Pedal to the Metal: How Fabricated Metal Manufacturers Can Accelerate Company Growth
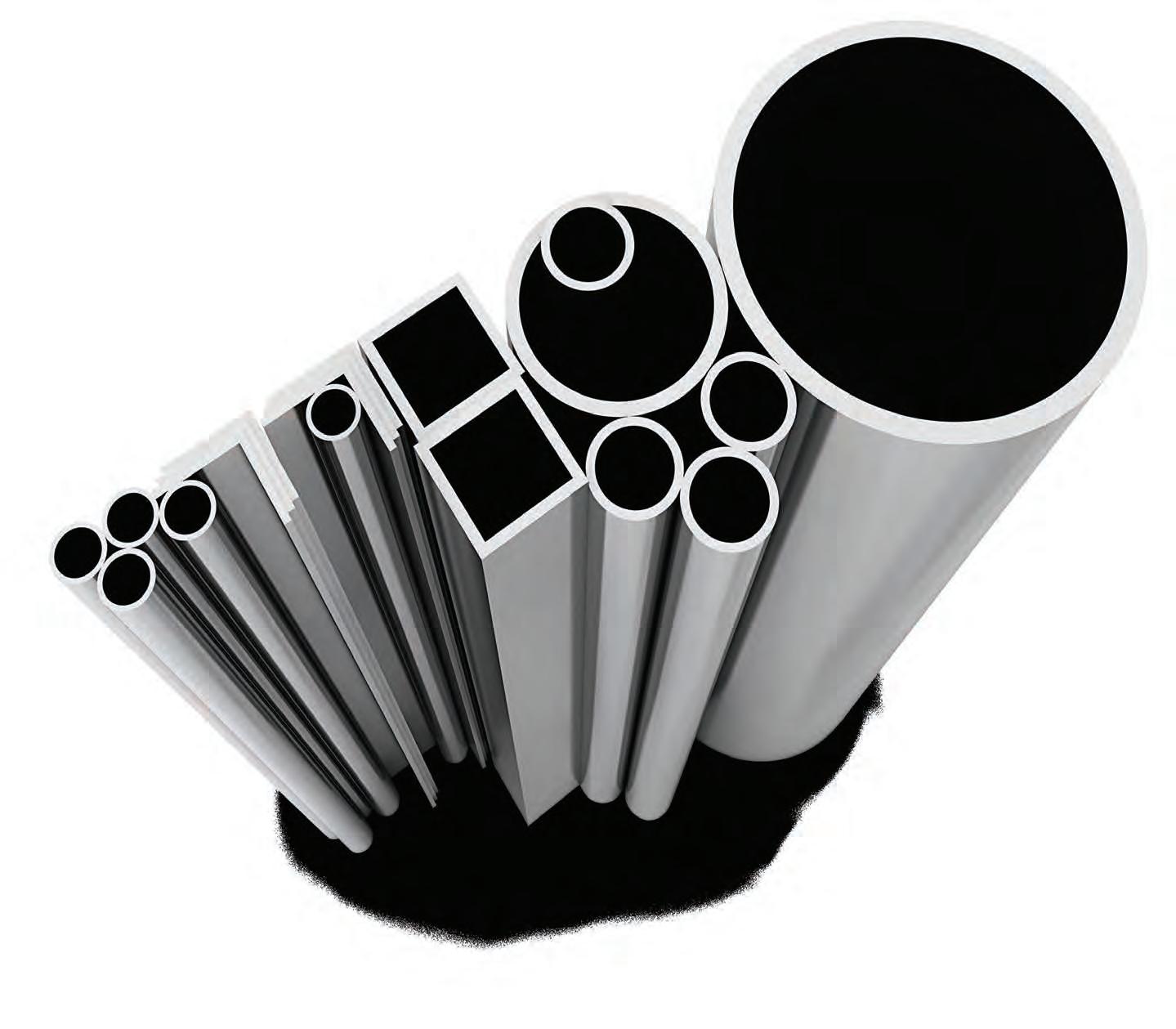
Like every manufacturing sector, metal fabrication has experienced major disruption over the past 24 months – which has changed both operational expectations and which customers and products can be relied on to provide a steady income stream.
