CRITICAL MINERALS
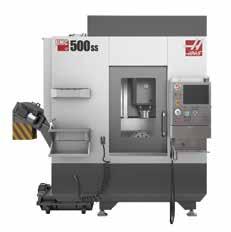
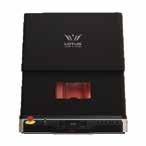
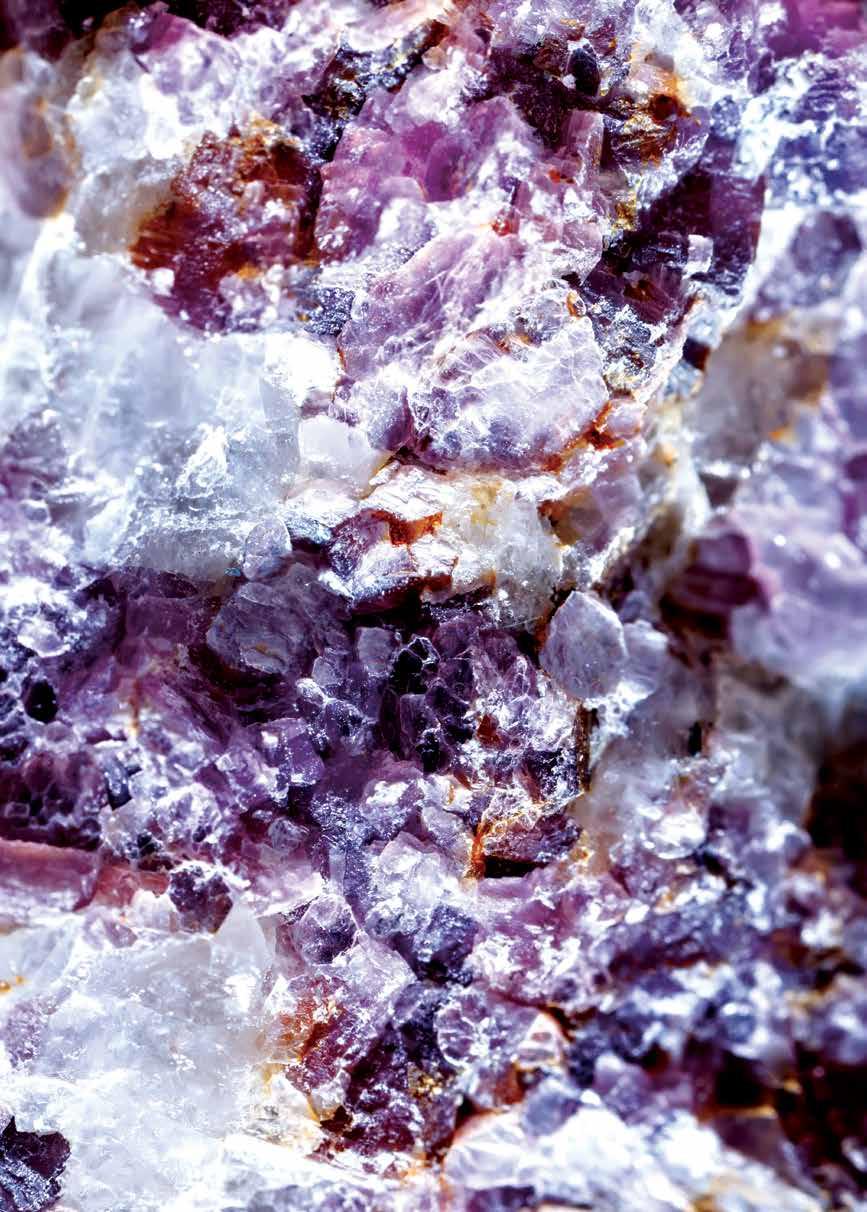
MINING & RESOURCES
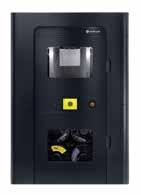
Transport & Logistics
State Spotlight: Queensland
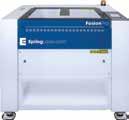
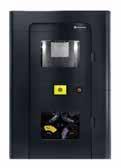
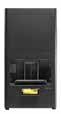
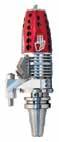
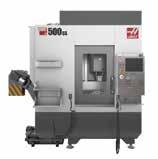

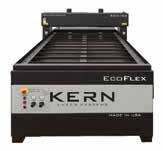

CRITICAL MINERALS
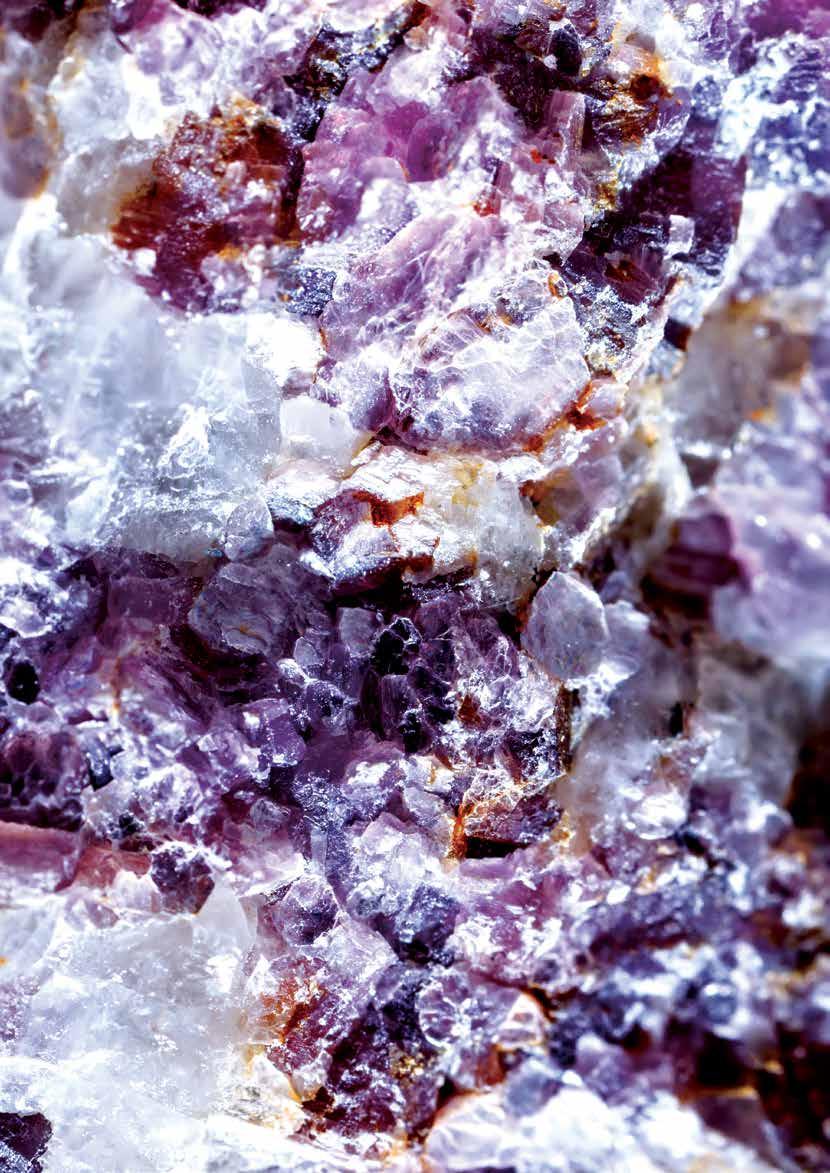
MINING & RESOURCES
Transport & Logistics
State Spotlight: Queensland
SHOWCASING 7 PRODUCT ZONES
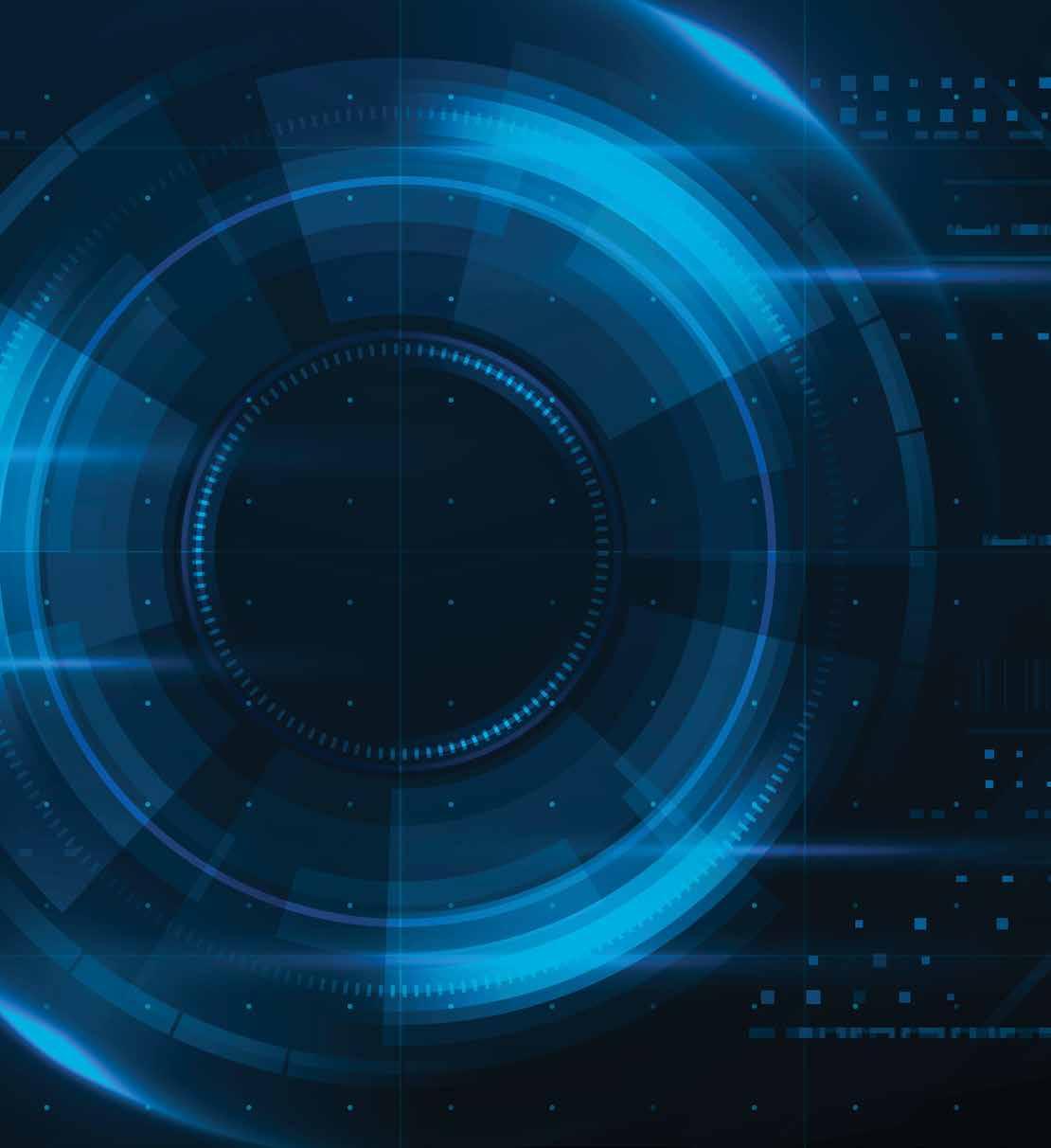
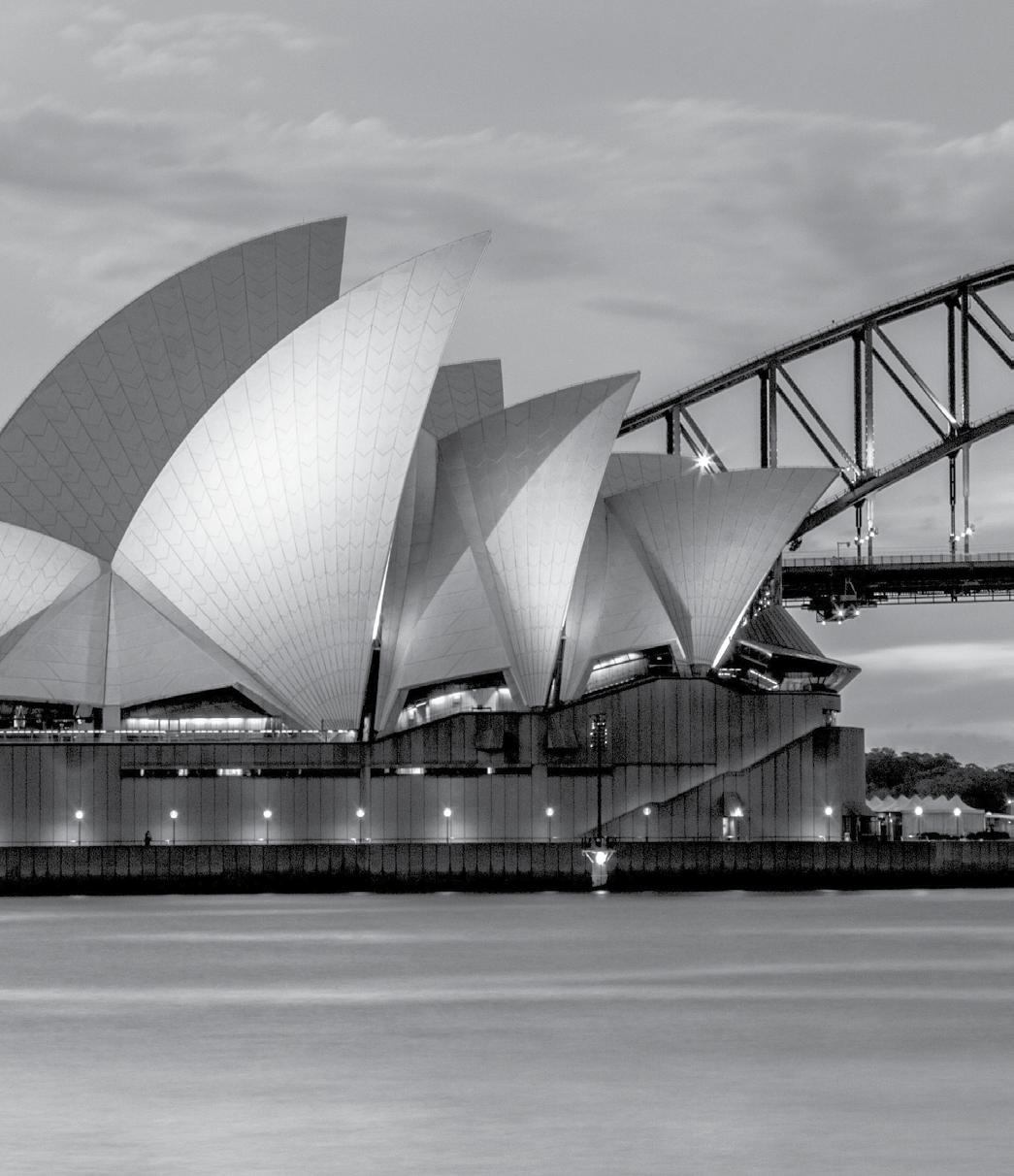
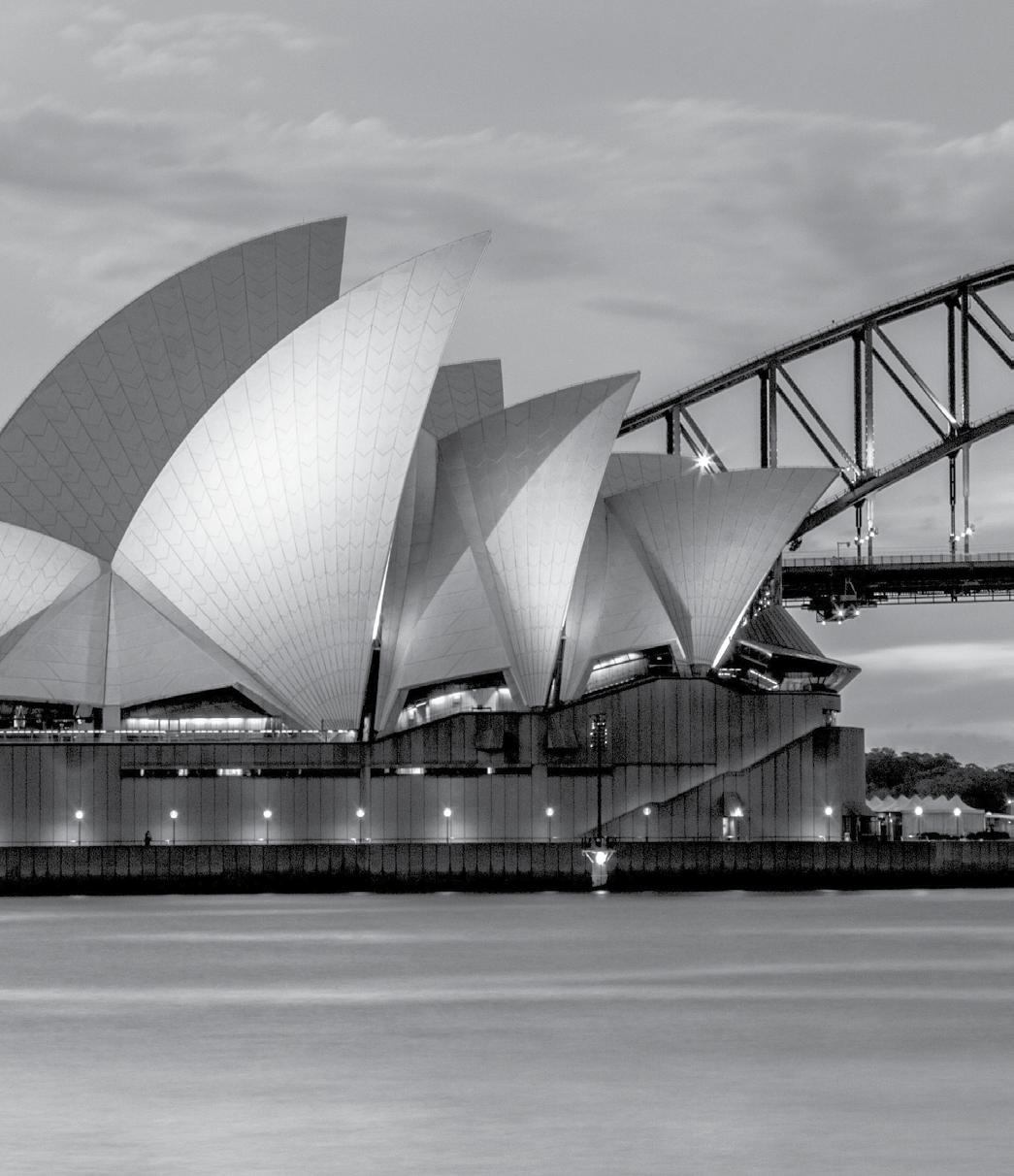
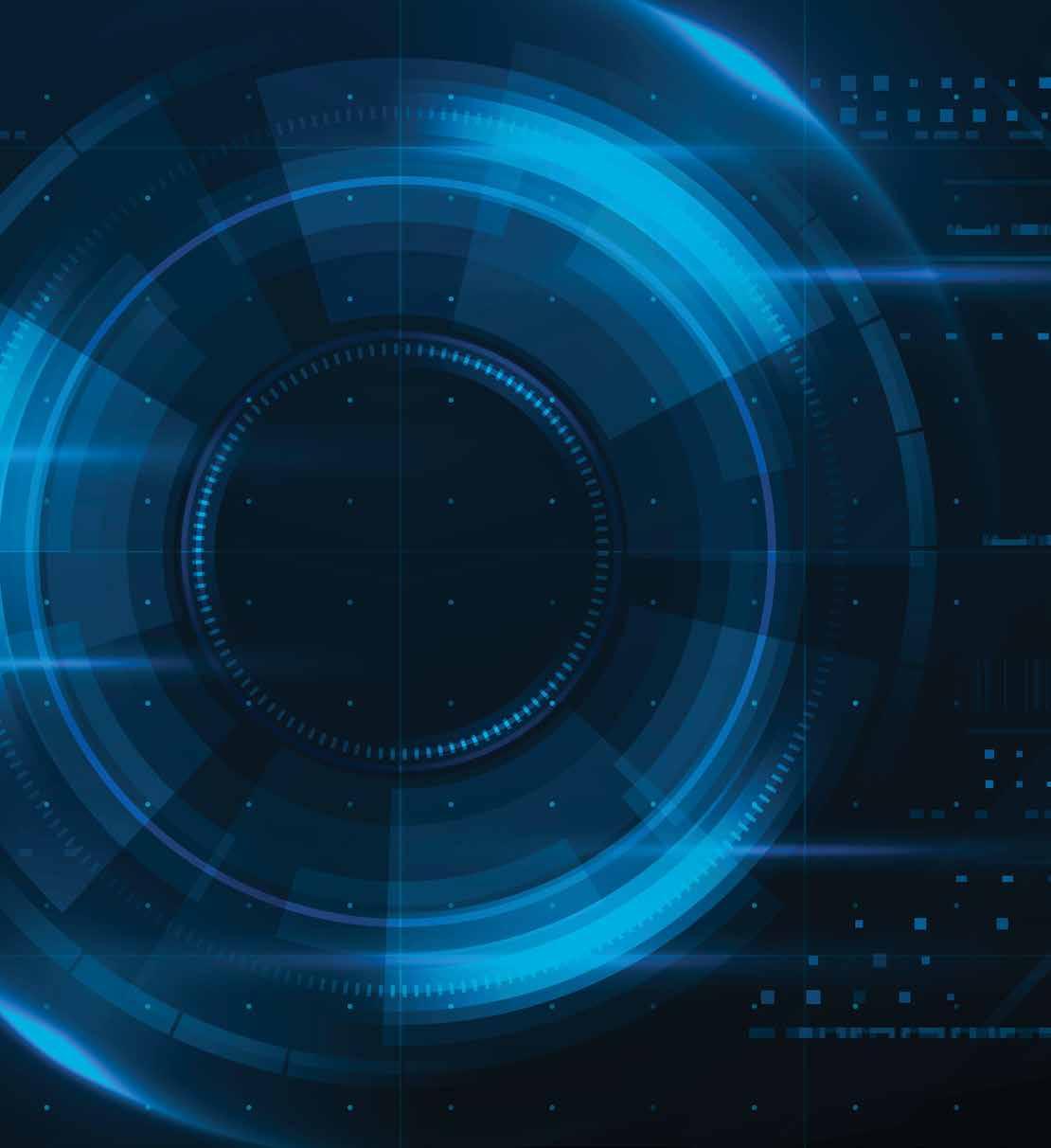
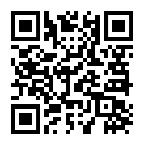
MINING & RESOURCES
Transport & Logistics
State Spotlight: Queensland
MINING & RESOURCES
Transport & Logistics
State Spotlight: Queensland
SHOWCASING 7 PRODUCT ZONES
Australia's most popular CNC plasma, With Swiftcut tables made in the UK & Hypertherm Plasma units made in the USA there is no compromise on quality.
Swift-Cut PRO is a feature packed plasma cutting table with the ability and power to cut for as long as required. With a robust steel fully welded frame and free standing operators console, making it ideal for workshops, metal fabricators, educational establishments, designers and artists.
With gantry parking to allow a full sheet to be loaded overhead and a dropped rail for ease of loading, not to mention the simple on-going maintenance, the Swift-Cut PRO really is the answer to all your cutting needs.
POWERED BY
Height Sensing
Four Machine Sizes
1250 x 1250mm
2500 x 1250mm 3000 x 1500mm 4000 x 2000mm
Heavy Duty Gantry
• Up to 25mm Cutting capacity depending on the Hypertherm unit selected
• DXF & JPEG photo import for creation of cutting files
• Soft sense Digital Torch-Height Control (DTHC)
• Quick response for improved cut quality and improved consumable life.
Operator Control
Optional Engraving Tool
Heavy Duty Welded Base
Priced from $34,900 ex GST $38,390 inc GST (P9010)
The Metalmaster Synchro series pressbrakes adopt a heavy duty integral welded steel structure that is furnace tempered post welding to relieve residual stresses and ensure accuracy & longevity of the machine. The hydraulic cylinders are manufactured from high resistance steel incorporating chromium plated ground & lapped pistons to ensure longevity of the Swedish brand SKF hydraulic seals.
The hydraulics system consists of electronically controlled proportional valves with independent 3 point closed loop safety monitoring of the two cylinders as well as the main hydraulic system.
Features
• 5 CNC Controlled Axis (Y1, Y2, X, R, V) as standard.
• Y1 & Y2 Axis is controlled by advanced safety monitored hydraulic proportional valves ensuring accuracy in movement.
• Bending compensation & accuracy is maintained using GIVI (Italy) Linear scales mounted on either end of the machine bed to measure any frame deflection
• CNC controlled auto crowning table (V) adjusts accordingly based on material, length & thickness specified in program.
CYBELEC CybTouch CNC Controller
• Touch Draw profile programming
• Automatic Bending Sequence
• 2D Interference Simulation
Electro-hydraulic servo synchronous control
The advanced Hydraulic system containing safety monitored proportional valves is integrated into the CNC control. Receiving real time feedback from the Y axis linear scales to the controller can compensate for deflection during bending, providing repeatable & precise control of the machine tool.
We offer the leading edge of ‘full service’ distribution and lifetime support for Okuma CNC machines. Solution focussed, our team work with our customers to provide machining realities, with exceptional results.
Our team gives you immediate access to decades of industry experience and a network of local and global machine tool experts. We partner with you from the very first meeting, guide you through project planning and support you through implementation, training and after sales care.
Quality
Support
Technology
Reputation
Activating the Industrial-scale Reconstruction Fund should be used to kick start the next stage of metals processing supply chain, right here in Australia.
The US Administration’s Inflation Reduction Act (IRA) converts $800bn of tax breaks and subsidies over the next decade to boost high-tech manufacturing throughout the US. That kind of investment would turbocharge any industry, and this is what is required here in Australia.
“There has been a renaissance in American manufacturing,” said American Council of Renewable Energy CEO and President Gregory Wetstone in a recent Goldman Sachs report. “I don’t think I have ever seen a law have greater impact on economic development in this country.” Australia’s Climate and Energy Minster Chris Bowen said he believed the US IRA might one day be viewed as significant a moment in the fight against Climate Change as the signing of the Paris Agreement in 2015.
In fact, the IRA has put everyone on notice. The beauty of it is that the majority of the incentives go to the consumers. That’s good politics. Here, the Safeguard Mechanism was brought in, which is just an incredibly complex way for industry to buy ‘credits’.
But just like the US, the powergrid as it stands cannot keep up with the projected load over the next decade. Australia is also way behind in being able to source the steel, build and deploy the high voltage towers and transmission lines, taking the current to those power-hungry industries. This is somewhere in the vicinity of 10,000 kilometres of extra high-voltage cable and towers.
Australia could power 60% of our domestic and manufacturing industry energy through rooftop solar, by saturating the market and pumping it back into the grid. Rewiring Australia’s Saul Griffith wrote that Australian rooftop solar is the cheapest electric power in the world, at three to four cents per kWh after financing.
Now, Prime Minister Anthony Albanese said it is “absolutely critical” to have a strong manufacturing industry in Australia. “During the global pandemic, we were reminded of the problems that can arise with global supply chains,” Albanese said. “And the need for us to be more self-reliant and more resilient, the need for us to make more things here, the need for us to have a manufacturing industry here in Australia.”
Treasurer Jim Chalmers released the latest Intergenerational Report in late August, warning that Climate Change threatens to devastate the economy over the next 40 years, but that Net Zero reforms offer lucrative opportunities, the same as mentioned above. The last Intergenerational Report by the Coalition hardly mentioned Climate Change.
The lucrative opportunities are the Critical Mineral Strategy and the National Reconstruction Fund deals, extracting the critical minerals for batteries, panels, towers and inverters, mined in this country. We sold 55% of the world’s required lithium brine in 2022. Critial minerals are essential to help cover the growing cost of health, NDIS, defence and servicing government debt, which together will rise from a third of GDP to 50% by 2060.
We also need to process our own iron ore into steel, here. Half of the cost of steel-making is the energy used in making it. We need to mine and process our ore into steel here, with the cheapest electrical power in the world. It could be more than a $1Tn industry, ten times larger than our fossil fuel industry. Imagine if we could process iron ore into green steel to deliver us home-grown metals to manufacture everything, here. Imagine the turbocharging this would do for Australian manufacturing.
Australia has the largest ore bodies of all the vital elements required for the next Net Zero steps the whole world needs to take. Australia has to stop being tauted as just the “world’s quarry” and it needs to get suited up pronto to be the “world’s foundry”.
Editor Paul Hellard phellard@amtil.com.au
Contributors
Paul Hellard
Wendy McWilliam Dr Cameron Tsai
Sales Manager
Nicholas Raftopoulos nraftopoulos@amtil.com.au
Publications Co-ordinator
Caroline Robinson publications@amtil.com.au
Publisher Shane Infanti sinfanti@amtil.com.au
Designer
Franco Schena fschena@amtil.com.au
Prepress & Print Printgraphics Australia
AMT Magazine is printed in Australia under ISO140001
Environmental Certification using FSC® Mix certified paper sourced using sustainable tree farming practices.
Contact Details
AMT Magazine
AMTIL
Suite 10, 5 Corporate Boulevard Bayswater VIC 3153
AUSTRALIA
T 03 9800 3666
F 03 9800 3436
E info@amtil.com.au
W www.amtil.com.au
Copyright
© Australian Manufacturing Technology (AMT). All rights reserved. AMT Magazine may not be copied or reproduced in whole or part thereof without written permission from the publisher. Contained specifications and claims are those supplied by the manufacturer (contributor).
Disclaimer
The opinions expressed within AMT Magazine from editorial staff, contributors or advertisers are not necessarily those of AMTIL. The publisher reserves the right to amend the listed editorial features published in the AMT Magazine Media Kit for content or production purposes.
AMT Magazine is dedicated to Australia’s machining, tooling and sheet-metal working industries and is published bi-monthly.
Subscription to AMT Magazine (and other benefits) is available through AMTIL Associate Membership at $190.00 (ex GST) per annum. Contact AMTIL on 03 9800 3666 for further information.
At the time of writing this article I was in Hannover, Germany, visiting the EMO Exhibition. Under the banner of ‘The Future of Business’, EMO is the world’s largest machinery technology exhibition, with 1,850 exhibitors from 42 countries.
AMTIL had a stand in the International Association pavilion alongside 26 other national associations from around the world, forming an excellent network of global machine tool and manufacturing technology bodies. One of our activities each year is a half day ‘General Managers’ meeting where all countries discuss a particular topic given to us. This year the subject was – Impact of New and Enabling Technologies.
Below is a summary of these discussions. The conversation went from traditional manufacturing to new and finally emerging technologies. We live in a world of acronyms so I will explain some of them for the uneducated!
Traditional manufacturing covered off CNC machining, robotics and automation, controls, lean manufacturing, six sigma, lights out machining, etc, etc. The focus was on fast spindle speeds, quick changeover time, high productivity and sustainability. I won’t delve too deeply into this area as the majority of our readers are in this space and know it better than me. Needless to say, being labelled as a “traditional manufacturer” is not a bad thing and certainly not a reason to change. However, being aware of new and emerging technologies is a must see and how it will impact a traditional business is also worthy of exploration.
New technologies probably focused on what was new over the past few years so included amongst other things mobility technologies, manufacturing as a service, materials science, additive manufacturing, 3D simulation, ICME (Integrated Computational Materials Engineering), digital manufacturing, industrial internet of things, Industry 4.0 and the list goes on. Mobility technologies is an interesting one as it encompasses everything from tablets and phone apps on the factory floor to connected and self driving vehicles and every other way that information and products can be mobilised. Additive manufacturing has been around for a long time and it can be argued whether it fits into this category but recent
advancements in 3D printing of metal in a production capacity rather than a prototyping technique lands it here. There is no doubt we are living in a data driven world and the impact that Industry 4.0 and IIoT are having in areas such as predictive maintenance, are significant. There is so much to learn and explore – far too much to try and explain on one page – I am merely sowing the seed for what might be looked in to. The focus here is on smart manufacturing, data analysis, processes improvement and not to be afraid to look at whether there is a better way to make something. I may be overstating things but companies that have taken steps in this space could be labelled as an “advanced manufacturer”.
Emerging technologies is a never ending list as by the time you read this there will be a myriad of other names to look into. But let’s start with AI (artificial intelligence), ML (machine learning), HPC (high performance computing), AR (augmented reality), drones, blockchain, cobots, virtual reality, low code or no code platforms, RPA (robotic process automation), embedded sensing controls, 5G networks, edge computing, quantum mechanics and, definitely, cyber security. Try and wrap your head around any or all of those! And if you have gone down any of these paths and implemented change I think you can call yourself a “manufuturer” – a manufacturer for the future. By the way, I would love to hear from you if you are, as these are the good news stories we want as editorial in this magazine.
Finally, taking all of these traditional, new and emerging technologies into account we also need to take into consideration today’s industry issues such as the circular economy, carbon neutral requirements, Smart and Green Manufacturing and ecodesign. In fact, a new International Standard ISO14955 has been updated with the heading Design Methodology for Energy Efficient Machine Tools. Sustainable competitiveness is one key to the future. As I said at the start, the world of manufacturing is evolving very fast, so try and keep up if you can.
The current local job market is incredibly competitive. Businesses need to find ways to stand out from the rest and attract the best talent.
If you’re looking for a needle in a haystack, Ripe Recruitment has access to a talent pool that you may not be able to reach.
We pre-screen candidates and send you the most qualified applicants who fit your specific needs, saving you time and energy.
CNC Machinist NSW
Technical sales Engineer NSW
Field service Engineer VIC
Technical Sales Representative NSW
Internal Technical Sales VIC / NSW
Field service Technician QLD
Field Service Engineer NZ
A more personal approach to recruitment
Helping you achieve more with solutions tailored to your needs
The Australian Government’s decision to support the growth of a high-end manufacturing sector was not a difficult one to make.
We have a world-class R&D sector which has delivered technological breakthroughs like Wi-Fi, the ultrasound scanner, colour xerography, spray-on skin, and the pacemaker. Our scientists and researchers continue to deliver globally important advances in areas like quantum computing, robotics, software development and renewable technologies. We have talented, savvy entrepreneurs who are commercialising these great ideas and building thriving new businesses.
We believe Australia can and should be more ambitious when it comes to manufacturing – for strategic as well as economic reasons. Backing our research strengths and comparative advantages to develop complex, knowledge-intensive industries will position us to become a nation of price-takers rather than price-makers.
Boosting domestic value-adding activities will also make us less vulnerable to external shocks and instability. And it will lesson our reliance on price-volatile exports of bulk raw minerals and commodities. We recognise, however, that growing our manufacturing sector will rely as much on maximising capital investment options as it does on generating innovative ideas and innovations.
More so.
The centrepiece of our plan to make more things in Australia using Australian expertise, the National Reconstruction Fund (NRF), will facilitate increased flows of finance into priority areas of the Australian economy. The NRF will provide co-investment finance alongside and in conjunction with the private sector, much like the successful Clean Energy Finance Corporation.
That will leverage a far greater amount of total investment into Australian industry. To elaborate on what is possible with a coinvestment model, the $10bn co-invested by the Clean Energy Finance Corporation since 2012 has supported total investment in clean energy projects of $36.5bn.
The CEFC’s success at crowding in private sector finance for renewable energy generation has help spur record levels of largescale wind and solar farms and rooftop PV uptake in Australia.
The Australian Government announced the seven independent NRF Board members in August. All have extensive banking, venture capital, banking, and financial services experience.
Crucially, they also have specialist knowledge spanning the NRF’s seven priority investment areas – renewables and low emissions technologies; medical science; transport; value-add in the agriculture. Board Chair Martijn Wilder established investment and advisory firm Pollination and has over 20 years’ experience as a leader in sustainable finance.
He is also a founding director of the CEFC.
Ahmed Fahour, who is currently chair of Invest Victoria, has occupied senior executive and board roles across banking, financial and other services in a career spanning three decades. Dr Katharine Giles is the current CEO and Managing Director of OncoRes Medical, a growth-stage medical device development and manufacturing company based in Western Australia.
She is also a Venture Partner at Brandon Capital Partners, and a member of the Curtin University Commercialisation Advisory Board. With their fellow Board members, they will bring a truly national perspective to the NRF’s activities – ensuring the benefits of economic diversification reach all parts of Australia.
Right now, they are working to set up the corporation as soon as possible, and to finalise policies and procedures around evaluating potential investments. These will be made public as soon as possible.
To expand the pipeline of quality, investment-ready projects for the NRF, we announced a $392m Industry Growth program in our May Budget. The initial stages of commercialisation and business growth can be high risk and high cost, presenting significant challenges for many SMEs.
To help mitigate such risks, the IGP will offer matched grant funding of $50,000 to $5m to eligible projects in NRF priority areas. Access to industry-led specialist advisory services will also be on offer. Besides facilitating a better investment climate for our emerging tech firms, the Australian Government is also clarifying long-term R&D objectives that support industry growth.
Earlier this year, we released Australia’s first National Quantum Strategy, a document setting out how to better translate Australia’s research edge into creating leading industries.
We’ve developing a new National Battery Strategy with the goal of establishing a globally competitive end-to-end domestic battery manufacturing ecosystem. And our forthcoming National Robotics Strategy will lay out how we can grow our robotics and automation companies and integrate these technologies across the wider economy – potentially adding between $170bn to $600bn per year to GDP by 2030.
The decline of Australian manufacturing over the past three decades was not pre-destined or inevitable. It was not because our research and development ecosystem underperform – or because our businesspeople are risk-averse. Far from it.
We have all the ingredients needed for re-industrialisation and our Future Made in Australia Policy – of which the NRF is a central feature – will ensure a stronger, more future-focussed manufacturing sector. One that creates good secure jobs for Australians and delivers long-term economic prosperity. industry.gov.au
The team at Krueger transport where after a replacement plasma machine and through conversations they also outsourced a lot of laser cutting.
The Marvel 2.5m x 10m with Transfer table o ered both solutions in 1 machine - meaning no outsourcing - no waiting times, reduced oor space, reduced power consumption, reduced handling time and higher control of the quality of nish. Which Krueger jumped on and now is taking advantage of the increased e ciency the new machine has supplied.
MACHINERY OPTIONS FROM FARLEY LASERLAB AUS
LASER WELDERS
LASER CLEANERS
LASER MARKING
2D FIBER LASER CUTTING
2D CO2 LASER CUTTING
2D + PIPE FIBER LASER CUTTING
PIPE FIBER LASER CUTTING
PRESS BRAKES
AIR PLASMA CUTTING
HD PLASMA CUTTING
HD PLASMA, BEVEL & DRILLING
DROSS DEBURRING MACHINES
Advantage isn’t enough: How can Australia turn energy superpower dreams into reality?
This is a contradictory time for clean economy visions in Australia. Our opportunities are becoming tangible. Major economies are making huge investments. Markets for minerals, energy and products are shifting. Governments are backing targets with the money and the nitty gritty needed to deliver them.
At the same time Australians feel intense doubts about our own ability to deliver. Supply chains are stretched. Project delivery costs surged for all forms of energy in 2022. Slow approvals and NIMBY grumpiness risk throttling transition. Against that contradictory background the Federal Government is considering how to respond to the US Inflation Reduction Act (IRA). Big decisions are needed soon.
Australia has plausible hopes of a clean energy advantage that will propel us to long-term success. But right now advantage isn’t enough. Mega-subsidies by the largest economies could make us irrelevant. There are three big reasons why Australia should take a bold approach.
First: the urgency of advancing our domestic energy transition, meeting emissions commitments and keeping the lights on. We need investment and expanded supply chains in globally scarce products. Keeping crumbling coal generators open because replacement projects are lagging would mean rolling the dice on whether these antiques will still work when we need them to.
Second: the path to cheaper cleantechs lies through deployment. Hydrogen will get cheaper through learning-by-doing, just like wind, solar and batteries have. Industry makes a thousand little improvements as it gains experience. Lower costs open more niches, driving more deployment and hence more cost reductions. That powerful dynamic gets going by paying to deploy expensive young technologies. Australia hopes to benefit greatly from future green industries. Our interest lies in accelerating that future, not reclining in a hammock while others build it.
Third is the risk that others do build the future and leave no place in it for Australia. Late entrants to green metals production may struggle without the experience, supply chains or customer relationships of early movers.
Decarbonising our economy is doable but not easy. Our opportunities in a net zero world are tantalising but we face intense competition. Our interest lies in minimising our costs and maximising our benefits over the full sweep of the transitions before us. Abatement with higher unit costs in the near term can be worthwhile where it enables larger savings over the longer term.
Our peers are implementing ambitious energy and industrial policies to make their own transitions and to build positions in new industries. We should match this while catering to our own economic circumstances, policy options, anticipated advantages and trade relationships.
We’ll need to be willing and able to build. If we can’t manage the social license and logistics to build transmission lines fast enough
just for our domestic transition, we can certainly kiss export visions goodbye. Facilitative reforms and capacity-building in private supply chains and public agencies can speed industrial development, boost productivity, and ensure access to skills.
We’ll also need large policy signals, amounting to tens of billions of dollars in incentive-equivalent, to promote investment in both domestic decarbonisation and initial partnerships for clean exports. “Contracts for difference” that top up the difference between market prices and clean product costs can offer investable certainty while phasing Budget support down and out over time.
And we’ll need to focus our financial efforts. Clean energy intensive products for the domestic market are the place to start. Green metals and chemical facilities would pull through large consequential investments in hydrogen production and renewable energy generation. That offers a large and certain market for component suppliers, locally and overseas, to scale up their own production. Maintaining our domestic industrial capacity is essential in its own right, and a stepping stone to the experience, scale and price point needed for clean export markets.
Challenging minimum goals for 2035 will help. So here are some starters for consideration.
We should maintain our share of world production of critical minerals as world demand steeply increases, and substantially increase processing in line with our trade and security partners’ need for trusted supply chains.
We should establish near-zero emissions production capacity for aluminium, ammonia and steel with output equivalent to at least half of Australia’s current primary production of those products. That requires large-scale near-zero emissions hydrogen production capacity at least equal to what’s needed for those clean products –roughly 300,000 tonnes per annum.
All that requires deployment of electricity assets sufficient to meet the needs of the above activities at the necessary pace, with globally competitive end-user costs. That’s likely at least six gigawatts of renewable generation just for the hydrogen, and much more for aluminium and alumina.
In the process we need to ensure we lay the foundations for export expansion through international customer and supply chain partnerships; local infrastructure, experience and planning; and the resolution of technical challenges including the direct reduction of hematite with hydrogen.
It’s a tall order at a time when we are full of angst about whether Australia can build anything at all. But as Bill Gates says, most people overestimate what they can do in a year and underestimate what they can do in ten years.
If we can be farsighted without tripping over our own feet, Australia has huge opportunities. If we can combine realism and aspiration, those opportunities can become reality.
This is an edited version of a speech delivered to the Hydrogen Connect Summit in Brisbane on 7 September 2023 aigroup.com.au
The National Reconstruction Fund is just part of the most significant industrial transformation in generations.
As we draw closer to the last quarter of 2023, Australia faces multiple challenges, including a cost-of-living crisis, responding to climate change and a changing geo-political environment, which has generated a significant shift in strategic defence priorities. Integral to these challenges are major opportunities to ease families' financial burden, reduce Australia’s emissions, secure our longterm economic prosperity, and develop a sovereign shipbuilding capability that will serve the nation for decades to come.
At its recent National Conference, the Australian Labor Party made several important commitments that set a path to transitioning Australia to clean and renewable energy and delivering 20,000 new shipbuilding jobs over the next decade.
While changes to Labor’s National Platform lay the foundations for this major reform, the work remains to build the policy detail and substance that turn those principles into tangible action.
The spiralling cost of food, energy and consumer goods has hit family budgets harder than at any time since the early 1990s. While the cost of groceries has increased by 10% in the past year, electricity prices have risen a staggering 25% in just 12 months. The inflation crisis is not unique to Australia, and countries worldwide are taking decisive and comprehensive action to ease the pressure on families, reduce industry costs, and lay the foundations of an economy aligned to tackling the challenges of climate change.
In the US, the Biden Administration has launched its A$550bn Inflation Reduction Act (IRA), the most significant climate legislation in US history, offering funding, programs, and incentives to accelerate the transition to a clean energy economy. Given that energy is a crucial input for economic production and a major cost for households, cheaper renewable energy will help to drive down inflation while reducing emissions.
Here in Australia, the federal Labor government’s National Reconstruction Fund, a $15.2 billion investment in helping local industry take advantage of opportunities in a net zero economy, and Labor’s commitment in its National Platform to transitioning the economy to renewable energy is an excellent first step.
But given the strong policy focus and substantial commitment of other nations to creating green economies, it’s clear that our government will need to invest at least ten times this amount in renewables and clean energy if Australia is to become globally competitive, and the Australian people and industry are to see benefits in lower energy prices fuelled by green energy.
Rather than a ‘cost to government’, all stakeholders across business and politics should see this for what it truly is: a wise investment in our nation’s people, its economy and a sustainable future for generations to come.
Renewable energy is simultaneously Australia’s greatest source of economic potential and our greatest untapped resource. Taking just one example, despite receiving 40% less sun than Australia, Germany produces over ten times more solar energy, meeting 50% of their energy needs.
Australia is well-placed to take full advantage of the global boom in renewable energy production. We enjoy the greatest access to natural resources in terms of sun, wind and waves, among other resources, compared with any other developed nation. But to realise
this, Australia will require a more muscular policy focus on behalf of the government. This includes major investments in developing renewable energy resources, capitalising on emerging renewable energy sectors such as hydrogen and investing in research and development into advanced green manufacturing methods.
The changing geo-political environment in Australia’s region has prompted a significant shift in Australia’s strategic priorities, and this will translate into renewal and new investment for Australia’s longneglected shipbuilding capability.
The changes to Labor’s National Platform promise around 20,000 local jobs in the shipbuilding sector over the next decade. These jobs will come as we rebuild our shipbuilding capabilities to produce new submarines and ships over the following decades. Importantly, it will also require rebuilding our training capabilities to create the next generation of highly skilled manufacturing workers we need to build and maintain Australian ships, and that’s good news for our manufacturing sector as a whole.
Another significant win for Australia’s manufacturing industry to emerge from the Labor’s National Conference was the creation of a Defence Industry Council focused on ensuring that local communities and industries capture the maximum benefit of national defence expenditure.
The Council will ensure we create tens of thousands more additional jobs in supply chains and local defence manufacturing, broadening the economic benefits across our cities and regions.
Australia stands at the threshold of an incredible opportunity to create national prosperity and adapt our economy to the realities of climate change and regional geopolitics. But in meeting the unique challenges our times present, government, business and unions must embrace new ideas and adopt robust and decisive action to succeed. amwu.org.au
Boosting digital skills in manufacturing to create future jobs.
