
25 minute read
Machinery Repairs
The Wes Amelie
Wessels’ containership to operate on SNG
Advertisement
MAN Energy Solutions and German shipowner Wessels Marine have announced a technical showcase whereby the 2017-retrofitted Wes Amelie, a 1,036-teu feeder container ship, will use liquefied SNG (Synthetic Natural Gas) produced from renewable electrical energy as drop-in fuel. The companies are co-operating on the Wes Amelie project with Nauticor, the LNG transportation company, and Unifeeder, the charter company. According to Stefan Eefting, head of MAN PrimeServ, Augsberg, there will be no alterations to the vessel’s main propulsion system to use SNG instead of LNG. The Wes Amelie, owned and managed by Wessels Reederei (Haren/Ems), was previously converted in 2017 when its MAN 8L48/60B main engine was retrofitted to its current, four-stroke MAN 51/60DF unit that enables dual-fuel operation – the first such conversion of its type throughout the world. The work was carried out in Bremerhaven by German Dry Docks (GDD). To demonstrate that SNG can successfully be used as shipping fuel, 20 of the 120 tonnes of LNG that the Wes Amelie typically uses for each round trip will be replaced by climateneutral SNG. As a result, CO 2 emissions are expected to decline by 56 tonnes for this trip. Automobile manufacturer Audi’s Power
to-Gas facility in Werlte, where a liquefaction plant is currently under construction, will provide the SNG, which will be generated by wind energy and is thus 100% climateneutral. The SNG trip will take place after the completion of the liquefaction plant in Q2 2020. Eefting said, “This is another important milestone and proof of concept for the Maritime Energy Transition, the initiative we have been driving since 2016. We strongly believe that a roadmap based on LNG and SNG as fuels can lead the way to a decarbonised future for shipping and, in Wessels Marine, we have the perfect partner.” “The Wes Amelie project has always been about demonstrating the technologically doable while pointing out the regulatory actions necessary to make it possible,” said Christian Hoepfner, Managing Owner of Wessels Marine, Hamburg. “The initial retrofit to LNG took support from the German Government to be financially viable, but it was a huge success for the environment in that it drastically reduced emissions. As a consequence, there now is a retrofit programme in place to make more retrofits happen.” He continued, “In another world-first, we will now demonstrate that SNG can successfully be used to reduce harmful emissions even further as the fuel is climate-neutral. However the costs are still way too high. Going forward, governments and regulators will have to work together to make this a viable and available option for ship owners.” Eefting added, “To bring down future emissions generated in the global-trade supply chain, synthetic fuels play a crucial role. Especially in shipping, the use of batteries alone is not a viable option and any successful decarbonisation efforts need to address the fuel. Power-to-X technology allows the generation of 100% climate-neutral natural gas from renewable energy. This technology has tremendous potential and needs to be freed from regulatory burdens and to be developed on an industrial scale to bring down costs.” A pioneer of this technology, MAN Energy Solutions commissioned the Werlte-based methanation plant, in partnership with Audi, in 2013. While the 6 MW methanation unit is still the largest of its kind in Europe today, MAN now offers a 50 MW EPC Power-to-X solution to ramp up the generation of synthetic fuel. “We need Power-to-X out of the labs and into the market in order to produce more competitive, renewable fuels by using scaling effects,” concluded Eefting.
Low-sulphur solution from CSSC
China’s CSSC Marine Service (CMS), the world-wide equipment service subsidiary of China State Shipbuilding Corp (CSSC), is
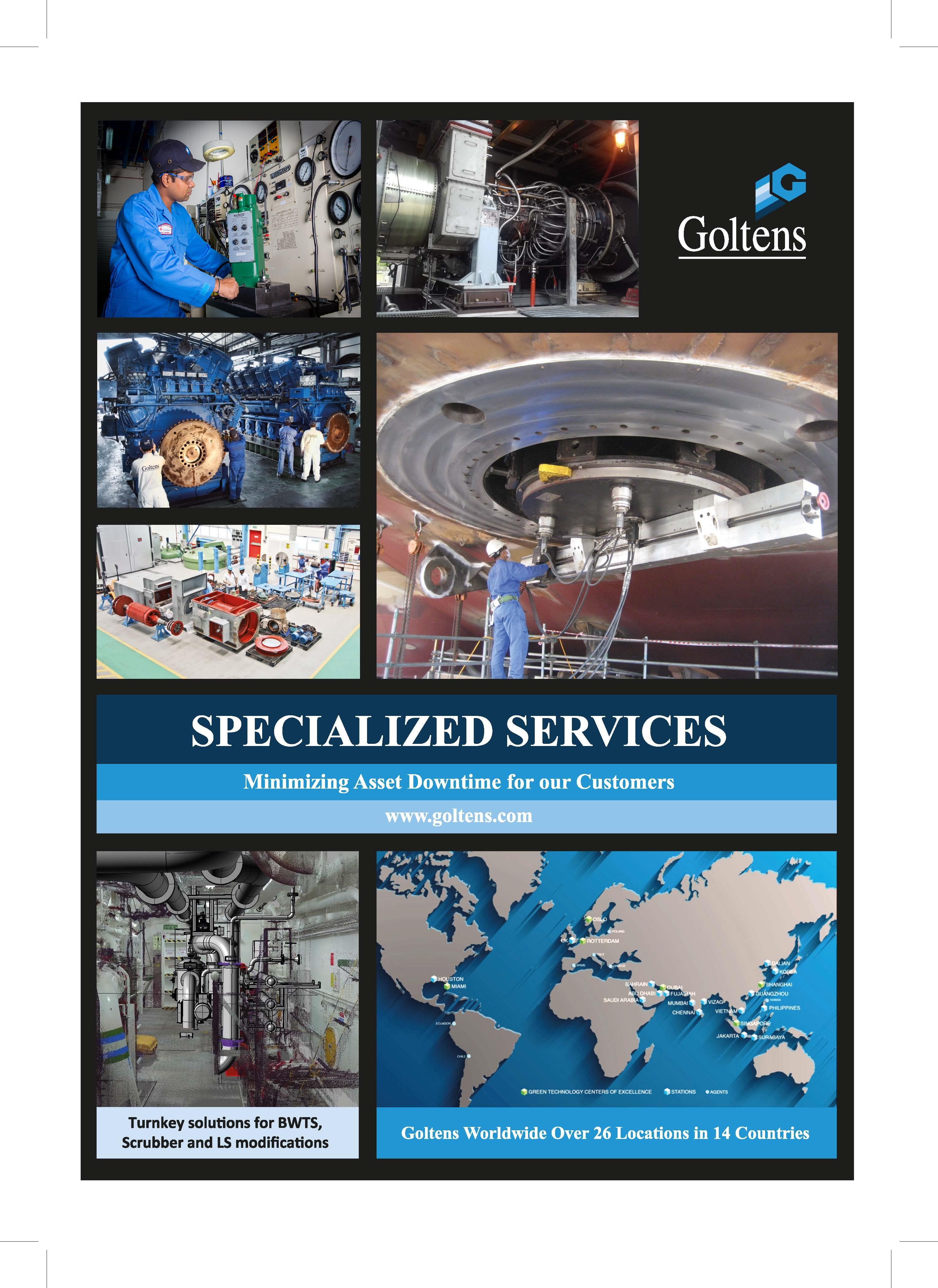
