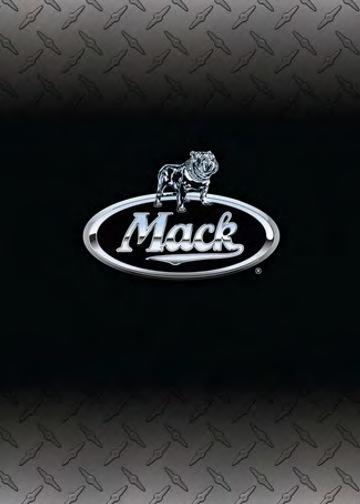

The descriptions and service procedures contained this manual are based designs and methods studies carried out March 2010.
The products are under continuous V ehicles and components produced after the above date may therefore have dif ferent specifications and repair When this believed have a significant bearing this supplementary service bulletins will issued cover the
The new edition this manual will update the service procedures where the title incorporates operation number , this a reference a Labor Code (Standard T ime).
Service procedures which not include operation number the title are for general information and reference made a Labor Code (Standard T
Each section this manual contains specific safety information and warnings which must reviewed before performing any a printed copy a procedure sure also make a printed copy the safety information and warnings that relate that The following levels cautions and warnings are used this Service Documentation:
Note: Indicates a condition that must followed order have the vehicle component function the manner intended.
Caution: Indicates unsafe practice where damage the product could occur
W arning: Indicates unsafe practice where personal injury severe damage the product could occur
Danger: Indicates unsafe practice where serious personal injury death could occur
All rights part this publication may stored retrieval transmitted any forms any recording without the prior written permission Mack T
Design and Function
Engine Control Module (ECM) 3
Board Diagnostic (OBD) Monitors 4
Engine Control Module (ECM) Diagnostic T rouble Codes (DTCs)
The manufacturer scan tool the preferred tool for performing diagnostic work. Contact your local dealer for more information visit .premiumtechtool.com” .
Note: The use a scan tool necessary perform diagnostic work well clearing any diagnostic trouble codes DTC(s) can longer cleared using the vehicles instrument cluster digital display and stalk switch
Six electronic control units (ECUs) are used; the engine control module instrument control module V ehicle Electronic Control Unit transmission control module the gear selector control module (GSCM) and the aftertreatment control module T ogether , these modules operate and communicate through the SAE J1939 (CAN data link control a variety engine and vehicle cab
The use a scan tool necessary perform diagnostic work well clearing any diagnostic trouble codes DTC(s) can longer cleared using the vehicles instrument cluster digital display and stalk switch Additional data and diagnostic tests are available when a scan tool connected the Serial Communication
For diagnostic contact your local dealer
The ECM controls such things fuel timing and delivery , fan engine protection engine brake operation, the exhaust gas recirculation (EGR) valve and the turbocharger nozzle. The VECU controls cruise control accessory relay controls and idle shutdown
The ICM primarily displays operational parameters and communicates these the other All have the capability communicate over the SAE J1587 data link primarily for diagnostics and data
The ECM a microprocessor based controller programmed perform fuel injection quantity and timing control, diagnostic fault logging, and broadcast data other ECUs. The fuel quantity and injection timing each cylinder precisely controlled obtain optimal fuel economy and reduced exhaust emissions all driving
The ECM controls the operation the engine brake EGR turbocharger nozzle and cooling fan clutch based inputs from many sensors and information received over the data links from other
addition their control the modules have board diagnostic (OBD) The OBD designed detect faults abnormal conditions that are not within normal operating parameters. When the system detects a fault abnormal condition, the fault will logged one both the memory , the vehicle operator will advised that a fault has occurred illumination a malfunction indicator lamp (MIL) and a message the driver information display , The module may initiate the engine shutdown procedure the system determines that the fault could damage the some situations when a fault the system will enter a The derate mode allows continued vehicle operation but the system may substitute a sensor signal value that may result reduced performance. some the system will continue function but engine power may limited protect the engine and Diagnostic trouble codes (DTCs) logged the system memory can later aid diagnosing the problem using a diagnostic computer through the instrument cluster display , When diagnosing intermittent DTC may necessary use a scan tool connected the Serial Communication
The VECU and ECM are dependent each other perform their specific control functions. addition switch and sensor the broadcast data between modules also includes various calculations and conclusions that each module has based the input information has
The engine control module (ECM) monitors and models (using physical principles) engine parameters monitor the engine s performance real This performed aid the ECM with its self diagnostic Many sensors are used for input the emission control
The system contains the following ECUs that are monitored;
• Engine Control Module (ECM)
• V ehicle Electronic Control Unit (VECU)
• Aftertreatment Control Module (ACM)
• Aftertreatment Nitrogen Oxides (NOx) Sensors
• Engine V ariable Geometry T urbocharger (VGT) Smart Remote Actuator (SRA)
These ECUs all communicate with the ECM via data links. The VECU communicates across the SAE J1939 (CAN1) data link while the others use the SAE J1939 - 7 (CAN2) data
The OBD systems use SAE J1939 data link protocol for communication with scan tools MACK trucks still are capable communicating via the SAE J1587 data link for The use a scan tool necessary perform diagnostic work well clearing any diagnostic trouble codes DTC(s) can longer cleared using the vehicles instrument cluster digital display and stalk switch
There are other ECUs such the Instrument Control Module T ransmission Control Module (TCM) and Anti - lock Brake System (ABS) Module that provide data the emission control system the diagnostic system but are not .
