Think… The life science shift: A new era for buildings
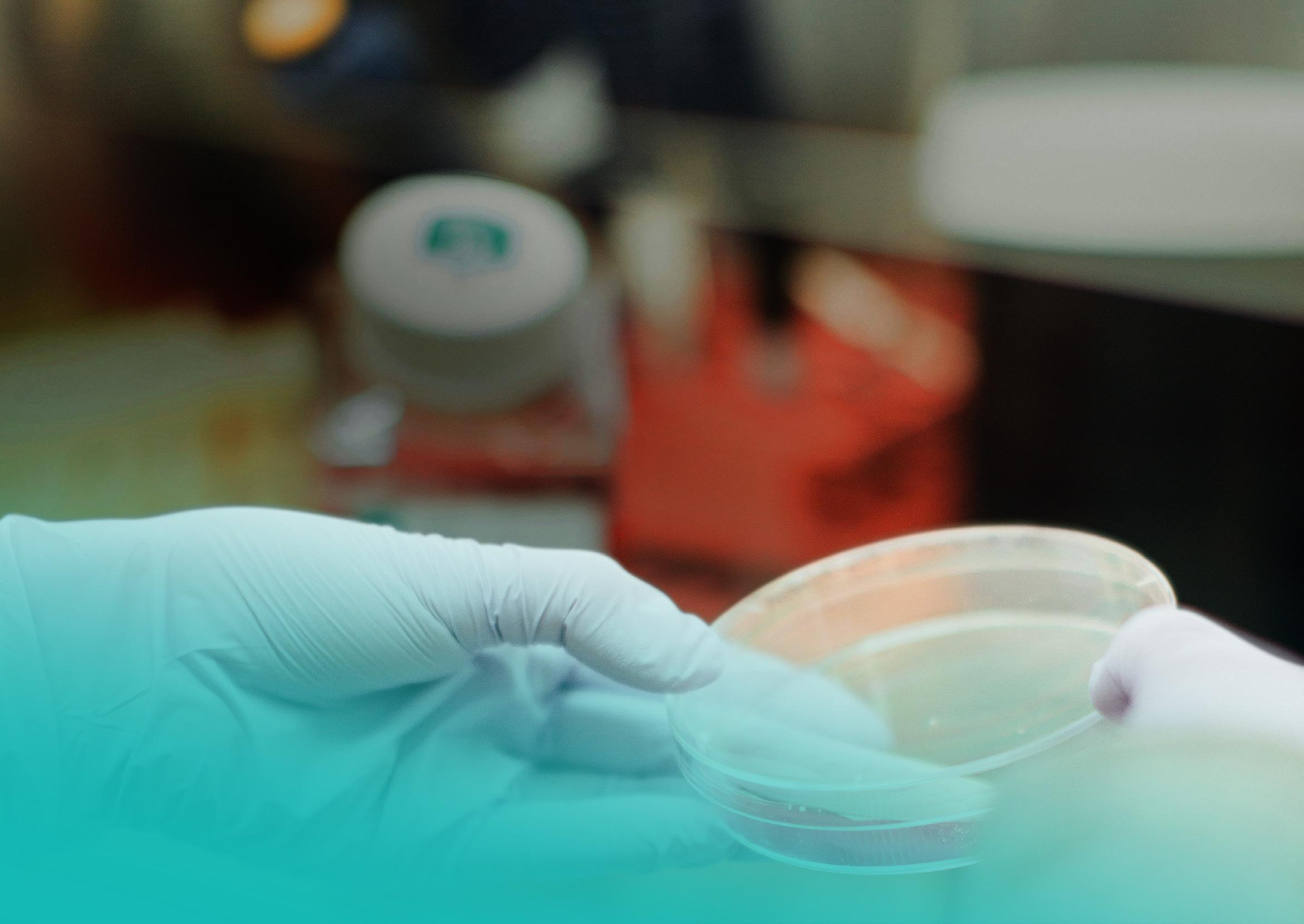
Inspire a better world through influence and design
Inspire a better world through influence and design
Life sciences are under the spotlight.
In the race to produce vaccines and treatments for COVID-19, the wider benefits of life science became crystal clear.
An industry which spans biomedical devices and pharmaceuticals, is now caught in several tailwinds as populations age and health budgets expand, and as demand for research and development into new drugs and treatment options grow.
Investors around the world are on the hunt for real estate dedicated to life science as they reallocate capital to diversify their portfolios and spread their risk. They are also scrutinising the sustainability of their investments through a risk lens.
At the same time, many of the world’s cities are overweighted in office stock. Can vacant office buildings be transformed into life science labs?