The CMS Marine Service network
using its expanded network of service stations to deliver a retrofit solution to engine starting problems that may occur with less viscous lowsulphur fuels. Some two-stroke engines using commonrail injection report problems reaching and maintaining high enough fuel rail pressure due to wear of fuel pumps, starting air problems or leaking injection control units. The concern is amplified when using fuels that are lighter and less viscous than heavy fuel oil, such as many of the very low sulphur fuel oil blends ship owners are likely to use to comply with IMO’s sulphur cap from January 1 st 2020. Less viscous fuels require higher pumping pressure or engines can fail to start. CMS’ solution is available for common-rail RT-Flex engines with five to seven cylinders of 48-60 mm bore deploying two or more fuel pumps. The Fuel Rail Booster pump upgrade guarantees and maintains fuel rail pressure required for a clean, first-time start. The system draws on the same fuel pump as the engine’s fuel supply unit, offering redundancy and reducing vessels’ spare parts inventories. It also reduces starting air consumption, enables planned maintenance and can reduce maintenance costs and potentially extend time between overhauls. CMS President Andrew Stump said, “We developed this solution following reports received from our customers of engine starting failures encountered when using low sulphur fuels. Our Fuel Rail Booster pump upgrade service greatly reduces the risk of an emergency during manoeuvring and pays for

itself if just one missed start is avoided.” CMS has already installed the solution on several vessels and is delivering the retrofit through an expanded number of service stations worldwide. The company has opened three service hubs – in South Korea, Singapore and Hamburg – and five service stations since it was founded in 2017. It has previously stated its ambition to open six service hubs and 28 stations by 2020. Service stations are located in China (Qingdao, Gaungzhou, Chengxi and Shanghai), South Korea, Singapore, Hamburg and Switzerland. CMS also has partner stations in countries including Brazil, Turkey, Poland, South Africa, Oman, Qatar, Dubai, US, New Zealand and Greece.
New Blueday Technology power system for trawler
The renovated Nordnes Gruppen trawler Nordbas will feature an integrated power system that will allow the ship to go diesel free for hours and run on renewable electricity. The new hybrid power system is being designed by Blueday Technology. Blueday’s team have worked with Nordnes Gruppen to design a bespoke, hybrid energy system for Nordbas, which will be refitted at Kleven shipyard in Norway. When deciding to rebuild Nordnes, Nordnes Gruppen decided to focus on reducing the environmental footprint of the renovated trawler and asked several companies to put forward proposals. Blueday’s design covers the ship’s automations and power system and uses the power generated by the Danish seine system’s winches to regenerate the on-board energy storage system, or battery. The innovative system will mean that Nordbas could run on 100% renewable electricity for up to several hours. Hans Petter Heggebø, CEO at Blueday Technology, said, “Nordnes Gruppen wanted to optimise the performance of their new trawler while making it more sustainable. There is a high level of innovation going into the Nordbas, and with this design we are proving that fleets can use renewable energy to improve existing ships’ performance. “We are experts in the development and delivery of environmentally friendly and energy efficient products and systems for offshore, marine and aquaculture industry. Lost productivity caused by poor performance or failure of a power or automation system can significantly reduce our customers’ revenue and profitability. Our SMART Hybrid Solutions establish the systems and processes necessary to improve energy performance, including energy efficiency, use and consumption.”
