DSNY Brooklyn District 3 Garage
Project Report
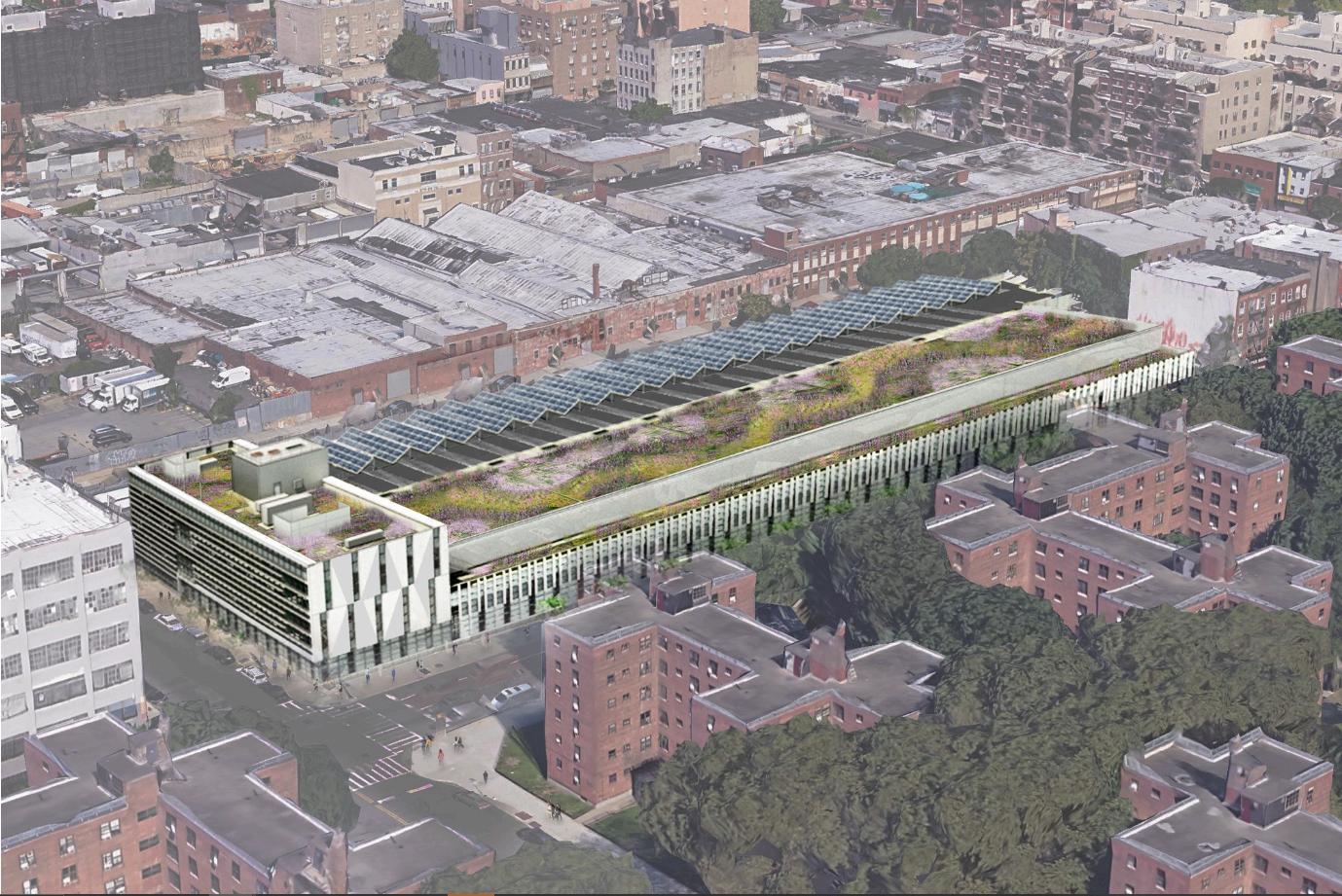
Source: Dattner Architects
Project Information
Design: Dattner Architects
Construction Manager: LiRo
General Contractor: NPCC
Client: DSNY
Address: 559 Park Avenue, Brooklyn NY 11205
Project Size: 135,000 sf
Project Cost: Estimated $175 Million
Notice to proceed: April 15, 2019
Expected Completion: December 2024
Ryan Castillo
Pre-construction Planning
Pre-Construction planning involves various different aspects of work. These include, but are not limited to: model coordination, material takeoff, construction estimating, bidding process, pre-construction meetings, and defining the construction budget.
