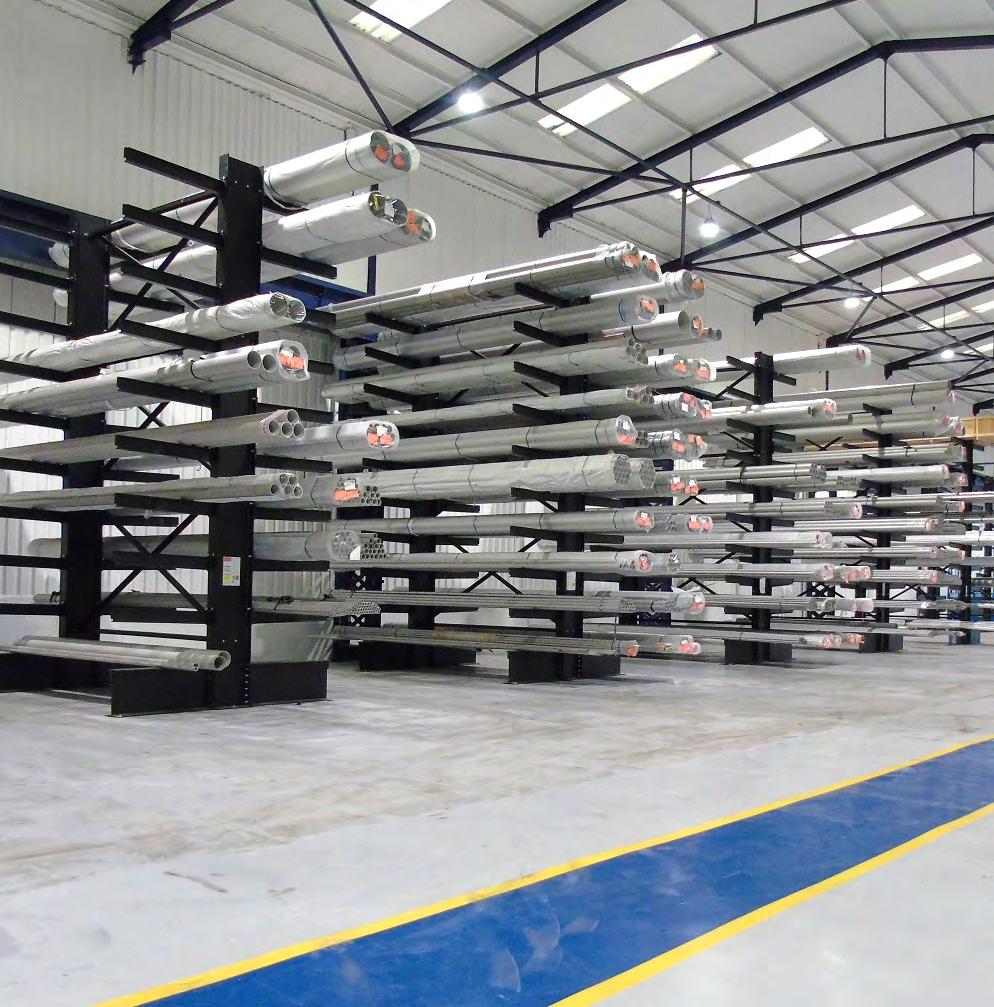
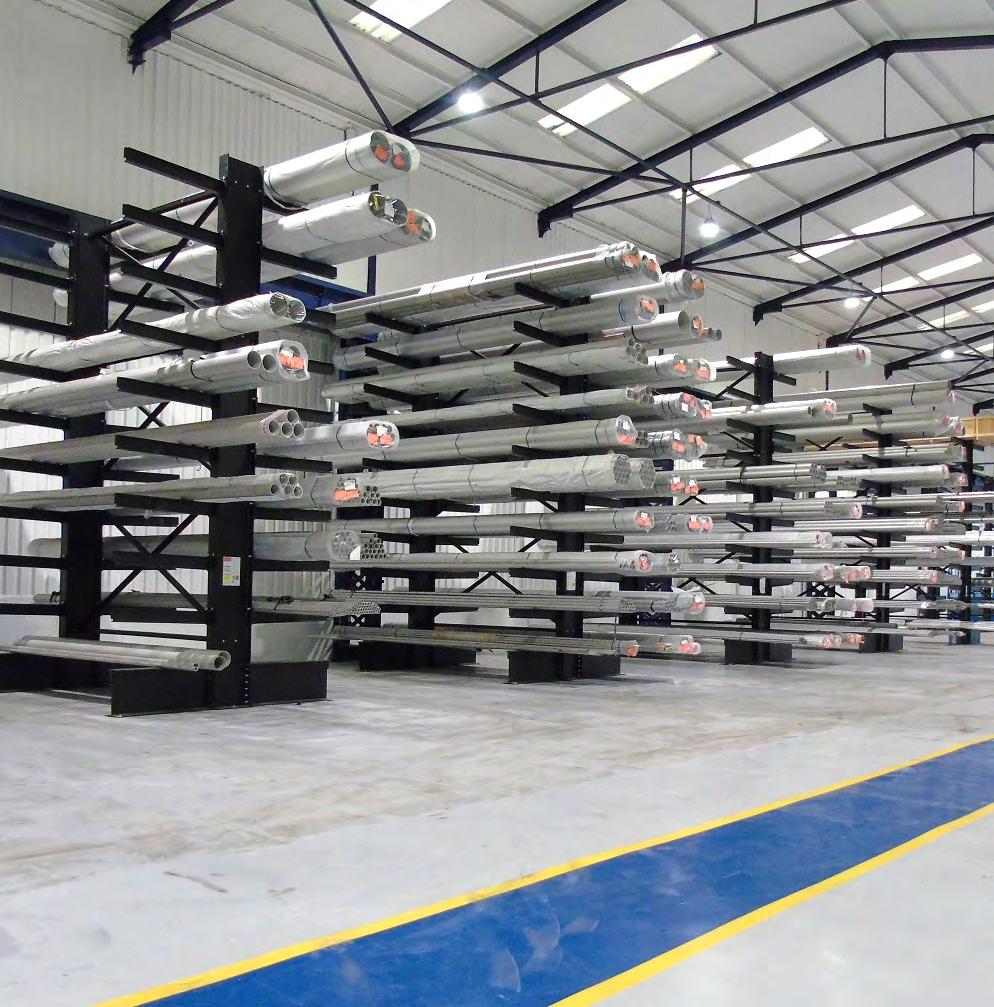
From passive connectors to active system components
Interfaces for medical device technology require an enormous variety of functionalities in a very small IP-protected space. The signal and data pins, power and protective earth contacts, as well as shielding and protective measures often pose design problems to developers. High-frequency electronics integrated into the circular connector can help reduce the density of electromechanical functions inside the component’s housing, promote miniaturization, and still create more space for optimized power transmission.
Miniaturized interfaces for signals, data, and electrical power are an engineering challenge per se. When it comes to components for medical technology, developers face even more stringent requirements: Failure protection, signal integrity, as well as functional, operator, and patient safety make their design tasks even more complex.
The increasing functional complexity places tight physical limits on the miniaturization of interface components. In state-of-the-art M12 circular connectors, for example, which comply with the draft standard 63171-7, power pins, protective contacts, shielding, and data ports coexist in a very small space. Although this is appropriate and desirable for overall functionality, it immensely restricts freedom in the design of individual functions. In the case of medical devices, this is particularly challenging. The compactness of the connectors is thus generally limited here, and many of these interfaces have already reached the boundaries of practical feasibility.
Questioning the contacts
Traditionally, in connectors, signals, data, and power are all linked via electrical contacts, whose mechanical and chemical properties fundamentally determine the performance, quality, and efficiency of transmission. In order to keep losses to a minimum, such direct electrical connection is absolutely essential for the power supply –but is not required for signals and data.
In the world of data transmission, there are proven standards for both wired and wireless connectivity. The use of the corresponding technologies depends mainly on the type and amount of data to be transferred, but also on the environmental conditions. While broadband wired Ethernet is becoming more and more established in instrumentation and automation technology, the low-energy Zigbee and Bluetooth LE – or high-speed WiFi – are good examples of widespread wireless communication standards. For data rates above this spectrum or in environments with electromagnetic interference, optical transmission methods such as fiber optics are also used.
In view of this variety of possibilities, the question arises as to what extent they can contribute to solving the problem of limited miniaturization of interface components in combined signal, data, and power connections. For example, what if signals and data could be transmitted between the male connector and the device without occupying space for electrical contacts? Without having to shield them from supply pins and from supply wires? What if the IP-protected installation space inside a connector housing could in future be used exclusively – or at least much more than before – for power transfer? What if the connector could accommodate an even wider range of functions?
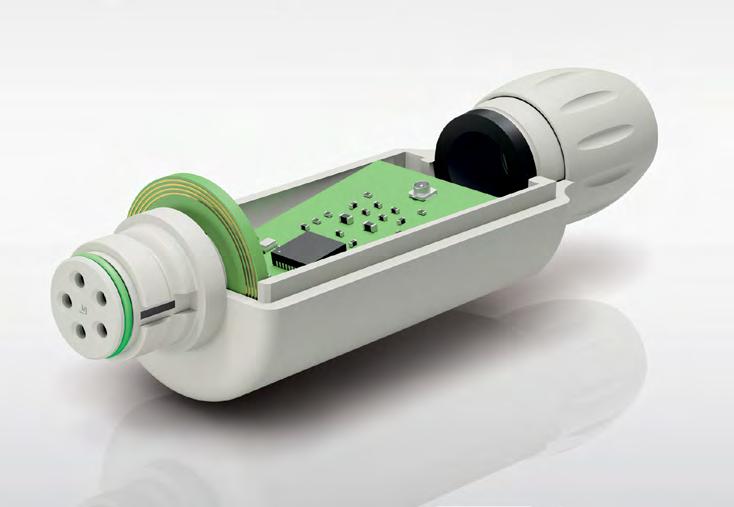
Formerly a connector, now a micro device
With the NeaCo² technology demonstration, binder explored this question and successfully merged the two worlds of electromechanical and wireless interfaces. Using NeaCo², the engineers from Neckarsulm/Germany have shown how electromechanics and Radio Frequency (RF) electronics can be combined in a small hybrid connector. While power is transmitted via the traditional pins, they have implemented
Hybrid connectors with NFC – developers can use the entire installation space inside the connector for the power pins, expanding the design options. Photo: binder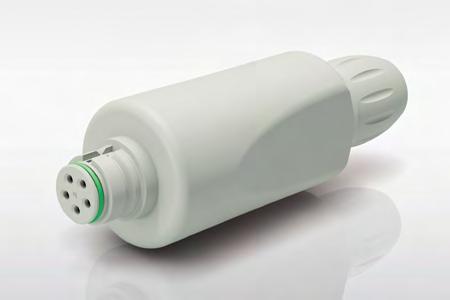
wireless Near-Field Communication (NFC). NFC has a significantly shorter range than Bluetooth or WiFi, for example, but allows the NeaCo² to be used in numerous new applications, such as device identification, predictive maintenance, and fault prevention. In short, binder has used the integration of RF electronics to transform passive hybrid connectors into active system components, so-called micro devices.
These offer tremendous advantages. Developers can use the entire installation space within the connector for the power pins, widening their design options. And this helps them optimize the efficiency of the compact and protected power port. Electronics integration also adds options to the development of product variants. The respective connector itself can be equipped with additional features, but can also act as a communication node – or even as a controlling device.
The possible new features that can be integrated into the hybrid connector thanks to NFC include:
· Identification of approved devices; only approved devices receive power
· Identification of devices for optimized power transfer
· Counting of mating cycles and recording of electrical resistance in order to predict faults
Metering transmission power and temperature
The function as an access point for live data traffic
Safety shutdown if operating limits get overrun
Minimized susceptibility to errors caused by contamination thanks to contactless data transmission
· The use of an additional data channel for migration systems
Conclusion
By integrating RF electronics, engineers are able to transform passive connectors into active system components. Thus, these receive new characteristics and distinctive features. The performance and communication capabilities of the hybrid interfaces may improve, and additional application scenarios arise. The new connectors can be used across all industries beyond medical technology – from industrial automation to e-mobility.
About binder
binder, headquartered in Neckarsulm, Germany, is a familyowned company characterized by traditional values and one of the leading specialists for circular connectors. Since 1960, binder has been synonymous with the highest quality. The company works with more than 60 sales partners on six continents and employs around 2,000 people worldwide. The binder group includes the binder headquarters, 16 affiliated companies, two system service providers as well as an innovation and technology center. In addition to Germany, the binder sites are located in Austria, China, France, Hungary, the Netherlands, Singapore, Sweden, Switzerland, the UK, and the USA.
Fields of application:
· Home care
Remote monitoring, Industrial IoT
Flexible power supply systems
Predictive maintenance
Mobile applications
Monitoring
Features:
· IP-protected interface
· Connector selectable from the binder portfolio
· Customized additional functionalities may be implemented
· Contactless communication is possible
· Very good media resistance
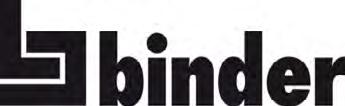
Binder UK Ltd
Unit D, ATA House, Boundary Way, Hemel Hempstead, Hertfordshire, HP2 7SS, UK
Tel. +44 1442 257339
Fax. +44 1442 239545
info@binder-connector.co.uk www.binder-connector.com/uk/
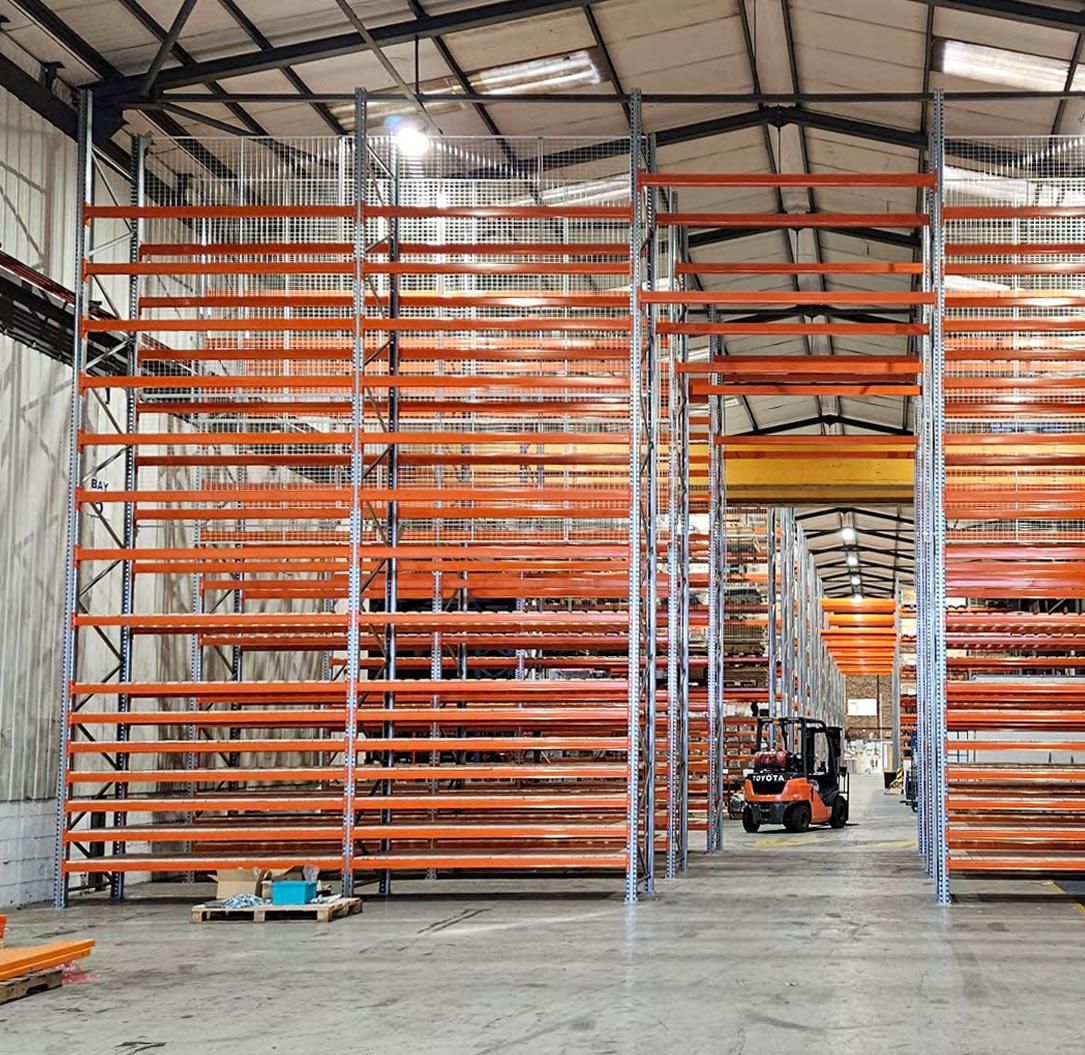
[click here]
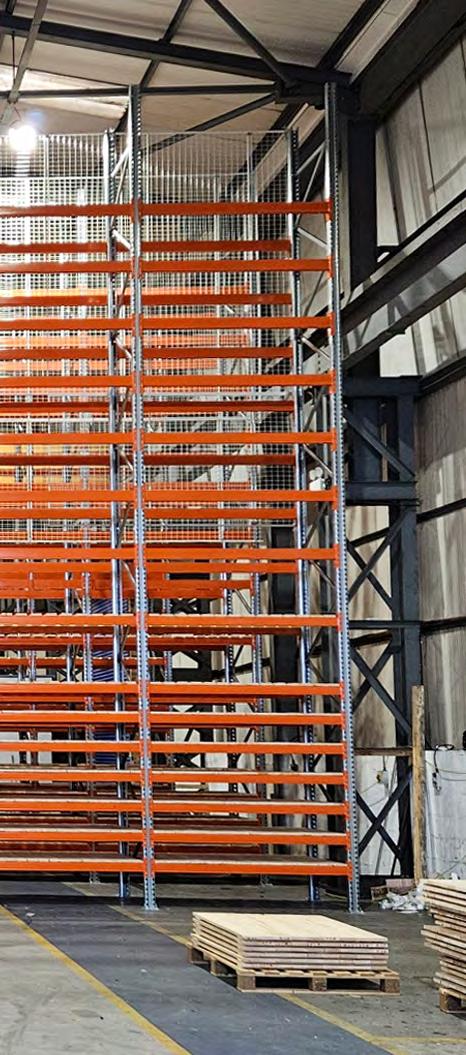
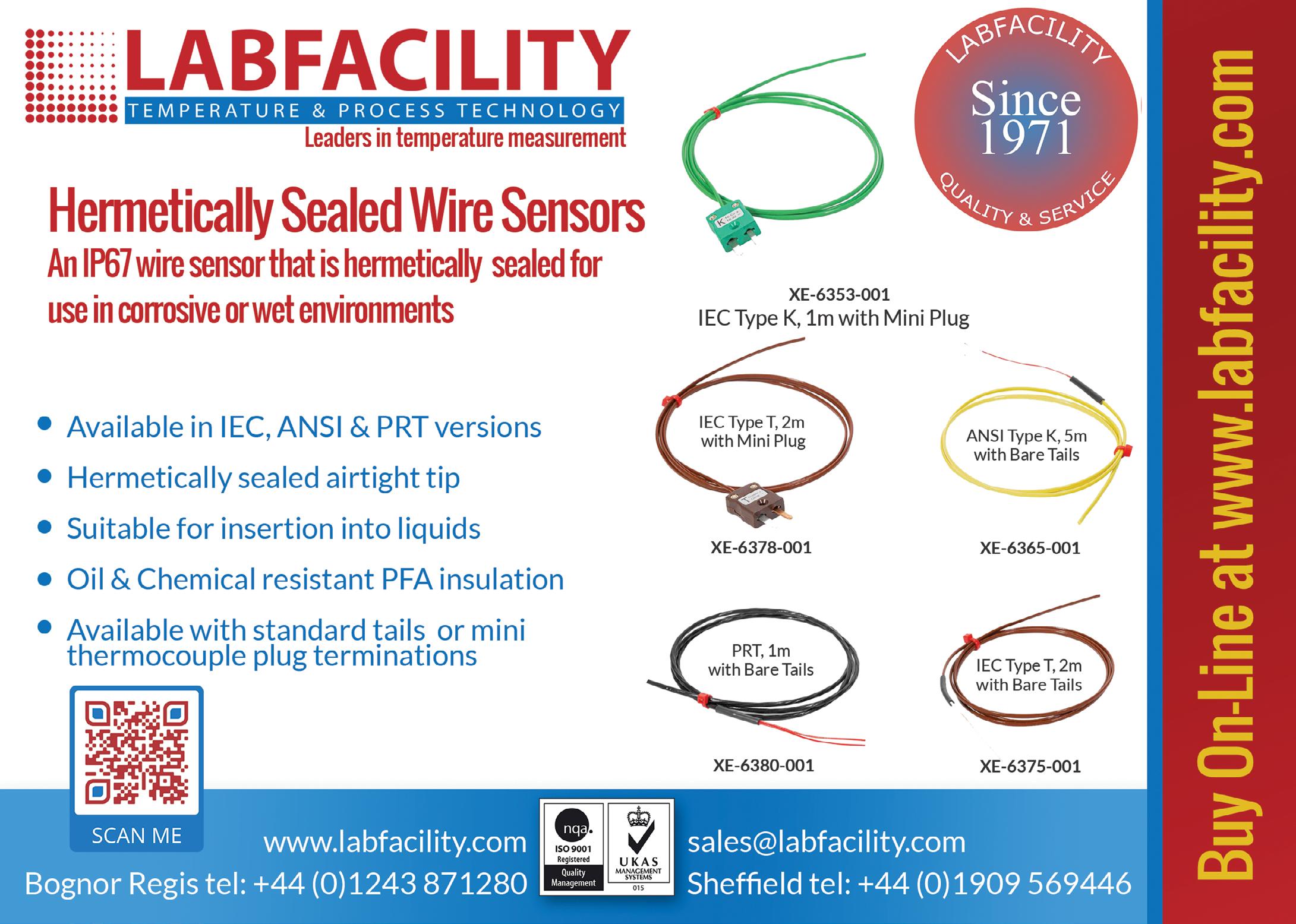
Delta Showcases D-Bot Series Collaborative Robots and IIoT Solution for Industry 4.0 at SPS Italia 2024
Delta, a global leader in power management and a provider of IoT-based smart green solutions, announced its participation in SPS Italia 2024 to present its latest innovations in factory automation, including the revolutionary D-Bot Series collaborative robot portfolio, which offers models capable of handling payloads as heavy as 30 kg with reach up to 1,800 mm.
