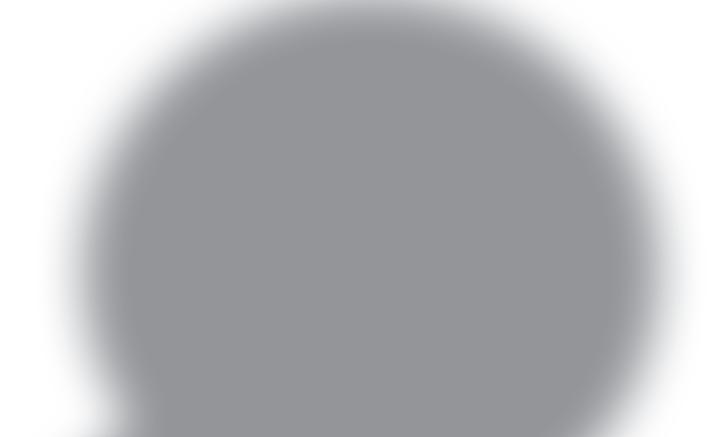
14 minute read
DfAM
Design for Additive Manufacturing
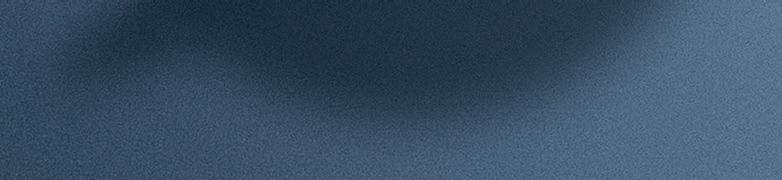
Material considerations when moving to 3D printing
Jon Eric Van Roekel • process engineering manager for 3D printing • Protolabs
Developments in 3D printing have made it a proven, industrial-grade manufacturing practice for end-use parts. At Protolabs, we see this evolution fi rsthand as customers leverage new additive manufacturing (AM) processes and expand material options to make more complex, lightweight, or sustainable products. However, the integration of additive manufacturing (AM) into the product design process is not without some tradeoff s along the way. A common decision point to overcome for many is choosing the right material, an evaluation step that is more complex with 3D printing practices. Or at least requires a new set of considerations. A material must be well-suited for the application in order to achieve design goals. And as we see 3D printing emerge as a manufacturing method for end-use part production, the properties of any material become increasingly important. AM benefi ts tremendously om recent investment and R&D eff orts dedicated to the creation of materials specifi cally designed for industrial-grade 3D printers. In terms of mechanical and physical properties, material selection hinges on the prioritization of design and desired quality requirements. Compared to traditional manufacturing practices, materials for 3D printing are still advancing to include rich sets of performance data that characterize materials over a range of conditions. Another factor to consider is that 3D printing produces anisotropic properties where the values diff er for the X, Y, and Z axes. The degree of anisotropy varies by technology, but it should always be a consideration. Both can be overcome by designing for
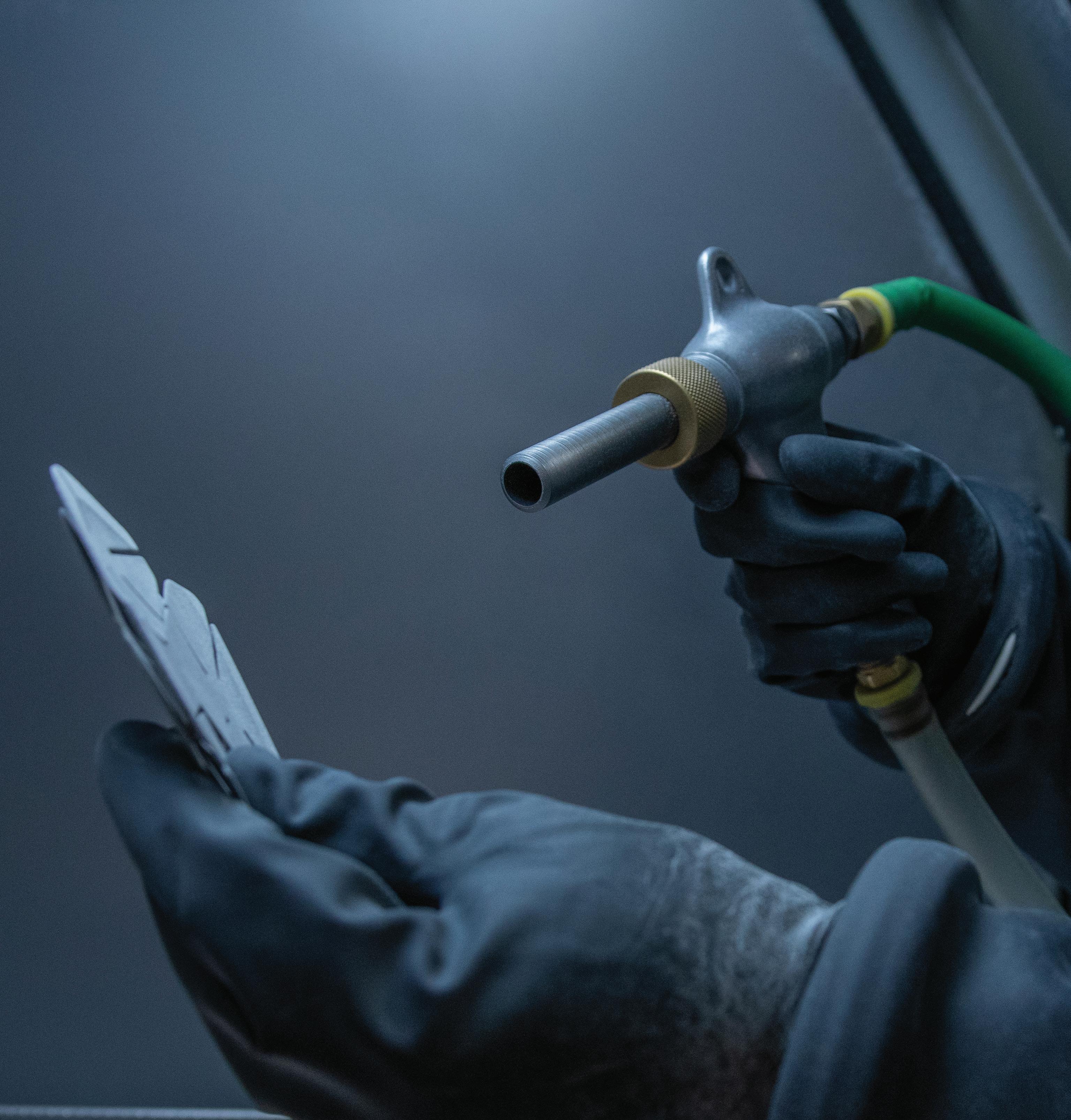
Design for Additive Manufacturing
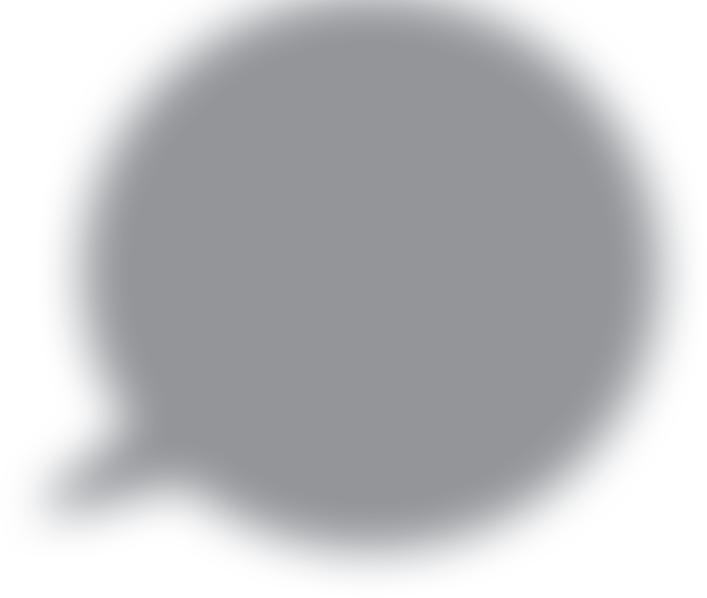
additive manufacturing and leveraging the experience of knowledg-eable service bureaus that have worked on millions of parts.
