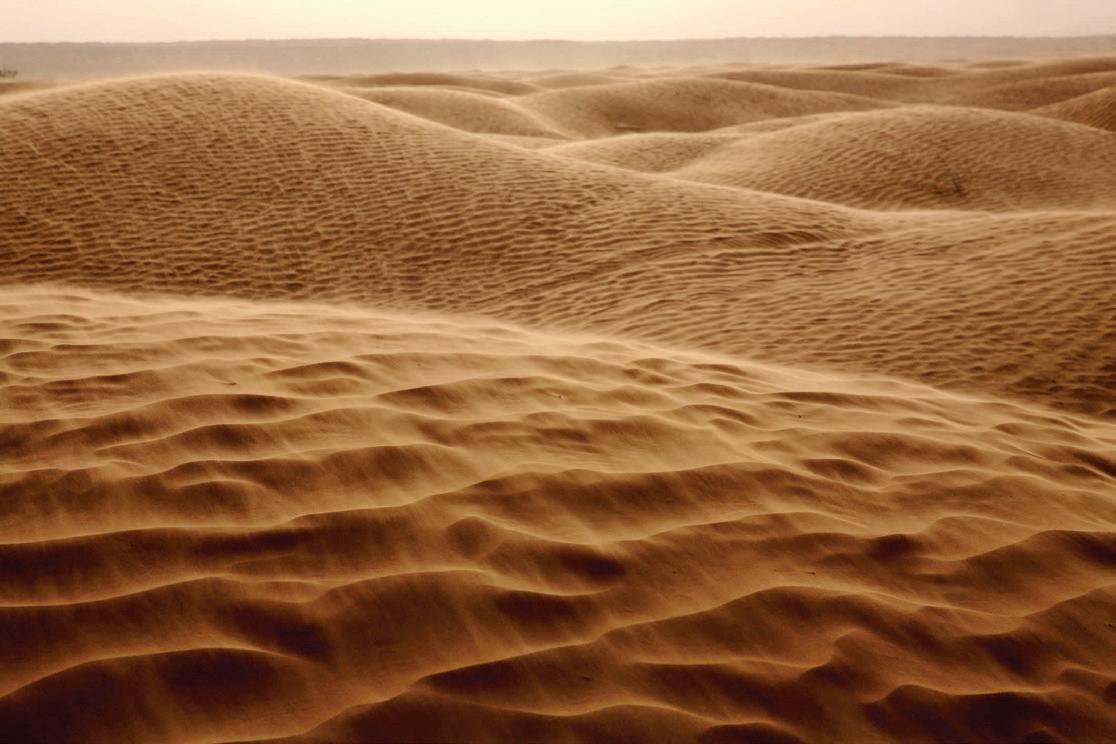
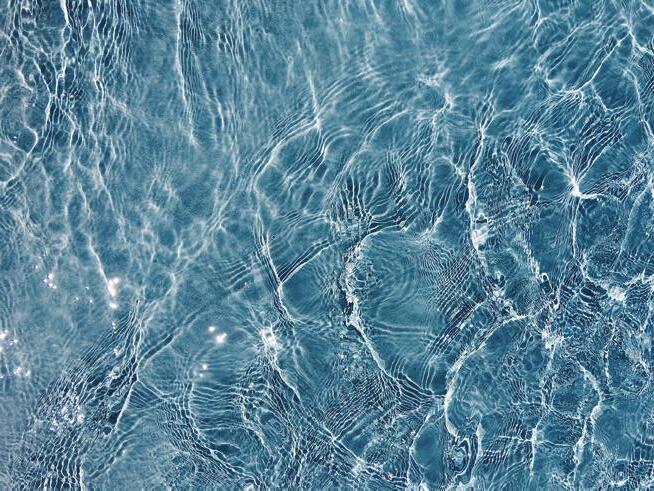
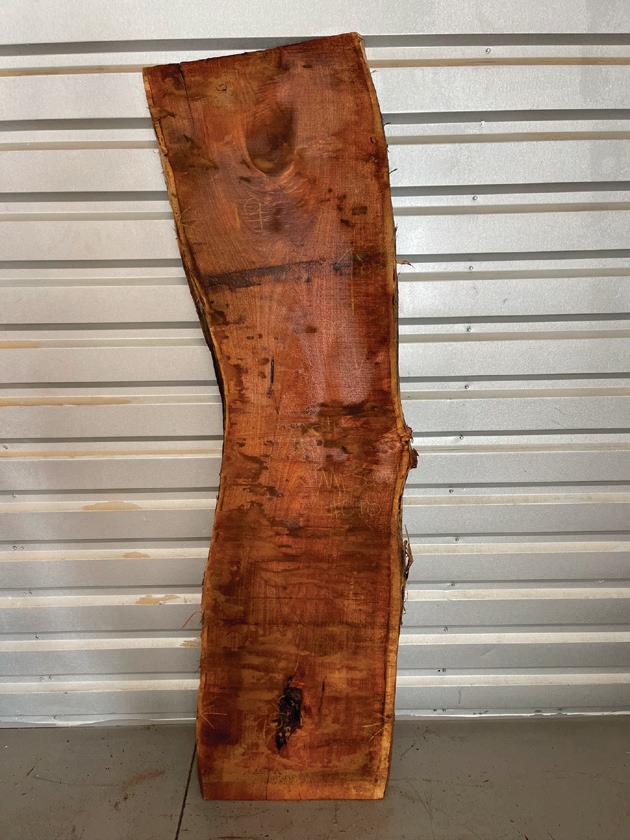
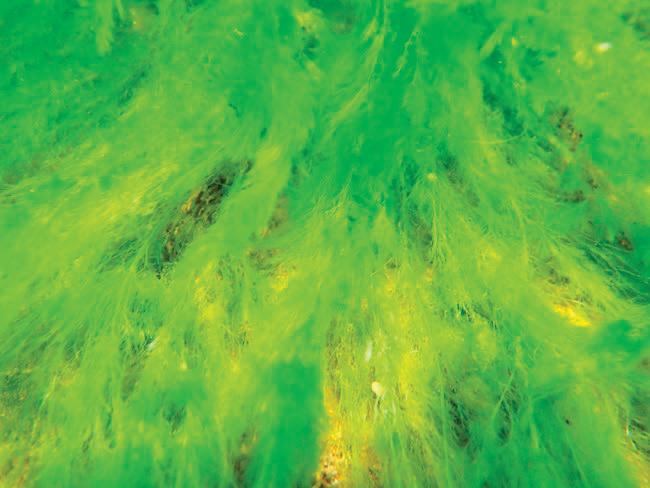
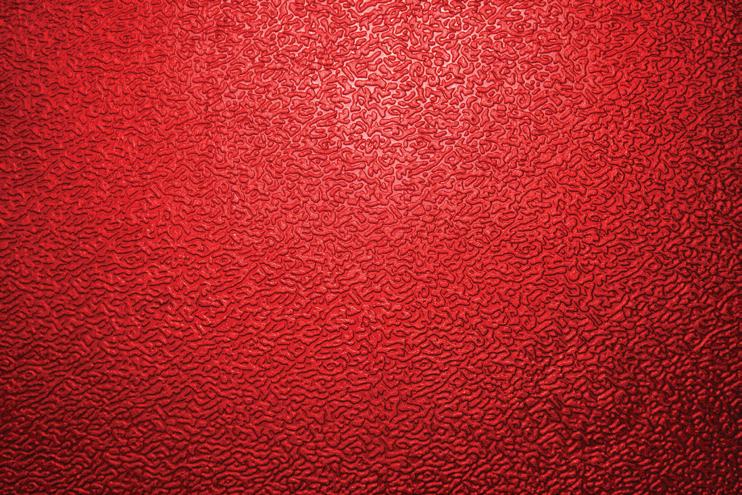
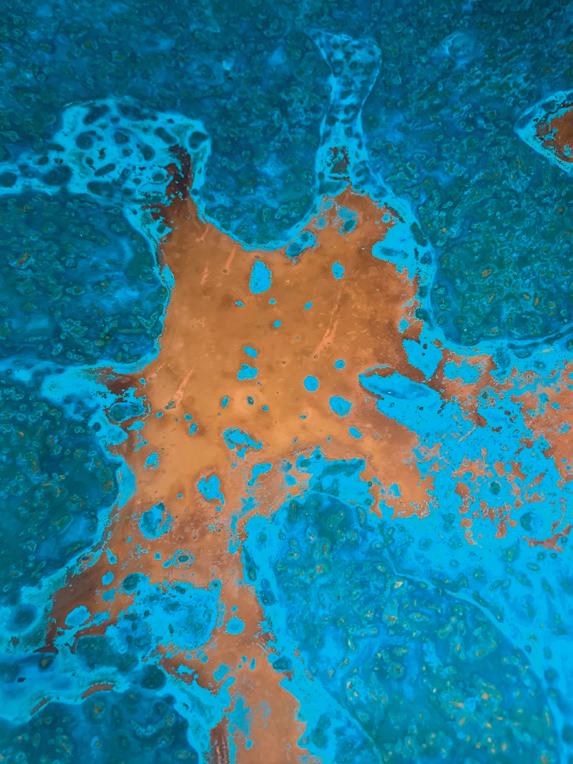
MESSAGE FROM DEAN HAHN
MESSAGE FROM NANCY BERGE
PROJECT DESCRIPTIONS
ENGINEERING DEGREE PROGRAMS
ACKNOWLEDGMENTS
THANK YOU TO OUR SPONSORS
THANK YOU, MENTORS & STAFF
DESIGN TEAMS
For the first year ever, students have access to a dedicated design center.
Craig M. Berge Design Day is a story of remarkable student success and the ways engineers improve lives.
We have much to be thankful for this year, including a dedicated Engineering Design Center for students, which bolsters the college’s commitment to experiential learning over all four years. Every engineering student now has 24-7 access to a spacious, well-equipped, safe place to collaborate and build.
Our seniors are thrilled to tell you about their projects. Not only are the designs a testament to their technical agility and creativity, but also the projects show why the college’s graduates are highly sought after in industry and government.
Students worked on ways to make mining and farming more sustainable: 3D-printed construction materials from tailings, an autonomous spider for collecting agricultural data, algae to reduce greenhouse gases, and solar energy covers for canal water evaporation. Teams developed a basketball shooting robot and an interactive model of the Tucson power grid to educate children. They created a haptic imaging device for blind scientists and airplane controls for armless pilots. They designed ways to keep people and animals safer – a drone to monitor wildfires, throw phone for hostage negotiations, and pet and livestock tracker, to name just a few. There are medical devices, robots for space exploration, and wastewater recycling projects, not to mention a BattleBot!
If you miss anything at Design Day, you can still learn about the 99 projects online in the students’ presentation videos, which will be available following the awards ceremony, where $47,000 in prize money will be presented.
Design Day and the Interdisciplinary Capstone Course are part of a lineup of competitions, maker fests, design courses, entrepreneurial and business instruction, and industry and community projects in the Craig M. Berge Engineering Design Program. The program immerses undergraduates at all levels in real-world experiences that integrate design, manufacturing and commercialization.
None of this would be possible without all the hard work behind the scenes. We are grateful to the donors, program mentors, university and industry partners, sponsors, judges, faculty, staff and alumni who help make the program and event a highly successful enterprise.
A special thank you to Nancy Berge and her family for their generosity, and to Larry Head, director of the Craig M. Berge Engineering Design Program, for his dedication to this unparalleled experiential learning and design curriculum in higher education.
Bear Down, and support our Wildcat engineers!
I love Design Day! It’s the best day ever to see our future. Our future in technology and our future in engineers who will make that technology a reality.”
MARLA PETERSON, alum, judge, Honeywell
The LightBrush
Feeding the Future: Student-led Design at the Nexus of Food, Energy and Water
AIAA Design/Build/Fly Competition
Let’s Boil a Computer Again!
Automated Universal Part Singulator (AUPS)
Throw Phone for UAPD/FBI Crisis Negotiation Team
Optical Scatterometer
Battery Powered Remote Communications via Cost-Effective Satellite Links
Medical Grade Leak-Proof Spigot For Diagnostic Reagents and Waste
Wireless Emergency Lighting System (WELS) Battery Tester
Large Tractor Ladder Latch Design
Cytology Slide Prep and Vial Storage System
Airfoil Cascade Hub Injection II
Mobile Reagent Filling System
Fluid Volume Measurement on a Microscope Slide
Launch Vehicle Ground Support Equipment Frontend
Novel Inspiratory Muscle Strength Training (IMST) Device
Autonomous Mechanical Spider (AMS) Platform for Crop/Turf Management
Autonomous Maintenance Identification Vehicle
Virtual Subject Matter Experts (SME) Training, Critical Asset Control
Telemetry and Data Logging System for the Wildcat Formula Racing Car BattleBots
My Health Navigator
Mechanical Energy Storage System
Automated Oil Dispenser
Pulsed Detonator Ignition System Optimization
Live Silage Analyzer and Mini-Fermenter
Arch Reactivator Brace
Comprehensive Modeling of Beam Propagation in Multimode Fiber and Experimental Validation (Year 2)
Vision-Based Agricultural Implement Awareness
Cyclesafe: An Automobile Proximity Sensing, Warning and Reporting Device for Bicycles
Broadband Tunable Fabry-Perot Spectrometer for Remote Sensing
Rotating Detonation Engine Heat Management System
Spin Balance Mechanism
Directed Energy Deposition (DED) Repair With Integrated Machining
Lightning Protection Garments for Injury Prevention
Smart Medical Drainage Catheter
Design of Remote-Controlled Automation of the Transformer Bioreactor (T-Bioreactor)
Mirror Distortion Measurement
Airplane Controls for Armless Pilots
Pressure Sensing Self-Regaining Retractors
An IoT-Based System for At-Home Behavioral and Physiological Health Interventions
Atto-Grid
SIPhTR: Small Item Photographing Triage Robot
REDIEM 2.0 – Renal Extremity Device to Measure Impedance, Edema and Movement
Sustainable Building Materials Using Mine Tailings
Miniature Animal Health Status Tracker (MAHST)
The Wired Room - Automated Digital Sound, Image and Motion Analysis for Enhanced Medical Diagnostics From a Patient Encounter
Ultra-Low Power RF Communication for Industrial IoT Sensors
Row, Row, Row Your Trike Gently Down the Street
Perio-Dx: Bad Gums = Bad Kidneys + Bad Heart
AQUABOT C3 - Aquatic Drone Coordination, Communication and Control
Snorpheus
Automated PVC Tube Winding
Smart Rocks - A Network of Covert Smart Sensors (Joint UArizona UMass Project)
Basketball Shooting Robot
Mixed Reality (MR) Diagnostic and Treatment System
Lunar Surface Transporter Vehicle (L.V.S.T.) - Team 1
Evaluation of Tensegrity Telescopes for Small Satellites on Asteroid Recon Missions
ElectroDose: Wearable Sensor for Quantitation of Pulsed Electromagnetic Therapy (PEMF)
Supplement Recommending Mobile App with Handheld Measuring Device for Saliva
pH and Calcium Levels
Understanding the Normal Aging Brain So That the Puzzle of Alzheimer’s Can Be Solved
Autonomous Robotic Racecars
PODBot Print on Demand Robots
STAR - Short Term Aerial Recognizance
Desktop Automated Powder Processing Station
Biomedical Sensor Board
Spacecraft Platform at L1 for Future Space Development - Team 1
Lunar Surface Transporter Vehicle - Team 2
Spacecraft Platform at L1 for Future Space Development - Team 2
Tissue Therm: Testbed System for Analyzing Thermal Effects of Pulsed Electromagnetic Therapy on Tissues
Flowing Robotic Surface - Haptic Imaging Device for Blind Scientists
Autonomous Mine Design
Vumbula Resources - Optimizing Geological Exploration in Uganda
SME Metallic Mine Design Competition
Railveyor
Spatial Exploration with Robotic Operators (SpERO)
Support Aerial Incendiary Locator (SAIL)
Irrigation Water Requirements Forecast Tool
Biofuels from Lignocellusoics
AZ Water Competition: Rainbow Water Reclamation Facility
Expansion Project
Liquefied Natural Gas (LNG) Receiving Terminal
Algae Photobioreactors for Carbon Dioxide Removal
Microbial Electrolysis Cell for Hydrogen Production and Electricity
Generation
Solar Panels Over the Central Arizona Project (CAP)
Bio-Aviation Fuel
Wafer Rinse Chamber Ultrapure Water (UPW) Recycling Stream
Dial-Assist
Perfume Manufacturing Process
Re-injection & Extraction Process for Simulated Crude Oil Plant
In-House Foam Part Production
AZ Water Competition: Rainbow Valley Water Reclamation Facility
Expansion Project
Bioplastic Synthesis Using Organic Waste Material
Dealcoholization of Red Wine Using Osmotic Distillation
It’s our dream, and we’re going to go and make it happen together. It’s going to be very exciting to see.”
YOUSUF CHOUDHARY, member of the BattleBots team
This award recognizes the project that embodies the best attributes of engineering design and the engineering profession. The winning project shall have an outstanding design approach and implementation, excellent system modeling and/or analysis that support the design, comprehensive system testing that verifies system requirements, and a superior presentation of results to Design Day judges. Team members of the winning project shall present themselves professionally and clearly demonstrate engineering knowledge of the design. The winning project shall clearly be the best project at Design Day.
While several designs may meet the judging criteria, this award is given to the design that does so the most effectively. The project that receives this award excels in many ways. The design is well thought out and its implementation is of high quality. It accomplishes all key design requirements and is supported by rigorous analysis and testing. Its poster and presentation are professional and easy to understand.
- $1,000)
This award recognizes the best project related to sustainable, cost-effective and environmentally friendly energy production, distribution or use. Winning projects could focus on developing new energy sources, reducing energy costs, improving efficiency or reducing cost of energy distribution, adapting existing energy distribution methods to better integrate new energy sources, and increasing efficiency of energy use.
Software has become an integral part of the operation, management and control of complex systems comprising mechanical, electrical, and optical elements. This award recognizes the best use of software in a system design to enable task automation, object recognition, system robustness, data collection, or other impressive features that would be difficult to achieve without software. Teams will be judged on the reliability, robustness, maintainability, reusability, originality and testability of software embedded in their designs.
The Systems Engineering perspective is based on systems thinking. When a system is considered as a combination of system elements, systems thinking acknowledges the primacy of the whole (system) and the primacy of the relation of the interrelationships of the system elements to the whole. This award goes to the team that most robustly addresses all aspects of the project from the systems perspective.
The French philosopher Voltaire is credited with the saying “Le mieux est l’ennemi du bien,” which means “the best is the enemy of the good.” Similarly, Leonardo da Vinci is credited with the saying “Simplicity is the ultimate sophistication.” This award recognizes the design team that best emulates these ideals and resists the temptation to overly complicate the design to yield a clean, simple, elegant, lowest-cost design that simply works well.
This award recognizes the most innovative use of optoelectronics and optomechanics in a design and is given to the team that demonstrates the most thorough approach to the design and engineering of its optical system. This award recognizes complete understandings of the optical design, system requirements, tolerance analysis, and optical component usage. Important criteria are integration of optics into the overall system, novel use of optical components, creative use of commercial off-the-shelf items, verification of optical components, meeting system requirements, use of standard optical design software, and manufacturability of optical design and components.
Rincon Research Award for BEST PRESENTATION ($1,500)
This award reflects the quality of the overall verbal and poster presentations. Verbal presentations should be well structured to describe efficiently the overall problem being solved and the specifics of how the team accomplished its design. Answers to questions should be direct and demonstrate mastery of the project. Presenters should speak in a clear and easily audible voice, making good eye contact with the judging pod. The poster board should be visually interesting and graphically well organized to tell a standalone story of the project.
($1,500)
This award recognizes a design solution that goes above and beyond the project design requirements and produces results that may impact and/or be useful for other products and applications. Teams competing for this award must show that they have met all project design requirements and have produced an innovative solution that may lead to other products or applications. Solutions that are sufficiently innovative for a potential patent application and that may form the basis of a new start-up will be given special consideration in the selection process.
($1,500)
Innovation may include the novel use of existing components or the creation of entirely new components to meet customer requirements. The most innovative design will not only be a creative solution to a problem but also an effective solution that is well implemented. This award recognizes the team that has created or made use of components in the most innovative way, or demonstrated excellence in the implementation of innovative design in its project, or both.
($1,250)
This award honors a student team that has improved or enhanced the quality of life for individuals through the outcome of their project. It recognizes the improved standard of health, comfort, environment, community, and happiness experienced by an individual or group. Projects are judged on the ability to promote the well-being of humans through togetherness and the practicality of the implementation. Teams should be able to effectively communicate their design and how it will improve lives.
