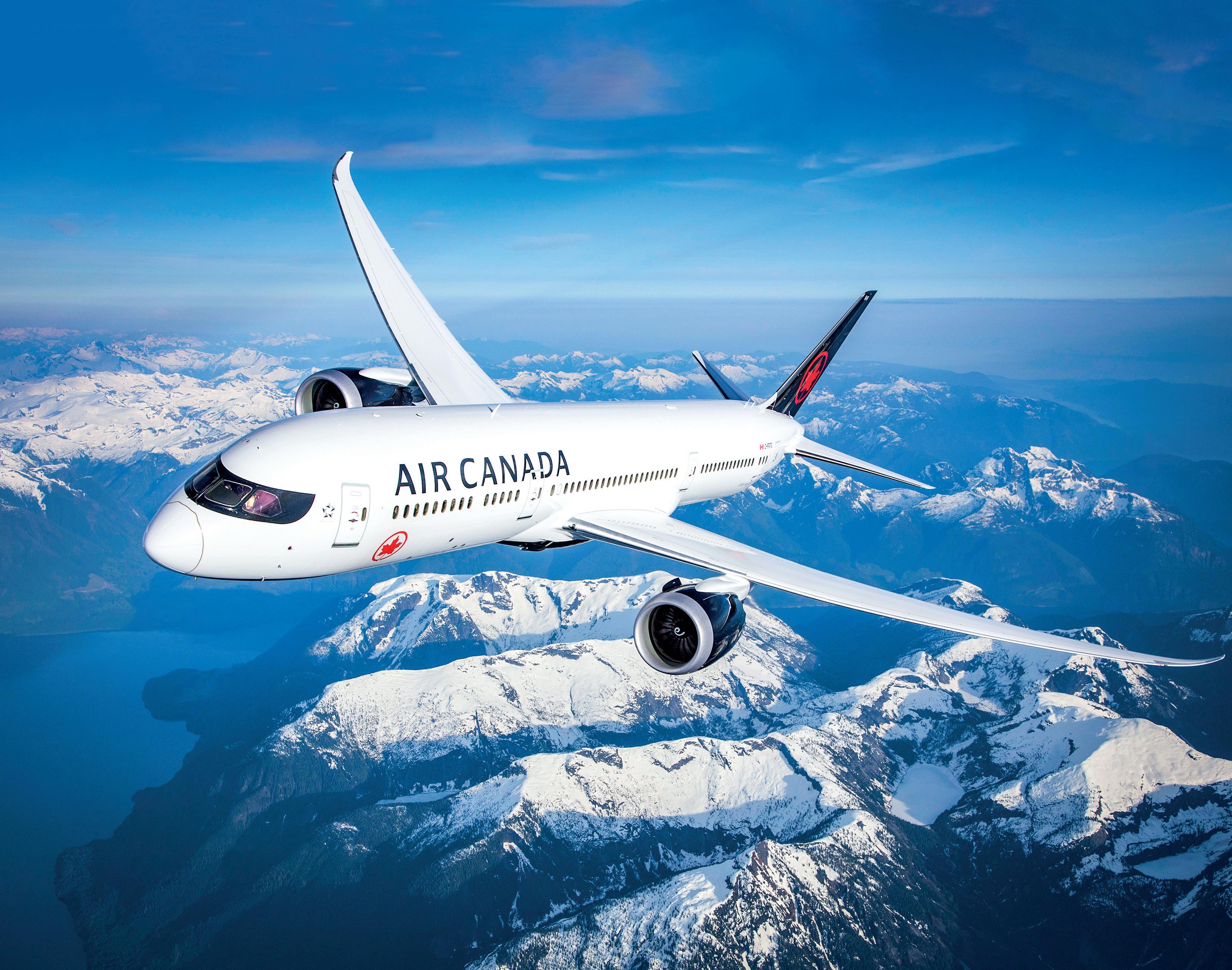
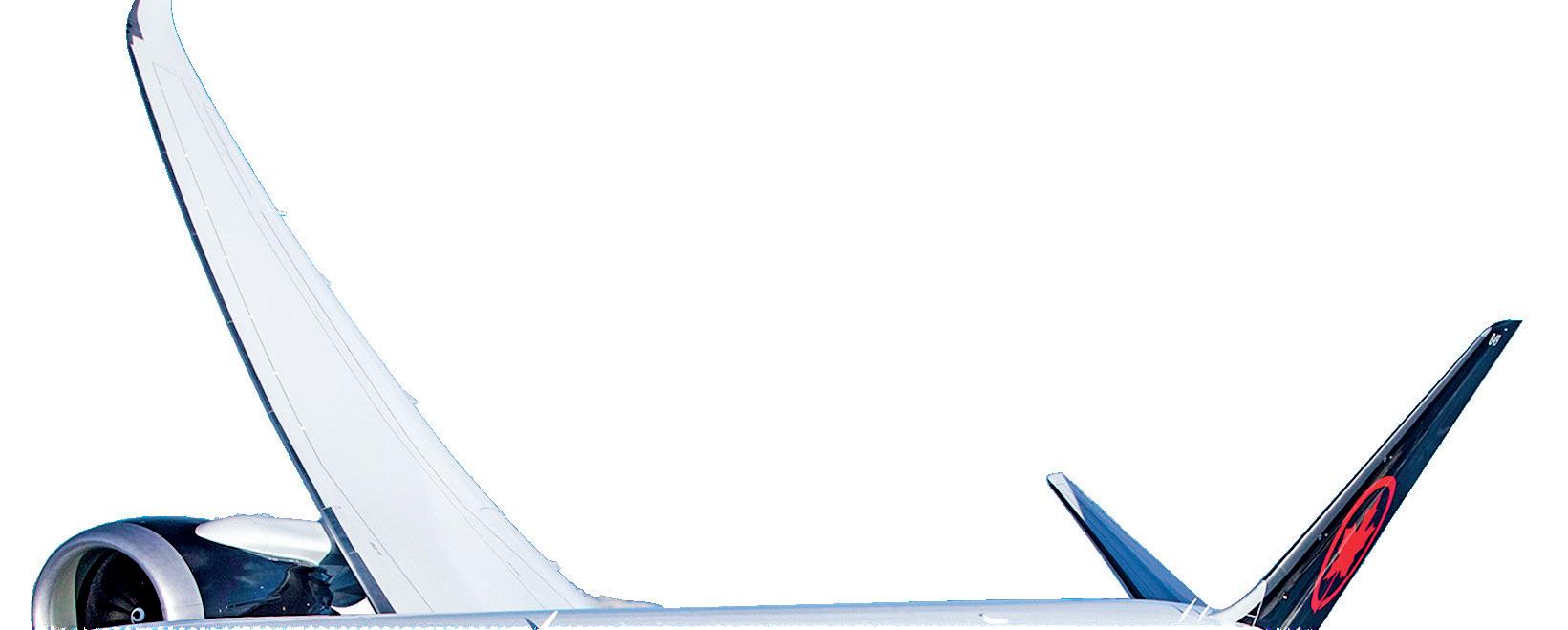
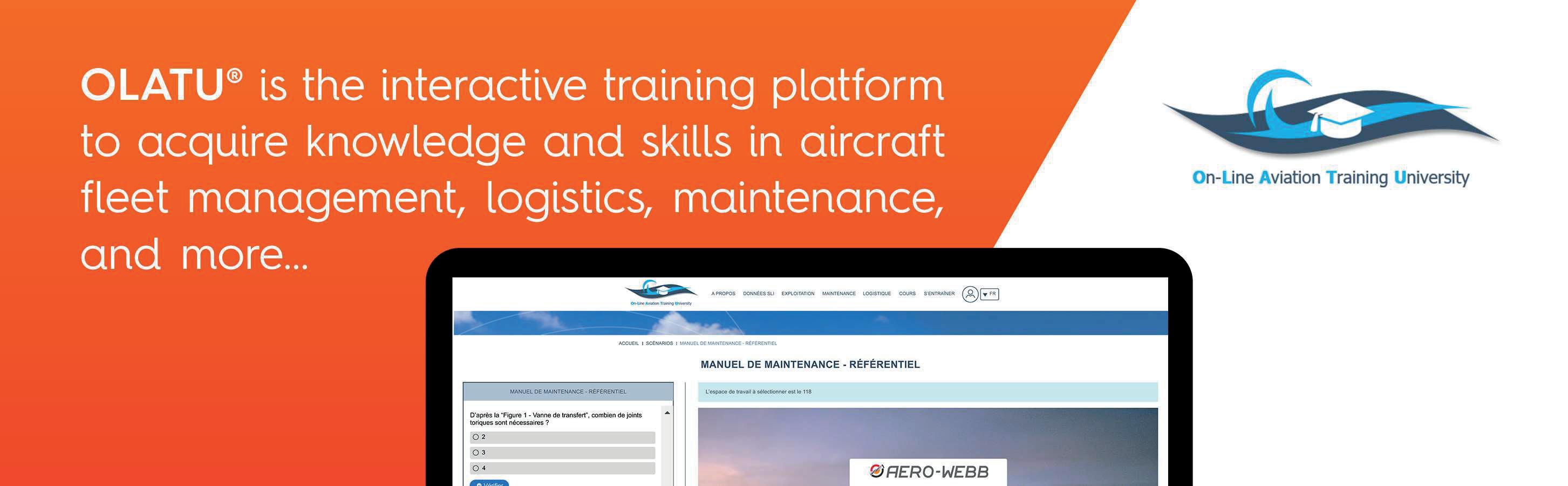
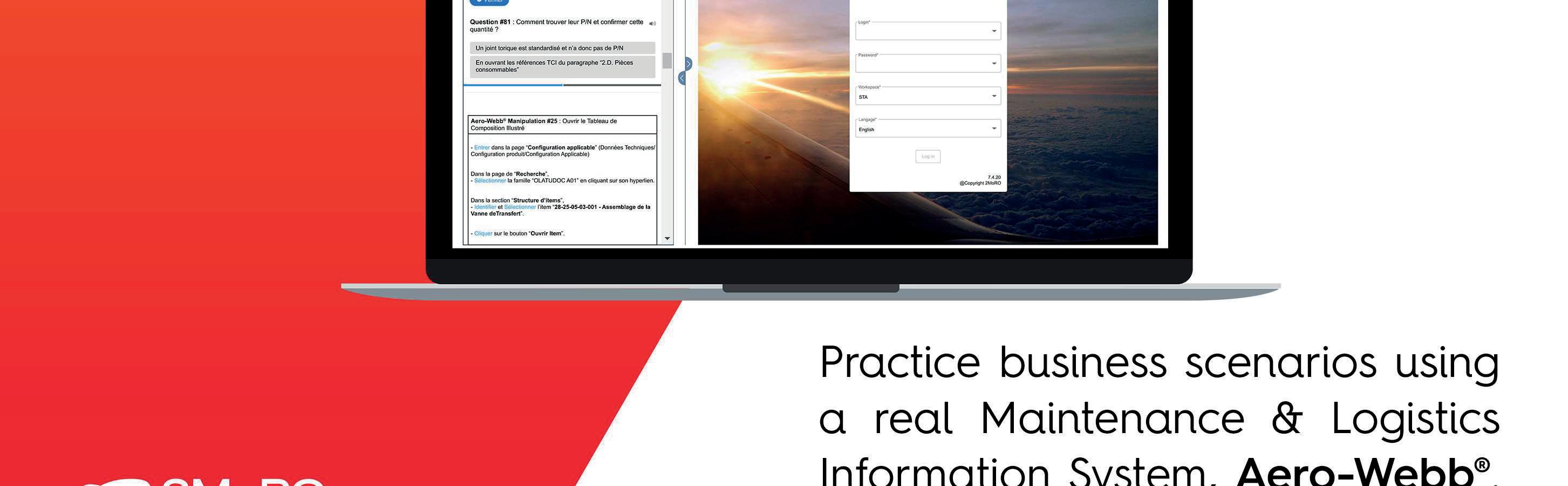
Publisher/Editor
Ed Haskey
E-mail: ed.haskey@aircraftit.com Telephone: +44 1273 454 235 Website: www.aircraftIT.com
Chief Operating Officer
Scott Leslie E-mail: scott.leslie@aircraftit.com
Copy Editor/Contributor
John Hancock E-mail: john@aircraftit.com
Magazine Production
Dean Cook
E-mail: deancook@magazineproduction.com
AircraftIT MRO is published bi-monthly and is an affiliate of Aircraft Commerce and part of the AviationNextGen Ltd group. The entire contents within this publication © Copyright 2021 AviationNextGen Ltd an independent publication and not affiliated with any of the IT vendors or suppliers. Content may not be reproduced without the strict written agreement of the publisher. The views and opinions expressed in this publication are the views of the authors and do not necessarily reflect the views or policies of their companies or of the publisher. The publisher does not guarantee the source, originality, accuracy, completeness or reliability of any statement, information, data, finding, interpretation, advice, opinion, or view presented.
As we approach the end of 2022, we might be tempted to heave a sigh of relief but maybe we’d better not tempt providence. We started the year still living with the effect of a pandemic and, more importantly, with the changes it had brought about for the airline and operator industry. Solutions and technologies that had once been ‘nice to have one day’ were now ‘must have in order to be able to operate’. Apart from anything else, there has been a significant change in the proportions of fleets that could be described as intelligent aircraft which generate huge quantities of data; but data is of little value if it cannot be sent to the right place and applied usefully. In this issue, we look at several aspects of digital technology, data and connectivity.
Our article from Lufthansa is about their A350 aircraft which use Rolls-Royce Trent XWB engines that generate large volumes of data which Rolls-Royce can use to improve performance and reliability; but the trick is how to get the data from the engines to Rolls-Royce and get the results back to the users. The article examines the high-quality data exchange solution that does the job. Air Tahiti is in a unique situation being geographically distant from almost anywhere else which means that they have to be self-reliant when it comes to MRO and stores. The airline needed a solution that would improve productivity in maintenance planning, stores management, airworthiness and utilization of the fleet.
An integrated M&E system has delivered all of that. With digitalization and mobile working comes a growing fleet of tablets and smart phones as well as the airline’s usual IT devices. From Air Canada you’ll read about the challenges of running several fleets of different devices and how they were resolved by a third-party device management solution that not only controls the devices but also ensures they are all synchronized for efficiency and regulatory compliance. Finally, we have an article about how Air Europa managed to implement a suite of software and mobile apps during the pandemic. Not just that but also what benefits the airline has gained and its plans for the future of the solutions.
The column in this issue, ‘What IT can do’, focuses on the challenge of getting ever larger volumes of data to ever growing numbers of applications which can turn it into useful information and get that information back to the people who need it. As usual, it wouldn’t be Aircraft IT without our vendors and, in this issue, Ultramain Systems, Swiss AviationSoftware, QOCO Systems and Exsyn Aviation Solutions all complete their Job Cards for you. Add to that our regular round-up of news and technology developments and the comprehensive ‘MRO Software Directory’ and you have Aircraft IT MRO: ideas and new developments that will improve your business today.
Wishing all readers a very happy New Year 2023.
Aircraft IT MRO: In so many ways, connectivity is the key component in successful use of IT solutions
Keeping up with what is happening in a complex and evolving business world is a challenge. At Aircraft IT MRO or here in the Aircraft IT MRO e-journal the latest developments are sorted and ready to read.
Keith Dugas, Director, Maintenance AI & Connected Operations, Air Canada
How Air Canada took control of the management of several fleets of devices and how synchronicity was achieved to meet exacting commercial and regulatory requirements.
Rutger Krom, shares the continuing drive within EXSYN to help airlines and MROs manage aircraft airworthiness and maintenance data
In the first of our Q&A pieces, Rutger Krom, Senior Aircraft Data Consultant and NEXUS Solution Architect, Exsyn Aviation Solutions, completes his ‘Job Card’ for Aircraft IT.
Julien Lebeau, Project Manager, Air Tahiti
How an integrated M&E system has enhanced productivity and efficiency for Air Tahiti and how IT has played key role in improving maintenance planning, stores management, airworthiness and utilization of the fleet.
John Warren explains how Ultramain’s pioneering commitment to paperless processes has freed clients to concentrate on what matters
In the next of our Q&A pieces, John Warren, Executive Vice President, Ultramain Systems, completes his ‘Job Card’ for Aircraft IT.
Lena Duken, Airworthiness Engineer, Deutsche Lufthansa AG and Jeff Winter, Senior Consultant, Deutsche Lufthansa AG
Lufthansa has a modern fleet of smart aircraft with connected Rolls-Royce engines and a new MRO/M&E management system. To get the best return from both needed a high-quality data exchange. This is what was implemented.
Andy Graham, knows that honesty and a continuing focus on quality have made QOCO the success it is today
In another of our Q&A pieces, Andy Graham, Chief Commercial Officer and Partner at QOCO Systems, completes his ‘Job Card’ for Aircraft IT.
Juan Miguel Sánchez García and Francisco De Borja Mas Boned
The process and challenges of implementing a suite of software and Mobile Apps during the world’s worst pandemic are covered, along with the benefits Air Europa is seeing from the new system and plans for the future.
Henrik Ollus, Customer Success Manager at QOCO Systems ltd. While unprecedented volumes of data are available to airlines and operators today, getting that data to a place where it can be used is a challenge.
Fabiano Faccoli, shares the enduring commitment to quality and customer service that has made Swiss AviationSoftware successful
In our final Q&A piece, Fabiano Faccoli, CEO of Swiss AviationSoftware Ltd., completes his ‘Job Card’ for Aircraft IT.
A detailed look at the world’s leading MRO IT systems
We were very pleased to welcome two new vendors to the Aircraft IT panel RecoSense Infosolutions Pvt Ltd offers an AI-powered platform for document analysis and data centralization. The platform powers Process Automations and Compliance Management with MROs in the Aviation Industry. RecoSense works as an Engineering partner with customers to build enterprise-specific solutions. Users can automate processing of manuals, process forms, M&E/MRO Records, job cards (Routine/Non-routine even handwritten), Logbooks, EOs, Technician reports, SFR’s, compliance, inspection reports, etc. with context, and can extract key Aviation metrics for analysis. The NLP-backed DocuSense platform swims through millions of documents to extract and consolidate the most relevant, insightful information for valuable investment data. It automates the process, which might take 1000s of manual hours, thus reducing Turn Around Time (TAT) while increasing operational performance and compliance through user-friendly interfaces. The platform not only evaluates the data but also can understand context through its unique knowledge graph.
ADE is a wholly-owned subsidiary of Capital A Berhad and based in Kuala Lumpur, Malaysia. The business leverages the AirAsia’s Engineering Department’s best practices and unsurpassed combined experience in the region. ADE offers a range of aircraft services focused on the Airbus A320, A321 & A330 for
engineering maintenance services, component and warehouse services, and engineering support services.
Equipped with state-of-the-art infrastructure and facilities and vast experience in airline engineering managing the world’s best low-cost airline, ADE aims to uphold the highest standards when it comes to professional integrity, quality and reliability; driving greater efficiencies and safety, for customers.
The operation is driven by big data, innovation and state-of-the-art digital technologies. Being a fully integrated digital company, ADE strives for operational excellence through enhanced visibility, intelligence, and decision making enabled by data. By combining data from their daily operations with other external data sources, ADE can provide customers with the most comprehensive end-to-end solutions to meet their needs. Supporting customers with the best, tailor-made solutions will always be ADE’s approach.
As a customer-driven company, your satisfaction is always ADE’s number one priority. They will remain nimble and agile to deliver the very best in the market when it comes to safety, reliability and customer service, which are the key components to their success.
Aircraft IT COO, Scott Leslie welcomed the new vendors stating, “Our vendors are the lifeblood of Aircraft IT and what RecoSense and ADE offer are very relevant solutions for our times.”
Perhaps it’s time to consider a new solution…
ENVISION and its mobile apps combine intuitive user-interfaces with streamlined workflows to help your teams work faster and more effectively.
The time saved on day-to-day tasks coupled with efficiencies gained from intelligent planning and analytics, allow you to increase profitability across your operations.
