and confidence, to name a few, are all part of the mix to varying degrees.
In this issue, we asked a dozen emerging leaders along the 10/12 corridor–all under the age of 40–how they handle the rigors of leadership, and to share what they’ve learned during their journey.
Each has earned the respect of their peers, in their own way, while leading teams in petrochemical facilities, oilfield service companies, ports, engineering firms and others in the industrial space. Meet these emerging leaders and get their insights on page 17.
For years, the beleaguered trucking industry has struggled to find the drivers it needs. Unfortunately, the problem has only worsened in recent months to include service technicians and back-office workers.
It’s forcing the industry to
consider new approaches to proactively addressing the problem, including lowering the driving age from 21 to 18 and launching local industry-sponsored CDL classes to attract Millennials and Gen Zers.
A fledgling CDL class at Baton Rouge Community College got off to a rocky start last year, with only a single student, but it’s beginning to gain momentum.
Instructor Jason Butcher is using classroom theory and behind-the-wheel training to teach USDOT rules and regulations; pre- and post-trip inspections; backing and maneuvering; driving on rural, urban and interstate highways; handling cargo; hours of service; and defensive driving.
Of course, these initiatives by themselves won’t solve the problem. At its core, the trucking industry suffers from an image issue that must first be overcome before it can attract and retain the workers it needs.
It’s estimated that more than 80,000 drivers will be necessary to fill a U.S. shortage in 2024, a number that is expected to grow to 160,000 by 2030. Get the latest on the chal lenges on page 41.
supply and demand.
National ABC President Michael Bellaman sums up the dangers of ignoring the problem: “Not addressing the shortage through an all-of-the-above approach to workforce development will slow improvements to our shared built environment, worker productivity, living standards and the places where we heal, learn, play, work and gather.”
Louisiana is the literal epicenter of industrial construction in the U.S., with three of ABC’s top five performers based in Baton Rouge. As a result, the impacts of the labor drain will likely be felt here more than anywhere else.
Some are attempting to stay ahead of the curve. In 2019, a group of industrial owners created an offshoot of the Greater Baton Rouge Industry Alliance to provide a more unified industrial voice for the New Orleans area.
The New Orleans Regional Industry Alliance, or NORIA, is currently mapping out its purpose and mission.
The numbers are daunting. Associated Builders and Contractors estimates that the U.S. construction industry will need to attract about 500,000 new workers in 2024 to balance
And ABC’s Bayou Chapter in New Orleans has plans to open a new temporary training facility near Venture
Global’s megasite in Plaquemines Parish.
Construction of the LNG facility has already ramped up significantly, and it’s depleting the local workforce of welders, pipefitters and other skilled laborers. Get the details on page 27.
WE KNOW THE IMPORTANCE of the maritime industry to the economic well-being of our state. This includes the five deep-draft ports on the Mississippi River that can accommodate large, ocean-going ships – the ports of Greater Baton Rouge, South Louisiana, New Orleans, St. Bernard, and Plaquemines.
When the total tonnage of cargo shipped from these five ports is combined, it qualifies the area from Baton Rouge to the mouth of the Mississippi River as one of the largest port complexes in the world.
To become more competitive with other ports in the U.S. and globally — and to attract more of the infrastructure money coming from Washington, D.C., it’s important for the five ports to work together.
That important work has already begun, with cooperation among Louisiana legislative leaders, port directors, and port staffs.
It’s been said, “A rising tide lifts all ships.” At the Port of Greater Baton Rouge, we look forward to the opportunity to lift all of Louisiana through increased economic developments made possible by this spirit of cooperation among our deep-draft ports.
THE FIVE DEEP-DRAFT PORTS OF SOUTH LOUISIANA ON THE MISSISSIPPI RIVER:
• Port of Greater Baton Rouge
• Port of South Louisiana
• Port of New Orleans
• St. Bernard Port, Harbor and Terminal District
• Plaquemines Port, Harbor and Terminal District
Healthy energy systems should be secure, equitable and environmentally sustainable, but maintaining a proper balance between the three is a challenging proposition for most countries.
That’s particularly true as the market transitions, with increasing speed, to decentralized, decarbonized and digital systems.
Gretchen Watkins, president of Shell USA in Houston, says it’s one of the biggest dilemmas
countries faces in combating climate change: how to transition to cleaner forms of energy while also making them affordable and reliable.
Watkins spoke recently at the Energy Transition North America Conference in Houston.
“Those (security, equity and environmental sustainability) don’t always go together in harmony,” she says. “In fact, at times they’re very much in tension. As we think about the energy transition, we should recognize that there
• Energy Security: Measures a nation’s capacity to meet current and future energy demand reliably as well as withstand system shocks with minimal disruption to supplies. Covers the effective management of domestic and external energy sources, as well as the reliability and resilience of energy infrastructure.
• Energy Equity: Assesses a country’s ability to provide universal access to reliable, affordable and abundant energy for domestic and commercial use. Captures basic access to electricity and clean cooking fuels and technologies, access to prosperity-enabling levels of energy consumption, and affordability of electricity, gas and fuel.
• Environmental Sustainability: Represents the transition of a country’s energy system to mitigate and avoid potential environmental harm and climate change impacts. Focuses on productivity and efficiency of generation, transmission and distribution, decarbonization and air quality.
THE PURPOSE:
• To learn from leading performers and best practice
are a lot of forces impacting the world’s ability to transition from traditional hydrocarbon fuels to cleaner energy, whether that be biofuels, wind, solar, hydrogen, carbon capture etc.
“There is an incredible need for collaboration in the energy transition space … collaboration between companies, governments, societies, academic partners etc. There’s also the need for good policy.”
Renewable forms of energy remain unaffordable for much
• To assess effectiveness of energy policies for enabling balanced transition management
• To analyze the urgency of competing priorities
• To test the relative impact of focus shifts and new directions
• To support dialogue on integrated policy innovation
of the world, while, conversely, traditional forms of energy are abundant and less costly.
And while the needle has been moved somewhat in the U.S. by the Inflation Reduction Act and the Infrastructure Investment and Jobs Act–both of which introducing incentives and funding for investments in clean energy–Watkins says the transition needs to be equitable across the globe.
“We will have failed if only part of the world’s population transitions, and the rest don’t,” she adds.
Since 2010, the World Energy Council has ranked the energy performance of 127 countries based upon energy security, energy equity and environmental sustainability.
Dubbed the “Energy Trilemma Index,” the ranking uses global and national data to recommend areas for improvements on policy coherence and integrated policy innovation, helping to develop well calibrated energy systems.
The index rankings provide comparisons across countries on each of the three dimensions, while historical indexed scores provide insights into the performance trends of each country over time.
UN-accredited, the World Energy Council is the world’s leading member-based global energy network and is an independent and non-political group working dynamically across the entire energy ecosystem.
Source: World Energy CouncilDeltak Manufacturing’s New Iberia, LA facility is strategically located 15 miles from the Gulf of Mexico with 150,000 sq. ft. combined under roof fabrication facilities and 19 overhead cranes.
PIPE AND PLATE PROCESSING & FABRICATION SHOP
• Building: 120' X 170'
• Computerized robotic CNC pipe coping/cutting equipment with up to 48” pipe capacity.
• Computerized robotic CNC plate cutting equipment, cuts up to 8” thick plate in sheets up to 10 ’X 40’, 400-amp plasma or oxy-fuel, with 5-axis bevel head.
STRUCTURAL SHOP
• Building: 150’ x 300’ x 70’
CLIMATE-CONTROLLED BLASTING & COATING SHOP
• Building: 95’ W X 265’ L X 38’ eave height
• Can process 18’ W × 15’ H × 40’ L structures
ROBOTIC BEAM AND STRUCTURAL SHAPES FABRICATION SHOP
• Building: 55’ W x 21’ L x 16’ eave height
• 7- axis robotic plasma cutting system cuts material to length, copes, compound miters, bevels, cuts weld access & bolt holes and etches piece marks, heat numbers and layout lines for weldments.
• Meets ANSI/AISC 360-05 standard specification on bolt holes for structural steel buildings.
• Equipped with 8 20-ton overhead cranes at a hook height of 56.5’, and has 75 welding stations.
• Overhead crane rails extend 50’ out from each end of the building to allow additional flexibility.
BARGE CAPABILITY
• 100’ × 400’ slip at a depth of 20-25’
• 800’ open-cell bulkhead with 6,000-ton load out capability
• 4,000 linear feet of additional waterfront
CUSTOM MAKE YOUR PRODUCT TODAY. 4418 Pesson Road, New Iberia, LA 70560 www.deltakmfg.com | (225) 435-7420
Regina Davis was introduced to the world of engineering during a scheduled STEM Day at her middle school. It ignited a spark in her that would never burn out.
“It put me on the path to becoming an engineer, even though at the time I didn’t really understand what an engineer did,” says Davis, who was appointed as ExxonMobil Baton Rouge’s refinery manager in September.
She would go on to earn a degree in chemical engineering at Louisiana Tech University as a first-generation college graduate, then land her first gig at ExxonMobil’s Chalmette Refining as a process contact engineer. While there, she would be promoted to roles of increasing responsibility, while also earning her MBA from the University of New Orleans.
In 2008, Davis was transferred to Fairfax, Virginia, and then in 2012 to the ExxonMobil refinery in Beaumont. In 2017, she relocated to the Strathcona Refinery in Edmonton, Alberta, where over a period of years she would be promoted from technical manager to operations manager, then eventually plant manager in 2021.
With the influence afforded by her plant manager’s role, Davis would be instrumental in the creation and sponsorship of the Women’s Interest Network and would become the co-chair of the inaugural Women United Initiative for the United Way Alberta Capital Region.
Nevertheless, Davis jumped at the opportunity to come back home to Louisiana. “This has been such a blessing,” she says. “Twenty-five years ago, I wouldn’t have believed you if you’d told me I would be here, as the first person of color in this role and only the second female.”
Since then, she has used her platform to promote the benefits of diversity in the workplace. She has also been active in recruiting,
serving as a member of both the ExxonMobil Louisiana Tech University and the ExxonMobil National Society of Black Engineers recruiting teams. “I feel having a diverse workforce gives us a competitive advantage,” Davis says. “It gives us the opportunity to be innovative and creative, while leveraging the unique perspectives that everyone brings to the table.”
What experience has most impacted your career?
When Hurricane Katrina slammed into the Gulf Coast in 2005, I was only six months into my first supervisory role at Chalmette Refining. I was just getting to know the ins and outs of being a new supervisor, while also dealing with people who had been significantly impacted by the
storm—including myself. My husband and I were in a FEMA trailer for well over a year, and my oldest daughter was in Houston with my parents because the schools were closed.
I learned a lot during that period. One of the things that impressed me the most was watching my plant manager focus on the people and their needs, even as we struggled to get our infrastructure up and running. At the time, I was the supervisor over the utilities complex, which was vital to getting the rest of the plant operational.