The Victorian Labor Government is supporting manufacturers across the state to equip their workers with the cutting-edge digital skills needed to boost competitiveness and create more jobs of the future. Minister for Industry and Innovation Ben Carroll today visited Ballarat manufacturer SEM Fire and Rescue, which is one the businesses benefitting from the Labor Government‘s $4.5m Digital Jobs for Manufacturing program.
Since launching in October 2022, the program has offered eligible manufacturing businesses grants of up to $5,000 per employee to enrol in a free 12-week course with Victoria’s top universities, TAFEs and training providers.
To date, the Digital Jobs for Manufacturing program has awarded nearly $775,000 in funding to 109 Victorian manufacturers, supporting 226 of their employees to enrol in a nominated training course. As one of the country’s largest manufacturers of emergency service vehicles, SEM Fire and Rescue is participating in the program to upskill staff and strengthen its digital capabilities to maintain a competitive advantage.
The program has allowed SEM Fire and Rescue to enrol mechanical engineer Mukesh Arella into an additive manufacturing course at the University of Melbourne. Through the course, Mukesh is enhancing his skills in new manufacturing technologies including 3D printing, helping to improve the design of vehicle components.
The program builds on the success of the $64m Digital Jobs program that is retraining 5,000 mid-career Victorians and supporting them to transition into digital-focused jobs.
The Government is backing the state’s advanced manufacturers through initiatives including the new $15m Made in VictoriaIndustry R&D Infrastructure Fund and $20m Manufacturing and Industry Sovereignty Fund. business.vic.gov.au/djfm
FSO established to equip Australia’s Training System as Finance, Technology and Business Jobs and Skills Council.
The Future Skills Organisation (FSO) has officially launched with a powerful remit to address Australia’s critical skill shortages.
Minister for Skills and Training, The Hon. Brendan O’Connor, has announced that the Future Skills Organisation (FSO) will be established as the Finance, Technology and Business Jobs and Skills Council (JSC). JSC's are at the forefront of implementing the government’s jobs and skills plan.
Building on years of industry knowledge and collaboration as the Digital Skills Organisation (DSO), the FSO has been tasked with not only developing strategies to help address skills shortages in critical areas such as digital, but also future-proofing skills and training for sectors - critical to advancing Australia’s economythe finance, technology, and business sectors.
“This is an exciting day for the future of skills, learning and training in Australia,” CEO of FSO, Patrick Kidd said. “As a JSC, we look forward to working with government, training providers, unions, employers and importantly, learners and employees, to deliver world-class outcomes and make Australia more competitive.”
Established by the Australian Government in 2022, JSCs will provide industry with a more strategic voice in ensuring Australia’s Vocational Education and Training (VET) sector delivers stronger outcomes for learners and employers.
“We have a significant responsibility to shape Australia’s skills and workforce future. Our mission is to collaborate with stakeholders across training, industry, unions, and government to grow Australia’s finance, technology, and business talent to benefit industries across Australia,” Kidd said.
“As we transform from DSO to FSO, we have a talented and passionate Board representing a cross-section of finance, tech and business, and from across Australia to drive us forward with our new remit,” Kidd added.
FSO Board Chair and non-executive director at ASX Ltd, Cochlear Ltd, Santos Ltd and QBE Ltd, Yasmin Allen AM, is passionate about integrating the learnings from DSO into new territory.
“This progression to a JSC is an important step in delivering our critical work in accelerating digital skills across Australia.
I want to see all Australians included in the digital transition. The only way we can do that is to ensure everyone has real access to training and development in a contemporary and timely way. Finance, Technology and Business intersect with our personal and professional lives every single day, it’s critical that we get it right.” Yasmin Allen AM said.
Mr Kidd also stated that support from government and industry stakeholders has been key in a landmark year ahead of this transition.
“We want to thank everyone that has seen the need for Australia to take future skills seriously and have invested in our mission. Particularly Minister O’Connor who has tasked the new JSCs to work with Jobs and Skills Australia so that we can together work to address Australia’s skill deficit. We are grateful for the essential tripartite support from industry, unions, and government.
We believe in Australia’s VET system and education. Together we have a unique opportunity to act as stewards across finance, technology, and business sectors to ensure our VET system is agile, responsive, and innovative.”
“FSO is committed to building a resilient workforce, working with both training institutions and industry to provide the skills that will prepare our economy for the jobs and opportunities of tomorrow – and beyond,” Patrick Kidd said. futureskillsorganisation.com.au
Global packaging company guarantees more jobs and investment.
A global manufacturing company and distributor of sustainable, innovative packaging has expanded its operations in Victoria as part of a multi-million-dollar project that is creating local jobs and boosting the state’s advanced manufacturing capabilities, with support from the Andrews Labor Government.
Minister for Industry and Innovation and Manufacturing Sovereignty Ben Carroll today visited Orora Beverages Dandenong facility, which is part of a $110m investment – backed by the Labor Government – to expand its manufacturing operations in the state, creating up to 18 new jobs. “We’re backing companies like Orora to expand, become more innovative and create jobs because we’re Australia’s advanced manufacturing state,” said Minister Carroll.
Orora’s expansion will allow the company to meet increasing demand from major global beverage customers across the industry including producers of craft and traditional beer, and non-alcoholic drinks.
Headquartered in Melbourne, Orora manufactures and distributes innovative packaging solutions including aluminium cans, glass bottles and corrugated board, with more than 250 employees in the state. “We’re proud of the contribution we make to the local economy as a responsible manufacturer and employer in the local community,” said Orora Beverage President Simon Bromell.
“We welcome the Victorian Government’s support for Orora’s important cans capacity expansion projects.”
The company has established a new aluminium beverage can manufacturing line at its Dandenong site to meet market demand for varying can sizes from slim and sleek 200ml to classic 500ml, while increasing production capacity. Orora has also increased capacity and warehousing for its production at its Ballarat facility. The environmentally sustainable aluminium can manufacturer produces its beverage cans on a conveying system, where aluminium coil made from mostly recycled content is mechanically and chemically treated and cured to solidify the can shape. The recyclable cans are then decorated, palletised and shipped to customer plants for filling.
The state’s $33bn manufacturing industry is a driving force of Victoria’s economy, made up of around 24,000 businesses, supporting more than 250,000 jobs, and providing around 30% of Australia’s manufacturing output.
The Government is supporting advanced manufacturers to innovate, build sovereign capabilities and take advantage of new opportunities through initiatives including the $15m Made in Victoria – Industry R&D Infrastructure Fund and the $20m Manufacturing and Industry Sovereignty Fund. ororabeverage.com
The RBA forecasts economic growth is going to slow considerably over the second half of 2023.
The July 2023 CreditorWatch Business Risk Index (BRI) has revealed the average value of business invoices has fallen by almost a third over the past 12 months, with a drop of 28% year-on-year. This massive drop in the value of invoices means Australian businesses are ordering less each month leading to a fall in revenues throughout the supply chain. CreditorWatch’s other key business indicators, trade payment defaults, credit enquiries, external administrations and court actions have also deteriorated. CreditorWatch Chief Economist Anneke Thompson’s says the Business Risk Index data supports the assessment of the RBA that economic growth is going to slow considerably over the second half of calendar year 2023.
“The RBA forecasts GDP to slow to 0.9% over the year to December 2023, down from 1.6% over the year to June 2023,” she says. “Household consumption has already slowed considerably, with the slowdown expected to worsen as more households come off fixed rate home loans. Household consumption is expected to have only grown by 1.6% to June 2023, and is forecast growth for the year to December is 1.3%.”
Average value of invoices for Australian businesses has dropped 28% over the past 12 months. B2B trade payment defaults continue to trend upward, with an 86% year-on-year increase. Credit enquiries dropped from June to July but are still up 66% year-onyear, reflecting the tightening of due diligence that businesses and lenders are performing on debtors. External administrations have increased 10% year-on-year, with most industries experiencing an increase in this measure. Court actions were flat from June to July but are up 17% year-on-year. CreditorWatch’s national default rate prediction for the next 12 months is for an increase from the current rate of 4.67% to 5.76%.
Businesses in the food and beverage services sector remains the most at risk of payment defaults (6.9%) by a considerable margin. Transport, Postal and Warehousing is the next riskiest industry at 4.4%. The regional Victoria regions of Ballarat, Yarra Ranges are in the top five regions in Australia for lowest risk of business failures. Ballarat in Victoria is the region with the lowest risk of business failure (across regions with more than 5,000 businesses), followed by Unley and Norwood-Payneham-St Peters in South Australia.
The regions with the highest insolvency risk continue to cluster around Western Sydney and South-East Queensland, with Merrylands-Guildford (NSW) recording a forecast default rate of 7.8% for this time next year. creditorwatch.com.au
For the fourth consecutive year, Bonfiglioli has announced the company has renewed its membership of APQP4Wind, a non-profit collective of the world’s leading wind turbine manufacturers and suppliers. This organisation helps companies achieve better quality solutions for wind power generation.
“Bonfiglioli’s membership of APQP4Wind highlights the company’s commitment to a sustainable future, and its role in the development of the world’s wind industry,” explained Martin Broglia, Managing Director Bonfiglioli Australia and New Zealand. “That one out of every three wind turbines globally use a Bonfiglioli gearbox, tells me we’re on the right track!”
Broglia points to the new 700TW Series planetary gearbox which is setting the standard for the growing wind turbine market. “This is the latest generation Yaw Drive planetary gearbox from Bonfiglioli, which offers reliable high radial/thrust load capacity and efficiency, in a robust and modular design,” said Broglia.
This gearbox was recommended for use by Spanish wind energy company, Siemens Gamesa Renewable Energy, when it sought out a wind turbine generator that could sustain a greater load for use in its 5G5x turbine. This is an onshore wind turbine that can reach up to 6.2 MW of power with a large rotor, obtaining one of the most competitive LCoE (Lower Cost of Energy) feasible.
“This demonstrates that Bonfiglioli’s dedicated integrated wind turbine solutions – developed over more than 30 years of co-engineering and collaboration with the world’s leading wind turbine OEMs – deliver reliable, superior performance, to maximise the customer’s productivity and ROI,” added Broglia.
Setting a new standard for offshore wind gearbox products, the cost- and space-saving 700TW series yaw drive with integrated moto-inverter delivers high performance even in low duty cycles. It features a wide range of reduction ratios, as well as high transmissible torque, radial/ thrust load capacity and shock resistance. With its rugged construction, including heat-treated steel alloy gears, this costefficient gearbox can handle heavyduty applications with ease.
It’s 8% lighter than its predecessors, and smaller; the integrated AC motor flange and brake decreases its height by 20%. It boasts a simplified design, with only a two piece housing and is IoT-ready, thanks to an in-built inverter.
“This gearbox is designed to reduce the lifetime cost of a wind turbine plant and offers improved energy consumption. It delivers great control both as a motor and as a generator, for regenerative braking action. In addition, it can be used as a battery backup solution. Installed and integrated with Bonfiglioli sensors, the solution provides real-time information on the load, speed and absorbed current of the system, making predictive maintenance easy,” explained Broglia.
“Bonfiglioli is the wind turbine one-stop shop, ensuring that customers enjoy the benefit of reduced complexity.”
In other Bonfiglioli news, Australia’s logistics market is estimated at over $139bn and with an annual growth rate of 4.04%, it’s expected to reach $173bn in the next four years. According to Broglia, “much of this growth stems from the rise of eCommerce - with the International Trade Administration ranking Australia as the 11th biggest market for eCommerce.”
“With the heightened demand and projected growth, Bonfigliol is wellpositioned to support the ever-changing needs of the logistics sector. Our team has decades of combined experience in the development of specialised and complete conveyor systems for material handling and warehousing applications.”
The local logistics and warehousing sector are facing significant challenges. Among these, the growing demand for rapid fulfilment, labour shortages, as well as climbing costs and the scarcity of warehousing space. “Customers are looking to reliable, compact conveyor solutions that offer variable speed control, and synchronisation with other equipment. Energy efficiency, scalability, safety and material flow control are essential in these applications,” explains Broglia.
“The goal for every business owner in the sector is to manage costs, while ensuring optimal throughput and efficiency”.
bonfiglioli.com/australia/en
Dongara Marine has come a long way from its initial focus on building boats for WA's cray fishing industry.
Since 1975, Dongara Marine has become a mainstay in West Australia's marine industry. Established by boat designer John Fitzhardinge in its namesake town, the business moved to a newly constructed waterfront shipyard in the port of Geraldton in 2022. Over the years, it has demonstrated exceptional prowess in boat building, maintenance, and marine services, emerging as a leader in the Australian maritime sector.
"Dongara Marine's success lies in our broad skillset, diverse workforce, and in-house capabilities," says managing director and part-owner Rohan Warr. “We’re continually developing our workforce and refining our trade skills, providing us greater control over scheduling, costs, performance, and quality.”
With highly experienced management, larger facilities, and an expanded, expert workforce Dongara Marine has the inhouse capabilities to undertake virtually every aspect of highly sophisticated vessel construction, repair/modification, and vessel support for commercial, government and recreational clients.
As a result of workload and projected demand, Dongara Marine is also operating from another established aluminium shipbuilding facility. Recent contract wins include two pilot boats for the Port of Fremantle for delivery next year.
With the capability to work on vessels made from Aluminium, fiberglass, composites, and timber, 85% of their work is aluminium. “All our hulls are aluminium. A lot of our work now pairs aluminium hulls with composite wheelhouses,” states Warr.
This focus on aluminium is justified considering the significant advantages this material offers. Warr explains, "Aluminium allows you to customise every boat. It's lightweight and easy to repair. It provides far better corrosion resistance than steel. If you maintain an aluminium boat well, it can last for 35 years plus.
"We are yet to discover the true lifespan of aluminium – if you maintain it properly, it will just about last forever."
Dongara Marine sources Capral aluminium for its projects. Since 2012, the company has enjoyed a productive relationship with Capral, acknowledging its capacity, product quality, and competitive pricing. "We use a lot of aluminium – an average boat would use about 15 tonnes of plate; a pilot boat would use 30 or
more. Capral aluminium not only meets our demand but enhances our work process, effectively providing us with a 'big Meccano set' that makes assembly easier," Warr elaborates.
Capral provides precision-routed plate products with intricate pen markings to streamline Dongara’s production process. These pre-cut and marked components are supplied to Dongara when needed ensuring the “kit” is ready to be assembled, minimising waste, and production times and reducing the risk of errors for the Dongara team.
As for the new shipyard in Geraldton, it's a significant upgrade. Developed on an approximately 9900m² site within the Fishing Boat Harbour precinct, the shipyard allows the firm to undertake multiple vessel construction and significant repairs simultaneously. This development has doubled Dongara's capacity, enabling the team to work on 14 boats simultaneously.
"Having a purpose-built facility on the waterfront is logistically a huge advantage," explains Warr. "We can bring a boat lifter into the sheds to move boats between the blasting bay or transfer from one shed to another for painting."
With earlier careers as a shipwright and a cray boat skipper, Warr’s love for Dongara’s craft is evident. "We start with a flat pack of materials, which goes out the door as a finished product. There's always a new set of challenges, a new set of problems to solve. And when you're out on the water or driving and see one of our boats, it makes you pretty proud."
Dongara Marine has come a long way from its initial focus on building boats for WA's cray fishing industry. With a dedicated workforce that thrives on challenges, an increasing capacity to deliver quality work, and a commitment to customer satisfaction, the company is not just building boats—it's creating a lasting legacy in the marine industry. Its partnership with Capral aluminium only strengthens its ability to deliver superior, customised vessels that will stand the test of time.’
"We're not just building boats; we're striving for continuous improvement across the business," Warr concludes. "With Capral's aluminium and our highly skilled team, every boat we build is better than the last one." capral.com.au
Hysata opens new electrolyser manufacturing facility in Port Kembla with $23m cash injection from QLD and Federal Government.
Australian electrolyser company Hysata has officially opened its new 8,000sqm global headquarters and electrolyser manufacturing facility in Port Kembla. This marks a significant milestone in Hysata’s journey, paving the way for commercialisation of its pioneering high efficiency electrolyser.
Hysata’s electrolysers are poised to transform the economics of green hydrogen production and accelerate decarbonisation of hard-to-abate sectors such as steel, chemical manufacture and heavy transport. The Australian Government, through the Australian Renewable Energy Agency (ARENA), has given a vote of confidence in Hysata’s technology by announcing a $20.9m grant from its Advancing Renewables Program. This funding will support commercial demonstration of a 5MW electrolyser unit to be trialled adjacent to the Stanwell Power Station near Rockhampton, Queensland.
Under a Memorandum of Understanding (MOU), Queensland Government-owned power company Stanwell Corporation will support the demonstration project with $3m, and provide the site and facilities for the field deployment of the electrolyser, which is being developed at Hysata’s new manufacturing facility. The project will create 44 new local jobs at Hysata.
Hysata CEO Paul Barrett said this is a pivotal moment in the company’s rapid technological and commercial scaling, as they work towards fulfilling a 9.4GW pipeline of signed conditional orders and letters of intent.
“Hysata’s new facility in Port Kembla signals the next phase of our scale-up journey. Our plan encompasses the construction of a 100MW per annum production line, with commercial-scale units scheduled for delivery in 2025, including the 5MW electrolyser unit for Stanwell's project. And we will ramp up rapidly to giga scale capacity thereafter,” said Dr Barrett.
“With exceptional 95% (41.5 kWh/kg H2) efficiency combined with cost-effective materials and minimised Engineering, Procurement and Construction (EPC) costs, Hysata’s electrolyser will deliver the lowest Levelised Cost of Hydrogen (LCOH) for green hydrogen producers. “We are proud to be partnering with ARENA and Stanwell to deliver the first commercial demonstration of our electrolyser. It is the first step towards Hysata reaching gigawatt scale by 2026 to fulfil burgeoning demand for our electrolysers.
“This site will also serve as the headquarters for our entire staff, fostering collaboration and fortifying our values-driven culture. We look forward to creating hundreds more local jobs and strengthening Australia’s sovereign manufacturing capabilities as we continue to grow.” Minister for Climate Change and Energy the Hon Chris Bowen MP officially opened the facility. “We’re delighted to support game-changing, homegrown innovation that will power our future as a clean energy manufacturer and a renewable energy superpower,” Minister Bowen said.
ARENA CEO Darren Miller said the project is a crucial step to enabling purchase orders for the technology. “Hysata is a great example of Australian innovation leading the way in renewable energy. This electrolyser technology could be a gamechanger for renewable hydrogen. The demonstration at Stanwell’s site will be key to unlocking commercial demand for Hysata’s product by proving the technology works at scale,” Miller said.
“ARENA has been involved in this technology since it was just a concept in a laboratory, so we’re pleased to be supporting this next step toward commerciality. Identifying promising renewable energy solutions and helping them along the innovation chain is what ARENA does best.”
Stanwell CEO Michael O’Rourke said the support for Hysata’s technology commercialisation was another important step in Stanwell’s goal to driving the development of Queensland’s renewable hydrogen industry.
“We are excited to support Hysata by facilitating the commercialisation of this innovative Australian-made technology through a field pilot,” O’Rourke said. “The development of a renewable hydrogen industry is a key component of our energy transformation. The potential to utilise high efficiency Australian technology in largescale hydrogen projects would be a real advantage.”
Hysata’s electrolysers boast the world's most efficient electrolysis cell, combined with a simplified balance-of-plant, achieving an impressive 95% system efficiency (41.5kWh/kg).
This efficiency has been verified in top-tier peer reviewed journal Nature Communications, surpassing incumbents by 20% and exceeding IRENA's 2050 electrolyser efficiency target.
Hysata is an Australian electrolyser company headquartered in Wollongong that is developing a completely new type of electrolyser, featuring the world’s most efficient electrolysis cell coupled with a simplified balance of plant. hysata.com
1968 to the 2023 Apprentice of the Year: ANCA’s Daniel Malone wins at the 2023 Victorian Manufacturing Hall of Fame Awards.
Daniel Malone, a fourth-year apprentice at ANCA in Bayswater North, has claimed the 2023 Apprentice of the Year award. This honour is especially gratifying to ANCA cofounder Pat McCluskey, who established the formal Apprenticeship program at ANCA and was himself the Apprentice of the Year in 1968.
ANCA has valued learning through apprenticeships since its beginning and the company has a proud history of investing in its people to develop a highly skilled and engaged workforce.
“Daniel makes all of us at ANCA very proud,” McCluskey said. “As Machine Tool builders it is important that we train our Apprentices in our own Apprentice School. For me especially, this win by Daniel warms my heart and gives meaning to why I set up the Apprentice School in the beginning. I’m a time served apprentice, and nothing pleases me more, than to see young men like Daniel, pay us back in spades.”
ANCA’s apprentices get exposure to CNC machining, precision fitting, electrical testing and grinding applications throughout their four-year program, which offers a range of technical training paths. This progressive learning pathway through the company gives a holistic understanding of how ANCA’s complex products are designed and manufactured.
No two days are ever the same for an ANCA apprentice.
Apprentice of the Year, Daniel Malone said, “From first learning about ANCA’s apprenticeship program, I knew it was something I wanted to pursue. Until that point, I was under the impression that the only way to have a career in engineering was to go to university and get a degree.”
“I like the dynamic aspect of being an ANCA apprentice, working to very fine tolerances that sometimes need to be within one micron is sort of mind blowing to think about. Some of the machines we build are equipped with the latest in innovative technologies for our industry and its always cool to see and work on new technologies and assemblies being developed and used on our machines.”
The program at ANCA includes fourmonth rotations, where the trainees experience building motors and spindles, sub-assemblies, and machines to testing, commissioning, and servicing. Every day can be different with hands on learning complementing formal study of Certificate III in Mechanical Trade. Further study is also encouraged, such as a Diploma in
Engineering Technology in Mechatronics. Daniel, who is completing a mechatronic fitting and turning apprenticeship said: “ANCA’s program helps connect the dots between the theoretical and the practical. First you learn engineering fundamentals through study and then you hit the shop floor and see those fundamentals reinforced in the tool work.”
“It is a community effort across ANCA to support the apprenticeship program and this win is a direct reflection on all those moving parts of the program. From the Apprentice Master to production managers to everyone on the shop floor – I want to say thanks to everyone who has been a part of the journey.”
“It feels good to be recognised for my contributions as an apprentice and I appreciate that ANCA has taken the time to nominate me. I am honoured to win, if a little bit shocked – it is a very humbling experience.”
ANCA aspires to create a thriving manufacturing industry. Training our own apprentices through a world-class program, is not only a way to fill a skills gap for our niche and complex industry, it also contributes back to the industry as a whole. There are not many companies or TAFEs, or universities that gives the experience you get a company like ANCA, where we have been successfully training highly skilled technicians for over 12 years. The skills in precision manufacturing apprentices accumulate adds value to any business they end up in.
Former apprentices have gone on to work in roles at ANCA including - Research and Technology Manager, Operations Manager,
Service Technician, Commissioner, Precision Fitter, CNC operator, Manufacturing Engineer, Engineering Manager, Regional Manager, and Technical Leader. Many trained apprentices travel and work in ANCA’s overseas branches to gain firsthand experience working with customers across the aerospace, automotive, 3C, woodworking and medical industries, delivering onsite service.
ANCA currently has 16 apprentices in the program Bayswater, with three to five new apprentices starting every year. The next intake will be advertised shortly.
In 2019, ANCA established an Apprentice Training Centre at our Thailand facility. With a similar training pathway to Australia, the program at ANCA Thailand upskills the local workforce.
The Apprenticeship Program has built a highly skilled team who can support ANCA’s business globally. The knowledge acquired through the program provides a deep understanding of machine tool fundamentals. As a niche industry, we recognise the importance of growing the technical knowledge and experience required to keep our position as a global leader in CNC tool and cutter grinding industry.
“Previously I had no idea that places like ANCA, that are a market leader in their field were manufacturing within Victoria,” Daniel added. “Now working at ANCA and seeing what we do, it has really broadened my perspective on Victorian manufacturing.”
Find out more about ANCA’s apprenticeship program at: group.anca. com/Careers/Apprenticeship-Program anca.com
Improving the supply chain had never been so crucial. Charlie Wood, CEO Wiise counts warehouses as integral to the ever-important supply chain.
Supply chains are still recovering from the pandemic disruption, and the continued shift towards e-commerce and onshoring resulted in the lowest national industrial vacancy rate, dipping to 0.8%, making Australia one of the tightest logistics markets in the world. Meanwhile, customer expectations around speed and transparency are becoming even more demanding.
Warehouses are integral to the supply chain as they bridge the gap between production and distribution, ensuring excellent customer service. To add value and provide a seamless supply chain, warehouses need to be as efficient and agile as possible while also keeping a cap on costs. While large enterprises have moved to automated warehousing with robotics and IoT, many others simply can’t afford the costs involved. So, many warehouses still rely on manual and slow processes with high human error rates. The flow-on effects are missed orders, incorrect inventory records that lead to over and under-buying of stock, and an inability to properly manage stock condition, spoilage/expiry and so forth.
As they grow, manufacturers are looking to new technology to stay competitive and transform how their warehouses work, and smartphone technology has been a saving grace.
While hardware scanners have been available for many years –and have evolved to become far more capable, smartphones have also opened new opportunities for more advanced functionality at a much more affordable rate. So, how does this new technology benefit manufacturers?
With pen and paper, stocktake is typically a slow and painful process, which means many businesses only do it annually. By digitising this process via a mobile device, businesses can save time, keep more accurate records, and see inventory in real time. Stocktakes can become a regular occurrence and potential issues can be identified before they become bigger problems such as overstocking, understocking, spoilage, or delays. These problems are particularly important for businesses expanding to multiple warehouses and locations where stock is moved from one location to another.
In many warehouses, orders start by being entered in the backoffice, pick lists are then printed, warehouse workers pick products
and mark items off the printed pick slip, then enter that data into the back-office system again before moving the items to delivery. This process is cumbersome and relies heavily on people. Mistakes are easily made, time is wasted running back and forth from the office to the warehouse, and the warehouse worker is the only one who knows the status of an order until it's completed. By using mobile devices, staff can easily scan barcodes, automatically update inventory records in real time, and manage all their activities from the palm of their hand. This helps eliminate mis-picks, delays, and inventory errors, all the while keeping business owners, warehouse managers, salespeople, and customer service teams on the same page, making life much less stressful for staff.
3. Keep customers happy
Customers today want up-to-date information on their orders, including shipping status and delivery times. Warehouse technology enables businesses to improve their DIFOT (delivery in full, on time). Urgent orders can be processed first by easily identifying order priority and filtering tasks by supplier, customer, and shipping dates. This not only improves customer satisfaction rates but also identifies any issues, such as shipping delays, much more quickly.
4. Grow with less overhead
Simple improvements to warehouse operations can save hours of admin, allowing staff to improve productivity or focus on more important activities.
With less time needed to process orders, manage inventory, and onboard staff, businesses can reduce the time wasted on inefficient processes, and focus on growth with far less overhead.
As manufacturers grow, it’s important they support their business with the right technology to improve efficiency and stay competitive. While robotics and automated warehousing are exciting developments, cloud and mobile-based software advancements can offer small and medium-sized businesses significant efficiency gains for a fraction of the cost.
Today, there is no reason for businesses to struggle with inefficient warehousing. There are fit-for-purpose solutions that can significantly improve operations, cut costs, and get orders to where they need to be sooner, helping businesses move forward with their expansion opportunities. wiise.com
Unlocking Australia's manufacturing potential through digitalisation. Matthew McKnight, the Senior Technical Manager, Design and Manufacturing at Autodesk.
The Australian manufacturing sector faces labour shortages, disrupted supply chains, and mismatched global supply relative to demand – a hangover from the COVID rapid boom. Resilience and adaptability have defined this industry, especially in light of the recent global pandemic.
Innovation and unplanned technology investments boosted the sector through lockdowns, and this adaptability to meet changing customer needs led to an all-time-high growth rate of around 10% during 2021.
However, as the global supply shocks ease, Australia’s manufacturing sector has returned to business as usual – and seen a productivity drop.
With the world's population predicted to reach 10 billion by 2050, and Australia to double in size, the sector is required to undergo a significant expansion to recover in order to tackle rising demand. Coupled with the substantial investments in advanced manufacturing for defence, and a $15bn contribution to the National Reconstruction Fund for green manufacturing, the opportunities are great.
However, there's no denying the limitations and challenges that come with manufacturing in Australia, including our remote location and high labour costs, which impact our export competitiveness. While government grants and incentives are available, the key to overcoming the current manufacturing barriers is tied to our ability to adapt, work with the resources we have, and prepare ourselves to take advantage of future resources. Accelerated digitalisation and improved sustainability are fundamental to this evolution.
Digitalisation is taking off globally, with the market for AI in manufacturing expected to rise by $14bn in five years. At home, CSIRO has launched a ‘Future Digital Manufacturing’ program to demonstrate the expansive nature of digitalisation in manufacturing, and explore new ways of working for manufacturers.
Technologies like generative design and machine learning are simplifying the design process, eliminating repetitive tasks, and providing invaluable environmental insights.
The interest in digitalisation isn't merely a response to current challenges, but an endeavour to future-proof businesses. The integration of automation and AI-powered insights into operations allows data to do some of the predictive and analytical heavy lifting.
We're living in a time of rapid change and digital transformation, which brings about its own set of challenges. To meet these challenges head on requires strategic thinking about what’s to come: be it digital or sustainability imperatives, or constantly fluctuating global trends.
However, the journey towards digitalisation is not without its hurdles. Australia’s skills shortage is significant in manufacturing, and the sector faces a significant hurdle in attracting and retaining skilled employees. Research shows 70% of firms are struggling to find people with the right skills and 68% believe that access to skilled employees is a barrier to growth.
To bridge this skills gap in advanced manufacturing, a two-pronged approach is required. Firstly, championing STEM education, starting from schools and continuing through to universities. Secondly, and in tandem, creating incentives to attract international talent to our shores, despite our high cost of living and tax rates.
For industry, collaboration is key, be it with industry partners, or further afield to learn how other sectors adapt to skills shortages, and other obstacles. The bespoke and flexible nature of construction may very well apply to manufacturing to provide insights into how to scale and shift with changing environments, and vice versa. Global instability and demand shocks have happened before, and if manufacturers look to the successes of industries which have come before, there might be nuanced, disruptive strategies to deploy. Further, it is critical to embed long-term mindsets into processes early. While it may not be possible to predict every change in government incentives, or world crises, comprehensive data collection and analysis can identify adaptable strategies that are resilient to changing conditions.
While the challenges are significant, the opportunities for growth and innovation in Australian manufacturing are equally so. Digitisation and a flexible, nimble approach are leading the industry's evolution. Looking ahead, the next 24 months promise a continuation of these trends. Manufacturing and construction sectors are poised to learn from each other's practices, merging the bespoke flexibility of construction and the repeatable efficiency of manufacturing.
Manufacturing in Australia has struggled to scale at the same rate as other countries which are better geographically connected with larger population and trade bases, but the manufacturing sector is well-positioned to lead the nation into the future, provided it can adapt in time to the challenges it faces and seize the opportunities that lie ahead.
We need to be playing the long game: building resilience in manufacturing isn’t just about solving immediate problems. The future of the Australian manufacturing industry hinges on our ability to drive change, not merely adapt to it. autodesk.com.au
Manufacturing companies need to go digital to stay competitive, says Scott Rigby, Chief Technology Advisor & Principal Product Manager at Adobe.
As B2B e-commerce evolves, the dynamic manufacturing industry increasingly leverages digital technologies to propel growth and streamline complex business processes. Yet, there still seems to be a gap in understanding digital commerce. As the landscape evolves, the manufacturing industry must embrace digital transformation, especially commerce applications, to help market its brand and products via a digital platform.
APAC B2B e-commerce is projected to grow at a compound annual growth rate (CAGR) of 15.2%, reaching $253bn by 2030. The pandemic has pulled the future forward, especially in the manufacturing sector, where digital adoption was slow. Digitalisation has transformed the industry, and new expectations have emerged in a post-covid world. B2B buyers report an increased frequency of online purchasing post-covid (43%), which is why three in five (61%) B2B manufacturers are investing more in digital commerce. In another study by Adobe, 40% of top-performing manufacturers believe they will generate at least half of all product sales through digital platforms within two years.
However, the journey towards digital transformation is not always seamless. Manufacturers are struggling to achieve their vision of a robust digital buying experience. This struggle is compounded by the shifting profile of manufacturers' buyers, supply chain instability, and labour market issues. To navigate these challenges and drive growth without incurring additional costs and complexities, businesses are seeking ways to simplify processes. Addressing these complexities, commerce technology emerges as a solution that offers industry-leading customisation and flexibility.
The profile of manufacturers' buyers is undergoing significant changes. Most buyers now are digital-first millennials who want to procure and solve problems digitally. This influential market segment alters the landscape and shapes how businesses engage with customers. Digital-first millennials exhibit distinct needs and purchasing practices that diverge from previous generations. There’s a degree of comfort in buying online, with users wanting more personalised experiences. For example, digital natives would expect to be able to use their mobile to browse products, to be recommended products to them based on information they’ve provided, and to be able to make a purchase on their phone.
Leaders understand this and are shifting their priorities towards digital transformation. However, many are starting a long way back, still taking orders over the phone and email. Furthermore, macroeconomic hurdles hinder the industry. Manufacturers face mounting costs, which are squeezing their already narrow profit margins. The industry also faces supply chain challenges impacting operations. The industry is also grappling with labour skills gaps and shortages, on top of legacy systems. Businesses are seeking ways to grow without the added costs and complexities, driving to consolidate technologies. This emphasises the need for simplification and frictionless self-service.
Commerce technology offers industry-leading customisation and flexibility, enabling businesses to span across both B2B and D2C from a single platform. It also provides opportunities for growth and enterprise at scale.
Liebherr is one of the largest construction machinery manufacturers in the world, and it needed an advanced B2B e-commerce platform for digital purchasing of spare parts across eight global divisions. With a significant revenue coming from service partners, Liebherr also needed to easily integrate partners into the solution, while engaging directly with customers and service partners. Liebherr chose to build the platform using Adobe Commerce and today more than 1,600 customer companies and service partners access the system. Each customer has a personalised, frictionless shopping experience, while Liebherr has better transparency in tracking and greater efficiency thanks to the reduction of support calls.
Commerce is becoming a valuable investment for businesses as it can mature over time. As they mature, companies can deepen their feature functionality and refine the buyer experience to drive results. For example, packaging company Signet wanted to provide a greater personalised experience on their website. They started with customers being able to create accounts where employees can access relevant company account information. Then it matched tiered mega-menus to customer profiles to create a more tailored browsing experience. Unique check-out flows were also created to align with different account creation processes. As a result of these optimisations, web revenue increased 25%, driven by 18% more shopping sessions and user experience improvements that have reduced cart and checkout abandonments by 27%.
Digital transformation represents more than just incremental progress. It is a path to creating value and improving the servicing of business partners and customers alike. Changes and shifts in the landscape are here to stay. As a result, successful firms are embracing Industry 4.0 technology, connecting industrial equipment to the cloud, promoting interoperability between modern and legacy systems, and evolving digital capabilities rapidly. adobe.com.au
A new report has found that Australia’s manufacturing sector is in sharp decline, with no other industry shrinking more in the last 15 years – from 10.7% in 2006 to just 6.2%
speaks of solutions.
Historically, the sector has struggled to secure key funding necessary for growth, despite many of our core industries relying on hardware to scale at the rate needed to service the country — agriculture, transport, and energy, to name a few. Melt Ventures, Australia’s first private venture capitalist fund specialising in the investment of clean technology startups, dedicated to advanced manufacturing, was founded from this recognised struggle, with an aim to revitalise an industry that is integral to domestic and international growth.
The benefit to regional communities — a significant proportion of advanced manufacturing companies are emerging in nonmetropolitan areas to capitalise on the existing skill sets already found in the regions (agriculture, logistics, power and resources), helping to bolster the economy and create jobs.
The longer we ignore the role Advanced Manufacturing will play in our transition to a green economy, the harder it will become for Australia to achieve our net zero goals. Decarbonisation will not be software-led. Rather, it will be innovation in hardware solutions that propel us towards our emissions reduction targets. As such, it is crucial that we make continued and sizable investments into Industry 4.0 technologies like robotics, automation and advanced materials, which will play a key role in furthering the next generation of our core industries — namely renewable energy like solar and wind. Adequate investment into these sectors will help to ensure better economic and environmental security now and in the future. Traditionally, Advanced Manufacturing companies have struggled to scale due to the higher initial investment required to get their products off the ground. However, the industry is now at an inflection point, with many of the tools and technologies developing to a state of greater reliability and lower costs — leaving them primed for investment opportunities.
Investment in long-duration energy storage companies like Endua, Allegro Energy and MGA Thermal will make a significant impact as Australia transitions away from coal-powered energy. Endua’s renewable energy power banks, Allegro’s flow batteries, and MGA’s thermal blocks are able to store energy for longer periods of time than traditional means, and deliver this across the grid as
needed. This is crucial to both Australia’s long-term energy security, and achieving our net zero goals, as incumbent power suppliers like Liddell Power Station prepare to close, leaving a 6,000GWh energy gap. Australia uses $565bn worth of manufactured products each year, but we only produce $380bn — 68% of total use. This is less than any other OECD economy and is a waste of the wealth of resources and experience we have at our disposal. Increasing our production levels to match consumption could generate an additional $50bn in GDP and more than 665,000 direct and indirect jobs in the sector.
Manufacturing job multipliers are also consistently higher, with the NSW Government’s job multiplier tool ranking specialised manufacturing at a multiplier of 1.9. Increased investment into the sector is key as we look to grow industries like clean energy — which will require significant people power to create the infrastructure needed to hold and distribute consistent power.
Melt Ventures is Australia’s first fund dedicated to Advanced Manufacturing. We committed to investing in hardware companies after we found that, of the 106 early stage funds in Australia, 103 of those were dedicated to software development. This has left a major gap in the financial backing available to companies that make physical products — and is one that we are helping to shrink.
Melt Ventures was launched in 2022 and backed by organisations including EnergyLab, Robotics Australia, and The Melt Accelerator.
To date, we have raised $15m for our first fund — investing in key long-duration energy storage companies Endua, MGA Thermal, and Allegro Energy. Melt Ventures provides seed and pre-seed funding, with a goal of investing between $100,000 and $1m into each company we back. Our focus is on seed and pre-seed raises as this is where Advanced Manufacturing companies require the greatest amount of capital to get up and running.
It’s time to double down on investing in Advanced Manufacturing in Australia. Our fund is dedicated to helping to build incredible hardware companies that are doing everything from sustainable and thermal energy storage, solving grid stability, and using Hydrogen to replace the need for diesel generators. melt.ventures
Co-led by the Department of Biomedical Engineering, researchers employed a novel approach to ‘tissue engineering’ blood vessels. By combining materials and fabrication technologies, they developed a method to create blood vessels with complex geometries.
Blood vessels serve an important function in sustaining life, by carrying oxygen-rich blood and essential nutrients to all parts of the body while removing toxic products. Illness and dysfunction in blood vessels, on the other hand, can result in life-threatening disorders such as heart attacks, strokes and aneurysms, making cardiovascular disease the number one killer globally.
While bypass surgery has proved a life-saving alternative for replacing severely damaged blood vessels, it has limitations, particularly for smaller diameter blood channels such as the coronary artery. Non-living synthetic grafts can cause blood clotting and obstruction, making them unsuitable in some circumstances. As a result, patients who have limited options due to past surgery or comorbidities such as diabetes face significant problems.
To overcome these limitations, the researchers investigated developing 'tissue-engineered' blood vessels, which are made from human cells and tissues. These created vessels have the potential to treat cardiovascular illness, as well as construct built-in blood supply for larger tissue creations.
Professor O’Connor said the research is an exciting step in scientists’ ability to engineer human blood vessels. “We are now able to rapidly and cheaply manufacture blood vessels using living tissue that has appropriate mechanical properties and mimics the cellular orientation of the inner-most layer of blood vessels,” Professor O’Connor said. ACS Applied Materials and Interfaces
The drone called Bat Bot, is capable of autonomous, flapping flight and weighs only 93 grams. Bat Bot uses a morphing skeleton array and a silicone-based membrane skin to mimic the flight of bats. The robot can move each wing independently and constantly change each wing's shape to perform complex manoeuvres that would be impossible otherwise. The flapping motion also conserves battery power, making it both quieter and more efficient than fixedwing or quadcopter drones. Bat Bot flaps its wings for better aerial manoeuvres, glides to save energy, and dive bombs when needed. Bat-inspired aerial robots also offer a number of benefits over current aerial robots, like quadrotors. The greatest advantage of these robots is their soft wings. Other rotorcraft are considered
inherently unsafe for humans due to their materials and sharp rotor blades and noise. Robots with the pliable wings of bats, on the other hand, are comprised primarily of flexible materials and can flap their wings at much lower frequencies. These robots are considered much safer to operate and fly as they navigate through different environments, with little chance of causing any damage.
CalTech
New research from Edith Cowan University (ECU) shows batteries built from zinc and air could be the future of powering electric vehicles. The project tested zinc-air batteries using a combination of cheaper, safer and sustainably sourced materials, which allowed for improved lifespan and performance. ECU’s Dr Muhammad Rizwan Azhar led the project which discovered lithium-ion batteries, although a popular choice for electric vehicles around the world, face limitations related to cost, finite resources, and safety concerns. “Rechargeable zinc-air batteries (ZABs) are becoming more appealing because of their low cost, environmental friendliness, high theoretical energy density, and inherent safety,” Dr Muhammad Rizwan Azhar said. “With the emergence of next-generation longrange vehicles and electric aircraft in the market, there is an increasing need for safer, more cost-effective, and high-performance battery systems that can surpass the capabilities of lithium-ion batteries.”
ECU’s breakthrough has enabled engineers to use a combination of new materials, such as carbon, cheaper iron and cobalt based minerals to redesign zinc-air batteries. "In addition to revolutionising the energy storage industry, this breakthrough contributes significantly to building a sustainable society, reducing our reliance on fossil fuels, and mitigating environmental impacts.”
Dr Azhar said while renewable resources such as solar, wind, and hydro energy play a critical role in the future of green energy, they are not completely reliable solutions as they are intermittent sources of energy. “Due to the abundance of zinc available in countries such as Australia, and the ubiquity of air, this becomes a highly viable and reliable energy storage solution,” Dr Azhar explained.
Eco-Mat
What happens in femtoseconds in nature can now be observed in milliseconds in the lab. Using a trapped-ion quantum computer, Scientists at the University of Sydney have witnessed the ‘Conical intersections’, the interference patterns of a single atom. These are vital to rapid photo-chemical processes such as light harvesting in human vision or photosynthesis. Scientists used a quantum computer to engineer and directly observe a process critical in chemical reactions by slowing it down by a factor of 100 billion times. Joint lead researcher and PhD student, Vanessa Olaya Agudelo, said: “It is by understanding these basic processes inside and between molecules that we can open up a new world of possibilities in materials science, drug design, or solar energy harvesting. “It could also help improve other processes that rely on molecules interacting with light, such as how smog is created or how the ozone layer is damaged.”
Chemists have tried to directly observe such geometric processes in chemical dynamics since the 1950s, but it is not feasible to observe them directly given the extremely rapid timescales involved.
Nature Chemistry
In a new partnership between iLAuNCH Trailblazer universities, the University of South Australia (UniSA) and the University of Southern Queensland (UniSQ), Adelaide-based clean energy technology company entX is set to change the landscape of sustainable energy solutions that will power space missions of the future.
The sustainable energy project is twofold for iLAuNCH. The first project will see UniSA and entX focus on the flow of thermal energy to ensure spacecraft can survive multiple nights in temperatures that can reach down to -180°C on the dark side of the lunar surface.
The second project with UniSQ will look to commercialise longterm power sources to spacecraft where solar energy cannot be relied upon. “We are thrilled to announce entX as another Trailblazer partner and program for the space industry,” said iLAuNCH Trailblazer Executive Director, Darin Lovett.
“Together we are working to commercialise two truly disruptive space energy technologies that will pave the way for global exports and give Australia a sovereign capability to excel on the world stage.” As Australia is becoming a global participant in lunar-based payload missions, there is an emerging need for sovereign capability to support applications that will need to survive a lunar night cycle
of 14 days at temperatures approaching -180°C.
In the first project with UniSA, entX will prototype a Radioisotope Heater Unit (RHU) supported technology platform, to provide thermal management for multiple lunar night survival. The RHU will possess a half-life that is more sustainable, and ideal for shorter duration missions (1-5 years) such as small payloads that will fly to the Moon on the emerging series of commercial landers.
UniSA
Epson and its subsidiary EXI have made an additional investment in GITAI, a startup company that develops general-purpose space robots. GITAI is a startup that envisions providing safe and affordable labour in space. Their goal is to develop and sell versatile space robots that will serve as a workforce for tasks both inside and outside space stations, in Earth's orbit, as well as on the Moon and Mars. Additionally, they aim to provide services in space.
With the acceleration of space development, including lunar resource development, Mars exploration, and the commercialisation of the International Space Station (ISS), a rapid increase in various types of work within space is anticipated, such as the construction of new space stations, lunar bases, and Mars bases. This work is potentially dangerous and is currently being performed by astronauts, who must be trained and transported at tremendous expense. GITAI is developing general-purpose robots that can significantly reduce the risk and burden on astronauts while also dramatically reducing the overall cost of transportation and training associated with space labour. By doing so, GITAI aims to make space exploration and development both safe and affordable. Since 2021, they have been steadily building a strong track record by developing lunar work robots and extravehicular robots, as well as by successfully completing on-board experiments using demonstration models on the ISS.
EpsonPacific Automation has announced a new Australian partnership with German manufacturer BERNSTEIN.
This new national distribution deal makes BERNSTEIN switching safety and innovation available to all Australian industrial operators, along with technical support provided by Pacific Automation. “We’ve been supplying BERNSTEIN products since 2006, so our team is well familiarised with the quality of their products.” says Stephen Armstrong, CEO at Pacific Automation. “Our goal is to represent BERNSTEIN in Australia how they would represent themselves. That means ensuring that our customers receive high quality customer service and technical support, just like they would from an OEM.”
Key product ranges now accessible through this new partnership include:
• Limit switches
• Safety rope pull switches
• Door interlock switches
• Foot switches
BERNSTEIN switches are utilised in factory automation and for machine and operator safety across Australian industry. Their products are highly modular and can often be customised to suit the requirements of an individual customer or unique application. “We intend to keep growing and distribute our products around the
globe. Therefore, we are pleased to have found a partner like Pacific Automation, who supports us professionally and trustfully in this intention.” says Mrs. Nicole Bernstein, Member of the Executive Board of BERNSTEIN AG.
“The added value for our customers is to have a competent contact person incountry who is just as convinced of the quality and functionality of our products as we are ourselves.”
Customers can now shop online with Pacific Automation and access the full ranges of BERNSTEIN switching technology.
