
15 minute read
Features
especially in the southern region. The blistering heat has broken record highs this year alone. Those working outside in construction or agriculture are especially at risk. Workers’ exposed to extreme heat are at greater risk of heat-related disorders like heat stroke and heat exhaustion. Employers and employees must know the signs and symptoms of heat stroke and heat exhaustion, and have a plan for first aid and emergency response (please refer to the Heat Illness Guideline.) Another concern is heat fainting (called syncope), which occurs when an employee is standing for long periods of time or standing up quickly after sitting or lying down for long periods. During a recent site visit with an employer, as we began to discuss prevention strategies related to this particular risk, the employer recalled one summer in particular in which the company faced four different instances. Two of which were recordable. He was relieved to see that as a result of training; his employees were now capable of responding in a manner that reduced the severity of injuries in all of these accounts. Employees immediately sprang into action, offering additional water sources and Dr. Thomas Bernard, USF Faculty moving the affected to cool rooms on-site. I would venture to say that proper training and effective emergency planning helped keep those employees alive that day. Failure to implement an effective injury and illness program can result in monetary fines from OSHA enforcement. Under General Duty Clause 5a1 OSHA can fine an employer for items discovered in an inspection that are known hazards (see OSHA and NIOSH websites). Additionally, loss of consciousness, regardless of the duration, is a recordable injury that would need to be included in your OSHA logs. Any injury or illness could result in a workers’ compensation claim that could potentially increase an employer’s modification rate and increase insurance premiums. It is imperative to ensure that employees are properly trained on what to expect and what signs to look for. Prevention of heat stress in workers is key. Adequate training should be provided so that employees are familiar with what heat stress is, how it can impact their safety, and how it can be prevented. Providing water, rest and shade is necessary to allow employees sufficient time to cool down. More importantly, employees need to be granted the ability to stop any processes necessary to prevent
Cruel Summer: The Dangers of Heat Stress
Although summer has officially ended and autumn is here, the hot weather has been relentless in the sunshine state,
David Ashman, Safety Consultant a more serious injury from occurring. According to the National Safety Council, workplace injuries and illnesses cost our economy $198.2 billion per day. Employers who invest in injury and illness prevention programs can expect to see significant cost savings in addition to reducing fatalities, injuries, and illnesses. USF SafetyFlorida, the state of Florida’s official small business consultation program provides employers with a FREE web-based tool known as the SafetyWriter. SafetyWriter allows employers to customize an injury and illness prevention program specific to their industry. To access the free tool or to request a complimentary consultation, visit www.usfsafetyflorida.com or call 1.866.273.1105.
For more information regarding heat stress: https://www.osha.gov/heat/index.html https://www.osha.gov/ Publications/osha3154.pdf https://www.osha.gov/SLTC/ heatstress/heat_illnesses.html https://www.weather.gov/safety/heat https://www.osha.gov/OshDoc/data_ Hurricane_Facts/heat_stress.html Tags: cruel summer, Heat Index, heat stress, USF Health, USF SafetyFlorida
Job Hazard Analysis in the Workplace
Employees are exposed to hazards in the workplace on a daily basis and employers have the responsibility of protecting employees from these hazards. Some hazards can lead to worse outcomes than others and some jobs are inherently more hazardous than others, but one thing they all have in common is that there are ways to reduce or possibly eliminate hazards using one of several control methods that are outlined in the National Institute of Occupational Safety and Health’s (NIOSH) hierarchy of controls. In order of preference and effectiveness, they are as follows:
Elimination – removing the hazard so employees are not exposed to the hazard. An example of this would be to move a noisy piece of machinery to another area where no one works or outside the building.
Substitution – substituting a hazard with something less hazardous. A common example of this is substituting a less toxic chemical for a more toxic chemical when both chemicals work equally as effectively.
Engineering controls – reducing the hazard through physical means such as barriers, ventilation, isolation, and enclosures. An example of this would be installing a spray booth for spraying solvent-based liquids.
Administrative controls – reducing the hazard through work practices or policies. An example of this would be having a policy that requires two employees to lift objects that weigh more than 50 lbs.
