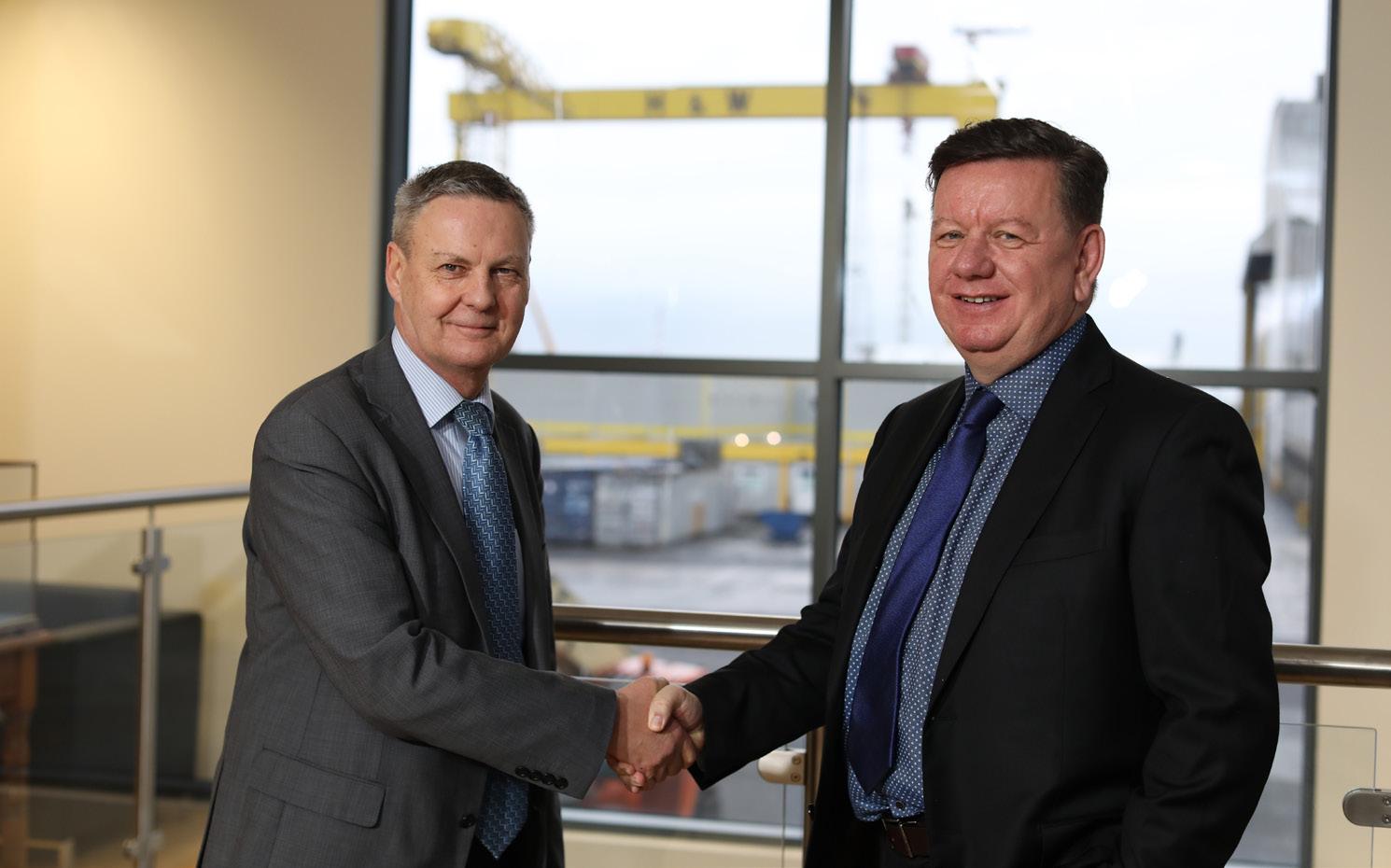
13 minute read
Shipyards
Mark Giles (left) and John Petticrew
Harland & Wolff re-opens
Advertisement
It was announced on December 5 th last year (2019) that InfraStrata plc completed the acquisition of the assets of Northern Ireland’s iconic shipyard Harland and Wolff (H&W), Belfast. InfraStrata now has 100% ownership of the assets following a £3.30m payment to the administrators of H&W - BDO LLP. An additional £1.45m is payable by April 30 th 2020. John Wood, Interim Chairman and Chief Executive Officer, commented at that time, “H&W is once again open for business. We will be seeking to bring in a few near-term revenue generating opportunities as quickly as possible which will strengthen our technical and operational capabilities for significantly larger projects in the future including our on-going gas storage and other energy infrastructure projects.” Then as soon as December 11 th , it was announced that H&W has been awarded contracts for the drydocking and repair of a total of five vessels from two owners to carry out annual inspections and maintenance. The first of these ships arrived on December 20 th 2019 and the second on December 27 th . John Wood commented, “The award of these first contracts is a crucial milestone in the life-cycle of the Company. The Board is committed to being revenue generating in 2019 and has now fulfilled that commitment to its shareholders. The fact that the completion of the acquisition of the assets of H&W was immediately followed by revenue generating
contracts validates this acquisition. This is the beginning of a transformational shift in the Company’s position to being revenue generative and ultimately cash-positive in the future.” The first two ships are both owned by Seatruck Ferries - the 19,722 gt ro/ro freight ferry Seatruck Performance and her sistership Seatruck Precision. Meanwhile, InfraStrata is involved in the Islandmagee Energy gas storage project located in Northern Ireland. Steel fabrication work for this project is likely to start in spring 2020, with modules