Pacific Automation is a leading provider of automation, electrical & control solutions in Australia. Since 1969 the company has specialised in delivering cutting-edge technology, exceptional customer service and full technical support to industrial operations. Founded in 1947, BERNSTEIN AG employs more than 500 people in ten countries today and is managed as an internationally active family business in its third generation. As a supplier of industrial safety and enclosure technology, their product portfolio ranges includes switches, sensors and housings, suspension systems and operator terminals, and system solutions for operating and safeguarding entire machines and plants. pacificautomation.com.au
Hexagon introduces automated turnkey vision measurement system.
Hexagon’s Manufacturing Intelligence division today announced the launch of OPTIV Scope, an innovative vision Coordinate Measuring Machine (CMM) that simplifies quality inspection across industries. OPTIV Scope combines efficiency, accuracy, precision and ease of use enabling businesses to save time and reduce the costs of quality inspection. The system is ideal for inspecting high volumes of parts with similar shapes.
Speed is of the essence in today's fast-paced manufacturing environment, and OPTIV Scope is designed for the challenge. With its ability to simultaneously measure multiple parts in seconds at the click of a button, OPTIV Scope eliminates the time-consuming process of manual part alignment before each measurement, allowing machine tool operators and quality professionals to focus on their critical tasks and maximise productivity.
Accuracy and precision are at the core of OPTIV Scope's capabilities. With accuracy of up to ± 0.7 microns, OPTIV Scope provides reliable and repeatable measurement data, independent of the operator, at the press of a button.
“Hexagon is committed to empowering manufacturing teams with cutting-edge measurement solutions that optimise efficiency and enhance productivity,” said Joerg Deller, general manager of stationary metrology devices and machine tool measurement at Hexagon. “OPTIV Scope completes our multi-sensor lineup, offering an entry-level, easy and precise machine that streamlines high-volume measurement for machine tool operators and quality professionals alike, saving time and costs.”
OPTIV Scope is available in six models with varying work volumes and camera resolutions, with a maximum 300 x 200 mm field of view. The system ensures comprehensive coverage of dimensioned features on a part, minimising the need for multiple measurements and improving workflow efficiency. Equipped with a double telecentric optical lens with a large depth of field, the system offers reliable edge detection with automatic focus. It captures sharp and clear images, even in complex measurement tasks.
OPTIV Scope caters to a broad range of industries and diverse manufacturing applications. Its versatility makes it an indispensable tool across sectors such as electronics, injection moulding, lowvoltage electrical appliances, mobile phone accessories, printed circuit boards, medical equipment and many more. No matter the application, OPTIV Scope provides accurate, repeatable measurements and streamlines processes. hexagon.com
Photonis iNocturn ultra-sensitive intensified camera.
The iNocturn from Photonis is an intensified camera combining an image intensifier tube with a sensitive, low-light camera. It features a unique combination of ultra-sensitivity, low SWaP, high frame rate, high-QE photodetectors, and nano-second gating. The intensified camera can detect different wavelength ranges from deep UV to NIR and is suited for applications in fluorescence imaging, electrical discharge detection, microscopy and spectroscopy. The camera’s high-resolution sensor is also equipped with a high frame rate for high-speed moving objects in applications such as industrial monitoring.
Small, compact and lightweight, the iNocturn intensified camera offers 1280x1024-pixel resolution, frame rates up to 100fps at full resolution, spectral range from 200 – 1100nm, however this is subject to photocathode choice. With either gated or non-gated options the minimum detection capability is up to a single photon. Connection is via PAL/NTSC, CameraLink, HD-SDI, USB 3.0, LVCMOS, C-mount and operational temperature -10C to +55C.
Thanks to the Smart Tube Management, the iNocturn range of camera produces high quality images and videos supporting the ability to perform single photon detection, with an ultra-low read noise reached without the need for any additional cooling.
The High QE image intensifier comes with different range of wavelength spanning from deep UV to Near Infrared enabling the user to focus on a specific range of wavelength for a particular application. For example, spark and electrical discharge detection application is very suitable with the iNocturn SUV, while the iNocturn Blue or Green can be used for other applications that include wafer inspection, spectroscopy, and microscopy. scitech.com.au
Turck's TBEN-S1-4DXP improves cost efficiency in distributed systems that have a low I/O density and a compact 4-I/O Module for Intralogistics.
Turck now offers the TBEN-S1-4DXP Ethernet I/O module which is specifically designed for use in applications with a low I/O requirement – such as in many logistics applications. The compact block module provides four channels that can be used flexibly as inputs or outputs in the same housing as the TBEN-S, which comes as standard with eight channels. With a temperature range from -40 to +70 ° and protection to IP65/IP67/IP69K, the new I/O module has a wide range of applications.
In applications where a small number of I/Os are collected and transferred over long distances, users benefit from the full flexibility of the TBEN-S compact module design, but with additional cost efficiency. The robust IP69K TBEN-S1-4DXP is ideal for decentralised automation, which reduces commissioning and wiring effort. As a Turck multiprotocol device, it can be used automatically in Profinet, Ethernet/IP or Modbus TCP networks without any intervention by the user.
Turck is presenting new optocouplers for transmitting fieldbus communication via fiber optic cable (FOC). The single or dualchannel devices of the FOC series transfer fieldbus protocols such as Profibus-DP or Modbus RTU as light signals along fiber optic cables. The zone 1 IECEx variant of the FOC couplers is unique on the market as it can be installed in zone 1 and can transmit intrinsically safe signals in accordance with RS485IS. The FOC media converters can cover large distances, more than 2500 meters, depending on the fiber optic cable used. FO cables are also immune to electromagnetic interference. Users
can also configure ring topologies for maximum availability with the devices in addition to point-to-point connections. All devices are provided with a universal shielding concept which can be easily adapted to individual processes. The integrated alarm output of the FOC converters can considerably shorten the time required for troubleshooting. turck.com
Laser Induced Breakdown Spectroscopy (LIBS), is now a viable technique for large scale analysis of geological materials with the ability to contribute to ore body knowledge and directly influence exploration geology programs and process metallurgy operations. The technique has some similarities to spark OES which has been used for many years in the metals industry to confirm or identify alloy grades.
While LIBS is not a new technology, it really came to the fore in 2012 when NASA employed it on the MARS Rover Curiosity. Their LIBS system called ChemCam is mounted on top of the mast and can analyse materials as far as seven metres away, where it was used to determine the composition of Martian geology samples. In July 2021 it was reported to have collected over 800,000 spectra from more than 2,500 individual targets. In the process, it has been responsible for some of the Rover’s most significant discoveries. In recent times, Canadian-based ELEMISSION Inc. developed the technology for similar applications with a more terrestrial focus.
LIBS employs a high intensity pulsed laser directed at the surface of a sample. The surface is transformed into a micro-plasma cloud consisting of atoms, ions, molecules and electrons in an excited electronic state. As these particles return to their ground state,
they release energy in the form of characteristic wavelengths of light. The emitted light is collected using a highly sensitive onboard spectrometer, enabling simultaneous detection of multiple wavelengths related to a specific element or group of elements. With the intensity of the spectral lines being proportional to the elemental concentration, scientists have been able to use this to identify and quantify elements in the material under study. The right combination of laser energy, advanced calibration techniques and high-performance spectrometers allows the technique to reach great sensitivity, with detection limits that can go as low as ppb in concentration levels.
X-Ray Fluorescence (XRF) is a staple analytical technique in the mining industry, mainly used to provide elemental analyses on bulk materials. Despite XRF’s extensive use, it is insensitive to light elements such as lithium, beryllium, carbon etc. XRF’s inability to detect light elements is tied to their atomic weight, with light elements such as lithium not able to be detected due to their X-ray fluorescence being too weak to detect. LIBS on the other hand is able to detect every element in the periodic table.
Continued next page
Driving informed mining decisions using high-speed LIBS core analysis. An article by Dr. Cameron Chai, Alejandro Fayad, Rowena Duckworth and Melissa Narbey.
Continued from previous page
An analogous technique to LIBS mapping is the fairly new micro XRF mapping. Both techniques have similar spatial resolution, however the LIBS mapping is orders of magnitude faster and is more sensitive to more elements, providing microanalysis on a macro scale.
Infrared Hyperspectral scanning utlises light from the visible, near-infrared (NIR) and short-wave infrared (SWIR) portion of the spectrum. By measuring the reflected light across numerous narrow and contiguous spectral bands, the scanner can capture the distinct absorption features of various minerals. These features have their own absorption pattern and algorithms can be used to deconvolute spectra to reveal the nature of the minerals within a drill core. While hyperspectral measurement scanners can capture data very quickly, they are best used for identifying fine grained sheet silicate alteration minerals rather than overall mineralogy and textures.
In comparison to other core scanning technologies:
Using drill core and rock chips loaded into core trays, the ECORE provides ultra-fast automated mineralogy with the aid of artificial intelligence. The system scans 30µm spots at variable resolutions (i.e. distances between spots), typically in the range 50 to 1000µm, with larger spacings possible if required. Core is usually scanned strip-wise, analysing a section down the length of the sample with a width of up to 40mm. At a standard sampling rate of 1300 spots per second and a one cm strip width, a full tray can be scanned in about 20 minutes at low resolution, while specific areas of interest can be identified and scanned at higher resolution if desired. This type of analysis generates highly detailed analyses which can be completed within a matter of minutes, with data available shortly after scanning.
Measurement
Outputs Elements and Elements Minerals only minerals and minerals
Elemental Entire periodic Na to Urange table
Limits of Low ppm
detection to ppb
Low ppm ~ 5%
Resolution 30µm 5-50µm 250µm
LIBS generates a spectrum from every spot scanned. By scanning many spots, typically many thousands, a detailed analysis of the sample can be generated, extending from elemental composition (similar to XRF), through to quantitative mineralogy.
ELEMISSION, who have been developing LIBS-based systems for geochemistry since 2014, recently launched the ECORE, a revolutionary laser-based core scanner designed for fast and efficient scanning of drill core and other geological materials. Using technology refined in the ECORE Flex that is currently being used by the CSIRO, the ECORE offers automated workflows enabling core samples to be analysed at a rate of up to 1000m/day.
The first commercial ECORE installation has recently taken place the Automated Mineralogy Incubator (AMI) in Perth where it is at home with other automated mineralogy systems. At the AMI, this cutting-edge analytical tool is available for use by the mining industry where clients can also benefit from the expertise of the AMI’s in-house mineralogists.
Traditionally, core samples are logged by geologists who have learned to identify minerals with the naked eye, but this is highly subjective and depends on the geologist’s skill. Often minerals that are quite different in composition are very similar in colour, density and texture. Additionally, there are microstructures relating to the rock formation that are not obvious to the naked eye or even under a hand lens. Complications in the natural world also extends to variations in chemistry in minerals that cannot even be determined by optical techniques.
The Geological Survey of Western Australia (GSWA) has a mandate to provide the most detailed geological information possible to aid mineral exploration and the mining industry in Western Australia. They have an extensive core library containing donated core and core that has been co-funded between exploration companies and the Government of Western Australia. Below is data from the cofunded Exploration Incentive Scheme (EIS) and Pilbara Minerals from the Pilgangoora area of Port Hedland in WA.
The ECORE has a camera that not only helps it to navigate the samples, but also provides valuable optical images that provide the basis for the chemical and mineralogical data to be overlayed. A skilled geologist could probably look at these core samples and identify the presence of phases such spodumene, K-feldspar, quartz etc., but quantifying how much is there, and identifying trace phases is much more difficult to determine.
The image below shows a full tray of drill core and overlayed is the elemental strip map for lithium. These samples were scanned using 50µm spots at high resolution i.e., 100µm spacings, with the entire tray taking about 90 minutes to scan. The scan time could be reduced by increasing the spot spacings.
There are clear zones of high lithium concentration throughout each core sample indicating areas of potential commercial value. Of interest are the zones of high lithium content where the mafic zone intersects the pegmatite and host rock.
As each element has a unique spectral fingerprint, the spectra from a multi-element material can be deconvoluted by looking at specific peaks from individual elements and hence the elemental composition derived. The image below shows element maps for the elements Li, Cs, Rb, Be, Na and K, with the dark red regions containing the highest concentration and dark blue the least concentration of each element, calculated on a pixel by pixel basis. In this case, it is easy to see the presence of lithium with some regions containing noticeable quantities of Cs and Rb, which is consistent with Li-bearing micas. The provided logs indicated significant spodumene content, so the high lithium content observed was expected. However, the logs did not provide any quantification, which can be easily achieved using the ECORE.
While elemental analyses are important, and the presence of high lithium content extremely promising, the ECORE can also generate automated mineralogical maps and determine quantitative mineralogy. This is achieved using the entire spectral fingerprint
of all of the elements present. The resultant data can be of great interest to exploration geologists and mining engineers. The ECORE minerology image below shows the mineral maps generated by the ECORE software. These maps clearly show which minerals are present, and where. Spodumene-rich regions are evident (green zones) in close association s K-feldspar and quartz, which is to be expected from this type of deposit. Interestingly, a small amount of lithium bearing bityite is also observed which could be easily overlooked during a visual inspection.
The mining industry has to embrace the latest technologies to both remain competitive and also utilise best practices to positively influence their decision-making processes. The decision-making processes need to be driven by definitive data. The ELEMISSION ECORE is able to provide reliable data at a rate that is commercially
relevant and can be used to target mining exploration projects or optimise process metallurgical operations. Especially suited to lithium-bearing minerals such as spodumene or lepidolite that are outside the realms of XRF, the ELEMISSION ECORE LIBS scanning excels with its ability to directly detect and quantify lithium minerals. By analysing millions of micro-sized points along the length of core samples, the ECORE is able to provide elemental and mineral maps. In addition, the ECORE has demonstrated its value to the mining industry with the ability to rapidly analyse large quantities of drill core without subjectivity. Geologists will have time for data interpretation rather spending their time manually acquiring the data. Access to this technology is now available at the Automated Mineralogy Incubator in Perth. elemission.ca automatedmineralogy.com.au
Raymax new technologies advance the analysis of ‘green minerals’.
Mineral exploration plays an important role in society. Today, with the drive for a low carbon economy there is pressure to discover mineral deposits such as nickel, lithium, cobalt, zinc and copper that are required to build renewable energy sources such as solar panels, wind turbines and batteries for homes, industry and electric vehicles. Without access to ‘green metals’ a low-carbon world won’t be possible.
In support of mineral exploration are two technologies that offer improved mineral identification techniques through reliable analysis. One of these technologies is LIBS or Laser Induced Breakdown Spectroscopy. A rapid minimally destructive chemical analysis technique used to identify and detect mineralogical samples. A leading laser system is the J200 LIBS instrument from Applied Spectra designed specifically to handle the most demanding trace element analyses — those requiring high sensitivity and accuracy. With a single-digit ppm (parts per million) level of detection (LOD) limit for many elements in the periodic table, the J200 LIBS is an ideal instrument for challenging quantitative elemental analysis with many sample matrices and capable of monitoring single or multiple elements of analytical interest.
“Already Australian organisations are applying LIBS to analyse the chemical construct of sample rocks for the detection the mineralogical content,” says Chris Lay, from Raymax Applications Pty Ltd who distribute Applied Spectra Inc laser systems. “Using LIBS has enabled the identification of essential mineral deposits and even enable better mapping of mine sites,” Lay added.
LIBS technology advances existing technologies currently used for the direct analysis of mineralogical samples such as infrared spectroscopy or IR. However, while IR identifies the mineralogy of a rock sample it does not identify the elemental composition such as rare earth elements (REEs) needed for identification and mining of ‘green minerals.’ XRF is a technology currently used to determine the concentration of basic metals such as copper, zinc, and nickel. However, XFR is known to be challenged when it comes to quantifying precious metals such as gold due to the low sensitivity and poor limit of detection. Additionally, portable X-ray systems used in situ in the field, have shown they are not sensitive enough to detect gold, for example in the ppm range – or parts per million, and often incur substrata interference with other minerals giving false values compromising determinations.
Compared to XRF techniques, the J200 LIBS instrument developed by Applied Spectra, offers attractive analytical advantages to the mining industry, detecting elements from H – Pu, including nonmetals such as H, N, F and O, that are often difficult or impossible to discern with other types of analysis. The J200 LIBS laser system can measure a large number of elements, simultaneously as well as detecting lighter elements such as B, Li, C, K, Ca, Mg, Al, Si, etc, that are beyond the capabilities of other techniques. “Little to
no sample preparation is required, meaning quick access to the system for analysis using Applied Spectra’s software package. Precise elemental analysis is fast, for instance a single spot analysis can be achieved in a few seconds,” Lay says. The J200 laser system offers high reliability for important elemental analysis. To support this highly complex process Applied Spectra have developed very powerful chemometric software for LIBS data analysis: Principal Component Analysis. “What we are seeing is that accurate, effective LIBS elemental analysis, has the potential to revolutionise the mining industry,” said Lay who would be delighted to explain the LIBS process and its importance to mining ‘green minerals’ to members of the mining industry. In addition, Lay can explain the process of laser ablation in the J200 Tandem LA-LIBS instrument of capturing the emitted light from laser ablation plasma for rapid spectroscopic analysis.
A second and complimentary technology is hyperspectral imaging, offered by HySpex NEO an established industry leading brand for both airborne and ground-based hyperspectral imaging supplied by Raymax Applications for customers in Australasia. This powerful tool is used in various fields revolutionising the way we analyse and understand materials. One application is in core scanning a technique used to analyse the composition and properties of sediment and rock cores. With a growing demand on ‘green’ metals essential for producing low carbon technologies such as electric cars and smart phones, a variety of natural resources have assumed greater importance in mining, increasing the demand for better samples from mine sites for geological analysis to achieve more accurate, detailed mineral maps.
wavelength bands to identify and characterise core samples. Hyperspectral imaging takes this process to a whole new level by capturing a spectrum of information for each pixel in an image. Instead of just a few discrete colour channels, hyperspectral systems collect data across hundreds of narrow and contiguous spectral bands. This results in a detailed spectral fingerprint for each pixel, providing unparalleled insights into the composition and distribution of materials within the core.
Using HySpex NEO hyperspectral imaging systems for core scanning has several key advantages. First, it allows the identification and differentiation of minerals, organic matter, and other components that might be challenging to distinguish using conventional methods leading to more accurate lithological and mineralogical classifications, aiding in the interpretation of geological history and environmental conditions. Second, hyperspectral imaging enables the detection of subtle changes in composition particularly valuable for identifying variations in mineralogy, porosity, and other physical properties across the length of a core sample.
In addition, using HySpex hyperspectral core scanning can provide insights into environmental conditions and processes. However, the use of hyperspectral imaging for core scanning also presents challenges. The vast amount of spectral data generated requires sophisticated data analysis techniques to extract meaningful information. This demands specialized software and algorithms that can process, interpret, and visualize the multidimensional data effectively. To meet this requirement, HySpex have partnered with Prediktera, whose premiere software solution, Breeze, enables a wide range of hyperspectral imaging applications for application development, routine analysis and real-time industrial analysis solutions.
“This complimentary technology to LIBS for core drill analysis incorporates HySpex VNIR and SWIR cameras which provide scientific-grade hyperspectral imagery,” explains Dr Cédric Chaminade from Raymax Applications, “Working together with the new Breeze Geo software tools, mineral mapping of the highest quality and highest resolution can now be undertaken.” In addition, the platform is linked to the USGS libraries and allows for mineral identification and quantification using many customisable algorithms such as minimum wavelength mapping, and spectral angle mapper, providing great resources for the end user.
HySpex NEO’s drill core scanner allows you to achieve a seamless user experience as the tools to implement hyperspectral imaging of mineral analysis in the laboratory, core shed, mine site, or even
a mineral processing environment are provided with the hardware. Realtime interpretation and visualisation of the scanned cores identifies areas of significance, such as alteration mineralisation, and highlighting sections requiring assay or geochemical sampling. The resulting mineralogic interpretation can be optimised for core boxes, it can handle drill chip boxes, loose samples, and rock mass. Due to the quality of data acquisition hyperspectral imaging will minimise misclassification of false allocations of material that may have yielded itself using other technologies such as hand-held devices or lower fidelity and resolution systems. “With HySpex NEO cameras,” says Dr Chaminade, “Each pixel in a hyperspectral image has a continuous spectrum, a technique that has wide geological applications, including the identification and classification of mineralogical alteration assemblages and correlation of geological units.” Using VNIR and SWIR cameras, imaging spectroscopy can help both identify and evaluate mineral or deposit specific geological materials. The data can also provide planning information in the form of a 3D model to help with on the ground activities, prior to extraction.
“At Raymax, we have extensive experience with HySpex NEO cameras, in the field, at mine sites, and for agricultural and defence applications. But the opportunities to assist with mining ‘green minerals’ to help the carbon-free economy is very exciting,” concludes Dr Chaminade. raymax.com.au
Using Gallium to target silver-based antimicrobials for nanomanufacturing.
Scientists from the ARC Centre of Excellence in Future LowEnergy Electronics Technologies (FLEET) at RMIT have developed a Gallium-based liquid metal in the form of nanodroplets, similar in form to our planet Earth. The nanodroplets feature an outer ‘crust’, a liquid metal ‘mantle’, and a solid ‘core’. Aside from the curious form it takes, the discovery creates new research opportunities in fundamental liquid metal chemistry as well as applications in flexible electronics, catalysts and fuel cells, and silver-based antimicrobials. Just another revolution in nanomanufacturing in Australia.
The solid intermetallic core is the key to securing the same amount of ‘target’ metals in each alloyed droplet.
“At the moment, materials like gallium are heavily under-utilised,” said Associate Professor Dr. Torben Daeneke, from RMIT’s School of Engineering, “these days it is only being used in niche applications, and in mining, most of it is not recovered and lost in the tailings.”
The developed planet-like nanostructures are expected to have a significant impact on renewable technologies such as fuel cells as well as chemical processing more broadly. The team demonstrated that the nanostructures are effective as ethanol oxidation catalysts which is a key process occurring within ethanol fuel cells. With ethanol being a renewable resource, these particles may help with decarbonising the transportation sector. Similar nanostructures can also be used in petrochemical processing where low-cost components of natural gas are converted into hydrogen and polymer feedstock.
The RMIT research
This FLEET research included previous methods attempting to dissolve the metals at relatively low temperatures, near room temperature. “Just as it’s possible to dissolve more sugar in warm water than in cold water, more copper can be dissolved in warmer gallium,” says lead author Caiden Parker, a PhD candidate at RMIT.
In the new study, RMIT researchers resolved the problem of dealloying by significantly heating the synthesis process (as high as 400°C) to ensure the solute metal is completely dissolved and introducing a carefully selected molten-salt suspension fluid.
“We were immediately struck by the nanodroplets’ similarity to an Earth-like planet, with a solid outer shell, a liquid metal mantle, and a solid metal core,” says Caiden. That solid core is the key to the success of the new technique, ‘locking up’ the same amount of solute in each alloyed droplet. “We were also delighted to see that our new metallic planet-like nanodroplets were everywhere!” continues Caiden.
The copper-gallium nanodroplets studied provided promising results in electrocatalytic oxidation of ethanol, which could be applied in ethanol fuel cells.
“In our paper we demonstrate that our liquid metal nano-planets hold promise as a fuel cell catalyst,” adds Daeneke. The noble metals could in future “be replaced by cheaper gallium alloys. These nanostructures also hold promise for catalysis more broadly and may help with breaking down hazardous contaminants or the production of commodity and fine chemicals. Work on these topics [is] ongoing in our labs.”
“These nanostructures can help us understand dissolution and crystallisation processes that occur in liquid metals in much more detail,” said Dr. Daeneke. “With an increased understanding of processes that occur in molten metals we may be able to lower energy requirements during metal refining while also improving the properties of the final metal product.”
Liquid metals are extraordinary materials that feature properties which arise due to their cloud of delocalised electrons and the
simultaneous liquid state of the individual atoms. Featuring excellent electrical and thermal conductivity, negligible vapor pressures and low viscosities, the metallic elements are in low oxidation states, thus rendering liquid metals ideal for many applications, including catalysis, inorganic synthesis, electronics, and biomedicine. Their ability to form a myriad of alloys is also crucial, allowing them to design a wide array of tailored liquid metals with engineered properties. A small amount of platinum can be added for a significantly enhanced catalytic activity in a range of model reactions.
“A key advantage of liquid-metal systems is the ability to adjust the metal mix for certain applications, dependent on the properties of the constituent metals,” says Caiden.
“For example, copper is a great electrical conductor. When we combine copper with gallium, we not only save significant cost in material consumption, but also open the way to flexible electronics, such as what you might have seen in sci-fi movies.”
The system was homogenously spread, with output yield significantly improved. Transmission Electron Microscope (TEM) analysis confirmed the core structure is observed in almost every droplet.
The presence of the solid core also promotes a very interesting use for the planet-like nanodroplets in catalytic reactions, ‘speeding up’ chemical reactions. Gallium has a low melting point of 29.76˚C but boils at 2,400˚C. Removal of the sodium acetate is important prior to this catalytic reaction, with the salt easily cleaned away in simple water baths.
The promising new technique opens up the potential use of highsurface area nanodroplets in a wide range of future applications, including, but not limited to, electronics or catalytic materials. The physical scale of the nanodroplets will also assist fundamental studies of liquid-metal chemistry, including looking into the precise nature of bond formation within liquid metals, solvation capabilities, crystallisation dynamics and the general colloidal chemistry that may occur within various molten metal systems.
“The planet-like structures are like little miniature laboratories, allowing us to study how molten metals behave at an atomic level,” adds Torben.
While the study proved viability of the new technique using a coppergallium system, the scientists expect further work to confirm that the technique will be successful using other combinations of solute and solvent alloy systems, beginning with silver, zinc, or bismuth in liquid gallium, tin or indium. rmit.edu.au fleet.org.au
CSIRO launches national data and information tool for soil.
Australia’s national science agency, CSIRO, has launched a new tool that will help Australia sustainably manage a critical natural resource which sustains lives and livelihoods. Now live and available for use, the Australian National Soil Information System (ANSIS) brings together soil data from across Australia, connecting multiple data sources to provide access to nationally consistent soil data and information.
It will equip farmers, policy makers and researchers with the data and information they need to better manage, restore, and protect Australia’s soils. Speaking at the Soil Science Australian conference in Darwin, ANSIS project lead at CSIRO, Peter Wilson, said it was an important step forward for the future sustainable management of soils in every part of the country.
“Soil is the backbone of our food security, and it is critical that we manage it effectively for climate change adaptation and economic and environmental prosperity to support national and global agrifood priorities,” Wilson said.
“Until now, it’s been exceptionally difficult to find, access, integrate and compare soil data. This new system brings together all this information providing easy access to soil data and information that will underpin the effective management of soil.”
ANSIS will be a valuable tool for farmers and farm advisors, allowing them to compare the condition of their soil with other soils in their region; monitor how their soil has changed over time; and inform opportunities for change or improvement in land management practices. Governments and industry bodies will be able to use data and information through ANSIS to support the development of effective policies to ensure our soil is sustainably used and enhanced for future generations, and to inform policy decisions in areas such as drought resilience, climate adaptation, natural capital accounting and biodiversity conservation.
Australia’s National Soils Advocate, the Hon Penelope Wensley AC said the launch of the new national soil information system was an exciting development.
“It represents a major advance in implementation of the National Soil Strategy. Good data, available in a consistent, accessible form, is essential for better understanding and management of Australia’s soil. “I know development of the system has been a challenging task and extend my compliments and thanks to CSIRO and everyone involved in delivering this important new tool for soil stakeholders and policy makers,” she said.
Wilson said ANSIS would enable researchers to better understand the way our soil works, its role in climate change adaptation and mitigation, and the impacts we have on this valuable natural resource.
ANSIS is supported by funding through the Australian Government National Soil Strategy (Department of Agriculture, Fisheries and Forestry) in collaboration with CSIRO and partner organisations. ansis.net csiro.au
It’s no longer a question of whether the mining sector is ready for the fourth industrial revolution, but rather, are the right foundations in place?
Australia is a global leader in mining – not just as a source for critical minerals, but as an innovation leader. As a nation where mining is conducted in particularly harsh and remote terrain, it’s undoubtedly the qualities of adaptability and inventiveness that have enabled the industry to fare well amidst the challenges brought forward by the COVID pandemic. It’s also these characteristics that will set the Australian mining sector apart in the race to both Mining 4.0 and Net Zero.
Both require radical changes in digital connectivity, electrification and automation. And that’s exactly what the whitepaper ‘Mining 4.0 – how do we get there in Australia’ does. It asks and addresses this critical question through an Australian lens.
It also examines what role Australia will play in this global paradigm shift – because this is a momentous time for mining. There has been a seismic shift in focus where sustainability is not just an auxiliary goal but an indicator of survival.
As a nation where mining is conducted in particularly harsh and remote terrain, it’s undoubtedly the qualities of adaptability and inventiveness that have enabled the Australian mining industry to fare well amidst the challenges brought forward by the pandemic. It’s also these characteristics that will set the Australian mining sector apart in the race to both Mining 4.0 and Net Zero. As both require radical changes in digital connectivity, electrification and automation. With research-based commentary from Australian mining experts as to the trends promoting change and the challenges that come with the disruptions, this ABB paper explores what sustainable solutions look like when there is connectivity of people and secure digital integration across operations.
Importantly, it includes insights from leading global mining company, Gold Fields, in regard to its digitalisation experience at the Australian Granny Smith mine, and from Caravel Minerals as to the planning of a 4.0 greenfield copper mine in Western Australia.
It’s a momentous time for mining. There has been a seismic shift in focus where sustainability is not just an auxiliary goal but an indicator of survival. This is reflected in the annual reports of Deloitte, EY, KPMG and PwC, for 2022, where Environmental, Social and Governance (ESG) concerns rank high on industry trend and risk lists. Notably, each investor group’s report recognises that ESG is no longer optional, but a minimum operating standard.
Globally, mining companies have been under increased pressure to reduce emissions with the sector responsible for up to 7% of Scope 1 and 2 emissions and up to 30% of Scope 3 emissions. Locally, the 2022 Climate Change Bill calls for a 43% reduction in Australia’s 2005-level emissions by 2030, with a net zero target of 2050.
Propelled by these goals, Australian mining companies have quickened the pace on decarbonisation. What should be explicitly clear, however, is that digitalisation is fundamental to decarbonisation; it underpins the energy system transition. Decarbonisation is not possible without the data, transparency, collaboration and control that digitalisation provides. In essence, the journey to decarbonisation and Mining 4.0 are one and the same.
And while Australia’s mining sector has been digitising assets and automating aspects of their operations for some time, the pandemic has been a key accelerant of digital transformation. With the restrictions that COVID-19 brought, miners got first-hand experience as to the effectiveness of their remote capabilities, and the connectivity and exponential technologies required for this were better established. They are now fast becoming embedded into operations. ABB.com
Next step to Net Zero copper mining with the MPR.
A new Minerals Processing Roadmap lays out a vision for sustainable copper mining, the third in the International Copper Association Australia’s— ICAA—Roadmap to Zero Project following earlier reports on Water and Material Movement.
Launched by Courtney Houssos, NSW Minister for Finance and Minister for Natural Resources, Minerals Processing is a unique collaboration between the resources sector, government, universities and the mining technology industry to reach net zero copper mining.
Copper is key to decarbonisation, helping to deliver clean energy and electrification that will double global demand for refined copper by 2050. Soaring demand brings new development and employment opportunities for Australian, state, territory and regional economies, but must be done sustainably in a climate critical world.
Minerals processing is the most energy intensive part of upstream copper production and can contribute significantly to a site’s emission profile. Minerals Processing identifies how mining companies, working in partnership with stakeholders, can embrace innovation using a ‘systems approach’ to speed collaboration, knowledge and impact.
The Roadmap identifies five mineral processing themes with accessible solutions for now and into the future. These include emerging novel processing solutions, digital and automation technologies like artificial intelligence, mixed realities or machine learning applied across comminution, concentration, extraction, or waste stream processes to better optimise ore liberation, enrichment, recovery, sustainability and asset performance. “Copper is key to a greener, smarter world but mining has to embrace innovation to cut emissions going forward,” ICAA CEO, John Fennell said. “The Minerals Processing Roadmap accepts this isn’t going to be easy, but shows what can be achieved with widespread collaboration, knowledge sharing and a systems thinking approach. Machine Learning and AI is supporting, and predicted to support, a range of applications that could improve plant performance and resource recovery. These include process optimisation technologies and systems, equipment optimisation including predictive maintenance, energy management, etc.”
Optimising energy, waste, water use and equipment performance at sites can be achieved through cutting edge grinding, flotation, leaching, ore chemistry, process optimisation and advanced recovery solutions. Future innovations are wide reaching and include coarse particle flotation, gravity separation, microwave fracturing, novel leaching, bio-mining, artificial neural networks, and ESG mapping.
A key challenge for innovation adoption is systemic barriers that exist in the industry. This includes a lack of collaboration and knowledgesharing models and structures that bring together industry stakeholders, researchers, technology providers, and policymakers together to tackle technical challenges. A lack of collaboration can inhibit the exchange of information, best practices, and lessons learned, all required to accelerate innovation and technology adoption. The MPR works to address this by outlining a range of solutions and pathways across five emission impact themes, and supported by significant industry wide initiatives to commit to a sustainable copper industry. The industry are demonstrating commitment and the MPR provides guidance to achieve a sustainable future. The Roadmap to Zero Project emphasises the importance of knowledge being available to mining companies in a way that is intuitive, quick, comprehensive, forward-looking, and accurate. Knowledge, combined with catalyst models of collaboration and partnership within and between mining companies and across the public, research, mining technology, and community sectors, will advance the likelihood of success for innovation uptake. Mining systems vary between sites and producers, and innovation and development are ever-changing. Currently, no independent and dynamic platform hosts knowledge, captures technology scoping efforts, and provides guidance on the technologies and emerging research that could deliver a zero-emission operation in the future. CollaborateOre is one such initiative that seeks to establish a platform beyond the resources of a single producer, researcher, or solution provider. ICAA, in partnership with Amira Global and others are demonstrating that through cooperative action, knowledge can be shared in accordance with FAIR (Findable, Accessible, Interoperable, and Reusable) principles of scientific data management. There is a need to act with urgency to master complexities and to achieve operational resilience against future pressures that are likely to eventuate. CollaborateOre demonstrates that the presentation of complex systems is possible, whether that be from the outcomes of research, data, tools, emerging technologies and trends, learning, directories, or communities of practice.
“Every copper producer and each copper operation will face its own pathway to decarbonisation, but the Minerals Processing Roadmap suggests just what can done together,” said Fennell.
The MPR report has many pertinent chapters for manufacturers, metal fabricators, producers and processers of critical minerals fort industrial markets. This is downloadable from the website below. copper.com.au
Sustainable solutions such as peristaltic pumps offer a competitive edge to mining companies amid a demand for lithium.
One of the world’s largest lithium producers is benefiting from using peristaltic pumps in its refining operations in Chile, with a reduction in leaks and downtime achieving cost savings at a time of expanding production for the mining company.
To meet rising demand from the burgeoning lithium-ion battery market and amid the global push towards electrification of vehicles, the Chile-based mining company has recently increased its focus on lithium with aims to hit production capacity of 180,000 tonnes of lithium carbonate in 2023.
To ensure its production is at full capacity during this expansion, the mining company is using Bredel Hose Pumps from WatsonMarlow Fluid Technology Solutions (WMFTS) at its lithium processing plant, where lime dosing is the main application. The peristaltic pumps have stopped leaks and cut maintenance downtimes that were experienced with an alternative pump principal that the mining company previously used, which has resulted in chemical costs savings.
The lithium extraction process in Salar de Atacama, the largest salt flat in Chile, begins with brine being pumped out of the ground and into evaporation ponds where the remaining brine is slowly enriched in lithium. Brines high in lithium content are then transported to the mineral processing and refining plant, where pure lithium carbonate and lithium hydroxide are produced. Lithium carbonate and lithium hydroxide are an essential input in the production of the cathode material in batteries used in electric vehicles (EV).
The mining company has used WMFTS peristaltic pumps at its lithium processing site in Chile for the past five years and has recently increased the number it uses to over 50 Bredel and Qdos pumps.
“The reliability of the pumps keeps the work area clean, with no lime, compared with the centrifugal pumps that leak all the time,”
said Pablo Silva, Applications Engineer for WMFTS in Chile. “The company has expanded its lithium operations and Bredel pumps have been part of the increase in production. During the last year when this company has doubled its production, Watson-Marlow has sold eight Bredel 65 pumps to them.”
Pump solutions for lithium production
For lithium carbonate production, this Chile-based mining company uses Bredel 65 pumps to transfer lime to the reactors, with a flow and discharge pressure of 8m3/h and 5 bar (2.2 litres/second and 72.5 PSI) to:
• Avoid maintenance issues caused by lime solidification
• Eliminate leaks experienced with other pump technology
• Ensure an accurate dose according to the pH required
The same pump also transfers lime during the production of lithium hydroxide from the reaction of lithium carbonate and lime, with a flow and discharge pressure of 12m3/h and 6 bar (3.3 litres/second and 87 PSI).
During lithium sulphate production in the press filter, the mining company uses Bredel 40 pumps to transfer lithium sulphate at 2m3/h and 7 bar as the pump avoids leaks and has the ability to handle low flow rate with 30-40% solids.
Bredel is widely used in mining applications to transfer corrosive liquids, such as hydrochloric acid. The Chile-based mining company uses Bredel 25 and 32 models and a Watson-Marlow 621 closecoupled pump to pump hydrochloric acid in the lithium carbonate reactors to avoid expensive and toxic leaks, and to get the correct dose according to the process.
Australia is also seeing increased lithium mining activity. In Western Australia, seven Bredel 2100 Duplex and one Bredel 80 peristaltic pumps have been used by a lithium mining company for the thickener and underflow process.
Water conservation is vital in countries such as Australia and good water management reduces disruption to mining operations as well as damage to the environment. Bredel hose pumps can be considered water-saving devices in their capabilities, in the way they handle undiluted tailings and thickener underflow.
Jose Longo, General Manager (Australia and New Zealand) for Watson-Marlow, said: “Bredel pumps and hoses are the right solution for abrasive slurry. Our hoses perform well in that application.
“Western Australia mines are in the middle of a desert, so water savings can also be a key for mining companies to use Bredel products, as our pumps can pump solids content up to 80%. Our products present very high reliability, an important factor when the closest town and service staff are more than four hours away.”
At the other end of the scale to major lithium suppliers in places like Chile and Australia, peristaltic pumps are also playing a key role as companies scale up their operations or try to establish a profitable lithium production site.
With prices of lithium—called “white gold” by investors—rocketing recently amid increased demand for lithium from the EV battery market, existing supply sites are ramping up production and there has been a birth of pilot projects aiming to mine and refine lithium in places like Nevada, United States, and Cornwall, England.
Getting it right at the pilot plant stage is crucial as savings can be made through water, chemical and energy use with the right pump for the transfer of slurries or for dosing, as well as being environmentally responsible.
Engineering and mining consultancy company Wardell Armstrong International Ltd has recently provided a lithium pilot plant as well as a modular mineral processing pilot plant for Elementos, an Australiabased pure tin exploration and development company.
“We built a pilot plant that was looking at recovering tin and since then we have done multiple pilot plants, including one for lithium,” said Dominic Conybeare, Principal Metallurgist at Wardell Armstrong. “We achieved the targets we set out to meet in terms of grades and with Wardell Armstrong able to demonstrate production of a highgrade, low-impurity tin concentrate.”
A modular design is at the heart of the Wardell Armstrong pilot plant assembled at its facility in Wheal Jane in Cornwall, England. WatsonMarlow 600 and 700 series peristaltic pumps are being used for the transfer of material between the various processing stages.
“The bigger pumps we have are all involved in the transport of slurry from one piece of equipment to another; for example, from conditioning tanks to flotation cells, from flotation rougher cells to flotation cleaner cells etc,” said Conybeare. “The main benefit is
the ease in which flowrates can be monitored and adjusted. For example, we usually feed the flotation circuit at two litres per minute. We use a lot of the smaller series pumps (Watson-Marlow 300s and 500s) to dose reagents, including flotation activators, depressors, frothers, collectors, pH modifiers, to the flotation circuit. The small adjustments we can make on these make them ideal. For example, for the lithium pilot plant it was important to keep the pH at 2.5 with sulphuric acid by dosing at various locations.”
Pilot plants like this from Wardell Armstrong test the equipment, chemical engineering methodology, and operations on a small scale before full production.
“The main benefit of pilot plant testing is to provide metallurgical proof that what has been achieved at a laboratory scale,” Conybeare added, “using a sample a few kilos in mass, in terms of final concentrate grade and recovery can be successfully scaled up, using samples a few tonnes in mass, without detriment to the final outcomes. We are also asked for pilot plants when clients need large quantities of concentrates produced for further downstream processing, like environmental testing and thickening/dewatering test work.”
Grinding Solutions, another metallurgical laboratory and consultancy service, produced a pilot project for Cornish Lithium, a mineral exploration and development company, which used Watson-Marlow 500 and 600 series pumps for reagent dosing, to dose sulphuric acid in pH adjustment and for slurry transfer. A Qdos 30 metering pump from WMFTS was also used for accurately dosing flocculant into settling tanks at a rate of 10-15 ml/min.
Cornish Lithium, which has developed advanced eco-friendly lithium extraction technology from geothermal waters underground, and Geothermal Engineering Limited (GEL) together have set up a pilot facility at United Downs, to demonstrate its methods, verify processes, understand costs and minimise risks. Their aim is the sustainable extraction of lithium and other battery metals in Cornwall. The plant uses five 500 series cased peristaltic pumps from WMFTS as part of the processing equipment. The 530SN/R2 pumps serve two different parts of the test plant, the first of which extracts lithium from the waters by pumping the brine from a container up through a column containing a large number of beads.
Bredel and Qdos pumps can achieve significant savings in water usage. On average, water savings of 71% can be achieved in comparison with typical centrifugal pumps.
Whether handling polymers, flocculants, reagents, abrasive lime slurries, or corrosive chemicals, Bredel and Qdos peristaltic pumps can accurately control the flow, with minimal downtime for maintenance and very low cost parts inventory.
wmfts.com/en-au/brands/watson-marlow-pumps/
An American view on US investment in critical-mineral mining in Australia. Shubham Dwivedi and Gregory
bring their expertise to Australian manufacturers.
This article appeared in The Strategist magazine in late July and is being republished with kind permission from the Australian Strategic Policy Institute.
In May, the United States and Australia signed a climate, critical minerals and clean energy transformation compact that establishes a framework for collaboration on climate issues, clean-energy technology and critical-mineral supply chains. It mainly discusses critical minerals in the context of their necessity in manufacturing clean-energy technologies.
The intent of the framework is to ‘coordinate policies and investments to support the expansion and diversification of responsible clean energy and critical minerals supply chains’. In this case, diversification basically equates to reducing dependence on China, in which various links in the critical-mineral supply chain are heavily concentrated. While the compact establishes a new ministerial dialogue, the Forum on Clean Energy Industrial Transformation, and an Australia–US taskforce on critical minerals, the most vital component of strengthening critical-mineral supply chains is investment in critical-mineral projects.
The critical minerals industry often cites a lack of capital as a barrier to stronger and more diverse supply chains. Mines are capitalintensive projects that can cost tens of billions of dollars. Therefore, any compact that seeks ‘an unprecedented expansion’ in critical mineral supplies must provide capital for mines. The need for government capital is further heightened given the lack of privatesector funding for mining.
The compact commits to using ‘domestic financial instruments and incentives to foster greater integration of responsible clean energy supply chains’, which includes critical-mineral supply chains. It also says the US and Australia will seek industry input on financial incentives, and it lists the US Export–Import Bank as a possible financing agency. Notably, in a joint statement with Australian Prime Minister Anthony Albanese, US President Joe Biden said that he would ask Congress to add Australia as a ‘domestic source’ under Title III of the Defense Production Act, enabling Australian projects to access significant US government funds.
Beyond those measures, the compact doesn’t offer funding specifics—but that was always going to come next, with industry input. To ensure the compact’s success, the US should consider a range of policies for funding mines in Australia.
First, the US should fund Australian mines under the compact, not refineries, which it should invest in domestically to diversify the critical-mineral supply chain. Mining is geographically constrained by the location of mineral deposits, but refining is largely determined by capital and regulations. For example, China has only 3% of global cobalt reserves and produces just 1% of global cobalt ore, yet it controls 77% of global cobalt refining capacity. Similarly, the US could fund enough refining capacity to satisfy domestic demand even without comparably large mineral reserves—especially with Australia on board. By funding Australian mines and the minimum level of crude refining required to economically ship critical minerals to the US to be refined, the US could effectively diversify the criticalmineral supply chain.
That said, the US should only fund Australian mines that produce minerals that are lacking in the United States and Canada. US critical-mineral supply chains are most secure when they are in or near the US and under friendly control. US taxpayer dollars should not be expended on distant mines when nearby mines are available and can meet demand. Importantly, this provision could make the proposal for funding Australian mines more palatable to Congress.
D. WischerSecond, the US should allow companies to partner in a US-funded mine only if they are not owned in any way by foreign entities of concern, including all Chinese entities. The US should not fund Australian mines where Chinese entities can benefit financially or influence the project at the expense of US taxpayers. To protect US national security, if an Australian company is seeking to participate in a US-funded mine in Australia, it should have to first divest any shares held by entities of concern.
American companies should have a controlling interest in US-funded mines, so that the US government can enforce compliance with US regulations, such as blocking Chinese companies’ involvement or investment in the mine. Partnering with experienced Australian partners will also enable less experienced US companies to build valuable mining skills, effectuating two of the compact’s goals: ‘to encourage stronger industrial collaboration’ and ‘to support workforce development in critical minerals’.
Lastly, the US should require that mined materials from Australia be refined by American companies in the US because diversifying the critical mineral supply chain is the primary reason for funding mines in Australia. That requirement will grow the country’s refining capacity and downstream processing for applications like the production of alloys for permanent magnets and cathode material for electric vehicle batteries. The US should also require that the mined material have an end use in a strategic US sector like aerospace or transportation, not consumer electronics like televisions and mobile phones.
The US should also require all companies participating in the mine to stop operating in China and selling their products to Chinese entities. Nor should the US allow companies to use earnings from a US-funded mine to support their operations in China or sales to Chinese entities. The US should not effectively subsidise companies that operate in China or sell products to Chinese mineral companies, which are beholden to the Chinese government.
The compact is a satisfactory starting framework for strengthening critical-mineral supply chains between the US and Australia. How the two countries deploy capital to mineral projects will determine the compact’s success, and US funding for mines in Australia could help achieve the compact’s goals. The stipulations attached to such an arrangement would help to ensure that US–Australia supply chains are diversified, protected from Chinese influence, and forged by a workforce in both countries.
