Introduction To Wire And Cable Insulating Materials
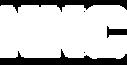
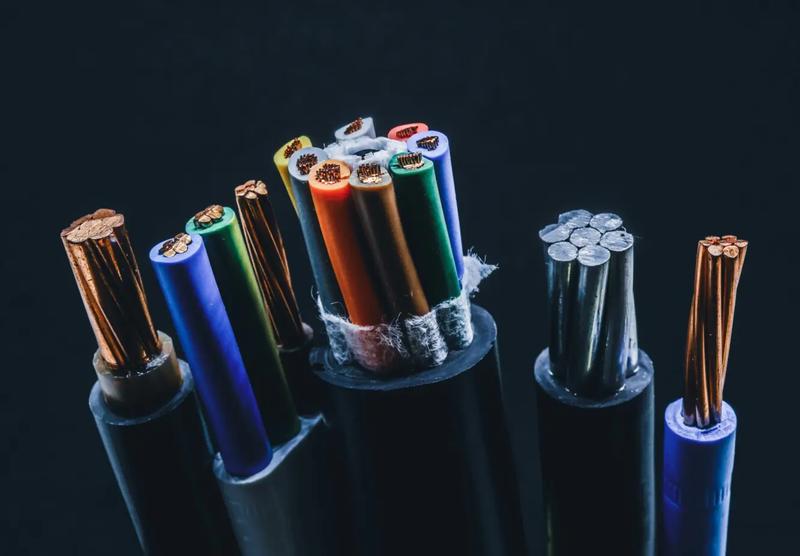
Cable insulation is a non-conductive material, or a material resistant to electric current, used to cover the conductive core of a cable or a wire.
It protects the cable from physical damage, prevents the conductors from coming in contact with one another, and prevents the cable from the impact of the environment
Insulating materials are also used for the cable jacket, which serves as a protective layer of mechanical protection against physical and environmental hazards like impact, abrasion, moisture, chemicals, and temperature extremes
This book presents a guide to the types of insulations used for electrical cables.
CHAPTER I
The three most popular groups of insulating materials for cables are thermoset, thermoplastic, and fluoropolymer Let's look into their main properties
Are polymers that can be heated and cooled multiple times without altering their chemical properties. This makes them highly versatile and recyclable. However, they typically have lower heat resistance compared to thermosets and fluoropolymers. Thermoplastic is a costeffective material for various residential, commercial, and industrial applications.
Are polymers which cannot be remelted or reformed once cured. This makes them extremely heat resistant and less likely to deform under load at high temperatures. However, it also means they cannot be recycled in the same way as thermoplastics. These insulations are suitable for high-voltage cables and harsh environments
is a type of polymer that contains fluorine atoms in their chemical structure. Fluorine gives these polymers exceptional resistance to heat, chemicals, and electrical conductivity. As such, they are often used in highperformance applications, such as aerospace and industrial equipment.
CHAPTER II
1.Polyvinyl Chloride (PVC):
Characteristics: Good insulator, flexible, flame-resistant, cost-effective resistant to oxidation and degradation. One of the most popular insulations on the market. SR-PVC is the version with improved abrasion resistance.
Temperature Rating: Up to 105°C.
Applications: Used in residential, commercial, medical,and industrial wiring.
2.Polyethylene (PE):
Characteristics: Excellent electrical properties, high-insulating capacity, moisture resistant. Not for high temperatures and outside applications. Can be low-density or high-density. A low-density one is more flexible.
Temperature Rating: Up to 80°C.
Applications: Used in low voltage applications, coaxial cable, and Ethernet cables.
3.Nylon (polyamide):
Characteristics: Good toughness, abrasion-resistant, chemically resistant, good dielectric properties. Resistant to cut-through.
Temperature Rating: Up to 105°C.
Applications: Often used in THHN building wire as a protective outer cover over the PVC insulation. Most often used as a jacket. Used in automotive wire and appliance wiring.
