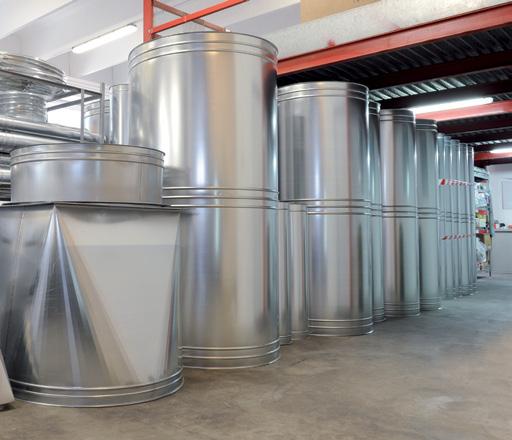
10 minute read
COMPONENTI PER IL TRASPORTO DELLA SEMOLA E FARINA
Utilizzata nel settore molitorio per il passaggio del prodotto (semola, farina etc.) viene realizzata in acciaio inox aisi 304 BA sp. 10-12/10 elettrosaldata e saldata a tig con trattamento di lucidatura esterna, nei diametri 105-120-150200-250-300 mm e nei vari componenti quali tubi, settori, settori girevoli, valvole, giunzioni.
Components
Advertisement
Used in the milling sector to convey the product (durum wheat flour, ), these items are made of 10-12/10 gauge 304 BA grade stainless steel, electrically and TIG welded and polished externally; available in 105-120-150-200-250-300 mm diameters and a range of components including tubes, fixed segments and rotatable segments, valves, splices.
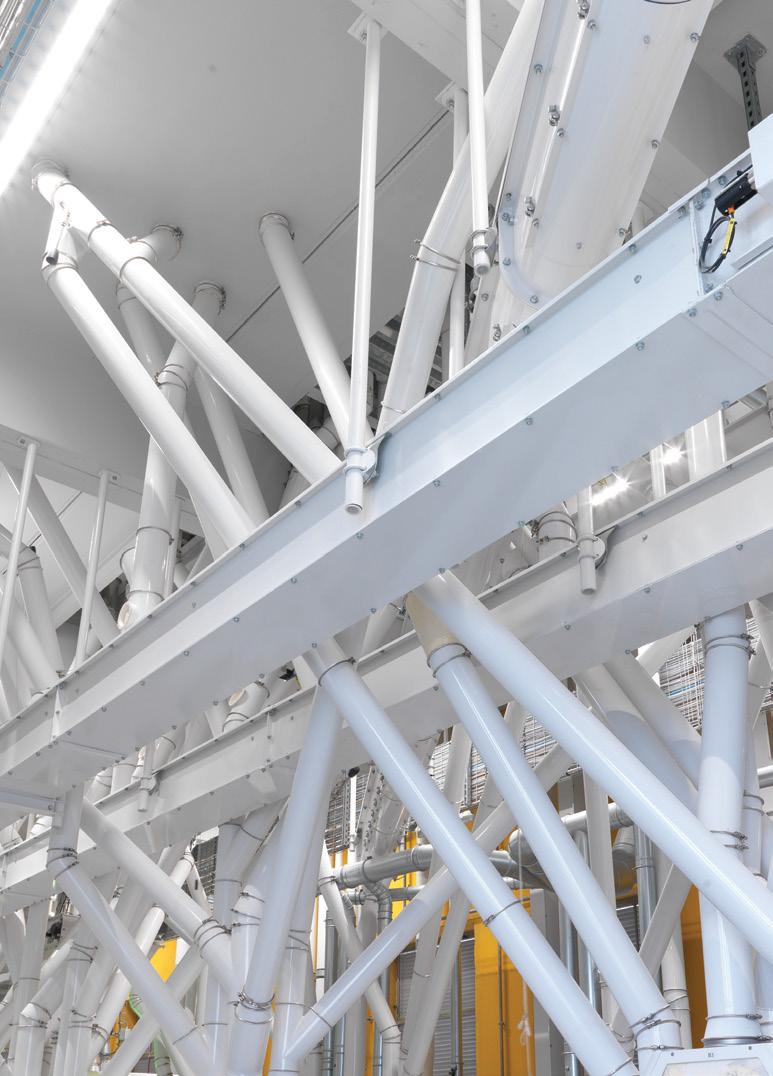
COMPONENTI PER L’ASPIRAZIONE MOLITORIA COMPONENTS FOR MILLING SYSTEM
Utilizzati nel settore Molitorio e Generico Industriale, vengono realizzati in Acciaio
Zincato Gr.ra Z200 o a richiesta in Acciaio della rete di magazzini e silos per lo stoccaggio dei cereali italiani è, in linea generale, la vetustà.