Luca Cavagnari, Head of Sales Italy, Industrial Automation Business Group, Delta Electronics EMEA region, expressed his enthusiasm for the event, stating, “Our showcase at SPS Italia 2024, is part of Delta’s strategic initiative to empower industrial evolution with high-efficiency, high-flexibility solutions that address the growing demand for advanced automation across various industries. Moreover, we are excited to present our new collaborative robot solutions, designed to transform traditional manufacturing into intelligent, automated production lines”.
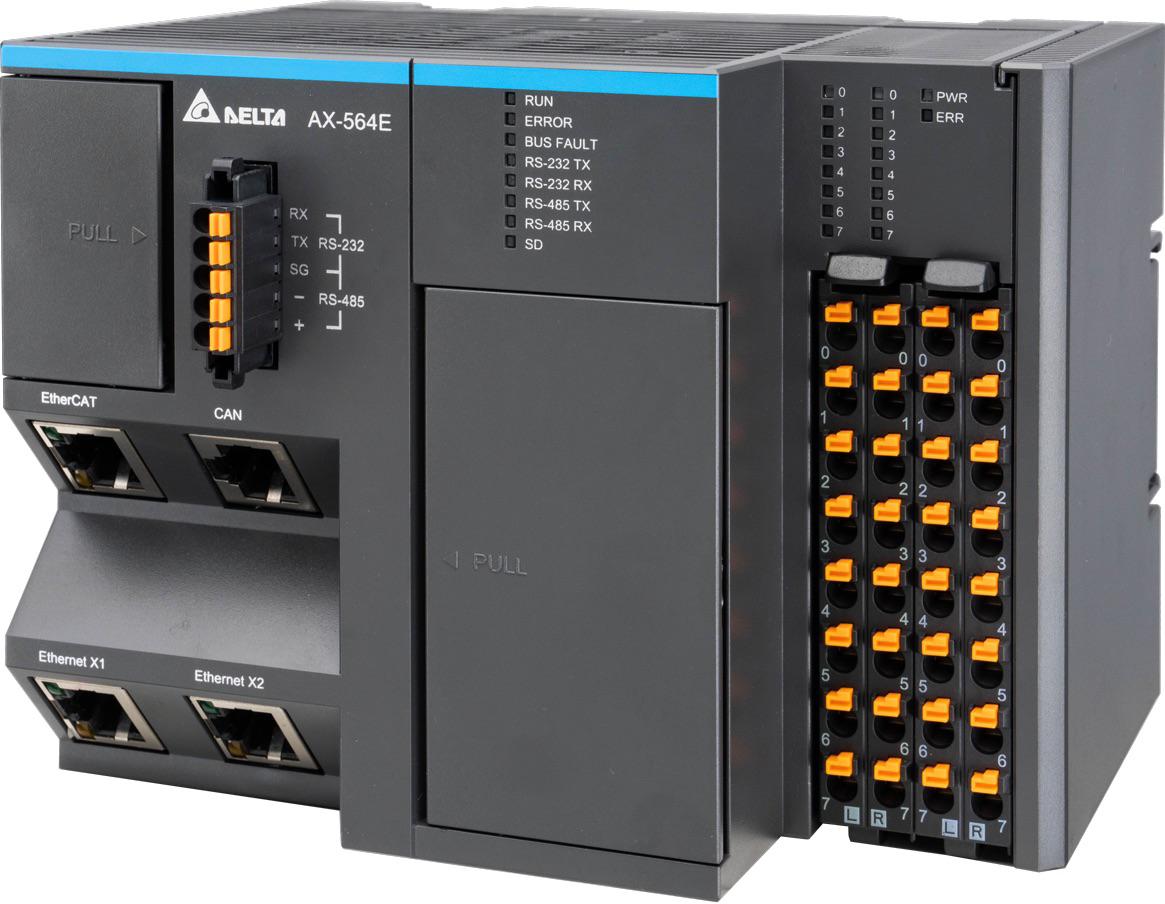
For more information about Delta, please visit www.delta-emea.com/en-GB/landing/sps-parma-2024
Click here to read the full article >
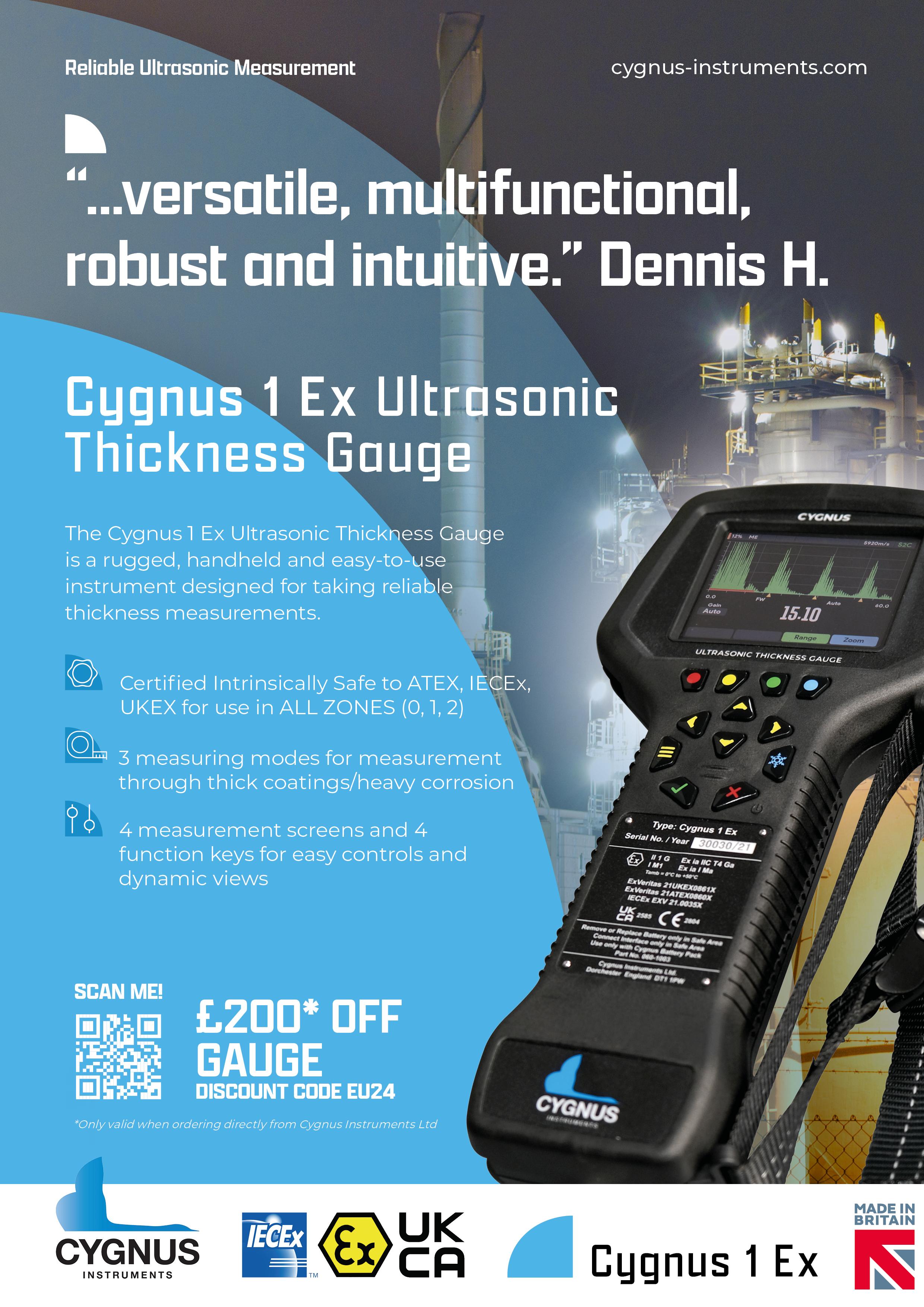
Vision Engineering celebrates 30 years of Mantis
Vision Engineering, the world-leading provider of innovative inspection, metrology, and digital 3D visualisation solutions, is celebrating the 30th anniversary of its best-selling and award-winning Mantis range of ergonomic optical stereo microscopes.
In 1994, Vision Engineering revolutionised the field of microscopy by introducing the first-ever ‘eyepiece- less’ stereo microscope, Mantis. This innovative instrument was meticulously crafted to bridge the gap between a bench magnifier and a traditional microscope, offering users an unparalleled ergonomic experience.
Its pioneering design not only earned Mantis widespread acclaim but also secured numerous industry-recognised design and innovation awards. As a result, Mantis quickly established itself as the industry standard for high-performance ergonomic stereo magnification, redefining precision and user comfort in industrial microscopy applications within the electronics, medical device, aerospace and automotive industries.

In 2005, Vision Engineering unveiled the second generation of Mantis. Soon after its introduction, Mantis manufacturing moved from Woking to a new manufacturing facility in Connecticut, USA. This iteration featured notable enhancements, such as a sleek and modern design, improved LED lighting, an expanded field of view, increased magnification capabilities of up
to 20x, and stand and accessory options. In 2009, Vision Engineering expanded the Mantis range by introducing the Mantis Elite HD Cam with a built-in camera for image capture.
The third generation Mantis was introduced in June 2023. The newest edition includes improved optics for both hand-to-eye coordination and excellent depth perception, a 3-position turret to house up to 3 objectives ranging from 3x to 15x, an 8x super long working distance lens, and five different illumination options providing flexibility to optimise the lighting to view the perfect image. The Mantis PIXO offers an improved, higher-resolution image and ‘designed-in’ integrated video camera. The system also features an option to switch between white and UV light.
Mantis is designed for precision engineering, electronic engineering, medical device manufacture, and a wide range of other applications that require high-quality images and superior ergonomics and is used in tens of thousands of R&D, manufacturing, and analytical sites worldwide.
For more information, please visit www.visioneng.com/mantis
Articulated Pipework Torsion In Hoses
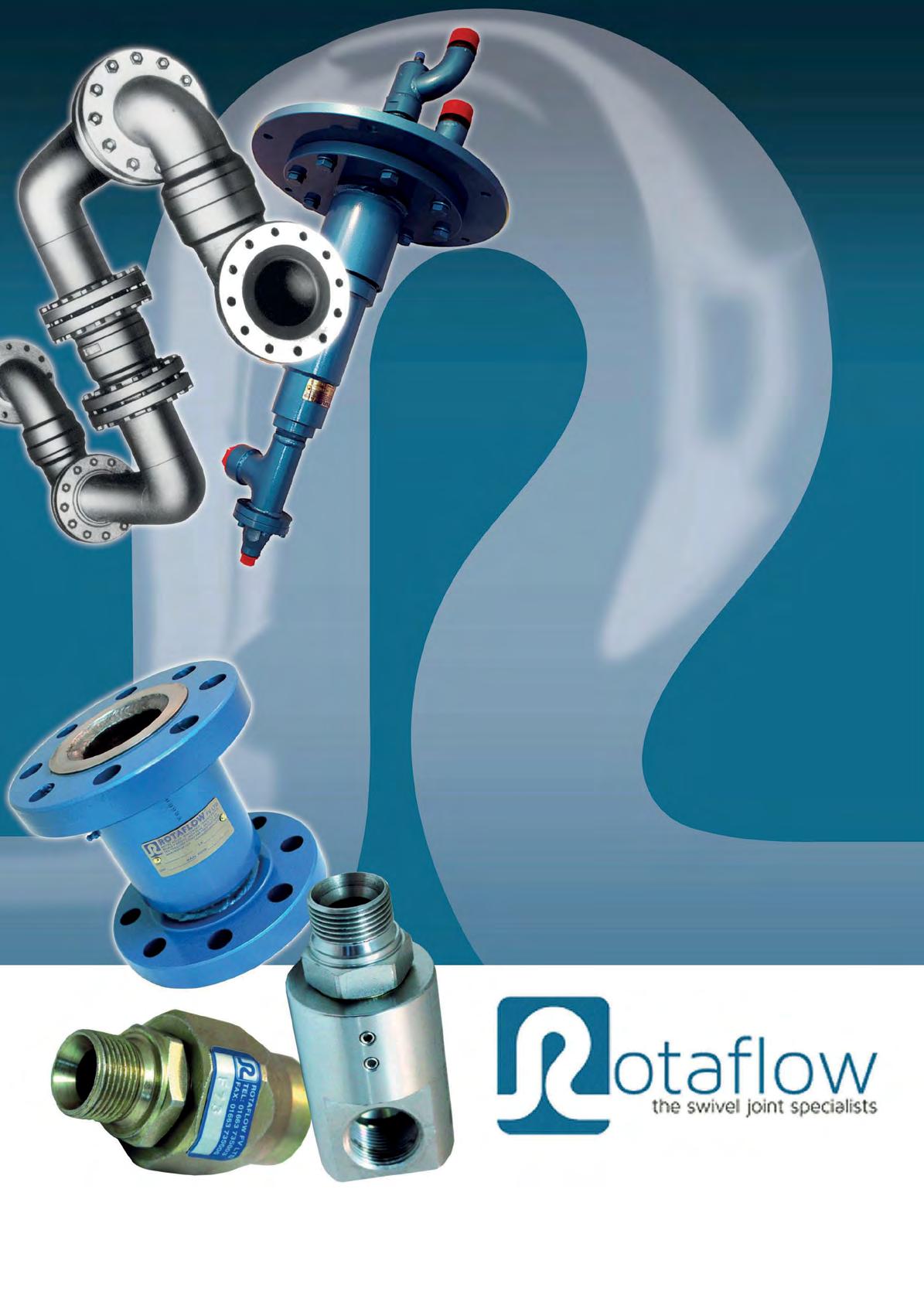
Rotating Cylinders
Fluid Carr ying Flexibility Swivel Joints
Swivel joints allow pipework to pressure 1/4” to 40” and beyond.
Vacuum to over 20,000psi.
Stock and bespoke production.
Unique bearing/seal design for longer life.
ISO 9001 CE marked where applicable.
Tel: +44(0)1663 735003
E-mail:
Positive Lock Terminals
Reliable and convenient connection
This week, we recommend to you Positive Lock terminals, including their compact versions. The showcased products are supplied by a well-known, specialist connector manufacturer TE Connectivity.