4.Thermoplastic Polyurethane (TPU):
Characteristics: High abrasion resistance, good flexibility at low temperatures, excellent tear strength, and resistance to oil, grease, and various solvents
Temperature Rating: Up to 125°C
Applications: Widely used in robotic and automation cables, industrial applications, and cables requiring superior abrasion resistance
5.Polypropylene (PP):
Characteristics: A thermoplastic polymer has excellent chemical resistance, low dielectric constant, lower heat resistance than PE
Temperature Rating: Up to 105°C
Applications: Mostly used in telecommunications, low voltage cables, and radio frequency signal transmission
6.Polystyrene (PS):
Characteristics: Low-cost, good dielectric properties, brittle
Temperature Rating: Up to 75°C
Applications: Used in capacitors, cable spacers, and insulating panels
8.Polycarbonate (PC):
Characteristics: High strength, excellent heat resistance, and good electrical properties It's also transparent
Temperature Rating: Up to 125°C
Applications: Used in connectors, fiber optics, and other high-temperature applications.
CHAPTER III
1.Cross-Linked Polyethylene (XLPE):
Characteristics: High dielectric strength, chemically stable, moisture resistant, excellent resistance to most solvents, and has better heat resistance than PE
Temperature Rating: Up to 90°C for normal operation, 130°C for emergency overload conditions, and 250°C for short-circuit conditions
Applications: Used in power cables, control cables, and applications where heat resistance and mechanical strength are important
2.Ethylene Propylene Rubber (EPR):
Characteristics: Excellent dielectric strength, flexibility, good resistance to heat, oxidation, ozone, and weather, and a wide operating temperature range
Temperature Rating: Up to 90°C
Applications: Widely used in MV and HV cables, mining applications, and flexible cords
3.Silicone Rubber:
Characteristics: Very common insulators good at high temperatures, flexibility, good electrical properties, resistance to weather, ozone, and UV light
Temperature Rating: Up to 180°C
Applications: Used in appliance wiring, automotive wiring, and medical applications
4.Neoprene:
Characteristics: Good flame retardant properties, excellent physical toughness, and resistance to oil, ozone, and oxidation
Temperature Rating: Up to 90°C
Applications: Used in mining cables, portable power cables, and other heavy-duty applications
5.Chlorosulfonated Polyethylene (CSPE or Hypalon):
Characteristics: Outstanding resistance to ozone, oxidizing chemicals, oils, and flame spread. Good physical properties and color stability.
Temperature Rating: Up to 90°C.
Applications: Used in control cables and power cables, especially for outdoor applications due to their superior weather resistance.
5.Polyurethane
Characteristics: This polymer has excellent resistance to abrasion, oil, and ozone, good flexibility at low temperatures.
Temperature Rating: Up to 80°C.
Applications: Used in robotic and automation cables, coil cords, and other applications requiring high flexibility and toughness.
6.Silicone:
Characteristics: Excellent flexibility at low temperatures, good heat resistance, good electrical properties
Temperature Rating: Up to 180°C, some special types can withstand up to 250°C
Applications: Used in cooking appliances, medical devices, and other applications requiring high heat resistance and flexibility
CHAPTER IV
1.Polytetrafluoroethylene (PTFE/ Teflon):
Characteristics: Exceptional resistance to heat, chemicals, and electrical interference.
Temperature Rating: Up to 260°C.
Applications: Used in aerospace, telecommunications, computer wiring, and military applications.
2.Fluorinated Ethylene Propylene (FEP):
Characteristics: Similar to PTFE but with lower heat resistance and slightly different electrical properties Excellent resistance to chemical attack
Temperature Rating: Up to 200°C
Applications: Used in data communication and instrumentation cables
3.Ethylene Tetrafluoroethylene (ETFE):
Characteristics: Excellent resistance to heat, radiation, and chemical attack, good electrical properties
Temperature Rating: Up to 150°C
Applications: Used in aerospace and solar cell applications
4.Polyvinylidene Fluoride (PVDF/ Kynar):
Characteristics: Excellent resistance to abrasion and impact, good resistance to most chemicals and UV radiation, good flame and smoke properties.