Personal Protective Equipment (PPE) – when no other controls are available the last line of protection is PPE. Common PPE are gloves, welding masks, respirators, ear protection, safety glasses, etc. The primary means to identifying and controlling hazards is to conduct a job hazard analysis (JHA). In OSHA Publication No. 3071 titled Job Hazard Analysis, a JHA is defined as “a technique that focuses on job tasks to identify hazards before they occur. It focuses on the relationship between the worker, the task, the tools, and the work environment.” Or more simply put: every step of a specific task is evaluated for potential hazards, control methods are identified to eliminate or reduce the hazards, and if no controls are available then identify what PPE is needed. JHA’s are thought exercises that attempt to identify what can go wrong, what the consequences are if something went wrong, the scenarios in which potential hazards lie along with their respective contributing factors, and how likely would it be to occur. A JHA need not be overly complex, but it does need to be effective. The task of conducting JHA often falls on the employees in positions of authority, such as the safety manager/coordinator or a supervisor/foreman; however, the best resource for completing JHAs is often overlooked – the employees themselves. Involving employees engaged in the job task or exposed to its unique hazards utilizes knowledge that can often be gained only by performing that job task. It also has the added benefit of having employees actively participate in the safety and health program, which is key in having them “buyin” to the safety and health program.
Ideally, JHAs are completed before a job task or process is introduced into the workplace. Conducting JHAs beforehand maximizes the opportunity to consider all types of controls and is more cost-effective as it allows hazards to be controlled before they can even occur, rather than modifying a job task or process that is already active. More often, though, JHAs are conducted well after a job task or process has been implemented and if an employer has several job tasks, all with varying types of equipment and hazards, conducting JHAs can seem overwhelming and employers may not
Garrick Johnson, MSPH, CIH
Health Consultant
even know where to begin. In this situation, JHAs can be prioritized based on: • Jobs with the highest injury or illness rates; • Jobs with the potential to cause severe or disabling injuries or illness, even if there is no history of previous accidents; • Jobs in which one simple human error could lead to a severe accident or injury; • Jobs that are new to your operation or have undergone changes in processes and procedures; andJobs complex enough to require written instructions.