For decades, terminal connectors have been among the most popular ways of connecting wiring to electromechanical components such as relays, contactors, switches, programmers. They are also applied in power circuits and controllers, whether in domestic appliances (white goods, audio/video devices), computers, the automotive industry or even industrial machinery. Flat terminals are easy to plug in and remove, which facilitates the maintenance and servicing of equipment, especially when such work involves replacement of its parts.
In applications where terminal connections are exposed to shock and vibration, there is a risk of electrical connection disruption. In such cases, snap-on terminals are used, among which the Positive Lock series from TE Connectivity deserves a special mention. These models differ from the competing solutions at first glance. Beside their sturdy design, the locking mechanism fitted with a special depressor is their distinguishing feature. The mechanism has two purposes. First of all, it makes the connection firm and safe. When connected, the latch snaps into the opening in the male connector, establishing a secure link. The terminals do not require a great deal of force to connect, and disconnecting them is just as easy – provided that it is done when the depressor is deflected. In addition to easy mating, the locking mechanism features an audible and tactile click. Thanks to that, the installer can be sure that the electrical connection has been made correctly and will achieve the expected rated performance (in many devices, visual inspection of the connection is either difficult or downright impossible). The manufacturer has also ensured special housings for the Positive Lock terminals. Note that the housing does not affect the operation of the locking mechanism, and the depressor can be operated freely.

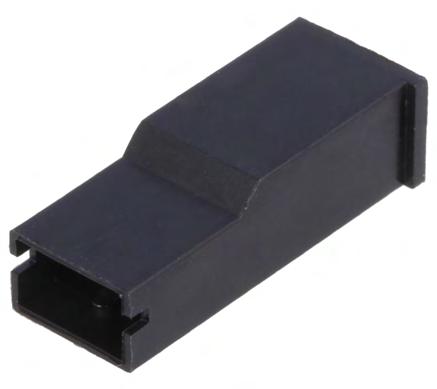
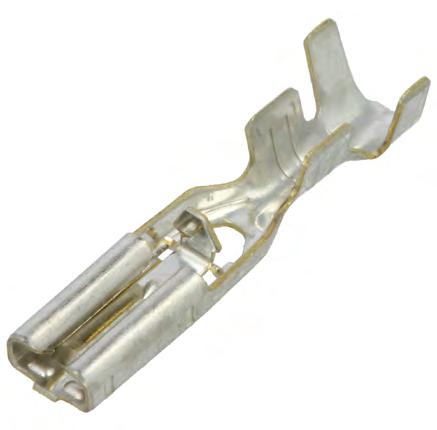
Terminals by TE Connectivity
The largest group of Positive Lock terminals are the 6.3 mm wide, 0.8 mm thick models. Finally, we would like to point out that the range of Positive Lock terminals in the TME catalogue has recently been expanded to include smaller, 2.8 mm wide terminals, as well as compatible housings. The latter feature an extended body with a grip which facilitates connections in hard-to-reach areas.
Positive Lock terminals 2.8 mm terminals
Type of terminal flat flat
Width 6.3 mm 2.8 mm
Thickness 0.8 mm 0.5 mm
Kind of terminal female female
Wire cross-section 0.5...6 mm2 * 0.5…1.5 mm2
Wire size 20...9 AWG * 20…16 AWG
Electrical mounting crimping crimping
Mechanical mounting wire-mount wire-mount
Ferrule variant uninsulated uninsulated
Contact plating tinned tinned
Contact material brass brass
Kind of packaging bulk bulk
Locking system latch latch
Manufacturer series Positive Lock Positive Lock * depending on the model
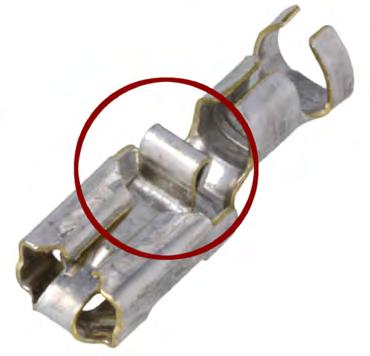
The illustration shows the depressor which releases the locking mechanism.

174779-1 2.8 mm Positive Lock housing
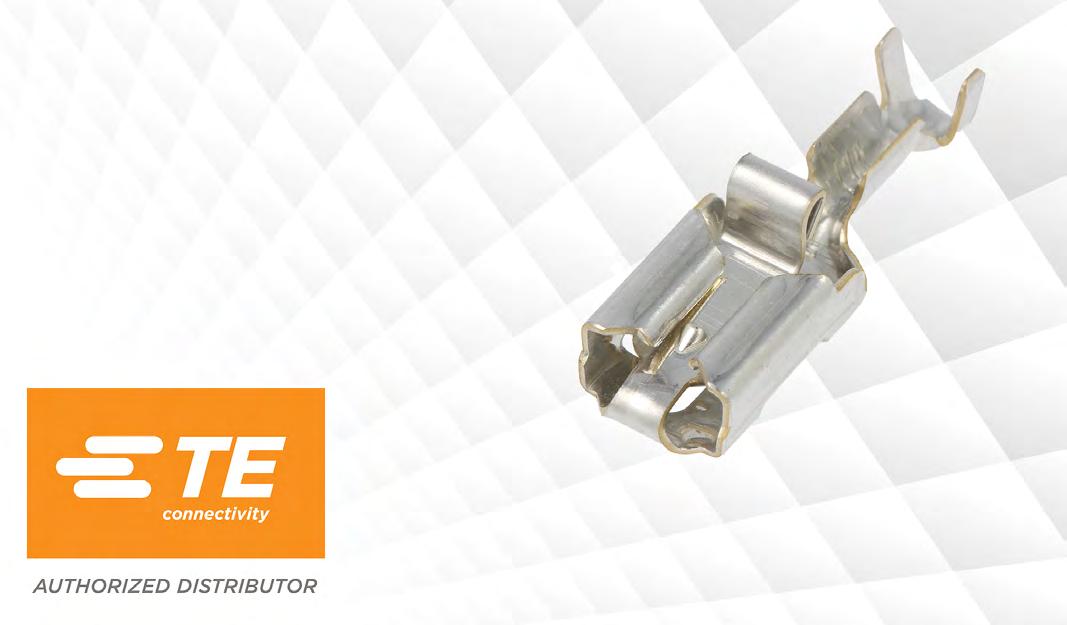
For more information, please click here
ODU Connectors - More Power, more Power!!!
With electrification on the rise, high-current and high-voltage are now fundamental requirements.
As electrification has increased, many existing connectors have been found wanting, creating a demand for connectors with larger contacts in order to transmit higher currents and higher voltages. Often these larger contacts have necessitated larger housings, creating a further problem.
This is why development of the ODU-MAC® Power Connector began around two years ago. Initial concept drawings were discussed with potential customers, product development began – from prototype to series production. Multiple test series were successful. Positive feedback is being received from the field.
Until now, this latest product concept has been listed on our website under the heading “Products you dream of” for specific applications.
Now the ODU-MAC® Power Connector has become a dream come true among modular connectors.
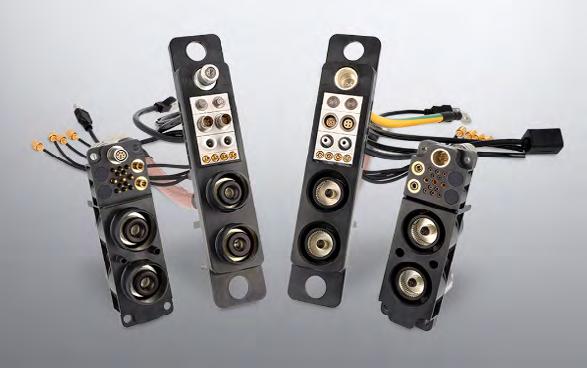
What makes the ODU-MAC® Power Connector so special?
• The ODU-MAC® Power Connector connects high-voltage and high-current transmission with up to 600 A per connector, with two bridged contacts using a busbar.
• The IP2X touch protection ensures increased safety for users.
• Thanks to the ODU LAMTAC® Flex contacts, low mating and de-mating forces can be achieved.
• This modular design – ideal for testing, with possible applications including eMobility, end-of-line testing and high-voltage testing.
• Depending on requirements, the docking connector can contain two or three power contacts combined with inserts from the ODU-MAC® D216 and D316 modular series.
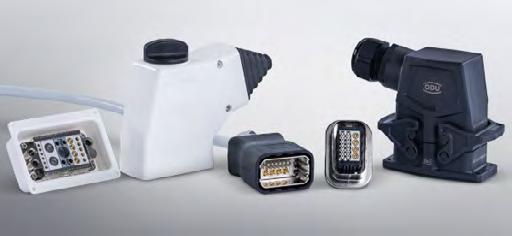
Customised Connectors
A customized connector for manual mating or automatic docking can also be created by combining these ODU-MAC® Power Connectors within housings from the ODU-MAC® BlueLine range.
Several locking options are available for manual mating via lever, transverse, spindle, push-pull. Easy handling with 10,000 mating cycles minimum.
The compact hybrid block ODU-MAC® Power Connector HB16 can also be integrated into enclosures thanks to its even smaller design.
More info at: https://odu-connectors.com/uk/products/ modular-connectors/odu-mac-blue-line/
The ODU Group is one of the world’s leading suppliers of connector systems, retaining all relevant areas of expertise and key technologies in-house, including cable assembly.
ODU connectors ensure a reliable transmission of power, signals, data and media for a variety of demanding applications including medical technology, military and security, automotive, industrial electronics, and test and measurement.
ODU-UK Ltd
tel: 0330 002 0640
email: sales@odu-uk.co.uk
web: www.odu-connectors.com/uk
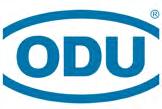

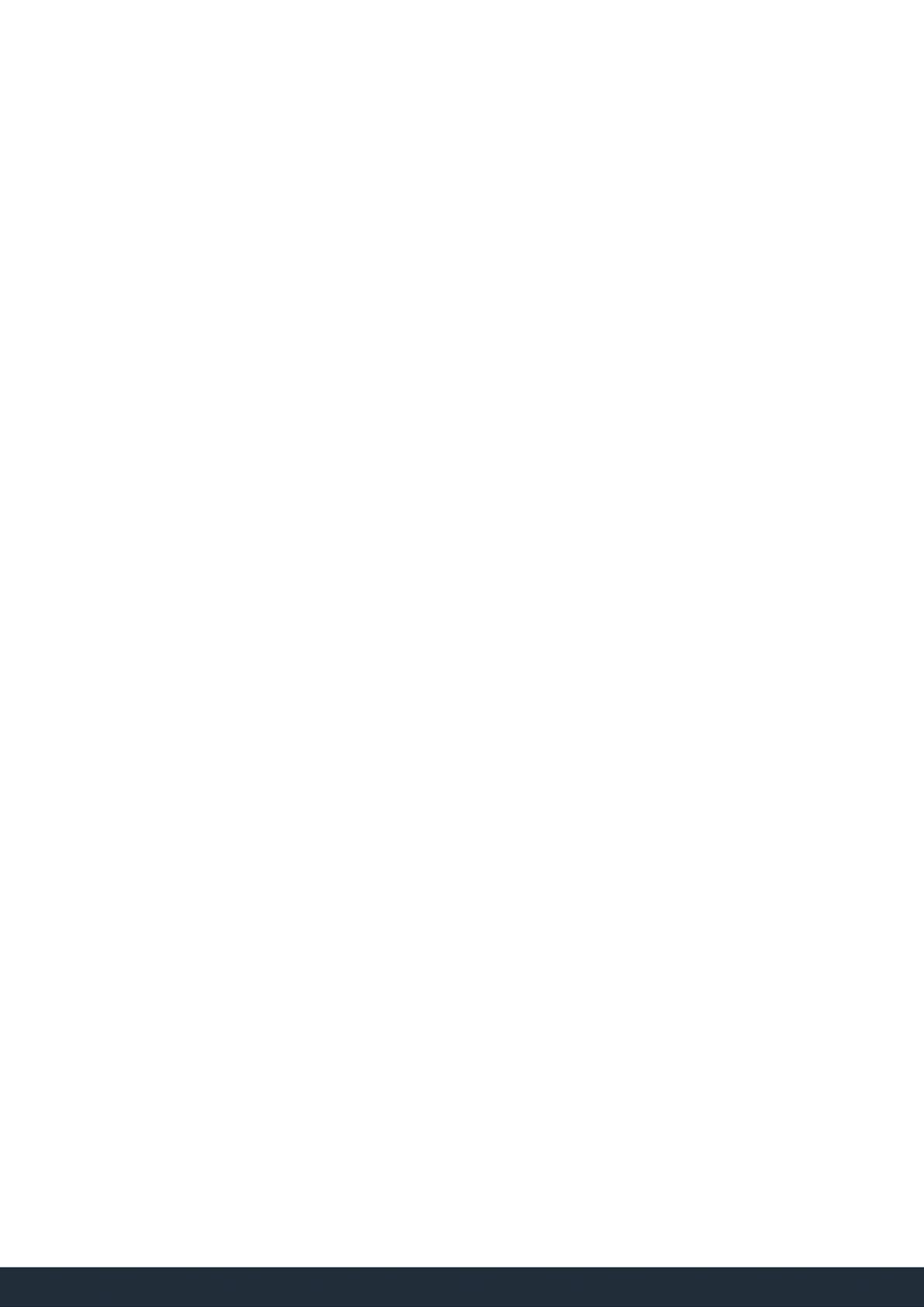
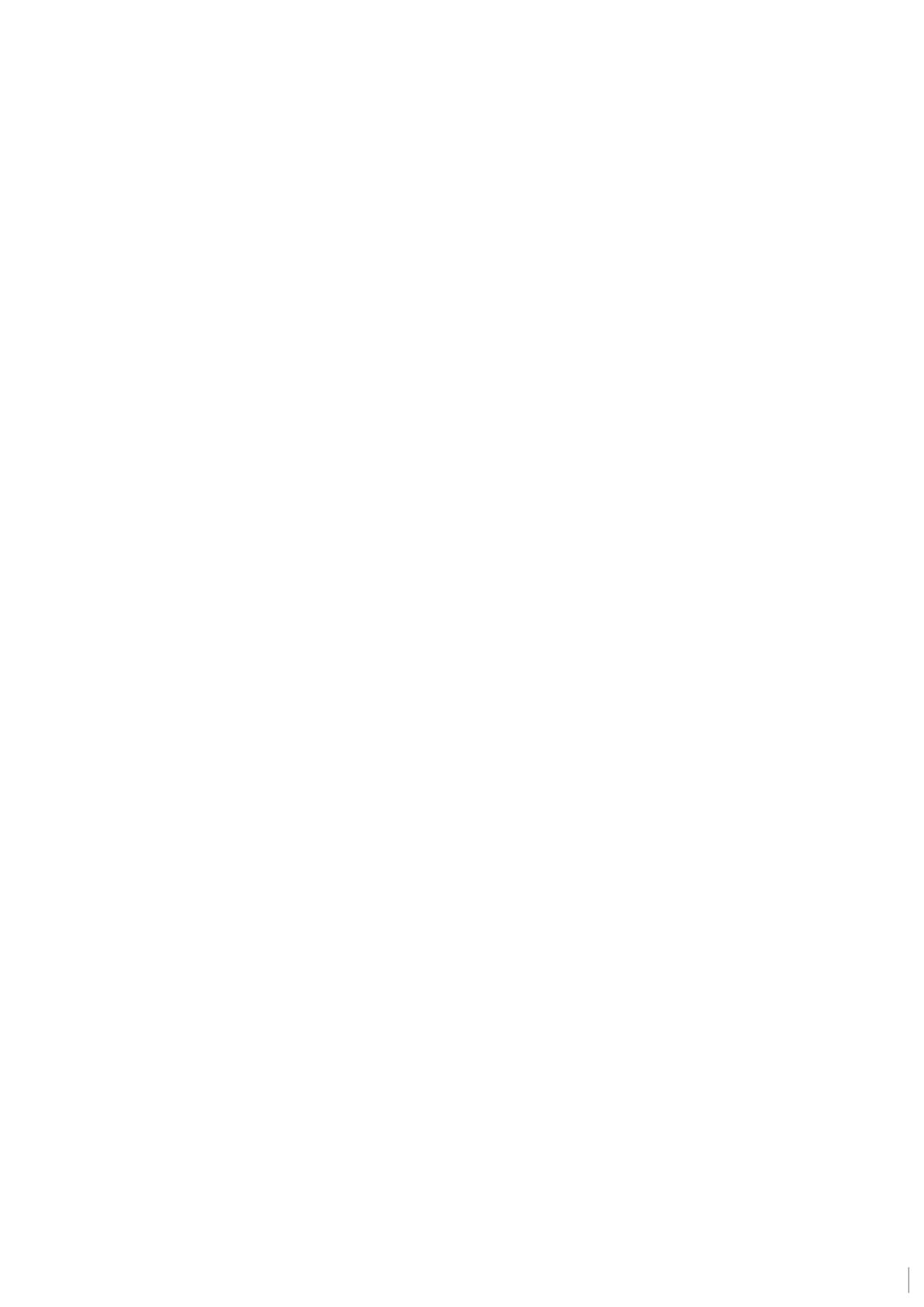
Titan Enterprises’ Ultrasonic Flow Meter Performs “Great” in Microgravity
Titan Enterprises’ flowmeters have been put through the wringer in various harsh environments, from high speed on an F1 racetrack, to deep mining and offshore oil rigs. Titan’s Process Atrato® ultrasonic flow meter is now taking a leap forward and proving to be ‘rock solid’ in tests within a totally unique environment - microgravity.
Multiple space agencies and private space companies around the world, such as Blue Origin, Nasa, Virgin Galactic, and SpaceX, continually explore new technologies and ways to solve specific issues encountered in ultra microgravity situations. NASA, for example, has conducted a number of laboratory experiments on the orbiting International Space Station to explore the effects of microgravity on water and other liquids.
The investigation of fluid flow processes in low gravity or microgravity environs is hugely important, helping to improve processes essential in the production of plastics and other polymers, to manufacturing medicines and operating machines. In space, liquids behave very differently than on Earth, with processes that are usually masked by the Earth’s gravity becoming much more evident. For example, in microgravity, liquids held together by surface tension can achieve sizes much larger than liquids on the ground. Also, when these liquids move, the motions are much slower in microgravity than on the ground.
