

IN THIS ISSUE
FEATURES
The Effectiveness of Welding Fume Product Controls
16
The intent of the scientific study recently undertaken by AWS was to compare the effectiveness of different welding fume product control methods in reducing exposure to welding fume.
20
Privacy Act Reforms: What Small Businesses Need to Know Following a two-year review of Australia’s privacy laws, the Federal Government has proposed reforms to the Privacy Act that will impact on businesses of all sizes. It’s expected the reforms will become law in late 2023.
32
Australia at Risk of Exclusion from Renewable Manufacturing Boom According to a report by the Centre for Future Work, Australia risks being left out of lucrative new markets for renewable energy-related manufacturing unless government provides an urgent response.
12
TAFE NSW Skills Underwater Welding Experts to Fill In-Demand Roles
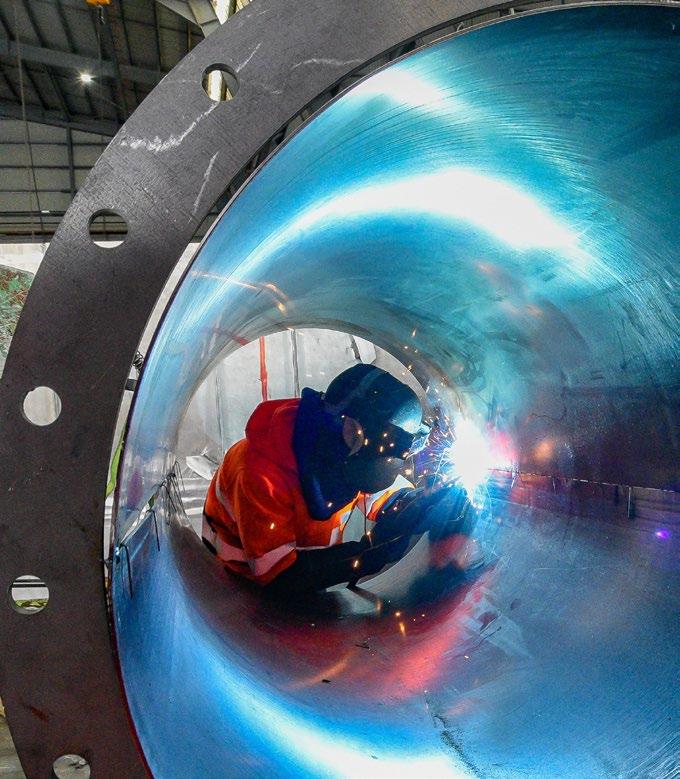

34
Triple Threat UNEEK Shapes Industry When it comes to quality and a customer-first approach, UNEEK is a leader across the welding and fabrication space. The company began almost 60 years ago, and has since become a key service provider for the defence sector. 41
Forging A Skilled Workforce Over the last couple of months, Port Moresby in Papua New Guinea was home to a suite of successful welding training programs, bringing together ten citizen employees from both Monadelphous and Santos.
42
Weld Australia Launches National Resources for MEM Training Package Weld Australia has designed and created a suite of resources for delivery of the 12 welding and fabrication units of competency in the Manufacturing and Engineering (MEM) Training Package.
22
2023 National Manufacturing Summit: Manufacturing the Renewable Energy Revolution
REGULAR COLUMNS
WELD AUSTRALIA CONTACTS
National Office PO Box 197 Macquarie Park BC NSW 1670 1800 189 900 office@weldaustralia.com.au weladustralia.com.au
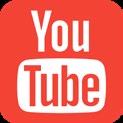
Chief Executive Officer
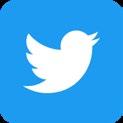
Geoff Crittenden 02 8748 0100 g.crittenden@weldaustralia.com.au
ENGINEERING
Victor Blain, Engineering Team Manager 0409 823 991 v.blain@weldaustralia.com.au
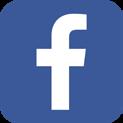
TRAINING
Guy Brooks, Training Manager 0488 743 322 g.brooks@weldaustralia.com.au
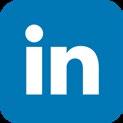
MARKETING
Michelle Bignold, National Manager, Sales & Marketing 0437 106 726 m.bignold@weldaustralia.com.au
MEMBERSHIP
David Choudry, Membership Manager 0417 878 104 d.choudry@weldaustralia.com.au
QUALIFICATION & CERTIFICATION
Deniz Yalniz, Qualification and Certification Team Manager 0487 487 170 d.yalniz@weldaustralia.com.au
BECOME A MEMBER
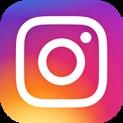
Subscription to Australian Welding is a Weld Australia member benefit included in annual membership fees. All rights reserved. No part of this publication may be reproduced or copied in any form without the written permission of Weld Australia. Weld Australia and its agents are not responsible for statements or opinions expressed by contributors in this publication, which are not necessarily those of Weld Australia. Publication of any advertisement does not constitute endorsement by Weld Australia of any product, nor warrant its suitability.

A MESSAGE FROM WELD AUSTRALIA’S CHAIR
IIW Annual Assembly
The IIW Annual Assembly provides an opportunity for IIW Technical Commissions and Working Units to meet. There are currently 18 IIW Commissions, each of which is focused on a specific area of interest, from additive manufacturing and power beam processes, through to structural performance of welded joints, pressure vessels, boilers and pipelines.
In late July, I travelled to Singapore to represent Australia at the 76th International Institute of Welding (IIW) Annual Assembly and International Conference on Welding and Joining.
An Overview of the IIW IIW is recognised as the largest worldwide network and centre of reference for welding and allied joining technologies. It operates as the global body for the science and application of joining technologies, providing a forum for networking and knowledge exchange among scientists, researchers, industry and educators, and disseminating leading-edge information and best practices.
Researchers, industry, educators, students and young professionals from over 51 countries worldwide are all part of the collaborative working platform of the IIW. Weld Australia is the Australian representative member of the IIW. Through the work of its Technical Working Units, the IIW’s focus encompasses
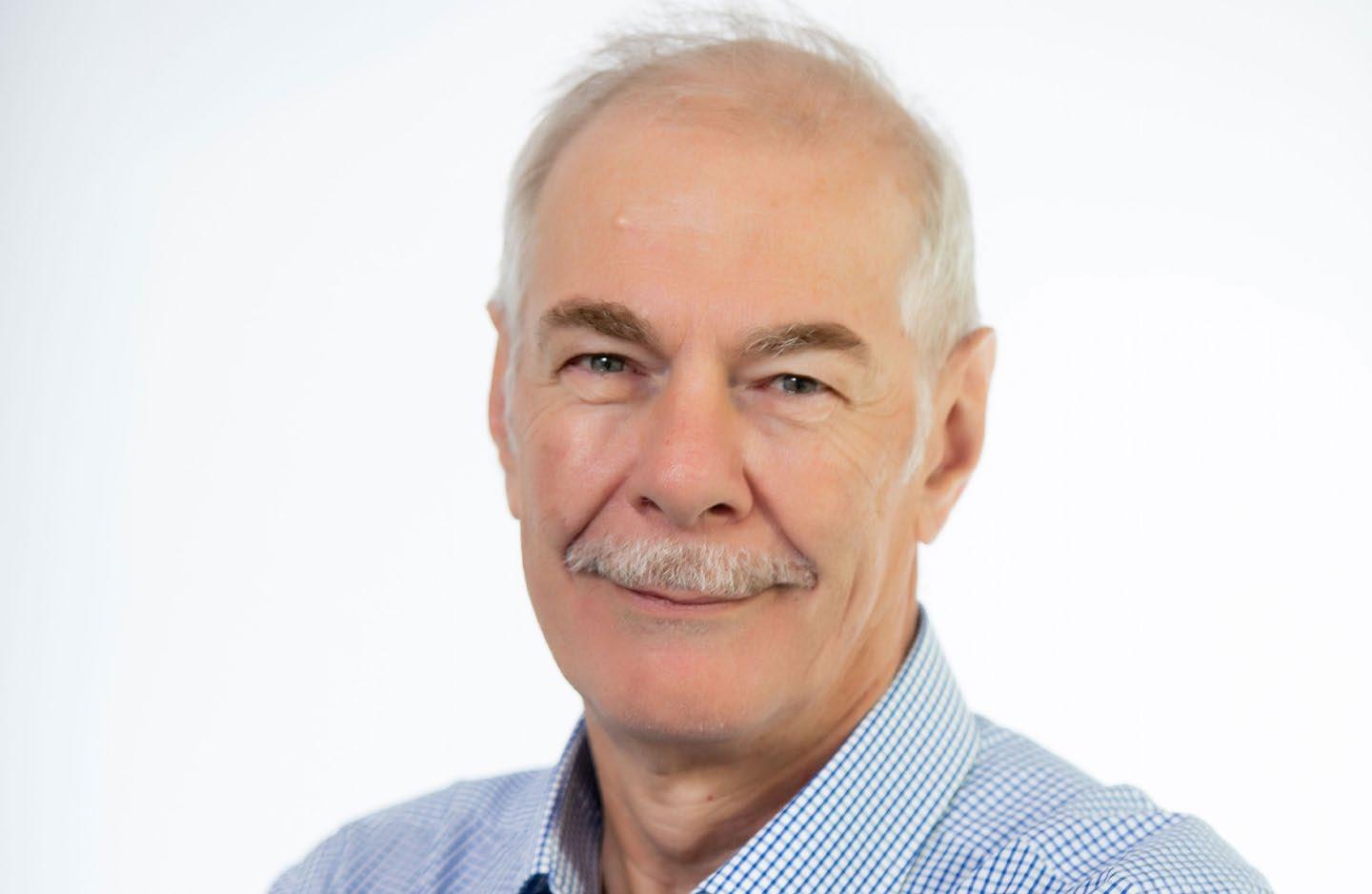
the joining, cutting and surface treatment of metallic and non-metallic materials by such processes as welding, brazing, soldering, thermal cutting, thermal spraying, adhesive bonding, microjoining and additive manufacturing. IIW’s work embraces allied fields including quality assurance, non-destructive testing, standardisation, inspection, health and safety, training, qualification, certification, design and fabrication.
IIW International Conference
The theme of this year’s International Conference was Advances in Welding, Joining and Additive Manufacturing. The program featured a range of engaging presentations.
The program demonstrated the important role manufacturing plays in Singapore’s economy; it accounts for approximately 20% of the nation’s Gross Domestic Product (GDP). Over the years, Singapore has built a diverse base of industries, occupying leadership positions in the aerospace, semiconductor, chemicals, and biomedical sciences sectors.
Weld Australia representatives attended and participated in many of the Commissions and have developed contacts from many parts of the world, with Weld Australia having access to the working of all 18 Commissions. It is worth noting that there were 46 member countries represented at the Assembly and over 800 attendees (17 of whom were from Australia).
I am pleased to report that Weld Australia received two commendations at the IIW Annual Assembly. The first recognised our donation to the Ukraine charitable fund. In 2022, Weld Australia suggested that the IIW Board establish a charitable fund to help ensure that the Ukraine could continue to participate in IIW activities amid the conflict with Russia. The IIW enthusiastically adopted the suggestion, established the fund, and waived all fees for Ukrainian members. Although we are one of the smallest members of the IIW, Weld Australia was the first organisation to donate to the fund.
The second commendation Weld Australia received was in recognition of our collaborative working relationship with the Italian Institute of Welding on establishing the Paolo Corronca Scholarship. When our friend and colleague, Paolo, passed
away earlier this year, Weld Australia created a Scholarship to fund an exchange program that will enable an Italian welding engineer to work in Australia each year.
One of the IIW’s strategic objectives is to foster closer collaboration between its member organisations. Historically, Weld Australia has had a very strong relationship with the Italian Institute of Welding, which first commenced when implementing the EN 15085 certification scheme in Australia.
Weld Australia has been taking a leadership role within the IIW IAB (International Authorisation Board) for internationally recognised qualification and certification of personnel and companies. Doug Hawkes (Director, Weld Australia) has been the IAB Board representative for the Oceania and Africa region and has stood down this year. We are proud to announce that the newly elected representative is Simon Doe again a Director of Weld Australia. The IIW Qualification and Certifications Systems have been developed and implemented worldwide with the main goal of supporting industry needs.
Bruce Cannon (Principal Welding Engineer, Weld Australia) gave two presentations to IIW Commission VIII Health, Safety and Environment. The first presentation focused on the work done by David Chippendale (Director Sales and Marketing, AWS Welding) on the effectiveness of welding fume product controls. See the article on page 16 for further information.
Bruce’s second presentation focused on welding and related safety in Australia, including an update on safety standards, fire precautions, welding electrical safety and welders’ clothing. Bruce provided details of the two Safety Alerts published by Weld Australia—one regarding welders’ clothing, and the other on hand-held laser welding machines This generated much discussion, with several attendees requesting copies of the alert on handheld laser welding machines, with similar problems in their home countries.
Bruce spoke briefly about the weld fume update and cancer awareness campaign being conducted by the AMWU and weld fume hazard levels currently under review by SafeWork Australia.
Finally, Bruce presented a sample of the two welder safety training videos that Weld Australia is currently developing. These courses cover a raft of activities across a range of welding processes, from electric arc welding and flame cutting, through to topics like welding fume safety, and welding in confined spaces, at heights, or in hot and humid conditions. These courses will be completed at the end of the year and made freely available via the Weld Australia website.
LASTING CONNECTIONS
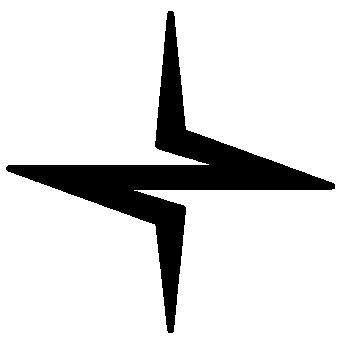
Böhler Welding offers a globally unique and complete product portfolio of welding consumables; these products are from our own production facilities. Our extensive range of approximately 2,000 products is continuously adapted to the current specifications of the industries and market requirements, considering the highest quality standards.

