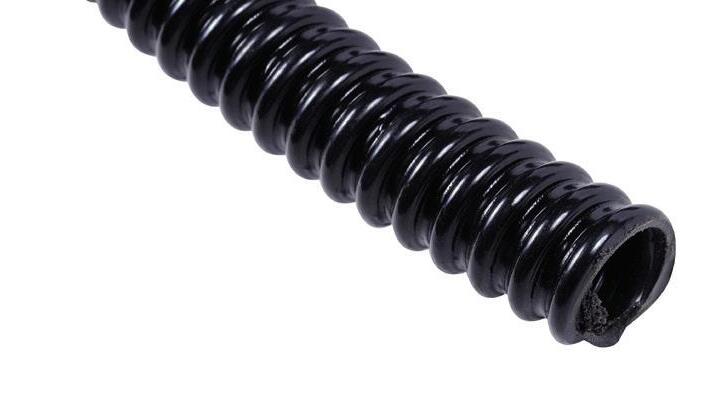
3 minute read
AVOIDING CORROSION — IT’S A MATERIAL CHOICE
from ECN August 2023
When specifying a cable management system, you need to understand the environment in which your customer will install it and advise them about the best material choice. In this article, Paul Nolan, Projects Director for the Hudson Group, takes a closer look at the factors you should consider.
We have all seen cable management and containment systems that suffer the ravages of corrosion because someone selected the wrong material. Equally, there is little point in choosing an unnecessarily expensive material if the system is for an office or similar benign environment.
Advertisement
The system needs to provide a long-term solution and protect against corrosion, but your customer needs to balance this against cost and not over specify a material if it’s not needed.
The first step is to understand where they will install it. Thankfully, at this point we can refer to EN ISO 12944-2, which provides classifications for corrosion and examples of where you may find them – see table.
Looking at the table, let’s run though what materials you might suggest.
Where you have very low corrosivity or C1, you should recommend either electro zinc plated or pre-galvanised steel. This would typically be for an indoor environment, such as in an office, school, hotel or shop.
One subject that you might hear about is zinc whiskers. These form on the underside of galvanised products or electroplated metals. These thin whiskers can eventually grow up to 1cm in length, break off and become a problem to electronics.
Also, hot dipped galvanised products will have a standard coating of 45 to 65 microns after being dipped in a bath of molten zinc. This is the average coating; the product is not evenly coated along its length. Deep galvanised products use a different steel which allows it to apply a thicker zinc coating for extra protection, but the process is more expensive.
• EXAMPLE INDOOR: Areas with high air humidity and high
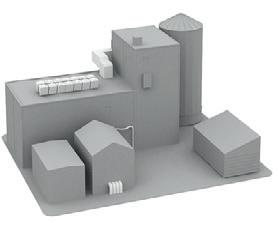
Raising the stakes slightly higher, a low to moderate C2 corrosive environment might be found in industrial premises, sports halls, warehouses or partially outdoor applications. Hudson Group would suggest a pre-galvanised steel cable management system.
For C3, where there is moderate environmental corrosivity, think outdoors or in a light industrial area, then you need to go beyond a pre-galvanised solution. For these applications, think about hot dip galvanised, CPC (Clear Plastic Coated) coated or powder-coated steel or PVC systems.
HALLS / WAREHOUSES
• EXAMPLE OUTDOOR: Environments with low levels of atmospheric pollution e.g
RURAL AREAS
• EXAMPLE INDOOR: Areas with moderate air humidity and some atmospheric pollution from production processes e.g.
BREWERIES / DAIRIES / LAUNDRIES
• EXAMPLE OUTDOOR: Environments with low salinity or moderate atmospheric pollution e.g.
URBAN AREAS / LIGHT INDUSTRIAL / SOME COASTAL INFLUENCE
And when your customer faces a highly corrosive environment, or C4, then they should use hot dip galvanised or powder coated steel, 304L stainless steel, PVC or GRP systems.