of some 50 – 100 tonnes in weight being transported by barge from the yard to the gas storage site. This project is likely to last for some 18 months – two years. During December, InfraStrata Plc announced the appointment of Clive Richardson, who was previously CEO of one of the world’s largest providers of commercial ship management services, as Chairman of the Company. John Wood, CEO of InfraStrata, said, “Clive has a very impressive CV and a demonstrable track record of adding serious value to businesses he is part of, so we are delighted that he has agreed to join our Board as Chairman. His wealth of experience and global network will be invaluable to InfraStrata as we focus on delivering significant contracts for our newly acquired Harland & Wolff assets and advancing our Islandmagee gas storage project in Northern Ireland. We look forward to 2020, which is set to be characterised by exciting new revenue opportunities and progression of our energy infrastructure portfolio, and I am confident that Clive will play a key role in our future success.” John Wood is also putting together an impressive H&W management team with John Petticrew joining as Managing Director. John Petticrew has decades of experience running fabrication and ship-building facilities around the world. Until recently, he was Vice President Operations at Seaspan Shipyard in Vancouver, Canada. John had 2,000 employees reporting into him with five divisional directors. In this role, John implemented the national shipbuilding strategy for Canada, building six vessels for the Navy and Coast Guard. Prior to this, John was the Vice President of Engineering for Seaspan, Technical Director for Gulf Marine Services and the Senior Project Director for Lamprell Energy Limited and held the position of New Building Manager for Dubai Dry Docks (now Drydocks World). Commencing his career in 1987, John spent a decade at Saint John Ship Building, serving as Superintendent and Production Manager. He has a wealth of experience across fabrication, oil & gas, defence, ship repair and vessel construction. He