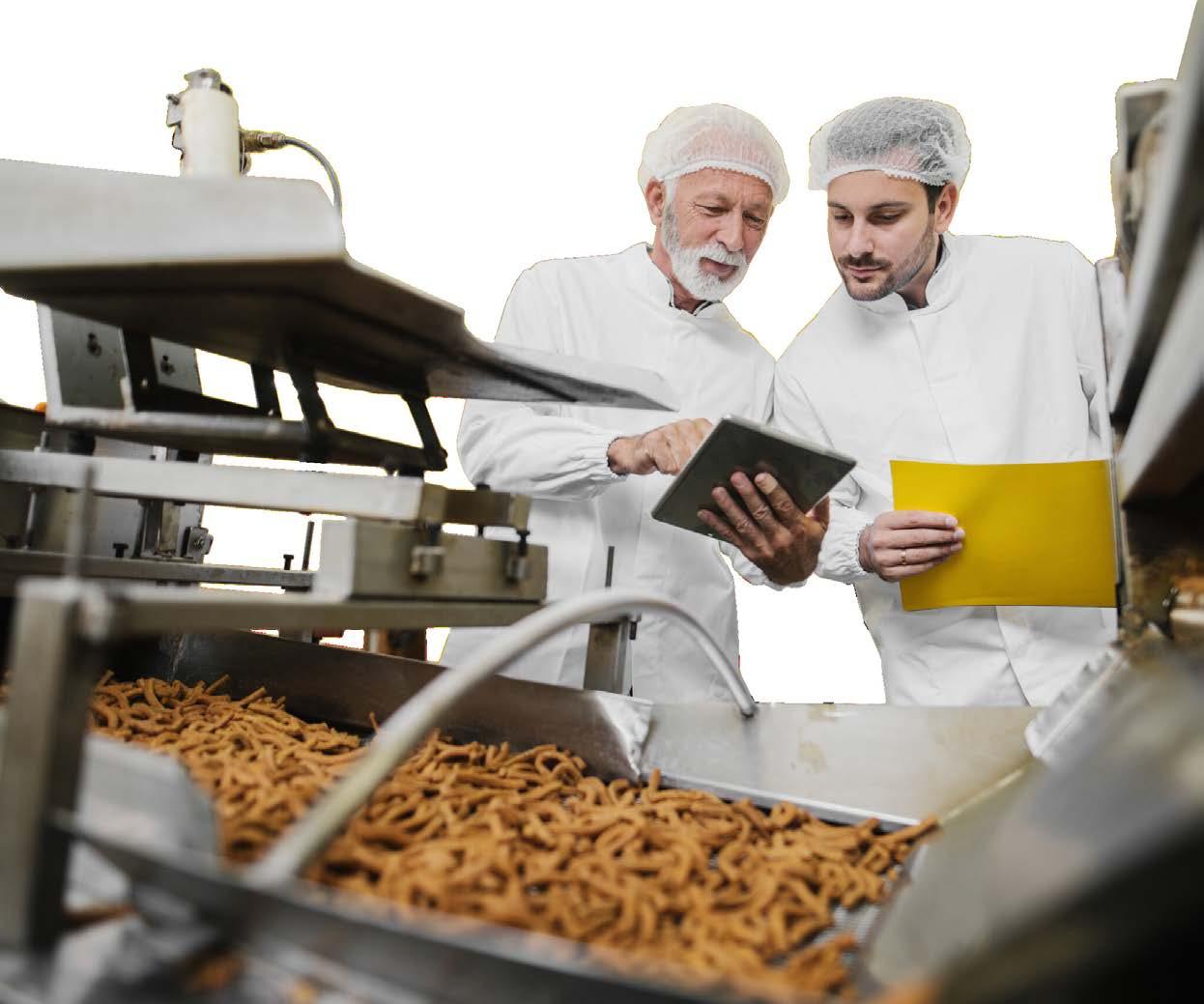
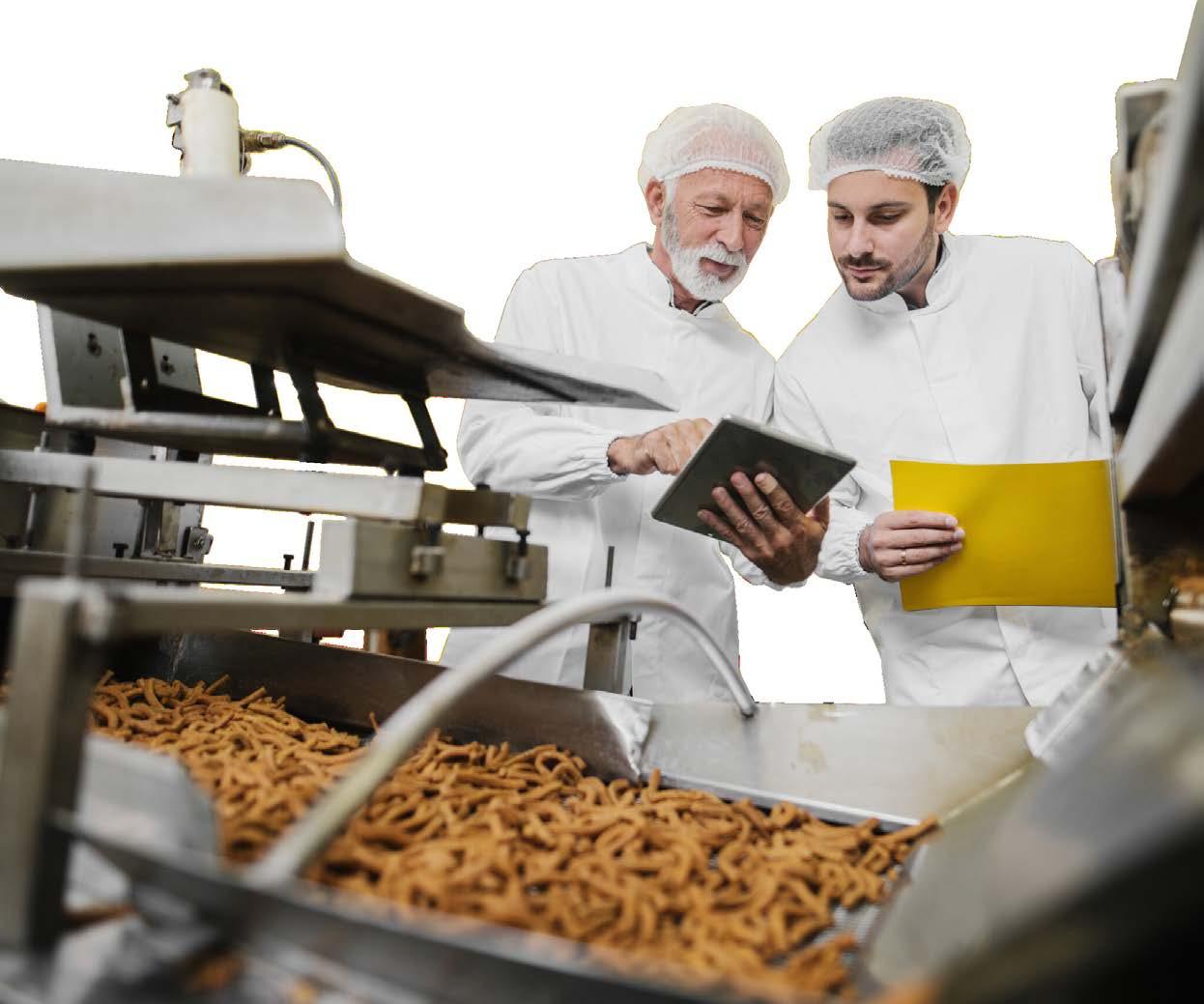
The Food Value Chain: 4 Topics you should keep in mind
Collaboration among stakeholders in the food value chain is more crucial than ever. With the global nature of food supply chains and the increasing frequency of recalls, food safety and traceability have become major concerns. Every stakeholder must take responsibility for sourcing, handling, and quality control. As a result, food safety policies and regulations now rely on the active participation of all parties involved. Sharing knowledge and data has become essential to managing the growing complexity of the industry.