A MIL located the instrument cluster This amber colored lamp used inform the driver that a malfunction signal has
•
Pedal Position (APP) Sensor , , page 6
•
Gas Recirculation (EGR)” , page 8 •
• Injection (Aftertreatment Hydrocarbon Doser , page 6
•
Diesel Exhaust Fluid (DEF) Feedback , page 6
• Diesel Exhaust Fluid (DEF) Quality ” , page 6
•
Diesel Particulate Filter (DPF)” , page 6
Gas Recirculation (EGR) Low , page 8 • Gas Recirculation (EGR) High , page 8 •
Gas Recirculation (EGR) Slow , page 9 • Gas Recirculation (EGR) Feedback , page 9 •
• Diesel Particulate Filter (DPF) Regeneration , page 6
•
Diesel Particulate Filter (DPF) Incomplete Regeneration ” , page 6
Gas Recirculation (EGR) Cooler , page 9 • , page 9 • , page 9 • , page 9 •
•
Diesel Particulate Filter (DPF) Regeneration Feedback , page 6
• Fuel Rationality , page 7
• Non - Methane Hydro Carbons (NMHC) , page 7
• Nitrogen Oxides (NOx) Sensor(s) , page 7
• Selective Catalytic Reduction (SCR)” , page 7
• Selective Catalytic Reduction (SCR) Conversion , page 7
• Air T emperature (AA Sensor , , page 7 • Air Cooler (CAC)” , page 8 • , page 8 • V , page 8 • V entilation Diagnostic , page 8 • Control Module Rationality , page 8
• Coolant T emperature (ECT) Sensor , page 8
Rationality , page 9 • Manifold Pressure (IMP) Control , page 9 • , page • , page •, page • Brake Switch, , page • T ake - f (PT Enable , page • “SAE J1939 (CAN1) Data , page • , page • ime/Date , page • ariable Geometry T urbocharger (VGT) Feedback , page • ehicle Speed Sensor (VSS), , page •, page • ariable Geometry T urbocharger (VGT) Slow , page
The APP sensor input analog voltage signal proportional the pedal position that read the vehicle electronic control unit (VECU). The angular position the pedal divided three dif ferent areas used for fault detection and/or recovery The value that transmitted under normal
conditions (value 0 - directly proportional the s angular The physical accelerator assembly also supports a digital voltage (On/Of generated idle validation (IV) switch that also powered the same regulated reference voltage
This diagnostic based the checking the aftertreatment diesel particulate filter (DPF) intake temperature during aftertreatment DPF active parked regeneration the aftertreatment DPF intake temperature does not reach a
minimum regeneration temperature within a specified time then the aftertreatment hydrocarbon doser considered
The aftertreatment DEF control consists a feedforward control together with a feedback The feedforward control value how much urea that must injected order
obtain the demanded nitrogen oxides (NOx) conversion ficiency The feedback controls the ammonia (NH3) buf fer the aftertreatment selective catalytic reduction
Aftertreatment DEF quality evaluated and determined through conversion ficiency the aftertreatment SCR system ficiency below the specified a fault
The aftertreatment DPF collects particulate and soot a ceramic wall - flow The strategy manage the accumulation soot take advantage natural aftertreatment DPF passive regeneration whenever
and invoke operating mode that enhances aftertreatment DPF passive regeneration when necessary Aftertreatment DPF active regeneration performed using aftertreatment hydrocarbon doser
This function detects the aftertreatment DPF regeneration frequency increases a level that would cause the non - methane hydro carbon (NMHC) emissions exceed the legal limitation the frequency exceeds the design
the number aftertreatment DPF regenerations are above the threshold the end the time period a fault
The aftertreatment DPF regeneration strategy reduce the soot level the DPF using passive However , the driving conditions not enable enough exhaust heat for passive regeneration keep with the soot loading active parked aftertreatment DPF regeneration will required.