started his career on Clydeside with Scott Shipbuilders. Paul Blake joins the management team as Operations Director. Until recently Paul was the Head of Projects at ASRY, Bahrain. Prior to this, he held the position of Project Manager at Grand Bahamas Shipyard, specialising in cruise vessel upgrades. Paul also held posts as Director and General Manager at Atlantic & Peninsula Pty Ltd in Australia and the General Manager/ Ship Repair Director at Topaz Energy & Marine in Dubai. Also in the new management team is Mark Giles (Director of Sales – Commercial and Defence), Stephan Mills (Director of Sales &
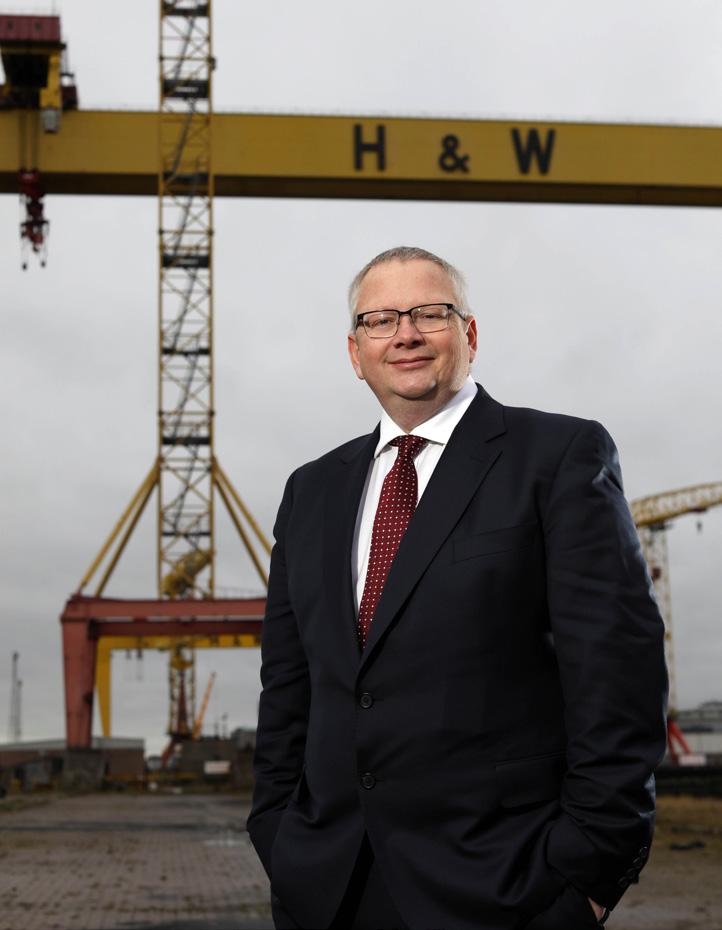
Marketing – Cruise & Ferry). H&W is also part of a group, including Spain’s Navantia and UK’s BMT, bidding for the UK Government’s FSS Programme involving a series of Fleet Solid Support Ships for the Royal Fleet Auxiliary (RFA). John Wood says, “We are to operate in as many as six different ‘streams’, including shiprepair and conversion, industrial projects, such as Islandmagee Energy, naval work, such as the RFA work currently under a joint bid with Navantia and BMT, and the renewable industry. This will allow H&W to maintain consistency in its workload.” H&W’s facilities comprise two main graving docks, the largest being the Main Dock, which has dimensions of 556 m x 93 m, making it one of the largest drydocking facilities in Europe. It was originally built as a building dock but has the ability of drydocking all types of ships. It is served by two massive Goliath cranes, with a capacity of 840 tonnes each. The cranes have been a recognisable feature of Belfast’s landscape for many years. This dock has seen semi-submersible rigs, large bulk carriers and FPSOs under repair, and has also been used for steel construction in the renewable industry. The second drydock is the Belfast Dock, a more traditional repair facility, with dimensions of 335 m x 50 m. This dock has seen several FPSOs under repair and was the location of the famous Sea Empress repair, following extensive grounding damage repairs in Milford Haven.