JHAs are included in OSHA’s Recommended Practices for Safety and Health Programs and employers are not required to conduct JHAs, but all employers should strongly consider conducting JHAs as they can help reduce injuries and illnesses, which in turn corresponds to reduced worker’s compensation costs and increased productivity. The exception to the requirement for conducting JHAs is if employees are being provided PPE. Since PPE’s effectiveness lies in its suitability for use in the specific application, OSHA’s PPE general requirements standard 1910.132 explicitly states employers need to have a written certification that a JHA has been performed, and that the proper PPE is being provided.
Now that the concept and process of conducting a JHA has been described, let’s look at a simple example I use when talking to employers about JHAs.
Example: Conducting a JHA for making a pot of coffee
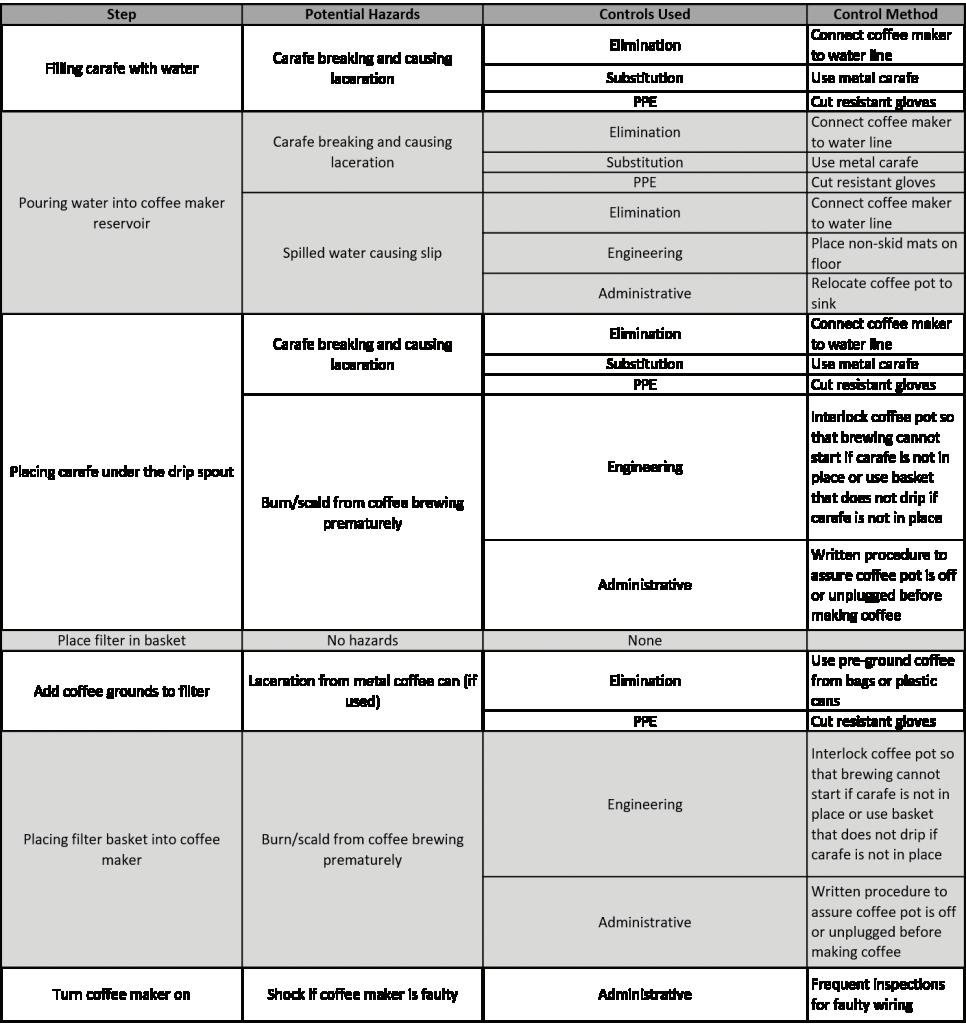
Now obviously this is overkill for a task as simple and relatively low hazard as making a pot of coffee, but it is illustrative of a comprehensive JHA. Now back to the question of effectiveness. How do you know if a JHA is effective? Simply put: if an employer has conducted a JHA on a job task or process, implemented controls, and employees are still sustaining injuries while engaged in that job task; then the JHA has overlooked something or identified improper PPE, and is not effective. In the coffee making example above, let’s imagine that only a very specific type of glass carafe can be used, the only source of water is from a 5 gallon dispenser due to the coffee maker being in a remote location, and that a carafe breaks which leads to an employee suffering a laceration. In this scenario, substituting the glass carafe is not an option, nor is eliminating the need to fill the carafe since it must be filled from a 5-gallon dispenser. The original JHA would show that the only option to protect employees from lacerations is to provide them with cut-resistant gloves; but since they are still being injured (assuming that they are actually wearing the gloves), the gloves identified are not effective. In this case, a new JHA would have to be performed and a different type of glove evaluated.
A properly conducted and effective JHA is a powerful tool in eliminating or reducing hazards in the workplace and can provide big returns in terms of cost savings and increased productivity. I would encourage all employers to download a copy of OSHA’s guidebook Job Hazard Analysis from https:// www.osha.gov/Publications/osha3071.pdf for further information. Consultants with the USF SafetyFlorida Consultation Program are readily available to help employers navigate the ins and outs of OSHA standards, and to assist employers provide a safe and healthy working environment for their workers. Call toll-free at 1-866-2731105 or visit www.usfsafetyflorida.com to request a free and confidential consultation visit.
COVID-19 Small Business Resources
January 2020 started with news of a novel disease in a country half way around the world. This novel disease would become what is known as COVID-19. Six months later, the United States has experienced over 1.8 million cases of COVID-19, over 100,000 fatalities attributed to the disease, led to stay-at-home orders, and shuttered non-essential businesses across the country. Indeed, this new disease has impacted virtually every aspect of American life.
