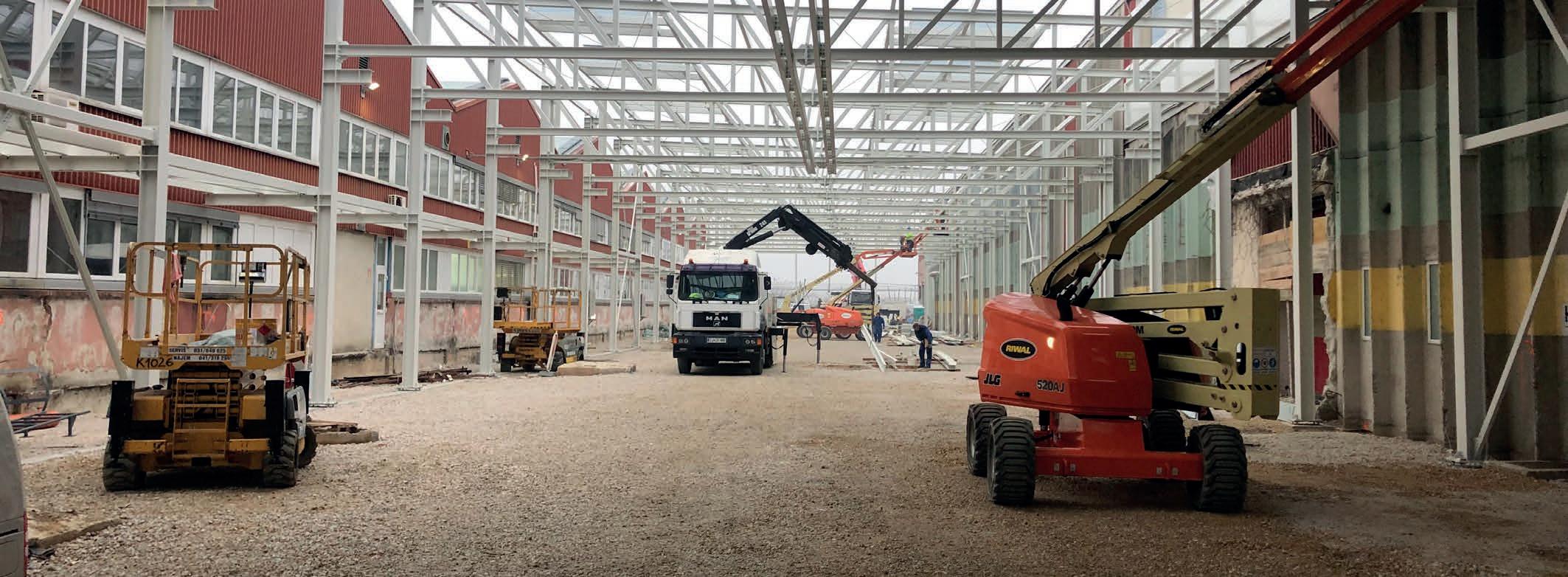
11 minute read
SIP business
by webblineltd
SIP business An investment-intensive year is behind us
One of the most important business decisions of a company is to what extent and in what areas to invest in. In SIP, despite the difficult period during the pandemic, planned investments did not stop.
Advertisement
The second half of 2020 was extremely active in terms of investment. Below, we and the employees who are most involved in them present the areas in which we have updated the premises and equipment.
New hall Generations before us have provided us with premises which we have used to a great extent to this day. In order to continue to grow and adhere to our plans in the future, we provided everything necessary last year to be able to start building a production hall today. We are entering a demanding market segment that requires greater specialisation of machines as well as a higher degree of flexibility. Therefore, the new covered areas will be used primarily for the preparation of machines before shipment and interphase storage of accessories. As the new hall is located between the storage and production facilities, we will simultaneously solve most of the current logistics challenges, namely the physical receipt of deliveries and the commissioning of spare parts.
The hall will be entirely at the same level with a floor area of 21 x 140 m and a height of 9 m. Thus, we acquire 2,709 m2 of new surface area. The main personnel passages and sectional industrial doors are planned on the north and south sides, where the building ends with a canopy. Several personnel and transport crossings are planned to connect with the existing facilities. The facade of the building will be made of aluminium sandwich panels, and the roof will be single-pitched with a slope of 6 ° and will incorporate light portals. The entire premises will be heated/ cooled via wall convectors of the VRF system and forced ventilated (summer and winter mode with energy recovery). All heat and cooling energy needs will be provided by a VRF type heat pump installed on the roof of the building. Two crane tracks will be installed along the entire length of the hall, and five bridge cranes with a load capacity of two tons will be installed along each of them.