What to consider with 3D printing materials One or two material properties can distinguish one additive material om another. The fi rst step in identi ing a material is defi ning the mechanical and physical properties critical for the application.
Common measured properties of interest to designers can include: • Ultimate tensile strength (UTS): The maximum stress the material can withstand before breaking. • Tensile modulus, or elastic modulus: Measures stiff ness, the higher the modulus, the stiff er the material. • Elongation (%): Measuring ductility, a higher elongation percentage indicates a material is more likely to be able to stretch or elongate into a thin wire shape. • Hardness: The higher the number, the harder the material. Hardness is typically measured and reported in HRC or HRB on the Rockwell scale for metals. For polymers, like PolyJet materials, durometers are typically reported. • Heat Defl ection Temperature (HDT): Sometimes called heat distortion temperature, the temperature at which deformation occurs when a rigid material is placed under a specifi c load.
The following takes a look at the information to consider in the selection of materials for the most popular 3D printing processes: direct metal laser sintering (DMLS), stereolithography (SLA), Carbon DLS, selective laser sintering (SLS), Multi Jet Fusion (MJF), and PolyJet (PJ).
Direct Metal Laser Sintering (DMLS) Materials DMLS, a type of metal 3D printing, uses pure metal powder to produce parts with properties that are generally accepted to be comparable to wrought metals when comparing them in the heat-treated condition. Unique in 3D printing, it also produces parts with material properties that approach an isotropic state, meaning similar properties independent om direction of measurement.
Some commonly used materials to consider: • Aluminum AlSi10Mg is comparable to a 360.0F aluminum alloy, which is commonly used for die-casting. The material features good strength-toweight ratio, high temperature and corrosion resistance, and good fatigue, creep, and rupture strength. • Stainless steel is available in two grades at Protolabs: 17-4 PH and 316L. Select 17-4 PH (precipitation hardened) for its signifi cantly higher tensile strength and yield strength, but recognize that it has less elongation at break than 316L, which means that 17-4 is less malleable than 316L.
Stereolithography (SL) & Carbon DLS Materials SL off ers the broadest selection of 3D-printable plastics with a large range of mechanical properties. It is also a go-to process for parts that require fi ne features and cosmetics, as well as a quality surface fi nish. Compared to injection-molded plastics, impact strengths are o en lower, and exposure to moisture and UV light may alter the appearance, size, and mechanical properties of SLA-printed parts over time.
Some commonly used, all-purpose materials to consider: • ABS-like White and ABS-like Gray are two of the more widely used durable SLA materials. In terms of fl exibility and strength, both materials fall between molded polypropylene and molded ABS, which makes them an easy choice for functional prototypes. • Ceramic-like Advanced HighTemp (PerFORM) is a stiff material option
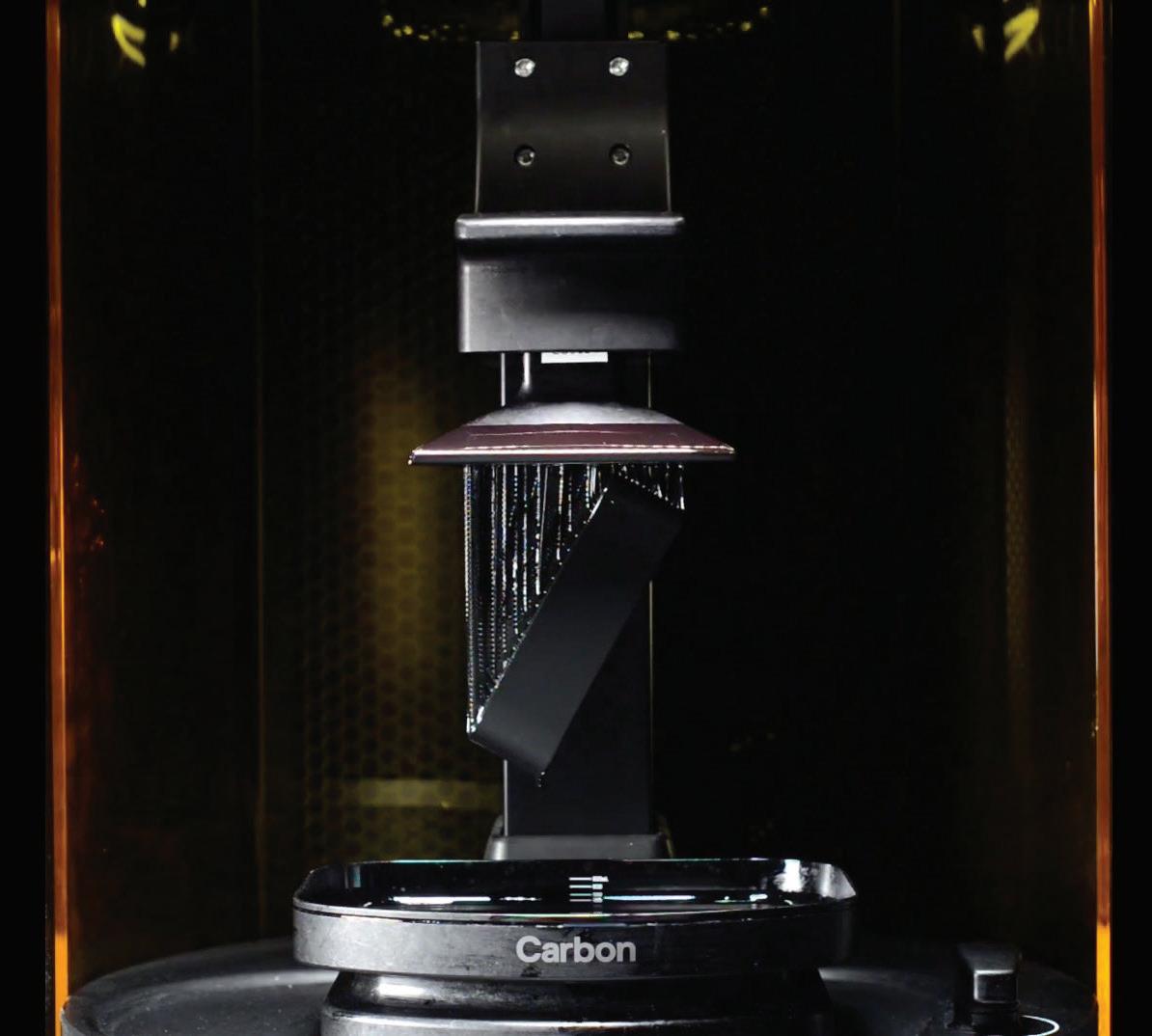
that is superior to similar injectionmolded thermoplastics when HDT (heat defl ection) is critical. • RPU 70 Rigid Polyurethane is a tough, all-purpose material. When manufactured using Carbon DLS, it can be categorized as an ABS-like material. Due to the post-build thermal baking process, materials paired with Carbon DLS can achieve heightened mechanical properties.
