
8 minute read
Vanliga ytdefekter på anodiserat aluminium
Dr. Anne Deacon Juhl - AluConsult och AnodizingSchool
Vanliga ytdefekter på anodiserat aluminium
– och hur man undviker dem
Tillverkare av aluminiumprodukter är inte alltid nöjda med ytkvaliteten på de anodiserade profil- och plåtprodukter som sänds tillbaka till dem från en anodiserare. De anodiserade produkterna kan vara fläckiga, ha färgvariationer eller korrosionsgropar, vilket orsakar reklamationer, ökade kostnader och frustration. Därför är det viktigt att aluminiumprodukttillverkare förstår grunderna i anodiseringsprocessen för att kunna kommunicera effektivt med sina anodiserare. Denna artikelserie kommer att ge en introduktion till den övergripande anodiseringsprocessen, inklusive vilka egenskaper som är möjliga, vilka som är rätt för en specifik produkt, och hur ett aluminiumföretag kan komma överens med sin anodiserare om specifikationer för att garantera ett riktigt resultat varje gång.
Att ta emot anodiserade detaljer med oacceptabelt utseende är förmodligen den vanligaste konfliktorsaken mellan anodiseraren och kunden. Defekter såsom matt utseende, korrosionsgropar, färgvariationer eller andra defekter handlar inte bara om att hitta en bra anodiserare – utan det handlar mycket mer om en bra kommunikation mellan anodiseraren och kunden.
Anodiseringskärl ses ofta som magiska lådor - där aluminiumdetaljer doppas och kommer upp med ett oxidskikt. Naturligtvis är anodisering inte magi, utan ett system med många variabler som bör nalkas vetenskapligt. Om variablerna inte är specificerade i förväg kommer kundens förväntningar inte att uppfyllas. Det är därför viktigt för aluminiumtillverkaren att komma överens med anodiseraren om processpecifikationerna. Denna artikel behandlar de sex vanligaste anodiseringsdefekterna som kan inträffa under de olika processtegen (uppsättning, etsning, anodisering, infärgning, eftertätning och ombearbetning samt vilka de rätta specifikationerna är för att undvika dem är.
Uppsättning, kallas även rackning
Anodisering är en elektrokemisk process, vilket innebär att kemikaliebadet måste ha en bra och pålitlig elektrisk kontakt med aluminiumdelarna. När man sätter fast delarna på upphängningsanordningen (rackningen) kommer kontaktmärket mellan dem oundvikligen att att synas som en fläck som inte är anodiserad. Detta innebär också att kontaktpunkten saknar skydd av oxidskiktet. Om aluminiumdelen är infärgad kommer denna fläck att vara ofärgad, och metallen syns igenom. Därför är det väsentligt att anodiseraren väljer den optimala rackningsmetoden. Kontaktmärket ska vara så osynligt som möjligt, men ändå se till att den elektriska kontakten är stabil och pålitlig genom hela processen, även vid kraftig omrörning i badet

Fig 1. Rackning med tråd och krokar
Fig 1 visar ett exempel på en dålig rackning med tråd och krokar som kunden inte bör acceptera. Aluminiumdelarna kommer att dingla fram och tillbaka, vilket kan leda till att kemikalierester fastnar i hålen mellan delar och aluminiumtråden. Detta orsakar också variation i tjocklek och färg och ger dålig eftertätningskvalitet.
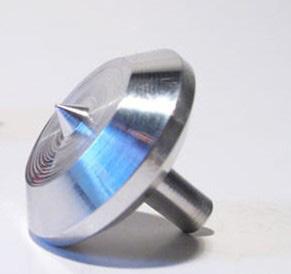
Fig 2. Vissa aluminiumprodukter kan vara svåra att racka, till exempel denna snurra, som nästan helt består av kritiska ytor.
Men vad händer om aluminiumdelen inte har några hål att hänga i och ingen sida som inte ska synas? Fig 2 visar en snurra som endast består av en kritisk yta. Hur ska anodiseraren racka en sådan aluminiumdel där hela ytan syns? Det finns inget enkelt eller entydigt svar eftersom allt beror på vad aluminiumdelen ska användas till. Eftersom kunden kan sin produkt bättre än anodiseraren är det helt avgörande att lösa detta tillsammans och hitta en smart och effektiv lösning.