As a CM on this project, advising the use of a BIM model would have a significant positive impact on the project since a comprehensive BIM model can streamline some of the other tasks involved in pre-construction planning. Problems that need to be addressed such as material takeoff, estimating, as well as defining the construction budget can all be helped tremendously with access to a BIM model of the project In actuality, there was no use of a comprehensive BIM model for this particular project, which meant that much of the other pre-construction planning tasks had to be done traditionally The client wanted things done in a certain manner that, as the CM on this project, we would be inclined to pushback in favor of innovating the pre-construction process in order to not only benefit the project but also to give DSNY the framework for approaching all future projects with a more updated approach as well as providing them with the knowledge and training necessary to utilize a comprehensive BIM model for any future projects they embark on
While the size of this project is quite large, the complex aspects of the construction project are realistically only limited to the special systems that are being installed such as the PV roof and electrical system needed to use such a system as well as the rainwater management system that the client requested The rest of the project scope is much more predictable when it comes to material takeoff. Material to be accounted for includes the cement that will be used for the floors, steel rebar, the steel beams and columns for the structure, the curtain wall system that runs along Nostrand Avenue, the precast concrete panels that line the elevation along Warsoff Pl, the steel support structure for the awning that covers the ramp on Warsoff Pl that leads to the basement, the ducts for HVAC, conduit for electrical, pipes for plumbing, the specialty equipment such as the girder crane and boilers, as well as the roll-down garage doors and the curtains used in conjunction with the garage doors that help with limiting heat loss from the interior
Construction estimating will also be conducted after material takeoff in order to estimate the overall cost of construction, which will be important to determining the overall construction budget. Without a BIM model, digital tools for this work are not available and thus this labor intensive work must be done by cost estimators on the CM team as part of our services as a CM as agent
As the CM as agent, we then advise DSNY on the different GC bids that are made after a RFP is made After leveling the bids, the contractor we advised the client to select for the project was NPCC
After the bid is accepted, we then organize a pre-construction meeting with all the parties involved in order to define responsibilities as well as discuss the project in a holistic manner When coming to the pre-construction meeting, we must set an agenda so that, at minimum, we can cover topics such as:
● Plan Reviews
● Site Conditions
● Utilities Review
● On-Site Storage
● Contract Reviews
● Quality Controls
● Safety Reviews
● Schedule Reviews
● Document Handling
● Communications Plan
For this project, some of the major issues that were addressed during the pre-construction meeting involved the site conditions and the utilities review The site conditions of the project posed issues with regard to material delivery and so solutions were discussed during this meeting The utilities review revealed that we would need to request the local utilities company, ConEdison, to conduct work in order to get power to the building. Due to the fact that the location for electrical equipment would be on a portion of the site that was previously a parking lot, we would need to coordinate the extension of ConEd service to this portion of the site
In addition to all of these tasks, a construction budget must be determined. At the onset of the project, the budget was estimated to be $169 million However, as we will discuss later, this budget was no longer sufficient due to changes in scope as well as unforeseen circumstances due to the COVID-19 pandemic.