COVID-19 and public health have been a constant part of the news cycle since the outbreak began. Social distancing has become a household term. And wearing a face mask in public has become the norm. The public health practices that have been implemented over the last few months have helped to turn the tide on the disease. Disease rates have stabilized or declined in many parts of the country. Many governors are beginning to lift their stay-athome orders.
As businesses begin to re-open, it is important for companies to implement disease prevention measures aggressively so that re-opening America can be done safely. Such measures could include establishing and implementing a COVID-19 prevention plan. Although not specifically required by the Occupational Safety and Health Administration (OSHA), implementing a COVID-19 prevention plan could be required under the OSHA general duty clause. The OSHA general duty clause requires that each employer provide a workplace that is free from recognized hazards that are causing or likely to cause death or serious physical harm to its employees. Surely COVID-19 is a recognized hazard likely to cause serious physical harm to employees in many industries. But establishing a prevention plan for a new, previously unrecognized disease may seem like a daunting task. Fortunately, there are resources available to assist a business in establishing a COVID-19 prevention plan.
Every business should be, or become, familiar with the OSHA 3990-03 2020 booklet “Guidance on Preparing Workplaces for COVID-19”. The document contains a wealth of information about COVID-19, how an outbreak could affect the workplace, and steps employers can take to reduce workers’ risk of exposure to the disease. The steps include measures that all employers can take such as implementing basic infection prevention measures, developing policies and procedures for COVID-19, and implementing basic workplace controls. The document is especially useful in that it provides an employer a means to classify their workers’ risk of exposure to the disease and also provides specific workplace controls based on that risk classification. The OSHA booklet can serve as the basis for developing a workplace specific COVID-19 prevention plan.
Also, every business should be, or become, familiar with the OSHA safety and health topics on the dedicated COVID-19 webpage. The webpage also has good information that can be used in developing a COVID-19 prevention plan. The webpage contains OSHA “Alerts” that are industry-specific designed to keep workers safe. The webpage provides guidance and resources for employers and workers on the control and prevention of COVID-19 in specific industries such as construction, dentistry, healthcare, and
Adam Marty, PhD, CIH
Health Consultant
retail operations, to name a few. An employer doing business within a listed industry would be wise to consider those industry specific control and prevention measures and incorporate them into their plan. The webpage also has useful posters and videos in the “News and Updates” tab to assist with employee training. Lastly, the webpage contains links to additional resources including worker training tools, webinars, and presentations about COVID-19.
Every business has a responsibility to take the precautions necessary to re-open America’s businesses safely. Every business should first implement a COVID-19 prevention plan and then use the “Workplace Decision Tool” developed by the Centers for Disease Control and Prevention (CDC) to assist in making re-opening decisions. Taking the necessary precautions will minimize employees’ risk of exposure to the disease and keep workers, their families, and their friends safe and healthy. Taking the necessary precautions will also reduce the chances of having painful re-instatements of stay-at-home orders due to an upswing in infection rates.
If your business needs assistance in developing a COVID-19 prevention plan or understanding what may be required by OSHA, the University of South Florida (USF) SafetyFlorida Consultation Program can provide free assistance. USF SafetyFlorida can provide a sample prevention plan, training materials, and resources. If there are questions about COVID-19 or if assistance is needed in developing a plan, please contact USF SafetyFlorida Consultation, www. usfsafetyflorida.com, for a free review and evaluation.
