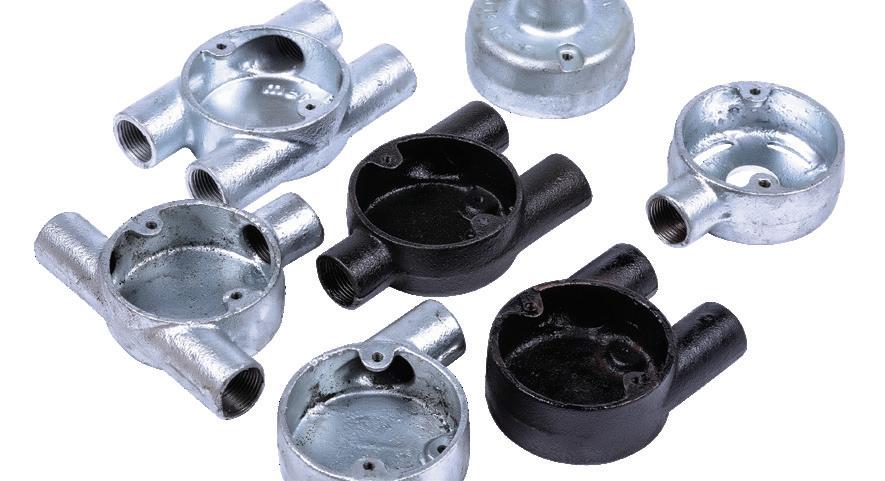
3 minute read
RETROFIT AND REFURBISH — EASY OPTIONS FOR CABLE PROTECTION
from ECN August 2023
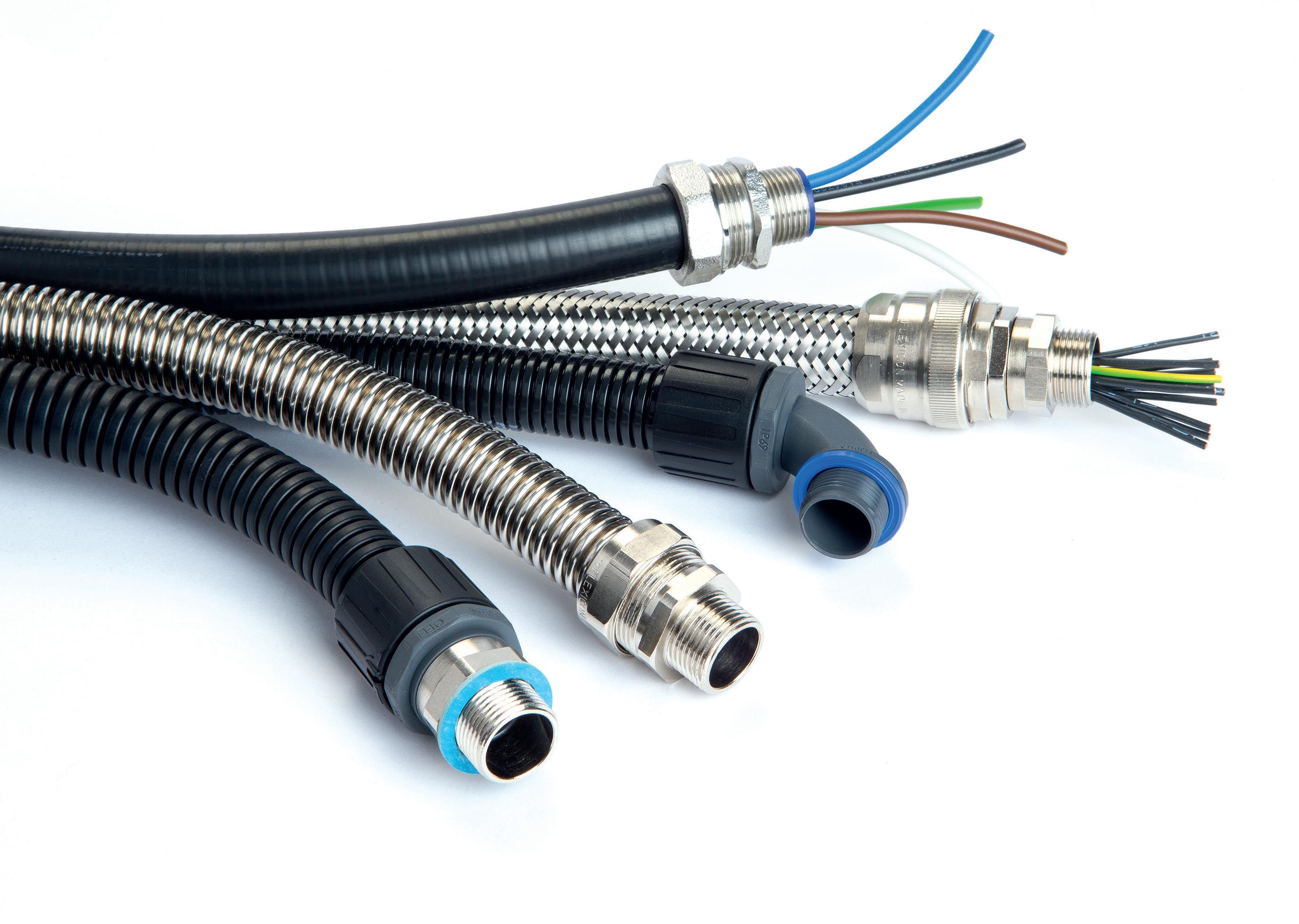
Alex Smith, Technical Director at Flexicon, identifies some of the areas to consider when specifying retrofit cable protection and how the right system can help speed up time on the job while protecting vulnerable or existing cabling.
Advertisement
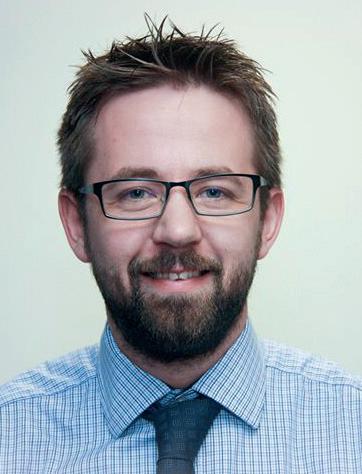
When it comes to upgrading the electrical infrastructure of existing properties, retrofit cable protection options can help electrical contractors capitalise on a growing refurbishment market.