With no moving parts, Titan’s Process Atrato® ultrasonic flowmeter offers benefits including high reliability, fast response, high-speed batching and precise liquid dispensing, such as in potable water dispensers. Even with restraints on orientation to avoid trapped gas bubbles, the Atrato® sensor’s low-flow capability and through bore design, are showing good results in fluid dispensing tests in microgravity environments for the potential of delivering water to astronauts in space.
Trevor Forster, Managing Director of Titan Enterprises, said: “Our company philosophy has always been about pushing boundaries – of our ideas, materials and technology – so knowing that our pioneering Atrato® ultrasonic flowmeter is being trialled in microgravity and tested to its limits, is incredibly exciting for us.”
To discuss an optimised flow measurement device for your specific application or process please contact Titan Enterprises on +44 (0)1935 812790 or email sales@flowmeters.co.uk. Or visit our website for further information.
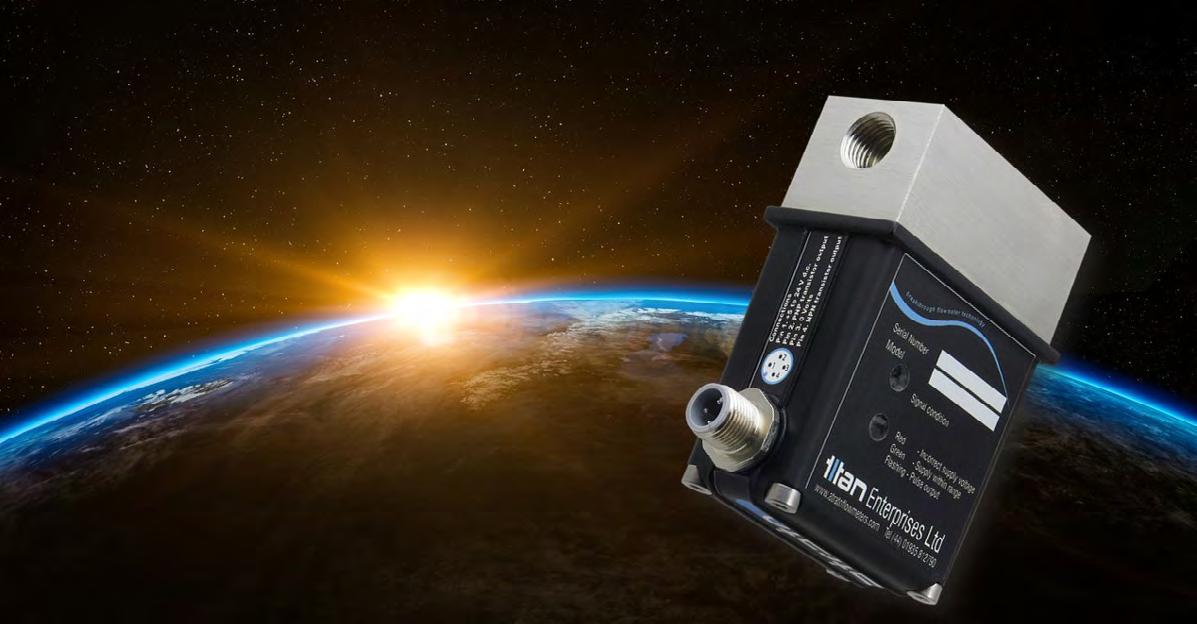
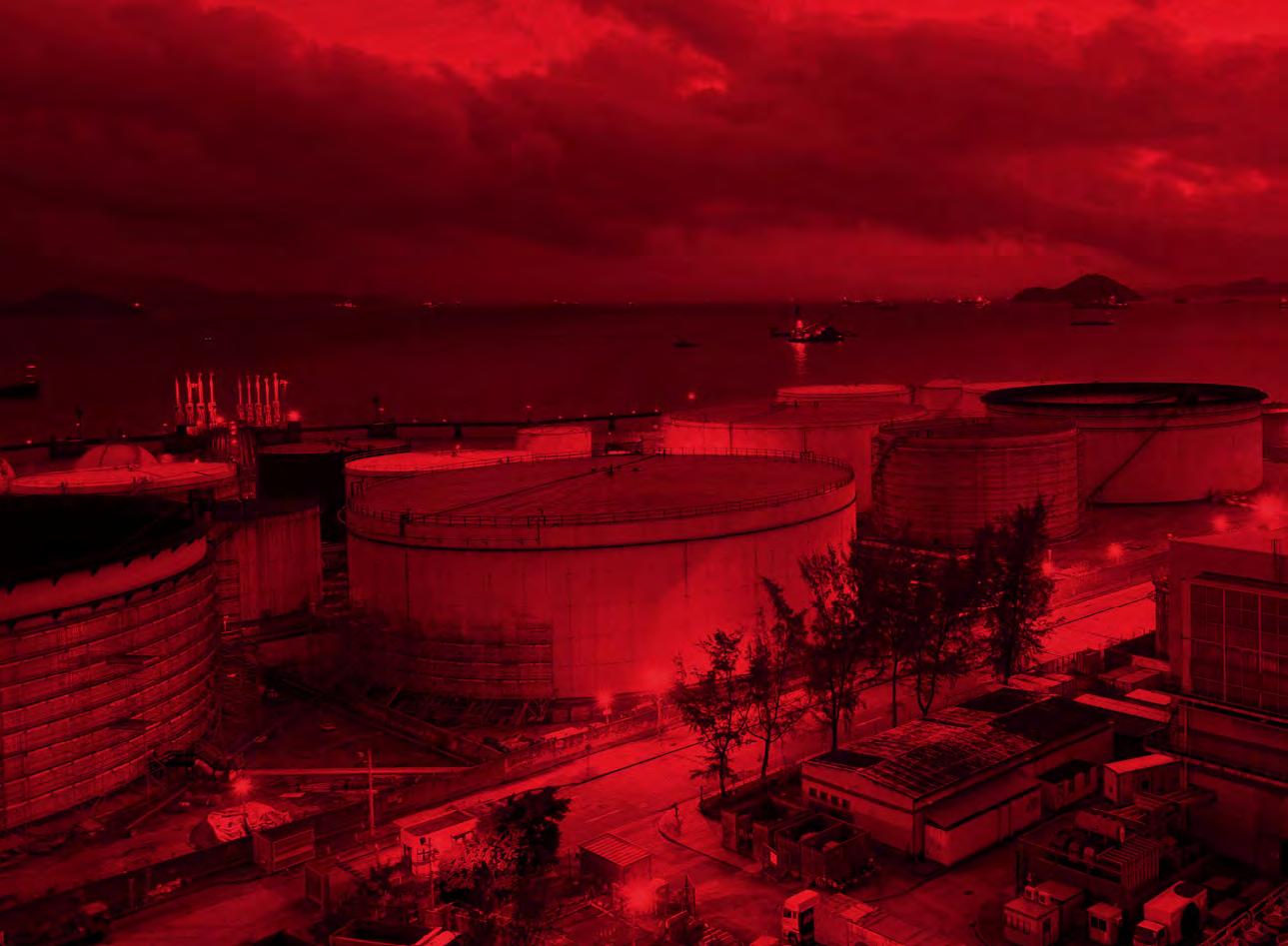
Specialist Training for the Storage Tank Industry Live online
, classroom, blended, e-learning or
in-house

• Gain or renew your 5-year Certificates of Competence*
• Courses based on EEMUA 159
• English, Dutch, German and French language options
• Select from courses throughout year, including:
TankAssessor courses*
9-12 September 2024 – in English
– classroom – Manchester, UK
30 September - 3 October 2024
– in French – classroom – Lyon, FR
14-17 October 2024 – in Dutch – classroom – Rotterdam, NL
4-7 November 2024 – in German
– live online
TankBasics courses
16 September - 25 October 2024
– in English – blended learning (live online, e-learning, and more)
Also...
TankInspector courses*
16-18 September 2024 – in French
– classroom – Paris, FR
16-18 September 2024 – in English
– live online – Houston time
23-25 September 2024 – in Dutch – classroom – Rotterdam, NL
28-30 October 2024 – in English – classroom – London, UK
Storage Tanks e-learning
On-demand – in English or Dutch
In-house courses
By arrangement for your choice of: time, language, location
EEMUA Seminar – Engineering the Energy Transition 6 June 2024 – London, UK
EEMUA Seminar – Storage Tanks
5 September 2024 – Birmingham, UK
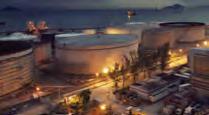
A guide to inspection, maintenance and repair Publication 159 Edition5
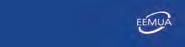
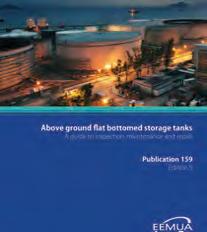
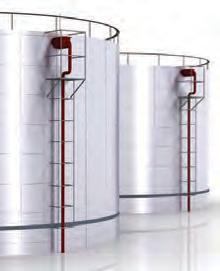
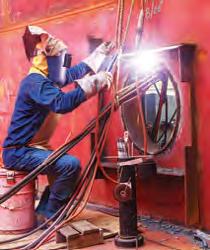
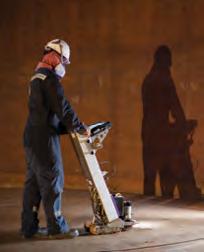
More choices, information and registration at www.eemua.org and events@eemua.org
of radio frequency identification (RFID)-equipped static fuel tanks and hand pumps, combining to complete the FuelServe solution. The self-service system eliminates the need to leave a jobsite to refuel vehicles and plant.
The launch follows an overhaul of fuelling strategy in the wake of revised legislation and the switch from red to white diesel last year. The manufacturer of custom-built bowsers (tankers) is already installing FuelServe units; each FuelServe unit pumps 80 litres per minute and has an automatic safety shut-off nozzle as standard.
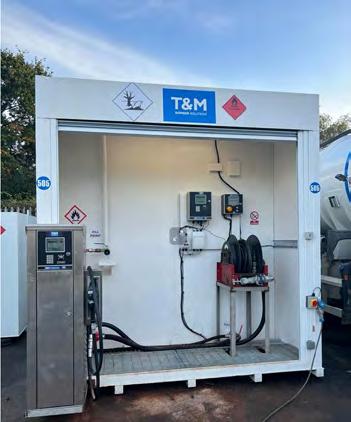
Terry Beasley, managing director at T&M, said: “The system prevents the principal contractor from having to send its trucks, vans, and pick-ups to the local petrol station. Where is the nearest station when you’re working on a stretch of the M25, for example? The disruption to site productivity in these situations is significant.
“We’re providing the entire product to all our customers who take up fuel solutions with plant hire, whether they use our bowers, fuel, or both. There is nothing like this available to construction sites; it can be fitted to any size of static tank. Feedback to date has been incredibly positive.” Click here to read the full article >
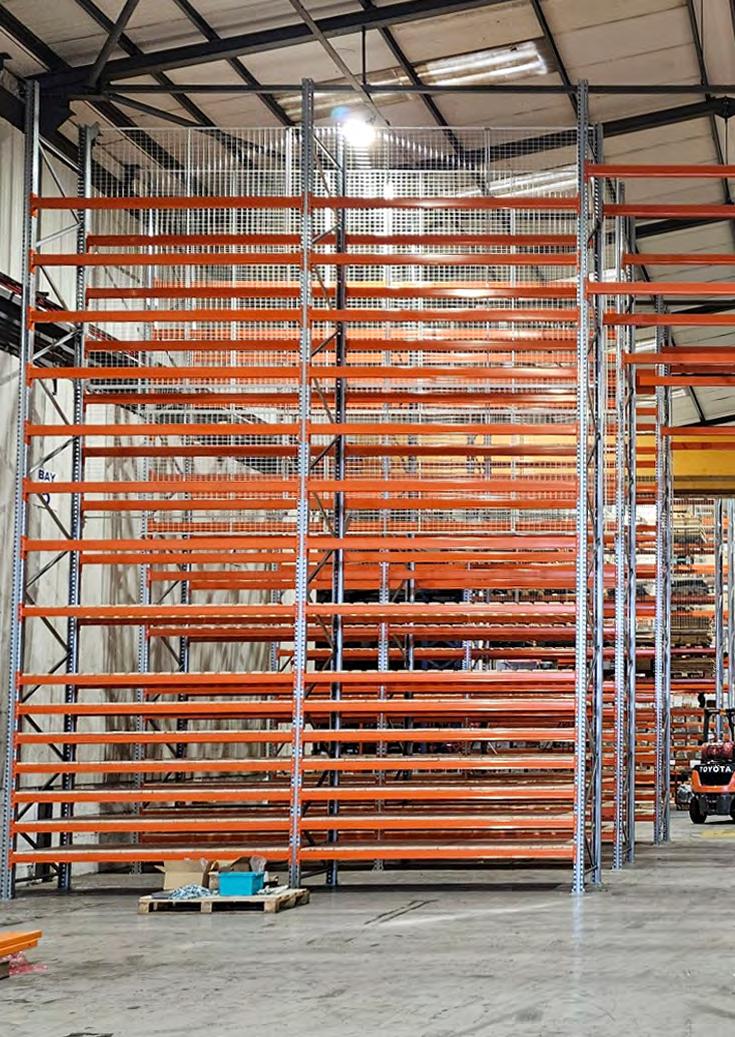
NERO DOUBLES ITS OPERATIONS TO MEET CUSTOMER DEMAND
Nero, a leading stockholder of stainless steel pipes, fittings, valves and flanges, has expanded its operations to meet a growing demand for its products.
Following over £250,000 of investment, the company has doubled the size of its West-Midlands warehouse.
Spanning 40,000 sq ft, the facility enables Nero to stock new products, including stainless steel push-in fittings and instrumentation fittings. It also has capacity to stock a larger range of pipe sizes, which are now available from ½ inch through to 16 inches along with suitable butt weld fittings and flanges.
An adjoining unit has been refurbished and remodelled to increase the space. The expanded warehouse features high level racking, a new overhead crane to handle larger product loads, and a saw providing a pipe cutting service.
Speaking about expansion, Darryl Spencer-Hicks, Nero’s Operations Director, said: “As a business, we have experienced year-on-year growth for a decade. In response, we have introduced a raft of new products to meet our customers’ needs, so the time was right to increase our stockholding capacity.
“A lot of this growth has been driven by the chemical industry which requires larger bore pipes and fittings to move higher volumes of fluid. Sales of push-in fittings are also rising as these are used in the air pneumatics of machinery, including control panels for mixing chemicals and fluids.
“As Nero continues to expand, so will our products to ensure we keep up with the pace of customer demand.”
For more information, visit: www.nero.co.uk
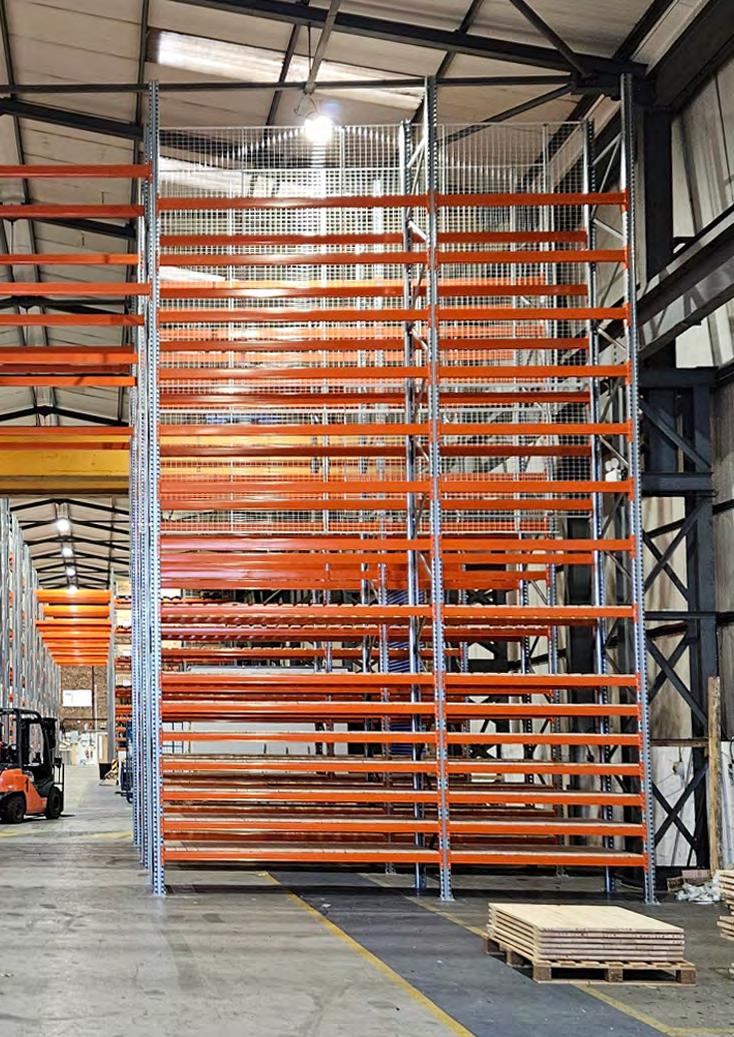
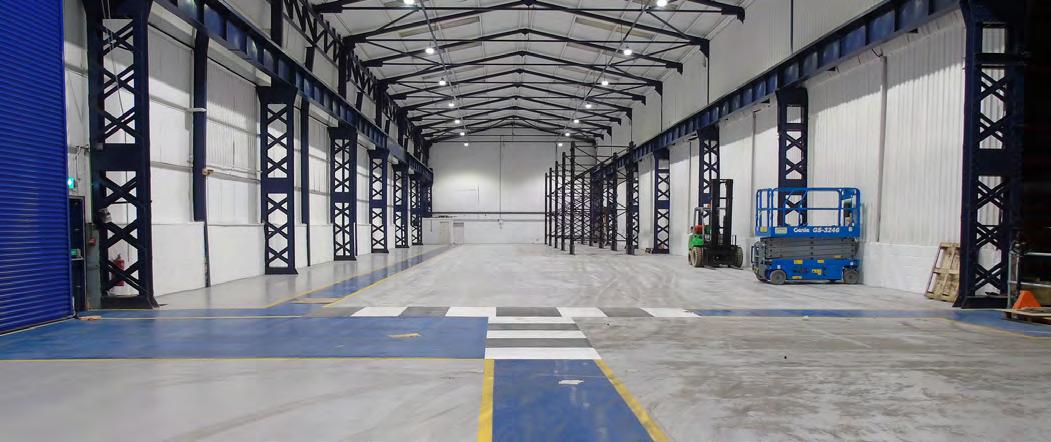


How to Transition to a Successful Nearshoring Operation for Fastener Acquisition
Making the strategic decision to transition to a nearshoring operation can bring about transformative benefits in how you acquire fasteners.
