

Advanced Tracking Technology
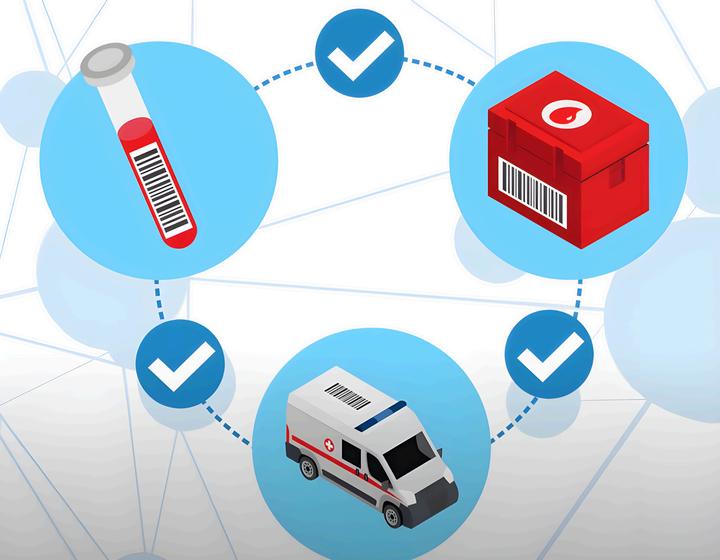
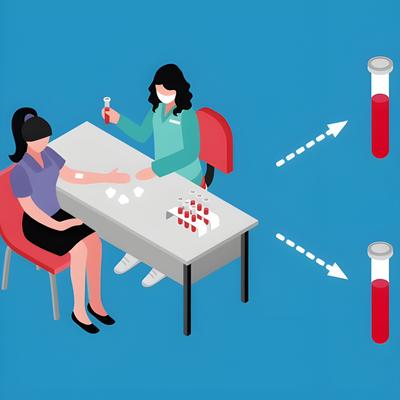
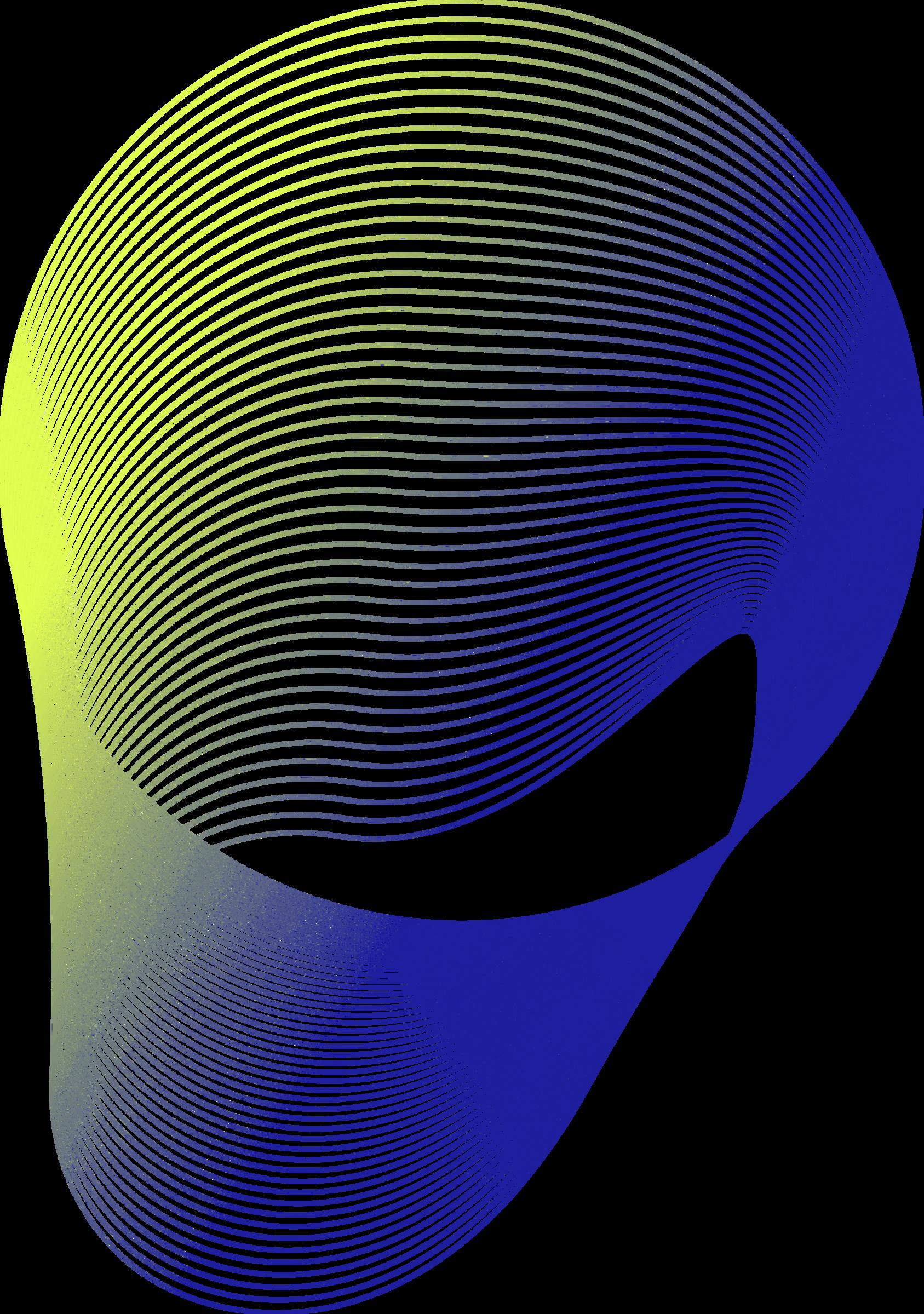
See how it works:
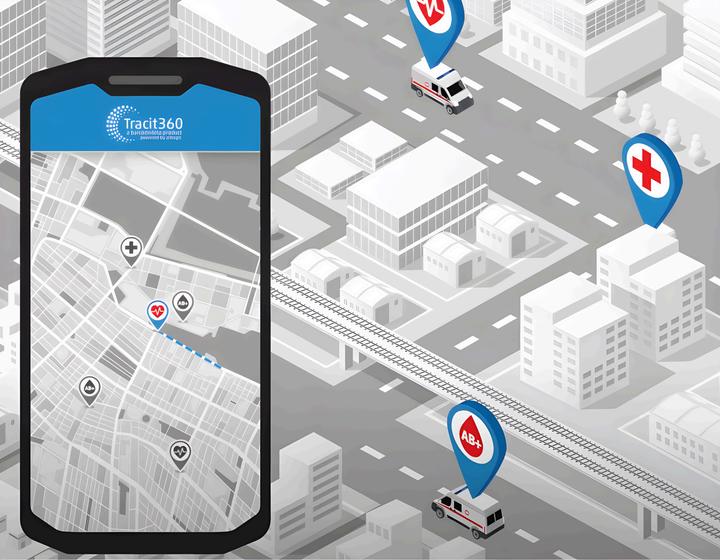

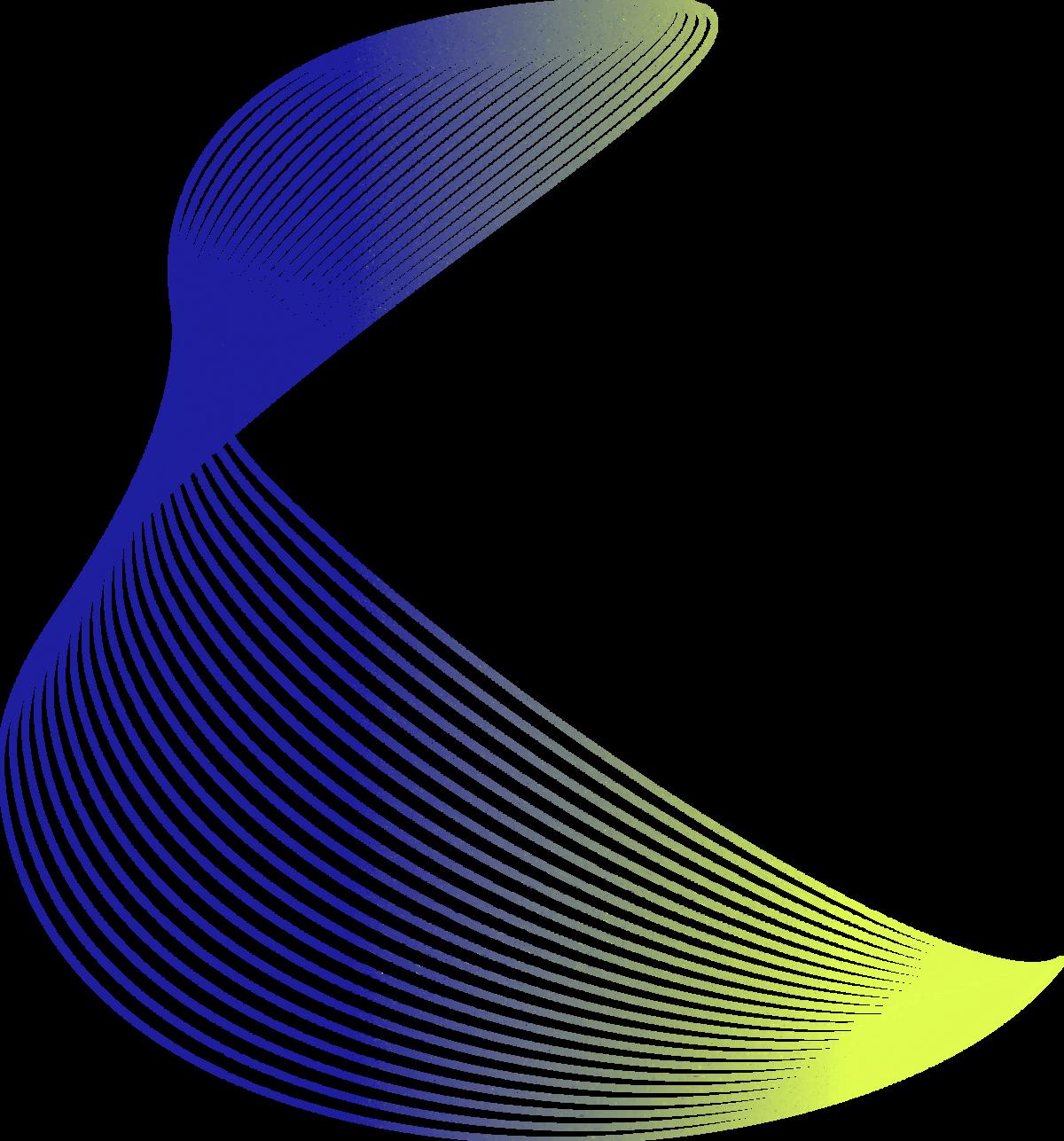
What is Tracit360?
Tracit360 is an intelligent, cloud-based asset-tracking solution for the NHS and Enterprises that need to track high-value assets, specimens, and inventory. It has been developed jointly with our longstanding software partner, Alternative Logic, to provide an easy-to-use, GS1 compliant, end-to-end solution that ensures your assets are visible in real-time throughout their lifespan.
Tracit360 incorporates the following technology:
Wi-Fi technology
A robust solution that leverages existing infrastructure, making it easy to deploy across healthcare facilities, warehouses, manufacturing, and distribution centres. It provides real-time location tracking, enhances workflow efficiency, and ensures optimal equipment utilisation. This technology helps prevent loss and theft, supports maintenance and compliance, and integrates seamlessly with existing host systems.
Bluetooth technology
Tracks assets and equipment by attaching Bluetooth Low Energy (BLE) sensors to items, utilising active IoT technology throughout the facility These sensors capture signals from the tags and transmit data to a centralised system, providing real-time location tracking, a full audit trail and status This integration with existing host systems enhances workflow efficiency, automates inventory management and ensures timely access to critical equipment.
Radio Frequency Identification (RFID) technology
RFID uses electromagnetic signals to read data from an RFID tag. It contains two components for identification: a tag and an RFID scanner. RFID tags contain a memory chip that stores a unique code to identify any object, as well as an antenna that is used to read the tag from the nearest distance based on its frequency. It is possible to identify the object from up to 20 feet away using passive RFID tags. Passive RFID technology provides lower ongoing maintenance costs and improved Total Cost of Ownership (TCO)