Yet, despite market turbulence, the future of fabricated metal manufacturing looks buoyant. And many organizations feel confident that their sales and revenue will increase throughout 2022.
But prosperity relies on manufacturers embracing a new world in which operations, people and relationships behave differently – not reverting to legacy systems and processes, hoping to weather future disruption.
To better understand how the metal fabrication sector is evolving and how organizations can grow their business in a post-pandemic world, Aptean surveyed 275 North American manufacturers.
Through our findings, we’ve identified four core challenges affecting the fabricated metal manufacturing sector – and how industry leaders are facing these challenges head-on to drive business expansion in 2022.
72% of fabricated metal manufacturers increased their annual sales and revenue in 2021, and 96% forecast further improvement in 2022.
As metal fabricators serve a wide variety of industries, manufacturers have been well-positioned to diversify their product and customer base during recent trading periods. And as result, they have navigated the pandemic better than some other manufacturing sectors.
Almost three quarters (72%) of the fabricated metal manufacturing companies that Aptean surveyed said their year-on-year revenue increased in 2021, and 48% are now in a place of business prosperity.
Confidence is even higher for the year ahead, with 96% of metal fabricators forecasting sales and revenue increases. But which sectors provide the best prospects for securing new business?
72% of fabricated metal manufacturers have recovered from the pandemic, and 48% say their business is now prospering.
The recovery of wider sectors is directly benefiting metal fabricators, with growth in aerospace and construction providing lucrative revenue streams for the next 12 months and beyond.
After two difficult years, the aerospace industry is getting back on its feet, with commercial airline passenger capacity set to grow by 47% in 2022 – driven predominantly by activity in Asia. And this will create new manufacturing and maintenance opportunities for metal fabricators.
As Deloitte notes, “recovery in air travel demand should drive an increase in aftermarket activity as higher aircraft utilization usually corresponds with increased maintenance, repair, and overhaul (MRO) work.” After significant financial losses during the pandemic, commercial airlines will be keen to maximize operational activity and ensure high maintenance standards to satisfy returning customers.
Another key sector driving manufacturing revenue this year will be construction, where output is now 1.7% higher than December 2017 thanks to record activity in the real estate market.
2021 was a year like no other for homebuying, with demand seemingly increasing month-on-month and properties reaching record prices in many areas. While this trajectory is not sustainable, construction will remain consistent throughout 2022 – providing ongoing revenue opportunities for fabricated metal manufacturers. As ITR Economics’ Senior Forecaster, Connor Lokar, summarizes, “I look at it as taking our foot off the accelerator, not slamming on the brakes and moving backwards.”
One thing worth noting, however, is that commercial construction isn’t recovering as quickly as the residential sector, due to many companies continuing to work remotely. This underlines the importance of metal fabricators understanding how customer demands are evolving, to capitalize on every new opportunity.
Like any sector, fabricated metal manufacturing must adapt to market disruption, optimize operations for current demands, and prepare for future change. But numerous challenges stand in the way of achieving this.
Our research identified four critical areas where metal fabricators want to strengthen and improve, to create the conditions for company growth.
Whether it’s colleagues or customers, personal relationships play a huge role in manufacturing success – yet these aren’t always easy to maintain.
The nature of metal fabrication means that many manufacturers are small businesses (SMBs), run by a limited number of staff and reliant on significant contracts from a small number of customers.
The loss of a customer or employee is felt deeply in terms of productivity and profitability. Our research found that people-based problems – employee availability/skills shortages and customer retention – are fabricated metal manufacturers’ biggest barriers to growth in 2022.
Even keeping hold of the current workforce is proving a challenge to many organizations, as 69% of fabricated metal workers expect a pay rise of 2% or more this year.
After months of material shortages and delays, the manufacturing supply chain is starting to recover. But it’s going to be a while before normality resumes.
56% of the fabricated metal manufacturers Aptean surveyed say they are still experiencing long lead times; a much higher number than the manufacturing industry baseline of 32%.