Temperature Rating: Up to 150°C.
Applications: Used in plenum cables, aerospace, and other highperformance applications.
5.Polyvinyl Fluoride (PVF):
Characteristics: Excellent resistance to heat, radiation, and chemical attack, good electrical properties.
Temperature Rating: Up to 150°C.
Applications: Used in aerospace and solar cell applications.
6.Perfluoroalkoxy Alkane (PFA):
Characteristics: Excellent heat resistance, chemical inertness, and electrical properties. It's very similar to PTFE and FEP but with better heat resistance.
Temperature Rating: Up to 260°C.
Applications: Used in high-temperature, high-frequency applications such as computer wiring, medical equipment, and aerospace applications.
7.Ethylene Chlorotrifluoroethylene (ECTFE):
Characteristics: High mechanical strength, excellent chemical resistance, good electrical properties.
Temperature Rating: Up to 150°C.
Applications: Used in aerospace and chemical processing industries for wire and cable insulation.
8.Perfluoroalkoxy Alkane (PFA):
Characteristics: Very similar to PTFE in terms of its excellent resistance to heat, chemicals, and electrical interference, but with better mechanical properties.
Temperature Rating: Up to 260°C.
Applications: Used in hightemperature, high-corrosion applications, such as semiconductor manufacturing, aerospace, and chemical processing industries.
CHAPTER V
Several Underwriter Laboratory Standards (UL) ensure the safety of common insulation materials Let's look into them in more detail
UL 44: Standard for Thermoset-Insulated Wires and Cables
This is the standard for thermoset applications, covering power and lighting circuits. It sets requirements for insulating materials' physical, electrical, and flame-retardant properties Most popular insulators that comply with UL 44 are XLPE, EPR, silicone rubber, PUR, and neoprene
UL 83: Standard for Thermoplastic-Insulated Wires and Cables
The standard for thermoplastic insulations in general-purpose electrical wiring applications.
Insulations that comply with the standards outlined in this requirement include PVC, PE, PP, TPE.
UL 758: Standard for Appliance Wiring Materials (AWM)
Сovers insulation materials used in appliance wiring, including flexible cords and cables. It ensures that cables perform well and are safe in appliances. The standard focuses on temperature rating, and flame resistance, among other factors The standard must be met by thermoset, thermoplastic, and fluoropolymer insulations
UL 83A: Standard for Thermoplastic-Insulated Underground Feeder and Branch Circuit Cables
UL 83A applies to thermoplastic-insulated underground feeder and branch circuit cables used in residential and commercial applications. The cables that fit these requirements are resistant to UV and moisture Many popular insulators fit these standards, including PVC and PE
UL 1277: Standard for Electrical Power and Control Tray Cables
UL 1277 covers electrical power and control cables installed in cable trays or raceways. Fitting insulators include PVC, XLPE, and EPR. The materials are expected to resist moisture, sunlight, oil, chemicals, and other factors that cables may encounter in cable trays or raceways
UL 1441: Standard for Systems of Insulating Materials - General
UL 1441 provides general requirements for systems of insulation materials, such as those used in motors, transformers, or other electrical equipment. It covers factors such as electrical properties, thermal aging, moisture resistance, and flame resistance Fitting materials include PVC, PI, and Mica