Holiday Safety: Seasonal and Temporary Workers
As the holiday season quickly approaches employers should focus on their responsibility to protect all employees, to include full time, part-time and temporary employees during the busy holiday season. Whether employees are stocking shelves, packing boxes, delivering products, or selling merchandise, temporary or seasonal employees hired to provide additional help have the right to a safe workplace. During this time of year, hiring seasonal workers increases and more employees are in unversed job settings. With increased merchandise sales, employees are expected to meet high demands. It is important to focus on employees who may not be as familiar with their new scope of work. Additionally, employers need to understand the different rules that involve seasonal/temporary workers. Industries such as retail employers should take precautions to keep workers safe while managing large crowds during sales events. Shopping increases during this time of year dramatically which directly impacts worker safety. It is important to address potential workplace safety hazards by implementing safety guidelines, such as using trained security personnel and barricades or rope lines for pedestrians and implementing crowd control measures and emergency procedures. According to the Bureau of Labor Statistics “Employer-Reported Workplace Injuries and Illnesses – 2018” the retail trade was the only private industry sector where the TRC (Total Recordable Cases) rate increased in 2018, rising from 3.3 cases to 3.5 cases per 100 full-time equivalent (FTE) workers. This was the first increase in the TRC rate in retail trade since the series began in 2003. Retail trade accounted for 14 percent of all injuries and illnesses in private industry in 2018. OSHA offers many resources that provide information and guidance for protecting those employed in various aspects of the retail industry, including warehousing, tractor trailer drivers, forklift safety, and crowd management. Please visit https://www.osha.gov/holidaysafety. html and https://www.osha.gov/temp_workers/ for additional information.
