ALLEN
INDEPENDENT SCHOOL DISTRICT
TECHNICAL
INTRODUCTION
The Allen Independent School District (AISD) provides this guide of administrative and technical guidelines for those involved in the planning, design, and construction of new school facilities and additions, expansions, or renovations of existing schools.
This document comprises Technical Design Guidelines (TDGs) that state the general principles to be used in the design of schools to achieve design consistency, equity, and quality, facilitating the timely completion of buildings, that can be effectively, efficiently, and economically managed through their life cycle.
The goal of these standards is also to provide safe, functional, and sustainable environments conducive to learning.
This document, in conjunction with Allen ISD Education Specifications, is intended both as a design road map for the District and Design Team and as part of a set of reference documents for the evaluation of contract compliance. All Architect/Engineering firms, and other consultants/vendors, under contract with the AISD are required to abide by these guidelines.
These TDGs are periodically reviewed and updated to address the inclusion of new products, construction methods, applicable building codes, and reference standards. AISD welcomes comments and suggestions on how to improve these guidelines. For comments and suggestions or further advice on these guidelines or any other matters relating to this document, please contact:
Brent Benningfield Assistant Superintendent of Operations
Allen Independent School District
612 E. Bethany Drive
Allen, TX 75002
ALLEN ISD FACILITIES DEPARTMENT CONTACT
Brian Neely
Executive Director of Operations
Allen Independent School District 1451 N. Watters Drive Allen, TX 75013
Email: brian.neely@allenisd.org Phone: 972-727-0363
ALLEN ISD FACILITIES DIRECTORY
Administration Building Administration (972) 727-0511
612 E. Bethany Drive Allen, TX 75002
Allen High School Grades 10-12 (972) 727-0400
300 Rivercrest Blvd. Allen, TX 75002
Anderson Early Childhood School
EE - Pre-Kindergarten (972) 396-6924
305 N. Alder Drive Allen, TX 75002
Athletics Department
Allen ISD Activity Complex (972) 727-0437
301 Rivercrest Blvd. Allen, TX 75002
Bolin Elementary School
K - 6th Grade (214) 495-6750 5705 Cheyenne Drive Allen, TX 75002
Boon Elementary School K - 6th Grade (972) 747-3331 1050 Comanche Drive Allen, TX 75013
Boyd Elementary School
K - 6th Grade (972) 727-0560
800 Jupiter Road Allen, TX 75002
Chandler Elementary School
K - 6th Grade (469) 467-1400 1000 Water Oak Drive Allen, TX 75002
Cheatham Elementary School K - 6th Grade (972) 396-3016 1501 Hopewell Drive Allen, TX 75013
Curtis Middle School Grades 7 & 8 (972) 727-0340 1530 Rivercrest Blvd. Allen, TX 75002
Dillard Special Achievement Center Special Programs (972) 727-7163
601 Main Street Allen, TX 75002
Ereckson Middle School Grades 7 & 8 (972) 747-3308
450 Tatum Drive Allen, TX 75013
Evans Elementary School
K - 6th Grade (972) 747-3373
1225 Walnut Springs Drive Allen, TX 75013
Ford Middle School Grades 7 & 8 (972) 727-0590 630 Park Place Allen, TX 75002
Green Elementary School
K - 6th Grade (972) 727-0370 1315 Comanche Drive Allen, TX 75013
Kerr Elementary School
K - 6th Grade (214) 495-6765 1325 Glendover Drive Allen, TX 75013
Lindsey Elementary School
K - 6th Grade (972) 908-4000 5730 Wilford Drive McKinney, TX 75070
Lowery Freshman Center 9th Grade (972) 396-6975
368 N. Greenville Avenue Allen, TX 75002
Marion Elementary School K - 6th Grade (214) 495-6784 1595 Stablerun Drive Allen, TX 75002
Norton Elementary School K - 6th Grade (972) 396-6918 1120 Newport Drive Allen, TX 75013
Olson Elementary School K - 6th Grade (972) 562-1800 1751 E. Exchange Parkway Allen, TX 75002
Preston Elementary School K - 6th Grade (972) 727-0511 2455 Hilliard Drive Allen, TX 75013
Reed Elementary School K - 6th (972) 727-0580 1200 Rivercrest Blvd. Allen, TX 75002
Service Center School Support (972) 908-8900 1451. N. Watters Drive Allen, TX 75013
STEAM Center Specialty Campus (469)-675-2700
1680 Ridgeview Drive Allen , TX 75013
Story Elementary School K - 6th Grade (972) 727-0570 1550 Edelweiss Drive Allen, TX 75002
Vaughan Elementary School K - 6th Grade (972) 727-0470
820 Cottonwood Drive Allen, TX 75002
Updates for the Allen ISD Attendance Zoe Map can be found through the following link: 1_Allen_ISD_Attendance_Zone_Map_2024_2025_Wall_Map.png (2160×1440)
0.01 CONTRACTING REQUIREMENTS
A. Agreement between Owner and Architect
AISD utilizes an AIA B101 Standard Form of Agreement Between Owner and Architect, as amended by AISD. The Assistant Superintendent of Operations is responsible for facilitating the execution of this contract. Contracts are to be approved by the Board of Trustees and signed by the Board’s designee.
B. Agreement between Owner and Contractor
AISD utilizes an AIA A133 Standard Form Agreement between the Owner and Construction Manager as Constructor, as amended by AISD. The Assistant Superintendent of Operations is responsible for facilitating the execution of this contract. Contracts are to be approved by the Board of Trustees and signed by the Board’s designee.
C. Supplementary Conditions
Any Supplementary Conditions required by AISD are to be coordinated through the Assistant Superintendent of Operations.
D. Current Forms
The Architect / Engineer shall, before publishing or incorporating any of the above forms, confirm with AISD that the forms to be published or incorporated are the latest revisions.
E. Rights Reserved
AISD reserves the right to make changes to any of these published documents and amendments prior to the execution of any agreement.
Storage
ALLEN ISD - RESPONSIBILITY CHART
RESPONSIBILITY MATRIX CONTINUES
ISD - RESPONSIBILITY CHART
Intercom System
Computers
Copy/Fax/Scan Machines
Large Format Printers
Computer Printers
Refrigerators w/ Water Line
Microwaves
Coffee Makers
Coffee Makers w/ Water Line
Dishwashers
Determined per project
to provide electrical and data
to provide electrical and data
GC to provide electrical and data
GC to provide electrical and data
Non-fixed provided by Allen ISD
provide electrical
to provide electrical and water line
RESPONSIBILITY MATRIX CONTINUES
0.03 PROJECT INFORMATION FORM
This form is to be filled out at the beginning of every project by the Architect and distributed to the Owner and project team.
Project Name: Address:
Project Budget:
Construction Budget:
Scope of the Project:
Substantial Completion Date:
Architect: Contact:
Contract Status: Complete Incomplete
Comments:
District Procured Consultants
Geotechnical Engineer: Contact:
Materials Testing Tab: Contact:
HVAC Testing and Balance: Contact:
Other: Contact:
Other: Contact:
Is property platted? Y N
Status of Soils Investigation Report: Complete Incomplete
Status of Survey: Complete Incomplete
Municipality:
Governing Jurisdiction(s):
Utility Providers
Electricity:
Gas: Water:
Waste:
TxDot?: Y N
Construction Procurement Method:
Construction Manager:
Construction Manager Contact:
0.04 GEOTECHNICAL / MATERIALS TESTING
A. Geotechnical and materials testing services have been previously selected based on qualifications and per Government Code, Chapter 2254, Professional and Consulting Services. Contact AISD for the geotechnical and materials testing services provider for each project.
B. Scope of services:
1. Geotechnical testing shall include verification of sub-surface conditions with respect to soil structure, bearing strata, seismic site class, and coefficient and groundwater observations. The geotechnical engineer is responsible for making recommendations for construction on the basis of observed conditions. Recommendations shall include a range of options.
2. Materials testing services shall include inspection, sampling, and testing necessary to confirm construction meets specified standards. Materials testing services shall ascertain compliance of materials and mixes with the requirements of contract documents. Responsibilities include promptly notifying AISD, architect, appropriate consultants, and contractor and authority having jurisdiction of observed irregularities or non-conformance of work or products.
3. All Testing Lab Reports shall be posted in the project’s project management software by the Testing Lab. Hard copies are not required. Testing Lab to flag any non-compliant reports. Testing Lab is to provide a digital copy of all reports at the end of each job.
4. Contact the Executive Director of Operations for details and clarifications.
0.05 STORM SHELTER
A. Procurement of storm shelter review services have been previously selected based on qualifications and per Government Code, Chapter 2254, Professional and Consulting Services. Contact AISD for the storm shelter review services provider for each project when applicable.
0.06 LAND SURVEY SERVICES
A. Land survey services, when applicable, are typically provided on a project basis through the Civil Engineer assigned to the project.
B. Scope of services:
1. Area to be surveyed shall be developed with AISD, architect, and civil engineer. The land survey shall commence immediately upon start of the project or as soon as scope of survey is determined. Draft copy of the land survey is required prior to start of Design Development phase.
a. Scale shall not be smaller than one-inch equals forty-feet and where practical shall be oneinch equals thirty-feet. Confirm scale requirements with Owner’s architectural firm.
b. Terrain contours shall be shown at one-foot intervals.
c. Identify on the drawing the benchmark used to establish contour elevations. Relate benchmark to local jurisdictions benchmark as required.
d. Property lines shall be shown.
e. All existing easements, building set-back lines, required landscape “buffer” yards, and other statutory legal or technical restrictions shall be show.
f. The location of all physical improvements to the property such as roads (gravel or paved), other paving, buildings, fences, wells, water tanks, drain fields, septic tanks, cisterns, signs, etc. shall be shown.
g. All on-site overhead and underground utilities, lines and piping shall be accurately located on the survey in accordance with the surveyor’s field inspection and examination of actual
development construction documents on file with the municipality in which they are located. Note meters, boxes, clean-outs, etc.
h. Identify any special flood hazard areas which occur on-site. Also note any contiguous, off-site special flood hazard areas. Identify location of 100-year flood plain, and official “floodway” based on the most recent FEMA map update, if applicable.
i. Off-site utilities located adjacent to the property including water, sanitary sewer, storm sewer, natural gas, electrical, cable/data, and telephone shall be shown. These utilities shall be accurately located on the survey in accordance with the surveyor’s field inspection and examination of actual development construction documents on file with the municipality in which they are located. Note meters, boxes, clean-outs, etc.
j. The existing location of those utilities listed above which do not lie adjacent to the property shall be documented separately with photocopy exhibits from City utilities plans, telephone company diagrams, etc.
k. Spot elevations shall be provided at adjacent streets’ centerlines, gutter and top of curb (where curb and gutter exist), slabs at existing entrances, and edge of paving and bottom of “borrow” ditch (where ditch exists) at intervals frequent enough to allow later detailing of matching on-site approaches and/or curb cuts.
l. Provide invert elevations and flow-lines at all sanitary and storm sewer clean-outs, manholes, inlets, and culverts on-site and adjacent to site. (Provide same information on nearest piping if not located adjacent to site).
m. Provide flow-line and invert elevations at any existing culverts or approach drain piping adjacent to site.
n. Locate trees on site. Call out species and caliper in inches. Boundaries of dense tree clusters and other heavy brush shall be shown on the survey.
o. Zoning of subject property and adjacent property shall be also noted on the survey.
p. Provide Auto-Cad format disk to AISD, architect and civil engineer.
q. Confer directly with Owner to obtain “Owner’s record drawings”, and other documents or knowledge which Owner may have, to establish all on-site “as-built” underground and overhead utility locations. This is of great importance on topographic surveys of sites that include existing buildings or other structures.
r. Provide perimeter dimensions of all existing structures.
s. Provide a legal description of the property
0.07 ENVIRONMENTAL SERVICES
A. Environmental quality testing services, when applicable, have been previously selected based on qualifications and per Government Code, Chapter 2254, Professional and Consulting Services. Contact AISD for the Environmental quality testing services provider for each project when applicable.
B. Scope of services: Investigation of hazardous materials shall include the following, but not limited to: 1. Asbestos
Asbestos consulting activities--Consulting activities in public buildings include: the designing of asbestos abatement projects; the survey for asbestos-containing building materials; the evaluation and selection of appropriate asbestos abatement methods and project layout; the preparation of plans, specifications and contract documents; the review of environmental controls and abatement procedures for personal protection that are to be employed every day of the asbestos abatement activity, from the start through the completion dates of the project;
the design of air monitoring of the project; any survey, management planning, air monitoring, or project management performed by or for the consultant or consulting agency; consultation regarding compliance with various regulations and standards; recommending abatement options; and representing the consultant agency or consultant in obtaining consulting work.
2. Mold
Mold assessment - Activity that involves:
A. An inspection, investigation, or survey of a dwelling or other structure to provide the Owner or occupant with information regarding the presence, identification, or evaluation of mold;
�. The development of a mold management plan or mold remediation protocol; or
�. The collection or analysis of a mold sample.
3. Lead Paint
Any lead-based paint inspection conducted in target housing or child-occupied facilities must be conducted by a certified Lead Inspector or Risk Assessor in accordance with the TELRR. A lead based paint inspection is a surface-by-surface investigation using approved documented methodologies to determine the presence of lead-based paint in these facilities. If only an assumption is made that lead-based paint may be present (no testing or sampling conducted), a certified Inspector or Risk Assessor is not required. Paint-chip collection and/or XRF (X-ray fluorescence) analysis are common ways to determine the presence of lead-based paint while chemical test wipe (swab) kits are not an approved method as they give inaccurate results for TELRR purposes. Paint-chip, soil, or dust samples must be sent to an EPA-Recognized Laboratory (accredited through the National Lead Laboratory Accreditation Program - NLLAP) for analysis to determine the presence of any lead in the sample. To inquire about these EPA-recognized laboratories, call the National Lead Information Center toll-free at (800) 424-LEAD or search for certified firms through the EPA website at: https://cdxapps.epa.gov/ocspp-oppt-lead/firmlocation-search.
A written lead inspection report must be developed by the certified Lead Inspector or Risk Assessor that includes the information specified in Section 295.212(a)(4) of the TELRR, such as, among other things, the date of inspection, address of building sampled, specific locations (building components) tested for lead-based paint, and copies of all lab analysis reports and downloaded XRF data.
0.08 STANDARDS FOR DISTRICT SYSTEMS
A. All access controls are to be coordinated with Allen ISD approved access control vendor. Owner and Architect to meet at the start of Construction Documents for the purpose of coordinating these requirements. Refer to Division 28 of the TDG for additional information.
B. All energy management systems shall be coordinated with district standards and controls. Architect to meet at the start of Construction Documents for the purpose of coordinating these requirements.
C. All surveillance systems shall be coordinated with Allen ISD approved access control vendor. Architect to meet at the start of Construction Documents for the purpose of coordinating these requirements. Refer to Division 28 of the TDG for additional information.
0.09 MEETINGS
A. NOTICE TO PROCEED MEETINGS: At the Notice to Proceed meeting the following shall be decided as a minimum:
1. Process for providing construction documents to the public.
2. Required deposits and return of checks and specifications.
3. Communication at the pre-solicitation meeting (if applicable).
4. Timeline for Addenda.
5. Timeline for last day for questions.
6. Communication throughout the CSP bond/construction solicitation.
B. REVIEW MEETINGS
1. Weekly or bi-weekly meetings with AISD and the project team during schematic design & design development.
2. Coordination meeting at the beginning of the construction document phase with ISD Access Controls and AISD Safety and Security representatives.
3. Construction Document review at 50%, 90%, and 100%, with AISD Facilities Coordinator and AISD Construction Coordinator. AISD Security representatives and AISD Access Control representatives are to be included at 50%.
4. Coordination meeting during design development with AISD Construction Coordinator to establish locations of all power and data.
C. DOCUMENT SETS FOR MEETINGS
1. At each CD’ review point provide E1 (30” x 42”) size .pdf files of the drawing sets to the relevant parties four days in advance of the meeting. The Architect is responsible for bringing appropriate printed material to the review meeting.
2. 100% CD’s are to be posted with ALL addendum and city review comments. Architect to provide to AISD representatives one E1 (30”x42”) size set, two half-size sets, and one set of printed/ bound set of project manuals.
3. Digital Copy of 100% CD’s and project manuals
0.10 CONSTRUCTION DOCUMENT STANDARDS
A. Drawing Standards:
1. Drawings shall be produced using a current CAD software program which can export and import to AutoCAD’s current version at a minimum. BIM software is required for projects over new projects and additions over 25,000 s.f.
2. Drawings must include the following:
a. Full floor plan at minimum scale of 1/8” = 1’-0”
b. Site plan at minimum scale of 1” = 40’-0” (projects with no sitework)
c. Site plan at minimum scale of 1/16” = 1’-0” (projects with site work)
d. Enlarged partial plans at minimum scale of 1/4” = 1’-0” (renovated interior spaces)
e. Exterior elevations at a minimum scale of 1/8” = 1’-0”
f. Interior elevations at a minimum scale of 1/8” = 1’-0”
g. Details at a minimum scale of 1” = 1’-0”
h. Door, Hardware, Window, Finish, and Signage Schedules
i. MEP drawings, schedules and details
i. Structural drawings and details
j. Food services
k. Landscape
l. Civil
m. Technology
n. Security
o. Life safety
p. Roofing drawings and details
B. Specification Standards
1. Specifications should be produced in a word processing format that can export and import Microsoft Word’s latest version.
2. Architects and Engineers must follow the Construction Specifications Institute (CSI) MasterFormat CSIMasterFormat 2004-2011.
C. Miscellaneous
1. Spreadsheets should be produced in a format that can export and import Microsoft Excel’s latest version.
2. Electronic documents shall be transmitted in the latest version of Adobe, unless the original editable format is necessary.
3. Enscape model provided at Owners request.
0.10 DESIGN SUBMITTALS
The following is an overview of the design submittals required of the A/E team at each design phase, subject to the requirements stipulated in the A/E’s agreement with the District. Note that the District may choose to combine phases for certain projects, and the A/E should confirm the District’s desired design process model, schedule, and deliverables at the initiation of each project. Each Architect shall provide a letter stating that these District Design Guidelines and Standards have been read and understood prior to starting the project. Written confirmation of submittal completion from the District is required before moving on to the next phase.
A. Schematic Design:
1. The Schematic Design Documents shall consist of drawings and other documents including a site plan, if appropriate, and preliminary building plans, sections and elevations; and may include some combination of study models, perspective sketches, or digital modeling. Preliminary selections of major building systems and construction materials shall be noted on the drawings or described in writing.
2. Schematic cost estimate, that may include some items as square foot costs.
B. Design Development:
1. The Design Development Documents shall illustrate and describe the development of the approved Schematic Design Documents and shall consist of drawings and other documents including plans, sections, elevations, typical construction details, and diagrammatic layouts of building systems to fix and describe the size and character of the Project as to architectural, structural, mechanical and electrical systems, and such other elements as may be appropriate. Interior and exterior elevations, building sections; door, window, hardware, finish, and signage schedules; details.
2. The Design Development Documents shall also include outline specifications that identify major materials and systems and establish in general their quality levels.
3. The Design Development package shall be submitted in two components:
a. Sign-off portion to include:
i. site plan
ii. plans
iii. elevations
iv. building sections
v. renderings
vi. preliminary color board
b. Additional detailed information as outlined above.
C. Interim Construction Documents (for example, 50% or 75% CD’s, per the A/E’s agreement with the District):
1. Construction documents: site, floor, demolition, reflected ceiling, and roof plans for all disciplines.
2. Architectural interior and exterior elevations, building sections; door, window, hardware, finish, and signage schedules; details.
3. Comprehensive 3-part technical specifications for all products and systems.
4. Final color and materials board – sign off by AISD representative.
5. When applicable, an updated cost estimate.
D. 100% Construction Documents: Submit design drawings after incorporating the District and any District consultant/peer review comments on the interim CD submittal. These drawings and specifications are for review, input, and approval from the District before the City of Allen drawing submittal, back check, approval, and bidding. Documents submitted to the City of Allen are required to meet the standard of being “buildable” and “biddable.”
1. Comprehensive and fully coordinated construction document site, floor, demolition, reflected ceiling, and roof plans for all disciplines.
2. Fully annotated and coordinated interior and exterior elevations, building sections; door, window, hardware, finish, signage schedules, details and integration of colors and materials.
3. Project manual with comprehensive, thoroughly complete 3-part technical specifications for all products and systems. Division 0 and 1 “front-end” specifications shall not be included in the project manual, including but not limited to the following sections:
a. 00001 Project Title and Signature Page
b. 00008 Deferred Approvals
c. 00009 Testing and Inspection Sheet
d. 00010 Table of Contents
4. Copies of Drawings and Specifications Furnished to Requesting Offerors:
a. (1) electronic copy of the Drawings and Specifications to Purchasing Department
b. (1) electronic copy of the Drawings and Specifications to the District Architect’s Department
c. (1) electronic copy of the drawings and specifications will be provided directly to a reprographic vendor of District choice to facilitate hard copy distribution to offerors upon request.
d. (1) electronic copy of the Drawings and Specifications to each prospective General Contractor. Copies, including electronic files, will not be sent directly to subcontractors.
E. Bid Set: City of Allen, Inspections Department approved set incorporating all back check comments and final District constructability review comments:
1. Comprehensive and fully coordinated construction document site, floor, demolition, reflected ceiling, and roof plans for all disciplines.
2. Fully annotated and coordinated interior and exterior elevations, building sections; door,
window, hardware, finish, and signage schedules; details.
3. Approved project manual with the addition of Division 0 and 1 “front-end” specifications, including color construction phasing plans. Equipment cut sheets provided separately shall not be included in the bid set.
4. Addendum may need to be issued during the bidding process. The addendum should be formatted on letter size or tabloid size paper whenever possible. All addendum items should be communicated to the District PM prior when formalizing and distributed to the Construction Manager for distribution.
F. For documents required during construction (Change Orders (CO), Requests For Information (RFI), material submittals, etc.), documents required after completion of the project (warranties, guarantees, training manuals, record documents, etc.), and the number of copies to be submitted at each phase, coordinate with the District Project Manager.
0.11 CONSTRUCTION COST ESTIMATE
The construction estimate shall be in CSI Master Format utilizing Microsoft Excel spreadsheet software. The estimates shall be itemized listing all materials, quantities, labor, equipment, and considerations for administrative costs such as bonds, insurance, contingencies, and escalation. Include a summary page that reflects the use of allowances and alternates (deductive or additive).
Provide an estimate format that parallels and provides a level of detail equal to the CSI division format of the A/E specifications. Do not group the headings to reduce the length of the estimate unless it is appropriate to the scope of the Work.
0.12 PROJECT RECORD DOCUMENTS
1.1
SUMMARY
A. Section Includes: Maintenance and submittal of record documents and samples.
B. Related Requirements:
1. General Conditions of the Contract for Construction: Documents at the site.
2. Section 01 33 23 - Shop Drawings, Product Data, Samples and mock ups.
3. Section 01 77 00 - Closeout Procedures.
4. Section 01 78 23 - Operation and Maintenance Data.
5. Individual Specifications Sections: Manufacturer's certificates and certificates of inspection.
1.2 MAINTENANCE OF DOCUMENTS AND SAMPLES
A. In addition to requirements in General Conditions, maintain at the site for the Owner one record copy of:
1. Contract drawings.
2. Specifications.
3. Addenda.
4. Change orders and other modifications to the contract.
5. Reviewed shop drawings, product data, and samples.
6. Field test records.
7. Inspection certificates.
8. Manufacturer's certificates.
B. Store record documents and samples in field office apart from documents used for construction. Provide files, racks, and secure storage for record documents and samples.
C. Label and file record documents and samples in accordance with section number listings in table of contents of this project manual. Label each document “PROJECT RECORD” in neat, large, printed letters.
D. Maintain record documents in a clean, dry and legible condition. Do not use record documents for construction purposes
E. Keep record documents and samples available for inspection by Architect.
1.3 RECORDING
A. Record information on a set of opaque drawings, and in a copy of a project manual. All changes made in these drawings in connection with the final construction and installation shall be neatly made in red ink on the prints.
B. Provide felt tip marking pens, maintaining separate colors for each major system, for recording information.
C. Contractor shall include with the record documents, all changes and modifications made by addenda, change orders, supplementary instructions, or other forms of documentation, written or verbal, which alter the documents.
D. Record information concurrently with construction progress. Do not conceal any work until required information is recorded.
E. Contract drawings: Legibly mark each item on the drawings to record actual construction, including:
1. Measured depths of elements of foundation in relation to finish first floor datum.
2. Measured horizontal and vertical locations of underground utilities and appurtenances, referenced to permanent surface improvements.
3. Measured locations of internal utilities and appurtenances concealed in construction, referenced to visible and accessible features of construction.
4. Field changes of dimension and detail.
5. Changes made by addenda and modifications.
6. Details not on original contract drawings.
7. References to related shop drawings and modifications.
F. Specifications: Legibly mark each item in the specifications to record actual construction, including:
1. Manufacturer, trade name, and catalog number of each product actually installed, particularly optional items and substitute items.
2. Changes made by addenda and modifications.
G. Other Documents: Maintain manufacturer’s certifications, inspection certifications, field test records, and other documents required by individual specifications sections.
H. Maintain these documents to reflect the current conditions of the work. Changes shall be reviewed on a monthly basis with the Architect’s representative. The Contractor’s updating of the “installed condition drawings” shall be a prerequisite to the monthly review of the Contractor’s payment request by the Architect’s representative.
1.4 SUBMITTALS
A. At contract closeout, deliver record documents and samples under provisions of SECTION 01 77 00 - CLOSEOUT PROCEDURES.
B. Transmit with cover letter in duplicate, listing: 1. Date.
2. Project title and number.
3. Contractor’s name, address, and telephone number.
4. Number and title of each record document.
5. Signature of Contractor or authorized representative.
0.13 SPARE PARTS AND MAINTENANCE MANUALS
A. Coordinate with AISD Project Manager regarding instructions for delivery, inventory and sign off.
B. Spare materials shall be stored in a conditioned storage room in each project. Coordinate the location of the storage room with the Owner.
C. Furnish maintenance materials from same manufactured lot as materials installed and enclose in protective packaging with appropriate identifying labels. Include material type, manufacturer, color, location of use, and associated accessories on the label.
D. Minimum spare items required:
1. EXPANSION JOINT COVER ASSEMBLIES - Provide 25% overage of resilient joint filler and 25% expansion joint assemblies, and special tools required for servicing components.
2. CERAMIC TILING - Upon completion of work, deliver to the project site 10% for each type, color, pattern, and size of ceramic tile installed.
3. MATERIAL TRANSITIONS - Upon completion of work, deliver one unit but not less than 5% of each type, model, color, and size of material transitions including metal trims to the project site.
4. TILING - Upon completion of work, deliver to the project site 10% of each type, color, pattern, and size of tile including ceramic tiles, porcelain, quarry tile installed.
5. ACOUSTICAL CEILINGS - Upon completion of work, deliver to the project site 10% of the typical acoustic ceiling type used in classroom and offices. Furnish two boxes of full size acoustical ceiling units of other types installed.
6. CEILING GRID - Upon completion of work, deliver not less than a box of ceiling grid for each type and colors to the project site.
7. STAGE FLOORING SYSTEM - Provide 5% spare 4’-0” x 8’-0” panels of tempered hardboard to the Owner for future replacement. Spare panels are to be painted and neatly stacked on a 2 x 4 frame supporting the pieces 24” o.c. both directions. Cover spare panels with a plastic drop cloth.
8. RESILIENT FLOORING - Upon completion of work, deliver to the project site not less than 10% for each 50 boxes or fraction thereof, for each type, color, pattern, and size installed.
9. ATHLETIC RUBBER FLOORING – Provide additional 5% of the total floor surface of each type and color.
10. CARPETING - Upon completion of work, deliver to the project site not less than 10% sq. yds. of each type, color, and pattern of carpet, exclusive of materials required to properly complete installation. Other remnants, usable scraps, and overage in carpeting shall be packaged in appropriate wrapping, labeled, and delivered to the Owner.
11. PAINTING - Upon completion of the work, deliver to project site 2 gallons of each type and colors of paint applied to interior and exterior surfaces. Provide formula for custom match colors.
12. TELESCOPING BLEACHERS, BLEACHER AND FIXED SEATING - Provide a 3% Attic Stock, or at least one unit of each style/type and size of seat. Confirm the percentage of spare for other types of fixed furniture with the Owner.
13. ACOUSTIC CEILING/WALL PANELS & DIFFUSERS: Confirm the quantity of acoustic wall panels and
diffusers spares with the Owner.
14. LOCKERS: Confirm the quantity of lockers spare parts with the Owner.
15. WINDOW BLINDS – Upon completion of work, deliver to the project site not less than 5% of each classroom size window blind unit and not less than one box of slats in typical classroom window width.
16. DIVISION 21:
SPARE SPRINKLER HEAD BOX: Provide baked enamel steel box to store 36 sprinkler heads (Minimum of 3 of each type used) for emergency replacement. Provide sprinkler wrench.
17. DIVISION 22:
Pumps - Provide the following spare parts and material to the Owner for his use after the warranty period:
• A mechanical seal for each pump
• A set of bearings for each pump
18. DIVISION 23:
a. Pumps - Provide the following spare parts and material to the Owner for his use after the warranty period:
1. A mechanical seal for each pump
2. A set of bearings for each pump
b. Fan-powered VAV boxes: Provide one spare motor for each size box.
c. Filters - Provide the following material to the Owner for use during the warranty period:
i. Sufficient media of each thickness, in original cartons, for a complete change.
d. Units - Provide the following spare parts and material to the Owner for use after the warranty period:
ii. One spare fan motor for each size of fan motor on the project.
iii. One spare set of filters or filter media for each fan coil unit on the project.
19. DIVISION 26:
a. Switchboards - Install fuses, of ratings shown, in each switchboard. Provide spare fuse cabinet with three fuses of each size provided. Locate in main electrical room as directed by the Owner.
b. Lighting Controls - Spare Parts: Provide minimum of 1 unit up to 5% of each hardware device product used, whichever is greater.
c. Provide exit sign directional arrows as required. Provide a minimum of two and a maximum of 10% spare exit signs to be installed as directed by the Architect.
20. Division 27:
a. Provide 10-percent spare patch cables of each type.
21. Division 28:
a. Fire Alarm - SPARE PARTS AND TOOLS:
i. Interchangeable Parts: All spare parts furnished shall be directly interchangeable with the corresponding components of the installed system. Spare parts shall be packaged and identified by nameplate, tagging, or stamping. Spare parts shall be delivered to the site in unopened cartons for storage as directed by the Owner.
ii. Spare Parts: Provide minimum of two, or 5% of building total, whichever is greater unless noted otherwise.
1. Spare shut down modules
2. Spare detectors of each type in the system
3. Spare alarm indicating devices of each type in the system
4. Spare manual pull stations
5. Spare protective covers of each type in the system.
6. Spare relays/controls required for connection to smoke and fire/smoke damper.
7. Devices listed above are to be installed as directed by the Architect/Engineer or local code authorities at no additional cost to the Owner. Unused spare parts are to be parts for Owner’s cabinet.
22. Division 32:
a. Synthetic Turf:
i. Provide (1) towed, non-powered “Turf Sweeper” with hitch.
ii. Upon completion of work, deliver to the project site 10% for each type, color, pattern, and size of Synthetic Turf installed.
E. Staff training on equipment operation and maintenance is required in written documentation and video. Where possible, training to be provided by the manufacturer. Initial training should be 6 weeks before CO and secondary training should be 2 weeks before CO and follow up training as required by the District in 3 months if necessary.
F. One year warranty date should be provided to the Owner in writing and the scheduled 11 month walk should include a training request.
01.01 LOCAL JURISDICTIONS
City of Allen
Planning Department
Building and Permitting
Fire
Health and Food Safety
214.509.4100 coa@cityofallen.org
214.509.4139 permits@cityofallen.org
214.509.4400 firecad@cityofallen.org
214.509.4180 health@cityofallen.org
All Allen ISD facilities, as indicated in Section 00 are located in the City of Allen except for Lindsey Elementary School, which is located in the City of McKinney. Throughout these Technical Design Guidelines, the City of Allen is referenced as the municipal Authority Having Jurisdiction (AHJ). When planning a project for Lindsey Elementary School, Allen ISD requires that the Architect/Engineer provide contacts for the City of McKinney Planning, Building and Permitting, Fire, and Health and Food Safety Departments on the Project Information Form found in Subsection 0.03. When referencing the Allen ISD Technical Design Guidelines, the Architect/ Engineer shall take note that when the City of Allen is referenced, it is understood that the City of McKinney will be substituted as the required AHJ for any work associated with Lindsey Elementary School.
Utilities Reference Section 26.02.
State
TxDoT
214.320.6200 Dallas District Engineer
TDLR Note: all registration must be done through a Registered Accessibility Specialist Elevators cs.elevators.escalators@tdlr.texas.org
Boilers
800-722-7843 boilers@tdlr.texas.gov
01.02 PURPOSE AND CODES
A. The purpose of this document is to assist the Architect/Engineer in the planning, design, and administration of construction projects for which the Architect/Engineer has been commissioned by the Allen Independent School District (AISD).
B. Unless noted o noted otherwise herein or in the AISD-Architect/Engineer Agreement, the scope of each phase of the work and the recommended procedures and practices of the Architect/Engineer during the performance of the work shall be provided as published in the latest edition of the following documents: The Architect’s Handbook of Professional Practice, The American Institute of Architects Manual of Practice, The Construction Specifications Institute. Uniform Drawing System, The Construction Specifications Institute.
C. These Design Guidelines are to be coordinated with and used in conjunction with all applicable codes and ordinances. All AISD projects shall be designed in compliance with the provisions as applicable:
1. International Building Code, as amended by the City of Allen.
2. International Plumbing Code, as amended by the City of Allen.
3. International Mechanical Code, as amended by the City of Allen.
4. International Fire Code, as amended by the City of Allen.
5. International Energy Code, as amended by the City of Allen.
6. National Electrical Code, as amended by the City of Allen.
7. Texas Accessibility Standards (TAS)
8. Collin County Public Health Department Standards
9. Texas Boiler Code
10. ASHRAE 90A
11. Texas Education Agency (TEA) - School Facility Standards for New Construction
12. City of Allen Zoning Ordinance
13. City of Allen Sign Ordinance
01.03 SCHEDULE AND ACTIVITIES
A. The Architect/Engineer shall schedule all activities to comply with the approved project schedule. Allow sufficient time to complete each task and submit to AISD for review. Schedule activities with consideration for review time and response time in acquiring approval for each project phase.
B. Phasing of services shall be determined by the Architect/Engineer and AISD immediately after selection of the Architect/Engineer. Key events shall commence with program review and end with AISD’s acceptance of the completed project. Due to the unique nature of predefined periods of occupancy of school facilities, it is mandatory that the Architect/Engineer cooperate with AISD in establishing a schedule of services and activities that minimize disruption to educational programs. As an example, it is not practical for extensive internal remodeling to occur in a facility during educational sessions without carefully planning for the attendant disruptions. Additionally, it is not desirable to complete a facility out of sequence with AISD semester periods and have the building remain vacant for an extended period of time.
01.04 CRITICAL SITE INFORMATION
A. Determine if the property is properly platted and zoned. If platting or zoning is improper, notify AISD to allow for this work to occur in conjunction with the topographic survey. The Architect / Engineer is to be familiar with Allen Stormwater Large Construction project standards and their requirements. Where
possible, projects on larger campuses should explore whether the activities are or can be grandfathered.
B. If no topographic survey exists, notify AISD in a timely manner to initiate acquisition. Specifically, request any unusual site data required for the project.
C. After new facilities have been “sited,” work in conjunction with the geotechnical engineer to provide a base site drawing locating all required test borings. Once complete, request that AISD procure geotechnical investigations.
D. All site and geotechnical data will be provided to the Architect/Engineer by AISD. In order to assure that project schedules will be met, the Architect/Engineer shall initiate request for this data at outset of project. The Architect/Engineer shall cooperate with AISD and provide required documentation to facilitate contracting for these services at the earliest possible date and shall periodically review the status of required services with AISD to prevent potential delays.
E. If required, an Environmental Survey Assessment (ESA) shall be furnished by AISD.
01.05 ARCHITECTURAL CONSIDERATIONS
A. Program Review: The Architect/Engineer shall review the program prepared by AISD in relation to the following listed criteria. The Architect/Engineer shall report any discrepancies or incomplete data to AISD as soon as practicable and prior to commencing the Schematic Design Phase.
1. Interrelationships/Adjacencies of all program components
2. Coordination of new program components with existing to ensure a cohesive and effective design solution.
3. New square foot efficiency of existing or planned facilities, e.g. compare the recommended program area to actual area required.
4. Analysis of existing/functional facility requirements by teachers and students during addition and renovation work to provide uninterrupted campus operation.
5. Outline potential problem areas in existing buildings that need attention and list in order of priority. In addition to deficiencies identified by AISD, the Architect/Engineer shall identify deficiencies in existing buildings/sites and record to AISD a prioritized list of potential remedial work.
6. Determine the historical value of the existing structure (if renovation/addition project) and assess the need for preservation.
B. On projects where a great deal of renovation or addition to an existing project is part of the program, the Architect/Engineer is responsible for verifying the adequacy of existing building plans furnished by AISD. If plans are not adequate, notify AISD. Architect/Engineer to ‘field verify’ existing conditions during the design phase.
C. In general, allowances shall not be considered as part of the contract or estimate. If there is a special case, the Architect/Engineer shall submit, on a per-project basis, any inclusion of allowances that it recommends being introduced into the Contract Documents.
D. It is expected that the architect will engage a commercial kitchen consultant to be included in the Architect’s fee as part of the consultant group except where specifically relieved by the Owner’s written direction. The Architect/Engineer shall be required to provide coordination through the Facilities and Maintenance Department for consultation with the Student Nutrition Department for all work conserving food service design.
01.06 STRUCTURAL CONSIDERATIONS
A. The structural design should consider simplicity, economy of construction, and buildability. Innovative structural designs or methods of construction may be considered only when the end product is suitable
for use in schools and the cost is comparable to traditional structural systems.
B. The building structure should allow for flexibility e.g. future change of function of rooms.
01.07 MECHANICAL CONSIDERATIONS
A. The Mechanical engineering installation comprises heating, ventilation, water, soils and wastes, and fire protection services. Among other considerations, the mechanical design must take into account the site microclimate, the building form and orientation of spaces, the thermal performance characteristics of the building, the occupancy trends and restrictions on pollutant emissions.
B. Thermal insulation standards shall meet or exceed the applicable codes, but shall also be considered in the context of the balance of heat loss and gain to minimize operational costs while maintaining comfort conditions.
C. The use of passive energy measures to achieve a comfortable internal environment should be employed where possible. Coordinate the form of the building with the Architect to minimize energy consumption, e.g. maximize the use of natural ventilation and day-light and minimize heat losses.
