CRAIG M. BERGE
ENGINEERING
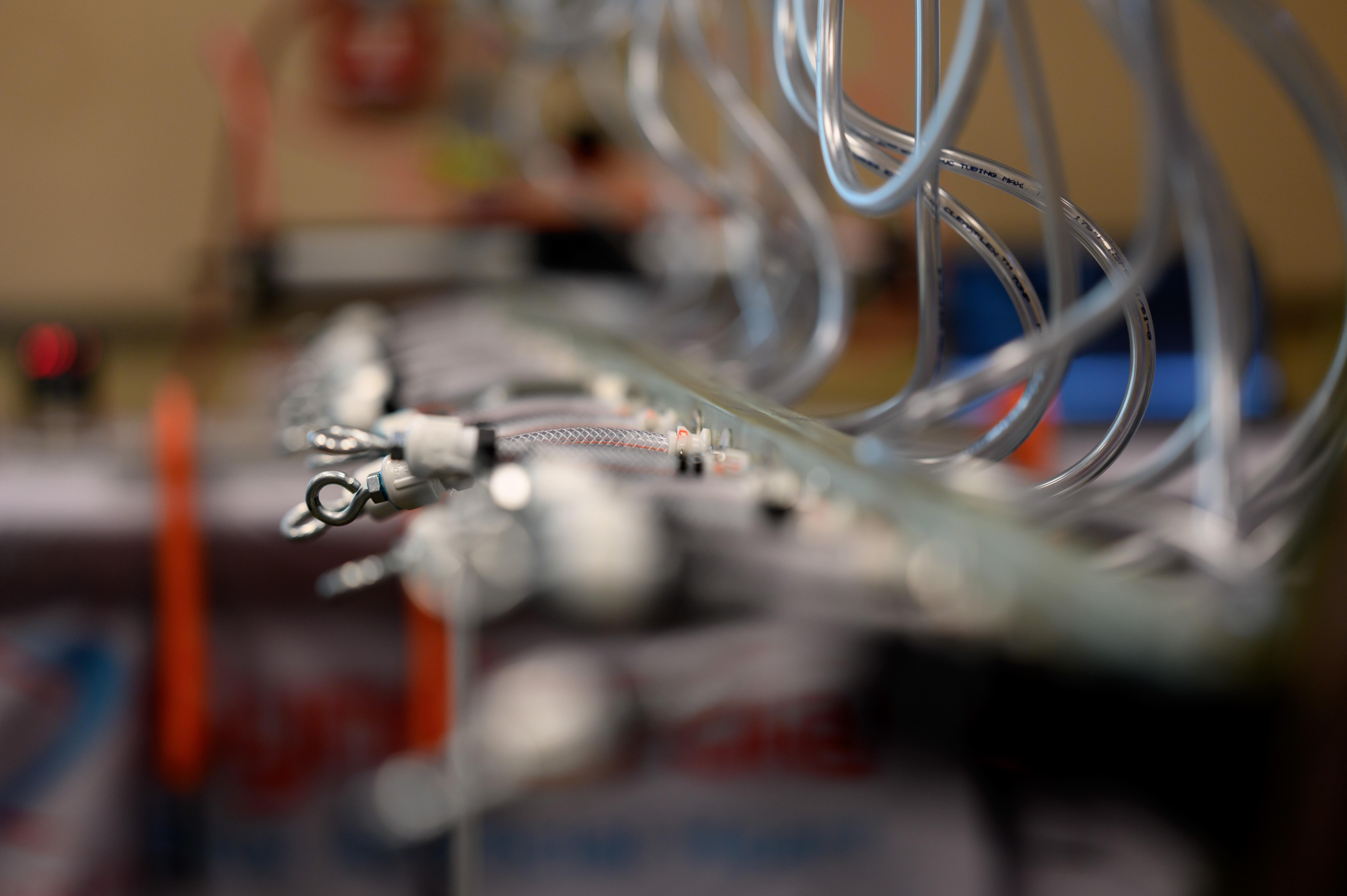
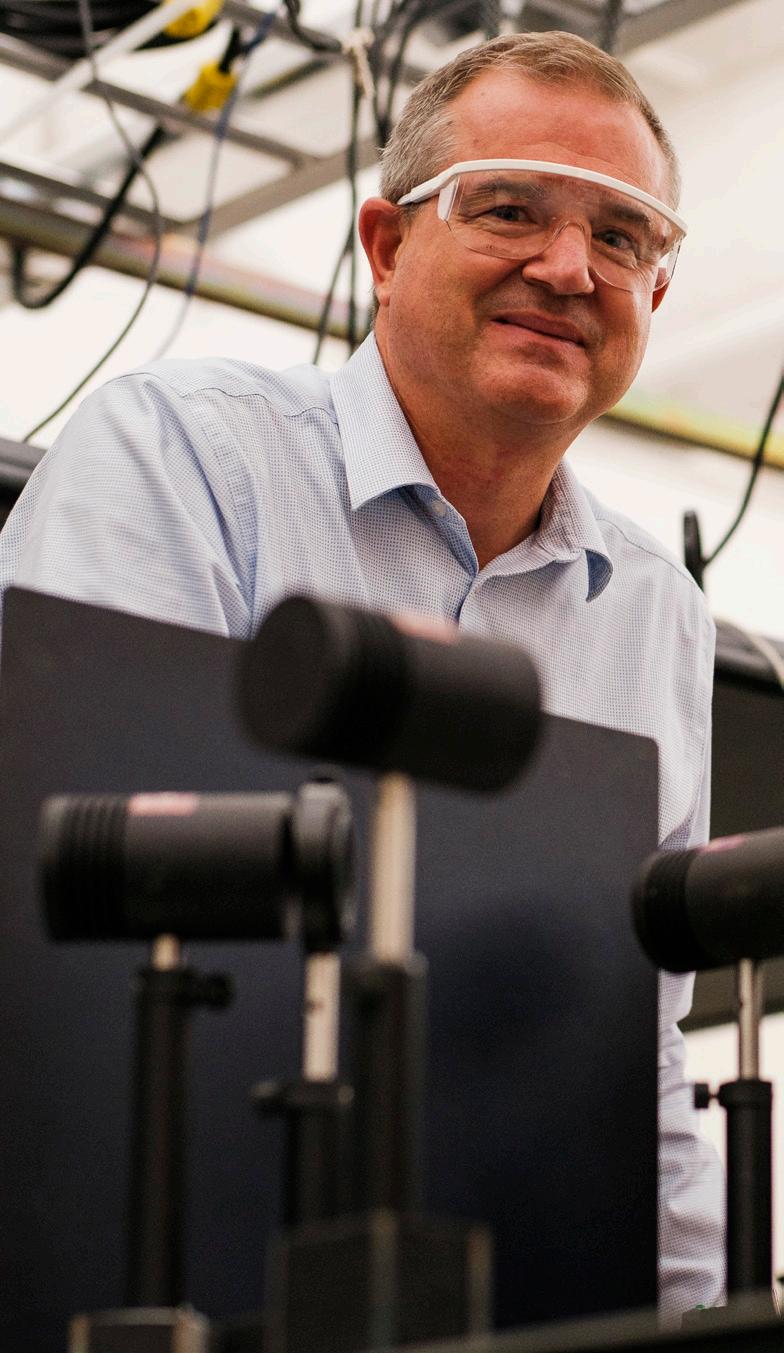
Welcome to 2025 Craig M. Berge Engineering Design Day
Teams display projects ranging from an autonomous amphibious delivery system to a golf robot.
Craig M. Berge Design Day is a story of remarkable student success and all the ways engineers help people.
Something for Everyone
As they looked toward engineering careers, the members of the class of 2025 collaborated in labs and workshops on aircraft designs, medical devices and diagnostics, communication networks and recycling methods.
Their designs are a testament to the technical agility and creativity of our students and mentors. Teams furthered space exploration efforts with a lunar base water collection system and a more efficient rocket engine. They manipulated light to grow coral and sterilize face shields used by health care workers. Students improved a mining shovel and designed a process for removing heavy metals from water using fungi.
Many of the seniors here will graduate this month with impressive job offers or graduate school plans. These accomplishments demonstrate why Engineering Wildcats quickly attain roles in which they can influence and build the systems, technologies and solutions humanity needs most.
I recommend you ask questions as you take in the dazzling displays of ingenuity. Students are thrilled to tell you about these fantastic projects they’ve worked on throughout the academic year. If you miss anything, you can learn about the projects in the students’ presentation videos, which will be available online (b.link/DesignDay2025) following the awards ceremony.
Join us for the 4 p.m. Design Day Awards Ceremony, where standout seniors will collect 35-plus prizes in all, from the Fish Out of Water to the Most Outstanding Project.
Thank You for Your Support
Design Day and the Interdisciplinary Capstone Course are part of a lineup of competitions, maker fests, major-specific design classes, entrepreneurial and business mentorship, and industry and community projects in the Craig M. Berge Engineering Design Program. The program immerses undergraduates at all levels in real-world experiences that integrate design, manufacturing and commercialization.
We are especially grateful to the donors, program mentors, university and industry partners, sponsors, judges, faculty, staff and alumni who help make the design program and Design Day a highly successful enterprise.
I’d like to extend a special thank you to Nancy Berge and her family for their generosity, as well as Larry Head, director of the Craig M. Berge Engineering Design Program, for his commitment to an unparalleled experiential learning program and design curriculum in higher education.
Bear Down, and support our Wildcat engineers!
David W. Hahn
Craig M. Berge Dean, College of Engineering
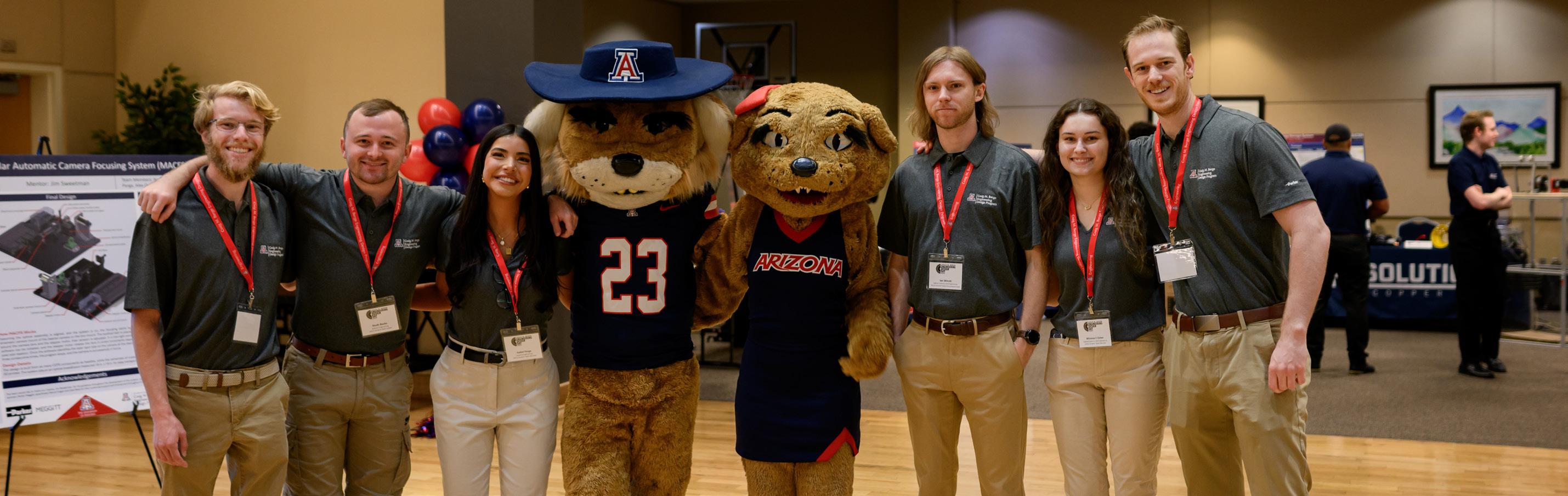

AWARDS
Sponsorship is a great way to get real engineering development work done and help projects come to fruition that may not otherwise have seen the light of day due to a lack of internal resources.”
STEMPLE, alum and Raytheon SPONSOR ADVISOR
Craig M. Berge Dean’s Award for MOST OUTSTANDING PROJECT
($7,500)
This award recognizes the one Design Day project embodying the best attributes of engineering design and the profession. The winning project has an outstanding design approach and implementation, excellent system modeling and/or analysis supporting the design, comprehensive testing that verifies system requirements, and a superior presentation of results to Design Day judges Team members of the winning project effectively demonstrate engineering knowledge of the design and present themselves professionally. The winning project clearly is the best at Design Day.
Raytheon Award for BEST OVERALL DESIGN
($5,000)
While several designs may meet the judging criteria, this award is given to the design that does so the most effectively. The project that receives this award excels in many ways. The design is thoughtful and its implementation is of high quality. It accomplishes all key design requirements and is supported by rigorous analysis and testing. Its poster and presentation are professional and easy to understand.
Bly Family Award for INNOVATION IN ENERGY PRODUCTION, SUPPLY OR USE
(1st prize - $2,000; 2nd prize - $1,000)
This award recognizes the best project related to sustainable, cost-effective and environmentally friendly energy production, distribution or use. Focus areas for winning projects include developing new energy sources, reducing energy costs, improving efficiency or reducing cost of energy distribution, adapting existing energy distribution methods to better integrate new energy sources, and increasing efficiency of energy use.
RBC Sargent Aerospace & Defense VOLTAIRE DESIGN Award
($3,000)
The French philosopher Voltaire is credited with the saying “Le mieux est l’ennemi du bien,” which means “the best is the enemy of the good.” It has also been noted that “simplicity is the ultimate sophistication.” This award recognizes the design team that best emulates these ideals and resists the temptation to overly complicate the design, yielding a clean, simple, elegant, lowestcost design that simply works well.
BAE Systems Award for BEST SYSTEM SOFTWARE DESIGN
($2,500)
Software has become an integral part of the operation, management and control of complex systems comprising mechanical, electrical and optical elements. This award recognizes the best use of software in a system design to enable task automation, object recognition, system robustness, data collection, or other impressive features that would be difficult to achieve without software. Teams are judged on the reliability, robustness, maintainability, reusability, originality and testability of software embedded in their designs.
Acron Aviation Award for MOST ROBUST SYSTEMS ENGINEERING
($2,500)
The systems engineering perspective is based on systems thinking. When a system is considered as a combination of elements, systems thinking acknowledges the primacy of the whole and the interrelationships of the system elements to the whole. This award goes to the team that most robustly addresses all aspects of the project from the systems perspective.
Honeywell Award for EXCELLENCE IN AEROSPACE SYSTEM DESIGN
($2,000)
This award recognizes excellence in overall system design in a project with an aerospace emphasis. Verbal presentations for the winning project are well structured to effectively describe the overall system and the specifics of how the team implemented its design. A key feature of the presentation is representative data demonstrating thorough testing of the system. Answers to questions are direct and indicate a high level of team competency about the details of the project. The presentation shows how all team members contributed, exhibiting core values of teamwork and professionalism.
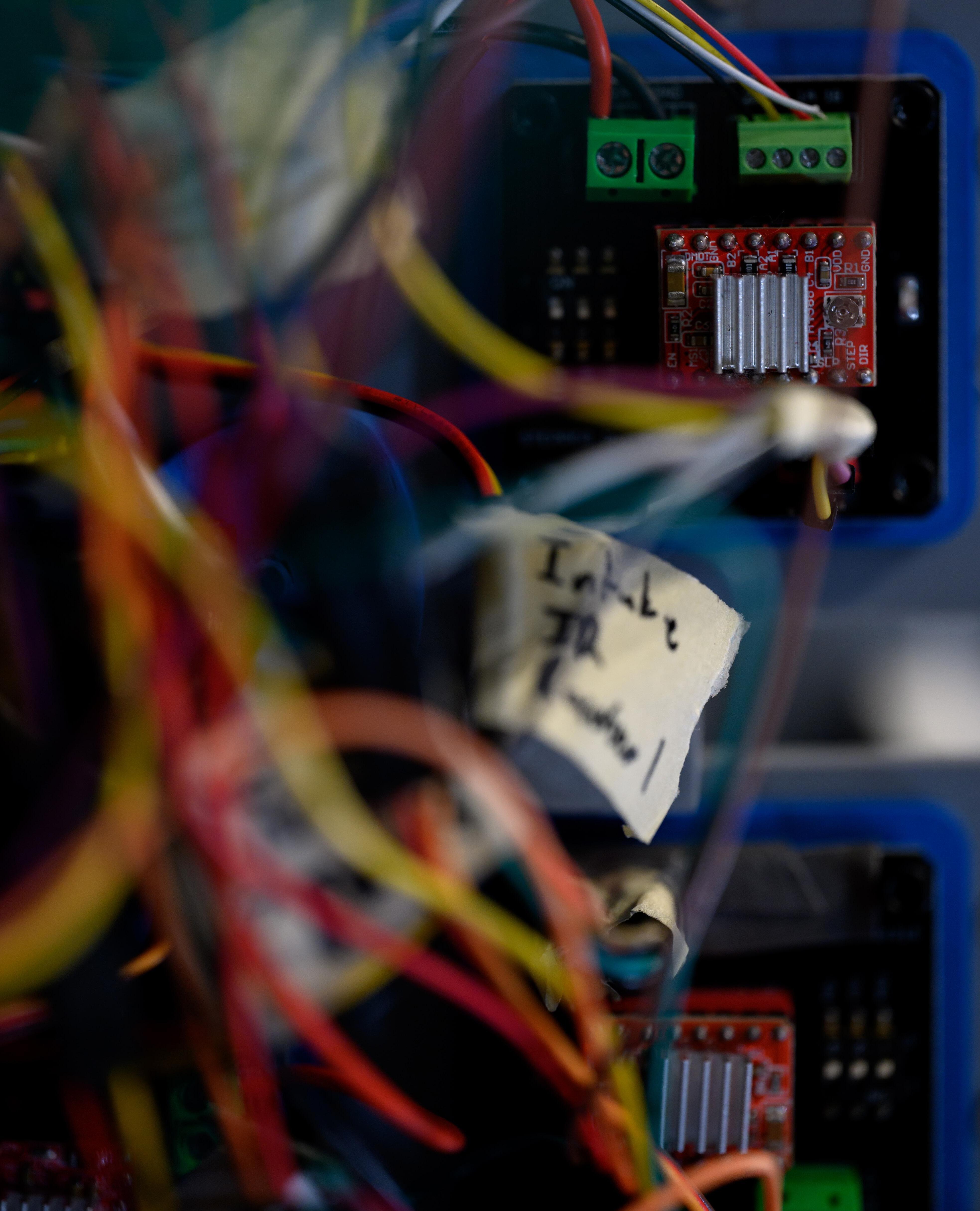
Coherent Award for BEST OPTICAL SYSTEMS DESIGN
($1,500)
This award recognizes the most innovative use of optoelectronics and optomechanics in a design. It is given to the team that demonstrates the most thorough approach to the design and engineering of its optical system. The winning team conveys complete understanding of the optical design, system requirements, tolerance analysis, and optical component usage. Important criteria are integration of optics into the overall system, novel use of optical components, creative use of commercial off-the-shelf items, verification of optical components, achievement of system requirements, use of standard optical design software, and manufacturability of optical design and components.
Rincon Research Award for BEST PRESENTATION
($1,500)
This award reflects the quality of the overall verbal and poster presentations. Verbal presentations are well structured to efficiently describe the overall problem being solved and the specifics of how the team accomplished its design. Answers to questions are direct and demonstrate mastery of the project. Each presenter speaks in a clear and easily audible voice, making good eye contact with the judges. The poster is visually interesting and graphically well organized to tell a standalone story of the project.
School of Mining and Mineral Resources Lowell Award for INTERDISCIPLINARY SOLUTIONS FOR MINING
($1,500)
The Lowell Award recognizes the best interdisciplinary solution that supports the mining industry, whether it is the improvements of optics and visibility for safety, reducing personnel exposure while working in the mine or mill, developing the next generation of high-altitude drones for mineral surveys, or a novel way of extracting minerals from space. This award requires the skills of all engineering disciplines. While expanding frontiers in resource development, the winning team demonstrates how its design makes quantifiable improvements to safety, the community and the environment.
School of Mining and Mineral Resources Lundin Award for INNOVATION IN MINING
($1,500)
The Lundin Award recognizes design innovation in the safe and economical extraction of mineral commodities. A key focus for this award is a written, well-documented mineral resource report, a well-developed mine plan, and an economic model to demonstrate the project’s viability. True innovation will illustrate the sustainability of the resource and its relationship with the environment and community. The written report and oral presentations for this project should demonstrate collaborations across the team members’ disciplines.
Roche Tissue Diagnostics Award for MOST INNOVATIVE ENGINEERING DESIGN
($1,500)
The recipient of this award demonstrates novel use of existing components or the creation of entirely new components to meet customer requirements. The most innovative design not only is a creative solution to a problem, but also the winning project is a well implemented, effective solution. This award recognizes the team that creates or makes use of components in the most innovative way or demonstrates excellence in the implementation of innovative design, or both.
W.L. Gore and Associates Award for LIFELONG INNOVATION
($1,250)
This award honors a team demonstrating excellence and innovation in biomedical engineering design. It recognizes outside-thebox thinking that pushes boundaries and hands-on approaches to creative solutions. Projects are judged on the elegance and creativity of the technical solutions and their implementation. The winning team effectively communicates the design, expresses how the project will improve lives, describes the current environment or paradigm, and generally speaks toward the economic reality of a possible implementation.
Mark Brazier Award for BEST BIOMEDICAL SYSTEM DESIGN
($1,000)
Biomedical engineering advances knowledge in engineering, biology and medicine. It improves human health through multidisciplinary integration of the engineering sciences with biomedical sciences and clinical practice. This award recognizes a design demonstrating excellence and innovation in biomedical engineering. It rewards outside-the-box thinking that pushes boundaries and hands-on approaches to creative solutions. Projects are judged on the elegance and creativity of the technical solutions and their implementation. The winning team effectively showcases the project’s design and clearly communicates its processes for creativity.
Henry & Suzanne Morgen Award for BEST CONSIDERATION OF THE END USER
($1,000)
This award goes to the team that best considers the needs of the end user/client. The winning team demonstrates consideration of the end user’s needs throughout the design process. The team has a list of end user concerns and shows how they are addressed. Many times, a physical prototype is created to understand and study the fit, form and function of the device or system, and usability testing is conducted with a sample group of end users to validate or improve the design. Teams are judged on the appropriateness of the prototyping, effectiveness of prototyping to improve the design, and how well the needs of end users are considered. Prototypes are made using rapid fabrication technology, traditional manufacturing or construction by hand.
Technical Documentation Consultants of Arizona Award for BEST DESIGN DOCUMENTATION
($1,000)
Successful implementation of any innovative design requires that all members of the design and production team communicate effectively. Design intent must be communicated to the rest of the team using documentation, with a clear map for others to reproduce the design based on that documentation only. The mechanical portion of the design is evaluated on the use of drawings with geometric dimensioning and tolerancing, solid models, illustrations and presentations that can be used to manufacture and inspect design hardware. Software and other systems are evaluated on the use of documentation that clearly and fully describes the system and illustrates the approach to testing.
Ana Needham Award for BEST EXTERNAL COLLABORATION BY A SINGLE-DISCIPLINE TEAM
($1,000)
This award recognizes the single-discipline design team that best demonstrates external team collaboration. Like real-world problems, senior design projects require skills from multiple sources, and students should learn the value of leveraging the strength of a diverse team, as well as seeking out external guidance and support to succeed. These skills are foundational to a successful engineering career.
Frank Broyles Award for BEST UAS DESIGN
($1,000)
This award recognizes the UAS project with the highest quality of design and construction that succeeds in or makes a good attempt to achieve the sponsor objectives.
The Institute of Electrical & Electronics Engineers (IEEE) Tucson Section Award for BEST USE AND IMPLEMENTATION OF ENGINEERING STANDARDS
($1,000)
The Institute of Electrical & Electronics Engineers is the world’s largest technical professional organization dedicated to advancing technology for the benefit of humanity. IEEE and its members inspire a global community through its highly cited publications, conferences, technology standards, and professional and educational activities. The society is a leading developer of international standards underpinning telecommunications, information technology, and power-generation products and services. This award recognizes the team that best shows the standards used in its project and how the use of those standards facilitated or improved the overall design and/or performance outcome.
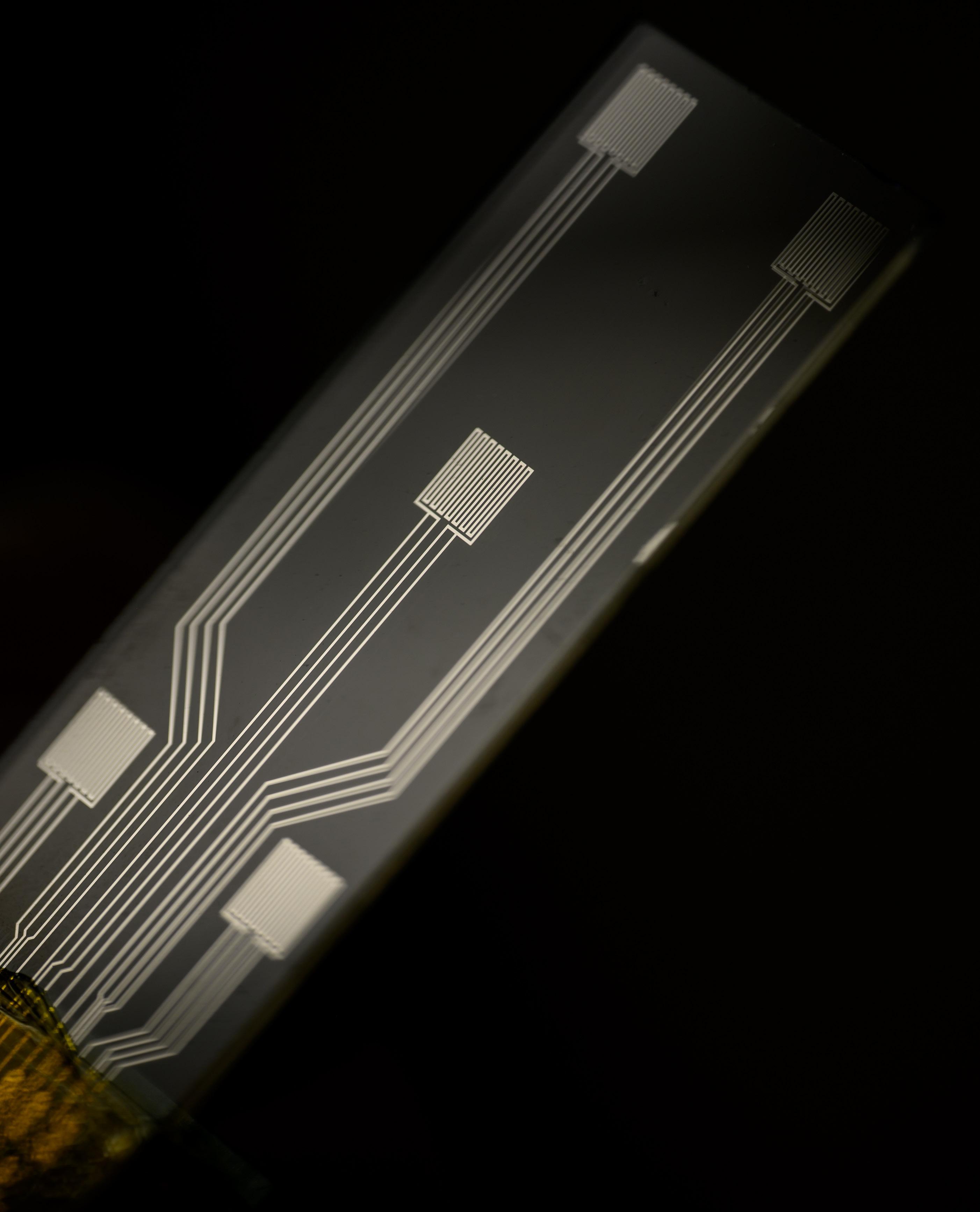
Mensch Foundation Award for BEST USE OF EMBEDDED INTELLIGENCE
($1,000)
The Mensch Award recognizes the team that best integrates embedded intelligence into a potential product, building a smart connected prototype with commercial value. Embedded Intelligence is characterized as the ability of a product to sense, process, communicate and actuate based on information gained from an understanding of itself and others and for the benefit of many. Preference is given to designs with SPCA capabilities demonstrably surpassing human abilities to perform the same function.
Larry Head Award for BEST VIDEO CAPTURING THE PROJECT STORY
($1,000)
The winning video best captures the sponsor’s need, the process used to develop the solutions, final solution – including testing and evaluation – and how the project meets the sponsor’s needs.
Lawrence Livermore National Laboratory Award for IMPACTFUL APPLICATION OF SCIENCE & TECHNOLOGY
($1,000)
This award recognizes a team that thinks big, applying science and technology to make a significant difference in the world – an enduring principle of Lawrence Livermore National Laboratory.
Steve Larimore Award for PERSEVERANCE & RECOVERY
($1,000)
The engineering design process is often rife with roadblocks. While these issues can be distressful, they represent opportunities for learning and can lead to designs that otherwise might not have been conceived. This award recognizes a team’s ability to learn from challenges and overcome hurdles during the design process. Judges consider the ingenuity of recovery factors as they relate to a successful final project.
Greg Lorton Award for PRACTICAL PROCESS DESIGN
($1,000)
Effective design of processes sets the stage for the success of chemical and environmental engineering projects. This award recognizes the best application of process design and economic principles to a chemical or environmental process. These principles include process synthesis through flow diagrams, material and energy balances, preliminary equipment sizing, and the determination of the economic viability of the project.
Sharon ONeal Award for SOFTWARE DEVELOPMENT WITH EMERGING TECHNOLOGIES
($1,000)
This award celebrates transformative projects that harness emerging technologies – artificial intelligence, machine learning, DevOps (or DevSecOps), augmented reality or virtual reality (AR/VR), and other forms of automation, for example. The winning team revolutionizes user experiences, optimizes business processes, or pushes the boundaries of what is possible in software engineering.
Phoenix Analysis & Design Technologies Award for BEST USE OF PROTOTYPING ($750)
This award goes to the team that best uses a physical prototype model to understand and study the fit, form and function of the device or system design. Teams are judged on the appropriateness of the prototyping technology, success in improving design, and effectiveness in communicating the need for prototyping. Prototypes can be made using rapid fabrication technology, traditional manufacturing or construction by hand.
Dataforth Corporation Award for BEST UTILIZATION OF THE INTERNET OF THINGS ($750)
Some estimates put the number of Internet of Things devices in 2025 at 40 billon worldwide. This award recognizes the team that best integrates modern IoT hardware, networking, data storage and analysis in a data acquisition and control system. The winning project’s data acquisition involves at least two sensors and a communication protocol, while algorithms, analysis and actuators provide feedback and control. Projects are judged on use of IoT devices and connectivity to provide simple, robust and efficient data acquisition and control to accomplish all or part of the project requirements.
Coherent FISH OUT OF WATER Award
($750)
This awards honors students successfully accomplishing tasks outside their realm of expertise. Senior design projects draw on multiple disciplines, and sometimes students must learn new subjects in areas outside their majors to accomplish project objectives. A student acquiring knowledge and applying newfound skills to help a team thrive shows dedication and initiative, integral traits of successful engineers.
Sharon ONeal’s SOCIAL IMPACT Award
($750)
This award celebrates engineering as a force for good, recognizing the capstone project that demonstrates the greatest potential to create positive change for society. The winning team’s engineering solution addresses critical social, environmental or humanitarian challenges. The project exemplifies not only technical excellence and creativity but also a commitment to improving lives, advancing sustainability or fostering community wellbeing.
Simpson Family Award for BEST SIMULATION AND MODELING
($500)
This award recognizes the project that makes the best use of computer-based simulation or modeling. The simulation may be the project itself or a tool used to model the performance of the design. Winning criteria include scope of the simulation, fidelity compared to real-world performance, and the engineering judgement exercised in determining the complexity of the model.
AZ Technica MANUFACTURING READINESS Award
($500)
This award is given to a team that goes beyond sponsor requirements, designing and building the best system considering usability and manufacturing readiness. Winning criteria are as follows:
• Reviews alternative designs, with the solution – one that can be used immediately – meeting or exceeding sponsor requirements.
• Considers producibility, ease of assembly and cost.
• Assesses reliability and maintainability while in the design/model/prototype phases as well as build phases.
• Considers user operation and includes operator instructions.
• Incorporates complete technical data package.
Dragoon Technology Award for MOST UNINTUITIVE DESIGN DRIVEN BY PHYSICS
($500)
While some designs are intuitive, others apply basic physics without necessarily conveying an understanding of the underlying principles, at times resulting in a rejected, or even laughable, design. This award recognizes a design that only an engineer could love.
AZ Technica Award for SUSTAINABLE MANUFACTURING INNOVATION ($500)
This award goes to the team whose design best incorporates a manufacturing method to reduce carbon emissions. Projects can introduce manufacturing techniques or use existing methods to lower cost and improve the quality of a product while reducing carbon footprint.
Honeywell Award for TEAM LEADERSHIP
(two individuals at $250 each)
This award recognizes students who best exemplify teamwork. Winners work cooperatively with others to produce a high-quality project; take initiative; give and receive feedback, supporting and respecting the opinions of team members; demonstrate effective leadership; keep their team focused; and elevate the work of team members. Teammates nominate potential winners.
Having access to the tools and resources at the Engineering Design Center has made a huge difference, and it’s fulfilling to think that our final product might improve the very space and tools that helped us build it.”
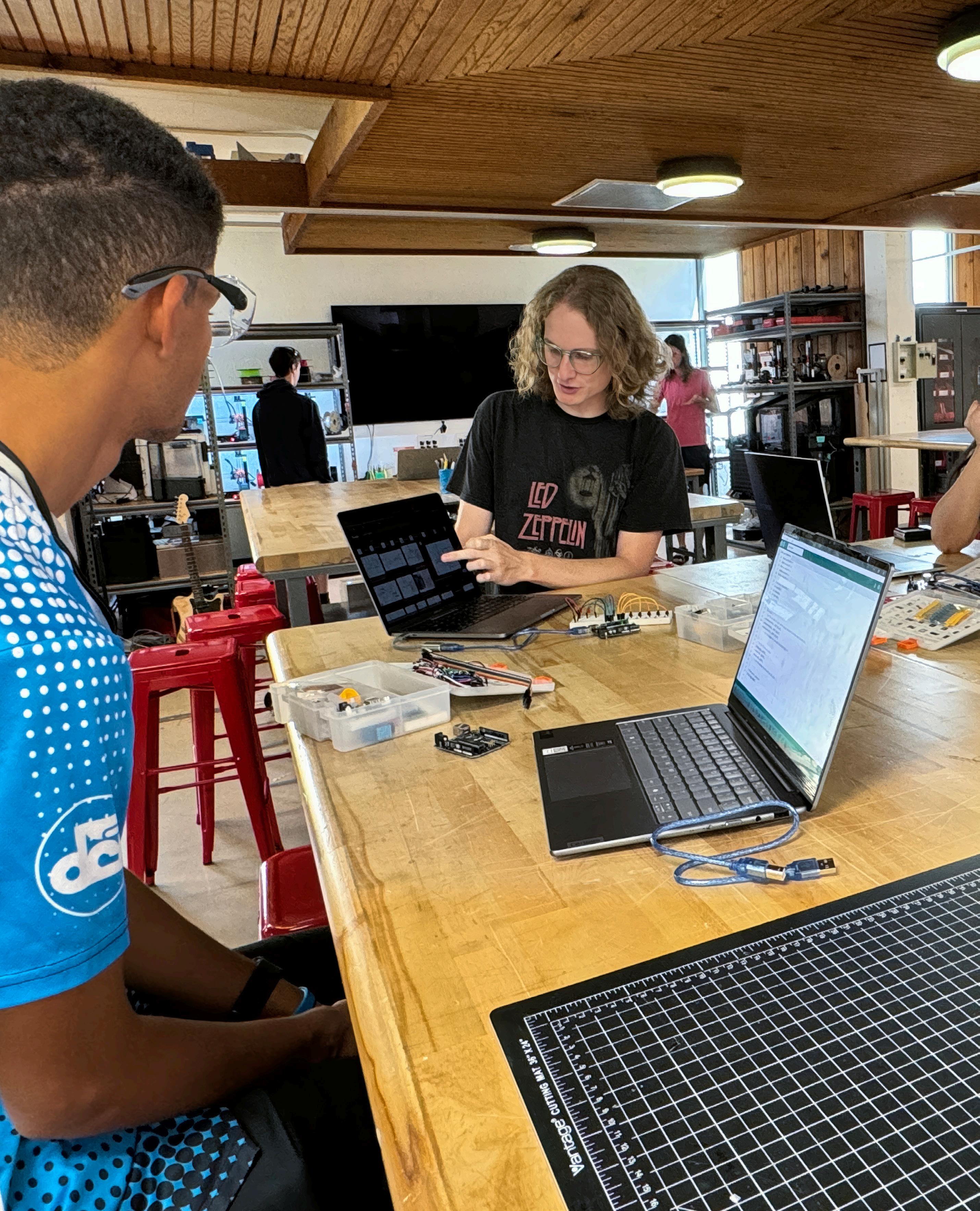
PROJECTS
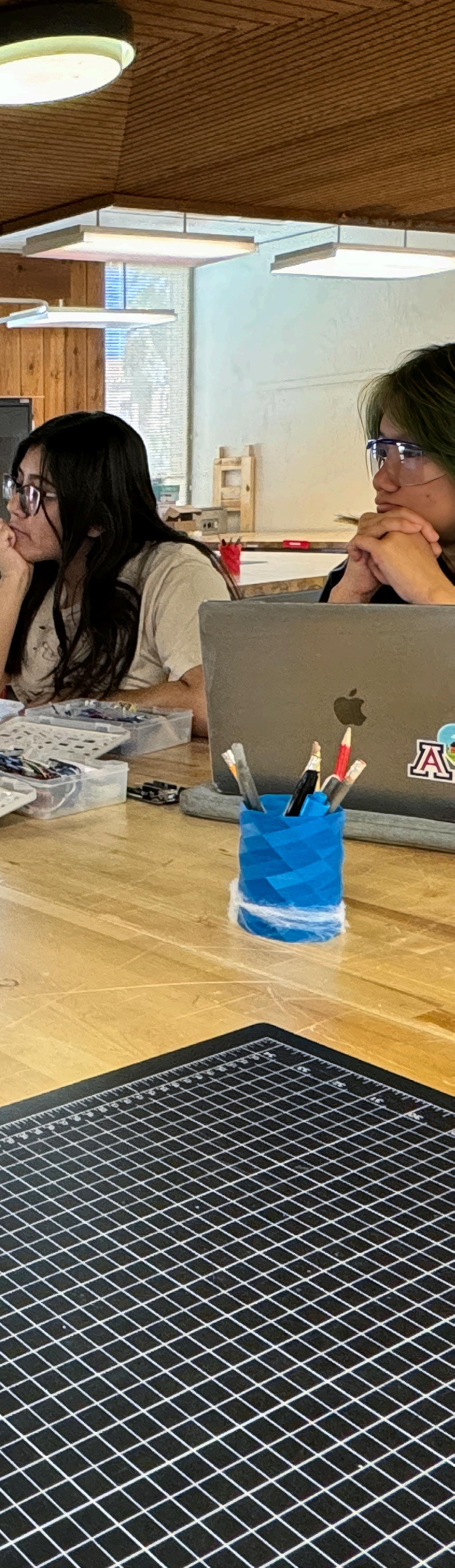


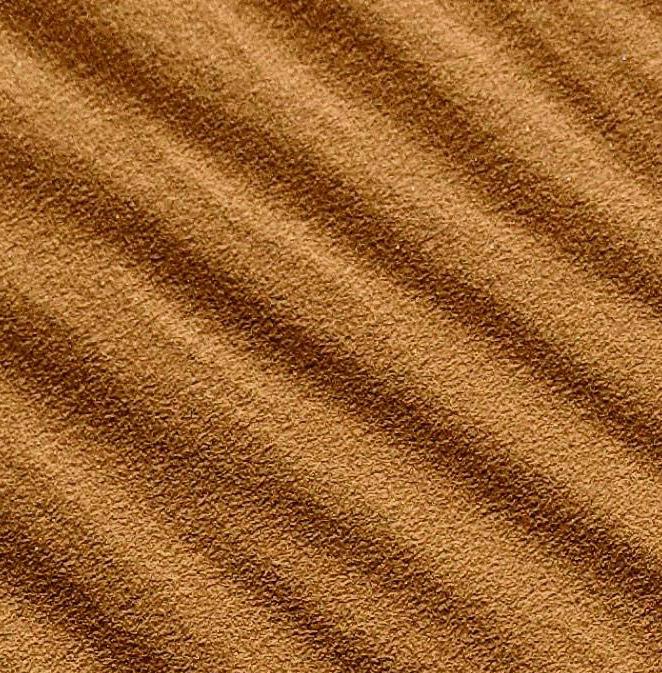
Drone-Based Object Awareness and Avoidance
Upgrade of Algae Optical Sensor Device
Aerospace Radome Impingement Test (Year 2)
Airplane Fuel Selector Valve Control for Armless Pilots
Treadmill with Soft Ambulatory Surface
Active Shooter Response, Door Breaching System
Ocean Light Control
SPIDER: Semi-Autonomous Precision Intelligent Detection and Elimination Robot, Phase 3
3D Printer Plastic Filament Verification System
309 AMARG Advanced Modules
Preliminary Design Study for a Blended Wing Body Seaplane
Self-Sterilizing Enclosed Face Shield for Health Care Workers
CASA Device for Carpal Tunnel Syndrome Treatment
Camera for Aerospace Situational Awareness (CASA)
Navigating a River of Glass and Plastic
Controlled Release Microparticle Process Design
Development of a Pediatric Foley Catheter with Safety Release Mechanism
PODBot Phase 2
Small Autonomous Amphibious Delivery System (SAAD)
Clean Hydrogen Power Generation Project
Optimizing Drip Line Harness Design for Use with Helicopters in Slope Leaching
Advanced Fluidics for Cancer Diagnostics
Slide Geometry and Safety in Pathology Automation
Fourth Generation Ground Support Equipment Design
Automated Slide Transfer
Parcel Identification and Trackability (PIT)
New Cart and Connector Design for SynCardia Total Artificial Heart Hospital
Driver Unit
Avionics Size Reduction and Thermal Reliability Enhancement
Lunar Automated Regolith Processing (LARP)
AQUABOT Fluence - Advanced Sleek Hydrodynamic Hull Design for Aquatic Drones
Dual Output Recon Camera (DORC)
Solar Performance Estimation Kit (SPEK)
MD-Sensei
Broadband All-Fiber Depolarizer
Hydraulic Mining Shovel Panel Re-Design with Adhesive Bonds
Wavefront Performance Measurement on Small Numerical Aperture (NA) Lenses
Liquid Propellant Rotating Detonation Rocket Engine (RDRE)
Hybrid Electric Demonstration Engine for Heavy-Lift UAV
WATER-BADDIES - Microplastic, Heavy Metal and Inorganics Water Detection System for Environmental and Human Health
The Room Knows - The Smart Patient Exam Room
Optical Metrology Module
Powder Conveyance for Sustainable 3D Printing
Automated Weight Bearing 3D Ultrasound Foot Scanner
NEO-CATH - Smart Urinary Catheter System - Analgesic, Anti-Inflammatory, Anti-Infective
Fiber-Coupled Package Test Station
3D Printing Temperature/Humidity Control Filament
Golf Putting Robot
AZ Heat Medicine - Reduce Renal Failure in Arizona - Fly, Measure, Treat
CycleSafe: A Bicycle Handlebar Mounted Automobile Proximity Sensing, Warning and Reporting Device - Phase 3
Pyrolysis Oil Refining for Plastic Recycling, Carbon Capture and Disaster Relief
Suspension Bath for Severely Burned or Injured Patients
The Exploration of Thermal Diode Effects of Nitinol-Based Shape Memory Alloys
Hybrid Electric Retrofit Demonstration for a Drilling Rig
Self-Disinfecting Urinary Catheters Using Safe Antimicrobial Light
Kay-Phos - A Point-of-Care Potassium and Phosphorus Diagnostic System for Kidney Patients
Vibration-Powered IoT Sensors with Ultra-Low Power RF Communication
Enhancing Monitoring Systems for Critical Feeders at the Capstone Copper Concentrator
Design, Build and Fly a Modular UAV for Autonomous Flight Tests
Local Hypothermia in Spinal Cord Injury
Heap Leach and Open Pit Optimization
Underground Mine Design
2024-2025 SME Metallic Design Competition
Heavy Metals Remediation Using Fungi
Fish Feed From Insects
Bomb Calorimeter Lab Experiment
PFAS Removal for Municipal Drinking Water
Nonalcoholic Anxiety Reducing Beverage
Bioethanol Production from Agricultural Waste
Process Optimization for Pyrolysis Oil Refining for Plastic Recycling and Disaster Relief
Extraction of Valuable Salts from Produced Water
Helium Recovery from Natural Gas
Improving Energy Efficiency in Semiconductor HVAC Systems
Naptha Methaforming
Hydrogen-Solar Residential Microgrid
Hydro-Desulfurization Unit
Inulin Production
AZ Water Competition
Radio Network Optimization
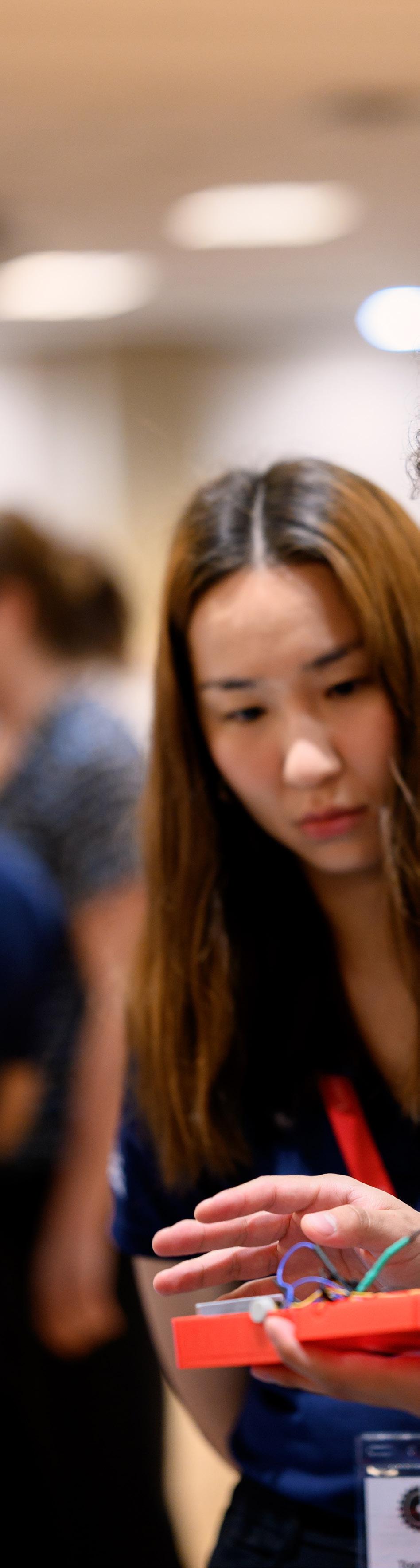

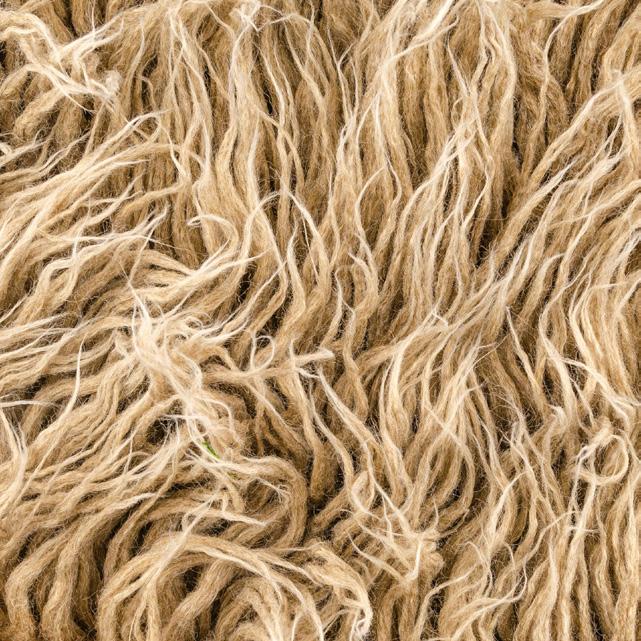
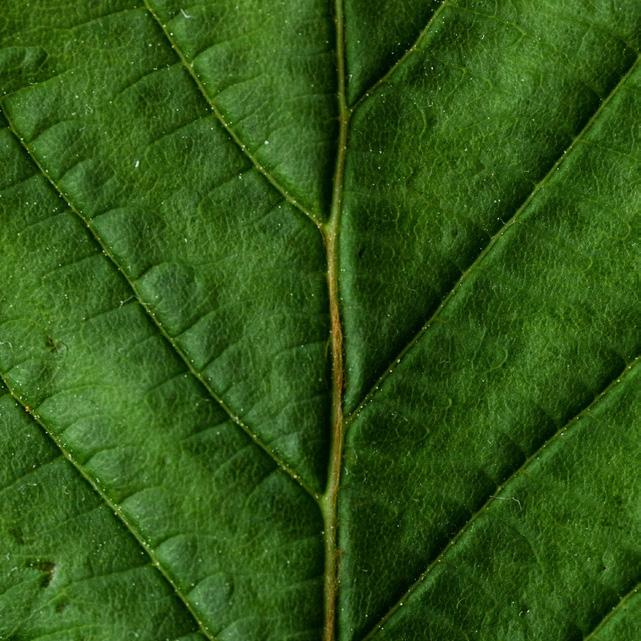
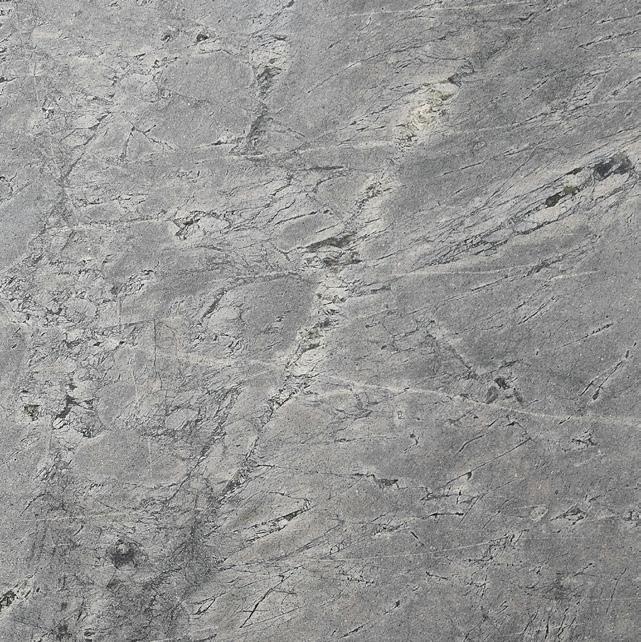
This project gives us the ability to go and do something not constrained by an assignment. It gives us the opportunity to be engineers and be creative.”
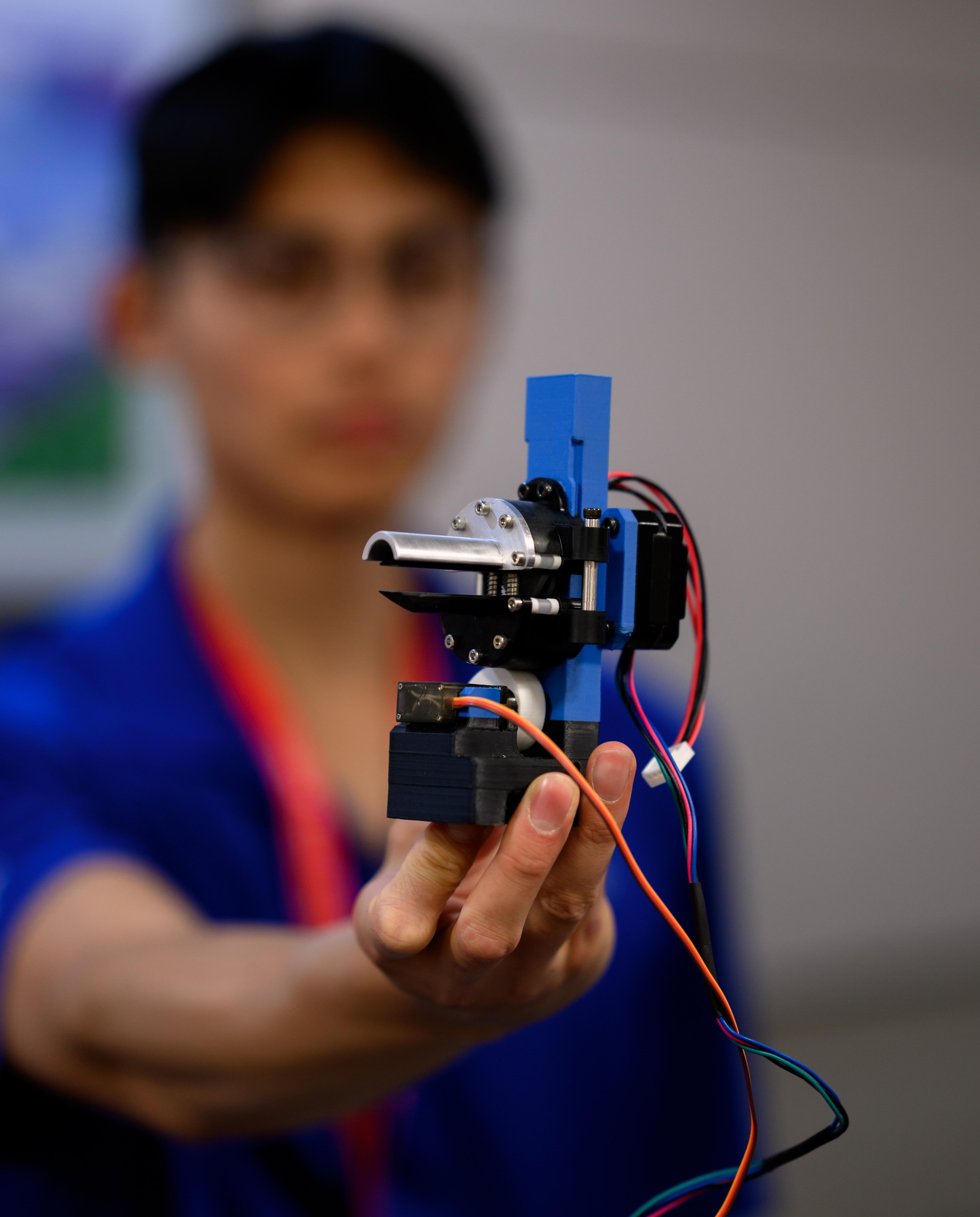
PROJECT DESCRIPTIONS
Drone-Based Object Awareness and Avoidance
Team 25001
PROJECT GOAL
Develop a simplified drone degraded visual environment pilotage system (DVEPS-Lite) that enables autonomous drone navigation in degraded visual environments (DVE).
Drones often struggle in applications where visibility is limited. This project provides a lightweight, costeffective, and highly reliable solution for enhancing drone performance in challenging environments. The team developed a simplified drone DVEPS-Lite system that enables autonomous drone navigation in these DVEs. By integrating lidar, or light detection and ranging, and video camera sensors, the system maps the drone’s surroundings in real time and allows the drone to navigate safely while avoiding obstacles, even in low-visibility conditions.
The team’s solution was to design and build a custom mirror mounting system that reflects the lidar laser. This creates a crosshair pattern, which allows more precise object detection at distances of up to 20 m. The team also included an actuator system that stabilized this mount by counteracting drone tilts and vibrations. This stabilization was necessary to ensure accurate environmental mapping and obstacle detection. The drone operates autonomously while transmitting telemetry and visual data back to a ground control station, providing operators with critical situational awareness. Additionally, the system features manual override capabilities so the operators can stop or land the drone when necessary.