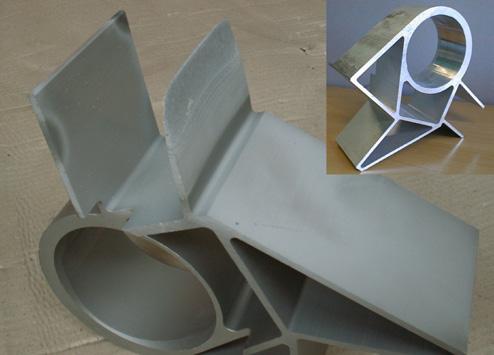
Fig 3. En aluminiumdel fotograferad före och efter anodisering, vilket visar synlig bränning av delen.
Etsning
Nästa defekt att diskutera inträffar när aluminium utsätts för en sur eller alkalisk lösning under etsningen, vilket har behandlats tidigare under avsnittet om förbehandling. Etsning av aluminiumytan, vare sig den är sur eller alkalisk, skapar en etsbild som ger ett specifikt utseende. Kvaliteten på detta utseende är mycket beroende av sammansättningen och temperaturen hos etslösningen, såväl som processtiden.
Koncentrationsskillnader i etsbadet kan leda till fläckiga områden på grund av en blandoxid på 6000-seriens aluminiumlegeringar. Etsningen börjar först lösa upp aluminiumoxiden och inte magnesiumoxiden, vilket då ger ett vitt, fläckigt utseende på ytan – ibland kallat ”vit etsblomma”.
Bästa praxis för aluminiumtillverkaren är att bestämma ett önskat glanstal för ytan och arbeta med anodiseraren för att skapa ett definierat värde med en glasmätare. Detta tal bör inkluderas i specifikationerna för att definiera önskat ytutseende. Likaså bör kunden fråga om det finns testplåtar som visar etsbilden på regelbunden basis, tillsammans med den kemiska analysen för etsbadet. Detta hjälper både anodiserare och kund att bedöma om förhållandena är under kontroll och säkerställa att resultaten under hela anodiseringsprocessen är acceptabla.
Anodisering
Under anodiseringsfasen bildas ett poröst aluminiumoxidskikt. Detta uppnås genom att applicera en stabil och fast elektrisk ström till aluminiumdelen. Missfärgning av delen uppstår ofta under infärgningsstadiet, när färgämnen berör det porösa oxidskiktet. Men variation i färg sker inte bara när den bildade porösa aluminiumoxiden färgas in. Missfärgning kan även ske på naturanodiserade delar, där det naturliga aluminiumet syns igenom. Denna typ av defekt kan ses som en regnbågsmissfärgning på den anodiserade ytan, vilket mestadels orsakas av dålig elektrisk kontakt som ger områden med mycket tunn skikttjocklek. I andra fall kan ojämn anodisering också leda till förbränning, där en del av aluminiumprodukten har ätits upp av kemikalierna, se fig 3.
Oregelbundna kontaktmärken och rackningar kommer också att leda till variationer i porstrukturen vilka skapar svårigheter för en jämn infärgning senare. För att bilda samma porösa oxidstruktur i charge efter charge krävs att alla parametrar hålls konstanta - såsom strömtäthet, temperatur mm.
För att säkerställa detta bör anodiseraren köra processen strömstyrt. För att uppnå detta är det nödvändigt att känna till delens totala yta. Det är också lämpligt att racka delarna på samma sätt varje gång. För absolut bästa anodiseringspraxis bör specifikationerna begära en bild av varje färdig charge. Dessutom bör man investera i ett virvelströmsinstrument för att mäta skikttjockleken på de mottagna anodiserade delarna.
Infärgning
När man använder färganodisering på en aluminiumprodukt är den vanliga proceduren att använda två infärgade provbitar (max och min) för att visa det acceptabla färgintervallet. Denna procedur – hur vanlig den än är i olika branscher – är dock opålitlig eftersom människor har olika förmåga att bedöma färgvariationer.
I stället bör man mäta färgerna. Färgskillnaden kan utvärderas med ∆E, vilket är ett tal som består av ljus/mörker, hur blå/gul och hur grön/röd en färg är. Till exempel är den vänstra delen av fig 4 mer gulaktig med ett b+-värde = 1,47. I jämförelse har den högra sidan ett b+-värde = 1,038.
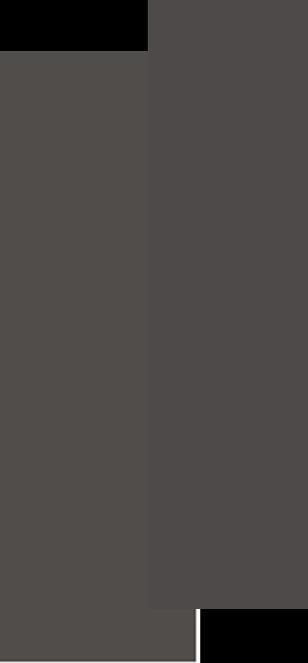
Fig 4. Två svartfärgade provbitar, där den vänstra sidan har ett mer gulaktigt utseende.