CHAPTER VI
In this table, we compare thermoplastic materials based on their most important properties that contribute to different aspects of their performance
Thermoplastic Insulation
Polyvinyl Chloride (PVC)
Polyethylene (PE) Nylon
Excellent
Moderate thermal stability
Good thermal stability
Flexible, durable
Can release harmful dioxins when burnt
Thermoplastic Polyurethane (TPU)
Polypropylene (PP)
Acrylonitrile Butadiene Styrene (ABS)
Polycarbonate (PC)
Good insulation
Good insulation
Good insulation, low dielectric constant
Moderate insulation
Good thermal stability
Moderate thermal stability
Good thermal stability
Moderate thermal stability
Tough, flexible
Tough, high tensile strength
High abrasion resistance, excellent tear strength
Tough, flexible
Tough, impact resistant
Recyclable, but not biodegradable
Recyclable, but not biodegradable
Can be recycled, not biodegradable
Recyclable, not biodegradable
Difficult to recycle, not biodegradable
Good insulation
Good thermal stability
High strength
Difficult to recycle, not biodegradable
Thermoplastic Insulation
Polyvinyl Chloride (PVC)
Polyethylene (PE)
Nylon
Thermoplastic Polyurethane (TPU)
Polypropylene (PP)
Acrylonitrile Butadiene Styrene (ABS)
Polycarbonate (PC)
Good against acids, alkalis, alcohol
Good against most acids, alkalis
Good against many chemicals
Excellent against oil, grease, various solvents
Excellent against most acids, alkalis
Good against many chemicals
Good against many chemicals
CHAPTER VII
In this table, we compare thermoset materials based on their most important properties that contribute to different aspects of their performance.
Thermoset Insulation
Heat Resistance
Electrical Properties
Thermal Properties
Mechanical Properties
Environmental Impact
Cross-Linked Polyethylene (XLPE)
Ethylene Propylene Rubber (EPR)
Silicone Rubber
Excellent (Up to 90°C, 130°C overload, 250°C short circuit)
Excellent (Up to 90°C)
Excellent (Up to 180°C)
Excellent insulation
Excellent insulation
Good thermal stability
Good thermal stability
Tough, durable
Flexible, durable
Not easily recyclable, not biodegradable
Can be recycled, not biodegradable
Neoprene
Chlorosulfonat -ed Polyethylene (CSPE)
Polyurethane (PUR)
Good (Up to 90°C)
Good (Up to 90°C)
Good insulation
Excellent thermal stability
Flexible, good tensile strength
Can be recycled, not biodegradable
Good (Up to 80°C)
Good insulation
Good insulation
Good thermal stability
Tough, good impact resistance
Can be recycled, not biodegradable
Melamine
Excellent (Up to 155°C)
Good insulation
Good insulation
Good thermal stability
Good thermal stability
Good thermal stability
Tough, durable
High abrasion resistance, excellent tear strength
High mechanical strength
Can be recycled, not biodegradable
Can be recycled, not biodegradable
Difficult to recycle, not biodegradable
Thermoset Insulation
Cross-Linked Polyethylene (XLPE)
Ethylene Propylene Rubber (EPR)
Silicone Rubber
Neoprene
Good against many chemicals
Good against many chemicals
Excellent against many chemicals
Excellent against oil, ozone, oxidation
Chlorosulfonated Polyethylene (CSPE)
Polyurethane (PUR)
Melamine
Excellent against many chemicals
Excellent against oil, grease, various solvents
Good against many chemicals
CHAPTER VIII
In this table, we compare thermoset materials based on their most important properties that contribute to different aspects of their performance.