Steve Larimore Award for PERSEVERANCE & RECOVERY ($1,250)
Issues and roadblocks always occur during the engineering design process. Although they cause panic and distress, they also represent great opportunities to learn and often lead to designs that would otherwise be impossible to conceive. This award recognizes a team’s ability to learn and to overcome issues or roadblocks encountered during the design process. The award is judged based on the ingenuity of solutions to problems caused by issues or roadblocks and the features in the final design that contribute to recovery from them.
Mark Brazier Award
Biomedical engineering is a discipline that advances knowledge in engineering, biology and medicine, and improves human health through cross-disciplinary activities that integrate the engineering sciences with biomedical sciences and clinical practice. This award recognizes the team the has demonstrated excellence and innovation in biomedical engineering design. It recognizes outside-the-box thinking that pushes boundaries and hands-on approaches to creative solutions. Projects are judged on the elegance and creativity of the technical solutions and their implementation. Teams should be able to communicate effectively their design and the processes they use for creativity.
This award goes to the team that best considers the needs of the end user/client. The team should demonstrate that they considered the end user’s needs throughout the design process. The team should have a list of end user concerns and show how they addressed them. Many times, a physical prototype is created to understand and study the fit, form and function of the device or system and usability testing is conducted with a sample group of end users to validate or improve the design. Teams are judged on the appropriateness of the prototyping used, how effectively prototyping is used to improve the design, and how well the needs of end users are considered. Prototypes can be made using rapid fabrication technology, traditional manufacturing, or can be hand built.
Successful implementation of any innovative design requires that all members of the design and production team communicate effectively. Design intent must be communicated from the design activity to the rest of the team using design documentation with a clear map for others to reproduce the design based on documentation only. The mechanical portion of the design is evaluated on the use of drawings with geometric dimensioning and tolerancing, solids models, illustrations and presentations that can be used to manufacture and inspect design hardware. Software and other systems are evaluated on the use of documentation that clearly and fully describes the system and illustrates the approach to testing.
This award recognizes the single-discipline design team that best demonstrates external team collaboration. Like real-world problems, senior design projects require skills from multiple sources and students should learn the value of leveraging the strength of a diverse team as well as seeking out external guidance and support to succeed. These skills are foundational to a successful engineering career.
This award recognizes the team that best executes project design using a flexible and incremental approach. Final project outcome is achieved through several test and evaluation iterations in collaboration with the customer. The project team should continuously review and assess results and quickly adapt to any changes or problems encountered.
IEEE is the world’s largest technical professional organization dedicated to advancing technology for the benefit of humanity. IEEE and its members inspire a global community through its highly cited publications, conferences, technology standards, and professional and educational activities. IEEE is a leading developer of international standards that underpin many of today’s telecommunications, information technology, and power-generation products and services. This award recognizes the team that best shows the standards used in their project and how the use of those standards facilitated or improved their overall design and/or its performance outcome.
The Mensch Prize for Best Use of Embedded Intelligence recognizes the engineering innovation team that best integrates embedded intelligence into a potential commercial product. Specifically, the award will be granted to a student team that has built a smart connected prototype that may have a commercial market. Embedded Intelligence is characterized as the ability of a product to sense, process, communicate, and actuate (SPCA) based upon information gained from an understanding of both itself and others and for the benefit of many. Preference will be given to designs with SPCA capabilities that can demonstrably surpass human abilities to perform the same function.
This award recognizes the interdisciplinary team that creates the best video telling the project story. The video must capture the sponsor’s need, the process the team followed to develop the solutions, the final solution including test and evaluation, and how it meets the sponsor’s needs.
This award recognizes excellence in overall system design in a project that has an aerospace emphasis. Verbal presentations should be well structured to describe effectively the overall system and the specifics of how the team implemented its design project. A key feature of the presentation must be representative data that demonstrate how the system was thoroughly tested. Answers to questions should be direct and demonstrate a high level of team competency about the details of the electronic system for the project. The presentation should demonstrate how all members have contributed to the project to exhibit core values of teamwork and professionalism.
This award recognizes excellence in overall mechanical system design in a project that has an aerospace emphasis. Verbal and written presentations should be well structured to describe effectively the overall system and the specifics of how the team implemented its design project. A key feature of the presentation must be representative data that demonstrate how requirements were analyzed, documented, designed against and tested. Answers to questions during the presentation should be direct and demonstrate a high level of team competency about the details of the mechanical system for the project. The presentation should demonstrate how all members have contributed to the project to exhibit core values of teamwork and professionalism.
Phoenix Analysis & Design Technologies Award for BEST USE OF PROTOTYPING ($750)
This award goes to the team that best uses a physical prototype model to understand and study the fit, form and function of the device or system designed. Teams are judged on the appropriateness of the prototyping technology used, how effectively prototyping is used to improve design, and how effectively the use of prototyping is communicated. Prototypes can be made using rapid fabrication technology, traditional manufacturing, or can be hand built.
The Fish Out of Water award congratulates students for successfully accomplishing a task that was not in their realm of expertise. The projects for senior design require skills from many disciplines, and students must sometimes learn a new subject or skill in an area outside of their major to help the team succeed. A student who not only learns this new subject or skill, but also uses it to effectively help the team thrive, shows dedication and initiative, gains that will continue to help in an engineering career.
This award recognizes the design team that best implements a modern data acquisition and control system. Recognition is given for the use of the system to collect data that characterizes project performance and assists in project optimization and, ideally, uses the same data acquisition system to perform feedback and control operations.
L3Harris
($500)
Some engineering problems are straightforward: optimal solutions are found through the application of engineering best practices. Sometimes, however, the best design choices are not obvious, and only reveal themselves after a thorough analysis of the underlying physical principles. This award recognizes a design that could only have been arrived at after careful study and creative application of physics.
Simpson Family Award for BEST SIMULATION AND
This award recognizes the project that makes the best use of computer-based simulation or modeling. The simulation may be the project itself, or a design tool used to model the performance of the project design. Criteria for this award is based on scope of the simulation, the fidelity of the simulation compared to real-world performance, and the engineering judgement exercised in determining the complexity of the model.
Frank Boyles Award for BEST UAS DESIGN ($500)
This award recognizes the unmanned aircraft systems (UAS) project with the highest quality of design and construction that succeeded in, or made a good attempt to, achieve the sponsor objectives.
Ergo Dave Award for BEST USE OF HUMAN FACTORS ENGINEERING ($500)
This award recognizes the team that makes the best use of HFE (human factors and ergonomics) design principles (understand, design, evaluate) iteratively. The winning team will provide evidence that they collected and understood both tasks and users, and showed significant reduction of fatigue and workload to users.
AZ
This award is given to a team whose system goes beyond sponsor requirements and best considers usability and manufacturing readiness. Teams will be judged on whether they did the following: considered alternative designs and selected the best choice; met or exceeded sponsor requirements; considered producibility, ease of assembly and cost; considered reliability and maintainability in both prototyping and build phases; considered user operation and included operator instructions; and included a complete design technical data package.
This award is given to the team whose design incorporates the most innovative manufacturing method addressing reduced carbon emissions. Projects could include introducing a new technique for manufacturing or an innovative use of an existing technique that reduces the cost and improves the quality of a product while reducing carbon footprint.
This award recognizes students who best exemplify teamwork skills, including the ability to work cooperatively with others to produce high-quality work, to take the initiative, to support and respect the opinions of fellow team members, to give and receive feedback, to demonstrate effective leadership, to keep their team focused, and to elevate the work of their fellow team members. Nominees for this award are selected by their teammates.
Thank you to everyone who has participated in this wonderful event, the Craig M. Berge Design Day which bears our family name. My family and I are delighted to see and learn about your design projects. They are truly outstanding.
Much of my husband’s life and engineering career was all about designing. As a student, he built and designed his dragster. Later in life, as a mechanical engineer, he worked for a company that paid for his education. The company loaned him to the U.S. Navy to design the starter for a jet airplane named the Intruder. That plane is on aircraft carriers to this day. Knowing that the Navy is still using something he created is truly remarkable.
My husband would expect remarkable things from each of you, too. He would be so proud of your creativity and all you have accomplished.
In my husband’s memory, I am honored to support the Craig M. Berge Engineering Design Program and these student experiences that move you toward the next chapters in your lives and careers.
All the Best,
Nancy BergeIt brings me a lot of joy being able to work with students on real-world problems.”
NITIN PATEL, alum and Caterpillar project advisor
“
Improve oral health and surface appearance of the oral cavity using LEDs.
For those who have mental or physical limitations or aversions to traditional toothbrush use, photodynamic therapy can improve overall oral health and decrease plaque bacterial colonization. This project presents a waterless, bristleless alternative to traditional mouth cleaning devices. It allows the user to select a light mode for three individual LED treatments using blue light, red light or a combination of the two.
The LightBrush design uses an Arduino Nano Every microcontroller to power the high-wattage LEDs, which are located on a custom-designed printed circuit board in the head of the brush. Custom code controls the LEDs according to the selected light mode, and it delivers a specific lux dosage amount over a set treatment time. For safety, an accelerometer ensures the user or caregiver is properly holding the LightBrush and automatically shuts off the device when the LEDs are shining upwards, preventing ocular damage. A piezo buzzer notifies the user when the treatment begins and is completed to prevent light exposure outside of the mouth. The lithium polymer battery can be recharged when voltage is low. The team 3D printed a prototype of the LightBrush to verify functionality of the complete system. Further research into potential environmentally sustainable materials for large-scale production of the device was also completed, and instructions for use were developed for customers.
Team 23014
Design an agrivoltaic system to provide power to the Greenery S Freight Farm at Biosphere 2 and create a functional demonstration model.
The project team developed an agrivoltaic system design and established solar production estimates to determine the renewable energy off-set for the Freight Farm located at Biosphere 2. Additional goals included structural design, operational guidelines, design of a secondary freight container to house electronics for the solar components, and a functional model. The design can work in any offgrid system located in arid regions where there is no or limited electrical grid connectivity.
The agrivoltaic system consists of 61 solar panels, a structural support system for the panels and an electrical system that controls the flow and storage of energy. While the team built a functional, smaller-scale prototype, they also created various models and electrical diagrams, worked with structural applications, and performed calculations to verify the full-scale design. The demonstration model incorporates the key components of the Freight Farm-Agrivoltaic System, including a structural assembly, electrical and solar components, and system monitoring.
TEAM MEMBERS
Ismael Ballesteros, Electrical & Computer Engineering
Jazmine Barraza, Engineering Management
Natalie Hall, Biomedical Engineering
Haley Renee Johnson, Biomedical Engineering
Fernando Romero, Industrial Engineering
Sovenna Emily Thorn, Systems Engineering
COLLEGE MENTOR
Mike Nofziger
SPONSOR ADVISORS
Shoshi Almog, Judith Macias-Harris
TEAM MEMBERS
Brooke Elizabeth Bykowski, Engineering Management
Lynn Carroll, Biosystems Engineering
Logan Eaton, Electrical & Computer Engineering
Stephanie Beatrice Orchard, Biosystems Engineering
Alejandro Quijada, Mechanical Engineering
Hailey R Schleining, Biosystems Engineering
COLLEGE MENTOR
Michael Madjerec
SPONSOR ADVISOR
John Adams
TEAM MEMBERS
John Roger Allen, Aerospace Engineering
Charles James Fischer, Aerospace Engineering
Keegan Kelaher, Aerospace Engineering
Kyle Ryan Peabody, Aerospace Engineering
Aidan Petrie, Electrical & Computer Engineering
Will Wong, Aerospace Engineering
COLLEGE MENTOR
Sergey Shkarayev
SPONSOR ADVISOR
Adrien Bouskela
Team 23015
PROJECT GOAL
Create a unique radio control aircraft that will compete in the American Institute of Aeronautics and Astronautics (AIAA) international Design/Build/Fly (DBF) competition.
The annual AIAA DBF competition is an international event, hosted in Tucson and Wichita, Kansas, that invites schools from all over the world to design, build and fly an aircraft according to the design requirements that are set each year. Each team must attempt to maximize their possible points earned via scoring guidelines set by the competition. Flight envelope attributes such as endurance, speed and payload weight must be balanced accordingly to create an aircraft that will obtain the highest score.
This year, the schools were tasked with designing an aircraft that is capable of flying three missions, each with their own stipulations. Based on the scoring and competition guidelines, this design must be able to carry a heavy internal payload, mount a vertical antenna to one wingtip and have an endurance of around eight minutes. In addition, the aircraft must be able to disassemble and fit into a box that is compliant with FAA carry-on regulations, limiting battery size and aircraft dimensions. By employing computational fluid dynamics, advanced composite building techniques and rigorous aerodynamic design processes, the University of Arizona team developed a competitive aircraft to represent the school on the international stage.
Team 23016
TEAM MEMBERS
Jesus Arias, Electrical & Computer Engineering
Chris William Bremser, Electrical & Computer Engineering
Sean Brown, Systems Engineering
Prasanna Raut, Mechanical Engineering
Rusty D Rinehart, Electrical & Computer Engineering
COLLEGE MENTOR
Bob Messenger
SPONSOR ADVISOR
Nicholas Keehn
PROJECT GOAL
Create a two-phase immersion cooling and filtration system with Fluorinert to significantly reduce computer server farm power and water usage.
The rapid growth in smartphone usage has led to a surge in demand for cloud services. Major data centers, which store information for cloud service providers, have replaced traditional local computer storage with large data storage facilities. These facilities require a huge amount of energy to power and drinkable water is used to keep them cool.
To address these issues, the team designed hardware and software to cool the computer servers using FC-72 Fluorinert as an alternative to current swamp cooling forced air systems. Flourinert was selected for its low boiling point of 132.8 degrees Fahrenheit. They also designed a custom filtration system to reduce and mitigate dendritic salt growth, which can lead to electrical shorting. This system eliminates vulcanizers and plasticizers that cause the damaging growth.
The team built a test system for data center applications, which required finding a suitable pump that handles the low boiling point and low viscosity of Fluorinert. Finally, they created an interactive graphical user interface to allow technicians to monitor cooling system efficiency. The team then measured progress toward the goal of reducing power and water consumption.
Team 23017
Design and build a flexible part feeder with a cartesian robot and high-resolution camera for use in automated assembly lines.
With millions of dollars being spent on tooling for automated assembly lines, companies are relying more on reconfigurable part feeding and sorting mechanisms to save costs. This project provides a solution by being easily adaptable to any assembly process without compromising effectiveness or reliability.
The AUPS consists of a cartesian robot, a high resolution camera, a gripping mechanism and a vibrating table. The robot is controlled using the CtrlX Machine Controller developed by Rexroth and an Arduino is used for controlling the sensors and gripper. Parts are fed manually onto the vibrating table, where the camera identifies and locates them, allowing the robot to travel, pick up and sort them correctly. If no parts are detected, the system uses the vibratory table to disperse parts until the camera can locate one. The gripping mechanism is attached to the end of the Z-axis of the robot and is capable of handling parts between 2-10 cm3 with a weight limit of 0.5 kg.
The system can automatically sort parts based on their shape and size. It is designed to operate in an enclosed factory floor environment and is therefore shielded from external interference with a metal frame and acrylic walls.
Team 23018
supported by Craig M. Berge Dean’s Fund
Deliver a rugged, reliable and secure audio-visual communication system for law enforcement to negotiate with hostage-takers and de-escalate situations.
During hostage situations, SWAT teams toss “throw phones” into buildings and encourage hostage-takers to initiate communication with a negotiator at a remote command center. These phones must be rugged, reliable and provide clear communication. However, the current 20-year-old system is hard-wired, cumbersome and intimidating to hostage-takers.
The team has advanced the technology to a more robust, reliable and friendly wireless solution. The solution consists of two major components, the throw phone and the command module. The design utilizes a 4G cellular network to ensure wireless connectivity and full-duplex communication across long distances. Low-light cameras controlled by a multiplexor provide video surveillance of the phone’s surroundings. Audio and video data is wirelessly sent over antennas, processed by a Raspberry Pi microcontroller and recorded onto a micro SD card capable of storing over six hours of audio and video footage. The data can then be quickly uploaded to an external thumb drive. All the components are contained in hard and soft plastic casing that is rugged enough to withstand throwing through windows.
Results of the project have shown the system provides real-time audio and video and a clear line of communication from as far as 300 feet for up to six hours. The device has proven to be nonintimidating to focus groups, which invites users to pick up and handle the phone without worry.
TEAM MEMBERS
Abdullah Albar, Systems Engineering
Kevin Dennis Gilman, Electrical & Computer Engineering
Nafisul Huq Khondaker, Electrical & Computer Engineering
Daniel Mack, Mechanical Engineering
Anthony Phillips, Optical Sciences & Engineering
Esmeralda Pimentel Enriquez, Mechanical Engineering
COLLEGE MENTOR
Pat Caldwell
SPONSOR ADVISOR
Brett Dooley
TEAM MEMBERS
Tanner Birecki, Optical Sciences & Engineering
Reid Clark, Industrial Engineering
John Paul LaRue, Electrical & Computer Engineering, Mechanical Engineering
Thaddeus Propper, Mechanical Engineering
Marcus Tal Wieser, Mechanical Engineering
COLLEGE MENTOR
Jeff Scott Wolske
SPONSOR ADVISOR
Joseph Berriman
TEAM MEMBERS
Nate Thomas Bushong, Systems Engineering
Daulton R Fox, Optical Sciences & Engineering
Ethan Lance Potthoff, Electrical & Computer Engineering
Will Reynolds, Optical Sciences & Engineering
Chase A Toncheff, Optical Sciences & Engineering
Rachel R Turner, Optical Sciences & Engineering
COLLEGE MENTOR
Mike Nofziger
SPONSOR ADVISOR
Benjamin Cromey
Team 23019
PROJECT GOAL
Build an optical scatterometer that measures how light interacts with the surface of a material.
Light scatters differently as it interacts with varying surface properties. Scattered light poses a problem for optical applications as it contributes to undesired stray light reaching the focal plane of a system. Understanding how light scatters helps predict stray light paths and prevents them from compromising system performance. To further this goal, the team designed an inexpensive optical scatterometer to measure the light scattering properties of a material.
The device shines a laser through an optical system which outputs a converging chopped beam onto a test sample and accurately measures the scattered power emitted as a function of angle in the plane of incidence. The focused spot is incident on a high-sensitivity detector, processed through a variable-gain transimpedance amplifier built from scratch, with noise reduction utilizing a lock-in amplifier. Recorded data are then plotted as a bidirectional scattering distribution function (BSDF). The BSDF characterizes the scatter distribution of optical radiation from the test surface, facilitating the analysis and mitigation of stray light in the system.
Team 23020
TEAM MEMBERS
Rahul Chowdhary, Electrical & Computer Engineering
Isabel Mary Dailey, Electrical & Computer Engineering
Carson Hayes, Electrical & Computer Engineering
Benson Hsieh, Engineering Management
Jeffrey T Sillers, Engineering Management
COLLEGE MENTOR
Pat Caldwell
SPONSOR ADVISOR
Randy Montgomery
Study the feasibility and relationships between satellite links and battery powered systems in order to design and optimize a system to control and monitor remote irrigation systems.
Traditional wired irrigation systems come with many challenges, including costly components, such as wiring, installation, maintenance and troubleshooting. With wireless technology, command and control is possible via a low-cost satellite network provided by Swarm Technologies. Battery powered devices allow the system to operate in any environment, regardless of access to external power sources.
The design includes a mobile application capable of connecting with an end device that communicates wirelessly to the irrigation equipment using a hub and spoke model. The mobile application uses various parameters to control and configure a remote irrigation system via the Swarm satellite network. The end device consists of a microprocessor, modem, antenna and power system. Fueled by a solar panel and batteries, it manages and monitors its own power capacity via intelligent wake and sleep cycles. A power model anticipates other energy sources such as hydroelectric. The team developed embedded software to communicate via Swarm satellites back to the hub and control irrigation rotors locally. The system can wirelessly connect to multiple irrigation rotors, where each rotor can be scheduled to turn on and off at specified times.
Team 23021
PROJECT GOAL
Design and prototype a medical-grade spigot to mitigate safety hazards in laboratory settings, ensuring secure and safe dispensing of chemical reagents.
At Roche Tissue Diagnostics, the current method for tissue staining involves dispensing chemicals through a spigot, which regulates the flow of reagents from chemical storage containers known as carboys. This existing system has recently been beset with leaks and issues, which are rooted in a faulty spigot connected to the carboy. The problems arose from a combination of mechanical failure, chemical degradation and incorrect operation.