New US West Coast yard
A new west coast US shiprepair yard was established in Everett, Washington in October – Everett Ship Repair LLC. The new repair yard has been set-up by Ice Cap Holdings and local shipbuilder Nichols Brothers Boat Builders. The new repairer will focus on the repair and maintenance of local commercial vessels, government-owned vessels and military craft. The yard will operate the 7,800 tonnes lifting capacity floating dock Faithful Servant, which previously operated in Bellingham, Washington. This floating dock, measuring 492 ft (150 m) x 148 ft (45 m), arrived in Everett on October 1 st and is being readied for service.
New apprentices at A&P Group
UK’s A&P Group has recruited a total of 20 new apprentices – 10 at its Tyne facility and a further 10 at A&P Falmouth. The new intake of apprentices includes two Health and Safety Apprentices – Rebecca Kitts at Falmouth and Anthony Innes at Tyne – who are among the first two HSE apprentices in the country. The other new apprentices are training to be engineers, electricians, welders, platers with additional training in procurement & supply. David McGinley, Managing Director Atlantic and Peninsula Marine Services Ltd, said, “Our management team is committed to building a sustainable future for A&P and our apprentices will play a significant role in developing our business in the future. We will
years of excellence
Maritime Manpower
SHIPYARD PERSONNEL OIL & ENERGY PERSONNEL RIDING SQUADS CREWING
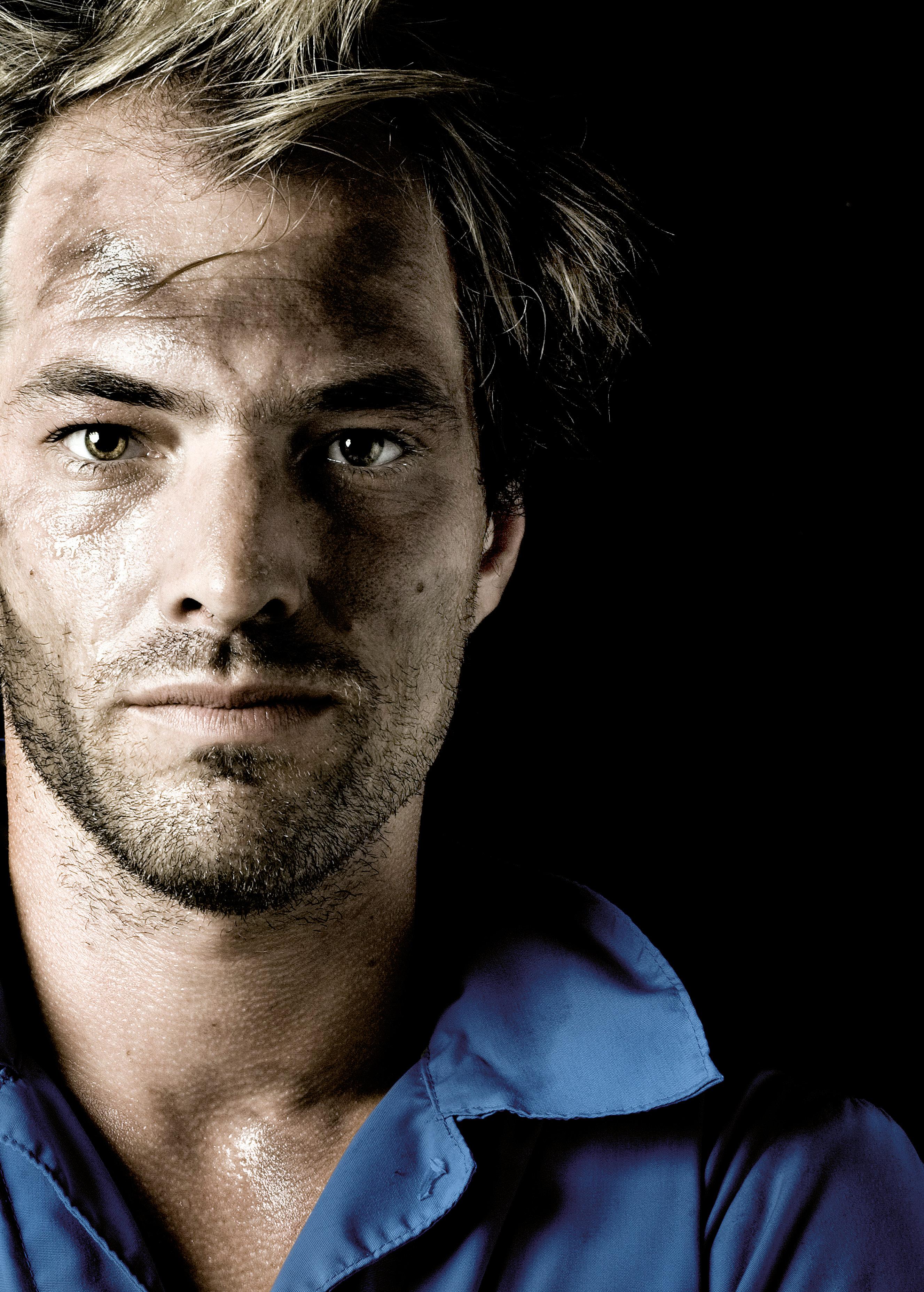
9 Puskin Street, Constanta, Romania T +40 241 586810 F +40 241 586805
www.nedcon.ro
Follow us on:
MLC 2006 Approved
Certified by Lloyd’s Register
