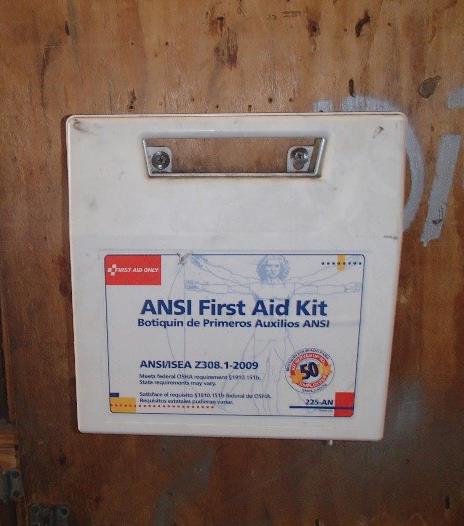
3 minute read
What We See
Each day, our consultants are out in the field visiting small employers in high-hazard industries. From a hazard standpoint, we see it all. On this page are photos of hazards we have identified this year. More importantly, our consultants assisted these companies with correcting the hazards so their employees can work safely.
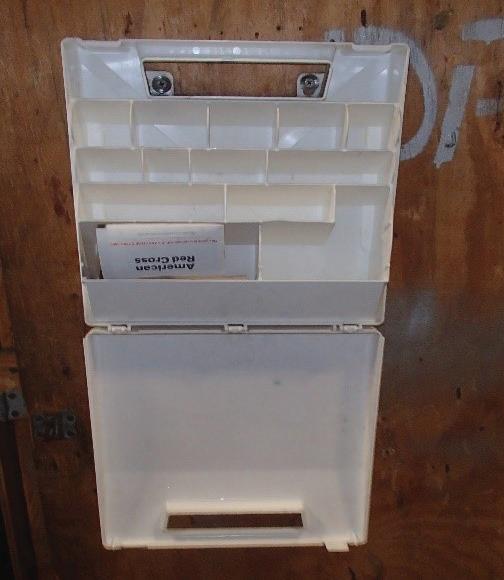
Adding additional counterweights to increase the lifting capacity of the forklift shifts the center gravity outside of the stability triangle of the forklift. This modification can result in decreased stability, handling, and steering ability, resulting in the forklift tipping over, the operator losing control of the forklift, the forklift dropping the load, and ultimately struck by and crushing injuries and fatal accidents. All respirators should be stored to prevent damage, contamination, dust, sunlight, extreme temperatures, excessive moisture, and damaging chemicals. It is important that employers ensure that employees clean, inspect, and properly store all respirators after each and every use. Adam Marty, PhD, CIH Michael Tartal It is a requirement