Method of Contracting
As the CM for this project, we came on as a CM as agent after design to advise DSNY on the construction of the garage. This means that we had no contracts with the GC or any of the subcontractors and only had a contract with the owner Our role as CM agent means that we oversee the overall project and provide services such as quality management, risk management, time management, and cost management to ensure that the project is delivered to the expectations of the client The benefits of our presence as an agent on this project are that we can provide expertise and solutions for some of the issues present with a project in this particular context. Some of the issues, which will be elaborated on in later sections of this document, include the site conditions which demanded effective coordination in order to work around the issues present in the given site as well as the quality management of a construction project which was going to be implementing some innovative but highly technical systems such as the photovoltaic system and the rainwater management system One of the issues associated with our contracting on this project is most present in the fact that we were brought on after design As a consequence, we could not provide the client with our services during pre-design and design phases of the project lifecycle
Joey Yuen
Quality Control Plan
There is no defined documented quality control plan instead there are constant on-site monitoring of construction activities daily by LiRo Superintendents There are 4 established superintendents, 2 superintendent that oversees the General Contractor, 1 that specializes in the mechanical systems, and 1 that specializes in the electrical systems These superintendents will ensure that the contract drawings and specifications matches the design intent and is properly executed. In addition, the NYC Department of Sanitation hires a third-party independent testing agency that is managed by the CM to conduct inspections, testings, and sign offs on various aspects of the construction which would require the DOB’s approval There is a Non-Compliance Report that is issued to the contractors and subcontractors when the completed work is not up to standards As a result, the contractors and subcontractors would have to submit a solution or remediation plan to the non-compliant work performed to receive payment
In addition to a Non-Compliance Report, the use of SiteManager as means of conducting daily work reports to monitor daily work activities, labor usage, equipment usage, and etc is a great software for quality control It is effective and efficient in ensuring that all parties involve review the daily work reports for record-keeping and proof of engagement This gives the benefit of having a record and is able to verify all work is completed, to-be completed, and on-going activities
Tests and Inspections
For testing and inspections, through the independent testing agency hired by the Owner being DSNY, the following tests would be monitored and performed
● Smoke Control Systems
● Mechanical Systems
● Fuel-Oil Storage and Fuel-Oil Piping Systems
● High-Pressure Fuel-Gas Piping (Welding)
● Mechanical Demolition
● Private On-Site Stormwater Drainage Disposal Systems, and Detention Facilities Installation
● Sprinkler Systems
● Standpipe Systems
● Heating Systems
● Chimneys
● Concrete Design Mix
● Concrete Sampling and Testing
● Energy Code Compliance Inspections
The largest change order to date is for $1.2 Million which was classified as a “Non-Material Scope Change” Essentially this type of change order means that it does not
substantially change the initial scope of work but rather as an additional expense The additional costs was for an additional telecom equipment and additional vehicle chargers which was originally suppose to be added on after construction was completed, but the Owner decided to amend the construction contract via a bulletin to include extra work.
For document control processes for procurement, there is the industry standard use of submitting RFIs, RFPs, and RFQs RFIs are request for information which allows all parties involved to request information that can help them about unknown conditions, further steps, or any additional information RFPs are request for proposal that will be requested from subcontractors, trades, manufacturers, etc for them to provide an estimate or bid to perform such works. RFQs are request for quotations that allows companies to requests a quote from a supplier for specific products or services
For contract drawings, shop drawings, RFIs, and any documentation record keeping, would all be printed out and carefully filed with a hardcopy. They are all located with a network database accessed via File Explorer which requires direct connection of internet to be able to have access and view all contract drawings and as previous mentioned documents. In addition the E-builder CM project management program assists as well with the paperwork scanned and documented as a bonus Stand Excel Spreadsheets are also used for recordkeeping and tracking completed repairs and other listed construction activities. This is extremely important for coming towards the end of the project with punch-list to see which construction activities are left to be completed
Recommendations for a quality control plan is to have a recorded documented quality control plan This allows for good practice and ensures that there is a standard to uphold to which would pertain to the quality control plan Having LiRo Superintendent constantly monitoring and the construction activities is efficient but following a system using as mentioned before SiteManager allows for good record keeping of daily work reports, material usage, labor usage, any street closures, etc.