strive to provide the best training possible to the next generation of apprentices. “At A&P we want our apprentices to grow in stature, learn from our current employees and build their lives upon a good work ethic that promotes a good team ethos. This is what this industry is all about. The development of highly skilled trades’ people has been a major contributor to obtaining the high level of credibility A&P has within the ship repair industry.”
Swedish Coat Guard contract for Damen Oskarshamnsvarvet
Sweden’s Damen Oskarshamnsvarvet has signed an engineering, procurement and construction (EPC) contract with Kustbevakningen, the Swedish Coast Guard (KBV), for a modernisation and modification project on the KBV 181. The vessel was built as a patrol boat, but will, after modification, serve as a combination vessel, for both patrol and oil recovery. It is used also by Umeå Marine Forskningscenter (UMF) for research and environmental monitoring in the Gulf of Bothnia. The KBV 181 is scheduled to arrive at Damen’s Swedish yard on April 21 st this year (2020), where she will remain until December, undergoing a scope of work that will extend her lifetime by 15 years and ready her for oil recovery work. Damen Oskarshamnsvarvet managing director Flip der Waal says that the two parties have worked closely in order to find a solution that matches the client’s budget and requirements. “The Coast Guard is a good customer of ours, we’ve worked together before on numerous occasions. Our co-operation during the process has been extremely pleasant and constructive. They think along with us, helping us to find solutions. As always, we have worked together as a team - in the end we both have the same objective – to get the project done as efficiently as possible.” The Swedish Coast Guard has been developing the plans for the project for some