TEAM MEMBERS
Dean Burross, Optical Sciences & Engineering
Jorge A Del Rio, Electrical & Computer Engineering
Declan Loomis, Aerospace Engineering
Andrew Mineau, Mechanical Engineering
Aidan Javier Roig, Software Engineering
Dorian Shay, Software Engineering
Eliana Stilson, Optical Sciences & Engineering
COLLEGE MENTOR
Mike Nofziger
SPONSOR ADVISOR
Benjamin Cromey
Upgrade of Algae Optical Sensor Device
Team 25002

PROJECT GOAL
Measure overall algae health in commercial raceway systems and provide real-time data within field conditions.
As algae-based industries – including biofuels, agriculture, and pollution management – continue to grow, precise and scalable monitoring of algal growth is becoming increasingly vital. However, existing assessment methods are energy-intensive, time-consuming, and limited to laboratories. This project addresses these challenges by improving a benchtop sensor designed to take real-time, in-field measurements and develop it into an in situ sensor for continuous deployment in raceways, which are cultivation environments.
The team focused on key improvements, including extending the sensor’s temperature range, boosting durability, and improving user-friendliness. Using spectrophotometry at 650 and 780 nanometers, the team’s system applies Beer’s Law to measure algae concentration and turbidity.
Data from the device is transmitted via ethernet to an external acquisition device. Once there, a digitalto-analog conversion stage ensures seamless integration with standard data collection systems. To mitigate temperature-induced fluctuations in laser output, the system includes a double-beam design that calibrates all measurements with simultaneous sample and reference readings. The team applied all these design improvements to both the original benchtop sensor and to the new in situ sensor. In addition, the team created a compact, hydrodynamic housing for the in situ version.
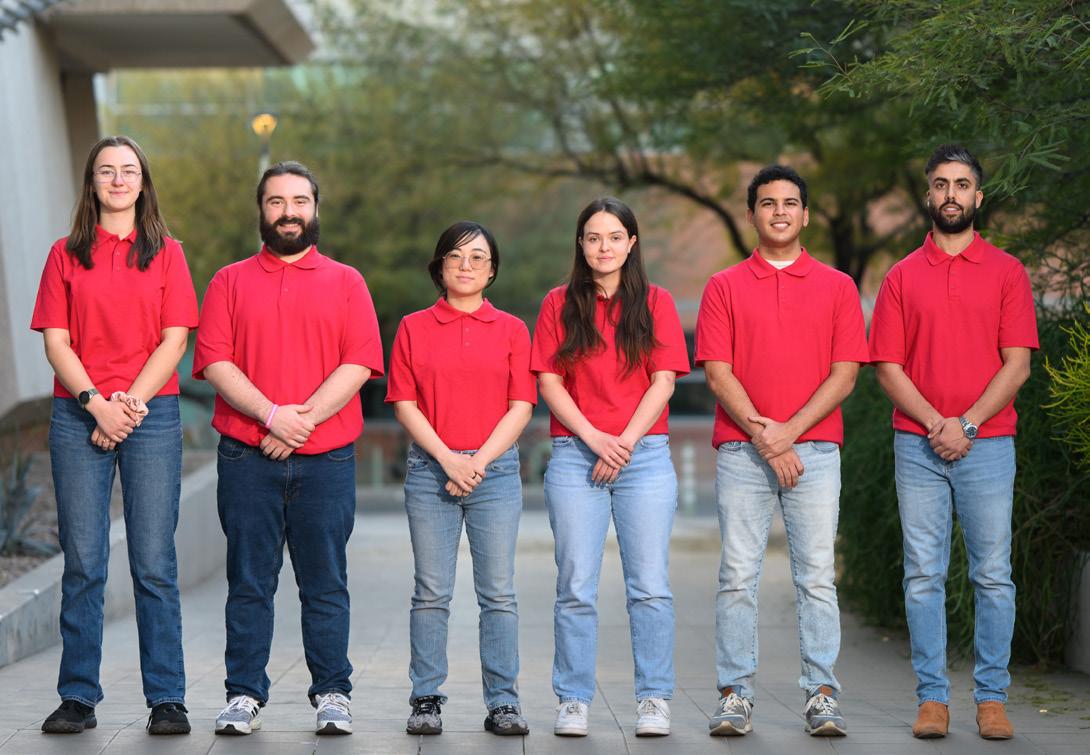
TEAM MEMBERS
Nawel Joachim Fajardo, Biosystems Engineering
Aliah Haigh, Electrical & Computer Engineering
Ellie Laton, Biosystems Engineering
Waled Nwaish, Mechanical Engineering
CJ Reda, Software Engineering
Emma Grace Heckert, Electrical & Computer Engineering
COLLEGE MENTOR
James Sweetman
SPONSOR ADVISOR
Gregory Ogden
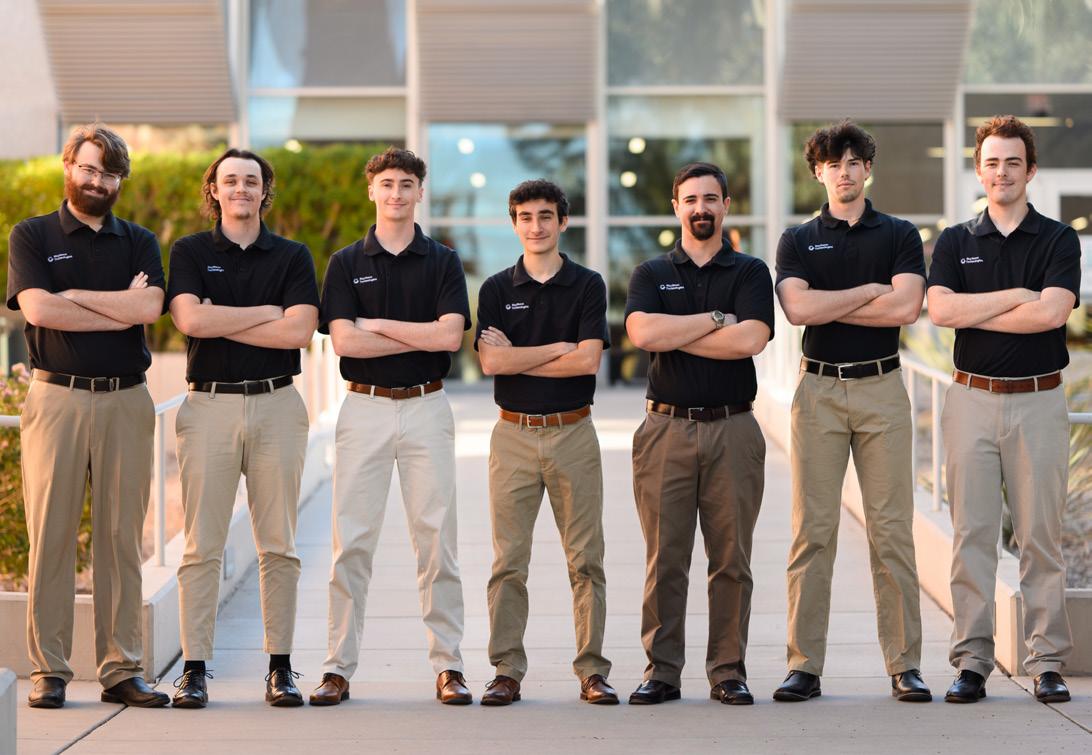
TEAM MEMBERS
Tanner Lensing, Mechanical Engineering
Hank Michael Erickson, Aerospace Engineering
Tyler Michael Fleming Bleed, Aerospace Engineering
Luke Garman, Applied Physics
Hunter Gray, Aerospace Engineering
Ryan Ramsden, Mechanical Engineering
Owen Sutherlin, Aerospace Engineering
COLLEGE MENTOR
Jeff Scott Wolske
SPONSOR ADVISOR
Chris Carbonneau
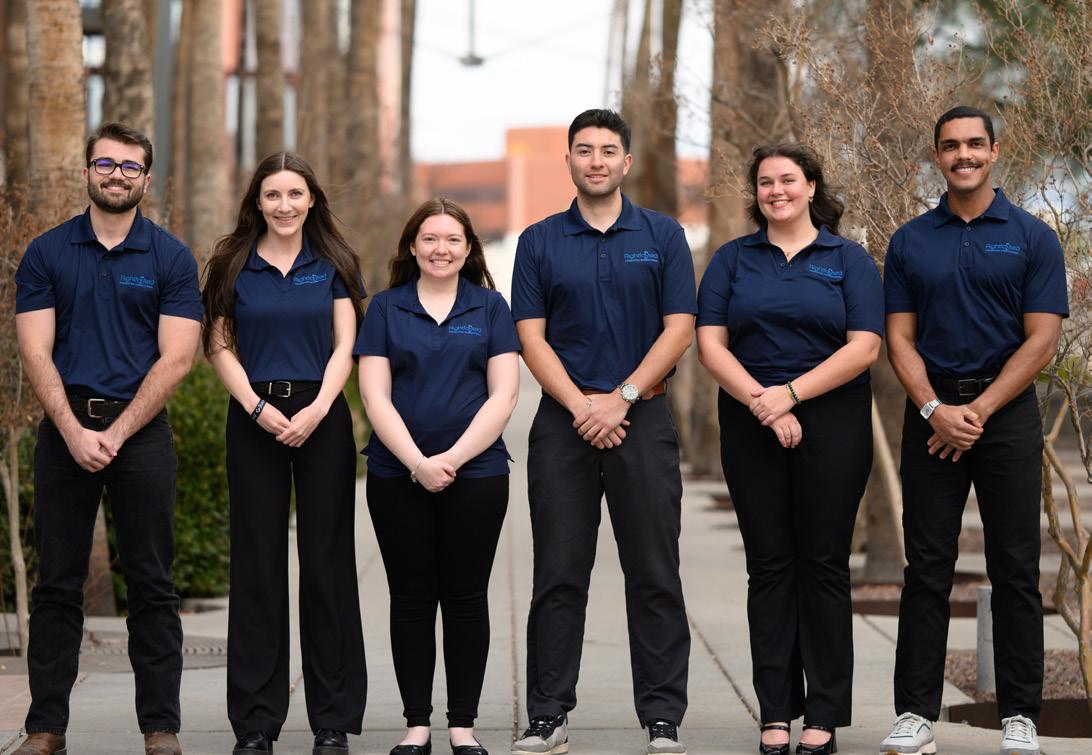
TEAM MEMBERS
Mason Marrero, Electrical & Computer Engineering
Abdulaziz Alrandi, Electrical & Computer Engineering
Luis Barnett, Aerospace Engineering
Hunter Fiore, Systems Engineering
Natasha Oler, Aerospace Engineering
Anja Ziegler, Aerospace Engineering
COLLEGE MENTOR
Carey Jeannette Jones
SPONSOR ADVISOR
Patrick Chamberlain
Aerospace Radome Impingement Test (Year 2)
Team 25003
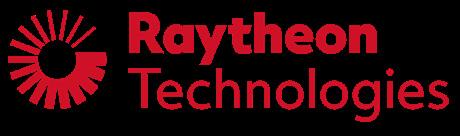
PROJECT GOAL
Create a cost-effective testing apparatus and methodology to evaluate the damage caused by high-speed water droplet impact to a radome, or missile nose cone.
Supersonic missile nose cones are designed to minimize aerodynamic drag at ultra-fast speeds while protecting sensitive electronics. These nosecones, or radomes, are often made of advanced materials that are transparent to the missile’s radar so it can track targets but are sensitive to impacts. Current testing methods for evaluating high-speed rain impacts on these radomes require very expensive and time-consuming methods. Furthermore, simulating a water droplet impact at supersonic speeds is challenging due to the complexities of deformable liquids.
The team’s solution is the Radome Impingement Test Apparatus (RITA) which uses pressurized gas to propel a nylon bead down a barrel at high speeds into a sample radome. This system affordably and accurately simulates the damage water droplets inflict on radomes. RITA uses an articulating mount to precisely adjust the angle and location of the testing sample to create varied impacts. It can evaluate the resulting damage to the radome and convert it into a damage score. This score becomes a metric to evaluate which radome materials perform better under high-speed rain impacts. Verification test results show promise for RITA as a rapid-turn and inexpensive evaluation solution.
Airplane Fuel Selector Valve Control for Armless Pilots
Team 25004
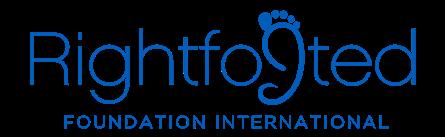
PROJECT GOAL
supported by Craig M. Berge Dean’s Fund
Redesign and automate the current fuel selector valve in an experimental RV-10 aircraft to ensure safe, reliable, and accessible fuel control for an armless pilot and any copilot.
In aircraft with multiple fuel tanks, pilots must regularly switch between tanks to maintain balance and prevent fuel starvation. However, pilots with disabilities are often unable to operate the fuel selector handle in its current design. The team worked with Jessica Cox, an armless pilot, to create a custom redesign that accommodates her needs. Additionally, the team integrated additional automated systems that allow her to focus on other critical flight tasks while ensuring proper fuel control.
The redesigned system consists of four primary functions: an automated fuel selection, an electronic override, a redesigned fuel selector handle, and a means of error detection. The pilot can enable automatic fuel switching as desired. When activated, the system automatically switches between tanks every 30 minutes. An electronic override allows the pilot to manually change the valve’s position with the push of a button. Cox can use the redesigned handle to move the valve without electronics. It is ergonomically optimized for Cox while remaining accessible to a nondisabled copilot. Finally, error detection alerts the pilot or copilot of any system issues using a display and light-emitting diodes that offer constant visual feedback. This project was specific to Cox, but the results enhance flight safety, reduce pilot workload, and ensure accessibility for all pilots regardless of physical ability.
Treadmill with Soft Ambulatory Surface
Team 25005

PROJECT GOAL
Design a specialized treadmill with a soft ambulatory surface to study rat gait on diverse terrains – including simulated extraterrestrial regolith – for research in biomechanics, rehabilitation and space exploration.
Bone health metrics, such as bone strain and gait patterns, provide critical insights into conditions like osteoporosis and spaceflight-induced bone loss. This project presents a specialized treadmill system with a soft ambulatory surface designed to advance this research by simulating diverse terrains and reduced-gravity environments. By studying rat gait under conditions that mimic lunar or Martian gravity, researchers can analyze how different gravitational forces impact bone density and strength. The treadmill also allows for controlled experiments on the effects of walking on various aggregates to provide insights into bone strain and potential rehabilitation strategies.
The project involved extensive mechanical, electrical and software engineering. The team designed mechanical components using OnShape software and fabricated them with 3D printing, machining and laser cutting. The students integrated electrical systems into a custom printed circuit board. Software development focused on creating an intuitive user interface and ensuring precise control of treadmill speed and harness height.
Verification testing confirmed the system’s performance including treadmill velocity accuracy, harness weight capacity and aggregate recirculation efficiency. The final prototype is compact, fits inside a fume hood, and is powered by a standard 120V wall adapter, making it suitable for laboratory use. Additionally, it can connect to implanted devices for data collection via an antenna.

TEAM MEMBERS
Alexis Barber, Mechanical Engineering
Juan Campista, Electrical & Computer Engineering
Alicia Enriquez, Electrical & Computer Engineering
Avery Marie Miller, Biomedical Engineering
Will Chambers Stephenson, Biomedical Engineering
Gabe Vogt, Mechanical Engineering
COLLEGE MENTOR
Sardar R Mostofa
SPONSOR ADVISOR
David Margolis
Active Shooter Response, Door Breaching System
Team 25006
supported by Craig M. Berge Dean’s Fund
PROJECT GOAL
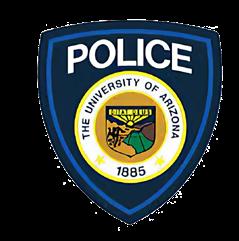
Develop a portable, next-generation tool capable of breaching steel-reinforced doors in under two minutes, operable by a single officer of any size.
Law enforcement professionals must be prepared to rapidly and effectively respond to active shooter events. This includes breaching any barriers that may stand in the way. In schools and hospitals, many doors are of high-security, reinforced metal types that render traditional breaching tools – such as the Halligan and battering ram – ineffective and inefficient. When every second counts, these tools require multiple officers and valuable minutes to gain entry.
To address this limitation, the team created a new tool that can breach these reinforced doors quickly and can be operated by a single officer. The design uses a common hydraulic actuator with a maximum column load of 2.5 tons. It is encased in an aluminum shell and equipped with steel teeth to breach both inward- and outward-opening doors by warping the door’s hinges and breaking the door frame.
The team used CAD software analysis to ensure the device can withstand the expected forces, and prototype testing results were promising. It is also lightweight and portable, featuring a backpack so the user can carry the hydraulic pump and 12V battery during use. This device provides an effective, durable and low-weight door breaching capability for first responders. These features make it a successful tool for breaching any security door an officer might encounter.

TEAM MEMBERS
Ethan Matthew Yock, Electrical & Computer Engineering
Fahad Almutairi, Industrial Engineering
Emily Ayala, Systems Engineering
Ian Harrell, Mechanical Engineering
Ximena Peregrino, Industrial Engineering
Brooke Risley, Mechanical Engineering
Daniel Larry Wolgemuth, Mechanical Engineering
COLLEGE MENTOR
Jeff Scott Wolske
SPONSOR ADVISOR
Joseph Berriman
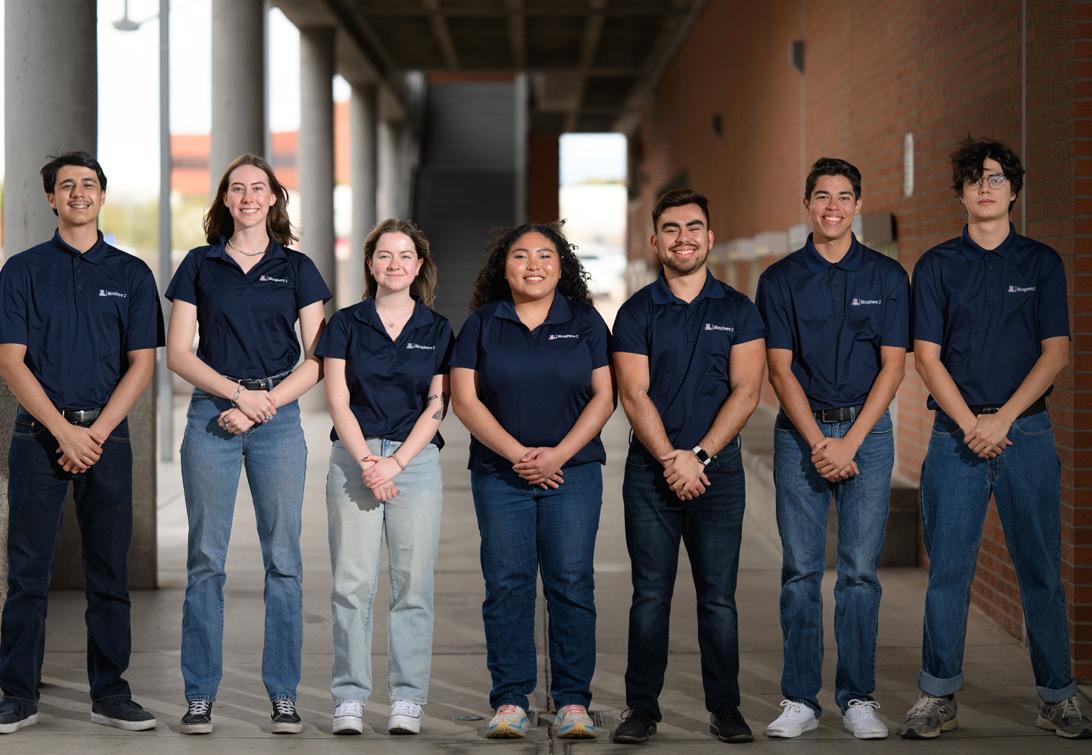
TEAM MEMBERS
Sarina Kaelyn Blanchard, Mechanical Engineering
Malia Edmonds, Software Engineering
Darwin Escobar, Electrical & Computer Engineering
Akira Y Jones, Biosystems Engineering
Maximilian Matthew Mace, Software Engineering
Samuel Moreno, Software Engineering
Ethan Tyler Smith, Mechanical Engineering
COLLEGE MENTOR
Michael Madjerec
SPONSOR ADVISOR
Lia Noel Crocker
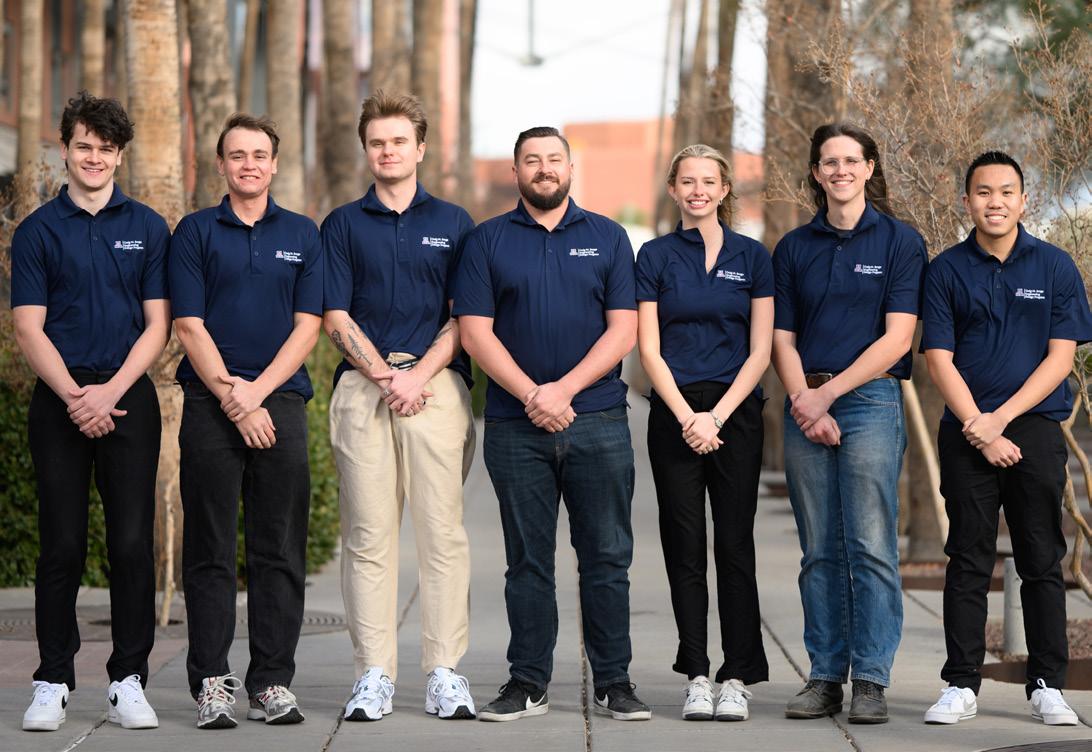
TEAM MEMBERS
Lachlan Craddock, Biosystems Engineering
Braden Joe Curtis, Software Engineering
Kevin Vi Dinh, Mechanical Engineering
Coty Norcross, Mechanical Engineering
Maddie Grace Carlson, Software Engineering
Alex Caulin-Cardo, Electrical & Computer Engineering
Robert Tkaczyk, Electrical & Computer Engineering
COLLEGE MENTOR
Carey Jeannette Jones
SPONSOR ADVISOR
Brian Little
Ocean Light Control
Team 25007

PROJECT GOAL
Design a microcontroller-based system that enables users to control a large network of Maxspect 500W LED commercial floodlights to assist with coral conservation research.
Coral conservation research depends on the ability to reliably and accurately control lighting. This project aimed to develop a personalized website that gives users the ability to send color and intensity commands to a series of Maxspect 500W LED commercial floodlights at Biosphere 2’s coral research space.
The team’s design works by sending light settings from the main system to individual controllers on the lights via controller area network bus communication protocol. The design includes one Raspberry Pi 5 and three Raspberry Pi Picos that serve as the main and individual controllers, respectively. Each light is equipped with a Raspberry Pi Pico integrated with two digital potentiometers that allow operators to precisely adjust lighting parameters based on given commands.
Users can also apply 24-hour lighting schedules and receive real-time feedback from a photosynthetic active radiation sensor. This allows them to monitor and detect out-of-range intensity values. Additionally, the team gave each microcontroller a housing unit to protect it from the environment and the capability to dissipate heat produced from the electronics. This system enables enhanced lighting control and data collection to support coral conservation research at the U of A Biosphere 2 facility.
SPIDER: Semi-Autonomous Precision Intelligent Detection and Elimination Robot, Phase 3
Team 25008

PROJECT GOAL
Improve turfgrass maintenance through advanced and semi-autonomous weed detection and elimination.
Weed overgrowth on golf courses presents a significant challenge to turf management. It requires frequent maintenance that is both labor-intensive and costly. Traditional methods rely on manual labor or widespread herbicide application. Both of these methods can be inefficient and environmentally harmful. To address these challenges, the team developed SPIDER, an autonomous, data-driven agriculture robot. SPIDER can streamline turfgrass maintenance with precise weed detection and elimination, particularly for environments like golf courses.
SPIDER’s system uses both software and hardware to enable autonomous movement, object avoidance and weed detection. Its mechanical assembly includes a main body that houses all electronic components and four legs on each side of the main body for mobility. A mechanical arm mounted on a rotational surface atop the main frame operates within a 90-degree arc between the front legs for precise weed removal. The weed detection software uses machine learning technology with PyTorch’s ResNet18 model. It is integrated with the mechanical elimination system by the repository running on an NVIDIA Jetson Nano AI platform to ensure seamless communication between software and hardware components.
3D Printer Plastic Filament Verification System
Team 25009

PROJECT GOAL
Reduce plastic waste in academic makerspaces, including the Engineering Design Center, by developing a plastic filament verification system for 3D printers.
Plastic waste is a major problem in academic makerspaces such as the Engineering Design Center at U of A. Novice users often employ incorrect material settings. This leads to failed prints, wasted material, excess material for recycling and additional time spent on cleanup and reprinting. This project aims to reduce plastic waste by developing a filament verification system for 3D printers.
The team designed a spectroscopy system to identify common filament materials used in 3D printing like PLA, ASA and PETG. Once it determines what material is loaded into the printer, the system checks for mismatches between the filament and the user’s selected print settings. These settings include material, nozzle temperature, bed temperature and print speed.
If the system detects a mismatch, it will automatically adjust the printer settings and notify the user. Ensuring the loaded material matches the print settings will improve print success rates and reduce waste. Additionally, since the primary focus of this project is makerspaces, the team will share the project as an open-source resource for the maker community as a cost-effective, efficient and sustainable solution for makers to replicate.
309 AMARG Advanced Modules
Team 25010
supported by
Craig M. Berge Dean’s Fund
PROJECT GOAL
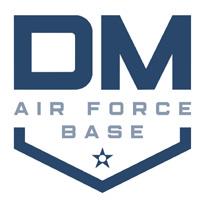
Study the cost and life cycle of decommissioned aircraft storage modules, design alternative modules using additive manufacturing, and report on the feasibility of replacing the current design.
The 309th Aerospace Maintenance and Regeneration Group (AMARG) at Davis-Monthan Air Force Base oversees a “boneyard” of decommissioned military aircraft. These aircraft sit on large wooden modules in storage. The modules are effective but outdated. In this multifaceted project, the team conducted a life cycle study on the current modules, developed a novel additive-manufactured replacement for the block, and reported on the feasibility of replacing the current modules with the new design.
The team first explored the cost of materials, production and implementation of the current modules. One of the key findings was that the current wooden module was designed under the limitations of additive manufacturing at the time. Conducting a trade study comparing cost, strength and environmental resistance of the current module and new materials, the team determined that acrylonitrile styrene acrylate, a thermoplastic polymer, is an optimal replacement material.
The team then carried out finite element analysis and topology studies to optimize material mass and mechanical strength. Finally, the team tested the new design and completed a feasibility study to determine whether the replacement is fiscally responsible. AMARG can use these results to inform their decision about which module design is better suited for their goals.
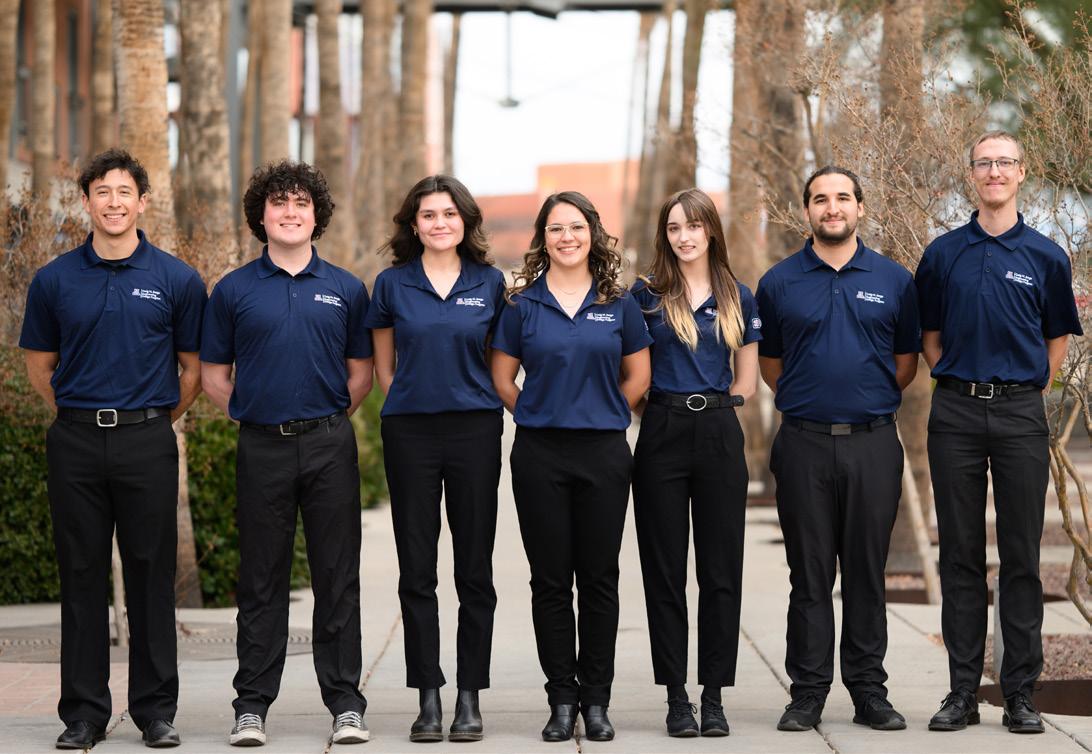
TEAM MEMBERS
Tej Ferron Scott, Electrical & Computer Engineering
Lauren Elizabeth Froberg, Engineering Management
Shelby Brooke Janssen, Materials Science & Engineering
Erian Armando Perez-Gamboa, Mechanical Engineering
Samantha Perry, Software Engineering
David Sepulveda, Electrical & Computer Engineering
Malcolm West, Mechanical Engineering
COLLEGE MENTOR
Mike Nofziger
SPONSOR ADVISOR
Matthew J Briggs
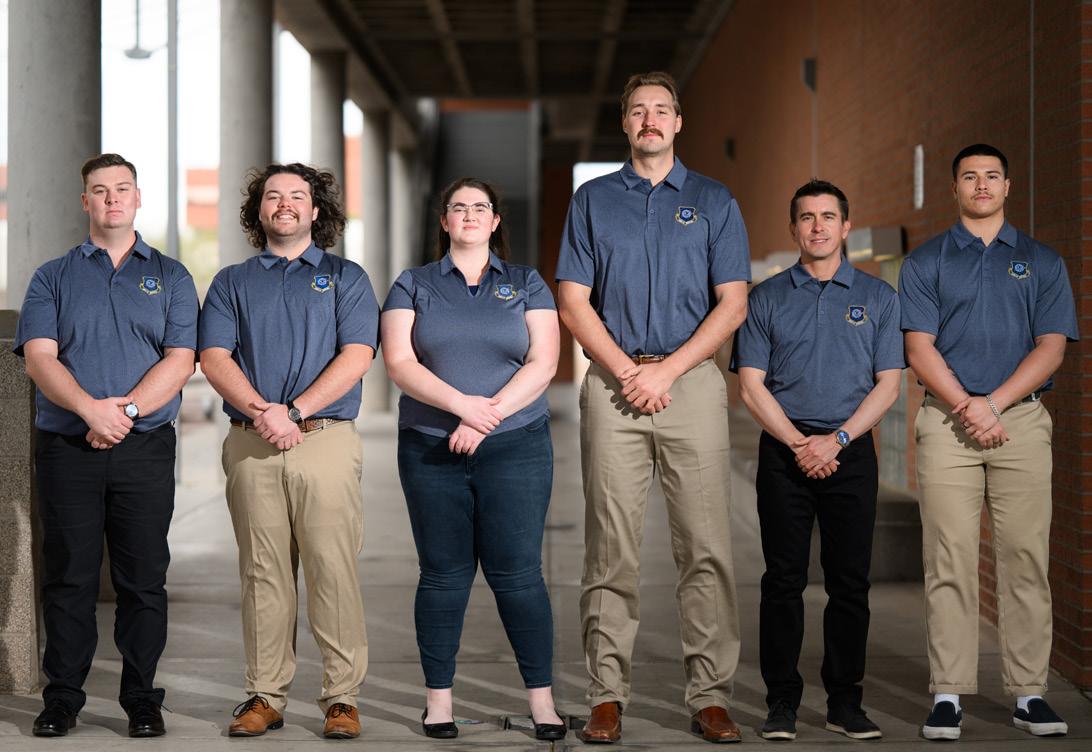
TEAM MEMBERS
Katheryn Garrett, Materials Science & Engineering
Matthew Jaworski, Materials Science & Engineering
Landen Lee, Mechanical Engineering
Will Menaugh, Mechanical Engineering
Andrew Peabody, Systems Engineering
Alex Reinert, Industrial Engineering
COLLEGE MENTOR
Michael Madjerec
SPONSOR ADVISOR
Ryan Stapleton
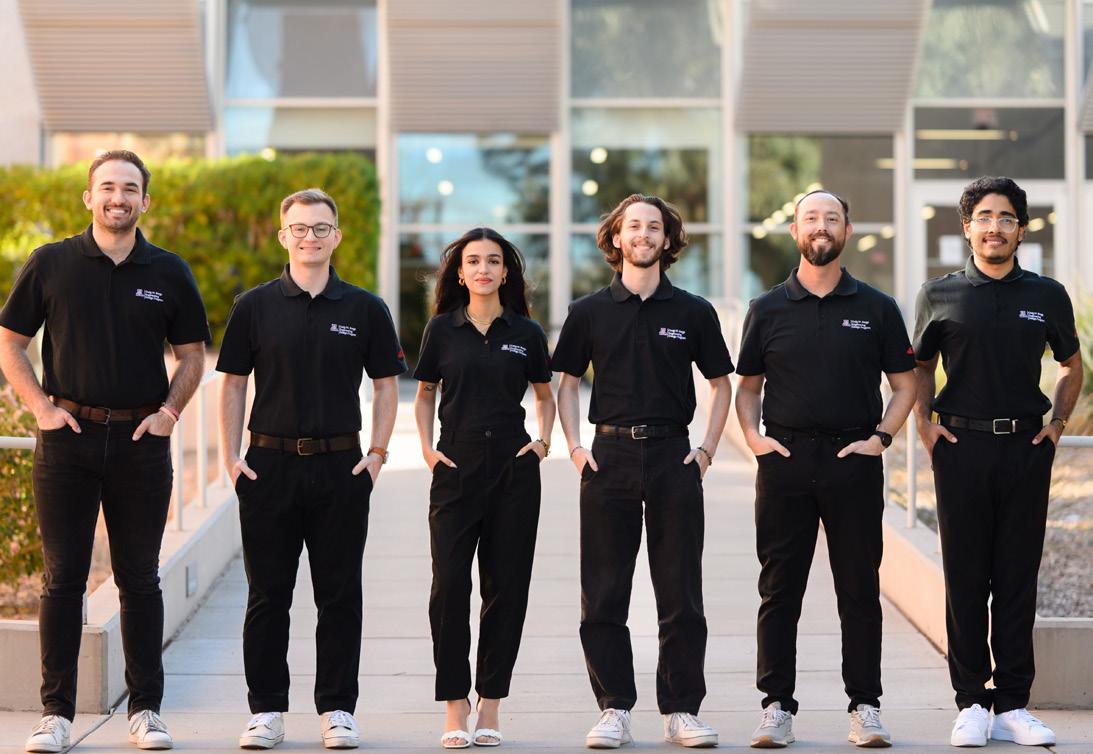
TEAM MEMBERS
Theo Altneu, Aerospace Engineering
Eric Clark, Mechanical Engineering
Alex Higuera Pierre Noel, Aerospace Engineering
Patrick Kupiec, Aerospace Engineering
Nyhel Sekulic, Systems Engineering
Gavin Vetro, Aerospace Engineering
COLLEGE MENTOR
Doug May
SPONSOR ADVISOR
Charles Simpson

TEAM MEMBERS
Anna Lindsey, Optical Sciences & Engineering
Jesus Equihua, Mechanical Engineering
Skye Morgan Garrett, Biomedical Engineering
Harsha Jaiganesh, Systems Engineering
Wesley Newman, Electrical & Computer Engineering
Sophia Rojas, Optical Sciences & Engineering
Caitlin Ruhland, Biomedical Engineering
COLLEGE MENTOR
Sardar R Mostofa
SPONSOR ADVISOR
Neal Brock
Preliminary Design Study for a Blended Wing Body Seaplane
Team 25011
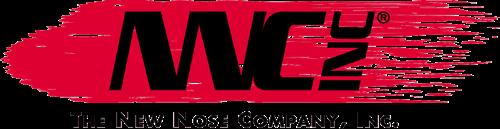
PROJECT GOAL
Investigate the feasibility for a long-range amphibious seaplane using a blended-wing body (BWB) configuration to support offshore missions.
The primary mission for this project was to develop better ways to deploy divers, submersibles and other payloads at sea. Secondary missions include maritime surveillance and search and rescue. To reach this goal, the team investigated the aerodynamic characteristics of two configurations of a BWB amphibious cargo seaplane: a baseline design and a variant equipped with catamaran-style floats. These configurations are intended for long-range offshore mission support, so the team optimized the design to meet these performance requirements and to maximize the coefficient of lift and minimize the coefficient of drag.
The team quantified the drag penalty introduced by the floats with computational fluid dynamics simulations and low-speed wind tunnel testing with a force balance and 3D-printed models. The students evaluated aerodynamic performance over a range of angles of attack at constant Reynolds numbers, which yielded key metrics such as lift, drag, pitching moment coefficients, and lift-to-drag ratios.
The team also explored alternate strategies for drag reduction and improved longitudinal stability. The results of these tests highlighted the aerodynamic penalties of float configurations and revealed opportunities for reducing drag while enhancing lift and stability through design refinements. These findings demonstrate the feasibility of optimizing the BWB seaplane concept for improved performance in future iterations.
Self-Sterilizing Enclosed Face Shield for Health Care Workers
Team 25012
LumiVici
PROJECT GOAL
Create an enclosed face shield that self-sterilizes using far-ultraviolet C (UVC) light for health care workers to wear in a clinical setting.
The COVID-19 pandemic underscored the critical need for advanced personal protective equipment (PPE) to shield health care workers and individuals in high-risk environments. The team developed a fully enclosed, self-sterilizing face shield designed to mitigate pathogen exposure and improve respiratory protection. This shield incorporates an integrated sterilization system featuring 222 nanometer light, a range of far-UVC light with germicidal properties. The shield automatically disinfects the external surface at timed intervals, reducing contamination risks and eliminating the need for manual cleaning.
The light effectively inactivates pathogens while remaining safe for human exposure, unlike traditional 254 nanometer UVC light. Additionally, the face shield fully encloses the user’s face and includes a builtin powered air-purifying respirator that achieves 99.97% filtration efficiency. This ensures continuous airflow while filtering out airborne contaminants.
The team’s engineering efforts focused on optimizing the light dosage for maximum pathogen inactivation while maintaining user safety. The final prototype demonstrates a practical and innovative solution for pandemic preparedness, offering sustainable protection for health care workers, laboratory personnel and frontline responders while reducing reliance on disposable PPE.
CASA Device for Carpal Tunnel Syndrome Treatment
Team 25013

PROJECT GOAL
Develop an affordable, streamlined brace to arch the transverse carpal ligament and relieve the everyday symptoms of carpal tunnel syndrome (CTS).
CTS affects 1% to 5% of adults globally (between 81 and 405 million people). It occurs when the median nerve in the wrist is compressed and leads to symptoms such as pain, numbness, tingling and weakness. CTS presents a significant challenge as there are currently no noninvasive technologies that specifically and quantifiably treat it.
This team aimed to relieve symptoms of CTS by designing a wearable brace that could apply 10 to 12 N of force to the carpal arch while stabilizing the thumb to prevent hand collapse. The design emphasizes simplicity, ergonomic comfort and affordability. It also accommodates a wide range of hand sizes and determines the applied force without user input.
The brace consists of a solid piece which wraps around the hand leaving a gap on the lateral side for the force applicator. This is a triangular structured force design. The end result of this project is the carpal arch space augmentation (CASA) wearable brace. It is constructed from 3D-printed thermoplastic polyurethane filament and a medical wrap and offers an effective and comfortable solution for alleviating the symptoms of CTS over an extended period of time.
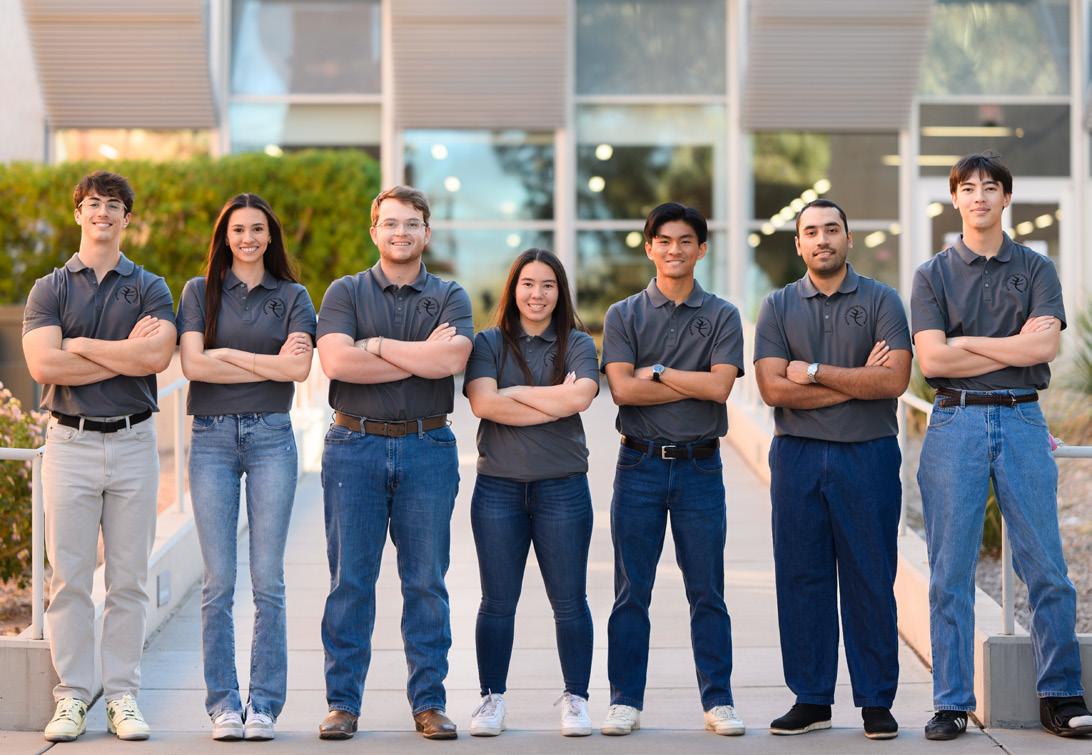
TEAM MEMBERS
Ali Alrashidi, Industrial Engineering
Brooklyn Fremin, Mechanical Engineering
Allen Z Lin, Mechanical Engineering
Ryan Henry Walton Mitstifer, Biomedical Engineering
Alex Moncada, Biomedical Engineering
Eric Pineda, Mechanical Engineering
Sabina Romero, Biomedical Engineering
COLLEGE MENTOR
Sardar R Mostofa
SPONSOR ADVISOR
Zong-Ming Li
Camera for Aerospace Situational Awareness (CASA)
Team 25014

