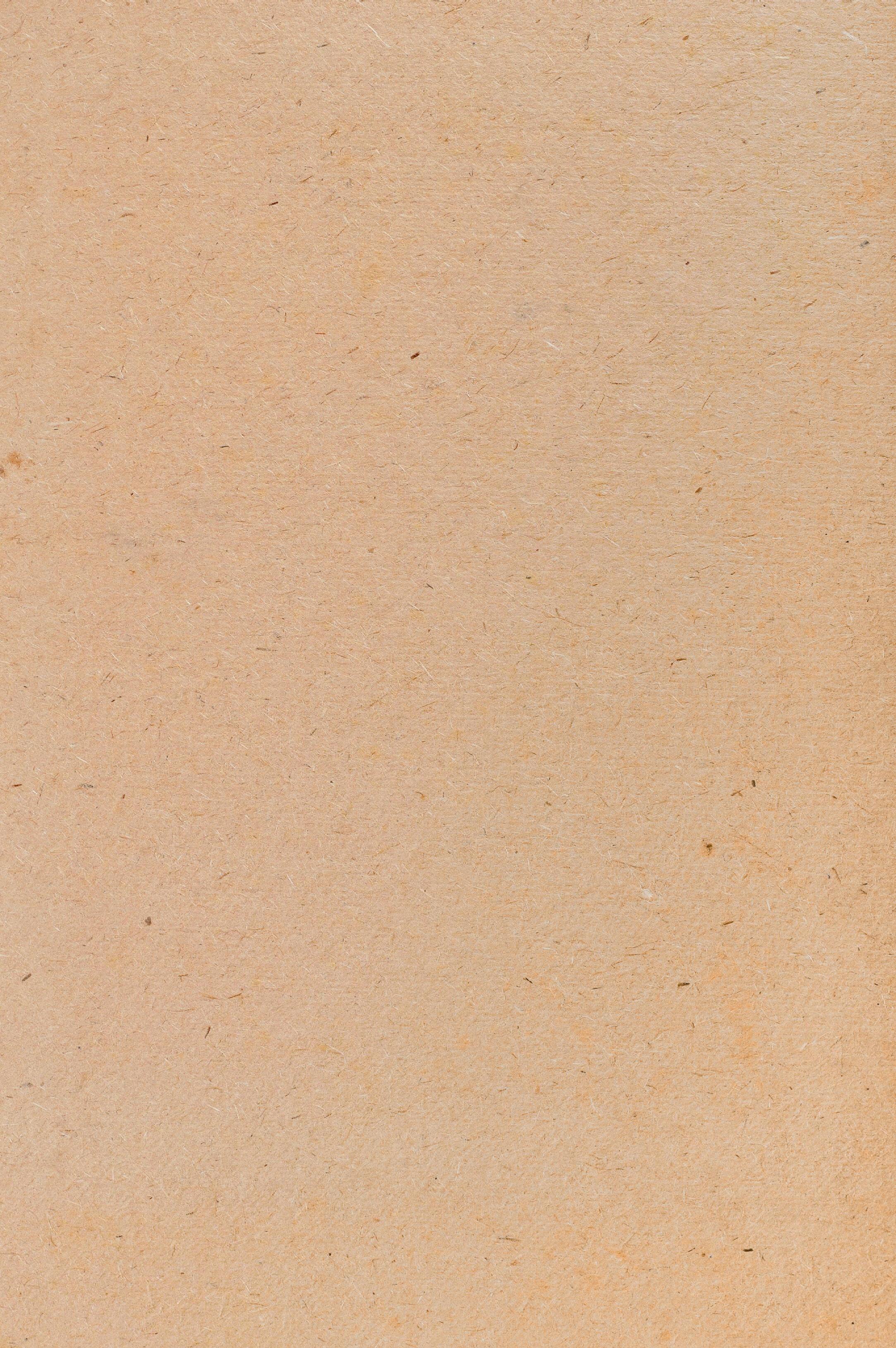
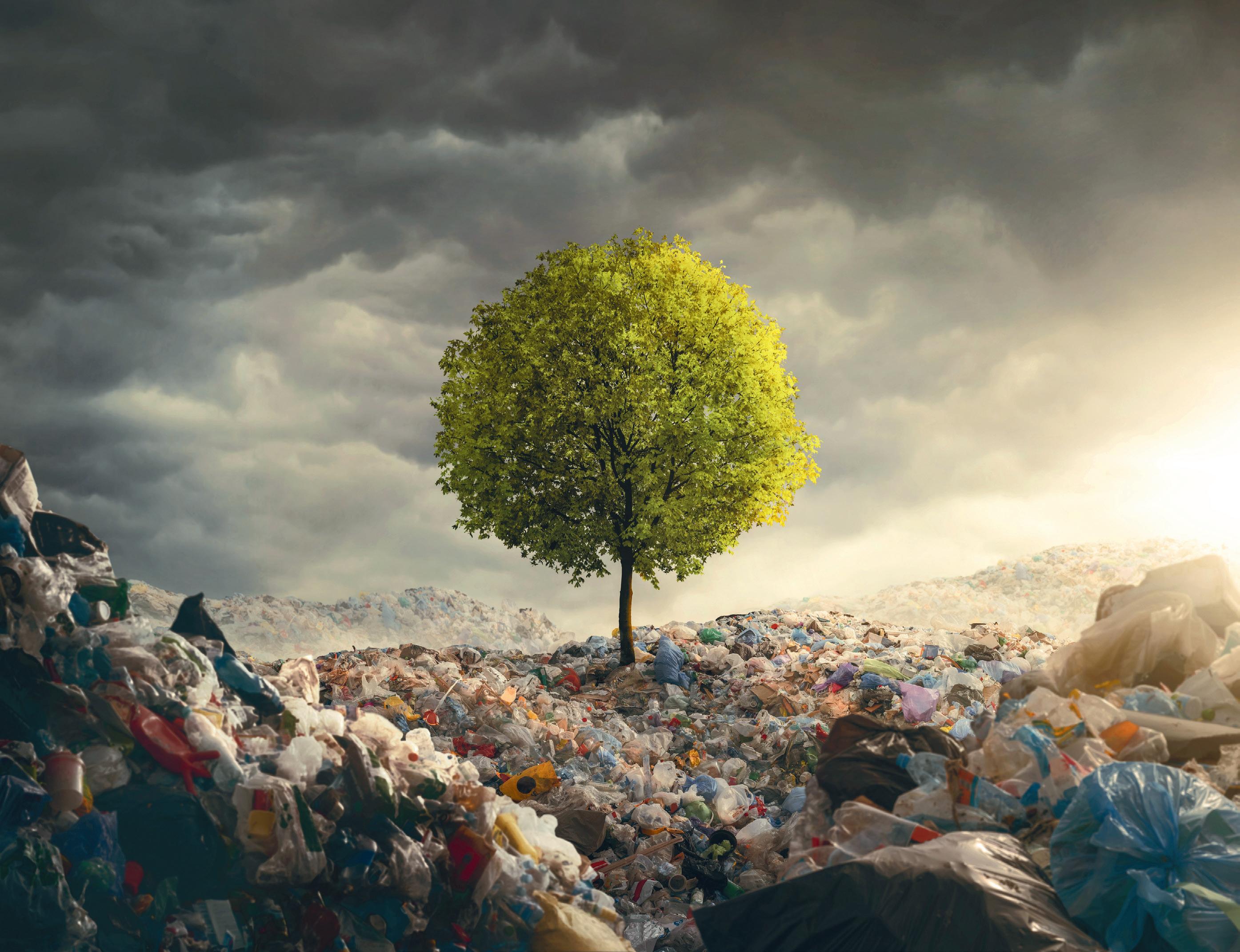
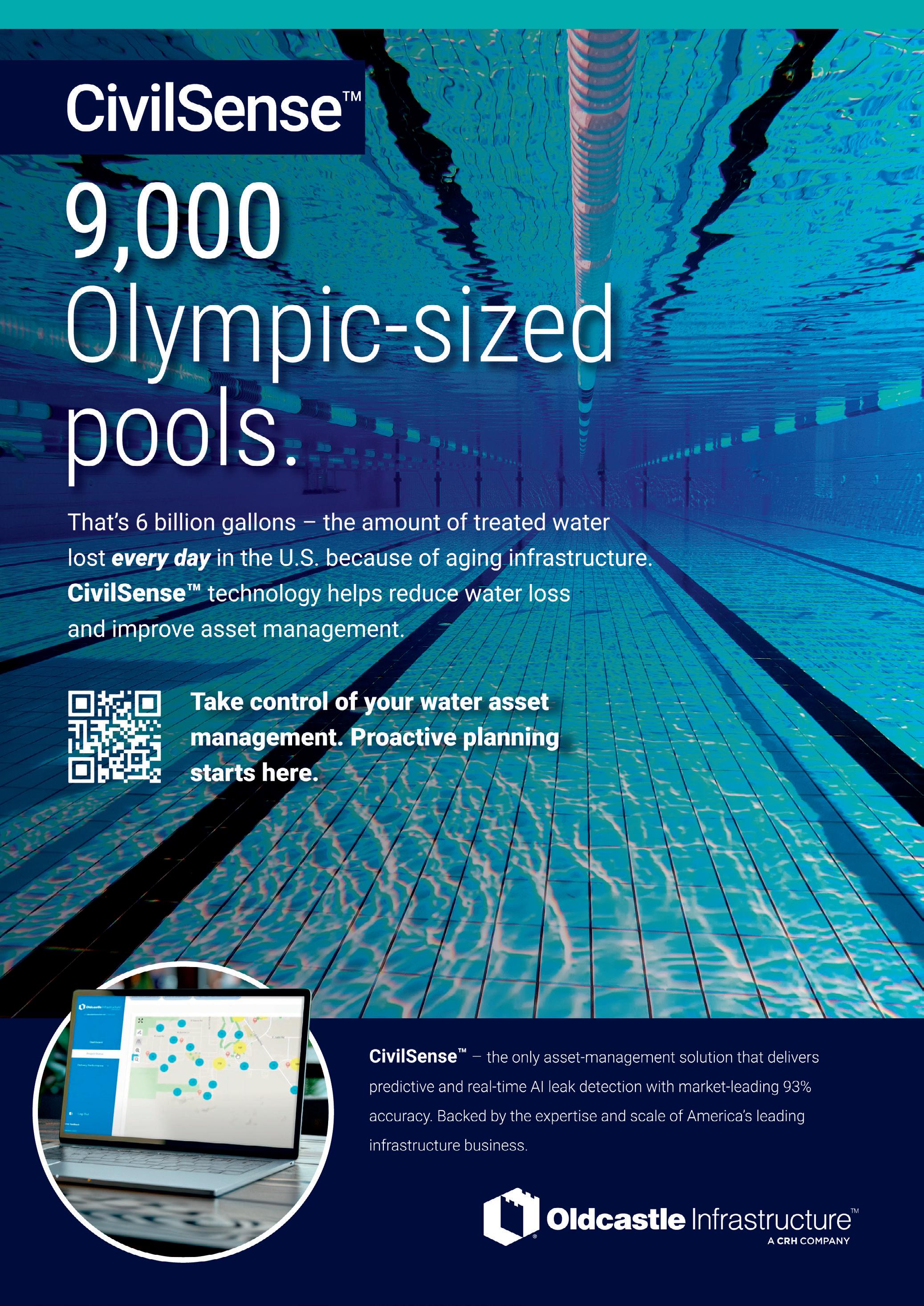
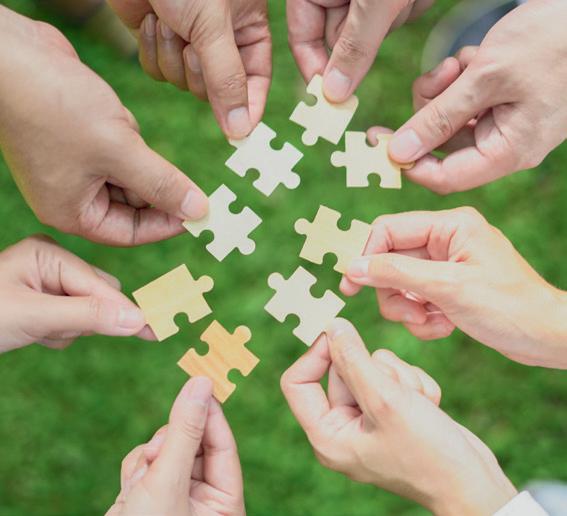
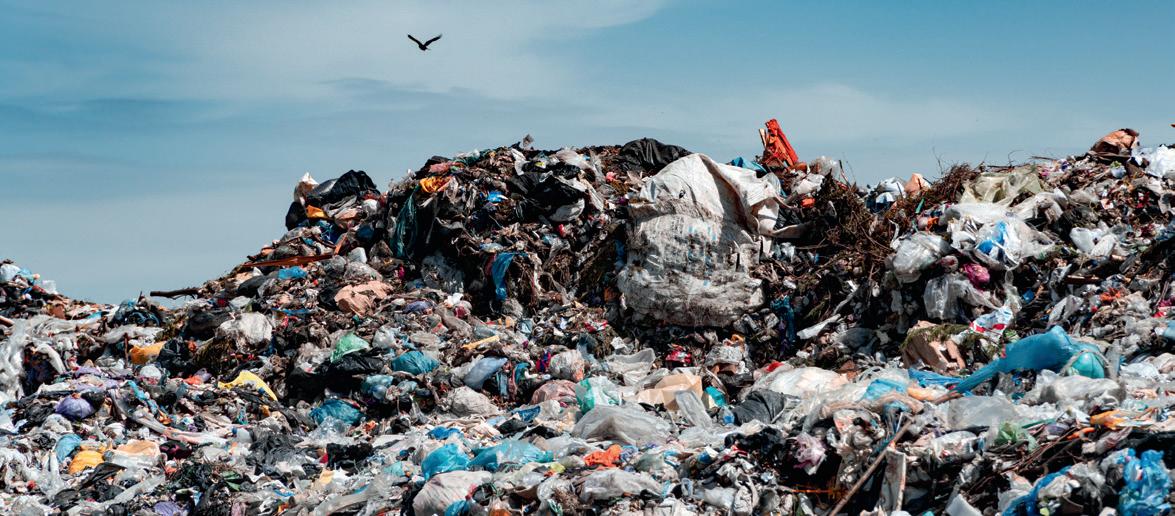
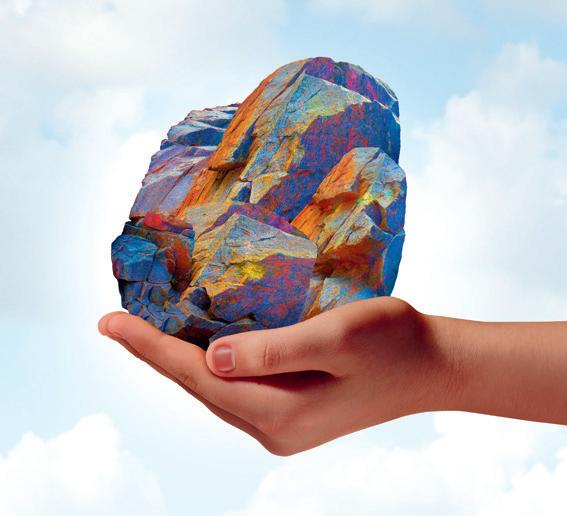
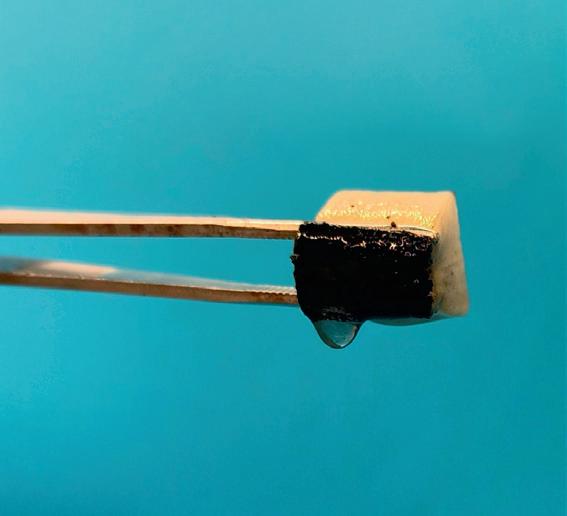
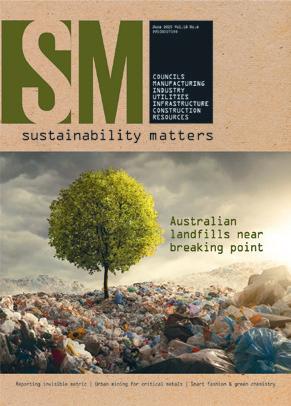
Every year, over a trillion dollars’ worth of food is wasted globally, which accounts for approximately 24% of all food produced. This waste not only represents a significant loss in food production but also contributes to pollution. If food waste was classified as its own category, it would rank as the third-largest emitter of greenhouse gases.
There has been considerable discussion about sustainable packaging as a strategy to reduce waste sent to landfills. However, if designed correctly, smart packaging could enhance food safety and help reduce the amount of food wasted in landfills.
According to the AIP, we need to shift our approach and create optimal packaging to minimise food loss. The ideal packaging solution varies for each product, as underpacking leads to food waste while overpacking results in excess packaging waste. Thus, achieving optimal design is essential.
With Australian cities facing landfill capacity issues by 2030, Mike Twemlow, Senior Sustainability Manager at Edge Impact, shares his insights on the main contributors to this problem. He discusses how packaging reform and stricter compliance measures may provide solutions. Additionally, don’t miss the case study on page 20, which explores how a smart fashion factory of the future could also help reduce waste sent to landfills.
We also examine a pioneering environmentally responsible process developed by two researchers at Monash University for extracting rare earth elements from secondary resources. Find out more about this innovative urban mining method on page 8.
Head Office Unit 5, 6-8 Byfield Street, (Locked Bag 2226) North Ryde BC NSW 1670, AUSTRALIA Ph: +61 2 9168 2500
If you have any queries regarding our privacy policy please email privacy@wfmedia.com.au
Editor
Carolyn Jackson sm@wfmedia.com.au
Assistant Editor Kylie Baracz
Publishing Director/MD Janice Williams
Art Director/Production Manager Linda Klobusiak
Art/Production Marija Tutkovska
Circulation
Alex Dalland circulation@wfmedia.com.au