There was a lot of pressure on me, and we did things that were very innovative to make it happen. Through it all, I really felt cared for by the company, and I tried to exhibit that same level of caring to my own team.
What’s your leadership style?
I think of myself as a servant-leader, so I lean into authentic engagement with my employees. While managing the Strathcona refinery in Alberta, I made a point to engage with our workers at a personal level as best I could.
That’s difficult to do in Baton Rouge, where the refinery has 1,200 employees and there’s another 800 on the chemical side.
With an organization of this size, the biggest challenge for me is figuring out a way to engage in an authentic manner. I’ve intentionally set aside time in my calendar for field tours so that I can interact with senior leaders, operations and others. And I’ve made sure that my direct reports are multiplying those efforts.
What’s your professional passion?
I am deeply committed to mentoring the next generation. That gives me a lot of energy. I was introduced to engineering at a young age, so I find it rewarding to create or support programs that promote STEM, or when I mentor others.
Recently, we sponsored an ‘Introduce a Girl to Engineering Day’ and we had some 70 to 80 young ladies from north Baton Rouge come to our facility. They were able to do experiments, hear from other engineers, and I got to share my journey. We’re also working to strengthen our connection with Southern University to attract more folks to our workforce.
Tell us about the future.
I am so proud of the way ExxonMobil has leaned into the energy transition. At the end of the day, we must continue meeting our customers’ needs, while doing it in a way that creates a more sustainable environment. We’re taking a very strategic approach in that regard, but it’s the right one.
common thread of optimism runs through Louisiana’s rising stars of industry. In their various positions of influence, these emerging leaders have overcome their own unique obstacles and taken calculated risks to become guiding forces in their companies.
Meet the next generation driving Louisiana’s industrial future.
At their core, they’re dreamers who take action. They tend to rise to the occasion, especially when a crisis hits, and have an unrelenting internal drive to make a difference. They also have a strong desire for growth and lifelong learning, and the energy and ability to inspire.
These young leaders have a message to share: that they’re ready, willing and able to carry the industrial market into a bold new future. In the following pages, 10/12 Industry Report features a dozen of these rising leaders, each nominated by their industry peers or colleagues.
TYLER ABADIE is doubling down on oil and gas. Even though some market segments are transitioning to renewables, he feels traditional forms of energy will continue to play a significant role for years to come.
That’s why he rebranded and repurposed his engineering and consulting firm into ABADIE, a nationally recognized firm focused on the development, investment, operations and management of midstream assets and energy-related portfolio companies.
Abadie’s upward trajectory has been swift. A few years after graduating from LSU with a degree in civil engineering, he saw an opportunity: there weren’t many engineering, consulting and field management firms servicing smaller, independent oil companies. “At 26, I began to serve that niche,” he says.
Abadie wasn’t a traditional engineer. He didn’t mind going out in the field to understand his clients at a macro and micro level, and that made him an invaluable resource. He took on various critical roles, such as engineering and operations lead for Harvest-Marks Pipeline, a private equity joint venture acquiring Chevron and British Petroleum Cypress Pipeline assets in southeast Louisiana. While there, he worked directly with ownership to achieve revenue benchmarks and managed daily operations.
The oil bust of the mid 2010s dropped another opportunity in his lap. As major oil companies began divesting their assets, his clients were in a position to acquire them. “So, they turned to me, 27 years old at the time, to help them,” he adds. “That was a real catalyst for us, and we kept growing and growing.”
Eventually, Abadie moved to Mandeville and re-branded the firm as ABADIE. “I decided that if people were going to exit these traditional energy spaces, we were going to re-enter as a different entity,” Abadie says. “That’s how ABADIE was formed.” To date, he has been involved as an owner’s representative, strategic consultant and due diligence advisor for more than $1 billion in acquisitions and divestments between major corporations and independent operators.
Abadie has been careful to maintain his company’s identity throughout its various iterations. That, he admits, can be a complex dance. “The individuals who get you from Point A to Point B are often not the same ones that get you to Point C, but you want to make sure you don’t lose your identity and that you stay loyal and valued to those individuals that helped you get to where you are.”
Fabiola Campoblanco has left a mark on Worley’s trajectory and played a pivotal role in shaping the strategic direction of the company’s North America West and Gulf Coast regions. Her initiatives have moved the company into various sustainable sectors, including battery materials, CCUS, hydrogen and offshore wind. As a member of the global transformation group focusing on the CCUS Growth Unit, she was key in building the unit, bridging global capabilities with regional needs and supporting critical CCUS pursuits worldwide. She has been selected as one of 12 participants in Worley’s prestigious Future Leaders program.
Rebecca Chandler has led Halliburton’s Geismar plant through multiple senior leadership changes over the years, while maintaining a culture of responsiveness. Running a chemical plant safely and with no recorded spills or injuries is no small feat. In fact, Chandler’s team has achieved several years without any incidents. Her projects have also created significant cost savings for the company. Chandler’s leadership has allowed for rapid response to the industry’s emergency needs for specialty chemicals. She is also a voice for diversity and individual development in the industry.
INSTRUMENT INSTALLATION & TECHNICAL SERVICES
ELECTRICAL CONSTRUCTION | POWER DISTRIBUTION
ENHANCED PANEL & MODULAR CONTROL BUILDING SERVICES
TELECOMMUNICATIONS & SECURITY SYSTEMS | MISSION
CRITICAL CONSTRUCTION | COMMISSIONING & START-UP
MAINTENANCE SERVICES | POWER DEVELOPMENT
POWER ENGINEERING & DESIGN | PIPE FABRICATION
Chief Operations Officer |
PALA, Baton Rouge
A Baton Rouge native, Adam Landry has been on an upward trajectory at PALA ever since joining the company in 2011 after graduating from LSU. Over the years, he’s been promoted from estimator to project manager to operations manager, and ultimately to his current role as chief operating officer. Landry is deeply committed to serving the industrial construction industry. Through Associated Builders & Contractors – Pelican Chapter, he serves as a member of the board of directors and the Young Professionals Executive Committee. He is also a member of the Advisory Council for the North Baton Rouge Industry Training Initiative and the Student Enhancement Committee for LSU’s Construction Industry Advisory Council.
Plastics Plant and Resin Finishing Plant Manager | ExxonMobil, Baton Rouge
AN EMBARRASSING moment early in her career forced Laura Eiklor to appreciate the importance of what she was doing for ExxonMobil. She was in her first leadership role as an operations supervisor, and her team had to respond to an urgent reliability issue one weekend.
“By the time I arrived, my operations team had already been in the field for a few hours fighting this issue, and I showed up dressed in shorts and sandals,” Eiklor says. “I was extremely embarrassed. There they were working to solve the problem, and I showed up in my weekend gear.”
As the current manager of ExxonMobil’s plastics and resin finishing plants, Eiklor’s shorts and sandals days are over. She’s more likely to be seen wearing FRCs,
even when she’s not planning to be in the field.
A chemical engineering graduate from Pennsylvania State University, Eiklor began her career as a contact engineer at the Baton Rouge Chemical Plant. At the time, becoming a plant manager was nowhere near her radar. “My goal was to get a job about three doors down, and that was my aspiration,” she says. “That sounded like a great career to me.”
But in 2010 her manager, John Kovich, came to her with an opportunity: A planning role had opened at ExxonMobil Chemical Headquarters in Houston. “I remember being scared and excited at the same time, but he saw it as an opportunity and believed that I could accomplish something bigger.”
Since then, she’s become more accustomed to change, as she recognizes the opportunities that it often brings. That’s particularly true of her current position. “I’m excited about the things I can do for the company,” Eiklor says. “I care a lot about the people who work for me, and I care a lot about these sites.”
Eiklor’s leadership credo is simple: listen, care and do your job. “Caring means getting to know my employees by name, asking them about their lives and families, and being wherever my employees are so I can relate to what they’re doing,” she says. “That could mean spending an hour walking with operations or mechanical teams to ensure there are no barriers standing in the way of them doing their job safely.”
Eiklor is also an advocate for women in industry. She sponsors the Women’s Interest Network at ExxonMobil and reaches out to area high schools to introduce female students to STEM careers. “Doing that is a big part of my personal mission,” she says. “We have an awesome opportunity having five female plant managers here in Baton Rouge, and there’s an obligation to a be a strong mentor.”
Her plant manager’s role doesn’t end when she leaves the plant each day. “I carry this place with me no matter where I am. I work hard when I’m here, and while I enjoy my time away from work with my family and children, ultimately my role is 24/7.”
AT JUST 30 years of age, Megan Landry found herself managing people old enough to be her parents. It was a difficult transition, as she went from being a co-worker to their boss virtually overnight. Landry admits that at the time, “people skills” weren’t her strong suit. She found it easier to manage a budget or engineer a solution to a problem than to manage people.
Fortunately, her manager offered some valuable advice that still guides her today. “He told me, ‘Not everyone is you,’ meaning you can’t communicate with everyone in the same way,” Landry says. “The way we communicate with one individual might be completely different from the way we approach someone else, even when the message is the same. In other words, there’s no one-size-fits-all approach to managing people.”
With a career spanning some 10 years, Landry has become a driving force in the chemicals industry, demonstrating a passion for enhancing processes that marry efficiency, compliance and sustainability. Beginning her journey as a process design engineer for capital projects, Landry quickly distinguished herself with a keen ability for technical design and problem-solving.
Over the following five years, she became a technical support engineer, where her responsibilities expanded to include day-to-day operations, project development and the successful commissioning and startup of three new chemical assets – all part of a large-scale expansion project at the Sasol Lake Charles Chemicals Complex. “Commissioning those units was one of the high points of my career so far,” Landry says. “In those three years, I think I got six years’ worth of experience. The skills and the growth during that period … you can’t put a price on it.”
Landry – who holds a bachelor’s degree in chemical engineering and master’s degree in business administration – currently oversees a spectrum of critical aspects, including personnel management, fixed and variable cost control, budgeting, forecasting and the overall production of assets. She feels that integrity and resilience are critical in her role as a leader. “I’m not afraid to get my hands dirty and go and work alongside someone when it’s necessary,” Landry says. “I feel it’s important to lead by example and will get out there.”
Beyond the confines of her professional duties, she is a member of the Leadership Southwest Louisiana Class of 2024 and contributes to company initiatives such as Junior Achievement, Chem Expo and Lake Area Industry Alliance Paint Recycling Day. She is also deeply committed to nurturing the next generation’s interest in the STEM fields.
Head of Key Accounts | Port NOLA, New Orleans
Janine Mansour has been on the commercial team at the Port of New Orleans since 2010 and currently serves as the head of key accounts. In her role, she works with Port NOLA’s key shipper, ocean carrier, inland transportation and logistics clients to provide client support, supply chain solutions and drive business growth across the port’s cargo and rail business lines. She also serves as a board member on the Louisiana District Export Council and is an active participant in many industry associations, including the International Freight Forwarders and Customs Brokers Association of New Orleans, the American Cotton Shipping Association and the American Metals and Supply Chain Institute.