In this latest instalment of ‘Think’, ADP explores some of the issues real estate owners, investors and building designers can consider when weighing up the obstacles and opportunities of life science laboratories.
“Life science studies living organisms, including biology, botany, zoology, microbiology, physiology, biochemistry and medicine – ‘living’ being the key word.”
Nigel Doxey, ADP Consulting
Life science is a popular branch of science and research that covers a broad range of streams. Most streams are usually undertaken in controlled laboratory environments that provide ‘containment’.
The economic contribution of life science to Australia is burgeoning. The market capitalisation of ASX-listed life science companies grew from $233 billion in 2022 to $255 billion in 2023, according to industry body AusBiotech.
In the UK, the life science sector contributes an estimated £43.3 billion in gross value add, with pharmaceutical manufacturing responsible for £19.2 billion, according to PwC analysis.
In real estate terms, ‘life science’ describes buildings specifically designed for biological science, medicine and healthcare.
Everything from biotechnology and pharmaceuticals to medical device companies and genomics are investigated in ‘life science’ buildings.
CBRE estimates that Asia Pacific life science real estate surpassed 9.29 million sqm (100 million sqf) in 2023, including hubs in Melbourne and Sydney. Investment funds have raised more than US$18 billion to invest in life science real estate in the past five years; however, there is a shortage of assets available for sale.
In an environment where science, research and development is cutting edge, spaces to enable this work are in high demand.
Identifying, designing and fitting out spaces that offer the function and flexibility to support the science, encourage innovation and collaboration whilst achieving green and sustainable features has opened up new opportunities for the property and construction industry, especially considering current office vacancy rates.
Australia’s national office vacancy is now at a three decade high, with 13.5% of all CBD stock and 17.9% of non-CBD stock lying empty, according to the January 2024 Property Council Office Market Report.
In the United Kingdom, office vacancy across central London and the ‘big five’ cities of Birmingham, Bristol, Edinburgh, Leeds and Manchester is 9.5%, according to January 2024 analysis from Cushman & Wakefield. This translates into a massive 34.8 million square feet of empty space, or 3.2 million square metres.
The divergence between older, low-quality stock and new premium offices with the highest green ratings is turning owners’ heads towards retrofitting and repurposing.
Where once institutional investors allocated their property portfolio to retail, industrial and office, they are now looking further afield –and life science is now hot property.
Asia Pacific life science real estate surpasses 9.29m sqm in 2023
+9.29M
Australia’s national office vacancy is at a three decade high years
Investment funds raise more than US$18 billion to invest in life science
“A laboratory is any building or part of a building used for scientific and related work that may be hazardous, including research, quality control, testing, teaching or analysis.”
Australian / New Zealand Standard
AS/NZS 2982: 2010
The laboratory landscape
> Wet labs – use of liquids for research or experiments
> Dry labs – computer-based research or analysis
> Extreme hazard – for work with flammable material, explosives, high toxicity material, highly infectious organisms, biological or radioactive
> Education – used for training in health and science at secondary schools, colleges and universities
> Containment – microbiological work (may include any of the above)
COVID-19 laid bare the vulnerability and fragility of our infrastructure, supply chains and global communities. Biological threats, whether accidental or deliberate, can endanger lives and disrupt economies.
What is containment?
The term ‘containment’ describes a combination of laboratory procedures, worker practices, equipment and engineering infrastructure that, together, support safe and secure handling of microorganisms or biological agents that might otherwise be hazardous to human or community health.
There are four classifications of infectious microorganisms according to degree of risk:
> Risk / Hazard Group 1 ‘low individual and community risk’.
> Risk / Hazard Group 2 ‘moderate individual risk, limited community risk’.
> Risk / Hazard Group 3 ‘high individual risk, limited to moderate community risk’.
> Risk / Hazard Group 4 ‘high individual and community risk’.
There are four levels of ‘containment’:
> Australia: Physical Containment levels –PC1, PC2, PC3 and PC4.
> UK: Containment Level –CL 1, CL2, CL3 and CL4.
> USA: Biosafety Level –BSL 1, BSL 2, BSL 3 and BSL 4.
Lack of knowledge, behaviour and complacency is quite often the biggest risk to biocontainment. This is referred to as ‘delusion of control’.
There are two types of containment measures: primary and secondary
Primary containment
Primary containment measures protect people working in the immediate laboratory environment from exposure to hazardous or infectious agents. This is achieved through good laboratory practices and the use of appropriate safety equipment and personal protective equipment.
At the lowest level, precautions may consist of regular hand-washing and minimal protective equipment. At higher biosafety levels, precautions may include airflow systems, multiple containment rooms, sealed containers, positive pressure personnel suits, established protocols for all procedures, extensive personnel training and high levels of security to control access to the facility.