Innovation for Sustainable Growth
As the global population continues to rise, food manufacturers face the ongoing challenge of improving productivity. So far, the food supply chain has proven adaptive to changing consumer demands, but future success will require even greater agility. Manufacturers must adjust to shifting demographics and consumer preferences while navigating an increasingly global and complex business environment. Leading global food producers are already addressing diverse dietary needs, sustainable supply chain practices, and evolving consumer demands. However, achieving these goals requires strong collaboration across the entire value chain, as both upstream and downstream cooperation is critical in food manufacturing.
Ensuring Food safety
Consumers are more concerned about food safety than ever before, and this anxiety is shared by food industry executives. Product quality failure is considered one of the industry’s biggest risks. Food safety has become a critical focus for companies that rely on public trust in the national food supply and the products they offer. New regulations, increasingly complex supply chains, and ongoing scientific advancements present both challenges and opportunities. Leading companies are investing in securing their supply chains, developing recall management plans, and improving product labeling and traceability. Compliance systems are being built to ensure that products meet the regulatory standards of all markets where they are sold.
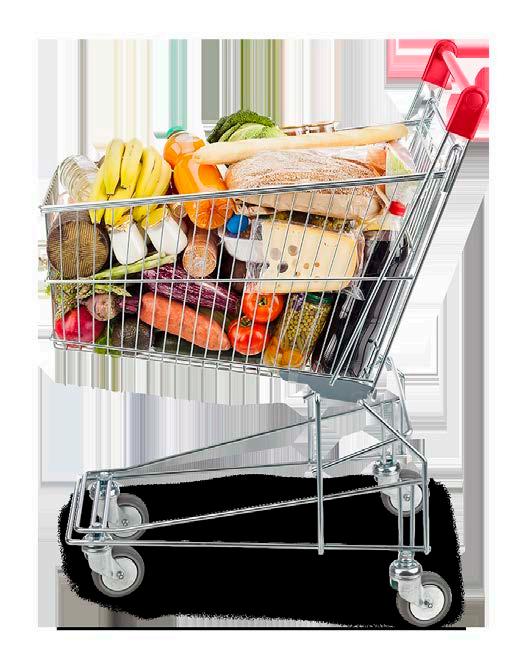
Globalization in the Food industry
The globalized food industry has led to greater specialization in processing and increased variety at lower prices. Over the past decade, consolidation across all food industry sectors has become the norm. As demand for food grows, particularly in developing regions, a significant shift in production and distribution methods will be necessary. Increased international trade will play a key role in meeting this demand. Countries must adopt modern farming, processing, and distribution practices to support large-scale trade. The timely sourcing and delivery of raw materials with minimal waste is a pressing challenge, one that can only be resolved through unprecedented collaboration across the value chain.
Addressing Waste Management
Waste management is a top priority for food manufacturers. In the developed world, total losses along the value chain can reach 40-50%, while in developing countries, food waste is estimated at 30-50% of total food expenditure. Although manufacturers and retailers have improved efficiency, it is becoming increasingly important to minimize waste during production to reduce losses throughout the value chain. Addressing waste caused by transportation will require manufacturers to find creative solutions for improving infrastructure and logistics.