Reducing commercial carbon emissions
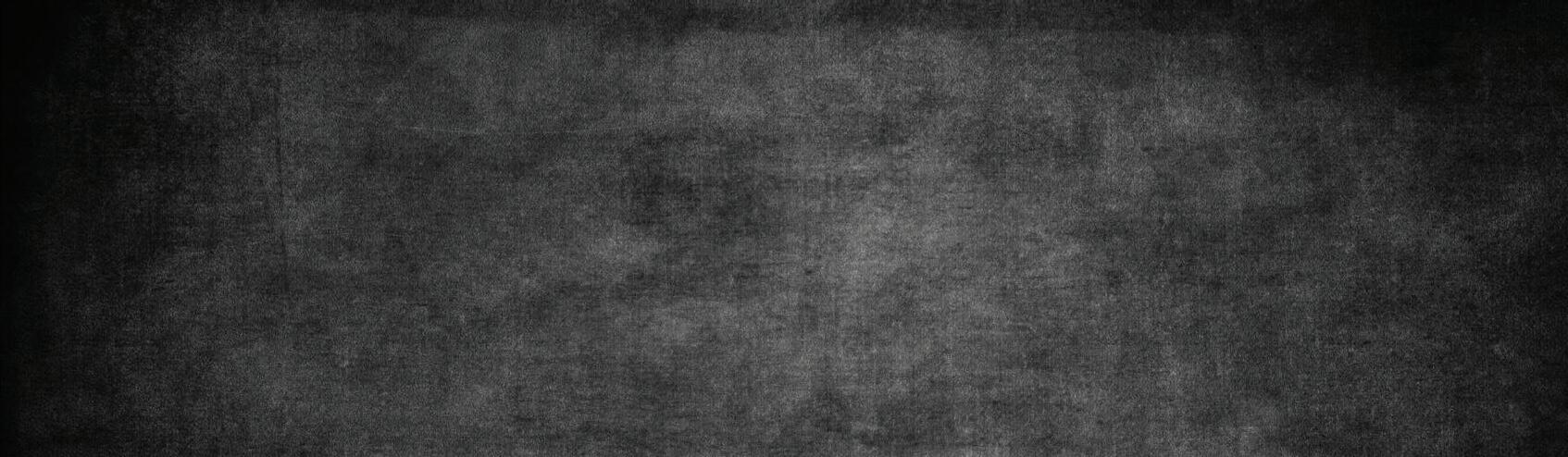
The UK Green Building Council reports that the built environment accounts for a staggering 40% of UK emissions. Environmentally friendly retrofit solutions such as new heating, ventilation systems and enhanced energy management control and monitoring are increasingly specified – but all will require electrical cabling installations and infrastructure to be upgraded.
In the 2021 Vision report, 96% of electrical contractors interviewed stated that new products to enable sustainable new build and renovation of existing properties represent an opportunity for their business growth. And elsewhere, homeowners are being encouraged to upgrade to energy-efficient solutions, such as solar panels and heat pumps. These drivers are all leading to increased demand for retrofit electrical wiring systems that will avoid major disruption to the building fabric or fixtures.


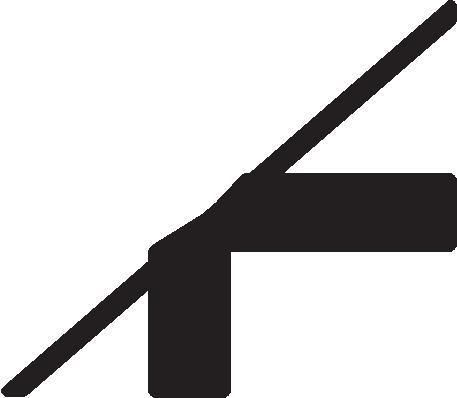
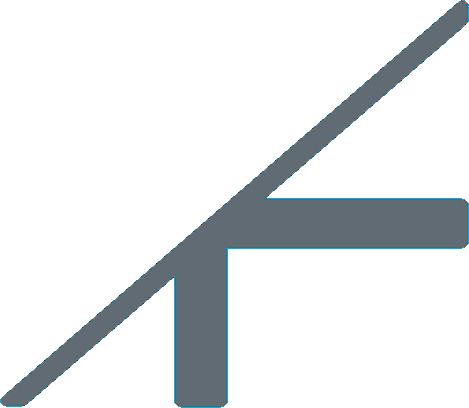
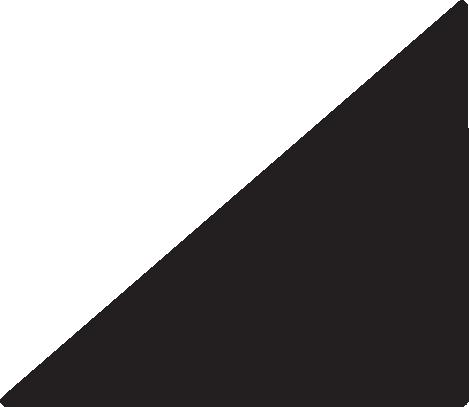
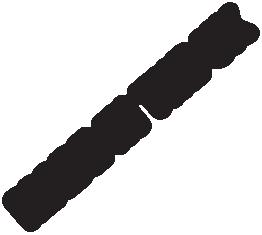
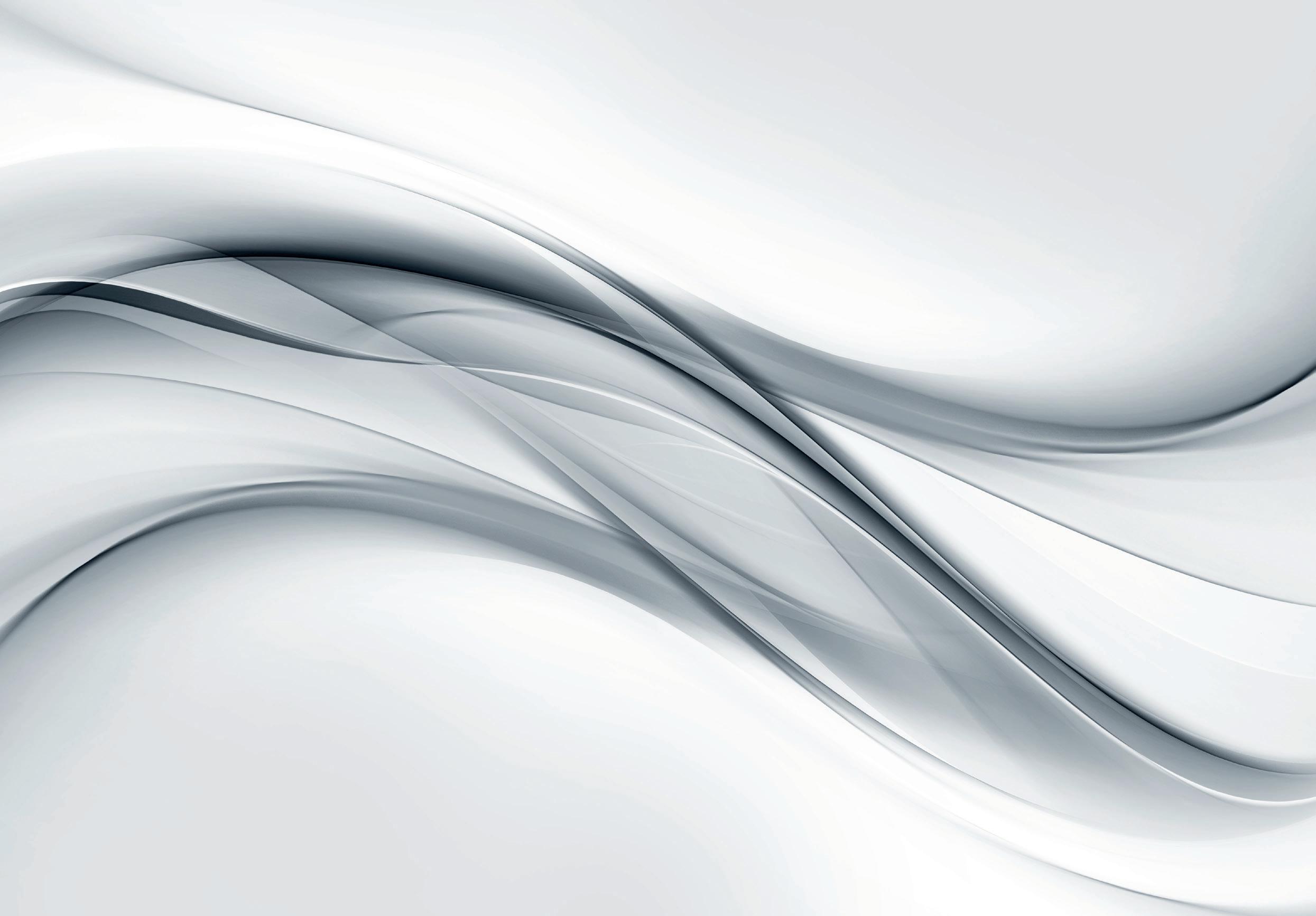
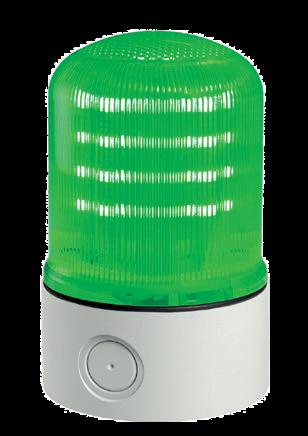

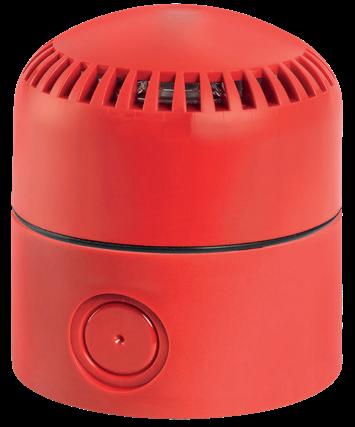
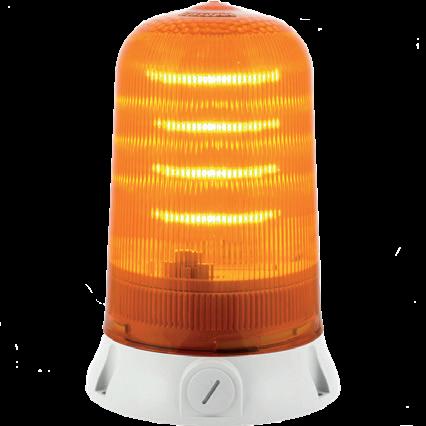


It is important to minimise the duration of installation programmes to avoid unnecessary delay and disruption, meaning many contractors are seeking new cable protection solutions that help reduce time on the job.
How to retrofit?
Most contractors are familiar with the complexity of traditional retrofit cable protection solutions, with the installation team required to pull existing cabling through the open end of a conduit system.
Conduit system manufacturers have been offering slit conduit options for some time, enabling installers to wrap insert the existing cabling to avoid disruption. However, it is important to ensure that the choice of flexible conduit system continues to offer the appropriate levels of protection for the environment and does not leave any areas of cabling or the installation exposed.