Nordnes Gruppen’s trawler Nordbas

Ulstein Blue Boxes installed on two offshore vessels
Norway’s Golden Energy Offshore has decided to install Ulstein Blue Boxes on-board two of their vessels. “With Blue Box we will manage to reduce our fuel consumption and environmental footprint further, which is very important to us,” says ship owner Per Ivar Fagervoll. Golden Energy Offshore, together with Ulstein, are now entering into a Blue Box pilot project on two of their vessels. “With this pilot project and the programmes
Norway’s Golden Energy Offshore has decided to install Ulstein Blue Boxes on-board two of their vessels
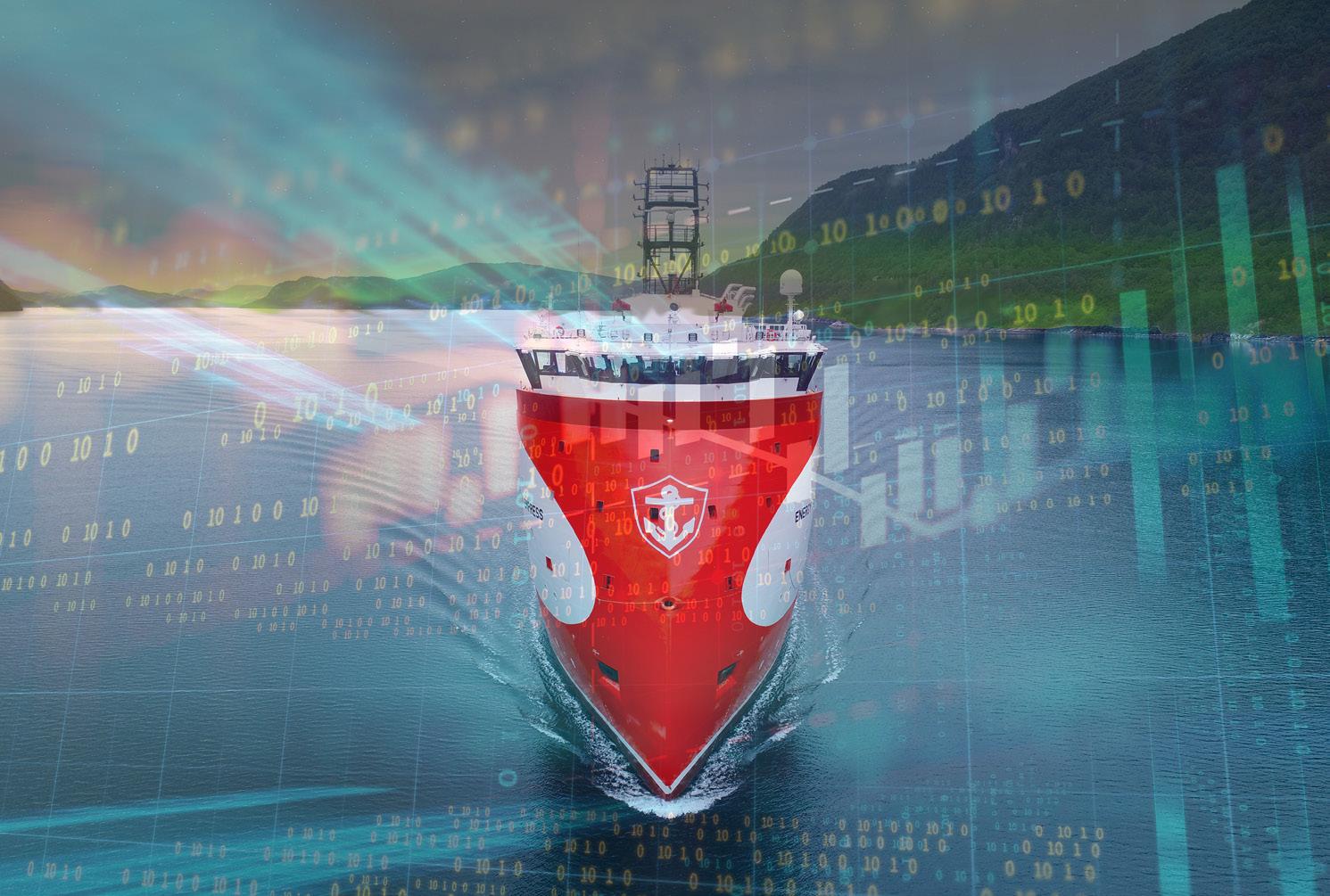
aligned with this agreement we will be enabled to consolidate, process and analyse data and target our focus on energy efficiency. This will have an impact on our environmental profile and sustainability adaptation, as it will identify optimised ‘green’ operations,” says Fagervoll. Blue Box is a system which is easy to set up. It connects the vessels’ data system to the cloud for direct access to important information such as engine configuration and speed. The ship’s crew and the ship owner’s land-based personnel will have easy and intuitive access to the data. Golden Energy Offshore will install Blue Box on the two sisterships Energy Duchess and Energy Empress. These are of the same ship design, have the same systems on-board, and work in the same geographical area. Their data can easily be compared. Through analyses of data the ship owner will be able to assess the most effective types of operational modes. By analysing their data as a decision support, the ship owner stands a better chance of getting the best out of the ship’s (or fleet) capabilities. This will lead to a reduced eco-footprint. By retrieving the data from the Blue Box cloud services, the ship owner can either access raw data for their own analyses or receive pre-analysed data via the report module. The intuitive user interface and alarm system give real-time advice to the ship operators on the most optimal way, economically and environmentally, to run the vessel. Thus, the system opens up to a big potential for fuel savings and reduced emissions.
Thordon bearing and seal installation perfect after three years
Canada’s Thordon Bearings has notched up another success story for a customer in the demanding offshore sector, with a bearing and seal installation in ‘perfect condition’ after over three years of operation. The crew/supply vessel Global Tiger, operated by UAE-based Global Marine is a 42 m vessel currently in service in the Middle East. It is one of a pair of all-aluminium crewboats built by Grandweld of Dubai in 2015/2016. The vessel, with 83-person capacity, is powered by a triple-screw Caterpillar propulsion plant, each engine rated at 1,450 bhp, to give a maximum speed of 26 knots. Since the vessel was intended for operation in the Middle East, with few shipyards offering full facilities for replacing stern gear seals and bearings, Global Marine was looking for a low-maintenance solution. Previous experience with gland packing had highlighted the need for regular tightening and re-packing, along with wear to the shaft in the packing area. The customer discussed alternative seals and bearings with Thordon, through its distributor Ocean Power International (OPI) of Dubai, and decided to use Thordon’s SXL propeller shaft bearings with TG100 seals. Global Marine and OPI worked with builder Grandweld to ensure that the design of the vessel was optimised for the Thordon products. The ship designers modified the original design in accordance with Thordon’s recommended minimum length for seal installation. Global Tiger was delivered in 2016 with SXL bearings and TG100 seals on each of the three 114.3 mm A22 Aqualloy Aquamet stainless steel shafts. After three years of operation, Thordon’s engineers inspected the seals and bearings during a routine docking, and found no sign of wear, with the seals in perfect condition. Meanwhile, Thordon Bearings is alerting its customers to the recent publication of a DNV GL study that concludes the recent surge in propeller shaft bearing failures is indeed related to the use of certain environmentally acceptable lubricants (EALs). In conclusion to the first phase of an ongoing investigation, DNV GL reported that, “there are transient conditions involving high oil film pressures and/or low oil temperatures where [synthetic] EALs will have a reduced load-carrying capacity. The vast majority of stern tube bearing failures in recent years occurred in the same type of transient conditions – during hard manoeuvring at high ship speeds, during mooring trials, and when operating with a partly submerged propeller.” In the Middle East, Abu Dhabi’s The National Marine Dredging Company (NMDC) has replaced the rubber cutter shaft bearings on the 89 m cutter suction dredger Al Khatem, marking a step closer to the dredging company’s fleet-wide conversion to Thordon Bearings’ seawater lubricated Composite cutterhead bearings and cutterhead intermediate lineshaft bearings. The 1979-built Al Khatem is the latest

TG100 seal after 3.5 years of stellar service on the Global Tiger
dredger NMDC has converted to the Thordon solution, following the success of similar conversions to the Al Sadr, Al Mirfa, Al Hamra, Umm Al Zemoul, Umm Al Anber and the beaver Dredge 2. Three more beaver dredgers Embarka 2, Embarka 5 and Embarka 6 are scheduled for conversion at an Egyptian yard later this year. Since China Ocean Shipping Company (COSCO) first specified a water lubricated propeller shaft arrangement for two 5,000- unit pure car/truck carriers (PCTC) in 2007, more and more shipowners and shipbuilders in China are rejecting oil lubricated propeller shaft and greased rudder bearing systems as a way of supporting their country’s commitment to environmental sustainability. COSCO now has Thordon Bearings’ COMPAC seawater lubricated propeller shaft bearing systems installed on about 70 ships, including heavy lift ships, bulk carriers, semisubmersibles and ro/pax ferries, with other shipowners following COSCO’s lead. China Oilfield Services (COSL) and China National Offshore Oil Corporation (CNOOC) are other Chinese owners to favour a water lubricated shaftline configuration.