That is why Optimas customers are excited to discuss the cold form manufacturing facility we plan to open in Monterrey, Mexico in 2024. Last year, Mexico overtook China as the United States’ largest goods exporter base on recent trade figures, and we are excited to be giving our customers a competitive edge by getting their fasteners produced locally in the second half of 2024.
However, the process requires careful planning, evaluation and execution to ensure a seamless transition that maximizes the advantages of geographical proximity, cultural compatibility and costeffectiveness.
Here’s a valuable guide we use to help customers navigate the shift to a nearshoring operation.
1. Assess Current Operations:
Before making the shift, conduct a thorough assessment of your current operations. Identify pain points,
challenges, and opportunities that could be addressed through nearshoring. This evaluation will help you understand the specific areas where nearshoring can bring the most value.
2. Define Objectives:
Clearly define your objectives for nearshoring. Are you aiming to reduce lead times, improve collaboration, or cut costs? Defining your goals will guide your decisionmaking process and help you measure the success of the transition.
3. Research Potential Nearshore Locations:
Research potential nearshore locations that align with your objectives. Consider factors such as political stability, infrastructure, skilled labor availability, and legal regulations. Choose a location that offers the right balance of advantages for your business.

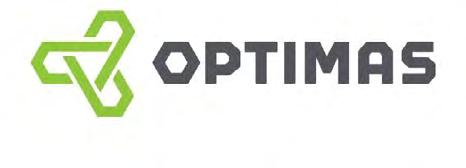
• ‘By Industry, For Industry’, practical guidance for everyday and irregular situations and tasks
• Readily accessible for all in the industry –wherever they are, whatever time they have
• FREE task and procedure checklists



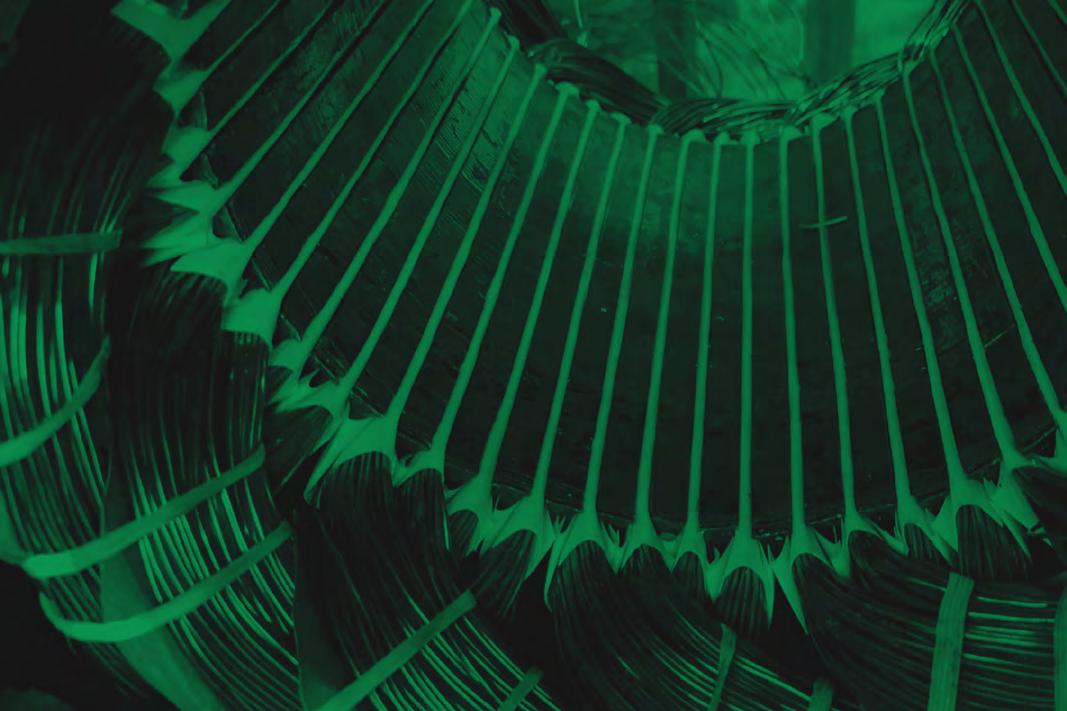
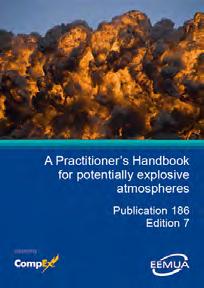
• professional development
• Webinars and seminars for knowledge sharing
• This selection of specialist publications and many
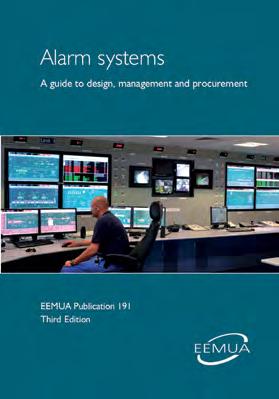
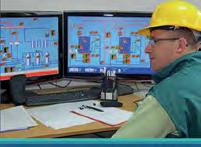
Also... EEMUA Seminar – Engineering Energy Transition – London, UK – 6 June 2024
To make EEMUA’s guidance, training, events and other practical resources work best for you and your team
– ask@eemua.org or visit www.eemua.org
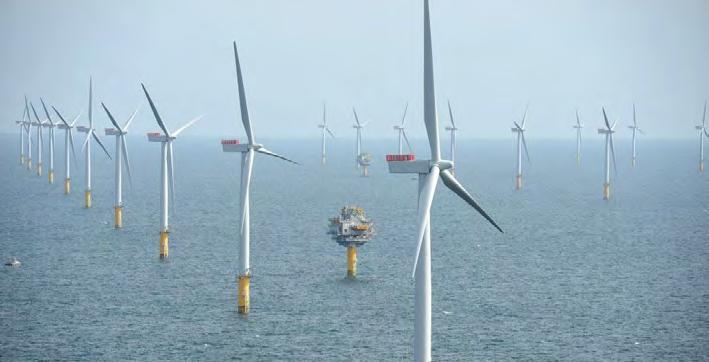
Drainage engineers from Lanes Group plc have carried out high pressure water jetting to clean tanks at an electricity sub-station for a giant off-shore wind farm in the North Sea.
The tanks have been installed to collect and store surface water run off at the sub-station near Wisbech, in Cambridgeshire, which serves the Race Bank wind farm 17 miles off the coast of Norfolk.
When fully-operational, the 573 Mega-Watt wind farm,

Water jetting power cleans tanks at wind turbine site
owned by Danish utility company Orsted, will have 91 turbines and capacity to generate electricity for 400,000 homes.
Engineering and construction firm J Murphy & Sons, which built the sub-station, commissioned Lanes to clean the newly-installed water tanks which form part of the site’s drainage management system.
www.lanesfordrains.co.uk
Protection & life extension of your critical components throughout any crisis!
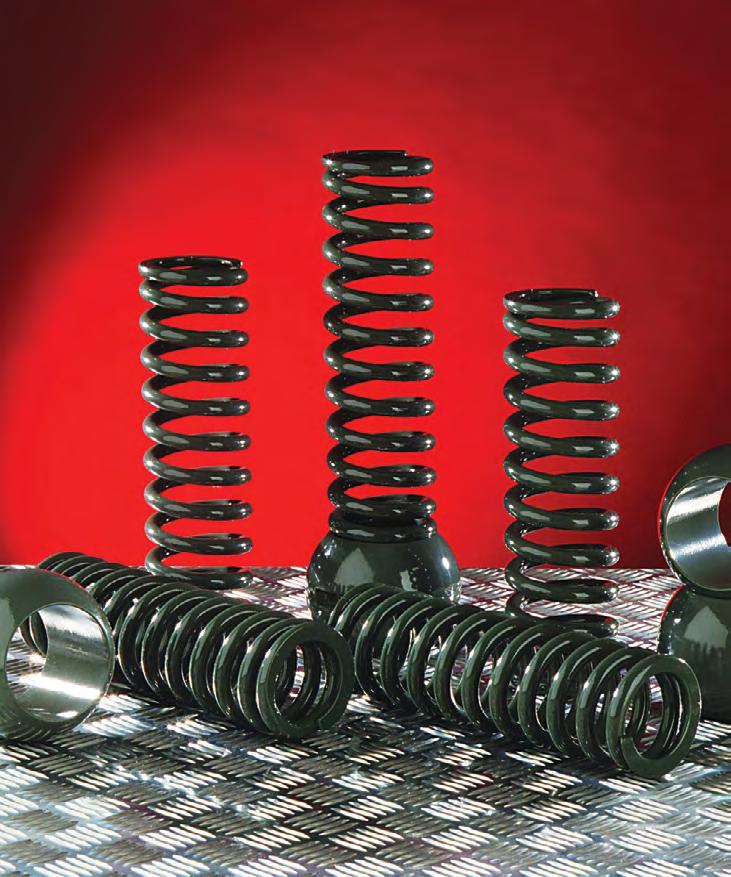
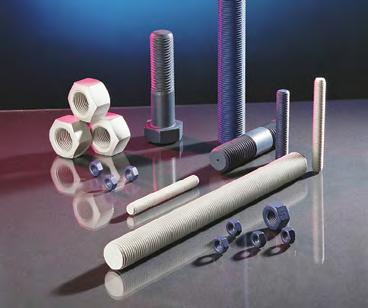
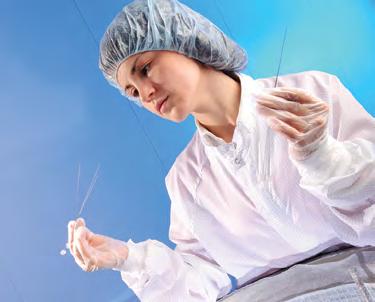
COATING SERVICES:
l Thermal Spray & HVOF Coatings
l Dry film lubricants - MoS2, PTFE, Graphite, WS2
l Coatings for corrosion, chemical & environmental protection
l Titanium anodising
l Zinc rich coatings for corrosion protection
l Impingment coating processes for ultra thin solid film lubricants
l Nonstick/release coatings for low coefficients of friction
l Primers for rubber and plastics for sound absorbing and dampening materials
l High temperature resistant coatings
l Rare earth magnet coatings
l Coatings for EMI/RFI shielding provide highly conductive coatings and platings to control electromagnetic interference
l Ultra thin conformal parylene coating to reduce friction and protect against contamination
l Pre-treatments including Ti Anodising, Phosphate Conversion Coating and Chilled Iron Blasting, Aluminum Oxide Blasting and Vapour Degreasing
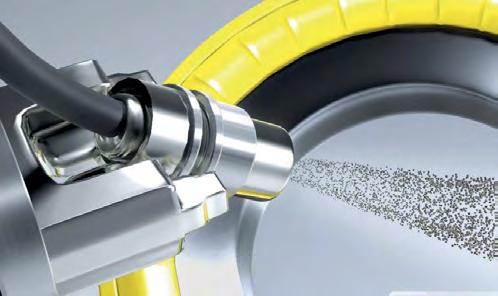
Popular Nor Ray Vac heat system relaunched with efficiencies to cut costs and eco impact
A heating system has been relaunched by leading manufacturer Reznor UK to give users greater control to boost efficiency levels and reduce running costs.
The Nor Ray Vac system, a gas fired continuous radiant tube heating system, has modulating burners for improved efficiency and control, provides better uniformed heat coverage thanks to its continuous radiant tube, with a filtered burner air inlet helping keep the burner head and components clean.
Boasting an aesthetically pleasing, bespoke appearance it can be tailored to suit building shape and size, while its NR40 rating means noise levels are lower than other systems on the market.
Offering a larger rated burner than before, it has more burners per fan which means less flue points. With a long continuous tube which can reach 84m, the Nor Ray Vac system can be used in rail sheds and aircraft hangars or other large open spaces.
Richard Leese, European General Manager at Reznor UK, said: “Reznor UK has always been committed to providing premium heating solutions combining comfort, efficiency, and reliability, so with the relaunch of the Nor Ray Vac system, we are taking these principles to new heights.
“Installation is quicker, it is easier to maintain and it is easier on the eye, all while maintaining the functionalities that make Nor Ray Vac an industry name.
“The Nor Ray Vac has been popular so when we put production on hold in 2022 we took the opportunity to simplify the system to manufacturer, ensuring we kept to its original great design.
“We are looking forward to building upon the system’s heritage by engaging with consultants, end consumers and contractors to demonstrate how the Nor Ray Vac system is tailored for both small and large buildings.”
The Nor Ray Vac System have been used in a range of premises including aircraft hangars, garages and showrooms, greenhouses, museums, factories, warehouses, distribution centres, sports halls and large retail outlets.
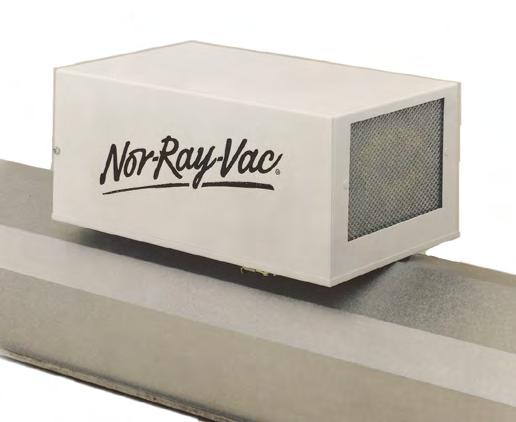
Its reliability and safety of operation meets the latest European standard for multi-burner systems.
Reznor UK is a trusted supplier of efficient industrial and commercial HVAC solutions, specialising in warm air heating, radiant heating, air curtains and more.
It is part of the most trusted worldwide HVAC manufacturer group, Nortek Global HVAC.
Operating for more than 100 years, Nortek works to a commitment to excellence and industry-leading innovations has set us apart.
Get in touch for more information, visit www.reznor.co.uk/nor-ray-vac/ or call 01384 489700
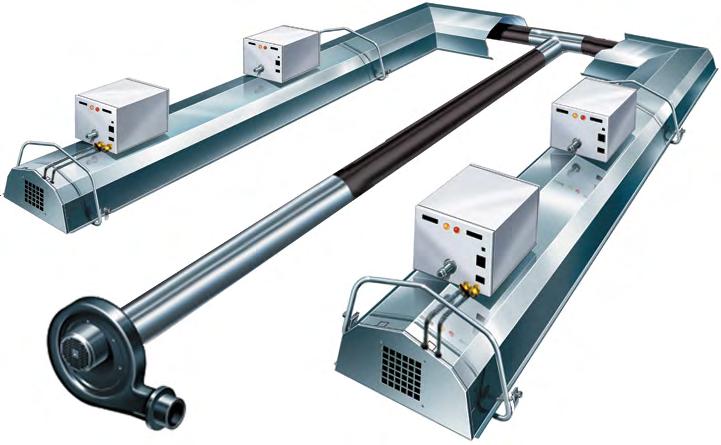
Staying power: wear protection solutions in Energy from Waste plants
Changing attitudes and regulations are making efficient, long-lasting operation more important than ever for Energy from Waste plants (EfW). Martin Trenk, Head engineer for Boiler coatings and EfW applications at Castolin Eutectic, explains.
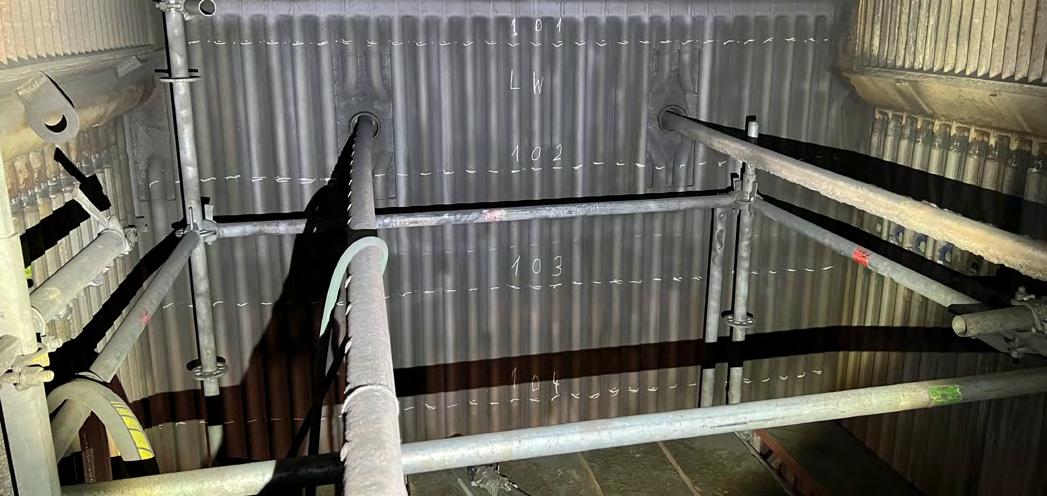
To fulfil the role of baseload in the power generation mix, thermal power plants must prioritise consistent power output. Maintaining consistent operation and output is a particular challenge for EfW plants, whose fuel –municipal waste – does not necessarily always yield the same amount of energy per tonne. The last thing an EfW plant operator wants, while closely monitoring and finely calibrating the boiler temperature and turbine speed, is an unplanned stoppage.
Yet many EfW plants do contend with frequent stoppages, both planned and unplanned, to replace worn parts or to mitigate emissions. With the European Union tightening its rules around burning municipal waste, EfW operators need to prove their plants can be efficient and play their assigned role in their nations’ power systems. It’s a question of industrial sustainability.
Which is why Castolin Eutectic has its own role to play in the EfW industry. Pioneering Industrial Sustainability is a long-held philosophy of Castolin Eutectic, one that has driven more than a century of innovation to improve the lifespan and efficiency of industrial parts – both outcomes with the potential to reduce the number of stoppages EfW plants need to endure.
Waste handling – unpredictable abrasion and wear
Most EfW plants burn mixed municipal waste that would otherwise be sent to landfill. The waste can include food, paper, textiles, wood and plastic – but also significantly more abrasive materials like metal, glass and electronic waste.