D. In determining how a room is ventilated, consider performance and comfort levels, acoustic factors, safety, ease of operation, conformance with current codes, and maintenance factors.
E. Air-tightness is a major factor in controlling heat loss due to unwanted air infiltration into buildings. Attention to construction detail and proper supervision of the work are necessary in achieving this goal.
F. Verify that toilets are ventilated by natural permanent ventilation means. In addition, changing areas and toilets shall be mechanically ventilated. A permanent natural vent to the exterior, either directly or ducted should be provided.
G. Provide for after-hours operation of certain areas as identified by the Owner.
01.08 ELECTRICAL CONSIDERATIONS
A. The Electrical Engineering installation comprises electrical supply, electricity main distribution, power distribution services, lighting services, communication services, transport services, and protective services.
B. An integrated design approach should provide opportunities for energy efficiency. The design team should be aware that energy efficiency strategies can support each other or can conflict and thus individual measures should not be considered in isolation.
C. In order to provide natural lighting review the site, plan form, orientation, passive ventilation, and passive solar strategies, and daylighting opportunities.
D. Verify that all teaching spaces and habitable rooms have natural daylight as the principal source of light. Artificial lighting shall be used to supplement the available daylight per AHJ.
E. Coordinate the geometry and distribution of glazed areas to provide a high level of natural light while avoiding glare and ensuring a good quality day-lighting distribution in the room.
F. If provided, windows in Computer rooms shall be designed as “wide and low” rather than “narrow and high” to minimize the area of bright and visible sky. For security reasons, they must be placed higher on the wall.
01.09 ACOUSTICAL CONSIDERATIONS
A. A good acoustic performance improves the quality of the learning environment. Noise producing and noise-sensitive spaces shall be located, designed, and detailed to minimize noise interference between them.
1. Sound Quality Considerations
a. Control excessive reverberation
b. Eliminate or minimize echoes
c. Shape rooms to create a uniform sound field in audience areas
2. Sound Isolation Considerations
a. Separate noisy and quiet spaces
b. Control noise transfer from noisy spaces
c. Provide adequate speech privacy
d. Isolate from exterior noise
e. Isolate impact noise
3. Equipment Noise and Vibration Considerations
a. Locate mechanical equipment with acoustical considerations
b. Specify noise emissions of equipment
c. Provide adequate vibration isolation. All equipment with moving parts will need to be isolated from the building structure to avoid vibration transfer.
01.10 MISCELLANEOUS DESIGN CONSIDERATIONS
A. All solicitations and contracting for testing laboratory services shall be furnished by AISD. Carefully review specified Contractor testing procedures with AISD to prevent duplication of services.
B. The Architect/Engineer shall establish additive or deductive alternates as a means of bringing the proposed project budget at least 5% under its estimated construction cost. These alternates shall be reviewed and approved by AISD.
01.11 SITE DESIGN REQUIREMENTS
A. The Architect/Engineer shall visit the site with an AISD representative and review and document existing conditions. The following listed items are to be considered in both new and existing construction conditions. Existing facilities may limit or prohibit the full implementation of these items.
1. Consider traffic patterns, staging areas, student drop-off and pick-up from cars and buses, parking areas, the safety of children while crossing streets or drives, and convenient access to office entry.
2. Preserve existing trees and shrubs (consider the City of Allen ordinance requirements).
3. Provide adequate service and staff parking.
4. Consider topography and existing drainage structures, creeks, swells, etc.
5. Consider existing easements, building lines, parking encroachments, communications, and electrical, utility, or gas/oil transmission lines.
6. Locate the Contractor’s site access points, work area, and staging area.
7. Locate existing structures, their size, and if they are portable or permanent.
01.12 SUSTAINABILITY
Allen ISD strives to provide the best atmosphere for learning and growth. We also have an integral partnership with the community, which not only charges us to be good stewards of taxpayers’ money, but to also work in concert with others for a better world. Green, sustainable, high performance, and energy efficient are all terms used to express an environmentally friendly approach to design and construction. This is a general overview of how the district is looking towards making our buildings more sustainable, hence reducing overall operating costs and providing a positive, healthier working and learning environment.
01.13 SAFETY AND SECURITY
A. The criteria set forth in this section are to be taken merely as considerations during the design process and shall not override local building codes or Texas Administration Code Title 19, Chapter 61, Subchapter CCs.
B. The design team must stay abreast of the latest development in the area of safety an security of school buildings and work in coordination with the District and local law enforcement to incorporate features intended to improve the health, safety and security of all occupants.
C. The design team must include in the design all current regulations relating to safety, health and welfare. In particular, the team members must both individually and collectively identify, at all stages of the design process, any hazards that the design or the facility may present during construction and subsequent use and maintenance. Where possible the hazards should be eliminated or the risk reduced. Any outstanding risks, together with any design assumptions, must be provided to the District so that they can be dealt with in the School’s Safety and Health Plans.
D. The Design Team should anticipate any potential danger to the school occupants and visitors as a result of work taking place near to, or within areas where educational activities are conducted, and seek to eliminate those hazards or reduce the risk through design, choice of location, phasing, programming of works, etc. In particular, the arrangements for safe entry and egress of building construction traffic during construction and the staging area should be considered. The approved phasing plan must be submitted with the construction documents for final validation by the Contractor.
E. Resources
1. Web Links
a. Texas School Safety Center
b. National School Safety Center
c. Crime Prevention Through Environmental Design (CPTED)
d. National Institute of Crime Prevention (NICP)
e. American Crime Prevention Institute (ACPI)
2. In Print
a. AIA Guide - Security and Design
b. Building Security - Barbara A. Nadel, FAIA
c. Let None Learn in Fear - Michael Dorn
d. Texas Senate Bill 11
e. Security Design Considerations for Instructional Facilities
F. Site Design
1. The designer shall consider the three layers of defense for the building.
a. First layer – location and understanding behaviors of physical context. Buildings & businesses located outside of site perimeter are of particular concern.
b. Second layer – Pertains to the space between site perimeter and building. Considers location of building on site and natural resources that provide protection. Design of access points, parking, roadways, pedestrian walks, lighting and signage are of importance.
c. Third layer – Pertains to protection of building itself. Consider design and location of utilities, mechanical systems, and surveillance equipment.
2. Proper site perimeter sets a pleasant first impression, is welcoming but controlled. Provide a buffer
between the perimeter and building. Fences and gates should be considered. Provide site restriction during school hours. Access points should be minimized
3. Overall campus should have maximum visibility from within the building. Provide shallow porches appropriate landscaping and open canopies to eliminate hiding places. At vehicular circulation points provide concrete barriers, benches, bollards or landscaping as a barrier.
4. Site entrances should be limited and controlled. Parent and bus drop-off should be separate, distinct, and well-marked with clearly defined areas of pedestrian circulation. Special needs drop-off areas should be protected from traffic flow to allow for prolonged loading. On-site queuing allows students ease of access to parents.
5. Site lighting should be provided at parking and pedestrian routes to reinforce after-hour visibility. Sidewalks are designed to support peak loads and reduce congestion.
6. Design playgrounds to allow visual surveillance by neighbors and police patrols. Provide transparent separation with fences. Site signage should mark the intended purpose of each entrance and post rules governing access.
G. Building Design - Exterior Considerations
1. Provide good illumination at the exterior of the building. Lighting should be continuous from dusk to dawn.
2. Building should be raised on site to improve visibility. Maximize windows for exterior surveillance. Control access to crawlspace by installing grates.
3. Consider signage at access points designating main entry, cafeteria, gymnasium and auditorium. Number each building entrance to assist emergency responders. At entry points provide multiple points of visibility. Entrances should be designed so they are easy to recognize.
4. Consideration should be given to conduits and gas pipes that lead to the roof. Provide sheet metal cover to deter climbing. Refrain from low walls that can allow access to the roof.
5. Design to accommodate appropriate coverage of surveillance PTZ cameras, including, at a minimum, one at each egress.
H. Building Design - Interior Considerations
1. Provide visibility to visitor parking and main entry from reception area. Consider the use of video surveillance for parent drop-off and bus drop-off.
2. Provide a secure vestibule at the main entrance in which visitors must enter administration area prior to admission to school.
3. Provide wide corridors that allow for increased visibility. Open stairs with see-through rails allow for ease of control. Avoid enclosed stairwells when possible.
4. Design to accommodate appropriate coverage of surveillance PTZ cameras, including, at a minimum, full coverage of corridors, cross corridors and interior side egress doors.
I. Construction Security
1. All employees of the general contractor and his subcontractors shall be badged. Temporary badges shall be issued by the general contractor for deliveris and other visitors.
2. There shall be no interaction between students and faculty, and construction workers. Contractor shall take such reasonable means necessary, including constructon fencing and interior dust partitions to separate the work and workers from the school.
3. Architect / Engineer, General Contractor and Subcontractors must be compliant with Texas Senate Bill
9 which requires school district contractors (those who provide services to school districts) to obtain state and national criminal history background searches on their employees who will be on school district properties for any purpose whatsoever, and to receive those results through the Department of Public Safety criminal history clearinghouse FACT (Fingerprint-based Applicant Clearinghouse of Texas).
01.14 SPACE NUMBERING
A. From the 50% Construction Document forward, drawings shall display the Construction Room Number and the Permanent Room Number for rooms. Do not assign Permanent Room Numbers to Restrooms, Mechanical Rooms, Electrical Closets or Custodial Closets. They should be labeled by function.
B. Rooms should be numbered according to the floor in which they are located.
1. 1st floor rooms -100s, 2nd floor - 200s and so on. Basement level preceded by a B, such as B01.
2. The first floor should be the level of the main entrance.
C. The main administration office in each facility should be the start, and then a logical sequence proceeding down the corridors preferably in a clockwise fashion should follow.
1. Even numbers on one side of a corridor and odd numbers on the other is good for organizing but may be hard to achieve.
D. Numbered rooms opening from the corridor shall be considered main rooms. E.g.: Room 100. Small rooms contained within larger rooms can be considered a sub part of that room. They should be numbered 100A, 100B, 100C and so on corresponding to the room they are in.
E. Additions should respect the numbering systems of the existing system.
F. Room numbers should not change once established by the architect; all systems (fire alarm, public address, mechanical, electrical, plumbing, etc.) must use the same numbers and names.
G. Number exterior exits prominently and sequentially to enable easy identification. Numbering to start at the building primary entry, and numbered in a clockwise direction of the building.
H. Display street address number in conformance with Allen Fire Department requirements, at a minimum.
02.01 PROJECT CONDITIONS
A. The design team shall field verify existing conditions to confirm the accuracy of any as-builts provided by Allen ISD. This is to include verification of property lines and easements in accordance with the most recent survey and or plat. If an applicable survey or plat is not available or in the design team’s opinion is out of date, the design team shall advise AISD of the need for a new topographic survey and or legal plat. AISD can require that updated drawings of existing conditions be submitted for AISD records and use.
B. When AISD will be continuously occupying portions of the existing building. A phasing plan should be developed in order for work to be carried out carefully and in an orderly manner to minimize interference with the daily operations and with adjacent portions of the structures to remain.
C. It is essential that there be minimal interruptions of existing mechanical and electrical systems in addition to the normal operation of facilities. Phase existing utilities indicated to stay in service and protect against damage during demolition operations. Except when authorized in writing by AISD, existing utilities serving occupied or used facilities are not to be interrupted. Architect/Engineer shall note for Contractor to locate, disconnect, remove and cap designated utility lines within demolition areas or any locations where adjacent work is to be performed.
D. Architect/Engineer shall consider location of existing trees on the site if an addition is planned. Design building to minimize the number of existing trees to be disturbed or removed.
E. Architect/Engineer shall phase demolition operations to ensure minimum interference with roads, streets, walks, and other adjacent occupied and used facilities. Streets, walks, or other occupied or used facilities shall not be closed or obstructed without AISD’s permission.
F. Phase operations to prevent damage to adjacent buildings, structures, and other facilities.
G. Architect/Engineer shall review existing drawings and survey (provided by AISD) for underground utilities where additions are being located. If utilities are located beneath the new addition, design of the building should include the relocation of existing utilities.
H. The design team shall identify all items required to be temporarily removed, stored and reinstalled and or relocated as part of the project.
02.02 DESIGN PHASES
A. Additions and Renovations
1. AISD shall furnish an asbestos report to the Architect/Engineer.
2. If electronic files of the existing building are available, AISD shall furnish them to the Architect/ Engineer.
3. Architect/Engineer shall perform a field investigation of the existing building.
4. Architect/Engineer shall coordinate an ADA/TAS review of the existing building based on the proposed scope of the project.
02.03 ASSESSMENT
A. Site Documentation
1. The Architect/Engineer shall document the site with photographs prior to construction. Photos are especially important for additions and renovation projects as they will allow before and after assessment at various stages of demolition and construction.
2. Documentation should include overall assessment, evaluations, calculations, and photographs of the existing conditions, prior to commencement of the work.
3. It is recommended that all disciplines participate in the site visit/survey(s) and documentation.
B. Site analysis of surrounding site considerations that may impact design and cost of project development, including but not limited to: surrounding land uses, mass transit routes, and utilities, zoning ordinances, easements, aircraft flight patterns, flood hazards, wetlands, topography, and biological and other environmental considerations.
C. Site analysis of on-site considerations that may impact design and cost of project development including but not limited to: Site access/circulation, ingress/egress by pedestrians (including persons with disabilities), passenger vehicles, delivery vehicles, emergency vehicles, and mass transit, if applicable as well as building access for fire apparatus, site security requirements, etc.
D. Evaluate existing and proposed number of parking spaces, accessible parking spaces, and handicapped van parking spaces for surface and structured parking allotment as per City and State accessibility standards.
E. Documentation of the local flooding potential and all other soil conditions.
F. Investigation of the conditions and capacities of the existing storm water management system. Review of local, state, and federal storm water regulations, and third-party sustainability storm water design requirements, when required. Perform a preliminary drainage analysis of existing and proposed site conditions to assess potential options for storm water management strategies. Generally locate areas where storm water storage facilities shall be, if needed.
G. Identify all conditions that will influence project schedule, including:
1. Site conditions that require mitigation
2. Availability of utilities, roadways, etc.
3. Approvals from regulatory agencies (historic, environmental, etc.)
4. Platting of both developed and undeveloped property.
H. The District’s budget includes all on site and off site development costs incurred, including parking, curb cuts, drives, paved play areas, walks and sidewalks at the street, unloading zone, landscaping, and exterior furniture and equipment.
I. The Architect/Engineer shall show concern for neighborhood scale, visual impact, aesthetics of proportion and color, good drainage, and the safety and comfort of the students.
02.04 SURVEYS
A. Architect/Engineer shall consult AISD for existing survey information regarding the project. If any additional boundary topographical survey work should be promptly requested by the Architect/Engineer. Refer to Survey procurement form.
02.05 SUBSURFACE INVESTIGATIONS/GEOTECHNICAL
A. If a building addition is planned, the Architect/Engineer shall promptly request a soil engineering investigation report and shall assist in suggested boring locations/quantities.
B. Engineer shall include the boring logs from the geotechnical report in the bidding and construction documents (as a section) of the specifications.
C. The geotechnical design values and parameters used to design the foundations shall be enumerated on the structural drawings.
D. Additional Geotechnical Considerations:
1. Architect/Engineer shall take into consideration the effects of local soils.
2. Architect/Engineer shall consider Geotechnical Engineer’s Report when designing foundation.
3. Regarding a building addition, the Architect/Engineer shall consider differential settlement between
new construction and existing construction.
02.06 HAZARDOUS MATERIAL AND ABATEMENT
A. The design team shall specify that no asbestos containing material (ACM) is to be utilized on any AISD new construction.
B. The design team shall specify that the General Contractor shall agree contractually to not utilize materials containing ACM and a letter of certification that no ACM was used shall be provided by the General Contractor at the end of the project.
C. If during construction, any suspect ACM or other hazardous materials are encountered during field verification, demolition or construction, the Design Team and the General Contractor agree to contact AISD immediately and to not disturb those materials.
03.01 GENERAL CONSIDERATIONS
A. All structures shall have their structural components designed by a structural engineer, licensed to practice in the State of Texas, and all structural drawings shall have the structural engineer’s seal affixed.
B. It is not the intent of these guidelines to limit the ability of the design skills or of the design professional’s expertise; however, structural designs other than conventional foundation and frame designs must be reviewed and approved by Allen ISD. The use of proprietary or patented structural systems should be avoided.
C. All concrete members shall be designed in accordance with the Building Code Requirements for Structural Concrete and Commentary ACI 318 – current edition adopted by the City of Allen.
D. If ACI Specifications conflict with local code, the local code shall govern.
E. The preferred ground floor construction is structural slab and/or piers with suspended floor or crawlspace. The architect/Engineer shall specifically address under-floor drainage and ventilation where required by code.
F. Structural engineer, Architect, and Mechanical engineer should coordinate any special requirements to assure adequate support is provided for special conditions, and equipment loads shall be designed to resist impact or dynamic load characteristics.
G. Prevention of loss of moisture from surface of concrete shall be accomplished by keeping the surface or forms continuously wet for as long as conditions require. Wet curing shall extend for not less than seven (7) days.
H. Test slabs for moisture and alkaline content and include remediation procedures within specifications to prevent finish-flooring failures. Follow manufacturer’s guidelines for recommended practices for preparation of subfloor for finish materials.
I. All concrete Work shall be performed in accordance with ACI 301 – Specifications for Structural Concrete Buildings.
1. Comply with ACI 304 – Recommended Practice for Measuring, Mixing, Transporting, and Placing Concrete.
2. Comply with ACI 305 - Specifications for Hot Weather Concreting.
3. Comply with ACI 306 – Standard Specification for Cold Weather Concreting.
J. Provide logs of geotechnical test borings in project specification.
Tilt Wall Construction
1. Minimum thickness of panels shall be 5.5 inches.
2. The requirements of section “Concrete Work” apply to work of this section.
03.02 GEOTECHNICAL INVESTIGATIONS FOR FOUNDATIONS
A. The primary purpose of a sub-surface investigation for foundation design is to accomplish an engineering use of the in-place materials for the support of imposed structural loads and to provide the contractor a guide on how achieve the required soil capacity.
B. Sub-surface exploration for foundation design shall delineate the horizontal and vertical limits of the investigation and establish the engineering properties that will affect the foundation design.
C. The spacing of borings, the establishment of boring depth, and the selection of engineering tests are the responsibility of the geotechnical engineer with consultation of the Architect/Engineer. These services must be provided by a geotechnical engineer licensed to practice in the State of Texas, and the report will have his or her seal.
03.03 TESTING - BY OWNER
A. All construction materials engineering services will be provided by a firm registered by the State of Texas to provide construction materials engineering services. The firm must comply with the requirements of ASTM E329 “Agencies Engaged in Construction Inspection and/or Testing.” Services are to be provided under the direct supervision of a professional engineer as required by the State of Texas Engineering Practices Act.
B. All concrete, soils, masonry, asphaltic concrete, structural steel, and other required services should be provided in accordance with the applicable ASTM and ACI standards as referenced in the project specifications.
C. Structural and compliance testing required as Special Inspections under the latest IBC Code as amended by the City of Allen shall be provided.
03.04 STRUCTURAL DESIGN CRITERIA TABULATION
A. The following data shall be shown on the first sheet of the Structural Drawings:
1. Note bearing strata for footings and/or piers, and allowable bearing capacities used for foundation design by engineer.
2. If concrete frame, indicate design was prepared in accordance with the latest edition of ACI-318.
3. Indicate required 28 day concrete strength, in PSI, for each concrete member classification and any Special Inspection or Special Testing requirements.
4. Indicate ASTM specification and grade of reinforcing used for design.
03.05 Concrete Forming and Accessories
A. Note all concrete beam and wall faces shall be formed full height each side. Earth forms shall not be permitted except at interior, unexposed faces of beams at slab-on-grade construction.
B. Note to construct and maintain concrete formwork tolerances as required by ACI 347 –Recommended Practice for Concrete Formwork.
C. Note corrugated fiberboard void forms shall be of a square shape and design. Trapezoidal shaped void forms shall not be used. This is only required is a suspended structural slab is designed.
D. Note: for Slab on Grade, provide an approved Vapor Barrier System. Install the vapor barrier per geotechnical requirements.
03.05 CONCRETE FORMING AND
ACCESSORIES
A. Note all concrete beam and wall faces shall be formed full height each side. Earth forms shall not be permitted except at interior, unexposed faces of beams at slab-on-grade construction.
B. Note to construct and maintain concrete formwork tolerances as required by ACI 347 –Recommended Practice for Concrete Formwork.
C. Note corrugated fiberboard void forms shall be of a square shape and design. Trapezoidal shaped void forms shall not be used. This is only required is a suspended structural slab is designed.
D. Note: for Slab on Grade, provide an approved Vapor Barrier System. Install the vapor barrier per geotechnical requirements.
03.06 CONCRETE REINFORCING
A. Reinforcing bars shall meet ASTM A615, Grade 60 deformed billet steel.
B. Reinforcing fabric shall meet ASTM A185, Grade 65 welded steel wire fabric. Supply welded wire fabric in flat sheets, not in rolls.
C. At slab-on-grade construction, provide reinforcing bolsters or chairs with sand plates where base material will not support chair legs.
03.07 CONCRETE MATERIALS
A. Portland Cement shall meet ASTM C150, Type I, unless job conditions or Work to be completed require alternate cement type.
B. Chemical admixtures used in concrete mixes shall be selected per job conditions or Work requirements. Concrete mix designs shall be reviewed by the Engineer of Record.
C. Fly ash shall be in accordance with ASTM C618, Type C or F. Fly ash may be substituted for up to a maximum of 25% by weight of cementitious material.
D. Calcium chloride shall not be used.
04.01 ARCHITECTURAL CONSIDERATIONS
A. Face Brick: Select a minimum of two face brick samples for the project and submit samples with preferred selection to Allen ISD for approval. Endeavor to select brick that is readily available from multiple sources to prevent delays and future color matching problems. Selection for renovation and addition projects shall match existing brick as closely as possible or provide compatible integration with existing materials. Specify face brick by manufacturer’s name and number. Do not use an allowance.
1. Face brick shall be grade SW, modular size.
2. Provide brick dimensions that minimize brick cuts and waste. Dimensions shall allow brick to be cut in half so both pieces are used in the design. Small and irregular brick cuts are discouraged. 3. EFFLORESCENCE Particular care must be taken in the selection of materials and in design and detailing of exterior walls to prevent efflorescence in brickwork. Certification shall be provided that brick and any masonry trim material have passed the “wick” test (ASTM C67).
B. Split face CMU, burnished block, cultured stone, and any other masonry exterior veneer shall only be used upon written approval by AISD.
C. Consider the use of sound absorbing CMU in Gymnasiums and Activity Rooms.
D. Rock shall be native stone, fieldstone or quarried, free of loose or friable incisions.
E. Exterior stucco is to be integrally colored and finished with an appropriate paint coat.
F. Cast stone units are to be manufactured by a current producer in good standing of the Cast Stone Institute. Manufacturers shall be required to design and provide reinforcement and anchorage systems.
G. Applied masonry without cavity wall construction is not acceptable.
H. Consider the use of masonry units manufactured within 500 miles of the building site.
I. For masonry veneer, provide adjustable anchors to allow for movement. Provide joints for expansion and contraction typically at inside and outside corners (within 5’-0”), offsets, and other changes in the wall plane, and at regular spacing (typically 20 to 30 feet on center, maximum). Refer to guidelines for expansion joint design/layout from the Brick Industry Association (BIA).
J. Design veneer walls with a ‘drainage plane’ to allow water that penetrates the wall to flow freely and drain through weep holes to the exterior. Provide cellular plastic weeps made from UV-resistant material. The recommended cavity width behind the masonry veneer is 2 inches.
K. Provide through wall flashing at the base of wall, at openings and other locations as recommended by the BIA (reference Division 07).
L. Architect shall specify for full masonry mock-up, including all masonry at exterior veneer, mortar, sealant, and window assembly. Provide colored mortar for new additions. When patching, masonry mortar shall match existing.
M. At brick veneer retaining walls and dumpster enclosures, provide cast stone or metal coping at top of wall.
N. DISIMILAR MASONRY VENEER MATERIALS A bond break material shall be provided between dissimilar masonry veneer materials; such as between clay brick, stone, cast stone and CMU courses.
O. Single wythe exterior construction is not permitted.
P. Detail the return of masonry veneer at all door and window jambs. Due to increase in wall thickness from continuous insulation requirements standard 4 1/2” aluminum storefront does not span from back-up wall system to masonry veneer without returning the veneer.
04.02 STRUCTURAL CONSIDERATIONS
A. Structural masonry design shall be in accordance with Building Code Requirements and Specifications for Masonry Structures with Commentaries – latest edition.
B. Note all cells containing reinforcing, bolts or other metal anchors shall be grouted solid.
C. Note all cells at or below grade shall be grouted solid whether reinforced or not.
D. Note reinforcing bars shall meet ASTM A615, Grade 60 deformed billet steel.
E. Masonry cement shall not be used in mortars.
F. Note to provide Type ‘S’ mortar in accordance with ASTM C-270 for all exterior and interior load- bearing masonry construction.
G. Note reinforced masonry grout shall be in accordance with ASTM C-476.
H. Note where horizontal joint reinforcement is used, reinforcement shall be pre-fabricated and conform to ASTM A951, minimum 9 gage wire, galvanized.
05.01 STRUCTURAL DESIGN CRITERIA TABULATION
A. The following data shall be shown on the first sheet of the Structural Drawings:
1. If steel frame design was prepared in accordance with the latest edition of the AISC Steel Construction Manual.
2. All structural steel shall meet the appropriate ASTM standard for strength and grade.
3. Include yield strength for each steel member type used in the design.
4. All Structural Steel Inspection and Testing Requirements
05.02
GENERAL CONSIDERATIONS
A. Structural steel design shall be in accordance with the AISC Steel Construction Manual – current edition adopted by the City of Allen.
B. Open–web steel joists and joist girders shall be designed and fabricated in accordance with the latest edition of the Steel Joist Institute.
C. Bolted connections shall conform to the RCSC Specification for Structural Joints Using ASTM A325 or A490 Bolts – latest edition.
D. All welded steel construction shall be noted to be in accordance with the latest edition of the ANSI/ AWS D1.1 Structural Welding Code.
E. Metal decking design shall in accordance with the Specifications of the Steel Deck Institute.
F. Cold-formed metal framing shall conform to the latest edition of the AISI Specification For The Design of Cold-Formed Steel Structural Members.
G. Design requirements for steel stair assemblies shall conform to the latest adopted building code by the City of Allen.
05.03 STRUCTURAL
STEEL
A. Provide headed anchor rods, threaded at one end for nut attachment, for column anchor bolts. J-shaped anchor bolts shall not be used.
B. Exterior steel members exposed to weather, including lintels, shall be galvanized.
C. Note to provide a minimum of 2 bolts at bolted steel connections.
05.04
METAL DECK
A. Provide galvanized metal deck at all steel roof and floor decking units. Galvanizing shall maintain a minimum coating class of G60.
B. Note metal deck welding shall be in accordance with ANSI/AWS D1.3 Structural Welding Code – Sheet Steel. Use E60XX electrodes.
C. Consider the use of acoustical deck at Activity Rooms and Gymnasiums.
05.05
COLD-FORMED METAL FRAMING
A. Exterior cold-formed metal stud framing shall be a minimum of 18 gauge material thickness.
B. Metal stud framing used as a back-up for brick veneer shall be sized to limit lateral deflections to a maximum of L/600 at exterior conditions. Deflections shall be based on steel stud properties only.
06.01 ROUGH CARPENTRY
A. All composite wood products (particleboard, MDF, and hardwood plywood) must comply with new limits on formaldehyde emissions.
B. Pressure-preservatives are to be used on all wood in contact with concrete or masonry, exposed to the weather, or prone to insect attack, in conjunction with roofing, under parapet caps, vapor barriers and waterproofing – sills, sleepers, furring, blocking, and stripping).
C. No wood products treated with (a) pentachlorophenol, (b) arsenic compounds, and/or (c) creosote shall be used in either interior occupied spaces or for exterior applications where there is a possibility of student contact. Borates are the preferred protective if available.
D. For exterior applications where students contact is not possible, wood treated with (a) pentachlorophenol, (b) arsenic and/or (c) creosote may be used Borates are preferred protective if available.
E. Must be water-borne, inorganic type and comply with the limit on volatile organic compounds (VOCs) for wood preservatives of 350 grams/liter using EPA Test Method 24.
F. Provide fire retardant treated wood as required by current code.
06.02 FINISH CARPENTRY
A. General:
1. Millwork shall be designed as maintenance-free as possible. Countertops shall be plastic laminate over plywood substrate and stabilizing backing sheet. At wet areas and areas prone to moisture, use solid surface countertops. Cultured marble is not acceptable. All shelves shall be plywood with hardwood edges. For typical casework construction, utilize AWl custom grade fabrications, plastic laminate clad. Particleboard is prohibited in casework; MDF is an allowable substrate. Economy grade shall be acceptable for custodial closets and storage rooms with owner’s prior written permission.
2. Specialty woodwork is to be stain-finished and in accordance with AWI Premium Grade. Wood species as selected by the architect.
3. Fabricate casework stiles and rails of solid lumber, firmly secured to cabinet ends, partitions, and bottom. Partitions, vertical dividers, and shelves shall be solid plywood. All exposed surfaces shall be plastic laminate clad. Semi-exposed surfaces may be themo plastic faced plywood or MDF.
4. Cabinet doors shall be lumber core plywood with solid edge bands, clad in plastic laminate. Thermo plastic facing is not acceptable on the interior side of cabinet doors. Door thickness shall be based on door size, but not less than 3/4”. Door design and species shall match existing construction in renovation/addition projects. Drawer fronts shall be 3/4” lumber core plywood with solid edge bands, clad in plastic laminate. Side and backs shall be 1/2”-thick solid lumber, slightly rounded on top edge, dove-tailed or dado glued, and nailed in the drawer fronts. Allow for nominal 1/2” clearance between doors and drawer fronts for overlay construction.
5. Shelves shall be a minimum of ¾” thick lumber core plywood with thermoplastic faces and solid edge band. Shelves of 36” in length up to 48” should be 1” thick lumber core plywood with thermoplastic faces and solid edge band. Lower shelves should be the full depth of the cabinet. Upper shelve and open book shelves shall be no less than 12” clear depth.
6. Typical hardware for casework shall include adjustable shelf standards routed into cabinet end walls, 75# capacity full extension drawer slides, 4”-long wire door pulls, and heavy-knuckle hinges or match existing hinges on renovations. Locks within anyone room shall match, except that teacher’s cabinet shall be keyed differently. Elbow latches should be used on offset doors.
7. Plastic laminate to be NEMA LD#, PF42 post forming, GP50, color and texture as selected.
8. Architect shall coordinate with owner for location of locks in each project. At a minimum, locks shall be provided at teacher cabinets, clinics, and offices.
9. Fabricate wall-hung cabinets with nailing cleat built into back of wall-hung cabinets. In new construction, provide solid wood blocking (fire resistant where required) in walls to which cleat shall be attached. In existing construction, provide wood cleats on surface of wall to which cabinet shall be attached. Fabricate wall cabinets to allow for a minimum depth of 12” clear inside.
10. Adjustable Shelf Supports: Shall be designed with pin supported with anti-tip-up shelf restraints for both 3/4” and 1” shelves. Design shelf to mate properly with the style of support selected to retard shelf slide-off, and slot for ability to mechanically attach shelf to clip. Load rating to be minimum 200 lbs. each support without failure. Cabinet interior sides shall be flush, without shelf system permanent projection.
11. Architect shall designate on the drawings for the contractor to provide a mock-up of the casework. The mock-up should represent a typical installation of casework with both base and upper cabinets. If acceptable to the architect and owner, the mock-up may be installed as part of the project.
12. Architect shall specify that the work be performed by a company licensed by the AWI Quality Certification Program. Certification shall be evidenced through the application of AWI Quality Certification labels and/or the issuance of an AWI letter of licensing for the project.
13. Wood Base and Handrails: Shall be Maple solid lumber. Joints shall be accurately cut to provide a close, flush fit with no visible end grain.
07.01 DAMPROOFING
A. Bituminous Damproofing: Provide semi-mastic asphaltic emulsion reinforced with non-asbestos fibers. Products shall comply with ASTM D 1227, Type II.
07.02 VAPOR PERMEABLE AIR/MOISTURE BARRIERS
A. Acceptable System: Provide an air retarder with air leakage of 0.06cfm/sq-ft at 25 mph per ASTM E1677 Type I. Water Vapor Transmission of greater than 20 perms. Vapor Barriers should be avoided. It should have a minimum water penetration resistance of 200 cm in accordance with AATCC-127.
B. Acceptable alternative: Fluid-applied vapor permeable membrane air barrier should be specified for use in cavity wall systems based on the type of rain screen material being provided. Such products should have certified air leakage and vapor permeance rates that exceed the requirements of ASTM E2178. All ancillary products for the system should come from a single manufacturer. If thru-wall flashings are specified in Division 4 it should be noted that they need to be supplied by the selected manufacturer of the vapor permeable membrane air barrier.
C. On larger projects a mock up should be specified to include typical flashings associated with the vapor permeable membrane.
07.03 SELF-ADHERING SHEET WATERPROOFING
A. It is Allen ISD’s preference that buildings should be designed with no soil placed above finished floor (basement condition). If it is determined by the Architect that the best design solution is to provide finished grade above finished floor, the design professional shall seek written approval from Allen ISD. If approval is granted, provide self-adhering membrane of rubber asphalt integrally bonded to polyethylene sheeting, formed into uniform flexible sheets not less than 56 mils thick. Provide organic fiberboard, treated for resistance to fungus and insects for a protection board over them membrane. Perforated pipe surrounded by gravel should be installed at base of membrane and tied into the storm sewer to collect ground water. The installation and extent of installation shall be in conformance with the geotechnical investigation recommendations.
B. Provide termination bar with anchors at 6 inches on center along top edge of all waterproofing which should terminate below finished grades. Allow for some soil subsidence since below grade waterproofing membranes should not be exposed to sunlight.
C. Prior to installing the protection board and drainage mat and prior to backfilling against the below grade waterproofing system have the installed membrane inspected by the waterproofing membrane’s technical representative.
7.04 MECHANICAL ROOM FLOOR COATING
A. Provide an interior urethane elastomeric pedestrian traffic coating with silica sand evenly broadcasted. Architect should also consider the addition of concrete curbs and floor drains.
a. Provide at all mechanical mezzanine where occupied rooms are located immediately below.
07.05 WATER REPELLENTS
A. Water repellent coatings are not required to achieve water resistance on brickwork subjected to normal exposures where proper material selection, detailing, construction and maintenance have been executed. Any application of repellents that also serve as a graffiti guard shall be approved in writing by the Allen ISD.
B. Case stone shall have a silane or siloxane water repellent applied in accordance with the Cast Stone Institute and the respective manufacturer’s requirements.
07.06 BUILDING INSULATION
A. Typical Learning Spaces: At all gypsum board dividing walls that extend to floor or roof deck above, provide batt acoustical insulation between studs and acoustical sealant at all joints on one side of wall to reduce sound transmission.
B. Administration, Conference rooms and Special Education rooms: Where gypsum board partitions are utilized, extend walls to floor or roof deck above and provide batt acoustical insulation between the studs and acoustical sealant at all joints on one side of wall to reduce sound transmission.
C. Insulation for Exterior Walls: Insulation for exterior walls shall meet the requirements of the governing International Energy Conservation Code.
07.07 METAL PANELS
A. Metal panels shall be installed a minimum of 4’-0” above finish grade and shall be installed with a continuous drainage plane.
07.08 ROOFING CONSIDERATIONS
A. Existing roofing systems shall be evaluated based on the following Categories as they best apply to each project.
1. Roofs installed 9 years or less shall be repaired matching the existing roofing system.
a. Warranty: Contractor’s Warranty: Two-year system warranty. Manufacturer’s Warranty: Ten- year No Dollar Limit Warranty that runs concurrent with Contractor’s Warranty.
2. Roofs installed 10 - 15 years, if after evaluation it is determined that 25% or more of roof area requires repair, the roof shall be replaced in its entirety. Repairs must match the existing roofing system.
a. Warranty: Contractor’s Warranty: Two-year system warranty. Manufacturer’s Warranty: Ten- year No Dollar Limit Warranty that runs concurrent with Contractor’s Warranty.
3. Existing roofing systems 16 years or older, that are showing signs of failure, shall be replaced in its entirety.
B. Preferred System: Single-ply fleece-backed thermoplastic polyvinyl chloride (PVC) membrane
roof system over SBS base sheet installed over mechanically attached ¼” coverboard and (2) layers of polyisocyanurate insulation mechanically fastened to metal decking in accordance with FM 1-90 requirements or adhered to structural concrete decking in accordance with FM 1-90 requirements. The minimum R-value of all roof systems shall be R-20. The PVC membrane shall be 60 mils and white in color.
1. Warranty: Contractor’s Warranty: Three-year system warranty. Manufacturer’s Warranty: Twenty-year No Dollar Limit Warranty that runs concurrent with Contractor’s Warranty.
*Acceptable Manufacturers: other manufactures with equal products will be considered with approval of Allen ISD.
Single-ply PVC: Johns Manville, Flex Membrane International, and Carlisle.
C. General Roofing Standards:
1. Roof design shall be in compliance with applicable building codes, manufacturer recommendations, and industry standards.
2. Design simple roof planes avoiding complex and varying roof levels or changes. Consider impact of structural expansion joint on roofing related details. On new low slope roofs provide ¼ inch slope per foot in structural deck except for small roof areas and canopies. Provide positive drainage on existing dead level roof decks in accordance with code requirements for existing buildings. Design roof slopes to minimize parapet heights where
possible. Utilize roof drains with overflow scuppers for roof drainage in accordance with applicable codes. Coordinate locations of overflow scuppers on exterior elevations. Use overflow roof drains where the use of overflow scuppers are not desired aesthetically.
3. Provide shop fabricated sheet metal expansion joints. Any alternates must be approved by Allen ISD.
4. All sight exposed sheet metal shall be prefinished galvanized sheet metal. All other sheet metal not exposed to normal views shall be galvanized sheet metal. Form thru-wall scupper sleeves out of Zincgrip Paintgrip sheet metal to allow for all joints to be soldered. Prime and paint to match adjacent prefinished sheet metal face trim.
5. Where present provide cast iron downspout boots (minimum 24 inches above finished grade) at all downspouts that discharge storm water at grade or where downspouts are piped into storm drainage system. Prime and paint all cast iron downspout boots. Install precast concrete splash blocks installed over an additional ply of adhered cap sheet where downspouts discharge storm water onto roofing unless such roofing is metal.
