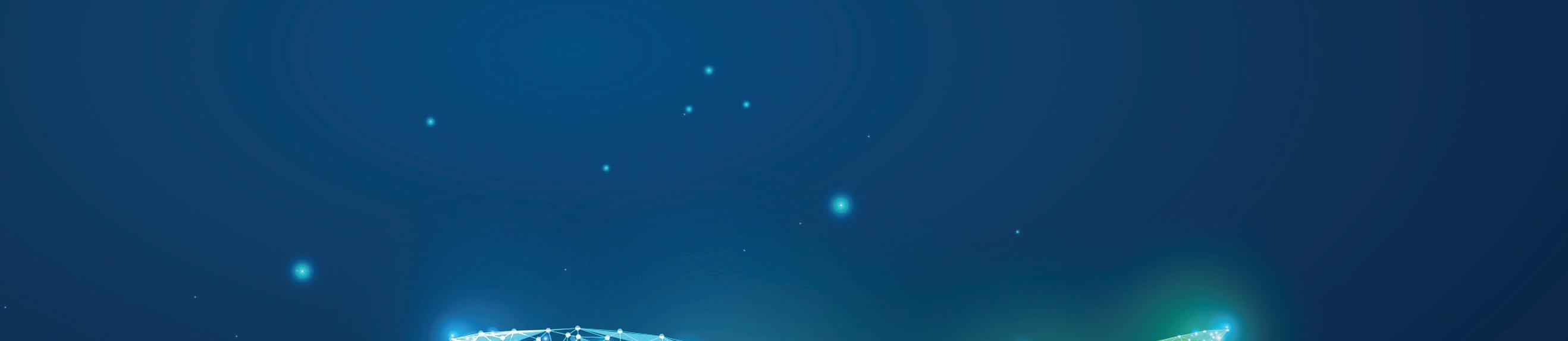
Breakthrough Technologies for Sustainable Biomanufacturing
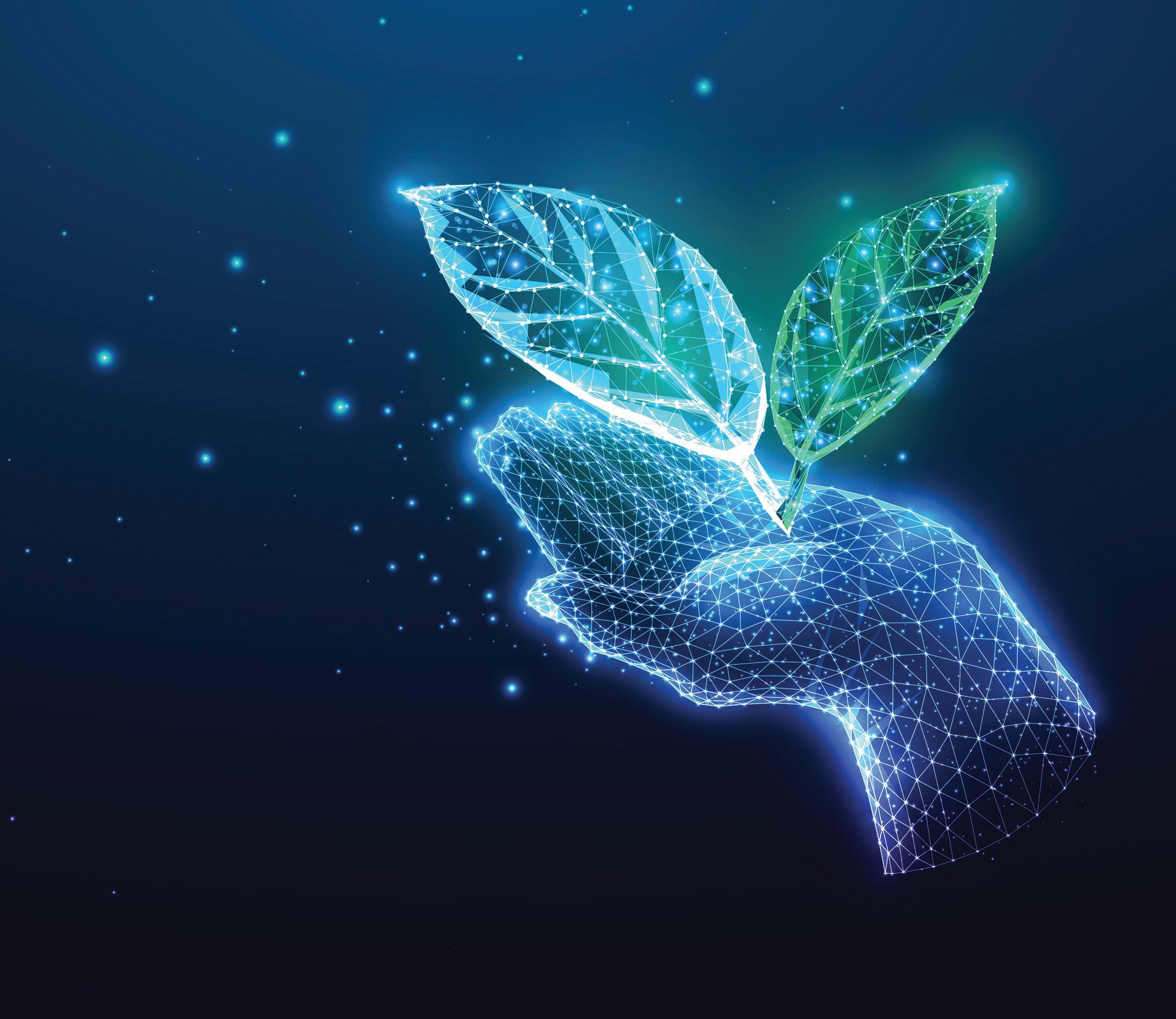
Astrea Bioseparations has a passion for delivering high-performance, monodispersed agarose beads for biopharmaceutical separation processes. Although the PuraBead portfolio is renowned for exceptional performance, what’s truly exciting is the remarkable sustainability woven into the PuraBead supply chain and manufacturing process.
Sustainable Harvest of Seaweed: The journey begins with farmers harvesting sustainably managed red seaweed (red marine algae of Gelidium and Gracilaria species). Not only does the seaweed capture dissolved carbon (carbonic acid) from seawater, thus enhancing water quality and biodiversity, but it also provides a buffer against ocean acidification. After harvesting, seaweed is solar-dried before undergoing an extraction and purification process to produce high-purity agarose perfect for crafting into agarose beads.
Innovative, Ecofriendly Manufacturing: Astrea Bioseparations stands out from other chromatography-resin suppliers with a unique aqueous manufacturing process for creating PuraBead media (Figures 1 and 2). Our innovative approach requires no oils or oil-derived solvents while ensuring impressive manufacturing efficiency. Highly uniform bead sizes produce minimal waste, with unwanted bead sizes eliminated through
Seaweed absorbs CO2 by photosynthesis
Seaweed dried, shipped for processing into agarose Agarose beads made in a
sieving. The biopolymer structure is naturally biodegradable, offering a superior and greener alternative to synthetic resin products.
Why Choose Agarose? Agarose stands out for its inert and hydrophilic properties, minimizing nonspecific binding and maximizing product purity. Derivatized agarose beads boast an optimal mix of high porosity, extensive surface area, and (after cross-linking) sufficient rigidity to support high flow rates. This set of features ensures not only increased binding capacity, but also significantly reduced processing times. Opting for agarose as the base matrix isn’t simply about achieving optimal performance; it’s a conscious decision you can make toward a sustainable biomanufacturing future.
Looking Forward: Over the past two years, Astrea Bioseparations PuraBead base beads have expanded their market greatly, outpacing other product ranges
to meet the resulting demand and reinforce a commitment to sustainability. Astrea Bioseparations has shifted to a semicontinuous beading process running 24 hours a day, seven days a week. Construction of a new agarose-bead manufacturing plant is underway, adjacent to the company’s existing facilities on the Isle of Man, UK, to support ongoing and projected growth of PuraBead products. The facilities’ design allows for easy expansion, securing future scalability and reducing power use through shared services. Astrea Bioseparations remains dedicated to innovation, collaboration, and sustainability, driving continuous improvement to meet the evolving needs of the biopharmaceutical industry. With the upcoming expansion, Astrea Bioseparations is not simply preparing for the future, but also shaping it to ensure that customers can benefit from the highest quality products and the most sustainable practices.
Environmental sustainability is an important goal for the bioprocessing industry, which is also under increasing pressure to decrease costs and boost productivity. Traditional chromatography adsorbents have served the industry well for many years, but meeting those combined demands requires more than maintaining the status quo. Enter AstreAdept chromatography adsorbents, which are based on a composite electrospun nanofiber technology (Figure 3 and 4). The innovative material provides novel advantages, with a potential to revolutionize multiple aspects of sustainable biomanufacturing.
Intensification of bioprocessing involves adopting technologies that can enhance processing performance while improving environmental impacts significantly. Using AstreAdept adsorbents contributes to achieving those goals by increasing productivity, reducing footprint, and lowering energy and water consumption. That positions AstreAdept products as an integral part of the bioprocessing industry’s journey toward sustainability.
Increased Productivity: Nanofibers naturally boast high ratios of surface area to volume due to their nano-scale dimensions. This unique characteristic provides nanofiber adsorbents with increased binding capacities, enabling them to
Figure 3: Schematic of composite nanofiber production
Polymer A
Syringe pump
Polymer solution
Metallic needle
High voltage supply
Polymer B
capture more target bioproduct than other media can. The structure of AstreAdept adsorbents provides almost immediate access to the binding surfaces and a wide flow path for fast-flow processing. This allows rapid binding with a residence time of under 1 second to achieve saturation capacities. By decreasing processing time and increasing adsorbent capacity, productivity is significantly enhanced. That in turn reduces the need to expand bioprocessing equipment, leading to substantial positive effects on process economics.
Bioprocessing: Because of the large binding surface area provided by low nanofiber density, a lot can happen in a small space. Devices incorporating this advanced material require smaller physical footprints than those of other technologies. The reduction in size brings multiple benefits, including decreased facility space requirements, lowered water consumption, and reduced waste generation. Minimizing such needs lessens the overall environmental impact of a biomanufacturing process, contributing to a greener and more sustainable manufacturing approach than was possible using previous technologies. Adoption of AstreAdept adsorbents represents a significant stride
toward more efficient and ecofriendly biomanufacturing practices. The technology offers a comprehensive suite of improvements that extend beyond mere process efficiency to encompass broader environmental and economic benefits.
Achieving optimal productivity and efficiency is crucial to the fast-paced world of biopharmaceutical production. Facilities that develop and manufacture biologics increasingly rely on ready-to-use disposable systems and technologies to streamline their processes. Single-use solutions solutions offer benefits such as faster turnaround times, simplified product release procedures, and faster product changeovers. Implementing ready-to-use technologies can reduce R&D costs and capital investment requirements significantly while enhancing environmental sustainability by cutting energy consumption, space requirements, water use, and cleaning chemical needs by up to 75% (Figures 5 and 6).
Leading the Way in Downstream Bioprocessing:
Astrea Bioseparations is at the forefront of providing ready-to-use solutions for downstream bioprocessing, with offerings including prepacked small- and largescale columns and the Evolve Process range of repackable chromatography columns. Capable of accommodating column volumes up to 130 L in scale, they are ideal for multiproduct facilities and smalland medium-scale production campaigns. Evolve Process columns can be packed quickly and easily with Astrea Bioseparations chromatography media or other preferred resins. These columns provide the ability to recover resin after use.
Innovative Solutions for
and Efficiency: Complementing the Evolve Process portfolio is the innovative Refresh Kit concept. Designed to facilitate replacement of process-wetted column elements while retaining components that don’t need to be replaced, these kits cut down on waste and equipment expenditures. Crosscontamination risks are reduced by enabling quick replacement of all process-contact components, minimizing time spent on column cleaning and validation and decreasing the use of organic solvents and hazardous substances (Figure 7).
Ideal for Multiproduct Facilities: Evolve Process columns and Refresh kits are especially beneficial
Figure 5: As supplied, Refresh Kits and all spare parts are fully recyclable. To comply with your local regulations/guidelines, check with local authorities before disposing of any parts.
Environmentally friendly Minimize use of harsh solvents and acids. Retain resins after use. Prevent crosscontamination.
Figure 6: Economical assessment based on contrasting 70-mm and 100-mm Refresh Kits against column storage footprint
Economical Average 65% cost savings compared with purchasing new Evolve columns
Increase storage space ≤75%.
Reduce inventory burden.
Figure 7: Efficiency and time savings increase with column size.
Diameter
Turn downtime into uptime. Increase facility flexibility, capacity, and efficiency. Save time on hardware cleaning.
for multiproduct facilities, such as those operated by contract development and manufacturing organizations (CDMOs) and contract manufacturing organizations (CMOs). These solutions reduce chromatography preparation times and resource needs, eliminating the necessity for dedicated columns and extensive inventories, thereby cutting downtime between batches.
Revolutionizing the Biomanufacturing Process: Ready-to-use disposable systems hold immense potential for revolutionizing biomanufacturing processes. By enhancing efficiencies, reducing contamination risks, and providing economic and environmental benefits, such innovative solutions will enable biomanufacturers to thrive in a competitive industry.
Steven J. Burton, PhD, is chief scientific officer; Daniella Steel is senior manager of product strategy; Nicol Watson is vice president of corporate and market strategy; all at Astrea Bioseparations, a Biotage Company, Unit 2, Freeport, Ballasalla, Isle of Man, United Kingdom, IM9 2AP; https://www. astreabioseparations.com. PuraBead, AstreAdept, Evolve, and Refresh are registered trademarks of Astrea Bioseparations.