Divisible conduits, such as the new Flexicon FPADS range, allow existing cabling to be inserted laterally via a slit opening. This product consists of two open conduit profiles, which then interlock to form a protected IP40 system around the cables. It is also important to consider the cable routing. Traditional split conduit options can potentially expose cabling when bent or routed around corners, whereas the newer, divisible conduit options will maintain more mechanical strength and continuous protection of the cabling, irrespective of orientation or routing due to their interlocking design.
Termination and fittings
All cable protection should be specified as a complete end-to-end system, considering not only the flexible conduit used, but also the range of termination and fittings required.
To make it easier to terminate cabling in retrofit applications, Flexicon now offers its new Flexicon FPADS range, with a hinged fitting and locknut to wrap around existing cabling, meaning no disruption and easy and secure termination.
Protecting new cabling
As well as considering retrofit options, specifiers may also be tasked with installing new electrical cabling at the same time.
In this scenario, there is a broader range of options available, and specification should consider the range of external
Many contractors are seeking new cable protection solutions that help reduce time on the job hazards that the cabling may be exposed to – whether that is to meet a certain IP rating, enhanced fire performance properties, resistance to chemicals or UV exposure, to name a few.
Where fatigue life or impact resistance is important, installers should consider nylon polyamide (PA) corrugated flexible conduit, which can offer high impact strength and recovery if crushed, combined with excellent temperature performance.