For very highly corrosive environments, such as chemical or water treatment plants, heavy industry, swimming pools or perhaps dockyards, then they will need a material that will stand the test of time. For this C5-I classification, you should suggest 304L or 316L stainless steel, deep galvanised steel or GRP.
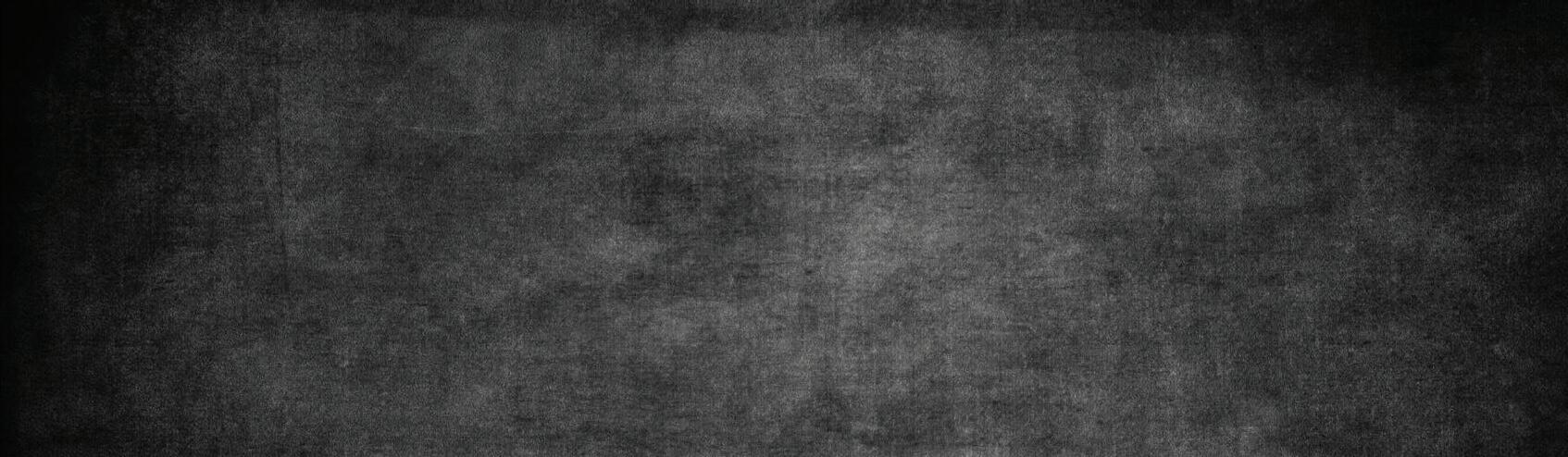
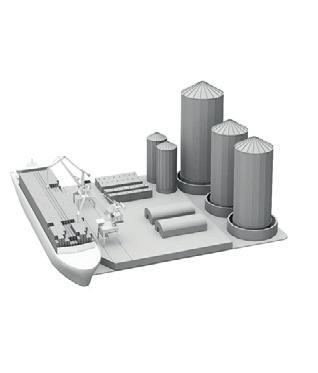


And finally, there is a special classification for marine environments (C5-M), which are notoriously corrosive. Here your customer will need a 316L stainless steel or a GRP system.
Even with the above suggestions, there are still some things that you should be aware of.
And Paul says that if a manufacturer tells you that they double dip their products, then ignore them. A steel will reach its maximum zinc absorption after one coating, a second coating will make no difference.
Remember that materials science does not stand still; someone will develop a better solution. One example is a new finish called Magnelis. This magnesium zinc alloy finish provides better corrosion resistance than galvanised options, is self-healing for cut edge protection and it is more cost effective.
Aluminium is not new, but it provides a lightweight, strong option for some applications, however, it can be hard to perforate and add fixing slots to.
For really extreme environments, GRP, or glass reinforced polymer, is the go-to material. Even here you need to be aware of different characteristics, as the mechanical properties of this material can vary. Delving deeper, there are four main resin types of GRP cable management products which will suit different specific atmospheric environments.