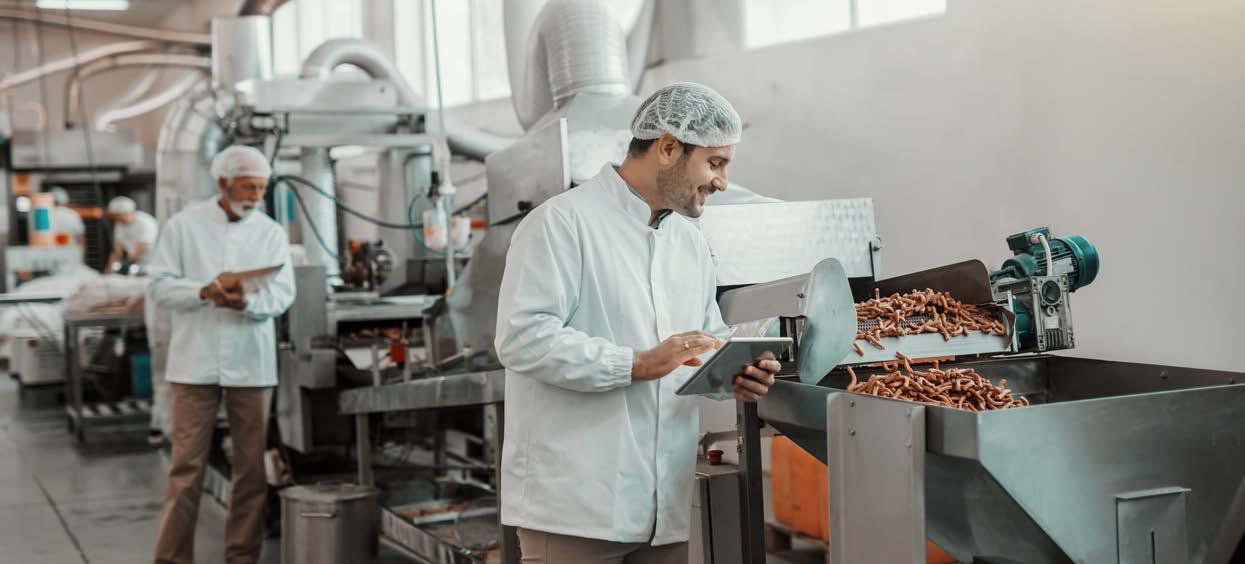
Food 4.0: Increasing Special Customer Needs as an Opportunity
Product development cycles are becoming shorter, customer requirements more stringent, quality standards higher, and at the same time, regulatory pressure on food manufacturers is increasing. These factors pose significant challenges for food producers.
Production Scheduling: Optimizing Processes Amidst Complexity
Production scheduling involves planning production orders on specific production lines at designated times and tracking the progress. It helps you stay on schedule and anticipate potential delays. By using production scheduling, you ensure that products are made at the right time. The sequence of production is pre-determined, allowing operators to focus on execution without needing to decide what to prioritize. This ensures the optimal use of production lines.
One key advantage of a digital planning solution is the ability to sort and schedule production orders efficiently. You can, for instance, plan based on order intake or when items need to be ready. Additionally, optimization can occur during the planning process, such as sorting by product color. For example, a sweets manufacturer must avoid making white sweets immediately after colored ones to prevent color contamination, which can compromise product quality. Failing to do so would require extensive cleaning, leading to wasted time.
Digital production scheduling optimizes the entire production process by linking all production steps. A production order can involve multiple stages. For example, when producing a mixed salad with carrots: washing the lettuce, cutting the lettuce, grating the carrots, cutting the carrots, and finally mixing all the ingredients in a jar. Although these steps may occur on three different production lines, digital scheduling ensures seamless coordination and efficiency across the entire process.
Special Dietary Requirements: Gluten-Free, Lactose-Free, or Kosher?
The demand for food products catering to specific dietary needs, such as gluten-free, lactose-free, or kosher, is on the rise. Alongside recipe management, it’s essential to maintain production lines suited to these specific conditions. A digital solution becomes crucial in managing and fulfilling these requirements.
For instance, when producing kosher products, you can define a specific recipe version that meets kosher standards. Additional instructions can then be added to ensure that all conditions for producing a kosher product are met. This applies not only to the ingredients but also to the production process itself. Whether you’re working with kosher, gluten-free, or lactose-free products, these specifications can be set as parameters for an article. These parameters are clearly and visually communicated to operators via their terminals.
Operators can easily see if an order is kosher or gluten- or lactose-free. Planners can then ensure that gluten-free products are not scheduled immediately after products containing gluten, avoiding cross-contamination. This guarantees that all special dietary orders are produced under the correct conditions.
MES and WMS: Bring your Production in the Perfect Flow
The combination of MES and WMS solutions allows for complete traceability of your goods and material flow—from receiving raw materials, through production, to the storage and delivery of finished products. Your logistics and production processes are seamlessly aligned, ensuring fast and accurate execution. This means the right products are delivered to the right production line at the right time.