The team used CAD software, 3D fabrication techniques, chemical compatibility testing, and mechanical and fluid analyses to develop multiple design iterations. Each iteration was tested extensively to ensure that the design is ready for mass production. The improved spigot not only enhances safety by eliminating mechanical failures and chemical degradation, but it also promises better ease of use. Additionally, the modular design approach offers cost efficiency in the manufacturing process.
Team 23022
Develop an easily manufacturable and modular device that will safely charge, discharge and test the batteries that power the Boeing 787 Dreamliner’s Wireless Emergency Lighting System.
In the event of an emergency, the WELS guides passengers to safety with luminescent signs and directions. To power this system, a WELS Battery Unit (WBU) must always be on board, fully charged, and safely operable. Currently, the Combined Ganged Battery Tester is used to verify the functionality of WBUs, but there is an issue with parts obsolescence. To keep up with the growing demand for WBUs, the WELS Battery Tester (WBT) has been designed with safety, reliability and manufacturability in mind.
The project centers around the electrical design which utilizes a custom circuit to interface with the WBU. This allows for charging, discharging, measuring battery temperature, reading internal memory and setting the WBU to a safe charge level for storage and shipping. These tests are implemented in the firmware of the microcontroller, which serves as the link from hardware to software. The packaged software application for the WBT confirms connection with a system, sends commands for which test is to be run and processes the data. The mechanical enclosure is lightweight, easily portable and ensures the WBU can make a secure connection with the device.
TEAM MEMBERS
Mohammed Almousa, Biomedical Engineering
Hector Flores, Biomedical Engineering
Rebecca Ger, Systems Engineering
Alec Jordan Blaauw Mills, Systems Engineering
Daniel Ramos Flores, Mechanical Engineering
Jason Zhang, Materials Science & Engineering
COLLEGE MENTOR
Pat Caldwell
SPONSOR ADVISOR
Ian Aguilar
TEAM MEMBERS
Ellie Griesemer, Mechanical Engineering
Marcel Merrill, Systems Engineering
Ary Nath, Electrical & Computer Engineering
Harrison Jay Pearl, Software Engineering
Ashton Rowe, Electrical & Computer Engineering
Luis Ruiz, Mechanical Engineering
COLLEGE MENTOR
James Sweetman
SPONSOR ADVISOR
Tyler Gleesing
TEAM MEMBERS
Harsh Bansal, Mechanical Engineering
Dom Jelenkovic, Engineering Management
Blake Andrew Rosen, Mechanical Engineering
Albert Isaiah Rubalcava, Mechanical Engineering
Kasey Spradling, Engineering Management
Matthew Villanueva, Mechanical Engineering
COLLEGE MENTOR
Jeff Scott Wolske
SPONSOR ADVISOR
Lloyd Becker
Team 23023
Improve and simplify the mechanical latching mechanism for the safety-boarding ladder on Caterpillar’s large track type tractors, while meeting structural durability and reliability requirements.
The boarding ladder attachment for Caterpillar’s D9 through D11 tractors enables operators to access the cab of the machine safely. However, the current actuator-driven latching mechanism that secures the ladder in the stowed position fails at low operating hours, creating downtime of the machine and loss of production. This project presents a motor-driven redesign of the latching mechanism to improve reliability and ensure backward compatibility for machines already in the field.
In this design, the access ladder swings up from the ground to the side of the tractor and is secured by two pins that firmly hold the ladder to the latching assembly on the machine. These pins are engaged by custom linkages driven by a geared motor and keyed shaft. This motor removes the linear actuator, the key source of failure from the current design. The redesigned linkages consist of a pivot link that interfaces with a shaft and connecting rods that drive the pins. The new system adds holding pads which adjust to the optimum stopping location of the stowed ladder. It also integrates limit switches with the current system of relays to stop actuation of the latching pins. This, in turn, interfaces with the switches, proximity sensor and rotational actuator that controls ladder movement. The new latching mechanism shows higher natural frequencies and reduction of stresses, ultimately improving structural reliability.
Team 23024
TEAM MEMBERS
Paige Bayze, Engineering Management
Collin Garard, Mechanical Engineering
Filiberto Quintero, Biomedical Engineering
Andrew K Tapia, Biomedical Engineering
Jackson Alexander Webb, Mechanical Engineering
Ibrahim Saad Zaky, Biomedical Engineering
COLLEGE MENTOR
Steve Larimore
SPONSOR ADVISORS
Michael Selep, Mansur Olaitan
Design a storage and sensing device for liquid-based cytology sample vials and slides in order to improve ergonomics, stability and usability for cryptotechnicians, reducing the risk of sample damage and human error.
The Slide Prep Utility for Roche (SPUR) is a new system that prepares slides for tissue staining from liquid-based cytology samples instead of tissue. Cytotechnicians manually stack hundreds of the slide and vial samples for processing, which presents the risks of damage and human error. The team developed a tray that allows cytotechnicans to keep the patient samples and slides safe and organized, resulting in a more efficient process.
The design includes a mechanical assembly and an electronic assembly. The mechanical portion consists of 12 holes designed for vial placement and 12 slide holders designed to fit two slides each. The electronic assembly includes an Arduino Nano, a temperature sensor and an E-Ink display, all powered by two 10Ah rechargeable batteries. The device temperature and sample storage age are monitored and presented on the display. If the temperature of the device moves outside a particular range, or if the sample storage exceeds six months, a visual alarm will be displayed, indicating the samples are no longer usable.
Team 23025
Develop a system that mitigates turbo fan engine surges by preventing backflow through compressor rotor gaps.
During critical stages of flight, when turbo fan engines perform at their operating limits, unfavorable atmospheric conditions can cause the direction of airflow through the engine to reverse through gaps between the engine casing and compressor rotor blades. This reverse flow is called a surge, and it can allow high temperature gases in the combustion chamber to back-flow into the compressor. This may cause catastrophic failure of the engine, necessitating an emergency landing.
To address the issue, the team designed a system to prevent backflow and 3D printed a prototype portion of a compressor with rotor blades and engine casing. It was tested by injecting a stream of high-pressure air into the gap. The team used a wind tunnel to measure changes in pressure across the airfoil when controlled by the injected stream of air. The design improves aircraft safety and reduces man-hours and costs required to repair engines after an occurrence of engine surge.
Team 23027
Design a mobile fluid detection system that identifies bulk fluid levels and is compatible with both a human user and an autonomous mobile robot.
The BenchMark ULTRA, an automated tissue staining instrument used in the detection of diseases such as cancer, requires several fluid reagents to perform its analyses. Detecting and maintaining adequate bulk reagent levels currently requires technicians to manually log usage, a process which is burdensome, time consuming and subject to error.
The team developed a cart-mounted, contactless vision system to automatically sense reagent fluid levels. The vision system includes a high-quality camera connected to a Raspberry Pi. An LED strip is used in conjunction with induced light blockers on the custom designed cart to stabilize the environmental conditions and improve measurement accuracy. The Raspberry Pi processes the camera image using gamma correction and performs fluid level estimation using pixel intensity comparisons, resulting in detection of fluid levels within 5% of the true volume. The analysis results are displayed on the system graphical user interface and saved for later use. A rechargeable power supply allows for 30 minutes of uninterrupted use.
TEAM MEMBERS
Becky Burns, Mechanical Engineering
Alhasan Haliru, Mechanical Engineering
Jake David Petersen, Aerospace Engineering
Abishek Sreenivasan, Aerospace Engineering
Avery Stockdale-Stephens, Aerospace Engineering
COLLEGE MENTOR
Doug May
SPONSOR ADVISOR
Nick Nolcheff
TEAM MEMBERS
Adrian Isaiah Alvarado, Biomedical Engineering
Jarod Mate, Mechanical Engineering
Divyansh Harendra Rathod, Biomedical Engineering
Samantha Mata Robles, Biomedical Engineering
Adrian Gildardo Rodriguez, Systems Engineering
Amanda Villegas, Optical Sciences & Engineering
COLLEGE MENTOR
Steve Larimore
SPONSOR ADVISOR
Matt Mette
TEAM MEMBERS
Taron Bashar, Biomedical Engineering
Roman P Golota, Electrical & Computer Engineering
Jacob Jones, Optical Sciences & Engineering
Misa Soto, Biomedical Engineering
Chloe Wetzel, Industrial Engineering
Nathan Yenerich, Biomedical Engineering
COLLEGE MENTOR
Mike Nofziger
SPONSOR ADVISOR
Bryan McKay
Team 23028
Design a system that measures the volume of residual fluid on a microscope slide with minimal user interaction.
Roche’s BenchMark ULTRA staining instrument has a variety of internal conditions, and it controls multiple chemical and physical parameters of the tissue staining process. The residual fluid volume on a microscope slide must be known and controlled. Currently, a technician measures the volume using a Kimwipe and an analytical balance. The team designed an optical approach to measure the volume of residual fluid on the microscope slide with less user interaction than the existing method.
The new system captures side-view images of fluid on a microscope slide and processes the images, measuring the height of the fluid at different points. A Raspberry Pi microcontroller directs the image processing, and a machine learning algorithm is trained to estimate and display the fluid volume onto an LCD screen.
The team designed and manufactured a plastic housing for the camera module that integrates directly onto the slide drawer of the staining instrument. They also manufactured an external housing for the Raspberry Pi and its associated components. Designed for simplicity, this system will greatly reduce the amount of time spent measuring residual fluid volumes.
Team 23029
TEAM MEMBERS
Kyle Ambrose Ambrose, Systems Engineering
Cody Truong Chi, Systems Engineering
Kevin Sean Grady, Electrical & Computer Engineering
Colin Herbert, Electrical & Computer Engineering
Braxton Montgomery Ulmer, Systems Engineering
COLLEGE MENTOR
Michael Madjerec
SPONSOR ADVISOR
Mark Hansen
Transition Northrop Grumman launch vehicle ground support equipment from a Javabased frontend to a web-based one. Apply a systems engineering approach for development of the Human-computer Interface design.
The defense industry typically uses software-based applications to test missiles and other types of flying projectiles. But as technology advances, the software requires numerous updates. By introducing a web-based frontend, the development, testing and release cycles of the system will be faster. The design provides the ability for multiple contributors to automate the integration of code and updates for new software.
By using a systems engineering approach, the team created a user-friendly interface prioritizing safety, performance and user satisfaction. A single client-side application receives data from the launch vehicle sensors and engineers, while simultaneously sending data packets back to the sponsor servers on any occasion of user interaction. With a graphical user interface paired with a backend, data forwarding allows the code to be maintainable and put in a single package. This design is a foundation for the transition to web-based applications for the launch vehicles.
Team 23030
Develop an innovative inspiratory muscle strength training device with enhanced user feedback, improving accessibility and impact for clinical and public applications.
Cardiovascular disease (CVD), the leading cause of death globally, results in over 19 million deaths annually, according to the American Heart Association. High blood pressure is directly linked to increased risk for CVD. While an abbreviated daily IMST regimen has been shown to significantly reduce systolic blood pressure, the exercises are difficult to perform effectively using current devices, which offer limited user feedback.
Our respiratory training system, ReTrain, is comprised of an ergonomic, handheld device containing a one-way breathing valve, pressure transducer and ESP32 microcontroller. It senses and transmits the user’s breathing pressure over a Bluetooth Low Energy interface to a paired smartphone application. The accompanying smartphone application monitors breathing pressure and provides live feedback. The device requires minimal user interaction, and the intuitive framework of the app enhances user experience. For standard training and calibration, a real-time waveform of the user’s pressure and current target level are displayed with an accuracy of 3.5%. Additionally, data from each session is stored on the user’s device and transmitted to a clinical program via Amazon Web Service.
Team 23031
Create a mid-sized autonomous utility robot with a simple, scalable and easily iteratedupon design, able to be adapted to a variety of missions, such as data gathering in industrial agriculture.
The Fourth Industrial Revolution is the idea that efficiency will be revolutionized by mass-data analytics fueling decisions made by AI. Large-area industries, such as agriculture, are racing to design a versatile drone capable of gathering this information. In this effort, ground based, hexapodal platforms have advantages over both flying drones and tracked/wheeled designs. These include the ability to mount heavier and more robust sensor packages, easy modification, longer loitering times, movement below and around foliage, and low impact on soil.
The AMS design uses off-the-shelf electronics, 3D printed parts and open-source software for simplicity, modularity and ease of modification. It includes a Raspberry Pi running the robot operating system, which has an abundant range of packages allowing for the easy integration of additional sensors, missions and parts. This current iteration uses lidar, or Light Detection and Ranging,=4ew31nd supersonic ranging devices, which provide robust obstacle detection and path planning. In addition, a GPS is used to define a roaming area for the robot, so this platform is ready to be adapted to large-area data gathering, especially within the agricultural sector.
TEAM MEMBERS
Tommy M Carder, Systems Engineering
Dylan McGuire, Biomedical Engineering
Collin Alexander Preszler, Biomedical Engineering, Electrical & Computer Engineering
Nicholas Sherwood Quatraro, Biomedical Engineering
Saul Silva, Systems Engineering
COLLEGE MENTOR
Steve Larimore
SPONSOR ADVISORS
Elizabeth F Bailey, Philipp Gutruf
TEAM MEMBERS
Ali Alaqeel, Electrical & Computer Engineering
Eli J Bitzko, Mechanical Engineering
Tam Friedman, Biosystems Engineering
Kaleb Gabriel Lucero, Engineering Management
Shambhavi Singh, Electrical & Computer Engineering
Ismail Abdul-Aziz Zaki, Mechanical Engineering
COLLEGE MENTOR
Pat Caldwell
SPONSOR ADVISORS
Pedro Andrade Sanchez, Brian Little, Mark C Siemens
TEAM MEMBERS
Alan Loreto Cornídez, Electrical & Computer Engineering
Jack T Moffet, Engineering Management
Victor Ferreira Silva, Mechanical Engineering
Nick Tolmasoff, Mechanical Engineering
Viru Vilvanathan, Mechanical Engineering
COLLEGE MENTOR
Bob Messenger
SPONSOR ADVISOR
Joseph Mueller
Team 23034
TEAM MEMBERS
Ahmad Ashraf Eladawy, Electrical & Computer Engineering
Milad Ghaemi, Optical Sciences & Engineering
Salman Mohammed Khashoggi, Industrial Engineering
Wilson Liao, Electrical & Computer Engineering
Rafael Lomeli-Navarro, Optical Sciences & Engineering
COLLEGE MENTOR
Bob Messenger
SPONSOR ADVISOR
Joseph Mueller
PROJECT GOAL
Design a system of sensors that automates the rapid detection of material handling equipment degradation or failure in high-usage warehouse facilities.
The equipment in Amazon fulfillment centers across the globe are susceptible to premature degradation and failure. These issues include bearing overheating and failure, conveyor belt misalignment and debris. To combat these problems, the team developed an autonomous, self-powered maintenance unit that can rapidly identify supply chain issues and streamline maintenance. The design will dramatically reduce the time and cost of critical repairs.
A maintenance worker might need up to eight hours to walk and inspect just one conveyor. But the autonomous robot design can do the task in as little as 15 minutes, while costing less than $600. The system uses a suite of low cost, state-of-the-art commercial sensors and is capable of accurately identifying equipment issues on the conveyor line. The hardware and software quickly detect possible failures and provide near-real-time reporting capabilities to factory maintenance technicians and engineers. The system sends a user-friendly, intuitive report to the local team while being completely customizable and modular, all while adhering to safety protocols required to reduce the hazards to personnel in these industrial settings.
Team 23035
PROJECT GOAL
Provide remote or in-person hands-on training to Amazon SMEs using virtual reality technology.
This project provides a VR training environment that simulates the conveyor belts that are critical to the operations of Amazon fulfillment centers. The system is designed to allow technicians to interact and gain experience with maintenance and repair of these assets. The company needs highly trained technicians because damage to critical assets can cost the company millions of dollars if the issue is not fixed quickly. Training in person is expensive because of travel, instruction costs and lack of experts for each specific asset. This project presents a more cost-effective method of training the technicians.
Through VR development in Unity, the team developed a training platform in which the user can perform functions that are critical to understanding the operation, repair, maintenance and part breakdown of the asset. Technicians can measure distances on an accurate 3D model of the asset. They can also identify part breakdown information of critical components, such as manufacturing, part number, part description and identification, allowing them to quickly procure replacements. The program also provides examples of faulty parts along with customizable procedures that allow technicians easier troubleshooting, repair, replacement and maintenance of the physical asset.
Team 23036
Develop a modular system to sense, transmit and display real-time racecar data.
In motorsports, data is paramount. Having the ability to gather information about the track, environment and car allows a team to better tune a vehicle optimally for a race. Technology that helps gather this data is available, but it is expensive and not compatible with all configurations of vehicles. To tackle these issues, the team created a modular system that is configurable with multiple sensors and usable in a wide variety of scenarios and environments. It provides critical real-time data for the Wildcat Formula Team.
The system has two Raspberry Pi computers that communicate with each other. One of them is onboard the race car for the driver, and the other is at the team’s chosen position, typically the pit lane. The onboard Raspberry Pi is connected to GPS, accelerometers and strain gauges, all gathering information on the car during a race. The remote subsystem has a Grafahan data plotting suite that converts the data into easily read figures. Use of this telemetry system allows setup of the car on race days to improve performance and safeguard against critical issues becoming safety hazards.
Team 23037
Design, build and verify a 250 lb. combat robot with active telemetry sensors capable of competing on the BattleBots TV show.
The BattleBots competition provides a space for builders to forge robots of destruction. As long as robots are under the weight limit and adhere to the BattleBots rules, they can fight. High achieving combat robots deal damage, survive deadly blows and look good while doing it. This project is a leap in the University of Arizona’s robotic community involvement and creates a space for future students to learn and have fun.
The team’s robot design integrates over 400 parts in six major subsystems – drive, weapon, armor, electronics, frame and telemetry sensors. The drive system uses four brushed motors to propel the robot to 20 mph. The weapon spins 45 lb. over 250 mph in eight seconds with a belt system. The stingray exterior is made of ultra high molecular weight plastic and AR400 ballistic steel for defense. The design includes an electronic system with kill switches, safety fuses and critical part protection. Holding it all together, the frame interlaces steel, aluminum and neoprene rubber to absorb impacts. Lastly, the combat robot houses speed, temperature and current sensors to ensure the driver is as informed as the robot is tough.
TEAM MEMBERS
Shayan N Afzal, Biosystems Engineering
Lukas Matthew Baker, Mechanical Engineering
Christian Copic, Electrical & Computer Engineering
Isaac Carlos Gloistein, Mechanical Engineering
Luke Kobran, Mechanical Engineering
Nicholas J Smith, Electrical & Computer Engineering
COLLEGE MENTOR
Doug May
SPONSOR ADVISOR
Michael W Marcellin
TEAM MEMBERS
Yousuf Choudhary, Electrical & Computer Engineering
Al Hurworth, Mechanical Engineering
Knudson Karson, Electrical & Computer Engineering
Mathias Micah Ramirez, Aerospace Engineering
Nick Scott Sivertson, Mechanical Engineering
Alex Tynan Wait, Mechanical Engineering
COLLEGE MENTOR
Steve Larimore
SPONSOR ADVISOR
Michael W Marcellin
TEAM MEMBERS
Dylan Etson, Electrical & Computer Engineering
Jerry Klosterman, Electrical & Computer Engineering
Brandon Kron, Biomedical Engineering
Isabella Martinez, Systems Engineering
Lauren Meloche, Biomedical Engineering
Nathan Owens, Systems Engineering
COLLEGE MENTOR
Elmer Grubbs
SPONSOR ADVISORS
Arun Rao, Lacey Rao
Team 23038
PROJECT GOAL
Develop a mobile phone application to improve outcomes and experience during inpatient hospital stays.
Many hospitals still rely on outdated communication techniques, ultimately leaving patients in the dark. The team designed My Health Navigator to improve the inpatient experience. It consists of two interacting systems, a database and an internet application. The database acts as the central storage of all information passing through the hospital system, while the application is responsible for the major functionality.
The application incorporates three distinct views, for patients, doctors and administration. Patients can see their care team members, schedule and rounding alerts, while physicians control that data using the doctor view. All functionalities are supported by the admin view, where accounts are created and patients are assigned their doctors and care team.
The team began with in-depth stakeholder analysis, operational concept development and requirements engineering. Then they created graphical user interface wireframes along with UML model components to map out the design for future development. The system information and files are securely hosted on a Liquid Web server. Stored HTML and CSS files direct the application front end, while Javascript and routing files dictate all backend functionality.
