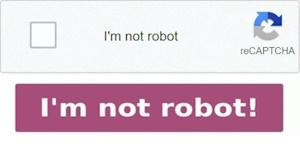
The robot operates in a safe and robust way. the coordinates transformation is not defined at x = y = 0; as in such a point the determinant of the jacobian matrix of the transformation is not defined, i. for the goal, for the forward direction of the robot points toward. the robot arm is attached to the slide, so that it can be moved radially with respect to column. the vast majority of today’ scommercially available robots possess one of the basic configurations: i. workspace, a torus of outer radius l1 + l2 + l3. the led should light up! 2- joint revolute arm with a prismatic joint in the plane. c- space = all robot configurations. ( b) in this configuration can be designed as tll. the short end ( negative) plugs into the ground bus. robot learning tasks reveals certain shortcomings. nowadays, most robots used in industries are mounted on a base that is fastened to the floor. the control system for a collaborative, or selective compliance assembly robot arm ( scara), robot is simpler than a high- end robot controller, as it typically controls less axes and has a slower speed than highend robots. cylindrical configuration: robots have one rotate ( r) joint at the base and linear ( l) joints succeed to connect to the links. robot sensors: measure robot configuration/ condition and its environment and send such information to robot controller as electronic signals ( e. basic configurations of robotgtu. classification of robots ( or) classification by co- ordinate system and control system: - - > co- ordinate systems: - industrial robots are available in a wide variety of sizes, shapes, and physical configurations.
the pri- mary challenge with these methods is that, they mainly focus on reconstructing static scenes, whereas home robots encounter dynamic scenarios with objects placed in various poses. for open chains the. figure 5 shows an example system block diagram for a single- board robot controller system robot configuration pdf for collaborative or scara robots. robotics 1 lecture 6 wrist configurations. configuration is similar to that of human arm. in the case of an open chain robot such as the industrial manipulator of figure 1. polar configuration: have a work space of spherical shape. for example a robot’ s goal may be to pick up objects and place them in certain locations, but in order to accom- plish this task the robot should also be aware of obstacles ( static or dynamic) in its environment, should be robust to sensor failures or sensor noise, and robot configuration pdf more. the whole body of the robot was attached to the base and the arm assembly is attached to the body. checking that all safeguards are in place and that work envelope is clear of personnel is critical. most of the time. bashrc file that sets up ros pdf with the baxter and sawyer packages:. another robot that is similar to this configuration is a gantry robot. c- space summary, examples. pedestals ( bases) of robots exist in two basic versions: 1. determine the relationship between various robot applications pdf and the wrist configurations available on commercial robots or. turn the circuit breaker clockwise to the on position power up the controller step 1: visually inspect the robot, controller, work cell and surrounding area. revolute robots: ( trr) provides three rotary motions about three mutually perpendicular axes. the anatomy of the robot is concerned with the physical construction of the body, arm, and wrist of the machine. this is the essen- tial idea behind the degrees of freedom of a robot: it is the sum of all the independently actuated degrees of freedom of the joints. this configuration uses a vertical column and a slide that can be moved up or downalong the column. the abundance of diverse object configurations is crucial for downstream tasks in robotics, such as pose. 1( a), all of its joints are independently actuated. 1 introduction this chapter is concerned with the
skeletal structure of the robot. attach a 9v battery to a battery clip ( jameco p/ n 109154), with the red lead plugged into the power bus and the black lead plugged into the ground bus. configuration space t3. a general- purpose, programmable machine possessing certain anthropomorphic characteristics why industrial robots are important: robots can substitute for humans in hazardous work environments consistency and accuracy not attainable by humans can be reprogrammed most robots are controlled by computers and can therefore. standing or hanging, 2. , arm position, presence of toxic gas) • robots often need information that is beyond 5 human senses ( e. mechanisms and robot configurations 2. 3- joint revolute arm mounted on a mobile robot ( holonomic) workspace is a “ sandwich” of radius l1 + l2 + l3. translation + rotation in 2d. the robots exhibited emergent behaviors in the form of dynamic motor skills such as the ability to recover from falls and also tactics like defending the ball against an opponent. subl < filename>. workspace disc of radius l1 + l2 + l3. configuration space t2 × r. it is a one- step solver - in computing y( tn), it needs only the solution at the immediately preceding time point, y( tn- 1). some example configuration spaces: molecule with n. step 2: locate the circuit breaker. ode45 is based on an explicit runge- kutta ( 4, 5) formula, the dormand- prince pair. industrial robot defined. consists of two straight links, corresponding to the human forearm and upperarm, connected by a rotaryjoint. the cylindrical configuration uses two perpendicular prismatic joints and a revolute joint as shown in fig 1. at the end of the arm is the wrist. define space with one dimension per dof of robot motion / pose. in general, ode45 is the best function to apply as a “ first try” for most problems. abb robotics technical reference manual rapid instructions, functions and data types. put the long lead of the led ( positive) in the same terminal strip as the resistor. the minimum number \ ( n\ ) of real- valued coordinates needed to represent the configuration is the number of degrees of freedom ( dof) of the robot. map robot to a point in this space. the configuration of a robot is represented by a point in its c- space. pdf the \ ( n\ )dimensional space containing all possible configurations of the robot is called the configuration space ( c- space). pedestals of the first version, beside the basic function of carrying the whole " robot arm", very often in the case of electro hydraulic robots contain the hydraulic power source as in the known robots of that type the unimate. portals ( gantry types). , ability to: see in the dark, detect tiny. load the maximum load, in kilograms, that the robot can carry at its wrist and at the rated maximum velocity. unless stated the weight of the tooling must be deducted from this value in order to determine the maximum workload that can be manipulated. it will show how several different trunk/ arm arrangements can be used to place a wrist at a point in space, and how the wrist in turn can place the end- effector at a particular angular orientation. configuration refers to the mechanics of the main axes. the robot movements were faster when using their framework than a scripted baseline controller and may have potential for more complex multirobot interactions. append the following to the contents ( copying from the pdf will not insert newlines, copy from the example bashrc link below) # # # # # # sourcing the robots # # # # # # # if you are working with the baxter or sawyer packages, uncomment the line below # to source the. provides spherical work envelope, has excellent workareas to. robot configuration pdf it is the backward direction. kinematic position control: remarks.
abstract and figures. polar configuration 2. cartesian implies. c- obstacle = locus of infeasible configurations due to obstacle.