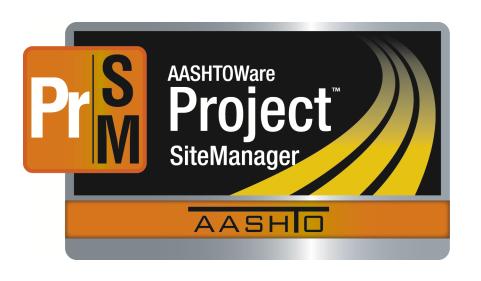
In addition to recommendations is with the utilization of Procore which is a construction management software that assists with Preconstruction, Project Execution, Financial
Management, Workforce Management, and Construction Intelligence It provides a centralized collaboration hub for DSNY, LiRo, and all project collaborators through the projects entire lifecycle Procore also allows for integration and collaboration with BIM, accounting, analytics, bidding, CRM, document management, estimating and takeoffs, quality and safety, progress documentation, and etc.
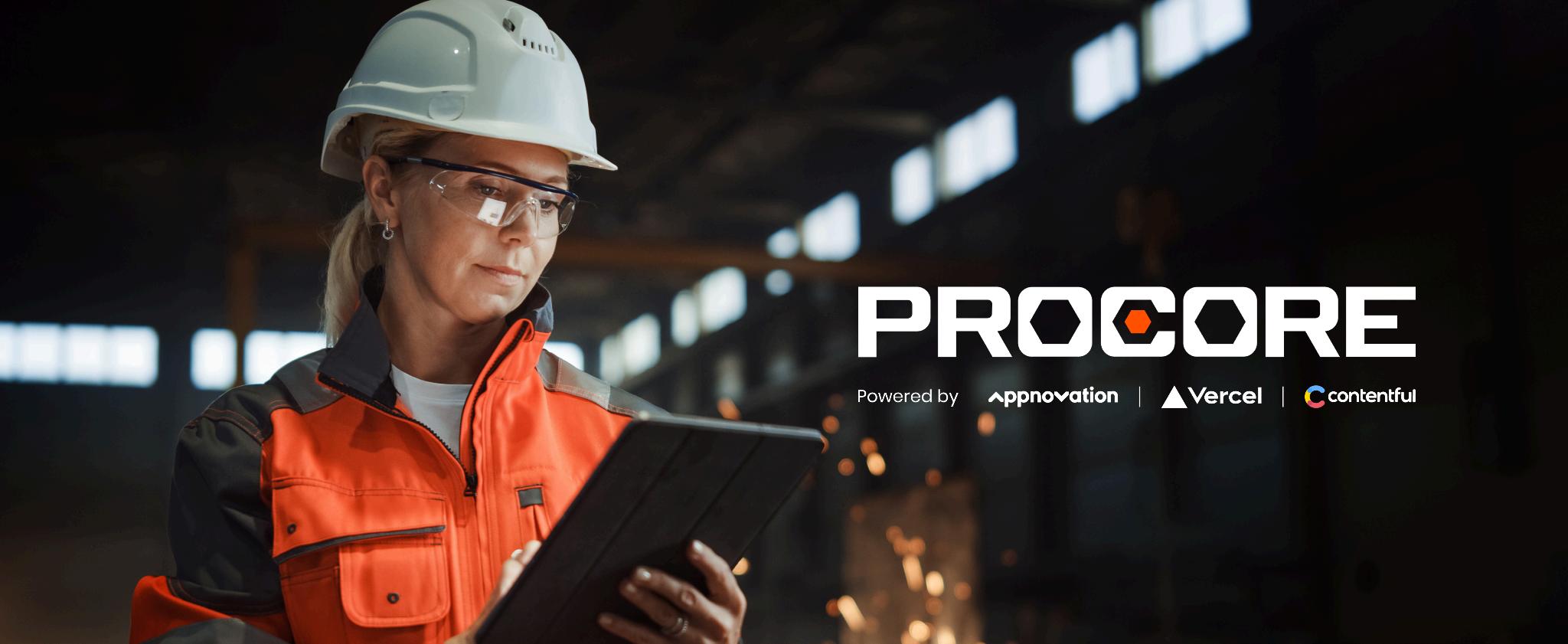
Communications Protocol
Communications on this project is via meetings and emails, whilst E-builder is used as mentioned earlier to communicate tasks and requests via attaching documents with descriptions and details. Meetings are arranged weekly on Wednesdays to allow key stakeholders such as an owner’s representative (city agency), the design team, the general contractor and CM team to discuss any issues and plans regarding the project and any upcoming work. Wednesdays are a useful time as early in the week, the supers are more busy kicking off work, whilst late in the week, like Friday, would mean any issues discussed or addressed in the meeting will have to wait until Monday to be implemented and some thoughts and ideas may have faded from the participants’ memory