Team 23039
TEAM MEMBERS
Thomas Carroll, Electrical & Computer Engineering
Jesse Koontz, Electrical & Computer Engineering
Yudong Liang, Mechanical Engineering
Keegan Michael Pierson, Engineering Management
COLLEGE MENTOR
Michael Madjerec
SPONSOR ADVISOR
Michael Hemphill
Design a gravity battery, and characterize the efficiency of such a system for applications in existing vertical mineshafts.
When using renewable energies, storage is essential due to the significant variance in power produced throughout the day. Resolution Copper is evaluating alternatives to battery arrays for on-site power in their facilities. The solution must be cheaper and have less environmental impact, while still being reliable. To answer this need, the team designed a gravity battery that uses Resolution Copper’s existing vertical mine shafts.
The proof of concept is a tower-like structure that uses a brushless motor, a permanent magnet generator and a belt system. It turns electrical energy into potential energy by suspending a mass, which can then be converted back into electrical energy when gravity pulls the mass and drives the generator. Push-button user inputs relay commands to an Arduino microcontroller that interfaces with the motor and braking systems. The design uses proximity sensors to detect the position of the mass and terminate cycles automatically. Additionally, the system uses AC voltage and current sensors to calculate the total energy and efficiency produced by the system.
Team 23040
Design and build an automated oil dispenser to eliminate cross contamination, reduce waste and notify the user of low fluid level for a standard 55-gallon drum.
Machine shops use devices such as computer numerical control (CNC) machines to cut all types of material. These CNC machines can require a variety of lubricant types in different amounts for their operations. They are often filled by the operator manually pumping from a 55-gallon oil drum. This regularly leads to spillage, wasted oil, cross contamination and safety hazards within the workshop.
The team designed the Automated Oil Dispenser to decrease the amount of spillage, time and work required due to manual pumping. This will result in a cleaner, safer and more efficient work environment. The design uses a color-coded categorization system to minimize cross contamination and ensure each machine gets the correct oil. A sink basin filters the oil to eliminate spillage, reduce waste and prevent contamination, while a microcontroller and electric pump fill the oil safe containers. This microcontroller is programmed to detect the amount of oil dispensed and alerts the user when the drum reaches a low level.
Team 23041
Design and optimize a pulsed detonation tube as an igniter for a Rotating Detonation Engine (RDE).
Innovations in propulsion presently are focused on supersonic combustion of propellants to increase the useful energy yield in the cycle of an engine. In contrast, this technology adapts supersonic combustion in an RDE.
Traditional engines and nozzles have subsonic combustion called deflagration, and shock waves travel around a ring-shaped chamber to combust propellants. To successfully start an RDE, a shock wave must propagate within the combustion chamber itself.
This project focused on creating and inserting supersonic combustion waves into an RDE. Geometric and chemical factors dramatically impact the efficiency and reliability of the detonation process. The team designed and fabricated a modular system to conduct an extensive test campaign varying numerous factors, including internal geometry, fuel-oxidizer ratio, pressure, and timing of spark plug ignition.
The result was enhanced supersonic wave velocity measured at the outlet of the system, yielding an optimized design with favorable shock wave generation, reliability and velocity.
TEAM MEMBERS
Harry Chhieu, Mechanical Engineering
Marco Andres Lopez, Mechanical Engineering
Cameron John Frost Meehan, Electrical & Computer Engineering
Tania Mitnasala, Electrical & Computer Engineering
Mandeep Singh, Mechanical Engineering
COLLEGE MENTOR
Michael Madjerec
SPONSOR ADVISOR
David Saucedo
TEAM MEMBERS
Chad Aykroyd, Mechanical Engineering
Ryan Curtis-Sanchez, Aerospace Engineering
Curtis Dodd Goldin, Aerospace Engineering
Weston Cole Meyers, Aerospace Engineering
Jacob Thomas Roschak, Aerospace Engineering
COLLEGE MENTOR
Doug May
SPONSOR ADVISOR
James Villarreal
TEAM MEMBERS
Fahad Mohammad Alrashed, Electrical & Computer Engineering
Martin Calderon, Mechanical Engineering
Canyon Charles Cooke, Mechanical Engineering
Erick F Dzeketey, Biosystems Engineering
Alex J Hillman, Electrical & Computer Engineering
COLLEGE MENTOR
Michael Madjerec
SPONSOR ADVISORS
Duarte Diaz, Brian Little
Team 23042
TEAM MEMBERS
Sebo Diaz, Biomedical Engineering
Vinamra Kumar, Biomedical Engineering
Kenzi Marie McNeil, Biomedical Engineering
Aaron A Ramos, Materials Science & Engineering
Alex Joseph Sciortino, Mechanical Engineering
COLLEGE MENTOR
Justin James Hyatt
SPONSOR ADVISOR
Dan Latt
Build a better research tool for silage analysis.
Silage is a long-storage-life cattle feed created through the fermentation of various agricultural products. The study of silage fermentation and additive processes affects commercial enterprises, such as dairies and feedlots, including the environmental impact of these enterprises. This project redefines silage research.
The current method of silage study wastes large quantities of disposable bags and silage. This team set out to build a research tool to replace the existing wasteful method of analyzing silage as well as simplify the data collection and analysis process.
The team’s design builds on an off-the-shelf pressure cooker modified to collect scientific data. The pressure cooker base is ideal, as it already facilitates successful fermentation with little modification. Students installed several sensors integrated into the lid of the pressure vessel to analyze trends in pH, temperature, humidity, oxygen and volatile organic compound (VOC) content. This information is then processed by an onboard Raspberry Pi before being uploaded to a GitHub repository for ease of access.
Team 23043
Using an energy return mechanism to support normal human gait while maintaining adequate range of motion in the affected foot, design and build a comfortable, wellfitting, brace that corrects Adult Acquired Flat Foot (AAFD).
AAFD is a potentially debilitating condition that affects up to 5 million people in the United States. Left untreated, AAFD can cause limiting pain and arthritis. Mild to moderate AAFD can be addressed using braces and orthotic supports. However, the design of available products to treat AAFD may be impeding their effectiveness.
This team designed a novel brace to address common complaints about available products: high temperatures within the brace, discomfort, poor fit in readily available footwear, inadequate correction of the deformity, and reduced range of foot motion.
Combining previously proven static archplate geometry with an adjustable springpack system, the Arch Reactivator allows a user to step down naturally then get dynamic support via the lifting of a springpack system at the upper portion of the brace. All of this is contained within a sleek, comfortable sleeve that is easy to put on.
Team 23044
Develop a graphical user interface (GUI)-enabled, experimentally verified optical fiber beam propagation software package that accurately models how fiber bending, twisting and ambient temperature impact performance.
Optical fibers are waveguide conduits that transport light. Due to their unique optical confinement mechanisms, optical fibers can only carry a finite number of modes, or electromagnetic (EM) field distributions. Although the physics of straight fibers is well understood, many applications require the waveguides to perform in more complex environments, which significantly alter the behavior of the modes and, therefore, the guided field.
Engineers can compensate for these environmental perturbations, but only with accurate computational modeling. This team based its approach on the software simulation package from last year’s Team 22041, improving the package usability and fiber bending accuracy with verification through a rigorous experimental study.
The simulation can be accessed through a fully functioning GUI that allows the user to propagate Gaussian, flat top, annular and custom EM fields through step index or photonic crystal fibers with arbitrary bending/twisting geometries and ambient temperatures. During the simulation, the GUI displays the fiber layout, propagation loss, and real-time updates of the EM field as it propagates through the fiber, providing the user with enhanced analysis and streamlined fiber-based optical design.
Team 23046
Using various sensors, identify and track the position of any implement attached to an autonomous tractor.
Adding the capabilities of implement recognition and positioning to a tractor dramatically increases the scope of what tasks its autonomous system can perform. This design serves as a cost-saving alternative to adding automation equipment to each of the several implements that a single tractor pulls.
The system, which is completely powered by the tractor itself and can withstand agricultural conditions, sits on top of the tractor cab to visually recognize and track the towed implement. It uses an OAK-D-PoE camera with machine learning models to perform implement detection and identification and a Livox Mid-40 sensor with lidar, or Light Detection and Ranging, and traditional algorithms to accomplish positioning relative to the tractor. All of the visual information is compiled and calculated on an NVIDIA Jetson in conjunction with the OAK-D, with on-board processing capabilities. The Oak-D performs the Neural Network computing on the camera itself, while the NVIDIA Jetson processes the outputs from the neural network and lidar data as well as the overall system code.
The result is a complex network of embedded software and hardware integrated to accurately identify and locate implements, effectively advancing the future of automation in agriculture.
TEAM MEMBERS
Francisco Javier Flowers, Optical Sciences & Engineering
Oscar Hsueh, Electrical & Computer Engineering
Atkin David Hyatt, Optical Sciences & Engineering
Lauren McCaffrey, Optical Sciences & Engineering
Oliver Wu, Optical Sciences & Engineering
COLLEGE MENTOR
Mike Nofziger
SPONSOR ADVISOR
Tao Chen
TEAM MEMBERS
Gavin M Caldwell, Electrical & Computer Engineering
Jessica S Grove, Industrial Engineering
Brett Miller, Biosystems Engineering
Kees Passon, Optical Sciences & Engineering
Everett Schafer, Optical Sciences & Engineering
Howard James Yawit, Electrical & Computer Engineering
COLLEGE MENTOR
James Sweetman
SPONSOR ADVISOR
Darcy Cook
TEAM MEMBERS
Omar Al Hilal, Electrical & Computer Engineering
Young Cho, Mechanical Engineering
Dan S Darnell, Mechanical Engineering
Shane Henry Jordan, Optical Sciences & Engineering
AJ James Sterner, Electrical & Computer Engineering
Jake Timothy Wern, Systems Engineering
COLLEGE MENTOR
Steve Larimore
SPONSOR ADVISOR
Dan Latt
Team 23047
PROJECT GOAL
Design and create an automobile proximity sensor for cyclists to ensure safety on the road and provide potential traffic violation information.
Every year in the United States nearly 1,000 cyclists die, and more than 130,000 cyclists are injured in road accidents. Regulations such as ARS 28-278 guarantee cyclists 3 feet of space on the road, but these laws are often ignored because there isn’t a clear way to determine this traffic violation.
The Cyclesafe, a lightweight device mounted inside the handlebar of a bicycle, employs LEDs to alert drivers of the cyclists’ location and uses a microcontroller and an ultrasonic proximity sensor to detect within milliseconds a driver crossing into the 3-foot boundary of the cyclist.
If an intrusion is detected, the device captures a picture of the offending driver’s license plate as well as the location of the incident using GPS. The photograph and location are stored to an onboard SD card, where the user can later collect the data and report violators to the authorities.
Team 23049
TEAM MEMBERS
Carolina Corella, Optical Sciences & Engineering
Jason Dylla, Optical Sciences & Engineering
Adam G Lane, Optical Sciences & Engineering
Allen Miller, Engineering Management, Optical Sciences & Engineering
Justin Alexander Scott, Optical Sciences & Engineering
COLLEGE MENTOR
Doug May
SPONSOR ADVISOR
Casey Streuber
Develop a low-cost spectrometer that applies a Fabry-Perot Interferometer (FPI) –replacing a diffraction grating to perform hyperspectral imaging.
Objects on the Earth’s surface contain different chemical compositions from mineral deposits, wildfires and industrial emissions. Each chemical composition emits light at a unique color, or wavelength of light.
A system with a spectrometer that takes 2D images of Earth’s surface at specified wavelengths can characterize and identify objects by their spectral emissions. Such a system can also work with Lidar, or Light Detection and Ranging.
The team’s design has two mirrors facing each other in a configuration known as an FPI, or cavity. Light passing through the cavity interferes constructively or destructively depending on the wavelength, as determined by the spacing of the cavity’s mirrors. Filtration of sunlight and accurate wavelength distinction of the light is achieved by adjusting the mirror spacing digitally with a piezoelectric actuator.
Collection and imaging optics around the FPI help form a monochromatic image. Software then coordinates the actuator and camera for data collection.
Team 23050
Implement a heat management system within Nobel’s Rotating Detonation Engine (RDE) and collect data to allow for improved design.
The global energy crisis is one of today’s biggest problems. RDEs are a new type of engine that could increase fuel efficiency up to 15% over conventional combustion, a huge improvement for energy and aerospace industries. However, heat management challenges must first be overcome.
An RDE supersonically combusts fuel, rapidly increasing the pressure and temperatures within the combustion chamber. A mixture of fuel is injected into the bottom of the RDE combustion chamber, where it meets a single detonation from the ignitor. The detonation creates a shockwave that continuously propagates around the annular combustor. Resulting high temperatures and pressures generate thrust or drive the turbine. But long exposure to the high temperatures is detrimental to the internal components of the RDE itself.
To help Nobel advance its RDE, the team designed a heat management system for a split path fluid flow within the walls of the combustion chamber. The system cools the RDE while it runs, allowing Nobel to run the engine for longer and collect data to optimize its design.
Team 23051
Design a novel mass properties measurement system for calculating the center of gravity of various payloads.
Mass properties are crucial when designing hypersonic rockets because unexpected deviations in balance can lead to flight failure. Theoretical mass properties data, often derived from naturally idealistic CAD models, must be refined with real measurements.
Using the principle of the conservation of angular momentum, this team designed a low-cost system to calculate the center of gravity for varying payloads. Imagine how figure skaters move their arms closer to or away from their bodies to change rotational velocity.
In this design, a system of three nested shafts moves two translation plates to shift the payload and maintain the system’s center of gravity. DC motors drive the system, and an electrical suite controls the motion. The system measures the current being drawn by the rotation motor as the plates are moved in two axes. The point at which minimum power consumption maintains rotational speed determines when the system’s center of gravity is in the rotational axis. Calculations determine how far the plates must shift the payload to establish its center of gravity.
TEAM MEMBERS
Nicolas Gross, Mechanical Engineering
Nathan Grossman, Aerospace Engineering
Sean Brian Harkins, Aerospace Engineering
Briannah Herman, Aerospace Engineering
Joseph Reid, Mechanical Engineering
Richie Ruicheng Ye, Aerospace Engineering
COLLEGE MENTOR
Pat Caldwell
SPONSOR ADVISOR
James Villarreal
TEAM MEMBERS
Hammad Al Hinai, Mechanical Engineering
Cameron Crowley, Aerospace Engineering
Aaron B Folkerts, Aerospace Engineering
Nicholas Gullo, Electrical & Computer Engineering
Casey J Kozlowski, Electrical & Computer Engineering
Wyatt Prentice, Aerospace Engineering
COLLEGE MENTOR
Doug May
SPONSOR ADVISOR
Sierra Rose
TEAM MEMBERS
Abdullah Almansour, Industrial Engineering
Blake Daniel Haines, Materials Science & Engineering
Rod mazda, Mechanical Engineering
Tania Ruiz, Mechanical Engineering
Brandon Robert St.Pierre, Mechanical Engineering
COLLEGE MENTOR
Michael Madjerec
SPONSOR ADVISORS
Brian Baughman, Jason Floor, Jalen Harrington, Clay Sutter
Team 23052
TEAM MEMBERS
Riley Cowling, Electrical & Computer Engineering
Victor P Frank, Biomedical Engineering
James Mark Gregory, Biomedical Engineering
Sebastian Alexander Oviedo, Electrical & Computer Engineering
Abi Swalander, Biomedical Engineering
COLLEGE MENTOR
Bob Messenger
SPONSOR ADVISOR
Dan Schlager
PROJECT GOAL
Evaluate the effects of parameters in the wire-fed DED process on the produced material properties in relation to a repair.
In the aerospace industry, many parts are made from super alloys, such as Inconel 718, to withstand the extreme temperatures of turbine engines and other commercial applications. Over time these parts wear out and have to be replaced. Honeywell is interested in performing a repair on these parts to return them to service with the original material properties.
This process uses a DED engine from Meltio, integrated with a Haas VF-2 CNC machine for hybrid manufacturing. The University of Arizona acquired this machine combination to evaluate this process. However, technical difficulties occurred during installation, rendering the equipment unavailable to the design team. Thus, the team had a third party prepare DED printed test specimens and used a factorial design of experiment to analyze grain structure and porosity in relation to specified printing parameters.
The team has cut the samples using a wire electrical discharge machine and is currently polishing and etching the samples for microscopic inspection and analysis.
Team 23055
Test and measure the protection provided by specially designed Lightning Protection Garments.
Globally, approximately 24,000 people per year are fatally struck by lightning. This team’s system measures the voltage across the chest wall and to the heart to determine the efficacy of the Lightning Protection Garments Zolt developed to minimize the risk of death from a lightning strike.
The design uses a mannequin to model the human physique. A circuit is created from head to toe to mimic the human body. The mannequin has a resistance approximately equal to the human body. A surge protection subcircuit and measurement subcircuits are placed in the chest cavity to measure the voltage and current within the system while also protecting the electronics.
A high-speed FPGA, or Field Programmable Gate Array, device, acting as an oscilloscope, is used to measure the voltage within the system at a rate of 100 samples per microsecond. This data is stored locally and downloaded for evaluation after the lightning tests.
At DNB Lightning Lab in Anaheim, the team struck the system with thousands of amps – in a variety of configurations. Measured values stored on a micro SD card were compiled to generate a graphical visualization of the voltage, current and energy values to determine the efficacy of the garment design.
Team 23056
Develop a functional prototype of a smart medical drainage catheter for improved analytics and diagnostics.
Becton Dickinson Peripheral Intervention is looking to improve medical drainage catheters. This prototype to integrate sensors is expected to benefit future products.
This team was tasked with prototyping a smart implantable medical drainage catheter to collect and safely dispose of excess fluid from a bodily cavity. In addition, the prototype automatically measures, records and wirelessly communicates parameters during the process of fluid inline removal. The parameters to be evaluated included the total quantity of fluid drained over time, time and duration of drainage procedures, detection of clogs, and the standard biometric measurements of fluid (pH and temperature).
The system collects the data and transmits the information in real time to physicians. Specified data can also be made available to patients, who currently must drain their catheters up to seven times a week and manually track drainages. The smart medical drainage catheter reduces patient responsibility, improves shared data reliability, and provides significant feedback – flow rate and time, clog detection, pH and temperature of the fluid.
Team 23057
Design and fabricate a remotely automated prototype T-Bioreactor capable of producing a range of hydrodynamic mixing patterns to facilitate growth of living organisms.
Bioreactors facilitate growth of living organisms that produce a wide range of food, pharmaceutical and energy alternatives. Stirred-tank bioreactors on the market contain a static impeller for mixing that provides one hydrodynamic mixing pattern. These types of bioreactors, when scaled to higher volumes, produce nonuniform distribution of nutrients and gases, which can reduce yields.
This team’s prototype T-Bioreactor adds an automated variable-pitch impeller. A linear actuator and mechanical linkage that provides varying amounts of axial flow drives the impeller transformation. Additionally, the bioreactor contains a variable speed motor to alter the impeller’s rotational speed. An Arduino Mega connected to a Raspberry Pi 4b with a touchscreen LCD display controls the system’s motors. A graphical user interface (GUI) allows easy control of the mixing speed and T-impeller angle. This GUI also has a section to import mixing profiles, changing speeds and angles at user-set times and enabling the system to work autonomously. With the wireless capabilities of the Raspberry Pi 4b, users can remotely access and control the T-Bioreactor via simple Virtual Network Computing, or VNC, software.
Results show the system’s variable-pitch impeller and variable-speed motor have the potential to improve hydrodynamic mixing patterns for larger-volume bioreactors.
TEAM MEMBERS
Mohammed Al Dallal, Mechanical Engineering
Karis Juliette Brackpool, Biomedical Engineering
Cynthia Ge, Biomedical Engineering
Kathryn T Hoang, Electrical & Computer Engineering
Bianca Rodriguez, Electrical & Computer Engineering
Hasina Shir, Biomedical Engineering
COLLEGE MENTOR
Don McDonald
SPONSOR ADVISOR
Chad Van Liere
TEAM MEMBERS
Greg R Burke, Biosystems Engineering
Alex Cantor, Biosystems Engineering
Angelo Mauro, Mechanical Engineering
Xingye Peng, Electrical & Computer Engineering
Yoni Wulf, Electrical & Computer Engineering
COLLEGE MENTOR
Jeff Scott Wolske
SPONSOR ADVISOR
Joel L Cuello
TEAM MEMBERS
Reem Alruwaih, Mechanical Engineering
Karen Jicel Bermudez Valdez, Engineering Management
Caroline Ann Humphreys, Optical Sciences & Engineering
Cameron James Sexton, Electrical & Computer Engineering
Clayton T Smith, Optical Sciences & Engineering
COLLEGE MENTOR
Justin James Hyatt
SPONSOR ADVISOR
Nitin Patel
Team 23058
TEAM MEMBERS
Alejandro Lopez, Aerospace Engineering
Simon Quang Minh Ly, Aerospace Engineering, Mechanical Engineering
Renatto Miguel Ramos, Aerospace Engineering
Zachary Thach, Mechanical Engineering
Sheehab Zaman, Electrical & Computer Engineering
COLLEGE MENTOR
Doug May
SPONSOR ADVISOR
David Margolis
Design an efficient and repeatable device that quantitatively measures the distortion in mirrors with spherical radius.
