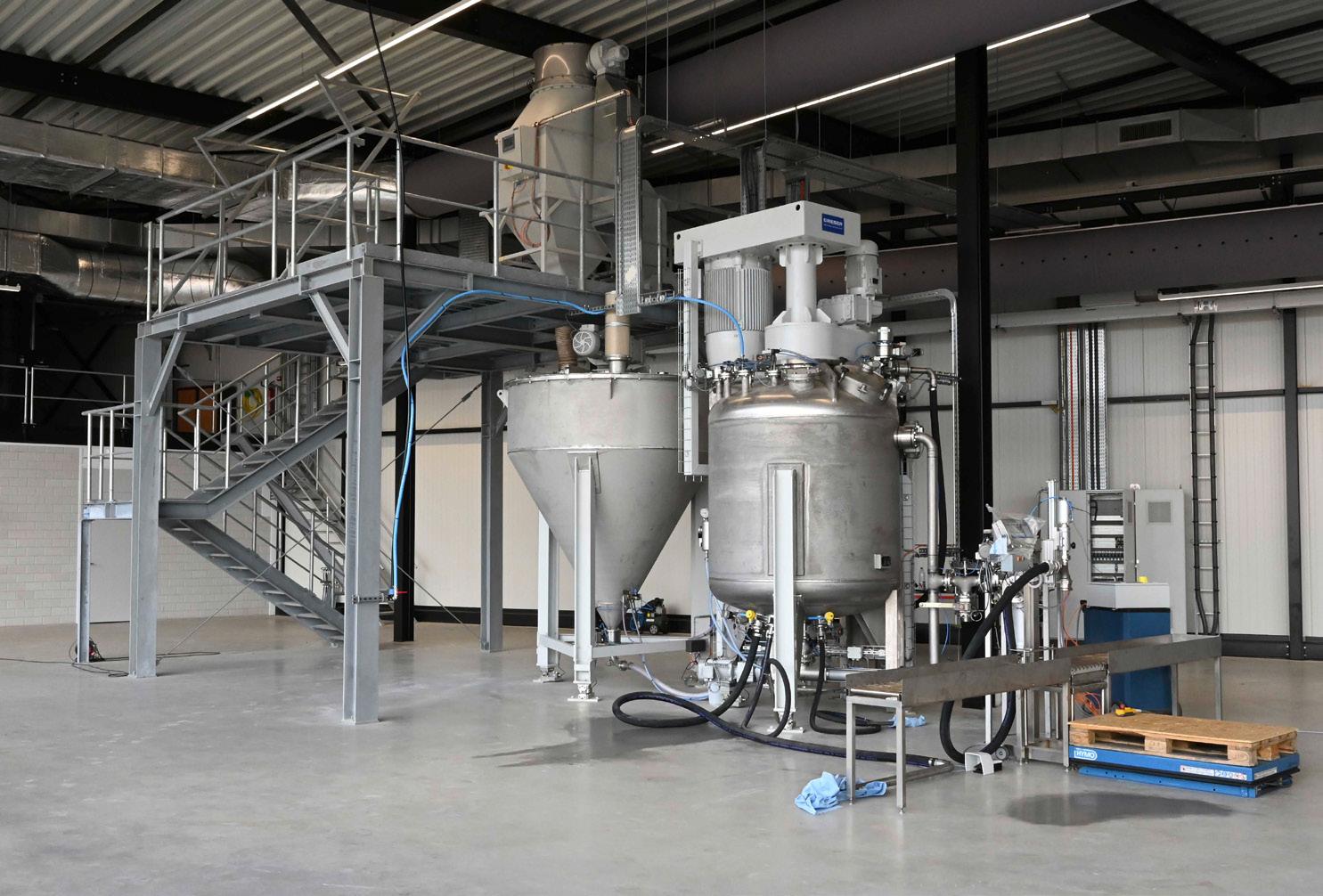
12 minute read
Paints & Coatings
The new Beele FISSIC equipment
New fixing and filling line at Beele
Advertisement
Only a few months after the first machines in Sealing Valley were commissioned, an entirely new mixing and filling line has now been put into operation as well. The line was specifically developed for one of Beele Engineering’s recent products - FISSIC coating. FISSIC is a new, high-quality coating that provides for a high degree of fire resistance. Furthermore, the FISSIC coating can be applied to provide thermal protection of cable and pipe transits. The coating can be applied with a brush or spraying system. For applications where FISSIC is used for its insulating properties, a lower density version with improved insulating properties is also available. The new filling and mixing line has a production capacity of about 2,500-2,750 litres/batch. The machine is used to fill standard 15-litre containers (approximately 22 kg). Other quantities are available on request. The new line consists of a fill-up and intake unit, a mixer and a filling and dosing unit. Separate controls among other things ensure the FISSIC coating is accurately dosed. Elaborate tests and practical trials have demonstrated the FISSIC coating’s high quality. The coating has been successfully tested for flame spread characteristics and toxicity. Bureau Veritas has issued the MED 39278/A0 EC certificate for the coating. Research by KIWA Nederland has demonstrated the product’s fire resistance and salt water resistance. Furthermore, the coating is gastight up to 30 mbar.
Paints & Coatings
The start-up of FISSIC production represents a next step in the realisation of Sealing Valley, Beele Engineering’s Centre of Excellence for sealing technology. The centre’s kick-off took place two years ago with initial production starting up six months ago. The construction of other components, such as office, training, education and demonstration areas is on schedule. Now that the contours of a large part of the planned buildings are visible and the production hall is in use, the enormous size of the 45,000 m 2 campus is also clearly visible. However, Sealing Valley will not only be impressive because of its size. In the recent past, a lot of effort has been devoted to expanding partnerships with other parties for accelerated innovation relating to fire safety and water tightness, and optimising field applications.