The project mostly always has an owner’s representative on site at the job office so that most clarifications and decisions can be made rapidly, saving time for correspondence and allows contractors to plan early on the agreed plan of action This proved useful during the period post COVID where various supply chain issues have to be addressed and changes or requests for extension of time and cost have to be processed. Although the fixed meeting schedule provides good predictability and consistency, it has occasionally caused some issues to be delayed until the following week to be addressed. To overcome this, a possible alternative is to set up an online video conference with only the required meeting participants to address a specific issue This will expedite the project when problems are detected
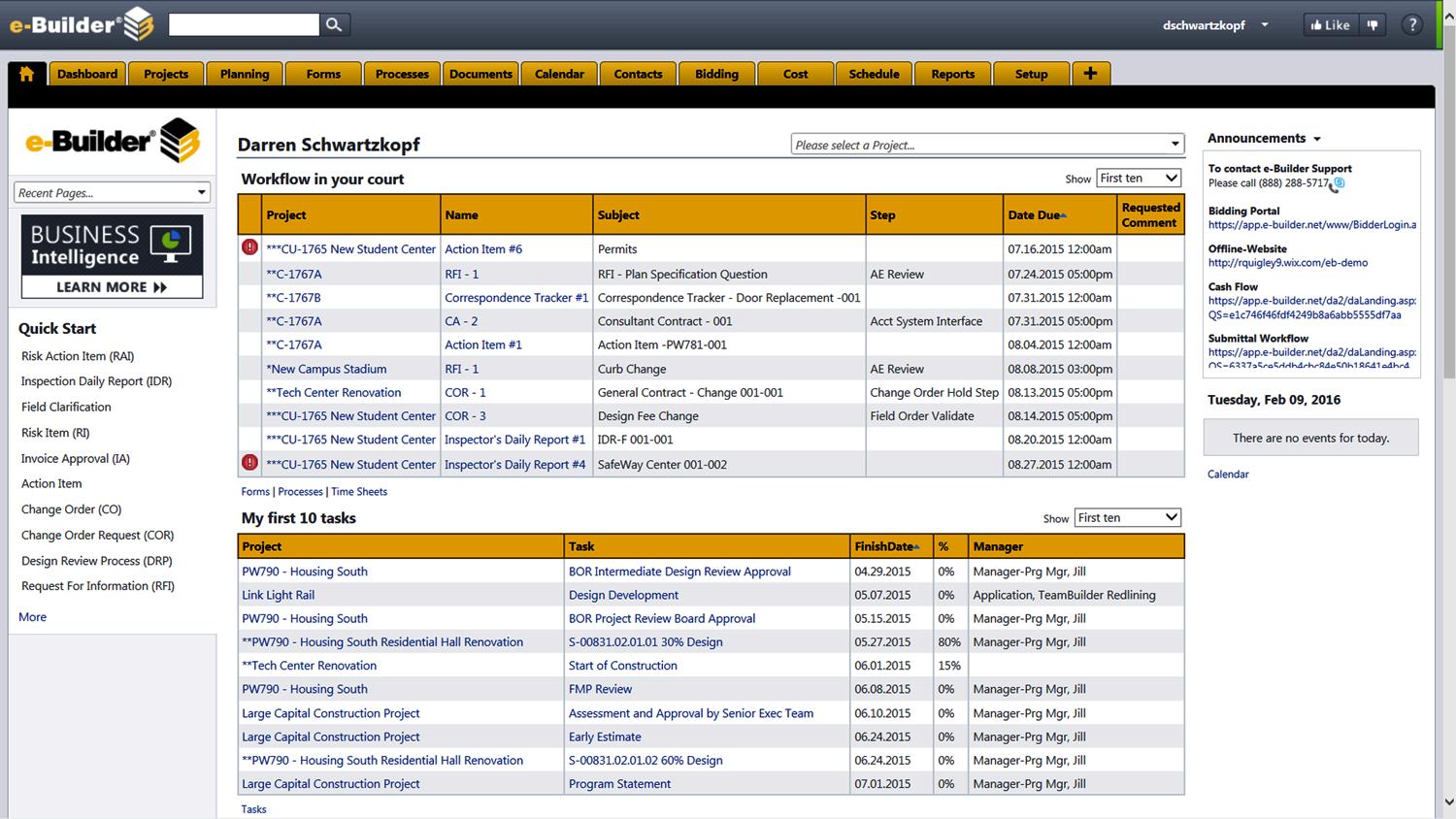
b t a i sort the sent tasks or contents, meaning the receiver will be presented with a list of messages, the attached documents and data, but without a way of making certain things stand out when needed other than by reading through the list. Some improvements can be seen here by utilizing software with a more optimized communications capability such as Procore
The project team makes announcements to the community and invites opinions via telephone from the local community who will be impacted by the lane closures and occasional road closure during the delivery of certain products This has been handled well with the community not severely opposing or hostile towards the project. Hours of noisy work are negotiated with the community as well to prevent complaints to the city that may result in a stop work order
Project Schedule
Regarding the schedule, the project groundbreaking started towards the end of 2019 with an original planned finish date of July 1, 2022 This planned finish date was impossible to achieve with the start of COVID which resulted in a stop work order from April 2020, and a very slow return to work with limited workers allowed on site
From mid 2020 to mid 2021, work continued slowly as new procedures have to be put in place for COVID. There are severe supply chain issues which have to be addressed one by one A time extension was applied for and approved with a new date of February 7, 2024 This proved to also be difficult to achieve, as at the start of February 2024, the schedule was nearly 99% through and the tasks were only 70% complete. Delays range from supply issues such as with the switchgear supplier A second extension was applied for with a finish in December 2024 Having the customer rep on site was very useful in applying for time extension and extra cost from the delays due to COVID and supply issues. The owner needs to submit the request for funding to the NYC comptroller office to approve, therefore documentation is important
Another source of delays was from Con-Ed being slow in coming to provide the mains connection to the site The lack of power prevented some activities from proceeding, such as
installing elevators as these required electrical power to operate and maintain Without power, the elevators would have to be held on the emergency brakes, which will eat into the product’s life cycle (brake wear, replacement cycles required) and go against customer specifications for a new installed elevator.