Selective Laser Sintering (SLS) & Multi Jet Fusion (MJF) Materials Primarily using polyamide nylon materials, both processes off er the most economical choices with o en greater toughness and high impact strengths when compared to SLA. The density of SLS/MJF parts are also closer to traditionally manufactured parts; however, both processes lack the ability to provide the surface fi nish and fi ne feature details off ered with SLA. When compared to injection-molded materials, polyamide has similar HDT values but less robust mechanical properties. SLS/ MJF material properties also have a known degree of anisotropism when measured in the x-y plane or the z plane.
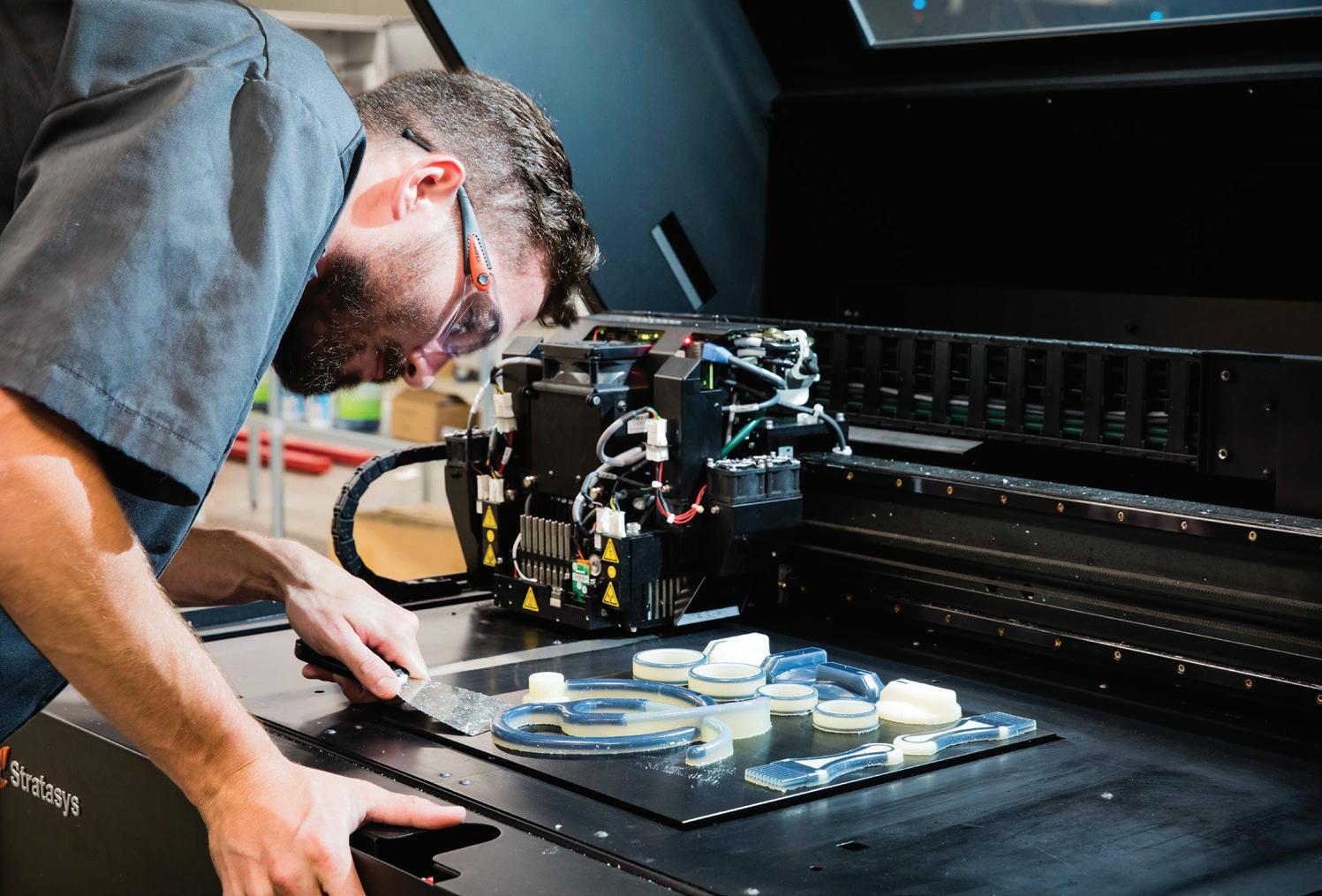
Some durable materials to consider: • Nylon PA 11 Black is a popular, general-purpose material that delivers on ductility and fl exibility without sacrifi cing tensile strength and temperature resistance. It also off ers the highest elongation of all AM nylons. A stiff er option is PA 12 White, which features slightly higher elastic modulus. These PA nylons can be mineral or glassfi lled to further improve stiff ness.
PolyJet (PJ) Materials The PJ printing process produces digital photopolymer parts with varying fl exibilities, durometers, and colors. Compared to injection-molded liquid silicone rubber (LSR), the mechanical properties are similar with one important distinction: digital photopolymers show more viscoelastic creep than an equivalent LSR material, meaning it may feel so er over time when under constant stress.