So if you’re ready for an upgrade, why not discover what ENVISION could do for you
in their MRO software as the legacy software was no longer in the position to support today’s airline maintenance requirements. Among others, the airline was looking for fully integrated end-to-end support for all processes for fixed and rotary wing aircraft combined with the capability to support a paperless operation. The operation of their aircraft is far from standard, the mixed fleet brings with it a mixed utilisation with its own challenges. A combination of scheduled, charter medical and SAR flights have to be accommodated when managing all ground activities and supporting business areas. With these requirements in mind, Air Greenland started an in-depth selection process to get a clear picture of the capabilities and gaps on the available software solutions. AMOS was able to
off the requirements and having a proven track record of successful implementations around the world for helicopters as well as fixed wing aircraft so, in late September 2022, Air Greenland and Swiss AviationSoftware were pleased to announce that the airline had chosen AMOS for its new MRO software.
“Air Greenland joins the evergrowing helicopter group within the AMOS Community and their mixed fleet is a perfect showcase of how AMOS allows customers to manage fixed and rotary wing aircraft within one MRO software” stated Fabiano Faccoli, CEO of Swiss AviationSoftware Ltd.
The implementation project is in full swing with workshops and training
being delivered both on-line and on-site. While the project started during the pandemic and all services from Swiss-AS had to be performed online, on-site travel is now possible again to the benefit of both, Swiss-AS and Air Greenland. Flexibility, creativity, and the lessons learnt from the beginning of the pandemic ensured that the travel ban did not block the implementation progress.
As with any project, one of the key paths to success is collaboration. Being able to support the dedicated and highly knowledgeable team from Air Greenland with in-house experts from Swiss-AS Business Consulting and Training, who bring years of experience and expertise, not only in regards to AMOS, but also in rotary wing operations and maintenance as well as airline and MRO activities, has continued to build on the strong foundations built during the selection process.
Greenland is not only a unique project geographical location for Swiss-AS staff, it has also had an impact on the implementation set-up: Contrary to the strong trend within the AMOS Community, and industry, due to its remoteness Air Greenland will not rely on cloud hosting, but will instead run the server on premise.
With the AMOS Airline Edition, Air Greenland will perform most of its maintenance inhouse and rely on the industry best practice processes that come with the MRO software.
AMOSmobile/EXEC is also in the scope of the project and will complete the AMOS user experience in the hangar.
In early October 2022, Ghana’s second largest airline, Pisces Aviation Ltd DBA PassionAir, announced that it had opted for Rusada’s ENVISION software to manage its airworthiness, maintenance, and flight operations.
From their base in Accra, PassionAir utilize a fleet of De Havilland Dash 8’s to serve destinations across Ghana. With plans in place to expand their routes and fleet, the operator has selected Rusada’s software solution to manage their operational activities going forward. They will adopt seven of ENVISION’s modules including Fleet Management, Base & Line MRO, Flight Operations, and Human Resources, which will be used to ensure regulatory compliance, effectively manage maintenance activities, and support day-to-day operations.
“We were looking for a more professional system that would bring our airline together and make our activities more efficient as we grow.” said Philip Nartey, Technical Services Manager at PassionAir “We are now looking forward to working with Rusada to get the system in place and prepare for go-live” he continued.
Rusada’s web-based solution will be implemented by their in-house deployment experts, with a view to go live early next year.
“PassionAir are another very welcome addition to our growing customer base in Africa. With their planned growth in mind, now is the
modern software solution that can streamline their operations. I know our teams are eager to get started on what promises to be another exciting implementation project.” stated Julian Stourton, CEO at Rusada.
Rusada: Rusada is a leading provider of aviation software with over 35 years of experience in the industry. Its ENVISION software manages over 2,000 fixed and rotary wing aircraft for 150 operators, maintainers, and manufacturers in 45+ countries. With its headquarters in Switzerland and offices in the USA, UK, UAE, India, Singapore, and Australia, Rusada provides global support for a global industry. Specialising in the management of airworthiness, maintenance, and flight operations, ENVISION is developed solely for aviation. Its modern, web-based platform features a suite of integrated modules, enhanced by a series of native mobile apps. ENVISION’s easy-to-use interface provides users with clear, actionable information, enabling processes to be carried out quickly and efficiently, and all without the need for paper or spreadsheets.
Air Atlanta Icelandic has been successfully running its global charter and ACMI operation for 36 years. For 25 of those years Air Atlanta has been a TRAX Maintenance & Engineering software customer. The company is now ready to transition to the TRAX eMRO product to allow its employees to be connected no matter where they are with access to real-time information. So, in early October 2022, Air Atlanta announced that it is turning to eMRO as a proven web-based device-agnostic solution with a modern user interface and a zeroinstall client. It matches how aviation works today.
Air Atlanta has a fleet of 15 Boeing 747-400 aircraft. Its core business has always been ACMI (Aircraft, Crew, Maintenance, and Insurance) leasing of their aircraft to other airlines. They provide their customers with a dedicated aircraft, which is fully crewed, maintained, insured, and managed under Air Atlanta’s Air Operator Certficiates (AOCs) for an agreed period of time. They’ve recently begun setting up a CMI hybrid service that manages the day-to-day operations for a customer’s aircraft. Air Atlanta also has management services that can provide maintenance and planning training, quality, safety and security, as well as the daily operation of multiple types of customer’s aircraft.
Together with the TRAX eMRO cloud-based aviation maintenance
solution, Air Atlanta can continue to provide the efficient and high level of service for its customers that it has been known for these many decades.
Air Atlanta: based in Kópavogur, Iceland, Air Atlanta is a charter and ACMI airline that has been operating for 36 years. It specializes in leasing aircraft on an ACMI and wet lease basis to airlines worldwide needing extra passenger and cargo capacity, as well as taking passengers to the sky with its own airline operation and charter services. The company operates in different countries and has bases worldwide.
TRAX: TRAX provides comprehensive software solutions designed to manage all aspects of aircraft maintenance. TRAX is the premier provider of aviation maintenance mobile and cloud products in the global market today. TRAX products support digital signatures, paperless Workpacks and manuals, RFID-capability for logistics, Biometric security, offline capability for its suite of mobile apps, web-based applications, and the ability for users to work anywhere with easy access to real-time information.
SafetyNet DocuNet
The world’s most trusted solution built to optimise your technical authoring, document distribution and compliance processes.
A single platform that streamlines SMS processes and enables a proactive safety culture.
Vistair Intelligence
A simplified path from data to insight that increases safety and drives decisive competitive advantage.
www.vistair.com
QOCO Systems Ltd were delighted to announce in late October 2022 that Widerøe has chosen to partner with QOCO Systems Ltd and will be using MROTools.io, the most advanced and dynamic tooling management software on the market. Tooling control has often been an after-thought and Widerøe was impressed with how MROTools.io addressed many of the challenges they had around the tooling environment.
MROTools.io will optimize and digitalize Widerøe’s tool management starting in November 2022. Widerøe was seeking better visibility and control of all the tooling processes and a must was a reliable and proven connection to its M&E system, AMOS.
within our core product functionality. We look forward to a long, and mutually supportive relationship with Widerøe”, said Andy Graham, Chief Commercial Office & Partner at QOCO Systems.
Widerøe: Widerøe, is a Norwegian airline, and is the largest regional airline operating in the Nordic countries. Widerøe Technical Services
InForm combines document & content management with process improvement in our tightly regulated industry. InForm seamlessly integrates with OEMs and M&E Systems to reduce any redundant work.
A completely paperless solution, making task card authoring & management highly efficient and requiring minimal technical expertise. InForm takes advantage of the latest OEM digital Maintenance Planning Document (MPD) and Task Card data (AMM). Support for iSpec2200 & S1000D import is built-in to the Task Card template, allowing imports of the entire deck without hassle.
IDMR offers unified Web-based applications with a centralized platform with no installations required. Our secure web application integrates with federated ADFS access and offers fast performance operating across OS, platforms, devices, and terminals.
Our advanced accessibility functionalities allow our applications to be mobile and work anytime, anywhere; key features for inspectors, technicians, and personnel working in hangars.
Management enjoys real-time access to dashboards to track the progress of checks, run reliability reports, and optimize turn-around time.
www.IDMR.com
“QOCO Systems is very proud to be associated with one of Europe’s oldest and most respected airline operations. Widerøe immediately understood the benefits of moving its tooling process to a digital platform, to ensure they have complete visibility across its diverse engineering operations, whilst ensuring connectivity to its M&E platform, AMOS. QOCO was able to demonstrate our superior control around tooling with enriched analytics in order to make critical decisions on operational investments and efficiencies, as well as rich offering
AS is a fully owned subsidiary of Widerøe AS and a daughter company in the Torghatten ASA Group and Fjord1 ASA. Widerøe Technical Services AS provides technical services in five airports and access to 42 airports throughout Norway. WTS provides Heavy Maintenance, Line Maintenance, Component Maintenance, Ground Support, AOG and training. The main office is located in Bodø.
QOCO: QOCO Systems, a trusted partner of leading airlines, MROs, and aircraft OEMs for over 12 years, helps the aviation industry to succeed in the changing world by creating new ways to work, to communicate, and to utilize data. We enable operational excellence and efficiency in the aviation industry with disruptive SaaS solutions. QOCO is committed to a high level of quality and information security, which is supported by ISO 9001 and ISO 27001 compliant management system certification.
IDMR, the leader in aviation document management software, presents a true web-based end-to-end paperless task cards
EXSYN were delighted to announce at the start of November 2022 that ASL Aviation Holdings has expand its relationship with EXSYN to utilize #NEXUS across ASL’s European airlines. The integration of NEXUS will allow ASL to closely manage the migration of #aircraft #data into AMOS and provide ongoing and extensive data #healthmonitoring capabilities. This agreement reflects the growth of a long-standing support arrangement between ASL and EXSYN around AMOS. “The adoption of NEXUS at ASL underpins the long-term relationship between EXSYN and ASL. In addition, it’s a best-practice industry example of how strong aircraft #datamanagement capabilities support an aircraft operator in #airworthiness #compliance as well as #operationalefficiency” said Sander de Bree, CEO of EXSYN Aviation Solutions.
NEXUS: NEXUS is a software solution in conjunction with an operator’s MRO/M&E system landscape to manage, collect and exchange data in
On-time delivery of aircraft parts is the difference between getting your fleet to the air and tens of thousands of dollars in lost revenue.
Skip the RFQ. Get your parts on-time.
We make it happen. www.aerotrade.ade.aero
© ASL Aviation HoldingsAircraft painting specialist Aviation Exteriors Louisiana (AvEx) announced, at the beginning of November 2022, that it has selected Rusada’s ENVISION software to manage its new line of heavy maintenance activities.
With over 30 years of painting experience under its belt, AvEx, located in New Iberia, Louisiana, recently made the decision to expand its service offering by adding heavy maintenance, and aircraft passenger to freighter conversion to its service
This increase in operational activity highlighted their need for a state-ofthe-art system to manage the new business lines. As such AvEx conducted an extensive research project, and after demonstrations and meetings with multiple providers, Rusada’s ENVISION was selected as the solution of choice.
“Our new additional operations will only be able to grow if we are able to manage the increased activity volume, and analyze effectively, something ENVISION will allow us to do with ease.” Said Jerry Hernandez, CEO at AvEx. “We were very impressed with the intuitiveness of the system. This coupled with Rusada’s professionalism and intellectual knowledge base, made ENVISION a sound choice for AvEx.”
AvEx will use ENVISION to manage the planning, assigning, and execution venture. Implementing ENVISION from
the get-go will allow them to make the best possible start with these new service lines. Our teams will now work hard to get the system up and running, to ensure AvEx’s continued growth in the MRO marketplace.” stated Julian Stourton, CEO at Rusada.
Rusada: Rusada is a leading provider of aviation software with over 35 years of experience in the industry. Its ENVISION software manages over 2,000 fixed and rotary wing aircraft for 150 operators, maintainers, and manufacturers in 45+ countries. With its headquarters in Switzerland and offices in the USA, UK, UAE, India, Singapore, and Australia, Rusada provides global support for a global industry. Specializing in the management of airworthiness, maintenance, and flight operations, ENVISION is developed solely for aviation. Its modern, web-based platform features a suite of integrated modules, enhanced by a series of native mobile apps. ENVISION’s easy-to-use interface provides users with clear, actionable information, enabling processes to be carried out quickly and efficiently, and all without the need for paper or spreadsheets.
ASQS were pleased to announce at the beginning of November 2022 that Jazeera Airways has taken off with IQSMS.
ASQS’s first customer in Kuwait, is also the first non-government owned airline in the Middle East established in April 2004. Jazeera serves to more than 50 destinations across the Middle East, Central and South Asia, and Europe, operating a reliable fleet of Airbus A320 and A320neo aircraft — all fitted with their signature leather seats.
In June 2018, Jazeera was the first airline in the Middle East to introduce the A320neo into its fleet.
Jazeera owns and operates its own terminal at Kuwait International Airport — Terminal 5 (T5) ensuring an enhanced passenger experience with dedicated check-in, fast immigration and short transfer distances. The IOSA certified operator raises the total number of IOSA certified IQSMS customers
to 64 operators.
IQSMS is therefore pleased to support the Kuwaiti airline with our integrated quality and safety management solution, simplifying vital operational processes for higher efficiency and safety. With the IQSMS core modules for reporting, quality and risk management, including the respective offline applications and the Document Distribution Module, Jazeera Airways is making a deliberate choice to promote a sound communication and safety culture throughout the entire organization. Facilitated reporting procedures and the possibility to file reports even without internet connection strengthens the safety accountability of each and every employee in the company and result in an overall increased operational safety performance.
The ASQS team is pleased to welcome Jazeera Airways as their first Kuwaiti customer on board.
In early October 2022, Seabury Solutions, a market leader in providing Information Technology solutions for the aviation industry, announced the integration of AI solutions through strategic partnerships.
“Aurora’s intelligent scheduling technology improves MRO throughput, resulting in improved transparency and reduced costs, while also resulting in superior operations management. Aurora was developed to help tackle difficult, mission-critical scheduling problems—by using artificial intelligence technologies to encode extensive expert domain knowledge with advanced algorithms to generate more efficient schedules. Today, Aurora manages the most demanding operations for organizations such as The Boeing Company, Mitsubishi Heavy Industries, Bombardier Learjet, Spirit AeroSystems, General Dynamics Electric Boat, Korea Aerospace Industries, and the US Air Force, US Space Force, and US Navy,” said Richard Stottler, President, Stottler Henke.
“Having seen OEMs and Tier 1s invest in predictive maintenance driven AI channels, it was crucial that AI found its way into enhancing data quality and integrity using data driven models. This acts as a segway into helping organizations visualize commercial impact of decisions using an Aircraft, Engine or Component’s Airworthiness and Maintenance data. KeepFlying sees great potential for Airlines, MROs, Lessors and Banks to create financial twins for the Assets they operate, lease, maintain and finance to predict costs, revenues, asset placement commercial potentials and risks using Machine Learning models trained across different Aircraft and Engine types.” remarked KeepFlying CEO, Sriram Haran.
“Our decision to include AI into our Functional Architecture was taken right before the Pandemic started and it was included in our road map together with a 5-year plan to execute it. After understanding the necessity of tools driven by AI in areas such as Scheduling, Planning, Revenue Forecasting (specifically for Airframe and Engines MROs, lessors and Financial Institutions) we took the challenge of inviting specialized strategic partners to deliver a set of solutions that will only improve our digital transformation platform and benefit not only current but also future customers,” stated Seabury Solutions CEO & President, Bijoy Mechery.
State-owned emergency medical operator FinnHEMS, announced in early November 2022 that it has opted for Rusada’s ENVISION software to manage its airworthiness and maintenance activities.
FinnHEMS operates Helicopter Emergency Medical Service (HEMS) flights for hospital districts from its seven bases across Finland. They utilize a fleet of nine helicopters, Airbus H135s and H145s, primarily for the deployment of emergency specialists to incidents, rather than the transportation of patients. As such, their callout rate is typically higher and more frequent than standard air ambulance services. With this high volume of flights and need for constant aircraft availability, FinnHEMS was seeking a greater level of confidence in their operational data and determined that ENVISION met all the requirements for the job.
“We are looking forward to relying on ENVISION to give us more certainty around our operations, as well as increased visibility on the readiness of our fleet.” said Tony Ellonen, Continuing Airworthiness Manager at FinnHEMS. “A key desire was to enable our maintenance teams to effectively plan for upcoming events. With ENVISION, vital information will be readily available to our main base and outlying deployment stations so that our helicopters can be strategically maintained, to be available at a
consolidating their current systems into ENVISION, using its airworthiness and maintenance modules to manage their activities going forward. The solution will be accessible via the cloud from any of their operating locations, and its live dashboards will ensure key information is available and consistent company wide. This will significantly reduce user’s workloads and avoid any potential human factors conflicts.
“Visibility and control are two words we are hearing a lot lately. Operators are finding it hard to manage complex operations with their data and processes spread across multiple different systems. ENVISION has been designed specifically to eliminate this problem, but nevertheless it is always gratifying when dynamic, forward thinking companies such as FinnHEMS select us to help out. In the coming months we will go above and beyond to deliver the oversight and control they seek.” stated Julian Stourton, CEO at Rusada. Read the full story on Aircraft IT Website
Seabury Solutions, a market leader in providing Information Technology solutions for the aviation industry, announced at the start of November 2022, the addition of Sky Airline, Chile, to their growing customer base of Alkym users.
“Through a meticulous evaluation process, Sky Airline chose Seabury Solutions’ Alkym to replace its current Aircraft Maintenance Management tool. It filled us with pride to be chosen by the client most known in the region for their innovation, growth, and adaptive business model. Our teams are currently working on an implementation project that will surely conclude successfully,” noted VP Sales Latin America, Manuel Roche.
“As Engineering & Maintenance Managers, we couldn’t be oblivious to the huge digital transformation process the company is undergoing. All internal processes and passenger-related
processes are being automated and the airline is experiencing remarkable growth. Due to this, we’ve been looking into replacing our current Management Information System (MIS) with a new system that can support our growth and the new challenges we must face as an airline. The system will allow us to streamline all our maintenance processes and, as a result, simplify our daily work and interaction with
our “skyers” through the system. The evaluation process to choose the new system was very thorough. Before launching the RFP, every department that interacted in one way or another with the system was consulted to make an internal list of prerequisites; this way, we could satisfy the diverse needs of our local clients. Alkym stood out as the one who fit most of those prerequisites while also being willing to fulfill all the leftover requirements in the middle-term,” remarked Sky Maintenance and Engineering Director, Cecil Davidson Tölg.
Dir. Davidson continued to comment, “One of the most important features that we need from our new MIS is the ability to work outside of the office and through intelligent devices, meaning it needs a mobile function, which Alkym provides. It is also very intuitive, which makes it easy to use and offers us
the possibility to improve the execution and management processes of our productive areas. Finally, it’s important to mention that Seabury has shown flexibility through the whole process and has worked tirelessly to find a solution that fits our needs. We are sure that the implementation process will provide us with many advantages to develop and smooth our maintenance processes; in that way, Alkym will support us in reaching one of our company goals, which is to continue progressing to a complete digital transformation of our processes.”
“It’s always rewarding to welcome a customer with such fleet growth as Sky Airline, who already has 28 aircraft and is waiting on more to arrive in the near future. It means we are on the right path to becoming the most comprehensive M&E Solution in the market, something that we’ve been striving for the last 20 years. There will be other airlines and MROs that eventually will move away from their existing, outdated M&E Solution, and we will be there to welcome them as well,” asserted Seabury Solutions VP & Head of Sales & Marketing, Carlos Bianchi.
Sky Airline: Sky Airline, is based at Comodoro Arturo Merino Benítez International Airport in Santiago, Chile and at International Airport Jorge Chavez de Lima, Peru. It is the second largest airline in both countries, behind LATAM Airlines and the first airline to operate under a low-cost model in Chile. It serves international routes to Argentina, Brazil, Chile, Colombia, Peru, Mexico, the Dominican Republic, and The United States of America. It also operates charter flights in Chile and South America.
Seabury Solutions: Seabury Solutions is a leading global aviation software
Eauthority® (a safety management software for aviation authorities), and a range of airline performance analysis tools within the Enterprise Performance Analysis System (EPAS). The EPAS® suite has models that include capabilities in determining current and future route profitability, maintenance performance, budget planning, fuel planning and distribution channel performance. Read the full story on Aircraft IT Website
„Implementing AMOS as our M&E software was a strategic project for Lufthansa and Lufthansa Cargo. We now have a solid platform to continue our digital push towards more increased mobility, leaner processes and easier data integration across our multiple systems.”
says VP Technical Fleet Management Lufthansa
Lufthansa and Lufthansa Cargo are live with AMOS, the worldclass M&E software solution. Both carriers have implemented AMOS including AMOSmobile, enabling paperless maintenance operations from the beginning.