There were originally around 1000 Construction Change Directives as the project began, but after the delays due to COVID, this number rose to over 1600 Part of the delay is due to i
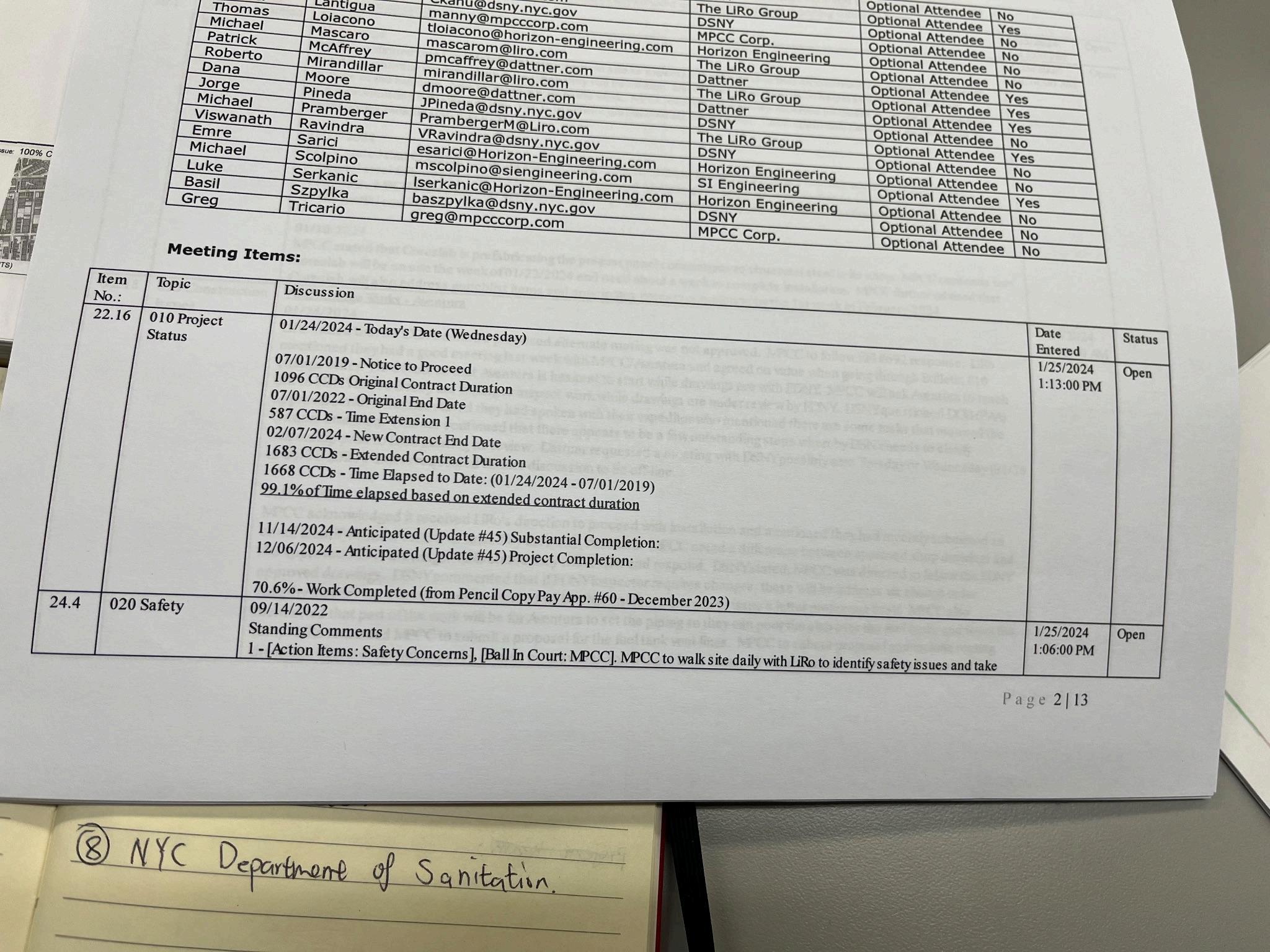
entrance is on the less busy road, there are still issues with smooth access. Numerous school buses are parked near the main entrance, making it difficult for trucks transporting materials to enter the site This situation necessitates extra work in terms of communication and cooperation with the community to manage traffic.
The second challenge is LEED certification Both the design process and the selection of construction materials follow LEED requirements, aiming for a more sustainable building However, this requires specific types of materials and has additional restrictions. During construction, a precast panel delivered to the site did not meet LEED standards Consequently, the construction manager decided to send it back, causing delays while waiting for the new
panel to be manufactured This incident underscores the importance of thoroughly checking material selection and double-checking decisions at every step.