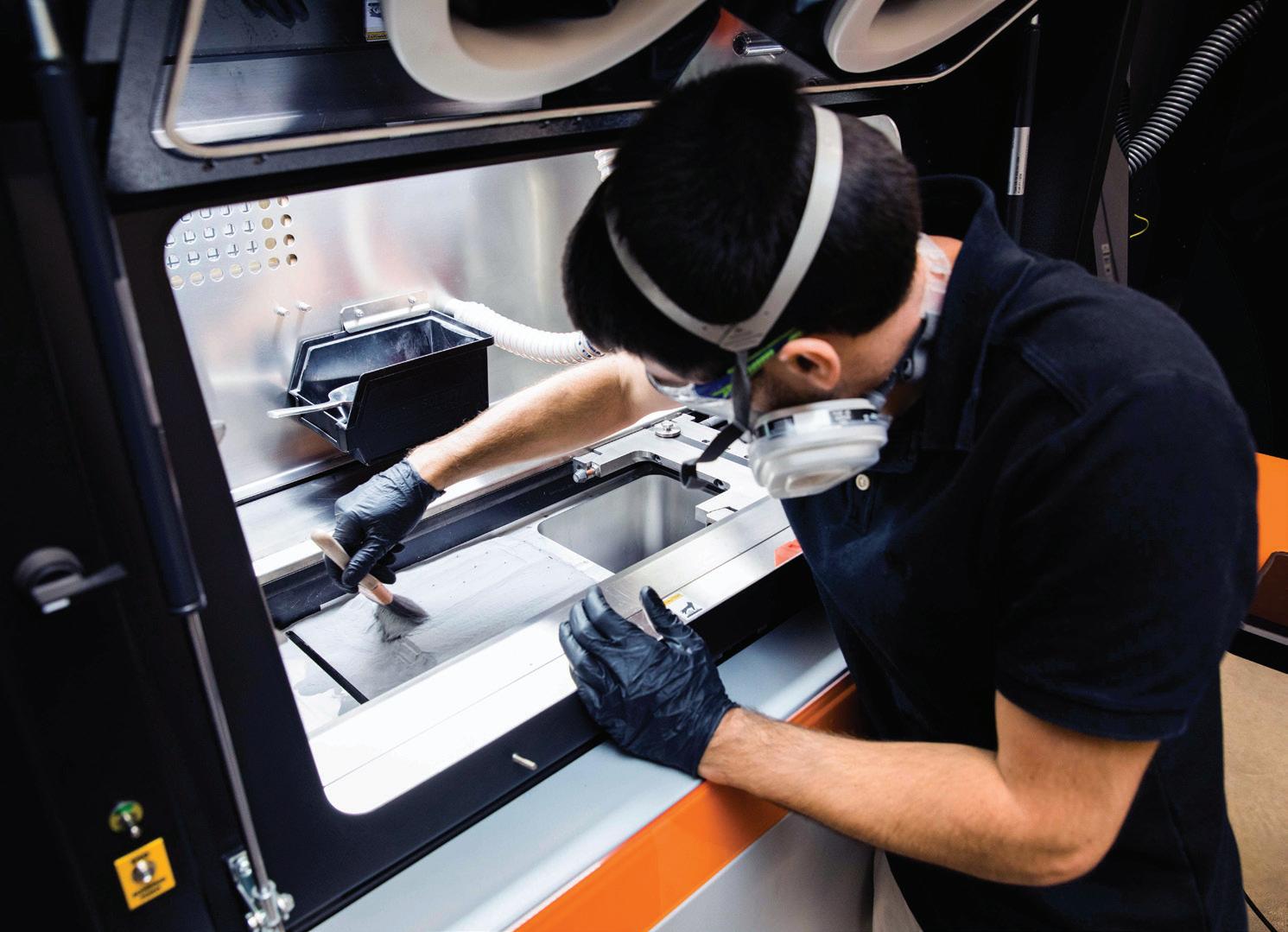
In conclusion, the wealth of 3D printing materials available today across all processes makes additive manufacturing more accessible than ever, and that library of materials is ever-expanding. As more companies turn to additive manufacturing for production parts,
DMLS uses pure metal powder to produce parts
the ecosystem is also better defi ning the capabilities and development opportunities for each material. DW
Protolabs www.protolabs.com
Design for Additive Manufacturing
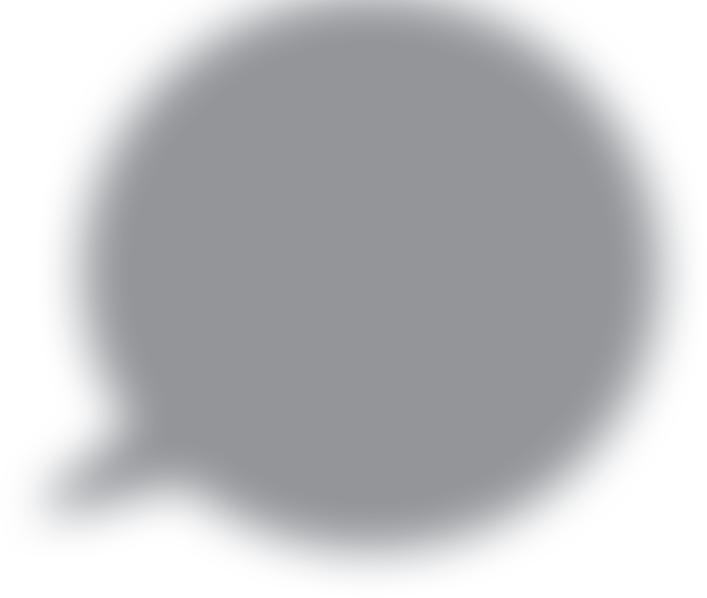
Rodin Cars 3D prints a custom metal gearbox for its Supercar

An 8 speed sequential, 68kg, additively manufactured from grade 23 titanium; the Rodin Cars gearbox is designed to set a new standard in automotive manufacturing.
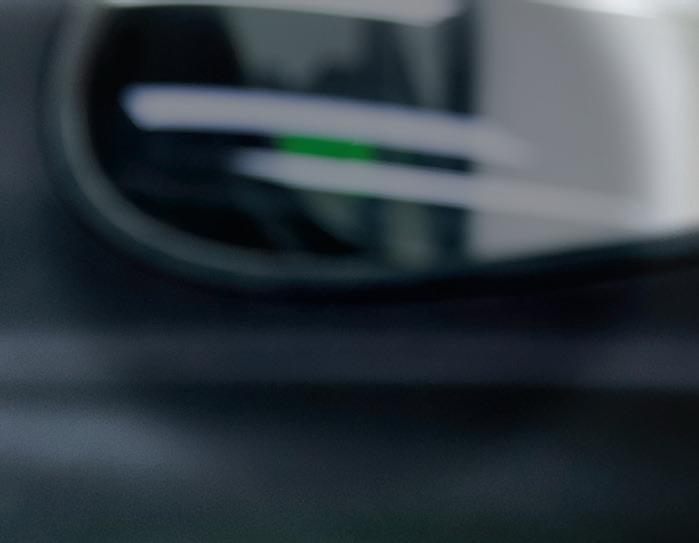
| Courtesy of Rodin Cars
Rodin Cars, a New Zealand-based manufacturer of the ultimate track car, designs and builds completely custom single-seat, open-wheel, high-performance vehicles that are designed to be faster than contemporary Formula 1 cars. The company is about to release a hypercar, the Rodin FZero. Among the hundreds of metal parts Rodin Cars is additively manufacturing for the Rodin FZero is a fi rst-of-its-kind 8-speed sequential gearbox with a hydraulically controlled diff erential. This completely custom component can only be produced using additive manufacturing. A gearbox created using traditional manufacturing methods would be cast out of magnesium or machined om billet material. The resulting component would take considerable time to produce, and be heavier and not withstand the rigors presented by the track. Rodin