Inox aisi 304 2b nei spessori 6-8-10-12/10 nei vari Diametri e dimensioni sia per i prodotti standard Seven che per le richieste personalizzate da parte del Cliente.
Used in the Milling and General Industrial fields. Made from Z200 basis weight galvanised steel or, on request, AISI 304 2b stainless steel with thicknesses of 6-8-10-12/10 and various diameters and sizes for both standard Seven products and for customised productions.
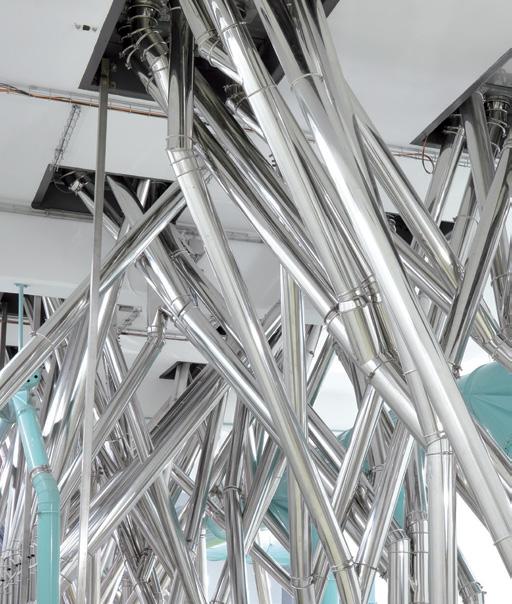
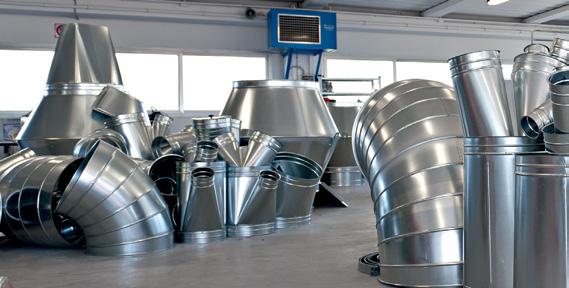

Riferisce il Piano Cerealicolo Nazionale che, a oggi, in circa il 40% di queste strutture sono stati realizzati interventi di ampliamento e, per la stessa quota, ammodernamenti e/o ristrutturazioni. Una proporzione che risulta omogenea tra tutte le macro aree geografiche della Penisola, a eccezione del Sud e delle Isole, cuore della produzione del grano duro per la pasta. In queste zone, poco più della metà delle strutture ha effettuato ammoderna- menti mentre oltre i due terzi non hanno mai proceduto con ampliamenti della capacità. Su scala nazionale, il 66% del totale delle strutture di immagazzinamento è dotato di una sola fossa di scarico e il 63% di una sola linea di carico. Il dettaglio regionale evidenzia uno scenario più favorevole solo per i centri censiti in Puglia. In realtà, sulle strutture vengono fatti continuamente degli interventi di manutenzione dal momento che i centri di stoccaggio hanno un’operatività costante durante tutto l’anno poiché si trovano, da un lato, a dovere rispondere alle modalità operative delle aziende agricole che lavorano con tempi strettissimi dato che la raccolta avviene in un mese con la conseguenza che questo può creare delle congestioni delle partite in entrata, provenienti dai campi. D’altro canto, è anche vero che devono riuscire a rispondere alle richieste da parte dell’industria di trasformazione che, per contro, lavora tutto l’anno e richiede un flusso costante delle forniture di materia. Questo processo, in pratica, vede la filiera operante su due parametri temporali completamente diversi. Da un lato, quello della raccolta (che avviene tutta in una volta), dall’altro quello della trasformazione (continua e costante durante tutto l’anno). Questo sfasamento presta il fianco a meccanismi che talvolta arrivano a vere e proprie distorsioni del regolare funzionamento del mercato aprendo margini a operazioni anche speculative. Dentro que- sti margini si gioca la partita della competitività dei centri di stoccaggio, spesso legati a commercianti e intermediari, più o meno piccoli, coinvolti nella stessa compravendita di derrate primarie. Secondo i dati del Piano Cerealicolo Nazionale, la metà degli stoccatori detiene la proprietà del prodotto stoccato. In pratica, il 50% stocca prodotto proprio; il 35% prodotti di terzi, pratica diffusa soprattutto nel Sud Italia, e il 16% entrambi.