Convex mirrors on heavy equipment in the construction industry are extremely important to safely operate vehicles. Therefore, it is crucial to have a mirror with acceptable levels of image distortion.
This project deliverable is an efficient and repeatable testing system that examines the mirror’s spherical radius distortion.
The design uses a machine vision camera to capture the reflection of concentric circles. These concentric circles are manufactured into a cone shape, which sits above the mirror. The camera sits at the top of the cone and can image the entire mirror. The team created a custom baseplate to hold the mirror to prevent movement, and the outer frame of the system is made out of extruded aluminum. The camera takes an image of the mirror, and this image is passed through an image processing algorithm. The algorithm is coded using the Python language and its associated image-processing libraries. The algorithm detects the edges of the image and from those edges calculates the circularity of each circle in the image. If the circles are misshapen, distortion is present. The algorithm determines if the distortion is above or below the accepted level.
Team 23060
PROJECT GOAL
Develop a control system that allows an armless pilot to safely operate a plane with rudder pedals.
Jessica Cox, the world’s first armless pilot, is building a foot-controlled airplane. Presently, she flies an Ercoupe that she can fly with her feet alone, but it has limitations. She intends to modify and fly a Van’s RV-10, a faster airplane better suited to her needs. However, in its current design, rudder pedals and the yoke are required making it unsafe for her to pilot. Team 23060 developed, prototyped and tested a system for six-axis control by feet alone of the RV-10 while also allowing Jessica to control the navigation and communication radios.
The team designed two identical pedals to replace the control stick. A mechanism directly connects to the elevator pushrods such that tilting the pedals controls airplane pitch. Another mechanism connects to the ailerons to control roll by rotating the pedals left and right. For yaw control, a link connects to the existing system such that pushing the pedals fore and aft moves the rudder. An added linkage directly connects to the existing brake system so squeezing the thighs controls braking. All these linkages were designed and tested to ensure that Cox has the strength to apply the necessary force to control the airplane.
Team 23061
Create a pressure-sensing and recording device to measure the tissue-retractor interface in surgery.
When surgeons use self-retaining retractors, the feedback of the tissue pressing on the retractors is lost once they are set. If the pressure is too high for too long, the retractors can cause permanent nerve damage to the patient.
This project created a user-friendly and sterilizable product for real-time pressure measurement during such operations.
The design incorporates two separate systems: one sterile and one nonsterile. The sterile system includes the retractor, to which two high-temperature force sensors are adhered. Siliconeinsulated wires connect the sensors to a ceramic connector plugged into the nonsterile system. The nonsterile system includes the analog signal processing, Arduino board, and graphical user interface tablet. The Arduino board calculates the pressure from the force exerted over the sensor area at the tissue-retractor interface then sends the data to the tablet via Bluetooth. The tablet uses a simple application the team created to simultaneously display the duration of retractor use and pressure data, allowing for control of thresholding and recording.
Team 23062
Create an IoT system integrating an Alexa and Fitbit device to improve patient compliance in at-home clinical trials and provide a physiological intervention system.
The results of clinical trials are sometimes compromised when participants do not comply with requirements. And, redoing trials can be time-consuming and costly. This team’s design allows researchers to remotely send participants surveys through an Alexa device and capture their responses. This smart speaker system streamlines the data collection process, increasing survey completion and improving data quality.
Surveys are sent out on a regular schedule or when triggered by certain physiological data obtained passively through wearable devices. The system sends reminders to complete any pending or unfinished surveys and compiles responses for analysis.
The team developed an Alexa Skill, a webserver, a front-end to back-end communications architecture and a database infrastructure to support these functionalities. The team also integrated existing entities, such as MyDataHelps for participant enrollment, REDCap for survey generation, and sensor fabric for processing wearable device data.
TEAM MEMBERS
McKenzie Leigh Bieg, Biomedical Engineering
Mark Andrew Bosset, Biomedical Engineering
Dania Laura Perez, Biomedical Engineering
Timor Shahin, Electrical & Computer Engineering
Evan Smith, Biomedical Engineering
COLLEGE MENTOR
Justin James Hyatt
SPONSOR ADVISOR
David Margolis
TEAM MEMBERS
Khaled Abdullah, Industrial Engineering
Wesley Chiu, Systems Engineering
Son Mac, Electrical & Computer Engineering
Darianne Sanchez, Biomedical Engineering
Julianne Chania Setiadi, Biomedical Engineering
COLLEGE MENTOR
Bob Messenger
SPONSOR ADVISOR
Shravan Guruprasad Aras
TEAM MEMBERS
Konner A Curtis, Electrical & Computer Engineering
Corey Hadley, Mechanical Engineering
Adam Hauck, Industrial Engineering
Rohit D Kalluri, Mechanical Engineering
Stafford Lorenzo Lewis, Electrical & Computer Engineering
Ariadna Michelle Rivera Gutierrez, Electrical & Computer Engineering
COLLEGE MENTOR
James Sweetman
SPONSOR ADVISOR
Sabrina Huaraque
Team 23065
TEAM MEMBERS
Alvaro Ballesteros, Mechanical Engineering
Cora M Davy, Optical Sciences & Engineering
Ruben Diego Fuentes Gutierrez, Electrical & Computer Engineering
Duncan Henry Robbins-Gennerich, Optical Sciences & Engineering
Julian Tellez Osuna, Mechanical Engineering
Kevin Lee Wolfe, Mechanical Engineering
COLLEGE MENTOR
Mike Nofziger
SPONSOR ADVISOR
Matthias Whitney
Design and build an interactive model of the Tucson power grid to educate children about the generation, storage and distribution of power.
The power grid is essential to everyday life. Compared to a century ago, electric power is a major necessity today. The main distributor of electricity in town is Tucson Electric Power (TEP). Through renewable and nonrenewable sources, TEP generates, stores and distributes power to various facilities all around Tucson.
This project illustrates the various methods and strategies TEP has implemented in recent years and highlights future goals. The outcome is a straightforward interactive, educational experience for children.
The team used CAD to design major components of the model. LEDs, representing location and motion of power transmission, are controlled by users interacting with buttons, cranks and a pump. Accuracy is measured with encoders and a multimeter.
Team 23066
Design an open-frame implementation of an automated system capable of sorting small objects by color, shape and size, or optical character recognition (OCR).
The Small Item Photographing Triage Robot (SIPhTR) is an automatic sorting mechanism that physically and electronically sorts small items according to user-defined characteristics, such as color, size and shape, or OCR. SIPhTR, which contains its own electrical hardware, lighting and outlet connections, is useful in several industries that rely on engineering processes.
This team designed and developed a system to intake a large sample of small items and organize them efficiently and accurately into separate storage units.
The device uses object recognition algorithms to identify characteristics such as color and shape. Once an object enters the field of view of the internal camera, an on-board computer analyzes the video output, and the software identifies the object by the chosen characteristic. The software then controls a mechanical system to isolate and store the object in its corresponding storage bin.
Team 23067
Develop a wearable device to quantitatively track and analyze edema, water content and leg movement for management of kidney disease.
Chronic kidney disease often results in comorbid conditions, which commonly include edema (excess swelling of the extremities) and restless leg syndrome (RLS). These conditions vary in severity throughout the day, sometimes preventing in-office medical providers from accurately monitoring their progression.
This team designed a wearable device to quantitatively track edema and RLS in a home setting.
The design integrates biosensors into a flexible stocking that records and transmits data to a smartphone for graphical interpretation by a clinician. Edema is quantified by two markers: 1) the isolated water content of the extremity measured using impedance biosensors, and 2) the circumference change due to swelling measured using flex sensors. Electromyography biosensors and accelerometry are used to identify and differentiate RLS-specific movements to determine their frequency. This data is sent to a smartphone application where it is analyzed and displayed graphically for easy interpretation by the patient as well as the clinician.
Team 23069
Create a prototype gantry system that moves a concrete 3D printer and acts as a proof of concept for a larger version.
This project aims to move around a concrete printer to produce cement-like material made of mine tailings, the leftover rocks and metals. The prototype has a small printing area, but it is designed to be replicated at a larger scale, including to print house-sized buildings.
The design is a gantry system that moves that 3D printer back and forth in the X-, Y-, and Z- directions. It uses 1-inch x 1-inch and 1-inch x 2-inch aluminum T-slot framing rails to make up the main body of the system. These rails can be assembled without welding, allowing for strong and adjustable formations. The main body is separated into truss beams that slide back and forth in a certain direction. This motion is controlled by stepper motors that connect to each truss and move them via roller chains or wheels.
Directions for how the system will move are given in G-code to Duet Web control, an online interface built specifically for this project’s 3D printer. A stepper motor controller from the same brand is used to translate the G-code to stepper motors. After inputting the building code to the system and receiving the mixture, the printer produces the structure with no further instructions needed.
TEAM MEMBERS
Haley R Alden, Electrical & Computer Engineering
Levi Jekabs Kerns, Systems Engineering
Emma Katelyn Mason, Biomedical Engineering
William Harrison McKay, Biomedical Engineering
Andrew Michael Nelson, Mechanical Engineering
COLLEGE MENTOR
Don McDonald
SPONSOR ADVISORS
Bijin Thajudeen, Marvin J Slepian
TEAM MEMBERS
Angel Aguilar, Engineering Management
Cody S Butler, Industrial Engineering
Cassidy LiMing Hodge, Mechanical Engineering
Tyler J Kral, Mechanical Engineering
Joel Harrison Trexler, Materials Science & Engineering
COLLEGE MENTOR
Justin James Hyatt
SPONSOR ADVISOR
Abraham Jalbout
TEAM MEMBERS
Ally Baker, Systems Engineering
Kali Elise Jasso-DeMontigny, Systems Engineering
Bryce Johnson, Electrical & Computer Engineering
Jake Michael Klonsinski, Electrical & Computer Engineering
Zachary Schawelson, Optical Sciences & Engineering
COLLEGE MENTOR
Elmer Grubbs
SPONSOR ADVISOR
Daniel O’Connor
Team 23070
Using sensors and products already on the market, create a small, inexpensive, disposable way to track an animal’s heart rate, location and velocity.
Millions of people around the world own some kind of animal, whether it’s a pet owner who has cats and dogs or a farmer with cattle and horses.
This team produced a simple and affordable way to track an animal’s well-being. A small device, the MAHST, is attached to any animal’s collar to track its location, speed and heart rate, then output the data to a simple mobile app for the animal’s owner.
The ultimate design uses two sensors: a GPS, or Global Positioning System, to track location and speed and a pulse sensor to monitor heart rate of the animal. An Arduino microcontroller collects and transfers the data to the app. The MAHST uses velcro to attach to the outside of an animal’s collar. The device is small, affordable, comfortable and easily removable.
Team 23071
TEAM MEMBERS
Youssif Abdelkader, Biomedical Engineering
Ben James Albright, Biomedical Engineering
Sophia Ippolito, Optical Sciences & Engineering
Michael Lauria, Electrical & Computer Engineering
Madeline A Procter, Electrical & Computer Engineering
COLLEGE MENTOR
Don McDonald
SPONSOR ADVISORS
Bijin Thajudeen, Marvin J Slepian
Develop a clinical data capture-and-analysis system for enhanced in-person health care encounters.
As digital modern medicine continues, physicians are spending less and less time interacting directly with their patients. This can lead to a loss of information as the medical provider cannot observe every physical symptom. Therefore, the Wired Room serves to collect and analyze visual and auditory patient inputs and supplement conclusions made by the provider.
The Wired Room consists of a set of microphones and cameras to record actual sound and video during a clinical visit. A newly developed graphical user interface, or GUI, controls the equipment. Additionally, Google MediaPipe with neural networks analyzes limb angles and acceleration to identify symptoms of interest. Sound can also be analyzed for correlation to various medical symptoms.
After the appointment, the GUI presents this data, along with normal video and audio of the visit, to the physician. The system is easy to transport and assemble in a multitude of settings such that out-of-clinic visits are also possible. The system will help guide a more informed and personalized health care plan in a digitally dominated environment.
Team 23072
Redesign and prototype a new radio frequency (RF) communication protocol for an IoT sensor system to lower power consumption and increase throughput and transmission distance.
Ridgetop Group’s Sentinel Motion suite employs accelerometers on bearing housings to capture, measure and process vibration signals, enabling condition-based maintenance in the railroad industry.
This project redesigns Ridgetop’s RotoSense circuitry, implementing a new RF protocol and new electrical components to decrease the power consumption, increase the throughput, and increase transmission distance.
The team designed a multilayer printed circuit board that integrates last year’s capstone project, an Energy Harvesting System. A new Nordic dual-core System on a Chip (nRF5340) is featured in the design to run the RF protocol, Bluetooth Low Energy. The microcontroller uses a serial peripheral interface and I2C to communicate with an accelerometer, gyroscope, analog-to-digital converter, and memory modules. The team wrote firmware that integrates RotoSense’s four different operating modes.
Team 23075
Design and develop a trike powered by rowing mechanics and maneuvered by leaning side-to-side.
Most recreational human powered vehicles primarily target the lower body in terms of physical conditioning. Rowing machines target nine different muscle groups throughout the body, accounting for more than 80% of the total muscles in the human body.
This Land Rower takes heavy inspiration from common rowing machines, like in a gym. It has a similar internal pulley system to reset the stroke of the user. Since there is no handlebar connected to a rigid fork like on a regular bicycle, the team developed a system that allows the user to steer by leaning. The steering system operates by pushing and pulling on separate tie rods that connect to each front wheel’s control arms as the user leans. Ackermann steering geometry is implemented in the design to prevent the leading wheels from scrubbing as they turn about different radii.
Typical bicycles and recumbent bicycles do not come in a-one-size-fits-all configuration. The Land Rower, in contrast, accommodates riders ranging from 5 feet to 6 feet 6 inches and up to 300 lbs.
TEAM MEMBERS
Nicolas Blanchard, Electrical & Computer Engineering
Quentin Johnson, Electrical & Computer Engineering
Harrison Kominski, Mechanical Engineering
Lucca Magalhaes, Electrical & Computer Engineering
Chris Westerhoff, Electrical & Computer Engineering
COLLEGE MENTOR
James Sweetman
SPONSOR ADVISORS
Arsh Rudra Nadkarni, Wyatt Pena
TEAM MEMBERS
Chase Anthony Finney, Mechanical Engineering
Diego Gonzalez, Mechanical Engineering
Jeremy Duane Heath, Mechanical Engineering
Calvin Keedi-Rodriguez, Electrical & Computer Engineering
Bryan Sprouse, Mechanical Engineering
Kassi Sreerama, Mechanical Engineering
COLLEGE MENTOR
Justin James Hyatt
SPONSOR ADVISOR
Ben Blehm
TEAM MEMBERS
Christian Niels Enevoldsen, Biomedical Engineering
Chris Hedgecoke, Biomedical Engineering
Cameron Matsumoto, Electrical & Computer Engineering
Joy Niu, Electrical & Computer Engineering
Abigail Prescott, Biomedical Engineering
COLLEGE MENTOR
Don McDonald
SPONSOR ADVISORS
Bijin Thajudeen, Marvin J Slepian
Team 23076
PROJECT GOAL
Develop a paper microfluidic wick enzyme-linked immunosorbent assay system to analyze gingival crevicular fluid (GCF) for the presence of six different biomarkers, plus a companion app to interpret test results.
Inflammation within the body is a known driver of chronic kidney and heart disease. Presently no rapid testing method exists to readily diagnose systemic inflammation. The team designed and developed an inexpensive, at-home testing kit that uses a paper microfluidic device for immunodetection and a cell phone app for colorimetric detection and readout of the microfluidic device. This system determines relative amounts of inflammation markers present in a GCF sample.
The design uses a paper microfluidic lateral flow assay system composed of a laminated card, a nitrocellulose (NC) membrane, and cellulose fiber pads to capture and collect GCF. Capillary action carries the sample to the conjugate pad, where binding occurs between inflammation biomarkers present in the sample and pre-loaded gold nanoparticle tagged corresponding antibodies. Further capillary action carries the antigen-antibody complex to the test line of the device located on the NC membrane. Secondary binding between the tagged complex and untagged antibodies incites a color change within the test line, the intensity of which depends on the amount of antigen present in the sample. This intensity is read by a color detection algorithm on the app utilizing the cell phone camera. Based on the intensity of the color, the app classifies the risk level for heart and kidney disease and displays the results on a live dashboard.
Team 23077
TEAM MEMBERS
Cristian Daniel De Gante Hernandez, Mechanical Engineering
LD Dukes, Mechanical Engineering
Garrett Austin Fenderson, Electrical & Computer Engineering
Austin Greif, Systems Engineering
Sidhant Gulati, Electrical & Computer Engineering
Siwen Wang, Systems Engineering
COLLEGE MENTOR
James Sweetman
SPONSOR ADVISORS
Joellen L Russell, Eddy Stocker
PROJECT GOAL
Create a communication, coordination and control system for a swarm of aquatic drones. This project presents a proof-of-concept (C3) system for a swarm of aquatic drones. The drones’ purpose is to monitor the state of oceans and recover plastic and other contaminants. To increase the devices’ efficiency, they will operate in a swarm or fleet mode.
The team designed and built eight drones with a central control unit and user interface. These drones are capable of autonomous navigation; individual and swarm movement patterns such as grid searches; collision avoidance with other system drones; monitoring water temperature, pH, and salinity; and communicating commands and data with the central control unit via a proprietary mesh radio frequency network.
The control system for a real-world ocean drone swarm with the ability to monitor ocean health metrics and remove plastics from the ocean will be built upon the C3 system from this project.
Team 23078
Detect and record patient snoring audio during an overnight sleep study, then analyze the audio in conjunction with sleep position for sleep apnea management.
One in five U.S. adults has obstructive sleep apnea (OSA), a condition that can lead to many serious medical issues. Snoring and its effects are a key indicator of OSA development. The Snorpheus is a wearable device that records snoring audio and position data and facilitates the transfer of data to the physician and patient.
The Snorpheus system has two components: 1) a wearable device to accurately detect and record patients’ snoring audio and correlated body position over a night’s sleep and 2) data processing software that indicates when patients snore and in what body position it occurs, while remaining compliant with health and privacy laws.
The design uses a Raspberry Pi as the core microcontroller to prompt data collection from an attached lavalier microphone when audio within the snoring frequencies of 100-600 Hz are detected. An external inertial measurement unit constantly records time-stamped data on a 180-degree axis. A micro SD card records data and transfers it to a clinic computer for data processing. External software uses a convolutional neural network to process audio and identify snoring events. Processed audio and body position data are synced using time stamps and exported to clinician and patient interfaces for data visualization.
Team 23080
Design a low-cost, tabletop automatic tube coiling machine that intakes pre-cut 7-inch long tubes and coils them into individual 4.5-inch diameter spools.
The current manual process of winding a PVC medical tube is tedious and repetitive. Operators must individually coil each tube, then complete bonding and final assembly. Automation can improve this process, eliminating the repetitive operation action while also decreasing build time, thereby increasing the production of medical products to hospitals, clinics and infirmaries across the world.
The tabletop mounted automated PVC tube winding machine intakes pre-cut PVC tubes into a hopper assembly. Two subsystems perform in unison to feed one tube at a time into the mainframe of the system to begin the coiling process. An Arduino Uno microcontroller controls stepper motors and actuators moving each tube through the coiling process. The total cycle time to move one tube from the hopper to coil to the position ready for operator retrieval is 10 seconds. The only operator labor required is refilling the hopper with pre-cut 7-inch long PVC tubes and retrieving the completed coiled tube from the machine. The operator interface uses three buttons: an emergency stop button, a start button that initiates the process, and a reset button that resets all systems to the starting point.