CHASE MELANCON knows how to face down a challenge. Since he was old enough to talk, he’s had to deal with a debilitating stutter. But instead of it stopping him, the stutter gave the St. Amant High School graduate a strong desire to get his message across – whether as a production supervisor at Occidental Chemical in Gonzales or as current chairman of the Ascension Parish Council.
“Moving up professionally and as an elected official and having people listen even when I sometimes don’t communicate clearly … that means a lot to me,” Melancon says. “Quite frankly no one cares. It doesn’t change their opinion of me as a leader one bit.” In fact, his colleagues on
the Ascension Council recently re-elected him as chairman for the second consecutive year.
Melancon feels it has made him a more empathic leader as he manages his team of 27 operators. He has an innate ability to listen and accept new ideas. On the parish council, he often assumes a mediator’s role, looking for the middle ground where “everybody is a little bit happy and a little bit mad. When you find that middle ground, that means everyone’s doing their part.”
Originally hired by OxyChem in 2014 as a process operator, Melancon was promoted to subject matter expert in 2020, then to shift supervisor for production in 2021. He landed his current role as production supervisor in
November 2022, where he has direct supervision in one of the plant’s eight process areas. “After three new positions in the last four years, I’m hoping to stay here for a little while and get my footing,” he says. “It’s been a lot of change in a short amount of time.”
His entry into politics came naturally. In 2015, Melancon began attending parish council meetings once or twice a month, then in 2019 he ran for parish council, with the full support of his wife. His only opponent eventually dropped out of the race, enabling him to run unopposed. Following his election, he aggressively pursued various roles, ultimately serving in leadership positions on the drainage,
strategic planning and utilities committees.
Melancon says OxyChem has provided him with an invaluable pathway for success. “The ability to have this type of career without a four-year degree is something that Ascension and all of south Louisiana offers you,” he adds. “Our industry gives us so many alternatives with the technical schools and vo-tech schools here.”
OxyChem is like a family to him. “There’s not a manager, superintendent or anyone else that you can’t sit down with and talk to. We have 450 employees across a 500-acre site and almost everyone knows each other in some form or fashion. If you work hard and do a good job here, they notice it. I’m living proof of that.”
As a former quarterback of the McNeese State University Cowboys, Cody Stroud knows the importance of teamwork. That has served him well in the industrial construction space, first as director of workforce development for Associated Builders and Contractors – Pelican Chapter. In 2016, he transitioned into a business development role at Triad Electric & Controls, where he develops and maintains new business opportunities with industrial and commercial clients. Stroud serves multiple professional and community organizations, and is on the SWLA Chamber Foundation board of directors.
Senior Manager, Supply Chain Management | Danos, Gray
Scott Theriot, a senior manager in supply chain management at Danos, has more than 18 years of experience in the energy industry, predominantly supporting major international oil companies in the Gulf of Mexico. At the age of 31, he received Danos’ prestigious Staff Employee of the Year award for his contributions to materials management. In 2020, Theriot partnered with other subject matter experts to develop and implement Intelligent Integrated Materials Solutions (i2ms) –Danos’ revolutionary supply chain service offering.
Corporate Relations Advisor | Shell, Geismar
With nearly 20 years of government relations, communications and external relations experience in the petrochemical and energy industry, Jordan Tremblay is a valued member of Shell’s corporate relations team in Louisiana. Since joining Shell, his experience and leadership continue to make positive impacts on Shell’s reputation and license to operate in the southeast Louisiana region, specifically Ascension and St. James parishes. He is also an active member in the Louisiana Midcontinent Oil and Gas Association and Louisiana Chemical Association, where he represents Shell on their Public and Government Relations committees. Tremblay is also a member of the Baton Rouge General Foundation’s board of directors.
CLAYTON WILLIAMSON got his feet wet in the oil and gas business working summers offshore while in college. His father and godfather got him the job so he could gain some experience in the industry. “I got to spend a couple of hitches offshore, long enough to realize I didn’t want to work offshore,” Williamson jokes. “But I got to see some of our equipment being used on those operations.”
It was an invaluable learning experience for the young Williamson. He came to respect the workers, and to admire their ability to work as a team – despite coming from diverse backgrounds, ethnicities and age brackets. “Seeing how the crews were run, how the site supervisor treated his people … that impressed me,” he says. “From the roustabouts to the drillers, deck hands, engineers and cooks … they were all out there working together. It was good to see how such a large group of people on different teams all work could together to make the job happen.”
A native of Morgan City, Williamson didn’t originally envision himself working for Petroleum Specialty Rental, the oilfield equipment company his uncle founded in 1979. After graduating from high school, all he wanted to do was play college baseball. But after brief stints as a pitcher at LSU and McNeese State University, he tore his rotator cuff and had to hang up his cleats. He ultimately graduated from the University of Louisiana – Lafayette with a degree in business.
Today, he does a little bit of everything in his role as COO. “I handle the business side of things, but I also handle most of our sales,” Williamson says. “I’m in Houston about every other week, because most of my customers are there.”
In recent years, he has become a vocal advocate for the oil and gas industry as chairman of the Professionals of LAGCOE and as a member of the American Association of Drilling Engineers. He’s also a Leadership Youngsville graduate.
Williamson is optimistic about the future of the industry, although he admits that the challenges of the last decade have tested its resilience. The oil bust in the mid-2010s was the biggest test, as it forced his company into bankruptcy. “It was a slow build back,” he says. “When the downturn happened, most of our business was focused on the Gulf of Mexico shelf, but companies were selling off their assets. Everything changed, so we had to change as well.”
Today, they’re a leaner, less vulnerable company. “It forced us to change the way we look at business and change the way we operate,” Williamson says. “We’re still providing the same equipment and quality, but we had to take a hard look at the pricing structure. Today, I feel better about where we are financially. We’re less susceptible to market downturns.”
Bengal supporting contractor, Performance Contractors meeting tight deadline of large process modules from module yard in Port Allen, LA and transloading to barge, barge transport to Amelia module yard for final offloading/ staging.
To successfully overcome your challenges, it takes more than a truck. It takes people with know-how.
Bengal maintains an extensive fleet of trucks to meet every hauling requirement including flat beds, step decks, RGN lowboys, extendable trailers, and tilt beds. All equipment is air-ride equipped to offer added protection to those sensitive shipments. We also handle arrangements for any escorts and permits that may be required.
We expertly handle time-sensitive heavy and oversize loads. With our large and diverse late-model equipment base, we can provide transportation solutions from standard flatbed and step deck freight, to specialized loads requiring unique attention. We make sure we have the equipment you require utilizing our network of dependable pre-screened carriers to get the job done safely and reliably. Our commitment to superior maintenance of our trucking fleet and cranes shows in our service department that consists of skilled technicians, parts professionals, and shop support staff that make our fleet the most reliable in the industry.
Our service department is on call 24/7 to quickly respond to an equipment call. We utilize a stateof-the-art computerized maintenance system that enables us to meet all customer and manufacturer compliance requirements. Our scheduled preventive maintenance program ensures that equipment is proactively managed, and we meet the critical demands of our customers.
Bengal provides solutions for all types of projects ranging from a single pallet to oversized heavy-haul loads. Our team’s ability to strategically plan and develop blueprints for turnkey projects has created time and cost savings for our clients.
With over 50 years of experience in logistics and freight, the team at Bengal can lower your cost and create efficiencies for customers by combining our network of qualified carriers. You can count on Bengal Logistics to help give your business the strategic advantage you deserve.
supported a chemical plant. We lifted a pressure vessel from a paint yard in St. Gabriel, LA, then transported a column to a plant using steerable equipment to support tight quarters at site.
Concrete infrastructure structures moving from south Mississippi facility down to mega Leeville, LA road expansion project.Venture Global kicks off Louisiana’s construction ‘thrill ride’ as more projects reach the final investment decision stage.
BY SAM BARNESAn unfathomable procession of up to 6,000 workers enters the gates of Venture Global’s Plaquemines LNG site every day. At $21 billion, the around-theclock, two-phased project is touted to be the largest in the nation.
Unfortunately, construction of the mammoth facility is draining the local skilled labor force and could continue to do so for years to come should the company’s equally substantial third phase – dubbed Delta LNG – reach a Final Investment Decision (FID) soon.
It seems Louisiana’s long-predicted construction surge is really happening.
The Venture Global job, as large as it is, is merely a bellwether of things to come, unlike previous years when reality didn’t quite live up to expectations. While other LNG projects might have tapped the brakes a bit across south Louisiana, there are plenty of other projects announced along the 10/12 corridor either breaking ground, in design or expected to reach FIDs soon.
“Of the $120 billion in announced projects, about half of them are evenly divided between Lake Charles and the Baton Rouge to New Orleans corridor,” says economist Loren Scott with
Loren C. Scott & Associates in Baton Rouge.
The reason for the unprecedented surge is simple. Industrial plants in Europe and Asia can’t compete with those in the U.S., which benefit from significantly lower natural gas prices. “We’re making stuff from natural gas that costs $2 per million BTUs and they’re having to pay $12 to $20,” Scott adds. “There’s no way they can compete with that. That’s why you’re seeing so many of these firms expanding here.”
As a result, industrial construction was the most significant contributor to jobs growth in Louisiana last year, with Baton Rouge – which supports the largest concentration of industrial contractors – leading the pack. Lake Charles and New Orleans weren’t far behind. “About 22 percent of the jobs created in Louisiana from December 2022 through December 2023 were in construction,”
“There is a lot of nontraditional construction that’s going on in the U.S. right now. It’s hitting at the same time as the traditional projects.”
MATT SHORIAK, executive vice president, EXCEL
Scott says. “And in Baton Rouge, construction accounted for a whopping 78 percent of the total jobs created.”
That’s not news to Pepper Rutland, president and CEO of
MMR Group. His Baton Rougebased electrical and instrumentation firm closed out 2023 with $1.4 billion in revenue, a 50% increase over the $920 million they earned the previous year. The work isn’t concentrated in one place, either. “It’s consistent in every area that we work, and we’ve got 30 offices from California to Pennsylvania, as well as Mexico and South America,” Rutland says.
MMR currently has about 1,000 workers at the Plaquemines LNG site, as well as a commitment to work on Venture Global’s upcoming CP2 (Calcasieu Pass
2) project in Lake Charles. All totaled, MMR employs about 7,000 craftspeople, nearly double what it employed in 2020. “Once we got past the pandemic, it seemed like all the work that was pent up was cut loose,” Rutland says. “Projects that were put on hold were restarted, and new markets emerged. And it’s continuing in most of the sectors that we’re in – industrial, manufacturing and ‘mission critical’ work. All those sectors seem to be in the same general mood. We don’t see that slowing down at all, at least for the next five to six years.”