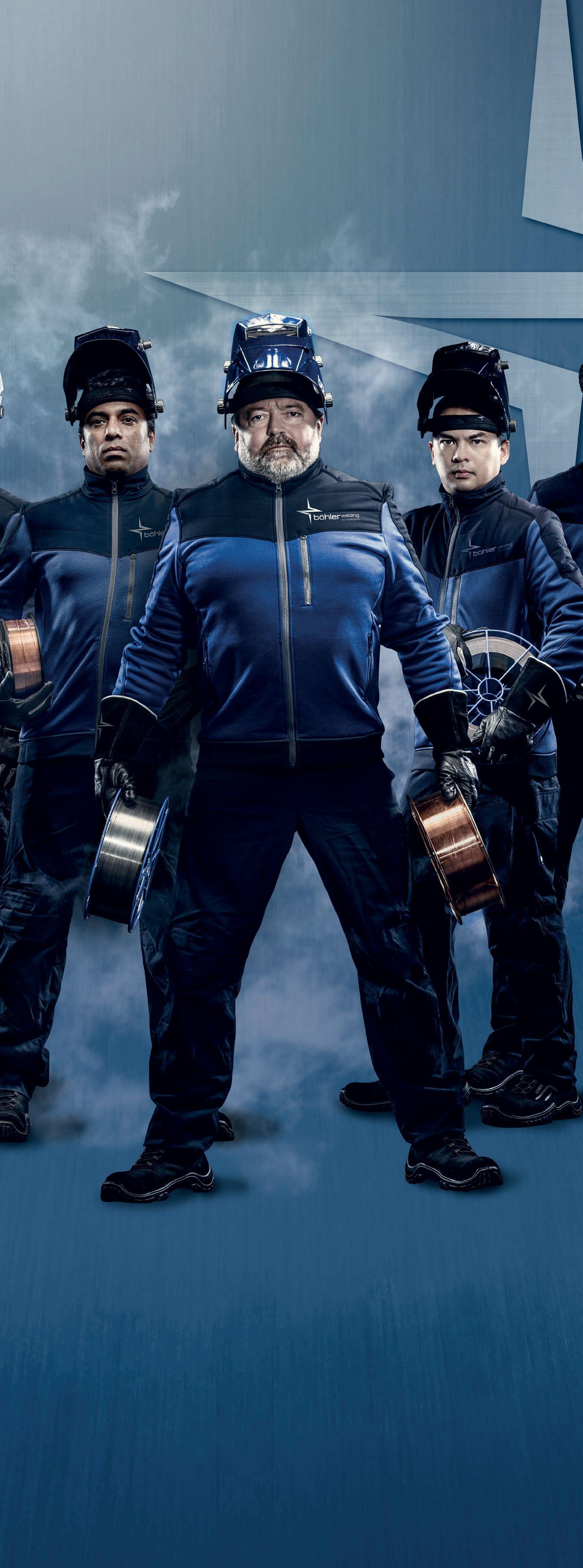
INDUSTRY CALLS FOR RADICAL NATIONAL STRATEGY TO MAKE AUSTRALIA’S RENEWABLE ENERGY REVOLUTION A REALITY
Australia’s manufacturing industry is calling on the Federal Government to take action now and implement a radical national strategy to make Australia’s renewable energy revolution a reality.
Manufacturing and energy industry leaders—from union representatives, developers and business owners, through to academics, economists and government ministers—gathered in Canberra in early August at the 2023 National Manufacturing Summit.
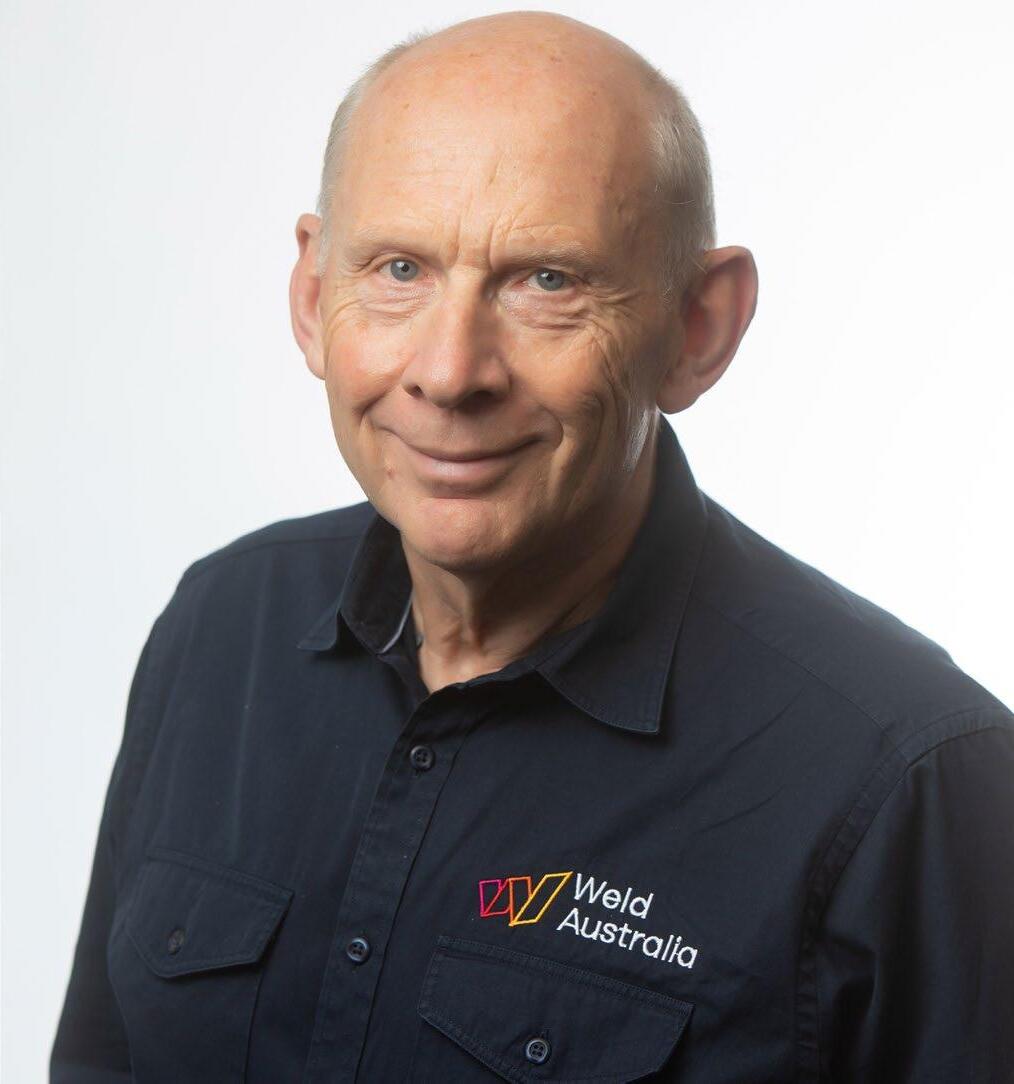
The message was clear: if Australia is to meet its net zero targets by 2050, our Federal Government must enact transformative national policy that delivers secure supply chains and a diverse renewables and clean energy economy, all of which can be sustained by the manufacturing industry. Australia must take inspiration from the United States, and their Inflation Reduction Act (IRA), which allocated upwards of US$500 billion in new spending and tax breaks that aim to boost clean energy.
The Imperative
We are now at the stage where even the most obtuse observer must
realise that global warming is real and is coming at us much faster than we imagined it could. Last year, Australia experienced record floods, with countless people losing their homes. This year, we’re expecting a record bushfire season, with the Northern Hemisphere already experiencing some of its hottest temperatures on record. The climate crisis makes manufacturing the renewable energy revolution an imperative.
In fact, the Australian Government has already legislated emissions reductions targets of 43% (on 2005 levels) by 2030 and net zero by 2050.
Importantly, these targets will necessitate the construction of new infrastructure on a massive scale. Australia’s existing renewable energy generation of 64GW is forecast to grow to over 218GW by 2050.
This will comprise 90GW of wind, 39GW of solar, 18.7GW of water, and 35.9GW of battery storage. For example, it is expected that over 11,000 wind towers will need to be produced, each requiring 500 tonnes of plate steel (for onshore wind towers) or 750 tonnes (for offshore wind towers). The annual
production of plate steel in Australia is currently 400kt.
To connect all this new generation to consumers, AEMO estimates that more than 10,000km of new transmission lines and 25,000 transmission towers (at 30 to 60 tonnes of steel per tower) will need to be constructed around the country.
Australia’s renewable energy industry will need a raft of additional resources to deliver on these ambitious projects, including: manufacturing and fabrication capacity, raw materials (particularly steel), and contracting and contractor resources. Plus, new technologies will need to be developed and deployed.
While our governments can wish, and hope, and make public pledges about Australia’s transition to renewable energy, we simply do not have the sovereign manufacturing capability to make this a reality. The Federal Government and state governments can wish their renewable energy policies into existence, but without a massive investment in local manufacturing, it will not be achievable.
The US Model
The Inflation Reduction Act (IRA) came into effect in August 2022 in the United States, with the central goal of reindustrialising and decarbonising the US. It is estimated that the IRA’s provisions will facilitate a 43% reduction in US carbon emissions by 2030.
The United States, through the IRA, has taken shown tremendous leadership, enacting a plan to tackle the challenges of the renewable energy revolution; a plan with manufacturing at its heart; and a plan that is already delivering unprecedented growth in the sector.
A combination of tax credits, loans and subsidies, the IRA is driving private sector investment in clean electricity and electric vehicle manufacturing. The IRA is an investment in—not a cost to—the US economy.
When announced, the IRA was expected to amount to US$391 billion on energy and climate change provisions. However, independent research estimates that this may rise to $1.2 trillion.
This is estimated to pave the way for some $3 trillion of private capital investment in renewable technology and manufacturing—an investment without which the US economy and society could suffer catastrophic and irreversible damage.
The IRA has already had remarkable beneficial impacts: in its first six months in operation, over 100,000 new clean energy jobs have been created across 90 projects, investment in clean tech and semiconductor manufacturing has doubled, and real spending on manufacturing has also more than doubled.
The International Context
It is little wonder that these bold government-led investment plans have already been echoed in China, Europe, Canada, India, Japan and South Korea.
It is estimated that the Chinese government has invested between eight and ten times more than the US and Europe combined into energy transition technology and development of renewable technology manufacturing capacity.
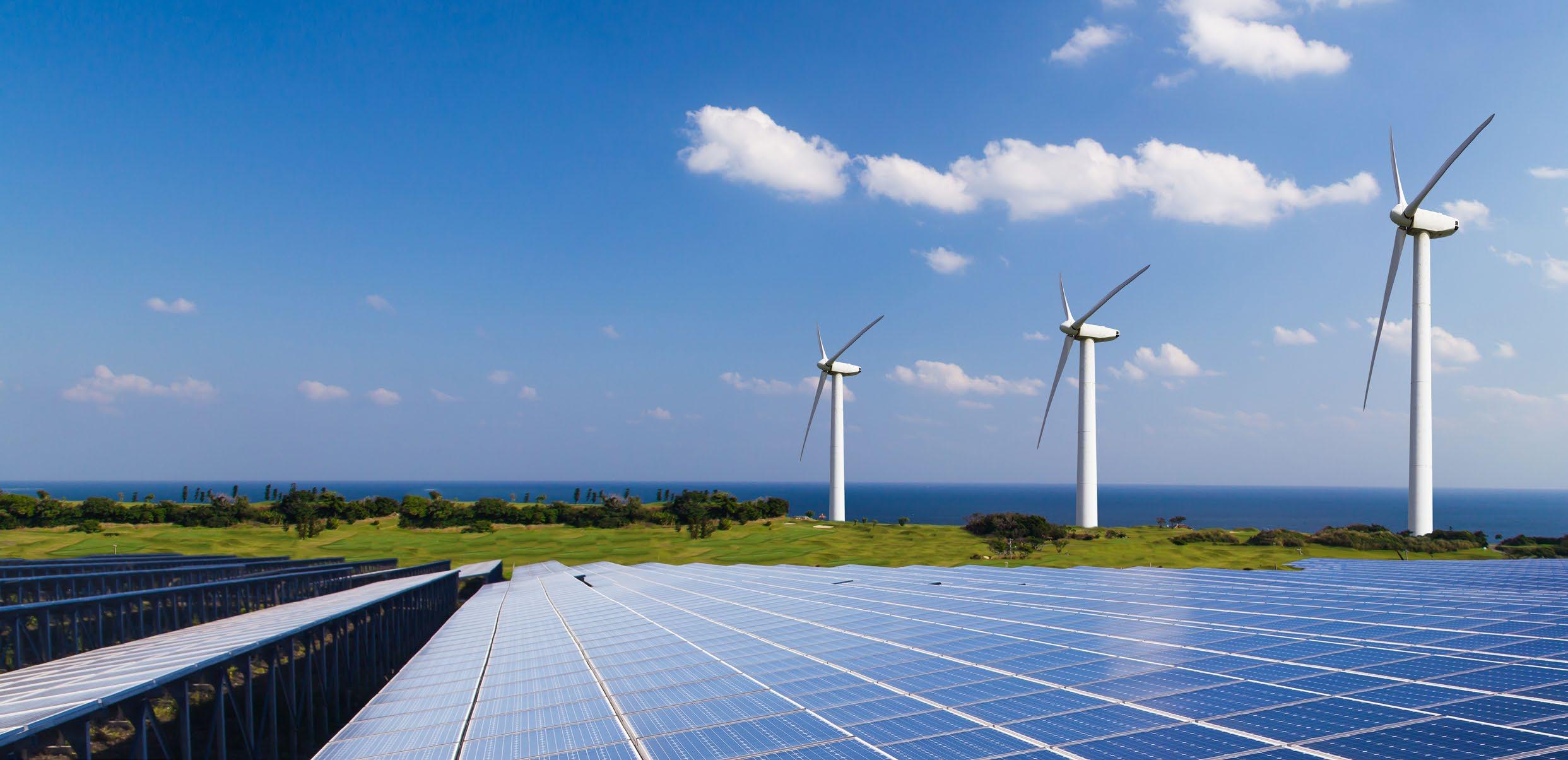
For example, thanks to its fast start and sustained, powerful industrial strategies, China has already secured a dominant position in all downstream segments of EV manufacturing.
The European Union recently announced the Green Deal Industrial Plan, which provides a framework for green technology and critical mineral supply. In addition, in July 2023, approval was confirmed for the European Chips Act, which will support an estimated €43 billion of investment between now and 2030 in measures such as next-generation technologies, and certification procedures for energy-efficient chips.
To achieve national decarbonisation goals, the Japanese government has formulated the Green Development Strategy through Achieving Carbon Neutrality in 2050. The South Korean government is set to embrace the economic opportunities of decarbonisation through its landmark Korean New Deal. In a landmark March 2023 federal budget, the Canadian government unveiled C$80 billion worth of fiscal programs to accelerate clean energy investments and developments.
“
If Australia is to ever achieve net zero, we must have our own version of the IRA, tailored to our local conditions. Australia simply has no choice. The alternative is unthinkable. We have half the net debt as a percentage of GDP as the US, so why are we even hesitating?”
“Australia must embrace the golden opportunity that the renewable energy revolution presents. We must become a clean energy manufacturing powerhouse, that exports value-added products to world.”
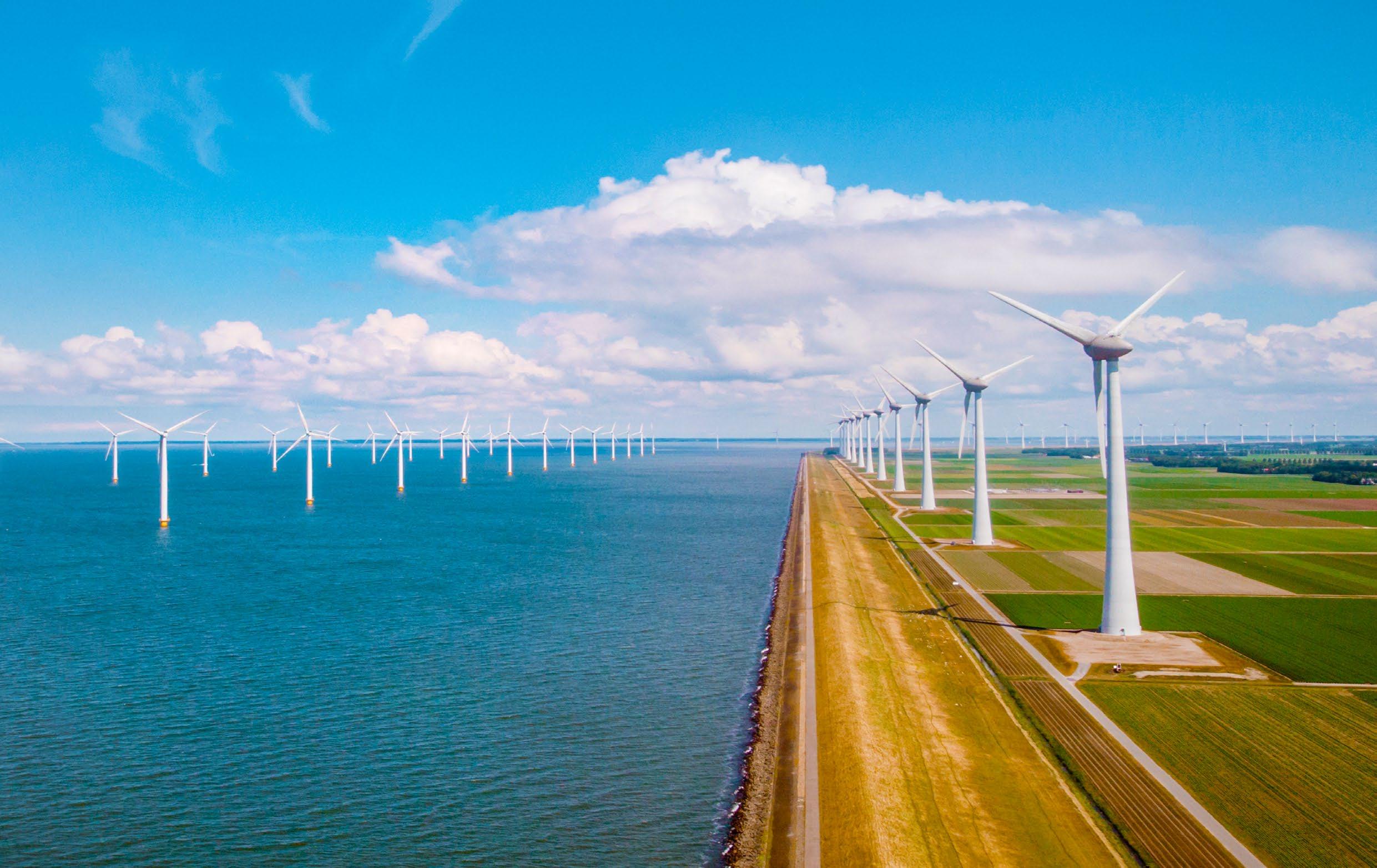
The (Lack of) Australian Response Meanwhile, Australia is still considering its response.
In Australia, the task of responding to the IRA seems to have created such an insurmountable challenge that we have ground to a halt. A policy of fiscal conservatism driven by Treasury is obstructing any type of progress. We are defeated before the first shot is fired.
Australia has many advantages in the global race for sustainable manufacturing, including an unmatched endowment of primary renewable energy sources, and ample deposits of critical minerals that are essential to production of renewable energy equipment. However, the painful legacy of decades of policy neglect for domestic manufacturing has left Australia’s industrial base in poor shape to seize the opportunities being opened up by the global energy transition.
Australia must stop debating the fiscal policy and act. We must become a valued partner within
international renewable energy supply chains. We must overcome our traditional ‘dig and ship’ mentality and leverage our critical minerals supply to manufacture complex, value-added renewable energy products onshore.
If Australia is to ever achieve net zero, we must have our own version of the IRA, tailored to our local conditions. Australia simply has no choice. The alternative is unthinkable. We have half the net debt as a percentage of GDP as the US, so why are we even hesitating?
Adjusted for the scale of the Australian economy, the Australian Government must commit $300 billion—approximately $12 billion a year to 2050—to a program similar in size and scale to the IRA. This sum is equivalent to current carbon subsidies, inconsequential when compared with the anticipated mining royalties from rare earth minerals, and less than the $368 billion we plan to spend on nuclear submarines.
With an IRA-type program that combines subsidies and incentives,
commercially viable procurement procedures and a sensible national strategy, the manufacturing industry will be able to respond and carry its share of the load. Industry will be able to invest in its own facilities and create more high-quality jobs. We will not be able to manufacture everything we need but we will be able to deliver enough to provide a buffer to gaps in the global supply chain and ensure reasonable pricing.
Australia must embrace the golden opportunity that the renewable energy revolution presents. We must become a clean energy manufacturing powerhouse, that exports value-added products to world. In this way, Australia will create thousands of new jobs, reduce our risks to volatile international markets, reduce the cost of living for Australian families, and play an essential role in global decarbonisation.
It is already too late. Australia must act now. We must act bravely and fund our renewable energy revolution properly. Australia’s governments must have the courage to act now.
BREAKING NEWS
Novarc Technologies Completes Series A Fundraising Round With Caterpillar Venture Capital
Novarc Technologies, a leading provider of advanced robotics solutions, recently announced that they have successfully completed a Series A fundraising round with Caterpillar Venture Capital, a whollyowned subsidiary of Caterpillar (a global leader in the manufacturing of construction and mining equipment).
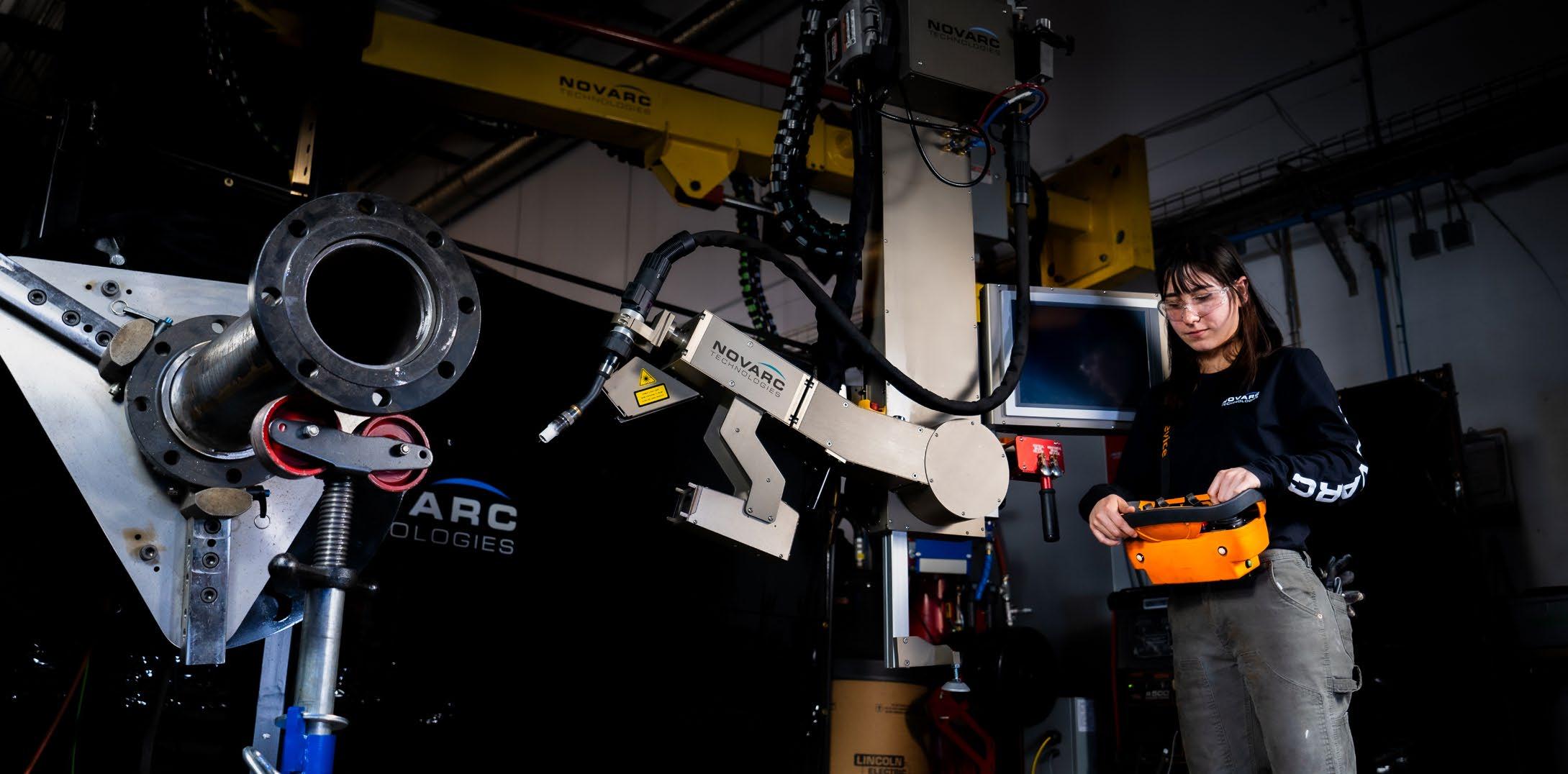
Caterpillar joins Graham Partners, Export Development Canada (EDC) and other syndicate investors, and provides strategic support to Novarc’s vision to accelerate the development of a ground-breaking AI-powered robotics platform.
“We are thrilled to welcome Caterpillar as an investor in Novarc. Their extensive industry expertise and global presence align perfectly with our goals. This investment will fuel the development of Novarc’s AI robotic welding solutions, enabling us to revolutionise the future of welding
in manufacturing automation and beyond,” said Soroush Karimzadeh, CEO of Novarc Technologies.
Novarc plans to leverage this strategic relationship to further enhance disruptive technology and expand its global reach. The adoption of a welding solution enhanced by artificial intelligence is fast becoming a necessity among fabrication facilities that want to remain competitive. The additional funds will be instrumental in advancing the development of Novarc’s AI-powered robotic solutions which provide a major step forward in manufacturing, precision, efficiency, and flexibility.
“With Caterpillar’s support, we are well-positioned to unlock new opportunities and transform the way manufacturing processes are executed,” said Karimzadeh.
“Together, through this relationship, we look forward to delivering innovative solutions that provide productivity, quality, and safety for our customers across the globe.”
Stanwell Clean Energy Hub Kicks Off with Training Cash
Queensland’s publicly owned energy company Stanwell Corporation will build a Future Energy and Innovation Training Hub (FEITH) valued at up to $100 million as step one of the state’s investment in a Stanwell Clean Energy Hub at Rockhampton.
The size of a shopping centre, the hub will provide the ‘sandbox’ to test out innovative new energy technology including wind, solar, hydrogen and battery storage, according to the government. It will also provide a reallife, hands-on training environment for Queensland energy employees to develop the skills needed to work on renewable energy technologies.
The project is proposed to be delivered in phases, starting with the establishment of common infrastructure and civil works in late 2023. Future phases include a skills academy and demonstration centre where the community can come to learn about new energy technologies.
BREAKING NEWS
Australia’s First Service Station Hydrogen Refueller Opens
Leading gas and engineering company BOC, a Linde company, and bp Australia recently celebrated the official opening of Australia’s first hydrogen refuelling station at a service station at the bp Port of Brisbane Truckstop in Lytton.
This milestone marks the completion of BOC’s Bulwer Island end-to-end renewable hydrogen demonstration project funded by BOC, Australian Renewable Energy Agency (ARENA), Queensland Government and bp Australia.
BOC is producing renewable hydrogen at its Bulwer Island production site with a 220 kW electrolyser powered by solar energy generated onsite. It is then transported in hydrogen tube trailers to the Linde hydrogen refuelling station located at the bp Port of Brisbane Truckstop.
Queensland Government’s QFleet will use the facility to refill its current fleet of five-hydrogen powered Hyundai Nexos in approximately three to five minutes. Any member of the public with a hydrogen car can also register with bp to refill their passenger vehicle with a bp plus card.
Binod Patwari, Managing Director of BOC South Pacific said the project is an excellent example of two leading companies working together to leverage skills and existing infrastructure to progress the renewable hydrogen industry.
“BOC is proud to officially open this hydrogen refuelling station with bp Australia, which is a critical part of our Bulwer Island end-to-end renewable hydrogen project and demonstrates our commitment to progress hydrogen as a zero emissions fuel for transport.”
“Our Bulwer Island production site is strategically located to supply renewable hydrogen to industrial and transport customers in Queensland. We are committed to scaling our hydrogen capabilities at this site in the future to support decarbonisation of high-emitting industries and working with government and industry to activate demand for hydrogen across Queensland.
“The successful integration of a hydrogen refuelling station at an existing service station has delivered key learnings that will pave the way for more hydrogen refuelling infrastructure across Australia’s service station network. Leveraging this existing infrastructure will be important to support the uptake of heavy transport particularly on major freight routes across Australia.
“We would like to thank our partners ARENA, Queensland Government and bp Australia for their support on this project, and look forward to delivering more hydrogen refuelling, production and supply projects in the future.”
Thales Opens Lithgow Advanced Manufacturing Centre
Defence manufacturer Thales Australia has continued its revitalisation of the historic former Lithgow small arms works with the opening of the company’s new advanced manufacturing facility in the regional New South Wales city.
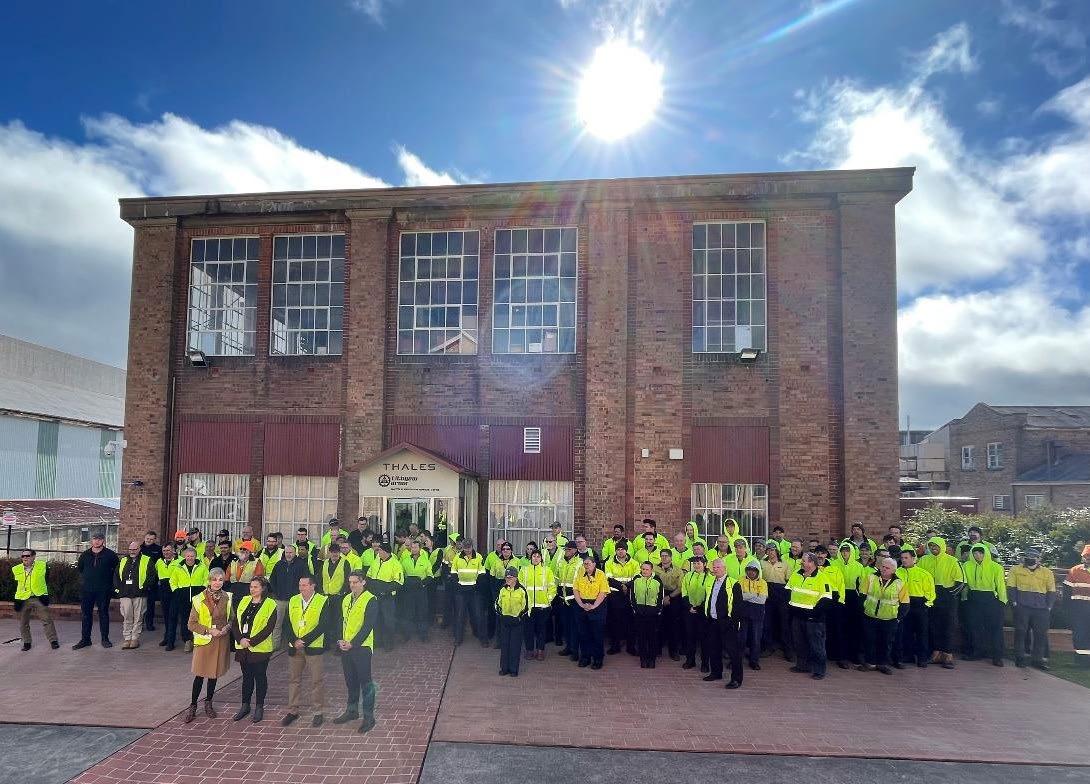
Defence Minister Pat Conroy officiated and opened the new Lithgow Arms facility which has been a centre of Australia’s defence industry since it opened in 1912.
The opening of the new facility is a milestone in the first phase in an ambitious plan to transform its Lithgow Arms site into an advanced manufacturing 4.0 and integration hub for the precision manufacture of Australian designed weapon systems.
The plant will integrate both traditional precision manufacturing and digital technologies, including 3D printing, and the installation of automated electro-plating and other metal treatment capabilities.
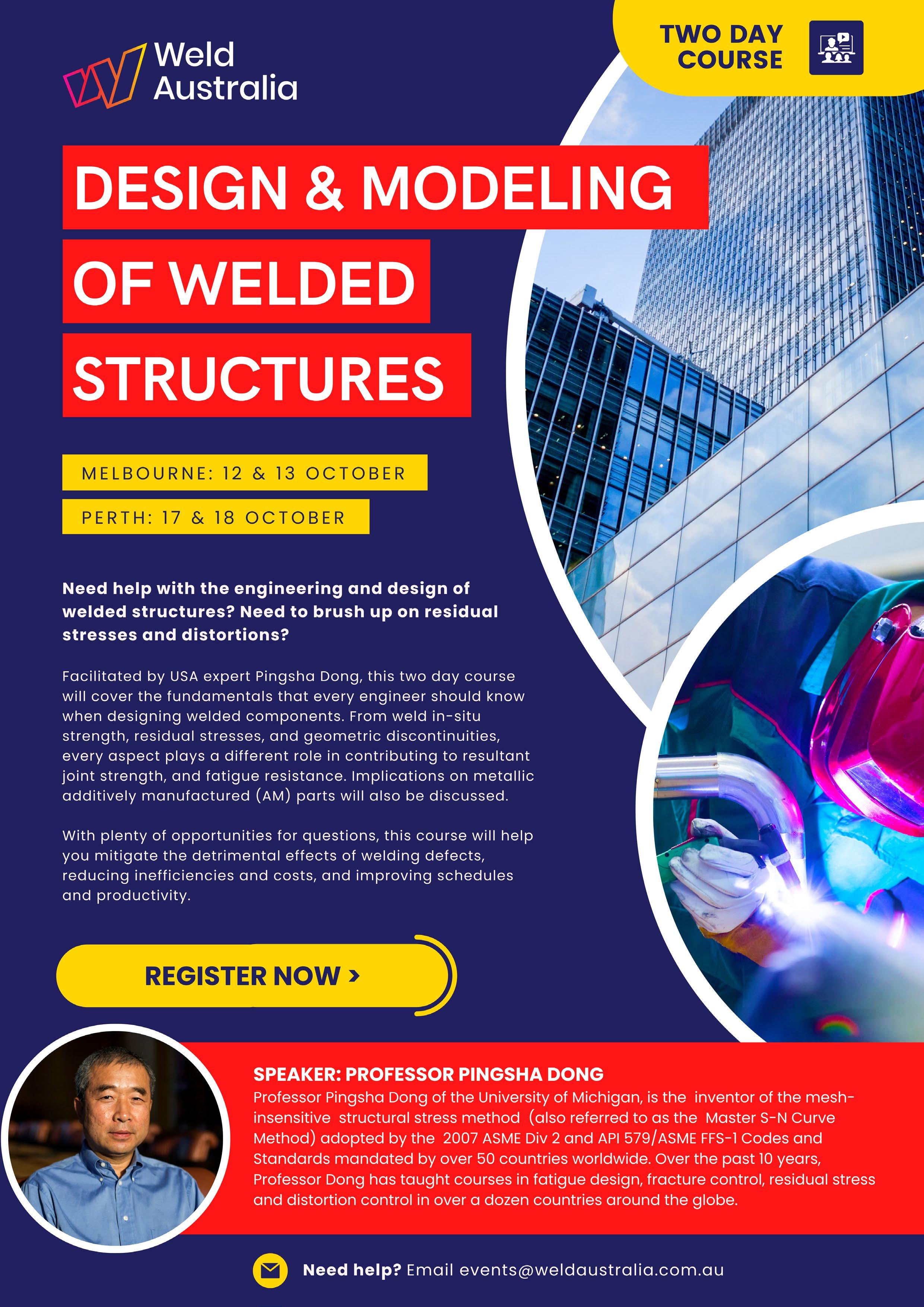
TAFE NSW SKILLS UNDERWATER WELDING EXPERTS TO FILL INDEMAND ROLES
As demand for graduate fabrication trade engineers in Australia skyrockets, TAFE NSW is supplying the industry with job-ready underwater welders who are quickly gaining lucrative jobs in the field.
With the large number of infrastructure projects underway across the country, opportunities for skilled fabricators and welders are expected to increase. According to Australian labour market insights, structural steel and welding trades workers is the largest employing
occupation in the manufacturing industry1
Adding diving experience to fabrication trade skills can significantly increase earning potential, with Salary Expert predicting the average Australian underwater welder salary to increase from $127,000 to $150,000 by 20272
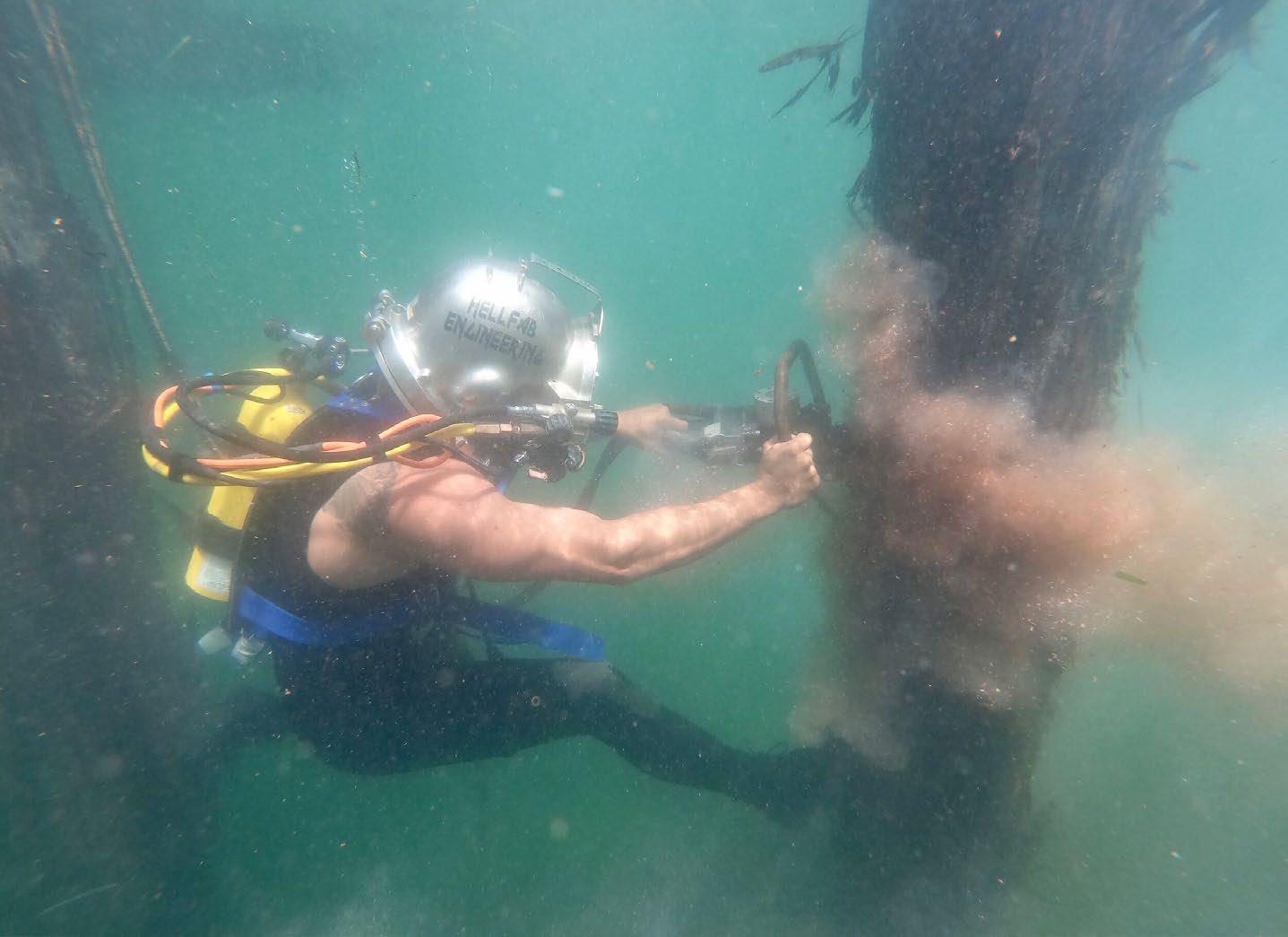
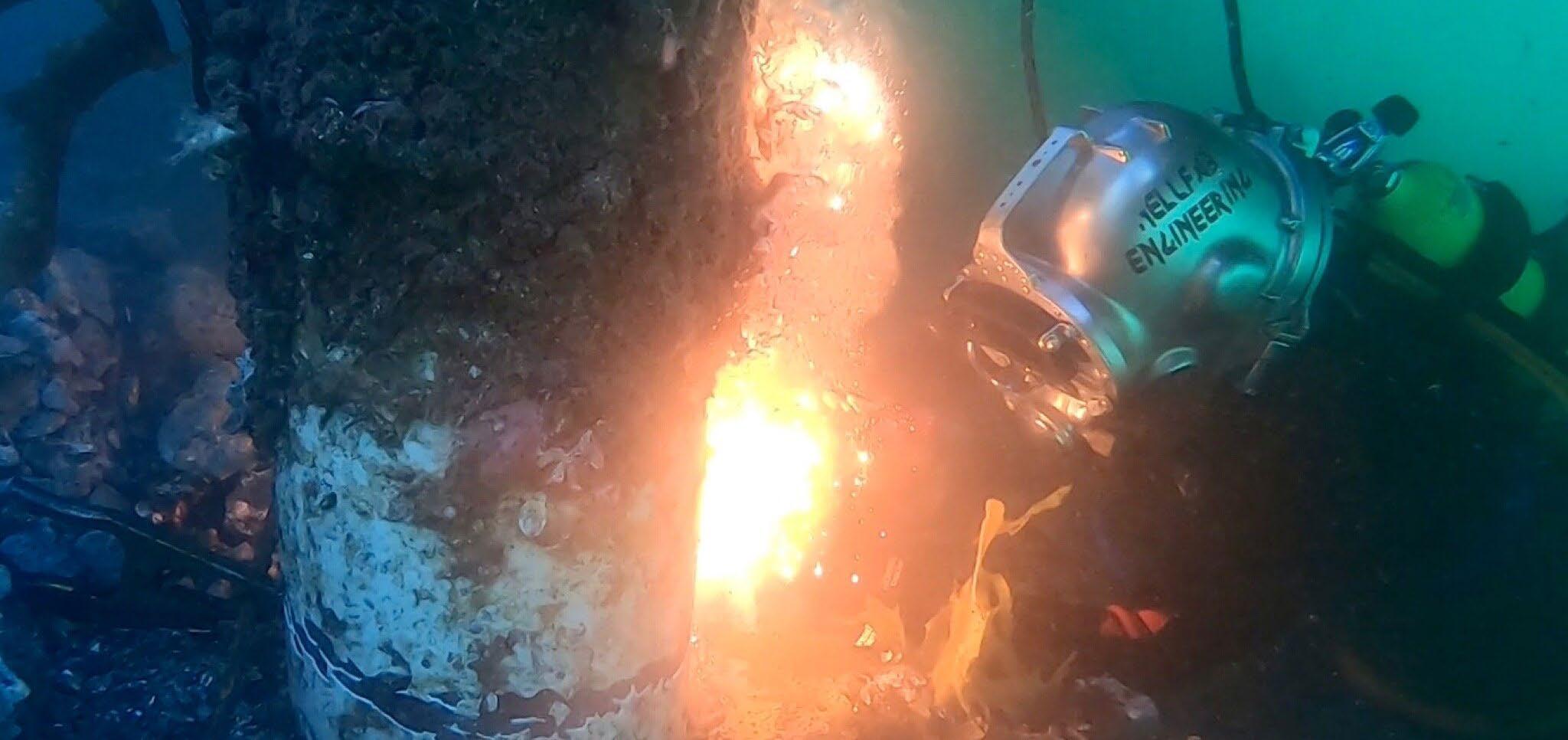
Kirrawee local Shaun Pyne seized on this opportunity to maximise his earning potential by pairing his boilermaker skills with a commercial diving license. “I started my career in the heavy marine industry in 2007 as an apprentice boilermaker with a
passion for competitive spearfishing and bodyboarding at an international level,” Shaun said.
“After completing my apprenticeship, I worked predominantly in the oil and gas industry as a boilermaker and rigger.”
Shaun completed his Certificate III in Engineering - Fabrication Trade at TAFE NSW Ultimo in 2019 and combined his skills as as a Certified Australian Diver Accreditation Scheme (ADAS) Commercial Diver, licenced to work up to a depth of 50m, to gain employment specialising in in-water repairs to ships, inland dams and marine structures. Shaun has now opened his own business – Hellfab Engineering – where he and his team service all aspects of civil, marine and subsea engineering works.
“The technical skills I gained at TAFE NSW set me up with an incredible foundation to take my career in any direction I chose,” Shaun said.
“Welders are in hot demand due to the number of construction works going on across New South Wales and there are many lucrative career paths in the industry. I’m lucky to lead a team of like-minded people who have combined their love of engineering with diving and my career choices have set me up for life.”
Gary Hibbert, Head Teacher ofMetal Fabrication and Welding at TAFE NSW said Shaun thrived on the combination of TAFE NSW’s specialised accredited training in metal fabrication and his personal ambition to take his career to the next level.
“The Certificate III in Engineering - Fabrication Trade teaches a combination of theoretical and practical skills in technical drawing and geometric development, fabrication including forging and founding, welding and thermal cutting and more,” Gary said.
“Graduates can go on to have a career as a boilermaker, welder, engineering patternmaker or blacksmith.”
“Shaun was a naturally good welder who consistently achieved great marks, and once he had his TAFE NSW fabrication trade under his belt, knew how he could maximise his skills in combination with his ADAS certification as a pathway to gain entry into the lucrative field of underwater welding,” said Gary.
TAFE NSW is currently offering a number of fabrication and welding certificate level engineering qualifications fee-free*.
Fee-free* TAFE is a joint initiative of the Australian and New South Wales Governments, providing tuition-free training places aligned to the state’s priority industry growth sectors for people wanting to train, retrain or upskill.
About TAFE NSW
As one of the leading providers of education and training in Australia, TAFE NSW has an extensive network of industry qualified and experienced teachers bringing up-to-date, realworld skills directly to the classroom.
With over 130 years of experience and more than 170 learning locations across the state, TAFE NSW offers flexible training options and a 90% student satisfaction rating. Each year, more than 430,000 students enrol in their courses and training. TAFE
NSW aims to skill the workforce for the future through high quality, personalised education and training.
TAFE NSW has a great reputation for industry and business partnerships. These connections ensure their students get the highest level of practical training, meaning they can provide a high quality, job-ready workforce. TAFE NSW is constantly adapting their courses and facilities
to suit local community and industry needs.
* Eligibility criteria apply. RTO 90003 I CRICOS 00591E I HEP PRV12049
Sources
1. https://labourmarketinsights.gov. au/occupation-profile/StructuralSteel-and-Welding-TradesWorkers?occupationCode=3223
2. https://www.salaryexpert.com/salary/job/ underwater-welder/australia
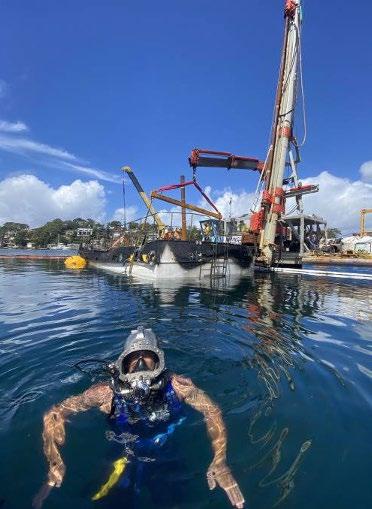
Further Information
To find out more about studying engineering trades at TAFE NSW visit: tafensw.edu.au/engineering or scan the QR code opposite.
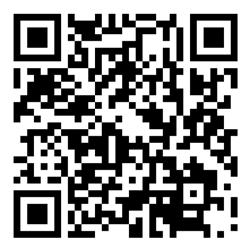
“
Welders are in hot demand due to the number of construction works going on across New South Wales and there are many lucrative career paths in the industry.”60 foot vessel salvage at Burraneer Bay.
Weld Australia’s Excellence Awards are one of the most prestigious events on the welding industry calendar. The Awards embody and promote the highest standards of craftsmanship, quality and professionalism. The 2023 Welding Excellence Awards are a fantastic opportunity for welders, fabricators and educators across Australia to showcase their people and their operations. Winners will be awarded in each state for each of the award categories below. Award entries close on 15 September 2023.
Company of the Year
The Company of the Year Award recognises superior performance across a comprehensive range of business metrics including: innovation, quality assurance, market success, corporate social responsibility, health and safety, sustainability, and training and development of employees. There are three sub-categories:
• Company of the Year – Fabrication Award Criteria | Enter Now
• Company of the Year – Gas & Gear Award Criteria | Enter Now
• Indigenous Company of the Year Award Criteria | Enter Now
Welding Professional of the Year
This Award recognises professionals who are making a valuable contribution to the Australian welding and fabrication industry. The individual should demonstrate a high level of skill, knowledge or craftsmanship, be dedicated to their profession, and have professional development plans in place. There are three sub-categories:
• Welding Professional of the Year – Welding Coordinator
Award Criteria | Enter Now
• Welding Professional of the Year – Welding Supervisor Award Criteria | Enter Now
• Welding Professional of the Year – Welding Inspector Award Criteria | Enter Now
How to Enter the Welding Excellence Awards
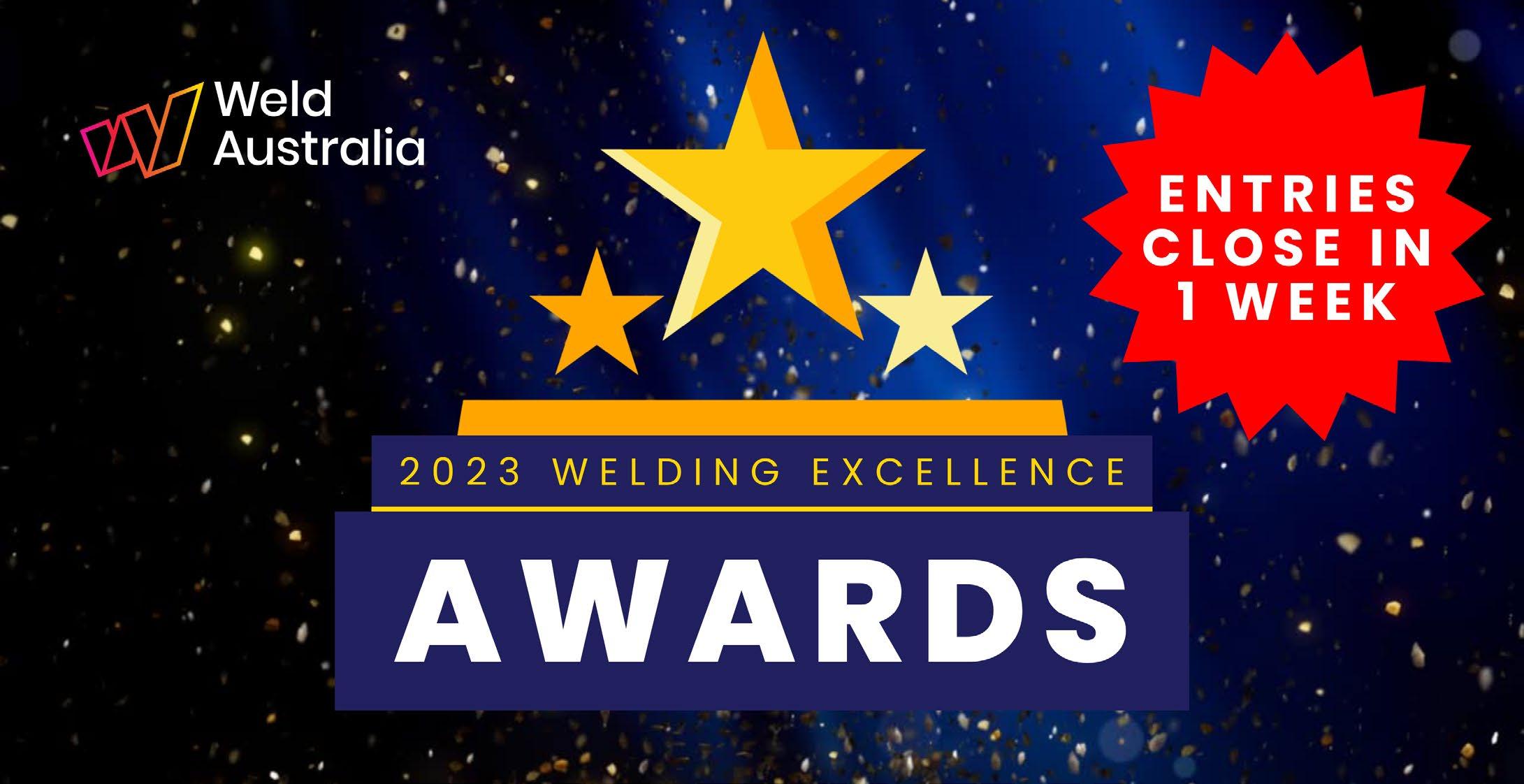
Entries must be submitted via the specific online form for each category by 15 September 2023. These forms can be found via the Weld Australia website, by clicking on the relevant red button.
Entry forms can be saved. However, before starting your entry, it is recommended that you download the Award Criteria (also available via the Weld Australia website). You will need the information outlined in the Award Criteria on hand to complete your online entry form.
Project of the Year
Award Criteria | Enter Now
The Project of the Year Award recognises excellence in welding and fabrication projects, with a focus on exceptional craftsmanship, a commitment to Australian and International Standards, environmental sustainability and innovation. Projects must have been completed in the 12 months preceding 1 October 2023.
Health and Safety in Welding
Award Criteria | Enter Now
The Health and Safety in Welding Award recognises organisations that are leading the way in encouraging and promoting health and safety throughout the Australian welding industry, and ensuring the health and safety of their own team. Organisations will be judged on criteria such as design and implementation of innovative programs or initiatives, the outcomes of these programs, and the health and safety of their team.
Trades Person of the Year
This Award recognises tradespeople who are making a valuable contribution to the welding and fabrication industry. The individual should demonstrate a high level of skill, knowledge or craftsmanship, be dedicated to their profession, and have professional development plans in place. There are three sub-categories:
• Young Trades Person of the Year Award Criteria | Enter Now
• Young Indigenous Trades Person of the Year Award Criteria | Enter Now
• Trades Person of the Year Award Criteria | Enter Now
Training and Education Award – Organisation Award Criteria | Enter Now
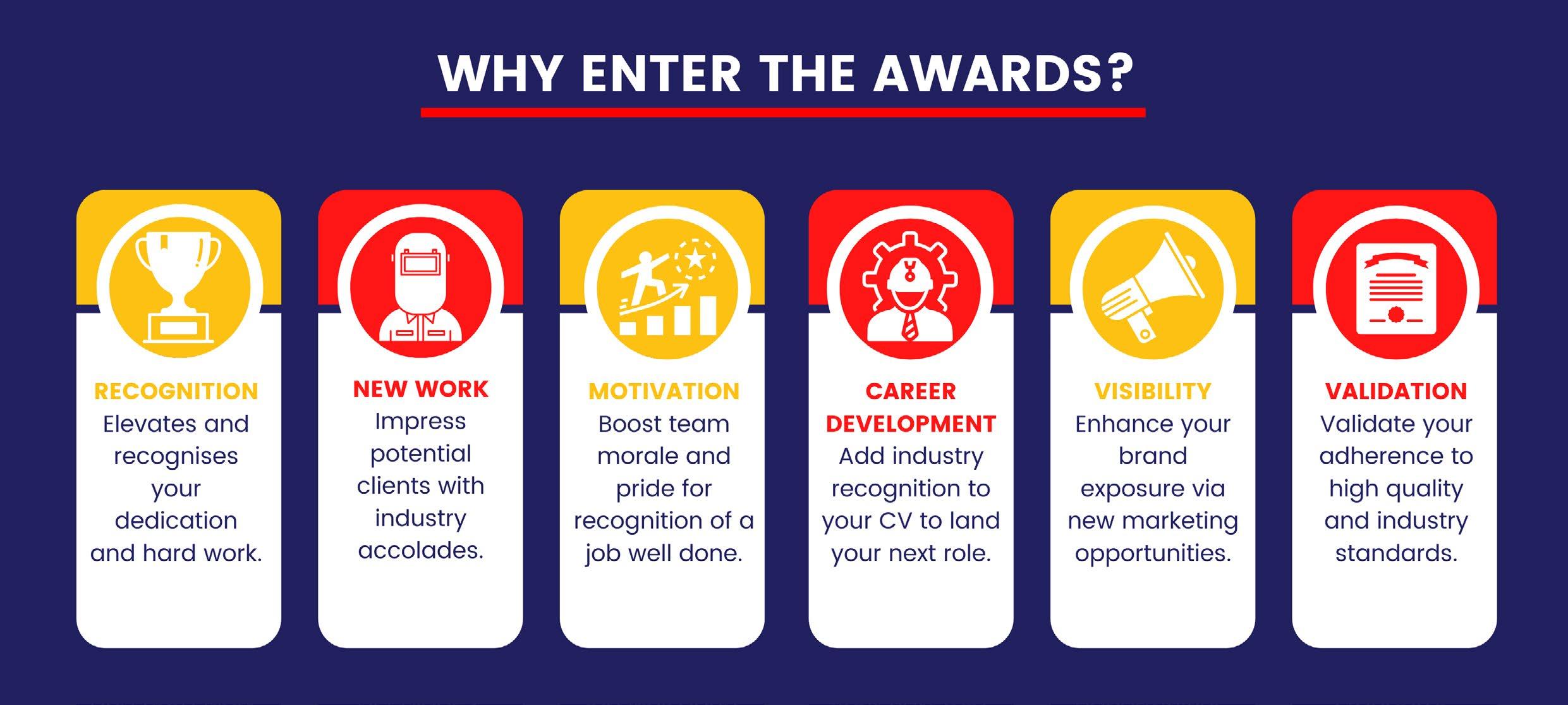
The Training and Education Award recognises the outstanding achievements of a STEM or VET provider or program. Entrants may include secondary education and tertiary education providers. Criteria include delivery of quality, innovative training programs, involvement with industry, recruitment and retention of students, and corporate social responsibility.
Training and Education Award – Individual Teacher Award Criteria | Enter Now
This Award recognises the outstanding achievements of a STEM or VET teacher. Entrants will be judged on criteria such as delivery of quality, innovative training programs, high level of knowledge or craftsmanship, strong links with students, and dedication.
Attend the Awards
• Perth: Wednesday 18 October at Beaumont on the Point
• Sydney: Wednesday 25 October at Waterview in Bicentennial Park
• Adelaide: Wednesday 1 November at Glenelg Golf Club
• Brisbane: Wednesday15 November at Indooroopilly Golf Club
• Melbourne: Wednesday 29 November at Huntingdale Golf Club
Registrations for the events are now open, and can be booked by clicking on the links above. The 2022 award events sold out in record time, so be sure to register early to avoid disappointment.
Ken Trevena Award – South Australia Only Award Criteria | Enter Now
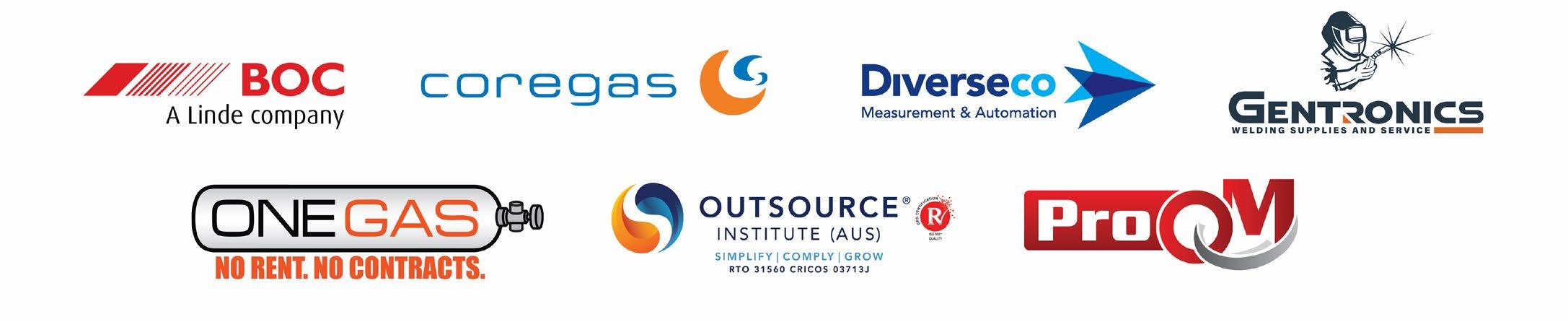
This Award recognises someone who has demonstrated an outstanding welding expertise on a particular project, attained meritorious skill in a Weld Australia Course, made a contribution to the art and science of welding, or developed a welding principle, technique or process.
Further Information
For further information, contact: Michelle Bignold on 0437 106 726 or m.bignold@weldaustralia.com.au
WITH THANKS TO OUR SPONSORS
A scientific study THE EFFECTIVENESS OF WELDING FUME PRODUCT CONTROLS
Welding fume has been linked to multiple forms of cancer, classified as a carcinogen by the International Agency for the Research on Cancer, and studies have concluded that “welders run an increased risk of lung cancer of up to 43% when compared with those who have never welded or been exposed to welding fume”. Welding fume is also linked to other short and long-term adverse health effects. There are countless studies that conclude that welding fume is bad for health, yet there seem to be few that provide practical guidance on how to effectively control welding fume exposure. The intent of the Scientific Study undertaken by AWS was to compare the effectiveness of different welding fume product control methods in reducing exposure to welding fume.
THE METHODOLOGY
The methods analysed were:
• On-Gun Fume Extraction Local Exhaust Ventilation (LEV)
• Hooded Capture Local Exhaust Ventilation (LEV)
• Welding Helmet with a Powered Air Purifying Respirator (PAPR)
The study included taking air samples while welding under controlled conditions. Fourteen different test scenarios were assessed, including variations of welding techniques and controls commonly used in Australia and New Zealand. Over 1,300 responses were received. It should be noted that the study does not address welding in confined spaces.
THE RESULTS
Without adequate controls, research shows that typical welding fume exposures are highly likely to exceed the regulatory workplace exposure standard, placing workers at risk of irreversible lung disease and other adverse health effects.
Welder’s Exposure to Welding Fume
Objective: Compare the effectiveness of On-Gun Fume Extraction LEV,
Hooded Capture LEV, and a Welding Helmet with a Powered Air Purifying Respirator in reducing the welder’s exposure to welding fume.
With a reduction in exposure of at least 99.96%, the Welding Helmet with an Integrated Powered Air Purifying Respirator was by far the most effective control measure in protecting the welder from welding fume exposure when compared to On-Gun Fume Extraction and Hooded Capture LEV.
The Welding Helmet with an Integrated Powered Air Purifying Respirator provided an Effective Protection Factor (EPF) of at least 2,600. Meaning a PAPR could reduce welding fume exposure to at least 1/2,600th of the outside concentration.
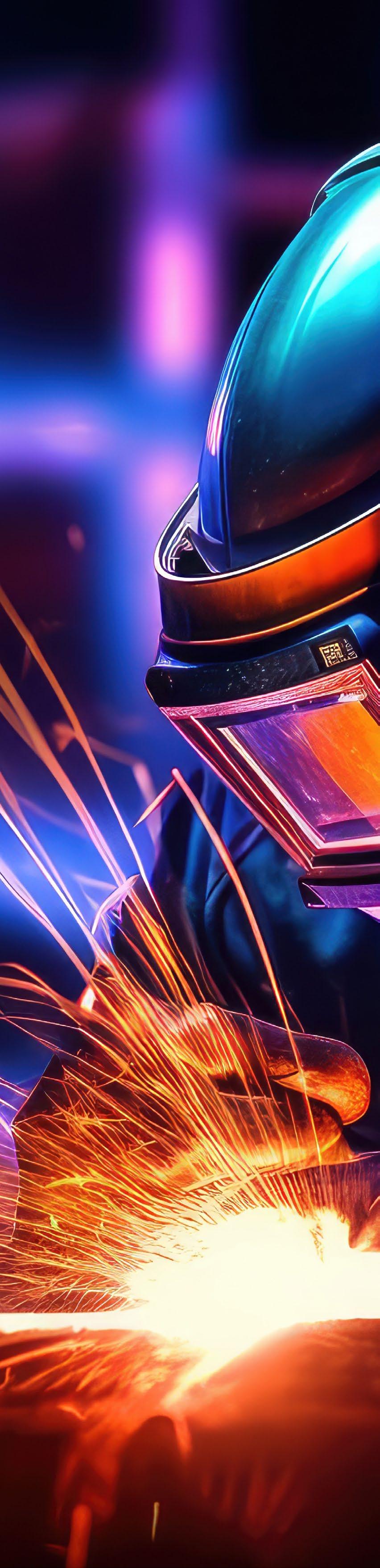
The results of the study show a level of performance at least 52 times better than the Required Minimum Protection Factor (RMPF) of 50 as specified in AS/NZS 1715:2009 Respiratory protective equipment.
A Welding Helmet with an Integrated
Without effective protection, welders are exposed to a carcinogenic substance. However, by law, it is the employer’s responsibility to reduce welding fume exposure to as low as reasonably practicable. The results of the study give clear and practical guidance on effective engineering and personal protective equipment (PPE) control methods to reduce welding fume exposure.
On-gun fume extraction, the most effective engineering control measured in the study, had an average capture rate of 90% across all tests. The law in Australia and New Zealand clearly states that if there is any remaining risk after higher controls, such as engineering controls, have been implemented, it must be minimised with suitable PPE. Based on the results of this study, a PAPR correctly worn and maintained, will ensure that the welder is well below all relevant Workplace Exposure Standards for most common welding applications, and can reduce welding fume exposure by a factor of at least 2,600 corresponding to a minimum 99.96% reduction.
Powered Air Purifying Respirator was found to be the most effective welding fume product control in reducing the welder’s exposure to welding fume based on the results of the study.
Compared to a half mask respirator, a welding helmet with a PAPR can offer:
• Superior respiratory protection.
• No breathing resistance.
• A cooling flow of fresh air to improve comfort.
• No requirement for fit testing.
• No requirement for a complete shaven condition (if relevant).
• Potential long term cost saving.
A PAPR should be considered a priority in situations where the welder is the only person requiring protection from welding fumes.
Removing Welding Fume from the Environment
Objective: Compare the effectiveness of On-Gun Fume Extraction LEV and Hooded Capture LEV in removing welding fume from the environment.
On-Gun Fume Extraction LEV was 33% more effective than Hooded Capture LEV in extracting welding
fume from the environment. On-gun fume extraction was able to extract up to 97% of the welding fume with an average of 90% across all tests.
On-gun fume extraction also has the added benefit of following the welder as the welder moves, unlike fixed LEV hooded capture that requires the welder to be perfectly positioned relative to the capture hood and for the welder and welding arc location to remain relatively stationary.
Measurements taken during the study suggested that exposure to welding fume can approximately double when the capture hood distance from the arc increased from 30cm (correct distance from the arc based on manufacturer’s instructions) to 50cm. This has large implications for welders who do not remain stationary or for those who are doing long welds.
On-gun fume extraction can also reduce the costs associated with maintaining welding helmet and PAPR consumables (such as outside cover lenses, particle filters) and workshop cleaning costs by capturing welding fume at the source.
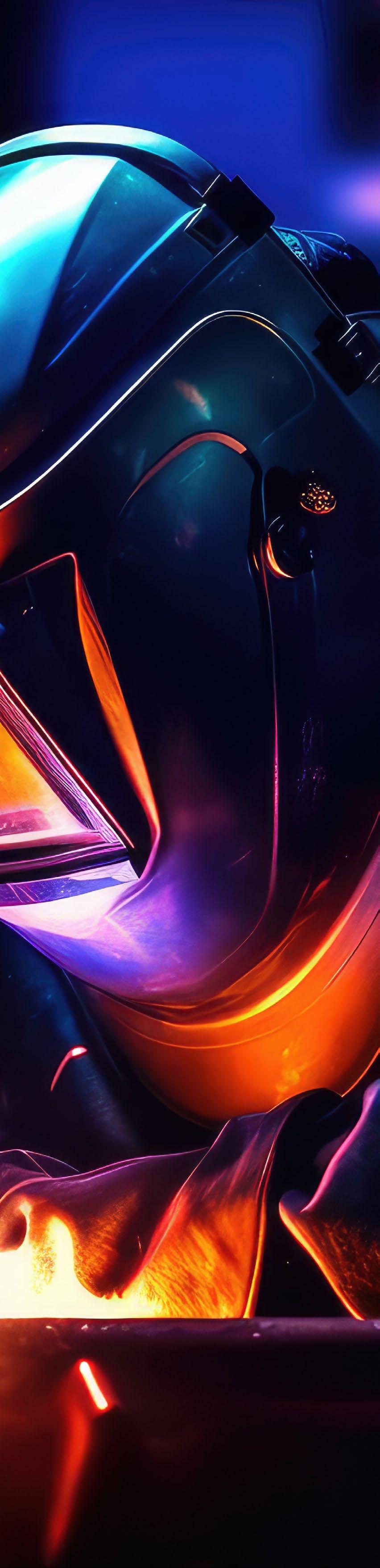
PRACTICAL TAKEAWAYS
Based on the conclusions of the welding fume product control study, the following product control guidance is offered to reduce welding fume exposure to as low as reasonably practicable when welding using the most common materials (aluminium, steel, stainless steel, galvanised steel etc.) in environments with good ventilation.
This guidance assumes that all efforts to mitigate risk associated with welding fume through elimination, substitution, and isolation controls have been carried out.
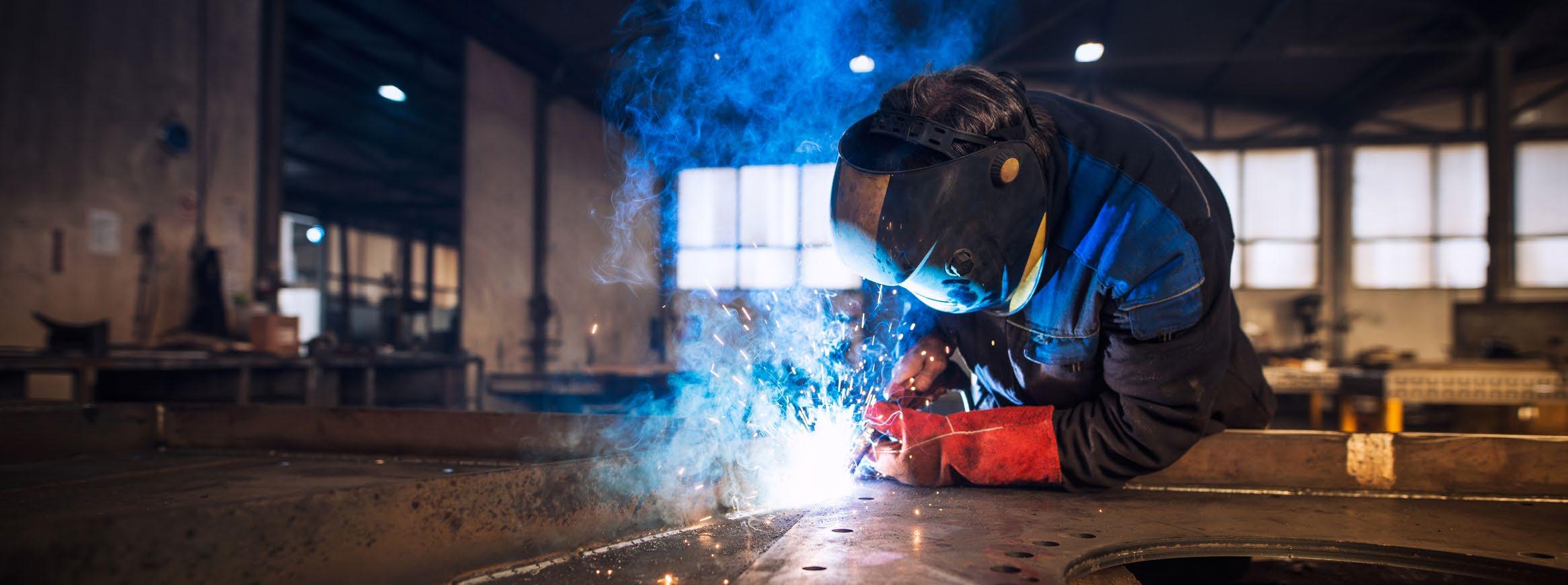
Protecting Only the Welder from Welding Fume
Introduce Welding Helmets with integrated Powered Air Purifying Respirators (PAPR).
Ensure staff are trained in the proper use and maintenance of the PAPR.
Many suppliers offer in-person and online training programs for free.
Remove surface coatings and look to mitigate risk by using a welding technique that produces less fume or introduce less hazardous materials where possible.
Welders should position themselves to ensure they keep their heads away from the plume where possible and take advantage of any ventilation available.
Protecting the Welder and Surrounding Workers from Welding Fume
Introduce a dedicated area for welding away from other workers and restrict access to this area where possible.
Introduce Local Exhaust Ventilation in combination with a Welding Helmet with an integrated
Powered Air Purifying Respirator to protect the welder and control the spread of welding fume throughout the environment. If suitable for the application, on-gun fume extraction is the most effective and practical engineering LEV welding fume control.
Have staff trained in the proper use and maintenance of the PAPR and LEV system. Many suppliers offer inperson and online training programs for free.
Remove surface coatings and look to mitigate risk by using a welding technique that produces less fume or introduce less hazardous materials where possible.
Welders should position themselves to ensure they keep their heads away from the plume (if applicable) where possible.
Download a Copy of the Study
For further information:
• Download a copy of The Effectiveness of Welding Fume Product Controls – An Australian Scientific Study
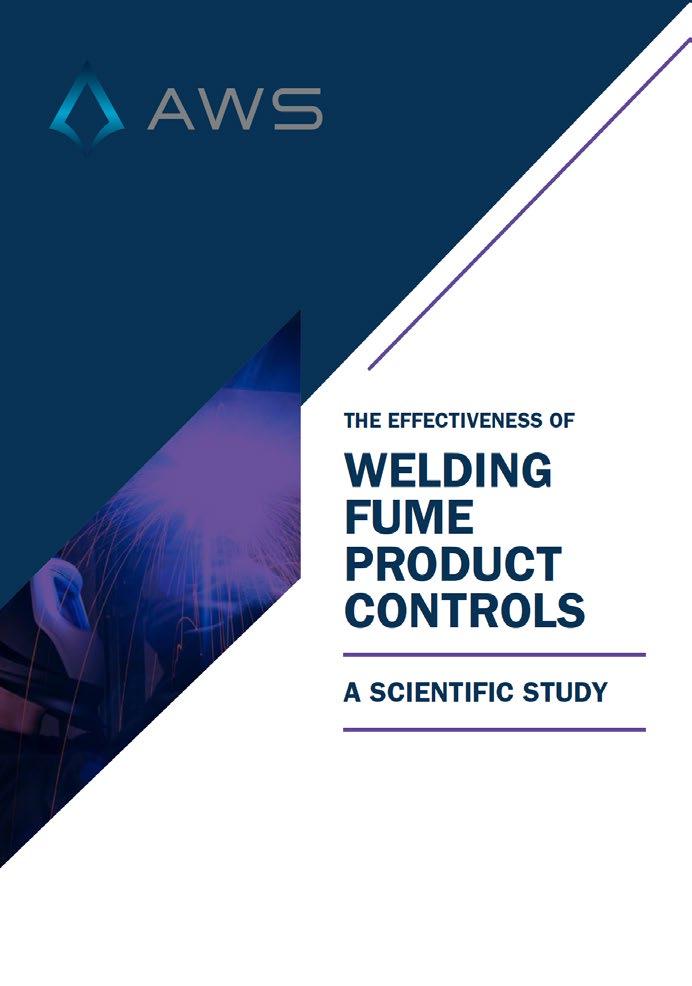
• Download a copy of the Key Fact Document
About AWS
AWS was established in 1994 and has played a key role in the welding industry ever since. As a company that specialises in welding safety equipment, it is AWS goal to raise awareness on the important issues that welders face. AWS supplies all forms of welding fume product controls including half mask respirators, auto-darkening welding helmets with powered air purifying respirators, hooded capture LEV, and on-gun fume extraction. For further information, visit: apexweldingsafety.com.au.
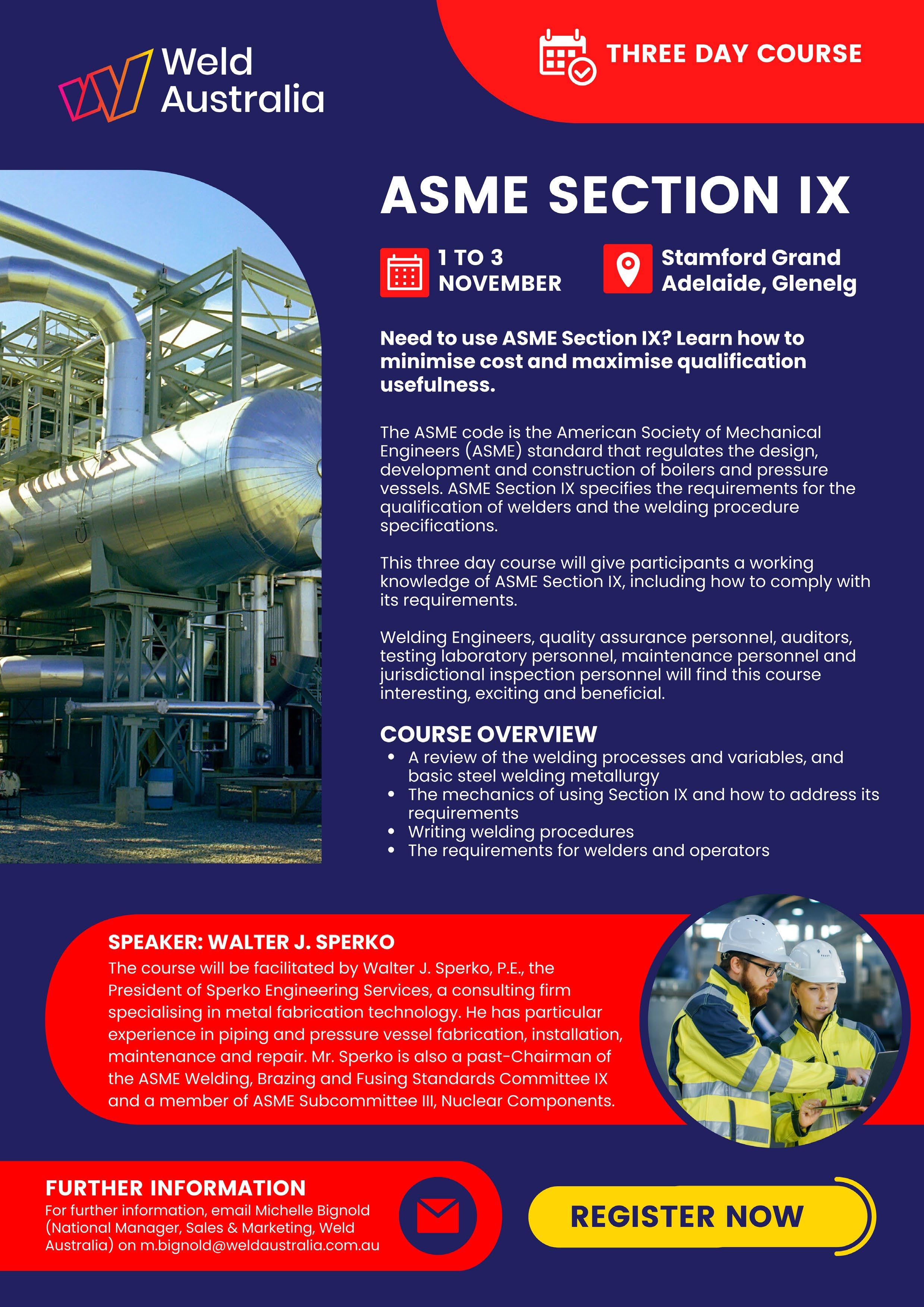
PRIVACY ACT REFORMS: What Small Businesses Need to Know
In Australia, businesses are responsible for protecting the personal information provided to them by customers under the Privacy Act. Following a two-year review of Australia’s privacy laws, the Federal Government has proposed a series of reforms to the Privacy Act that will impact on businesses of all sizes. It’s expected that the reforms will become law in late 2023. Here’s what the expected changes mean for your small business, and how to ensure compliance with the updated Privacy Act.
Understanding the Privacy Act
The Privacy Act was introduced in 1988 to regulate how businesses and federal government agencies handle personal information and protect their customers’ privacy. Organisations must adhere to 13 Australian Privacy Principles that govern the collection, use and disclosure of personal information.

