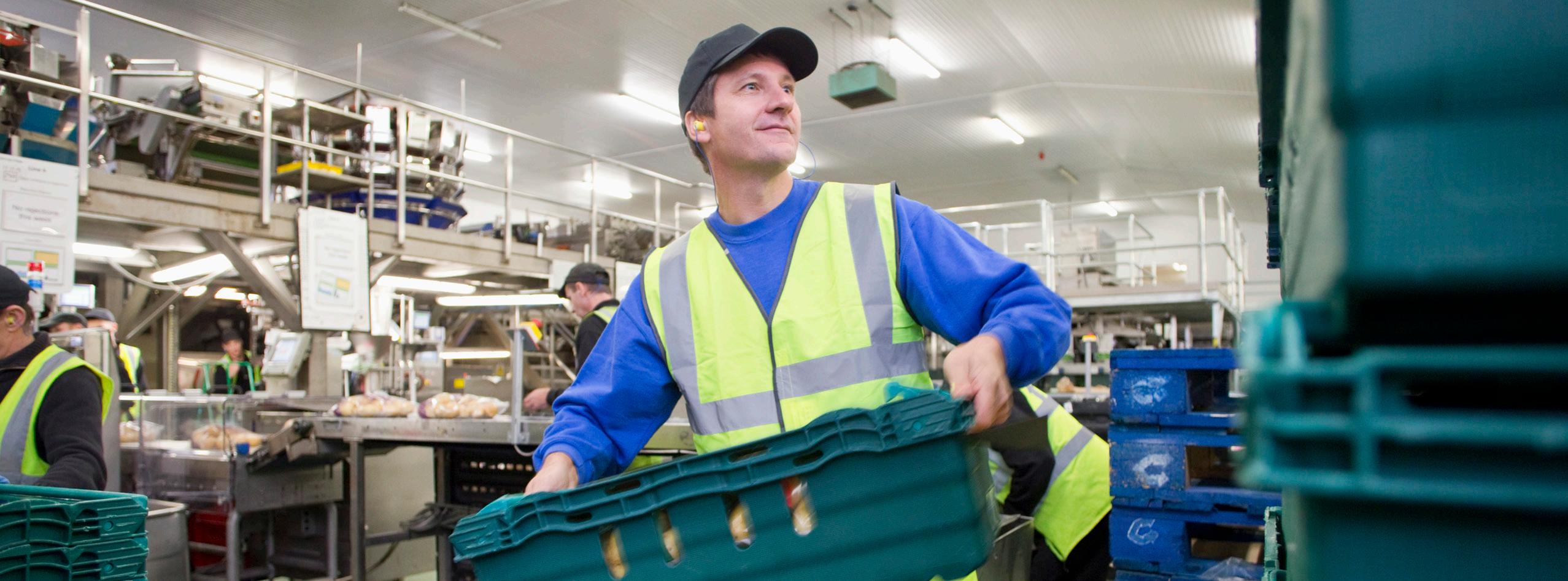
6 minute read
5 Tips for Preventing Back Injuries in the Workplace
EMC Insurance and CUI Agency
5 Tips for Preventing Back Injuries in the Workplace
Back injuries account for nearly 20% of all injuries and illnesses in the workplace, affecting more than one million workers annually. Whether your employees sit at a desk in an office setting or regularly lift and move heavy materials, back injury prevention is important.
What Causes Back Pain Several factors can contribute to back pain at work. For example:
• Force—exerting too much force on your back, such as by lifting or moving heavy objects
• Repetition—repeating certain movements, especially those that involve twisting or rotating your spine
• Inactivity—a desk job can contribute to back pain, especially if you have poor posture or sit all day in a chair with inadequate back support
Consult the Hierarchy of Hazard Control
Identifying and controlling safety and health hazards in the workplace is fundamental to the prevention of injuries and illnesses. Many different techniques are available to help identify hazards, such as workplace audits, supervisor observation, job safety analysis and injury claims analysis.
The hierarchy of hazard control is a system used to minimize or eliminate worker exposure to hazards, helping you prioritize possible safety measures to help ensure you’re getting the most impact. To use the hierarchy of hazard control correctly, start by looking for solutions at the top of the hierarchy and work your way down.