In exchange for its minerals, Australia would get investment and a diversified supply chain, and in exchange for its capital, the US would get access to those minerals and its own diversified supply chain. Such an arrangement would serve the needs of both countries and help achieve the compact’s goal of promoting a ‘responsible, sustainable, and stable supply of critical minerals.’
Shubham Dwivedi is a faculty fellow with Georgetown University’s program in science, technology, and international affairs. Gregory D. Wischer is a critical minerals analyst researching US–China supply-chain competition. aspi.org.au
DB Schenker is providing comprehensive Project Construction Freight Forwarding and Logistics services to Albemarle’s Kemerton Lithium Expansion Project (KEP) in Western Australia. The engineering contractor will be Hatch Australia.
The Kemerton Lithium Expansion Project is DB Schenker’s first foray into the rapidly growing battery metals mining industry globally. Lithium is a key ingredient in batteries to support global decarbonization efforts, offering a long-lasting and efficient alternative to traditional fuel sources such as gasoline, and having applications in electric vehicles. The Kemerton plant is located approximately 150 kilometres south of Perth, WA. It is located near the Port of Bunbury and close to one of the world’s largest hard rock lithium deposits the Greenbushes mine.
The work will be supported by the DB Schenker Project Control Tower office located in Perth, in conjunction with our global network of Project offices that are specialised and accustomed to the unique logistics service requirements of the industry.
DB Schenker is proud to be selected by Albemarle and Hatch to provide comprehensive international freight and logistics solution in support of this very important project.
“We have a proven track record of working safely and efficiently, even on the most remote sites and mega projects in the world,” says Frank Vogel, VP Global Projects & Industry Solutions APAC. This award will also provide exciting new local employment development and
opportunities for DB Schenker in Western Australia. DB Schenker is one of the world’s leading logistics providers with around 76,600 employees at more than 1,850 locations in over 130 countries. The company operates land, air, and ocean transportation services, and it also offers comprehensive logistics and global supply chain management solutions from a single source. To reach its ambitious goal of net carbon zero by 2040, the logistics service provider continuously invests in innovative transport solutions, renewable energies, and carbon-neutral products for its customers. dbschenker.com
World’s first autonomous MudMaster saving water use by up to 40%.
Phibion has launched the first of its fully autonomous mine tailings management systems capable of delivering around-the-clock operations in the most challenging waste environments.
The Australian-based solutions provider is delivering faster mine rehabilitation and safer tailings dam management through its unique methodology and MudMaster® amphibious technology coupled with their patented accelerated mechanical consolidation (AMC) at operations in Australia, Jamaica, Chile and Brazil.
The new driverless Dart MudMaster® means even greater efficiency and savings for mine operators, as well as improved safety and environmental outcomes for communities. Both the MudMaster and Dart MudMaster are manufactured in Australia. The Dart MudMaster can halve in-situ tailings volume and deliver a 40% improvement in water recovery for operational reuse.
Phibion’s Chief Executive Officer Jacques Janse said Queensland’s resource sector experience and world-leading advanced manufacturing capabilities made it the natural home of this technology.
“Our commitment to innovation and safety, along with the support of leading researchers and the Queensland Government, have enabled Phibion to take this technology to the world,”
“We are making tailings dams safer, smaller and more sustainable which means resource companies can deliver on their ESG ambitions and return land back to communities faster and better than ever before,” Janse said. “Tailings are part of virtually all mining and refining operations. If not managed correctly, they can become a high safety risk that creates legacy issues for the local community and the environment.”
The MudMaster® technology solution works to make tailings dams safer and smaller by rapidly dewatering and consolidating the material to create strength and free up volume for future deposition
at a fraction of the cost of traditional capital-intensive alternative systems. The new Dart MudMaster® will deliver even greater efficiencies. The autonomous machine can operate longer based on a remotely assigned operational plan, carried out in the most effective and efficient way before returning to a designated setdown area. This improves performance and results in greater fuel efficiency.
Janse said autonomous operations meant the Dart MudMaster® could operate in the most challenging tailings environments, normally unsuitable for workers due to potential exposure to toxic substances.
“We see this as a game-changer for mining tailings management and land rehabilitation projects around the globe,” Janse said. phibion.com
AMT: As the Queensland Minister for Regional Development, Manufacturing and Water, that is a lot of portfolio space to get your head around first off Minister. Promise I’ll stay within the walls of manufacturing. Do you find a bit of ‘crossover’?
Glenn Butcher: Definitely - there is lots of crossover and that’s what I want to see. I want to see local manufacturers benefitting from our significant investment in critical infrastructure like water projects, so that benefits to Queensland businesses are seen all the way down the supply chain. A significant amount of our infrastructure investment occurs outside Southeast Queensland given the decentralised nature of the state. And this is set to continue - as an example, 95% of our $62bn Energy and Jobs Plan will be invested outside SEQ.
That’s why we have a plan and why we keep investing in our grants and support programs so that our local manufacturing businesses can continue to innovate and grow so they can make the most of the opportunities that come through significant government investment in our regions. As a quick example - to kick off Manufacturing Month, I visited Austrack Equipment, a Queensland business that manufactures SafeVac pipe lifting machines. These machines are on site, lifting the pipes for the $983m Fitzroy to Gladstone pipeline. A great Queensland business, supplying to a Queensland project, and creating more jobs for Queenslanders.
AMT: Now I understand Queensland’s Manufacturing Month is well underway. Can you tell me what Manufacturing Month is all about?
GB: Absolutely, I love talking about manufacturing. As a fitter and turner by trade I have worked in manufacturing most of my life. I am really proud to be Queensland’s Manufacturing Minister and part of a government that’s dedicated an entire month to celebrating manufacturing. Manufacturing is a $20bn industry, that provides 180,000 Queenslanders with good, secure jobs so there’s a lot to celebrate
The Palaszczuk Government is a strong backer of local manufacturing. Between our Made in Queensland and Manufacturing Hubs Grant programs, we’re investing nearly $130m directly into local businesses, supporting over 6,500 jobs. That number is projected to grow to over 10,000 jobs in the next five years. Our investment is helping Queensland manufacturers grow, be globally competitive and increasing productivity and innovation. Because if we can make it here in Queensland – we should.
Our work to cement Queensland’s position as a global manufacturing leader includes increasing the profile of Queensland’s manufacturers. The industry has spoken loud and clear – they need more skilled workers and they want to attract school leavers and change traditional perceptions of what it means to be a manufacturer.
This is what Manufacturing Month is all about. Throughout September, manufacturing events are taking place across Queensland, showcasing what our manufacturers are capable of. That includes our expanded Inside Advanced Manufacturing Program, where some of Queensland’s top manufacturers opened their doors to showcase their innovative manufacturing practices to other manufacturers. I attended events at AMEC Plastics at the Gold Coast, Rheinmetall at Redbank, Zone RV in Coolum and Baywood in Maryborough and I can tell you the feedback was awesome. The manufacturers in attendance saw first-hand advanced manufacturing techniques and had an opportunity to build networks and foster collaboration between local manufacturers.
We then held a showcase at Parliament House attended by over 150 manufacturers and 24 exhibitors which was a huge success and we’ve got more great events planned throughout the rest of September.
Glenn Butcher is the Minister for Regional Development and Manufacturing, and the Minister for Water in Queensland.
With so much going on in the state under Palaszczuk Government, the very busy Minister found time to speak with AMT magazine.Gladstone News
AMT: I hear there has been a recent partnership with the Gold Coast Titans NRLW team?
GB: Yes, this month I was excited to combine two of my favourite things – manufacturing and NRL when I launched the Palaszczuk Government’s new partnership with the Gold Coast Titans NRLW team at Cbus Stadium. The new partnership will promote our Women in Manufacturing Mentor Program providing young women in school a chance to be matched with industry professionals to help them build confidence, develop their career and expand their networks. It will also promote the Diversity, Equity and Inclusion Toolkit, which is helping employers looking to diversity their workforce, improve resilience and reduce turnover.
We know more needs to be done to increase the number of women in manufacturing so this is a key focus for us. The Titans players are fantastic role models of success and resilience in traditionally male dominated fields. This is about increasing the profile of women because whether its strapping on footy boots or steel caps, you can’t be what you can’t see.
AMT: More broadly, can you elaborate on what the Women in Manufacturing Strategy is and why it is important?
GB: From the shop floor to leadership positions, we know women are valuable and crucial to innovation and growth, but the industry has historically faced challenges in attracting and retaining women.
On International Women’s Day this year, I launched the Women in Manufacturing Strategy, which is designed to address this very issue. It aims to attract, train and retain women in the manufacturing industry by focusing on increasing participation in traditionally male dominated roles and to reduce barriers.
We understand that the key to increasing numbers starts by promoting an inclusive culture, where employees feel valued and that is what our Strategy is all about. We’re achieving this through four priority areas:
• Supporting diversity, equity, and inclusion in the manufacturing industry;
• Building on our existing capabilities and skills to further women’s leadership and development;
• Boosting women’s participation in Vocational Education and Training, building the STEM pipeline, and promoting advanced manufacturing capabilities throughout secondary and tertiary studies; and
• celebrating and showcasing the women in Queensland’s manufacturing industry.
The numbers show women are still vastly under-represented in technician and trades roles – this is what we are working to change.
AMT: By 2026, Queensland will be international market leaders in the delivery of advanced manufacturing technologies, systems, products and services that are innovative, sustainable, and embedded in local and global supply chains. How is the ‘Advance Queensland Initiative shaping up?
GB: The Advance Queensland Initiative is a strategy to drive diversity, strengthen regional growth and create jobs. It has laid the foundation for innovation to happen in Queensland. It has supported the creation, scale up and international success of many Queensland researchers, innovators and businesses.
Now is the time to build on this success and further accelerate Queensland’s future economy and jobs growth through innovation. The Innovation for a Future Economy 2022-2032 Roadmap is for everyone in Queensland’s innovation ecosystem. It will help drive a strong, resilient and inclusive Queensland economy.
Some of the key achievements from the Roadmap in my portfolio area include:
• The delivery of the Made in Queensland Grants Program and the Manufacturing Hubs Grant Program;
• The delivery of the Commercial Manufacturing Accelerator Voucher Scheme. This is a partnership with James Cook University where local manufacturers can take their business to the next level, by offering them up to $25,000 to develop, test and modify prototypes, before going to production.
• The delivery of the Women in Manufacturing Strategy.
In the coming decades, Queensland’s manufacturing industry will face new challenges, realise new opportunities and continue to diversify. The revised Advanced Manufacturing 10-Year Roadmap and Action Plan sets a path for Queensland manufacturers to respond to these changes, drive economic growth and create jobs. It contains 19 actions in five key strategy areas to address these challenges and position manufacturers to grasp new opportunities to grow their business and create jobs.
This includes transitioning to a low carbon economy, increasing diversity and accessing supply chain opportunities in the emerging green energy sector as part of the Queensland Energy and Jobs Plan and the Olympics and Paralympics.
I know our manufacturers are at the forefront of innovative manufacturing processes. I see it when I visit manufacturers across the state. I recently visited Zone RV, a business that received a grant through our Made in Queensland grant program. The grant enabled them to purchase the largest 3D printer in the Southern Hemisphere. At 20 metres long, five metres wide and two metres high this equipment is impressive. It is allowing them to bring their innovative ideas to life by printing the castings used to create the moulds for the component parts for their caravans. Not only has it meant 99 more local jobs, but it’s making them global leaders in caravan manufacturing and opening doors to new possibilities.
AMT: Of course, we’re all looking ahead to the 2032 Olympic and Paralympic Games bringing more identification to the Queensland brand. Again, where can manufacturers become involved?
GB: As a government, our focus on local procurement has always been strong. We have had a local purchasing policy since 2017, focused on supporting local businesses. We know that as a Government, we have significant purchasing power and we must make sure it is working to create and support quality, secure jobs for Queenslanders – to buy from local businesses, suppliers, and manufacturers. We must also ensure that we secure increased value for Queenslanders from every procurement dollar spent. The Olympic and Paralympic Games will be no exception. There are incredible opportunities to be had for our manufacturers. With major upgrades happening to get Queensland Games-ready, we are going to need manufacturers building everything from the podiums, to the medals, to the cupboards in the athletes’ rooms, the chairs in the stadium, the food we are serving and everything in between.
Manufacturers are being urged to start the journey to being 2032-ready now. To be considered as a supplier, businesses will need to be able to report their carbon footprint and be able to demonstrate sustainability measures.
The Q2032 Procurement Strategy has been launched, explaining how businesses can get themselves ready now to become suppliers to the 2032 Olympic Games. qld.gov.au
The Sustainable Aviation Fuel Roadmap builds consensus on developing an Australian sustainable aviation fuel industry, identifying opportunities to produce and scale production using Australian feedstocks.
Australia has an opportunity to develop a sovereign sustainable aviation fuel (SAF) industry, with domestic demand for jet fuel expected to increase by 75% by 2050, according to a new roadmap released recently by Australia's national science agency, CSIRO and Boeing Australia.
Unlike conventional jet fuel, SAF is produced from renewable sources – like agricultural waste, animal fats and vegetable oils –and significantly reduces carbon emissions over the fuel’s life-cycle making it a more sustainable alternative for powering aircraft.
The Sustainable Aviation Fuel Roadmap builds consensus on developing an Australian sustainable aviation fuel (SAF) industry, identifying opportunities to produce and scale production using Australian feedstocks.
CSIRO Senior Manager and lead Roadmap author, Max Temminghoff, said Australia was in a prime position to develop a domestic industry.
“By actively working to liberate feedstocks, the roadmap estimates that Australia is currently sitting on enough resources to produce almost five billion litres of SAF by 2025. This could supply nearly 60% of jet fuel demand projected for that year,” Temminghoff said.
“That’s enough fuel to power 640,000 Melbourne to Sydney return flights on a Boeing 737.
“Through a combination of feedstocks and mature technologies, a large and growing portion of Australia’s jet fuel demand can be met with local materials such as agricultural waste and residues.
“To convert these feedstocks into viable jet fuel, the report identifies the Alcohol-to-Jet and the Fischer-Tropsch process – a process currently conducted at CSIRO’s Perth laboratory – as ideal technology options to propel a sovereign SAF industry.
“But Australian government, industry and research must work together to overcome key challenges to realise the economic and sustainability benefits of a domestic SAF industry.”
The challenges that the Australian SAF industry must address include feedstock availability, supply chain constraints, and aligning to international standards and regulation.
The roadmap points to biogenic materials in the near term, such as sugarcane, sawmill residues, and municipal solid waste, as well as hydrogen and CO2 in the medium to long term, as key feedstocks.
Boeing Regional Sustainability Lead APAC and Roadmap coauthor, Heidi Hauf, said the findings highlighted that a local SAF industry will contribute to decarbonisation and energy security while also generating more regional jobs and new export markets.
“The report identified the role the Australian Defence Force could play in kickstarting Australia’s SAF industry and also addressing Australian fuel security challenges,” Hauf said.
“Currently, Australia imports 90% of its liquid fuel, including jet fuel, through long supply chains exposed to geopolitical and climate change risks, and delays associated with quality issues, placing the country in a vulnerable position when it comes to jet fuel security.
“With alternative technologies such as battery and fuel-cell powered planes still limited in long haul capabilities and the increasing competition for carbon offsets, SAF offers the largest potential for reduced aviation emissions in the near-term.”
CSIRO Energy Director Dr Dietmar Tourbier said the roadmap aligns with the Federal Government’s recently established Jet Zero Council – of which CSIRO and Boeing are members – and supports the commercial aviation industry’s commitment to net-zero carbon emissions by 2050.
“The roadmap is part of the critical work CSIRO is undertaking to support Australia’s hardest to abate sectors to halve their emissions by 2035, and forms part of our Towards Net Zero Mission,” Dr Tourbier said.
Together, Boeing and CSIRO have a 34-year collaboration on joint research projects which has led to significant aerospace advances, including a focus on scaling SAF production across the region.
“While further technology development is expected to lead to fully synthetic fuels, biofuel is a critical component to help Australia advance its net zero ambitions now,” Dr Tourbier said.
“With the rest of the world transitioning to SAF, Australia should not miss out on the opportunity to become a major player in this space.” csiro.au boeing.com
The role of dynamic braking resistors in securing the EV power systems during the electric vehicle rollout. Here, Simone Bruckner, managing director of dynamic braking resistor (DBR) manufacturer Cressall, explains the role of resistors in supporting the e-mobility revolution.
Developments in the electric vehicle (EV) market are advancing at a rapid pace, with consumer uptake on the increase and the end of the road for newly manufactured ICE vehicles fast approaching.
A DBR is a vital component in the EV power chain, responsible for safeguarding the electrical system by removing excess energy from a vehicle’s braking system. This mechanism supports several applications in the EV space — regenerative braking, fuel cell power reliability and heavy goods vehicle emergency braking systems.
In EVs, a DBR’s ability to absorb and redirect energy facilitates regenerative braking. Regenerative braking uses the excess kinetic energy to recharge an EV’s battery. It is able to do this because the electric motor in an EV can run in two directions: one, using the electrical energy, to drive the wheels and move the car, and the other, using the excess kinetic energy, to recharge the battery.
When the driver lifts their foot off the accelerator pedal and steps on the brake, the motor starts to resist the vehicle’s motion, “swapping direction”, and begins putting energy back into the battery. As a result, regenerative braking uses the EV’s motor as a generator to convert lost kinetic energy into stored energy in the battery.
On average, regenerative braking is between 60 to 70% efficient, which means that around two thirds of the kinetic energy lost during braking can be retained and stored in the EV battery and used later for acceleration, drastically improving the energy efficiency of the vehicle and extending battery life.
However, regenerative braking cannot act alone. A DBR is needed to make the process safe and effective. If the car battery is full or there is a failure in the system, there’s nowhere for the excess energy to be dissipated, which risks the failure of the entire braking system. So, a DBR is installed to dissipate this excess energy unsuitable for regenerative braking and dissipate it safely as heat.
However, it’s not just in braking where DBRs come into play. We must also consider how they can positively impact the growing hydrogen fuel cell EV (FCEV) market. While FCEVs aren’t as viable for an imminent widespread rollout, the technology is there, and it certainly has more long-term promise.
FCEVs are powered by proton exchange membrane fuel cells. FCEVs turn hydrogen into electricity by combining the hydrogen fuel with air and pumping it into the fuel cell. Once inside the fuel cell, this triggers a chemical reaction, resulting in the extraction of electrons from the hydrogen. These electrons then create electricity, which is stored in a small battery used to power the vehicle.
If the hydrogen used to power them is produced using electricity from renewable sources, the result is a completely carbon-free transport system. The only end products of the fuel cell reaction are electricity, water and heat, and the sole exhaust emissions are water vapour and air, making them more aligned with the EV rollout. However, they do have some operational shortfalls.
Fuel cells are unable to work under heavy loads for a long time, which presents issues when rapidly accelerating or decelerating. Studies into fuel cell function have shown that, when an FCEV begins accelerating, the fuel cell’s power output increases gradually to a point, but then it begins to oscillate and drop despite velocity remaining consistent. This unreliable power output presents a challenge for automakers.
The solution is to install a fuel cell for a higher power requirement than necessary. For example, if a FCEV needs 100 kilowatts (kW) of power, installing a 120kW fuel cell would ensure there is always at least the required 100kW of power available, even if the fuel cell’s power output drops. Opting for this solution requires a DBR to remove the excess energy when not required, by performing a “load bank” function.
By absorbing the excess energy, DBRs protect an FCEV’s electrical system and also enabling them to be very reactive to high power demands and accelerate and decelerate rapidly without storing excess energy in a battery.
To meet each EV application, Cressall’s EV2 DBR offers a tailored solution. When selecting a DBR, automakers must consider a few key design factors. For all vehicles powered by electricity — be it a battery or a fuel cell — making components as lightweight and compact as possible is a top design demand.
In response to these demands, Cressall’s EV2 is the most compact and lightweight solution available to the EV market, offering 10kW of power per cubic decimetre (dm3) and 9.3kW of power per kilogram. It’s a modular solution, meaning up to five units can be combined in a single assembly to meet power requirements of up to 125kW.
Being water cooled, heat can be dissipated safely without the need for extra components, such as fans, as is the case with air-cooled resistors. This means that the EV2 is 10% of the volume and 15% of the weight of a conventional DBR, lightening the load of the vehicle itself, meaning it can travel further on the same amount of fuel.
While DBRs are an essential element of an EV braking system, selecting the right one is essential to efficient operations. Offering unrivalled compact, lightweight qualities, the EV2 Cressall allows automakers to meet their design and safety requirements without forfeiting weight or size qualities.
cressall.com fortressresistors.com
Keeping climate hopes alive with sustainable logistic ecosystems. Garry Valenzisi, Vice President APAC, Global Industries & General Manager ANZ at Iron Mountain explains the complexities of the future.
Following a tumultuous few years, pressures facing Australia’s warehousing and logistics sector, from the pandemic, supply chain issues and energy prices, have started to ease. However, due to the enormous impact of the global supply chain on carbon emissions, sustainability progress still hangs in the balance as it becomes apparent that the UN Paris Agreement climate pledge is at real risk of being missed unless action is taken immediately.
Australia’s economy and lifestyle is dependent on the smooth operation of the $130bn supply chain and logistic sector. Thankfully, there are many ways in which the warehouse and logistics sector can act cooperatively to ensure progress is swift, substantial, achievable, and ultimately beneficial to all – business, customer and planet alike.
Supply chain operatives, by their very nature, are deeply embedded within the operations of a great variety of businesses of all sizes. This means that their scope 1 and 2 greenhouse gas (GHG) emissions form a large part of their partners’ scope 3 emissions.
Currently there are no requirements in Australia for companies to offset Scope 3 or 'downstream' greenhouse gas (GHG) emissions of a project as a precondition to obtaining planning approval for that project.
Whilst this is the case, the International Sustainability Standards Board (ISSB) recently announced companies across the globe will soon be required to report on their customers’ and suppliers' carbon emissions to further reduce greenhouse gas emissions. Reporting scope 3 emissions accurately can be difficult for organisations due to challenges with identifying and measuring emissions that are outside their control. When warehousing and logistics facilities, and other third-party service providers, prioritise reducing their own scope 1 and 2 emissions, scope 3 emissions are reduced for their customers, creating an ecosystem of collective responsibility, where the wider supply chain works in tandem to support carbon reduction throughout.
The desire to cut carbon and improve sustainability across the board has been demonstrated by many supply chain operators in recent years, with many taking steps to enhance energy efficiency by utilising green energy from renewable sources, ramping up recycling efforts, preserving natural resources and reducing the use of diesel fuel. However, there are several other ways in which warehouses can play a role, reducing not only their own carbon footprint, but also that of their suppliers and customers. Making a concerted effort to run more efficient buildings now, will support businesses’ wider ESG goals in the long-term.
The demand for warehouse space is currently far outstripping availability, so providers that can offer shared usage facilities with flexible and scalable contracts for customers, within an energy efficient building are crucial to supporting the net-zero growth of their supply chain, starting from the ground up.
The construction of new buildings can now be developed in accordance with low carbon specifications, ensuring that all assets have climate resilience measures installed, in order to directly impact upon the emissions profiles of all concerned.
Australia accounts for just 0.33% of the world’s population, yet is one of the highest emitters of greenhouse gas emissions per capita, globally. Additionally, the carbon emissions of materials used in building construction in Australia is 30 to 50 million tonnes of
carbon dioxide equivalent (CO2-e) – approximately five to 10% of Australia’s annual greenhouse gas emissions. Purchasing materials from local suppliers is another way that a provider’s carbon footprint can be closely managed.
Renewable energy accounted for 35.9% of Australia's total electricity generation, up from 32.5% in 2021. With a goal to increase the share of low-carbon power generation by 2030, with 82% to come from renewable energy, there is significant progress to be made within this space. Key to this is the understanding that cutting carbon makes good business sense, by updating operations with energy efficiency solutions, operations can save more money in the long run than the cost of the initial capital outlay.
For example, warehouses can implement an aggressive program to drive efficiencies such as re-lamping with LEDs with motion sensors to ensure usage only when needed, integrating thermostats for zoned atmosphere control, employing battery technology, using carbon neutral fire suppression systems, and employing reverse logistics to optimise your fleet and supercharge recycling. Furthermore, installing solar panels linked directly to electric vehicle charging stations creates a renewable-to-renewable loop, drastically reducing the need for grid energy.
Operating solely on energy generated from 100% renewable sources means that organisations are less reliant on fluctuating energy costs and electric logistics vehicles charged on-site are not susceptible to hikes in diesel prices and new regulations pertaining to which areas they are able to enter. This allows providers to reduce overheads, as well as mitigate organisational risks and remain resilient in light of external economic pressures affecting the supply chain.
Recycling or reusing plastic packaging and pallets, as well as continually monitoring the performance and condition of the inventory to identify goods, records and assets coming to the end of their lifecycle are just some of the ways that modern warehouses can innovate to tackle emissions and increase their productivity at the same time.
While organisations need to focus on reducing their own carbon footprint, ultimately, the key to cutting carbon is collaboration. As mandatory reporting on indirect emissions draws closer, businesses will soon find themselves obligated to support their suppliers and partner organisations to build ESG factors into every decisionhoping that it will set us on a 1.5 degree pathway to meet the goals of the Paris Climate Accord. ironmountain.com/au
Groundbreaking ABS study explores potential of commercial nuclear reactors on a container tanker.
The transformational impact of nuclear propulsion on the design, operation and emissions of a 14k TEU container vessel and a 157k DWT Suezmax tanker have been modeled by ABS and Herbert Engineering Corporation (HEC) in a groundbreaking study. ABS commissioned HEC to carry out the study to explore the potential of advanced modern reactor technology for commercial marine propulsion. The study is designed to help industry better understand the feasibility and safety implications of nuclear propulsion and to support future development projects.
The study, which involved input from leading nuclear reactor developers, modeled the impact of two, lead-cooled, 30MW fast reactors on the container carrier, finding it would likely increase cargo capacity and operational speed, while eliminating the need for refueling during its entire 25-year lifespan. On the Suezmax vessel, the study found the addition of four, 5MW, heat-pipe microreactors, while decreasing cargo capacity, would raise operational speeds and only require refueling once during its 25-year life. Both concept vessels would emit zero CO2.
“Our findings from this latest cutting-edge research underscore why the industry cannot afford to ignore the vast potential offered by nuclear propulsion both in terms of emissions reduction and operational efficiency. A net-zero world is more easily realized through nuclear propulsion, and we are putting in place the foundations for that future today. Turning this into a practical reality will require significant public sector support and ABS is well placed to bring governments and industry together,” said Christopher J. Wiernicki, ABS Chairman and CEO. “Advanced or small modular reactors address many of the issues traditionally associated with nuclear for commercial maritime use, with enhanced safety and efficiency, reduced cost and waste and proliferation prevention. Nevertheless, many questions need to be answered and it is critical that industry evaluate these technologies with a laser focus on safety.”
“HEC is pleased to be able to support ABS and explore the practical application of nuclear power on board. This study is helping us to understand in detail both the potential of modern reactor technology and how this will affect the design and operation of future vessels,” said Robert Tagg, Senior Principal Naval Architect at HEC.
ABS is playing a pioneering role in supporting the development of nuclear propulsion for commercial vessels. The U.S. Department of Energy (DOE) has awarded ABS a contract to research barriers to the adoption of advanced nuclear propulsion on commercial vessels. The DOE has also contracted ABS to support research into thermal-electric integration of a nuclear propulsion system on a commercial vessel being carried out by the University of Texas. abs.com hec.com
New roads mixed with recycled plastics at ten sites across Victoria will demonstrate a viable circular-economy solution to the nation, experts say.
The RMIT University-led project – supported by the Australian Research Council, Austroads and 10 Victorian councils – will incorporate recycled plastic from consumer and industrial waste, including notoriously stubborn soft plastics, into asphalt as a performance enhancer.
With Australians generating 2.6 million tonnes of plastic waste each year and landfill space expected to reach capacity by 2025, this project is helping to address an urgent challenge.
Project lead, RMIT Associate Professor Filippo Giustozzi, said the team will also produce best-practice guidelines on the use of recycled plastics in asphalt roads.
“These guidelines will enable local governments, which control 80% of the nation’s roads, to begin widescale adoption of this innovative recycling solution,” said Giustozzi from RMIT’s School of Engineering.
The City of Melbourne and nine suburban and regional councils will lead the way, each having sections of recycled road up to 900 metres long paved over coming months.
The 10 project sites will use an estimated 21,000kg of recycled plastic, but the potential scale of this solution is considerable given the several hundred thousand kilometres of roads across Australia, Giustozzi said. “If Australia’s 537 local governments each used a small amount of recycled plastic in the many roads they resurface each year, then nationally we’ll have created a large end-market for recycled plastic.”
Extensive laboratory studies conducted by RMIT for Austroads – the collective of the Australian and New Zealand transport agencies – show these mixes are mechanically, chemically, and environmentally sound, he said.
"The performance of roads can actually be improved with the additions of recycled material, such as plastic and rubber, to be more durable against traffic and resistant against ageing,” Giustozzi said. The team’s latest study, funded by Austroads and published in top journal Science of The Total Environment, found the recycled plastic asphalt mixtures had 150% less cracking and 85% less deformation under pressure testing than conventional asphalt.
“These studies tell us that adding specific types of plastic in the right way can generate greater rutting and fatigue resistance,” he said. “In some instances, the performance of the mix was similar to some of the more expensive polymers used in roads and substantially higher than conventional asphalt mixes.”
The partnership with Victorian councils and Austroads will now translate these findings into applied solutions that enhance the sustainability of our roads. “This is a critical step in demonstrating the feasibility of this approach to tackling a problematic waste stream in Australia, while establishing a trusted network for plastics recycling in road applications,” he said.
Austroads Chief Executive, Geoff Allan, noted increasing interest in exploring the viability of repurposing recycled waste plastic, and said Austroads was leading ground-breaking work to investigate the most suitable types of plastics for use in roads.
“This project builds on the work completed last year that confirmed recycled plastics can be successfully incorporated in road infrastructure without detrimental effects on the environment, the health and safety of the workers, or the future recyclability of plastic-modified asphalt,” Allan said.
“A major contribution of this project will be to develop evidencebased guidance that will provide certainty to road managers about the use of recycled plastics in road surfacing applications and thus lay the foundations for this solution to be embraced nationally.” Along with Austroads, the collaboration includes Australia’s leading pavement authorities and specialists, including public works and building bodies, recyclers and contractors.
It will be coordinated under the ARC Industrial Transformation Research Hub for Transformation of Reclaimed Waste Resources to Engineered Materials and Solutions for a Circular Economy (TREMS).
Local government areas involved in the project include City of Melbourne, Banyule, Bayside, Moonee Valley, Hobsons Bay, Baw Baw, Latrobe, Casey, Mornington Peninsula and Wyndham. rmit.edu.au
A new zero emission heavy transport vehicle has been created, which can remove the carbon impact of installing large infrastructure such as bridges, wind turbines and power station components. Mammoet – the world’s largest heavy lifting and transport company – is responsible.
It works by converting existing Self-propelled Modular Transporters - or SPMTs - from diesel to electric power. SPMTs are the workhorse of heavy industry, used in every large energy and construction project worldwide.
Mammoet developed a retrofit kit to replace diesel engines in the vehicles with electric motors. Once converted, each SPMT works in the same way as before: transporting objects up to thousands of tonnes at a walking pace, using a remote control.
The new vehicle shows Mammoet’s strong commitment to the energy transition, and to its own sustainability. Fitting new engines in existing SPMT fleets cuts down on both waste and additional construction, compared to purchasing new zero emission equipment.
The new SPMT can eliminate the carbon footprint of site transport. This allows our customers to reduce the impact of large infrastructure projects on surrounding people, businesses, and infrastructure. It reduces noise levels at project sites, making working conditions quieter and safer. Communication between staff is clearer, while work can take place for longer at sites with sound restrictions.
This solution was part-financed by the DKTI, a Dutch government program to develop climate technologies and innovations in logistics. Mammoet worked with a leading provider of zeroemission powertrains for heavy industry to bring the electric power pack solution to market.
Developed by Mammoet in 1984 and with over 40,000 axle lines in use globally, the SPMT, or Self-propelled Modular Transporter, revolutionized heavy industry by moving any heavy load safely, efficiently and with precision.
This next step in its story will be just as significant, reducing their CO2 and NOx (nitrogen oxide) emissions to zero and pointing the way toward a sustainable future for heavy transport. mammoet.com
Ferag AG and dereOida join forces to revolutionise intralogistics solutions.
Ferag AG, a renowned family-owned Swiss company with over 65 years of experience as a global market leader in material flow systems, and dereOida, an Australian pioneer based in Sydney, producing warehouse automation software with their revolutionary doWarehouse system, are uniting their strengths to offer an unparalleled intralogistics solution to businesses across various industries. dereOida's flagship product, doWarehouse, presents a holistic single view across the warehouse. With the freedom to select any automated system, customers can seamlessly integrate their chosen hardware into doWarehouse, all while benefiting from dereOida's outstanding support services. The doWarehouse system enables the user to streamline processes, enhance productivity, reduce costs and allows for continuous improvement through insightful analytics. Notably, it provides a single source of truth, revolutionises sortation management, replaces cumbersome spreadsheets, and optimises warehouse space utilisation.
Ferag AG's legacy as a family-owned Swiss company specialising in intralogistics solutions and the development, design and distribution of material flow systems is built upon innovation, quality, and a commitment to customer satisfaction. With a global presence across 18 countries and a team of more than 600 dedicated professionals, Ferag has consistently delivered cutting-edge sorting, conveying, buffering and order fulfillment solutions to a diverse range of industries.
The merger of these two industry innovators presents a transformative offering for businesses seeking to optimise their warehouse operations. By combining dereOida's state-of-the-art software solutions with Ferag's unparalleled expertise in material flow systems and design, customers can expect an end-to-end solution that addresses every aspect of intralogistics with unprecedented quality, reliability, and support.
dereOida is a trailblazer in warehouse automation software. Their doWarehouse system offers a comprehensive view of all warehouse operations, allowing customers to integrate various hardware options while benefiting from unparalleled support services. dereOida's commitment to innovation and efficiency has transformed how businesses approach warehouse management.
dereOida has solidified its position as a game-changer in the industry with successful implementations at two of Australia's leading retail giants, Myer and The Iconic.
“The combined expertise and resources of Ferag and dereOida will allow us to explore new horizons and drive innovation in every aspect,” Karl Friesenbichler, CEO dereOida said. “We are confident that this merger will lead to remarkable results and increase the value we provide to our customers, partners and stakeholders.” ferag.com
A final report for our country’s Digitisation in transport and freight: Lessons for Australia project, run with the Department of Infrastructure, Transport, Regional Development and Communications and Swinburne University of Technology.
The aim of the project was to undertake a comprehensive systematic literature review of international best practice in digitisation in the transport and freight sectors. Key case studies demonstrating the benefits and impacts in terms of enhancing network performance, efficiency and productivity will be identified and analysed.
A number of measures available in the literature indicate that Australia’s transport sector falls behind on digitisation trends compared to many other Organisation for Economic Co-operation and Development (OECD) countries, particularly in terms of the role of information and communications technologies (ICT) in enhancing the performance and efficiency of the transport and freight sectors.
This research undertook a comprehensive review of international best practice in the area of transport and freight digitisation, with a view to understanding how digitisation might enhance these sectors’ performance. The research identified learnings from the experience of countries with higher levels of transport and freight digitisation, and how these could be adapted to help Australian decision-makers shape the future directions of innovations in these sectors. Key case studies demonstrating the benefits and impacts in terms of enhancing performance and productivity were analysed. The research also included stakeholder consultations to ensure the findings reflected industry and government experiences of the barriers, opportunities and benefits of digitisation.
This study considered all users and transport modes that are part of the transport and freight sectors. These include road, public transport, freight and supply chain management, rail transport, maritime and shipping, active transport and aviation. Within each sector, a number of functional areas that are amenable to digitisation and technology solutions were identified. A total of 40 functional areas were analysed that included road safety, adaptive traffic signal control, managed motorways, public transport management, video surveillance and
monitoring, electronic ticketing payment systems, asset and cargo management, train signalling, airport safety and security, predictive asset management, port operations and safety of cyclists and e-scooters. The study also identified key emerging technologies that offer promise in addressing the key challenges facing the transport and freight sectors such as artificial intelligence (AI), CAVs, Internet of Things (IoT) and blockchain. Digitisation best practices in each of the 40 functional areas were evaluated taking into consideration the numerous benefits of tech-enabled smart mobility solutions such as improving safety, productivity, efficiency and user experience. The evaluations showed high benefit-cost-ratios (BCRs) for digitisation solutions compared to expanding physical transport infrastructure. On average, traditional transport capacity expansion projects (such as building new roads or tunnels) provided a BCR below 3.0. This is much lower than the benefits of technology and digitisation solutions that were found to exceed a BCR of 5.0 in many cases and reach as high as BCR of 30 in some cases. Digitisation investments were also found to require much lower capital investment compared to infrastructure building projects.
This study also included benchmarking of best practice transport and freight digitisation across OECD countries. Comparative evaluations were undertaken based on 10 international digitisation indicators in addition to 40 new indices developed in this research covering all functional areas. This information was used to develop best practice transport and freight digitisation indices based on three pillars that included productivity, industry and consumer acceptance, and policy and regulations. The benchmarking results showed Australia’s best practice transport and freight digitisation index to range between a score of 59 for the maritime sector up to a score of 81 for the road sector. Australia’s overall index score across all sectors was 72 which ranked Australia at number 13 amongst all OECD countries.
imoveaustralia.com
We
Projection Micro Stereolithography or PµSL for short, is a micro 3D printing process that is a variation on stereolithography (SLA) that enables users to microfabricate components with ultra-high resolution down to 2 µm. With a range of commercially available liquid polymer resins and the ability to tailor your own formulation, PµSL introduces new levels of freedom compared to other traditional microfabrication techniques. It has the added benefits of superior material integrity and surface finish compared to conventional polymer 3D printing.
With many manufacturers across a variety of industries pushing for miniaturisation in their product designs, micro 3D printing opens new possibilities for component manufacturers, offering design freedom and rapid concept to product timeframes. While 3D printing and desktop 3D printers have become extremely accessible, sometimes design specifications go beyond their capabilities and even those of micro injection moulding and micro CNC machining. In this article we explore Projection Micro Sterolithography (PµSL) as an alternative solution.
3D printing of polymers has really taken off in recent years. Interestingly, the driving force behind the growth has been noncommercial adopters or hobbyists who can get into 3D printing outlaying only a few hundred dollars, with systems available from any number of manufacturers and consumables being very affordable. That said, the ability to produce “rapid prototypes” has also seem industry also consume their fair share of 3D printers.
These highly affordable systems are based on Fused Deposition Modelling (FDM) or Fused Filament Fabrication (FFF). The process involves taking a thermoplastic polymer filament and extruding it through a heated nozzle. In doing so the polymer is melted and fused to the underlying later, effectively creating a 3D structure by depositing a series of 2D shapes.
While FDM can be used to print large components, small components and fine surface finishes are perhaps the Achillies heel of these systems. Another issue with FDM printing is the inherent weakness at the point where each layer comes together. While systems are being scaled up to produce larger components simply by increasing the travel of the gantry/print head, printing smaller components becomes a problem with nozzle diameters (typically of the order of 0.4 mm, and occasionally 0.2 mm) restricting with the level of surface finish they can achieve. So, what happens if you want to fabricate components with features smaller than that?
What if you need high precision, high resolution and high accuracy?
While it is possible to produce some components by processes such as micro injection moulding, this process is suited to high volume production runs as the tooling can be expensive, especially where the component is complex. However. micro injection moulding may not be able to fabricate components with internal structures such as microfluidics. Similarly, micro CNC machining is limited by the size of the tools that can be used, low throughput rates and also the inability to form internal structures, although it can be ideal for applications such as low volume production of components with simple geometries.
There is a growing need to produce small components with surface finishes that rival micro injection moulding. This is where micro 3D printing technologies come in, with the ability to fabricate structures with features in the single micron range or even in the sub-micron range, potentially with internal structures and at volume.
Projection micro-stereolithography (PµSL) is a form of
stereolithography (SLA) that incorporates a DLP® light engine, precision optics, motion control and advanced software. SLA produces parts in layers using a photochemical process, whereby a photosensitive liquid resin is exposed to light so that polymeric cross-linking and solidification occurs. In contrast, the PµSL process, patented by Boston Micro Fabrication (BMF) marries the benefits of SLA and DLP technologies and employs a flash of ultraviolet (UV) light which results in the rapid photopolymerisation of an entire layer of resin. PµSL technology also supports continuous exposure for faster processing.
Similar to other 3D printing processes, the process starts with a CAD file that is sliced into a series of 2D images called digital masks that show or hide specific areas of the layer. A 3D structure is then built up layer by layer. As each layer is laid down, it is photopolymerised using a flash of UV light projected into a DLP (Digital Light Processing) chip according to the layer’s mask pattern. By controlling the projection lens, PµSL technology can achieve resolutions from several micrometres or hundreds of nanometres.
BMF’s range of microArch 3D printers use the pµSL process which suits UV-curable materials such as polymers, hydrogels and composite resins that contain ceramic or metal particles. While the open platform allows the use of any (suitable) material, BMF have a range of polymers that offer e rigidity, toughness, high-temperature resistance, biocompatibility, flexibility or transparency.
Advantages of the PµSL process include:
• High precision
• High resolution – down to 2µm
• High accuracy
• No need for moulds or tools
• Can reduce time from concept to prototyping to low volume production
PµSL v competing technologies
PµSL is one of a number of available microfabrication technologies. In comparison, it offers unrivalled resolution, size and tolerance at relatively high speed. Although 2PP-DLW offers higher resolution, resolution of this level is not always required. 3D printing techniques lends them to rapid prototyping, reducing concept to prototype timeframes as well as time to production.
Technology Highest Speed Comments
XY Resolution
PµSL 2 µm Fast Fast + high-precision SLA ~50 µm Slow Slow + medium precision
2PP-DLW <50 nm Extremely Ultra-high precision, slow small overall size but very slow
FDM ~200 µm Slow Rough surface and low precision
PolyJet 600 DPI (42 µm) Fast Low precision, fast and large size
Note – 2PP-DLW = 2 photon polymerisation using direct laser writing. Compared to traditional techniques like micro injection moulding and micro CNC machining, PµSL does not require specialist tools or custom moulds, with the latter often being very expensive and timeconsuming to produce. These traditional processes, in particular micro injection moulding are also not well suited to prototyping, especially where a design may still need to be refined and will require large production runs to become economically viable.
The PµSL microfabrication process is suited to production of parts for a wide range of applications. Some of these are summarised in table 2.
Industry Component
Electronics Connector bases, chip sockets
Medical devices
Cardiovascular stents, blood heat exchangers, spiral needles
Microfluidics Valves for gene sequencing, lab-on-a-chip (LOC) devices
Filtration
Micro-electro- Micro switches, gears, latches, sensors, mechanical motors, valves, actuators, consumer systems (MEMS) electronics, accelerometers
Bio-MEMS Stents, micro needles, LOC devices
Optical Optical sensors, optocouplers, fiberglass connectors
Research Drug discovery, micro filtration
Summary
3D printing is gaining momentum as a commercial production process, especially in Australia where high value added, with lower volume production is more viable. It is often preferable to more conventional techniques, and the only viable option when components have complex geometries and containing features such as internal cavities which cannot be machined or moulded. Furthermore, with a trend towards miniaturisation, micro fabrication becomes an attractive solution and Projection micro stereolithography (PµSL) becomes an attractive proposition as an ultra-high resolution 3D printing technique that also brings high-speed production, accuracy and precision. AXT.com.au
Boston Micro Fabrication 3D printer that utilise PµSl technology. The benchtop microArch S240 with 10µm printing resolution
Large scale VSF-3D printing growing your business potential.
CNC Design, an established Australian company with core competencies in machine tools, engineered drives, robotics, and additive technologies, has recently commissioned a new range of largescale additive VSF-3D printers. These thermoplastic composite printers have the potential to revolutionise the manufacturing industry by enabling the production of a wide range of items such as plugs, moulds, fixtures, structural components, formwork, decorative pieces and architectural parts.
The VSF-3D printer uses a large area gantry to carry a patented multi zone extruder for melting and extrusion, providing the ability to rapidly print large structures with reinforced composites up to 220kg/hr. In addition, the printers offer an optional 5-axis machining head can provide smooth surface finishes.
The printers have several other features, including a nozzle rotation unit with a temperature-controlled roller to flatten and compress print bead, a vacuum pellet drying and conveying system with high performance and energy efficiency for continuous printing, axis print speeds up to 20 m/min with axis rapid speeds up to 60 m/min, changeable nozzles, and Siemens
SINUMERIK ONE controls, the leading platform for advanced manufacturing.
INNOMERIX Pty Ltd, a CNC Design subsidiary business, has been established to supply a wide range of thermoplastic composites. Equipped with a sophisticated compounding line and advanced dosing systems for incorporating powder and fibre into the polymers. This allows material properties such as strength, pliability, impact resistance to be adapted for each application. Other properties such as UV protection, low flammability, and biocides to avoid marine growth can also be added as part of the manufacturing process. The focus of INNOMERIX is on creating a green economy for 3D printing with low CO2 emission materials and recycling as a priority.
CNC Design has recently installed a new VSF-3D printer with a print area of 12m x 5m x 1.6m. Located on the same site as INNOMERIX, creating a fully integrated Application Centre. This facility supports proof printing and machining of client's projects, development of new advanced printing and machining technology, development, and testing of INNOMERIX
compounds, VSF-3D sales demonstrations, and production of specialty components on a commercial basis.
One of CNC Design's customers is Queensland manufacturer One Composites, a fully owned subsidiary of Zone RV, where their VSF-3D printing system is the largest in the Southern Hemisphere. The 22m x 5m x 1.6m system was initially established for both 3D printing and machining in composite materials for a wide range of off-road caravans that combine lightweight composite bodies with class-leading components. However, One Composites CTO, Dave Biggar says, “whilst investing in new advanced manufacturing technology may be perceived as a high risk, our experienced team quickly mastered the technology and identified a growing demand for large-scale 3D printed and/or machined components. The implementation of this technology has significantly increased our efficiency and versatility, enabling us to combine external project work with initial lightweight composite body production. As a result, our equipment is now being fully utilised, creating a need for additional production capacity and growth in our One Composites business.”
The ability to grow your business using largescale thermoplastics printing is immense, as companies like One Composites are now turning to this technology to complement their existing manufacturing processes whilst attracting new business opportunities. The technology provides the ability to innovate quickly, enhance or
replace materials, and develop interesting new shapes that create differentiation in the market.