Hempel joins Getting to Zero Coalition
Denmark’s Hempel has announced that it has joined the Getting to Zero Coalition, a multi-stakeholder group that aims to see the introduction of commercially viable zero emission shipping vessels by 2030. In 2018, IMO adopted a strategy to reduce greenhouse gas emissions from shipping by at least 50% by 2050 compared to 2008 levels. At the same time, IMO will pursue efforts to eliminate emissions from shipping altogether – the full decarbonisation of the industry. For this to be possible, zero emission vessels (ZEV) are essential, which is why the Getting to Zero Coalition was established. A partnership between the Global Maritime Forum, Friends of Ocean Action and the World Economic Forum, is bringing together industry stakeholders to work towards having commercially viable ZEVs operating along deep-sea trade routes by 2030. Hempel has committed to being a key player in achieving this goal. Christian Ottosen, Group VP, Head of Marine Business at Hempel, comments, “As a company, we have long played a key role in helping the shipping industry reduce emissions through our hydrodynamic hull coatings, such as Hempaguard MaX and our SHAPE propulsion efficiency measuring services. When creating ZEVs, we need to consider all aspects of design and operation – not just the fuel source – and our coatings are one of the most important components to achieve this reduction.” Launched in September 2019, Hempaguard MaX reduces a vessel’s drag in the water, which cuts fuel consumption and associated emissions. It is based on Hempaguard X7, a hull coating that has been applied to over 1,500 vessels since its launch in 2013, enabling those vessels to collectively reduce their annual fuel bill by US$500m and cut annual CO 2 emissions by over 10m tonnes. The Getting to Zero Coalition will begin by working with industry players in the maritime, energy and other related industries, as well as academics, think tanks and policy makers, to develop a roadmap that identifies the technologies, investments and actions needed to get commercially viable ZEVs operating on the water by 2030, including all necessary infrastructure around the new vessels.