time. It will involve a broad scope of work, including enlargement of the aft deck area which will provide the additional deck space needed to allow the vessel to fulfil her large diversity of tasks, ranging from hosting scientific research missions to oil recovery in ice. The hull reconstruction will be carried out above the waterline in order to maintain the vessel’s ability to manoeuvre in ice. Additionally, a new bulwark will be fitted, including a transom door which will fold outwards to become an additional deck extension able to support oil recovery equipment. Both of the vessel’s existing cranes will be replaced with new ones and an additional, 90 tonnes, crane will be installed. Damen will remove bulkheads from the main deck in order to incorporate a new laboratory, to be operated by Umeå University. This will include the construction and installation of a Ferry box for continual water sampling and Damen Oskarshamnsvarvet has signed an EPC contract with Swedish Coastguard
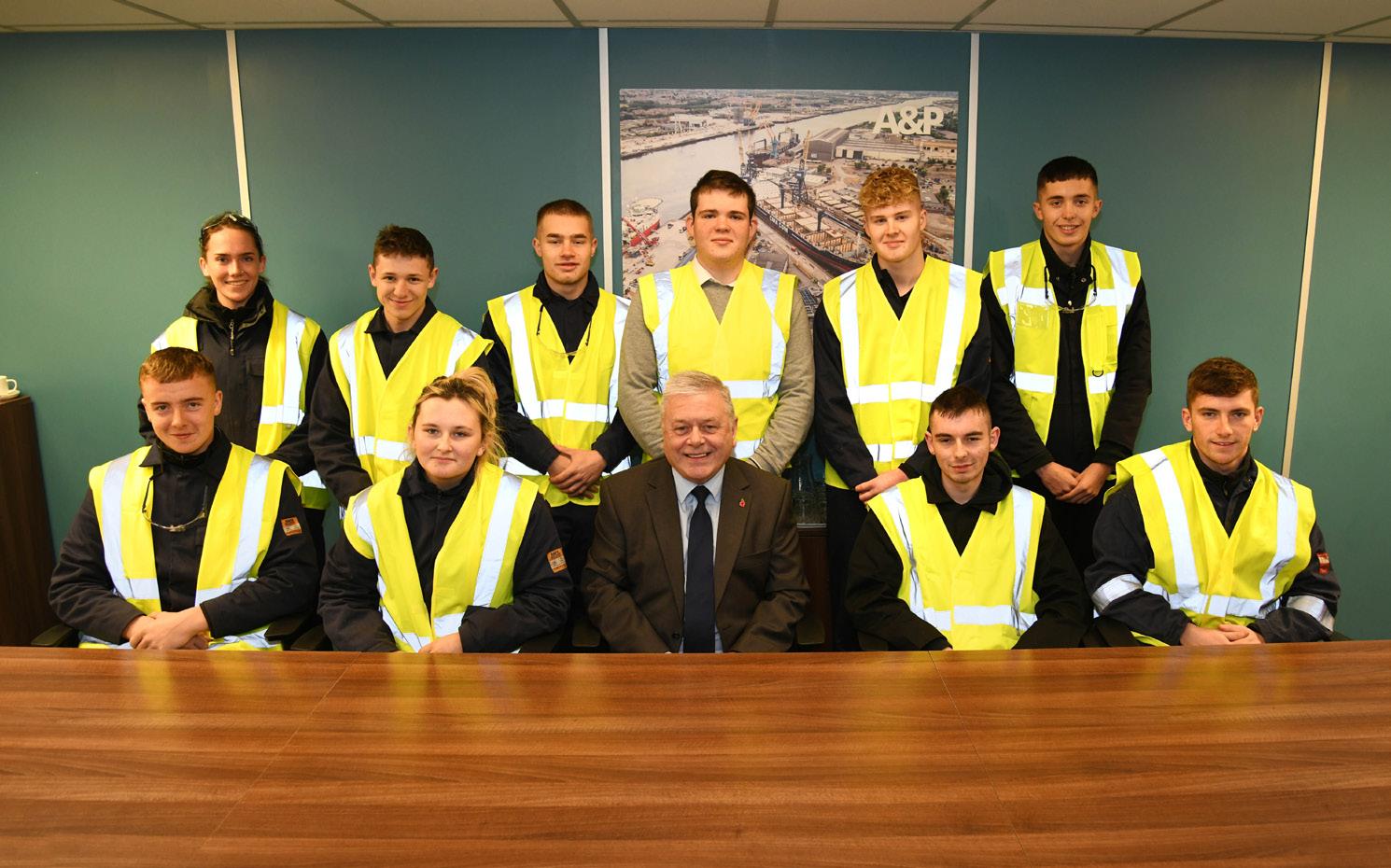

analysis for the Swedish Meteorological and Hydrological institute. In the modernisation of the bridge, Damen will replace all communication and navigation equipment and will modify the console, seating and entire layout in order to obtain improved ergonomics. Additionally installed CCTV cameras will also be monitored from the bridge in order to improve safety of work on the aft deck. Conditions on-board will be enhanced with a refurbishment of accommodation areas, renewal of HVAC equipment and a focus on reducing noise and vibrations throughout the vessel. Damen’s yard has already begun work on the project, beginning with the designs for the steel work, electrical integration, wheelhouse equipment and HVAC modification.
