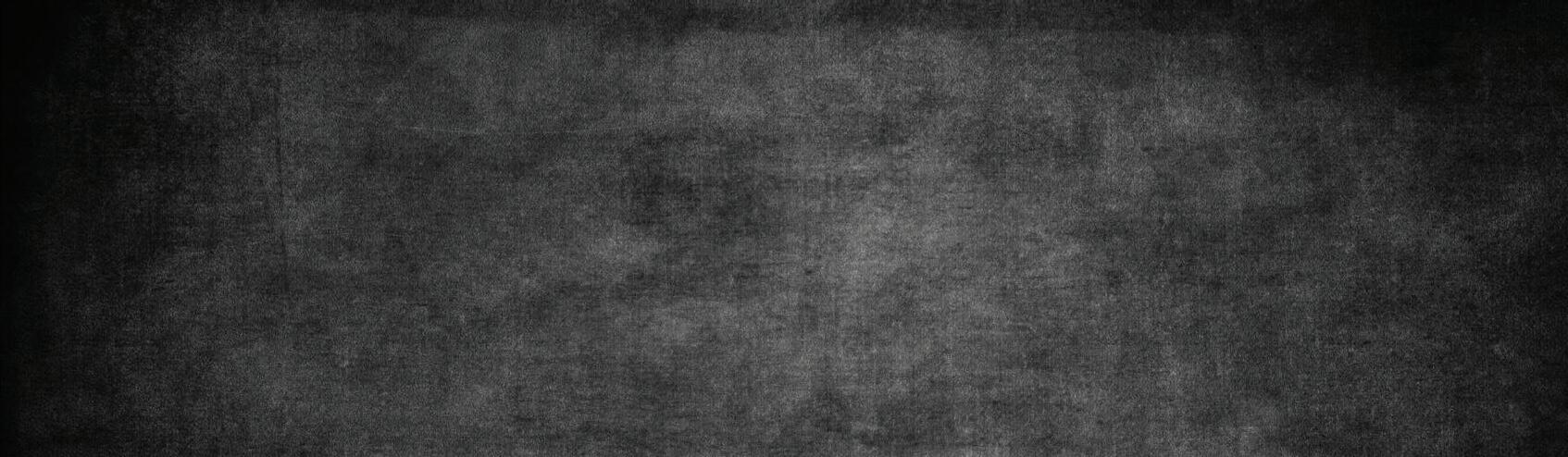
3 minute read
TRANSFORMING ELECTRIC UNDERFLOOR HEATING
from ECN August 2023
Designing away the potential for error and speeding up installation time is what the next generation of electric underfloor heating cables should achieve. Alistair Bell, Managing Director at ThermoSphere, explains how such a product can drastically transform installation to the benefit of customers, installers and merchants alike. This is vitally important as construction prices continue to rise.
The cost of labour and materials is contributing to the increase in renovation and construction prices, which are expected to rise by 17% in 2023. Installers, customers, and merchants cannot afford mistakes.
Advertisement
Revisiting finished jobs and reinstalling damaged heating cables costs time, and slow installations delay projects. Electric underfloor heating manufacturers can help by going back to the drawing board and redesigning their cables to remove the need for cutting membrane and insulation – speeding up installation times.
Sparking the next generation of electric underfloor heating cables
A common, if not the most common, point of failure in electric underfloor heating is the joint where the heating cable meets the ‘cold’ cable that connects to the thermostat. This is because these hot-to-cold cable ‘joints’ are big and bulky – often three times the size of the cables that they’re joining – so they have to be installed in a totally different way to thinner cables. To install a bulky hot-to-cold joint, installers must create cavities in the materials beneath the joints. They can do this by cutting into the membrane mat and insulation, creating a space for the joint to lay in, or by chasing out the wood or concrete sub floor if there’s no insulation being laid. Either way, tools are brought into the picture, increasing the risk of damage to the joints and cables. Grinders and Stanley blades can easily nick a joint, which can go unnoticed.
Once the installation is complete and the power switched on, the system will fail, and installers will have to troubleshoot and fix their work, sometimes returning to site much later to do so. The cavities can also create a problem that results in cable failure, months or years down the line. The air inside the cavities isn’t an efficient enough thermal conductor to dissipate the heat and stop the cables overheating and failing. So, a small air gap can easily ruin a project long after it’s installed.
Without gouging out holes for the joints, no installer can get a flush finish ready for tiling. So, as things currently stand, cable installation involves a risky, but necessary evil.
A change in the way next-generation underfloor heating cables are manufactured can head off these problems. For example, the hot-to-cold joints are currently created during a secondary manufacturing process. First, the hot and cold cables are created by separate processes, then later those cables are crimped or soldered together and reinsulated with heat shrink. By creating the connection in the primary manufacturing process, they can be made in-line, and crucially, the same diameter as the underfloor heating cable.