of OSHA that employees be given a safe and healthy workplace that is reasonably free of occupational hazards. However, it is unrealistic to expect accidents not to happen. Therefore, employers are required to provide medical and first aid personnel and supplies commensurate with the hazards of the workplace. In
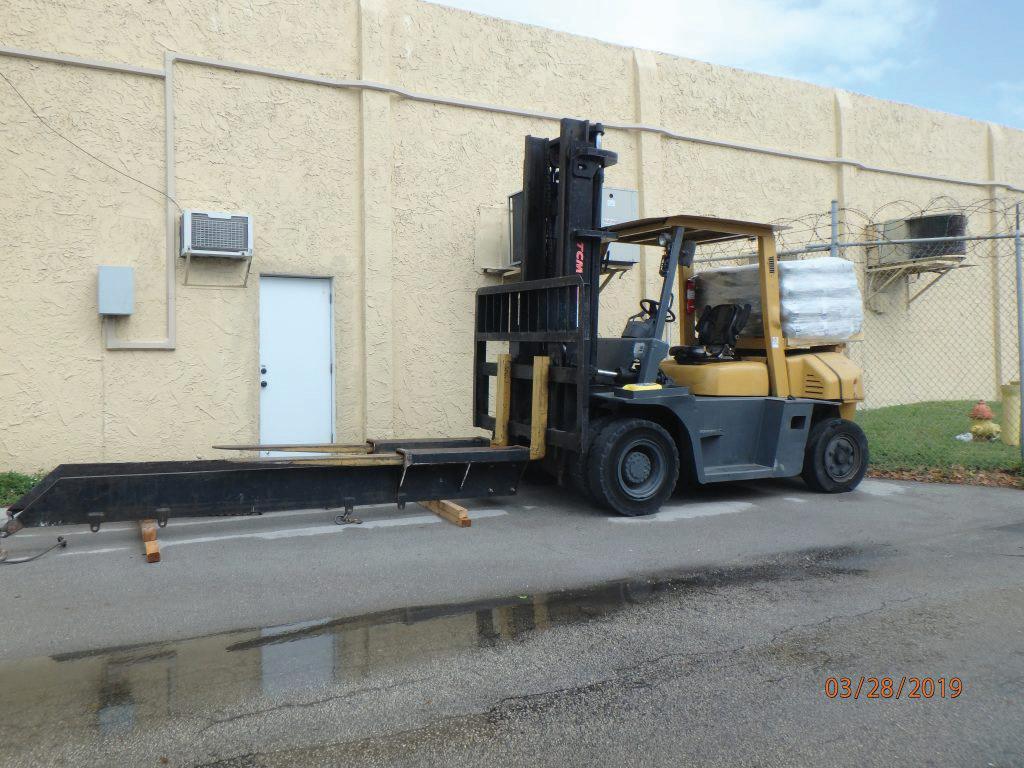
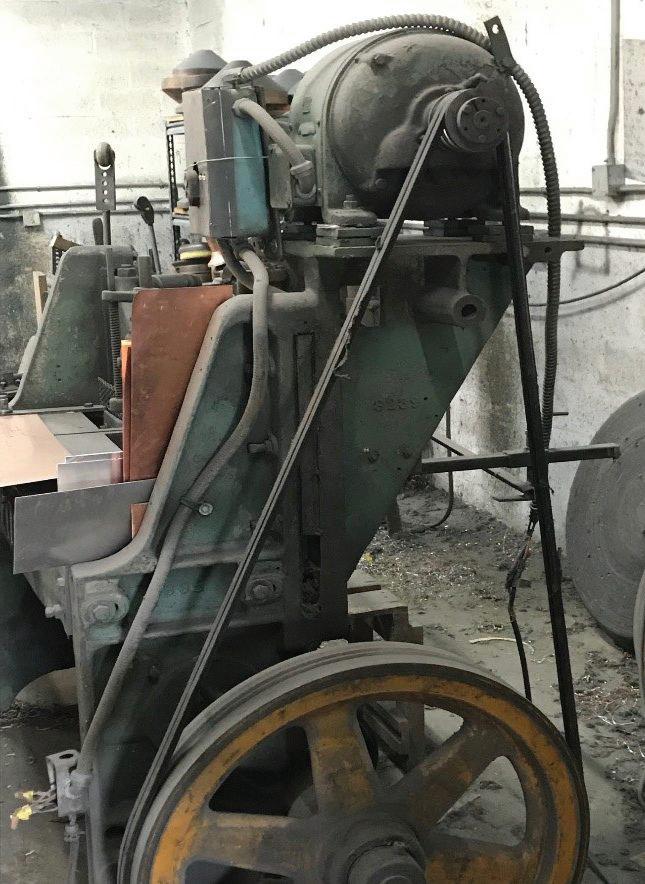
this instance, there were no supplies available.
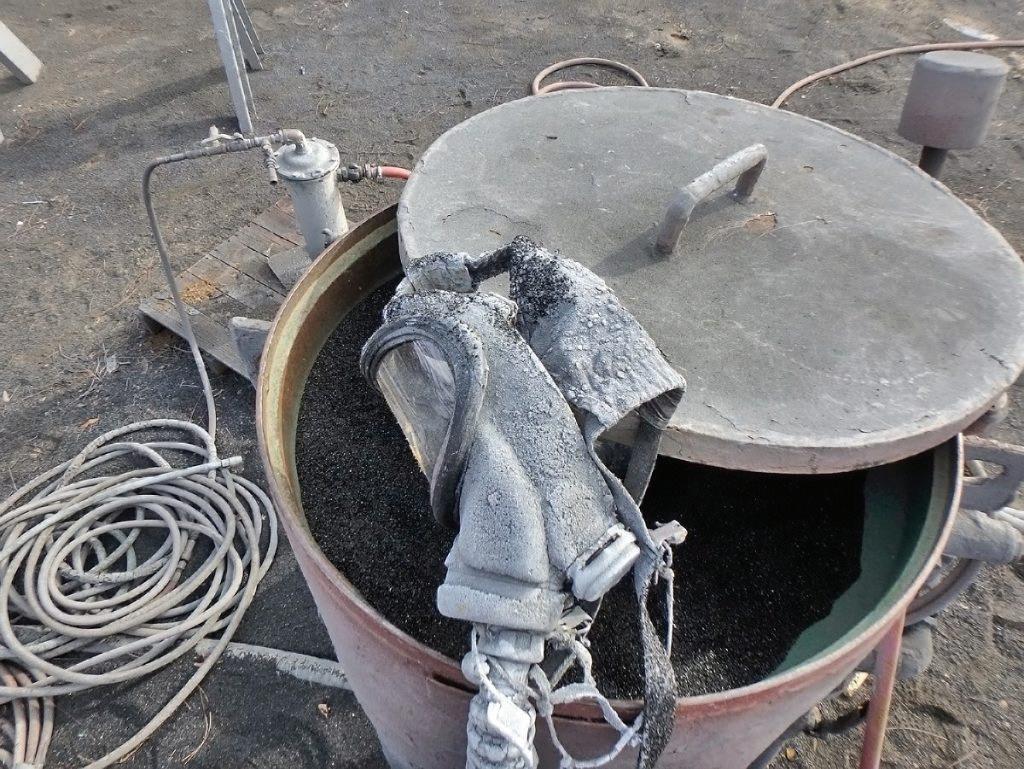
If there is a defect or evidence of damage that might expose an employee to injury, the defective or damaged item shall be removed from service until repairs and the equipment is rendered safe.
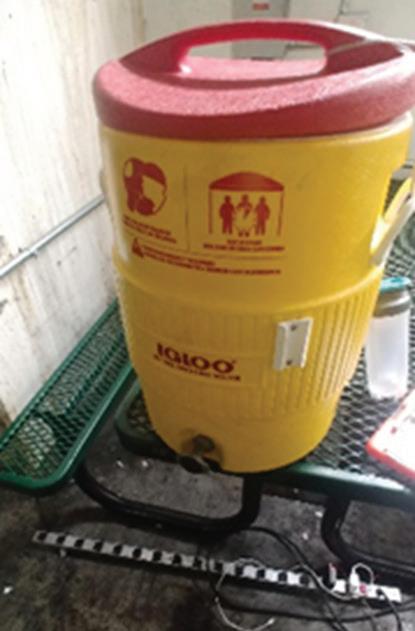
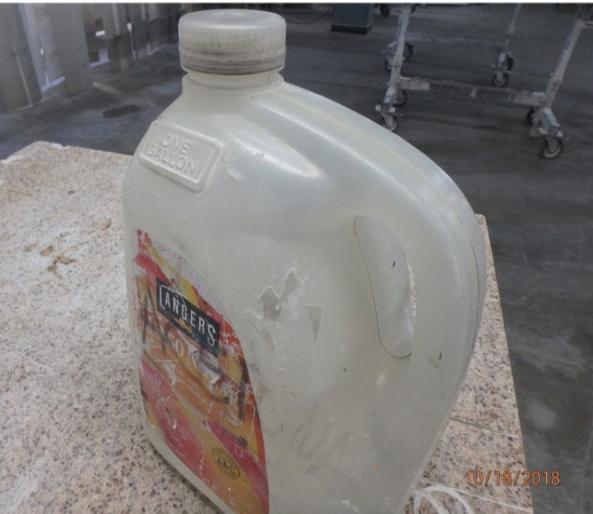
Electric equipment should be free from recognized hazards that are likely to cause death or serious physical harm to employees. Do a hazard assessment, remove the water cooler and or the electrical outlet; provide single service cups and ensure the cooler cover is locked and secured. It is important for employer to ensure that each container of hazardous chemical in the workplace is labeled, tagged or marked with the identity of its contents and hazards associated with exposure to those materials. Worker(s) may unknowingly be exposed to diesel, with potential for fire resulting in burns, smoke inhalation, or fatality. Gabe Garcia Keith Brown A one-gallon plastic juice container that contained acetone, a category 2 flammable liquid, was observed in a production area. The container had become brittle and was breaking apart at the top. Many flammable liquids are solvents which can degrade certain types of plastics causing the plastic to become brittle or soft. If the container fails, this can increase the risk of a fire or explosion resulting in employee burns, traumatic injuries, and/or fatalities. General purpose wiring and electrical equipment can cause explosions and fires in areas where flammable vapors and liquids are present. These areas require special electrical equipment which is designed for the specific hazard involved. Many electrical components arc, spark, or produce heat under normal operating conditions. In designing equipment for hazardous locations, these components are either replaced by lower powered substitutes or shielded from contact with the atmosphere or the equipment chassis.