PROJECT GOAL
Create a real-time bird’s-eye view of an aircraft’s surroundings to avoid potential collisions.
Ensuring situational awareness during ground operations is critical in modern aviation. This is especially true at busy airports where limited visibility increases collision risks. To address this need, the team developed CASA. It is a system that enhances safety and efficiency by providing a real-time bird’s-eye view of an aircraft’s surroundings using multiple high-resolution cameras strategically placed around the airframe. A Jetson Nano AI computer processes and fuses the camera feeds into a seamless 360-degree display that highlights nearby objects – such as vehicles, equipment and personnel – while generating real-time alerts for potential hazards.
The team implemented CASA on a scaled aircraft model and tested it in a simulated airport environment. This test confirmed CASA’s ability to eliminate blind spots and assist pilots and ground crews in navigation. CASA also provides environmental and sustainability benefits by preventing ground fuel spills and aircraft damage caused by operational incidents. By improving efficiency and reducing operational costs, the system presents a scalable and cost-effective solution for both business jets and commercial airliners.
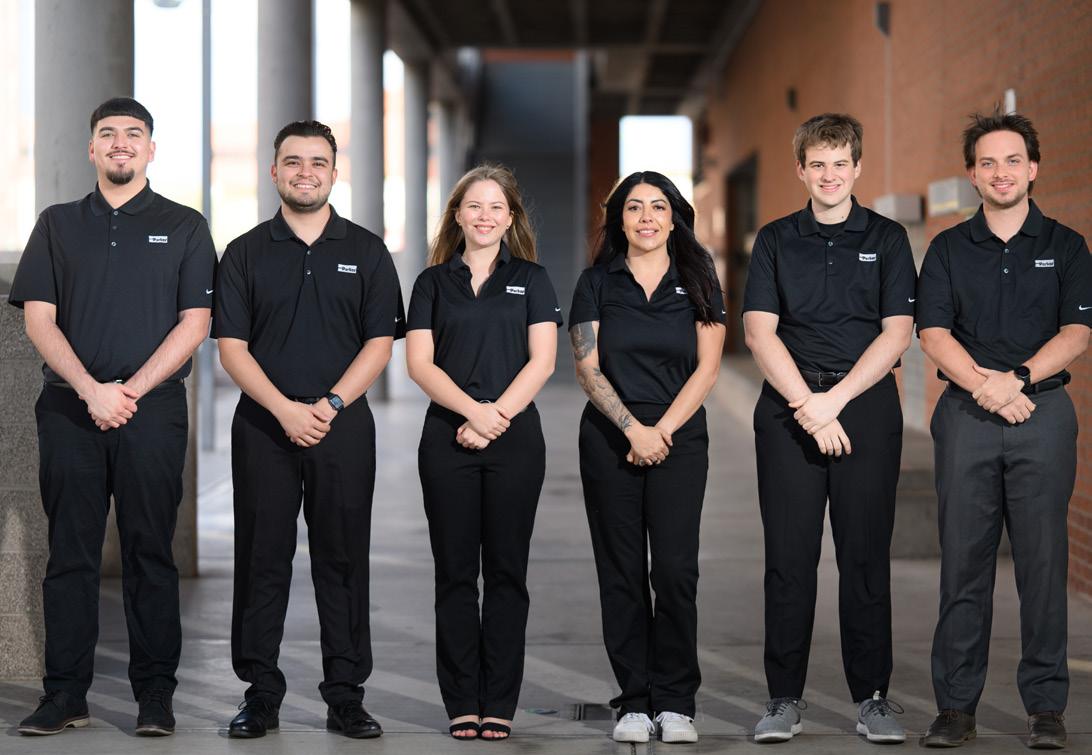
TEAM MEMBERS
Matthew Colson, Software Engineering
John E Dominguez-Trujillo, Mechanical Engineering
Diego Glenn, Systems Engineering
Amber Parker, Software Engineering
Carly Rose Wingness, Aerospace Engineering
Aidan Cler, Mechanical Engineering
COLLEGE MENTOR
James Sweetman
SPONSOR ADVISOR
Jake Reed
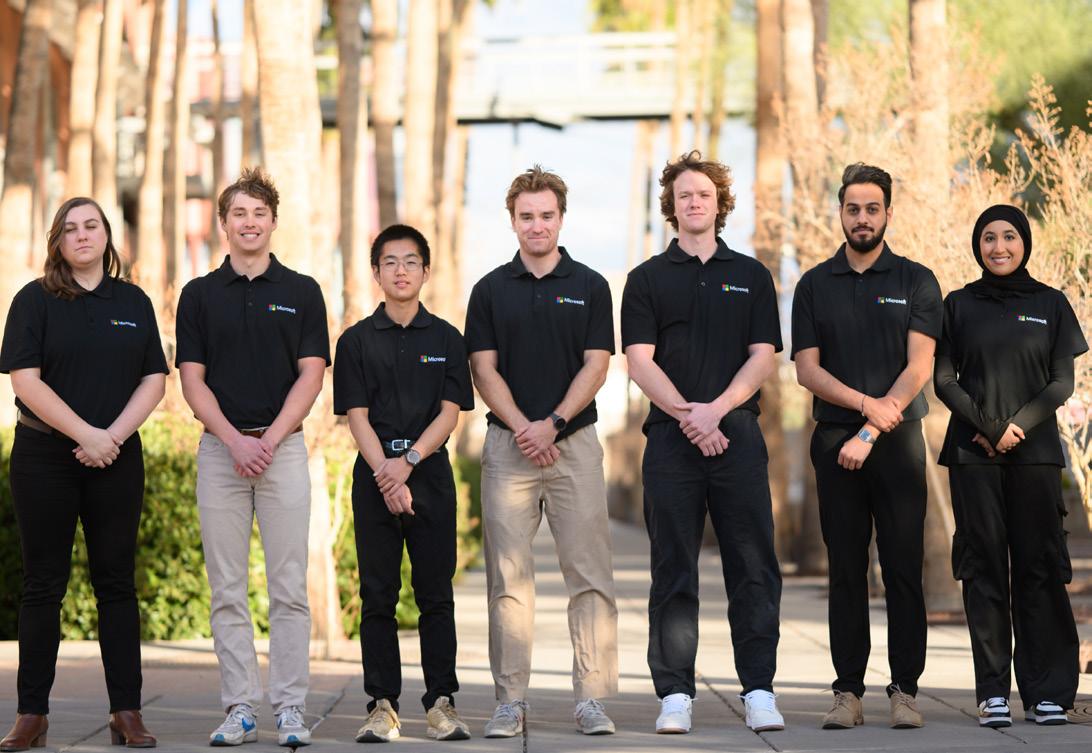
TEAM MEMBERS
Adam Beheathland, Optical Sciences & Engineering
Samantha Fisher, Systems Engineering
Ayesha Sajjad, Aerospace Engineering
Ali Ibrahim Alghareeb, Industrial Engineering
Joseph Lee, Mechanical Engineering
Dave Peddie, Mechanical Engineering
Will Zupancic, Engineering Management
COLLEGE MENTOR
Michael Madjerec
SPONSOR ADVISOR
Nicholas Keehn
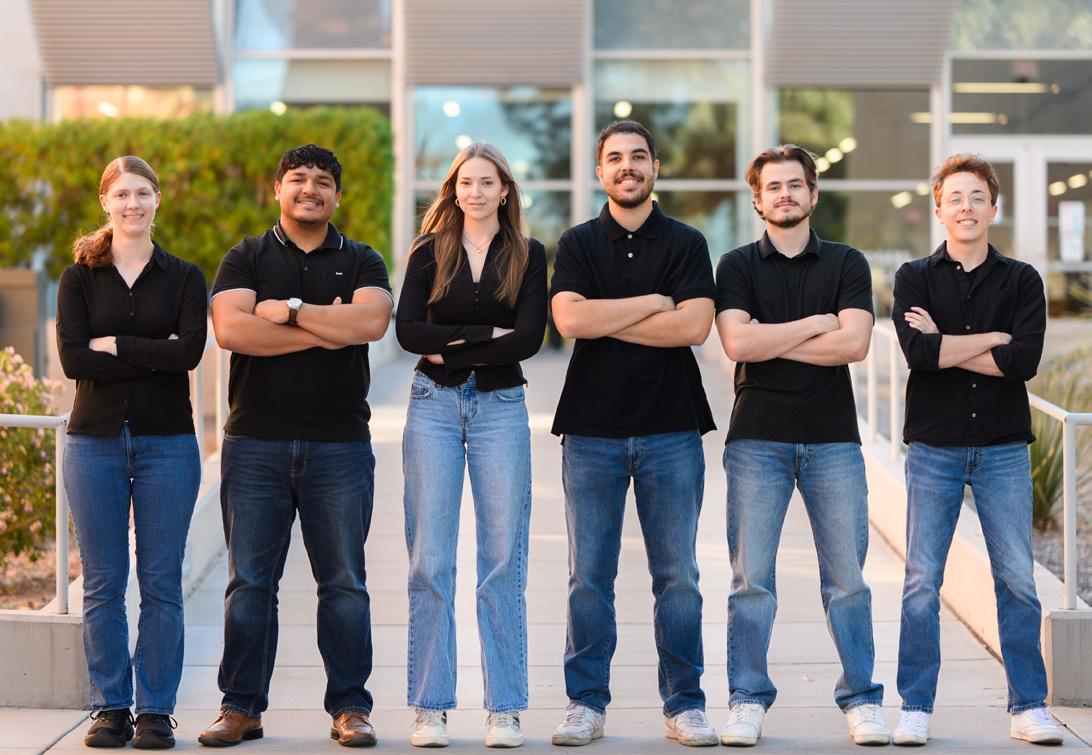
TEAM MEMBERS
Emre Devrim, Mechanical Engineering
Reed Michael Frankeberger, Biomedical Engineering
Desiree Phylicia Riley, Biomedical Engineering
Jackson Wisler, Biomedical Engineering
Jenna Childress, Industrial Engineering
Will E Roman, Biomedical Engineering
COLLEGE MENTOR
Don McDonald
SPONSOR ADVISOR
Peter Crapo
Navigating a River of Glass and Plastic
Team 25015
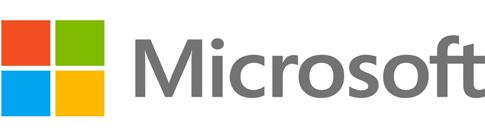
PROJECT GOAL
Develop a tool that efficiently and safely guides active optic cables (AOCs) to computer units in Microsoft data centers, minimizing manual labor and reducing safety risks to technicians.
AOCs are essential for high-speed data transmission in modern data centers. However, they are difficult to install. Traditionally, routing these fragile cables requires technicians to climb ladders and manually guide them through overhead trays. This poses safety risks and is inefficient. For this project, the team developed a pulley system that alleviates these problems.
The design features three main assemblies: the mounting assembly, the cable interface and the deployment system. The mounting assembly securely attaches to the standard 24-inch-wide cable tray to ensure stability during operation. The cable interface, designed to protect the delicate transceivers located at the end of AOCs, uses a boat-like structure with magnets and Velcro for secure transportation. Finally, the deployment system incorporates a pulley mechanism – which can be operated manually or with a power tool – to efficiently move cables along the trays. When these three components are combined, operators can use the system to safely and efficiently install AOCs by loading the cable transceivers in the cable interface and pulling it to its designated location using the deployment system.
Controlled Release Microparticle Process Design
Team 25016
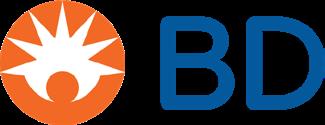
PROJECT GOAL
Develop a scalable process for producing poly(lactic-co-glycolic acid) (PLGA) microparticles with controlled drug release properties for catheters or other existing systems.
Many modern medical devices, such as indwelling catheters, incorporate drug-eluting coatings to prevent potentially life-threatening complications. Controlled drug release from PLGA microparticles enables prolonged therapeutic effects. This reduces the need for frequent and persisting interventions. In this project, the team aimed to optimize the microparticle fabrication process by analyzing key processing parameters and their influence on particle morphology – the study of particles’ shape, size and surface characteristics – and drug encapsulation efficiency.
The team chose a fabrication design that uses a microfluidic double T-junction system to precisely control emulsion droplet formation while a syringe pump delivers active and continuous phases at optimized flow rates. This produces microparticles ranging in size from 5 to 50 µm. After production, the team implemented various drying techniques, including lyophilization, to enhance particle smoothness and consistency.
Once the fabrication process was complete, the team used scanning electron microscopy for microparticle characterization to validate morphology and uniformity. By refining the process parameters, such as solvent selection and stir rates, the team established a reliable method for producing high-quality drug-loaded microparticles. These findings are a critical step toward advancing medical technology and improving patient outcomes.
Development of a Pediatric Foley Catheter with Safety Release Mechanism
Team 25017
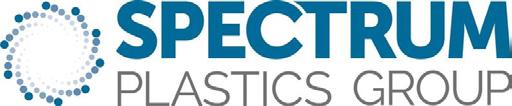
PROJECT GOAL
Design and prototype a pediatric Foley catheter that releases safely when significant force is applied.
A Foley catheter is a common medical device that helps a patent empty their bladder. It is inserted into the patient’s urethra and secured with a balloon in the bladder. The undue removal of Foley urinary catheters by patients is a critical issue in pediatric care that can cause significant pain, medical complications and additional hospital costs. To minimize this risk of urethral trauma, the team designed a device that automatically deflates the retention balloon when sufficient force is applied.
This modified pediatric catheter utilizes a plug and tether safety release mechanism. Excess force on the tether pulls the plug beyond its resting position, causing sterile water to flow from the balloon to the bladder. This deflates the balloon, allowing the catheter to be removed easily. The team optimized the deflation lumen’s flow rate and egress mechanism’s response threshold using computational fluid dynamics simulations to predict fluid flow.
Iterative prototyping methods – including stereolithography, fused deposition modeling, and extrusion simulations – supported the design decisions. Optimization ensured reliable deflation while maintaining normal functionality. The team completed a production run with prototype tooling and conducted verification testing including tensile force and flow rate testing to confirm performance. This device will soon undergo FDA approval for use in health care.
PODBot Phase 2
Team 25018
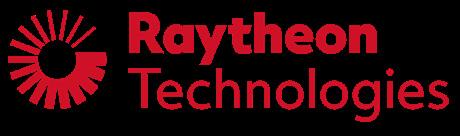
PROJECT GOAL
Deliver and verify a system that produces low-cost, durable and configurable airborne and ground-based robots that satisfy custom missions for intelligence, surveillance, reconnaissance and payload delivery.
Urban and desert reconnaissance is vital for first responders, search and rescue teams, and border patrol agencies. These professionals require low-cost, customizable and durable airborne and groundbased reconnaissance systems that can be built rapidly and deployed on-site just before a mission. 3D printing is ideal for this task.
The team designed, verified and delivered configurable airborne and ground-based bots that can operate in diverse operational scenarios. The designs incorporate video, audio and low-light capabilities, as well as design features to accommodate narrow spaces, varied terrain and dense infrastructures. The bots’ abilities to navigate tunnels, operate in urban areas, and transmit audio and video in restricted areas provide enhanced visual surveillance, reconnaissance and payload delivery while mitigating risk to operators.
Beyond hardware, the team also developed the PODBot configuration system. This is a scalable, software-driven platform that provides a mission-customizable list of parts for bot configuration, assembly instructions, graphical user interaction, and 3D printer integration. The system also provides users with control of the bots during missions, manages user input, and streams live video and audio. The team’s testing demonstrated rapid deployment capability and real-world functionality that address the sponsor’s three distinct use cases and meet the demands of modern reconnaissance and payload delivery missions.
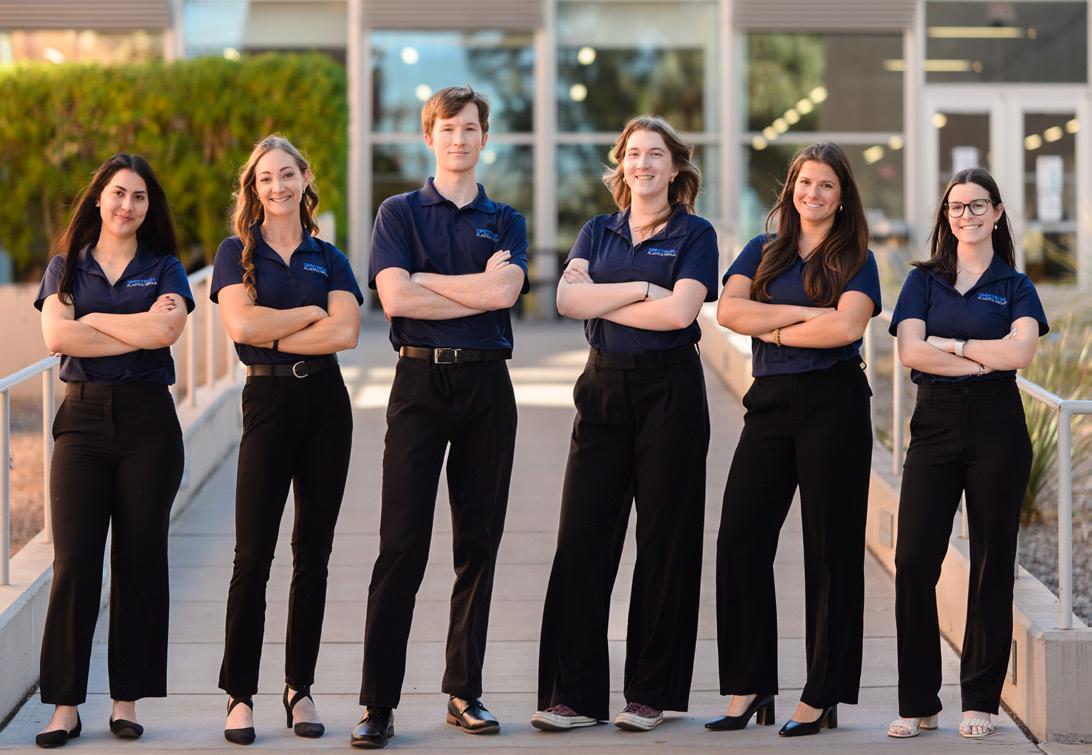
TEAM MEMBERS
Julia Magdalene Amato, Biomedical Engineering
Hannah Elisabeth Lehrfeld, Engineering Management
Isabelle O’Grady, Biomedical Engineering
Sean Runkle, Mechanical Engineering
Taylor Schreiber, Mechanical Engineering
Xochitl Triana, Biomedical Engineering
COLLEGE MENTOR
Doug May
SPONSOR ADVISOR
Jordan McEldowney
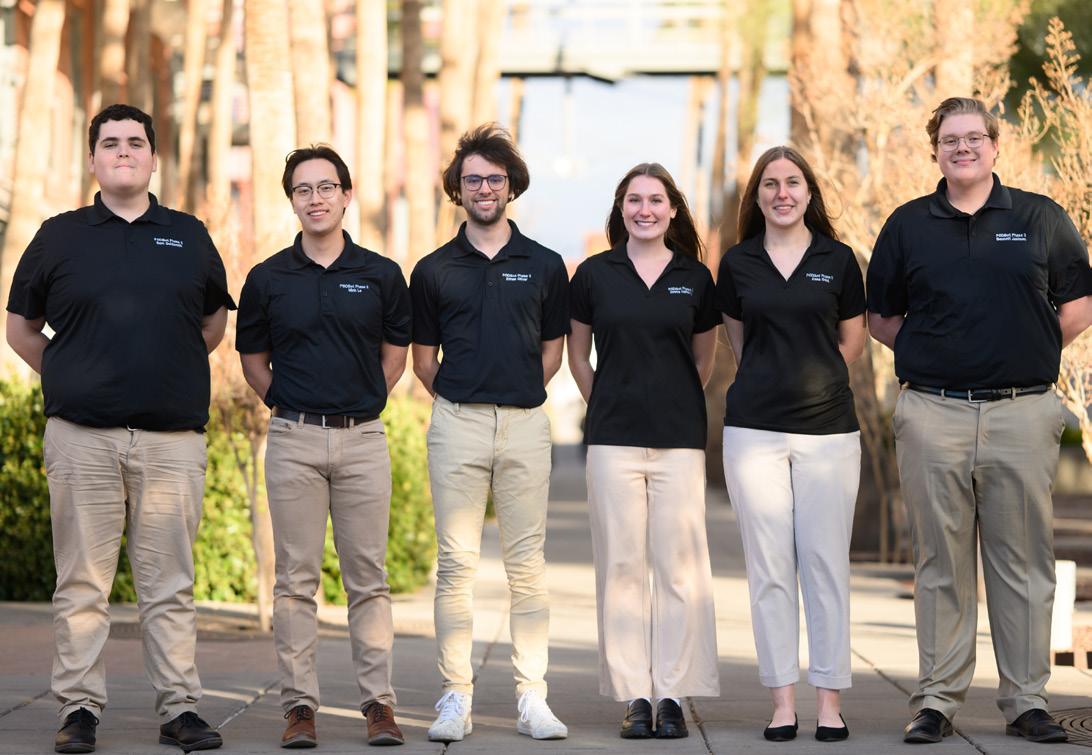
TEAM MEMBERS
Anna Gold, Aerospace Engineering
Sam Victor Goldsmith, Systems Engineering
Emma K Halferty, Electrical & Computer Engineering
Bennett Jackson, Software Engineering
Minh Le, Software Engineering
Ethan Oliver, Aerospace Engineering
COLLEGE MENTOR
Jeff Scott Wolske
SPONSOR ADVISOR
Jim Bakarich
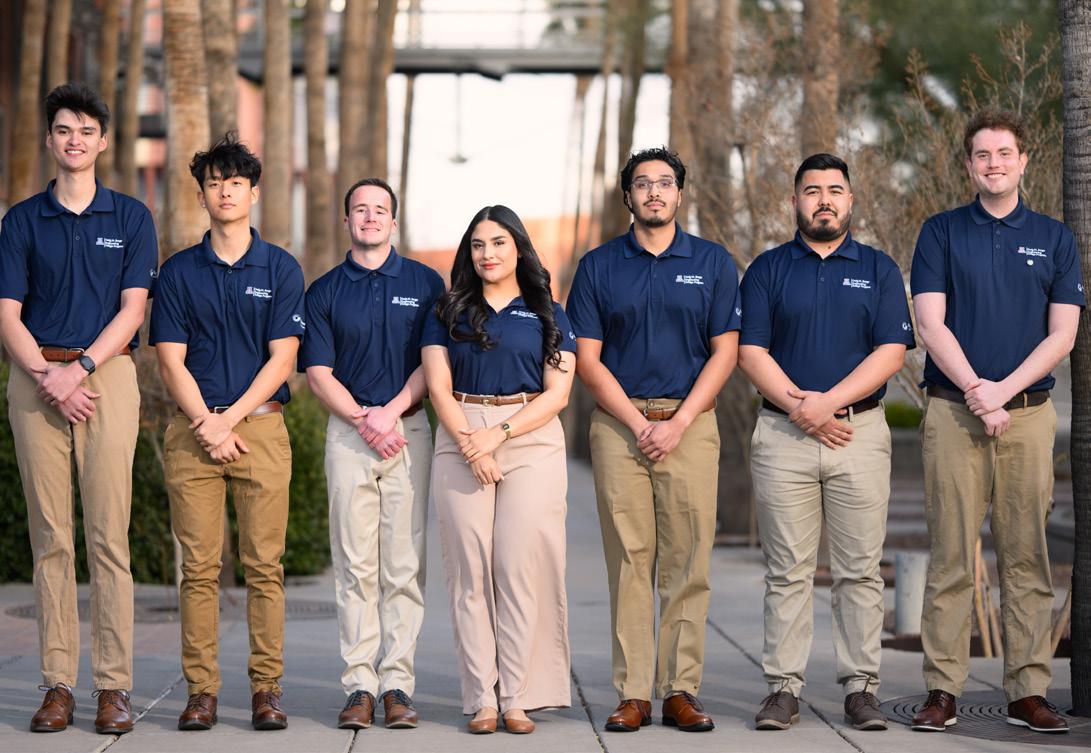
TEAM MEMBERS
Deven Aggarwal, Mechanical Engineering
Miguel Jonathan Ayala, Mechanical Engineering
Caleb Chang, Software Engineering
Raymond Martinez Robles, Electrical & Computer Engineering
Drew Smith, Electrical & Computer Engineering
Andrea Torres, Systems Engineering
Griffith Ray Wiele, Software Engineering
COLLEGE MENTOR
Steve Larimore
SPONSOR ADVISOR
Jim Bakarich
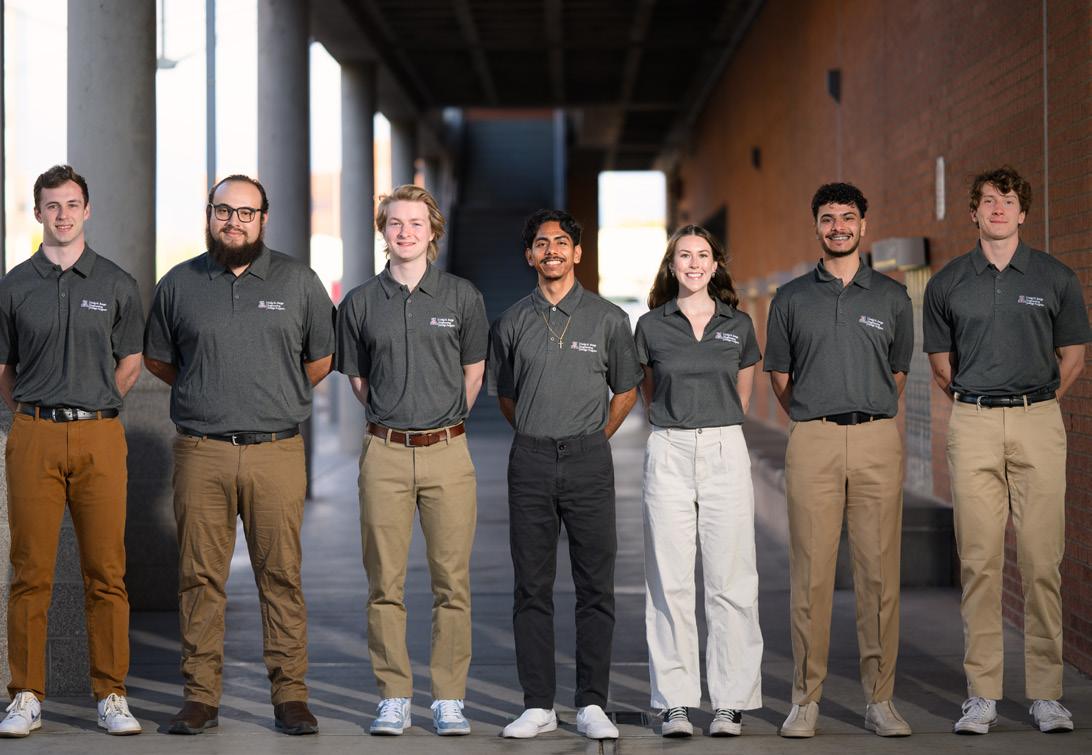
TEAM MEMBERS
Luke Lange, Mechanical Engineering
Christian Alcaraz, Mechanical Engineering
Abdulwahab Al-Qenaei, Electrical & Computer Engineering
Utah Bryant, Engineering Management
Lauren Goodrich, Software Engineering
Eli Jacobson, Electrical & Computer Engineering
Daniel David Kaitel, Engineering Management
COLLEGE MENTOR
Steve Larimore
SPONSOR ADVISOR
Vahan Garboushian
Small Autonomous Amphibious Delivery System (SAAD)
Team 25019
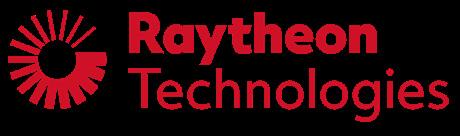
PROJECT GOAL
Develop an autonomous system for transporting small payloads across water and land with reliable round-trip delivery.
The SAAD system enhances emergency response by transporting supplies to dangerous or inaccessible areas. Designed for both aquatic and terrestrial use, it is compact, easy to deploy and capable of navigating lake-type environments. It supports manual control and sets the groundwork for full autonomy in later stages.
The system features a durable hull for housing electronics and payloads, two water thrusters for propulsion and six wheels for land mobility. Equipped with LiDAR, ultrasonic sensors, GPS, magnetometers, and a live-stream camera, the system continuously gathers real-time data for navigation and obstacle avoidance. A Raspberry Pi 5 manages processing, controlling thrusters, wheel motors, and electronic speed controllers to ensure seamless transitions between land and water.
Users control the system through a graphical user interface accessible on a tablet, smartphone or computer. The SAAD system can deliver a small 10-lb payload and complete a 500-m round trip on a single charge while maintaining stable communication. It provides a safe, low-cost and efficient solution for emergency supply delivery in challenging environments.
Clean Hydrogen Power Generation Project
Team 25020
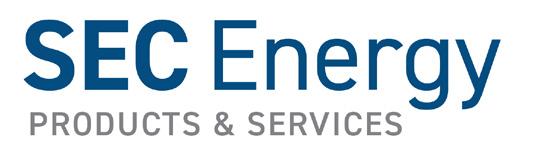
PROJECT GOAL
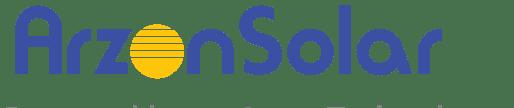
Create a prototype and theoretical scaled-up design for solar powered hydrogen generation and storage with a focus on efficiency throughout the process.
This project addresses a critical challenge in renewable energy: developing efficient and sustainable energy storage for intermittent energy sources like solar and wind. Despite the massive growth of renewable energy in the past decade, its utility will always be limited unless there is a way to store the energy to align production with demand. Conventional battery storage is effective, but it is limited by lifespan and environmental impact. Clean hydrogen offers a promising alternative.
The team designed and prototyped a system that generates hydrogen through solar-powered water electrolysis using a 900 W photovoltaic array. It stores the hydrogen at pressures of up to 40 psi in a gravity-fed water tank. A solenoid valve regulates flow to a fuel cell that converts hydrogen back into electricity for future use. An Arduino microcontroller monitors temperature and pressure sensors to ensure system safety and optimal operation.
This integrated renewable energy cycle provides key insights into scaling the design to a 50 kW solar system and a full-scale hydrogen generation plant. With this project, the team has demonstrated hydrogen’s potential as a scalable, reliable and environmentally friendly energy storage solution.
Optimizing Drip Line
Harness Design for Use with Helicopters in Slope Leaching
Team 25021

PROJECT GOAL
Optimize the irrigation system for hillside leaching operations at the Morenci Mine by designing a drip line harness and spool system.
Slope leaching is a common and effective method for extracting copper and other ores at mines. However, the current method for preparing and deploying the necessary dripline harnesses is laborintensive, and the helicopters used for deployment have limited capacity. This leads to inefficiencies and space constraints. The team developed a dripline harness and spool system to address these challenges. This system reduces the on-site footprint and enhances dripline deployment efficiency. It also enables scalability in slope leaching operations.
The team developed an improved drip line harness by incorporating flexible construction fencing into the design to maintain spacing within the system. The associated spool design consists of two triangular stands as supports and a cylindrical spool design that can accommodate the 24,000-squarefoot harness that will be furled on this design.
The team performed finite element analysis, Instron testing and mathematical analysis to confirm that the design would perform well in its intended environment. By implementing this harness and spool design, mine operators can enhance copper production efficiency and maintain a sustainable, scalable process for future operations. Thanks to these improvements, this system will likely increase annual profits for the mining operation.
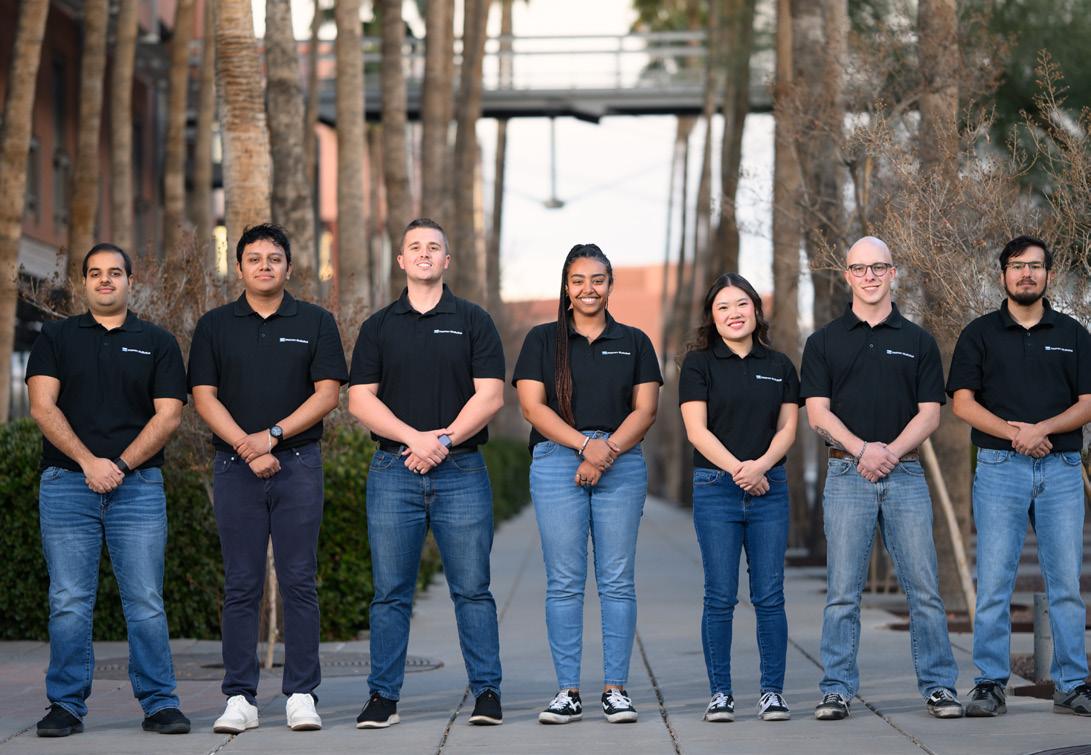
TEAM MEMBERS
Emiliano Morales, Industrial Engineering
Abdullah Alkandari, Industrial Engineering
Alex Hyte Johnson, Mechanical Engineering
Lemia Mohamed Salih, Aerospace Engineering
Lucas Schweers, Mechanical Engineering
Blaise Wilson, Materials Science & Engineering
Annie Wilson, Engineering Management
COLLEGE MENTOR
Michael Madjerec
SPONSOR ADVISOR
Joel Russell
Advanced Fluidics for Cancer Diagnostics
Team 25022
PROJECT GOAL
Create an integrated testing system that will perform fluidics delivery repeatedly and precisely to characterize a pump and optimize existing processes for reagent application.
A fast and accurate diagnosis is essential for providing therapeutic results to cancer patients. A key part of this process is creating stained microscope slides. Roche (Ventana Medical Systems) has provided over 10,000 BenchMark ULTRA and ULTRA PLUS instruments to health providers. These devices use specific immunochemistry reagents for fast and automated staining of microscope slides. This project creates a system that can repeatedly and precisely characterize and optimize the reagent rinse and drain cycles of the Fenyx pump used in these devices. It integrates the microfluidic pump with stepper motors, a weight scale and an optical sensor using custom Python code.
The team built the BencH20 prototype to improve upon reagent cycles in the standard benchtop Fenyx pump. BencH2O includes a mechanical frame that supports pump tubing, a pressurized chamber, a weight scale, a slide bed and multiple stepper motors that allow the team to finely adjust the nozzle position relative to the slide. A Raspberry Pi 4 and Triple-Axis Trinamic controller will complete system commands by working mutually to communicate software code and firmware.
The Raspberry Pi stores weight data for further flow rate analysis. The team can run multiple tests in sequence to simplify the microfluidic delivery. This makes it ideal for diagnostic workflows.
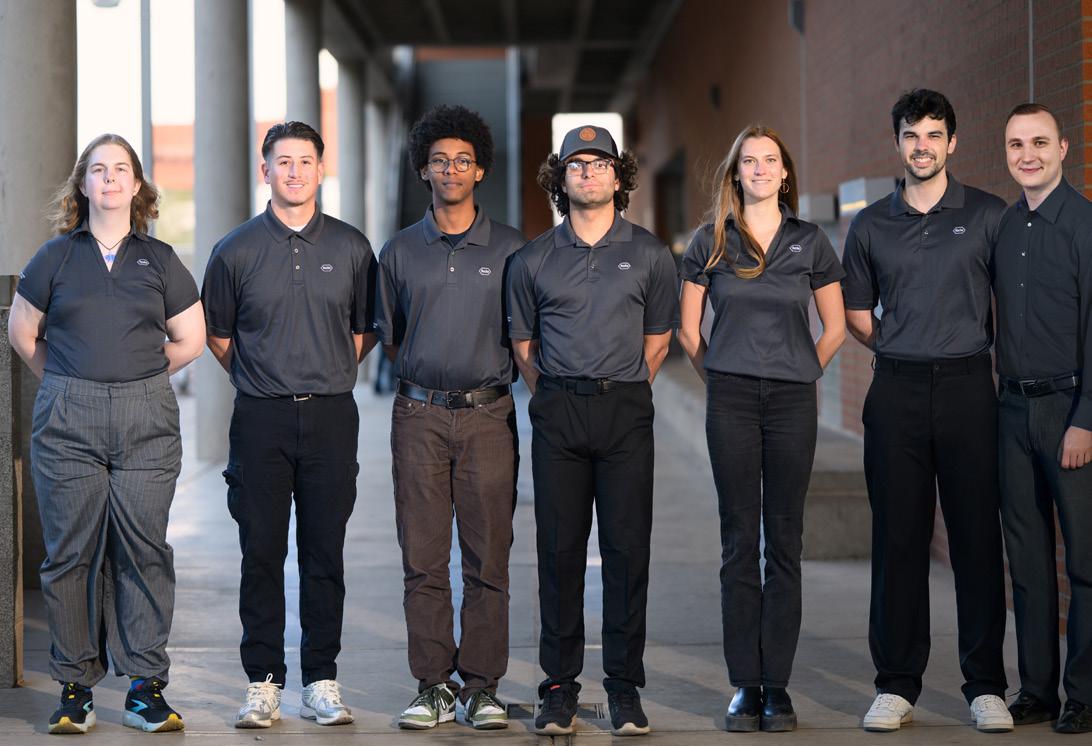
TEAM MEMBERS
Danielle Connacher, Biomedical Engineering
Enoch Dew, Electrical & Computer Engineering
Niko A Martell, Software Engineering
Daniel M Meles, Mechanical Engineering
Luis Fernando Morales, Systems Engineering
Marie Juliette Sheehan, Mechanical Engineering
Gabriel Leonard Galahad Declercq, Biomedical Engineering
COLLEGE MENTOR
Pat Caldwell
SPONSOR ADVISOR
Dustin Charamut
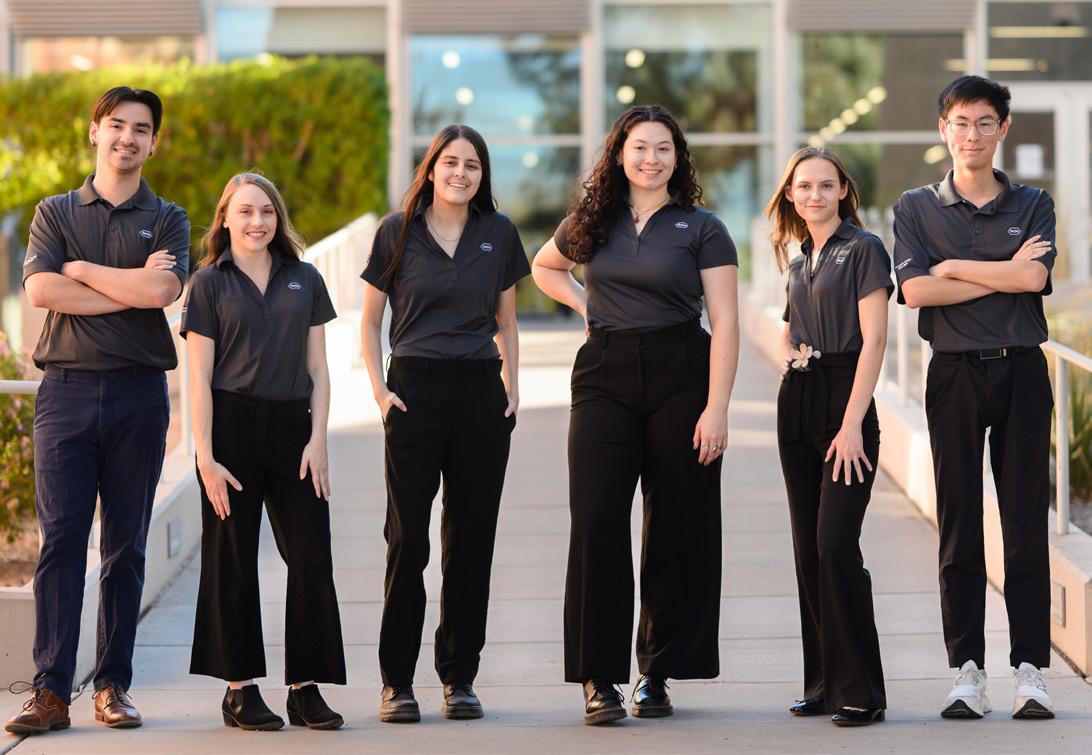
TEAM MEMBERS
Juliette Jacelle Nevarez, Software Engineering
Eleni Canez, Systems Engineering
Phoenix Rey Garcia, Software Engineering
Trinity Jade Hardy, Biomedical Engineering
Katelyn Owens, Mechanical Engineering
Ryan Joseph Thien, Biomedical Engineering
COLLEGE MENTOR
Pat Caldwell
SPONSOR ADVISOR
Peter Horsfield
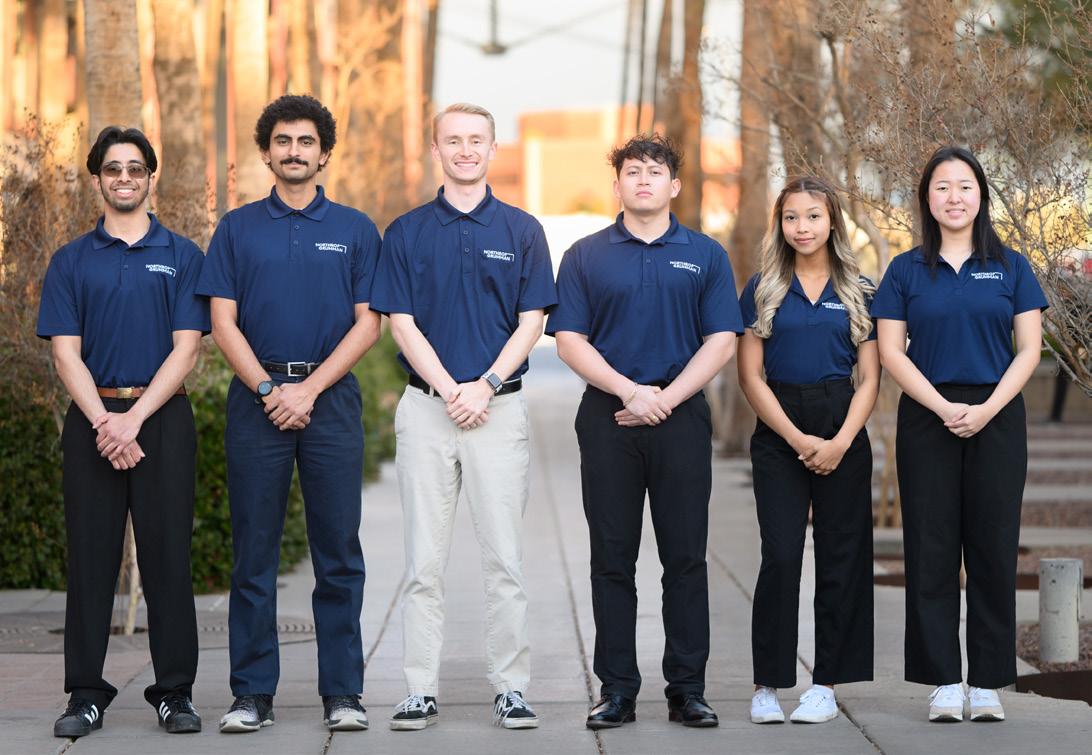
TEAM MEMBERS
Ashlee Sokha Diggles, Electrical & Computer Engineering
Veer Nayyar, Mechanical Engineering
Drew Philip Wilson, Aerospace Engineering
Ishan Adhikari, Electrical & Computer Engineering
Sue Min Kwon, Software Engineering
Luis Soto, Software Engineering
COLLEGE MENTOR
Pat Caldwell
SPONSOR ADVISOR
Kristel Basra
Slide Geometry and Safety in Pathology Automation
Team 25023
PROJECT GOAL
Design and develop a fully integrated histology coverslip misalignment detection system. Roche Tissue Diagnostics is developing the Histobot system for safe, efficient and automated transfer of tissue sample histology slides. These histology slides are currently prepared by technicians who add coverslips to the slides or equipment that automatically places coverslips. Both of these methods can cause inconsistencies in coverslip alignment. A misaligned coverslip can cause damage to both the slide and the human tissue being processed. This increases the time for patient diagnosis. Roche needs a precise, modular and safe system to ensure that histology slides always have aligned coverslips.
To meet these goals, the team developed the Slide Labeling for Integrity and Defect Evaluation System (SLIDES). It is an entirely automated system that can detect misaligned slides. The main design is a turntable with a rotating disk supported by an outer frame and placed above a plate. A stepper motor spins the disk around to different positions via a pulley system. It can house up to four slides simultaneously, and Roche’s Histobot system can load and unload these slides from SLIDES as it moves around. The frame design includes a camera and lighting system positioned above the slides for viewing and analysis.
Fourth Generation Ground Support Equipment Design
Team 25024
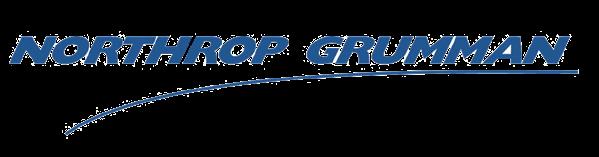
PROJECT GOAL
Update and complete a prototype 16-channel power switching printed circuit board (PCB) and integrate a separate daughterboard with a microcontroller for external graphical user interface (GUI) communication that allows for individual control of each power channel.
Power distribution and control are essential for efficient operation in various applications, including power delivery, equipment testing and product launching. The ability to selectively switch power on and off for multiple channels improves flexibility, safety and efficiency. The largest bottleneck with these systems is procurement and component manufacturing. As demand increases, manufacturers are seeking new designs that emphasize modularity, component and wiring consolidation onto PCBs, part interchangeability, sustainability, and reduced lead and build times.
This project achieves these goals by enhancing an existing power switching design. It adds features to the schematic, refines the PCB layout and adds advanced communication capabilities. The complete design is also much easier to assemble and rework. The team’s updated system consists of three identical 16-channel power switching assemblies housed within a standard rackmount enclosure. All components used in the assembly will be available for the foreseeable future and adhere to Automotive Electronics Council standards. Each assembly is controlled by an easily removable microcontroller on a daughterboard that communicates with an external GUI. This allows users to toggle individual channels remotely via ethernet for secure communication.
Automated Slide Transfer Team 25025
PROJECT GOAL
Design and automate the slide handling, imaging, and transfer processes in histology labs at Roche Tissue Diagnostics, Tucson Division.
Histology labs remain one of the least automated environments in health care. Due to a shrinking pool of professionals, highly trained pathologists and histotechnicians are often required to perform these tedious and repetitive tasks, reducing their ability to focus on complex diagnostics. Additionally, tissue staining can leave residue on slides that can interfere with microscope analysis and digital scanning.
The team developed the Automated Slide Transfer System (ASTS) that combines the precision of a 3D printer with the functionality of a forklift to streamline laboratory workflow. ASTS accepts an input tray of up to 20 slides, individually removes and inspects each slide, detects excess reagent dots, reads barcode identifiers, and places slides into an output rack. It then generates a comma-separated values file containing barcode data and general slide quality information.
A Raspberry Pi 5 controls ASTS’s high-precision gantry system equipped with a custom-designed gripper for slide manipulation, offering 0.05 mm accuracy. A Blue Series M12 lens and a Raspberry Pi HQ camera analyze slides during transfer. This enables rapid barcode scanning and reagent detection. With adjustable gantry speeds of up to 1 ft per second, the system can process 20 slides in under 400 seconds.
By automating tedious histology tasks, the ASTS reduces workload, improves efficiency and enhances slide quality. This supports Roche’s mission of “doing now what patients need next.”