The close cooperation of the Lufthansa group members will be further promoted by AMOScentral, which enables the exchange of data between AMOS instances while nevertheless allowing each group member to keep control over their individual AMOS environments.
At the endo of November 2022, Aviation software leader Comply365 was pleased to announce that its newest partner, Spright, will leverage Comply365’s document and compliance management system to support its growing drone operations, delivering medical supplies for rural and underserved communities across the US.
Spright uses state-of-the-art UAS technology to provide advanced BVLOS drone solutions tailored to medical delivery and utility inspection applications.
Drone pilots at Spright will use Comply365’s mobile app to access their operational manuals, flight safety, and maintenance documents and provide compliance to required content.
“Commercial drone operators must meet many of the same requirements and certifications as
commercial airlines to ensure safe and reliable operations, so it made sense for us to turn to a longtime, proven solution in the aviation industry with Comply365. We needed a system to manage our operational content and compliance and be able to target the distribution of these documents to our pilots, and we found Comply365 to be a perfect fit.” stated Spright President Joe Resnik
Pilots will always have the most updated content with revision control and automated syncs, and they’ll be able to quickly find content and easily filter and search across all their manuals. They’ll also be able to personalize their documents with annotations, bookmarks, and highlights, which are retained when files are updated. Users will be able to easily see what’s changed in a document and can read and sign in the same place, providing automatic compliance tracking for Spright, with built-in
reporting for regulators.
Spright is the second drone-based operator to join the community of Comply365 users, which includes many major airlines around the globe.
“While we’ve previously transformed existing industries with our solutions, it’s exciting to be part of the new, rapidly growing drone industry. We are thrilled to welcome the innovative team at Spright to our global community of users,” Comply365 CEO Tom Samuel said. “Spright is solving many access and efficiency challenges with the latest technology, and we are proud to partner with them to offer a solution that will scale with Spright as they grow their operations to serve critical needs.”
Comply365: Comply365 is the leading provider of enterprise SaaS and mobile solutions for content management and document distribution in highly regulated industries. Having played an
instrumental role in the FAA’s approval of replacing the traditional, paper-based, pilot flight bags with electronic flight bags (EFBs), Comply365 partners with clients to transform their industries.
Spright: Spright is the drone division of Air Methods, helping to solve many of the toughest challenges facing communities across North
America. This innovative, drone-based solution is tasked with leveraging emerging aeronautical technology to create operational solutions that can be implemented locally. Based in Gilbert, AZ, Spright is a stand-alone Part 135 Operator with a leadership team with more than 70 years of aviation operational experience.
Read the full story on Aircraft IT Website
Towards the end of November 2022, OASES was pleased to announce the launch of OASES Knowledge Base, the ultimate resource for all things OASES related. Initially the new platform will offer articles, product information, instructional videos, updates, webinars and FAQs with added customer interaction and networking in a community environment including:
• Training content accessible 24/7/365;
• 10 October 2022Access to Live Streaming sessions;
• Archive of all webinars and OASES online events;
• A safe environment for content related questions and feedback;
• We will continue to upload and create insightful content in collaboration with our customers and will be offering;
• Self-learning online courses;
• Individual product modules;
• Customised material for organisations.
OASES Knowledge Base will be accessible for free but will also offer ‘advanced content’ with a pay-as-yougo or subscription model offered to customers.
“We’re looking at diversifying our training offer at OASES to embrace more flexible solutions that allow customers, wherever they are, access to a world-class suite of training content based on their needs.”
Explained OASES Operations Director, Alessandra Palmer-Tilley.
“In addition we believe that by presenting this information in a collaborative, community-based environment we can achieve a much better understanding of our customers’ requirements and as such better improve and evolve our product portfolio.” he continued.
OASES Customers that haven’t already received their invitation to access OASES Knowledge Base should contact their Customer Success Manager directly.
Read the full story on Aircraft IT Website
Since switching to Aerros, our customers have:
• Increased fleet size with minimal increase in overhead
• Increased plan detail by 9x and plan length by 4x
• Reduced time to budget by half
Learn how Aerros can dramatically improve your planning results today.
aerostratsoftware.com info@aerostratsoftware.com
■
face in a post-pandemic world is the shift to automating key operational processes such as maintenance auditing and vendor interpretation issues.
South East Asian Airlines, a reputed name in the aviation industry, announced in early October 2022 that it had entered a Maintenance Repair and Overhaul (MRO) agreement with Collins Aerospace for its fleet of 55 Boeing 787s, which also extends to the airline’s budget carrier section, Scoot. The airline has clocked an impressive journey throughout its growth trajectory and has won several accolades for its high in-flight service standards. The airline even runs a subsidiary, the South East Asian Airlines Engineering Company (SIAEC), which undertakes MRO for
began its digital transformation journey in 2018. Since then, they have made extensive progress. However, they were yet to digitize and automate maintenance audits and vendor interpretation. Due to missing data, the sale encountered difficulties when the airline found it challenging to process aeroplane maintenance records. Maintenance checks needed to be completely redone to help plug the gaps. The entire process would need to be undertaken from scratch, resulting in an unnecessary expense and a mammoth effort. Another challenge was the lack of an incumbent mechanism to validate the Shop Finding Reports provided by the vendors. There was no way to check whether the assessed damages were
airline saw it as an opportunity to course-correct and avail itselfof an AI-based solution to address the issue.
This was when AI-solutions provider RecoSense stepped in. After detailed discussions with South East Asian Airlines, RecoSense identified key areas where smart solutions could be applied to simplify the entire aircraft maintenance audits and vendor analysis process and bring efficiency and cost-effectiveness to the process. This comprised AI-based auditing of hand-written maintenance records, standardisation of damages and their classification, and detailed vendor analysis.
The maintenance records at South East Asian Airlines had all been manually created and managed, causing several gaps in the information. Due to inefficient maintenance audits, gathering corresponding MRO data proved
susceptible to inefficiency and data gaps. The second challenge was addressing vendor interpretation to curb unnecessary expenditures. There was no way to tell if the vendors’ Shop Findings Report submitted was accurate. The damages mentioned in the reports often exceeded the actual scope of work, thus resulting in overbilling and revenue leakage, which impacted the airline’s profitability.
Automation via a unified, simplified platform could bring end-to-end transparency and accountability to maintenance audits and vendor interpretation processes. RecoSense implemented its AI Transformation and Content Intelligence Solutions, specifically customised for the aviation industry. The tools used created a niche knowledge graph, interlinking various stages and activities of the MRO and vendor-related operations. This formed the foundation for Natural Language Processing (NLP) and the cognitive engines to function.
When we think about a paper logbook on an aircraft, we think about a piece of paper that is accessible by 1 person at a time. The paper logbook usually consists of notes handwritten by the pilot, technician, or cabin attendant which various parties then transport to the back-office system, hangar, MRO, or relevant destination. Copies must be created, faxed, or emailed and records should be stored or returned to the aircraft. This process can create issues with illegible handwriting, errors, and vital missing information. A digital replacement, in this case the Electronic Tech Log, maximises time efficiency when completing mandatory documents and the app can be configured to input repetitive data or pre-fill date/time automatically. The completed documentation can then be sent to a handler on the ground when the device has a connection. It is no longer necessary to store paper copies (although paper can always be used as a
backup). The data can be structured clearly and easily read.
Producing accurate, consistent and near real-time data means that the recipient of this data has an easier job. Let’s look at maintenance engineers as this is an area that can produce costly delays. A pilot that is using an electronic tech log can enter faults, defects or squawks as they happen (or soon after). These updates are transmitted to the relevant maintenance department, either in real-time or when the aircraft touches the ground. This transmission simplifies the control of maintenance on the line and decreases the chance of parts being wrongly replaced whilst also enabling faster turnaround times. The Electronic Tech Log provides a system that can manage the more dynamic needs of line maintenance by sending timely data in an organized fashion. Longer-term analysis of data can also reveal
accordingly. Finally, there are also benefits to external maintenance teams planning to accept an aircraft at a remote station.
Handwritten entries cannot be searched, used in analytics, or mined for information. The data inside of an ATL is useless until it reaches the hands of the next person in line. An Electronic Tech Log provides a connected system that can be used by multiple people, from anywhere, at the same time. The full influence of an eTechlog can only be seen when we
look at all the areas it affects in an airline. It has often been described as the ‘beating heart’ of an airline due to the range of departments that are affected. An effective eTechlog allows a pilot to communicate with the airline’s MCC both directly or indirectly, line maintenance, 3rd party maintenance and aircraft records without these departments having to depend on each other to pass on data. Not to mention providing back-office teams with real-time views of the Electronic Tech Log in the cockpit, connecting all mission-critical personnel on any given day of operations.
The fact that more stakeholders can see an up-todate view of the aircraft’s status allows for anticipation and forward planning for upcoming maintenance activity. The Electronic Tech Log replaces the paper-based ATL complete with the capability to record approved signatures (under EASA NPA/2016-12), license numbers and to sign off on the airworthiness the aircraft. It can therefore be
treated like the ATL when it comes to the airline’s designated CAA. The recording of defects and MEL items is also something that gets closely monitored by the regulator. The REDiFly Electronic Tech Log comes equipped with a fully searchable digital MEL which automatically provides deferral processes and related information at the click of a button. Furthermore, we at REDiFly use our experience and expertise to provide support for the air operator through the entire approval process.
Although an Electronic Tech Log is not free, its implementation can result in significant cost reductions and savings throughout the entire organization. Paper-based systems can be expensive, time-consuming and physically heavy. Time and money are spent on the storage, printing, entering, and processing of data as well as searching for errors and identifying trends for analytics. Digital data entry is significantly faster, more accurate and instantly searchable, saving team members time and
minimizing costly errors. Data is automatically transferred and stored, meaning technicians get defect information directly and office staff no longer engage in time intensive data entry and processing. The efficiency of defect management is enhanced with access to real time data giving technicians the ability to identify and resolve defects with greater speed and accuracy, resulting in less delays and quicker turnaround times.
Maintaining records, allotting task cards, and extracting detailed information from the records is a laborious task for the aviation maintenance team. The amount of time and resources taken to run the maintenance process and update the records leave the aviation maintenance team wondering if only an automation system exists to help them.
A leading aviation leasing entity came to RecoSense with the same requirement. They needed an intelligent automation system that could analyze the incoming work pack, split the work packs into task cards. Post completion to process/validate the task cards for quick engine dispatch there by optimizing TAT’s.
RecoSense is one of the fast-growing AI-powered data intelligence solution providers. With the
proprietary NLP engine and efficient machine learning & intelligent deep learning system, RecoSense’s AI solution helps organizations better handle tons of data, structure them, and get better insights accurately in a shorter time frame.
• Automated Compliance
• Reduced Turn Around Time (TAT)
• Plugging of Revenue Leakage
• Accelerating Process with higher accuracy
When the aviation leasing entity receives the engine or other major aviation component, a work pack containing thousands of pages regarding the tasks to be performed will be given. Then the maintenance team has to manually extract the data point and add it to the MRO software and Planner excel sheet. Similarly, all the updated task cards from various
technicians during the engine/other major aviation component visit must be collected. Then the task cards must be manually scanned, reviewed, and clubbed together as one whole set for engine dispatch.
Since various human resources are used at each stage, the consistency of the end result varies. It takes months to plan the resources for maintenance, and the team has to wait for the entire set of task cards to arrive to complete the engine dispatch process.
Using legacy systems caused high operational costs, manual errors, and revenue leakage for the leading aviation leasing entity. To overcome the shortcomings, the entity required —
1. Automation for analyzing the incoming Work Packs.
2. Automation in processing the completed Task cards.
While the legacy system takes months to complete and despatch an engine, the AI system can perform the same tasks in a relatively shorter duration. Once the aircraft maintenance team collects the flight records, the records will be fed into the AI system. Later the AI system will-
• Extract data from the records
• Analyze the data and correlate them
• Execute the desired automation task
The task card may contain unstructured data like handwritten data, stamp seals, signatures, etc.; This is where the cognitive AI engine & Natural Language Processing (NLP) engine kicks in. Irrespective of the format, language, and information structure, the NLP engine extracts the proper information without any errors.
The AI system uses deep learning to analyze the extracted data and get progressively higher-level features from the data. These extracted data will be used to perform data classification and correlation, which will help the AI system to automate the desired task, such as extracting the
data and updating the info on MRO software.
Let’s see how RecoSense’s AI-based solution helped the leading aviation leasing entity accomplish its goal.
The goal is to leverage NLP’s full potential to process the work packs and split work packs in a logical order based on the Task card number. Later the extracted data points should be uploaded to the MRO software & Planning excel sheets. Typical process followed on receipt of Work Pack is:
• Print the entire Work Pack.
• Segregate the Work Pack into individual Task cards.
• Populate the Planning XLS.
• Update Task Card Data into MRO Software.
All this work is manually done by the Planning Engineer. A senior resource doing manual work is an anachronism in today’s world.
Thankfully the DocuSense AI platform from RecoSense is powerful enough to perform the complex task of processing the docs and extracting all types of structured and unstructured data. Since the Docusense platform handles thousands of data regularly using high-end Optical Character Recognition (OCR), the system can effortlessly identify the key entities and tag them.
Read the full story on Aircraft IT Website
Air Canada is the largest airline in Canada by fleet size and passengers carried. Keeping aircraft in optimal condition is a critical part of everyday operations. For that, the Maintenance team must optimize aircraft maintenance procedures to ensure security and meet regulatory requirements while minimizing turnaround time between flights to limit the costs of having an aircraft grounded. Essential to meeting regulatory requirements is ensuring that maintenance engineers have mobile tools with the latest documentation always available plus achieving optimal aircraft security. However, maintaining synchronicity across all devices throughout multiple sites presents numerous challenges which can add significant costs and delays that can result in longer aircraft turns.
With the challenges of managing mobile devices, Air Canada looked for a partner to help ensure that their teams always had up-to-date and ready-to-use devices. The best match identified was M3 Solutions and this case study explains how that worked. Of course, different airlines will have different needs but this article highlights the fundamental reasons for having a solution to manage devices, how one such solution works and was implemented plus, of course, what Air Canada gained from implementing the solution.
teams always had up-to-date and ready-to-use devices. The best match identified was M3 Solutions…”
Air Canada first introduced iPads on its Boeing 787 Dreamliners for their entry into service. The goal was to maximize flying time for the 787, which meant maintenance turnaround time needed to be the lowest it could be for any widebody aircraft. To achieve that, gaining as many efficiencies as possible was essential.
Prior to the introduction of iPads, when an aircraft landed, the engineer would take the aircraft defect paper logbook to the closest desk-top terminal to look up the applicable references and determine whether the defect could be deferred and the aircraft dispatched or whether the aircraft would have to be grounded until that defect was resolved. Mobility allowed the adoption of Apps to access information pertinent to the airworthiness of the aircraft; and offered the flexibility to complete all maintenance tasks safely on board the aircraft (as images above) without having to disembark or lose time walking to a desktop computer. It has allowed engineers to fix or legally defer defects faster, which has led to an increase in ‘first-time fix’ rates and a reduction in deferrals into the planning process; ultimately improving aircraft reliability.
The 787 represented a step change in aircraft technology and was well suited to the introduction of a proof of concept for new technologies and processes. As a result of successful implementation of the proof of concept, Air Canada rolled out these new technologies and solutions to all other aircraft types.
As an entirely new concept in aircraft design and the ‘smartest’ aircraft to date at its time, the 787 presented a challenge in the maintenance turnaround and, as Boeing acknowledged, Air Canada achieved the highest levels of reliability among operators of the type. Much of that has to do with the amount of time that has been given back to the aircraft maintenance engineers who can now stay with the aircraft throughout a turn as opposed to spending time on a desk-top terminal.
Initially, the Proof of Concept (PoC) was to showcase the benefits of having all maintenance procedures/recordings done on the wing. The benefits were clear, but the PoC helped iron out several core issues.
One of the biggest criteria for any aviation regulatory body is to maintain synchronicity across all technical publications. Working from the latest and same documentation is a requirement of Transport Canada. Once the OEM publishes a revision to the aircraft maintenance manual, it would be impossible for the revision to be adopted across every platform that an airline operates that same day. When those revisions are sent, operators will also add airline specific content to the revisions and then publish them. This set of documentation can be as large 35GB, making it virtually impossible to synchronize a large fleet of devices seamlessly and efficiently. With the 787’s entry into service, Air Canada found that maintaining synchronicity on all iPads in the fleets was much too cumbersome. In addition, the IT team needed to plan the OS update and the application update, and ensure their compatibility. This is where the partnership with M3 Solutions and their Platform was introduced. It fully automated all of these processes.
Notwithstanding that, the original business case was proven in the sense that our technical dispatch reliability improved. Engineers no longer had to spend time returning to the desktop computer to ensure compliance when deferring defects: now, everything can be done on wing. Engineers have all the maintenance manuals in their hands, with the ability to action a defect on wing which has increased our proficiencies.
We discovered that it would take an IT resource one week to implement revisions or updates on just 25 devices. Air Canada sees approximately three revisions per month (36 per year) for different fleets. That fact alone supported a good business case to introduce third-party management of the devices even before taking account of the regulatory aspect.
Today, Air Canada Maintenance has more than 500 iPads in operation making it simply impossible to manage that large a fleet without appropriate automation enabled by the M3 Platform. Also, although this article refers to the Technical
“One of the biggest criteria for any aviation regulatory body is to maintain synchronicity across all technical publications. Working from the latest and same documentation is a requirement of Transport Canada.”
publication updates, there are, of course, many more to consider such as the software suite of Trax (Quickturn and Task Control), updated daily, as well as iTIMS which is an app built by Interfacing to allow for the housing of our component maintenance manuals as well as our engineering authorization work flow.
Running several fleets of different devices poses several challenges for IT management.
Today’s aircraft are increasingly sophisticated and technically advanced. The amount of documentation needed to outline every aspect of an aircraft’s maintenance has increased tenfold since the days of printed maintenance manuals. Aircraft manufacturers are constantly updating their maintenance documentation to ensure compliance and adherence to safety regulations. In addition to monthly technical publications which are regularly supplied by aircraft manufacturers, there are also unscheduled releases as often as required to catch critical maintenance deficiencies in the equipment and prevent any failures. In both instances, the challenges surrounding how the information is transmitted and how quickly it can be distributed across MRO teams, in every location around the world, to ensure proper compliance across the entire fleet of aircraft, become critical.
With Air Canada maintenance crews operating in multiple locations worldwide and servicing several aircraft models, maintaining synchronization across all of their mobile devices can pose a significant challenge. This is not only to ensure the aircraft’s maintenance documentation is up to date, but that the devices’ OS matches the requirements of the mobile app which provides that information, most often provided from the aircraft manufacturer. If different tablets have different OS versions, then errors may occur which can impact the smooth operation of maintenance teams and result in longer aircraft turns, not to mention added strain on IT resources tasked with resolving those errors.
Updating every device so they have the right operating system, app version and latest documentation is often a time-consuming process. Doing this manually can put an enormous strain on any I.T. department and require multiple people to achieve it in a timely manner. Furthermore, because of the delays associated with this update process, ensuring that maintenance crews all have synchronized documentation on their device, right when the update is scheduled for release, is virtually impossible.
also be able to track each device and have detailed reports of where it was used and by whom.
M3 Solutions’ innovative technology eliminates the legwork involved in synchronizing a mobile device ecosystem by streamlining content deployment, complex data structures and installations required for maintenance crews to perform their jobs. The platform hosts each device and is uniquely tailored to process updates, install certificates, wipe clean after each use, charge the devices, and much more. The moment a user picks up the device they know it will have the same installations and same version of technical documentation that any other user would have in their organization. Within the M3 platform, access is controlled to devices via RFID, barcode and NFC readers – ensuring all devices are physically secured and traceable (figure 1). Ultimately, it’s a platform that bears the load of an IT team, with a worldwide support network ready to troubleshoot from anywhere.
Figure 1
Air Canada saw significant gains as a result of using the M3 Platform, including current functionality:
• Seamlessly manage multiple device-types including tablets and UMD running different OS, in the same installation.
• Deploy new OS or configuration images remotely and unattended, across the entire network. Manage the content on all devices and ensure it is complete and always up to date.