6. Provide minimum 2’-6’ x 3’ roof hatch with ladder safety posts for each roof area through a lockable maintenance area where possible. When not possible, provide roof access ladders to allow for access to all roof areas from roof areas having a roof hatch at all elevation changes of 24 inches or greater. Legs of such roof access ladders shall not require flashings to be installed in the field of the roof. Provide permanently installed steel access ladder for all roof hatches. Ladders and roof hatches shall be no closer than 10’-0” from edge of roof.
7. Replacement of Existing Roofs:
a. Repair and replacement of existing roof systems and associated assemblies should only be performed after discussion with Allen ISD. Items to be evaluated include, as a minimum, the existing condition of the ballast, if any, membrane, insulation and roof deck or substrate assembly, flashing components, expansion joints, roof drainage and slope. Architect shall perform a roof survey with Allen ISD maintenance staff when evaluating an existing roof membrane and shall secure a history of the roof installation, roof maintenance and leak history. No mopped overlay roof systems will be considered. Single ply overlay systems can be considered if maintenance traffic warrants such a system and after infrared moisture survey, moisture probes and possible roof cores have been completed to confirm any areas containing suspected wet insulation. All wet insulation shall be replaced prior to any overlay system being installed. Architect shall confirm that existing structural system can support the additional load of any overlay system.
b. Standing/Ponding Water: Design of new roof systems shall include measures to ensure that positive drainage is present for all roof areas to eliminate the presence of ponding water 48 hours after rainfall occurs.
8. Metal Roofs: Metal roofs are not preferred but will be considered through a design variance request. Metal roofs should only be used as a design feature and not as the primary roofing material. Any metal roof should have a slope of 2:12 minimum. Provide a high temperature self-adhering rubberized asphalt underlayment beneath the metal roof. The metal should be prefinished with a fluorocarbon polymeric coating containing 70% PVDF Hylar 5000 or Kynar 500 finish. The finish shall have a Solar Reflective Index of 29 or greater.
9. Support roof level piping with pre-manufactured pipe supports installed at a maximum of 8 feet on center and within 2 feet of each change in direction. Install each pipe support over an additional layer of adhered modified bitumen membrane or single ply membrane as required by roofing manufacturer. No wood blocking shall be used for pipe supports. Specify pipe supports with rollers under all gas piping to allow for expansion and contraction. Pipe supports should be at a height that maintains roof warranty and complies with MEP requirements.
10. Locate roof penetrations a minimum of 36 inches away from vertical roof system flashing or other vertical roof penetrations.
11. Install roof level condensing units on pre-manufactured roof curbs (i.e. ThyCurb by Thybar) with galvanized sheet metal caps installed over plywood sheathing. Shim such curbs to provide a level surface for condensing unit. Secure condensing units to metal caps with galvanized sheet straps anchored to the unit and through the vertical face of the sheet metal caps. If possible, anchor the required electrical disconnects for the condensing units to the condensing unit.
12. Eliminate roof penetrations of any kind through the roof system base flashings.
13. On existing modified bitumen roof systems where repairs are being made, install the cap sheet after all roof level work has been completed by other trades and after the roofing manufacturer has inspected the base ply installation with all items being addressed and inspected, and the base ply has been installed and after it has been confirmed that all low areas that pond water beyond the 48 hour limitation have been largely eliminated through the installation of additional base ply material.
14. Install roofing manufacturer approved and warranted roof walk pads on all sides of all roof hatches, at the base of all roof access ladders and around rooftop equipment that will require periodic servicing.
15. Install continuous termination bars 12” min above roof surface, with fasteners at 6 inches on center along the leading edge of all roof system base flashings.
16. Install a minimum of two fasteners per side to anchor all exhaust fans to rooftop curbs. Such fasteners shall be installed in the vertical face of the exhaust fan base.
17. Install sheet metal counter flashing at all vertical flashings. Utilize 2-piece counter flashing with reusable receiver where possible. Exception: Counter flashings are not needed below sheet metal copings.
18. Install prefinished sheet metal wall panels at all parapet walls that are in excess of 36 inches high while providing minimum 8 inch high roof system base flashings.
19. Avoid concealed gutters where possible. If required, form out of stainless steel or copper to allow for all joints to be soldered. Install EPDM or high temperature self-adhering rubberized asphalt underlayment under all concealed guttering.
20. Provide butt type expansion joints at 50 feet on center at all guttering. Install downspouts with expansion joints taken into account.
21. Where multiple pipe penetrations occur in close proximity provide at least 1 inch of separation between each pipe, each to be properly flashed. Include removable flashing hood at pipe penetrations flashed with pourable sealer installed in galvanized metal penetration dams with soldered joints to allow for the pourable sealer to be serviced. Where resin flashings are to be installed provide a minimum of 6 inches between penetrations to allow for resin flashings to be installed.
22. When a rooftop equipment screen is required it shall be designed so as to limit the number of roof penetrations. Install sheet metal flashing hoods over all screen support flashings.
23. Install tapered insulation crickets, sloped at a rate of ½ inch per foot on the high side of all roof curbs in excess of 30 inches wide when the field of the roof is sloped at ¼ inch per foot.
24. Install thru-wall flashings with weeps at 24 inches on center above roof system counter flashings when new or existing cavity wall construction is present.
25. Review changes in metal deck direction with roofing manufacturer to confirm if roof expansion joint or separation curb will be required.
26. At locations where gas piping must extend up and over the face of a structure in an exposed condition install prefinished sheet metal cover to discourage individuals from climbing gas piping to gain roof access.
27. Provide underlayment under all roof level copings. Copings shall be fabricated in accordance with ANSI/SPRI ES-1 requirements and SMACNA.
28. Provide minimum 12” high roof system base flashings with such height being measured from the field of the roof to the top edge of the roof system flashings.
7.09 FIREPROOFING
A. Architect should design building in order to eliminate the need for fireproofing. If due to the building size or other considerations fireproofing is required by code, provide cementitious fireproofing in lieu of mineral fiber fireproofing. All fireproofing shall be designed per UL requirements and shall be detailed and specified. All facilities shall be of Type I or Type II construction.
07.10 FIRESTOPPING
A. Detail and or specify the installation of fire stopping at all penetrations through all fire-rated construction where required by code.
07.11 EXPANSION JOINT COVER ASSEMBLIES
A. Wall and Floor Locations: Provide all metal joint covers, aluminum frame construction, free of gaskets and fillers and designed to permit 50% joint movement at all interior conditions gaskets and fillers shall be allowed at exterior conditions.
B. Ceiling Locations: Provide flexible multi-layered rubber extrusions with continuous internal baffles to fit in an extruded aluminum frame.
08.01 HOLLOW METAL DOORS & FRAMES
A. Provide primed steel doors and frames to comply with all the requirements of the Steel Institute SDI100.
1. Interior Steel Doors should be provided at cafeteria/kitchens, locker rooms, gymnasium and athletic areas, etc. which are subject to high abuse. Provide 18 gage steel doors and 16 gage steel frames. (Use 2” frames at head of doors. Do not use 4” head for door frames unless to match existing construction.)
2. Exterior Steel and Glass Doors & Frames should generally be provided at all Exterior Entrances, except where Main Entry doors should be in keeping with the architectural style of building. See 08.02 for an alternate door type to be used in lieu of a Hollow Metal Door as a replacement for a Paneled Wood Door. Provide 16 gage steel doors and 14 gage steel frames. Use 2” frame at head of doors. Do not use 4” head for door frames unless to match existing construction.
a. All exterior doors/frames to be prepped for card readers. Card readers shall be installed at locations as coordinated with Allen ISD. All unused boxes shall be covered with gasket and faceplate.
3. Fire-Rated Door Construction should conform to NRPA 252 or UL 10C. Fire rated doors for area separations at egress corridors shall be as large as allowed by code pair 4’-0” x 8’-0” with no center mullion or as condition allows.
4. Door heights typically shall be 7’-2”. Other door heights or use of transoms require written approval of Allen ISD. Minimum door widths shall be 3’ with 3’-6” maximum for single-leaf door (4’-0” wide door is permitted at kitchen loading dock, band rooms, athletic rooms or at fire-rated door which will primarily be held in the open position). Upward only vertical rods are allowed at double doors.
08.02 ALUMINUM & GLASS-PANELED DOORS AND FRAMES
A. All doors at primary entrances will be replaced with Prefinished Aluminum and Glass-Paneled Doors.
08.03 WOOD DOORS
A. Typical Interior Doors should be flush solid core doors premium grade, 1-3/4” thick, clear pre- finished stain grade, plain sliced hardwood as approved by Allen ISD. Door finish shall be stained hardwood veneer at the Elementary School, Middle School and High School levels. Frames should be 16-gage welded steel. All glass shall be tempered unless fire-rated glass is required by Building Code. Fire-Rated Door Construction should conform to NFPA 252 and NFPA 80. No wood doors shall be used at exterior.
08.04 SOUND CONTROL DOOR ASSEMBLIES
A. At Auditorium Band, Choir, Ensemble, adjacent offices, practice rooms, and other Fine Arts areas in need of sound control, provide door and frame fabricated as a sound-retardant unit. The assembly should be tested according to ASTM E90 and Certified with an STC rating minimum of 48. At Middle and High School levels, an acoustical consultant should be part of the design team to determine sound control door locations.
08.05 ALUMINUM-FRAMED ENTRANCES AND STOREFRONT
A. Aluminum Entrances: For exterior installations, use 2” x 4½” profile, flush glazed (inside glazed at elevated floors). Door frames should have 3/16” thick wall construction and aluminum doors shall be wide-style type with 5” stiles, 6½” top rail, 5” intermediate (centered on panic device) and 10- 1/4” bottom rail beveled. Preferred finish is Architectural Class 1 Clear Anodic Coating. Other anodic and prefinished coatings will be considered through a design variance request. Where exterior or
interior pairs of doors are required, provide a keyed removable mullion. The maximum size of glass panel shall be 4’-0” x 4’-0”. Deflection of glass framing members under exterior design loads shall not exceed L/175 or ¾”, whichever is less. If allowed by building code requirements, aluminum storefront is acceptable to be used at interior areas such as Library, Administration, and Cafeteria entrances.
B. Aluminum Storefront Windows for exterior installation shall use 2” x 4½” or 2” x 6½” IECC profile at additions and new buildings, It is Allen ISD’s preference that all window locations for windows to be fixed. Preferred finish is Architectural Class 1 Clear Anodic Coating. Other anodic and prefinished coatings will be considered through a design variance request. Deflection of glass framing member under exterior design loads shall not exceed L/175 or ¾”, whichever is less. Per Allen ISD approval, light shelves shall be considered in classrooms. Exterior storefront windows shall be thermally broken. Aluminum subsills with preformed watertight end dams shall be provided.
C. Glass:
1. Entrance Doors: Tempered ¼” thick with tinting to either match existing construction or on new construction, as selected by Architect/Engineer.
2. Storefront and Exterior Windows: Double-glazed, 1” thick minimum, with tinting to either match existing construction or on new construction, as selected by Architect/Engineer. Unless noted otherwise, provide with hard-fired, low-emissivity coating. For security considerations, all glass shall be inside glazed. Provide shading for west and south facing glass.
3. Interior Doors and Borrowed Lights: In vision panels or borrowed lights, provide ¼” laminated or fire glass as required by code.
4. Skylights are prohibited unless required by Energy Conservation Code. Clerestory glass is allowed with approval of Allen ISD.
08.06 GLAZED ALUMINUM CURTAIN WALL
A. Limit the use of glazed aluminum curtain wall systems. If system is required for structural requirements, restrict its use to the main entrance. System should be designed for permanent resistance to air and water leakage. Preferred finish is Architectural Class 1 Clear Anodic Coating. Other anodic and prefinished coatings will be considered through a design variance request. Deflection of framing members perpendicular to the plane wall shall not exceed L/175 of its clear span or ¾”, whichever is less. System shall be thermally broken.
B. Glass: Refer to the Aluminum Framed Entrances and Storefront for requirements.
08.07
TRANSLUCENT FIBERGLASS SANDWICH PANEL ASSEMBLIES
A. At Middle School and High School gymnasiums, translucent fiberglass sandwich panels (Kalwall or equal) for window openings. Translucent Fiberglass Sandwich Panel Assemblies will only be considered through a design variance process. Translucent fiberglass faces shall be manufactured from glass fiber reinforced thermoset resins. The exterior face shall have permanent glass erosion barrier.
08.08 DOOR HARDWARE
A. General
1. All exterior doors, toilet room doors, and other doors required by codes shall receive closers. All doors shall be furnished with stops (wall mounted preferred). All doors shall have rubber silencers. The preferred hardware finish at new facilities shall be BHMA-626 Satin Chrome (US26D).
B. Preferred Hardware: 1. Locks
a. The specified mortised door hardware for all Classrooms is to be Corbin Russwin, ML2075 function, no substitution. This function is keyed on the exterior side and a thumb latch on the interior side. Full mortise locks at storage rooms shall be Corbin Russwin ML2057.
b. New door hardware at additions/renovations could be the same manufacturer as the existing hardware (Note: Contact Allen ISD for other manufacturers acceptable to the district). Match existing finish.
c. Schools with Cylindrical Type Hardware should be retrofitted with cylindrical locks.
1) Classrooms: provide C/W 3351.
2) Storage rooms: provide C/W 3357.
d. Include Allen ISD in the Door Hardware submittal review process.
2. Closers: Norton 8501 BFH – interior. LCN 4111 – exterior. Do not install manual hold-opens on fire- rated doors. Utilize electromagnetic hold-open devices wired into fire alarm system.
3. Panic Devices: (Corbin Russwin) 5200-S series on aluminum and glass storefront doors and series on wood and hollow metal doors with dogging feature with plugs at exterior doors.
4. Provide ball bearing butt hinges on all doors with closers. Provide continuous geared hinges on band room, athletics, and aluminum and glass doors.
5. Protective plates shall be provided at all the following locations: Classrooms, Athletics, Band, Restrooms, Gymnasium, Exterior doors and Kitchen.
6. Provide intumescent smoke seals at all fire-rated doors.
7. Security Arrangements: All machine and equipment rooms shall have locks and a common key system to allow access only to maintenance and custodial personnel.
8. Key cabinets shall be furnished with each building and shall have capacity to store all keys plus 25” additional stock. Each school shall be keyed, master keyed, and/or grand master keyed to existing Corbin Russwin key system, no acceptations will be considered. Provide bitting list with all locks. Provide three keys for each number.
08.09 LOUVERS
A. At new buildings, provide aluminum louvers with Architectural Class 1 Clear Anodic Coating. Other anodic and prefinished coatings will be considered through a design variance request. Architect should coordinate with Engineer to determine free area requirements for mechanical equipment. For additional/renovations, alternate material and finishes to match existing building may be considered with approval by Allen ISD.
FINISHES MATRIX CONTINUES
Locker Room
Showers/Restroom Resinous or Ceramic Mosaic Tile Resinous or Ceramic Mosaic Tile
Band/Choir/ Ensemble Modular Carpet
Painted Concrete or Painted CMU
Orchestra Modular Carpet Painted Concrete or Painted CMU
Activity Room Indoor Resilient Athletic Flooring
Library Modular Carpet
Office/ Administration Modular Carpet
Workroom/Lounge LVT
Ceramic Tile Painted Water-resistant Gypsum Board
Concrete or Painted CMU
Concrete or Painted CMU
Acoustical Ceiling Tiles and Diffuser Panels
Acoustical Ceiling Tiles and Diffuser Panels
Rubber Concrete or Painted CMU Painted Exposed Structure
Rubber Painted Gypsum Board Acoustical Ceiling Tile and Painted Gypsum Board
Rubber Painted Gypsum Board Acoustical Ceiling Tile and Painted Gypsum Board
Rubber Painted Gypsum Board Acoustical Ceiling Tile
Vestibules Walk-Off Carpet Ceramic Tile or Exterior Material
Entrance Lobby LVT
Main Corridor LVT
Stairs Ceramic Mosaic Tile or Rubber Treads and Risers
Academic Corridor Modular Carpet/LVT at Drinking Fountain Alcoves
Single-user Restroom
Porcelain Tile
Group Toilet Porcelain Tile
Restroom/Shower Slip Resistant
Porcelain Tile
Mechanical Sealed Concrete
Electrical/MDF/IDF Sealed Concrete
Custodial Sealed Concrete
Storage Sealed Concrete or LVT
Ceramic Tile Wainscott with Paint Above
Rubber Ceramic Tile Wainscott with Paint Above
Rubber Ceramic Tile Wainscott with Paint Above
Ceramic Tile or Rubber Ceramic Tile Wainscott with Paint Above
Rubber Ceramic Tile Wainscott with Paint Above
Porcelain Tile
Porcelain Tile
Porcelain Tile
Rubber
Ceramic Tile (full height)
Ceramic Tile (full height)
Ceramic Tile (full height)
Painted CMU or painted concrete.
Rubber Painted CMU or Gypsum Board
Rubber Painted CMU or Gypsum Board
Rubber Painted CMU or Gypsum Board
Acoustical Ceiling With Hold Downs and Gypsum Board
Acoustical Ceiling Tile and Painted Gypsum Board
Acoustical Ceiling Tile, Painted Gypsum Board (Exposed Structure upon AISD approval)
Acoustical Ceiling Tile, Gypsum Board (Exposed Structure upon AISD approval)
Acoustical Ceiling Tile, Painted Gypsum Board (Exposed Structure upon AISD approval)
Painted Water-resistant Gypsum Board
Painted Water-resistant Gypsum Board
Painted Water-resistant Gypsum Board
Painted Exposed Structure
Painted Exposed Structure
Acoustical Ceiling Tile
Acoustical Ceiling Tile
*Recommend sound consultant for design and use of materials
*Recommend sound consultant for design and use of materials
Tile backer board at showers
Ceramic tile wainscot at mop sink.
Painted plywood for panel mount
Prior to installing any floor covering using moisture-sensitive adhesives, the Contractor shall perform moisture testing on concrete slab. If moisture is elevated, apply appropriate sealing applications to prevent moisture penetration.
09.02 INTERIOR MATERIAL APPLICATIONS
A. The Architect/Engineer shall select finish materials from a palette of materials approved by AISD. In general, materials shall be selected for durability, minimum maintenance and ease of repair/ replacement with the AISD’s maintenance personnel.
B. Only impact-resistant, graffiti-resistant materials shall be used on walls in corridors, restrooms, mechanical rooms, kitchens, dressing rooms, shower rooms, locker rooms, and other areas subject to heavy use, abuse, and vandalism.
C. Minimum ceiling heights shall be 9’-0” unless otherwise required to match existing construction or as approved by AISD.
D. Acoustical Control: Minimize sound transmission between classrooms and other spaces, and to maximize the privacy of offices, conference rooms toilet rooms, walls around these spaces shall extend and seal the deck above.
1. Do not locate mechanical rooms or restrooms adjacent to classrooms, offices or library.
2. Minimum 55 NRC ceiling tiles.
3. The sound insulation should be either located within the wall cavity, or be achieved by wall mass, such as solid masonry.
4. All other partitions shall extend a minimum of 8” above the finished ceiling.
5. In special instructional spaces requiring specific acoustical control, such as band and choir rooms, isolate these areas acoustically from adjacent rooms, with special acoustical treatment, vestibules, isolation walls extending and sealed to deck above, sound traps/liners in mechanical systems, and acoustical seals on all doors. Utilize Acoustical Consultant for design.
09.03 PLASTER ASSEMBLIES
A. Provide cement plaster soffits at building entrances and cement plaster ceilings at locker room shower areas. Plaster should be installed on metal lath with scratch, brown and finish coats.
B. Apply plaster in accordance with ASTM C 926, PCA Plaster Manual and Manufacturer’s instructions. Utilize the most stringent if conflicts exist.
C. Exterior Insulation & Finish Systems (EIFS) shall not be used for either new or renovation projects.
09.04 GYPSUM BOARD
ASSEMBLIES
A. Install as recommended by U.S. Gypsum Co., “Gypsum Construction Handbook”.
B. Use Type X or better at all interior conditions.
C. Use 20 ga. min. metal studs at all interior partitions. Maximum stud spacing 16” on center.
D. Gypsum wall board shall be 48 inches wide by 5/8” thick by maximum permissible length, with tapered edges.
E. Utilize 5/8” thick water-resistant gypsum board in wet areas, meeting ASTM C1396.
F. Gypsum sheathing shall be 4’ x 8’ x ½” thick water-resistant treated core with glass mats front and back.
G. At shower locations provide a tile backer board per ASTM C 1178.
09.05
ACOUSTICAL CEILINGS
A. Acoustical Tile
1. 24” x 24” x 5/8” thick, non-directional, Fine Fissured tile.
2. NRC range of 0.50 – 0.60.
3. Acoustic panels shall be Class 25 (non-combustible).
4. Basis of design product is Fine Fissured Humiguard, manufactured by Armstrong World Industries, Inc.
B. Where required by code, provide fire-rated ceilings per UL assemblies. Architect shall coordinate with local jurisdiction for building code compliance.
C. Vinyl Covered Lay-in Panels, At Kitchens, Concessions and when required by code.
1. ½” thick, fine-textured, white vinyl-faced.
D. Fiberglass Acoustic Lay-in Panels, when a high level of sound control is required and as approved by AISD.
1. NRC range of 0.90 – 1.00.
E. Suspension Assemblies
2. Intermediate duty structural classification per ASTM C 635.
3. 1” wide white enamel finish.
4. Suspended ceiling systems should be of the type that allows the ceiling materials to be removed from its supporting framework, or otherwise removable, and replaceable, without refinishing.
5. Provide design to prevent uplift at vestibules.
F. Warranty
1. Minimum 30 year warranty against visible sag and resistance to mold/mildew and bacteria.
09.06 CERAMIC TILE
A. Tile for floor applications should have a Dynamic Coefficient of Friction that exceeds 0.42 when wet.
B. Tiles shall have a minimum hardness of 7 on the MOH’s scale.
C. Grout shall be sealed at the following locations:
1. Wall tile in wet areas
2. Floor tile
Epoxy grout were budget allows.
D. Install metal trim at outside corners, exposed edges and floor transitions to other materials. Basis of design is Schluter.
E. Install minimum 40-mil waterproof membrane at shower pans.
1. Provide a 40-mil thickness crack isolation waterproofing sheet membrane.
2. Crack Isolation Membrane: Chlorinated Polyethylene sheet of non-plasticized elastomer with non-woven polyester laminated to both sides, nominal 0.030” t hick or comply with ANSI A118.12.
3. Provide at Slab on Grade and 2nd Floor installations in compliance with ANSI A108.17.
F. Install 5/8” Type X Tile Backer board behind ceramic tile walls at shower location. Georgia-Pacific DensShield, or equal.
G. Toilet Rooms and Custodial Closets
1. Tile size to be approved by AISD. Prefer large format 8”x8” or larger.
2. Latex Grout in all tile.
H. Floor Tile shall be thru body porcelain.
I. Provide coved trim tile at wall base.
J. Damp cure Portland Cement grout for minimum of 72 hours.
09.07 QUARRY TILE
A. Seal with slip resistant, low lustre, non-buffing type sealer.
B. Damp cure grout minimum of 48 hours.
C. Epoxy grout were budget allows.
09.08 RESILIENT WOOD FLOORING
A. At gymnasiums in Middle and High School levels provide resilient wood flooring with vented base. Minimum thickness shall be 25/32”.
B. Maple flooring is preferred using mixed grain with Third and Better Grade D. Product should comply with sports-floor assembly manufacturer’s written recommendations of MFMA applicable to flooring type indicated.
C. Provide perimeter gap for ventilation and expansion.
09.09 WOOD STRIP
FLOORING
A. At Middle School platforms and the front of Middle and High School auditorium stages (public side of curtain) provide wood strip flooring.
B. Product should be solid maple, tongue and groove, Select and Better Grade, with random lengths but no strip less than 2’-0” in length.
C. Minimum thickness shall be ¾”.
09.10 TEMPERED HARDBOARD FLOORING SYSTEM
A. At middle and high school stages (located behind curtain) provide Masonite floor underlayment. Color selection shall be black.
09.11 RESILIENT FLOORING
A. Rubber Base and Accessories
1. Type TS (rubber, vulcanized thermoset) rubber base, 1/8” thick x 4” high.
2. Manufacture in continuous rolls.
3. Outside corners shall be matching, factory formed, pre-molded units.
B. Vinyl Composition Tile
1. 12 x 12 x 1/8 inch thick size.
2. ASTM F1066, Class 2 (through pattern construction.
3. Minimum 5 year warranty.
4. Provide slip-retardant, textured vinyl composition tile on sloped surfaces.
C. Luxury Vinyl Tile
1. Minimum 5.0mm thick
2. Minimum 0.55mm wear layer.
3. 10 year wear warranty.
D. Rubber Flooring – Requires district approval.
1. Homogeneous construction with non-porous texture.
2. Sheet or tile, minimum 3mm thick.
3. Rated for heavy traffic.
E. Slip Resistant Resilient Sheet Flooring
1. Basis-of-Design: Altro Stronghold 30 by Altro USA, Inc.
2. Wear Layer/Overall Thickness: 3.0mm, with slip retardant particulate suspended evenly throughout the product thickness.
3. Slip Resistance: ADA compliant, ASTM D 2047 James Machine, SCoF Dry 1.03 / Wet 0.88 DIN 51130 Ramp Test – R 12.
4. Accessories:
a. Vinyl Welding Rod.
b. Stainless Steel cap strip.
c. Stainless Steel Corner Guard – 5” high.
09.12 INDOOR RESILIENT ATHLETIC FLOORING
A. At weight room, provide Spartus as manufactured by Tuflex Rubber Flooring, Div. of Rubber Products, Inc, 27” x 27” x 3/8” thick tiles, or equal.
09.13 EPOXY-RESIN TERRAZZO
FLOORING
A. Provide terrazzo flooring with the matrix comprised of two-part 100% solids thermosetting epoxy resin. Aggregate shall be marble and recycled glass chips. Chip size 0 shall be used per NTMA grading standards.
B. Full coverage flexible membrane shall be Terroxy® Iso-Crack or approved equal.
1. Epoxy terrazzo sealer shall be slip-resistant (min. 0.5) and stain-resistant water based surface sealer that is chemically neutral with pH factor between 7 and 12, does not affect color or physical properties of terrazzo type indicated, and complies with NTMA Guide Specification for epoxy terrazzo.
2. Provide a terrazzo control joint at spacing recommended by manufacturer and over building slab control joints.
C. Specify non-slip finish.
09.14
PRECAST TERRAZZO STAIRS
A. Provide epoxy tread/risers for installation over concrete or steel substrate. Materials shall consist of white Portland cement (ASTM C 150), aggregates that meet ASTM C33, and marble chips that conform with NTMA gradation standards.
B. Reinforce precast with deformed rods or wire mesh as recommended by manufacturer.
C. Provide three lines of abrasive inserts at each tread.
9.15 MODULAR TILE CARPETING
A. Textured or level loop, tufted or woven, pile height shall be between 0.107 and 0.187, with maximum pile height variation of 1/32 inch.
B. Pile Density of minimum 7000 oz per cubic yard, for moderate to heavy traffic, as defined in HUD/ FHA publication UM-44d:
1. Pile density = [36 x pile yard weight (ounces per square yard)] / pile thickness.
C. Class 1 flammability rating.
D. Flooring Radiant Panel Test, NFPA-253, ASTM E 648.
E. Smoke Density, NBS Smoke Density Chamber NFPA-258, 450 or less.
F. Static Test, AATCC Test Method 134-1979, 2.5KV or below under standard test conditions 70°F, 20% R.H.
G. Appearance Retention Characteristics:
1. Appearance Retention Rating (ARR): Carpet and Rug Institute (CRI) test TMI101 graded in accordance with ASTM D-5252 (hexapod). Rating shall be a minimum of 3.0 after 12k revolutions.
2. Colorfastness to Light: Test Method AATCC-16E with a rating of 3 minimum, 4 for heavy light exposure locations, after 40 AATCC fading units using AATCC gray scale for color change.
3. Soiling Resistance: AATCC 171 (HWE) for 2 washings to simulate removal of topical treatments by hot water extraction, followed by AATCC 175. Minimum rating of 7 using AATCC Red 40 Stain Scale.
H. Durability Characteristics: Provide carpet meeting or exceeding the following:
1. Tuft Bind / Edge Ravel: ASTM D1335, minimum of 8 lbs-force or higher, wet.
2. Delamination Strength of Secondary Backing: ASTM D 3936 minimum 2.5 lbs per inch width.
I. Dye method: minimum 80% solution dyed, 100% preferred.
J. Backing:
1. Broadloom Carpet Backing:
a. Primary Backing: woven polypropylene or approved equal.
b. Secondary Backing: vinyl or urethane backing system.
2. Hard-Backed or Modular Carpet Backing: Primary Backing: Reinforced synthetic. Secondary Backing: vinyl or urethane backing system.
a. Cushion Backed allowed where acoustical dampening is desired. Pre-approval of use required by District. Secondary backing: PVC Free polyurethane cushion.
K. Lifetime warranty, with a 10 year, non-prorated warranty against delaminating, edge ravel, zippering, moisture penetration and maximum 10% wear.
L. Recycle excess/removed carpet.
9.16 WALLCOVERINGS
A. Vinyl wall covering shall in no case be used on any wall surface.
9.17 PAINTING
A. Provide paint as manufactured by one of the following:
Kelly-Moore Paints
PPG Paints
Sherwin-Williams Co.
B. Paint and finish the following materials, fittings, and equipment items which are exposed-to-view.
1. Iron, steel, and galvanized metal.
2. Unstained Wood.
3. Concrete masonry units.
4. Interior concrete ceiling and beam surfaces.
5. Gypsum board.
6. Interior caulked joints.
7. Portland cement plaster.
C. Bare and insulation covered piping and ductwork, conduit, hangers, grilles and registers, and primed metal surfaces and factory-finished surfaces of mechanical and electrical equipment.
D. Do not paint prefinished items, concealed surfaces, finished metal surfaces, operating parts, and labels, including the following:
1. Factory-finished metal lockers and finished light fixtures.
2. Architectural aluminum and stainless steel.
3. Interior concrete floors and steps and all exterior concrete.
4. Acoustic panel ceilings, unless noted on drawings.
5. Pre-finished cabinets.
6. Operating parts: Moving parts of operating mechanical and electrical equipment, such as: valve and damper operators, linkages, sensing devices, motor and fan shafts.
7. Labels: UL, FM, or other code-required labels or equipment name, identification, performance rating, or nomenclature plates.
E. V.O.C. (Volatile Organic Compound) Compliance: Products listed in the schedules and/or substitutes proposed for use by Contractor must be formulated to meet all applicable ordinances and regulations regarding maximum V.O.C. content. Utilize products which have been specially formulated to meet such requirements.
F. Painting: All wall surfaces shall be water based unless no suitable water-based coating is available for the particular substrate. Hollow metal frames shall be oil based.
1. Interior coatings that are required to be highly scrubbable shall be in a gloss sheen.
2. Oil-based paint is preferred for exterior metals.
3. Block Filler: Utilize block filler only of type and quality approved by primer and top coat manufacturer.
G. Doors: Doors shall have a clear finish with two coats of sealer and two coats of stain.
9.18 STAINING
A. Clear wood finishes, floor coatings, stains, primers and shellacs applied to interior elements must not exceed the VOC content limits established in South Coast Air Quality Management District (SCAQMD) Rule 1113, Architectural Coatings, rules in effect on January 1, 2004.
9.19 HIGH IMPACT WALL COATING
A. High performance coating as manufactured as PolyShield Plus by Colortex Coating with two step water-based system and ASTM scrub rating of a minimum of 11,000 rubs.
10.01 MARKERBOARDS & TACKBOARDS
A. Markerboards: Provide porcelain enamel steel liquid chalk writing system, 4’-0” high by length indicated in the Educational Specifications. Face sheet shall be 24 gage, leveled enameling steel with porcelain enamel writing surface. Core material of nominal ½ thick fiberboard or double-ply hardboard. Panel backing of 0.015” sheet aluminum or 26 gage sheet steel. Manufacturer shall factory assemble and bond together the face sheet, core and backing sheet. Color shall be white and panel shall be up to 16’ in length without joints. Mounting heights from finished floor to bottom of the chalkrail shall be:
Kindergarten 30”
Elementary 30”
Middle School 36”
High School 36”
Adult 36”
Note: writing wall surfaces will be considered by written approval prior to incorporating within the project.
B. Tackboards: Vinyl shall be heavy duty, self-healing laminated under high pressure to ¼” thick cork. Rigid backing panel of ¼” hardboard and cork shall be factory assembled and bonded together. Colors shall be recommended by Architect and approved by AISD. Tackboards shall be up to 16’ in length without joints. Provide tackboards at Elementary School academic corridors.
C. Tackstrips: Cork tackstrips shall be provided at Middle School and High School corridors located adjacent to Art Classrooms.
D. Frames & Trim: Marker and tack boards should have extruded aluminum frames and trim. Finish shall be Architectural Class II natural anodic coating. Provide 1” wide map rail made of aluminum with cork insert. Provide two flag holders for each room. Marker troughs should be of tubular extruded aluminum with cast aluminum end caps.
E. Provide permanent stenciled horizontal lines or horizontal/vertical grid lines on marker boards per school request and approval by Allen ISD Facilities and Maintenance Department
F. Marker board resurfacing is not allowed.
10.02 DISPLAY CASES
A. Provide manufacturer’s standard recessed display case, consisting of the display housing with extruded aluminum perimeter frame, sides and back, tackable surface, tempered glass shelves and sliding doors with lock and hardware, fully recessed florescent light fixtures, and operable transparent covers with hardware. Key all locks to district master system and provide tempered glass at doors.
B. Locations: Provide as follows
1. Elementary Schools: One display case near the administrative offices and gymnasium.
2. Middle & High School: In Corridor near main entrance, administrative offices, main entrance to the cafeteria, art classroom, music classroom, athletic areas and gymnasiums, and in areas of the library or resource center.
10.03 BULLETIN BOARDS
A. Provide 3” deep display case with clear, tempered safety glass. Architect and AISD to determine height and width. Finish shall be Architectural Class II natural anodic coating. Tackboard shall be seamless sheet ¼” thick cork with a resinous binder and washable vinyl surface. Color and texture should be recommended by Architect and approved by AISD. Furnish each cover with the manufacturer’s standard lock, keying all locks alike.
B. Location: In Corridor adjacent to teacher sign-in area, lounge and workroom area, cafeteria and in administrative office.
10.04 IDENTIFYING DEVICES
A. Interior Room Signage
1. Interior Graphics: All rooms and areas within a building shall be identified with a number. This includes stairs, restrooms, storage and mechanical rooms, etc. Elevators and wheelchair lifts are also required to be numbered. Rooms and areas that open directly onto a corridor shall be given a number designation (no letters) irrespective of whether or not they also have a room name. Rooms within other rooms (i.e., rooms without direct access from a corridor) shall have a letter designation following the room number (example: 214A, 214B, etc.) All rooms shall receive a sign. Architect/Engineer shall design a system of interior graphics consisting of signage attached to walls adjacent to doors to identify room numbers and room names for areas that are not classrooms, such as administrative, mechanical, toilets, resource rooms, and other areas. For renovation work, DO NOT change the room numbers which are already in place. Room numbering for additions and renovations should match existing room numbers. All signs shall comply with the Texas Accessibility Standards (TAS) and all other laws, ordinances, and authorities having jurisdiction. Braille shall be Grade II, having dimensions as required to meet TAS. Provide engraved or pre-molded lettering. Signs shall be mechanically fastened. Final interior room signage shall be approved by AISD.
2. Exterior exits shall be numbered to correspond with exterior exit signage.
B. Exterior Building Signage:
1. Cast Aluminum Letters: Cast aluminum alloy, smooth flat faces, sharp corners, true lines and accurate profiles. Provide at least two points of attachment for each letter. Finish shall be anodized or baked-on enamel, bonderized to aluminum, as selected by Architect and approved by AISD. Letters shall be fully fabricated before enameling. School name and address to be located at front of building. At MS and HS level, identify Gymnasium and Auditorium. Final exterior building signage layout and locations shall be approved by AISD.
2. Exterior exits shall be numbered to correspond with exterior exit signage.
C. Building Dedication Plaque:
1. Provisions for the inclusion of a dedication plaque shall be included in the construction documents for each project. Plaque will be developed by the Architect based on a template design and specification approved by AISD. A sufficient allowance may be used as the means of making provision for the plaque.
10.05 TOILET COMPARTMENTS
A. Provide floor-mounted, overhead braced 1” thick, solid HDPE (high density polyethylene) with rounded corners. Hardware shall be vandal-resistant satin stainless steel hardware. Provide ADA compliant sliding door latches, twisting catch operation is not acceptable. Continuous piano hinge and coat hooks should be installed on doors.
B. Provide backing within walls and ceilings to withstand partition loading.
C. Finish: Textured gloss finish, color to be selected by Architect and approved by AISD.
D. Overhead braces with sloped and contoured profile that makes them difficult to grip.
E. Urinal screens are required between fixtures and adjoining surfaces.
10.06 CORNER GUARDS
A. At outside corners in Corridors, provide flush-mounted (fire rated where required) brushed finish stainless steel, 4’-0” long min., 0.028 and 0.040-inch thick, medium duty or better.
B. At outside corners in Kitchens provide cement-on Guards 4’-0” long Type 430, 18 gage stainless steel corner guards, 90°, 1/8” radius. Mount with premium adhesive.
10.07 CUBICLE CURTAINS
A. Located at Clinic, provide cubicle curtain, track and hanger system that can isolate each cot individually. Track shall be extruded anodized aluminum. Carriers shall be an assembly with body and wheels that are self lubricating. The eye and hook assembly shall have a 2” drop from the bottom of the track. Curtains shall be the length on track plus 10% and height of ceiling to 15” maximum above the floor. Light shall be placed inside curtain area and individually switched. Fabric shall be flame resistant, polyester reinforced, anti-bacterial vinyl fabric.
10.08 TOILET ACCESSORIES
A. A/E shall indicate all accessories on both floor plans and interior elevations. All accessories shall be mounted in compliance with applicable IBC and ADA requirements. When the code-required mounting dimension is a minimum or maximum, the A/E should locate the accessory and indicate a dimension so as to provide for appropriate construction tolerance.
B. Owner shall provide and contractor to install accessories, including but not limited to the following listed items:
1. Soap dispenser, one at every two lavatories, breakrooms, and at classroom sinks.
2. Paper towel dispenser and receptacle or electric hand-dryers as directed by AISD in the following locations:
a. Paper towel dispenser and receptacle shall be located in employee restrooms, nurses’ office, breakrooms, and classroom sinks only.
b. Electric hand dryers (World Dryer XRA5E or approved equal) shall be located in public accessed group restrooms and locker rooms.
3. Wall mount or partition mount roll toilet paper holder shall be used and installed one per stall. 4. Coat hook and doorstop for each toilet stall.
5. Sanitary napkin receptacle shall be installed at women’s restroom in secondary schools and faculty facilities. One per stall.