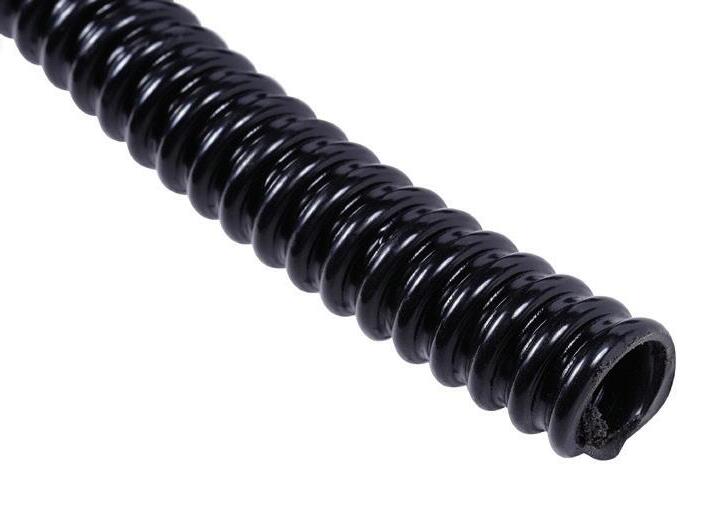
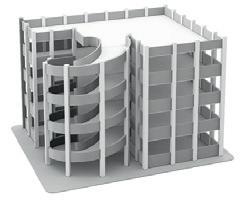
It pays to know the basics about different materials and when you should suggest using them, but always remember that you can always phone the manufacturer to ask for their advice, especially if they offer a wide range of different materials.