In conclusion, CNC Design's large-scale VSF-3D additive printers offer an exciting opportunity for manufacturing businesses to grow their potential by providing innovative and cost-effective solutions to a cross section of industries including defence, education, aerospace, vehicle manufacturing, mining and marine. cncdesign.com.au
Sydney Head Office and Technical Centre Unit 7/16 Lexington Dr, Bella Vista NSW 2153
Perth Service Centre Butler, WA 6036
Melbourne Office and Technical Centre Unit 1/3-4 Anzed Ct, Mulgrave VIC 3170
Brisbane Service Centre Stafford Heights, QLD 4053
Auckland Office and Technical Centre Unit 2/67 Business Parade South, East Tamaki, Auckland 2013
Adelaide Service Centre Lockleys, SA 5032
3D printing’s evolution beyond prototyping sparks collaboration between Abilitymade and 3DExplorer.
The 3D printing revolution has transcended its initial role as a mere prototyping tool. 3D Explorer is creating robust, cost-effective, and tailor-made products harmonises seamlessly with the distinct needs of businesses and their clientele.
At the heart of this transformation lies the cutting-edge technology driving 3D Explorer. This technological marvel has democratised production capabilities, empowering enterprises of all sizes. From specialised research and development items to rapid prototyping and full-scale production, businesses now possess the prowess to craft singular pieces or mass quantities without compromising on quality, economic feasibility, or punctuality.
The versatility inherent in 3D printing technology has ignited a surge of interest across diverse sectors, including healthcare and medical device production. For instance, 3D Explorer has established itself as a pivotal player in medical device printing, with the ability to respond swiftly to urgent demands. This was clearly evident in a recent collaboration with Abilitymade, where 3D Explorer seamlessly 3D printed and vapor-smoothed a SAFO (Standard Ankle Foot Orthosis) in just three days. This prompt response proved incredibly beneficial to both patients and healthcare providers.
However, it's not solely their rapid response that sets 3D Explorer apart. Their unswerving dedication to superior material quality and unparalleled customer service has earned them accolades from industry professionals. The endorsement from Hugo Marchant, Quality, Production & Development Engineer, resonates powerfully: "Your company has had the largest improvement in material properties that I have seen for impact strength out of all the companies I’ve tested. You have also been able to match the impact properties of some of our top-tested companies."
The impact of rapid, full-colour prototyping reverberates in the manufacturing domain. Designers and engineers wield this technology as a transformative tool, expediting concepts into fully functional, precision-engineered components, all under rigorous timelines. Beyond this, the technology's utility extends to creating electronic modules, bespoke fixtures, jigs, and guides, all pivotal in ensuring precision and consistency throughout the manufacturing journey.
The influence of 3D printing extends even into architecture, design, and the realm of art. Architects, builders, and
property developers harness its prowess to construct intricate architectural models, bolstering marketing endeavors and providing clients with vivid projections of forthcoming projects. Meanwhile, artists infuse their creations with newfound depth by incorporating 3D textures, culminating in life-sized, chromatic sculptures that were once the realm of dreams.
Venturing into consumer goods, 3D Explorer introduces venEyes, a brand specialising in 3D-printed, bespoke eyewear. Each pair conforms harmoniously to the contours of the wearer's visage,
epitomising the beauty of personalisation. This on-demand innovation resonates in sidestepping overproduction, enhancing environmental consciousness – a crucial facet in sectors like health and fashion, which often grapple with surplus waste. The glimpses provided above are mere teasers of 3D Explorer's boundless potential. For those embarking on a journey of exploration and innovation, partnering with the adept team at 3D Explorer holds the key to realising the ambitions of your next endeavour.
3dexplorer.com.au
The Additive Manufacturing Cooperative Research Centre (AMCRC) is an industry led collaborative research funding organisation focused on advancing Australia’s additive manufacturing sector.
The centre brings together industry partners, developing the next generation of products and services, and research institutions to conduct cutting-edge research, develop new technologies, and drive innovation to foster a globally competitive innovation ecosystem for advanced manufacturing. The CRC matches dollar-for-dollar Industry Partner cash for collaborative manufacturing R&D and innovation projects with CRC Research Partners. This is a potential fit for Industry Partners (e.g. manufacturing and related businesses) where their strategy includes:
• investing in an eligible transformative manufacturing R&D project with a CRC Research Partner of between two and five years in duration, that can commence from 2025 onwards;
• spending at least $250,000 cash per project to fund the cost of researcher salaries and operating costs at a CRC
Research Partner (which, if eligible, the CRC can match dollar for dollar up to a maximum of five million dollars per business);
• with the Research Partner(s) conducting at least 50% of the overall project research effort;
• utilising and/or developing new manufacturing technologies and business models aligned with the CRC Research Programs to deliver commercial outcomes, including within Australia, ideally within three years of completion of the project;
• collaborating with other Australian manufacturing SMEs through the project.
Some of the unique problems that Australian manufacturer’s face including a heavy reliance on overseas supply chains with massive shipping costs and associated emissions are a huge opportunity for AM to solve by allowing the localisation of volume sensitive production of complex, high value, and customisable components. AM also gives product designers and engineers incredible freedom to light
weight the next generation of transport and aerospace components driving fuel efficiency and emission reduction, while Increasing electric vehicles range. EV battery technology is rapidly evolving and AM’s ability to print high surface area to weight ratio parts in almost any critical mineral opens up opportunities for those very minerals to be converted into high value products that could unlock net zero pathways for Australian manufacturing. Couple this with our growing access to affordable renewable energy, means there will be long term sustainable opportunities for ambitious manufacturers to build new product portfolios for export markets.
The development and application of next generation AM technologies coupled with innovation and capability building will be the catalyst for manufacturing growth and transformation and the focus of the Additive Manufacturing CRC.
John Croft – 0414 747 636 john.croft@amcrc.com.au amcrc.com.auThere is nothing to be worried about, says David
Alatorre, Chief Technical Officer, Rivelin Robotics.This article aims to explore the challenges being faced by manufacturing organisations across industries. A societal and cultural shift away from manual, craftsmanship-based roles, coupled with the perception of health risks in manufacturing occupations has led to a significant skills shortage in the sector. Various other challenges include regulatory pressures, unstable supply chains, and unprecedented uncertainties — all of which are exacerbating the situation and threatening the competitiveness of manufacturing enterprises. However, this article posits that the solution to these escalating issues lies within the realm of digitalisation and automation technology. Our analysis is rooted in the evolution of job market trends, and the opportunities presented by innovations such as Rivelin NetShape, a frontrunner in the digital revolution of manufacturing. By harnessing machine learning, advanced sensors, and proprietary algorithms, this technology transforms skilled manual tasks for post processing and finishing metal parts and components into repeatable, traceable digital procedures that significantly boost productivity and reduce costs.
The article will go on to present a future where the burdens of manual labour can be alleviated by robotics and AI and show how a 'local for local' production model - the strategy of manufacturing goods in proximity to their intended customers to promote regional selfsufficiency - can become a reality thanks to digital manufacturing. Furthermore, we posit that these changes in the industry make roles like 'Digital Manufacturing Engineer' increasingly appealing to a new generation of computer-literate, technically minded jobseekers. The objective of this communication is to assess the impending shift from manual craftsmanship to digital procedures, and from low-cost overseas production to local digital manufacturing, offering insights for industry stakeholders and business leaders navigating these changes.
Despite recent advancements in industrial safety standards and protocols, manufacturing occupations are still associated with a multitude of health risks such as exposure to harmful substances, repetitive strain injuries, hand-arm vibration syndrome, dust inhalation, hearing loss, vision deterioration, and risks related to machinery accidents, fire, and electrical hazards. It is possible to eliminate these risks through comprehensive safety measures; but, even then, trends suggest that this alone will not prevent the looming skills shortage. Over recent years, the allure of traditional skilled workforce sectors such as manufacturing has been diminishing. As pointed out by Muro et al. in their research at Brookings Institution, societal progression and technological development have catalysed an evolution in the job market, shifting the focus from manual, craftsmanship-based roles to those centred on digital skills and intellectual stimulation.
One of the key factors contributing to this shift is the rapid advancement of technology and digitalisation across various industries. The digital revolution has created new and exciting opportunities in fields like artificial intelligence (AI), data science, software development, robotics, and automation. These professions are attractive as they involve working with innovative technologies to solve complex problems, and push through new boundaries. Organisations of all sizes increasingly rely on digital technologies to enhance their operations, improve efficiency, and gain a competitive edge. Safety considerations are also a significant factor in career choices, along with physical exertion. As a result, traditional industries like manufacturing and construction are typically associated with being physically demanding and higher risk. For younger people entering the workforce, manufacturing jobs are less
likely to attract them for the above reasons. This is supported by a survey conducted by Deloitte, which found that millennials and Gen Z workers prioritise purpose and meaning in their careers and avoid higher risk industries.
Consequently, across the global workforce, but particularly in Western cultures, millions of physical and skilled positions remain unfilled, not necessarily due to salary constraints or flawed policies but because of a pronounced shift towards more fulfilling and safe professions.
This skills shortage is only one among a growing list of factors escalating manufacturing costs. The manufacturing sector is grappling with a multitude of other challenges such as unstable supply chains shaken by global events, regulatory pressures tightening the requirements for quality and traceability, and unprecedented uncertainties. The combination of these factors leads to spiralling costs, threatening the competitiveness of manufacturing enterprises. Here we will expand further on these challenges and their implications:
Supply Chain Susceptibility to Shocks: More than any event in recent history, the COVID-19 global pandemic crystallised how vulnerable global supply chains are. During the height of the pandemic years almost one third (30%) of United Kingdom manufacturing companies struggled with disruptions across their supply chains and sourcing essential goods and components. Almost every industrial manufacturer (97%) reported some form of negative effect. Western economies found themselves heavily reliant on distant suppliers who were also in chaos due to lockdowns, workers in isolation and reduced transportation/shipping capacity. This has led directly to companies looking to reduce supply chain risks by reshoring certain industries in the west. Extraordinary events such as the blockage of the Suez Canal in March 2021 also demonstrate the potential fragility of global trade routes. Individually and together, these events serve as indicators for manufacturing companies to diversify – and shorten — their supply chains, promote national and regional production, and mitigate the risks associated with relying on a single transportation route or region.
Geopolitical Factors: Geopolitical tensions are nothing new and neither is their effect on global trade. The world is currently grappling with the fallout from conflict in Ukraine following the Russian invasion, which has had a considerable impact on the economic landscape, particularly in terms of energy supply (with average prices of nonhousehold electricity up 131% and gas 215% in the European Union over the conflict period) and manufacturing. Western economies, seeking to reduce dependency on foreign powers for such critical resources and industries may prioritise re-industrialisation efforts to enhance self-sufficiency and reduce vulnerabilities to potential disruptions. As President Biden put it at the recent G7 summit in Hiroshima, countries should “push to build a more resilient and
inclusive global economy that can better withstand the kinds of shocks that we’ve experienced over the last few years, including by building a more secure and more diversified supply chain”. Countries are looking at ways to invest in domestic industries to regain economic strength, to maintain a competitive edge, to protect national security and to advance technological leadership.
Government Policy Priorities: A strong industrial base is one way that governments can look to protect resilience against potential risks. This can include prioritising policies that support the revitalisation of key industries, such as defence, energy, telecommunications, and critical infrastructure. This can also bring the benefits of stimulating job creation and economic growth by supporting domestic production and innovation. The recent signing into law of the CHIPS and Science Act of 2022 in the United States is one example of targeted reshoring policy, and the President’s statements in Hiroshima about “protecting a narrow set of advanced technologies critical for national security” further reinforces this pattern. The European Union is also showing interest in sectorspecific policies to promote reshoring, both indirectly - such as through carbon taxes and public procurement rules - and directly - such as through stockpiling mandates and trade/tariff policy. As more governments experiment with sector-specific reshoring initiatives, consensus will gradually form on how to effectively drive reindustrialisation. Some potential solutions to these challenges lie in the technological advancements of the last decade, particularly in automation technology. The convergence of advanced software tools, artificial intelligence and robotics offers a promising path towards re-industrialisation. As the experienced workforce edges towards retirement and the global west steers away from inexpensive foreign labour, manufacturing enterprises are turning to the digital paradigm; a world where humans shape ideas, and technology crafts them into reality.
There are critical issues plaguing the manufacturing sector, ranging from a significant skills shortage to unstable supply chains, regulatory pressures, and unprecedented uncertainties. The situation necessitates urgent innovative solutions to maintain the competitiveness of manufacturing enterprises. Automation and digital manufacturing technologies such as Rivelin NetShape® can help address these issues. By capitalising on machine learning, advanced sensors, and proprietary algorithms, these digital platforms transform skilled manual tasks into repeatable, efficient, and safer digital procedures. This not only boosts productivity and reduces costs but also makes the manufacturing sector more appealing to a digitally oriented, safety-conscious workforce.
The unfolding digital revolution in manufacturing is painting a future where robotics and AI can significantly alleviate the demands of manual labour. It enables the transition to a 'local for local' production model, where goods are manufactured close to their intended customers, promoting regional self-sufficiency, and reducing supply chain vulnerabilities. The digitalisation of the manufacturing industry has profound implications, particularly in reindustrialising western economies, enhancing resilience, and diversifying supply chains. In conclusion, as societal, technological, and economic dynamics continue to evolve, embracing digitalisation and automation technology in manufacturing emerges as an effective strategy to navigate and mitigate the challenges confronting the sector. It lays a sustainable foundation for the industry, marrying human creativity with technological precision to ensure a safer, efficient, and productive future for manufacturing. The journey from manual craftsmanship to digital procedures is not merely a transition but a transformation offering immense possibilities for businesses, workforce, and economies at large. rivelinrobotics.com
In a fast-paced manufacturing environment, maintaining quality and consistency in high volumes of output can be easily achieved through collaborative automation.
According to Masayuki (Masa) Mase, Country Manager for Universal Robots Oceania, “the simple truth is that human error can be costly and for this reason, companies are handing more meaningful tasks over to humans and letting robots handle the rest.”
Collaborative robots (cobots) are designed to handle repetitive, dull and even dangerous tasks. “They are cost-effective, safe and flexible to deploy in companies both big and small. Unlike traditional robots, they are easy to program and can work in small spaces too,” he said. “Manufacturers can rest easy knowing that tasks are carried out without any errors time and time again.”
“Every manufacturer is trying to achieve a competitive advantage and this comes down to efficiencies. The more efficient and errorfree your production line is, the more output you can achieve,” said Masa. Cobots offer the precision and consistency needed to achieve these efficiencies. “A robot will consistently and repeatedly follow exact processes and pre-defined workflows with miniscule deviation, providing optimum conditions for study or analysis.”
It requires superhuman abilities to repeat the same movement over and over again for many hours with exactly the same precision. Automating quality inspection lets you increase measurement consistency and maintain high product quality levels. The repeatability of down +/- 0.03 mm (30 micron) of the UR robot arm is perfect for automating quick-precision handling in quality inspection and testing applications.
“A robot arm with a UR+ certified vision camera offers easy plug-andplay integration for non-destructive testing and 3D measurements, further guaranteeing the quality of your products. It can objectively identify and pinpoint defective or faulty parts before they are packed or shipped.”
Masa breaks down a few recent examples of cobots being deployed globally to help improve efficiencies and enhance quality on the factory floor.
More than 70 cobots are currently being used by Siemens to relieve staff from repetitive and tiring actions. At Siemens GWE, the automation of manufacturing processes has been a great success. Using cobots not only increases productivity and improves the company's cost position but also increases the motivation of the entire workforce.
“Thanks to the cobots from Universal Robots, we have managed to ensure that automation has arrived to take its place right next to all employees on the production floor,” said Harald Ell, Production Planner at Siemens Gerätewerk Erlangen.
Hwa-Hsia Glass introduced 11 cobots in its plant as of its digital transformation strategy. Requiring no changes to existing floor space and other resources, UR cobots save Hwa-Hsia Glass six times the space compared to traditional industrial robots - effectively freeing up 25% of the manpower. The cobots allow operators to focus on skilled tasks, diminish their fatigue from repetitive work, and improve overall productivity and quality. The introduction of UR cobots further reduced revenue loss due to customer complaints by USD54K-72K annually and helped achieve the company’s vision of becoming an employee-friendly workplace.
Olympus - Singapore
Olympus is a leading manufacturer of test and measurement solutions used in aerospace, oil and gas, automotive, and other industrial applications. Olympus' inspection systems can be used to detect and characterise defects, and non-destructively measure elemental compositions in a range of materials such as metals, plastics and composites.
Inspection tasks are often carried out over an extended period of time, in uncomfortable or even unsafe positions, presenting scenarios that may lead to incidents or accidents caused by fatigue, repetitive stress, and bad human factors. By incorporating cobots, Olympus provides a complete and efficient automation solution to their clients.
These solutions relieve operators from potential health and safety hazards due to long hours of repetitive work in uncomfortable positions, and enable them to focus on activities such as optimising inspection methods, analysing data, and other value-added tasks.
“It’s great to see cobots being deployed across the globe to help enhance companies’ value propisitons and work alongside their teams to reduce the workload,” said Masa. “We look forward to seeing where automation is headed in the years to come.”
universal-robots.com
Failing to keep track of tank farms can be costly. Here, Ian Loudon, International Sales Manager at remote monitoring specialist Omniflex explains why tank monitoring is not just essential, but simple too.
When considering the potential consequences of inadequate tank farm monitoring, images of disasters like the Buncefield fire probably spring to mind first. However, with the development of safety regulations and equipment, these catastrophic events are becoming far less common over time. Instead, those who rely on functional tank farms as part of their supply chains are more likely to suffer from inefficiency and resultant financial setbacks., Without accurate information, businesspeople are in the dark. Keeping track of supply levels in tank facilities is crucial both to regulate your incoming materials and provide the required product quantities on demand. This is as true for hazardous chemicals and flammable petroleum storage as it is for paint and water. But how can decision-makers access that critical data?
In parts of the developing world, a calibrated dipstick and crossreferencing table or a sight glass and internal floats are still used to determine levels inside each tank. Across farms with tens or even hundreds of tanks, this is slow, expensive and involves an inherent lag in data reporting. Furthermore, this brings no safety oversight for tank levels.
In more technologically equipped regions, advanced methods like remote monitoring have been used for many years. Here, tank farms will use whatever infrastructure is available to transmit information to a central collection point, whether a physical facility or cloudbased storage. This might be done by wired internet connection if it exists on-site, if not then mobile networks or even satellite-based communication.
The major challenge exists not in transmitting the data, but in gathering it in the first place. In chemical or petrochemical settings, this collection process is often costly because of the expensive instrumentation required to assess the tank levels in hazardous environments. The measurement equipment often represents up to 80 per cent of the overall project costs to implement remote monitoring at tank farms.
Although these costs can raise eyebrows, perspective is key. The ramifications, both financial and safety-related, of missing an overflowing tank can be severe. Forcing an emergency shutdown can lead to days and even weeks of expensive downtime in production. Research from the Aberdeen group showed that unplanned downtime at refineries and petrochemical plants costs between $10,000 and $250,000 per hour. Serious environmental damage like petroleum fires or chemical pollution is also a frightening consequence. When Dulux engaged Omniflex to help provide direct access to vendors in the management of bulk chemical supply and on-site storage, the world-leading paint brand had complex, monitoring-based needs. The company wanted to monitor the tank levels of various paint ingredients stored onsite, such as the pigment, binder and additives. This site consisted of 76 tanks with various contents and Dulux’s procurement team shared this cloud based data with its 23 different vendors, who are located around the globe, to improve the logistics and resupply timelines.
To meet these needs, Omniflex provided a solution based around its Data2Desktop® service. All the data described was made available to Dulux’s vendors using conventional internet browsers, anywhere in the world. Dulux and its vendors can monitor the tank status to stay abreast of chemical supply and usage trends. In the case of Dulux’s tank farms, it already had technology that pumped the bulk material chemical components into the mixing tank in the correct quantities, so the initial instrumentation costs were avoided. Omniflex’s remote monitoring solutions ‘bolted on’ to the existing measurement instrumentation, saving on engineering and installation costs, and so Dulux management personnel could determine the amount of each ingredient they needed to procure. Although the installation costs for tank monitoring are not insignificant, the cost/benefit relationship easily justifies the expenditure. Those who could benefit from this remote data collection are asking the wrong question. Instead of saying “Can I afford to implement this technology,” they should be asking “Can I afford not to?”. omniflex.com
As industry 4.0 gains momentum, an increasing number of businesses are looking for ways to create and capture value through the computerisation and networking of their manufacturing and maintenance processes.
Firms considering the introduction of a computerised system are generally driven by the promise of increased efficiency, quality and cost savings. One area that is often overlooked however is safety, even though increased safety also has a significant impact across all areas of the business.
Research and industry experience has found that organizations that prioritise safety experience a return on investment that extends beyond purely financial returns, with benefits including:
• Improved risk management, by making it easier to comply with regulations, laws, and standards;
• Increased productivity, by automating critical processes;
• Enhanced reputation. A reputation for safety is extremely important, particularly for industries that are involved in, or produce products for high-risk industries. It is often a critical factor in winning contracts and tenders.
Safety is also often narrowly defined and examined separately from quality. However, safety is both an attribute and an objective of quality particularly in the world of Industry 4.0. We will be examining the relationship between the two through the lens of networked tool solutions, particularly screw tightening operations.
The decision to invest in computerised infrastructure has often been driven by the desire for increased productivity, efficiency and quality, but this has been increasingly balanced by the need for flexibility, the ability to respond to increasingly individualised customer requests and to be able to master small batch sizes. It is no longer just large companies that are investing heavily in high tech production. At the same time there is increased pressure on the upstream supply chain, the suppliers who provide parts and components, to meet the high standards of their customers, to look at their own processes to reduce error and deliver verifiable quality.
There is also the need to ensure the stringent requirements of the production environment can be transferred to the downstream servicing environment. Maintaining standards can be seen as a quality issue but in many industries, they are also a safety issue. For example, vehicle brakes must be bolted to a defined torque during production, but how are these same standards maintained in a service environment in a way that can be verifiably documented.
In an increasingly complex environment, there is a need for a greater attention to standards, and often narrowing margins of tolerance. However, this is balanced by an increased demand for flexibility. It is often the human that is best placed to react quickly to change. The quality standard for humans is often a qualification. A qualification does not guarantee that those standards will be put into practice in a real-world environment. In some factory environments the workers are largely unqualified. This has implications for quality and of course safety. These issues can be counteracted using the digital definition of screw-tightening processes via Digital Worker Assistance Systems, which not only shortens the learning process but guides the worker through the specified processes, avoiding unintentional errors. Steps are not missed, and bolts are precisely tightened to a preset torque. The aim is not to replace the worker but to support them by providing direct feedback and Guidance.
Traditional production operations have relied exclusively on mechanical (analogue) torque wrenches with manual processes from setting up the torque wrench to creating paper-based instructions, quality control and manual logging. There is obviously considerable potential for error within these systems. The next stage is companies that have transitioned to digital torque wrenches but have not networked them. There is the benefit of the higher precision of digital torque tools and the ability of direct fastener evaluation. However, there is still the need to assign the displayed or logged tightening values manually and process control is still largely paper based.
In both scenarios the quality of the final product is largely dependent on the experience of the user. And while electronic torque wrenches provide feedback on the quality of the completed joint, compliance and safety standards are still at risk if that information is not registered by the user.
Many companies try to overcome these risks through the use of cost intensive torque wrenches for random quality and safety checks, however the time lag before quality issues can be identified leads to additional risks.
Other companies try to ensure compliance by assigning an additional person to check processes are followed. The additional costs incurred are generally excessive when compared to the costs of an intelligent worker system in conjunction with the use of electro-mechanical torque tools.
It is relatively simple to connect integration capable torque tools to a subordinate system such as assembly software or a production control system and then enable data exchange. In the simplest scenario a worker assistance system can be installed to a single PC. Digital control begins with the worker and the product being assigned a barcode. The worker is then guided through the entire process, including assistance in selecting the necessary parts and tools. In the case of torque controlled bolted connections, the worker assistance system presets the corresponding tool to suit each fastener in turn. The worker can see through the software interface which fastener is to be tightened in which sequence. Most importantly the torque wrench transmits the tightening values measured back to the assistance system where they are automatically monitored and logged.
The implications for both quality and safety are obvious:
• The opportunity for error is reduced to an absolute minimum;
• The quality and reliability of the joints and the resulting product are greatly increased;
• There is seamless traceability at both a product and individual worker level with reliable logging and traceability inherent to the system;
• The highest possible standards of safety and quality can be achieved with the minimum of training because digital processes reduce the effort required to create and maintain paper-based worker instructions.
The benefits of installing an autonomous worker assistance system are obvious. They are easy to install and represent a low threshold entry to Industry 4.0. In addition, the system can be easily rolled out to multiple workstations after a successful trial.
Safety and quality very much go hand in hand at Stahlwille, a German manufacturer renowned for producing tools that are amongst the finest on the market. Made to exacting specifications Stahlwille tools are made to such high specifications that they are widely used in safety critical industries such as defence, aviation and aerospace. Stahlwille is also the gold standard in the automotive industry. Stahlwille tools feature several safety innovations and features that are applicable to various machinery and vehicles, which are of critical importance in an environment like the defence force.
Stahwille have stated that anything that can be digitalised will be digitalised. Anything that can be interconnected will be interconnected. As a leading innovator and pacesetter in the field of torque technology, Stahlwille have been developing torque tools, measurement devices, calibration devices and software solutions to meet the requirements of Industry 4.0 for some time. The result of this is DAPTIQ, the new standard for interconnective systems to enable users to reap the benefits of digitalisation and considerably increase efficiency and process capability by integrating them in their own systems.
The Manoskop® 766 DAPTIQ® can be easily integrated into existing workflows and infrastructures even when they do not come from the same manufacturer using Open Protocol. Where workflows cannot be mapped via Open Protocol the Manoskop® 766 DAPTIQ® has its own protocol to allow flexible and simple integration. Even where there are numerous networked tools from different manufacturers it is still possible to obtain a uniform overall
picture of all production cells by simply connecting to a central database or a superordinate manufacturing system (MES) that consolidates and evaluates the data.
Aside from the benefits to quality and safety control sytems through the logging functionality the system provides other benefits.
Process related errors can be prevented in advance by applying the poka yoke principle which ais to keep all the necessary materials and tools in the right place at all times amongst other benefits. Examples of applications include:
• Stacklights for status display according to the traffic light principle;
• Socket trays to ensure the correct insert tool is selected;
• Position tracking to ensure the correct fastener is being tightened.
As Industry 4.0 gains momentum there is little doubt that, “anything that can be digitalised will be digitalised and anything that can be interconnected will be interconnected.” While the financial costs and benefits have been examined in depth there has been less of a focus on the quality and safety gains. In the case of screw tightening applications, those gains are enormous, particularly when considered alongside the speed and ease of implementing a digital worker assistance system. Stahlwille have made it even easier with premium tools, a stellar reputation in safety critical industries, and a system that can be easily integrated with existing systems and tools even when they come from a variety of manufacturers. Safety and Quality are very much intertwined, and both a focus and a benefit of Industry 4.0. whiteint.com.au
Enhancing manufacturing operations in Australia and New Zealand with the right ERP system. Rob Stummer, Director of Growth at SMC asks us to understand the Digital Transformation Blueprint.
In the fast-paced world of Australian and New Zealand manufacturing, remaining agile, efficient, and innovative is paramount. Over recent decades, digital technologies have continued to pave the way for manufacturers, enabling them to streamline business processes, anticipate customer needs, and respond quickly to an evolving market. As manufacturers modernise, the role of technology, particularly Enterprise Resource Planning (ERP) systems, has become more critical than ever.
Manufacturing enterprises represent intricate systems involving numerous departments, workflows and processes. Tasks range from managing intricate inventory details, coordinating production schedules, ensuring top-tier quality control, to maintaining compliance with stringent industry standards. To manually coordinate all these moving parts or employ disconnected systems is not just inefficient, but it's a breeding ground for costly mistakes that can hinder growth.
This is precisely where ERP systems step in. These digital marvels centralise and harmonise core business operations, offering realtime oversight and control across an entire organisation. For manufacturing units seeking to establish a significant presence in the competitive markets of Australia and New Zealand, the integration and automation offered by ERP software are absolutely essential.
SMC recommends organisations do a comprehensive analysis to understand what issues you are trying to solve with a new ERP system, and to identify the business-critical opportunities they are trying to achieve. In doing so you will have a clearer view of your organisation’s business and strategic process, data and people requirements and are better able to determine which software tools are best suited to achieving these. At SMC we call this understanding your Digital Transformation Blueprint. The two distinct manufacturing modes supported by modern ERPs that help distinguish fit are whether your organisation engages in discrete or process manufacturing. Mixed mode manufacturing if relevant to you, also helps determine fit.
over the years ERPs have taken on industry verticals, specialising and investing in functionality more suited to the industries that they have experience and customers in. Understanding the undeniable influence of ERP in manufacturing is just the tip of the iceberg. Here are the pivotal factors to keep in mind when navigating the vast sea of ERP solutions:
Business-specific requirements: Every manufacturing unit has its distinct needs and operational methodologies. The ERP system, therefore, should be an extension of the company’s ethos, catering explicitly to its industry, product range and workflows. A rigorous assessment of business needs, understanding pain points and bottlenecks, and identifying areas ripe for automation will guide the ERP evaluation process. Growth and scalability: The manufacturing landscape of Australia and New Zealand is dynamic, and growth is inevitable for businesses that adapt. The chosen ERP solution should not only cater to present requirements but should scale seamlessly with expanding production, increasing user count, and broadening product lines.
Seamless integration: In an era where business functions are heavily interconnected, an ERP system’s integration capabilities can't be ignored. The ERP should effortlessly mesh with current software tools and systems, such as CRM platforms, e-commerce systems, and even the production machinery. A prime example of this integration is linking ERP with shop floor control systems, which offers a real-time peek into production processes, promoting optimal resource use and informed decision-making.
The future of manufacturing in Australia and New Zealand is exciting, with technology playing a leading role. And in this evolving narrative, the ERP system stands out as a game-changer, transforming how businesses operate, grow, and thrive. With partners like SMC, manufacturing businesses can confidently navigate the digital transformation journey, ensuring that their ERP system not only enhances productivity but also positions them firmly for future success.
Another key distinction that impacts the functionality and ultimately the ERP most suited to your organisation is the method of production your business uses: Unique Job Production or Lean Job Production (Engineer to Order or Make to Order). Whether you manufacture standard products to order (Lean Job Production) or manufacture individualised products to order, (Unique Job Production) determines which ERP functionality is more important for your organisation.
Finally, the industry in which your business operates impacts the ERP solutions best suited to your organisation. This is because
Rob Stummer is currently the Director of Growth at SMC. He has over 15 years of experience as a CEO and Managing Director for global ERP and Enterprise Software companies throughout the Asia Pacific region. He brings extensive knowledge in implementing ERP solutions and delivering digital transformations that propel business innovation, with particular expertise in the construction and manufacturing sectors. Rob has a proven ability to develop and implement technology strategies for accelerated growth, supported by a strong commercial acumen and an agile mindset that focuses on optimising operations and improving service quality. Recognised as a thought leader in ERP and Enterprise Software across the region, Rob has been successful in maintaining a strategic, bigpicture perspective while fostering innovation and smart business practices to enable his clients to stay competitive. His career also includes executive leadership roles in technology advisory at KPMG and Accenture. Beyond these responsibilities, Rob also serves as Chairman and Non-Executive Director for several technology companies, bringing a multidimensional view of the industry to his roles. sm-c.com.au
'Understanding the undeniable influence of ERP in manufacturing is just the tip of the iceberg.'
Embracing cloud technology to improve workplace health and safety in the manufacturing sector.
The new Australian Work Health and Safety Strategy has identified manufacturing as one of the priority sectors for safety management, as workers are exposed to major health and safety risks in the line of work. According to Safework Australia, 11% of all workplace fatalities recorded in 2021 occurred in the manufacturing sector.
“Manufacturers are generally aware that they must comply with the applicable workplace safety legislation, to ensure their employees are safe at work. However, not having adequate safety management systems in place can impact a business,” explained Mary Nizamis, Chief Relations and Governance Officer at Skytrust, a cloud-based safety and compliance software system providing users with a holistic approach to safety compliance. “Cloud-based health and safety software resolves these issues fast, putting the employer and employees firmly in control of workplace safety.”
• Quick and easy implementation: Unlike traditional software packages, cloud-based software solutions don’t rely on the download or installation of IT infrastructure. “The Skytrust software, for example, can be configured and operational within 48 hours,” said Nizamis.
• Cost-effective, flexible packages: A monthly subscription enables a cost-effective package that also provides ongoing enhancements to the platform at no cost to the client.
• Easy access: Employees can easily access the software, at any time, through smartphones, laptops and other devices. An App also offers the ability to report incidents, hazards, and conduct inspections even when offline.
• Software enhancements: As part of the package, continual enhancements ensure the business is always utilising the latest version of the software, without the time (and additional IT costs) associated with purchasing updates.
• Collaboration and data sharing: Cloud-based software enables employees to edit and share data collaboratively, in real-time. It also ensures data consistency, resulting in fewer errors. “This makes teams more productive, especially in environments or industries involving remote work,” Nizamis elaborated.
• Data and reporting: Cloud-based software can collect and collate business data which, in turn, can be used to enhance business operations and performance. “The Skytrust reporting features allow you to track and measure the effectiveness of your WHS management systems and gain a global overview of how the business is performing,” said Nizamis.
• Security: Cloud-based software requires dedicated strict security protocols to be put in place by the provider, to reduce the risk of data being compromised. “Similarly, the data recovery and backup functionality of the cloud prevents data losses and downtime,” added Nizamis.
“Cloud-based workplace safety software allows risk controls to be implemented company-wide, and these controls to be constantly reviewed and monitored as required. The safety manager can evaluate whether current safety management systems are effective in mitigating risks,” explained Nizamis. She pointed to Skytrust’s work health and safety software, which enables management and staff to track, monitor and record incidents online with quick and easy access via smartphone or tablet, using QR codes. Her advice when considering safety management software is to choose a solution that’s easy to use, offers easy-to-understand dashboards with real-time data, and with the functionality to
manage everything from training to machinery licences and employee information in one place. “The implementation of new technology solutions can be daunting but, with careful planning, it’s easier to get the whole team on board,” she added.
Laying the foundations for technology adoption
Mary Nizamis reiterated that a company’s technology adoption plan shouldn’t be any different to other strategic business plans. Follow the standard principles of strategic planning:
1. Set your vision: Collaborate with key personnel to outline shared long-term goals. This helps get all stakeholders on board and can avoid potential barriers.
2. Build your plan: Everyone in the business needs to be aware that digital transformation will initially have various implications for different personnel when moving from existing systems. Good communication is essential in managing expectations.
3. Involve your IT department: Moving to cloud-based technologies sometimes relies on the input of your IT team to efficiently manage the transition. To reduce any challenges or barriers with the process, get your IT team involved from the start for a smoother transition.
4. Develop a business case: Evaluating your return on investment will help create a clear business case and rally stakeholder support. Businesses that have whole team support and customer understanding, experience positive outcomes from their digital transformations.
5. Get into the Cloud: Online software services are the next logical step for any business. This is because they not only enable remote use, but also provide many benefits around efficiencies, productivity, and reduced IT operating costs through not having to manage your own servers or maintain systems. “Your provider should ensure that all your cybersecurity requirements are met and there is also the added benefit of reducing your carbon footprint,” added Nizamis. skytrust.com.au
With the current uncertain business climate impacted by high inflation, pressure on wages and the need to provide an exemplary customer experience to win new customers, many companies have turned to technology to digitise their sales operations.
Almost every organisation has been impacted by the work-fromanywhere or hybrid work patterns where employees are no longer required to work from the office and have turned to digital solutions to assist in their transformation to meet these challenges. Those companies that have provided their workforce with the capability to continue their daily duties via remote access are the companies that have been able to survive, if not thrive, during unpredictable times.
No matter what your industry, sales drive success.
Digital transformation is about finding areas and processes where you can make the biggest impact with the least effort, and a great place to start is with your selling process. This is where money comes into the organisation. If you can make a positive impact within the selling process and insulate it from disruption, you will be well on the way toward transforming your entire enterprise. Positively impacting the selling process offers immediate results that are highly visible. Stabilising or improving sales revenue translates into stability for the enterprise.
Here are six signs your selling process could benefit from digital transformation.
1. You’re not seeing improvements.
First, if improvement is not possible with existing tools and processes, it’s likely that you need to explore digital transformation. It’s common for improvement recommendations to be greeted with scepticism, reluctance or outright defiance; this is human nature. Change is often received as a threat.
Effective managers understand this and know how to work around or over obstacles and motivate reluctant employees to embrace new processes.
Stagnation is indicative of process problems.
2. You’re always behind your competitor.
The second sign is centred on market share and success. If you are always coming in behind your competitor, relegated to the role of bid fodder and watching your competition close deals that you didn’t even know were there, you know you have process problems. Today, buyers are educated, and they know more about what they want to buy than ever before. If your competitors get a quote in before you, the buyer may well decide that the issue is closed and not even consider a second offer.
Customer experience is the number-one area where organisations look to differentiate their offerings. If you have a good starting process with your quotation that is fast, efficient, reliable, and accurate, you can get a head start from the get-go.
3. Configuration errors are common.
When you quote or propose a solution for your customer, you know how important it is for your solution to be demonstrably effective. If you are finding out late in the sale or even after the product is installed that your solution is not addressing the needs of the customer, this is a common sign that digital transformation is needed.
4. Extended pricing and price-justification discussions
Are you having difficulty in justifying why your product is priced the way it is?
Almost any buyer will ask if you can “do better” on the price, but when the entire sales conversation is dominated by price and your explanations are not resolving your prospect’s concerns, something is wrong.
It doesn’t matter if you are pricing by value received, cost plus or discounting off list, if the price is not understood and accepted, it probably means you are way out of line with other solutions under consideration. This has less to do with being the lowest price than it does with offering an explainable price.
5. Complex or opaque quotation documents
Closely related to price-justification are issues related to the inscrutability of your quotation documents. Complex products frequently do not lend themselves to bottom-line quotations. However, buyers will likely compare solutions using drive-away prices. If you have trouble summarising the pricing that drive the bottom line in your quotation, you are going to have a prospect with little confidence in the numbers you quote.
If you can’t equip your buyer to explain your price, you have process problems.
6. Tribal knowledge is not built into configuration and pricing processes.
If your product configuration and pricing require esoteric knowledge to effectively propose and quote a useful solution, you will likely swing and miss at many opportunities. This is especially true if you are working with new sales reps or trying to serve contactless quotes to your customers.
As products evolve, exceptions, special considerations and other minutiae associated with how your product is configured and priced will creep into your sales knowledge base. This information should be documented but instead is passed along outside of the price list or options catalogue.
This will lead to process problems. At Cincom, we have had great success with transforming these processes for complex manufacturers in Australia.
As a global leader in configure-price-quote (CPQ), Cincom’s solutions are geared towards enhancing organisation’s capabilities, optimising processes and delivering a better experience for customers. Cincom has a suite of software solutions that is designed to help businesses operate more efficiently and effectively.
Contact James McDougall, Business Development Manager, at 0408 488 709 cincom.com/au
Artificial intelligence is best taken one step at a time. Barry Urquhart is Managing Director of Marketing Focus.
It is easy to do. And it comes with consequences and costs. The latter may be financial, social, political, cultural and operational. Take pause, the business landscape is littered with the fallout of past rushes centred on mass production, just-in-time, cloud computing and online sales. More contemporary examples feature production zero-emissions, greenenergy, algorithms, renewable fuels and autonomous operations. And now, there is AI – artificial intelligence.
There are lessons to be learnt. Sugar rushes effect changes in behaviour, waistlines, eating habits and attention spans. Many of those were not considered, anticipated, or subjected to rational cost: benefit equations at the time of purchase. Value is difficult to measure, monitor and control. It can be, and often is a weighty issue. Few want to be left behind… behind what? The sentiments evolve into truisms, founded on emotions and well-intended intensions and idealisms which typically lack objective, substantive and rational reasoning. Generative AI is representative of the subject matter. The term is both explicit and implicit. Generational, strategic and quantum change, if not progress, advancement and competitive advantage, is significant in scale.
Enhanced efficiency, effectiveness and productivity of innovations, technologies and disruptive processes may not result in better outcomes, advantages, benefits and rewards for clients, customers, service providers, business managers and stakeholders. Indeed, they can have profound impacts on morale, cohesion, job security, employee attrition rates, customer service and service delivery. Skill-gaps become evident rapidly. Internal and external satisfaction levels can decline.
Therefore, installing innovations and change is only an initial phase. Ensuring and optimising “fit” may require attention, time and resources to facilitate, install and support changes in structures, systems, processes and skill sets. Australia, Australians and Australian businesses are beneficiaries of the mining resources. We are foremost in operations, profitability and adaptability. Autonomous trucks and trains are examples. Admittedly, the sector is populated with risk-takers, entrepreneurs and opportunists.
A commonly applied philosophy is founded on three pillars:
Each, and all, have relevance and application to commerce at large, particularly when addressing artificial intelligence.
A key preceding phase is: EXPLORE.
Artificial Intelligence has many dimensions. Some are customised. Others have been commoditised. None can be secured, installed and left to its own devices. Inevitably deficiencies, shortfalls and errors become apparent – with potentially significant implications, complications and consequences. Therefore, mining the marketplace for the “right’ or most appropriate AI is imperative. One size does not fit all. Mining, scoping and documenting the potential will identify the needs for complementary, contributing and supportive infrastructure.That will enable pre-emptive refinement
to the intended introduced artificial intelligence and the existing operations. Gaps will need to be filled, only then can outcomes, intended and unintended, advantages and disadvantages, enhancing and improving be identified, analysed, documented, implemented, monitored, measured, improved and provided with optimal infrastructural support.
ChatGPT, or similar, are timely case studies. Pre-existing phone, computer and online systems maybe incompatible or limiting.
Human overview checking, verification and approval are advisable, if not mandatory. Legal practitioners, medical specialists, engineering experts and psychology consultants will attest to that. Set and forget is fraught with potential pending or inevitable non-identifiable consequences.
Artificial Intelligence should be secured and implemented for specific purpose or intended outcomes. Accordingly, goals, outcomes and key performance indicators need to be determined and qualified first, with input from relevant internal and external stakeholders.
Variances and refinements may be necessary. They should be tolerated, recognised, respected and actioned. Delegated authorities and responsibilities need to be determined and agreed upon, implemented and enforced. Transparency and accountability are important. There should be no space to hide.
The process is called: Rhyme and Reason
ALERT: Beware AI snake-oil-salespeople. They abound.They seem to appear without invitation or solicitation, then disappear. Followup, follow-through and accountabilities are difficult to implement.
Artificial Intelligence works best from a broad and extensive existing database. It is those that determine parameters and content. Therefore, original and unprecedent thought, texts, expressions, responses and actions have severely restrained scopes.
AI is fundamentally a tool which complements existing human, systemic and structural resources. It does not and should not be employed to replace such. Operating in or from a void is, well, hollow.
Artificial Intelligence, in its many guises, represents exciting prospects. Commerce at large should be open, positive and enthusiastic about the prospects. However, it comes with inherent costs, strengths, weaknesses, limitations and needs.
Each phase, step if you will, needs to be explored, mined, refined and defined before acquisition, introduction, implementation and operation. We at Marketing Focus have contributed to many deliberations on how customer service will be affected, can be effected and improved because of AI. The circumstances are situational and individualised. The benefits are immense, when perceived through client and customer perspectives, particularly personalised customer service.
Think about it – That is intelligent, but not artificial. marketingfocus.net.au
Considerations when choosing an ERP system and provider. John Gellel from WMSSoft Australia brings his experience and guidance.
The decision to implement or change your Enterprise Resource Planning (ERP) system is one of the largest information technology innovations you will make to your business. It can either propel your business into information nirvana or leave you weeping in the pit of technology failure. The associated effort, costs and business disruption are significant, so it is worthwhile to perform your due diligence.
The ideal scenario for your ERP implementation would be one all encompassing system managing your information processing needs via one central information repository, seamlessly inter-connecting your customer e-commerce portal through to sales, scheduling, manufacturing, warehouse, dispatch, finance, accounts, dispatch, CRM and much more. When implemented correctly it's poetry in motion.
There will be two major decisions required in moving forward with implementing an ERP: Which ERP and who will install and support it.
Typical ERP choice considerations are an ERP’s features, fit for purpose, licensing, hosting and implementation costs, upfront and hidden costs, scalability, capability, access, customisation(ability) and quality, support, security, ease of integration, ease of use and flexibility.
Typical ERP provider/implementor choice considerations are upfront and hidden costs, capability, relevant industry experience, professionalism, certifications, office location, IT project best practice (management, analysis, documentation, sign-offs, project control), training, support/communication quality and level of care. Many factors will influence your choice of ERP and provider. Meeting with different ERP providers will be a time of discovery, knowledge and power. Devoting your time and efforts in the selection process will be worthwhile in the long run.
The following are worthy areas to discuss when meeting with ERP providers. If the providers don’t cover these, prompt them and gauge capability based on their answers.
Initial scoping: What business modules do you intend to implement and what is the base functionality required of each module? Sales, Purchasing, Manufacturing, CRM, finance, etc. By defining the ERP modules from the outset and asking questions about your basic workflow and functionality required, an ERP implementer will gain information to provide an implementation cost estimate. An implementation project requires these to be defined from the outset. Analysis and Requirements: During initial meetings with an ERP provider, they can gain an understanding of what you need in each module (from the scope) to determine a rough estimate. Actual costs can vary greatly based on the complexity required in each module, the ability of an ERP’s base (vanilla) functions to meet your business needs and the work required if development (code customisations) are made to get the system to a state where it works for you. Correctly analysing and designing your manufacturing requirement and solution is going to be the most complex task, and by itself, generally equal to all other business modules combined and also the area where failure to correctly implement occurs.
Once you have chosen your ERP provider, the real work begins. Be confident that your potential ERP provider has ERP certified consultants, experienced business analysts capable of understanding your business, analysing your workflow, documenting each and every requirement, comparing those requirements to the vanilla ERP system and designing solutions when a requirement does not match the vanilla out of the box software. Even without IT knowledge, you can gauge capability by how they answer.
Do they answer in a manner that explains a defined, phased, project structure or is the approach ad hoc? Are they simply developers with no business analysis and project management skills? An ad hoc approach with no clear boundaries can open the door for open ended costs without finalized solutions.
Lack of ERP knowledge: Will the ERP consultants provided to build your solution be adequately trained in the ERP system and modules that they will be working on? What training and certifications do they have? Are they local? What is the format of communication? Face to face, video meets, phone, email.
Lack of Manufacturing knowledge: Manufacturing workflow is complex. You know it well. Be sure they do too. Ensure the solution they provide is aligned with your business workflow.
Bad Data/Data migration: Ensure the ERP provider asks questions about your current data, identifying your data issues and how they will resolve them. Ask how they will assist in the identification of bad data, clean, it, transform and load the data to the new ERP system. If unresolved data issues are moved to the new ERP system, you will have trouble.