Andrew Lawrence, CEO and founder of de.iterate— experts in data privacy and cyber security compliance—explained, “Business owners are required to handle customers’ personal information in a clear and transparent way, and safeguard against theft, loss, misuse, interference, modification, and unauthorised access.”
“Under the Privacy Act, businesses need to have a clear privacy policy outlining the information they collect, what they use it for, and how they protect it. They may only collect information where it is necessary for business activities, and must destroy or de-identify personal data once it is no longer needed. The Privacy Act also gives individuals greater control over how their personal information is handled.”
What is Considered Personal Information?
Personal information is any information that allows you to identify an individual – regardless of whether it is true or what form it is in. This might include your customers’: name; contact details, such as address, email, or phone number; date of birth; signature; banking and credit information; IP address; employee records; medical or health records; photos or videos; voice print or facial recognition biometrics; location information from a mobile device; and opinions that are identifiable.
Privacy Act Reforms: What Small Businesses Owners Need to Know
The Federal Government recently released its highlyanticipated Privacy Act Review Report, containing some of the most sweeping reforms to the privacy landscape in Australia, including 116 proposals to amend the Privacy Act. The proposed changes are aimed at bringing our privacy regime in line with equivalent overseas laws, and strengthening protection and control of personal information in the digital age.
“Broadly speaking, these reforms will increase the types of information governed by the Privacy Act and the obligations of businesses when handling personal information, as well as the rights of individuals, and the penalties for privacy breaches,” Andrew said.
The most significant change is the removal of the small business exemption – so that all Australian businesses will be required to meet minimum data privacy standards, regardless of turnover. Currently, businesses with turnover of less than $3 million are exempt.
In addition, employee data is currently exempt from protections in the Privacy Act. This is set to change with privacy protections being extended to cover company employees. This means businesses will have increased obligations around transparency and security of employee records. They’ll also be required to notify staff and the Federal Government’s Office of the Australian Information Commissioner (OAIC) of data breaches affecting employee personal information. Other key reforms include:
• A broader definition of personal information
• Introduction of a ‘fair and reasonable’ test for use of information
• New collection and consent requirements
• Established data retention periods
• New rights for individuals
• Limitations on direct marketing and trading
• New requirements for children
• Transparency about automated decision making
• New measures for cross-border disclosures
• More efficient data reporting
• Greater penalties and enforcement
How Businesses Can Ensure Compliance
When the changes become law (which is expected to occur in late 2023), to comply with the Privacy Act Australian businesses will have to:
• Have a Privacy Policy on their website that is clear and unambiguous
• Have a data access request process that enables a response within 30 days
• Provide notice that data is being collected at specific points
• Have a register of what data is collected and stored
• Know how long data is stored and why
• Have a process to delete or de-identify data when it is no longer needed
• Keep a register of suppliers
• Know what data they’re sharing with suppliers
• Know where their suppliers are storing data
The Australian Cyber Security Centre (ASCS) has developed a set of mitigation strategies that organisations can use to protect themselves against possible cyberattacks and protect sensitive information in line with the Privacy Act. The key strategies are known as the Essential Eight, and are recommended as a baseline to build cyber resilience and minimise the risk of systems being compromised. The Essential Eight are designed to protect Microsoft Windows-based internetconnected networks – although they may also be
applied to cloud services and other operating systems.
What is the Essential Eight?
1. Application control: prevent the execution of unauthorised programs or malware.
2. Patch applications: improve security by fixing known vulnerabilities in applications.
3. Configure Microsoft Office macros: only allow vetted macros in and block entry of other macros.
4. Application hardening: disable high-risk functionality in Flash, ads, and Java.
5. Restrict admin privileges: give fewer accounts a high level of access to operating systems and applications.
6. Patch operating systems: check frequently for security vulnerabilities, and apply patches and updates.
7. Multifactor authentication: verify users when they perform a privileged action or access highly-sensitive data.
8. Regular backups: store copies of files offline where they can’t be accessed by a hacker.
How de.iterate Can Help
Until now compliance has only been a Big Business Problem. New legislation makes compliance essential for businesses of all sizes – but existing solutions can be expensive to procure and require specialist skills, putting them out of reach for many small businesses.
de.iterate is a turn-key online compliance platform that streamlines compliance with the Privacy Act, and the ACSC Essential Eight. Accessible via desktop, or through our fully-featured mobile app, it simplifies implementation and management of cyber security and privacy controls, via small, easy to manage tasks.
For further information, visit: deiterate.com.au

Manufacturing the Renewable Energy Revolution
Weld Australia, in collaboration with the Australia Institute’s Centre for Future Work, hosted the National Manufacturing Summit at Old Parliament House on 2 and 3 August. With the theme of Manufacturing the Energy Revolution: Industrial Opportunities from Renewable Energy , the event was a great success.
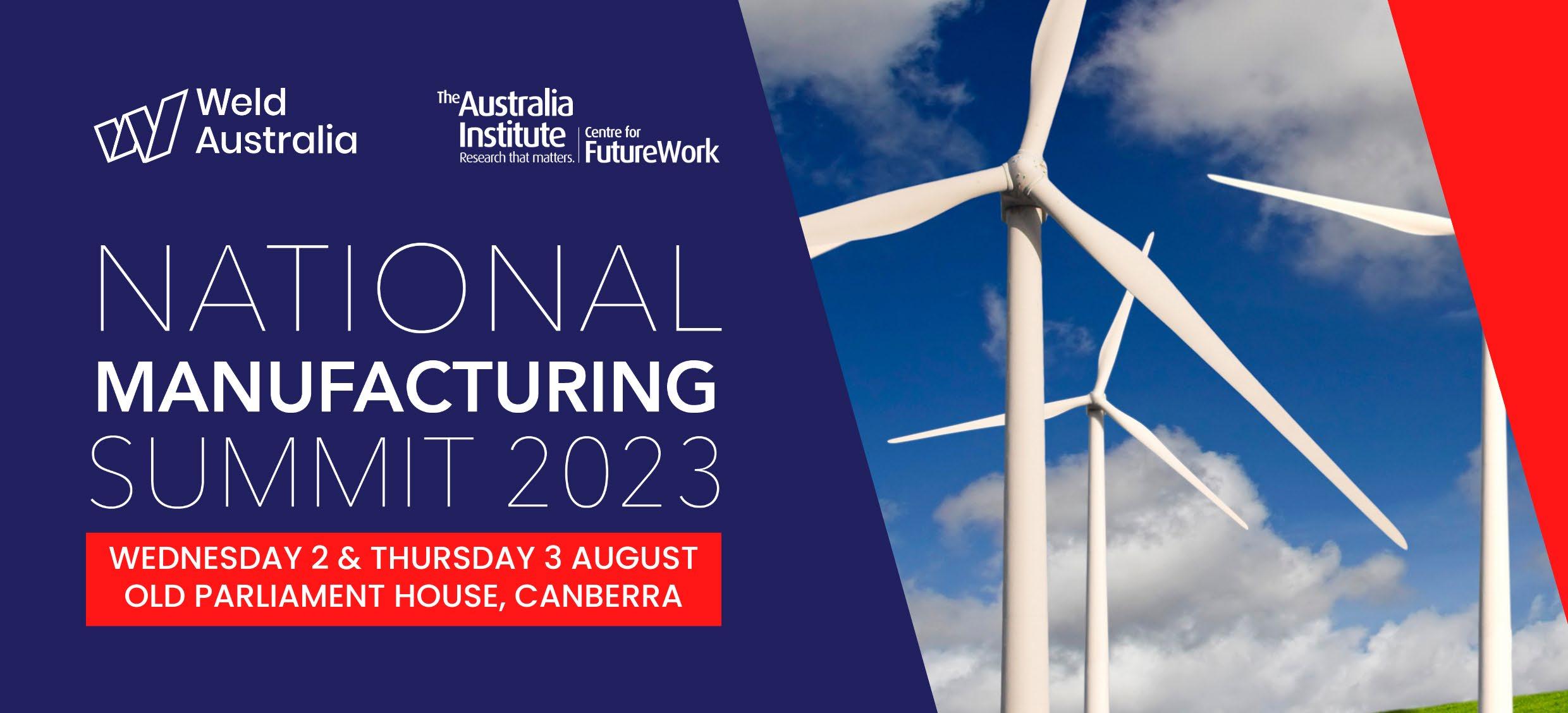
The Summit kicked off with a Gala Dinner, sponsored by Oceanex Energy. Emily Scivetti, Chief Operating Officer at Oceanex, gave an insightful overview of their operations. An Australian company, Oceanex is progressing the development and construction of up to five offshore wind farms off the coast of Australia. These wind farms will provide a new source of largescale, clean and reliable electricity that creates huge new investment, jobs and innovation opportunities, especially in key regional centres.
An Australian offshore wind industry will need more than 1,000 steel foundations in the next 10-20 years. New South Wales, particularly the Hunter and the Illawarra regions, are primed to take advantage of this growing sector and become a leader in the deployment of floating offshore wind farms. NSW provides an ideal home for offshore wind farms with existing transmission infrastructure, reliable wind resources and a workforce experienced in developing and delivering large energy projects. But the workforce needs to be much more significant.
Construction needs to begin by 2028 to get first wind into the national electricity grid by the early 2030s.
WITH THANKS TO OUR SPONSORS
If Oceanix was to build at a pace of one floating foundation a week, it would need up to three million tonnes of steel over 12 to 15 years and create 1,000 fulltime jobs in fabrication.
Oceanex estimates that each NSW offshore wind farm will require at least 750,000 tonnes of steel. With larger components, offshore wind will require a sizeable skilled labour force and can provide a catalyst for significant growth of local manufacturing and engineering capabilities. These manufacturing opportunities are real but Australia needs to act now to capitalise on these opportunities.
Keynote Address by Adam Hersh
International expert, Adam Hersh, gave the keynote address on Industrial Policy: Past, Present and Future. A Senior Economist from the Economic Policy Institute in Washington DC, Adam focuses on international trade and US-China relations. According to Hersh, “We have entered a dangerous and fragile inflection in the planet’s climate systems.” He also cited the unprecedented Chinese economic rise as “the biggest economic rise in the history of human existence.”
Hersh compared the industrial policies of ‘Trump-onomics’ (described as capital and top-income tax cuts, trade-tech war, trickle down and anti-worker) with Bidenomics, which features the:
• Infrastructure Investment and Jobs Act: provides approximately $550 billion in new federal investment in America’s roads and bridges, water infrastructure, resilience, internet, and more.
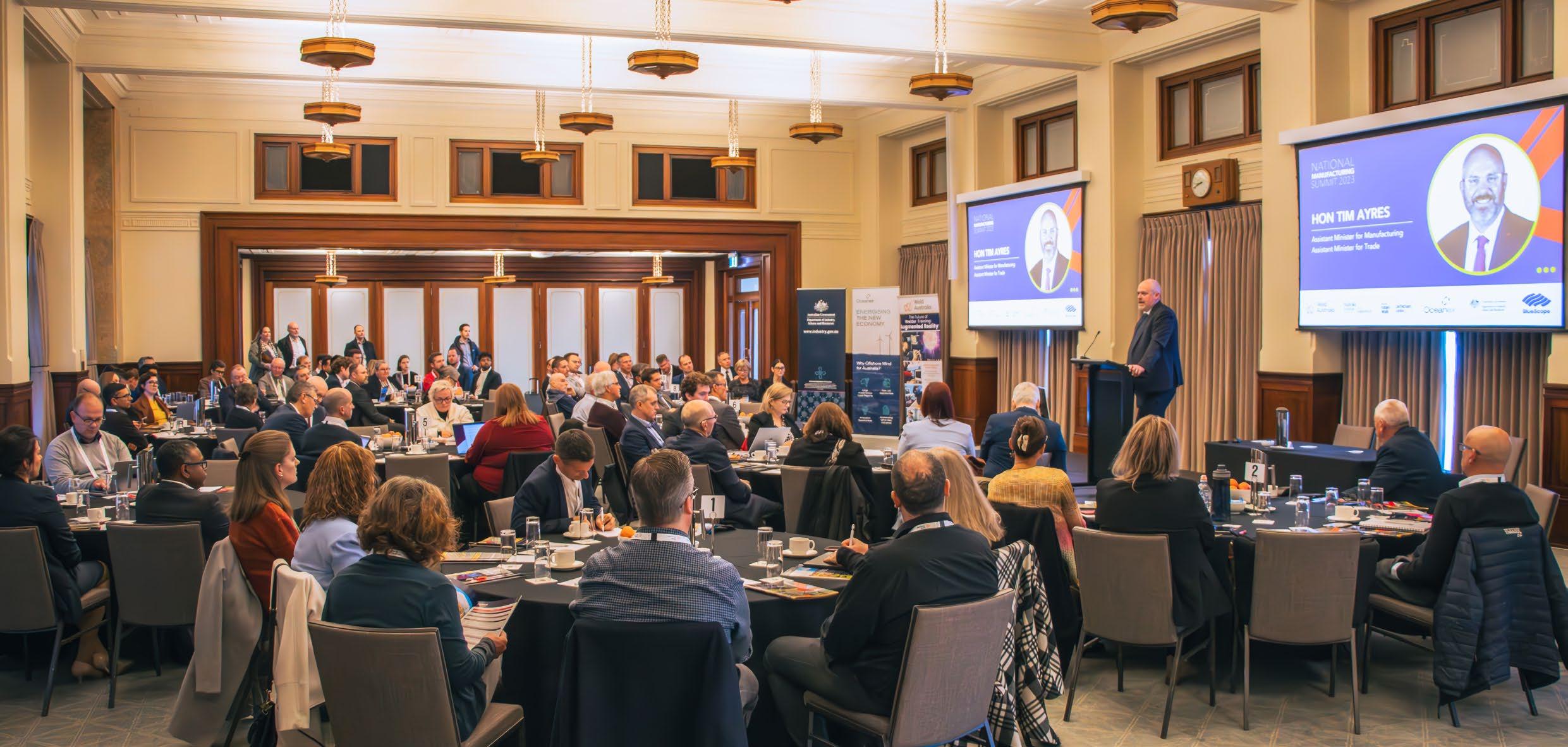
• Inflation Reduction Act: provides US$370 billion in investments and aims to curb inflation by reducing the federal government budget deficit, lowering prescription drug prices, and investing into domestic energy production while promoting clean energy.
• CHIPS and Science Act: provides approximately US$52 billion for American semiconductor research, development, manufacturing, and workforce development, as well as a 25% investment tax credit for capital expenses for manufacturing of semiconductors and related equipment.
The introduction of these three pieces of legislation has seen investment in manufacturing boom in th United States. According to Hersh, just some of the results of these budget deficit negative policies (raises new revenues) include:
• Fastest economic recovery in US history
• Largest ever investment in public transit
• Largest investment in passenger rail since Amtrak
• Largest investment in bridges since the interstate highway system (1950s)
• Policies to transition all key sectors: energy, transportation, industry, agriculture, and commercial and residential buildings
• Policies targeting investments with equity in all regions and communities
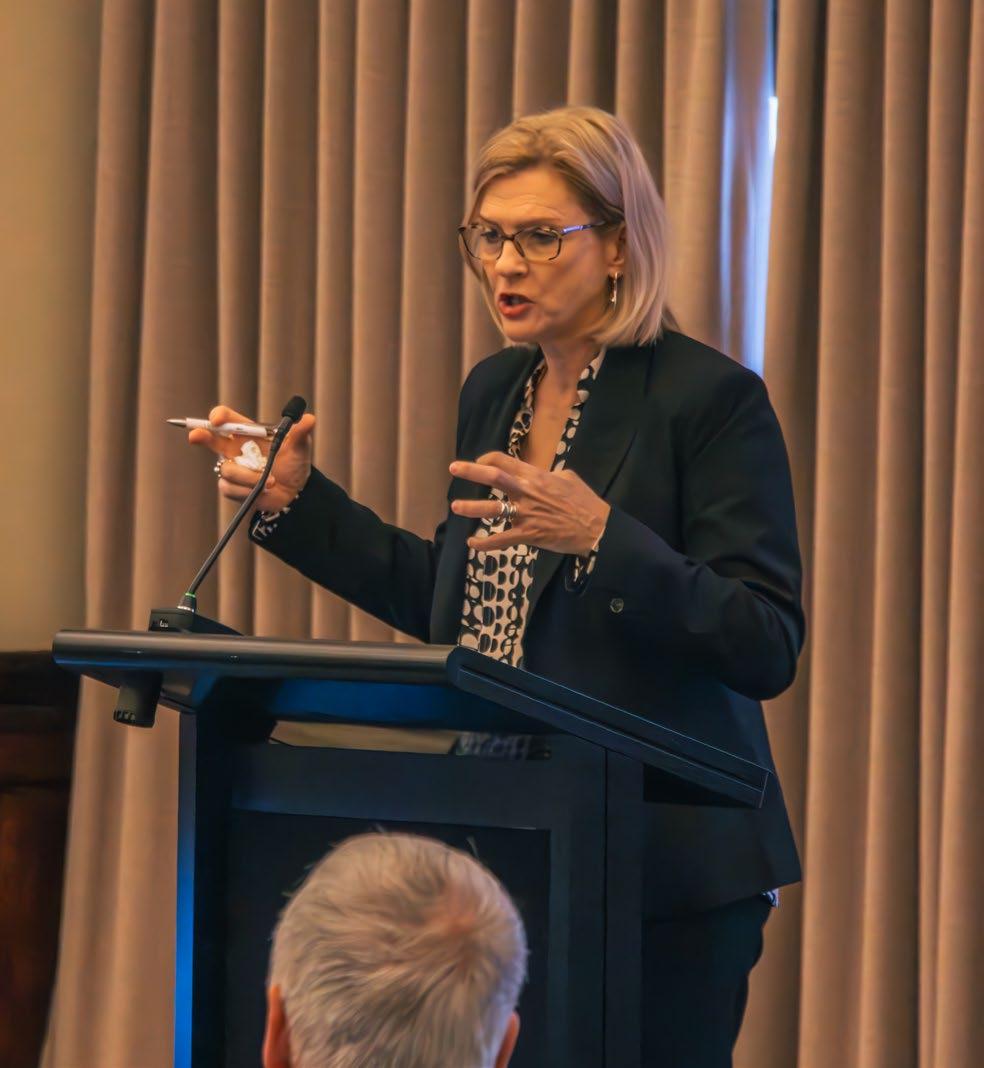
• An expected 40% Greenhouse Gas (GHG) emmissions reduction by 2030