Because the different materials present can yield widely different amounts of energy, it is important to mix the waste well before incineration, to achieve a stable boiler temperature. All this naturally causes significant wear on the hoppers the waste is delivered into, the crusher rotors that mix and break it up, and the apparatus that conveys it to the incinerator (which may be a grabber or a screw, depending on the plant design).
Not only can the wear on these fuel handling parts be significant, but it is also often unpredictable, because the fuel loads are not uniformly abrasive. The composition of the waste being sent to EfW plants can vary considerably depending on the composition and habits of the feeder municipalities, and even on the season. However well mixed the waste is, some loads will contain more glass, metal and hard plastic, and some will contain less.
This has historically posed an economic conundrum for EfW plant builders, owners and operators. A plant’s waste handling systems ideally need to be hardwearing enough to stand up to significant abrasion – but may not need to be that hardwearing a hundred percent of the time.
If the plant handled only the most abrasive materials, the case for up-front investment in harder-wearing parts would be obvious: the plant would be unable to operate for long without them. But because not all of the fuel is significantly abrasive, and because not all plants are costed on a lifecycle basis, it can be tempting to gamble on less hardwearing parts. If the loads they handle happen to be mostly less abrasive, they might outlast their designed service life.
But it could also go the other way. And when it does, a planned stoppage in six months’ time can become an unplanned stoppage tomorrow, bringing with it all the challenges of quickly and safely shutting the incinerator and turbine, and later ramping back up to a stable boiler temperature.
A typical example of the difference that wear protection can make is on fuel crusher rotors that needed to be rewelded on a yearly basis because of high wear. In many cases the crusher casings are also affected by wear. An effective solution is refurbishment with SAFE-HARD 600 Chromium free welding wire applied to the rotor, while a composite material known as CastoDur Diamond Plate (CDP) is applied to the casing. The result is that the lifetime of the crusher is always increased, but the level depends on the type of waste. The improvement can range from 2 up to 10 times the life without wear protection.
The very abrasive fuel in waste to energy plants also creates wear issues for hydraulic garbage grabs. As the edges wear away, more waste falls back into the bunker. This leads to the need for more lifting movements and more energy and time required for fuel filling. The solution is to fit CDP wear plates on the inside of hydraulic garbage grab. The outcome is a 200% increase in lifetime.
Case study: Boiler coatings - ChromeClad
In March 2021, Castolin Eutectic perfomed a boiler coating job at a chemical plant in Germany, applying wear protection on 740 m² of boiler panels. More than one year later, in November 2022, the exposed surfaces were still visually flawless. The solution applied through Twin Wire ARC Spray was a coating called ChromeClad XC, a nickel-based coating providing superior resistance within extreme corrosive environments. The proprietary alloy top coat is applied over an extremely dense bond coat which literally seals the weak ferrous substrate and ensures excellent bonding. Subsequently, a ceramic layer called TubeArmor, is applied over this coating to densify it and prevent slag build-up. It is a non-porous, nonreactive shield that resists ash, oxidation, erosion, iron sulfide corrosion, sulfur and chlorine permeation and hazardous chemical byproducts. TubeArmor is applied on the prepared surface one coat at a time until the recommended thickness is achieved. Its green color is a perfect indicator that provides excellent contrast for drone inspections. As a result of TubeArmor’s high emissivity, significantly more heat can be absorbed in areas where it is needed than, for example, cleaned surfaces clad with Inconel.
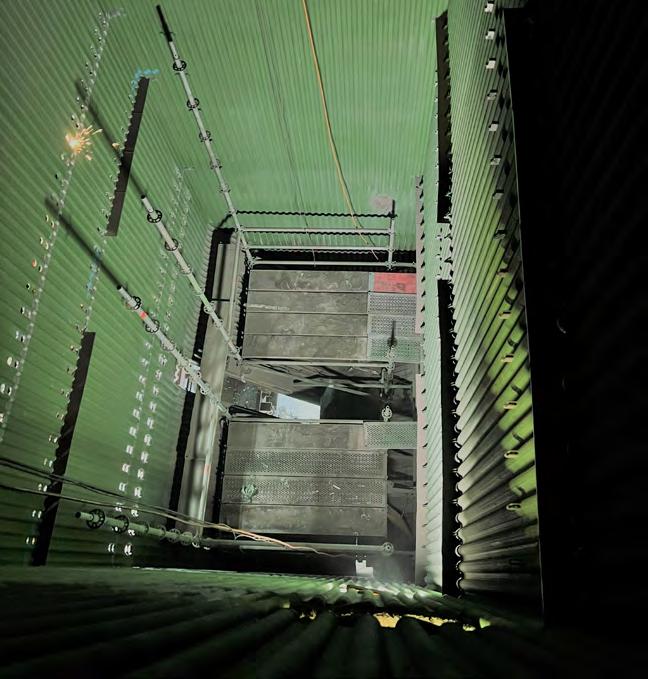
Ash handling – time to raise the industry standard?
Not all the waste delivered to EfW plants is combustible. Nonferrous metals and some other non-combustible materials form slag, which must be removed from the incinerator along with ash.
In most EfW plants, the chutes, chain conveyors and sieves of the ash handling system are manufactured from steel or manganese steel. Without protection from additional plating or specialist coatings,
these industry standard parts are vulnerable to high abrasion wear from the ash and non-combustibles in the slag. Manganese steel de-slagger chutes and slagsorting sieves usually need replacement after only a year in operation.
Why are EfW plants still being constructed as standard using parts that cannot stand up to the normal stresses of their operations? Using harder-wearing materials or adding wear-facing solutions for materials like manganese steel, would undoubtedly increase the upfront investment needed to construct an EfW plant –but the historical performance of these standard parts suggests strongly that these up-front costs would pay off over the life cycle of the plant.
One example of the possibility for improvement is found in the high level of wear on the gliding strips, the chain and depending on the construction also on the bars, which are made normally from standard or manganese steel. This is due to ash and non-combustibles in the slag. The solution is to use cut CDP plates for the strips and bars. The Chromium carbides and Borides content provides protection against abrasion and reduces friction and consequently wear of the chain. The result is that the lifetime for strips increases up to 10 times, for the bars up to 6 times.
Flue gas cleaning – the influence of attitudes and regulation
As well as the engineering challenges of incinerating unsorted municipal waste, EfW plants must deal with changing attitudes to waste among regulators, businesses and the public. These trends do not progress uniformly in all territories, so EfW operators in different parts of the world face different challenges. However, the direction of travel for the world as a whole is tending towards:
• reduced carbon dioxide and equivalent emissions
• a circular economy, featuring increased recycling and reuse, and so less waste being sent to landfill and EfW
One significant consequence of increasing enthusiasm for recycling and reuse is that people throw away less plastic. The caloric value of plastic is high relative to many of the other types of waste that EfW plants use as fuel. So, when people try to throw away less plastic, the overall caloric value of local EfW plants’ fuel starts to fall.
As established, it is vital for EfW plants to maintain a stable boiler temperature, and therefore a steady
turbine speed and energy output. With less energy available in the fuel being delivered, EfW plants must use bigger fuel loads to obtain the same energy output.
At the same time, operators must keep close watch on their plants’ emissions. The European Union regulates emissions from all thermal power plants and has specific rules about allowable emissions from incinerating municipal waste. For example, if the percentage of particulates emitting from an EfW plant’s flue exceeds the allowed limit, the plant must shut down to investigate and mitigate the cause.
To protect the environment and avoid these unplanned regulatory stoppages – which compound planned and unplanned stoppages to replace worn parts, further reducing a plant’s annual uptime – EfW plants incorporate flue gas cleaning systems, which combine filters, cooling and chemical processes to capture particulates and harmful gases from the incineration process before they can be emitted to the atmosphere.
Because their purpose is to process hot, acidic exhaust gases, these crucial systems are prone to various forms of corrosion, as well as erosion by fly ash carried in the flue gas. Wear and damage to the flue gas cleaning systems can reduce their effectiveness, potentially leading to regulatory stoppages on top of the stoppages needed to replace the damaged parts themselves. A key area for attention is the flue gas deflectors that get damaged by erosion due to fly ash particles in the flue gas at around 170˚ C within a year. Covering the deflectors with a laser cladded LC8 half pipe provides protection against erosion by the fly ash particles. When assessed after a year in operation no damage was found.
The priority for EfW – extending service life
It is more important than ever for EfW plants to operate as efficiently as possible.
Efficiency means extracting the maximum energy possible from each hopper of fuel, to compensate for its decreasing plastic content and caloric value.
And efficiency means operating at a stable boiler temperature, turbine speed and energy output for as much of the year as possible, with stoppages – planned or unplanned, for repairs, maintenance or regulatory reasons – kept to a minimum.
To achieve this, EfW plant operators must prioritise extending the service life of parts throughout their plants. Parts that last longer before wearing out will cut
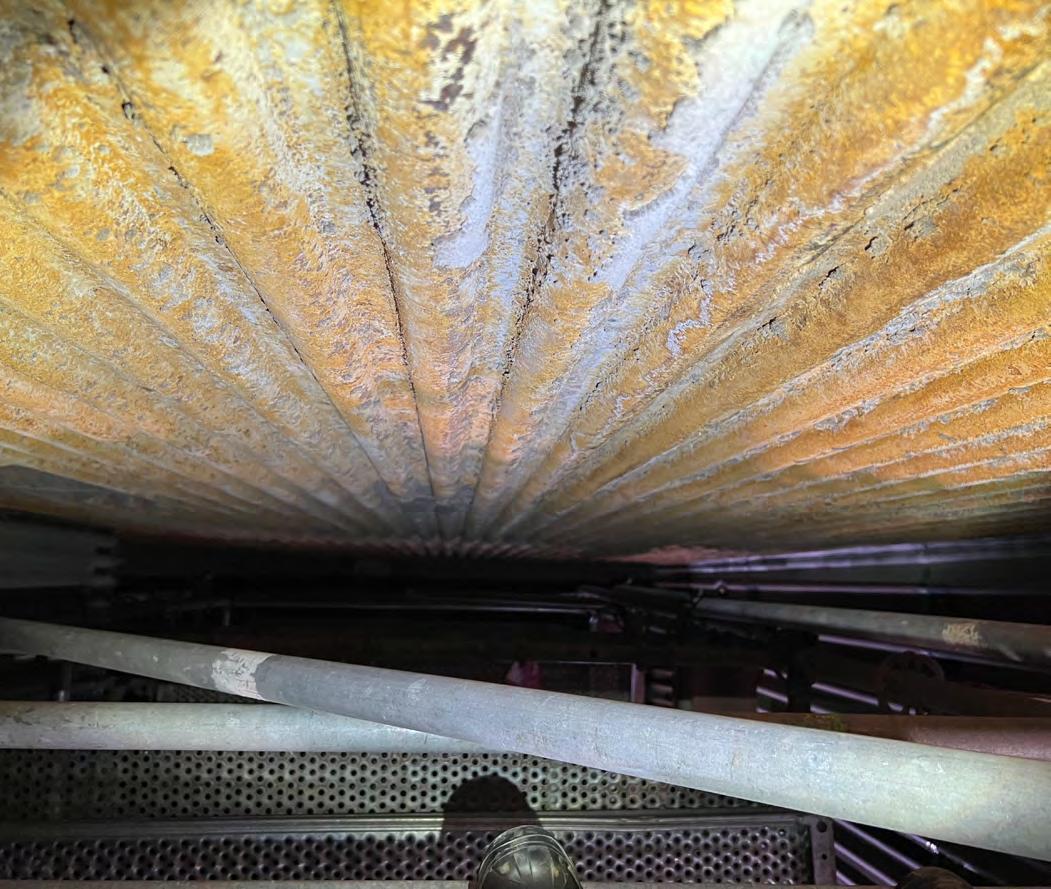
down on stoppages for maintenance and repairs. And parts that perform at peak for longer will maintain the efficiency of the plant’s systems, converting more waste to energy, cleaning up the flue gases more successfully, and reducing the chance of regulatory stoppage and damage to the environment.
Castolin Eutectic is determined to support the EfW industry in its mission to reduce landfill, make good use of waste and protect the environment. The company’s global network of technical advisors takes a whole life-cycle approach that maximises the efficiency of systems, the service life of parts, and long-term cost-effectiveness.
From fitting CDP strips and wear plates to waste handling apparatus, to arc-spraying waste incineration and flue gas cleaning system components with heatand corrosion-resistant coatings, Castolin Eutectic offers solutions for every element of a modern EfW plant. Case studies show that customers in this sector have seen the service life of waste grabbers
double, and fuel ducts and grate bars operate for eight years and counting with very low wear, after being enhanced with Castolin Eutectic wear-facing solutions.
Staying power
EfW plants already in operation need to make the most of upcoming scheduled maintenance periods to apply wear-facing solutions to extend the life of parts in service.
And for any new EfW plants currently in the planning stages – now is the time to rethink the accepted industry standards, in light of the real-life experiences of existing plants, and build these systems to last.
Training to prevent loss of hazardous substances…
From day one, Learners on the EEMUA MIPC® training build a unique workbook of mechanical integrity know how tailored to each Learner, site and company. Combining live online classes, e-learning, and one-to-one sessions with expert Tutors, enhanced by Mentor support and guidance throughout, EEMUA's Mechanical Integrity Practitioner Certificate course gives professionals the flexibility to learn on-site or on-call.
Developed and verified by industry to satisfy industrial engineering’s requirements for primary containment in old and new equipment – including pressure systems.
K Keeps practitioner-level engineers on top of industry developments and good practice – so that valuable practitioners are most effective wherever they’re needed on-site.
E Enterprise-class, blended, live online system for productive learning – on-site or on-call.
A Adapts to the engineering needs of each Learner and their company via an Induction of 2 hours prior to the course – to fit work schedules from September 2024
I In-depth training to fit work schedules – 4 hours per week for 27 weeks.
Registration open now. Learning starts 21October 2024.
For more information please contact online-learning@eemua.org
+44 (0)20 7488 0801 www.eemua.org
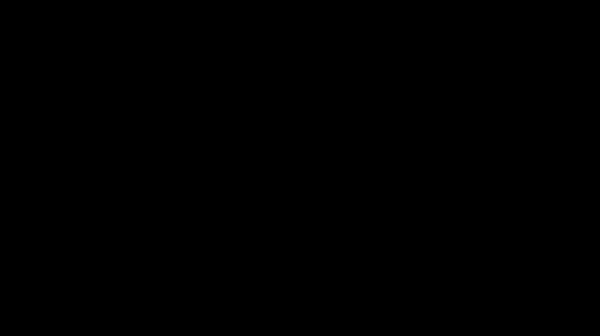


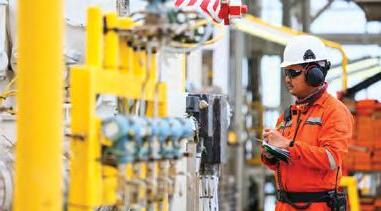
C CPD-approved with industry recognised 5-year certification via robust exam.
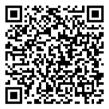
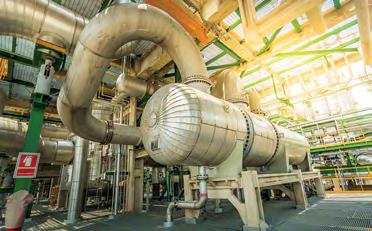
Smart-Ex® 03 – the new intrinsically safe 5G smartphone from Pepperl+Fuchs for future-oriented digitalization of hazardous areas
Pepperl+Fuchs presents the intrinsically safe Smart-Ex® 03, a new and future-proof 5G- and Wi-Fi 6-enabled smartphone that was developed entirely in-house in Europe. The 6-inch device combines all the expertise and know-how of Pepperl+Fuchs subsidiaries ECOM Instruments as a pioneer in intrinsically safe mobile devices and Aava Mobile as an expert in industrial tablets and wireless technologies.
The smartphone with the cutting-edge AndroidTM 13 operating system complies with the latest technical standards such as 5G, Wi-Fi 6 and eSIM and is therefore ideally equipped for flexible worldwide use in public and private networks of mobile network providers or companies. Thanks to fast and secure transmission of large amounts of data, users benefit from state-of-theart functions for communication and collaboration such as remote support, video conferencing or push-to-talk.
The Smart-Ex® 03 is predestined for a wide range of applications such as communication, digital workflows and work order management, operational safety, scanning, asset management, predictive maintenance,
augmented reality applications or IoT integration. Employees along the entire value chain in the process industry, the hydrogen industry, the energy industry or battery production thus benefit from end-to-end digital processes right into hazardous areas.
Thanks to the technical standard 5G, the Smart-Ex® 03 provides outstanding connectivity. The technology enables fail-safe transmission of high data rates of up to 10 Gbit per second with a latency of less than 5 milliseconds.
www.pepperl-fuchs.com
SICK’s unique NOVA software platform delivers AI-powered, user-friendly machine vision
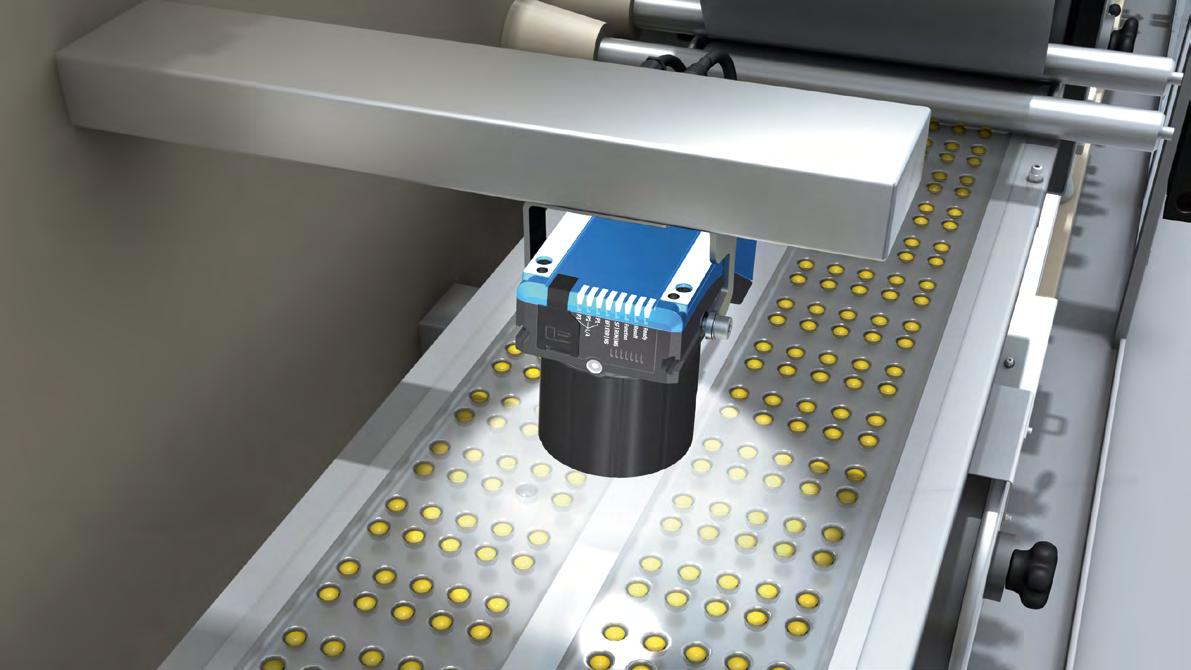
SICK is constantly expanding the capabilities of its unique NOVA platform, providing users with even more options for developing smart, scalable machine vision solutions.