I contratti di filiera e i centri di stoccaggio
Anche per questo, non è semplice riuscire a coinvolgere gli stoccatori dentro i contratti di filiera dove, per definizione, si stabilisce un prezzo stabile all’origine. A oggi, questi contratti sono applicati, per lo più, dalle grandi aziende di trasformazione, in funzione soprattutto della necessità di approvvigionarsi costantemente, durante l’anno, con materia prima la cui qualità risponda sempre agli stessi standard. La chiusura delle filiere attraverso i contratti “di filiera”, ad esempio, oppure con le certificazioni di grano 100% italiano, sono oggi temi di attualità strettamente connessi ai centri di stoccaggio. Temi che nascono dalle richieste del consumatore che è sempre più consapevole e attento all’origine della merce e alla qualità della materia prima. Peraltro, questi strumenti giuridici, sono a oggi quelli considerati più efficaci per l’equa distribuzione del

REALIZZAZIONE DI SILOS IN CALCESTRUZZO ARMATO PER LO STOCCAGGIO DI PRODOTTI FARINACEI


RIVESTIMENTI DI CELLE E SILOS CON RESINE EPOSSIDICHE CERTIFICATE PER IL CONTATTO CON ALIMENTI
RIVESTIMENTI DI PAVIMENTI CON RESINE MULTISTRATO E AUTOLIVELLANTI
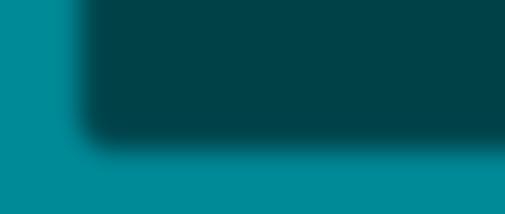
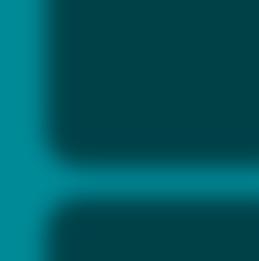
TINTEGGIATURA SUPERFICI INTERNE ED ESTERNE DI OPIFICI INDUSTRIALI
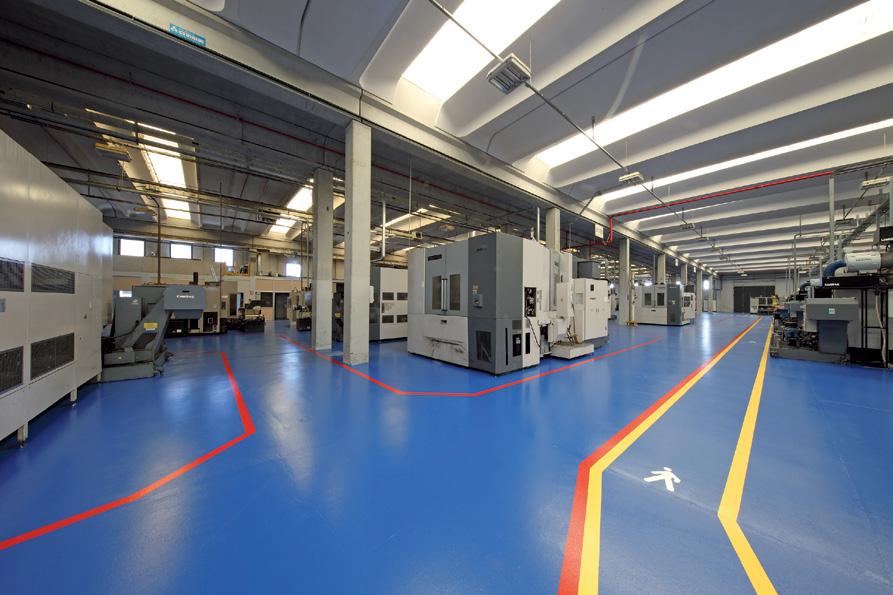
RINFORZI E MIGLIORAMENTI SISMICI MEDIANTE L’USO DI INTONACI ARMATI, NASTRI IN FRP E STIRATURE ARMATE s.p. Andria-Trani km 1,500 Andria (BT) t 0883.251661 info@pi-sa.it www.pi-sa.it

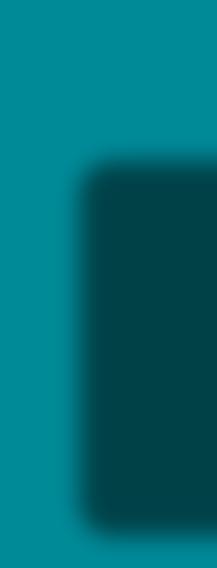
Differenziazione
valore lungo la catena di fornitura. Un valore che oggi, in parte viene determinato dal ruolo dei centri di stoccaggio anche se, negli ultimi anni, l’Italia ha registrato una progressiva compressione degli stock cerealicoli.