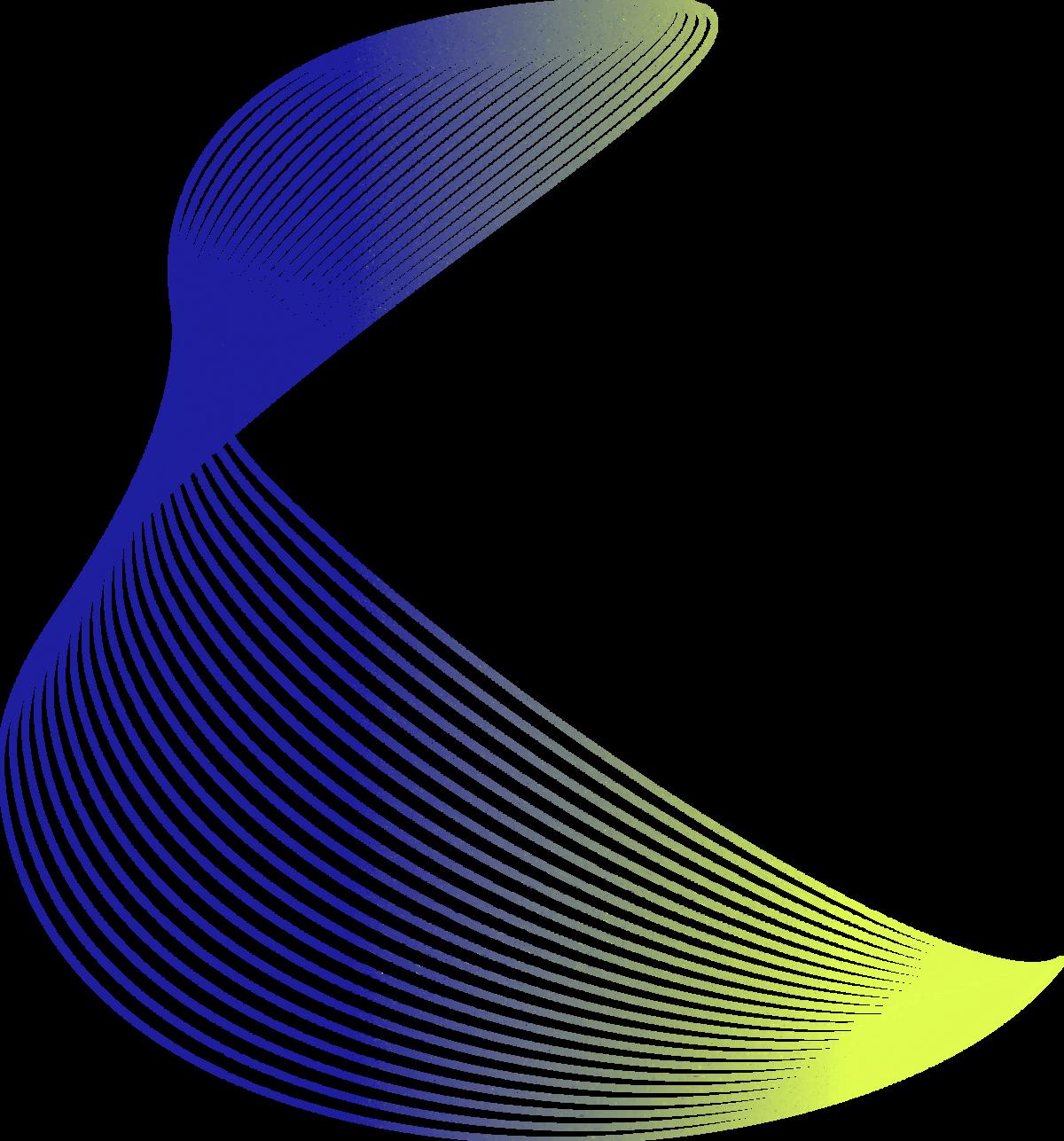
Tracit360 Use Cases
Tracit360 improves a hospital workflow in the following areas:
Tracking Medical Devices
Specimens Tracking Medical Records Tracking Surgical Instruments Tracking Pharmacy Medication
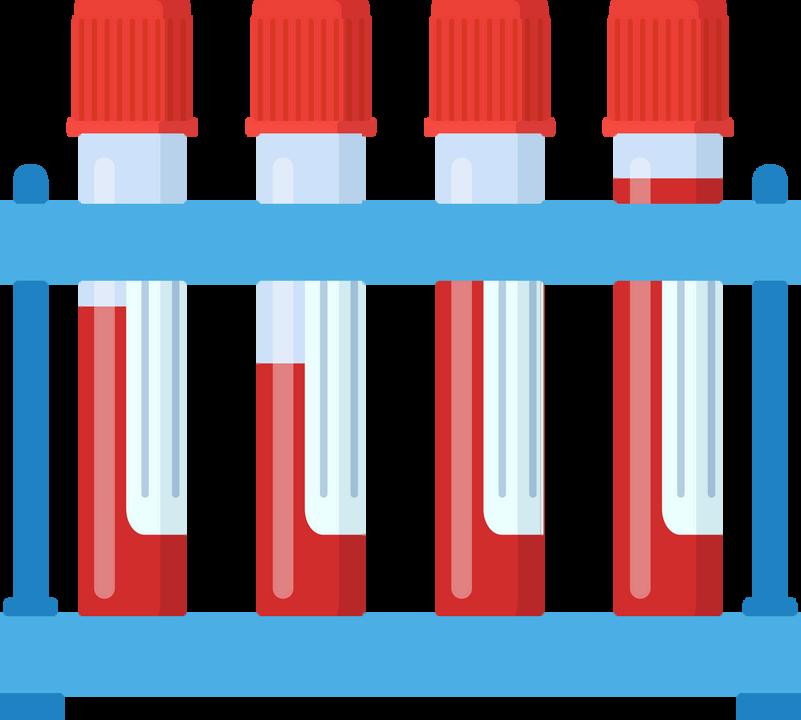