Tim Ayres, Assistant Minister for Manufacturing and Trade
The Hon Tim Ayres, Assistant Minister for Manufacturing and Trade, opened the 2023 National Manufacturing Summit. According to Ayres, “If we are to rebuild Australia’s industrial base and seize the opportunities of our net zero future, we will need everyone working together to transform our economy.”
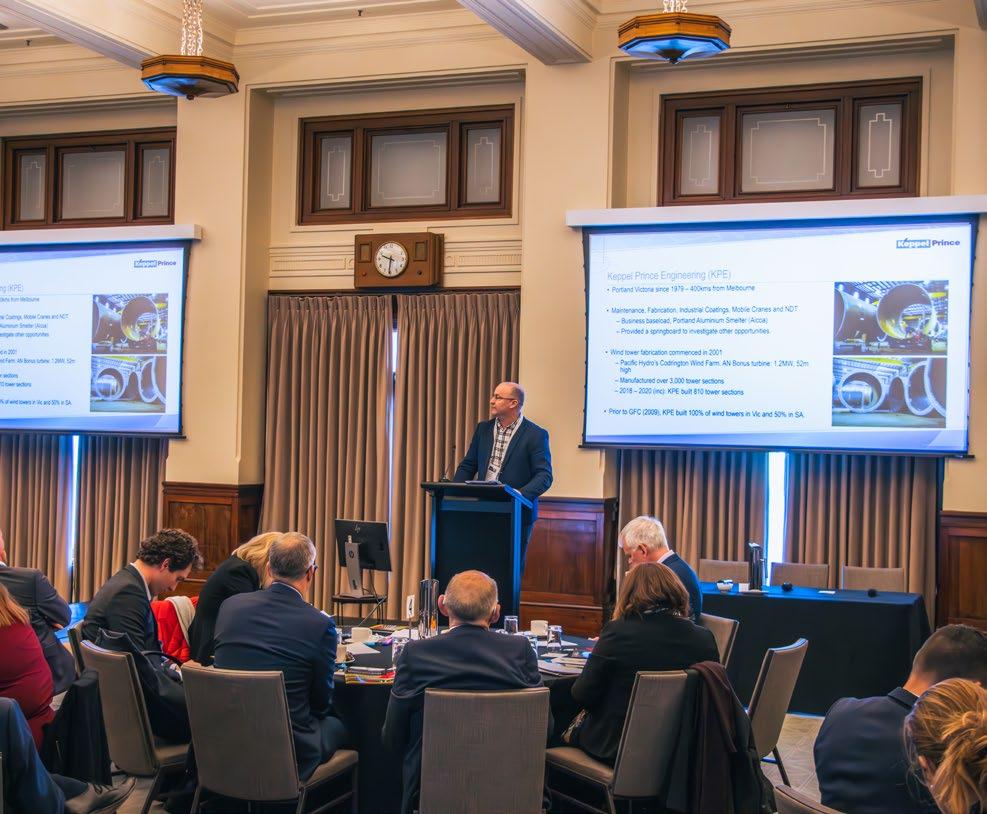
“Australia has all the ingredients that would make us a renewable superpower. This includes: limitless solar and wind reserves, globally significant supplies of critical minerals, advanced critical technology capabilities, and close proximity to the fastest growing region of the world in human history.”
“Australia simply cannot afford another wasted decade... This week’s update of the Harvard University Economic Complexity Index demotes Australia further down international rankings, from 91st to 93rd in the world for 2021 – between Uganda and Pakistan.”
“Australia’s product exports are dominated by raw commodities rather than value-added products. The need to drive Australian exports up the value chain has never been more significant, or more urgent.”
“Australia will work cooperatively with our key trading partners like the United States, Japan and the Republic of Korea on our shared clean energy and green industrial objectives. Because the global challenge of decarbonisation requires a global solution. And Australia is set on playing its part.”
“The Australian Government will support our trading partners in their own transition to net zero – including by being a reliable supplier of the resources they need during the process.”
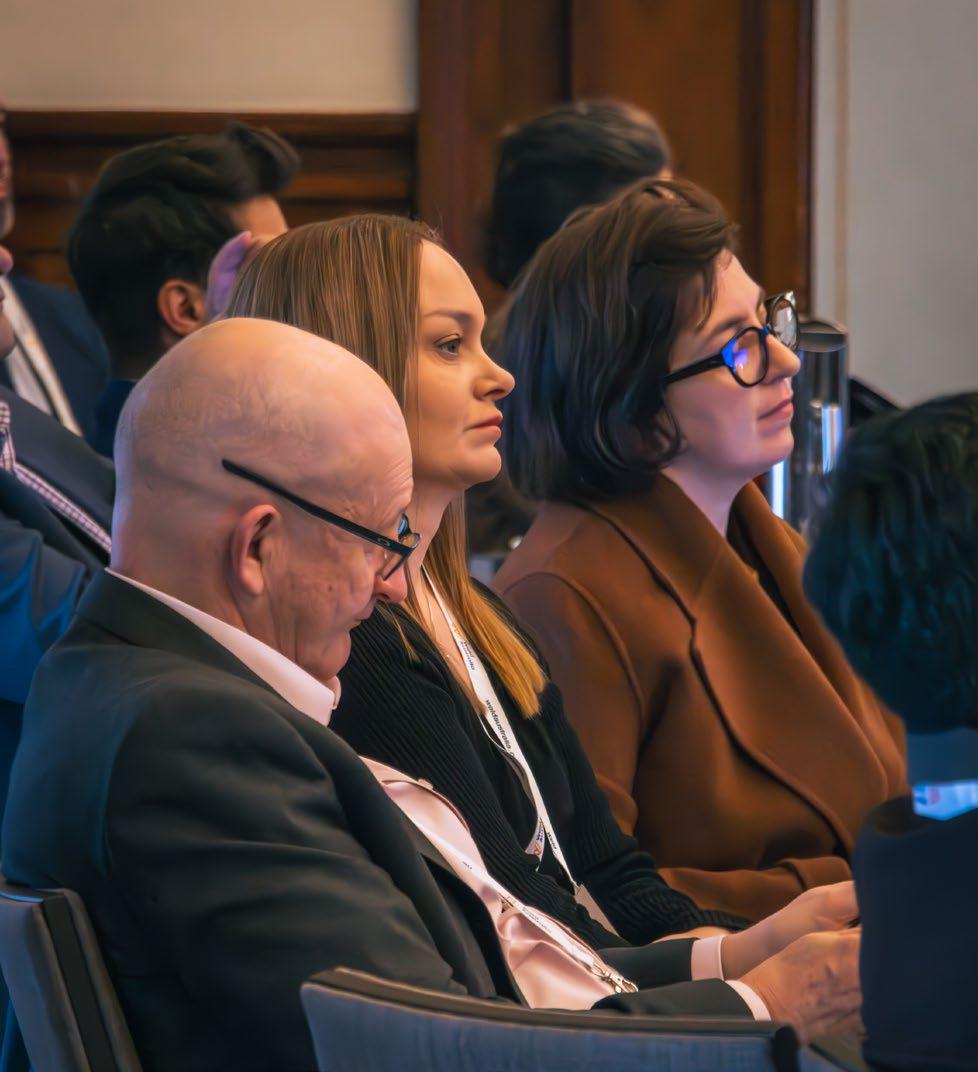
“Ensuring the transformation of our nation into a highvalue, high-wage modern green economy needs to be a collaborative effort. It will involve governments, industry, unions, the research sector and other stakeholders. If we work together Australia will reach our emissions reduction goals while placing ourselves in the forefront of advanced manufacturing nations. Because there is too much at stake to simply retreat or be resigned to another decade of slipping down the global value chain.”
Manufacturing the Renewable Energy Revolution
The second session of the day saw Dan McKinna (General Manager, Keppel Prince) speak about the opportunities and challenges in manufacturing onshore wind towers
According to McKinna, “Australia requires a nine-fold increase in grid-scale wind and solar to meet our 2050 targets under AEMO’s step change scenario. The opportunity for local manufacture of wind towers is massive. An onshore wind tower requires 7km of weld
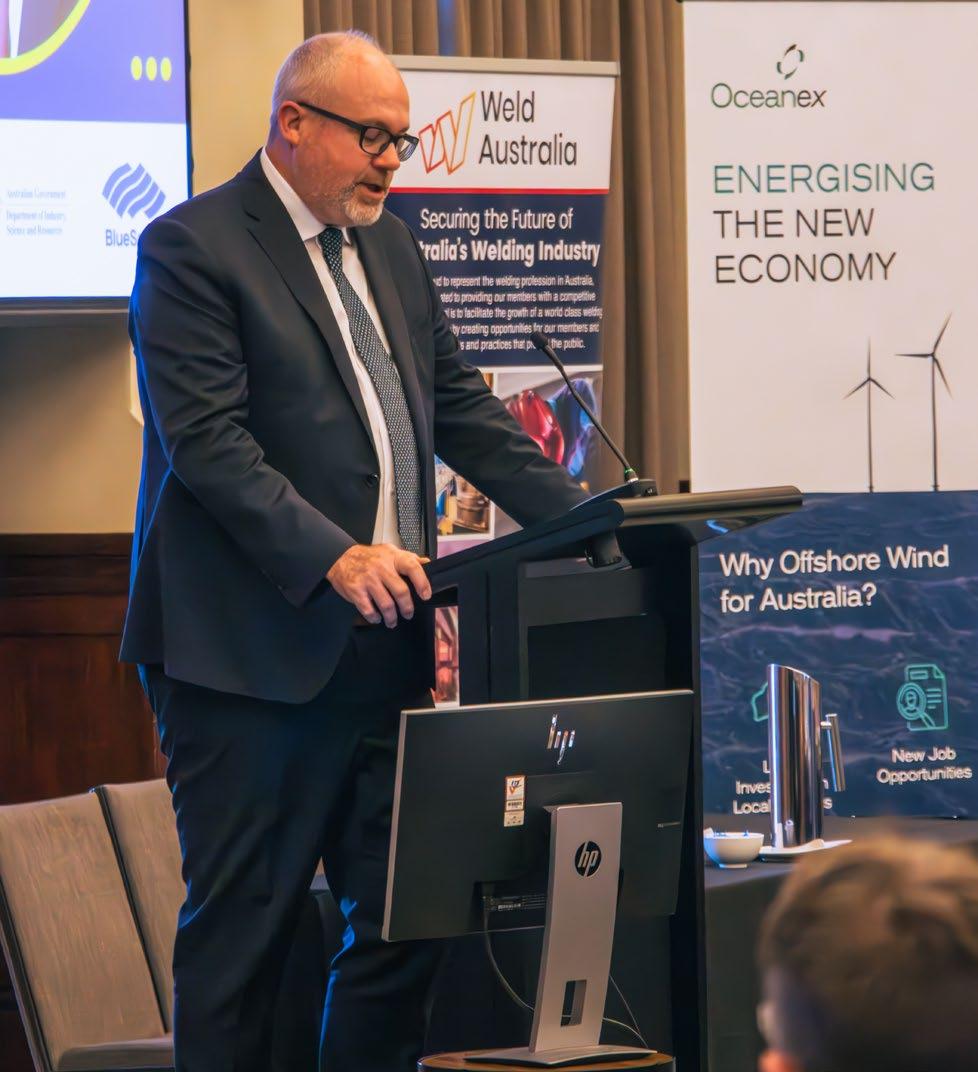
MANUFACTURING THE ENERGY REVOLUTION
Opportunities in Offshore Wind

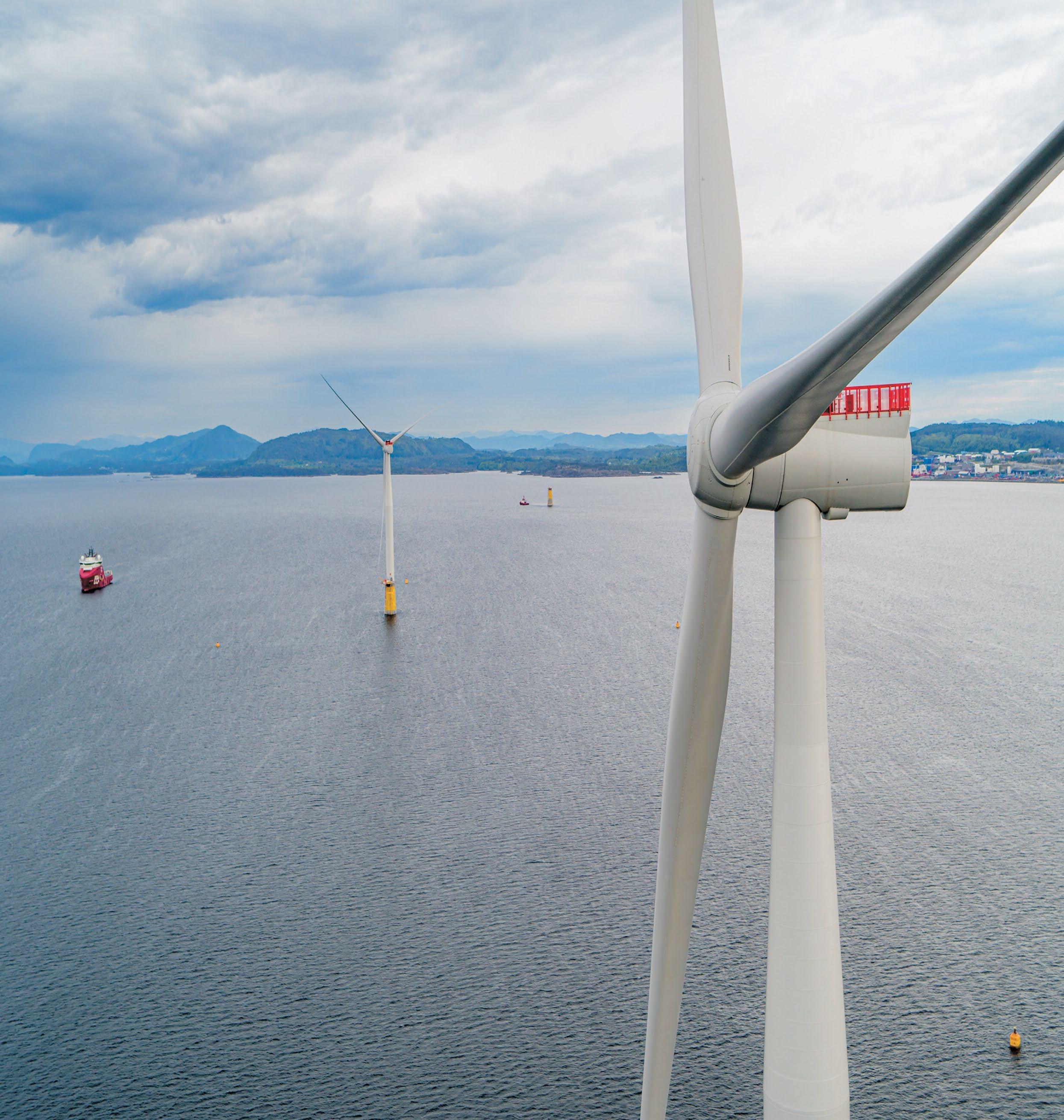
Floating technology
Oceanex Energy’s NSW offshore wind farms will utilise floating technology rather than fixedbottom foundations. The introduction of this new technology to Australia offers a significant opportunity to scale up manufacturing and develop and grow new and robust supply chains. It also creates an ideal environment for Australian steel producers and NSW steel fabricators to work with designers to shape, optimise and undertake manufacturing in NSW.
Given the size of floating foundations and the modularity of most designs, there is significant opportunity for foundations to be manufactured close to existing port infrastructure, with many subcomponents spread across a local fabrication ecosystem. For example, smaller workshops undertaking small subcomponent fabrication and large workshops with water access fabricating and assembling the biggest subcomponents.
Advanced capabilities
NSW and in particular, The Hunter and Illawarra regions, have deep experience in steelmaking, ship building and world class advanced welding capability. These are ideal heavy manufacturing attributes to kickstart a dedicated supply chain. Large companies such as BlueScope Steel, Civmec, Ampcontrol, Precision OxyCut and many others with regional operations, are well established. These companies can adapt or expand operations to help service the design and manufacture of floating foundations for the Australian market and beyond. There is also significant potential for innovative manufacturing processes to develop with this innovative new technology and reduce costs. Achieving this will ensure Australia not only establishes its own supply chains, but makes us competitive against overseas supply.
Manufacturing the energy revolution also creates an immense opportunity for offshore wind to share the available workforce that possess complementary manufacturing skills from heavy industry including capturing those wishing to transition to a new industry.
in each unit, to manufacture the towers for 40GW of installed onshore wind capacity requires in excess of 22 million person-hours of manufacturing. Offshore wind expands this even further, we estimate that to manufacture the towers and foundations for 40GW of fixed foundation offshore wind will require in excess of 53 million person-hours of manufacturing. All this manufacturing is going to be completed somewhere, Australia needs to ensure that we play a significant part in this opportunity.”
“We need to incentivise investment. We must have certainty of demand—if local manufacturers are going to invest in factories, we need certainty that those factories will be fed. We need local content targets. The potential demand need not be 100%. We need to remove the peaks and troughs; we need a baseline demand for an extended period of time,” said McKinna.
Simon Preston, Group General Manager at Allthread Industries, presented a case study focused on the Murra Warra II wind tower project.
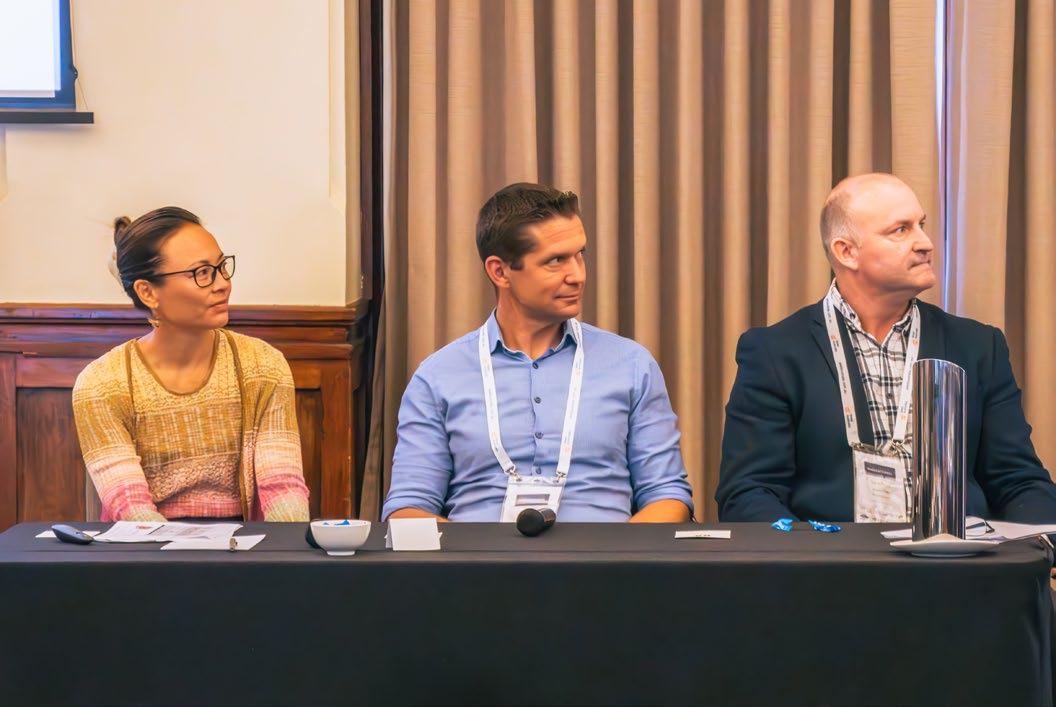
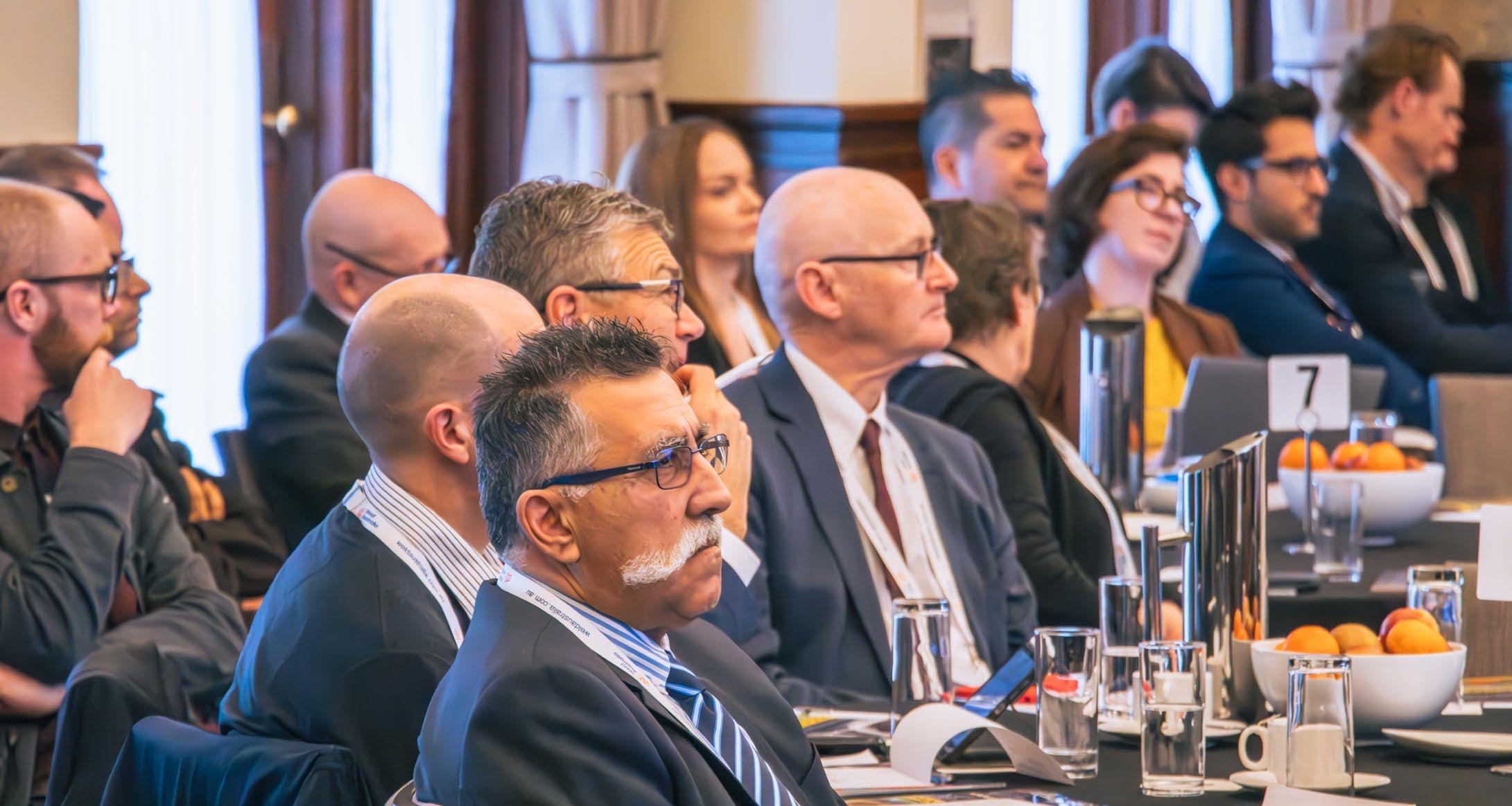

Given the size, scale and weight of the turbines, a robust anchor cage solution was required; the expertise of Allthread Industries was required. Allthread Industries supplied a unique solution that competed with cheaper overseas imports based on the value delivered throughout the construction phase—not just on the cost of steel.
“We were able to provide an Australian-made solution. Our solution used all Australian steel, and on analysis used 97% Australian content and 50% recycled content,” said Simon.
industry.gov.au/major-projects-and-procurement

The Changing Policy Landscape
The Hon Lance McCallum, Assistant Minister for Energy Queensland, provided an overview of the Queensland state government’s work in renewables. Queensland has set a bold clean energy future—a 70% renewables target by 2032—as part of the $62 billion Queensland Energy and Jobs Plan.

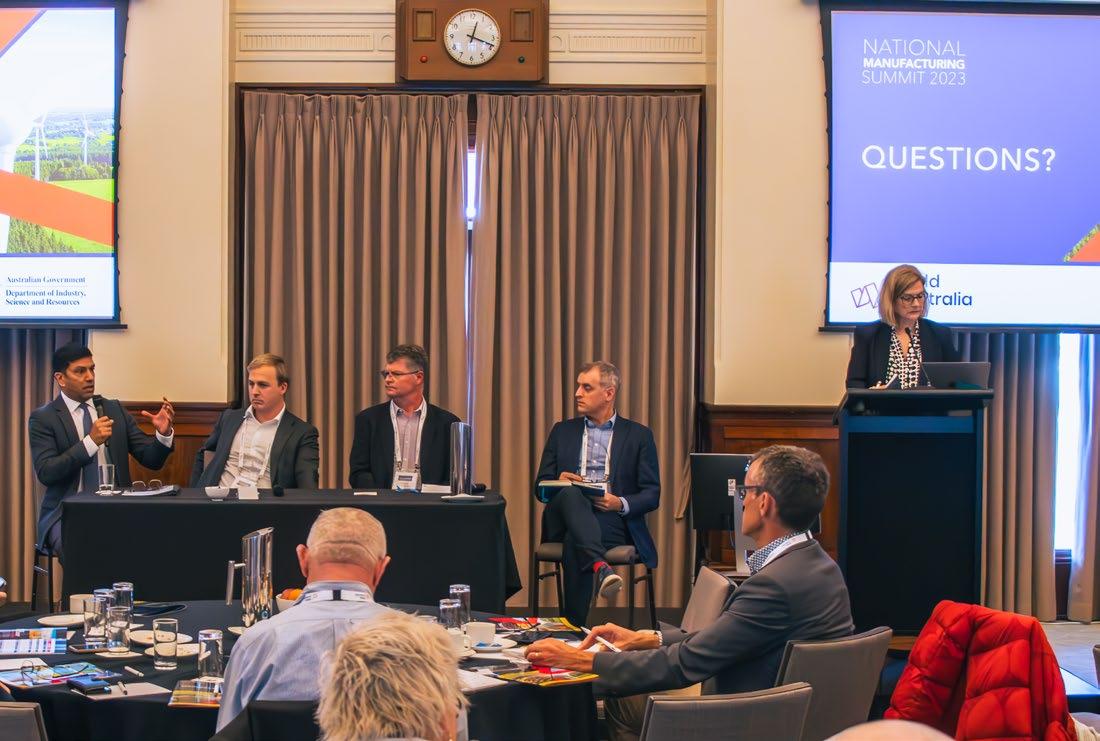
The Plan includes initiatives such as: a commitment to progress two new pumped hydro projects by 2035; a pathway to build the new Queensland SuperGrid, which will connect solar, wind, battery and hydrogen projects across the state and unlock new capacity and storage; a commitment to convert all of Queensland’s publiclyowned coal-fired power stations into clean energy hubs by 2035, backed by a Job Security Guarantee for workers; and substantial investment across the state, with 95% of clean energy infrastructure investment anticipated to be in regional Queensland.
“We are sending a very clear message to manufacturers—those already established in Queensland, or looking to the future—you are welcome in Queensland. We have a renewable energy plan, a myriad of opportunities directly related to the plan (and indirectly related to the plan throughout the supply chain), as well as opportunities for the 2032 Olympics and everything associated with that,” said Minister McCallum.
Tim Buckley, Director, Climate Energy Finance, also gave a highly informative and engaging presentation during this session. According to Buckley, the installed cost of solar energy development globally will halve in price this decade. “We have all the critical minerals and the know-how, but it is now a global technology and investment race to the top. Indonesia isn’t ignoring it. Chile, Vietnam, and India aren’t either. Australia would be crazy not to grab the opportunity stemming from the US IRA with both hands, and to do it fast, and at an unprecedented scale,” he said.
“...it took the world 183 years to generate the first terawatt of energy through solar installs, and it’ll take only three years to generate the second terawatt. Then only 15 months to generate the third. Can we do it? Of course, we can do it. But we have to do it fast,” said Buckley.
Developing an EV Supply Chain in Australia
Kirk McDonald (Project Manager, Supercharge Australia) kicked off the first session post-lunch at the National Manufacturing Summit. According to Kirk, despite producing almost 60% of the world’s lithium, Australia retains less than 1% of the US$200 billion and rising annual product value, with 98% of the lithium mined in Australia being refined overseas. Australia can do more than “dig and ship” lithium: it can be a leader in lithium battery technology, from extraction
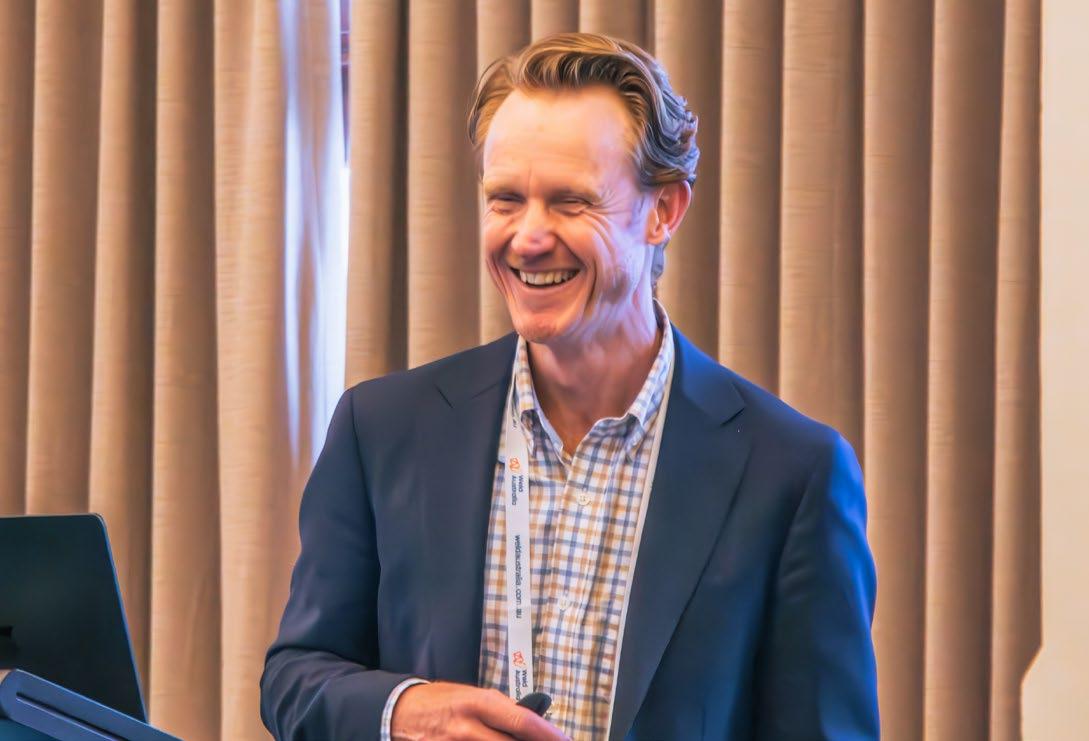
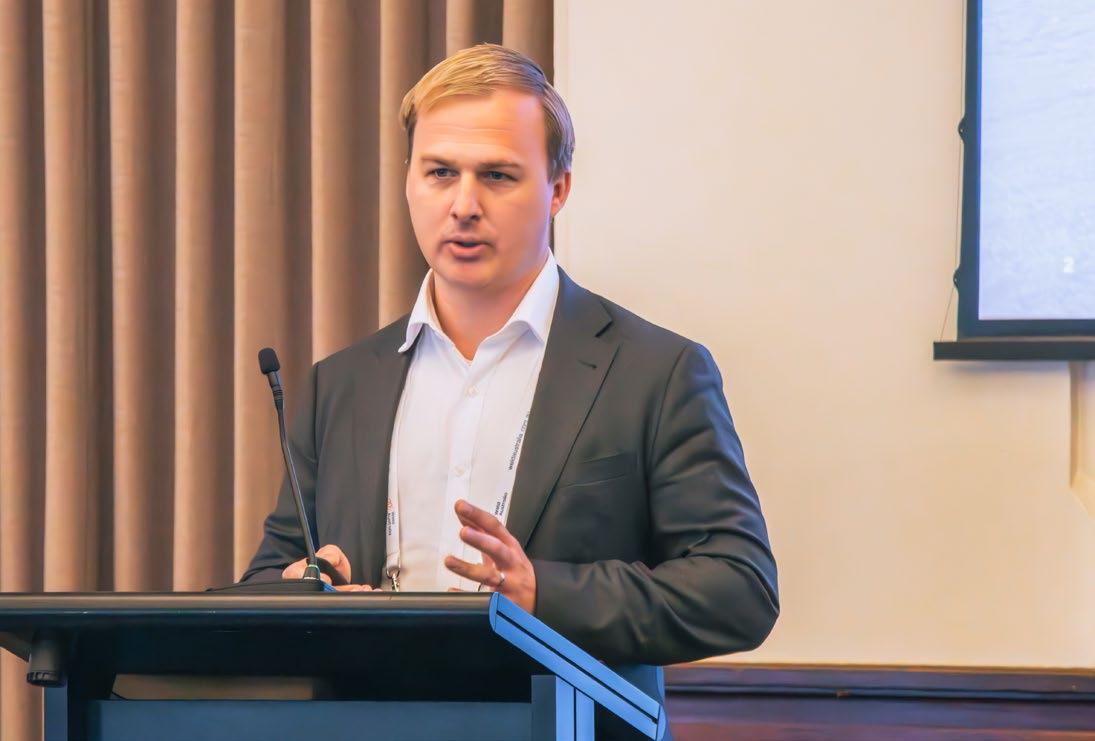
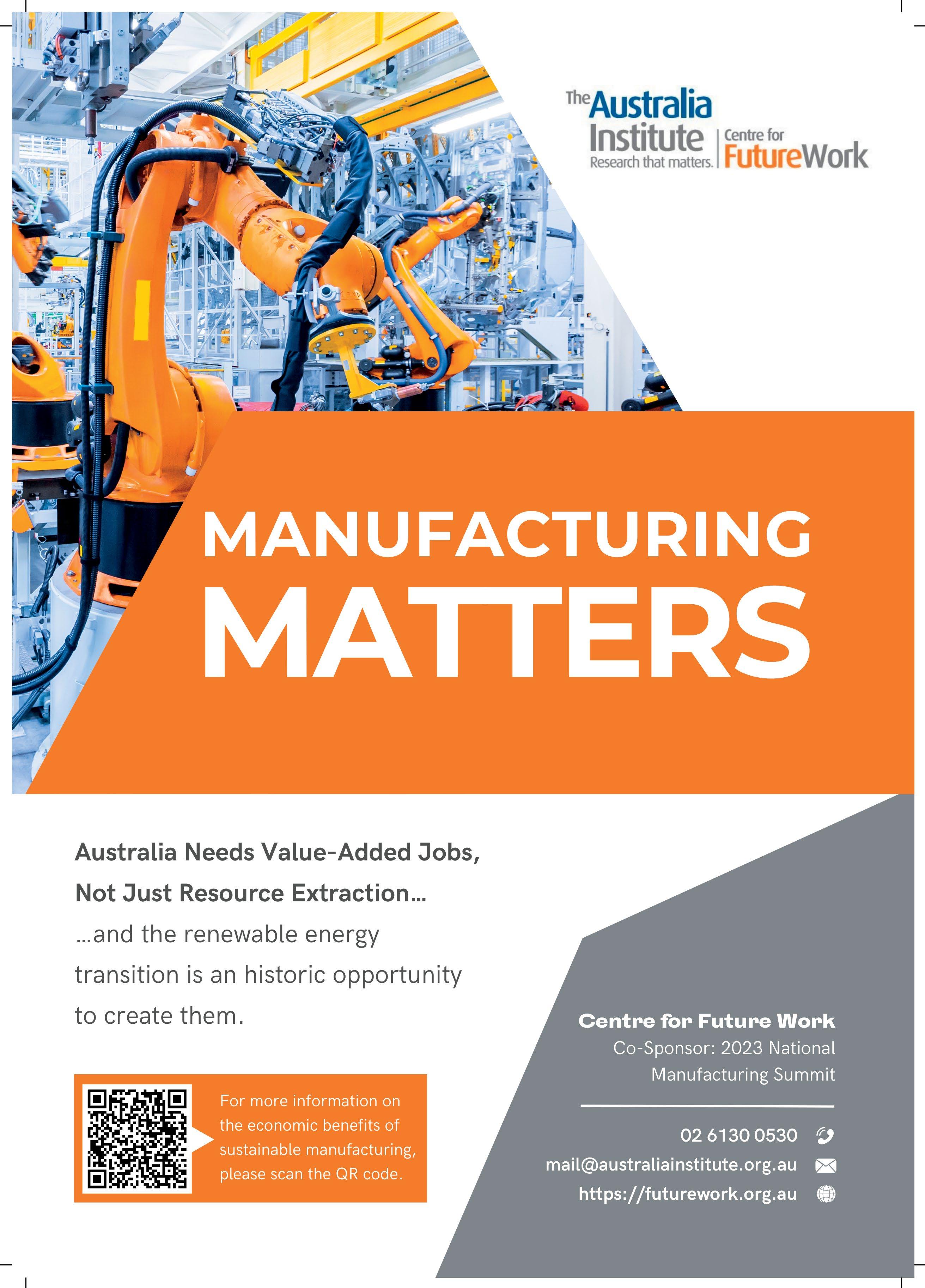
to advanced battery and EV manufacturing. This is good news for the global climate, but also for the thousands of jobs that will be created in the process. Kirk provided an overview of the range of opportunities available to startups, as well as how countries around the world fund and support the start-up ecosystem.
Katie Hepworth (Political and Strategic Advisor, Australian Manufacturing Workers Union) presented on the heavy vehicle manufacturing industry at the 2023 National Manufacturing Summit.