All construction and assembly works are expected to be completed in the first week of March next year. After completing all the necessary formalities, we expect to be granted the permit a month later. Currently, several infrastructure projects and renovations are underway. After the construction of the toilets in logistics, the toilets on the floor of the annex of the Trimo 2 hall are now being built, and the works on the ground floor will soon follow. In the immediate vicinity, premises are being renovated which in the future will be intended for the maintenance team (workshop and offices) and on the first floor, premises are being prepared for the offices for operational managers of production, planning, quality control and finalisation technology.
Eccentric press Toni Udrih
In July, we installed an eccentric C-shaped press by one of the world's leading manufacturers of eccentric presses.
One of the advantages of the new press with reduction is the transmission of energy—in addition to the flywheel and shaft—via a gear. Such a system allows large tonnages at reduced speed, so it is suitable for more demanding work. Its nominal force is 130 tons. The press is equipped as standard with an OMPI brake-clutch unit, a Siemens PLC control panel, a Pilz safety system, an automatic lubrication device and a hydraulic overload system. With the new press, we gained faster clamping of tools and greater precision in workpieces. Another great advantage of the press is the CNC adjustment of the plow and stroke, and it is also equipped with a bar code reader to search for programmes, which allows the programme to be loaded correctly.
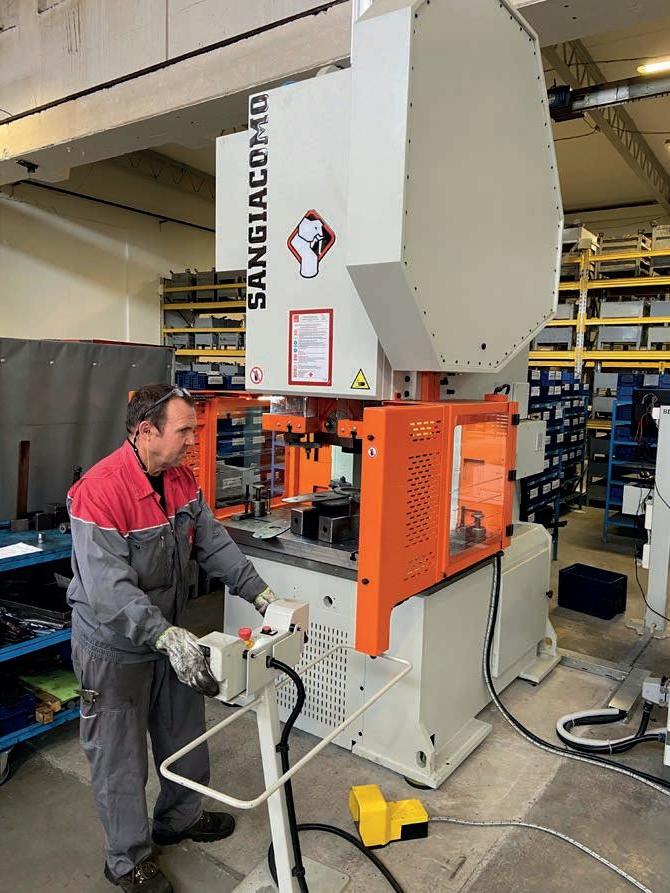
Measuring machine Peter Kračun
At the end of September 2020, we commissioned a new 3-coordinate measuring machine in the measuring laboratory, which will slowly replace our previous measuring machine, whose technology has become outdated and was taken over by new technologies in metrology. We decided on this brand on the basis of good references and excellent support provided by Slovenian company representatives. This machine is the most widespread in the automotive industry, used by most European car brands, and SIP is the first user among companies engaged in agricultural activity using it.
In addition to greater accuracy (repeatability of measurements is in the range of 0.4um), the new machine enables automatic measurement of workpieces, and higher measurement speed. On the previous measuring machine, the measuring protocol lasted 40 minutes or more, and when the same protocol is performed on the new machines, it is done in two to three minutes, fully automatically. All this allows us to achieve a larger range of measurements and thus a higher level of quality assurance.