Copy Control
Ashna Mehta copy@wfmedia.com.au
Advertising Sales
Tim Thompson Ph: 0421 623 958 tthompson@wfmedia.com.au
All material published in this magazine is published in good faith and every care is taken to accurately relay information provided to us. Readers are advised by the publishers to ensure that all necessary safety devices and precautions are installed and safe working procedures adopted before the use of any equipment found or purchased through the information we provide. Further, all performance criteria was provided by the representative company concerned and any dispute should be referred to them. Information indicating that products are made in Australia or New Zealand is supplied by the source company. Westwick-Farrow Pty Ltd does not quantify the amount of local content or the accuracy of the statement made by the source.
Major Australian cities are said to be heading towards landfill capacity by 2030, with fast fashion seen as one of the main culprits. Australian sustainability consultancy Edge Impact said this kind of waste is partly why the federal government will strengthen its packaging reforms in Australia — with businesses forced to comply or face hefty fines.
Edge Impact, an RSK company, predicts that new national regulations will apply to all companies trading in Australia — from global e-commerce platforms to homegrown brands. It said these businesses will be required to overhaul their entire approach to their packaging ecosystem, with every step needing to be reviewed, from product design and material selection to consumer disposal and recycling, to ensure each component is sustainable and resource efficient.
Landfills across Australia are said to be fast approaching crisis levels. Perth is the most critical and expected to reach capacity this year. Melbourne’s Hampton Park is said to reach capacity by 2028, Sydney by 2030, and Brisbane’s is also stretched with the Council of Mayors (SEQ) aiming to target a diversion of one million tonnes of landfill waste by 2030. Adding to the problem is ‘wishcycling’ — the well-intentioned but incorrect recycling
of materials. Confused consumers often throw non-recyclable packaging into the recycling bin, contaminating entire batches and contributing to approximately 21% of the recycling materials sent to landfill.