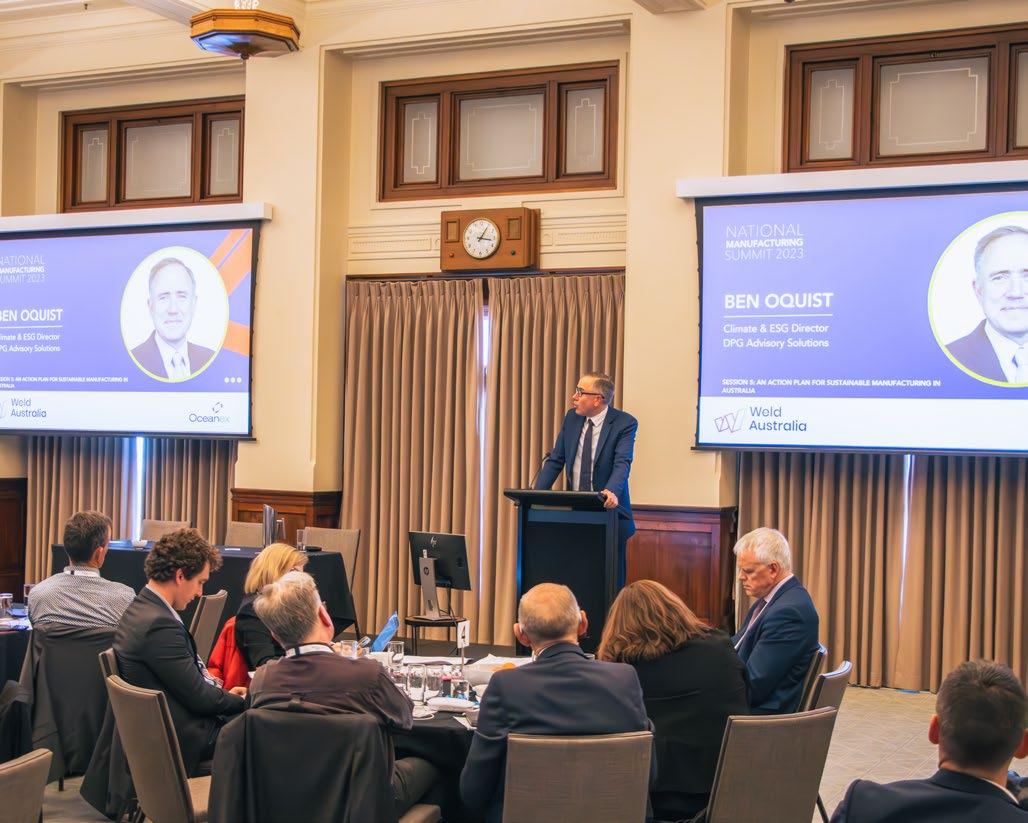
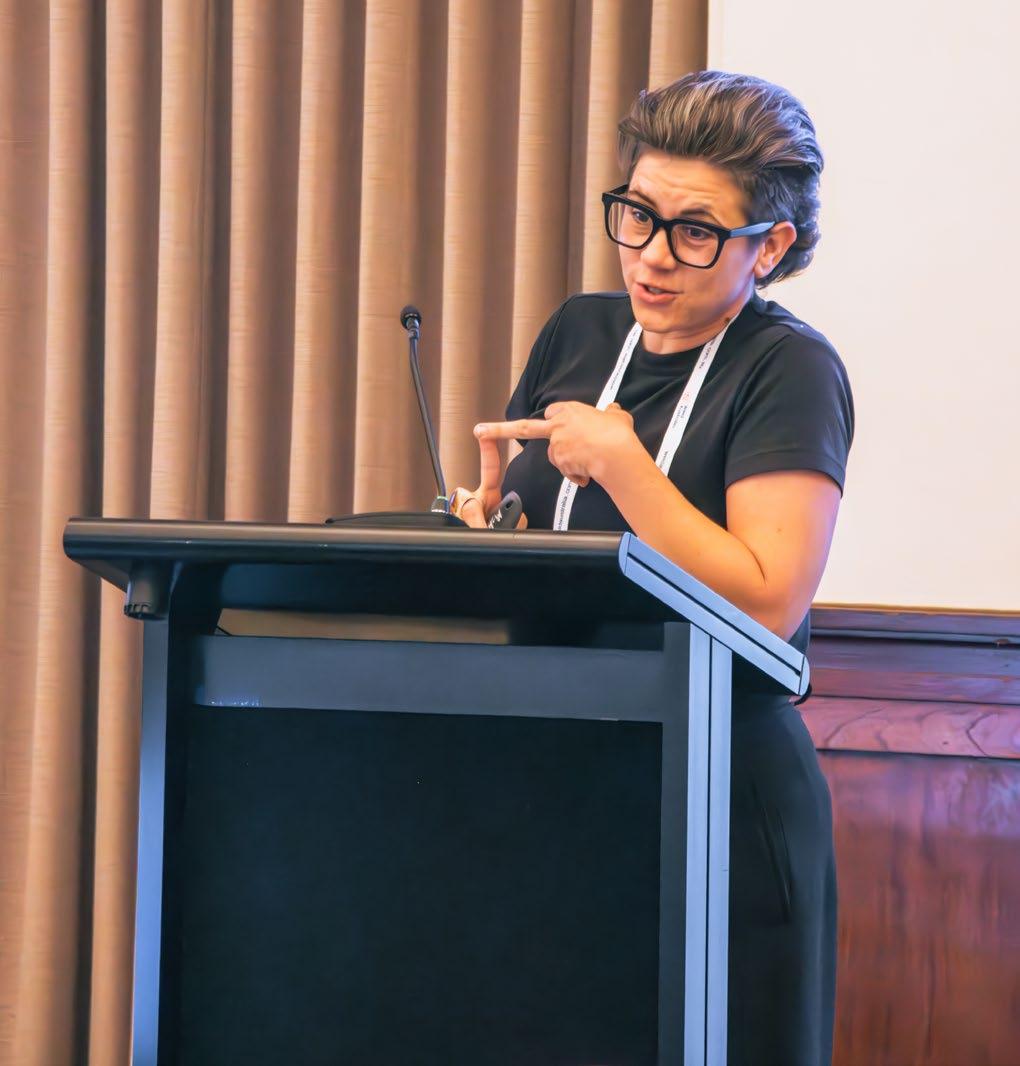
According to Katie, there is a real need for regulatory certainty and harmonisation of standards, a steady supply of work and a smoothing of demand, and workforce skills development in both R&D at a high level and in trade skills.
“We cannot rely on narrow local content rules. While these are an important part of the equation, we need to determine how we target funding. Where are we funnelling the money? We cannot just ask for government funding and tax credits, the money needs to be targeted to gain a competitive advantage,” said Katie. “We need a response that is commensurate to the US Inflation Reduction Act. We’re calling for $150 billion.”
Making it Happen: An Action Plan for Sustainable Manufacturing in Australia
Australian Council of Trade Unions President, Michelle O’Neil, made it clear that there shouldn’t be a single worker made redundant by the phase-out of fossil fuels. “If we miss out on this opportunity to become a renewable manufacturing powerhouse, we’ll be leaving jobs and wealth on the table. Don’t leave behind those people who make everything you use every day,” she said. “There are so many manufacturing sectors hitting the new learning curve.”
According to Geoff Crittenden (CEO, Weld Australia), “We are now at the stage where even the most obtuse observer must realise that global warming is real and is coming at us much faster than we imagined it could. Last year, Australia experienced record floods, with countless people losing their homes. This year, we’re expecting a record bushfire season, with the Northern Hemisphere already experiencing some of its hottest temperatures on record. The climate crisis makes manufacturing the renewable energy revolution an imperative.”
“In Australia, the task of responding to the IRA seems to have created such an insurmountable challenge that we have ground to a halt. A policy of fiscal conservatism driven by Treasury is obstructing any type of progress. We are defeated before the first shot is fired.”
“Australia must stop debating the fiscal policy and act. We must become a valued partner within international renewable energy supply chains. We must overcome our traditional ‘dig and ship’ mentality and leverage our critical minerals supply to manufacture complex, value-added renewable energy products onshore.”
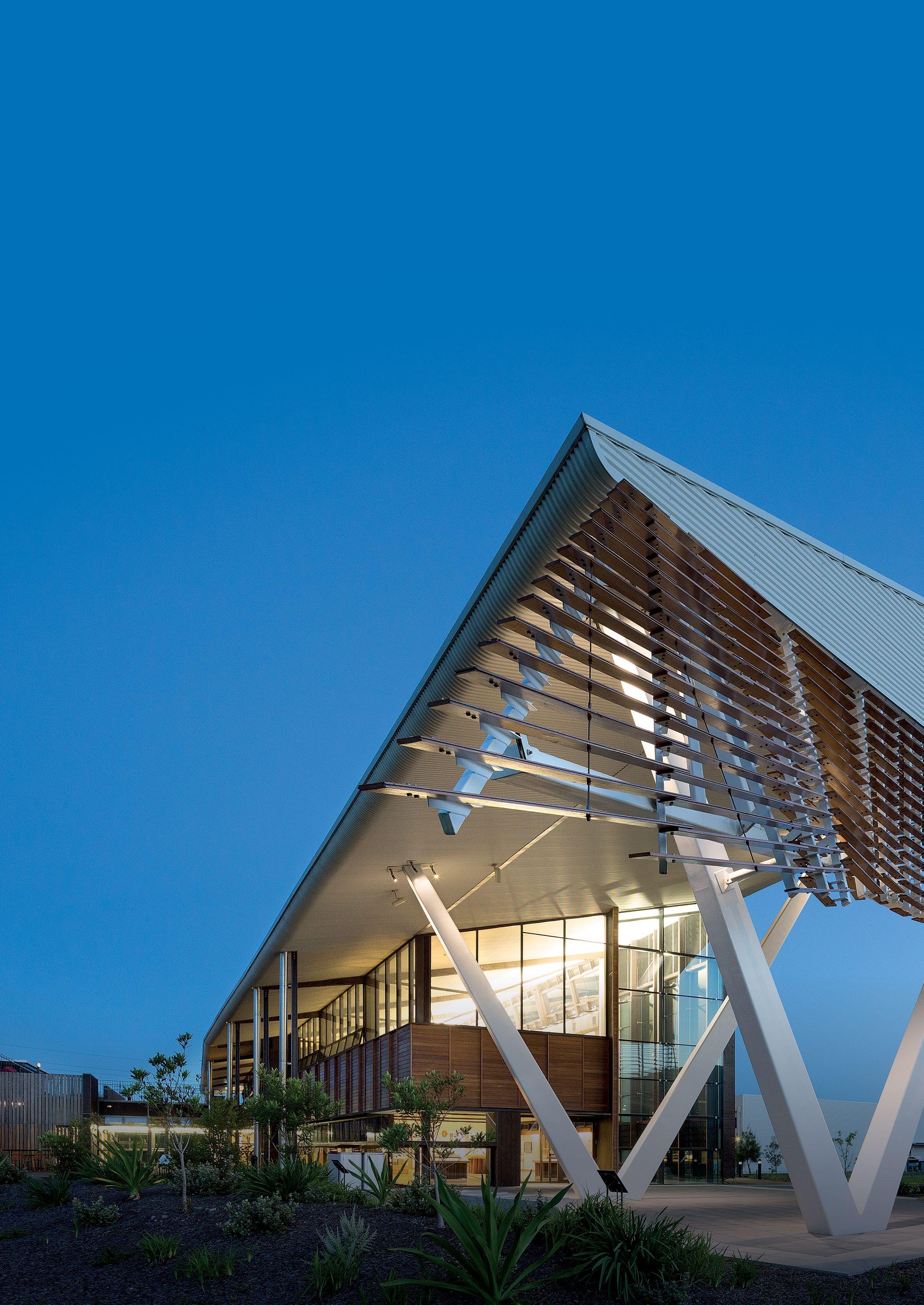
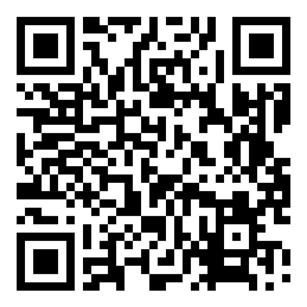
New report reveals: AUSTRALIA AT RISK OF EXCLUSION FROM RENEWABLE MANUFACTURING BOOM
Australia risks being left out of lucrative new markets for renewable energy-related manufacturing unless government provides an urgent, domestic response to match powerful incentives introduced by the US and several other industrial nations. The finding was published in a new report released by the Australia Institute’s Centre for Future Work, as part of the 2023 National Manufacturing Summit. The report reviews the new incentives for production of batteries, electric vehicles, renewable energy generation and transmission equipment, and other renewable energy products provided under the Biden Administration’s Inflation Reduction Act and parallel public programs.
According to the report, there is an overseas manufacturing boom in the productions of batteries, electric vehicles, renewable energy generation and transmission equipment, and other renewable energy products.
This boom is being driven by incentives provided by the Biden Administration’s Inflation Reduction Act, and similar supports in the European Union, China, Japan, Korea, and Canada.
Meanwhile, Australia is considering its response, but no clear strategy has been announced.
The report estimates the proportional investment required to match the American Inflation Reduction Act in the Australian context at between $83 to $138 billion over 10 years in fiscal supports and incentives to match US benchmarks.
Several qualitative best practices should also be included in the
Australian response to the IRA to generate maximum economic, social, and environmental impact. These include strong labour and environmental standards attached to subsidised projects, public equity participation, and parallel investments in training for workers.
“The extraordinary response by industry to the US measures confirms that these policies are having an outsized effect on the volume and location of sustainable manufacturing investment,” said Dr Jim Stanford, Director of the Centre for Future Work and co-author of the report.
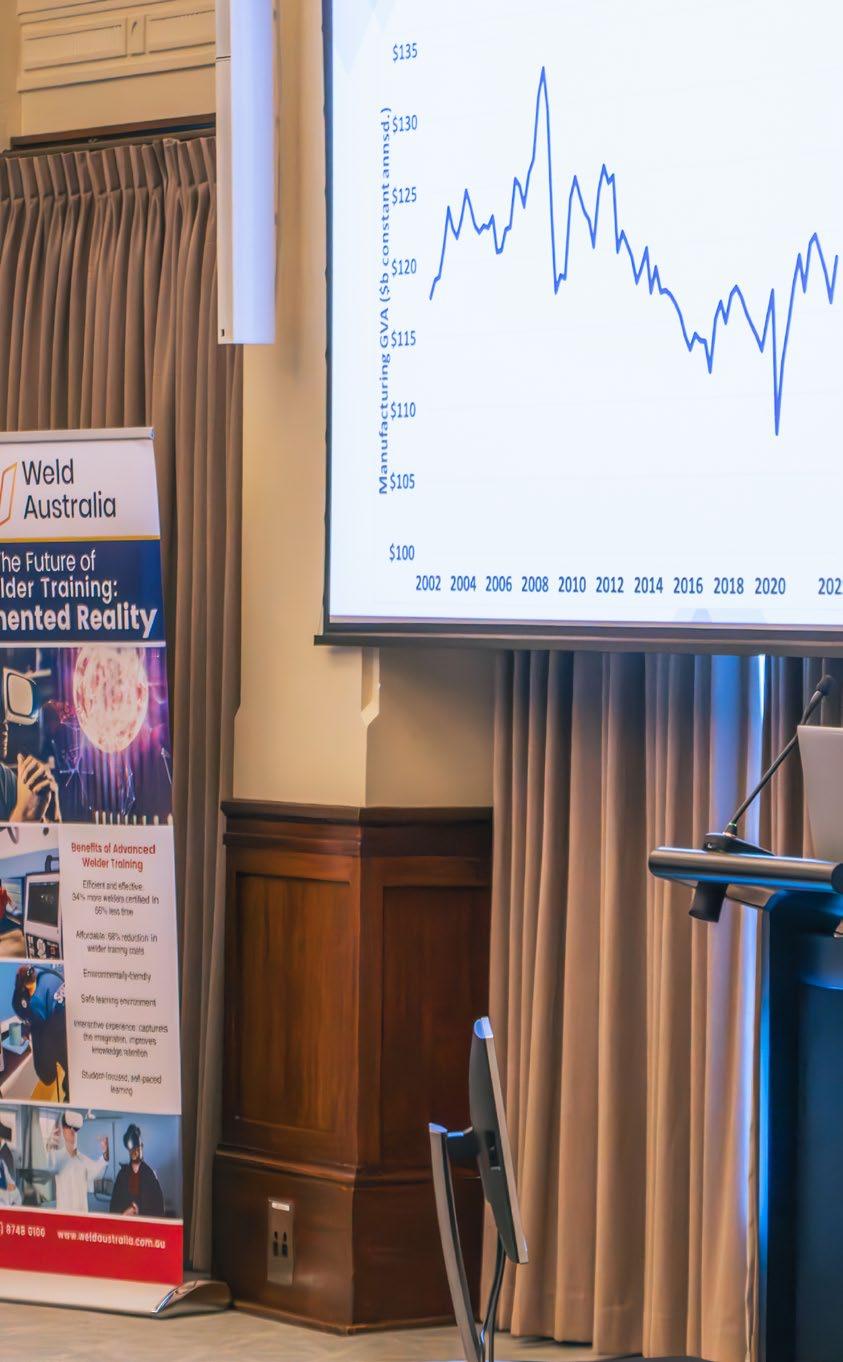
“It also confirms that Australia must move quickly with its response to this new industrial landscape, or risk losing its chance to leverage our renewable energy resources into lasting, diversified industrial growth.”
Charlie Joyce, a research fellow at the Centre and co-author of the report, noted: “The global race for clean technology manufacturing is
well underway, and Australia is barely on the track.”
“Australia has many advantages when compared to other competitors in this market, including an unmatched endowment of renewable energy sources and ample deposits of critical minerals. However, the painful legacy of decades of policy neglect for domestic manufacturing has left our industrial base in poor shape to seize the opportunities opening up ahead of us.”
“If we don’t support domestic manufacturing to quickly enhance its production, skills, and technological capabilities, all that will happen is we will replace one set of unprocessed minerals: coal, oil and gas; with another: raw lithium and related critical minerals.”
“Without action, most of the spinoff benefits of the renewable energy revolution for industry, technology, value-added and diversification will pass us by,” said Joyce.
The report estimates the proportional investment required to match the American IRA in the Australian context at between $83 to $138 billion over 10 years in fiscal supports and incentives to match US benchmarks.
“That is a big fiscal ask by any standards, but not out of reach for Australia,” said Dr Stanford. “But the common claim that Australia cannot afford to undertake proportionately equivalent measures is not convincing.”
“Our federal budget is in much better shape than the US And the government has committed to other, less pressing priorities which are just as expensive – such as nuclear submarines, Stage 3 tax cuts, and ongoing fossil fuel subsidies.”
The common claim that Australia cannot afford to undertake measures that are proportionately equivalent to the IRA is not convincing. Enhancing Australia’s capability to produce the
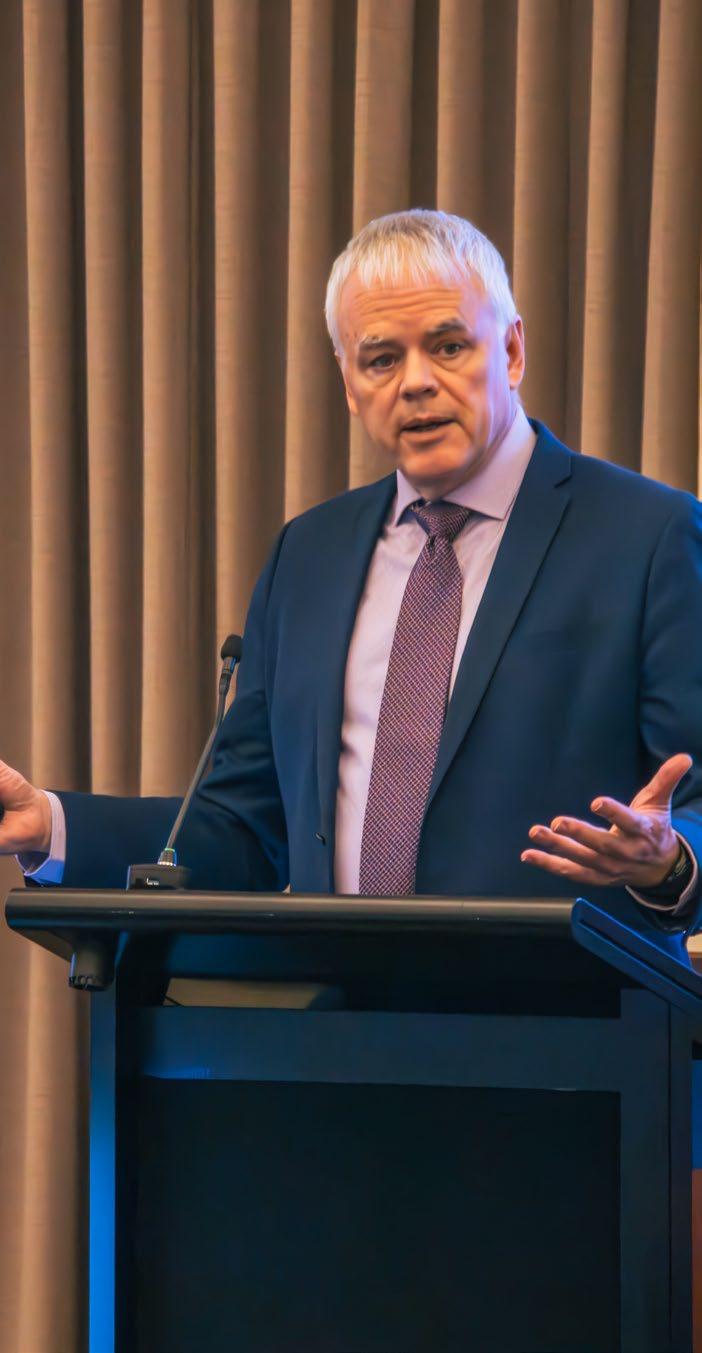
manufactured products required by the renewable energy revolution, and to position other manufacturing to take advantage of growing supplies of clean energy (such as green steel and aluminium production), would pay off in stronger economic and employment growth, less vulnerability to volatility in global fossil fuel markets, and a stronger political constituency to support the renewable energy transition.
The report also recommends several qualitative best practices that should be incorporated into the Australian response to the IRA, to generate maximum economic, social and environmental impact, including:
• strong labour and environmental standards attached to subsidised projects
• public equity participation
• parallel investments in training for workers to fill the new jobs
To download a copy of the report, visit: futurework.org.au
About the Centre for Future Work
The Centre for Future Work is a research centre, housed within the Australia Institute, to conduct and publish progressive economic research on work, employment, and labour markets.