Wärtsilä wins offshore and fishing vessel refits
Finland’s Wärtsilä has been selected to engineer, supply, and commission a hybrid propulsion system for an offshore sector vessel. Norway’s Eidesvik AS has contracted Wärtsilä to carry out the upgrade project on its Viking Neptun construction vessel. This latest order follows two similar hybrid upgrade contracts awarded to Wärtsilä in recent months. The 15,900 dwt Viking Neptun was built in 2015. It is fitted with Wärtsilä engines and Wärtsila’s Low Loss Concept (LLC) electrical systems. By choosing Wärtsilä’s battery hybrid solution, the ship will be able to operate on a single generator set together with batteries during dynamic positioning (DP) operations. Integration of the new system with the existing Wärtsilä control systems will be seamless. The Wärtsilä hybrid solution will deliver customer benefits in the form of fuel cost savings and better environmental performance. Furthermore, maintenance costs will also be reduced since the load on the engines will be more efficient and the running hours will be less. The Wärtsilä scope includes two 870 kWh battery packs and two 2.7 MW drives for the hybrid system pre-installed in containers. Wärtsilä will also upgrade the existing switchboard, as well as the integrated automation and power management systems. The project is expected to be completed within a six months period. Meanwhile, Wärtsilä is to supply a 12-year old fishing vessel with a Wärtsilä 32 engine, a NOx Reducer (SCR) selective catalytic reduction system, and a shaft generator. The new engine will replace an existing one from another supplier on-board the Brennholm, a 75 m long vessel owned by Norway-based operator Brennholm AS. The installation will take place at the Orskov Yard in Denmark at the end of 2020. The order with Wärtsilä was placed in November 2019. According to measurements carried out in various operating modes, the fuel-efficient Wärtsilä engine will save approximately 13% in fuel costs compared to the vessel’s
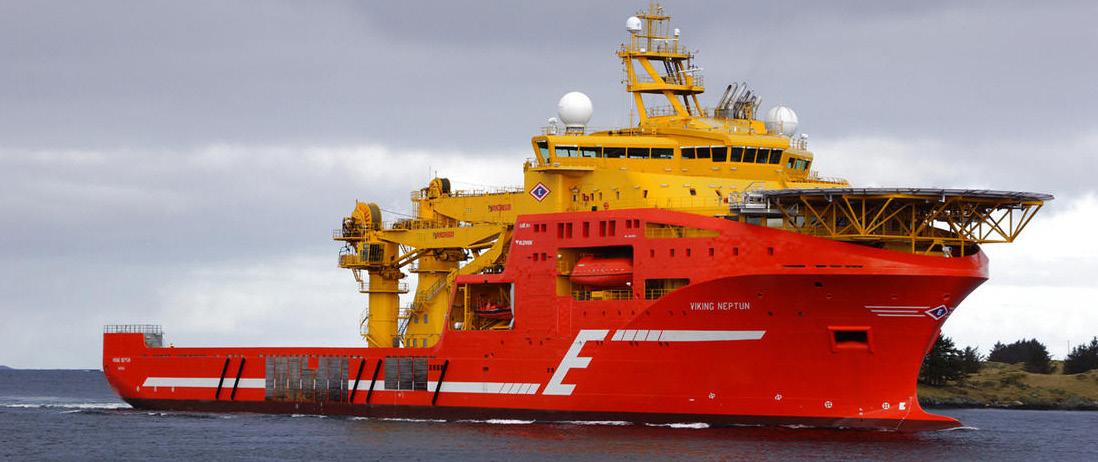
A Wärtsilä hybrid upgrade will enable Eidesvik’s Viking Neptun to become more environmentally sustainable and fuel efficient existing engine. Wärtsilä will also deliver a NOx Reducer (SCR) system that will reduce nitrogen oxide emissions to the atmosphere by approximately 51,000 kg/year. These installations will enable the vessel to comply with IMO’s Tier III regulations. The Wärtsilä scope also includes a shaft generator to produce electrical power for the ship’s network. At Orskov Yard the focus is very much on environmentally-friendly solutions, so this fuel and eco-optimised package for the Brennholm is something we are pleased to install,” says Lars Fischer, CEO at Orskov Yard. Wärtsilä is scheduled to deliver its equipment to the yard in October 2020. Wärtsilä has recently established its latest Expertise Centre (EC) in Singapore. Based within the company’s Acceleration Centre facilities, the EC provides various value-adding support functions, including for example, operational support and dynamic maintenance planning, for those Marine and Energy business customers having Lifecycle Solution agreements with Wärtsilä. Wärtsilä Expertise Centres currently monitor some 900 installations with more than 2,000 engines around the world. Meanwhile, Wärtsilä and Singapore-based PSA Marine have agreed to collaborate in the co-creation of smart technologies for the marine sector. The focus will be on solutions that are human-centric and deployable. The LoI was signed during November as part of the events celebrating the anniversary of the opening of the Wärtsilä Acceleration Centre in Singapore.