In addition to the new measuring machine, we obtained two hardness testers in the heat treatment department. The first, allows measurement based on the Rockwell scale and the second, on the Vickers scale. The new testing machines enable serial measurement of samples, which speeds up the control time and increases the volume of the measured parts, thus achieving greater repeatability during heat treatment and higher quality of heat-treated parts.
Manufacture of hydraulic pipes Aljaž Ožir
Due to increasingly complex machines, which no longer have only a few hydraulic pipes, but as many as 150 or more, the need arose in the process to manufacture hydraulic pipes for our own machines. We started in-house production in September 2020 and we produce all hydraulic pipes up to DN19 in the company.
With the acquisition of new hydraulics, the number of purchasing elements was reduced by as much as 95 per cent. As the pipes are manufactured for the needs of the next day, the interphase stocks have been reduced and space in the warehouse has been freed up. Hydraulic pipes that are needed for spare parts, can be made on the spot when required. If there is a problem with pipe length, we can make a new pipe in five to ten minutes,

Example of ovality measurement printout with surface scanning
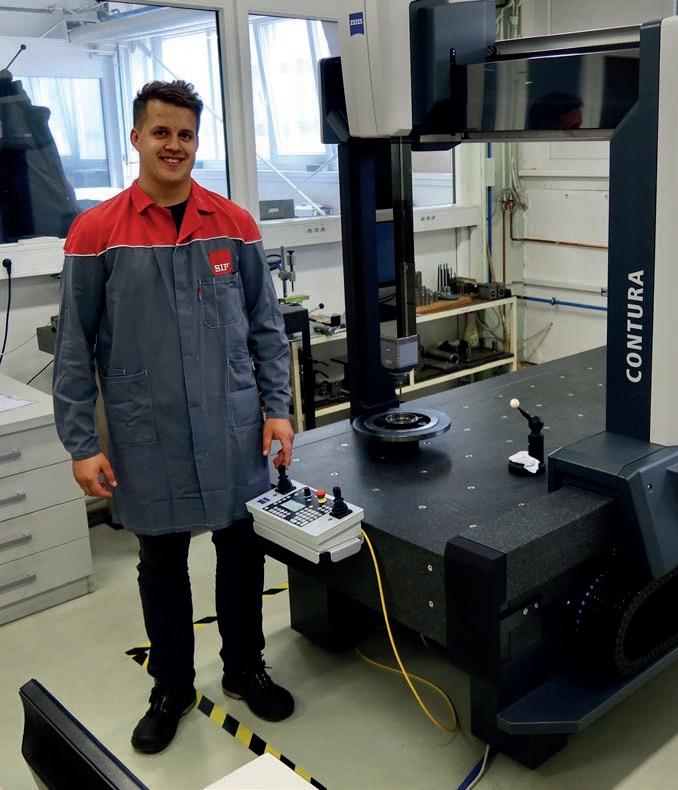
Tilen Ramšak, head of measuring laboratory