It serves as a unique centre of excellence on the economic issues facing working people: including the future of jobs, wages and income distribution, skills and training, sector and industry policies, globalisation, the role of government, public services, and more. The Centre also develops timely and practical policy proposals to help make the world of work better for working people and their families.
For further information, visit: futurework.org.au
“
If we don’t support domestic manufacturing to quickly enhance its production, skills, and technological capabilities, all that will happen is we will replace one set of unprocessed minerals: coal, oil and gas; with another: raw lithium and related critical minerals.”Dr Jim Stanford (Director, Centre for Future Work). Charlie Joyce (Research Fellow, Centre for Future Work).
TRIPLE THREAT UNEEK SHAPES INDUSTRY THROUGH EXCELLENCE IN QUALITY & INNOVATION
When it comes to quality and a customer-first approach, UNEEK is a leader across the welding and fabrication space. The company began almost 60 years ago, and has since become a key service provider for Australia’s defence sector. In addition, UNEEK caters to a range of other industries across automotive, oil and gas, renewable energy, and transportation. UNEEK recently certified to AS/NZS ISO 3834, EN 15085 and DIN 2303, which is already taking the company into a new stratosphere of quality and service. Weld Australia spoke with UNEEK’s Quality Manager and Welding Coordination, Mathew Billman, who said the certifications are paving the way for the company to compete in an increasingly globalised market.
UNEEK Bending is behind some of the most state-of-the-art engineering solutions in Australia. Based in Dandenong in Melbourne’s southeast, the company was born in 1964.
According to Mathew Billman, “In the early 1960s, there were very limited capabilities within Australia for bending and forming of metallic parts. So it was seen as a niche market. We initially only had one competitor, so there was plenty of opportunity.”
In the early 2000s, UNEEK was bought out by a multi-national. However, one of the original owners soon bought the company back. Today, UNEEK’s design department, research and development engineers, welders and metalworkers are all committed to quality.
UNEEK has become one of Australia’s leading bending, rolling
and welding company. “We can bend, roll and form a huge range of metallic products—everything from structural materials through to tubes and piping.”
“We are specialists in the industry. We supply to a diverse range of industries, including rail (both trains and trams) and transport like buses and trucks. We also have a large footprint in power generation all around Australia,” said Billman.
UNEEK has supplied crucial parts for the F-35 fighter jets, which are exported to the United States.
“We put a significant amount of research and development into the parts to make them more repeatable and raised the quality to a high standard; we have never received any NCRs. We are looking to supply 100% of these parts worldwide.”
“These strike fighter jets all have our parts, which is unusual for the defence industry as there is always a back-up supplier,” Billman said.
Modern Technology Brings
UNEEK’s Dream to Life
Over 40 staff members call UNEEK’s 4,500m2 facilities their home. The company has invested in, and implemented a range of modern welding technologies, including brand new welding equipment throughout the workshop. UNEEK also intends to add a laser welding system to their capabilities early next year.
“We weld our defence parts with an automated orbital TIG welding process, using cutting edge technology that we imported from Europe. The technology is capable of welding 3.2 diametre tube up to 6 inch diametre,” Billman said.
Photos (clockwise from top left):
Solar power plant at Australian National University in Canberra.
Super heater elements in stainless steel 310.
Artists’ impression of the X’trapolis 2.0.
Thermal fluid heater 150Nb Sch40 Twin start coil in carbon steel.
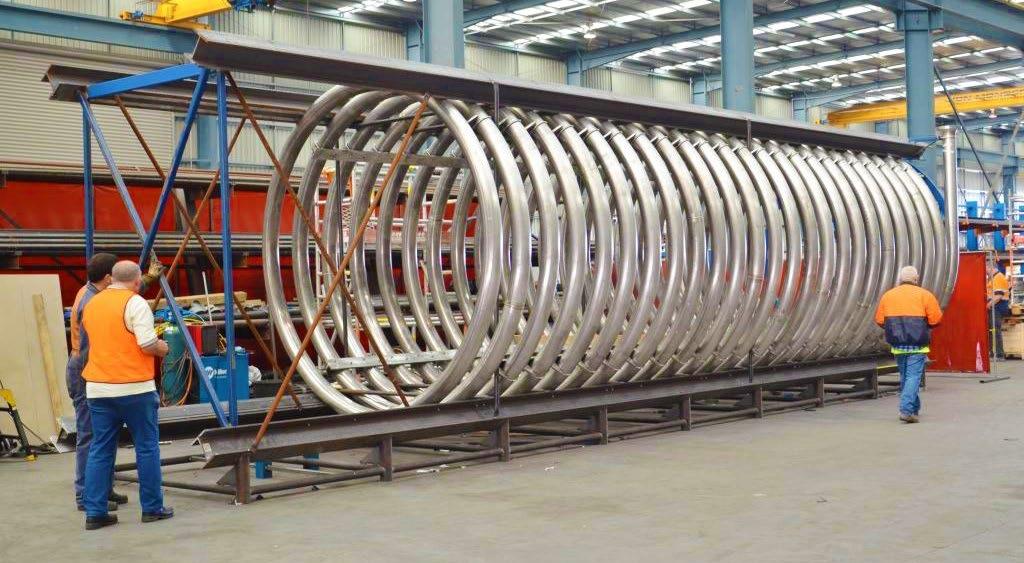
“What really sets us apart from our competitors is our experience with different materials. We weld all common materials, but also have extensive experience with exotic materials, gained over the last 20 years. It is not uncommon for us to weld materials such as Inconel, Hastelloy and Titanium to name a few.”
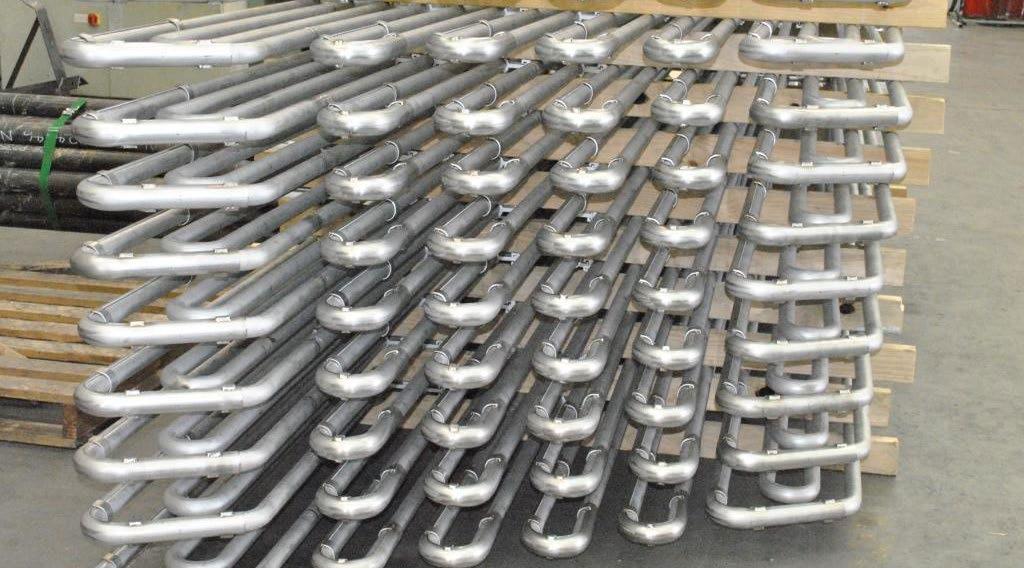
All UNEEK team members—from welding operators through to Welding Supervisors—hold Weld Australia qualifications. “We have the right people, in the right roles, with the right qualifications, skills and experience.”
Bulk Certification Sees UNEEK’s Quality Increase
UNEEK recently underwent certification for AS/NZS ISO 3834 Quality requirements for fusion welding of metallic materials, EN 15085 Railway applications — Welding of railway vehicles and components and DIN 2303 Welding and allied processes – Quality
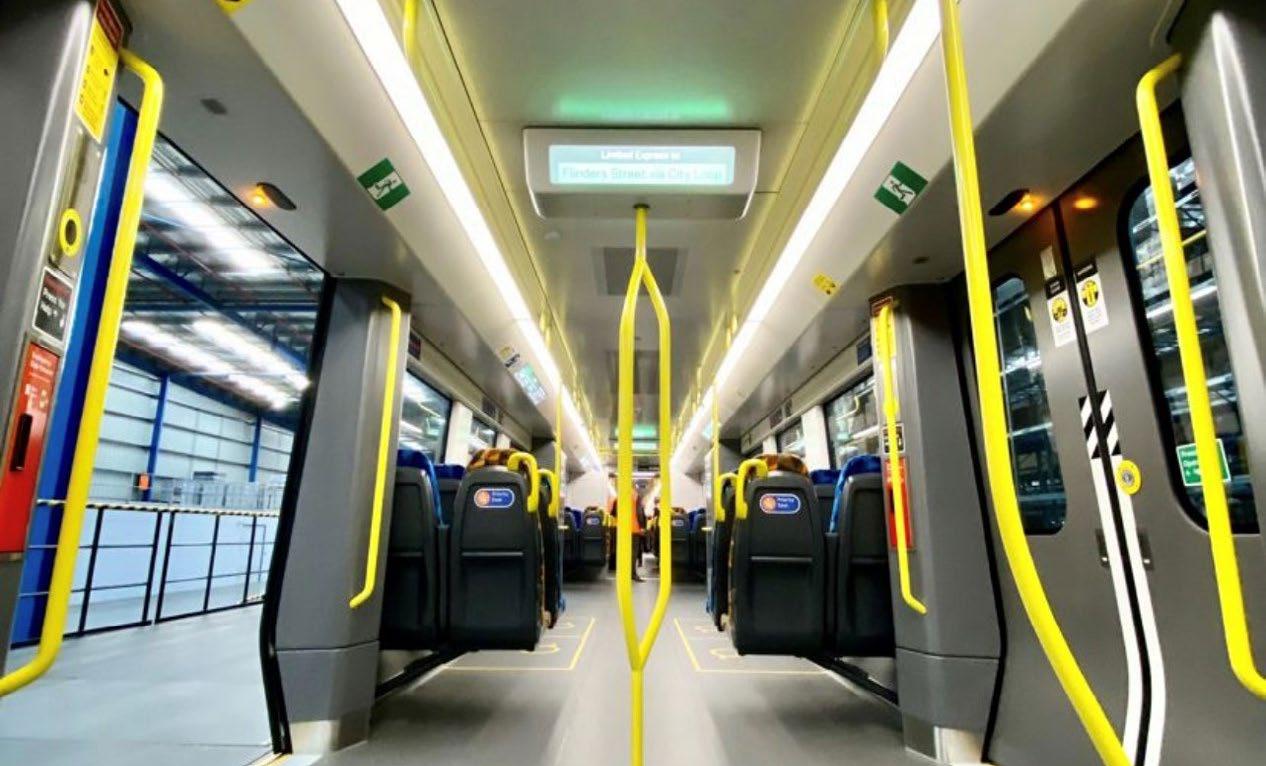
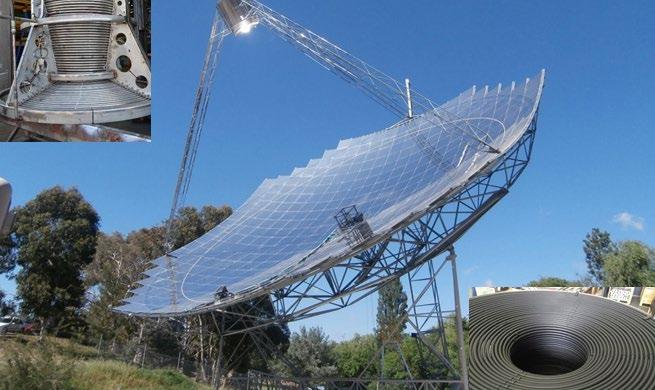
requirements to be met by production and maintenance companies for military products. These certifications form part of UNEEK’s constant quest for perfection.
Billman, who has been with UNEEK for two years, said certification is a huge undertaking. However, he believes it is a crucial part of implementing and improving several quality management systems. “When I first started at UNEEK, I implemented AS 9100 Quality systems for aerospace. This was quickly followed by AS/NZS ISO 3834, EN 15085 and DIN 2303.”
“The reason we undertook certification to all of these systems is that manufacturing is a really competitive market. So, we like to ensure that our capabilities remain diverse. We want our capabilities to be leading edge, whether we’re bending, rolling or welding for the aerospace, rail or defence industry,” he explained.
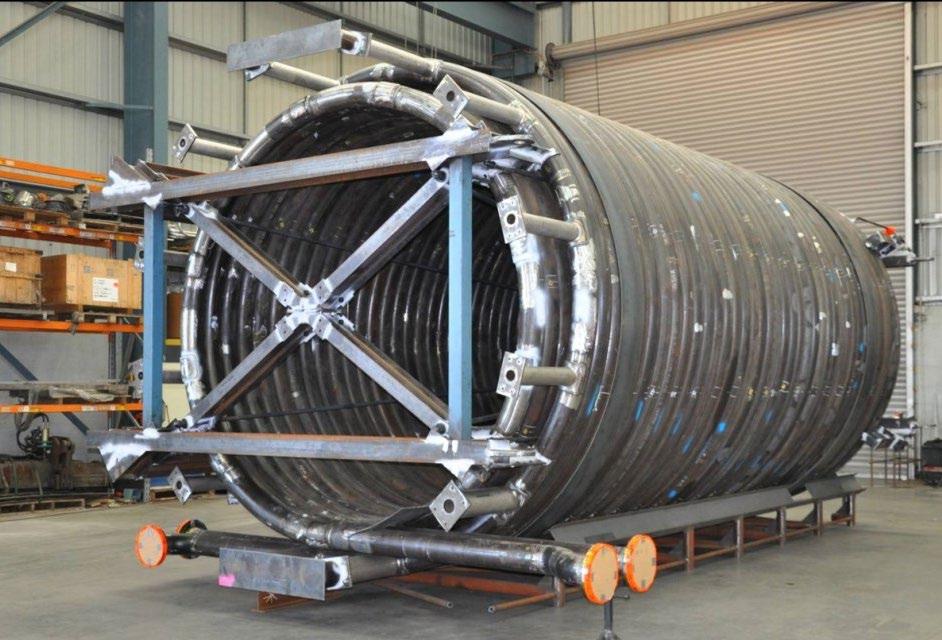
“Having worked with Weld Australia previously, I knew the process would be trouble free and very smooth. The Weld Australia team made the job very easy and answered all the questions we had.”
When it comes to other organisations embarking on the same certification journey, Billman said it will improve the systems already in place.
“A lot of people get scared about implementing new systems because of the work involved, but the process is very beneficial for your company overall. Company owners and managers have more confidence in the parts produced, and customers are confident that their parts will all be correct and of the highest quality, and employees have clear processes to follow, streamlining their workflow,” Billman said.
CONSTRUCTION OF BIOMASS ENERGY PROJECT
Uneek Energy is an Australian advanced-waste technology provider specialising in processing and converting selected waste, timber waste and commercial and industrial waste to energy.
Biomass for energy can be obtained from the remains of forest harvesting, from the industries of the first and second transformation of wood, from agricultural and forestry products, from residues from livestock farms, from the organic fraction of urban solid waste, of crops implanted and exploited for the sole purpose of obtaining biomass, the so-called energy crops, and in general, of any product of organic origin capable of energy use.
Recently, Uneek Energy completed the turnkey construction of a 3MW biomass energy project for a client on a turnkey basis.
The biomass energy project was used to dry timber and heat treat pallets, crates and cases to the standard ISPM-15 Regulation of wood packaging material in international trade , which sets out the requirements for phytosanitary standards for overseas export.
The project features Australia’s only bioenergy powered heat-treatment kilns. The client switched from LPG gas to renewable woodchip, sourced from shredding waste timber packaging and recycled pallets.
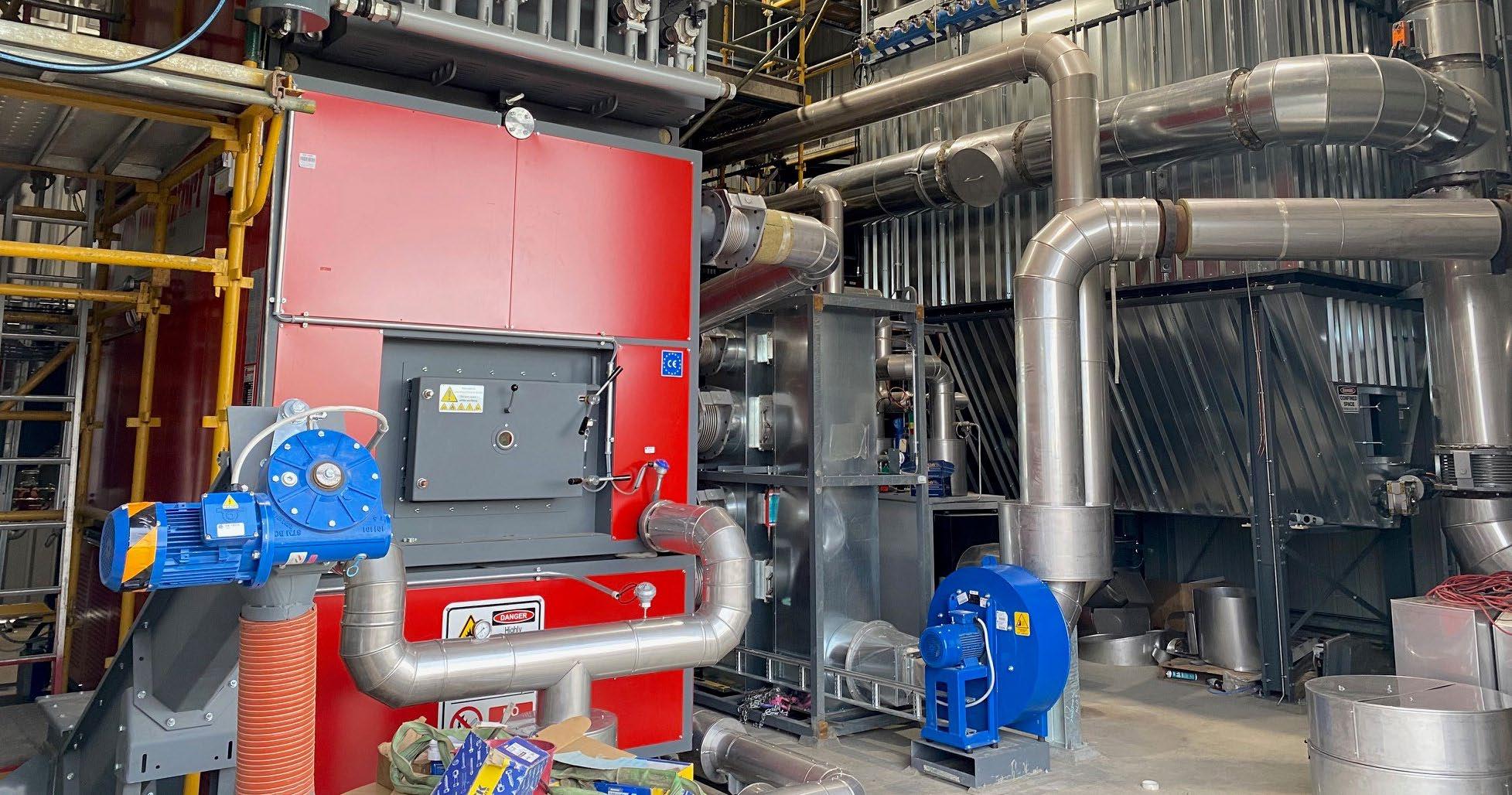
The biomass boiler supplies hot water at 90°C to an insulated structure where fin fans convert hot water to hot air for the heating and curing of timber pallets. This process ensures that the pallets to pass strict Australian Quarantine and Inspection Service (AQIS) requirements, enabling the pallets to be used for the export market.
A Broad Scope of Work
Uneek Energy took full responsibility for broad scope of work for the project under a turnkey arrangement with the client.
During the initial stages of the project, Uneek Energy delivered full plant layout designs and detailing, civil design of foundations and bulk earthworks design and site works.
Uneek Energy undertook electrical design, supply and installation of:
• Power supply to energy island
• Internal distribution and supply to all consumers
• Instrumentation supply and installation
• PLC for control of all equipment including integration with vendor supplied PLC for 1 button operation
Uneek Energy was also responsible for: insulation and cladding of all hot surfaces including piping, ducting, tanks and so on; design, supply, installation and commissioning of the fire detection and suppression system; and precommissioning and commissioning of the plant.
Welding Excellence
With UNEEK ranked as one of Australia’s leading bending, rolling and welding companies, they were also responsible for all structural steel design, fabrication and erection on the project, including:
• A heat storage tank
• All piping, encompassing a feed system with FW pumps and lines, supply lines to the heat storage tank and return lines from the heat storage tank to feed pumps
• Installation of all vendor supplied equipment, such as boiler, fans, baghouse, feeders and so on
• Two exhaust stacks
Uneek Energy conducted all welding both off-site and on-site for the piping systems. All piping was PN16 SS 316L, with the pipe size ranging from 150NB down to 15NB at instrument tapping points. All piping was fully butt welded between equipment terminal points, necessitating a percentage of field fit welds with 100% inert gas purging for all joints. All joints were fully TIG welded.
All welding and materials had full traceability, including welder qualifications, weld procedure qualification, consumables and materials (both pipes and fittings).
All piping was fabricated and welded in accordance with AS 4041 Pressure piping Class 3 and AS 4458 Pressure equipment - Manufacture. All piping was then inspected in accordance with AS 4037 Pressure equipmentExamination and testing and subject to 100% visual inspection followed by full hydrostatic pressure testing. To the credit of Uneek’s project management personnel and the highly skilled welding team, the final weld repair rate was zero.
About Uneek Energy Solutions
Uneek Energy Solutions, in partnership with SIEA Biocal in Spain, provides engineering solutions for smaller, stand-alone modular biomass projects in
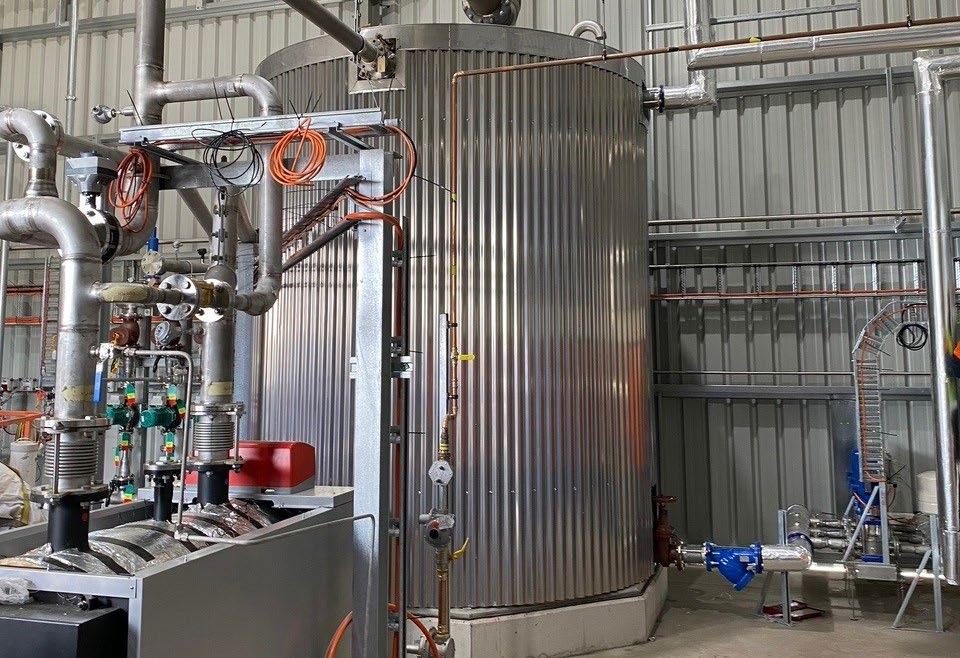
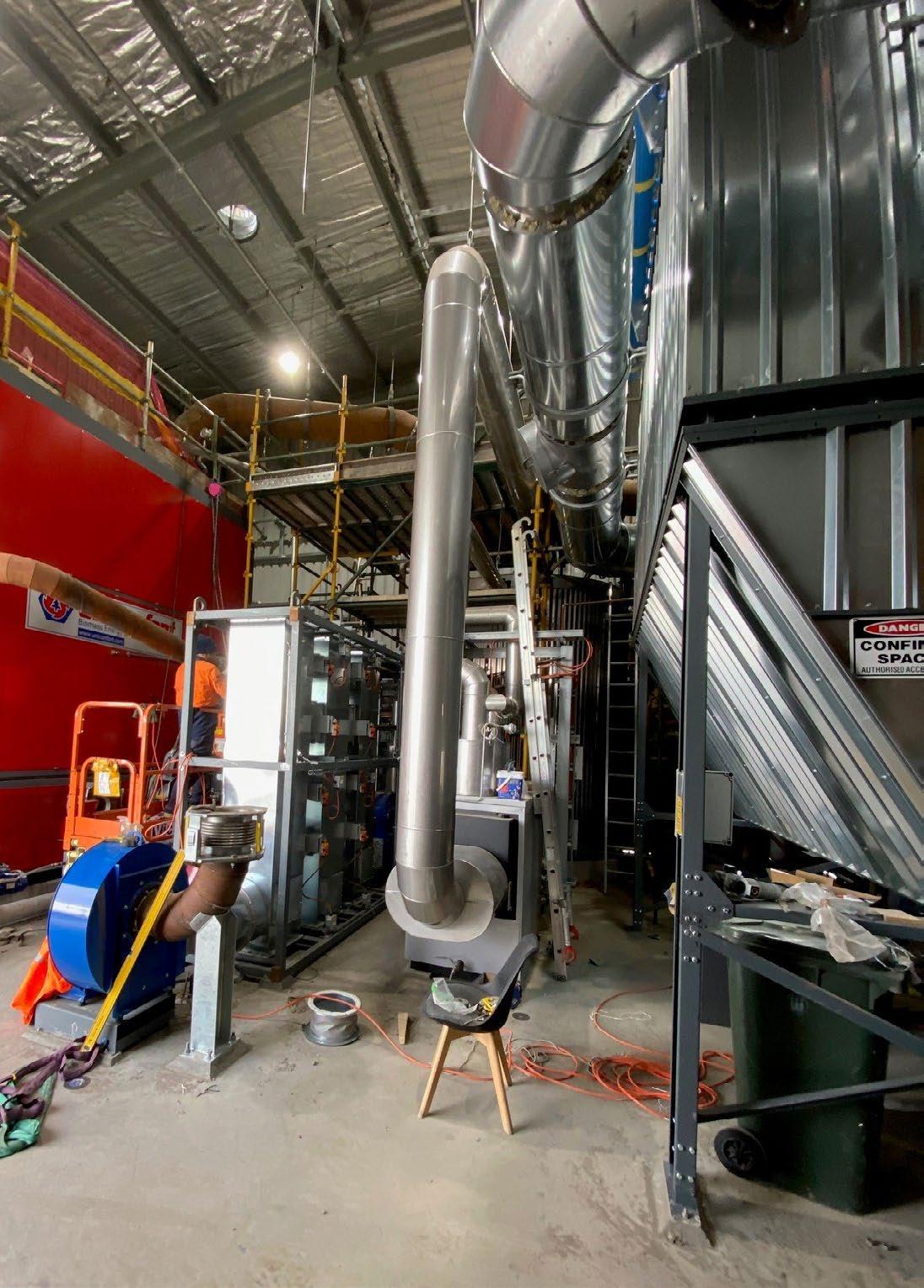
Australia. Electric power generation can be provided from 80kW up to 16MW, with steam generation from 100kg/h to 20,000kg/h Uneek’s specialty.
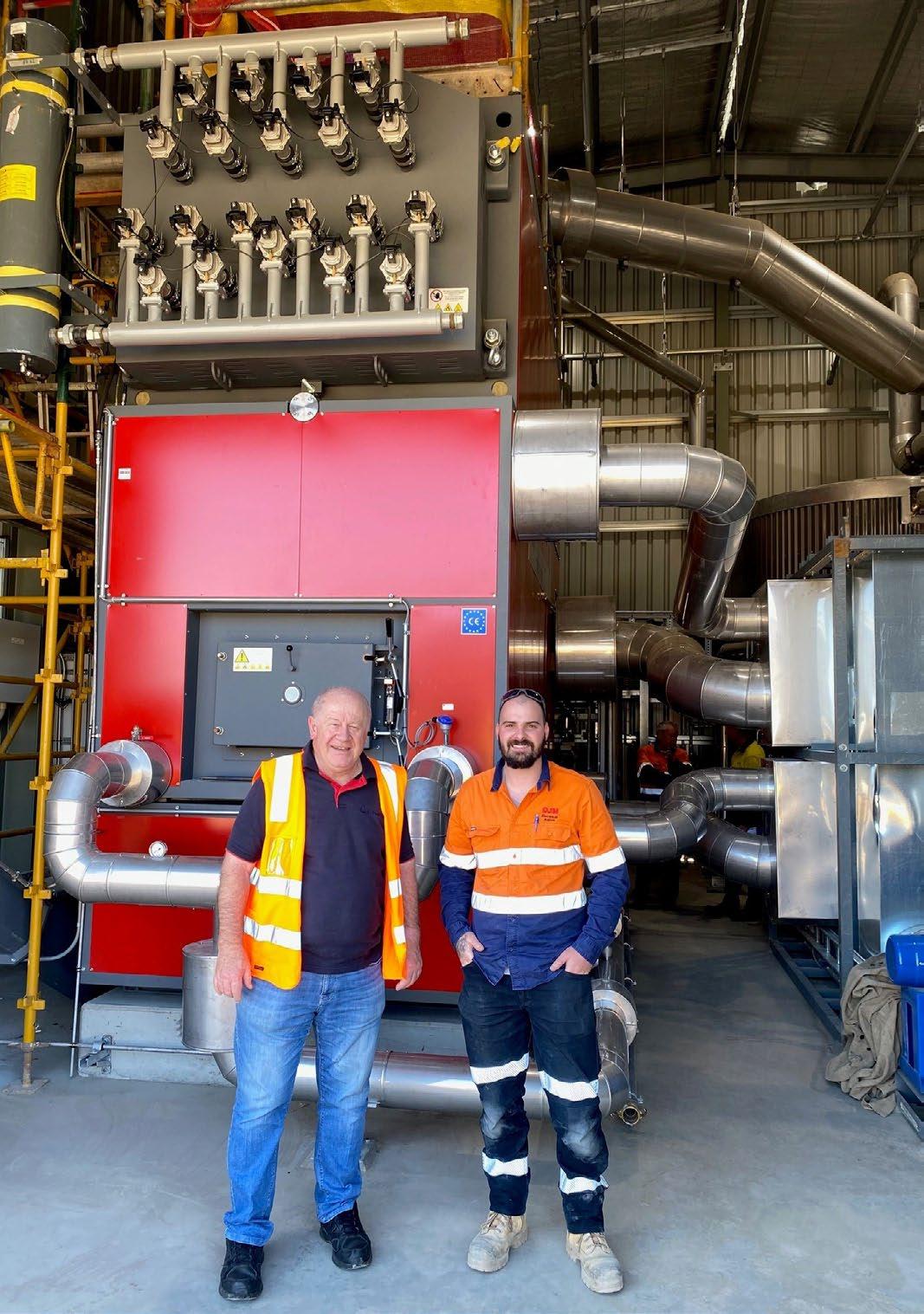
Uneek Energy also supplies the AGAM furnace temperate measurement system by Bonnenberg Drescher, which enables real time two dimensional measurments in furnaces up to 2000°C.
In collaboration with Steinmuller Engineering Germany, Uneek Energy offers life extension, efficiency and reliability improvements, emission reductions and specialised design works for the power generation industry.
Further Information
For further information about Uneek Energy Solutions, visit: uneekenergy.com.au
Q&A WITH A WELD AUSTRALIA MEMBER

Kohan Hanby, Hanby Welding & Engineering
Kohan Hanby knew he wanted to be a welder early on, starting his boilermaker apprenticeship at just 15 years of age. Throughout his apprenticeship his focus and determination have been unwavering. During the second year of Kohan’s apprentice, he completed ISO 9606 Fusion Welding. At the time, he was the youngest recipient in the southern hemisphere to do so. In the same year, Kohan went on to complete Non-Destructive Testing training in Dye Penetrate and Magnetic Particle Inspection. Kohan was recognised for his exceptional work at the TAFE Queensland 2022 Cairns Trade Excellence Awards, winning the Engineering Apprentice of the Year Award, as well as the event’s top accolade, the Outstanding Apprentice of the Year Award. He also took home Weld Australia’s 2022 Young Tradesperson of the Year Award and was a Queensland Training Award regional finalist.
Can you describe your job?
I am a Boilermaker / Pressure Welder at Hanby Welding & Engineering Pty Ltd. Although we are located in Cairns we travel all over Australia fabricating and install predominately fuel and LPG pipe spools. There is no such thing as a normal work day for us, with a huge variety of work from fabricating simple brackets, to working on heavy machinery or trains all the way through to hygiene process tubes and certified welding.
What inspired you to choose a career in welding?
My Dad has worked extensively in the industry since he left school, and has gone from a Boilermaker to a Pressure Welder and then onto a Welding Supervisor and Inspector. His knowledge and experience in the industry has certainly inspired and assisted me in my career.
What do you enjoy most about your job and welding?
There are a few aspects I particularly enjoy. I enjoy seeing a project through to completion; that rewarding feeling of transforming raw material into a finished project. I also enjoy training and help out our apprentices and networking with clients and supporting companies.
Why do you think other young people should consider a career in welding?
Now is a great time to get into the industry with a recognised skill shortage not only here in Australia but also internationally. As a result the demand for skilled boilermakers is at an all-time high with a lot of financial benefits offered to both the employer and apprentice. Additionally if you can lay a weld here in Australia, the same process and technique is used pretty well much everywhere else around the globe, therefore the opportunity to see the nation or world is on offer if that’s what you’d like to do. Not to mention the financial stability at a young age is a real bonus.
Do you have any advice for young people considering a career in welding?
Bring a great attitude. Like anything, enter into your career with the attitude of trying to achieve the highest quality standard in every job. A positive attitude and the willingness to learn with make up for any shortcoming in your abilities. Aptitude is great but a great attitude with ace aptitude every time! Plus I don’t think it needs to be said, but a desire to be there and being a genuinely good person goes along way.
What is the most interesting project you’ve worked on?
Installing the LPG pipe spools at a gas terminal in Tasmania. At the time I wasn’t qualified as certified welder, but seeing the team pre-fabricate the pipe spools here in Cairns and then flying down to Tasmania to assist in the install was really enjoyable. It definitely encouraged me to knuckle down and commit to studying with Weld Australia earlier this year for my AS1796 Cert 7 ticket.
On a completely different level, I’ve also fitted out a new work vehicle for a local veterinary. I kitted out the ute tub with lockable drawers and then fabricated a dog box that sat onto of the drawers and topped it off with installing a roof top tent for their all remote travelling. I really enjoyed this project because of the freedom and creativity the client provided.
Who has inspired you professionally?
Obviously my dad, but all world class leaders in their respective fields. Seeing their high standards and how they apply themselves is an inspiration. You can learn some much from watching and listening to the advice of others. As an apprentice, I remember working with Mikey, a truck driver who we used prior to his retirement. He was genuinely a great guy full of awesome advice. He’d provide advice on everything from lifting and stacking loads all the way through to getting a splinter out of your finger.
What do you believe is the biggest challenge for the welding industry?
That would have to be the skill shortage facing Australia.
What about the biggest opportunity for the industry? There’s plenty of demand in the industry at the moment creating some good opportunities for individuals and businesses to expand.
RAPID FIRE
What are your top 3 ‘bucket list’ items?
1. Become a commercial helicopter/ videographer pilot for Red Bull.
2. Tour Australia in a coil converted 79 series Landcruiser.
3. Travel the east coast of Australia on a jet ski.
If you could be famous, what would you want it to be for? Innovation of a new product or adrenalin/travel lifestyle.
If you could meet anyone, who would it be? Matt Baker from Explore Life.
What is your pet peeve? Imperfections in products.
What is your favourite:
• Food: Mum’s Vietnamese chicken wraps
• Song: Joker and thief
• Sport: Downhill/Enduro mountain biking and island hopping & exploring the Great Barrier Reef with mates on jetski’s.
What is your top tip for welding excellence? Patience, persistence and perseverance.
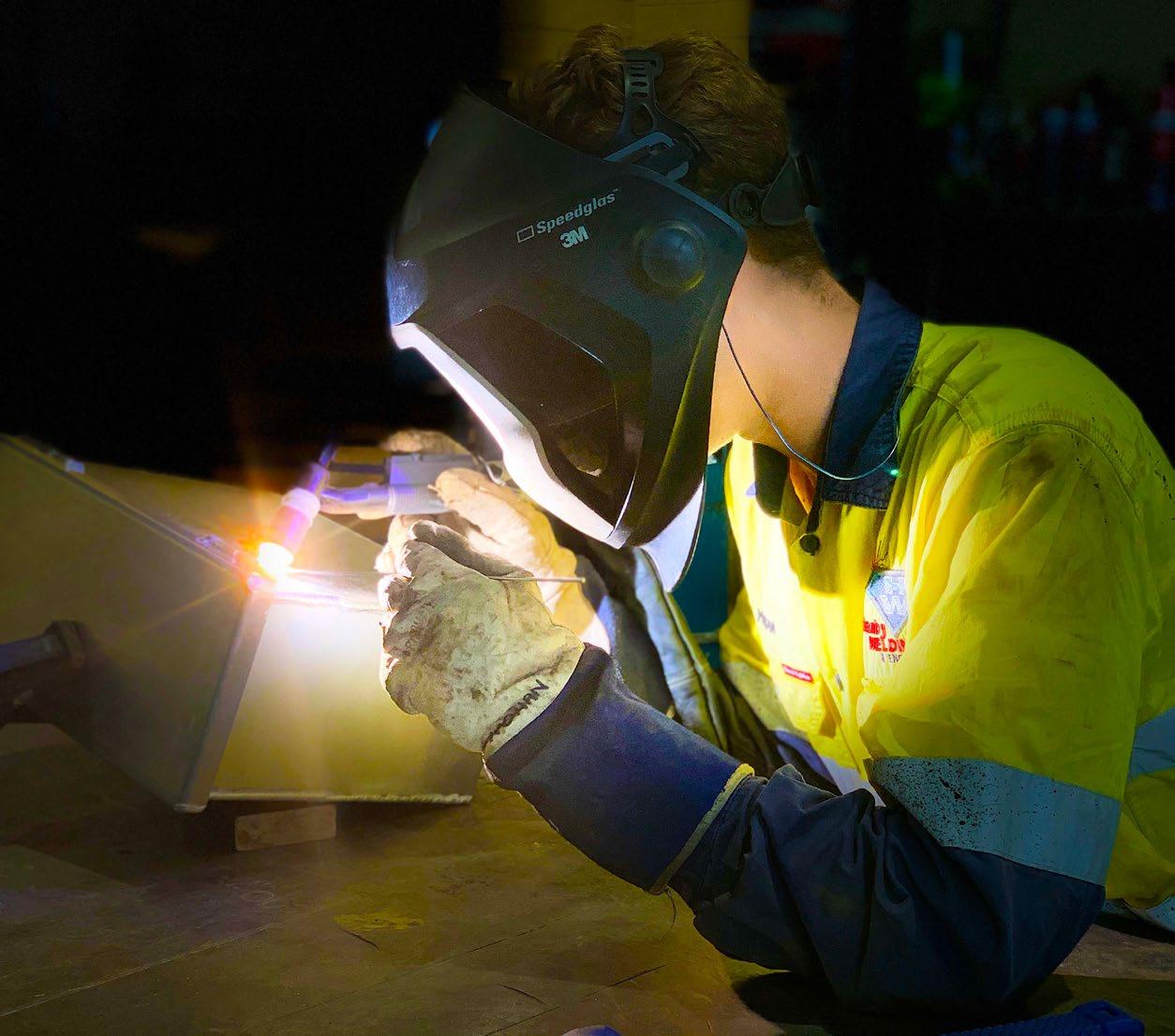


FORGING A SKILLED WORKFORCE Industry comes together to develop local welding talent in Papua New Guinea
Over the last couple of months, Port Moresby in Papua New Guinea was home to a suite of successful welding training programs, bringing together ten citizen employees from both Monadelphous and Santos across their Lihir and Monadelphous Worley Joint Venture (MWJV) operations. In collaboration with Weld Australia, Monadelphous conceptualised and coordinated two welding upskilling programs including Welding Technology Basics and International Welding Inspector - Basic (IWI-B).
Led by Weld Australia’s experienced trainer, Joe Sandor, the comprehensive program covered welding processes, codes, standards, inspection techniques, and safety protocols. Participants engaged in theoretical sessions and practical demonstrations, gaining handson experience and a deep understanding of welding inspection procedures.
Mark Potts, Quality and Welding Manger for Monadelphous said, “This is a first for us all in PNG, and a fantastic example of our commitment to corporate social responsibility by training some of our national employees in welding inspection. By investing in the development of local talent, Monadelphous is not only bridging the skills gap but also empowering the local workforce to make significant contributions to their communities, and the broader nation. I’m proud of our ongoing dedication to creating sustainable opportunities and fostering economic growth in PNG.”
The success of the IWI-B course in Port Moresby was further bolstered by the proactive support and engagement of the site teams across Lihir and MWJV. The collaboration between the site teams, Weld Australia, and the participants fostered a strong sense of teamwork, highlighting the collective effort to advance welding inspection practices.
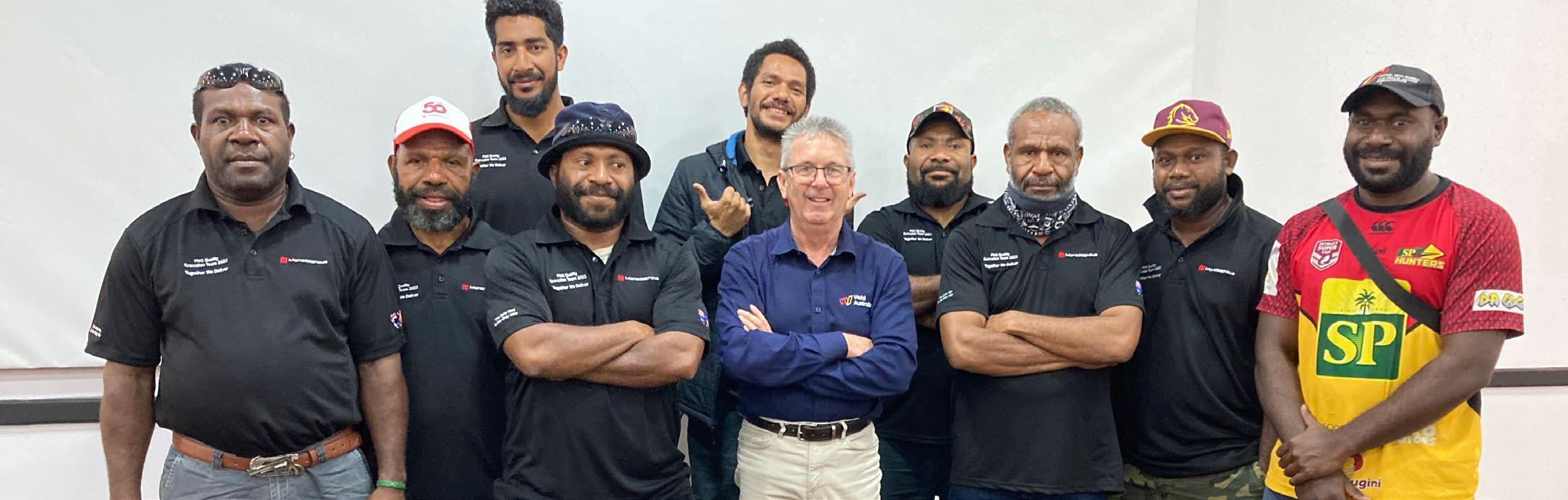
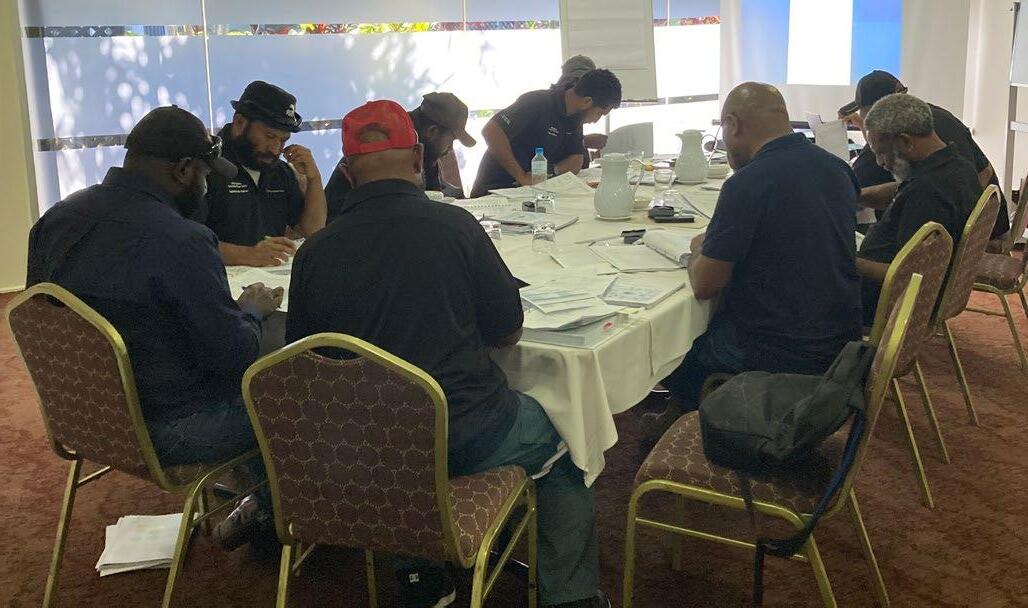
“Upskilling initiatives like this showcases the value of professional development opportunities in PNG, allowing
employees to acquire essential skills and expand their knowledge in line with international best practices. We anticipate that the newly acquired expertise will have a positive impact on welding inspection practices across our operations, promoting higher quality standards and safety measures – which is great for everyone,” said Sean Lavin, Learning and Development Advisor (Eastern Region), Monadelphous.
The successful conclusion of the course resulted in the participants being awarded internationally recognised certifications as Welding Inspectors, acknowledging their enhanced skills and competence in welding inspection. These certifications will further empower the employees from Lihir, MWJV, and Santos to contribute significantly to their respective organisations and promote higher standards of quality control.
WELD AUSTRALIA LAUNCHES NATIONAL RESOURCES FOR MEM TRAINING PACKAGE
Weld Australia is pleased to announce the launch of a new suite of learning resources for the Manufacturing and Engineering Training Package.
Weld Australia has designed and created a suite of resources for delivery of the 12 welding and fabrication units of competency in the Manufacturing and Engineering (MEM) Training Package.
According to Geoff Crittenden (CEO, Weld Australia), “Our resources help simplify the learning process for students, teachers and training institutes and—most importantly— place the student at centre of the learning process.”
“Weld Australia believes that a national industry, which has a national learning package, needs national learning resources. Whether you’re an apprentice in Kalgoorlie, Ultimo or
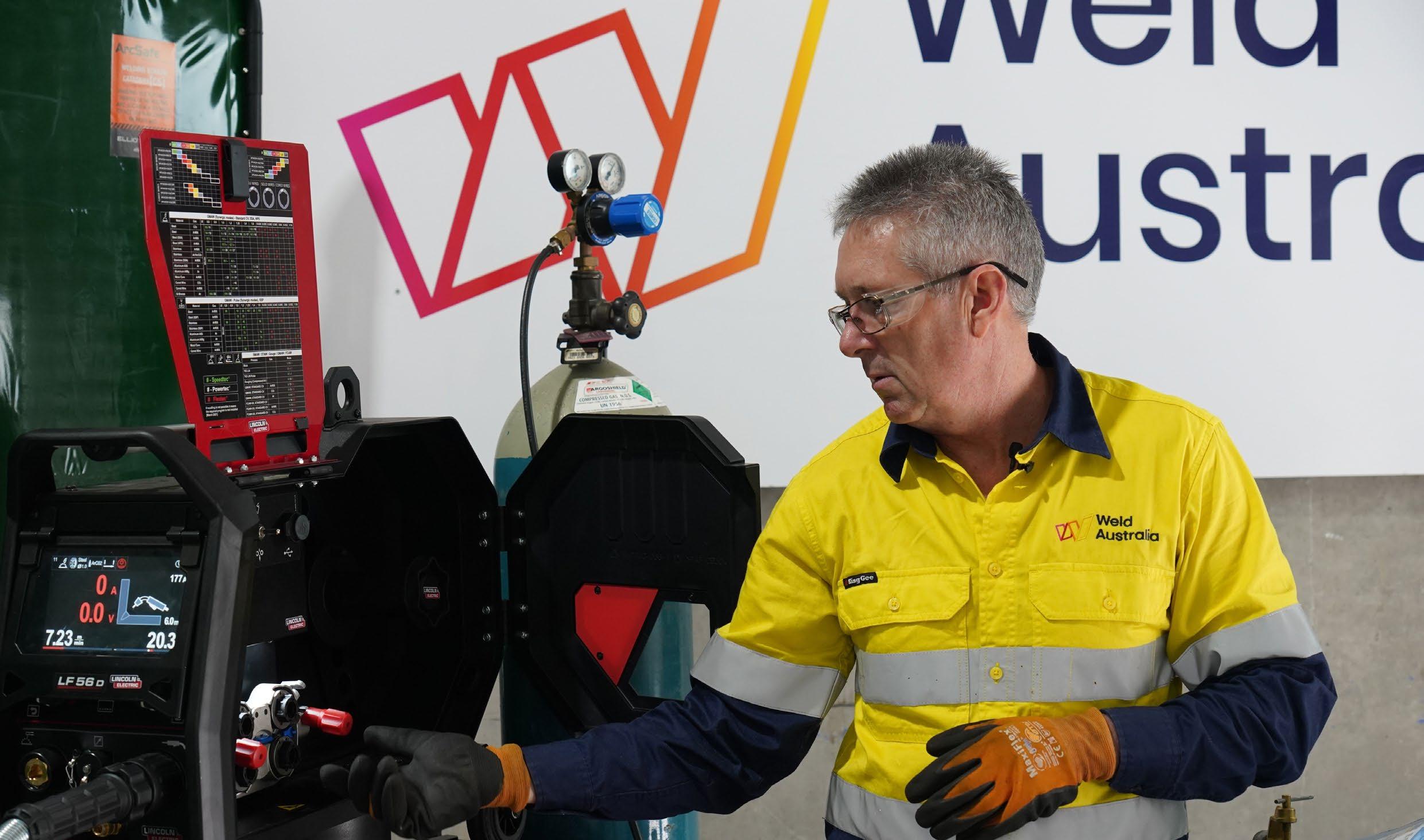
Davenport, you should have access to the same, high-quality training. Our goal is to help ensure that highquality welder learning is consistent across the country.”
Welders are more in demand than ever—labour shortages are inhibiting the growth of Australia’s welding industry. According to Weld Australia’s members, 50 per cent of Australia’s welding workshops are currently operating at 80 per cent of their capacity or below. When asked why this is, a lack of skilled workers was the overwhelming answer.
“This labour shortage comes as no surprise. Weld Australia has been calling for urgent action for over five years. We estimate that Australia will be at least 70,000 welders short by 2030,” said Crittenden.
“And yet, the number of welding trade workers in Australia dropped
by 8 per cent in the course of just five years, and completion rates of welding apprenticeships continue to fall by as much as 23 per cent annually. It is essential that welder training is revolutionised with online, accessible and engaging learning resources.”
Weld Australia formed a national consortium of TAFEs to work on the project. Over the last two years, the consortium has collaborated with us to develop the most engaging, upto-date resources possible. Members of the consortium piloted use of the resources, and some TAFEs have already permanently adopted them.
Weld Australia’s MEM Resources have been built with students, teachers and training organisations in mind. It reimagines the learning process with its user-friendly interface, diversified delivery methods, and audited and accurate
material. The new MEM resources are completely online and accessible via phone, mobile device or computer. This allows students to access learning at the time, place and pace that suits them best.
South Metropolitan TAFE Pilot South Metropolitan TAFE in Fremantle, Western Australia was the first training organisation to facilitate an official pilot. The feedback received from students and lecturers alike was extremely positive.
According to Jonathon Maile (Executive Director – Engineering, Transport and Defence, South Metropolitan TAFE), “The resources have been terrific, not only for our team here at South Metro TAFE, but we’ve also upheld these and shared these with some external customers as well. So from a quality perspective, the resources have been tremendous.”
“Being able to link in with Weld Australia and other TAFEs, improved training outcomes—there is a better consistency from a technical perspective Australia-wide. It has improved our focus on digitisation and eLearning, and the increased the flexibility of how we deliver. We’re
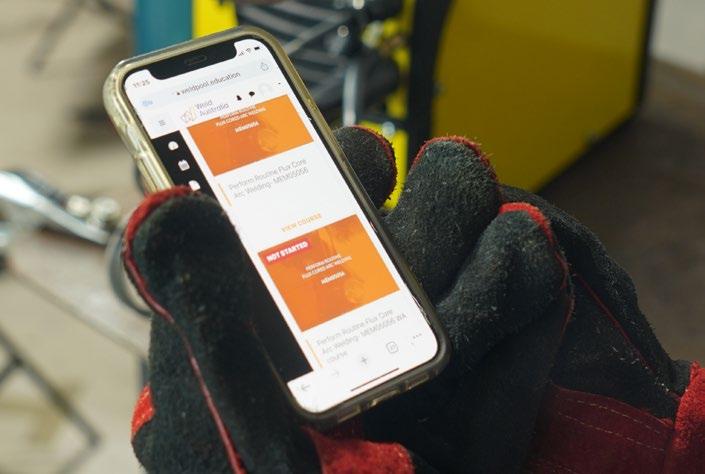