End products also move efficiently through the warehouse to their final destination. Together, these components form—an all-encompassing tool for managing production and logistics in the food and beverage industry. It is the ultimate step towards achieving Operational Excellence.
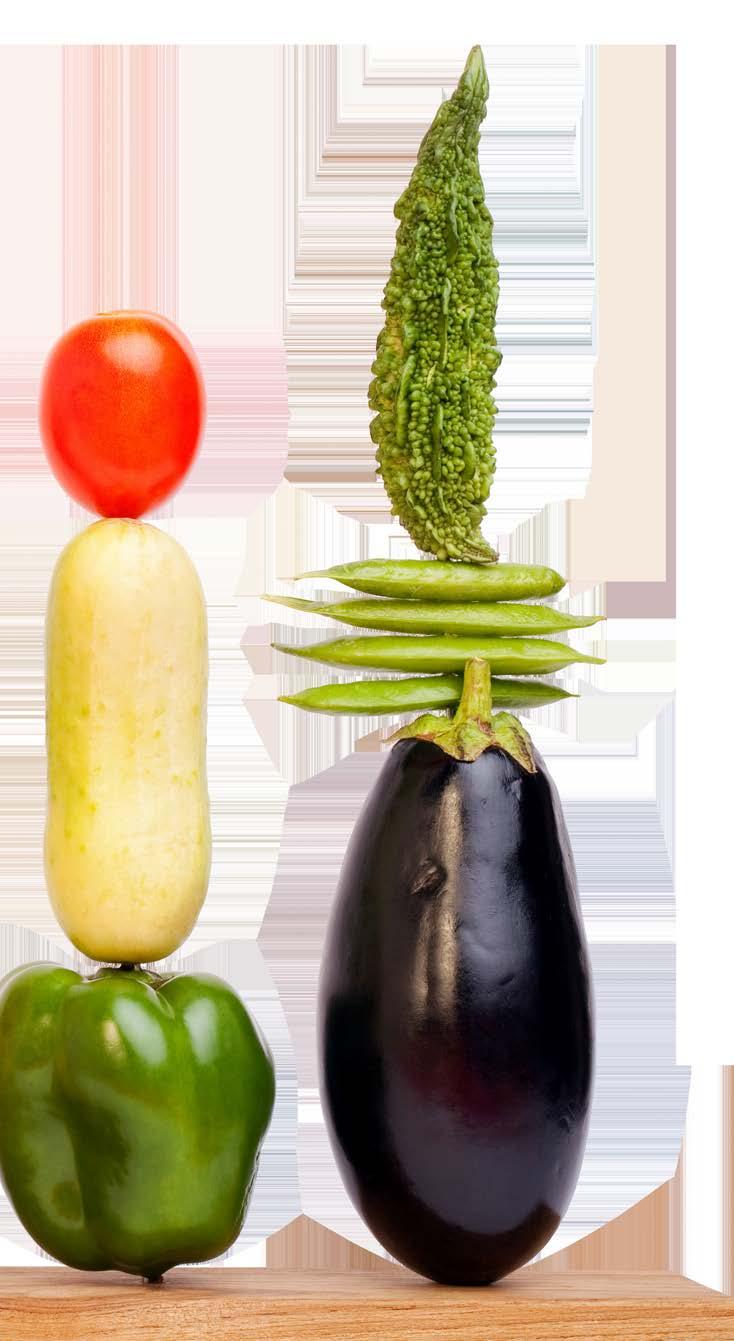
Aptean MES Objective Edition for the Food and Beverage industry
Our MES solution streamlines production processes and material flows, from handling raw materials and components to the creation of finished products. Aptean MES Objective Edition is composed of functional modules that can be implemented on a scalable basis, tailored to your specific needs. The core Production Management modules provide essential functions required to run your production operations, including:
Product Definition
Scheduling and Execution
Resource Management
Data Collection and Analysis
Our MES solution helps you to use your machines and production devices more efficiently, thereby providing you quantifiable advantages:
Deliver finished products with high quality and consistency with our recipe management
Reduce the amount of waste and surplus through the first-expired, first-out principle and save costs on ingredients
Get a real-time overview of your production progress and manage your schedule using the graphical plan board
Quickly find the cause when there’s a problem or complaint with a finished product in the event of a recall
Lower operational expenses
Continuous improvement through management of your machine settings
Aptean WMS Objective Edition for the Food and Beverage industry
Our WMS solution streamlines your logistics processes and flow of goods in your warehouse and even in your production environment - from receiving and storing the goods to picking, Value added logistics, kitting, repacking and on to shipment.
The basic Warehouse Management module provides optimal control over your daily operations:
› Warehouse-Modelling
› Order Management and Scheduling
› Task Management
› Inventory Management
Aptean WMS Objective Edition enables you to use your people, machines and logistic devices more efficiently, thereby helping you realise quantifiable advantages:
› Track and trace all transactions and movements from the receipt of goods to the shipping of finished products
› Keep track of your inventory levels and have your goods brought at the right time to the production lines
› Process higher volumes with the same amount of resources
› High degree of accuracy and punctual deliveries
› Limit inventory levels
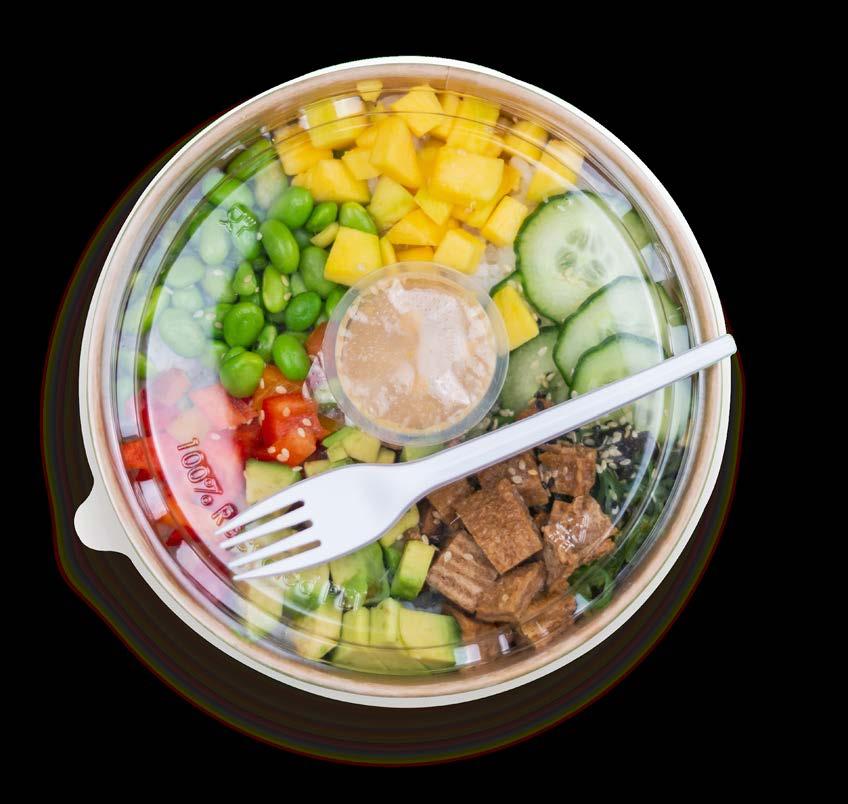
About Aptean
› Lower operational expenses of your machine settings
Do you have specific questions about how you can take your manufacturing and warehouse management to the next level?
Aptean is one of the world’s leading providers of purpose-built, industry-specific software that helps manufacturers and distributors effectively run and grow their businesses. With both cloud and on-premise deployment options, Aptean’s products, services and unmatched expertise help businesses of all sizes to be Ready for What’s Next, Now®. Aptean is headquartered in Alpharetta, Georgia and has offices in North America, Europe and Asia-Pacific.
To learn more about Aptean and the markets we serve, visit www.aptean.com.