Sulzer Mixpac announces weld coating
Sulzer Mixpac has announced that its MIXPAC MixCoat Flex and MixCoat Spray cartridgebased two-component dispensing systems are ideal for touch-up and repair work of weld seams and difficult to reach areas on Navy ships. With their consistent mix quality, the systems reduce labour time and increase efficiency by decreasing the need for hand painting. Naval vessels at sea are constantly exposed to a harsh environment, including salt water, rain, hail, and extreme heat and cold. Sailors battle the elements with a routine of daily shipboard maintenance including painting,
Applying MIXPAC MixCoat Flex and MixCoat Spray cartridge-based two-component dispensing systems
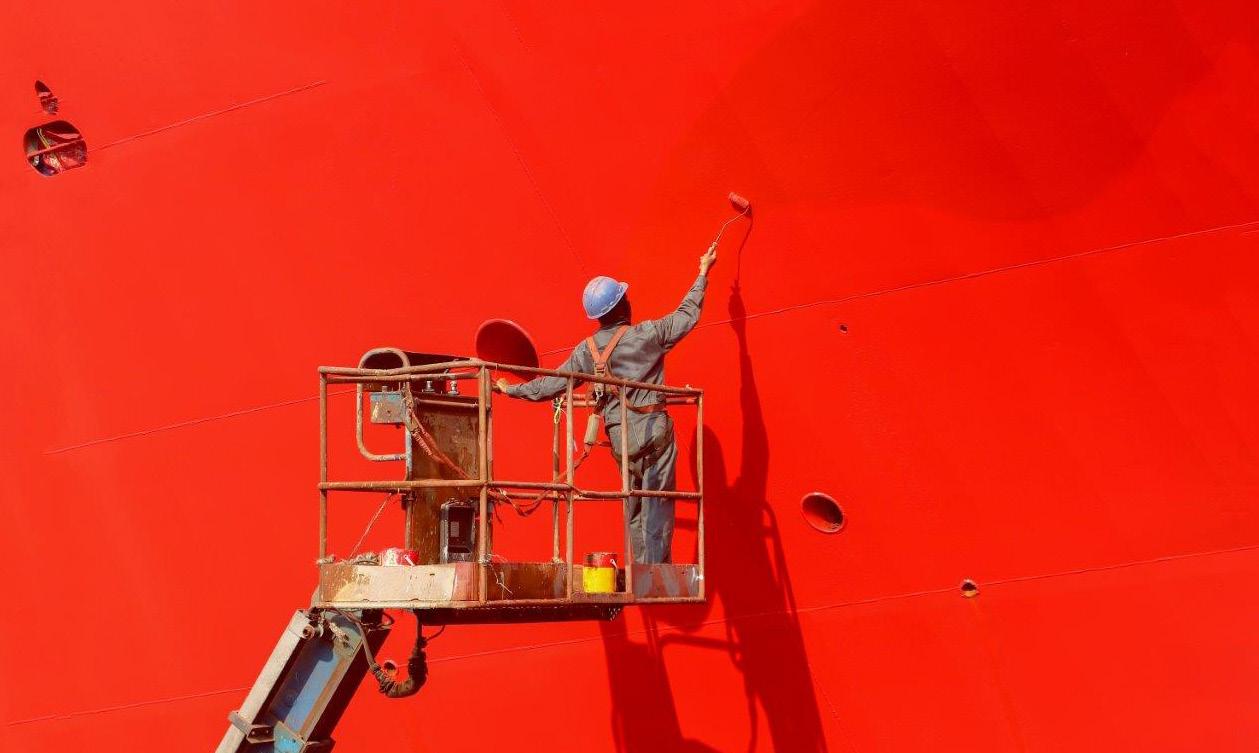
touch-ups, and repairs. Historically touch-up paint solutions involve time consuming and inaccurate hand mixing and frequently result in surplus unused mixed paint that must be disposed of. With the MixCoat Flex and MixCoat Spray cartridgebased systems, materials are more easily stored and dispensed. The proper ratio is dispensed into the static mixer, so it can be consistently mixed, and cartridges can be resealed and stored for later use, so nothing goes to waste. MixCoat Flex is a great choice for Naval coating applications in areas with limited accessibility for standard spray equipment. It offers maximum flexibility to reach into tight and angled spaces, like tanks and bilges, and in and around tight areas for weld seams, eye beams, nuts, bolts, and rivets. The hose enables workers to spray all these angles and tough to reach areas instead of painting them by hand with a brush. The MixCoat Flex allows tasks to be completed sooner and offers a consistent and superior mix quality. Also useful is the MixCoat Spray model, a portable pneumatic dispensing system designed for small volume applications, touch-up, and repairs. Unlike large and expensive plural component spray equipment that is difficult to transport, the MixCoat Spray system is extremely lightweight and manoeuvrable. The MixCoat Spray system offers an added benefit in that it is fast and easy to assemble, clean up and break down, so users lose very little time for the maintenance cycle. Using MIXPAC MixCoat Flex and MixCoat Spray cartridge-based two-component dispensing systems provides the Navy with an excellent and economical option to reduce its hazardous waste stream and the cost of waste disposal for excess unmixed paint, especially for weld seams and tough to reach areas.