able to utilise these training resources in class to support lecturers. If apprentices miss classes, they can access the resources and catch up a lot more quickly than trying to reschedule another block later on.”
Brenda Micale (General Manager, Training Services at South Metropolitan TAFE) agreed. “The resources have improved our delivery across the fabrication area quite significantly. We’ve had some really great feedback from our industry partners too.”
“On our own, we could have developed an adequate suite of materials for the qualification. Through the national collaboration, we got a much higher quality resources. On a TAFE budget, we never could have got all the bells and whistles—the videos, the eLearning— it’s just financially out of our reach.”
“It’s great when I go out to Rockingham, the Thornley and Naval Base campuses where fabrication is taught and you can see apprentices engaging with the technology. They’re able to download it onto their mobile phones, they can play the videos, its interactive.”
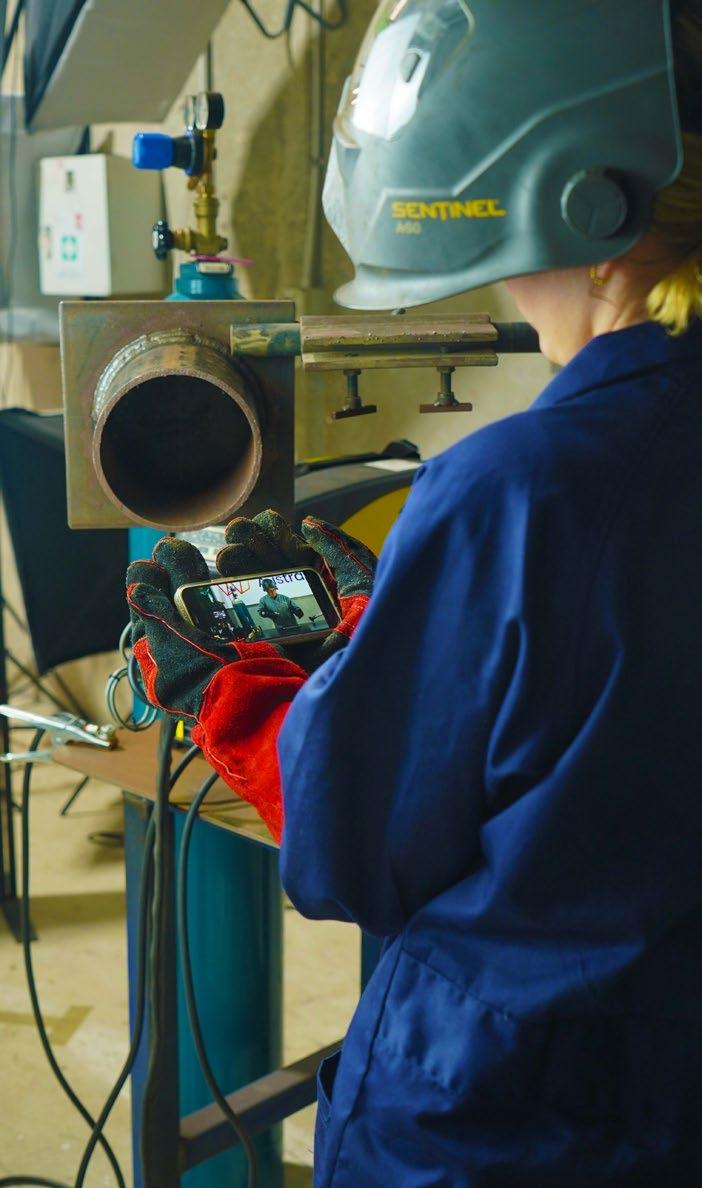
FURTHER INFORMATION
To find out more about Weld Australia’s new MEM learning resources, email training@weldaustralia, and watch the video above.
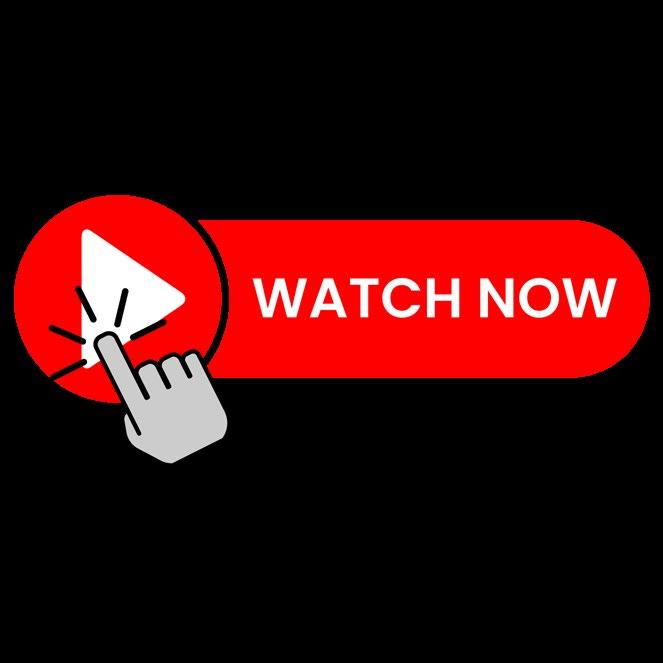
“ On our own, we could have developed an adequate suite of materials for the qualification. Through the national collaboration, we got a much higher quality resources. On a TAFE budget, we never could have got all the bells and whistles—the videos, the eLearning— it’s just financially out of our reach.”
Why Choose Weld Australia for Certification?
Weld Australia is a highly respected and independent third-party, and is proud to be the International Institute of Welding Authorised Nominated Body for Company Certification. When Weld Australia conducts your certification audits and assessment, you have access to our highly qualified team of experts. Our team values you and your business to improve your existing workplace structures and operations. We will enhance processes and procedures to ensure they’re in-line with all Australian and International Standards requirements. In turn, this delivers better results, including enhanced productivity, greater customer satisfaction and increased profitability.
All our assessors are:
• Qualified and experienced in quality system auditing and experienced in welded fabrication
• Certified in Integrated Management System (IMS) Certifications
• Either IWE or IWT qualified, with at least three years’ experience in welded fabrication
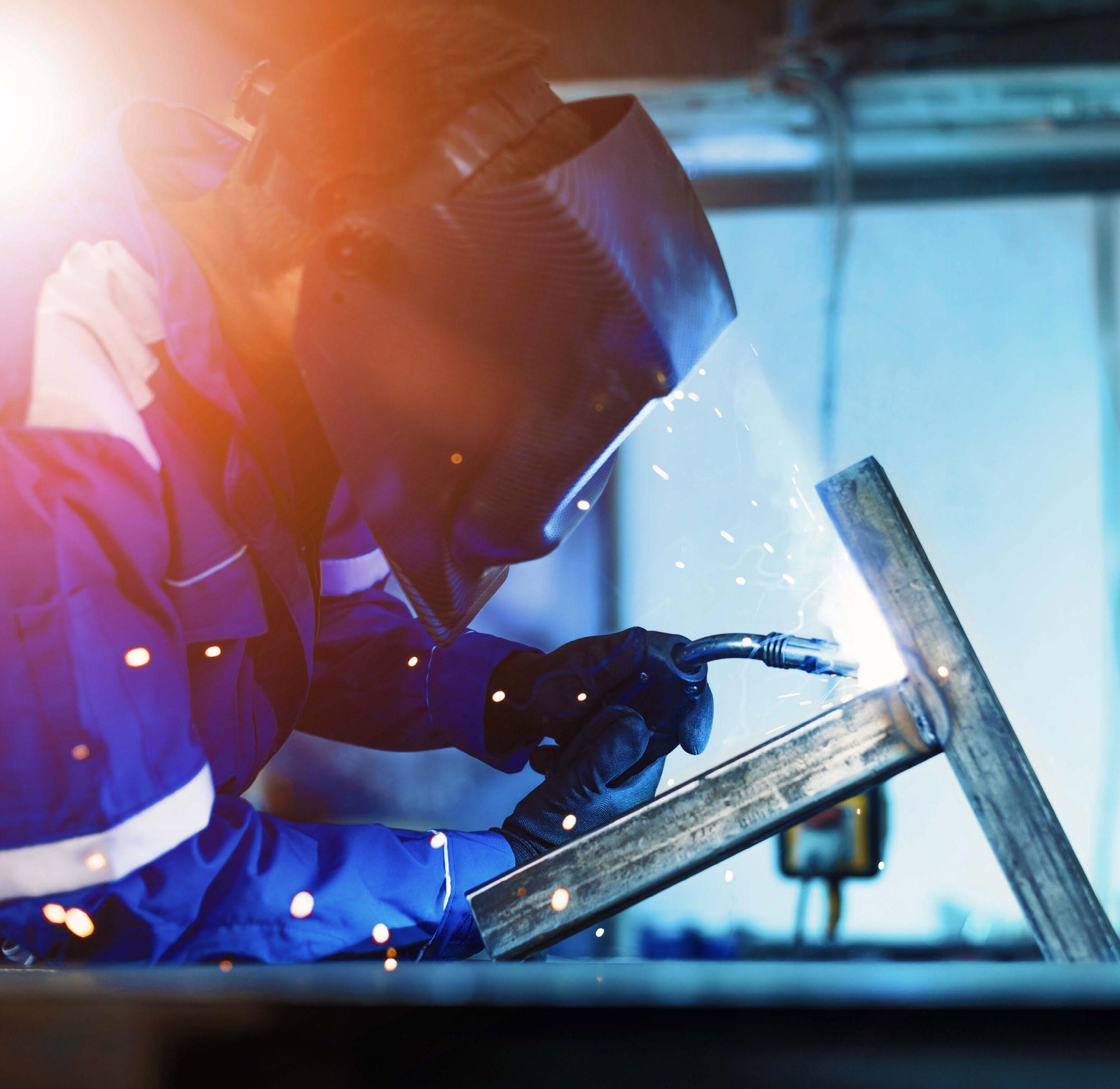
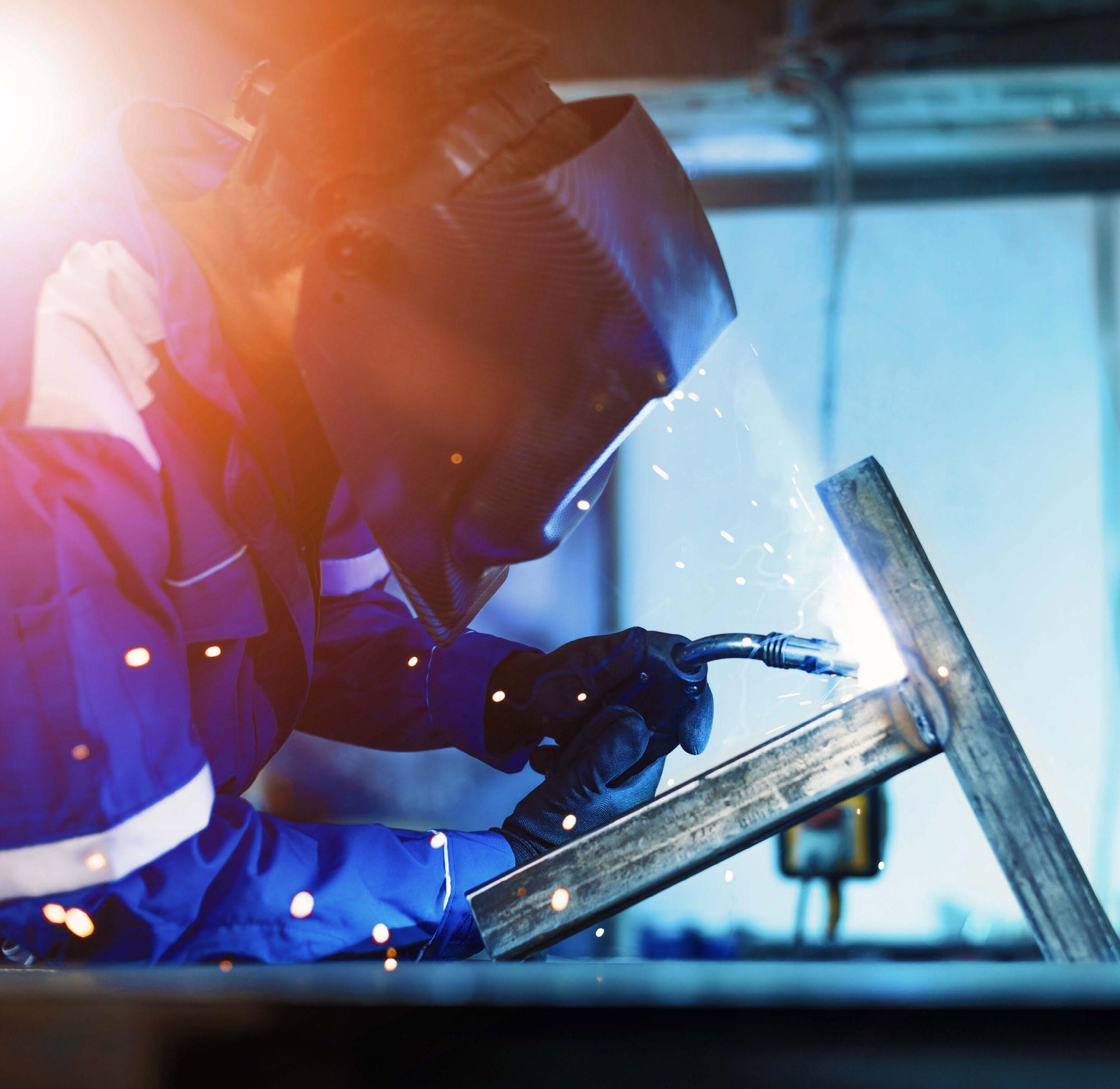
• Extremely familiar with factory production control systems, quality management systems, auditing principles and AS/NZS ISO 19011 – Guidelines for auditing management systems.
For more information, email qnc@weldaustralia.com.au or visit: weldaustralia.com.au/qualification-certification
WELD AUSTRALIA LAUNCHES NEW COMPANY CERTIFICATIONS
We are pleased to announce that companies can now be certified by Weld Australia to three new Standards:
AS/NZS ISO 9001 Quality Management System;
AS/NZS ISO 14001
Environmental Management; and AS/NZS ISO 45001
Occupational Health and Safety
AS/NZS ISO 9001
AS/NZS ISO 9001 is a crucial certification for a quality management system. It is used by organisations to demonstrate their ability to consistently provide products and services that meet customer and regulatory requirements.
First adopted in 1987, over one million organisations from more than 160 countries have certified to ISO 9001 to meet quality management objectives.
Obtaining ISO 9001 certification offers several advantages. It showcases a commitment to quality, assuring clients of
standardised, consistent outcomes. This recognition differentiates you in a competitive market, elevating your business reputation.
The certification processes can help streamline your operations, reducing wastage, and improving efficiency, to translate into cost savings. It also emphasises continual improvement, promoting innovation and adaptability. This certification enhances customer trust and satisfaction, potentially increasing client retention and referrals.

Lastly, some clients mandate ISO 9001 certification for contractual purposes, widening market opportunities. In essence, ISO 9001 can accelerate growth and boost credibility.
AS/NZS ISO 14001
ISO 14001 is one of the most recognised and advanced environmental management systems in the world. It provides a framework for companies, including welding businesses, to minimise their environmental footprint, ensure compliance with applicable legal regulations, and continually improve in these areas.
For welding businesses, the benefits are manifold. Besides promoting eco-friendly operations, the certificate process can help reduce waste and energy consumption, leading to cost savings. Achieving this certification differentiates a company in the marketplace, highlighting its commitment to sustainability. This attracts environmentally conscious clients and enhances reputation among stakeholders.
Moreover, by adhering to ISO 14001, businesses are better equipped to anticipate and manage environmental risks, ensuring long-term resilience and sustainability. This is essential in an evolving climate, where safer environmental practices should be at a business’ core.
AS/NZS ISO 45001
AS/NZS ISO 45001 has wellbeing and safety at its core to minimise workplace-related injuries and poor health. The leadership-lead approach means AS/NZS ISO 45001 meets moral, legal, ethical and industrybest practice when it comes to an employers’ duty of care over staff.
The certification shares principles with a range of other essential standards within the welding, fabrication and manufacturing space.
This certification offers numerous benefits. It not only helps reduce the incidence of accidents and health-related absences but also demonstrates your commitment to the safety of your workforce. This proactive approach to health and safety can enhance a firm’s reputation, boost employee morale, and potentially decrease insurance premiums. Moreover, ISO 45001 helps businesses to ensure compliance with legal and regulatory requirements, reducing the risk of penalties and lawsuits.
AN UPDATE FROM OUR HOTLINE
Weld Australia offers a ‘Hotline’ service to all Corporate Members. The purpose of the Hotline is not to provide a solution, but to advise the enquirer on practical next steps. For further advice, Weld Australia’s highly experienced welding consultants can speak to you over the phone or visit your site in person. If you have a Hotline query, complete our online form: weldaustralia.com.au/hotline
With the availability of hand held laser welding machines in Australia, Weld Australia recently received an enquiry on the application of Australian welding standards for the welding of light gauge aluminium and steels using these machines.
Weld Australia advised that the scope of AS/NZS 1665 Welding of aluminium structures and the AS/NZS 1554 Structural steel welding series of standards do not preclude the use of these standards for laser welding. However, the standards were not drafted with the intention of addressing specific issues that may be applicable for laser welding.
Looking at AS/NZS 1665, within the innovation provisions (Clause 1.3) specific mention is made that laser welding is not excluded but is not directly addressed in the standard. To consider the use of laser processes
using this standard, consideration needs to be given to:
1. Joint design
2. Qualification of weld procedures
3. Qualification of welders
4. Essential variables
5. Weld Quality
Aside from butt joints and fillet joints, laser process are commonly used for through-thickness lap joints and ‘stake’ joints (welding through a flange into a web to create a T piece). Fillet joints can be made with the assistance of a filler wire, whereas butt joints can be autogenous joints made with a square edge preparation.
Weld procedures can be qualified in the usually manner and tested for conformance as specified with AS/NZS 1665. Welders can similarly be qualified by testing against their ability to reproduce a qualified weld procedure as detailed in the standard.