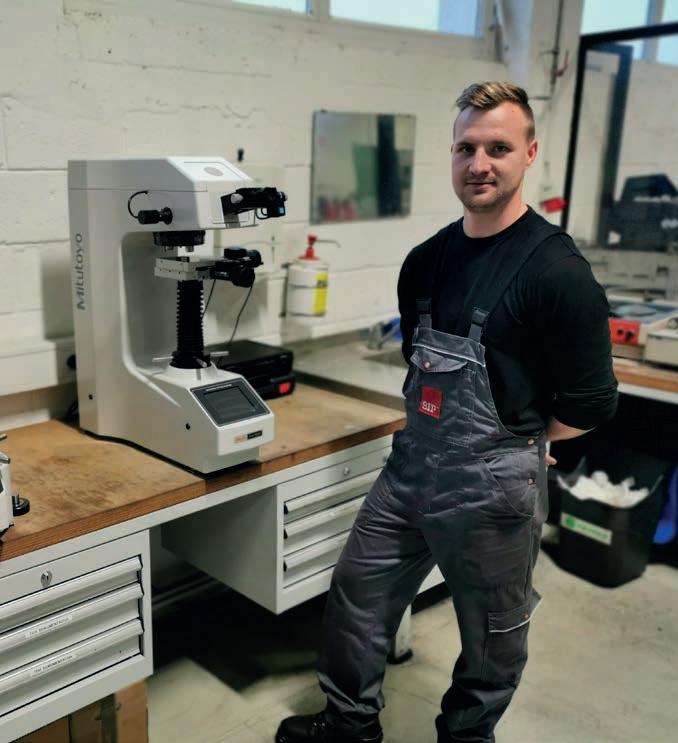
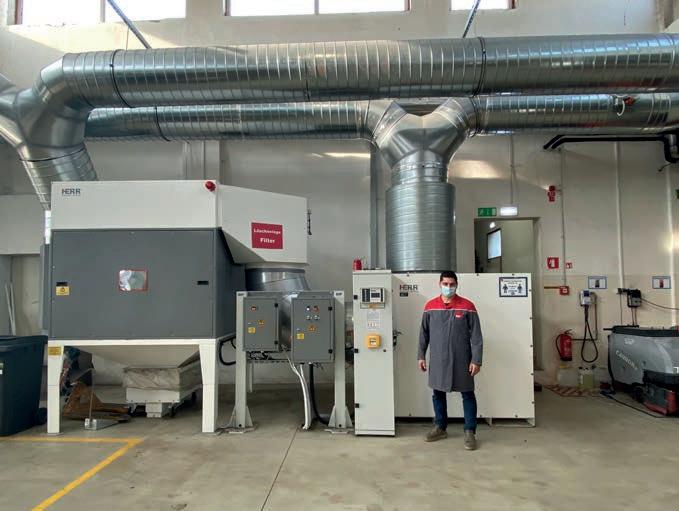
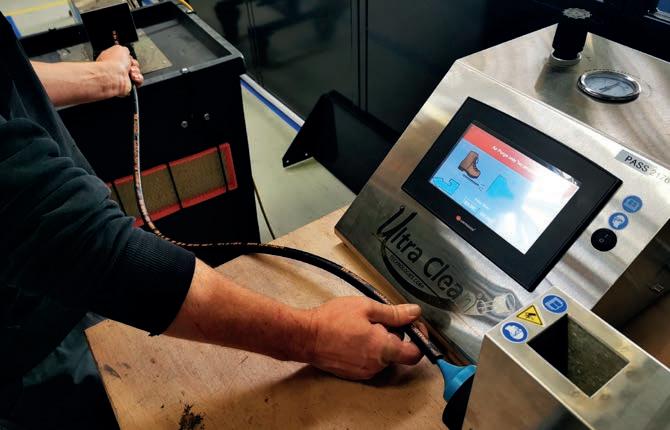
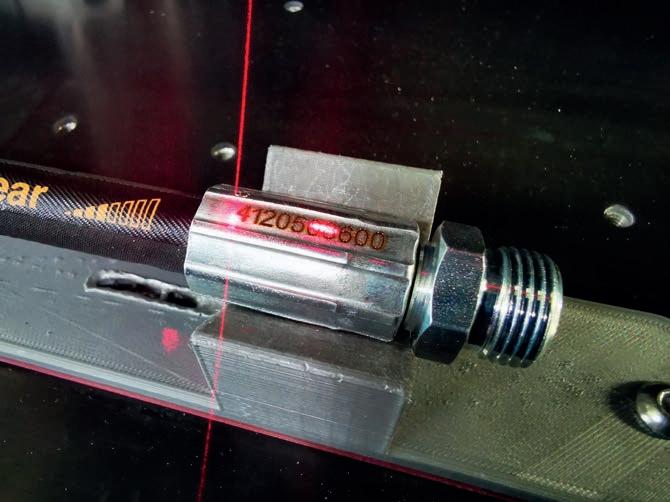
“One of the acquisitions enables us to engrave nameplates on machine parts by laser. This means cheaper production and incomparably better quality of plates.
which saves us from assembly line delays. We can now also make pipes for prototype machines and laser engrave pipe IDs on the connectors, which the current supplier could not provide. Laser engraving of machine plates is another of the acquisitions. This means cheaper production and incomparably better quality of plates. With arranging in-house production of hydraulic pipes, we lowered stock cost of bigger hydraulic sets as they are produced on demand and on time.
The workplace is a U-shaped cell. In the middle of the U-shaped cell are storage bins with all the necessary elements for the assembly of hydraulic pipes and sets. Since all the elements are at hand, there is minimal transport of material involved. On the right side of the cell, we have space to make metal pipes. The space is separated by a metal wall with plexiglass, which prevents the passage of dirty particles from the metal pipes to the space of rubber pipes. The space for the production of metal pipes is currently being renovated. New tables, preparations, lighting and more are being made.