Training: How will the ERP provider ensure that key stakeholders and all staff will be trained and ready prior to the ERP going live? Training is another area that is commonly under resourced in ERP implementations. A clearly communicated and executed training plan is required.
I hope the above points will help you on the start of your ERP journey. Good luck!
John Gellel is the Implementation and Sales Manager at WMSSoft Australia with over 35 years experience in IT development, business analysis and project management. wmssoft.com.au
IFS has announced it has signed a definitive agreement to acquire Falkonry, Inc. a California-based Industrial AI software company that provides automated, high-speed data analysis to the manufacturing and defence industries. The AI-based, self-learning solution continuously monitors large volumes of data for assets, machines, systems, and industrial processes to discover and analyse unusual behavior and causes of failures.
Acquisition positions IFS as the only vendor with leading ERP, EAM, FSM and ESM functionality now able to provide AI-generated anomaly detection to drive automation and optimisation of processes and workflows across its entire platform.
The addition of Falkonry’s self-learning anomaly detection solution to IFS’s existing enterprise simulation and AI based scheduling and optimisation capabilities further evidences the company’s strategy to use AI pervasively to provide end-to-end intelligent insights in EAM (Enterprise Asset Management) across ERP (Enterprise Resource Planning), MES (Manufacturing Execution System), PSO (Planning, Scheduling, Optimisation), FSM (Field Service Management) and ESM (Enterprise Service Management) technology to increase people and asset productivity.
Headquartered in California, USA, and regional presence in Mumbai, India, Falkonry was founded in 2012 by CEO Nikunj Mehta. The company has customers across North America, South America, and Europe, including the US Navy and Air Force, Ternium, North American Stainless, Harbour Energy, and SSAB, demonstrating its focus on industries in industrial manufacturing and Defense agencies.
“Falkonry is unique in the market because its technology is agnostic and also it does not require data scientists,” said IFS CEO, Darren Roos. “These are great differentiators for Falkonry that means the solution is both scalable and low-cost to implement – two fundamental attributes that very much align to our own values,” Roos added. “Falkonry’s technology can be applied in all industries, and whilst the team has some hugely impressive references in IFS’s focus markets on asset performance management, manufacturing execution systems, servitisation, and configurable workflows, we see a really broad addressable market to capitalise on.”
“The convergence of artificial intelligence and industrial processes has become increasingly crucial for organisations seeking to enhance productivity through data,” Nikunj Mehta, CEO of Falkonry said. “We are thrilled to join forces with IFS and looking forward to combining our unique strengths to provide a truly compelling value proposition to our existing customers as well as IFS’s customers. Becoming part of IFS will enable us to further innovate and extend the value we create for our customers.”
“Today's enterprise is continuously collecting asset performance data, making it a challenge across a multitude of industries from manufacturing to service to put it in the right context and take action in real- time,” said Brian O’Rourke, IDC Research Manager, EAM and Smart Facilities. “Organisations using artificial intelligence and machine learning models with their data for self-learning asset performance anomaly detection will generate critical insights faster, boosting productivity and business performance.” ifs.com falkonry.com
Injectronics Industrial offer a unique service to business owners, manufacturing line managers and service repair agents alike - a fault analysis and repair service for many applications including difficult to source and obsolete items.
Introducing a new, time sensitive and cost-effective option when it comes to making a decision on your industrial repair.
The range of repairs available include:
QLD company makes an industry-leading switch to LocAl lower carbon aluminium for their Elipso aluminium louvres and plantation shutters.
In today's increasingly eco-conscious world, businesses are taking significant steps to reduce their carbon footprint and contribute to a sustainable future. Ozroll, a leading provider of high-quality external shading solutions, has embraced this ethos by revolutionising its Elipso aluminium louvres and plantation shutters with a switch to LocAl® Green lower carbon aluminium supplied by Capral.
"By switching to LocAl Green lower carbon aluminium, Ozroll is not only prioritising environmental stewardship, but they are also setting a new benchmark for sustainable manufacturing practices," said Peter Bulka, Capral’s Industrial Manager for Southeast Queensland. This strategic move aligns with Ozroll's commitment to minimising carbon emissions and fostering a greener planet.
"Energy efficiency and sustainability are a big part of what we do,” added Jack McDonald, General Manager of Ozroll Queensland. “The products we offer to the market, including our louvres and plantation shutters, can deliver real efficiency benefits within the built environment.”
McDonald explained that sustainability is an essential philosophy within the company. With growing demand from clients to deliver more sustainable solutions, moving to LocAl® Green lower carbon aluminium was a natural decision.
"When we heard about LocAl and understood it was an option for our product, we moved quickly to introduce it to our range. The product delivers the same structural and performance characteristics with the added benefit of lower CO2 emissions," added McDonald.
Capral introduced LocAl™ in November 2022 and was the first local extruder and distributor of aluminium products to offer a lower-carbon aluminium option for Australian manufacturers. The local™ Green option, which is now standard on all Ozroll's Elipso Aluminium Louvres & Plantation Shutters, is up to 50% lower in carbon emissions than the current global average for aluminium. Ozroll will reduce its carbon footprint by 1200t CO2e annually in this single move.
Aluminium is often touted as the “Sustainable metal”, its versatility and recyclability earning it this reputation. However, there are significant variations in the carbon emissions generated by smelters during the production of primary aluminium - one might argue that some aluminium is more sustainable than others.
The main contribution to the carbon emissions of aluminium comes from the electrolysis process used in aluminium smelting. Around 60% of the aluminium sector's GHG emissions are from the production of electricity consumed during the aluminium smelting process.
The carbon emissions in primary aluminium production range from under 4kg CO2e/kg Al to over 20kg CO2e/kg Al, largely dependent upon the energy sources used. The current global average carbon emission for primary aluminium is approximately 16.8 kg CO2e/ kg Al.* By contrast, carbon emissions associated with Capral’s LocAl™ Green product are only 8kg CO2e/kg Al.
"At eight kilograms of carbon emissions per kilogram of aluminium, Capral's LocAl Green offer has 50% lower carbon emissions than the current global average for primary aluminium,” added Bulka. “It gives Australian manufacturers like Ozroll an important opportunity to make more responsible procurement decisions when they source extruded aluminium. Capral is so proud to be able to support Ozroll in the supply of lower carbon aluminium, we really congratulate Jack and his team on this industry-leading decision.”
The switch to LocAl™ Lower Carbon Aluminium by Ozroll in their Elipso aluminium louvres and plantation shutters exemplifies the importance of sustainable choices by Australian manufacturers. By prioritising environmental stewardship and actively reducing its carbon footprint, Ozroll sets a new benchmark for sustainable manufacturing practices in the external shading industry.
*These figures are based on Scope 1 and Scope 2 emission ex smelter. ozroll.com.au capral.com.au
Additive manufacturing – described as the more complex and industrial-scale implementation of 3D printing manufacturing techniques – is on the rise across Australia and the globe, with industry experts SmarTech Analysis forecasting the market to be worth $37bn by 2025. To support the forecasted growth in domestic capabilities in this area, two class-leaders have signed a landmark partnership.
The renowned Vocational Education and Training (VET) provider TAFE Queensland, have teamed up with Core Additive an Australian leader in the sale, support, and supply of class-leading Markforged additive manufacturing equipment to increase Queensland and Australian capabilities in the additive and advanced manufacturing sectors.
The agreement sees Core Additive and TAFE Queensland committing to a two-year collaboration set to accelerate the development of training programs specific to the 3D printing, composites, and additive manufacturing industries. Key training programs for local industry members will ensure Queensland and Australian businesses do not fall behind in the age of advanced and additive manufacturing.
James Staples, the Chief Executive Officer of Core Additive, expressed immense pride in the partnership between Core Additive and TAFE Queensland. Recognising the significant role played by TAFE Queensland in vocational education and training, Staples highlighted the value of this collaboration in advancing the additive and advanced manufacturing sectors.
“We are excited to see what this partnership can deliver across the next two years and know we have chosen a like-minded partner in TAFE Queensland that will work to ensure this industry is supported by necessary training in years to come,” Staples said.
TAFE Queensland Business Development Manager of Emerging Industries Shawn O’Sullivan said as the largest training provider in the Sunshine State, TAFE Queensland has the resources required to support the growing need for training in the industry and are excited to help shape the next generation of skilled manufacturers.
“TAFE Queensland is constantly developing and adapting training to meet the current and future needs of the industries we service. Our teachers are experts with deep connections to their industries and they provide training across 60 campus locations from Cairns to Coolangatta and out to Mt Isa with industry-standard equipment and materials,” O’Sullivan said.
“This partnership is one of many that TAFE Queensland holds across a range of industry sectors to develop the training needed to future-proof local industries. With a class-leading advisor in Core Additive, we can develop training safe in the knowledge that it is what serves Queenslanders best,” he said.
Core Additive offers cutting-edge additive manufacturing solutions to the educational sector. This commitment extends to supporting TAFE Queensland in the development of the critical training needed to support Queensland's future workforces and economy. As part of the Queensland Government’s VET Emerging Industries initiative, which sees $15m invested in new skills and training strategies across identified emerging industry needs in the manufacturing, energy, agribusiness, and screen and digital sectors, this training development is a clear demonstration of how TAFE Queensland is connecting Queenslanders with the work they want and supporting employers to grow stronger workforces.
coreadditive.au
Kemppi launches new robotic welding machine for automated environments.
Kemppi has released the AX MIG Welder, a powerful robotic welder with seamless integration, an easy-to-use interface and the latest welding technology.
The AX MIG Welder is purpose-built for high-intensity, 24/7 automated welding environments. With 400 or 500A power and a robotic wire feeder, it is engineered to perform difficult tasks and meet demanding production targets.
The AX MIG Welder has fine-tuned ignition and a precise seam tracking signal to ensure repeatable, high-quality welds. For challenging materials, Kemppi MAX or Wise arc performance welding processes can be used to increase speed, lower heat input, and ensure penetration. Designed for easy integration, the AX MIG Welder is compatible with most robot brands and comes with software and hardware components for fast and seamless blending. It lets you start continuous, precision welding in no time. Featuring an intuitive user interface and simple controls, the AX MIG Welder is easy to use and can be operated with basic welding knowledge. Machine controls and real-time performance data can be accessed with a browser on a laptop or mobile phone – the user interface can also be integrated into an existing control system. Plus, the web browser-based user interface lets the operator adjust machines remotely, saving time while delivering convenience.
Flexibility is key with the AX MIG Welder, and it can be configured to suit varying applications. This allows users to tailor the robotic welding system to their needs, while implementing a cost-effective solution.
With the new Kemppi AX MIG robotic welder, fast integration, easy operation, cutting edge performance and exceptional welding quality are a given. kemppi.com
A new era of full-face protection and visibility with Kemppi’s Zeta welding and grinding helmets.
Kemppi has also released its new Zeta range of welding and grinding helmets. The Zeta helmets set a new benchmark in fullface protection with a lightweight design and top-of-the-line visibility features. Designed for multifunctional use where the face and eyes need protection, the Zeta helmets provide an excellent work experience for welding, grinding, inspection and cutting processes. With an emphasis on improved visibility and eye protection, the four models within the Zeta range are equipped with the most advanced auto-darkening filter for welding or a wide visor for grinding, along with many other must-have features.
The Zeta welding helmets have a significantly large viewing area with the ADF filter. It measures 110mm in width and 60mm in height. The Zeta grinding helmets feature a large 200 mm high visor with a 180° horizontal view for greater visibility.
In addition, the Zeta ADF is an improved version with VISION+ technology increasing the quality of vision and work accuracy. The ADF DIN 2.5 light-state means you can enjoy sharp colours and visibility through the filter when the welding arc is inactive.
The shell construction of the Zeta helmets is strong and robust but lightweight. This, together with the helmet’s well-balanced design, helps relieve the strain on the neck and shoulders.
The well-balanced, narrow-shaped design of the Zeta helmets, combined with the perfect weight distribution, offers extra comfort and endurance resulting into better work accuracy.
Both the Zeta G200X and Zeta W200x helmets feature integrated LED lights. The user can manually switch the LED lights off and on. Or they can select the automatic button which switches the lights off in bright conditions and then back on to help improve visibility and safety.
The battery pack is located on the neckband, which further improves the balance of the helmet. The battery pack is easy to charge using a USB charger, and you can check the power level by simply pushing the button outside the shell.
Designed and constructed with a smooth inner surface, the Zeta helmets are easy to clean which enables improved hygiene.
Users can choose from 4 helmet models within the range. These include the:
• Zeta G200 grinding helmet
• Zeta G200x grinding helmet with integrated LED work lights
• Zeta W200 welding helmet with automatic darkening welding filter (ADF)
• Zeta W200x welding helmet with ADF and integrated LED work lights
Kemppi.com
New Miller Vortex HDV provides the next level of welding respiratory protection.
In recent years, there has been increased body of research and general awareness around the long-term respiratory health hazards of welding fumes.
As a result, there is a growing demand for personal respiratory protection that not only offers increased protection, but also enhanced comfort, visibility, and capability to the operator. These advantages are particularly important within industries such as mining, mineral processing, oil and gas, petrochemical, and structural steel manufacturing. These industries within Australia in particular rely heavily on the use of filler metals such as stainlesssteel, nickel or manganese alloys, aluminium, hard-facing, and self-shielding wires throughout their welding processes. In addition to other contributing factors, these wires can generate far more hazardous fumes while welding, thus the typical fume ventilation and extraction methods are no longer considered adequate protection to the welding operator.
In these environments, the operator must utilise a Personal Air Purifying Respirator (PAPR) like the new Miller Vortex HDV system from Welding Industries of Australia (WIA) to protect themselves from short term respiratory irritation and long-term illness.
The Miller Vortex HDV PAPR System complies with Australian and New Zealand Standards AS/NZS 1716.2012, AS/NZS 1338.1 (Auto-Darkening) and AS/NZS 1337.1 B (High Impact)
Designed to take respiratory protection to the next level, the Miller Vortex HDV PAPR System offers a range of features and exclusive technologies that set it apart from other systems, says Product Manager Aleksandr Koshelyev, who consults extensively with users of welding equipment concerning their industries’ particular and evolving needs.
“The Vortex HDV PAPR system standout is its HDV technology which provides a sharp, detailed view at any angle with minimal distortion. This feature makes it easier for welders to see their work with increased visibility,” says Koshelyev. Other technologies include:
• ClearLight™ 2.0 which offers a second-generation view through the lens, providing advanced high-definition optics for a clearer, brighter, and more realistic weld view.
• X-Mode is another benefit to welding operators. Designed for outdoor usage, it eliminates sunlight interference, as the lens only darkens when the welding operator strikes an arc. Described as game changing it’s also ideal for low amp TIG and out-of-position welding.
• InfoTrack™ 2.0 technology is also exclusive to Miller, allowing users to track arc time and arc counts, as well as store and switch between two custom preset memory settings.
With comfort and visibility in mind, Miller’s Vortex PAPR system includes a lightweight blower unit. Only1362 grams, it provides long-term comfort so that welders can wear it for extended periods without causing strain. While the large 174x126mm integrated grind shield offers a larger, clear viewing area for grinding and other tasks. From a productivity perspective, Miller have integrated a quick release one-piece HDV cover lens to simplify lens changes and reduce downtime, and a brighter 2.5 Light State so welders can keep their hood down for improved safety and productivity.
The unit’s lightweight and low profile blower unit, above, and LCD interface, below, which allows users to see fan speed, filter time, battery level, and current time. Included in the technology package are two lithium-ion batteries, one to use and another for charging, eliminating downtime when it’s time for a recharge.
The Vortex HDV PAPR System provides protection against solid particles, welding fumes and mists, making it an ideal choice for welders searching to improve safety and reduce health risks associated with grinding and welding operations. Six air distribution points ensure that the air is evenly distributed, providing maximum cooling and comfort, while the three air speeds allow the operator to control the volume of air to meet their work conditions. The audible and vibrating alarm increases safety by notifying the user in noisy environments of low battery due to reduced air flow. Included in the package are two lithium-ion batteries, one to use and another for charging, eliminating downtime when it’s time for a recharge.
Usage of the Vortex HDV PAPR System is easy, thanks to the LCD display that provides an easy-to-read screen for viewing fan speed, current time, and battery level, and a filter timer to remind the welder when it's time for it to be replaced.
With all of these features and technologies combined, the Miller Vortex HDV PAPR System provides the ultimate respiratory protection for welders, ensuring greater clarity, comfort, and safety,” says Koshelyev. “The Miller Vortex HDV PAPR System is a gamechanger in respiratory protection for welders, providing exclusive technologies and top features that offer the next level of protection, comfort, and visibility. Its lightweight design and industry-leading features make it a must-have for welders in various industries to provide clean, comfortable, and compliant work environment.” welding.com.au
Welding unseated – cold spray technology a cool new contender for repair.
Welding has long been the go-to method for repairs and restoration of metal parts. Although it’s a well-established and great method for joining metals, when it comes to repair, welding may not always be the most suitable solution. Unfortunately, with limited alternatives available, it has often been the common or default choice. However, a new technology is now emerging that promises to revolutionise the repair process and offer a more versatile and efficient solution: low-pressure cold spray technology.
Cold spray – also known as supersonic particle depositionis a groundbreaking technology for repairing geometries and applying functional coatings. Unlike welding, which involves high temperatures and can result in distortion, residual stress, and damage to surrounding materials, cold spray operates without the need for extreme heat. Instead, it propels metal particles at supersonic speeds onto metal surfaces. As they collide, the kinetic energy of the particles causes them to deform and interlock with the metal surface, creating a strong, metallurgically bonded coating. When it comes to repair and maintenance, the advantages of lowpressure cold spray over conventional welding are numerous. Firstly, the absence of high temperatures during the cold spray process eliminates the risk of distortion, annealing, and warping, saving more parts from damage. This characteristic is particularly beneficial for intricate and heat-sensitive components, such as crank cases, tooling such as dies, or where precise heat management is crucial.
Secondly, cold spray technology offers superior material compatibility, making it possible to repair and restore a wide range of metals. Unlike welding, which is often limited to joining similar metals, the cold spray system can utilise dissimilar metals such as nickel for repairing cast iron parts or aluminium for repairing steel structures and protecting them from corrosion.
In welding, the joining of metals relies on melting the base metals and adding a filler material that is compatible with them. The success of the weld largely depends on the metallurgical compatibility between the base metals and the filler material. If the metals being joined have significantly different compositions, properties, or melting points, achieving a strong and durable weld can be challenging or even impossible. Welding dissimilar metals often requires specialised techniques, such as the use of intermediate layers or interlayers, to promote bonding and prevent the formation of brittle intermetallic compounds.
On the other hand, cold spray technology offers a distinct advantage when it comes to joining dissimilar metals. In the cold spray process, metal particles are accelerated to supersonic speeds and impact the surface of the substrate material. These particles undergo plastic deformation upon impact, causing them to interlock and form a strong bond with the substrate. Unlike welding, cold spray does not rely on melting the base metals or using a filler material. Perhaps the most promising aspect of cold spray technology is its ability to restore worn or damaged parts without compromising their original properties. By selectively depositing material only where needed, cold spray extends the lifespan of components, reducing the need for costly replacements. This feature presents significant cost savings for industries that heavily rely on maintenance and repair operations, such as oil and gas, mining, and marine. One company commercialising cold spray is called Titomic, located in Melbourne. Titomic is bringing cold spray technology to the market, and is focused on adding value to machine shops, engineering firms, and maintenance firms alike.
“Welding is sometimes used where it shouldn’t be, as welding is often the best – sometimes only – solution available. We’ve spoken to many engineering shops who’ve gone to repair parts with
welding, whether it's crank cases, shafts, or bearings, only for them to spend time welding which might lead to cracks. As well as having to ditch the part, they’ve spent the time welding too,” said Dominic Parsonson from Titomic.
This emerging technology represents a potential shift in the field of metal part repair and restoration. With its ability to overcome the limitations of welding, it offers a more versatile, efficient, and cost-effective solution. By eliminating distortion, offering superior material compatibility, and extending the lifespan of components, cold spray technology is set to transform the way a range of industries approach repairs. As this innovative technology continues to evolve, it opens new possibilities and paves the way for a future where metal part repair becomes faster, more precise, and more economical than ever before.
titomic.com
Empowered Women in Trades: women in welding.
This unique program aimed to empower women by providing them with an opportunity to explore the world of trades. Participants were engaged in formal training, provided with individualised coaching and support and equipped with tools to help them thrive in a career in a male-dominated industry.
In collaboration with the Local Jobs Program (North East Melbourne), SYC, and Melbourne Polytechnic, Empowered Women in Trades facilitated this innovative initiative that combined accredited welding units in OXY, MIG, and ARC welding with a focus on positive psychology and human skills training.
Throughout the course, eight enthusiastic women donned protective gear and immersed in comprehensive lessons on the PERMA concept by Martin Seligman as a part of the framework for applied positive psychology and effective communication. Expert instructors, Tony, Sam and Dave, provided hands-on training and guidance in the workshops, ensuring each participant gained practical knowledge and expertise in welding techniques. The course covered a variety of welding techniques, including:
• the MMAW process, identification, and technology,
• uses, advantages, and limitations of MIG and Oxy Welding.
• Emphasis was placed on safe operations and adhering to Occupational Health and Safety (OH&S) protocols. Upon completion of the program, participants achieved the necessary skills and knowledge required to pursue entry-level welding positions within the industry. Key outcomes included identifying welding technology, implementing safe practices, and mastering various welding techniques such as depositing beads, butt, and fillet welds.
Beyond the three days a week at Melbourne Polytechnic, participants were also provided with additional opportunities to enhance their career prospects. They had the chance to embark on a site tour at Atherton and see the skills being applied in industry, benefit from career coaching & mentoring sessions, and participate in a mini-careers expo at the conclusion of the course with six organisations who will help them connect with the next stages in their career journeys.
“Wonderful program that has opened up so many doors. I am very excited to continue my path,” was feedback provided by one of the participants. Another expressed gratitude for the learning experience: “Thank you for this amazing program and everything I now know that I can achieve because of it.”
Empowered Women in Trades is proud to announce that seven out of the eight participants successfully graduated from the program, with two already securing employment. We extend our thanks to all the individuals and organizations involved in making this program possible, including the Local Jobs Program, SYC, Melbourne Polytechnic, instructors Tony, Sam and Dave and all our industry specialists including AMTIL, AiGroup, Squad, AGA, Northlink, Atherton, and Kwill Constructions who added value to the program with their expertise and industry knowledge.
Most importantly - we congratulate each participant on their outstanding achievements and wish them continued success in their welding careers. ewitrades.com
Gigantic onshore windfarms, massive offshore windfarms on floating pontoons. Australia needs huge amounts of steel, skilled labour and power in equal measure to even begin these projects. Paul Hellard reports from Canberra.
The Hon Tim Ayres, the Assistant Minister for Industry and Science appeared at Weld Australia’s National Manufacturing Summit, on an unnervingly mild mid-winter morning in Canberra. He spoke of the challenges ahead for Australia. “We must move fast in this changing environment. And everything needs to work together,” he said. After a decade of inaction by the LNP governments, Minister Ayres said his government was ready to sign on to actionable plans. There are some positive moves in the Powering the Regions Fund, the National Reconstruction Fund, Rewiring the Nation, and the Capacity Investment Scheme which has been the start of the transformation of industry policy in Australia.
What’s needed though, as stipulated by other speakers at the event was the biggest piece of economic policy since the post-WW2 Marshall Plan. The EU, Canada, and the US have all brought their programs into action, pushing manufacturing and construction in the States with their IRA and CHIPS Act.
According to the CEO of Weld Australia, Geoff Crittenden, host of the Canberra event, “We are now at the stage where even the most obtuse observer must realise that global warming is real and is coming at us much faster than we imagined it could. Last year, Australia experienced record floods, with countless people losing their homes. This year, we’re expecting a record bushfire season, with the Northern Hemisphere already experiencing some of its hottest temperatures on record. The climate crisis makes manufacturing the renewable energy revolution an imperative.”
“The United States, through the IRA, has taken shown tremendous leadership, enacting a plan to tackle the challenges of the renewable energy revolution; a plan with manufacturing at its heart; and a plan that is already delivering unprecedented growth in the sector. A combination of tax credits, loans, and subsidies, the IRA is an investment in—not a cost to—the US economy. An investment without which the US economy and society could suffer catastrophic and irreversible damage.”
“In Australia, the task of responding to the IRA seems to have created such an insurmountable challenge that we have ground to a halt. A policy of fiscal conservatism driven by the Treasury is obstructing any type of progress. We are defeated before the first shot is fired.”
Emily Scivetti is the Chief Operating Officer at Oceanex Energy. Offshore wind power generation is experiencing rapid growth globally and the opportunities for Australia are significant. She outlined her wish to build a massive workforce as soon as possible. Oceanex is developing a portfolio of offshore wind farms in waters deeper than 70 metres off New South Wales and New Zealand, and in shallower waters off Western Australia. The scale of these ventures is eye-watering. Offshore wind farms will provide a new source of large-scale, clean and reliable electricity that creates huge new investment, jobs and innovation opportunities, especially in key regional centres. A single rotation of an offshore wind turbine can supply a day’s worth of energy for an average NSW household. Each NSW project is estimated to generate up to 2GW of electricity which is a similar scale to the power provided by a NSW coal-fired power station.
An Australian offshore wind industry will need more than 1,000 steel foundations in the next 10-20 years. New South Wales, particularly the Hunter and the Illawarra regions, are primed to take advantage of this growing sector and become a leader in the deployment of floating offshore wind farms. NSW provides an ideal home for offshore wind farms with existing transmission infrastructure, reliable wind resources and a workforce experienced in developing and delivering
large energy projects. But the workforce needs to be much more significant. Oceanex estimates that each NSW offshore wind farm will require at least 750,000 tonnes of steel. With larger components, offshore wind will require a sizeable skilled labour force and can provide a catalyst for significant growth of local manufacturing and engineering capabilities. These manufacturing opportunities are real but Australia needs to act now to capitalise on these opportunities. Scivetti’s plea supported Weld Australia’s estimate that Australia needs 70,000 more trained work-ready welders before 2030. She wants to see Australia’s steel industry fabricate floating foundation substructures on shore, but securing suppliers and workforce is critical to success and timing is everything. A new offshore wind industry will need suction pile anchors, columns, pontoons and braces – large-scale steel components that could be manufactured across the local fabrication ecosystem using BlueScope steel.
Dan McKinna, General Manager of Keppel Prince concurred on the massive challenges ahead. “Australia requires a nine-fold increase in grid-scale wind and solar to meet our 2050 targets under AEMO’s step change scenario. The opportunity for local manufacture of wind towers is massive. An onshore wind tower requires seven kilometres of weld in each unit, to manufacture the towers for 40GW of installed onshore wind capacity requires in excess of 22 million person-hours of manufacturing. Offshore wind expands this even further, we estimate that to manufacture the towers and foundations for 40GW of fixed foundation offshore wind will require in excess of 53 million person-hours of manufacturing. All this manufacturing is going to be completed somewhere, Australia needs to ensure that we play a significant part in this opportunity.”
Adam Hersh is a Senior Economist from the Economic Policy Institute in Washington DC where he focuses on International Trade and US-China relations. Hersh was one of a number of international speakers at the National Manufacturing Summit recently in Canberra. “We have entered a dangerous and fragile inflection in the planet’s climate systems,” he said. He also cited the unprecedented Chinese economic rise as “the biggest economic rise in the history of human existence.”
“China can make, pretty much anything,” he added.
“We have a historic opportunity to rebuild Australia's manufacturing industry through renewable energy,” said Charlie Joyce from the Carmichael Centre, Australia Institute, releasing a Centre of Future Work report on the day with Dr. Jim Stanford, which states Australia needs to respond much quicker to the powerful new incentives on offer in the US and several other industrialised countries. “The Albanese government needs to go big and go now on climate industrial policy to seize the full opportunities of the renewable energy revolution or risk missing out completely. Australia risks being cut out of lucrative new markets for manufactured products linked to renewable energy systems,” he said.
The Biden administration in the US reacted to China’s rise, with the Inflation Reduction Act (IRA) and the CHIPS Act. “In recent years, Chinese investment in clean tech manufacturing has been eight to ten times greater than the US and Europe combined,” Joyce added. “Cleantech manufacturing has become a national development priority in China. There is a global race for clean tech manufacturing, and Australia is barely on the track.”
Geoff Crittenden was tuned into the heavy consequences of not moving fast enough. “We need to train many more welders to cover the requirements of these projects, otherwise we will be left in the dust,” he said.
Among the field of companies with skin in the game attending the Summit here in Canberra was Vestas. I spoke with Fredrik AndrenSandberg, Head of PA in Asia-Pacific. He said the Danish wind turbine manufacturer could see Australia really had a big job ahead of it. “We only install 20% of what we need globally to reach net zero and achieve energy security, for offshore wind we even need to ten-fold installations. In Australia, we only install 20-25% of what's needed to reach the 2030 targets. Energy also reaches into each country’s important national security measures.” Vestas knows about having obstacles in the way of business. They used to have turbine construction projects in Russia. Now they don’t. They have also lately experienced the impact of COVID-related issues within a global supply chain. Vestas has so far supplied 40% of all the Australian wind farm capacity installed and are open to utilising Australian-made steel if the market allows for it.
ACTU President Michelle O’Neil made it clear that there shouldn’t be a single worker made redundant by the phase-out of fossil fuels. “Don’t leave behind those people who make everything you use every day,” she said. “There are so many manufacturing sectors hitting the new learning curve.”
AEMO expects the surge in renewable energy generation by 2050 will need to be connected using 10,000km of new transmission cables and 25,000 towers, each using 60 tonnes of steel. “But without a massive investment in local manufacturing this will not be achievable in Australia,” said Crittenden. “If Australia is to ever achieve net zero, we must have our own version of the IRA, tailored to our local conditions. Australia simply has no choice. The alternative is unthinkable. We have half the net debt as a percentage of GDP as the US, so why are we even hesitating? Adjusted for the scale of the Australian economy, the Australian Government must commit $300bn—approximately $12bn a year to 2050—to a program similar in size and scale to the IRA. This sum is equivalent to current carbon subsidies, inconsequential when compared with the anticipated mining royalties from rare earth minerals, and less than the $368bn we plan to spend on nuclear submarines.”
Tim Buckley, the Director of Climate Energy Finance Australasia, added that the installed cost of solar energy development globally will halve in price this decade. “We have all the critical minerals and the know-how, but it is now a global technology and investment race to the top. Indonesia isn’t ignoring it. Chile, Vietnam, and India aren’t either. Australia would be crazy not to grab the opportunity stemming from the US IRA with both hands, and to do it fast, and at an unprecedented scale,” he said. BNEF’s Jenny Chase states it took the world 183 years to generate the first terawatt of energy through solar installs, and it’ll take only three years to generate the second terawatt. Then only 15 months to generate the third. Can we do it? Of course, we can do it. But we have to do it fast.
weldaustralia.com.au
In today's dynamic manufacturing landscape, Australian companies are seeking innovative ways to address capacity constraints without significantly increasing their workforce. Challenges such as workforce shortages, rising labour costs, and skill gaps are common pain points. A subtle yet transformative solution is emerging - a technological advancement that complements human capabilities rather than supplanting them. Orbimax Cobot Welders; a robot taught by movement and a simple smartphone app that can be realised and implemented immediately into your existing workforce, bringing instant investment gains.
The Australian manufacturing sector faces an array of hurdles. Workforce scarcity, escalating labour expenses, and skill deficiencies continue to challenge operations. Moreover, maintaining precision, consistency, and productivity places a considerable burden on existing teams. These obstacles can impede the ability to scale production in response to market fluctuations.
A quietly revolutionary solution is quietly gaining traction. It operates in tandem with human workers, alleviating their burden. This technology marks a pivotal shift, automating repetitive and physically taxing tasks, enabling human workers to focus on tasks necessitating creativity, problem-solving, and higher-order decisionmaking. This augmentation in human capacity leads to increased productivity without the imperative of hiring additional staff.
Manufacturers are accustomed to the capricious nature of market demands. Seasonal shifts, abrupt surges in orders, or unforeseen disruptions can unsettle production schedules. The adaptable nature of this technology allows manufacturers to flexibly scale operations. This adaptability empowers businesses to react promptly to market shifts, without rigid staffing constraints.
Safety and quality assurance remain paramount concerns. Advanced sensors and AI-driven algorithms equip this solution, enabling it to work alongside human operators seamlessly and securely. By handling repetitive welding tasks with impeccable precision, this technology guarantees consistently high-quality output, mitigating the risk of defects or rework.
A shortage of skilled labour persists in Australian manufacturing. Orbimax Welding Cobots offer manufacturers an opportunity to upskill their existing workforce. The Cobot Welder is driven and programmed by a smartphone app – if you can send a text message you can program this robotic welder. By integrating this solution, workers gain experience in collaborating with advanced automation systems. This not only enhances their proficiency but also futureproofs their careers in an industry embracing automation.
Embracing automation is more than mere operational refinement; it's about maximising profitability. By leveraging this technology, manufacturers can significantly augment their output, thereby reducing the overall cost per unit. The return on investment is measured not only in terms of operational efficiency but also in the enhanced competitiveness and sustainability of the business.
In the face of evolving market dynamics, Australian manufacturers must adopt forward-thinking strategies to empower their workforce while addressing capacity constraints. A technological advancement is quietly reshaping operations, allowing manufacturers to expand their capacity without ballooning their staff. By automating routine tasks and ensuring precision, this technology redefines operational efficiency. It's time to embrace this subtle yet transformative paradigm shift and unlock new levels of productivity. orbimax.com.au
EMC are the choice for high quality, precise and easy to use edge breaking and corner rounding machines.
Variable speed edge breaking or corner rounding up to 2mm rad 650mm working width
Compact machine to replace hours of manual angle grinding No manual movement of grinding head required
Edge breaking, corner rounding and oxide removal
From 1 to 4 stations within the machine
Easy to use touch screen
1350mm wide working table
Vacuum table with optional magnetic section
Flexible configuration, from 2 to 4 stations within the machine
Corner rounding, edge breaking and/or surface finishing
1350mm or 1650mm working table width
Connect multiple machines together in one production line
Selecting the right stretch forming equipment for your application. Del Williams is a renowned technical writer for the manufacturing industry in the US.
The stretch forming process can create stronger parts, increase production, and reduce processing steps, but selecting a machine with best-in-class capabilities is essential.
For manufacturers striving to increase profitability while expanding their capabilities and improving their processes, adding stretch forming to their repertoire may be the answer.
Stretch forming is a unique process where material such as steel, stainless steel, aluminum, or even titanium is stretched beyond its yield point and simultaneously wrapped around net shaped dies. Forming sheet or extruded material using this method essentially shifts the neutral axes of a part to the perimeter of the die resulting in a smooth, wrinkle-free contour that closely retains the shape of the die, improves the mechanical properties, and eliminates many post process steps used to attain dimensional accuracy.
Initially developed as an efficient means to produce components with complex curved profiles in the aircraft industry, stretch forming is now widely used for similar components in automotive, aerospace, construction, rail, and rocketry.
“As part producers seek to expand their capabilities, many have approached us with new stretch forming applications. Combining modern CNC technology with our precise digital die mapping technology and historically robust machine structure provides for the finely tuned automated motion control necessary to maintain constant strain in the part throughout the cycle, all resulting in industry leading dimensional stability.” says Dave Gardner, Senior Mechanical Engineer at Erie Press Systems, a company that manufactures custom-engineered hydraulic presses for applications including metal forming, stretch forming, composite compression molding presses, cold extrusion, and forging. Park Ohio acquired Erie Press Systems in 2020 and is now a part of Ajax-CECO-Erie Press (ACE), with over a century of experience in custom designing and building presses and forming machines.
Manufacturers that are unfamiliar with stretch forming as well as those with special requirements often require guidance to select equipment that meets their specific needs.
Drawing on Erie Press’s decades of experience in aerospace applications and ACE’s century of fabricating machinery, Gardner covers the basics of stretch forming and provides tips for selecting equipment that can help to maximize product quality, reliability, and productivity.
According to Gardner, stretch forming machines may be classified into three primary design types, depending on the client’s intended production requirements. Sheet stretch forming machines are used to produce complex curved sheet metal parts such as exterior panels and leading edges on aircraft, high-speed trains, RVs, buses, and commercial rockets. Extrusion stretch forming machines are used to produce extruded structural components with complex cross sections and curved profiles such as stringers and support beams for aircraft, skeletal components for locomotive, buses, transportation structures, and various curved shapes used in the elevator and architectural (building) industry. High-speed, highvolume stretch forming machines are generally reserved for forming extrusions in automotive or other high production applications.
Each design type classification can be further broken down into a series of machines with specialised features that are better suited for producing specific types of parts.
“Due to the wide range of features and options that are available, we work with our clients to develop the technical details of a machine that will fully meet their unique production requirements,” says Gardner.
Stretch forming offers numerous advantages, including the ability to accurately form complex shapes while maintaining the part’s total volume. Once the component is stretched into the yield state, less force is required to wrap the part around the die than with other forming methods. Part cost is substantially reduced by the ability to form accurate and repeatable components with little wasted material and, in most cases, a scuff-free quality finish that doesn’t require dimensional or cosmetic improvement. Additionally, the process induces work hardening in many materials, which increases strength while reducing internal residual stress and spring back as compared to conventional bending operations.
From Gardner’s decades of machine design experience in various applications, he advises purchasing stretch forming machines with structural integrity, longevity, and precise motion control.
Stretch forming is not a high impact process, but forces involved can be over 3,000 tons in some aerospace applications. Highquality stretch forming machines with very precise motion control and the ability to digitally map the contour of the die with respect to the forming axes will form the part with nearly constant strain throughout the process and create very precise, consistent parts for many decades. Consequently, it is important to select a machine with these features to extend its accuracy, longevity, and reliability.
Whether manufacturers are new to stretch forming or industry veterans that want to extend their capabilities, thoughtful selection of a machine specifically engineered to satisfy their unique requirements will result in the most robust, reliable, and costeffective solution for expanding their capabilities and improving their processes.
ajaxerie.com
Del Williams is a technical writer based in Torrance, CA, USA
New face-milling cutter to produce aluminum battery racks.
Automotive original equipment manufacturers (OEMs) are getting more involved in battery cell production, which is moving physically closer to vehicle assembly plants. McKinsey & Company reports that battery technology, durability, and performance will be key differentiators that set OEMs apart. Here, Fernando Oliveira, Global Manager for Automotive Aluminium at metal cutting specialist Sandvik Coromant, explains how its new concept M5F90 face-milling cutter could be crucial for helping OEMs get ahead of their peers. Battery systems will continue to evolve over the coming years and new developments and shapes will be required. For OEMs, this will entail producing near-net shaped battery system parts based on more complex designs. Machining these designs will require efficient and lighter-cutting tools, to minimize impact on the machine tool and ensure the component stays in shape.
The role of OEMs is also evolving as they get more involved in battery production, which McKinsey & Company attributes to “the backward integration of OEMs from packs and modules up to cell production.” At the same time, the race is on to build lighter and more efficient electric vehicles (EVs) that travel for longer distances with a maximised vehicle range per charge.
Furthermore, manufacturers must produce these more complex components to the highest quality and with high productivity. How can manufacturers achieve this while maintaining a low cost-percomponent? The answer lies in more efficient cutting tools, which have good accessibility and are as light as possible to allow quick tool changes.
Manufacturers are turning to ‘lightweighting’, which entails building cars and trucks that are less heavy to achieve better fuel efficiency and handling.
Another McKinsey & Company study, Lightweight, heavy impact, calculates that “Lightweight measures can help reduce CO2 emissions to a certain extent (approximately 0.08 g CO2 reduction per kilogram saved).” It concludes that “If an OEM manages to reduce the vehicle weight by 100kg, it saves approximately 8.5 g CO2 per 100km.”
As one of the lightest metals in the world, aluminium is an established lightweighting solution. Aluminium is almost three-times lighter than iron and, although of lower strength than iron, is still very strong and corrosion resistant. From a design engineering perspective, it has been found that placing conventional cast iron parts with aluminium alloys can reduce the overall weight of the engine block by up to 40–55%. A further advantage of aluminium is that it is very recyclable and can be melted and reused without any harm or change to its mechanical properties. In fact, approximately 75% of all aluminium ever produced is still in use today, which is testament to the material’s usefulness in OEMs’ sustainability strategies.
The power train of a European passenger car typically contains around 80 kilograms of aluminium, which means these parts the engine, gear box, suspension parts, housings are an obvious area of
interest for light weighting measures. Aluminium may also be used in the batteries themselves: the EU-China Energy Cooperation Platform (ECECP) recommends aluminium-air (AIair) batteries as an “inexpensive, light and powerful” alternative to lithiumion (Li-ion) batteries.
Here, let’s focus on aluminium battery racks. These components generally have smaller faces with more threads, holes and other features. Another important consideration is electric battery racks for trucks, specifically larger models driven away from built-up areas, which measure up-to two metres in length. Battery racks require an assortment of machine tools and applications like milling, rimming and more. Yet even larger battery racks don’t require large tools and are, instead, made up of smaller faces with more features, threads, and holes. Therefore, they require shoulder and face milling tools or reamers that can produce components to the required quality and tolerances.
For machining battery racks, Sandvik Coromant recommends using its M5 family of dedicated automotive aluminium milling cutters, including the M5F90 face-milling cutter designed to machine parts without burring, scratching or chipping. The cutter is dedicated to machining thin-wall aluminium parts and, to achieve this, it is equipped with a smaller cutter body of 25–80 mm or 0.98-3.15 inch in diameter. The M5F90 also contains brazed Polycrystalline Diamond (PCD) tips, so requires no adjustment and secures very reduced runouts. This enables high feed rates while also eliminating cutting vibrations.
In one instance, the M5F90 was used to machine an aluminium battery tray. This was an ideal application for the new concept face-milling cutter because the application required that the tool be used to clean surfaces in the first machining stage of the newly-cast aluminium part in a single operation, without burring.
Its dimensions were approximately 980x600x130mm. Overall, 48 tools were used to machine the component including solid carbide drills, solid carbide end mills, high-speed steel (HSS) taps, brazed PCD reamers, brazed PCD milling cutters and, lastly, the M5F90 cutter. The aluminium component was machined in a 5-axis machining centre, equipped with a HSK 63 high-speed tool holder.
The M5F90’s brazed PCD inserts have stepwise cutting edges in both senses, radially and tangentially. This characteristic lowers the power consumption allowing to run with higher cutting parameters, which eliminates burrs and reduces vibrations during machining. The latter advantage, in particular, helps give reliable performance with improved tool life and increases the number of components machined. In the end, the battery tray machining application demonstrated a key advantage of the M5F90. Specifically, that it enables roughing and finishing in a single operation, thus saving time. This was demonstrated with in the machining of the aluminium battery tray; the component was machined in 20.3 minutes. With this enhanced tool performance, OEMs can get more involved in producing battery systems, while setting themselves apart from competitors.
sandvik.coromant.com
Originally founded in New Zealand in 1974 by Keld and Vivi Sorensen manufacturing specialised machine tools, Sorensen Engineering relocated to Sydney in 1981. Although continuing to manufacture machine tools until the early 2000’s, this second-generation family business diversified into production of precision component parts and assemblies in the mid-1980’s and has continued to innovate and was recently recognised in the top 100 most innovative companies in Australia.
Today, with a total staff of 30, the company is a highly competent precision engineering business with more than 40 years’ experience. Sorensen services diverse markets such as mining, pump & fluid controls, film & TV equipment, and biomedical & scientific equipment. More recently, in response to the COVID crisis, they have been supporting critical projects with components for ventilators and PCR instruments involved in large-scale COVID testing.
The first Okuma lathe was purchased by Sorensen Engineering in 2006 and today it has nine Okuma machines including CNC lathes, horizontal and vertical machining centres, plus automation and robotics.
“The selection of Okuma machines came down to the precision and reliability of these machines and the excellent service offering provided by Okuma Australia who have skilled engineers and technicians in the field plus a resident engineer from the Okuma Japan based in Australia,” said Sorensen Engineering Managing Director Julius Sorensen. “With technology leading industry today and continuing to advance, we are always looking for the next step to improve efficiency and service to our clients. Our company continues to invest, with in excess of $3 million spent in the last five years, as each new machine brings additional advanced features consistent with our innovative approach to business. Okuma’s professional advice of the most suitable equipment to meet our needs now and for the future has always worked for us,” he said.
As well as the engineering business, the Sorensen Product Lab has been established adjacent to the existing factory as a purposebuilt workshop for prototyping, product development, and the fabrication of pilot runs. The Product Lab team combine design,
engineering, materials, and machining experience to experiment, collaborate in creating new products, or to further develop and enhance existing products for product development now and into the future. In this area we attract engineering graduates, who come directly from leading universities and who bring new and exciting concepts and challenge current ideas, bringing skills in engineering analysis etc., especially in areas such as cutting-edge software and additive manufacturing.
The on-going introduction of new technology challenges our engineers who see advantages with the many new features and new ways in which jobs can be approached with the latest advanced machining centres. The addition of robotics and automation has freed up skilled staff providing much more flexibility and allowing Sorensen Engineering to undertake shorter runs competitively.
“We have made radical changes into automation pushing the advantages these new Okuma machines offer and although there is a learning period as our engineers adapt to new concepts, the long-term benefits are there as we modernise and advance,” said Julius Sorensen.
Engineering and achievements of this company, which sits within Australia’s top 100 most innovative companies, has been the success of the Product Lab where engineers are not restricted by processes, have passionate ideas, and the freedom to explore these within a culture to push the limits particularly in the area of automation.
The key outcome has been an increase in capacity and output using the skills and innovative ideas we have without increasing staffing levels. A number of machines are now capable of running without supervision 24/7 with less quality issues on all machining centres.
“Such innovation and the readiness to explore the latest advances Okuma can offer in technology and at the same time embracing 4.0 manufacturing concepts with challenging minds within all levels of the company is proving to be exceptionally successful,” said Steve Norbis, Okuma Northern Regional Manager NSW & QLD. “Encouragement from the top down is a success story in itself,” he said. okumaaustralia.com.au sorenseneng.com
The nanometre control system implemented in ANCA’s ULTRA machines represents a significant advancement in precision machining.
ANCA has introduced a groundbreaking nanometre control system that sets new standards in precision machining. This cutting-edge technology enables silky smooth movement of all linear and rotary axes, resulting in exceptional surface finishes on cutting tools. The nanometre control system offers unmatched accuracy, flexibility, and performance, empowering manufacturers to produce a premium range of cutting tools with the utmost precision. By leveraging ANCA’s expertise and deep industry knowledge, the ULTRA range of machines equipped with this revolutionary control system opens up new possibilities for the grinding industry.
The nanometre control system implemented in ANCA’s ULTRA machines represents a significant advancement in precision machining. The system incorporates ANCA's best-in-class technology and leverages the company's vertical integration, enabling robust and scalable improvements throughout the machine. This holistic approach ensures optimal design and functionality, resulting in an unrivaled level of accuracy, performance, and tool life.