TEAM MEMBERS
Noah Butler, Electrical & Computer Engineering
Christine M Carlson, Biomedical Engineering
Logan Deane, Biomedical Engineering
Evan Bradley Rains, Electrical & Computer Engineering
Nisha Anjali Rajakrishna, Biomedical Engineering
COLLEGE MENTOR
Mike Nofziger
SPONSOR ADVISOR
Nirav Merchant
TEAM MEMBERS
Hector Francisco Castro Martinez, Industrial Engineering
Salman Marafie, Electrical & Computer Engineering
Joseph Nimrod, Industrial Engineering
Miguel Sebastian Quintero-Cardenas, Industrial Engineering
Nick Williams, Mechanical Engineering
COLLEGE MENTOR
Steve Larimore
SPONSOR ADVISOR
Rick Lopez
TEAM MEMBERS
Ethan Alexander Cowsky, Mechanical Engineering
Brian James Glaser, Electrical & Computer Engineering
Abby Renee Gookin, Systems Engineering
Benjamin Kopiec, Engineering Management
Adam Kosinski, Electrical & Computer Engineering
Evan Wright, Electrical & Computer Engineering
COLLEGE MENTOR
James Sweetman
SPONSOR ADVISORS
Scott Fiore, Milan Patel
Team 23081
PROJECT GOAL
Provide covert data collection in a variety of environments to monitor for human and vehicular activity.
The University of Arizona and University of Massachusetts Lowell partnered with Raytheon Technologies to deliver a low-risk and cost-effective mesh network of Smart Rocks for surveillance data collection in remote areas like state borders and hiking trails.
Each Smart Rock node uses a combination of auditory and seismic sensors to analyze the environment for human and vehicular activity, with the collected data being shared across the network via long-range communication protocols. With the Smart Rock graphical user interface, users can locate individual nodes and extract crucial data seamlessly. Each node has the capability to be modified with a variety of different seismic and auditory sensors to satisfy the user’s individual needs and budget.
The ESP32 microcontroller is responsible for managing all subsystems including each individual sensor, batteries, GPS and both communication protocols. The system is designed for a variety of remote areas and can withstand harsh climates for a minimum of two weeks without user maintenance. The Smart Rock system hosts the state-of-the-art technology necessary to meet all the demands of many critical areas of surveillance and security.
Team 23082
TEAM MEMBERS
Adrian Cruz, Mechanical Engineering
Zaid Darwish, Systems Engineering
James Ryan Fulton, Electrical & Computer Engineering
Finnley Hartz, Applied Physics
Tanner Moore, Mechanical Engineering
Tylor Dale White, Mechanical Engineering
COLLEGE MENTOR
Bob Messenger
SPONSOR ADVISORS
Jim Bakarich, Luke Baer
Build a robot, BALL-E, that can consistently launch a basketball into a standard hoop from the free-throw line and inspire interest in STEM among youth.
As the older generation of STEM professionals leaves the workforce, the new generation must take their place, and demand is expected to soon surpass the amount of workers available. The team designed a robot to intrigue and enrich the minds of middle school and high school students and demonstrate the possibilities of an exciting career in the STEM field.
BALL-E is a robot that uses a tire-drive mechanism to launch a basketball from the desired position to consistently make shots. BALL-E was designed from the ground up using 3D modeling software such as Fusion 360. BALL-E can autonomously determine the distance from the hoop and adjust the launching force and angle using cameras, computer vision algorithms, and software that is run on a PC. The team designed BALL-E to display its internal mechanisms while shooting a basketball in real time so that students may easily follow how the robot operates. Students will also have a chance to control Ball-E using a gaming controller.
Team 23083
Develop an MR application capable of diagnosing vertigo in a patient and directing them through vertigo treatment maneuvers to relieve adverse symptoms.
Vertigo, a vestibular balance disorder most commonly caused by a disruption to the inner ear, affects roughly 40% of all American adults. Common symptoms include dizziness, spinning, and nystagmus, the involuntary rhythmic movement of the eye. Traditional diagnostic and treatment methods require a patient to travel for professional assistance. This system provides a more accessible and affordable option for those with mild to intermediate symptoms.
The team developed an MR program in Unity using the onboard accelerometer, magnetometer, gyroscope, and infrared camera of the HoloLens 2 augmented reality headset to emulate traditional vertigo diagnostic and treatment procedures. A multi-point input system accompanies the MR overlay within the headset to record, calculate and archive the patient’s head orientation and eye movement in real time. Control thresholds from a healthy model are used to determine whether the patient is afflicted with vertigo. Afterward, the patient is prompted to follow a healthcare-backed treatment process. The healthcare professional and patient can access the patient’s data via a website.
Team 23084
Develop a concept for a lunar surface transporter and extend the exploration capabilities to offload habitats at various locations on the south pole of the moon.
NASA has ambitious plans to return humans to the moon through the Artemis Program. A future human mission will set the stage for permanent colonization, but it will require extraction and utilization of lunar resources to be feasible. This year’s NASA RASCAL Competition calls for a lunar surface transporter vehicle that would extend astronaut exploration capabilities and perform a variety of functions. The project request was for two competing teams.
Team L.E.T.O. (Lunar Explorer and Transportation Off-loader) developed a model version of an L.V.S.T. for the assistance of space operations, recognizing the mass, power, volume and costs for all elements. The team documented the total mass launched from the Earth, as well as the accompanying risks from its structural design. The team was also tasked with identifying various contingency strategies for failure upon each system that would impose an early end to the crewed surface mission.
TEAM MEMBERS
David Adkins, Electrical & Computer Engineering
Shaylan R Bera, Biomedical Engineering
Hayden Kim, Optical Sciences & Engineering
David Chibuikem Mazi, Electrical & Computer Engineering
Jason Zhang, Electrical & Computer Engineering
COLLEGE MENTOR
Elmer Grubbs
SPONSOR ADVISOR
Ian Jackson
TEAM MEMBERS
Brandon Carpenter, Aerospace Engineering
Connor M Dobbins, Aerospace Engineering
Abraham E Ochoa, Aerospace Engineering
Gustavo Edwin Sodari, Aerospace Engineering
Nick Tiffany, Aerospace Engineering
COLLEGE MENTOR
Jekan Thangavelauthum
SPONSOR ADVISOR
Harshad Kalynaka
TEAM MEMBERS
Javier Alday, Aerospace Engineering
Quinn P Lamey, Aerospace Engineering
Hilliard Wegner Paige III, Systems Engineering
Jared Pavek, Aerospace Engineering
Matthew Christopher Walton, Aerospace Engineering
COLLEGE MENTOR
Jekan Thangavelauthum
SPONSOR ADVISOR
Adrien Bouskela
Team 23085
PROJECT GOAL
Design, develop, manufacture and test a small spacecraft formfactor 2 mirror deployable tensegrity telescope for Near Earth Asteroid (NEA) detection.
Detection of NEAs is important for scientific and planetary defense applications. Currently, most NEA detection is conducted with ground-based telescopes due to cost and logistical constraints. However, these stations can be limiting due to atmospheric disturbances, light pollution and increasing amounts of space debris in orbit.
The team fabricated an orbiting deployable telescope for asteroid reconnaissance, enabling the use of lower-cost CubeSat spacecraft for NEA detection. The project’s objective is to demonstrate the capability to detect NEAs approximately 0.3 astronomical units from Earth with very low albedos, a measurement of the fraction of light that a surface reflects, for scientific and planetary defense applications.
Team 23086
TEAM MEMBERS
Hassan AlRabia, Biomedical Engineering
Xiangnan Huang, Biomedical Engineering
Guransh Mann, Electrical & Computer Engineering
Julio E Trejo, Biomedical Engineering, Mechanical Engineering
Zhehao Zhang, Electrical & Computer Engineering
COLLEGE MENTOR
Jeff Scott Wolske
SPONSOR ADVISORS
Erica Tassone, Marvin J Slepian
Design and build a wearable sensor system that detects and reports the frequency and duration of a patient’s PEMF therapy treatments.
PEMF therapy has been shown to produce significant therapeutic benefits for a variety of biological and physiological responses, especially increased wound healing and chronic pain reduction. The ElectroDose complements Regenesis’ existing therapeutic technologies by adding diagnostics and treatment monitoring. This allows for real-time data processing, which reduces follow-up times for patient reevaluations and leads to optimization of further treatment.
This wearable system consists of several key assemblies. The PEMF sensor assembly registers the raw PEMF signal and digitally converts it for processing. The circuit assembly forms the sensor system’s foundation via basic electrical components such as resistors.
The system also contains a state-of-the-art Infineon programmable system-on-chip microcontroller and a Bluetooth radio. The microcontroller processes and measures the PEMF treatment. The radio communicates the frequency and durations of treatments to Regenesis for future patient check-ins. The 3D printed polylactic acid mechanical assembly protects the circuitry and makes the device comfortable, light and durable. Testing results show the ElectroDose measures administered treatments within 2-3% of the specified treatments.
Team 23088
Develop a mobile app for interpreting blood test results, a website for administering a health quiz, and a device for analyzing saliva samples to prepare for the launch of the student startup Gesund Me.
Many people in the United States are deficient in their diets and dependent upon big pharmaceutical companies to suppress their ailments with targeted treatments. Holistic methods and nutritional supplements offer a preventive method to treat illnesses, heal deficiencies, and potentially cure diseases, but require adequate knowledge to use properly and effectively. The purpose of this team’s consumer products and services is to provide individuals with the tools they need to interpret their own lab results and biometric data in order to develop an intimate understanding of their personal nutritional needs, thus allowing them to take advantage of this alternative approach to healthcare.
The team built an iOS mobile application with an original blood value interpretation algorithm that was modeled on techniques from established medical books. They also developed a website with a low-barrier-to-entry health quiz and a back end with full support for machine learning. Lastly, the team succeeded in designing and building a saliva testing device that uses modern ion selective electrodes for a fast and convenient user experience.
Team 23089
Improve the Instantaneous Cue Rotation (ICR) arena by adding a uniform food distributor, designing and building a new open platform arena for rats to traverse, and improving the food reward robot – all to enable the mapping of brain cells.
The Evelyn F. McKnight Brain Institute uses the ICR arena as an experimental system to collect highdensity cellular recordings directly from the brains of lab rats. The rats navigate around a ring-shaped testing environment, and the data collected is used to advance the understanding of Alzheimer’s disease and how it degrades organisms’ ability to maintain spatial orientation.
The team modified the ICR to allow researchers to collect a more robust data set by requiring rats to navigate the new open arena. The uniform food distributor is a critical component, including a pair of mechanisms to drop sprinkles onto the platform randomly and uniformly across the full area to incentivize rats to explore the entire space. The food distributor software was built using an Arduino and the pre-existing reflective photo microsensor. This is crucial for collecting data on the rats’ navigation in all directions and enables the identification and mapping of grid brain cells, as this is not accomplished in the current arena.
Additionally, the food reward robot used in the existing setup was redesigned, making it lighter, more compact, and with wheels that have a higher coefficient of friction, allowing it to stop and respond faster to the rats’ positional data. The redesign also reduced the likelihood of the robot colliding with a rat during testing.
TEAM MEMBERS
Anett Marian Garcia, Biomedical Engineering
Keegan Daniel Godfrey, Electrical & Computer Engineering
Nathan Herling, Electrical & Computer Engineering
Raphael Lepercq, Electrical & Computer Engineering
Elliot Zuercher, Electrical & Computer Engineering
COLLEGE MENTOR
Elmer Grubbs
SPONSOR ADVISOR
Raphael Lepercq
TEAM MEMBERS
Elizabeth M Connacher, Electrical & Computer Engineering
Gerry Flores, Mechanical Engineering
Gabriel Marquez, Systems Engineering
Alec Mitchell, Optical Sciences & Engineering
Claire Pedersen, Biosystems Engineering
Efrain Torres, Electrical & Computer Engineering
COLLEGE MENTOR
Don McDonald
SPONSOR ADVISOR
Don McDonald
TEAM MEMBERS
Nico Cornejo-Lopez, Electrical & Computer Engineering
Leon Farhaj, Engineering Management
Malcolm Neifeld, Mechanical Engineering
Ezra Depineda, Mechanical Engineering
Ryan Prather, Electrical & Computer Engineering
COLLEGE MENTOR
Elmer Grubbs
SPONSOR ADVISOR
Jonathan Schwab
Team 23090
PROJECT GOAL
Design and build two high-speed robotic racecars, with the sensing and processing electronics packaged in a sub-chassis called the Removable Autonomous Control Electronics (RACE) package.
Autonomous vehicles are becoming increasingly more common, and the technology is creating safer driving conditions. Similarly, small-scale autonomous vehicles can perform numerous tasks including cleaning, moving heavy objects, and performing dangerous tasks. The team demonstrated the possibility of developing a small-scale autonomous racecar from readily available, off-the-shelf parts.
The two designs use a sensor and computer to scan surroundings and navigate through a track autonomously. The team also developed the RACE package that houses all components necessary for autonomous driving. The computer uses a lidar, or Light Detection and Ranging, sensor, to collect data and runs an algorithm, which then controls the steering and drive motors. Simulation and testing demonstrated the differences between the theoretical fastest track speed, manual driving speed, and various autonomous driving algorithms. The two cars serve to show the iterative process – the first car served as an initial proof of concept, which the team then upgraded using a more powerful computer, optimized autonomous algorithms, and an optimized RACE unit to house all the parts.
Team 23091
TEAM MEMBERS
Buddy Bacheller, Systems Engineering
Robert Jeffrey Dyer, Industrial Engineering, Systems Engineering
Joe Manas, Mechanical Engineering
Nick Alexander Miller, Aerospace Engineering, Mechanical Engineering
Brian John Sanderson, Mechanical Engineering
COLLEGE MENTOR
Jeff Scott Wolske
SPONSOR ADVISOR
Jim Bakarich
Develop and prove out a user-specified system that produces on-demand, low-cost, configurable and durable air/ground remote-controlled bot vehicles that are customconfigured for end users such as SWAT teams, border patrol officers, and first responders.
Urban and desert reconnaissance has become invaluable to first responders and those who work in such fields as search and rescue and border patrol. These professionals could benefit from a low-cost, configurable, durable, airborne and/or ground-borne reconnaissance solution that is printable on demand, on site just prior to mission.
The team was tasked with developing the blueprints for a basic, scalable quad copter or rugged ground bot design that can be 3D printed, assembled, programmed and operated the next day. They proved out this system with the production of a working aerial-bot prototype and a working ground-bot prototype.
In use, the end user opens the PODBot application on a computer or tablet, then selects the mission type, vehicle scale and vehicle functionality through a series of interview questions. The graphical user interface provides a list of pre-purchased components, a list of parts to 3D print, and tailored assembly instructions. The user then launches a 3D printing application. The user waits no more than 12 hours for the vehicle frame of the vehicle to be printed, or in the case of urgent missions, chooses a pre-printed frame. The user then assembles the structural and electrical components according to the instructions. Each scenario produces a remote-controlled vehicle to provide reconnaissance, small supply transport or emergency communication to overcome real-world challenges.
Team 23092
Prove the feasibility and performance of five critical components to a tube-launched aerial reconnaissance drone that provides first responders and government agencies with rapid situational awareness for safe and effective response.
STAR is an aerial drone pneumatically launched from a tube that hovers over an area and streams video to a user device. The team developed and proved out the five main subsystems of the drone for future integration by follow-on engineering capstone teams.
The system is made up of these subsystems: camera, durability, autopilot, arm deployment and power distribution. The camera subsystem employs a high-resolution analog camera, transmitter and receiver that displays video on the user’s device. The durability subsystem demonstrates a drone mock that is able to withstand launch loads. This “slug prototype” is made of durable 3D printed CarbonX Nylon 12 and machined aluminum parts. The autopilot subsystem demonstrates stable flight through an altitude-hold feature for user-controlled information-gathering. The arm deployment subsystem demonstrates the transition from launched “slug” configuration to the deployed quadcopter configuration. This subsystem employs microswitches and a flight controller to demonstrate power delivery to the four brushless motors as the arms are deployed and locked. Finally, the power distribution subsystem relays enough power for a minimum of five minutes of operation.
Results independently show the feasibility and performance of each of the five critical subsystems. This gives confidence for future integration work to ensure the system is durable, stable and able to provide valuable information to the user.
Team 23093
Automate the media blasting process for selective laser sintering (SLS) 3D printed parts.
The product printed with an SLS 3D printer and recovered from a hardened Nylon 12 shell takes hours of manual labor to remove. The team automated the SLS finishing process by designing and fabricating an automated desktop powder processing station that removes at least 98% of the excess SLS powder.
The autonomous system effectively removes excess Nylon 12 powder from the printed parts by combining a tumbling mechanism with traditional media blasting. A motor attached to a basket tumbles the part in the enclosed cabinet, while the blasting process is automated by replacing manual valves with electrical solenoid valves. The finishing cycles are performed automatically based on the user’s input via the graphical user interface. A Raspberry Pi controller allows the system to execute the processes for a desired user-specified time.
TEAM MEMBERS
Cesar Armando Bours, Aerospace Engineering
Caleb William Eubanks, Biosystems Engineering
Josh Ray Forrest, Systems Engineering
Tyler Stephen Monlux, Electrical & Computer Engineering
Gabby Parks, Aerospace Engineering
COLLEGE MENTOR
Jeff Scott Wolske
SPONSOR ADVISOR
Dmitry Knyazev
TEAM MEMBERS
Khalid Al-Suleimani, Mechanical Engineering
Blake Davis Ashton, Mechanical Engineering
Tim Le, Electrical & Computer Engineering
Tyler Moldovan, Electrical & Computer Engineering
Dalal Ben Nakhee, Industrial Engineering
COLLEGE MENTOR
Pat Caldwell
SPONSOR ADVISOR
Michael Futch
TEAM MEMBERS
Barbara Bruno, Biosystems Engineering
Margaret Erin Gile, Biomedical Engineering
Tony Koulong, Electrical & Computer Engineering
Diana Picon, Biosystems Engineering
Rylie Watson, Biomedical Engineering
COLLEGE MENTOR
Elmer Grubbs
SPONSOR ADVISOR
Urs Utzinger
Team 23094
TEAM MEMBERS
Casey Cash, Aerospace Engineering
Nicholas Cooley, Aerospace Engineering
Alexander Jaquith, Aerospace Engineering
Shane Jones, Aerospace Engineering
Spencer Shedd LaFoley, Aerospace Engineering
Sean Martin Fearhgus Simila, Aerospace Engineering
COLLEGE MENTOR
Sergey Shkarayev
SPONSOR ADVISOR
Sergey Shkarayev
Develop a Raspberry Pi hat that integrates five biomedical sensors for educational learning.
The University of Arizona Department of Biomedical Engineering tasked the team with developing a sensor hat compatible with a Raspberry Pi 4. The board integrates sensors for skin impedance, electrocardiogram, blood oxygenation, sound and temperature and applies these sensors to clinical settings.
College students within the medical fields will use the cost-effective biosensor package for in-class experimental purposes. The board interfaces with a Raspberry Pi’s general purpose input output pins and integrates the sensors cohesively with software, within the connection capacity of the device. The fully integrated board can depict signals and measurements to the user intuitively.
The team has designed and built an all-in-one package that makes use of these sensors with the Raspberry Pi in a simple and intuitive way, allowing for easy data collection, visualization, and analysis of physiological signals.
Team 23095
Conceptualize, design and prototype key subsystems of a space refueling platform at the Earth-moon L1 Lagrange point.
In the next 30 years, cislunar space – the area between Earth and the moon – will become crowded with debris and diverse space development activities. Next-generation platforms that provide services such as refueling, repair, cislunar observation and communication capabilities are needed. Two student teams are competing in this year’s NASA RASCAL Competition to conceptualize, design and prototype critical elements of the L1 space platform envisioned at the Earth-moon first Lagrange point.
The Lagrange Area Refueling Station (LARS) is this team’s answer to NASA’s question of how to get spacecraft from Earth to the lunar surface and back again with heavier useful payloads to put humanity’s colonization of the moon on the fast track. LARS can autonomously refuel incoming spacecraft with a novel fuel source, liquid water, using advanced robotics and AI technology. Situated at the Earth-moon L1 Lagrange point, LARS provides water to incoming client craft so that they may convert it to superheated steam and propel themselves to their destination, be that the lunar surface or back home to Earth.
The team created a tech demonstration of the robotic arm refueling system, showcasing the ability for the arm to autonomously locate and refuel customer spacecraft while also demonstrating the ability to restock its own fuel reserves to extend its mission life.
Team 23096
Design a vehicle capable of offloading, transporting and deploying various systems and equipment on the surface of the lunar south pole in support of crewed mission operations.