Secondo le stime Fao per il 2023, confermate dall’andamento della campagna cerealicola, quest’anno la produzione mondiale di cereali sarà in calo dell’1,7%. I dati sono stati corroborati dai controlli in campo appena conclusi nelle pianure produttive statunitensi che, per colpa della siccità rischiano di vedere ridotte le rese del 30%, se va bene. In ragione di ciò, l’Onu ha stimato per quest’anno, un ridimensionamento delle scorte mondiali dei cereali del -1,6% rispetto all’inizio del 2022. Ciò influirà anche sugli scambi commerciali mondiali, stimati in riduzione del 2,4%.

Guerra in Ucraina e rafforzamento del dollaro Usa vanno individuate come le prime due cause del fenomeno.
Procedere all’ammodernamento della filiera di stoccaggio comporta investimenti importanti. Gli esperti stimano che, per un impianto con una capacità di circa 200mila quintali, ad esempio, servirebbero dai tre ai cinque milioni di euro per apportare migliorie funzionali all’innalzamento dell’asticella della qualità della materia prima, come, ad esempio, l’installazione di un laboratorio di analisi interno, un siste- ma di pre-pulitura della merce in entrata e un sistema di stoccaggio differenziato per tipologia di partite. Ad esempio, in base all’apporto proteico del grano. Maggiore è questa variabile, migliore è la qualità della derrata.
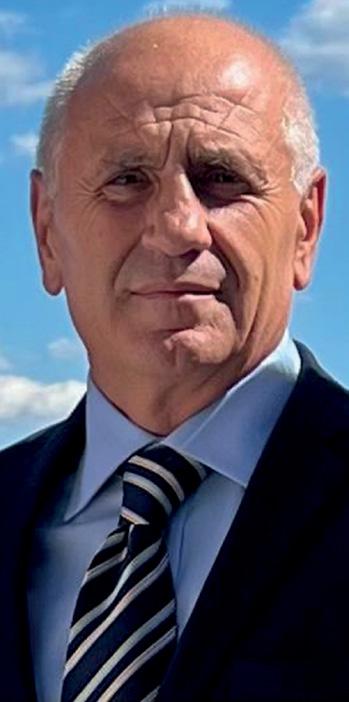
Aggiornare la mappa delle strutture esistenti
“Almeno il 70% dei centri di stoccaggio in Italia ha bisogno di essere ammodernata”, spiega Antonio Minicozzi, amministratore unico di Agrisemi Minicozzi Srl di Benevento, azienda che lavora per l’80% con Barilla nel quadro di un contratto di filiera con materia prima 100% italiana. Gli investimenti che rivoluzionerebbero l’efficienza del comparto sono impegnativi ma garantiscono benefici di lungo termine che si traducono, negli anni, in importanti risparmi di risorse. Ad esempio, per costruire un centro di stoccaggio in muratura, con fondo conico per la pulizia del prodotto, servirebbero dai 3 ai 4,5 milioni di euro. Si tratta di una cifra superiore di circa il 40% rispetto ai tradizionali silos in metallo. Ma i vantaggi di lungo periodo che si otterrebbero sono molti. Innanzitutto il cemento armato si mantiene meglio negli anni e ha bisogno di minore manutenzione. Poi, una struttura in muratura disperde meno aria fredda e quindi implica un abbattimento dei costi dell’energia usata per il raffreddamento degli ambienti. Bisogna ragionare sul lungo periodo, nel senso che quello che si spende oggi con l’investimento, si traduce, negli anni, in efficientamento a cominciare dal risparmio effettivo sulla bolletta elettrica. Basti pensare che la dispersione termica nei silos di metallo determina qua- si il 60% in più dei consumi energetici rispetto alle strutture di stoccaggio in cemento armato”.