Meanwhile, 40% are being challenged by fluctuating prices as a result of limited material availability. Manufacturers have been hit by two years of surging metal prices, with high demand seeing metals such as steel reach their biggest cost-price detachment in history.
Not only is supply chain disruption making operations, logistics and profit margin harder to manage, it’s having a direct impact on the customer relationships that manufacturers are trying so hard to protect.
64% of fabricated metal manufacturers have needed to extend customer delivery deadlines over the past 12 months as a result of supply issues, and 32% have cancelled some orders to prioritize high value customers.
There is some respite on the horizon; metal prices seem to be stabilizing, helped by the lifting of international trade tariffs on importing steel and aluminum, and supply chain bottlenecks are beginning to ease. However, manufacturers realize that their supply management model needs to change if they want to safeguard their business against future disruption.
64% of fabricated metal manufacturers have needed to extend customer delivery deadlines due to supply issues.
Supply chain disruption isn’t just impacting customer relationships; it’s causing critical problems elsewhere in manufacturing operations, which is challenging metal fabricators in other ways.
With material and component deliveries unpredictable, many fabricated metal manufacturers are struggling to maintain appropriate inventory levels. 3 in 10 organizations told us that aligning their production schedule with available inventory is a major business challenge – particularly for jobs involving purchased components such as microchips, where there have been global shortages.
These inventory management challenges have made production very stop/start for many manufacturers, and also impacted metal fabricators’ ability to accurately forecast workload.
When we asked organizations how far they could track raw materials through their production line, only 56% could trace them from supplier through to distribution. And this lack of end-to-end visibility is affecting areas such as quality control and industry regulation.
Without complete traceability, it’s difficult to prove regulatory compliance – or to respond quickly to any issues affecting product quality and legality. And fabricated metal manufacturers in North America will face further pressure to improve visibility as international regulations change; in the UK for example, regulatory bodies recently launched national health and safety inspection program to ensure that workers are not being unnecessarily exposed to metalworking fluids and welding fumes.
We’ve outlined the key challenges fabricated metal manufacturers face in 2022. But how are organizations solving these issues, to mitigate risk and realize their predicted profit potential?
Our research identified four key strategies that metal fabricators are prioritizing in order to enhance their business growth this year.
While fabricated metal manufacturers can work across multiple industries, demand is rarely consistent in each sector. To capitalize on every new business opportunity, fabricators need the agility to ramp production up and down in line with market activity.
Digital transformation is critical to achieving operational flexibility, and many companies are already implementing software to make them more flexible. For example, 44% of the fabricated metal manufacturers we surveyed have already automated production management, and 48% of those who’ve invested in smart factory software say it has increased their speed of production.
Another key aspect to becoming more agile is improving inventory management. Some metal fabricators have taken to holding ‘safety stock’ in order to combat material shortages, but this isn’t the most resourceful or costeffective solution to supply chain constraints.
A smarter alternative is to make inventory control a priority area for digital transformation; deploying software that can make smarter use of available inventory by aligning material supplies with current and forecasted orders. And this is exactly what 64% of fabricated metal manufacturers plan to do.
Smarter inventory management doesn’t just safeguard against stock-outs; it enables manufacturers to reconfigure production schedules based on what’s available, to keep production running even when certain jobs are on hold.
Strong supply chain management unlocks value throughout the manufacturing process. And many metal fabricators recognize the need to widen their supplier networks in order to increase resilience.
When the pandemic hit and brought global trade routes to a standstill, any manufacturers reliant on a small number of suppliers were badly affected – especially fabricators reliant on Chinese imports.
Our study revealed that more than a third (36%) of metal fabricators struggled with a lack of vetted alternative suppliers when trying to manage their supply chain in 2021, while 32% experienced issues with onboarding new suppliers.
To overcome this, 56% of fabricated metal manufacturers plan to spread their orders across a wider number of suppliers in 2022 – with many considering nearshore sourcing alongside international suppliers to further mitigate risk.
Digital transformation will also influence supplier management and decision-making capabilities over the next 12 months. Only 28% of fabricated metal manufacturers have automated their supply chain operations, compared to the manufacturing industry average of 42%.