Medical Device Tracking
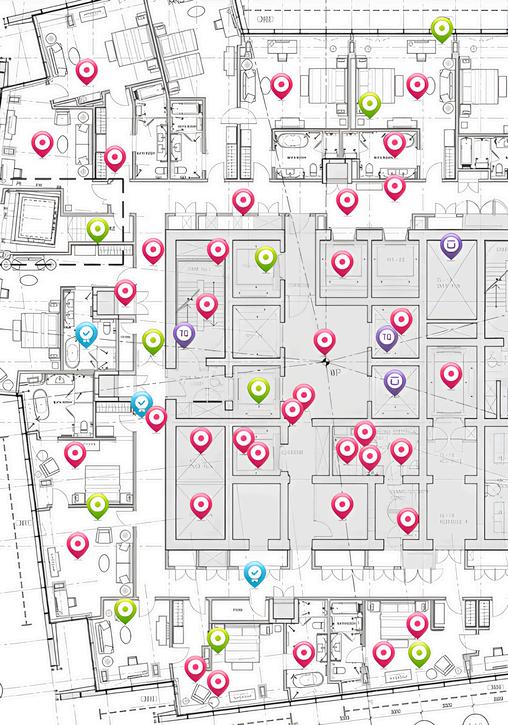
Why is Tracit360 beneficial for tracking medical devices?
Bringvisibilitytothelocationandstatusofyour medicaldevicesusingRealTimeLocationSystem (RTLS)technologiestoimproveuptime,optimise resourceutilisationandminimisewastage.
Accurateassetvisibilitycanextendthelifespanof assetsandmaximisetheirutilisation;asa consequence,healthcareorganisationscan achievesignificantcostsavings.
Eachcategoryofmedicaldevicerequires trackingcapabilitiesforpatientneeds Itisour jobatBarCodeDatatofindtherightsolutionfor eachenvironment.
Tracit360's RFID Solution
Tracit360 promotes a Hybrid Technology Solution After analysing the medical devices and the current technology within the hospital, we will recommend the right solution, for the right application, in the right location
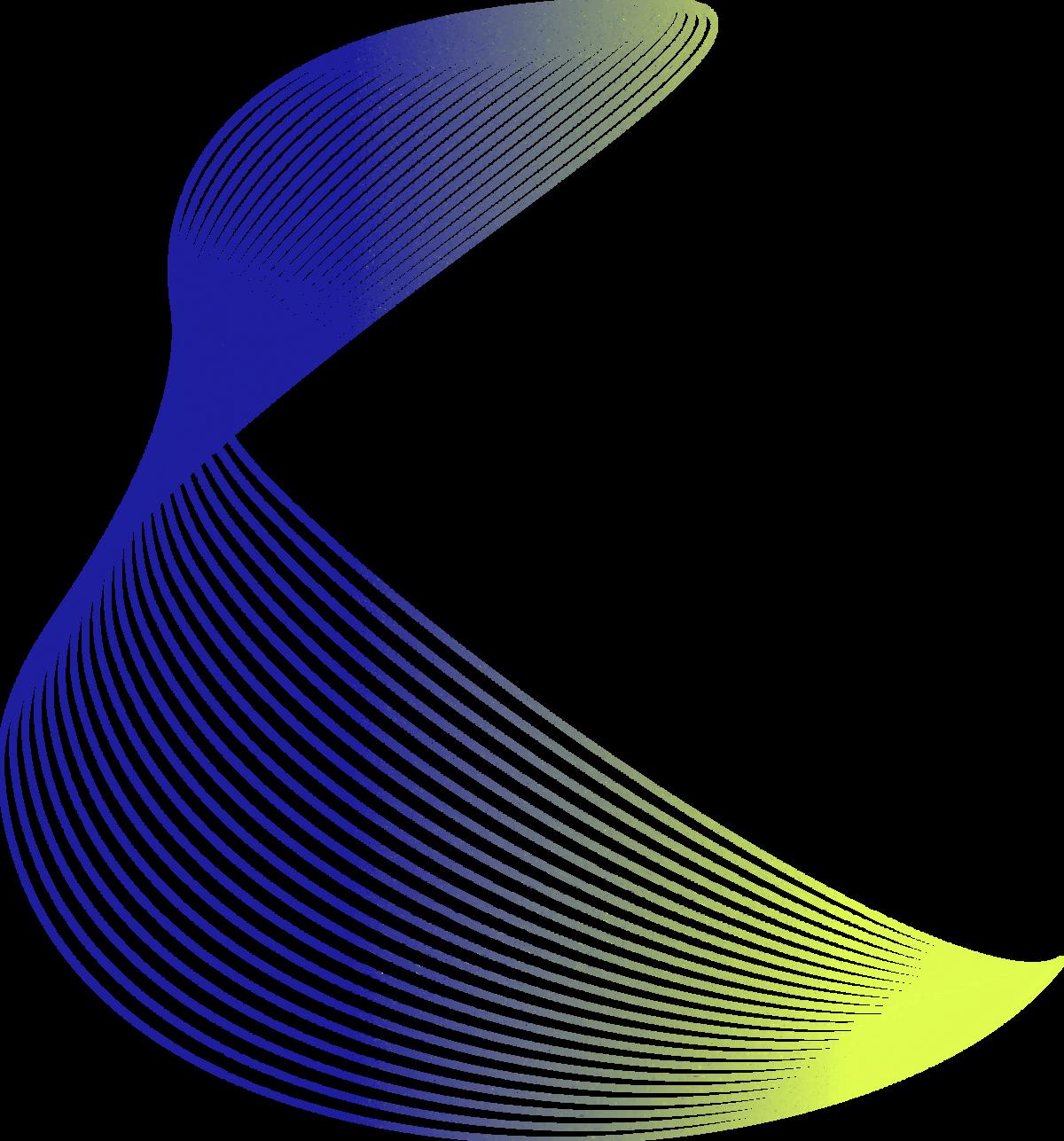
Using a combination of active and passive RFID technology, we offer a secure and cost-effective solution for tracking medical devices to meet CQC requirements. Passive RFID tags are variable in size, low cost, require no battery, and are GS1 compatible. They offer flexibility and accuracy through the combination of mobile and fixed RFID readers.
Active RFID technology uses BLE sensors or beacons connected to network infrastructure, such as Cisco Spaces, to track high-risk, high-dependency items and their status for compliance purposes
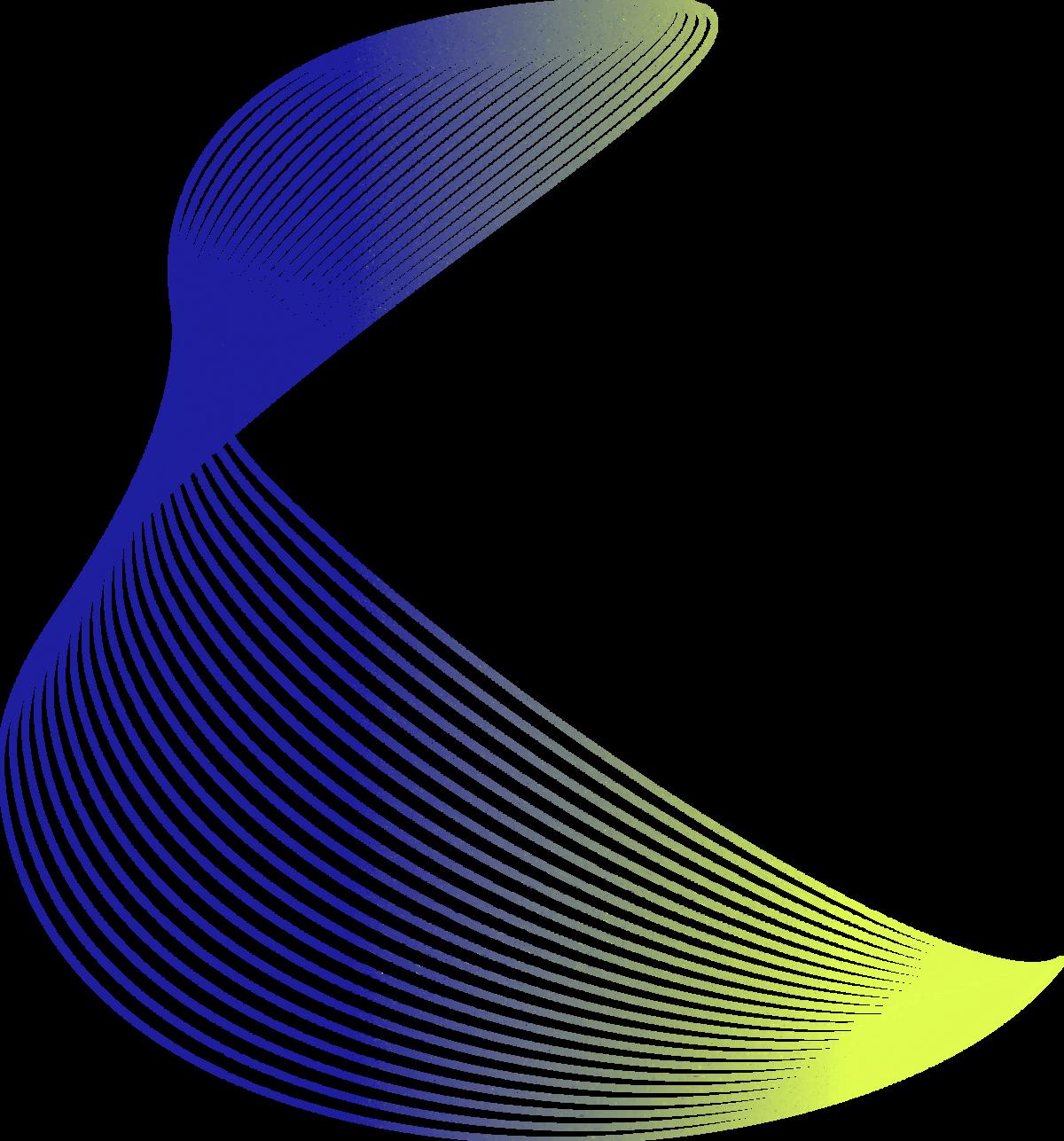
The benefits of tracking medical devices:
1. Asset Inventory and Tracking:
Utilising systems that employ real-time tracking of assets can significantly improve efficiency Barcode and RFID tagging using GS1 standards help automate the process, providing accurate data on asset location, condition, and maintenance requirements.
2. Preventive Maintenance and Calibration:
Regular maintenance schedules and calibration protocols are essential to extend the lifespan of assets and ensure accurate functionality. Implementing a preventive maintenance programme can help identify issues before they escalate.
3. Asset Utilisation and Optimisation:
Asset utilisation data can provide insights into equipment usage patterns, identifying under or over-utilised assets This information can guide decisions on equipment acquisition, retirement, or reallocation, optimising asset usage and minimising unnecessary purchases
4. Integration with Technology:
Integrating asset management systems with other systems, such as Computerised Maintenance Management Systems (CMMS) and inventory management software, streamlines operations and enhances data accuracy.
5. Vendor and Contract Management:
Effective asset management includes maintaining accurate records of equipment warranties, service contracts, and maintenance agreements. Ensuring contract timelines and conditions are adhered to prevents costly contracted non-compliance penalties
6. Sterilisation of Devices:
The management of devices used in Sterile Services is as essential as the maintenance of the devices themselves. Tracking instruments used in theatres identifies the equipment used in the surgical process, providing an accurate audit trail.