5 Tips to Prevent Back Injuries
There are steps you can take to avoid and prevent back injuries at work. Here are five tips to reduce strain on your back while working:
1. Workplace improvements: Elimination of a hazard is the most effective means of controlling it. Start by figuring out how to avoid lifting in the first place. Consider redesigning a workstation to relieve physical stress and remove ergonomic hazards, or introduce mechanical aids (lift tables, hoists, etc.) to minimize material handling injuries.
• Picture this: Recycling collectors have historically faced high injury rates due to the repetitive task of lifting recycling containers and emptying them into recycling trucks. In recent years, companies have adopted mechanical side arms to lift the bin of recyclables into the truck, eliminating the need for employees to manually lift recycling containers entirely.

• Bonus tip: Consider what new risks or hazards are created in the event of a substitution. For example, while using a side arm to lift the bin of recyclables into the truck eliminates lifting for the employee, using a joystick for 10+ hours a day to control the arm introduces another overexertion risk—stress on the hands and wrist. Albeit not as great as the lifting exposure, you still need to be cognizant of it and consider alternatives, such as a button instead of a joystick.
2. Modify repetitive tasks: If you cannot eliminate the need to lift, try modifying the task to reduce the force and frequency of lifting. Can you change the way the job is done to limit the lifting? Can you alternate physically demanding tasks with less demanding ones?
• Picture this: Considering the example above, replacing a fleet of recycling collection vehicles takes time and money to implement. In the meantime, the company could shorten routes or limit the number of hours an employee spends doing the physically demanding task. To limit the number of hours, drivers can alternate their time between driving and completing other required tasks at the processing facility or partake in a job rotation. The company can also consider hiring additional drivers to allow for shorter shifts. Be careful not to substitute one task that stresses the back for another.
3. Lift properly: If you cannot eliminate the lifting task, make sure to protect yourself by lifting properly—this is an “administrative control” according to the hierarchy of hazard control.
When lifting and carrying a heavy object, get close to the object, bend your knees and tighten your stomach muscles. Use your leg muscles to support your body as you stand up. Hold the object close to your body. Maintain the natural curve of your back. Don’t twist when lifting. If an object is too heavy to lift safely, ask someone to help you.
• Use this resource: The National Institute for Occupational Safety and Health (NIOSH) Lifting Equation mobile application, NLE Cal, is a tool that looks at specific tasks and calculates the overall risk index for single and multiple manual lifting tasks— giving you an idea of whether it’s a safe lift for the worker.
4. Stretch regularly: Daily stretching exercises can improve flexibility, which allows the body to turn and twist the back with less chance of injury. Although this tactic is less effective than the ones above, implementing a stretching program it is relatively inexpensive in the short-term.
5. Engage with employees: One of the most effective ways to involve employees in your ergonomics program is to consult with them. For example, organizations can discuss ergonomics during safety meetings and the group can identify ergonomic risks and brainstorm ways to improve a process. Employees are a great resource to tap into to find ergonomic solutions.
Picking the Right Recommendation
The recycling collector is a good example of a critical hazard where multiple recommendations could be made. Often organizations gravitate toward lower levels of the hierarchy of hazard control (such as personal protective equipment) because they appear to be less costly and time consuming.
While they be less effort in the short run, they are not as effective long-term. Remember, the highest levels of control on the hierarchy are the most reliable at addressing hazards.
With the proper planning, training and tools any facility can create an environment that enables workers to avoid back injuries.
Find More Online
Visit EMC’s website for free loss control resources, including a customizable industrial ergonomics program template.
Free Industrial Ergonomics Training
Preventing back injuries is just one part of the ergonomics equation. Learn how you can effectively manage industrial ergonomics in your operation during a free virtual training session with EMC’s Senior Risk Improvement Representative, Nic Benson.
Nic will discuss how you can detect and address ergonomic issues to reduce operational expense and downtime. The session is free for all UMA members.
Industrial Ergonomics with Nic Benson Wednesday, Sept. 28 10 – 11 a.m. MT Register
Free Industrial Ergonomics Training
Preventing back injuries is just one part of the ergonomics equation. Learn how you can effectively manage industrial ergonomics in your operation during a free virtual training session with EMC’s Senior Risk Improvement Representative, Nic Benson.
Nic will discuss how you can detect and address ergonomic issues to reduce operational expense and downtime. The session is free for all UMA members.
Industrial Ergonomics with Nic Benson Wednesday, Sept. 28 10 – 11 a.m. MT Register: https://emcins.zoom.us/meeting/register/tJ0ocOqvqT8rG9cMR2nfdm85b8kmb3OVSNUU