Yanmar work for Royston Marine
A programme of engine health checks on generators on an OSV operated by Marine Platforms has been completed by diesel power specialist Royston. Engineers from the company’s operation in Lagos undertook the work on the four Yanmar 8N280L-EV generator engines, which have each completed more than 24,000 running hours, on-board the 93 m, 4,850 gt African Vision, as part of an assessment of critical power systems. The move was necessary to extend the engines’ maintenance period by 12 months, enabling the vessel to complete essential offshore work in the Gulf of Guinea. The work was completed by Royston in a threeday maintenance period, while the vessel was
The African Vision
docked at Onne port in Nigeria. Work saw cylinder head covers, camshaft covers, fuel injectors and pumps removed, and inspections carried out along with leakage testing of fuel parts and timing checks. Inspections of the pistons, liners, cylinder head faces, and valves were carried out using a borescope to assess levels of pitting and carbon build-up. Incremental load testing in line with the engine manufacturer’s specification was also completed. Marine Platforms is an offshore oil service company focused primarily on providing services to the upstream sector of the oil and gas industry in Nigeria and the wider African continent. The African Vision is a Marin Teknik MT 6012 design with a 1,000 m 2 deck space, including mezzanine deck. It is equipped with a 100-tonnes AHC crane, aux 22 tonnes crane and accommodation for 66 people. Meanwhile, a new series of engineering health checks and service work carried out by diesel power specialist Royston on deactivated marine engines has enabled Azerbaijan-based Caspian Marine Services (CMS) to bring laidup vessels back into operational service. Initial investigations into the condition of the power units were carried out and a plan for engine overhaul prepared. Rather than complete the engine work in the UK, the owners decided to tow the vessels to drydock facilities in Baku on the Caspian Sea. Engineers travelled from Royston UK to undertake extensive service and repair work, which has seen engines running now on the PSVs Khojaly (formerly the FD Untouchable), Guba (formerly the FD Unbeatable), Savalan (formerly the FD Honorable), Murovdag (formerly FD Indomitable) and Shahdag (formerly FD Incomparable). Three of the vessels are back in operation while the other two are completing sea trials as demand for vessels operated by CMS from customers across the Caspian Sea region grows. The work in Baku, undertaken by a fourstrong Royston engineering team, saw engine power packs removed, main and bottom end bearings fully inspected and where necessary, replacement parts fitted. The fuel injection systems were fully stripped and cleaned, and all fuel pumps replaced with new, before comprehensive timing checks were completed.

More repair advice available from Sulzer
On-going investment by Sulzer is widening the services available to customers and reducing the time to deliver repair projects. The opening of the new service centre, just outside Houston, Texas, has delivered a large pump repair shop that is equipped with lift capacity to handle the largest of machines along with enhanced repair technologies and equipment to provide fast-paced, turnkey repairs. This will ensure pump repairs, upgrades and retrofits are delivered to the highest standards in accelerated timeframes. Sulzer’s new Houston Service Centre for pump services offers a wide range of services and expertise, especially in the oil and gas sector. The facility is adjacent to the company’s electromechanical services (EMS) centre, enabling customers to access a wide range of services from a single location. As a pump OEM, Sulzer has decades of experience in the design and manufacture of pumps, including large scale, high-energy equipment, that enables the company to repair pumps of any design. Certified welding facilities offer the ability to weld pressure vessels and carry out nondestructive testing (NDT) to ensure a highquality repair. The engineers have experience of dealing with a wide range of materials and ensuring that the best possible solution is delivered to the customer. A complementary investment in automated welding provides highest quality welds in reduced timeframes. Extensive machine tools, both manual and automated, are used in the manufacturing of new parts as well as modifying existing components to improve performance and efficiency. Installation of additional vertical boring mill and lathe machinery supports multiple project execution. With support

Specialists from Sulzer have worked day and night to replace damaged coils in a 170-tonne, 19 MW (25,500 hp) propulsion motor
from the experienced design team utilising the latest laser scanning technology, reverse engineered parts for legacy equipment can be manufactured on site, even if the original manufacturer no longer supports the pump under repair. All of these services are available via Sulzer’s global network of facilities. The company’s single point of contact philosophy means that a customer’s local service centre is able to manage any repair project and ensures that it is delivered on time by using the extensive resources within the Sulzer network. Sulzer has also extended its global network of service centres with the opening of a new facility in Balikpapan, Indonesia. The new service centre is positioned in a prime location to serve customers in oil & gas, mining, power and general industries, which dominate the surrounding area.
