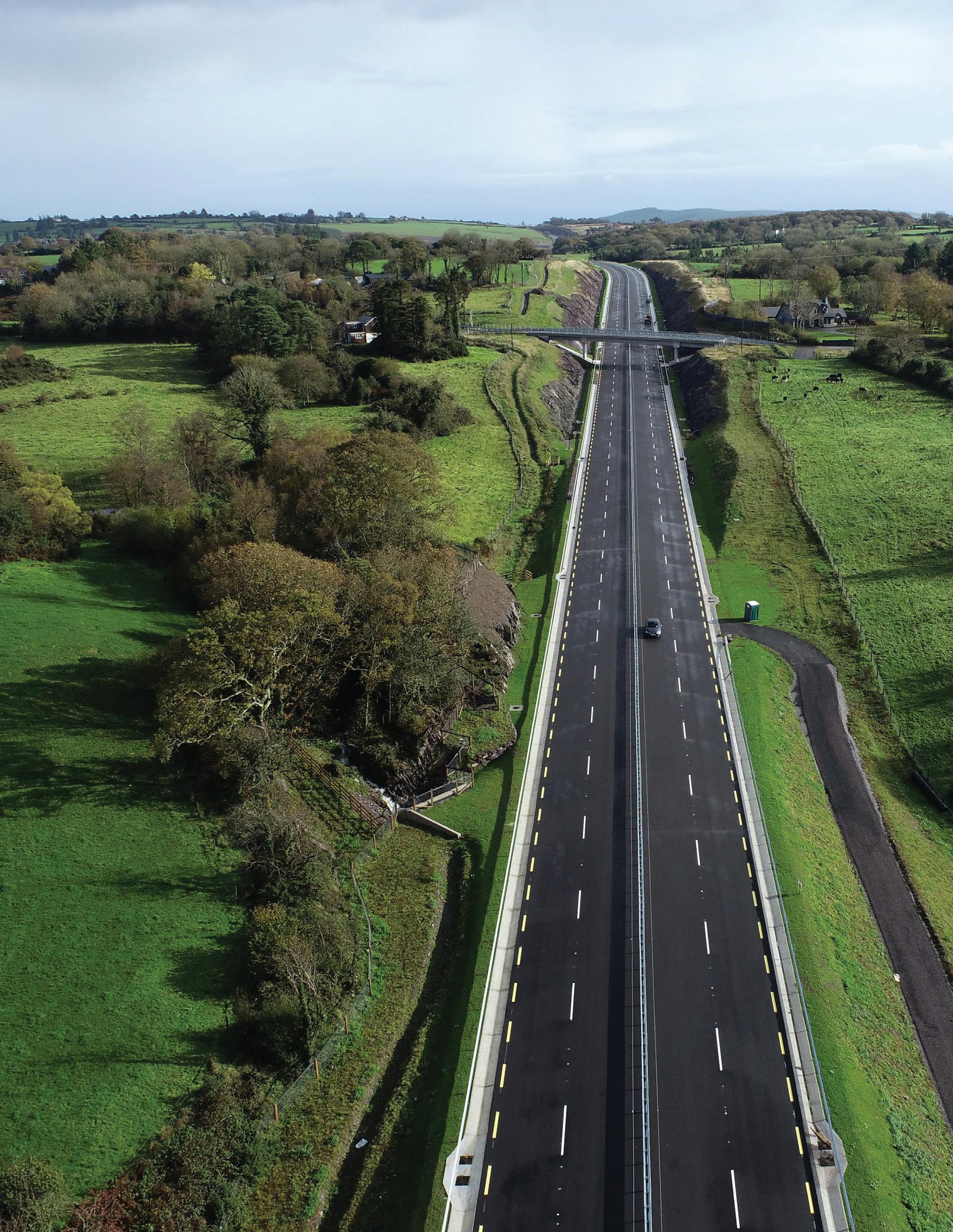
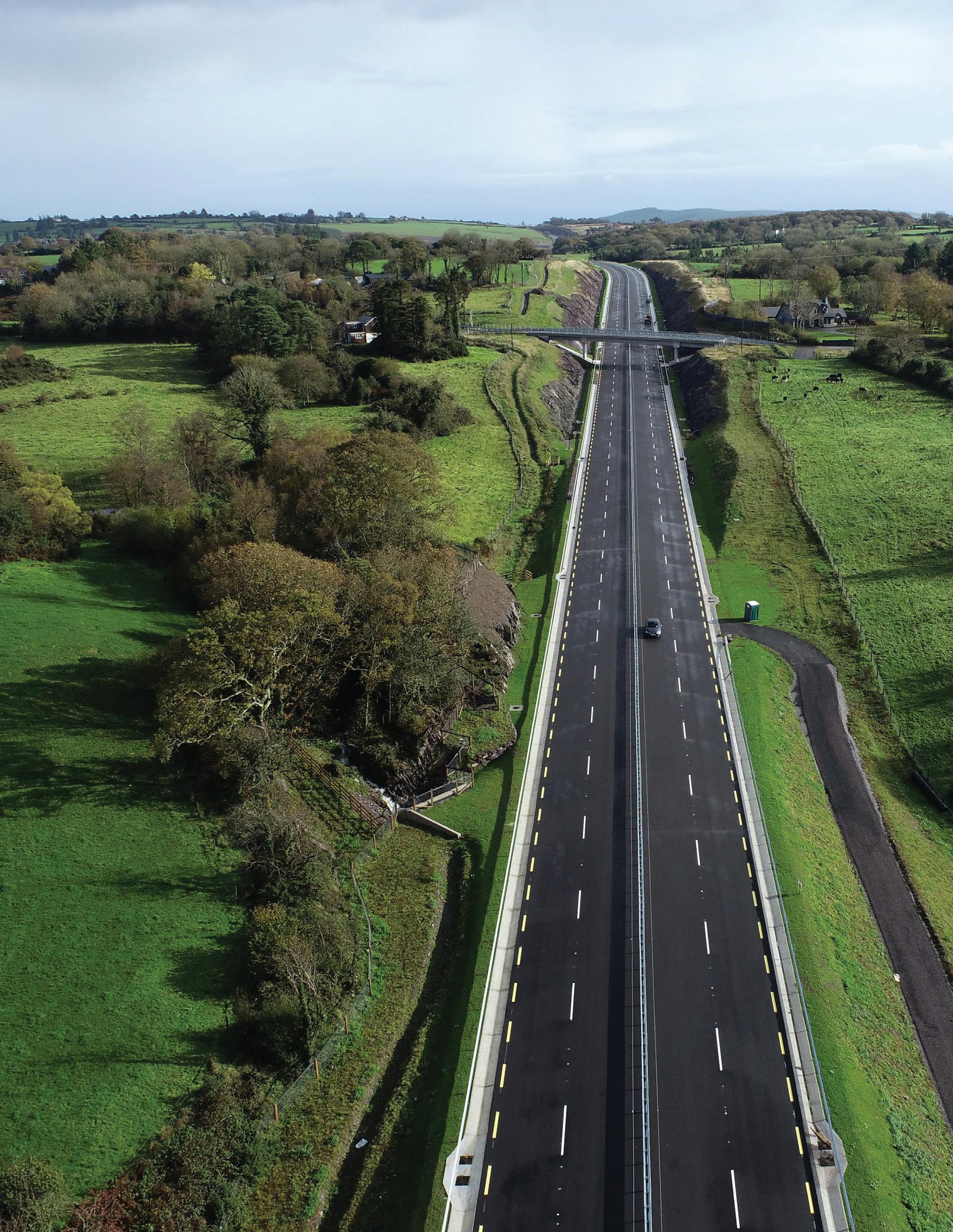
DISPATCH
ASH GROVE
Message from Serge
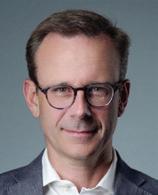
As we enter the second quarter of 2024, I want to express our heartfelt gratitude for your continued support and partnership throughout the year.
This year started off with three acquisitions added to the Ash Grove family. In early February, we closed on purchasing a cement plant and four terminals from Martin Marietta’s South Texas business. The purchase includes the Hunter Cement Plant located in New Braunfels, Texas, with a capacity of 2.1 million tons, more than 140 years of limestone cement reserves and four terminals: three in the Houston metropolitan area and one in Beaumont, Texas. We are excited to welcome the Hunter employees to our team and look forward to working together to achieve our ambitions (read more on page 4).
At the end of February, Sapphire Americas closed on an acquisition called Cadence Environmental Energy, headquartered in Michigan City, Indiana. Cadence Environmental Energy was the first company to use carbon-rich waste as fuel in cement kilns. Today, this fuel, called Chem-Fuel®, has helped industries large and small manage their hazardous wastes in the most cost-effective and environmentally responsible way possible. Since Chem-Fuel® replaces coal and other fossil fuels, these non-renewable resources can stay in the ground.
Cadence operated two state-of-the-art analytical laboratories: one in Foreman, Arkansas, and one in Chanute, Kansas. Both labs are equipped with the latest technology and staffed with
fully-trained professional chemists. These labs can quickly and accurately analyze waste to ensure it meets the nation’s number one alternative cement kiln fuel standards.
In January, we closed on an acquisition called DE-Source in Eastern Oregon, approximately 90 miles south of our Durkee plant. This acquisition provides the West Region with access to over 100 million tons of pozzolanic materials that will be used to produce low-carbon cement and sold across Eastern Washington and Idaho, as well as in Portland, Oregon and Elko, Nevada.
We also held our annual Ash Grove conference in Charlotte Harbor, Florida, in February. This year, we combined our conference with our colleagues at IPG, an incredibly successful CRH business providing full-scale infrastructure solutions for water, communications, energy and transportation infrastructure with a focus on sustainability. The conference theme was “Driving Growth Together” and we focused on areas where we can maximize our full potential to deliver high-quality sustainable binders for concrete solutions.
It already has been a busy year indeed, and I am excited about Ash Grove’s path ahead, which is full of opportunity now and for years to come. Our teams are delivering daily on our purpose of shaping a sustainable future through the services we provide to our customers and how we operate our business. Thank you for your continued partnership with Ash Grove and for our mutual success.
Serge Schmidt Ash Grove PresidentCRH GTA Employer Recognition
It is an honour and privilege to announce that CRH Canada has been named as a Greater Toronto Area Top Employer for 2024!
Every year, Mediacorp Canada Inc., a benchmark for workplace best-practice in the GTA, critically analyzes hundreds of Canadian companies based on a plethora of criteria, such as employee communication, benefits, employee development
programs, workplace environment & atmosphere, among other things. Over the years, this prestigious list has become extraordinarily competitive. So we would like to extend our gratitude to every individual who has worked hard to ensure CRH Canada excels in every aspect as a top employer with great benefits, unparalleled career development opportunities and high young talent retention across all our businesses.
Solutions for a Sustainable Future
At CRH, we are leading the transition to smarter, more sustainable construction to help reinvent the way our world is built.
Our ability to deliver more sustainable solutions for our customers is underpinned by our strong sustainability foundations – protecting the natural world, helping our people and communities to thrive and ensuring we operate as a responsible business. Our 2023 Sustainability Performance Report outlines our progress and how our framework for a sustainable future is helping to solve three complex global challenges: water, circularity and decarbonization.
By focusing on developing products, services and solutions that help to solve these global challenges, we are creating value for all stakeholders and driving future growth for CRH.
Our Framework for a Sustainable Future focuses on how we can contribute to tackling some of the greatest challenges facing society and the built environment, as well as making progress on our other material sustainability issues.
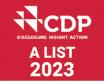

We are extremely proud to be recognised as a GTA Top Employer for the past six consecutive years with over 3,000 employees, striving everyday to uphold our values of prioritizing health, safety and overall well-being of our people. This accomplishment would not have been possible without the determination and incredible work ethic of every individual at CRH Canada.
By partnering closely with our suppliers and customers like you, we further drive decarbonization upstream and downstream of our operations to create a more sustainable supply chain.
In our commitment to people, we are continuing to develop our culture and talent, while driving our ambitions for a safer, more inclusive and diverse workforce. In our communities, we are working to create positive change. Finally, our strong governance structures, processes, and policies play a vital role in embedding sustainability throughout our organization and uniting us in the way we work.
Our 2023 Sustainability Performance Report highlights our continued commitment to providing sustainable solutions and outlines our initiatives to promote sustainability and environmental stewardship around the world. Scan this QR code to see the entire report.