TEAM MEMBERS
Andres Galvez, Software Engineering
Carson McDaniels, Biomedical Engineering
Derek Tien Nguyen, Mechanical Engineering
Alex Romero-Lozano, Electrical & Computer Engineering
Sebastian Saucedo Alcantar, Systems Engineering
Kerwin Dewberry Jr, Mechanical Engineering
Aaliyah Thompson-Mazzeo, Mechanical Engineering
COLLEGE MENTOR
Steve Larimore
SPONSOR ADVISOR
Matt Mette
Parcel Identification and Trackability (PIT)
Team 25026
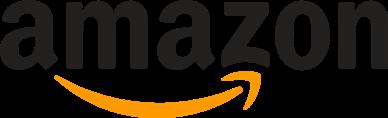
PROJECT GOAL
Accurately identify totes and non-totes in real-time and promptly stop a conveyor belt when a non-tote is detected.
Ambaflex spiral conveyers are designed to work with specific types of containers referred to as totes. The presence of non-totes causes severe jams and expensive repairs. These incidents lead to immense cost impacts including direct repair costs, lost production hours that affect multiple downstream processes, and labor costs. This project prevents non-totes from advancing further through the Ambaflex conveyors at an Amazon facility. This saves Amazon operational expenses and improves cycle times and customer satisfaction.
This design relies on two key components to distinguish between totes and non-totes: a Cognex IS2000M camera and an Orange Pi 5. Using color and dimension detection, these two components and their associated software work together to identify objects on the conveyor belt and stop it when necessary. Totes are bright yellow with specific dimensions; anything else on the conveyor line is classified as non-tote. The device is bolted to the floor via a sturdy rectangular metal frame that encloses the conveyor belt. An interface screen on the frame’s side allows Amazon associates to monitor the system’s status, understand stoppages and restart operations as needed. The PIT system integrates with Amazon’s existing setup to illuminate an Andon stick when a non-tote is detected and alert associates to remove it from the conveyor belt line.
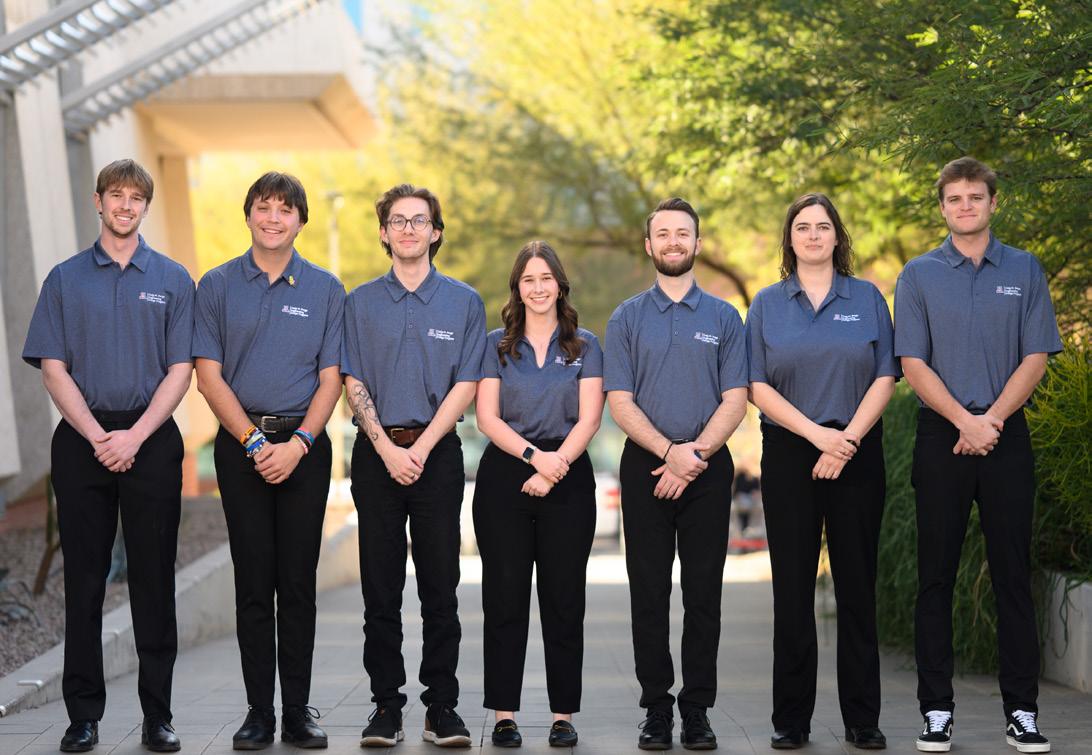
TEAM MEMBERS
Adam Feasel, Systems Engineering
Chris Karceski, Software Engineering
William Tyler Rains, Software Engineering
Ryan Wells, Industrial Engineering
Andre William Fanning, Engineering Management
Casey Fulbright, Industrial Engineering
Rebecca Gehring, Industrial Engineering
COLLEGE MENTOR
Sardar R Mostofa
SPONSOR ADVISOR
Jessica Grove
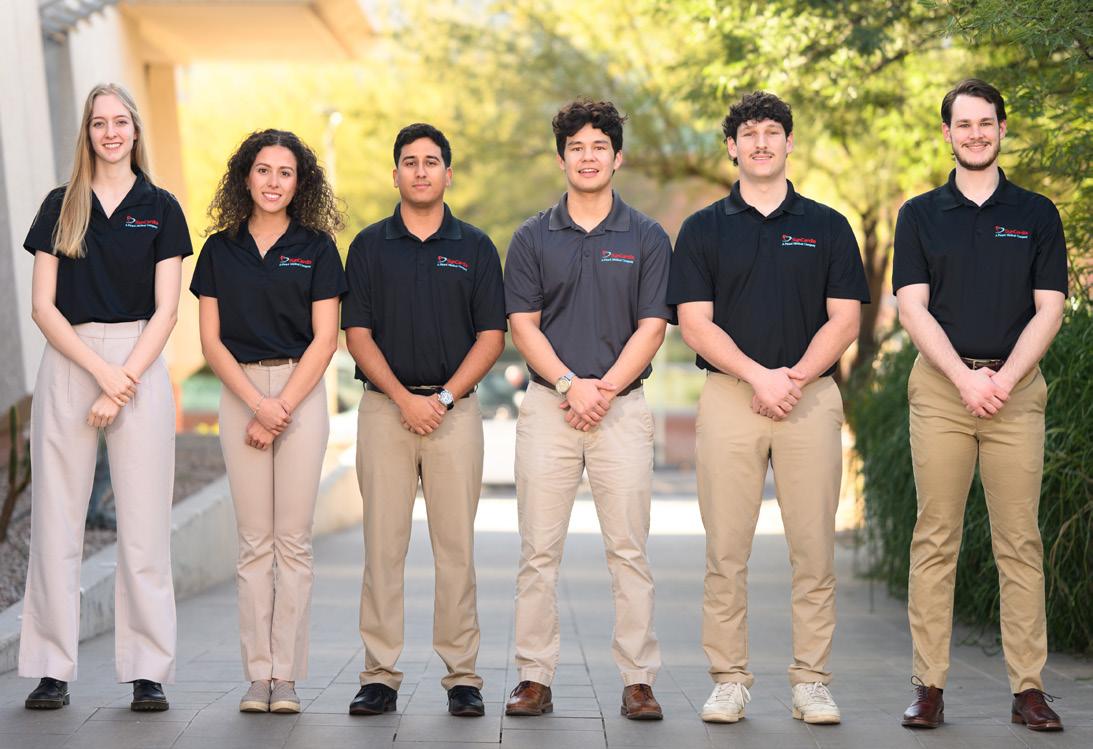
TEAM MEMBERS
Suraj Bharaj, Biomedical Engineering
Matt Conrad Greenfield, Biomedical Engineering
Alexa Hoover, Electrical & Computer Engineering
Lynette Kay Valenzuela, Biomedical Engineering
Zach Tran, Mechanical Engineering
Christopher Kelly, Systems Engineering
COLLEGE MENTOR
Pat Caldwell
SPONSOR ADVISOR
Duffy Elmer
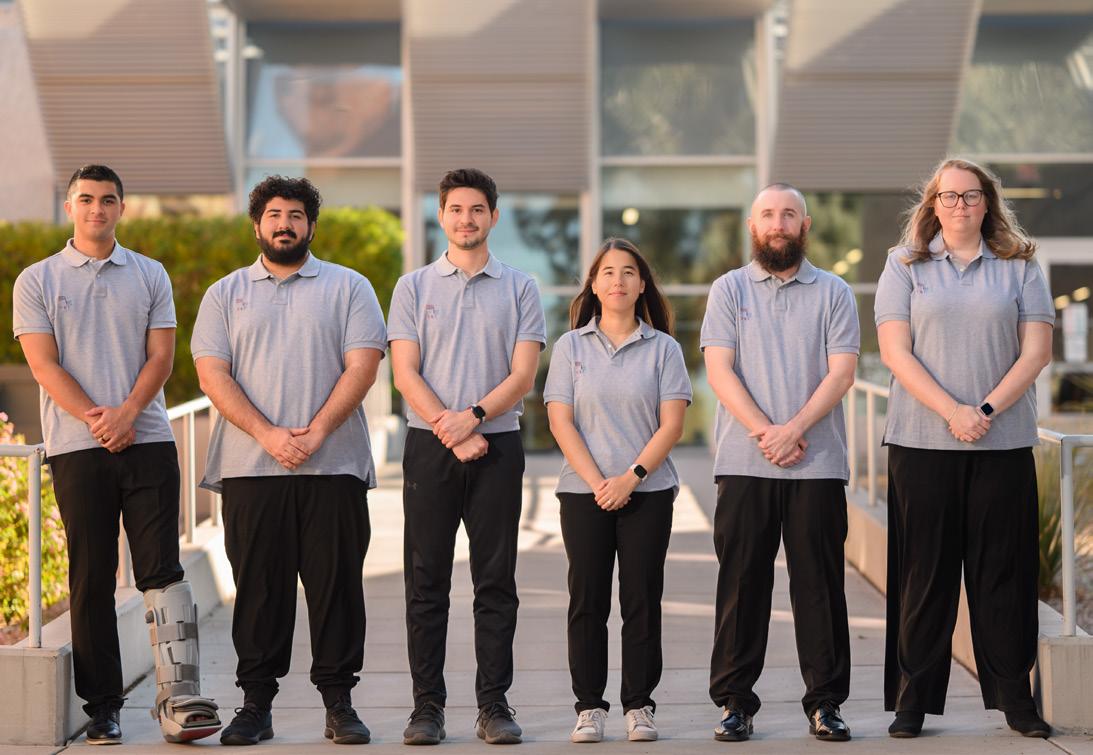
TEAM MEMBERS
Raul Samuel Dominguiano, Aerospace Engineering
Ahmad Malik, Electrical & Computer Engineering
Cody McManus, Mechanical Engineering
Stevie Robbins, Aerospace Engineering
Sarah Li, Systems Engineering
Miguel Angel Barrera Coronado, Aerospace Engineering, Mechanical Engineering
COLLEGE MENTOR
Doug May
SPONSOR ADVISOR
Jay Crossman
New Cart and Connector Design for SynCardia Total Artificial Heart Hospital Driver Unit
Team 25027
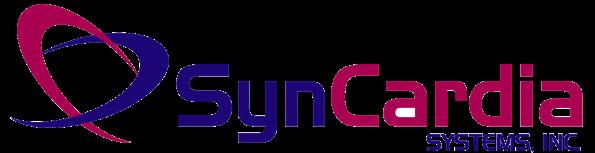
PROJECT GOAL
Address component obsolescence issues in the existing fleet of SynCardia’s hospital carts, and provide a redesign of the entire hospital cart to enact future cosmetic and human factors improvements.
The team focused on replacing obsolete components and enhancing existing design elements for the Syncardia hospital cart. Phase I involved modifying the current hospital cart to accommodate a new C2 Driver connector and touchscreen. This included integrating a projected capacitive touchscreen optimized for use with gloves and resistant to fluid interference. The team updated the cart design to accommodate these components by modifying the sections of the frame that house them. These new components passed all verification testing and successfully addressed the pressing obsolescence issue.
Phase 2 of this project was to redesign the hospital cart itself. This redesign further enhanced the cart’s performance by improving hospital elevator accessibility. The team accomplished this by adding larger wheels, increasing the touch screen’s mobility with modified mounting, and reducing the overall form factor. Additionally, the team redesigned the frame to meet new human factors requirements. This addressed issues associated with inserting the C2 driver, which required lifting the 602lb. cart over 2 ft. The new design configuration reduced this height to only 2.5 inches.
The team also added new features including storage hooks for managing power and air hoses and a modified drawer to house spare batteries. These improvements provide greater efficiency and functionality for hospital use.
Avionics Size Reduction and Thermal Reliability Enhancement
Team 25028
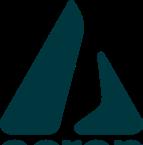
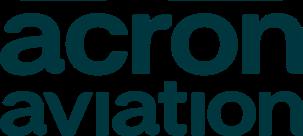
PROJECT GOAL
Develop a passive thermal management system to enhance operations of size-reduced avionics in urban air mobility (UAM) applications.
UAM is an emerging market that includes electric vertical takeoff and landing (eVTOL) aircraft, which prioritize compact, space-efficient, integrated systems. However, the small volume and close proximity of heat-generating components result in high thermal concentrations. This degrades avionics performance and longevity. Passive thermal management strategies are key to enhancing system reliability and avoiding the design complexities, energy usage and maintenance requirements that come with active cooling solutions.
The team created a passive thermal management system that integrates copper heat pipes, an aluminum heat sink and thermal interface materials to efficiently dissipate heat. The team designed, assembled and tested a compact hardware enclosure featuring this thermal management system and used polyimide heaters to simulate internal heat loads based on expected operating conditions. Computational fluid dynamics and thermal analyses were performed using SOLIDWORKS Flow Simulation followed by experimental testing in a thermal chamber to validate the design’s performance across an ambient air temperature range of -32°C to 70°C. The final design offers a compact, lightweight thermal management solution with no moving parts. This ensures reliable avionics performance in weight- and size-constrained environments like eVTOL aircraft.
Lunar Automated Regolith Processing (LARP)
Team 25029
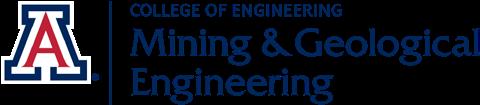
PROJECT GOAL
Design and build a proof-of-concept system for collecting icy lunar regolith and processing water from it for use in space exploration.
Constructing a habitable lunar base is a significant step in the advancement of space exploration. In situ resource utilization is one of the best options for obtaining water safely and economically. LARP is a multi-year project that presents a solution for water acquisition in a lunar base by using the ice present on the lunar surface.
The system is composed of two separate units: a mobile excavation unit (MEU) and a stationary extraction unit (SEU). The MEU uses a bucket elevator to excavate and collect regolith and store it in a load bed. It utilizes an Arduino-based microcontroller with an on-board Wi-Fi chip to allow for user control on a phone app graphical user interface. The user can control the height of the bucket elevator and load bed via linear actuators and the speed of the wheels and elevator using DC motors.
The MEU deposits regolith into the SEU’s heating chamber through a funnel and motorized ball valve. Here, pipe heating tape heats the regolith until the water inside evaporates into the condensation subsystem. The steam passes through a heat exchanger, condenses back into water, and drips into a storage container that can be removed for water collection and later use. The team’s proof-of-concept system can produce 0.5 L of water per day and can be scaled up to provide more as needed.
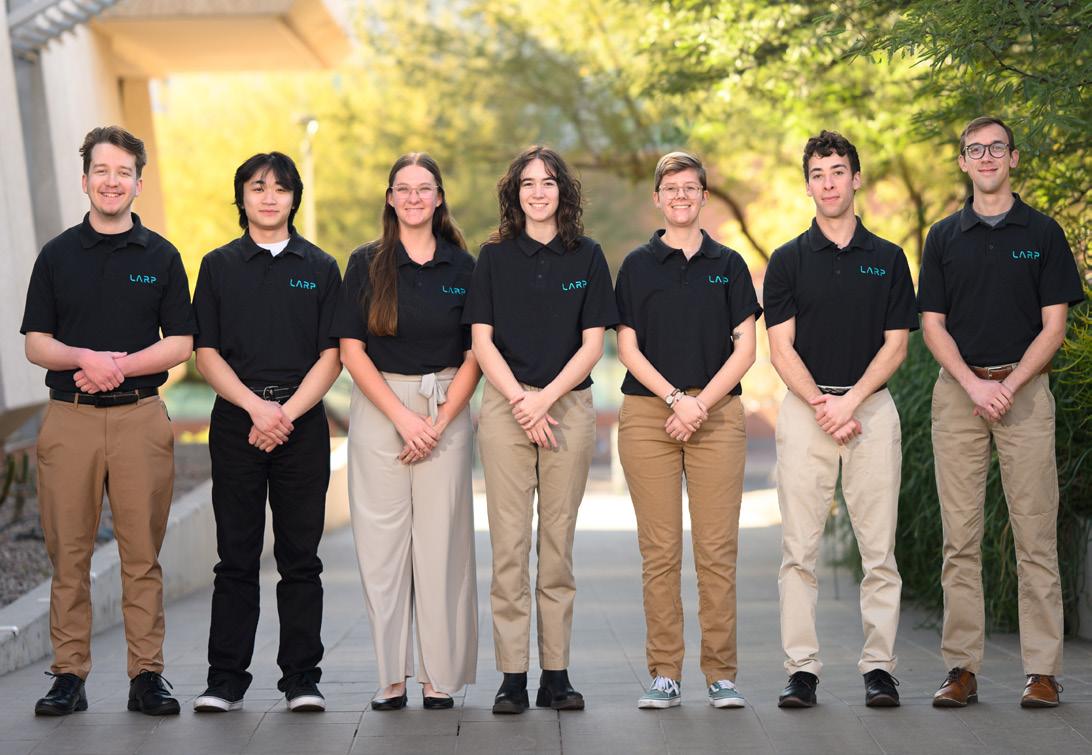
TEAM MEMBERS
Elian Alvarez, Systems Engineering
Chad Cantin, Aerospace Engineering
Alex Liang, Electrical & Computer Engineering
Gracy Raben, Aerospace Engineering
Ellie Wolcott, Aerospace Engineering
Emerson Moser, Aerospace Engineering
Rachael Pabst, Mechanical Engineering
COLLEGE MENTOR
Pat Caldwell
SPONSOR ADVISOR
Nathalie Risso
AQUABOT Fluence - Advanced Sleek Hydrodynamic Hull Design for Aquatic Drones
Team 25030

PROJECT GOAL
Design a sleek, hydrodynamic hull for an autonomous ocean drone that is optimized for minimal drag, self-righting capabilities and reduced energy consumption.
Monitoring ocean health is an essential part of understanding how climate change affects the oceans. To address this critical need, the team developed the AQUABOT Fluence system. This aquatic robot provides a safe and cost-effective way for organizations to effectively study ongoing issues. The team integrated several features into the AQUABOT that make it ideal for operating in a harsh ocean environment. These include a self-righting hull design to ensure stability in turbulent oceans, a propulsion system for mobility, and sensors to collect and transmit ocean health parameters in real time. Operators can remotely control the system using autonomous waypoint navigation.
The team’s engineering efforts focused on minimizing drag through hydrodynamic optimization and incorporating robust materials so AQUABOT can withstand marine conditions. This ensures energy efficiency for extended battery life and durability for a longer product lifetime. The team also developed a temperature data collection and transmission system using Starlink satellite internet service and implemented a user-friendly interface for remote operation.
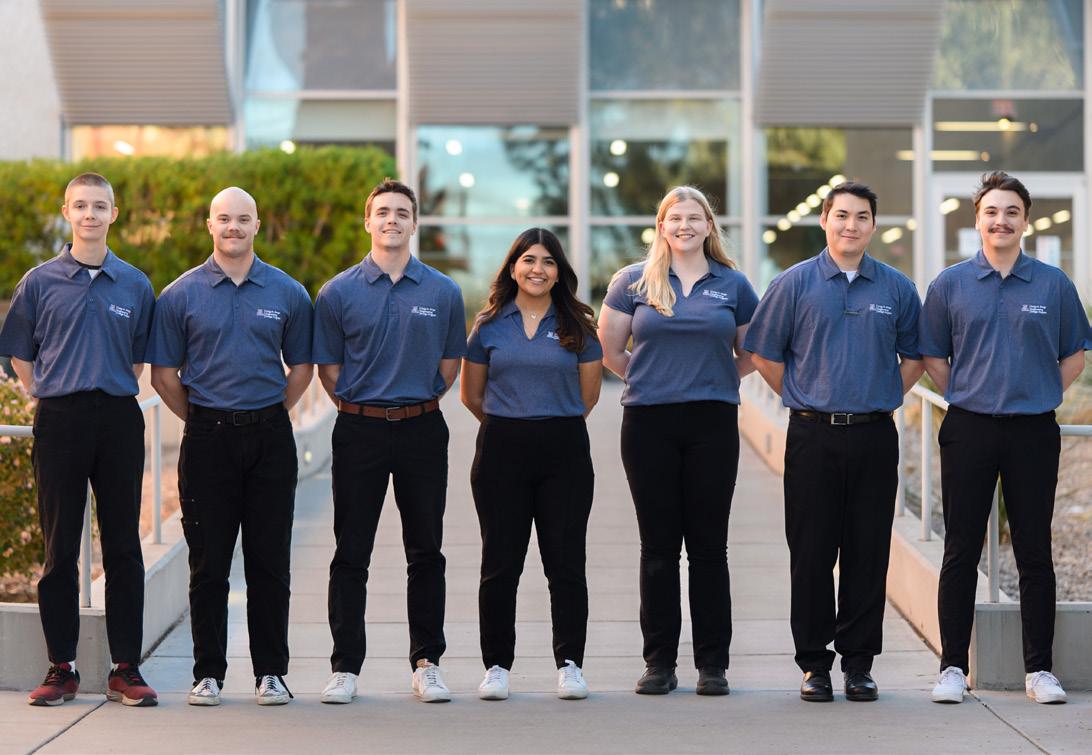
TEAM MEMBERS
Jack Paul Goodale, Systems Engineering
Yadi Jimenez, Biomedical Engineering
Cooper Mauldin, Mechanical Engineering
Jason Alexander Mayhall, Aerospace Engineering
Zach Wollerman, Electrical & Computer Engineering
Quinlan Reed, Software Engineering
Jennifer Hall, Mechanical Engineering
COLLEGE MENTOR
James Sweetman
SPONSOR ADVISOR
Eddy Stocker

TEAM MEMBERS
Lucas Bernal Dent, Software Engineering
Abigael Doyle, Mechanical Engineering
Olive McCay Mehrer, Optical Sciences & Engineering
Stewart Nickel, Optical Sciences & Engineering
David Ramsayer, Mechanical Engineering
Arjun Dalal, Systems Engineering
COLLEGE MENTOR
James Sweetman
SPONSOR ADVISOR
Matthias Whitney
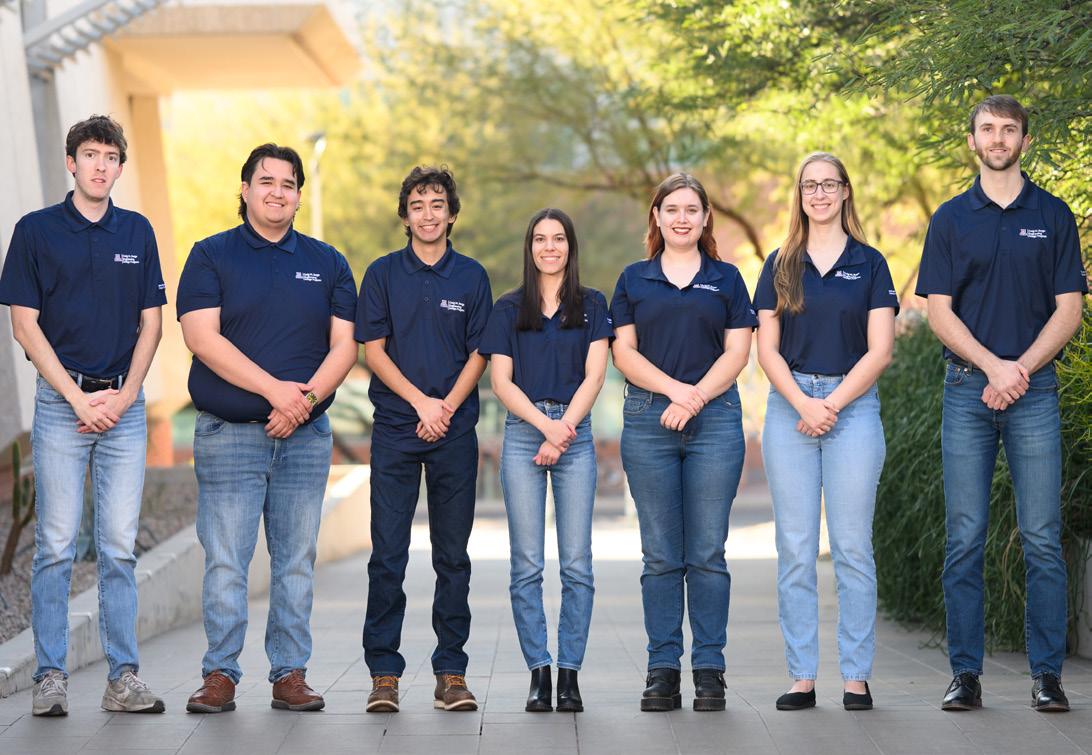
TEAM MEMBERS
Kari Cordes, Software Engineering
Jacob Duran, Mechanical Engineering
Sebastian Alexander Longoria, Software Engineering
Hannah Alexandra Spallas, Electrical & Computer Engineering
Matthew Wasko, Electrical & Computer Engineering
Jack T Hughes, Software Engineering
Natalie Barnhouse, Mechanical Engineering
COLLEGE MENTOR
James Sweetman
SPONSOR ADVISOR
Glen Abousleman
Dual Output Recon Camera (DORC)
Team
25031
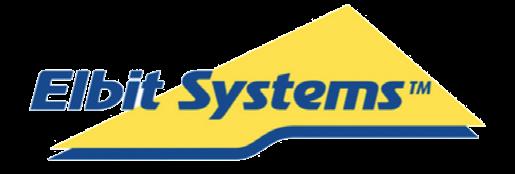
PROJECT GOAL
Evaluate the performance of production electro-optical sensors by designing a camera that will illuminate a target with visible and near-infrared (NIR) lasers and capture video imagery.
Reconnaissance is a key part of situational awareness and improves strategic decision-making. Elbit Systems of America (ESA) – a provider of tools for defense, aviation, and medical instruments – tasked the team with designing DORC. It will use visible and NIR laser technology to illuminate and capture video feeds of targets up to 500 m away. It must also be able to operate during twilight and low-light settings and resist basic outdoor operational conditions such as high temperatures and dust. The overall goal is to create a device that can serve as test equipment for ESA’s development of future electro-optic devices.
The team designed DORC with four subsystems: optical, mechanical, electrical and software. DORC can project visible or NIR light onto the target depending on the powered laser diode. A sensor then captures the target and sends the information to a Raspberry Pi for processing and display. A handheld 3D-printed shroud that can be mounted on a standard tripod houses these subsystems. This allows a user to control light output and camera field of view. The DORC can run for six hours on battery or indefinitely on wall power.
Solar Performance Estimation Kit (SPEK)
Team 25032

PROJECT GOAL
Accurately estimate solar power availability and cost savings based on electricity consumption at a residence using a portable kit.
Solar power is an increasingly efficient method of electricity generation and has become an attractive prospect for many homeowners. However, customers have no way to corroborate estimates from a solar power provider and cannot know if the investment in solar panels truly makes sense for them. To address this unknown, the team designed the SPEK, a portable kit that users can rent to accurately measure the solar power potential of their home. It monitors the power output of a small, built-in solar panel throughout the day and transfers that information to a cloud-based application. It also includes a frame and electronics enclosure to ensure the SPEK will remain securely on homeowners’ roofs, insulated from rain and excessive heat.
The team developed an electronic system to accurately measure the power output of the solar panel, while also using the panel as a power source. The design includes an ESP32-C6 microcontroller, which controls the data collection and sends it to the team’s database via the homeowner’s Wi-Fi network. Users can access this data on both the website and the app, allowing convenient access to calculated usage statistics and savings estimations.
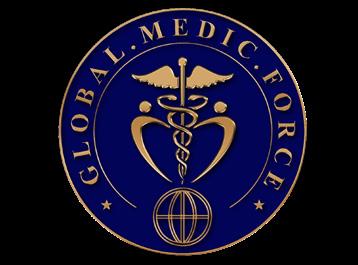
PROJECT GOAL
Develop an advanced AI-driven digital clinical mentor that delivers concise, situationally relevant, real-life clinical guidance to health care workers in remote areas.
Many people around the world live in places where their dedicated health care workers do not have access to advanced medical expertise. MD-Sensei is a mobile app designed to support health care workers in remote and developing areas by providing AI-powered medical guidance, with or without internet access. It is available on iOS and Android and features an intuitive chatbot trained on decades of clinical expertise. This allows health care workers to quickly access real-time diagnostic support and treatment recommendations. When users need additional expertise, they can escalate cases to on-call medical doctors through the app. These physicians log into a secure admin website where they can review AI-generated responses, join conversations, and provide direct guidance in real time. The admin website allows clinic administrators to monitor AI-assisted interactions, track analytics, perform quality assurance checks and manage user accounts.
By seamlessly integrating AI-driven assistance with human expertise, MD-Sensei empowers frontline workers to deliver more informed, reliable care. The system bridges the gap between local clinics and experienced medical professionals so that even the most remote health care facilities have access to expert support when they need it most.
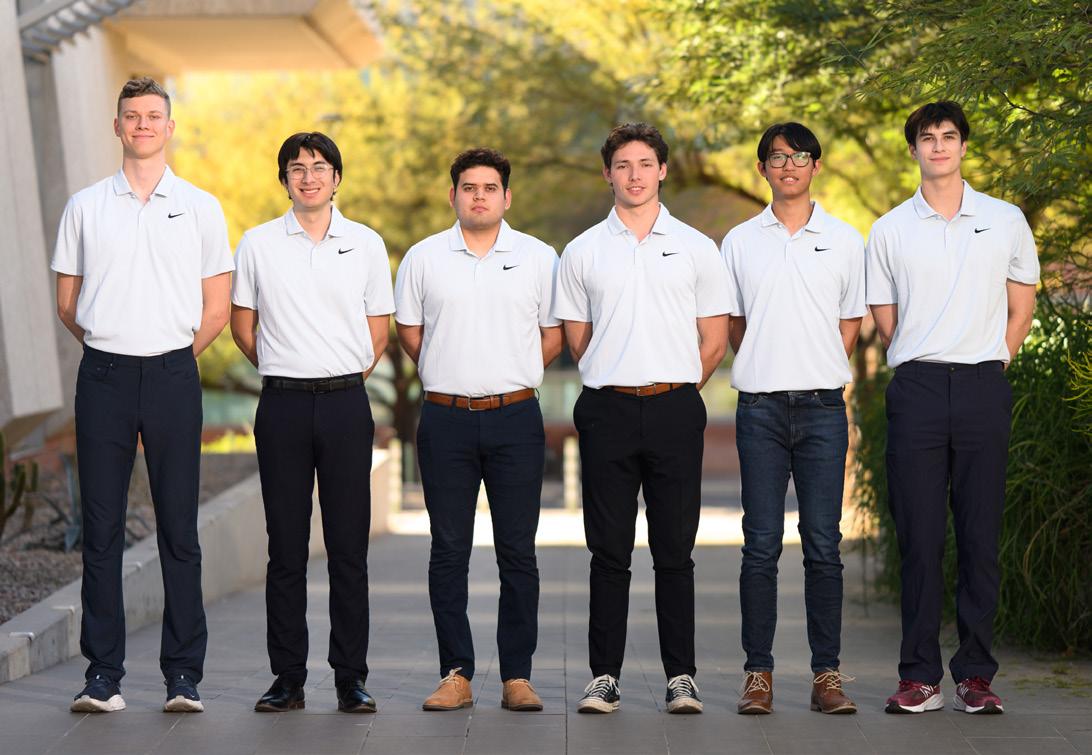
TEAM MEMBERS
Cameron Brown, Software Engineering
Dominick Rudolph D’Emilio, Software Engineering
Ruben Galdean, Software Engineering
Hsin-Wei Lin, Software Engineering
Oliver Philipp Liam Seymour, Software Engineering
Marco Arturo Manzo, Systems Engineering
COLLEGE MENTOR
Doug May
SPONSOR ADVISOR
Marie Charles
Broadband All-Fiber Depolarizer
Team 25034
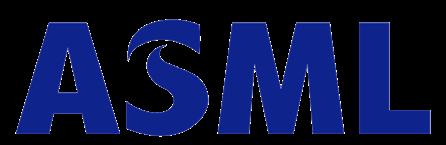
PROJECT GOAL
Design, prototype and experimentally verify a depolarizer made entirely of fiber optic cable to improve the accuracy of wafer alignment.
Photolithography machines use optical alignment sensors to precisely position and overlay photomask layers by detecting the reflection of polarized light from silicon wafer gratings. High alignment accuracy is crucial for wafer pattern transfer quality. This can be optimized using unpolarized light, which has the potential to maximize total signal detection. It is achieved by using coherent light sources and a depolarizer.
The team developed two theoretical models for depolarizing a broadband, visible/near-infrared input beam of any polarization state: Fiber Ring and Lyot. They chose the Lyot depolarizer and conducted experimental verification on a prototype of this passive, all-fiber model.
The Lyot depolarizer is made of two lengths of polarization-maintaining fiber spliced together, with one rotated 45 degrees relative to the other. The team selected a red fiber-coupled superluminescent diode as the coherent source for experimental setup. The light from this diode is routed through free space to control its polarization state, coupled into the depolarizer, and emitted back into free space, where the team took measurements with a Stokes polarimeter to verify the degree of polarization.
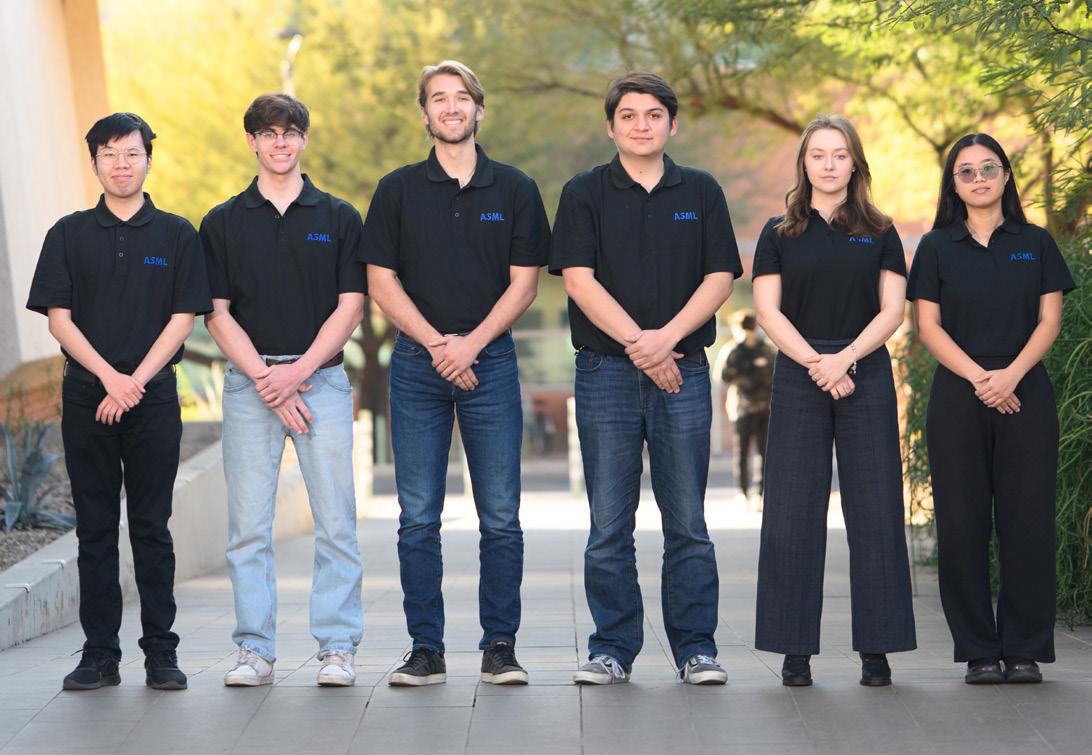
TEAM MEMBERS
Liam Falk, Applied Physics
Jack D Nguyen, Electrical & Computer Engineering
Joseph Edmund Campion Roa, Optical Sciences & Engineering
Adeline Tai, Optical Sciences & Engineering
Sophia A Golota, Electrical & Computer Engineering
Jimmy Payan, Electrical & Computer Engineering, Systems Engineering
COLLEGE MENTOR
Mike Nofziger
SPONSOR ADVISOR
Tao Chen
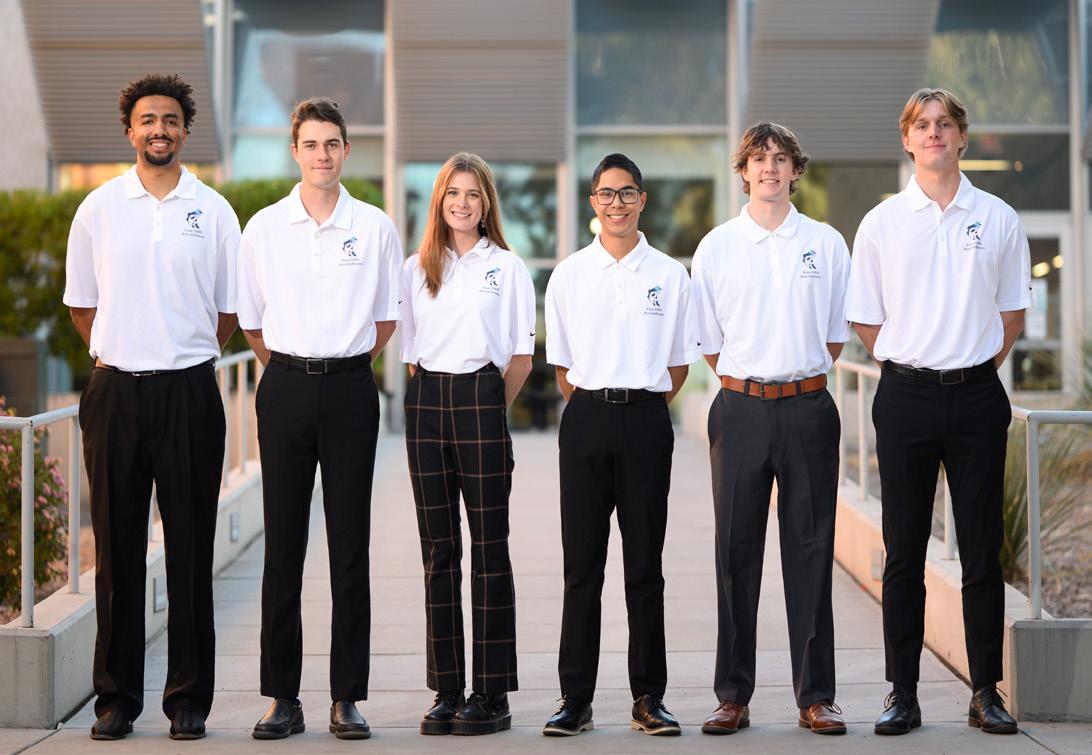
TEAM MEMBERS
Elyse Dilbeck-Stover, Biosystems Engineering
John Esparza, Biosystems Engineering
Jake Weithas, Electrical & Computer Engineering
Nate Hunter Williams, Mechanical Engineering
Isaak Ulm, Mechanical Engineering
Anthony John Saunders, Electrical & Computer Engineering
COLLEGE MENTOR
Steve Larimore
SPONSOR ADVISOR
Scott A Bonar
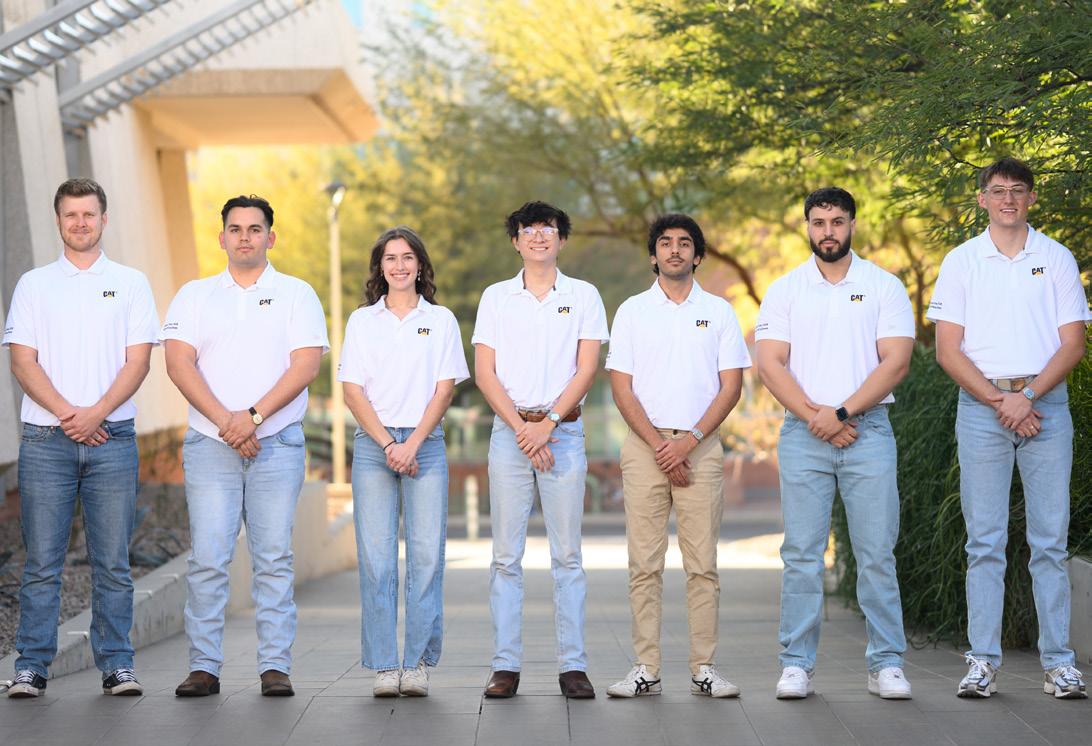
TEAM MEMBERS
Ahmed Ayad Al Mohammed, Engineering Management
Joseph Aumick, Mechanical Engineering
Dante’ Dixon, Mechanical Engineering
Emma Geneve Miller, Mechanical Engineering
Camden Nelson, Mechanical Engineering
David Rumph, Mechanical Engineering
Musab Ali, Industrial Engineering
COLLEGE MENTOR
Michael Madjerec
SPONSOR ADVISOR
Lloyd Becker
Electrofishing Unit Designed Specifically to Remove Large Numbers of Fish from Waterbodies
Team 25035