70 years celebration at Damen Oranjewerft
Holland’s Damen Shiprepair Oranjewerf (DSO) is celebrating 70 years of delivering repair, maintenance, conversion and refit services to the maritime industry. Short turnaround times, a wealth of knowledge from its personnel and a dedicated focus on clients’ needs have been the key characteristics of the yard’s modus operandi over the last seven decades. Oranjewerf’s location – just north of Amsterdam and close to the Amsterdam-Rhine Canal and the North Sea Canal – is also a significant factor in its success - this has earned it a respected position serving both the inland and seagoing shipping sectors. Throughout DSO’s long history, the yard’s services have remained very much unchanged. Founded in 1949 by a consortium of local shipping companies and shipyards, the yard’s


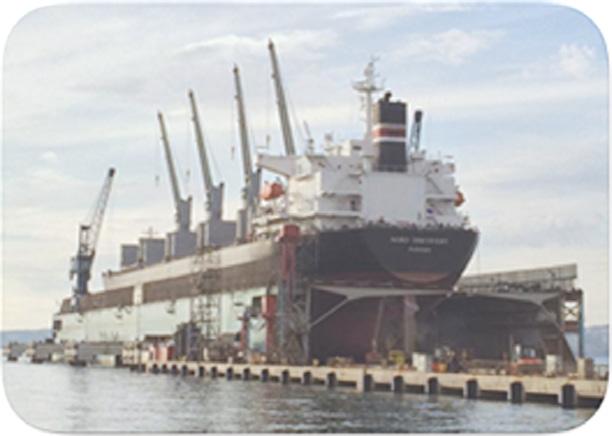
Damen Shiprepair Oranjewerf
major aim was to offer repair services to inland and coastal vessels. Now, 70 years later and part of the Damen Shipyards Group since 1989, DSO is able draw upon that vast amount of experience to continue its work for numerous maritime markets. A look at the yard’s current workforce illustrates this continuity of skills - some of the team have worked there for more than 20 years, one of them for 40 years. The inland cruise sector is particularly important for DSO. Every year, for example, some 2,400 inland cruise vessels visit the city of Amsterdam. “About 25 to 30 of these come to us and Damen Shiprepair Amsterdam (DSAm) for some sort of docking,” says Jeen van der Werf, sales manager at the yard. The common factor required by these clients is a quick turnaround, something that DSO can reduce to less than six hours. “This is our specialty – inland cruise vessel operators can drop passengers off at nine o’clock in the morning for a nice day exploring Amsterdam, and then be in our drydock at 1000 hrs. We make sure that the work is done in time so that the vessel can pick up the passengers at three in the afternoon.” DSO still works with inland cruise vessels in the off-peak season, but then this is typically for more lengthy jobs such as special surveys or more intense maintenance tasks. For all its work, the yard utilises one drydock (135 m x 23 m), with a 6,000 tonne lifting capacity) and one slipway (100 m x 11 m, 1,500 tonne capacity). These are occupied 95% of the time. Joining the Damen Shipyards Group 30 years ago saw DSO increase its coverage to more maritime sectors. Today, this most notably includes clients from the offshore industry,
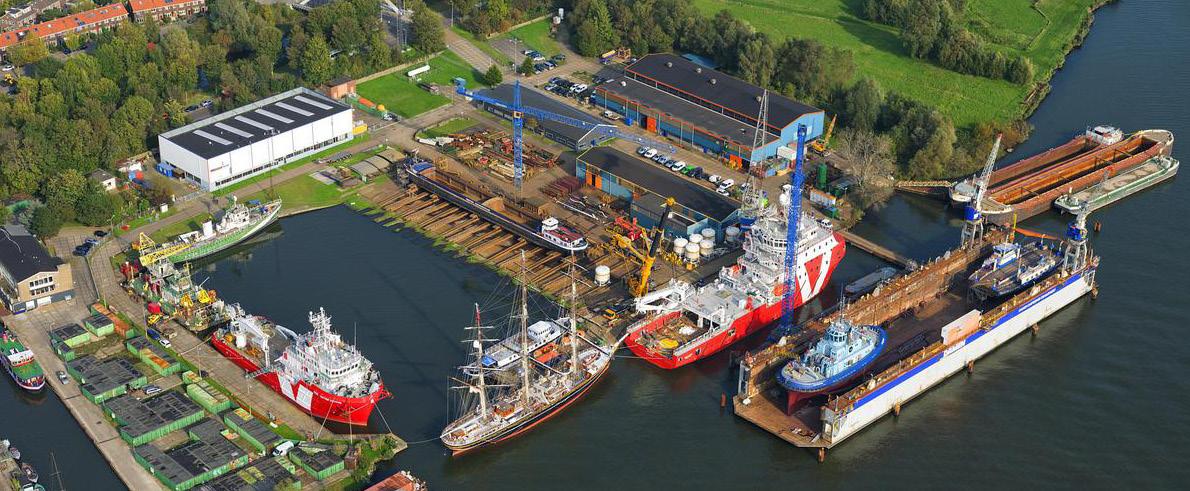
with ships operating out of IJmuiden and Den Helder, in addition to vessels working in the dredging and cargo sectors.