Matt Shoriak, executive vice
“It is the number one challenge that most industrial contractors are facing right now. Everyone is in the same boat.”
PEPPER RUTLAND, president and CEO, MMR Group
president of EXCEL Group in Baton Rouge, says he has been through boom times before, but this is different. “There is a lot of non-traditional construction that’s going on in the U.S. right now,” Shoriak says. “It’s hitting at the same time as the traditional projects.”
And unlike before, it’s impacting both unskilled and skilled labor. “For whatever reason, it’s harder now to get the unskilled people than the skilled, which was the complete opposite five years ago,” he adds. “These workers possess skills, but they’re learning on the job and advancing, and there aren’t people to take their places.”
When necessary, MMR pulls workers from other branches in Texas, Louisiana, Florida, Alabama and Mississippi to support mega-projects such as Plaquemines LNG. MMR’s Workforce Development Department assists with the logistics of it all. “Those workers will get transferred if they want to come,” Rutland says. “You
have to do that. You can’t just hire people off the street.
“It is the number one challenge that most industrial contractors are facing right now. Everyone is in the same boat. There are massive expansions in all industries, and that’s putting the burden on finding qualified craftsmen.”
Meanwhile, new RV parks and campgrounds are already cropping up across south Louisiana to support an ever-increasing influx of out-of-state workers. “There’s a certain segment of the industrial construction workforce that is very nomadic,” Scott says. “They might live in Iowa or West Texas, but they have an RV or trailer and they go wherever the work is.
“When you cross the Sunshine Bridge there’s an RV park full of construction workers, and you’ll see more of them as time goes by. With a shortage of workers,
there will be a big enough increase in wage rates to entice people to come here to work.”
Data recently released by the Greater Baton Rouge Industry Alliance shows a concerning gap between the needs of industry and the available supply of skilled crafts people over the next three years. Adding to the burden, some of Louisiana’s skilled labor workforce migrated to other states during previous market downturns.
“We’re forecasting a nearterm need for 50,000 people in Louisiana and Texas, and up to 100,000 between now and the end of 2026,” says Connie Fabre, GBRIA’s president and CEO. “The biggest needs will be for pipefitters, welders, millwrights, instrumentation technicians and electricians.”
To get ahead of the problem, GBRIA, along with Associated Builders & Contractors, various chambers of commerce, the Southwest Louisiana Construction Users Council and Lake Area Industry Alliance in Lake Charles launched the Louisiana Skilled Craft Workforce Development Resource Initiative last fall. The group is seeking more state financial and legislative support to create a pipeline of Louisiana-based skilled laborers. “There’s a lot of investment in Louisiana, and with that a lot of opportunities for people living in the state,” Fabre says.
Elsewhere, ABC Pelican Chapter is looking to shorten the length of select courses at its Baton Rouge training center. David Helveston, president & CEO, says they’re currently piloting a 100 percent “hands on” pipefitting class that takes only six months, instead of the previous two years, by eliminating the classroom component. It’s an attempt to im-
prove student retention rates and increase the number of pipefitters coming out of the program.
The first cohort of about a dozen students is expected to graduate in June. “Industry was involved in the development of the program,” Helveston says. “They narrowed it down to the most important elements, and focused on what was really needed out in the field. They got to the core of what was important.
“They’ll still need to pass the NCCER assessment test,” he adds. “If few pass, we’ll have to make some tweaks before moving forward.” If they’re successful, however, ABC will likely begin revamping its heavy equipment operator course as well to decrease its duration and increase “seat time.”
These days, though, contractors can’t rely solely upon traditional
The following Top 10 projects are either under way, have an FID issued or are expecting an FID in 2024:
1 $21 billion: Plaquemines LNG, Venture Global, Port Sulphur
2. $16.8 billion: Driftwood LNG, South of Lake Charles
3. $10 billion: Energy Transfer LNG, Lake Charles
4. $9.4 billion: Gron Fuels Renewable Diesel Fuel, Port of Greater Baton Rouge
5. $7.5 billion: Ascension Clean Energy/Clean Hydrogen Works, Donaldsonville
6. $7.5 billion: St. Charles Clean Fuels, St. Rose
7. $7 billion: Delfin LNG, Off the Coast of Cameron Parish
8. $4.6 billion: Lake Charles Methanol, Calcasieu Ship Channel
9. $4.5 billion: Louisiana Clean Energy Complex, Air Products, Burnside
10. $4.35 billion: Magnolia LNG, Calcasieu Ship Channel
“The biggest needs will be for pipefitters, welders, millwrights, instrumentation technicians and electricians.”
CONNIE FABRE, president
Industry Alliance
methods for worker training, MMR’s Rutland says. “We’re having to do a lot of the training ourselves,” he adds. “We have master trainers, and in some instances, we have portable training facilities at the sites. As good as ABC is, the training is falling to the contractors themselves.
“Either you’re going to train your people or you’re not going to have trained people.”
Two years ago, they launched MMR University, an internal learning and development program tailored to augment higher education and professional skillsets over a 2.5-year period. Complemented by new classroom facilities at MMR’s Baton Rouge headquarters, MMR-U combines in-person instruction with handson lessons, virtual learning opportunities, two summers of field experience and personal mentorship from MMR professionals.
“We’re taking interns from LSU and Southeastern and training
them up so that when they graduate, they’ll step into a higher role,” he adds. “Because, quite honestly, we just can’t wait.”
Meanwhile, contractors at Plaquemines LNG are having to play catchup in the workforce development space. The project is also testing the limits of local infrastructure, as LA 23 is the only way in and out of the Port Sulphur site. “The project is a behemoth,” says Jeb Bruneau, president/ CEO of ABC Bayou Chapter. “Cajun’s down there with over 1,000 people, Performance with over 1,000 people, MMR with 1,000, and Triad and Baker Gulf Coast Industrial folks are down there … these contractors are all en masse at that site.”
Fortunately, a sizeable portion
of the project is being prefabricated in modules off site. Performance Contractors recently added a modular fabrication facility in Amelia, in part to support the work. They’re fabricating the modules, then loading them onto barges for transport up the Mississippi River to the site. Turner industries is performing similar work at its New Iberia fabrication yard, and Baker Hughes is manufacturing and testing pre-assembled and fully integrated modular turbomachinery units from its facilities in Italy.
Should Venture
Global’s third multibillion-dollar phase – dubbed Delta LNG – reach an FID, the strain on the local workforce could continue through 2030. And it won’t be the only game in town. “IMTT is talking about a mega-hydrogen project,” Bruneau says, “and
Valero, Shell, Dow & Occidental Chemical have upcoming work as well, so we’re expecting a pickup in the industry in general.”
Recently, Bruneau reached out to the Plaquemines Parish Learning Center in Port Sulphur about potentially establishing a satellite training center 10 minutes south of the Venture Global site. If they reach a deal, PPLC would hold classes for the local community during the day and at night ABC would train workers for the Venture Global site.
While not the size and capacity of ABC’s training center, the satellite facility is logistically necessary. “Many of them can’t get to St. Rose in time because there’s such a bottleneck of traffic,” Bruneau says. “The additional training will come nowhere close to meeting the demand, but it will help. You’re talking thousands of additional people that we could train over the next six years.”
Spurred by the Venture Global
project and a general rise in investment in the area, GBRIA recently reenergized the New Orleans Regional Industry Alliance (NORIA), a “subcommittee” it created in 2019 to provide a more cohesive voice for New Orleans area industry. Before the advent of NORIA, there was no centralized entity for coordinating workforce development or industry advocacy efforts.
and sponsored by seven area plants and contractors advertising careers in industry.
“The industrial community in the New Orleans area needs to have their own voice,” says Tom Yura, vice president of operations – Americas at Mitsubishi Chemical in Geismar, and one of the founders of NORIA.
The Greater Baton Rouge Industry Alliance is forecasting a near-term need for 50,000 skilled workers in Louisiana and Texas, and up to 100,000 between now and the end of 2026
On March 5, NORIA sponsored an inaugural “Journey to Industry Event,” which was attended by 200 area 10th graders
“As an industry, we have a huge impact on so many things, but we don’t walk with the kind of swagger that matches the billions of dollars that we generate. We need to make sure that we’re reasonably represented.”
Congratulations
Kate MacArthur is worried about the roads in her parish. If most of the industrial projects planned for Ascension Parish break ground in the next year or two, the resulting surge in contractors and plant workers traveling down area highways could become unmanageable.
At last count, there were some 22 planned projects in Ascension and St. James parishes – 11 above $1 billion in cost – representing the highest concentration of industrial investment in the state.
“All these jobs we’re adding are great, but they’re projecting some 1,400 new permanent jobs over the next five years,” says MacArthur, president/CEO of the Ascension Economic Development Corp. “That means 1,400 more cars.”
“The big question at the moment is where can we park people so that there aren’t 2,000 to 4,000 additional cars driving into the same area every day?”
KATE MACARTHUR, president and CEO, Ascension Economic Development Corp.
The number is exponentially higher when accounting for construction traffic. “The big question at the moment is where can we park people so that there aren’t 2,000 to 4,000 additional cars driving into the same area every day?”
While the parish’s infrastructure needs are glaringly obvious, progress toward a solution has been slow.
In April 2022, a group of stakeholders comprised of local government officials, industry representatives and community leaders created the Highway 30 Coalition for the purpose of securing funding and potentially accelerating the expansion of the heavily traveled highway.
“LA 30 needs to have an additional lane in each direction, and so does LA 73,” MacArthur says.
“They provide the main access to the interstate and other areas. That’s the number one challenge.” Strains on the power grid are another concern, says economist Loren Scott of Loren C. Scott & Associates in Baton Rouge. “Entergy is making the case that more transmission lines need to be built along that corridor,” Scott says.
“That’s because out of the dozens of projects announced from West Baton Rouge to St. Charles … most of them are in Ascension and St. James parishes.”
Fortunately, there has been some recent progress on the infrastructure front. A section of LA 70 is currently being widened as part of a $53.2 million project stretching from LA 22 in Sorrento to the base of the Sunshine Bridge. And another $29 million is being spent to construct two-lane roundabouts at the on- and off-ramps on both sides of the I-10/LA 30 interchange and farther west at the intersection of LA 30 and South St. Landry Road.
“We’re also optimistic about a new economic development district the parish created around the LA 30 industrial corridor,” MacArthur adds. “That will provide a pathway for receiving matching funds to widen LA 30 and move
“People will welcome us, but they won’t get too excited if we’re negatively impacting traffic.”
projects along faster.”
Tom Yura, vice president of operations – Americas, Mitsubishi Chemical Group in Geismar, says anyone who has worked in Ascension Parish long enough knows that roads are an issue. “People will welcome us, but they won’t get too excited if we’re negatively impacting traffic,” Yura says.
Mitsubishi plans to build a $1 billion facility on a 77-acre site in Geismar that could produce up to 385,000 tons annually of methyl methacrylate, a chemical used in a variety of paints, adhesives, building panels and other acrylic polymers.
The project, to be located on LA 30 between BASF and Rubicon, is expected to create 125 direct jobs and 669 indirect jobs. Construction could begin as early as this summer.
“Dealing with road congestion and how to get construction folks and employees to the jobsite without negatively impacting the community … those are important issues to us,” he adds.
Yura, who is also chairman of the Greater Baton Rouge Industry Alliance, plans to work with local officials and other owners to find solutions, which could include staggering shift schedules, locating
off-location parking lots for workers and using mass transportation.
“We have to find ways to minimize the impact through traffic solutions and supporting long term road improvements … because there are a lot of people there now.” He plans to join the Hwy. 30 Coalition to help support their efforts.
When Air Products recently needed help transporting construction workers to and from its new blue hydrogen facility in Darrow, T3 Industrial Solutions of Baton Rouge came up with a decidedly unique idea. Why not use double-decker buses – the same kind used to transport tourists in New Orleans, New York and London –to carry employees to the site?
As a first step, they contacted the Lamar Dixon Expo Center about constructing a parking lot on their property.
“They loved the idea,” co-owner Trent Davis says, “since there were about 40-plus acres of unused land that we were going to develop at no cost to them. We entered into a Cooperative Endeavor Agreement to facilitate the parking and busing – not just for Air Products, but for any other major project or event in the area.”
Today, there are some 4,500 parking spaces at Lamar Dixon. Additionally, the contractor has procured 10 of the double-decker buses from an overseas seller –with the first arriving in February. They estimate that each bus will take some 81 cars off the road.
T3 Industrial Solutions is asking for 60-day lookaheads from their clients to ensure they have an adequate number of buses to meet the need. “We’re trying to stay out ahead of it,” he says, because you can’t just snap your fingers and get a double-decker bus.”
With the scarcity of the workforce, Davis feels the buses will help owners attract workers. “These aren’t just old beat-up school buses,” he adds. “They have individual bucket seats, so the workers will feel like they have their own space. It’s going to change the employee bussing and transportation game.”
AEDC shares project timeline information with its industrial members, as well as the local sheriff’s department and parish administration, “so they know what’s going to be happening on the roads,” MacArthur says. “We
“Out of the dozens of projects announced from West Baton Rouge to St. Charles … most of them are in Ascension and St. James parishes.”
LOREN SCOTT, economist
serve as a connector piece so we can help them in their planning, traffic management etc. They try to stagger events as best they can, but that’s not always possible.”
They also work with GBRIA and River Parishes Community College to identify future work-
force needs and to ensure that adequate recruitment and training is under way. “If a project is going to create 50 new jobs, the plant owner will give GBRIA the full breakdown and they’ll loop in the technical colleges,” she adds. “We meet with RPCC quarterly to
“As market conditions change and more announcements are finalized there will be a big demand on craft labor, whether welders, pipefitters or boilermakers.”
JOSH WIGGINS, plant manager, Koch Methanol St. James
make sure that they’re providing the right classes and training for now and the long term. That way, we ensure all those numbers are aligning.”
Josh Wiggins, plant manager at Koch Methanol St. James, says he doesn’t expect any issues finding available workers for his plant’s two-year, $150 million optimization project just now ramping up, “but of course as market conditions change and more announcements are finalized there will be a big demand on craft labor, whether welders, pipefitters or boilermakers.
“We’ll ask our contractors for a labor escalation forecast and see if we’ll need to pivot or adapt our current timeline.”
The Koch Methanol Optimization Project is a collection of projects intended to achieve a 25 percent increase of the facility design production rate from about 4,950 to 6,200 metric tons per day of refined methanol.
The project will require some 400 temporary construction jobs at peak. “We’re keeping a close eye on turnarounds and industrial activity in the area to look for any potential future constraints,” Wiggins says. “Ultimately, it’s going to
depend on the level of expansion going on around the plant.”
Koch Methanol frequently hires from the local community and offers scholarships through RPCC to area high school students and adult learners, who then receive skills training during a two-year program. They also recently donated $70,000 to St. James Parish Schools.
Yura says even though there aren’t any shovels in the ground yet, Mitsubishi has already begun cultivating a local workforce.
“During this quiet time, we’re visiting people in the community, introducing ourselves and letting them know what types of jobs are coming,” he adds. “We’ll be partnering with RPCC and local high schools and trying to figure out how we can support as many local people as possible to fill the jobs we’re going to need filled.”
For its part, T3 Industrial Solutions hopes to provide transportation to those living in disadvantaged areas, possibly funded by the federal Inflation Reduction Act and/or Justice40 initiatives.
“Transportation can be the difference between having a job and not having a job,” Davis says. “We would love to set up some type of
transportation arrangement with the parish or private sector where we would transport these people and give them the same access as everyone else to getting a job.”
At present, they’re determining the best way to structure the effort. “It’s literally one of those things that would benefit everyone,” he adds. “The dollars would stay in the community, and we wouldn’t have to bring people in from Texas.”
A host of economic and regulatory variables will ultimately determine just how many projects become reality in the coming months and years. Lingering inflationary pressures, for example, could cause delays or prevent some owners from pulling the trigger altogether.
Mitsubishi’s Yura is actively seeking to partner with other plants to share the cost of some expenses, such as infrastructure, and thereby alleviate the impacts of inflation.
“If you have to build a bridge over a levee to bring in modules for your project, for example, that’s a sunk cost. But if there are multi-
alition in Geismar,” he adds, “and we’re beginning active discussions to see how we can help each other.”
Wiggins says Koch Methanol is using mostly existing assets during its optimization project, so he doesn’t expect significant impacts from material price increases or supply chain disruptions. Much of that, he says, has already been factored into the overall project cost and timeline.
Of course, not everyone’s happy with the proliferation of work coming down in the pike in Ascension and St. James.
ple companies that can utilize that bridge, instead of one company having to bear all the costs they can spread it around and lower the overall project costs for everyone.”
That could also help reduce traffic disruptions, as only a single bridge would need to be constructed.
“We have a strong industry co-
A years-long battle waged by environmental and community groups has been under way to stop Formosa from building a massive petrochemical complex along the Mississippi River in southern Louisiana. The Taiwan-based chemical giant hopes to build the $9.4 billion petrochemical complex – dubbed the Sunshine Project – on a sprawling 2,400acre site in St. James Parish.
By and large, though, Ascension Parish has been more welcoming. “Ascension has been very open armed toward industry,” Scott says. “They recognize what it means for their school system and that these plants provide good paying jobs, and they’re going to town.”
10/12 Industry Report shines a light on companies and organizations that make an impact in their fields and in their communities.
“Well done is better than well said.” This is Delta Owner Cody Odom’s quote to live by from founding father Benjamin Franklin. Tenacity and a willingness to say yes to almost any job is what has set Delta Machine & Ironworks apart from the competition for the past 40 years. As a result, Delta is celebrating several milestones in 2024. The company is having its best year in business, and as icing on the cake, received the “Safest 70 Award” from the state’s largest workers’ comp provider LWCC.
“One piece that has remained the same as the industry has gotten more complex and diverse is our hard work,” says Odom. “That seems to resonate with all of the folks we do business with. We want to thank our loyal customers for supporting us for the past 40 years.”
Delta started out as a machine shop in 1984 and
transitioned into a fabrication company over the years as the need for smaller steel jobs grew. Today, Delta manufactures custom pipe supports, piping accessories and plate products from two shop and three office locations. No matter how large or small the job, Delta will find a way to get it done.
“We’ve had a lot of customers think a scope was too big for us, but so far we’ve been able to meet the challenge,” says Engineering Director Heidi
Holmes. “We don’t like to send our customers somewhere else. We like to do it all, start to finish, so we can make sure that it’s done right.”
Clear communication, listening to customer needs, and being relentless on quality have made up Delta’s customer service mission from the start. “Whatever we say we’re going to do, we’re going to make it happen,” Heidi adds. “We keep our word. I think our customers find that’s a rare thing nowadays. Sometimes that means really late nights and a lot of weekends and pulling resources from one place or another to help out.”
While the company has grown, its core team of experienced fabricators and machinists has stayed the same. Customers know who they’re talking to when they call Delta and can look forward to being part of a team from the start to the finish of a project.
We aren’t going to let anyone work harder than us,” Cody says.
“Everybody’s involved in energy, either making energy, moving it, trading it or using it,” says Pierre Conner, Executive Director of the Tulane Energy Institute. “We are all in the business of energy.”
It’s for this reason that the Tulane Energy Institute added a Master of Management in Energy (MME) program in 2011. This unique one-year program equips new college graduates with the knowledge and skills they need for leadership roles in energy and enables early to mid-career professionals to transition into new roles, such as going from engineering to management.
With a focus on applied knowledge and the option to specialize in areas including analytics, electric power, renewable energy or trading, the MME program has a record-high employment rate of 93
percent. “No matter where you come to us from, you’re leaving at a higher level with a better trajectory,” explains Conner, who brings to his role nearly 40 years of experience in energy finance and operations. “We estimate almost $200 trillion will be spent in energy and changing energy systems between now and 2050. There needs to be lot of people who understand the business and can make good investments.”
Of course, there’s a strong focus on sustainability and renewables in regard to climate change and the adoption of clean energy. Experiential and practical learning offer real-time information, projects with real companies and hands-on exercises. Industry immersion includes visits to solar fields, production platforms, power plants and refineries to deepen students’ understanding of all things energy. Students even experience actual market conditions
in the classroom by doing simulations in Tulane’s $3 million Trading Center.
“We consume a lot of information around energy, because we are going to do something about it,” says Conner. “Prices, policies … we incorporate that into the coursework. We are working on real-world problems, incorporating current events and trends.”
The Tulane Energy Institute is housed within Tulane’s Freeman School of Business and is also closely connected with Tulane Law School and the School of Science and Engineering.
“We continue to stay on the forefront of emerging technology, and I envision we’ll continue to make sure that our MME program can reach a broad spectrum of potential students,” Conner adds. “Our focus on energy education is to prepare our graduates for the energy future.”
The transportation industry is charged with meeting rising demand for drivers. Here’s what stands in the way.
Louisiana’s beleaguered trucking industry blames systemic issues for a worsening driver shortage and hopes to cast a bigger net to entice more non-traditional workers to the industry.
There’s growing evidence that something must be done. More than 80,000 drivers are currently needed to fill a U.S. shortage, according to a recent study by the American Journal of Transportation—a number that’s expected to increase to 160,000 by 2030.
Renee Amar, executive director of the Louisiana Motor Transport Association in Baton Rouge, says the most impactful change would be lowering the federal driving age from 21 to 18 years old for interstate trucking. Younger drivers can currently drive within the state, but not across state lines.
“And that’s where they make the most money,” Amar says. “They might drive regionally and make $40,000 to $50,000 a year, but it’s
when they drive longer hauls that they make upwards of $100,000 or more.”
As it is, the current law excludes the trucking industry as a viable career option for graduating high school seniors.
“If they’re not going to school, they’re going to work somewhere else, and by the time they’re 23 or 24 they’ve already picked a profession,” she adds. “We’ve already lost a couple of generations of potential truck drivers due to the law.”
IN SEARCH OF A SOLUTION: Congress created a pilot program that would test the plausibility of giving CDL’s to younger truckers and to develop a Women of Trucking Advisory Board to attract and support women in the trucking industry. Industry advocates in Louisiana say it has been largely ineffective.
Attracting more women to the industry would be another option. “We need to understand the psychology of why we have such a hard time recruiting women into the profession,” Amar says. “They are often excellent truck drivers because of their attentiveness to details and their hyper safe nature. It’s just a matter of convincing them to make it a career.”
The U.S. Congress responded to the trucker shortage problem in 2022 by adding provisions in the Infrastructure Investment and Jobs Act to create a pilot program that would test the plausibility of giving CDL’s to younger truckers and to develop a Women of Trucking Advisory Board to attract and support women in the trucking industry.
The pilot program designates various locations across the nation where 18- to 19-year-olds can drive while accompanied by a driving instructor and equipped
with enhanced safety equipment. Data is then collected by a designated testing agency to determine if the drivers are as safe as their older counterparts.
Unfortunately, the program has been largely ineffective, Amar says, due to restrictions written into the process, such as designating mostly union-funded apprentice groups to run the program and mandating driver-facing cameras in the trucks.
“The agency wrote the rules so tough that no one wants to apply,” she adds. “Most of the big trucking companies wouldn’t go for that. We’re in the process of working with ATA (American Trucking Associations) to get some of that pulled back.”
Cully Frisard, CEO of Frisard’s Trucking Co. in Gramercy, welcomes a younger driving age, but also has issues with the way the pilot program is being handled.
“They are only allowing certain entities to train these drivers,” Frisard says. “They’re also saying they need only 400 hours of driver
training. That’s not enough time. They need to spend at least a year behind the wheel of that truck. The way it is, they’re not giving new drivers the chance to be successful.”
Amar is more hopeful about WOTAB’s efforts.
The group, operating under the Federal Motor Carrier Safety Administration, is charged with reviewing and reporting on policies that recruit, retain or advance women in the trucking industry through scholarship opportunities, enhanced training, mentorships, education and outreach.
She admits there are a few hurdles to clear before women will consider trucking as a viable option, not the least of which is their personal safety.
“We’ve already lost a couple of generations of potential truck drivers due to the law.”
RENEE AMAR,
“When a trucker ‘times out’ they must pull over, and for every 11 trucks on the road there’s only one parking space on average,” Amar says. “Sometimes they
As the marketing division of Melara Enterprises, we seamlessly fuse creative storytelling with performance data to craft compelling content and cultivate influential brands. With decades of collective experience, our team of creatives and strategists specializes in forging meaningful connections between your business and its audience, consistently elevating brand engagement and impact with every project we undertake.
must search for an hour or two to find a parking space. That’s difficult for everyone, but things like that make it incredibly challenging for us to recruit women.”
To help prospective students overcome the typically pricey tuition for CDL courses – some $5,500 on average – in 2022 LMTA began offering $100,000 in scholarships through Louisiana’s Community and Technical Colleges. Thus far, 18 students have received scholarships. “We felt like if we were going to complain about this, we should put our money where our mouth is,” Amar says.
“At the moment, we can only take five students at a time because that’s all I can put in the truck.”
JASON BUTCHER, CDL instructor, Baton Rouge Community College
a second truck, so we’re looking to eventually hire another instructor.”
And last summer, Baton Rouge Community College launched a CDL program at its Port Allen campus. Upon completing the program, students will be eligible to test for either a CDL Class
A tractor-trailer license or CDL Class B straight truck license, with the final skills test administered by BRCC’s state-approved examiners.
CDL instructor Jason Butcher designed the program to address
new federal Department of Transportation guidelines. He’s now teaching his second eight-week class. “At the moment, we can only take five students at a time because that’s all I can put in the truck,” Butcher says. “We do have
Ultimately, he hopes to expand the program to include three instructors, each teaching 15 students at a time, as well as add an evening class that would span 12 weeks. “Once we get established and our classes running, the word is going to get out and we’ll start building our clientele and getting more people in,” he adds.
The local trucking industry isn’t actively involved in recruiting any of his graduates at the moment,
CIVIL CONSTRUCTION
CIVIL CONSTRUCTION MATERIAL SUPPLY TRANSPORTATION & LOGISTICS
YOUR TURNKEY PROVIDER FOR CIVIL CONSTRUCTION SITE DEVELOPMENT
All rising professionals, entrepreneurs, executives, and small business owners are invited to join us in taking their leadership up a notch. Business Report’s Executive Leadership Academy is a transformative program that will take your career and your organization to new levels of success.
THE BATON ROUGE BUSINESS REPORT’S Leadership Academy was outstanding! I took away some things that I had not previously considered, and I acquired insight about my style as a leader that I really was unaware of.”
KEVIN HUSSEY, United Fire & Water Damage of LA, LLCEACH CLASS HAD PRACTICAL INFORMATION that I could immediately take back to the office and apply. I also enjoyed being surrounded by incredible classmates that led to great discussions and sharing of perspectives. I have many pages of notes that I know I will reference for many years to come.
THE EXECUTIVE LEADERSHIP ACADEMY is one of the best things I have done in my career for professional development. The course content was excellent with a ton of practical applications. Being able to network and collaborate with other professionals across industry type was of great value.”
Lee & Associatesso Butcher is aggressively trying to connect graduating students with jobs. “On my own, I invited a recruiter from McElroy Truck Lines in Cuba, Ala., to talk to our students and potentially recruit them,” Butcher says. “They have a good program for new drivers.”
Unfortunately, some local trucking companies simply don’t hire students fresh out of CDL school. The insurance risk is often too great, so most recent CDL graduates go to large national trucking companies.
Randy Guillot, president of Triple G Express Inc. in New Orleans and a former ATA chairman, says all his drivers must have experience before they can be hired. Triple G Express primarily transports containers in and out of the Port of New Orleans across a 200-mile radius.
“We have a mix of drivers where the median age is a bit less than the average, but I haven’t been able to take advantage of any new drivers,” Guillot says. “They typically start with the larger
trucking companies, then as they gain more experience they come here.
“Of course, we support the driving schools and the recruitment of more drivers, but we don’t hire them directly out of school.”
Similarly, Frisard only hires drivers with a minimum of one year of experience. Insurance requirements are the primary reason. “It’s hard for us to hire a new driver,” Frisard adds.
“One year is required with a clean history with the previous company, and it must only be one company.”
Guillot says it has been an ongoing challenge for him to find truckers. “It’s a problem that has always been there,” he adds.
“The challenge my entire career has been recruiting enough qualified drivers for our roster. I am not minimizing that ongoing issue.”
His need for truckers will likely increase in the coming
BY THE NUMBERS80,000
Number of truck drivers currently needed to fill a U.S. shortage
160,000
Number of truck drivers needed to fill a U.S. shortage by 2030
SOURCE: American Journal of Transportation
years, should one or more planned container terminals be constructed in the New Orleans area and Plaquemines Parish. The successful completion of Port NOLA’s proposed Louisiana International
Terminal in St. Bernard Parish would have a significant impact on his business, so Guillot currently serves as a logistical consultant on the project for the New Orleans Regional Planning Committee.
As for Frisard, any difficulties he might have had finding drivers has been alleviated by inflationary drags on the economy. His business has slowed somewhat as people buy less of the products he hauls, including food products, pharmaceuticals, and paper, among other finished goods.
Nevertheless, “every industry needs new people because a lot of the workforce is going to age out,” Frisard says. He’s hopeful that the younger generation will see trucking as a good career choice.
“You don’t have to go through years of schooling, and the financial gain from it is a lot more than you would see coming out of a two- or four-year college. And if they find the right company, they’re looking at even better money.”
‘Scope 3’ emissions are often overlooked in the quest for carbon neutrality.
It’s a frequently ignored, but critically important, piece of the carbon neutrality puzzle.
As industrial owners aggressively pursue their own internal environmental goals, the emissions from shipping, trucking, rail, air and pipeline are often overlooked or not accurately gauged as part of the process.
That’s significant, as the supply chain produces an estimated 60% of emissions in the U.S., says Stuart Page, a senior consultant in the U.S. Department of Energy’s Loan Programs Office in Houston.
By SAM BARNES“It’s a big chunk of where our emissions come from, which means there’s real opportunity there,” says Page, who moderated a panel at the recent Energy Transition Conference in Houston, sponsored by Reuters Events. “But when looking at the
Issue Date: Spring 2023
“We believe that until companies comprehensively understand their carbon footprints, the problem isn’t going to be solved.”
top 2,000 companies in the world, only about one-third of them have credible, science-based net-zero 2050 targets.”
And of those, he adds, only 10% are tracking “Scope 3” emissions –those that result from the moving of assets not owned or controlled by the reporting organization.
Zach Scott, head of U.S. Carbon for global oil and gas shipper Trafigura in Houston, says his office focuses exclusively on decarbonizing processes in the supply chain.
“We believe that until companies comprehensively understand their carbon footprints, then the problem isn’t going to be solved,” says Scott, also speaking at the Energy Transition Conference.
It will ultimately require a significant amount of collaboration at every stage of the process, but “that just isn’t happening in the energy value chain,” he says.
In 2022, Trafigura partnered with Palantir Technologies to launch Agora, a secure, independent platform delivering enhanced
INCOMPLETE PICTURE: When looking at the top 2,000 companies in the world, only about one-third of them have credible, science-based net-zero 2050 targets. And of those, only 10% are tracking “Scope 3” emissions – those that result from the moving of assets not owned or controlled by the reporting organization.
visibility, reporting and analysis of commodity supply chain carbon intensity. The platform combines Trafigura’s knowledge of commodity markets, including data on shipments and trade routes, with Palantir’s software for data-driven
operations and decision-making.
The resulting tool brings greater transparency to the carbon intensity of commodity supply chains.
In turn, this helps companies understand how existing trade flows and routes can be decar-
bonized to hit emissions reduction targets faster. It also allows for collaboration across supply chains, benchmarking, analysis of alternative scenarios for carbon intensity reductions and carbon price impact modeling. Users’
Recycling you can rely on:
Extract value from your used materials
Experience gold standard, speedy service Services tailored around your business Prompt and competitive payment
Together, we can transform today’s materials into the ones we’ll all need tomorrow.
primary data can be supplemented with industry data to map new simulations and pathways.
Scott says companies can make better-informed decisions when equipped with accurate data.
“That’s why we rolled out the tool,” he adds. “If you can’t measure it, you can’t manage it.”
Dom Peré, chief executive officer of Baton Rouge-based logistics company Marex Services Group LLC, says owners should embrace carbon-reducing strategies in their supply chains, since they often go hand in hand with a significant savings in cost and time.
Unfortunately, many companies don’t see the need for a logistics strategy and instead lean on familiar, and often inefficient, ways to schedule shipments. Peré says Marex uses technology to look for efficiencies throughout every stage of the logistical process. Founded in 2011, the company provides freight management, transportation consulting, and a range of do-
mestic and cross border logistics services.
“Logistics can comprise up to 10 to 30 percent of a project’s budget,” he adds. “Everything should be planned out up front. If you can move to a more digital, automated, tech-centered platform where you’re centralizing everything, you can optimize your processes. And when you’re able to optimize – by maximizing the space on that flatbed truck or ship or optimizing a route – that can have a pretty big impact on carbon.
“For example, by keeping a truck’s wheels turning in an efficient manner, a driver won’t have to ‘deadhead’ from Baton Rouge to Shreveport to grab a load before going back to Houston. They can grab something within a threeto-five-mile radius. All of that reduces the overall impact to the environment … and your business. That’s what we do as a transportation management firm.”
In recent years, “nearshoring” the manufacture of materials has also become an increasingly pop-
ular way to improve supply chain efficiency. McKinsey & Company’s annual survey of supply chain leaders revealed that the share of companies making moves to nearshore their production was expected to nearly triple in 2023, primarily the result of the supply chain disruptions during and following the pandemic.
Nearshoring comes with other benefits, not the least of which is a reduction in supply chain emissions, says Laura Zapata, co-founder and CEO of Clearloop in Nashville. Clearloop provides carbon solutions for a variety of organizations, as well as invests in solar projects across the U.S. to expand access to clean energy.
“Nearshoring also creates more domestic jobs and reduces supply chain expenses,” Zapata says.
The company nearshores its supply chain when possible, and recently entered into a supply agreement with First Solar to provide solar panels from its New Iberia manufacturing facility currently under construction. The
$1.1 billion plant is expected to be operational in 2026. Clearloop also plans to use U.S.-made steel for the steel tubing in the solar panel mounting systems.
By localizing the supply chain, Clearloop hopes to cut emissions while also increasing the security of their supply chain. “We’re lowering the carbon intensity of building the modules,” Zapata says. “And as more of that happens, we’re creating job skills that will help grow that part of the economy.”
Some banks are outright declining to finance projects that they expect will increase carbon levels, or that fail to account for their supply chain emissions.
Ravina Advani, head of the Low Carbon Transition Group Americas for BNP Paribas in New York, says her international bank is pairing back on investments in certain carbon emitting industries such as coal and conventional oil and gas, while
doubling down on evolving and clean technologies.
BNP Paribas is one of the founding members of the NetZero Banking Alliance, consisting of more than 100 financial institutions who banded together to measure the carbon footprint of their portfolios, with an eye on achieving net-zero by 2050.
“We’re looking at the carbon emissions from every single loan that we lend,” Advani says, speaking during the Energy Transition Conference. “Any time we expect that a natural gas fired plant or pipeline project will create an uptick in carbon emissions, we’re saying ‘no’ to those deals. We have targets goals of our own and we want to ensure that we get there by mid-century.”
“If there’s a decarbonization angle for us we will certainly look to support that client with their decarbonations plans, but if it’s a cement plant, for example, that isn’t looking to decarbonize in any way we’ll have a harder time supporting that.”
We invited industry and construction leaders to share their organizations’ perspectives on the challenges and opportunities they anticipate in 2024 and the lessons they have learned in the past year.
OWNER - PRESIDENT
Delta Machine & Ironworks
FOR 40 YEARS, Delta has found that the keys to success in business aren’t too different from the keys to success in life. Keep your word, work hard, and remember who you are. At Delta, we build pipe supports and machine blinds all based on those foundational commitments. What’s more, we don’t hold any patents or own any proprietary information. We sell the same products as many other suppliers and our customers have plenty of options. We’re grateful for our loyal customers who continue to choose Delta for their important projects. We know that tomorrow’s business is no guarantee, and we aim to earn our spot on every project by being the best teammates.
Issue Date: Spring 2024 Ad proof #1
Our customers’ objectives haven’t changed much throughout the years. They want a knowledgeable fabricator that can bring real-world construction experience to the table, asking the right questions and delivering the right supports, on time, every time. We’re relentless on quality and resolved to deliver on our promises. We won’t be outworked by anyone. No matter what projects come next, we’ll be here, and doing what’s worked for the last 40 years. Huge THANK YOU to our loyal partners!
• Please respond by e-mail or phone with your approval or minor revisions.
• AD WILL RUN AS IS unless approval or final revisions are received within 24 hrs from receipt of this proof. A shorter timeframe will apply for tight deadlines.
• Additional revisions must be requested and may be subject to production fees.
check this ad for:
ad design © Melara Enterprises, LLC.
Rex Industrial
ANY TYPOS
2023 AND THE beginning of 2024 have been a “goldilocks” scenario with economic indicators not too hot, not too cold. This along with pending Fed rate cuts and AI hype has driven markets to new highs and created good conditions for business investment. On the flip side, we continued to see wage inflation and natural gas prices have been depressed.
This is an “outlook” after all so the question is, where do we go from here?
There is no shortage of business metaphors ranging from “Scared money doesn’t make money” to “Don’t leave the port when a storm is brewing”. Things do seem to slow down in an election year, and we may look back at this time as a bubble, but that does not mean we can sleep on 2024. Each business will make risk/reward decisions and the future will tell.
It is important to separate internal and external factors. External factors like elections affect everyone and we often have little control over them. Focusing on internal factors like being disciplined, team building, and good old-fashioned hard work will make all the difference for your company and clients.
Check us out at RexIndustrial.com if you would like to know more about how we can support your projects. See you in the field!
PRESIDENT & CEOIssue Date: Spring 2024 Ad proof #2
• Please respond by e-mail or phone with your approval or minor revisions.
• AD WILL RUN AS IS unless approval or final revisions are received within 24 hrs from receipt of this proof. A shorter timeframe will apply for tight deadlines.
2024 IS SHAPING up to be another great year for GBRIA. Demand for industry products is growing to meet the world’s needs for modern conveniences. Louisiana is a location of choice to invest in energy transition and carbon reduction projects, and over $100 billion in projects are planned to build clean energy solutions to make cleaner batteries for electric cars, solar panels, and wind farms. The products made right here in our backyard are fueling the energy transition. Our partnerships with area educational institutions including area high schools, ABC, BRCC, RPCC, and the Alliance Safety Council are working to recruit and train needed skilled craftspeople. Our latest labor forecast shows that demand is higher than ever for skills such as welders, scaffold builders, millwrights, pipefitters, electricians, engineers, and technology professionals of all types. Over 100,000 skilled people will be needed between now and the end of 2026, and although Louisiana’s industrial workforce is globally competitive, we need many more. GBRIA also continues to work on local infrastructure solutions, like the I-10 widening and a new bridge, advocacy in the public, improved plant safety and advancing the latest technologies for continuous improvement in operations. We are proud to coordinate the amazing partnerships that GBRIA and its members have with education, government, and our community, and we’re excited about the year ahead.
• Additional revisions must be requested and may be subject to production fees.
Carefully check this ad for: CORRECT ADDRESS • CORRECT PHONE NUMBER • ANY TYPOS
This ad design © Melara Enterprises, LLC. 2024. All rights reserved. Phone 225-928-1700
AS A FOUNDING member of the Association of Reciprocal Safety Councils (ARSC), Alliance Safety Council is dedicated to continually refining and ensuring the integrity of the reciprocal training model within industry. ARSC delivers more than 300,000 units of Basic Orientation Plus® (BOP) and BOP Refreshers on behalf of hundreds of facilities across the nation annually. BOP plays a crucial role in eliminating redundant training. Options are good and change is inevitable, but with new process safety management training options, it’s critical to recognize that sudden shifts in site requirements present considerable obstacles for industry’s transient workforce - increased deployment times and costs. Continuing to accept BOP as baseline training by simply adding “or” to a site’s requirements will result in significant savings by leveraging reciprocal courses offered by ARSC. Skilled labor shortages also continue to be a challenge. Ensuring that training is accessible 24/7/365 can offset this. At Alliance, we’ve broadened our remote learning capabilities with Al-assisted remote identity verification and participant monitoring, and remain committed to offering industry the most effective remote verification methods while upholding reciprocity.
Active Louisiana industrial projects announced or proposed, with projected capital investment of $25 million to $250 million. Second line shows projected capital investment and direct new jobs. List is representative, not complete; statuses and costs change frequently.
1 CF Industries Green Ammonia
$198M | 10 jobs
Location: Donaldsonville Status: FEED stage
2 BP Lightsource Prairie Ronde Solar Farm
$170M | 1,300 jobs retained
Location: Pointe Coupee Parish Status: Construction begins late 2024
3 Weyerhaeuser lumber mill upgrades
$157M | 4 jobs
Location: Holden Status: 2024 completion
4 Kinder Morgan Louisiana Pipeline expansion
$151M | 0 jobs
Location: Southwest Louisiana Status: December 2023 completion
5 IMTT terminal upgrades
$150M | N/A
Location: Geismar Status: 2023 completion
6 Delek Refinery
$150M | 30 jobs
Location: Krotz Springs Status: 2024 completion
7 Shell catalyst plant output boost
$121.7M | 17 jobs
Location: Port Allen Status: Equipment installation September 2024; final testing Q4 2024
8 International Matex Tank Terminals storage tanks, pipelines + dock
$100M | 8 jobs
Location: Geismar
Status: 2023 completion
9 Cornerstone hydrogen cyanide plant
$100M | N/A
Location: Jefferson Parish Status: Pending
10 Delta Biofuels renewable fuels from bagasse plant
$100M | 126
Location: Jeanerette
Status: In progress
11 Acadia Gulf of Mexico Access Channel deepening
$96M | N/A
Location: Port of Iberia Status: Underway
12 Eastman Taminco expansion
$70M | 5 jobs
Location: St. Gabriel Status: Underway
13 Placid Refining Headquarters + Port Allen facility modernization
$66M | 20 new jobs; 215 retained jobs
Location: Baton Rouge, Port Allen Status: Completion in 2027
14 International Paper Modernization
$52M | Retain 492 jobs
Location: Bogalusa
Status: N/A
15 Syngenta Crop Protection expansion
$52M | 3 jobs
Location: Iberville Parish Status: N/A
Sponsored by
16 Georgia Pacific revitalization
$50M | N/A
Location: Zachary
Status: N/A
17 CF Industries nitrogen fertilizer plant expansion
$41.4M | 7 jobs
Location: Donaldsonville
Status: 2023 completion
18 I,4 Group Plant
$35M | 35 jobs
Location: Ascension
Status: N/A
19 South Lafourche Leonard Miller Junior Airport corridor project
$35M | N/A
Location: Lafourche Parish
Status: Completion late 2024/early 2025
20 Deere & Co. manufacturing expansion
$29.8M | 70 jobs
Location: Thibodaux
Status: Production begins in 2024; full capacity by 2025
Active Louisiana industrial projects announced or proposed, with projected capital investment of $250 million or more. Includes projects that are underway, awaiting FID, and proposed. Second line shows projected capital investment and direct new jobs. List is representative, not complete; statuses and costs change frequently.
1 Venture Global LNG export facility
$21 billion | N/A
Location: Plaquemines Status: Phase 1 & Phase
2 FIDs issued
2 Driftwood LNG
$16.8B | 498 jobs
Location: West bank of the Calcasieu River, south of Lake Charles Status: Pending
3 G2 Net Zero LNG
$11B | 250 jobs
Location: Cameron Parish
Status: Production in 2027
4 Energy Transfer LNG
$10B | 250 jobs
Location: Lake Charles Status: Pending
5 Formosa Sunshine Project
$9.4B | 1,200 jobs
Location: St. James Parish Status: Delayed
6 Grön Fuels Renewable diesel facility
$9.4B | 1,025 jobs
Location: Port of Greater Baton Rouge Status: In progress
7 Delta LNG + Delta Express Pipeline
$8.5B | 300 jobs
Location: Plaquemines Parish Status: FID late 2025
8 Ascension Clean Energy/ Clean Hydrogen Works
$7.5B | 350 jobs
Location: Donaldsonvlle Status: FID 2024
9 St. Charles Clean Fuels
$7.5B | N/A
Location: St. Rose Status: FID and construction start in 2024
10 Delfin LNG
$7B | 400 jobs
Location: Off the coast of Cameron Parish Status: FERC approved; September 2027 deadline to build
11 Lake Charles Methanol
$4.6B | 200 jobs
Location: Calcasieu Ship Channel Status: Final investment decision projected in 2022
12 Air Products Blue Hydrogen Complex
$4.5B | 170 jobs
Location: Burnside Status: Operational 2026
13 Magnolia LNG
$4.35B | 70 jobs
Location: Calcasieu Ship Channel Status: Pending
14 Commonwealth LNG
$4B | N/A
Location: Cameron Parish Status: FID 2024
15 IGP Methanol Gulf Coast Methanol Park
$3.6B | 325 jobs
Location: Plaquemines Parish near Myrtle Grove
Status: FID mid-2024
16 Lake Charles Methanol
$3.24B |123 jobs
Location: Port of Lake Charles Status: FEED study, permitting
17 Pointe LNG
$3.2B | 200 jobs
Location: East Bank of the Mississippi River in Plaquemines Parish Status: N/A
18 DG Fuels Sustainable Aviation Fuel Complex
$3.1B | 1,055 jobs
Location: St. James
Status: FEED study in process; FID Q4 2023
19 CF Industries + Mitsui & Co. blue ammonia plant
$2B | 102 jobs
Location: Geismar
Status: FID 2023
20 Nutrien clean ammonia plant
$2B | N/A
Location: Acension Parish
Status: FID 2023; production in 2027
21 Mitsubishi Chemicals methyl methacrylate complex
$1.9B | 125
Location: Geismar
Status: FID 2024
22 Port NOLA
Louisiana International Terminal
$1.8 billion
Location: Violet, St. Bernard Parish
Status: Construction in 2025; first berth opens in 2028.
23 Proman Big Lake Fuels
$1.6B | 243 jobs
Location: Lake Charles
Status: FID second half of 2023; commercial operations 2025
24 EuroChem amonia/urea plant
$1.5B | 200 jobs
Location: St. John Parish Status: Pending
25 Methanex Corp., Methanex 3
$1.6B | 25 jobs
Location: Geismar
Status: Commercial operations Q4 2023
26 Shell Chemical olefins facility expansion
$1.2B | 12 jobs
Location: Geismar
Status: FID 2024; production in 2026 or 2027
27 Shell renewable diesel and sustainable avidation fuels facility
$1.3B | 42 jobs
Location: Convent Status: FID mid-2024
28 Shintech Louisiana Expansion of manufacturing and packaging facilities
$1.3B | 30 jobs
Location: Iberville and West Baton Rouge parishes Status: Completion in 2023
29 REG renewable energy expansion
$1.2B | %0 jobs
Location: Ascension Parish Status: Construction complete by 2023; full commissioning in 2024.
30 Burge seed oil production facility
$1B | N/A
Location: Destrehan Status: FID pending
31 Mitsubishi Chemical Corp Methacrylate manufacturing complex
$1B+ | 125 jobs
Location: Geismar
Status: Final investment decision in mid-2022
32 Energy World USA
$888M | 150 jobs
Location: West of Belle Pass in Lafourche Parish Status: Completion 2023
33 St. Bernard Renewables biorefinery
$835M | N/A
Location: PBF Chalmette Refinery Status: Startup first half of 2023
34 Koura lithium ion battery components
$800M | 100 jobs
Location: St. Gabriel Status: FID pending
35 Arbor Renewals gasoline and green hydrogen plant
$800M | N/A
Location: Port Allen Status: N/A
36 BASF MDI production facility
$780M | 22 jobs
Location: Geismar
Status: Construction began January 2023; complete in 2025
BLUE = ADDED SINCE PREVIOUS EDITION
Sources: LED, LEO, 10/12 research
37 Origin Materials biomass manufacturing facility
$750M | 200 jobs
Location: Geismar
Status: Complete in late 2025/early 2026
38 Kindle Energy Magnolia Power Generating Station
$740M | 25 jobs
Location: Plaquemine Status: Commercial operations in May 2025
39 Project Cypress carbon capture hub
$603M | 100 jobs
Location: Southwest Louisiana Status: Pending
40 Southern Cross Transmission Project/HVDC converter station + transmission line
$600M | N/A
Location: DeSoto Parish Status: Completion 2026
41 Nutrien Ammonia Plant Expansion
$560M | 15 jobs
Location: Ascension + Iberville Parishes Status: FID 2022
42 Enable Midstream Partners Gulf Run Pipeline
$550M | N/A
Location: Westlake
Status: Projected in service by Q4 2022
43 Westlake Chemicals expansion
$512M | 12 jobs
Location: Geismar
Status: FID 2024
44 Shell Chemical lubricant plant
$519M | 7 jobs
Location: Geismar
Status: Under construction
45 UBE Corp. lithium icon battery components
$500M | N/A
Location: Jefferson Parish Status: Operations late 2026
46 APM Container Terminal
$500M | 56 jobs
Location: Plaquemines Parish Status: Letter of intent signed with Plaquemines Port Harbor and Terminal District.
47 Element25 manganese sulfate manufacturing plant
$480M | 65 jobs
Location: Ascension Parish Status: FID 2024
48 Monarch Energy green hydrogen production facility
$426M | 44 jobs
Location: Ascension Parish Status: FID 2025
49 Entergy Bayou Power Station
$411M | N/A
Location: Leeville in Lafourche Parish
Status: Awaiting Louisiana Public Service Commission review
50 Enbridge Gator Express Meter project& Venice extension project
$400M | N/A
Location: Plaquemines Status: Gator Express Meter Project in service 2023; Venice Extension Project in service, 2024
51 Freepoint Ecosystems
$350M | 35 jobs
Location: Burnside Status: FID 2023
Anative of Tampico, Mexico, Paola Alvarado graduated from the University of Monterrey in 2004 as an industrial engineer.
While in college, she began working for a boiler manufacturer as a project manager overseeing the design and manufacture of industrial boilers. Later, she moved with her husband to the U.S. and began working for a similar company as a quality control manager.
When a larger firm purchased the company, she discovered that the new owner was concerned more about the bottom line than the quality of work. Seeing an opportunity, Alvarado set out on her own to create CORE in 2019.
In 2020, her husband joined her in the business, and they moved CORE from their house to a building in Gonzales. The company relocated again in 2022 to its current Airline Highway facility in Prairieville.
Before Paola Alvarado could realize her dream, she first had some formidable hurdles to clear. The biggest was financial in nature, as she had only $50,000 in seed money to set up the business.
Finding a lender was a challenge, too, although she eventually acquired a $350,000 Small Business Administration loan. Alvarado didn’t want any additional debt, so she didn’t take a paycheck for the first two years that CORE Boiler & Mechanical Services was in business–it all went to her workers and overhead.
At first, Alvarado had big dreams but no work. She began knocking on doors, but no one was answering. “In the industrial field, you need three years of safety records to ensure that you’re a safe company, so there’s a high barrier to entry when you’re starting from scratch,” Alvarado says.
A few customers, though, knew
POSITION: Founder & President
COMPANY: CORE Boiler & Mechanical Services, Prairieville
WHAT THEY DO: CORE Boiler & Mechanical Services’ earnings have skyrocketed by nearly 3,000% in the five years since the contractor was founded, making it the fastest growing Louisiana company in last year’s Inc. 5000. CORE clocked in at No. 182 after its revenue increased from roughly $250,000 in 2019 to $8.1 million in 2022. And the growth continues. Owner Paola Alvarado estimates that the company’s revenues were some $10 million in 2023. CORE’s “bread and butter” is industrial boiler repairs, but it also offers pipe fabrication, turnaround services and specialty welding.
of Alvarado through her former employer and decided to give her fledgling company a chance. She says American Styrenics in St. James was her first client.
“They were willing to issue a deviation because we didn’t have the safety hours,” she says. “We did a small, quick repair and everything looked good, then there was another one and then another. It just grew from there.”
That’s when Alvarado had an epiphany. By focusing her attention on those companies that had given CORE a chance, she could provide more tailored services and develop long-term partnerships.
It proved to be a winning formula. “Even without a sales team, we were able to start from nothing and grow to $10 million in sales a year … and we’re debt free,” Alvarado says. “But we’ve been careful about growth. We didn’t say ‘yes’ to everything in the beginning; we made sure we had the infrastructure and resources before we committed to a job.”
CORE does what it does and does it well. Its 24-hour response service is particularly attractive to customers.
“It never fails, it’s usually a Friday afternoon when they call,” she says. “We’re known primarily as a boiler company, but we notice other things when we’re there, and we
assist them whenever it’s possible. Still, we won’t commit ourselves to something that we can’t do.”
Alvarado says she’s “still on the journey,” but if there’s one prevailing lesson that’s she learned it’s that nothing is given and everything must be earned. “If you have the commitment and ambition, along with the right business model, you can succeed,” she adds.
The company’s name sums up its “secret sauce” for success. “We wanted to create a company that, at its ‘core,’ is about the people, both our employees and customers,” Alvarado says. “That’s our purpose; that’s our mission.”