Svitzer contract for Rolls-Royce
Rolls-Royce has signed a 10-year service agreement with leading global towage and marine services operator Svitzer A/S. The agreement – named Global Frame Value Care Agreement (VCA) – covers spare parts deliveries in six countries for a fleet of 17 tugs powered by MTU-brand Series 4000 engines. In it, the cost of maintenance services is being tied to the engine up-time. This is the first maintenance contract of its kind to be signed by Svitzer. The preventive maintenance arrangement preserves engine availability for Svitzer while contributing to optimal life-cycle costs. Denmark’s Svitzer currently operates 17 One of the Svitzer tug fleet
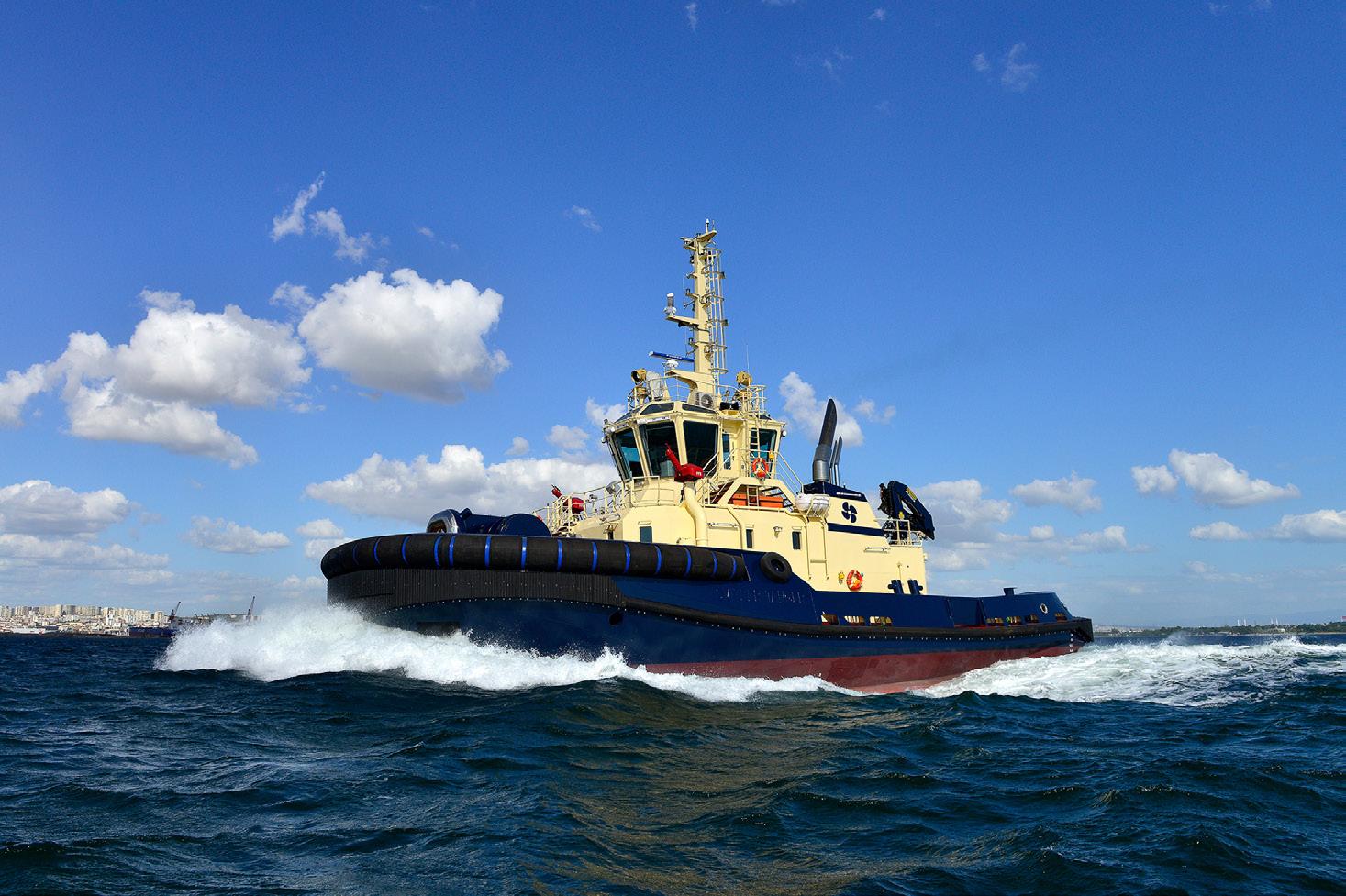
vessels with MTU Series 4000 units on-board. Among them are the world’s first harbour tugs with 90 tonnes bollard pull powered by high-speed diesel engines. These have been in service in the Tanger-Med cargo port in Morocco since 2018. Other vessels are deployed in Brazil, CostaRica, Denmark, Great Britain and Germany. Also included in the fleet is the tug Svitzer Hermod, the first commercial vessel to demonstrate remote operation, which is likewise powered by twin MTU 16V4000 M63 diesel units. As part of the agreement, the RollsRoyce business unit Power Systems will ensure that exactly the right spare parts for a vessel are made ready in the right place at the right time, for each scheduled maintenance. This approach will allow Svitzer to have focus on efficiency in the technical management and operation of the vessels in scope, while spare parts planning, scheduling and deliveries are handled by Rolls-Royce.
MHI-MME offer modifications for LSFO use
As the new IMO sulphur caps comes into operation, Japan’s Mitsubishi Heavy Industries Marine Machinery & Equipment (MHI-MME) has made available two kinds of modifications of LSFO to the main boilers and Exhaust Gas Scrubber (EGS) to the auxiliary boilers in 2019. Application of LSFO - MHI-MME has carried out the modifications of the boiler firing facility, boiler control system and fuel supply line. MHI-MME will complete the modification of
EXPERIENCE MATTERS!
Delighting Customers Since 1999
One Year Warranty
Extensive New & Reconditioned
True 24/7 Whenever & Wherever
Installing Turbocharger Confidence
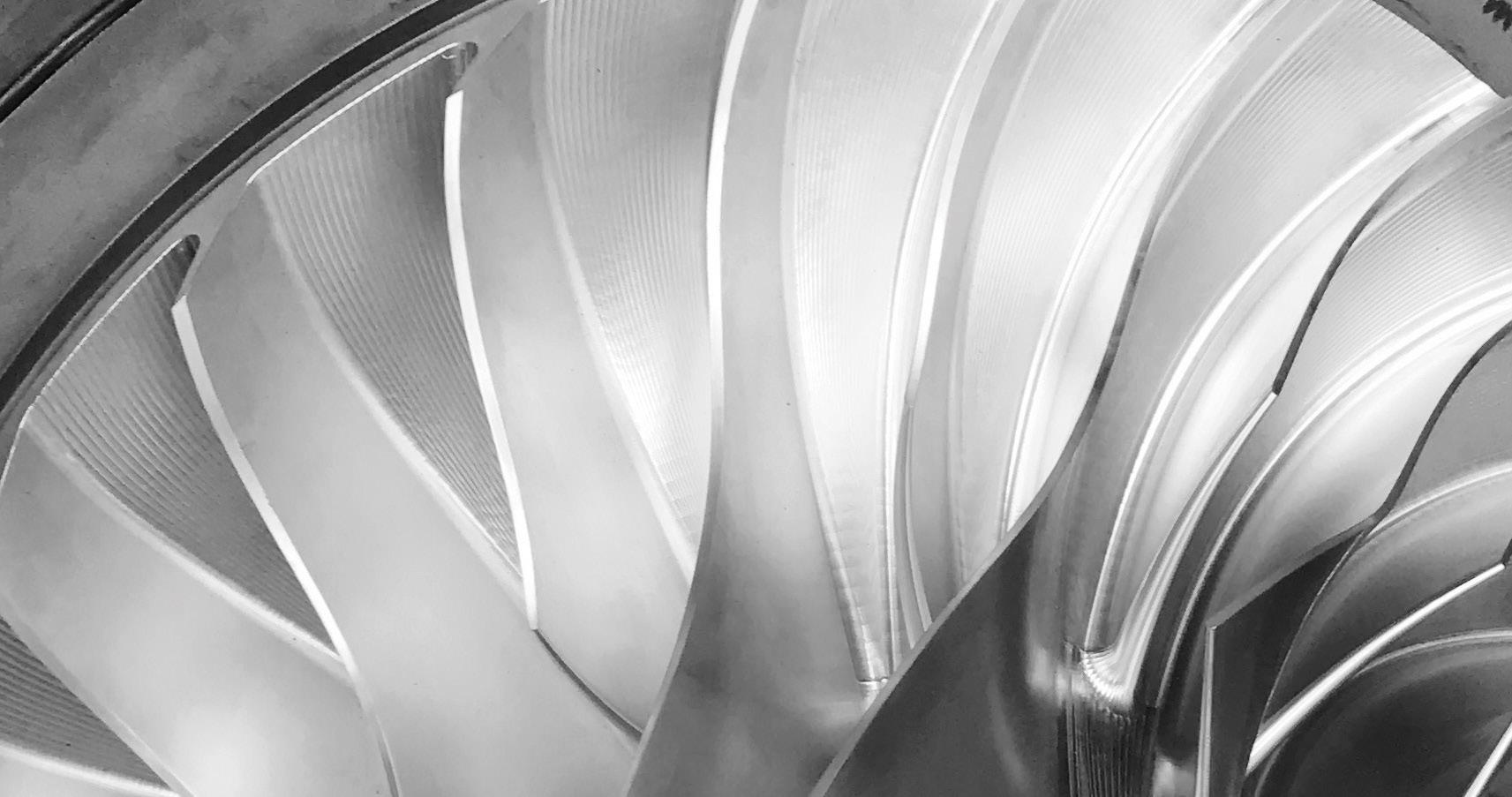
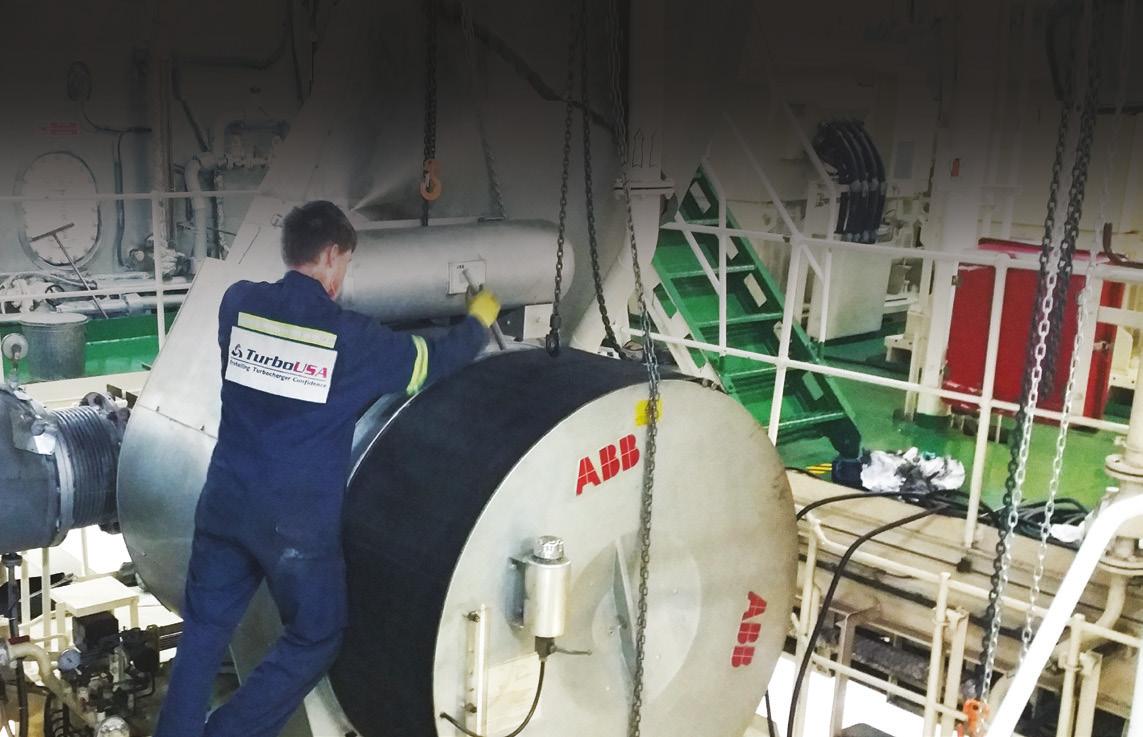
TurboUSA, Inc. - Office & Technical Center 2950 SW 2nd Avenue • Ft. Laud., FL 33315 • U.S.A. Toll free: 877-887-2687 • Telephone: 954-767-8631 Fax: 954-767-8632 • Email: info@turbo-usa.com www.turbo-usa.com
MHI-MME has made available two kinds of modifications of LSFO to the main boilers and Exhaust Gas Scrubber (EGS) to the auxiliary boilers in 2019
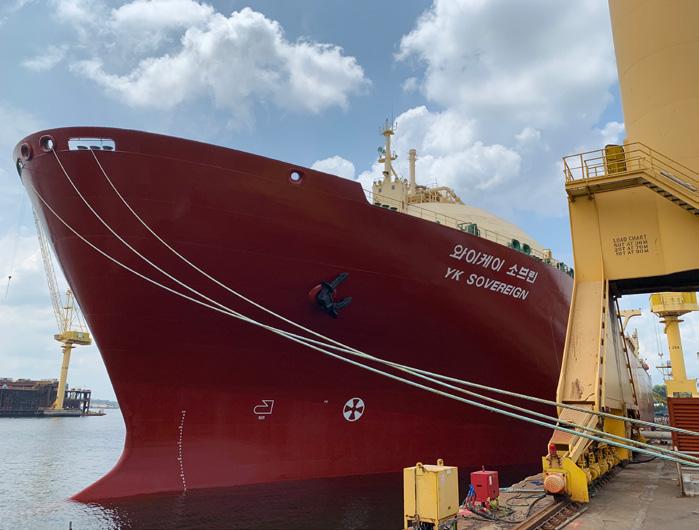
approximately 50 LNG tankers during this year (2019). LSFO has been supplied on a worldwide basis since September 2019, and there are many kinds of fuel specifications, which vary in fuel viscosity from lower content, being a characteristic of LSMGO made from gas oil, to a higher version, and identifying to ULSHFO made of de-sulphurised residual oil. Boiler firing characteristics are not affected by oil viscosity directly, but by oil temperature at the burner inlet. MHI-MME’s modification includes a control system so that all types of LSFO are ready to be put into practice with ease. Installation of EGS - Auxiliary boilers onboard conventional oil tankers are modified in connection with EGS for SOx reduction. A part of the combustion gas from the boiler is supplied to the Inert Gas System (IGS), however, IGS is not approved to reduce SOx as is the function of EGS. Therefore, in case of a two boiler-system, one boiler supplies combustion gas from LSFO for the IGS and the other boiler works on HFO for EGS. It is essential to modify the gas duct between boilers and EGS as well as boiler-controlsystem to prevent reverse flow of exhaust gas into engines and boilers. Meanwhile, MHI-MME is delivering MET turbochargers for the world’s largest two-stroke dual-fuel X-DF engine 12X92DF developed by Switzerland’s Winterthur Gas & Diesel (WinGD) and being built by China’s CSSC-MES Diesel (CMD). These engines are scheduled to be mounted on a total of nine 23,000 teu containerships to be built at a shipyard that is under the China State Shipbuilding Corporation (CSSC) group. Many MET Turbochargers have already been mounted on WinGD’s X-DF engines, and this major project further confirms the compatibility between MET Turbochargers and X-DF engines. A ceremony to unveil the project’s first completed unit will be held on December 2 nd at a CMD, where the engine was built. The combination of the MET Turbocharger with the 12X92DF engine achieves the uniform lean combustion of gas mixed air in the engine. At the same time, the effective utilisation of the exhaust gas enables both cleaner emissions and high efficiency. It makes it easy to accommodate the strict IMO NOx and SOx emission regulations on specified ships, while also reducing CO 2 emissions with the contribution changing the fuel from diesel to dual fuel. IMO’s NOx Tier III standards, which require an 80% reduction in NOx emissions from Tier 1 standard, have been in effect since 2016 in Emission Control Areas (ECA). The waters subject to these standards are expected to expand going forward. As for SOx, in addition to the ECA where strict emissions regulations are already in effect, the requirements will be intensified in all other waters from 2020, reducing the allowable sulphur content in marine fuels from the current limit of 3.5% to 0.5% or less. The combination of MET Turbochargers with X-DF engines will realise a powerful option for meeting these stricter rules. MHI-MME developed new models of small, lightweight and high-efficiency turbochargers in 2018, aiming to complete the first such turbocharger in 2020. The MET-MBII turbocharger series are available to install the turbocharger on WinGD diesel engines as well as former MET-MB series.
Fishing vessel refit for Høglund
During late August 2019, Ocean Venture contacted Norway’s Høglund to replace its smoke damaged integrated automation system (IAS) on-board the fishing vessel Prowess. When it comes to automation systems, owners must often balance a speedy retrofit against long-term reliability. This was the challenge presented to Høglund with the retrofit of the Prowess. The IAS is an essential part of vessel operations – it enables integration between the various systems and components with an overarching computer system. For example, in the engine room alone, the systems monitoring a vessel’s engine temperature, fuel levels, viscosity and flow control will all be managed by a comprehensive automation system. A damaged, ineffective or unreliable automation system can incur a significant cost and great difficulties for the shipowner. As these systems communicate, there are optimisations to be found as the systems work together. Power can be managed more effectively, saving fuel, and alarm systems can be integrated to track performance and give further visibility into a vessel’s electronics. However, the proper integration of our ships is something that has historically been overlooked. The reason is simple - the budget for automation is small, and hence, there is little incentive to optimise, rather than sticking with solutions bundled in with other systems. At the design stage, ship designers might have a low level of understanding of electronics and automation, so this design element is overlooked. Later in a vessel’s life, the apparent complexity involved in replacing and upgrading a system is a barrier to improving or replacing an automation system. During the summer of 2019, the old Autronica IAS of the Prowess was damaged after the back-up batteries in the Engine Control Room (ECR) started smoking – rendering the IAS completely unusable. Making things worse, all of this occurred less than two weeks before it was due to sail to the Barents Sea to fish for snow crabs. Thanks to Høglund’s flexible approach, experience and expertise, the Prowess returned to its fishing grounds with a new, fully functioning IAS just over a week later. Projects of this nature on vessels similar to the Prowess would typically take between two to three weeks to complete Børge Nova, CEO of Høglund commented, “The impressive work on the Prowess is a good example of how our expertise makes an impact. We were able to save a considerable amount of time by creating software tailored to the vessel before going on-board, which meant that we had more time to install and test equipment when we were on site. Consequently, we understand the ship owner’s need for urgency and always strive to tackle complex technical challenges in a matter of days.” SORJ
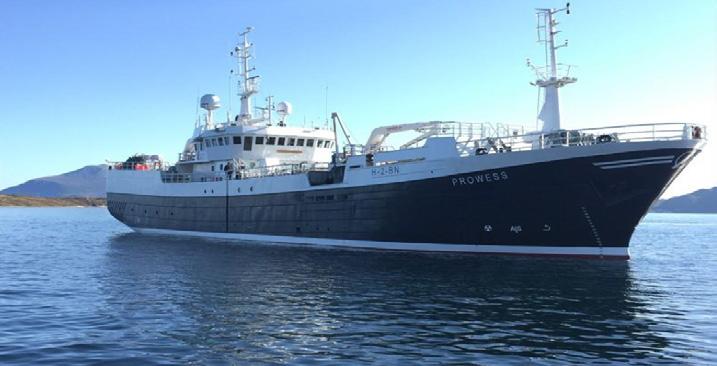
The fishing vessel Prowess