Secondary containment
Secondary containment protects the external environment through a combination of facility design, engineering infrastructure and operational practices. Some of these include:
How do we ensure an asset appeals to a wide spectrum of life science streams? Flexibility and adaptability are the key.
As life science activities vary, so do the needs, equipment and regulations of each enterprise. For this reason, leases are rarely simple or straightforward, and a space designed for one tenant many require adapting to suit another.
At level 2, containment is largely achieved through good sealing, directional airflows, the use of specialist equipment, personal protective equipment and the ability to access and clean surfaces.
Containment level 2 generally allows the most flexible outcomes to undertake differing life science streams.
Very bespoke ‘targeted’ long term science / expensive
Very bespoke ‘targeted’ long term science / very expensive
The ability to conduct research anywhere in the world and to collaborate with projects, partners and institutes across disciplines and markets is elevating research to new heights.
1. Start-ups race for space: There is a growing demand for co-working labs that connect early-stage companies to capital and resources.
2. Demand outstrips supply: Everyone is on the hunt for the right space, with ‘location, location, location’ the familiar catchcry.
3. Life science move fast: The typology of lab users is diversifying, and social networks and tech platforms are transforming scientific research.
4. Flexible first: The emphasis in on agile and adaptive labs capable of being repurposed and restructured to meet a range of research types.
5. A long wish list: Sustainability, connectivity, modular design, techenabled processes, automation and digitisation are on every tenant’s wish list.
6. The great unknown: Expect growth ahead in lab-enabled spaces for unknown tenants and undefined research.
“‘Lab enabled space’ is a new term that refers to a space that is designed, equipped and configured to support various laboratory and reseach activities”.
Nigel Doxey, ADP Consulting
A critical shortage of laboratory space is a big challenge for small start-ups which often lack the funding to lease or fitout their own space.
The incubator model offers a flexible and affordable ready-to-go laboratory solution with limited upfront capital with no longterm commitment from the tenant.
Lab enabled spaces, while great in principle, aren't always easy to achieve in practice. Differences between traditional offices and lab environments mean conversions aren’t always straightforward.
The usual challenges encountered during retrofit projects – heritage overlays, planning restrictions, spatial limitations and hazardous materials – are intensified.
Some considerations include:
> Mechanical, electrical and plumbing: Standard labs use around double the amount of electricity of an office, and almost all labs require a standby power generator. Building upgrades usually need to uplift ventilation and airflow systems to increase the amount of fresh and exhaust air. Plumbing must factor in additional water and sewerage services, as well as accommodation of specialty gases.
> Structural capacity: Floor-to-floor heights must be able to accommodate essential lab design features such as air ducts for additional ventilation. Load capacity must also increase to meet the needs of heavy, vibration-sensitive equipment.
We are seeing that traditional office floorto-floor heights are typically adequate for containment level 2 facilities.
> Codes: Change of use may require development approval, and projects must comply with laboratory codes and fire safety measures.
> Logistics: Life science work often requires additional equipment, so loading docks and freight lifts must be able to accommodate this.
> Hybrid work: Many processes can now be conducted without human intervention, which means researchers don’t always need to be physically in the lab. Spaces need to be connected so people can collaborate both remotely and in person.
> Architecture and planning: laboratories require safe discharge of dangerous exhaust air and this may require the addition of high stacks above the building.
5: Key considerations in life science building revitalisation
Large roof area with structural capability and room for expansion.
Architectural character and attributes to attract workers.
All electric and high efficiency plant.
Structural loading and high floor-to-floors to allow service distribution and heavy equipment.
Utility connections and trade waste provisions.
Good daylight, views and facade designed for high indoor environment quality.
Fume exhaust stacks –consider safe discharge and height.
Large flexible core with service lifts.
Large HVAC plant for high air change rates. Loading dock access for equipment, deliveries and specialist waste. Access to public transport and cycle access.
End of Trip facilities.
Function, breakout and and meeting spaces to increase collaboration.
Figure 6: Key considerations in life science building revitalisation
Additional fresh air for exhaust make-up and higher air-change-rates.
Dedicated general exhaust for containment and directional air-flow.
Dedicated specialist pipe and gases risers with spare capacity and access.
High floor to floor heights to allow flexible services.
Spare capacity in electrical risers & trunking for future connections and high load equipment.
Base building air conditioning to to not impede highly serviced lab area.
Structural loads to be assessed for heavy equipment and vibration.
Localised sanitary drainage and specialist drainage as required.
Flexible HVAC systems capable of tight temperature bands.
Nominated or dedicated services zones for high weight equipment located adjacent to ventilation and piping risers.
Lighting with high lux levels and variable controls as required to suit lab application.