A game-changing foundation software platform for configuring machine vision solutions, NOVA can run on a wide range of 2D and 3D vision sensors, creating countless potential applications for machine vision technology. The platform’s advanced AI functionality removes the need for complex manual setups by enabling users to teach through examples.
NOVA is continually evolving and SICK has enhanced its capabilities to better meet customers’ needs, with recent updates including tools for anomaly detection, 3D height detection and box detection.
Suitable for industries, applications and users of all kinds
SICK’s NOVA is suitable for a wide range of industries, including logistics, automotive, FMCG and robotics, and it runs on a multitude of 2D and 3D vision cameras, leveraging different imaging technologies. NOVA provides both machine vision experts and non-experts with the ability to develop bespoke applications and use ready-made plug-ins to configure machine vision solutions to meet their needs.
The cost-effective NOVA foundation software platform enables users to teach through examples for ease-of-use and scalability. Featuring a user-friendly web interface, NOVA can utilize a variety of imaging techniques to handle even the most challenging requirements.
Nathaniel
SICK UK’s Market Product Manager, says, “SICK’s NOVA provides the AI-powered capabilities to enable all companies and users to harness the potential of 2D and 3D machine vision and enhance their operations. Starting with just one camera, NOVA enables end users, OEMs and integrators to expand solutions and even create advanced custom developments using Lua programming and HALCON.
“At SICK, we provide full spectrum machine vision solutions, combined with our extensive expertise and legacy as a machine vision pioneer, to create bespoke solutions for countless applications.”
For more information, visit: www.sick.com/gb/en
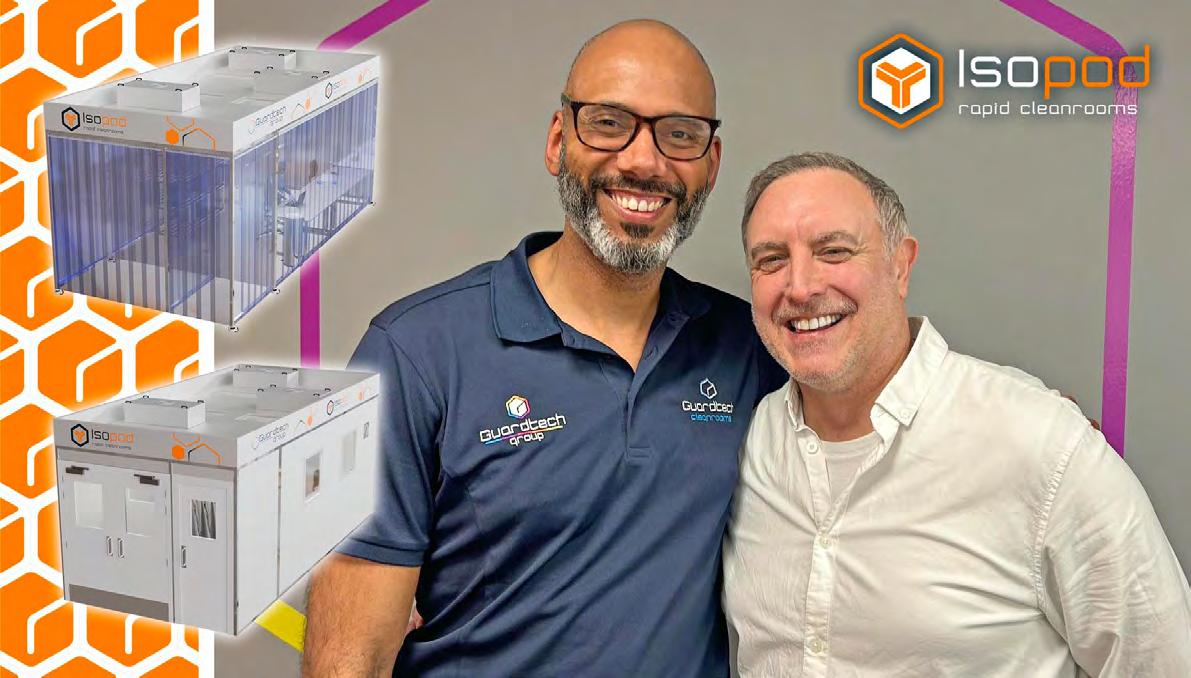
Guardtech elevate rapid cleanroom offering as new era of Isopod takes shape
Suffolk-based cleanroom construction experts back up new website with a string of exciting developments for the quick-assembly brand
THE GUARDTECH GROUP are ushering in a new era of quick-assembly cleanroom excellence with a series of exciting developments regarding their Isopod Rapid Cleanrooms brand.
The Haverhill-based controlled environment construction specialists recently launched an exciting new website for Isopod – www.iso-pod.co.uk – an innovative site that takes clients through the most comprehensive, small-scale cleanroom procurement process on the market.
Guardtech’s new site hosts their revolutionary ‘build your own cleanroom’ Isopod Configurator alongside in-depth Isopod model pages, helpful Technical component content and illuminating case studies.
What’s more, there are also now all-new Configurations pages for the Shell (Hardwall), Flexi (Softwall) and Hybrid (Genus) models, which outline the standard 2x3m, 3x3m, 3x4m, 4x4m and 5x3m pod options, as well as standard PAL/MAL dual airlock Configurations for each size.
Guardtech have invested significantly in R&D over the
12 months to develop what they believe are their most compelling Shell, Flexi and Hybrid model prototypes yet.
The latest Isopods promise to be the most robust, reliable, high-performance modules in the brand’s history – a process led by Isopod/CleanCube Manufacturing Manager Michael Burton and Guardtech Group ISO Commercial Manager Andrew Cressey.
“Isopod, as a high-quality, quick-assembly cleanroom product, is now better than ever before,” says Cressey.
“The idea with this newly streamlined and standardised process is to make buying a rapid, small-scale cleanroom pod as straightforward as possible.”
Cressey has been delivering smaller scale cleanroom pods, alongside more large-scale, complex facilities, for more than a decade.
He’s utilised his wealth of experience to help the Group develop the most efficient, customer-friendly service in the history of Isopod.
“I’ve been providing cleanroom systems like Isopod for a long time now, so I know better than most what
clients need – and how they want the process to unfold in terms of procuring these units.
“Ultimately, many customers will still require a bespoke system, but the idea with these new standard Configurations is that a potential new client can quickly and easily see what options they’ve got, in terms of basic process room plus Personnel and Materials Airlocks layouts, and then make a super-quick, informed decision as to how they want to move forward.”
Guardtech’s Isopod Rapid Cleanrooms Brochure has also been given an update as part of the brand refresh, with more in-depth focus on the three base models, Configurations content and much more.
And the brand now has a newly established twopronged, dedicated sales team in the form of Jack Pummell and Steve Bawa.
The Guardtech Group Business Development Managers will offer a more concentrated client-centred service in the North (Bawa) and South (Pummell), taking the brand’s streamlined approach to a whole new level.
Bawa, who joined Guardtech three months ago and, like Pummell, also provides Cleanroom Service Plans, facility Decontamination Agreements and cleanroomgrade furniture & equipment, is thrilled to have joined Guardtech at such an exciting time.
“I’m delighted to be involved with Isopod – it’s such an amazing, innovative product,” he says. “Guardtech have a long history of excellence in terms of cleanroom construction – and you can see all the hallmarks of their expertise in the quality of the modules.
“Establishing that level of trusted intellectual property has obviously come over years and years of building complex cleanrooms – and you can really see that in Isopod.
“I’m looking forward to providing these brilliant units for clients across the realm of Life Sciences, High-Tech Engineering and Manufacturing.”
For more information on Isopod Rapid Cleanrooms, call 0330 113 0303, email sales@guardtech.com or visit www.iso-pod.co.uk.
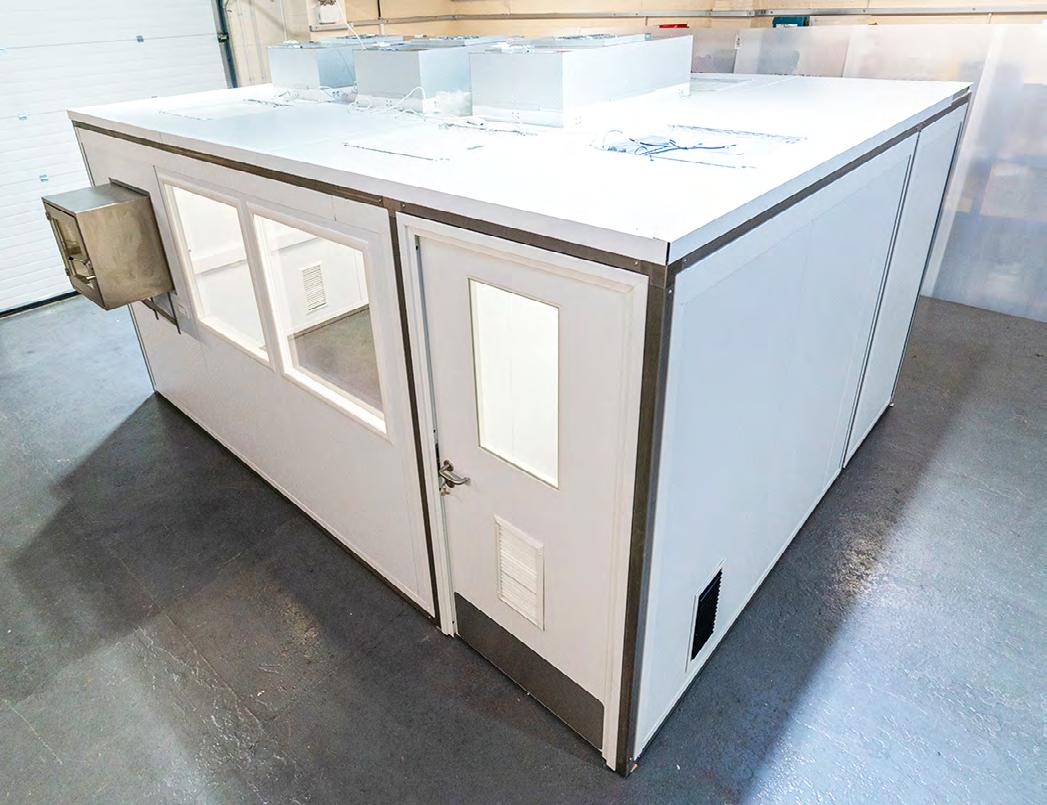
Deltek profile: We speak to Neil Davidson, Group Vice President, Deltek.
What inspired Deltek’s founding and how has the company’s vision evolved over time?
Deltek was founded based on a passion for providing innovative solutions to the unique challenges of running a project-based business. It is how we came about and over the past 40-plus years, Deltek has never wavered from its focus on our customers, and we continue to develop our solutions in line with their unique requirements to realise the fastest and most comprehensive time to value. As a result, the company delivers the most complete industryspecific solutions for professional services firms, government contractors and over 30,000 of them worldwide use Deltek, helping them achieve maximum performance when delivering their projects.
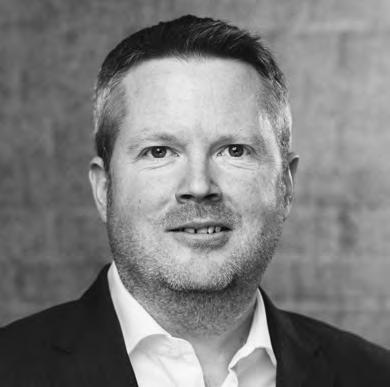
How does Deltek differentiate itself from competitors in the project-based software solutions market?
The difference between us and our competitors is that Deltek is the largest pure-play project-based solution provider. Our products are purpose-built for project-based businesses and users in that community, giving them more specificity, depth and breadth than our competitors. Whether it is cultivating or managing your opportunity pipeline or leveraging AI to pull together smart summaries, project solutions are where we focus all our innovation muscle.
Fundamentally, our mission is to deliver the most complete industry specific solutions that maximise our customers’ performance at every stage of the project lifecycle. Day in and day out, we’re committed to delivering on this mission.
How does Deltek approach customer feedback and incorporate it into product development?
We know that our customers are key to identifying areas of project improvement – we’re there to power their project success and as such, they know what they need better than anyone else. We only succeed if our customers succeed. To capture this insight, we have multiple channels to intake customer feedback – including our Idea Portal, in-person events like Deltek Project Nation Live and Deltek ProjectCon, one-on-one conversations, and online feedback opportunities.
We take customer and partner feedback on enhancements and new features very seriously, with ongoing assessments of our clients, as well as staying ahead of industry trends and emerging technology. As a result, we’ve been keenly aware of our clients’ interest and the increasing industry focus on Artificial Intelligence. With our research showing that almost two-thirds (64%) of engineering firms are confident that investing in AI will expand the services that they can deliver to the market, and 47% believe that successful AI implementation will increase profits, we wanted to help our customers unlock its innovation.
Our recent launch of AI-powered intelligent business companion Dela™, unveiled our umbrella of AI capabilities available across our product suite, making it easy for users to access business intelligence, get assistance, and apply automation to increase the efficiency of project delivery. From speaking to customers every day, we know that they need solid data as a foundation to use AI. Our platform provides that data, and AI helps them to leverage it in a way that brings tangible value to their businesses.
What are the biggest challenges facing project-based businesses today, and how does Deltek address these challenges through its solutions?
Our annual industry research report, Clarity 2024: Trends & Insights for Architecture, Engineering & Consulting Firms, reveals that, in 2024, there has been an increase in concerns about perceived business risks to organisations, compared to 2023, which highlights the growing uncertainties and challenges facing project-based businesses. The top concerns for engineering firms include cyber-security risks/breaches (79%), global political uncertainty (72%), and being able to recruit/retain effective employees (71%).
Engineering firms have positive ambitions for 2024, with 81% expecting to increase their profits this year.
Of course, technology will play a major role, with 45% of engineering firms recognising that investing in technology innovation and IT infrastructure delivers their biggest growth opportunities during the next 12 months.
Our industry-focused expertise powers project success by helping firms achieve performance that maximises productivity and revenue. As of today, thanks to our team of project experts and insights from customers, we’re proud to be the leading global provider of enterprise software and information for project-based businesses.
How does Deltek foster a culture of innovation and continuous improvement within the company?
At Deltek, we live each day based on core company values that help drive our people and our company to success. These values are fundamental principles that we use to guide our business processes and interactions with each other, our customers, and our community. Our values include being customer-focused, having a collaborative environment, being curious and innovative, working and delivering with speed, and having high integrity and passion.
In every project we undertake, we seek to add value at every stage. We challenge the way we’ve always done it and we create new ideas. We don’t believe in innovation for the sake of innovation; we innovate to provide our customers and users with more value within the Deltek solution. Purposeful innovation is our tagline, and it runs true throughout all tech and feature changes.
Across the business, we’re always exploring the latest developments and innovations in technology, considering how we can evolve our solutions to enable better projects. To keep our purpose front and centre throughout this process, we have core pillars of focus which evolve over time as we work to make the project lifecycle smarter. The pillars are currently workforce 3.0, industry automation, cloud-first and pervasive connectivity, process automation (RPA), alongside AI and machine learning (ML).
How does Deltek envision the future of project management and project-based businesses, and what role does the company aim to play in shaping that future?
The engineering industry is undergoing a transformation in the digital age, and businesses need to embrace technology as the catalyst for growth, productivity, and innovation. In fact, our research reveals that two-thirds (67%) of engineering firms believe they will lose market share within two years if they fail to make significant progress with digital transformation, cementing its significance.
To unlock the next level of project success, firms need to respond to the challenging needs and expectations of their clients, employees, and regulators. Adopting and
leveraging the right digital tools will enable professional services firms to attract and retain the best talent, deliver value to their clients, and differentiate themselves in a crowded market.
Deltek’s role is to make the project lifecycle smarter. Whether that be through process automation or leveraging artificial intelligence to enhance operations, we are and will continue to be a partner that helps make complex projects successful with innovation that is aligned with customer needs.
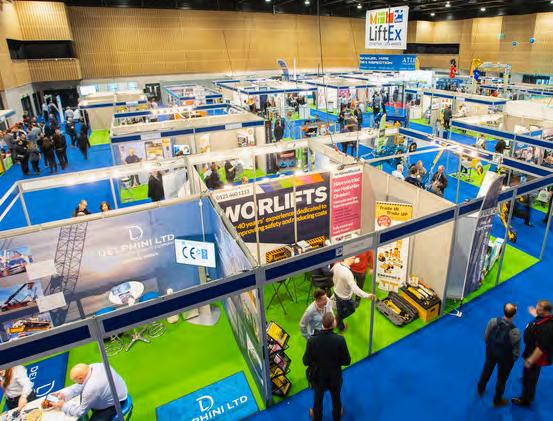
Visit LiftEx 2024 to boost lifting
LiftEx 2024, the flagship event of the Lifting Equipment Engineers Association (LEEA), will take place on 16-17th October 2024 at the new West Hall at Olympia in London – a great central location for a truly global industry.
The exhibition floor at Olympia will be packed with almost 100 exhibitors showing their solutions to improve productivity, efficiency and safety for end users. These will feature the latest lifting products including hoists, mobile and overhead cranes, steel chains, wire rope, winches, shackles, web slings, rigging, spreader beams, height safety and load monitoring equipment, IT solutions and more.