Improved Study results from PPG
Holland’s PPG has announced results from a study that concluded vessels using its fouling release and anti-fouling coatings show improved speed and power performance. PPG conducted the study in collaboration with DNV GL, a provider of risk management and quality assurance services to the global maritime industry that is based in Oslo, Norway. The study used the hull performance analysis methodology developed by DNV GL to analyse the performance of various major vessel types. These included LNG tankers, bulk carriers, crude oil tankers and cruise vessels that use PPG anti-fouling and fouling release solutions in a variety of operating conditions.
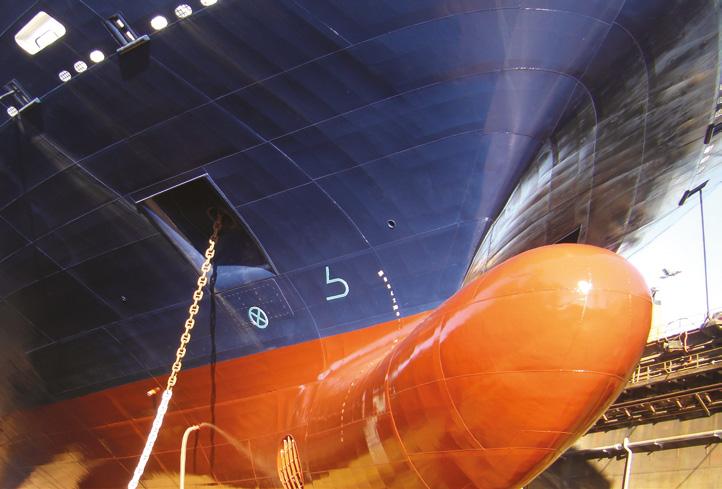
A ship with PPG Sigmaglide The results demonstrate noteworthy hull performance, with less than 1.5% average speed loss across the variety of ship types and operational conditions. In addition, vessels using PPG Sigmaglide 1290 fouling release coating demonstrated notable speed and power improvement over the baseline sea trial conditions. PPG selected DNV GL to partner in the study due to the accuracy of the company’s vessel performance analysis methodology, which is more rigorous than the ISO 19030 standard for measuring changes in hull and propeller performance. DNV GL’s testing procedures introduce advanced filtering and normalisation methods that increase the usability of data and yield more accurate results.