We also started engraving the factory plates of the machines with a laser. With this project, we switched from previous aluminium plates to black eloxiated aluminium plates. The raw plates of the cut-out are cut by us and then engraved on the station shown.
The portal crane in the welding section David Štraus
In August, we installed a portal crane and a crane track in production. The frame is 30 metres long, 7.5 metres wide and has a load capacity of 3.2 tons. It has four gantry cranes equipped with anti-collision sensors at a distance of 4 metres. It is equipped with an operational hours meter, an overload audible signal and a final press for lift and drop. The acquisition of a gantry crane was necessary so that we could move the “black line” from the assembly department to the welding department. With the portal crane, it is now possible to weld larger elements in weight and dimensions, such as various chassis for trailers and manure spreaders, directly in the welding department.
Hydraulic lifting platform for storage of welding devices David Štraus
In October, we installed a hydraulic lifting platform in the welding department for storing welding equipment. We decided to buy it in order to ensure easier transfer of welding equipment to the upper floor. Prior to the investment, the welder had to take the devices up the stairs himself or use a forklift. The load capacity of the lifting platform is 1.2 tons and one person. It is equipped with a cabin made of quality sheet metal, with cabin safety keys, ceiling light and a floor made of corrugated sheet metal. It is hydraulically operated and automatically lowers in the event of a power failure.
Horizontal machining centre Nejc Trampuš
In the first week of December, we took over the new horizontal machining centre in the machining department. The new machine will take over the work of old machining centre in about a month, when a comprehensive service will be performed. After the service is completed, both machines will increase the flowability and flexibility of mechanical machining, as the machining capacity at the horizontal centre will double. The machining centre has working strokes of 730x730x880mm and a workbench of 500x500mm. We will install a quick-clamp system for holding devices onto it. This will make it possible to machine the pieces currently being machined at the old machining centre. The centre also has an additionally increased cooling pressure through the spindle, 70 bar, which ensures a higher quality of processing and better tool life. shift due to the changed machine fleet and the nature of the work. As a result, a larger compressor that did not have a regulated drive had to be turned on and off too often. All this has resulted in increased electricity consumption and fluctuations in operating pressure between 6.6 and 7.6 bar, which of course is not good for work plants, machines, devices and preparations.
With the new compressor, the frequency control with a 75kW HPM hybrid engine allows the adjustment of air consumption with the highest efficiency in the entire range from 3.23 to 14 m3/ min. Therefore, the pressure in the entire network is practically constant at 7.1 bar, which is a big gain compared to the old compressors.
The new, patented type of electric motor uses permanent magnets in the rotor, has virtually no wear parts, is very small, has minimal heat loss and is particularly suitable for use with a frequency regulator and allows an infinite number of starts.
In the compressor station, the old compressors are still in operation from time to time. After two months of operation, it is evident that with the normal need for compressed air, the new compressor operates with a capacity of 65 to 70 per cent. The control mode is set so that only the new compressor operates, and the old two turn on automatically in the event of a new compressor failure and in the event of an abnormal current load, which has happened in the past.
As part of the renovated compressor station, a new energy distributor R-VARILNICA-2 was made for the distribution of electricity for all consumers in this part of the hall (compressors, boiler room, CO2 station, future new air conditioner). We expect that with the investment in the new compressor, the compressed air supply will be of high quality and reliable, the pressure in the system will be constant, and the savings in electricity consumption due to frequency regulation in the entire operating area will be reduced by 20 per cent.
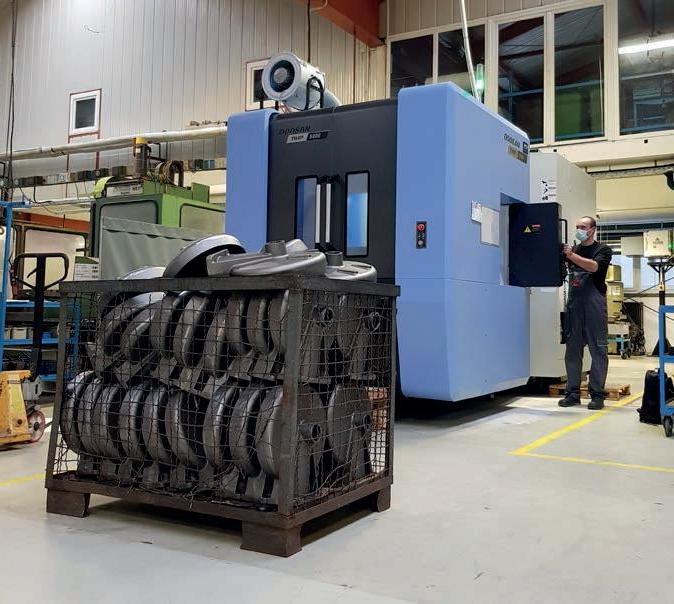
Compressor Verner Perin
Energy investments this year include the purchase of a new compressor. The purchase was urgently needed, as the existing compressors collected 112,000 and 65,000 operating hours in 15 years of operation.