NASA has ambitious plans to return humans to the moon through the Artemis Program. A future human mission will set the stage for permanent colonization, but it will require extraction and utilization of lunar resources to be feasible. This year’s NASA RASCAL Competition calls for a lunar surface transporter vehicle that would extend astronaut exploration capabilities and perform a variety of functions. The project request was for two competing teams.
Building infrastructure on the moon requires transporting large and heavy equipment and other cargo from lunar landers to their intended destination. The team designed the LETO-1 (Lunar Equipment TranspOrter 1) vehicle to achieve this functionality and meet the competition requirements. LETO-1 is an expandable, remotely operated, six-wheeled surface vehicle. It uses existing and in-development space technology, including a lightweight, scalable crane system, shape memory alloy spring tires, brushless motors and a robust sensor suite.
The team scaled the prototype to 18% of the fully extended length and 0.1% of the full mass with limited functionality and sensors. The structures were made primarily of aluminum with pneumatic tires, passive shock suspension, brushed DC motors and a powered winch crane. A LiFePO4 rechargeable battery powers active components, which are remotely controlled through an Arduino Mega with custom software. Testing verified the prototype’s ability to load, transport and offload payloads effectively in relevant terrain.
Team 23097
Design and prototype key elements of an orbital refueling station concept.
In the next 30 years, cislunar space – the area between Earth and the moon – will become crowded with debris and diverse space development activities. Next-generation platforms that provide services such as refueling, repair, cislunar observation, and communication capabilities are needed. Two student teams are competing in this year’s NASA RASCAL Competition to conceptualize, design and prototype critical elements of the L1 space platform envisioned at the Earth-moon first Lagrange point.
This team created an in-depth solution for refueling spacecraft during their extended mission lifetimes. While OASIS as a whole will require a large team, budget and time frame to complete, the team made two prototypes to showcase and act as inspiration for future development.
The “Smart Tank” focuses on varying volume control. To avoid fuel sloshing in a half-empty tank in zero gravity, the tank uses a plate and rotating rod to alter the volume as fuel either enters or leaves the vessel. This allows for smooth, continuous dispensing due to the lack of empty space.
As a proposed solution to the dangers that micrometeorites present to the station, the team implemented a multi-layer solution where each layer is spaced out to provide a buffer. The layers are made of fiberglass, Kevlar and aluminum. The protection system has been thoroughly tested with various rounds fired from an AK-47, thanks to Richard Wagner.
TEAM MEMBERS
Jared Bartunek, Aerospace Engineering
Jacob F Bessette, Aerospace Engineering
Steele Lawrence, Aerospace Engineering
Kevin Michael May, Aerospace Engineering
Stephen M Phemester, Aerospace Engineering
COLLEGE MENTOR
Jekan Thangavelauthum
SPONSOR ADVISOR
Harshad Kalyankar
TEAM MEMBERS
Jasem Mohammad Amoudi, Aerospace Engineering
Matt Guerra, Aerospace Engineering
Ruby Lee Huie, Aerospace Engineering
Nico Austin River, Aerospace Engineering
Justin Saxon, Aerospace Engineering
COLLEGE MENTOR
Jekan Thangavelauthum
SPONSOR ADVISOR
Sergey Shkarayev
TEAM MEMBERS
Rhea Carlson, Biomedical Engineering
Kellys Kerubo Morara, Biomedical Engineering
Kati Patterson, Electrical & Computer Engineering
Alex Casey Sullivan, Biomedical Engineering
Brendan Tobin, Biomedical Engineering
COLLEGE MENTOR
Don McDonald
SPONSOR ADVISORS
Erica Tassone, Marvin J Slepian
Team 23098
PROJECT GOAL
Create a biocompatible test platform to analyze the effects of pulsed electromagnetic field (PEMF) radiation and the temperature effects on different tissues in order to assist in furthering research on tissue therapy.
PEMF is a new form of therapy that aids healing of lesions and reduces soreness in human tissue by energizing the cells and influencing them to self-repair. However, the thermal effects of PEMF have not been studied to the fullest extent. This project presents a testbed for analyzing the temperature change that PEMF causes in tissues. This change is studied in a controlled environment using an array of temperature sensors, electric field (E-Field) sensors, and magnetic field (H-Field) sensors to display the relation between EMF strength and temperature change neatly in a graphical user interface.
The system test tissue uses an array in which resistance temperature detectors interface with an Arduino to send temperature data to the system computer. Two E-Field and two H-Field sensors work with an oscilloscope to process the incoming signal. Data is then sent through Python code, which in turn displays a 3D thermal map as well as an EMF field map. Finally, the data exports to an Excel file for record keeping and reporting/analysis.
The design also uses a 3D printed sample tank that submerges a tissue in saline. Inside the tissue holder, a coiled vinyl tube circulates water from an external heating bath, ensuring that the saline remains the standard temperature of the human body.
Team 23099
TEAM MEMBERS
Sabrina Alexis Contreras, Mechanical Engineering
Valeria Roxana Martinez, Biosystems Engineering
Samantha Schatz, Biomedical Engineering
Ira Stokes, Mechanical Engineering
Jackson Wyatt Wood, Electrical & Computer Engineering
YiYun Wu, Optical Sciences & Engineering
COLLEGE MENTOR
Justin James Hyatt
SPONSOR ADVISOR
Justin James Hyatt
Design and build a flowing robotic surface to display 3D continuous data on a physical surface for visually impaired scientists.
In the past, astronomers have included visually impaired people in their research by converting data to sound or 3D printed models of astronomical objects. These are laudable efforts, but they are slow processes and cannot present holistic 3D data. This project presents a three-dimensional surface that changes its shape to make data accessible through the sense of touch.
The team designed and constructed a working prototype that consists of a 20x20 array of independently actuated pins, a continuous surface overlaid on top of the pins, and an electronic control system. The team implemented image processing algorithms to reduce input data to the limited system resolution. This device is capable of displaying data, such as heat maps, laser beam profiles and even the astonishing black hole photo, in 3D. Blind scientists can use this device for feedback when analyzing 3D data and images. Pairing with the Arizona State School for the Deaf and the Blind and a visually impaired teammate allowed for reliable user feedback and future advancements for this device.
Team 23100
Design and economically compare three case models for implementing autonomous haulage trucks into an operating mine environment.
Nevada Gold Mines tasked the team with identifying the best-fit option for implementing autonomous haulage systems into an operating mining sector. Autonomous haulage trucks are a young technology that is constantly undergoing developmental changes to best fit differing mine environments, which presents a valuable opportunity to research possible implementation methodologies.
The project encompasses three major sections: 1) identifying and compartmentalizing data obtained from three separate cases – baseline, aftermarket and original equipment manufacturer; 2) researching and theorizing the best possible implementation process for autonomous haulage trucks; and 3) economically analyzing and comparing each case model and making a final determination.
The team procured project data through given baseline parameters, as well as through researching aftermarket autonomous options, or retrofitting, and options available through original equipment manufacturers. They then conducted a risk assessment analysis for safety and economic risks associated with the implementation of autonomous haulage. The final economic model comparison allows for a determination of whether autonomous implementation is economically optimal.
Team 23101
Design and deploy a streamlined method for identifying new mineral resources in underexplored Uganda to avoid the current pitfalls of mineral exploration.
Demand for mineral resources, metals in particular, far exceeds available and projected supplies. Mining engineers need to discover and exploit new mineral deposits to fill the demand gap. This process of mineral exploration is plagued by slowness, inefficiency and disconnection from later mineral production, along with the broader implications of mineral resource exploitation.
This team designed and piloted a new model of mineral exploration that places many of the later production concerns early in the process. Piloted in Uganda through the Next Generation Explorer Award Competition, the project uses mining engineering, mineral processing and systems engineering inputs to focus resources on the most economical and feasible mineral deposits. The team defined and prioritized three mineral deposits of high potential for further resource allocation.
TEAM MEMBERS
Daouda Berthe, Mining Engineering
David Gowan, Mining Engineering
Henry Cartright Hilliard, Mining Engineering
Rodrigo Martinez, Mining Engineering
Hunter Mattocks, Mining Engineering
Rhett Hale Sutherland, Mining Engineering
COLLEGE MENTOR
Brad Ross
SPONSOR ADVISOR
Jonathan Jazwinski
TEAM MEMBERS
Caelen Ross Burand, Mining Engineering
Zubin S Soomar, Mining Engineering
COLLEGE MENTOR
Brad Ross
SPONSOR ADVISOR
Herve Rezeau
TEAM MEMBERS
Alex Bullinger, Mining Engineering
Ben Dale Champie, Mining Engineering
Adolfo Sebastian Hog, Mining Engineering
James Nickels, Mining Engineering
David John Raihala, Mining Engineering
Katie Elizabeth Slaughter, Mining Engineering
COLLEGE MENTOR
Brad Ross
SPONSOR ADVISOR
Brad Ross
Team 23102
TEAM MEMBERS
Celma Olicia Antonio, Mining Engineering
Jake Jeffrey Bedlington, Mining Engineering
Jason J Ellett, Mining Engineering
Abraham Estopellan, Mining Engineering
Ana Santa Masie Masie, Mining Engineering
Juanita Joy Parkerson, Mining Engineering
COLLEGE MENTOR
Brad Ross
SPONSOR ADVISOR
Tim Wiitanen
Design and propose a feasible mine design for a metallic mineral deposit based on real-world constraints provided by the Society for Mining, Metallurgy, & Exploration (SME) Metallic Mine Design Competition.
This team participated in SME’s international collegiate competition requiring teams to create a mine plan and evaluate its feasibility using real-world data.
In Phase 1 of the competition, the team designed a metal mine based on a given resource model, processing data and equipment restrictions. The final design considered multiple economic, environmental, equipment, processing and risk tradeoffs to determine the best mine plan. They created a report from their results and presented it to the judges. Based on their Phase 1 report, this team was selected as one of six teams internationally to participate in Phase 2.
During Phase 2, the team updated the mine plan under additional constraints and presented to a panel of judges at the MINEXCHANGE 2023 Conference in Denver, where they won second place overall.
Team 23103
Determine if Railveyor is a productive and economical alternative to traditional haulage.
This team conducted a feasibility study involving the design of an open pit mine using the Railveyor conveyance system. The goal is to determine what aspects of an open pit mine would make Railveyor an economic and productive alternative to traditional haulage, or whether a combination of Railveyor and haul trucks could be more beneficial.
Team 23104
Design a robotic system to enter and explore Martian lava tubes for the purpose of geological survey.
There are more than 1,000 suspected lava tubes on Mars, which could someday provide shelter from the Martian environment for human inhabitants.
SpERO consists of a solar balloon that travels across the Martian surface in search of lava tubes and lowers an inflatable rover to collect photographic samples and point maps of the lava tube environment. It uses lidar, or Light Detection and Ranging, to collect 3D point maps of the lava tubes and entrances, cameras to take images of the environment, and sensors to measure temperature and radiation. An antenna relay system sends the data to Earth to be analyzed by scientists.
The prototype aims to validate this system using an autonomous octocopter drone that carries a rover on a lowering garage. A spool-motor system lowers a rover on the garage to autonomously maneuver around obstacles without the use of GPS. It navigates using lidar and inertial measurement units and collects a 2D point map and images of the environment. The data is communicated from the rover to the drone through an antenna on the garage. SpERO will demonstrate navigation capabilities, the rover lowering system and a three-antenna communication relay.
Team 23105
Build a paraglider drone for thermally monitoring wildfires semi-autonomously with high endurance.
SAIL aims to assist first responders by addressing how to monitor wildfires and other large disaster areas over long durations.The ideal system would allow for visually tracking fire progression, the spread of residual embers, fire containment, and wind conditions, then using the data to predict the spread of the fire and any danger it poses. The secondary objective is supporting search and rescue operations to locate missing persons, and the tertiary objective is collecting data that can improve our understanding of wildfires and how to manage them.
Addressing this problem requires a platform that can observe vast swaths of land, enhance the detection of people and other heat signatures compared to traditional cameras, requires minimal training to operate, and is less expensive to implement than other available platforms. This team’s solution is the SAIL drone, a paraglider unmanned aircraft system (UAS) that relays live thermal video and telemetry data to a portable ground station from which the operator commands the autopilot. The drone can be launched traditionally or deployed from a high-altitude balloon for vertical launch and longer flight time.
TEAM MEMBERS
Roman Joseph Anthis, Aerospace Engineering
Anna Elizabeth Dinkel, Aerospace Engineering
Andrew Gabriel Frisch, Aerospace Engineering
Elijah West Greenfield, Aerospace Engineering
Nicholas Scott Mammana, Aerospace Engineering
Kylar Joshua Nietzel, Aerospace Engineering
COLLEGE MENTOR
Sergey Shkarayev
SPONSOR ADVISOR
Harshad Kalyankar
TEAM MEMBERS
Max Chen, Aerospace Engineering
Katelyn E Hackworth, Aerospace Engineering
Maanyaa Kapur, Aerospace Engineering
Yash Vardhan Singh, Mechanical Engineering (Grad Student)
Alton Matthew Zhang, Aerospace Engineering
COLLEGE MENTOR
Sergey Shkarayev
SPONSOR ADVISOR
Adrien Bouskela
TEAM MEMBERS
David Coulter, Systems Engineering
Ramon Garcia, Systems Engineering
Miguel Rocha Sanchez, Systems Engineering
Daniela Ruiz Cabuto, Systems Engineering
Lam Hai Tran, Systems Engineering
COLLEGE MENTOR
Samuel Peffers
SPONSOR ADVISOR
Nick Bahr
Team 23106
PROJECT GOAL
Develop a computer program capable of predicting irrigation water requirements for Bard’s near-18,000 acre district with 90% or greater accuracy. This program shall continuously refine its forecast through machine learning.
Continuous depletion of water from the Colorado River due to chronic overuse and continuous drought necessitates more precise water management methods. Bard Water District currently runs at 73% forecast accuracy. The design team developed a Python-based program capable of forecasting the necessary amount of irrigation water for the entire district at +/- 1% accuracy. The variables were identified through a full factorial design of experiment and continuously refined with machine learning.
Project deliverables include a fully functioning irrigation water forecasting program with webbased user interface, an implemented integration plan transitioning the system into its operating environment, new operator training, a user instruction document and a technical data package.
Team 23107
PROJECT GOAL
Design a process to convert wood biomass into bio-oil and upgrade the bio oil to biodiesel.
The aim of this project is to maximize biomass conversion into alternative energies by developing a process that includes a pyrolysis reactor and bio oil upgrading process. This reactor converts the wood lignocellulosic biomass into bio oil and other byproducts such as char. The bio oil can then be further refined and sold as biodiesel to power diesel combustion engines.
TEAM MEMBERS
Omar Hany Abutaleb, Chemical Engineering
Armeen Pajouyan, Chemical Engineering
Ronnie Joseph Sabatino, Chemical Engineering
Nebyate Seged, Chemical Engineering
COLLEGE MENTOR
Kimberly L Ogden
SPONSOR ADVISOR
Bob White
Team 23108
Improve the Rainbow Valley Water Reclamation Facility by implementing new techniques for treating wastewater, in compliance with environmental regulations, in response to population growth and increased interest in environmentally safe disposal of waste.
The team designed facility upgrades for the Rainbow Valley Water Reclamation Facility to meet population growth projections while producing Class A+ effluent. The upgrade designs allow the facility to continue operation during construction, and also incorporate odor mitigation measures to improve nearby residents’ quality of life. Improved solid waste treatment is included to produce Class B sludge.
Team 23109
The team designed an LNG receiving terminal to be sited in the Gulf Coast. They designed the unloading and tankage to offload LNG from 125,000 m³ ships. The nominal sendout capacity of the receiving terminal will be 1,050 million standard cubic feet per day (MMSCF/D) measured at the ship’s rail. After vaporization, natural gas will be delivered to the pipeline at 1,250 pounds per square in gauge (psig) and 40 degrees Fahrenheit.
TEAM MEMBERS
Mojisola Adebusola Ajayi, Environmental Engineering
Claudia B. Alvarez, Environmental Engineering
Ethan Lord, Environmental Engineering
Saadia Sajjad, Environmental Engineering
COLLEGE MENTOR
Adrianna Brush
SPONSOR ADVISOR
Thomas Olden
TEAM MEMBERS
Dana Al Marzouq, Chemical Engineering
Wahab Sami Alsharaf, Chemical Engineering
Santiago Fernandez Falcon, Chemical Engineering
Alex Charles Welch, Chemical Engineering
COLLEGE MENTOR
Adrianna Brush
SPONSOR ADVISOR
Fred Brinker
TEAM MEMBERS
Abdullah Monzer ALQallaf, Chemical Engineering
Dhari AlShammari, Chemical Engineering
Sierra Gobert, Chemical Engineering
Antonio Murrieta, Chemical Engineering
COLLEGE MENTOR
Kimberly L Ogden
SPONSOR ADVISOR
Charles Stack
Team 23110
PROJECT GOAL
1. Increase the purity of biogas.
2. Reduce greenhouse gas emissions caused by carbon dioxide.
3. Improve the economic viability of biogas production for renewable energy.
This project centers around the use of an algae photobioreactor to upgrade biogas into high-quality biomethane. The production of biomethane offers numerous benefits, including its ability to be seamlessly integrated into existing natural gas systems and equipment. Biogas, which is produced from the decomposition of organic material, typically contains 60% methane and 40% carbon dioxide. However, through a cutting-edge biogas upgrading process, the team aimed to maximize the percentage of methane present in the biogas, resulting in a highly pure and valuable form of renewable natural gas.
Using an algae photobioreactor, the team efficiently and sustainably enhanced the quality of biogas through the removal of impurities such as carbon dioxide. This project aims to contribute to the expansion of renewable energy production, reduce dependence on fossil fuels and mitigate greenhouse gas emissions.
Team 23111
TEAM MEMBERS
Abraham Joaquin Arvizu, Chemical Engineering
Claire Bukowski, Chemical Engineering
Zachary Joseph Fine, Chemical Engineering
Gabriel Schirn, Chemical Engineering
COLLEGE MENTOR
Adrianna Brush
SPONSOR ADVISOR
Caitlin Schnitzer
Investigate hydrogen production through microbial electrolysis. Hydrogen can be stored and sold to consumers or utilized in a hydrogen fuel cell as an environmentally conscious form of electricity generation.
This project explores using a microbial electrolysis reactor in tandem with a hydrogen fuel cell in a water treatment facility to generate electricity. A microbial electrolysis reactor uses an anode and a cathode to produce hydrogen gas from microbial growth within wastewater. The hydrogen gas is then sent to a fuel cell, where it combines with oxygen to produce electricity. The team researched both hydrogen production and hydrogen fuel cells to create a system that would generate electricity from only wastewater. The generated electricity could be used for many applications, including powering different machinery in a water treatment plant or adding power to the grid. The system is optimized to be both economically and environmentally friendly.
Team 23112
Develop a model that can be used to determine if solar energy covers for the CAP canal are economically and environmentally worthwhile.
There is a growing need to find creative ways to conserve water in Arizona. The Colorado River, which supplies the water for Phoenix and Tucson through the CAP canal, is currently in a Tier 2 drought, causing Arizona’s water allotment to be cut by 21%. This project aims to evaluate how solar covers placed over the CAP canal could suppress evaporation and offset the energy costs associated with moving the water along 336 miles of canal.
The model allows the user to input seasonal weather trends and data corresponding to any section of canal and calculates the suppressed evaporation losses and energy collection. The team applied principles of heat and mass transfer, as well as photovoltaic energy collection, for estimation. The photovoltaic collectors also contain no toxic or hazardous materials, to abide by requests from farmers who use the CAP canal water.
Team 23113
Design a process for manufacturing aviation fuel using little or no fossil fuel precursors.
The team designed a process to produce aviation fuel from an algae feedstock. The process includes growing of algae, fermentation of algae products and conversion to aviation-grade fuel.