This article is based on a CPD seminar run by the Hudson Group called ‘Selecting the Correct Environmental Material’.
Hudson Group, hudsoncmg.com
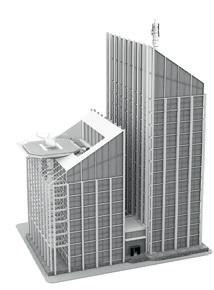
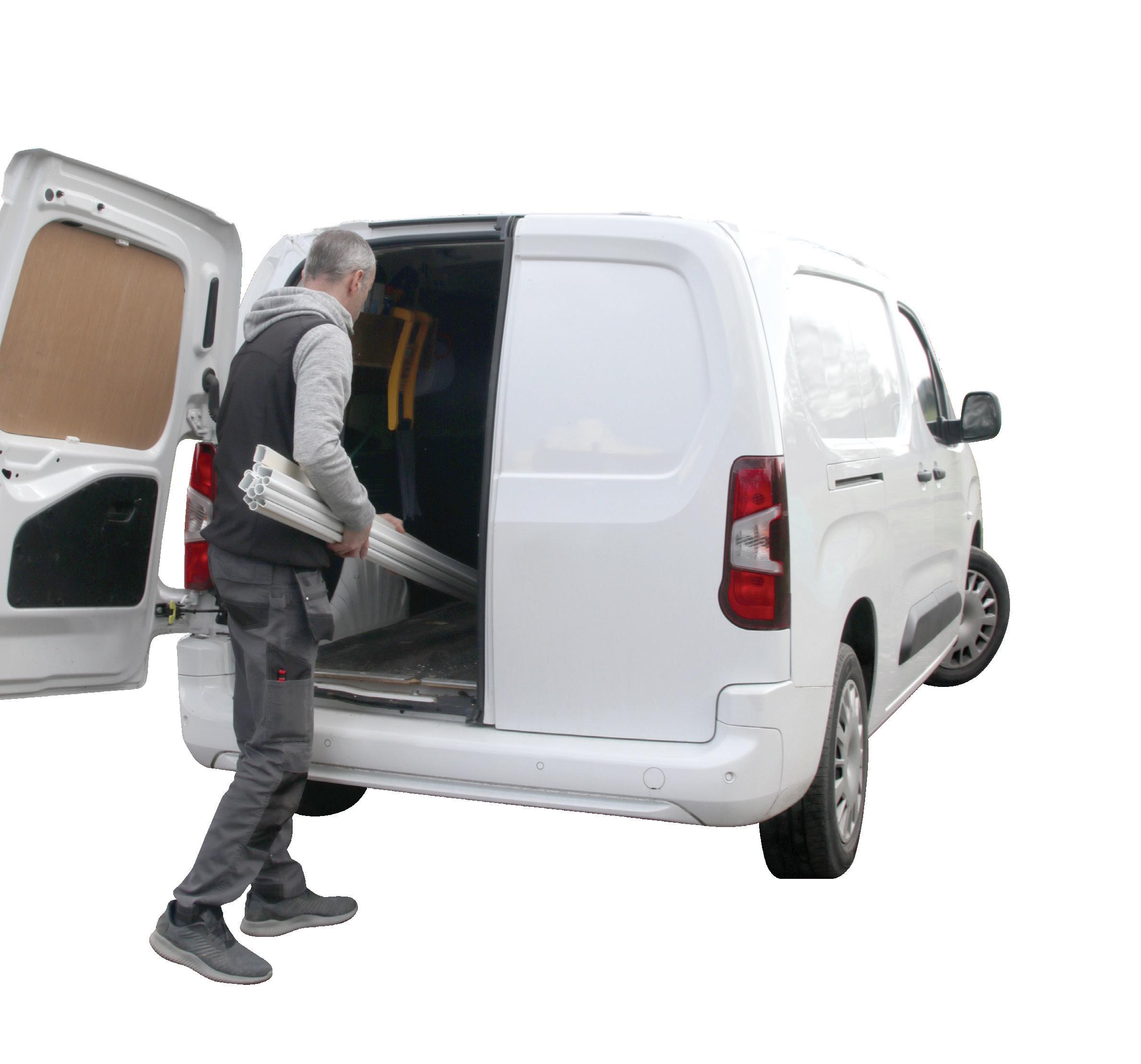
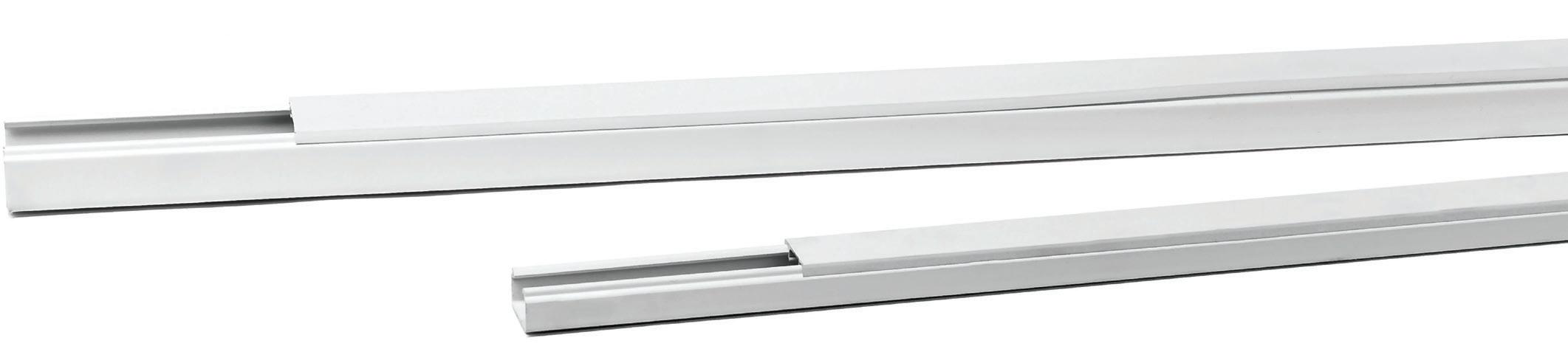
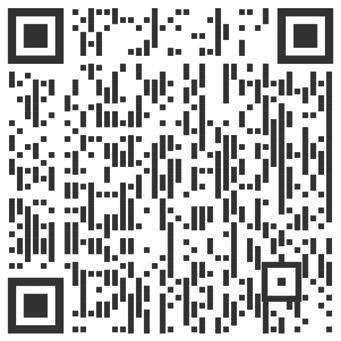