“We’re dealing with a public awareness gap,” said Mike Twemlow, Senior Sustainability Manager at Edge Impact. “Many consumers believe they’re doing the right thing, but inconsistent labelling and nonrecyclable materials make proper disposal impossible. This is why businesses must go beyond compliance and invest in clear, packaging instructions to help consumers correctly dispose of waste.”
The government’s new mandatory packaging regulations are on the horizon, which will require businesses to comply with mandatory sustainability standards. The new regulations will likely include design standards to ensure all packaging is recyclable or compostable, minimum recycled-content requirements to reduce reliance on virgin plastics, bans on harmful chemicals in packaging materials and even eco-modulated fees where businesses are charged based on their environmental impact.
The reforms, which aim to cut waste, are also key to moving Australia towards a packaging circular economy.
“A circular economy is about breaking the ‘take, make, waste’ model that dominates our
supply chains,” Twemlow said. “It’s about creating closed-loop systems where packaging can be reused, repurposed or fully recycled without degradation.”
With these new regulations on the way, Twemlow said that businesses can no longer afford to delay action.
“At the least, businesses should be complying with current APCO sustainable packaging guidelines,” he said. “This will make it easier for businesses when the tough reforms are in play. Businesses need to audit their packaging materials, redesign wasteful supply chains, and clearly label products to eliminate consumer confusion. Otherwise, they’ll be left scrambling when these regulations take effect.
“Fast-product platforms are fuelling a disposable culture that Australia simply cannot sustain. But any company using non-recyclable packaging is at risk. The government is done waiting, it’s only a matter of time before the compliance crackdowns are here.”
Mike Twemlow, Senior Sustainability Manager at Edge Impact. With expertise in circular economy strategies, waste minimisation and regulatory frameworks, Edge Impact works with companies to design sustainable packaging solutions that meet Australian and global compliance standards while reducing environmental impact.
Alexey Lebedev, VP Pacific, AVEVA
In April, we witnessed one of the more heated climate change conferences on record — not in terms of temperature, but debate. Australia seemingly rejected the nuclear overtures of its allies as it aims to continue to focus on solar, wind and other renewables. Meanwhile, the nation has begun developing its 2035 Nationally Determined Contribution (NDC) — effectively its new emissions reduction target — after COP30 host Brazil and other nations introduced theirs.
In short, there’s a lot left to discuss, legislate and more in the coming 12 months. But what’s not up for debate is the need for, and importance of, data, particularly with the requirement for environmental, social and governance (ESG) reporting foisted upon industry.
Since 1 January this year, Australia’s largest organisations have been required to deliver mandatory climate-related reporting, including disclosures on climate-related risks and opportunities, and on greenhouse gas emissions across the value chain. This will soon begin for medium-sized companies as well.
The legislation also includes a phased-in approach for Scope 3 reporting, allowing companies an extra year from the beginning of their disclosure requirements to report on the quantity of their indirect value chain emissions, in addition to three years of protection from litigation concerning Scope 3 disclosures.
The challenge many businesses face is quite apparent: how does one measure emissions? When reporting on financials, that’s simple, at least relatively speaking, compared to emissions reporting: it’s a paper trail of purchases, receipts and more, including pipeline of business and other metrics. In effect, everything is recorded – and it’s a matter of collating everything from there — with experts in finance teams now having perfected it into a fine art.
But how does one measure an emission, let alone tons of them? And when we get
down to Scope 3 emissions, how do we apply this to the entire value chain?
Again — and this is not to minimise the challenge organisations face — but it comes down to the data. And the ability of experts to record and report on emissions has improved immensely as the need to report on these data becomes ever more important.
We’re now able to accurately determine how energy-efficient various technologies are, their carbon footprint and more. The issue for businesses is that their systems are so vast — but with the right systems in place, these emissions can be recorded in the background.
AGL is one such example — it is leveraging a thermodynamic performance-optimisation system, which aims to reduce fuel consumption by 0.5% and reduce CO2 emissions, a marginal improvement that translates to savings of millions of dollars per year. The second is a wind-yield-optimisation system, which targets a 1–2% increased yield in AGL’s wind portfolio.
In addition, with the right technologies in place, organisations can more easily connect their systems to speak to each other, which not only helps to record emissions, but to reduce emissions and the silos within organisations and with their partners.
For example, Talison Lithium is one of the largest lithium producers in the world with complex processes, multiple plants and sites, and many data sources. To address this level of complexity and scale, it created a unified system with cloud capabilities for production reporting and tracking from pit to port. This integration has resulted in reduced downtime and increased end-of-month reconciliation efficiency and accuracy.
Organisations can also use digital twins, which are, in short, a virtual representation that serves as the real-time digital counterpart of a physical object or process. There are two types of digital twin: the engineering digital twin helps companies optimise the design and build of a new plant with energy
efficiency and sustainability in mind, while the operational digital twin is focused on building a replica of operations to streamline efficiencies including energy usage.
Leveraging both ensures businesses can improve every stage of the operational life cycle, ranging from improved design fidelity and decision-making to optimised construction and management. This ultimately helps organisations make more informed decisions that can help them achieve their sustainability goals as they are able to model site operations or energy usage via the digital twin.
When it comes to ESG reporting, having a consolidated holistic view of data inputs, inclusive of emissions, helps organisations harness their data and make accurate analysis in line with legislative requirements.
The point is that there are methods to report on something that, to the naked eye, is invisible — but an emission, ultimately, is another data point that now can and must be recorded.
We’re heading into an election year and much may change — but what is certain is that reporting on our emissions is to begin — and organisations need to prepare for the new standard.
If organisations don’t get on the front foot on this, the fines could be immense, and the pressure from an increasingly environmentally conscious public will be equally immense. But empowered with the right data and tools at their fingertips, the people charged with undertaking such a monumental task will eventually see the ESG reporting mountain as a proverbial molehill in the end, all while helping their businesses become more efficient and sustainable.
Rare earth elements (REEs) — comprising the 15 lanthanides, along with scandium and yttrium, are essential to modern technology. Often described as the “vitamins of the 21st century industry”, these metals play a critical role in sectors ranging from renewable energy and national defence to semiconductors and consumer electronics, including smartphones and electric vehicles. The global REE market is currently valued at approximately US$12 billion, with a projected compound annual growth rate (CAGR) of 12.3%, reflecting their increasing strategic and economic importance.
For decades, a handful of countries has maintained a dominant position in the global supply chain, accounting for approximately 70% of worldwide production. However, recent geopolitical tensions and trade disputes have exposed the fragility of this dependence, prompting a re-evaluation of global sourcing strategies. The strategic importance of these materials has rendered their supply highly politicised and increasingly monopolised by a limited number of processing nations, underscoring the urgent need for diversified and resilient supply chains.
Australia plays a pivotal role in this landscape, accounting for 5.14% of global REE production and holding around 4% of the world’s reserves. It ranks as the fourthlargest producer after China, the United States and Myanmar. China continues to dominate the midstream and downstream segments of the value chain, controlling nearly 90% of global refining capacity and over 50% of downstream applications.
The extraction and separation of rare earth elements demand advanced technical expertise and sophisticated infrastructure, rendering it a high-barrier industry. In response, resource-rich nations such as
Australia are prioritising the development of independent processing capabilities to reduce strategic vulnerabilities. The Australian Government, under Prime Minister Anthony Albanese and supported by the Hon. Madeleine King (Minister for Resources and Minister for Northern Australia), has committed AU$22 million to advance domestic REE processing infrastructure.
Currently, global demand is met primarily through the commercial mining of rare earth-rich ores. However, these resources are finite and insufficient to sustain long-term demand, with projections suggesting only two to three decades of viable production at current rates. This raises two critical questions: what volume of REEs is available in national stockpiles? And how can Australia safeguard its economic interests in an increasingly competitive global landscape?
In a volatile, uncertain, complex and ambiguous world, national self-sufficiency and resource sovereignty are paramount. It is therefore imperative to conserve Australia’s limited natural endowment while strategically diversifying supply chains, investing in technological innovation and embedding circularity into resource management systems.
Motivated by the imperative to develop sustainable critical mineral supply chains, two researchers at Monash University have pioneered an environmentally responsible process for extracting REEs from secondary resources. These secondary resources — comprising end-of-life products and legacy
industrial waste — form the basis of what is known as urban mining. Bennet Thomas and Professor Sankar Bhattacharya, from the Department of Chemical and Biological Engineering, have developed a novel, provisionally patented process that recovers REEs from mine tailings, coal fly ash and electronic waste. Their approach integrates first principles of thermodynamics and mass and energy balance to achieve high extraction efficiencies across all 17 REEs, while significantly reducing environmental impact.
In their recent publication in Hydrometallurgy and Journal of Environmental Chemical Engineering, the researchers demonstrate the viability of using coal fly ash — a low-cost, abundant waste by-product — as a feedstock for REE recovery. In Victoria alone, approximately 1.3 million tonnes of brown coal fly ash have been generated annually since the late 19th century, much of it stored in ash dams. Remarkably, the REE concentrations in some of these ashes are comparable to
those found in commercially mined ores, yet without the radioactive by-products typically associated with uranium and thorium found in REE mineral ores. This makes urban mining not only environmentally advantageous but also commercially compelling.
Their process has the potential to produce an additional 45,000 tonnes of REEs per year from coal fly ash alone — more than double of Australia’s total REE output in 2021 (19,958 tonnes), and nearly one-third of China’s production (~152,407 tonnes), the current global leader. This innovation could position Australia to play a transformative role in reshaping the global rare earth supply chain.
The process technology developed by Thomas and Bhattacharya represents an engineering breakthrough, with laboratoryscale results demonstrating good efficiency in REE recovery. Initially developed at a 100 mL reaction scale, the team has scaled the process to 30 L with over 90% extraction of rare earth metals into leachate. The work has won Thomas a prestigious Victorian Royal Society Young Scientist prize. Further processing of leachate has so far resulted in 40% separation of selected rare earth metals. The team is currently finalising the engineering design for continuous operations at the 100-litre scale with plans to construct a demonstration facility at Monash University, marking a critical step towards commercialisation. The results will enable credible economic analysis.
