Cold welding
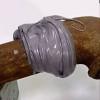
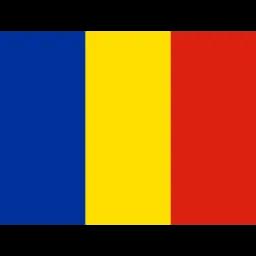
For decades determined welders have proudly worked hard through the cold winters. If you have ever struggled to produce a quality weld amid inclement weather, it becomes easy to respect the old-timers. Compared to regular MIG short-circuit welding CMT emits about 90 less heat into the workpiece. These can?t be fusion welded because they tend to crack under heat, and they are challenging to join with welding methods other than cold welding. For this reason, it is not typically used in applications where high strength is required. Cold welding or contact welding helps do away with this challenge because they work on the principle of physics and material science. In her free time, She enjoys reading up on the latest advancements in the industry, as well as exploring new ways to innovate and improve upon existing processes. Without these temperatures present during welding, it can be difficult to ensure that all parts are properly bonded together if they have different surface qualities or thicknesses. Welding in an enclosed space or room increases chances of fume accumulation thus increasing the chances of hexavalent chromium exposure.The frost that develops during normal weather is the result of condensation. In addition, coldwelded joints can be just as strong as those created using traditional welding methods. I personally prefer a welding jacket like this one by Lincoln Electric. With practice, I've learned what welding equipment works and what doesn't via firsthand experience. The potential exposure to hexavalent chromium during welding is necessitated by the following factors. Welding process. Different welding processes have different fume generation rate and thus the amount of hexavalent chromium produced will also differ.Through these innumerable months of cold weather, welders, whether welding in welding shops or in an oil field somewhere up north have found ways to mitigate the effects of welding in cold weather. Once pressed together, the nanoscale distance becomes irrelevant, and metal atoms jump from one piece to another. On the other hand, spot welding is fast and efficient, making it ideal for mass production. Unlike fusion welding, such as arc welding and friction welding, cold welding doesn?t have a molten or a liquid metal phase, which is why it?s referred to as cold welding. It’s a process where two pieces of metal are joined together without the use of heat or any other bonding agent. It works by compressing the metals together and allowing their atoms to interlock, which produces a strong bond between the two pieces. If so, then you know how the cold can affect them, even during this. Cold welding can produce neat welds and be as effective as the original materials worst component. One of the biggest disadvantages is that cold welding can only be used on metals that are compatible with each other. In addition, cold welds can be used to create strong and durable joints without the use of heat or filler material. This can cause metals to fail to join together, or lead to weak or cracked welds. Heat is used in the welding process to make the two metals soft enough to diffuse with each other or with a third metal (filler). One element that you can take control of is the temperature of your welding gas tank. Advantages, Limitations andApplications of Cold WeldingAdvantages of Cold Working: 1.This results in a nearperfect bond with almost no repercussions, and the two separate pieces of metal become a homogeneous mass.