Coppercoat has outperformed its rivals in a re-examination of anti-fouling test panels to determine the quantity of copper loss from different anti-fouling products to the environment. The assessment, which was carried out by Plymouth Marine Laboratory (PML), found that Coppercoat leached significantly less copper over five years than the other coatings on test. The panels are the basis of a previous PML report in which Coppercoat emerged as the best-performing anti-fouling. In the in situ trial of protective coatings – conducted by the Energy Technologies Institute – two 3.5-tonne test pods covered in panels coated with a wide variety of anti-fouling systems were submerged in a tidal stream in the Fall of Warness, Orkney, Scotland. A meticulous recent re-examination of the test panels has revealed that while conventional (selfpolishing) anti-fouling paints typically exhibited a mean product loss rate of 0.099µm/day, the Coppercoat showed a mean product loss rate of just 0.0071µm/day. And when the PML team examined the copper content alone – the active biocide – the loss from the Coppercoat was found to be a mere 1.42µg/cm 2 /day. What this means, in more basic terms, is that the Coppercoat’s total product loss – over a five-year period of constant immersion in an area of strong tidal flow with mineral scour – was just 1/14 th of that shown by traditional anti-fouling paint. Expressed as a percentage, the Coppercoat demonstrated a coating loss
The PML test rig
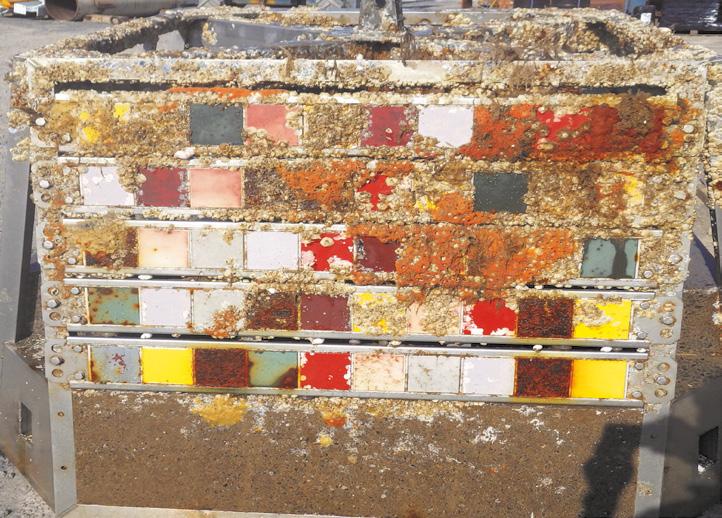
of approximately 4.3% over the five years - in comparison, the conventional anti-fouling paints on test lost 90-100% of their copper-containing topcoat. From the tidal flow rate measurements taken at the test site, PML Project Co-ordinator Dr Tom Vance and his team calculated that the test equated to subjecting the coatings to a voyage of more than 283,000 kms at a speed of 3.5 knots over the five-year period. This statistic helps to illustrate why the Coppercoat officially supplied for the race boats on the 2017/18 Clipper Round the World Race yachts looked as good as new when the boats were lifted out following their 40,000 NM circumnavigation. The results of the re-examination speak volumes about Coppercoat’s inarguable benefits for the environment and clients alike, in a milieu where regulations concerning biocide leach rates from anti-fouling systems are set to become ever more stringent. The fact that Coppercoat leaches far less biocide into the sea than its competitors – and therefore protects for longer the boat hulls, diffusers, subsea coolers and wind turbine transition pieces to which it is applied – is of immense significance.
Renewal of JV agreement between Jotun and COSCO
Norway’s Jotun A/S and China’s COSCO Shipping International Hong Kong have reinforced their commitment to one another with the renewal of their long-standing JV agreement. The JV, first signed in 2005, secures the future of Jotun COSCO Marine Coatings (JCMC), a 50-50 owned entity that holds a clear market leading position as China’s number one marine coating supplier. The signing of the joint venture took place at a special ceremony held at COSCO Shipping’s headquarters in Shanghai. A high profile gathering of business and political leaders witnessed the signing, including Xu Lirong, Chairman of COSCO Shipping Group, Torbjorn Roe Isaksen, the Norwegian Minister of Trade, Industry and Fisheries, the top management teams from COSCO Shipping Group and Jotun, and further attendees from the Norwegian government and embassy. “Jotun COSCO Marine Coatings has established a clear market leading position in the provision of high-quality products to the shipping industry in China,” states Morten Fon, CEO, Jotun. “The company marries the innovative, high performance coatings technology of Jotun with the infrastructure, industry expertise and valued reputation of COSCO Shipping in this key domestic market. We are proud of what we have
(Left to right) Standing - Signe Brudeset, Norway’s Ambassador to China, Torbjørn Røe Isaksen, Norwegian Minister of Trade and Industry, Xu Lirong, China COSCO Shipping Group, Zhu Jianhui, COSCO Shipping International (Hong Kong) Sitting - Morten Fon, Jotun A/S, Liu Gang, COSCO Shipping International (Hong Kong)
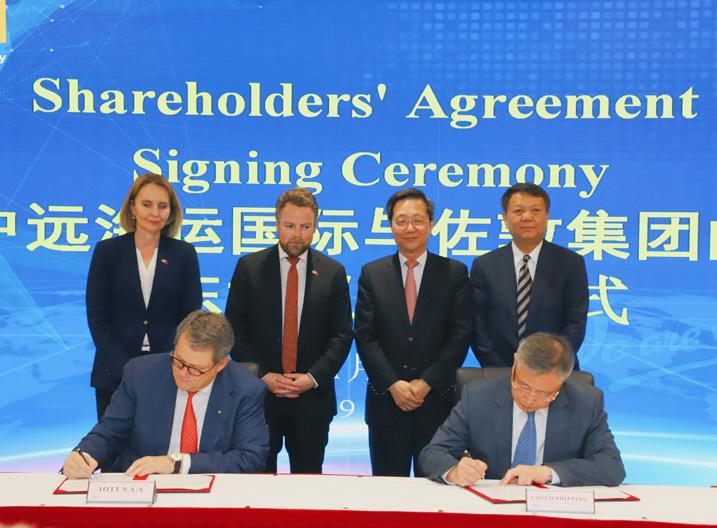
achieved together so far and look forward to a continuation of the excellent progress, partnership and market development.” COSCO Shipping International Executive Director and JCMC Chairman, Liu Gang comments, “We are happy to continue this solid, productive and valued partnership into the future. Jotun is a quality supplier and a preferred partner to the COSCO Shipping fleet. It is a venture that delivers mutual value, and we believe it can go from strength to strength in the years to come.” Jotun, headquartered in Norway, is the world’s number one provider of advanced marine coatings and has a long history in China, establishing its first base in the country in 1983. It has since expanded to operate five companies and two factories, with 1,600 employees and domestic revenue of NOK4.5bn (US$494m).
Increase in drydocking contracts for Nippon Paints
The total number of vessels applying Japan’s Nippon Paint Marine hull coatings at drydock increased by 9% this year compared to the company’s 2018 figures. In the 12-month period to June 2019, the marine coatings supplier, a division of Japan’s Nippon Paint, registered increased applications across all ship sectors, with growth in supply of underwater coatings to gas tankers, in particular, rising more than other types of vessels. The number of gas tankers applying Nippon Paint Marine products jumped significantly by more than 30% during the period, followed by a 15% increase in the number of passenger vessels and cruise ships using the company’s coatings. Bulk carrier and general cargo vessel applications increased by 7% and 4%, respectively. Studying the detailed statistics of the products’ applications revealed that the company’s unique self-indicating epoxy coating NOA10M was the coating most frequently applied during the period. In fact, numerous Nippon Paint Marine’s drydocking applications used the selfindicating coating during 2019. Significant growth was also seen with the class-leading fuel saving coating A-LF-Sea and the company’s standard anti-fouling Ecoloflex, both of which saw an application increase of 15%. The number of ships using Nippon’s highend copper silyl-acrylate anti-fouling Ecoloflex HyB, meanwhile, increased steadily. SORJ
There has been a marked increase in orders for the NOA PC700 coating to shipyards retrofitting exhaust gas cleaning systems