Specimen Tracking
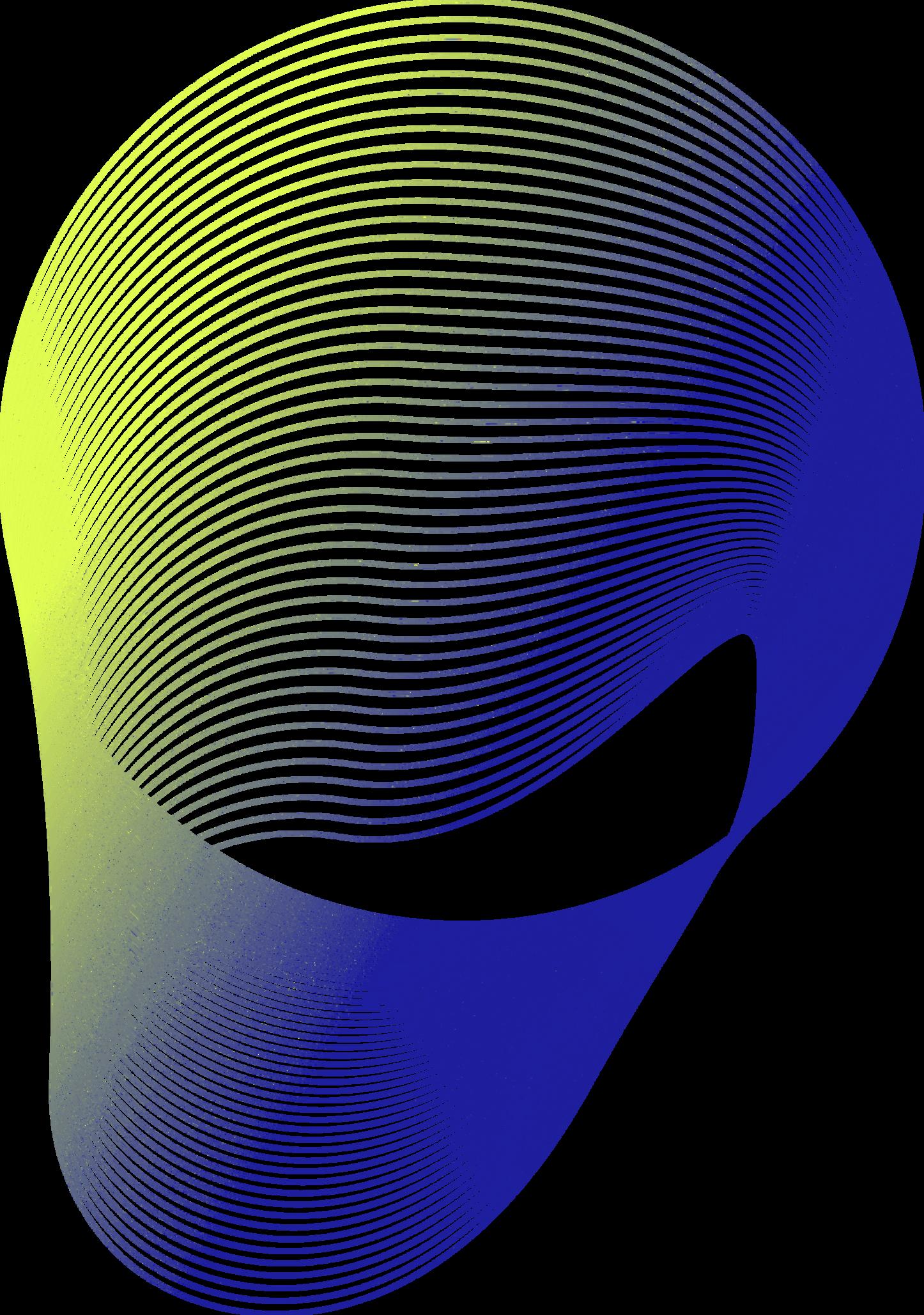
Specimen tracking is a vital process in the healthcare sector; ensuring correct sample identification and tracking from collection to the laboratory is critical to diagnosis and treatment. 62% of sample errors associated with labelling and processing occur before samples reach the lab¹.
Manual systems and data collection along with paper records are inefficient and problematic, causing errors
Pre-printed labelling of sample tubes can contribute to incorrect patient identification for samples In 2022, 23,584 rejected blood samples were reported by 179 sites in 1 month by NHS Blood and Transplant.²
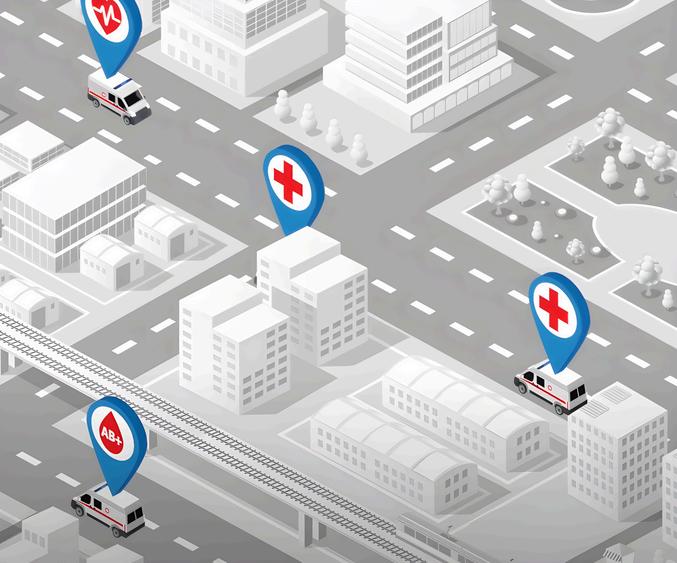
Our fully integrated Tracit360 solutions track each step of the specimen's journey, from collection using Positive Patient ID (PPID). The easy-to-view dashboard allows visibility of samples from the point of collection through to their arrival at the laboratory, with the potential to integrate with existing 3rd party LIMS systems.
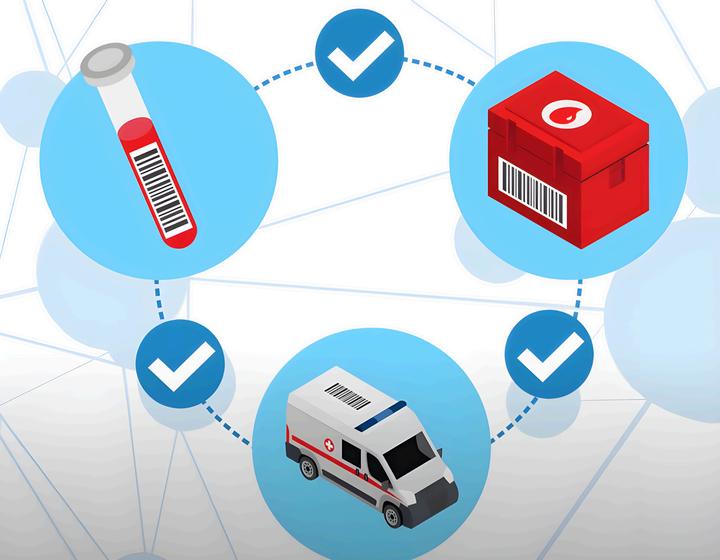
TheuseofRFIDtechnologyprovidesfullvisibility whilethesampleisintransit,enablinglaboratory stafftoeffectivelyandefficientlyplan workloadsandpriorities
Hospitalstaffor3rdpartyproviderscanalsobe re-routedaccordingtoservicedemands, eliminatingunnecessarytrips.RFIDoffersthe optionforautomaticsamplereceiptandcheckin,eliminatingmanualprocesses.
from pre-analytical quality indicators and how should we J Lab Precis Med 2018;3(6)
2 - 2022-blood-sample-labelling-key-pointspdf (nhsbtdbeblobcorewindowsnet)
1 - Cadamuro J, Gaksch M, Mrazek C, Haschke-Becher E, Plebani M How do we use the data
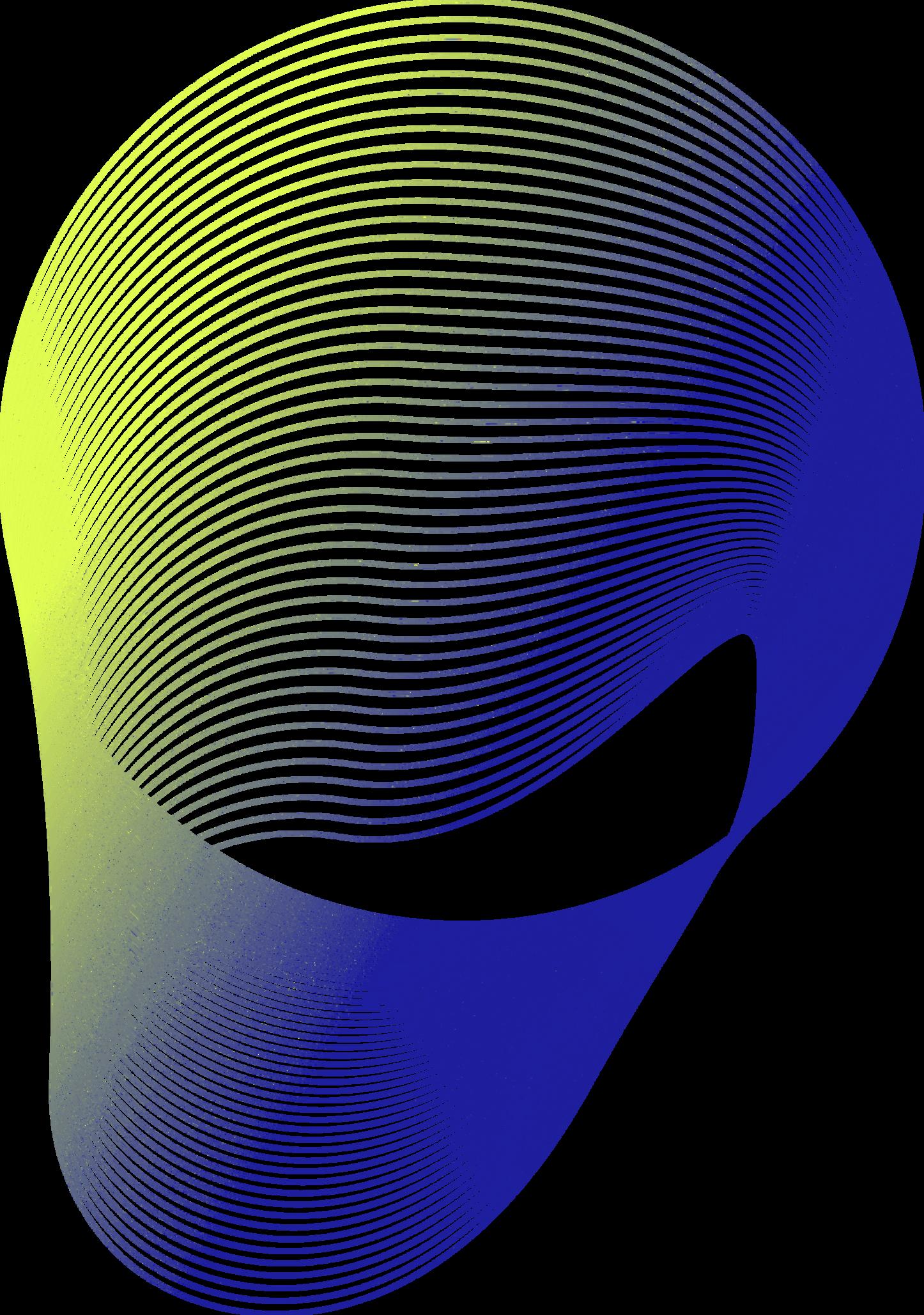
The Samples

Trackingsamplescorrectlyandefficientlyisthecore functionalityoftheTracit360solutionUsingbarcodes andRFIDtechnologyprovidessignificantbenefitsfor real-timevisibilityonallsamples.
Scanningeachuniqueidentifierkeepsthedriver informedonthesamplestheyaretransporting.This decreasesthechancesofsamplesbeinglostornot beingreceivedatthelaboratoryintimefortesting. Real-timevisibilityprovidesafullaudittrail,minimising errorsinsamplecollections.
Reporting and Dashboards
Sharing information with the sender, the courier or porter, and the receiving laboratory, ensures that no sample is overlooked. From the point of collection to delivery to the laboratory, reports and acknowledgements can be shared automatically, saving staff time previously spent chasing deliveries.

Collection
Correctly identify sample with RFID

RFID Sample Journey
Pick-Up
Drivers carry smart devices, which provide collection details.
Delivery
Deliver and validate the correct location.
A C B E D
Storage Transport
Temperature controlled storage
Track ETA’s and expected collection and delivery times.

Surgical Instrument Tracking
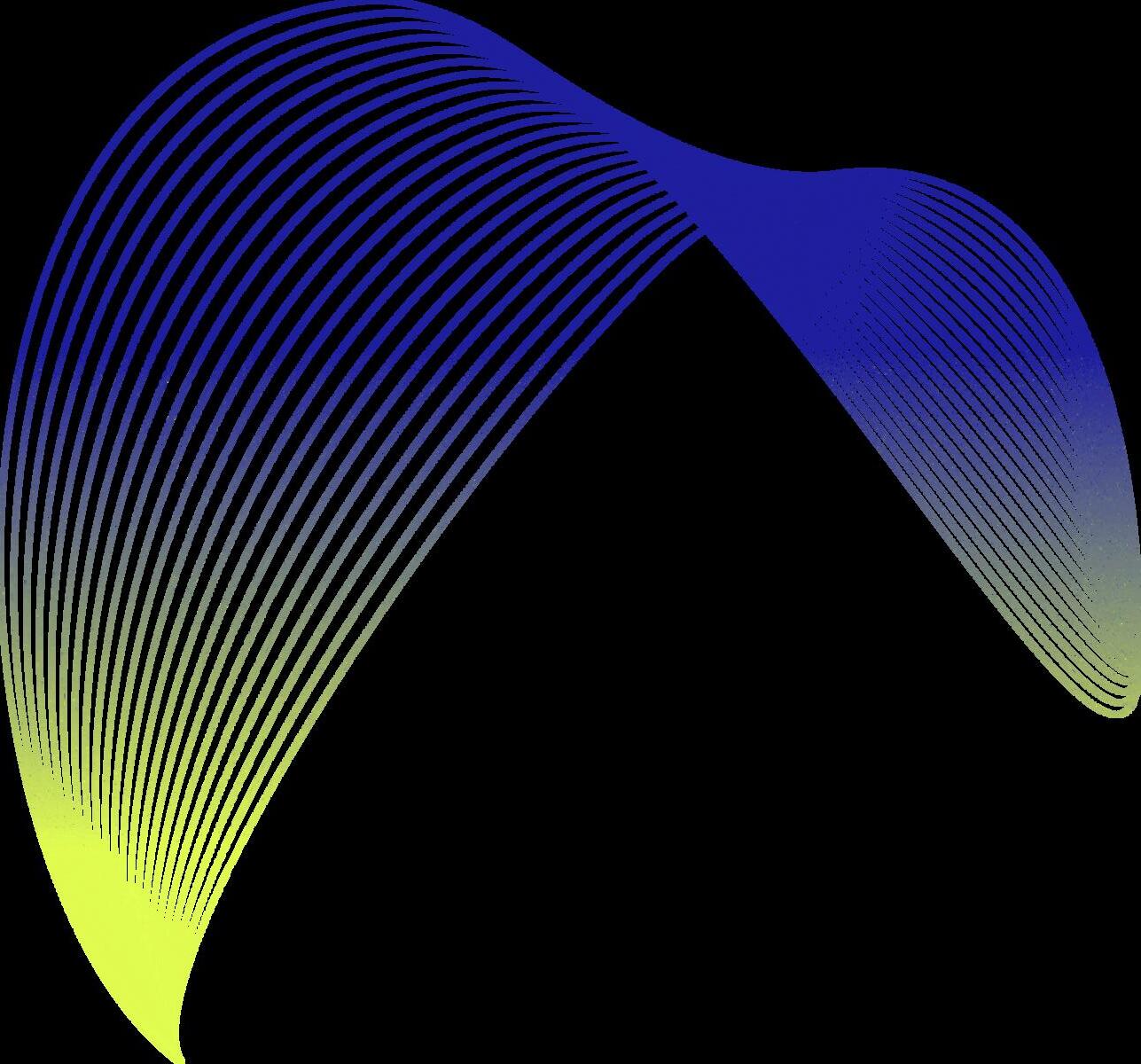
Tracit360 ensures a more organised, safer and time-efficient procedure within the operating theatre.
The hospital documentation process is typically manual and labour-intensive With Tracit360 efficiency is greatly improved, providing hospitals with higher quality and accuracy in documenting crucial surgical instruments and their condition and usage each day
Tracking surgical instruments using Tracit360
Surgical instruments arrive at the medical facility
Instruments are tagged with a UI and scanned into Tracit360.
Instruments used and are scanned to update their location and condition
Instruments sanitised and returned; this is logged in Tracit360
Instrument records are finalised, ready for the next procedure
How passive RFID is integrated into the process

The reader detects signals from these tags and sends the location data to Tracit360, improving visibility and enabling quick location of tagged items.
RFID Readers are installed at decontamination area entrances, exits, autoclaves, sterile storage rooms, and theatres to track surgical equipment. Each item has a specialised RFID tag designed to withstand standard sterilisation procedures