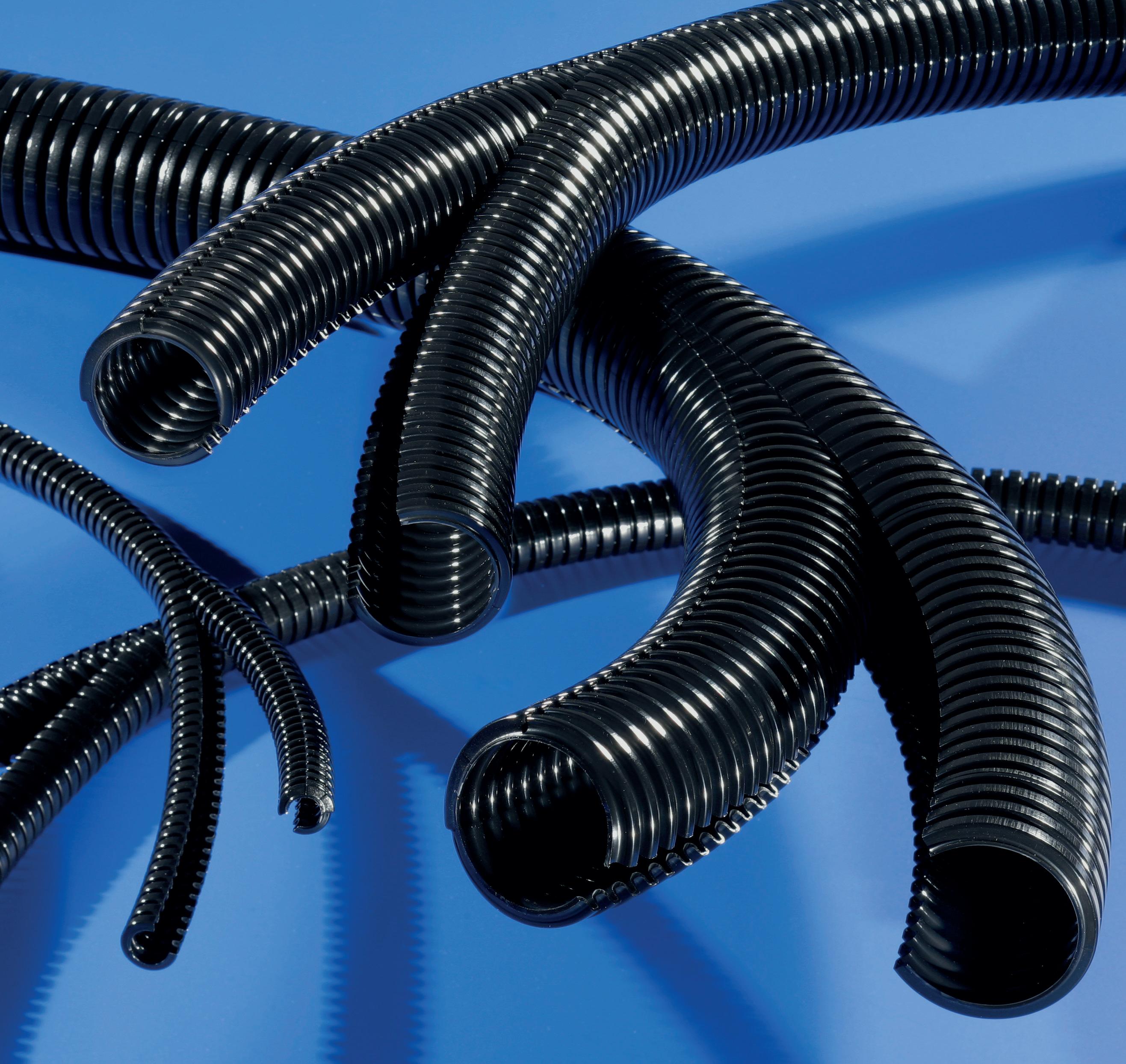
Polypropylene and PVC conduit systems are available, however, both systems are inferior to nylon polyamide (PA) when it comes to fire performance, resistance to solvents and their abrasion resistance properties.

With no exposed metallic content, non-metallic conduits do not rust or corrode, thus maintaining performance and appearance over time. In addition, it is worth considering labour and installation time. Non-metallic