Fluoropolymer Insulation
Polyvinyliden e Fluoride (PVDF)
Polytetrafluo roethylene (PTFE)
Fluorinated Ethylene Propylene (FEP)
Ethylene Tetrafluoroeth ylene (ETFE)
Perfluoroalkox y Alkane (PFA)
Polyvinyl Fluoride (PVF)
Ethylene Chlorotrifluoro ethylene (ECTFE)
Good (Up to 150°C)
Excellent (Up to 260°C)
Excellent (Up to 200°C)
Good (Up to 150°C)
Excellent insulation
Excellent insulation, low dielectric constant
Excellent insulation, low dielectric constant
Excellent insulation, low dielectric constant
Good thermal stability
Excellent thermal stability
Excellent thermal stability
Good thermal stability
Tough, resistant to abrasion and impact
Tough, flexible
Flexible, resistant to most chemicals
Tough, resistant to abrasion
Difficult to recycle, not biodegradable
Difficult to recycle, not biodegradable
Difficult to recycle, not biodegradable
Difficult to recycle, not biodegradable
Excellent (Up to 260°C)
Good (Up to 150°C)
Good (Up to 150°C)
Excellent insulation, low dielectric constant
Good insulation
Excellent insulation
Excellent thermal stability
Good thermal stability
Good thermal stability
Tough, flexible
Tough, flexible
High mechanical strength
Difficult to recycle, not biodegradable
Difficult to recycle, not biodegradable
Difficult to recycle, not biodegradable
Fluoropolymer Insulation
Polyvinyliden e Fluoride (PVDF)
Polytetrafluo roethylene (PTFE)
Fluorinated Ethylene Propylene (FEP)
Ethylene Tetrafluoroeth ylene (ETFE)
Perfluoroalkoxy Alkane (PFA)
Polyvinyl Fluoride (PVF)
Ethylene Chlorotrifluoro ethylene (ECTFE)
The three tables below grade thermoplastic, thermoset, and fluoropolymer materials based on the high school grading system to illustrate how different insulators compare to each other in terms of performance. In this grading, A+ stands for exceptional, A for excellent, B for great, C for adequate, D for below average, and F for poor.
Pricing is assigned the number, where 1 stands for the cheapest and most readily available insulation, while 5 stands for the most expensive one. Insulations are then assigned an average grade, where A+ = 4.0, A = 4.0, B = 3.0, C = 2.0, D = 1.0, F = 0.0.
These tables are only for educational purposes, and do not represent an objective score. Depending on the applications, insulating materials might have different requirements, which would deem some factors more important than the others.
CHAPTER XI
Insulation Name
CrossLinked Polyethylen e (XLPE)
Ethylene Propylene Rubber (EPR)
Silicone Rubber
Neoprene
Chlorosulfona -ted Polyethylene (CSPE)
CHAPTER XII
Insulation Name
PTFE (Polytetrafluo -roethylene)
FEP (Fluorinated Ethylene Propylene)
PFA (Perfluoroalko -xy)
ETFE (Ethylene Tetrafluoroeth -ylene)
PVDF (Polyvinylidene Fluoride)
PTFE (Polytetrafluoroethylene)
FEP (Fluorinated Ethylene Propylene)
PFA (Perfluoroalko -xy)
ETFE (Ethylene Tetrafluoroeth -ylene) PVDF
CHAPTER XIII
Biodegradable cable insulations are being developed in the 21st century because of the need to reduce environmental impact, improve safety, and contribute to the improved waste management cycle.
As it stands in 2023, no biodegradable cable insulations are effective enough to be used on a mainstream level.
Here are some of the insulations that are currently in development:
Polylactic Acid (PLA): PLA is a biodegradable thermoplastic monomer derived from renewable resources such as corn starch or sugar cane. It is commonly used in packaging and biomedical devices. However, its application in the field of electrical insulation still needs to be studied due to issues like moisture absorption and lower temperature resistance compared to traditional insulation materials.
As it stands right now, polylactic acid demonstrates good insulation properties at temperatures between room and 70°C. For higher temperatures, PLA does not prove to be an effective insulator at higher temperatures, as suggested by research. Despite this, PLA demonstrates good electrical properties compared to its petroleum counterparts.
Thermoplastic Starch (TPS): TPS is produced by destructuring starch under heat and shear in the presence of plasticizers like water and glycerol. It's a fully biodegradable and renewable material. The negative side of the material is that it has limitations in terms of moisture resistance and thermal stability, which make it less suitable for use in highperformance electrical applications.