6. Framed mirror over each sink. 18 gage Type 430 stainless steel mirror with bright polished finish and frame at middle and high schools. Mirrored glass surface with satin stainless steel frame at administrator’s teacher’s restrooms, and elementary schools.
7. Stainless steel grab bars in accessible stalls installed per ADA/TAS requirements. Provide wood blocking in walls at mounting locations.
8. Reversible Folding Shower Seat shall be water resistant, ½” thick solid phenolic with stainless steel frame, mounting brackets and self-locking mechanism.
9. Shower Curtain Rods shall be heavy duty with stainless steel finish. Shower curtain shall be heavy duty, opaque, matte white vinyl containing antibacterial and flame retardant agents.
10.09 FIRE PROTECTION SPECIALTIES
A. Provide as required by the AHJ Fire Marshal in public spaces. Coordinate with AISD as required to achieve a vandal-resistant installation.
B. Fire Extinguisher Cabinets: Preferred style: Semi-recessed (less than 4” projection from wall for ADA compliance). Provide white trim and door with window and continuous piano hinge.
C. Fire Extinguishers: Provide 10 lb. extinguisher that conforms to NFPA-10.
D. Fire Hose Cabinets are not approved.
10.10 LOCKERS
A. Secondary Student Personal Lockers: Pre-finished metal, 12” x 18” x 36” mounted two tiers high with a four-digit standard numbering system. Each locker shall have handle-hasp to receive a student-provided lock. Provide with coat hooks and book shelf. Lockers shall have a sloping top to prevent dust accumulation or shall be built in a wall recess. When existing lockers are to be replaced, consideration shall be given for locker size and quantity in a given footprint. Architect shall coordinate locker layout with AISD.
B. PE Areas: Gym clothes lockers shall be 12” x 12” x 12” and all-welded construction. Provide one locker for each student enrolled. 50% of the lockers will be for boys and 50% for girls. Street clothes lockers shall be 12” x 12” x 36”. Provide one locker per student assigned per class period. Each locker shall have handle-hasp to receive a student-provided lock. Finished end panels at lockers should be minimum of 18 gage. Lockers shall have a sloping top to prevent dust accumulation or shall be built in a wall recess.
C. Athletic Lockers: Size shall be determined by individual sport and level. Provide all-welded and ventilated construction. Each locker shall have handle-hasp to receive a student-provided lock. Finished end panels at lockers should be minimum of 18 gage. Lockers shall have a sloping top to prevent dust accumulation or shall be built in a wall recess. Middle School Football lockers shall be double-tier 18” x 24” x 36” with sloping top. High School Varsity Football lockers shall be open with integrated seat for lockable storage. Tops shall be flat for above-locker storage and be tight to adjacent wall.
D. Kitchen Lockers: Provide 12” x 12” x 36” and 12” x 12” x 12” lockers in an appropriate area near the kitchen restroom. Quantity of lockers to be determined by AISD. All lockers shall have a sloping top to prevent dust accumulation or shall be built in a wall recess. Lockers shall be heavy-gage steel with a baked-on enamel finish. Each locker shall have a handle hasp to receive a user-provided padlock. Provide a minimum of six lockers or as directed by AISD.
10.11 EXTERIOR SUN CONTROL DEVICES/PREFABRICATED WALKWAY COVERS
A. Exterior sun control devices and prefabricated walkway covers are not required by AISD, however acceptable for consideration as a project develops.
B. Sunscreens for playgrounds and play structures is prohibited.
10.12 FLAGPOLES
A. External halyard style only (do not use internal halyard style) 30’ tall, aluminum construction. AISD will provide flags.
B. Flag pole(s) should be located near and assist in identifying the main entrance to the building. A tapered, ground set, pole is preferred (manual operation). Flag pole should be furnished with one rope, with two sets of clips to facilitate flying both U.S. and Texas flags.
10.13 MOTORIZED PROJECTION SCREENS
A. Provide ceiling-recessed, motorized projection screens at Cafetorium, Library, and Auditorium. Screen size shall be determined by projector location and room size. Provide extra drop to lower screen within 2’-0” above finish floor. Screen shall be operated by 3-position control switch.
11.01 ENERGY EFFICIENCY REQUIREMENTS
A. All equipment shall comply with the highest Consortium for Energy Efficiency (www.cee1.org) tier available for that product category. Where no CEE rating is available, equipment should meet Energy Star criteria. All equipment should be cross-referenced with available PG&E rebates and the Project Manager should be alerted to their existence where applicable.
B. Any proposed equipment that is not eligible for either standard above must be approved in advance by the District’s Director of Sustainability.
11.02 AUDITORIUMS
A. To be developed per project with AISD, the Architect, and the Theatrical consultant.
11.03
FOOD SERVICE CONSIDERATIONS
A. To be developed per project with AISD, the Architect, and the Food Service consultant.
11.04
APPLIANCES
A. Architect/Engineer shall specify appliances including but not limited to the following item and location:
1. Refrigerator: Teacher Lounge, Special Education areas, Culinary, and Science Labs. Water connection should be provided at planned location. Under counter refrigerator to be provided within building nurse station.
2. Dishwasher (coordinate ADA): Science Prep, Life Skills, Family and Consumer Science, and Teachers’ Lounge.
3. Range: Family and Consumer Science, Life Skills.
4. Exhaust Vent: Family and Consumer Science, Life Skills. Exhaust must exit to the exterior of the building.
5. Microwave (Built-in): Family and Consumer Science, Life Skills.
6. Oven: Family and Consumer Science, Life Skills.
7. Under counter Refrigerator: Clinic, Concessions, Science Prep.
8. Clothes Washer/Dryer (commercial at athletic laundry): Family and Cons. Science, Life Skills.
9. Laundry Equipment:
a. When washing machines are specified for schools, consider the following:
1) Minimum 3.0 cubic feet capacity
2) Consortium for Energy Efficiency (CEE) Tier 3 rated
3) Front loading feature
4) White porcelain finish, galvanized steel shell construction
5) 115V, 60hz, 10A electrical power capacity. Assign a separate circuit for this equipment.
6) Should have a variety of selections for wash and spin cycles.
7) Acceptable manufacturers: Maytag, Whirlpool, Kenmore, General Electric
b. Coordinate location of such equipment with custodial services of school site. Location shall have water supply and drain line available, in addition to the electrical power, preferable at the custodial room or boiler/mechanical room.
c. Preferably washing machine should be near a service utility sink.
10. Cooktops: Life Skills.
B. The preferred color selection for appliances is black.
C. Architect shall coordinate with MEP engineer for electrical, mechanical, and plumbing requirements of appliances. Casework shall be designed for appliances to be installed with proper fit and trim. Review ADA/TAS for height and reach range requirements.
11.05 ATHLETIC EQUIPMENT
A. Basketball Backstops: Provide tempered glass backstops for full-court play on secondary school basketball courts. Also provide two additional sets of glass backstops for half-court play and equip these backstops with motorized operating lifting devices so that they may be parked in the up position for full-court activities. Provide retractable backstops at multi-purpose gyms. Backstops at elementary schools shall be height adjustable.
B. Volleyball Inserts: Install inserts into concrete slab under wood gym floor for volleyball net posts. Approved manufacturer is Sports Imports, No Substitutions unless approved by AISD.
C. Gymnasium Wall Padding: Provide protective mats on walls behind and adjacent to basketball backstops.
D. Roll-up Gymnasium Divider: At secondary school gymnasiums provide an electrically operated roll-up divider to section area in half. The bottom 8 feet of curtain shall be opaque solid vinyl coated polyester fabric. Upper curtain section shall be vinyl coated polyester mesh. Vinyl and mesh to be low emitting VOC.
E. Scoreboards:
1. Provide Fair-Play scoreboards (or approved equal) with durable, high-contrast LED digits to ensure optimal legibility with low maintenance. Wide angle LED’s allow for viewing from any location. Neoprene gaskets and polyurethane coating protects against outdoor moisture and corrosion. Acrylic cover and conformal coating protect indoor components. Provide wireless controller as standard equipment. Manufacturer shall include a 5-year warranty/ maintenance agreement that includes all electronics and labor. Coordinate with AISD scoreboard model, features, and locations for each project.
2. At High School and Middle School exterior fields, provide Daktronics scoreboard (or approved equal) at Stadium locations. Coordinate with AISD scoreboard model, features, and locations for each project.
11.06 SAFETY EQUIPMENT
A. Evacuation Chairs: Provide evacuation chairs as follows: one evacuation chair per stair, whether the floor exists to grade or not. It is recommended that evacuation chairs be distributed so that an approximately equal number of chairs are located on each floor above grade. The architect shall propose locations to the District for approval. Each evacuation chair should be located outside and adjacent to the stair enclosure, clearly visible within the corridor but without obstructing access to the stair or reducing the required exit width.
1. Do not place evacuation chairs inside the stair enclosures as this violates Fire Department requirements
2. Avoid building alcoves for the placement of the chairs. Each chair comes with a storage cabinet that shall be anchored to the wall.
3. Evacuation chair manufacturer and product: Basis of Design: Stryker Model Number 6254-070000.
B. AED and Cabinet: Coordinate AED cabinet quantities and locations with AISD.
1. Identification: Provide wall sign and cabinet identification lettering on the cabinet door
2. Cabinet Alarm: Actuation when door is opened. Powered by low voltage, complete with transformer.
3. AED Accessories: AED unit, carry case, adult pads, infant/child pads, lithium battery (with one extra battery), and rescue-ready kit.
4. AED manufacturer and product: Basis of Design: AED Plus by Zoll Medical Corporation
5. AED cabinet manufacturer and product: Basis of Design: Semi-recessed, Model 80000-0814 by Zoll Medical Corporation, color: white.
C. First Aid Kit: metal, wall-mounted cabinet without medications.
1. Design capacity: 150 people
2. First Aid Kit: manufacturer and product: Basis of Design: First Aid Only 90829 XL Metal SmartCompliance General Business First Aid Cabinet, ANSI 2021 Class B without Meds.
11.07 PROJECTION SCREENS
A. Projection Screens
1. Housing and Operation:
a. Metal casing
b. Surface mounted, manual operation is standard for all classrooms. Motorized operation is allowed and preferred only for screens wider than 10’-0”. For motorized applications, provide standard power to screen housing and low-voltage service to wall-mounted controls when possible. Controls shall include a lockable, keyed cover. When unlocked, the controls shall allow push-button operation without turning a key.
c. Spring rollers when housing is exposed (surface-mounted).
d. Controlled screen return for screens 10’-0” or wider.
2. Material: Vinyl/fiberglass, Green Guard certified, matte white with black backing and black border, flame-retardant, mildew-resistant, 1.0 gain, min. 60-degree half-gain angle. Glassbeaded screens are not allowed.
3. Mounting:
a. Screens shall be wall-mounted whenever possible. Mount sufficiently high to allow full viewable area to be visible when bottom is 4’-0” above finish floor. Specify extension brackets when necessary to so that the screen will clear any projecting obstructions.
b. Screens at assembly spaces with stages or raised platforms may be suspended from the ceiling structure in order to be near the stage curtain or edge of stage as appropriate.
4. Sizes:
a. All projection screens shall be standard manufacturer dimensions allowing images that have a 16:10 width-to-height aspect ratio. No custom sizes are allowed without prior approval from the District Project Manager and the District Architect.
b. Projection screens shall be specified to include extra black drop at the top of the screen when necessary to allow the bottom of the screen to rest 4’-0” above the finish floor. The A/E shall determine the required black drop based on the mounting height and height of the viewable screen area.
c. Classroom screens shall have a viewable area of approximately 96” W. x 60” H.
d. Screens at assembly spaces, including theaters, multi-purpose rooms, and libraries shall be sized so that the height of the viewable area is no less than 1/6 the distance from the screen to the last row of seats.
11.08 LABORATORY FUME HOODS
A. Laboratory fume hoods are to meet or exceed Cal/OSHA requirements per section 8 CCR 5154.1.
B. Provide ONLY ducted laboratory hoods exhausting air to the exterior of the building. Ducting shall be negatively pressurized inside the building envelope. Re-circulating or “ductless” (filter-equipped) hoods are NOT ALLOWED.
C. Do not incorporate demonstration (two-sided) laboratory hoods into any designs.
D. Position laboratory hoods away from doors, operable windows, and other air sources that can create turbulence and/or contaminant re-entrainment from the hood.
11.09 KILNS
Regardless as to whether fired by gas, electricity, or other means, kilns can emit potentially hazardous air contaminants including carbon monoxide, oxides of nitrogen, metal fumes, and halogen gases (chlorine and fluorine as examples).
A. All kilns must be purchased with the manufacturer-designed mechanical (fan-powered) ventilation (“venting”) kit. Care should be taken in preparing the order for the kiln as manufacturers may sell the venting kit as an optional added-cost accessory rather than as part of the basic kiln assembly.
1. Ventilation must be exhausted directly to the exterior of the building at a location away from foot traffic, play areas, windows, or building air intakes.
2. The exhaust system is to have a separate electrical circuit.
B. Through the use of the venting kit, points where firing and combustion products may escape from the kiln’s firing chamber and into the room must have air flowing into the firing chamber, unless the kiln itself is housed inside of an exhaust hood or ventilated enclosure. Such exhaust hoods or ventilated enclosures must have air flowing into them from the surrounding room in sufficient volume and velocities to capture firing and combustion products emitted from the kiln and prevent their escape into the room.
C. During kiln operation fans in venting kits must be operated in strict accordance with the manufacturer’s recommendations.
D. Pottery rooms need clay traps in sinks and storage for the work.
E. Anchor kilns securely to their working surface.
F. High temperature sprinkler heads required at kiln rooms.
G. Kiln manufacturer and product:
Paragon TnF-24-3 with Auxiliary Output (AOP.) The electrical power option is to be 208v / 3 Phase. The AOP is a relay-powered electrical receptacle mounted to the kiln that operates an Orton Vent Master Blower Unit during kiln firing. This is a sole source item and no substitutions will be allowed.
11.10 BOOK DEPOSITORY
A. Installation shall be ADA compliant.
B. Book Depository manufacturer and product:
Model No. 15-8951 Kwik Drop™ Through-Wall System “Book Return” as manufactured by Kingsley Library Equipment Co. This is a sole source item and no substitutions will be allowed.
11.11 PLAYGROUND EQUIPMENT
A. Playground equipment is typically provided in the construction contract. Coordinate with AISD playground equipment requirements and required site considerations for systems to be provided.
12.01 HORIZONTAL BLINDS
A. Provide 1” wide x 0.0085” thick, slat-type aluminum blinds in classrooms, science labs, library, and administration areas. Provide 1” valance for each blind. Unit shall tilt the slats to any desired angle and hold them at that angle. Operation shall be by wand of sufficient length and swivel for easy operations. Lift cord shall be of adequate diameter, braided of high-strength synthetic fibers.
12.02 WINDOW SHADES
A. Window shades shall be provided at cafeterias, libraries, rooms with floor to ceiling windows, and where black out conditions are required.
B. Recessed ceiling shade pockets at suspended acoustical ceiling or dropped drywall ceilings are discouraged.
C. Side and Sill Channels: For room darkening shades or blackout shades, provide 2-piece extruded aluminum side and sill channels to eliminate left, right and bottom edge light gaps. One-piece side channels will not be acceptable.
D. Shade Cloth Material:
1. All shades shall be made of interwoven non-combustible fiber, inherently flame-retardant and permanently flame-resistant. Material shall pass test per NFPA 701-1999, Test Methods 1 and 2. Fire rating: NFPA Class A.
2. Room-darkening shades shall be hemmed top and bottom, with both hems double needle stitched and backstitched at edges. Hems must be turned so that stitching passes through three thicknesses of fabric.
3. Sufficient length of materials to allow two complete wraps around roller when shade is fully extended Roller in hem construction prevents fabric from being pulled off roller. Fabric is to be attached by double wide staples. No adhesive is allowed.
4. Material for general shading shall be Greenguard certified, PVC-free.
5. For black-out shading, material shall be Greenguard certified, PVC-free.
6. Fabric Openness Factor: 3% where blackout shade not required.
E. Cord: Shall be stainless steel chain. Nickel plated steel chain not acceptable. Include cord clasp to be mounted at appropriate height above window sill side wall. Chain shall be rated for 90 lbs. breaking strength.
F. Fascia:
1. Continuous extruded aluminum “L”-shaped profile to conceal the roller shade tube mechanism. It shall be attached to the tube mounting brackets by snapping it in place on a hinge rib clip, without the use of adhesives, magnetic strips, or exposed fasteners. It shall be able to be installed across two or more shade bands in one piece as specified.
2. Fascia minimum thickness of 5/16-inch with paint finish in color as selected.
3. Provide bracket/fascia end caps where mounting conditions expose outside of roller shade brackets.
4. Notching of fascia for manual drive chain shall not be acceptable.
12.03 LABORATORY CASEWORK AND EQUIPMENT (MIDDLE AND HIGH SCHOOL)
A. Casework: Provide Red Oak Premium Grade veneer at all exposed exterior and semi-exposed surfaces of casework. Cabinet front and drawer style shall be flush overlay with vertical matching grain direction. Classroom upper and base cabinets shall be lockable with stainless steel wire finger
pulls. Use 1” thick epoxy-resin countertops at base cabinets, tables, sinks and workstations. 4” high epoxy-resin applied curb backsplash where base cabinets, tables, and workstations are adjacent to a wall. All sinks to be 1” thick epoxy-resin.
B. General: At Teacher’s demonstration table provide valve to shut off gas and water from student work stations. Provide separate switch to shut off electrical at student work stations. Located on the wall, behind Teacher’s demonstration table, provide emergency shut off button that disables all utilities in the labs (water, gas and electric) including teachers demonstration table. Dedicated computer outlets and Owner provided equipment outlets should not be tied to emergency shut-off. Provide reset button for utilities in adjacent prep room.
C. Equipment: For each science lab provide fire blanket, handheld emergency eyewash (teacher station), emergency shower/eyewash station, fire extinguisher, goggle storage (provide electrical outlet), acid storage cabinet, and flammable liquid storage cabinet.
D. Fume Hoods: Provide a constant volume fume hood in Chemistry and Integrated Physics and Chemistry. The Services included to the fume hood shall be gas, power and water. Provide a combination vertical and horizontal sliding sash. The countertop shall be epoxy resin.
12.04 LIBRARY FURNITURE AND EQUIPMENT
A. Architect shall coordinate with AISD for library furniture layout. Architect shall coordinate electrical and data requirements at circulation desk and computer stations. Furniture shall be provided by Owner FFE package. The General Contractor will furnish circulation desk and casework where included.
12.05
MUSICAL INSTRUMENT CABINET SYSTEM
A. At middle and high school level provide storage cabinets for musical instruments that are chip and abrasion resistant under normal usage and protect instruments and cases from damage. Shelving should withstand continuous use without surface or front edge breakdown. Provide heavy duty doors. Provide Wenger cabinets or approved equal. Each locker shall have handle-hasp to receive a student-provided lock.
12.06 FIXED AUDIENCE SEATING
A. Auditorium
Provide the Citation by the Irwin Seating Company or approved equal. Seating shall be comprised of an enclosed aisle end panel with veneer surfaced insert panel, a one-piece injection molded polymer high impact-resistant rear panel that shall be not less than 25” in length, extending down to the rear of the seat. Backs shall be rectangular shaped, padded and upholstered on their face. The seat pan shall be self-lifting with a torsion spring seat lift mechanism and have a 3” formed cushion over an ergonomic-formed polymer substrate. The seats shall be supported by a 14 ga. steel standard chair platform with a solid wood arm rest. Row and seat shall have identification plates. Provide ADA accessible seating as required. Seats shall be 20”-22” wide with color selected from manufacturer’s standard and premium colors.
B. Lecture room seating in secondary schools shall be fixed tables with integrated wire management system and grommets.
12.07 TELESCOPING BLEACHERS
A. Telescoping Bleachers: Provide multiple-tiered seating rows comprised of seat and deck components, risers, and supportive understructure. It shall be operable on the telescoping principle, stacking in minimum floor area when not in use. Vendor information and parts list should be included as part of the close-out documents. For bleachers greater than 5 rows provide a non-
friction electrical power system. Operation shall be keyed to remote wall switch panel with view of bleachers. Provide first tier accessible cutouts per requirements of ADA and Texas Accessibility Standards.
12.08 SITE FURNISHING
A. Bicycle Rack Design:
1. Racks shall be designed to accommodate “U”-shaped locking devices and support the bicycle horizontally in two places.
2. The racks shall be constructed of durable materials to withstand permanent exposure to the elements, such as powder-coated metal or stainless steel.
3. All Bicycle parking spaces must be hard surfaced and dust free and consist of at minimum a compact gravel base.
4. Refer to City Zoning Ordinance for additional requirements.
B. Seating and Tables: Adjacent to Building Entry, Cafeteria and play areas the architect should consider the use of Owner provided outdoor trash receptacles, seating and tables. Units should be mounted to pavement for permanent installation. Provide suitable area for seating and tables for (High School, Middle School, or Elementary School) students with a position meeting ADA/TAS requirements
12.09 CASEWORK
A. General casework: Provide plastic laminate tops and faces on all exposed surfaces. PVC edges applied with hot melt. Drawers and cabinets to be locked are to be keyed differently, with locks in individual rooms keyed alike. Provide a masterkey. Shelf supports for adjustable shelves shall be twin pin design with anti tip-up shelf constraints for both ¾” and 1” shelves. Design to include keel to retard shelf slide-off and slot for ability to mechanically attach shelf to clip. Load rating to be a minimum 300lbs at each support without failure. Hinges shall be 170 degree six-way adjustable self-closing concealed. Acceptable manufacturers of casework include: Case Systems Inc., TMi Systems Design Corp, Concepts in Cabinetry, or LSI Corp of America.
12.10 ENTRANCE FLOOR MATS
A. Building entrances to be walk-off carpeting, entry mats are not allowed.
12.11 CHANGING TABLES
A. Coordinate with AISD changing table locations in restrooms that serve the public such as restrooms near gymnasiums and auditoriums.
B. Changing Table manufacturer and product:
Koala Kare KB310-SSRE Horizontal Stainless Steel Recessed-Mounted Baby Changing Station. This is a sole source item and no substitutions will be allowed.
13.01 GENERAL
A. The design team shall coordinate with Allen ISD to establish minimum performance requirements for all items, including the following items listed below within this chapter as defined by the CSI Master Format. The minimum performance standards are to be developed on a per project basis and reviewed with Allen ISD prior to the issue of Construction Documents for bidding or permitting.
1. Pools
2. Insulated Rooms
3. Tensioned Fabric Structures
4. Green Houses
5. Grandstands
6. Frame-Type Bleachers
7. Metal Storage Buildings
8. Metal Building Systems
9. Storm Shelters
10. Special Education spaces that exceed standard requirements.
13.02 SOUND-CONDITIONED ROOMS
A. Design Requirements: Provide modular, sound-isolating enclosures with internal acoustical environments suitable for music instruction and rehearsal, voice announcements, tape recording, private consultations, testimony and remedial instruction.
1. Rooms shall be modular in 15” increments with individual panels that are removable and replaceable with only partial disassembly of module.
2. Standard module should include perimeter neoprene floor seal, door with vision light, corner posts with integrated speakers, enclosures and wiring. Wall panels shall have integrated wiring and mountings for microphones. Ceiling grid and panels shall be included with integrated ventilation, illumination, power and signal distribution systems. Components should allow for upgrade to V-Room Practice without disassembly. Manufacturer shall be Wenger Corporation or approved equal.
3. AISD will also consider built-in-place sound conditioned rooms where budget is a concern.
13.03 MODULAR BUILDINGS
A. The use of modular classroom buildings is discouraged and will only be considered if time constraints are an issue on the project. If modular classroom buildings are approved, the buildings components must comply with and follow the District Standards and meet code and TEA standards.
14.01 HYDRAULIC ELEVATOR
A. Provide hydraulic, holeless passenger/stretcher (Offset Entry) elevators at all multi-story facilities, including existing facilities so designated. Provide 3’-6” clear opening for door and inside of cab dimension of 4’-9” x 6’-8”. Car speed shall not exceed 150 feet per minute. Capacity shall be a minimum of 3000 lbs. Walls shall be high pressure laminate with hooks for removable pads. Floor shall be vinyl composition tile and ceiling a suspended white translucent diffuser. Provide 1-1/2” round handrail with stainless steel finish. Elevator shall have keyed hall switch for access at all levels. Pit shall have a ladder and permanently installed sump pump that complies with State of Texas Elevator Code and Local Municipal requirements.
Design Basis: TK Elevator’s Evolution 100 verify EOX Self-Supported Machine Room-Less elevator or approved equal.
B. Elevator shaft shall be rated as per the building code requirements.
C. Elevators, hoistway shafts, and machine rooms shall comply with IBC Chapter 30, including all standards referenced therein.
D. Per ASME A17.1, article 8.4.11.1, where buildings are designed with expansion joints, the machine room and the hoistway shall be located on the same side of an expansion joint.
E. Isolate pumping plant and piping from building structure.
F. Submittals are to be reviewed by the District and Project Architect.
G. Emergency telephone shall ring the main site office and after four rings shall roll over to the emergency repair line weekdays 7:30 to 4:00 and after hours and weekends.
H. Provide telephones and have them identified at the main telephone board with a durable, permanently marked tag with assigned phone number and “Elevator Emergency Telephone.”
I. Keys for elevators, elevator machine room, and elevator fire recall are to be standardized; verify with the Allen ISD prior to bid.
J. Maintenance service
1. Initial Maintenance Service: Beginning at Substantial Completion, provide twelve (12) months’ full maintenance service by skilled employees of the elevator Installer to include:
a. Monthly preventative maintenance, repair or replacement of worn or defective components, lubrication, cleaning, and adjusting as required for proper elevator operation at rated speed and capacity.
b. Provide parts and supplies as used in the manufacture and installation of original equipment.
c. Provide emergency callback service 24 hours-per-day, 7 days-per-week with a response time of 2 hours or less. Provide emergency callback service 24 hours-per-day.
I. On renovation projects, verify with AISD if an elevator modernization/refurbishment is required. A modernization/refurbishment typically consists of upgrading the elevator systems and can include new equipment, technologies, methods of operation, and updating the elevator’s interior finishes.
14.02 OVERHEAD BARRIER-FREE LIFT
A. For use in Life Skills restrooms, provide a ceiling mounted Personnel Transfer System that includes hand control, battery charging system patient sling, lifting module and rail system. Rail system shall be rigidly attached to structure above.
14.03 WHEELCHAIR LIFTS
A. Provide manufacturer’s standard wheelchair lift system to meet IBC, ADA, TAS Standards, and State Elevator Code. The rated load shall be 750 lbs. minimum with a speed of 9 feet per minute. The
station controls shall be push button with key operated on/off switch. Provide key operated call- send controls at upper and lower stop. Platform shall be non-slip. Finish to be electrostatically- applied powder coat selected from manufacturer’s standard and optional colors.
B. Vertical platform lifts are the preferred product for most applications.
C. Incline lifts mounted along existing stairs are discouraged and acceptable only in extreme hardship situations with prior approval by Allen ISD. If used, select option for manufacturer-provided handrail. Design layout so that when lift platform folds up and stores away it does not infringe upon required exit width or create an obstruction or hazard at either top or bottom of stairs for people entering or exiting.
D. Provide appropriate signs related to ADA, TAS, and State Elevator Code. For type of signs, mounting heights and other related information, refer to Division 10 for signage.
E. Proposed substitutions for approved equal products must be approved by the AISD Operations Dept. representative and authorized in writing by the District Architect.
F. Provide emergency power back-up and same maintenance/operation and certification submittals as required for elevators.
G. Avoid exterior lifts.
H. Vertical platform lifts shall be pit mounted.
I. Paint a “keep clear” zone on the floor, adjacent to the top and bottom landings. The “keep clear” zone includes the floor area needed to access the lift controls.
J. The first two years of lift maintenance are to be included in the Construction Contract. Contact telephone numbers and maintenance records must be made available to the District. A final service and inspection is required three weeks before the expiration of the two-year warranty period.
21.01 GENERAL PROVISIONS
A. All new facilities, new additions to existing facilities and remodeled facilities for Allen ISD shall be provided with full and complete fire suppression systems as required for practical operation and in conformance with all applicable regulations, codes, and ordinances.
B. All materials shall be UL and FM approved and shall manufactured in the United States and/or shall comply with the most current North American Free Trade Agreement (NAFTA)/United States-Mexico Canada Agreement (USMCA).
C. All Fire Suppression System equipment and installation shall meet the requirements of NFPA No. 13, 14, 20, 24, 25, 70 and 72.
D. Architect/Engineer shall coordinate with the Local AHJ the specific requirements for the following:
1. Standpipe Systems
2. Fire Department Connection location
3. Floor Control Valve Assemblies
4. Roof Mounted Test Hydrants
5. Backflow Requirements
E. The Fire Suppression System shall be designed to provide a minimum of 10 psig safety factor into all the hydraulic calculations.
F. The maximum velocity in the pipes shall not exceed 32 ft./sec.
G. Standard pressure piping system components shall be listed for 175-psig minimum working pressure.
H. Engineer shall coordinate with local AHJ the exact requirements of the following:
1. Location backflow device.
2. Location of Fire Department Connection, in relation to the building, fire lane and fire hydrants.
3. Locations of Hose Valves/Standpipes (when required).
I. All materials shall be readily available by local suppliers.
J. Piping material shall be provided by a single source.
K. Engineer shall specify that the Contractor shall provide a list of all the installed Equipment and Associated Warranty items in their Operating and Maintenance (O&M) manuals. The list shall identify which equipment has a one-year warranty and a separate list that shall identify which equipment has an extended warranty and the length of that warranty. Provide start dates for all warranties and note when warranty is parts only or includes parts and labor.
21.02 FIXTURE AND EQUIPMENT DETERMINATION
A. General design criteria and preferred manufacturer requirements are as required by this document and as required by AISD.
21.03 PIPE ROUTING
A. In general, piping shall be run parallel or perpendicular to the lines of the building. No fire suppression piping shall pass through elevator machine rooms, transformer vaults, electrical rooms, telephone rooms, MDF room, or IDF room. The only fire suppression piping allowed will be for the specific devices required to serve those spaces.
B. Where existing fire suppression systems are being renovated for new additions or renovations it shall be noted: “The Fire Sprinkler Contractor shall rework the existing fire suppression system as required to accommodate all areas of new construction, including all areas of renovation and additions. Contractor shall rework the existing fire main, distribution piping and branch piping
as required in order to accommodate the renovated areas and areas of new construction.
Relocate and/or replace existing sprinklers as required. Provide new sprinklers as necessary for complete coverage. Contractor shall match existing building materials & methods unless otherwise noted in the specifications. Where sprinkler piping is removed disconnect & cap above ceiling. Contractor shall field verify scope of work prior to bid submittal.”
21.04 FUTURE EXPANSION
A. If there is a known future expansion the fire suppression area of coverage and piping systems shall be sized to accommodate the known future expansion.
21.05 UTILITIES
A. Architect/Engineer shall coordinate with local AHJ in order to obtain a Fire Flow Test for all new projects or projects where the fire suppression systems are affected. If the local AHJ will not provide this information free of charge, the Architect/Engineer shall coordinate with AISD to pay for having a Fire Flow Test completed. The Architect/Engineer shall coordinate the location of the Fire Flow Test to be completed “across” the project property. This information shall be utilized to determine if a Fire Pump will be required at the property.
21.06 DESIGN CRITERIA
A. A wet system shall be installed in heated areas and dry pipe systems in areas subject to freezing. When heated areas are not available and dry pipe system not used, provide heat tracing and/or insulation installed per NFPA and per local Fire Marshal Requirements.
B. Steel Pipe and Fittings:
1. The minimum fire main size shall be 6”. This is the minimum size and may need to be increased in order to comply with NFPA requirements and flowrates.
a. The fire riser shall be a single welded 304 stainless steel riser with flanged ends and tie-rod brackets. Unit shall be UL and FM approved. Equal to Ames, IBR Series.
2. Threaded pipe: 1-1/2” and smaller shall be Sch. 40 black steel, ASTM A 53 Grade B.
3. Fittings 1-1/2” and smaller shall be minimum Class 150 malleable iron threaded fittings. Fittings shall be UL listed and FM approved. Acceptable manufacturers: Tyco or Anvil.
4. Grooved pipe: 2” and larger shall be Sch. 10 black steel, rolled groove (NO THIN WALL, EDDYFLOW, OR EDDYTHREAD PIPING SHALL BE ALLOWED). Standard weight, black-steel pipe: ASTM A 53/A 53M, Type E, Grade B. ASTM A 53 Type F pipe should not be used for grooved joints. Acceptable manufacturers: Bull Moose, Allied, or Wheatland Tube.
5. Fittings 2” and larger shall be mechanical grooved. Fitting shall be UL listed and FM approved. Mechanical grooved fittings shall be the flush sealed gasket style equal to Victaulic “AWWA Flush Seal” with a minimum pressure rating of 300 psig. Acceptable manufacturers: Victaulic, Tyco, or Anvil.
6. No Mechanical Tees shall be utilized.
7. Where required by local AHJ, provide a double detector check valve assembly with indicating butterfly valves. Ames Maxim, M300-BFG Series.
8. Where required by local AHJ, provide a reduced pressure zone detector valve assembly with indicating butterfly valves. Ames Maxim, M500-BFG Series.
C. The installation of the entire Fire Suppression Systems shall comply with all rules and regulations of the National Board of Fire Underwriters, the Local Building Code, Local Fire Marshall, and the latest Requirements of NFPA Pamphlet 13, and other local authorities exercising jurisdiction.
D. Valves:
1. Ball Valves: Shall be UL and FM approved, 350 psig rated with bronze body and grooved or threaded end connections. Acceptable product: Victaulic 728 or equal by Tyco or Anvil.
2. Butterfly Valves: Shall be UL and FM approved, 300 psig rated with ductile iron body and grooved end connections. Acceptable product: Victaulic 705 or equal by Tyco or Anvil.
3. Gate Valves: Shall be UL and FM approved, 250 psig minimum pressure rated with ductile iron body and grooved end connections. Acceptable product: Victaulic 771 and 772 or equal by Tyco or Anvil.
4. Check Valves: Shall be UL and FM approved, spring-assisted swing check for vertical or horizontal installation. Valves are rated for 250 psig minimum, ductile iron body and grooved end connections. Acceptable product: Victaulic 717 and 717R or equal by Tyco or Anvil.
5. Universal Manifold Assembly: Shall be UL and FM approved, NPS 1-1/4” up to 8” where the universal manifold check valve assemblies are specified for use in wet-pipe sprinkler systems as floor control manifolds or shotgun riser check valves they shall be listed for such use. The body shall be ductile iron with a pressure rating of 300 psig minimum that incorporates a control valve, check valve, flow switch, test & drain assembly, adjustable relieve valve and gauges into a compact footprint. The test and drain assembly shall contain an adjustable relief valve with a range from 175 to 310 psig and a universal test orifice. Acceptable product: Victaulic Globe UMC or equal by Tyco or Anvil.
6. Alarm Check Valves: Ul and FM approved, the valve shall be ductile iron with grooved end connections and 300 psi pressure rating. The valve internal parts shall be replaceable without removing the valve from the installed position. Acceptable product: Victaulic 751 or equal by Tyco or Anvil.
7. Tamper Switches: Provide tamper switches equal to Potter Type OSYSU or PCVS Series on all control valves for connection to the fire alarm system.
8. Water Flow Detectors: Provide a water flow detector equal to Potter Type VSR Series at the main fire protection piping entrance to the building or system, in addition to other locations required, to detect any flow in the system from any cause. If flow is detected, sound a local alarm.
9. Floor Control Valve Assembly: Provide a floor control valve assembly where a single sprinkler alarm valve assembly controls more than one floor level. Unit shall be monitored by a flow switch. Drain line from control valve shall be routed to the exterior portion of the building wherever possible and terminated open sight a minimum of 6” above the finished grade.
10. Dry and Preaction Valves: Shall be UL and FM approved, low differential and latched clapper design with ductile iron body and grooved end connections. Pressure rating shall be 300 psig minimum. Valve internal parts shall be replaceable without removing the valve from the installed position. Valve shall be externally resettable. Acceptable product: Victaulic 768 and 769 or equal by Tyco or Anvil.
11. Where a Dry or Pre-Action system is provided a Nitrogen Generator shall be provided for the volume of the system.
12. Nitrogen Generator:
a. The nitrogen generator shall have an air compressor system that is sized appropriately for the application and capable of achieving system supervisory pressure within 30 minutes in accordance with requirements of NFPA 13. The air compressor system may include an external compressor.
b. The nitrogen generator shall provide a minimum of 98% purity nitrogen to the fire sprinkler system.
c. The nitrogen generator shall be equipped with a filtration system to remove residual water and all hydrocarbons from the air stream.
d. The nitrogen generator shall have a nitrogen control panel capable of monitoring compressor runtimes, nitrogen generator pressure, as well as its operational mode locally and via the internet.
e. The nitrogen generator shall have a leak detection system capable of determining sprinkler system leak rates, giving alerts if leaks develop within the sprinkler piping, nitrogen generator system or air compressor.
f. The nitrogen generator shall be able to indicate trouble alerts: locally via nitrogen control panel, via BMS trouble alert relay, via internet, and via email.
g. The nitrogen generator system shall automatically switch between air bypass mode and nitrogen generating mode based on the demands of the sprinkler system.
h. The nitrogen generator shall have a nitrogen storage tank that conforms to the ASME standard for pressure vessels.
i. Acceptable Manufacturers: Potter Signal or ECS (Engineered Corrosion Solutions).
E. Sprinklers:
1. Provide standard coverage quick-response Bulb-Type, (“O-Ring” water seal design not acceptable) automatic fire sprinklers with 155 Deg.F. or as required by NFPA-13, operating temperature of the following style and finish (all sprinkler heads shall be centered in the ceiling tiles). Acceptable manufacturers: Victaulic, Tyco, Reliable or Viking.
Style:
U - Upright C - Flat Concealed
P - Pendant D - Dry (e.g. ‘DF’ is Dry Flush)
S - Sidewall T - Flat Concealed Institutional Tamper Proof
F - Flush
Finish:
CB - Cast Brass
CP - Chrome Plated, Bright Polished
P - Paint as directed by Arch.
R - Recessed (or ceiling; max 1” drop below ceiling)
Type:
AS - Automatic Sprinkler
OO - On-Off Sprinkler
Sprinkler System Type:
WP - Wet Pipe
DP - Dry Pipe
NF - Non-fire-protection connections on automatic sprinkler system
AF - Anti-freeze
2. For ceiling with a finish other than “off-white” sprinklers shall have adjustable drop-down deflector type concealed sprinkler heads with manufacturer painted cover plate. Final color selection shall be approved by the Architect and shall be submitted for approval prior to ordering the cover plates.
F. Accessories:
1. Victaulic Flexible Sprinkler Hose Fittings are allowed but shall not exceed 36” in length. Victaulic VicFlex AH2 or AH2-CC with approved bracket or equal by Easy-Flex or FlexHead Industries.