Various mechanical and chemical methods are used to remove the oxide layer. Other commonly used materials that can be joined using cold welding are stainless steel, aluminum, zinc, and nickel. Unlike in fusion welding no liquid or molten phase is present in the joint. Firstly, one must remove enough oxide layers from both working metals. Cold welding is commonly used in the electrical and electronics industries, particularly for semiconductor manufacturing, bonding electrical leads, and welding cable ends. Welding rate.The fumes generated during a welding process tend to increase with increased welding rate.Additionally, pulse welding is ideal for welding large surface areas such as tanks, heavy machinery, and other equipment. This is because Chromoly metals are sensitive to temperature and thus exposure to heat during welding should be done gradually This welding method is particularly useful for thin materials, as it can join them together without any risk of warping or deformation. It works by compressing the metals together and allowing their atoms to interlock, which produces a strong bond between the two pieces. This welding process is relatively new and constantly under development by teams of engineers. Gold: Gold is a soft, malleable metal frequently used in jewelry and electronics. It is very important that your first pass achieve good penetration. You may ?experience fewer headaches and possibly some cost savings after covering your machine.? Check and change the anti-freeze if needed. When dissimilar metals are melted in points to fuse them, they don’t actually join well and can thus lead to weak welds and cracks. On the other hand, scientists have discovered that very thin nanowires of gold having a diameter of 10 microns can be cold-welded within seconds of bringing them in contact by applying minimal pressure. Cold welding or contact welding is a solidstate welding process that requires little or no heat or fusion to join two or more metals together.This causes the atoms on the surface of each metal to interlock, forming a bond. This requires additional preparation steps and can take some time to achieve. Treat your fuel. Stabilizers will help when the machine is not going to be used for a few weeks. Weldingmastermind.com is compensated for referring traffic and business to these companies. Both welding methods are effective in their respective fields and produce stronger and more durable metal joints. Different cold-pressure welding machines can be used to achieve the required pressure and temperature to weld metals together The weld produced under such conditions is characterized by crack resistance and durability You can tell that you have achieved the correct temperature in the workpiece by using a special heat sensitive marking crayon, a laser-equipped heat sensor gun, or by simply using your hand if you are experienced enough. In essence, cold welding is a welding process that needs little to no heat to fuse two metals together. Upon welding, one should avoid cooling the weld rapidly as it can lead to cracking of the weld. When a weld cools too rapidly directly after application it will be very susceptible to cracking. However, during the winter, regulators can become frozen both inside and out.Accessibility, UserAgreement, Privacy, PaymentsTerms of Use, Cookies, CAPrivacy Notice,Your Privacy Choices andAdChoice.
Although both have similar terms, they differ in terms of processes and applications. Without these temperatures present during welding, it can be difficult to ensure that all parts are properly bonded together if they have different surface qualities or thicknesses. Both welding methods are effective in their respective fields and produce stronger and more durable metal joints. By understanding the capabilities of cold welds, welders can open up a world of possibilities for their projects. However, thicker metals would require a preheat to temperature between 300-400 degrees Fahrenheit. Staying comfortable in cold weather might sound like a namby-pamby goal. Scientifically the process of using pressure is called solid. WeldingMastermind.com is a participant in theAmazon Services LLC Associates Program, an affiliate advertising program designed to provide a means for sites to earn advertising fees by advertising and linking toAmazon.com.This site also participates in affiliate programs with other sites. The metals should not have undergone any hardening process, including work hardening. Welding rate.The fumes generated during a welding process tend to increase with increased welding rate. Once prepared, the two metal parts are brought into contact at high pressure under a vacuum and at ambient temperature. Properties, Uses and Application What is Cartridge Valve. Leave a Reply Cancel reply Your email address will not be published. Some of the most common uses for cold welds include repairing pipelines, joining dissimilar metals, and fabricating delicate structures. In addition, cold welding can only be used on metals that are compatible with each other. In fact, sometimes the strength of cold welding can be a real nuisance, such as during space applications, as NASAhad to learn it the hard way during the 1960s and 1970s. Cold welds are particularly well suited for joining metals that are difficult to weld using traditional methods.Acold welding machine can cost anywhere from 400 to 1000. Cold welds are typically used to join two pieces of aluminum or stainless steel. Most of these machines are portable and can handle wires, rods, and strips. However, it is important to note that cold welding can only be used on metals that are compatible with each other This bond is strong enough to create a permanent connection between the two metals that can withstand high levels of stress and vibration. Equipment maintenance should be a year-round endeavor This is called cold welding, and it’s actually more fascinating than it sounds. Cold welding is a process that combines two metals by creating enough pressure to form metallurgical bonds. For this reason, cold welding is also quite commonly used in laboratories or industries such as aerospace.An electric current is passed through the metal, which heats and causes it to melt. Their welders are used in a variety of industries, including aerospace, automotive, and medical. While doing the strength calculations, the designer should consider at least 50% thickness of one of the sheets lost because of the pressure applied. Cold welding is the process of joining two metals or materials together without using any heat.