Sono ancora molti, inoltre, i player della filiera costituiti da piccoli commercianti che ritirano il prodotto dagli agricoltori e lo stoccano senza differenziarlo, semplicemente ammassandolo sul pavimento dei loro magazzini. In questo senso, gli esperti considerano strategico e, soprattutto preliminare, un aggiornamento della mappa delle strutture esistenti e attive in Italia.
“Bisogna superare la visione a macchia di leopardo che da sempre domina questo settore - precisa Minicozzi -, che si basa su un’aspra concorrenzialità tra le piccole e le grandi aziende. Occorrerebbe fare un’inversione di rotta che sia prima di tutto culturale. Si sta iniziando ad affrontare questo discorso, per esempio, fra i centri aderenti ai consorzi agrari che rappresentano circa il 30% del totale. Il problema è che il 60% dei centri di stoccaggio sono in mano alla rete commerciale privata che non viene certificata. Servirebbe una mappa dettagliata, regione per regione. Si sta iniziando a lavorarci”. Sarebbe un passo avanti anche per armonizzare l’andamento del mercato ed evitare le conseguenze di prezzi troppo volatili che penalizzano, in prima battuta, il produttore. Oggi per calcolare il prezzo al primo conferimento, si prendono a riferimento i valori di mercato alla consegna in magazzino, mentre: “per garantire un’equa remunerazione ai produttori - specifica Minicozzi - proprio in virtù dell’alta volatilità del prezzo di questi prodotti, che ha visto quest’anno, ad esempio, un’oscillazione dai 560 euro a tonnellata all’inizio della campagna, fino a 320 euro a tonnellata delle ultime settimane, le liquidazioni al cerealicoltore andrebbero fatte sulla base della media dei prezzi annuali con chiusure dei prezzi calcolate su nove o dieci mesi. Con l’attuale sistema di calcolo, oggi il produttore ci rimette molto. In questa fase di mercato, si sta lavorando ai limiti del sottocosto”.