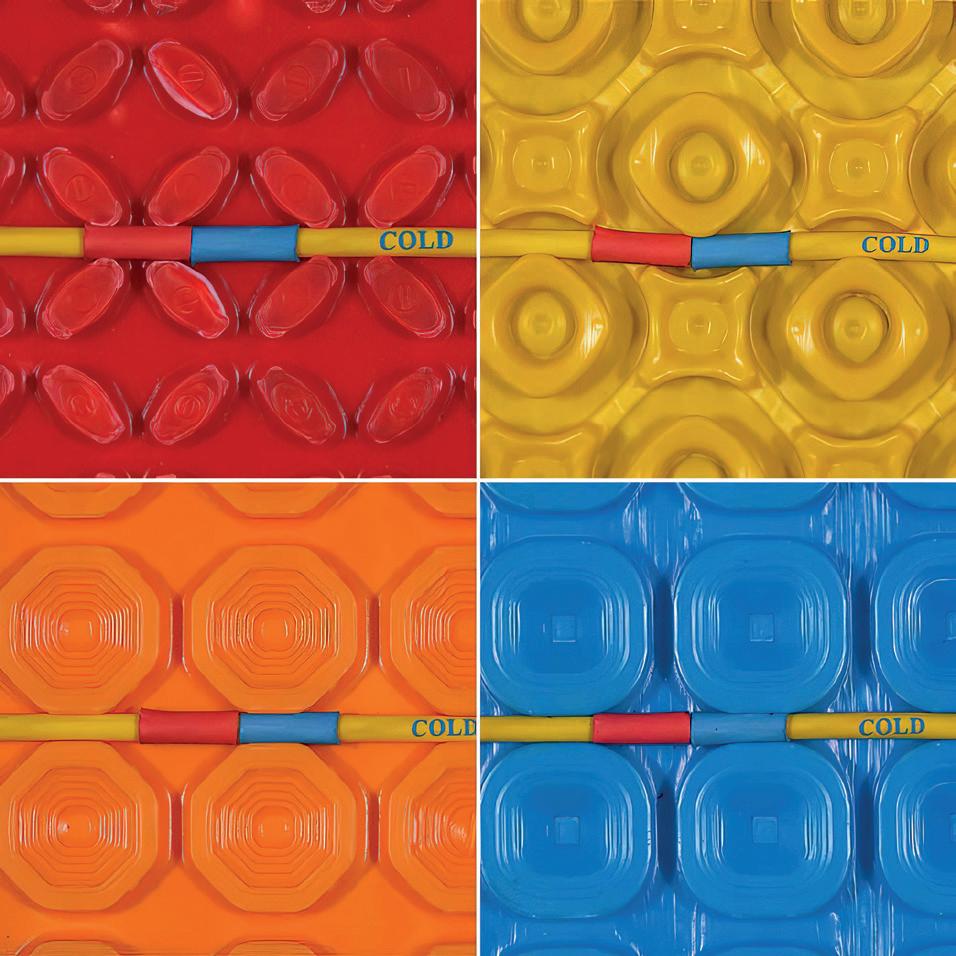
Creating the hot/cold connection during the primary manufacturing process removes the risk of damage and gives installers the peace of mind that a job is truly complete. There is less likelihood of returning to repair or reinstall a project, ripping up tiles or flooring that will also have to be replaced. For both installers and merchants, using products that are virtually impossible to damage helps to enhance their reputation for providing quality installations or materials.
Power in installers’ and merchants’ hands
By changing the manufacturing process and redesigning their cables, underfloor heating companies can design away one of the biggest risks and costs for installers, merchants and customers. What’s more, they can also drastically transform the installation process to make it quicker and simpler, while also providing quality installations for customers.
A heating cable that has in-line connections can be manufactured to be uniform in thickness end-to-end, which allows the full length of the cable to be installed within the membrane in the exact same manner. If the cable is an easy to install membrane heating cable that only requires installers to press the cable into the membrane mat, then the whole of the cable, including the hot/cold connection and cold tail can be pressed in, which removes the need for tools altogether. No-tool installation is quicker, less complex and less risky. Speeding up installation reduces the disruption to a customer’s home or time required on a construction site, enabling other phases of the project to progress quicker.