At this pivotal stage, the researchers are actively seeking engagement with investors and government stakeholders to initiate strategic dialogues. The team is collaborating with multiple partners to advance the technology and facilitate its deployment within Australian markets, contributing to national efforts to build a resilient and sovereign rare earth supply chain.
New membranes made at the University of Michigan (U-M) could help desalination plants minimise or eliminate brine waste produced as a by-product of turning seawater into drinking water.
Currently, liquid brine waste is stored in ponds until the water evaporates, leaving behind solid salt or a concentrated brine that can be further processed. But brine needs time to evaporate, giving it a chance to potentially contaminate the groundwater.
For every litre of drinking water produced at a typical desalination plant, 1.5 litres of brine is produced. According to a UN study, over 37 billion gallons of brine waste is produced globally every day. When there is no space for evaporation ponds, desalination plants inject the brine underground or dump it into the ocean. Increasing the salt levels near desalination plants is a problem as it can harm local marine ecosystems.
To eliminate brine waste, desalination engineers would like to concentrate the salt so it can be easily crystallised in industrial vats rather than ponds that can occupy over a hundred acres. The separated water could be used for drinking or agriculture, while the solid salt could then be harvested for useful products.
Seawater not only contains sodium chloride — or table salt — but valuable metals such as lithium for batteries, magnesium for lightweight alloys and potassium for fertiliser.
“There’s a big push in the desalination industry for a better solution,” said Jovan Kamcev, U-M Assistant Professor of Chemical Engineering and the corresponding author of the study published in Nature Chemical Engineering . “Our technology could help desalination plants be more sustainable by reducing waste while using less energy.”
Desalination plants can concentrate brines by heating and evaporating the water, which is energy intensive, or with reverse osmosis, which only works at relatively low salinity. Electrodialysis is said to be a suitable alternative because it works at high salt concentrations and requires relatively little energy. This process uses electricity to concentrate salt, which exists in water as charged atoms and molecules called ions.
Water flows into many channels separated by membranes, and each membrane has the opposite electrical charge of its neighbours. The entire stream is flanked by a pair of electrodes. The positive salt ions move towards the negatively charged electrode, and are stopped by a positively charged membrane. Negative ions move towards the positive electrode, stopped by a negative membrane. This creates two types of channels — one that both positive and negative ions leave and another that the ions enter, resulting in streams of purified water and concentrated brine.
However, electrodialysis has its own salinity limits. As the salt concentrations rise, ions start to leak through electrodialysis membranes. While leak-resistant membranes exist on the market, they tend to transport ions too slowly, making the power requirements impractical for brines more than six times saltier than average seawater.
The researchers overcome this limit by packing a record number of charged molecules into the membrane, increasing their ionrepelling power and their conductivity — meaning they can move more salt with less power. With their chemistry, the researchers can produce membranes that are 10 times more conductive than relatively ‘leak-proof’ membranes on the market.
The dense charge ordinarily attracts a lot of water molecules, which limits how much charge can fit in conventional electrodialysis membranes. The membranes swell as they absorb water, and the charge is diluted. In the new membranes, connectors made of carbon prevent swelling by locking the charged molecules together.
The level of restriction can be changed to control the leakiness and the conductivity of the membranes. Allowing some level of leakiness can push the conductivity beyond today’s commercially available membranes. The researchers hope the membrane’s customisability will help it take off.
“Each membrane isn’t fit for every purpose, but our study demonstrates a broad range of choices,” said David Kitto, a postdoctoral fellow in chemical engineering and the study’s first author. “Water is such an important resource, so it would be amazing to help to make desalination a sustainable solution to our global water crisis.”
Opal, a recycling, paper and packaging business, has partnered with textile recycling expert BlockTexx to recycle its company’s uniforms.
BlockTexx’s technology recovers valuable fibres from end-of-life textiles, transforming them into new materials that can be used in a variety of applications.
The initiative will see old and unused uniforms from Opal’s Paper & Recycling Botany Mill collected and recycled, reinforcing the company’s commitment to sustainability.
As part of the pilot program, a 660 L container of uniforms has already been collected from Botany Mill team members. These uniforms will undergo BlockTexx’s textile recycling process, which breaks down garments into reusable fibres.
Environment, Testing and Management Systems Manager at the Botany Mill Karen Jones said the partnership shows how businesses can play a pivotal role in addressing the environmental challenges posed by textile waste.
“Opal’s Botany Mill is one of Australia’s largest and most advanced cardboard recycling operations, and over the years we’ve implemented processes to support a circular economy and close the loop in our operations,” Jones said. “By partnering with BlockTexx to give our uniforms a new life, we are extending our waste reduction and recycling efforts beyond the production line.”
Opal hopes that the partnership with BlockTexx will inspire other organisations to explore similar solutions for their own workplace waste.
“We’re thrilled to be working with the Botany Mill on this exciting initiative,” said Adrian Jones, BlockTexx co-founder.
“It’s fantastic to see a major manufacturer in the paper and packaging industry taking proactive steps to further reduce its waste and demonstrate leadership in sustainability. This initiative not only helps divert textile waste from landfill but also shows how textile recycling can be an integral part of corporate responsibility.”
Opal
www.opalanz.com
Chris Cummings, Smart Water Consultant, Digital Water Market, Oldcastle Infrastructure
Nearly 40 million people — roughly 12% of the U.S. population — rely on the Colorado River for water. This iconic river, which stretches across seven states, supports irrigation, generates power, and serves as a vital source of drinking water. Yet its flow has diminished by about 20% over the past century — a seemingly modest decline that carries significant consequences. A mere 10% reduction in flow jeopardizes $1.4 trillion in economic activity.
Three critical factors compound the challenges facing the Colorado River: overdependence, climate change, and aging infrastructure. Together, they create a pressing need for innovative water management solutions as water scarcity becomes a growing regional crisis.
The impacts of water scarcity are particularly visible in states like Arizona and California. A 2023 Arizona Department of Water Resources report predicted a groundwater shortage of 4.6 million acre-feet over the next century. For perspective, one acre-foot of water can support up to three households for a year, depending on the community. This looming shortfall could disrupt new development approvals in the Phoenix metropolitan area, home to 4.6 million people, unless alternative water sources are secured.
California faces similar challenges. The 2023 State Water Project Delivery Capability Report estimated that by 2043, the state’s water delivery capacity could decline by 23% due to shifting water flow patterns and extreme weather events. This reduction — equal to 496,000 acre-feet annually — represents enough water to supply 1.7 million homes for a year.
Beyond shortages, water loss due to leaks, theft, or metering inaccuracies — referred to as Non-Revenue Water (NRW) — exacerbates the crisis. Worldwide, approximately 35% of treated drinking water is lost each year as NRW. In the U.S. alone, six billion gallons of treated water are wasted daily, adding up to two trillion gallons annually. This staggering loss of resources costs municipalities around $8 billion every year, according to the American Society of Civil Engineers (ASCE).
Aging infrastructure further compounds the issue. The Environmental Protection Agency (EPA) estimates that $625 billion will be needed over the next two decades to address deteriorating drinking water systems. Leaks and inefficiencies drive up costs for utilities, hampering their ability to invest in critical infrastructure upgrades. The burden often falls on consumers, as utilities are forced to raise rates, adding financial pressure on households and businesses.
To address these challenges, Oldcastle Infrastructure has developed CivilSense™, a cutting-edge water infrastructure asset management solution that combines advanced artificial intelligence with decades of expertise. CivilSense uses network and acoustic data to identify leaks and predict pipe failures before they occur, offering municipalities a proactive and sustainable way to improve their water management. By leveraging datadriven insights, this solution helps cut operational costs, prevent major line breaks, and reduce water loss effectively, making it an invaluable tool for communities struggling with water scarcity.
CivilSense is particularly impactful as municipalities face staffing shortages, skill gaps due to retirements, and tight budgets that hinder necessary repairs. By providing a scalable and efficient solution, water utilities can mitigate resource loss and plan for the future with greater confidence.
Forward-thinking communities are seeking ways to cope with water scarcity today with innovative measures like CivilSense. Consider Bartow County, a community about 50 miles north of Atlanta that buys about 95% of its water from neighboring cities and counties.
In an Oldcastle Infrastructure pilot program, CivilSense analyzed the water distribution network and identified nine separate leaks, varying from small (1–4 gallons per minute) to medium (5–9 gallons per minute) and large (more than 10 gallons per minute). Of the nine, two were small, three were medium, and four were large. The total water lost from these nine leaks totaled 83 gallons per minute, which translates to nearly 120,000 gallons a day or 43 million gallons per year.
“Repairing small leaks that are three-to-five gallons per minute may not sound exciting, but having the ability to fi nd and fi x leaks before they create more damage is a much more proactive and less costly approach,” said Lamont Kiser, director of Bartow County Water. “Our proactive approach is working for Bartow County and our citizens.”
Water scarcity is no longer a distant threat — it’s a presentday reality demanding action. With CivilSense, municipalities of all sizes can adopt smarter water management practices to protect their most vital resource. As the challenges grow, so do the opportunities to innovate and secure a sustainable water future for future generations.
Specializing in software solutions and go-to-market strategy, Chris Cummings is dedicated to advancing sustainable water management technologies.
Oldcastle Infrastructure www.oldcastleinfrastructure.com
Sydney Water has removed over 300,000 kg of debris and rubbish from Sydney’s waterways during a week-long operation to prevent flooding, protect fish populations and maintain the health of connected waterways.
The heritage-listed stormwater basin in Sydenham, known as ‘The Pit’, holds stormwater as part of Sydney Water’s extensive network. It is a large-scale trap which prevents silt and waste from polluting connected waterways, such as Cooks River, and the surrounding biodiverse environments.
The Pit is located next to Sydenham Station and its sandstone walls and pumping station were constructed in the 1940s.
Sydney Water’s Integrated Stormwater Team Manager, Robert Allen, said emptying The Pit was crucial, taking a crew of more than 10 people armed with trucks and excavators over a week to complete.