• Gate the deployment of new revisions of apps to ensure compatibility with the OS version deployed.
• Physically control access to portable devices, monitor the users and their usage with administrator permissions and the system management dashboard.
• Schedule or deploy content in real-time, to some or all devices, anywhere in the world, within minutes and without IT resource intervention (remote and unattended content deployment).
• Retrieve accurate device and system monitoring, ad-hoc reporting, and transaction auditing.
• Reduce IT and device inventory costs immediately. Overall system ROI (return on investment) was achieved within months of installation.
The requirement to maintain synchronicity with technical publications and the latest reference documents is a Transport Canada requirement. With 35
gigabytes of monthly updates, we quickly discovered it would not be possible to maintain synchronicity unless we had a controlled mechanism such as the M3 Platform.
In addition to physical security, access control, and inventory tracking capabilities, deploying the M3 Platform significantly helped streamline Air Canada’s maintenance operations by eliminating delays to synchronize all devices for various teams to use. We would be hard-pressed to find another industry where the adage, ‘time is money’ is as applicable as it is in aviation. For Air Canada, the M3 Platform helped us save both time and money.
Keith Dugas, Director, Maintenance AI and Connected Operations has the current mandate to build AI solutions for Air Canada’s Operations. Keith has worked for Air Canada for 14 years, where he has had business lead responsibility for Air Canada’s Supply Chain transition to Trax from the airline’s legacy maintenance system, as well as responsibility for deployment of logistics and operations continuous improvement initiatives. Most recently, before AI, Keith was the business lead to digitalize Air Canada’s line maintenance paper-based processes, having started his career in AOG operations and progressed into management from there.
Air Canada is Canada’s largest airline, the country’s flag carrier and a founding member of Star Alliance, the world’s most comprehensive air transportation network, celebrating its 25thanniversary in 2022. Air Canada provides scheduled passenger service directly to 51 airports in Canada, 51 in the United States and 86 internationally. It has a fleet of more than 332 aircraft (179 mainline, 39 Rouge and 114 Express), which is also one of the youngest, most fuel efficient and environmentally friendly in the world. It includes, Boeing 737, 767, 777 and 787 types; Airbus A220, A319, A320, A321 and A330; Embraer 175; Mitsubishi CRJ; and De Havilland Dash 8-400.
“The moment a user picks up the device they know it will have the same installations and same version of technical documentation that any other user would have in their organization.”
Rutger Krom is Senior Aircraft Data Consultant at EXSYN Aviation Solutions, being responsible as Lead Solution Architect on EXSYN’s flagship solution NEXUS. As Lead Solution Architect, he oversees all development activities of NEXUS and supports customer onboardings onto NEXUS. Rutger joined EXSYN in 2014 as a graduate intern and has ever since played a vital role in the continued development of the business, various high profile airline data migration projects and EXSYN’s overall footprint in the aviation industry.
Aircraft IT: Your name, your job title, and the name of the business?
Rutger Krom: Rutger Krom, Senior Aircraft Data Consultant and NEXUS Solution Architect
Aircraft IT: How did EXSYN get started?
RG: EXSYN started out in 2011 as a consultancy company focused on supporting airlines implementing MRO systems. Over the course of several projects, use cases were encountered that triggered the development of what is now EXSYN’s aircraft data management platform. Within this platform we provide solutions to manage aircraft data, analytics to drive business value, and technical support services to help clients adopt our technology. The platform itself is centred around the two core applications, NEXUS and AVILYTICS. This resulted in EXSYN’s unique positioning as being a niche leader in offering digital solutions for aircraft maintenance and engineering data
Aircraft IT: What is the guiding business principle that drives EXSYN?
RG: Transparency and flexibility have been at the core of our team since the beginning. Whatever we do, we strive towards a full cooperation to achieve the project’s goals, instead of two entities sitting on different sides of the table. Everyone in the business is encouraged to speak their mind, both internally but also externally, to ensure nothing is missed and all ideas have been heard.
Aircraft IT: What has EXSYN’s greatest business achievement been to date, and why?
RG: During the pandemic, the aviation industry was, as a whole, hit hard. At EXSYN we have been able to continue to support our customer base during this difficult time. As well as keeping our entire team on board, we have simultaneously invested heavily in our technology to even better support airlines and MROs to manage data in critical airworthiness processes.
“EXSYN offers the AOG risk monitor that uses data from MRO systems as well as onboard aircraft data to create risk profiles of aircraft in the fleet and the probability of component failures.”
Aircraft IT: What have been your disappointments and what have you learned from them?
RG: Predictive maintenance is a hot topic within the aviation industry. Within Avilytics, EXSYN offers the AOG risk monitor that uses data from MRO systems as well as onboard aircraft data to create risk profiles of aircraft in the fleet and the probability of component failures. However, we had to accept a rather slow adoption as we underestimated that data at many airlines is not yet ready to really adopt predictive analytics and a predictive maintenance philosophy. Based on this experience, our focus in this area is now more helping airlines to manage their aircraft data and have a continued level of data accuracy to become ready for using predictive analytics. To achieve this, we offer our customers data health checks to continuously validate their system, ensuring their system remains clean, up-to-date and
Aircraft IT: In a sentence, how would you summarize what EXSYN does for aircraft maintenance customers?
RG: We help our customers to efficiently manage aircraft data, retain continued trust in the accuracy of their data and empower digitization of their technical operations to derive value from their aircraft data.
Aircraft IT: What do you feel will be the next big thing in maintenance Aviation IT?
is still too much ‘waste’ in these processes, where data is registered manually in different places/ systems. This is not only a next step for individual airlines per se, but something that will happen industry wide and between all stakeholders in the aircraft maintenance value chain.
Aircraft IT: What do you want your customers to say about EXSYN
RG: That EXSYN made a difference and is a valued partner that seeks the best solutions together with the customer.
Aircraft IT: Rutger Krom, thank you for your time.
“…we offer our customers data health checks to continuously validate their system, ensuring their system remains clean, up-to-date and efficient.”
As with any case study, a key part of the story will be the subject of the article which, in this case, is Air Tahiti. So, before we look at the case study, let me first tell you something about Air Tahiti.
Operating from and in French Polynesia, in the middle of the Pacific Ocean, halfway along a line between San Francisco and Sydney, Air Tahiti works in a unique environment. The network is as large as Europe but largely over water (figure 1). To travel to anywhere outside of the territory always entails a five- or six-hour flight — in short, it’s quite remote. There are 1,200 people working in the company and just ten aircraft. The reason why there are so many employees is that we undertake all of the ground handling for the network as well as the catering plus the usual airline divisions of Flight Ops and Technical department to do the maintenance with our own C-checks and Heavy checks, because it’s easier for the airline to do its own work in such a remote place. Air Tahiti carries almost 800,000 passengers a year, twice the population of French Polynesia, with a fleet of nine ATR-72 and one -42 aircraft.
•
•
•
•
Figure 1
Tahiti itself is right in the middle of the territory with the Marquesas Islands as far away as Sweden is from Paris. Air Tahiti connects 48 destinations within the 120 islands of French Polynesia; we have ETOPS (Extended Twin Engine OPerationS) flights as well as having both the shortest (at just seven minutes) and the longest (at four hours) flights operated by ATR aircraft. Because of the wide variation in flight lengths, the aircraft are rotated to different flights in order to roughly
equalize wear and tear across the fleet. The airline has only one maintenance base in Tahiti with around 90 people working there. All maintenance is carried out at that base; there is no line support to the other destinations but we do carry out our own C-checks, as I mentioned above.
Working with a legacy system to manage maintenance and stores, Air Tahiti experienced a number of pain points (Figure 2).
Multiple disparate systems data inconsistencies and repeated data entry
Figure 2
We were using multiple disparate systems which led to data inconsistencies and the need for repeated data entry. There were also capability voids when it came to the airline’s adherence to regulatory requirements; as well as planning and execution of maintenance, the upkeep of the manuals was the responsibility of the Hangar department. Finally, there was a lack of real-time stock visibility.
“We were using multiple disparate systems which led to data inconsistencies and the need for repeated data entry. There were also capability voids when it came to the airline’s adherence to regulatory requirements…”
that can be used to repair parts or from where uses can purchase, for example, a starter generator, with all of the suppliers and their costs plus some historical information with links to go into historical transactions for more information, also some parts on the screen where users can see the parts that are on order as well as where parts have been used. This was a game changer for us with its good visibility of the data and history allowing users to focus on their work.
There are also some workflows that users can reconfigure in the application to set authorization levels for purchasing and repairing parts (figure 5).
Figure 5
Some workflows can be defined to include, depending on the price of the part, who can authorize its procurement. Workflows can also be defined for purchase and repair orders. Ramco empowers the user to configure each warehouse and segregate, for instance, serviceable and not serviceable parts as well as to define some strategies for the warehouse in terms of picking parts when they are required for mechanics or the planning department (figure 6).
“Some workflows can be defined to include, depending on the price of the part, who can authorize its procurement. Workflows can also be defined for purchase and repair orders.”
Versatile Warehouse Configuration
• Full control on stock: Ability to set part conditions and transactions applicable to a Warehouse
• Warehouse level definition of Part Planning parameters to ensure automatic completion of the stock
Figure 6
Some screens, that are called Hubs, offer a good view on activity (figure 7.1)
Hubs : Activity at a Glance
Figure 7.2
Users can see that it focuses on external receiving for several warehouses and if the user picks one warehouse, as illustrated in the figure, it can be seen that there are three transactions to be inspected with the transactions and what they are about. This helps give a very good view of activities at a glance but it also it allows end users to work directly from the screen, so they can launch the transaction for, say, inspecting the part, direct from the screen. It can be used by management but also by end users to pick up that transaction that they have to do.
Having implemented a system, the question always has to be, how has the business benefitted? I’m glad to report that we can see clearly the benefits that the Ramco solution has delivered for Air Tahiti (figures 8.1 and 8.2).
Figure 7.1
For example, figure 7.1 shows the fleet availability with all the aircraft on one screen. Users can see the next due date for the aircraft’s maintenance and some later dates. That’s one example and another one is for the inventory operations (figure 7.2).
“… with all the aircraft on one screen. Users can see the next due date for the aircraft’s maintenance and some later dates.”
Figure 8.1
Maintenance
•
Effective Discrepancy deferral process
• Management workflows to monitor user authorizations based on the transaction & its total value Figure 8.2
For the future, having this system which is running smoothly gives Air Tahiti confidence, should we need to grow the fleet and/or increase the number of destinations. We are also considering going more mobile, using Ramco tools, and would like to reduce paper in the business because paperwork is timeconsuming. The Ramco application is modular and is what we are looking for, because it could help in reducing paperwork, plus the application provides some AI/ML (Artificial Intelligence / Machine Learning) functionalities that Air Tahiti does not use right now but that could help the processing of the mechanics’ work.
I hope that this article will inform readers and encourage any who face particular and non-standard challenges such as those faced by Air Tahiti, to consider that step to a more modern way of doing things. At Air Tahiti, we have enjoyed considerable benefits from our solution.
Julian joined Air Tahiti in 2006 to manage the transition between an old legacy IT system and an off-the-shelf. He is experienced at implementation and administration of M&E/MRO systems into an operational environment. He also has knowledge of various functional areas from engineering and planning through maintenance reporting and fixing to logistic and store management. Julian has also worked on the analytic and KPIs side of such projects.
stock levels with inventory stock analysis that has enabled the airline to reduce the incidence of excess procurement and to move to a perpetual inventory stock take. Previously, we were undertaking wall to wall inventory stock takes which was very time-consuming and inaccurate plus, it isn’t feasible to do a real wall to wall stock check in just one or two days. Now, with perpetual inventory, we are able to count 20 to 50 parts a day which is less time consuming and more accurate than before.
We have been able to improve maintenance execution with the Ramco solution because of the tools it makes available plus, for the mechanics, the screens are clear and useful so that they can record several tasks and discrepancies in the same few clicks. For procurement management, the solution supports everything including part modifications, advanced and standard exchanges and other transactions which are all covered in the system. Also, the workflow management, as previously noted, offers managers the opportunity to manage who does what, i.e., to monitor user authorizations so that the right people do the right tasks; it also shows the total value of each transaction.
Air Tahiti, the main carrier in French Polynesia, covers a network as vast as Europe. Connecting Tahiti to the outer islands for more than 60 years, the airline is inspired by the lives of legendary Polynesian heroes. There is an emphasis on reducing the business’s impact on the environment as well as supporting culture and communities in French Polynesia. The fleet includes seven ATR-72, two ATR-42 and three Beechcraft King Air B200 aircraft.
Ramco Aviation software offers Maintenance solutions on cloud and on premise with multi-tenant capability and next-gen mobility, catering to the needs of Heli-Operators, MROs, Airlines, Defense and Charter operations. Next-gen mobility solutions for maintenance operations are available through an app ecosystem where MRO supervisors, mechanics, pilots, storekeepers and customers can seamlessly execute critical operations on the go, from anywhere, anytime.
John Warren has been in the aviation industry for nearly 40 years and holds a BBA in computer science from the University of New Mexico. For more than 38 years, he has served as the Executive Vice President over the M&E division, IT, and QA at Ultramain Systems. Mr. Warren is the Chief Architect of ULTRAMAIN.
Aircraft IT: Your name, your job title, and the name of the business?
John Warren: John Warren, Executive Vice President, Ultramain Systems
Aircraft IT: How did Ultramain Systems get started?
JW: ULTRAMAIN® was first developed in 1980 with the goal of providing best practices and efficient operations to the aviation industry. Since that time, the business has undergone several technology enhancements to ensure we continue to provide the industry and our customer base with a best-in-class, integrated, comprehensive and easy-to-use system.
Aircraft IT: What is the guiding business principle that drives Ultramain Systems?
JW: A fundamental belief that aviation software serves more than a utilitarian purpose. Everything we do should help the industry be more efficient, reduce costs, and improve compliance.
Aircraft IT: What has Ultramain Systems’s greatest business achievement been to date, and why?
JW: It would have to be the leadership role that we have played in paperless operations. Paperless has been promised for decades but no-one put together a comprehensive end-to-end solution that allowed operators and third-party maintainers to get there. Ultramain changed that with ULTRAMAIN ELB™ and ULTRAMAIN Mobile Mechanic™. Ultramain has been in the paperless business for a long time. Today, when you look at the landscape of vendor offerings, everyone is touting paperless offerings.
Aircraft IT: What have been your disappointments and what have you learned from them?
JW: We were surprised and disappointed at how long it took the industry to recognize the advantages of paperless operations. Today, due to the lack of manpower, operators and maintainers are seeking out paperless solutions as fast as they can.
Aircraft IT: In a sentence, how would you summarize what Ultramain Systems does for aircraft maintenance customers?
JW: ULTRAMAIN makes you more efficient.
Aircraft IT: What do you feel will be the next big thing in maintenance Aviation IT?
JW: We believe there is more work to be done in the areas of optimization and (transactional) automation. Maintainers are still somewhat enslaved to IT systems. Our belief is that this will be reduced over the next few years.
Aircraft IT: What do you want your customers to say about Ultramain Systems?
JW: That we understand their business, what makes them unique, and we helped them become a better competitor by using our products.
Aircraft IT: John Warren, thank you for your time.
This article is a case study of how QOCO has enabled a continuous data exchange between Lufthansa and Rolls-Royce Digital Services. That said, it is always useful when sharing a case study such as this, for readers to understand something about the business to which the implementation has been applied. So, first, some information about Lufthansa and Lufthansa Industry Solutions and ourselves.
Lena is part of the business department with some thirty airworthiness engineers who undertake everything related to fleet lifetime control. That includes requirements for the engines when they have to be taken off the wing or when which part has to get what type of sub-task plus everything regarding standard duty cycle counters for the Trent XWB engines on the Airbus A350 aircraft, through which we came into contact with QOCO: this case study is specifically about the Airbus A350 and Trent XWB engines. We came into contact with QOCO when Lufthansa introduced, in collaboration with Lufthansa Industry Solutions, AMOS as their new MRO/M&E IT solution. Introducing that new IT solution in May 2022 was a significant and ambitious project for Lufthansa.
Jeff works with Lufthansa Industry Solutions, a Lufthansa company delivering IT services for a variety of customers in air travel, logistics, transport and more, with locations in Germany, Switzerland, Albania and USA, and with more than 2,300 employees. Jeff’s role is to deliver to the customer a consultancy experience based on AMOS and other IT applications.
MROTools.io
MROTools.io is a leading tool management software designed to simplify the process of borrowing, returning, reporting and tracking tools.
It was originally developed in close collaboration with a client to fulfill their requirements for centralized tool management and optimized usability.
• Entire audit trail and compliance overview
• Integration capability with all major M&E systems
• Up to €2 000 000 in annual savings*
*Savings calculated with actual customer data. Reference is a European airline with 63 aircraft.
data exchange. DACs (Direct Accumulation Counts), used by Rolls-Royce for lifing Trent XWB engines, allow the engines and engine components to be monitored
DACs and back in order to integrate the AMOS system with the Rolls-Royce service, an integration that had not been there before.
“The initiator of the change was the introduction of AMOS. The implementation of a new MRO/M&E IT system enabled Lufthansa to get a new way of managing data exchange.”
EngineData.io by QOCO is an automated data exchange platform which helps operators and, as in this case, the OEM, Rolls-Royce to exchange data. The solution manages the bi-directional data flows between Lufthansa and RollsRoyce systems (figure 1).
Figure 1
In addition, QOCO does comprehensive data controls and data validations to promptly alert the airline to any data issues. EngineData.io is always running in the background and keeping the AMOS and Rolls-Royce systems synchronized but invisible to users. After the implementation, QOCO provides a fully managed service that ensures undisrupted continuous data exchange, validates data quality and fulfills set requirements.
The implementation of the solution for Lufthansa IT was a quick and easy one since QOCO delivered documentation to Lufthansa along with examples, tests and more. Fifteen interfaces had to be updated from the AMOS system in the Lufthansa IT environment.
We opted for a ‘big bang’ go-live (see above) so everything had to go online in just a few hours which was not that easy. During the migration, the standard duty cycle counters that go with the Trent XWB also had to be migrated plus, also before the go-live, it was necessary to adjust processes with some tiny changes that had to be done in AMOS. Other than that, for Lufthansa, the less we have to deal with the new solution, the happier we are as an operator and it has proved robust and reliable.
Due to the Covid-19 pandemic, there were no face-to-face meetings until the go-live and the weeks that followed. Much of the preparatory work had to be conducted remotely. Also, we have to remember that Lufthansa was implementing two new systems with both AMOS and EngineData.io. The project in its entirety was very ambitious and it was good to find that this part of the project was very straightforward with not too many problems encountered on the part of the airline. For QOCO, there was more testing than is usually required with other operators
“The implementation was time critical as Lufthansa was already using the DACs System exclusively which meant that we couldn’t afford a long delay in the data exchange which had to be up and running reasonably quickly after the AMOS go-live.”
because Lufthansa had to complete quite a few data migrations; as a result, the data quality analysis had to be done a couple of times to ensure that the data was good. Also, testing standards needed to be rigorous because the airline was already using the DACs and it was important to avoid any hiccoughs when going live. QOCO always tries to arrange its resources to be available when customers need it. The implementation was time critical as Lufthansa was already using the DACs System exclusively which meant that we couldn’t afford a long delay in the data exchange which had to be up and running reasonably quickly after the AMOS go-live.
The major factor and dependency, during the QOCO EngineData.io implementation project, was the ongoing AMOS MRO/M&E system
has a large fleet of twenty-one Airbus A350’s with Trent XWB engines. For this reason, managing the data exchange manually was not an option, not even as a backup solution.”
in place between the Lufthansa’s previously utilized MRO/M&E system and Rolls-Royce DACs and that Lufthansa was already using the Rolls-Royce DACs.
“Lufthansa
A further challenge was data quality. Data exchange testing was done in multiple iterations; data quality improved with each data migration round from Lufthansa’s old MRO/M&E system to AMOS. Some of the data quality findings were identified by QOCO’s team performing the data quality analysis (DQA) and reported to the operator. DQA is an inherent part of the implementation project. The final DQA was completed after the last data migration run just before the go-live.