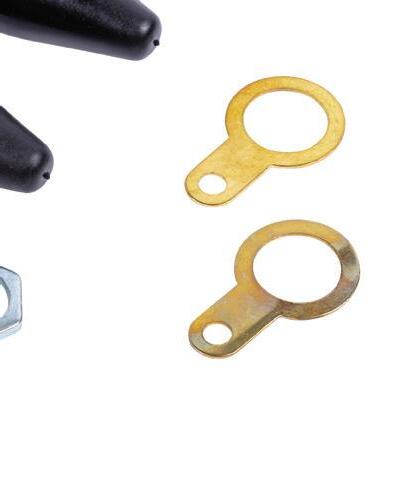

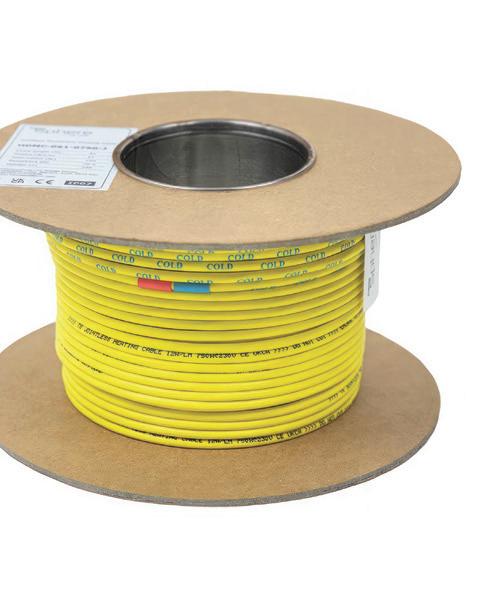
For larger projects, or for installers with many smaller projects, the improvements in installation speed allow them to lay more cable in less time. And, if heating cable companies offer a cable for every project size, then installers can avoid multi-cable installations.