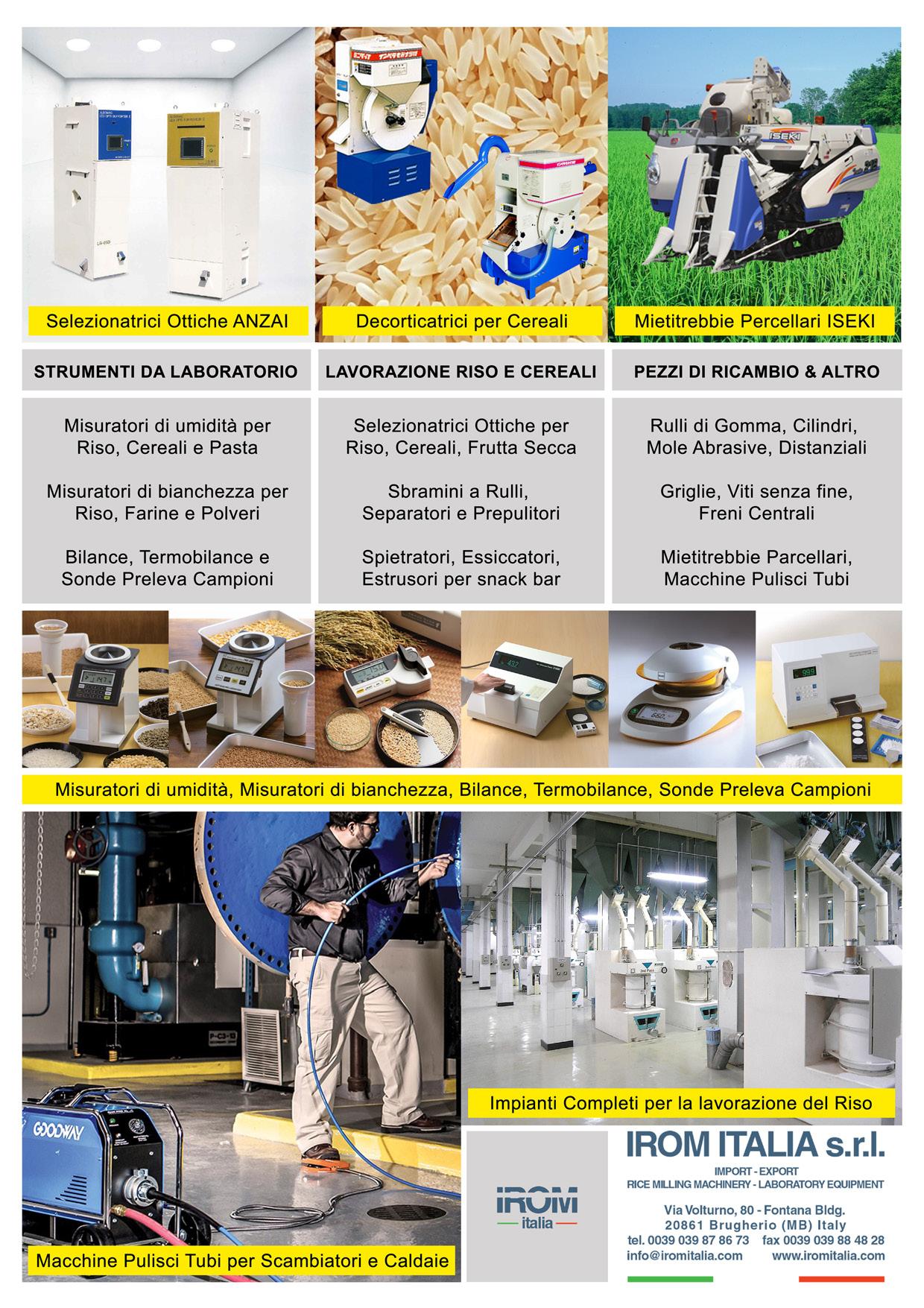
L’impellente necessità di differenziare il grano in stock
Con la spinta di tutto il comparto allo sviluppo di nuove varietà e al miglioramento di quelle esistenti, la necessità di potere differenziare il grano in fase di stock diventa sempre più cogente. Le vecchie cultivar nostrane, non arrivavano a una percentuale di apporto proteico superiore al 12% ma erano preferite dai produttori per la loro maggiore resa per ettaro.
Quelle nuove, tra le quali molte ancora allo studio, hanno un contenuto proteico più alto (fino al 14,5%), e sarebbero certamente competitive con i grani di provenienza d’Oltreoceano, tuttavia non garantiscono, per ora, la resa necessaria per diventare concorrenziali con le mega economie di scala che si riescono a ottenere nelle grandi pianure statunitensi o canadesi dove le varietà vengono selezionate (e trattate) con criteri completamente diversi da quelli europei e dove il problema della resa non è un fattore critico stanti gli ingenti volumi che si producono. Per abolire l’uso di prodotti chimici per la disinfestazione del grano in fase di stoccaggio, si sta sviluppando un crescente in- teresse per le celle di refrigerazione, dal momento che le basse temperature sono un fortissimo deterrente per gli infestanti. Secondo le stime degli esperti, il numero dei centri di stoccaggio attrezzati per mettere in piedi delle celle di refrigerazione, oscilla tra il 10 e il 15% del totale.