2. Furnish sprinklers with cage guards in gymnasiums, locker rooms or activity center. Provide where exposed sprinklers are installed at or below 8’-0”. Cage guards shall be a UL listed and engineered products which shall be listed by the sprinkler manufacturer for specific use on the exact sprinkler installed.
3. Wall Mounted Weather-Proof Horn/Strobe or Water-Motor Gong (As required by local AHJ): Provide wall mounted weatherproof, red finished, 120V exterior horn/strobe UL listed FM approval with back box equal to Potter SH-120 Series or Provide a 10” weatherproof, red enameled finish, water-motor gong, UL listed, FM approved Victaulic 760 Water Motor Alarm or equal by Tyco or Potter.
4. Tamper - Flow Switches: Provide tamper switches equal to Potter Type OSYSU or PCVS Series on all control valves for connection to the fire alarm system.
5. Automatic Air Vents: Provide as required by NFPA 13, shall be UL listed, FM approved rated up to 175 psig. Provide with ball valve and union upstream of the y-strainer. Potter PAV or pre approved equal.
G. Engineer shall coordinate fire suppression inspector test connection and drain down locations with Architect prior to approval of shop drawings. In general, avoid areas of flatwork that could be stained by the testing process.
22.01 GENERAL PROVISIONS
A. All new facilities, new additions to existing facilities and remodeled facilities for Allen ISD shall be provided with full and complete plumbing systems as required for practical operation and in conformance with all applicable regulations, codes, and ordinances.
B. All piping materials shall be manufactured in the United States and/or shall comply with the most current United States-Mexico-Canada Agreement (USMCA).
C. Architect/Engineer shall coordinate with the Local AHJ the specific requirements for the following: 1. Backflow Requirements.
D. All materials shall be readily available by local suppliers.
E. Piping material shall be provided by a single source.
F. All faucets and flush valves shall be manual. No automatic infrared sensors shall be used.
G. Engineer shall specify that the Contractor shall provide a list of all the installed Equipment and Associated Warranty items in their Operating and Maintenance (O&M) manuals. The list shall identify which equipment has a one year warranty and a separate list that shall identify which equipment has an extended warranty and the length of that warranty. Provide start dates for all warranties and note when warranty is parts only or includes parts and labor.
22.02 FIXTURE AND EQUIPMENT DETERMINATION
A. General design criteria and preferred manufacturer requirements are as required by this document and as required by Allen ISD.
22.03 ENERGY CONSERVATION
A. Projects for all new facilities, new additions to existing facilities and remodeled facilities, where appropriate, shall conform to the current codes as adopted by the local AHJ.
22.04 PIPE ROUTING
A. In general, piping shall be run parallel or perpendicular to the lines of the building. No plumbing piping shall be installed in or pass through transformer vaults, elevator machine rooms, electrical rooms, telephone rooms, MDF room, or IDF room.
B. Where existing facilities are being renovated and sawcutting of the floor is required in order to accommodate underground utilities, the Architect and Engineer shall review available structural documents for existing slab conditions. Any sawcutting of structured slabs, post-tension slabs or slab on carton forms shall be coordinated between the Architect, Structural Engineer and MEP Engineer.
22.05 FUTURE EXPANSION
A. In sizing the various plumbing systems, ample provisions shall be made for anticipated future additions to the building, including, but not limited to, the required equipment spaces needed to accommodate the future additions.
22.06 UTILITIES
A. Verification: Architect/Engineer shall, where practically possible, verify the affected utilities for the size, location, direction of flow, and depth of all sanitary sewer, storm sewer, water, and gas mains adjacent and/or available to the project. Verify the pressure for all water and natural gas lines. Where existing documentation is not available and where verification is not practically possible, the Architect/Engineer shall coordinate with AISD for obtaining this information through AISD maintenance personnel, video scoping (to be paid for by AISD) and/or DIGTESS.
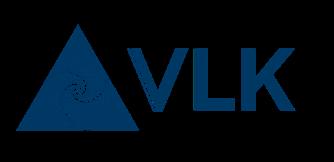
B. Architect/Engineer shall coordinate with local AHJ in order to obtain a Fire Flow Test for all new projects or projects where the plumbing systems are affected. If the local AHJ will not provide this information free of charge, the Architect/Engineer shall coordinate with AISD to pay for having a Fire Flow Test completed. The Architect/Engineer shall coordinate the location of the Fire Flow Test to be completed “across” the project property. This information shall be utilized to determine if a Domestic Water Booster Pump will be required at the property.
C. Construction Documents:
1. Indicated Services: Indicate location, depth, size, and direction of flow of existing or proposed new sanitary sewer and storm sewer mains and indicate location, pressure, and size of existing and proposed new water and gas mains.
2. Elevations: Finished floor elevation(s) for the building shall be clearly and prominently indicated. Building sanitary and storm water lines shall indicate approximate flowline elevations below finished floor. In addition to approximate flowline elevations at critical junctions underneath the building slab. Where possible, building shall be designed to permit gravity drainage of sanitary sewer and storm water.
3. Existing Conditions: Plans shall indicate all known existing underground work that is in the area related or systems related to the project, including piping, valves, manholes, pits, vaults, transformers, electrical wiring, telephone facilities, etc.
22.07 DESIGN CRITERIA: ALL PLUMBING SYSTEMS SHALL BE DESIGNED IN ACCORDANCE WITH THE FOLLOWING CRITERIA:
A. Domestic Water Systems:
1. Piping systems within 5’-0” of the Building:
a. Shall be Type K below slab or grade and Type L copper above slab or grade.
b. Pipe sizes 2” and larger shall be soldered, brazed or pressed
c. Pipe sizes 2” and smaller may utilize ProPress – Viega
d. Underground riser, welded 304 stainless steel one-piece riser assembly with flanged end and tie-rod bracket, UL and FM approved, AMES In-Building Riser Model “IBR2 Series” for 3” and smaller or “IBR Series” for 4” and Larger.
2. Piping systems beyond 5’-0” of the Building:
a. Piping 4” and larger shall be Blue Brute, Class 200 C900 (DR 21) piping.
3. Isolation valves:
a. 2-1/2” and smaller shall be full port, lead-free bronze or red brass, 1/4 turn ball valves w/ stainless steel ball and stem manufactured with dezincification resistant material with less than 15% zinc. Equal to Nibco, Apollo or Hammond, Milwaukee
b. Isolation valves 2-1/2” and larger shall be lead-free
i. Ball – Full-Port Flanged, FDA approved epoxy coated with stainless steel ball and stem.
c. Valve stems shall be installed parallel to floor.
4. Isolation valves shall be located:
a. Walk-In Chases Restroom (Where Provided) – Provide an individual shut-off valve to each side of the chase, as close as possible, to the chase opening. No piping shall cross the chase below 7’-6”.
b. Gang Restroom without a Walk-In chase – In the chase behind an access panel, shall be a minimum 18”x18” access panel. One valve may turn off the entire restroom. Locate the main shut-off valve and access panel on the wide side of the Men’s ADA stall.
c. Individual (private) restrooms - In the chase behind an access panel, shall be a minimum 18”x18” access panel.
d. Individual fixtures – Shall be located above the ceiling within 24”of the fixture water risers.
e. Isolation valves located above ceilings shall be set no higher than 24” above the ceiling. The water piping shall offset as required to meet this mounting requirement. Valve stems shall be set parallel to the finished floor. Insulation at valves shall be chamfered or valve handle extensions shall be provided to avoid damaging the pipe insulation.
f. Kitchen Equipment – Each piece of kitchen equipment supplied with water shall have isolation valves located above the ceiling within 24” of the water risers where the ceiling is accessible. Provide access door and frame where ceiling is not accessible.
g. Isolation valves on the domestic hot and cold water system shall be provided in corridors to allow for the isolation of building zones (wings, sections, and areas of the building). Avoid the use of wall access to valves and other plumbing devices. Where possible, locate valves and other devices above lay-in ceiling.
h. Isolation valves on the domestic cold and hot water system shall be provided to isolate classrooms and showers. Valves shall be located in the corridor where possible.
i. Isolation valves shall be provided to isolate male and female locker rooms separately.
j. Isolation valves on the domestic cold and hot water system shall be provided at individual sinks/fixtures at the supply risers above the ceiling.
k. Isolation valves for non-freeze wall hydrants shall be located within 24” of riser drop to non freeze hydrant.
l. Isolation valves for roof hydrant or other equipment that is mounted high in the structure shall be set no higher than 24” above the ceiling.
m. A map of the zone valves (floors, wings, sections, future additions, etc.) shall be provided to the owner at the completion of the project. Provide one (1) copy of this valve map in the Main Mechanical Room. The map shall be installed in an aluminum frame and Lexan cover.
n. All valves shall have a minimum 1-1/2” diameter brass valve tag equal to Seton Style 250- BL, secured with brass ‘S’ hook. A valve tag chart shall be located immediately adjacent to the plumbing Zone Valve Map located in the Main Mechanical Room. This chart shall be installed in an aluminum frame and Lexan cover.
5. Backflow Protection:
a. The design engineer shall coordinate the location and type of backflow devices that shall be required by the local AHJ.
b. Backflow devices for both potable and non-potable water systems shall be (stainless steel) manufactured by Watts, Wilkins or Ames. These devices shall be located in the building, in a Mechanical space where possible, and shall be mounted at a minimum of 3’-0” and a maximum of 5’-0” above the finished floor. Valve shall be provided upstream and downstream of backflow devices for isolation and maintenance. Provide backflow device at ice makers where required by the local AHJ. All backflow devices shall be USC tested and approved for installation orientation.
6. Horizontal Y-Strainers shall be located on the domestic water main entry into the building downstream of the building isolation valve and upstream of the backflow device.
7. Provide Pressure Gauges, upstream and downstream of:
a. Backflow devices
b. Pumps
c. Y-strainers
d. Pressure Reducing Valves (PRV)
e. Booster Heaters in the kitchen
f. Filters
8. Cartridge Filters shall be installed as follows:
a. Provide with shut-off valve, pressure gauge, backflow device, pressure gauge, shut-off valve, union, filtration system, union, pressure gauge, shut-off valve.
b. Filters shall be provided at ice makers.
9. Provide “Angle Stops” where fixture supply stops are provided.
a. Lead-Free Quarter Turn stops with Heavy Duty Stainless Steel Braided Flexible Risers.
10. Provide “Check Stops” in shower mixing valves, mop sink faucets, kitchen sink faucets or any other fixture where a cross connection between hot and cold water could occur.
11. Trap Primers shall be designed to deliver potable water to floor drain p-traps. Trap Primers serving floor drains shall be automatic operation. (No Trap Guards)
PPP Model Smart-Prime SMP-500, Mini-Prime MP-500 or Prime-Time PT/S Series. Sioux Chief Hyrda-Rester Unit provided will depend on quantity of fixtures being served and on manifold size.
12. Shock Arrestors shall be provided per the manufacturer’s installation instructions and shall be sized per manufacturer’s recommendations. At a minimum shock arrestor shall be placed at individual fixture risers, just downstream of the isolation valve in a walk-in chase and between the last two fixtures within a walk-in chase.
13. Access Doors – Shall be stainless steel with a minimum size shall be 18”x18”, with screw driver cam lock.
14. Provide hose bibbs in mechanical rooms.
15. Do not provide hose bibbs in restrooms.
16. Provide a non-freeze wall hydrant near exterior clean-outs.
17. Provide non-freeze roof hydrants when roof mounted equipment is provided. Provide at 100’-0” centers.
18. Provide non-freeze wall hydrants around perimeter of building. Provide as close as possible to 100’-0” centers.
19. Provide isolation valves for all hose bibbs, non-freeze wall hydrants and non-freeze roof hydrants. Refer to “Isolation Valve” information above for valve locations.
B. Utility Markings:
1. Ceiling Grid - At all above ceiling locations the contractor shall, at the end of construction, mark the ceiling tile grid with a self-adhesive ceiling markers. Use a Seton Ceiling Markers. Mark as follows:
Domestic Cold Water Valves – Single Blue Dot.
Domestic Hot Water Valves – Single Yellow Dot.
Fire Dampers – Single Red Dot (Marked on Wall Mold under Damper).
HVAC Controllers – Double Green Dot.
HVAC Chilled Water Valves – Double Blue Dot.
HVAC Heating Water Valves – Double Yellow Dot.
Duct Smoke Detectors – Double Red Dot.
Natural Gas Valves – Single Orange Dot.
2. Ceiling Grid – Where VAV boxes are located they shall be marked with a Phenolic Equipment Tag mounted to the ceiling grid. Shall be Black with White Lettering.
3. Pipe Markers:
a. Provide flow arrows at each marker location.
b. Markers shall be spaced not more than 20 feet on center and at each change of direction but not more than 4 feet in each direction from each elbow and tee. Markers not required on piping runouts less than four feet (4’) in length and 1-1/4” or smaller in size.
c. Identification markers shall be installed on all new piping; indoors, outdoors and in the crawl space except for drain and waste lines 3/4” and smaller.
d. Install markers on exposed piping systems only after jacketing systems.
C. Domestic Water Heating and Accessories:
1. Electric Storage type water heaters (Where multiple heaters are used, the hot and cold water shall be piped in the reverse parallel, first-in/last-out method) –
a. Under 100 Gallons:
i. Rheem
ii. A.O. Smith
iii. American
2. Gas Fired water heaters shall be Tankless (Where multiple heaters are used, the hot and cold water shall be piped in the reverse parallel, first-in/last-out method)
a. Condensing Water heaters shall be provided with acid neutralization kit to handle condensate from the flue.
b. Where system input is greater than 199,000 BTUH:
i. The system shall be considered a boiler and the cold water supply shall be served by a dedicated RPZ.
ii. A carbon monoxide monitor and interlock shall be provided. Shall be equal to AGS Mini Merlin.
c. Acceptable heater manufacturer: Noritz CR60-FS-NG NCC199CDV
3. Thermostatic Mixing Valves:
a. Master mixing valves shall be manual and/or automatic (if provided with open user interface) and shall be ASSE 1017 certified. These valves shall be provided with inlet check stops and inlet y-strainers.
1) Caleffi 6000 Series
2) Digital Mixing Valve with open user interface allowing for manual control without a laptop – Leonard Proton
b. Point-of-use mixing valves shall be ASSE 1070 certified. These valves shall be provided with inlet check-stops, unions on all sides, and inlet y-strainers. These shall only be used in location where +140 degree water required (i.e. kitchens, culinary labs, etc..)
4. Circulation Pumps: Where domestic hot water supply to a fixture exceed the requirements of the IECC a circulation pump shall be provided.
a. Acceptable Manufacturers:
i. Taco
ii. Grundfos
iii. Bell & Gossett
D. Storm/Overflow Drain Systems:
1. Piping Systems:
a. Above & Below Slab/Grade and in Crawlspace:
i. Schedule 40 PVC pipe with solvent welded joints. Where hung in the crawlspace provide hangers spaced a minimum of ten (10) feet on center and within two (2) feet of each fitting or change in direction.
ii. Where installed in return plenum spaces, provide schedule 40 cast iron No hub pipe and fittings.
2. Roof/Overflow drains shall have cast iron dome strainers.
a. Acceptable manufacturers:
i. Jay R. Smith
ii. Josam
iii. Wade
iv. Zurn
v. Watts
3. Storm Shelter Roof/Overflow drains (where provided):
a. Roof Penetration Housing, Cyclone Vault, CRD/COD
4. Downspout Nozzles: Shall be a stainless steel nozzle with a hinged stainless steel perforated operated cover, loose wall flange and no-hub connection.
5. Downspout Boots: Where provided, downspout boots shall connect to the underground storm system and shall be constructed of cast iron with factory applied rust inhibitor primer or cast aluminum. Engineer shall coordinate with Architect for length of boot.
6. Final Smoke Test: (At the completion of every project where new storm/overflow piping is installed and/or existing storm/overflow piping is modified, the entire system for the facility shall be tested as indicated below.) AISD construction manager shall be notified (2) days in advance of when the test shall occur. Contractor shall document testing procedures, start time and time of completion. This information shall be included into the O&M manuals as part of the final close out documents.
a. Produce smoke by smoke machine.
b. Maintain pressure equal to 1 inch water column for 15 minutes before inspection starts.
c. Repair leaks discovered during test.
d. Repeat test until system holds smoke for ten (10) minutes without showing leaks.
E. Sanitary Sewer Systems:
1. Piping Systems:
a. Above & Below Slab/Grade and in Crawlspace:
i. Schedule 40 PVC pipe with solvent welded joints. Where hung in the crawlspace provide hangers spaced a minimum of ten (10) feet on center and within two (2) feet of each fitting or change in direction.
ii. Where installed in return plenum spaces, provide Schedule 40 No Hub Cast Iron piping and fittings
iii. PVC pipe material shall not be allowed to serve fixtures, drains, or equipment subject to receiving fluids with temperatures of 140 Deg F. or higher. Provide cast iron service weight pipe and fittings as specified above and extend a minimum of 20’ (twenty feet)
or to main waste line to assure high temperature cools in cast iron pipe before entering PVC piping material.
iv. Service Weight ASTM A74 Cast Iron Bell and Spigot for below grade and No-Hub for crawl space shall be used where sanitary sewer or grease waste discharge can be 140 deg.F or greater.
1) Cast Iron acceptable manufacturers:
(a) Tyler Pipe
(b) AB&I
(c) Charlotte Pipe
2. Cleanout locations:
a. Duplex Outlet shall be provided within 24” of clean-outs. Where located inside a walk-in chase. A single duplex outlet shall be provided near the chase door.
1) End of Line Clean-outs set 12” above flood line of the water closets.
2) At Urinals – provide sweeping wye off vent a minimum of 2” above fixture flood rim to the side of the fixture.
3) At lavatories or washfountains – provide sweeping wye off vent 2” above fixture flood rim.
4) Provide main stack clean-out (where sewer line drops below the floor), this shall be set 12” above flood rim of lowest water closet. Where a vertical carrier is utilized for the main stack drop, provide a clean-out 12” above the flood rim of the water closet on a 4” vent stack.
5) Cleanouts should face into the restroom from the fixture being served. If back-to-back fixture is served, provide towards Boys/Mens RR
b. Floor Clean-Outs:
i. Avoid installation of floor clean-out in corridors and walkways.
ii. On straight runs inside the building provide cleanouts 50 feet on center.
iii. Provide double cleanouts at each point at which the sanitary sewer exits the building.
Two-way cleanouts are not acceptable.
iv. Provide wall clean-out where waste pipe in chase wyes down to below grade.
v. Coordinate with AISD for strategic locations of clean-outs within the kitchen to provide as much access for service as possible.
3. Map of all Clean-Outs shall be provided by the plumbing sub-contractor as part of the Close-Out Documents. One (1) shall be provided in the Main Mechanical Room and one (1) shall be provided main Custodial Room. The maps shall be installed in an aluminum frame and Lexan cover.
4. Provide a minimum of one (1) floor drain in each walk-in chase.
5. Provide high flow floor drains or floor sink in mechanical rooms.
6. Provide floor drains in all group restrooms and all student restrooms. Unless, required by code, do not provide floor drain in single staff restrooms.
7. Provide top access, cast aluminum plaster traps with stainless steel strainers at each individual art sink.
8. For group showers, provide perimeter trench drains.
9. Clean-Out plugs shall be raised head bronze plugs.
10. Two-way cleanouts are not acceptable.
11. Long sweep tees shall be utilized at sanitary sewer connections.
12. Fixture p-traps shall be 17 ga. chrome plated cast brass with cleanout.
13. Vent through roof locations shall be located a minimum of 25’-0” from any outside air intake, 5’-0” from the inside edge of the parapet, and extended above the roof to terminate, a minimum of 18” above the roof deck or 6” above the parapet height, whichever is greater.
a. For existing facilities where vent are closer to OAI than noted above – Provide with activated carbon filter vent cap. Equal to Odor Hog or Studor Maxi-Filtra.
14. Floor drains located in the kitchen shall be type 304 fabricated stainless steel 8” with stainless steel grate. Equal to Josam 43450-VP.
15. Floor sinks located in the kitchen shall be type 304 fabricated stainless steel 12”x12”x8” with stainless dome strainer and 3/4 stainless steel grate.
16. Clean-Out, Floor Drains and Floor Sinks:
a. Acceptable manufacturers:
i. Jay R. Smith
ii. Josam
iii. Wade
iv. Zurn
v. Watts
17. For construction at existing facilities:
a. Prior to start of construction, contractor shall video scope the existing sanitary sewer mains in and around the area of construction. Any breaks, separations, bellies, or abnormality to sewer main shall be reported to the AISD project manager.
b. At the completion of construction, the contractor shall video scope the sanitary sewer mains and provide copies of video scope to the AISD project manager.
c. Both videos shall be reports and videos shall be with the O&M Manuals as part of the final close out documents.
18. Final Smoke Test: (At the completion of every project where new sanitary sewer piping is installed and/or existing sanitary sewer piping is modified, the entire sanitary sewer system for the facility shall be tested as indicated below.) AISD project manager shall be notified (2) days in advance of when the test shall occur. Contractor shall document testing procedures, start time and time of completion. This information shall be included into the O&M manuals as part of the final close out documents.
a. Produce smoke by smoke machine.
b. Maintain pressure equal to 1 inch water column for 15 minutes before inspection starts.
c. Repair leaks discovered during test.
d. Repeat test until system holds smoke for ten (10) minutes without showing leaks.
19. Sewage Ejectors (ONLY WHERE PRE-APPROVED BY AISD):
a. If sewage ejectors are required for grey or black water removal, the ejector basin shall be located on site, outside the building footprint. Pumps shall be provided with a bronze impeller, stainless steel shaft and shall be designed to provide a 100% redundant system (N+1). Sewage ejector basins shall be designed to have a dry and wet well Sewage ejector controls shall be wired to the EMS and shall have an audible and visual alarms. Dual pumps
shall be provided and shall be wired for lead/lag control.
If the sump basin is greater than six feet (6’-0”) deep, the basin shall be provided with a stainless steel rail system and quick release devices on the pumps. Pumps shall be equal to Weil, Flygt or Armstrong.
F. Natural Gas Systems:
1. Engineer shall coordinate with the local gas utility provider to confirm that availability and proximately of the gas main to the campus. Where possible, a minimum 5 psig gas service shall be provided. Once confirmed the Engineer shall coordinate the gas meter location with the local gas provider, architect and civil engineer.
2. Piping Systems (above grade) shall be ASTM A53, Grade A, Sch. 40 black steel pipe.
a. 2” and smaller shall be threaded and coupled, Class 150 malleable iron for pressures 2 psig and less.
b. 2-1/2” and larger shall have butt welded joints.
c. All gas piping in sleeves shall have welded joints, regardless of size.
3. Valves shall be 125 psig, flat or square head, non-lubricated plug with resilient double seal, listed for natural gas service. Acceptable Manufacturers: SMG Global, Milwaukee, Hammond, or McDonald.
a. Valves shall be located on gas main piping on roof at major branch lines or legs to allow for isolation of areas, wings, sections, and future additions.
4. Unions and Valve shall be provide at each piece of equipment. Valves shall be located immediately upstream of the equipment dirt (drip) leg.
5. Piping Systems (below grade beyond the building footprint) shall be ASTM D2513, D2683 & D3261, Type PE 2306 SDR 9 polyethylene pipe and thermally bonded fitting.
a. Shall be provide with underground trace wire equal to Seton, Underground Warning Tape.
6. Gas pressure regulators shall be installed per manufacturer’s instruction, upright. Regulators shall be noted for the contractor to provide the spring color and orifice size as required to meet the required downstream pressure and required downstream flow. Acceptable Manufacturers: Equimeter, Fisher, Sensus or Itron.
7. The Engineer shall utilize the Long Length methodology for designing the gas piping system.
8. Where intermediate pressure, 5 psig or greater, is available the Engineer shall design the intermediate pressure on the roof and shall design to have this pressure and regulator as close as possible to concentrated loads on the campus. For low pressure branch piping downstream of regulators at these concentrated loads the Engineer shall utilize bulk main sizing across the piping system, not reducing the low pressure main line size.
9. Exposed gas piping shall be painted to match the building finish on exterior walls or painted “Safety Yellow”.
10. Underground gas piping shall be provided with detectable aluminum foil plastic backed tape or detectable magnetic plastic tape manufactured specifically for warning and identification of buried piping or utilities. Tape shall be detectable by an electronic detection instrument.
Provide tape in rolls, 3 inches minimum in width, color coded for the utility involved with suitable warning and identification imprinted in bold black letters continuously and repeatedly over entire tape length.
11. Gas piping on the roof shall be supported on 10’-0” centers, within 3’-0” of all equipment connections, and within 2’-0” of every change in direction. Supports shall be Mapa MS-5RA with stainless steel all-thread and traffic pad, Mapa WP1016. Acceptable manufacturers: Mapa, Erico or Miro.
G. Acid Waste Systems:
1. Piping Systems (As manufactured by Orion, Enfield, Fuseal, Zurn):
a. Above Grade (In open plenum ceilings):
i. Piping shall be ASTM E84 rated:
ii. CPVC with solvent welded joints
b. Above Grade (In ducted return systems):
i. PVDF with electrofusion welded joints
ii. CPVC with solvent welded joints
iii. Durion with mechanical joints
iv. Polypropylene with electrofusion welded joints.
c. Below Grade/Slab or in Crawlspace:
i. PVDF with electrofusion welded joints
2. Acid Dilution Basin shall manufactured of acid resistant seamless, molded polyethylene materials and shall be filled with minimum 90% Calcium Carbonate Limestone chips. Basins shall be located outside the building footprint in accessible location.
H. Plumbing Fixtures:
1. All faucets shall be manual mechanical metering. No automatic infrared sensors shall be used.
2. All flush valves shall be automatic battery powered.
3. Individual lavatories shall be utilized, washfountains shall not be used.
4. Vitreous China Fixtures:
a. Acceptable manufactures:
i. Gerber
ii. Kohler.
iii. Zurn
iv. American Standard.
5. Water Closets shall be wall mounted with manual 1.28 GPF flush valves.
6. Urinals shall be rated at 0.5 GPF wall mounted with floor mounted carriers.
7. Manual Flush Valves:
a. Acceptable manufacturer:
i. Sloan
ii. Zurn
iii. Delta
iv. American Standard
8. Lavatories shall be wall mounted with floor mounted carriers.
a. Faucets shall be single lever manual.
b. Faucets shall be the commercial grade type using heavy duty chrome plated cast brass.
c. Student and adult lavatories shall have 4” cast brass centers with a single lever manual faucet. Fixture shall be supplied with a cold and tempered line and minimum 4-3/4” spout.
d. Clinic lavatory shall have 4” centers with a gooseneck spout, 4” wrist blade quarter turn ceramic cartridge handles with tempered and cold supply.
e. Faucets for mop sinks shall be provide with quarter turn ceramic check stops.
f. Supply stops shall be lead free quarter turn ball valves with braided stainless steel flexible risers.
g. Acceptable manufacturers:
h. T&S Brass
ii. Delta
iii. Zurn
iv. Central Brass
9. Fixture Carrier Acceptable Manufacturers:
a. Josam
b. Jay R Smith
c. Wade
d. Zurn
10. Electric Water Coolers shall be manual vandal resistant all stainless steel units.
a. Units shall be all stainless steel.
b. Units shall be manual push operation, no electronic push operation.
c. Units shall not be wired to building EMS.
d. Engineer shall note that the Contractor shall clean air cooled condenser coils on EWC’s at end of the project.
e. Reset button for GFCI circuit shall not be installed behind the EWC.
f. Provide shut-off valve for each group of EWC’s located above the adjacent ceiling.
g. One unit within the EWC group shall have a bottle filler on ADA side.
h. Do not provide filter on EWC.
i. Acceptable manufacturers are:
i. Halsey Taylor
11. Showers shall be pressure balancing complying with ASSE 1016.
a. Do not provide column showers.
b. Showers heads for students shall be vandal resistant institutional type chrome plated with maximum flow of 1.5 gpm.
c. Showers for staff/adults shall be chrome plated, brass construction with a maximum flow of 2.0 gpm.
d. Wall mounted group showers units shall be a stainless-steel enclosures with severe service vandal resistant shower heads, no soap dish, with vertical shroud that extend up to the ceiling.
e. Acceptable manufacturers:
i. Acorn
ii. Bradley
12. Emergency Shower/Eye Wash Stations (For Labs):
a. Each unit shall have a 20 gpm flow restrictor valve installed on the 1 ¼” supply line downstream of the isolation valve.
b. The eyewash portion of the unit shall be piped directly to the acid waste. This shall occur
through a factory modified tee outlet at 24” A.F.F. on the standpipe that is connected to an acid resistant p-trap.
c. A floor drain shall be provided for the shower portion of the unit and it shall be a high flow drain with minimum 10” stainless steel grate directly below the shower head.
d. A test funnel from the emergency shower manufacturer for shower testing shall be provided. Provide one test kit per station.
e. Acceptable manufacturer: Bradley or Guardian
13. ADA sinks in Teacher Lounges shall be no greater than 5.5” deep with offset drain to back and be provided with disposal that is less than 12” deep in order to meet ADA wheelchair front approach. Where no disposal is provided sink depth shall be 6.5”.
14. Hose bibbs shall be provided in mechanical rooms. These shall be anti-siphoning with a vacuum breakers.
a. Acceptable manufactures:
i. Woodford.
ii. Jay R Smith
iii. Josam.
15. Exterior Non-Freeze Wall Hydrants:
a. Units shall be the flush in wall type with keyed operation, with a coverplate.
b. Units shall be located 100 feet on centers.
c. Provide unit at loading docks.
d. Shut-off valves shall be provided for each NFWH within 24” of the hydrant riser.
e. Acceptable manufactures:
i. Woodford
ii. Jay R Smith
iii. Josam
16. Non-Freeze Roof Hydrants (Where Roof Top/Make-Up Air Units are provided):
a. Units shall not require a drain and shall utilize venturi technology to drain down below the roof deck.
b. Units shall be located 100 feet on centers. Isolation valves for roof hydrant shall be set at 24” above the ceiling below the hydrant being served.
c. Unit shall be installed with underdeck framing and clamps per manufacturer’s installation instructions.
d. Depth of hydrant shall be based on roof deck insulation. The hydrant shall extend a minimum of 24” above the final roofing membrane/insulation.
e. Acceptable products:
i. MAPA Products MPH-24-FP
17. Undercounter Ice Makers shall be provided with a floor drain and in-line filters which shall be located in accessible location (under adjacent sink where possible). Provide ice makers at all Clinics.
18. Kitchen Ice Makers shall be provided with in-line water filters which shall be located in an accessible location.
19. Kitchen Equipment that is connected to the domestic water system shall be provided with a
backflow prevention device as required by the local Authority Having Jurisdiction (AHJ). A RPZ shall be provided at in-line water filters and shall be installed in an accessible location.
20. Shut-off valves, unions and pressure gauges shall be provided upstream and downstream of in line filters.
21. Where plumbing fixtures are installed on an island. Conventional island venting is required that is compliant with the International Plumbing Code and local AHJ. Air admittance valves (AAVs) shall not be used.
I. Lab Utility Controls:
1. Control system shall be connected to EMS.
2. High School – Students shall receive cold water and gas only.
3. Middle School - Engineer shall confirm with the architect if both water and gas are to be provided or if cold water only is to be provided.
4. Solenoid Enclosures shall be below the ceiling in an accessible location and shall be Fully Recessed stainless steel enclosures in the wall.
5. Solenoids shall be 24V.
6. Teacher’s demonstration table utilities shall be controlled through individual normally closed solenoid valves that shut down through operation of the classroom EPO.
7. Computers, ice makers, aquariums shall not be wired through the lab utility control system.
8. Lab Utility Controls shall be provided by Isimet, Lab Safety Systems or Lab Automation Control Systems.
23.01 CODE RELATED GUIDELINES FOR HVAC
A. Mechanical Code
1. Consult with the Architect and the local authority having jurisdiction to determine the mechanical code to govern the project.
2. Consult the local authority having jurisdiction to determine if the AHJ has any amendments or unique mechanical requirements for projects in their jurisdiction.
B. Energy Code
1. Consult with the Architect and the local authority having jurisdiction to determine the energy code to govern the project.
2. Consult the local authority having jurisdiction to determine if the AHJ has any amendments or unique energy requirements for projects in their jurisdiction.
23.02 HVAC DESIGN PARAMETERS
A. Site Conditions
1. Note the geographical location of the project.
2. Consult the Civil Engineering survey and grading plans to determine the site elevation.
3. Determine which meteorological weather station is closest to the project site and from that station’s weather data establish the ambient outdoor air conditions to be used in HVAC load calculations.
4. Coordinate with the Architect and Owner for geotechnical data related to the soil on site.
a. A geotechnical report should be provided for reviewing soil movement on site.
b. If the project’s HVAC systems require it, a ground-coupled heat-exchanger test well may be required. Depending on the site conditions and building size, more than one test well may be recommended.
c. MDF / IDF Rooms
i. MDF and IDF Rooms are to be provided with cooling by means of decentralized, direct expansion systems. These systems are to only serve the designated MDF or IDF space and no others. (LG Preferred)
23.03 HVAC SYSTEM GUIDELINES
A. Evaluate the project’s requirements and design criteria in coordination with the architectural plans, Owner project goals, and these design guidelines. Propose HVAC systems applicable to the project.
B. Typical HVAC Systems in the AISD include the following. Preferences are noted where appropriate to the system.
1. Controls Systems (Alerton by Logical Control Services (LCS).
a. Energy / building management system (EMS / BMS BACnet) with direct digital control (DDC) to control HVAC systems and integrate with other systems (power monitoring, lighting controls, etc.). The EMS includes local and remote control panels, temperature control field devices, and other appurtenances necessary to perform required sequences of operation for the project’s HVAC systems. The EMS includes devices and instruments required for a complete and operational system. Many sequences of operations will be fully automatic, some operate manually (for example, by means of a push-button switch), and the system offers remote surveillance of operations, adjustment of operations, status updates, alarms, data collection, and other features requested by the Owner for the particular project.
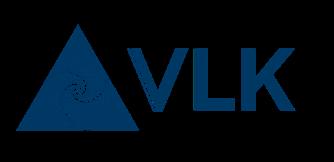
b. New projects shall be: Alerton by Logical Control Services (LCS). Where existing DDC systems are on a site, consult with the District regarding expansion of the existing system and if the existing control system manufacturer on that site shall be closed specified.
c. DDC Control System shall be integrated into the Owner’s existing energy management system for complete local and remote communication. System shall be Windows-based and Web-based control configuration with dynamic graphics operator interface for all point monitoring, setpoint adjustments, calendar-based operation, special event calendaring, etc. d. Primary control communication shall be through District high-speed Ethernet network integrated through central DDC global controller. System shall also include backup telephone communication via phone modem.
i. The system shall be capable of “stand alone” operation of the building HVAC system and also capable of operation as part of a central energy management system (EMS) located at the District administrative center.
ii. The stand-alone DDC electronic control system shall be fully compatible and addressable by the District system.
2. Testing, Adjusting, & Balancing for HVAC (TAB)
a. Projects shall be: Alerton by Logical Control Services (LCS). Where existing DDC systems are on a site, consult with the District regarding expansion of the existing system and if the existing control system manufacturer on that site shall be closed specified.
3. Hydronic Systems
a. GCHE Systems: Ground-coupled heat-exchanger (GCHE) / geo-thermal systems. Consult with the District regarding their preferences for GCHE systems on a project. Should a GCHE system be designed for a project, the following design guides are provided.
i. Well Fields
1. 300’ deep wells spaced 20’-0” apart (on center).
2. Thermally enhanced grout with the grout mixtures’ minimum thermal conductivity being 1.20 BTU/hr•ft•°F.
3. Provide geolocation devices placed at the corners of each well field, in pipe trenches every 40’-0”, and suspended from valve covers. A geolocator device should be provided that can locate these devices. Provide geolocation ball type markers and/or tape makers are also placed above buried GCHE pipe.
4. Provide isolation valves in both the return and supply pipes of rows in the well field. Additionally, a normally closed valve has been provided at the end of well field header piping to allow for flushing of the pipes. Provide a 1’x1’ concrete paver below the valves. A PVC pipe sleeve is typically provided for operator rods to extend to the valves from the valve box located at grade.
5. The piping in the well fields is typically arranged in a reverse-return configuration.
ii. Pumping Scheme
1. Distributed pumping with push/ pull pump packages installed for each heat pump.
2. Evaluate the project and discuss with the Owner which pumping scheme is best suited for the project.
iii. Piping
1. GCHE risers shall be located near exterior walls with accessibility for purging. In addition to normal butterfly type isolation valves in the riser, the following appurtenances shall also be provided.
• Thermometer
• P/T Test well
• P/T Test well for EMS pressure sensor
• P/T Test well for EMS temperature sensor
• 2” connection with ball valve for purge valve assembly
• Pressure gauge
• 4” flanged, 150# ANSI rated, single piece cast bronze body sight flow
indicator equal to John C. Ernst Co., Inc. Rotator Model 241
2. Provide normally closed ball valve at the end of the piping loop in the building to be used for purging / flushing purposes.
3. Depending on the type of pumping arrangement, coil connection details will vary. A centralized pumping scheme will include a control valve (two-way or 3-way at the last coil on the loop) and automatic flow control device in addition to other appurtenances.
iv. Make-Up Water
1. Provide an automatic fill for make-up water to each loop.
2. Provide a pressure reducing valve on this make-up water line.
3. Provide a quick fill bypass line around the pressure reducing valve to allow for manual fill.
b. Four-Pipe Chilled & Heating Water Systems
Chilled Water System
1. Source of Cooling: Water-cooled chillers are preferred. Consult with the District regarding redundancy and capacity of the chilled water plant. Existing campus renovation projects shall be evaluated for system replacement and verified with AISD prior to implementation.
2. Chilled water systems are a primary/secondary arrangement with primary water pumps, variable flow distribution pumps, and decoupling bypass line. Secondary distribution pumps should be controlled by variable frequency drives (VFD) to modulate pump speed based on pressure differential in the main chilled water loop. An additional, redundant distribution pump may be provided (also with VFD) with a separate electrical service for stand-by operation.
3. Variable primary system (preferred in retrofit projects. Verify with AISD prior to implementation) may be considered where there is sufficient load and limited space in the central plant. In this case, flow meters shall be provided at each chiller to maintain minimum flow in the system and bypass valves at the end of the loops shall be sized to provide minimum flow across the active chiller.
4. Provide two-way control valves at load coils in the system with 3-way bypass valves at the coil at the end of a loop.
5. Water-cooled chillers located in mechanical rooms will require a refrigerant monitoring system and associated room exhaust.
ii. Condenser Water System
1. Where a water-cooled chiller is used, a condenser water system is needed.
2. The condenser water system shall include cooling towers. The capacity provided by the towers be decided upon with the Owner’s approval. The towers shall have VFDs to vary the speed of their fan.