Putting digital workflows in place will enable organizations to understand which customer orders are impacted by supplier setbacks, and also identifying alternative partners that can provide the volume of materials they require within the necessary timeframe.
56% of manufacturers plan to use more suppliers in 2022.
Digital transformation delivers more than just operational value. It plays a pivotal role in innovating company culture and improving employee productivity, which are essential to driving growth.
The employee experience is central to many manufacturers’ 2022 business development strategies. 52% of metal fabricators plan to use software to streamline the hiring process and recruit stronger talent this year. And the same percentage want to implement more effective training through manufacturing technology, to upskill and inspire their existing workforce.
In parallel with this, many fabricated metal manufacturers are looking at which current manual tasks can be automated using smart factory software – with a third (32%) of those who’ve implemented digital transformation projects seeing an improvement in productivity within the first 12 months.
Manufacturers also appreciate the value of each employee to their business and want to take steps to mitigate the impact of people leaving the company or changing their role.
62% want to capture more data to prevent employee changes resulting in knowledge loss – particularly where experienced fabricators are retiring and being replaced by young professionals. And 52% want to use technology to improve contingency planning, so employees can work more productively, even in difficult circumstances.
62% of manufacturers want to capture more data to prevent knowledge loss when employees leave or change roles.
Although there are day-to-day challenges to solve, metal fabricators recognize the importance of innovation in an industry where there are multiple revenue streams to explore.
44% of fabricated metal manufacturers told Aptean they are prioritizing product innovation in 2022, which is much higher than the general manufacturing industry average of just 26%. And we’re already seeing fabricators using digital software to accelerate R&D.
For example, some manufacturers are now using CAD/CAM systems to create prototypes before metalworking begins – speeding up product development while limiting material wastage and managing costs.
Many front-running companies are also integrating operational processes, to create a seamless transition from concept to commercial execution. 52% of the metal fabricators who participated in our research have already automated quoting and estimating, and 48% are automatically calculating BOMs. This means their successful prototypes can be rapidly put into production with accurate costings and material requirements.
92% of fabricated metal manufacturers are even interested in exploring the potential of leading-edge technologies such as robotics to improve the accuracy, consistency and quality of production. However, this can only be seriously considered once essential processes have been optimized.
Metal fabrication is a transformational process, and manufacturing operations should be no different. To accelerate company growth, fabricators need to adapt quickly to both market challenges and customer opportunities.
Establishing a well thought-out digital transformation strategy is central to automating processes, improving speed and accuracy of production, and liberating employee value – all essential ingredients in improving business performance, and key to embracing change.
To create a digital transformation that can weather market conditions, here are six key things manufacturing executives can consider:
1.
Start with an audit – although a smart manufacturing set-up should enhance production endto-end, some operational areas will be more vulnerable than others. By conducting an audit you can identify areas that need immediate attention; these may have changed since you drafted your original transformation roadmap.
2. Make people central to the proposition – whenever you’re considering investment in new manufacturing technologies, focus on the value it will deliver to your employees and customer service. This is where transformation is needed most.
3. Understand the impact of change on other business areas – one small shift can have a major ripple effect. For example, expanding your supplier network might not seem like a top priority, but it could transform inventory management and speed up production.
4. Get your infrastructure right – innovation is important, but prioritizing optimization will enable you to put new concepts into production quicker. A strong operational infrastructure is pivotal to driving long-term success.
5. Think holistically – find solutions like fabricated metal ERP software, which allow you to enhance multiple business areas through one technology platform, rather than looking at your problems individually and sourcing separate solutions to solve each challenge
6. Constantly question and learn – with an integrated digital transformation strategy in place, your business will be generating valuable, joined-up data. Analyze this information to continuously question your systems, strategies and relationships, to strengthen your proposition and drive
Aptean is one of the world’s leading
grow
With
and on-premise
Aptean’s products, services
that helps manufacturers and distributors
of all sizes to be Ready for What’s
Now®. Aptean is headquartered in Alpharetta, Georgia and has offices in North America, Europe and Asia-Pacific.
www.aptean.com