As newer, innovative, next-generation cables transform electric underfloor heating, installers, merchants and customers will continue to benefit.
ThermoSphere, thermosphere.com
By changing the manufacturing process and redesigning their cables, underfloor heating companies can design away one of the biggest risks and costs
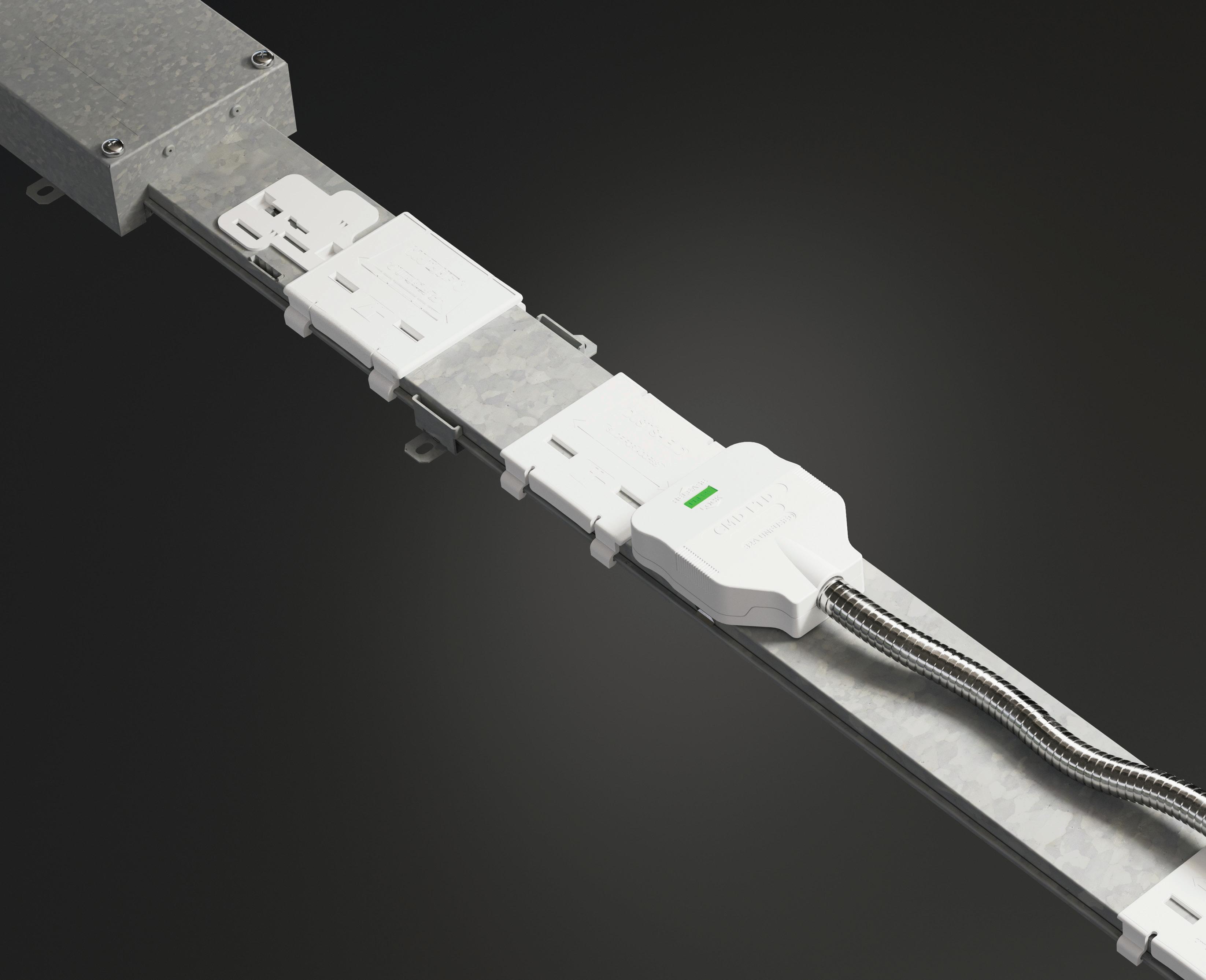
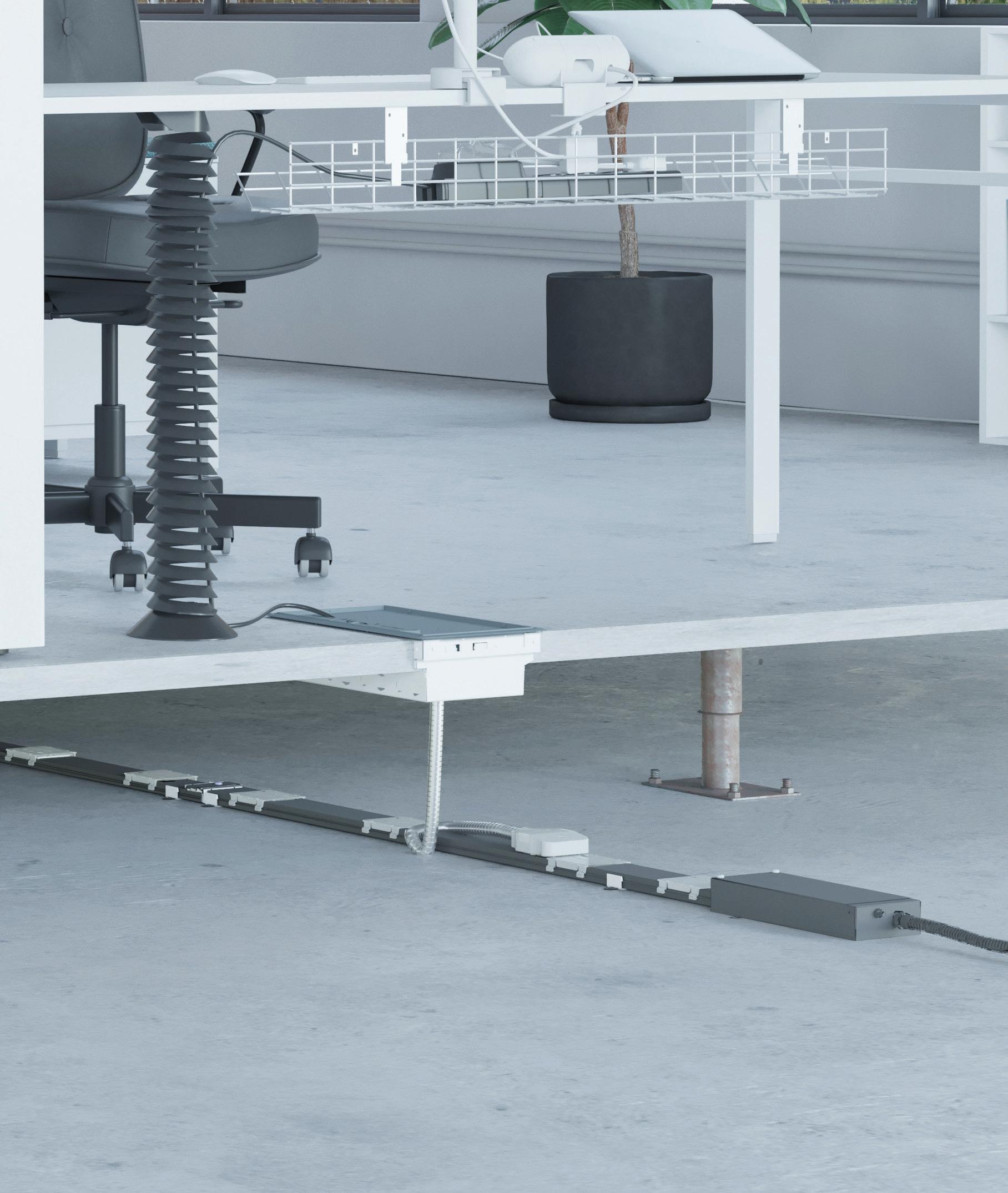