3. Cooling towers may be provided with a basin sweeper system. Consult with the District regarding their preference for this type of system.
4. A 2” water connection should be provided at the towers for blow down and cleaning.
5. Exterior piping with pressurized water shall be heat traced, insulated, and provided with aluminum jacketing.
6. Constant volume condenser water pumps shall be provided.
iii. Heating Water System
1. Heating water systems shall have high efficiency (95%+) condensing boilers with stainless steel heat exchangers. Boiler systems shall be designed for a minimum of two (2) boilers and some redundancy (to be confirmed by AISD). Typically where two boilers are provided, 33% redundancy is provided and where three or more boilers are provided the preference is to have N+1 redundancy.
2. Boiler isolation valves shall be provided where more than one boiler is provided.
3. The pumping scheme shall be a variable primary arrangement with variable flow distribution pumps and a bypass line or bypass at coils. Pumps will be controlled by VFD to modulate pump speed based on pressure differential in the main loop.
4. Boilers will be sequenced automatically based on variable load.
5. Provide two-way control valves at load coils in the system with 3-way bypass valves at the coil at the end of a loop.
6. Boiler flue piping shall be stainless steel or aluminum and shall be double wall. Where possible, individual venting is preferred.
7. Condensate neutralization kits shall be provided on the condensate connection from all boiler flues to the floor drains in the mechanical rooms.
8. Carbon monoxide sensors shall be provided in the boiler room in accordance with Texas State Boiler Law so that the boilers shut-down when carbon monoxide is detected at the prescribed parts per million.
9. Preferably, boilers and chillers do not occupy the same equipment room. Where they do need to occupy the same space, a boiler shut-down switch that shall close the gas valve to the boilers shall be provided and interlocked with the chiller refrigerant monitoring system.
iv. Chemical treatment
1. Chemical treatment for the chilled water, condenser water, and heating water systems shall be provided.
2. Consult with AISD for their current water treatment vendor and water treatment preferences.Chem-Aqua is current service provider.
4. Air Distribution Systems
a. Air distribution systems shall be provided to meet the requirements of the project.
b. All mechanical cooling systems shall involve forced air circulation of a “low- pressure” type 0.5” to 1.5” external static pressure) for single zone/constant volume systems and “medium pressure” type (2.5” to 4.0” external static pressure) for multiple zone/variable air volume (VAV) systems.
c. Variable Air Volume Systems
i. Variable air volume heating/cooling systems are preferable, utilizing low-pressure, single-inlet variable air volume terminals at controlled spaces.
ii. The preference is for parallel type fan powered terminal units throughout the facility except where high volume spaces or long throws are required, in which case series type fan powered terminal units would be utilized.
iii. Single duct VAV terminal with re-heat coils should only be used if fan powered terminal units cannot be utilized. Single duct VAV terminals should only be utilized where serving cooling only spaces.
iv. All classroom type spaces shall have fan powered terminal units.
d. Constant Volume:
i. Air handling systems incorporating heat and cooling shall be arranged to prohibit simultaneous heating and cooling generation.
ii. Provide for variable speed drives on fans where possible to allow for “single zone VAV” type application.
e. Ductwork: Ductwork shall be new, of galvanized steel construction installed in accordance with the latest editions of the SMACNA Duct Construction Standards. Flexible duct will only be allowed at the last five feet (5’) for diffusers.
f. Special exhaust systems: Special exhaust systems shall be provided as directed by the Owner and Architect and appropriate to the project. Such systems may include dryer exhaust, cooking hood exhaust, kiln room, kiln hood, or some other type of specialty exhaust for a process. Routing material and fan equipment shall be suitable for the application.
g. Air Outlets and Inlets: Grilles, registers, diffusers, and other air distribution terminal devices shall be provided suitable for the intended use and coordinated with Architectural designs and branding products.
h. Ventilation Openings: Ventilation openings may be provided through wall louvers or roof mounted hoods. Ventilation openings in the envelope of the storm shelter shall receive UL listed wind storm assembly storm louvers that comply with appropriate ICC 500 and FEMA requirements.
i. Fire Dampers: access to fire dampers shall be coordinated with owner and to be accessed above ceiling.
23.04 HVAC EQUIPMENT GUIDELINES
A. Pumps
1. Pumps shall be sized and selected appropriate for the application.
2. Distributed push-pull pumps on geo-thermal GCHE systems typically are equal to pump package assemblies provided by Geo Systems.
3. Floor mounted centrifugal pumps shall have mechanical seals and a drainable base. They may be end-suction or double-suction as appropriate for the application. Where specific space limitations exist, in-line type pumps may be used. In-line pumps may be required at air handler coils for freeze-protection operations. Individual pressure gauges on the suction
and discharge of each pump shall be provided. Pump manufacturers shall be Paco, Taco, Armstrong.
4. Where condensate drain systems require a pump, a pump may be provided by the air- conditioner manufacturer or one similar to LITTLE GIANT VCMA, VCMX, or VCL Series condensate pump, depending on the application’s needs.
5. All pumps shall be easily accessible for maintenance. Floor mounted pumps shall be located in mechanical equipment rooms.
B. Fans
1. Exhaust fans shall be roof-mounted (using curbs) where roof space is available. Such roof mounted fans shall be dome type, down-blast centrifugal fans, belt-driven or direct-
drive, and integrated with attendant air conditioning system, lights, thermostat, or shall be controlled by the Energy Management System as appropriate for the application.
Exhaust fans may be inline fans suspended from structure or mounted to ceilings where roof space is not available or it is appropriate for the application. Such fans shall be centrifugal fans, belt-driven or direct-drive, and interlocked as noted for roof mounted fans. All motors one horsepower or larger shall receive high (premium) efficiency motors. Fans shall be AMCA certified.
2. Special air systems will require fans appropriate for the application.
3. Fans shall be provided with safe and easy access for maintenance.
C. Air Terminal Units
1. See previous guidelines in air distribution systems for additional comments on air terminal units.
2. Parallel fan powered air terminal units shall be provided with a sound attenuator / baffle.
3. Heating water coils are typically provided on fan powered air terminal units. Where called for these coils are at a minimum, 2-row coils.
4. Acceptable manufacturers are Envirotech, Titus, Price,
5. Air terminal units (ATUs) shall be installed in accessible locations. In classroom applications, ATUs are preferably installed above corridor ceilings.
6. Ceiling labels for ATUs shall be provided.
D. Boilers
1. The District does have some existing copper fin tube boilers, but high efficiency (96%+) condensing boilers with stainless steel heat exchangers are preferred.
2. Boiler manufacturers shall be limited to Lochinvar preferred, LAARS, Raypack, RBI.
3. All boilers shall be provided with BacNET MSTP or ModBUS interface. Provide the District with a list of points that can be mapped and allow for the District to review or provide input on specific points to be mapped from MSTP or ModBUS interface.
4. Boilers shall be installed in mechanical equipment rooms with ample space for clearance and maintenance.
E. Chillers
1. Water-Cooled (Magnetic Bearing preferred, Centrifugal, Screw)
a. Water-cooled chillers shall be centrifugal type. Centrifugal chillers shall be selected to be non-surging with constant condenser water at minimum expected loads and shall unload down to a minimum of 20% of full load with constant condenser water. Provide the
district with options for chiller efficiency versus added cost to allow the district to determine if they would like a more expensive, higher efficiency chiller that they can use to apply for higher rebates with.
b. Chiller refrigerant circuit shall include charging valves, sight glass, filter/driers, and line strainers.
c. Chillers will be located in a manner to minimize unit noise to the building. Additional sound suppression or insulating type system shall be reviewed and implemented as needed to minimize high frequency sounds.
d. Chillers shall be provided with BacNET MSTP interface. If BacNET IP interface is used, coordinate data drop for chiller. Provide the District a list of points that can be mapped and allow District to provide input on which points to map to the EMS. The chiller controls shall be capable of remote control and monitoring by the EMS.
e. Chiller manufacturers are York preferred.
2. Air-Cooled (Magnetic Bearing preferred, Centrifugal, Screw)
a. Air-cooled chillers shall be packaged outdoor air-cooled type with screw or scroll compressors with 5-year warranties, ASME shell & tube heat exchangers, upflow condenser fans, coil hail guards, refrigerant and oil pressure switches, flow switches, pre- piped and pre-charged with all operating and safety controls for a complete assembly.
b. Chiller refrigerant circuit shall include charging valves, sight glass, filter/driers, and line strainers.
c. Chillers will be located in a manner to minimize unit noise to the building and not reduce operational capacity. Where chillers are located on roofs additional sound suppression or insulating type system shall be reviewed and implemented as needed to minimize high frequency sounds.
d. Chillers shall be provided with BacNET MSTP interface. If BacNET IP interface is used, coordinate data drop for chiller. Provide the District a list of points that can be mapped and allow District to provide input on which points to map to the EMS. The chiller controls shall be capable of remote control and monitoring by the EMS.
e. Chiller manufacturers are York preferred.
F. Cooling Towers
1. All cooling towers shall be elevated on structural supports.
2. Cooling towers shall be cross-flow type only. No counter-flow type shall be allowed.
3. All cooling towers shall have stainless steel cold and hot water basins, including all structural members. An Evertough type coating may be considered as an alternate to stainless steel basins if desired by the Owner.
4. Where possible, multiple cells shall be provided.
5. Towers shall have variable frequency drives (for condenser fans), basin heaters, sump outlets, equalization lines (with baffle plates where multiple cells are installed on common header), and bottom bypass connection with baffle plate. Provide bottom or side inlets where possible. Top inlets area acceptable where side or bottom inlets with internally pre- piped headers are not possible.
6. Cooling towers shall be provided with full access platform around entire perimeter of tower with access ladder to ground. Provide OSHA safety cage as required. Provide ladder to fan access deck with safety rails. Provide internal access platforms. Provide external motors
with gear drives with rain covers for all new towers. Provide individual overflow and make- up water per cell.
7. Acceptable manufacturers are REYMSA (preferred), BAC, and Evapco.
G. Air-Handling Units
1. General: Air handling units shall consist of factory-fabricated insulated steel casings housing heating coils and/or cooling coils, one or more blowers, air filters, damper assemblies (as necessary to type of unit), insulated drain pan, and blower motor with drive assembly. Central station type chilled water air handlers shall be specified with either housed centrifugal fans or multiple plenum/ plug type direct fans in a fan
array. Where air handling units are installed exposed to the weather, casings shall be specifically designed for weatherproof operation, and where installed on roofs, shall be provided with insulated roof- mounting curbs arranged for flashing into roof membranes and enclosing all ducts, pipe, and conduit penetrations associated with the unit.
2. Heating and Cooling Coils: Heating and cooling coils for HVAC equipment shall be constructed of copper tubes and copper or aluminum fins, with fins bonded to the tubes.
a. Test Pressures: Water coils shall be factory leak tested at not less than 200 psig and refrigerant coils for not less than 300 psig.
b. Selection Criteria: Cooling coils shall be selected for a face velocity over the active coil area of no more than 550’ per minute. Heating coils shall be selected similarly for no more than 800’ per minute. Except as otherwise specifically authorized by the District, cooling coils shall be selected for suction temperatures or entering chilled water temperatures no lower than 42°F to 46°F, and heating coils for entering hot water no higher than 180° F.
c. Scheduled Requirements: Minimum acceptable capacities for cooling and heating coils shall be scheduled on the plans in terms of total heat and sensible heat transfer, coil CFM, coil air entering dry bulb and wet bulb temperatures, for refrigerant coils or flow rate and entering water temperature for water coils.
d. Certification: Specifications shall require coil manufacturer to certify coil performance at scheduled conditions per appropriate AHRI procedures and to provide computer- generated verification of performance under specified conditions as a part of the submittal data for approval.
3. Fan Speed Control: Unless otherwise specifically authorized in writing by the District, variable air volume (VAV) delivery from VAV air handling units shall be accomplished by means of variable speed or variable frequency drive motor controller. In all cases where a variable frequency drive is used for motor speed adjustment the fan motor shall be premium efficiency type rated for use with a variable frequency drive.
4. Drives: Drive assemblies shall be adjustable pitch V-belt type for motors less than 10 horsepower and fixed sheave V-belt type for motors 10 horsepower and above, provided with protective guards where located outside housings.
5. Each air handling unit shall be provided with MERV 13 angle filter racks where space allows. Flat filter sections shall only be allowed where angle filter sections are not feasible due to space constraint.
6. Acceptable manufacturers are York preferred.
7. Air-Handling Units (AHUs) shall be installed in mechanical equipment rooms. If space is not provided, obtain approval by the Owner prior to considering mounting an AHU outside on a roof. If a roof mounted AHU is planned, then an insulated pipe chase shall be provided as noted previously.
H. Roof-Mounted Air-Conditioners
1. Factory-assembled, roof-mounted, self-contained air-conditioning units shall have one or more scroll refrigeration compressors, air-cooled condensers, direct-expansion (“DX”) evaporator coils, evaporator blowers, air filters, and all necessary and appropriate interconnecting piping, wiring, controls, insulation, refrigerant, etc., installed within a weather-proof housing that includes condenser coil hail guards and provided with a suitable insulated roof-mounting curb. Units shall also contain heating capability including gas-fired stainless steel heat exchangers, controls, and accessories wherever natural gas is realistically available. If gas is not available a discussion with the District shall be had regarding options for the site.
2. All units shall have direct drive ECM type fans on 3-5 ton units with external static pressures 0.5 in. wg. and below.
3. Two-stage or multiple compressors shall be provided for all units 3 tons and above.
4. Hot-gas re-heat type coils for de-humidification control shall be provided on all units.
5. Where larger units are provided with variable speed drives, the associated drives control interface shall be required to be provided by the unit manufacturer and not removed during balancing.
6. Gas heat size shall be reviewed for units with higher outside air requirements or at the upper end of a cabinet range and medium heat, in lieu of low heat, possibly used to meet a minimum discharge temperature.
7. Provide non-fused unit mounted disconnect switches for all units.
8. Provide non-powered service outlets on units where required by code.
9. All condensate drain connections shall be made outside of the unit, such that no drains from below unit allowed.
10. Each rooftop unit shall be provided with 2” metal filter frames. Each filter frame shall be constructed of minimum 24-gauge galvanized steel with a black metal lath backing.
11. The filter frames shall be provided with MERV 13 filters.
12. Sound transmission from rooftop units can create unacceptable levels of noise in a learning environment. All rooftop units shall have the following sound attenuating material installed in the roof curb. Where rooftop units are used for band halls, choir room or other sound sensitive areas, the design professional shall specify a vibration isolation type roof curb similar to Vibro-Acoustics, type VCR.
13. All units shall be equipped with air side economizers. Units shall be provided such that the District can control the economizer section for the unit independently from the main unit controller.
14. Provide powered relief or barometric relief with all units.
15. Acceptable Manufacturers are Aaon preferred, Trane, Lennox
I. Split-System Air-Conditioners
1. Condensers shall be factory-assembled units consisting of refrigerant coils, induced- draft fans, refrigerant piping, valves, controls, and/or receivers, mounted within a suitable casing or incorporated appropriately into HVAC equipment components. Coils shall be made of copper tubing and copper or aluminum fins, and fans shall be propeller types (with vertical discharge except for small package A/C units). All exposed condenser coil surfaces shall be provided with coil hail guards and all fans provided with fan guards. Fan motors shall be drip proof and suitable for operation in the low range of voltages for the system (i.e. 200 volt
for 208, 208 volt for 230, 460 volt for 480). Fan motors with non-standard voltage/ phase characteristics, such as 460/480 volt, single phase, or which utilize a single disconnect switch for multiple motors, are not acceptable.
2. Condenser Installation: All air-cooled condensing equipment shall be installed in such a way as to provide not less than the manufacturer’s recommended clearances for service and air circulation, but in no case less than 3’-0” horizontally from any side. Where enclosing walls inhibit the free flow of air for circulation to the equipment, the equipment shall be installed so that the discharge fan deck of the unit is level with the top of the enclosure.
3. Indoor units shall be either ducted or ductless type depending on application. Ducted indoor units are preferred in most spaces unless there are associated space constraints. Provide electric heat for units where needed when used for equipment rooms or other specific applications.
4. Acceptable manufacturers are Trane preferred, Mitsubishi, LG, and Lennox.
J. Water-Source
Unitary Heat Pumps
1. Water-source, water-to-air unitary heat pumps are typically high efficiency units. Each unit shall have a water-to-refrigerant heat exchanger and an air-to-refrigerant coil. Fans may have EC motors. These shall be controlled by the Building Automation System. Systems served by these units shall have fully ducted supply and return air systems.
2. These units shall be provided with condensate overflow protection with alarm contacts for all horizontal units suspended above finished spaces.
3. These units shall be integrated with the EMS and shall have the ability to be reset by the EMS whenever an alarm occurs.
4. Acceptable manufacturers are Trane preferred, Carrier.
5. Vertical heat pumps installed in mechanical equipment rooms. Ample space shall be provided for equipment clearances and maintenance accessibility.
K. Fan Coil Units
1. General: Fan coil units may be utilized where existing fan coil units are used, for small zones on chilled and heating water systems, or where ground source heat pump systems are converted to 4-pipe systems.
2. There is a preference to have heating water coils in the pre-heat position.
3. Acceptable manufacturers are Trane, Carrier, and York.
L. Unit Heaters
1. Electric unit heaters may be provided in electrical, mechanical, and fire riser rooms.
2. If gas piping is routed in the same space, a gas-fired unit heater may be used. Unit heaters shall be thermostatically controlled.
M. Radiant Heaters
1. Radiant heaters may be provided in such outdoor spaces as appropriate for the application, such as animal housing facilities.
2. Acceptable manufacturers are Re-Verba-Ray, Reznor, and Modine.
23.05 OTHER HVAC PREFERENCES
A. HVAC Identification
1. Equipment shall be identified by name plates similar and equal to Seton Name Plates, Style 15671(M4564).
a. Thickness: 1/16” (min.)
b. Size: 1”x3” (min.)
c. Beveled edges
d. Color: black satin with white core lettering
e. Attachment: nickel plated steel screws
f. Lettering: 3/16” tall, Gothic Normal font
2. Equipment and devices located above ceiling shall be identified by means of adhesive, vinyl, colored dots placed on ceilings where these items are located. Coordinate with the District for color usage.
B. Air Cleaning Devices:
1. Air-cleaning devices shall be needlepoint bi-polar ionization type devices such as provided by Global Plasma Solutions and Plasmas Air.
26.01 GENERAL PROVISIONS
A. All new and remodeled facilities for Allen ISD shall be provided with full and complete electrical, lighting, and related support systems as required for practical operation and in conformance with all applicable regulations, codes, and ordinances.
26.02 SERVICE CHARACTERISTICS
A. The electrical service characteristics for each project shall be determined specifically for the site involved, as approved by the PM (project manager).
B. Note that depending on the campus location, the service could be provided by multiple entities. Engineer shall confirm electric provider prior to commencing any design work.
Electricity: Oncor
Gas: Atmos, CoServ
Water: North Texas Municipal Water District (NTMWD) 214.509.4530
Waste: North Texas Municipal Water District (NTMWD) 214.509.4530
Data/Fiber: AT&T, Frontier, Earthlink
Underground Utility Locator 811 www.call811.com
C. Facilities: The electrical service characteristics shall be 480Y/277 Volt, three phase, four wire on all new projects (subject to confirmation by the local electric utility company). The primary service voltage shall be selected for economy of wiring based on anticipated loads and voltages of equipment being served.
D. Existing Facilities: Existing electrical service characteristics shall be maintained, when feasible, for all additions/renovations.
E. Building utilization voltages shall be as follows:
1. 480 or 208 Volt, three phase, for motors 3/4 horsepower and larger.
2. 120 Volt, single phase, for motors 1/2 horsepower and smaller.
3. 120 or 277 Volt, single phase, for general lighting.
4. 208 or 480 Volt, single phase, for exterior area lighting.
5. 208 Volt, single phase, for special purpose outlets.
6. 480 or 208 Volt, three phase for electric heating elements 3kW and larger.
7. 120 Volt, single phase, for electric heating elements smaller than 3kW.
8. 208Y/120 Volt, three phase, four wire for general purpose use.
9. All equipment shall be 120 or 208 Volt, single or three phase, for kitchen equipment, as designated by the kitchen consultant. Provide a 208Y/120 Volt, 400 AMP service as a minimum.
26.03 SERVICE INTERRUPTIONS
A. Construction Documents shall require that any and all service interruptions required for the project shall be coordinated with AISD prior to the scheduled shutdown. A written request shall be submitted 10 business days in advance of the scheduled outage. The contractor shall include a schedule of his work and an estimate of the time required to accomplish the work. All service outages shall be coordinated such that they shall occur at times other than school hours, and the system shall be re-energized prior to the start of the next scheduled school day.
26.04 ELECTRICAL DISTRIBUTION SYSTEMS
A. General: The type and location of the power company service transformer (i.e., pole- vs. pad-
mounted) shall be determined for each specific site based on input from the local electric company. Pad-mounted transformers are preferred, and metering provisions as required by the local electric utility shall be provided. Service charges from the local electric utility company shall be directed to AISD and not included in construction contracts.
B. Existing Service: If an existing power company service originates from a vault, below or on grade, additional loads shall be served from the existing vault if allowed by the local electric utility company.
C. Service shall be changed to pad-mount transformer above grade if performing major service renovations or required by the local electric utility company. Pad-mount transformers are preferred over pole-mount transformers. If a new power source is required, justification shall be made for any deviation from the existing design scheme. The Architect/Engineer shall coordinate all requirements with AISD.
D. New Service: New electrical service to any facility shall be run underground in type EC (encased burial) PVC conduit. Install in accordance with the manufacturer’s recommendations and provide 25% spare conduit capacity.
E. Provide concrete-filled steel pipe bollards around all transformer and service equipment as required by the local electric utility company.
F. Secondary electrical services shall be provided underground using copper conductors in concrete encased PVC raceways. Aluminum alloy conductors may be considered for secondary electrical services only when construction budgets do not allow for copper conductors to be provided.
G. Branch circuits to each classroom must be kept separate, and there must be a minimum of two receptacle branch circuits provided for each classroom. Computer lab shall have minimum seven 20 amp circuits. (Maximum six computers per 20-amp circuit).
H. The term “clean power” where used for technology equipment means that the source is derived from a dry-type transformer operating within normal commercial power tolerances having less than 5% total harmonic distortion (THD) on the secondary bus unless another THD figure is required for the equipment.
I. Isolated ground systems will only be required for audio visual and theatrical systems when required by the systems being specified. Isolated ground systems, branch circuits, and receptacles shall not be used unless specifically required by the equipment manufacturer.
J. Ground Fault Circuit Interrupter (GFCI) receptacles are preferred over GFCI circuit breakers. GFCI circuit breakers shall only be used when GFCI receptacles cannot be provided. Where a GFCI receptacle is not readily accessible, a remote test/reset button shall be provided in the nearest janitors’ closet.
K. Electrical equipment furnished by the district with verified loads should be placed on dedicated circuits, especially heating equipment such as electric ranges in the Home Economics Departments, shops and kitchen equipment.
L. Coordinate power requirements for equipment such as copiers with AISD during design. Some equipment may require 208 Volt, single-phase circuitry.
26.05 ELECTRICAL DISTRIBUTION EQUIPMENT
A. Busses in all switchboards and panelboards of any type shall be copper. Aluminum will not be acceptable for any current-carrying purpose. All terminations shall be rated for a minimum of 75°C. Acceptable manufacturers are Square-D, Eaton, General Electric, Siemens,
B. Electrical distribution equipment will not be permitted on the job site until it can be fully protected from weather, moisture, physical damage, etc.
C. Main Switchboards and Main Distribution Panelboards:
1. All bussing shall be copper.
2. AIC rating shall be as shown on the construction documents.
3. All main circuit breakers shall be molded case circuit breakers with adjustable LSIG electronic trip units.
4. All distribution circuit breakers shall be three-phase, thermal-magnetic, bolt-on type.
5. Indoor equipment shall be NEMA 1 rated. Outdoor equipment shall be NEMA 3R rated.
6. Equipment shall be located in electrical equipment rooms preferably with direct outdoor access.
7. Provide phenolic mimic bus.
8. Provide engraved nameplates for all equipment. Nameplate shall include equipment name, voltage, and available fault current.
9. Provide engraved nameplates for all main and distribution circuit breakers.
10. Provide an externally mounted transient voltage surge suppression device (TVSS).
11. Provide a surface mounted electronic metering device with energy management system
interface equal to Square-D Ion7400 series power meter.
12. Additional capacity in service feeders and main switchgear shall be included for 20% future expansion of all projects.
13. Acceptable manufacturers are Square-D, Eaton, General Electric, Siemens,
D. Distribution Panelboards:
1. All panelboard bussing shall be copper.
2. AIC rating shall be as shown on the construction documents.
3. All distribution circuit breakers shall be three-phase, thermal-magnetic, bolt-on type.
4. Indoor panelboards shall be NEMA 1 rated. Outdoor panelboards shall be NEMA 3R rated.
5. Panelboards shall be located in equipment rooms/spaces designated for such equipment.
Panelboards may not be located in corridors, toilets, and other student areas. Electrical spaces shall be designed to allow for access, maintenance and replacement of equipment, and future panel space.
6. Provide engraved nameplate on all panelboards. Nameplate shall include panelboard name, voltage, and panelboard power source.
7. Provide engraved nameplates for all main and distribution circuit breakers.
8. Acceptable manufacturers are Square-D, Eaton, General Electric, Siemens,
E. Lighting and Appliance Panelboards:
1. All panelboard bussing shall be copper.
2. AIC rating shall be as shown on the construction documents.
3. All circuit breakers shall be bolt-on type. Plug in circuit breakers will not be accepted.
4. Indoor panelboards shall be NEMA 1 rated. Outdoor panelboards shall be NEMA 3R rated.
5. Provide door within door construction.
6. Each panelboard shall have a minimum of 42-poles and provided with a minimum of 9 spare circuit breakers.
7. All panelboard directories shall be typed and mounted on the inside of the door behind a clear plastic sheet.
8. Load Balance: All panelboard circuits shall be balanced on all phases within 10%.
9. Panelboards shall be located in equipment rooms/spaces designated for such equipment.
Panelboards may not be located in corridors, toilets, and other student areas. Electrical spaces shall be designed to allow for access, maintenance and replacement of equipment, and future panel space.
10. Do not install panelboards in closets with sinks. Panelboards may be installed in kitchen areas provided they are in closets or in a separate area away from moisture.
11. All HVAC equipment shall be fed from separate panels and circuits from other building loads. Utilize 480 Volt power, if available.
12. Provide engraved nameplate on all panelboards. Nameplate shall include panelboard name, voltage, and panelboard power source.
13. Acceptable manufacturers are Square-D, Eaton, General Electric, Siemens, F. Dry Type transformers:
1. All transformer winding shall be copper.
2. Indoor transformers shall be NEMA 1 rated. Outdoor transformers shall be NEMA 3R rated.
3. All transformers shall be floor or ground mounted on concrete housekeeping pads.
4. Provide K13-rated type transformers where the usage warrants.
5. Dry type transformers shall have the minimum DOE 2016 efficiency ratings, not exceed 150 degree C rise and have copper windings.
6. Provide engraved nameplate on all transformers. Nameplate shall include transformer name, primary voltage, secondary voltage, and transformer primary power source.
7. Acceptable manufacturers are Square-D, Eaton, General Electric, Siemens, 8. Enclosed Switches and Circuit Breakers.
9. All switches shall be heavy duty.
10. All switches shall be fused or non-fused depending on the application.
11. Indoor switches shall be NEMA 1 rated. Outdoor switches shall be NEMA 3R rated.
12. Provide engraved nameplate on all switches. Nameplate shall include equipment name, voltage, and equipment power source feeder or branch circuit designation.
26.06 LIGHTING
A. General: In each application, the type of lighting best suited for the task shall be installed, with proper consideration being given to the efficiency of the source so that an overall energy- efficient system is provided that is compliant with the current energy code.
B. Illumination Levels:
1. Illumination levels shall be per IES recommendations or the following table unless limited by current energy codes.
C. Use lighting fixtures with favorable coefficients of utilization and maintenance factors, long life LEDs, and energy-efficient electronic drivers.
D. LED light fixtures shall be used for all areas. LED Fixtures shall be supplied from a manufacturer engaged in production of similar fixtures for at least five years and have the following certifications.
1. UL 1598 and 2043 listed.
2. LM79/LM80 compliant.
3. RoHS compliant.
4. Design Lights Consortium (DLC) qualified.
E. Installation, General: Light fixtures shall be suspended from structure and not from the ceiling system. Light fixtures shall be located in such a way as to reduce vandalism. Where 277 Volt lighting branch circuits supply classroom lighting, the branch circuits must not supply more than five adjacent classrooms. Where 120 Volt lighting branch circuits supply classroom lighting, the ranch circuits must not supply more than two adjacent classrooms.
F. General Lighting Criteria:
1. Exterior Lighting: Refer to currently adopted International Energy Code for compliance.
a. All exterior lighting shall be LED and be dimmable where required by Energy Code.
b. LED color temperature for exterior lighting fixtures shall be 4100, degrees Kelvin.
c. Recessed wall packs are prohibited; only surface-mounted fights allowed, except soffit lighting, which should be limited to exit locations and may be used for wall and limited site illumination.
d. Exterior lighting requirements vary with specific project locations – coordinate all requirements with AISD and the local authority having jurisdiction (AHJ). Exterior lighting design shall follow Illuminating Engineering Society of North America (IESNA) illumination guidelines.
e. Any exterior junction boxes in ground to the quartzsite concrete boxes.
f. Typical underground conduits shall be Sch. 40 PVC, with Rigid 90-degree bends with corrosion tape.
g. Provide stranded wire for all pole lights.
h. Exterior pole mounted Security and Parking Lot lighting is to be installed on square, straight steel poles with concrete bases. Light fixture and pole color and finish shall be as selected by the architect. Pole base height to be appropriate for location, i.e., pole bases located in vehicle parking areas shall be minimum 36” tall, pole bases located in pedestrian areas should be no higher than 1” above surrounding grade.
i. Provide glare shielding for fixtures located adjacent to residential zoned properties, and where otherwise required for conformance to local lighting ordinance.
j. All Outside and Parking lot lighting shall be circuited separately from other building loads and controlled from the lighting control system. For additions, add exterior lighting to existing EMCS where feasible and permitted, consult with owner.
k. Exterior lighting and parking lot lighting in the kitchen delivery and entrance area to be circuited separately from other building loads and controlled separately from the control system for operation at 5-5:30 am for kitchen staff.
l. Provide dimming controls for exterior site lighting areas as required per the adopted Energy Code.
m. Poles are to be of steel construction, bolted to the concrete base.
n. Exterior lighting designs should include design practices that control glare and split, and do not allow light to spill onto neighboring properties.
o. All exterior lighting to be controlled by photocell and time schedule controller for photocell ON, schedule clock OFF operation. Provide with manual override in location of control panels, through relay panels.
p. Flagpole lighting must properly light all flags, with dedicated flood light fixtures, provide photometric for owner review. Use in-ground flood lights. Do not use ground mounted flood lights. Control using photocell & timer.
q. No ground mounted, fixtures. Use alternatives including in-ground flood lights.
r. All parking lot fixtures are to have in-line fuses accessible through the hand-hole at the base of the pole.
2. Interior Lighting: Refer to currently adopted International Energy Code for compliance.
a. In all classroom areas, provide 2’x4’ lensed LED fixtures with native 0-10V dimming. Each room is to be equipped with a Vacancy Sensor, Lighting Controller and multi-button Low Voltage Wall Switches. Photosensors for daylighting shall be provided where required by Energy Code.
b. In Kitchens, provide 2’x4’ lensed LED fixtures with gasketed housing or other suitable food service area rated construction.
c. In all Science/Art areas, provide 2’x4’ lensed flat panel LED fixtures with native 0-10V dimming. Each room is to be equipped with a Vacancy Sensor, Lighting Controller and multi-button Low Voltage Wall Switches. Photosensors for daylighting shall be provided where required by Energy Code.
d. In shower areas or other areas with wet exposure, provide acrylic or poly lensed LED fixtures with gasketed housing UL listed for use in wet areas and showers.
e. Gymnasiums are to have LED “high bay fixtures”. All gymnasium lighting fixtures are to be provided with wire guards or high impact lens construction, and safety cable for secondary support.
f. Provide separate lighting control zones in gymnasiums and activity rooms to allow for zoned control zones, and dual level switching over seating.
g. Where applicable, at gymnatorium’s, provide suspended border light bar and star par spotlight in front of stage with portable dimmer and fluorescent fixtures above the stage. For theatrical efforts, task lights shall be fluorescent fixtures.
h. Exit signs are to be LED with red, vandal resistant lenses and white vandal resistant housings. Provide wire guards for exit signs in gymnasiums and other areas where signs may be impacted by sports activities.
i. Lighting in Life Skills, Cool-Down Room and other special needs spaces to be dimmable. Consider providing fixtures and controls with adjustable lamp color.
j. Stage areas are to have specialized lighting fixtures, to be verified per individual school project. Discuss specific Stage requirements during planning with AISD Program Manager and refer to latest District stage equipment design guidelines. (Consider using LED theatrical fixtures)
k. Provide lighting in all elevator hoistway, pit and in crawl spaces.
l. Light fixtures in stairwells shall be easily accessible for maintenance. It is preferred that wall- mounted lights be installed above the landings in stairwells such that extension type ladders or similar apparatus may be used on flat flooring. No lighting fixtures shall
be located such that maintenance will require standing on a ladder over stair treads.
G. Athletic Lighting
1. LED lighting by Musco is the preferring athletic lighting system, with Musco wireless controls.
2. Follow UIL Minimum lighting standards as a minimum starting point, and consult the district on a project-by-project basis for each venue.
3. Football Stadiums should have 70fc, average, on the field and 40FC on track measured horizontally at 5ft above the field. This may require additional fixtures for uniform track lighting at apex of the curves/
4. Indoor Practice Field should have 70FC average maintained on the field level.
5. Glare & spill control is the second priority over lighting levels. Fixture design should not cause undesirable glare to participants, or spectators.
H. Lighting Controls:
1. The AISD preferred lighting control system is by nLight, manufactured by Acuity.
2. Provide distributed lighting control system for all areas. Utilize systems with networked gateway for commons, and corridors areas. Control system strategies shall comply with the current State adopted International Energy Conservation Code.
3. During design, consult with AISD maintenance and facilities for corridor and commons area lighting controls, including locations for overrides, and networking of control zone areas.
4. Lighting control based on schedule for interior lighting shall be provided with override switch(s) for manual override control in the event of failure. This switch shall be installed in an approved location coordinated with AISD.
5. Designer to maximize natural daylighting to the extent possible.
6. Combination occupancy/vacancy sensors are required by the International Energy Conservation Code. Coordinate lighting sensors so they do not interfere with projection systems.
7. Switching, General. Multi-level switching shall be provided in all classroom and office areas. Provide separate lighting control zone for fixture at the teaching wall, and preset controls for dimming in an AV mode. All switching shall be in accordance with the current energy code requirements.
8. Provide wired solution for building interior, with stand-alone devices.
9. Battery powered switches are not permitted and should not be used.
10. Network control for corridors, and Common areas for control across the campus, Control by schedule with zone override switches in Reception, Main Electrical Room, other spaces as coordinated with the owner.
11. Group toilets should be on with corridor lighting, with occupancy control as require by the energy code.
12. Wireless control for parking lot pole lighting
13. Provide separate exterior lighting control zones for the following zones (wireless fixtures can be grouped in programming). Coordinate in review with owner early in design development: a. Parking areas
b. Pedestrian areas & Area lighting
c. Driveways
d. Building mounted exterior lighting
e. Kitchen exterior entry and Service areas
f. Canopies
g. Exterior lighting to be controlled by schedule
h. Exterior lighting, all zones to have manual overrides locally located
26.07 EMERGENCY POWER SYSTEM
A. Interior Emergency/Exit Lighting:
1. AISD, prefers to utilize a system that powers LED exit and emergency light fixtures with low voltage power from remotely located, central battery controllers. Approved manufacturer, Signtex Lighting Inc., Grasonville MD., no exceptions.
2. The central battery system should be comprised of both dedicated fixtures for exit & emergency lighting, as well as utilize architectural light fixtures as emergency light fixtures.
3. Emergency egress and exit lighting fixture (LED type preferred) shall be designed to provide not less than one foot-candle on the floor surfaces, served by a battery for not less than 1-1/2 hours duration independent of the normal service.
B. Classrooms & hallways shall utilize wall mounted fixture above the door.
C. Storm Shelter Emergency Power
1. In storm shelters, the emergency power supply for ICC-500 required, mechanical ventilation systems shall consist of a UL listed, emergency lighting inverter system sized to provide full power supply to respective mechanical equipment and any other required shelter electrical loads for a minimum of 120 minutes (2 hours).
2. ICC-500 required emergency lighting shall be provided the low voltage, central batter powered lighting system (Signtex Lighting Inc.), and shall be dedicated to only serving storm the storm shelter areas, and those respective shelter lighting fixtures for a minimum of 120 minutes (2 hours).
26.08 SWITCHES AND OUTLETS
A. Receptacles, General: Receptacles shall be three-wire, tamper resistant, grounding type, specification grade, “Pass and Seymour,” “Leviton,” or approved equal. All receptacle faceplates shall be 302 stainless steel device cover plates.
1. Maximum number of general-purpose receptacles per circuit should be limited to 8, unless otherwise approved by the AISD Program Manager.
2. Switches and receptacles should not be located in chalkboards, markerboards or tack boards. Coordinate all locations to avoid conflicts.
3. Normal mounting height of switches should be 45” above finished floor, complying with state and local requirements regarding access by the handicapped, coordinate with the architect.
4. Mounting height of wall receptacles should be 15” above finished floor. Mounting height of above-counter receptacles should be 45” above finished floor. Mounting height of TV/ Monitor receptacles should be 90” above finished floor, unless noted otherwise.
5. Standard switch and receptacle cover plates in Kitchens, Restrooms, Gymnasiums shall be s stainless steel
6. Standard switch and receptacle cover plates in Classrooms, Offices, other spaces shall be non-breakable lexan
7. Standard wall receptacles/switches should be “white”
8. Wall receptacles with dedicated isolated ground (IG) circuits shall be “orange.”
9. Provide IG ground conductor color, “green with yellow tracer”.
10. Wall receptacles served by generator backup circuits shall be “red.”
11. Provide two (2) “convenience” receptacles per wall in all teaching spaces.
12. Receptacles outside buildings should be located adjacent to each exterior door, provided with vandal-resistant, weatherproof in-use covers and be GFCI protected.
13. All receptacle installations shall comply with local AHJ requirements.
14. All receptacle and switch plates shall be labeled with the circuit number, both inside the plate and the face of the plate.