“This project has seen the equivalent of 4100 wheelie bins’ worth of silt and debris removed from The Pit. Considering we undertake this project every two years, this is a substantial volume of debris,” Allen said. “During heavy rain events like we are currently experiencing, this proactive work at The Pit has been crucial to help protect the nearby areas and waterways from flooding due to the massive volume of water in our stormwater network.
Overlay of sediment.
“For example, during a heavy rain event in 2022 we saw The Pit reach nearly 40% capacity — this is the fullest it has been in recent years. Thanks to this emptying work the teams have just completed, we are just above 20% capacity despite the huge deluge that has been battering Sydney this week.”
The Pit temporarily holds water from the Marrickville West channel before slowly pumping it to the Marrickville East channel, draining into the Cooks River. The presence of silt in The Pit decreases its storage capacity, increasing the risk of flooding during heavy rain
events. If the material moves further downstream, it could block other channels and impact aquatic habitats.
“Imagine every piece of rubbish, dust and dirt you see on the roads and in the gutters around your area ... all which is destined to end up in our stormwater channels eventually, as it washes down the stormwater drains you see on the side of the road,” Allen said. “Those drains ... mainline to our beautiful waterways and The Pit help us to clear some of the mess and protect our waterways as stormwater goes on the next stage of its journey.”
Emptying The Pit is a delicate operation involving a variety of pumps, a combination jet-vac truck, front-end loaders, posi tracks, excavators, and various additional trucks and trailers. It is heavily weather-dependent, as trucks risk being trapped in The Pit if there is sudden flooding.
The Pit holds 100,000,000 L of water at capacity. Creating an environment where it can hold stormwater without being impeded by silt and debris is said to be of great benefit to the surrounding area.
“The Pit has been operational for 80 years and is like a big bathtub, holding stormwater back and keeping it in the catchment so it doesn’t all flow into the channel at once and flood areas nearby,” Allen said. “It plays a big part in protecting the area and, by cleaning it out, we can increase the capacity of The Pit. This means it can hold even more stormwater if there is a big weather event.”
There are over 70 stormwater catchments managed by the Integrated Stormwater team at Sydney Water, including approximately 80 gross pollutant traps (GPTs), which catch rubbish in waterways so it can be removed from the environment.
“We see a lot of single-use plastic drink bottles and takeaway containers in the GPTs, demonstrating the personal impact of everyone’s litter disposal on our waterways,” Allen said. “The public can greatly impact the preservation of areas like the Cooks River by making little changes such as disposing litter appropriately.”
Sydney Water said that emptying The Pit is very important for the waterways which snake through Greater Sydney. Clearing these materials helps to prevent erosion and flooding downstream, and preserves the delicate ecosystems depending on the waterways to survive.
“So many people are surprised when they realise the huge structure they have been passing while on the train serves such an important role. It’s a very interesting piece of history in the area,” Allen said. “Removing this rubbish and sediment greatly impacts the creatures who call the Cooks River home, with the clarity of the Cooks River directly corresponding to the work done at The Pit.
“Too much sediment from these built-up areas can really choke up the waterways and create an uninhabitable environment where not enough sunlight is getting through, and this murkiness can directly impact fish populations.”
South Australia’s Nepenthe Wines has introduced fully removable aluminium tearaway capsules across all its still wines — a permanent shift aligned with World Environment Day 2025.
The new closure system, developed by packaging supplier Interpack, features a split-design capsule that can be easily separated from the glass bottle. Traditional wine sleeves are often missed during recycling due to poor separation, meaning many end up in landfill despite being made of infinitely recyclable aluminium.
“With something like aluminium, the recycling potential is enormous, but only if it’s sorted properly,” said Tamar Bourke, Senior Brand Manager at Nepenthe. “By making the cap fully removable and guiding people on what to do, we’re making the sustainable choice the easy one.”
With around 75% of all aluminium ever produced still in use today, proper sorting is essential to maximise its environmental benefit. Yet many Australians don’t realise wine closures affect the recyclability of the entire bottle.
“We knew our packaging could do more,” Bourke said. “When we reviewed our life cycle impact, closures stood out as a key area for improvement. CAPR offered a low-cost, practical solution that made a tangible difference without compromising wine quality.”
The decision followed a detailed life cycle analysis conducted by Nepenthe in 2023. As part of its review, Nepenthe switched to lighter bottles for its Altitude and Elevation ranges and adopted labels made from 100% recycled content.
CAPR closures were tested over three months to ensure they met the brand’s standards for product integrity and storage, and the cap designs themselves were updated to include clear removal instructions.
“Wine can be stored for years, so we needed to be confident the new cap wouldn’t compromise quality,” Bourke explained.
Nepenthe’s campaign ‘Naked in the Vines’, launched in March, supports this packaging shift with creative storytelling and consumer education across the company’s website, social channels and retail partners. “We’ve focused on education across all touchpoints,” Bourke said. “We want our customers to understand not just what we changed, but why.”
The change is part of Nepenthe’s broader sustainability journey. In addition to switching to lighter bottles and recycled labels, the brand is currently exploring the use of 100% recycled glass for its flagship APEX range — although sourcing in Australia remains a challenge, with most suppliers only able to achieve 70–90% recycled content.
Tips to recycle aluminium packaging correctly include:
• Fully remove aluminium sleeves or caps before placing bottles in glass recycling.
• Scrunch smaller pieces (like foil) into a tennis-ball-sized lump so they can be picked up by sorting equipment.
• Collect smaller closures like wine caps or kombucha lids inside an aluminium can before recycling.
Nepenthe’s Elevation and Altitude wines featuring the new closure are available nationally.
Swinburne University of Technology researchers have developed a process that converts cereal industry waste into high-value bacterial cellulose (BC) — a material used in medical dressings, food packaging and parts of electronics.
The technique, shown in this study published in uses a natural fermentation process to transform rice bran and cereal dust into BC, reducing production costs by up to 90% while maintaining quality, in an industry worth over $750 million globally.
Lead researcher Dr Vito Butardo Jr said this research could divert thousands of tonnes of agricultural waste from landfill while also addressing the high cost of producing bacterial cellulose using conventional methods.
“Despite containing valuable nutrients, excess rice bran and cereal dust typically end up as waste or as low-value animal feed. Our innovative process creates a sustainable circular economy solution that reduces waste and saves money,” Butardo said.
“Most importantly, extensive testing confirmed that our waste-derived bacterial cellulose maintains the same highquality characteristics as cellulose produced from expensive conventional media.”
The Swinburne team used stabilised rice bran from SunRice and cereal dust from Rex James Stockfeed Ltd to employ a natural two-step fermentation process where common food-grade fungi
Rhizopus oligosporus (also used in tempeh production) break down the complex fibrous structure of the cereal waste through solid-state fermentation.
This process makes nutrients more accessible for the second stage, where bacteria convert these nutrients into pure bacterial cellulose.
“Using rice bran pre-treated with Rhizopus oligosporus , we achieved a 22% increase in bacterial cellulose yield compared to untreated materials,” Butardo explained.
The research is said to have significant environmental and commercial implications for industries seeking sustainable alternatives to synthetic products.
The global bacterial cellulose market is experiencing rapid growth, projected to reach $1.5 trillion by 2028 (US$950 million) with applications spanning wound dressings, artificial skin, water filtration membranes, food packaging and components for flexible electronics.
Butardo hopes to scale up this technology to make a difference with sustainable biomaterials, implementing the process commercially and internationally with industry partners and other sectors.
“Our process demonstrates that agricultural waste can be viewed as an untapped resource rather than a disposal problem,” Butardo said. “This research showcases how innovative biotechnology can help close the loop in our food and materials systems.”
Electromagnetic flowmeters or magmeters are composed of a transmitter and sensor that together measure flow. The magnetic flowmeter’s sensor is placed inline and measures an induced voltage generated by the fluid as it flows through a pipe.
The principle of Electromagnetic Flowmeter (volumetric flowmeter) is based on Faraday’s law of electromagnetic induction. The coils of the flowmeter generate a magnetic field orthogonal to the flow direction. According to Faraday’s law of induction, a conductive liquid passing through the magnetic field induces a current between the two electrodes, which can be used to measure the voltage. The higher the flow velocity, the higher the induced voltage. This voltage signal is converted into a standard signal (eg, 4–20 mA or pulse) by the integrated electronics.
Electromagnetic flowmeters have basic applications for demanding flow and custody transfer (CT) measurements. They have designs and liner materials for various applications — from potable water to extremely adhesive, abrasive or aggressive fluids.
This electromagnetic flowmeter, being the non-intrusive type, can be used in general for any fluid that has a reasonable electrical conductivity greater than 5 µS/cm. Fluids like sand-water slurry, coal powder, slurry, sewage, wood pulp, chemicals, water other than distilled water in large pipelines, hot fluids, high viscous fluids specially in food processing industries, and cryogenic fluids can be metered by the electromagnetic flowmeter.
Modsen Electromagnetic Flowmeters with wafer and flanged versions have a large choice of nominal sizes from DN3 to DN3000.
Slentech Pty Ltd www.slentech.com.au
Vertiv has introduced the Vertiv CoolLoop Trim Cooler, in support of air and liquid cooling applications for AI and HPC (high-performance computing). This cooler supports diverse climate conditions for hybrid-cooled or liquid-cooled data centres and AI factories.
Integrating with high-density, liquid-cooled environments, the AI-ready cooler provides operational efficiency and aligns with the industry’s evolving needs for energy-efficient and compact cooling solutions. It provides up to a 70% reduction in annual cooling energy consumption leveraging free-cooling and mechanical operation, and 40% space savings compared to traditional systems. Designed to address the challenges of modern AI factories, the system supports fluctuating supply water temperatures up to 40°C and cold plate functionality at 45°C.
Straightforward water connections are said to provide smooth and direct system integration for the Vertiv CoolLoop Trim Cooler and the Vertiv CoolChip CDU coolant distribution units, for direct-to-chip cooling. The cooler can also connect directly to immersion cooling systems. This simplifies installation and operational complexity, allowing compatibility across a range of high-density cooling environments, providing time savings and cost efficiencies for customers.