L’ipotesi refrigerazione
Il tema della refrigerazione potrebbe, peraltro, portare, in un futuro non troppo lontano, a joint venture tra filiere agricole. Con quella ortofrutticola, ad esempio, che è stata particolarmente colpita dagli eventi calamitosi delle ultime stagioni (siccità, parassiti, grandinate, bombe d’acqua e al- luvioni) e dall’erosione netta della redditività dei produttori. Ci sono già alcune aziende agricole che si stanno guardando intorno con l’obiettivo di mettere a disposizione della filiera cerealicola, i propri magazzini refrigerati anche in considerazione del fatto che, almeno per quel che riguarda il grano duro, la produzione interna è in aumento e la nostra dipendenza dalle importazioni si è ridotta negli ultimi due anni, dal 40% al 32% anche se, quest’anno, le importazioni di grano dall’Ucraina sono aumentate del 318% rispetto alla campagna precedente. “La nostra azienda - dice Minicozzi - è relativamente giovane perché l’abbiamo costituita all’inizio degli anni Duemila. Noi lavoriamo sia come stoccatori sia come ditta sementiera. Lavoriamo con il grano duro proveniente da Campania, Puglia, Basilicata e Calabria. Tutti i carichi in ingresso sono analizzati partita per partita e poi suddivisi nelle varie celle di stoccaggio in base al peso specifico e all’apporto proteico. Le partite sono pre-pulite dalle impurità nella fase di ingresso e poi conservate in celle refrigerate con HCO2, acido carbonico, che ci permette di non ricorrere all’uso di prodotti chimici. L’80% del prodotto lo forniamo a Barilla nel quadro di un contratto di filiera in virtù del quale, oltre a non usare chimica, siamo in grado di tracciare il prodotto dal seme alla consegna al mulino del cliente. Sulla ricerca finalizzata al miglioramento varietale, in Italia siamo carenti. La ricerca ha subito un forte rallentamento perché è stata tolta la certificazione dell’uso del seme in Italia. Questo ha comportato che i nostri produtto-

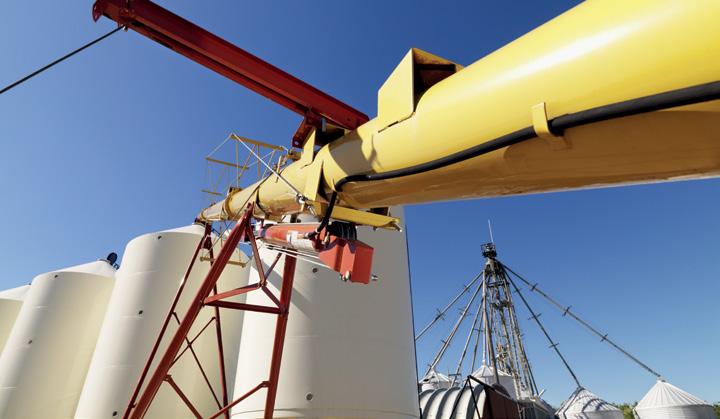

Occorre
ri sono dovuti andare a comprare le varietà da piantare all’estero, in Francia, ad esempio, o in Spagna, dovendo poi corrispondere royalties salatissime per la messa in produzione. Dobbiamo attivare una ricerca made in Italy per avere un settore competitivo, su questo punto si stanno iniziando a muovere le cose”. L’installazione di un impianto minimo di refrigerazione, comporta un costo che dipende dalla potenza installata. Si parte da 120mila a 150mila euro secondo quanto dicono gli esperti. Il prezzo si riferisce alla refrigerazione di un silos medio da 10mila quintali con uso del freddo per circa 10 ore, in base alla temperatura di entrata del gra- no, e il monitoraggio della temperatura. Il mercato offre già soluzioni adatte a questo scopo. Il problema, oggi più che mai, è quello del costo energetico, ma la refrigerazione a temperatura costante permette di ottenere ottimi risultati.

La posizione di Compag
“I centri di stoccaggio privati hanno sempre fatto fatica ad accedere ai finanziamenti pubblici regionali e/o comunitari - afferma Edoardo Musarò, vicedirettore di Compag -. Questo è principalmente dovuto alla complessità delle procedure burocratiche, all’incertezza dell’assegnazione dei fondi, oltre che alla limitatezza dei fondi gestiti dalle singole Regioni specificatamente per lo stoccaggio. In virtù di questo Compag, per il quinto bando dei contratti di filiera e di distretto, ha svolto un ruolo di coordinamento consentendo ai propri associati di poter partecipare a due progetti da cinquanta milioni ciascuno, per la metà rivolti ai centri di stoccaggio, entrambi risultati ammissibili. Il primo era localizzato nel Centro-Nord e riguardava il grano tenero, il mais e la soia. Il secondo era localizzato nel Centro-Sud Italia e riguardava prevalentemente il grano duro. Questa attività è stata di grande importanza in quanto sono misure che prevedono dei requisiti ben precisi, come ad esempio la multi-regionalità, alle quali le aziende non possono accedere in maniera singola. La nostra attività e il nostro impegno hanno consentito di integrare diversi soggetti e anelli della filiera. Riteniamo, infine, che il sistema delle filiere sia uno strumento di fondamentale importanza in quanto consente di poter programmare produzioni e investimenti e inoltre consente una equa distribuzione del valore lungo la catena di fornitura”.

Mariangela Latella