TEAM MEMBERS
Spencer J Babyak, Chemical Engineering
David William Czirjak, Chemical Engineering
Jack W Hughes, Chemical Engineering
Tyler Aaron Pearson, Chemical Engineering
COLLEGE MENTOR
Kimberly L Ogden
SPONSOR ADVISOR
Avelino E Saez
TEAM MEMBERS
Juliana C Baltram, Chemical Engineering
Eugenio Castillo, Chemical Engineering
Osama Almusallam Musallam, Chemical Engineering
Dorian J Werner, Chemical Engineering
COLLEGE MENTOR
Adrianna Brush
SPONSOR ADVISOR
Chris Dahl
TEAM MEMBERS
Kyle Garette Bartell, Chemical Engineering
Jesus Adan Chavez, Chemical Engineering
Garrett Tellez Romero, Chemical Engineering
Alfredo Valdez, Chemical Engineering
COLLEGE MENTOR
Adrianna Brush
SPONSOR ADVISOR
Farhang Shadman
Team 23114
TEAM MEMBERS
Izzy Marie Beeley, Chemical Engineering
Shane Shane Klemish, Chemical Engineering
Sophia Qamar, Chemical Engineering
Greyson Alexander St Pierre, Chemical Engineering
COLLEGE MENTORS
Kimberly L Ogden, Adrianna Brush
SPONSOR ADVISOR
Marvin J Slepian
PROJECT GOAL
Design a reuse process for wastewater to make a semiconductor plant more sustainable and reduce water utility costs.
The team designed a membrane filtration process to reuse wastewater from semiconductor rinse operations. The goal was to reduce overall water usage for semiconductor manufacturing facilities, helping them save money on utility costs in the long term.
Team 23115
PROJECT GOAL
Create a recyclable system for dialysis machines.
Hemodialysis functions to remove the build up of salts, water and toxins from the body when a patient’s kidneys are not working adequately. For many patients, receiving hemodialysis treatments means traveling to a hospital or dialysis center several times each week for hours at a time. With an increase in remote healthcare technology, hemodialysis has expanded to the home. Within the hospital or home setting, hemodialysis is still a water-intensive process that results in wastewater disposal.
Dial-Assist supplements commercial portable hemodialysis systems by recycling the effluent wastewater, also known as dialysate, to minimize the need for a tap water connection and increase patients’ independence. The system consists of a sorbent canister to remove salts and uremic toxins and UV sterilization to destroy bacteria. The effluent dialysate is recycled to a purity level that allows it to be reused by the patient once the prescribed amount of salts and other dialysate components are re-added. The entirety of the device fits in a compact container above the portable dialysis system. Dial-Assist will aid in the progression of more independent hemodialysis treatments so patients with kidney disease may have a higher quality of life.
Team 23116
Create a perfume with a popular scent that will produce profits while minimizing carbonbased energy. Optimization should increase efficiency, decrease energy requirements, and power the process with sustainable energy sources.
The first step is using steam distillation to extract the essential oils of orange peels and cinnamon bark in a semi-batch process. The product from steam distillation is cooled by a refrigeration cycle. The condensed exit stream is then pumped into two decanter centrifuge separators: one for orange and one for cinnamon. The oil and water mixtures separate due to differences in polarity. The floral water from each separator is pumped into a single floral water holding tank, while the essential oils are pumped into surge tanks, where they are held until needed for perfume formulation.
The perfume formulation process starts when the essential oils are combined with all other required ingredients: vanilla essential oil, water, ethanol, and the UV filter (ethylmexyl methoxycinnamate). From there, the final mixture goes into a chiller for 25 minutes before being pumped into a filter. The vibratory filter separates the final product from the precipitate wax that forms during the chilling process. The filter waste is transported into the previously mentioned waste tank. The final product leaves the filter and is pumped into the product holding tank to be held until transportation to be packaged.
The process will be powered by solar panels.
Team 23117
Design a vapor reinjection system that utilizes the separation of liquids and gases from the production well to increase the well’s oil and natural gas production.
In enhanced oil recovery, liquid and/or gas is reinjected into an oil reservoir to re-establish lost pressure and extract additional oil. This project focuses on the reinjection of gas into the oil well using the tertiary reinjection of methane, specifically in an Alaskan oil field. Before being reinjected into the reservoir, the methane must be separated from the oil and water that is entrained in it. This is done using a series of heat exchangers, separators and compressors to safely and efficiently separate out the different components for use in their own streams.
The safety of this process is of utmost importance, since many pieces of equipment are operating at high pressure and high temperature. To reduce operator injuries and prevent the need for maintenance, misters and control valves will be used to maintain safe operations at all times. Optimal operations for this process will yield an increased separation and recovery of oil and natural gas as well as increase safety and decrease the need for maintenance.
TEAM MEMBERS
John Siruzie Bergin, Chemical Engineering
Kale Teagan Burke, Chemical Engineering
Chloe Elizabeth Sarocka, Chemical Engineering
Makayla Marie Schilling, Chemical Engineering
COLLEGE MENTOR
Adrianna Brush
SPONSOR ADVISOR
Rodney Keith
TEAM MEMBERS
Hayden A Borden, Chemical Engineering
Alena Isabel Hermosillo, Chemical Engineering
Abby Regan Long, Chemical Engineering
Regan M Wagner, Chemical Engineering
COLLEGE MENTOR
Adrianna Brush
SPONSOR ADVISOR
Robert Siml
TEAM MEMBERS
Chandler Arden Canant, Chemical Engineering
Dallan D Graybill, Chemical Engineering
Sophia Mischke, Chemical Engineering
Jamie Nicole Scott, Chemical Engineering
COLLEGE MENTOR
Kimberly L Ogden
SPONSOR ADVISOR
Jared Gardner
Team 23118
TEAM MEMBERS
Kyle Thomas Churchman, Chemical Engineering
Morgan P Habkirk, Chemical Engineering
Ismael Q Hernandez, Chemical Engineering
Alejandra Hinojosa, Chemical Engineering
COLLEGE MENTOR
Adrianna Brush
SPONSOR ADVISOR
Andrea Achilli
PROJECT GOAL
Create a foam for marine applications with desirable material physical properties.
The team began by conducting research to identify foam candidates, then selecting and ordering raw materials. Next, they created a test plan; conducted safety analysis; and began test apparatus building, including CAD drawing and 3D printing. Finally, they began creating foam samples in the lab, testing the physical properties of the material, analyzing the data, and creating a theoretical scale-up process.
Team 23119
PROJECT GOAL
Provide a detailed expansion design recommendation for the Rainbow Valley Water Reclamation Facility located in Goodyear, AZ.
This project consisted of upgrading the Rainbow Valley Water Reclamation Facility’s water treatment capacity from 0.75 to 1.25 million gallons per day. Additional deliverables included expanding and upgrading the biosolids treatment to produce Class B biosolids for land applications, implementing an efficient odor control strategy to reduce odorous hydrogen sulfide emissions, providing an economic analysis on capital costs, and providing a plant layout that includes a hydraulic profile and construction sequencing plan.
Team 23120
Develop a recipe for a biodegradable plastic that is less wasteful and environmentally damaging than conventional, fossil fuel-based plastics.
The aim of this project was to design a biodegradable plastic using waste materials. The main sources of polymeric material were orange peel waste and plant stems. In addition to recycling food waste, the project also provided data on synthesizing alternatives to conventional plastics, which take many years to decompose.
The team tested multiple recipes to determine the optimal ratios for strength and plasticity. For instance, they tested cornstarch to orange peel waste ratios ranging from 0 to 1:5, the use of both hydrochloric acid and trifluoroacetic acid, and the plasticizers glycerol and acetyl tributyl ester. They then characterized all of the samples based on their tensile strength and glass transition temperature. Tensile strength testing followed the American Society for Testing and Minerals (ASTM) standards for plastics. The team measured the glass transition temperature using differential scanning calorimetry. This project represents a significant step forward in the pursuit of sustainable and environmentally friendly plastics.
Team 23121
Dealcoholize wine while retaining the visual, aromatic and flavor characteristics.
Climate change has caused the alcohol by volume (ABV) of wine to increase by 2% globally, resulting in undesirable flavor changes. Producing a low-alcohol wine would help to control wine quality and provide more options to consumers, as the demand for no- and low- alcohol drinks has been growing over the last few years. This project focuses on the dealcoholization of wine while attempting to retain the visual, aromatic and flavor characteristics. The team chose osmotic distillation to remove ethanol from red wine, as their research found it to be both the most affordable and most effective at retaining wine’s sensory characteristics. In this process, feed wine and stripping distilled water are run in counter-current flow over a hydrophobic polypropylene membrane. Ethanol moves from the wine into the stripping water, resulting in a reduced alcohol wine.
TEAM MEMBERS
Rudaina Jamal Alduaij, Chemical Engineering
Stephen Lee Farris, Chemical Engineering
Aakanksha Gadh, Chemical Engineering
Fatima Khan, Chemical Engineering
COLLEGE MENTOR
Kimberly L Ogden
SPONSOR ADVISOR
Victor Octavio Tenorio Gutierrez
TEAM MEMBERS
Kaylee E Franzel, Chemical Engineering
Jessica Ann Nicholls, Chemical Engineering
Daniella R Roberts, Chemical Engineering
Sarina A Tuskey, Chemical Engineering
COLLEGE MENTOR
Adrianna Brush
SPONSOR ADVISOR
Suchol Savagatrup
TEAM MEMBERS
Brendan Christopher Greene, Chemical Engineering
Samuel Herschler, Chemical Engineering
Bryce Sterling Long, Chemical Engineering
Arleth Adamaris Ortiz, Chemical Engineering
COLLEGE MENTOR
Adrianna Brush
SPONSOR ADVISOR
Lisa A Jones
Team 23122
TEAM MEMBERS
Meghan S Greenslade, Environmental Engineering
Mia Mai Migliore, Chemical Engineering
Caroline Renee Webster, Chemical Engineering
Gavin C Wolkon, Chemical Engineering
COLLEGE MENTOR
Kimberly L Ogden
SPONSOR ADVISOR
Yadi Wang
Produce HMF for potential use in other applications by using agricultural waste.
This project focuses on designing a process for year-round production of at least 95% pure (5-Hydroxymethylfurfural) HMF. It uses multiple agricultural waste inputs that are readily available in Arizona, while minimizing the use of hazardous reagents. This process will help farms and farm industries manage environmentally harmful agricultural waste while maximizing the production of HMF, a component used in the creation of the biofuel 2,5-Dimethylfuran (DMF), as well as potentially in polyester manufacturing.
Team 23123
PROJECT GOAL
Create a mobile photovoltaic system that provides shade to agriculture and grazing animals. This system will incorporate agrivoltaic concepts including evapotranspiration and solar tracking.
The team designed a mobile photovoltaic system to provide shade to agriculture and grazing animals while harnessing solar energy to produce electricity. The designed system consists of a hitched, moveable trailer carrying two 500-gallon open storage tanks to allow for evapotranspiration, 12 solar-tracking panels secured on top, and a water trough secured on the back for livestock. The agrivoltaic design will maximize the use of available land by combining solar energy production with agricultural activities.
Team 23124
Provide Hydronalix with a functioning heat transfer testbed and data analog system that provides live temperature data to reduce the chance of motor burnout while their unmanned boats are being operated.
The team designed and constructed a heat transfer test bed to find the necessary flow to cool the motors of unmanned boats, thereby improving lifespan and preventing burnout.
Team 23125
Improve the strip cleaning section of a steel manufacturing line by implementing a more environmentally friendly degreasing method. Maintain industry specifications for cleanliness and comply with industry safety standards and regulations.
This project focuses on replacing the degreasing system of a steel tube manufacturing line for Atkore Allied Tube & Conduit in Phoenix. The degreasing system removes the oil, rust and dirt from the surface of the steel coil before it is formed and welded into its final tube shape. A clean steel surface helps prevent bare spots during paint application and reduces scrap.
The current degreasing system consists of a series of four caustic tanks with decreasing concentrations of sodium hydroxide solution, with the fourth and final tank being a water rinse. The sodium hydroxide tanks are also equipped with natural gas heaters to heat the solution to the ideal temperature for caustic degreasing (140 degrees Fahrenheit). The sodium hydroxide binds to the oil, dirt and rust molecules on the surface of the steel strip and is washed off with the water. This system costs $1.15 million annually to maintain and requires HAZMAT processing.
The team explored more environmentally friendly strip cleaning solutions, including using lasers, steam, dry ice and induction heating degreasing methods. They concluded the best option was to conduct experiments on induction degreasing, and this is the focus of the new steel degreasing design.
TEAM MEMBERS
Lily N Heuertz, Chemical Engineering
Meg Vivian Richards, Chemical Engineering
Curtis Shoemaker, Chemical Engineering
Reese C Tomooka, Chemical Engineering
COLLEGE MENTOR
Gregory Ogden
SPONSOR ADVISOR
Dillon Allen
TEAM MEMBERS
Olivia Culbertson McNally, Chemical Engineering
Amelia Ryann Talkington, Chemical Engineering
John Joseph Totaro, Chemical Engineering
COLLEGE MENTOR
Kimberly L Ogden
SPONSOR ADVISOR
Thomas Babb
TEAM MEMBERS
Kayla A Bansback, Chemical Engineering
Ashley Duncan, Environmental Engineering
Annissa Lopez, Environmental Engineering
Diego Salido, Environmental Engineering
COLLEGE MENTOR
Kimberly L Ogden
SPONSOR ADVISOR
Patrick Pasadilla
Team 23126
PROJECT GOAL
Develop a sustainable and efficient system that combines aquaculture and traditional farming to provide a replenishable food source for long-distance space travel.
By combining aquaculture and traditional farming methods, the team developed a sustainable and efficient system to provide a replenishable food source for long-distance space travel. The aquaponic system comprises four rotating plant-growing towers mounted around an inner grow light. Each tower has a ball bearing and is belt-driven by a DC motor to expose the plants to the inner grow light at a specific number of revolutions per minute (RPM), ensuring even lighting in minimal space.
The effluent from a fish tank undergoes specialized built-in mechanical and biological filtration before being circulated to the grow towers and back to the fish tank. The growing columns spin through custom polyethylene terephthalate glycol (PETG) fittings, while the rest of the unit remains stationary. Ultimately, the SPADE project aims to demonstrate the viability of aquaponics as a sustainable food source for space travel, ensuring sustainable human nutrition in extreme conditions.
AEROSPACE ENGINEERING
ARCHITECTURAL ENGINEERING
BIOMEDICAL ENGINEERING
BIOSYSTEMS ENGINEERING
CHEMICAL ENGINEERING
CIVIL ENGINEERING
ELECTRICAL & COMPUTER ENGINEERING
ENGINEERING MANAGEMENT
ENVIRONMENTAL ENGINEERING
INDUSTRIAL ENGINEERING
MATERIALS SCIENCE & ENGINEERING
MECHANICAL ENGINEERING
MINING ENGINEERING
OPTICAL SCIENCES & ENGINEERING
SOFTWARE ENGINEERING
SYSTEMS ENGINEERING
After students are assigned to projects, teams work with their sponsors to generate structured lists of system requirements and metrics for evaluating nal designs and prototypes.
Following approval of the Systems Requirements Memo, teams conduct research and brainstorm to produce preliminary or conceptual designs.
In this structured document, against which all designs, tests and prototypes are gauged, students de ne requirements for completed projects in consultation with sponsors.
Based on feedback from sponsors and mentors at the Preliminary Design Review, teams modify their preliminary designs and create detailed manufacturable designs to create prototypes for Craig M. Berge Engineering Design Day.
In this formal review, sponsors and mentors critique conceptual designs –for which sponsor approval is required – challenge assumptions and help teams re ne their plans.
At this milestone, sponsors and mentors ensure their teams are meeting all requirements and have feasible plans to manufacture and test prototypes within budget.
Following the Critical Design Review and approval of the Critical Design Report, teams begin purchasing parts and manufacturing custom components to produce their prototypes.
In this formal exchange, sponsors and mentors provide project feedback as teams address any last-minute changes.
During the last phase of the program, teams collaborate closely with sponsors to assemble and test their prototypes. They also prepare their presentations and demonstrations for Craig M. Berge Design Day.
Capstone projects are the culmination of a year’s worth of work. Students have applied knowledge from the breadth of their undergraduate education, exercised out-of-the-box thinking and spent hundreds of hours producing the best solutions for their sponsors. We applaud your dedication and professionalism and congratulate you on your achievements.
Project mentors apply hundreds of years of collective engineering experience to guide students in the completion of their projects. They ensure the implementation of industry standards in the design process. Their expertise in devising solutions to challenging problems adds a critical dimension to students’ engineering knowledge. Thank you for your hard work, your commitment to excellence in engineering design and your role in the education of our students.
Sponsors provide students with real-world questions and allocate funds to the program. They designate technical staff and mentors to steer students through the intricacies and requirements of their projects. Sponsors are a big part of what makes the Craig M. Berge Engineering Design Program (which encompasses Interdisciplinary Capstone and other capstone courses) what it is today: one of the largest and best-quality programs of its kind in the nation. Thank you immensely for your continued support.
The external judges who participate in Craig M. Berge Design Day supply independent professional assessments of the quality of students’ work. They help maintain the accreditation of undergraduate University of Arizona Engineering degree programs by providing insight and suggestions for improving the Craig M. Berge Engineering Design Program. Thank you for volunteering your time and applying your knowledge to evaluate students’ capstone projects.
Dedicated professionals in the College of Engineering ensure the program’s smooth operation. They spend thousands of hours each year organizing events, communicating with sponsors, operating manufacturing areas, generating marketing materials and news, maintaining budgets and purchasing records, and performing a myriad of other tasks. Thank you all for your invaluable contributions and the excellence you bring to the program.
AGCO Corporation
Alpa Merchant, DDS PC
Amazon
Cliff Andressen
ASML US, Inc.
Atkore Allied Tube & Conduit
Auxilium Technology Group
Awareness Ranch
AZ Technica
Ball Aerospace
Bard Water District
BD (Becton Dickinson)
BFC Medical
Bly Family
Bosch Rexroth Corporation
Mark Brazier
Frank Broyles Caterpillar Inc.
Coherent
Competitive Engineering
Dataforth Corporation
Elbit Systems of America
Ergo Dave
GEOST
Gesund Me
Larry Head
Honeywell Aerospace
Hydronalix
IEEE Tucson Section
Jackson Medical
Kidney ADVANCE Project - NIH/ACABI
L3Harris Commercial Aviation Solutions
L3Harris Unmanned Systems
Steve Larimore
LED Dental Wellness
Lundin Mining Group
Meggitt
McDonald/Watt Projects
Mensch Foundation
Microentities Worldwide
Microsoft
Henry & Suzanne Morgen
NASA
Ana Needhan
NeoChloris
Nevada Gold Mines
Nobel
Northrop Grumman
Paragon Space Development Corp
Phoenix Analysis & Design Technologies
Railveyor
Rain Bird Corporation
Raytheon Technologies
RBC Sargent Aerospace & Defense
Regenesis Biomedical, Inc
Resolution Copper
Ridgetop Group
Rightfooted Foundation
Rincon Research
Rob Dollar Foundation
Roche Tissue Diagnostics
Simpson Family
SRP
SunMed
Technical Documentation Consultants of Arizona
TRAX International
Tucson Electric Power
Tucson Embedded Systems, Inc
Universal Avionics
W.L. Gore and Associates
Zolt Technology LLC
Craig M Berge Dean’s Community Fund
AIAA Student Branch
Biosphere 2
Center for Accelerated Biomedical Invention
Center for Biomedical Informatics & Biostatistics
Department of Aerospace and Mechanical Engineering
Department of Biomedical Engineering
Department of Biosystems Engineering
Department of Chemical and Environmental Engineering
Department of Electrical and Computer Engineering
Department of Mining and Geological Engineering
School of Animal and Comparative Biomedical Sciences
Steward Observatory Solar Lab
UA Police Department/FBI
Wildcat Robotics
Adrianna Brush
Pat Caldwell
Elmer Grubbs
Justin James Hyatt
Harshad Baswaraj Kalyankar
Steve Larimore
Michael Madjerec
Doug May
Bob Messenger
Don McDonald
Mike Nofziger
Gregory Ogden
Kimberly L Ogden
Samuel Peffers
Herve Rezeau
Brad Ross
Sergey Shkarayev
James Sweetman
Jekan Thangavelauthum
Jeff Scott Wolske
Larry Head – Craig M. Berge Engineering Design Program Director
Debbie Claggett – Engineering Design Capstone Coordinator
Cecilia Lopez - Business Manager
Nataly Islas - Student Worker
Alondra González - Student Worker
Monica Palafox - Student Worker
Special thanks to SRP for providing lunches for all of our students on Design Day.
From startups to Fortune 500 companies, a varied group of sponsors benefits from this outstanding interdisciplinary academic program each year.
Try out potential employees
Explore new technologies
Move products to market
Support engineering education
Boost company profile on campus
Teams of four to six seniors, mentored by industry liaisons and University of Arizona Engineering faculty, spend an entire academic year taking your design projects – many of which become patented technologies and commercial projects –from start to finish.
View the 2023 Design Day project presentations at b.link/DesignDay2023