15. Provide tamper-proof receptacles in rooms where required by the NEC based on age and grade level.
16. Provide at least three dedicated 120 Volt circuits and one dedicated 120/208 Volt, four-wire circuit in each communication closet. Provide power to the UPS’s as required by Division 27 Technical Design Guidelines.
B. Receptacles, Switched: Receptacles shall be switched using vacancy sensors and plug load controllers only where required by the International Energy Conservation Code, or ASHRAE 90.1. Switched receptacles shall be clearly labeled using approved AISD labeling standards.
26.09 CONDUIT AND RACEWAY
A. Installation, General: No conduit shall be run within 10” of the roof deck inside the building. Conduit shall be suspended from structural members, and not from ceiling systems or roof deck Conduits shall be located only in places approved for their use by the NEC. Circuits for lighting shall be provided with separate conduit runs from those for receptacles. Do not install conduits on the roof. Use appropriate fastening devices to mount conduits and boxes (Toggle bolts on plaster and sheetrock walls, etc.). Conduit shall not be routed directly on building roofs.
B. Materials: Conduit system shall be metallic throughout, UL labeled, and all steel shall be hot dip galvanized. Fittings shall be of similar construction.
C. Electrical underground feeders shall be encased in red concrete with a minimum cover of 36” in paved areas and 30” in unpaved areas. Typical underground conduits shall be Sch. 40 PVC, with Rigid 90-degree bends with corrosion tape. Provide Sch. 80 for risers at utility company power poles.
D. Underground: All underground primary and secondary electrical feeders shall be routed in concrete encased PVC conduit. At least one spare conduit shall be provided for each secondary electrical feeder.
E. Above grade exposed: All raceways above ground and exposed shall be galvanized rigid conduit.
F. Above grade interior to building: All raceways above grade and interior to the building shall be electrical metallic tubing with compression fittings. Set-screw fittings will not be allowed.
G. Final Connections: Flexible conduit may be used only for final connections to equipment and lighting fixtures, with a maximum 6’ length. All connections to mechanical equipment shall be made with flexible metal conduit. Flexible metal conduit used in damp or wet locations shall be PVC coated (Sealtight).
H. MC Cable: For final connections from junction boxes mounted on the building structure to recessed lighting fixtures. Type MC cable assemblies shall be permitted, with the cable assembly length not to exceed six feet and with supports as required by the NEC. Fixture-to-fixture chain wiring is not permitted. Type MC cable is also permitted to be used for vertical branch circuits
located in walls comprised of steel studs and drywall. All other locations are to be in EMT as specified, and EMT must be used to transition the branch circuit conductors into the wall at these locations. Continuous runs of MC cable above ceiling or horizontally in wall cavities are not permitted. NEC requirements for supporting from the structure will be strictly mandated. All home runs from the first box to the panelboard shall be in EMT.
26.10 CONDUCTORS
A. All feeders and branch circuits shall be copper type THHN/THWN-2 or XHHW in raceways. Aluminum alloy conductors will not be considered. MC cable shall be limited to 6’ lighting fixture whips from branch circuit junction boxes mounted to structure above lay-in ceilings.
B. Control Wiring: All control wiring shaft be 24 or 120 Volt (maximum) as appropriate to the use. AII control wiring shaft be run in conduit. ”HVAC Control Wiring” as associated with the automatic control system or AISD district-wide EMS shall be provided as delineated elsewhere in this manual.
C. Grounding: The electrical system shall comply with NEC rules for grounding. All panelboards/ distribution boards shall be provided with separate grounding bar. A separate green grounding conductor shall be run in each conduit. A Ufer ground shall be used as the system grounding electrode for all new construction projects. Electrical systems installed in additions to existing structures shall be grounded to the same grounding electrode as the existing system. Provide grounding for telephone service, and all other incoming low voltage services.
D. Conductor Color Coding: All conductors shall be color coded using factory pigmentation with the following color designations:
1. 208Y/120 Volt systems:
Phase A - Black
Phase B - Red
Phase C - Blue
Neutral - White
Ground - Green
2. 480Y.277 Volt systems:
Phase A - Brown
Phase B - Orange
Phase C - Yellow
Neutral - Gray
Ground – Green
26.11 LIGHTNING PROTECTION AND DETECTION
A. Lightning protection systems are not required on AISD projects.
26.12
ELECTRICAL STUDIES
A. A short-circuit, coordination and arc flash study shall be provided on all projects. The study shall be provided by a licensed electrical engineer registered in the State of Texas. The study shall require that the contractor adjust and set all adjustable circuit breakers as recommended in the coordination study.
B. Arc flash labels shall be provided by the contractor on all electrical distribution equipment including all switchboards, panelboards, transformers, and disconnect switches.
26.13 CONDUIT AND RACEWAY
A. Installation, General: No conduit shall be run within 10” of the roof deck inside the building. Conduit shall be suspended from structural members, and not from ceiling systems or roof deck. Conduits shall be located only in places approved for their use by the NEC. Circuits for lighting shall be provided with separate conduit runs from those for receptacles. Do not install conduits on the roof. Use appropriate fastening devices to mount conduits and boxes.
B. Materials:
1. Conduit system shall be metallic throughout, UL labeled, and all steel shall be hot dip galvanized. Fittings shall be of similar construction. All wiring shall be in EMT conduit with steel compression fittings – no set screw or aluminum type fittings allowed. In new construction no conduit shall be installed on the roof; all conduit shall be hung from structure.
2. On existing buildings conduit may be installed on roof using conduit supports and pads suitable for direct sunlight, conduit size, weight, quantity and roof system with Unistrut supports and accessories. Conduit supports shall allow for conduit expansion and contraction. Manufacturers shall be Portable Pipe Hangers, Eaton B-Line, Miro Industries or approved equal. Conduit on roof shall be Aluminum or X-Wall Reinforced Thermosetting Resin Conduit (RTRC).
C. Electrical underground feeders shall be encased in red tinted concrete with a minimum cover of 48” below finished floor and on select fill. Typical underground conduits shall be PVC Coated Galvanized Rigid Steel or Reinforced Thermosetting Resin Conduit (RTRC) long sweep elbows with PVC, RTRC or PVC coated galvanized rigid steel straight run conduits. Provide Galvanized Rigid Steel or X-Wall RTRC for risers at utility company power poles.
D. Flexible Metal Conduit or Steel MC cable may be used only for final connections to light fixtures with a maximum 6’-0” length.
E. Final Connections to equipment mounted on roof, rotating equipment, transformers, and kitchen or food processing equipment, or where flexible conduit is required outdoors shall be made with Liquid Tight Flexible Metal Conduit.
F. Minimum indoor conduit size shall be 3/4”.
G. The minimum conduit size between buildings for technology, voice, data, fire alarm, video, security, surveillance, BMCS, and other telecommunications shall be 2”.
H. Engineer shall include empty conduits to marquee/monument sign locations for power and data.
I. Engineer shall include (4) 4” empty conduits for future use from main building, under drives, to future portable classroom locations. Curbs shall be marked to identify locations of conduits.
J. Engineer shall include (4) 4” empty conduits for future use under sidewalks, drives, parking lot landscaped islands, etc. to allow for future work to be accomplished without having to sawcut existing concrete.
K. Provide surface-mounted, dual channel, aluminum raceway system equal to Wiremold AL5200 by Legrand for computer labs.
26.14 CONDUCTORS
A. General: Provide factory-fabricated conductors of the size, rating, material, and type as indicated for each use. Conductors shall be soft or annealed copper wires meeting, before
stranding, the requirements of ASTM B 3, Standard Specification for Soft or Annealed Copper Wire for Electrical Purposes, latest edition.
1. Conductors for control wiring sized #12 AWG through #10 AWG shall be stranded. All control wiring shall be 24 or 120 volt (maximum) as appropriate to the use. AII control wiring shall be run in conduit. HVAC Control Wiring as associated with the automatic control system or AISD district wide BMCS shall be provided as delineated elsewhere in this manual.
2. Conductors for power and lighting shall be solid excluding: HVAC equipment, Refrigeration Equipment, Pumps, Ventilators & fans. Stranding shall be Class B meeting the requirements of ASTM B 8, Standard Specification for Concentric-Lay-Stranded Copper Conductors, Hard, Medium Hard, or Soft.
3. Where authorized in writing by the Owner and Architect and not prohibited by local codes or the Authority Having Jurisdiction (AHJ), aluminum alloy compact stranded conductors may be allowed in AWG sizes 3/0 through 750 kcmil (150-358 Amps) for service entrance conductors and feeders exceeding 25-feet in length. Aluminum alloy conductors shall not be used for grounding or for branch circuits or any equipment terminations. Aluminum alloy conductor size shall meet or exceed the equivalent ampacity for the specified copper conductor using 75 C ampacities for both types of conductors.
B. Insulation for standard building conductors: Insulation shall meet or exceed the requirements of UL 83, Standard for Thermoplastic Insulated Wires.
1. All wiring inside lighting fixtures shall be temperature rated per NEC.
2. Insulation for copper conductors shall be UL Type THHN/THWN, 90 degrees C.
3. Insulation for aluminum conductors shall be UL Type XHHW-2, 90 degrees C.
C. Insulation for 2-hour fire rated power cables: Insulation shall meet or exceed the requirements of UL 2196 Fire Test for Electrical Circuit Protection Systems, and UL 44, Standards for Fire Resistive Cable.
1. Insulation for conductors shall be UL Type RHH/RHW, 75 degrees C for wet locations and 90 degrees C for dry locations.
2. Electrical Circuit Protective Systems (FHIT) – System 27 of the UL Fire Resistance Directory. Color Code Table (Use continuous color-coded insulaion throughout)
Notes:
1. 120/208, 120/240, and 277/480 Volt Systems shall be routed in separate raceways.
2. Switched legs of phase conductors for lighting and appliance branch circuits shall be of the same color as described above throughout the entire circuit.
3. Conductors shall be the same color from breaker to device or outlet.
D. Grounding: The electrical system shall comply with NEC rules for grounding and bonding. All panelboards/distribution boards shall be provided with separate grounding bar. A separate green grounding conductor shall be run in each conduit. A Ufer ground shall be used as the system grounding electrode for all new construction projects. Electrical systems installed in additions to existing structures shall be grounded to the same grounding electrode as the existing system. Provide grounding for telephone service, and all other incoming low voltage services.
27.01 GENERAL PROVISIONS
A. All new facilities, new additions to existing facilities and remodeled facilities shall be provided with Communication Systems as determined by Allen Independent School District. The primary function of these systems is to coordinate activities, facilitate staff communications and provide communications for the campus population for routine programming and safety and security information.
27.02 CODES AND STANDARDS
A. Federal, state, and local codes, rules, regulations, and ordinances governing the work are to be included in the specifications. Should items noted in the drawings or specifications create an installation that is in violation of codes, rules, regulations, or ordinances, promptly call them to the attention of Allen ISD’s Executive Director of Operations.
B. The division 27 systems shall comply with the system specific industry standards in addition to the Codes and Design Standards. The following industry standards shall apply as per applicable system:
1. NECA 1 – Standard for Good Workmanship in Electrical Construction, 2015
2. ANSI/TIA Standards:
a. ANSI/TIA-568.0-E – Generic Telecommunications Cabling for Customer Premises, 2020
b. ANSI/TIA-568.1-E – Commercial Building Telecommunications Cabling Standard, 2009 - Part 1: General Requirements, 2020
c. ANSI/TIA-568.2-D – Commercial Building Telecommunications Cabling Standard, 2009 - Part 2: Balanced Twisted Pair Cabling Components, 2018
d. ANSI/TIA-568.3-D – Optical Fiber Cabling Components Standard, 2016
e. ANSI/TIA-568.4-D - Broadband Coaxial Cabling and Components Standard, 2017
f. ANSI/TIA-569-E – Telecommunications Pathways and Spaces, 2019
g. ANSI/TIA-606-D – Administration Standard for Telecommunications Infrastructure, 2021
h. ANSI/TIA-607-D – Generic Telecommunications Bonding and Grounding (Earthing) for Customer Premises, 2019
i. ANSI/TIA-526.7-A – Measurement of Optical Power Loss of Installed Single-Mode Fiber Cable Plant, 2015
j. ANSI/TIA-526.14-C – Optical Power Loss Measurement of Installed Multimode Fiber Cable Plant, 2015
k. ANSI/TIA-758-B – Customer-Owned Outside Plant Telecommunications Infrastructure Standard, 2012
l. ANSI/TIA-942-B – Telecommunications Infrastructure Standard for Data Centers, 2017
m. Install infrastructure in accordance with the most recent edition of BICSI® publications:
n. BICSI – Telecommunications Distribution Methods Manual, 14th Edition
o. BICSI – Information Technology Systems Installation Methods Manual, 8th Edition
p. INFOCOMM / AVIXA audio-visual Standards:
q. AVIXA-V202.01:2016 - Display Image Size for 2D Content in AV Systems
r. AVIXA-F501.01:2015 - Cable Labeling for AV Systems
s. AVIXA-A102.01:2017 - Audio Coverage Uniformity in Listener Area
t. ANSI/INFOCOMM-2M-2010 - Standard Guide for AV System Design and Coordination Processes
u. INFOCOMM-3M-2011 - Projected Image System Contrast Ratio
v. INFOCOMM-4:2012 - Audiovisual Systems Energy Management
w. AVIXA-F502.01:2018 - Rack Building for Audiovisual Systems
x. INFOCOMM-10:2013 - Audiovisual Systems Performance Verification
3. Federal, state, and local codes, rules, regulations, and ordinances governing the Work, are as fully part of the specifications as if herein repeated or hereto attached. If the Contractor should note items in the drawings or the specifications, construction of which would be code violations, promptly call them to the attention of the Owner’s Representative in writing. Where the requirements of other sections of the specifications are more stringent than applicable codes, rules, regulations, and ordinances, the specifications shall apply.
4. American Society for Testing and Materials (ASTM): ASTM E. 814 – Standard Test Method for Fire Tests of Penetration Firestop Systems
5. Underwriters Laboratories, Inc. (UL): UL 1479 – Tests of Through-Penetration Firestop Systems
6. NFPA-70 – National Electrical Code, 2017
7. Americans with Disabilities Accessibility Guidelines, 2010.
8. Code of Federal Regulations, Title 29, Chapter XVII, Part 1910 (OSHA).
9. Uniform Building Code (UBC).
10. International Building Code (IBC).
11. Texas Department of State Health Services (TDSHS)
12. Applicable codes and directives of authorities having jurisdiction
27.03 CONTRACTOR’S
QUALIFICATIONS
A. The Contractor shall employ full-time, factory-trained, licensed, local technicians and installers for product installation, maintenance, support, service and warrant.
B. The proposed contractor, as a business entity, shall be a local authorized distributor and designated representative of the equipment manufacturer, with full extended warranty privileges. The proposed contractor shall have been actively engaged in the business of selling, installing, and servicing commercial building commercial cable systems for a period of at least 5 years. Selected contractor must be certified in specified system, subcontracting other companies certified in proposed product shall not be allowed.
C. The proposed Contractor shall have an office within 150-miles of the job site, staffed with factory- trained technicians who are qualified and licensed to supervise the installation, to be responsible that the system is installed as submitted, to conduct system start up, and perform a 100 percent operational audit of all installed devices. The technicians shall instruct the Owners’ representatives in the proper operation of the system, and to provide service throughout the warranty period. The contractor shall be capable of dispatching technicians to repair a system within six (6) hours of a service request.
D. The proposed contractor shall be fully experienced in the design and installation of the type of system and manufacturer herein specified and shall furnish with the contract proposal an itemized list of the installations of the type specified herein.
E. The contractor shall employ factory-trained technicians capable of supporting the maintenance of the system. No contract employees are allowed. All installing technicians shall be employed by the proposed contractor.
F. The Owner’s Representative or Owner may investigate, as they deem necessary to determine the
ability of the proposed Contractor to perform the work. The proposed contractor shall furnish to the Owner with any information or data requested for this purpose.
27.04 SUBMITTALS AND SHOP DRAWING REQUIREMENTS
A. Designers shall require that the contractor to produce Shop Drawings for each Division 27 specification section which provides such a requirement within. These sections include, but may not be limited to, sections 27 10 30, 27 41 31 and 27 51 41.
B. Provide Product submittals for all Sections which include the requirement. All product submittals must include all products, accessories, and options clearly identified within the submittal. Wiring diagrams which show all field connected wiring, termination points and labeling.
C. Contractors shall not utilize the Consultants’ original design drawings in the submittal or shop drawing process. Contractor shall develop their own original shop drawings.
27.05 TEST RESULTS
A. Designers shall require that 100% of all cables, conductors, and strands must be tested and certified according to the manufacturer’s recommendation. These test reports shall be provided to the Owner.
27.06 AS-BUILT DRAWINGS
A. Designers shall require that the Contractor provide updated shop drawings which reflect accurate as-built information including, but not limited to, cable routing and cabinet elevations
27.07 DATA CABLE PLANT
A. The owner’s standard manufacturers model numbers, functions, and features described in this specification section are those of the CommScope Uniprise Structured Cabling Solution with a 25- year warranty , and this shall constitute the quality and performance of the equipment to be furnished. Equivalent systems made by the following manufactures and covered by similar extended warranty programs are acceptable; any other proposed suppliers must be pre-approved:
a. CommScope Uniprise
b. Panduit
c. Superior Essex
d. Ortronics
2. The selected contractor must be a certified Integrator/Installer authorized by one of the Manufacturers listed below to provide an extended warranty to the Owner covering all network cable and connectivity hardware products comprising this installation site. All UTP cable, fiber optic cable, and all wiring devices installed shall be products of one approved manufacturer or joint manufacturers program and approved for use in their extended warranty program. The Contractor and Manufactured shall jointly provide the Owner an extended warranty of the installed system against defects in material or workmanship; provide a copy of contractor certification
3. All cabling and components shall be rated for the environment in which it is installed
B. Station Cabling
1. The data cable plant design shall provide Category 6A Local Area Network (LAN) circuits to the following locations, as well as locations of MEP and/or the Owner furnished Systems requiring LAN connectivity:
a. VoIP Telephones
b. Video Surveillance Cameras
c. Wireless access points
d. Workstations
e. Printers/Copiers
f. Main Distribution Frame (MDF) and Intermediate Distribution Frame (IDF)
i. Monitored Power Meters
ii. Local Conditioned Air Unit Controls
iii. Climate Monitoring Meters
g. Employee Time Clocks
h. Access Control System Controllers
i. Video Surveillance Servers
j. Local Sound System Head Ends
k. PA/Intercom Head Ends
l. Fire Alarm Control Panels
m. Intrusion Detection Control Panels
n. Mechanical Air Handling Units
o. Building Automation System Main and Remote Panels
p. Electrical Switch Gear and Branch Circuit Power Meters
q. Intelligent Lighting Controls
r. Emergency Generator Monitoring Controls
s. Sump Pump and Sump Pit Monitoring Controls
t. Building Water System Meters
2. The SCS cable shall route in corridors, parallel and perpendicular to the building, and enter each room above the room’s main entrance door.
3. All station cabling shall include 10’ service loop in each closet prior to the termination and a 10’ service loop prior to each field side termination.
4. Including service loops, vertical rise and/or drop, and cable route; no cable shall exceed 295’ from termination point-to-termination point (Permanent Link Distance)
5. Cable color shall comply with the EMS ISD Standard:
a. White – Voice d. Purple – Security
b. Blue – Data e. e. Yellow- AV
c. Green – Wi-Fi
6. Copper Patch Cords
a. Provide one 1’ distribution frame and one 12’ workstation/equipment per installed run shown on plans.
C. Backbone Cabling
1. One (1) 12-strand, armored OM4 fiber optic cable shall connect each IDF to the building’s MDF. 2. Each IDF shall have IDF shall have a one rack unit (1RU), rack mounted fiber optic enclosure, with LC connector adapter plates. All fiber shall terminate into the installed enclosure.
3. The building’s MDF shall have a minimum of one (1) two Rack Unit (2RU), rack mounted fiber enclosure with LC fiber optic connector adapter plates. All fibers feeding the associated IDFs shall terminate into this enclosure. Enclosure size and quantities shall be increased as required to
house 120% of the fiber terminated. Single Category 6A cable from the MDF to every installed elevator and fire alarm control panel is required for secondary dialer requirement.
27.08 TELECOMMUNICATIONS SPACES
A. Main Distribution Frame (MDF)
1. The MDF is the primary communications room for the building. This room shall house all Servers, Routers, Primary Fiber Switches, network equipment, television hardware, fire alarm main panel, access control main panel and power supplies, HVAC building automation, lighting control, Telecommunication Service Provider’s Demarcation Point and the Owner’s wide area network equipment
2. Location and Requirements:
a. The MDF shall not be used as a route for, or to hold other building systems. For example; Boilers Rooms, Air Exchange Rooms, Janitorial Closets, Water heaters, Wet Sinks, or Electrical rooms.
b. The MDF shall be centrally located within the building.
c. The Room size shall be as follows:
i. Elementary Schools – 12’ X 16’
ii. Middle School and High Schools – 14’ X 20’
iii. Rooms shall be open to deck with no ceiling.
d. Cover walls with 3/4” grade A/C plywood, painted with fire retardant paint on all six sides leaving the fire rating stamp exposed. Mount plywood 6-inches AFF vertically side by side.
e. Door shall be a minimum of 3’0” and shall swing out, from the corner of the room, on the corridor side and shall have the same fire rating as the room.
f. All conduit stub ups, sleeves, and cores shall be located within 6” of walls.
g. Provide detailed locations for all sleeves in wall indicating number of sleeves, sleeve sizes, and detail which sleeve is for which low voltage system such as fire, intercom, security, structured cabling, building controls, etc.
B. Intermediate Distribution Frame (IDF)
1. The IDF is space housing communication equipment serving network devices on an intermediate level. IDFs will be placed throughout the building and serve as intermediate connection points where the category 6 and 6A cable will be terminated. The LAN of copper signal will be converted to LAN over fiber, via network equipment, and routed to the MDF.
2. Requirements:
a. The IDF shall not be used as a route for, or to hold other building systems. For example; Boilers Rooms, Air Exchange Rooms, Janitorial Closets, Water heaters, Wet Sinks, or Electrical rooms.
b. IDF sizing shall be adequate to house the number of rack/cabinets being installed, plus one (1) additional rack/cabinet. Minimum size for these rooms shall be 8’ X 10’.
c. IDFs in multi-floor buildings shall be aligned vertically (stacked).
d. Rooms shall be open to deck with no ceiling.
e. Cover walls with 3/4” grade A/C plywood, painted with fire retardant paint on all six sides leaving the fire rating stamp exposed. Mount plywood 6-inches AFF vertically side by side.
f. Door shall be a minimum of 3’0” and shall swing out, from the corner of the room, on the corridor side and shall have the same fire rating as the room..
g. All conduit stub ups, sleeves, and cores shall be located within 6” of walls.
h. Provide detailed locations for all sleeves in wall indicating number of sleeves, sleeve sizes, and detail which sleeve is for which low voltage system such as fire, intercom, security, structured cabling, building controls, etc.
C. MDF/IDF MEP Requirements
1. HVAC
a. Provide 24x7x365 dedicate cooling system for room, sized for equipment installed. System shall be separate and independent from building air conditioning system. The system shall maintain a positive air pressure with minimum of one air change per hour.
b. Locate thermostat above light switch at entry door.
c. No floor drains shall be located inside any MDF, IDF, or any other location housing Technology Head End Equipment.
2. Electrical requirements:
a. Power for telecommunications equipment shall not be on same panel serving convenience receptacles, lighting or HVAC equipment.
b. Provide quadplex convenience outlet every 6’-0” along perimeter room wall.
c. Provide one (1) 30AMP/208V, L6-30R locking electrical receptacle at the primary equipment rack/cabinet installed in the backside of the vertical wire manager 18-inches AFF. Coordinate the nema configuration for the plug and receptacle.
d. Provide one (1) 20AMP/120v quad per every two (2) racks installed on the overhead ladder tray.
e. The following shall be considered the minimum requirements for Uninterruptible Power Supply system (UPS). The size and/or quantity shall increase as need to accommodate the equipment being deployed in each closet.
i. Provide one (1) 3000VA UPS in every network racks
3. Lighting
a. Lighting shall be provided in the aisels in front and behind all network cabinets, providing no less that 50 ft candles measured at 3’ AFF.
b. Lighting placement shall be coordinated with conduit, cable tray, and the rack system.
4. Fire Alarm shall utilize the base building system.
5. Fire Protection shall utilize the base building system.
D. Grounding and Bonding
1. Provide a 12-inch wide X 4-inch high Telecommunication Ground Busbar (TGB). Mount TGB on the wall behind the network racks at +84-inches AFF.
2. All racks, cabinets, and equipment enclosures shall be bonded to the TGB. Utilize #6AWG ground wire and copper two-hole compression ground lugs. Each rack, cabinet, and/or enclosure shall have a dedicated ground. Do not daisy chain.
3. TGB to be bonded to the building’s main entrance ground utilizing 3/0 grounding wire and two hole copper compression lugs.
4. Bond all incoming conduits, ductwork, piping, cable trays and termination frames with #6 AWG and two hole compression lugs.
E. Racks and Cabinets
1. All rack layouts shall be coordinated with the Owner’s Technology Department.
2. Patch panels and other components shall not consume more than 50% of the total rack/cabinet space, leaving 50% available for the Owner equipment.
3. Racks shall be 19-inch wide by 7-feet high (45U) 2-post racks.
4. 10” double sided vertical cable managers shall be placed at each end of the rack systems and between each rack. Cable managers shall allow management of cabling in the front and the rear of the racks.
5. Wall mounted cabinets shall be 19-inch wide and sized accordingly for the cable quantity in the serving area.
a. Wall mounted cabinets shall be mounted on fire-rated plywood
6. Ladder tray shall route across the top of all racks/cabinets and around the entire communications closet, providing pathway from each wall to each rack/cabinet in the system within the MDF. Ladder tray shall route across the tops of all cabinets and one piece of ladder
spanning the room opposite direction of the racks in each IDF. Ladder rack shall be sized either 12 or 18- inches based on the quantity of cables. Ladder rack accessories to be included:
a. Cable bend radius dropout transition from the ladder tray to be mounted above each vertical wire managers and shall be the same size as the ladder tray.
b. End cap to cover exposed ends of the ladder rack.
27.09 NETWORK AND IP TELEPHONE EQUIPMENT
A. Network Switches
1. All network switches are owner furnished, contractor installed.
B. Wireless Access Point (WAP)
1. All wireless access point are owner furnished, contractor installed.
C. Voice over Internet Protocol (VoIP) Telephones
1. All VoIP Telephones shall be owner furnished and installed.
27.10
INTERCOM SYSTEM
A. The IP based system is Singlewire Informacast with Atlas IED or CyberData devices.
1. The designed system shall provide complete public announcement throughout the entire building including outside playgrounds and Bus stops.
2. The designed system shall allow 2-way communications, direct dialing, and an IP speaker without the use of a press-to-talk-or talk to listen switch
3. The designed system shall integrate with the Owner’s VoIP telephone system, allowing paging to be initiated from any VoIP telephone with the appropriate permissions.
B. Approved Contractor
1. NetSync – Houston, TX.
27.11 AUDIO AND VIDEO SYSTEMS
A. General
1. All new facilities, new additions to existing facilities and remodeled facilities shall be provided with Audio and Video system as required to distribute audio and/or video content for instructional and event purposes.
B. Instructional Spaces (Classroom, Labs, Collaboration Spaces )
1. The AV system for these spaces shall consist of the following:
a. 75-inch Newline interactive or non-interactive monitors per district standards.
b. Extron Plenum Vault AV system.
C. Cafeteria, Library, and Gymnasium
1. The AV system for these spaces shall consist of the following:
a. Video Projector and screen as required for the space.
b. Extron control system with Symetrix control panel.
D. Audio Systems
1. Audio DSP
a. Provide audio Digital Signal Processors (DSP).
i. Contractor shall provide appropriate DSP based upon the required number of AEC channels and the available analog input/output capacity.
b. Audio DSPs shall feature:
c. Minimum of 4 input and 4 output
d. Minimum of one AEC Channel per Microphone
e. 128 x 128 AVB network audio interface
f. Voice Over IP (SIP) telephone interface
g. Network & Serial control interfaces
h. USB DSP Expansion Modules, where required
i. Five (5) year manufacturer warranty
j. Basis of design: TesiraFORTE AVB VT and TesiraFORTE AVB VT4, Tesira EX-UBT
2. Audio Amplification
a. Amplifier as required for space meeting owner requirements.
E. Recessed Ceiling Speakers
15. Provide speakers modeled and designed for space to meet owner requirements
G. Wireless Microphone System
1. System shall incorporate a wireless transmitter (microphone, body pack, etc.) with a rack mounted receiver that is tuned to receive radio waves and audio signals.
2. Approved Product
a. Shure QLX-D series or equivalent.
H. Assistive Listening System (ALS)
1. An assistive listening system shall be provided in assembly areas where audible communication is integral to the space and shall be in compliance with the Americans with Disabilities Act (ADA).
2. Twenty-five percent (25%) minimum of receivers provided, but no fewer than two, shall be hearing-aid compatible.
3. Each assembly area required to provide assistive listening shall provide signs informing patrons of the availability of the assistive listening system. These signs shall comply with the International Symbol of Access for Hearing Loss.
4. Approved Manufacturer
a. Listen Technologies
b. Williams Sound
5. Digital Signage
a. To be Newline displays, to be determined during the design coordination
28.01 GENERAL PROVISIONS
A. All new facilities, new additions to existing facilities and remodeled facilities shall be provided with Life Safety and Security Systems as determined by National and Local Codes and Allen Independent School District. The primary function of these systems is to create a Safe and Secure atmosphere by providing early detection, prevention, and notification. The System shall support the Standard Response Protocol Procedures established by the Owner while assisting first responders in communication and information as required to implement an appropriate and safe response.
28.02 CODES AND STANDARDS
A. Federal, state, and local codes, rules, regulations, and ordinances governing the work are to be included in the specifications. Should items noted in the drawings or specifications create an installation that is in violation of codes, rules, regulations, or ordinances, promptly call them to the attention of AISD’s Executive Director of Operations.
B. The division 28 systems shall comply with the system specific industry standards in addition to the Codes and Design Standards. The following industry standards shall apply as per applicable system:
1. Institute of Electrical and Electronics Engineers (IEEE):
a. IEEE 1100 Recommended Practice for Powering and Grounding Electronic Equipment.
2. Underwriters Laboratories, Inc. (UL):
a. UL 294 Access Control System Units
3. RoHS compliant
4. SIA AC-01-1996.10 - Access Control – Wiegand
5. International Electrotechnical Commission (IEC)
6. ISO / IEC 10918 - Information technology Digital compression and coding of continuous-tone still images: Requirements and guidelines; JPEG. AVIF is the latest and greatest compression format.
7. ISO / IEC 14496-10 - Information Technology - Coding of Audio-Visual Objects - Part 10: Advanced Video Coding; MPEG-4 Part 10 (ITU H.264).
8. ISO / IEC 23008-2 - High Efficiency Coding and Media Delivery in Heterogeneous Environments Part 2: High Efficiency Video Coding; MPEG-H Part2 (ITU H.265, HEVC).
9. FCC Part 15 – Radio Frequency Device
10. Electronic Industries Alliance (EIA)
a. RS485 - Electrical Characteristics of Generators and Receivers for use in Balanced Digital Multi-Point Systems
11. Federal Information Processing Standards (FIPS)
a. Advanced Encryption Standard (AES) (FIPS197)
b. FIPS201-2: Open Options DNA Fusion FIPS in conjunction with an E2-SSP-D2-FIPS, NSC-100 FIPS, RSC-2-FIPS and other listed components will provide an access control solution that is fully FIPS 201-2 compliant.
c. Personal Identity Verification (PIV) of Federal Employees and Contractors
12. Homeland Security Presidential Directive 12 (HSPD12)
C. The installation contractor shall hold a class B Security Contractor Company license issued by the State of Texas.
28.03 ACCESS CONTROL SYSTEM (ACS)
A. General
1. The ACS shall include the design as required to expand the Owner’s existing Continental Access platform to accommodate additional access control to addition/renovation spaces and/or to accommodate the addition of a completely new site.
2. The system architecture shall consist of:
a. Continental CICP2800 Door Controllers
b. HID Signo40 readers
B. Access Control Controller and Lock Power Supplies shall be backed up with batteries.
C. Access-Controlled doors
1. Access controlled doors shall be placed at strategic location identified during the design process. Each access-controlled door shall consist of the following:
a. One (1) Door Mounted Access Credential, HID Signo40.
b. One (1) door position sensor, GE 1076D-G, on single and double door active leafs and on each double door inactive leaf.
c. One request to exit (REX) motion detector programmed to log an access event as an authorized access upon exiting an access-controlled portal. REX device to be connected to the access management system control panel, by the access control integrator. Do we need this? They say here that it is to log people leaving the building. Do we actually use this feature, or are we just paying for motion detectors that do nothing for us. They don’t activate the access control because we have crash bars. Also, the DPS can perform the same monitoring function.
d. All electrified door hardware, wireless or hardwired, to be specified by the door hardware consultant. Access Control active devices (card Readers, motion detectors, door position switches) to be provided by the access control integrator.
2. All perimeter doors shall be either under access control or monitored by the access control system.
D. Monitored Doors:
1. When the occupied areas of the building are accessible by an exterior door that is intended for exit purposes and not access controlled, the door shall have a DPS on each leaf that will notify the ACS of the door position and be capable of alarming locally and notifying designated personnel when the door position state changes or is left in an open state beyond a designated period of time.
E. Remote Door Release:
1. A 2-way video-intercom system will be placed at the main entrance door, with the master station located at the front reception desk. Remote release of the main entrance door will be allowable through the video-intercom system as authorized by the front reception. A rollover feature will be programmed to roll over to the designated portable devices and/or PC workstations.
2. A remote portal release button shall be placed at the reception desk, to allow remote release of any door allowing access into any portion of the school, beyond the reception area. Each such portal will have a designated button for individual release.
F. System Integration:
1. The ACS shall be integrated with the VSS, allowing video of access control events to be viewed
via the access control management system
28.04 VIDEO SURVEILLANCE SYSTEM (VSS)
A. General
1. The VSS will consist of video surveillance cameras, servers, and software which will be utilized to provide capabilities of monitoring live video and recording video for investigative purposes.
2. The Owner’s existing Video Management Software (VMS) is Verkada. The VSS shall include the design as required to expand the Owner’s existing VMS to accommodate additional coverage of addition/renovation spaces and/or to accommodate the addition of a completely new site.
3. The design will accommodate for additional/new storage space, management servers, and licensing as required to support the quantity of cameras installed and maintain the required amount of storage days.
B. Video Surveillance Camera Placement:
1. The video surveillance system shall provide for video monitoring and recording of entrances, exits, and sensitive areas.
2. Exterior surveillance coverage shall be placed as required to provide detection coverage at the following locations:
a. Playgrounds
b. Outdoor collaboration/instruction areas
c. Bus pick-up/drop-off
d. Parent pick-up/drop-off
3. Exterior surveillance coverage shall be placed as required to provide general surveillance coverage at the following locations:
a. Student Parking Areas
b. Staff Parking Areas
c. Visitor Parking Areas
d. Sports Fields
A. Fire Alarm Design
1. All new facilities, new additions to existing facilities and remodeled facilities shall be provided with an addressable fire alarm system as required by International Fire Code, latest enforced edition.
2. Provide systems with voice evacuation as required for currently adopted code of requirements. For additions to existing buildings without these types for systems, confirm notification type requirements with AHJ.
3. For projects at existing facilities where existing fire alarm systems will be replaced, design considerations for phasing and continued operation of the existing fire alarm system until the new fire alarm system is installed, operational and accepted by the AHJ.
B. References
1. National Fire Protection Association (NFPA):
a. NFPA 70 National Electrical Code, latest enforced edition.
b. NFPA 72 National Fire Alarm Code, latest enforced edition.
c. NFPA 101 Life Safety Code, latest enforced edition.
2. Accessibility Codes:
a. American’s with Disabilities Act (ADA)
b. Texas Accessibility Standards (TAS)
C. Qualifications
1. Specifications should include prohibiting the fire alarm system installer from using installation subcontractors, for any and all scope of work.
2. Specifications should include qualifications for the fire alarm systems installer to have a minimum NICET Level II Fire Alarm Technician on site for the final check out.
28.06 FIRE ALARM SYSTEM DESCRIPTION
A. The fire alarm control panel shall Notifier NFS2-640, no exceptions. Larger buildings may require an NFS2-3030.
B. AISD prefers to have the control panel located in secured spaces, such as an MDF or IDF were permitted by the AHJ. When this occurs, locate a remote annunciator in a location that is normally occupied by staff, such as a reception area, with the annunciator being located in a secured area, within that space. Where remote annunciators are located in such spaces, provide a remote microphone adjacent to the annunciator.
C. A documents enclosure should be provided at the control panel location, for record documents in accordance with NFPA, including a 4gb USB drive for storing digital record of all as-built documents. Document enclosure shall be as manufacturers by Space Age Electronics, and shall be the red in color, and shall have the AISD logo printed by the manufacturer.
D. All addressable devices shall be labeled with applicable circuit identification number. Identification labels must be printed labels with black lettering on a clear background. Labels must be machine printed.
E. Show Location of Fire Alarm Control Panels and Remote Annunciators on plans where applicable.
F. All initiation devices shall be labeled with printed labeled indicating the device address.
G. Fire or smoke alarm “door hold open system” shall be 24v electromagnetic and connected into the building fire alarm system; 120 volt type and electromechanical systems are not acceptable.
H. Fire Alarm manual pull station shall be located at all exits. Where manual pull stations are provided, they shall have tamper proof pre-action covers, STI Series Stopper with audible alarm.
I. Smoke detectors are to be provided as required by codes and authorities having jurisdiction. Additional smoke detectors are to be avoided unless specifically required by AHJ.
J. Where duct smoke detectors are required at mechanical equipment above ceilings, such as air handlers or roof top mounted equipment, provide remote test/reset switches located on the ceiling below the equipment. Where such equipment is above the ceiling of a classroom, locate these in the corridor outside the classroom. Provide an engraved label indicating the device, system address and unit served equipment number.
K. Where duct smoke detectors are required, construction documents should indicate that the duct detectors are to be provided to the mechanical contractor for installation.
L. Fire alarm communication module shall be IP type with LTE cellular backup. Coordinate placement of required network outlets during design phase with technology systems provider.
M. Fire alarm and smoke detection devices shall be wired into the building systems (rather than battery operated) and placed at the appropriate spacing as recommended by the applicable codes.
N. Documents should include provisions for coordinated muting of all building local sound systems, in the event of alarm or emergency announcements.
O. Construction Documents shall require that any and all service interruptions required for the project shall be coordinated with AISD prior to the scheduled shutdown. A written request shall be submitted 10 days in advance of the scheduled outage. The contractor shall include a schedule
of the work and an estimate of the time required to accomplish the work. All service outages shall be coordinated such that they shall occur at times other than school hours, and the system shall be re- energized prior to the start of the next scheduled school day.