systems are often quicker to install than metallic options as they are easier and faster to cut. Non-metallic fittings will typically be one piece and simply push on and twist to secure.
For more complex application requirements, customers should speak to their supplier to discuss bespoke options.
These could include conduit supplied in non-standard or pre-cut lengths, in larger or smaller diameters or with different thread termination or fitting options. Additionally, more complex requirements, such as altering performance characteristics to meet a certain temperature requirement, compression strength or abrasion resistance, or to achieve a greater fatigue life may also be considered.
Flexicon, flexicon.uk.com
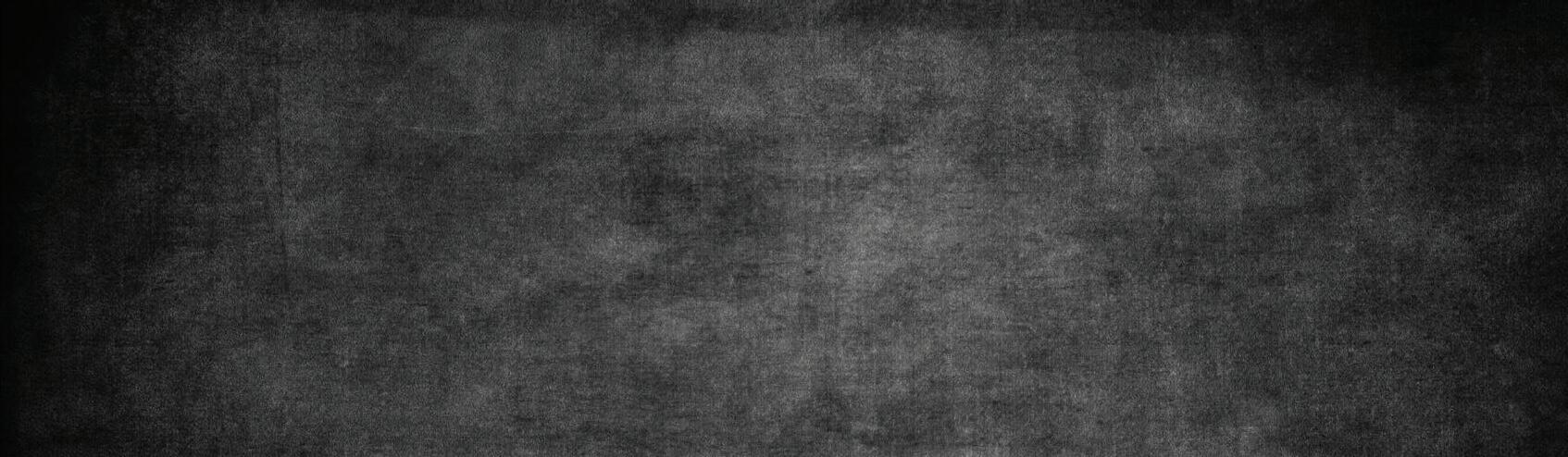
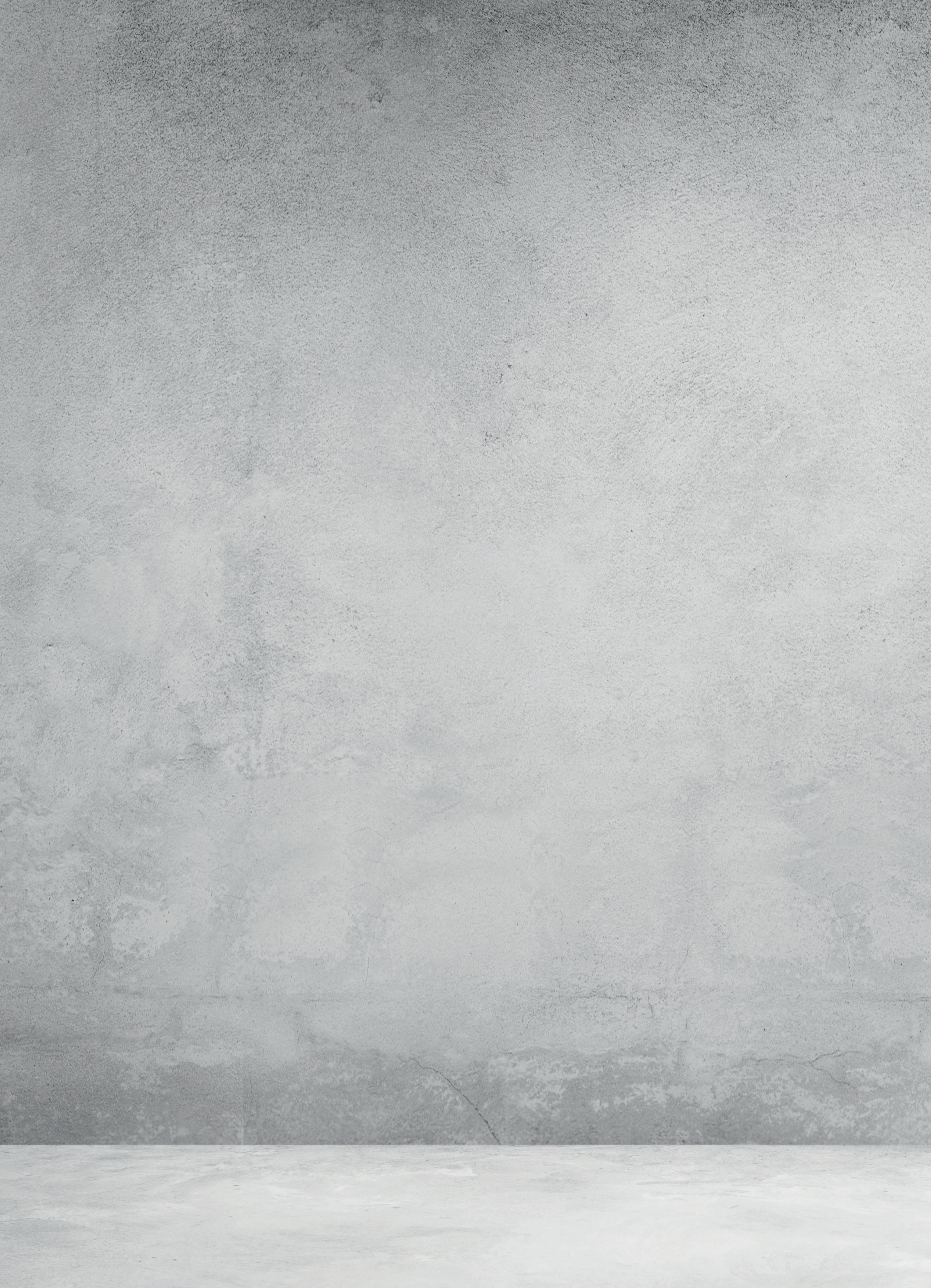
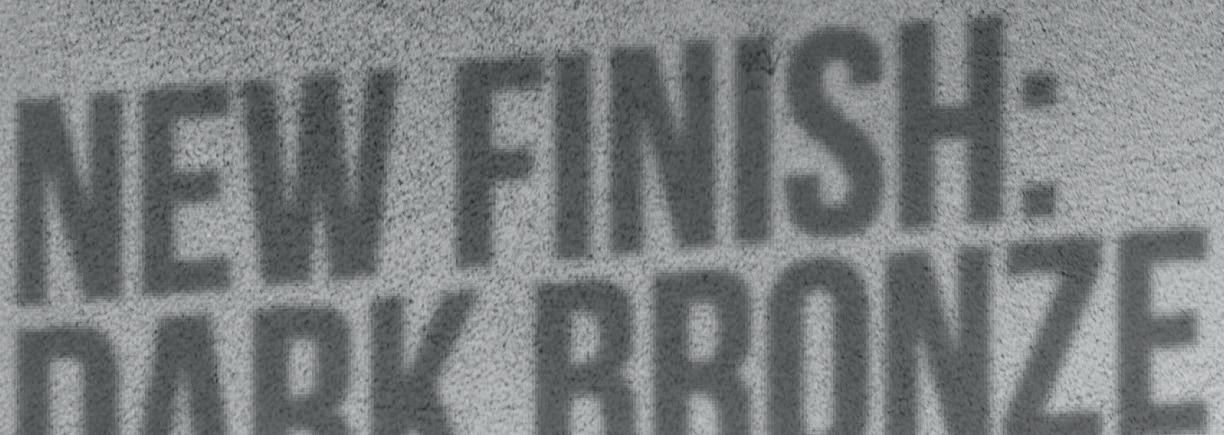
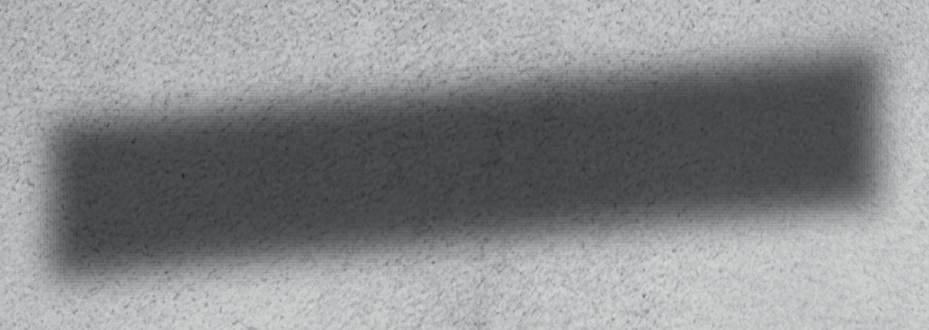

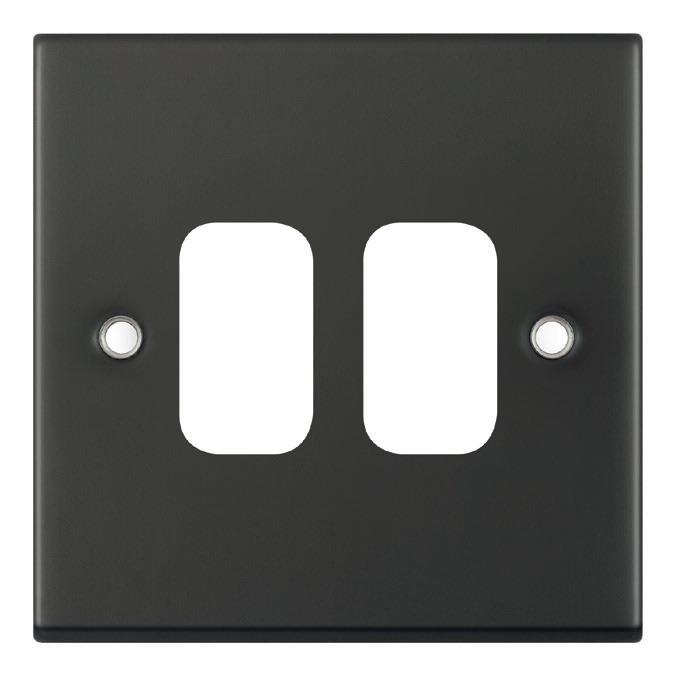