I personally urge you to be prepared and take special care to ensure your employees are trained and ready for the fast approaching holiday season. Communication is vital to everyone’s
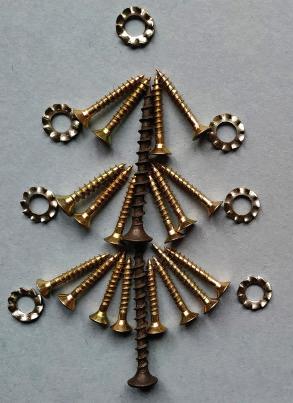
safety and the success of your business. Katlyn Thomas, BS, Health Consultant
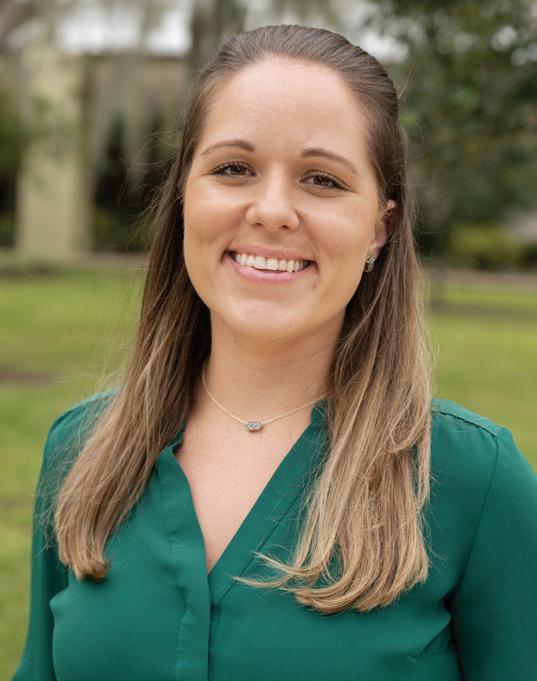
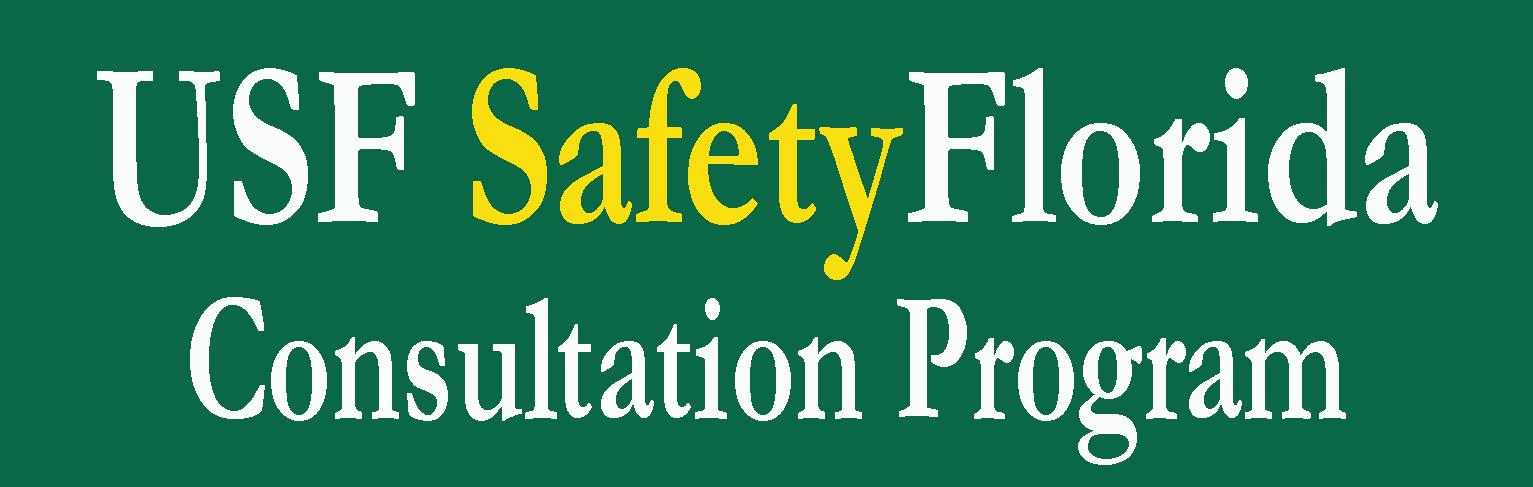
Consulting • Training • Education
USF SafetyFlorida Consultation Program’s primary purpose is to help your company prevent work-related fatalities, injuries and illnesses. In the short term, we do that by emphasizing hazard identification. In the long term, we do that by helping you develop a safety management program. Our strategies give you the results you’re looking for. If you are ready to take the next step towards safety in your business, contact us today to request a free and confidential safety consultation.
On-site Consultation
USF SafetyFlorida offers free and confidential safety and occupational health advice to small and medium-sized businesses, with priority given to high-hazard worksites. Our consultants work with employers to identify workplace hazards, provide advice on compliance with OSHA standards, and assist in establishing injury and illness prevention programs.
Training & Education
The OTI Education Center provides training and education on occupational safety and health subjects for federal and state compliance officers, state consultants, other federal agency personnel, and the private sector.
Online Management Tool
SafetyWriter, an online safety management tool developed by USF SafetyFlorida helps companies customize a written safety and health management program without the guesswork.
Award Programs
USF SafetyFlorida rewards small businesses who demonstrate strong, effective safety cultures with the opportunity to receive either the SHARP (from the OSHA national office) or the Sunshine State Safety Award (exclusively for Florida’s small businesses).
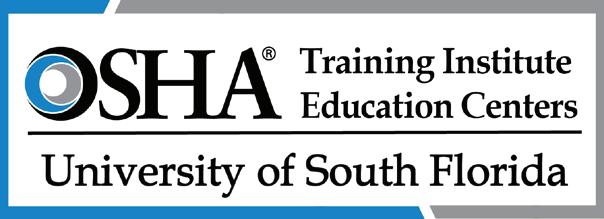
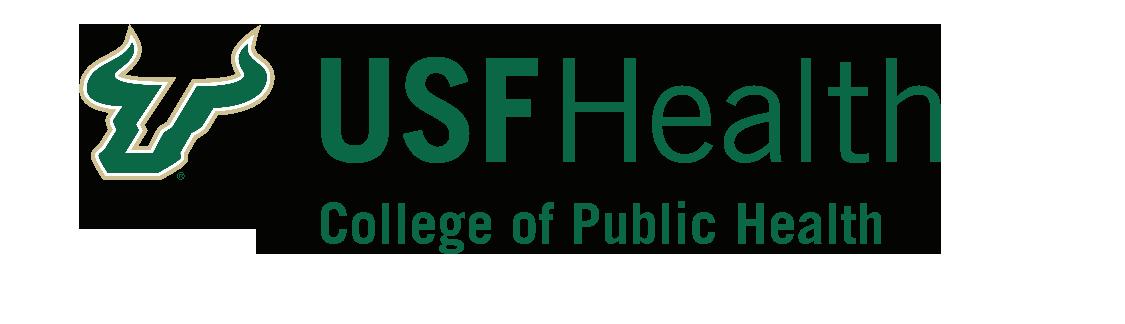