The final data challenge was the sheer volume of data to be handled. Lufthansa has a large and growing fleet with currently twenty-one Airbus A350’s with Trent XWB engines and more on order. For this reason, managing the data exchange manually was not an option, not even as a backup solution. Go-live for transition, from the previous MRO/M&E system, with in-house integration with DACs, to AMOS, with EngineData.io based data exchange with DACs, had to happen in just a matter of weeks after the AMOS go-live. That meant that the downtime of not having the data exchange running had to be minimized. In the event, EngineData.io end-to-end testing was completed right after AMOS go-live. After successful end-to-end testing, Lufthansa went live with EngineData.io just two weeks after the AMOS go-live.
As of today, QOCO ‘s Support Team is continuously keeping an eye on the data exchange that includes comprehensive data quality controls. Possible data quality findings are immediately analyzed and reported to Lufthansa and Rolls-Royce enabling rapid corrective actions that continuously ensure the continuity of core business operations.
As far as working with QOCO is concerned, we would change nothing. Of course, it would always be nice to get some more testing done to get a better feeling for any new solution but the whole project and implementation went well. Always, with big IT roll-outs, there is never the time to do everything that you might want to do but in truth we’d see no need to do anything differently if there were a next time. From the QOCO perspective, the project took a while to get started and it was necessary to wait for the AMOS implementation to get closer before this program could get underway. There were some small matters with the timeline having to change but that was only a matter of weeks, so small adjustments in the schedule were all that were needed. The main benefit for Lufthansa, of course, is the ability to improve engine time on wing.
Within Lufthansa, the interface is currently with AMOS but the plan is to have that interface working with other applications and systems. QOCO continuously extends data exchange capabilities driven by customer needs and improving EngineData.io experience.
Having a master’s degree in aeronautical engineering, Lena Duken has supported Lufthansa’s AMOS introduction as an airworthiness engineer over recent years. With a focus on powerplants, the setup of the configuration and requirements for the Trent XWB was one of her tasks. Lena started her career as a trainee at Lufthansa Technik before joining the engineering department as a process and systems engineer.
Jeff Winter is an IT Consultant at Lufthansa Industry Solutions (LH IND). Graduating with a master’s degree in aerospace engineering, he worked for Lufthansa Technik as a project engineer creating a system for an integrated AD/ Modification Compliance Status. Jeff then worked as a process and interface expert in the AMOS roll out project for DLH. There he was responsible for connecting AMOS to the DLH IT environment.
Deutsche Lufthansa AG, commonly shortened to Lufthansa, is the flag carrier of Germany. When combined with its subsidiaries, it is the second-largest airline in Europe in terms of passengers carried. Lufthansa is one of the five founding members of Star Alliance, the world’s largest airline alliance, formed in 1997. The fleet includes Boeing 747 and 787; Airbus A330, A340, A350 and A380 as well as A320 family; Embraer 190 and 195 plus Bombardier CRJ900
Lufthansa Industry Solutions is an IT service company for process consulting and system integration. This wholly-owned subsidiary of Lufthansa Group supports its customers with the digital transformation of their company. Its customer base includes both companies within Lufthansa Group and more than 150 companies in various other industries.
QOCO Systems Ltd helps the aviation industry to succeed in the changing world by creating new ways to work, to communicate, and to utilize data. The business’s solutions provide significant improvements to the industry’s complex processes. They enable customers to achieve more by doing less and to realize time-savings in labour-intensive tasks. They also bring visibility to customers’ operations to support decision-making based on real-time information.
Andy joined aviation industry when he was 21, starting within airline operations, and he was hooked on aviation from day one. The daily challenges are complex but also very rewarding working in a strong international team, seeking ways to problem solve and help customers succeed. In 2020, he joined QOCO as a Chief Commercial Officer and Partner, having been curious as to what QOCO was doing and what gave them a unique position with an iconic brand name like Rolls-Royce. At QOCO, Graham loves the culture of transparency, openness, honesty and respect as well as unique solutions used by some of aerospace’s best-known brands.
Aircraft IT: Your name, your job title, and the name of the business?
Andy Graham: Andy Graham, Chief Commercial Officer and Partner at QOCO Systems
Aircraft IT: How did QOCO get started?
AG: QOCO Systems was established in 2009 by Ilari Neitola, who is currently a Chief Technology Officer and Chairman of the Board. In QOCO’s vision, he combined his two main interests, aviation and IT. Ilari
saw opportunities to improve maintenance planning activities through software combining information from multiple sources with an easy and user-friendly interface. He thought that the best opportunity to drive the change was becoming an entrepreneur and that is when and why QOCO was established. Ilari ran the company successfully for many years delivering IT solutions for both the aviation and railway industries. In 2015 QOCO’s ownership was reorganized with Lauri Jämsén Ville Santaniemi and
Arttu Kataja joining company. I joined QOCO in the summer of 2020. Since then, due to rapid growth, the QOCO crew and operations have doubled.
Aircraft IT: What is the guiding business principle that drives QOCO?
AG: Transparency, trust and honesty guide us with our customers. We deliver what we promise and engage with our customers very proactively. QOCO has a unique combination of aviation and software development expertise that allows us to deliver high quality solutions for our customers. Our solutions focus on enabling seamless data exchange services for intracompany and intercompany purposes. Quality is at the heart of everything we do. We are proud to be an ISO 9001 and ISO 27001 certified organization.
it is today
“Transparency, trust and honesty guide us with our customers. We deliver what we promise and engage with our customers very proactively.”
Aircraft IT: What has QOCO’s greatest business achievement been to date, and why?
AG: The partnership with Rolls-Royce is the major achievement for us. We are utilizing our strengths to deliver seamless data exchange services, EngineData.io platform, for enabling high value digital services for Rolls-Royce customers, the world’s largest airlines. Our long-term partnership with Finnair enabled the development of MROTools. io, the leading digital tool management software. Working together with Finnair allows us to deliver solutions that are 100% fit for the purpose and significantly improve tool management. This year we are proud to announce new clients that use MROTools.io, such as Wideroe.
Aircraft IT: What have been your dis ppointments
us vulnerable to global events affecting the sector. I believe that following our passion for the aviation industry and utilizing our core competences for the benefit of our customers is the only way to succeed.
Aircraft IT: In a sentence, how would you summarize what QOCO does for aircraft maintenance customers?
AG: QOCO improves operational efficiency, compliance, and visibility of crucial data to help make critical business decisions.
Aircraft IT: What do you feel will be the next big thing in maintenance Aviation IT?
AG: Digitalization and getting rid of manual processes will prevail in the coming years. Aviation maintenance will become automated and based on
“We are utilizing our strengths to deliver seamless data exchange services, EngineData.io platform, for enabling high value digital services for Rolls-Royce customers, the world’s largest airlines.”
Aircraft IT: What do you want your customers to say about OQCO
We are writing this article to share with industry colleagues our experience because sharing successful experience benefits everybody. As with any case study, in order to fully understand the story, it’s useful to know something about the subject of the study, in this case, Air Europa. So, we’ll begin with an introduction to the airline.
With more than 60 destinations served in Europe and the Americas, Air Europa is Spain’s third largest airline with a fleet of Boeing 787-8 and -9, Boeing 737, Embraer E195 and ATR 72 aircraft. There are more than 3,000 employees across the three organizations within the business. But what were the reasons for undertaking this challenging project in the worst possible economic situation due to the Covid pandemic?
In 2017, Air Europa came to the realization that we needed to upgrade the maintenance and engineering IT solution used by the airline. There was an internal analysis carried out to establish the basis for the project and what we realized from that was that, the maintenance department had a different management eco-system that had been developed in-house with separate solutions for each department and their users; every one of those systems had their own database which meant that not all users could share information so were not working with the same information. This made engineering, logistics and planning very difficult. Furthermore, these systems were based on obsolete technology which did not allow improvement to the systems or the development of mobility tools. And, without mobility tools, it was going to be difficult to apply the paperless policies that we wanted or to improve the efficiency of processes, or work in real time.
The conclusion was that we needed a new IT tool; we needed to change but that change needed to be aligned with Air Europa’s broader digital transformation plan, the vision for that plan and its mainstays (figure 1). Based on that, we defined our goals and the requirements for the new system.
This decision should be, aligned with the Air Europa Digital Transformation Plan and its mainstays.
Based on this, we defined our goals and the requirements of the new system Figure 1
The vision is built on six mainstays: safety and quality assurance, cost control, continuous improvement, innovation, punctuality and, in the middle, people. Also, the decision to undertake a project like this must be aligned with the vision for Air Europa. Based on this, we defined our own goals (figure 2)
“We wanted to standardize Air Europa’s internal processes and align them with the vision as well as industry standards, and we wanted to work with a single platform accessing the same information at the same time…”
We wanted to standardize Air Europa’s internal processes and align them with the vision as well as industry standards, and we wanted to work with a single platform accessing the same information at the same time; that was very important. We wanted to be able to work in real time and to remove as much paper as possible from all processes. In a similar vein, we wanted to apply a digital signature capability while maintaining cost control and with improved internal communication using the same language — where there are different products or tools in use, they don’t always talk the same language.
After benchmarking, and analyzing different proposals, and the pros and cons of each one, we determined that TRAX was the solution that best met Air Europa’s requirements; not only because the tool met eighty or ninety percent of our digitalization requirements but also, they were open to the idea of modifying or adding new functionalities in order to cover the rest of our requirements.
To make things clearer, we’ve broken this article into two sections. First, before the GoLive, the planification of the project and how we arrived at that and then, what happened after the GoLive.
At the outset, we implemented the eMRO platform from TRAX for the back office, and we deployed the Air Mobility platform. We wanted to deploy a maintenance application to help us to better control defects management as well as task planning and manuals. We also wanted the plan to focus operations on the pilots and cabin crew.
At the top of figure 3, we can see the initial plan.
Starting on 1 April 2019 the expectation was that, in two years, we could have completed two phases of the plan; the first phase for Maintenance and the second phase for Operations, deploying the electronic Cabin Log App and electronic Technical Log Book with the Pilot App. Unfortunately, we encountered two problems during this process and that caused us to re-define the project.
The first was that we needed to re-define the elements in the project. Initially we had included not just the airlines in the group, Air Europa and Air Europa Express, but also included the MRO as part of Globalia Holdings. However, the process, currently underway, for selling the airlines to IAG does not include the heavy maintenance business. We had to re-define the project leaving out the MRO. The second problem probably needs no further explanation; we’ve all suffered the consequences of Covid and, unfortunately, many companies went out of business.
These problems together made re-defining the project necessary. One of our main visions at Air Europa is continuous improvement and we applied this philosophy in order to continually adapt the project and the planning. The result was, as can be seen on figure 3, after the seven months of delay proposed for phase 1, we went to GoLive.
We gave ourselves just seven months but, in the end, we did it. One of the most important things with this project and the reason we succeeded was the Team. We had to identify experts in order to train them on the new platform which is eMRO, redefine all of the processes in the company and help employees to understand the new processes that the company would be implementing (figure 4).
This Project has required us to redefine all internal Processes
More than 100 Processes and more than 603 Standard Works have been redefined.
This Process & Standard Work definition has followed the SIPOC definition process methodology
“… people just thought about the area in which they worked, they didn’t think globally. We needed to train them, in order to understand these new and connected processes, to think globally.”
When there were, in the past, systems that were not connected, people just thought about the area in which they worked, they didn’t think globally. We needed to train them, in order to understand these new and connected processes, to think globally.
This kind of project, as you can imagine, meant that the people in the company were out of their comfort zone, needing to re-define all the processes. If you have this kind of stress, as we faced it, in the middle of the pandemic, then you can imagine the impact and the consequences was a record of temporary employment regulation, an unfamiliar situation and all at the same time. It was very hard but the aptitude and attitude of the workforce, with hours of hard work, ensured that we got through the project.
During this project, we had to redefine more than one hundred internal processes at Air Europa, as well as more than 600 standard work procedures, all based on the SIPOC (Suppliers, Inputs, Process, Outputs and Customers) methodology for definition in order to ensure that all processes in the company were part of a big chain and compatible with one another. Another key task for this project was the migration of more than thirty years of data with some 576 million records across seven systems (figure 5).
Over 30 YEARS of data has been migrated from the LEGACY system
The second issue (figure 6.2) was the corner cases.
Data migration issues 1st Wave
Corner cases 2nd Wave
Helping new users
Avoid the “Valley of Despair”
Figure 6.2
accurate. The data was also cleaned before we were able to operate with it. There were different sources such as logistics from CAMO and tools that had to be separated and all put into the same system. Then, when all of that was in place, in July 2021 we completed the GoLive which took 36 hours; but that wasn’t the whole thing. It’s easy to think that, when you have completed a GoLive, everything has been done but that is not the case.
Just before GoLive the on-site TRAX consultant shared a video called ‘Life after GoLive’. It’s an interesting video because it shows the most important challenges and problems that are faced after deployment of a project. Although the video refers to an Office 365 deployment, the main problems that we faced in Air Europa were the same (figure 6.1).
After several monthsof hard work, July 13, 2021, was the GL, however we couldn’t say the Project was ‘done’ at thatmoment: “we started to face to real life”
Data migration issues 1st Wave
Corner cases 2nd Wave
Helping new users
Avoid the “Valley of Despair”
“After several iterationsyou might encouter data migrationerrors This can happen because not all data has been fully checked bykey users, or because scripts have failedduring themigration process”
Ø It’simportantto sort out theseerrors beforetoo many pile up
Figure 6.1
We faced for key issues.
The first one was data migration. We had completed several iterations and thought that all was now clear but it was impossible to be sure that all the information was ready. Some errors became apparent after the GoLive and it’s important to sort out any such issues because, if you don’t do it, they will pile up.
“It’s impossible to test every possible scenario prior to GoLive. The second wave of issues you might encounter are the outliers one off scenarios you didn’t have time to test”
Ø You must be sure that your project team handles these cases as soon they appear, then you should be fine.
We performed a lot of simulations, defined a lot of processes and tested them but it is quite impossible to test all the system and all possible cases that might arise. Therefore, it is important to prepare to face the processes and cases that might not have been tested because additionally, maybe, we might have created data in the wrong way which will lead you back to the first problem.
The next issue was helping new users (figure 6.3).
Corner cases 2nd Wave
Helping new users
Avoid the “Valley of Despair”
“Next thing to look out for are user errors. We consider these issues the most dangerous because if they aren’t dealt with swiftly, user errors can snowball into an avalanche of problems that affect the whole organization.”
Ø speed of resolution is key. If errors are being created faster than resolutions, that’s a problem.
Figure 6.3
Air Europa spent a lot of time training users but needed to GoLive with just sixty percent of users fully trained. That means that the forty percent who had yet to
“All employees are able to access the system to get information in real time and at the same time while all the engineers are also working in digital formats so most of the paper has been removed from Air Europa’s operations.”
complete their training could cause errors in the system that needed to be corrected as soon as possible because, if left unsorted, small errors can generate large problems.
Nowadays, we are facing the fourth issue which is trying to avoid the ‘Valley of Despair’ (figure 6.4).
“As a resultofthesortofissues in the previous item, users might get frustrated and disappointed, and wonder if the project was even worth it.”
Ø Speed of resolution is key. If errors are being created faster than resolutions, that’s a problem.
Figure 6.4
Not all systems are perfect and it’s true that not all users were fully trained which did cause some issues and led to people complaining. But, as a manager, you need to manage them in order to put them on the right path, to understand that the system is not perfect and needs an assimilation process until it is working. However, after that period of assimilation, today, we have succeeded and have started to work with the new standardized processes. All parts of the organization are working on a single platform which has delivered some great benefits.
All employees are able to access the system to get information in real time and at the same time while all the engineers are also working in digital formats so most of the paper has been removed from Air Europa’s operations. How was this achieved? Using ‘an App for every task approach (figure 7). Deploying a Maintenance Platform and eMobility Suite based on ‘an APP for every Task’ approach
We deployed a maintenance platform, eMRO from TRAX, the heart of the system, for the back-office plus every task has its own application. All of the applications were connected/integrated with the system.
8).
Figure 8
The first one is to have a plan, to be clear where you are going: the plan will need to be adjusted as the environment changes — for instance, Covid was not planned. It is important to identify and enroll the key users. It’s a challenging project and you won’t have all the knowledge necessary to carry it out: you’ll need to involve people in the company with the right experience. Communication is vital and we worked hard on this at Air Europa but we feel we could always further improve. For me, one of the most important lessons has been the need to lead by example, to be the first to be hands on with the new system. And, of course, be sure to have a committed provider; Air Europa had that committed provider in Trax.
During the project, we came across different situations that required us to create or perform side projects that had to be carried out in parallel with the main project. The first one was that Air Europa needed to replace the document management system plus integrate it with the new platform. We were able to migrate nearly 500 gigabytes of records related information and have created more than 200,000 linked documents to the eMRO platform.
Another project of which we are very proud, has been the deployment of a mobility system and application for mechanics and all of this system had to be deployed generating the need to manage a large quantity of devices. We needed
This Smart Locker is able to manage and update the system, identify who has access to the device, prove a smart delivery system, to know whether or not it needs updating, to update while charging and to know time of use. We are also able to quickly update and deploy the content for applications. That is quite important because, if a mechanic is working when a new version of a publication needs to be deployed, that means that, if the mechanic doesn’t have the correct application, he’ll be unable to do the work. We are able to deploy all new versions in less than twenty minutes for all devices in all of our facilities and we are able to monitor all devices; where they are, their status, their charge, the updating; all of which can be transferred into the platform. Plus, the cost has been less that solutions that we found in the market.
“We are able to deploy all new versions in less than twenty minutes for all devices in all of our facilities and we are able to monitor all devices; where they are, their status, their charge, the updating…”
Also, we realized the benefit of sharing experiences. At the start of the article, we said that one reason for the article is that we are here to share. We have realized the benefit of sharing experience, problems and doubts not only with providers but also with other customers, like ourselves, that are working with the same system. We share the decisions that help us to solve problems because we have the same restrictions, the same problems, authority requirements… all of us, in the end, work more or less in the same way. So, we decided to create a collaboration group initially to discuss the problems, experiences and solutions; but now there is a collaboration workspace in which members can share their different points of view and understand how each one thinks and solves problems. It started with TRAX customers in Spain but nowadays it is a bigger group (figure 10).
Figure 10
We are very proud of this because we have all learned a lot from other airlines which is to the benefit of us all.
Let’s look at what Air Europa will be doing during the last mile of the digitization process. This is not just a project for maintenance, but also affects the whole organization; many will benefit from it. This last mile has the highest visibility and impact on real daily flight operations. It doesn’t mean that this is the end of the project; it’s just another milestone and, once it has been passed, there will be a new lifecycle. Many scenarios are being considered and Air Europa is performing a lot of testing, but faciplusplus new problems in real life operation ands a certainty and is part of the cycle. Of course, this was not the priority but even working with the first phase of the project, the focus was already on this last mile
During this phase, we introduced two new apps, one for the Flight Crew and one for the Cabin Crew: even though they were only two applications, it was not an
easy task. These two apps will be to complete the whole process of this transformation project. Although new challenges will arise during this last mile, there is the opportunity to co-operate and collaborate with other customers, and to share experiences and problems and candmmon solutions. Also, there is strong support from Air Europa’s partner and, at the end, we’ll need to fulfil all the Authorities’ requirements that we come across. These working groups generate useful added value.
But, for the project to continue, there will need to be new working groups and that’s not an easy task. We need employees that are eager to share new ideas, to be able to collaborate with each other and sometimes undertake some testing because it can be hard to nail down what’s going on in the Apps or in the integration with the systems. A lot of this has been done during the pandemic, even while having to overcome physical separation distances, but we are proud of what has been achieved. Happily, we managed with a great team that delivered good results and are one hundred percent committed to the project.
The digitization process is mind blowing for which we had to be ready to prepare because sometimes these kinds of transformations are not welcome and sometimes they are a bit frustrating when things don’t go as expected.
There are some interesting benefits (figure 11) from which we want to highlight the speeding up of the operation and reducing maintenance transit times, always with safety standards in mind.
Figure 11
There is also reduced maintenance impact on passengers and no over information is provided. We did share some legacy information on the paper techlog which doesn’t make sense. What does make sense is for information to be updated in a real time platform with access to it as required. Addressing new challenges is also a benefit; it helps to improve processes and offers value to the whole project. And we are getting closer to the idea of a paperless cockpit.
One goal that we have in mind is to keep going and keep focusing on the passengers. For this, we are thinking about how to deliver real-time reports from the systems in the company and take advantage of this information to take action as soon as possible.