The third challenge is related to COVID-19 and budget overruns As mentioned in the project schedule, the unexpected outbreak of COVID-19 led to site closures and restrictions on labor density during the post-COVID period. These unforeseen external factors delayed construction and increased costs The delays also caused extra costs for storing materials in factories or other countries, and societal restrictions contributed to further delays in the project's close-out phase Additionally, weather conditions played a role, as continuous rain caused difficulties because the building lacked a completed roof To cope with the rain, the construction manager adjusted workdays to include weekends.
Other factors contributing to delays included taking over the existing building and supply chain issues At the beginning of the construction phase, the existing building was not as ready as expected, causing further delays. Supply chain disruptions, exacerbated by the effects of COVID-19 on factories, impacted the timely delivery of materials, leading to additional challenges on-site.
Unique Methods/Equipment
Regarding equipment, this project utilized a girder crane in the mechanics area instead of a traditional crane This choice was ideal due to the structure's design, which had beams installed to support crane runs. The girder crane has lower costs, is easier to install, and requires less maintenance compared to traditional cranes
This project also features interesting sustainability systems First, there's a rainwater recycling system that collects rainwater from the roof and stores it in the basement. The collected water can be used for flushing toilets and maintaining the green roof
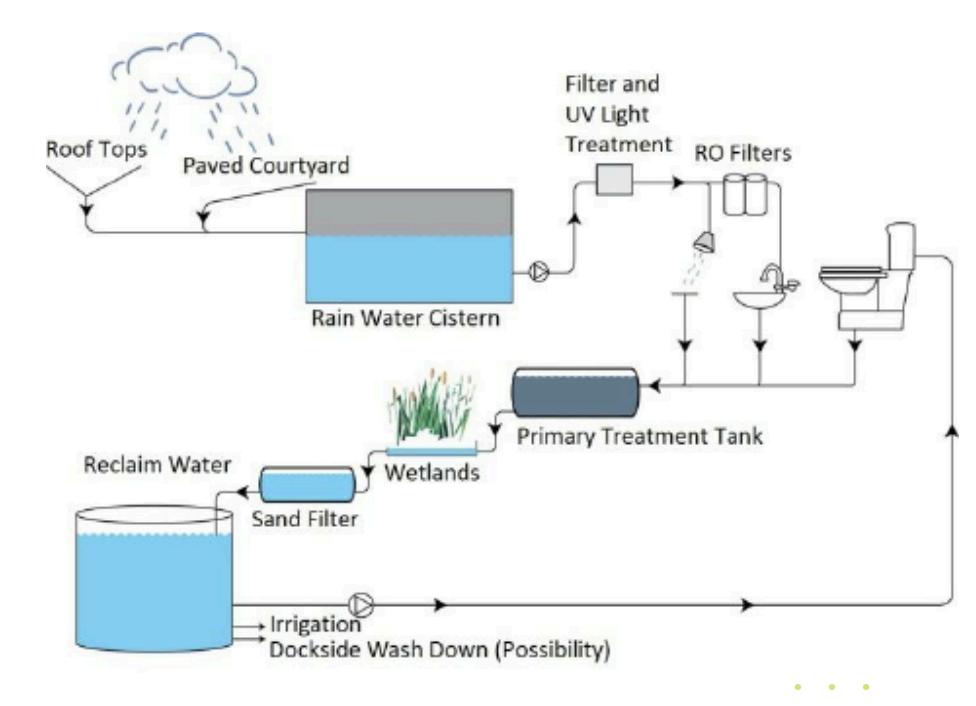
The photovoltaic (PV) roof is another sustainability highlight. It includes solar panels that collect solar energy, which is converted into electricity and stored in batteries for later use This electricity can also be used to charge electric vehicles in the future The building's design
follows LEED guidelines, incorporating numerous openings to increase energy efficiency by allowing more natural light, thus reducing electricity consumption during the day