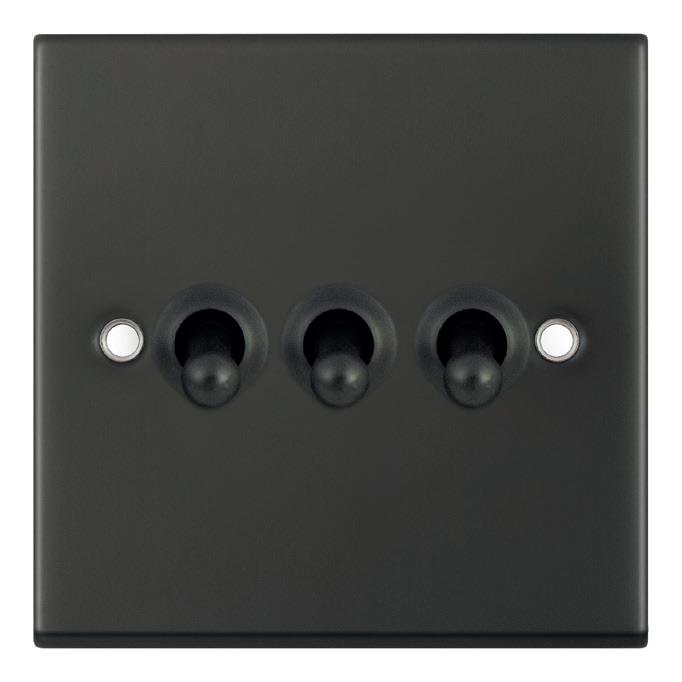

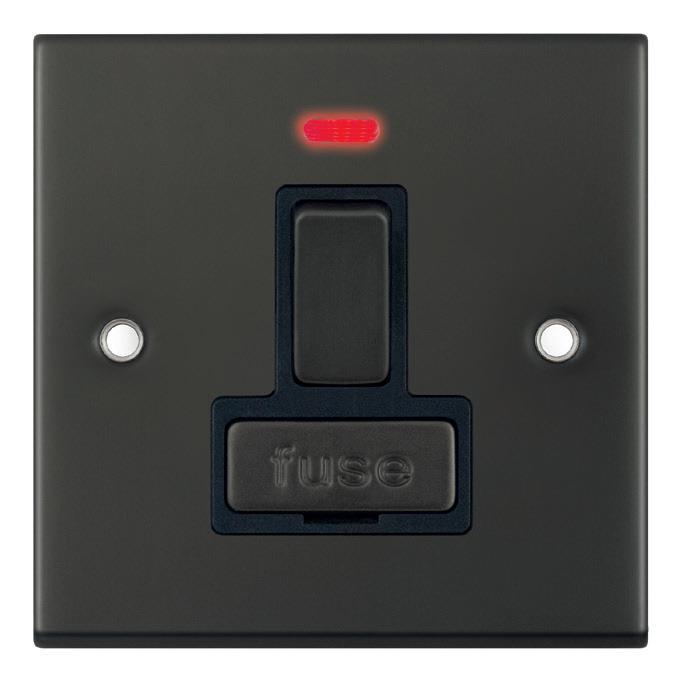
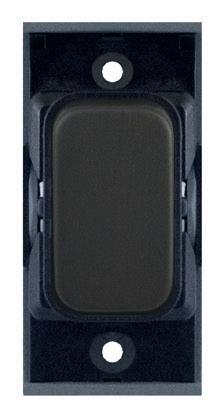
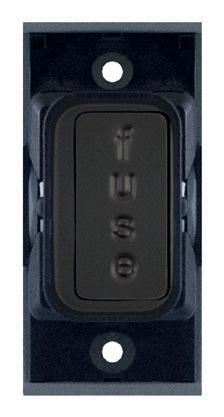
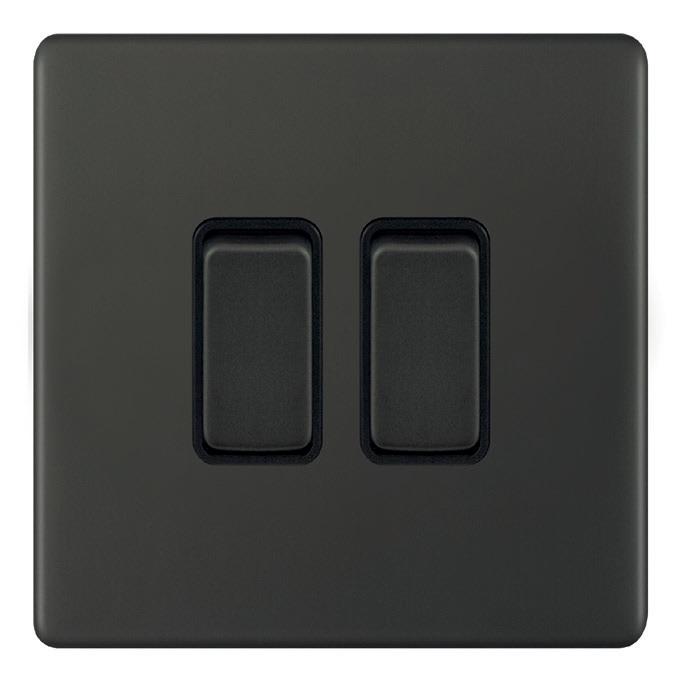

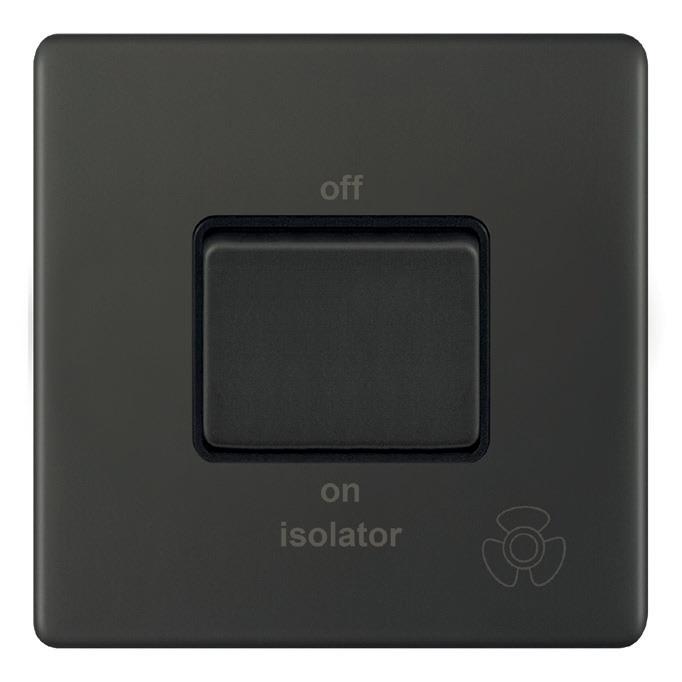
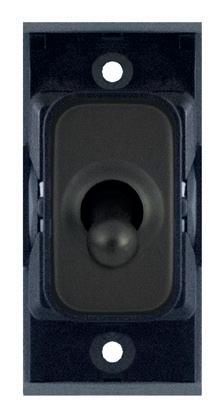
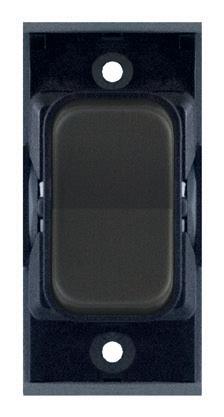
Two
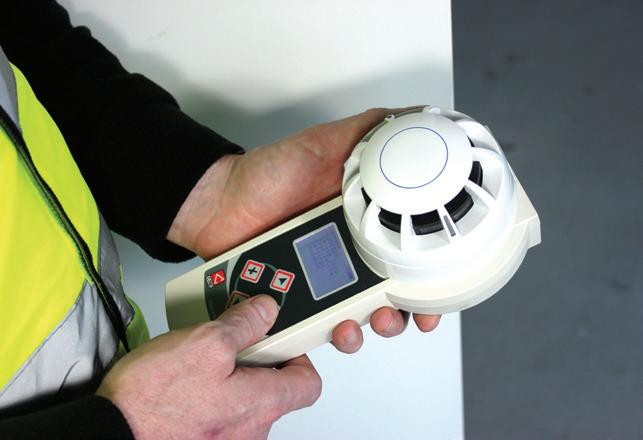
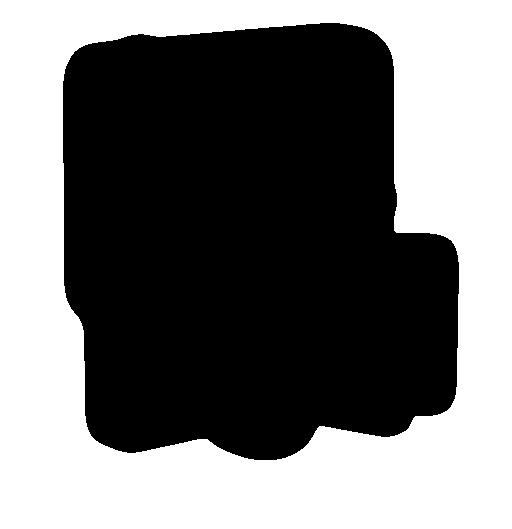
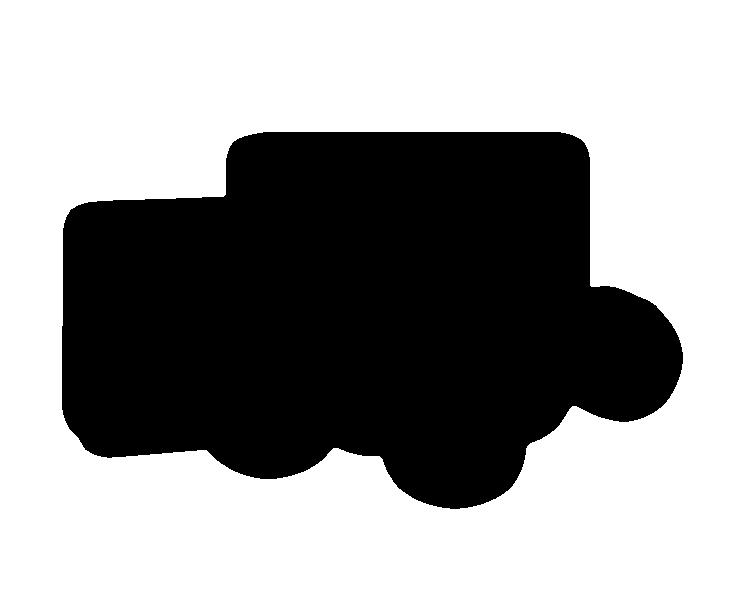