As we said before, we have faced new challenges during this project, and some of them have created work on side projects. Sometimes we uncover shortcomings which need to be faced — how to deal with a system failure or a lack of connectivity during an operation. So, it was necessary to build new procedures to deal with those sorts of contingencies that might happen during an operation. In case of a contingency, it is necessary to go back to basics and use the paper system but Air Europa wants to give support to these back-up procedures. For this reason, the IT department with Flight Operations has developed some interfaces to connect ACARS to the back-end of eMRO to fetch all maintenance data that pilots would need to handle a contingency scenario. We can retrieve information, collate it with the facts, such as maintenance checks, due dates and notices to crew. In addition, there are links to Jasper reports which is another way to retrieve this information. Both are powerful tools and we wanted to get the most from them since they add value and give support to the whole ecosystem.
In figure 12, you can see a real test flight.
Figure 11
There are some deferred defects and, on the other side of the figure a Jasper report. The Jasper report shows an example of a deferred defect with the minimum information that the pilot would need to dispatch the aircraft and, underneath the Jasper report, some snapshots from the ACARS report with the same information.
To conclude, the results so far. We have begun to test all this in the real environment and the results have been good. It’s a way to detect hidden details that might have been overlooked before. And here, the final key users gain a special relevance with their feedback. We need to detect any possible gaps in our processes, minor gaps with the app and with the integratioands. Looking over the work we have done at Air Europa, we are proud of it, we are achieving our goals
with minor changes which is normal. We hope this will have been useful for anyone considering embarking on a similar digital transformation and paperless maintenance project.
Head of Innovation in Air Europa Maintenance and Project Manager of eMRO and eMobility implementation
Borja is a Telecommunications Engineer who started at Air Europa Maintenance in 2017 as Innovation Manager. In addition to managing innovation projects, he has played a leading role in the implementation of eMRO and eMobility suite (TRAX) as project manager. This project was considered strategic within the company’s digital transformation plan, whose GoLive was in July 2021, marking a major milestone on Air Europa’s Maintenance digitalization roadmap.
Captain and Line Training Captain, and Engineer in Computer Science Juan Miguel has been in aviation for over 20 years and is a Captain on the Boeing 737: he was also type rated on Airbus 330 and Embraer 195. He is passionate about hardware and software programming skills due to his academic background as an Engineer in Computer Science and is involved in the digital transformation project in Air Europa to deploy TRAX eMobility.
Headquartered in Mallorca, Air Europa is Spain’s third-largest airline, flying non-stop to more than 60 destinations, including points within Spain as well as international destinations across Europe, Africa, Asia, North America and South America. The fleet of 48 aircraft includes Boeing 787-8 and -9 types as well as, Boeing 737-800, Embraer E195 and ATR72. Maintenance operations include part145 and CAMO.
TRAX eMRO is an enterprise software provider of aircraft fleet engineering & maintenance, MRO, planning, compliance and inventory management. The eMobility Suite is truly mobile with offline capability to ensure users can work in Wi-Fi/Cellular dead zones. Organizational capabilities and support solutions include: custom software development, software maintenance, mobile solutions, systems application integration, release upgrade support, SaaS cloud hosting, Project Management & implementation support, user training, business analyst consultation with business process mapping & documentation, gap analysis, data migration, and QA testing.
Irecently heard a metaphor in which data exchange was compared to water irrigation. Imagine modern aircraft and engines accumulating vast amounts of data from sensors and asset management processes. Most of that data then remains confined in the operator’s systems, as water in a reservoir. Little value is gained from that data, until a pipeline is built to distribute it to those who have the capabilities to extract data-driven value for both themselves and the data provider, as a canal providing water from the reservoir to the vineyard.
In my last column, we explored the value that OEMs (Original Equipment Manufacturers) can extract from digital twins of their assets when they are able to access the airlines’ up-to-date digital records and sensor data. In this context, digital records refer to the fleet and asset configuration data, maintenance records, part utilization data and flight records, all of which are typically maintained in the airline’s Maintenance & Engineering (M&E) system. In this article, I will discuss how the pipeline for that data can be built.
To determine how OEMs can establish a reliable data exchange solution, we first need to explore the requirements for that solution. There are three key requirements that need to be fulfilled for the OEM to effectively utilize the digital records data.
The OEM must receive the data from all their assets in the same format. One of the challenges in establishing regular and reliable data feeds from operators to data consumers is the lack of
standardization in how data is stored and managed by different operators using different M&E systems.
To ensure that OEMs can utilize the digital models of their assets, those models need to be up-to-date with the latest data from the operator’s system. To meet this requirement without unreasonable effort, manual processes for formatting and entering the data must be eliminated. Therefore, the data must be provided to the OEM in a format which can be automatically ingested by the receiving systems.
This requirement is obvious, but not trivial to meet. As digital records data is generated to a great extent by manual processes, data quality issues are inevitable, and data quality across different airline systems varies widely. To allow for this, the data exchange solution itself must include monitoring and data validation logic to ensure that only high-quality data is delivered to the OEM’s systems.
Taking into account these requirements, it becomes apparent that a centralized data exchange solution for automated transformation, validation and delivery of the data from the different airlines is needed. A centralized solution allows the OEM to tap into one data source that provides a continuous flow of formatted and validated data, separately for each of the OEM’s systems that require it. A centralized solution also allows effective monitoring of the data
streams from different airline customers, and enables the continuous development of data validation rules built into the data exchange solution.
Rolls-Royce is an industry leader in this area and provides data exchange enabled digital services for their airline customers through the Blue Data Thread program. Nick Ward, VP Digital Systems, Civil Aerospace at Rolls-Royce describes the program as follows: “Imagine a thin blue thread connecting every Rolls-Royce powered aircraft, every airline operation, every maintenance shop and every factory”. Read more about Rolls-Royce Blue Data Thread in the Aircraft IT article, ‘Rolls-Royce and QOCO: working together for PLM’.
Rolling out a working data exchange solution between any OEM and its hundreds of airline customers does not happen overnight. The challenge of onboarding airlines to the platform is two-fold. The first is the technical challenge of connecting to the airlines’ systems. Subject matter expertise in M&E systems integration and a deep understanding of the data in those systems are critical capabilities for the OEM to acquire.
The second challenge is to motivate the airlines to participate in the data exchange, which is a complex matter but can be broken down into a simple cost-benefit equation. To address the cost side of the equation, the airline’s burden to connect to the pipeline should be minimized. This is accomplished by providing support for the airline and designing the integration around existing M&E system data export capabilities. In practice, a light-scale integration project with each airline is needed and should be managed by the OEM or their integration partner.
To address the benefit side of the equation, the OEM must consider the business value it can generate for airline customers with access to the data. For example, this value could come from enhanced predictive maintenance techniques lowering maintenance costs, automated data management, or optimized operations.
When considering the value that can be generated by the right data consumer, and looking at the development of the industry in a broader sense, we can envision a future where several data consumers tap into the same centralized data exchange solution. In this vision, there are a host of airlines on one side of the platform, and several data consumers on the other side, together comprising an ecosystem of data exchange and value sharing. As owners of the data, the full control of data sharing must remain with the airlines. In summary, the key ingredients in enabling data exchange between operators and data consumers are the technical integration capability, and a willingness to collaborate and create value for all involved parties.
Henrik is a Customer Success Manager at QOCO Systems ltd., with extensive experience in delivering data exchange solutions for collaborative parties in the aviation industry. In his current role, he is working within strategic relationships to oversee global deliveries of the EngineData.io SaaS solution, which enables OEMs, Airlines, MRO service providers and other key players in the aviation industry to share data and jointly create value.
VENDOR JOB CARD: SWISS AVIATIONSOFTWARE LTD.
Fabiano has a master’s degree in economics and computer science from the University of Zürich. He has spent the last 20 years working with AMOS and has been instrumental in developing a small team of visionary experts into the market leader of MRO software. Prior to his current role, he was responsible for customer success and customer-facing activities, besides ensuring that AMOS meets customer and market expectations. He wants to focus on fast tracking the industry’s digitalization, through intelligent and enjoyable-to-use software.
Aircraft IT: Your name, your job title, and the name of the business?
Fabiano Faccoli: Fabiano Faccoli, CEO of Swiss AviationSoftware Ltd.
Aircraft IT: How did Swiss AviationSoftware Ltd. get started?
FF: The history of AMOS goes back to the year 1989 when Crossair (predecessor of Swiss International Air Lines) decided to develop its own MRO software which laid the foundation for AMOS. In 2004, Swiss AviationSoftware was founded, a spin-off from Swiss International Air Lines. The new company was given the ideal set-up to develop its own strengths as an MRO software provider in this highly specialized
niche market while still being embedded in a strong and successful aviation context. To continue its story of success, Swiss-AS can draw on decades of experience as well as on a large customer community which contributes to the longevity and competitiveness of the product.
Aircraft IT: What is the guiding business principle that drives Swiss AviationSoftware Ltd.?
FF: Whatever we do, we do it with passion, while always keeping the main goal in mind: with AMOS we strive to give our customers the best-possible tools and all the necessary support to allow them to swiftly adapt to change and gain a competitive edge in the age of digital disruption.
Aircraft IT: What has Swiss AviationSoftware Ltd.’s greatest business achievement been to date, and why?
FF: Having successfully enabled over 200 customers in managing their Technical Operation more safely, effectively and efficiently while never losing a customer and being able to support small operators and flag carriers or LCCs with hundreds of aircraft. We have been profitable from the first day and have maintained that position over 30 years, eventually becoming the market leader. During these three decades we have successfully achieved two major technology changes and will continue to evolve AMOS allowing customers to exploit the opportunities that new technologies and digitalization will bring in the coming decades.
“…too often we’re too impatient or thrilled when introducing innovation. Very often smaller steps following agile principles are the right approach, although they might not be so shiny or grandiose.”
We strongly believe in honesty, transparency, and sticking to commitments. We have always been very keen to collaborate with other industry stakeholders and have focused on making AMOS able to seamlessly integrate with other systems. Finally, we have only been able to be successful through our customers, that positively challenge us every day and motivate our outstanding team of almost 300 colleagues to go the extra mile.
Aircraft IT: What have been your disappointments and what have you learned from them?
FF: Underestimating the right timing and respecting the organizational and human impact of introducing new technology. We all know about the chasm in the technology adoption life cycle, but too often we’re too impatient or thrilled when introducing innovation. Very often smaller steps following agile principles are the right approach, although they might not be so shiny or grandiose. It will help individuals to better adapt and reduce operational impact as well. However, the real key is to always include innovators and early adopters from within your customer base, when planning the introduction of innovation and new technology. We are very
fortunate that our customer base provides sufficient partners always thinking three steps ahead and having a desire to actively shape the industry’s digitalization.
Aircraft IT: In a sentence, how would you summarize what Swiss AviationSoftware Ltd. does for aircraft maintenance customers?
FF: We provide intelligent, best-in-class, highly secure and enjoyable-to-use software solutions and added value services, that allow our customers to run their MRO and Technical Operations processes safely, efficiently and effectively with state-of-the art technology in an increasingly connected world.
Aircraft IT: What do you feel will be the next big thing in maintenance Aviation IT?
FF: Before talking about the next big thing, all industry stakeholders should provide the foundation to truly exploit the current big things like predictive maintenance and big data. To truly exploit the potential of data, its quality (timeliness, completeness, accuracy, consistency, integrity, and validity) needs to greatly improve. The challenges that we need to jointly solve as a priority are moving
to paperless processes, making sure that data can be exchanged across companies and systems safely and fast, and eventually provide software that can cope with the varying digitalization maturity levels of industry players in the years to come.
We will put a strong focus on evolving AMOS in a way that can cope with the fact that not every airline or MRO can digitalize at the same pace. Once the data quality is high, then customers can benefit from AMOS’ growing automation features and high level of integrability. With AMOScentral we’ll facilitate and fast-track the industry’s digitalization by empowering collaboration and data exchange across all market players.
Aircraft IT: What do you want your customers to say about Swiss AviationSoftware Ltd.
FF: Swiss-AS provides software and services that help to run our operation reliably and achieve our ambitious business objectives. Whenever we have issues, we know that we can count on Swiss-AS and its staff. They are fun to work with and genuine.
Aircraft IT: Fabiano Faccoli, thank you for your time.
“The challenges that we need to jointly solve as a priority are moving to paperless processes, making sure that data can be exchanged across companies and systems safely and fast, and eventually provide software that can cope with the varying digitalization maturity levels of industry players in the years to come.”
Key ‘at-a-glance’ information from the world’s leading MRO software providers.
IT is a powerful force but, to leverage its greatest value, it must be harnessed and directed. It must also be able to handle huge and growing data streams that record every aspect in the lives of aircraft and the processes by which they fly. This challenge has attracted the best brains and most innovative enterprises to create IT solutions for one of the most demanding working environments, Aircraft MRO and M&E. Inevitably, there are many such developers and vendors offering solutions ranging from single function `Specialist Point Solutions’ to complete `End-to-End’ solutions covering the whole process. Only readers will know the specific requirements of their businesses but we have assembled a directory of the best MRO software providers and listed them alphabetically to make it easier for you to undertake a brief-ish (there are 37 providers and the number continues to grow) survey of the market, as a preliminary to starting on any specification and selection process. Or you might simply read it to keep up to date with what is available today.
W: www.2moro.com
T: +33 (0)559 013 005
E: sales@2moro.com
Locations: France (HQ), Canada and Malaysia
W: www.adsoftware.fr
T: +33 (0)4.50.89.48.50
E: contact@adsoftware.fr
Location: France, Thailand, South Africa, Brazil
NAME OF PRODUCT MARKETED
• Aero One, Aero-Webb, BFly
KEY BUSINESS/SOFTWARE AREAS
• MRO: Line, Base, Engine maintenance
• Airworthiness and Fleet Management
• Flight and Crew management
• Material Management
• ERP: Finance, Purchasing, Sales, HR
2MoRO is a software development company dedicated to the aviation market. Our teams are located in Europe, America and Asia. We work with partners and resellers worldwide and our software solutions are used in more than 20 countries.
We propose 3 different software solutions in order to fit every type and size of Aviation, Aerospace and Defense companies. Our solutions have been chosen by aircraft and engine manufacturers such as Airbus Helicopters, Dassault Aviation or Safran Group but also by aircraft operators, airlines or independent MROs. We also have a R&D department and can help you in data migration.
Aero One® and Aero-Webb® have been designed to complement your ERP solution regarding aviation and MRO specific needs. They are certified by SAP®, and Aero-Webb® can also be used as stand-alone. BFly®, our latest software, is a new way to create customized software for aviation and enables users to collaborate, design personalized screens, workflows and business processes.
At 2MoRO, we are proud to offer a very dedicated customer service, as reflected by our 95% retention rate. We work mainly on a fixed-price base and we are ISO 9001 certified for aviation software development, maintenance and support.
•
KEY BUSINESS/SOFTWARE AREAS
• AIRTIME — Fleet management & CAMO
• AIRSTOCK — Inventory control & Logistic
• AIRDOC — Documentation management
• AIRSTAT — Reliability and statistic reports
• AIRWORK — Time Tracking Software
ADSoftware has developed an integrated fleet management system and logistic package called AIRPACK. This 6 module system answers to the needs of aircraft and helicopters operators, as well as MRO and CAMO centres. It meets all requirements in terms of functionality, traceability, performance, aviation legislation and regulations. Today, ADSoftware counts more than 54 clients worldwide. The strength of ADSoftware is the simplicity of its products; they are Microsoft Windows® ready, Web-enabled, available in various languages and a complete training program can be done in just five days. The company also provides a 24/7 online technical support and extremely competitive pricing conditions.
W: www.adbtech.com
T: +1 (425) 466-5013
T: +1 (614) 377-9644
E: sales@adbtech.com
Location: Bellevue, Tampa USA; Istanbul, Turkey
•
KEY BUSINESS/SOFTWARE
• Fleet Management
• Maintenance Engineering
• Material Management
• Production Planning
• Labor Collection, Billing
APPLIED DATABASE TECHNOLOGY (ADT) is a professional services and software development firm that provides MRO software solutions for aircraft operators as well as aircraft repair and overhaul organizations. Our commitment to this business segment is proven with our software package, WINGS, designed specifically for aerospace companies. ADT has been in the software business since 1992 and has built an excellent customer reference base. Our first priority is always customer satisfaction; thus we have obtained 100% customer satisfaction since 1992. ADT has a proven record to develop reference accounts in the Aviation industry along with other high technology companies which are considered to be leaders in their fields.
W: www.aeroxchange.com
T: +1 972 556 8500
E: support@aeroxchange.com
Location: Texas, United States
W: www.aerostratsoftware.com T: +1-888-558-2860 E: info@aerostratsoftware.com
Location: Seattle, USA
• Aeroxchange
KEY BUSINESS/SOFTWARE AREAS
• MRO
• Supply Chain efficiencies
• Exchange of documents
• Commercial trancactions
• Procurement
Aeroxchange is the only electronic business network that supports all MRO business processes within the aviation industry for buyer and sellers. Aeroxchange provides a complete lifecycle of electronic communication from order creation to final invoice. The Aeroxchange service accelerates repair, replenishment, sourcing, inventory pooling and other critical operations in the aviation supply chain.
Aeroxchange automates the exchange of documents and information for commercial transactions. Our electronic platform dramatically reduces manual activity for transaction processed by fax, telephone and email, and increases the accuracy and timeliness of information and document exchange.
For airlines and buyers, Aeroxchange creates supply chain efficiencies for complex procurement of MRO goods.
For sellers and repair service providers, Aeroxchange creates sales channel efficiencies by broadening visibility of inventory and capabilities and streamlining the order process.
NAME OF PRODUCT MARKETED
• Aerros
KEY BUSINESS/SOFTWARE AREAS
• Heavy/Base Maintenance Planning
•
•
•
•
Aerostrat is based in Seattle, WA and offers one product called Aerros, a one-of-a-kind program that manages an airline’s or MRO’s aircraft maintenance schedule. Aerros enables users to optimize the maintenance program by managing various maintenance and operational constraints, which maximizes event yield, drives costs down, and enables the organization to plan proactively, not reactively.
Aerros provides robust ‘what-if’ scenario capabilities that allow users to see the effect of different variables. This aids in making sound business decisions concerning the maintenance and fleet plan. Some of these variables are maintenance programs limits, min/target/max yield, aircraft hr/cy utilization, track/requirement compatibility, and maintenance allocations. To forecast an optimal maintenance plan within an operation, Aerros also provides a Capacity Planning feature. This feature allows users to input and view vendor capacity available and labor hour demand to better manage the labor force.
Aerros also provides easy-to-navigate scenarios with drag and drop event movement and manipulation. Scenarios can be published so others (including vendors or operators) can view the plan. Aerros provides excellent system stability and reliability with standard IT practices. It is also integrationready and designed to work as an extension of a user’s existing information systems.
W: www.asqs.net
T: +43 1 306 1234
E: sales@asqs.net
Locations: ASQS GmbH, Vienna, Austria; ASQS Ltd., Bangkok, Thailand; Calgary, Canada
NAME OF PRODUCT MARKETED
• IQSMS (Integrated Quality and Safety Management System)
• Flight Data Monitoring (FDM) Service
• The IQSMS Suite consists of a total of 10 modules, varying according to the operator. (Airlines, Business Jets, Helicopter, Airports, MROs...)
KEY BUSINESS SOFTWARE AREAS
• Quality Management Module
• Reporting Module
• Risk Management Module
• Document Distribution Module
• Emergency Response Planning Module
ASQS (Advanced Safety and Quality Solutions) is a global supplier of highly innovative QMS and SMS software for the aviation industry, supporting more than 200 large and small operators, including airlines, business jet and helicopter operators, groundhandling agents/FBOs, airports and maintenance organizations, in creating a safe and productive work environment.
The company specializes in intuitive, integrated, web-based solutions with exceptional customer support. ASQS’s core product IQSMS allows clients to manage operational data 24/7 online and offline with a single integrated tool which significantly simplifies daily tasks. The easy handling of the software creates a positive reporting culture, enables comprehensive quality management and proactive risk management to maximize productivity, reduce operating costs, and optimize internal and external working procedures. IQSMS automates laborious processes like the submission of ECCAIRS or IDX compliant incident reports which, combined with a consolidated, up-to-date regulations database, ensures legal compliance with national and international requirements and standards.