Regarding the operating hours, the smaller compressor has exceeded the threshold at which servicing still makes economic sense. The network operation of both compressors was no longer optimal, as the smaller frequency-regulated drive was no longer sufficient to cover the afternoon or night
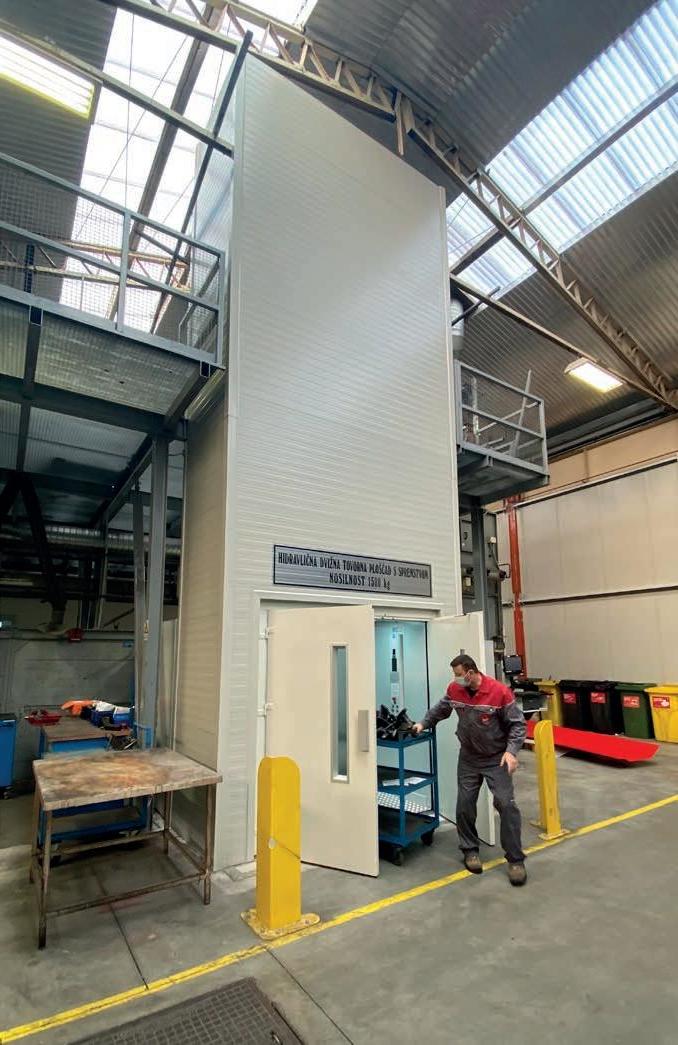

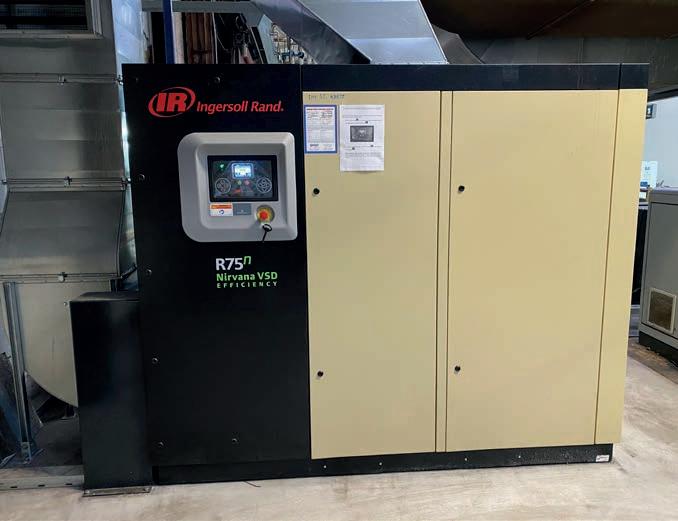