interrupted parked aftertreatement DPF regeneration detected this This not a fault mode but handled the aftertreatment the ratio between the uncompleted and completed regenerations above the specified limit, a fault reported.
This function monitors the particulate matter regeneration feedback control and detects:
• the system fails begin feedback control
• a failure deterioration causes open loop
• the feedback control has used all the allowed adjustment
When the aftertreatment hydrocarbon doser used, the feedback control monitored for a saturated controller a saturated actuator A saturated controller actuator means that all allowed adjustment has been used The monitors detect a malfunction the controller saturated more than a given percentage the time and the target temperature can
not reached the actuator saturated more than a given percentage the time.
http://manualplace.com/download/man-ecm-dtc-truck-guide-manual-actros-etc/
The aftertreatment fuel system consists a aftertreatment fuel shutof f valve, a separate aftertreatment hydrocarbon doser (injector), and aftertreatment fuel pressure sensor . The aftertreatment fuel shutof f valve diagnostic function look the aftertreatment fuel pressure when the valve opened and When conditions are proper for the the function requests opening the aftertreatment fuel shutof f valve order pressurize the aftertreatment fuel
This action should increase system When the aftertreatment fuel shutof f valve closed the system pressure should decrease since the valve has internal drain pipe that constantly depressurizes the For more information about these components refer Fuel Pressure Sensor , Circuit , page , Fuel Shutof f V Circuit , page Hydrocarbon Doser , Circuit , page
T o detect when the hydrocarbon conversion fails the aftertreatment diesel oxidation catalyst the temperature reaction the aftertreatment DOC outlet monitored when fuel injected the exhaust. The amount hydrocarbon supplied the aftertreatment hydrocarbon doser will determine the expected increase temperature after the aftertreatment The aftertreatment hydrocarbon doser
injection rate (duty cycle) monitored and used calculate whether there should a corresponding heat Once has reached acceptable accumulated duty cycle the expected temperature dif ference can calculated. This dif ference should then above a certain limit the hydrocarbon conversion was
The NOx sensors consist of:
• Housing holding the sensing
• electronic control unit interfacing the sensor and the engine control module
• A electrically connecting the sensing element with the ECU.
There are two aftertreatment NOx one before and one after the aftertreatment selective catalytic reduction (SCR)
Aftertreatment NOx sensor diagnostics monitor the sensors signal quality and The purpose this function detect the
• Bad signal quality
• Removed sensor
• Missing signal
Circuit integrity the aftertreatment NOx sensor checked the sensor itself and the status transmitted the engine control module (ECM) over the CAN data The following can
The aftertreatment NOx sensor before and after SCR catalyst have unique CAN identification numbers hence can not The sensor before the SCR catalyst monitors the engine out NOx The sensor after SCR monitors system out NOx
• open circuit
• high voltage
• circuit low high
The aftertreatment SCR system a catalyst system that used reduce exhaust Nitrogen Oxides (NOx) emissions. This reduction performed injecting diesel exhaust fluid (DEF) urea solution) into the exhaust fumes prior the aftertreatment SCR A chemical process performed aftertreatment SCR catalyst and DEF , converts NOx
The aftertreatment SCR catalyst diagnosis calculates the low temperature performance the aftertreatment SCR system and compares the performance when the catalyst warm enough reach high nitrogen oxides (NOx)
nitrogen oxide (NO) and water The aftertreatment control module (ACM) used control the aftertreatment SCR components and relays system information the Engine Control Module The ECM controls the overall system
This based the premise that a deteriorated catalyst can considered a catalyst with less The volume critical reach the low temperature performance the aftertreatment SCR
The T sensor analog input that read the instrument cluster electronic control unit. The instrument cluster processes the raw signal and transmits the T value the SAE J1939 data The vehicle electronic control unit (VECU) receives the T value and based certain vehicle conditions the value The VECU then transmits
the T value back the SAE J1939 data link where received the engine control module (ECM).