Certification for Sembcorp Marine’s 3D printing
Singapore’s Sembcorp Marine has received certifications qualifying its 3D printing procedures and specifications for components used in its construction and repair projects. This game-changing development paves the way for the Group to unlock significant efficiencies and reduce supply chain risks. Awarded by quality assurance and risk management company DNV GL, the certifications endorse Sembcorp Marine’s use of 3D printing technology for repairing non-critical parts such as worn-out metal sleeves used in pumps, and for fabricating bevel gear sets for machinery applications. More importantly, these certifications give Sembcorp Marine the experience to prepare for the validation and use of more 3D-printed components in its projects, which will reduce the Group’s reliance on external procurement. Sembcorp Marine President and CEO Wong Weng Sun said, “The DNV GL certifications help us work towards a 3D printing regime that lets Sembcorp Marine custom-make components, improve their design and quality, and mitigate external procurement constraints on cost, leadtime and availability – for instance, parts for a repair job that may be expensive, obsolete, not in stock or no longer in production.” 3D printing – also known as additive manufacturing – fabricates three-dimensional solid objects from a digital file by successively adding layers of material until the intended object is formed. This technology reduces material wastage and enhances the sustainability of Sembcorp Marine’s operations. Mr Wong said 3D printing can also expedite project turnaround at Sembcorp Marine shipyards and allow the wider offshore and marine (O&M) sector to become more selfsufficient. To develop 3D printing for O&M applications, he said Sembcorp Marine has been working closely with DNV GL, AStar’s Singapore Institute of Manufacturing Technology (SIMTech), National Additive Manufacturing Innovation Cluster (NAMIC), Nanyang Technological University and commercial additive manufacturer 3D Metalforge. Brice Le Gallo, DNV GL Regional Manager South East Asia and Australia and Director of the DNV GL Global Additive Manufacturing Centre of Excellence in Singapore, said, “It is very satisfying to award Sembcorp Marine the certifications for 3D printed parts - it has been a partnership, beginning in November 2017, which showed commitment and demonstrated the technical ability of the teams involved in achieving the certifications. I truly believe 3D printing can make a major impact in reducing cost, creating efficiencies and lowering supply chain risks. I am confident that the certifications awarded to Sembcorp Marine will encourage more collaborations and developments in the O&M sector.” SORJ