PROJECT GOAL
Create an electrofishing unit designed to aid in nuisance fish removal from waterbodies.
Non-native fish threaten local aquatic ecosystems and the economies that depend on them. Biological and chemical solutions are controversial and often don’t allow for selection between native and nonnative fish. Mechanical removal methods are promising and less controversial but need to be optimized to maximize control of non-native fish and minimize cost.
Electrofishing – a method of mechanical fishing that uses an electric field underwater to stun or herd fish via involuntary muscle contractions – has traditionally been used for sampling rather than population control. This project introduces a specialized electrofishing system designed specifically for efficient non-native fish removal in rivers and streams.
The team developed a system with a modular, width-spanning frame that operators drag upstream. Each section is equipped with anode and cathode droppers that generate a controlled electric field to guide fish into a bag seine for manual removal. The system is powered by a generator and managed through a control box. Users can adjust voltage, frequency and current to optimize effectiveness based on the target fish species.
By combining precision electrofishing with strategic fish herding, this solution provides a scalable, nonchemical approach to invasive fish management. This balances ecological preservation with practical implementation.
Hydraulic Mining Shovel Panel Re-Design with Adhesive Bonds
Team 25036
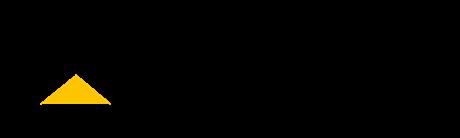
PROJECT GOAL
Redesign the slew ring cover of a hydraulic mining shovel to use structural adhesives in place of welds.
The slew ring assembly is a critical component of a hydraulic mining shovel which allows the machine to rotate smoothly. A slew ring cover sits atop the slew ring to retain grease within the assembly. Traditional welding techniques for adhering components of the cover often cause distortion within the thin sheet metal, leading to grease leakage. This reduces lubrication within the assembly, raises environmental concerns and increases maintenance costs. For every hour of downtime of these machines, a customer can lose over $200,000 in potential revenue. This project explores the use of structural adhesives as an alternative to welding to prevent any distortion within the slew ring cover.
The team’s design uses structural, acrylic adhesives to bond the components of the slew ring cover to preserve the surface flatness of the sheet metal. This required an entire redesign of the cover to limit welding and incorporate these structural adhesives throughout. A series of mechanical, environmental and virtual tests validated the adhesive bonds’ strength, lifespan and resistance to mining conditions. After further development, these adhesives can enter the Caterpillar ecosystem and be used on a variety of machines for years to come.
Wavefront Performance Measurement on Small Numerical Aperture (NA) Lenses
Team 25037
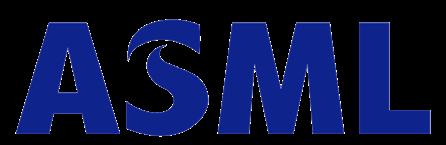
PROJECT GOAL
Determine the limits of accuracy and repeatability in measuring wavefronts of small NA lenses using a single-pass metrology setup.
ASML is a global leader in lithography for mass producing semiconductor chips. The company uses optical techniques to measure wafer topology in its commercial lithography systems. ASML’s current method for qualifying the lenses used in level sensors relies on a double-pass interferometer. While this method is effective, it also has serious limitations: It is complex, requires a large facility and is time-consuming. To address these problems, the team explored alternative single-pass metrology techniques that can improve efficiency while maintaining accuracy and repeatability.
The team evaluated three approaches and then selected the Shack-Hartmann Wavefront Sensor for its simplicity and availability. After confirming this sensor’s potential with extensive theoretical analysis and modeling, the team designed and built a test setup around the sensor to validate the theoretical findings through experimental testing. This testing confirmed that the system successfully measures and displays wavefront aberrations introduced by the test lens. Repeated measurements demonstrate the setup’s accuracy and repeatability, confirming its potential as a viable alternative to the more complex double-pass interferometer that ASML currently uses.
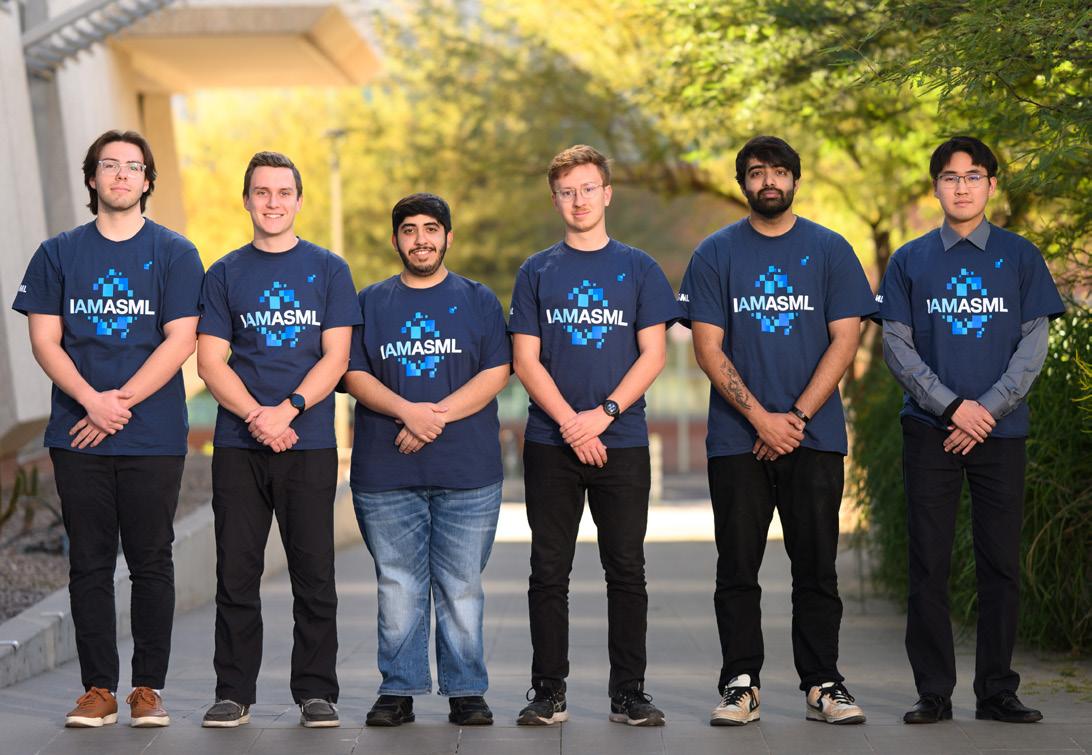
TEAM MEMBERS
Mohamed Almheiri, Mechanical Engineering
Kris Pawel Kuiper, Optical Sciences & Engineering
Miguel Sandoval, Software Engineering
JhihYang Wu, Electrical & Computer Engineering
Caleb Edward Brownlie, Engineering Management
Ricky Saxena, Optical Sciences & Engineering
COLLEGE MENTOR
Mike Nofziger
SPONSOR ADVISOR
Bart Kessels
Liquid Propellant Rotating Detonation Rocket Engine (RDRE)
Team 25038
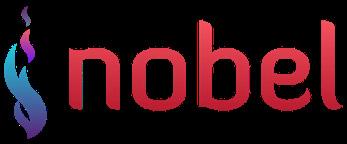
PROJECT GOAL
Design, fabricate and test an RDRE that uses a propellant mix of liquid oxygen and liquid ethanol.
The RDRE is an innovative approach to propulsion with the potential to be 25% more efficient than conventional rocket engines. This project will leverage this technology to reduce cost and improve sustainability. Conventional rocket engines use subsonic combustion – the same process as a car engine – while RDREs use supersonic combustion, also known as detonation. The key component of the RDRE is an annular combustion chamber where a detonation wave continuously propagates at supersonic speeds to efficiently burn the injected propellant.
The team designed, simulated, fabricated and tested a prototype RDRE. The focus was optimizing the detonation wave dynamics and ensuring the structural integrity of the engine under operating conditions. The team’s RDRE uses an injector plate designed to mix liquid propellants and ensure stable detonation in the combustion chamber. A deflagration-to-detonation transition tube starts a detonation wave which continuously travels around the chamber. The engine also features an aerospike nozzle to generate optimal thrust at various altitudes. The team’s tests demonstrated detonation-based propulsion’s potential to advance rocket technology, and the project has real-world applications in space exploration and defense.
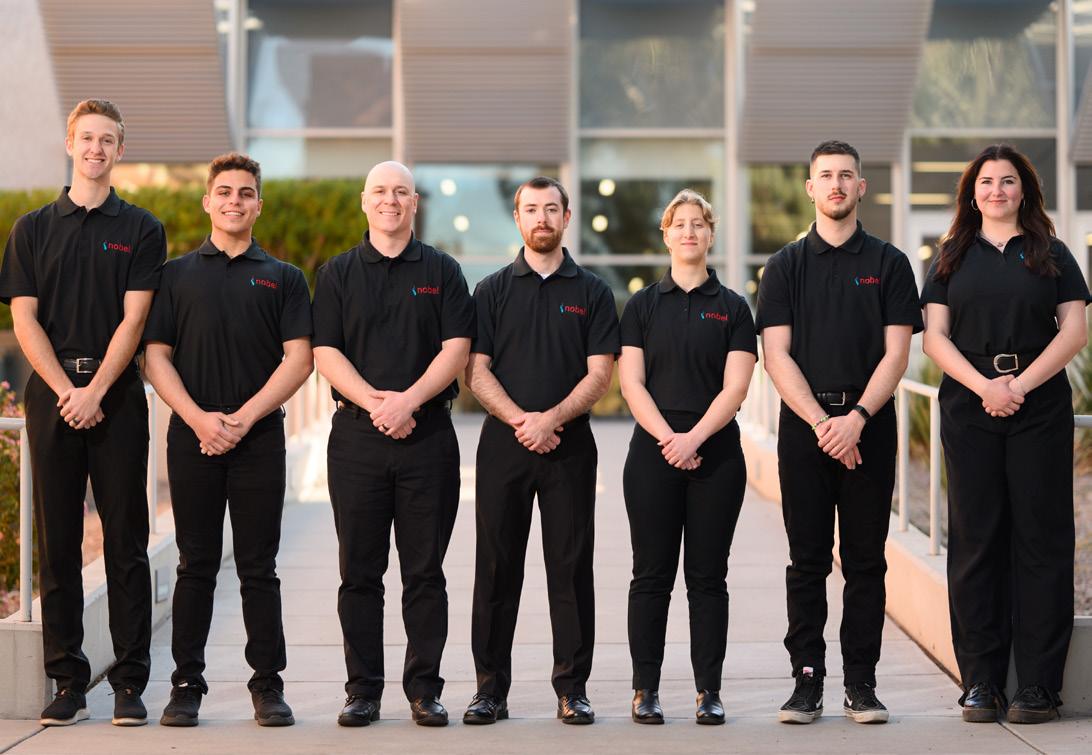
TEAM MEMBERS
Robert Lane, Aerospace Engineering
Christopher Mason, Aerospace Engineering
Brendan Perry, Mechanical Engineering
Marilyn Salome, Aerospace Engineering
Reed Christopher Spurling, Aerospace Engineering
Luis Molina Davila, Engineering Management
Gemma Smith, Aerospace Engineering
COLLEGE MENTOR
Carey Jeannette Jones
SPONSOR ADVISOR
James Villarreal
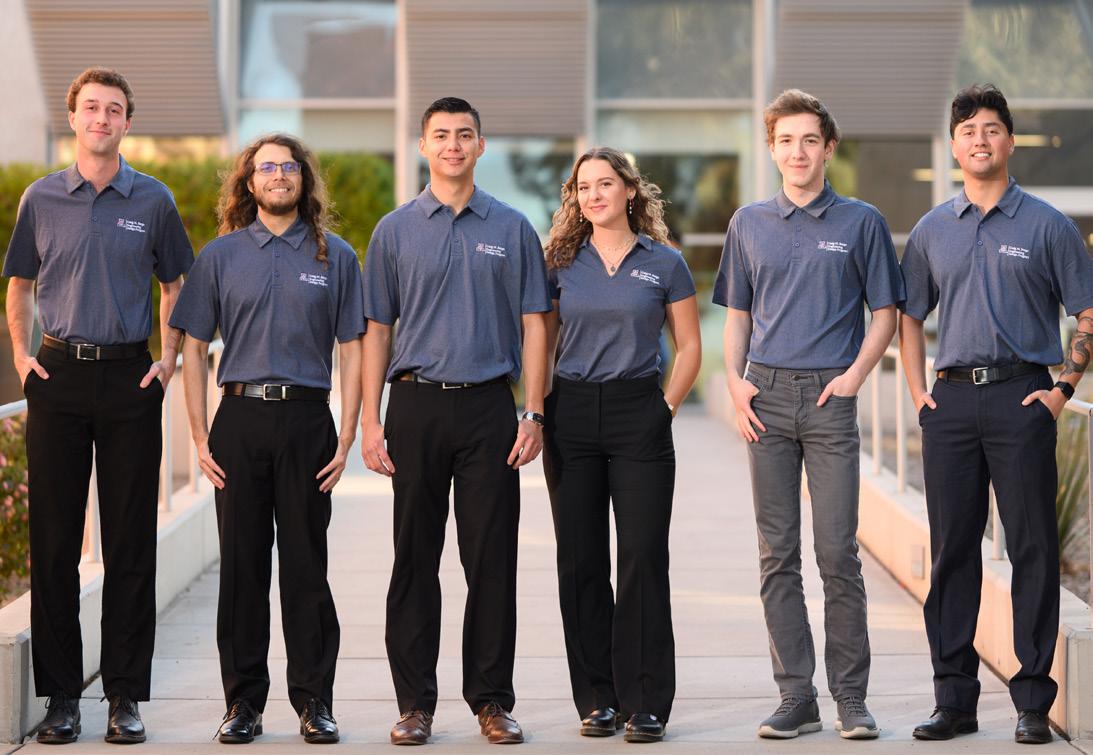
TEAM MEMBERS
Julian Jose Aleman, Mechanical Engineering
Brian Alberto Flores, Electrical & Computer Engineering
Korbin Hansen, Aerospace Engineering
Sebastian Robinson, Electrical & Computer Engineering
Rachel Rhomberg, Aerospace Engineering
Nathaniel Skiffington, Aerospace Engineering
COLLEGE MENTOR
Carey Jeannette Jones
SPONSOR ADVISOR
James Villarreal
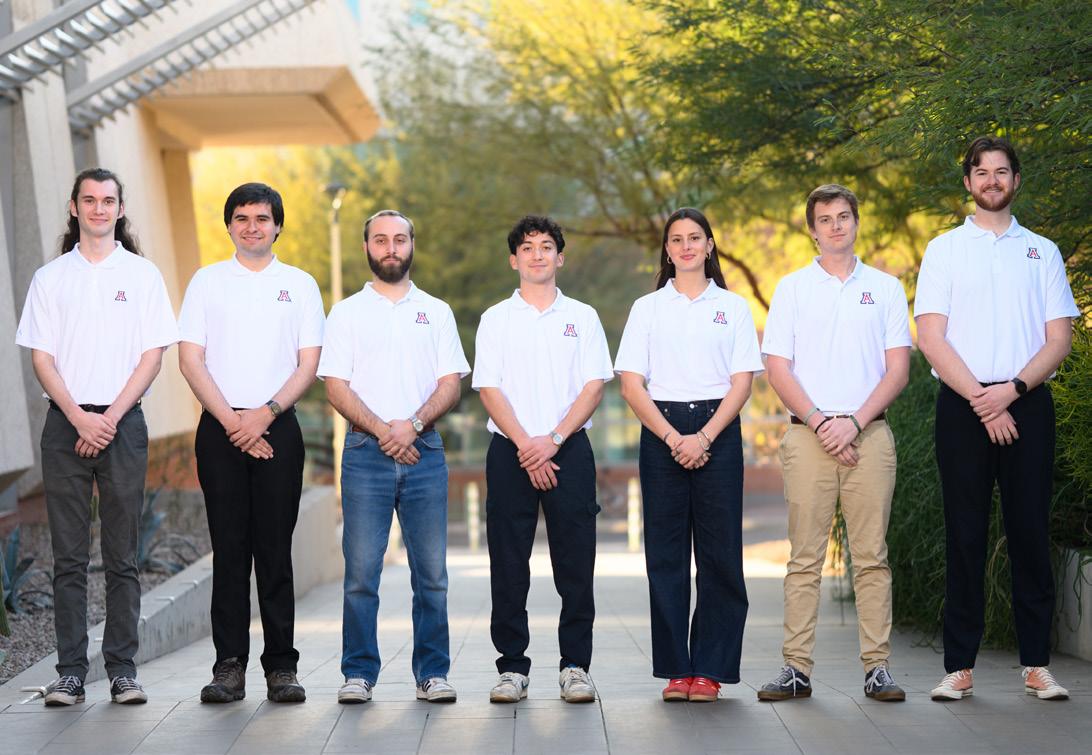
TEAM MEMBERS
Brendan Bamberg, Optical Sciences & Engineering
Austin Medina, Software Engineering
Alia Nichols, Optical Sciences & Engineering
Aidan Talucci, Mechanical Engineering
Tyler Thursby, Electrical & Computer Engineering
Danny Knaus, Biomedical Engineering
Jameson Teague Brehmer, Biomedical Engineering
COLLEGE MENTOR
Don McDonald
SPONSOR ADVISOR
Marvin J Slepian
Hybrid Electric Demonstration Engine for Heavy-Lift UAV
Team 25039
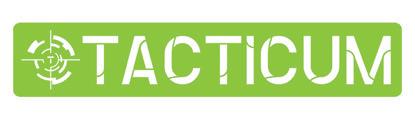
PROJECT GOAL
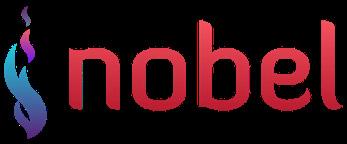
Develop a hybrid-electric powertrain system in tandem with a simulation to serve as proof-of-concept for a heavy-lift UAV that demonstrates viability for future missions.
The range and payload capacity of current UAVs are constrained by battery energy density limitations. This project addresses this challenge by building and testing a scalable hybrid-electric system that combines a combustion engine with electric propulsion to achieve the power-to-weight ratio required for cargo missions. The team began by simulating the powertrain in MATLAB Simulink to evaluate performance under flight conditions. Although the test system was not flyable, it was designed to scale to a UAV with a 2,200 lb. gross takeoff weight including a 1,000 lb. payload capacity with a two-hour runtime.
The team delivered two main components: a tabletop powertrain and a Simulink simulation. The powertrain is hybrid-electric with a complex data acquisition system connected to the powertrain that monitors diagnostics in real time. The simulation allows a user to customize the powertrain configurations and analyze performance over various flight profiles. Key subsystems include the power distribution system for efficient power management and the data acquisition system for user control and data collection. This proof-of-concept demonstrates the feasibility of hybrid-electric systems for heavy-lift UAVs and paves the way for future development.
WATER-BADDIES - Microplastic, Heavy Metal and Inorganics
Water Detection System for Environmental and Human Health
Team 25040
KIDNEY ADVANCE PROJECT
PROJECT GOAL
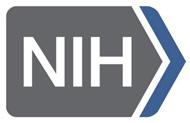

Develop a portable, low-cost point-of-care device for detecting and quantifying water contaminants.
Water pollutants – including heavy metals, inorganic contaminants, and microplastics – pose significant risks to both the environment and public health. A system for monitoring these “water baddies” is a necessary part of understanding this contamination and taking steps to correct it. Unfortunately, traditional water testing methods rely on laboratory-based analysis, which is expensive, time-intensive and often inaccessible to the general public. This project introduces a functional, small footprint/point-of care analysis system for detecting these water baddies to ensure clean water for a safe future.
The team used a colorimetric and fluorescence-based approach for rapid, on-site water monitoring in an easy-to-use desktop clinical device. The result is a novel paperfluidic device that uses commercial test strips to detect heavy metals and inorganic contaminants and fluorescent microscopy – using a digital microscope, blue LED, and a 520 nm bandpass filter – to identify microplastics. The system employs a dropper mechanism and conveyor belt to deliver samples precisely to detection zones. Results are captured via imaging, analyzed through software, and accessible via a Bluetooth-enabled mobile app. Through experimental calibration, the team determined that the device can successfully detect contaminants well below the limit of EPA National Primary Drinking Water Regulations.
The Room Knows - The Smart Patient Exam Room
Team 25041
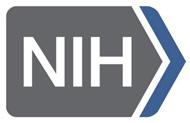
PROJECT GOAL

Systematically capture information that the physician might miss in a standard exam, as well as extract information to create verbal and digital biomarkers of disease.
Demand for primary health care is increasing as the population ages. Fewer medical doctors are available per patient, and the extensive manual data entry required by current electronic health record systems results in less time for meaningful patient interactions. Since a diagnosis is often determined by careful observation of verbal and nonverbal cues, these shorter appointment times can result in missed diagnoses. Therefore, a system that automates observation and documentation to enhance diagnostic accuracy and improve clinical efficiency provides value.
The team’s solution to this problem is a portable kit equipped to capture and record both visual and auditory data. Integrated software processes the data and provides suggestions for diagnosis. To do this, the audio analysis system first distinguishes speech between the clinician and patient, analyzes speech for diagnostic clues, and assesses the patient’s emotions based on verbal cues. Next, facial analysis detects any abnormalities in facial structure and determines the patient’s predominant emotions throughout a visit. Finally, the motion analysis takes in video of the patient’s movement during the visit and analyzes their gait, speed and sit-to-stand values. After recording and analysis, the system transfers the data into a final report with a summary of findings. The kit can accomplish this during the patient’s visit, allowing the physician to take this information into account while forming a diagnosis.
Optical Metrology Module
Team 25042
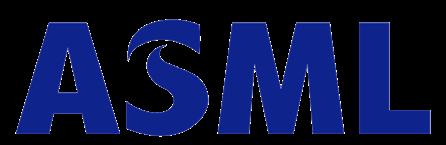
PROJECT GOAL
Design, build and test a prototype optical metrology module system that measures the size, velocity, and trajectory of microspheres with diameters less than 500 microns.
ASML US, Inc. is the world’s only supplier of extreme ultraviolet (EUV) lithography machines, which are crucial for manufacturing the most advanced semiconductor chips. Contaminants that may end up in the system can lead to extended downtime and costly repairs.
As an example, contaminants may arise during the vaporization of tin particles. ASML US, Inc. uses these particles in its laser produced plasma (LPP) EUV lithography tools. A powerful carbon dioxide laser needs to strike the particles at just the right time to produce the EUV light.
This project focused on designing, building and testing an optical metrology module that measures the size, velocity, and particle trajectory of glass soda-lime microspheres with diameters smaller than 500 µm. It used commercial off-the-shelf components supplemented by 3D-printed or locally machined parts. The system comprises a flow control unit, light source, and detector, all housed within a cube no larger than 3 feet per side, with supporting circuitry and display components mounted externally. The metrology module can detect and track particles similar to the ones ASML uses in its LLP EUV lithography processes. The team evaluated the system through iterative testing and collaboration with ASML and demonstrated that the system improved the detection and positioning of microspheres that are critical for the operation of the LPP EUV tools.
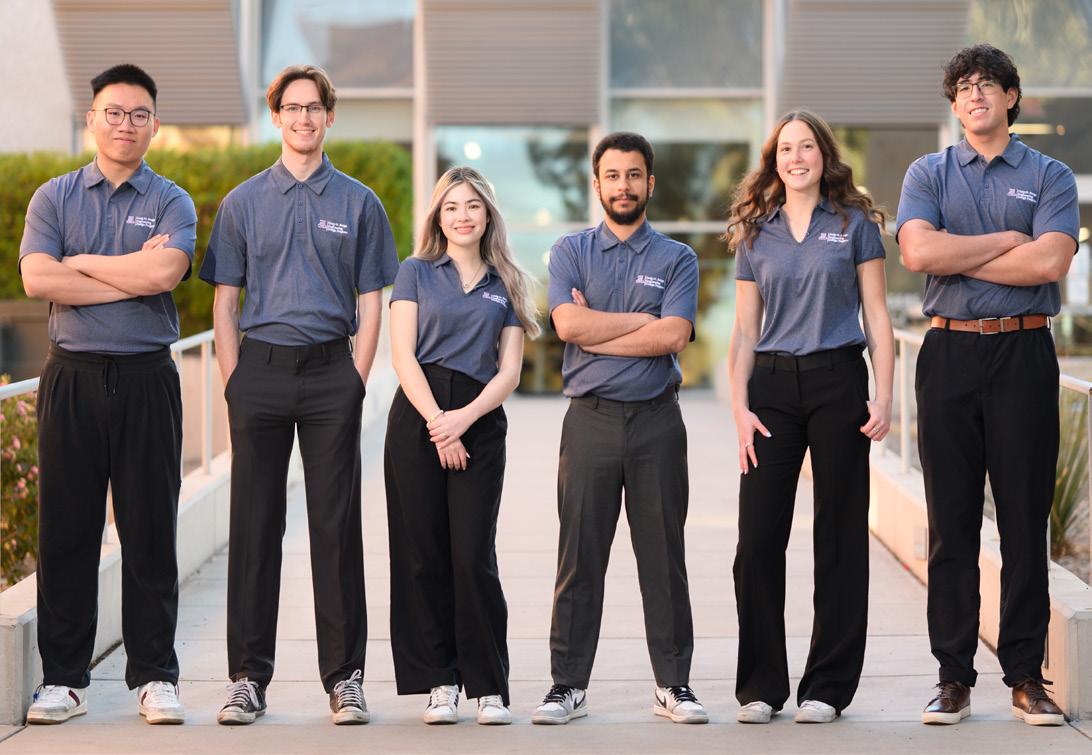
TEAM MEMBERS
Rashed Altammar, Electrical & Computer Engineering
Kaiyang Diao, Biomedical Engineering
Jorge Andres Lujan, Software Engineering
Elissa Chen Matlock, Biomedical Engineering
Bella Klein, Biomedical Engineering
Skyler DeVaughn, Software Engineering
COLLEGE MENTOR
Don McDonald
SPONSOR ADVISOR
Marvin J Slepian
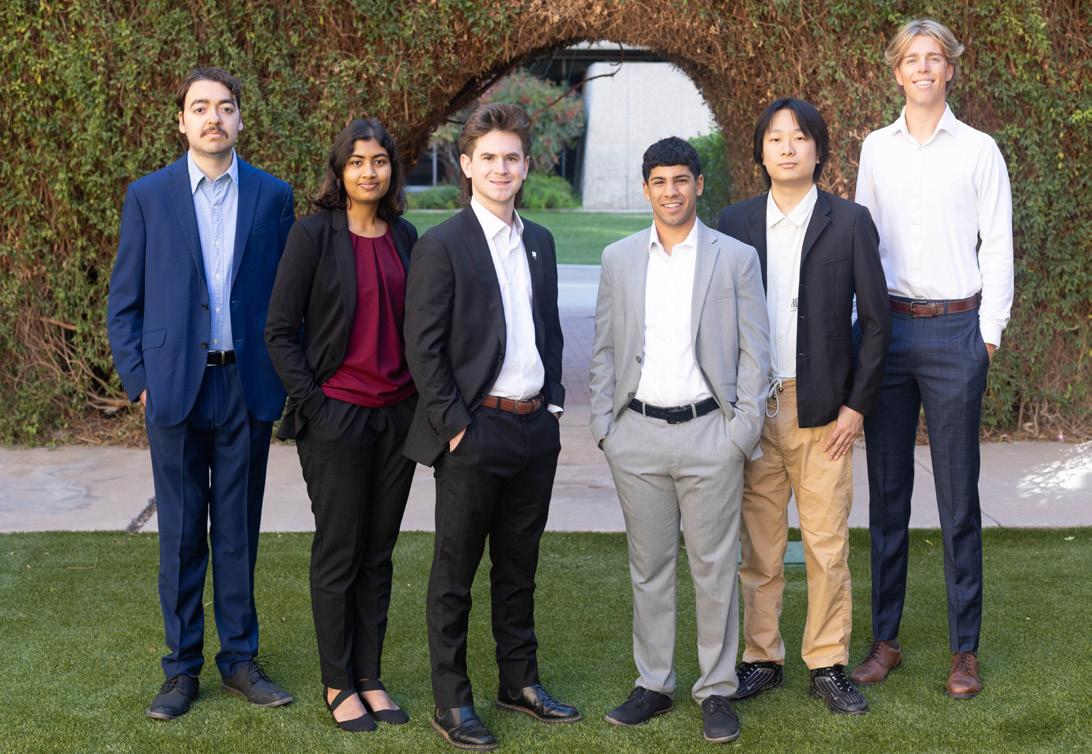
TEAM MEMBERS
Derek Kropp, Electrical & Computer Engineering
Nicholas Leonhard, Mechanical Engineering
Vaidehi Pujary, Electrical & Computer Engineering
Adam Wan, Optical Sciences & Engineering
Giancarlo J Duarte, Engineering Management
Noah Michael Hasegawa, Optical Sciences & Engineering
COLLEGE MENTOR
Don McDonald
SPONSOR ADVISORS
Erik Huerta
Sarah Kreikemeier
Bin Kim
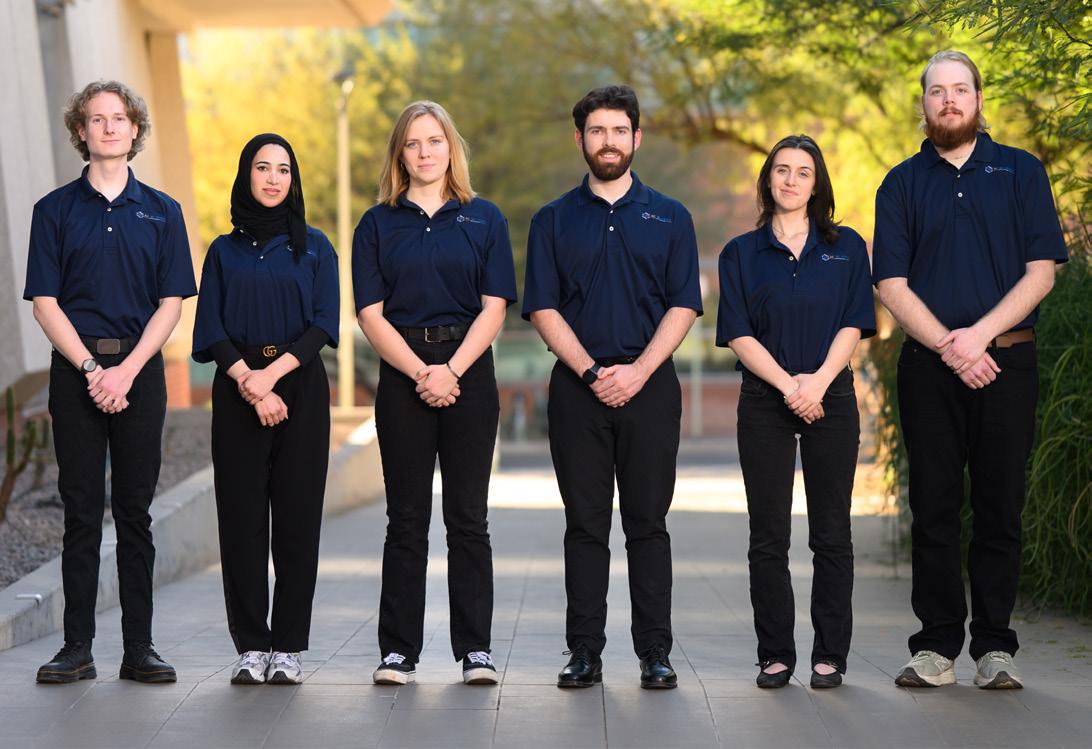
TEAM MEMBERS
Brenna Lisa Allen, Mechanical Engineering
Batoul Jassim Alqalaf, Industrial Engineering
Carson Di Maria, Mechanical Engineering
Caleb Kehret, Mechanical Engineering
Madison Migliori, Software Engineering
Seven Mathew Gilbert, Electrical & Computer Engineering
COLLEGE MENTOR
Sardar R Mostofa
SPONSOR ADVISOR
Barrett Locke
Powder Conveyance for Sustainable 3D Printing Team 25043
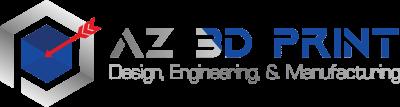
PROJECT GOAL
Create a system that automates the transfer and mixing of HP PA12 powder, a thermoplastic material, for 3D filament production to reduce powder exposure and improve efficiency.
Industrial HP-MJF 3D printers are revolutionizing manufacturing, but they produce excess PA12 glassnylon powder as a byproduct of the printing process. The current method for recycling this powder is to manually transfer it between barrels using a scoop. This requires extra labor and produces undesirable airborne particulates. To improve efficiency and workplace safety, the team created a material conveyance system that automates the recycling process by transporting, mixing and extruding PA12 powder into reusable 3D printing filament.
The team’s system consists of three primary subsystems: a cyclone-based transport system, a rotary mixing subsystem and a hopper-fed extrusion assembly. The transport system moves powder from a bulk storage barrel to the mixing chamber. Here, controlled rotation incorporates additives for color and stability. Next, the mixed powder is fed into a filament extruder via a hopper assembly. Users can control powder transfer and mixing parameters via a touchscreen interface. The system also automatically logs operational data for tracking and optimization. This system promotes material reuse, reduces manual handling, and provides a safer and more consistent method for producing recycled filament.
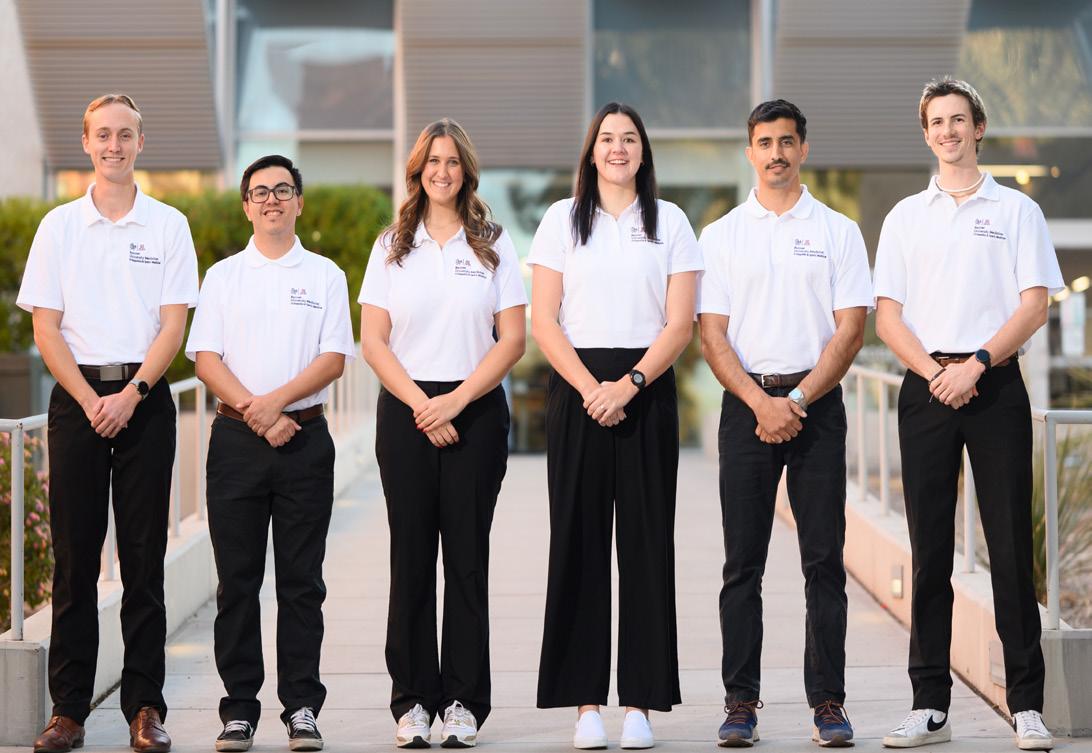
TEAM MEMBERS
A.J. Makkyla, Biomedical Engineering
John Paul Martin Encinas, Software Engineering
Brad Matheson, Mechanical Engineering
Noman Nabi, Mechanical Engineering
McKenna Lynn Nichols, Biomedical Engineering
Grace Guzinski, Biomedical Engineering
COLLEGE MENTOR
Don McDonald
SPONSOR ADVISOR
Dan Latt
Automated Weight Bearing 3D Ultrasound Foot Scanner
Team 25044

PROJECT GOAL
Develop an automated, weight-bearing 3D ultrasound foot scanner that uses shear wave elastography (SWE) to accurately assess plantar ligament stiffness for early detection of arch collapse.
The team created the Automated Weight-Bearing 3D Ultrasound Foot Scanner. It is a novel diagnostic tool designed to be used in a clinical setting to measure the stiffness of arch-supporting structures in a weight-bearing position. This system integrates SWE and brightness mode imaging to provide a precise, real-time assessment of plantar ligament stiffness. Using this system, a clinician can accurately detect early signs of arch collapse.
The team’s engineering efforts focused on refining the mechanical structures of the device for improved patient adjustability, developing advanced data acquisition and processing software, and enhancing the graphical user interface for real-time visualization. The final design features an automated ultrasound probe positioning system, pressure sensors for load distribution feedback, and a compact, user-friendly platform that can accommodate various foot sizes and patient weights. The team’s testing confirmed that the system has a ±5% accuracy in stiffness measurements. This is sufficient accuracy to improve preventative care in podiatry and orthopedic clinics. This scanner also standardizes foot stiffness assessments, which gives clinicians an efficient, reliable and noninvasive diagnostic tool for enhancing patient outcomes.
NEO-CATH - Smart Urinary Catheter System - Analgesic, AntiInflammatory, Anti-Infective Team 25045
KIDNEY ADVANCE PROJECT
PROJECT GOAL
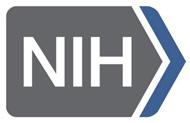

Develop a urinary catheter system with integrated analgesic, anti-inflammatory, and anti-infective properties to enhance patient comfort and reduce catheterassociated infections.
Urinary catheters are essential medical devices, but they are prone to causing pain, inflammation and infection. To address these challenges, the team developed an improved, patient-friendly urinary drainage catheter system. The team’s design integrates advanced biomaterials, localized drug delivery, and real-time health monitoring. This system will reduce medical morbidity and mortality in patients who need these catheters.
The team began by identifying the limitations of current Foley catheters. They determined the importance of including a way to administer analgesic, anti-inflammatory and anti-infective agents, as well as the need to monitor patient vitals through the device. The resulting design features a threeway lumen catheter made of medical-grade silicone. It incorporates a polymer dip-coating that allows medical professionals to administer a controlled release of ibuprofen and dexamethasone to reduce pain and inflammation.
A solenoid-generated electromagnetic field (EMF) also inhibits bacterial biofilm formation. Integrated temperature and pH sensors continuously monitor patient health and wirelessly transmit the data to the system. This enables health care providers to track patient health and system functions –including anti-inflammation release, temperature, pH and time and application of EMF – remotely on a mobile application.
Fiber-Coupled Package Test Station
Team 25046
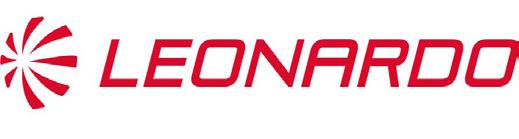
PROJECT GOAL
Develop an enclosed, automated station for testing fiber-coupled laser diodes, significantly reducing manual testing time while prioritizing safety.
Fiber-coupled laser diodes are part of many defense and commercial applications. Users must properly test these lasers, but that can be expensive and pose risks to the testers. The team developed an enclosed, automated station for testing fiber-coupled laser diodes. This will significantly reduce manual testing time while prioritizing safety.
Since this setup uses powerful Class 4 lasers, the team enclosed it and included an emergency power-off circuit to ensure safe operation. An automated fiber-alignment system provides precise fiber positioning, while integrated cooling and vibration isolation maintain stable operating conditions. The cooling system features closed loops for the aperture, screen, device under test carrier, and laser diode driver for efficient thermal management. Operators can control the system with a programmable logic controller to collect data on electrical inputs, cooling performance and optical outputs. This includes power measurements with and without cladding light blocked by an aperture. The system also measures the laser’s far-field pattern and spectrum using an off-axis camera and spectrometer.
This test station ensures that laser measurements meet specified criteria and automatically assigns a pass or fail based on predefined thresholds. By automating data collection and analysis, this system streamlines testing, improves accuracy, and guarantees repeatable results for high-power laser diode characterization, all within a safe and controlled environment.
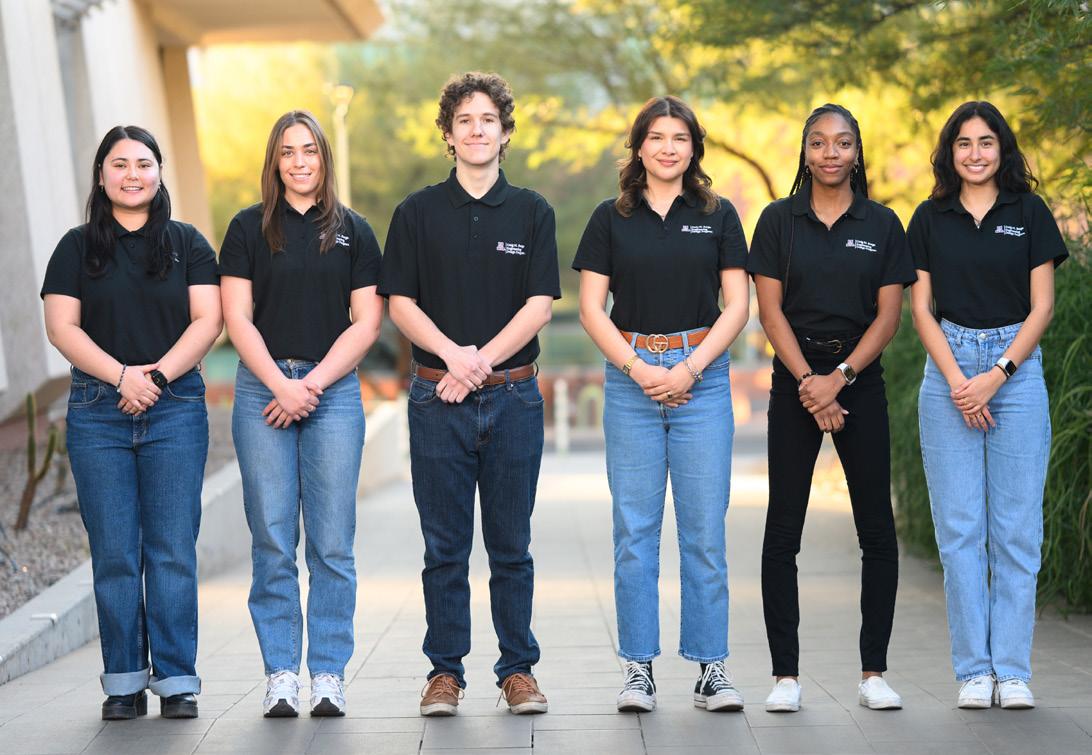
TEAM MEMBERS
Cameron Alexander Balderrama, Electrical & Computer
Engineering
Dalia Castro-Fimbres, Software Engineering
Enka Hysaj, Software Engineering
Cassidy Little, Biomedical Engineering
Khushi Praveen, Biomedical Engineering
Kaitlyn Hbr McKnight, Biomedical Engineering
COLLEGE MENTOR
Don McDonald
SPONSOR ADVISOR
Marvin J Slepian
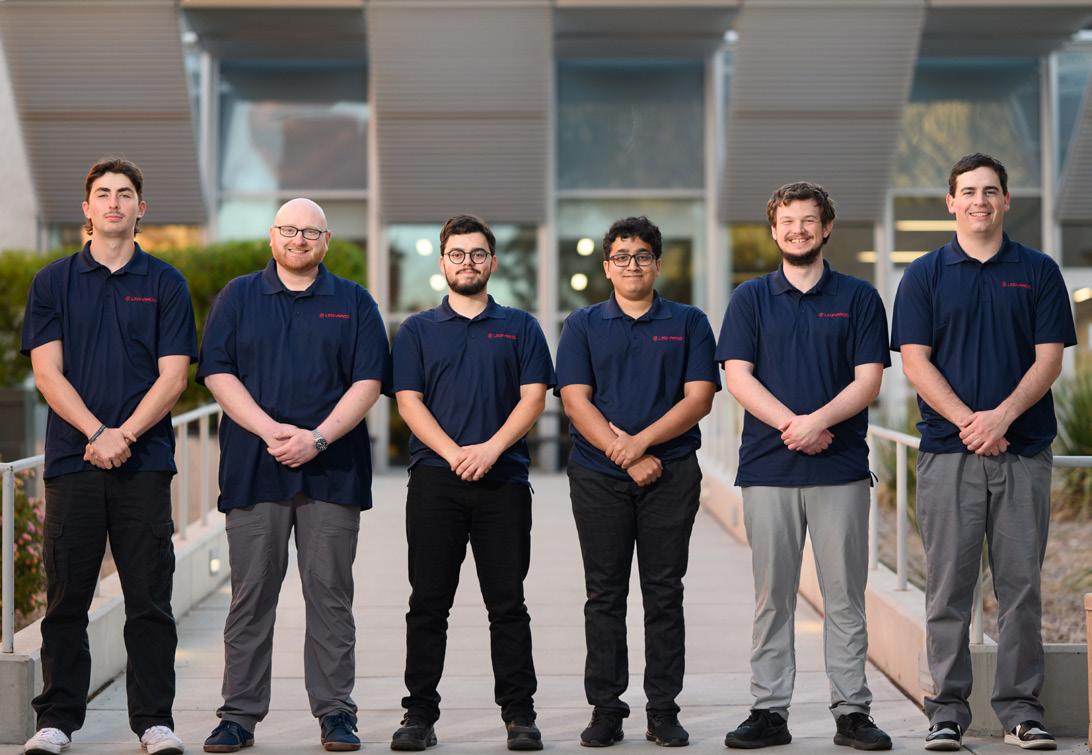
TEAM MEMBERS
George Malone Davis, Electrical & Computer Engineering
Aditya Vijaykumar, Optical Sciences & Engineering
Jason Bradley Walls, Engineering Management
Cutter Reed Williams, Mechanical Engineering
Max Betaille, Applied Physics
Kobe Mercea, Optical Sciences & Engineering
COLLEGE MENTOR
Mike Nofziger
SPONSOR ADVISOR
Brian Caliva
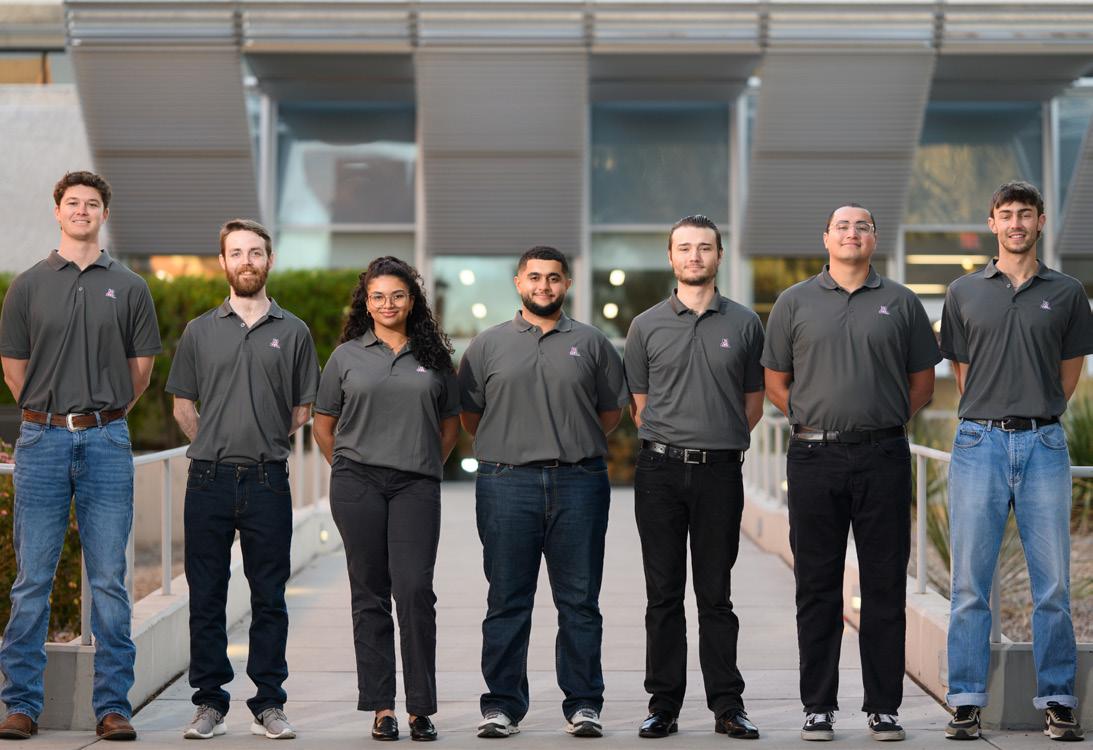
TEAM MEMBERS
Cole Rogers, Electrical & Computer Engineering
Esteban I Salazar, Materials Science & Engineering
Roman Sharp, Industrial Engineering
Devin Taylor, Mechanical Engineering
Allison Jade Williams, Aerospace Engineering
Ryan Raad, Electrical & Computer Engineering
Mohanad Alyamani, Industrial Engineering
COLLEGE MENTOR
Michael Madjerec
SPONSOR ADVISOR
Alexander Rudisill
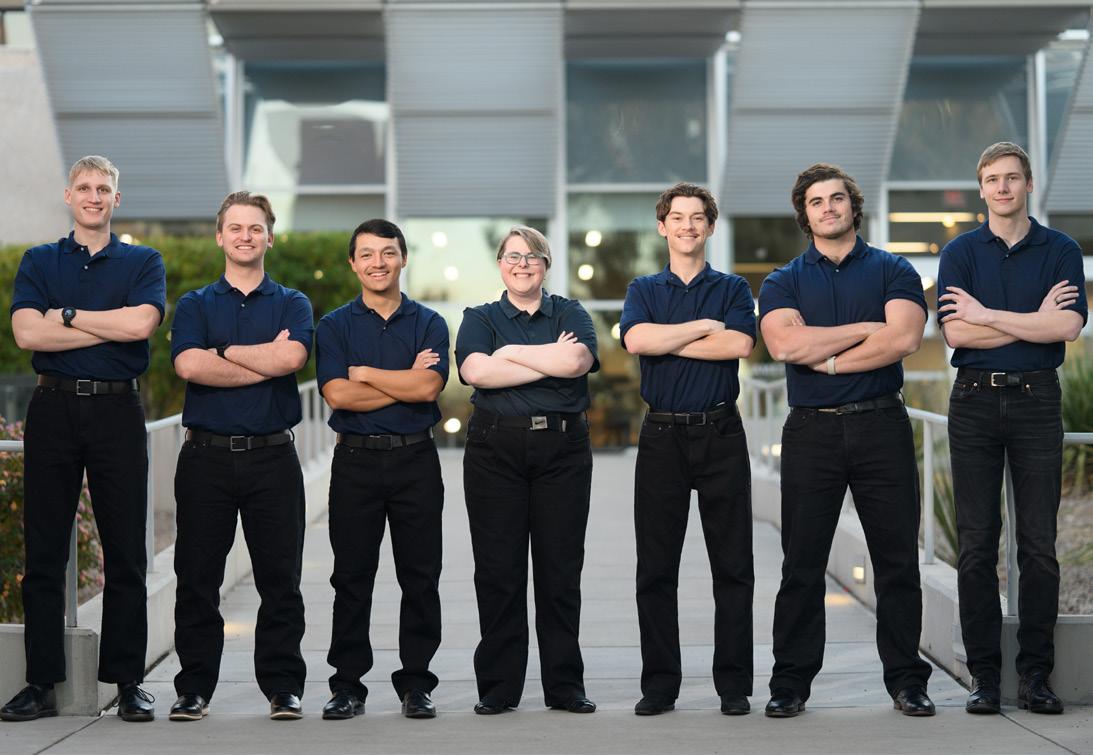
TEAM MEMBERS
Alex Choi, Electrical & Computer Engineering
Davin Schlak, Mechanical Engineering
Matthew Schultz, Systems Engineering
MiLee Alexandra Vogel, Software Engineering
Carson Winn, Mechanical Engineering
Evan Scott Shiel, Industrial Engineering
Tyler Wilson, Electrical & Computer Engineering, Mechanical Engineering
COLLEGE MENTOR
Jeff Scott Wolske
SPONSOR ADVISOR
Luke Baer
3D Printing Temperature/Humidity Control Filament
Team 25047
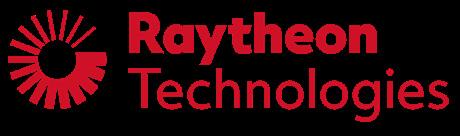
PROJECT GOAL
Design a storage unit that is capable of preheating and storing an industrial amount of 3D printing filament to be ready for use at a moment’s notice.
Raytheon’s Additive Manufacturing (3D printing) Lab produces thousands of parts each year of varying materials and sizes. The company’s printers use various filaments with a wide range of preferred temperature/humidity conditions. Having the ability to effectively store these materials, control temperature and humidity, and quickly prep multiple different filament types means reducing waste and improving lead times for customer prints.
The team designed and built a multi-compartment temperature/humidity chamber that can accommodate these different filament types. A low humidity and warm temperature environment is ideal for effective printing. The team also found that spending time to preheat the material can slow down projects and lead times, and damaged filament can ruin a print or the printer.
The controlled environment of the team’s chamber can store various filament types and ensure material integrity by protecting against moisture absorption and temperature fluctuations. The system includes integrated heating, dehumidification and air circulation components to provide precise environmental control within a defined temperature range and humidity levels. The unit is also durable, mobile and optimized for use in a fabrication shop environment with a focus on long-term reliability and energy efficiency.
Golf Putting Robot Team 25048
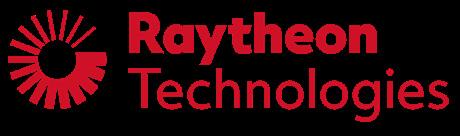
PROJECT GOAL
Create an advanced and engaging golf putting robot that inspires the next generation of engineers and problem-solvers by showing how engineering principles can solve realworld challenges in sports and beyond.
This project demonstrates how engineering can replicate the fine control and decision-making required to accurately and consistently putt a golf ball. It leverages concepts from various engineering disciplines from robotics to sensor integration and many more complex and fun learning opportunities. The goal of showing off these engineering skills and applications is to engage young students in STEM fields.
The Golf Putting Robot, fondly referred to as GoPheR, is a design project aimed at perfecting the complex human task of putting on a golf green. The system utilizes a lidar, or light detection and ranging, sensor to create a detailed map of the green. This allows the robot to assess slope, surface variations, and optimal paths for a successful putt. GoPheR also uses two on-board cameras for object recognition of the ball and flag and for alignment and tracking. The robot has on-board stepper motors to precisely adjust GoPheR’s position relative to the ball and the speed at which GoPheR’s putter contacts the ball. This simulates human-like putting motions. With these core components, GoPheR can ensure completing a hole in two putts or fewer from any point on a regulation putting green.
AZ Heat Medicine -
Reduce Renal Failure in Arizona - Fly, Measure, Treat
Team 25049