Cars wanted to fl ip this design into a true innovation – the ultimate component produced om 3D printed titanium that would be compact, light, strong, and durable. For the Rodin FZero, the engineers envisioned a brand new gearbox with specifi c gear ratios and diff erential. The 18-month design process resulted in a gearbox with a hydraulically
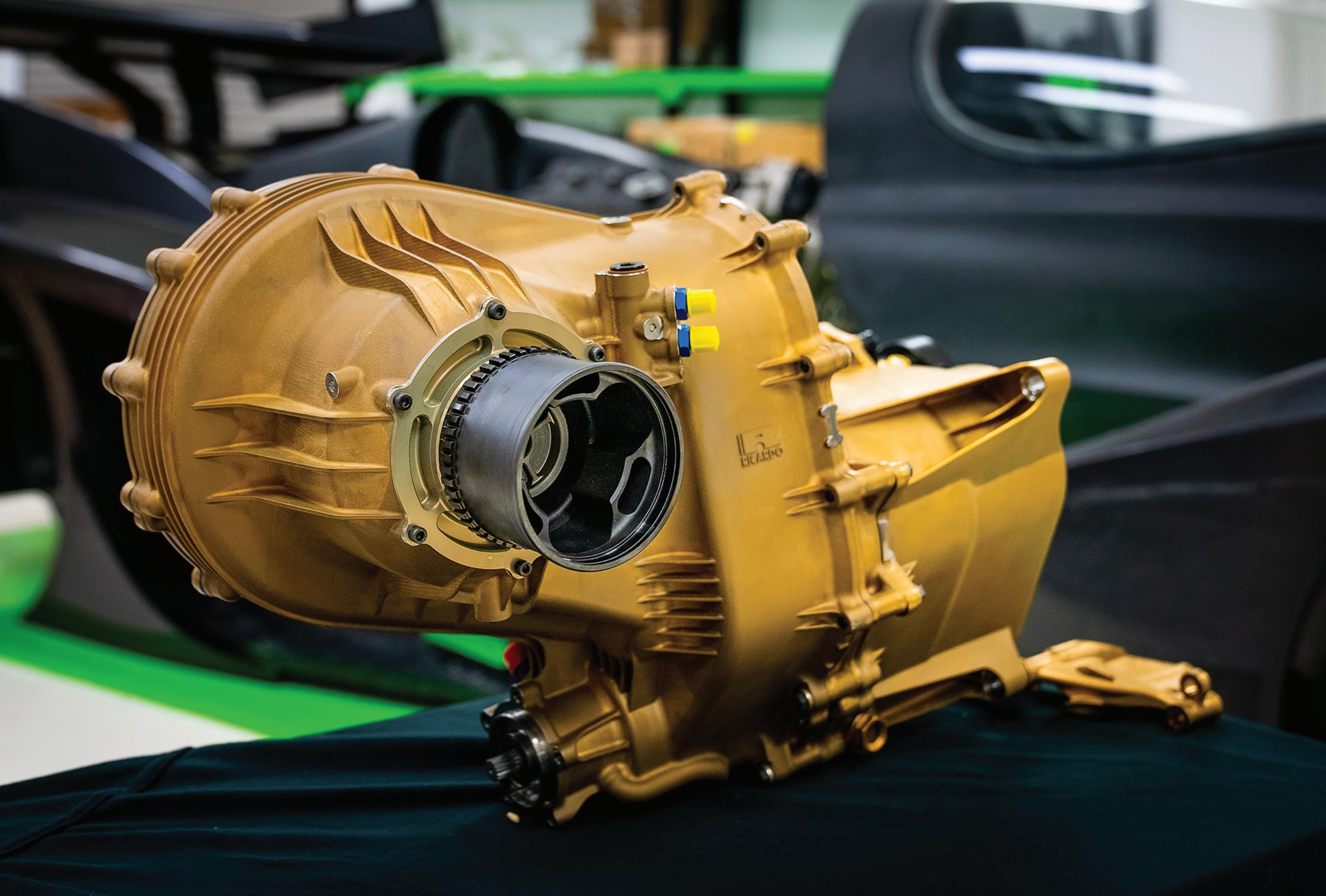
The Rodin Cars bespoke gearbox, uniquely designed specifi cally for manufacturing using state-of-the-art metal 3D printing technology.
| Courtesy of Rodin Cars
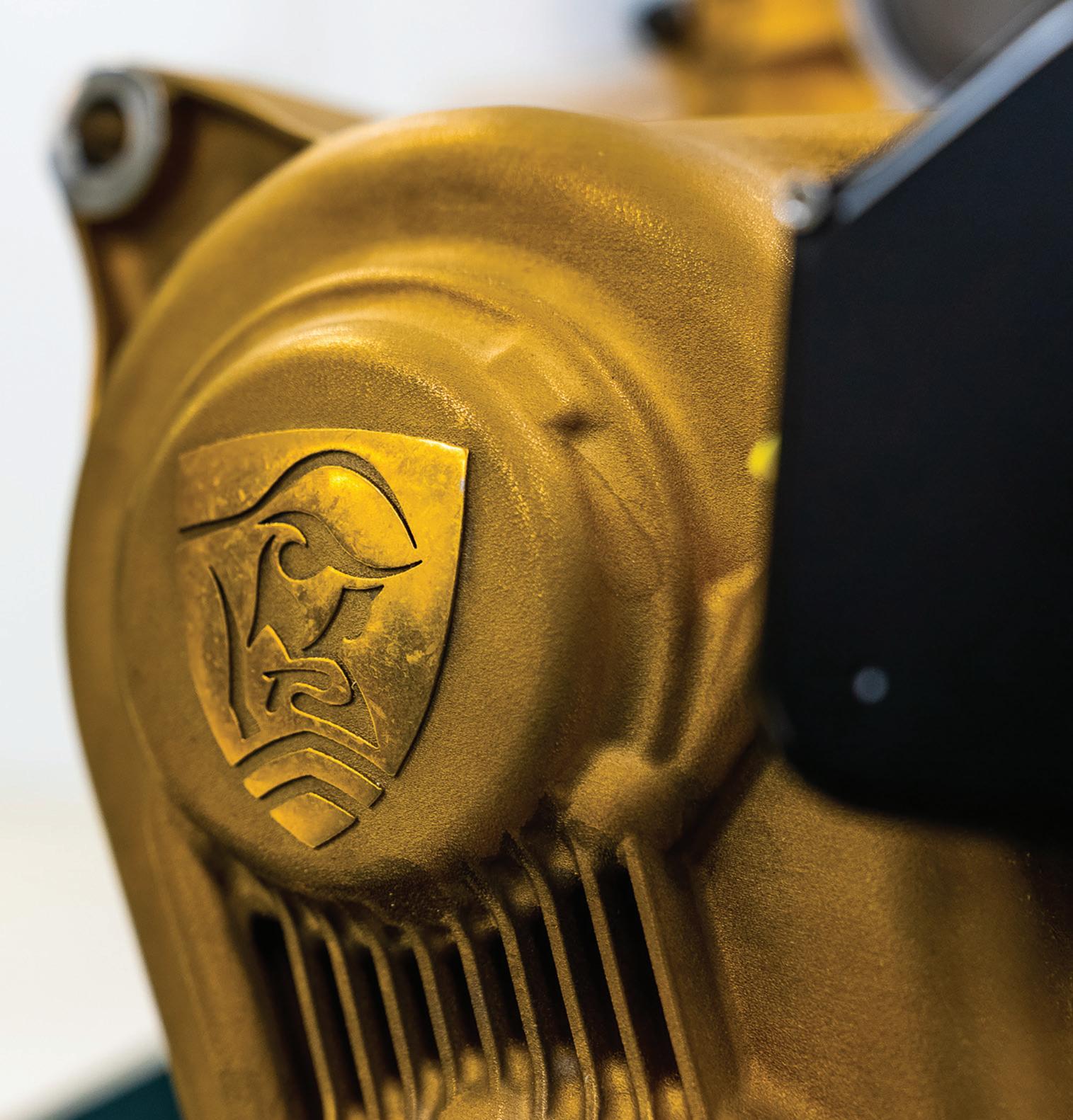
controlled diff erential with internal galleries and thin-wall bearing and mount structures. The engineers worked alongside members of 3D Systems’ Application Innovation Group (AIG) in Littleton, Colorado, and Leuven, Belgium to bring this unique design to life. The team used direct metal printing (DMP) technology to produce the new gearbox that includes 2-mm thick walls and weighs 68 kg. The application engineers in Littleton optimized the gearbox print design details for additive manufacturing at the large scale achievable on the DMP Factory 500 and produced the fi rst part on its DMP Factory 500 in Leuven. The additive system includes a vacuum chamber to ensure the lowest O2 content and can make seamless large parts as large as 500 mm x 500 mm x 500 mm. Rodin Cars recently installed a DMP Factory 500 on-site at its newly expanded facility and will produce the gearbox, as well as hundreds of other bespoke parts, for the Rodin FZero. “3D printing allows us to design and create components otherwise unachievable using traditional methods of manufacturing,” said David