The cooler uses low-GWP refrigerant and provides a scalable cooling capacity up to almost 3 MW in the air-cooled configuration. With free cooling coils optimised for high ambient temperatures, the system is designed to operate in free cooling mode across more seasons and conditions, for reduced electrical consumption and CO2 emissions. It is compliant with 2027 EU F-GAS regulations ban, avoiding the need for redesigns or infrastructure upgrades to meet the regulatory requirement.
Vertiv Australia Pty Ltd www.vertiv.com/en-asia/
The Slentech DZK transmitter has a modular design with high accuracy that is easy to install. The probe and transmitter can be used in any combination, making them suitable for multiple installation situations and applications.
The plug-in probes provide quick and easy exchange with no interruption in the measuring process. Only a single screw is required to close it securely.
The integrated HX processor uses the values for relative humidity and temperature to calculate the dew point, enthalpy, mixing ratio, absolute humidity or wet bulb temperature. Depending on customer preferences, any two of these values can be captured at two analog outputs using standardised signals.
The output variables can be freely configured via the USB port. The transmitter is automatically registered in Windows via the USB cable after connecting to the PC. No drivers are required.
The physical measuring values and analog output scaling can be changed based on the measured sizes of relative humidity and temperature. All temperature values can be displayed in degrees Fahrenheit or Celsius. The sensor is powered via USB for configuration — no power supply unit is required.
A typical application of the DZK series sensor can be for use in a smokehouse, where the sensor features a replaceable probe, making maintenance easy for all staff.
The probe withstands temperatures of up to 125°C, offers IP65 protection with a PTFE-coated filter, is washdown-resistant and includes a 25 m cable for extended reach.
Slentech Pty Ltd www.slentech.com.au
The Australian Fashion Council (AFC) and Epson Australia have launched an initiative to evaluate the potential for an AI and digitally powered smart factory to advance Australia’s clothing manufacturing capabilities. The organisations are seeking a qualified research partner to conduct a six-month feasibility study that will create a detailed blueprint for a pilot facility combining digital design and print, automation and AI technologies to rebuild local production.
A clothing smart factory is an automated production facility that enables on-demand, customisable garment manufacturing with minimal waste and fast turnaround times. By bringing together digital design and print and advanced manufacturing technologies with AI-powered systems and analytics, smart factories can enable quick, flexible production runs that respond rapidly to market trends without the high minimum order quantities that can result in overproduction.
Jaana Quaintance-James, CEO of the Australian Fashion Council, said: “This smart factory initiative addresses multiple challenges facing Australian fashion manufacturing, from supply chain disruptions to skills shortages. Our sector is at a critical tipping point. The feasibility study will validate whether a smart factory pilot program can be commercially viable while delivering broader benefits as part of an integrated advanced manufacturing ecosystem.”
Research commissioned by the AFC has estimated that for every $1m invested in returning production to Australia, approximately $1.2m in economic returns could be generated through job creation, technology adoption, strengthened local supply chains and reduced import dependencies.
Craig Heckenberg, Managing Director of Epson Australia, said: “Epson is committed to supporting innovation in Australian manufacturing as we believe Epson’s digital textile printing technology can help build a more sustainable world and improve lives. Our partnership with the AFC and this blueprint and initiative will help local brands, big and small, have access to smart manufacturing capabilities that match their scale and ambition. For smaller brands, it means producing high-quality garments locally, on demand. For larger companies it offers a blueprint to implement smart factory practices within their
operations. As a result, we see a future where Australian-made sustainable fashion will set the global standard, leading not just in design, but also in ethical, high-tech manufacturing.”
Before committing significant resources to establish a smart factory, the AFC and Epson recognise the importance of thoroughly validating the concept and learning from other local and international examples. The comprehensive six-month study will assess market viability, technical requirements, operational models, financial projections, and social and environmental considerations to create a detailed implementation roadmap.
“This isn’t just a research exercise, it’s the foundation for action,” Quaintance-James said. “Following completion of the study toward the end of 2025, we’ll develop a detailed implementation plan to secure investment partnerships, finalise specifications for an initial pilot, develop training programs with educational institutions, and create a governance framework to maximise benefits to the Australian fashion industry.”
“The smart factory concept represents a transformative shift toward ‘rapid agile’ on-demand manufacturing,” Heckenberg said. “Rather than speculative production, this approach enables creating products in response to actual consumer demand, simultaneously addressing profitability challenges and environmental concerns.”
The initiative aims to retain sovereign manufacturing capability, rebuild local supply chains, drive digital innovation, and upskill the workforce through educational partnerships.
Research partners may be Australian-based or international organisations with the capacity to conduct a thorough feasibility study that delivers actionable recommendations. Interested parties should submit their expressions of interest by 15 June 2025.
Epson Australia Pty Ltd www.epson.com.au
Emerson has released the Rosemount 490A Optical Dissolved Oxygen Sensor, a digital Modbus-enabled measurement device designed to improve operational flexibility, simplify installation and reduce maintenance costs across many industrial applications in the water/wastewater treatment, biopharmaceutical manufacturing, food and beverage processing, and steam power generation industries.
Most dissolved oxygen probes for industrial applications are made for installation in specific and relatively benign conditions. These sensors are often only capable of communicating process values via analog signals to control systems, and they require frequent calibration to maintain accuracy and avoid sensor drift. To address these issues, the sensor provides suitable dissolved oxygen measurements in demanding environments, while simplifying integration into existing control systems with digital and universal Modbus RTU communication via an accompanying transmitter. In addition to producing readings within 90 seconds of transition from dry to wet conditions, the sensor is capable of measuring process media in both liquid and gas phases, without requiring separate calibrations.
The sensor employs Environmental Protection Agency-approved luminescence-quenching technology, reducing the need for electrolyte refills to reduce maintenance requirements compared to traditional amperometric sensors. Its two-year sensing cap lifespan further minimises downtime and associated costs, and it can be calibrated in free air.
Additionally, the chemically resistant IP68-rated design enables reliable performance in challenging environments. Its small form factor, coupled with forward and rear facing 1-inch NPT threaded connections, simplifies installation in a variety of settings.
Unlike amperometric sensors, the 490A uses an optical sensor, which does not consume oxygen or require water flow for accurate measurements. Furthermore, guard cap options provide weighted orientation, anti-fouling protection, and air blast cleaning, catering to a wide breadth of applications.
Emerson www.emerson.com/au/automation
Trina Solar has launched the Elementa 2 Pro 5 MWh battery energy storage solution. The product builds on the Elementa 2, providing greater efficiency, flexibility and safety.
It features Trina’s self-developed 314 Ah high-performance Trina Cell, supporting 15,000 cycles (up from 12,000 cycles offered in the Elementa 2) to extend system lifespan and reduce life cycle costs, enabling a higher return on investment for users.
It provides enhanced advanced cooling technology, incorporating an intelligent hybrid air-liquid cooling system.
Trina Solar Australia www.trinasolar.com/au
Designed for demanding and/or dirty plant environments, ECD’s OIW80 oil-in-water analyser’s sensor features a built-in wiper cleaning system to remove biosolids and films that might cloud the sensor window’s visibility. The sensor features a built-in automatic screen window wiper, to reduce technician manual checks and the frequency of scheduled maintenance cleanings. The intelligent analyser is designed to measure oil over a wide range of 0 to 30 ppm (mg/L) and can be factory preconfigured to measure oil in multiple ranges or easily set in the field. The rugged, high-performance analyser’s responsive sensor operates over a broad temperature range from 5 to 45°C to quickly detect leaks and alert plant technicians.
The heavy-duty construction of the sensor’s housing uses strong, corrosion-resistant stainless steel (standard) or optional titanium, and meets the IP68 water ingress standard. Every aspect of the sensor’s design has been tailored for years of operation and trouble-free service in the demanding wet environments typical of industrial and municipal water and wastewater treatment applications.
The sensor uses fluorescence sensing technology for measurement of oil in water, which is typically proportional to its concentration. The sensor communicates directly with ECD’s versatile T80 universal transmitter when oil is detected.
During installation, the system is connected to the ECD T80 transmitter and the sensor’s calibration range information is automatically uploaded to the analyser. It then automatically configures the displays and outputs of the transmitter to the values appropriate to the oil sensor’s measurement parameters.
Transmitters are available as either single- or dualchannel devices, allowing one analyser to measure up to two parameters or two ranges. The transmitter is available in a 24 VDC or a 100/240 VAC power configuration. All versions are available with an optional HART output to support integration with larger control systems. AMS Instrumentation & Calibration Pty Ltd www.ams-ic.com.au
Deakin University’s Institute for Frontier Materials (IFM) has partnered with Australian fashion brand Country Road to trial a fully domestic process to transform low-grade Merino wool into high-value yarn.
The ‘Mud to Marle’ project provides a new step in Australia’s textile industry, made possible after IFM and Full Circle Fibres secured a grant as part of the Country Road Climate Fund.
In collaboration with textile manufacturer Loomtex, the team has demonstrated how low-value wool can be spun into fine yarn perfect for fashion garments.
The project sought to prove the viability of end-to-end onshore production, conducting innovative trials at various locations including Deakin University’s Future Fibres Facility at the IFM.
Despite producing world-renowned wool, Australia has limited infrastructure to process raw fibre on a commercial scale. However, giving new life to low-grade fibres fits perfectly with IFM’s sustainability mandate and technical capacity.
“Deakin University is at the forefront of cotton processing and spinning innovation in Australia and has an array of textile processing equipment,” Associate Professor Christopher Hurren said.
“During the project we wanted to explore methods that reduce resource use while still delivering a viable, high-quality textile product. One of the ways we did this was by dyeing only the wool fibres within the wool–cotton blend, reducing water and energy
consumption in this process. The project shows the potential to
Meriel Chamberlin, the owner and founder of Full Circle Fibres, explains that about 3–5% of Merino fleece consists of short fibres known as locks.
“These shorter fibres are perceived as having a lower value than the rest of the fleece and tend to be used in homeware and chunkier knit garments as it is difficult to process them into fine yarn,” Chamberlin said.“In our project, we sourced locks from South Australia and blended the fibres with cotton from Queensland. The wool–cotton blend yarn we’ve created is finer than yarn normally made with locks. We wanted to explore methods that reduce resource use while still delivering a viable, high-quality textile product.”