Many of the essential variables will also apply. However, given that welding current and voltage is not applicable, other parameters will be applicable. Guidance is available from ISO 15614-11 Specification and qualification of welding procedures fir metallic materials — Welding procedure test — Part 11: Electron and laser beam welding
Weld quality and inspection requirements can be managed in the usual way as defined in the standard.
For the welding of steels to the AS/NZS 1554 series, a similar approach can be taken. It should be noted that the prequalified joints given in the various parts of the AS/NZS 1554 series are unlikely to be applicable and full qualification testing is recommended.
This Hotline update covers a specific query encountered during the last few months. Whilst accuracy in welding is critical, it is impossible to report in detail the full circumstances of the query. As such, Weld Australia recommends that further technical advice is sought in relation to specific, individual circumstances.
SAFETY ALERT
WASA-2023-02 | ISSUED: 10 JULY 2023
HAND-HELD LASER WELDERS
Hand-held laser welder devices are being imported into Australia in increasing numbers from a variety of sources. These devices transmit invisible laser light energy via fibre optic cables to a welding torch similar in design to a conventional GMAW or Mig welding torch. They are typically used for the welding of light-gauge sheet metals on a range of materials, some of which are highly reflective e.g. carbon and stainless steels, titanium and aluminium.
• Hand-held laser welding devices are Class 4 lasers, capable of inflicting severe burns and permanent blindness on unprotected personnel who may be directly or indirectly exposed to the laser radiation.
• Welders and personnel performing laser welding should wear clothing designed for welding that covers all exposed skin. Laser safety glasses designed for the wavelength of laser light in use must be worn at all times including under the welding helmet incorporating a laser resistant face shield.
• Hand-held laser welding should only be conducted in a fully enclosed absorptive booth designed for laser welding with safety interlocks on the door(s), or in areas that prevent direct and indirect beam exposure including by reflection.
ISSUE
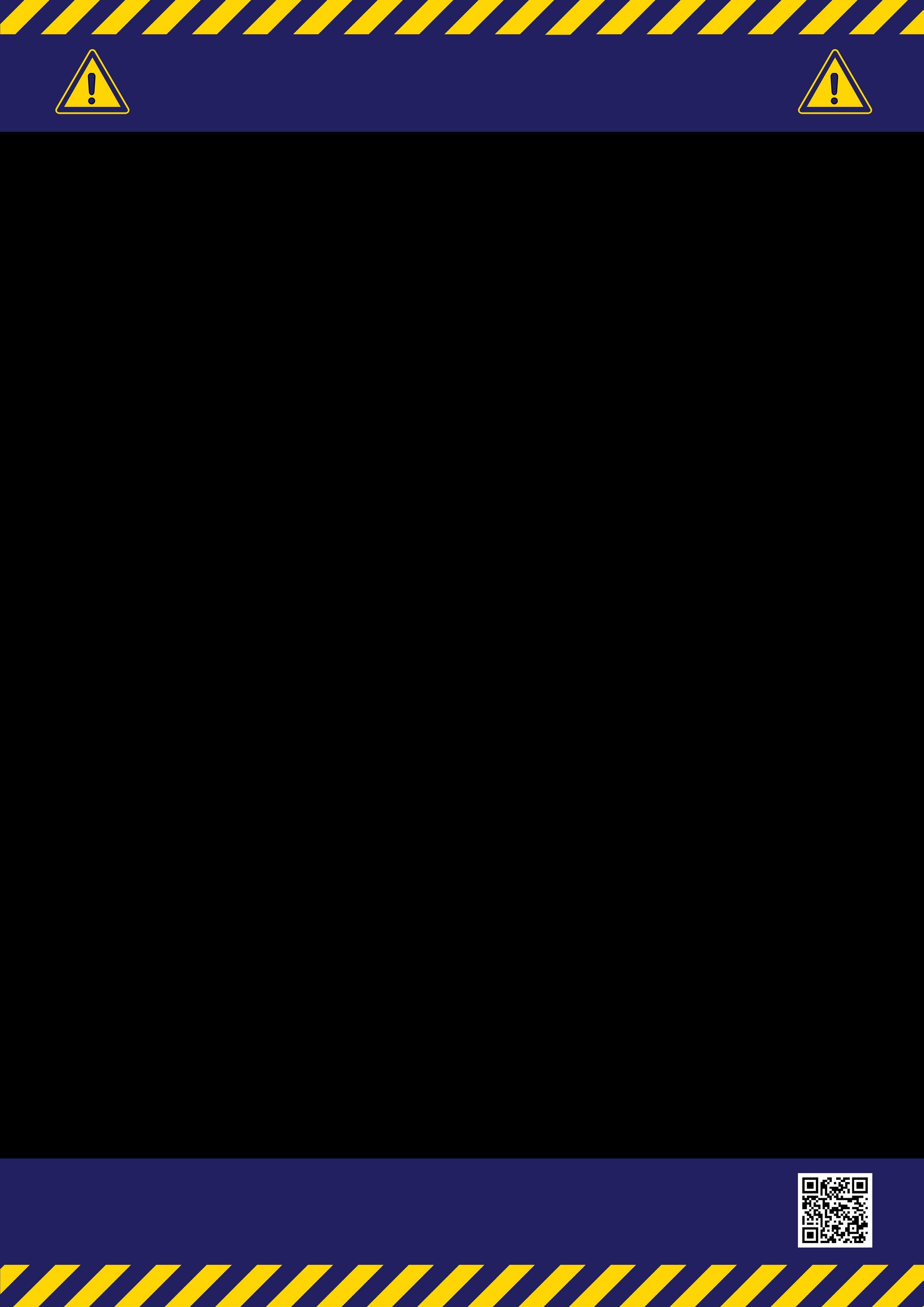
The high energy (up to 8kW peak) laser light transmitted by these welding machines is often invisible, and is capable of inflicting severe burns and permanent blindness upon personnel who may be either directly or indirectly exposed without suitable protection. Accordingly, they are classified as a Class 4 laser product under AS/NZS IEC 60825.1 Safety of laser products - Part 1: Equipment classification and requirements
SAFETY PRECAUTIONS
Hand-held laser systems are available with inbuilt safety features ranging from minimal, through to models with integrated systems designed to ensure that the laser can only be activated when intended. It is recommended that only hand-held laser systems which incorporate switching and other interlocking safety features designed to prevent inadvertent operation or operation when the welding torch is not in direct contact with the workpiece, be purchased and used. This includes:
• Lock out key operation
• Emergency stop (Estop)
• Door safety entry switch interlocks for the welding booth
• Work piece clamp to prevent operation when the torch is not in Contact with the workpiece
• No-plasma cut-out (when work piece clamp is connected to welding touch, unit will not emit a beam for any longer than 5 milliseconds i.e. machine cannot go into “star-wars” mode)
• Laser radiation hazard labels.
It is also recommended that hand-held laser welding only be conducted in a fully enclosed absorptive booth designed for laser welding, or in areas that prevent direct and indirect beam exposure including by reflection.
Protective clothing for welders using hand-held lasers should be suitable for welding and cover all exposed skin. Laser safety glasses designed for the wavelength of laser light in use must be worn at all times including under the welding helmet incorporating a laser resistant face shield.
REGULATIONS
Workplace health and safety regulations throughout Australia impose severe penalties upon any person controlling a business or undertaking that results in a person being exposed to direct or indirect laser radiation. The Regulations requires that:
1. Laser equipment intended for use on plant is designed, constructed and installed so as to prevent accidental irradiation of any person
2. Laser equipment on plant is protected so that any operator of the plant or other person is not exposed to direct radiation, radiation produced by reflection or diffusion or secondary radiation
3. Workers operating the laser equipment are trained in the proper operation of the equipment.
Welders operating hand-held laser welders must be suitably trained in the safety requirements and operation of the laser equipment.
WARNING
1. Direct exposure to laser radiation can cause severe skin burns and immediate and permanent loss of vision.
2. Exposure to reflected laser radiation is similarly hazardous and capable of causing permanent blindness and severe burns.
FURTHER INFORMATION
Refer to Weld Australia’s Technical Guidance Note TGN-SW02 Laser safety for further information. It can be download free of charge from https://weldaustralia.com.au
THE CHANGING FACE OF AUSTRALIAN STANDARDS
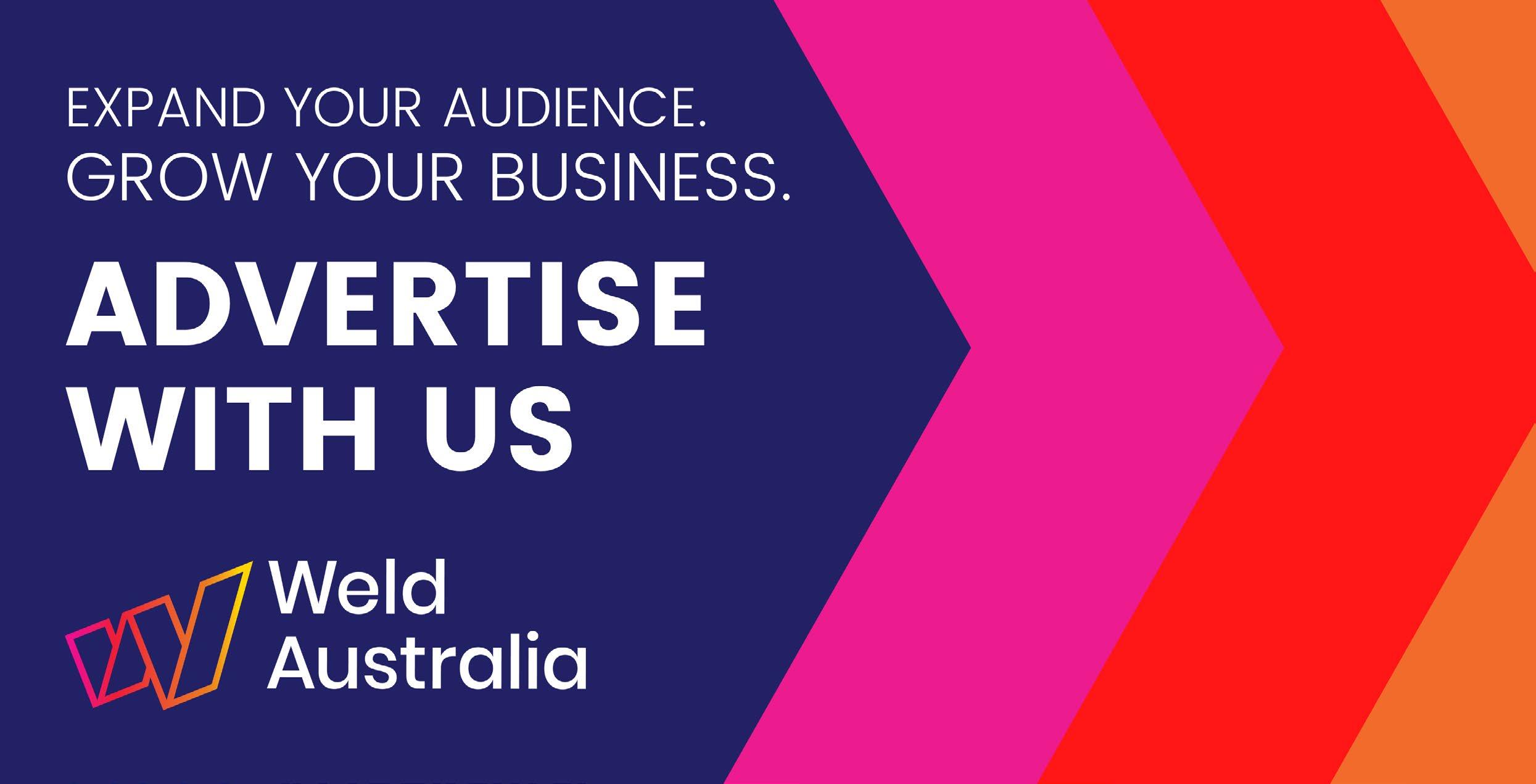
Australian Standards are living documents. They reflect progresses in science, technology and systems
To maintain their relevancy, all Standards are periodically reviewed, with amendments and revised editions published. The last few months have seen several developments, including an urgent review into Standards related to rubber hoses for welding, cutting and allied processes, and ongoing reviews into Standards related to pressure equipment and steel structures.
Pressure Equipment
The revision of AS/NZS 3788 Pressure equipment—In-service inspection is progressing well and public comment closed in June. Comments received are currently being resolved by the drafting committee. While the large number of comments received will take time to resolve, the project remains on schedule.
Welding Consumables
Committee WD-002 has reviewed the aged AS/NZS 1167 suite (Welding and Brazing — Filler metals) and the adoption of the relevant ISO consumable standards is progressing.
The Committee has also resolved to revise AS 2576 Welding consumables for build-up and wear resistance and project consultation is currently underway.
Welding Safety
The revision of AS 1674.1 Safety in Welding and allied processes— Part 1 Fire precautions is underway. Initial drafting has been completed, with a public review draft now being prepared by Committee WD-004.
The standard is used extensively in industry to establish fire preventative measures whilst welding in locations not necessarily designed for hot work.
Separate to this project, Committee EL-019 has commenced the revision of the sister standard AS 1674.2 Safety in Welding and allied processes—Part 2 Electrical with the kick-off meeting held in August.
Associated with these projects is the revision of AS 2812 Welding, brazing and cutting of metals — Glossary of terms by Committee WD-003. The project is currently being prepared for public comment.
Bridges
The revision of AS/NZS 5100.6 Bridge design — Part 6: Steels and composite construction is well
advanced and following a period of public comment, comments are currently being resolved. The revision will align the requirements of the standard with the latest revision of AS 4100 Steel structures, AS/NZS 5131 Structural steelwork — Fabrication and erection, and the New Zealand steel structures design standard NZS 3404.1. The revision will resolve known conflicts and anomalies via an amendment.
Steel Structures
Standards Australia has commenced a major revision of AS 4100 Steel structures in May. Committee BD-001 is managing the project. Cognisance will be taken on the relevant amendments to AS/NZS 5100.6.
WD-003’s project to revise AS/NZS 2214 certification of welding supervisors —Structural steel welding has been approved. The project will see the standard split into parts and renamed. The existing standard will become Part 1 and will be revised to accommodate welding inspection, similar to the latest revision of AS 1796.
Part 2 will cover bolting supervisors and will be drafted with the assistance of members of BD-001. Project kick-off is anticipated in September. As previously advised, the long term intention is to add additional parts to cover the qualification of key personnel relevant to AS/NZS 5131.
Committee BD-023 is currently revising AS/NZS 1594 Hot-rolled steel flat products. Formerly managed by Committee MT-001, this standard primarily relates to grades of steel used in hot rolled coil product form but also relates to lighter gauge plate manufactured from hot rolled coil for structural purposes. The draft is currently being prepared for public comment.
ISO Update
ISO TC44/SC10 has completed the revision of ISO 3834 Quality requirements for fusion welding of metallic materials series of standards primarily taking cognisance of changes to ISO 9001 Quality management systems — Requirements and the 2019 edition of ISO 14731 Welding coordination — Task and responsibilities
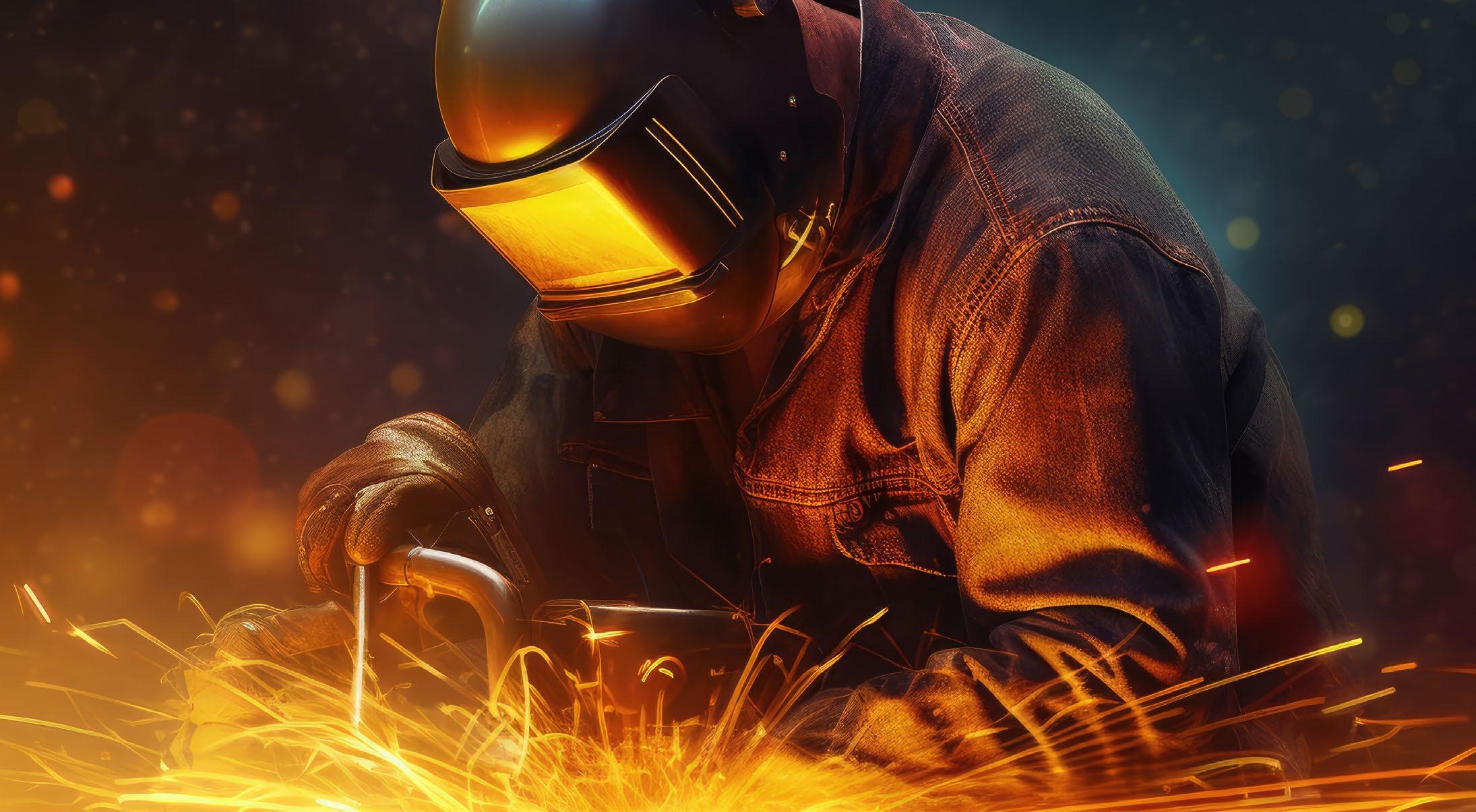
Parts 1 to 5 inclusive have been published and adopted by Standards Australia as direct text adoptions. Revision of Part 6 of ISO 3834 is now well advanced and is being prepared for FDIS ballot. Consideration for adoption in Australia will commence after finalisation by ISO.
TC44/SC10 has also been revising ISO 17660 Welding—Welding of reinforcing steel. This edition is planned to combine the two existing parts into a single document. Work is ongoing.
Similarly, ISO TC44/SC11 has been revising ISO 9606-1 Qualification testing of welders—Fusion welding— Part 1: Steels to combine all 5 parts into the one standard. This will simplify the ongoing maintenance and review requirements for the standards currently published as Parts 2 to 5 of ISO 9606-1. A CD draft has been released for ballot and comment by National Committees with the drafting committee next scheduled to meet in November 2023 during TC44 week.
AN UPDATE FROM WELD AUSTRALIA’S INDUSTRY GROUPS
Weld Australia’s Industry Groups provide a forum for technology transfer and research and development, linking members with industry and research organisations. Weld Australia works with Technology Network members to ensure they remain diverse and resilient in the ever-changing and increasingly challenging global markets.
POWER GENERATION ASSET INTEGRITY BOARD
The Power Generation Asset Integrity Board met in late July, with representatives from EnergyAustralia, Loy Yang N, CS Energy, Delta Electricity, Synergy and Weld Australia in attendance.
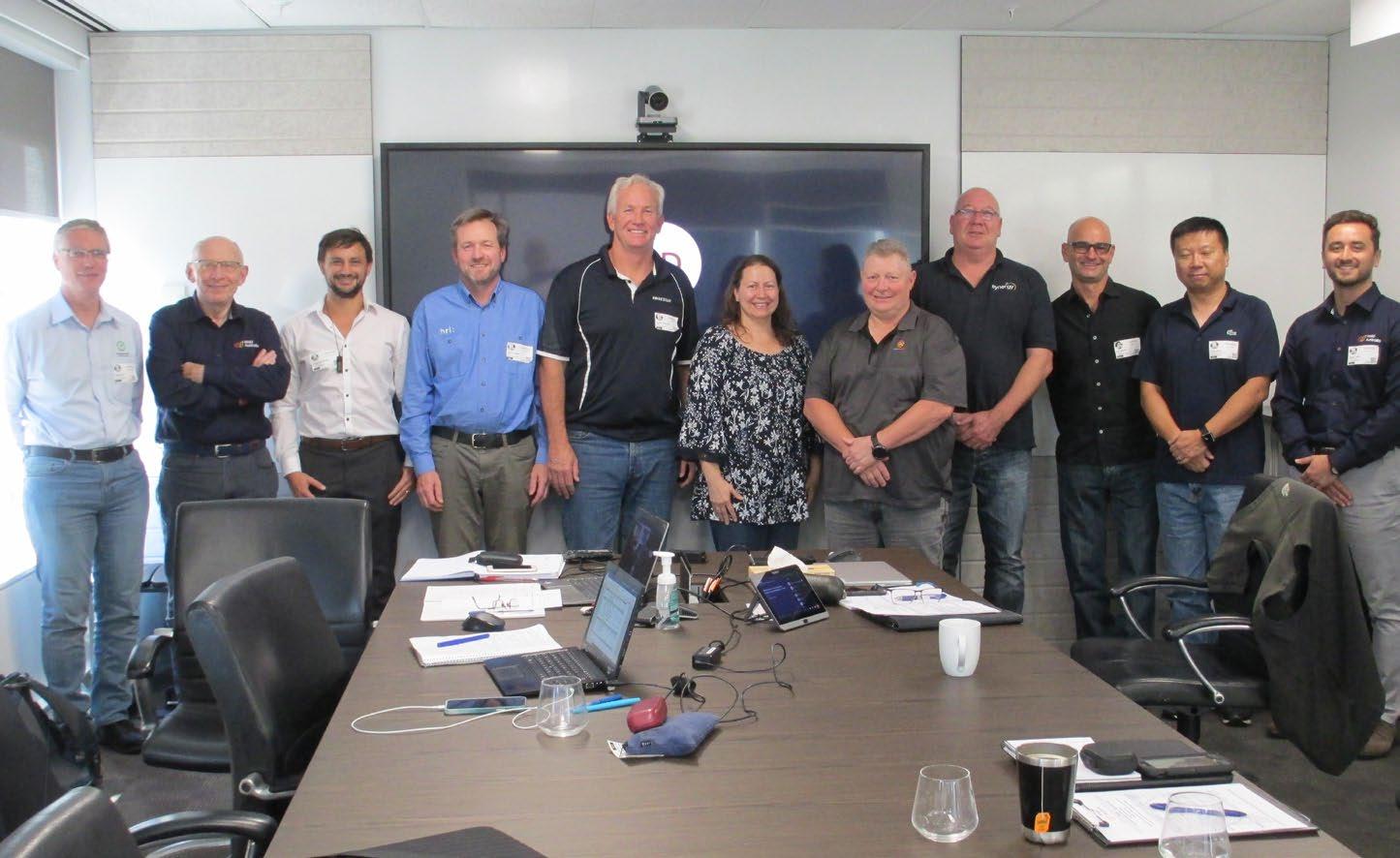
The purpose of the meeting was to review the strategies and future directions for the Power Generation Industry Group. A draft Charter was circulated and discussed, including provision for renewable energy and a Turbine Industry Group.
The Boiler Industry Group discussed several topcis, including Integrity management, advanced analytics, management of data, flexible operations, low load operations, lay-up procedures and ramp rates. Skills shortages were also discussed, with members indicating that it is difficult to attract and retain young people, and there is general
shotage of labour for specialist positions. As such, there is a real need for graduate development programs for young people.
Finally, renewable energy was discussed. Many generators are in the process of planning, building and operating wind assets and battery energy storage systems (BESS). It was suggested that BESS Working Group be formed.
DEFENCE INDUSTRY NETWORK
Weld Australia recently launched the Defence Industry Network. The purpose of the Network is to support, grow and sustain the local Australian defence Industry. Meetings have been attended by representatives from Austal, Baker & Provan, Bisalloy, the Department of Defence, DVR Engineering, HRL, Lincoln Electric, Marand, Precision Metal Group, Thales, Uneek and Weld Australia. The meetings have featured lively
discussions of several topics, including skills and labour shortages and ways to help overcome these shortages; the importance of collaboration within Defence supply chains to mitigate risk, share resources and learnings and create sovereignty; and the importance of a range of different certifications and qualifications.
Interested in Joining?
The Defence Industry Network will focus on companies who are either already operating in the defence supply chain, or have ambitions of joining. Our aim is to ensure that contractual commitments to Australian Industry Content and Indigenous Participation are honoured.
The Network will also focus on:
• Contracting issues and the supply chain issues
• Compliance with Australian Standards, and certification and accreditation to Australian Standards
• Australian local manufacture and equal opportunity
• Advocacy to Government
Membership of the Defence Industry Network is free of charge for all Weld Australia Premium Corporate Members. Just some of the benefits include: networking with others in the defence industry, addressing technical and welding issues, discussing supply chain issues and solutions and accessing Weld Australia training, resources and specialist personnel.
To join, contact: Andrew Davies (Manager Technical Industry Networks) on 0438 428 966 or a.davies@ weldaustralia.com.au
REGISTER NOW: NEW RENEWABLE ENERGY INDUSTRY GROUP
Weld Australia is proposing to establish a Renewable Energy Industry Group to bring together existing generators, new players, manufacturers, suppliers, specialists and consultants.
REGISTER YOUR INTEREST
Interested in joining? To register your interest, please contact Andrew Davies (Manager Technical Industry Networks, Weld Australia) on 0438 428 966 or a.davies@weldaustralia.com.au
The Federal Government has established a policy and targets to reduce carbon emissions by 43% by 2030, and reach net zero by 2050. These targets will play a key role in limiting global temperature increases and ensuring Australia’s transition to a low carbon future consistent with our commitments under the Paris Agreement.
These targets will necessitate the construction of new infrastructure on a massive scale. Local manufacturing and supply chains will need substantial growth to provide resources and materials for the planned renewable infrastructure. A massive increase of skilled workers will also be required.
Australia’s renewable energy industry will need to deal with raft of issues to deliver on these ambitious projects, including:
• Manufacturing and fabrication capacity
• Raw materials (such as steel and copper)
• Skills and labour
• Contracting and contractor resources
• Regulatory approvals
• Connection to the grid
All this is within the context of several broader Australian energy market issues, including:
• Market volatility
• Grid stability
• Thermal electricity generation operational limitations
In face of these challenges, Weld Australia’s new Renewable Energy Industry Group will bring together existing generators, new players, manufacturers, suppliers, specialists and consultants to:
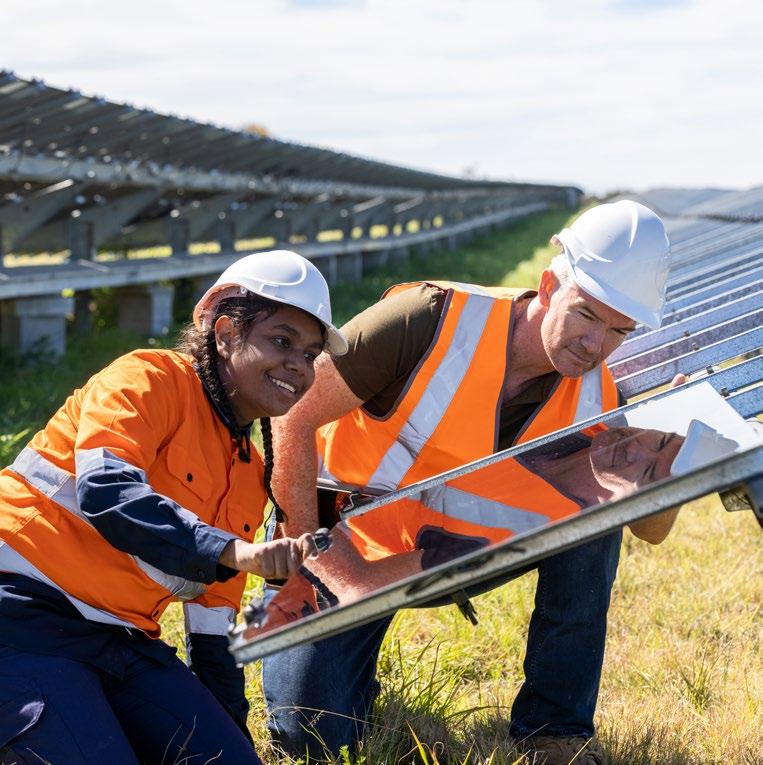
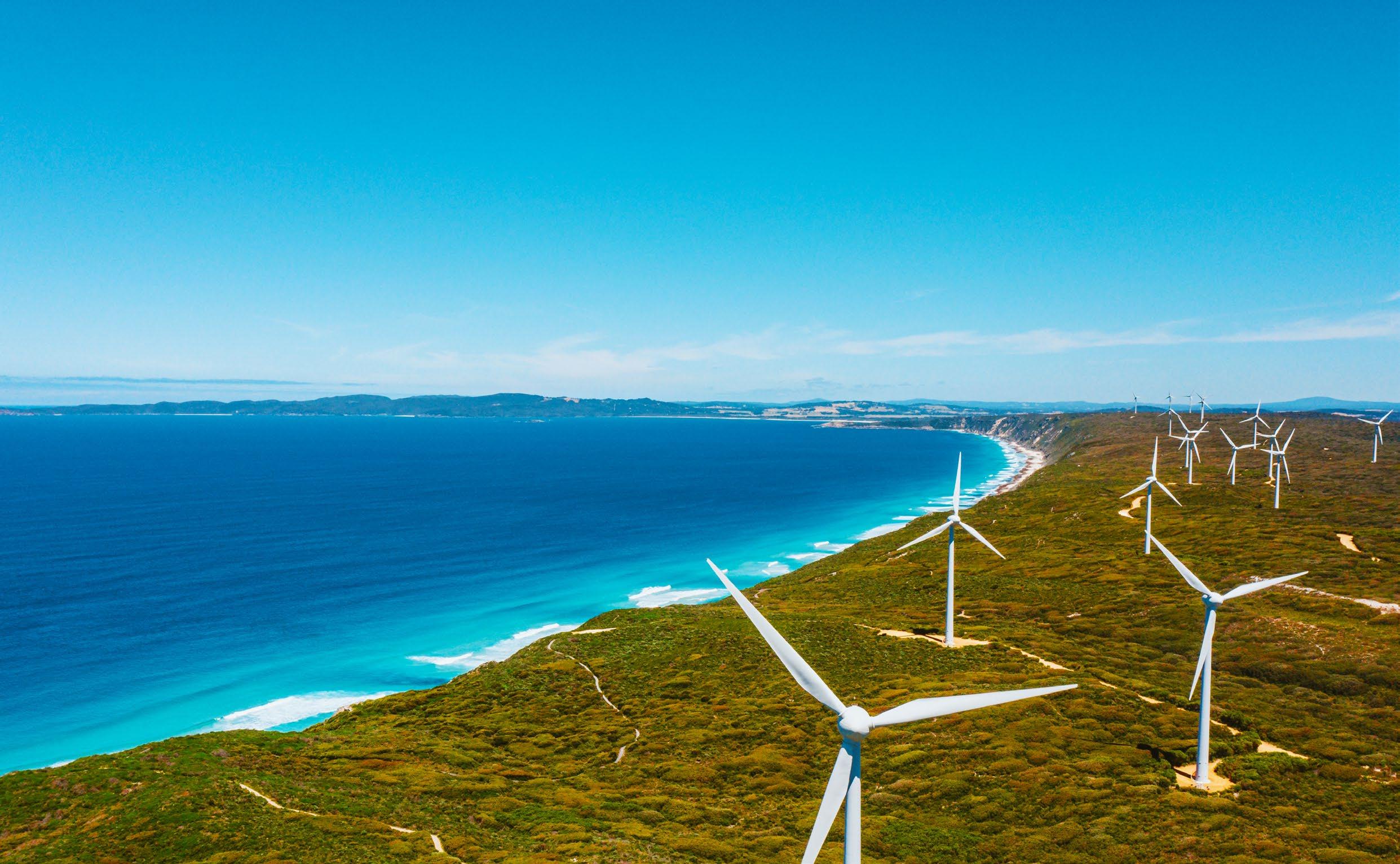
• Share knowledge experience, and learnings
• Discuss and workshop renewable energy issues
• Network and collaborate with like-minded industry colleagues
• Develop younger and less experienced staff
The purpose of the Weld Australia Renewable Industry Group will be to grow, strengthen and support the local Australian Renewable Energy Industry. The Renewable Energy Industry Group will bring together like-minded companies in the renewable energy sector to meet and discuss issues facing the industry. Weld Australia will also manage and facilitate meetings and act on behalf of its members in addressing issues that arise from the Group.
FIRST MEETING: 28 SEPTEMBER
The Renewable Energy Industry Group will commence with an online webinar on Thursday 28 September from 10:00am to 12:00 noon. A broad agenda for this meeting will include:
• Introductions and group overview
• Technical presentations
• Open discussions of issues and group structure
• Details for the next meeting
I N - H O U S E
T R A I N I N G
C o n s i d e r e d i n - h o u s e t r a i n i n g
f o r y o u r t e a m ? I t ’ s c o n v e n i e n t ,
t a i l o r e d , c o s t - e f f e c t i v e a n d
c o l l a b o r a t i v e .
T A K
E Y O U R B U S I N E S S
T O T H E N E X T L E V E L
Weld Australia currently has a few very rare one-week blocks available in October, November and December. All our in-house training courses need a minimum of 10 students
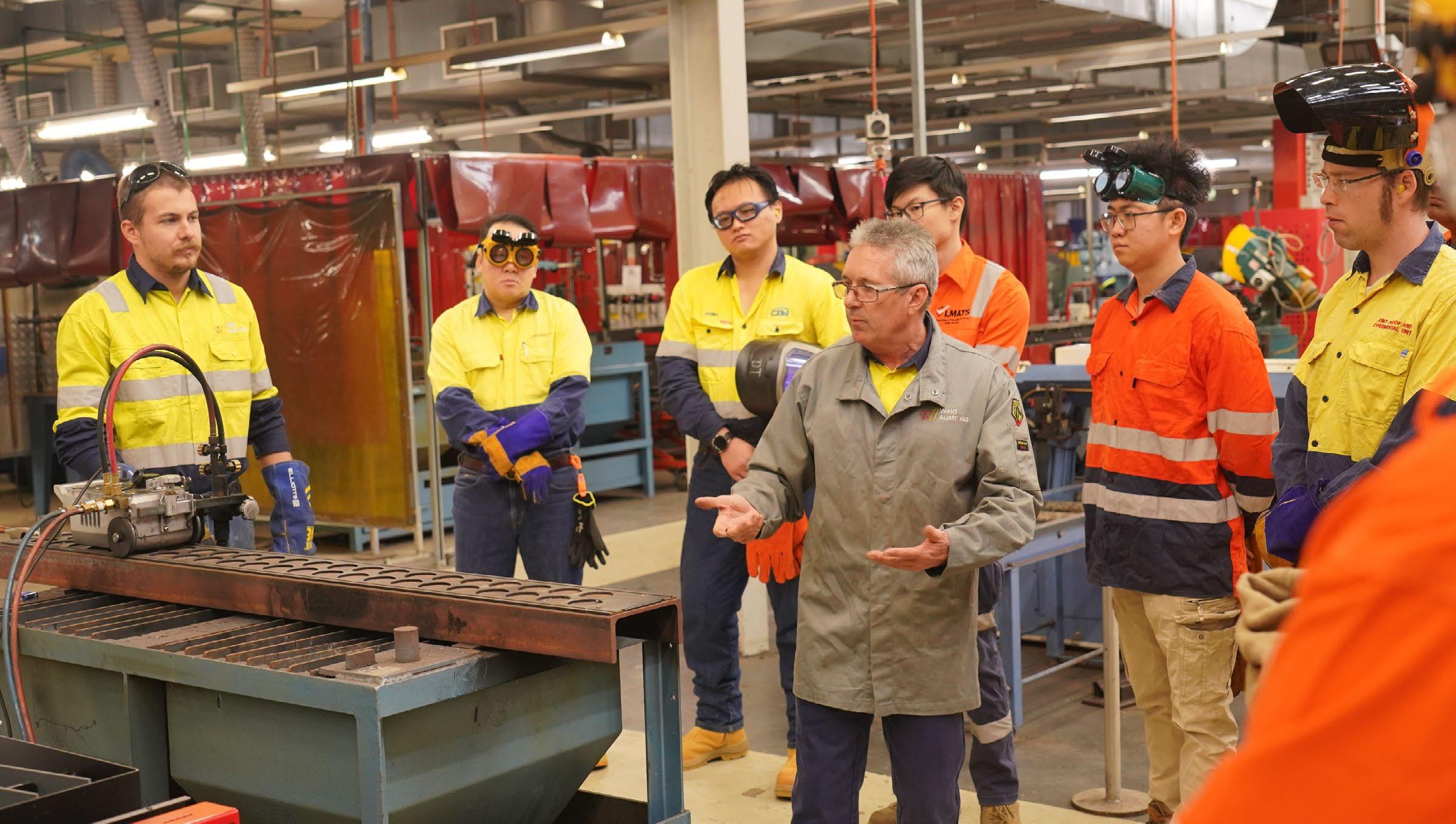
OUR MOST POPULAR IN-HOUSE COURSES
IIW International Welding InspectorBasic (IWI-B)
This internationally recognised course provides extensive knowledge surrounding welding, inspection theory and application
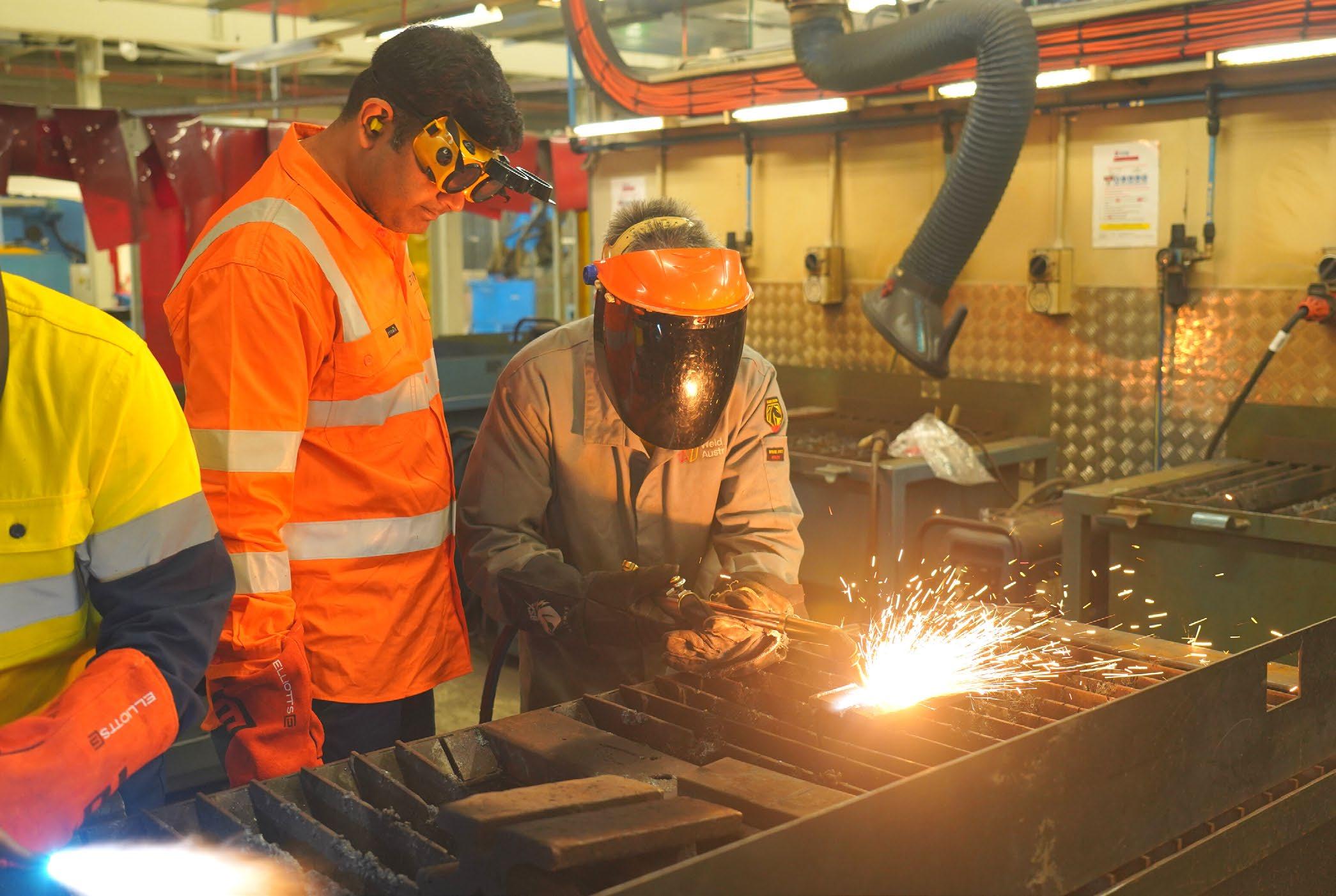
Welding Fundamentals
This course covers significant issues that may arise with welded components, welding processes, weld defects and testing, and welder qualification
Welding Supervisor - AS 2214 and AS 1796 Cert 10
Our course covers welding processes, terminology and technology; welding metallurgy; weld testing and inspection; standards and specifications; and more
For information, or to book your in-house course, contact us via 1800 189 900 or training@weldaustralia.com.au
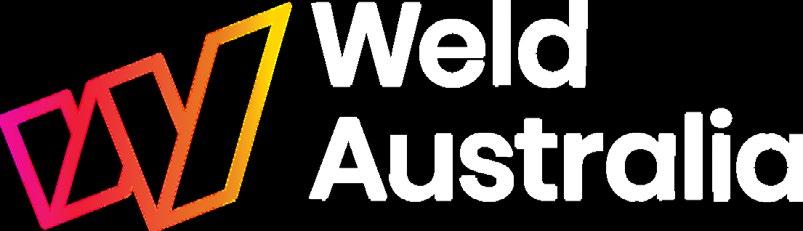
FUSION WELDING COURSES
There are two fusion welding courses that adhere to ISO 9606 Qualification testing of welders on Training.gov.au. This is the authoritative source of nationally recognised training and Registered Training Organisations (RTOs). These two courses were developed in Victoria in 2018 and use augmented reality welding simulators as a key component of the training.
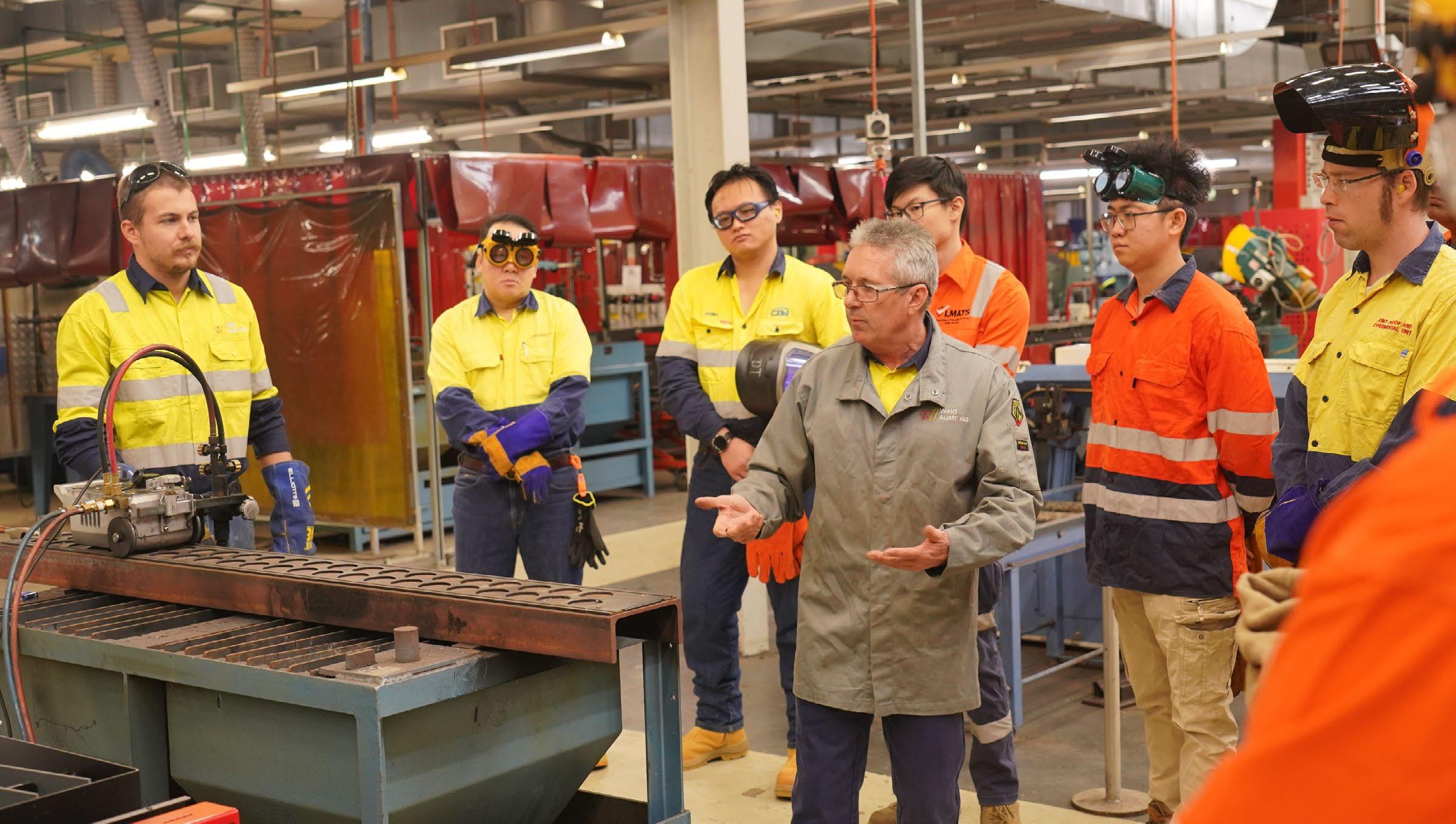

TRANSITION WORKERS
To be awarded a certificate for the Course in Fusion Welding to AS/NZS ISO 9606 for Transition Workers, you must successfully complete seven units of competency (four core and three elective). Core units: Simulate fusion welding processes using augmented reality equipment
Identify welding processes, safe welding practices and use of hand and power tools
Interpret and apply AS/NZS ISO 9606 for fusion welding processes
Perform fusion welding procedures to meet the procedures of ISO 9606-1 (Steels – carbon steels)
EXPERIENCED WELDERS
To be awarded a Statement of Attainment for the Course in Fusion Welding to AS/NZS ISO 9606 for Experienced Welders, you must successfully complete three units of competency (one core and two elective). The core unit is: Interpret and apply AS/NZS ISO 9606 for fusion welding processes.
FURTHER INFORMATION
For further information, contact: training@weldaustralia.com.au
Enrol in a fusion welding course through any Advanced Welder Training Centre below.
ACT
Canberra Institute of Technology cit.edu.au
81 Mildura Street, Fyshwick
Queensland
TAFE Queensland tafeqld.edu.au
• Cairns Campus: Gatton, Newton, Eureka and, Wilkinson Streets, Manunda
• Townsville (Trade Centre Bohle) Campus: 763 Ingham Road, Bohle
• Toowoomba Campus: 100 Bridge Street, Toowoomba City
• Ashmore Campus: Benowa Road & Heeb Street, Ashmore
• Nambour Campus: 91 Windsor Road, Burnside
• Bundaberg Campus: 118 Walker Street, Bundaberg West
Tasmania
Tasmanian Minerals and Energy Council
tasminerals.com.au
13 Wellington Street, Burnie
Victoria
Box Hill Institute boxhill.edu.au
465 Elgar Road, Box Hill
Bendigo TAFE
bendigotafe.edu.au
23 Mundy Street, Bendigo
Federation University federation.edu.au
Lydiard Street South, Ballarat

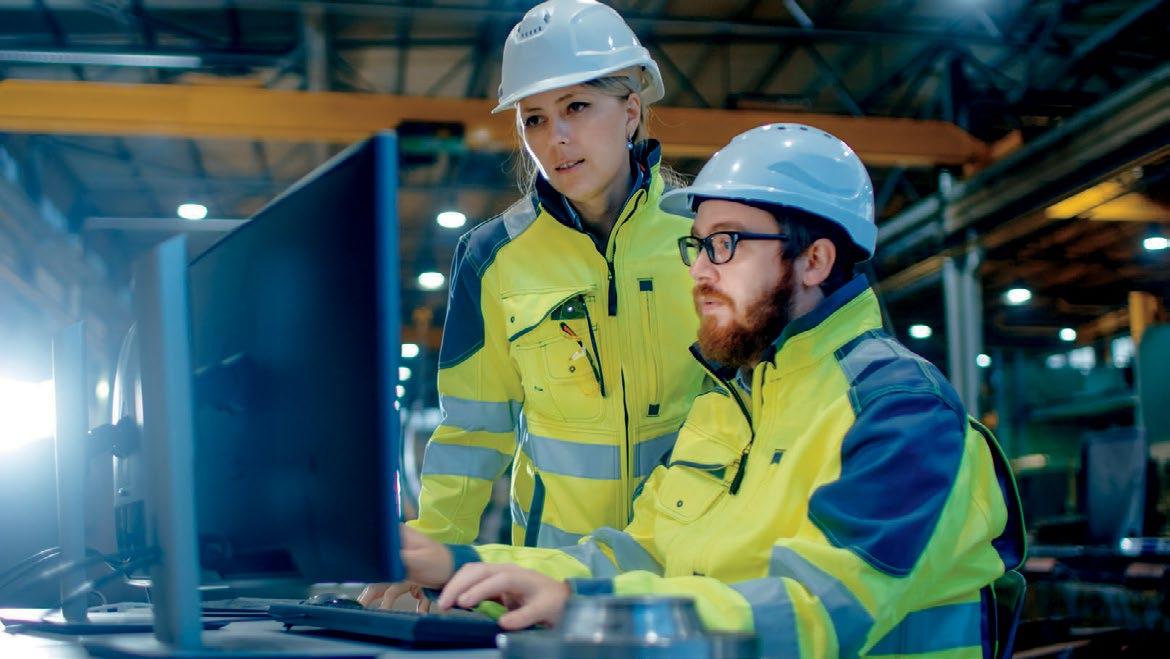
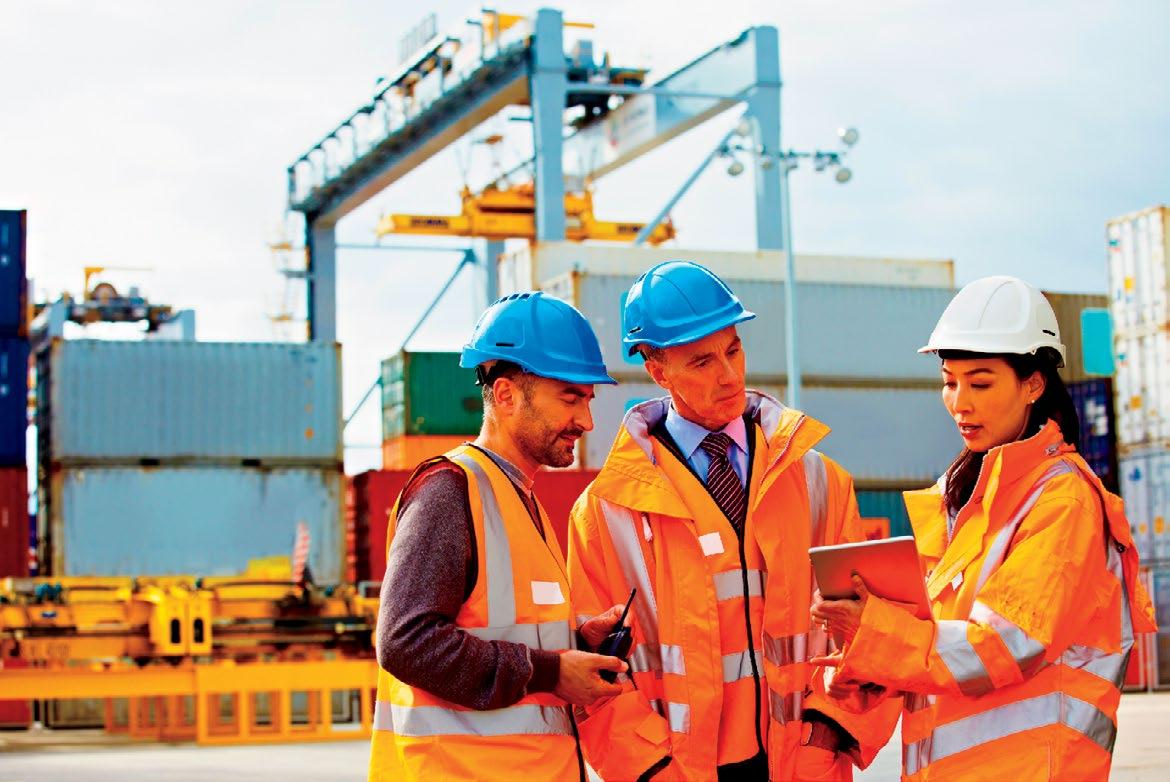
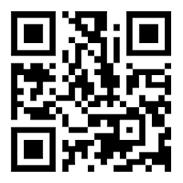