Dicker, founder, Rodin Cars. “With the Rodin FZERO gearbox, we had specifi c criteria we wanted to meet in terms of weight and durability. Because of the size and quality required for such a large component, it was only possible to print it on 3D Systems’ DMP Factory 500 machine. We couldn’t source another AM supplier who was able to off er a similar solution for our needs - the print quality, volume capacity, testing facilities in Leuven, and continued technological support.” In addition to 3D Systems’ DMP technology, Rodin Cars is also using the company’s selective laser sintering (SLS) technology for production parts and stereolithography (SLA) to produce tooling for carbon fi ber forms. “Additive manufacturing is enabling industry leaders to de limitations and stand apart,” said Kevin Baughey, segment leader, transportation & motorsports, 3D Systems. “This is a shining example of how additive manufacturing not only enables parts to be produced that couldn’t be created through conventional methods, it is also delivering a lighter, more durable, beautiful vehicle. It’s the blending of the art of design with the science of hyper-performance cars and motorsports.”
DW
3D Systems www.3dsystems.com
Design for Additive Manufacturing
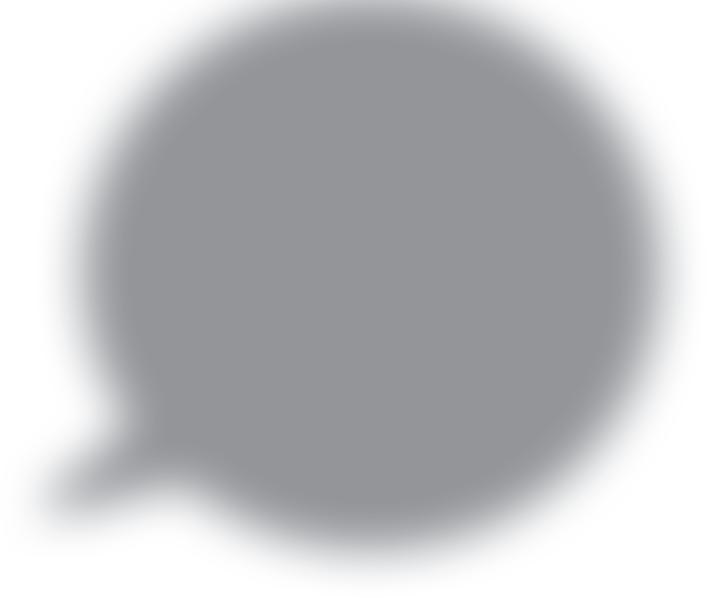
3D printed gra helps the hearing impaired
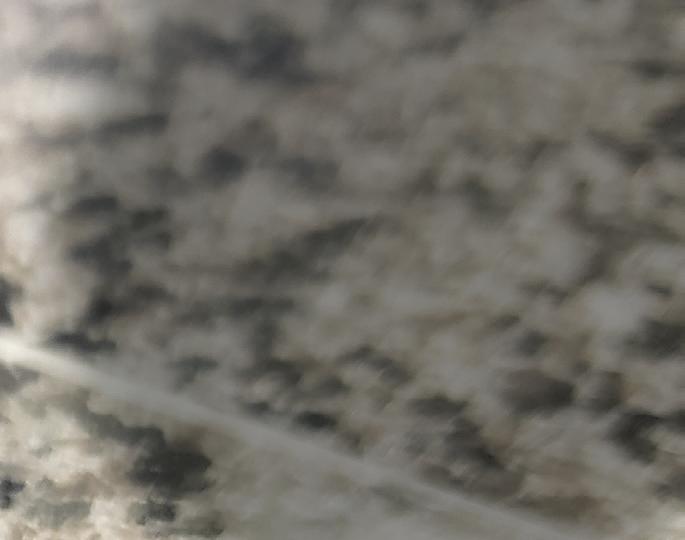
The PhonoGraft device is a biomimetic graft that has the potential to enable high-quality and long-lasting eardrum reconstruction. It is a 3D printed biodegradable elastomer in the form of customizable biomimetic circular and radial sca olds, and is intended to function like the native eardrum.