28.07 INSTALLTION CONSIDERATIONS
A. All wiring in locations without ceiling shall be installed in a continuous conduit system.
B. Device manufacturers wire guards are to be provided for any and all devices located in Gym, Activity Rooms or similar locations where devices could be subject to damage.
C. Tamper resistant covers to be installed at all manual pull stations except the station next to main fire alarm control panel.
1. A smoke detector shall be installed at all locations where field power supply units are installed including the main fire alarm control panel.
D. Project documents shall include at least 8 hours of factory training with designated owner representatives on the fire alarm, and its proper operation, following successful acceptance testing, and prior to project closeout.
31.01 GENERAL REQUIREMENTS
A. Allen Independent School District (AISD) budget includes all site development costs incurred, including parking, on site utilities, storm water detention, drainage facilities, erosion and sediment controls, curb cuts, drives, paved play areas, walks and sidewalks at the street, unloading zone, landscaping and exterior furniture and equipment. Street, curb, gutters, and utility extension beyond the immediate site are generally not included but rather as a separate allocated budget amount. It is therefore essential that economy of means be a prime consideration in designing site improvements such as pavements, walks, utility distances, drainage and other elements affected by layout and location.
B. Minimize cut/fill operations at site and try to maintain a balanced site. Discuss cut/fill quantities when requiring import or export of material with authorized AISD official to determine if other sites can use excess material. Also verify with AISD on other sites in the District that may have excess materials when needing import to see if existing recourses can be feasibly reused.
C. Other Design Disciplines: The consultant shall coordinate his work with other consultants throughout development of the project to eliminate conflicts.
31.02 EARTHWORK
A. Excavation: Control runoff and limit erosion during construction, excavation, and grading. Stockpile good topsoil and store. Excess fill material, subsoil, and materials which are deemed unsuitable for fill shall be removed from the AISD property at the Contractor’s expense.
B. Fill: Provide guidelines based on Geotechnical Engineer’s report for acceptable fill. Consider native soil to be utilized in planting areas. Importation and stockpiling of fill and topsoil materials shall be shown in staging plan.
31.03 SOILS
A. Top Soil: Top soil removed during grading or excavation of site shall be stockpiled on site for re-use during landscape work. The top soil that is stockpiled shall be clean and free of debris. If quantity of stockpiled topsoil is insufficient, provide additional topsoil, as required, to complete landscape work. Provide direction to contractor that new topsoil shall be obtained from local sources or areas having similar soil characteristics from naturally well-drainage sites. Provide recommendations to add soil amendments as necessary to meet fertility and pH level requirements of selected plantings.
31.04 SUBTERRANEAN TERMITE TREATMENT
A. Design of the buildings shall include consideration of Integrated Pest Management principles per the Texas Department of Agriculture Texas Structural Pest Control Service. Provide termite treatment below all new construction and additions.
31.05 SEDIMENT CONTROL
A. Consider existing and proposed site grading, topography, adjacent properties, downstream conditions and drainage features. Provide a plan to guide the contractor through the construction process to maintain site sediment runoff. Refer to TCEQ regulations. Provide areas and plan for sedimentation basins during construction. Ensure requirements that the contractor will provide a Strom Water Pollution Prevention Plan for the site and will be responsible for maintenance and day to day operation in accordance with all local, state and federal requirements.
31.06 CRITICAL SITE INFORMATION
A. Determine if the property is properly platted and zoned. If platting or zoning is improper, notify AISD to ensure that this can be corrected at the same time the site topography field work is being performed.
B. If no topographic survey exists, notify AISD immediately to initiate acquisition. Specifically request any unusual site data required for the project.
C. After new facilities have been “sited,” work in conjunction with the Geotechnical Engineer, Structural Engineer and Civil Engineer to provide a base site drawing locating all required test borings. Once complete, request that AISD order geotechnical investigations.
D. All site and geotechnical data will be provided to the Architect/Engineer by AISD. In order to assure that project schedules will be met, the Architect/Engineer shall initiate request for this data as soon as predictable. The Architect/Engineer shall cooperate with AISD and provide required documentation to facilitate contracting for these services at the earliest possible date and shall periodically review the status of required services with AISD to prevent potential delays.
31.07 SITE PLANNING
A. The Architect/Engineer shall be concerned with all improvements within the property line boundaries, including, but not limited to, parking, drives, walks, all-weather play areas, drainage, and utility and/or service entrances. In all instances, the Architect/Engineer shall design drive approaches, walks, and similar municipal-required facilities crossing public rights of way in accordance with local ordinances and standards. The design and implementation of off-site utility and street extensions in the public right of way shall be the responsibility of AISD. All site development shall be done in an efficient manner and shall weigh initial cost in relation to long term maintenance.
32.1 PURPOSE
A. This document is a narrative describing AISD Basis of Design for grounds and exterior improvements. The information contained herein shall be used by the Project Design Team to develop grounds and exterior improvements that help the District meet its goals of creating an environment that is conducive to learning; provides a safe and secure environment for physical activity and promotes physical fitness; is easy to maintain; and helps the District meet its goals for sustainability. The document shall be used as part of the District’s Construction Design Standards. The Architect/ Engineer shall be responsible for bringing to the attention of the AISD Representative any variances in design from these guidelines and any opportunities for value engineering that provide long term benefit to the District.
32.2 GENERAL
A. Site work, landscaping and other exterior improvements are to be designed to be durable, low maintenance, and vandal resistant, while creating an aesthetically pleasing, safe, and secure environment. The cost of site maintenance is kept to an absolute minimum. Low maintenance cost is to be a primary consideration during selection of materials, plantings, and site equipment.
1. Locate and orient building to make best use of site conditions. Account for ground water, soil conditions, and wind and weather exposure. Ensure properties of the building materials are appropriate for site conditions. Typically, orient the building with a north-south axis for natural lighting opportunities. Consider architectural appearance, future expansion, and functional requirements when locating utility service entrances, cooling towers, pad mount transformers, gas meters, manholes, and other mechanical items. Flagpoles shall be located near the main entrance of the building in order to identify its location. Verify and receive approval from AISD for any other location.
2. Design shall provide for safety, accessibility, and durability. Where possible, slopes and equipment shall meet, and exceed, ADA accessibility requirements. Provide accommodations for the addition of portable classroom buildings at a later date.
3. Landscape design is to be developed as a part of the overall project design. Courtyards shall have direct outside access without passing through halls or rooms. Architectural design is to include a service entry for all courtyards. Adequate drainage shall be incorporated into all designs.
32.3 SITE REVIEW / EXISTING CONDITIONS
A. Architect/Engineer shall determine location of, field verify, and identify on drawings, all underground utilities, vaults, tanks, fiber optics, etc. Contact an AISD Representative for assistance in locating existing services and irrigation. Consultant and surveyor shall call for utility locates and verify location of underground utilities. The surveyor shall locate all visible and marked utilities in coordination with local utility locates. The consultants should determine any existing utilities that may require potholing to verify elevation and location. SUE investigation of existing utilities on the site shall be coordinated with District. Coordination of these efforts should be done with the AISD.
1. The Architect/Engineer shall visit the site with a AISD representative and review existing conditions. The following listed items are weighted in relation to modification of existing facilities but shall apply equally to new schools sites.
a. Consider traffic patterns, staging areas, student drop-off and pick-up from cars and buses, parking areas, safety of small children while crossing streets or drives, and convenient access to office entry.
b. Preserve existing trees and shrubs.
c. Provide adequate services and staff parking.
d. Consider topography and existing drainage structures, swells, etc.
e. Consider existing easements, building lines, parking encroachments, and electrical, utility, or gas/oil transmission lines.
f. Locate contractor’s work and staging area.
g. Locate existing structures, their size, and if they are portable or permanent
32.4 PAVING
A. To conserve land available for green areas, recreational spaces, and future expansion, consider consolidation of drive, parking, and service drives.
B. Provide precast concrete bumper stops in parking lots wherever curbs are not used. At new schools, provide typical site furnishings, including bike racks, basketball backstops (4”-diameter steel pipe, steel backboards, goals, and chain nets), trash containers, etc. AISD will provide all playground equipment.
C. Use local jurisdictions standard guidelines for all drive layouts and requirements. Circulation patterns should be simple and non-confusing. Consider separation of bus and vehicular circulation. Provide sufficient parking for staff and visitors. Parking spaces to be the standard size of 9' x 18.' Entrances and exits into parking areas should be located so as not to create a traffic hazard. Consider fire lane requirements for width, clearance and pavement design capable of accommodating emergency vehicles. Refer to local jurisdiction for required sizes of parking, drive isles and fire lanes. Painted pavement markings shall utilize thermal plastic pavement markings. Particular attention shall be paid to turning radius for buses to enter and exit the facility without crossing over lanes. Provide for a minimum inside turning radius of 30’ on all bus lanes. Design all roadways in accordance with soils report/geotech. Design sidewalks with reinforcement adequate to withstand accidental vehicular traffic. Benches, retaining walls, and other surfaces shall be designed to discourage vandalism and skateboarding on school property.
D. Pavement designs should be based on recommendations of the soils engineering report and published weights for various vehicle classifications. A reinforced concrete apron drive at transition with the street should be provided. All driveways shall be Portland cement reinforced concrete for new and renovation construction. All parking areas shall be concrete paving for new and renovation construction. Architect/Engineer shall check with local jurisdiction having authority to confirm paving requirements. Asphalt paving should meet TxDOT Standards ITEM 340, 247, and 300.
E. Use of exposed aggregate concrete (poured-in-place) as a “finish” material is discouraged and must have prior written approval from the District.
1. Utilize concrete mixes with a high percentage of fly ash content as a substitute for Portland cement up to 20% will not affect finishing conditions, but may change appearance. Coordinate with the District all fly ash content prior to Design Development.
2. Utilize recycled aggregate in concrete design mixes where possible.
3. Curing compounds used at school sites should contain no more than 10% solvents.
Establish top elevations of manhole covers and cleanouts flush with pavements and in grass areas at an elevation, which will allow unobstructed mowing and which will assure good positive drainage.
F. At street unloading zones, where permitted, provide for reinforced concrete sidewalk continuous with curb to permit stepping directly from an auto to an all-weather surface. Provide sidewalks along the street frontage of all facilities from property line to property line, including connection to building.
G. Minimize the use of curbs in loading dock areas.
H. Paved areas shall be provided with curbs and gutters, unless directed otherwise by AISD.
I. Vehicular access to restricted areas or controlled parking areas shall use tubular steel gates. Gates shall cantilever or clear span all openings. Intermediate posts are not allowed. If route is part of a fire lane, provide necessary KNOX locks or KNOX boxes.
J. All paving joints shall be sealed with self-leveling silicone type sealants.
K. Special consideration shall be given to all entrance sidewalks and paving. Design should minimize the likelihood that paving will buckle and/or move causing the doors to the entrance to not open. Porches and sidewalks immediately located next to entrances shall be integrated into the structural design rather than being independent of the facility.
L. A provision for access by the handicapped is required including provisions for drop-off and unobstructed entry into the building from parking area or point of drop off. Provide loading areas as required by Code. Ensure curb ramps do not collect water. Refer to the Architectural Barriers Act, Article 9102, Texas Civil Statutes, including the Texas Accessibility Standards (TAS); and the Americans with Disabilities Act, Public Law 101- 336, including Part 36 as amended, (ADA).
M. Lighting: Provide adequate site security lighting during early morning and late evening activities for safe egress around buildings and in parking lots. Site lighting and plantings shall be placed so that mature plants do not obstruct or obscure security lighting.
N. Transportation: Design Documents shall provide details and sections for pavement and fill designed to support: 1) bus, fire, and service truck traffic and 2) automobile traffic, parking, and paved playgrounds. Separate bus loading and service traffic from parent drop off and other parking areas. Layout so that bus queuing does not interfere with deliveries and service vehicles. The layout must address pedestrian and bicycle safety by providing safe routes for access that minimizes interaction with vehicular traffic. Site specific designs must be review and approved by AISD.
O. Parking Lots: To ensure there is safe access into and out of the school grounds and to provide the maximum flexibility in scheduling of school hours and deliveries, the service entry should not be shared with bus traffic or parent/student drop off lanes. Traffic patterns and parking lots shall be evaluated to ensure that service traffic does not interfere or conflict with other vehicular or pedestrian traffic. Provide entry to the service yard for kitchen deliveries and trash pick-up separate from bus traffic, staff parking, and parent/student drop off areas. Refer to city minimum requirements for off-street parking for elementary, middle and high schools. Consultant shall confirm in writing with AISD all parking requirements. In certain situations, AISD may require additional parking above city minimum requirements. At High School sites, separate visitor, employee and student parking. Consult with AISD on required bus parking for each site. Pre-cast concrete bumper stops are required where no curb is present. Precast concrete splash blocks shall be provided at all exterior downspouts.
1. Service yard shall be designed to allow easy access by large delivery vehicles and waste disposal trucks. Provide adequate turning radius to accommodate tractor/ trailer deliveries and access to dumpsters by disposal service. The dumpster location and access route require review and approval by the service provider.
P. Dumpster, Loading Dock, and Service Areas: Provide reinforced concrete pad and approach that shall withstand traffic of service trucks and support dumpsters and/or compactors without cracking or rutting as recommended by the Geotechnical report. Design dumpster and/or compactor pad so that trash receptacles do not roll while being filled or emptied. Pad shall have between 1% and 2% slope to provide drainage. Minimum design requires bus rated pavement for all service areas; concrete pad for approach and service area is preferred. Provide parking for 2 service vehicles near loading areas. Provide an exterior hose bib at all loading area locations and dumpster enclosures. Provide separate receiving areas for food service and general deliveries. Provide separate exits for food service and custodial access to dumpster locations. Provide slab area and screening as required by
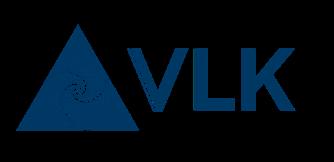
the City of Allen for recycling dumpster and trash dumpster. End post shall be made of at least a Sch. 40 steel with enough strength to support the weight of the gates. Gates for dumpster enclosures shall be light weight durable material to prevent food service and custodial personnel injuries when opening. Verify with AISD the number and size of containers required for dumpster enclosures for each project.
Q. Bollards: Bollards shall be concrete-filled steel pipe. Bollards shall be painted safety yellow. Provide bollards to protect utilities and transformers. Where bollards block access by service vehicles, the center bollard shall be sleeved to allow removal. See Exhibit 1 for dumpster layout design requirements.
R. Sidewalks: Concrete sidewalks and walkways shall be a minimum of 5’ wide. Finished grade of sidewalks and walkways shall be no more than 1” above surrounding grade and have a cross slope of less than 2%. Sidewalks by bus drop-off shall be a minimum of 8’ wide.
S. Mowing Strips: A hard surface mowing strip shall be installed adjacent to vertical barriers such as buildings (2Ft. min.), fences, and retaining walls. Mow strips must be flush with the grass.
32.5 RETAINING WALLS
A. All retaining walls over 4’-0” shall be engineered and have fencing/guardrail installed at the top of the wall in such a way that access is blocked for fall protection.
B. When using a decorative concrete masonry unit, all caps and corner pieces shall match decorative units. All caps shall be secured in place using the manufacturer specified adhesive for that product.
32.6 FENCES AND GATES
A. Fencing material is determined by the jurisdiction and there may be other requirements or materials than those listed below. Consultant shall verify with the City of Allen requirements as to allowable fencing materials.
B. All chain link type fences used in the District shall be galvanized 12-gauge steel. Tension wire shall be spiraled or crimped at tops and bottoms. Top rails to be used at all locations, with bottom rails used at athletic locations. Fence ties and fabric edges shall be appropriately knuckled and tied back so that there are no protruding sharp edges. Fence ties are to be at industry-standard minimum spacing and twisted (no looped).
C. Entire perimeter of site should be fenced with 6’ high fencing, 10’ fencing at tennis courts including lockable vehicular gates. Wrought Iron Fencing shall be use at front of sites and chain-link fencing shall be used for sides and rear of site. Coordinate with AISD for wrought iron fence pattern and details. Adequate pedestrian gates shall be provided, 5’ minimum in width. Gate stop shall latch over gate. Gate within hard surface areas shall be designed with wheels located 3’ maximum from end.
D. Gate Access
1. Maintenance access shall have a minimum of a 10’ clear opening. Any opening over 10’ shall be double gate.
2. Gates shall not be constructed of solid steel. Gates shall be constructed with light weight durable materials such as wrought iron. Wheels shall be included on all gates greater than 8’. Wheels shall be of adequate strength to support the weight of the gate.
3. Gates sized at 10’ shall be provided on all retention ponds. Pedestrian access shall be 24” with offset post to keep motorized vehicles off of school grounds.
4. Follow ADA guidelines for facility access points.
5. Fire Department must be notified for installation of Fire Department Connection (FDC) for all fire lane access gates to facility sites.
6. If ornamental fencing is used, it shall be powder coated tubular steel. No powdered coated aluminum or aluminum chain link shall be used. The minimum height on ornamental fencing shall be 6’. Coordinate with AISD for ornamental fencing detail and requirements.
7. 12-gauge fencing shall be used around soccer field and bleacher area. All baseball and softball back stops shall have the bottom 6’ from the ground in 12-gauge steel. All end posts for back stops shall be set to a minimum 4’ depth or greater so that backstops can tolerate strong winds and weight of ice, especially if the goal has an overhang as part of the construction.
8. End post shall be a minimum of Sch. 40 gauge steel. Aluminum end post will not be allowed. End post shall be strong enough to support the weight of the gate.
E. Gate Hinges: Hinges shall be structurally capable of supporting the gate and allow the gate to open and close without binding. The hinges shall be designed to permit the gate to swing a full 180 degrees.
F. Single Gate Latch: The gate latch shall be capable of retaining the gate in a closed position and shall have a provision for a padlock.
G. Double Gate Latch: The gate latch shall be a drop rod or plunger bar arranged to engage the gate stop. Locking device shall be constructed so that the center drop rod or plunger bar cannot be raised when the gate is locked. The latching devices shall have a provision for a padlock. Holes shall be provided to drop the drop rod or plunger bar when gate is fully open to prevent gate unintentionally closing.
H. Keepers: Keepers shall be provided for each gate over 4’ so they do not swing unintentionally.
32.7 GRADING
A. There must also be concern for neighborhood scale, visual impact, aesthetics of proportion and color, good drainage, the safety and comfort of the students, and the satisfaction of parents and constituents.
B. Care should be taken to prevent sheet flow and drainage from intersecting with walk ways from student, staff, and visitor parking lots.
C. If an addition results in an enclosed courtyard, provide drainage analysis, provide for primary and overflow drainage. Provide positive slope from enclosed courtyards to interior catch basins or French drains.
D. Grade crawl spaces with a positive slope from perimeter grade beam to interior catch basins or French drain system.
E. Provide surface drainage of storm water to off-site discharge points.
F. When practical, provide surface drainage of storm water to off-site discharge points. Provide underground drainage structures only when surface drainage is not feasible.
32.8 PLAY FIELDS
A. Play Fields: Play fields shall be designed with positive drainage at a minimum of 2% slope and maximum of 5% slope. Provide a drainage system on site to ensure play field can be usable in wet weather.
B. Athletic Fields and Surfaces: Consultant shall coordinate and verify in writing with AISD staff on materials on all athletic facilities including, turf, fencing, field events, types of goals, size of fields, striping, marking and logos. Also discuss what appurtenances shall be required with the
development of athletic facility and all planned uses. Artificial turf may be considered with written approval from AISD. At tennis courts, provide typical exterior slats at fencing, poles, and cranks.
C. Backstops: Provide structural engineering for backstops. Vendor should be able to provide specifications/engineering calculations or a structural guideline. Minimum height for backstops at elementary schools shall by 12’ play an additional angled cantilever of 6’ to help prevent foul balls from leaving playing area. Consultant shall coordinate the height and materials to be used for high school baseball and softball fields with AISD.
32.9 ON-SITE TRAFFIC SIGNS
A. Provide traffic and regulatory signs for parking and drives mounted as required by the City of Allen, Fort Worth, Southlake, Colleyville, or Watauga and the Texas MUTCD. Signage shall include pavement markings. Signs shall be mounted at a minimum 7’ measured from the bottom of the sign if in grass areas or a minimum of 7’ to bottom of sign if mounted in pavement. All signs shall be located and installed to comply with all TAS & ADA standards and requirements.
32.10 SITE WORK
A. Site Grading: Engineering plans shall show:
1. Surface drainage, detention areas, and discharge points
2. Subsurface drainage (if required), footing drains, and under-floor drainage systems
3. Total amount of disturbed area showing hard surface and non-hard surface area amounts (previous, non-previous)
4. Include a site plan showing existing and finish grades for entire site
5. Include an erosion control plan showing location and details of proposed erosion devices. All temporary erosion control devices shall be removed prior to final project completion.
a. Natural features, such as drainage ways, wetlands, and hillside slopes, shall be incorporated into the overall design and landscape design for the property.
b. Site building and design grading to minimize cut and fill requirements. Cut and fill should be balanced to reduce the need for import or export of soil. Limit gradients to provide slope capable of supporting landscape materials, that can be reasonably maintained, and mitigate potential impacts such as erosion, deposition, and drainage flows on adjacent properties.
c. Finish grades shall be designed to provide positive drainage away from buildings and to approved drainage systems.
d. No site grading or work shall be allowed to create potential drainage problems to neighboring properties.
e. Prior to any construction of buildings or site paving, topsoil shall be stripped from the areas to be covered by buildings or paving, and stockpiled for later on-site redistribution in those areas where there shall be landscape plantings.
f. Maximum grades shall not exceed 4’ horizontal to 1’ vertical on any earthen surface. Refer to local codes for maximum grades for emergency vehicles
g. 0.50% grades is the minimum grade for paving and shall not be used unless required. Grass and earthen areas shall have no less than 2% grade unless approved in writing from AISD. Consultant grade areas throughout the site such that it is not adverse to the function it will serve. Playgrounds should not have hostile slopes.
h. Consultant shall consider ADA accessibility to all functions of the facility such that it may be use by all staff and students. Coordinate accessible routes with AISD and TAS specialist.
At existing sites, the consultant shall review the TAS reports for the site and coordinate improvements required to bring site into current ADA compliance.
B. Drainage
1. Provide an engineered drainage plan for the site conforming to all applicable state, local, and federal regulations. Drainage system shall be designed to manage water on the site without flooding or erosion. The drainage plan shall address surface roof, foundation, subsurface, and under-floor drainage. Proposed landscaping shall reflect provisions to minimize erosion both during construction and after occupancy. Footing and foundation drains shall be rigid, perforated, non-corrugated PVC, and surrounded by drain rock.
2. Hard surface play areas shall be designed to support vehicles and landscape service equipment. Hard surfaces shall be sloped to provide drainage. Provide drainage system to prevent flooding or play areas and to collect and manage runoff from hard surfaces. Drain hard surfaces away from the building. Provide 2% slope away from building wall to a distance of 10’ from outside wall or as specified in geotechnical report. Design drainage so it does not create tripping hazards. Locate drain grates, catch basins, and manhole covers out of the area of play. Trench drains should be designed with high strength metal grate to withstand vehicle traffic.
C. Stormwater Conveyance and Detention Ponds
1. Detention and retention areas shall be integrated into the total design when required. Slopes shall not exceed 4:1. Coordinate slope stabilization treatments with AISD. All ponds shall be designated to promote water quality of storm water run-off. Manage runoff to minimize impacts on flooding, erosion and water quality. Consider and discuss use of bio swells, downspouts discharging to grade, rain gardens, saw tooth curbs, raised inlets, wet ponds, porous pavement/ pavers and grass channels. Ensure whenever possible that utility lines and facilities are not located in detention and retention areas.
32.11 PLAYGROUND AND SURFACING REQUIREMENTS
A. Playground areas vary from campus to campus. Coordinate the requirements with the District.
B. Provide accessible path from school to playgrounds.
C. Place playground in close proximity to main building.
D. All new playground equipment must meet the latest published standards/guidelines for both the American Society for Testing and Materials (ASTM) and the U.S. Consumer Product Safety Commission (CPSC).
E. All equipment installations shall be performed by factory authorized and trained installation personnel and will be completed per ASTM and CPSC standards.
F. Soft Surfaces shall be provided around all playgrounds. Wood chips are not allowed. All surface material shall meet state and federal requirements and shall be approved in writing by AISD. Clarify with AISD for material selection.
G. All play areas shall have on-site signage indicating use guidelines for the equipment. Example: “This play area is designed for children 2 to 5 years of age (or 5 to 12, or whatever is appropriate for the play area). Adult supervision is recommended.”
H. Play equipment area boundaries (retaining walls) shall be located a minimum of 20’ from any street, driveway, parking lot, etc. where vehicles are likely to drive or park. If they must be located nearer than this, a fence shall divide the area, in its entirety, from vehicular traffic.
I. Play areas requiring fencing shall have the fabric installed on the play equipment side of the fence, with the posts outside the play area for safety.
J. Paved play areas at school sites must not be contiguous with vehicular traffic areas. If in close proximity, an adequate barrier should be provided.
K. All playgrounds shall have positive drainage around them. Sites where equipment is to be installed should be have enough slope to provide positive drainage of water per manufactures recommendations. Playgrounds shall be ADA accessible.
L. All playgrounds shall be inspected to ensure that full zones are met, complies with all safety requirements, and meets all ADA and accessibilities requirements.
32.12 ATHLETIC FACILITIES
A. All athletic facilities and appurtenances shall be designed and marked according with UIL, National Federation of High Schools (NFHS) and NCAA regulations as required. Consultant shall coordinate with the AISD on the material, layout, size and seating for all athletic facilities. Where possible parking for athletic venues should utilize existing parking around the site in the required parking counts prior to adding parking. All methods to determine provided and required parking shall be approved by city and AISD. If artificial turf or paving is required for an athletic facility, the consultant shall design the subgrade and paving in accordance with the geotechnical recommendation.
1. Track Surfacing - Provide red structural surface at the middle and high school level. All tracks shall be polyurethane with pavement and sub-grade as specified in the geotechnical report. All tracks shall have an interior and exterior 12” wide by 24” deep reinforced concrete curb and cross AISD tracks shall be sloped to drain according to field elevations. All tracks shall have a storm sewer system to convey storm water away from the track. Sub-grade and paving for the track shall be designed in accordance with the geotechnical recommendations. All tracks should be 8 lanes at the high school level.
2. All athletic fields shall be crowned properly to provide good drainage, and baseball and softball fields shall be crowned to drain to sideline areas.
3. Athletic fields in conjunction with track shall provide for positive drainage off of the track and onto the field where it is collected and discharged in the storm drainage system. Rain water or irrigation overspray shall not pond on track.
4. Access for maintenance equipment to athletic fields shall be considered in fencing and gate locations and sizes. Typical maintenance gate: Pair 10’ -0” clear.
5. Football fields shall have a conduit installed for electrical power. The location shall be coordinated with AISD.
6. All athletic fields shall have a buffer around the perimeter for auxiliary activities such as cheerleading. The type of material shall be coordinated with AISD.
32.13 SITE SECURITY / FENCING
A. Fencing as required by the City of Allen ordinances shall be provided in the contract. All new fence installations shall be reviewed with AISD to evaluate existing trees and fences that AISD may need to coordinate with adjacent owners. At a minimum, chain link fencing shall be provided at all perimeter property lines with the exception of the main frontage road entrance. Provide steel gates to allow remote areas of the site to be secured. Typical perimeter fence height shall be 6’-0”.
32.14 IRRIGATION
A. Irrigation System Design Parameters
1. System shall be designed with a single mainline, using the necessary quantity and type of backflow prevention devices, water meters, and valves required to comply with TCEQ, and the application requirements listed in Item B (Irrigation Operation Parameters). A Looped Mainline
should be used with addition of valves to create individual Flow Zones for better control of multiple zones that may operate simultaneously. Any looped Mainline shall have isolation valves designed in the main to prevent a total loss of irrigation capabilities during a major line break.
2. System shall have a rain/freeze sensor at each site.
3. Provide separate irrigation and domestic meter(s).
4. System shall have individual zones designed to irrigate athletic turf, landscape beds, and other turf areas separately.
5. System shall have a rain/freeze sensor at each site.
6. Provide separate irrigation and domestic meter(s).
7. System shall have individual zones designed to irrigate athletic turf, landscape beds, and other turf areas separately.
8. Irrigation zones may not utilize both rotor and spray heads in any single zone.
9. Irrigation zones shall may utilize rotor and spray heads in any single zones.
10. All proposed control systems shall be approved by AISD before bid.
11. Sprinklers, control boxes, manhole covers, and catch basins are to be at a height where they do not present a trip hazard or interfere with mowing. When possible, do not locate these items on playing fields or in play areas.
12. All holes and trenches to be backfilled and compacted to the original density.
13. Provide irrigation for all ground cover areas.
14. All elementary and middle schools should have an irrigation system at the front yard; at the sides only when possible. Playfields should be irrigated via sprinkler systems or if not possible, via quick couplings. Grass to be irrigated.
15. Flower beds shall have an irrigation system.
16. (2) wire systems are not allowed.
B. Irrigation Operation Parameters
1. Precipitation: 1.5” per week for lawns and plantings; Athletic fields: 2” per week or as specified.
2. Water Frequency: Per Allen Water Utilities guidelines.
3. Available Time: 8 hours (10:00 PM to 6 AM)
4. Seasonal Conditions: Peak irrigation demand during the summer school break shall hold to the identified parameters. Discretion is given to operation not the design of the system unless otherwise approved by the District.
5. The Owner is to be notified if the design requires the use of an irrigation pump.
C. Provide athletic irrigation materials as follows:
1. No irrigation mainline or valve shall be located within the field-of-play. Provide either hose bibs or underground waterline with quick-couplers, including shut off isolation valves, in boxes with lockable covers a grade level for athletic facilities. Verify quantity and location with AISD.
2. Preferred: Rainbird ESP-LXME controllers with IQ4 Cellular card installed with external antenna run outside of the building for reception. Acceptable alternates: None.
3. Natural Grass Softball Field:
a. Provide spray heads along each baseline to the far corner of the dugout as separate zones.
b. An additional zone of spray heads shall follow the infield to outfield transition.
c. Quick-couplers (4) shall be located near each base within the turf area, location verified with AISD.
d. Provide rotors in the outfield
e. Provide spray heads to each pitcher warm-up area as separate zones.
4. Natural Grass Baseball Field:
a. Provide spray heads along each baseline to the far corner of the dugout as separate zones.
b. An additional zone of spray heads shall follow the infield to outfield transition.
c. Quick-couplers (4) shall be located near each base within the turf area, location verified with AISD.
d. Provide rotors in the outfield.
e. Provide spray heads to each pitched warm-up area as separate zone.
5. Natural Grass Football Field:
a. Provide 5 rows of rotors from inside edge of track to inside edge of track.
b. Provide rotors on hash lines.
c. Set watering sequence to water from the middle of the field out.
d. Locate all valves beyond the end zone.
e. All zone lateral lines shall be aligned to run with field.
6. Natural Grass Practice Fields:
a. Provide a rotor layout that is symmetrical from sideline to sideline and avoids a head location in the soccer goal or goalie box.
b. Locate all valves beyond the end zone or sideline fence.
c. All zone lateral lines shall be aligned to run with the field.
7. Shot Put:
a. Provide rotor coverage with no head located within 50 foot of the pad.
8. Controller Location:
a. Coordinate the controller location with the AISD. Provide communication/data line to all controllers. Provide complete systems on all new projects. Provide controller per AISD requirements. Refer to guide specifications for special product preference for heads, valves and backflow preventers.
b. Provide temporary controllers for use during construction.
c. Irrigation main lines and laterals shall be sleeved under all paving. Jetting is not allowed.
Coordinate with paving plan.
d. Provide pavement marking in concrete curb (saw cut of two parallel lines 2-inches in length and 1-inch apart) designating the location of all irrigation sleeving.
e. All ground valve boxes shall be supported by a 2 inch thick solid paver that extends beyond the limits of the box bottom.
f. System shall have individual zones designed and grouped to irrigate athletic turf, landscape beds, and other turf areas separately.
g. Deviations from any part of this irrigation section should have the District approval and documented in writing.
D. Drip systems to the athletic tracks both inside (natural grass) and outside. Two to three small (1/2”) lines buried parallel to the track. These should be on an automatic time controller and hooked to a
City irrigation piping system. This is essential in controlling movement of the subgrade in areas of hi PI (clays) that essentially will destroy the integrity of the tracks. This is a low cost method of installation. Also inline irrigation controllers 6-12 of these.
32.15 LANDSCAPING
A. On new schools, Architect/Engineer is responsible for landscape and irrigation systems design. On existing schools, consideration should be given to landscape design at the front of each building. Repair existing systems and remove any landscape timbers and replace with environmentally friendly solution.
1. Where landscaping is being provided at an existing campus (i.e., an addition), the plant material selection should generally conform to complement existing plant material. Coordinate plant location with utilities so as not to conflict with utility lines.
2. Use of native drought resistant plant material is required. Plant material requiring excessive irrigation or maintenance shall be avoided. Design should be based on the most extreme water restrictions imposed by city requirements.
3. Ground cover shall be planted in such a manner and quantity that full coverage can be achieved within 12 months.
4. Trees shall be planted far enough away from sidewalks and buildings so that they cannot be used to access roofs. This will also minimize the accumulation of leaves and debris on the roof and in gutters.
5. All tree and plant material shall be readily adaptable to area soils, reasonable disease resistant, and require low maintenance. Tree and plant material shall be approved by AISD. The use of Bald Cypress trees and other water intensive trees is prohibited.
6. All trees shall require a minimum of three (3) stakes. All trees and planting areas shall be properly mulched to a depth of two (2) inches. Use safety stake with high visibility. Post and guy wires shall not be permitted in these areas.
7. Trees shall be planted to allow a minimum of 11’ -0” between tree and any object to allow for lawn equipment. Trees shall not be placed in close proximity of sidewalks where buckling is likely to occur due to tree growth. Trees shall not be placed within 35’ of building.
8. Where existing turf areas are to be converted to bed or planting areas, the turf shall be chemically eradicated to minimize re-growth in the future. These areas shall be properly prepared with amended organic matter.
9. Landscaped areas shall be kept to a minimum. Aggregate size location shall be coordinated with AISD.
10. Final grades shall be smooth and consistent at proper elevations prior installation of aggregate.
11. Courtyard landscape shall not contain grass or deciduous trees. Topsoil imported to the site shall come from naturally well-drained local sources having similar soil structure and characteristics.
12. Sloped areas shall maintain a grade to provide safe operation of six (6) foot wide mowing equipment.
13. Areas with slopes of 4:1 or greater shall be landscaped to be stable, provide for erosion control and special protective measures shall be implemented. These measures shall be reviewed with AISD Maintenance.
14. Athletic fields and other competition areas shall be sodded with 419 Bermuda grass. Playfields and other areas shall be sodded with common Bermuda grass. In well-sunlit areas (6 or more hours a day of direct sunlight), St. Augustine or Zoysia shall be utilized in shady areas. Any reinforcing mesh or grid must be removed from sod before installation. No backing material of any kind will be accepted for installation..
15. Consideration shall be given to the maintenance requirements of tree islands.
16. Hardy plant materials shall be utilized, including Nandinas, Dwarf or regular Yaupons, Indian Hawthorne, and Dwarf Crape Myrtles.
17. All hedges shall be planted at least five feet from building walls.
18. Preferred tree species: Live oak, Red Oak, Chinese Pistachio, Cedar Elms, Lace-Bark Elm.
Bradford Pear is not allowed.
19. Groundcover: Decomposed Granite.
20. Limit the use of metal edging and hundreds of small shrubs. Use larger diameter trees and a lesser amount of small trees.
21. Contractors’ proposals shall include an alternate price for a one (1) year warranty and maintenance contract to include fertilizer, trimming, and irrigation of all shrubs and trees.
33.01 GENERAL REQUIREMENTS
A. Design professional shall consider low impact design strategies LID for the site drainage.
B. Avoid routing water, sewer or drainage lines and utility lines under the building structure and under reinforced concrete pavement.
C. Careful attention should be given to planning the location and detailing of utility service entrances and service equipment such as, stacks, grease traps, manholes, cleanouts, hose bibs, valves, service vaults, transformers, backflow preventers, and gas and water meters. A successful design requires a careful balance of aesthetics, functional operating features, and cost.
D. Careful consideration shall be given to avoid drainage near playground equipment. Drainage must be routed away from playground equipment and safety surfacing.
E. Provide steel pipe bollards around all electric transformers, gas regulators, or meters where exposed to vehicular traffic.
F. Require provision in plans for the requirement of Trench Safety plan for the specific site.
G. Required installation of tracer wire or tape capable of tracing in all utility trenches.
H. Coordinate with other disciplines for gas, electric, communication lines.
33.02 WATER SYSTEM
A. Conform to City of Allen Water Utilities Standards for materials, backfill and embedment.
B. Provide isolation valves at all outside hose bibs.
C. Obtain fire flow test data prior to any water design for domestic, fire or irrigation. Provide information to MEP, Landscape Architect, Architect and AISD for review and consideration of existing conditions.
D. Have separate water meter for domestic and irrigation. Coordinate with City of Allen Water Utilities. A surface mounted reinforced concrete apron shall be provided on all valves not in pavement.
33.03 SANITARY SEWER SYSTEM
A. Conform to City of Allen Water Utilities Standards for materials, backfill and embedment
B. Provide isolation valves at all outside hose bibs.
C. Obtain fire flow test data prior to any water design for domestic, fire or irrigation. Provide information to MEP, Landscape Architect, Architect and AISD for review and consideration of existing conditions.
D. Have separate water meter for domestic and irrigation. Coordinate with City of Allen Water Utilities. A surface mounted reinforced concrete apron shall be provided on all valves not in pavement.
33.04 STORM SEWER SYSTEM
A. Conform to City of Allen Stormwater Standards for materials, backfill and embedment.
B. Concrete pipe - C-76, Class III for minimum of 2’ of cover or IV for cover less than 2’.
C. Consider design of appurtenances with City of Allen Standards.
D. Provide steel downspout boots at all downspouts that discharge above grade.
E. Provide pre-cast concrete splash blocks at each downspout.
F. Minimum slopes of closed conduits shall not be less than 0.50%.
G. Consider pilot flumes in the bottom or detention ponds or channels where grade is less than 2%
H. Flumes crossing sidewalks shall have metal covers with rigid connection to pavement sufficient to carry projected loads and shall have a non-slip surface.
I. All exposed grates for inlets shall be cast iron and capable of carrying intended loads.
J. Consider ADA compliance for inlets in pedestrian paths.
K. Consider opening sizes of inlets for use.
L. Minimum cover on storm sewer pipes shall be 2’.
M. Primary and headwall drains should not empty across parking or sidewalks.