The project has unlocked an additional $300,000 for a threeyear industry partnership to accelerate Deakin’s research into wool–cotton products.
“The commercial spinning capacity in Australia is incredibly limited, but the learnings from this project have helped demonstrate demand and investment potential,” Chamberlin said. “There is growing momentum to revive Australia’s textile manufacturing capabilities.”
With samples of the Mud to Marle wool–cotton blend now tested in prototype garments — including T-shirts, jumpers and pants — the project is said to have set the stage for further innovation in circular Australian textile production.
water resource management
Driven by the need to adapt to climate change, demographic and environmental challenges, and to optimise water resource management, Australia and New Zealand are taking strategic steps towards the digitalisation of the integrated water cycle.
Both regions, with advanced regulatory frameworks and growing awareness of sustainability, are implementing digital technologies to improve the management of drinking water, sanitation, wastewater treatment and stormwater. It is worth noting that Australia is not only the driest inhabited continent on Earth, it also has one of the highest per-capita water consumption rates in the world — 493 L per day, according to UN-Habitat.
New Zealand, on the other hand, has a relative abundance of water resources. However, intensive agriculture, excessive
water extraction for irrigation, droughts and outdated infrastructure — resulting in water loss through leaks — are among the key challenges it must address to ensure equitable and sustainable access to water. As a result, the sector is undergoing a profound transformation aimed at modernising and unifying the management of drinking water, wastewater and stormwater services through the Three Waters program.
In this context, water resource management — integrating IoT sensors, artificial intelligence (AI) and predictive analytics, among other technologies — is emerging not just as an option but as a key solution
to enhance operational efficiency and reduce environmental risks.
According to Joan Carles Guardiola, Business Development Manager, Xylem Vue at Xylem ANZ, “The digital tsunami we are immersed in must be leveraged by all industries and sectors — especially the water sector, which can rely on multiple digital tools to help utilities improve their operations and efficiency.”
The role of digitalisation: predictive management
Digital transformation, therefore, is a tool that helps utilities optimise operations, retain institutional knowledge, reduce the use of natural resources, improve service quality, and anticipate water crises and extreme events — such as the numerous floods that have affected Eastern Australia in recent years or the 2023 floods in Auckland.
Several digital applications being implemented in the region are proving useful in facing these challenges:
• Real-time monitoring of water networks: Digitalisation allows for a shift from reactive maintenance to a predictive approach. Smart networks collect realtime infrastructure data through various sensors, which are then analysed using AI algorithms to detect anomalies and anticipate failures.
• Predictive analytics and big data: Advanced data analysis makes it possible to process massive volumes of historical data to identify behavioural patterns, anticipate infrastructure failures, improve responses to extreme events, and plan investments more effectively.
• Digital twins of infrastructure: Digital twins are virtual replicas of plants, networks and treatment systems that simulate different operational scenarios and support decision-making through real-time simulations. These systems can also generate recommendations or even automate certain processes to optimise performance while meeting required service levels.
• Smart agriculture and efficient water use: Agriculture plays a fundamental role in the economy of both countries, which are global agri-exporting powers. (In New Zealand’s case, agriculture is a key economic pillar.) For this reason, digital irrigation — through sensors, satellite imagery and
AI — is transforming water management in agriculture, enabling more precise and sustainable use of the resource. Benefits of predictive management are:
• Cost reduction: Data-driven interventions lower operational costs by avoiding unnecessary maintenance and emergencies.
• Improved service: Service continuity is enhanced by preventing network outages or sewer overflows that affect communities.
• Environmental sustainability: By reducing resource consumption and minimising untreated discharges, natural ecosystems are better protected.
• Extended infrastructure lifespan: Detecting failures before they occur increases the durability of assets.
• Knowledge retention: Predictive management allows for the structuring, systematisation and preservation of operational and historical knowledge. Through predictive models fuelled by historical and realtime data, the accumulated expertise of technicians, operators and managers is captured, avoiding its loss due to staff turnover or retirement.
• Data democratisation: With the integration of predictive platforms, data moves out of isolated departmental silos and becomes accessible and understandable to various profiles within the organisation. This breaks down traditional barriers to knowledge management and fosters a more transparent and participatory approach.
• Value generation: Predictive management not only optimises processes but also transforms data into strategic insights, enabling anticipation of critical events, cost reduction and improved asset performance. In doing so, it turns information into a competitive advantage, allowing utilities to offer better service, reduce risks, and maximise the economic, social and environmental value of water.
However, the digital transformation of water utilities, in pursuit of smart water management, must consider three key aspects:
• Cybersecurity: With digitalisation come new threats and connected networks must be protected accordingly.
• Corporate culture and digital skills: One of the cornerstones is staff training. As mentioned earlier, digitalisation adds value to society, but achieving this requires developing and encouraging digital skills among operational teams.
• Public–private collaboration: Continuous cooperation between governments, technology companies and water operators is essential to enhance customer service and integrated water cycle management. The integration of AI and predictive maintenance not only optimises the present but also prepares cities for a resilient future in the face of climate change. In regions like Queensland and New South Wales — where extreme weather events are increasingly frequent — these tools will be essential for anticipating risks and ensuring service continuity.
Smart wastewater networks, powered by AI and IoT sensors, represent a quiet yet crucial revolution in water management across Australia and New Zealand. For example, in Adelaide, the implementation of Xylem Vue to detect hydraulic transients in its distribution network has enabled improved asset and operational management, reducing the number of incidents and extending infrastructure lifespan by minimising stress.
This demonstrates that predictive maintenance is not only possible but also highly cost-effective and sustainable. As technology continues to advance and costs decrease, broader adoption is expected — transforming the sanitation system into a central pillar of resilient urban water management.
Monash University engineers have developed a water-based battery that could help Australian households store rooftop solar energy more safely, cheaply and efficiently than ever before.
‘Flow batteries’ have been around for decades but have traditionally been used in large-scale energy storage due to their large size and slow charge speeds. Yet, this next-generation flow battery is said to open the door to compact, high-performance battery systems for homes, and is expected to be much cheaper than current $10,000 lithium-ion systems.
Wanqiao Liang, the study’s first author and PhD candidate at the Department of Materials Science and Engineering, said the team’s new membrane design fixes the speed problem, making it ideal for households and a promising key player in the energy transition market.
“We’ve taken a safe, affordable chemistry and made it fast enough to capture rooftop solar in real time,” Liang said. “We’ve engineered a membrane that finally makes organic flow batteries competitive for residential and mid-scale storage. It opens the door to systems that are not only cheaper, but also safer and simpler to scale.”
While some companies already produce flow batteries, Monash’s design is said to stand out for its combination of safety, low cost and high-speed performance.
“The key was improving ion selectivity; letting the good ions through quickly while keeping unwanted ones out. Our new membrane achieves this balance, allowing fast, stable operation even at high current densities,” Liang said. “We outperformed the
industry-standard Nafion membrane in both speed and stability — running 600 high-current cycles with virtually no capacity loss — that’s a major leap forward for this kind of battery.”
Wanqiao said a careful balance was crucial to making these batteries work for rooftop solar at home.
“This is the kind of battery you’d want in your garage,” Liang said. “It’s non-toxic, non-flammable and made from abundant materials, all while keeping up with solar power on a sunny day.”
The team is now 3D printing prototype systems and testing them under real-world conditions.
“If the prototypes keep performing the way we expect, this could be on the market in a few years’ time,” Liang said.
Flow batteries store energy in liquids rather than solid materials like those found in lithium-ion batteries, making them cheaper to manufacture, safer to operate and easier to scale.
“We’ve developed a new type of membrane inside the battery that guides the flow of materials better — kind of like adding lanes to a highway. That means faster charging, longer battery life and better performance overall,” Liang said.
Monash University’s new flow-battery membrane is designed to be:
• safe: water-based, non-flammable liquids;
• low-cost: expected to be significantly cheaper than current $10,000 lithium-ion home systems;
• sustainable: made from abundant materials without critical minerals like lithium or cobalt;
• flexible: suitable for households, commercial buildings and large-scale energy storage.
Hydro Innovations was approached by Western Sydney Meat Works and SJ Plumbing Industries to provide a pump solution to replace the existing submersible pump operating in the abattoir’s wastewater (green and red lines) collection pit.
The existing submersible pump was continually blocking due to the large quantities of paunch, stomach linings, grit and other foreign materials ending up in the pit. As a result of these blockages, constant vigilance of the submersible pump was required to ensure its continuous operation.
In the event of a blockage and the submersible pump stopping, it meant the submersible pump would have to be lifted from the pit, with the impeller/suction end dismantled to remove the offending material, reassembled and returned to operation; an often lengthy, messy and difficult exercise.
Phil Rothheudt, Hydro Innovations’ NSW Regional Manager, attended the site and quickly realised this was a perfect situation for a Gorman Rupp self-priming pump.
The Gorman Rupp self-priming pump would sit at the surface of the pit (not submersed), where instant and safe access to the pump’s internals (and the blockage) was available to the operators; regular service and maintenance is also simplified with the easy access, all carried out at the surface.
The Gorman Rupp self-priming pump requires no foot valve (to block or leak); just an open suction pipe into the liquid is all
that’s required. The result is an easy pump to install, operate and maintain.
Rothheudt also recommended the pump be fitted with the Gorman Rupp Eradicator ‘Solids Management System’ to deal with the often-stringy intestines, tough gut linings, undigested hay or any material that might find its way into the pump that could result in blocking, jamming or wrapped around the impeller. Gorman Rupp self-priming pumps fitted with the Eradicator system have been deployed in many abattoir sites around Australia and municipal sewage treatment plants with excellent results.
The abattoir decided to proceed with the purchase of a Gorman Rupp Super T3C60SC-B fitted with the Eradicator ‘Solids Management System’.
Within a day of operation, the waste material that had built up in and around the pit was being steadily pumped to the separator screen.
The initial startup was so successful that an excavator was deployed to dig and loosen the heavy settled material in the bottom of the well, mixing it with the incoming flow; the pump then sent the mixture to the separator screen.