Smooth and precise motion of machine axes is crucial for achieving high-quality surface finishes on cutting tools. ANCA’s nanometre control system utilises a state-of-the-art servo control algorithm, allowing for silky smooth axis movement. This unique algorithm, combined with nanometre-level measurement capabilities, ensures ultra-fast response to internal and external disturbances. By effectively mitigating irregularities originating from linear rails, bearings, or friction, ANCA’s control system guarantees outstanding tracking performance. Furthermore, it accomplishes this without the need for complex and expensive mechanical systems, thereby streamlining the manufacturing process.
One of the remarkable features of ANCA’s nanometre control system is its ability to reduce reversal errors to the nanometre scale when an axis changes direction during grinding. This precise control eliminates any reversal marks that could potentially affect the tool's quality. Consequently, the need for secondary operations such as finishing or sparkout is significantly reduced, resulting in improved cycle times and increased productivity for the production of highquality cutting tools. The system's ability to eliminate reversal marks, combined with its smooth and precise motion control, ensures superior surface quality. The reduction in secondary operations not only saves time and resources but also enhances productivity.
ANCA’s nanometre control system represents a groundbreaking development in precision machining and sets a new benchmark for the industry. By incorporating advanced servo control algorithms and nanometre-level measurement capabilities, this cutting-edge technology enables silky smooth movement of machine axes, resulting in exceptional surface finishes on cutting tools. The system's ability to eliminate reversal errors and reduce the need for secondary operations enhances productivity and overall efficiency.
ANCA’s ULTRA range of machines equipped with the nanometre control system empowers manufacturers to achieve new levels of accuracy, flexibility, and quality in the production of cutting tools, solidifying ANCA’s position as an industry leader in CNC grinding technology. anca.com
In the world of metal cutting tools, tool holding is perceived to be stagnant. Jason Allen from Iscar gives his thoughts.
Experts may claim that true revolutionary changes in tool holding associated with the HSK adaptation ended three decades ago. In the world of cutting tools, tool holding is the most conservative field, where groundbreaking ideas are rare. Have tool holding systems reached a cul-de-sac, with no new trends in sight?
In spite of slow progress, tool holding systems continue to develop naturally. The progress of these tools is evolutional and reflects modern-age metalworking requirements. New technologies form new demands for machine tools and cutting tools, resulting in tool holding solutions that remain an integral link to machining processes. This essential link physically connects the cutting tool with the machine. Although there are no substantial changes in this branch of metal cutting, major strides are being made to stay abreast of new technologies.
New developments aim to enhance the capabilities of toolholders and their mechanical systems. Improving the main functional characteristics of the mechanical systems is attributed to strength, rigidity, gripping forces, accuracy, and vibration damping properties. Another advancement relates to the new age metal cutting techniques which pave the way to new horizons within this field. High-velocity tools characterise high-speed machining referred to as HSM. Consequently, the balanced and robust performance of the toolholder is required to function under escalated centrifugal loads and characterises contemporary HSM toolholders that align with advanced machining centers. This has placed heat-shrink toolholders at the forefront of machining technologies and focuses on the engineered balance concept by considering essential theoretical balance parameters before production. 3D modeling in contemporary CAD system environments significantly expands engineered balance possibilities. As the engineered balance relates to virtual objects, it cannot relate to the “physical” balancing of a real toolholder. However, an engineered balance design diminishes the mass unbalance of potential products and makes “physical” balancing much easier.
When cutting diverse materials, effective coolant supply significantly improves cooling and lubrication. This results in improved machining parameters and prolonged tool life. Increasing cooling capabilities is an additional direction for toolholder technology advancement. The growing popularity of additive manufacturing (AM) in combination with computer flow modeling opens new prospects for optimising coolant supply.
In addition, advanced coolant concepts also exist in coolant-driven speeders, enabled by the coolant system of machining centers. This phenomenon upgrades the abilities of the machine for HSM, consequently providing new levels of machine efficiency.
A modular tooling principle enables quick toolholder customisation using a limited number of standard elements. This principle facilitates the reduction of tooling stock and diminishes the dependence of special toolholders. Therefore, versatile, and reliable modular tooling systems continue to be the subject of new developments in metalworking.
The improved dynamic behavior of the machining system includes a machine, toolholder, clamping fixture and workpiece, all of which contribute to better performance. The vibration damping properties of a toolholder play an important role in this process, especially in long-reach applications. Increased cutting speeds and growing rotational velocities require toolholder manufacturers' engineering solutions.
The digitization of modern manufacturing creates the basis for the smart factories of tomorrow and highlights the digital components of a toolholder. It is not physical sensors and traditional devices alone, but the evolution of digital twins for computer modeling incorporated in CAD/CAM and virtual manufacturing systems, and the Internet of Things (IoT) that comprise the new trends in machining metal. The desire to achieve improved machining processes has forced toolholder manufacturers to reinvent their portfolios with virtual toolholder models.
ISCAR’s X-STREAM SHRINKIN tool holding family now includes the SRX-CX heat-shrink chucks with coolant jet channels along the shank bore.
The chuck design is intended first and foremost for high-speed machining operations, characterised by the slimmest thermal shrink chuck with direct coolant to the cutting edge. ISCAR’s new chuck design expands the toolholder application range especially when milling deep cavities and shoulders. Pinpointed coolant contributes to effective chip evacuation, prevents recutting, and eliminates chip sticking to the cutting edge. This enables applying CNC machines with the low external flow to achieve efficient milling in closed deep pockets and cavities.
As a continuation of the slim thermal shrink concept, ISCAR has introduced heat-shrink toolholders with a tapered shank for direct mounting on standard ER collet chucks and driven units. The holders are designed for clamping relatively small-in-diameter tools (3-12 mm). The shank design provides a rigid and reliable connection in a chuck. The holders that combine thermal shrink advantages, optimised coolant flow, and robust mounting in a chuck ensure high tool performance.
The concept of mounting compact toolholders in ER chucks has been successfully adopted also in NEOCOLLET – a new tool holding family that provides an alternative to clamping cutters with spring collets.
The high-pressure coolant-driven Micro 90 Jet spindle is a smallin-size speed increaser for accurate work in difficult-to-reach areas and is assembled from only six parts. It enables rotational velocities from 35,000 to 53,000 rpm while the main spindle of the machine remains idle.
WHISPERLINE boring bars have a built-in antivibration mechanism with an auxiliary mass immersed absorbent. The bars facilitate stable cutting at high overhangs. ISCAR has expanded bar clamping solutions by power chucks with polygonal taper adaptation according to ISO 26623, holders with VDI adaptation, and sleevetype tool blocks.
“Conventional” products in ISCAR’s tool holding lines have been enriched by ultra-precise spring collets for ER11 chucks, and a new design of sealed reduction sleeves for hydraulic chucks.
Virtual assembly
ISCAR’s electronic catalogue provides virtual assembly and digital representation options for ISCAR standard products, including toolholders and accessories such as pull studs, setting screws, etc. Apparently, the talk of stagnation in the metalworking communities is premature. The new developments are not a breakthrough, yet they systematically bring toolholders to a new orbit in accordance with the growing demands of the metalworking industry.
The future of tool holding technology is exciting and full of potential. With the continued development of innovative solutions, toolholders will become increasingly sophisticated and able to meet the demands of the modern metalworking industry. iscar.com
Walter presents the DC166 Supreme with innovative new web thinner.
In the field of aluminium machining, operators often look for more specialist tools as their requirements are often very specific. Now, with the new DC166 Supreme, premium tool manufacturer Walter has demonstrated just how special a standard drill can be.
The solid carbide drill with internal coolant has been specially developed for machining aluminium and other ISO N materials, which is why it boasts certain distinctive features. All the key surfaces on the drill, such as flutes, lands or clearance angles are polished. This reduces friction and prevents adhesion when machining the highly adhesive material. This increases the tool life and the process reliability of the drill. The highly innovative, patentpending thinner web of the DC166 Supreme is like nothing else on the market. It prevents the edge from building up and improves the chip removal and the supply of cooling lubricant.
The aluminium specialists' innovative design facilitates exceptionally high cutting speeds in conjunction with excellent drilling quality –especially in terms of the roundness of the hole and the surface quality. The arrival of the Walter DC166 Supreme is a product that can be used with emulsion, oil or minimum quantity lubrication (MQL), in 5XD, with a diameter of three to 12mm.
By having the Walter DC166 Supreme available as standard, the Tübingen-based company can quickly show the drill's performance in action to potential users. At the same time, Walter also offers the drill as a special tool up to 30XD in diameters from three to 20mm via the Walter Xpress Service. This provides a shorter delivery time of maximum of two weeks. The DC166 Supreme is of interest for all areas of application dealing with ISO N materials, especially the automotive sector and aircraft construction. walter-tools.com suttontools.com
Australian technology is satisfying a global need for sustainably sourced hardwood. By Dr. Cameron Chai.
Have you ever been told to surround yourself with experts to help you grow professionally? Let the story of Peter Torreele and 3RT be a case study for you as he and his collaborators developed a technology and a complete manufacturing solution despite being told it couldn’t be done.
The technology they developed enables the production of hardwood timber materials that appear and behave just like natural timber using sustainably sourced juvenile plantation raw materials and nanotechnology. As a result, they avoid the need to log old growth forest that often contain trees over 100 years old. 3RT’s timber is now squarely aimed at filling a market need with technology that can be adopted anywhere in the world.
The 3RT journey started back in 2014 when Peter Torreele, now Managing Director of 3RT, identified a growing demand for timber building materials while native forests logging was increasingly being banned. This was also being driven by a need for an alternative to the high energy intensive materials such as metals and concrete to reduce carbon emissions. While hardwoods are very desirable, the supply of these timbers is diminishing as governments seek to comply with the international forestry certifier, Programme for the Endorsement of Forest Certification (PEFC) banning the import of timber derived from old growth forests. PEFC went further in 2022 and banned “conflict timber”, timber imported from Russia and Belarus. To illustrate the impact that will have on local supplies, Australia imported $80m worth of timber from Russia alone. Torreele was inspired by the concept of strandwoven bamboo flooring and sought to replicate this type of product using other sustainable timber species. He partnered with Flinders University’s department of Nanotechnology and Materials Science to biomimic the growing of a tree.
Working with researchers from Flinders University, they developed technology that allows them to convert abundantly available, juvenile wood into products with properties that exceed those of mature trees from old growth forests. Henkel assisted in the development of the water-based Nanoglue. The raw material can be sustainably sourced from juvenile plantations, which would be otherwise used for low value applications like woodchips used to create low value materials like particle board and MDF which utilise formaldehyde adhesives. In contrast, their newly developed timber uses no toxic chemicals or solvents and is completely recyclable and culminates in a higher value product.
By 2016 they had applied for Global Provisional Patents to protect their intellectual property and had begun designing the equipment required to take their manual lab-based process to the pilot plant scale. By 2018, they had been granted 14 patents globally, with another 10 pending. Recognising the potential, the South Australian government awarded them a grant which enabled them to establish their own research facility in Adelaide, which has become the 3RT Innovation Centre. This includes an R&D line and a first generation Digital Production Unit. In doing so, they were able to prove their production concept and demonstrate the commercial viability having tested it on many dozens of timber species with many local customers.
At this point, 3RT were ready to scale their process and they turned to Bosch Australia Manufacturing Solutions (BAMS), part of the multinational Bosch organisation with a history extending over more than 137 years. This particular business unit has an interesting history as well. Originally servicing the automotive industry, they needed to pivot with the demise of local car manufacturing.
As it turned out, BAMS was an ideal fit for 3RT, having many years of expertise in process design, automation and Industry 4.0. They also brought to the table the instant credibility of their global parent organisation along with their global footprint which could be called upon to support installation across the globe. 3RT’s name stems from the three R’s of sustainability, reduce, reuse and recycle. This mentality and the potential to roll out sustainable technology internationally resonated with the Bosch ethos and culture who were excited to partner with 3RT.
When asked about how they approached the 3RT project, Andrew Bartlett, Strategic Project Manager at BAMS responded, “3RT’s process is unique. The process and equipment blocks required were known quantities and we were still able to apply our automation experience around this. For us the real challenge was working with a natural product as opposed to an engineered product which introduced more variability.” He went further to add, “the technology was fairly well-defined, so there was no need to redesign the core processes. Rather, we applied our industrial knowledge to refine the process to improve cycle times, create a robust and reliable system and reduce scrap. In doing so, we optimised throughput and created a reliable process that is capable of 24/7 production.”
The industrialisation project ended up taking longer than expected as it took place during the height of the COVID pandemic. While the lockdowns were inconvenient, their issues were a consequence of supply chains and obtaining equipment due to delays in production and shipping. However, the importance of a local partner was highlighted with international travel off limits. Close collaboration kept the project in motion and the entire integration was completed domestically.
Working together, 3RT and BAMS were able to design a highly automated production workflow with a compact footprint that is easily deployable globally. Sourcing best in class pieces of equipment from around the world, these were integrated and automated by BAMS using advanced robotics and smart automation. The resultant modular manufacturing plant is capable of producing timber slabs 2600x300x500mm weighing in the vicinity of 300kg each at the rate of two blocks every nine minutes. The highly automated nature of their process means it only needs three people to run it. In fact the only human intervention required is loading of raw materials, unloading finished product and quality control. The process itself is customisable and can be adapted for locally sourced materials.
These resultant scientifically engineered blocks can then be cut down into smaller sections which can be used for both decorative and structural applications such as:
• Beams and posts
• Doors
• Paneling
• Flooring
• Indoor and outdoor furniture
• Window and door frames
• Decking
• Cladding and battens
• Step treads and handrails
3RT’s process has a recovery rate of over 80% which compared to 31% for a traditional sawmill. As would be expected from an engineered product, the properties of 3RT’s timber are more consistent and reliable, with less defects. The absence of saw dust
also represents a step change for the industry. Their product also inherits the natural characteristics such as termite resistance, fire resistance etc. of the source timber. Another advantage of their process is the ability to tailor products by mixing timber species to achieve specific properties or appearances.
The plug and play digital production units have also been designed such that they can be rolled out anywhere in the world. The modular design allows them to be installed near the source materials to minimise the carbon footprint of the process by minimizing transport. Increasing production capacity is simply a case of adding additional modules.
Ashraf Abdelmoteleb, Head of IoT Technology and Business Operations at 3RT also added, “3RT are actively looking to license their technology. We are interested in building long-term partnerships with companies who want to implement our technology. We will be offering full support for any installation. Using the latest IoT technology, we can remotely monitor any plant, offer preventative maintenance and ongoing process optimisation.” In addition, the 3RT innovation Center provides customised R&D support, allowing customers to develop their own bespoke wood products.
At present 3RT is in the growth phase. Their pilot plant in Adelaide has successfully demonstrated that their patented process can produce timber products that mimic look, feel and properties of hardwoods. They can achieve in one day, what nature takes 50 to 100 to produce, while preserving forest and natural habitats. They can also use the pilot plant to demonstrate to potential clients how the process can be applied to source timbers from anywhere around the world.
The Adelaide plant is also geared up to produce decorative and structural timber products for a select group of customers in Australia. While their first plant is due to be commissioned in Belgium before the end of the year, 3RT have plans to have 50 plants up and running around the world in the next ten years, a goal that seems achievable with the increasing demand for timber as a sustainable and carbon-friendly building material. This is no doubt the beginning of long-term relationship between 3RT and BAMS that will see Australian manufacturing technology exported the world over.
Peter Torreele had the final word, adding “we are extremely proud of the technology that we have developed working with Flinders University, Henkel and BAMS. Our solution fulfils the demand for low carbon, toxin-free building materials, reduces native forest depletion and helps to secure the reliability of global supply chains.” 3rt.com.au henkel.com.au bosch.com.au flinders.edu.au
MASPRO Engineering Pty Ltd has a strong reputation in the industry for delivering operational efficiencies to some of the world’s best-known mining companies.
Recently the Australian engineering business has turned this skill inward, investing in not just one, but two Agile Flex 35D robotic loading systems for CNC machine tools.
The two Agile Flex 35D systems at MASPRO are 4-drawer models with the top pallet option, both tending DMG NLX 2500/700 dual spindle turning centers. One of the systems was installed at MASPRO’s Condobolin manufacturing facility and the other at their Wetherill Park facility, in New South Wales, Australia.
The Agile Flex 35D systems are being used in the manufacture of hydraulic cylinder pistons but will ultimately handle a wide variety of machined parts for the mining equipment sector.
The Agile Flex 35D robotic loading systems have allowed MASPRO’s machinists to focus on more complex roles such as programming rather than the timeconsuming and difficult manual loading and unloading of parts. Removing the need for manual handling has also eliminated the risk of repetitive stress injury.
Established in Condobolin in 2006, MASPRO is a family-owned and operated mining technology business with a history spanning three generations.
MASPRO are leaders in manufacturing quality spare parts for OEM equipment and have leveraged reverse engineering to understand how to manufacture highquality products, delivering precisionengineered mining parts to the world. With a culture of innovation, MASPRO have continually tested and trailed different means of manufacturing to meet demand, ultimately investing in cuttingedge technology, highly skilled people and rigorous quality processes.
This culture of innovation was the motivation behind MASPRO’s decision to employ CNC automation.
Whilst some industry sectors may be concerned about robots replacing humans and a decrease in work opportunities, MASPRO Managing Director Greg Kennard is optimistic about the benefits of automation that are often missed amongst scaremongering headlines.
“Automation offers faster, safer, more precise production, and can give us economies of scale, however skilled employees will always be in demand,” says Greg.
“Innovation via robotic equipment, programming and automation will help manufacturing free up time for their skilled
engineers and operators by removing monotonous manual tasks, and will clear the decks for creative thinking and design. This is what the manufacturing industry desperately needs,” says Greg.
“We work in a high-risk industry. Any new technology that can reduce the risk of harm to employees – even by a fraction –is worth looking into. Safety is our primary focus from a manufacturing and production perspective, so removing high-risk tasks from our process is helping to drive our investment in automation,” explains Greg. As a leader in mining drill parts, MASPRO is determined to keep pace with world trends and embrace the benefits of technology, machine learning and automation where there is a clear benefit to its employees and customers.
Agile Flex is a range of out of the box robotic loading systems for CNC machine tools. Rapid to deploy, compact and easy to use, Agile Flex has been developed to add lights out machining at a very affordable price to any brand of CNC machine. The Agile Flex 35D is a system suitable for heavy parts
and large CNC machines, with a multilayer drawer system that increases overall capacity and unmanned run time. With up to eight drawers and an optional top mounted pallet, the Agile Flex 35D can process up to 9 unique part numbers unattended. Combined with the ability to process castings and uneven parts, the Agile Flex brings real agility to CNC automation.
The Agile Flex state of the art user interface requires no robot programming knowledge and is specifically designed to be intuitive for the CNC machine tool user. It could not be simpler to configure complex robot motion and sequences in minutes on an Agile Flex CNC machine loading system.
Rapidly deployed on any CNC machine, compact and affordable, Agile Flex offers maximum productivity out of the box.
Agile Robotic Systems is part of the John Hart group of companies and has drawn upon a heritage of over 70 years in machine tools and over 40 years in automation and robotics to become a leading supplier of innovative machine loading systems. agilerobotics.com maspro.com.au
This major hydraulics supplier wanted to minimise emissions and waste as well as increasing productivity and reduce customer lead time.
Cross Hydraulics is a global leader in the distribution and manufacturing of customer and application specific hydraulic system solutions for mobile and industrial applications. Their extensive inventory includes pumps, motors, valves, power units, transmissions, and controls. Since 1976, their proficiency, the quality of individual components, and their operational dependability have garnered market recognition.
Through ASA’s partnership with Okuma Australia, Cross Hydraulics came to ASA looking for a machine tending solution to tend to an Okuma LT3000 EX 3T3MY. ASA designed the complete automation cell after consulting with Cross Hydraulics to determine the existing pain points and desired outcomes for this investment, including a Modula Vertical Storage System and Hi-Tech Metrology Shop Floor Coordinate Measuring Machine (CMM).
Cross Hydraulics adheres to environmentally responsible production practices and were looking for ways to reduce raw material, minimise emissions and waste as well as increasing productivity and reduce customer lead time. They were looking for a solution that not only offered an ability to add a second machine to the cell in the future, but also capability for 24hour lights out operation. “From the get go,” said Michael Finck, Senior Engineer at Cross Hydraulics, “I was blown away by ASA and the knowledge and experience with machine tending systems and their overall professionalism.”
Pat Green, Director of ASA chose a FANUC R2000iD/100FH, Hollow Wrist robot with a reach of 2605mm and a payload of 100kg for this bespoke solution. “The hollow wrist robot allows for a neat and compact machine tending solution, which mitigates the need to manage externally routed cables to the dual handed gripper,” he said. The cell included the robot, dual handed gripper, guarding, PLC and safety control system as well as a vertical storage system to store billets and finished goods for long periods of unmanned production.
A two-handed gripper with integrated quick change adapters was specifically designed for the system to complement the FANUC R2000iD/100FH robot. ASA supplied 14 grippers and a gripper change station that allows seamless transition between billets and finished goods of different sizes.
The solution
As the robot entered the machine at the end of a cycle, one gripper was already holding
a raw billet to insert into spindle ONE while the other gripper was empty and prepared to receive the finished part from spindle TWO. After commencing the next cycle, the robot would offload the completed parts into the Modula Storage System which featured 17 individual trays to handle the Cross Hydraulics parts or place it to the CMM for Quality and Inspection assurance. ASA’s HMI software enables the selection of different types of tending sequences such as loading billets and unloading finished parts from the integrated machine bar feeder. ASA’s HMI software makes setting up new parts a breeze and walks the operator through the process while at all times, logic checking the input values to avoid potential collisions. “The HMI is so
easy to use and flexible to accommodate all our different machining operations and part configurations,” noted Michael Finck, “including the different loading and unloading sequences.”
The result? Cross Hydraulics and ASA were able to reduce cycle time, increase overall productivity as well as enhance safety and flexibility. Michael Finck mentioned that, “this automation project, being a combination of the purchase of the Okuma machine serviced by a FANUC robot, has increased our productivity by three times on some parts, and up to around 6.5 times on others.”
crosshydraulics.com.au
automatedsolutions.com.au
Tynbell Sheetmetal's latest acquisition powers future defence work.
Tynbell Sheetmetal is an Adelaide-based provider of fabricated metal products, has invested in new cutting-edge equipment to accommodate growing industry demands. The strategic investment allows Tynbell to operate at the forefront of complex Defence and Aerospace projects.
The family-owned sheet metal manufacturer has recently taken significant steps toward expansion and growth, as it looks to the future of precision manufacturing in Australia.
Tynbell has taken delivery of a new Bystronic Xpert Pro Press Brake Machine, representing a significant investment in the future while also improving output, safety and energy efficiency.
“Our new press brake is designed to process and bend metal faster, with greater flexibility, repeatability and accuracy,” said Tynbell Managing Director, Raymond Fenech. “The machine incorporates cutting-edge technology to meet the demands of the Defence Industry,” he added.
Tynbell Sheetmetal extended their manufacturing facility six months ago, in a strategic move to enhance their capabilities, creating more space to accommodate the specific requirements of Defense customers.
This expansion was the first milestone in Tynbell's longterm growth journey, as the manufacturer continues to forge its reputation for unmatched quality and precision within the Defence and Aerospace sectors.
With the introduction of the Bystronic Xpert Pro Press Brake Machine, Tynbell is poised to revolutionise their production processes, boost productivity, and offer more job opportunities.
“This machine will significantly elevate our productivity, reduce the risk of human error and ensure the consistent delivery of highquality products,” said Mr Fenech. "We have big plans, and the introduction of the Bystronic Xpert Pro Press Brake Machine is just a beginning."
Tynbell’s recent growth trajectory is a testament to its willingness to invest in the future. The manufacturer has plans to further cement its commitment to quality, by installling a new ERP system and working towards ISO 9001 certification, with a targeted achievement date set for the end of this year.
The ISO 9001 certification will further reinforce Tynbell’s dedication to maintaining the highest standards across its manufacturing processes and customer service.
Tynbell’s fabricated metal services include full product design, prototype development services and turnkey solutions from concept to completion. With the technology to customise projects, the Australian manufacturer has completed a broad scope of projects, from decorative artwork in the local community to lasercut tubes for pumps in the mining industry.
As a resilient, family-run business based in Adelaide, Tynbell has earned a reputation for quality. Demand for services has grown, with the Tynbell workforce expanding from 9 to 15 employees across the past two years.
The manufacturer is now expanding its operations to better serve clients within the defence, aerospace, and space industries with an ongoing focus on customised solutions. tynbellsheetmetal.com.au
The high-performance Mitsui Seiki J350G jig grinder offers a combination of application flexibility, accuracy, reliability and operator-friendly operation. The machine’s grinding infeed stroke is the largest available among competing machines, with a U-axis range of -3mm to +50mm relative to the spindle center. This provides the flexibility to grind small and large diameter holes, as well as multiple features, using a single wheel in a continuous, automatic mode.
According to Mitsui Seiki, many legacy jig grinders are currently coming offline in shops and manufacturers are looking to replace them with those featuring advanced CNC controls. To that end, the J350G’s Fanuc 31i-B control has a 15" touch panel LCD screen and is preloaded with G-MAPS conversational-style programming software. The control also permits easy manual programming via graphic icons, data entry, or conventional methods.
“Jig grinders are the most common machine type in small shops and large factories. Most have at least one. Our CNC J350G provides the ability to grind a wide variety of features automatically, without changing wheels,” said Mitsui Seiki USA chief operating officer Bill Malanche, “It provides the flexibility required in today’s manufacturing environment.” To maximize accuracy, the X- and Y-axes of J350G are hand scraped and incorporate needle roller bearings.
Left and right slide ways are V-F flat shaped, and the Y-axis (spindle head motion) is V-V shaped to maximize positioning accuracy. The machine bed consists of a thick, highly rigid casting supported by three level points, assuring consistent perpendicularity and parallelism. Builtin, custom-designed Heidenhain scales contribute to +/- 0.0007mm accuracy on the X-, Y- and Z-axes.
Table longitudinal travel (X-axis) is 500mm, transverse travel (Y-axis) is 300mm, and quill travel (Z-axis) is 100mm. Maximum distance from the table surface to the grinding spindle nose is 450mm. The machine’s work surface is 700mm x 350mm and permissible table load is 300kg. Table and saddle maximum rapid feed rates are 2,000 mm/min and grinding feed rates are variable from 0.1mm/min to 2,000 mm/min. The standard high-frequency spindle motor operates from 9,000rpm –45,000rpm. A variety of spindle motor options include an air-turbine motor with 75,000rpm capability.
The machine’s 3m2 (2,220mm x 2,610mm) footprint is 50% smaller than that of the previous model, maximizing floor space efficiency. A standard total enclosure machine cover permits easy operator access while fully addressing safety and environmental concerns. mitsuiseiki.com
Business purchase a leap of faith, kept alive with CNC machines from OKUMA.
To understand the rich story behind South Fence Machinery and where it fits in New Zealand’s history, is to appreciate the passion that Ben Byers and Marty Neill had for the iconic business when they put their hands up to buy it in the challenging period following the GFC. Business South’s Richard Loader goes on the journey to South Fence Machinery.
Located in Christchurch, South Fence Machinery is the world leader in designing and building the complex machinery that fabricates a broad range of fencing wire. Any fence wire that you see anywhere in the world is highly likely to have originated from a machine built by South Fence.
The company’s origins go back to 1932 and a small business called New Zealand Fencing Gate Works, which was founded by William Ullrich, and sold to his 19-year-old nephew Fred in 1936. Always the innovator, Fred became the driver behind the Hurricane brand of fencing, building production plants all around New Zealand, and selling Hurricane fence wire products throughout Australasia, PNG, and the United Kingdom.
To support the wire making operation, Fred imported older wire making machines that were largely past their use-by-date, reengineered them and either used them in his production plants or returned them overseas, thus developing machine making IP that would become the hallmark of the business.
Early on, Fred purchased plans for a machine, enabling the company to engineer a bigger and better type of machine to fabricate wire products more efficiently. A new engineering division was set up to manufacture the machines, and the company’s international reputation grew.
In the early to mid 2000s the wire products manufacturing division was sold, and the engineering division became South Fence Machinery Ltd. This enabled the company to concentrate all its resources on the design and manufacture of machinery for the wire industry worldwide, and supply of spare parts. South Fence Machinery continued as a family owned and operated business, with Fred’s son Peter joining the business, followed by third generation Jeremy.
Supplying 80% of the world’s wire making machines, when the GFC hit in 2009, international orders for new machines plummeted, and by 2010 South Fence Machinery went from a team of fifty to about twenty. By this time the business was being managed by Peter and Jeremy and due to other business commitments, the decision was made to sell.
Ben and Marty had both been working in the business for long periods of time and knew its operations and customers very well.
Ben says the IP side of the business and deep institutional business knowledge made it very difficult for an outsider to walk in and take the business over successfully. “It really needed to be carried on by people within the business. We had been in the business for a long time, and we knew what the business was about, and what it meant.
“We knew a lot about the family history and the people who had come before us, and I think in some respects we felt a responsibility to steer the ship as temporary guardians until the next people came along. So, in 2012 we purchased South Fence Machinery.
“We rented the building off the Ullrich family, bought the IP and machinery and took on ten staff. It was a tough call. We didn’t have any machine sales going forward, but we were producing spare parts to service the many machines we have around the world. We were also doing a lot of local engineering work around Christchurch to keep the business going for a year or two after the GFC credit crunch.
“Peter and Jeremy Ullrich and our bank were also very supportive of us, but it was a very scary time for a while. To have walked away from it and see the business collapse would have been a shame.
“I think Marty and I both felt responsible to get stuck in and have a crack, and it has turned out very well.”
Ben and Marty put a lot of effort into ensuring the world knew that South Fence Machinery had survived the GFC, and that its doors were open for business. “This company is built on reputation, and we always stand behind what we do, always take responsibility, and back our customers up,” Ben says.
“Our machine brands are very well known, and a turning point came when we were approached by someone starting a new business in Australia who needed a specific type of wire making machine.
“On a handshake deal we designed and built that machine. Very quickly after that, another order came, and then another and that’s how we’ve grown — with a reputation for ensuring the customer is getting what they need, and we can fix any problems very quickly, which is what we’re very good at.”
Ben says the real turning point came in 2015 when a couple of large corporate pro jects were taken on requiring a lot of investment and effort put into R&D, and over 12 months the development of that machinery changed the wire fencing industry. “We have brought about a lot of change, just as the people before us adapted and put their money back into the business, with innovation and staff training. One of the biggest changes which we have been part of is the ergonomics of how tasks are done when fabricating fencing wire. If you go back twenty-five years, the operator could be seriously injured, or worse, if they did something wrong. Because we’ve been working with large corporate customers, there has had to be the highest level of safety in the machine design. We’ve driven safety in the design of these machines, and the ergonomics in how they are operated to improve machine operation and prevent RSI injuries. So, we’ve been working to improve those things for the customer and end user, so that our customers machine operators can go home safe every night.”
While South Fence Machinery does have a small domestic fence machine market, and services the original wire machines now owned by Summit Steel & Wire, along with some CNC machining for other engineering firms in Canterbury, designing and manufacturing wire fabricating machines for the global market forms the bulk of the company’s work.
Those customers range from small one-man operations right up to a significant number of very large corporates. “Depending in what we’re building and the specifications required by the customer, these machines could be two to three million dollar plants, so you need a huge cash flow to build them. You need a big crew of really smart people, and you need a lot of equipment to do it. “The machinery we have here is very specialised and there’s only a few of them in the Southern Hemisphere. But the customer is not just buying the machine. They are buying the service and support that they get after the machine has been installed.
“We build about five or six of these big machines each year, along with three or four of the smaller ones. “The machines are built here in their entirety, we set them up, commission them and test them. Then strip them apart and put them in five 20’ containers and ship them off. The knowledge our team have is immense and it takes us about five years to train someone before we can send them on site. So you need a lot of really good people around you. “We also service the machines onsite, and in some cases we can assist our customers remotely on-line with the late model machines.”
“Responding to market changes and customer needs with agility; staff development; embracing innovation; and investment in stateof-the-art machinery have been the cornerstones of success for South Fence Machinery,” says Co-Director Ben Byers.
“We have tried to be smart about training. We couldn’t get staff and so we have put a lot of emphasis on training young people. Since we started this initiative we have trained twelve engineering apprentices and are now training a further seven apprentices in the team. We’ve grown the team to forty-two staff, including three contractors.
“There is a mix of qualified tradesmen, welder fabricators, planning / purchasing staff, and university qualified design engineers. We have a big R&D team including three core designers, with another seven team members with hands on manufacturing experience involved on a part time basis to provide balance and a good sounding board. The three contractors are in electrical and programming roles.”
The introduction of new CNC machinery is designed to remove production bottlenecks, and streamline the manufacturing processes. “If you called us pre-COVID and ordered a fence machine it would go into a queue with a lead time of twenty-four months, which is ridiculous.
“We identified that we needed to make ourselves more productive manufacturing wise and the only way to do that was to increase manufacturing real-estate by investing in new technology and new machinery.
“We looked at our existing machinery and broke it down into square metres. For example, we had these huge machines which have a machine table of five metres by two metres, machining a part that was 400mm square. I thought, I only have one spindle cutting head and I’m using a huge machine to cut this tiny part, and all the big parts are sitting there waiting to be machined.”
To remove the bottle neck and speed up the machine delivery time, South Fence Machinery invested $4.5m in new technology including new CNC machinery specifically designed around the size of the task.
“The old machinery is still there but complements the new machinery, creating a lot of operational efficiency. The new machinery is used for the smaller work it is designed to do, while the old machinery is doing the larger work it should have been doing in the first place. That was an interesting journey for us and now we have a turnaround time of about nine months, depending on the machine and specs required. We have also bought automated machinery that operates autonomously. There are parts that we can machine a lot more efficiently, because we’re not paying labour for the twelve hours the machines are running unmanned.
“Our new equipment is all Japanese Okuma machinery. South Fence has always bought Okuma machinery. It’s excellent machinery; they are a bit like the Bentleys of the CNC world — we rely on them and trust them to accurately produce the great fence machines we are known for.”
Ben says another key focus for the company’s R&D team is the development of some new wire making machinery projects. “These machines are twelve months away from completion and testing. Once tested and released our team will again challenge what’s possible in the wire manufacturing industry. The future is all pretty exciting, to be honest.” southfence.co.nz
Why Autonomous Mobile Robots are the key to workplace safety, by Matthew
Hunter, National Manager Emerging Technology, Konica Minolta.Achieving workplace safety and operational efficiency are essential objectives for any supply chain and logistics organisation. However, scarce labour availability, low unemployment rates, and rising labour costs are creating challenges in these business-critical areas. Traditionally, logistics businesses have relied on forklifts, pallet jacks, trolleys, or pallet tuggers, all of which require safety equipment, processes and controls, as well as human intervention. Even autonomous guided vehicles (AGVs) need to follow specific paths and often require a human to watch over them.
To bridge the labour gap, and to improve the speed, accuracy, and security of their operations, businesses are increasingly turning to autonomous mobile robots (AMRs), which can work on their own and are more flexible than AGVs.
AMRs provide efficient, cost-effective alternatives to traditional material movements, and, while no machine can offer absolute safety, AMRs come close. They can navigate complex environments while maintaining safe interactions with human employees. Advanced sensors let AMRs predict and avoid obstacles, ensuring a smooth flow of operations. This adaptability is crucial, especially since a significant percentage of manufacturers cite collisions and shop floor accidents as a major challenge in the warehouse.
AMRs can feature all-around vision and can detect objects up to 20 metres away, irrespective of lighting conditions. They’re also capable of skilfully manoeuvring around both people and obstructions, maintaining preset speed limits, and can even adjust those limits and issue auditory alerts in areas deemed high-risk. They also remain focused and are not subject to fatigue, making them less prone to distractions compared to humans.
AMRs are equipped with proximity sensors and wheel encoders, letting them create dynamic maps of their surroundings. They plan their movements to sidestep obstructions and off-limit areas, ensuring that operations proceed without hitches. Adhering to standard operating procedures (SOPs) also minimises the likelihood of accidents involving AMRs, especially those that could potentially harm human workers.
There are three main reasons why these robots are crucial to the future labour force:
Enhanced operational efficiency. In addition to elevating workplace safety levels, AMRs play a transformative role in augmenting operational efficiency and streamlining business processes. With the ability to operate around the clock without requiring breaks, AMRs not only improve speed but also add a layer of consistency and reliability that is often challenging to achieve with a human workforce.
Their integration into existing systems allows for real-time tracking and analytics, which in turn facilitates process optimisation and resource allocation. As a result, they contribute to significantly reduced downtime or idle periods in operational settings. Importantly, the role of AMRs is not to replace human employees but to act as collaborative agents. They handle repetitive and laborious tasks, liberating human workers to focus on complex problem-solving, quality control, and other intellectually stimulating activities.
Significant cost savings. The financial benefits of implementing AMRs in the workplace extend beyond the obvious savings on labour costs. One often overlooked advantage is the reduction in capital expenses related to traditional material handling equipment like forklifts, as well as the ongoing costs of maintenance, repairs, and operator training for such machinery. AMRs, being highly adaptable
and low maintenance, offer a fiscally prudent alternative. Their flexibility allows them to be easily reconfigured for different tasks or workflow changes, effectively future-proofing the investment.
On the safety front, their precision and reliable operation significantly cuts down the likelihood of workplace accidents, offering a dual benefit: reducing costs related to workers’ compensation claims and maintaining a higher standard of safety. By fostering a safer and more efficient environment, AMRs not only directly contribute to the bottom line but also improve company reputation and employee satisfaction, offering an invaluable advantage in today’s competitive business landscape.
AMRs also contribute to a more sustainable operational model for companies. By automating tasks traditionally performed by humans, these robots reduce overall energy consumption and resource allocation in the supply chain. They can even be configured to optimise routing and scheduling, minimising fuel or energy expenditure.
Health and safety. The use of robotic technologies contributes to a healthier workforce by mitigating the risk of musculoskeletal disorders, which are common in jobs requiring repetitive motions or heavy lifting. Robots can also prevent falls by taking over tasks that would require workers to operate at heights, and they can help reduce worker fatigue by performing tasks that are physically demanding over long periods.
There are many sectors where AMRs are proving to be particularly beneficial, including:
Transporting goods: AMRs equipped with sensors and computer vision technology can navigate through complex warehouses and production floors. This capability minimises the risk of collisions with human workers or other equipment during the transportation of goods, parts, and materials. By automating this part of the workflow, not only is the operation more efficient, but it’s also safer as it reduces the chances of accidents related to manual handling of heavy loads.
Machine handling: manual operation of machinery comes with its own set of risks, including the handling of moving parts, high levels of noise, and the potential for human error. Leveraging robotic arms and AMRs can dramatically reduce these risks. By automating these processes, workers are less likely to suffer from musculoskeletal disorders related to repetitive tasks or be exposed to other machine-related hazards.
Precision tasks: robotic arms can execute tasks that require a high level of precision, such as cutting, welding, and the handling of hazardous materials. These arms can work with materials that are toxic, have high temperatures, or are potentially explosive, all without exposing human workers to the risks involved. This advanced capability protects employees from harmful substances and dangerous tasks, improving overall workplace safety.
In the face of current challenges such as labour shortages, cost pressures, and workplace safety, AMRs are emerging as an essential solution. Thanks to ongoing advancements in technologies like artificial intelligence (AI), these robots are continually improving, making them a long-lasting asset for businesses. They don’t just offer immediate gains in efficiency and cost reduction; they also pave the way for sustainable and adaptable operations in an increasingly automated world.
Far from being a luxury, these robots are swiftly becoming a core component for any organisation focused on both safety
and operational excellence. Failing to adopt this transformative technology could mean missing vital opportunities to boost both safety and productivity. More significantly, such a delay could jeopardise an organisation’s ability to compete effectively in a fastchanging industrial landscape.
Adopting AMRs is no longer optional for businesses striving for safety and efficiency. Any delay risks missed opportunities and a weakened competitive position. It’s time for businesses to fully embrace the advantages that AMRs bring in creating a work environment that’s both safer and more productive.
When choosing a provider for autonomous mobile robots, it’s vital to look for solutions that offer more than just productivity gains. The right partner can help your business elevate efficiency levels, empowering your employees to focus on more meaningful activities, while also optimising workflow to reduce bottlenecks and lead time. Especially in industries where work can be physically demanding, the right robotic solution becomes a cornerstone in a fully automated and more efficient production line.
Selecting AMRs isn’t just a purchase; it’s an investment in a safer, more efficient, and more sustainable future. The choice made today can set the stage for long-term competitive advantage and operational excellence. This investment provides benefits that go far beyond the initial costs, making them a cost-effective solution for dynamic business environments.
konicaminolta.com.au
Safeguarding Australia and New Zealand's Industrial Systems: The importance of operational technology cybersecurity.
Rockwell Automation, the world’s largest company dedicated to industrial automation and digital transformation, has partnered with cyber-physical systems protection company, Claroty, to release a white paper on safeguarding Australia and New Zealand’s industrial systems.
In the face of an ever-growing climate of cybersecurity attacks, operational technology (OT) security specialists bear the weight of safeguarding Australia and New Zealand's most critical infrastructure. Ensuring uninterrupted essential services such as energy, food and beverage, healthcare, data processing, and mining industries demands utmost vigilance. However, the recent Rockwell Automation and Claroty survey of 42 C-suite executives and heads of security exposes a concerning truth – many OT systems remain exposed and vulnerable.
“A lot of the challenges organisations face today can be traced back to the fact that OT has traditionally been operated and managed as a separate entity from conventional information technology (IT) environments,” says Anthony Wong, regional director, South Pacific, for Rockwell Automation.
The survey bears this out with 26% of respondents admitting that there is a low or medium level of collaboration between OT and IT, and the two units could do better.
“Increasingly, cybercriminals are exploiting sometimes lax OT security as springboards to launch a wider attack across an organisation,” says Wong. For example, a recent cyber-attack on a major Australian meat packing company, forced the temporary shutdown of 47 sites across Australia and a ransom demand of $14.2m.
• 65% of respondents detected at least one OT-related cybersecurity incident in the last 12 months.
• 60% of cybersecurity leaders believe their budget is not enough to protect their operations
• 29% of respondents were concerned that an OT security incident could disrupt their production.
• 26% of respondents admitted having low or medium levels of visibility into the operations of their network.
• 26% of respondents worry that attacks could compromise the safety of their employees or others
• Just 14% of respondents feel well equipped to identify an OT cybersecurity incident.
The survey reveals a significant challenge faced by companies – the ongoing disconnect between teams managing OT and IT systems. A quarter of respondents admit that their IT and OT business units are not collaborating as effectively as they should be. This lack of cohesion poses risks to the integrity, availability, and business continuity of critical infrastructures.
“Segregating OT and IT responsibilities used to be manageable because disconnected OT systems were seen as being functionally separate from mainstream systems. But with casual connectivity now built into nearly every device installed into corporate networks, these assumptions no longer hold true,” said Wong.
To confront these pressing issues, it is imperative to bridge the gap between OT and IT teams and secure the infrastructure against relentless exploitation. Implementing full-spectrum IT/OT/Internet of Things (IoT) visibility and detection capabilities becomes essential to combat threats that transcend the IT/OT boundary.
rockwellautomation.com/en-au/capabilities/industrialcybersecurity/state-ot-security-sp.html
Prime Minister Anthony Albanese has opened CSL’s new global headquarters and R&D Centre.
The Prime Minister of Australia, Anthony Albanese has opened CSL’s new Global Headquarters and Centre for Research and Development (R&D) in the Parkville biomedical precinct in Melbourne.
Part of a $2bn infrastructure investment program in Australia undertaken by CSL over the past four years, the facility will house more than 850 professionals dedicated to protecting public health and bringing life-saving innovative therapies to those in need. “Today, we stand here proudly as a trailblazing force in innovation, with global scale and Australia as our home and Melbourne as our headquarters. We own and develop our own IP and we forge collaborations with the brightest minds in academia in Australia and beyond. We see our future completely integrated with the biomedical precincts, and recognise our long-term success is tied to Australia’s excellence in biomedical research and tertiary education,” said Dr Brian McNamee AO, Chairman of CSL.
The new site will place CSL in close proximity to its many valued partners, including the University of Melbourne, the Walter and Eliza Hall Institute, the Royal Melbourne Hospital, the Doherty Institute and the Murdoch Institute.
“This very building stands as a testament to our transformative journey from our century old Royal Park site. It is a realm of discovery and development, offering possibilities to Australia's local researchers and becoming a source of ground-breaking
medicines for patients across the globe,” Dr McNamee said. The state-of-the-art facility spans 18 floors, each designed with a specific purpose to drive innovation and progress. It also has two levels dedicated to the Jumar Bioincubator, which offers office and laboratory space for up to 40 Australian biotech start-ups to progress the commercialisation of their research.
“We hope that with the addition of this world-class facility the scientific and commercial output of the Parkville Biomedical Precinct here in Melbourne can continue to be much more than the sum of its parts. Our aim is to catalyse even more research, more development and ultimately deliver more products that can help people in serious need all over the world,” said Dr Paul McKenzie, CSL’s Managing Director and Chief Executive Officer.
“CSL is one of Australia’s most essential and successful biotech companies – and I am so pleased to be opening this world-class facility in Melbourne.
“This magnificent facility will help position CSL to compete in the global marketplace. The work that CSL does right here will continue to be integral to Australians’ health and quality of life,” said Prime Minister Anthony Albanese.
The Green Building Council of Australia bestowed a five-star rating for its design features that represent ‘Australian Excellence’ in environmentally sustainable building practices. csl.com.au
Rigby Cooke Lawyers has been advising manufacturers on their commercial needs for decades. And, that’s why we are the ‘go-to’ legal advisors for AMTIL members and the manufacturing industry.
At Rigby Cooke Lawyers, we can assist with all your business legal needs and have the expertise to advise on the following:
> Commercial transactions
> Business structuring (companies, joint ventures and partnerships)
> Commercial contracts
> Employment and workplace relations
> Occupational health and safety
> Succession planning and family business
> Personal property securities law
> International trade (import and export)
> Intellectual property
> Privacy and data protection
> Property sales, purchases and leasing
> Planning and environment
> Building and construction
> Litigation and dispute resolution
> Insolvency, asset protection and reconstruction
> Tax
For more information on how we can assist you and our exclusive benefits for AMTIL members, please contact Julia Cameron, Lead Partner of our Manufacturing group, on +61 3 9321 7807 or JCameron@rigbycooke.com.au.
Australian companies teaming up to pursue international projects funded by the US and Australian governments aimed at accelerating commercial adoption of quantum computing.
Q-CTRL, a global leader in developing useful quantum technologies through quantum control infrastructure software, and Diraq, a leading innovator in Silicon-based quantum computing, today announced they will be partnering on three multi-million-dollar projects to expand the commercial adoption of quantum computing. It represents the first stage of an anticipated partnership delivering new, high-impact quantum computing capabilities to the global market, from Australia.