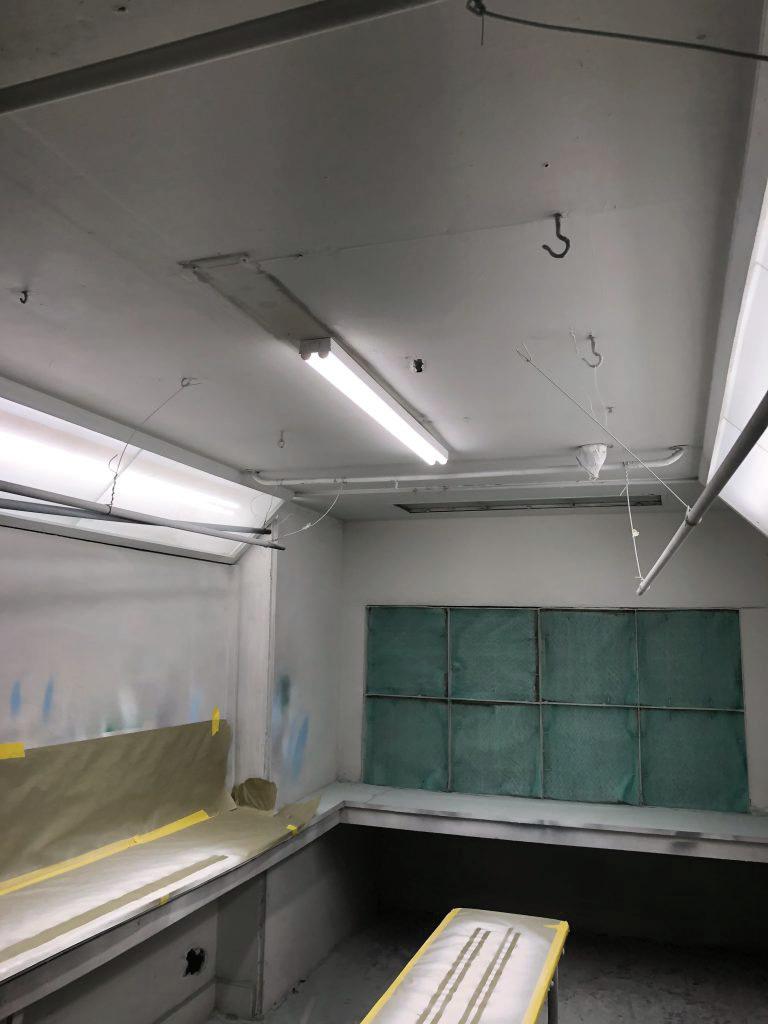
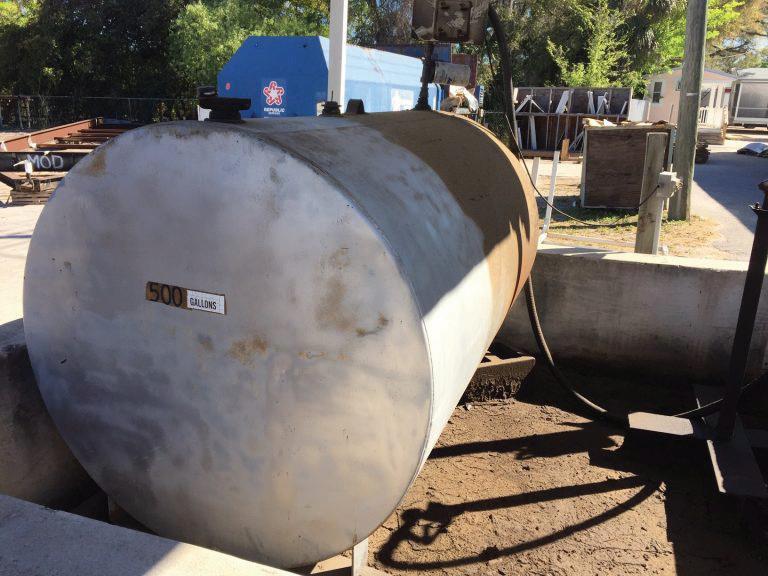
Adam Marty, PhD, CIH Garrick Johnson, MSPH, CIH