
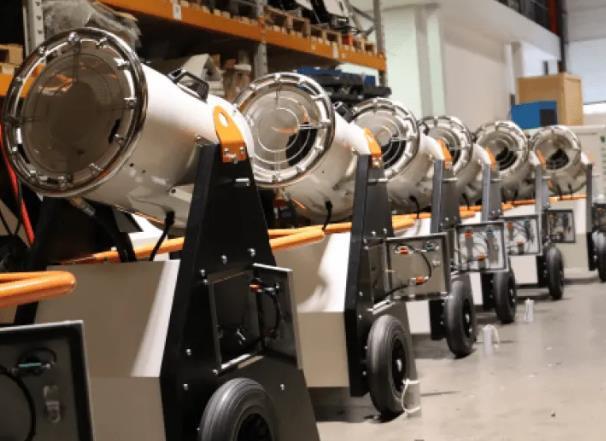
Introduction:
Dust is a common byproduct of many industrial processes, including mining, construction, and manufacturing. While it may seem like a harmless annoyance, dust can actually pose a serious health and safety risk to workers and the environment. Not only can dust lead to respiratory problems, but it can also cause explosions and fires in certain situations. To combat this problem, many industries turn to dust suppression systems, which are designed to minimize the amount of dust that is released into the air. In this article, we will explore how dust suppression systems work and why they are an essential tool for any industry that produces dust.
A dust suppression system is a set of equipment and techniques that are used to reduce the amount of dust that is released into the air during industrial processes. There are several different types of dust suppression systems, including:
Wet Suppression Systems: Wet suppression systems use water to dampen the dust particles, causing them to stick together and fall to the ground. This type of system is commonly used in mining and quarrying operations, where large amounts of dust are generated.
Dry Suppression Systems: Dry suppression systems use chemicals or other agents to capture and neutralize the dust particles. This type of system is often used in manufacturing and processing plants, where the dust is generated from materials like wood, paper, and plastics.
Enclosure Systems: Enclosure systems involve enclosing the dust source in a sealed container or room, which prevents the dust from escaping into the air. This type of system is commonly used in manufacturing and processing plants, where the dust is generated from equipment like crushers, grinders, and conveyors.
The specific method that a dust suppression system uses will depend on the type of system being used. However, in general, dust suppression systems work by:
Identifying the Dust Source: The first step in any dust suppression system is identifying the source of the dust. This is typically done by conducting a site assessment and identifying the areas where dust is most likely to be generated.
Applying the Suppression Technique: Once the dust source has been identified, the appropriate suppression technique is applied. This may involve spraying water, chemicals, or other agents onto the dust, or enclosing the dust source in a sealed container or room.
Monitoring and Adjusting: Dust suppression systems must be monitored and adjusted regularly to ensure that they are working effectively. This may involve adjusting the amount of water or chemicals being used, or making changes to the enclosure system to improve its effectiveness.
Why Are Dust Suppression Systems Necessary?
Dust suppression systems are necessary for a number of reasons, including:
Health and Safety: Dust can pose a serious health and safety risk to workers, as well as to nearby communities. Exposure to dust can lead to respiratory problems, and in some cases, can even cause lung cancer. In addition, certain types of dust can be explosive and can lead to fires and explosions.
Environmental Protection: Dust can also have a negative impact on the environment, particularly on air and water quality. By reducing the amount of dust that is released into the air, dust suppression systems can help to protect the environment and ensure that local ecosystems are not damaged.
Regulatory Compliance: Many industries are subject to regulations and standards that require them to minimize their impact on the environment and protect the health and safety of workers. By implementing a dust suppression system, industries can ensure that they are in compliance with these regulations and avoid potential fines or penalties.
Dust suppression experts for Construction, Demolition, Mining, Waste and Scrap Recycling.