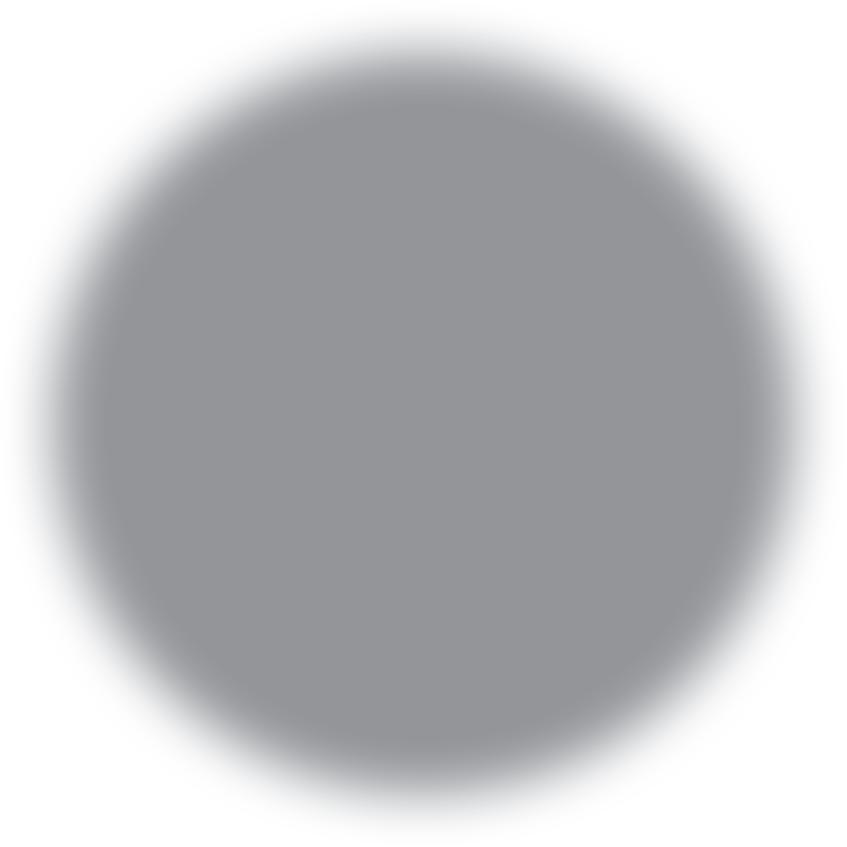

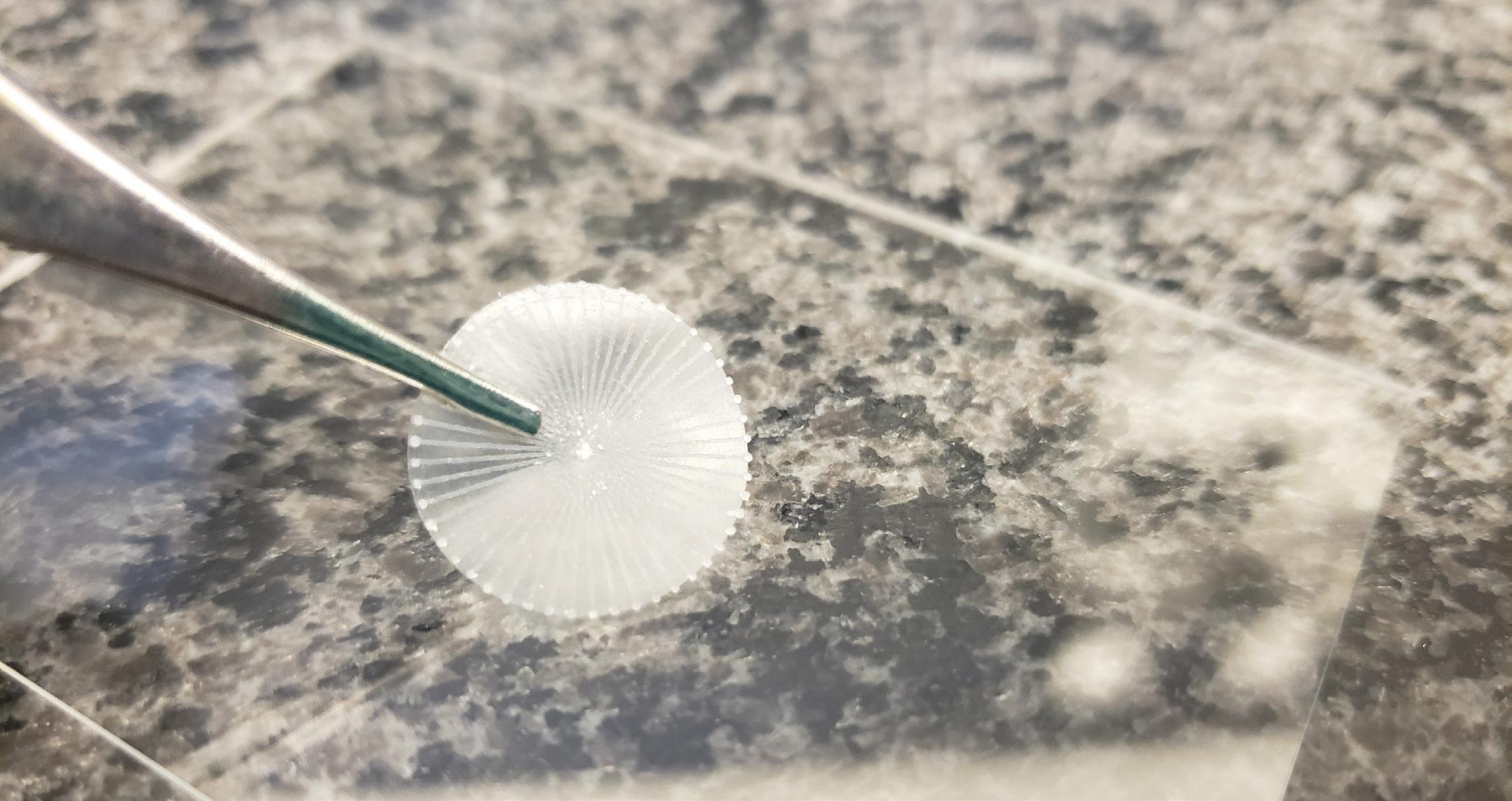
Thousands of people suff er om damage to their tympanic membranes, compromising their hearing. A biofabrication technology has led to the development of PhonoGra technology—a promising pathway for so tissue regeneration for a range of healthcare applications. The PhonoGra technology was initially developed by researchers at the Wyss Institute for Biologically Inspired Engineering at Harvard University, Harvard John A. Paulson School of Engineering and Applied Sciences (SEAS), and Mass Eye and Ear in Boston (Mass Eye and Ear is a member of Mass General Brigham). Harvard’s O ce of Technology Development has granted Desktop Metal and its subsidiary business, Desktop Health, an exclusive license to commercialize the platform. The PhonoGra technology is being studied for possible use in an implantable device for repairing damaged eardrums, with a programmable biodegradable 3D printed gra that has the potential to be minimally invasive and off er patients decreased procedure times and improved healing and hearing outcomes. The concept for the PhonoGra device arose a er the 2013 Boston Marathon bombings, when many individuals sustained eardrum perforations due to the blast injury. Nicole Black, PhD, then a doctoral student in Lewis’ Harvard lab, recognized an opportunity to explore ways in which 3D printing might be used to improve outcomes following eardrum reconstruction. Lewis and her research group, in collaboration with ear surgeons Dr. Aaron Remenschneider and Dr. Elliott Kozin om Mass Eye and Ear, assembled a multidisciplinary team of material scientists and otolaryngologists. “One of the most prevalent injuries of the Boston Marathon bombing was perforated eardrums,” said Dr. Remenschneider. “This is also common in military personnel a er blast injury and in children and adults with ear infections. Surgical repair of the eardrum is unfortunately necessary for many patients to restore hearing and create a ‘safe’ ear.” Six years of research and development, with an infusion of focused translational funding om the Wyss Institute, led to the creation and
Design for Additive Manufacturing
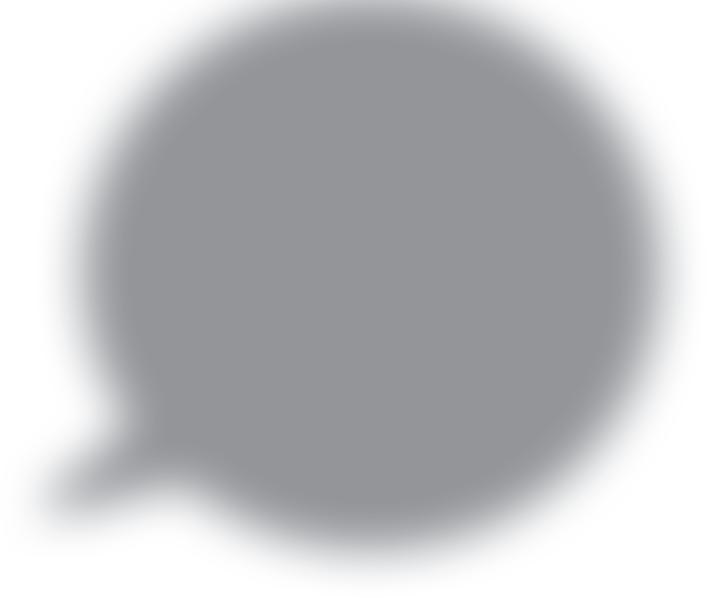
A biometric 3D printer is used to print the PhotoGraft.