PROJECT GOAL
supported by Craig M. Berge Dean’s Fund
Develop an integrated drone-delivery, diagnostic test and software system to identify, test and treat dehydration that will mitigate heat-related health risks in the community.
Dehydration and other heat-related health risks are a major concern in Arizona. In this community and population project, the AZ Heat Medicine team created a surveillance system that combines a drone, a point-of-care test, and a software platform to monitor, address and potentially treat dehydration.
The system uses visual cues, regional temperature data and historical hydration results to assist a drone operator in locating individuals in the community that are at risk of heat-related injury. Once the operator has identified an at-risk individual, they can assess the individual for dehydration. This pointof-care test employs a conductivity sensor to analyze a provided urine or saliva sample for hydration levels. Depending on the assessment, the operator can also dispatch fluids for rehydration via a small deployable parachute system. A software platform allows for the communication between the drone and operator. It also tracks community hydration trends and securely stores the collected data for further analysis.
By merging these advanced subsystems, the team has created a data-driven solution that promptly assesses and responds to dehydration. This will ultimately help mitigate heat-related health risks, enhance community well-being, and potentially reduce mortality and morbidity for thousands of people in Arizona.
CycleSafe: A Bicycle Handlebar Mounted Automobile Proximity
Sensing, Warning and Reporting Device - Phase 3
Team 25050
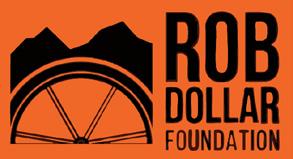
PROJECT GOAL
Design and develop a compact, high-precision bicycle handlebar-mounted device for automobile proximity detection, real-time warning and incident reporting. It features seamless smartphone integration and superior accuracy and reduced size compared to the previous version.
Arizona law A.R.S. 28-735 mandates that vehicles maintain a minimum 3 ft passing distance when overtaking cyclists, yet no enforcement mechanism currently exists. This project seeks to develop a handlebar-mounted detection device that identifies and documents violations to provide evidence and improve cyclist safety.
This phase of development focused on high-speed detection methods to ensure accurate data capture for vehicles traveling at speeds of up to 45 mph relative to the bicycle. The goal was to deliver five functional prototypes for sponsor testing.
The system uses a time-of-flight sensor for rapid sampling. If a vehicle encroaches within the 3 ft threshold, an ESP32-S3 Sense microcontroller triggers a forward-facing camera to capture a burst of images and activates an LED alert for the cyclist. The device integrates with a companion smartphone app that logs GPS location, uploads images and auto-selects key frames from the incident.
Designed for versatility, the modular housing supports both drop-bar and flat-bar handlebars to ensure broad compatibility across different bicycle types. This innovative system provides a practical enforcement tool to enhance cyclist safety and promote compliance with driving laws.
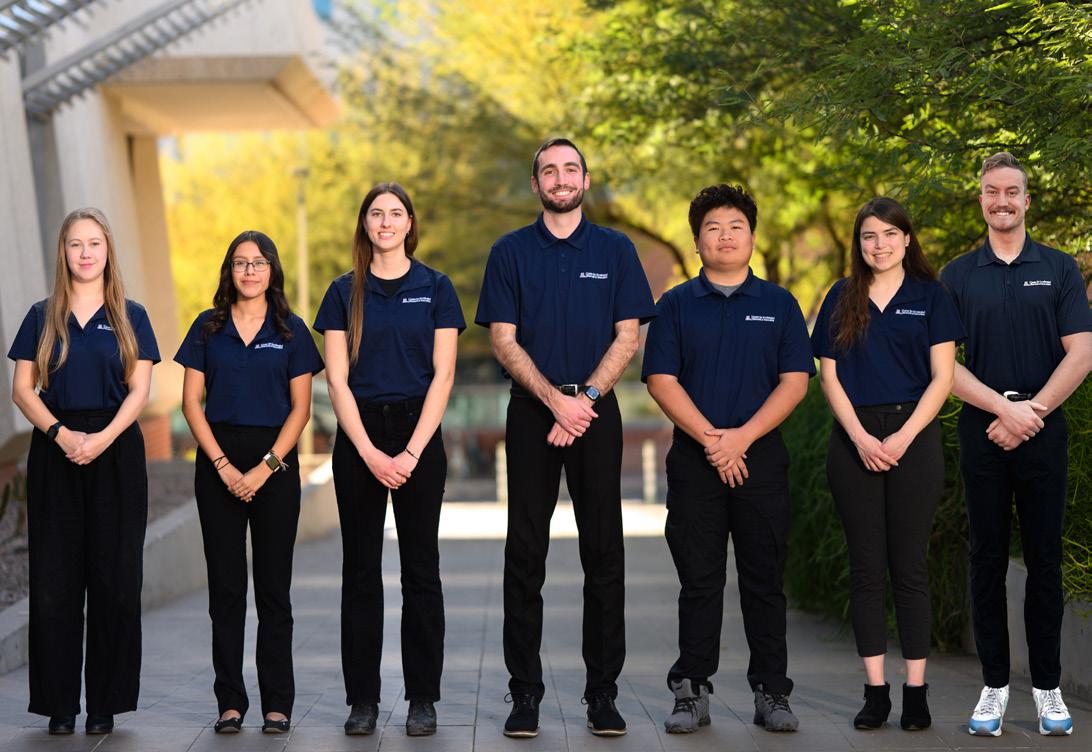
TEAM MEMBERS
Lily Finnegan, Aerospace Engineering
Jennifer Galvan, Software Engineering
Nam Le, Systems Engineering
Elizabeth Provencio, Aerospace Engineering
Bethany Radtke, Mechanical Engineering
Dalton Hoverson, Biomedical Engineering
Sean Diehl, Biomedical Engineering
COLLEGE MENTOR
Carey Jeannette Jones
SPONSOR ADVISOR
Marvin J Slepian
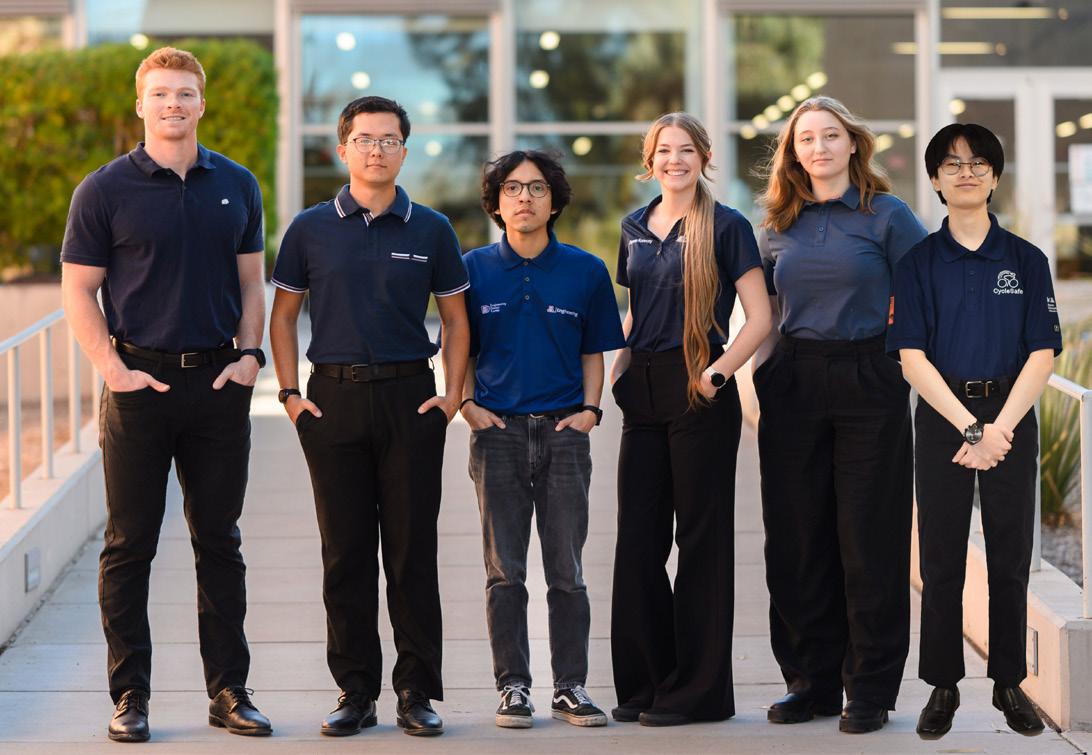
TEAM MEMBERS
Jay DeFrangesco, Electrical & Computer Engineering
William Hiroaki Grobe, Mechanical Engineering
Grace Grace Peltan, Software Engineering
Christian Pickerel, Mechanical Engineering
Noah L Richey, Software Engineering
Angel Perez, Electrical & Computer Engineering
Kayma Konecny, Optical Sciences & Engineering
COLLEGE MENTOR
Steve Larimore
SPONSOR ADVISOR
Dan Latt
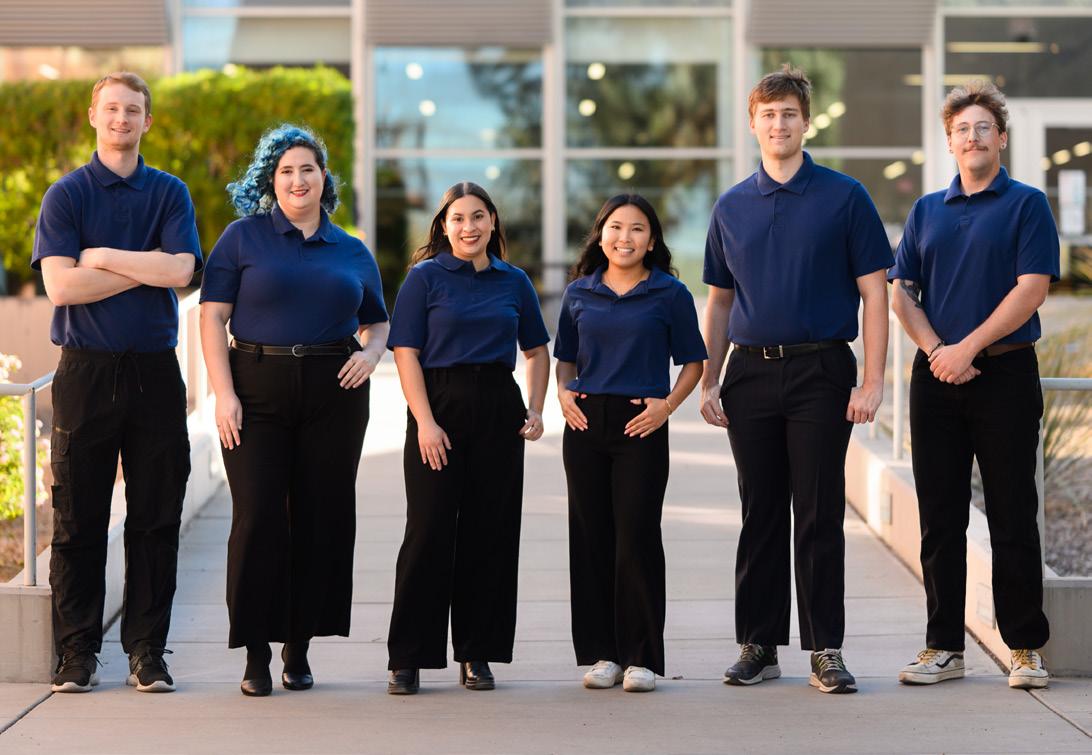
TEAM MEMBERS
Alex Brown, Biosystems Engineering
Joseph Jacobs, Mechanical Engineering
Michael McDonald, Mechanical Engineering
Alfani Quintero, Electrical & Computer Engineering
Abigail Simon, Materials Science & Engineering
Maddy Mayumi Kogachi, Biosystems Engineering
COLLEGE MENTOR
Doug May
SPONSOR ADVISOR
Raphael Lepercq

TEAM MEMBERS
Juan Dabdoub, Biomedical Engineering
Trevor C Limbaugh, Mechanical Engineering
Joselyn Toothaker, Biomedical Engineering
Chengji Zhang, Materials Science & Engineering
Levi McCluskey, Biosystems Engineering
Joshua A Capel, Electrical & Computer Engineering
COLLEGE MENTOR
Jeff Scott Wolske
SPONSOR ADVISOR
Quent Augspurger
Pyrolysis Oil Refining for Plastic Recycling, Carbon Capture and Disaster Relief
Team 25051
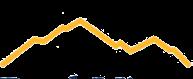
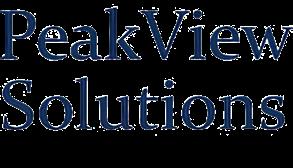
PROJECT GOAL
Develop a bench-scale oil separation module to process raw pyrolysis oil into light, medium and heavy fractions, optimizing fuel recovery for disaster relief and remote energy use.
Fuel scarcity and plastic waste pose major challenges to the environment and human health. This is especially true in disaster areas. One solution is pyrolysis oil, which converts plastic waste into fuel but requires further processing. In this project, the team developed an oil separation module to refine pyrolysis oil into five fractions to improve output oil usability.
The team’s solution uses a heating mantle to heat crude pyrolysis oil in a flask. The system first purges the flask with nitrogen to remove oxygen. It then applies a vacuum to regulate pressure. As the oil heats, it vaporizes and enters a Vigreux column where separation occurs. Lighter fractions rise, condense and collect in a receiver, while heavier fractions remain for further processing. The flask rotates for batch processing, and the cycle repeats at different temperatures to extract all fractions.
To ensure control, the system uses two thermocouples to monitor temperature and a vacuum pressure gauge to verify precise conditions. The team confirmed safety and fuel viability using gas chromatography mass spectrometry analysis to determine the chemical composition of each fraction. This portable and scalable system is an effective waste-to-energy solution that can be used in off-grid and disaster recovery applications.
Suspension Bath for Severely Burned or Injured Patients
Team 25052
ROY MEDINA
PROJECT GOAL
Create an effective method and deliver a scaled prototype for assisting the treatment of victims of fires or other traumatic events by suspending them within a medicated fluid.
Many patients need to spend a long time in hospital beds. However, the friction and pressure of long-term bed rest can cause discomfort and further injury to severely burned or injured patients. Suspending a patient in fluid could potentially eliminate these issues and facilitate healing with the right mixture of medications. In this first-year project, the team demonstrated a half-scale model to show how some parts of the system will work in a fully realized system.
This project relied on biomedical, mechanical, electrical, materials and hydraulic engineering. All of these disciplines came together to create a completely original suspension tank. The tank includes temperature and pH sensors to monitor the state of the fluid. This ensures the comfort and safety of the patient and provides care for them in this sensitive state. The suspension tank operates on a rotating axis to allow for easy ingress and egress and to allow health care workers to monitor the patient’s recovery. It is also equipped with a waste-evacuation system that senses and removes human waste. The results of the half-scale model show promise and display the potential for future teams to build a full-scale solution.
The Exploration of Thermal Diode Effects of Nitinol-Based Shape Memory Alloys
Team 25053
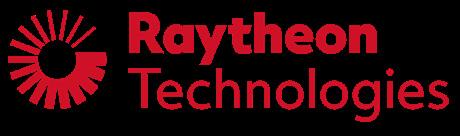
PROJECT GOAL
Design and test a rig to measure the thermal diode effect of certain shape memory alloys and determine the alloys’ potential for controlling heat flow into and out of sensitive electronics.
Keeping electronics cool isn’t just about performance, it’s about survival. Excess heat can cripple efficiency, shorten lifespan or even trigger catastrophic failures. Enter the nitinol-aluminum (NiTiAl) thermal diode, a potentially cutting-edge solution designed to preferentially control heat flow and directionally. It is analogous to the one-way electron flow of an electric diode. The NiTi-Al thermal diode could revolutionize heat management, ensuring that critical systems operate at peak performance and enhancing everything from military technology to next-generation computing and nanotechnology.
A paper by Dr. Franziskonis proposed this theory. It asked, can phase-transforming smart materials like nitinol – an alloy made of nickel and titanium – create a highly effective thermal diode? To find out, the team designed and built a specialized rig to experimentally test and analyze heat flow and thermal rectification efficiency. An insulated firebrick enclosure housed the test samples to ensure controlled thermal conditions while a patch heater simulated the thermal temperatures encountered in missile flights. Thermocouples attached to the samples sent data to a laptop through a data logger so the team could analyze the thermal diode’s performance versus control samples. Based on the test results, the team concluded that these NiTi-Al thermal diodes could be highly effective in specialized applications.
Hybrid Electric Retrofit Demonstration for a Drilling Rig
Team 25054
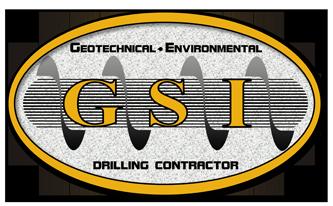
PROJECT GOAL
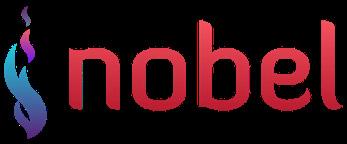
Design, build and implement a hybrid electric power system to replace the 115 HP Cummins 5.9 L diesel engine in a CME75 geotechnical drilling rig to reduce emissions, improve fuel efficiency and support net-zero goals while maintaining drilling performance.
Geotechnical drilling rigs like the CME 75 rely on diesel engines for high power output. However, conventional systems generate significant emissions and require frequent maintenance. To address these limitations, the team designed the Hybrid Electric Drill Retrofit (HEDR). It is a system for exploring the feasibility of using hybrid electric power as a sustainable alternative to conventional engines. By integrating multi-disciplinary engineering design, analysis and rapid prototyping, the team aimed to reduce emissions, lower maintenance costs and optimize energy use while maintaining drilling performance.
The team developed a system that integrates an electric motor, a generator and a battery stack to optimize power usage and extend operational lifespan. The electric motor directly interfaces with and drives the drill bit through a five-speed transmission. A battery stack powers the motor while the generator supplies supplemental energy to the batteries. A microcontroller controls this process. It manages power distribution, ensures optimal efficiency and collects real-time performance data.
The HEDR project offers a more sustainable and cost-effective alternative for field operations and demonstrates the feasibility of hybrid-electric solutions in geotechnical drilling.
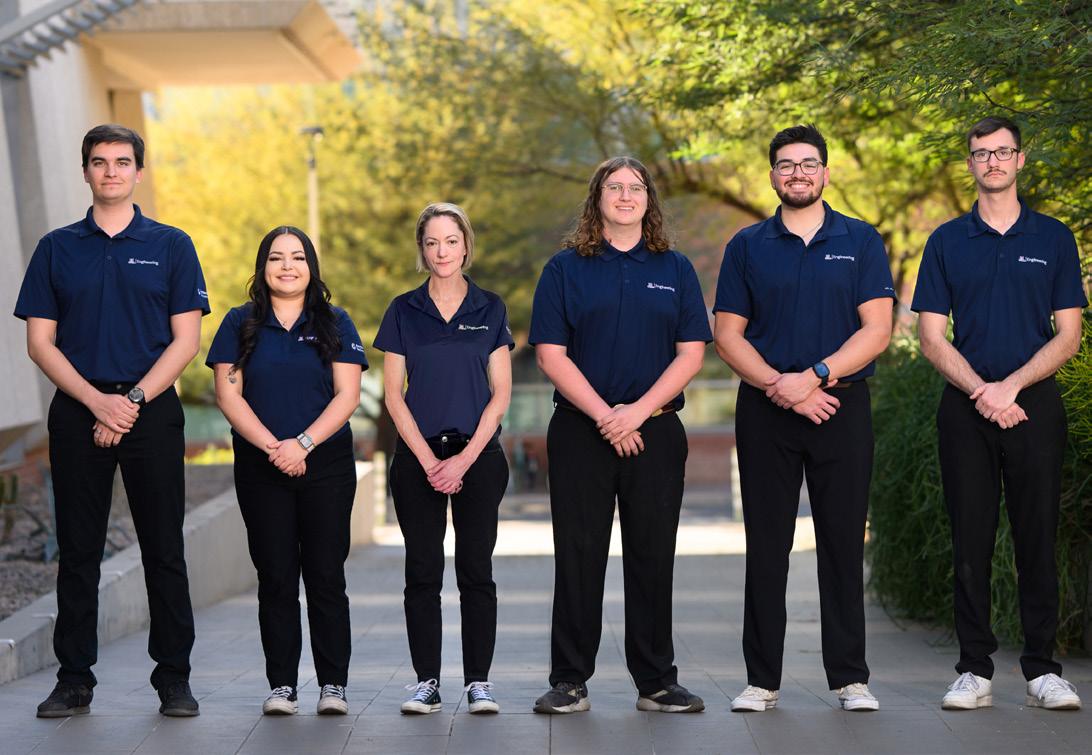
TEAM MEMBERS
Adam Bejarano, Materials Science & Engineering
Tara Brady, Electrical & Computer Engineering
Iliana Carpio, Engineering Management
Nicholas DeAnda, Mechanical Engineering
Ranger Stevenson, Materials Science & Engineering
Michael Pfaff, Aerospace Engineering
COLLEGE MENTOR
Jeff Scott Wolske
SPONSOR ADVISOR
Dave Staggers
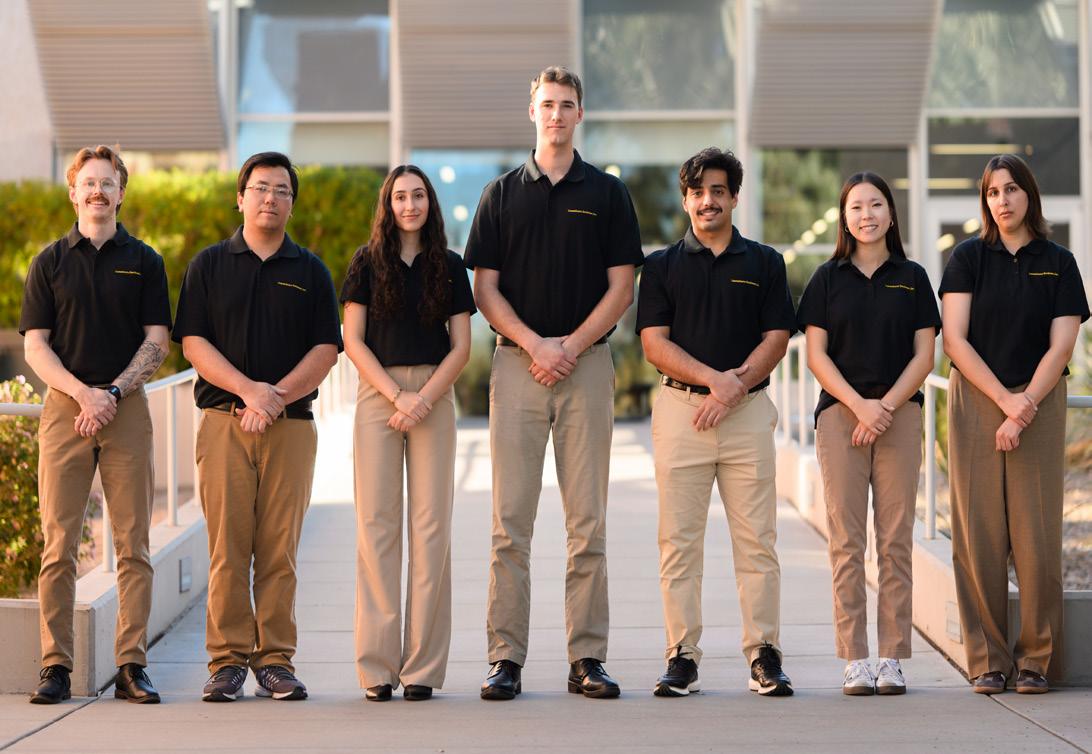
TEAM MEMBERS
Ahmad Fahad AlKhezzi, Electrical & Computer Engineering
Steven Crellin, Mechanical Engineering
Alicia Marie Diaz, Mechanical Engineering
Thuan Nguyen, Electrical & Computer Engineering
Matthew Wright, Mechanical Engineering
Zeah Zimpleman, Engineering Management
Kira McKay, Mechanical Engineering
COLLEGE MENTOR
Pat Caldwell
SPONSOR ADVISOR
Steve Bradshaw
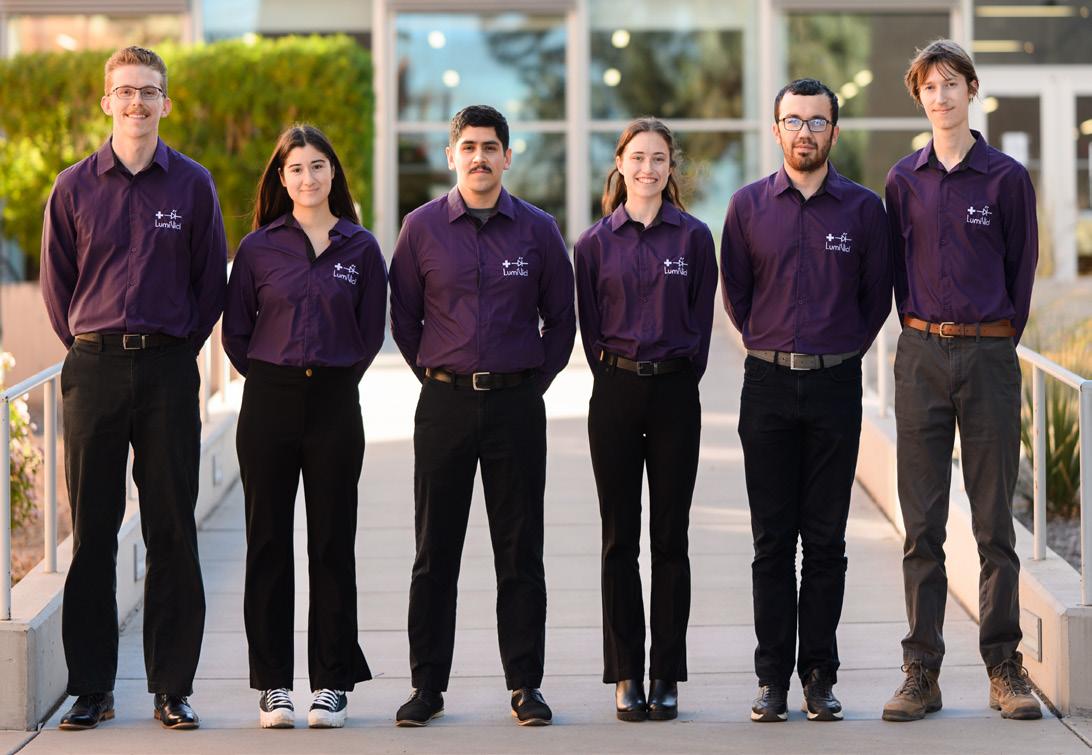
TEAM MEMBERS
Gabi Hope Andreakis, Biomedical Engineering
Omar Corona Ramos, Electrical & Computer Engineering
Kyle McIllece, Mechanical Engineering
Sarvarbek Soporboev, Systems Engineering
Ella Elizabeth Marshall, Biomedical Engineering
Dennis Timothy Shaw, Optical Sciences & Engineering
COLLEGE MENTOR
Mike Nofziger
SPONSOR ADVISOR
Neal Brock
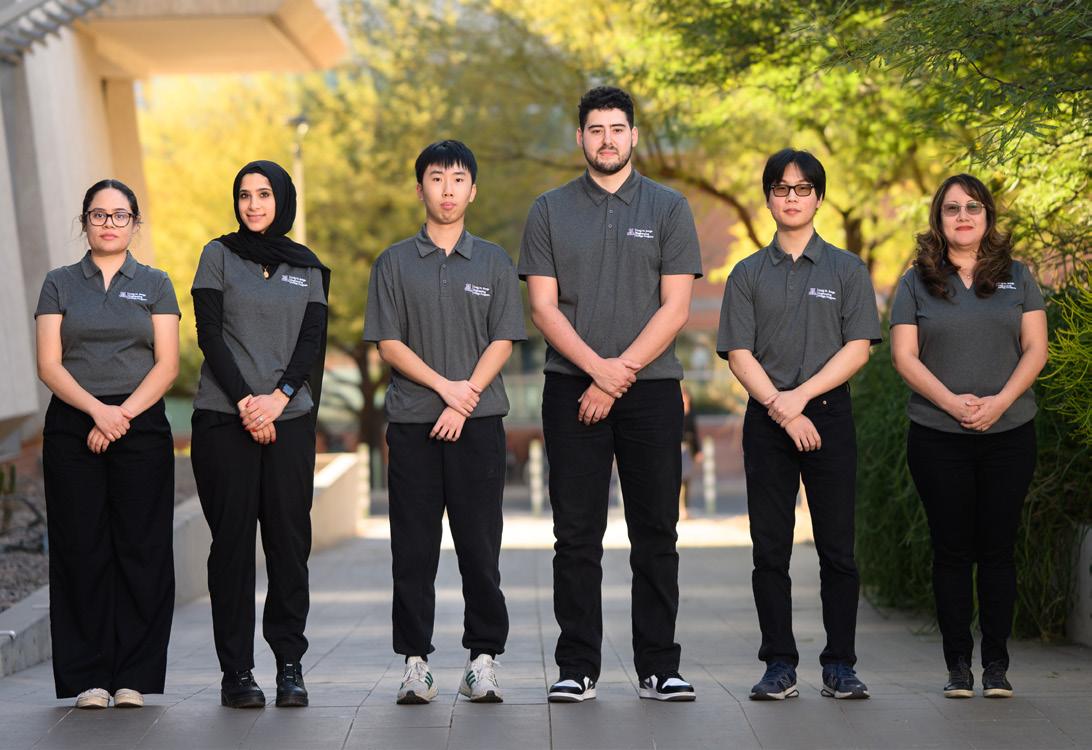
TEAM MEMBERS
Maria Sara Arvizu Velazquez, Electrical & Computer Engineering
Abrar Wael El Farmawi, Biomedical Engineering
Allen Fan, Electrical & Computer Engineering
Shawn Kim, Software Engineering
Joey Wallace, Software Engineering
Perla Gutierrez, Software Engineering
COLLEGE MENTOR
Sardar R Mostofa
SPONSOR ADVISOR
Marvin J Slepian
Self-Disinfecting Urinary Catheters Using Safe Antimicrobial Light
Team 25055
PROJECT GOAL
Develop a urinary catheter that reduces bacterial colonization using embedded 405 nm antimicrobial light to achieve a 99% bacterial reduction rate over an extended period.
Catheter-associated infections are a major health care concern. These infections often lead to prolonged hospital stays and increased patient morbidity. One solution is to coat the catheter with antimicrobials. However, traditional antimicrobial coatings degrade over time, making them ineffective in the long term. In this project, the team designed and tested a self-disinfecting urinary catheter that uses low-dose 405 nm light to continuously reduce bacterial colonization for several hours.
The team’s solution integrates fiber-coupled 405 nm LED light sources. These effectively impede bacterial growth while remaining safe for human tissue in controlled doses. A clear catheter material ensures efficient light transmission, and a low-power, embedded control unit regulates continuous light exposure at key disinfection points. The team carried out efficacy testing on the final prototype to assess its effectiveness in reducing infection risks.
This solution provides a long-term, non-chemical infection prevention method for catheterized patients. It is easy for medical staff to apply and safe for use within a hospital environment. With this design, the team has succeeded in the goal of reducing hospital-acquired infections and antibiotic reliance in human and veterinary catheter use.
Kay-Phos - A Point-of-Care Potassium and Phosphorus Diagnostic System for Kidney Patients
Team 25056
supported by Craig M. Berge Dean’s Fund
PROJECT GOAL


Estimate and determine the potassium and phosphorus content in food for chronic kidney disease (CKD) patients.
CKD affects approximately 37 million adults in the United States. Many of these patients also experience abnormal electrolyte levels that can lead to further comorbidities. Hyperkalemia (high potassium) occurs in 40% to 50% of patients. This condition can result in dangerous heart rhythm problems. Additionally, hyperphosphatemia (high phosphorus) occurs in 70% to 80% of patients and contributes to bone disease and increased cardiovascular risk. Knowing CDK patients’ potassium and phosphorus levels is therefore critical.
The team addressed this need by creating a dual-measurement, AI-based approach to determining food electrolyte content. The system combines image recognition technology for rapid, everyday assessment with physical measurements via “grind and find” for high-accuracy validation. The image recognition system leverages machine learning and web-based information to continuously improve its accuracy in classifying food items and estimating their potassium and phosphate levels. The grind and find method represents the team’s ongoing research to establish precise measurement standards for potassium and phosphorus in food items. This in turn helps validate and improve the image recognition system’s accuracy.
Vibration-Powered IoT Sensors with Ultra-Low Power RF Communication
Team 25057

PROJECT GOAL
Provide a communication interface system so multiple railcar health monitoring systems can daisy chain their data and send it to the master control unit.
Preventing train derailments is a critical challenge in railroad maintenance. It requires advanced monitoring systems that can detect potential issues before they escalate into catastrophic failures. The existing Sentinel Motion Internet of Things (IoT) system addresses this challenge by monitoring vibration and temperature data from railcar wheel bearings. While it is effective in identifying critical faults, its current IoT hub device is constrained by a limited transmission range. This project enhances the Sentinel Motion system by extending its data collection and transmission capabilities to improve predictive maintenance.
The team developed a vibration-powered, wireless train network (WTN) node which meets low size, weight and power constraints. The WTN node serves as an intermediate network host between Ridgetop’s Sentinel Gateway IoT hub and RotoSense sensor nodes. In this role, the WTN node facilitates seamless data collection and transmission. An integrated SAM R21 microcontroller efficiently routes data packets across multiple communication interfaces while optimizing power consumption for maximum operational longevity. A piezoelectric transducer array-based vibration energy harvesting system powers the device and incorporates safeguards against extreme vibrations and excessive voltages. This ensures complete energy self-sufficiency while facilitating communication.
Enhancing Monitoring Systems for Critical Feeders at the Capstone Copper Concentrator
Team 25058

PROJECT GOAL
Develop a working model of a conveyor belt system for the Capstone Copper Mine using data from electrical and mechanical sensors to optimize performance and predict future failures.
Capstone Copper is an open pit mine that operates 24/7. It serves as a key contributor to Arizona’s copper production by processing 22 million tons of ore annually. Conveyor belts transport this ore to various phases of processing within the mine. Failure of these conveyance systems leads to excessive downtime and major economic loss. To minimize these failures, the team designed a system which will monitor the conveyor belts that deliver mined ore from the primary to a secondary crushing facility.
The team determined that the key areas of concern – the ones that produce the highest economic loss and downtime – are the belt and the driving pulleys. The team simulated the belt’s status of abnormal side travel, temperature gradients, and the quality of the belt’s surface. They then designed and built a proof-of-concept small-scale conveyor with a range sensor and an infrared temperature sensor integrated with two microcontrollers. An intuitive graphical user interface in the system allows operators to view the real-time condition of the belt and sends an alert when conditions indicate a failure. Operators can also access a historical data log.
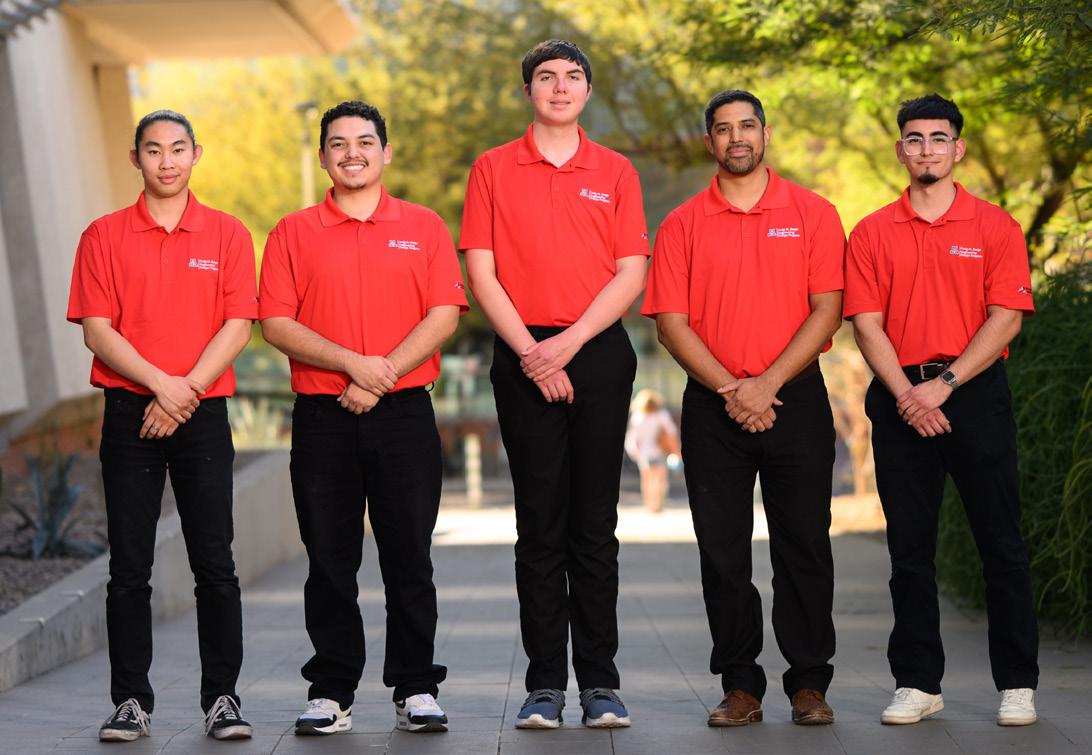
TEAM MEMBERS
Ethan Wesley Burnett Nguyen, Electrical & Computer Engineering
Miguel Hurtado, Software Engineering
Pedro Sanchez, Aerospace Engineering
Matthew David Nolan, Software Engineering
Dalian Meraz, Electrical & Computer Engineering
Jeffrey Richardson, Electrical & Computer Engineering
COLLEGE MENTOR
James Sweetman
SPONSOR ADVISOR
Arsh Rudra Nadkarni
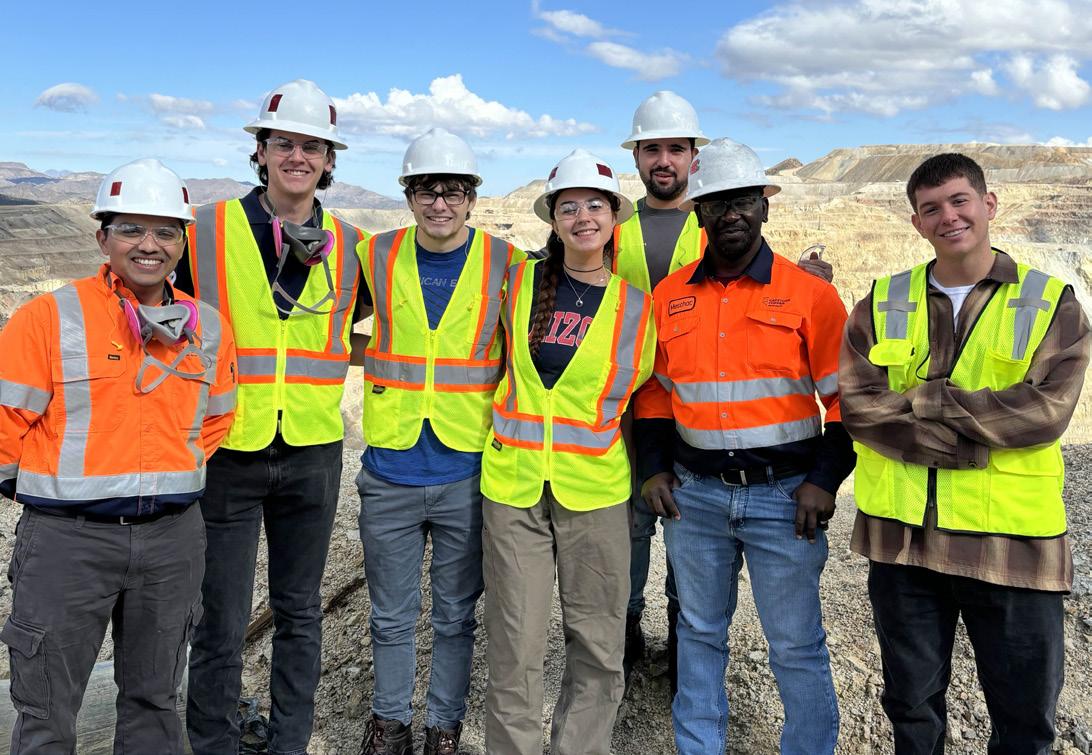
TEAM MEMBERS
Roshan Adhikari, Aerospace Engineering
Joshua Connor Kimble, Electrical & Computer Engineering
Soltane Loudhabachi, Software Engineering
David Parker Wigton, Electrical & Computer Engineering
Katelyn McLean, Industrial Engineering
Eladio Pena, Aerospace Engineering
COLLEGE MENTOR
Doug May
SPONSOR ADVISOR
Paul Villaorduna
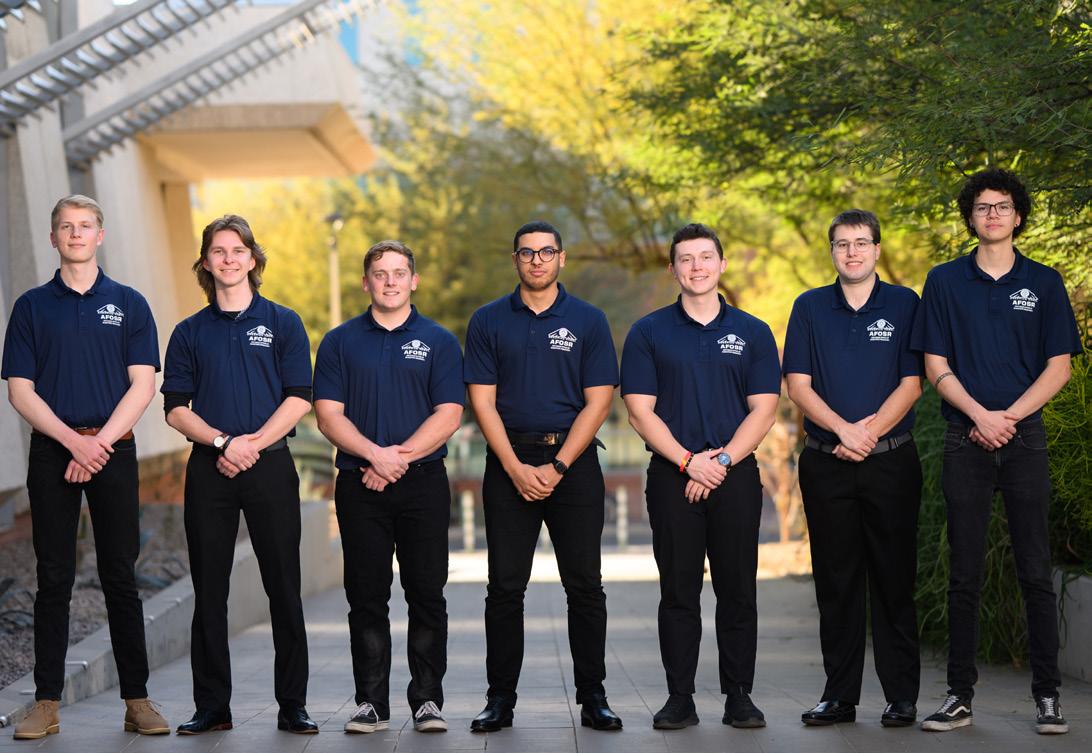
TEAM MEMBERS
Cougar K Bellinger, Software Engineering
Teegan Cook, Aerospace Engineering
Cooper L Dickerson, Aerospace Engineering
Logan Stonehouse, Electrical & Computer Engineering
Unai A Urreiztieta, Aerospace Engineering
Tyler Cook, Aerospace Engineering
Adam El Houmaidi, Aerospace Engineering
COLLEGE MENTOR
Steve Larimore
SPONSOR ADVISOR
Elijah West Greenfield

TEAM MEMBERS
Anna Lucille Fravel, Systems Engineering
Janna Said, Biomedical Engineering
Makena Verdugo, Biosystems Engineering
Jesus Ivan Zazueta, Mechanical Engineering
Darya Pershina, Biomedical Engineering
Amir Sobhan Haghiri, Biomedical Engineering
COLLEGE MENTOR
Carey Jeannette Jones
SPONSOR ADVISOR
Urs Utzinger
Design, Build and Fly a Modular UAV for Autonomous Flight Tests
Team 25059

PROJECT GOAL
Design, build and fly a highly modular, mid-size, fixed-wing UAV.
This project introduces a versatile UAV testbed designed to support on-demand analysis of various flight configurations with a single aircraft with the goal of enhancing flight research capabilities at U of A.
The team developed the UAV testbed through extensive research into construction techniques and aircraft performance to ensure the design aligns with conventional aerodynamics while maintaining modular adaptability. The resulting airframe prioritizes ease of assembly and positive stability across a wide range of configurations. To optimize performance, the team estimated the flight envelope using numerical analysis and simulations and ensured structural integrity before fabrication using finite element analysis.
A hands-on manufacturing approach played a key role in development. Prior material testing helped determine the optimal fabrication methods for carbon fiber composites, which were primarily produced in-house. Pre-manufactured carbon tubes and outsourced machined aluminum parts complemented the custom-built components. This resulted in a lightweight yet structurally robust aircraft.
The UAV features a speed range of 45 to 200 mph, a wing sweep angle adjustable from 0 to 60 degrees, and a 10 ft wingspan at 45 degrees sweep. With a flight time of five to seven minutes, it meets all research requirements set by U of A and provides a highly adaptable platform for advanced aerodynamic testing.
Local Hypothermia in Spinal Cord Injury
Team 25060

PROJECT GOAL

Develop a localized cooling system for spinal cord injuries to mitigate secondary trauma and inflammation.
Spinal cord injuries cause permanent damage that impacts mobility and quality of life. Inducing hypothermia can significantly improve surgical repair of the spinal cord injury after traumatic or complete spinal cord injury. Lowering the body temperature by between 5 and 12°C for four to five hours, followed by controlled rewarming at 1°C per hour over a 20-hour period, slows metabolism, decreases cellular stress and inflammation and prevents edema. However, systemic hypothermia comes with risks such as cardiac arrhythmias and coagulation issues. In this project, the team designed a method for applying targeted hypothermia to the injured spinal cord rather than the traditional systemic hypothermia.
The design integrates a compact chiller, a disposable cooling paddle, and a thermal monitoring subsystem. The chiller circulates distilled water through the paddle which the surgeon positions and secures on the dura (the tough layer surrounding the spinal cord) after surgery to remove part of the vertebrae. An LCD interface displays real-time temperature data via paddle-integrated thermistors. Health care providers can manually adjust the device to maintain the target cooling profile. A surgeon will surgically remove the paddle after treatment.
Heap Leach and Open Pit Optimization
Team
25061

PROJECT GOAL
Generate a surface mine open pit and create a geometric-designed dump leach pad alongside appropriate economic justification, permitting and reclamation work.
Industry consortium the Next-Generation Design Alliance conducted a prefeasibility study for a copper leach-only operation in central Arizona. These operations rely on detailed plans and carefully designed drainage pads for leaching out copper from the ore to maximize production and minimize waste. Using provided project parameters and block models, the team developed a mine plan and leach pad design that leverages advanced mine planning software for pit optimization. This project challenged team members to use their mineral processing expertise and apply industry-relevant methodologies for optimizing operational efficiency to create the leach pad design.
The team began by evaluating the economics of a leach pad expansion. The design included location selection for the leach pad and collection pond, liner design, and the sequence and stacking for the pad. The team also conducted a stability assessment and incorporated environmental and permitting considerations. In addition, the project includes a process flow sheet, tons, mass balance, time rate and recovery estimates for metal recovery. Finally, the team conducted a trade-off study for trace mineral recovery including gold, silver and molybdenum.
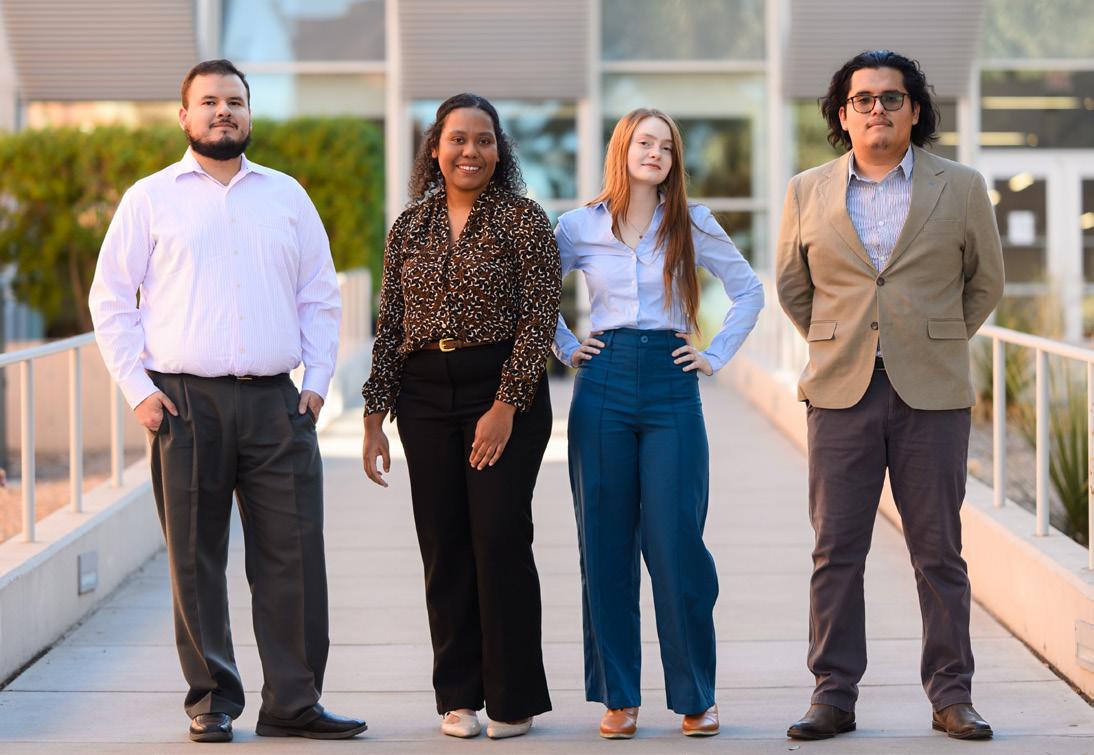
TEAM MEMBERS
Israel Armando Bernal Diaz, Mining Engineering
Damian Marin, Mining Engineering
Sarah Marquez, Mining Engineering
Fransiska Pogolamun, Mining Engineering
Thi Truong, Mining Engineering
COLLEGE MENTOR
Edward Clifton Wellman
SPONSOR ADVISOR
Andrew Wunderlich
Underground Mine Design Team 25062