W: www.atp.com
T: +1 415-330-9500
E: marketing@atp.com
Location: Brisbane, California; Toronto, Canada; Austin, Texas; and Bonita Springs, Florida
W: www.aviationintertec.com
T: +1 807-625-9260
E: info@aviationintertec.com
W: www.boeing.com/supportandservices
E: BoeingSupportandServices@Boeing.com
W: www.comply365.com
T: +1 (877) 366 2365
E: info@comply365.com
Location: USA
• ChronicX
• SpotLight
• ATP Libraries
• ATP Aviation Hub
• Flightdocs
• Maintenance Operations Solutions
• Maintenance Tracking
• Flight Operations
• Reliability Tools
• Aircraft Troubleshooting
• Business Intelligence for Aircraft
• Recurring Defect
•
•
•
•
•
•
ATP is a global information services and software solutions company focused on making flying safer and more reliable. ATP Information Services is the general and business aviation industry’s source for aircraft technical publications and real-time regulatory information. ATP Software Solutions is the leading provider of maintenance tracking, flight operations, inventory management, repetitive defect analysis, and troubleshooting software. The company’s applications help reduce operating costs, improve aircraft reliability, and supports technical knowledge sharing and collaboration within the general and business aviation, military/defense, commercial aviation, and OEM industries.
The company has deployed solutions for multiple Fortune 100 companies, supporting more than 75,000 aircraft maintenance professionals worldwide. As a global company, ATP has more than 7,500 customers in 137 countries, with nearly 50 years of experience in the information services and software industries.
RAAS is an MRO and CAMO software system designed to meet the needs of mid-tier commercial fleet operators. Enabling modern, high-efficiency workflows in a powerful and straightforward package, RAAS is the best fit for midsize fleets and user groups. Scalable, intelligent and 100% browser-based, RAAS includes efficiency-creating features such as automated real time airframe time updating and exchange of aircraft next due items, electronic technical dispatch, MPD/MRB driven program management and check package creation, purchase order e-approval and e-signature, integration with finance/accounting for payables or inventory value management, and of course approved paperless and e-signature maintenance processes from the hangar floor to the cockpit.
RAAS customers enjoy the benefits of a widely accessible and easy-to-use inventory management and maintenance support system that through continued use is able to reduce maintenance costs by increasing maintenance procedure efficiency, reducing held inventory, providing proof of quality for inspection escalations, and by directly reducing clerical manpower requirements. The quick deployment, ease of support, and low TCO inherent in cross-platform browserbased information systems coupled with high levels of integration, easy-to-use user interfaces, and many automated reporting and data analysis features make RAAS a leader in its field.
NAME OF PRODUCT MARKETED
• Airplane Health Management
• Business Consulting
• Maintenance Performance Toolbox
• Optimized Maintenance Program
KEY BUSINESS/SOFTWARE AREAS
• Technical Content Management
• Vehicle Health Mana gement
• Maintenance Optimization Consulting
Boeing is the world’s largest aerospace company and leading manufacturer of commercial jetliners and defense, space and security systems. Boeing Support and Services combines airplane design and manufacturing expertise with unique access to fleet-wide operational data to offer optimization solutions.
With these offerings, Boeing addresses the evolving need for integration and optimization of data and information across the aviation ecosystem to empower smart decision-making. The portfolio includes services and solutions for flight operations, maintenance & engineering and procurement organizations to optimize the operational efficiency of airplanes and operations.
Boeing has more than 250 customers for its optimization solutions. The portfolio draws on solutions from a family of Boeing companies: AerData, Inventory Locator Services and Jeppesen, serving operators of Boeing and non-Boeing airplanes.
NAME OF PRODUCT MARKETED
• ProAuthor (XML-Based Authoring Solution)
• Electronic Flight Bag (EFB)
• Digital Briefing
• Document & Communication Manager
• Training Solution (LMS Learning Manager)
KEY BUSINESS/SOFTWARE AREAS
• XML-Based Authoring Solution (ProAuthor)
• Electronic Flight Bag (EFB)
• Digital Briefing Flight Release
• Document Mgmt. and Distribution Platform
• Targeted Distribution w/ Compliance Tracking
Comply365 delivers secure, cloud-based solutions, focusing on Authoring, EFB and Digital Briefing Solutions, as well as Targeted Distribution of Mobile Manuals.
The Authoring Solution, features ProAuthor: the aviation industry’s first and only XML-based solution for authoring, revising and distributing publications.
Comply365’s proven Electronic Flight Bag (EFB) solution lets crews access mission-critical information throughout each phase of flight.
Digital Briefing helps turn planes faster for more on-time departures with instant feedback to dispatchers when the flight crew accepts a release and signs Fit for Duty.
Comply365’s full-featured Document Management and Targeted Distribution Platform boosts productivity by delivering any type of manual or document directly to any mobile device or stationary workstation.
W: www.oases.aero
T: +44 1621 817 425
E: info@oases.aero
Location: UK
NAME OF PRODUCT MARKETED
• OASES Modules
• OASES Mobile
• OASES Techlog
• OASES Cloud
• OASES Web
• Continuing Airworthiness
• Material, Warranty & Commercial Management
• Planning & Production
• Line Maintenane
• Complete MRO workflows
Commsoft’s Open Aviation Strategic Engineering System (OASES) is the all-in-one software for airworthiness maintenance control, meeting strict regulatory requirements. It enables airlines, fixed wing and rotary operators, MROs, and CAMOs to increase efficiencies in the management and monitoring of every procedure or intervention.
OASES is used by 130 aviation organisations — national carriers, large third-party maintenance providers, and independent operators — and supported in 55 countries across 6 continents. Commsoft is an MIT group company, part of the Valsoft Corporation portfolio.
W: www.conduce.net
T: 0044 333 888 4044
E: info@conduce.net
Location: Nuneaton, UK
W: www.crossconsense.com
T:
NAME OF PRODUCT MARKETED
• eTechLog8
• eCabinLog8
• eCentral8
• eTraining8
• eForm8
• eDoc8
KEY BUSINESS/SOFTWARE AREAS
• Electronic Logbook (ELB)
• Cabin Log
• Electronic Forms Designer
• Document Viewer
Conduce pioneer mobile aviation solutions.
eTechLog8 is our world leading Electronic Log Book (ELB), fully approved by multiple Airworthiness Authorities and trusted by customers worldwide.
eTechLog8 eliminates the paper technical, cabin, and deferred defect logbooks, and replaces these with an easy to use, workflow controlled mobile solution. Available on both Windows and iOS, eTechLog8 is fully integrated with all the leading MRO and M&E systems. All eTechLog8 customers report significant benefits, ranging from improved efficiency, data accuracy and consistency to faster turnarounds, all contributing to reduced costs.
Conduce also offers a fully integrated suite of companion applications, which provide mobile paperless solutions for the cabin log, CBT training, custom forms, and ensuring key documents are at your fingertips.
Conduce has a sliding pricing scale, depending on fleet size and operates as a subscription model, with one flat fee, per tail, per month covering everything: hardware, software, 24/7/365 support, mobile data, future proofed upgrades and more. There are no hidden costs. Ask us today for a tailored proposal.
CrossConsense’s portfolio runs from AMOS Support, BI-Management, Data Migration and Hosting to the products Aircraft Fleet View, ACSIS and AviationDW. As a wholly owned subsidiary of Canadian’s FLYHT Aerospace Solutions Ltd., CrossConsense also offers solutions for Fuel Management, Turn Process Management and other software applications as well as AFIRS hardware that collects data during flight.
AMOS Support: CrossConsense has a long tradition in providing support for AMOS with one single point of contact for 1st and 2nd level; also realizing well-planned and organized data migration projects for airline customers and Reporting and Business Intelligence Analytics.
Aircraft Fleet View is a user-friendly App that gives an always up-to-date view on an airline’s fleet status. It indicates AOGs, delays and other important information with the right level of detail to be useful but not crowded with information.
ACSIS is a powerful predictive maintenance software tool developed to assist any airline, operator, MRO facility and OEM to avoid AOGs, delays and turnbacks, improve aircraft utilization, and enhance safety.
AviationDW is a managed data warehouse, tailor-made for use with your backend system, e.g. AMOS. AviationDW simplifies KPI creation based on MRO System data.
W: www.empowermx.com
T: +1 866-498-3702
E: info@empowermx.com
Location: Frisco TX, USA
• FleetCycle® Execution Suite — MRO Manager (FCXM)
• FleetCycle® Execution Suite: Production Manager (FXPM), MRO Manager (FCXM) and Line Manager (FCXL)
• Maintenance Program Manager (FCMPM), Planning Manager (FCPM), Reliability Manager (FCRM), Material Manager (FCMM), and Maintenance Intelligence (FCMI), Electronic LogBook (FCELB)
• Coming Soon: FleetCycle® Executive Suite — Shop Manager (FCXS))
EmpowerMX is an aviation industry-recognized software development/consulting-services business. We are purely focused on empowering our customers with the ability to decrease the costs of making air travel safer by equipping their decision makers with reliable, real-time/globally available intelligence for minimizing maintenance turn times/ OpEx while maximizing airworthiness/profits. FCXM allows MROs, airlines, and lessors to effectively control the entire maintenance lifecycle or only the portions for which they are responsible. Airlines can jointly manage their outsourced and insourced activites like engineering reliability, QA and maintenance programs at the line, heavy and shop levels with an expected reduction in cycle times and increase in labor productivity on the magnitude of 16-30 percent. Third-party MROs can run their entire operation from bidding through contracting to invoicing.
W: www.ettaviation.com
T: +1 208-424-9424
E: info@ettaviation.com
Locations: Boise, ID, USA
W: www.exsyn.com
T: 0031-20-760 8200 E: hello@exsyn.com
Location: Amsterdam
NAME OF PRODUCT MARKETED
• MISA: Complete Aviation Management Information System
BUSINESS/SOFTWARE AREAS
• Accounting
• Maintenance
• Inventory Management
• Purchasing
• Human Resources/Payroll
The Management Information System for Aviation (MISA), is a fully integrated, and expertly supported product that provides extensive tools for an aviation company to manage all aspects of their business, including accounting, maintenance, inventory management, purchasing, flight operations, employee training, human resources, payroll, labor collection, government contracting, and flight school management.
It is a common practice for aviation companies to use multiple applications to manage their operations. Often, such applications have limited interfaces necessitating duplicate data entry — a recipe for inducing errors and decreasing efficiency. And even when interfaces exist, they can be difficult to manage and require resources to build, maintain, and support them.
MISA provides the solution for these issues by standardizing, streamlining, and integrating business processes across all the various departments and functional areas within the company; and this integration improves the bottom line while providing employees a user-friendly and consistent application experience across the whole organization and access to real-time, comprehensive, and relevant information from a single system rather than from disparate sources. MISA boasts impressive customer loyalty as evidenced by a number of aviation companies who have used MISA as their ERP system for more than two decades.
EXSYN Aviation Solutions is a leading industry provider of aviation engineering and data solutions. Located in Amsterdam, the Netherlands, the team comprises of aircraft engineers with deep IT & data skills. Allowing to combine industry expertise with technology knowledge.
EXSYN’s aircraft data management platform (NEXUS & AVILYTICS) is deployed with more than 20 different airlines and MROs across 20 different countries globally. Overall, it has already integrated with more than 10 different MRO software’s and 29 different aircraft types. Combining EXSYN’s aircraft data management platform with any MRO software provides airlines and MROs the ability to not just record airworthiness and maintenance data but also drive value from their data through business optimization, maintenance costs reductions and higher fleet availability.
W: www.flatironssolutions.com
T: +1.303.627.6535
E: info@flatironssolutions.com
Locations: Europe, Asia, USA, Middle East
NAME OF PRODUCT MARKETED CORENA Suite
KEY BUSINESS/SOFTWARE AREAS
• Content Management System (CMS)
• Interactive Electronic Technical Publisher (IETP)
• Maintenance & Engineering
• Flight Operations
• Tablet Solutions & Mobility
Flatirons provides consulting, technology, and outsourcing for content lifecycle management (CLM). For more than 20 years, we have served global Fortune 1000 customers in aerospace, automotive, electronics, financial services, government, healthcare, and publishing. Our customer engagements help organizations efficiently deliver the right information, at the right time, to the right people by leveraging structured content and digital media — Turning Content into Knowledge®. The CORENA Suite by Flatirons is the leading content lifecycle management (CLM) solution developed specifically for organizations that rely on missioncritical data to design, manufacture, operate, or maintain complex assets over their product and service lifecycles as well as across multi-echelon business networks. For more than 25 years, the world’s leading airlines, aerospace manufacturers, OEMs, and defense organizations have relied on the CORENA product suite to create, manage, and deliver large volumes of technical information throughout its lifecycle. Today, CORENA customers rely on the CORENA suite to modernize their IT infrastructures, improve customer satisfaction, and maintain their competitive advantage.
W: www.gamit.co.uk
T: +44 1279 818800
E: roam@gamit.co.uk
Location: London UK (HQ), Basel Switzerland, Beirut Lebanon
• ROAM — Online digital airworthiness records archive and records complance manager.
• RDOC — ROAM Document OCR & Classification engine, through the use of configurable algorythems RDOC can recorgnise your documents easily, accuratly and fast.
• Airworthiness records archive
• Status Builder
• Document Indexing
• Communication module
• Outsourcing
Gamit was founded in 1990 to provide technical support for operators, MRO’s and leasing companies, including on spare parts, technical support, records auditing, on site representation, and technical consultancy. Through years of experience, Gamit developed ROAM, airworthiness records management solution and an online enterprise solution that is more than scanning a document into a PDF and storing on the company server. It uses advanced technologies to deliver an aviation specific document management solution. ROAM is highly scalable making it beneficial for an engineering team looking after 5 or 500 aircraft.
One of the key benefits is allowing users to have full access to an entire library of records from birth, online. This means its users can simply navigate and identify key documents and prepare an aircraft for sale, lease or lease redelivery. The user can package up records quickly and easily, either themselves, or outsourcing the task to the ROAM support team.
W: www.IDMR-Solutions.com
T: +1-347-565-4367
E: sales@IDMR-Solutions.com
Location: New York/Tel Aviv
W: www.ifs.com
T: + 613-576-2480
E: AndInfo@ifsworld.com
Locations: 60+ Worldwide
NAME OF PRODUCT MARKETED
• InForm
KEY BUSINESS/SOFTWARE AREAS
• Technical Publication
• Engineering Orders
• Task Cards
• Planning
• Maintenance Programs
• Electronic Signatures
IDMR Solutions Inc. is a global leader offering enterprise SaaS and mobile solutions for content management, document distribution, electronic task cards, and e-signatures in the highly regulated aviation industry. InForm is a software engineered to provide end-to-end comprehensive business solutions integrated with leading M&E systems. InForm supports the industry leaders’ remote and mobile workforces enabling safe and efficient operations. Every day, thousands of engineers, maintenance planners, technical writers, and maintenance technicians rely on InForm for digital delivery of operational content, replacing paper-based documentation. With aviation leaders trusting IDMR, InForm is the solution of choice for several national carriers, Heli-operators, e-commerce, defense and logistics contractors, and MRO organizations.
NAME OF PRODUCT MARKETED
• IFS Cloud, IFS Maintenix
KEY BUSINESS/SOFTWARE AREAS
• Fleet and Asset Management
• Maintenance, Repair and Overhaul (incl line, heavy, complex assembly, component repair)
• 3rd-party MRO bidding, quoting, invoicing, product lifecycle management, enterprise operational intelligence
IFS is a globally recognized provider of software solutions for global aerospace & defense (A&D), including airlines and fleet operators, A&D manufacturers, defense in-service support and independent MROs. IFS’s solutions support project and program-centric manufacturing; a complete spectrum of maintenance management capabilities for sea, land and air assets, from heavy, complex, and component MRO, to line maintenance or at-platform/asset support; as well as all types of procurement models. IFS’s innovative enterprise solutions are designed for the regulated A&D industry and markets where manufacturing, MRO, project and service functionality are business- and operationally-critical whilst also supporting global, core enterprise capabilities for managing finance, inventory and human resources. With flexible, modular and enterprise breadth, IFS solutions empower A&D organizations to quickly adapt and manage change whilst delivering bottom-line value, increasing efficiencies and cost savings, and safeguarding compliance. IFS customers include BAE Systems, Lockheed Martin, General Dynamics, SAAB, GE Aviation, Pratt & Whitney, HAL, Emirates, LATAM, Qantas, China Airlines, Air France-KLM, and Southwest Airlines.
Maximize the value of your aviation assets by simplifying and automating asset management. For both MROs and Engine lessors, Jetraxx’s asset management solutions simplify compliance, standardize data, and streamline processes, with up-to-the-minute views into your entire portfolio anytime, anywhere. Record keeping for aviation assets has long been time-consuming, cumbersome, and inconsistent. Lease returns were stressful for everyone involved, with disagreements about documentation and responsibilities lengthening the process. Whether you are managing a single asset or a fleet, Jetraxx can simplify and streamline all aspects of records management — saving you both time and money.
Jetraxx is your behind-the-scenes partner, providing technical records assistance and portal-based records management, customized with your brand’s look and feel. With customizable workflows and auto-generated data packs, Jetraxx’s cloud-based, proprietary records management system automates document acceptance, approval, and rejection to ensure data integrity and compliance with your process. MROs can benefit from Jextraxx’s proven digital work order management system, which eliminates burdensome paper handling, automates workflows, and provides real-time updates to clients. The streamlined system is convenient for clients and ensures clear communication from the outset.
• Engine Shop FinTwin™
• Hangar FinTwin™
• Operator FinTwin™
• Lessor FinTwin™
• Shop / Hangar Visit Models
• Asset Driven Capacity Planning
• RUL Revenue Models
• Asset Risk Analytics
• Asset History Data Wrangling
The Digital FinTwin™, powered through an Aviation DSaaS (Data Science as a Service) platform, is a data-to-dollar enabler.
The KeepFlying™ platform allows:
• Operators, Financiers and Lessors visualize their Asset’s Revenue Potential over its Remaining Useful Life (RUL)
• MROs to capitalize on an Artificial Intelligence driven Analytical platform for Profitability & Capacity Planning of an Asset’s Maintenance Visit (Hangar, Shop).
The Data Wrangling layer absorbs, transforms, classifies and categorises every Aircraft, Engine & Component’s historic, dynamic data using unique mathematical techniques.
The Digital FinTwin™’s highly configurable Finance and Risk models use the processed data to assist commercial decisions by generating deep financial insights.
Eliminate Guesswork. Reimagine Revenue Hours.
W: www.laminaar.com
T: +65 6239 0150
E: contact@laminaar.com.sg
Location: Singapore, Denver, Bangalore, Mumbai
W: www.lufthansa-industry-solutions.com
T: +49 40 5070 30000
E: marketing.sales@lhind.dlh.de
Location: Germany, Switzerland, USA
NAME OF PRODUCT MARKETED
• ARMS®2.5, ARMS®NS, ARMS®on the TAB, InfoPrompt 2.5
• Network / Commercial Planning with Optimizers
• Flight Operations / Fleet Following
• Flight Planning & Dispatch
• Crew Operations Management with Optimizers
• Maintenance, Engineering & Logistics
A future-ready and fully integrated software applications suite for the aviation business: airlines, non-scheduled operators, MROs, airport operators, regulators and training facilities, with in-built optimizers, business intelligence (BI) & Data Analytics. Our offerings may either be accessed as a complete suite covering the full spectrum of operations, or as a stand-alone module addressing a specific functional area, e.g., Network Planning, Flight Ops, Crew, Maintenance, Logistics or Safety or Analytics. The suite has a unified database that allows a seamless flow of data and information between operational functions. Our product is highly customizable and designed to adapt to clients’ specific requirements. We do our own implementations, on a turnkey basis, and also provide prompt, reliable and economical technical support in-life.
NAME OF PRODUCT MARKETED
• DocManage Product Suite, DocSurf Mobile, EFFOM, DocCreate
• IT Solutions and Process
• Consulting for MRO
• Electronic Flight Operation Manuals
• Airline Job Card Content Management
• Predictive Analytics and Maintenance
• RFID
Lufthansa Industry Solutions is an IT service company for process consulting and system integration. This wholly-owned subsidiary of Lufthansa Group supports its customers with the digital transformation of their company. Its customer base includes both companies within Lufthansa Group as well as more than 150 companies in various other industries.