preclinical de-risking of the PhonoGra material and device platform. Black became an entrepreneurial champion for the technology; she and several colleagues founded a startup, Beacon Bio, to advance the technology into commercial development. Beacon Bio has now been acquired by Desktop Metal. The PhonoGra device is a biomimetic gra that has the potential to enable high-quality and long-lasting eardrum reconstruction. Partnering with surgeons to develop the technology and understand critical features, such as the acoustic and mechanical properties of the gra material, has been important in its development, Black said. “This device, which is manufactured om a biodegradable elastomer in the form of customizable biomimetic circular and radial scaff olds, is intended to function like the native eardrum. Preliminary bench studies show that the PhonoGra device not only closed the eardrum perforation; it supported the body’s regeneration of the complex eardrum structure,” said Black, who has joined Desktop Health as the Vice President of Biomaterials and Innovation. “Such gra architectures benefi t om the use of 3D printing and permit the eardrum to transmit both low- and high equency sound waves.” The PhonoGra platform has been validated in preclinical studies in animal models. These studies have shown that as the eardrum heals, native cells and blood vessels grow into the biocompatible PhonoGra material. Since the gra material is biodegradable, it is expected to be replaced by native tissue over time. “This technology has potential to ‘intelligently’ support the regeneration of so tissues in other areas of the body,” said Black. “We believe that this platform may one day off er a groundbreaking solution to the millions of patients impacted by tympanic membrane perforation (TMP),” said Michael Jafar, President and CEO of Desktop Health. “PhonoGra material technology, coupled with our biofabrication capabilities, has tremendous potential across a range of healthcare applications in so tissue – om cardiovascular and neuronal gra s to plastic surgery.” “I’m delighted for the members of my lab at Harvard and our collaborators at Mass Eye and Ear who jointly developed this innovative technology, and who successfully applied their entrepreneurial drive to demonstrate its potential. In addition to TMP relief, this advanced gra technology could pave the way for a multitude of healthcare products in the fi elds of cardiac, vascular, and plastic surgery,” said Jennifer Lewis, ScD, who is a Core Faculty member at the Wyss Institute, a Hansjorg Wyss Professor of Biologically Inspired Engineering, and Jianming Yu Professor of Arts and Sciences at Harvard SEAS. PhonoGra technology is in advanced-stage research and development, and currently not available for sale anywhere in the world. Black and her team at Desktop Health intend to conduct additional preclinical studies and pursue FDA review. DW
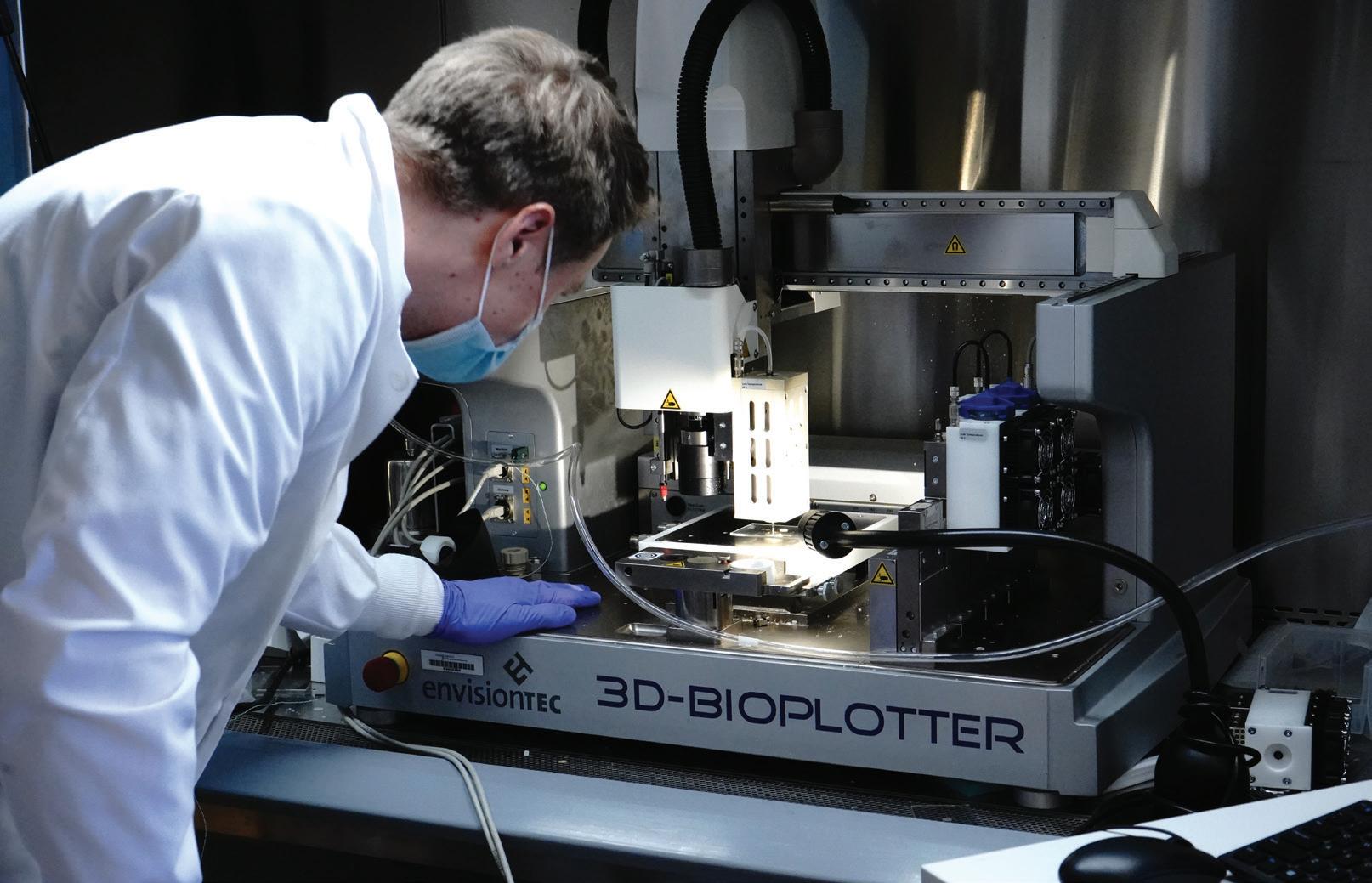
Desktop Health www.desktophealth.com