The two Australian quantum technology companies will deliver three projects together: two from the NSW Office of the Chief Scientist and Engineer’s Quantum Computing Commercialisation Fund (QCCF) and one from the US Army Research Office. Q-CTRL and Diraq are sharing responsibilities on the projects: Diraq will develop and provide access to its Silicon quantum computing hardware and Q-CTRL will build and integrate its quantum infrastructure software solutions to deliver maximum end-user value from the hardware.
Q-CTRL and Diraq highlight Australia’s leading role in the global quantum technology industry. Diraq’s hardware is constructed using a novel technology known as spins in silicon, offering true scalability in the number of qubits to the many millions, and ultimately billions per chip. Q-CTRL is a category-defining business focused on developing quantum infrastructure software to improve the utility and performance of quantum hardware. Michael Biercuk, founder and CEO of Q-CTRL, and Andrew Dzurak founder and CEO of Diraq, have been colleagues for over 20 years – first in academia and later in industry – and are recognised pioneers in their technical specialties.
The Australian quantum ecosystem is flourishing, and with the recently announced National Quantum Strategy, the Government has taken steps to be an active supporter in growing the industry.
The Quantum Computing Commercialisation Fund is an initiative from New South Wales to empower Australian quantum computing hardware and software companies. The projects focus on increasing the commercial and technological readiness of quantum computing technologies in order to support long-term commercial activities. The projects shared between Diraq and Q-CTRL will help deliver Australia’s first cloud-accessible silicon quantum processor, and help orient this technology towards providing cutting-edge capabilities to Australia’s globally leading financial services sector. “The partnership between Diraq and Q-CTRL exemplifies our shared commitment to driving the next era of innovation in the quantum
computing industry, both locally in Australia and globally,” said Diraq CEO and Founder, Andrew Dzurak. “We are delighted to collaborate with Q-CTRL, leveraging our specialised areas of expertise to jointly drive successful outcomes across these transformative projects.”
Australian companies and University teams have long engaged with the US Army Research Office in support of quantum computing capability development. In the current project led by Diraq, the two teams will focus on developing novel techniques to operate and optimize next-generation Silicon quantum processors. The ARO R&D program now aligns with quantum technology initiatives supported under the trilateral AUKUS agreement’s Pillar II. AUKUS Pillar II is aimed at enhancing capabilities and interoperability with a focus on cyber capabilities, AI, quantum technologies and undersea capabilities. In July, Q-CTRL announced a separate deal with the Australian Department of Defence, centering around quantum sensors for navigation; the technological breakthroughs would be shared with AUKUS partners in the US and UK.
“It’s exciting to see Australia’s two leading quantum computing companies collaborating to deliver true sovereign capability in one of the most profound technical fields of the century,” said Q-CTRL CEO and Founder, Michael Biercuk. “We’re thrilled to be helping accelerate the work of our friends at Diraq, and ensuring these powerful new systems deliver value broadly across the Australian and global economies.”
Diraq is a world leader in building quantum processors using silicon ‘quantum dot’ technology, leveraging over two decades in engineering and research expertise at UNSW Sydney and backed by an extensive IP portfolio. Diraq’s goal is to revolutionise fullstack quantum computing by driving qubit numbers on a single chip to the many millions, and ultimately billions needed for useful commercial applications.
Q-CTRL’s quantum control infrastructure software for R&D professionals and quantum computing end users delivers the highest performance error-correcting and suppressing techniques globally, and provides a unique capability accelerating the pathway to the first useful quantum computers and quantum sensors. Q-CTRL operates a globally leading quantum sensing division focused on software-level innovation for strategic capability. Q-CTRL also has developed Black Opal, an edtech platform that enables users to quickly learn quantum computing diraq.com q-ctrl.com
Artificial Intelligence is by no means a new phenomenon and is already doing what think might one day do. Anders Billesø Beck, Vice President Strategy & Innovation, Universal Robots talks about what’s next.
For decades we have been talking about AI as a technology with the potential to radically disrupt our society and impact the future of mankind – some being optimistic, others dystopic in their view on AI.
But with the emergence of technologies like ChatGPT, it looks like the future is now and it’s hard to think of a time when AI has been a hotter topic than at present.
One of the key reasons why AI is now being discussed in workplaces all over the world is because computer processing has taken giant leaps forward in recent years. We now have the processing power to handle the vast amounts of information and data required for AI technology, something we simply didn’t have before. This hardware development has paved the way for an AI breakthrough, including new software programs like ChatGPT. But while chatbots are still in the early stages of transforming how we communicate and gather information on the internet, AI technologies is already making a real-life difference in another arena – manufacturing.
Here are four examples of how AI is impacting industrial automation today, and how it can be used to benefit manufacturers all over the world by making it simpler to automate complex and diverse tasks - even in unstructured environments.
Humans can look at disordered objects – such as parts in a binand immediately see the difference and understand which of them can be handled without interfering with other objects. Automation engineers know that this isn’t always the case for robots, to put it mildly. As a result, bin-picking of unstructured items has traditionally been thought of as a notoriously difficult problem to solve. But this is changing with AI.
Take for example Apera AI’s ‘4D Vision’ technology, which is challenging the status quo by providing cobots with “humanlike perception” – a claim that sounds hyperbolic at first, but is borne out on several levels and enables faster, more effective robot performance - especially in bin-picking applications. With the use of scanners and cameras, ‘4D Vision’ can identify the “most pickable” objects and inform the cobot of the fastest and safest path to handle them. The cobot is provided with pose estimation and path planning data ensuring that the robot takes a safe, collision-free path to accomplishing its goal.
The mainstream understanding of AI is a technology that’s able to “think” by itself and make decisions without prior teaching or instructions. Even though this is not always the case, these upsides are exactly what you get with the robobrain.vision kit from Robominds designed for the logistics industry for e.g. kitting, order picking or de-palletising tasks.
Simplified, most automation solutions within manufacturing are programmed to handle a specific object with set dimensions. Of course, these solutions can be programmed to handle further variations, but they rely on humans telling the robot which objects to handle and what to do with them.
With this kind of camera-based AI technology, the robot can pick up different - objects regardless of their shape or size. And by not having to spend time on teaching or programming the robot, customers are given even greater flexibility and can change the objects being handled without spending time on re-programming.
Another example of how AI enables industrial robots to deal with variance in position, shape or movement is MIRAI from Micropsi Industries.
Instead of being dependent on specific measurements being preprogrammed, it’s able to generate robot movements in real-time. This means the robot can do e.g. assembling, gripping, screwdriving or testing tasks, even if the position of machines or objects fluctuate from time to time.
Inbolt's AI-based Inbrain is another technology using AI to handle variations and moving parts. It processes massive amounts of 3D data at high frequency and identifies the position and orientation of a workpiece, adapting the robot trajectory in real-time, which makes it ideal for assembling, handling, finishing, and testing. To see it in action, see this video.
AI can also be used to give robots touch senses. The AI control software from AICA enables the robot to learn precise tasks such as assembly of gears, even when the task varies every time.
Another important upside of AI in industrial automation is that its constantly improving - automatically. The more your robot is working, the more data the AI application is gathering, and with this data the underlying algorithm can continously optimise, adjust and improve the robot’s performance.
This level of self-learning means that, as a customer, your automation solution will improve by the day – without you having to spend time and money on updates or upgrades to your solution.
The upsides of this new synergy between AI and cobots are evident. Manufacturers looking to cobot automation to overcome their business challenges – whether its labor shortage, improving employee’s wellbeing or raising quality or productivity – are now able to solve extremely complex tasks, even in unstructured environments. And, at the same time, AI products are presenting manufacturers with an unforeseen level of flexibility and simplicity, as well as raising quality and reliability.
It's clear AI is already making an impact on industrial automation, but the best part is we’re only just scratching the surface. The future might be here, but the best is yet to come.
universal-robots.com
Sophos, a global leader in innovating and delivering cybersecurity as a service, today announced a new sectoral survey report, “The State of Ransomware in Manufacturing and Production 2023”, which found that in more than two-thirds (68%) of ransomware attacks against this sector, the adversaries successfully encrypted data. This is the highest reported encryption rate for the sector over the past three years and is in line with a broader cross-sector trend of attackers more frequently succeeding in encrypting data. However, in contrast to other sectors, the percentage of manufacturing organisations that used backups to recover data has increased, with 73% of the manufacturing organisations surveyed using backups this year versus 58% in the previous year. Despite this increase, the sector still has one of the lowest data recovery rates.
“Using backups as a primary recovery mechanism is encouraging, since the use of backups promotes a faster recovery. While ransom payments cannot always be avoided, we know from our survey response data that paying a ransom doubles the costs of recovery,” said John Shier, field CTO, Sophos. “With 77% of manufacturing organisations reporting lost revenue after a ransomware attack, this added cost burden should be avoided, and priority placed on earlier detection and response.”
In addition, despite the growing use of backups, manufacturing and production reported longer recovery times this year. In 2022, 67% of manufacturing organisations recovered within a week, while 33% recovered in more than a week. This past year, only 55% of manufacturing organisations surveyed recovered within a week.
“Longer recovery times in manufacturing are a concerning development. As we've seen in Sophos' Active Adversary reports, based on incident response cases, the manufacturing sector is consistently at the top of organisations needing assistance recovering from attacks. This extended recovery is negatively impacting IT teams, where 69% report that addressing security incidents is consuming too much time and 66% are unable to work on other projects.”
Sophos provides a look at a large-scale ransomware attack against a manufacturing company in its newly released three-part “Think You Know Ransomware?” documentary series. In episode 2, Sophos interviews the chief information security officer of Norsk Hydro, a
major aluminum production company, to learn about the aftermath and investigation of the attack against the company.
Manufacturing reported a low propensity to pay the ransom (34%) to get their data back, with almost double the number that paid the ransom using backups for data recovery (73%). Encouragingly, the use of backups for data recovery increased by 15 percentage points from the 58% reported a year before.
While this is a welcome improvement, manufacturing has the lowest rate of data recovery (88% got back encrypted data vs. the 97% cross-sector average), suggesting that the sector should continue to focus on strengthening backup use.
The proportion of manufacturing organizations paying higher ransoms has increased from our 2022 study, with 40% paying a ransom between $100,000 and $999,999 v 29% who paid this amount the year before. In addition, 20% reported payments of $1m or more compared to just 8% the year prior.
Sophos experts recommend the following best practices for organisations in manufacturing and across all other sectors:
Strengthen defensive shields with:
• Security tools that defend against the most common attack vectors, including endpoint protection with strong anti-exploit capabilities to prevent exploitation of vulnerabilities, and Zero Trust Network Access (ZTNA) to thwart the abuse of compromised credentials
• Adaptive technologies that respond automatically to attacks, disrupting adversaries and buying defenders time to respond
• 24/7 threat detection, investigation and response, whether delivered in-house or by a specialist Managed Detection and Response (MDR) provider
• Optimise attack preparation, including making regular backups, practicing recovering data from backups and maintaining an up-to-date incident response plan
• Maintain good security hygiene, including timely patching and regularly reviewing security tool configurations sophos.com
Building a smart factory requires a smart approach. Lucas Hale, ANCA’s Global Marketing Manager bring it all together. to make informed decisions is a substantial component of the smart factory. With data gathering at the very heart of smart factory procedures, utilising the cloud is fundamental to its operation. Using a cloud service provider (CSP) removes the need to invest in on-site server infrastructure, maintenance, and IT staff.
Over the past decade, new technologies have increasingly permeated the factory floor. Automation, always a part of manufacturing, has quickly escalated thanks to ever increasing computer processing power and data storage. At the same time, technologies such as artificial intelligence, the Internet of Things connectivity, cloud computing, big data analytics, 3D printing, and many others that were previously complex to install and configure have become affordable and scalable. They too have found their way into industrial applications.
This rapid acceleration of digital transformation has been termed Industry 4.0—the Fourth Industrial Revolution. A major outcome of this period has been that the truly connected factory, or smart factory, is a reality. As more machines begin to communicate with each other, productivity increases. Gains in efficiency, using analytical tools that can predict maintenance needs, improve it even more. But the real benefits of a smart factory are far beyond mere productivity. It provides the ability to predict and adjust to changes, both internal and external, to offer unprecedented agility and flexibility, and create real competitive advantages for a business.
While it's easy to see how automation increases productivity by speeding up processes, streamlining product movement between machines, and reducing errors, the real benefits of a smart factory come from a far broader concept.
Smart factories offer complete transparency by integrating machines, processes, and people into a single, digitally connected system. Sensors feed data from every element of the manufacturing process all the time, so the information reflects current conditions. It's then integrated with data from suppliers and customers to create a holistic view of upstream and downstream supply chain processes. This means any change from the expected can be instantly recognised and acted upon. Whether it's a difference in the availability of raw materials, a bottleneck in production, a shift in market demand, or an infinite number of other variables. And, of course, any necessary changes can be actioned either by human intervention or by autonomous decision-making.
The ability of the smart factory to predict future outcomes based on historical and real-time data offers benefits in all sorts of ways. From anticipating issues with inventory, to predicting quality problems, to monitoring areas of safety concern.
One significant opportunity offered by smart factories is predictive maintenance. Until now, organisations had to choose between maximising the life of a part at the risk of it failing and causing machine downtime or incurring the cost of replacing parts early, perhaps unnecessarily.
Predictive maintenance means, data gathered from connected, smart machines enables accurate prediction of when and where failures could occur, maximising the life of parts and minimising unnecessary downtime.
The pandemic has only accelerated the use of cloud applications around the world. The ability to access information from anywhere
The benefits include unlimited scalability, making it easy to grow without the need for additional infrastructure. Cost is usually tied to consumption, so you're only paying for what you use. And the CSP is responsible for updating and maintaining the operating systems.
While some people are concerned about security, the fact is that a reputable CSP is going to have much greater resources to put into cybersecurity to protect your data in its cloud than you could ever hope to have in an on-site system.
A smart factory is capable of optimising the use of every asset. It should result in lower downtimes, greater capacity, reduced changeover time, and more.
Detecting quality defects faster and identifying the cause, results in lower scrap rates and lead times, as well as better quality products. Just about every benefit of running a smart factory is likely to lower costs, increase efficiency, expand optimisation, establish more predictable inventories, improve predictive maintenance, and so on. There will also be benefits for both the environment and staff. Operational efficiencies may result in a smaller environmental footprint, while a reduction in the potential for human error should reduce the likelihood of industrial accidents.
It's also worth acknowledging that likely changes in labour markets means moving towards a smart factory operation can insulate you from a potential skills shortage in the future.
While the technology for building a true smart factory certainly exists today, it's unnecessary to change everything at once. In fact, an important attribute of the connected factory is that it'll continue to evolve as technology and requirements change. Build it incrementally, adding elements as you can. And ensure that you adapt the system to suit your business,
around.
The ANCA Integrated Manufacturing System (AIMS) is a modular manufacturing system that lets you add automation to one specific process or build an entirely connected production line. Custom built to your needs, it connects machines and processes to maximise productivity, improve quality, and free operators from doing simple tasks so they can be redeployed to more valuable projects.
Everything is controlled by an AIMS server, which manages data flows and machine programs, displays real-time machine activity and continuously gathers production data.
Investing in smart factory capability, at whatever speed, makes sense for your business, it really is inarguable. The benefits of agility, connectedness, and transparency are essential to enable you to function more effectively and efficiently in an ever-increasingly complex and rapidly shifting market. machines.anca.com
Siemens’ partner APS to manufacture and adapt critical technology for Australia’s energy transition in Adelaide.
Siemens and its national distribution partner APS Industrial (APS) announced the opening of a new manufacturing facility in Adelaide. The new facility will manufacture and assemble a range of critical technology, including Siemens' air circuit breakers (ACBs), and inject over 150 technology jobs into the local industry over the next 10 years.
Local Australian manufacturing will also help reduce current ACBs product availability lead times by as much as 50% and increase the footprint of locally manufactured systems.
Speaking at the announcement, Siemens Australia and New Zealand CEO Peter Halliday said, “This is the first time in the world that these Siemens products will be assembled and certified outside of a Siemens factory, giving the same quality assurances. This demonstrates the trust and ability of our national distribution partner APS Industrial. APS will adapt and assemble Siemens ACBs and peripheral equipment right here in Adelaide, which is good for jobs, good for industry and good for the economy.”
The ACBs are a critical component of energy transition across industries, helping provide safe power supply, protecting valuable equipment at manufacturing sites, built environments, mine sites, commercial buildings and any other infrastructure requiring a safe and secure source of electricity.
South Australian Deputy Premier Dr Susan Close welcomed the local investment saying, “Siemens and South Australia share a long history that goes back over 150 years. As South Australia continues to grow, we need like-minded partners like Siemens and APS that help build our sovereign capability and protect critical infrastructure and industry. This investment and commitment to future jobs further cements the technological prowess and capabilities of our state.”
The facility will enable APS to accelerate the delivery of ACBs to switchboard builders and electrical contractors who install and serve the Australian and New Zealand markets.
Speaking at the launch event in Adelaide, APS CEO David Hegarty said, “This is a significant investment for all of us – APS, Siemens and for local industry. Five years ago, APS was formed as Siemens’ master distributor in Australia and since then, we have grown significantly in size and scale as we’ve helped electrify and digitalise industries. One of the biggest challenges to the growth of our industries over the last few years has been global supply chain issues. The establishment of this new facility will reduce the reliance of global supply chains for a product that is critical to many applications and industries. We’re proud to support local industry and jobs and keep giving them access to best-in-class global technology.”
The new facility is conveniently located in Clarence Gardens, just a short distance from Adelaide’s CBD.
“Since we started our Australian operations in Adelaide in 1872 with the establishment of the Overland Telegraph, we’ve achieved several technology firsts with South Australia,” said Halliday. “I’m proud of our relationship with APS Industrial, and how this decision demonstrates an expansion of the Siemens footprint in South Australia and our long-term commitment to the state. With APS we are helping progress Australian industry and economy. We can’t expect industries to innovate and continue growth trajectories without access to the right resources. This is a significant move that helps address one of the most critical challenges being faced by industry today,” added Halliday. siemens.com
Full range of industry standard measuring equipment with many popular sizes supplied with calibration certificates.
Specialist range of digital ultrasonic & laser measuring instruments and gauges.
www.accud.com.au
Garth O’Connor-Price illustrates a tool to revive your manufacturing business. O’Connor-Price is a Director at William Buck, a leading firm of accountants and advisors.
In times of economic uncertainty, SME businesses are generally squeezed harder than larger ones, with fewer levers to help them navigate financial distress. This is particularly relevant for SME manufacturing businesses, which have faced headwinds in recent times caused by high inflation, increasing interest rates, supply chain issues and challenges sourcing skilled people.
This uneven playing field was improved with the introduction of the Small Business Restructuring (SBR) regime in 2021. SBR is a tool exclusively available to SME businesses to restructure their affairs, break the cycle of funding historical losses and set themselves up for future profitability.
To be eligible for the small business restructuring regime, a company must have:
• Liabilities of less than $1m
• No outstanding employee entitlements (i.e., superannuation), and
• Lodged and returned all outstanding lodgments to the ATO. It is also worth noting that a director can only use the SBR regime once every seven years.
• Assessment of eligibility criteria.
• Director makes declaration that company is insolvent or likely to become insolvent and appoints an SBR practitioner (registered liquidator) – this process mirrors that of the process to appoint a Voluntary Administrator.
• Director remains in control of business whilst the restructuring plan is finalised.
• SBR practitioner works with the company to prepare plan, makes reasonable enquiries into the affairs of the company, assesses debts and provides a report to creditors on the plan.
• Creditors are generally restricted from exercising enforcement rights during this period.
• Creditors consider plan, confirm or dispute assessed debt and cast their vote.
• Plan is accepted if at the end of the voting period the majority in value of creditors (exc. related creditors) vote in favour of the plan.
• The ATO has disclosed that to 30 June 2023, they were majority creditor in 92% of SBR matters and have voted in favour of 91% of SBR proposals.
• Company no longer subject to SBR regime and Director continues to control business without oversight of SBR practitoner.
• SBR practitioner monitors compliance with plan, collects contributions and distributes dividend to creditors.
A manufacturing business in distress is likely to have an escalation of trade and statutory creditors as declining performance requires that creditors are pushed out. However, it is also likely that the business may have equity locked up in equipment which could be used to address the build up of creditors. Below is an example of how this might work:
The above outlines the potential upside to a manufacturing business of creating a restructuring plan with its creditors. Factoring in current working capital and costs, unlocking $100k in equity to fund the SBR contribution could lead to an improvement in the company balance sheet of $350k. This result is based on the secured creditor increasing the company’s facilities with preservation of their security (i.e., plant and equipment) and unsecured creditors accepting a dividend of 26c on the dollar for their claims.
This result is likely to be a better one for all creditors than liquidation. If the company ceases to trade, employee entitlements will crystalise and the value of the plant and equipment would decrease, reducing the equity available to pay creditors.
The SBR contribution can be generated in several ways including a third-party injection of funds or future trading profits.
As noted above, the SBR is exclusively available to SME businesses. The alternative for larger distressed businesses or those that don’t meet the eligibility criteria for the SBR regime include a formal restructure through a Voluntary Administration or an informal restructure under Safe Harbour.
Please contact your local William Buck Restructuring and Insolvency advisors for further information.
Garth O’Connor-Price is a Director at William Buck.
William Buck is a leading firm of accountants and advisors. Ph: 03 9824 8555 williambuck.com
On 1 July 2023, the Australian government established the National Anti-Corruption Commission (NACC) under the National Anti-Corruption Commission Act 2022 (NACC Act) to combat corruption and lack of transparency within the federal government and address growing public concerns about corruption of public officials.
Given the potentially significant implications for various sectors, businesses that deal frequently with federal government agencies, including those in the manufacturing industry, should be particularly vigilant about its impact.
Established due to declining public trust in Australian institutions, the NACC's main objectives are:
• detecting and addressing corrupt conduct;
• investigating potential serious or systemic corruption; and
• educating the public about corruption and its effects.
Operating independently from government, the NACC has the authority to probe allegations within the Australian government public sector. It can investigate matters that adversely impact a public official's integrity, including misuse of office or mismanagement of information.
The NACC’s key powers include:
• accessing Commonwealth data and premises without a warrant;
• applying for search warrants to search other places, vehicles and people;
• compelling document production and appearance at hearings to give evidence;
• utilising covert investigative and surveillance techniques; and
• conducting public hearings, if in the broader interest. However, not all issues will be investigated with only cases of suspected serious or systemic corruption falling within the jurisdiction of the NACC.
The definition of 'public official' in the NACC Act is extensive. Including but going beyond members and staff of federal government agencies and the Australian Parliament, it encompasses contracted service providers – consultants, independent contractors, labourhire agents, and others linked to government services.
Corruption, per the NACC Act, is defined as instances where a public official breaches trust, misuses their role, or mishandles information. Such cases of corrupt conduct can include:
• misuse of information by a public official obtained in the course of performing official duties;
• bias or dishonesty by a public official in the course of conducting official duties; and
• private businesses or individuals trying to influence a government official to engage in corrupt conduct.
Referral of matters to the NACC are made through:
• voluntary referrals, which are open to anybody to refer a potential corruption issue to the NACC; and
• mandatory referrals, including Heads of Commonwealth agencies and Public Interest Disclosure officers, who are obligated to notify the NACC about any suspicious and serious corrupt activities.
Typically, under Australian law, individuals can decline to provide evidence regarding an offence they might have committed due to the privilege against self-incrimination. However, the NACC Act generally mandates that people must supply information, documents, or items to the NACC even if it might incriminate them. In addition, a person will not be excused from providing information, or a document required by a notice or direction to produce at a hearing, on the grounds that doing so would disclose legal advice given to a person, or a communication, that is protected against disclosure by legal professional privilege.
However, the NACC Act does include a safeguard which ensures that such incriminating details will not be admissible as evidence against the individual in criminal proceedings, proceedings for the imposition or recovery of a penalty, or confiscation proceedings. There is also a protection against enforcement of contractual, or other remedies or rights, based on the disclosure made to the NACC.
On concluding investigations, the NACC Commissioner will release a report detailing findings and recommendations. These might range from individual actions to policy rectifications. Some evidence might be shared with the police or prosecutors if deemed criminal. Agencies must respond to these recommendations within a set timeframe.
The NACC’s scope of jurisdiction is not limited to public officials. Any action made by a private entity influencing, or trying to influence a public official to engage in corrupt conduct can be considered a breach. This may include unduly pressuring an official during a tender process or offering any kind of reward, financial or otherwise, to a public official in return for a ‘favour’.
It is important for businesses in manufacturing industries that deal with various federal government agencies and officials on a regular basis to be aware of the implications of the NACC Act. We urge businesses to educate their teams about NACC regulations, ensuring compliance and safeguarding against potential breaches.
With the arrival of the NACC, businesses, including those in manufacturing, must be cautious and informed about their engagements with government officials.
If you are an Australian company or individual requiring advice on any aspect of the NACC Act, or would like to discuss the NACC in greater detail, please contact Andrew Hudson, Partner, on (03) 9321 7851 or Alexander Uskhopov, Lawyer on (03) 9321 7806. rigbycooke.com.au
AMTIL recently attended the EMO Exhibition in Hannover and manned a stand in the International Association pavilion. With over 1,850 exhibitors from 42 countries, EMO is the largest machine tool and manufacturing technology exhibition in the world, recording over 100,000 trade visitors.
Once again ANCA held the fort for Australian manufacturing, highlighted by the release of their latest machines, the MicroX and EPX-SF. Unveiling the MicroX machine was a big deal as it was the first time the market has seen this premium technology that is a dedicated machine for micro tools. ANCA’s EPX-SF is a specialised solution for precise edge preparation. Both machines are backed by almost 50 years of ANCA innovation.
Back at the AMTIL stand we had a steady stream of visitors wanting to know more about the industry, looking for agents or just having a chat with some Aussies. We also had many great catch ups with our equivalent associations from 26 countries around the world, making it a very worthwhile show for us. I attended the International General Managers meeting which created some lively discussion on new and emerging technologies (see page 10 for more information). I am also on the Steering Committee for the Oxford Economics Global Machine Tool Forecast which we commission to have produced every six months. This report contains a lot of interesting overseas information around machine tool sales, industry sectors and growth opportunities and is available free of charge to AMTIL members by accessing the Members Portal of our website.
Of course like most overseas events there was the customary Gala Dinner, Welcome Reception and Exhibitor parties to attend. Social networking at its very best. All in all a great event and one I would encourage most machine tool buyers to visit at least once in their career.
AMTIL site visit to Eilbeck Cranes in Ingleburn, hosted by Charlie Eilbeck.
Midway through August, AMTIL’s Corporate Manager Greg Chalker took a group of AMTIL members on a visit out to Ingleburn in New South Wales to an open-site day with Charlie Eilbeck at Eilbeck Heavy Machining. About 12 AMTIL members came along to tour the facilities alongside a representative from the Department of Employment and Workplace Relations (DEWR).
“We saw some of the finest heavy CNC machines kicking around. Big machining centres, one was a double column with an eight metre by three and a half metre travel on its table. A very nice machine. Another was a nice multi-tasking lathe with full 5-axis milling and six metres between centres. We then went over to Charlie’s second
machine and fabrication shop where he has new borer 13 metres on its x-axis, six metres on its y-axis and an 80 tonne rotary table. Big fabrications and big machining,” said Chalker.
Greg invited the DEWR representative along to get a taste of what our members are always talking about. “I wanted our colleague from DEWR to have the opportunity to get it firsthand,” he said. “I wanted DEWR to see some of our better machine shops, and to make certain that Canberra knew that manufacturing is not dead in Australia. It's very much alive and this is what it looks like.” eilbeckcranes.com amtil.com.au
There was a great turn-out at the Tonsley Innovation Precinct in Adelaide for the AMTIL site tour.
AMTIL ran a very successful networking function at Tonsley Innovation Precinct on August 17th in Adelaide, SA. Ten years ago, the South Australian Government converted the entirety of the old Mitsubishi vehicle assembly plant into a venue for startups, established companies and education hubs. The concept was brave, inspiring, and ultimately, very successful. In fact, around 2,000 people across 140 companies are now employed at Tonsley – more than double than when Mitsubishi closed. 8,500 students study alongside this highly skilled and specialised workforce each year at anchor academic institution Flinders University, and TAFE SA. And more than 500 residents call Tonsley home as part of its growing community.
Around 26 particpants came along to attend the AMTIL session and the feedback from our members has been excellent. Philipp Dautel, the Tonsley Precinct Director was a very capable tour director and MC as well, showing us all through the sectors where companies opened up for the group and speaking about the history, the work being done now and the future plans in store. A few of the participants in the walk in fact stepped forward to extol some stories from back when the place was still a car factory.
Stuart Davis, the Acting Deputy Director of Industry Programs at the Australian Industrial Transformation Institute, at the Factory of the Future also spoke about the South Australian and National program to assist SMEs in exploring technologies within Factory of the Future. We also heard from Callan Marwick, the Executive Director, Industry and Workforce Capability in the Department of Industry Innovation and Science in South Australia, speaking about the many ways the SA Government is stepping up to help manufacturers with industry advice and direction.
This industry district is located 12km south of Adelaide, and has made dramatic strides since opening in 2012. From its initial remit to re-ignite a stalling manufacturing sector in Adelaide’s southern suburbs following the closure of the Mitsubishi plant in 2008, to now solving some of the world’s most complex problems through creative innovation.
As a hub for cutting-edge research and development, Tonsley has driven Adelaide’s transition from traditional to high-value manufacturing and with it, built out the state’s sovereign capability. sa.gov.au flinders.edu.au tonsley.com.au amtil.com.au
Aim high with the help of a Global Footprint Scholarship.
If you are a Vocational Education and Training (VET) student trained in agriculture, horticulture or a trade like metalwork or another field of manufacturing, this may be for you. Since 1983, more than a thousand young Australians have travelled the world with this scholarship program and returned to Australia ready to share ideas, knowledge, skills, and networks to inspire others.
Ryan Hepplewhite was the 2018 Sheet Metal Scholar with Global Footprints Scholarships and Big Brother, and winner of the $8,000 travel grant to go overseas for a unique industry experience. This program, previously known as BBM Scholarships, is all about sustainability and supporting young people to create the future they want for themselves and their planet.
Hepplewhite first started his journey to be a metal fabricator when he was 13 years old, playing around in the yard at home in Mt Keira, NSW. First came a trolley for his cycle to help move his shovels around when creating dirt bike jumps. Simple things. Next came his passion to create parts to make a go-kart.
“I picked metalwork as an elective at high-school and enjoyed making useful hand tools for myself,” he said. He loved making things he knew would last a lifetime. He did some work experience at Coastwide Engineering once he was old enough and was offered an apprenticeship by them. They’d seen his enthusiasm to get back to work as soon as possible.
“Once working, I soaked up all the knowledge I could,” Hepplewhite continues. He doesn’t know how he found out about Global Footprints, but he won First Place at the regionals, and won Gold at the National WorldSkills competition.
In 2018 as a fourth-year apprentice, Ryan applied for a scholarship to travel overseas with his skills. His workplace selection was the WEC Group in Darwen UK.
“My Global Footprints Scholarship gave me an opportunity to travel and learn my trade in another country,” he said. “I was able to travel on my own and continue seeing parts of the world I’d never been to.” Ryan was learning a broad range of techniques, industry standards and sustainability in his trade. “I met a lot of smart people who were willing to give me advice and guidance to better me as a tradesman," Hepplewhite said. “The history of fabrication dates back such a long time in the UK. It was a great experience seeing the craftsmanship in even the smallest of details.”
“I’ve become a more knowledgeable and better tradesman, leader, and person. I am enormously proud of what I’ve been able to achieve in my trade with the help of many others,” he said. “I have now been given the opportunity to pursue another trade in the industry, that being an industrial electrician. My skills as a fabricator have already helped me so much learning another trade.”
“I cannot wait to see what the future holds or where I’ll end up, but I know I’m lucky to have had the opportunity with my scholarship to explore what another part of the world could teach me,” he added. Global Footprints Scholarships open every year at the start of May. Ryan Hepplewhite first started his journey to be a metal fabricator when he was 13 years old, playing around with things in the yard at home in Mt Keira trying to figure out how he could improve around him. First came a trolley for his cycle to help move his shovels around when building dirt jumps. Simple things. Next came his passion to create bits and pieces to make a go-kart. globalfootrpints.org.au
Please join us for breakfast at the AMTIL 2023 AGM and hear our guest speaker, Taylor Nugent, from the National Australia Bank, presenting an ‘Australian Economic Overview.’
Presenter Taylor Nugent is an Economist within the Global Markets Research team at the National Australia Bank (NAB). In this role, he provides commentary and insights for our clients on the domestic and global economy and financial markets, with a focus on the Australian economy. Taylor studied economics at the Australian National University and began his career at the Reserve Bank of Australia, where he worked as an economist and financial markets analyst.
Following the guest speaker presentation, the AGM is an opportunity to hear about AMTIL’s latest plans and initiatives plus reports on the previous year’s activities. We will also be recognising and awarding our 10 and 20 year members.
Details:
Date: Thursday 26th October, 2023
Time: 8:00am - 11:00am
Breakfast served at 8:00am
Venue: Riversdale Golf Club, Mount Waverley, Victoria
Presentation: 8:45am, followed by Annual General Meeting
Pricing: Free for AMTIL and AM Hub Members
Non-members $49
Registration essential
Parking: Free parking is available at the venue.
AMTIL would like to welcome the following companies who have signed up as new members of our association.
ABRASIVESTOCKS PTY LTD
53 Bainbridge Street ORMISTON, QLD 4160 abrasivestocks.com.au
ACCENTIS PTY LTD
Suite 10, 82 Buckland Road NUNDAH, QLD 4012 accentis.com.au
ACCURPRESS AUSTRALIA PTY LTD
P.O Box 504 MOOLOOLABA, QLD 4557 accurpress.com.au
ALLIED TELESIS
Suite 301, 448 St Kilda Road MELBOURNE, VIC 3000 alliedtelesis.com.au
ALLOYS
40 Koornang Road
SCORESBY, VIC 3179 alloys.com.au
AMCCS PTY LTD
9A Pembury Road
MINTO, NSW 2566 aesenvironmental.com.au
BARON RUBBER
Suite 5, 15 Lakeside Drive BROADMEADOWS, VIC 3047 baronrubber.com.au
BAR’S LEAKS AUSTRALIA 41A Bay Road TAREN POINT, NSW 2229 barsleaks.com.au
BIESSE 473 Victoria Street WETHERILL PARK, NSW 2164 biesse.com
CGB PRECISION PRODUCTS PTY LTD
Unit 9, 32 Silkwood Rise CARRUM DOWNS, VIC 3201 cgb.com.au
CLEAR21
Level 1, 6-8 Compark Circuit MULGRAVE, VIC 3170 clear21.com
It was close right to the very end –much like the football onfield, but a HUGE congrats goes to Porsche Man – crossing the finish line ahead of AMTIL's CEO Shane Infanti with D-Ricks coming in third – a great effort by all. At the time of print the Preliminary Finals will be hottly contested by the Pies and GWS at the MCG, with Brisbane ready to take on the fairytale of the season that is Carlton on on their home deck in Brisbane. The Blues were ready to sack the coach and since their win against the Suns have hardly put a foot wrong. Melbourne out in straight sets for the second time in two years has really has missed on the opportunity – play a better brand and system – win instead of whine! I myself think the Pies might edge out Brisbane for the chocolates, but who knows. Thanks for the fun during the year. Till next season… Sanchez
ROUND 24
1 Porsche Man 150 (751)
DULL LTD
Level 17, 447 Collins Street
MELBOURNE, VIC 3000 dull.net
2 Shane Infanti 149 (695)
3 D-Ricks23 149 (749)
4 blsmithy 148 (687)
5 BrickyP 148 (706)
6 Rokay Raggy! 147 (713)
7 Motörhead 147 (735)
8 Pmart9 146 (770)
AXT Pty Ltd
1/3 Vuko Place
WARRIEWOOD, NSW 2102 axt.com.au
EMBEDDED LOGIC SOLUTIONS 5/23 Hunt Street
NORTH PARRAMATTA, NSW 2151 emlogic.com.au
9 SondogsV2 146 (808)
10 Jas255 145 (708)
Due to the ongoing Coronavirus pandemic, many industry events world-wide have been postponed, rescheduled or cancelled. Readers are advised to check with all event organisers for the latest information. For the latest international travel advice, please visit health. gov.au/health-topics/novel-coronavirus-2019-ncov – For more events, please visit amtil.com.au/events
INTERNATIONAL
METALEX
VIETNAM, Ho Chi Minh
4-6 October 2023
metalexvietnam.com
METAVAK NETHERLANDS, Gorinchem
10-12 October 2023 metavak.nl
3D PRINT CONGRESS & EXHIBITION
FRANCE, Paris
11-12 October 2023
3dprint-exhibition-paris.com
AI EXPO
JAPAN, Tokyo
25-27 October 2023
nextech-week.jp/hub/en-gb/exhibit/ai.html
CAMX
USA, Atlanta
30 October-3 November 2023 thecamx.org
WESTEC
USA, California
7-9 November 2023
westeconline.com
MACTECH EGYPT, Cairo
9-12 November 2023 mactech-eg.com
PLAST IMAGEN
MEXICO, Mexico City
12-18 November 2023 plastimagen.com.mx
METAL MADRID
SPAIN, Madrid
15-16 November 2023
advancedmanufacturingmadrid.com
METALEX
THAILAND, Bangkok
22-25 November 2023 metalex.co.th
MANUFACTURING INDONESIA
INDONESIA, Jakarta
6-9 December 2023
manufacturingindonesia.com
SEMICON, JAPAN
JAPAN, Tokyo
13-15 December 2023
semiconjapan.org
STEELFAB
UAE, Sharjah
8-11 January 2024
steelfabme.com
EUROGUSS
GERMANY, Nurnberg
16-18 January 2024
euroguss.de/en
IMTEX FORMING
INDIA, Bangalore
18-23 January 2024 imtex.in
SEMICON KOREA
KOREA, Seoul
31 January-2 February 2024 semiconkorea.org
ATX WEST USA, Anaheim
6-8 February 2024 imengineeringwest.com
SIMODEC
FRANCE, La Roche-Sur-Foron
4-8 March 2024 salon-simodec.com
ASIAMOLD CHINA, Guangzhou
4-6 March 2024 asiamold-china.cn.messefrankfurt.com
ALL ABOUT AUTOMATION
GERMANY, Friedrichshafen
5-6 March 2024 allaboutautomation.de
KONEPAJA
FINLAND, Tampere
19-21 March 2024 konepajamessut.fi
CCMT MACHINE TOOL FAIR
CHINA, Pudong
8-12 April 2024 ccmtshow.com
MACH
UK, Birmingham
15-19 April 2024 machexhibition.com
SIMTOS
KOREA, Goyang
22-26 April 2024 simtos.org
NPE USA, Florida
6-10 May 2024 npe.org
3D PRINT CONGRESS & EXHIBITION
FRANCE, Chassieu
4-6 June 2024
3dprint-exhibition-lyon.com
INTERTOOL
AUSTRIA, Vienna
4-7 June 2024 intertool.at
MMMM
INDIA, New Delhi
29-31 August 2024 mmmm-expo.com
AMB
GERMANY, Stuttgart
10-14 September 2024 messe-stuttgart.de
BI-MU
ITALY, Milan
9-12 October 2024 bimu.it
EUROBLECH 2024
GERMANY, Hanover
22-25 October 2024 euroblech.com
JIMTOF 2024
JAPAN, Tokyo
5-10 November 2024 jimtof.org
ADVANCED DESIGN & MANUFACTURING EXPO
CANADA, Montreal
13-14 November 2024 admmontreal.com
METEC INDIA
INDIA, Maharashtra
27-29 November 2024 metec-india.com
ICC SYDNEY, DARLING HARBOUR
17-19 APRIL 2024
The ONE event that showcases the latest innovations, technologies and equipment in the advanced manufacturing sector. Explore new opportunities, meet and network with industry leaders and technology experts, all under ONE roof at ONE show. australianmanufacturingweek.com.au
IMARC
ICC SYDNEY
31 OCT–2 NOV 2023
The International Mining and Resources Conference (IMARC) is where the most influential people in the mining industry come together, delivering ideas, inspiration and serving as a meeting ground for industry. From ground-breaking technology, worldclass content, to a vivid showcase of all the elements that make the mining industry great. imarcglobal.com
WA MINING
PERTH EXHIBITION CENTRE
11-12 OCTOBER 2023
As technology accelerates, it has never been more important for mining companies to connect with suppliers. WA Mining’s exhibition will showcase the latest technical and digital innovations across the entire mining value chain. waminingexpo.com.au
WASTE EXPO AUSTRALIA
MCEC, MELBOURNE
25-26 OCTOBER 2023
Waste Expo Australia is the country's largest gathering of waste management and resource recovery professionals, which brings together leading solution providers in the waste management, recycling, resource recovery and sustainability sectors. wasteexpoaustralia.com.au
AUSBIOTECH
BRISBANE, QUEENSLAND
1-3 NOVEMBER 2023
Biotechnology Industry Forum in Australia. AusBiotech is dedicated to the development, growth and prosperity of the Australian Biotechnology Industry. ausbiotech.org
AUSRAIL
ICC SYDNEY
13–16 NOVEMBER 2023
AusRAIL Plus has always been a highlight on the rail industry calendar and 2023 is set to be bigger than ever as we welcome rail leaders from Australia, New Zealand and the world to discuss the achievements, opportunities and emerging trends in the industry. ausrail.com
WA MAJOR PROJECTS CONFERENCE PERTH CONVENTION & EXHIBITION CENTRE
28-29 NOVEMBER 2023
Western Australia’s largest major projects & infrastructure conference attracting over 250 delegates each year. Topics covered –Transport, housing, health, education, energy & water. waconference.com.au
MELBOURNE CONVENTION & EXHIBITION CENTRE
12-15 MARCH 2024
Australasia’s Processing and Packaging Expo is an exhibition that will truly represent all sectors of the industry, including machinery, ancillary equipment, materials and packaging, food processing and industry services. It will provide a comprehensive range of all processing and packaging equipment and services under one roof. appex.com.au
I told them if private enterprise doesn't build an Australian car, the Australian Government will.
We set out to impress them with a presentation that would run like a well-drilled floor show at the Diamond Horseshoe. For three weeks we worked on our production, with a staff of GM people seconded to us to help “get the show on the road”. We had them all working flat out: eighteen stenographers, seven photographers and photographic reproduction men, two statisticians, plus experts from GM finance, materials and manufacturing divisions. Huge blowup pictures showing Australian scenes and views of GMH plants in operation in Melbourne, Adelaide and Sydney, some measuring five feet by four feet, were made. Big coloured charts of production costs, freight costs, output increases and sales increases were prepared to add to those we had brought with us from Australia. Movie films and pictures of Australia, with special synchronised commentaries, were prepared. The visual story would be just as important as the spoken one in this project. At the end of three weeks of non-stop work it was finished. If it wasn’t the finest presentation of Australia ever prepared for the enlightenment of Americans, I’ll eat my hat.
The title of our show was, Australia-GM’s Performance and ResultsManufacture of Complete Motor-Cars in Australia Hollywood might have called it Pacific Powerhouse, and they wouldn’t have been inaccurate. It was scheduled to go before the committee for the first time on 20 September, 1944. On 17 September, after we’d checked over the whole of the presentation, I wrote a personal note to J. K. Jensen, in Australia.
“So far, all of our arranged facts look unbeatable,” I wrote. “However, you can never tell with these fellows. They only have to hear some stupid radio report or read in a newspaper, ‘Wharf Strike in Australia: Soldiers have to Unload Ships’, and they’ll just as likely go off in the wrong direction.
“I intend boring hard on getting GM to do the job. If I fail, I will leave General Motors, and if I can get a hearing with the Government, get the capital in Australia and England and get it done under my own banner. I’ve set my course on getting a car made, as you know. I believe it is a sound and good proposition. I feel there is a fifty-fifty chance that GM will say ‘Yes’. But if they don’t, count me in under some other heading.”
That, I think, proves the measure of my conviction that the car should be made.
Our big day, 20 September, was another heat-wave day. When I went into the executive conference-room to put forward our case, everyone had his coat off. Some of the men were fanning themselves. At a long table, facing the big blown-up pictures and a large map of Australia, sat the top executives of the General Motors Corporation. I had spent weeks planning the tactics I would adopt. I decided the best opening gambit would be to outline the potential for development in Australia and to tell of the country’s great wealth of natural resources.
Jack Horn and I had spent weeks planning the tactics I would adopt. We decided the best opening gambit would be to outline the potential for development in Australia, and to tell of the country’s great wealth of natural resources. The higher up the ladder in the managerial structure of General Motors, the more experienced, practical and technical the top men are. My strengthand I was playing it to the full-was that I knew in every detail what was involved in designing a body, in designing dies and tools, and then producing them. I felt myself fortunate that here at the top of General Motors were men who would take facts and statements, and, if convinced, would accept them and decide fairly. They didn’t give weight to ‘airy-fairy’ generalisations. Nor did I.
So I led off on the iron-ore deposits and the coal and lime-stone, the steel and the character of that steel, the lead, zinc, copper and tin. I told them of the long ocean hauls to bring things into the country, and how
Australia in the war had shown its ability to fend for itself industrially. I told them that 82% in value of all the spare parts we sold in Australia were made in Australia: the radiator cores, valves, pistons and rings, and so on. I discussed population growth, economic wealth, the importation of motor chassis and components, the wastefulness of having to keep pace with overseas body designs. Step by step I went through my story: it was the best, most fervent “sell-Australia” story ever told.
Half way through my address, the chairman of GM, Alfred P. Sloan, a crusty old Tory, who, I always thought, considered me too venturesome, interrupted me with the remark, “I don't like this country, Australia. It’s a socialist sort of place: the Government owns the railroads, doesn’t it?”
I said, “Yes, Mr. Sloan. Because private enterprise didn’t want to build railroads, the Government had to. The Government also owns the telephones.” “There you are, you see,” he said, turning to the other members of the committee. “It’s a goddaqi socialist set-up. That’s just what we don't stand for in the United States.”
I said, “Mr. Sloan, private enterprise in Australia simply couldn’t tackle a job like the telephone system. Nobody would do it but the Government.”
He said, “And I suppose you’re going to say that about the automobile, too?” “Yes, I am. I’m quite sure of it,” I said. “If private enterprise doesn't build an Australian car, the Australian Government will. They really believe it’s essential.”
To be continued…
Recent legislative changes all point to a shift towards promoting innovation and entrepreneurship and away from a penal system that stigmatises failure. In times of economic uncertainty, this shift should encourage company directors to seek assistance at the first sign of distress.
William Buck's restructuring experts can take you through the options available to deal with financial distress, including: