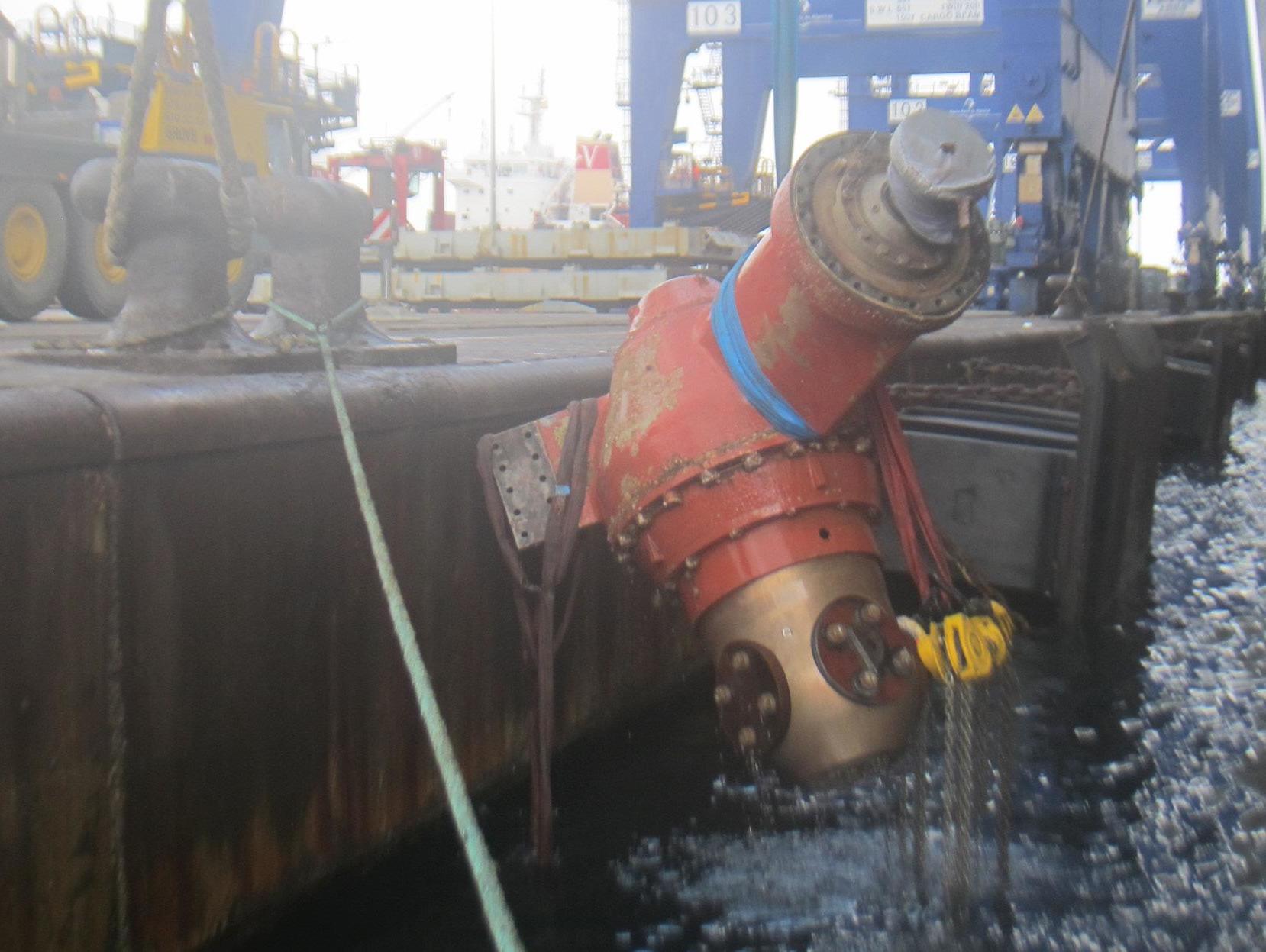
20 minute read
Underwater Repairs
News from Hydrex
A 208 m cruise vessel sailing in the Caribbean recently suffered steering problems after one of its two bow thrusters malfunctioned. Having to depend upon assistance every time the ship berthed will quickly become very expensive. Going off-schedule, however, to have the bow thruster replaced would cost the owner both financially and its reputation. A solution was therefore needed that could be carried out on-site without interrupting the vessel’s schedule. Enter the Hydrex tried and tested flexible mobdock technique and experienced diver/technicians. There was only a time frame of eight hours at each port of call during the ship’s cruise in the Caribbean. It was therefore important that the operation was split up in parts that could be finished before the vessel had to leave again. A Hydrex team also recently travelled to Tenerife for an underwater propeller blade straightening on a 246 m cruise ship. The crew of the ship had noticed that the engine was overloading. This was the result of damaged propeller blades that were performing below average. The engine had a higher workload, leading to increased fuel consumption and added stress. A detailed survey of the ship’s two propellers revealed that the four starboard side propeller blades of the vessel were bent. A fast, on-site solution to restore the propeller’s balance and
Advertisement
Underwater Repairs
efficiency was needed. Luckily the port side propeller blades were in good condition and did not require any repairs. Recently a Hydrex team of Hydrex mobilised to Oslo, Norway for an underwater bow thruster operation on a large ferry. A seal in the gearbox was leaking and needed to be replaced. A small window was made available for the operation, but the repair had to be finished before the next scheduled trip. The Hydrex technical department proposed to replace the defective seal underwater with a tailormade cofferdam. The cofferdam was designed by their R&D department and fabricated at the Hydrex headquarters in Antwerp. This allowed the divers to remove the damaged seal ring and replace it with a new one in a dry environment. Hydrex teams have recently carried out several rudder repairs on ships in Belgium and
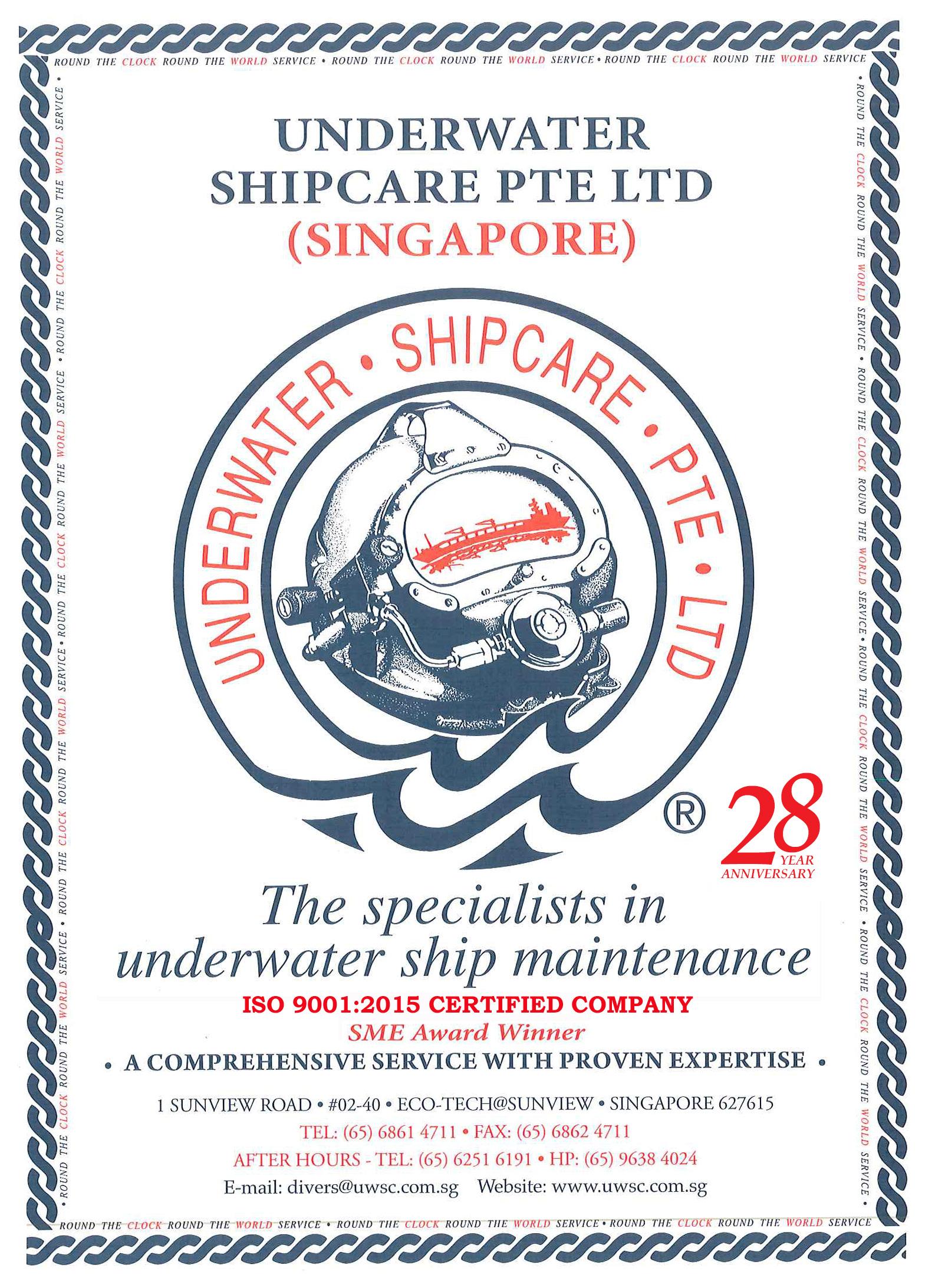
France. In all cases cracks were found that needed to be repaired to prevent them from spreading and causing further damage to the rudders. A 230 m ro/ro ship in Zeebrugge had suffered cracks on both sides of the rudder flap. On the starboard side a branching crack was found while a single crack was present on the port side. Hydrex divers first drilled arrests on all extremities of the cracks to prevent them from spreading. They then positioned C-shaped plates over the crack arrests and secured these with wet welding. On-board two 229 m bulk carriers (sisterships) in Le Havre and Dunkerque, cracks were found on the upper pintle corner of the hinge that connects the rudder flap to the main rudder blade. Fortunately these cracks could be repaired by grinding them out after a crack arrest had been drilled. The affected area was then filled with clad welding. The cracks on these rudders were spotted during an underwater inspection before they caused problems for the ship. This once again shows the benefits of having regular inspections carried out by competent divers, followed by comprehensive and accurate reports.
Recently one of Hydrex’s diver/technician teams carried out underwater stern tube seal repairs on a 192 m ro/ro vessel in Rotterdam. The vessel was suffering from an oil leak, making a fast repair necessary. The team carried out the entire operation on-site and underwater using a Hydrex flexible mobdock. Meanwhile, the four blades of a 190 m bulk carrier’s propeller were severely bent. An on-site solution was needed to restore the propeller’s balance and efficiency. A team was therefore mobilised to CamPha, Vietnam. An oil tanker needed its four propeller blades overhauled during a stop in Ghent, Belgium. Hydrex sent a team to the vessel’s location to remove the blades on-site and reinstall them when they returned from the workshop. The operation was carried out while the vessel was alongside and trimmed so that the blades could be surfaced one by one. The team started the repair with the installation of chain blocks to rig the first blade. They then removed the blade bolts and lifted the blade. A blind flange was installed to prevent water ingress during the overhaul. The ship crew then turned the propeller 90° to surface the second blade. The Hydrex technicians repeated the same procedure on all four blades A Hydrex team recently removed a bow thruster from a 229 m bulk carrier. Two weeks later the overhauled unit was reinstalled. Both operations were done during stops in Algeciras, Spain and had to be carried out within the tight schedule available to the charterer. SGS acquires UWC US-based Subsea Global Solutions (SGS) has announced that it has acquired Singapore’s Underwater Contractors (UWC) and Australia’s Gray Diving Services (GDS), through separate transactions. With these two tandem acquisitions, SGS expands its global footprint in the Asia-Pacific region beyond Busan, South Korea, where it had a local office for the last seven years and increases the number of its home ports worldwide to 13. Commenting on the acquisitions, Paul Peters, CEO of SGS said, “This is a significant milestone in the history of SGS. We are absolutely delighted to expand our global footprint to Singapore, a strategic commercial shipping hub where most of our clients visit regularly, as well as to Sydney, a critical port for our cruise business. With well-known brands like UWC and GDS joining our organisation, we will solidify our leadership in our market segment and will be able to truly support our clients from these key locations with our own personnel, boats, gear, and equipment. We look forward to joining our forces.”
Seal replacements by SGS
Over the past few months, SGS has performed a number of high capacity underwater repairs across the globe. The majority of these repairs have focused on seal replacement. Face and Lip type seals can be completely renewed and serviced with OEM and Class approved procedures. Face type seals can be completely rebuilt ‘wet’, where lip type seals can be renewed, including the bonding of new seal rings, completely underwater using the TransHab - the transportable habitat designed by SGS. Bonding new seal rings, removal or installation of spacer rings, and even complete replacements can be performed at anchor or during cargo handling operations without interference with the vessel’s schedule - thereby avoiding unnecessary off-hire and drydocking.
TransHab is a lightweight, inflatable habitat that is fitted around the stern seal between the stern tube and propeller, thereby providing a dry environment large enough for two technicians to carry out repairs. Using stock adapters, TransHab is designed to fit any seal arrangement, including azipod drives, with liner sizes from 480 mm – 1,200 mm. In the Far East, SGS Busan answered the call of a cruise vessel. With passengers on-board, keeping the schedule was of obvious concern and importance to the cruise line. The port time allocated for Busan was only 32 hours, though crews generally need 48 hours to complete the repair - especially on both port and starboard shafts. To save time, SGS dive technicians met the vessel in Hong Kong first to remove the rope guard and take stern arrangement measurements, before meeting the vessel again in Busan. The vessel had very limited space for the TransHab system due to the struts and propeller blades, but the dive team was able to modify habitat adaptor plates according to the vessel’s particular stern tube shape, thereby maximising workspace within the habitat (and thus creating the space necessary to perform such complex tasks). SGS dive technicians worked diligently to complete the repairs successfully within 29 hours, ahead of schedule,
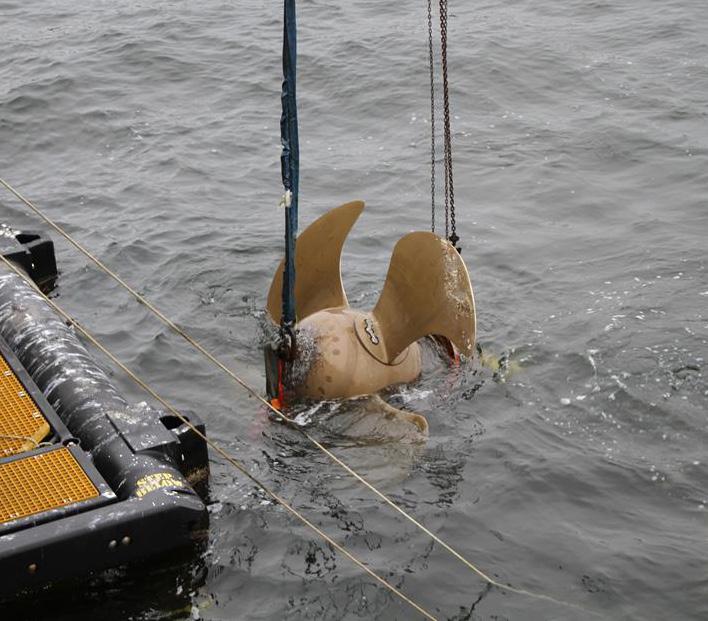
enabling the vessel to sail away at its scheduled departure time. Not long after, another cruise vessel was experiencing shaft seal issues in Japan. SGS crews had only five days in which to prepare for the job - 13 dive technicians were flown in from various offices around the US and Canada, SGS’ fly away kit (approximately 12 m ≠ , 3,000 kg) was prepared and shipped to Japan the following day, and work permits were obtained with the help of the vessel’s local agent. The vessel had a four-lip system, consisting of a dirt seal, water seal, air seal and oil seal - and all four needed replacing. This sealing system was also one of the more complex types that require experience, attention to detail, and effective time management to be able to complete within the allotted time frame. The overhaul of the seal system required a complete disassembly, including the seal housing flange. The seal housing flange, it should be noted, is several hundred kilograms and must be carefully removed, realigned, and reinstalled to avoid damaging the sealing gaskets. Upon relocation of the flange, the forward split cover ring can be removed to expose the oil seal. New seals must be bonded precisely to avoid any defects and subsequent complete re-disassembly (seals cannot be pressure tested without reinstallation of the flange). During the repair, SGS crews had to pump out more the 1,000 litres of oil out from the habitat - delaying the start of the repair as crews were focused on taking extra precautions not to release any oil out to the ocean. Due to the experience level of the technicians however, SGS was able to work quickly and efficiently (even bonding the first seal while still disassembling the last seal) - the full shaft seal repair was completed on time, as quoted, and allowed the vessel to depart on schedule with zero delays. SGS Long Beach recently received an emergency request from the Superintendent of a large cruiseship to inspect the vessel’s stern thruster. SGS dive technicians were dispatched and attended the ship the following day in Los Angeles with one of seven fully equipped dive vessels. Upon initial inspection, it was found that a mooring line had been pulled into the thruster. The line had wrapped so tightly around the propeller that it crushed the rope guard into the thruster propeller shaft. The line had also wedged itself in the tiny gap between one of the propeller blades and the tunnel plating, rendering the thruster inoperable.
ECOsubsea’s cleaning technology approved
Norwegian brothers Tor and Klaus Østervold finally have proof of concept for their revolutionary ECOsubsea hull cleaning

technology, transforming a pressing environmental problem into potential business profit – both for them and forward-thinking shipowners, ports and service suppliers. Here Tor explains how this young business will help maritime rid itself of an age-old problem, “Some challenges you can fix overnight, some might take a week or a month, and some take 11 years.” Tor Østervold is laughing down the line from the ECOsubsea business base in Southampton. The affable 36 year old is describing how, after setting up shop with his younger sibling Klaus in 2008, it’s taken this long for ‘everything to fall into place’. But, considering the ambition and innovation that define the business, the wait is hardly surprising. “We’re addressing a problem that impacts upon shipowners, ports and, bearing in mind the environmental implications, upon society itself,” states the ECOsubsea CEO (Klaus is COO). “So, it was never going to be an overnight fix! “We have developed revolutionary technology here, and I firmly believe it can be the ‘missing piece of the jigsaw’ in terms of the industry’s quest for greater sustainability. But before we get on to that solution, what exactly is the problem?” In short, bio-fouling is organic matter that attaches to vessel hulls creating friction on otherwise smooth surfaces, leading to loss of speed and a decrease in fuel efficiency. This in turn causes greater fuel consumption, higher operational costs and increased emissions spilling out into the atmosphere. In fact, studies have shown that maintaining clean hulls could help the world fleet reduce costs and emissions by up to 15-20%. A hugely compelling figure in an era of both reduced margins and greater environmental awareness. However, traditional cleaning methods that centre on diving teams scrubbing vessel surfaces are problematic. Not only is the job itself time and labour intensive, but it also leads to the organic matter being deposited on the seabed and this, through the spread of potentially invasive species, impacts upon local ecosystems. As a result, many ports have banned - or are in the process of looking into banning - established hull cleaning practices altogether. And then there’s the scrubbing action itself, which can be damaging to the expensive coatings shipowners invest in. “This is a major issue for our industry,” Østervold argues, “It hits every stakeholder in one way or another, impacting upon business performance, local communities, broader society, and the health and well-being of our planet. That’s the scale of the problem. And, for ECOsubsea, that’s also the opportunity.” Established in Norway, but with a main operational base in the port of Southampton (which itself banned hull cleaning back in 2010) and a growing international footprint, the Østervold family business utilises complex technology to offer a simple solution – ‘clean hulls and no crap’. Picture an underwater vacuum cleaner, an automated lawnmower, or even an Oxpecker (the bright billed little birds that scour the backs of rhinos, zebras and other large mammals eating parasites). ECOsubsea’s technology shares qualities with all of them. A remotely operated underwater vehicle, it clings to ships and works over the entire hull area, removing all biofouling, before sucking it down a tube for on-shore collection, filtration and, in a neat innovation, use for biogas (thanks to a project with waste and energy management giant Veolia). The entire process takes an average of 8.5 hrs, with the ‘Collector’ unit amassing over 97.5% of everything that is removed from the hull. “This far exceeds the most stringent local and international regulations, meaning ECOsubsea cleaning can be done in any port, anywhere,” Østervold explains. “And as our solution uses high pressure ‘soft jets’ of water, instead of abrasive brushes, the integrity of vessel coatings is completely safeguarded, while the quality of cleaning far out strips what is possible through manual scrubbing. “It is a game changer,” he adds. “It is proven, reliable, and we see huge demand for the benefits of clean hulls, greater efficiency and environmental protection worldwide.” The foundation for the business may have taken time to build, but it appears to be rock solid. The brothers initially disclosed their plans to Moller/Maersk in April 2008 and were invited to stay in Denmark for three months to research the concept. Four years of development followed before, in 2012, the first prototype emerged. The technology was a success from its very first date with a vessel, but, unfortunately, it got a little too attached. “The cleaning quality was excellent,” Østervold reveals, “but it took its time! In fact, the unit took 61 hours to clean a hull. So, in terms of efficiency, it wasn’t quite what we’d hoped for!” Seven years of intensive testing, refinements and partnerships have followed – with cleaning projects for leading owners such as Carnival, WWL Ocean and Hoegh Autoliners. The company has now completed over 500 assignments, with the Southampton unit accumulating more than 4,000 hours of service. “We have the optimal technology, operational expertise and business understanding to take the next step and really begin scaling up,” enthuses the ECOsubsea head. “It’s a process that is now underway.” The company has recently reached agreement with the ports of Antwerp and Zeebrugge, giving it the green card to roll out the system in these busy hubs, greatly increasing access to the world fleet. In a demonstration of the flexibility of ECOsubsea’s business plan, the team is working with existing local diving companies who will carry out the cleaning as a service provider, with full training and certification to be undertaken at the Southampton base. “In the UK we work with our own team on operations,” Østervold explains, “but to meet demand and grow market share we’re very open to establishing expert partnerships with both service providers and forward-looking ports, which can then offer this as a part of port infrastructure and create a new revenue stream. “In addition, we also see demand coming from larger shipowners who may want their own cleaning hubs for fleets, ensuring continually smooth hulls and optimal business and environmental performance.” Does he see the possibility for smaller machines that are permanently attached to individual hulls, constantly crawling over them to maintain standards? Yes, it’s certainly possible,” is his coy answer. “We are looking at different unit sizes, but for the time being we have an ideal universal size for ships of any type ranging between around 150 and 400 m. The future business potential within that context is enormous.” ECOsubsea has recently won another port over to offer its services - the Dutch, national regulatory body, Rijkswaterstaat has given the Norwegian company the green light to start offering hull cleaning services to vessels at all Dutch Ports including Europe’s biggest port, the Port of Rotterdam, a move that is helping the firm solidify its position in Europe following similar permissions in Antwerp, Zeebrugge, Ghent and Southampton. “Ports want evidence that our system works,” says Tor Østervold. “We can now give it to them. They also want evidence that vessels
have active hull biofouling plans, and we are helping operators and ports with the digital implementation of that too,” he added. “At the end of last year we were only in Southampton,” adds Østervold. “Now we are in a growing number of ports including Amsterdam and Rotterdam.” For Østervold a giant port such as Rotterdam, with a strong environmental benchmark, is an important step in the evolution of the company. The port of Rotterdam’s Breakbulk Business Manager Irene Bennett points to the role the Authority plays in generating a healthier environment, primarily concerning air quality, noise and the natural environment and biodiversity and water quality. “We recognise that efficient cleaning of ship hulls is better for the water quality in the port and reduces CO 2 emissions and fuel costs,” she says. “The advantages of initiatives like ECOsubsea will enhance the sustainability of the entire transport chain. The Port of Rotterdam is therefore happy to promote initiatives that fit in well with our corporate social responsibility goals.”

ECOsubsea has been working closely with a number of major ship operators, including Carnival, Wallenius Wilhelmsen and Hoegh Autoliners, that recognise the need for clean hulls, and the additional need to clean their vessels’ hulls responsibly. Vessel operators are increasingly under pressure to operate their vessels with the lowest fuel consumption, and fouled hulls are a leading cause of poor operational performance.
Phoenix divers Assist with vessel in New Zealand
In the early hours of December 23 rd , an urgent inquiry was received from a Phoenix client requesting a proposal and timeline for a dive team to mobilize immediately to international waters 12 miles from the city of Auckland, New Zealand. The situation was complicated as the vessel had undergone an underwater inspection in a previous port with the subsequent report and findings forwarded to the New Zealand Government for review prior to entry. The Government quickly rejected approval for the vessel to enter due to fouling evident on the hulls niche areas. It is a strict requirement that all vessels entering New Zealand territorial waters must be cleared by the New Zealand Ministry of Environmental Protection and be 100% free of any and all bio-fouling to dissuade the introduction of invasive species into New Zealand waters. Due to the schedule urgency, the impending holiday, and potential revenue loss, the client requested a Phoenix dive team immediately mobilize to the vessel to perform a niche area cleaning and subsequent underwater video inspection. The Phoenix team arrived in a timely manner, performed the work, and submitted the evidence to the New Zealand Environmental Protection Authorities so that the vessel was able to be cleared in time to fulfil is obligated charter on December 28 th in Auckland. Meanwhile, Phoenix International Holdings
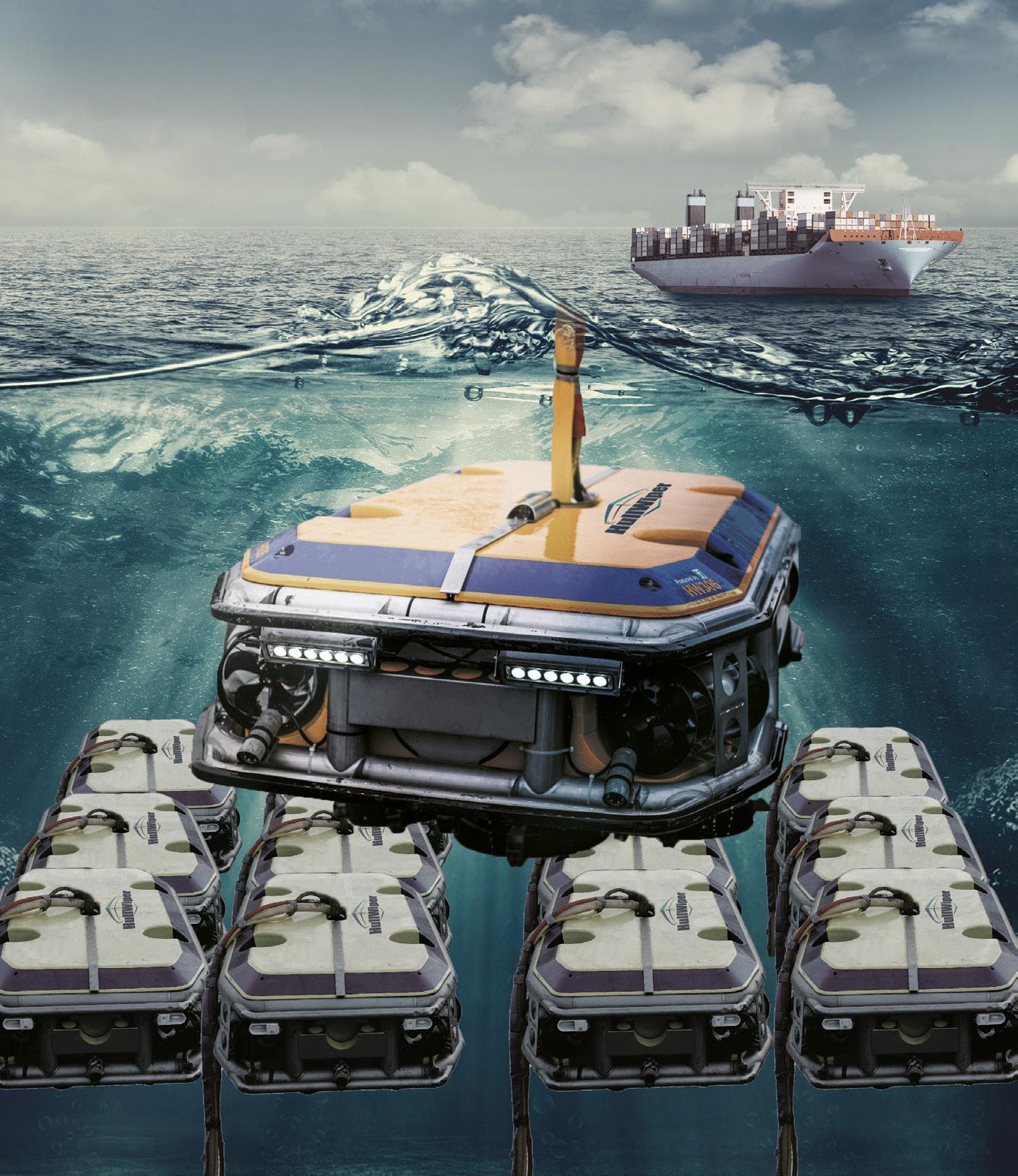
HullWiper operating in Gibraltar Port.
has announced that Matthew Long has been promoted to Corporate Vice President. Matthew will retain his current duties as General Manager of Phoenix’s Largo, MD operations, and in his additional role as Corporate VP will assume responsibilities for company-wide financial forecasting, reporting and budgeting.
HullWiper signs partnership with SCAMP
HullWiper is expanding its operations in Gibraltar in partnership with SCAMP, with a second underwater hull cleaning unit that will be operational in the first quarter of 2020. About 60 hull cleans have been carried out in the Port of Gibraltar by HullWiper since its launch there in 2017. Growing demand for safe, eco-friendly in-port hull cleans will be met with HullWiper’s Remotely Operated Vehicle (ROV) operating in the Strait of Gibraltar day or night, quickly, cleanly and efficiently. With the second unit, cleaning operations will start on the east side of Gibraltar. HullWiper’s underwater diverless- and brush-free cleaning technology uses adjustable natural seawater jets to dislodge and remove biofouling without the abrasive scrubbing

or harsh chemicals employed by traditional methods. The ROV collects marine fouling removed from hulls, rather than releasing it into port waters and risking the spread of invasive marine species. Captured residues are pumped into the ROV on-board Filter unit and deposited into dedicated drums onshore, protecting both the marine environment and the customer from potential fines or penalties. And as no divers are involved, the ROV also saves costs and reduces the risk to human life. Freddie Pitto, SCAMP General Manager Shipping Services, says, “This second HullWiper ROV enables us to provide even more vessels with reliable and efficient hull cleans to ensure they leave for their next destination foul-free.” Traditional hull cleaning methods generally restrict requirements for hull cleans with deep drafts or during harsh weather conditions. Deep draft restrictions do not apply to HullWiper and cleaning can be carried out even in adverse weather conditions. Since its launch in late 2013, HullWiper has expanded from its first base in Dubai to include key locations across the Middle East, as well as ports in Australia, Denmark, Egypt, Gibraltar, Norway, Singapore, Sweden and – most recently – Panama and Mauritius. Plans are in the pipeline for new locations including Sri Lanka, Korea, South Africa, Chile and Bahamas. HullWiper is also available for lease where the company does not have its own base. To date, HullWiper has attended more than 1,000 vessels for hull cleans worldwide. Meanwhile, HullWiper is joining forces with GAC Qatar in preparation to launch its hull cleaning solution at the Qatari port of Ras Laffan in early 2020 to meet growing demand for safe, eco-friendly hull cleaning solutions. GAC Qatar is the only company to have been granted a license by the country’s Environment Ministry to operate hull cleaning equipment in its waters. HullWiper’s Remotely Operated Vehicle (ROV) complies with Qatar’s strict regulations, which include the collection of 100% of biofouling removed during cleaning for safe disposal at the Qatar Petroleum (QP) facility after a QP test, and the maintenance of proper cleaning records for monthly submissions to the QP Environment office. All fouling removed from the hull during cleaning is captured in its unique on-board filter unit, and a detailed report of the operation is produced. The agreement with GAC Qatar was signed under HullWiper’s leasing programme, which was introduced in 2017. The programme enables HullWiper to work with partners around the world to offer ship owners and operators a cost-efficient, brush- and diver-free alternative to traditional hull cleaning methods, which also protects both the ocean and expensive anti-fouling vessel hull coatings. Owners and operators benefit from a clean hull without any extra downtime or harm to the marine ecosystem. SORJ