PROJECT GOAL
Create and optimize a panel caving drawbell drill and blast design to determine the feasibility of automated blasting technology, reduce operational costs and cycle time, and comply with health, safety and environmental standards.
Panel caving is an underground mining method that relies on continuous rock breakage using gravity. It provides an efficient and controlled method of excavating ore into a catchment, called a drawbell. These drawbells eliminate the need for continuous drill and blast operations in a single panel and allow for loading and hauling of ore. Optimizing the design and technology features ensures productive drawbells throughout the mine and reduces operational and construction costs.
Resolution Copper asked the team to construct a drill and blast drawbell design for a panel caving operation located 5,000 to 7,000 ft underground. The primary objective was to design both a typical drawbell and a drawbell with newer blasting technologies and free face reduction or elimination.
The team prioritized safety while optimizing the number of drillholes, charging cycles, operational efficiency, cost and sustainability to maximize productivity per unit cost. To do this, the team collaborated weekly with the project sponsor and periodically with external resources, used empirical methods for design validation, and synthesized a risk assessment matrix. The team completed a tradeoff analysis and created an iterative and adaptable quality assurance and quality control program. The program contains a list of systematic procedures for meeting and verifying product quality and a corrective decision-making process to identify, fix and prevent errors.
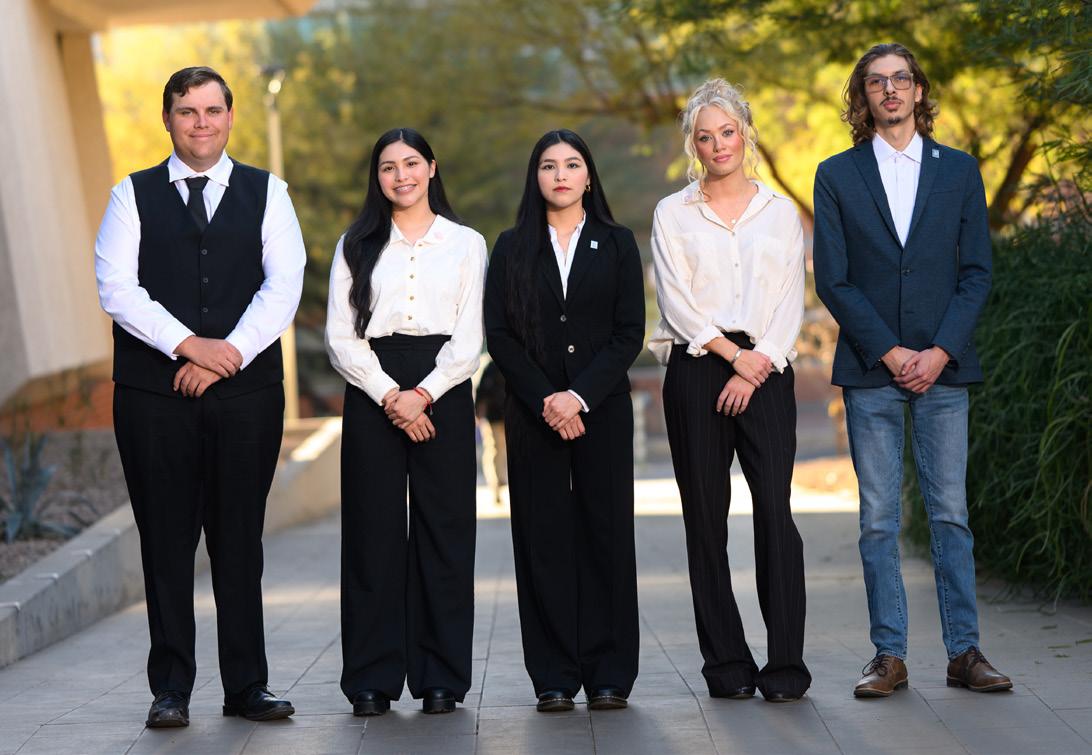
TEAM MEMBERS
Thomas Gage Buza, Mining Engineering
Carolina Gamez Gonzales, Mining Engineering
Casandra Gamez Gonzales, Mining Engineering
Evamarie Scarlet Penney, Mining Engineering
Jose Alberto Quintero, Mining Engineering
COLLEGE MENTOR
Edward Clifton Wellman
SPONSOR ADVISOR
Carlos Dipas
SPONSOR
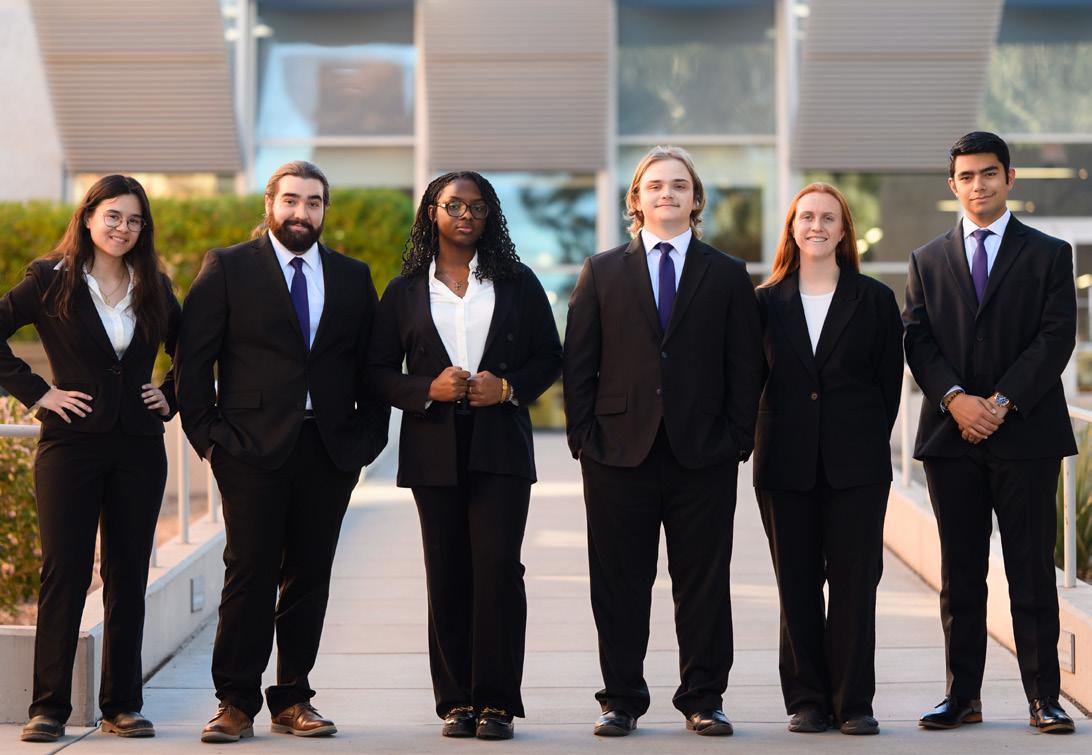
TEAM MEMBERS
Jake C Pacheco, Mining Engineering
Carter Max Brown, Mining Engineering
Greatness H Ojum, Mining Engineering
Matthew Lee Patterson, Mining Engineering
Alexis Noel Rylaarsdam, Mining Engineering
Karla Trinidad Togawa, Mining Engineering
COLLEGE MENTOR
Edward Clifton Wellman
SPONSOR ADVISOR
Kray Luxbacher
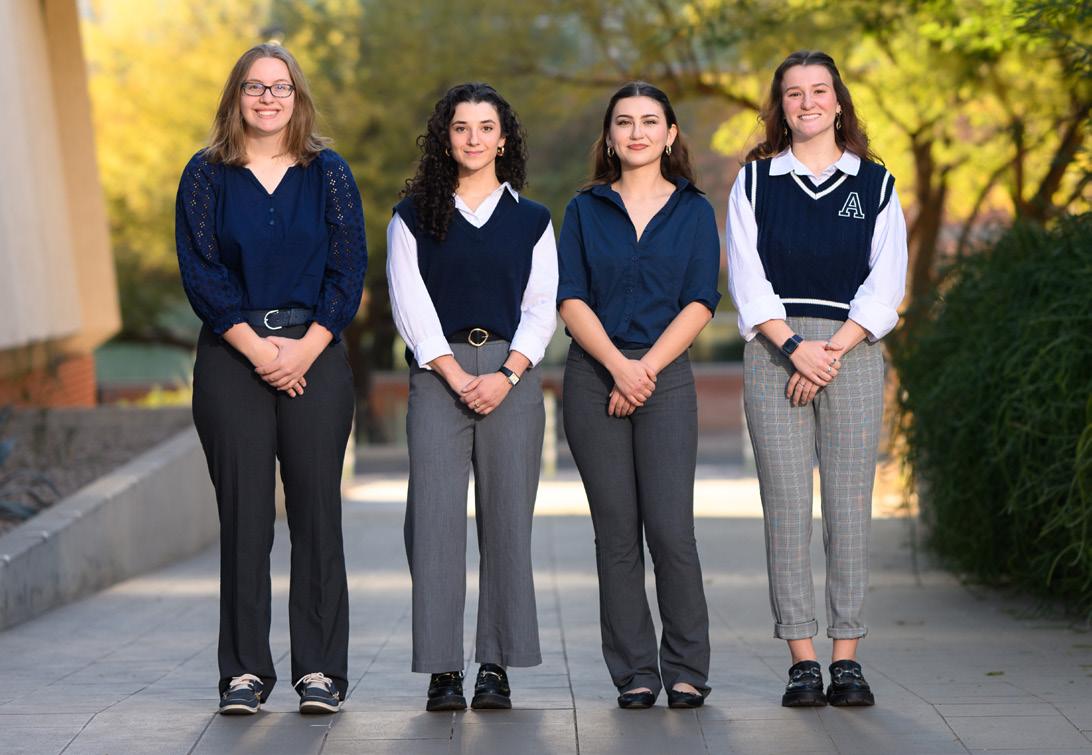
TEAM MEMBERS
Xavia Raquel Gutierrez, Environmental Engineering
Kate Sophia Hartke, Environmental Engineering
Jess Rose Mazza, Environmental Engineering
Macy K Winn, Environmental Engineering
COLLEGE MENTOR
Adrianna Brush
SPONSOR ADVISOR
Cherie De Vore
2024-2025 SME Metallic Design Competition
Team 25063

PROJECT GOAL
Complete and submit a scoping study for an open-pit lithium mine in Australia during Phase 1 and represent the University of Arizona at the SME MINEXCHANGE conference, where the team will present a Phase 2 summary.
The team, MAGJCK Metals, prepared a scoping study regarding the design and feasibility of an open-pit lithium mine located in the Pilbara region of Australia, as prescribed in the 2024 SME Metallic Design Competition Problem Statement. This report comprised Phase 1 of the project and was completed within the three-week window in October 2024.
During Phase 2, the team modified the project to account for the decline in lithium carbonate equivalent prices and projections of continued downward trends in 2025 and beyond due to oversupply and subdued growth in the electric vehicle sector. The team revised the mine plan, made major revisions to the process plant, and updated the environmental and permitting sections of the technical report they submitted to the project’s board of directors. The team represented U of A at the SME MINEXCHANGE Conference held in Denver in February 2025. Team members delivered a thorough presentation of both phases of the project – highlighting the changes to Phase 1 based on updated information and requirements gathered during Phase 2 – and earned second place in the international competition.
Heavy Metals Remediation Using Fungi
Team 25064

PROJECT GOAL
Design a passive treatment system for mining-influenced water (MIW) contaminated with heavy metals using inactivated fungi as a sorption medium.
Heavy metal contamination, from both natural and anthropogenic sources, affects millions of people worldwide. This problem is particularly difficult for Native American communities impacted by abandoned mines. As current heavy metal removal methods can be costly and generate secondary waste, costeffective, environmentally friendly bioremediation alternatives are needed.
The team’s solution is a passive treatment system that uses fungal-based bioremediation (mycoremediation) to remove heavy metals with minimal energy inputs. To develop this system, the team first performed batch experiments to assess the biosorption capacity (milligrams of metal removed per gram biomass) and adsorption rates of the Fusarium fungus in a mixed heavy metal solution designed to emulate acid mine drainage. The team’s treatment system is based on the findings from these experiments.
MIW first flows through a limestone pond to precipitate aluminum and iron. Next, the water enters a passive packed-bed reactor containing inactivated fungal media. Here the heavy metals adsorb onto the surface of the media during chemical, physical and electrostatic interactions. The system operates at a target flow rate of 10 gallons per minute, relies on gravity-driven flow, and aims to reduce heavy metal concentrations to meet EPA discharge standards.
Fish Feed From Insects
Team 25065

PROJECT GOAL
Identify the ideal insect-based fish feed formulation by optimizing protein content, buoyancy, water stability and fish feed preference while aiming for an eco-friendly, scalable solution.
Conventional fish feed often contributes to overfishing, environmental degradation and significant challenges for small-scale farmers in developing countries, particularly in countries like South Africa. To meet the increasing global demand for fish while ensuring environmental sustainability and addressing the economic challenges posed by conventional fish feed, the team experimentally compared three innovative insect-based fish feed alternatives.
This project focused on two specific insect sources: mealworms and black soldier flies. The team developed a careful process for cultivating, blending and producing these insects into pelletized fish feed designed for tilapia farming. This method enhances the nutritional value of the feed and reduces its environmental impact, as these insects require minimal land, water and cost.
By prioritizing the needs of small-scale farmers, the team aimed to offer an alternative to traditional feed that enhances economic viability and boosts food security. Moreover, this insect-based feed’s production scalability means it can extend beyond South Africa where it can contribute to more sustainable practices in global aquaculture. The team’s findings provide valuable insights that could significantly reshape fish farming practices and balance productivity with ecological responsibility, even on an industrial scale.
Bomb Calorimeter Lab Experiment
Team 25066

PROJECT GOAL
Develop experiments, experimental procedures and instructional materials for the CHEE 401A lab course using the advanced reactive system screening tool (ARSST) bomb calorimeter to better student understanding of reaction kinetics, thermal hazards and industrial pressure relief design.
The ARSST bomb calorimeter provides precise data on temperature, pressure and reaction rates so students can assess runaway reaction risks and industrial safety considerations. In this project, the team integrated the ARSST into a two-week lab series that teaches students to analyze reaction kinetics, thermal hazards and pressure vent scaling.
The team selected two key reactions for experimental study: the decomposition of hydrogen peroxide and the production of ferric sulfate through hydrogen peroxide oxidation. The hydrogen peroxide experiment focuses on understanding how heating rate and pressure influence reaction rate and conversion. This provides students with insight into runaway reaction prevention.
The second experiment explores ferric sulfate production by optimizing catalyst ratios and reaction conditions to improve efficiency and minimize peroxide decomposition. Students will be responsible for making effective alterations to the experimental parameters while remaining compliant with safe lab practices. Safety will be a chief requirement because of the high temperature and pressure environments found in the ARSST. Through these labs, students will learn to apply theoretical concepts to real-world safety and process optimization challenges.

TEAM MEMBERS
Fahad Alarbeed, Chemical Engineering
Adrian Carlos Jimenez, Environmental Engineering
Trisha Jean Lane, Environmental Engineering
Bobby Luna, Chemical Engineering
COLLEGE MENTOR
Adrianna Brush
SPONSOR ADVISOR
Kim Ogden
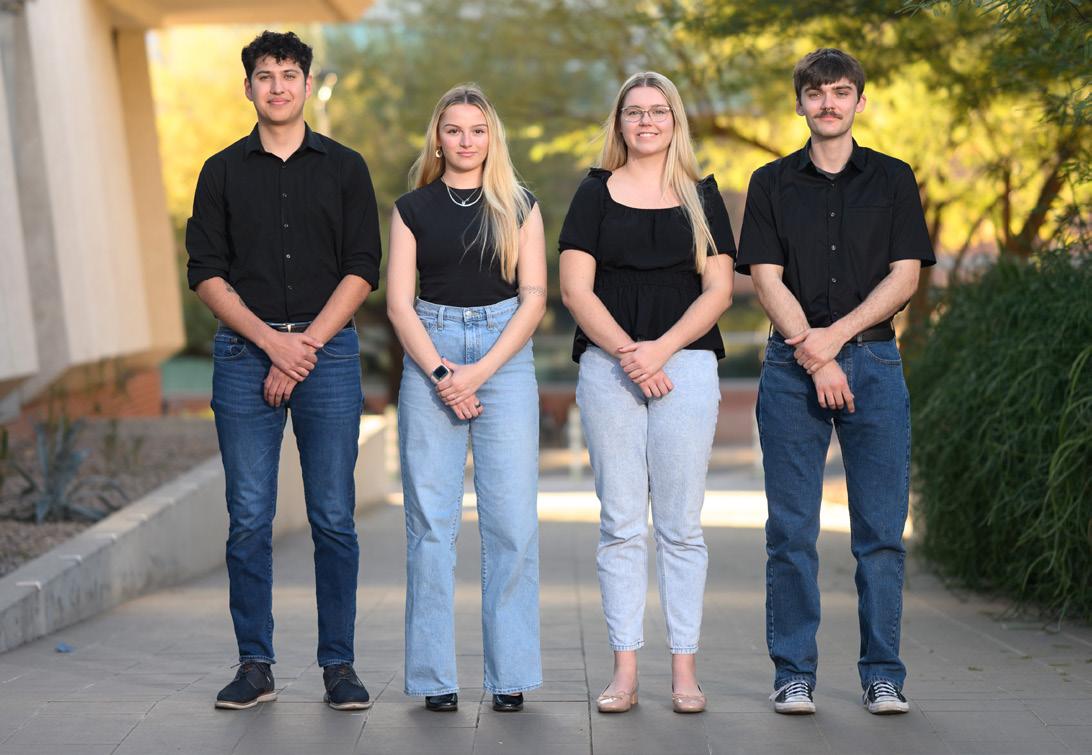
TEAM MEMBERS
Angel Phelan-Quinn Vega, Chemical Engineering
Maddy G Rahman, Chemical Engineering
Connor G Wilson, Chemical Engineering
Johnna Jo Zarndt Buettner, Chemical Engineering
COLLEGE MENTOR
Adrianna Brush
SPONSOR ADVISOR
Greg Ogden
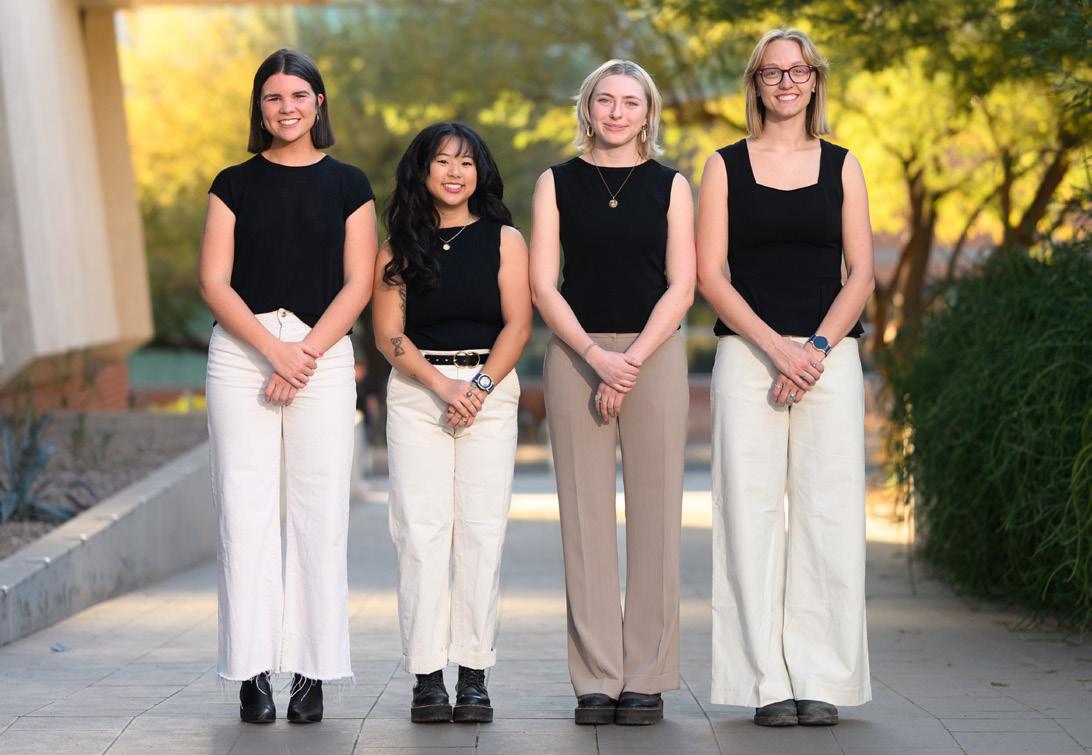
TEAM MEMBERS
Reese Arbitelle, Chemical Engineering
Abigale Marie Bahnick, Chemical Engineering
Ellie Rose Holicky, Chemical Engineering
Lizzy Grace Somer, Chemical Engineering
COLLEGE MENTOR
Adrianna Brush
SPONSOR ADVISOR
Adrianna Brush
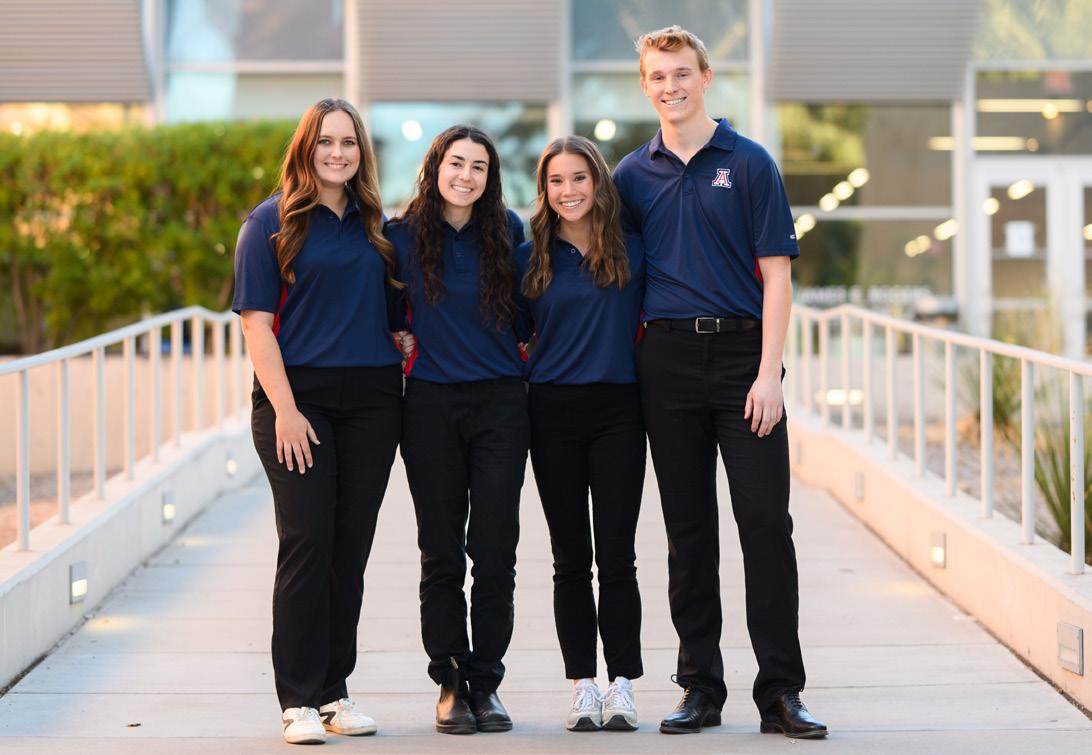
TEAM MEMBERS
Tucker Ryan Blanksma, Chemical Engineering
Heather Noelle Carr, Chemical Engineering
Callie Paige Carrejo, Chemical Engineering
Alexandra Henri Wolff Winkelman, Chemical Engineering
COLLEGE MENTOR
Adrianna Brush
SPONSOR ADVISOR
Adrianna Brush
PFAS Removal for Municipal Drinking Water
Team 25067

PROJECT GOAL
Design a large-scale process to deliver clean water to Southern Arizona through innovative poly- and per- fluoroalkyl substances (PFAS) treatment with adsorption kinetics.
This project aims to develop a treatment system for water contaminated with PFAS, also known as “forever chemicals.” These synthetic chemicals were once commonly used in firefighting foams at Arizona’s Davis-Monthan Air Force Base and are still used in many products that resist heat, grease or water. However, PFAS – particularly perfluorooctanesulfonic acid (PFOS) and perfluorooctanoic acid (PFOA) – have been linked to serious health risks, including cancers and infertility, and are found throughout the environment in concentrations far exceeding EPA safety limits. The team addressed these rising concerns by designing a scalable groundwater treatment plant in Summit, Arizona, an area that is heavily affected by PFAS pollution.
The complete groundwater treatment plant includes a dedicated PFAS removal zone and incorporates advanced treatment methods such as UV oxidation and granular activated carbon (GAC) filtering. The team worked to understand the adsorption kinetics of PFOS and PFOA on GAC, which are essential for scaling the treatment plant to meet regulatory standards. Additionally, the team emphasized engagement with the local community, particularly those involved with the Unified Community Advisory Board, who have long advocated for addressing PFAS contamination in the region.
Nonalcoholic Anxiety Reducing Beverage
Team 25068

PROJECT GOAL
Create a nonalcoholic beverage with natural ingredients that may reduce users’ symptoms of anxiety as an alternative to alcoholic drinks.
This project’s aim was to create an enjoyable, nonalcoholic (≤0.5% ABV) social beverage that produces a calming effect for the consumer. The drink uses only natural ingredients, has no aftertaste and contains supplements backed by research. The team chose Ashwagandha, L-Theanine and Lion’s Mane after thorough evaluation for calming and mood effects, safety, natural occurrence and taste profile. An at-home procedure extracted the supplements by dehydrating, pulverizing, soaking and boiling. The team tested the extracts using high-performance liquid chromatography to determine the efficiency of the extraction process and ensure a safe, effective and high-quality tincture.
Once the tincture was optimized, the team designed an industrial-sized, scaled-up processing plant based on experimental findings and Aspen simulations. The design was structured around parallel extraction lines. Each line’s product can be combined, carbonated and packaged for sale. The team optimized the design so that the active compounds could be effectively extracted while keeping the drink nonalcoholic. This portion of the project had additional profitability, scalability, and limited water and energy consumption criteria. The team also aimed to adhere to OSHA guidelines and produce a product that would be approved by the FDA.
Bioethanol Production from Agricultural Waste
Team 25069

PROJECT GOAL
Design a bioethanol production facility that uses agricultural waste as the feedstock.
Ethanol is a renewable energy source commonly used as a fuel and fuel additive in cars. Currently, ethanol is not produced or used on a large enough scale to challenge fossil fuels’ dominance. This is largely due to its technically challenging and inefficient production process, which results in lower energy density, higher production cost and limited availability.
The team identified a method of converting agricultural waste into bioethanol that improves efficiency and sustainability. The goal was to find a solution that simultaneously addresses the harmful emissions produced by fossil fuel consumption and the wasteful disposal of agricultural byproducts.
The proposed process serves as an outlet for 82,500 metric tons of corn waste annually sourced from farms in southeastern Nebraska. The stover – leftover inedible material – undergoes pretreatment, where a rolling disc mill physically breaks it down, then a steam explosion further breaks down lignin. The cellulose and hemicellulose contained in the treated stover are then hydrolyzed into glucose and xylose. Saccharomyces cerevisiae, or baker’s yeast, then ferments this mixture to produce ethanol in an aqueous solution. Finally, this solution passes through a series of distillation columns and a molecular sieve. The final product is fuel-grade ethanol.
Process Optimization for Pyrolysis Oil Refining for Plastic
Recycling and
Team 25070
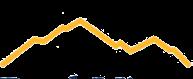
Disaster Relief
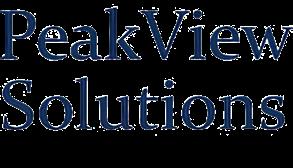
PROJECT GOAL
Design a refinement process for pyrolysis oil that can be deployed in disaster-struck areas to process plastic waste into usable fuel for vehicles and generators at the disaster cleanup site.
Two problems often plague disaster sites: an excess of plastic waste and lack of fuel. This project simultaneously solves both using pyrolysis – breaking down a substance by heating it in an oxygendeprived atmosphere to prevent combustion. Plastic polymers are ideal for pyrolysis because they break down into a combustible liquid that is much more volatile than their plastic source. This liquid can be distilled into usable fuel.
This multi-year project already has a portable device for pyrolyzing plastic in disaster areas to produce emergency liquid fuel. It reaches temperatures of up to 500°C while maintaining an inert environment to produce gaseous and liquid products by pyrolyzing a pure polypropylene plastic sample.
This year’s team focused on refining this crude product into fuel for use in combustion engines. The team conducted research and lab testing to characterize the product and determine its chemical composition. Simulations on ASPEN software revealed the best distillation methods and parameters. Through these simulations, the team developed a batch distillation column to separate the product oil into different keys based on molecular weight. These separate keys, along with the necessary additives, have potential as fuels for different purposes – e.g. lighter key for gasoline engines and heavier key for diesel engines. Findings from this project also advised Team 25051’s experimental design and execution.
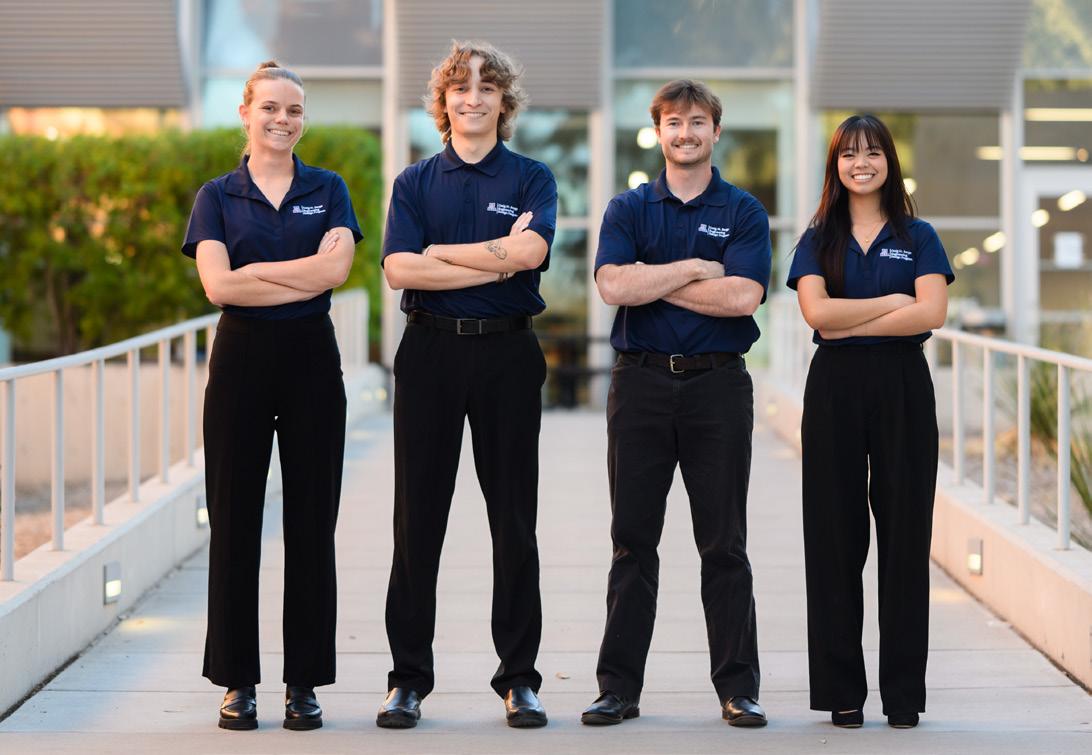
TEAM MEMBERS
Logan Emma Chung, Chemical Engineering
Franco Osvaldo Daluisio, Chemical Engineering
Abby Mae Haan, Chemical Engineering
Justin Smith, Chemical Engineering
COLLEGE MENTOR
Adrianna Brush
SPONSOR ADVISOR
Adrianna Brush
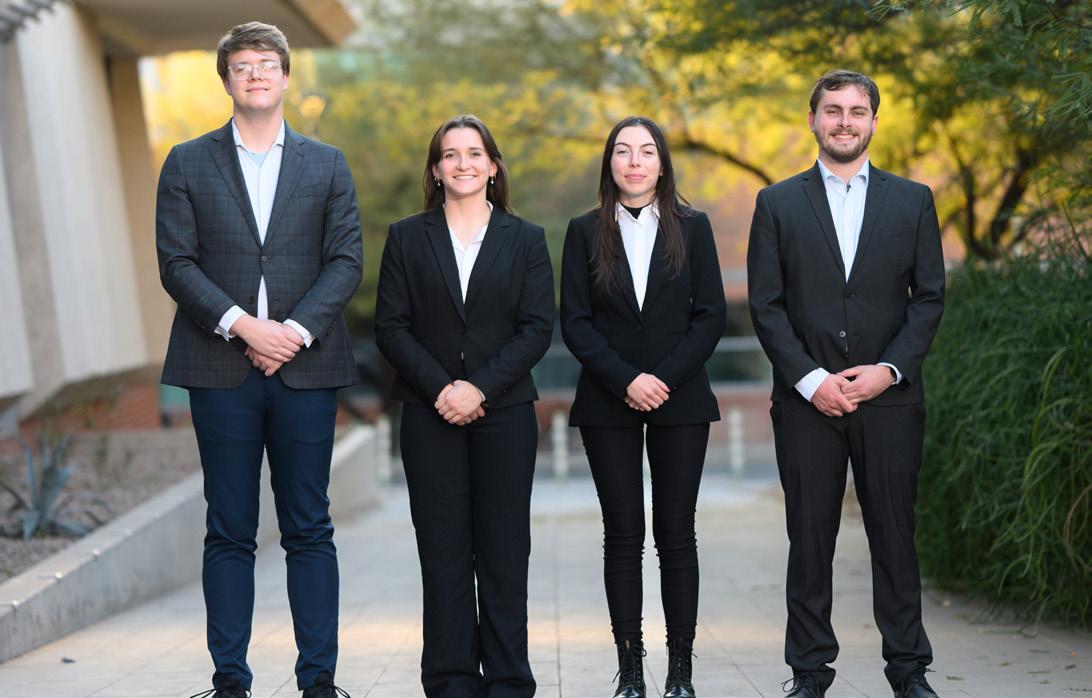
TEAM MEMBERS
Mirina Elizabeth Enderlin, Chemical Engineering
Kyra Elle Glassey, Chemical Engineering
Gabriel Leebrick Lowery, Chemical Engineering
David Pinegar, Chemical Engineering
COLLEGE MENTOR
Adrianna Brush
SPONSOR ADVISOR
Manny Miera
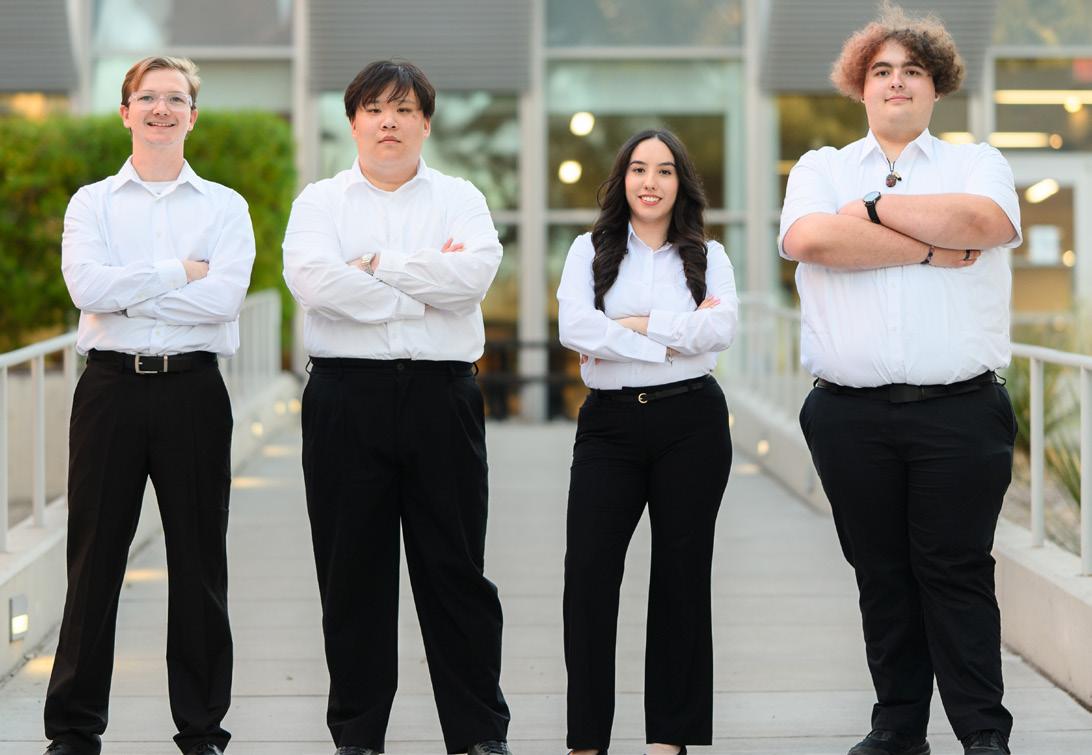
TEAM MEMBERS
Victoria Ariana Franco, Chemical Engineering
Sylas Ginnis, Chemical Engineering
DoHeon Kim, Chemical Engineering
BT Matthew Terry, Chemical Engineering
COLLEGE MENTOR
Adrianna Brush
SPONSOR ADVISOR
Adrianna Brush
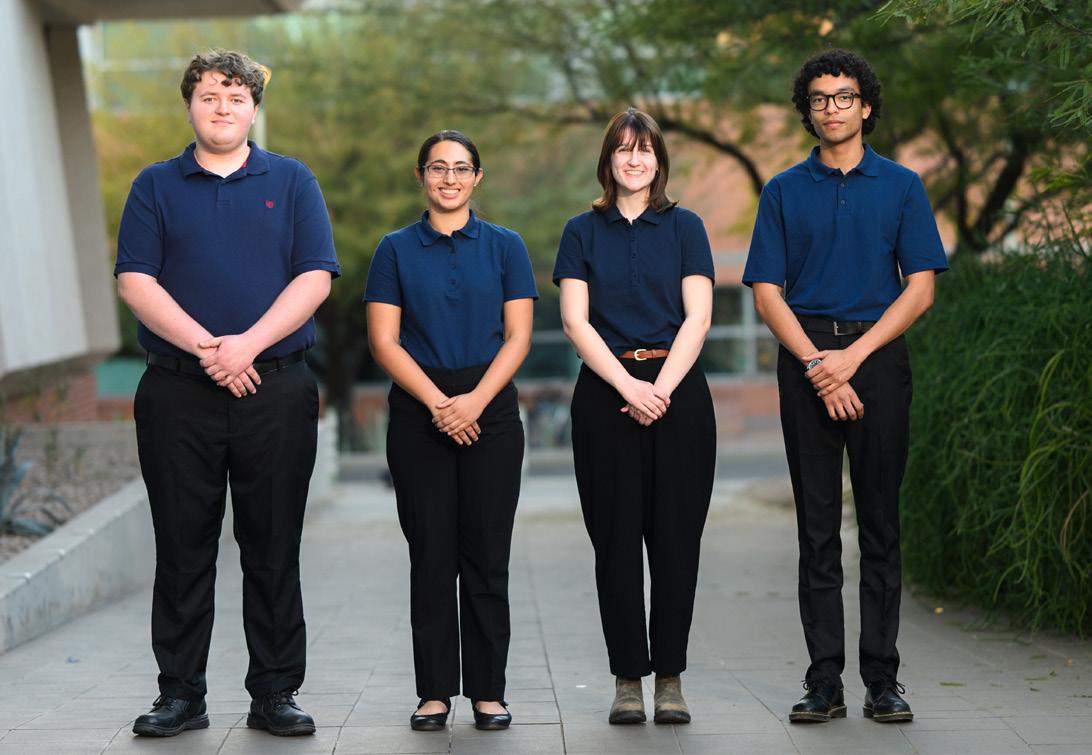
TEAM MEMBERS
Ezra David Harris, Chemical Engineering
Catherine Priya O’Brien, Chemical Engineering
Landon C Shimskey, Chemical Engineering
Emma Kathryn Walker, Chemical Engineering
COLLEGE MENTOR
Adrianna Brush
SPONSOR ADVISOR
Adrianna Brush
Extraction of Valuable Salts from Produced Water Team 25071

PROJECT GOAL
Extract high-value constituents from a pretreated brine concentrate in the Permian Basin to transform waste into a revenue-generating resource while mitigating operational and disposal expenses.
Produced water is a key byproduct of oil and gas extraction via hydraulic fracturing. This process injects water at flow rates of 100 barrels per minute and pressures of up to 15,000 psi to release hydrocarbons trapped in underground formations, primarily shale. If not handled properly, produced water poses environmental risks through spills, leaks or excessive use. Its complex composition – which includes various chemicals, salts, minerals, and additional additives and varies based on a company’s fracturing process and location – is a significant concern that makes managing produced water a critical challenge for the industry.
Hazardous materials – such as heavy metals and naturally occurring radioactive substances, as well as high salinity levels – make this water unsuitable for reuse without purification. Saltwater disposal wells (SWDs) are the primary treatment solution, but they come with limitations. The sheer volume of produced water can overwhelm SWDs, creating inefficiencies and delaying purification. Hydraulic fracturing can be particularly costly in arid regions where water is scarce. This makes water recycling essential.
The shale gas industry is increasingly focused on converting produced water into profitable byproducts before it reaches SWDs to offset purification costs. Extracting constituents such as sodium chloride, potassium chloride, calcium chloride, strontium chloride and strontium sulfate represent valuable opportunities for sustainable resource management.
Helium Recovery from Natural Gas
Team 25072

PROJECT GOAL
Design a nitrogen removal unit (NRU) with helium recovery using a two-column cycle to process pipeline gas to ensure low nitrogen content in the output, high helium purity and recovery, and optimized energy efficiency.
This project centers on designing an NRU model with helium recovery to process nitrogen-rich natural gas and meet strict product specifications. The goal is twofold: deliver pipeline-quality natural gas with minimal nitrogen and produce a crude helium stream at a high recovery rate. To achieve these targets, the team employed a double-column cryogenic distillation cycle – first removing most hydrocarbons at high pressure, then separating helium from nitrogen at lower pressure.
The design utilizes the cold nitrogen and helium output streams to pre-cool incoming feed gas. This reduces the need for external refrigeration, lowers overall power consumption and maximizes heat recovery. It also decreases operating costs and enhances the overall efficiency of the cryogenic separation cycle.
The team used modeling software, focusing on recapturing energy using turboexpanders and lowering the operating pressures of the two columns. The model successfully achieved a high helium recovery rate while maintaining low nitrogen content in the pipeline gas. The team then conducted extensive sensitivity analyses to fine-tune column pressures, optimize heat exchanger performance and evaluate the impact of different process configurations. Additionally, trade-off studies between turboexpanders and Joule-Thomson valves identified the most efficient method for reducing power consumption without compromising separation efficiency. Through these efforts, the team successfully developed a robust and energy-efficient NRU design that meets all specifications while balancing performance, cost and feasibility.
Improving Energy Efficiency in Semiconductor HVAC Systems Team 25073

PROJECT GOAL
Design multiple HVAC air configurations for semiconductor cleanrooms in series to minimize energy consumption while meeting strict environmental conditions.
Semiconductor manufacturing requires cleanrooms that maintain precise environmental conditions regardless of conditions outside the facility. This includes strict control over temperature, humidity and air quality. These conditions are essential for ensuring the quality and reliability of sensitive semiconductor products. HVAC systems in these facilities are primary contributors of energy consumption and thus environmental degradation. With the goal of minimizing energy consumption and environmental impact, the team set out to optimize the recirculation of air while ensuring industry standards are met.
The team designed and calculated energy consumption of the HVAC system for several different air configurations. The focus was on maximizing the use of recycled air in each system. The team used Matlab to automate hourly energy calculations over an entire year using historical weather data. They then compared each configuration and determined the most energy efficient designs that met the strict air quality needs of semiconductor cleanrooms considering outside conditions. At the end of this process, the team extrapolated climate change data to predict how the energy consumption needs and cost of HVAC systems in semiconductor fabrication facilities will change in the future.

TEAM MEMBERS
Isaiah M Hernandez, Chemical Engineering
Ivan Hernandez, Chemical Engineering
Nick Travis Patton, Chemical Engineering
Addison Seckar-Martinez, Chemical Engineering
COLLEGE MENTOR
Adrianna Brush
SPONSOR ADVISOR
Adrianna Brush
Naptha Methaforming Team 25074

PROJECT GOAL
Design and optimize a methaforming unit to convert full range naphtha and ethanol into gasoline blending stock, liquefied petroleum gas and hydrogen-rich gas.
The demand for liquid fuel has risen in the last decade while environmental standards for greenhouse gas emissions have become stricter. In response, the fuel production industry developed an innovative alternative to conventional refinery methods known as methaforming. This process converts full range naphtha – a by-product of crude oil distillation – and ethanol into gasoline, blending stock to reduce costs and a lower environmental impact.
This project aims to help meet the growing demand for fuel by developing a methaforming unit within an existing refinery in Texas. The unit utilizes full range naphtha and ethanol to create the methaformate product, and the main byproducts are hydrogen rich gas and liquefied petroleum gas. The process uses a catalytic bed reactor to increase the gasoline blending stock’s research octane number to 90 with an output rate of 5,000 barrels per standard day.
The team used modeling software to simulate the reactions that take place in a methaforming unit: dehydration of alcohol, aromatization of olefins, alkylation of aromatics, aromatization of paraffins, and isomerization of paraffins. The team iterated the unit operation conditions to meet market specifications of liquefied petroleum gas and hydrogen-rich gas and adhere to product specifications for gasoline blending stock. Introducing expander/compressor pairs – for pressure integration and maximizing the heat flux values of heat exchangers – further optimized energy efficiency.
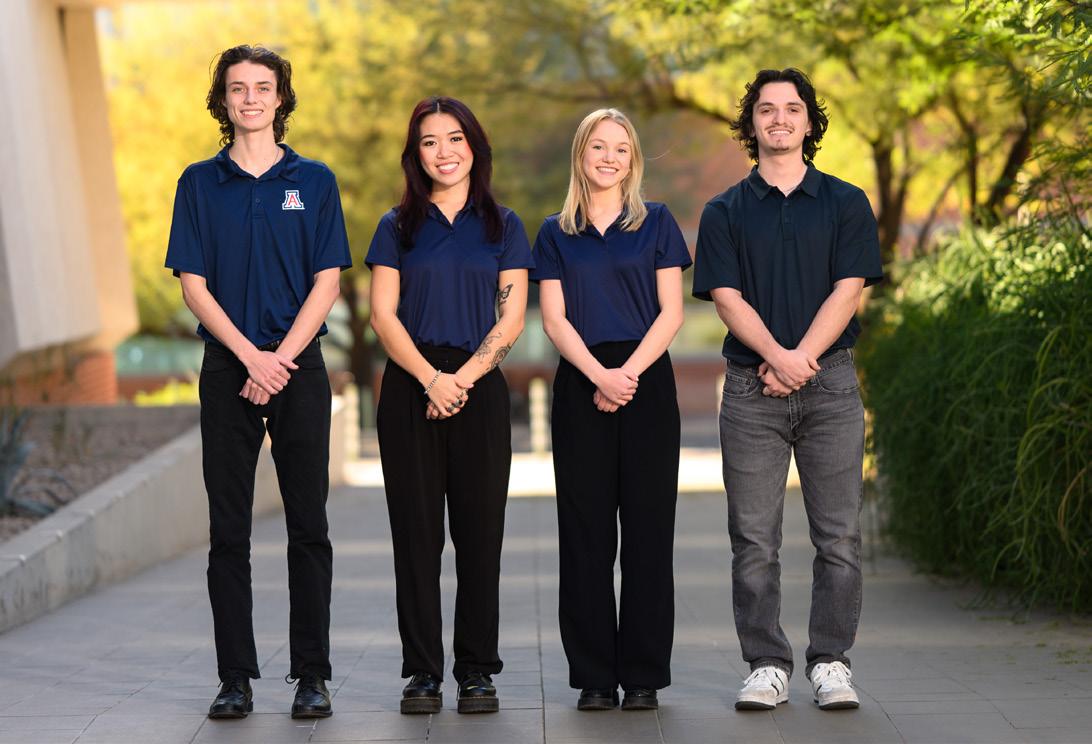
TEAM MEMBERS
Rachel Michelle Jurek, Chemical Engineering
Tiffany Thao Mi Nguyen, Chemical Engineering
Luis E Pesqueira, Chemical Engineering
Sam J Webster, Chemical Engineering
COLLEGE MENTOR
Adrianna Brush
SPONSOR ADVISOR
Adrianna Brush
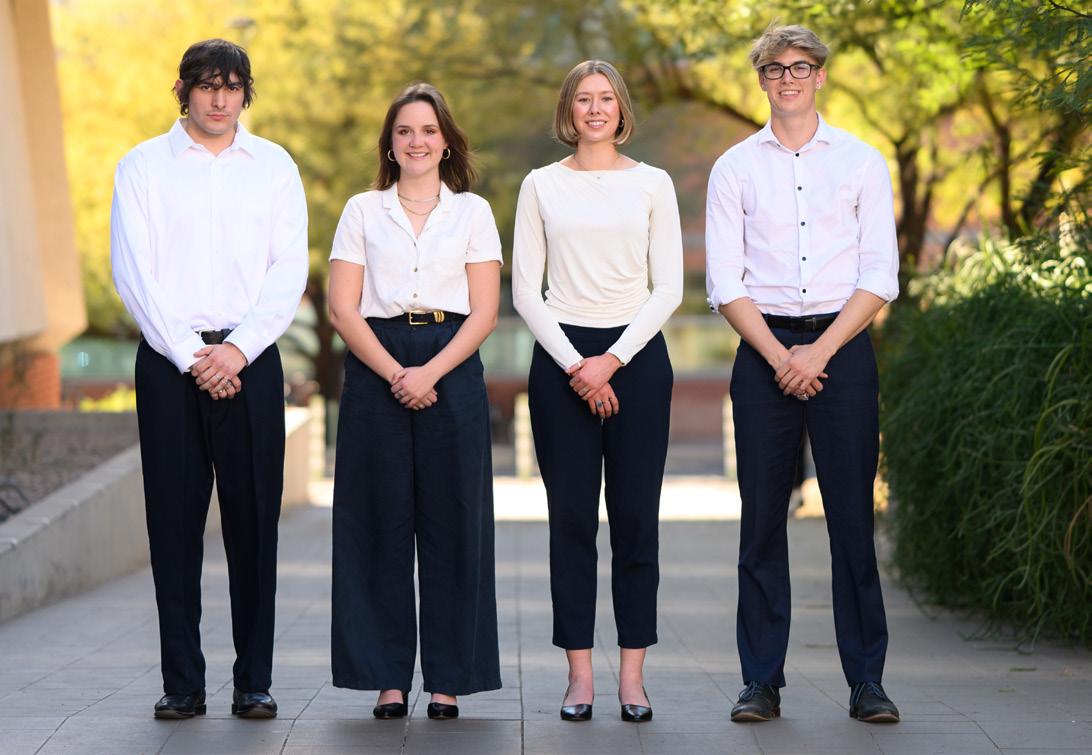
TEAM MEMBERS
Liana Parker Kingston, Environmental Engineering
Leo Partida, Chemical Engineering
Brayden Arthur Vos, Environmental Engineering
Elizabeth Butler Wilson, Environmental Engineering
COLLEGE MENTOR
Adrianna Brush
SPONSOR ADVISOR
Adrianna Brush
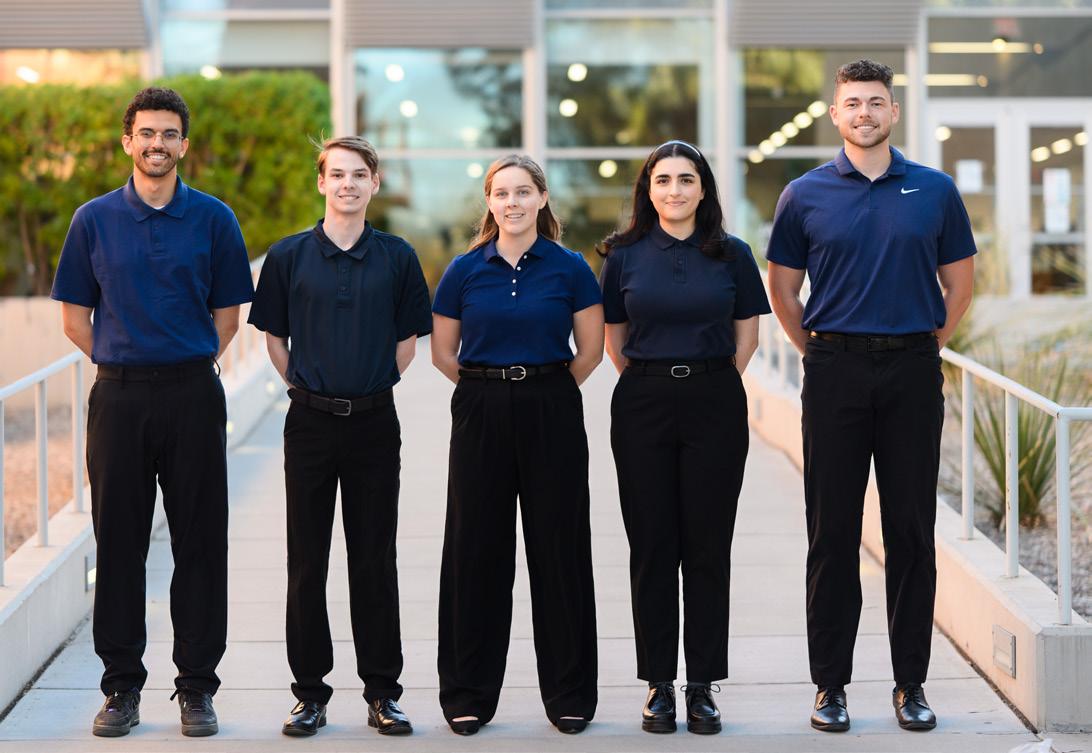
TEAM MEMBERS
Mohammad Alherz, Chemical Engineering
Aisha Ahmad Anoohi, Chemical Engineering
Brock Bailey, Chemical Engineering
Cameron Allen Morrison, Chemical Engineering
Amanda Ruth Whalen, Chemical Engineering
COLLEGE MENTOR
Adrianna Brush
SPONSOR ADVISOR
Adrianna Brush
Hydrogen-Solar Residential Microgrid
Team 25075