Polyhydroxyalkanoates (PHAs): PHAs are polyesters produced by bacterial fermentation of sugar or lipids in nature They are fully biodegradable and are used in packaging, medicine, and agriculture However, their cost and performance characteristics, such as long downtime for polymer recovery, have limited their use
Bio-based Polyethylene (bio-PE) and Bio-Polyamides (bioPA): Bio-PE is similar to conventional PE but is made from renewable raw materials such as sugarcane Likewise, biopolyamides bio-PA reflect the properties of bio-nylon While it's technically not biodegradable, it is recyclable and has a lower carbon footprint compared to conventional PE The strength of this type of insulation is that it is the most similar in properties compared to traditional types of insulation
Materials like bio-PE and bio-PA have the most potential as long as their biodegradability can be improved because their physical properties are the closest to those of their petroleum counterparts.
So far, biodegradable materials are far from achieving mainstream status because more research, testing, and development is required.
As far as sustainability, the materials that are easily recyclable are the best in terms of environmental impact because recyclability is easier to achieve. These materials include PE, Nylon, and PP, among others. Most recyclable materials are thermoplastics, even though PVC, the most popular thermoplastic, is not recyclable.
With the abundance of various insulating materials on the market, there is a coverage for any kind of application/cable in residential, commercial, and industrial applications of any complexity. In the future, we will see new types of insulations and improved/ optimized types of existing insulating materials. The developers of cable insulations will be looking into improving flame retardance, high-temperature resistance, and environmental sustainability. With existing insulations, like the highly popular PVC, the experts will be looking at optimizing the formulation electrical, thermal, and mechanical properties. This includes using heat stabilizers and flame retardants to improve its performance at high temperatures in fire-prone environments, and improving its photostability with additives. Improving recycling properties of the PVC insulation.
Industrial insulations, only better. TPS Industrial Insulations. (2020, May 27). https://tps-industrial-insulations.com/?
fbclid=IwAR2PvUr6Ot1TBbnd7BNRECPZIIbDa4rFUiPHz7bUnxNDyeACqBF2MM yf6yk
Oi, T., Shinyama, K., & Fujita, S. (2012). Electrical properties of heat‐treated polylactic acid. Electrical Engineering in Japan, 180(1), 1-8.
Poltronieri, P., & Kumar, P. (2017). Polyhydroxyalkanoates (PHAs) in industrial applications. Handbook of ecomaterials, 4, 2843-2872.
Saleh, T., Yousif, E., Al‐Tikrity, E., Bufaroosha, M., Husain, A., & Al-Mashhadani, M. H. (2022). Modification of PVC with captopril and complexation reaction for preparing photostability and thermal stability of PVC. Materials Science for Energy Technologies, 5, 311-323.
UL 44. UL 44: UL Standard for Safety Thermoset-Insulated Wires and Cables. (2018). https://global.ihs.com/doc_detail.cfm?item_s_key=00097088
UL 83. UL 83: UL Standard for Safety Thermoplastic-Insulated Wires and Cables. (2017). https://global.ihs.com/doc_detail.cfm?
item _ s _key=00097256
UL 758. UL 758: UL Standard for Safety Appliance Wiring Material. (2022).
https://global.ihs.com/doc_detail.cfm?item_s_key=00330815
UL 1277. UL 1277: UL Standard for Safety Electrical Power and Control Tray Cables with Optional Optical-Fiber Members. (2022).
https://global.ihs.com/doc_detail.cfm?item_s_key=00096869
UL 1441. UL 1441: UL Standard for Safety Coated Electrical Sleeving. (2022).
https://global.ihs.com/doc_detail.cfm?item_s_key=00096907
Xu, X., Zhu, D., Wang, X., Deng, L., Fan, X., Ding, Z., ... & Makinia, J. (2022). Transformation of polyvinyl chloride (PVC) into a versatile and efficient adsorbent of Cu (II) cations and Cr (VI) anions through hydrothermal treatment and sulfonation. Journal of Hazardous Materials, 423, 126973.