The products EFOM and DocSurf Mobile were developed together with Lufthansa Airlines based on 15 years of common experience and excellence in electronic flight operations manuals and processes to fulfill both current and future requirements. EFOM — A manufacturer independent Content Management System. Functionally mature and based on 17 years of experience, EFOM makes it possible to fulfill FlightOps requirements, e.g. expandable for new publishing backends; flexible to integrate new documents; open for customized enhancements or to integrate business processes such as Compliance Management. DocSurf Mobile — A Library Viewer for MRO and FlightsOps documents is available as a native iOS app or Windows application. The revision service allows change lists to be checked and content to be compared with a previous version. Navigation is intuitive and includes a fast and easy search. A user independent management of favorites and notes is provided, keeping this information revision safe and available.
W: www.m3-solutions.net
T: +1 888-318-4808
E: sales@m3-solutions.net
Location: Fort Lauderdale USA, Europe, Asia
W: www.mrxsys.com
E: contact@mrxsys.com
Location: Luxembourg/Monaco
NAME OF PRODUCT MARKETED
• M3 Platform – Mobile Device Synchronization and Asset Management Solution
• MRO Maintenance Mechanics — Device Synchronisation & management.
• Above & Below the Wing Specialists — Device (asset) management
• Device Management (SW) — Tablet, Laptop, Desktop, Scanner, Radio running MacOS, Windows, iOS & Android.
• Device Management (HW) — Charging, Access Control & Surveillance.
M3 Solutions is the company and innovator behind the powerful and versatile M3 Platform, a comprehensive hardware and software solution for portable device and content management. M3 solutions has sales and distribution offices in North America, Europe and Asia, as well as a global partner network to service customers worldwide in various environments including Airlines, Military and training.
The solution allows administrators to fully control the managing, distributing, charging, and monitoring of an organization’s portable device inventory and enables easy remote and unattended content distribution including OS, App & Content deployments, across all devices in the network, anywhere around the world, within minutes. The M3 Platform supports most laptops and tablets and can work with different device types running any OS, within the same installation. For access control, inventory management, security, privacy, user identification, content deployment, networking administration, and reporting regarding your portable devices and their content, the M3 Platform provides the ideal solution.
NAME OF PRODUCT MARKETED
• Blue EYE, Blue MRO, Blue STOK
KEY BUSINESS/SOFTWARE AREAS
• Quotation & Invoicing
• Project Management & Reporting
• Work Report Automatic Generation
• eJobCard iPad App
• Supply Chain Management
The MRX Systems software solution is a fully-integrated digital platform enabling aviation professionals to access real-time data and take control over their fleet and their operations.
Thanks to more than 10 years of customer feedback and perpetual development, MRX Systems brings a complete, secure and scalable solution to challenges faced by operators, CAMOs and MROs. The system is divided into three modules, each of them designed to meet the specific operational needs of their users.
Blue MRO — designed for MRO management, this module enables you to digitalize maintenance process from issuing quotations, assigning jobs to technicians, reporting repairs and findings until compiling all related paperwork into one exhaustive and automatically-generated full work report.
Multi-User, 100% paperless, always up-to-date, and Cloud based, all data is accessible at any time worldwide enhancing operation and maintenance efficiency
W: www.nvable.com
T: +44 141 280 0050
E: contact@nvable.com
Location: Glasgow, UK
NAME OF PRODUCT MARKETED
• ConNVerge for Aviation
KEY BUSINESS/SOFTWARE AREAS
• Electronic Techlog
• Electronic Forms (Assessments)
• Document Management
• Operational Analysis
• Station Operational Compliance
The concept behind our CoNVerge platform is simple. We believe that businesses should have the flexibility to easily innovate and add new applications to their toolbox, without being stifled by legacy technology or a single technology brand.
CoNVerge is all about minimising risk, fuss and capital costs and maximising efficiency. Provided as a service, it combines a hosted environment and web portal with mobile applications and data interfaces to virtually any system.
The platform is easily integrated into your existing business systems and brings together the best tools to handle data acquisition and data analysis — all on scalable infrastructure. Best of all, we even take the day-to-day management off your hands.
Our CoNVerge platform is blazing a trail in the aviation sector. In a hi-tech industry, where the stakes are even higher, long-standing clients such as British Airways Cityflyer know they can rely on NVable and our custom-designed software to make things simple, safer, more secure and streamlined. We provide airlines with technology solutions that reduce effort, improve processes and produce useful information, with one simple goal — to change things for the better.
Bring everything together and do IT better when you bring onboard CoNVerge and NVable.
QOCO Systems Ltd helps the aviation industry to succeed in the changing world by creating new ways to work, to communicate, and to utilize data, having been a trusted partner of airlines, MROs, and aircraft OEMs for over ten years.
QOCO Systems’ solutions provide significant improvements to the industry’s complex processes. They enable our customers to achieve more by doing less and to realize time-savings in labour-intensive tasks. They also bring visibility to customers’ operations to support decision-making based on real-time information.
Solutions offered include the following SaaS solutions: MROTools.io for tool management in aircraft maintenance, EngineData.io for intelligent integrations between collaborating players in aviation, and OpsMetrics.io for fully transparent collaborative decision making. QOCO also provides a wide range of consulting services for customers’ unique needs in the areas of digitalization, process improvement, data analytics, and more.
All this is realized by the business’s team of professionals with expertise in aviation and software development. Agility and customer-centricity is built into QOCO’s way of working, which allows them to quickly and cost-efficiently deliver solutions that fulfill the customer’s real needs.
Ramco Systems offers Aviation Maintenance solutions on premise and on cloud, with multi-tenant capability and nextgen mobility for Airlines, Heli-Operators, MROs and Charter operations. Its comprehensive scope spans the spectrum of organizational needs, including Finance, HCM, Manufacturing, Planning and Optimization, in one integrated platform.
Ramco Aviation’s latest Next-Gen digital technologies include: Mobility Solutions: Ramco’s next-gen mobility solutions for maintenance operations are available through an app ecosystem wherein everybody involved can seamlessly execute critical operations on the go, from anywhere, anytime; The BOTS Revolution: Ramco intelligent CHATBOTS deliver parts data, manage AOGs, and perform daily admin tasks for a more personalized and immersive ERP experience; HyperConnected Ecosystem: B2B integrations with AeroXchange, Gains, Logistics providers and OEMs bringing Suppliers, Customers and Logistics providers together on ONE platform
Ramco Series 5 reduces Turn Around Time (TAT) while increasing operational performance and compliance through user-friendly interfaces. Ramco has always been an innovator in maintenance IT — enabling clients to focus more on business-critical activities, while the solution processes transactions and decision support, based on intelligent rules. Powering 4000+ aircraft and 21,000+ end-users, Ramco is used by more than 75 operators world-wide.
W: www.recosenselabs.com
T: +1 206 451 350
E: Info@recosenselabs.com
Location: United States, Canada, India
NAME OF PRODUCT MARKETED DocuSense
KEY BUSINESS/SOFTWARE AREAS
• AI Transformation & Content Intelligence Solution
• Intelligent Document Processor
• Maintenance, Repair & Overhaul
• Automate Maintenance Audit
• Compliance Management
RecoSense offers an AI-powered platform for document analysis and data centralization. The platform powers Process Automations and Compliance Management with MROs in the Aviation Industry. RecoSense works as an Engineering partner with customers to build enterprise-specific solutions.
Automate processing of manuals, process forms, M&E/MRO Records, job cards - Routine/Non-routine even handwritten, Logbooks, EOs, Technician reports, SFR’s, compliance and inspection reports, etc. with context and extract key Aviation metrics for analysis.
The NLP-backed DocuSense platform swims through millions of documents to extract and consolidate the most relevant, insightful information to obtain valuable investment data. It will automate the process, which might take 1000s of manual hours to process, thus reducing Turn Around Time (TAT) while increasing operational performance and compliance through user-friendly interfaces.
The platform does not only evaluate the data but also can understand context through RecoSense’s unique knowledge graph.
W: www.redifly.com
T:
W: rota.technology
T: +1 321 710 7682(ROTA)
E: info@rota.technology
Location: Melbourne, FL USA and global
NAME OF PRODUCT MARKETED
• Consulting, MXF Software, PDS(Process Development System) and custom applications
KEY BUSINESS/SOFTWARE AREAS
• MRO IT Software Implementations
• MRO IT Software Upgrades
• MRO IT Software Support/Managed Services
• MX Long Range Planning
• MRO IT Custom Software Development
W: www.rusada.com
T: 03333 440730
E: information@rusada.com
Location: Switzerland, USA, UK, UAE, India, Singapore, Australia
NAME OF PRODUCT MARKETED
• Envision
KEY BUSINESS/SOFTWARE AREAS
• Fleet Management
• Base Maintenance
• Line Maintenance
• Flight Operations
• Materials Management
Rusada develops ENVISION - an industry leading MRO and Flight Operations solution. With over 100 customers worldwide and a combined fleet of 2,000 fixed wing and rotary aircraft, ENVISION is used by aircraft operators and MRO’s to successfully manage their operations.
REDiFly delivers a sleek and modern Electronic Technical Logbook. We are an independent, data-driven company that offers bespoke software solutions for the aviation industry. We provide a comprehensive framework that can integrate with an airline’s current systems, including MRO, flight scheduling, and crew management, amongst others.
What does REDiFly do? REDiFly works with the key people involved in digitizing a client’s current paper-based aircraft technical logbook. In doing so, the solution increases levels of safety and regulatory compliance, streamlines flight-toground connectivity and enables digital archives of secure and searchable aircraft records. REDiFly provides a seamless intersection between flight operations and aircraft maintenance to minimize communication errors while maximizing the efficiency of daily operations.
What makes REDiFly different? It is an independent company that applies a user-centric approach by working closely with customers through the onboarding, trial and go-live phases of an implementation. Its flexibility means that REDiFly adapts to a client’s current processes rather than the other way around.
With MRO systems projects and support spanning both the military and commercial markets ROTA brings proven experience to all sides of aviation. Our team has been embedded for years in the business functions we support. In both military and commercial. Specializing in system implementations and upgrades ROTA brings deep knowledge of aviation business processes, integrated into custom built software, to provide not only all testing documentation but also leave customers with a full manual of SOPs moving forward. Aside from upgrades ROTA has completed a number of data projects from cleaning up aircraft configuration to system security overhauls. After these upgrades or projects, training and ongoing admin support can be provided for any MRO IT needs.
The latest version of ENVISION is web-based and deviceagnostic with an intuitive and user-friendly interface. Modules, which can be purchased individually or as part of an integrated solution, include: Fleet Management, Base Management, Line Maintenance, Component Maintenance, Materials Management, Financial Management, Resource Management, Quality & Safety Management and Flight Operations.
W: www.seaburysolutions.com
T: +353 860 621311
E: mkt@seaburysolutions.com
Locations: Ireland, Argentina, Australia, Canada, Germany, Kenya, Korea, Netherlands, Philippines, and the USA
NAME OF PRODUCT MARKETED
• Alkym, EPAS, eAuthority
KEY BUSINESS/SOFTWARE AREAS
• Technical Operations
• CAMO
• MRO
• Performance
•
Seabury Solutions is a leading global aviation software development and consultancy company. It was established in 2002 and forms part of the Seabury Capital. Seabury Solutions has built its reputation in the market by delivering industry leading aviation IT solutions catering for some of the largest airlines across the world, down to the smallest operators. We have built upon decades’ of aviation expertise in-house, to leverage this knowledge into a suite of products, that enhance the decision making process for Airlines, Regulators and MROs.
With a truly global reach, the network of offices are located in Argentina Australia, Canada, Germany Ireland, Kenya, Korea, Netherlands, Philippines, and the USA. Our integrated aviation software range from Maintenance Systems for Airlines & MROs, Safety Management Software for Aviation Authorities and a range of performance analysis tools within the Enterprise Performance Analysis System (EPAS) Suite. The suite includes modules for Route Profitability, Maintenance Performance, Contract & Invoice Verification Budget Planning, Fuel Planning and Distribution Channel Performance.
W: www.staffnow.aero
T: +35 987 857905
E: info@staffnow.aero
Location: Las Palmas de Gran Canaria, Spain
NAME OF PRODUCT MARKETED
• StaffNow
KEY BUSINESS/SOFTWARE AREAS
• Staffing
• Engineering
• Production
• Quality
StaffNow is the first digital platform connecting aviation maintenance technicians with MRO/OEM companies in a fast, transparent, reliable and streamlined way.
StaffNow transforms the real staffing industry processes into digital ones following EASA/FAA regulations. All available contractors in StaffNow are pre-checked to ensure their eligibility to work. The profiles are ready for your Quality and Production departments’ review. This ensures that you get the contractors you need exactly when you need them.
Ready to streamline the way you source? Try StaffNow - your digital contracting workforce source.
W: www.swiss-as.com
T: +41 61 582 72 94
E: marketing@swiss-as.com
Location: Basel, Switzerland; Miami, FL, USA; Singapore; Tokyo, Japan
•
KEY BUSINESS/SOFTWARE
• Material Management
• Engineering
• Planning
• Production
• Maintenance Control
• Component Maintenance
• Commercial
• HR
• QA
• Financial Management
• Mobile suite
• Flight simulators
• Multi-entity functions
W: www.trax.aero
T: +1 305.662.7400 E: sales@trax.aero
Location: Miami, FL, USA; West Sussex, UK; Tokyo, Japan; Riyadh, Saudi Arabia
Swiss-AS positions itself not as a pure software house, but as a company tightly linked to airline business. Being in touch with active aircraft maintenance on a daily basis and therefore able to capture MRO trends at a very early stage, Swiss AviationSoftware unites more than 30 years of IT experience with profound MRO expertise and offers its customers a functionally unsurpassed and technologically state-ofthe-art maintenance system. AMOS is a comprehensive, fully-integrated software package that successfully manages the maintenance, engineering and logistics requirements of modern airlines and MRO providers by fulfilling demanding airworthiness standards. To date, over 190 customers from all over the world steer their maintenance activities with AMOS, which makes AMOS one of the industry-leading MRO software solutions worldwide. The ever growing ‘AMOS community’ ranges from pure operators, major charter, regional and low-cost carriers up to large airline groups and MRO providers — proof that AMOS is fit for any environment, regardless of size or geographical origin.
• eMRO
• eMobility
• Engineering & Planning
• Production & Shop
• Technical Records & Reliability
• TRAXDoc Document Control
• Supply Chain Management
• E-enabled Aircraft Capabilities
• Aircraft Mobility apps
• Maintenance Mobility apps
• Paperless Maintenance
• Warehouse Mobility apps
TRAX is the global leader in the aviation industry for MRO ERP software, with over 200 airlines and MROs using their products. TRAX has the most advanced maintenance software solutions available for airlines and MROs worldwide with fleets consisting of all types of aircraft. TRAX eMRO is a completely integrated product, in addition, the eMobility suite offers a range of iOS apps to provide mobile accessibility. Organizational efficiency gains can be substantial when using TRAX eMRO and eMobility, and ROI is quickly realized. TRAX maintains its advantage over the competition by developing software that works for customers through modern technology, world class support and strong customer relationships.
W: www.trustflight.io
T: 44 (0) 330 229 0219
E: info@trustflight.io
Location: Leamington Spa, UK; Edinburgh, UK; Luton, UK; St Helier, Jersey
NAME OF PRODUCT MARKETED
• Tech Log, Task Cards
• Digital Logbook
• CAMO (service)
• Aircraft Registry (service)
KEY BUSINESS/SOFTWARE AREAS
• Aircraft log books
• Aircraft maintenance task cards
• Digital and paperless working
• CAMO support
• Aircraft Registry support
From inception, TrustFlight has been ingrained in the aviation industry. Founded by two commercial pilots with a proven track record at the intersection of technology and business, the business has grown considerably and with stability, having recently celebrated the opening of a fourth office.
Throughout, TrustFlight gained an incredible team with backgrounds spanning different areas of aviation and technology, ensuring a solid presence in the industry. Now offering a range of products and services within the sector, TrustFlight helps to remove costly paperwork and associated errors, preserve aircraft value, and increase efficiency and safety in aircraft operations.
Five values shape TrustFlight’s culture, guide the business’s work and the way it grows. Integrity Transparent and open: offering trust to partners and assuming it from them. Responsibility Owning the work they do and taking responsibilty for it: striving to make it the best possible.
Leadership Leading from within: providing support for the team to do incredible work and drive the industry forwards.
Innovation Products are crafted for the future needs of the industry, going beyond what exists in the market. Excellence Every one of TrustFlight’s values contributes towards the excellence in their products.
W: www.vistair.com
T: 01454 550663
E: info@vistair.com
Location: United Kingdom and USA
NAME OF PRODUCT MARKETED
• ULTRAMAIN® v9™ M&E / MRO
• ULTRAMAIN Mobile Mechanic™
• ULTRAMAIN Mobile Inventory™
• ULTRAMAIN ELB™
• ULTRAMAIN M&E / MRO: 31 modules including: Configuration Management; Line/Base Mx Planning; Line/ Base Mx Scheduling; GATe; Quality Assurance; Asset Management
• Maintenance & Engineering
• MRO
• Military Maintenance
• Maintenance Planning & Scheduling
• Paperless Customer Care on Mobile Devices
• Electronic Technical Logbook
Ultramain Systems, Inc. develops M&E / MRO and ELB software for the aviation industry and is the only aviation software provider with customers running full, end-to-end paperless operations from the cockpit to the ground.
ULTRAMAIN v9, featuring Mobile Mechanic and Mobile Inventory enables real-time paperless data collection for the full maintenance and inventory process. Combine ULTRAMAIN v9 with ULTRAMAIN ELB, the easy-to-use electronic logbook, and the entire maintenance process becomes paperless. Contact us to learn what you need to equip your organization with customer mobile devices and see why elite aviation customers around the world are choosing ULTRAMAIN to reduce costs and increase aircraft up time.
NAME OF PRODUCT MARKETED
• DocuNet
• SafetyNet
KEY BUSINESS/SOFTWARE AREAS
• Aviation Document Management (All format types inc. PDF, XML, S1000D, I Spec 2200)
• Electronic Flight Bag (EFB)
• Document Management and Distribution Platform
• Maintenance & Engineering
• Flight Operations
• Compliance Tracking
• Form Creation and Management
• Aviation Safety Management Software
Vistair provides document, safety, and quality management technology solutions to support the delivery of improved safety, compliance, and operational efficiency that results in significant commercial savings to aviation organizations. Combining technology, development expertise and service delivery, Vistair’s suite of aviation technology solutions provides both commercial airlines, aerospace and defense organizations with an approach that helps demonstrate a clear link between increased reporting and a change in procedures and behaviors, which fundamentally drives a safer organization.
Document Management: DocuNet is the aviation industry’s leading end-to end document management solution, providing a coherent, single point of control for editing, publishing, distributing, and viewing all operational documentation. It provides the flexibility to access documents via the web and mobile devices and can also manage documents in all formats.
W: www.yonder.info
T: +41 43 215 27 94
E: contact@yonder.info
Location: Zurich, Switzerland
NAME OF PRODUCT MARKETED
• Yonder Mind
KEY BUSINESS/SOFTWARE AREAS
• Content Management System
• Workflow-based Content Distribution
• Compliance Tracking
• Content-based Learning
Stay in control of your content and bring reliable, rolespecific information to frontline employees — with one fully customizable content management solution. Yonder Mind is an easy-to-use content management solution designed specifically for controlled information like operation manuals, guidelines, rules, or regulations. Our unique approach allows users to work with dynamic content instead of static documents. Dynamic content will display the right information at the right time, depending on the user profile and on the context of use. A powerful search function further improves end-user satisfaction.
Yonder Mind brings operational documentation and manufacturer manuals together in one solution. Pilots work with the easy to use YM Offline App and enjoy role-specific revision updates instead of having to go through hundreds of revised pages. Editors create and enhance content in the YM Editor while revisions become manageable again thanks to the fully integrated YM Workflow. Company guides (e.g. Winter Ops Guide) can be created without having to worry about duplicates anymore since information is only contained once in Yonder Mind. And never miss a change in regulation again thanks to our IQSMS Connector.
We have over 15 years of experience with electronic documentation in aviation that we can leverage to our customers’ benefit. Our team has a diverse background ranging from a former EFB administrator for a large international airline to a long-haul captain knowing, from his own experience, what crews need.