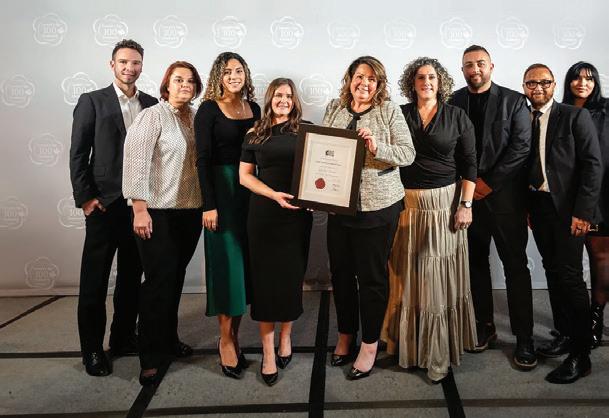
CRH Agrees to Acquisition of Material Assets in Texas
In November 2023, CRH agreed to a $2.1 billion acquisition of material assets in Texas.
We are thrilled and honoured to announce that as of February 2024, CRH has completed its acquisition of Martin Marietta’s cement business in South Texas. This acquisition marks our underlying focus on the commitment to serve the Texas construction industry through strategic growth and expansion of Ash Grove Cement.
The key material assets of this acquisition for Ash Grove include:
• Hunter Cement Plant: A robust facility with a capacity of 2.1 million tons and 140 years of limestone cement reserves strategically located in New Braunfels, Texas
• Cement Distribution Terminals: Three active terminals (two in the Houston metro area and one in Beaumont) and one idle terminal (in Houston) will enhance Ash Grove's distribution capabilities
• 20 vertically-integrated ready-mix concrete plants in San Antonio and Austin, Texas: CRH has requested approval to acquire these plants, which will be managed by our Americas Materials colleagues

The acquisition of these high-quality assets further strengthens our marketleading position in Texas and increases our exposure to attractive, high-growth markets. Our ability to leverage our cement expertise and technical capabilities will enable us to enhance and optimize our existing position in Texas, resulting in significant synergies and self-supply opportunities. This transaction reflects our disciplined approach to capital allocation, as well as our commitment to deliver further growth and value creation for our shareholders. We also believe there is significant potential to unlock additional growth opportunities across an expanded footprint in this attractive growth market.”
– Albert Manifold, Chief Executive of CRHThis acquisition stands as a transformational opportunity for CRH to acquire a high-quality operating business strategically positioned in the burgeoning Austin and San Antonio metro markets.
We would like to extend our gratitude to our teams for their relentless hard work and dedication to make this transaction possible. We would also like to take this opportunity to thank you, our customers, for your trust and commitment, as we try to improve our product and service to guarantee your satisfaction.

CAC Net Zero Action Plan Follow Up
Achieving Net Zero with the 5 Cs
As Ash Grove continues to strive towards our sustainability goals, we look at the 5 Cs to sustainability for guidance. The 5 Cs to sustainability include: Clinker, Cement, Concrete, Construction and Carbon Uptake. Each category presents a different and unique challenge towards achieving our goals.
Clinker
The key ingredient that gives our cement its binding properties. This is the most carbon-intensive component of cement. Listed below are our plans to reduce clinker emissions:
1. Replacing fossil fuels – higher uses of natural gas
2. Clinker substitution – lower clinker content cements
3. Carbon capture – sequestering carbon in product to increase its reactivity
4. Thermal efficiency – reducing heat loss during the process
5. Decarbonated raw materials – exploring new raw materials with less bound CO2
Cement
The most energy-intensive phase of the concrete value chain that occurs at the cement plant. By introducing new materials into our products, we can continue to maintain the highest quality products while reducing our emissions. We will continue to use and optimize the following to reduce emissions:
1. Portland-limestone cement (GUL)
2. Supplementary cementitious materials (SCMs) – SLAG, Fly Ash, Silica
3. Blended cements – 75/25 GUL/SLAG blends
Concrete
As an essential building material, concrete must be produced to ensure the highest quality and performance, but we also must work to reduce emissions. We will implement the following to reduce concrete emissions:
1. Concrete mix optimization
• Larger aggregate to minimize paste (cement and water)
• Aggregate gradation optimization
• Recycled concrete aggregate
• Utilize chemical admixture
2. Optimize concrete designs
• Ensure not to over-specify strength and durability requirements
3. Powering concrete with clean energy
Construction
There are many opportunities to reduce the volume of admissions throughout the construction/design process. The achievement of emission reduction through construction is out of the direct control of the cement/concrete industry and requires a shared commitment of achieving net-zero emissions:
1. Through design optimization
• Material efficiency
• Avoidance of over-designing
2. Waste reduction
Carbon Uptake
Emissions in this area can be reduced significantly. Concrete naturally sequesters Carbon Dioxide from the atmosphere. Through research conducted at the Swedish Environmental Institute, an average of 20% of the Carbon Dioxide calcination emissions can be permanently sequestered when a concrete structure has been built. Maximizing Carbon Uptake is in the hands of architects/ engineers to ask to use exposed concrete wherever possible.
If you would like us to go over these in more detail with your team, feel free to reach out to your technical services team at Ash Grove.

Ask The Tech Team
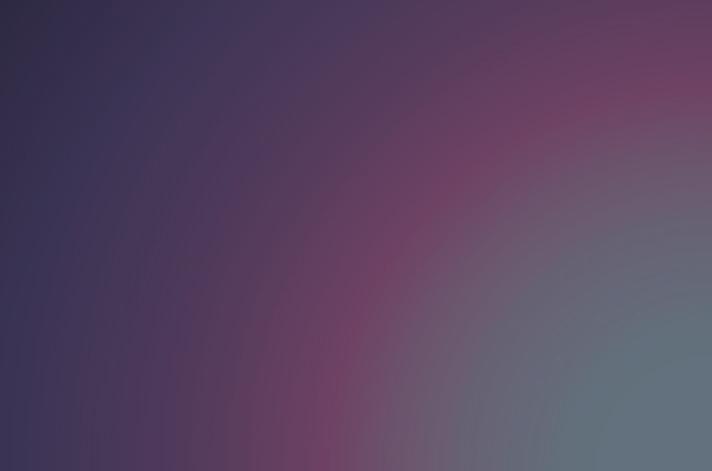
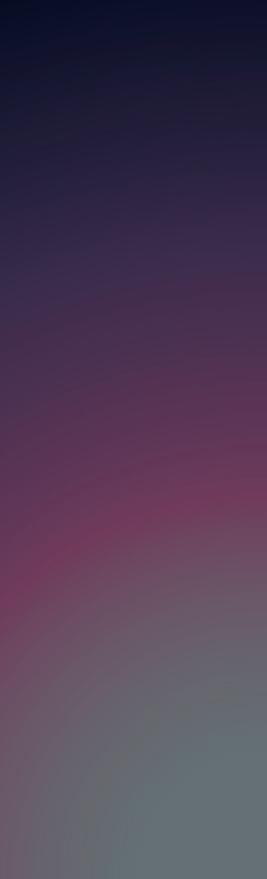


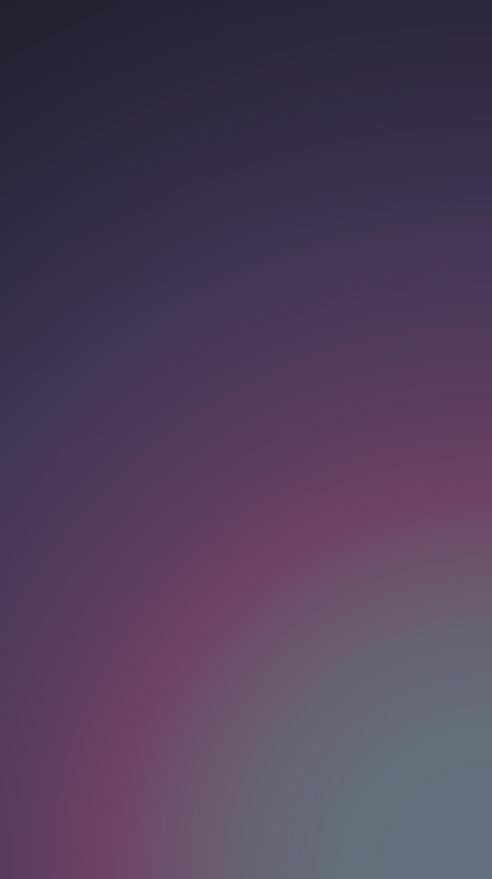
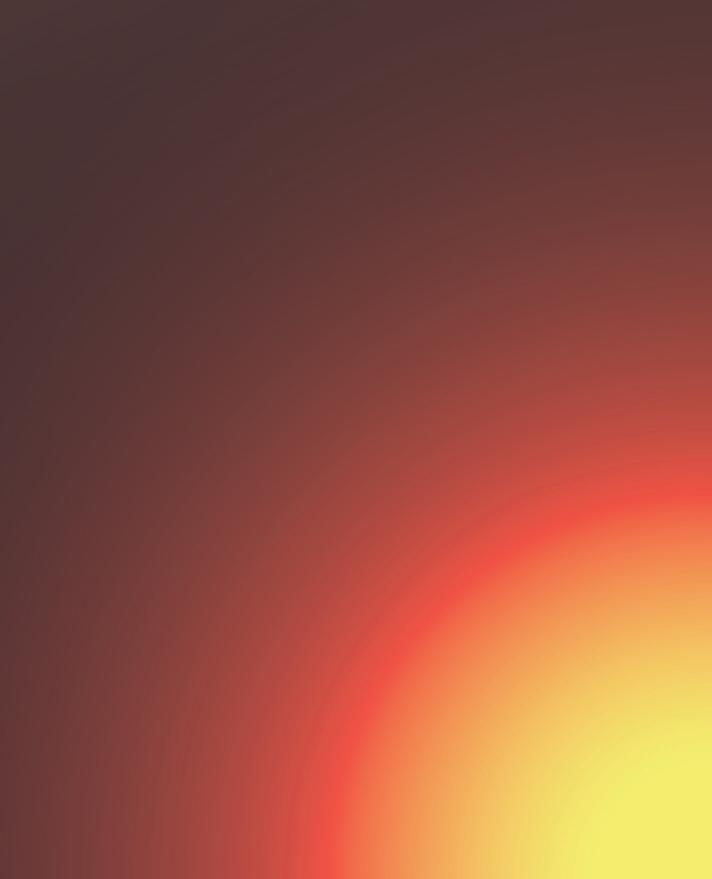
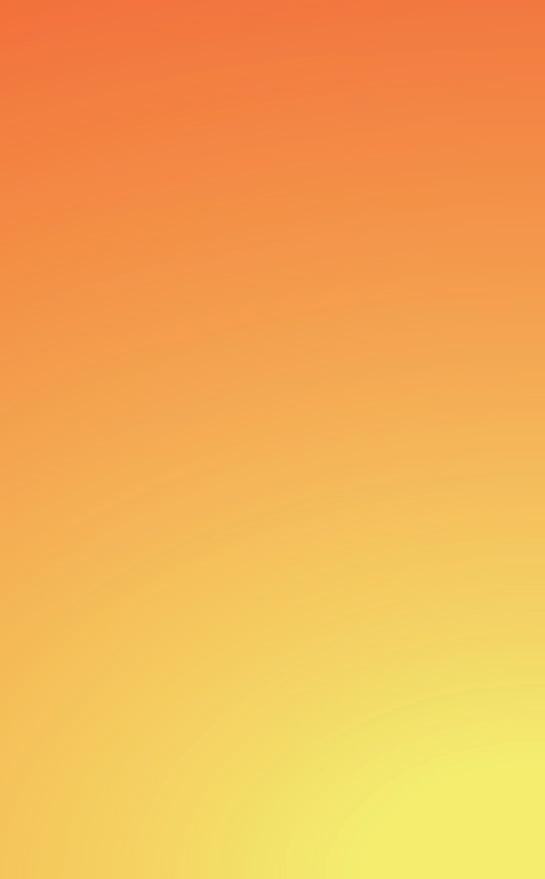



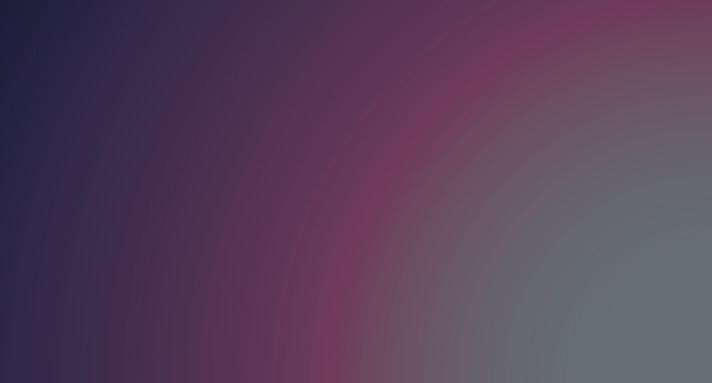
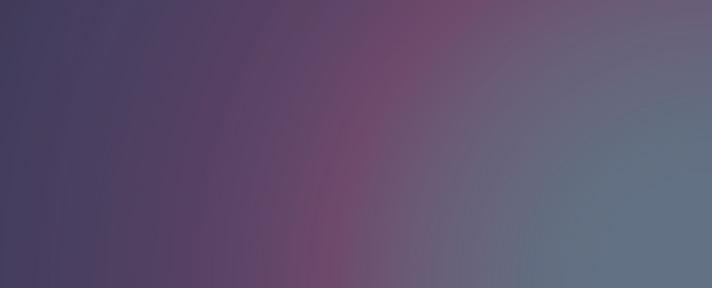


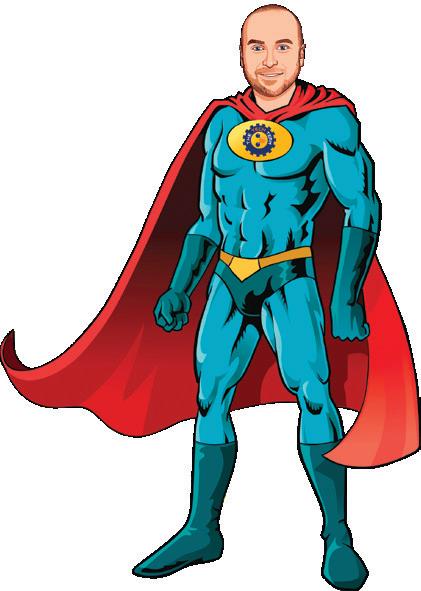
Tech Team help!
Sincerely,
Edward-Parker Davidson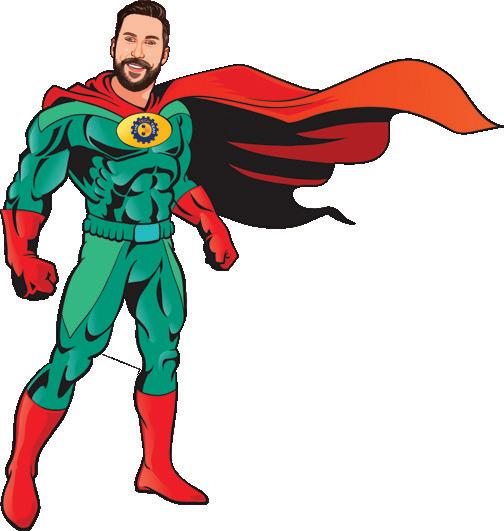
I need to show I can make green concrete, but it keeps coming out grey!
How to Calculate your Concrete’s Embodied Carbon
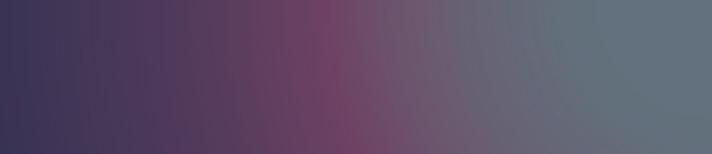

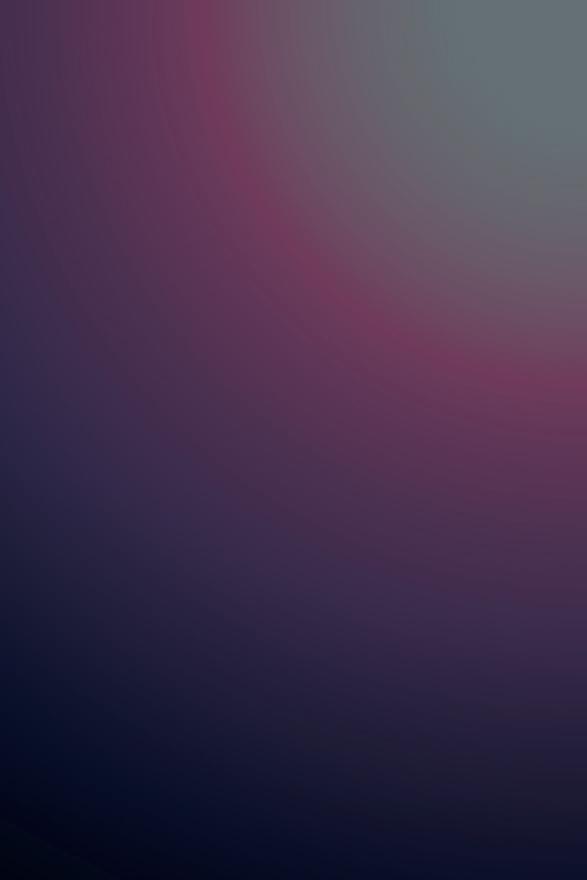
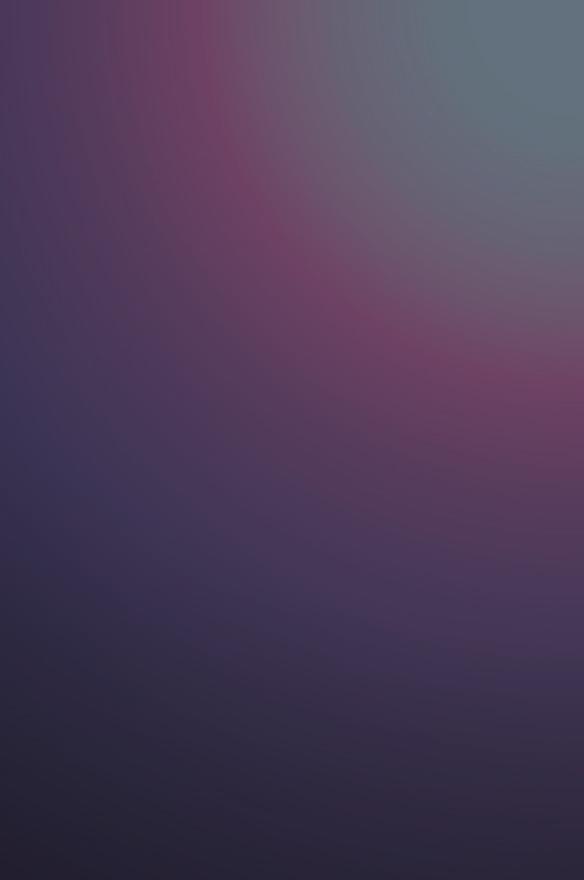
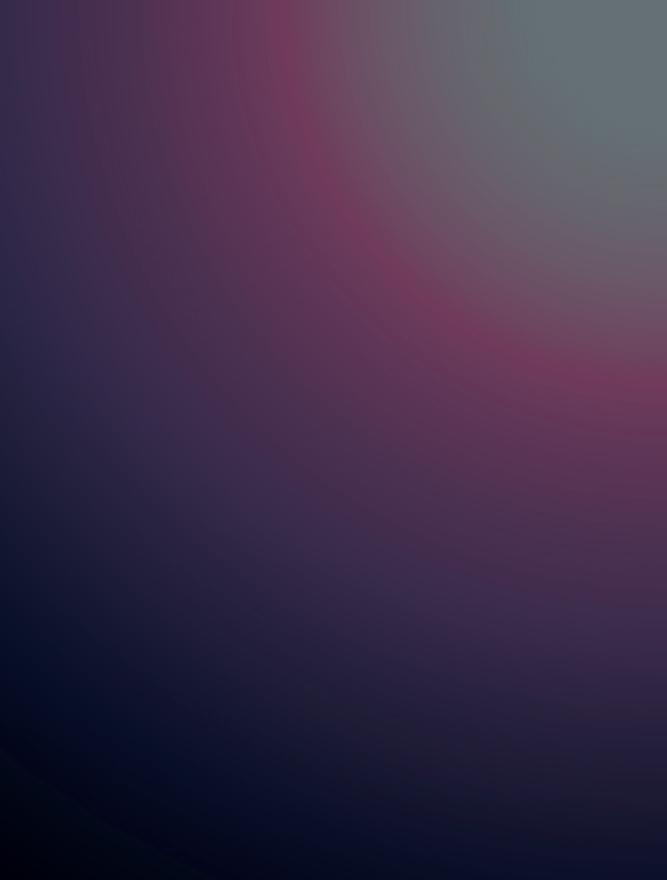
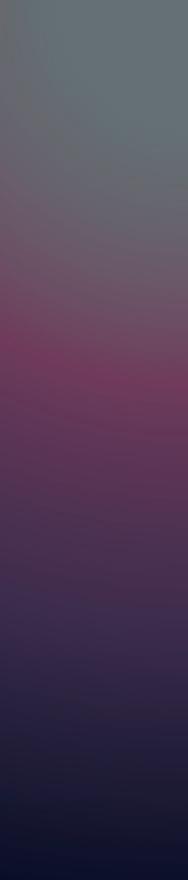
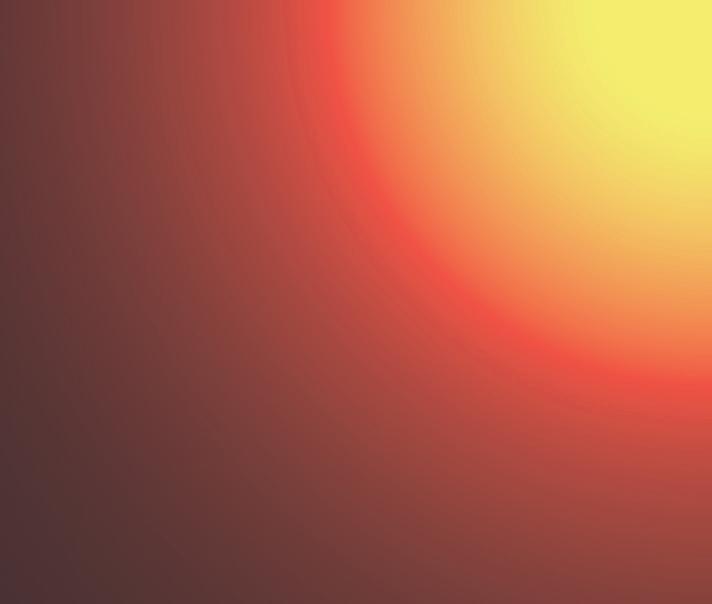
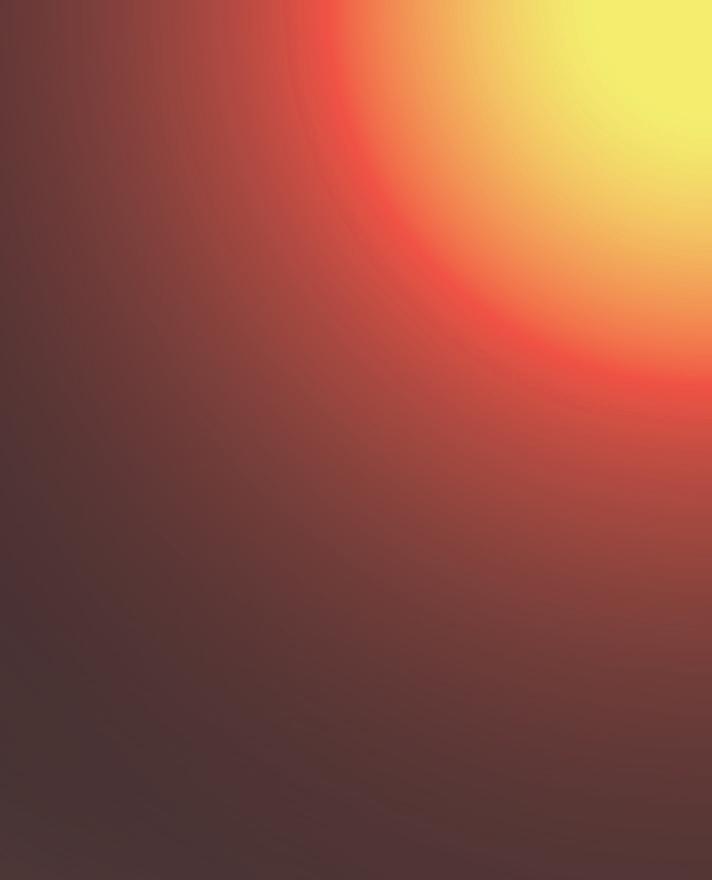
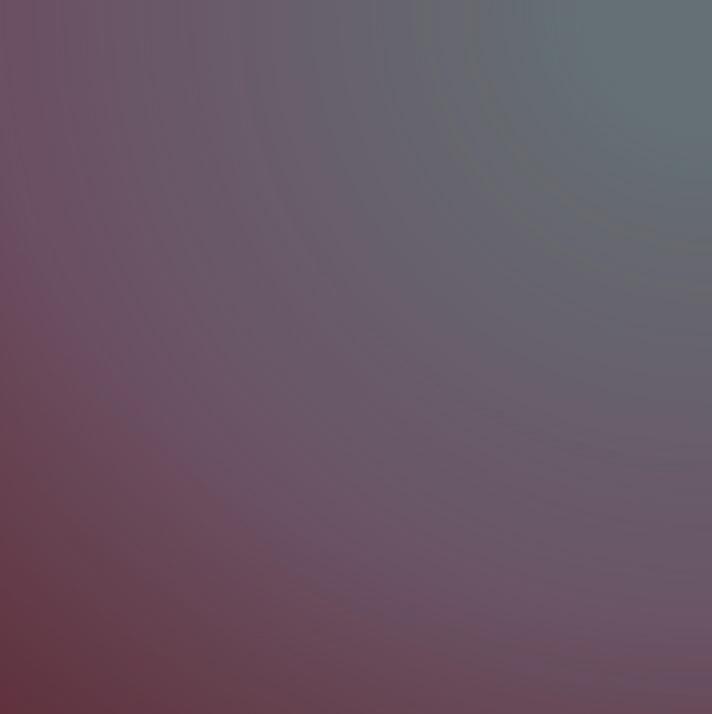



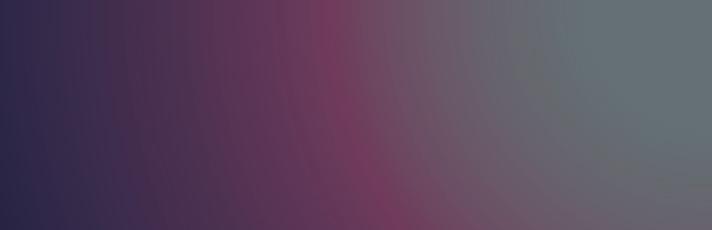


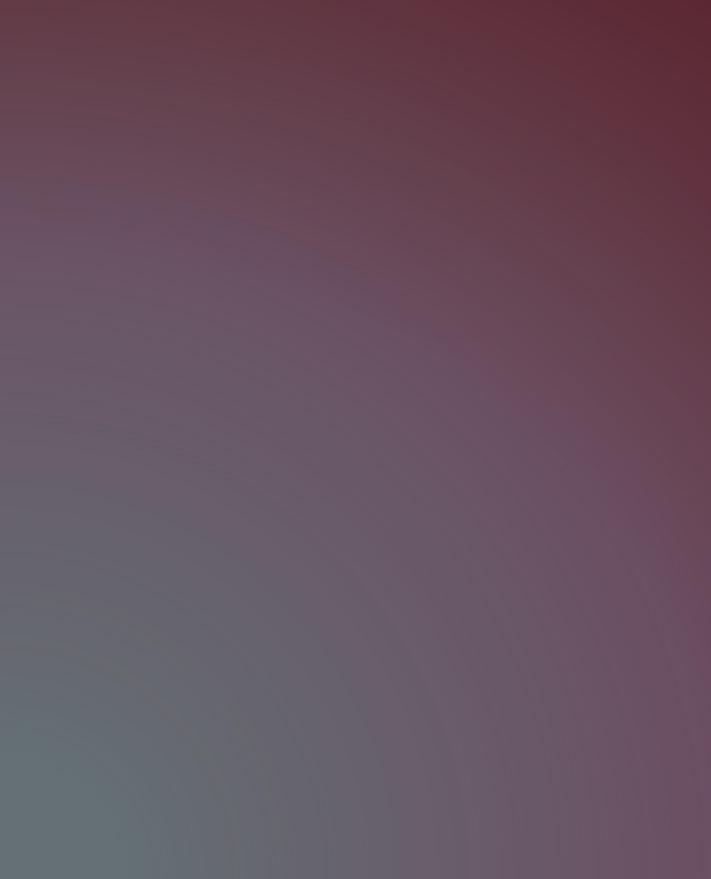
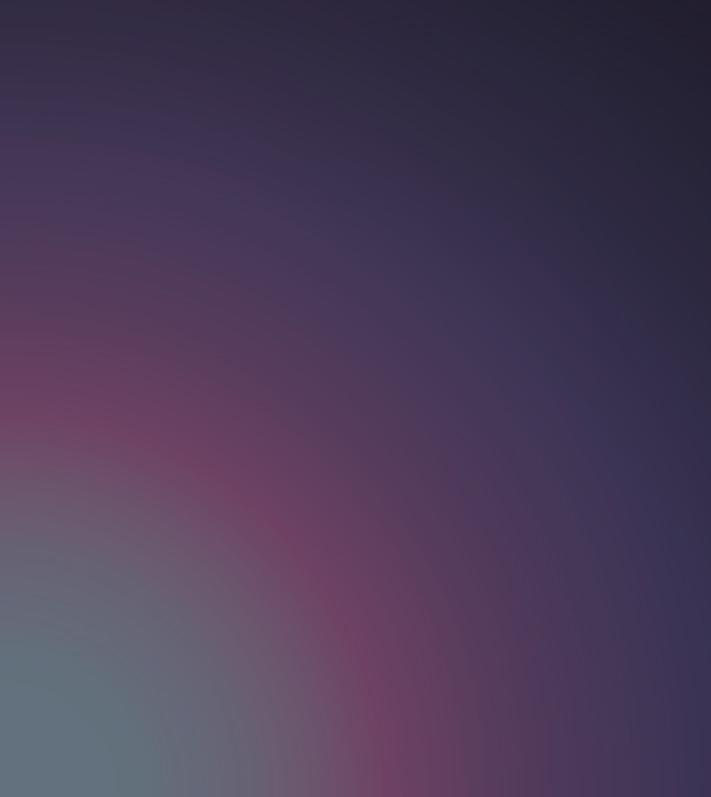
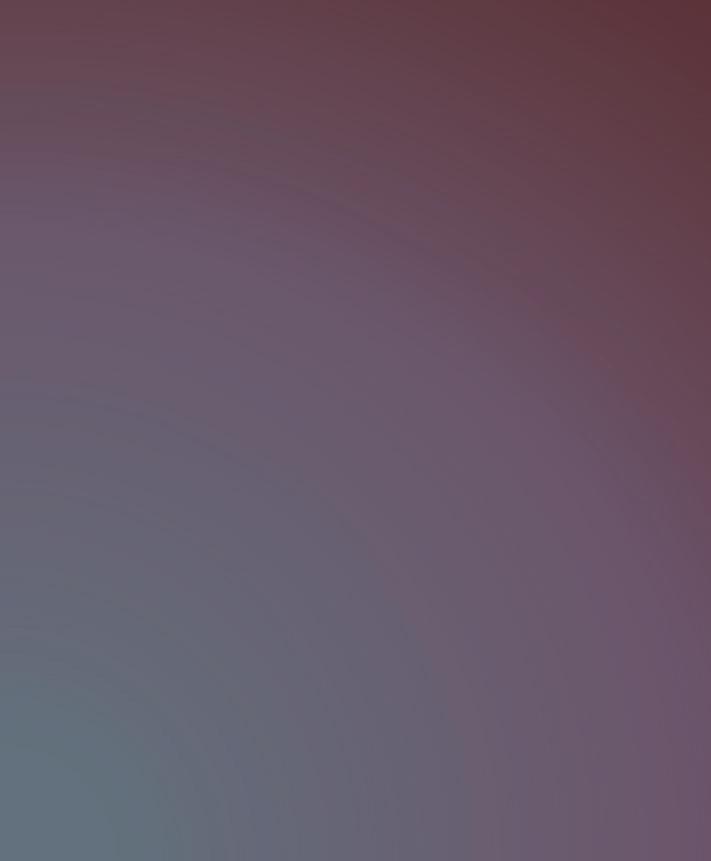
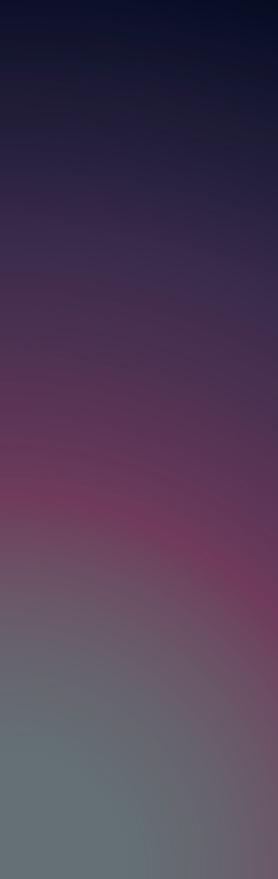
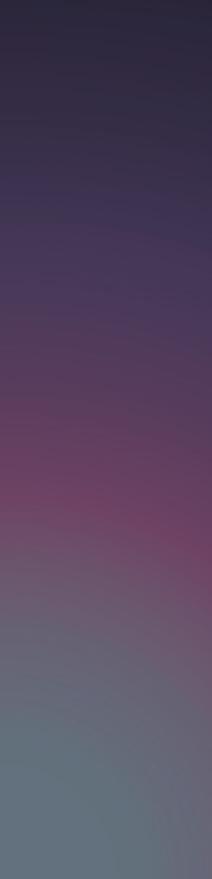
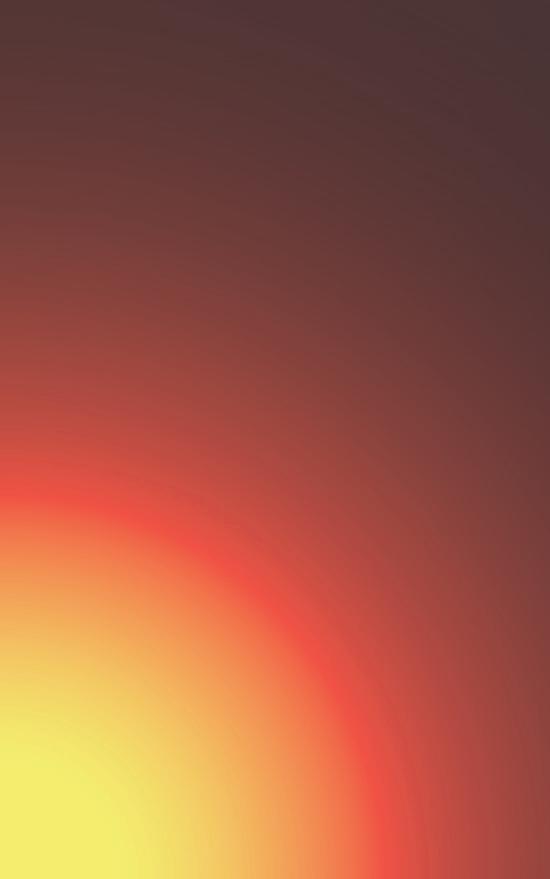
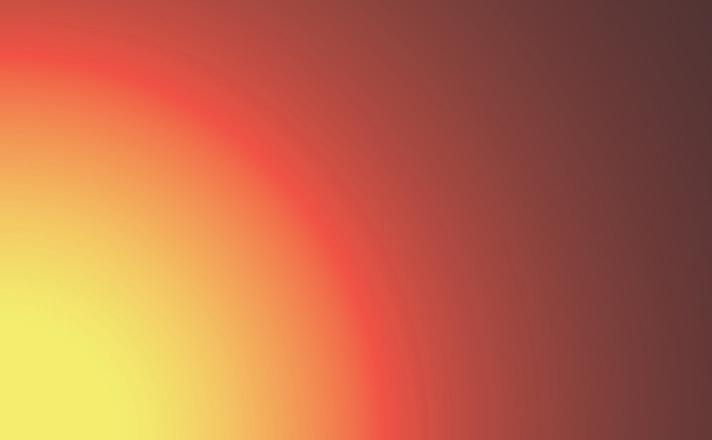
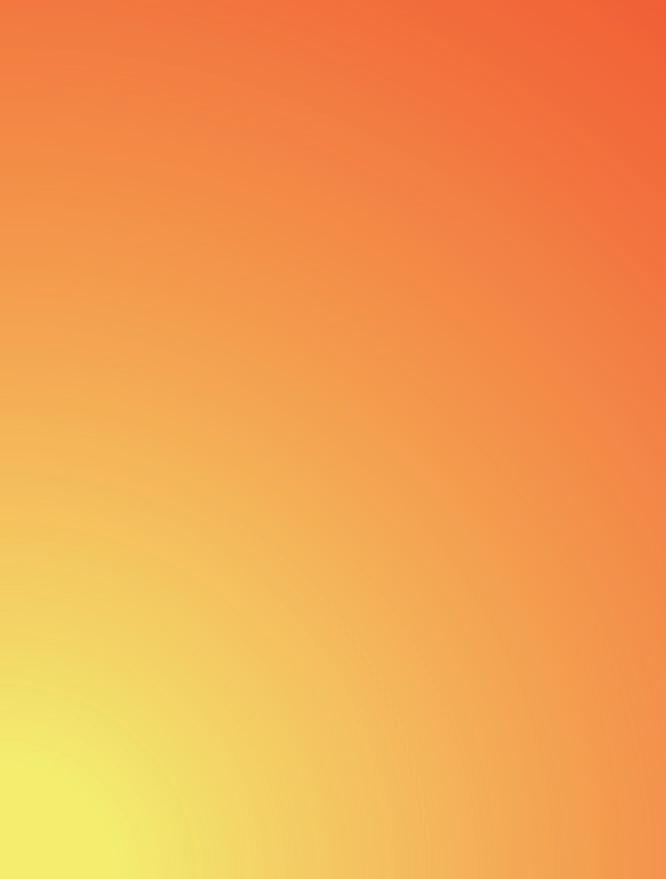
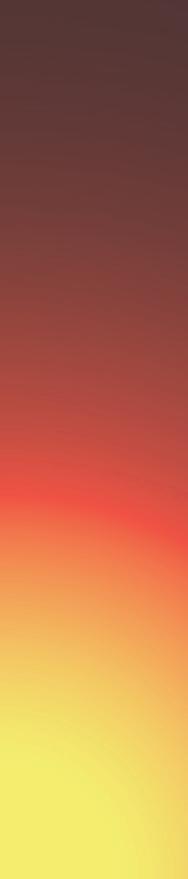
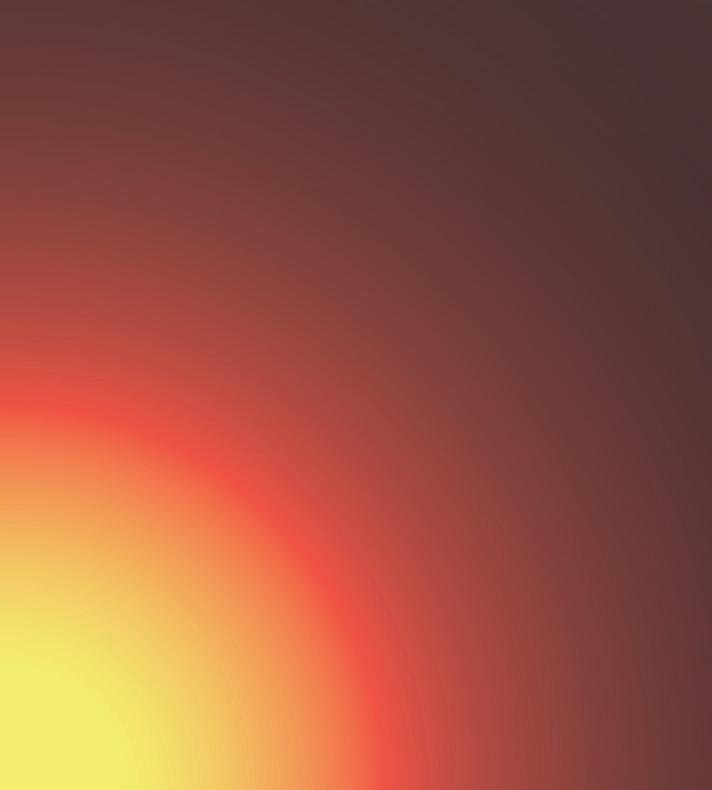

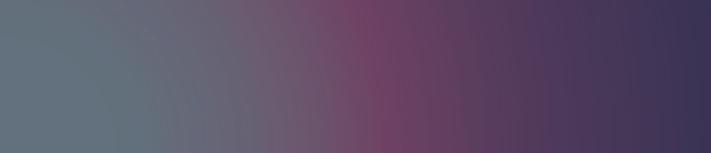
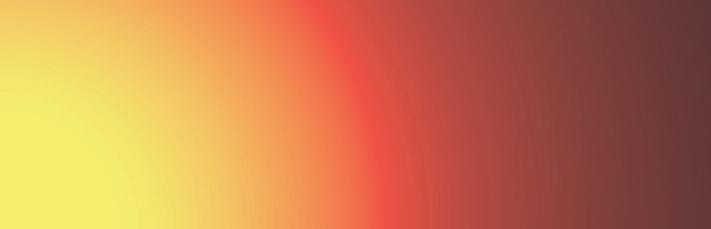
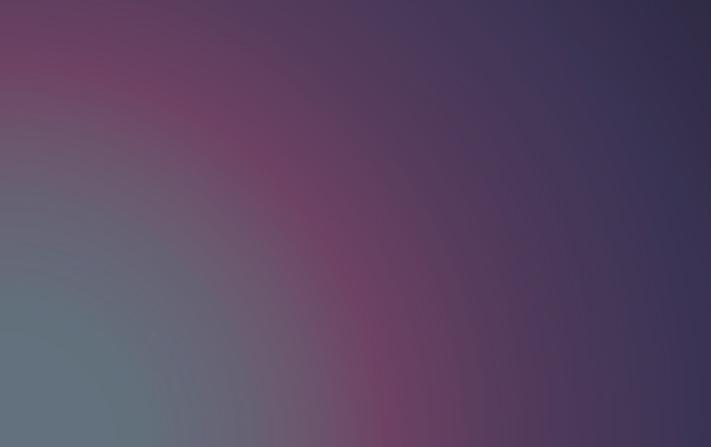
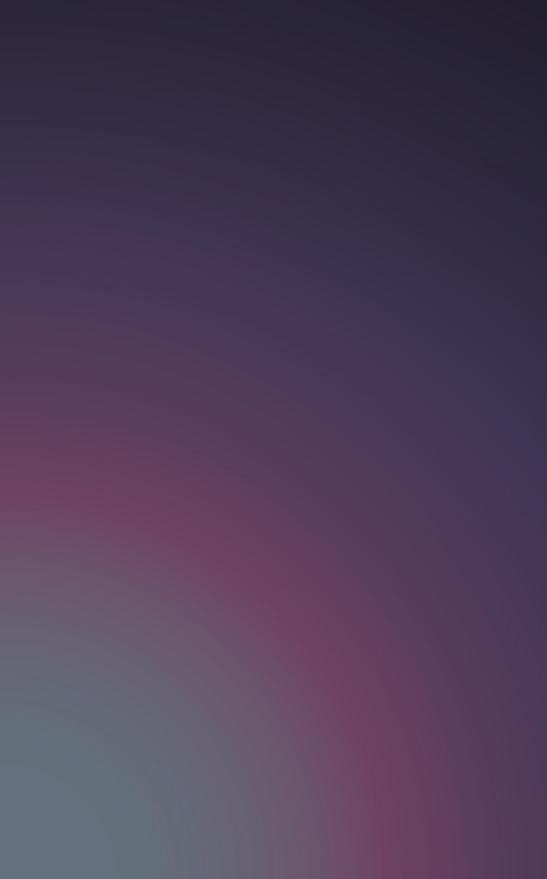
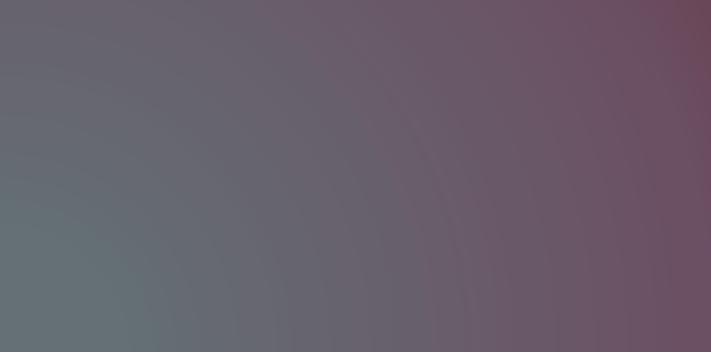
Companies have adapted to developing a concrete carbon project budget approach. This allows for flexibility in the concrete mix designs used because of a demanding schedule and special applications.
GHG reduction = CO2e Baseline − CO2e Project
The important number is the percentage Green House Gas reduction:
% GHG reduction = (GHG Reduction) ∙ 100 CO2e Baseline

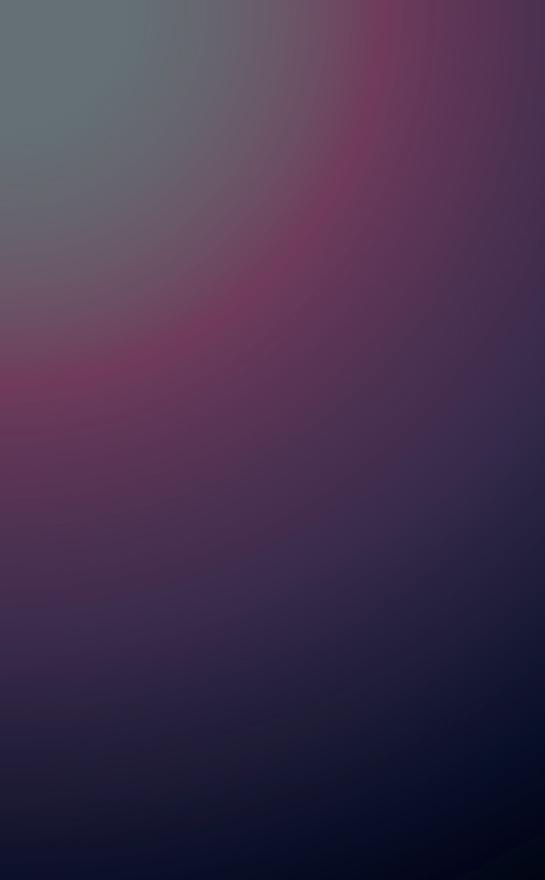
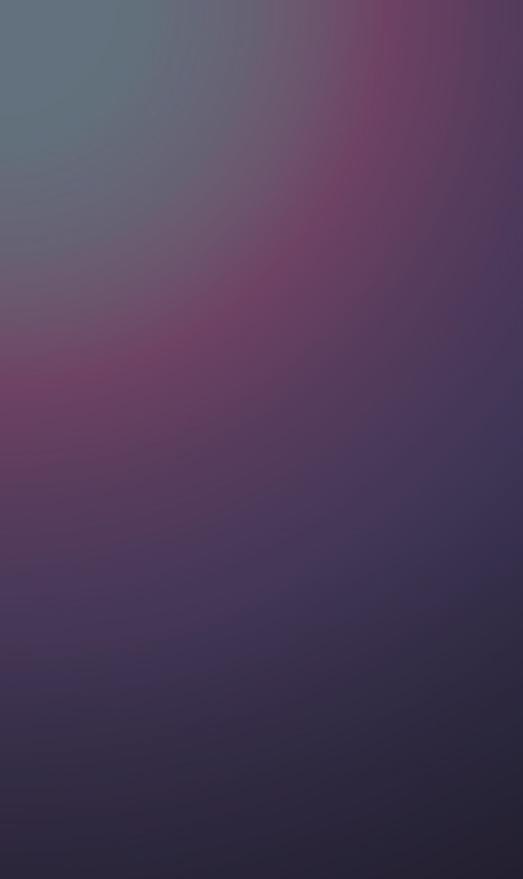


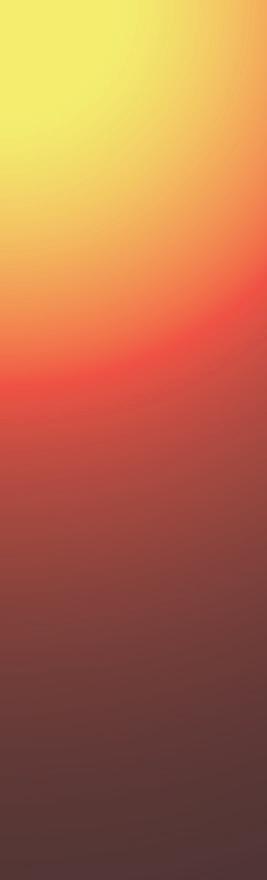
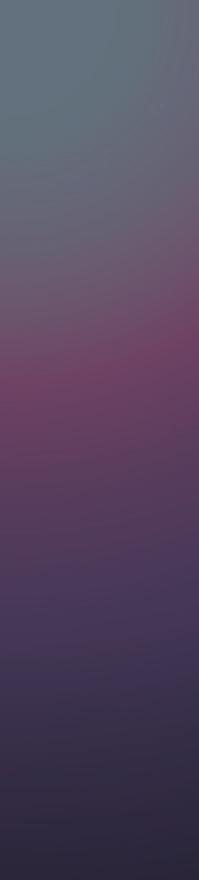
Through several calculations and considerations, a concrete carbon project budget can be reached. To find a project’s Green House Gas reduction:
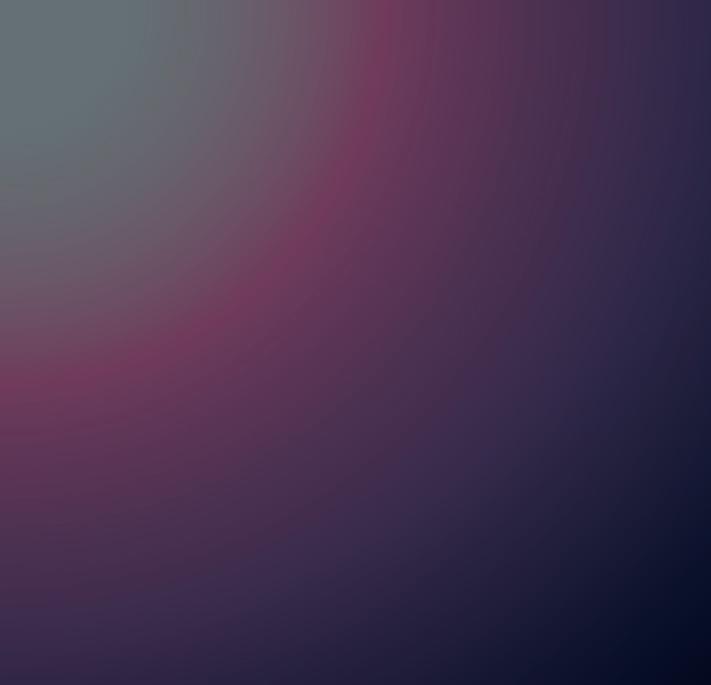
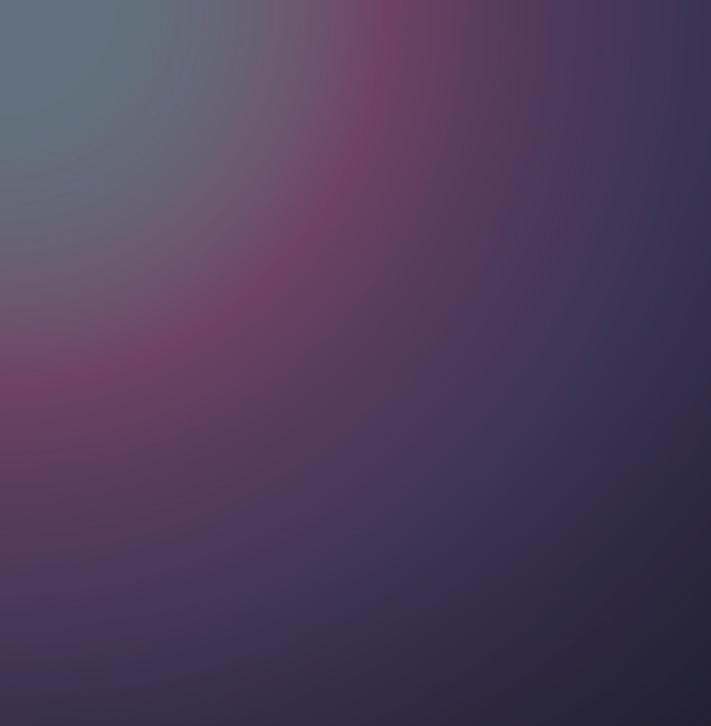
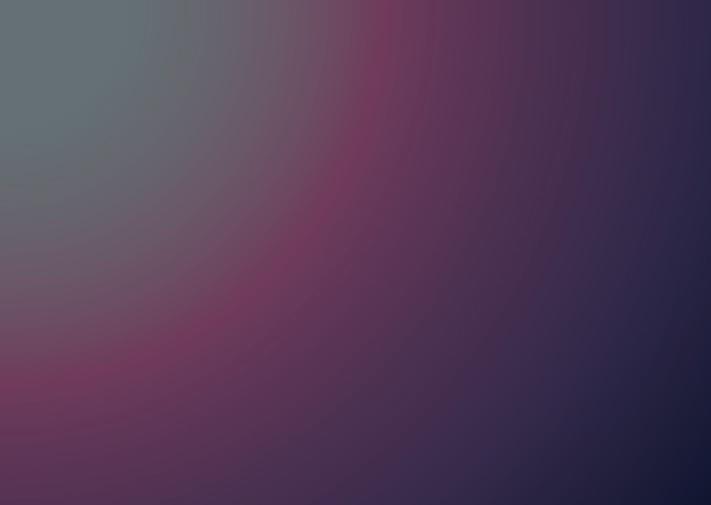
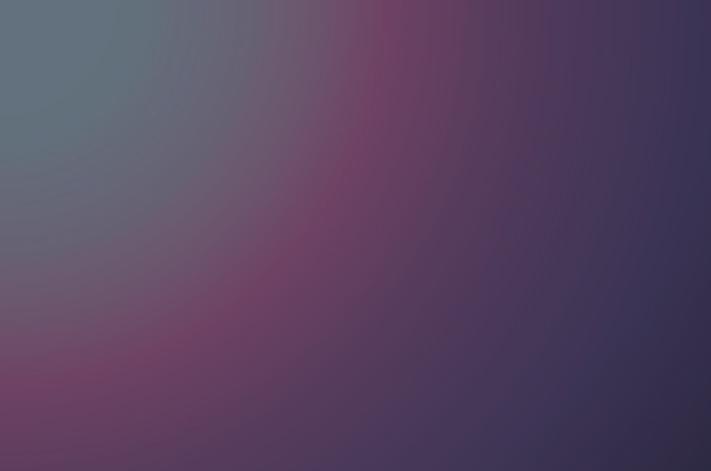
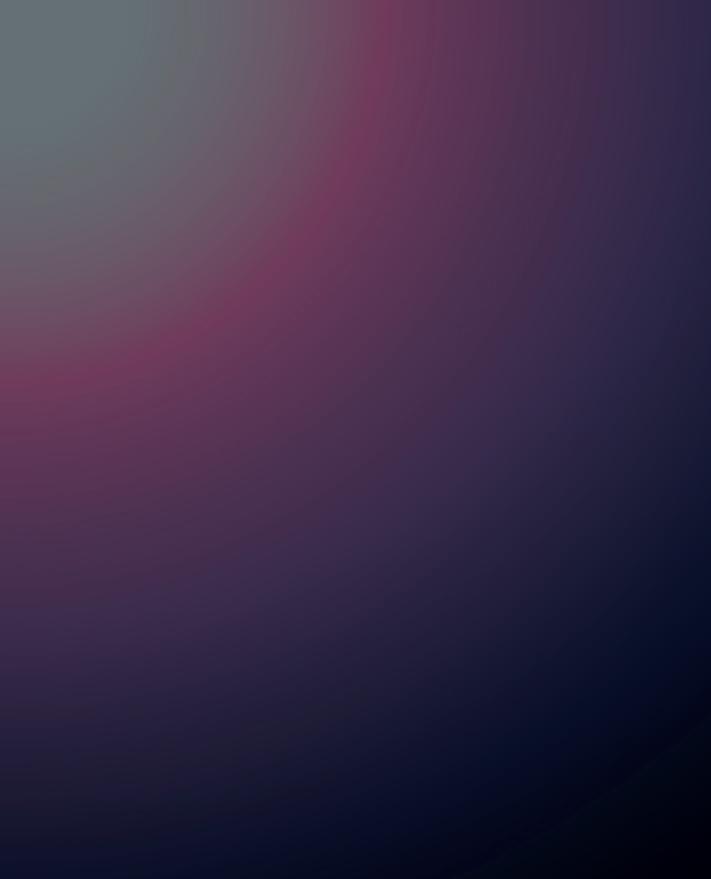

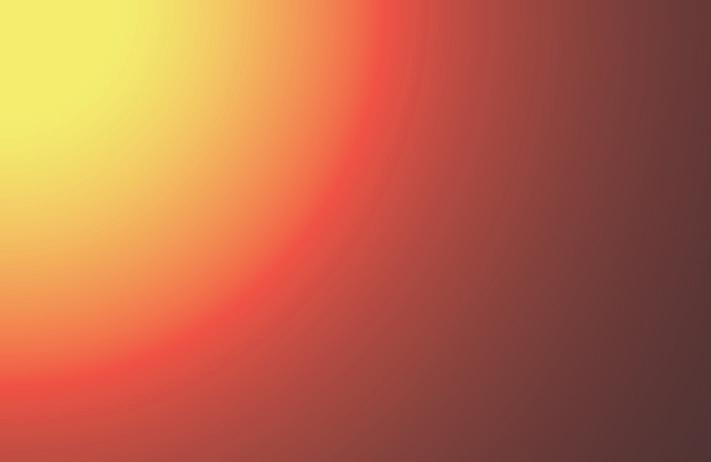

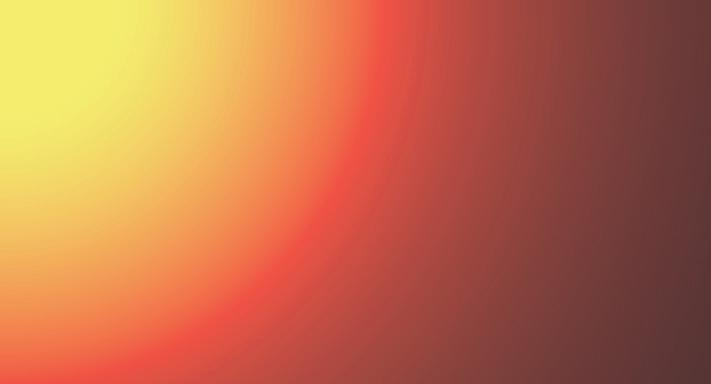
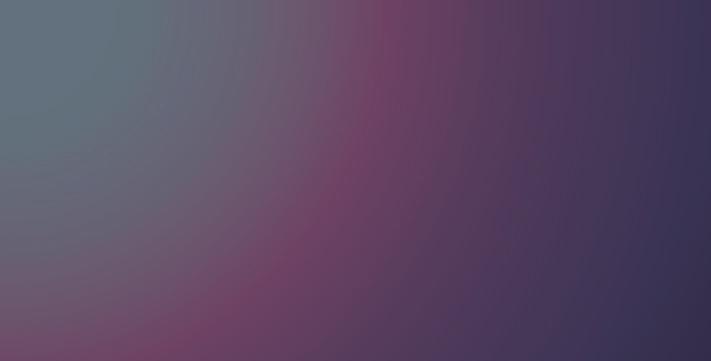
Carbon dioxide equivalent (CO2e) Baseline: The emissions calculated by the volumes of all the anticipated mixes used in the project multiplied by their regional average GWP.
CO2e Project: The emissions from the concrete used in the project calculated by the volumes of all the mixes used in the project multiplied by their GWP.
Example of a Carbon Project Budget Produced by Concrete Ontario
For this project, the anticipated CO2e Baseline was 9,294.9 tonnes CO2. As the project progressed, additional mix designs and specialty applications had to be used due to accelerated strength requirements to meet project deadlines. This increased the CO2e Baseline to a final Baseline of 10,661.9 tonnes CO2 The treasury board has allowed a 30% increase in GWP baseline for accelerated and cold concreting applications. This can help accelerate a project or allow it to run year-round without drastically impacting its GHG reduction capability.
After the placement of concrete is finished, the actual CO2e Project is calculated to be compared with the CO2e Baseline. In this case, the CO2e Project was calculated to be 9,032.4 tonnes CO2, significantly lower than the baseline, meaning the project had a large GHG reduction. Using the equations listed prior, the GHG reduction was calculated to be 1,629.5 tonnes CO2 and an overall GHG Reduction of 15.3%.
Anticipated Baseline vs Final Baseline for Different Mix Designs
CO2e Baseline Final CO2e Baseline
Concrete Carbon Project Summary (Type GUL)
Summary
Total Concrete Carbon Project Budget 10,661.9 tonnes CO2
Total Carbon Project Impact 9,032.4 tonnes CO2 84.7% of Project Carbon Utilized
Total Carbon Savings 1,629.5 tonnes CO2 15.3% GHG Reduction
Proposed Changes to the GWP Calculation
With potential new changes to the GWP calculation in the near future, one of the big changes to be discussed is the move from kg CO2e/m3 to kg CO2e/m2. Ontario has recognized that most of the embodied carbon comes from concrete, steel, insulation and wood. A new approach
is to evaluate the average on a per floor or surface area perspective of the entire building. It would appear that the goal here is to give a bit of flexibility on having various levels of carbon footprint floors with the goal of being below a specific level. Larger buildings would have a higher specification for kg CO2e/m2 than smaller ones. The issue is that project coordinators must now evaluate all the raw materials and ensure that the combination is lower
than the target kg CO2e/m2 target spec. This is now creating a lot of confusion for the raw material suppliers, such as ready-mix, as they can no longer use industry standards to show GHG reduction levels with their current mixes. Concrete Ontario is diligently working with the ministry and parties involved with this change to help educate them on the implications it could cause amongst the raw material suppliers.
Mississauga Technical Sessions
The Mississauga cement plant is opening its doors to all customers. Our goal is to provide an interactive and educational day to build your knowledge on cement and its affects in concrete. This one-day educational session will include a detailed tour of the cement plant, lunch and lectures.
Cement Plant Tour
The walking tour will take about two hours and will enable you to see how cement is made, from the entrance of the raw materials to final products leaving the door.The five key subjects we will cover during the tour are:
material extraction
Classroom Session
Once the tour is complete, we will return to the classroom for further discussion and lunch. Some of the key topics we will discuss during the classroom session include:
Introduction to Ash Grove
Cement manufacturing
SCMs and their importance
Cement reactions in concrete
Aggregates and admixtures
How to read a mill cert
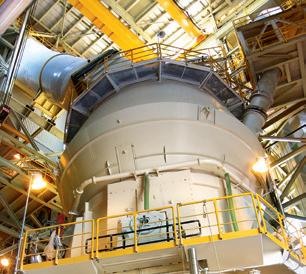
Common concrete plastic and hardened issues
Sustainability in the industry, including topics on EPDs, calculators and 2050 net-zero targets
We are hoping this training session will be informative for new employees to your company, as well as a refresher to more seasoned ones.
Looking to provide training at your location? We are happy to come out to you as well!
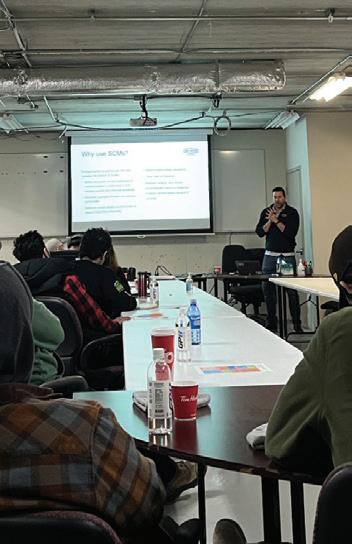
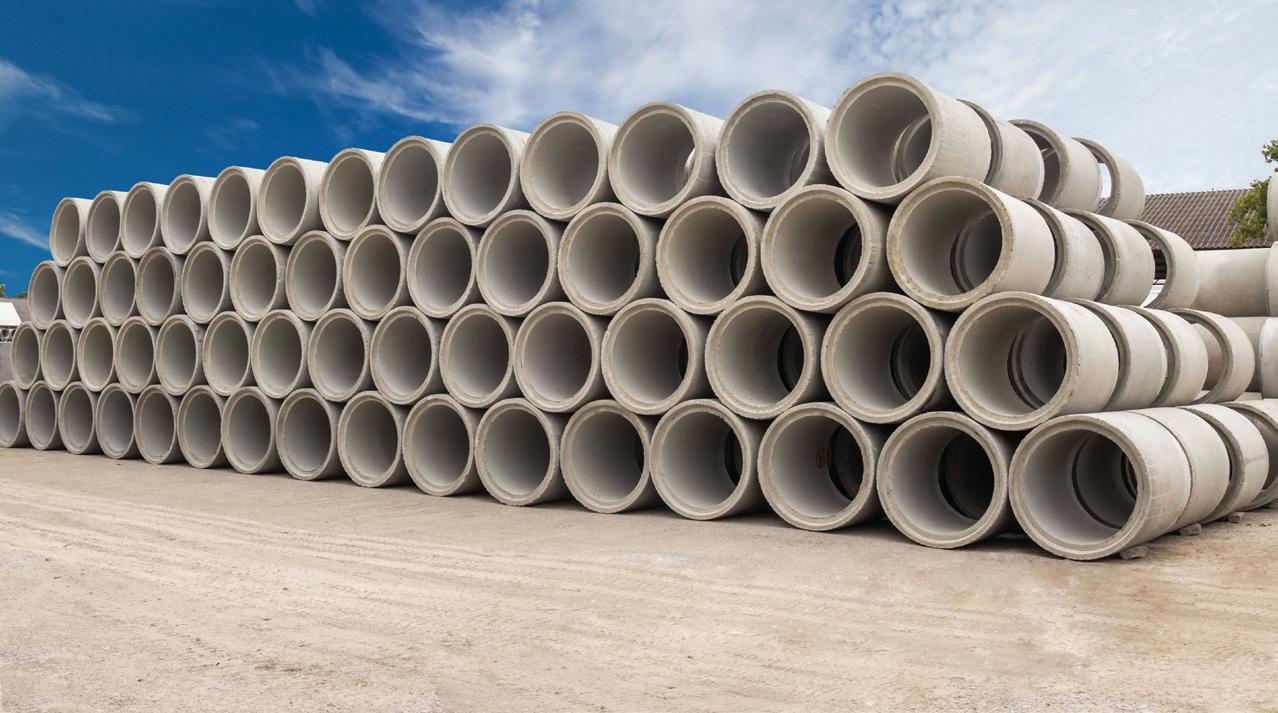
Manitoba / Saskatchewan Update
Ash Grove had the pleasure of joining our customers and colleagues during a meeting with the Ministry of Transportation Manitoba (MTI) in February this year to discuss the use and acceptance of GUL in both ready-mix and precast applications.
Currently, MTI has limited acceptance of GUL in precast/prestressed concrete. This is a concern given Ash Grove’s goal of net zero by 2050. Our message was clear. Given the elimination of GU in the market, we expressed what needs to be done for the Ministry to gain confidence in the product to approve it across all Department of Transportation (DOT) applications. The main specifications mentioned for GUL acceptance were:
• 1030 – reinforced cast in place concrete
• 1031 – specification for ready-mix concrete
• 1032 – superstructure concrete
• 1040 – fabrication of precast prestressed concrete girders
• 1047i – fabrication of precast concrete panels
At the end of our meeting, MTI had agreed to GUL for precast applications in most classes except for S1 (high sulphate attack exposures, requiring HS / HSb
cements). As an additional measure, we contacted the Ministry of Transportation of Ontario (MTO) for further assistance and references on GUL acceptance in Manitoba.
Meanwhile in Saskatchewan, they require a low alkali cement given the large amount of reactive (high silica phases) aggregate in the province. This market can only take cements with an alkalinity value below 0.6. Ash Grove supplies this market from the Joliette cement plant in Montreal as it is able to produce a low alkali cement. With the recent acquisition changes, Ash Grove is exploring new low alkali options for the Saskatchewan market. As of now, our cement plant in Chanute, Kansas can produce low alkali cement and deliver to the Saskatchewan market. Ash Grove is working with the Saskatchewan DOT to get this product approved.
Up until recently, the Saskatchewan DOT was only accepting low alkali GUL. It has recently come to accept products that meet CSA A3000-18, which includes
GUL. The Saskatchewan DOT is in the process of updating its documents for wording around the use of GUL. As with all regions that are new to accepting GUL, the first approach will likely be to allow it in residence and lower structural requirement works, such as curbs and pavements.
As requested by Saskatchewan DOT, we will follow its cementitious materials requirements and all testing involved to get an Ash Grove low alkali cement, such as the one in Chanute, approved. Our second step for the Saskatchewan market will be to get blended products approved. In most provinces and states, a blended product with either SLAG or Fly Ash is the easiest and tested method to help avoid sulphate and alkali-silica attack. We are hoping that given the use in blended cements across neighboring provinces, that this prescriptive requirement will quickly be changed.
For further updates on the Manitoba and Saskatchewan provinces, feel free to reach out to Rob Richer, technical services engineer with Ash Grove.
Embracing Innovation: Mississauga Cement Plant's Investment in Onsite Blending
After much anticipation, Ash Grove’s Mississauga cement plant is thrilled to announce an innovative investment in onsite blending capabilities. This strategic move represents a significant milestone in our journey towards operational excellence, sustainability and customer satisfaction.
Currently, the plant relies on third-party services located off-site for blending products. However, the time has come to internalize blending operations and ship directly from our facility. This shift not only enhances efficiency, but also aligns seamlessly with our strategic plan to offer lower clinker factor products and binders to the commercial market.
With sustainability at the forefront of our priorities, the incorporation of Supplementary Cementitious Materials (SCMs) into our blends is a key focus. This investment unlocks the potential to provide a wide variety of blends in higher
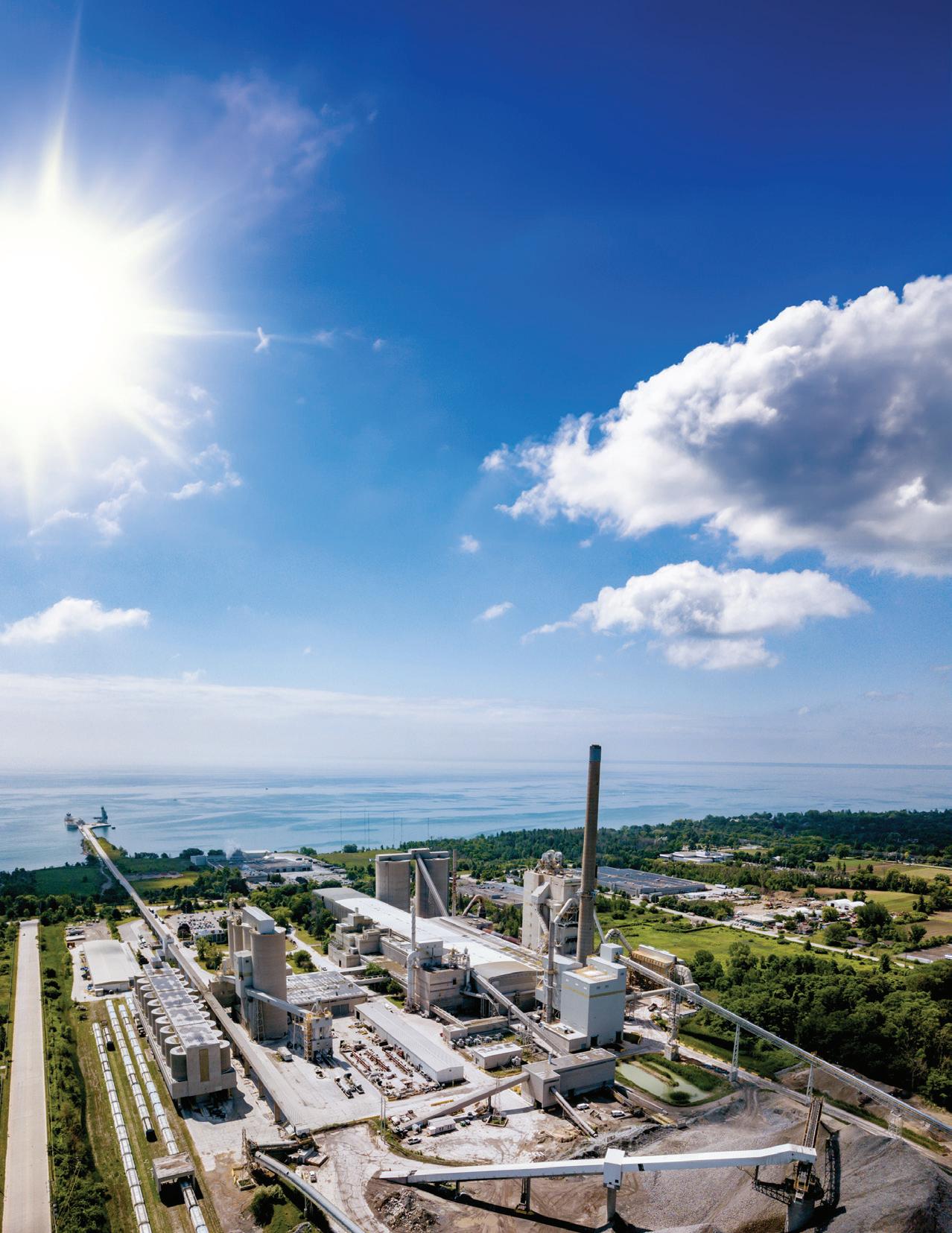
volumes, meeting evolving regulatory standards and mix designs.
The proposed system introduces a 'Dial-a-Blend' feature, allowing for custom mixes directly loaded onto trucks, eliminating the need for additional storage. This innovation not only streamlines logistics, but also boasts impressive loading times, ensuring swift and efficient service for our valued customers.
By bringing blending operations in-house, the Mississauga cement plant stands to increase throughput and capacity, providing increased blended
product solutions to meet the growing demands of the market. Furthermore, this initiative will indirectly improve our overall production capacity, unlocking opportunities for additional grinding of GUL cement and reinforcing our position as industry leaders.
In conclusion, Ash Grove’s Mississauga cement plant's investment in on-site blending heralds a new era of innovation and efficiency. This strategic investment not only aligns with our commitment to sustainability, but also enhances our ability to offer a diverse range of blends to the commercial market. The incorporation of SCMs into our blends underscores our dedication to meeting regulatory standards and evolving mix designs. By embracing innovation and efficiency, we are poised to deliver unparalleled value to our customers while reinforcing our position as industry leaders committed to sustainability and excellence.
Mississauga I&D Council
At Ash Grove, we thrive on bringing together many different backgrounds, trades and skills and stand as one force to be reckoned with, united in our pursuit of progress and equality.
Our employees are a vital part of our culture and we love the sense of being one community. We love to learn about new cultures, their backgrounds and, most importantly, have a taste of their cuisine (I mean food brings everyone together). Our spectacular team spiked the idea of bringing everyone to one table.
Formed in July 2023, the Mississauga Plant Inclusion and Diversity Committee meets monthly to discuss events and initiatives. It has supported a variety of monthly lunches to celebrate different cultures and holidays. Each lunch included food and decorations
for the holiday and/or culture and featured a short presentation on what the holiday meant, why it was celebrated and some background on the culture, such as music, religion(s), traditional foods, dress and unique facts for that holiday or culture. The teams leading the planning for the food ordered traditional foods and drinks so that the plant employees could enjoy food for that holiday or culture. Each event was well attended and thoroughly enjoyed by all employees, particularly by employees who had never had the chance to try some of the more traditional foods. Future events include things like the Lunar New Year, Nowruz (Iranian/Persian New Year) and other engagement events! The Committee also focuses on Employee Spotlights shown on our internal TV monitors. It highlights an employee’s likes, vision and certain information so employees can get to know each other at that location.
2023 Ontario Concrete Awards
Every year, the Ontario Concrete Awards Banquet recognizes some of the most innovative and exceptional projects among various companies in the concrete industry. Below are some of the winners for the 2023 Concrete Awards. We would like to extend our heartiest congratulations to all the winners of the Ontario Concrete Awards.
Architectural Hardscape
Innisfil Town Square
Material supplier: Champlain Ready-Mix
Location: Innisfil, Ontario
Date of completion: September 2022
Project type: Mixed-use public space
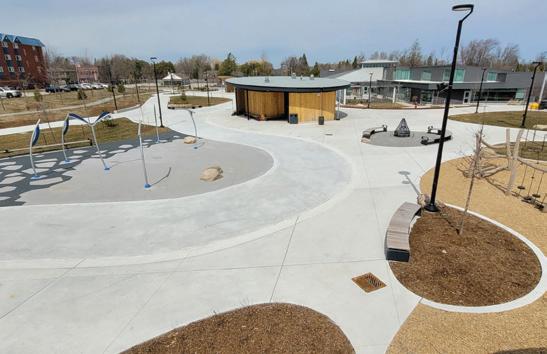
Approximately 1,200 m³ of concrete was used for this project, which included a skating trail, stage and event space, splash pad and walking trail.
Our focus is to be a place where everyone has the same opportunity to develop and progress, a place where everyone can feel personally and professionally fulfilled in their work. Our differences enable us to be a better team – one that makes better decisions, drives innovation and delivers better business results. Inclusion allows us to attract diverse talent and allows diverse voices to be heard. In practical terms, it is about creating an environment where everyone in the organization can be at their best. It involves all of us working together to make a difference by creating an environment that values the different contributions a diverse workforce can bring. An inclusive culture helps employees fulfill their objectives and maximize their potential irrespective of gender, race, creed, sexual orientation or ability.
At the Ash Grove Mississauga plant, we want to create and sustain a culture where fairness, inclusion and belonging are achievable for everyone.
To submit your project or check out other winners visit their websiteconcreteawards.ca
Infrastructure
Kingston 3rd Crossing
Location: Innisfil, Ontario
Date of completion: September 2022
Project type: Mixed-use public space
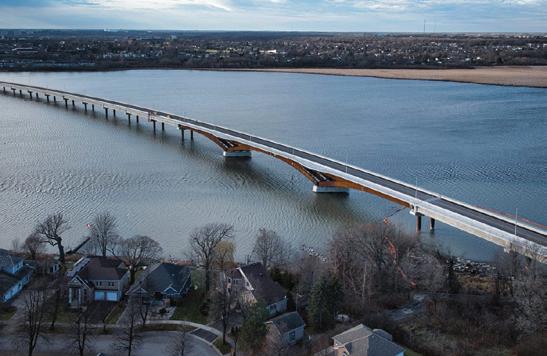
1.2 km bridge crossing the Cataraqui River, part of the Rideau Canal system Bridge Deck and diaphragm consists of 6,500m³ of ready-mix concrete with 95 precast girders that are 48m long and weigh 83 tonnes each.
In this model the budget of $180 million is set and the city, contractor and designer work together to deliver the project within that budget. Together all partners share the risk and reward to deliver the best possible project. The city is the first in Canada to use an Integrated Project Delivery model for building a bridge.
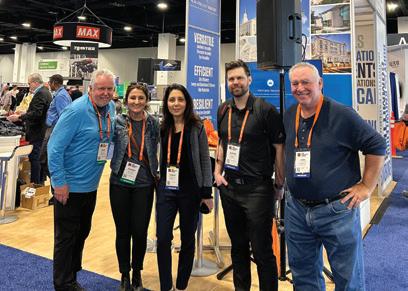
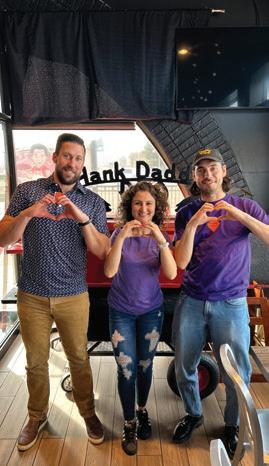
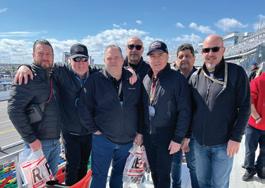
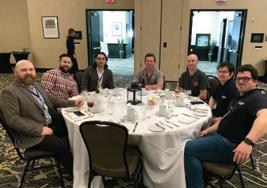



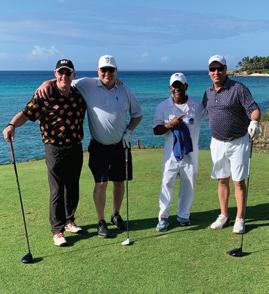
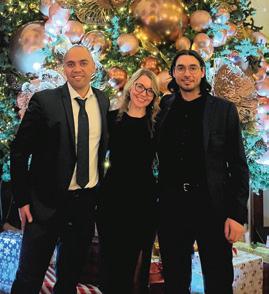
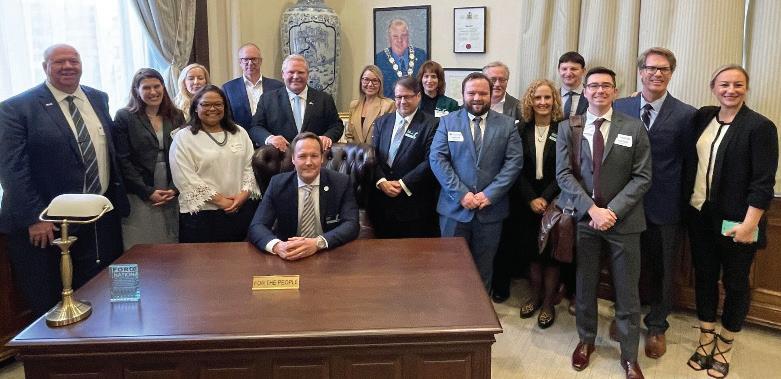