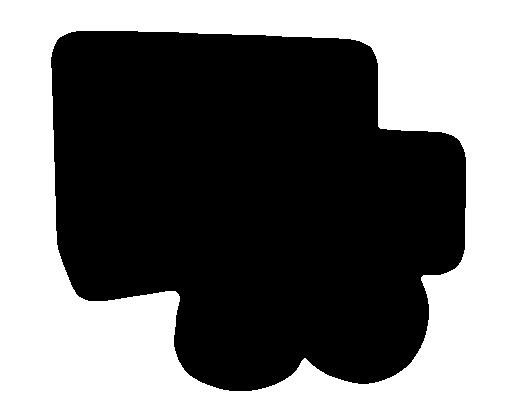
Distributed
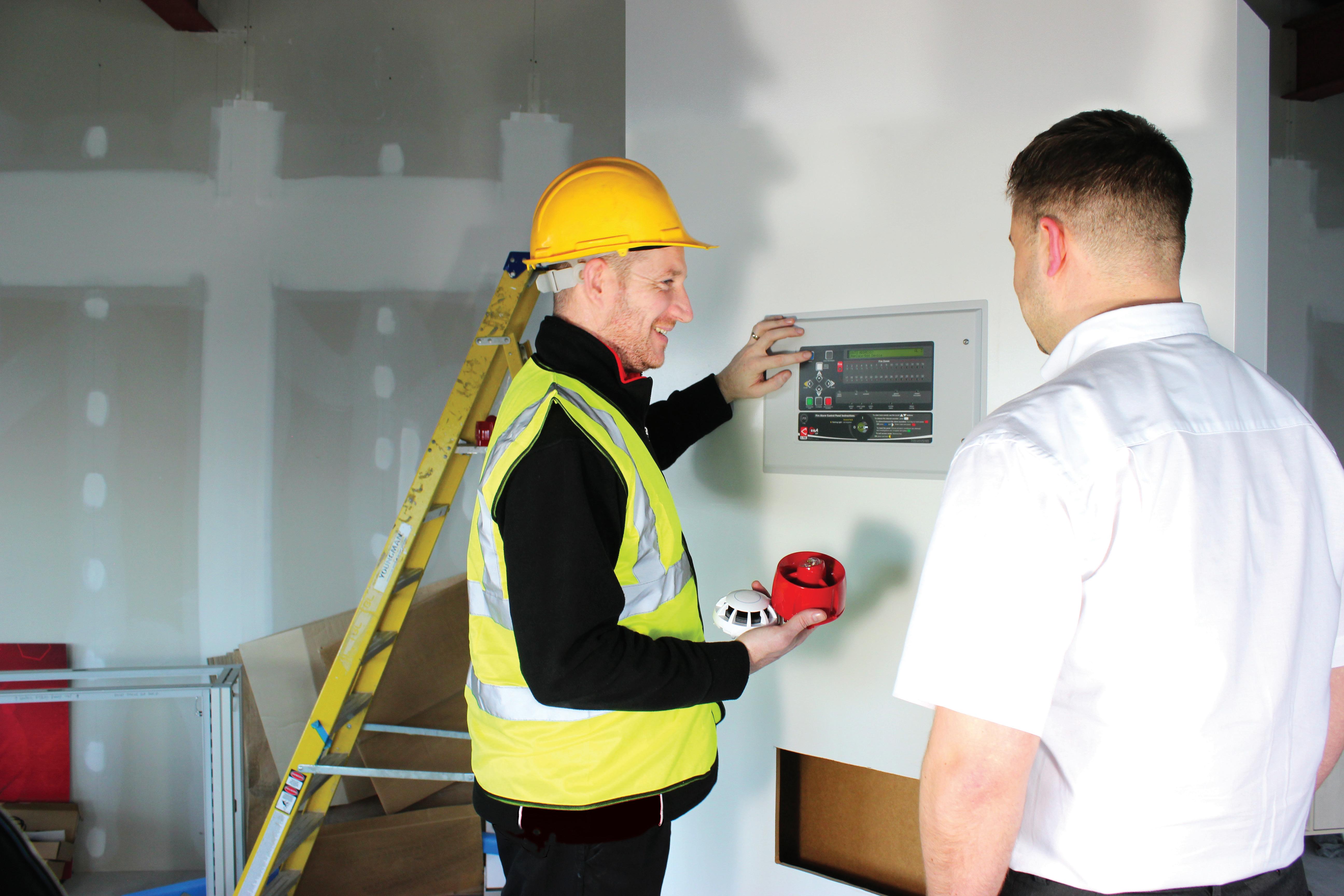
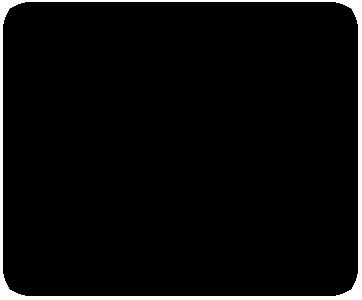


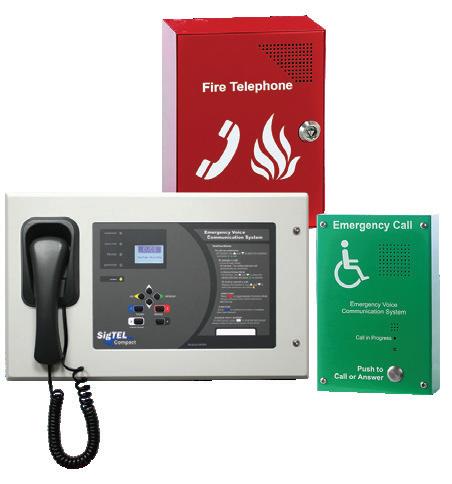
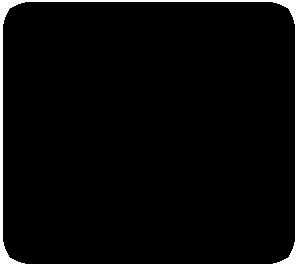
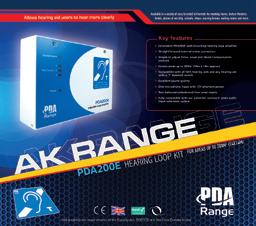
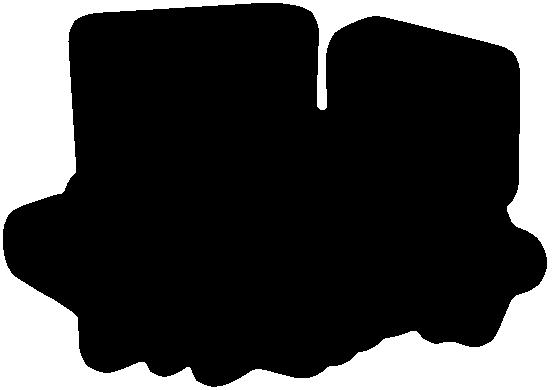
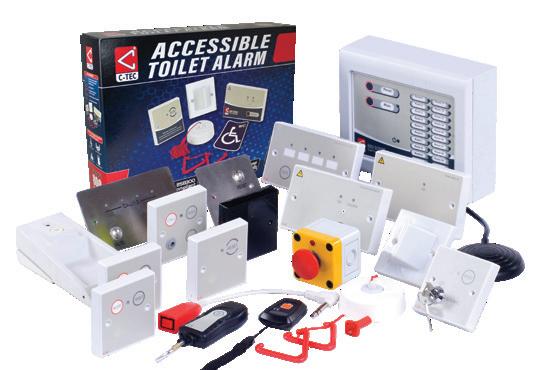

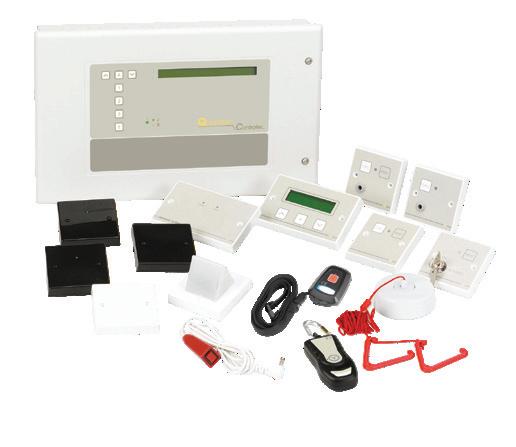
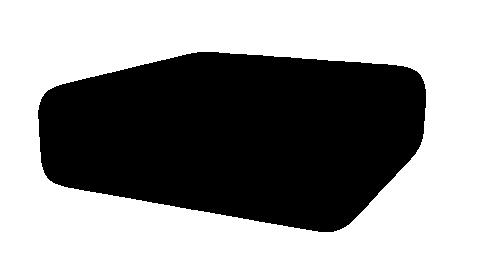

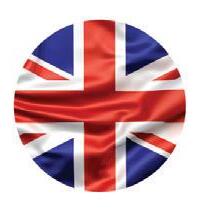