PROJECT GOAL
Integrate solar and hydrogen technologies to design and model a residential microgrid for sustainable, resilient energy delivery.
The energy production industry demonstrates a rising need for renewable infrastructure to replace aging equipment and increase system resilience. Microgrid technologies are an effective tool for combating these challenges. The combination of renewable resources and energy storage allows microgrids to provide energy to support demand despite the intermittency of solar and wind. However, energy storage remains a challenge. Hydrogen is an emerging energy storage solution that may offer higher efficiency and environmental sustainability than conventional batteries.
The team designed a neighborhood microgrid in Tucson that uses solar power from photovoltaic cells. To ensure reliability, the grid is backed up by hydrogen technology, which can supply further electricity when needed. Combining solar panels, an electrolyzer, hydrogen storage and a fuel cell allows the microgrid to provide energy to residents under any weather conditions. The team created a DERMS model to visualize energy flows and address challenges of widely fluctuating energy inputs and load requirements.
This design pioneers scalability and safe implementation of novel hydrogen technology. The team created tools and developed models that are designed for easy adaptation to diverse microgrid applications. Similar systems can be implemented in data centers, electric vehicle charging stations and universities.
Hydro-Desulfurization Unit
Team 25076

PROJECT GOAL
Design a catalytic hydro-desulfurization unit to process 30,000 barrels per standard day of blended straight-run gas oil and light cycle oil to produce a diesel product with sulfur concentration meeting the industry standard.
When gasoline and diesel hydrocarbon compounds are burned, naturally occurring sulfur forms compounds that damage respiratory health and contribute to toxic acid rain. For this reason, the government regulates the amount of sulfur allowed in fuel. In diesel, this limit is as low as 50 parts per million. To comply with these standards, oil refineries must remove sulfur before the diesel can be sold and used.
Hydrodesulfurization is the primary removal method. In this process, hydrocarbons from other parts in the refinery, e.g. straight-run gas oil and light cycle oil, are reacted with hydrogen in the presence of a catalyst at high temperatures and pressures to separate sulfur from the hydrocarbon chain and create hydrogen sulfide gas.
The team designed a reactor and a separation system to remove hydrogen sulfide and other gases from the diesel stream. An amine unit processes the gases to absorb hydrogen sulfide and recycle hydrogen back to the reactor. The diesel product is stabilized and separated from lighter hydrocarbons before being sold as a product.
The team simulated and optimized the hydrodesulfurization unit in Aspen HYSYS software. The goals were to reduce sulfur content in the final diesel product to a maximum of 50 parts per million to minimize energy usage, cost and the environmental impact of this process.
Inulin Production
Team 25077

PROJECT GOAL
Model and optimize the extraction and purification process of inulin from Jerusalem artichokes for future use in the pharmaceutical industry.
The pharmaceutical industry often looks to plants for effective treatments. Inulin is one of these plantbased potential therapies. It is a naturally occurring polysaccharide in plants such as dandelions, chicory root and Jerusalem artichokes. Inulin can be used as a prebiotic, a dietary fiber, an enhancement for vaccines, and in medicines targeting the colon and kidneys. Jerusalem artichokes contain a high inulin content and serve as a sustainable source for this biomaterial. However, the process for refining the inulin from Jerusalem artichokes is inefficient and expensive.
In this project, the team focused on improving this inulin refinement process. To reach pharmaceutical grade after extraction, the inulin undergoes an intensive purification process. This includes the use of reactors, desalination and moving bed chromatography units, a falling film evaporator, and a spray dryer. The team mathematically modeled each piece of equipment, comparing modeled values with prior research to determine the optimal conditions for purified inulin.
The result of this project is pieces of equipment that are optimized to improve yield and purity while still considering cost and environmental impact.
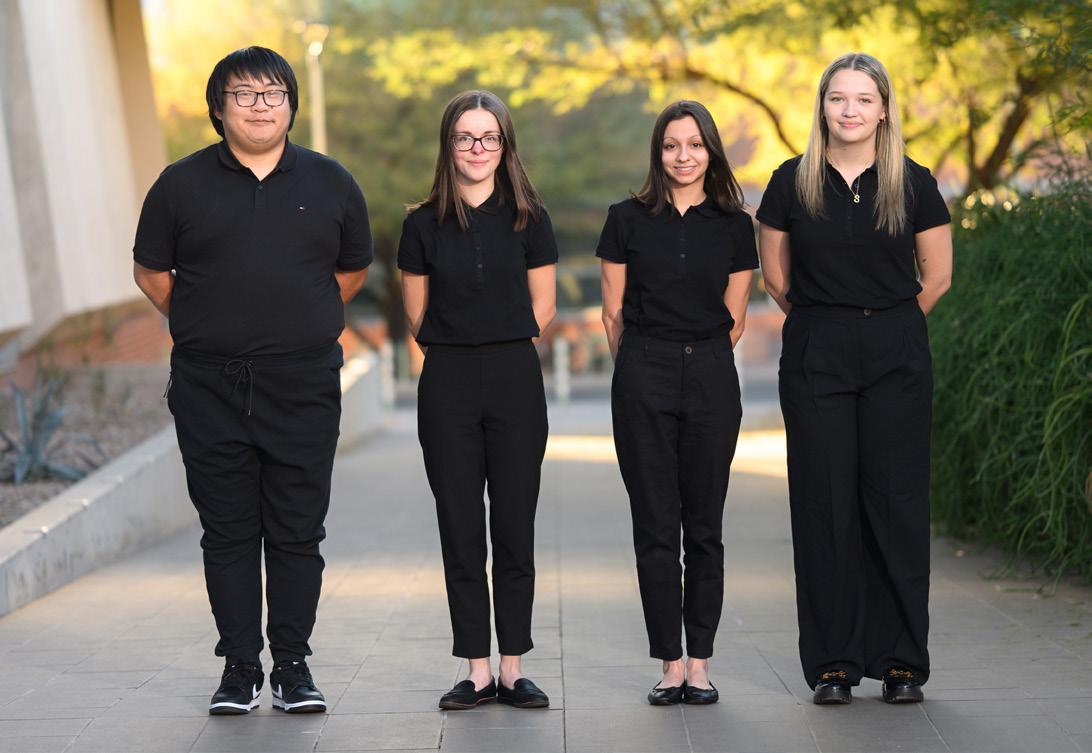
TEAM MEMBERS
Chopper Chi, Environmental Engineering
Sophie Anne Harrison, Chemical Engineering
Kayden Rylee Masters, Chemical Engineering
Jess Ann Sunclades, Chemical Engineering
COLLEGE MENTOR
Adrianna Brush
SPONSOR ADVISOR
Adrianna Brush
AZ Water Competition
Team 25078

PROJECT GOAL
Develop a design proposal to upgrade the city of Surprise SPA 1 Water Reclamation Facility (WRF) by increasing treatment capacity while ensuring compliance with regulatory discharge standards, optimizing plant operations, and integrating costeffective solutions for long-term sustainability.
The Arizona Water Association (AWA) hosts a yearly student design competition that tasks students with an engineering analysis and design project related to a water treatment facility. Teams created innovative and cost-effective solutions to meet the competition’s design goals.
This year, the AWA asked teams to propose an expansion plan for the SPA 1 WRF in Surprise, Arizona. The goal was to increase the facility’s treatment capacity from 12.8 million gallons per day to 16.3 million, while maintaining operational efficiency and regulatory compliance. The team evaluated four secondary treatment alternatives for Plants 4 and 5: the modified Ludzack-Ettinger process, a membrane aerated biofilm reactor, a membrane bioreactor (MBR), and the Four-Stage Bardenpho process.
After analyzing these options, the team determined that MBR is the best solution due to its ability to provide superior effluent quality, minimize hydraulic impacts, and maximize treatment capacity within the existing footprint. The MBR system enhances operational reliability and process control while reducing the facility’s overall environmental impact. Additionally, the team’s design includes a recommended construction timeline and an assessment of operational and maintenance costs.
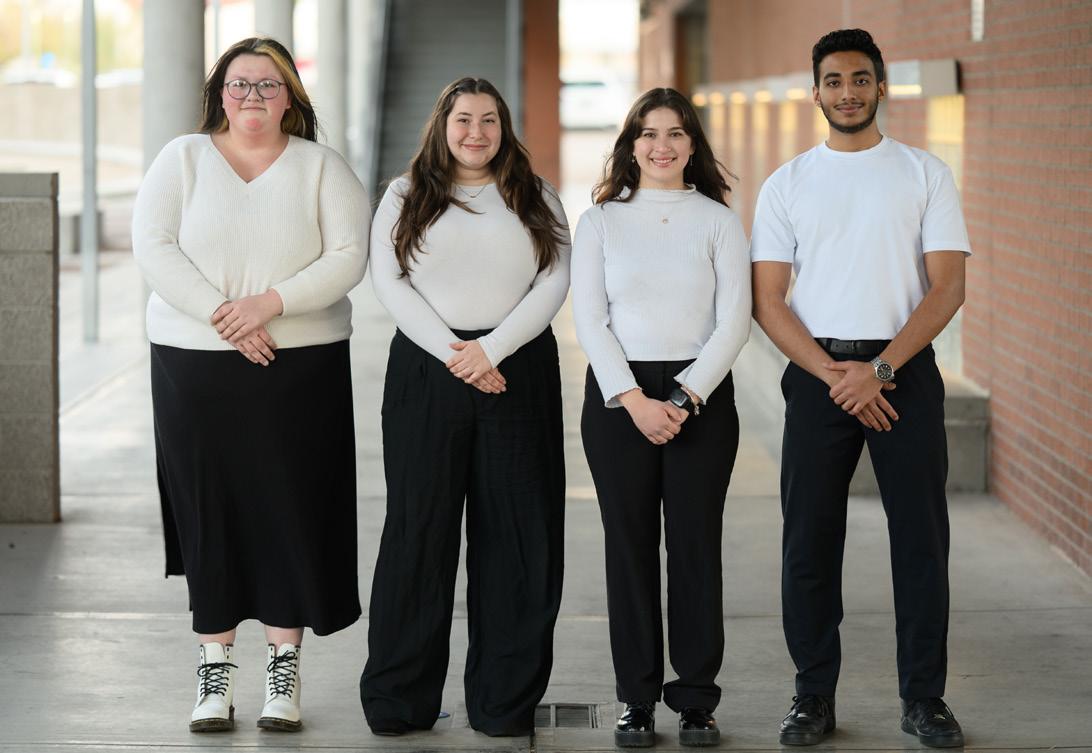
TEAM MEMBERS
Rayan Mohamed Elnewehy, Chemical Engineering
Sasha Paige Neyman, Environmental Engineering
Miranda Ashley Nitz, Environmental Engineering
Yixel Quevedo, Environmental Engineering
COLLEGE MENTOR
Adrianna Brush
SPONSOR ADVISOR
Adrianna Brush
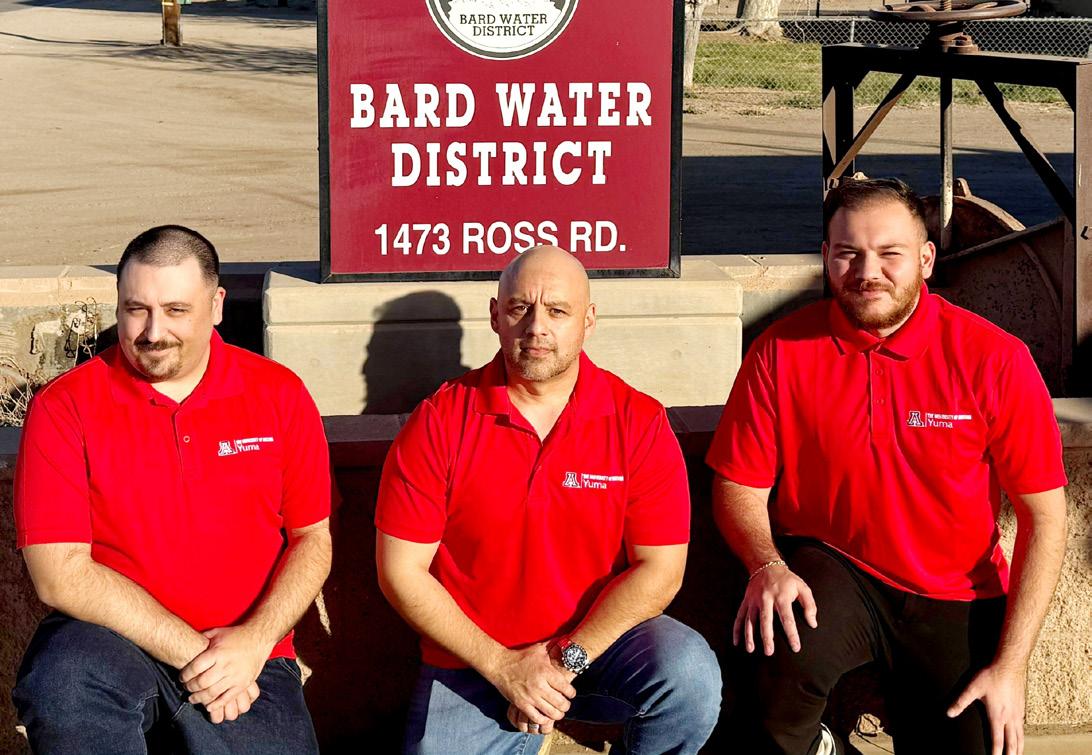
TEAM MEMBERS
Daniel Fiorella, Systems Engineering
Sergio Jesus Legy, Industrial Engineering
Anil Yamaner, Industrial Engineering
COLLEGE MENTOR
Samuel Peffers
SPONSOR ADVISOR
Nick Bahr
Working with the students keeps you young, keeps you engaged.”
Radio Network Optimization
Team 25079
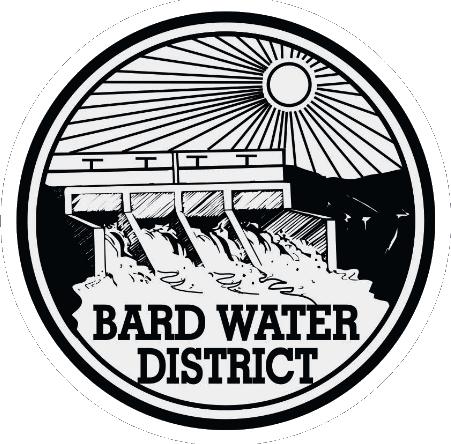
PROJECT GOAL
Determine the best method for improving the quality and reliability of the radio communication system for Bard Water District (BWD) and deliver an implementable plan to apply that method.
Radio communications relay data from and to sensors and actuators in the irrigation water distribution system across the 18,000-acre BWD. The district is expanding status monitoring and distribution control automation across its geographic footprint. However, obstructions within the terrain and fields of palm trees reduce or even completely block radio signals and line of sight (LOS) between existing antennae, limiting automation expansion.
The team used the Radio Mobile software to simulate the existing radio network and identified multiple technically viable solutions. Through close coordination with the project sponsor to define stakeholder needs and priorities, the team developed comprehensive analysis and comparison criteria to determine the optimal solution.
Following the sponsor’s concurrence with the design team’s initial recommendations, the team ran additional Radio Mobile simulations to solve a secondary problem: extending connectivity to the area southwest of the office just outside of the town of Winterhaven. The team achieved this by extending the main tower to attain LOS with a greater part of the southwestern area and installing the subscriber radios on 16 ft poles mounted on concrete bases. The district can place these hardware mounts near any of the sensors or actuators in the area and relay the radio signal to other areas with obstructions. This ensures LOS and signal integrity throughout the BWD area of operation.
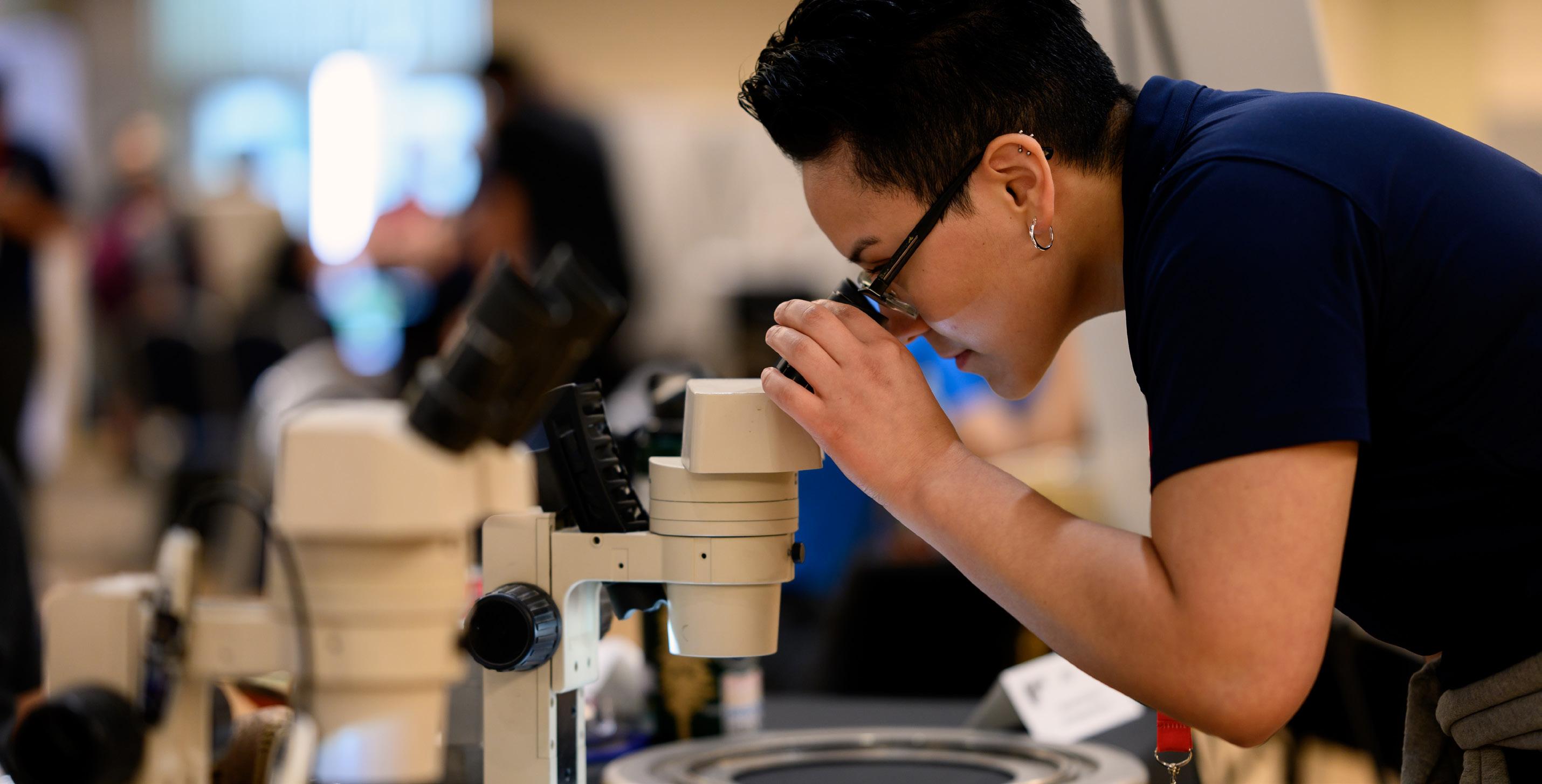
CHARLIE SIMPSON, project and prize sponsor
NANCY BERGE
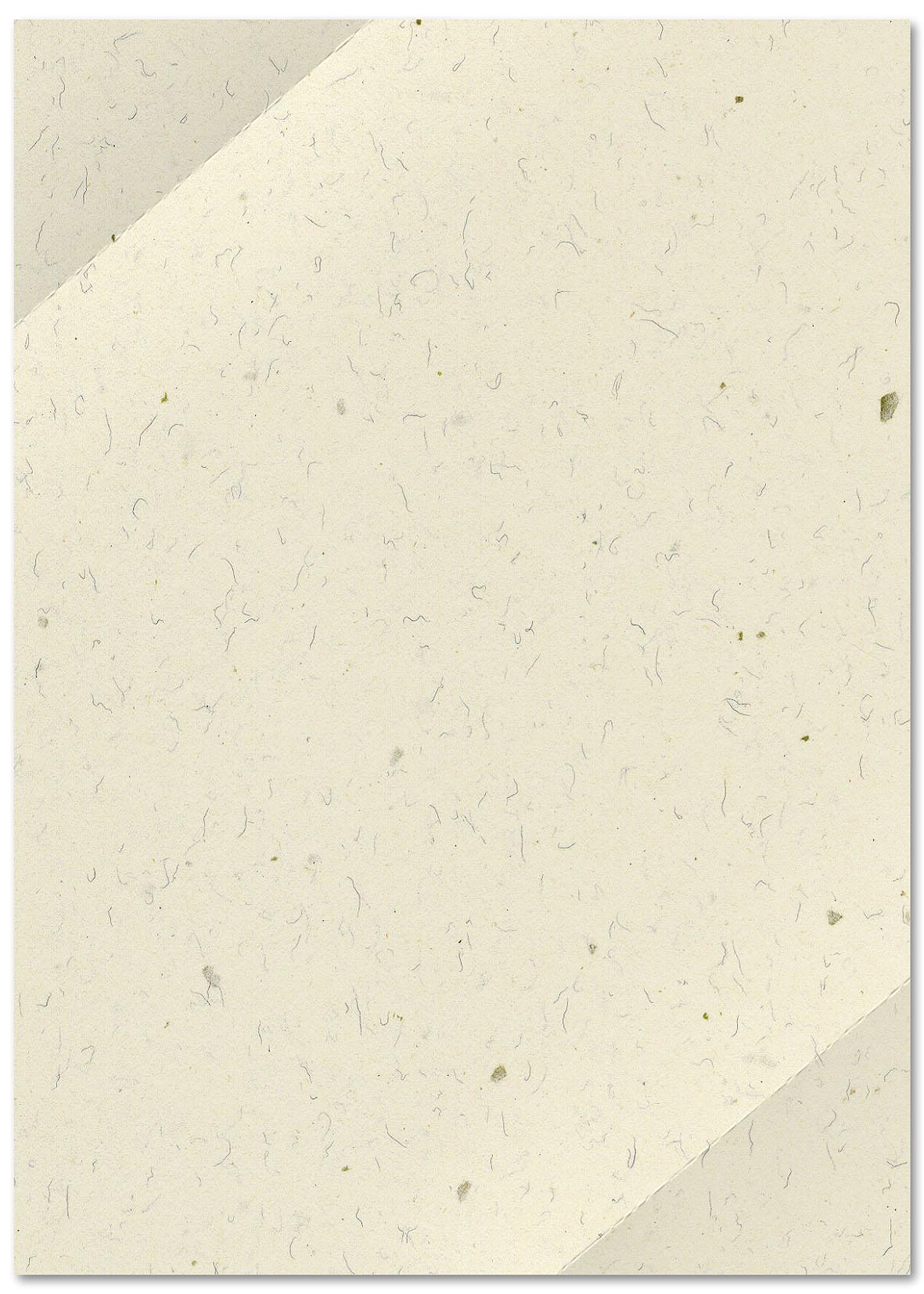
Dear students,
Thank you to everyone who has participated in this wonderful event, the Craig M. Berge Design Day which bears our family name. My family and I are delighted to see and learn about your design projects. They are truly outstanding.
Much of my husband’s life and engineering career was all about designing. As a student, he built and designed his dragster. Later in life, as a mechanical engineer, he worked for a company that paid for his education. The company loaned him to the U.S. Navy to design the starter for a jet airplane named the Intruder. That plane is on aircraft carriers to this day. Knowing that the Navy is still using something he created is truly remarkable.
My husband would expect remarkable things from each of you, too. He would be so proud of your creativity and all you have accomplished.
In my husband’s memory, I am honored to support the Craig M. Berge Engineering Design Program and these student experiences that move you toward the next chapters in your lives and careers.
All the Best,
Nancy Berge
Interdisciplinary Capstone Course and Senior Design Projects
YEAR AT A GLANCE
ENGINEERING DESIGN OPEN HOUSE
SYSTEM REQUIREMENTS 4 weeks
PRELIMINARY DESIGN 4 weeks
After students are assigned to projects, teams work with their sponsors to generate structured lists of system requirements and metrics for
DETAILED DESIGN 6 weeks
Following approval of the Systems Requirements Memo, teams conduct research and brainstorm to produce preliminary or conceptual designs
Based on feedback from sponsors and mentors at the Preliminary Design Review, teams modify their preliminary designs and create detailed manufacturable designs to create prototypes for Craig M Berge Engineering Design Day
WINTER BREAK
DESIGN CHANGES/ BEGIN BUILD 7 weeks FINALIZE BUILD/ ACCEPTANCE TESTING 9 weeks
Following the Critical Design Review and approval of the Critical Design Report, teams begin purchasing parts and manufacturing custom components to produce their prototypes
SYSTEM REQUIREMENTS MEMO
In this structured document, against which all designs, tests and prototypes requirements for completed projects in consultation with sponsors
PRELIMINARY DESIGN REVIEW
In this formal review, sponsors and mentors critique conceptual designs –for which sponsor approval is required – challenge assumptions and help
During the last phase of the program, teams collaborate closely with sponsors to assemble and test their prototypes. They also prepare their presentations and demonstrations for Craig M Berge Design Day
CRITICAL DESIGN REVIEW
At this milestone, sponsors and mentors ensure their teams are meeting all requirements and have feasible plans to manufacture and test prototypes within budget.
INTEGRATED STATUS REVIEW and FINAL ACCEPTANCE REVIEW
This review facilitates communication & collaboration among the engineering team and stakeholders, helping them make informed decisions about design changes and project progress.
17 ENGINEERING DEGREE PROGRAMS
AEROSPACE ENGINEERING
ARCHITECTURAL ENGINEERING
BIOMEDICAL ENGINEERING
BIOSYSTEMS ENGINEERING
CHEMICAL ENGINEERING
CIVIL ENGINEERING
COMPUTER SCIENCE & ENGINEERING
ELECTRICAL & COMPUTER ENGINEERING
ENGINEERING MANAGEMENT
ENVIRONMENTAL ENGINEERING
INDUSTRIAL ENGINEERING
MATERIALS SCIENCE & ENGINEERING
MECHANICAL ENGINEERING
MINING ENGINEERING
OPTICAL SCIENCES & ENGINEERING
SOFTWARE ENGINEERING
SYSTEMS ENGINEERING
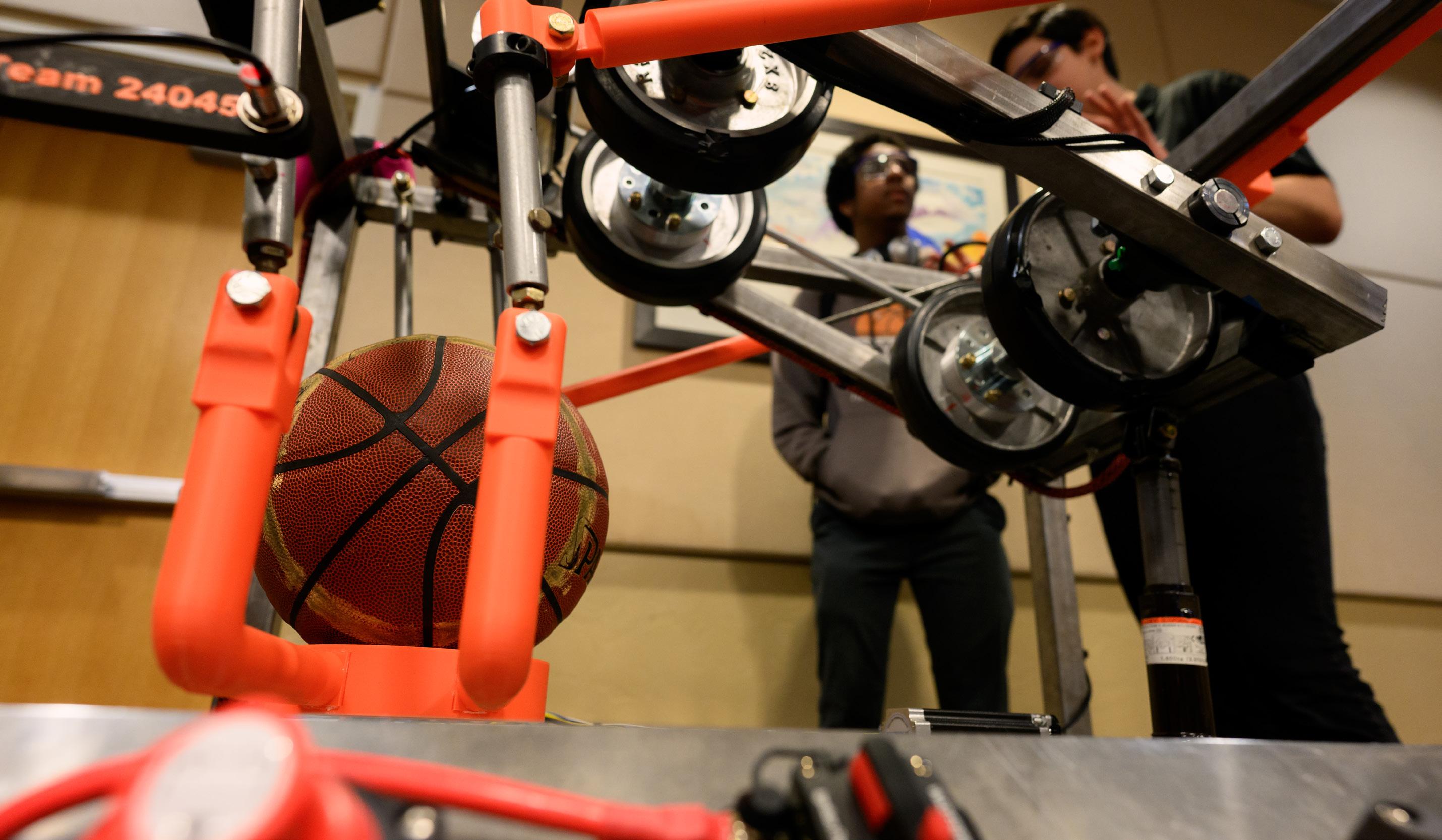
CRAIG M. BERGE DESIGN DAY
ACKNOWLEDGMENTS
STUDENTS
Capstone projects are the culmination of a year’s worth of work. Students have applied knowledge from the breadth of their undergraduate education, exercised out-of-the-box thinking and spent hundreds of hours producing the best solutions for their sponsors. We applaud your dedication and professionalism and congratulate you on your achievements.
MENTORS
Project mentors apply hundreds of years of collective engineering experience to guide students in the completion of their projects. They ensure the implementation of industry standards in the design process. Their expertise in devising solutions to challenging problems adds a critical dimension to students’ engineering knowledge. Thank you for your hard work, your commitment to excellence in engineering design and your role in the education of our students.
SPONSORS
Sponsors provide students with real-world questions and allocate funds to the program. They designate technical staff and mentors to steer students through the intricacies and requirements of their projects. Sponsors are a big part of what makes the Craig M. Berge Engineering Design Program (which encompasses Interdisciplinary Capstone and other capstone courses) what it is today: one of the largest and best-quality programs of its kind in the nation. Thank you immensely for your continued support.
JUDGES
The external judges who participate in Craig M. Berge Design Day supply independent professional assessments of the quality of students’ work. They help maintain the accreditation of undergraduate University of Arizona Engineering degree programs by providing insight and suggestions for improving the Engineering Design Program. Thank you for volunteering your time and applying your knowledge to evaluate students’ capstone projects.
STAFF
Dedicated professionals in the College of Engineering ensure the program’s smooth operation. They spend thousands of hours each year organizing events, communicating with sponsors, operating manufacturing areas, generating marketing materials and news, maintaining budgets and purchasing records, and performing a myriad of other tasks. Thank you all for your invaluable contributions and the excellence you bring to the program.
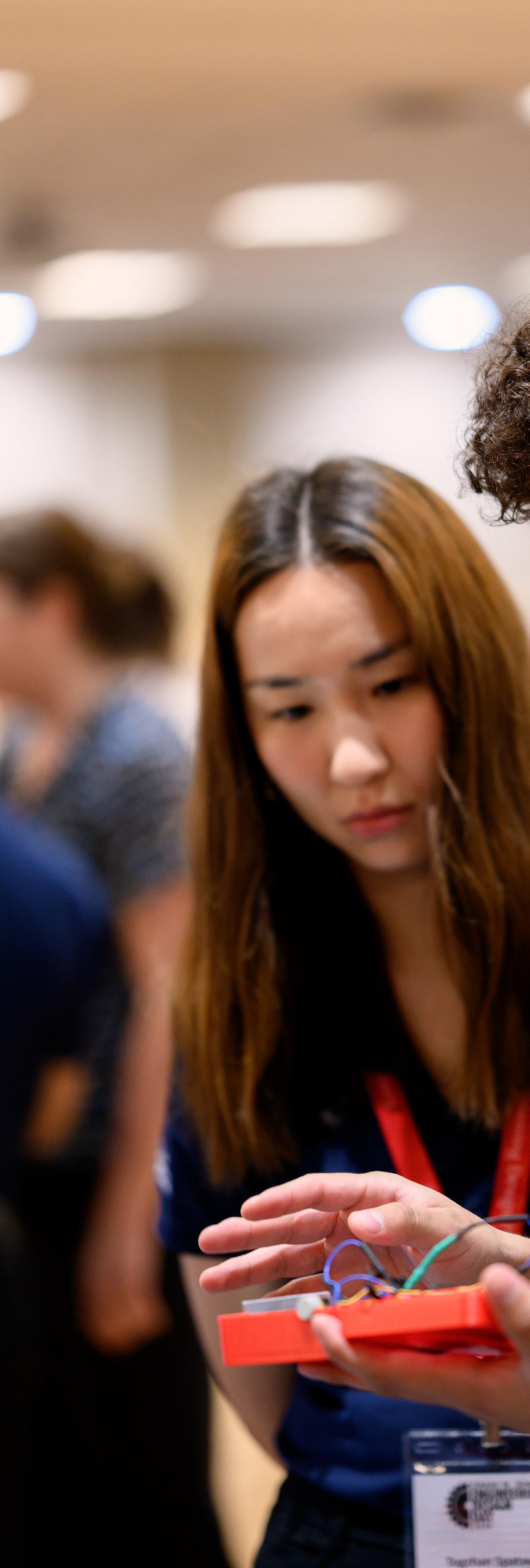
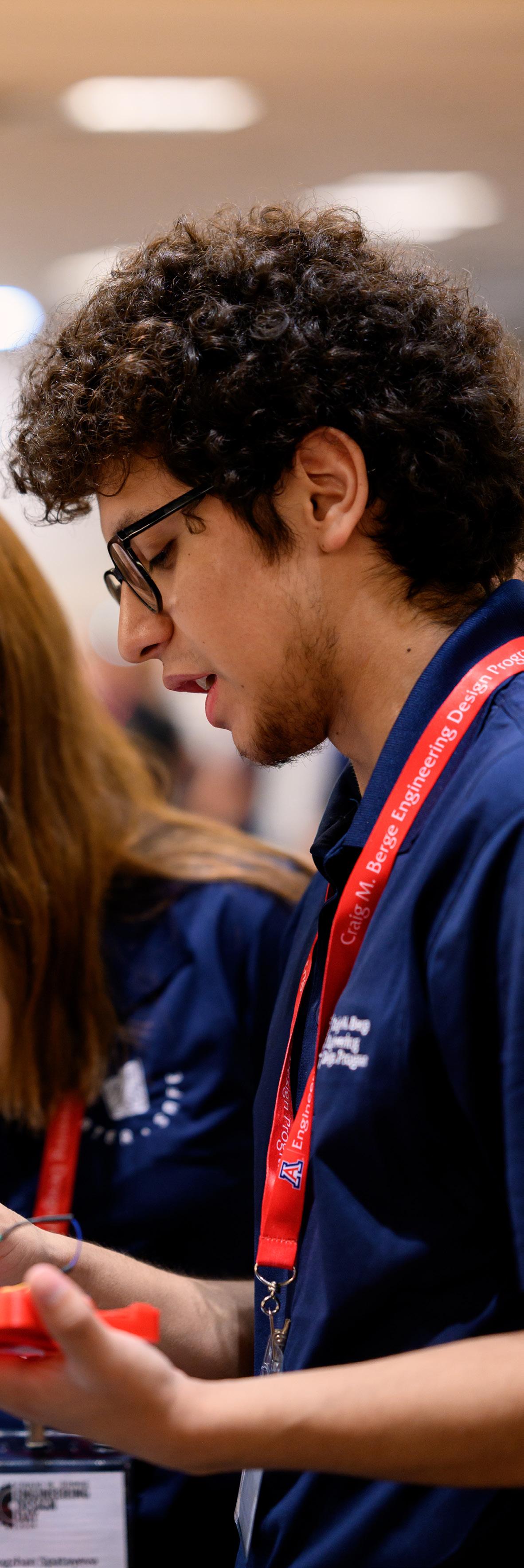
CORPORATE, GOVERNMENT & PRIVATE
Acron Aviation
Amazon
Ana Needham
Arzon Solar
ASML US, Inc.
AZ 3D Print
AZ Technica
BAE Systems
Bard Water District
BD (Becton Dickinson)
Capstone Mining Corporation
Caterpillar Inc.
Coherent
Dataforth Corporation
Davis-Monthan Air Force Base 309 AMARG
Donald Newman
Dragoon Technology
Elbit Systems of America
Frank Broyles
Freeport McMoRan
General Dynamics Mission Systems
Geomechanics Southwest, Inc.
Global Medic Force
Greg Lorton
Henry & Suzanne Morgen
Honeywell Aerospace
Institute of Electrical & Electronics
Engineers (IEEE)
Larry Head
Lawrence Livermore National Laboratory
Leonardo Electronics US - Laser Solutions
LumiVici
Mark Brazier
Mensch Foundation
Microsoft
National Institutes of Health
Nobel
Northrop Grumman
Parker Meggitt
PeakView Environmental Solutions
Phoenix Analysis & Design Technologies
R3 Aerospace
Raytheon Technologies
RBC Sargent Aerospace & Defense
Resolution Copper
Ridgetop Group
Rightfooted Foundation
Rincon Research
Rob Dollar Foundation
Roche Tissue Diagnostics
Roy Medina
Salt River Project
SEC Energy
Sharon ONeal
Simpson Family
Spectrum Plastics Group
Steve Larimore
SynCardia Systems
Tacticum
Technical Documentation Consultants of Arizona
The Bly Family
The New Nose Company, Inc.
W.L. Gore And Associates
THE UNIVERSITY OF ARIZONA
Arizona Center for Accelerated Biomedical Innovation (ACABI)
Craig M. Berge Dean
Engineering Design Center
Biosphere 2
College of Medicine
Department of Aerospace & Mechanical Engineering
Department of Biomedical Engineering
Department of Biosystems Engineering
Department of Chemical & Environmental Engineering
Department of Mining & Geological Engineering
Department of Orthopaedic Surgery
Police Department/ALERRT
School of Mining & Mineral Resources
School of Natural Resources & the Environment
THANK YOU, MENTORS & STAFF
MENTORS
Adrianna Brush
Pat Caldwell
Steve Larimore
Carey Jones
Michael Madjerec
Doug May
Don McDonald
Sardar R Mostofa
Mike Nofziger
Samuel Peffers
James Sweetman
Edward Clifton Wellman
Jeff Wolske
STAFF
Larry Head, Craig M Berge Engineering Design Program Director
Debbie Claggett, Engineering Design Capstone Coordinator
Nikki Heath, Operations Specialist
Neda Alihemati, Purchasing Office
Divya Dhole, Purchasing Office
Tina Tian, Purchasing Office
Matthew Briggs, Design Faculty
Urs Utzinger, Design Faculty
Alexa Armstrong, Engineering Design Center
Miguel Barrera, Engineering Design Center
Cienna Charron, Engineering Design Center
Carolina Ferreira Silva, Engineering Design Center
Seven Gilbert, Engineering Design Center
Amir Haghiri, Engineering Design Center
Caleb Maloy, Engineering Design Center
Brody Manas, Engineering Design Center
Caroline McCarthy, Engineering Design Center
Angel Perez, Engineering Design Center
Samantha Perry, Engineering Design Center
Josiah Rash, Engineering Design Center
Elias Thomas, Engineering Design Center
Ilana Valenzuela, Engineering Design Center
Gabe Vogt, Engineering Design Center

I love being an advocate for the development of young engineers. I believe receiving guidance from someone who was just in your shoes not too long ago helps define the next steps in your career.”
SIERRA ROSE, alum and Northrop Grumman Space Systems SPONSOR ADVISOR


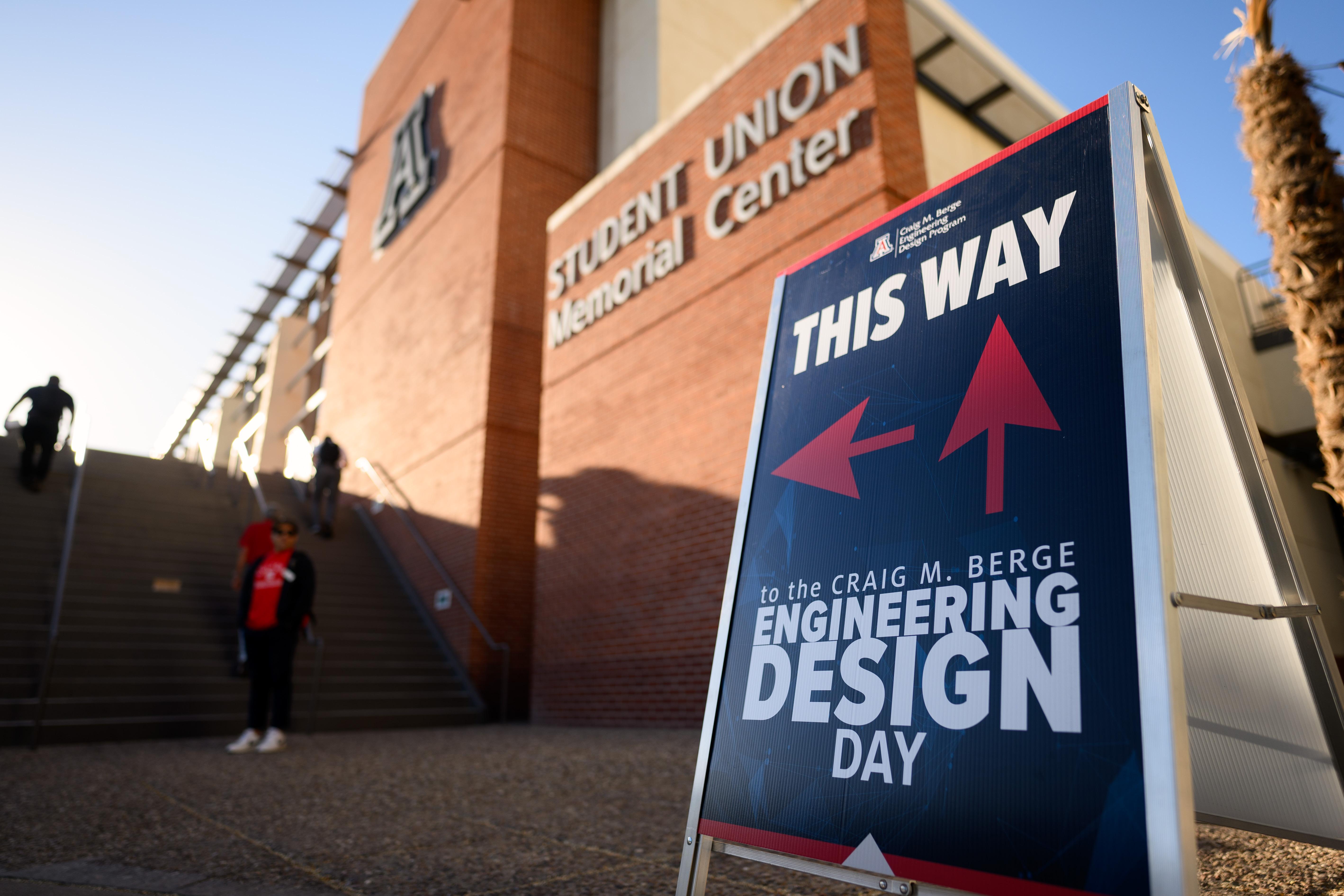
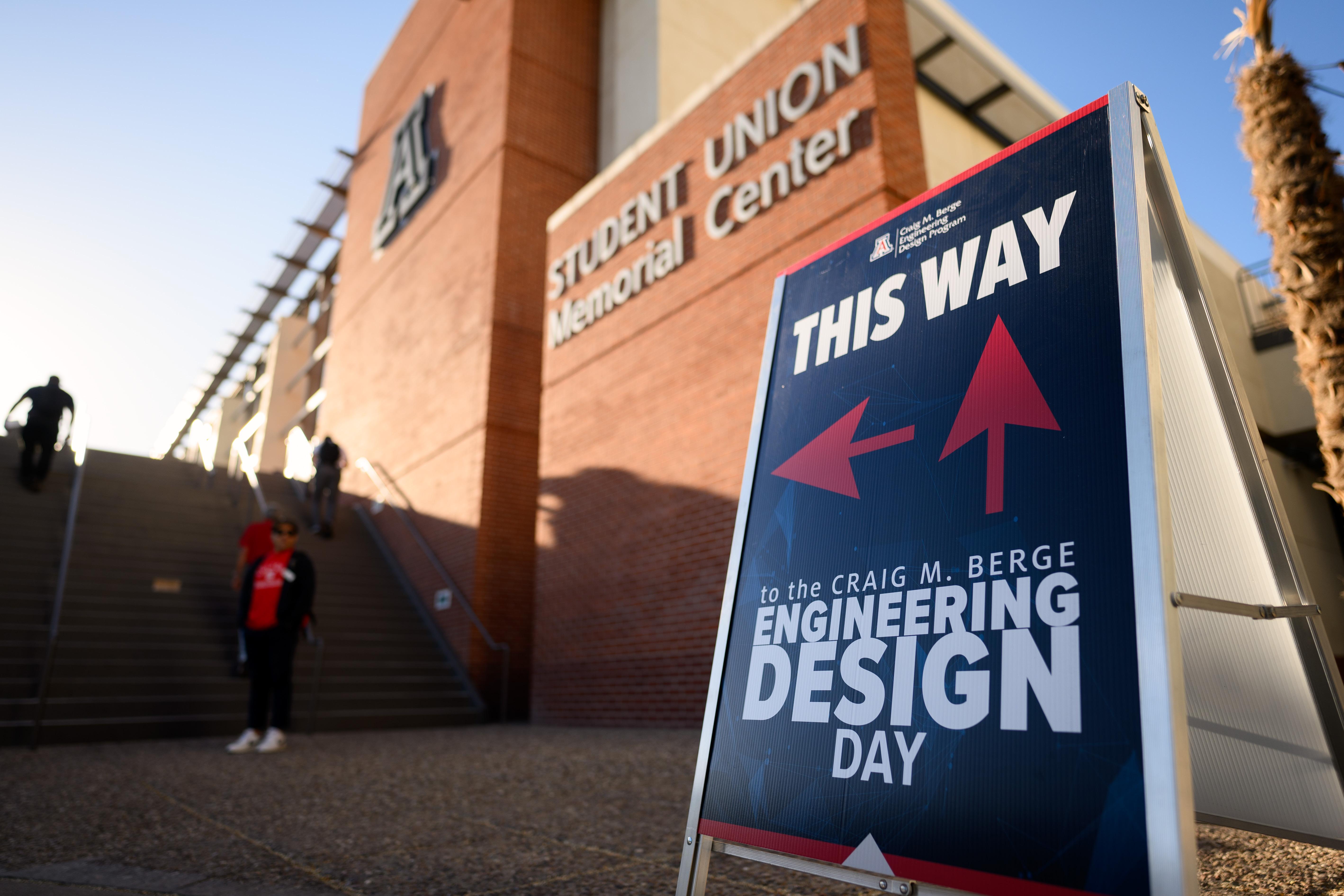
From startups to Fortune 500 companies, a varied group of sponsors benefits from this outstanding interdisciplinary academic program each year.
Try out potential employees
Explore new technologies
Move products to market
Support engineering education
Boost company profile on campus
TRANSFERRING SKILLS TO THE WORKFORCE
Teams of four to six seniors, mentored by industry liaisons and University of Arizona Engineering faculty, spend an entire academic year taking your design projects – many of which become patented technologies and commercial projects – from start to finish.
View the 2025 Design Day project presentations at b.link/DesignDay2025