Crucially, your visit will contribute to improving safety with advice from experts on the LEEA stand, while free training sessions and presentations will be delivered by LEEA Accredited Training Scheme members at the ATS Seminar, which is being held across both days.
Set to be the best yet, LiftEx 2024 is supported by sponsors including YOKE, the manufacturer of lifting fittings for chain, wire rope and webbing slings; Rope and Sling Specialists, one of the largest independent
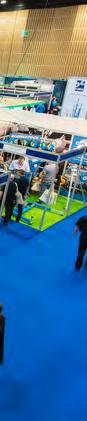
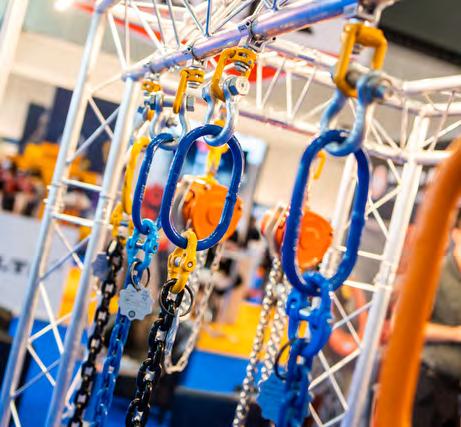
lifting standards in engineering
companies in the field of lifting equipment engineering in the UK; and Headline Sponsor RiConnect Inc, which offers powerful software known as RiConnect that is designed to streamline equipment management and ensure regulatory compliance and traceability.
The many networking opportunities during the event will include the annual LEEA Awards ceremony will be held at the iconic Dorchester hotel on the evening of 16 October 2024.
For engineers, LiftEx 2024 offers the perfect chance to gain vital lifting related knowledge and insights, as well as an opportunity to meet LEEA members
and discuss ways they can help achieve best lifting practice.
Registration will be open soon at the exhibition website at events.leeaint.com/liftex-london-2024.
For those interested in exhibiting, a few stands remain available. Sponsorship packages are also available for the exhibition and Awards Dinner.
Requests will be dealt with on a first-come, firstserved basis, so please contact Leah Phelps on +44 20 3488 2865 or at enquiries@L2Events.com or visit: events.leeaint.com/liftex-london-2024
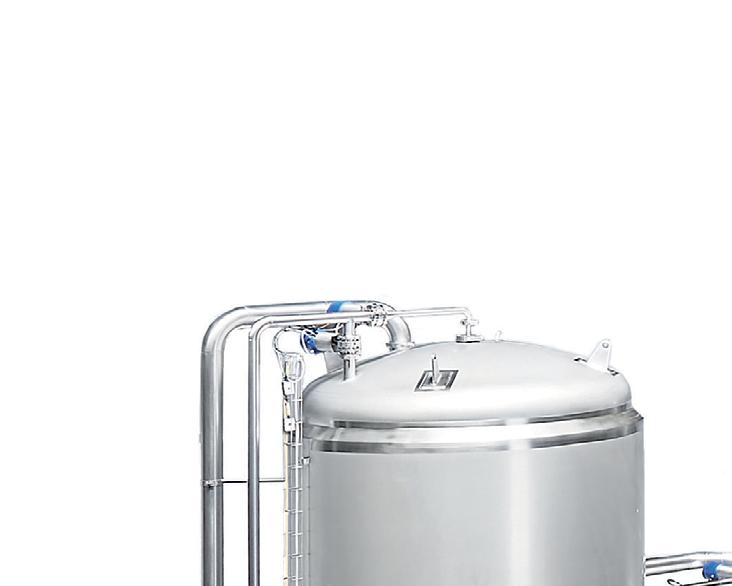
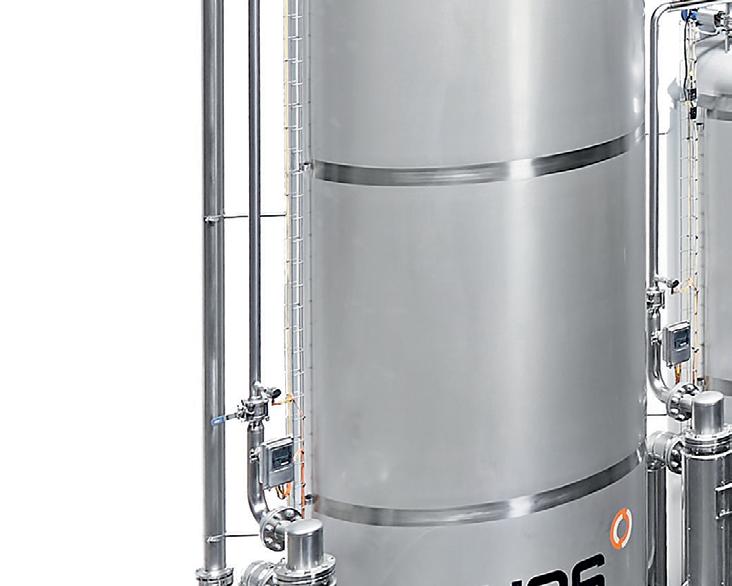
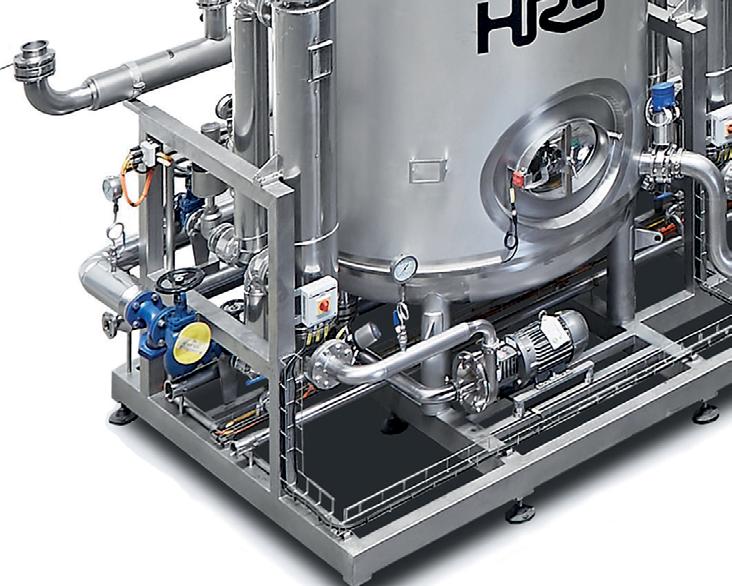
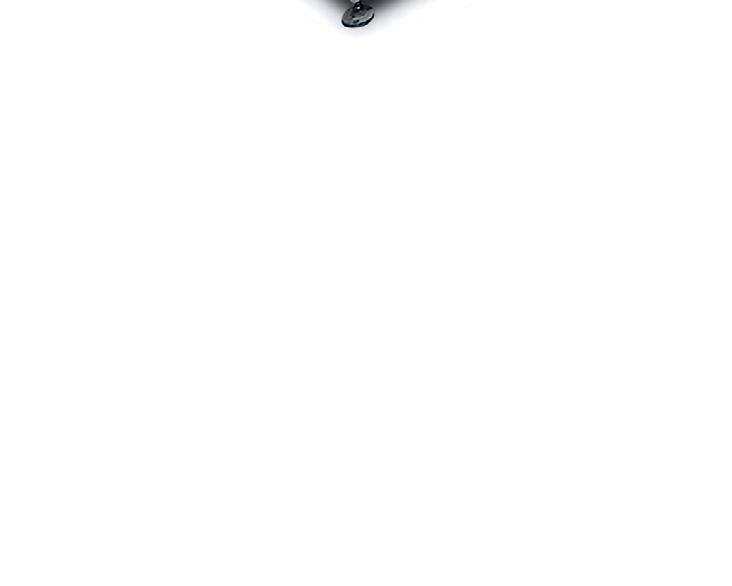
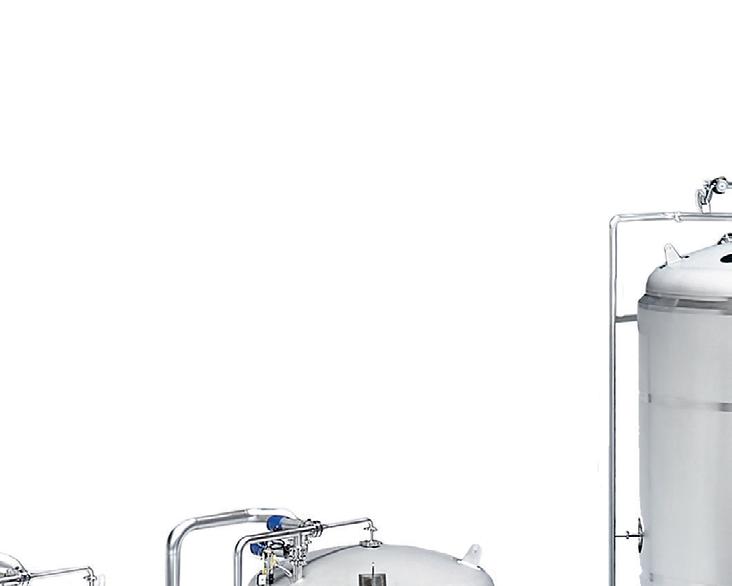
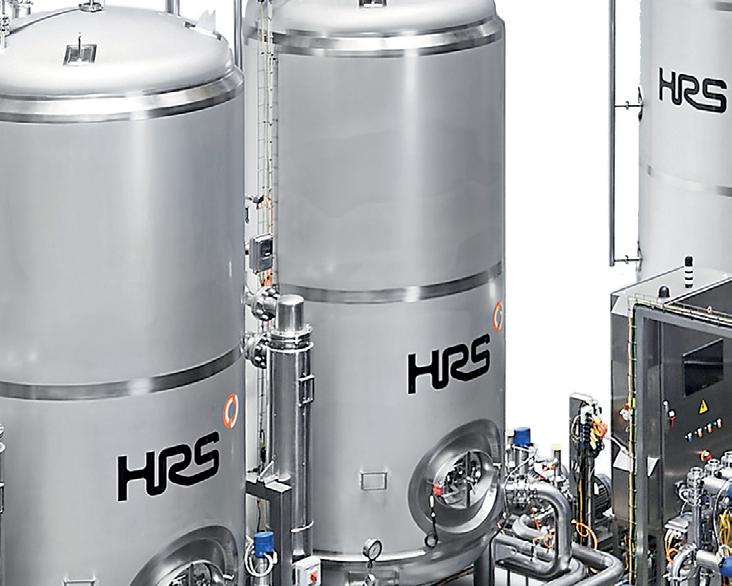
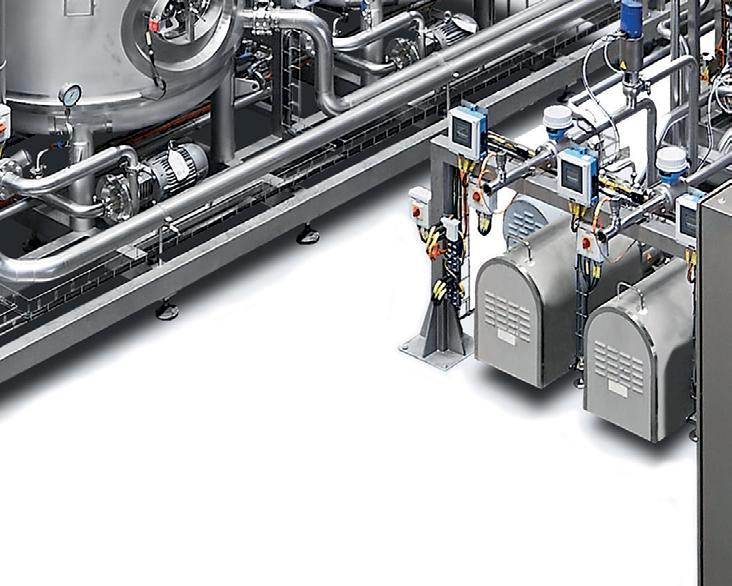
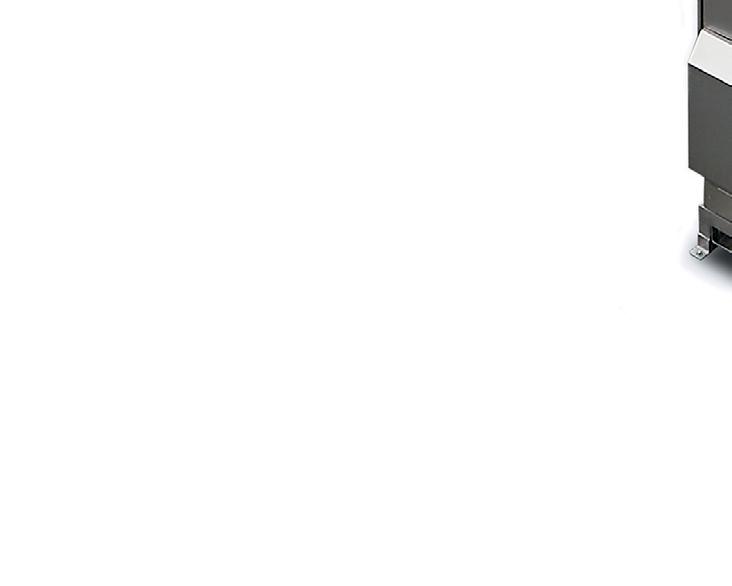
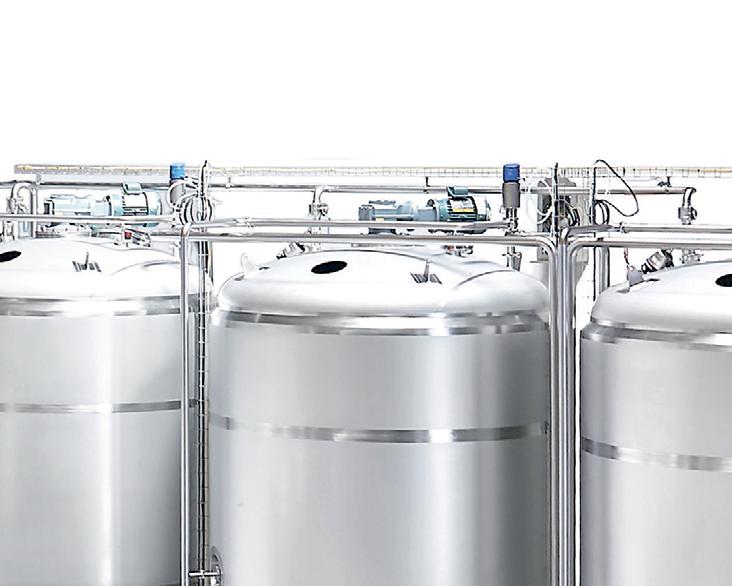

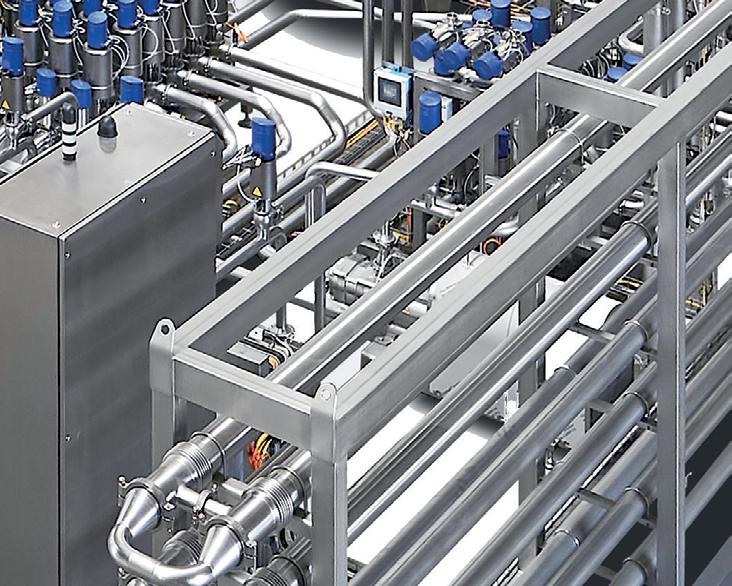
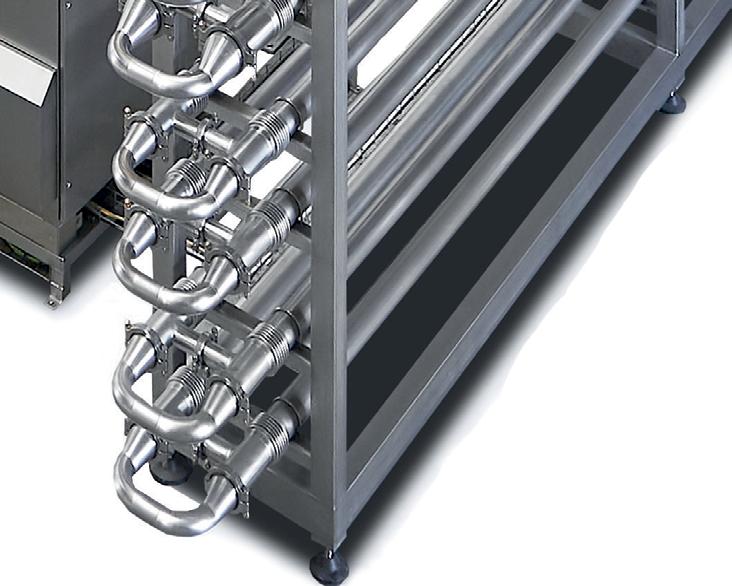

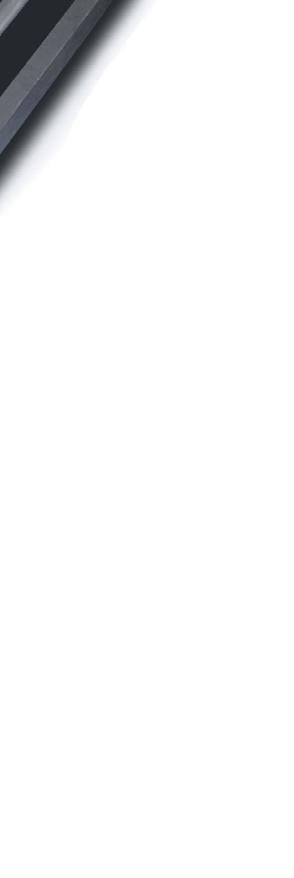