Fire zones, detector strategy, extinguishers and sprinkler requirements to be considered.
High performance facade for energy and glare reduction and thermal stability. Highly sealed facade with membranes when pressurisation is required.
Dedicated risers for fume cupboards and objectionable exhausts (explore manifolding) – avoid the need for fire dampers where possible.
Laboratories have an outsized impact on carbon emissions due to their energy-intensive nature, so it is vital to understand the steps that lab owners, managers, designers, and engineers can take to help decarbonize them.
Laboratory facilities require much higher ventilation rates than other commercial buildings. The heating and cooling energy needed to condition and move this air can be 5 to 10 times greater than the amount of energy used in most office buildings. Laboratories also tend to have tighter temperature and humidity controls.
Our first challenge is to integrate energy saving technology and design features that drive down energy consumption in operations without compromising safety, compliance or the science.
Energy usage increases as laboratories become more complex and specialised where there are high process loads. But there are solutions. I2SL, the International Institute for Sustainable Laboratories, has developed a series of resources, including a smart labs toolkit.
Our second challenge – one which can be addressed by adaptive reuse – is to consider the embodied carbon emissions in new laboratory development. The World Green Building Council estimates that 11% of the world’s energy-related carbon emissions come from the manufacture of building materials and during construction. Therefore, retaining old office buildings and repurposing them as life science spaces ticks many boxes.
When we are designing new life science facilities, we must consider adaptability from the outset which will be fit for many different futures.
Just as office workers expect a premium experience, so do those who work in laboratories.
One 2023 industry survey of more than 100 leaders in life science found talent scarcity was their top concern. And 86% of those leaders said their organisations were more focused on the talent experience than ever before — up from 77% the previous year.
The best lab spaces, therefore, aren’t just practical. They are also inspiring, promote health and wellbeing, encourage learning, collaboration and interaction between scientific communities.
86%
77% 86% of those leaders said their organisations were more focused on talent experience than ever before.
Up from 77% the previous year.
Must have the ‘wow factor’
Lab space must have the ‘wow factor’ to attract and retain today’s top scientific talent.
Overlooking London's Bloomsbury Square, Victoria House is a neoclassical treasure. Built in the 1920s, Victoria House has recently been upgraded and now offers an ‘ecosystem’ for London's life science sector.
Located in the UK’s ‘golden triangle’ of science excellence, Victoria House has been redeveloped by Oxford and Pioneer. The building is designed for start-ups to scaleups, and brings together a community of enterprises at similar stages of growth.
The grand lobby is more evocative of a five-star hotel than a science hub, with concierge services and comfortable seating in a plant-filled atrium.
The working spaces include everything from fitted incubators to Category Level 2 laboratories. Floorplans support bespoke fitouts and flexible operations. The seventh floor 23,000 sq feet incubator offers a spectrum of space from single benches in a co-lab to dedicated area.
There are meeting and breakout rooms with original wood-panelled interiors and state-of-the-art technology, health and wellness facilities, and a rooftop terrace for building occupants to soak up London's spectacular skyline.
Targeting BREEAM Excellent, the building is fully electrified, with an upgraded central plant, new smart meters and an air-source heat pump system.
Reusing the existing building saved embodied carbon emissions, while 95% of construction waste was recycled and single-use plastic entirely eliminated during construction.
24,637sqm
18,429sqm
Floor-toceiling heights of up to 4 metres 4m
Piped gases to each floor
lab to workspace ratio High CL2
Minimum of of laboratory space across eight floors
196 cycling spaces and premium end-of-trip facilities
6air changes per hour
Fume hood capacity designed at 1per 4,500 sq f.
Think is a thought leadership series developed by ADP Consulting to ask and answer some of the big questions confronting the property and construction industry.
About ADP Consulting
ADP Consulting’s vision is to inspire a beatter world through influence and design.
Founded in 2011 in Australia, ADP Consulting is a sustainability-led, multi-services engineering consultancy with close to 300 people, and a growing international footprint.
We provide building services engineering, structures, sustainability, ICT, acoustics, audio visual, security, vertical transportation, and specialist lighting design to the property and construction industry.
Always thinking, we push the boundaries in engineering and design to find the best solutions to the most complex projects.
Our experts
For more information, please contact:
Author: Nigel Doxey Technical Director
E: n.doxey@adpconsulting.com
Nikki Beckman Director
E: n.beckman@adpconsulting.com
M: +61 425 773 885
Alex Sear Director
E: a.sear@adpconsulting.com
M: +61 450 074 226
London Chancery House 53-64 Chancery Lane
London WC2A 1QS
adpconsulting.com
@adp-consulting-pty-ltd
@adpconsultingptyltd