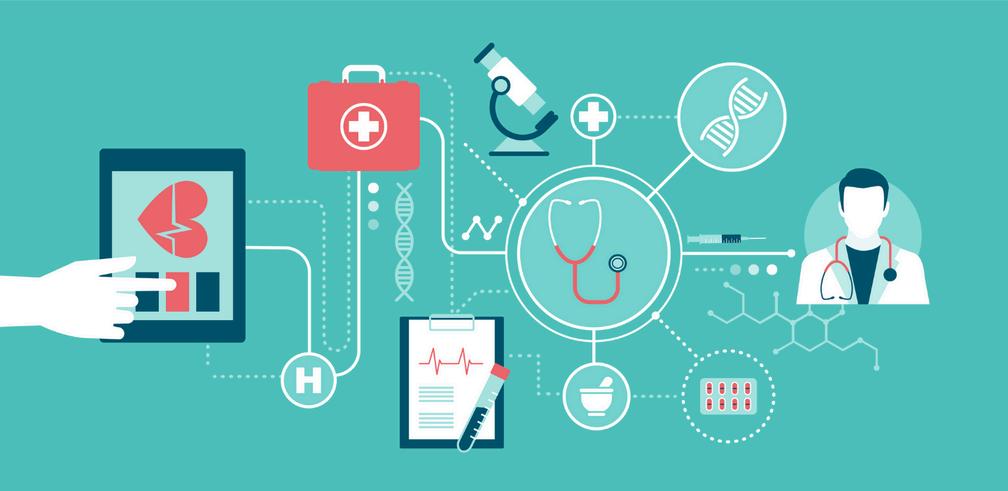
Increased visibility of sterile surgical equipment allows the hospital to monitor usage, availability, and spares, aiding in stock-level decisions.
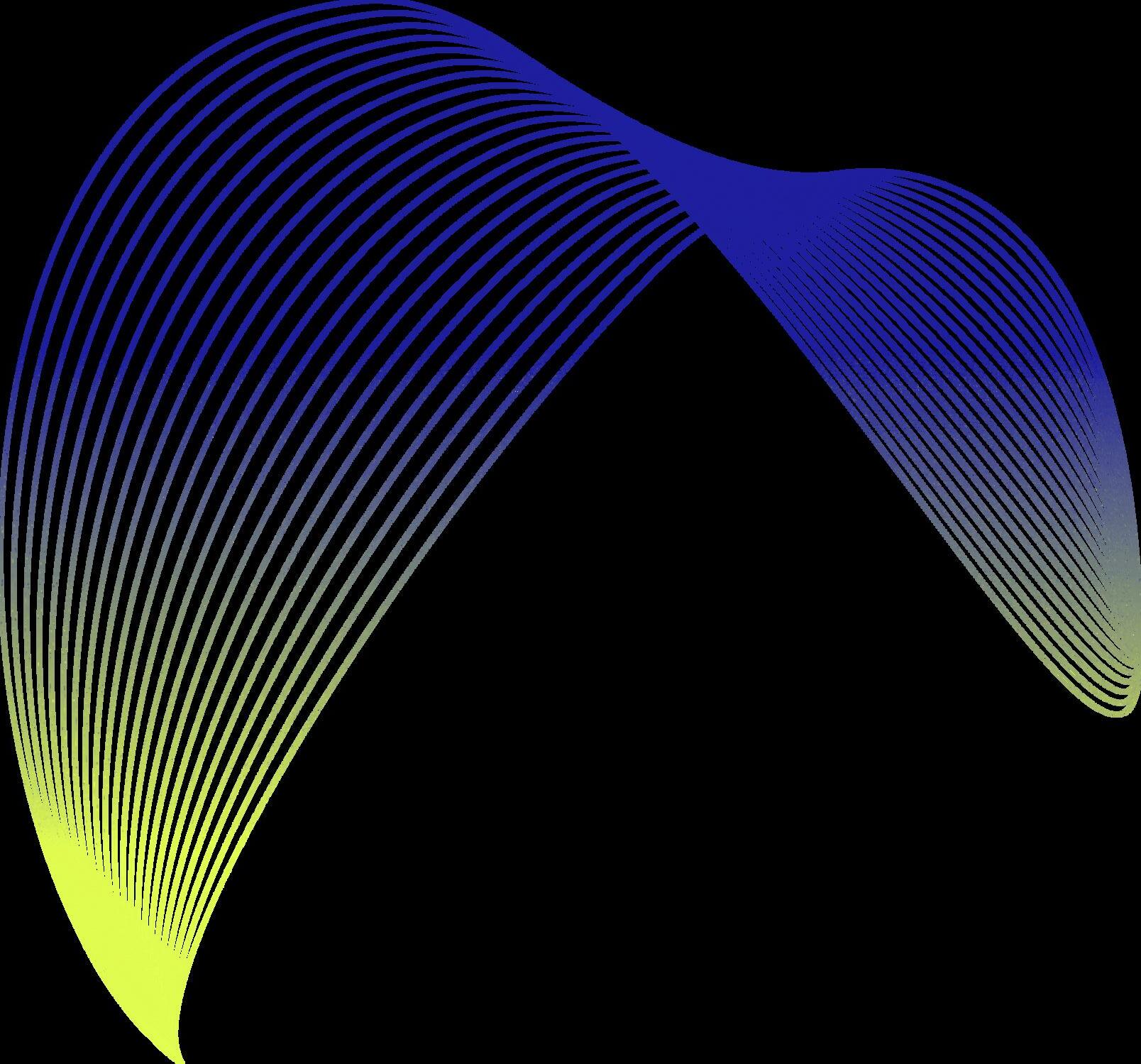

Medical Record Tracking
Tracit360 offers immediate efficiency savings in tracking, locating, re-filing, and auditing medical records, helping healthcare trusts to meet NHS directives and enhancing patient care and safety. Tracit360 accurately tracks all movements of patient medical records, each medical record, box, and shelf location will be equipped with a barcode or GS1-compliant RFID/EPC tag
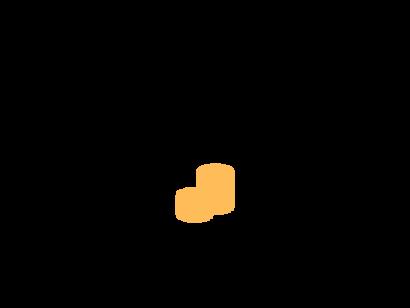
The Tracit360 platform and supporting technology can be used for multiple tracking purposes, while the affordability of barcode and RFID labels keeps the ongoing cost of consumables low
With Tracit360, improved efficiency and organisation of medical records ensures timely delivery to the right l idi li i i i making informed decisions g record loss.
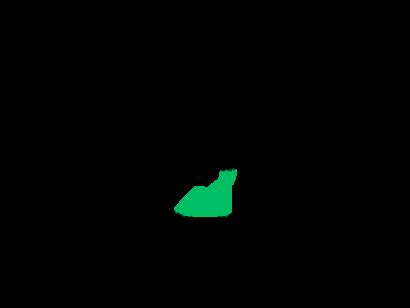
Tracit360 uses RFID technology, enabling staff to scan medical records as they enter or exit departments, creating an active audit trail. Passive RFID scanners track record movement within the hospital
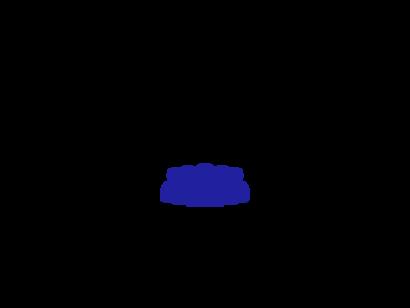
Records can be stored in the warehouse in any location
Simply scan the barcode on the record and on the shelf where it is being placed. Any misplaced records can be located using a mobile ‘point and find’ RFID reader.
The transfer of patient records is recorded on Tracit360 Detailed movement history including the requestor, who moved the record, and where it was taken, helps prevent lost and misplaced records.
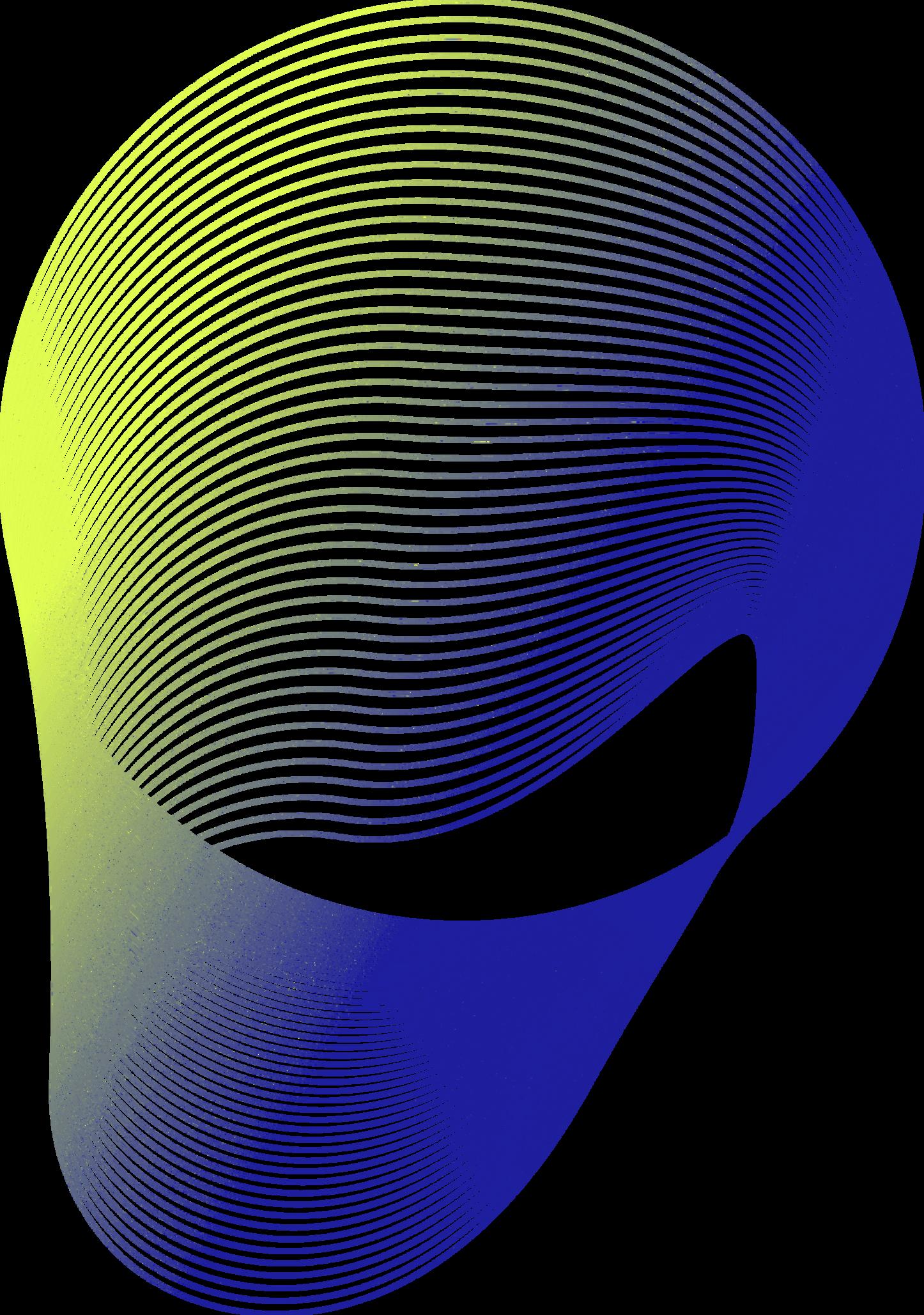
Once patient records are tagged, they can be registered at any hospital warehouse by scanning the barcode label and assigning a location. From there, each movement is automatically tracked using the embedded RFID tag, allowing for real-time monitoring with Tracit360 For patients with multiple records, all files are grouped and labelled consistently, ensuring easy identification and storage together after retrieval
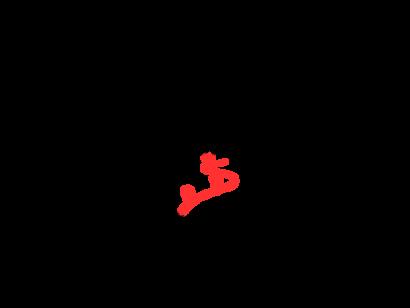
Tracit360 guarantees timely access to medical records, enabling staff to easily locate them across an Integrated Care System (ICS) This supports the push towards interoperability and shared care records
Misplaced medical records can delay patient appointments. Tracit360 stores and saves records, ensuring appointments proceed as scheduled
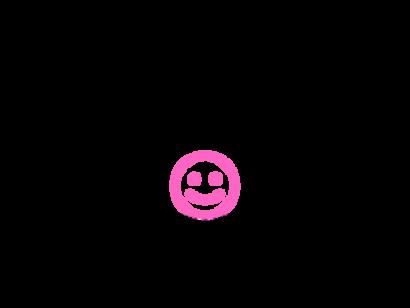
Tracit360 boosts the efficiency of medical record departments, minimising tedious searches and leading to a better working environment and improved staff morale.
Individual users are responsible for tracking and locating records in their sub-locations, but RFID readers will track any movements of records between departments using tags All sublocations operate as a satellite warehouse, using barcodes and RFID tags to track records
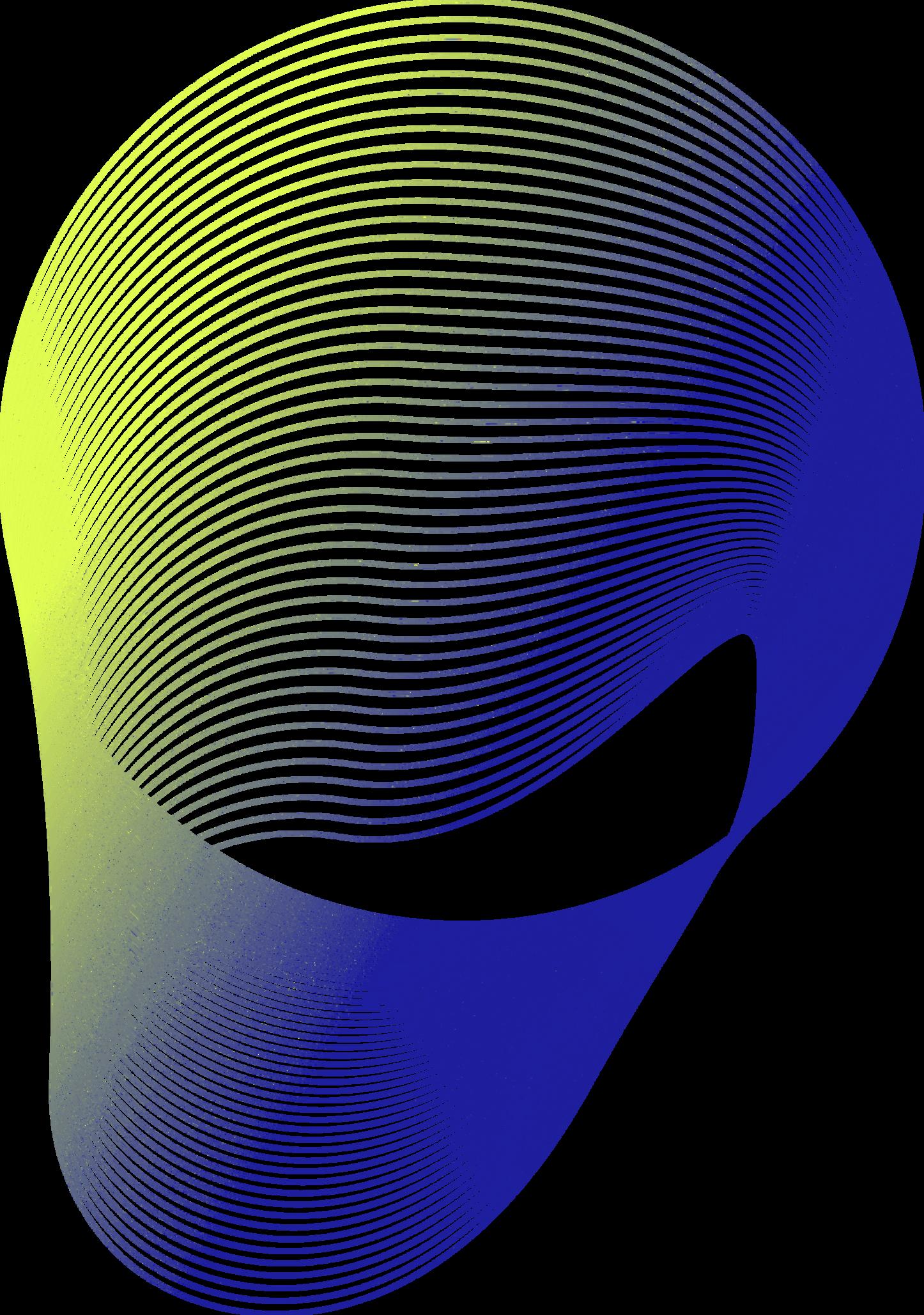
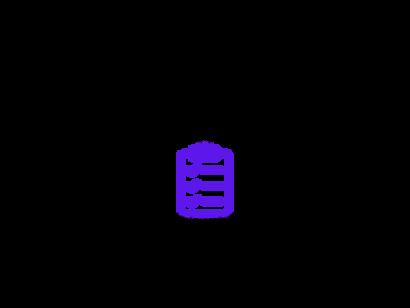

Pharmacy Medication Tracking
How Tracit360 enhances pharmacy operations:
Supply Chain Tracking:
Barcodes encoded with GS1 standards (GTINs) can be scanned to track medications directly to the patient. Tracit360 can identify when and where a product was produced, shipped, and received.
Prescription Packing:
Ensure the right medications are packed and are in the bag before they are made ready for collection.
Prescription Storage:
The creation of a mini-warehouse within the pharmacy for prescription storage ensures the right order is collected.
Share Alerts/Data:
Once a prescription is packed and placed in a pick location in the pharmacy, a message alerts staff that they are ready for collection
Recorded Collections:
Every prescription collection is recorded by signature or tapping the staff badge, capturing the date, time, who collected it, and from which location.
Delivery Tracking:
Track all deliveries using a smart device running the Tracit360 software, including the receiving location, the pharmacy and the porter service This helps to reduce the average collection and delivery time of 1hr 50mins
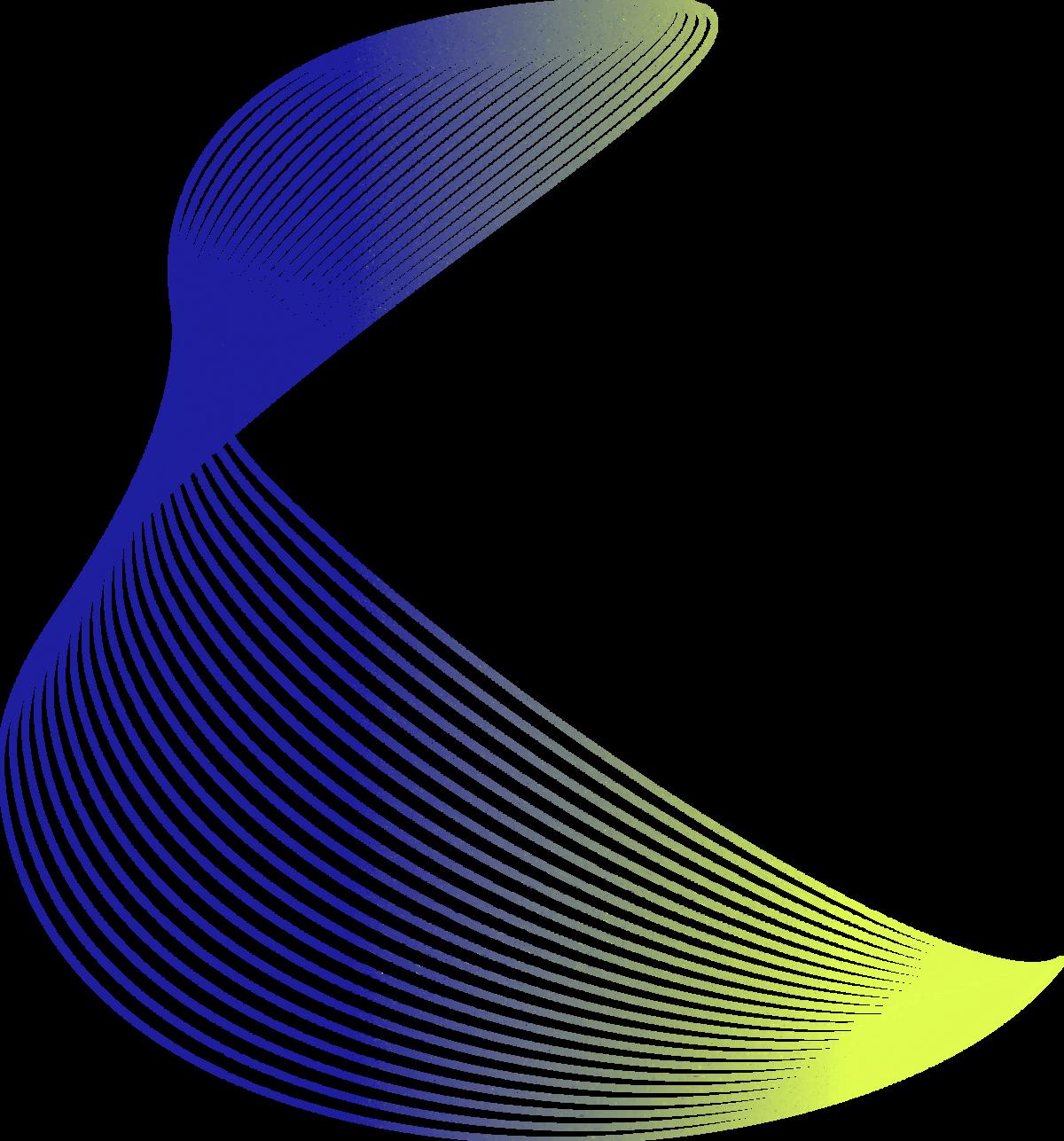
Tracit360 streamlines medication distribution providing instant track and trace capabilities Having greater control of medications as they leave the pharmacy is crucial Being able to establish their location within the distribution chain accurately increases reliability.
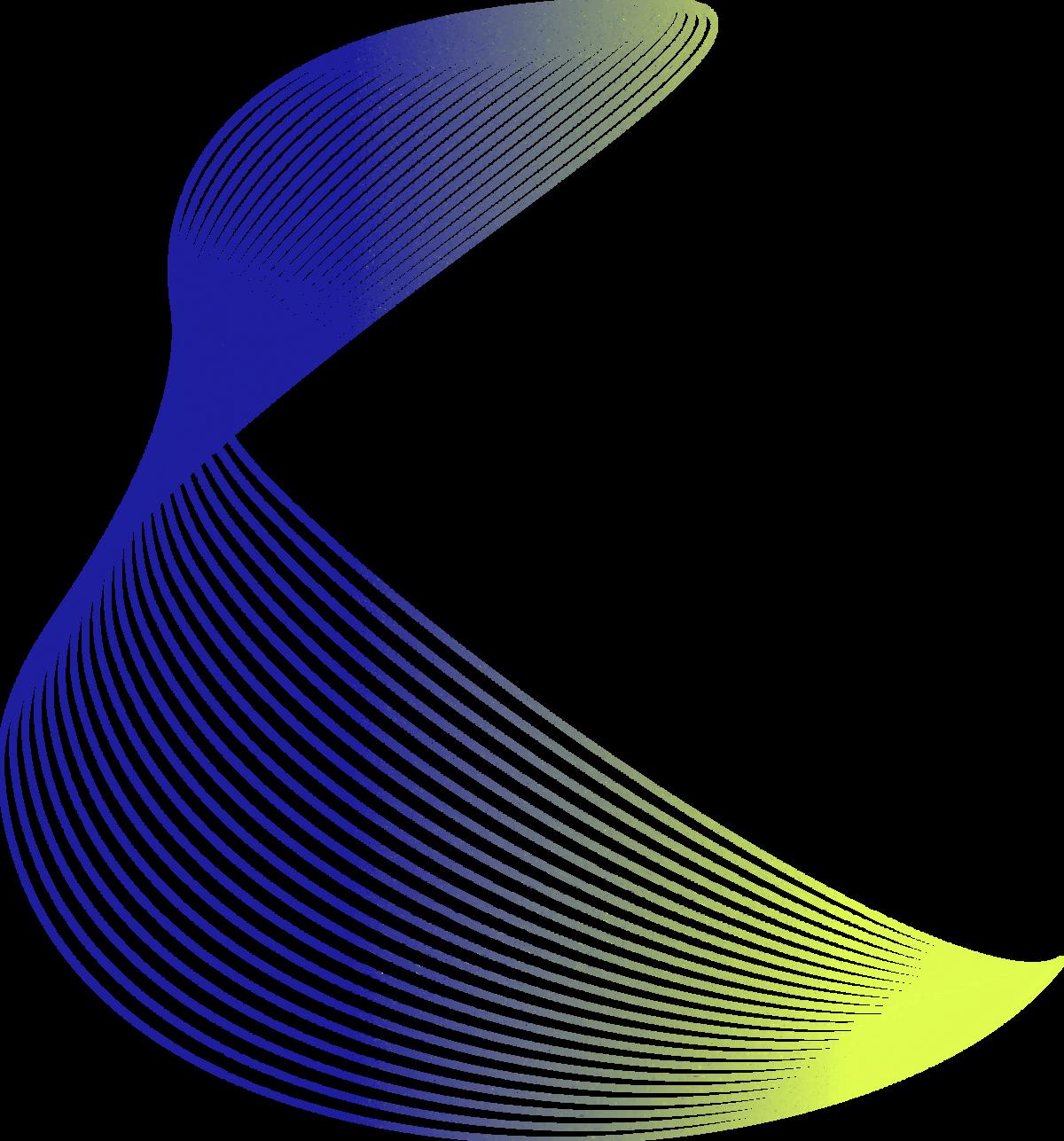
How RFID is implemented into pharmacy asset tracking:
RFID plates are placed in specialised pharmacy transport bags to track large sets of samples or specimens throughout their journey. At Bar Code Data, we provide healthcare trusts with a variety of bag and case types which are produced specifically for healthcare requirements.
Temperature Control Padded Cases:
In conjunction with ice packs, these validated cases allow the movement of pharmaceuticals at the correct temperature They can be manufactured using an antimicrobial PVC material that will combat 99 9% of bacteria
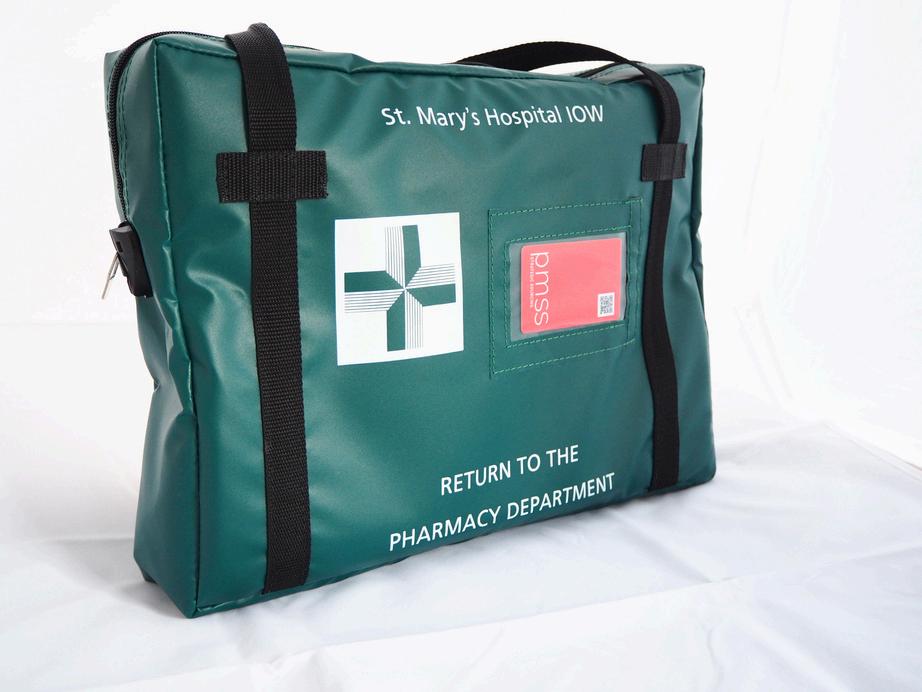
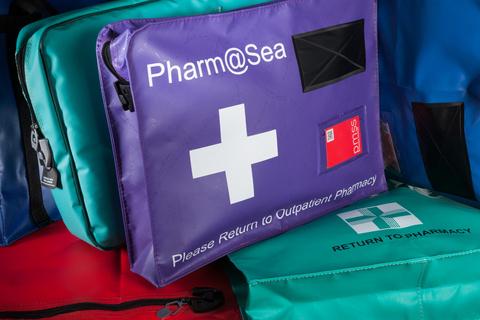
Pharmacy Security Pouches
Made from durable coated PVC nylon, the bags incorporate a strong zip to close the bag and the additional locking security housing ensures goods arrive at their final location tamper-free and fit for purpose
Bespoke Cases
We have a wide range of coloured PVCs available which allows users to create a colour coding system for designated routes Each case comes with a unique sequential barcode and eyereadable number for tracking purposes.
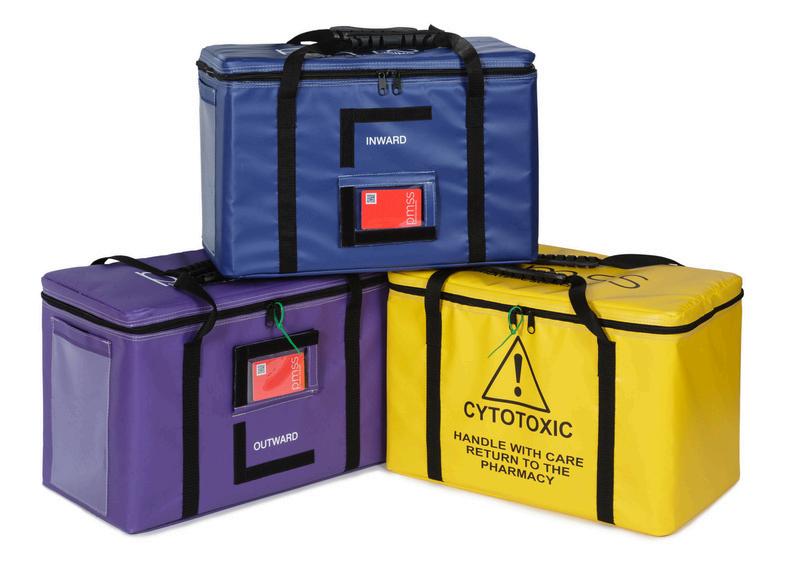

Inventory Management
Bar Code Data’s GS1 compliant Inventory Management solution coordinates the movement of goods through a seamless cycle of ordering, storing, producing, using, and replenishing goods It ensures the right items reach the right place, in the right quantity, at the right time Inventory Management maintains product availability at warehouses and local forward stock locations
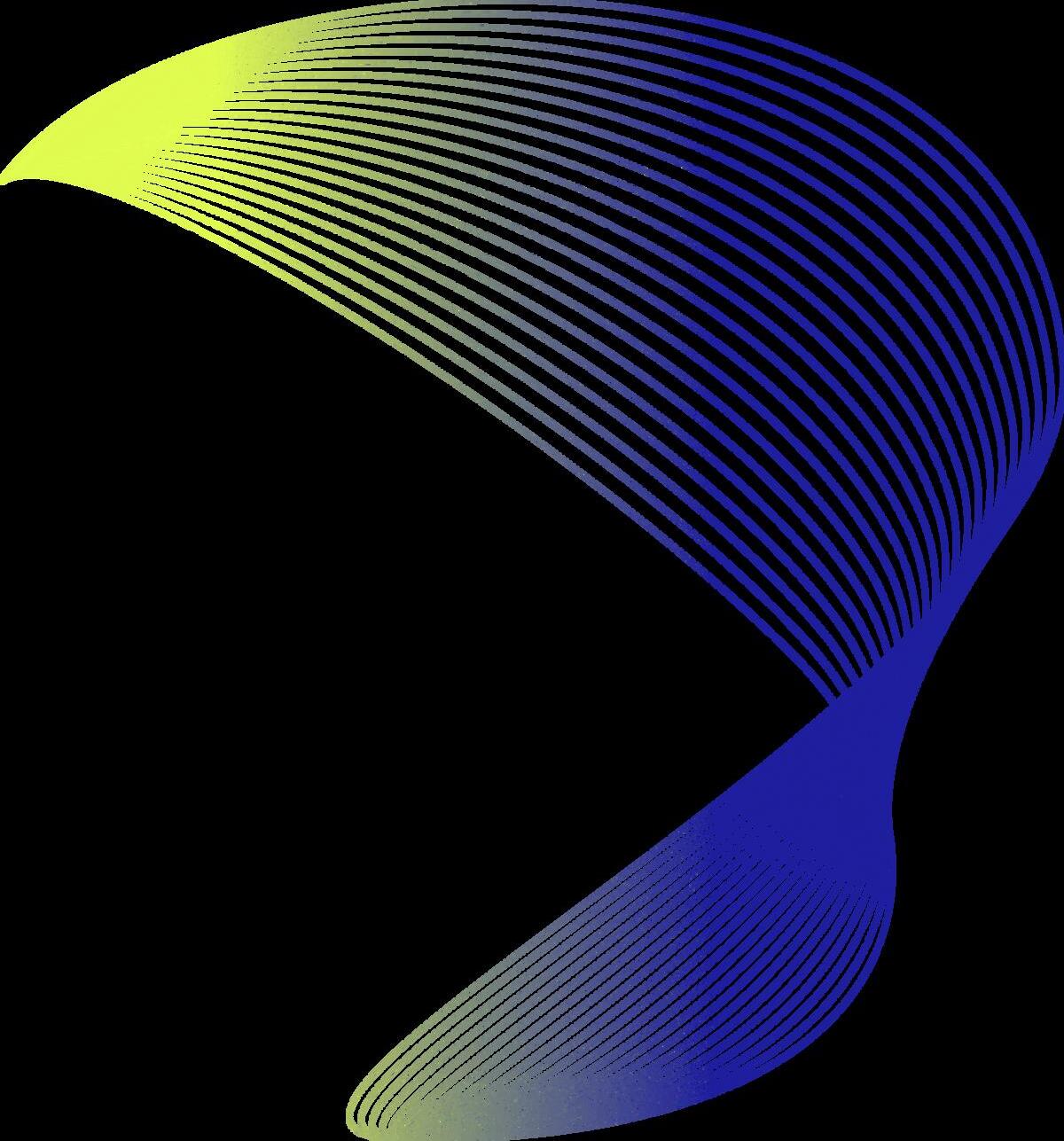
A modern Inventory Management System (IMS) should not only manage inventory but also bring visibility to inventory decisions in the warehouse. Bar Code Data’s Stock IMS streamlines processes using barcoding and RFID technology to produce real-time data for inventory and asset management. Pair with Bar Code Data’s extensive hardware range and you have a full end-to-end solution.
Combining technologies such as barcodes and RFID allow for effective management of expensive and mission critical items. Recording all the data at the point of use from the GS1 codes helps with compliance with the MHRA data requirements and supporting recalls.

Bar Code Data Inventory Management solutions
Greater inventory visibility:
Active inventory management ensures the right amount of stock is on hand, limiting the risk of stock shortages and overstocking
Improved workflow efficiency:
Inventory management ensures stock is on hand and in the right location for teams to use to treat patients. Automatic reordering can be implemented for the main warehouse and all sub-warehouses.
Effective stock management:
Understanding stock trends allows efficient use of existing stock Across NHSE, there is estimated to be over £1 billion of shelf stock. Using stock usage data and employing cycle counting to check problem stock lines in problem locations prevents stock outages.
Better use of technology:
Utilisation of technologies such as RFID can help manage high-value and critical items, such as implants and patient-specific items
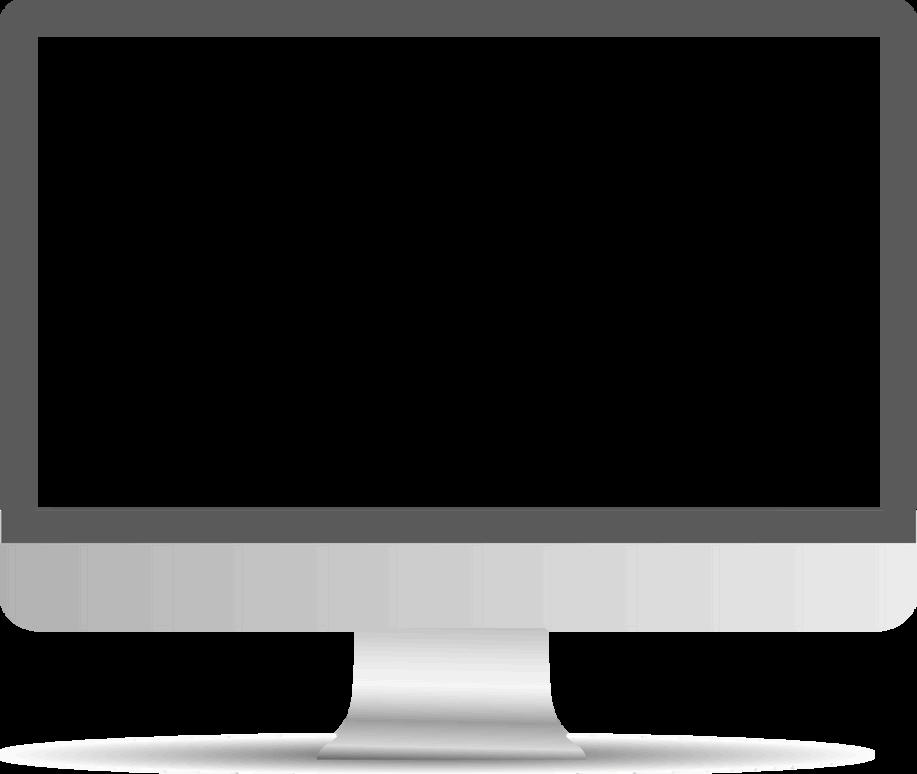
At-a-glance dashboards and management reporting provide:
Ultimate visibility for your business needs
Accurate financial reporting for better financial management
Improved focus on what needs attention by automating the everyday.

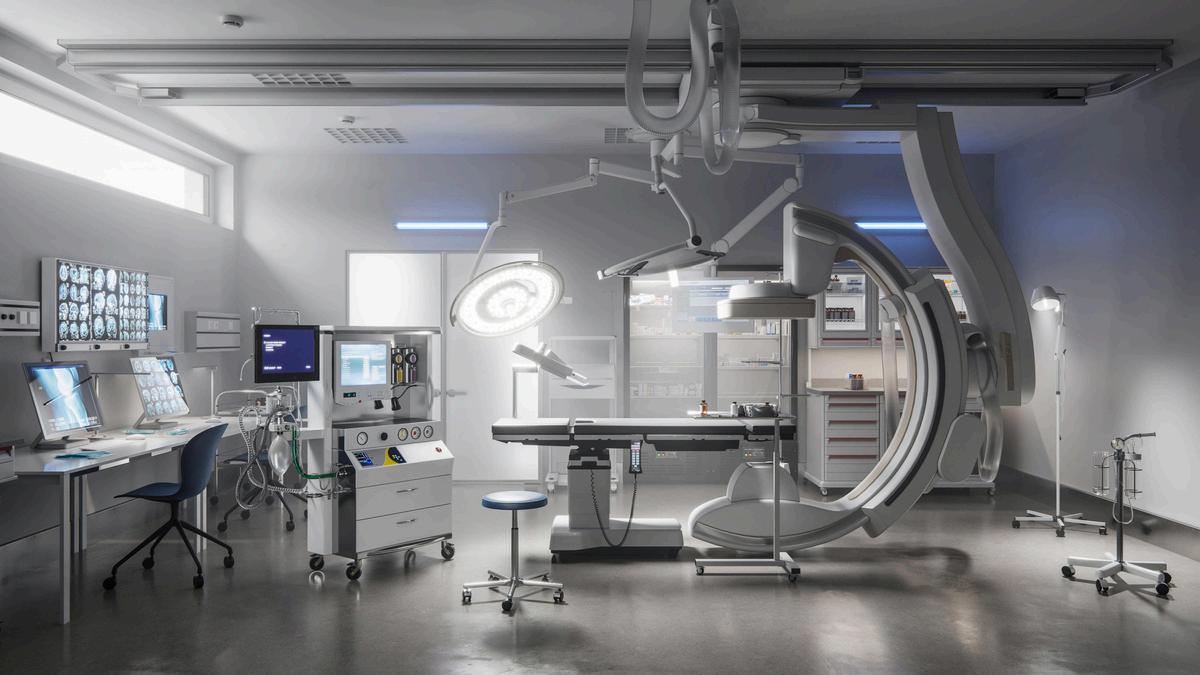
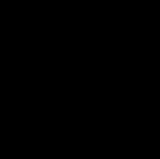
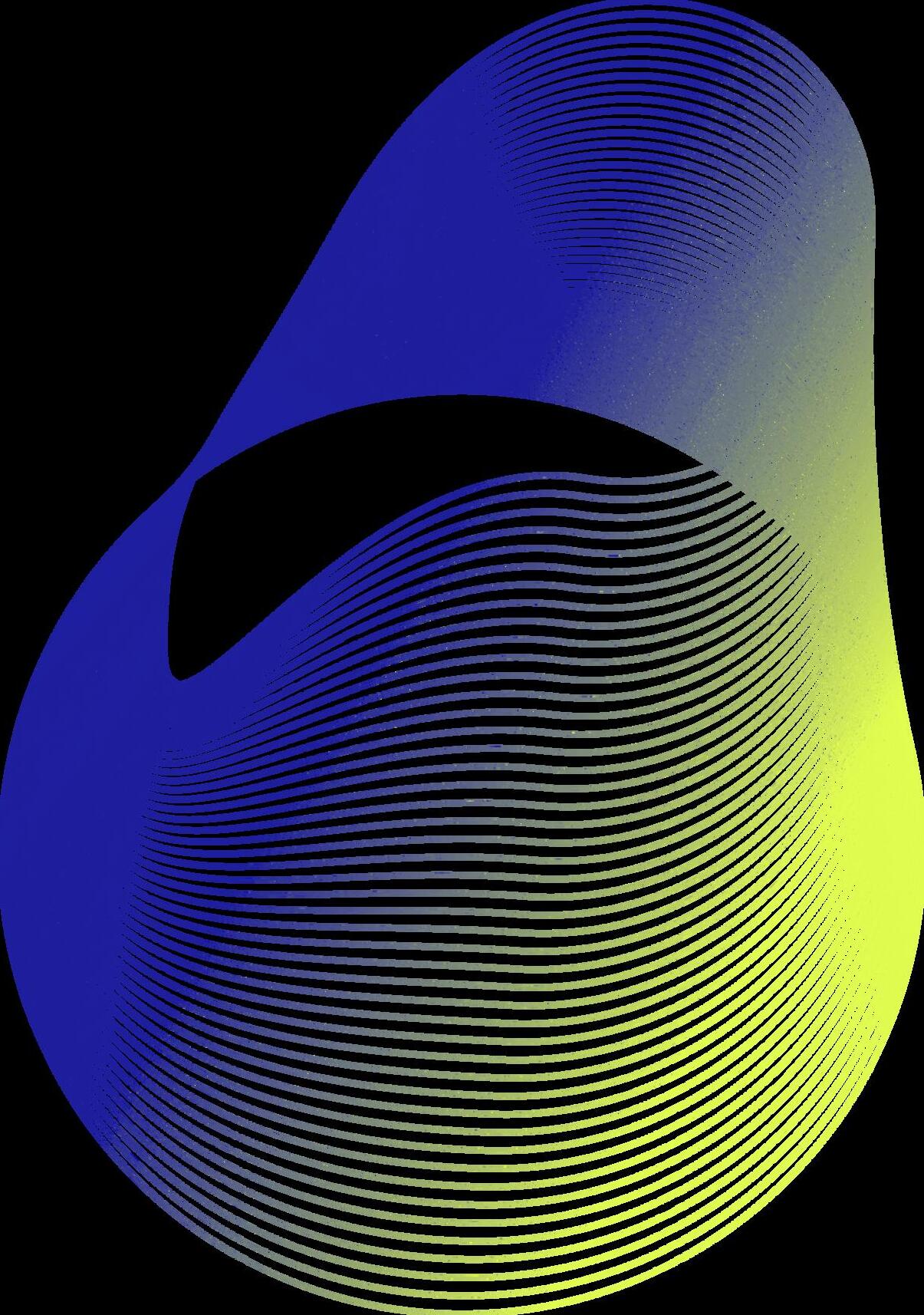
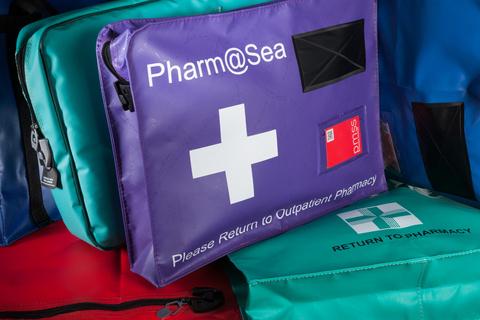
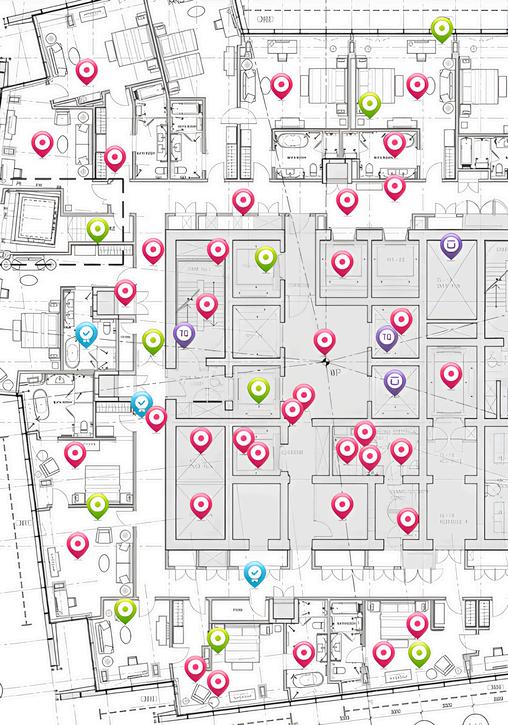