If the pump ever did block or jam, the operators simply opened the suction-end inspection cover and removed the offending blockage before getting back to work. Hydro Innovations www.hydroinnovations.com.au
Engineers from Australia and China have invented a spongelike device that captures water from thin air and then releases it in a cup using the sun’s energy, even in low humidity where other technologies such as fog harvesting and radiative cooling have found it difficult.
The water capture device is designed to remain effective across a broad range of humidity levels (30–90%) and temperatures (5–55°C).
Senior researcher Dr Derek Hao, from RMIT University in Melbourne, said the invention relied on refined balsa wood’s naturally spongy structure, modified to absorb water from the atmosphere and release it on demand. The wood-based composite developed by the team for their research fits into a cup with a dome lid and anti-pollution tray, a cooling mechanism and an activation system powered by the sun.
“Billions of people around the world lack access to drinkable water, and millions die from water-borne diseases every year,” said Hao, a materials scientist and environmental engineer in RMIT’s School of Science. Hao was corresponding author on the study, which was done in collaboration with five Chinese research institutions, led by Dr Junfeng Hou from Zhejiang A&F University.
“Our team has invented a device comprising wood’s spongy scaffolding, lithium chloride, iron oxide nanoparticles, a carbon nanotube layer and other specialised features,” Hao said.
The team used artificial intelligence for accurate prediction and optimisation of the device’s water harvesting and discharging performance under varying environmental conditions. The spongy material, which is an
The team used artificial intelligence for accurate prediction and optimisation of the device’s water harvesting and discharging performance under varying environmental conditions.
early-stage lab prototype, absorbs moisture from the atmosphere when the cup’s lid is open. When the lid is closed under sunlight, water is released into the cup.
Under laboratory conditions, the device absorbed about 2 mL of water per gram of material at 90% relative humidity and released nearly all the water within 10 hours under sun exposure — which is said to be higher than most other known methods and at less cost. With nine sponge cubes, each weighing 0.8 g, 15 mL of water can be absorbed and released into the cup.
“In outdoor tests, our device captured 2.5 mL of water per gram overnight and released most of it during the day, achieving a daily water collection efficiency of 94%,” Hou said. “At 30% humidity, our device absorbed water at about 0.6 mL per gram.
“These results highlight its potential use in off-grid, solar-driven water harvesting systems.”
Hao said the use of natural wood as a matrix not only reduced costs but also provided structural integrity and enhanced water transport through its porous architecture.
“These features enable the material to be manufactured in large quantities and
deployed in real-world applications such as water collection in remote or arid regions,” he said. “The device retained its flexibility and water-absorbing function even after being stored at -20°C for 20 days, demonstrating excellent freeze resistance.
“Its moisture absorption–release performance was stable across 10 consecutive cycles, with less than 12% decline in efficiency.”
Hao said the device would be suited to emergency scenarios, such as in the wake of natural disasters where water supplies have been compromised, if the team can scale up and optimise the modular innovation.
“The current demonstration unit size is 15 mm3. It would be very easy to prepare a larger unit, or we can use the units to form an array,” Hao said.
“Its ability to harvest potable water from the atmosphere using only sunlight makes it invaluable in disaster-stricken areas where traditional water sources are compromised. The system’s portability and reliance on renewable energy further enhance its applicability in such contexts.”
The material used by the team was designed with scalability and affordability in mind.
“The main component, balsa wood, is widely available, biodegradable and cheap, and the manufacturing process is not complex, which could enable mass production,” Hao said. “The demonstrated stable performance over multiple cycles and in various environmental conditions indicates longevity and cost-effectiveness.”
Hao said the team was in discussion with prospective industry partners on pilot-scale production and field deployment, integrating into modular water-from-air harvesting systems. “Solar panels combined with thermal energy storage could enable round-the-clock operation, particularly in areas with intermittent sunlight,” he said.
Hao said developing automated control systems using Internet of Things sensors to monitor relative humidity, temperature and solar intensity could further optimise water harvesting cycles. “Building on the artificially intelligent design used in the study, more advanced design platforms could be developed to screen new material combinations and predict long-term water absorption and release performance,” he said.
The team’s study has been published in the Journal of Cleaner Production.
Around 98% of lignin created as a forestry by-product from plants is discarded, but a new enzyme could be the key to extracting high-value molecules from this waste using a green chemistry approach.
These molecules are the building blocks for compounds like fragrances, flavourings, fuels and therapeutics, turning a waste stream into a valuable resource.
“Traditional chemical processes for synthesis of these types of chemicals rely on petroleum-based starting compounds and heavy metal catalysts, making them non-renewable and inherently toxic processes,” said Dr Fiona Whelan, a Cryo-electron Microscopist from Adelaide Microscopy at the University of Adelaide, whose study was published in Nature Communications
“This new catalytic processing method will support development of other new green chemistry ‘enzyme factories’ or biorefineries to turn the lignin and other biological waste streams into a valuable repository of fine chemicals.”
Lignin is the name given to the hard polymers that act as mechanical support in hard- and softwoods and is said to be one of the most abundant polymers on Earth.
Agriculture and forestry amass around 100 million tonnes of waste lignin per year, but this could be diverted to become a promising renewable and sustainable feedstock for chemicals currently obtained from fossil fuels.
“Strategies for using lignin involve a combination of chemical and biological processes,” said Associate Professor Stephen Bell, from the University’s School of Physics, Chemistry and Earth Sciences.
“High temperatures, high pressure, strong acids and poisonous solvents are used to break up the polymers in the waste stream.
“The valuable compounds trapped in the waste are then extracted and undergo further chemical processing at temperatures higher than 400°C to ‘valorise’ the lignin. These processes are expensive and bad for the environment.”
Hardwood lignin has two key chemical components that require processing to make useful compounds. Researchers had previously discovered an enzyme that could be used to break down one of these compounds, which is also found in softwood, but no biological breakdown process had been identified that could use the second more complex hardwood compound, comprising about 50% of the waste.
“Biological breakdown of lignin occurs in a complex microbial quorum, with fungal enzymes likely breaking up hard polymers, and bacteria taking the unreactive smaller compounds and processing them to get metabolic energy,” Whelan said.
“Looking to the microbial kingdom, we identified that a soil bacterium, Amycolatopsis thermoflava , contains enzymes that could process molecules from lignin cheaply, using hydrogen peroxide to drive the reaction — making valorisation much less harmful to the environment.”
The research team has used this new enzyme as a model for retrofitting the hydrogen peroxide driven activity into other enzymes to generate green chemistry approaches of the future for the generation of high-value chemicals of use in the flavour, fragrance and medicinal chemistry industries. University of Adelaide adelaideuni.edu.au
World Green Building Council (WorldGBC) has launched the Asia Pacific Regional Network (APN) Resources and Circularity Readiness Framework, presented at the WorldGBC hosted accelerator session, ‘Retrofitting buildings: Lessons from a global network’, as part of the World Circular Economy Forum 2025 (WCEF2025), a global event dedicated to the circular economy.
Developed by WorldGBC’s APN of 17 Green Building Councils (GBCs) as well as knowledge partners, the framework is a practical roadmap aimed at policymakers and businesses across the region to assess their circularity readiness and identify strategic priorities for action to decarbonise their building stock on both a national and regional scale.
The framework can be used as a tool to quantify the business case for circular, sustainable principles in the built environment, and support businesses and governments to reduce waste, conserve resources and lower carbon emissions. It shows the industry the practical steps it can take now towards circularity, based on its current capabilities. It sets out clear assessment criteria, specific readiness indicators and actionable guidance based on five interconnected elements:
• Government leadership: Policies and regulations driving circularity at all levels.
• Technical solutions: Innovative approaches enabling resource efficiency and circular material flows.
• Data: Measurement systems tracking resource use and circularity progress.
• Finance: Funding mechanisms supporting circular business models and infrastructure.
• Mindset: Cultural shifts prioritising resource conservation and sustainable consumption.
The Framework further supports WorldGBC’s 2025–2027 strategic plan, which outlines the vision for a sustainable built environment, guided by global 2030 decarbonisation goals.
Gai, Head of Asia Pacific Network, WorldGBC said, “The framework has been developed by sustainability experts from the Asia–Pacific, one of the most diverse regions in the world, which is defined by remarkable complexities of culture, building stocks and environmental conditions. Our network recognises that harnessing diversity is fundamental to shaping a more resilient, resource-efficient future — but we need a guide to show us how to put our ambition into action. That is why we developed the APN Resources and Circularity Readiness Framework.
“WorldGBC is proud to join our Green Building Councils and partners in launching this timely resource. It creates a common language to guide businesses through collaboration, identifying their needs and applying circular methods which support our shared vision for a sustainable and regenerative future for Asia–Pacific and beyond.”
Jeff Oatman, chair of the Asia Pacific Regional network, Head of Collaboration and membership at Green Building Council of Australia (GBCA), added, “The Resources and Circularity Readiness Framework is a timely and much-needed initiative to accelerate the transition to a more regenerative and resource-efficient built environment across our region. By offering a clear pathway for assessing readiness and driving action, it empowers governments, industry and communities to make smarter, more sustainable decisions around circularity. I’m proud to be part of this collaboration and to contribute to a tool that not only fosters innovation but
also supports practical outcomes that matter for people and the planet.”
Takuji Kohama, Chief Representative, AGC Group for Asia Pacific, also commented, “A resilient built environment relies on understanding ecological interconnections and making a conscious shift from linear consumption to cyclical resource stewardship. Designing buildings and infrastructures with their lifecycle in mind maximises material efficiency and minimises waste through a holistic approach from resource sourcing to end-of-life. Prioritising design for disassembly, material recovery, reuse and repurpose transforms buildings into dynamic material banks, significantly reducing construction’s environmental impact and fostering economic and environmental sustainability.
“Participating in the formulation of Resources and Circularity Readiness Framework offers a practical path to sustainable growth in our resource-constrained and climate-challenged region. This framework empowers built environment stakeholders to adopt a regenerative, resilient mindset focused on long-term value creation, redefining design, construction and living beyond waste minimisation. We aim to catalyse greater collaboration, innovation and systemic change, positioning AGC as a regional leader in circular economy practices and a model for urban sustainability.”
GBCs will use the framework to assess their own readiness to accelerate the transition to a circular economy in the built environment, as well as supporting the Asia–Pacific market.