Eftertätning
I eftertätningssteget sluts porerna i aluminiumoxiden. Detta är ett viktigt steg för att öka korrosionsbeständigheten och för att säkerställa att aluminiumdelen inte ändrar sina egenskaper när den används.
Fig 5 visar en svartfärgad anodiserad profil efter tre månaders användning. – Som man kan se har aluminiumdelen blekts till en ljusbrun färg, nästan gul – definitivt inte ett bevis på en bra anodiseringspraxis. Denna defekt inträffar om eftertätningen utförs dåligt och det porösa oxidskiktet blir adsorberande. Vatten och aggressiva ämnen kan då komma in i den porösa strukturen vilket minskar korrosionsskyddet och bleker färgerna.
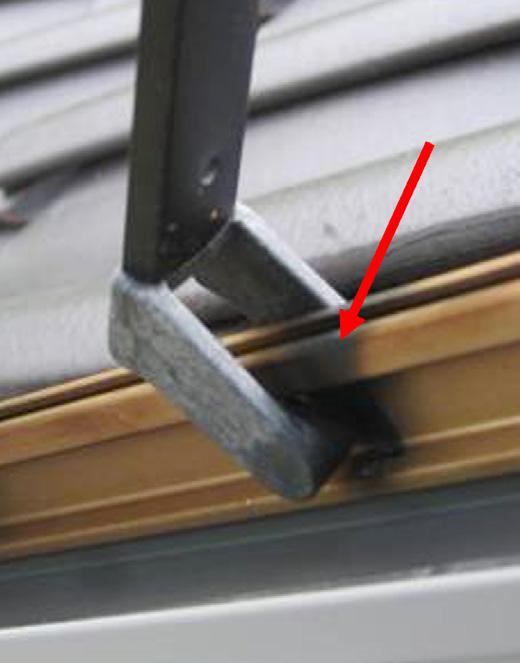
Fig 5. En svartanodiserad profil med dålig tätning, som visar färgblekning efter tre månaders utomhusexponering. Röd pil indikeraroriginalfärgen.
För att säkerställa en högkvalitativ eftertätning kan kunden göra ett enkelt slippapperstest efter att ha mottagit de behandlade delarna. Slippappret är en glasbelagd pappersremsa som ska gnidas över den anodiserade delen. Om tätningen är rätt utförd skadas den anodiserade ytan inte eftersom oxidskiktet är hårdare än glas.
Ombearbetning
Om anodiseraren upptäcker en ytdefekt innan det anodiserade godset skickas tillbaka till kunden, kan aluminiumdelen ”ombearbetas”. Att ombearbeta en defekt del innebär att alkaliskt etsa bort oxidskiktet. Med andra ord tas det felaktiga skiktet bort och aluminiumdelen anodiseras igen. Denna ombearbetning är skadlig för aluminiumytan eftersom den leder till en grövre yta, dimensionsförändringar och förändringar i porstrukturen. Det betyder också att ombearbetade delar kommer att få ett annat utseende än delar som endast har anodiserats en gång. Därför bör det i specifikationerna framgå att om en anodiserad del behöver ombearbetas ska anodiseraren kontakta kunden för att diskutera om delen ska ombearbetas eller tas bort från chargen.
Slutsats
Att ta emot aluminiumdelar med anodiseringsdefekter är inte bara en olägenhet – det är en affärsfråga. Ytdefekter gör att fler aluminiumdelar behöver anodiseras igen för att få önskad finish. Omanodisering kostar inte bara pengar utan också tid. Men hur kan kunden vara säker på att anodiseraren gör jobbet rätt? Svaret är att sätta upp de rätta specifikationerna från början. I stället för att bara skicka aluminiumdelarna bör kunden ha ett samtal med anodiseraren först. Specifikationerna kan omfatta: överenskommelse om bra kontaktanslutning vid rackning, uppmätning av önskat glanstal, identifiering av lägsta och högsta färgvärde, utföring av slippapperstestet på mottaget material, godkänna skikttjockleken och/eller diskutera felaktiga delar som ska ombearbetas eller underkännas. Med tydliga specifikationer kommer anodiseraren att vara bättre rustad för att undvika defekter och kunden får önskad ytfinish för varje beställning.